Механические испытания сварных — Справочник химика 21
Простейшие механические испытания сварного соединения с целью получения таких его характеристик, как предел прочности, относительное удлинение, угол изгиба, производят прн помощи портативной машины с разрывным усилием 200 кН. [c.103]Техническую документацию и изготовление сосудов Техническую документацию на изготовление и ремонт трубопроводов (акт приемки ведомость ревизии труб, фланцев, крепежа, фасонных деталей ведомость учета труб высокого давления после механической обработки ведомость учета гнутых труб высокого давления журнал сварочных работ протокол механических испытаний сварных образцов журнал проверки качества электродов, сварочной проволоки, флюса, аргона для проведения сварочных работ акт проверки технологических [c.562]
Протоколы механических испытаний сварных образцов…….. 17 -1- + + ц- [c.
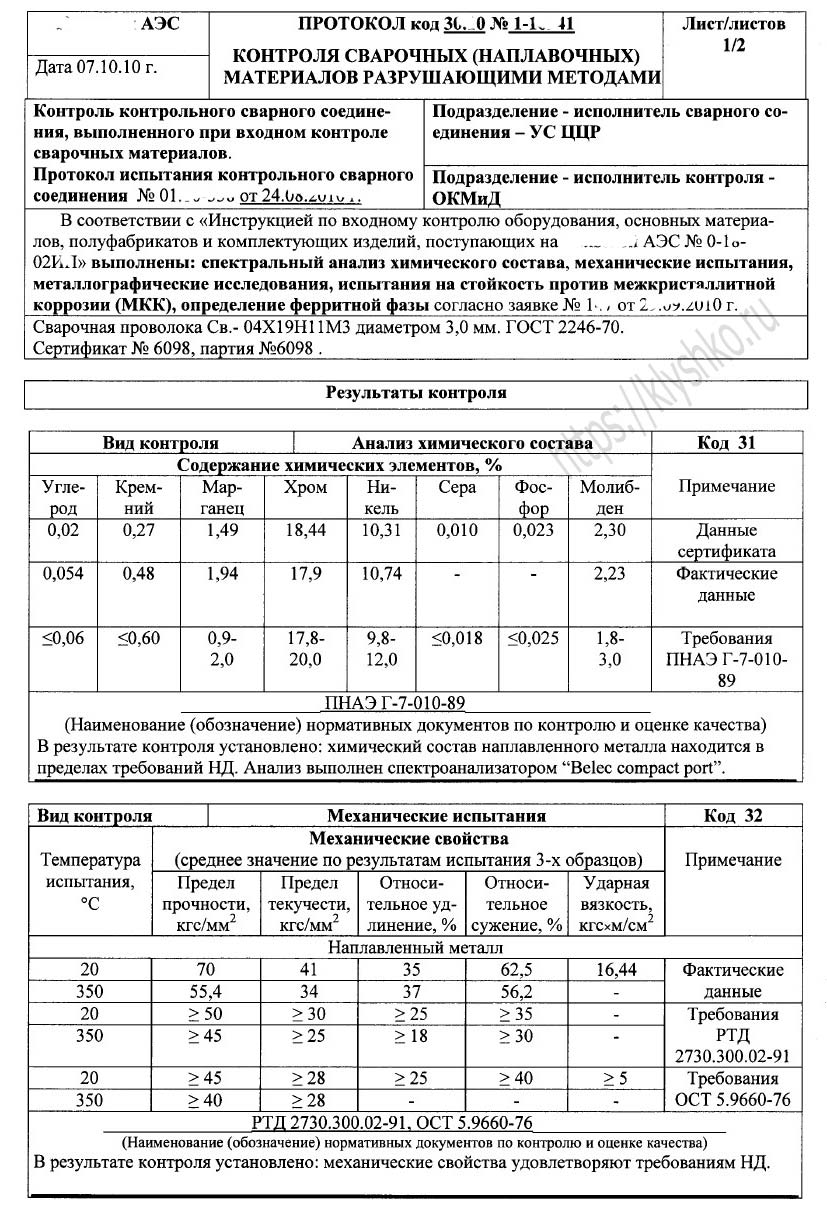
В табл. 176 даиы результаты механических испытаний сварных соединений, [c.183]
Механические испытания сварных соединений, а также измерение твердости металла различных участков сварного соединения и наплавленного металла проводят при нормальной температуре, равной (20 10) °С [(293 10) К]. Испытания различных участков сварного соединения на статическое растяжение, ударный изгиб и стойкость металла против механического старения проводят при нормальной температуре или при повышенных или пониженных температурах, если это предусмотрено стандартами или другой технической документацией. [c.261]
Форма и размеры образцов для механических испытаний сварных соединений должны соответствовать действующим стандартам [c.76]
Сварные соединения подвергают механическим испытаниям для определения их прочности и пластичности. Механические испытания проводят на растяжение, загиб и ударную вязкость. При проведении механических испытаний каждый сварщик обязан сварить контрольные стыки в условиях, аналогичных производственным.
Механические испытания сварных соединений производят для проверки соответствия их прочности и пластических свойств техническим условиям. Основные виды механических испытаний — испытания на растяжение, ударную вязкость, загиб или сплющивание. [c.129]
Механические испытания сварных швов газопроводов производят на специальных машинах. Для проверки из стыка должны вырезаться 3 образца с неснятым усилением для испытаний на растяжение (разрыв) и не менее 3 образцов со снятым усилением для испытаний на изгиб (загиб). Образцы вырезают из различных участков, равномерно распределенных по периметру стыка. Результаты испытаний считают удовлетворительными, если предел прочности шва будет не меньше нижнего предела прочности основного металла труб, а угол загиба — не менее 120 для электродуговой и не менее 100 для газовой сварки.
Контроль сварных соединений проводят в соответствии с требованиями Правил устройства и безопасной эксплуатации сосудов, работающих под давлением . Качество сварных соединений, выполненных при изготовлении баллонов, контролируют внешним осмотром 100% сварных соединений, механическими испытаниями образцов, просвечиванием проникающими излучениями, гидравлическими и пневматическими испытаниями. Обязательными видами механических испытаний сварных соединений являются испытания на статическое растяжение и загиб, при этом временное сопротивление на разрыв должно быть не менее 38 кгс/мм , а угол загиба— не менее 100°. [c.42]
Механическим испытаниям сварных стыков подземных газопроводов (наружных и внутри зданий), сваренных дуговой или газовой сваркой, независимо от рабочего давления газа должно подвергаться следующее количество стыков (помимо пробных), сваренных каждым рабочим в течение календарного месяца [c. 124]
Для механических испытаний сварных стыков, выполненных всеми видами дуговой и газовой сварки, вырезаются из каждого стыка а) три образца с неснятым усилением для испытаний на растяжение б) три образца со снятым усилением для испытаний на изгиб (загиб). При Dyмеханические испытания проводят на целых стыках на растяжение и сплющивание.
При механических испытаниях сварных стыков проверяют образцы, вырезанные из контрольных стыков, на растяжение, загиб, сплющивание и ударную вязкость. [c.54]
До настоящего времени еще не разработаны единые условия механических испытаний сварных соединений пластмасс. Методы прочностных испытаний, принятые для металлов, не могут быть целиком перенесены на испытания пластмасс и их сварных соединений. Поэтому многие организации при разработке технологии сварки пластмасс разрабатывают также методику испытания качества сварных швов [16]. При подготовке образцов для испытаний на растяжение усиление шва снимают, плоскости тщательно обрабатывают и выравнивают. [c.214]
Сварные соединения проверяют внешним осмотром, металлографическими исследованиями, химическим анализом, механическими испытаниями, просвечиванием рентгеновскими лучами, гамма-лучами, магнитными методами и с помощью ультразвука. Предварительно сварное соединение тщательно очищают от шлака, окалины и металлических брызг. Внешним осмотром выявляют наружные дефекты шва. Осмотр производят невооруженным глазом или с помощью лупы с десятикратным увеличением. Размеры сварных швов проверяют шаблонами и мерительным инструментом. Механические испытания сварного соединения осуществляют на специально сваренных контрольных образцах или на образцах, вырезанных из сварного соединения. Прн этом определяют предел [c.128]
Результаты механических испытаний сварных стыков оформляются Протоколом. [c.535]
Результаты механических испытаний сварных соединений должны удовлетворять требованиям табл. 7.8. [c.111]
В табл.
Объем представляемой документации исчерпывается актами испытания на прочность и плотность, а также актами механических испытаний сварных образцов. [c.193]
Помимо механических испытаний сварных соединений проверка качества таковых производится путем просвечивания рентгеном сварных швов. [c.203]
Механические испытания сварных соединений долл[c.139]
Нормы механических испытаний сварных стыков газопроводов должны соответствовать требованиям главы СНиП 111-29-76. [c.197]
Нормы механических испытаний сварных соединений трубопроводов из углеродистых сталей предел прочности — не ниже предела прочности основного металла угол загиба не ниже 100° при дуговой сварке и не ниже 70° при газовой сварке ударная вязкость — не ниже 6 кгс м/см . [c. 164]
Механические испытания сварных соединений трубопроводов производятся для определения их прочности и пластичности. Сварные швы испытывают на растяжение, загиб или сплющивание и на ударную вязкость. Испытание производится на образцах, вырезанных из контрольных стыков, которые завариваются каждым сварщиком в условиях, тождественных производственным, с применением тех же основных и присадочных материалов и в том же положении, в каком производится сварка стыков трубопроводов. Виды механических испытаний, количество контрольных сварных стыков трубопроводов и нормы механических свойств сварного шва определяются соответствующими техническими условиями или проектом. Порядок механических испытаний сварных швов регламентирован ГОСТ 6996—54. [c.289]
Методы специализированных механических испытаний сварных образцов (или «машинные» методы) (рис. 5.13) основаны на доведении зоны мегалла термического влияния или металла шва до образования холодных трещин под действием напряжений от внешней длительно 177]
Механические испытания. Сварные соедиЕюния по результатам механических испытаний отбраковывают в следующих случаях [c.490]
По результатам механических испытаний сварные соединения бракуют, если временное сопротивление ниже минимально допустимого ггредела для временного сопротивления основного металла по ГОСТам или техническим условиям на соответствующие полуфабрикаты (листы, трубы и др.) из стали данной марки для сварных соединений выполненных газовой сваркой на трубах из стали 20 по ГОСТ 8731—74 и ГОСТ 8733—74, временное сопротивление должно быть не ниже за кгс/мм для сварных соединений трубопроводов пара и горячей воды из стали 15ГС, подвергаемых термической обработке, — не ниже 46 кгс/см [c.243]
Необходимо соблюдать величины зазоров в стыках сварных соединений, следить за правильной стыковкой соседних лепестков, проверять внешний вид сварных швов и наличие подрезов, неироваров, трещин и других наружных дефектов, проводить механические испытания сварных соединений и их просвечивание радиоактивными препаратами. Строгое соблюдение принятой технологии сварки, высокое качество присадочных материалов и флюсов вместе с пооперационными методами контроля позволяют получить гарантированное высокое качество сварных швов. [c.247]
Однако, существующие стандарты на механические испытания сварных соединений не учкггьшают специфического влияния факторов механической неоднородности соединений. Поэтому условия подобия испьгганий ими не удовлетворяются. [c.190]
В табл. 154 представлены результаты механических испытаний сварных соединений, выполненных из сплавов марок АМгЗ и АМг5В аргоно-дуговой сваркой с присадкой сплава АМг5. [c.217]
Техническую документацию на изготовление сосудов Техническую документацию на изготовление и ремонт трубопроводов (акт приемки ведомость ревизии труб, фланцев, крепежа, фасонных деталей ведомость учета труб высокого давления после механической обработки ведомость учета гнутых труб высокого давления журнал сварочных работ протокол механических испытаний сварных образцов журнал проверки качества электродов, сварочной проволоки, флюса, аргона для проведения сварочных работ акт проверки технологических свойств электродов журнал режима термообработки сварных швов заключение по неразрушающим методам контроля сварных швов акт гидрав- лического испытания трубопоо-водов высокого давления ведомость проверки гнутых труб высокого давления) Техническую документацию на изготовление детален и запасных частей (акт приемки, паспорт, чертеж) [c. 562]
При получении неудовлетворительных результатов по какому-либо виду механических испытаний сварных стыков, предусмотренных пп. 5.18, 5.19 настоящих Правил, должно проводиться повторное испытание по этому же виду на удвоенном числе образцов. В случае получения при повторном испытаиии неудовлетворительных результатов хотя бы на одном образце проводится отбраковка стыков, сварен- [c.197]
Механические испытания сварных образцов — Энциклопедия по машиностроению XXL
Результаты механических испытаний сварных образцов на разрыв и загиб должны удовлетворять требованиям, приведенным в табл, 3, п. 2. [c.89]Результаты механических испытаний сварных образцов должны удовлетворять требованиям ГОСТ, ТУ и табл. 10 и И настоящих Правил. [c.220]
Результаты механических испытаний сварных образцов должны соответствовать требованиям табл. 8. [c.370]
Механические испытания сварных образцов проводят для определения стандартных механических характеристик материала — предела текучести, прочности, относительного удлинения и поперечного сужения (показатели пластичности), а также ударной вязкости. Кроме того, проводят испытания на изгиб плоского образца или на сплющивание (для труб диаметром менее 108 мм). Эти виды испытаний необходимы в следующих случаях
[c.378]
Количественная оценка сопротивления сварных соединений образованию холодных трещин основана на теории замедленного разрушения и предусматривает механические испытания сварных образцов. Испытания эти подобий испытаниям на длительную прочность. Наибольшее применение получил метод МВТУ на машине ЛТП. Метод основан на механическом испытании сварных образцов рекомендуемых размеров путем нагружения постоянными нагрузками. Нагрузки моделируют упругую энергию собственных напряжений в сварных конструкциях. За показатель сопротивляемости металла образованию холодных трещин при сварке следует принимать минимальное растягивающее напряжение от внешней нагрузки, при котором в сварном соединении образца образуются трещины после выдержки образца под нагрузкой в течение 20 ч. [c.49]
Механические испытания сварных образцов для определе-
[c. 355]
Наиболее простой качественный способ определения сопротивляемости сталей образованию холодных трещин заключается в сварке технологических проб (рис. 202). Количественный метод оценки сопротивляемости сталей образованию холодных трещин при сварке состоит в механическом испытании сварных образцов непосредствен- [c.424]
Методы количественной оценки сопротивления сварных соединений образованию холодных трещин основаны на теории замедленного разрушения [2] и предусматривают механические испытания сварных образцов или образцов из основного металла, обработанных по циклу околошовной зоны. Испытания эти по своему типу подобны испытаниям на длительную прочность. [c.159]
Характеристика переносной машины для механических испытаний сварных образцов [c.705]
На сварочные работы (включая выписку из сертификата на трубы и металл фланцев копию сертификата на электроды и сварочную проволоку копию диплома сварщика журнал сварочных работ протокол механического испытания сварных образцов)
[c. 727]
На сварочные работы (включая копии сертификатов на электроды н сварочную проволоку копии сертификата на трубы, термообработку сварных стыков копию удостоверения сварщика журнал сварочных работ протокол механического испытания сварных образцов и испытаний на межкристаллитную коррозию) [c.727]
В протоколе механических испытаний сварных образцов указываются лабораторный номер образца, фамилия, имя и отчество сварщика, диаметр трубопровода, марка стали, дата сварки, положение во время сварки, марка электродов или сварочной проволоки, маркировка образцов, результаты механических испытаний (предел прочности, угол загиба, ударная вязкость, характеристика металла в месте разрушения). Протокол подписывается лицом, выполнявшим испытания, и начальником контрольной лаборатории. [c.728]
Результаты технологических и механических испытаний сварных образцов, выполненных газовой сваркой по правилам Госгортехнадзора, признанные удовлетворительными, должны соответствовать нижеследующим показателям [c.

Методы разрушающего контроля позволяют определить количественные характеристики показателей качества (прочность, пластичность, твердость) путем механических испытаний сварных образцов или выборочного испытания сварных соединений штатных изделий. При испытаниях образцов или изделий выявляются дефекты в местах разрушения. [c.303]
Механические испытания сварных образцов (ГОСТ 6996-54, 1497-42 я 1524-42) [c.251]
Механизация погрузочно-разгрузочных работ па складах оборудования и материалов 484 Механические испытания сварных образцов 185 [c.556]
Контроль В процессе сварки включает систематическую проверку режима сварки, исправности работы сварочной аппаратуры и приспособлений, проверку соблюдения сварщиком установленного технологического процесса сварки, осмотр и обмер шва шаблонами. Данный вид контроля осуществляется мастером и контролером ОТК. Контролем готового изделия или узла определяется качество выполненной сварки. Для этого производится наружный осмотр и обмер швов, испытание на плотность (для швов сосудов, работающих под давлением), металлографические, физические и химические исследования, механические испытания сварных образцов.
[c.182]
Методы специализированных механических испытаний сварных образцов. Методы специализированных механических испытаний сварных образцов (или машинные методы) основаны на доведении зоны металла термического влияния или металла шва до образования холодных трещин под действием напряжений от внешней длительно действующей постоянной нагрузки [8]. При испытаниях серию образцов нагружают различными по величине нагрузками непосредственно после окончания сварки и выдерживают их под нагрузкой в течение 20 ч. За сравнительный количественный показатель сопротивляемости металла сварных соединений трещинам принимают минимальное растягивающее напряжение от внешней нагрузки сгр. min, при которой начинают образовываться трещины. [c.146]
Контроль готового узла, детали или изделия выполняется контролерами ОТК или мастером. Этот вид контроля включает наружный осмотр и обмер швов, испытание на плотность (для швов сосудов), механические испытания сварных образцов, просвечивание швов, если таковое предусмотрено техническими условиями на сварку. Наиболее сложные операции данного вида контроля выполняются с привлечением заводской лаборатории.
[c.403]
Прямые способы оценки склонности сталей к XT включают сварочные технологические пробы и специализированные механические испытания сварных соединений. Пробы представляют собой сварные образцы, конструкция и технология сварки которых вызывают интенсивное развитие одного или нескольких основных факторов, обусловливающих образование трещин. По назначению пробы разделяют на лабораторные и отраслевые, Лабораторные пробы дают сравнительную оценку материа- [c.538]
Механические испытания сварных соединений разделяют на статические (растяжение, определение твердости, загиб) и динамические (испытания на удар, усталость и вибрацию). Испытания проводят по утвержденным стандартам. Образцы, применяемые при испытаниях, также стандартизованы.
[c.568]
Механические испытания сварных соединений труб диаметром менее 100 мм при толщине стенки менее 12 мм могут проводиться с использованием как отдельных образцов, так и цельных стыков со снятым усилением и удаленным гратом. Испытания последних на статический изгиб заменяются испытанием на сплющивание. Достаточно испытания по одному контрольному стыку на сплющивание и растяжение. Металлографическое исследование в этом случае выполняется на специально свариваемых конт рольных соединениях. [c.217]
До настоящего времени еще не разработаны единые условия механических испытаний сварных соединений пластмасс. Методы прочностных испытаний, принятые для металлов, не могут быть целиком перенесены на испытания пластмасс и их сварных соединений. Поэтому многие организации при разработке технологии сварки пластмасс разрабатывают также методику испытания качества сварных швов [16]. При подготовке образцов для испытаний на растяжение усиление шва снимают, плоскости тщательно обрабатывают и выравнивают.
[c.214]
Примечания 1. Во всех случаях число контрольных стыков должно быть не менее одного. 2. Механические испытания сварных соединений труб малого диаметра производят путем испытаний целых стыков контрольных соединений. 3. При проведении механических испытаний и металлографического исследования на образцах, вырезаемых из стыка, число свариваемых контрольных стыков на первых двух машинах может быть сокращено в два раза, если обеспечена возможность вырезки всех необходимых образцов. [c.593]
Заблаговременно перед прихваткой вставки к барабану сварщики должны наплавить образцы для испытания наплавленного металла электродов и сварить пластины для испытания сварных образцов. Работу по сварке вставки нельзя начинать до получения удовлетворительных результатов механических испытаний образцов. [c.274]
После сварки пластин они отрезаются резаком и из них изготовляются контрольные образцы для механических испытаний сварного шва.
[c.274]
Проба на свариваемость производится путем механического испытания пяти образцов, сваренных встык со снятым усилением щва. Три из этих образцов испытываются на разрыв и два на загиб. Сварка образцов должна производиться теми же электродами, которые будут применяться в процессе основной сварки. Результаты испытаний образцов считаются удовлетворительными, если сварные соединения покажут следующие механические свойства прочность не менее 38 кг/мм и угол загиба не менее 100°. [c.437]
Механические свойства сварных стыковых соединений, изготовленных из листовой стали, проверяют испытанием сварных образцов, вырезанных из контрольных пластин, сваренных одновременно с изготовлением контролируемых изделий с применением тех же исходных материалов, метода сварки, режимов и термообработки. [c.368]
В связи с отличием механических свойств сварного соединения и основного металла возникает необходимость в их оценке. Для этого проводят обычные механические испытания, однако образцы часто изготавливают таким образом, чтобы можно было определить механические показатели отдельных зон основного металла, примыкающего к щву, наплавленного металла или сварного соединения.
[c.497]
Проведенные механические испытания сварных соединений многослойного материала показали, что их предел прочности находится на уровне 0,90. .. 0,95 предела прочности основного материала и составляет 270. .. 280 МПа. В отдельных образцах предел прочности соответствует прочности основного материала. Временное сопротивление на отрыв и срез слоев в стыковом соединений незначительно отличается от свойств [c.514]
Качественную оценку склонности сталей к образованию трещин повторного нагрева получают путем испытаний жестких сварных проб, которые после сварки подвергают высокому отпуску в течение 5… 15 ч. По результатам испытаний стали разделяют на склонные и несклонные к растрескиванию. Сравнительную количественную оценку получают путем механических испытаний сварных образцов по методу ЛТП2 или имплант , которые выполняют в условиях длительного нагружения при температуре высокого отпуска. Минимальные напряжения от внешней нагрузки, при которых начинается растрескивание, принимают за показатель сопротивляемости образованию трещин повторного нагрева.
[c.548]
Проверка механических свойств сварных стыковых соединений барабанов, паросборников и других аналогичных узлов паровых котлоз из листовой стали производится путем механических испытаний сварных образцов, вырезаемых из контрольных пластин, сваренных одновременно с изготовлением контролируемых сварных изделий с применением тех же исходных материалов, методов сварки н сварочных режимов, как и при изготовлении самих изделий. [c.971]
Результаты механических испытаний сварных образцов должны удовлетворять требованиям Госгортехнадзора, приведеиным в табл. 6-12. Показатели механических свойств сварных соединений определяются как среднее арифметическое результатов, полученных при испытании отдельных образцов, и должны удовлетворять приведенным в таблице нормам.
[c.297]
Проверке подвергается и проволока, предназначенная для механизированных способов сварки или для применения в ка честве присадочного металла. Каждая партия проволоки обязательно должна сопровождаться сертификатом, в котором указываются ее марка и диаметр, номер. плавки, химический состав, вес партии, номер стандарта и название завода — изготовителя л роволоки. Кроме того, к каждой бухте проволоки прикрепляется металлическая бирка с обозначением проволоки по стандарту, номером плавки и названием завода-изготовителя. На бирке ставится также клеймо завода-изготовителя и клеймо заводского ОТК. Кроме наличия сертификата и бирки в проволоке, поступившей в монтажную организацию, проверяют поверхность. В больших партиях можно проводить выборочный контроль, в небольших следует проверять каждую бухту. На поверхности проволоки не должно быть окалины, масла, ржавчины, грязн, краски на проволоке из высоколегированной стали не должно быть следов графитовой смазки. Проволоку с указанными дефектами применять не разрешается. Перед намоткой проволоки в кассеты полуавтоматов или автоматов все дефекты должны быть устранены. При отсутствии документации проволока перед применением должна пройти тш,ательный химический анализ. Для этого из партии одной плавки отбирают 3% общего количества бухт, но не менее двух. Стружку для анализа берут от обоих концов каждой отобранной бухты. Результаты химического анализа позволяют определить марку проволоки. После этого заваривают несколько образцов для определения технологических свойств проволоки. Желательно также выполнить механические испытания сварных образцов. По получении положительных результатов испытаний в соответствии с заданным технологическим процессом, в котором предполагается использовать проволоку, дают разрешение на ее применение. На каждое испытание обязательно оформляют акт. Без актов проведенные испытания считаются недействительными.
[c.259]
Метод ЛТП МВТУ [85]. Метод основан на механическом испытании сварных образцов путем нагружения постоянными нагрузками. Нагрузки моделируют упругую энергию собственных напряжений в сварных конструкциях. Образец для испытаний представляет собой сварной тавр небольших размеров (рис. 72). К вертикальной стенке тавра прикладывают нагрузку М, создающую напряжения растяжения в шве и околошовной зоне. Образец нагружают при температурах начала аустенит-ного превращения и выдерживают под нагрузкой в течение 20 ч и более после сварки. Одновременно испытывают серию образ-
[c.160]
Механические испытания сварных образцов (ГОСТ 699В-54 ГОСТ 1497 42 ГОСТ 1524-42) [c.693]
Цилиндрическая обечайка баллона имеет продольный шов и к ней круговыми швами приварены два штампованных днища. К верхнему днищу сплошным швом приварена горловина, а к нижнему — прерывистым швом приварен опорный башмак. Наибольшее распространение в промышленности имеют баллоны емкостью 50 дм (на 21,2 кг сжиженного газа). Баллон емкостью 50 дм имеет наружный диаметр 2991о мм, толщину стенки 3 лш и общую длину (с колпаком) 960 мм. Вес баллона (без вентиля, колпака и защитных колец) 22 1,5 кг, рабочее давление 16 кгс/см испытательное гидравлическое 25 кгс1см . Качество сварных швов при изготовлении баллонов контролируется внешним осмотром по ГОСТ 3242—69 — 100% механическими испытаниями образцов по ГОСТ 6996—66 просвечиванием проникающим излучением (ГОСТ 7512—69) или другими методами по согласованию с Госгортехнадзором СССР гидравлическими испытаниями пневматическими испытаниями. Результаты механических испытаний сварных образцов должны удовлетворять следующим требованиям временное сопротивление на разрыв — не менее 38 кгс/мм , угол загиба — не менее 100 . Баллоны для пропан-бутана окрашивают в красный цвет. Норма заполнения баллонов для пропана принимается из расчета 0,425 кг сжиженного газа на 1 дм номинальной емкости.
[c.58]
Наиболее простым качественным способом определения сопротивляемости сталей образованию холодных трещин является сварка жестких технологических проб (см. V. 66, б). Материалы, в которых при сварке проб образуются холодные трещины, считаются склонными к образованию трещин. Количественный метод оценки сопротивляемости сталей образованию холодных трещин при сварке состоит в механическом испытании сварных образцов непосредственно после сварки постоянной длительно действующей нагрузкой. В спецпальных установках сварные образцы небольших размеров нагружают грузами различных масс (рпс. V. 68). Под действием груза образцы выдерживают в течение 20 ч. Минимальные напряжения в образце, при которых возникают холодные трещины, являются критическими и служат для оценки сопротивляемости сталей образованию трещин.
[c.349]
В качестве присадки использовали сварочную проволоку из материала того же состава, что и основной (АД-1М), и флюс АФ-4Д. Механические испытания сварных образцов из алюминиевых сплавов, сваренных аце илено-кислородным пламенем и природным газом, показали, что прочность сварных швов одинакова. [c.42]
Применяемые в настоящее время методы оценки технологической прочности сталп в процессе превращений аустенита при сварке можно классифицировать по следующим приотакам по способу регулирования факторов, обусловливающих образование трещин, по характеру оценки полученных результатов и по назначению. По первому признаку они делятся на технологические пробы и методы, основанные на механическом испытании сварных образцов или образцов, подвергнутых термической обработке, с.тодной с тер.мическим воздействием прп сварке, по второму — на качественные п количественные (стр. 196 п 205), а по третьему — на лабораторные и отраслевые.
[c.212]
Для ошлаковывания окиси кремния 5102, образующейся прн сварке чугуна, во флюс необходимо вводить основные соли. Наиболее целесообразно в данном случае использовать углекислые соли натрия, обладающие низкой температурой плавления. Флюс для сварки-пайки чугуна латунными присадками содержит следующие вещества 50—60% буры или борной кислоты, 25—20% углекислой соды, 25—20% углекислого натрия. Такой флюс обеспечивает хорошую растекаемость присадочного металла и смачивание им основного металла, а также является индикатором температуры, так как его плавление происходит около 700 °С. Процесс сварки-пайки ведется по следующей технологии подготовленные механическим путем кромки прогревают газовым пламенем до 600—650 °С, затем на нагретую поверхность наносят слой флюса. Нагрев кромок продолжают до расплавления флюса. Конец присадочного прутка, на который предварительно нанесен слой флюса, прогревают горелкой до начала плавления, и пруток погружают под слой расплавленного флюса, находящийся на детали. Конец прутка все время должен касаться нагретой поверхности детали и расплавляться только под флюсом. После заполнения разделки шва пламя горелки медленно отводят от детали, шов накрывают листовым асбестом. Схема процесса сварки чугуна латунным прутком дана на рис. 85. Механические испытания сварных образцов, выполненных этим способом, показывают, что разрыв
[c.157]
Нагрев под калибровку, как правило, используется для нормализации цилиндрической части барабана. Нагрев производится следующим образом на выдвижной под нагревательной газовой печи устанавливаются чаще всего, чугунные опоры, затем под вводится в печь и последняя разогревается при помощи газовых горелок до температуры нормализации, т. е. до 900—920 . После этого под печи выдвигается, цилиндрическая часть барабана укладывается на опоры так, чтобы расстояние ее от пода было не менее 200—250 мм, и под снова вводится в печь. Вместе с этим загружаются в печь и сваренные одновременно с цилиндрической частью барабана контрольные испытательные пластины, из которых потом будут изготовлены образцы для механических испытаний сварного шва.
[c.134]
Проверка механических свойств сварных стыковых соединении из листовой стали должна производиться путем испытаний сварных образцов, вырезаемых из контрольных пластин, сваренных одновременно с изготовлением контролируемых изделий с применением тех же исходных материалов, метода сварки и сварочных рен имов. [c.219]
Испытательные машины состоят из приводного устройства, обеспечивающего плавное деформирование образца, и силоизмерительного механизма, с помощью которого измеряется сила сопротивления образца создаваемой деформации. По принципу действия приводного устройства различают машины с механическим и гидравлическим приводом. Гидравлический привод обычно применяется у машин большой мощности, предназначенных для испытания от 10-10 до 100-10 Н и выше. По конструкции силонзмерителя машины разделяются на машины с рычажным силоизмерителем и силоизмерите-лем, работающим по принципу измерения гидростатического давления [10]. На машинах с гидравлическим приводом труднее поддерживать заданную скорость деформирования образца, чем при использовании механического привода. По мере увеличения сопротивления материала образца деформированию растет давление масла в рабочем цилиндре. При этом усиливается просачивание жидкости через зазор между цилиндром и поршнем и скорость деформирования уменьшается. Для ее поддержания на постоянном уровне необходимо увеличивать подачу жидкости в цилиндр пропорционально ее утечке. Этот недостаток машин с гидравлическим приводом существен. Следует отметить, что в разрывных машинах рычажного типа (например, ИМ-4Р, ИМ-12Р и Р-5) обеспечивается необходимая скорость нагружения и запись диаграммы растяжений производится в большом масштабе, что увеличивает точность определения (То,2- Поэтому применение этих машин предпочтительнее при испытании образцов из основного металла.
Гидравлические машины с успехом применяются при испытании сварных образцов, для которых сдаточной характеристикой является временное сопротивление разрыву.
[c.16]
Форма протокола механических испытаний сварных стыков стального (полиэтиленового) газопровода
Лаборатория ________________________________________________________________ (наименование строительно-монтажной организации) |
Монтаж систем газоснабжения протокол механических испытаний сварных стыков стального (полиэтиленового) газопровода
№
__________
«__» _______________ 200_ г. Произведены испытания стыков стального (полиэтиленового) газопровода, сваренного ___________ из труб по ГОСТ (ТУ) ________, марки стали наружным диаметром _______ мм, толщиной стенки ______________ мм, сварщиком _____________________ (фамилия, имя отчество) ____________________________________ имеющим номер (клеймо) ____________. по адресу __________________________________________________________________________ (улица, привязки начального и конечного пикетов) в период с «__» ______________ 200_ г. по «__» ________________ 200_ г. |
Результаты механических испытаний сварных стыков стального газопровода
Номер образцов | Размеры образцов до испытаний | Результаты испытаний | Оценка стыка (годен, не годен) | ||||||
толщина (диаметр), мм | ширина (длина), мм | площадь поперечного сечения, мм2 | на растяжение | на сплющивание | на изгиб | ||||
разрушающая нагрузка, Н (кгс) | предел прочности, МПа (кгс/мм2) | место разрушения (по шву или основному металлу) | величина просвета между поверхностями пресса при появлении первой трещины, мм | угол
изгиба, град. | |||||
Результаты механических испытаний сварных стыков полиэтиленового газопровода
Номер стыка | Номер и тип образца, вырезанного из стыка | Тип разрывной машины | Предел текучести при растяжении, МПа (кгс/см2) | Относительное удлинение при разрушении, % | Характер и тип разрушения | Оценка стыка (годен, не годен) |
Начальник лаборатории ______________________________________________________
(подпись, инициалы, фамилия)
Испытания проводил ________________________________________________________
(подпись, инициалы, фамилия)
Примечание. Протокол испытаний следует составлять
на каждого сварщика отдельно и копию
представлять в составе исполнительной
документации на все объекты, на
которых в течение календарного месяца
работал этот сварщик.
Протокол механических испытаний сварных стыков полиэтиленового газопровода общие положения по проектированию и строительству газораспределительных систем из металлических и полиэтиленовых труб- сп 42-101-2003 (утв- протоколом от 08-07-2003 32) (приложения л — э) (2021). Актуально в 2019 году
размер шрифта
ОБЩИЕ ПОЛОЖЕНИЯ ПО ПРОЕКТИРОВАНИЮ И СТРОИТЕЛЬСТВУ ГАЗОРАСПРЕДЕЛИТЕЛЬНЫХ СИСТЕМ ИЗ МЕТАЛЛИЧЕСКИХ И ПОЛИЭТИЛЕНОВЫХ ТРУБ- СП. .. Актуально в 2018 году
N _____ «__» _________ 200 _ г. | ||||||||||
Произведены испытания сварных соединений полиэтиленового газопровода, выполненных | ||||||||||
(вид сварки) | ||||||||||
Из труб | ||||||||||
(маркировка) | ||||||||||
Сварщик | ||||||||||
(фамилия имя отчество) | ||||||||||
Тип сварочной машины (аппарата): | ||||||||||
Метод испытаний | ||||||||||
Тип испытательной машины: | ||||||||||
Газопровод построен (строится) по адресу: | ||||||||||
Период строительства: с «__» ________ 200__ г.![]() Результаты механических испытаний сварных соединений приведены в таблице. Форма таблицы при испытании на осевое растяжение по ГОСТ 11262 |
Номер стыка | Номер образца, вырезанного из стыка | Скорость движения зажимов | Предел текучести при растяжении, МПа | Относительное удлинение при разрыве, % | Характер и тип разрушения | Оценка стыка (годен, не годен) |
Форма таблицы при испытании деталей с закладными нагревателями на сплющивание или отрыв | |||||
Номер стыка | Номер образца, вырезанного из стыка | Тип испытательной машины и скорость движения зажимов | Зафиксированный процент отрыва или разрушающая нагрузка | Характер и тип разрушения | Оценка стыка (годен, не годен) |
Заключение: | ||||||
Начальник лаборатории | ||||||
(подпись, фамилия) | ||||||
Испытания проводил | ||||||
(должность, подпись, фамилия) | ||||||
Примечание.![]() |
ПРИЛОЖЕНИЕ Ш
(рекомендуемое)
Профстандарт «Специалист по механическим испытаниям сварных соединений и наплавленного металла» с 2020 года, утвержденный Минтруда
Организация работы и кадровые вопросы в связи с коронавирусомОбразцы основных документов в связи с коронавирусомНерабочие дни в связи с коронавирусом
Образцы заполнения кадровых документовФормы первичных учетных документовСведения о трудовой деятельности (электронная трудовая книжка)Ведение трудовых книжек в бумажном виде
Специальная оценка условий трудаНесчастный случай на производствеОбязательные медосмотры (профосмотры)Инструктажи по охране труда
Обязательные документы при проверкахКалендарь кадровика
Хранение и использование персональных данныхМеры по защите персональных данных работниковОтветственность за нарушения законодательства о персональных данных
Привлечение иностранцевОформление иностранцев
Оформление приема на работуТрудовой договор
График отпусковЗамена отпуска денежной компенсациейОформление ежегодного оплачиваемого отпускаОтпуск по беременности и родамОтпуск по уходу за ребенкомЛьготный (дополнительный) отпуск
График работыПривлечение, оформление и оплатаУчет рабочего времениВыходные и праздничные дни
Правила внутреннего трудового распорядка (ПВТР)Дисциплинарные взысканияПорядок увольнения за нарушение трудовой дисциплины
Заработная платаРайонные коэффициенты и надбавкиМатериальная ответственность работника
Оплата больничного листа (не пилотный проект)Оплата больничного листа (пилотный проект)Заполнение больничного листа работодателемРабота с электронными больничнымиПособие по беременности и родам
Порядок проведения аттестацииОграничения на увольнение из-за непрохождения аттестацииРасходы на подготовку и переподготовку кадров
Основания для увольненияПроцедура увольнения по сокращению
Перейти в telegram-чат
Испытания сварных соединений, швов, стыков, неразрушающий контроль в Москве
Воспользуйтесь нашими спецпредложениями!
- Скидка 10% на проверку качества сварных соединений
Проведение испытаний сварных швов и стыков выполняется для того, чтобы можно было контролировать образование всевозможных дефектов, которые в последующем могут привести к серьезным разрушениям. Выполнение испытаний конструкций должно проходить максимально качественно и точно. Для того чтобы провести контроль сварных стыков и соединений используют следующие методы:
- тщательный наружный осмотр;
- проведение специальных механических испытаний;
- осуществление гидравлических и пневматических испытаний швов, стыков и соединений;
- использование металлографического способа проверки, где применяются непосредственно физические (ручные) способы проверки.
Какой именно вид испытаний необходим, будет зависеть от материала, используемого для строительства. Так же играет роль и технология строительства.
Неразрушающие методы контроля
В случае если вы не желаете нарушать целостность уже готовых конструкций в процессе проверки, существуют специальные неразрушающие методы контроля состояния соединений и стыков. К ним можно отнести:
- контроль с использованием ультразвука;
- контроль сварных швов визуальным способом;
- радиографический метод.
Для проведения контроля состояния стыков, швов и соединений с помощью ультразвука используется специальный прибор под названием дефектоскоп. Если будет обнаружен дефект, передающаяся волна будет искажаться, что определяется датчиком прибора.
Ультразвуковой контроль
Данный метод является акустическим. В числе его преимуществ можно назвать высокую производительность, что позволяет за относительно непродолжительное время проводить контроль довольно большого объема соединений. Кроме того, у него большая проникающая способность, что незаменимо при работе с материалами большой толщины, и очень высокая чувствительность, позволяющая обнаруживать даже мелкие дефекты. Его едва ли не единственный недостаток – сложность определения характера дефекта, поэтому нередко его дополняют методом радиографического контроля.
Контроль сварных швов бака дозатора
Радиографический контроль
Он основан на такой особенности материалов, как различная степень поглощения рентгеновских лучей. Посредством данного метода можно с высокой точностью выявить наличие и точно определить расположение существующих дефектов или неоднородностей соединений, а также выявить их характер. Этот метод очень эффективен и широко распространен.
Вас интересует испытание сварных соединений, швов, стыков? Хотите узнать стоимость работ?
Закажите обратный звонок с сайта, мы перезвоним за 24 секунды и ответим на все вопросы!
Испытание сварных соединений
- г. Москва, Ул.Профсоюзная дом 97
- Детская спортивная школа 37, дворец «Хрустальный»
- ООО «Научно -производственная фирма «Химхолодсервис»
Визуальный контроль
Сегодня такой контроль осуществляется не только невооруженным глазом, но и при помощи специальных луп, перископов и эндоскопов, что позволяет довольно эффективно контролировать качество проведенной сварки. Однако, у него есть существенный недостаток, заключающийся в человеческом факторе. Так уровень достоверности полученной при таком контроле информации напрямую зависит от квалификации и добросовестности специалиста, его осуществляющего.
Достаточно дорогим, но весьма точным, является радиографический способ исследования соединения стыков и швов. Для осуществления подобного процесса необходим специальный аппарат — рентгенограф. Через срез пропускают гамма-лучи, которые воздействуют на специальную пленку, расположенную за швом. Для того чтобы определить наличие дефектов, детально рассматривается пленка.
Но перед тем как приступать непосредственно к конкретному способу исследования, необходимо провести тщательный визуальный осмотр. Выполняют подобные процедуры только квалифицированные специалисты.
Ультразвуковой контроль таврового сварного шва
- Здание ТРК по адресу: г. Москва, ул. Авиаконструктора Миля, Вл.7
- Многофункциональный центр «Променад», Московская область, г. Мытищи, микрорайон 17, кварталы 27-33
- ТЦ «Косино-Парк» ул.
Святоозерская, вл. 5 ( Москва, ВАО, район: Косино-Ухтомский )
- ЖК «Пироговская Ривьера», МО, Мытищинский район, Городское поселение Пироговский, деревня Пирогово
- ТЦ «Юго-Запад», Проспект Вернадского, пересечение с ул. Покрышкина
- ТЦ «Курский», Варшавское шоссе, вл. 148
- ЖК «Эталон-сити», улица Старокрымская, вл. 13
- ЖК «Яуза Парк», Краснобогатырская улица, вл. 28
- ЖК «LIFE-Митинская Ecopark», ул. Митинская, вл. 22
- ЖК «Тушино», Москва, СЗАО, район Покровское-Стрешнево, Волоколамское шоссе, вл. 67
- Многофункциональный административно-деловой центр проспект Мира, вл. 127-129
- ЖК «Павелецкая II», Павелецкая наб., вл. 8
- ТЦ «Ашан Пролетарский», Пролетарский пр., 30, Москва
- ЖК «Версис», Нахимовский проспект, 69 (угол улицы Вавилова)
- Клубный дом, ул. Менжинского, вл. 30, стр. 1
Трудовые действия | Выполнение трудовых действий, предусмотренных трудовой функцией A/02.3 «Выполнение работ по механическим испытаниям сварных соединений полимерных материалов» настоящего профессионального стандарта |
Разработка производственно-технологической документации по разрушающим испытаниям сварных соединений полимерных материалов | |
Подготовка образцов, определение условий проведения механических испытаний для разных температур | |
Определение соответствия данных, полученных при механических испытаниях сварных соединений полимерных материалов, требованиям документации, содержащей нормы оценки качества | |
Оформление протоколов механических испытаний сварных соединений полимерных материалов конкретным методом | |
Необходимые умения | Необходимые умения, предусмотренные трудовой функцией A/02. |
Анализировать данные, полученные по результатам механических испытаний сварных соединений полимерных материалов конкретным методом, на предмет их полноты и достаточности для принятия решения о соответствии механических свойств требованиям документации, содержащей нормы оценки качества | |
Производить необходимые расчеты при оформлении результатов механических испытаний сварных соединений полимерных материалов конкретным методом | |
Необходимые знания | Необходимые знания, предусмотренные трудовой функцией A/02.3 «Выполнение работ по механическим испытаниям сварных соединений полимерных материалов» настоящего профессионального стандарта |
Принцип расчета и составления схем для нестандартных испытаний сварных соединений полимерных материалов | |
Порядок выбора режимов и параметров испытаний сварных соединений полимерных материалов для конкретных методов | |
Нормы оценки качества образцов по результатам конкретного метода механических испытаний сварных соединений полимерных материалов | |
Требования к оформлению и хранению результатов механических испытаний конкретным методом | |
Другие характеристики | — |
Механические испытания — испытание на растяжение, часть 2
Для утверждения процедуры стыковой сварки большинство спецификаций, таких как ISO 15614 и ASME IX, требуют проведения испытаний на растяжение.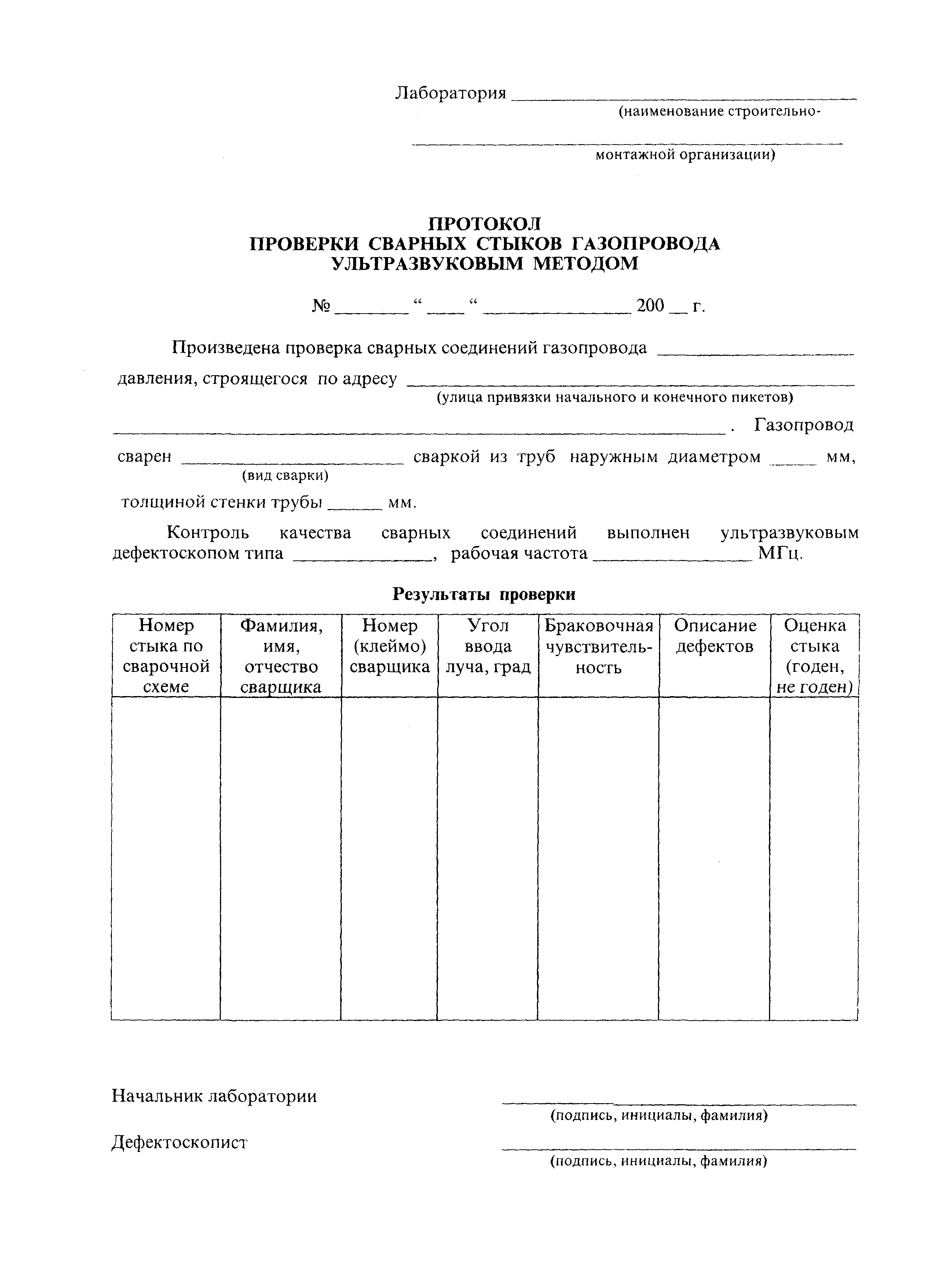
Обычно это испытания на растяжение поперечного соединения (CJ) квадратного или прямоугольного поперечного сечения, которые, как следует из названия, ориентированы поперек сварного шва, так что испытываются оба основных металла, обе зоны термического влияния (HAZ) и сам металл сварного шва ( рис.1 ). Излишек металла сварного шва в верхней части сварного шва можно оставить на месте или обработать механической обработкой.
Хотя можно измерить предел текучести, удлинение и уменьшение площади образцов CJ, тот факт, что имеется по крайней мере три различных участка с разными механическими свойствами, делает такие измерения неточными и ненадежными, хотя иногда это выполняется исключительно для информационные цели.
Указанные выше спецификации требуют, чтобы регистрировались только UTS и положение трещины. Прочность поперечного шва обычно должна превышать минимальный указанный UTS основного металла.В большинстве случаев металл сварного шва прочнее основного металла — он превосходит другие — так что разрушение происходит в основном металле или в ЗТВ при напряжении выше указанного минимума.
В случаях, когда сварной шов и / или HAZ слабее, чем основной металл — хорошим примером являются сварные алюминиевые сплавы, упрочненные старением или холоднодеформированные — это рассматривается в большинстве спецификаций.
Проектировщик должен также принять это во внимание при расчетах конструкции и предоставить какой-либо метод компенсации этой потери прочности.
Испытание на растяжение стыковых сварных швов плоских пластин не представляет особых проблем, связанных с формой образцов, но образцы, изготовленные из стыкового соединения труб, не являются плоскими, и эта кривизна может повлиять на результаты. В контексте аттестационных испытаний процедуры сварки это не имеет значения, поскольку испытание используется только для определения UTS и положения разрушения. Для получения более точных результатов образец для испытаний можно растянуть и обработать плоско, как показано на Рис. 2 .
Может возникнуть необходимость обработать несколько образцов по всей толщине сварного шва, особенно на очень толстых стыках, где мощность растягивающего устройства недостаточна для вытягивания образца на всю толщину, Рис. 3 .
Для испытания трубки малого диаметра в отверстие трубки вставляется сплошной стержень, чтобы предотвратить сжатие трубки, когда образец зажимается в растяжной машине.
Большинство испытаний сварных швов проводится с образцами CJ, но образцы с продольной ориентацией полезны, особенно там, где металл шва или HAZ очень прочный, но пластичность низкая.
В образце CJ основной металл может деформироваться и, наконец, разрушиться без значительного деформирования металла сварного шва или ЗТВ, тогда как в образце для продольных испытаний нагрузка распределяется более равномерно.
Хрупкий сварной шов или ЗТВ не будут вытягиваться вместе с основным металлом, но будут трескаться с открытием трещин, но не обязательно распространяться на основной металл по мере проведения испытаний.
Вышеописанные испытания соответствуют требованиям, предъявляемым к процедурам сварки. Они не дают уверенности в том, что сварные швы в конструкции будут подходить для своих целей, например, для работы в надземных или криогенных условиях, и многие стандарты применения, такие как необожженные сосуды под давлением PD 5500 и сосуды под давлением ASME VIII, требуют дополнительных испытаний.
Поскольку прочность металла падает с повышением температуры, эти спецификации требуют проведения испытаний на растяжение при повышенной температуре при максимальной расчетной температуре.
Эти испытания должны проводиться только на металле сварного шва с использованием ориентированного в продольном направлении образца круглого поперечного сечения, по которому может быть получено точное измерение предела текучести.
Многие прикладные стандарты, такие как PD 5500, требуют дополнительных испытаний, помимо тех, которые требуются, например, ISO 15614-1.Об этом следует помнить, когда документация по утверждению процедуры подается на утверждение контролирующим органом или клиентом.
Срок действия данных о растяжении
Предполагается, что взятые пробы являются репрезентативными для основной массы материала, но это не всегда так.
Предел прочности при растяжении отливки, например, часто определяется по образцу, изготовленному на станке из стояка, и размер зерна у него будет отличаться от размера зерна основной части отливки.
Прокатный стальной лист будет иметь различные свойства в продольном, поперечном и сквозном направлениях.Таким образом, технические требования к материалам, такие как BS EN 10028, Плоский прокат из стали для целей давления, требуют, чтобы испытание на растяжение проводилось поперек направления прокатки, чтобы сталь испытывалась поперек «зерна» — в направлении более низкой прочности и более низкой пластичности.
Размер продукта также может влиять на свойства, так как во время термообработки толщина секции будет влиять на скорость охлаждения с более медленными скоростями охлаждения и, следовательно, более мягкими структурами в центре более толстых секций.Это рассматривается в стандартах на материалы путем определения так называемого «ограничивающего правящего сечения», максимального диаметра стержня, при котором требуемые механические свойства могут быть достигнуты в центре.
В дополнение к вариациям свойств из-за формы образцов и температуры испытания, скорость нагружения также влияет на результаты.
На рисунке 4 показано, как прочность на разрыв увеличивается, но пластичность уменьшается с увеличением скорости испытания.Следовательно, необходимо контролировать скорость поперечной головки натяжного станка, и в стандарте BS EN 10002 указан диапазон скоростей напряжения от 6 МПа в секунду до 60 МПа в секунду. В спецификациях ASTM есть аналогичные, но не идентичные требования.
Само собой разумеется, что калибровка испытательного оборудования, чтобы гарантировать работу в пределах допустимых параметров, является обязательной.
Соответствующие спецификацииBS EN 10002 Методы испытаний металлических материалов на растяжение.BS EN 876 Разрушающие испытания сварных швов металлических материалов — испытание на продольное растяжение. BS EN 895 Разрушающие испытания сварных швов металлических материалов — испытание на поперечное растяжение. BS EN ISO 7500-1 Машины для испытания на растяжение / сжатие. ![]() ASTM A370 Механические испытания стальных изделий. ASTM E8 Испытание металлических материалов на растяжение. ASTM B557 Испытание на растяжение деформируемых и литых изделий из алюминия и магниевых сплавов. |
Эту статью подготовил Джин Мазерс.
Эта статья о вакансиях была первоначально опубликована в Connect, май / июнь 2004 г. Она была обновлена, поэтому веб-страница больше не отражает в точности печатную версию.
Физические испытания сварных швов: разрушающие и неразрушающие
Описанные ниже испытания были разработаны для проверки навыков сварщика, а также качества металла шва и прочности сварного соединения для каждого типа металла, используемого в боеприпасах.
Многие тесты обнаруживают дефекты, невидимые невооруженным глазом.
Разрушающие испытания Некоторые из этих испытаний, такие как испытания на растяжение и изгиб, являются разрушающими, поскольку образцы для испытаний нагружаются до тех пор, пока они не выйдут из строя, поэтому можно получить желаемую информацию.
Разрушающие испытания делятся на две категории:
- Заводские испытания
- Лабораторные испытания (коррозионные, химические, микроскопические, макроскопические / увеличительное стекло)
Другие методы испытаний, такие как рентгеновские и гидростатические испытания, не являются разрушающими (неразрушающий контроль).
Этот тип контроля также называется неразрушающим контролем или неразрушающим контролем и NDI или неразрушающим контролем.
Целью этих методов является проверка сварных швов без повреждения.
Подход к физическому испытанию каждого сварного шва описан ниже.
Разрушающее испытание физических сварных швов
Тест кислотным травлением
Этот тип или физическое испытание сварного шва используется для определения прочности сварного шва. Кислота воздействует на края трещин в основном металле или металле сварного шва или реагирует с ними и обнаруживает дефекты сварного шва, если таковые имеются. Он также подчеркивает границу между основным металлом и металлом шва и, таким образом, показывает размер сварного шва, который в противном случае может быть нечетким. Этот тест обычно выполняется на поперечном сечении стыка.
Растворы соляной кислоты, азотной кислоты, персульфата аммония или йода и йодида калия обычно используются для травления углеродистых и низколегированных сталей.
Управляемый тест на изгиб
Качество металла сварного шва на лицевой стороне и в основании сварного соединения, а также степень проплавления и проплавления с основным металлом определяют с помощью испытаний на управляемый изгиб.Это также показывает эффективность сварного шва.
Этот тип физических испытаний сварных швов проводится на зажимном приспособлении (рис. 13-1). Эти образцы для испытаний изготовлены из сварных пластин, толщина которых должна быть в пределах возможностей приспособления для гибки. Образец для испытаний помещают поперек опор штампа, который является нижней частью зажимного приспособления. Плунжер, управляемый сверху гидравлическим домкратом или другими устройствами, заставляет образец вдавливаться в матрицу и обеспечивать ее форму.
Чтобы выполнить требования этого испытания, образцы должны изгибаться на 180 градусов и, чтобы их считали пригодными, не было трещин размером более 1/8 дюйма.(3,2 мм) в любом направлении должны появиться на поверхности. Испытания на изгиб торца выполняются в зажимном приспособлении с лицевой стороной сварного шва в растянутом состоянии (т. Е. На внешней стороне изгиба) (A — рис. 13-2). Испытания на изгиб корня шва проводят, когда корень сварного шва находится в растяжении (т. Е. За пределами изгиба) (B — рис. 13-2). Образцы для испытаний на управляемый изгиб также показаны на рисунке 13-3.
Приспособление для испытаний на управляемый изгиб (Рисунок 13-1)Примечания:
- T = Толщина испытательной пластины
- Закаленные валки При желании можно использовать на плечах
- Особые размеры для пластины 3/7
- Все размеры указаны в дюймах
Испытания на свободный изгиб
Подход к испытаниям физических сварных швов со свободным изгибом был разработан для измерения пластичности наплавленного металла сварного шва. Образец для физических испытаний сварного шва вырезается из сварной пластины с расположением сварного шва, как показано в A, рис. 13-4.
Каждый угол образца по длине должен быть скруглен по радиусу, не превышающему одной десятой толщины образца. Следы инструментов, если таковые имеются, должны быть вдоль образца. Две линии разметки наносятся на лицевую поверхность на расстоянии 1,6 мм от края сварного шва. Расстояние между этими линиями измеряется в дюймах и записывается как начальное расстояние X (B, рисунок 13-4).Затем концы испытуемого образца сгибают под углом примерно 30 градусов, причем эти изгибы составляют примерно одну треть длины от каждого конца. Таким образом, сварной шов располагается по центру, чтобы гарантировать, что весь изгиб происходит в сварном шве.
Изогнутый образец затем помещают в машину, способную оказывать большое сжимающее усилие (C, рис. 13-4), и изгибают до тех пор, пока на лицевой стороне корпуса не появится трещина более 1/16 дюйма (1,6 мм) в любом размере. сварной шов. Если трещины не появляются, изгибание продолжается до тех пор, пока образцы не будут на 1/4 дюйма.(6,4 мм) толщиной или меньше могут быть испытаны в тисках. Более тяжелую пластину обычно испытывают на прессе или гибочном станке.
Независимо от того, используются ли при испытании на свободный изгиб тиски или устройство сжатия другого типа, рекомендуется обработать верхнюю и нижнюю контактные пластины оборудования для гибки так, чтобы поверхности были параллельны концам образца (E, рисунок 13- 4). Это предотвратит выскальзывание и выскальзывание образца из испытательной машины при его изгибе.
Испытание сварного металла на свободный изгиб (Рисунок 13-4) После изгиба образца до точки, где испытательный изгиб завершен, расстояние между разметанными линиями на образце снова измеряется и записывается как расстояние Y.Чтобы найти процент удлинения, вычтите начальное значение из конечного расстояния, разделите на начальное расстояние и умножьте на 100 (рисунок 13-4). Обычные требования для прохождения этого испытания состоят в том, чтобы минимальное удлинение составляло 15 процентов и чтобы на поверхности сварного шва не было трещин более 1/16 дюйма (1,6 мм) в любом размере.
Испытание на свободный изгиб в значительной степени заменяется испытанием на управляемый изгиб, при наличии необходимого испытательного оборудования.
Испытание на обратный изгиб
Испытание на обратный изгиб — это тип физического испытания сварного шва, который используется для определения качества металла шва и степени проплавления корня Y сварного стыкового соединения.Используемые образцы аналогичны образцам, необходимым для испытания на свободный изгиб, за исключением того, что они изгибаются корнем сварного шва со стороны растяжения или снаружи. Испытываемые образцы должны изгибаться на 90 градусов без разрушения. Этот тест в значительной степени заменяется тестом на управляемый изгиб.
Тест на разрыв ников
Испытание на разрыв с зазубринами было разработано для определения наличия в металле сварного шва стыкового стыка каких-либо внутренних дефектов, таких как включения шлака, газовые карманы, плохое плавление и / или окисленный или обгоревший металл. Образец получают из сварного стыкового соединения механической обработкой или резкой с помощью кислородно-ацетиленовой горелки. Каждый край сварного шва в месте соединения прорезан пропилом по центру (рис. 13-5). Подготовленную таким образом деталь соединяют перемычкой между двумя стальными блоками (рис. 13-5) и заклеивают тяжелым молотком до тех пор, пока участок сварного шва между пазами не сломается.
Раскрытый таким образом металл должен быть полностью расплавленным и без шлаковых включений. Размер любого газового кармана не должен превышать 1/16 дюйма.(1,6 мм) по большему размеру, а количество газовых карманов или пор на квадратный дюйм (64,5 кв. Мм) не должно превышать 6.
Испытание на разрыв на разрыв (Рисунок 13-5) Другой метод испытания на разрыв используется для определения прочности угловых швов. Это испытание на разрыв углового шва. К вершине V-образного образца прикладывают усилие с помощью пресса, испытательной машины или ударов молотка до разрыва углового шва. Затем поверхности трещины будут проверены на прочность.
Испытание на прочность при растяжении
Испытание сварного шва на растяжение, выполняемое в мастерской, представляет собой тип устройства для физического испытания сварного шваЭтот тип физического испытания сварного шва используется для измерения прочности сварного соединения. Часть a для размещения сварной пластины находится посередине между губками испытательной машины (рис. 1306). Ширина и толщина испытательного образца измеряется перед испытанием, площадь в квадратных дюймах рассчитывается путем умножения этих значений перед испытанием, а площадь в квадратных дюймах рассчитывается путем умножения этих двух цифр (см. Формулу на рис. 13-6).
Образец для испытания на растяжение физического сварного шва затем устанавливается в машину, которая будет прилагать усилие, достаточное для разрушения образца. Испытательная обработка может быть стационарной или переносной. Машина переносного типа, работающая по гидравлическому принципу и способная вытягивать и изгибать образцы для испытаний, показана на рис. 13-7.
По мере того, как образец испытывается на этой машине, на датчике регистрируется нагрузка в фунтах. В стационарных вариантах прилагаемая нагрузка может регистрироваться на балансировочной балке.В любом случае регистрируется нагрузка в момент разрушения. Образцы для испытаний, сломанные при испытании на разрыв, показаны на рисунке 13-3.
Образец для испытаний на растяжение и метод испытаний (рис. 13-6) Переносная машина для испытания на растяжение и изгиб (рис. 13-7)Прочность на растяжение, которая определяется как напряжение в фунтах на квадратный дюйм, рассчитывается путем деления разрывной нагрузки на образец по первоначальной площади поперечного сечения образца. Обычные требования к пределу прочности сварных швов на растяжение заключаются в том, что образец должен тянуть не менее 90% прочности на разрыв основного металла.
Прочность на сдвиг поперечных и продольных угловых швов определяют по растягивающему напряжению на испытательных образцах. Ширина образца измеряется в дюймах. Образец разрывается под действием растягивающей нагрузки, и определяется максимальная нагрузка в фунтах. Прочность сварного шва на сдвиг в фунтах на линейный дюйм определяется делением максимальной нагрузки на длину разорванного углового шва. Прочность на сдвиг в фунтах на квадратный дюйм получается делением прочности на сдвиг в фунтах на линейный дюйм на средний размер горловины сварного шва в дюймах.Образцы для испытаний делают шире, чем требуется, и обрабатывают до нужного размера.
Неразрушающий контроль
Гидростатические испытания
Это неразрушающий тип физических испытаний сварных швов, используемый для проверки качества сварных швов на закрытых контейнерах, таких как сосуды высокого давления и резервуары. Испытание обычно состоит из наполнения сосуда водой и приложения давления, превышающего рабочее давление сосуда. Иногда большие резервуары заполняются водой, которая не находится под давлением, чтобы обнаружить возможные утечки через дефектные сварные швы. Другой метод — это испытание маслом, а затем отпаривание сосуда. Видно обратное просачивание масла из-за гильзы.
Испытание магнитными частицами
Это метод физических испытаний или контроля сварных швов, используемый для сварных швов и деталей из магнитных легированных сталей. Он применим только к ферромагнитным материалам, у которых наплавленный сварной шов также является ферромагнитным. В проверяемом изделии создается сильное магнитное поле с помощью электрического тока большой силы тока.
Поле утечки будет создано любым разрывом, который перехватывает это поле в детали.Местные полюса создаются полем утечки. Эти полюса притягивают и удерживают магнитные частицы, размещенные для этой цели на поверхности. Рисунок частиц, нанесенный на поверхность, указывает на наличие неоднородности или дефекта на поверхности детали или вблизи нее.
Рентгеновское исследование
Это радиографический метод физического испытания сварного шва, используемый для выявления наличия и характера внутренних дефектов в сварном шве, таких как трещины, шлак, раковины и зоны, в которых отсутствует надлежащее сплавление. На практике рентгеновская трубка размещается с одной стороны сварной пластины, а рентгеновская пленка со специальной чувствительной эмульсией — с другой стороны. При проявлении дефекты металла проявляются в виде темных пятен и полос, которые может интерпретировать оператор, имеющий опыт работы с этим методом контроля.
Пористость и дефектное проникновение в корень, обнаруженное при рентгеновском обследовании, показаны на рис. 13-8.
Внутренние дефекты сварных швов, обнаруженные при рентгеновском контроле (рис. 13-8)Инструкции по обращению с рентгеновским аппаратом, чтобы не навредить обслуживающему персоналу, можно найти в: Американском стандартном кодексе промышленного использования рентгеновских лучей
Гамма-тест
Это испытание представляет собой радиографический метод физического испытания и контроля сварных швов, аналогичный рентгеновскому методу, описанному в параграфе о испытании кислотным травлением, за исключением того, что гамма-лучи исходят из капсулы с сульфатом радия вместо рентгеновской трубки.
Из-за коротких длин волн гамма-излучения возможно проникновение в участки значительной толщины, но время, необходимое для экспонирования металла любой толщины, намного больше, чем время, необходимое для рентгеновского излучения, из-за более медленной скорости, с которой гамма-излучение лучи производятся.
Рентгеновский контроль используется для большинства радиографических обследований, но гамма-оборудование имеет то преимущество, что оно чрезвычайно портативно.
Флуоресцентный пенетрантный тест (тест с красителем)
Типы испытаний на проникновение красителя в сварные швы Флуоресцентный проникающий контроль — это метод неразрушающего физического контроля сварных швов, с помощью которого в твердых материалах могут быть обнаружены трещины, поры, утечки и другие неоднородности.Это особенно полезно для обнаружения поверхностных дефектов в немагнитных материалах, таких как сварные швы из алюминия, магния и аустенитной стали, а также для обнаружения утечек во всех типах сварных швов. В этом методе используется смываемый водой материал с высокой флуоресценцией, обладающий исключительной проникающей способностью.
Этот материал наносится на чистую сухую поверхность металла, подлежащего проверке, с помощью кисти, распыления или погружения. Излишки материала удаляются ополаскиванием, протиранием чистой тканью, смоченной водой, или пескоструйной обработкой.Затем наносится проявитель влажного или сухого типа. Неровности на поверхностях, которые были должным образом очищены, обработаны пенетрантом, промыты и обработаны проявителем, демонстрируют яркие флуоресцентные индикаторы в черном свете.
Преимущества этого метода физических испытаний сварных швов:
- Для черных и цветных металлов
- Низкая стоимость
- Простота нанесения и интерпретации
- Минимальная подготовка
Недостатки:
- Может пропустить проблемы под поверхностью
- Не работает с пористыми материалами
Типы красителей:
- Тип A: Флуоресцентный, излучающий видимый свет при просмотре в черном свете
- Тип B: Яркий краситель, который можно исследовать при обычном освещении.
Прост в использовании и удобен для тестирования в полевых условиях.
Испытания на твердость
Твердость может быть определена как способность вещества сопротивляться вдавливанию при локализованном смещении. Проще говоря, устойчивость к вдавливанию, износу и истиранию. Обычно применяемое испытание на твердость является неразрушающим испытанием, используемым в основном в лаборатории, а не в полевых условиях. Испытания на твердость используются как средство контроля свойств материалов, используемых для конкретных целей, после того, как желаемая твердость была установлена для конкретного применения.
Испытание на твердость используется для определения твердости металла шва. Путем тщательного тестирования сварного соединения можно изолировать твердые участки и определить степень влияния тепла сварки на свойства основного металла.
Оборудование для испытаний на твердость
Тест файла:
Самый простой метод определения сравнительной твердости — это напильник. Это выполняется путем пропуска напильника вручную над испытуемой деталью. Можно получить информацию о том, тверже или мягче исследуемый металл, чем напильник или другие материалы, подвергшиеся такой же обработке.
Машины для определения твердости:
Есть несколько типов машин для определения твердости. Каждая из них уникальна тем, что ее функциональный дизайн лучше всего подходит для конкретной области или области применения, для которой предназначена машина. Однако на одном металле можно использовать более одного типа станков, и полученные значения твердости могут быть удовлетворительно коррелированы. В лабораторных испытаниях твердости металлов чаще всего используются два типа машин: твердомер по Бринеллю и твердомер по Роквеллу.
- Твердомер по Бринеллю При испытаниях по Бринеллю образец устанавливают на опоре станка и прикладывают нагрузку в 6620 фунтов (3003 кг) к шарику из закаленной стали, который находится в контакте с поверхностью исследуемого образца.
проверено. Стальной шарик имеет диаметр 0,4 дюйма (10,2 мм). Нагрузке дают оставаться в течение 1/2 минуты, а затем снимают, и измеряют глубину углубления, сделанного шариком на образце. Следует отметить, что для облегчения определения твердости по Бринеллю диаметр фактически измеряется депрессия, а не глубина.Таблицы значений твердости по Бринеллю были подготовлены для различных диаметров оттиска. Эти диаграммы обычно используются для определения чисел Бринелля. Результирующее число твердости по Бринеллю получается по следующей формуле:
HB = число твердости по Бринеллю
D = диаметр шарика (мм),
d = диаметр полученного, восстановленного круглого отпечатка ( мм)
P = приложенная нагрузка (кг) - Твердомер по Роквеллу Принцип действия тестера Роквелла по существу такой же, как и у тестера Бринелля.Он отличается от тестера Бринелля тем, что меньшая нагрузка оказывается на меньший алмаз в форме шара или конуса. Глубина вмятины измеряется и указывается на циферблате, прикрепленном к машине.
Твердость выражается произвольными цифрами, называемыми «числами Роквелла». Они имеют префикс в виде буквенного обозначения, такого как «B» или «C», чтобы указать размер используемого мяча, приложенную нагрузку и шкалу, используемую в испытании.
Другие тесты — это алмазная пирамида Виккерса и склероскоп.
Измеритель твердости по ВиккерсуMagnaflux Test
Это быстрый неразрушающий метод физических испытаний сварных швов для обнаружения дефектов на поверхности стали и ее магнитных сплавов или вблизи них путем правильного намагничивания и применения ферромагнитных частиц.
Основные принципы
Для всех практических целей контроль магнитофлюксом можно сравнить с использованием увеличительного стекла в качестве физического метода испытания сварных швов. Однако вместо стекла используются магнитное поле и ферромагнитные порошки.Метод контроля магнитных частиц основан на двух принципах: во-первых, магнитное поле создается в куске металла, когда электрический ток протекает через него или вокруг него; во-вторых, эти мельчайшие полюса устанавливаются на поверхности металла везде, где это магнитное поле нарушается или искажается.
Когда ферромагнитные частицы приближаются к намагниченной детали, они сильно притягиваются этими полюсами и крепче удерживаются на них, чем на остальной поверхности детали, тем самым образуя видимую индикацию.
Вихретоковый (электромагнитный контроль)
Испытание магнитными частицами в основном для дефектов поверхности и черных металлов. Вихретоковый (электромагнитный) контроль — это метод неразрушающего контроля, основанный на том принципе, что электрический ток протекает в любом проводнике, подвергающемся изменяющемуся магнитному полю. Он используется для проверки сварных швов магнитных и немагнитных материалов и особенно полезен при испытании стержней, угловых соединений, сварных труб и трубок. Частота может варьироваться от 50 Гц до 1 МГц, в зависимости от типа и толщины материала текущих методов.Первый относится к испытаниям, в которых магнитная проницаемость материала является фактором, влияющим на результаты испытаний, а второй — к испытаниям, в которых учитывается электрическая проводимость.
Неразрушающий физический контроль сварных швов методами вихревых токов включает индукцию электрических токов (вихревые токи или токи Фуко) в испытательном образце и измерение изменений этих токов, вызванных неоднородностями или другими физическими различиями в испытательном образце. Такие испытания можно использовать не только для обнаружения несплошностей, но и для измерения отклонений в размерах образца и удельном сопротивлении.Поскольку удельное сопротивление зависит от таких свойств, как химический состав (чистота и легирование), ориентация кристаллов, термическая обработка и твердость, эти свойства также можно определить косвенно. Электромагнитные методы подразделяются на магнитоиндуктивные и вихретоковые. Первый относится к испытаниям, в которых магнитная проницаемость материала является фактором, влияющим на результаты испытаний, а второй — к испытаниям, в которых учитывается электрическая проводимость.
Один из методов создания вихревых токов в образце для испытаний состоит в том, чтобы сделать образец сердечником индукционной катушки переменного тока. Есть два способа измерения изменений величины и распределения этих токов. Первый — измерить резистивную составляющую импеданса возбуждающей катушки (или вторичной испытательной катушки), а второй — измерить индуктивную составляющую импеданса возбуждающей (или вторичной) катушки. Электронное оборудование было разработано для измерения либо резистивной, либо индуктивной составляющих импеданса по отдельности или обоих одновременно.
Вихревые токи индуцируются в проводящем испытательном образце за счет переменной электромагнитной индукции или действия трансформатора.Вихревые токи имеют электрическую природу и обладают всеми свойствами, связанными с электрическими токами. При генерировании вихревых токов испытуемый образец, который должен быть проводником, помещается в поле катушки, по которой проходит переменный ток. Катушка может охватывать деталь, возможно, в форме зонда, или, в случае трубчатой формы, может быть намотана, чтобы поместиться внутри трубы или трубы. Вихревой ток в металлическом образце также создает собственное магнитное поле, которое противодействует исходному магнитному полю. Импеданс возбуждающей катушки или второй катушки, соединенной с первой, в непосредственной близости от образца, зависит от наличия наведенных вихревых токов.Эта вторая катушка часто используется для удобства и называется считывающей или считывающей катушкой. Путь вихревого тока искажается наличием неоднородности. Трещина и отводит, и накапливает вихревые токи. Таким образом, кажущийся импеданс катушки изменяется из-за наличия дефекта. Это изменение можно измерить и использовать для определения дефектов или различий в физической, химической и металлургической структуре. Подповерхностные неоднородности также могут быть обнаружены, но ток спадает с глубиной.
Испытания на акустическую эмиссию
Один из акустических методов — удар по сваренному объекту и определение качества шва по тону. Акустико-эмиссионный контроль (AET) Методы физических испытаний сварных швов в настоящее время считаются дополнительными к другим методам неразрушающего контроля. Однако они применялись во время контрольных испытаний, периодических проверок, обслуживания и изготовления.
Испытание на акустическую эмиссию заключается в обнаружении акустических сигналов, возникающих в результате пластической деформации или образования трещин во время нагружения.Эти сигналы присутствуют в широком частотном спектре наряду с окружающим шумом от многих других источников. Преобразователи, стратегически размещенные на конструкции, активируются поступающими сигналами. При использовании подходящих методов фильтрации внешний шум в составном сигнале заметно снижается. Любой источник значимых сигналов строится триангуляцией на основе времен прихода этих сигналов на различные преобразователи.
Тестирование феррита
Влияние содержания феррита
Полностью аустенитные наплавленные швы из нержавеющей стали имеют тенденцию к образованию небольших трещин даже в условиях минимального ограничения.Эти небольшие трещины, как правило, располагаются поперек линии плавления в сварных проходах и основном металле, который повторно нагревали до температуры, близкой к температуре плавления материала, при последующих проходах сварки. Трещины явно являются вредными дефектами и недопустимы. С другой стороны, влияние трещин на характеристики сварки менее очевидно, поскольку эти микротрещины быстро размываются очень прочной аустенитной матрицей. Наплавки с трещинами на сварных швах удовлетворительно работают в очень тяжелых условиях.Однако склонность к образованию трещин обычно идет рука об руку со склонностью к более крупным трещинам, поэтому часто желательно избегать металлов сварных швов, чувствительных к трещинам.
Присутствие небольшой доли фазы магнитного дельта-феррита в аустенитном (немагнитном) наплавленном шве влияет на предотвращение как растрескивания по средней линии, так и растрескивания. Количество дельта-феррита в сваренном материале в значительной степени контролируется балансом в составе металла сварного шва между элементами, способствующими ферриту (наиболее распространены хром, кремний, молибден и колумбий), и элементами, способствующими аустениту (никель, марганец, углерод и азот являются наиболее распространенными). Однако избыток дельта-феррита может отрицательно сказаться на свойствах металла сварного шва. Чем больше количество дельта-феррита, тем ниже пластичность и вязкость металла шва. Дельта-феррит также предпочтительно разрушается в некоторых агрессивных средах, таких как мочевина. При длительном воздействии температур в диапазоне от 900 до 1700 ° F (от 482 до 927 ° C) феррит имеет тенденцию частично превращаться в хрупкое интерметаллическое соединение, которое сильно охрупняет сварной шов.
Переносные ферритовые индикаторы предназначены для использования на объектах.Содержание феррита в наплавленном шве может быть указано в процентах феррита и может быть заключено в скобки между двумя значениями. Это обеспечивает достаточный контроль в большинстве приложений, где указано минимальное содержание феррита или диапазон ферритов.
Услуги по испытанию сварных швов | SGS
Если качество сварки не контролируется и / или сварка не соответствует ожиданиям отрасли, ваш продукт и репутация находятся под угрозой. Чтобы помочь вам избежать дорогостоящих задержек из-за нестандартных процедур сварки, мы предлагаем вам ряд услуг по испытанию сварных швов, обеспечивающих жизненно важную гарантию качества, которая имеет решающее значение для безопасности материалов и производительности.
Почему стоит выбрать услуги по испытанию сварных швов от SGS?
Наши услуги по испытанию сварных швов включают:
- Инспекция по сварке — наши аккредитации позволяют нам быть свидетелями квалификационных записей процедуры сварки и квалификационных испытаний сварщиков в соответствии с британскими, европейскими и американскими стандартами
- Лаборатории, аккредитованные UKAS 17025 — наши лаборатории, аккредитованные в соответствии с ISO 17025 UKAS, предлагают широкий спектр услуг по металлургическому, механическому, химическому анализу, испытаниям давления и коррозии
- Визуальный контроль сварки — у нас работают сертифицированные и опытные инспекторы по сварке, которые могут выполнять визуальный и размерный контроль труб и конструкционных сварных швов
- Металлургические испытания — мы проводим углубленный анализ стальных образцов для поиска микроструктурных дефектов и различных фаз, присутствующих в дуплексах и супердуплексах, а также во многих других свариваемых материалах.
- Механические испытания — мы проводим широкий спектр механических испытаний сварных образцов.Также известные как разрушающие испытания, они могут использоваться для целей проектирования и определения приемлемости переменных, используемых для создания сварного соединения. Механические испытания позволяют нам определить свойства материала, включая предел текучести, предел прочности при растяжении, пластичность, ударную вязкость, вязкость разрушения и твердость.
- Испытания стыковых сварных швов — мы можем выполнить ряд испытаний стыковых сварных швов, чтобы определить качество, прочность, твердость и пластичность сварного шва.Некоторые из проводимых нами испытаний включают неразрушающий контроль, испытания на растяжение, испытания на изгиб, испытания на удар, макроанализ и испытания на твердость. Эти, а также некоторые другие испытания могут использоваться для определения приемлемости процедуры сварки или аттестационного испытания сварщика .
- Испытание углового сварного шва — мы можем определить качество углового сварного шва, выполнив неразрушающий контроль и механические испытания. Макрообследования и испытания на угловое изгибание дают хорошее представление о профиле, плавлении и проплавлении, а также выявляют какие-либо дефекты, такие как пористость или включения, в сварном шве.Эти испытания используются для проверки способности сварщика сваривать угловой шов

Мировой опыт испытаний сварных швов
Как ведущий мировой поставщик металлургических услуг, мы предлагаем вам непревзойденный опыт и знания в области методов испытаний сварных швов. Вот почему мы — лучший выбор для широкого круга клиентов-производителей.
Наш механический цех площадью 10 000 кв. Футов, от квалификационных испытаний процедуры сварки до квалификационных испытаний сварщиков, полностью оборудован для обработки сварочных листов любого размера.Кроме того, чтобы гарантировать, что вы никогда не пропустите сроки из-за задержек тестирования, наша команда опытных инженеров обеспечивает быструю обработку заказов и непревзойденный контроль качества.
Свяжитесь с нами сегодня, чтобы обсудить ваши требования к испытаниям сварных швов.
свяжитесь с нами
Что такое разрушающий контроль сварных швов?
Разрушающий контроль сварных швов выполняется для нескольких целей, например: для квалификации спецификации процедуры сварки, для квалификации сварщика или оператора сварки или для проведения производственных испытаний.
Для соответствия Спецификации процедуры сварки (WPS)Процедура сварки написана на основе опыта и знаний в области сварки, но для ее квалификации необходимо провести некоторые механические испытания.
Например, вы пишете WPS для материала нержавеющей стали, такого как ASTM A240 TP 316L; вы определяете число P, число A, диапазон толщины, тип и диаметр присадочного металла, конфигурацию соединения, напряжение и силу тока сварочного аппарата и т. д.
Ваш WPS готов; Вам нужен сварщик, чтобы сварить вам тестовый купон. Образец сваривается, разрезается и отправляется в лабораторию механических испытаний. Выполняются два испытания на растяжение, два испытания на изгиб корня и два испытания на изгиб торца.
Если результаты тестов были удовлетворительными и соответствовали критериям приемки, то ваш WPS считается аттестованным. Итак, если ваша работа — сосуд высокого давления, трубопровод и резервуар для хранения, то эти испытания выполняются в соответствии с разделом IX ASME.
Если работа связана со стальной конструкцией, то разрушающие испытания сварного шва должны проводиться на основе AWS D1.1, и если работа находится в стадии разработки, ваши разрушающие испытания для WPS должны выполняться в соответствии с требованиями API 1104.
Чтобы получить квалификацию сварщика или сварщика Сварщики и сварщики обычно имеют квалификацию радиографического или ультразвукового контроля, но некоторые работодатели предпочитают проводить механические испытания (разрушающие испытания). Чтобы получить квалификацию сварщика, вам необходимо разрезать тестовый купон и выполнить одно испытание на изгиб корня и одно испытание на изгиб торца (на основе ASME IX).
Обратите внимание на то, что в некоторых сварочных процессах нам не разрешается проводить испытания RT или UT для аттестации сварщика или оператора сварки, и мы должны использовать разрушающие испытания сварного шва. Например, вы не можете квалифицировать сварщика по RT или UT для процесса сварки GMAW-S и FCAW.
Любой код или стандарт по сварке имеет собственные требования к механическим испытаниям для аттестации сварщика, например: ASME IX, API 1104, AWS D1.1 и т. Д.
Разрушающий контроль сварных швов для производственных испытанийИногда мы проводим разрушающие испытания, исходя из требований проекта.Например, есть проект технологических трубопроводов, а у вас есть 2000 тысяч стыков труб для сварки.
Спецификация проекта требует, чтобы из каждых 100 соединений для механических испытаний выбиралось одно соединение. Это разрушающее испытание, и вы потеряете это сварное соединение, но это способ убедиться, что сварные соединения имеют соответствующую пластичность и другие требуемые механические свойства.
Этот метод не очень распространен, но некоторые заказчики учитывают это требование в своей спецификации проекта.
Критерии приемлемости указаны в каждом соответствующем коде или стандарте. Например, ASME IX требует, чтобы предел прочности сварного шва на растяжение не был ниже минимального указанного значения прочности материала на разрыв.
Если образец для испытаний сломался по основному металлу и вышел за пределы сварного шва, то было бы приемлемо, если предел прочности при растяжении составлял более 95% минимального заданного предела прочности.
В том же стандарте после испытания на изгиб трещины не должны превышать 1/8 дюйма на напряженной поверхности.
Когда вы получили отчет о лабораторных испытаниях, вам следует обратиться к указанному стандарту, чтобы определить приемлемость теста. Вам необходимо сравнить измеренные значения в отчете об испытаниях с допустимым диапазоном в стандарте.
Вернуться в производственную инспекцию
Вы нашли эту статью полезной? Нажмите на кнопки «Мне нравится» и «G + 1» ниже!
У вас недостаточно прав для чтения этого закона в это время
У вас недостаточно прав для чтения этого закона в это время Логотип Public.Resource.OrgЛоготип представляет собой черно-белую линию улыбающегося тюленя с усами. Вокруг печати находится красная круглая полоса с белым шрифтом, в верхней половине которого написано «Печать одобрения», а в нижней части — «Public.Resource.Org». На внешней стороне красной круглой марки находится круг. серебряная круглая полоса с зубчатыми краями, напоминающая печать из серебряной фольги.Public.Resource.Org
Хилдсбург, Калифорния, 95448
США
Этот документ в настоящее время недоступен для вас!
Уважаемый гражданин:
В настоящее время вам временно отказано в доступе к этому документу.
Public Resource ведет судебный процесс за ваше право читать и говорить о законах. Для получения дополнительной информации см. Досье по рассматриваемому судебному делу:
Американское общество испытаний и материалов (ASTM), Национальная ассоциация противопожарной защиты (NFPA), и Американское общество инженеров по отоплению, холодильной технике и кондиционированию воздуха (ASHRAE) против Public.Resource.Org (общедоступный ресурс), DCD 1: 13-cv-01215, Объединенный окружной суд округа Колумбия [1]
Ваш доступ к этому документу, который является законом Соединенных Штатов Америки, был временно отключен, пока мы боремся за ваше право читать и говорить о законах, по которым мы решаем управлять собой как демократическим обществом.
Чтобы подать заявку на получение лицензии на ознакомление с этим законом, ознакомьтесь с Сводом федеральных правил или применимыми законами и постановлениями штата.
на имя и адрес продавца. Для получения дополнительной информации о постановлениях правительства и ваших правах гражданина в соответствии с нормами закона , тел. пожалуйста, прочтите мое свидетельство перед Конгрессом Соединенных Штатов.
Вы можете найти более подробную информацию о нашей деятельности на общедоступном ресурсе.
в нашем реестре деятельности за 2015 год. [2] [3]
Спасибо за интерес к чтению закона.Информированные граждане — это фундаментальное требование для работы нашей демократии. Благодарим вас за усилия и приносим извинения за возможные неудобства.
С уважением,
Карл Маламуд
Public.Resource.Org
7 ноября 2015 г.
Банкноты
[1] http://www.archive.org/download/gov.uscourts.dcd.161410/gov.uscourts.dcd.161410.docket.html
[2] https://public.resource.org/edicts/
[3] https://public.resource.org/pro.docket.2015.html
Разрушающие испытания — Услуги по механическим испытаниям
Собственные лаборатории MISTRAS выполняют разрушающие испытания ( DT ) и услуги механических испытаний компонентов в аэрокосмической, автомобильной, нефтегазовой, ветроэнергетической и инфраструктурной отраслях.
Разрушающий контроль ( DT ) — важный процесс в процессе выбора и утверждения материалов для высокоэффективных материалов.
DT часто выполняется на недорогих компонентах большого объема. В отличие от неразрушающего контроля ( NDT ), при котором проверки выполняются без существенного повреждения структурной целостности актива, разрушающие испытания растягивают, изгибают, ломают и иным образом деформируют компонент до механического разрушения в контролируемой среде.
Это делается для измерения, среди прочего, их прочности, твердости, жесткости и количества повреждений, которые они могут понести во время работы, в соответствии со спецификациями заказчика.Разрушающее тестирование предназначено для получения последовательных, повторяемых результатов, поэтому, если один компонент выйдет из строя определенным образом, можно ожидать, что другие, изготовленные с использованием аналогичного процесса, будут иметь аналогичные недостатки.
DT необходим для композитов, металлов и других материалов, которые используются в самолетах, автомобилях, резервуарах для хранения и во многих других областях. Им часто приходится работать в условиях экстремального стресса и высоких температур.
Служба разрушающего тестированияMISTRAS моделирует эти среды для испытания образцов вновь изготовленных компонентов до механического отказа, чтобы гарантировать их безопасную работу после запуска.Сервисы MISTRAS DT могут использоваться для различных материалов, включая:
- Сплавы
- Керамика
- Композиты
- Бетон
- Металлы
- Пластик
- Полимеры
Металлы или композиты, подверженные растущим уровням растяжения, сжатия, сдвига и отслаивания во время эксплуатации. MISTRAS использует различные методы механических испытаний, в которых e. грамм. добавление температуры, деформации, однонаправленной или сдвигающей нагрузки может дать полезные результаты о реакции материалов, работающих в условиях экстремального напряжения. Вы можете узнать больше о механических испытаниях MISTRAS ниже.
Испытание на твердость включает в себя несколько методов, в которых к материалу прикладывают принудительное вдавливание и измеряют глубину вдавливания; чем глубже вмятина, тем мягче материал. Это полезно для оценки качества материала и устойчивости к ударам.
MISTRAS использует различные методы измерения твердости для определения твердости материалов с помощью небольших вмятин. В сочетании с другими методами испытаний, такими как испытание на растяжение, испытание на удар, металлографический и химический анализ, вы можете обнаруживать материалы или узнать больше об их процессах термообработки.
Узнайте больше о проверке твердости от MISTRAS здесь.
Испытания на удар Ударные испытания включают в себя разрушение материала с высокой скоростью для определения ударной вязкости, ударной вязкости и способности поглощать энергию. Он часто используется для предоставления информации о сильных и слабых сторонах сварных швов. MISTRAS проводит испытания на ударную вязкость при различных температурах, чтобы воспроизвести среду, в которой находится материал, когда он используется в эксплуатации.
Испытания на ударную вязкость, такие как испытания с V-образным надрезом по Шарпи или U-образным надрезом, определяют ударную вязкость путем регистрации энергии, которую материал поглощает при разрушении. Для сварных материалов испытания на удар можно использовать для получения информации о прочности и поведенческих свойствах сварного шва.
MISTRAS проводит испытания на ударную вязкость при различных температурах, чтобы воспроизвести среду, в которой находится материал, когда он используется в реальных условиях.
Для композитных материалов MISTRAS использует ударные испытания для моделирования, например, повреждение в процессе эксплуатации, которое приводит к расслоению материала. После этого определяются остаточные механические свойства.
При испытании на сдвиг параллельные силы, приложенные к контактной поверхности, определяют свойства при напряжении сдвига.Испытания на сдвиг важны для таких компонентов, как болты или винты, которые испытывают силы сдвига, если скрепляемые вместе поверхности перемещаются из стороны в сторону.
Он также используется для испытаний образцов, полученных с помощью процессов аддитивного производства.
Испытания на растяжениеИспытания на растяжение часто проводятся для оценки прочности на разрыв, предела текучести и удлинения. Метод состоит в том, чтобы натянуть образец для испытаний, чтобы определить, насколько прочен материал и насколько он может удлиниться.
Специалисты MISTRAS применяют контролируемое напряжение к металлическим, композиционным и полимерным материалам с целью измерения их предела прочности на растяжение, максимального удлинения, предела текучести, эластичности, пластичности и других характеристик материала. Также называемый «испытанием на растяжение», испытание может проводиться в различных условиях, адаптированных специально для каждого эксперимента в зависимости от окружающей среды, в которой находится наблюдаемый материал.
Испытания на растяжение проводятся на металлических или пластмассовых изделиях, отливках, сварных швах, проволоке, арматуре и трубных изделиях.
Тестирование адгезии на отслаивание
Испытание на растяжение прочности клея, используемого для соединения компонентов. Это используется для контроля качества (QC) и определения адгезионных свойств, чтобы предсказать, как определенное вещество будет работать во время использования. Испытания на отслаивание под углом 90 и 180 градусов разрывают склеенные материалы и фиксируют среднее усилие, необходимое для полного разделения.
Во время общих испытаний адгезии на отслаивание определяется прочность на отслаивание клея, используемого для соединения компонентов между собой. Тестирование адгезии на отслаивание, проводимое нашим обученным персоналом, — это быстрый и надежный способ получить представление о поведении материала.
Тестирование на отслаивание барабана, обычно используемое в аэрокосмических компонентах, определяет сопротивление склеивания адгезионных материалов с гибкими и жесткими поверхностями. В этом испытании инструмент, известный как подъемный барабан для отслаивания, измеряет сопротивление путем приложения усилий отслаивания по мере разделения материалов.
MISTRAS предлагает специальный тест на отслаивание барабана, который широко используется для компонентов авиакосмической промышленности.Испытание определяет так называемую силу отслаивания барабана путем отслаивания металлического листа от сотового заполнителя. Затем мы используем подъемный барабан для определения сопротивления, прикладывая к компонентам только отслаивающее усилие.
Испытание с плавающим роликом Испытание на отслаивание, при котором гибкие и жесткие материалы разделяются с помощью приспособления для отслаивания с плавающим роликом для определения средних сил отслаивания. Испытание проводится под углом для негибких веществ.
Во время испытания с плавающими роликами лаборанты MISTRAS отделяют гибкие и жесткие материалы друг от друга с помощью специального приспособления для отслаивания роликов.Определенная средняя сила отслаивания позволяет операторам узнать об истинном поведении металла и о том, как компонент будет действовать в коммерческих условиях.
Испытание подшипниковИспытания на усталость подшипников качения для выявления тепловых воздействий, процессов чистовой обработки и т. Д. Из-за напряжений и деформаций, которым подвергается подшипник качения во время эксплуатации, важно знать его механические возможности.
В композиционных материалах — испытание на подшипник, определяющее эксплуатационные характеристики ламината, и образец подвергается либо растягивающей, либо сжимающей нагрузке через болт до разрушения.Затем испытуемый образец исследуется на наличие неисправности.
Прочность на межслойный сдвиг (ILSS)
Стандартные или готовые структурные слоистые материалы подвергаются давлению при испытании на сдвиг для возникновения разрывов. Тестируются ламинаты, состоящие из эпоксидной смолы или другого хрупкого материала. Тип возникающего разрыва может характеризовать материал матрицы или качество соединения матрицы.
MISTRAS используют испытание прочности на межслойный сдвиг или испытание на прочность короткой балки ( SBS ) для определения прочности ламината на сдвиг по толщине.Образец подвергается трехточечной нагрузке с коротким пролетом, что позволяет сделать выводы о качестве матрицы и производственном процессе.
Наши решения для испытания прочности на межслойный сдвиг ( ILSS ) помогают гарантировать, что прочность между пластинами из ламината определена. ILSS используется для стандартных ламинатов и ламинатов с готовой структурой.
Испытания на сдвиг внахлестку
Испытание клеевого соединения, при котором пластины соединяются вместе с помощью специального клея и разрываются на части, измеряется точка разрыва, в которой пластины разделяются. Тестирование на сдвиг внахлестку используется для определения правильности использования клеев.
MISTRAS использует испытание на сдвиг внахлестку для определения прочности клеев. MISTRAS оценивает максимальное усилие и оценивает поверхности излома. Это эффективный тест для наблюдения за процессами облигаций.
Испытания на вязкость при межслойном разрыве
Испытание на вязкость межслойного разрушения характеризует расслоение материалов и определяет вязкость разрушения армированных композитов.По мере того как образец разрывается, рост трещины измеряется до тех пор, пока образец не достигнет точки разрушения.
СпециалистыMISTRAS проводят испытания на вязкость межслойного разрушения как надежный и эффективный метод DT. Нагрузка осуществляется либо растяжением (режим I), либо сдвигом (режим II), либо их комбинацией.
Тестирование фоторамки
Метод испытания на сдвиг, который используется, в частности, для больших композитных материалов. В четырех краях панели просверливаются отверстия, и края панели зажимаются между направляющими.Во время испытания тянущие силы панели прикладываются по диагонали к противоположным углам рамы, когда пары рельсов вращаются относительно друг друга.
Испытание рамки для изображения — это надежный и надежный метод испытаний для больших образцов материалов, позволяющий определить данные о сдвиге, необходимые для проверки конструкции и конструкции. MISTRAS полностью подготавливает материалы к испытаниям и сверлит отверстия в зависимости от размера и толщины материала. Он завершает испытания сэндвич-панелей и помогает выявить драпирующие свойства материалов.
Испытания на изгиб
Испытание на изгиб — это качественное разрушающее испытание, которое оценивает пластичность и прочность материала. Изгиб материала можно анализировать для определения характеристик под давлением, сопротивления растрескиванию и способности выдерживать нагрузку. Этот тест часто используется для стыковых сварных соединений.
Испытания на прочность изогнутой балки позволяют измерить прочность изогнутой балки в композитных материалах.Это испытание состоит из двух опор, соединенных изгибом под углом 90 градусов, который обеспечивает постоянный изгиб поперек армированной волокном балки. Этот тест также может измерять прочность на разрыв между слоями.
MISTRAS испытание прочности изогнутой балки является популярным методом испытаний и высоко ценится за свою эффективность.
Испытание на разрыв ников Испытание на разрыв с зазубринами состоит из предварительного надреза поверхности материала с последующим приложением прямой силы, часто путем удара по поверхности молотком или вытягивания ее в приборе для испытания на растяжение.Затем материал с трещинами исследуют для анализа прочности на основе включений шлака, пористости, неполного разрушения, трещин и других характеристик трещин.
Испытание на разрыв на разрыв состоит из предварительного разрезания поверхности свариваемого материала с последующим приложением прямого усилия. Затем материал с трещинами исследуют для анализа технической надежности на основе включений шлака, пористости, неполного разрушения, трещин и других характеристик трещин. Испытание на разрыв на разрыв гарантирует, что любые существующие внутренние дефекты находятся в определенных пределах технических характеристик материала.Этот метод тестирования показывает внутреннее качество сварных швов.
Испытания подшипников качения
MISTRAS определяет величину усталости подшипников качения. Из-за напряжений и деформаций, которым подвергается подшипник качения во время эксплуатации, важно знать его механические возможности.
Испытания подшипников на усталость обеспечивают точный контроль качества компонентов. MISTRAS располагает полным набором оборудования, необходимого для правильного проведения испытаний подшипников.
Испытания композитных материалов на сдвиг
Существует два типа подходов к выполнению сдвига в случае композитных материалов: с использованием наклонного ламината или образца с V-образным надрезом, нагруженного сдвигом.В первом случае характеристики сдвига в плоскости определяются путем нагружения наклонного ламината при растяжении. В последнем случае приспособление нагружается либо в растяжении (метод сдвига рельса), либо в сжатии (так называемый «метод сдвига Иосипеску»). Свойства толщины ламината при сдвиге также могут быть определены в зависимости от экстракции образца.
Тест часто используется для контроля качества и обеспечения качества ( QA / QC ) или для сбора данных для определения характеристик материалов.
Испытания точечной сварки
MISTRAS использует разрушающие испытания для проверки качества точечной сварки и других компонентов оборудования. К точечной сварке снаружи прилагается сила, чтобы открыть зону сварки для дальнейшего осмотра и анализа. Этот тип тестирования позволяет техническим специалистам более тщательно проверять точечную сварку.
— SpotTrack
Наладка процесса точечной сварки
Как в автомобилестроении, так и в аварийном ремонте контактная точечная сварка является основным процессом соединения тонколистовой стали.Точечная контактная сварка — это очень быстрый и надежный процесс, который легко автоматизировать и не требует особых навыков оператора. Самым большим техническим требованием к контактной точечной сварке является обеспечение правильной настройки процесса в первую очередь.
Будет запущен новый процесс точечной контактной сварки:
- Первое изготовление компонента
- Изготовить существующий компонент из новой комбинации материалов
- Ремонт детали
Несмотря на кажущуюся простоту, точечная контактная сварка подвержена влиянию многих локальных переменных, вариации характеристик сварочного аппарата, а также влияние геометрии компонентов и монтажа означает, что универсальный набор параметров не может быть применен к данной комбинации материалов.
Хотя существует множество стандартов, рекомендующих диапазон параметров, которые обычно следует применять для конкретных материалов.
При настройке нового процесса контактной точечной сварки необходимо найти оптимальные параметры (обычно с использованием стандарта в качестве ориентира) и проверить качество сварного шва с помощью разрушающих испытаний.
Разрушающее (отслаивающее) испытание
Основным методом проверки качества точечной сварки является разрушающий контроль, при котором точечные сварные швы разрываются под действием приложенной извне силы, и основной металл отрывается от зоны сварки.Зона сварного шва выявляется и оценивается на предмет ее качества, чтобы убедиться, что она соответствует назначению.
Обычно применяются два основных метода разрушающего контроля:
Сварные швы разламываются при испытании на отслаивание путем зажима одного из сварных листов, обычно в тисках. Другой сварной лист захватывается одним из них; плоскогубцами, клещами или роликовым инструментом, и сила прилагается таким образом, что сварной шов нагружается перпендикулярно его первоначальной ориентации, таким образом, открывая сварной шов (рис. 1). Испытание на отслаивание может быть выполнено вручную или механизировано, в случае механизированного испытания можно измерить силу разрушения.
При испытании разрушающим долотом между листами, разделяющими их и нагружающими сварной шов, вбивают долото. Долото может иметь одно лезвие или два отдельных зубца, и усилие можно прикладывать вручную или с помощью механических средств. Если испытание на долото механизировано, можно измерить силу разрушения.
ISO10447 2006 Контактная сварка — «Испытание контактных точечных и выступающих сварных швов отслаиванием и долотом» описывает процедуру разрушающих испытаний и измерений контактных точечных сварных швов, разделы 5.2 и 5.3 подробно описано, как проводить испытание на отслаивание и как измерять сварной шов. Немецкий эквивалент — DIN EN ISO 10447: 2007-09
.
Рис. 1. Испытание на отслаивание
Рис. 2. Испытание на долото
Оценка качества сварного шва, измерение сварного шва
Разрушающее испытание долотом или отслаиванием приводит к тому, что зона сварного шва была оторвана от одного из металлических листов, открытая площадь сварного шва может быть измерена. Это измерение размера сварного шва обычно используется как показатель качества сварного шва, т.е.е. пригоден ли сварной шов по назначению.
Точечные сварные швы измеряются штангенциркулем. Поскольку точечные сварные швы не всегда точно круглые, следует проводить два измерения под углом 90 ° друг к другу. Наибольший и наименьший размеры точечной сварки следует измерять, как показано на рисунке 3. Средний диаметр сварного шва рассчитывается, как показано ниже:
Средний диаметр сварного шва = d1 + d2 / 2
d1 = наибольший размер сварного шва
d2 = наименьший размер сварного шва
Минимальный средний диаметр сварного шва часто используется в целях контроля качества; размер сварного шва обычно зависит от толщины листа.Типичный минимальный средний диаметр сварного шва часто составляет 4 или 5 дюймов, где t = толщина листа.
Рисунок 3. Измерение точечной сварки
Виды разрушения точечной сварки
В обычной низкоуглеродистой стали большинство точечных сварных швов, которые подвергаются деструктивным испытаниям, разваливаются как «пробка» или «вырывание», пробка характеризуется отрывом зоны сварки от одного из листов, оставляющим видимый выступ, который легко измерить , рисунок 4.
Высокопрочные стали и толстые листы могут разрушаться как «стыки» или «частичные пробки».
В случае выхода из строя границы раздела сварной шов будет срезаться прямо через его центр, оставляя половину сварного шва на каждом листе и без выступающей заглушки, рис. 5.
В случае частичной заглушки зона сварного шва сама частично разрушится, тогда окружающий лист также будет разрушаться, в результате чего только часть сварочной заглушки будет выступать из листа, рис. 6.
Разрушение границы раздела также характерно для более прочных и толстых сталей, в случае повреждения границы раздела сварной шов будет срезаться непосредственно через его центр, оставляя половину сварного шва в каждом листе и не выступающую заглушку, рис.
Рисунок 4. Неисправность пробки
Рисунок 5. a: Частичное повреждение пробки, b: поперечное сечение частичной пробки
Рисунок 6. Сбой интерфейса
При измерении среднего диаметра сварного шва важно убедиться, что указаны правильные размеры, необходимо учитывать несколько факторов.
При измерении полного разрушения электрозаклепки часть листового материала все еще может быть прикреплена к зоне сварного шва, этот лишний материал следует отогнуть назад, чтобы обеспечить точное позиционирование штангенциркуля, рис. 7.
Рис. 7. a: Поперечное сечение, показывающее излишки листового материала, b: размеры сварного шва, которые необходимо измерить, c: правильное расположение штангенциркуля
При измерении разрушения границы раздела следует измерить размеры зоны грубого разрушения, как показано на рисунке 8.
Рис. 8. a: Измеряемые размеры сварного шва, b: правильное расположение штангенциркуля на шероховатой поверхности излома
При измерении частичного разрушения электрозаклепки истинные размеры ядра сварного шва — это размеры шероховатой поверхности излома, эта область может быть частично покрыта сварочной пробкой.В некоторых случаях также может потребоваться средний диаметр площади плунжера, который измеряется путем позиционирования штангенциркуля на самом большом и самом маленьком размерах плунжера, таким же образом, как при обычном повреждении плунжера, рис.
Рис. 9. a: Измерение площади сварного шва частичной заглушки, b: правильное расположение штангенциркуля на шероховатой поверхности излома, c: измерение площади заглушки частичной заглушки, d: установка штангенциркуля на плунжере площадь
Частота испытаний
Разрушающий контроль обычно выполняется при настройке нового процесса сварки для проверки качества сварки перед производством или ремонтом компонента.В производственной линии всегда будут проводиться периодические разрушающие испытания компонентов. На автомобильных производственных линиях один автомобильный кузов, как правило, полностью подвергается разрушающим испытаниям, и все сварные швы измеряются с периодичностью от одного кузова в неделю до одного в месяц, в зависимости от практики отдельных компаний.
.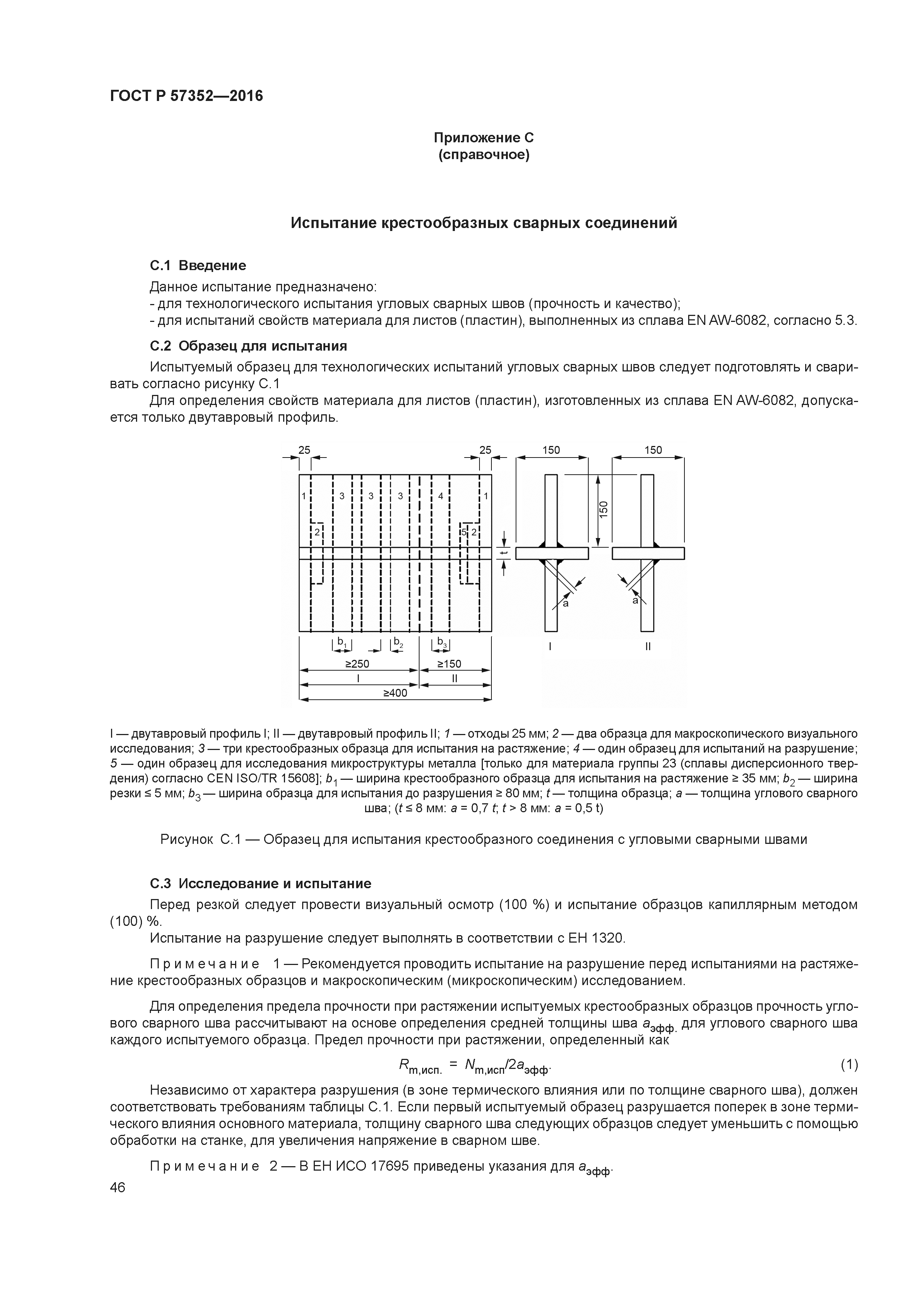