Расчет режима сварки под флюсом
Расчет режима сварки под флюсом производится по заданной глубине проплавления. Глубина проплавления йп определяется по формуле [c.326]Расчеты режимов сварки под флюсом [c.65]
В остальном, с учетом указанных особенностей, расчет режимов при сварке под флюсом аналогичен расчету режимов сварки в среде защитных газов (пункты 1 — 14). [c.55]
Для сварки изделий большей толщины рекомендуется разделка кромок. В зависимости от принятой формы разделки и режима сварки рассчитывают число слоев и устанавливают порядок их выполнения. Расчет площади поперечного сечения металла, наплавленного за один проход, и числа слоев проводится аналогично расчету при ручном процессе и сварке под флюсом. [c.224]
ЗОНЫ. Техника сварки первого прохода такая же, как и односторонних швов.
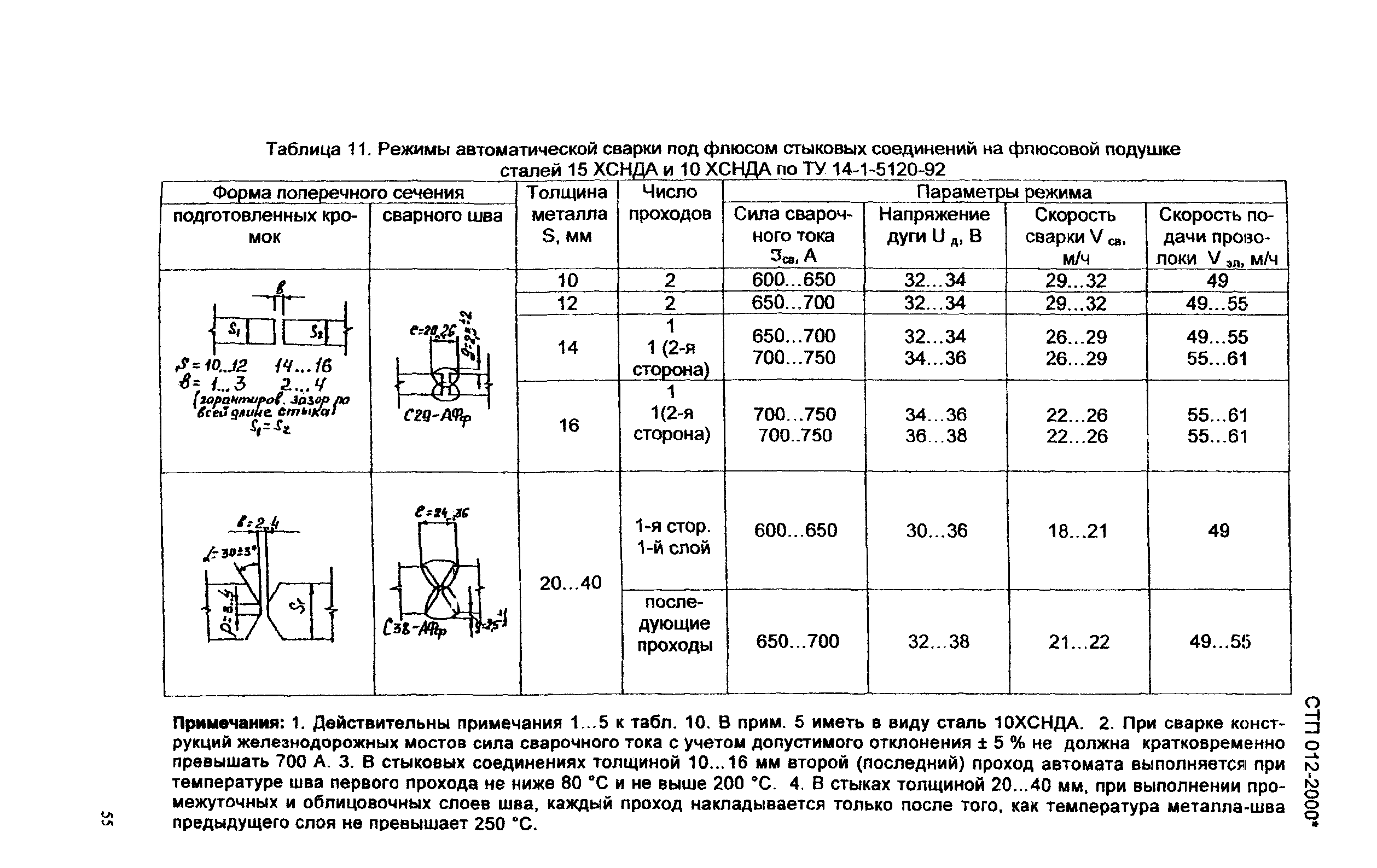
Приближенный расчет режимов автоматической сварки под флюсом [c.162]
Расчет режимов сварки стыковых швов под слоем флюса (эскизы соединений даны в табл. И). Для расчета принимаем напряжение на дуге 34 глубину проплавления Я = 9 мм величину усиления с — 2 мм, зазор а = 2 мм. [c.47]
Задача проектанта-технолога заключается в расчете режимов сварки соединений, обозначенных по ГОСТу 5263—58 на чертежах, заданных для производства в проектируемом цехе изделий. Обозначения на чертежах включают установленные стандартами для ручной дуговой сварки (ГОСТ 5264—58) и для автоматической и полуавтоматической сварки под флюсом (ГОСТ 8713—58) конструктивные элементы подготовки кромок и подлежащих выполнению швов для практически применяемых видов соединений.
Параметры режима автоматической сварки под флюсом могут быть выбраны либо по литературным (справочным) данным, либо расчетами. [c.48]
Типовой пример расчета режима автоматической сварки под флюсом стыкового соединения при толщине листов 5=10 мм. [c.49]
Пользуясь методикой расчета режимов автоматической сварки под флюсом, приведенной в разделе 3, решить следующие задачи [c.62]
Переход примеси из флюса в шов или, наоборот, окисление данного элемента из шва и переход его в шлак не является неизменным. Переход примеси зависит от режима сварки, состава и свойств флюса, а также от полярности при сварке на постоянном токе. Чем выше напряжение дуги, чем меньше ток, тем больше величина ДЛ. Однако для приблизительных расчетов для случая сварки под флюсами АН-348-А или ОСЦ-45 значения Д Л могут быть условно приняты следующими Д51=0,15 й ДМп = 0,20 й дС = —0,03 Д5=0 ДР = 0,008 6.
При расчете режима автоматической сварки под флюсом ток (/ ц) выбирают из расчета 100 а на 1 мм глубины проплавления. Скорость сварки (v J определяют по формуле [c.187]
РАСЧЕТ И ПРОВЕРКА РЕЖИМОВ АВТОМАТИЧЕСКОЙ СВАРКИ ПОД СЛОЕМ ФЛЮСА ПО ЗАДАННОЙ ГЛУБИНЕ ПРОВАРА [c.44]
Расчет режимов дуговой сварки под слоем флюса [c.51]
Процесс сварки ведется так, что к месту сварки впереди дуги подается флюс, количество которого определяется в зависимости от режима сварки с расчетом полного его расплавления. Толщина слоя флюса значительно влияет на формирование шва и глубину проплавления. Наибольшая глубина проплавления наблюдается при минимальной толщине слоя флюса, но в этом случае ухудшается формирование шва, а также затрудняется удаление шлака. С увеличением толщины слоя флюса выше определенного значения для данной толщины свариваемого металла в металле шва появляются поры и нарушается стабильность процесса.
Рассмотрим вопросы построения критериев подобия по методу анализа размерностей и основы теории многофакторного эксперимента. Формулы для выбора режимов сварки и приближенного расчета геометрических размеров сварных швов и их механических свойств приведены только для механизированной сварки под флюсом и только для низкоуглеродистых и пизколегированпых сталей. Для этих сталей и метода сварки указанные форму гы про1нли многократную опытную проверку и дают надежные результаты с точностью до 10 — 12%.
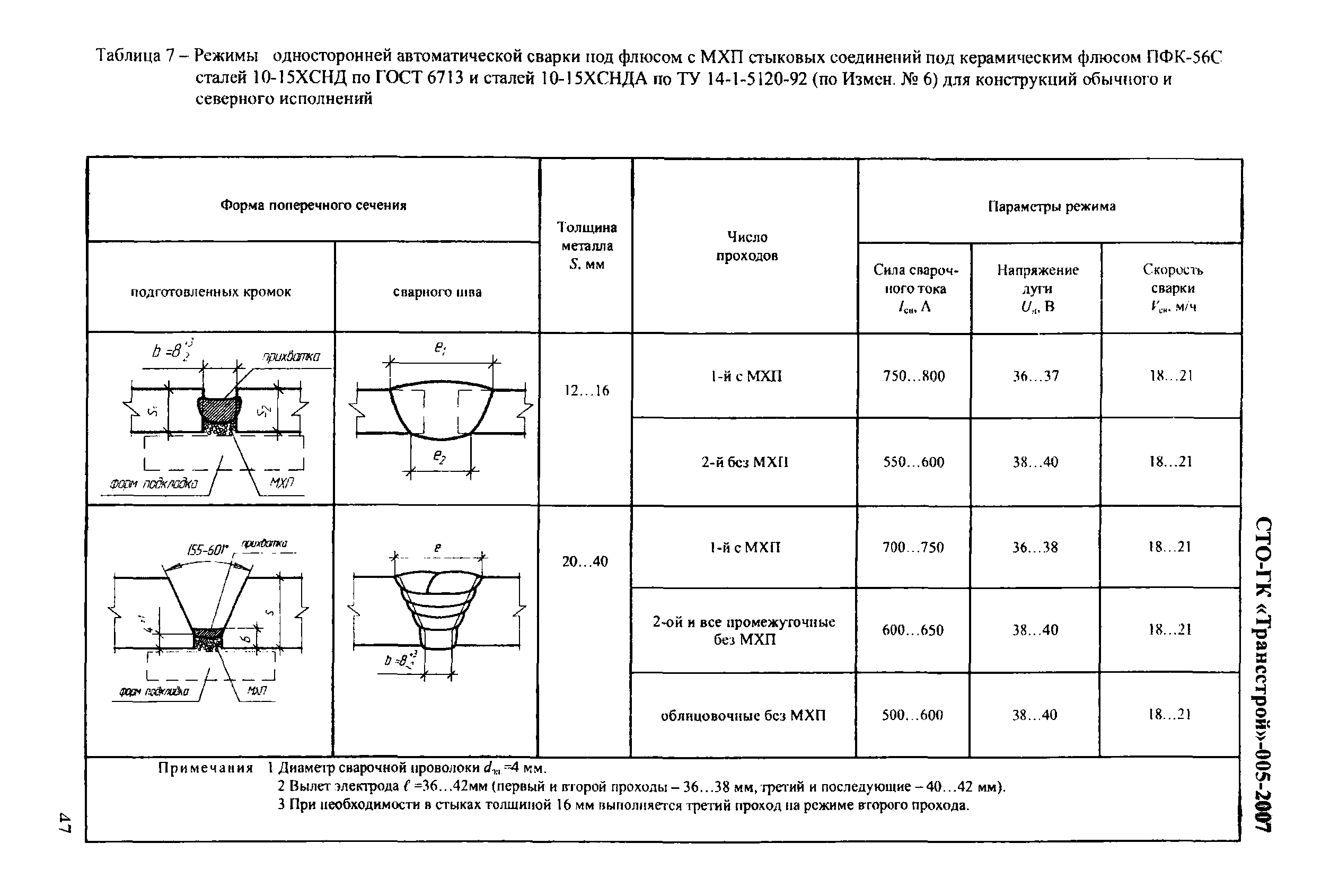
При использовании для сварки низкоуглеродистых проволок в полной мере можно реализовать преимущество сварки под флюсом получать швы с глубоким проплавлением, используя при однопроходной сварке стыковых соединений без разделки кромок повышенный сварочный ток и скорость сварки. Необходимый состав металла шва будет обеспечиваться повышением доли основного металла в шве, которую при выборе режима сварки во избежание перелегирования шва следует проверять расчетом. [c.253]
На рис. 100 схематически показаны форма разделки кромок и порядок выполнения слоев шва при однодуговой сварке под флюсом двухслойных сталей. Первый слой шва сваривают высоколегированной проволокой диаметром 1,6—2 мм на пониженных режимах с таким расчетом, чтобы усиление этого слоя шва было минимальным, но обеспечивался бы надежный провар. Этот слой целесообразно сваривать полуавтоматом на отдельном рабочем месте. Многие заводы успешно выполняют его автоматической сваркой проволокой диаметром 3 и даже4лгж.
При разработке технологии и техники сварки под флюсом пользуются двумя видами расчетов режимов сварки 1) расчетами, связанными с получением шва заданных геометрических размеров и 2) тепловыми расчетами. В первом случае определяют только режим сварки, т. е. ток, напряжение дуги, скорость сварки.
Расчет площади поперечного сечення шва, наплавленного за один проход, и числа проходов выполняется так же, как и при сварке под атоем флюса, но с учето.м разбрызгивания и угара, которые в данном случае намного больше. Ориентировочные режимы сварки в среде углекислого газа приведены в табл. 50—55. Реж1 Д ы сварки в среде аргона устанавливаются в каждом конкретном случае в зависимости от марки стали, назначения конструкции и других факторов. [c.151]
ВСН 375-77 Инструкция по автоматической дуговой под флюсом и электрошлаковой сварке с порошковым присадочным металлом (ППМ)
СТРОИТЕЛЬНЫХ РАБОТ СССР
УТВЕРЖДАЮ:
Заместитель министра монтажных
и специальных строительных
работ СССР
К. К. Липодат
10 февраля 1977 г.
ИНСТРУКЦИЯ
ПО АВТОМАТИЧЕСКОЙ ДУГОВОЙ
ПОД ФЛЮСОМ И ЭЛЕКТРОШЛАКОВОЙ
СВАРКЕ С ПОРОШКОВЫМ
ПРИСАДОЧНЫМ МЕТАЛЛОМ (ППМ)
ВСН 375-77
ММСС СССР
ЦЕНТРАЛЬНОЕ
БЮРО
НАУЧНО-ТЕХНИЧЕСКОЙ ИНФОРМАЦИИ
Москва — 1 9 78
СОДЕРЖАНИЕ
1. Общие положения . 2 2. Автоматическая дуговая сварка под флюсом с ППМ .. 2 Сварочные материалы .. 3 Технология сварки . 4 Сварка с предварительной засыпкой ППМ .. 5 Сварка с подачей ппм на вылет электрода . 6 Дефекты сварных швов, причины их появления и способы
устранения . 3. Электрошлаковая сварка с ППМ .. 10 Сварочное оборудование. Источники питания и монтажные приспособления . 10 Сварочные материалы .. 11 Технология сварки . 12 Подготовка и техника выполнения сварки . 13 Контроль качества сварных швов . 13 Дефекты сварных швов, причины их появления и способы устранения . 14 4. Техника безопасности при автоматической дуговой под флюсом и электрошлаковой сварке с ППМ .. 14 Приложение 1. Станок для рубки сварочной проволоки диаметром 0,8-2,0 мм на крупку . 14 Приложение 2. Расчет количества ППМ и скорости автоматической дуговой сварки с предварительной засыпкой ппм стыковых соединений листовых конструкций толщиной до 60 мм без скоса кромок . 16 Приложение 3. Методика и
номограммы для выбора параметров режимов автоматической дуговой сварки под
флюсом с подачей ППМ на вылет электрода стыковых с разделкой кромок и угловых
соединений низкоуглеродистых и низколегированных сталей . |
Инструкция разработана Всесоюзным научно-исследовательским институтом по монтажным и специальным строительным работам (ВНИИмонтажспецстрой) Минмонтажспецстроя СССР с участием Института электросварки (ИЭС) им. Е. О. Патона АН СССР и Московского высшего технического училища (МВТУ) им. Н. Э. Баумана Министерства высшего и среднего специального образования СССР.
Инструкция подготовлена кандидатами техн. наук И. И. Ивочкиным, А. И. Алексеевым, Б. Д. Малышевым, Ю. А. Черновым, А. Ф. Соседовым, Н. П. Рощупкиным; инженерами К. А. Илюковичем, Л. М. Матвеевой (ВНИИМонтажспецстрой) при участии докт. техн. наук О. И. Стеклова, канд. техн. наук Б. Ф. Якушина (МВТУ им. Н. Э. Баумана), доктора техн. наук Б. Ф. Лебедева, В. А. Богдановского (ИЭС им. Е. О. Патона).
Инструкция предназначена для специалистов сварочного производства,
работающих по изготовлению и монтажу металлических конструкций.
Минмонтажспецстрой СССР |
Ведомственные строительные нормы |
ВСН 375-77 |
Инструкция по автоматической дуговой под флюсом и электрошлаковой сварке с порошковым присадочным металлом (ППМ) |
ММСС СССР |
|
Впервые |
1.1. Инструкция распространяется на следующие способы сварки металлических конструкций:
автоматическую дуговую сварку под флюсом с применением порошкового присадочного металла (ППМ) в нижнем положении стыковых и угловых соединений из низкоуглеродистых сталей марок ВСт3кп, ВСт3пс, ВСт3сп и низколегированных сталей марок 09Г2С, 14Г2, 10Г2С1, 10ХСНД, 15ХСНД, 16Г2АФ и 14Х2ГМР толщиной до 60 мм;
электрошлаковую сварку с
применением ППМ низкоуглеродистых сталей марок ВСт3кп, ВСт3пс, ВСт3сп и
низколегированных сталей марок 10Г2С1, 09Г2С, 10ХСНД, 15ХСНД, 16Г2АФ толщиной
30-60 мм.
При обоих способах сварки с ППМ следует руководствоваться общими требованиями СНиП III-18-75 «Металлические конструкции. Правила производства и приемки работ» и положениями СНиП III — A .11-70 «Техника безопасности в строительстве», а также указаниями «Инструкции по изготовлению стальных конструкций из углеродистой и низколегированной сталей» МСН 97-65/ГМСС СССР и «Инструкции по электрошлаковой сварке кожухов доменных печей».
1.2. Введение в зону сварки ППМ повышает тепловую эффективность процесса и качество сварного соединения. Благодаря таким свойствам ППМ, как автономность, развитая поверхность и малая масса частиц, введение его в зону сварки позволяет значительно уменьшить потери тепла и повысить коэффициент полезного действия источника сварочного тепла.
Внесены |
Утверждены |
Срок введения |
1.3. В качестве ППМ используется крупка, приготовленная на простейшем станке (приложение 1) из сварочной проволоки диаметром 0,8-2,0 мм. При этом длина частицы крупки должна быть равна диаметру проволоки.
1.4. Сварочная проволока, применяемая для изготовления крупки, должна быть очищена от технологических и противокоррозионных смазок, масел, грязи и ржавчины.
1.5. ППМ должен иметь неокисленную поверхность и храниться в металлических закрытых сосудах в сухом помещении.
1.6. Изготовлять ППМ можно на любом стандартном и нестандартном оборудовании, обеспечивающем требуемые размеры металлической крупки.
1.7. Сварочный флюс АН-348А,
АН-60, АН-22, АН-8 по ГОСТ 9082-69 перед сваркой необходимо прокалить при
температуре 200-250 °С в течение 1,0-1,5 ч, если влажность флюса превышает 0,1
%, в соответствии с техническими условиями на эти материалы.
2.1. Автоматическая дуговая сварка под флюсом с ППМ производится на стандартном сварочном оборудовании: сварочных тракторах ТС-17МУ, ДТС-38, ТС-35, АДС-1000, сварочных самоходных автоматах подвесного типа АБСК, А-639К и др.
В качестве источников питания рекомендуются выпрямители ВКСМ-1000, ВДМ-1601, ВДМ-3001, ВСЖ-1600 и преобразователи типа ПСМ.
2.2. ППМ в зону сварки вводят двумя способами:
путем предварительной засыпки ППМ в зазор или разделку перед сваркой (рис. 1, а) простейшими устройствами;
путем подачи ППМ с ферромагнитными свойствами на вылет электрода в процессе сварки (рис. 1, б).
Дозировку и подачу ППМ на вылет электрода осуществляют дозатором конструкции ВНИИмонтажспецстроя, который устанавливают на любой сварочный трактор (рис. 2).
Сварочные материалы
2.3. Поставляемый для сварки
металл и сварочные материалы должны иметь сертификаты заводов-изготовителей.
2.4. Для обеспечения требуемых свойств металла шва необходимо применять ППМ и сварочную проволоку определенного химического состава (табл. 1), флюс марки АН-348А по ГОСТ 9087-69.
Рис. 1. Принципиальные схемы
сварки:
а — с предварительной засыпкой ППМ в зазор или
разделку; б — с подачей ППМ на вылет электрода в процессе сварки
Рис. 2. Сварочный трактор АДС-1000 с установленным на нем дозатором-приставкой для подачи ППМ на вылет электрода
Таблица 1
Сварочная проволока, используемая для приготовления ППМ в зависимости от свариваемого металла и марки электродной проволоки
Основной металл |
Электродная проволока |
ППМ в виде крупки из проволоки |
|
марка |
диаметр, мм |
||
Низкоуглеродистые стали |
Св-08А Св-08ГА |
4-5 4-5 |
Св-08А или Св-08Г2С Св-08А |
Низколегированные стали: |
|||
09Г2С |
Св-08ГА |
4-5 |
Св-08ГА или Св-08Г2С |
Св-10Г2 |
4-5 |
Св-10Г2 или Св-08Г2С |
|
10Г2С1 |
Св-08ГА |
4-5 |
Св-10Г2 или Св-08Г2С |
Св-10Г2 |
4-5 |
Св-10Г2 или Св-08Г2С |
|
14Г2 |
Св-08ГА |
4-5 |
Св-08Г2С или Св-10Г2 |
Св-10Г2 |
4-5 |
Св-10Г2 или Св-08Г2С |
|
16Г2АФ |
Св-08НМА или Св-08ХМ |
4-5 |
Св-08Г2С |
10ХСНД 15ХСНД |
Св-08ХМ |
4-5 |
Св-08Г2С или Св-08ГА |
Примечание . При сварке стали марки 14Х2ГМР необходимо
применять электродную проволоку марки Св-08ХН2ГМЮ с ППМ из проволоки Св-08Г2С,
флюс АН-17М.
Можно применять также флюсы АН-60 и АН-22 или смесь флюсов АН-348А и АН-60.
Технология сварки
2.5. Типы сварных соединений, конструктивные элементы подготовки свариваемых кромок (углы разделки, притупления и т.п.) должны соответствовать данным табл. 2 и 3.
2.6. При оборке деталей конструкции под сварку и подготовке поверхности необходимо руководствоваться указаниями СНиП III-18-75 «Металлические конструкции. Правила изготовления, монтажа и приемки» и «Инструкции по изготовлению стальных конструкций из углеродистой и низколегированной сталей» МСН 97-65/ГМСС СССР.
При подготовке под сварку стыковых соединений качество реза должно удовлетворять требованиям ГОСТ 14792-69. При этом допускается неперпендикулярность кромок реза к поверхности листов на величину h , которая не должна превышать значений, определяемых по формуле:
,
где lmin — минимальная ширина шва по ГОСТ;
b -
зазор по табл. 2.
Таблица 2
Швы стыковых соединений без скоса кромок, двухсторонние на стальной подкладке или флюсовой подушке
Тип шва по ГОСТ 8713-70 |
Подготовка кромок |
Выполненный шов |
|||
С2 |
|||||
Параметры , мм : |
|||||
S = S1 |
10 |
20 |
30 |
40 |
50 |
b |
4 |
6 |
7 |
8 |
9 |
l = l1 |
20 ± 4,0 |
22 ± 4,0 |
35 ± 5,0 |
34 ± 5,0 |
35 ± 5,0 |
q = q1 |
|
2,5 ± 2 , 0 |
|
|
|
Таблица 3
Швы тавровых соединений без скоса кромок, двухсторонние и односторонние
Тип шва по ГОСТ 8713-70 |
Подготовка кромок |
Выполненный шов |
||
T 1 и Т5 |
||||
Параметры, мм: |
||||
S 1 ³ S |
3-5 |
6-10 |
12-16 |
18-40 |
b |
0+1,0 |
0+1,5 |
0+1,5 |
0+1,5 |
При сборке стыкового соединения листы с неперпендикулярно обработанными
кромками необходимо размещать так, чтобы зазор в корне шва соответствовал
значениям b согласно табл. 2 (рис. 3).
Рис. 3. Сборка стыков с неперпендикулярно обработанными кромками
2.7. При сборке конструкций прихватки нужно выполнять ручной электродуговой сваркой электродами типа Э-42А с фтористо-кальциевым покрытием (марки УОНИ-13/45, УП-2/45 и др.), типа Э-46Т с рутилово-карбонатным покрытием (марки МР-3, ОЗС-4, АНО-3 и др.) или полуавтоматической сваркой в среде СО2, а также в смеси газов. Перед сваркой прихватки и свариваемые кромки должны быть тщательно очищены от шлака.
2.8. В тех местах, где зазоры в стыках деталей, собранных под сварку, превышают величины, указанные в табл. 2- 3, в виде исключения разрешается производить подварку стыков либо наплавку кромок ручной дуговой или полуавтоматической сваркой в среде СО2.
Сварка с предварительной засыпкой ППМ
2.9.
Способ сварки с предварительной засыпкой ППМ (см. рис. 1, а) предназначен для
двухсторонней сварки стыковых соединений без разделки кромок, а также для вы полнения соединений с
разделкой кромок и тавровых «в лодочку». Для предотвращения просыпания ППМ
сварку первого прохода стыков следует производить на металлическом листе. Для
этих целей разрешается применять флюсовую подушку или подушку из ППМ.
При сварке листов толщиной до 36 мм зазор в стыке следует заполнять ППМ заподлицо с поверхностью листов; для толщин 36-60 мм зазор заполняют на 2/3 толщины свариваемого металла.
Толщина слоя ППМ при сварке тавровых соединений «в лодочку» должна быть на 2 мм больше величины катета шва.
2.10. Режим автоматической сварки под флюсом с предварительной засыпкой ППМ стыков без разделки и «в лодочку» следует назначать в соответствии с табл. 4- 5.
При сварке стыковых соединений других толщин, не указанных в табл. 4, скорость сварки следует корректировать в соответствии с разделом «Расчет технологических параметров сварки» (приложение 2).
На режимах, указанных в
табл. 5,
сваривают соединения «в лодочку» из низкоуглеродистых сталей. Режимы сварки
низколегированных сталей «в лодочку» следует выбирать по методике, изложенной в
приложении 3.
Сварку за один проход угловых соединений «в лодочку» с катетом шва более 14 мм осуществляют на более мощных источниках питания.
При использовании источников сварочного тока ВДМ-1601, ВДМ-3001 и ВСЖ-1600 сварку швов тавровых соединений «в лодочку» до катетов 18-20 мм можно производить за один проход.
На режимах, указанных в табл. 4, сваривают стыковые соединения из низкоуглеродистых и низколегированных сталей без предварительного подогрева, кроме сталей 16Г2АФ и 14Х2ГМР толщиной свыше 40 мм, режимы сварки этих сталей следует выбирать по методике приложения 3.
2.11. Сварку стыковых
соединений толщиной до 60 мм следует производить с двух сторон, по
одному проходу с каждой стороны. Сварку второго прохода осуществляют в
соответствии с табл. 4 на режиме первого, при этом засыпки ППМ не
требуется. Сварку следует производить постоянным током обратной полярности.
2.12. Дозировка ППМ при сварке «в лодочку» осуществляется с помощью шаблона (рис. 4). Для выполнения сварки «в лодочку» необходимо заменить направляющее колесо трактора другим, более широким, имеющим выточку по окружности такой глубины, чтобы колесо не касалось слоя ППМ, предварительно засыпанного в разделку.
Таблица 4
Режимы однодуговой автоматической двухсторонней сварки стыковых соединений без скоса кромок под флюсом с предварительной засыпкой ППМ
Толщина металла, мм |
Оптимальный зазор, мм |
Диаметр электродной проволоки, мм |
Скорость подачи проволоки, м/ч |
Сила сварочного тока, А |
Напряжение, В |
Скорость сварки, м/ч |
Расход ППМ, г/см |
20 |
6 |
5 |
103 |
1000-1100 |
40-44 |
35 |
5,0 |
30 |
7 |
5 |
103 |
1000-1100 |
42-45 |
19,5 |
8,0 |
40 |
8 |
5 |
128 |
1200-1300 |
43-48 |
16 |
12,0 |
50 |
9 |
5 |
140 |
1300-1400 |
44-48 |
12 |
16,0 |
60 |
11 |
5 |
163 |
1350-1450 |
45-50 |
12 |
18,0 |
20 |
6 |
4 |
154 |
900-950 |
42-45 |
35 |
5,0 |
30 |
7 |
4 |
163 |
950-1000 |
42-46 |
19 |
8,0 |
40 |
8 |
4 |
163 |
950-1000 |
43-48 |
14 |
12,0 |
50 |
9 |
4 |
210 |
1100-1200 |
44-49 |
14 |
16,0 |
60 |
11 |
4 |
240 |
1300-1400 |
46-50 |
12 |
18,0 |
Таблица 5
Режимы однодуговой автоматической сварки под флюсом угловых соединений «в лодочку» из низкоуглеродистых сталей с предварительной засыпкой ППМ
Катет шва, мм |
Сторона шаблона для ППМ, мм |
Диаметр проволоки, мм |
Сварочный ток, А |
Напряжение, В |
Скорость подачи проволоки, м/ч |
Скорость сварки, м/ч |
Расход ППМ, г/см |
Количество проходов |
8 |
10 |
5 |
750-800 |
36-38 |
68,5 |
54,5 |
2 |
1 |
10 |
12 |
5 |
800-850 |
38-40 |
74,5 |
47,0 |
3 |
1 |
12 |
14 |
5 |
850-900 |
40-42 |
81,0 |
37,5 |
4 |
1 |
14 |
16 |
5 |
900-950 |
40-42 |
87,5 |
32,0 |
5 |
1 |
Техника автоматической сварки под флюсом – ООО «ЦСК»
Главная|Энциклопедия сварки|Т|Техника автоматической сварки под флюсомПеред началом автоматической дуговой сварки под флюсом проверьте чистоту, правильность сборки кромок и направление электрода по оси шва. Металл повышенной толщины сваривается многопроходными швами с необходимым смещением электрода с оси шва. Перед наложением последующего шва поверхность предыдущего шва тщательно очищается от шлака и проверяется с целью обнаружения наличия в нем внешних дефектов. В начале автоматической сварки под флюсом, когда основной металл еще не прогрелся, глубина его проплавления уменьшается,поэтому эта часть сварного шва обычно выводится на входную планку. В конце сварки на месте кратера образуется ослабленный шов, поэтому процесс сварки заканчивается на выводной планке. Планки входа и вывода шириной до 150 мм и длиной (в зависимости от режима и толщины металла) до 250 мм фиксируются на прихватках перед сваркой. После сварки под флюсом планки удаляются.
При автоматической сварке стыковых соединений под флюсом на весу практически невозможно получить шов с провариванием по всей длине стыка из-за утечки в зазор между кромками расплавленного металла и флюса и образования прожогов. Чтобы предотвратить это, используются различные методы, способствующие формированию корня шва. Сварка односторонних швов может проводиться по предварительной ручной подварке, если автоматическая сварка невозможна. Односторонняя сварка под флюсом на оставшейся стальной подкладке возможна в тех случаях, когда она приемлема с точки зрения эксплуатации.
Для сварки под обычными плавлеными флюсами требуется абсолютно чистая металлическая поверхность в зоне сварки. Любое загрязнение поверхности кромок, особенно ржавчина, даже в небольших количествах, часто приводит к пористости металла шва и трещинам. Поэтому кромки соединяемых деталей подвергаются особенно тщательной очистке. Процесс сварки должен следовать как можно быстрее после очистки и сборки. В дополнение к чистоте поверхности кромок, при сварке под флюсом предъявляются повышенные требования к химическому составу основного и электродного металлов. Небольшое увеличение содержания углерода, серы, фосфора, допустимое при ручной сварке, во время автоматической сварки под флюсом может вызвать трещины. Появление трещин также может вызвать ликвация – локальные скопления, например серу, с приемлемым средним ее содержанием в металле. Это одна из причин, почему кипящая сталь, склонная к ликвации, при автоматической сварке иногда образует трещины при удовлетворительном среднем химическом составе металла. Трудности, вызванные недостаточной чистотой поверхности кромок, отклонениями в химическом составе основного металла или наличием в нем ликвации, могут быть в значительной степени устранены некоторым увеличением легирования наплавленного металла специальной легированной электродной проволоки или использованием неплавленого легирующего флюса.
Автоматическая сварка обеспечивает глубокое плавление металла до 20-30 мм и более, поэтому характер разделки кромок для сварки должен измениться. При сварке на малых токах, ручной или автоматической открытой дугой, глубина проплавления основного металла мала и обычно варьируется в пределах 2-6 мм, поэтому при любой значительной толщине основного металла приходится прибегать к разделке кромок, чтобы обеспечить проплавление всей толщины.
Сварка под флюсом в большинстве случаев обеспечивает проваривание всей толщины без разделки кромок. Потребность разделки обусловлена требованием получения надлежащей формы сечения шва. При сварке под флюсом практически не происходит потери металла на угар и разбрызгивание, весь электродный металл переходит в шов. Во многих случаях при отсутствии разделки кромок электродный металл придает сечению шва уродливую форму с чрезмерным избытком наплавленного металла.
Наличие разделки кромок позволяет удалить избыточный наплавленный металл и придать сечение сварного шва надлежащую форму. Поэтому для дуговой сварки под флюсом размер разделки кромок в основном определяется количеством металла расплавленного электрода.
Сварочный флюс
Фактически, флюс представляет собой гранулированный порошок диаметром от 0,2 до 4 мм, используемый для защиты дуги, сварной ванны и наплавляемого металла от вредных внешних воздействий.
Во время работы создается подушка из флюса, основной целью которой является:
— создание надежной защиты сварочной ванны в виде газового облака и шлака от воздействия негативных факторов: сырости, пыли, низкой температуры воздуха и т. п.
— обеспечение стабильной дуги, во время которой будет проводиться непрерывный процесс формирования шва в сварочной ванне;
— улучшение качества соединения и обеспечение сварного шва необходимыми свойствами;
— выведение примесей из металла в зону шлака.
Флюсовые сварочные материалы подразделяются на несколько категорий, в зависимости от технологии производства, состава и прямого назначения.
По способу производства:
— плавленые флюсы или рудоминеральные, предварительно плавятся в печи, после подвергаются дополнительному прокаливанию и формированию в гранулы;
— неплавленые флюсы или керамические флюсы производят путем смешивания минералов и ферросплавов с добавлением жидкого стекла.
По химическому составу сварочного флюса:
— оксидные;
— солеоксидные;
— солевые.
По области применения сварки под флюсом:
— оксидные флюсы применяют для сварки низколегированных сталей;
— солевые флюсы применяют во время работ по переплавке шлака, обработки высоколегированных или углеродистых сталей, а также цветных металлов и для работ с титаном.
2.1 Расчет режима сварки. Разработка технологии изготовления колонны коробчатого сечения
Похожие главы из других работ:
Изготовление титанового короба методом сварки
3.1 Расчет и выбор режима сварки
К режимам сварочного процесса при автоматической аргонодуговой сварке неплавящимся электродом с присадочной проволокой относятся параметры: Сварочный ток, напряжение дуги, диаметр электрода, диаметр проволоки, скорость сварки, расход газа. ..
Обработка металлов сваркой
2.2 Выбор режима сварки
Выбор сварочного оборудования при ручной дуговой сварке сводится к выбору источника питания сварочной дуги. Источником питания сварочной дуги называют устройство, которое обеспечивает необходимый род и силу тока…
Паровая турбина
7. Расчет и выбор параметров режима сварки.
Режим сварки — совокупность основных характеристик сварочного процесса, обеспечивающего получение сварочных швов заданных размеров, форм и качества. При дуговой сварке такими характеристиками являются сварочный ток, напряжение на дуге…
Разработка технологии изготовления колонны коробчатого сечения
2.1 Расчет режима сварки
Режимы сварки под флюсом имеют основные и дополнительные параметры. К основным относят: ток, его род и полярность, напряжение дуги, диаметр электродной проволоки, скорость сварки. Дополнительные параметры режима — вылет электродной проволоки. ..
Разработка технологического процесса изготовления сварочного аппарата
2.3 Расчет режима сварки
Для сварки корпуса аппарата применяли двустороннюю автоматическую сварку под флюсом, так как применяются значительно большие токи, позволяющие получить большое проплавление основного металла. Рисунок 4 — Схема стыка без зазора…
Расчеты тепловых процессов при стыковой сварке
3. Подобрать параметры режима точечной сварки: выбрать геометрические параметры электродов, время сварки, расчитать силу сварочного тока и усилие сжатия электродов для точечноя сварки деталей из жаропрочного сплава ХН78Т толщиной 0,5+0,5 мм
Точечная сварка начинается с предварительного сжатия деталей электродами, что необходимо для получения электрического контакта между деталями и электродами. Через некоторое время после сжатия электродов включается сварочный ток…
Сварка левой половины корпуса редуктора мотоблока
Расчет параметров режима сварки
Сварку в защитных газах выполняют на постоянном токе. Сила тока зависит от диаметра и состава электрода, скорости подачи электродной проволоки, полярности, вылета электрода, состава газа. Рис. 4…
Совершенствование технологического процесса изготовления конструкции металлургической промышленности на ОАО «ЗСМК»
2.4.2 Расчет параметров режима механизированной сварки стыкового шва
Рассчитаем режим сварки стенки и полки толщиной 25 мм при изготовлении верхней и нижней рам опоки. Тип шва — двусторонний многопроходный. Если шов стыкового соединения с разделкой кромок выполняется за несколько проходов…
Совершенствование технологического процесса изготовления конструкции металлургической промышленности на ОАО «ЗСМК»
2.4.3 Расчет параметров режима сварки угловых швов при автоматической сварке тавровых соединений
Рисунок 3 — Тавровое соединение с разделкой кромок Если тавровое или угловое соединение выполнено с разделкой кромок, то расчет параметров режима сварки и размеров шва производится по методике. ..
Создание усовершенствованной существующей базовой конструкции ручки к кастрюле диаметром 250 мм
5. Расчет режима сварки
Исходными данными для расчета значений параметров режима являются: 1. Материал изделия и его теплофизические свойства. 2. Толщина, сечение соединяемых деталей…
Стыковая сварка уголков
1.3 Параметры режима сварки. Циклограмма сварки
…
Технологические процессы сборки и сварки трубопровода диаметром 50 мм в поворотном положении в базовых условиях
2.4 Выбор режима сварки
Для электросварки. Под режимом сварки понимают совокупность контролируемых параметров, обеспечивающих устойчивое горение дуги и получение швов заданных размеров, формы и свойств…
Технология автоматической сварки стали 18Г2АФпс автоматической сваркой под слоем флюса
3.4 Выбор режима сварки
К режиму сварки при автоматической сварке под слоем флюса необходимо отнести: силу тока, скорость подачи проволоки, скорость сварки. 1) Значение силы тока вычисляется по формуле: Iсв =80…100)*h, (А) где h- глубина проплавления, мм Iсв = 80*20 = 1600…
Технология сборки и сварки трубопровода диаметром 50 мм в поворотном положении
1.4 Выбор режима сварки
Для электросварки. Под режимом сварки понимают совокупность контролируемых параметров, обеспечивающих устойчивое горение дуги и получение швов заданных размеров, формы и свойств…
Характеристика стали, её свариваемости
3.2 Расчет параметров режима сварки
Расчет параметров режима сварки будем вести в соответствии с методикой, предложенной [1]. Оттуда же взяты все нижеприведенные формулы. Определяем величину сварочного тока Iсв(80…100) hр; (3) где hр — глубина проплавления, равна 7…
Справочник— Совместное проектирование и подготовка Справочник
— Совместное проектирование и подготовка 27 Базовый Введение в типы суставов Тип соединения, выбранный для любых сварочных работ, может существенно влияют на качество и прочность сварного шва; цена труда и материалов; время и затраты на подготовку, отсадку и позиционирование работы; и другие факторы такой же важности.
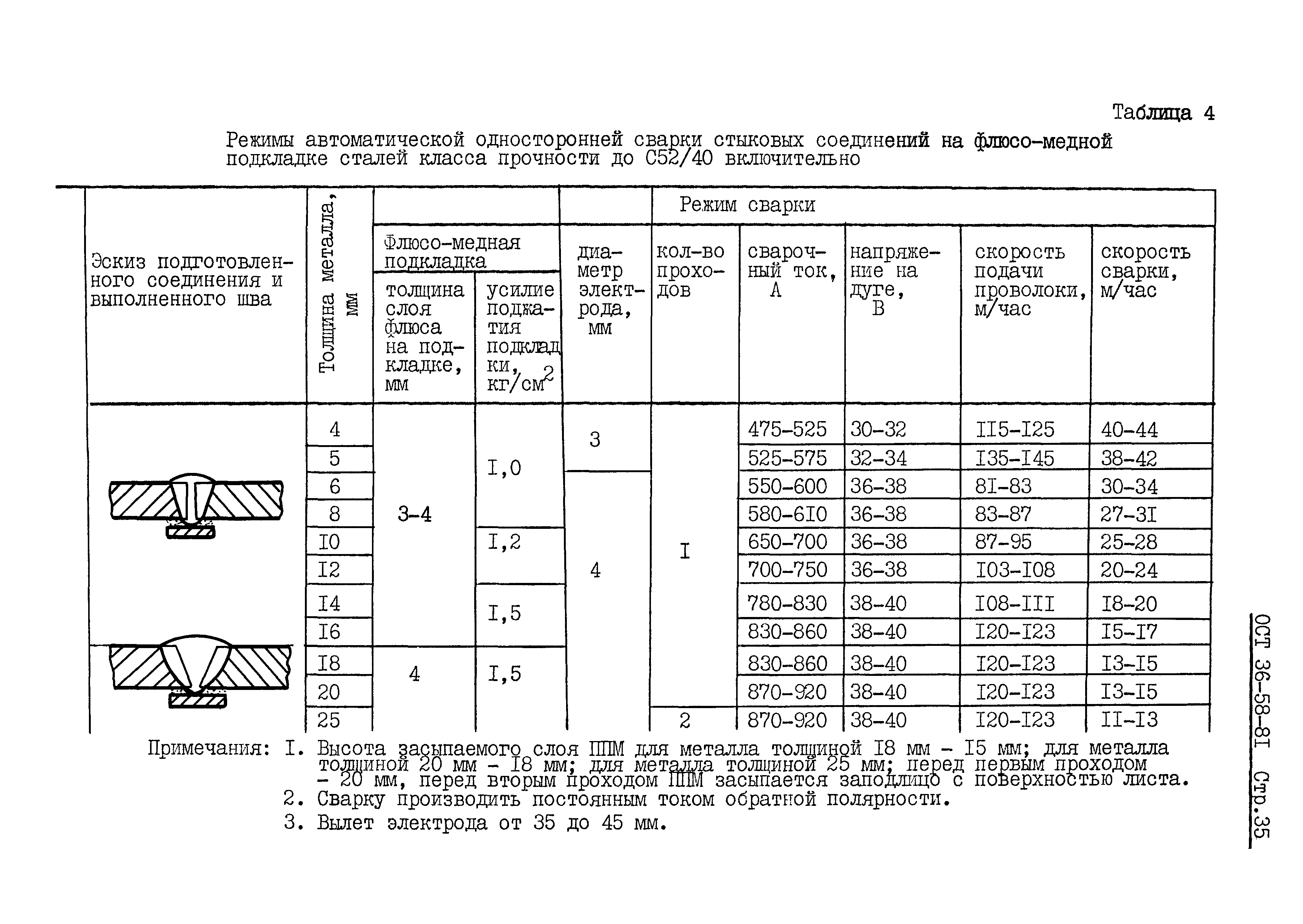
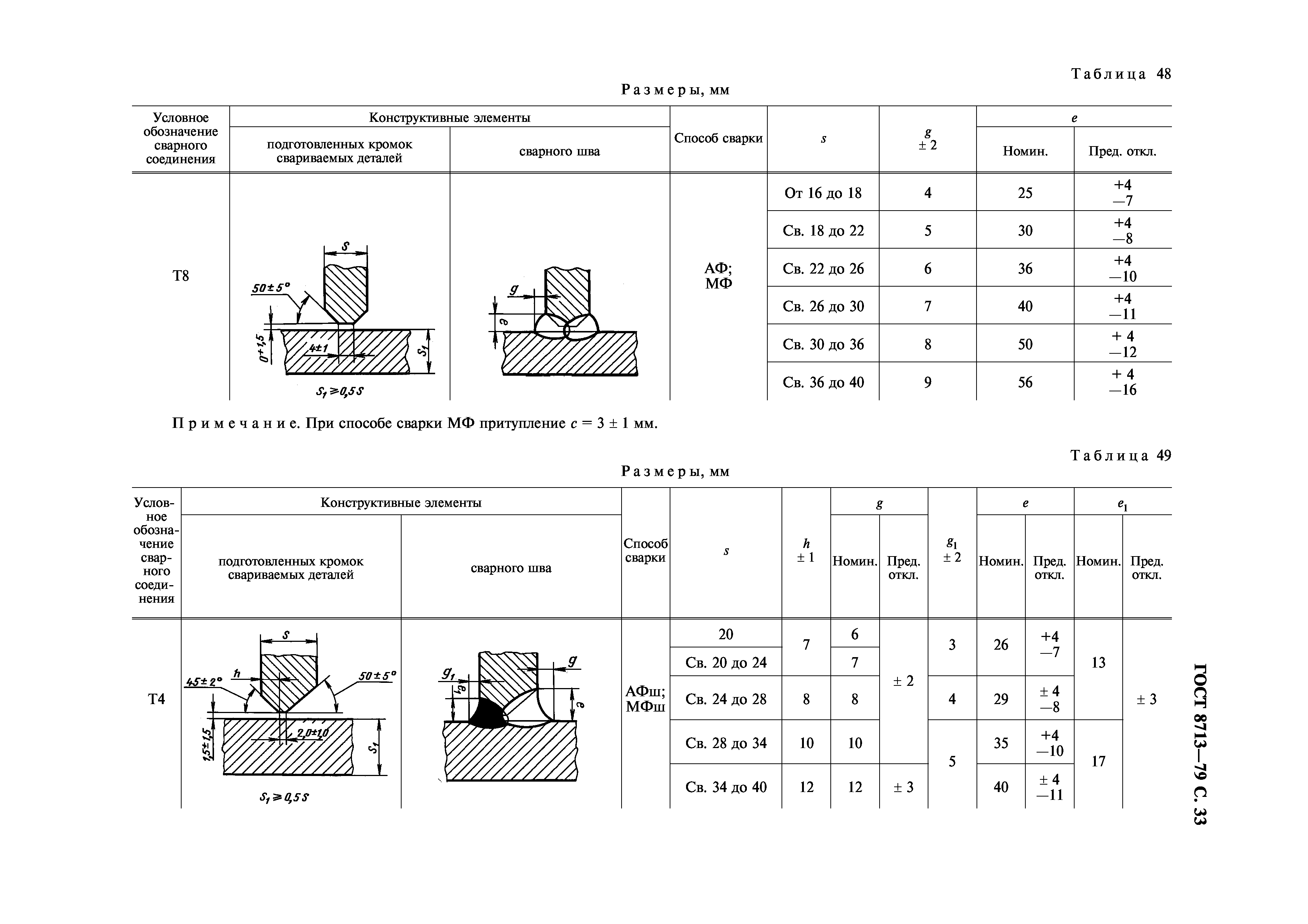
— Совместное проектирование и подготовка
]]> Общий Описание Соединение Дизайн & Подготовка Создание Сварка Операционная Подсказки и Процедуры Определение из Поддерживающий Расплавленный металл Край Подготовка Условия Соединение Уборка Основной сустав Типы 31 г) Стыковое соединение с одинарной U-образной канавкой (рис.12f.) Стыковое соединение с одинарной U-образной канавкой часто используется для многопроходной сварки под флюсом. Любой толщина материала может сваривать с использованием этой конструкции стыка. А небольшой ручной подкладочный шов часто делается с обратной стороны стыка. Если ручная сварка не производится, поверхности корня должны быть плотно стыкованы (максимальный зазор в корне составляет 1/32 дюйма). Для очень толстого материала, двойная U-образная могут использоваться стыковые соединения с пазом.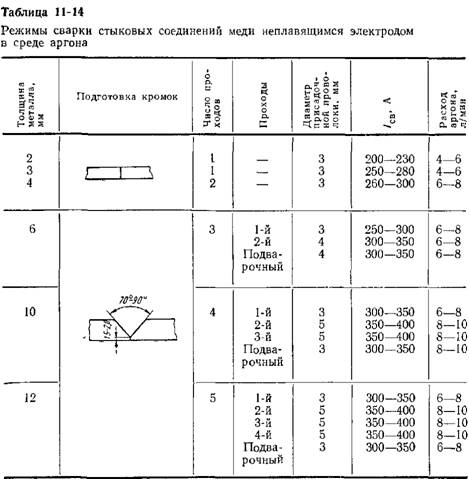

Что такое сварка? | Как работает сварка? | Виды сварки | Различные типы сварных соединений
Что такое сварка?
Сварка — это процесс изготовления или лепки, при котором материалы, как правило, металлы или термопласты, соединяются с использованием высокой температуры для плавления деталей друг с другом и их охлаждения за счет плавления. Сварка отличается от низкотемпературных методов соединения металлов, таких как пайка и пайка, которые не плавят основные металлы.
Помимо плавления основных металлов, в стык обычно добавляют присадочные материалы, чтобы сформировать ванну расплавленного материала.Зубной налет и т. Д. Может быть прочнее основного материала основного металла.
Давление также можно использовать с нагревом или для формирования самого сварного шва. Сварка также требует защиты, чтобы присадочные или расплавленные металлы не загрязнялись или не окислялись.
Для сварки можно использовать множество различных источников энергии, в том числе химическую газопламенную, электрическую электрическую дугу, лазер, электронный луч, трение и ультразвук, хотя зачастую это промышленный процесс; Сварку можно выполнять в самых разных средах, в том числе на открытом воздухе, под водой и на открытом воздухе.
Сварка — опасное занятие, поэтому необходимо соблюдать меры предосторожности, чтобы избежать ожогов, поражения электрическим током, повреждения зрения, вдыхания токсичных газов и паров, а также воздействия интенсивного ультрафиолетового излучения. Расходные материалы обычно выбираются так, чтобы они имели тот же состав, что и основной материал, и, таким образом, образовывали однородный сварной шов.
Однако это случаи, например, при сварке хрупкого чугуна, когда используются присадки с очень разными составами и, следовательно, свойствами.Эти сварные швы называют неоднородными. Хотя это часто промышленный процесс, сварку можно выполнять в самых разных средах, в том числе на открытом воздухе, под водой и на открытом воздухе.
Сварка — опасное занятие, поэтому необходимо соблюдать осторожность, чтобы избежать ожогов, поражения электрическим током, повреждения зрения, вдыхания токсичных газов и паров, а также воздействия интенсивного ультрафиолетового излучения.
Также читайте: Контактная проекционная сварка | Работы по контактной проекционной сварке
Как работает сварка?
Сварочные работы путем соединения двух материалов без разделения связующих материалов.В отличие от пайки и пайки, в которых используется связующее с низкой температурой плавления, при сварке две детали соединяются непосредственно вместе.
Сварка используется в нашем мире для создания многих современных конструкций, таких как небоскребы, автомобили, корабли и самолеты. Раньше строители применяли другие методы соединения металлических деталей.
Есть варианты пайки, пайки и сварки клепками. Сварочный пистолет или горелка плавят определенные части основных металлов. Этот процесс, обычно проводимый с использованием сильного нагрева с добавлением присадочного материала, создает ванну расплавленного металла, так что легче соединить новую металлическую деталь.
Вместо нагрева для сварки металлов давлением также используется давление, в зависимости от типа и толщины материала. Сварка металла: в большинстве случаев приложение одновременного давления и нагрева к основному материалу позволяет быстро и эффективно выполнять сварку металла.
Как упоминалось выше, защитный газ защищает расплавленный металл или сварочную ванну от загрязнения или окисления. Сварка пластмасс: при сварке пластмасс сначала подготавливают поверхности, а затем нагревают и прижимают.После этого материал охлаждается.
Сварка дерева: Сварка дерева заключается в том, чтобы подвергнуть материал давлению перед использованием того же тепла, которое создает линейное движение трения.
Также читайте: Техника газовой сварки | Части сварочной горелки | Работа газовой сварки | Виды газовой сварки | Типы пламени при газовой сварке
Виды сварки:
№1.
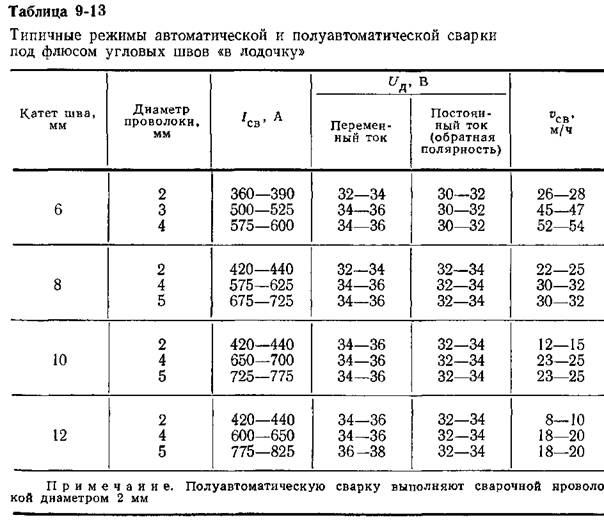
GMAW (газовая дуговая сварка металла) — самый простой вид сварки для начинающих.Сварка MIG — это на самом деле два разных типа сварки. Во-первых, используйте неизолированный провод и вторую флюсовую жилу. Оголенная проволока Сварка MIG может использоваться для соединения тонких металлических частей вместе.
Сварку MIG сердечникомFluxus можно использовать на открытом воздухе, так как она не требует расходомера или подачи газа. Сварка MIG обычно выбирают любители и сварщики-любители, у которых нет денег на приобретение дорогостоящего оборудования.
№2. Сварка TIG
GTAW (газовая дуговая сварка вольфрамовым электродом) чрезвычайно универсален, но это один из самых сложных методов сварки, и сварщики Lincoln Electric TIG являются квалифицированными специалистами.Для сварки TIG требуются две руки. Одна рука подает стержни, а другая держит горелку TIG.
Эта горелка создает тепло и дугу, которые используются для сварки большинства обычных металлов, включая алюминий, сталь, никелевые сплавы, медные сплавы, кобальт и титан. Это один из самых распространенных видов сварки.
Это вид дуговой сварки, в которой используется непрерывная проволока, называемая электродами. Вы также можете использовать защитный газ, который проходит через сварочный пистолет и защищает его от загрязнения.
№ 3. SMAW Сварка
Дуговая сварка экранированного металла, также известная как дуговая сварка экранированного металла, делает это по старинке. Сварка палкой немного сложнее для мастеров, чем сварка MIG, но вы можете купить оборудование для сварки штангой за очень небольшую плату, если хотите испытать себя дома.
Для сварки штангой используются сварочные стержни с электродом. Для этих типов сварки вы используете художественную сварку металлических экранов, более известную как сварка штангой. Вы используете расходные материалы и защищенный электрод или палку.
Стержень размягчает и соединяет металлы, нагревая их дугой между покрытым металлическим электродом и основной металлической заготовкой. Когда палочка плавится, ее защитная оболочка также плавится, защищая область потоотделения от кислорода и других газов, которые могут находиться в воздухе.
№4. FCAW Сварка
Дуговая сварка порошковой проволокой (FCAW) использует тепло, выделяемое электрической дугой постоянного тока, для плавления металла в области соединения. Между поданной расходной присадочной проволокой и заготовкой непрерывно зажигается дуга, в результате чего как присадочная проволока, так и заготовка плавятся в непосредственной близости.Вся область дуги покрыта защитным газом, который защищает расплавленные сварочные ванны от атмосфер.
FCAW — это высокопроизводительный процесс для ряда простых углеродных, легированных, нержавеющих и дуплексных сталей. Его также можно использовать для наплавки и наплавки. Дуговая сварка порошковой проволокой — это вариант процесса MIG / MAG, и, хотя у этих двух процессов есть много общих черт, это также несколько принципиальных различий.
Например, он обеспечивает большую пластичность с составами сплавов, чем MIG. Это обычно обеспечивает более высокую скорость осаждения проволоки и большую стабильность дуги, хотя эффективность процесса MIG, как правило, выше.
Также прочтите: Что такое пламя при газовой сварке? | Типы пламени при газовой сварке
№ 5. MAG Сварка
MAG-сварка — это метод дуговой сварки в среде защитного экрана с использованием диоксида углерода (CO2) и электрода без покрытия. Сварка MAG применяется для: низколегированных сталей; Тонкий и средней толщины листовой металл.Хотя сварка MAG не подходит для всех материалов и сварной шов немного широкий, она чрезвычайно полезна для менее сложных работ и для обычной стали, поскольку этот метод сварки является самым дешевым.
Наши специалисты дадут вам самые лучшие советы о том, подходит ли этот процесс для ваших продуктов больше, чем сварка в свободной атмосфере или сварка в инертных газах — в целом, чтобы перейти от сварки MAG к сварке MIG, нам нужно только заменить газовый баллон. Так что изменить способ сварки довольно просто.
№ 6. Сварка под флюсом
Дуговая сварка под флюсом или SAW — один из наиболее часто используемых процессов дуговой сварки. Для этого требуется электрод, который может быть сплошным или трубчатым. Электроды следует использовать непрерывно. Его следует кормить непрерывно. Оххх. К сведению, трубчатый электрод — это тот, который экранирован от потока.
Основные особенности этой сварки: — зона сварки и дуги защищены от загрязнения окружающей среды с помощью гранулированного плавкого флюса.Сварочные ванны защищены слоем флюса. Так что эта область фактически погружена в этот поток.
Когда температура повышается и плавится, флюс становится проводящим. Таким образом, создается путь для электронного потока между электродом и деталями. Сварка под флюсом может выполняться вручную или автоматически. Но это можно сделать и с помощью полуавтоматического процесса, когда сварочный пистолет используется в ручном режиме.
Здесь дана подача гравитационного флюса под давлением. В качестве источника питания можно использовать как постоянный, так и переменный ток.Комбинация постоянного и переменного тока очень распространена во многих электродных системах. Источники питания постоянного напряжения используются очень часто.
№ 7. Плазменно-дуговая сварка
Плазменная дуговая сварка — это прецизионная технология, которая обычно используется в аэрокосмической отрасли, где толщина металла составляет 0,015 дюйма. Примеры такого применения могут быть на лопатках двигателя или воздушных уплотнениях. Плазменная дуговая сварка похожа по технике на сварку TIG, но электроды подключаются заново, а ионизирующие газы внутри дуги используются для выработки тепла.
№ 8. Электронно-лучевая и лазерная сварка
Электронно-лучевая сварка (EBW) и лазерно-лучевая сварка (LBW) — это процессы сварки с высокой плотностью энергии, которые предлагают множество потенциальных преимуществ, включая низкое тепловложение при сварке, высокое отношение глубины шва к ширине, узкую зону термического влияния (HAZ. ) включены. И меньше искажений. EBW использует динамически сфокусированный луч высокоскоростных электронов, в то время как LBW использует тепло от когерентного лазерного луча высокой плотности для воздействия на сварное соединение и создания коалесценции.
EBW обычно необходимо выполнять в вакууме без использования. Защитный газ, который обеспечивает отличную защиту от атмосферных загрязнений. LBW обычно выполняется с использованием защитных газов аргоном или гелием, чтобы предотвратить окисление расплавленных сварочных ванн.
Пористость может быть проблемой свариваемости из-за высокой скорости затвердевания и глубокой сварочной ванны, которая не позволяет легко растворенным газам выпадать в осадок; Этот эффект усиливается за счет более высоких скоростей движения сварного шва.Колебания или движение сварочной ванны из-за переплетения балки может обеспечить время, необходимое для выхода газов из сварочной ванны, и помочь уменьшить пористость.
Восприимчивости к жидкостным трещинам в «области шляпки гвоздя» ЗТВ способствуют условия напряжения / деформации в этой области. Низкая скорость перемещения сварного шва создает низкотемпературный градиент в ЗТВ и способствует снижению чувствительности к трещинам от жидкости.
Также читайте: Что такое садовые вилки? | 10 лучших садовых вилок
Различные типы сварных соединений:
№1.Сварка стыковых соединений
Стыковое соединение представляет собой соединение, при котором две металлические детали удерживаются вместе в одной плоскости, а каждая металлическая кромка соединяется сваркой. Стыковая сварка — это наиболее распространенный тип соединений, используемых в строительных конструкциях и системах трубопроводов. Его довольно легко приготовить, и для достижения желаемых результатов можно применять множество различных вариаций.
Стыковая сварка выполняется разными способами, и каждый из них служит для разных целей. К отличительным факторам относятся размер канавки, наслоение и ширина зазоров.Ниже приведены некоторые типичные примеры стыковых сварных соединений.
- Квадрат
- Одинарный скос
- Двойной скос
- Одноместный J
- Двойной J
- Одинарный V
- Двойной V
- Одинокая ты
- Двойные U-образные пазы
Участок металлической поверхности, плавящийся в процессе сварки, называется лицевой поверхностью. Перед сваркой облицовочной поверхности можно придать форму для повышения прочности сварного шва, что называется подготовкой кромок.Стыковое соединение или каждая сторона могут иметь разную форму. К причинам подготовки облицовочных поверхностей к сварке можно отнести следующие:
- Нормы и стандарты
- Металл
- Глубокий провар
- Гладкий внешний вид
- Повышенная сила
В некоторых случаях для канавки может быть указан точный размер, форма и угол. Если точные размеры не указаны, можно изготовить кабелепровод нужного размера. Однако важно помнить, чем шире желобок; тем больше сварки нужно будет выполнить.
По мере того, как металл становится толще, вам нужно будет изменить конструкцию соединения, чтобы обеспечить качественную сварку. На более тонких участках часто можно выполнить сварной шов с полным проплавлением, используя стыковые соединения квадратного сечения. При сварке толстого листа или труб сварщик часто не может добиться 100% проплавления без использования каких-либо канавок.
Когда дело доходит до стыковых соединений, обычно встречающиеся дефекты могут включать прожог, пористость, растрескивание или неполное проникновение. Однако этого можно избежать, изменив параметры сварки.
Также читайте: Что такое гаечный ключ? | Типы гаечных ключей | Типы гаечных ключей
№2. Сварка тройника
Т-образное сварное соединение образуется при пересечении двух деталей под углом 90 °. Это приводит к тому, что кромки сходятся в Т-образной форме в центре пластин или компонентов. Тройники считаются одним из видов углового сварного шва, и они также могут образовываться, когда труба или труба привариваются к опорной плите.
При использовании этого типа сварного шва всегда важно обеспечить эффективное проникновение сварного шва в потолок.Для изготовления тройника можно использовать несколько стилей сварки:
- Сварной шов
- Сварной шов с прорезью
- Сварной шов под фаску
- Угловой шов
- Сварной шов с J-образной канавкой
- Сквозной сварной шов
- Сварной шов с развальцовкой, скосом и канавкой
Тройники обычно не имеют канавок, если основной металл не толстый и сварка с обеих сторон не может выдерживать нагрузку, которую должно выдерживать соединение. Распространенным дефектом, который возникает в Т-образных суставах, является разрыв пластин, вызванный ограничением, которое испытывает сустав.Чтобы предотвратить это, сварщики часто используют стопор, чтобы предотвратить деформацию стыков.
№ 3. Сварка угловых стыков
Угловые соединения аналогичны сварным соединениям тройников. Однако разница в том, где находится металл. В Т-образном соединении он размещается посередине, а угловые соединения открываются или закрываются в «углу», образуя L-образную форму. Эти типы соединений наиболее распространены в индустрии листового металла, например, при производстве рам, коробок и других приложений.
Существует два способа подгонки внешнего углового соединения — с образованием V-образной канавки (A) или квадратного стыкового соединения (B), как показано на рисунке ниже. Стили, используемые для выполнения угловых соединений, включают V-образную канавку, J-образную канавку, U-образную канавку, пятно, кромку, галтель, угловой фланец, скошенную канавку, развальцованную V-образную канавку и квадратный канал или стык.
Также читайте: Что такое заклепка? | Как делается клепка? | Захватывающее определение | Типы заклепок
№4. Сварка внахлест
Сварное соединение внахлест представляет собой модифицированный вариант стыкового соединения.Он образуется, когда два куска металла накладываются друг на друга внахлест. Обычно они используются для соединения двух частей разной толщины. Сварные швы можно производить по одному. Соединения внахлест редко используются для толстых материалов и обычно используются для листового металла.
Возможные недостатки этого типа сварного соединения включают разрыв пластин или коррозию из-за перекрытия материалов. Однако, как и все остальное, этого можно избежать, используя правильную технику и изменяя переменные по мере необходимости.
№ 5. Сварка краевых стыков
В краевых соединениях металлические поверхности скрепляются так, чтобы края были ровными. Одну или обе пластины можно сформировать, повернув их под углом. Назначение сварных соединений — соединение деталей вместе с распределением напряжений.
Силы, вызывающие напряжение в сварных соединениях, — это растяжение, сжатие, изгиб, скручивание и сдвиг, как показано на изображении ниже.
Также читайте: Какие размеры шин? | 13 различных типов шин | Классификация шин
Типы сварных соединений:
№1.
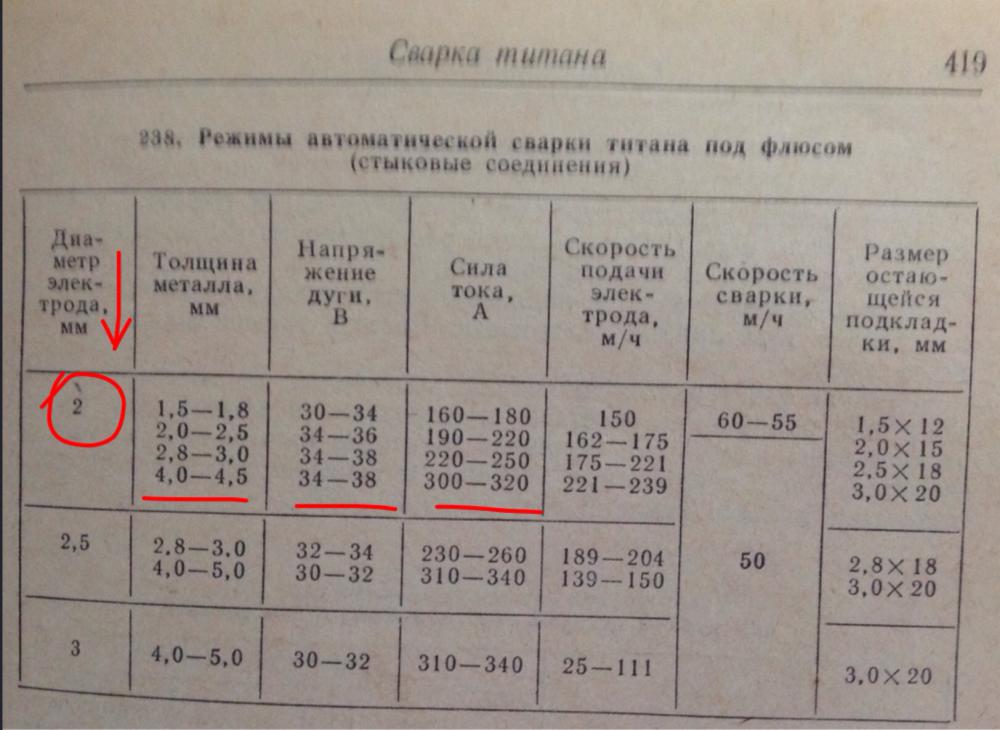
Соединения между двумя перекрывающимися компонентами выполняются путем наложения углового сварного шва по периметру отверстия в одном компоненте, чтобы его можно было прикрепить к поверхности другого компонента, открытого через отверстие.
Сварной шов выполняется заполнением отверстия в компоненте заготовки присадочным металлом таким образом, чтобы его можно было прикрепить к поверхности перекрывающегося компонента, открытого через отверстие; отверстие может быть круглым или овальным.
№2. На основе Penetration
Сварное соединение, в котором металл шва полностью входит в соединение инерционным плавлением. В США предпочтительным термином является шов с полным проплавлением (см. JCP, AWS D1.1).
Сварные швы, в которых проплавление намеренно меньше полного проплавления. В США предпочтительным термином является сварка с частичным проникновением в стык (PJP).
№ 3. Характеристики завершенных сварных швов
Металл, соединяемый или оголенный сваркой, пайкой или пайкой.
Металлы соединяются во время сварки, пайки твердым припоем или наплавки.
Во время сварки весь металл расплавляется и остается в сварном шве.
Часть основных металлов подвергается металлургическому воздействию тепла сварного шва или термической резки, но не плавится.
Граница между металлом сварного шва и ЗТВ при сварке плавлением. Это нестандартный термин для обозначения сварного соединения.
Область, содержащая сварочный металл и ЗТВ.
Поверхность сварного шва обнажается со стороны, с которой он выполнен.
Зона на стороне первого проходит дальше всего от сварщика.
Граница между поверхностью шва и основным металлом или между прогонами. Это очень важная характеристика сварного шва, потому что пальцы являются точками концентрации высоких напряжений и часто являются точками зарождения различных типов трещин, например, усталостных трещин, холодных трещин. Чтобы снизить концентрацию напряжения, пальцы ног должны плавно переходить в поверхность основного металла.
Металл, лежащий вне плоскости соединения пальцев ног.Другие нестандартные условия по данному признаку: армирование, перелив.
Примечание: — Термин «армирование», хотя и обычно используется, не подходит, потому что никакой дополнительный металл сварного шва поверх и выше поверхности основного металла не делает соединение более прочным.
Фактически, толщина, которую следует учитывать при проектировании сварного компонента, — это толщина расчетной горловины, которая не включает дополнительный металл сварного шва.
Металл плавится или накапливается при прохождении электрода, горелки или выдувной трубки.
Слой металла сварного шва, состоящий из одного или нескольких прогонов.
Понравился пост? Поделитесь этим с вашими друзьями!
Рекомендуемое чтение —
Возможность заполнения канавок стыкового соединения по сравнению с дуговой сваркой вольфрамовым электродом
Реферат
В данной работе исследуется возможность использования процесса сварки трением с перемешиванием (FSW) в качестве метода сварки с заполнением канавок для сварки дуплексной нержавеющей стали (DSS), которая широко используется используется нефтесервисными компаниями и морскими предприятиями. Для экспериментов FSW были разработаны три различных геометрии канавок без корневого зазора, которые были обработаны на пластинах DSS толщиной 6,5 мм. FSW выполнялись для изготовления стыковых соединений при постоянной скорости вращения инструмента 300 об / мин, скорости сварки в поперечном направлении 25 мм / мин и угле наклона 3 o с использованием инструмента из карбида вольфрама (WC). Для сравнения, те же самые пластины из DSS были сварены с использованием дуговой сварки вольфрамовым электродом в газе (GTAW). Полученные соединения были оценены и охарактеризованы с помощью радиографического контроля, оптической микроскопии, а также испытаний на твердость и растяжение.Дифракция обратного рассеяния электронов (EBSD) использовалась для исследования зеренной структуры и фаз до и после FSW. Первоначальные результаты показывают, что FSW успешно использовались для сварки DSS-соединений с различной конструкцией канавок с бездефектными соединениями, полученными с использованием V-образной канавки 60 ° с корневой поверхностью 2 мм без корневого зазора.
Это соединение, полученное сваркой трением с перемешиванием (FSWed), было дополнительно исследовано и сравнено с соединением GTAW. Микроструктура соединения FSWed в основном состоит из α и γ со значительным измельчением зерна; сварной шов GTWA помимо ферритной фазы (α) в зоне сварного шва (WZ) содержит аустенитную фазу различной морфологии, такую как межзеренный аустенит (GBA), внутризерновые выделения аустенита (IGA) и видманштеттенский аустенит (WA). используется высокая теплопроводность и присадочный стержень 2209.Предел текучести, предел прочности и удлинение соединения FSWed увеличены по сравнению с сваркой GTAW на 21%, 41% и 66%, а по сравнению с BM на 65%, 33% и 54% соответственно. Исследование EBSD показало значительное измельчение зерна после FSW со средним размером зерна 1,88 мкм для аустенита и 2,2 мкм для феррита.
Ключевые слова: конструкция пазового соединения , сварка трением с перемешиванием, дуговая сварка вольфрамовым электродом, 2205 DSS, механические свойства
1.
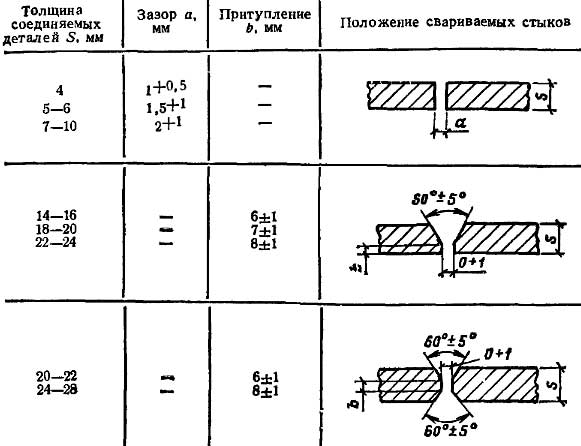
По сравнению с ферритными и аустенитными нержавеющими сталями, дуплексная нержавеющая сталь (DSS) имеет отличную прочность и коррозионную стойкость. сопротивление в тяжелых инженерных приложениях благодаря двухфазной структуре (почти 50% ферритной (α) фазы и 50% аустенитной (γ) фазы) [1,2,3,4,5].Эта уникальная микроструктура обеспечивает преимущества DSS по сравнению с каждой из аустенитных и ферритных нержавеющих сталей. Сообщается, что [4] коррозионное растрескивание под напряжением и предел упругости аустенитной нержавеющей стали улучшаются с присутствием α-фазы. Кроме того, присутствие γ-фазы приводит к повышению ударной вязкости дуплексных нержавеющих сталей, препятствуя росту зерен α-фазы [5]. Таким образом, DSS широко рекомендуется для использования во многих приложениях, таких как химическая и нефтехимическая промышленность, морская промышленность, трубы для опреснения воды и трубы для сжиженного природного газа, помимо использования во многих горнодобывающих приложениях [3,5].
Следовательно, DSS считается подходящим выбором для многих инженерных приложений вместо ферритных и аустенитных нержавеющих сталей [6]. Среди дуплексных нержавеющих сталей 2205 DSS считается наиболее распространенным типом сталей этого класса. Этот сорт широко используется в нефтяной и газовой промышленности, в компонентах морской воды и в электроэнергетике [4,6]. Эффективность соединения сварных деталей 2205 DSS в основном зависит от структуры и зависит от типа метода сварки. 2205 DSS можно сваривать с использованием методов сварки плавлением с высокой энергией дуги, таких как газовая дуговая сварка металлическим электродом (GMAW) [7], газовая дуговая сварка вольфрамовым электродом (GTAW) [8,9] и дуговая сварка в среде защитного металла (SMAW) [2] .Процесс GTAW обеспечивает эффективную и чистую сварку по сравнению с другими процессами сварки плавлением [10]. Сообщается, что зона сварки (WZ) GTAW-сварки может иметь приемлемое соотношение γ / α при использовании специального присадочного стержня. Однако особенности микроструктуры сварного шва не похожи на микроструктуру основного металла [11], а производительность низкая, поскольку максимальная толщина, которую можно сваривать за один проход, не может превышать 3 мм [2,12]. Процесс GTAW с использованием присадочного прутка ER 2209, обогащенного никелем, обеспечивает приемлемое соотношение α / γ в сварных деталях [13].Сообщалось, что химический состав присадочного стержня играет значительную роль в реформировании γ-фазы, чем применяемая скорость охлаждения [14].
FSW, как метод соединения в твердом состоянии, становится все более заметным при соединении и сварке дуплексных нержавеющих сталей (DSS) [15]. В 2205 DSS оптимальные свойства достигаются, когда материал имеет равные пропорции аустенита и феррита [16]. Это желаемое соотношение фаз изменялось во время процессов сварки плавлением и способствовало большему образованию феррита в зоне сварного шва в результате переплавки и затвердевания материалов [17].Кроме того, рекомендуется сваривать DSS в диапазоне 0,2–1,5 кДж / мм, чтобы избежать выделения хрупких интерметаллических фаз [18]. С другой стороны, методы твердотельной сварки, такие как FSW, кажутся подходящими в этом отношении [19]. Этот процесс сводит к минимуму проблему ферритизации DSS во время циклов термической сварки из-за их твердотельной природы и уменьшает общие проблемы, связанные со сваркой плавлением. Во время процесса FSW микроструктура основного материала испытывает как высокую температуру, так и сильную деформацию, вызванную перемешивающим инструментом.Сосуществование этих двух факторов активирует возникновение некоторых механизмов разупрочнения по всему материалу, что приводит к тонкой микроструктуре, обычно обнаруживаемой во время процессов горячей деформации [20].
Сварка трением с перемешиванием (FSW) мягких материалов, таких как алюминиевые и магниевые сплавы, стала обычным явлением при сварке из-за способности материала инструментальной стали сваривать такие материалы с минимальными затратами и риском отказа [21,22]. Однако риск отказа и стоимость все еще очень высоки в случае инструментальных материалов, используемых для СТП твердых металлов, таких как сталь [23], титан и никелевые сплавы [24]. В основном это происходит из-за высокой температуры и сильного стресса, испытываемого во время СТС [25]. Инструментальные материалы для СТП из жаропрочных сплавов должны демонстрировать отличные свойства при температурах выше 900 ° C [25]. В СТП материалов с высокой температурой размягчения используются различные типы материалов, такие как материалы на основе WC [26], W – Re [27] и материалы PCBN [28]. Однако инструмент FSW подвергается серьезным нагрузкам и высоким температурам, особенно при сварке твердых сплавов, таких как стали и титановые сплавы, и коммерческое применение FSW к этим сплавам в настоящее время ограничено высокой стоимостью и коротким сроком службы инструментов FSW [ 25].Однако из-за высоких температур и давлений, необходимых при производстве PCBN, стоимость инструмента очень высока [25]. Из-за своей низкой вязкости разрушения PCBN также имеет тенденцию разрушаться на начальной стадии погружения [25]. Таким образом, материал WC представляет собой экономичный вариант для СТП из твердых металлов [26] и твердых композитов [29,30], если можно продлить срок службы инструмента.
Важным параметром, который можно рассматривать для увеличения срока службы инструмента, является геометрия штифта инструмента и уступа [31]. Кроме того, уменьшение сил, испытываемых инструментом при врезании или во время FSW, может повысить стойкость инструмента WC.В этом отношении наличие канавок вдоль линии соединения значительно снизит эти силы. Кроме того, идея заполнения канавок с помощью FSW является почти новой и инновационной в отношении заполнения без использования присадочного стержня. Преимущество FSW перед другими методами сварки, такими как сварка лазерным лучом [32] в качестве метода сварки без использования присадочных стержней, заключается в более низком тепловложении. Таким образом, эта работа направлена на внедрение FSW в качестве метода соединения с заполнением канавок для сварки DSS в нефтесервисных компаниях вместо технологии сварки GTAW.
2. Материалы и методы
2.1. Материал
SAF 2205 В качестве основного материала использовались пластины DSS толщиной 6,5 мм. Заготовки для сварки были вырезаны из пластин в состоянии поставки для процессов GTAW и FSW, длиной 200 мм и шириной 100 мм. Химический состав основного материала DSS указан в. В процессе GTAW используется присадочный пруток AWS A5.9 ER2209, который содержит на 3,68% больше никеля, чем 2205 DSS. Повышенное содержание никеля в присадочном стержне стабилизирует аустенитную фазу в сварных деталях.Химический состав присадочного стержня приведен в. Химический состав основного материала и присадочного стержня указан в таблице данных, предоставленной поставщиком.
Таблица 1
Химический состав основного материала 2205 DSS (мас.%).
Cr | Ni | Mo | Mn | Si | N | C | P | S | Fe |
---|---|---|---|---|---|---|---|---|---|
3,15 | 1,51 | 0,38 | 0,17 | 0,015 | 0,025 | 0,001 | Бал.![]() |
Таблица 2
Химический состав присадочного прутка E2209 (в мас.%).
Cr | Ni | Mo | Mn | Si | N | C | P | S | Cu | Fe | 42 | 3,03 | 0,76 | 0,86 | 0,14 | 0,022 | 0,015 | 0,016 | 0,05 | Бал.![]() |
---|
2.2. Процедура сварки
Для FSW были спроектированы и обработаны канавки трех различных геометрий без корневого зазора, как показано на: (a) U-образная канавка под углом 60 ° с корневой поверхностью 2 мм, (b) V-образная форма под углом 60 °. канавка без корневой поверхности, (c) V-образная канавка 60 ° с корневой поверхностью 2 мм и (d) V-образная канавка 60 ° GTAW с корневой поверхностью и корневым зазором.Перед сваркой образцы были механически очищены проволочной щеткой из нержавеющей стали для удаления поверхностных оксидов и загрязнений.
Проекты соединений с пазами ( a — c ) для процесса FSW и ( d ) для процесса GTAW [33].
Инструмент FSW был разработан с конической геометрией штифта. Диаметры заплечика, угол сужения штифта, кончик штифта и длина штифта были выбраны как 20 мм, 30 °, 5 мм и 5,5 мм соответственно. Из-за высокого напряжения трения и нагрева при СТП DSS; Инструмент, буртик и штифт были изготовлены из карбида вольфрама (WC) [1]. а показаны чертежи инструмента WC.
Схема чертежей ( a ) инструмента WC FSW и ( b ) образца для испытаний на растяжение (размеры в мм).
На основании предварительных экспериментальных испытаний FSW, а также имеющихся данных в литературе [34], оптимальными параметрами сварки FSW были скорость вращения 300 об / мин, скорость перемещения 25 мм / мин и угол наклона 3 °. . Эксперименты по FSW проводились с использованием модели машины FSW (EG-FSW-M1) [35]. Для сравнения между FSW и сваркой плавлением была выбрана газовая дуговая сварка вольфрамом (GTAW), которая применялась для сварки DSS 2205 в стыковом шве.Среди методов сварки плавлением GTAW широко используется для сварки дуплексных материалов в нефтяной и нефтехимической промышленности. Используемая геометрическая конструкция соединения для процесса GTAW представляла собой V-образный угол канавки 60 ° с поверхностью впадины 2 мм и зазором 2 мм; d. Стык был подготовлен в соответствии с конструкцией стыка в соответствии с утвержденными техническими условиями на сварку.
Процесс GTAW проводили на установке DCEN-GTAW с вольфрамовым электродом 2,4 мм типа EWTh-2, длиной дуги 2,4 мм и расходом аргона 15 л / мин.Процесс GTAW проводился с использованием предварительно утвержденных технических требований к процедуре сварки (PQWPS) с параметрами сварки, как показано на рис.
Таблица 3
Проход | Приставной стержень | Ампер (A) | Вольт (В) | Скорость хода (мм / мин) | Тепловая нагрузка (кДж / мм) |
---|---|---|---|---|---|
1-й | ER2209 | 116 | 10 | 90 | 0,733 |
2-й | 159 | 13 | 90 | 1.![]() | |
3-й | 155 | 13,5 | 81 | 1,550 | |
Крышка1 | 150 | 14,5 | 76 | 1,717 903 9048 9048 9048 9048 9048 9048 0,516 | |
2.3. Оценка и характеристика стыков
Радиографический контроль (RT) был проведен в соответствии с ASME V и ASME VIII на сварных соединениях с использованием гамма-камеры (модель 880 MAN-027, NSW, Австралия) с источником иридия-192 с использованием Рентгенографические пленки D7. Микроструктурный анализ сварных швов был выполнен с использованием оптического микроскопа (модель Olympus: BX41M-LED, Токио, Япония). Поперечные сечения были подготовлены посредством основных этапов металлографии в соответствии с ASTM E-3 и ASTM E-2014 с зернистостью до 2400 и затем механически отполированы с использованием суспензии оксида алюминия 0,05 мкм. После этого следовала очистка ацетоном, сушка и электрохимическое травление с использованием 20 г КОН в 100 мл раствора H 2 O. Фазовый состав в зонах перемешивания и сплавления стыковых соединений FSWed и GTAWed исследовали методом рентгеновской дифракции (XRD, Siemens Incorporating, Мюнхен, Германия) с использованием Siemens-D5000 с Cu Kα-излучением (длина волны λ = 0.15406 нм) при 40 кВ и 30 мА в диапазоне 2θ 20–110 ° и шаге 0,03 o . Ферритное число основного материала (BM), зону термического влияния (HAZ) и зону сварного шва (WZ) оценивали для соединений, сваренных методом FSW и GTAW, с использованием ферритового прицела (FERITSCOPE MP30 — Fischer Company, Вустершир, Великобритания).
Модель твердомера по Виккерсу (модель Qness Q10 M, Голлинг, Австрия) использовалась для получения значений твердости по поперечному сечению на расстоянии 1 мм с нагрузкой 98 Н и временем выдержки 15 с.Чтобы оценить эффективность сварного соединения, образцы для испытаний на растяжение были вырезаны перпендикулярно направлению сварки в соответствии с ASTM E8. b показывает стандартные размеры образцов для испытаний на растяжение, которые использовались в качестве эталонов при приготовлении образцов соединений на растяжение; Толщина образца для испытания на растяжение варьировалась в зависимости от толщины зоны сварного шва, то есть толщина в зоне сварного шва использовалась в качестве толщины образца при растяжении в каждом случае, что означает, что материал с дополнительной толщиной выше, который был подвергнут механической обработке.Испытание проводили при комнатной температуре со скоростью напора 0,5 мм / мин с использованием универсальной испытательной машины (Instron 4208, усилие 300 кН, Норвуд, Массачусетс, США).
3. Результаты и обсуждения
3.1. Механизм сварки FSW с заполнением канавок
С момента изобретения процесса сварки FSW известно, что этот процесс сварки в твердом состоянии нельзя использовать для сварки с необходимостью заполнения канавок. В данной работе выполнено технико-экономическое обоснование использования СТС при сварке стыковых соединений с проточками.показывает инструмент FSW, погружающийся в канавку спереди (а) и сзади (b). Можно отметить, что наличие канавки облегчает этап погружения и, как ожидается, снизит износ инструмента и продлит срок его службы. После полного погружения, как показано в c, материал начинает обтекать инструмент, и вокруг инструмента образуется полюс, который становится устойчивым с небольшим потоком перед инструментом, который не влияет на соединение за инструментом. Можно заметить, что этот полюс становится устойчивым с перемещениями инструмента, как это видно из существующих изображений отверстий, показанных для U-образной канавки с хвостовиком (а) и V-образной канавки без хвостовика (b). Ожидается, что такая конфигурация соединения облегчит погружение инструмента, уменьшит силы сопротивления инструмента и уменьшит подвод тепла. Это напрямую увеличит срок службы инструмента и улучшит свойства соединения. а показан инструмент WC FSW с устройством держателя после восьми испытаний сварки 2205 DSS с некоторыми следами прилипания материала к инструменту WC. Кроме того, увеличенное изображение инструмента WC на b показывает стабильность характеристик инструмента, которые указывают на то, что при условии наличия канавок износ не происходил, и на внешней поверхности уступа можно отметить только окисление из-за высокой термической стойкости. циклы испытали.Стабильность WC после восьмикратного погружения и сварки можно объяснить наличием канавки, которая снижает силы сопротивления инструмента.
Фотографии, сделанные во время FSW 2205 DSS с заполнением бороздок. ( a ) Вид спереди во время врезания инструмента FSW, ( b ) вид сзади во время врезания инструмента FSW и ( c ) вид спереди во время FSW.
Шпоночное отверстие после FSW 2205 DSS ( a ) U-образная канавка с корнем. ( b ) V-образная канавка без корня.
( a ) Инструмент WC FSW с расположением держателя после восьми испытаний дуплексной сварки нержавеющей стали с помощью инструмента WC, увеличенного в ( b ).
3.2. Визуальный и радиографический осмотр
показывает вид сверху стыковых соединений FSWed 2205 DSS, изготовленных с самозаполнением канавок различной конструкции. Можно заметить, что во всех случаях канавки заполнялись успешно, с некоторыми дефектами, отмеченными в U- и V-образных канавках без поверхности корня, в основном из-за большого объема канавок, которые требуют большого объема материала для плотного заполнения. .Например, U-образное соединение обеспечивает хороший внешний вид поверхности с обширным заусенцем. Кроме того, было обнаружено уменьшение толщины сварного шва примерно на 2 мм по сравнению с основным материалом для достижения заполнения канавки; а. Эта потеря толщины происходит из-за отсутствия потока материала и большого объема конструкции соединительной канавки (а). Полученный сварной шов с V-образной канавкой без корня имеет частично хороший внешний вид с меньшим количеством заусенцев. Видны поверхностные пустоты по длине сварного шва на отходящей стороне; б.Кроме того, было измерено уменьшение толщины сварного шва примерно на 1 мм по сравнению с DSS BM. Эти особенности верхней поверхности также связаны с отсутствием наполнения и текучести материала в результате большого объема конструкции в форме паза (b). Полученный шов V-образной формы с дизайном поверхности корня показал хороший внешний вид поверхности с небольшим заусенцев и минимальным уменьшением толщины. Для сравнения, такое же соединение внахлест 2205 DSS было изготовлено методом GTAW с V-образной канавкой с основанием и корневым зазором 3 мм (d).d показывает вид сверху стыкового шва GTAW 2205 DSS. Можно считать приемлемым внешний вид без дефектов поверхности. Радиографический контроль выявляет внутренние дефекты стыковых соединений, изготовленных с использованием U-образной и V-образной формы без рисунка поверхности корня, как показано на a, b, соответственно.
Кроме того, были получены почти надежные стыковые соединения 2205 DSS для обоих стыковых соединений FSW с использованием конструкции с V-образной канавкой с корневым соединением и стыковым соединением GTAW, как показано в c, d, соответственно.
Вид сверху на сварные швы FSW ( a ) FSW, П-образный паз с корнем; ( b ) FSW, паз V-образный без корня; ( c ) FSW, V-образная канавка с корневой поверхностью; и ( d ) GTAW, V-образная канавка с корневой поверхностью и зазор, сварка GTAW для стыковых соединений 2205 DSS [33].
Рентгенографические пленки сварных швов СТШ: (а ) СТШ, П-образный паз с корнем; ( b ) FSW, паз V-образный без корня; ( c ) FSW, паз V-образный с корнем; и ( d ) GTAW, V-образная канавка с корневой поверхностью и корневым зазором GTAW-сварка для 2205 DSS [33].
3.3. Макроструктура и микроструктура
a – c показывает макроструктуры поперечного сечения стыковых соединений FSW, полученных с использованием различных конструкций канавок. d представляет собой макрофотографию поперечного сечения стыкового соединения GTAWed.Для стыков FSWed наблюдаются три выделенные зоны — зона перемешивания (SZ), зона термомеханического воздействия (TMAZ) и зона термического влияния (HAZ) [35]. Кроме того, граница между SZ и TMAZ очень заметна на наступающей стороне, в то время как она более разбросана на отступающей стороне, что связано с совмещением направления вращения, поперечного направления на этой стороне, а также более точным зерна на наступающей стороне, чем на отступающей [36]. Имеются туннельные дефекты и потеря толщины на 2 мм стыкового соединения 2205 DSS с использованием U-образной канавки без основания, как показано на а.Эти дефекты связаны с большим объемом паза стыка. Кроме того, наблюдаются внутренние дефекты (б) для стыкового соединения, сваренного с использованием V-образной проточки без корня; эти дефекты являются туннельными дефектами. Более того, уменьшение толщины этого соединения составляет примерно половину уменьшения толщины соединения, сваренного с использованием конструкции U-образной канавки с корнем.
Эти дефекты также могут быть связаны с неправильной конструкцией пазового соединения. Для сварного соединения с использованием V-образной канавки с корнем было отмечено, что поперечное сечение не имеет дефектов, и было обнаружено очень небольшое уменьшение толщины.Основываясь на визуальном осмотре, рентгенографическом исследовании и исследовании макрофотографии, можно сделать вывод, что V-образная канавка 60 ° с 2-миллиметровой поверхностью корня без корневого зазора является подходящей конструкцией соединения для процесса заполнения канавки FSW для создания прочного соединения. Для сравнения был получен бездефектный шов с V-образной канавкой с корневой поверхностью 2 мм и корневым зазором 3 мм, полученным с использованием GTAW, как показано d. Более того, две выделенные зоны, WZ и HAZ, могут быть обнаружены как признаки сварки плавлением [37].
Макроструктура сварных швов FSW: ( a ) FSW, П-образный паз с корнем; ( b ) FSW, паз V-образный без корня; ( c ) FSW, V-образная канавка с корневой поверхностью; и ( d ) GTAW, V-образная канавка с корневой поверхностью и корневым зазором, сварка GTAW для стыковых соединений 2205 DSS.
показывает микроструктурные особенности в различных зонах надежного соединения FSWed, полученного с использованием V-образной канавки, угла канавки 60 °, конструкции торцевого соединения 2 мм, (a) основной металл (b) TMAZ на продвигающейся стороне (AS), (c) SZ, и (d) TMAZ на отступающей стороне (RS). Типичная пластинчатая микроструктура 2205 DSS состоит из островков γ-фазы в матрице α-фазы. Эти γ-островки имеют ярко выраженную ориентацию в α-матрице, параллельную направлению прокатки, как показано в а. Эта пластинчатая структура α- и γ-фаз DSS BM рекристаллизована и измельчена, чтобы дать равноосные зерна (c) из-за сильной пластической деформации, вызванной инструментом FSW, и высоким нагревом при трении.Сообщается, что SZ является ядром зоны FSW, где инструмент FSW вызывает сильное перемешивание материала и нагревание. Следовательно, температура и деформация находятся на своих крайних значениях в СЗ по сравнению с ТМАЗ [38]. На небольшом расстоянии от средней линии прохода 2205 DSS FSW заметен TMAZ (b, d). Он характеризуется более низкими температурами и деформациями по сравнению с SZ [39,40]. Утонченные равноосные зерна в SZ и образование удлиненных зерен в TMAZ способствует резкой границе между двумя зонами (b, d).После того, как TMAZ движется к BM, появляется HAZ, как показано на b, d). Он находится далеко от зоны перемешивания инструментов (SZ). Таким образом, он подвергается только циклу нагрева и охлаждения без какой-либо деформации. Следовательно, особенности микроструктуры этой зоны близки к ОМ с небольшим ростом зерна в некоторых стыках СТП [34]. Затвердевание DSS во время сварки плавлением является разновидностью феррита. Это означает, что из жидкого состояния зерна α-фазы зарождаются и преимущественно растут, а затем образуются γ-зерна различной морфологии [41].Кроме того, термический цикл между сварными швами DSS очень неоднороден и сложен, особенно для многопроходной сварки, как и в процессе GTAW [42]. показана оптическая микроструктура поперечного сечения соединения GTAWed — BM (a) и различные зоны сварки: HAZ (b, c) и WZ (d – f).
Большое и малое увеличение ЗТВ показаны соответственно на b, c. Видно, что была получена относительно большая ширина ЗТВ. Зона крупнозернистой структуры HAZ (b), примыкающая к линии зоны плавления, могла быть образована почти полным растворением γ-фазы в цикле нагрева и последующим ростом зерен α-фазы.Микроструктура ЗТВ состоит из крупных α-зерен с непрерывными сетками γ-фазы на границах α-зерен (GBA) и крошечных зерен видманштеттенового аустенита (WA) (). Однако погонная энергия в WZ выше, чем в HAZ; следовательно, вероятно обнаружение различных морфологий γ-зерен, включая GBA, внутригранулярные γ-преципитаты (IGA) и WA. Eghlimi et al. [43] сообщили, что GBA образуется при температуре 800–1350 ° C. Зерна WA выпали из зернограничной γ-фазы, как показано на WZ (b, d).Боковые рейки WA, зарождающиеся из зернограничной γ-фазы, формируют ориентации по морфологии зерен в α-матрице. Рамирес и др. [44] сообщили, что WA образуется в интервале температур 650-800 o C. ИГА зарождается внутри α-зерен (d, e).
Он также сохраняет кристаллографическую ориентацию с α-фазой. Зерна IGA более мелкие по сравнению с зернами GBA и WA. Эти особенности микроструктуры в основном считаются микроструктурами 2205 DSS, сваренных методами сварки плавлением, как сообщалось во многих предыдущих работах [2].прост и состоит из мелкозернистого перекристаллизованного феррита и аустенита. Микроструктура после GTAW, показанная на рисунке, довольно сложна и состоит из различных морфологий аустенита, таких как GBA, IGA, и крупных зерен феррита с непрерывной сеткой аустенита.
Оптическая микроструктура стыкового соединения FSWed 2205 DSS с V-образной канавкой с корневой поверхностью: ( a ) BM, ( b ) SZ / TMAZ / HAZ на продвинутой стороне, ( c ) SZ, и ( d ) SZ / TMAZ / HAZ на отступающей стороне.
Оптическая микроструктура стыкового соединения GTAWed 2205 DSS с V-образным пазом с корневой поверхностью и корневым зазором: ( a ) BM, ( b , c ) WZ / HAZ / BM при большом и малом увеличении соответственно ( d — f ) WZ.
3.4. XRD Assessment
показывает дифрактограммы рентгеновских лучей на стыковых соединениях FSWed и GTAWed 2205 DSS. Видны только пики α- и γ-фаз. Похоже, что сигма-фаза (σ) не была обнаружена в WZ для обоих суставов или ее количество может быть ниже 5%, что, как известно, является средним пределом обнаружения методом XRD.Следует отметить, что при исследовании микроструктур σ также не наблюдалось. Сообщалось, что [13,45] термический цикл сварки DSS имеет решающее влияние на выделение σ-фазы. Σ-фаза обычно образуется после длительной выдержки при температурах от 650 до 950 ° C.
Рентгенограммы соединения 2205 DSS FSWed, полученного с использованием V-образной канавки 60 o с корневой поверхностью и стыковых соединений GTAWed.
3.5. Измеренное содержание аустенита
показывает содержание γ, измеренное с использованием ферритового зонда FERITSCOPE MP30 в сварных соединениях 2205 DSS, полученных методами GTAW и FSW.Содержание γ-фазы в BM, HAZ и WZ сварного соединения 2205 DSS GTAW составляет 49%, 46% и 59% соответственно, как указано в. Можно отметить, что процентное содержание γ-фазы в WZ соединения 2205 DSS составляет 59%, что выше, чем BM. Это увеличение γ-фазы можно приписать использованию присадочного стержня ER2209 во время метода 2205 DSS GTAW, содержащего больше Ni, чем 2205 DDS BM [46]. При этом содержание γ в ЗТВ составляет 46%, что несколько меньше, чем у БМ. Это снижение процентного содержания γ-фазы может быть связано с циклом нагрева / охлаждения во время процесса GTAW [46].Содержание γ-фазы в SZ в сварных соединениях 2205 DSS с использованием FSW показано на рис. Содержание γ-фазы составляет 54% в зоне SZ и 51% в зоне HAZ / TMAZ, что немного выше, чем в зоне BM. Увеличение содержания γ-фазы в СЗ объясняется воздействием высокой температуры во время процесса СТП при применяемых режимах сварки 300 об / мин и 25 мм / мин. Это высокотемпературное воздействие привело к превращению части α-фазы в γ-фазу при охлаждении [47].Можно сказать, что соотношение α / γ в зоне сварного шва больше подходит для соединений, сваренных методом FSW, чем GTAW.
Содержание аустенита (%) в микроструктурных зонах соединения FSWed, полученного с использованием V-образной канавки 60 o с корневой поверхностью и GTAWed 2205 DSS, полученного с использованием ферритового зонда FERITSCOPE MP30. Примечание: для образца FSWed WZ представляет SZ, а HAZ представляет как TMAZ / HAZ.
3.6. EBSD Investigation
показывает карты фазового цвета (аустенит зеленым и феррит красным) для основного материала (a и b) и зоны перемешивания соединения FSWed, полученного с использованием V-образной канавки 60 o с поверхностью основания (c ) с высокоугловыми границами (HAB)> 15 o с наложенными черными линиями.Можно заметить, что микроструктура основного материала состоит из сильно вытянутых зерен как ферритной матрицы (красный), так и островков аустенита (зеленый) с объемными долями 0,46 и 0,54 соответственно, как показано на карте. Здесь следует отметить, что объемная доля немного изменилась после изменения размера шага сбора данных, так как после использования шага 0,5 мкм в (b) она становится 0,49 и 0,51 соответственно, что почти достигает идеальной доли фазы 1: 1. Удлиненные зерна феррита более сплошные, в то время как удлиненные зерна аустенита разделены на более мелкие зерна с HAB.показывает гранулометрический состав основного материала аустенита (а) и феррита (б). Можно заметить, что аустенит имеет почти случайное распределение и размер зерна от 3 до 22 мкм, в среднем 6,5 мкм. В то время как феррит имеет неслучайное распределение и более широкий диапазон размеров зерен от 3 мкм до 60 мкм со средним размером 7,2 мкм. c показывает карту фазового цвета для зоны NG после FSW. Ясно, что морфология зерен в зоне NG полностью отличается от наблюдаемой в основном материале.Значительное измельчение зерна можно наблюдать при равноосной морфологии зерна как для феррита, так и для аустенита. Зона перемешивания в FSW испытывает очень высокую степень пластической деформации при высоких температурах, возникающих в результате перемешивания инструментом FSW материала, окружающего инструмент [19,48]. Это условие привело к процессу динамической рекристаллизации в зоне перемешивания и образованию равноосной мелкозернистой структуры.
Распределение размеров зерен после FSW показано в c, d для аустенитной и ферритной фаз соответственно.Обе фазы демонстрируют случайное распределение размеров зерен в диапазоне от 1,2 мкм до 4,7 мкм для аустенита со средним значением 1,88 мкм и от 1,2 до 6 мкм для фазы феррита со средним значением 2,2 мкм. Объемная доля двух фаз составляет 0,62 и 0,38 для аустенита и феррита соответственно. Можно отметить увеличение процентного содержания аустенита в зоне перемешивания, что согласуется с результатом, полученным с использованием ферритового прибора, с немного более высоким процентным содержанием, полученным с использованием EBSD.Это может потребовать меньшего размера шага, чтобы уменьшить процентное содержание аустенита, как это наблюдается, когда в случае BM используются два разных размера шага. Полученные результаты в отношении измельчения зерна и процентного содержания фаз согласуются с результатами, опубликованными в литературе [49].
Фазовые карты (аустенит — зеленый, феррит — красный) для основного материала ( a , b ) и зоны перемешивания соединения FSWed ( c ) с высокоугловыми границами (HAB)> 15 o с наложенными черными линиями. Данные в ( a ) получены с размером шага 1 мкм, а данные в ( b , c ) получены с размером шага 0,5 мкм.
Гранулометрический состав аустенита BM ( a ), феррита ( b ) и NG соединения FSWed ( c ) аустенита, ( d ) феррита.
Из распределения углов разориентации, показанного на, можно отметить, что в BM преобладают HAB с неслучайным распределением для обеих фаз, аустенита (а) и феррита (b).В аустените можно наблюдать высокую плотность двойниковых границ при 60 °, как это также можно наблюдать на картах GB, наложенных на. После FSW распределения углов разориентации обеих фаз (c) аустенита и (d) феррита показывают случайное распределение, которое является типичным распределением рекристаллизованного материала. Плотность двойниковых границ в аустените все еще можно наблюдать при том же угле разориентации, составляющем около 60 °.
Распределение углов разориентации аустенита BM ( a ), феррита ( b ) и NG соединения FSWed ( c ) аустенита, ( d ) феррита.
Кристаллографическая текстура до и после FSW представлена полюсными фигурами 001, 101 и 111 (a, b для аустенита BM и феррита соответственно) (c, d для аустенита и феррита зоны FSWed NG соответственно). И аустенит, и феррит BM демонстрируют типичную текстуру прокатки с ГЦК и ОЦК с более прочной текстурой (в ~ 11 раз случайной) в случае феррита, чем у аустенита (~ в 4 раза случайной). После FSW текстура для обеих фаз является слабой, только примерно с двукратной случайностью, напоминающей текстуру сдвига обеих фаз.
001, 101 и 111 полюсные фигуры аустенита BM ( a ), феррита ( b ) и NG соединения FSWed ( c ) аустенита, ( d ) феррита.
3,7. Распределение твердости
показывает изменение твердости в стыковых соединениях 2205 DSS, сваренных методом (а) FSW и (б) GTAW. В целом видно, что значения твердости в WZ соединения FSW выше, чем у соединения, сваренного методом GTAW. Для соединения FSWed из a видно, что твердость достигает максимального значения 280 HV в SZ и постепенно уменьшается при переходе от TMAZ и HAZ до 260 HV и 250 HV, соответственно. Сильная пластическая деформация, сопровождаемая максимальной температурой в SZ во время процесса FSW, приводит к наиболее эффективной модификации микроструктуры с точки зрения измельчения зерна (c) за счет динамической рекристаллизации [35,50], что оправдывает самое высокое значение твердости в этой области. . В TMAZ во время FSW вводятся более низкие пластическая деформация и температура, что приводит к меньшему измельчению зерна и более низким значениям твердости. В ЗТВ деформация отсутствует, и материал DSS только претерпевает термический цикл [51].Это подтверждает самые низкие значения твердости, близкие к твердости BM в этой области. Для соединения GTAWed из b видно, что твердость достигает максимального значения 265 HV в WZ и постепенно уменьшается при переходе от HAZ и BM до 250 HV и 240 HV, соответственно. Колебания значений твердости можно объяснить наблюдаемыми микроструктурными особенностями [13]. Наличие большего количества межкристаллитных зерен γ (d) увеличивает твердость WZ [52], в то время как наличие более крупных зерен α снижает твердость HAZ.
Такие же тенденции были получены и в других работах [46].
Карты твердости по Виккерсу сварных швов DSS 2205 ( a ) сварных швов FSWed, полученных с использованием V-образной канавки 60o с корневой поверхностью и ( b ) соединения GTAWed.
3.8. Свойства при растяжении
показывает свойства при растяжении с точки зрения предела текучести (Ys), предельного напряжения при растяжении (UTS) и удлинения (E%) сварных соединений, полученных в результате процессов FSW и GTAW, по сравнению с BM. Очевидно, что соединения FSWed имеют гораздо более высокие свойства при растяжении (Ys, UTS и E%), чем соединения, представленные как соединениями GTAWed, так и BM.Это согласуется с измерениями твердости, показанными на. Можно видеть, что Ys, UTS и E% соединений FSWed улучшены по сравнению с BM на 65%, 33% и 54%, а по сравнению со сварными деталями GTAW на 21%, 41% и 66% соответственно. . Это улучшение свойств при растяжении в основном объясняется основными особенностями модификации зерен в процессе FSW [53]. Ghadar et al. [38] сообщили о значительном улучшении предела прочности на разрыв и деформации разрушения при трении при перемешивании 3.5 мм 2205 DSS и приписал это улучшение свойств растяжения измельчению зерна. Можно сказать, что размер зерна в WZ является доминирующим фактором, определяющим механические свойства. Кроме того, только около 16% улучшения Ys обнаружено для соединений GTAWed по сравнению с Ys BM без заметного увеличения UTS. Это повышение предела текучести можно также приписать измельчению зерна в WZ [42].
Свойства при растяжении основного материала DSS 2205 и соединения FSWed, полученного с использованием V-образной канавки 60 o с корневой поверхностью и соединения GTAW.
Вклад авторов
Концептуализация, M.M.Z.A. и K.A.A .; методология, М.М.З.А .; M.M.E.-S.S. и K.A.A. программное обеспечение, M.M.Z.A. и K.A.A .; проверка, M.M.Z.A .; M.M.E.-S.S. и K.A.A .; формальный анализ, K.A.A .; H.M.A.E.-A. и M.M.E.-S.S .; расследование, К.А.А. и H.M.A.E.-A. ресурсы, Б.А., Нью-Джерси и К.Т. курирование данных, M.M.Z.A .; K.A.A. и H.M.A.E.-A .; письменная — оригинальная черновая подготовка, К.А.А. и M.M.E.-S.S .; написание — просмотр и редактирование, M.M.Z.A. и M.M.E.-S.S .; визуализация, H.М.А.Э.-А. и К.Т .; надзор, M.M.Z.A., I.G.E.-B. и H.M.A.E.-A .; администрация проекта, M.M.Z.A., I.G.E.-B. и H.M.A.E.-A .; финансирование приобретения, B.A., N.J., and K.T. Все авторы прочитали и согласились с опубликованной версией рукописи.
Расчет режимов дуговой сварки под флюсом двусторонних стыковых соединений
[1] А.Акулов, Г.А. Бельчук, В. Демьянцевич, Технология и оборудование сварки плавлением, Москва, Машиностроение, (1977).
[2]
Вен С. У., Хилтон П., Фарруджа Д.К.Дж., Конечно-элементное моделирование процесса дуговой сварки под флюсом, J. of Materials Processing Technology, 119 (2001) 203-209.
DOI: 10.1016 / s0924-0136 (01) 00945-1
[3]
Махапатра М.М., Датта Г.Л., Прадхан Б., Мандал Н.Р., Трехмерный анализ методом конечных элементов для прогнозирования влияния параметров процесса SAW на распределение температуры и угловые деформации в однопроходных стыковых соединениях с верхним и нижним усилением, Int. J. Сосуды под давлением и трубопроводы, 83 (2006) 721-729.
DOI: 10.1016 / j.ijpvp.2006.07.011
[4] Киран Д.В., Басу Б., Шах А.К. и др., Трехмерный анализ теплопередачи при двухпроводной тандемной дуговой сварке под флюсом, ISIJ Int., 51 (5) (2011) 793-798.
DOI: 10.2355 / isijinternational.51.793
[5]
Сумка S. , Де А., Разработка трехмерной модели теплопередачи для процессов газо-вольфрамовой дуговой сварки с использованием метода конечных элементов в сочетании с идентификацией неопределенных входных параметров на основе генетического алгоритма, металлургические операции и операции с материалами A, Vol. 39 А, (2008) 2698−2710.
DOI: 10.1007 / s11661-008-9607-1
[6]
Бибби М., Чакраварти А., Голдак Дж., Новая модель конечных элементов для сварочного источника тепла, Металлургические операции, Vol. 15, (1994).
[7] Дивис В.[и др.], Численное моделирование деформации сварочного процесса и прогноз остаточного напряжения, определение модели источника тепла, Численное моделирование процесса сварки, Том 49, Выпуск 11-12, (2005) 15-29.
DOI: 10.1007 / bf03266499
[8]
Миллс Г. С., Основные механизмы проплавления при GTA-сварке, Welding J., Vol. 58, № 1, (1979) 21-24.
[9] Сидоров В.П., Семистенов Д.А. Математическое моделирование геометрии сварного шва при сварке конструкционных сплавов и биометалла. Тольятти, Тольяттинский государственный университет, 2009.
[10]
Сидоров В. П., Мельзитдинова А.В., Определение допустимых отклонений режимов двусторонней дуговой сварки, Welding International, (2016) 1-4.
DOI: 10.1080 / 09507116.2016.1243748
[11] В.Фролов В. Теория сварочных процессов. М .: Высшая школа, 1988.
[12]
Андреев С. Б., Головченко В.С., Горбач Д.В., Руссо В.Л. Основы сварки морских конструкций. СПб .: Судостроение, 2006.
[13] Сидоров В.П., Семистенов Д.А., Хурин С.А., Новые факторы эффективности плавления металлов, Сборник докладов Всероссийской конференции с международным участием Современные проблемы повышения эффективности сварочной техники, Часть 1, Тольятти, Тольяттинский государственный университет, (2006) 128- 134.
[14]
Алексеев Ю. Э., Кушнарев Л.Н. Оборудование для дуговой сварки под флюсом. Л .: Энергия, 1977.
[15] Цвелев Р.А. Оценка погрешности воспроизведения температурного поля при сварке флюсом по эквивалентному источнику тепла, Сварочное производство, 6 (2013) 11-15.
[16]
DuPont J. Мардер Н. А. Термический КПД процессов дуговой сварки // Сварка. 74, № 12, 1995, стр. 406-416.
[17] Ерохин А.А., Основы сварки плавлением, М., Машиностроение, (1973).
[18]
Дьяконов В. П. Справочник по алгоритмам и программам на BASIC для персональных компьютеров, Москва, Наука, (1987).
[19] Сидоров В.П., Борисов Н.А., Вклад в переплав электродного металла для сварки под флюсом, Пайка-2013: сборник докладов конференции (Тольятти, 10-12 сентября 2013 г.), Тольятти, Тольяттинский государственный университет, (2013) 232-239.
[20]
Сидоров В. П. Влияние типа и полярности тока на проплавление электрода и основного металла при дуговой сварке под флюсом // Сварка и диагностика. 2013. № 3. 20-23.
[21] Сидоров В.П. Анализ условий сварки под флюсом двусторонних стыков без подготовки кромок, Серия конференций IOP: Материаловедение и инженерия, Vol. 253, Конференция 1, (2017).
DOI: 10.1088 / 1757-899x / 253/1/012011
[22]
Березовский Б. М., Стихин В.А. Расчет параметров распределения теплового потока поверхностной сварочной дуги, Сварочное производство, 2 (1980) 1-4.
[23] Сидоров В.П., Борисов Н.А. Критерии дуговой сварки при сварке // Сварка и диагностика. 2013. № 6. 24–27.
Влияние угла канавки в стыковых соединениях на угловую деформацию при дуговой сварке под флюсом | Махендрамани
Просмотры аннотации: 114 | Просмотры PDF-файлов: 3Авторы
г.
Кафедра машиностроения, UVCE, Университет Бангалора, Бангалор-560 001, Карнатака, Индия Н. Лакшмана Свами
Кафедра машиностроения, UVCE, Университет Бангалора, Бангалор-560 001, Карнатака, Индия
Абстрактные
При сварке стальных конструкций в сварном шве образуется локальная зона плавления из-за большого количества тепла, поступающего от дуги, а затем возникает неравномерное распределение температуры за счет теплопроводности.Угловая деформация является серьезной проблемой и наиболее ярко проявляется среди различных типов деформации пластин, сваренных встык, в обрабатывающей промышленности. Эта угловая деформация в основном связана с неравномерной поперечной усадкой по глубине свариваемых пластин. Ограничение этой деформации удерживанием может привести к более высоким остаточным напряжениям. Трудно получить полное решение для прогнозирования углового искажения, которое могло бы быть надежным для широкого диапазона процессов, материалов и параметров управления процессом. Таким образом, разработка надлежащих методов уменьшения и контроля деформации приведет к созданию более надежных сварных конструкций с уменьшением стоимости изготовления. Исследовано влияние угла канавки на угловую деформацию стыковых сварных соединений, полученных дуговой сваркой под флюсом. В этом исследовании образцы были подготовлены для различных углов канавки для разного раскрытия корня и толщины горловины в стыковых соединениях с одной V-образной канавкой, с косой канавкой и с двойной V-образной канавкой. Эти образцы были сварены методом дуговой сварки под флюсом с постоянными параметрами процесса.Угловая деформация была измерена и проанализирована для всех образцов. Было замечено, что угловая деформация уменьшается с увеличением угла канавки для данного отверстия корня и толщины горловины.
Ключевые слова
Угловая деформация, угол канавки, включенный угол, угол скоса, дуговая сварка под флюсом.
Что такое сварка? | Различные типы сварки и определения сварочных работ
Определение, процессы и типы сварных швов
Сварка — это процесс, который объединяет такие материалы, как металлы, термопласты и / или дерево, с использованием тепла или давления для плавления деталей вместе. Дать им остыть дает возможность слияния.
Различные материалы требуют уникальных процессов и технологий. Некоторые материалы считаются несвариваемыми. Хотя этот термин не используется в словаре, он хорошо известен инженерам как термин, означающий, что определенный материал не может свариваться.
Исходные материалы — это термин, используемый для описания отдельных частей, которые соединяются вместе. Примеры основных материалов — трубы и плиты. Он отличается от наполнителя или расходного материала, который добавляется для соединения основного материала.Примерами присадочных материалов являются проволока, металл или расходуемые электроды.
Обычно расходные материалы выбираются так, чтобы они были сопоставимы по составу с исходным материалом. Это позволяет им создавать однородный сварной шов. Однако есть обстоятельства, такие как сварка хрупких чугунов, для которых требуется другой состав. В этом сценарии эти сварные швы будут называться неоднородными.
Наконец, готовое сварное соединение называется сварной конструкцией. Сварная деталь — это единица, созданная путем сварки нескольких более мелких деталей.
Как работает сварка?
Соединение металлов
Сварка, пайка и пайка — все это приводит к прочному соединению основных материалов. Процессы пайки и пайки не плавят основной металл. По сравнению с пайкой и пайкой, сварка представляет собой высокотемпературный процесс, при котором основной материал плавится с добавлением сварочного присадочного материала.
Высокая температура создает сварочную ванну из расплавленного материала. Этот расплавленный материал охлаждают для образования соединения. В результате получаются чрезвычайно прочные соединения, иногда даже более прочные, чем у исходных материалов.Давление может использоваться в сочетании с нагревом для сварки двух материалов вместе.
При сварке металла, находящегося на прямом контакте с воздухом, кислород воздуха вступает в реакцию с металлом и образует оксид. Это загрязняет металл и приводит к плохой сварке. Лучший способ предотвратить это — использовать защитный газ.
Соединение пластмасс
Сварка пластмасс — это процесс, который создает молекулярную связь между двумя совместимыми термопластами. В этом процессе для соединения материалов обычно используется тепло, за исключением сварки растворителем.В зависимости от используемого процесса способы соединения пластмасс можно разделить на методы внешнего и внутреннего нагрева.
Соединение пластмасс происходит в 3 этапа:
- Давление часто используется на стадиях нагрева и охлаждения, чтобы удерживать детали в правильном положении и улучшить поток расплава по краям.
- Нагрев обеспечивает межмолекулярную диффузию от одной части к другой.
- Охлаждение создает сплав, который укрепляет вновь созданную связь.
Соединение дерева
Сварка дерева соединяет материалы за счет давления и тепла, создаваемых трением. Древесные материалы, которые должны быть соединены вместе, подвергаются давлению, а затем растираются взад и вперед с высокой скоростью, что создает тепло, которое связывает материалы вместе.
Это быстрый процесс, который создает высокопрочное соединение, которое происходит в течение нескольких секунд, и не требует использования какого-либо клея.
Общие конфигурации швов
стыковое соединение
Это соединение двух частей на концах или краях под прямым углом друг к другу от 135 до 180 градусов.Это самый простой стык, потому что он включает только разрезание материала на определенную длину и последующее соединение двух частей вместе.
Т-образный шарнир
Тройник обычно называют точкой сварки двух материалов. Это соединение между концом или краем одной детали и лицевой стороной другой. В результате детали в области стыка образуют угол 90 градусов. Это соединение образует букву T, как следует из его названия.
Угловой шарнир
Угловое соединение — это соединение концов двух сегментов. Это соединение образует друг с другом угол более 30 градусов, но менее 135 градусов в области стыка. Этот стык в образовании выглядит как буква L.
Кромочный стык
Краевой стык образуется путем объединения краев двух сегментов с образованием угла друг к другу от 0 до 30 градусов в области стыка.
Крестообразный шарнир
Крестообразное соединение образуется путем сварки двух плоских стержней или плоских пластин под прямым углом на одной оси.Этот сустав по форме напоминает крест.
Нахлест
Соединение внахлест — это соединение двух перекрывающихся сегментов, образующих угол между собой от 0 до 5 градусов в области соединения.
Типы сварных соединений
Сварные швы на основе конфигурации
- Сварка с пазом. Это соединение двух вышележащих деталей, которое создается путем наложения полностью или частично углового шва вокруг края отверстия в одном компоненте.Это соединяет деталь с внешней стороной другой детали, которая выходит через отверстие.
- Электрозаклепка. Этот сварной шов выполняется путем заполнения отверстия в цельной детали присадочным металлом, чтобы соединить его с внешней частью перекрывающейся детали, которая выступает через отверстие. Отверстие может иметь овальную или круглую форму.
Сварные швы на основе проплавления
- Сварной шов с полным проплавлением. Также известный как сварной шов с проплавлением, представляет собой сварной шов очень большой толщины.Этот сварной шов состоит из двух металлических частей, соединенных между собой без зазоров. Наплавленный металл полностью проникает в шов с полным проплавлением корня. Это приводит к более высокой прочности, чем сварной шов с частичным проплавлением.
- Сварной шов с частичным проплавлением. Также известный как сварной шов с частичным проплавлением, это сварной шов с бороздками, приводящий к неполному провару соединения. Этот сварной шов заполняет только часть зазора и используется только тогда, когда нет необходимости развивать полную прочность соединяемых частей для передачи нагрузки.
Сварные швы в зависимости от доступности
- Односторонний сварной шов. Это соединение, которое приваривается только с одной стороны. Его нельзя использовать для замены конструкций или панелей. Он чрезвычайно эффективен при косметическом исправлении.
- Двухсторонний сварной шов. Это соединение, сваренное с двух сторон.
Характеристики завершенных сварных швов
- Основной металл. Металлические компоненты, соединяемые вместе расплавленным присадочным металлом в процессе пайки, сварки или сварки твердым припоем.
- Присадочный металл. Металл, добавляемый при наплавке, сварке, пайке или сварке твердым припоем.
- Сварной металл. Это весь металл, который плавится и затвердевает во время образования сварного шва и сохраняется в нем.
- Зона термического влияния (HAZ). Это сегмент основного материала, будь то металл или термопласт, свойства материала которого изменяются в результате воздействия высоких температур в результате сварки или термической резки.
Этот сегмент не растаял.
- Линия Fusions. Этот термин обычно не используется для описания сварного соединения, но является границей между свариваемым металлом и ЗТВ при сварке плавлением.
- Зона сварки. Это область сварного шва, которая включает как металл шва, так и ЗТВ.
- Лицевая сторона сварного шва. Это открытая поверхность сварного шва на той же стороне, на которой была завершена сварка.
- Корень шва. Это область, где обратная сторона сварного шва пересекается с поверхностью основного металла.Подобно тому, как корни дерева глубоко проникают в землю, это та часть, которая имеет самое глубокое проникновение.
- Приварной палец. Это стык поверхности сварного шва и основного металла или между прогонами. Эта особенность имеет решающее значение, потому что пальцы ног — это области необычайной концентрации стресса. Зона носка сварного шва также является отправной точкой для различных видов трещин, таких как холодные и усталостные трещины.
- Избыток металла шва. Это также называется армированием или переполнением.Это лишний металл шва, который находится за пределами области, соединяющей пальцы ног. Несмотря на то, что его иногда называют усилением, этот термин на самом деле не описывает, что такое избыточный металл сварного шва, потому что избыток металла сварного шва не делает сварной шов более прочным. Расчетная толщина шва — это фактический термин, используемый для описания толщины сварного шва, который исключает излишки металла шва.
- Сварочный ход (проход). Этот термин используется для описания металла, который плавится во время одного «прохода или прохода» горелки, горелки или электрода.
- Сварной слой. Это результат сварного прохода или прогона.
Источники энергии
В зависимости от используемого источника энергии доступны различные процессы с различными технологиями. Одним из первых видов сварки была кузнечная сварка. Позже была создана дуговая сварка. Сегодня для сварки используются электрическая дуга, лазеры, газовое пламя, ультразвук, трение и электронный луч. При работе с каждым процессом человек должен быть очень осторожным, потому что он может вызвать ожоги, повреждение зрения, эклектический шок, вдыхание ядовитых сварочных газов и дыма, а также воздействие радиации.
Какие бывают методы сварки и для чего они используются?
Различные типы процессов с уникальными технологиями включают:
Дуговая сварка
- Включает: ручные, полуавтоматические и автоматические процессы.
- Включает: сварку металла в среде инертного газа (MIG), сварку в среде активного газа (MAG), сварку штучной сваркой, сварку в среде инертного газа вольфрама (TIG), сварку металлическим электродом в среде защитного газа (GMAW), сварку порошковой проволокой (FCAW), плазменную сварку , дуговая сварка в защитных слоях металла (SMAW) и сварка под флюсом (SAW).
- Использует присадочный материал.
- Используется в основном для соединения металлов, таких как нержавеющая сталь, никель, медные сплавы, алюминий, титан и кобальт.
- Процесс, используемый в энергетической, аэрокосмической, автомобильной, нефтегазовой и других отраслях промышленности.
Сварка трением
- Техника соединения материалов с использованием механического трения.
- Выполняется различными способами на различных сварочных материалах, таких как алюминий, сталь или дерево.
- Механическое трение создает тепло, чтобы смягчить материалы, чтобы их можно было смешать для образования связи во время охлаждения.
- Не требует присадочных металлов, защитного газа или флюса.
- Способ соединения зависит от таких процессов, как сварка трением с перемешиванием (FSW), линейная сварка трением (LFW), ротационная сварка трением (RFW) и точечная сварка трением с перемешиванием (FSSW).
- Идеально подходит для комбинирования несвариваемых легких алюминиевых сплавов и может использоваться для склеивания древесины без клея и гвоздей.
- Этот процесс обычно используется в аэрокосмической промышленности.
Электронно-лучевая сварка
- В процессе используются высокоскоростные электроны для объединения материалов.
- Кинетическая энергия электрона превращается в тепло при ударе по заготовке. В результате материалы плавятся вместе.
- Выполняется в вакууме для предотвращения рассеяния луча.
- Используется для соединения толстых профилей, поэтому его можно применять в различных отраслях промышленности, таких как аэрокосмическая, автомобильная, железнодорожная и атомная энергетика.
Лазерная сварка
- Используется для соединения деталей из металла или термопласта.
- В процессе используется концентрированное тепло, что делает его идеальным для сварки с высокими скоростями, а также узких и глубоких швов.
- Легко автоматизируется.
- Идеально подходит для автомобильной промышленности, поскольку процесс выполняется при высоких скоростях сварки, что делает его идеальным для применения в больших объемах.
- Выполняется в воздухе.
Сварка сопротивлением
- Процесс соединяет металлы путем приложения давления и пропускания через них тока в течение определенного периода времени.
- Процесс чрезвычайно рентабелен, потому что для образования сцепления не требуются другие материалы.
- Обычно используется в автомобильной промышленности из-за быстрой обработки.
- Процесс можно разделить на две формы:
- Точечная сварка. В этом процессе используется тепло, передаваемое между двумя электродами. Затем его наносят на крошечный участок, когда детали зажимаются вместе.
- Шовная сварка. Этот вид сварки сравним с точечной сваркой, но заменяет электроды колесами, которые вращаются, когда свариваемые сегменты проталкиваются между ними, чтобы создать сварной шов без утечек.
Где это используется?
Сварочные процессы обычно используются в самых разных отраслях промышленности, таких как автомобилестроение, строительство, энергетика и авиакосмическая промышленность.