Контроль качества сварных соединений
Содержание страницы
1. Виды контроля качества сварных соединений
Часто готовые сварные соединения имеют трещины и другие дефекты, не всегда находящиеся на поверхности шва. Для обнаружения дефектов применяются два метода контроля качества швов — разрушающие и неразрушающие.
Разрушающие методы применяются для определения физических свойств сварного соединения. В основном он применяется при оценке квалификации сварщиков. Иногда они находят применение и на производстве, когда из партии готовых изделий одно или несколько разрушаются, и по результатам их проверки делается заключение обо всей партии.
Неразрушающие методы используются для проверки качества швов без их разрушения. С их помощью можно узнать местоположение дефекта, его размер, характер. Этот способ удобнее всего применять, когда сваркой изготавливают ответственные изделия. Группа неразрушающих методов контроля качества включает в себя:
- визуальный метод;
- магнитнопорошковый метод;
- капиллярный метод;
- акустический метод;
- метод ионизированного излучения;
- вихретоковый метод;
- контроль герметичности.
2. Визуальный метод
Это наиболее общий вид проверки. Он включает в себя проверку размеров, формы, местоположения шва. С его помощью обнаруживаются такие дефекты, как выходящие на поверхность трещины, неметаллические включения, подрезы, непровары. Этот метод можно применять только после полного удаления шлака с поверхности шва.
Для проверки формы шва применяются шаблоны. У качественного сварного шва усиление должно совпасть с определенным шаблоном.
Также для проверки применяются увеличительные стекла, миниатюрные телекамеры, нутромеры и линейки.
Каждый сварной шов должен быть проверен сварщиком. Хороший сварщик сразу обнаружит внешние дефекты и впоследствии устранит их.
3. Магнитнопорошковый метод
Магнитнопорошковый метод очень эффективен для обнаружения поверхностных или расположенных близко к поверхности пор и трещин. Он применяется только на материалах, способных намагничиваться. Перед проверкой требуется тщательно очистить поверхность. Используется жидкий аналог магнитного порошка или флюоресцентный магнитный порошок.
Металл подвергается воздействию сильного магнитного поля. На краях трещин и раковин поле концентрируется, что вызывает притягивание порошка. После прекращения действия магнитного поля вокруг каждой трещины или раковины наблюдается концентрация порошка. При применении флюоресцентного порошка для обнаружения концентраций место проверки следует осветить ультрафиолетовым светом.
Так как направление трещин неизвестно, проводят два тестирования. Первый раз линии магнитного поля направляются по возможности перпендикулярно шву, второй раз параллельно.
После обнаружения трещины вскрываются для исправления.
4. Капиллярный метод
Метод применяется для обнаружения поверхностных трещин. Он основан на применении цветных красок. Способ может применяться не только на металле, но и пластмассах, керамике или стекле. Метод не применяется для обнаружения дефектов, не выходящих на поверхность.
Проверка проводится в следующей последовательности:
- проверяемая поверхность очищается;
- поверхность покрывается краской, которая должна проникнуть вовнутрь трещины или раковины;
- через некоторое время краска удаляется;
- поверхность покрывается проявляющей краской. Применяется краска, контрастная по цвету первой;
- через некоторое время, если есть трещины или другие дефекты того же характера, на краске появятся пятна первой краски, которые будут показывать положение дефекта;
- после проверки краска удаляется.
В качестве проникающей краски может быть использована флюоресцентная краска. Для обнаружения ее проникновения через проявляющую краску применяется ультрафиолетовый свет.
Время выдержки проникающей краски на поверхности может варьироваться от 3 до 60 мин. При комнатной температуре краску рекомендуется держать 3—10 мин. На рис. 1 показана поверхность краски при наличии дефекта сварного шва.
Рис. 1. Поверхность краски при наличии дефекта сварного шва
5. Акустический метод
В этом методе для обнаружения местоположения и размера дефектов используются звуковые волны. Он может быть применен практически для любого материала. Ультразвуковая дефектоскопия использует звук высокой частоты более одного мегагерца.
Электронное устройство, названное пьезоэлектрическим преобразователем, помещается на поверхность материала, вглубь которого преобразователь излучает ультразвуковые волны. Для лучшего проникновения волн требуется обеспечить хороший контакт между преобразователем и поверхностью материала.
Волны посылаются внутрь материала через очень малые промежутки времени. Длительность такого промежутка — от одной до трех микросекунд. Посланная волна проходит сквозь материал, отражается от границ материала и трещин, если они попадаются на пути волны. Отраженная волна возвращается обратно в преобразователь. После получения первой волны тут же посылается другая такая же. Этот процесс повторяется примерно 500 000 раз в секунду. Во время проверки преобразователь передвигается по поверхности. Каждая отраженная волна показывается на дисплее. Также на дисплее отображаются сигналы, отраженные от границ материала и от внутренних дефектов. На рис. 2 схематично показан процесс акустической диагностики сварного шва.
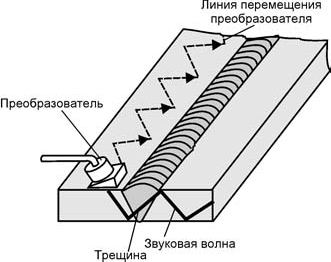
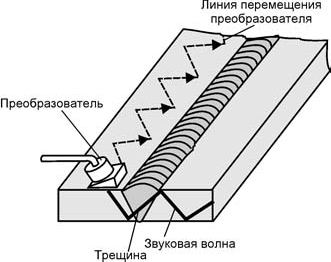
Рис. 2. Акустическая диагностика сварного шва
Преимущества акустической диагностики:
- быстрота, дает немедленные результаты;
- может быть использована на различных материалах;
- не требуется доступа к обоим сторонам шва. Недостатки:
- требуется хороший контакт преобразователя с поверхностью;
- трудно увидеть дефекты, параллельные звуковому лучу;
- требуется специальный навык для правильной интерпретации данных на дисплее;
- оборудование требует регулярной настройки.
- Вихретоковый метод
В вихретоковом методе используется катушка индуктивности, подключенная к генератору переменного тока с регулируемой частотой. Переменное магнитное поле катушки индуцирует переменные микротоки. Эти токи и являются вихревыми.
В процессе проверки катушка, настроенная на определенное значение полного сопротивления (значение полного сопротивления можно видеть на осциллоскопе) перемещается по поверхности детали. Если внутри материала детали есть дефекты, то происходит изменение вихревых токов. Это приводит к изменению полного сопротивления спирали катушки, что отображается на осцилоскопе.
Методом вихревых токов можно обнаружить дефекты, залегающие у поверхности. Глубина исследования зависит от частоты переменного тока и обычно не превышает 3 мм. Метод применяется для исследования как плоских поверхностей, так и круглых (например, труб). Кроме трещин и раковин таким способом можно обнаружить и различные вредные включения.
6. Метод ионизированного излучения
Внутренние дефекты могут быть обнаружены с помощью ионизированного излучения. Частный случай метода ионизированного излучения — контроль с помощью рентгеновского излучения. Рентгеновское излучение — это поток энергии, способный проникнуть сквозь многие материалы и воспроизвести их внутреннее состояние на фотопленке или на экране монитора.
Источником ионизированного излучения в природе являются радиоактивные изотопы. Некоторые изотопы могут использоваться в приборах для создания рентгеновских лучей, но их применение небезопасно для человека.
Рентгеновские снимки используются для исследования ответственных соединений, например на атомных электростанциях, трубопроводах, кораблях, подводных лодках, самолетах.
Данным способом можно контролировать различные материалы при их различной толщине. Чем больше толщина, тем больше энергии и времени требуется на просвечивание.
Рис. 3. Рентгенограмма сварного шва
По фронтальному рентгеновскому снимку можно определить местоположение и размеры трещины, но не глубину ее залегания. При обнаружении трещины производится еще один снимок под некоторым углом, что помогает определить точное положение трещины относительно поверхности детали. На рис. 3 показана рентгенограмма сварного шва.
7. Контроль герметичности
Герметичность любого сосуда проверяется по отсутствию утечки. Это наиболее общий метод проверки сварных швов на резервуарах и трубах, используемых для хранения неядовитых жидкостей или газов под давлением. Для этих целей наиболее подходит по свойствам диоксид углерода (углекислый газ). Он не ядовит и взрывоопасен. В проверяемом сосуде или трубе создается небольшое давление (170—690 кПа) от пневмокомпрессора, а вся поверхность шва покрывается раствором воды и мыла. Утечка обнаруживается по появлению пузырей. По завершению закачки газа записываются показания манометра, подача газа прекращается. Через сутки снова проверяют показания манометра. Падение давления будет сигнализировать об утечке. Это довольно простой способ проверки.
При другом способе контроля герметичности сварных швов поверхность сосуда покрывается известью. После того как известь высохнет, в сосуде создается давление. По осыпавшейся извести можно определить места утечки. Данным способом возможно испытывать конструкции и на утечку жидкости. Тогда в сосуде создается гидростатическое давление. Наиболее часто применяется вода, тем не менее, она не просачивается через очень маленькие трещины.
Для проверки на наличие мельчайших микроскопических утечек применяется метод гелиевого течеискания. Сосуд наполняется гелием, а на исследуемую область устанавливается датчик масс-спектрометра. Этот прибор способен обнаружить одну частицу применяемого для обследования газа в миллионе частиц воздуха.
Просмотров: 260
КОНТРОЛЬ КАЧЕСТВА СВАРНЫХ ШВОВ [труб и металлоконструкций]
[Контроль качества сварных швов] – необходимая процедура для определения качества металлоконструкции.
Если шов недостаточно плотный, с нарушенной герметичностью и другими деформациями – все это неминуемо скажется на сроке эксплуатации металлоконструкции.
Особенно быстро это произойдет в случае, если металлоконструкция будет находиться под постоянным давлением.
Для контроля качества и проверки соответствия швов ГОСТ существуют специальные процедуры, виды которых (ультразвуковой, визуальных и т.д.) будут подробно освещены в статье.
Назначение процедуры и метод визуального осмотра
Перед проверкой металлоконструкции на соответствие требованиям ГОСТ, сначала обязательно требуется проверить, насколько качественно сделаны швы – на этом этапе выявляются все внешние и внутренние недостатки швов, а также исправляются, если это возможно.
Тщательному контролю подвергается каждое готовое изделие перед тем, как его допустят к эксплуатации.
Первый и самый простой уровень контроля качества: визуальный осмотр.
Визуальный осмотр металлоконстуркции позволяет выявить внешние и самые явные деформации швов, такие, как трещины, непровары и прочие недостатки.
Большинство подобных деформаций позволяет определить обычный визуальный осмотр металлоконструкции без использования дополнительного оборудования, однако, в некоторых случаях практикуется применение специальных устройств.
Виды контроля сварных швов делятся на разрушающие и неразрушающие.
Первый вид контроля подразумевает только визуальный осмотр, все остальные, более сложные техники проверки относятся ко второму типу.
Второй вид контроля может быть капиллярным, ультразвуковым, радиационным, магнитным и проверкой на проницаемость.
При любом неразрушающем способе проверки внешний вид металлоконструкции не деформируется, что делает его более удобным и востребованным, чем разрушающий способ.
Разрушающий – визуальный – способ контроля используется только в том случае, если сварная деталь сварена постоянным типом сварки без изменения условий.
Методы контроля сварных швов также бывают разные. При проведении контроля по ГОСТ поочередно проводятся разные виды процедур, выявляющих качество сварного шва.
Видео:
Процедуры делят на химические, механические, физические, а также визуальный и ультразвуковой осмотр.
Наиболее бюджетным является визуальный осмотр, поскольку он не требует никаких финансовых затрат.
Однако он используется не в целях экономии, а ввиду необходимости, поскольку позволяет выявить самые значительные нарушения швов.
Визуальный осмотр необходим для совершенно всех видов металлических соединений, независимо от того, какие методы контроля последуют за ним.
Часто визуальный осмотр по ГОСТ проводят без применения всяких вспомогательных устройств, однако в некоторых случаях для того, чтобы проверка была более точной, используют лупу, которая способна увеличить осматриваемое пространство швов в 10 раз.
В этом случае можно заметить даже самые мелкие непровары, подрезы, наплывы и другие дефекты.
Внешний контроль швов включает не только непосредственно визуальный осмотр, но также обмер сварных швов, замеры кромок и прочие процедуры.
Если изделия для металлоконструкций, которые подвергаются контролю, выпущены массовым тиражом, то в этом случае для их создания используют специальный шаблон, позволяющий соблюдать точные и одинаковые замеры всех параметров сварных швов.
Если визуальный просмотр прошел успешно, то за ним следует физический осмотр, на котором выявляется качество шовного соединения и другие характеристики.
Цель подобного контроля в том, чтобы убедиться, что по своим характеристикам сварные швы полностью соответствуют ГОСТ.
Проверка физическими и химическими методами производится с подключением специального оборудования, например, электромагнитного сердечника, а также других устройств.
Главная цель проведения любого типа контрольной проверки – выявить не только непосредственное состояние швов, но также проверить, насколько качественно сама металлическая деталь, и не было ли нарушений во время сварочных работ.
В зависимости от типа металла, характеристики швов будут несколько отличаться между собой, однако все они должны соответствовать ГОСТу-6996-66, в котором отмечены все надлежащие к выполнению виды контрольных работ.
Другие методы контроля
Контроль качества сварных соединений трубопроводов и других металлоконструкций производится разными методами, однако все они необходимы для установления того, насколько выпускаемая продукция соответствует ГОСТ.
После того как визуальный осмотр завершен, следует его просвечивание. Эта процедура требует использования рентгена или гамма-лучей.
Видео:
При проверке рентгеном аппарат устанавливают с внутренней стороны металлоконструкции.
С помощью рентгена можно увидеть места, где сварочное оборудование оказало недостаточное воздействие – на пленке они будут отмечены пятнами более темных оттенков, чем основной цвет соединений.
С помощью подобного метода происходит выявление трещин в металлоконструкции, непроваров, шлаковых включений и других деформаций, незаметных при внешнем осмотре.
С помощью просвечивания можно оценить металлические соединения толщиной не более 6 см, при обнаружении дефектов просвечивается в два раза больше стыков.
Магнитографический способ проверки качества необходим, чтобы обнаружить поле рассеивания, образующееся там, где есть дефекты.
Способ заключается в намагничивании поверхности детали, после чего область полей появляется сверху магнитной ленты, которую прижимают на поверхность швов.
Весь процесс проверки металлоконструкции фиксируется с помощью дефектоскопа, а после информация считывается и, таким образом, устанавливается, есть ли на швах дефекты.
Подобный метод позволяет выявлять наличие трещин, пор, непроваров, шлаковых включений и других дефектов, возникающих в процессе сварки.
Также с помощью магнитографического метода можно определить наличие на поверхности швов поперечных трещин, широких непроваров или округлых пор, однако с поиском дефектов подобного рода данный метод справляется несколько хуже.
Использовать его можно только для металлических заготовок, толщина которых не превышает 1.2 см.
Ультразвуковой способ проверки качества часто используется для оценки на соответствие ГОСТ стали и изделий из цветного металла.
Ультразвуковой способ заключается в направлении звукового колебаний на поверхность металла и последующего отражения, чтобы выявить возможные дефекты.
Видео:
Для получения ультразвуковой волны используют несколько пьезоэлектрических кварцевых пластин, которые фиксируются в щупе.
После колебания ультразвуковой волны, которые отражаются от металла, улавливаются специальным устройством – искателем, который преобразует ультразвуковой луч в заряженный электричеством импульс, переходящий к усилителю, а затем воспроизводящийся с помощью индикатора.
Для того чтобы ультразвуковой способ был эффективен, перед тем, как ультразвуковой луч направляют на металл, его поверхность предварительно покрывают автолом или компрессорным маслом.
Вскрытие швов – более радикальный метод проверки, когда вероятность дефектов достаточно высока, но при этом ни ультразвуковой, ни другие методы не могут ее выявить.
Швы вскрываются специальным устройством только в том участке, где высока вероятность наличия дефекта.
Вскрытие происходит путем просверливания углубления, диаметр которого должен несколько превышать размер шва, а затем поверхность подвергается шлифовке и обрабатывается разведенной азотной кислотой.
Этот метод заметно деформирует металлическую заготовку, и после него граница прохождения швов проступает очень явно, поэтому без надобности этот способ контроля не используют.
Химический метод контроля на соответствие ГОСТ заключается в обработке поверхности швов фенолфталеиновым раствором, перед этим поверхность необходимо тщательно зачистить, удалив все шлаки и загрязнения.
После нанесения раствора место обработки накрывается тканью, которая пропитывается азотнокислым серебром (раствор 5%).
Этот метод позволяет выявить наличие локальных течей: на этих местах серебро приобретет серебристо-черный вид, а фенолфталеин – красный.
Для того чтобы определить, насколько плотность сварного шва соответствует ГОСТ, применяют метод пробы керосином.
Благодаря ему можно найти самые маленькие дефекты, размер которых может быть около 0.1 мм.
Для выявления дефектов качества швы покрываются каолином или мелом с одной стороны, и смачивается керосином с другой.
При наличии проницания в шве, на поверхности каолина или мела появятся жирные пятна желтого цвета.
Появляются они не сразу, поэтому проверка на ГОСТ этим методом проводится не менее 4 часов.
Как проверить сварной шов за 1 час!
Как проверить сварной шов
Почти все характеристики сварного шва могут быть оценены во время проверки сварки – некоторые относятся к размеру сварного шва, а другие – к наличию неоднородностей в сварном шве.
Размер сварного шва может быть чрезвычайно важным, поскольку он часто напрямую связан с прочностью и эксплуатационными качествами сварного шва.
Например, сварные швы меньшего размера могут не выдерживать нагрузки, прикладываемые во время эксплуатации.
В зависимости от их размера или местоположения неоднородности сварного шва (дефекты внутри или рядом со сварным швом) могут влиять в худшую сторону на качества сварного шва его запланированных рабочих характеристик.
Разрывы сварного шва часто называют дефектами сварки, и они могут иногда вызывать преждевременное разрушение сварного шва из-за снижения прочности или дополнительных концентраций напряжений внутри сварного компонента.
Проверка сварного шва проводится по нескольким причинам, наиболее распространенной из которых является определение того, соответствует ли качество сварного шва его предполагаемому применению. Чтобы оценить качество сварного шва, вы должны сначала иметь критерии, с которыми вы можете сравнить характеристики сварного шва.
ГОСТы, стандарты, разработанные специально для различных применений сварочного производства, используются во время проверок сварки, чтобы определить приемлемые уровни разрывов шва.
Важно выбрать стандарт и способ сварки, который предназначен для использования в вашей отрасли или области применения.
Критерии приемлемости качества проверки сварного шва могут быть получены из нескольких источников. Чертеж или чертеж сварочного производства, обычно предоставляют размеры и другую информацию о размерах, такую как длина и местоположение сварных швов. Эти требования к размерам, как правило, устанавливаются посредством проектных расчетов. Также они могут быть взяты из проверенных конструкций, которые, как известно, соответствуют эксплуатационным требованиям к сварному соединению.
Роль инженера инспектора по сварке.
Проверка сварочных работ требует широкого спектра знаний со стороны инженеров, включая понимание сварочных чертежей, символов и процедур; конструкция сварного соединения; код и стандартные требования; и методы проверки и тестирования.
По этой причине многие сварочные нормы и стандарты требуют, чтобы инженер по сварке был официально аттестован. Существует несколько учебных курсов по проверке сварочных работ и сертификационных программ.
Методы контроля сварки.
Визуальный осмотр.
При правильном выполнении визуальный осмотр часто дает возможность проверить сварной шов и является самым простым и наименее дорогим методом для многих соединений. Однако хорошо выглядящий сварной шов не всегда обеспечивает внутреннее качество, а внутренние разрывы не всегда видны невооруженным глазом. В этом случае, доступны дополнительные методы, в том числе перечисленные ниже.
Обнаружение поверхностных трещин.
Используемый для обнаружения мелких трещин, швов, пористости и других разрывов на поверхности, обнаружение поверхностных трещин обычно применяется с использованием одного из двух методов: инспекция проникающей жидкости или магнитная дефектоскопия.
Рентгенографический и ультразвуковой контроль сварного шва.
Чтобы проверить сварной шов и установить целостность без разрушения сварного элемента, эти два неразрушающих метода испытаний обнаруживают разрывы во внутренней структуре сварного шва.
Качественная сварочная работа требует создания и контроля надежно системы проверки сварки. Необходимо использовать надлежащую технику.
Очень важен опыт инженеров сварщиков, которые осуществляют контроль.
Проверка качества сварочных швов в системе неразрушающего контроля
Ультразвуковое обследование сварных соединений металлоконструкций.
Контроль проводился в соответствии с требованиями ГОСТ 14782-86.
Объект контроля: сварные соединения усиливающих деталей 7-4 в переходе из 2-го строения в 14-ое,1-й этаж.
СХЕМА ОБЪЕКТА КОНТРОЛЯ №1
ФОТО ОБЪЕКТА КОНТРОЛЯ №1
РЕЗУЛЬТАТЫ КОНТРОЛЯ ОБЪЕКТА КОНТРОЛЯ №1
№ П.П. |
№ Сварного соединения |
Типо размер соединения, мм |
Контроле доступность |
Оценка, балл |
Примечание |
1 |
1 |
5 |
1ДК |
Не годен |
Присутствуют недопустимые дефекты |
2 |
2 |
5 |
1ДК |
Годен |
|
3 |
1а |
5 |
1ДК |
Не годен |
Присутствуют недопустимые дефекты |
4 |
2а |
5 |
1ДК |
Годен |
|
Проверка сварного шва — сопровождение и завершение сварочных работ
Всесторонний и полный контроль сварных швов – ключевой компонент обеспечения надёжного и качественного соединения деталей в узел и работоспособности обследуемого объекта. Правильная оценка качества шва важна всегда, но в ответственных соединениях параметры шва нормируются. Регламентируется и контроль этого типа соединений.
Нормы государственных стандартов, отраслевые нормы задают все необходимые требования к сварке:
- Обработку кромок и деталей
- Сварочные материалы и технологии
- Регламент контроля.
Вот почему качество объекта, в котором предусмотрена сварка, закладывается на стадии проектирования. Грамотный дизайн конструкции любого объекта предусматривает удобство выполнения сварочных работ, обработку швов и их контроль, а впоследствии – антикоррозионные и отделочные мероприятия. Таким образом, качество сварного шва определяется до начала его исполнения — грамотным дизайнерским и конструкторским решением.
Качество сварного соединения
Соединения металлических деталей сваркой играют различную роль в общей работе конструкции. Ответственные соединения при деформации или разрушении делают невозможной эксплуатацию всего узла, изделия или конструкции. Очень часто угроза потери сварным соединением работоспособности неизбежно ведёт к крупной аварии и большой опасности для многих людей. Это – важные, ответственные соединения, контроль которых осуществляется самым тщательным образом, строго нормируемым соответствующими правилами и законами.
Измерение геометрии сварного шва
Во многих конструкциях использованы такие соединения сваркой, деформации и разрушение которых приведут к незначительным негативным явлениям без угрозы людям и без серьёзных убытков. Такие соединения должны соответствовать нормам самого общего характера. Проверка таких швов выполняется в общем порядке, без детального анализа и полной проверки.
Важная часть сварочной технологии – точная настройка режима каждой операции. Такое уточнение режима сварки реализуется выполнением пробных швов с использованием проектных материалов для будущего соединения. Эти образцы можно подвергать любому виду контроля, в том числе – со вскрытием (разрезкой) швов для анализа. Пробы позволяет уточнить параметры тока, проверить точность выбора электродов или других сварочных материалов.
Вся подготовительная работа значительно уменьшает риск брака в выполнении соединений сваркой, а проверка качества сварных швов всегда доказывает целесообразность пробных образцов.
Порядок проверки сварных соединений
Порядок выполнения оценки качества сварных соединений приблизительно одинаков для всех случаев применения технологии сварки. Проверку выполняют таким образом:
- Выполненный участок шва зачищают от шлака и окалины, а при необходимости – обрабатывают раствором кислоты для получения однородной поверхности шва
- Выполняют визуальный осмотр и замеры параметров шва
- Производят инструментальную проверку качества шва согласно регламенту, предусмотренному нормами для изготавливаемого изделия или конструкции.
На практике первые фазы такого контроля проводят в процессе выполнения сварки. Специалист-сварщик проверяет выполнение операции, добиваясь достаточного уровня качества, для чего требуется контролировать параметры сечения шва (величину катета), его длину и другие требования, например – к выполнению прерывистого шва.
Магнитный метод проверки образца сварного шва
Только добившись полного выполнения технологических требований, сварщик объявляет шов выполненным и предъявляет его к проверке, зачистив от шлака и окалины. На практике исполнение важных и ответственных швов делается в присутствии специалистов, отвечающих за качество такой работы. Эти специалисты выполняют текущий контроль процесса сварки, корректируют этот процесс, контролируют его.
Хорошая организация сварочных работ, участие в них компетентных специалистов нужного уровня обеспечивают высокое качество, которое почти всегда подтверждается точным инструментальным контролем.
Особенности контроля сварочных работ
Выполняемый контроль сварных соединений преследует цель не только выяснить качество шва, но и его соответствие особенным требованиям узла, изделия или конструкции, для которой он выполнен. Одно из основных таких требований – герметичность шва и его способность выдержать давление.
Особенности некоторых изделий, изготавливаемых с применением сварки таковы, что контроль под давлением осуществить невозможно. В таком случае эта проверка откладывается на момент испытания полностью готового объекта. Так поступают при испытаниях ёмкостей и трубопроводов, работающих под высоким давлением. Дефекты швов, обнаруженные при испытании давлением, исправляют и проверяют качество повторным испытанием.
Одна из главных особенностей проверки качества сварных соединений заключается в необходимости контролировать весь процесс, от разделки кромок до зачистки готового шва от шлака и окалины. Отчасти такая необходимость объясняется тем, что сварку выполняет один человек и надёжность многих сложных, дорогостоящих и опасных конструкций нельзя оставлять в зависимости от одного, самого ответственного исполнителя или подрядчика.
Небольшая группа специалистов, в которую хорошо включать инженера, способна обеспечить хорошую поддержку непосредственному исполнителю сварочных работ, квалификация которого в самом лучшем случае ограничена практическими навыками. В такой группе могут приниматься более точные решения о корректировке режима сварки, что в конечном итоге отражается на качестве готового шва. Важна мотивация сварщика и всей группы, заинтересованных в качественном выполнении сварочных работ.
Осмотр и замеры сварочных швов
При выполнении серьёзных, ответственных сварочных операций к контролю шва относят проверку разделки кромок соединяемых деталей, от которых зависит соответствие всей операции проектным требованиям.
Цель первой стадии контроля сварных соединений – проверка параметров шва и обнаружение видимых изъянов, а также – признаков внутренних дефектов. Вот что проверяет эксперт, выполняющий такую работу:
- Делаются замеры длины шва
- Шаблоном проверяют профиль (сечение) шва
- Оценивается равномерность шва, его внешний вид, свидетельствующий о качестве наплавленного металла
- Шов тщательно осматривается на предмет поиска непроваров, подрезов, следов обрыва дуги — основных дефектов сварочной технологии
- Уточняется характер последующих фаз контроля, учитывающих требования норм и характер операции.
Внешний вид шва многое говорит опытному специалисту, неспроста некоторые швы подвергают самому придирчивому контролю. В случае обнаружения недопустимого брака шов срезают или вырубают, после чего выполняют заново. Есть изделия и конструкции, в которых повторное выполнение сварочной операции не допускается, такие детали и узлы изготавливают заново.
Сварщик выполняет первые этапы визуального контроля в процессе сварки шва
Значительные дефекты, обнаруженные визуально, являются достаточным основанием для признания шва браком, другие виды диагностики при этом не требуются. После исправления дефектов проверку сварных швов выполняют заново.
Ультразвуковой контроль сварки
Проверка сварочных швов ультразвуковой аппаратурой – самый распространённый метод неразрушающего контроля соединений такого рода. Это объясняется самыми широкими возможностями такой аппаратуры, простотой и безопасностью её работы, пригодностью для применения в полевых условиях.
Ультразвуковые дефектоскопы предназначены для обнаружения мест с нарушением цельности и плотности металла, для поиска трещин, пустот, каверн, включений шлака и других дефектов.
Магнитная проверка швов
Ещё один достаточно распространённый способ контроля качества сварных швов основан на использовании свойств магнитного поля, на состоянии которого отражаются внутренние дефекты сварного соединения. Этот метод особенно хорош в стационарных условиях производства, но есть и портативная аппаратура для его применения «на выезде».
В зоне проверки выполненной сварки создаётся сильное магнитное поле, а на поверхность шва наносят мелкодисперсную смесь или взвесь со стальными опилками, которые занимают характерное положение, отражающее состояние магнитного поля в необходимом месте.
На равномерном фоне такого изображения отчётливо видны места, где магнитное поле неравномерно – это и есть место расположения дефекта или брака. Одно из важных достоинств этого метода – его наглядность и простота. Рисунок характера магнитного поля, отображённый на поверхности сварочных швов детали можно сфотографировать и включить в документацию о выполнении контроля.
Капиллярный контроль
Ещё один хороший способ проверки качества сварки – капиллярный контроль, который в старые времена назывался керосиновой пробой. Суть этого метода заключается в том, что керосин, обладающий очень высокой степенью текучести, способен проникать в самые тонкие зазоры и трещины, где он потом обнаруживается с помощью специальных вспомогательных материалов.
Эта технология применяется и сейчас, причём в старинном виде, с использованием керосина и мела, который наносят на обследуемое место. На поверхности, покрытой мелом, проявляются следы керосина, сохранившегося в дефектных местах – трещинах шва.
Интересны особенности выполнения сплошного шва нахлестом. Такая технология формирования стыка листовых материалов или заготовок приводит к образованию небольшого промежутка между двумя швами, расположенными с обеих сторон плоскостного (в пределах ограниченного участка) по характеру объекта.
Для выполнения капиллярного контроля проникающую жидкость, керосин или пенетрант закачивают в этот промежуток под небольшим давлением через специально сделанное для этого отверстие. Следы проникновения пенетранта стараются обнаружить с одной, иногда – с обеих сторон фрагмента объекта.
Так же работает и современная замена керосину – пенетрант, который сохраняется в трещинах, полостях и прочих дефектных местах. Кстати, во многих современных составах для капиллярного анализа пенетрант либо содержит керосин, либо является полноценным керосином с добавками.
Теоретически возможны ситуации, при которых керосиновая проба может не отреагировать на наличие полостей в теле шва, но вероятность такого дефекта ничтожна.
Сварка рельсов
Рельсы железнодорожных и трамвайных путей соединяют сваркой на сложных узлах пересечений и разветвлений, а также – для уменьшения количества стыков. Для этого применяют три основные технологии:
- Обычная ручная дуговая сварка электродом
- Контактная сварка, в том числе — в виде газопрессовой технологии
- Термитная сварка – оригинальная технология, аналогичная процессу плавки и литья.
В особенных условиях протяжённых рельсовых путей используют специальные передвижные установки, представляющие собой мобильный сварочный пост, в составе которого есть и аппаратура неразрушающего контроля сварных швов и стыков. Такая организация сварки и её проверки важна для оперативного выполнения всех работ. Скорость сооружения или ремонта рельсового пути – важный фактор экономического характера.
Другие методы проверки качества сварки
В производственных, а иногда – в полевых условиях применяют и другие методы контроля сварных швов. Ограничения в их использовании обусловлены дороговизной, громоздкой или опасной аппаратурой. Вот несколько таких методов:
- Радиационный (рентгенографический) контроль, использование которого ограничивает дороговизна и опасность радиационного поражения для человека. Точность и наглядный характер этой проверки не позволяют отказаться от его применения
- Проверка высоким давлением – этот метод применим только для испытания объектов, формирующих замкнутый порожний объём. Места, где шов «пропускает», обнаруживаются при помощи обычного мыльного раствора
- Испытание герметичности аммиаком – эта методика, применяемая для проверки герметичности швов, имеет ограниченное применение из-за опасности аммиака для человека, однако отличается очень высокой точностью. Идея такой проверки состоит в том, что пары аммиака, которым удаётся проникнуть в самых малых количествах через обследуемый шов, вступают в реакцию с индикаторным составом с обратной стороны.
Технологии проверки качества сварных швов приблизительно одинаковы для всех видов свариваемых материалов:
- Стали
- Нержавеющей стали
- Алюминия
- Чугуна
и некоторых других цветных металлов. Наибольшие сложности вызывает проверка результатов ручной дуговой сварки электродами, немного проще проверить результаты газосварки.
Более высокое качество сварного шва обеспечивает сварка полуавтоматом, выполняемая в среде углекислого газа. Настолько же качественными получаются швы, выполненные во многих современных технологиях автоматической сварки. Швы, выполненные в атмосфере аргона, отличаются мизерным количеством шлака и окалины, полноценным составом наплавляемого металла. Проверка таких сварочных соединений показывает лучшие, чем при ручной сварке электродами, результаты.
Общее качество сварочных работ принципиально выше на отлаженных производственных участках и линиях, работающих в стационарном режиме. В таком же постоянном, стационарном режиме работает и система контроля сварных соединений. Количество дефектов и брака в таких производственных условиях минимально.
Такой поточный режим применяют при изготовлении многих изделий и деталей в разных отраслях. Качественная наладка постоянного, стабильного режима сварки – гарантия высокого качества. В такой технологии серийного стационарного производства можно изготавливать даже крупноразмерные строительные конструкции.
В полевой обстановке, на стройплощадке, условия выполнения сварочных работ хуже, чем в производственном цеху, уровень качества швов также не так высок. Проверка в полевых условиях сложнее. Эти и многие другие факторы учитывают при разработке проектов тех объектов, где применяется сварка, а качественно запроектированный объект всегда будет доведён до завершения.
Контроль качества сварных соединений
Контроль качества сварных соединений
Контроль качества труб, помимо оценки и контроля качества отливок, должен включать контроль качества сварных швов, который проводится непосредственно при выполнении сварного соединения. Дефекты могут быть внешними и внутренними, и если первые можно обнаружить визуальным анализом или с помощью лупы, например, увеличительной линзы, то при поиске последней используются разные методы неразрушающего контроля качества, среди которых существует радиационный (рентгенографический) метод.
При неразрушающем контроле качества сварных изделий необходимо искать следующие дефекты, которые могут быть обнаружены в сварном шве и не видны на поверхности:
- скрытые трещины и абсцессы,
- пузырьки и поры газа,
- неисправные плавкие соединения,
- неплавкие сплавы,
- мест повышенной твердости (шлаковые, оксидные, металлические и др.),
- вогнутость и выпуклость корня шва,
- прожоги и поднутрения,
- превышение скорости плавки и другие дефекты сварки.
Оборудование для контроля качества сварных швов и стыков
Контроль качества сварных и сварных конструкций радиографическим методом может осуществляться с помощью рентгеновского оборудования , широкий спектр которого представлен на рынке. При этом дефекты сварных швов на полученных рентгеновских снимках проявляются в виде темных пятен, так как проходящие через них рентгеновские лучи теряют первоначальную интенсивность.
Часто визуальный анализ фотографий оказывается недостаточно эффективным и удобным, и фотографии обрабатываются и просматриваются на компьютере, для чего, помимо рентгеновского аппарата, используется система визуализации — камера, подключенная к ПК с установленное на нем управляющее приложение, а также для анализа и обработки изображений.
Программа контроля качества сварных соединений и швов
Программное обеспечение, разработанное специалистами Altami , используется для анализа и форматирования изображений, в том числе рентгеновских, и проведения измерений.В приложении Altami Studio есть все необходимые инструменты для повышения качества изображений (регулировка яркости и контрастности, гамма-коррекция, фильтр Псевдоцветов, разработанный специально для обработки рентгеновских лучей и многое другое), а также для измерений — длины, периметра, площади объектов. В приложении есть функция автоматического поиска необходимых объектов с последующим выводом статистики (периметр и площадь).
Кроме того, используя разработки в области автоматизации контроля качества, отдел разработок Альтами может обеспечить автоматизацию контроля качества сварных соединений и сварных швов с помощью программного продукта на базе Altami Studio .
Ультразвуковой контроль сварных соединений, методы и технология контроля
Практически нет промышленности, где бы проводились сварочные работы. Подавляющее большинство металлоконструкций монтируются и соединяются между собой сварочными швами. Конечно, качество подобных работ в будущем зависит не только от надежности возведенного здания, сооружения, машины или какого-либо агрегата, но и от безопасности людей, которые будут так или иначе взаимодействовать с этими конструкциями.Поэтому для обеспечения надлежащего уровня выполнения таких операций применяется ультразвуковой контроль сварных швов, благодаря которому можно обнаружить наличие или отсутствие различных дефектов на стыке металлических изделий. Об этом продвинутом способе контроля и пойдет речь в нашей статье.
История возникновения
Ультразвуковая дефектоскопия как таковая была разработана в 30-х годах. Однако первое реально работающее устройство появилось на свет только в 1945 году благодаря компании Sperry Products.За следующие два десятилетия новейшие технологии управления получили мировое признание, количество производителей такого оборудования резко увеличилось.
Ультразвуковой дефектоскоп, цена которого на сегодняшний день начинается от 100 000 -130000 тыс. Руб., Изначально базировался на электронных лампах. Такие устройства были громоздкими и тяжелыми. Работали исключительно от источников переменного тока. Но уже в 1960-х, с появлением полупроводниковых схем, дефектоскопы были значительно уменьшены в размерах и могли работать от батарей, что в конечном итоге позволило использовать устройства даже в полевых условиях.
Шаг в цифровую реальность
На ранних этапах работы описываемых устройств использовалась аналоговая обработка сигналов, из-за чего, как и многие другие подобные устройства, были подвержены дрейфу в момент калибровки. Но уже в 1984 году компания Panametrics дала старт первому портативному цифровому дефектоскопу под названием EPOCH 2002. С этого момента цифровые блоки превратились в высоконадежное оборудование, в идеале обеспечивающее необходимую стабильность калибровки и измерений. Ультразвуковой дефектоскоп, цена которого напрямую зависит от его технических характеристик и марки производителя, также получил функцию записи данных и возможность передачи показаний на персональный компьютер.
В современных условиях все больше и больше интересуют системы с фазированными решетками, в которых используется сложная технология, основанная на многоэлементных пьезоэлектрических элементах, генерирующих направленные лучи и создающих поперечные изображения, аналогичные медицинской ультразвуковой визуализации.
Область применения
Ультразвуковой метод контроля применяется во всех направлениях промышленности. Его применение показало, что его можно одинаково эффективно использовать для испытаний практически всех типов сварных соединений в строительстве, имеющих толщину сварного основного металла более 4 миллиметров.Кроме того, метод активно используется для проверки соединений стыков газонефтепроводов, различных гидравлических систем и систем водоснабжения. И в таких случаях, как контроль швов большой толщины, полученных в результате электрошлаковой сварки, ультразвуковая дефектоскопия является единственным приемлемым методом контроля.
Окончательное решение о пригодности заготовки или сварного шва к эксплуатации принимается на основании трех основных показателей (критериев) — амплитуды, координат, условных размеров.
В целом ультразвуковой контроль — это как раз тот метод, который наиболее плодотворен с точки зрения формирования изображения в процессе исследования шва (деталей).
Причины актуальности
Метод контроля с применением ультразвука хорош тем, что имеет гораздо более высокую чувствительность и надежность показаний при обнаружении дефектов в виде трещин, меньшую стоимость и высокую безопасность при использовании по сравнению с классические методы рентгенологического контроля.На сегодняшний день ультразвуковой контроль сварных соединений применяется в 70-80% случаев контроля.
Ультразвуковые преобразователи
Без использования этих устройств неразрушающий ультразвуковой контроль просто немыслим. Устройства служат для формирования возбуждения, а также для приема колебаний ультразвука.
Заполнители различаются и могут быть классифицированы по:
- Методу контакта с исследуемым продуктом.
- Способ подключения пьезоэлементов к электрической цепи самого дефектоскопа и смещение электрода относительно пьезоэлемента.
- Ориентация акустическая по отношению к поверхности.
- Количество пьезоэлементов (одно-, двух-, многоэлементные).
- Ширина полосы рабочих частот (узкополосная — полоса менее одной октавы, широкополосная — полоса пропускания более одной октавы).
Измеренные характеристики дефектов
В мире технологий и промышленности ГОСТ руководит каждым.Ультразвуковой контроль (ГОСТ 14782-86) в этом вопросе тоже не исключение. Стандарт устанавливает, что дефекты измеряются по следующим параметрам:
- Эквивалентная площадь дефекта.
- Амплитуда эхо-сигнала, определяемая с учетом расстояния до дефекта.
- Координаты дефекта в месте сварки.
- К условным размерам.
- Условное расстояние между дефектами.
- Количество дефектов на выбранной длине сварного шва или стыка.
Работа дефектоскопа
Неразрушающий контроль, который является ультразвуком, имеет свой собственный метод использования, который гласит, что основным измеряемым параметром является амплитуда эхо-сигнала, полученного непосредственно от дефекта. Чтобы отличить эхо от величины амплитуды, устанавливается так называемый уровень подавления чувствительности. Он, в свою очередь, настраивается с использованием стандартного корпоративного образца (СОП).
Начало работы дефектоскопа сопровождается его настройкой.Для этого устанавливается чувствительность отбраковки. После этого в ходе проведенных ультразвуковых испытаний полученное эхо-сигнал сравнивается от обнаруженного дефекта с фиксированным уровнем отклонения. В том случае, если измеренная амплитуда превышает уровень брака, специалисты решают, что такой дефект недопустим. Затем шов или изделие отклоняются и отправляются на доработку.
Наиболее часто встречающиеся дефекты свариваемых поверхностей: непровар, непровар, трещины, пористость, шлаковые включения.Именно эти аномалии эффективно обнаруживают дефектоскопию с помощью ультразвука.
Варианты ультразвукового исследования
С течением времени в процессе проверки появилось несколько эффективных методов исследования сварных соединений. Ультразвуковой контроль предоставляет достаточно большое количество вариантов акустического исследования рассматриваемых металлических конструкций, но наиболее популярными являются:
- Эхо-метод.
- Тень.
- Метод зеркала-тени.
- Эхо-зеркало.
- Дельта-метод.
Метод номер один
Чаще всего в промышленности и на железнодорожном транспорте используется эхо-импульсный метод. Именно благодаря ему диагностируется более 90% всех дефектов, что возможно за счет регистрации и анализа практически всех сигналов, отраженных от поверхности дефекта.
Сам по себе этот метод основан на звуке металлического изделия импульсами ультразвуковых колебаний с последующей их регистрацией.
Преимущества метода:
— возможность одностороннего доступа к товару;
— довольно высокая чувствительность к внутренним дефектам;
— высшая точность определения координат обнаруженного дефекта.
Однако есть и недостатки, среди которых:
— низкая устойчивость к помехам от поверхностных отражателей;
— сильная зависимость амплитуды сигнала от места дефекта.
Описанная дефектоскопия означает отправку ультразвукового генератора на изделие. Прием ответного сигнала происходит либо им, либо вторым искателем. При этом сигнал может отражаться как непосредственно от дефектов, так и от противоположной поверхности детали, изделия (шва).
Теневой метод
Он основан на подробном анализе амплитуды ультразвуковых колебаний, передаваемых от излучателя к приемнику. В е
.Строительство резервуаров для хранения| Монтаж резервуара для хранения
7.1. Методика контроля качества сварных соединений при монтажных работах
Контроль качества сварных соединений при строительстве резервуара должен включать:
- Применение способов сварки, способов и объема контроля сварных соединений, применимых к степени важности резервуара;
- Применение эффективных технологических процессов сварки и материалов согласно положениям плана металлоконструкций и плана выполнения работ;
- Осуществление авторского и технического надзора.
В таблице приведены сведения о методах контроля качества сварных соединений, применяемых в зависимости от контролируемого элемента резервуара:
Зона контроля | Метод контроля | |||||
визуально-измерительная | вакуум | радио | ультразвуковой | капилляр (цвет) | избыточное давление | |
НИЖНЯЯ | ||||||
Шарниры нижние | + | + | – | – | – | – |
Нижние швы на расстоянии 250 мм от внешнего края | + | + | + | – | – | – |
ОБОЛОЧКА | ||||||
Вертикальные стыки 1-й и 2-й зон | + | – | + | + ¹ | – | – |
Вертикальные стыки остальных зон | + | – | + ² | + | – | – |
Швы горизонтальные | + | – | + ² | + | – | – |
Перекрестие вертикальных и горизонтальных швов | + | – | + | – | – | – |
Патрубок-патрубок | + | + | – | + | – | – |
Стык между хомутом патрубка (люка) и 1м ремнем гильзы | + | – | – | – | + | + |
Стык между хомутом патрубка (люка) и стенкой (кроме 1-го пояса) | + | – | – | – | – | + |
Радиальные соединения колец жесткости | + | – | – | – | – | + |
Места снятия монтажных устройств, сварные соединения элементов конструкций после их термообработки | + | – | – | – | + | – |
Соединение днище с оболочкой | + | + | – | – | + | – |
КРЫША | ||||||
радиальные стыки опорного кольца | + | – | – | + | – | – |
Стыки кровли, щиты кровельные | + | + | – | – | – | + |
Соединение патрубка к кровле | + | + | – | – | – | – |
ПЛАВАЮЩАЯ КРЫША | ||||||
Стыки ящиков (отсеков) и заглушки стеллажей | + | – | – | – | – | + |
Стыки центральной части | + | + | – | – | – | – |
Отводы к кровле | + | + | – | – | – | – |
1 разрешено использование ультразвукового контроля 2 разрешено рентгенографическое исследование 3 контроль пробоя «мел-керосин» фиксация сварного шва с внутренней стороны |
Объем физического контроля сварных швов (в процентах от длины шва) оболочки резервуара в зависимости от класса опасности резервуара должен соответствовать требованиям таблицы:
ОБЪЕМЫ ФИЗИЧЕСКОГО КОНТРОЛЯ СВАРНЫХ СОЕДИНЕНИЙ ОБОЛОЧКИ БАКА , в% от длины шва | |||||
Зона контроля | класс опасности | ||||
IV | III | II | Я | ||
1 000 — 10000 м³ | 10000 –20000м³ | ||||
Вертикальные сварные соединения: | |||||
в зонах 1-2 | 20% | 25% | 50% | 100% | 100% |
в зонах 3-4 | 5% | 10% | 25% | 50% | 100% |
в зонах 5-6 | 2% | 5% | 10% | 25% | 50% |
зоны выше 6-й | – | – | 5% | 10% | 25% |
горизонтальных швов: | |||||
в зонах 1-2 | 3% | 5% | 10% | 15% | 20% |
в зонах 3-4 | 1% | 2% | 5% | 5% | 10% |
в зонах 5-6 | – | – | 2% | 2% | 5% |
в других зонах | – | – | – | 2% | 2% |
При выборе зон контроля преимущественное внимание следует уделять зонам пересечения стыков.
Монтаж стыков резервуаров, устанавливаемых спиральным способом, вместимостью от 1000 м³ и более необходимо контролировать по всей длине стыков.
Результаты испытаний и контроля качества сварных соединений фиксируются в актах и актах и являются существенными дополнениями к документации на резервуар.
7.2. Заключительные испытания после строительства резервуара для хранения нефти
Завершающим этапом испытаний резервуара является гидравлическое испытание под давлением, предназначенное для проверки герметичности соединений и прочности конструкции в целом.
Цистерны с несъемной крышей без понтона дополнительно подвергаются избыточному давлению и относительному давлению изнутри.
В приведенной ниже таблице указаны испытания, которые необходимо провести для резервуаров разных типов (1 — резервуары с неподвижной крышей без понтона, 2 — резервуары с неподвижной крышей и понтоном, 3 — резервуары с плавающей крышей).
№ | вид испытания | 1 | 2 | 3 |
1 | Испытание на водонепроницаемость | + | + | + |
2 | Испытание корпуса цистерны на прочность при гидростатической нагрузке | + | + | + |
3 | Испытание на герметичность неподвижной крыши | + | – | – |
4 | Проверить устойчивость корпуса резервуара путем создания относительно разрежения внутри резервуара | + | – | – |
5 | Испытание плавающей крыши на плавучесть | – | + | + |
6 | Тест производительности роликовой лестницы | – | – | + |
7 | Проверка устойчивости основания цистерны с определением абсолютной и неравномерной тяги по контуру днища, крен профиля цистерны центральной части днища | + | + | + |
Гидравлическое испытание резервуаров с плавающей крышей или понтоном под давлением проводится перед установкой краевых уплотнений.
Испытания цистерны любого типа проводятся на основании программы испытаний, включенной в проектный проект металлоконструкции и план выполнения работ.
Программа тестирования должна включать:
- Этапы испытаний, оговаривающие уровень загрузки / слива воды и время выдержки;
- Нормы избыточного и относительного давления, время выдержки при испытании;
- Схема визуального осмотра;
- Требования к замерам необходимых геометрических параметров элементов конструкции резервуара и его фундамента;
- Обработка результатов испытаний, контрольные расчеты (при необходимости), итоговый отчет о пригодности и режиме эксплуатации цистерны.
7.2.1. Гидравлические испытания бака под давлением
В процессе гидравлического испытания под давлением бак постепенно наполняется водой до запланированного уровня. Нагружение осуществляется поэтапно с определенными временными интервалами, предназначенными для контроля его осадки и состояния сварных швов, а также для проведения других измерений и контроля, предусмотренных программой испытаний.
Если в ходе испытания обнаруживается утечка из-под края днища или в первом кольце корпуса, вода полностью сливается (удаляется).При обнаружении трещин в швах оболочки вода сбрасывается до уровня ниже обнаруженного дефекта. Если дефект появляется в кольце 2 nd -6 th , вода удаляется до уровня на одно кольцо ниже дефекта. При появлении дефекта в кольце 7 -е и выше — вода удаляется в кольцо 5 -го . После устранения дефектов тестирование продолжается.
Резервуары для хранения жидких материалов с массовой плотностью, превышающей плотность воды, а также резервуары, устанавливаемые на участках без наличия воды, могут испытываться с самим продуктом.Перед такими испытаниями все сварные соединения кожуха, днища, крыши и труб люка / фитингов, а также соединения кожуха с крышей и днищем должны быть проверены на герметичность.
Резервуар, наполненный до запланированного уровня, должен находиться под нагрузкой в течение следующего периода:
- Резервуар стальной вертикальный V≤10000 м³ — 24 часа;
- Резервуар стальной вертикальный V = 10000-20000 м³ — 48 часов;
- Резервуар стальной вертикальный V≥20000 м³ — 72 часа.
Цистерна считается выдержавшей испытание, если в течение периода испытаний на ее поверхности или по краям дна не возникнет протечки, если уровень испытуемого продукта не снизился, если осадка (проседание) фундамента и фундамента стала стабильный.
Гидравлическое испытание под давлением рекомендуется проводить при температуре не ниже +5 ° С. Если испытание проводится в зимний период, воду следует подогреть или обеспечить ее постоянную циркуляцию, чтобы предотвратить ее замерзание в трубах и задвижках, а также не допустить обмерзания корпуса резервуара.
7.2.2. Испытания под давлением корпуса и крыши резервуара под давлением:
Неподвижная крыша резервуара без понтона испытывается на избыточное давление с резервуаром, заполненным до уровня, который на 10% ниже планового, с выдержкой груза 30 минут.Давление обеспечивается за счет потока воды при плотно закрытых крышах люков. В ходе испытаний проводится полный визуальный контроль сварных швов несъемной кровли.
Устойчивость корпуса резервуара проверяют относительным давлением внутри резервуара, наполненного водой до уровня 1,5 м, выдерживая резервуар под нагрузкой в течение 30 мин. Относительное пониженное давление обеспечивается сливом жидкого продукта при плотно закрытых люках. Если признаков неустойчивости не обнаружено (отсутствие заклинивания, застревания), считается, что корпуса и крыши выдержали испытание на относительное давление.
Избыточное давление применяется на 25% выше планового уровня, относительное пониженное — на 50% выше планового, если проектная документация не содержит иных требований.
После проведения приемочных испытаний приваривать к резервуару какие-либо элементы конструкции не разрешается. Возможно выполнение антикоррозионных работ, утепление и монтаж оборудования, предусмотренного проектной документацией.
После проведения гидравлических испытаний под давлением необходимо оценить фактическое техническое состояние металлического каркаса резервуара, фундамента и фундамента.
7.2.3. Основные требования к организации и проведению испытаний:
Окончательное испытание резервуара на прочность, устойчивость и герметичность проводится после завершения всех сварочно-монтажных работ, проверки качества всех элементов конструкции, в том числе сварных швов, и принятия организацией технического надзора.
Все испытания проводятся в соответствии с технологической схемой, включенной в План выполнения работ. В технологическую карту включить:
- Порядок и режим гидравлических испытаний под давлением;
- Порядок и режим испытаний на избыточное давление и вакуум;
- Устройство временных трубопроводов для погрузки и выгрузки воды с установкой Безопасность и запорные клапаны;
- Панель управления;
- Требования безопасности труда при испытаниях.
Временный трубопровод для отгрузки и отвода воды должен быть проложен вне зоны насыпи. Схема отвода воды разрабатывается для каждого конкретного случая. В процессе испытаний вода часто перекачивается из одной емкости в другую, а из последней — в пожарную емкость временного водоема.
Диаметр трубопровода для погрузки-разгрузки воды должен соответствовать расчетному уровню эффективности погрузочно-разгрузочных работ.
Кроме схемы работы потока и слива воды, следует предусмотреть схему аварийной разгрузки на случай появления трещин на корпусе резервуара. В аварийных целях рекомендуется использовать один из трубопроводов заборно-раздаточной арматуры и технологический трубопровод с задвижкой вне зоны насыпи.
Обязательно установить и специально обозначить предупредительными знаками границы опасной зоны на период испытаний. Если вокруг резервуара устроена насыпь или защитная оболочка, они считаются границей опасной зоны.В случае установки резервуара без насыпи пределы опасной зоны определяются радиусом, проведенным от центра резервуара на расстояние, равное двум диаметрам резервуара.
Испытания проводит монтажная организация в сопровождении представителей службы технического надзора и руководителя строительного проектирования. По окончании испытаний специалисты по установке и заказчик подписывают акт (акт) о завершении монтажа металлоконструкций и приемке резервуара на дальнейшие антикоррозионные процедуры, монтаж оборудования и другие работы.
.