Зажимы для точечной сварки
Для того, чтобы соединить металлические элементы, чаще всего используют сварку. Для неё есть масса подходов и методов, и каждый используется в зависимости от ситуации и имеет свои плюсы и минусы.
Но основными критериями для выбора технологии всегда была скорость работы, свойства шва и, конечно, характеристики используемого металла.
Один из методов — точечная сварка (которую еще называют контактной) — соединяет в себе большинство преимуществ: быструю пайку, высокую точность, а также качество соединения, несложное исполнение.
Эту технологию можно использовать и в производственных цехах, и для домашнего ремонта. Лучше всего она проявляет себя при соединении тонких листов металла, поэтому часто является основной на автомобильных заводах.
Точечная сварка имеет один секретный нюанс. Чтобы сформировать точку сварки, мастер использует контактные сварочные клещи (зажим). Они могут не только прижимать элементы, но и нагревать их импульсами тока.
Это дополнение обеспечивает прочность сварного шва. Мы расскажем, как вы можете сделать сварочные клещи для точечной сварки дома самостоятельно, чтобы не платить лишнего за заводские в строительных гипермаркетах, тем самым сделать сварку дешевле.
Общая информация
Зажимы для точечной сварки бывают ручные и подвесные. На типах этого инструмента нужно остановиться на пару минут, чтобы понимать нюансы их ручной сборки.
Ручные сварочные клещи имеют простую конструкцию. Также, как и весь остальной ручной инструмент (пассатижи, плоскогубцы, щипцы), в основе их системы рычаг, который регулирует открытие и закрытие клещей.
Главный нюанс сварочных клещей — возможность применить трансформаторную систему. К одной рукояти клещей подсоединяется трансформатор, который передает на инструмент ток для того, чтобы создать соединение.
Через одну из рукояток трансформаторный механизм передаёт генерируемый сварочный ток на электродные стержни. В этом заключается основная работа механизмов для зажима. Вы руками прижимаете детали из металла клещами, через них идёт ток.
Электрическая сила и сила сжатия создают точку сварки (поэтому сварка точечная). Процесс не механизированный, он от начала до конца выполняется руками сварщика, поэтому только он решает, насколько быстро будут свариваться элементы.
Подвесные зажимы для контактной сварки в быту используются редко. Но их часто можно встретить на заводах и у профессиональных мастеров, использующих узкоспециализированное оборудование для точечной технологии.
Эти клещи встроены в сам аппарат, и принцип их работы другой. Да, они созданы, чтобы сжимать детали друг с другом, но не вручную. Потому производительность работ вместе с подвесными клещами выше, чем с ручными.
Собирать такие дома нет смысла, так как, скорее всего, у вас нет оборудования, с которым их можно было применить.
Поэтому далее речь будет идти о сборке именно ручных клещей для точечного метода сварки.
Изготовление
Вы проведете меньше времени в магазинах, сделав сварочные клещи для точечной сварки своими руками. При этом вы тратите намного меньше, и сэкономленные деньги можно «пустить» на качественные материалы для сварки.
Делать и использовать ручные клещи для контактной сварки несложно. Но при этом они подходят для любого вида металла. Им найдёт место и человек, ремонтирующий своё авто в гараже, и мастер выездных работ. Себестоимость их радует экономных людей.
Первый этап изготовления самодельного инструмента — создание основы. Для неё подойдут материалы, которые есть у каждого под рукой. Это может быть любая сталь или сплав, толщина которых не больше пяти миллиметров.
Из листа материала сделайте несколько полосок по двадцать мм в ширину. Длина их может быть разной, она зависит от ваших пожеланий. Для основы подойдут и широкие стержни из металла. Кончикам заготовок придайте очертания щипцов.
Наложите изготовки наискось относительно друг друга и состыкуйте. По центру сделайте отверстие, которое будет точкой регулировки открывания и закрывания клещей. В месте отверстия проложите между пластинами диэлектрическую прокладку.
С конца одного стержня/пластины также нужно просверлить дырочку, чтобы можно было крепить на болты медный провод. Противоположная заготовка тоже просверливается. Отверстие в ней нужно, чтобы крепить кабель аппарата и фиксировать клемму.
Изолируйте металл клещей для точечной сварки с помощью изоленты вместе с резиновой накладкой (это может быть кусок шланга) после того, как соедините и просверлите нужные компоненты.
Эти материалы защитят вас во время работы с электричеством, а держать их в руках станет удобнее. Такой конструкции хватит, чтобы поддерживать сварочные зажимы на весу, но для их закрепления нужно будет добавить пружину между ручками.
Ток к зажиму подводится тоже с учётом правил. Его лучшим источником станет трансформаторный механизм со второстепенной наложенной обмоткой. Можно обмотать кабель на сердечник три раза.
Для того, чтобы повысить мощность точечной сварки, объедините пару трансформаторов, генерирующих ток.
Схемы для создания ручных клещей найти нелегко, поэтому постарайтесь продумать их устройство сами. В помощь вы можете взять видео уроки по созданию не подвесных клещей или советы знакомых мастеров.
Заключение
Мы рассказали вам всё, что знали о изготовлении ручных клещей для контактной точечной сварки. Для этого вам не придётся искать особые материалы, так как можно обойтись и теми, что у вас уже есть.
Несмотря на простоту такого инструмента, он не хуже дорогих заводских клещей из магазинов. К тому же, самодельные инструменты не требуют особых условий хранения и ухода.
Если вы будете использовать их не на постоянной основе, они тем более «проработают с вами» не один год.
Как вы собирали клещи для точечной сварки вручную? Какую схему придумали? Вы можете помочь своим советам новичкам в комментарии под этой статьей. Возможно, именно благодаря вам кто-то решится собрать свой первый инструмент. Желаем вам удачи!
Время чтения: 5 минут
Сварка — это самый распространенный метод соединения металлов на данный момент. Сейчас существует масса технологий сварки, каждая из которых обладает как достоинствами, так и недостатками. Но в конечном итоге подбор технологии зависит от типа металла, его характеристик, предполагаемой скорости сварки и ее качества.
Одна из технологий, сочетающая в себе высокую скорость и качество работ, при этом относительную простоту процесса — это контактная точечная сварка. Она применяется как в быту, так и на крупных производствах. Контактная точечная сварка хорошо зарекомендовала себя при сварке тонколистового металла, например, кузова авто. Весь секрет кроется в технологии. Для формирования сварной точки применяются специальные сварочные клещи для контактной сварки, которые не только сжимают детали, но одновременно подогревают их с помощью короткого электрического импульса.
Благодаря этому формируется прочный сварной шов. В этой статье мы расскажем, как сделать клещи для сварки в домашних условиях, чтобы удешевить сварку и сэкономить на приобретении заводских клещей.
Общая информация
Клещи для сварочных работ могут быть ручными и подвесными. Давайте подробнее поговорим про типы клещей, поскольку это важно для их самостоятельной сборки.
Ручные клещи контактной сварки вы можете видеть на картинке ниже. Как видите, конструкция ручных клещей крайне проста, и во многом схожа с любым других ручным инструментом (с теми же плоскогубцами или щипцами), где используется рычажная система открытия/закрытия. Основное отличие ручных клещей для контактной сварки заключается в дополнительном применении трансформатора. Трансформатор подключается к одной из рукояток клещей и генерирует сварочный ток, необходимый для формирования шва.
Суть работы клещей контактной точечной сварки заключается в том, что трансформатор генерирует сварочный ток, который затем подается через рукоятку клещей на сварочные электроды.
Также есть подвесные сварочные клещи для точечной сварки. Они используются на производстве либо при изготовлении профессиональных аппаратов для контактной сварки. Такие клещи встраиваются в сварочный аппарат и работают по иной схеме. Они все так же сжимают обе детали, но этот процесс происходит не вручную. Именно по этой причине подвесные клещи гораздо производительнее, чем ручные. Тем не менее, в домашних условиях подвесные клещи не собираются. Это нецелесообразно и для их применения нужно специальное оборудование.
Поэтому далее мы расскажем, как собрать своими руками ручные клещи для контактной сварки.
Самодельные клещи
Ручные клещи для точечной сварки, сделанные своими руками — это отличный способ сэкономить, и при этом получить рабочий инструмент.
Состыкуйте заготовки крест-накрест и просверлите отверстие. Оно необходимо для соединения двух металлических заготовок и их дальнейшего раскрывания/закрывания. Не забудьте про прокладку из диэлектрика. Ее нужно установить между двух заготовок. Затем на торце одной заготовки нужно сделать отверстие для крепления медных проводов с помощью болта. На другой заготовке сверлится отверстие для крепления сварочного кабеля и фиксации клеммы.
Обмотайте ручки клещей изолентой или наденьте резиновый шланг, если использовали металлический стержень при изготовлении приспособления. Так клещи будут более безопасными и удобными в применении.
Что касается подвода тока к клещам, то для этих целей сгодится любой трансформатор с вторичной перемотанной обмоткой. Вы можете уложить в три витка сварочный кабель на сердечник. Если вы хотите получить контактную сварку повышенной мощности, то соедините два трансформатора и используйте их для генерации тока.
В интернете есть чертежи только подвесных клещей, так что вам придется самостоятельно продумать конструкцию своего самодельного приспособления. Но это не вызовет затруднений, поскольку в многочисленных видеороликах подробно рассказывается, как сделать ручные клещи.
Вместо заключения
Теперь вы знаете, как можно сделать клещи для точечной сварки своими руками буквально из подручных средств. Себестоимость таких клещей невысока, поэтому вы сможете сэкономить и при этом получить полноценного помощника в быту или в хозяйстве. Как показывает практика, самодельные клещи очень надежны и неприхотливы к хранению. Это очень важные достоинства, поскольку вам не придется беспокоиться об их сохранности. Ну а если вы и вовсе нечасто пользуетесь клещами, то они без проблем прослужат долгие годы.
А вы когда-нибудь собирали ручные клещи для контактной сварки? Поделитесь своими советами в комментариях ниже. Они пригодятся всем, кто только начинает собирать самодельные аппараты и приспособления для сварки. Может быть, вы знаете некоторые особенности, которые нужно обязательно учесть при сборке самодельных клещей. Расскажите и о них тоже. Желаем удачи в работе!
Известно, что подготовка любых деталей к свариванию требует ничуть не меньших усилий, чем непосредственная их сварка. Причём «львиную» долю подготовительных мероприятий составляет сборка рабочей схемы (в которую входят и зажимы для сварки) с фиксацией всех составляющих в удобном положении. Указанный процесс нуждается в особом внимании, поскольку от него зависит качество изготавливаемого изделия.
Необходимость в фиксации
Действительно, мало кому понравится, когда собранная после долгих стараний конструкция от одного прикосновения электрода сварочного аппарата разваливается на части и нуждается в повторной сборке.
Заметно сложнее выглядит ситуация, когда из-за неправильно собранной схемы элемент приваривается не так как надо, что заставляет разбирать её и начинать сварку заново
Существует большое количество различных механизмов и специальных зажимов, используемых для сварочных работ с целью повышения производительности и удобства их проведения.
Все эти изделия по своему прямому назначению делятся на установочные детали и закрепляющие (фиксирующие) струбцины или зажимы.
Виды зажимных приспособлений
Рабочие зажимы, применяемые в сварке, могут иметь следующие конструктивные исполнения:
- обычная клемма в виде металлической прищепки с рабочим названием «крокодил»;
- специальный зажим с фиксатором для сварки;
- так называемые винтовые стыковочные прижимы, к которым можно отнести и угловую струбцину;
- магнитные клеммы и другие виды фиксирующих зажимов.
На практике чаще всего используются сварочные зажимы первых трёх типов, как хорошо зарекомендовавшие себя при работке с любым видом сварного оборудования.
Регулируемые зажимные клещи с фиксирующим механизмом обеспечивают надёжный контакт с заготовкой и массой во время сварки. Простейший вариант винтового прижима– это обычный болт с накручиваемой на него гайкой, соединяющий две обжимные пластины.
Значительно реже при организации сварки применяется так называемая «магнитная клемма», относительно которой мнения специалистов по сварке заметно расходятся. Ей будет посвящён отдельный раздел статьи.
Зажимы выпускают в широком ассортименте. Регулярно занимаясь сваркой, можно выбрать такой зажим, которым будет удобнее всего пользоваться. Встречаются зажимы в виде клещей, пассатижи, удлиненные и другие разновидности.
Подключение «массы»
Так называемая «масса» (или обратный провод, подключаемый к свариваемой заготовке) отличается от прямого кабеля меньшей гибкостью и изготавливается из более дешевого металла.
Иногда его просто приваривают к заготовке или к металлической конструкции, на которой ведутся работы. Съёмный зажим массы применяется лишь в ситуациях, требующих частой смены места подсоединения обратного кабеля или же при необходимости повышения качества электрического контакта.
Для формирования такого соединения в процессе сварки обычно используется винтовой зажим, обеспечивающий контакт, близкий к идеальному. Этот вариант удобен тем, что позволяет быстро произвести смену места подсоединения, необходимость в которой возникает довольно часто.
По мнению некоторых специалистов клеммы для массы вместе с проводами (при проведении сварки в стационарных условиях) могут заменяться медными, алюминиевыми или стальными сплошными шинами.
При этом в случае, когда для сварки используется переменный ток, необходимо принимать во внимание поверхностные эффекты, приводящие к неравномерности его распределения в проводниках.
Чтобы самостоятельно изготовить клеммы-прищепки для сварки типа «крокодил» потребуется:
- отрезок стального профиля типоразмером 25х25 и толщиной стенок порядка 2-х миллиметров;
- медная пластина толщиной 2 миллиметра с размерами 2 на 10 сантиметров;
- стальная пружина диаметром около 2-х сантиметров;
- ручные инструменты по металлу.
Со всеми нюансами изготовления такой клеммы своими руками можно будет ознакомиться по видео.
Магниты
К основным достоинствам этого класса зажимных механизмов следует отнести не только быстроту и удобство фиксации подводящего кабеля на элементах свариваемых конструкций, но и возможность их лёгкого снятия.
По мнению ряда сварщиков, такие устройства заметно облегчают монтажные операции и сокращают время, затрачиваемое на подготовку к сварке.
Они могут рассматриваться как полноценная замена достаточно громоздких и занимающих много места зажимов и струбцин, однако не следует забывать и об имеющихся у этих приспособлений недостатках. К одним из таких минусов, согласно отзывам пользователей, относится ослабление крепления при сильном разогреве поверхности контакта во время сварки.
Помимо этого, большинство покупателей считают цену на такое оборудование завышенной и не в достаточной мере оправдывающей его преимущества. Однако при общей оценке качественных и эксплуатационных показателей этих зажимов чаша весов склоняется в сторону их полезности и удобства для работы.
Угловые струбцины
Струбцины традиционно относят к вспомогательным инструментам, используемым для жёсткого соединения деталей между собой или же для надёжной фиксации заготовок при сварке.
Их также можно назвать зажимами, так как функция состоит в фиксации детали. Характерной особенностью этих механизмов является применение в них угловой фиксации соединения между элементами конструкции.
Некоторым «народным умельцам» удаётся изготовить их самостоятельно, что заметно экономит домашний бюджет и позволяет сделать зажимы для сварки, исходя из своих вкусов и предпочтений.
Преимущество такого зажима проявляется в том, что на нём имеются несколько монтажных овальных отверстий, с помощью которых его корпус может надёжно закрепляться на рабочем верстаке или столе.
Практическое использование механических струбцин, как правило, связано с необходимостью фиксации деталей свариваемой рамы, например, или других деталей, нуждающихся в угловой фиксации.
Важнейшей составляющей конструкции такой струбцины является подвижный механизм упора. Он размещается на массивном металлическом кронштейне с пазами для фиксации свариваемых заготовок, расположенными под прямым углом.
Следует обратить внимание на то, что для подключения сварочного аппарата (импульсного инвертора, например) целесообразнее применять готовые зажимы и фиксирующие приспособления, выпускаемые отечественной промышленностью.
И лишь в крайних случаях, когда указанные механизмы недоступны сварщику – удобнее воспользоваться возможностью их самостоятельного изготовления.
Самодельные струбцины из разных материалов и для разных задач
Самодельные струбцины удобны в тех случаях, когда нет поблизости строительных магазинов или рынков.
Кроме этого, самодельный инструмент можно сделать тех размеров и форм, которые требуются для выполнения определенных задач.
И конечно же мастер изготавливающий своими руками инструмент, экономит на его покупке.
В быту этот инструмент используют достаточно редко, однако, бывают ситуации, когда без них не обойтись.
Если вдруг зажим понадобился, но нет возможности его приобрести, имеет смысл изготовить собственный вариант из подручных материалов:
Содержание статьи
Вариант 1
Основанием послужит рамка обыкновенной ножовки по металлу.
С обеих сторон находятся крепления для полотна.
Их необходимо заменить длинными винтами соответствующей толщины.
Если использовать шпильки немного меньшего диаметра, придется использовать контргайки.
К торцам винтов привариваются металлические пятаки, но можно обойтись без сварки и использовать их в качестве подложки.
Вариант 2
Можно использовать швеллер (в поперечном разрезе напоминает букву “П”). Отрезается поперек кусочек шириной 3 – 5 см.
Одна сторона выполнит функцию фиксированной губы.
С противоположной стороны (ножка буквы “П”) просверливается отверстие, нарезается резьба и вкручивается винт, под торец которого подкладывается или приваривается плоский пятачок.
Как вариант, можно использовать два сваренных буквой “П” уголка.
Вариант 3
Имея под рукой неиспользуемый пистолет для герметика скелетного типа, можно изготовить быстросъемную самодельную струбцину.
Сам по себе он уже может быть использован, как зажим для заготовок небольшой ширины.
Для большей универсальности, от пистолета необходимо отпилить рамку, а на ее место приварить к рукояти прочную металлическую полосу, изогнутую буквой “Г”.
Так как дерево поддается обработке лучше, можно изготовить простейшую струбцину из этого материала.
Деревянные струбцины
Простейший вариант самодельного деревянного зажима – две планки, которые стягиваются двумя болтами с гайками.
Можно улучшить конструкцию, прикрепив к болтам ручки, изготовив деревянные губы различных форм и размеров.
Еще один вариант – вырезать из березовой фанеры толщиной 12 – 16мм 4 – 5 идентичных П-образных заготовки, которые после склеивания послужат рамой.
С одной стороны ножки просверливается внутрь корпуса отверстие под винт, под него подкладывается пятак.
При необходимости можно к винту приделать деревянную рукоять, или же для прижима использовать соответствующий шляпке ключ.
Если изготовление этого инструмента своими руками вам не очень подходит, в этом случае всегда можно приобрести магазинный вариант.
Для правильного выбора хороших струбцин нужно знать их виды и важные отличия.
Важно знать при выборе струбцин
Выбирая струбцину, необходимо обратить внимание на следующие особенности:
Материал
Для изготовления зажимных инструментов используется либо чугун, либо же инструментальная сталь.
Первый вариант обладает меньшей прочностью, не способен выдержать чрезмерное прижимное усилие.
Чугунные струбцины используются, как правило, при работе с деревом.
В любом случае, на самом инструменте должна быть соответствующая пометка.
Вид и конструкция
Оба параметра должны соответствовать работе, которую инструмент будет выполнять.
Большим прижимным усилием обладают G-образные варианты с винтом, в то время, как быстрозажимным инструментом удобнее пользоваться.
Для работы с широкими деталями, чтобы прижимное усилие распределялось по большей площади, используются струбцины с удлиненными губами.
Количество
Для фиксации любых заготовок понадобится сразу несколько струбцин, что позволит равномерно распределить прижимное усилие на заготовках большой площади.
Рекомендуется покупать сразу набор.
Накладки
Многие домашние мастера подкладывают под контактирующие с заготовками элементы зажима брусочки, дощечки, металлические пластины, резиновые обрезки.
В этом нет необходимости, так как хороший инструмент изначально должен иметь качественные накладки.
Работоспособность и отсутствие дефектов
Инструмент, естественно, должен быть исправен.
Прижимные губы должны плотно прижиматься, легко и с первого раза.
Элементы не должны болтаться и люфтить.
Конструкцию нужно осмотреть на наличие повреждений (трещин, сколов).
Все углы, во избежание травматизма, должны быть округлые и отшлифованные.
В некоторых случаях имеет смысл к комплекту стандартного прижимного инструмента докупить струбцины глубокого захвата.
Они предназначены для фиксации, захвата и удержания деталей.
Будут полезны и для сварщиков, и для столяров, так как особая форма губ позволяет захватывать и прижимать заготовки за основание в обход выступающих элементов.
Со временем у любого мастера накапливается много разного инструмента, в том числе и большое количество струбцин.
В этом случае для их хранения очень удобно использовать специальные стойки.
Стойки для струбцин
Для удобного хранения прижимных инструментов рынок предлагает широкий выбор стоек для струбцин.
Они могут быть выполнены из дерева и металла, а их размеры варьируются от нескольких десятков сантиметров (переносные варианты), до полноценных инструментальных рам и шкафов на колесиках.
Среди мастеров популярны стойки – карусели, которые позволяют хранить большое количество зажимов и струбцин на сравнительно малой площади, при этом обеспечивают простой доступ к инструменту, который размещается со всех сторон.
Наиболее распространенный и востребованный вариант – металлическая стойка на колесиках с рамочной конструкцией, отдаленно напоминающая стремянку.
Рама, при необходимости, складывается.
Она имеет съемные перекладины, посредством которых можно регулировать просвет.
Подходит для хранения зажимов любых типоразмеров, за счет чего успешно используется и в домашних мастерских, и в крупных производственных цехах.
Наличие колесиков со стопорами позволяет легко передвигать весь комплект прижимного инструмента и неподвижно его устанавливать возле рабочего места.
Подробную информацию об основных видах струбцин смотрите здесь
Зажимы своими руками. Самодельные зажимы. Самодельные струбцины – разновидности и технологии изготовления
Опытные мебельщики, столяры, слесарных дел мастера справедливо считают, что струбцина является не менее важным инструментом, чем удобный верстак, хорошо сбалансированный рубанок или набор острых, как бритва, стамесок из шведской стали. Приспособление можно купить, взять в аренду, но лучше всего сделать струбцину своими руками. В этом случае будет уверенность, что нехитрое устройство не подведет в самый ответственный момент.
Суть устройства струбцины
Конструктивно струбцина представляет собой простейшее устройство, позволяющее прижать деталь, заготовку, несколько составных частей в одно целое для установки крепежа — саморезов, болтов с гайками, заклепок, или пока сохнет клей.
К устройству струбцины, независимо от конструкции, материала и размеров приспособления, предъявляют два основных требования:
- Рама струбцины не должна деформироваться под нагрузкой, жесткость каркаса приспособления должна быть достаточной, чтобы сохранить параллельными плоскости прижимных губок;
- Конструкция прижимного винта должна обеспечивать регулируемое и плавное прижатие подвижной опоры струбцины на фиксируемой поверхности.
Существует достаточно большое количество всевозможных схем струбцин, и, хотя устройство любой струбцины примитивно по сути, никто не пытается сделать универсальную конструкцию, которой можно было бы пользоваться в любой ситуации. Устройство получается очень тяжелым, неудобным и сложным в работе.
Поэтому размеры и схему приспособления подбирают, исходя из габаритов соединяемых деталей и требуемого усилия прижатия. Условно струбцины делят на три большие группы:
- Столярные и мебельные линейчатые струбцины, их стараются сделать из твердых сортов древесины и металла;
- Монтажные струбцины большой жесткости;
- Слесарные упорные струбцины.
Кроме классических струбцин-линеек, широко используют заказные струбцины нестандартных схем, большинство из них изготавливается под выполнение одной-двух операций повышенной сложности.
Например, сверление в массиве из нескольких досок на большую глубину, обрезка или склеивание бруса фигурным способом под прямым или нестандартным углом, сварка деталей сложной конфигурации. Вариантов более чем достаточно, лучший способ обеспечить самое высокое качество соединения — это все же сделать струбцину нужного размера и формы.
Деревянная универсальная струбцина своими руками
Проще всего сделать струбцину из деревянной планки и бруса. Дерево — достаточно демократичный материал, поэтому, если выполнить правильную разметку деталей и использовать надлежащие инструменты, то без особых усилий можно сделать зажим любого уровня сложности.
Для изготовления деревянной струбцины потребуются следующие инструменты и приспособления:
- Настольный сверлильный станок мощностью 400-500 Вт под сверла от 1-15 мм. Вертикальный ход сверлильного патрона должен быть не менее 120 мм;
- Электрический шлифовальный круг. Его можно сделать самостоятельно, для этого на электроточиле вместо абразивного камня устанавливают круг из фанеры, толщиной 10 мм и диаметром 350 мм, на котором с двух сторон наклеены полотна наждачной бумаги;
- Ручная дисковая пила по дереву с диаметром диска не менее 150 мм. Можно использовать болгарку или ленточную пилу.
Все остальные операции можно сделать с помощью ручного инструмента. Разумеется, сверлить отверстия и нарезать пазы можно также и ручными дрелью и ножовкой, только достичь требуемого качества и точности изготовления с использованием ручных инструментов будет очень непросто.
Классическая F образная струбцина
Конструкция простейшей деревянной струбцины выглядит, как латинская буква F. Вертикальная и верхняя горизонтальная планка представляют собой одно целое — неподвижную направляющую, соединенную упором одной из губок. Центральная перемычка буквы F — это подвижная или ответная часть губок, которая приводится в движение ходовым винтом. Третья часть струбцины с приводным винтом изготавливается в съемном варианте. Зажим можно переставлять по длине направляющей планки, расстояние между губками сделать меньше или больше, насколько позволяет длина базовой рейки.
Общий вид струбцины приведен на фото.
Первоначально нужно сделать направляющую рейку. Для этих целей подойдет лиственница или еловая доска. Все остальные детали струбцины можно сделать из любой древесины, кроме мягких сортов, — тополя, липы, березы.
Важно!
Для изготовления любых приспособлений и вспомогательной оснастки используют только бездефектную древесину. Если нет таковой, то лучше всего сделать струбцину из обычной фанеры толщиной 15-20 мм.
Базовую планку вырезают по длине будущего приспособления. На опорную неподвижную часть губок зажима приходится львиная доля нагрузки, поэтому лучше всего сделать направляющую из самой прочной древесины или применить небольшую хитрость.
По боковому торцу рейки вырезают полукруглый паз, в который укладывают стальной прут, диаметром 8-10 мм. С одной стороны конец загибается вокруг торца, на другом конце прут соединяют с неподвижной губкой гайкой, навернутой на предварительно нарезанную резьбу.
Неподвижную часть губок приклеивают к направляющей планке столярным клеем, после высыхания клея опорную поверхность тщательно подрезают по углу в 90 о к направляющей планке. Эту деталь можно сделать клееной, или пропилить монтажный паз с помощью ручной циркулярной пилы.
Ответную или подвижную часть губок вырезают вместе с опорой под винт из одного бруска. Далее в обеих заготовках нужно сделать П-образные пропилы, позволяющие посадить детали на направляющую планку. После снятия заусенец заготовки устанавливают пакетом в сверлильный станок и сверлят отверстие под ходовой винт.
Если предполагается достаточно интенсивное использование струбцины, то в отверстие под винт необходимо запрессовать латунную трубку, сделать подшипник скольжения. В противном случае ходовой винт достаточно быстро разобьет отверстие на 2-5 мм, что сделает инструмент непригодным для работы.
Струбцина, собранная из дерева и стали
Деревянной струбциной удобно работать, если нужно сделать небольшой прижим, чтобы зафиксировать пакет из нескольких планок или склеить две детали. Если предполагается обработка бруса или доски столярным инструментом, рубанком или шлифмашиной, то струбцину для фиксации материала лучше всего сделать с металлической направляющей.
Процесс изготовления струбцины из дерева и стали выглядит следующим образом:
Остается собрать струбцину, переставляемую часть засверливают под фиксирующий болт, устанавливают болт или шпильку и затягивают гайкой. По окончанию сборки нужно сделать два-три холостых прогона, чтобы осадить стенки и облегчить вращение винта.
Деревянная струбцина для фиксации и стяжки наборов
В 40% случаев работы в столярной или мебельной мастерской требуют использования длинных струбцин для стягивания целых наборов или пакетов из планок, формирования мебельных щитов, столешниц и дверного полотна. Процесс изготовления струбцин для нужд стяжки практически не отличается от обычного деревянного F-образного приспособления.
В отличие от других схем приспособлений, струбцина для стяжки изготавливается из массивного бруса, сечением 50х50 мм и длиной не менее 100 см. В направляющей планке из бруса сверлят на станке ряд отверстий для перестановки ответной части губок.
Кроме того, потребуются три блока из дуба или бука, для того чтобы сделать неподвижную опору с ходовым винтом и две части губок — переставляемую и подвижную.
На ответной переставляемой опоре прорезают установочный паз и сверлят отверстие, в которое запрессовывается гайка под крепежный болт. Расстояние между опорами можно сделать больше-меньше, если губку переставить на следующее отверстие и зафиксировать ее болтом.
Деревянный зажим из деталей вешалки
Небольшое приспособление, очень напоминающее стягивающий тип струбцин, можно запросто изготовить из обычных костюмных плечиков. Деревянная основа вешалки изготавливается из двух одинаковых половинок трапециевидной формы.
Первым делом, чтобы изготовить зажим из вешалки, необходимо сложить две половинки плечиков в один пакет и зажать в тисках сверлильного станка.
Не раскрывая станочных тисков, потребуется сделать четыре отверстия диаметром 8 мм. Получаются две заготовки, в каждой из которых есть пара сквозных отверстий. Остается сделать зажим, для этого необходимо отрезать две шпильки с резьбой М8, длиной по 25 см каждая. Шпильки можно вклеить в одну из половинок или сделать симметричный вариант, как на фото.
Из зажима можно сделать фиксирующее устройство для склейки досок, удержания труб или стягивания пакета из нескольких планок.
Быстрая С образная струбцина для дерева
Кроме классических вариантов столярных струбцин и зажимов, в работе с мебелью и деревоматериалами приходится использовать малоразмерные фиксаторы. Одним из таких приспособлений является С-образная струбцина, изготовленная из дерева, фото.
Прежде чем сделать зажим, необходимо подыскать подходящую заготовку из дерева. С-образные струбцины требуют очень прочной древесины, поэтому для изготовления используют акацию, вяз или степной дуб. П-образный корпус вырезается болгаркой. При общем размере корпуса 100х100 мм ширина боковин должна быть не менее 2,5 см.
В одной из боковин нужно сделать сквозное отверстие диаметром 12 мм, в которое запрессовываются две стальные гайки, М8 или М6. Проще всего навернуть гайки на резьбовой шток, смазать клеем и вставить в отверстие. Нужно сделать несколько несильных ударов киянкой, чтобы гайки с небольшим натягом вошли в сквозное отверстие. Остается сделать ручку, и С-образная струбцина готова.
Струбцина из металла своими руками
Большую часть слесарных и столярных струбцин изготавливают из металла, чаще всего стали или алюминиевых сплавов, причин для подобной избирательности всего две:
- Высокая прочность металлических деталей;
- Длительный срок службы даже при большой нагрузке.
Чтобы сделать струбцины из металла, потребуется сварочное оборудование, болгарка и обычная электродрель и электролобзик.
Длинная стягивающая струбцина
Наиболее логичным будет сделать струбцину, у которой направляющий брус или планка из дерева заменены квадратной профильной трубой. Метровую струбцину можно сделать из квадрата 20х20 мм, для двухметровой потребуется профиль 30х30 мм. Использование трубчатого квадратного профиля позволяет сделать конструкцию очень жесткой без «тянучек» и усадки, как это бывает у пиломатериалов.
Проще всего сделать длинную струбцину по классической схеме. Стационарная, подвижная и переставная части изготавливаются из толстой фанеры.
Каждая деталь состоит из двух половинок, которые вырезаются лобзиком и стягиваются болтами на длинной квадратной трубе. Ходовой винт можно сделать из двух частей резьбовой шпильки и обычного куска арматуры.
Самодельная сварная струбцина из арматуры
Вместо дерева можно использовать обычный арматурный пруток, сечением 8-10 мм. Чтобы сделать корпус струбцины из арматуры, потребуется вырезать две заготовки длиной 65 и 55 см. Прутки греют на паяльной лампе и загибают на стальной оправке под прямым углом согласно чертежу.
Согнутые заготовки сваривают в одну Г-образную конструкцию, обязательно соединяются сварочным швом носик и линейные участки арматуры.
Следующим этапом из отрезка в 20 см изготавливают стойку под ходовой винт, к которой приваривают гайку. Если усилие зажима на струбцине более 50 кг, то стойку можно сделать гнутой или укрепить дополнительным подкосом.
Самодельная G-образная струбцина
Конструкцию с G-образным корпусом еще называют винтовым прессом за огромное усилие, которое можно получить с помощью ходового винта. Сделать G-образную струбцину достаточно просто. Для этого необходимо нарезать болгаркой заготовки корпуса из толстого металла, не менее 7-8 мм толщиной.
Корпус сваривается буквой П. На верхней полке нужно сделать отверстие под гайку, далее навинтить ее на ходовой винт и установить на место сварки. На нижней полке укладывают небольшой кусочек металла — столик, который прижимают вывернутым винтом. Нужно только сделать несколько сварочных точек или швов, чтобы приварить столик и гайку, и струбцина готова.
Деревянная прокладка для опоры металлической струбцины
Важной деталью любой струбцины считается подкладка, устанавливаемая под опорные поверхности зажима. Делается это для достижения двух целей:
- Не допустить повреждения зажимаемой струбциной детали, так как в металлических приспособлениях давление зажима может легко достигать нескольких сот килограммов;
- Равномерно передать и распределить усилие от ходового винта на поверхность мебельного щита или фиксируемой детали.
Лучше всего сделать прокладку из обычной березовой фанеры или мягкой древесины с нешлифованной поверхностью.
Зажим для наворачивания проволоки на оправку
Очень непростой задачей считается надежная фиксация стальной проволоки на круглой заготовке, например, резиновой трубе или оголовке штуцера. Конструктивно такое приспособление состоит из двойного корпуса и намоточного штифта.
Проволоку оборачивают вокруг трубы и зацепляют на штифте с болтовой головкой. За 2-3 поворота ключом намотанная полуторная петля натягивается до нужного состояния. Остается сделать поворотом корпуса закрутку проволоки на шланге в несколько витков и обрезать ее концы.
Угловые струбцины своими руками
Использование специализированных струбцин на сегодня остается единственно возможным способом собирать любые прямоугольные или квадратные конструкции из дерева и металла с идеально выставленным прямым углом.
Например, система из готовых треугольников, которые охватывают плоскости стыкующихся сторон и прочно удерживают их в нужном положении, до момента установки крепежа или окончания сварочных работ.
Зажим универсальный под любой угол
Прямой угол, как правило, не представляет особой проблемы при работе со струбцинами, значительно сложнее сделать угол произвольной величины. Для решения подобных задач нужно сделать приспособление к струбцине, как на фото.
В основе дополнительного устройства используется обычный сосновый брусок с вырезанным по центру сектором прямого угла. Второй деталью является обычный прямоугольный треугольник, который можно сделать из еловой или сосновой рейки.
В вершине угла сектора высверливается сквозное отверстие, диаметром 5-6 мм. Именно отверстие позволяет треугольнику качаться и менять угол наклона струбцины на 3-7 о.
Угловая стальная струбцина для сборки
Соединить две детали под прямым углом намного проще, если закрепить их в угловой струбцине. В простейшем случае приспособление представляет собой две направляющие из обрезанной профильной трубы или стального уголка.
Направляющие необходимо выставить с помощью угольника под углом в 90 о и соединить дополнительными накладками из листового металла.
Для того чтобы заготовки при работе не выпадали из приспособления, на каждой из направляющих дополнительно устанавливают по две G-образных струбцины.
Струбцина быстрозажимная своими руками
Иногда в работе с деревом требуются струбцины, с помощью которых можно сделать фиксацию или прихват детали к рабочему столу или месту в течение буквально нескольких секунд.
Для того чтобы сделать быструю струбцину, потребуются деревянные доски или фанера толщиной 16-18 мм. Первоначально калька деталей переносится на дерево и вырезается с помощью электролобзика. В ведомых частях потребуется сделать пропилы под заход ответной детали.
По размеченным точкам осей нужно сделать отверстия диаметром 20 мм.
Из круглой заготовки вырезаются шарнирные оси, шлифуются и запрессовываются в отверстия. Получается конструкция струбцины, чем-то напоминающая ножницы. Для привода используется стандартный ходовой винт диаметром 6 мм.
Зажим для удержания и фиксации мелких деталей
Аналогичным способом можно сделать зажим для фиксации особо мелких деталей. Предварительно потребуется разметить и вырезать из ОСБ или фанеры две половинки устройства, похожего на пинцет или медицинский зажим.
Серповидные заготовки соединяются между собой с помощью деревянной оси, поэтому в каждой из деталей струбцины необходимо сделать отверстие соответствующего диаметра. Для корпуса зажима можно использовать ясень или ель, ось необходимо сделать из более твердого материала — дуба или бука.
Струбцина из прута арматуры и дерева
Используя арматурный прут, длиной 50-60 см и диаметром 8 мм, можно сделать очень прочную и одновременно легкую рамку универсального назначения.
В основе конструкции используется опорный деревянный блок из твердых сортов древесины. Размеры блока 150х50х30мм. Размеры могут изменяться в зависимости от толщины и радиуса изгиба арматурного прута. Крючок из куска арматуры можно согнуть тяжелым молотком на стальной трубе. Изгиб нужно сделать так, чтобы согнутая арматура была плоской.
Ленточная универсальная струбцина
Одна из наиболее интересных необычных конструкций струбцин использует в качестве силового элемента толстый ремень из полиэфирной ткани. Ленточная струбцина используется там, где необходимо равномерно стянуть несколько деталей.
Чтобы изготовить ленточную струбцину, необходимо сделать угловые элементы и устройство для натяжения полиэфирного ремня. Три уголка вырезают из обычной сосны по распечатанной кальке. Четвертый элемент — натяжное устройство изготавливается из двух блоков и натяжного винта.
Лента пропускается вокруг блока, если выкручивать винт ключом, расстояние между блоками увеличивается, и ремень устройства натягивается, прижимая все четыре блока к детали.
Кулачковые быстрые струбцины
Зачастую деталь или заготовку в струбцине необходимо зафиксировать быстро, причем сделать зажим без лишних движений. Например, при сушке или окрашивании партии панелей или рамок. Для этих целей лучше всего сделать специализированное приспособление с кулачковыми зажимами, фото.
Отличие данного приспособления заключается в том, что вместо традиционного ходового винта на вертикальных губках зажима устанавливают эксцентрики из фанеры.
Для этого на деревянных стойках предварительно необходимо сделать пропил по толщине эксцентрика.
Телескопический раскладной зажимной хомут
В основе идеи телескопического приспособления для зажима используется набор труб, входящих друг в друга с минимальным зазором, как у раскладной удочки, и набора кольцевых хомутов с винтовым фиксатором.
От каждой трубы отрезают колечко, к которому приваривается брусочек металла с нарезанной резьбой. Завернутый винт или болт фиксирует трубу, расположенную внутри, что позволяет зажать всю конструкцию в одну раздвинутую штангу.
Крепежные универсальные зажимы
Кроме струбцин, для фиксации склеиваемых деталей сложной конфигурации широко применяются двухполочные универсальные зажимы, фото.
Идея зажима — струбцины позаимствована у переплетного пресса, размеры и количество фиксаторов выбираются в зависимости от размеров детали.
4-х ходовые полизажимы для деревянных панелей
Отсутствие надежной фиксации остается одной из проблем, с которой приходится сталкиваться при сборке и склейке щита из нескольких широких и плоских планок. Сделать сборку даже из пяти -шести проклеенных планок и стянуть материал обычными длинными струбцинами не получится, при малейшем увеличении усилия щит выгибает дугой.
Решением проблемы будет приспособление с четырьмя струбцинами, фото.
Панель фиксируется двумя парами зажимов. На концах каждой пары нужно сделать крестообразный зажим из гайки и металлических пластин. На ответном конце крепления устанавливают регулируемый по высоте шарнир. Ходовой винт каждой струбцины упирается в деревянную накладку. Достаточно сделать несколько оборотов винта, чтобы пара брусков прочно сжала склеиваемые детали.
Зажимная коробка для установки на верстаке
Если нет специального монтажного ложемента, детали сложной конфигурации не так просто закрепить на ровной поверхности верстака. В этом случае для обработки деревянной детали сложной пространственной конструкции лучше всего сделать зажимную коробку.
Сделать конструкцию довольно просто:
- Из фанеры собирается коробчатый остов;
- Вдоль длинных сторон коробки нашивают два бруса, лучше всего сделать из сосны, сечением 50х50 мм;
- Набивается ряд монтажных поперечин из того же материала.
Коробка позволяет с помощью зажимов обеспечить удержание любой, самой сложной детали. Если для ее обработки планируется использовать мощные электроинструменты, для коробчатого основания нужно также сделать струбцину или зажим, фиксирующий приспособление на столе.
Самодельный зажим для журнального стола
Серьезной проблемой всех деревянных столов журнального типа была и остается невысокая поперечная жесткость рамы, даже без нагрузки столешница частенько имеет небольшой, но крайне неприятный люфт.
Устранить проблему можно установкой самодельного зажима или стягивающей пружины. Две планки или брусочка из дерева соединяют между собой длинной металлической скобой.
Приспособление можно сделать с винтовым зажимом или самоподжимным. В любом случае, бруски усилят и зафиксируют каркас с ножками, тем самым устранят имеющийся люфт.
Недорогой простейший зажим из колечка трубы ПВХ
Иногда приходится искать подручные средства, чтобы удерживать при переноске, но чаще при сверлении или обработке детали и предметы круглого сечения. Самый простой вариант зажима можно сделать из кольца полихлорвиниловой трубы.
Достаточно просверлить два сквозных отверстия, вставить пару отрезков арматуры и в одном месте разрезать стенку кольца. Приспособление рассчитано на определенный диаметр детали, поэтому для работы придется сделать целый набор зажимов.
Стойки для набора струбцин
Рабочие приспособления и струбцины в первую очередь должны храниться в специально отведенном месте. Вместо сваленного кучей инструмента, из которого сложно найти и выбрать необходимое устройство, лучше всего сделать несколько разрезных стоек или полок. В этом случае на то, чтобы быстро выбрать несколько наиболее подходящих по размеру и устройству струбцин, уйдет всего лишь пара минут, а не полдня, как ранее.
Импровизированные зажимы
Зачастую в столярной работе или при сборке деревянных конструкций не хватает времени на изготовление полноценных струбцин и зажимов. Тогда на помощь приходит смекалка и опыт.
Например, заготовку круглого сечения можно зафиксировать с помощью нескольких колец, набитых на рамку.
Арматурный прут или водопроводную трубу можно зажать с помощью импровизированной струбцины из нескольких брусков и скотча.
Обычный фиксирующий шнур багажника поможет стянуть подобно ленточному зажиму набор из десятка деревянных планок.
Время чтения ≈ 5 минут
Струбциной называют инструмент, напоминающий ручные тиски, который используют для надежной фиксации или склейки двух элементов. Например, в столярном ремесле ее применяют, чтобы соединить две плоскости на время высыхания клеевого раствора. Однако не всегда этот инструмент есть под рукой, поэтому можно самостоятельно прибегнуть к изготовлению быстрозажимной конструкции. Чтобы правильно сделать струбцину своими руками из металла, нужно следовать пошаговым инструкциям с фото и видео мастер-классам.
Особенности конструкции
Струбцина может быстро выйти из строя, поэтому так важно знать, как смастерить самодельный инструмент. Составными частями данной металлической конструкции являются рычажная часть, рама, губы зажима и подвижная деталь.
В чем преимущества зажимных инструментов:
Струбцину можно сделать и из древесины, однако металлическая конструкция практичней и надежней. Ее изготовление не потребует особых знаний и навыков, понадобится лишь применение сварочного оборудования, ножовки и горелки. Весь процесс с пошаговой инструкцией показан на видео.
Модели зажимных инструментов делятся на следующие классы по работе механизмов и структурным особенностям:
Технология изготовления
Струбцина, сделанная своими руками из металла, значительно надежней и практичней деревянной конструкции. Для изготовления самодельных агрегатов потребуется сварочное оборудование и слесарные агрегаты.
Инструменты для изготовления струбцины любого типа
1 вариант
Следуя инструкции, можно сделать самодельную струбцину из металлической арматуры.
2 вариант
Чтобы сделать своими руками угловой инструмент для зажима, нам понадобятся следующие материалы: стальные обрезки от уголка 40*40, 50*50 и 30*50 по 200 мм, 2 F-образные струбцины и полоса 10*50 до 250 мм длиной.
Приступим:
Приобретать струбцины в строительных магазинах достаточно накладно. Всем хочется избавить себя от лишних затрат, если есть альтернативные варианты. Таких инструментов может понадобиться сразу несколько, особенно это актуально при сборке, изготовлении или ремонте предметов мебели. Самодельные струбцины заменят вам ручные тиски, так как есть возможность выбрать модель, тип и размер инструмента. Следуя инструкциям на фото и видео, можно быстро разобраться с механизмом изготовления и быстро сделать ручной зажим из подручных материалов.
Начинающему мастеру не помешает узнать, что на первых этапах обойтись одним лишь молотком или пилой вряд ли получится. Впоследствии придется прибегнуть к применению тисков или быстрозажимной струбцины, чтобы зафиксировать заготовку или склеить отдельные фрагменты. Сделать ее своими руками довольно просто. Нет ни одного достаточно универсального зажима, который позволял бы удовлетворить все потребности при выполнении различных типов работы.
Применение деревянных струбцин
Они бывают различных стилей, моделей и размеров. А потому можно запастись различными моделями, которые всегда пригодятся. Мастер может закупить несколько моделей струбцин Assistent, к тому же они там стоят не так уж и дорого. Если человек не хочет платить за такую покупку, он может сделать деревянную или трубную струбцину своими руками. Модели из древесины очень популярны, их можно изготовить самостоятельно. Такая модель простая в эксплуатации и легко регулируется.
Модель F — деревянная струбцина, которая слегка усовершенствована. Здесь используется планка из клёна шириной 5 см и толщиной 0,6 см. А также в конструкции присутствует металлический стержень, на который нанесена резьба. Чтобы изготовить ручку, надо взять деревянную заготовку. Для этого подходит лиственная порода без дефектов.
Подвижные детали должны быть хорошо высушены, чтобы без проблем скользить на планке. На стержне должно присутствовать две гайки. Они располагаются на конце и затягиваются потом друг против друга. Благодаря этому они не расходятся во время использования. Можно использовать отдельную стопорную гайку или простую модель с постоянным замком. И ещё две гайки необходимо, чтобы зафиксировать снаружи зажимные колодки вместе с шайбой.
Допускается использование контргайки и других способов крепления. Двойные изделия заклинивают друг друга. Это самый надежный и простой способ. Он же самый дешёвый. Важно оставить некоторое пространство для винта, чтобы он мог свободно вращаться.
Из древесины и стали
Обрезают при помощи ножовки резьбовой шток до 30 см. Сначала необходимо обустраивать дополнительный разрез на блок размером 9 на 7 см, если речь идет о нефиксированных концах. Как только все углы будут срезаны, надо просверлить отверстие и вставить затяжные болты.
Надо убедиться, что отверстия довольно велики, чтобы подогнать головку болта. Фиксируется резьбовой стержень в верхней зоне фиксированного конца. Отверстие должно быть довольно большим, чтобы гайку можно было вставить гайку в штангу. Устанавливают фиксированный конец, когда намереваются сверлить отверстия. Производя сборку, необходимо убедиться, что концы закреплены под прямым углом. Резьбовой шток благодаря этому будет становиться параллельно стержню.
Перед сборкой необходимо обустроить отверстие, где проходят гайка и резьбовой стержень. Делают это в том же положении блока, что и для фиксированного конца. Надо убедиться, что отверстие довольно широкое и глубокое, чтобы разместить гайки. Нижняя зона маленькая, а потому сюда трудно вставить достаточное количество винтов. Это необходимо для предотвращения скручивания.
Размеры полки определяются в соответствии с желаемой длиной и имеющимся оборудованием. После этого распиливают компоненты системы до необходимого размера, вырезают подушечки для губки и сверлят необходимые отверстия, ручки наклеивают пятиминутной эпоксидной смолой. Когда стержень винта зазубрен напильником или наждачной бумагой, фиксируют ручки посредством эпоксидного клея.
Лёгкие самодельные варианты
Легкая струбцина, сделанная своими руками, изготавливается на основе металлического стержня. Эти зажимы, хоть и не такие мощные, как стальные, всё равно дают возможность создавать сильное прижимное давление для любого клея. Соответственно, срок службы у них довольно внушительный. Штанга может быть сделана в любой длине. Единственное, надо запомнить, что по всей длине основного стержня не должен проходить резьбовой стержень. Головка струбцины не испытывает необходимости в нём на этом конце, что значительно упрощает сборку. Зажимные губки делают из фанеры.
Стопорная гайка представляет собой элемент, который фиксирует прижимную губку на стержне. При этом он не должен пребывать под давлением. Гайку можно срезать обычной ножовкой. Эпоксидной смолой его закрепляют на пятке. Выемка должна получиться довольно широкой и подходить к шайбе и глубокой, чтобы гайка и шайба могли без проблем поворачиваться.
Здесь надо использовать гайку 35 мм, так как необходимо просверлить отверстие в поперечнике 38 мм с донной частью и 15 мм глубиной. После сверления углубления делают сквозное отверстие. Оно требуется для зажимного винта. Фиксируют подвижную головку на неподвижной позиции и отмечают места, где должно располагаться отверстие.
Рукоятка, винт и основная сборка
Изготавливают квадратные заготовки по 25 мм и отрезают для каждой ручки по 100 мм. Обозначают центральную часть и высверливают с помощью сверла фрагмент 10,5 мм 60 мм. В качестве аналога можно высверливать довольно широкое отверстие, после чего покрывать эпоксидной смолой. Но такой способ считается недостаточно надежным.
Шлифуют заготовку, чтобы сделать более удобную ручку и приклеивают к данному зажимному винту. Приступают к основной сборке. Это простая задача, позволяющая наклеить плёнку к неподвижной головке. Укрепляют стопорную гайку и делают торцевые колпачки. Они должны не допускать соскальзывания головки со штанги. Потому желательно прикрутить небольшую пластинку на пятку. Благодаря этому выскальзывание гайки с места исключается . Это действует, как крюк.
Кулачковый зажим
Это устройство не только полезное, но и предельно простое. Надо помнить, что кулачковые зажимы быстродействующие, но не способны гарантировать большой силы зажима деталей. Вот почему их используют тогда, когда требуется сравнительно небольшая сила резания. Они не годятся для работы под большим давлением, как это возможно с крупной струбциной. Но при этом они чрезвычайно просты в использовании.
Для приготовления используют специальный шаблон. Он необходим для создания кривых. Шаблон изготавливается из металла, пластмассы или древесины. Его используют, чтобы подтянуть гладкие кривые. При этом кулачковые механизмы не являются прямым отслеживанием французской кривой. Правильный кулачок должен иметь профиль , увеличивающий расстояние между осью вращения и постоянной скоростью. В этом он напоминает спираль, прочерченный карандашом.
Начинающему мастеру не помешает узнать, что на первых этапах обойтись одним лишь молотком или пилой вряд ли получится. Впоследствии придется прибегнуть к применению тисков или быстрозажимной струбцины, чтобы зафиксировать заготовку или склеить отдельные фрагменты. Сделать ее своими руками довольно просто. Нет ни одного достаточно универсального зажима, который позволял бы удовлетворить все потребности при выполнении различных типов работы.
Применение деревянных струбцин
Они бывают различных стилей, моделей и размеров. А потому можно запастись различными моделями, которые всегда пригодятся. Мастер может закупить несколько моделей струбцин Assistent, к тому же они там стоят не так уж и дорого. Если человек не хочет платить за такую покупку, он может сделать деревянную или трубную струбцину своими руками. Модели из древесины очень популярны, их можно изготовить самостоятельно. Такая модель простая в эксплуатации и легко регулируется.
Модель F — деревянная струбцина, которая слегка усовершенствована. Здесь используется планка из клёна шириной 5 см и толщиной 0,6 см. А также в конструкции присутствует металлический стержень, на который нанесена резьба. Чтобы изготовить ручку, надо взять деревянную заготовку. Для этого подходит лиственная порода без дефектов.
Подвижные детали должны быть хорошо высушены, чтобы без проблем скользить на планке. На стержне должно присутствовать две гайки. Они располагаются на конце и затягиваются потом друг против друга. Благодаря этому они не расходятся во время использования. Можно использовать отдельную стопорную гайку или простую модель с постоянным замком. И ещё две гайки необходимо, чтобы зафиксировать снаружи зажимные колодки вместе с шайбой.
Допускается использование контргайки и других способов крепления. Двойные изделия заклинивают друг друга. Это самый надежный и простой способ. Он же самый дешёвый. Важно оставить некоторое пространство для винта, чтобы он мог свободно вращаться.
Из древесины и стали
Обрезают при помощи ножовки резьбовой шток до 30 см. Сначала необходимо обустраивать дополнительный разрез на блок размером 9 на 7 см, если речь идет о нефиксированных концах. Как только все углы будут срезаны, надо просверлить отверстие и вставить затяжные болты.
Надо убедиться, что отверстия довольно велики, чтобы подогнать головку болта. Фиксируется резьбовой стержень в верхней зоне фиксированного конца. Отверстие должно быть довольно большим, чтобы гайку можно было вставить гайку в штангу. Устанавливают фиксированный конец, когда намереваются сверлить отверстия. Производя сборку, необходимо убедиться, что концы закреплены под прямым углом. Резьбовой шток благодаря этому будет становиться параллельно стержню.
Перед сборкой необходимо обустроить отверстие, где проходят гайка и резьбовой стержень. Делают это в том же положении блока, что и для фиксированного конца. Надо убедиться, что отверстие довольно широкое и глубокое, чтобы разместить гайки. Нижняя зона маленькая, а потому сюда трудно вставить достаточное количество винтов. Это необходимо для предотвращения скручивания.
Размеры полки определяются в соответствии с желаемой длиной и имеющимся оборудованием. После этого распиливают компоненты системы до необходимого размера, вырезают подушечки для губки и сверлят необходимые отверстия, ручки наклеивают пятиминутной эпоксидной смолой. Когда стержень винта зазубрен напильником или наждачной бумагой, фиксируют ручки посредством эпоксидного клея.
Лёгкие самодельные варианты
Легкая струбцина, сделанная своими руками, изготавливается на основе металлического стержня. Эти зажимы, хоть и не такие мощные, как стальные, всё равно дают возможность создавать сильное прижимное давление для любого клея. Соответственно, срок службы у них довольно внушительный. Штанга может быть сделана в любой длине. Единственное, надо запомнить, что по всей длине основного стержня не должен проходить резьбовой стержень. Головка струбцины не испытывает необходимости в нём на этом конце, что значительно упрощает сборку. Зажимные губки делают из фанеры.
Стопорная гайка представляет собой элемент, который фиксирует прижимную губку на стержне. При этом он не должен пребывать под давлением. Гайку можно срезать обычной ножовкой. Эпоксидной смолой его закрепляют на пятке. Выемка должна получиться довольно широкой и подходить к шайбе и глубокой, чтобы гайка и шайба могли без проблем поворачиваться.
Здесь надо использовать гайку 35 мм, так как необходимо просверлить отверстие в поперечнике 38 мм с донной частью и 15 мм глубиной. После сверления углубления делают сквозное отверстие. Оно требуется для зажимного винта. Фиксируют подвижную головку на неподвижной позиции и отмечают места, где должно располагаться отверстие.
Рукоятка, винт и основная сборка
Изготавливают квадратные заготовки по 25 мм и отрезают для каждой ручки по 100 мм. Обозначают центральную часть и высверливают с помощью сверла фрагмент 10,5 мм 60 мм. В качестве аналога можно высверливать довольно широкое отверстие, после чего покрывать эпоксидной смолой. Но такой способ считается недостаточно надежным.
Шлифуют заготовку, чтобы сделать более удобную ручку и приклеивают к данному зажимному винту. Приступают к основной сборке. Это простая задача, позволяющая наклеить плёнку к неподвижной головке. Укрепляют стопорную гайку и делают торцевые колпачки. Они должны не допускать соскальзывания головки со штанги. Потому желательно прикрутить небольшую пластинку на пятку. Благодаря этому выскальзывание гайки с места исключается . Это действует, как крюк.
Кулачковый зажим
Это устройство не только полезное, но и предельно простое. Надо помнить, что кулачковые зажимы быстродействующие, но не способны гарантировать большой силы зажима деталей. Вот почему их используют тогда, когда требуется сравнительно небольшая сила резания. Они не годятся для работы под большим давлением, как это возможно с крупной струбциной. Но при этом они чрезвычайно просты в использовании.
Для приготовления используют специальный шаблон. Он необходим для создания кривых. Шаблон изготавливается из металла, пластмассы или древесины. Его используют, чтобы подтянуть гладкие кривые. При этом кулачковые механизмы не являются прямым отслеживанием французской кривой. Правильный кулачок должен иметь профиль , увеличивающий расстояние между осью вращения и постоянной скоростью. В этом он напоминает спираль, прочерченный карандашом.
С помощью таких тисков очень удобно и надежно зажимать небольшие детальки. А для того, чтобы наш зажим при развинчивании гайки автоматически разжимался, то можно внутрь на болт, между створками петли надеть пружину. Ее не нужно брать очень мощную, для того чтоб без особого труда она позволяла зажимать нужные детали.
Для работы необходимо:
— небольшая дверная петля;
— болт;
— гайка-«барашек»;
— отвертка;
— плоскогубцы.
Зажим своими руками делается достаточно просто. Мы берем дверную петлю, в которой должно быть по 3 отверстия с каждой стороны. Соединяем оба ее края и одну дырку рассверливаем под болтик, если у вас нет маленького, который сможет подойти под уже имеющиеся отверстия.
Вставляем болт в подготовленное для него отверстие и с другой стороны зажимаем гайкой-«барашком». Чтобы зажатие предметов было максимальным, можно воспользоваться отверткой и плоскогубцами.
Самый элементарный зажим из подручных материалов готов.
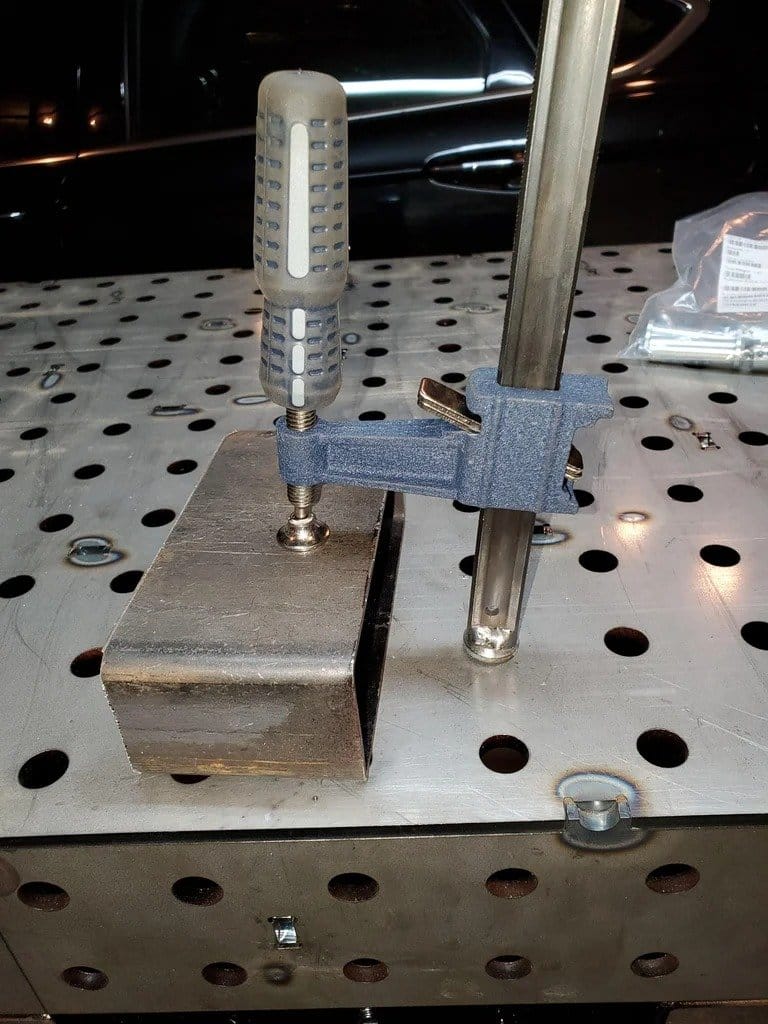
Теперь можно провести его испытания, для этого возьмем два материала, которые нам необходимо склеить. Наносим на их поверхности клей, прикладываем друг к другу. Затем раскрываем наш зажим, вставляем туда склеиваемые материалы и при помощи гайки-«барашка» и болтика зажимаем. Затягиваем при помощи плоскогубцев и отвертки. Теперь ждем, пока застынет клей.
Магнитная масса для сварки — инструкция по изготовлению
Магнитная масса для сварки — это удобное приспособление, позволяющее закрепить ее на свариваемых деталях, и хорошая альтернатива стандартным прищепкам.
Часто дополнительные приспособления к сварочному аппарату либо плохого качества и ломаются, либо же могут отсутствовать вообще. Магнитная масса для сварки — это удобное приспособление, позволяющее закрепить ее на свариваемых деталях, и хорошая альтернатива стандартным прищепкам.
Из чего состоит такой контакт, какие положительные качества у него имеются и как его изготовить самостоятельно. Об этом дальше в статье.
Магнит или зажим
Обычно сварочные аппараты комплектуются кабелем массы с держателем зажимного типа. С первого взгляда, это удобно, такое приспособление можно надежно закрепить к практически любой поверхности (листы, металлопрокат и прочие).
Но бывают ситуации, когда нет возможности установить такую массу на заготовку или, еще чаще, она перегорает. Неплохой альтернативой станет магнитный контакт сварочного кабеля.
В чем его преимущества перед стандартным зажимом-прищепкой?
- Это возможность закрепить контакт практически на любые поверхности без особых хлопот.
- Простая конструкция практически вечна в использовании, не сломается, так как нет никаких пружинок и механизмов.
- Такая масса отлично выдерживает перепады напряжения и нагрузку, вследствие чего не перегорает.
- Большая площадь контакта обеспечивает надежное замыкание.
Но есть и свои недостатки у такого вида крепления контактов. Главный недостаток — это то, что магнитная масса для сварки будет плохо устанавливаться на маленькие по площади детали, например, пруток или арматуру. Вторым отрицательным свойством будет невозможность закрепления на свариваемые части из цветных металлов: алюминия, меди и прочих. Также со временем магнит будет загрязняться металлической стружкой и его периодически нужно очищать.
Без учета двух последних факторов, это довольно удобное приспособление, которое можно даже изготовить своими руками без лишних затрат.
Конструкция магнитного контакта
Само устройство состоит из двух частей.
- Контакт. Это точка, где к держателю закрепляется кабель массы.
- Магнит. Может быть разнообразных форм и размеров.
Эти две части соединяются между собой креплением. Вес магнитная масса для сварки будет иметь в зависимости от размеров. Например, магнитная клемма для сварки от компании ESAB весит около 850 грамм.
Главное в такой конструкции — простота, за счет которой обеспечивается надежность функционирования и бесперебойная работа.
Самостоятельное изготовление
Конечно, такой крепеж сварочной массы можно просто приобрести. Производители, которые изготавливают сварочное оборудование, выпускают и дополнительные приспособления в виде креплений. Но это лишние финансовые потери, такой контакт можно изготовить самостоятельно.
Изготовление магнитного контакта для сварочного кабеля своими руками довольно простое. Понадобится минимум инструментов, а детали могут быть под рукой.
Что для этого нужно:
- Во-первых, магнит. Это главная деталь всего устройства, которая обеспечит надежность крепления. Чаще всего можно увидеть самоделки, сделанные из магнита от автомобильных динамиков.
- Во-вторых, две шайбы по размеру магнита. Если использовать автомобильный динамик, то на одну из шайб можно наварить болт для дальнейшей сборки.
- В третьих, болт и гайка для зажима кабеля.
Сборку всей системы проводят таким образом:
- Шайбы можно изготовить из листового металла, по размеру магнита.
Если это динамик, то он обычно имеет круглую форму. Соответственно и шайбы должны быть такими же.
- У нижней (та, что будет служить непосредственно контактом) сверлят отверстие по диаметру шляпки болта.
- Саму верхушку болта нужно сточить до толщины шайбы.
- Теперь эту конструкцию сваривают и зачищают. Должна получиться деталь в виде гриба с ножкой из резьбы.
- Магнит надевают на болт, а сверху — вторую шайбу.
- Теперь на шток с резьбой крепят конец кабеля массы и всю конструкцию стягивают гайкой.
Так с простейшего материала собирается элементарная масса для сварки на магните. Ее бесперебойная работа будет доказательством правильной сборки. Размеры такого контакта будут зависеть от габаритов магнита. Круглые массы заводского изготовления обычно имеют диаметр около 50-60 миллиметров.
Для опытного сварщика, знающего принцип работы массы на сварочном аппарате, изготовить требуемое крепление не составит труда. Самым примитивным контактом может стать закрепленный к кабелю кусок прутка, который закрепляют к заготовке парой точек сварки. Но, конечно, такое приспособление очень неудобно в использовании.
Также можно сделать самостоятельно и магнитный держатель для электродов. Что тоже уже зависит от личных предпочтений в удобстве работы.
Самодельная клемма на магните хороший вариант экономии средств. Хотя использовать такое крепление или нет — это уже смотрят на личные удобства в работе. Если сварка используется редко (как обычно в быту), то можно попросту обойтись стандартным зажимом.
Что Вы думаете по поводу удобства такого приспособления? Насколько целесообразно покупать или изготовить такую клемму массы? И стоит ли приобретать такое крепление заводского изготовления, если можно сделать его самостоятельно в своей мастерской? Возможно, у Вас иметься личный опыт по использованию, тогда просим поделиться им в блоке комментариев и принять участие в обсуждении.
чертеж и как сделать своими руками Зажимы своими руками
Струбцина — это инструмент позволяющий фиксировать деталь во время обработки. Мастера часто используют различные виды струбцин в своей работе. Будь то столяр, или слесарь, обрабатывающий металл – всегда есть необходимость ее использования.
Это приспособление выпускается в разных вариантах, от универсальных до специализированных. Сравнительно недавно появилась новая модификация: быстрозажимная струбцина. Развивает усилие сжатия до 450 кг.
Задача у всех видов общая – зафиксировать заготовки для обработки или соединения между собой.
Как и любой другой инструмент – струбцины можно приобрести в магазине или изготовить самостоятельно. Второй вариант часто выбирают профессионалы. Проще придумать собственную конструкцию, чем искать вариант для индивидуальных задач.
Самодельные струбцины – разновидности и технологии изготовления
Угловая струбцина
Такие приспособления применяются для фиксации двух предметов (не обязательно одного размера) под прямым углом, для соединения их между собой любым способом. Это могут быть деревянные заготовки при склеивании, или сборке при помощи уголков и конфирмата.
Однако чаще всего, угловая струбцина используется в качестве кондуктора для сварки металлических деталей под прямым углом.
Для изготовления понадобятся:
- стальной уголок 40 мм, толщиной 3-4 мм;
- стальные пластины шириной 40-50 мм;
- шпильки с резьбой, желательно закаленные;
- прутки для воротков;
- гайки для червячного механизма;
- сварочный аппарат;
- дрель, метчики.
Уголки привариваем к стальным пластинам строго под углом 90°.
На каждую сторону крепим при помощи сварки червячную конструкцию. Это такой же уголок с наваренной упорной гайкой или утолщением, в котором нарезана резьба в соответствии со шпилькой-воротком. Ширина рабочего зазора подбирается под потенциальные заготовки.
ВАЖНО! Если диапазон размеров обрабатываемых деталей слишком широк – лучше изготовить несколько струбцин. Слишком большой ход воротка не способствует прочной фиксации.
В рабочую гайку вкручивается шпилька-вороток, после чего на ее конце собирается упор. Как правило, это конструкция из двух металлических шайб разного размера. Упор должен свободно прокручиваться на шпильке.
Начинающему мастеру не помешает узнать, что на первых этапах обойтись одним лишь молотком или пилой вряд ли получится. Впоследствии придется прибегнуть к применению тисков или быстрозажимной струбцины, чтобы зафиксировать заготовку или склеить отдельные фрагменты. Сделать ее своими руками довольно просто. Нет ни одного достаточно универсального зажима, который позволял бы удовлетворить все потребности при выполнении различных типов работы.
Применение деревянных струбцин
Они бывают различных стилей, моделей и размеров. А потому можно запастись различными моделями, которые всегда пригодятся. Мастер может закупить несколько моделей струбцин Assistent, к тому же они там стоят не так уж и дорого. Если человек не хочет платить за такую покупку, он может сделать деревянную или трубную струбцину своими руками. Модели из древесины очень популярны, их можно изготовить самостоятельно. Такая модель простая в эксплуатации и легко регулируется.
Модель F — деревянная струбцина, которая слегка усовершенствована. Здесь используется планка из клёна шириной 5 см и толщиной 0,6 см. А также в конструкции присутствует металлический стержень, на который нанесена резьба. Чтобы изготовить ручку, надо взять деревянную заготовку. Для этого подходит лиственная порода без дефектов.
Подвижные детали должны быть хорошо высушены, чтобы без проблем скользить на планке. На стержне должно присутствовать две гайки. Они располагаются на конце и затягиваются потом друг против друга. Благодаря этому они не расходятся во время использования. Можно использовать отдельную стопорную гайку или простую модель с постоянным замком. И ещё две гайки необходимо, чтобы зафиксировать снаружи зажимные колодки вместе с шайбой.
Допускается использование контргайки и других способов крепления. Двойные изделия заклинивают друг друга. Это самый надежный и простой способ. Он же самый дешёвый. Важно оставить некоторое пространство для винта, чтобы он мог свободно вращаться.
Из древесины и стали
Обрезают при помощи ножовки резьбовой шток до 30 см. Сначала необходимо обустраивать дополнительный разрез на блок размером 9 на 7 см, если речь идет о нефиксированных концах. Как только все углы будут срезаны, надо просверлить отверстие и вставить затяжные болты.
Надо убедиться, что отверстия довольно велики, чтобы подогнать головку болта. Фиксируется резьбовой стержень в верхней зоне фиксированного конца. Отверстие должно быть довольно большим, чтобы гайку можно было вставить гайку в штангу. Устанавливают фиксированный конец, когда намереваются сверлить отверстия. Производя сборку, необходимо убедиться, что концы закреплены под прямым углом. Резьбовой шток благодаря этому будет становиться параллельно стержню.
Перед сборкой необходимо обустроить отверстие, где проходят гайка и резьбовой стержень. Делают это в том же положении блока, что и для фиксированного конца. Надо убедиться, что отверстие довольно широкое и глубокое, чтобы разместить гайки. Нижняя зона маленькая, а потому сюда трудно вставить достаточное количество винтов. Это необходимо для предотвращения скручивания.
Размеры полки определяются в соответствии с желаемой длиной и имеющимся оборудованием. После этого распиливают компоненты системы до необходимого размера, вырезают подушечки для губки и сверлят необходимые отверстия, ручки наклеивают пятиминутной эпоксидной смолой. Когда стержень винта зазубрен напильником или наждачной бумагой, фиксируют ручки посредством эпоксидного клея.
Лёгкие самодельные варианты
Легкая струбцина, сделанная своими руками, изготавливается на основе металлического стержня. Эти зажимы, хоть и не такие мощные, как стальные, всё равно дают возможность создавать сильное прижимное давление для любого клея. Соответственно, срок службы у них довольно внушительный. Штанга может быть сделана в любой длине. Единственное, надо запомнить, что по всей длине основного стержня не должен проходить резьбовой стержень. Головка струбцины не испытывает необходимости в нём на этом конце, что значительно упрощает сборку. Зажимные губки делают из фанеры.
Стопорная гайка представляет собой элемент, который фиксирует прижимную губку на стержне. При этом он не должен пребывать под давлением. Гайку можно срезать обычной ножовкой. Эпоксидной смолой его закрепляют на пятке. Выемка должна получиться довольно широкой и подходить к шайбе и глубокой, чтобы гайка и шайба могли без проблем поворачиваться.
Здесь надо использовать гайку 35 мм, так как необходимо просверлить отверстие в поперечнике 38 мм с донной частью и 15 мм глубиной. После сверления углубления делают сквозное отверстие. Оно требуется для зажимного винта. Фиксируют подвижную головку на неподвижной позиции и отмечают места, где должно располагаться отверстие.
Рукоятка, винт и основная сборка
Изготавливают квадратные заготовки по 25 мм и отрезают для каждой ручки по 100 мм. Обозначают центральную часть и высверливают с помощью сверла фрагмент 10,5 мм 60 мм. В качестве аналога можно высверливать довольно широкое отверстие, после чего покрывать эпоксидной смолой. Но такой способ считается недостаточно надежным.
Шлифуют заготовку, чтобы сделать более удобную ручку и приклеивают к данному зажимному винту. Приступают к основной сборке. Это простая задача, позволяющая наклеить плёнку к неподвижной головке. Укрепляют стопорную гайку и делают торцевые колпачки. Они должны не допускать соскальзывания головки со штанги. Потому желательно прикрутить небольшую пластинку на пятку. Благодаря этому выскальзывание гайки с места исключается . Это действует, как крюк.
Кулачковый зажим
Это устройство не только полезное, но и предельно простое. Надо помнить, что кулачковые зажимы быстродействующие, но не способны гарантировать большой силы зажима деталей. Вот почему их используют тогда, когда требуется сравнительно небольшая сила резания. Они не годятся для работы под большим давлением, как это возможно с крупной струбциной. Но при этом они чрезвычайно просты в использовании.
Для приготовления используют специальный шаблон. Он необходим для создания кривых. Шаблон изготавливается из металла, пластмассы или древесины. Его используют, чтобы подтянуть гладкие кривые. При этом кулачковые механизмы не являются прямым отслеживанием французской кривой. Правильный кулачок должен иметь профиль , увеличивающий расстояние между осью вращения и постоянной скоростью. В этом он напоминает спираль, прочерченный карандашом.
Начинающему мастеру не помешает узнать, что на первых этапах обойтись одним лишь молотком или пилой вряд ли получится. Впоследствии придется прибегнуть к применению тисков или быстрозажимной струбцины, чтобы зафиксировать заготовку или склеить отдельные фрагменты. Сделать ее своими руками довольно просто. Нет ни одного достаточно универсального зажима, который позволял бы удовлетворить все потребности при выполнении различных типов работы.
Применение деревянных струбцин
Они бывают различных стилей, моделей и размеров. А потому можно запастись различными моделями, которые всегда пригодятся. Мастер может закупить несколько моделей струбцин Assistent, к тому же они там стоят не так уж и дорого. Если человек не хочет платить за такую покупку, он может сделать деревянную или трубную струбцину своими руками. Модели из древесины очень популярны, их можно изготовить самостоятельно. Такая модель простая в эксплуатации и легко регулируется.
Модель F — деревянная струбцина, которая слегка усовершенствована. Здесь используется планка из клёна шириной 5 см и толщиной 0,6 см. А также в конструкции присутствует металлический стержень, на который нанесена резьба. Чтобы изготовить ручку, надо взять деревянную заготовку. Для этого подходит лиственная порода без дефектов.
Подвижные детали должны быть хорошо высушены, чтобы без проблем скользить на планке. На стержне должно присутствовать две гайки. Они располагаются на конце и затягиваются потом друг против друга. Благодаря этому они не расходятся во время использования. Можно использовать отдельную стопорную гайку или простую модель с постоянным замком. И ещё две гайки необходимо, чтобы зафиксировать снаружи зажимные колодки вместе с шайбой.
Допускается использование контргайки и других способов крепления. Двойные изделия заклинивают друг друга. Это самый надежный и простой способ. Он же самый дешёвый. Важно оставить некоторое пространство для винта, чтобы он мог свободно вращаться.
Из древесины и стали
Обрезают при помощи ножовки резьбовой шток до 30 см. Сначала необходимо обустраивать дополнительный разрез на блок размером 9 на 7 см, если речь идет о нефиксированных концах. Как только все углы будут срезаны, надо просверлить отверстие и вставить затяжные болты.
Надо убедиться, что отверстия довольно велики, чтобы подогнать головку болта. Фиксируется резьбовой стержень в верхней зоне фиксированного конца. Отверстие должно быть довольно большим, чтобы гайку можно было вставить гайку в штангу. Устанавливают фиксированный конец, когда намереваются сверлить отверстия. Производя сборку, необходимо убедиться, что концы закреплены под прямым углом. Резьбовой шток благодаря этому будет становиться параллельно стержню.
Перед сборкой необходимо обустроить отверстие, где проходят гайка и резьбовой стержень. Делают это в том же положении блока, что и для фиксированного конца. Надо убедиться, что отверстие довольно широкое и глубокое, чтобы разместить гайки. Нижняя зона маленькая, а потому сюда трудно вставить достаточное количество винтов. Это необходимо для предотвращения скручивания.
Размеры полки определяются в соответствии с желаемой длиной и имеющимся оборудованием. После этого распиливают компоненты системы до необходимого размера, вырезают подушечки для губки и сверлят необходимые отверстия, ручки наклеивают пятиминутной эпоксидной смолой. Когда стержень винта зазубрен напильником или наждачной бумагой, фиксируют ручки посредством эпоксидного клея.
Лёгкие самодельные варианты
Легкая струбцина, сделанная своими руками, изготавливается на основе металлического стержня. Эти зажимы, хоть и не такие мощные, как стальные, всё равно дают возможность создавать сильное прижимное давление для любого клея. Соответственно, срок службы у них довольно внушительный. Штанга может быть сделана в любой длине. Единственное, надо запомнить, что по всей длине основного стержня не должен проходить резьбовой стержень. Головка струбцины не испытывает необходимости в нём на этом конце, что значительно упрощает сборку. Зажимные губки делают из фанеры.
Стопорная гайка представляет собой элемент, который фиксирует прижимную губку на стержне. При этом он не должен пребывать под давлением. Гайку можно срезать обычной ножовкой. Эпоксидной смолой его закрепляют на пятке. Выемка должна получиться довольно широкой и подходить к шайбе и глубокой, чтобы гайка и шайба могли без проблем поворачиваться.
Здесь надо использовать гайку 35 мм, так как необходимо просверлить отверстие в поперечнике 38 мм с донной частью и 15 мм глубиной. После сверления углубления делают сквозное отверстие. Оно требуется для зажимного винта. Фиксируют подвижную головку на неподвижной позиции и отмечают места, где должно располагаться отверстие.
Рукоятка, винт и основная сборка
Изготавливают квадратные заготовки по 25 мм и отрезают для каждой ручки по 100 мм. Обозначают центральную часть и высверливают с помощью сверла фрагмент 10,5 мм 60 мм. В качестве аналога можно высверливать довольно широкое отверстие, после чего покрывать эпоксидной смолой. Но такой способ считается недостаточно надежным.
Шлифуют заготовку, чтобы сделать более удобную ручку и приклеивают к данному зажимному винту. Приступают к основной сборке. Это простая задача, позволяющая наклеить плёнку к неподвижной головке. Укрепляют стопорную гайку и делают торцевые колпачки. Они должны не допускать соскальзывания головки со штанги. Потому желательно прикрутить небольшую пластинку на пятку. Благодаря этому выскальзывание гайки с места исключается . Это действует, как крюк.
Кулачковый зажим
Это устройство не только полезное, но и предельно простое. Надо помнить, что кулачковые зажимы быстродействующие, но не способны гарантировать большой силы зажима деталей. Вот почему их используют тогда, когда требуется сравнительно небольшая сила резания. Они не годятся для работы под большим давлением, как это возможно с крупной струбциной. Но при этом они чрезвычайно просты в использовании.
Для приготовления используют специальный шаблон. Он необходим для создания кривых. Шаблон изготавливается из металла, пластмассы или древесины. Его используют, чтобы подтянуть гладкие кривые. При этом кулачковые механизмы не являются прямым отслеживанием французской кривой. Правильный кулачок должен иметь профиль , увеличивающий расстояние между осью вращения и постоянной скоростью. В этом он напоминает спираль, прочерченный карандашом.
Обработка заготовок на столярном верстаке будет удобной при использовании различных приспособлений, фиксирующих детали на поверхности стола. Своими руками реально сделать как простейшие упоры и прижимы, так и универсальные системы, позволяющие закреплять заготовки любых конфигураций.
Простые деревянные упоры для столярного верстака — чертеж, пример
Самодельные верстачные упоры из древесины не тупят инструмент и не портят торцы деталей. Приспособления разделяются по типу стержня и вставляются в отверстия соответствующей формы.
Прямоугольные клинья не вращаются и обеспечивают абсолютную неподвижность заготовки. Сами упоры изготовить легко, но на выдалбливание квадратных гнезд уйдет много времени и усилий. Эти отверстия целесообразно устраивать в столешницах из массива доски на стадии изготовления столярного верстака.
В рабочих поверхностях, сделанных из листового материала, правильнее использовать упоры с цилиндрическим стержнем. Такие приспособления удобны для закрепления криволинейных деталей, а отверстия для них всегда можно высверлить в нужном месте. Жесткая фиксация прямоугольных заготовок достигается установкой дополнительной планки с двумя стержнями.
Как сделать упор с круглым стержнем
Для стержня верстачного упора подходит береза, вишня, клен или орех. Верхняя планка изготавливается из той же твердой древесины или из фанеры. Низкопрофильный упор можно сделать из ламинированной панели высокой плотности, оставшийся после укладки напольного покрытия.
Определитесь с диаметром стержня. Если планируете позднее приобретать готовые фиксаторы, выберите стандартный размер 19 мм. В случае уверенности в дальнейшем самостоятельном изготовлении приспособлений для столярного верстака используйте диаметр 21 мм. Такой наружный размер имеют полудюймовые водопроводные трубы, из которых изготавливают самодельные прижимные струбцины. Примерно такой же величине соответствует условный проход трех четвертных труб, подходящих для изготовления круглых стержней из дерева.
Возьмите обрезок трубы диаметром 3/4 дюйма, длиной в 60–80 мм и с резьбой не менее 20 мм. Заточите кромки с одного торца и наверните гайку на другой.
Вставьте приспособление в дюймовую трубу и прогоните через него березовую палку, ударяя сверху тяжелым молотком.
Подрезайте древесину, когда щепки упрутся в гайку. Может показаться, что проще взять трубку длиннее, но пробивать тогда будет намного тяжелее.
Прогнав палку, снимите заусенцы наждачной бумагой. Сделанные таким образом деревянные стержни могут иметь незначительные изъяны, не влияющие на общую форму цилиндра. В начале обустройства домашней мастерской, когда еще нет специальных станков, вы не найдете более простого способа изготовления круглой палки своими руками.
Начертите на заготовках верхние части упоров в нужном количестве и отметьте центры сверления отверстий.
Сделайте перовым сверлом углубления в половину толщины материала. Начинайте сверлить на небольших оборотах, слегка нажимая на дрель. В момент касания на поверхности появятся риски, по которым будет видно, куда следует отклонить инструмент для перпендикулярного сверления.
Распилите заготовки, отшлифуйте торцы и раззенкуйте отверстия под шурупы.
Нанесите столярный клей на стержень и в углубление.
Соедините детали, прижмите их руками и вытрите излишки клея. Вставьте стержень в отверстие столешницы и закрутите шуруп.
Через десять минут осторожно вытащите упор, выталкивая снизу и не сдвигая детали. Оставьте приспособление до полного высыхания клея.
Сверлите отверстия для верстачных упоров там, где считаете необходимым. Чаще всего они нужны в левой части стола для строгания заготовок и рядом с тисками для совместного использования. Расстояние между центрами отверстий должно быть везде одинаковым и соответствовать размеру длинных упоров. Перед высверливанием прикрепите снизу ненужную доску, чтобы не было сколов при выходе сверла.
Как сделать упор для распила досок
Расположенный сбоку столешницы упор удобен для поперечного распила досок. Когда он не нужен, его поворотная часть опускается и не мешается. Используйте приспособление вместе с длинным верстачным упором, надежно прижимая доску одной рукой, а другой, работая ножовкой.
Вырежьте деревянные элементы упора из остатков твердой древесины. Сделайте два раззенкованных отверстия в неподвижной части и одно в поворотной планке, точно соответствующее диаметру используемого шурупа.
Отметьте на торце стола месторасположение подвижной детали на одной линии с верстачным упором.
Закрепите сначала поворотную планку, добавив при необходимости брусок для увеличения толщины столешницы. Далее перпендикулярно ей установите неподвижную деталь.
Универсальные верстачные прижимы
Подвижные крепления позволяют фиксировать на столярном верстаке различные заготовки и съемные рабочие панели. Прижимы передвигаются во врезанных заподлицо с поверхностью стола металлических направляющих с т-образным желобком (Т-слотах), которые могут быть алюминиевыми или стальными.
Как сделать направляющие своими руками
Аналог заводских рельс с т-образным пазом легко изготовить из металлической трубы прямоугольного или квадратного сечения. Подходит профиль высотой не более половины толщины столешницы. Сразу подберите болты и разметьте вырез на одной стороне трубы соразмерно диаметру болта.
Вырежьте паз болгаркой, подровняйте края напильником и закруглите кромки наждачной бумагой.
Подберите подходящие обрезки профилей для изготовления слайдеров, если шестигранная головка меньше желоба и проворачивается в нем.
Просверлите отверстия для болтов и нарежьте скобы, рассчитывая их высоту на 1–2 мм меньше, чем внутренний проход профиля.
Как врезать направляющие в столешницу
Используйте ручной фрезер для выборки углубления в столешнице. Если врезаемый профиль шире фрезы, делайте паз за два подхода.
Начертите на поверхности разметку и установите параллельно ей ровную панель. Для предотвращения сколов при выходе фрезы прикрепите вплотную к торцу деревянную рейку.
Настройте ограничитель глубины фрезерования и выберите паз за несколько проходов.
Переставьте панель, вырежьте оставшийся материал и отшлифуйте углубление абразивной шкуркой.
Закрепите направляющие шурупами, сделав в металле углубления под шляпки.
Как сделать простую прижимную планку
Настраиваемые системы зажимов предоставляют множество вариантов закрепления деталей на столярном верстке. Самая простая конструкция – прижимная планка, фиксируемая скользящими в Т-образных треках болтами.
Напилите полосы фанеры, прибавив 20 мм к указанной на чертеже ширине деталей, чтобы позднее обрезать склеенную заготовку и получить идеально ровные торцы. Для средней части сгодятся фанерные обрезки одинаковой толщины.
Склейте детали, просверлите зенковкой отверстия на удаление 25 мм от краев и закрутите саморезы с обеих сторон. После высыхания клея отпилите заготовку до чистовых размеров циркулярной пилой.
Вырежьте фанерные шайбы диаметром чуть больше ширины прижимной планки.
Аккуратно рассверлите в них отверстия под болты.
Разместите приспособление на поверхности столярного верстака, наденьте шайбы и закрутите гайками барашкового типа.
Прижимная планка отлично подходит для удерживания больших заготовок, а также в качестве бокового упора, вдоль которого можно направлять инструмент, например, при фрезеровании продольного паза.
Как сделать прижимные скобы из фанеры
Простые и удобные прижимы в виде скоб закрепляются на верстаке в тех же Т-слотах, легко перемещаются и позволяют фиксировать разнообразные детали в любых положениях.
Приспособление состоит из фанерной части с пазом, болта со слайдером, шайб, гайки-барашка и металлической втулки.
Для изготовления деревянных элементов потребуется шаблон, его легко начертить на бумаге руководствуясь нашей инструкцией.
Порядок изготовления шаблона
Обведите шаблон на фанере и отметьте шилом центр сверления.
Сделайте отверстие перовым сверлом диаметром 22 мм.
Подготовьте остальные заготовки и соедините их вместе с помощью столярного клея и шурупов. Отшлифуйте торцы, уделяя особое внимание верхней полуокружности и нижним закругленным частям.
Возьмите полудюймовую трубку, отмерьте на ней отрезок длиной в толщину фанерной скобы. Высверлите по центру отверстие для болта и обрежьте втулку по размеру. Сточите напильником металлические заусенцы и зачистите наждачной шкуркой поверхности.
Соберите прижим, подложив под гайку шайбы.
Прижимная скоба на фото ниже более проста и изготавливается подобным образом. При использовании этой конструкции приходится класть под второе плечо рычага подкладку примерно такой же толщины, иначе будет перекос болта, приводящий к деформации направляющей рельсы.
Увеличьте возможности прижимной системы, изготовив из профильной трубы еще один Т-образный трек. Располагая направляющую между врезанными в столе рельсами, вы сможете закреплять детали в любом месте столярного верстака.
Фиксируется такая дополнительная планка по краям короткими болтами, а во внутри профиля находятся небольшие фанерные вкладыши с отверстиями.
Рассмотренные приспособления для столярного верстака просты в изготовлении и подходят для закрепления большинства обрабатываемых заготовок. Дальнейшее занятие столярным делом потребует новых упоров или прижимов, придумать которые поможет смекалка, а сделать позволит приходящий постепенно опыт.
Струбцина – это вспомогательный инструмент, который используется для фиксации досок при их соединении в заданном положении. Также струбцина подойдет для удержания досок во время их распиливания, для разводки ножовочного полотна, соединения различных элементов. В инструмент могут вкладываться требующие обработки детали. Затем, используя подвижной элемент, их зажимают при помощи губок и приступают к работе. Для надежного удержания деталей в нужном положении рекомендуется применять два и больше зажимов.
Самодельные скрепы чаще изготавливаются из металлов или древесины, и по своим характеристикам они мало в чем уступают покупным, фабричной сборки. Поскольку конструкция прижимного устройства простая, то понять принцип его работы, чтобы изготовить самостоятельно, будет несложно.
Изготовление винтовой металлической струбцины
Перед началом работ потребуется подготовить необходимые материалы. Для основы конструкции подойдет стальной лист толщиной один сантиметр, любые ровные обрезки той же толщины. Длина заготовки произвольная, но ее стараются выбрать с учетом рабочего расстояния струбцины.
Основные материалы изготовления:
- стальной лист;
- длинные болты;
- гайки.
Составляется чертеж. На материале заготовки размечается будущее тело инструмента, которое по виду напоминает букву «С». Вместо стального листа можно использовать отрезок профилированной трубы, согнутый в виде буквы «С». Особых требований к толщине заготовки нет, но конструкция должна быть надежна. Выбор длины производится с учетом размеров рабочей зоны, обрабатываемых деталей.
После нанесения разметки деталь вырезают из металла. В домашних условиях заготовки небольших размеров можно вырезать при помощи болгарки. Но при изготовлении зажимов больших габаритов рекомендуется воспользоваться газовым резаком, ацетиленовой горелкой. Следующий этап – обработка, шлифовка заготовки. Все острые края, наплывы, образовавшиеся при работе с газосварочным оборудованием, сбиваются при помощи напильника, а поверхность шлифуется наждачной бумагой. Это необходимо сделать, чтобы, зажимая заготовки, не порезаться об острые края.
Подготовив длинные болты М 8, М 10, приступают к креплению подвижного элемента. Для чего на одной стороне заготовки привариваются гайки под выбранные болты. При отсутствии болтов можно подобрать шестигранники, стальные пруты нужной длины с предварительно нарезанной резьбой.
На внутреннем рабочем конце винта приваривается плоская ровная деталь, на которую возлагается функция губок. На обратной стороне винта при помощи сварки крепится рычаг из обрезков шпильки. Его наличие ускорит процесс зажима заготовок, дополнительно снизив величину прикладываемых усилий. На этом сборка струбцины своими руками завершена.
Устройство углового зажима
При изготовлении углового инструмента для сборки мебели важно точно выдержать прямой угол 90°. Основными доступными материалами являются уголки со стальными полосами. Для работы понадобятся:
- 40-миллиметровый стальной уголок толщиной 3-4 мм;
- стальные пластины 40-50 мм;
- шпильки с резьбой;
- прутки для воротков;
- гайки;
- сварочный аппарат;
- электродрель, метчики.
Угловая струбцина самая сложная в изготовлении, но при проведении некоторых видов работ без нее не обойтись. На начальном этапе к стальным пластинам под прямым углом привариваются уголки, а на каждый из уголков – гайки, которые послужат для создания червячной конструкции. Еще один вариант – просверлить отверстие в уголке и нарезать в нем при помощи метчика внутреннюю резьбу. Ширину рабочего зазора подбирают с учетом величин потенциальных заготовок, но слишком большой ход прижимного воротка снижает прочность их фиксации.
Для обработки деталей различного размера рекомендуется подготовить несколько зажимов!
Шпилька вкручивается в приваренную гайку. На ее конце собирается упор из металлических шайб различного диаметра, который должен свободно прокручиваться при вращении шпильки. С обратной стороны воротка просверливают отверстие под металлический прут. Используемый в качестве рычага, он передаст большее усилие, поэтому будет надежнее удерживать рабочие заготовки.
Деревянная струбцина – сделаем из остатков досок
Наибольшей популярностью пользуется деревянная быстрозажимная струбцина, но инструмент аналогичной конструкции можно изготовить и из металла. Несмотря на простоту конструкции, она очень удобна при выполнении различных работ.
Наличие двух одинаковых струбцин расширяет область их применения!
Для сборки потребуется подготовить следующие материалы:
- кусочки досок;
- шпильки с заранее нарезанной резьбой;
- гайки и барашки, соответствующие резьбе шпилек;
- рейки.
Вначале подготавливаются две шпильки одинакового диаметра с нарезанной резьбой. Они должны иметь длину 200 мм. Гайки подбираются под резьбу шпилек. Заготавливаются две рейки, желательно из древесины твердых пород. Лучшим выбором будет дуб, бук, береза, ясень. Рейки подгоняются под одинаковый размер. Для этого лишнюю длину отпиливают, а срез подвергают шлифовке. После этого в каждой из реек просверливают по два отверстия с небольшим допуском. Причем расположения отверстий на каждой из заготовок должны идеально совпадать, а их диаметр соответствовать диаметру шпилек.
На поверхность реек можно наклеить полоски фанеры. Их подгоняют по габариту деревянных заготовок, просверливают отверстия. Шпильки вставляют в полученные отверстия и надежно фиксируют при помощи гаек на одной из реек с обеих сторон. Чтобы исключить продавливание материала, под гайки подкладывают шайбы. Эта планка всегда будет неподвижной, но другая сможет свободно перемещаться по направляющим в виде шпилек.
Устанавливается другая планка. Для этого ее, продев через шпильки, осаживают на место. Прижим осуществляется при помощи обычных гаек и рожкового ключа, но для удобства и повышения производительности необходимо установить гайки-барашки. Проверяют ход скрепы, если он затруднен или требуется дополнительная подгонка деталей, обнаружились другие дефекты, то их устраняют. Работы по сборке прижимного устройства из дерева можно считать завершенными, осталось опробовать его в деле.
Правильно собранные прижимные устройства позволяют надежно крепить деревянные детали при проведении столярных работ. Конструкции перечисленных видов скреп пользуются популярностью и настолько простые, что их можно изготовить самостоятельно из подручных материалов с привлечением минимального количества инструментов.
типы и разновидности, область применения
Создание точных и качественных металлоконструкций сложно себе представить без использования таких приспособлений, как струбцины. Это специальные зажимы, позволяющие надежно фиксировать и точно стыковать компоненты металлоконструкций во время сборочных или ремонтных работ.
Зажим заготовок осуществляется чаще всего губками, но могут использоваться и другие органы захвата, все зависит от типа струбцины.
На сегодняшний день различают свыше десятка разновидностей струбцин:
- F-образные
- G-образные
- Трубные
- Ленточные
- Угловые
- Распорные
- Крестовинные
- Двух- и трехосевые
- и пр.
Помимо типа конструкции струбцины для сварки различаются между собой и по принципу сжатия:
- Винтовые
- Триггерные
- Рычажные
- Пружинные
- и т.д.
Ниже будет описана четверка самых распространенных струбцин, без которых не может обойтись ни один сборщик/ремонтник металлоконструкций. Итак, какие виды струбцин сегодня востребованы.
G-образные струбцины
Это простейший вариант струбцин. Конструкция таких приспособлений представлена обыкновенной скобой с винтовым прижимом. Пример на фото ниже.
G-образные струбцины используются для фиксации заготовок к краю столешницы слесарного верстака или сварочного стола. Такие струбцины актуальны в основном для работы с негабаритными деталями.
При помощи G-образных струбцин можно обездвижить и расположить в правильном направлении: уголок, швеллер, листовой металл, трубу с прямоугольным профилем, шестигранник и прочие типы проката. Вместе с тем G-образные струбцины дают возможность надежно прижимать к друг другу и детали: труба к трубе, труба к металлическому листу и пр.
Главным недостатком G-образных струбцин является возможность прижима заготовок только у края столешницы, так как скоба имеет заметно ограниченную глубину профиля. Какие еще существуют виды струбцин.
F-образные струбцины
Если G-образные струбцины имеют всего одну регулировку (высоты прижима), то в F-образных струбцинах предусмотрено несколько регулировок. Это непосредственно сама высота прижима и так называемый «дожим», дающий гарантию максимально надежной фиксации. Пример F-образной струбцины на фото ниже.
Как и в случае со струбцинами G-типа, F-образные приспособления рассчитаны на прижим заготовок либо между собой, либо к краю столешницы.
F-образные струбцины регулируют высоту прижима посредством направляющей планки, по которой ходит нижняя прижимная губка. Принцип фиксации в таких струбцинах прост. Упираясь в заготовку нижняя губка клинит на направляющей планке. Для усиления клина нужно просто закрутить вспомогательный винтовой прижим.
F-образные струбцины для сварки и столярных операций обычно отличаются направляющей планкой. В сварочных струбцинах планка обычно ровная, а в столярных приспособлениях направляющая планка чаще всего использует ребристую поверхность.
В отличии от G-приспособлений струбцины с F-образным профилем позволяют крепить достаточно высокие заготовки. Разумеется, есть и совсем небольшие F-прижимы. Высота разведения губок в F-струбцинах может составлять от 100 до 300-500 (мм). Конкретная высота прижима будет зависеть от модели струбцины. Из выложенного ниже видеоролика можно узнать, как выбрать струбцину для сварки.
Угловые струбцины
Это серия узкоспециализированных струбцин. С их помощью можно точно стыковать фасонный прокат под прямым углом. Такие струбцины являются незаменимыми при изготовлении рам и каркасов. Угловая струбцина позволяет приваривать торцы труб, уголков, швеллеров и пр.
Различают мобильные и стационарные струбцины. Зажимы мобильного типа можно использовать по месту, то есть непосредственно на самой металлоконструкции. Стационарные же струбцины жестко крепятся к столешнице слесарного верстака или сборочного/сварочного стола. Стационарные зажимы позволяют стыковать прокат на одном месте, что позитивно отражается на точности изготавливаемых конструкций. Приспособления стационарного типа хорошо себя зарекомендовали при серийном и массовом производстве металлоконструкций.
Классические струбцины углового типа фиксируют заготовки при помощи зажимных губок. В более современных моделях фиксация проката реализована за счет магнитных сил. Достаточно просто разместить заготовки на направляющих, прокат сам «прилипнет» к струбцине. Магнитные зажимы отличаются простотой и надежностью конструкции.
Слабым местом магнитных угловых струбцин является возможность работать только с металлическими заготовками, которые проявляют магнитные свойства. Струбцины же с зажимными губками могут стыковать алюминий, легированную сталь, медь и всевозможные сплавы, которые не реагируют на магнит.
Прижимные струбцины
Отдельная категория струбцин, которая предназначена для установки на сварочные или сборочные столы. Струбцины этого типа нередко называют «прижимами быстрого действия». В отличии от G- и F-образных зажимов прижимные струбцины позволяют фиксировать заготовки не только у края столешницы, а в любом месте рабочей зоны.
Струбцины прижимного типа монтируются либо посредством специальных технологических разъемов (круглых или Т-образных), либо переставных плит.
Существует множество разновидностей прижимных струбцин. Внизу выложен видеоролик, автор которого демонстрирует широкий ассортимент прижимов быстрого действия. В видео есть и рекомендации, как выбрать струбцину для сварки.
Прижимные струбцины можно условно разделить на несколько обширных категорий:
- С винтовым прижимом
- Рычажные/шарнирные
Как понятно, в струбцинах с винтовым прижимом губка перемещается на резьбовом штоке. Рычаг же прижимает эксцентриковым механизмом. В продвинутых струбцинах силу эксцентрикового прижима можно регулировать.
Дополнительная информация
При выборе струбцин для сварочных работ следует особое внимание уделить используемым в конструкции прижима материалам. Для фиксации металлических заготовок предпочтение следует отдавать струбцинам с металлическими губками. Дело в том, что при сварке заготовок металл собираемой детали может разогреваться до покраснения. Если губки будут пластиковыми или резиновыми, они сразу же «поплывут».
Пластиковые и резиновые губки хороши только для столярных операций.
Не следует ограничиваться заказом струбцины одного единственного размера. В закромах у опытного сборщика металлоконструкции каждый из типов струбцин представлен тремя, а то и четырьмя типовыми размерами.
Если сварочные работы проводятся в рамках серийного или массового производства, то следует отдавать предпочтение струбцинам заводского изготовления. Самодельные прижимы в этом случае не обеспечат высокой точности стыковки заготовок. Для единичного же домашнего использования опытные сварщики нередко используют самодельные струбцины. Среди таких прижимов встречаются и уникальные экземпляры, не имеющие аналогов на рынке промышленной продукции.
Угловой зажим под прямым углом 90 градусов, самодельные Угловые зажимы, быстрая фиксация, аквариум, стекло, дерево, фоторамка, деревянный угловой зажим|Крепления|
информация о продукте
Характеристики товара
- Применение: Other
- Индивидуальное изготовление: Да
- Товары для ремонта: Woodworking
- Структура: Угловой зажим
- Происхождение: Китай
- Наличие стандарта: Other
- Номер модели: /
- Материал: Алюминий
отзывах покупателей ()
Нет обратной связи
Professor Hammer: самодельные зажимы для панелей
Это простой самодельный зажим, который очень эффективен для надежного удержания больших панелей, обеспечивая точное выравнивание и жесткость, необходимые для стыковой сварки.
Q.
Я делаю много топов, разрезаю пирог на капоте, и я планирую разделить пару машин. Я очень внимательно отношусь к качеству своей работы и использую исключительно стыковые соединения и сварку TIG. Благодаря этому сварные швы остаются мягкими и обрабатываемыми, с минимумом деформации, и позволяет мне идеально выпрямлять панели, поэтому требуется лишь небольшое количество наполнителя.
У меня есть широкий ассортимент зажимов, в том числе несколько 18-дюймовых зажимов с глубоким горлом, которые позволяют мне зажимать панели заподлицо для прихваточной сварки, но если мне нужно сделать сварной шов по всей большой панели, мне нужно выровняйте участки, недоступные для зажимов.
Я знаю, что для этой цели есть коммерчески доступные зажимы, но мне нравится делать свои собственные инструменты. У вас есть предложения, как надежно закрепить большие гибкие панели при подготовке к стыковой сварке?
Брюс Карпентер
Через Интернет
A.
Прежде всего, я рекомендую вам работать с осторожностью. Как вы знаете, стыковые соединения внахлест более распространены для этого типа работ, но если вам нужна максимальная обрабатываемость сварного соединения, позволяющая довести панели до совершенства, стыковые соединения, выполненные сваркой TIG, определенно подходят.
Я видел много способов выравнивания панелей под сварку. Некоторые люди используют маленькие ремни с дырочками на каждом конце. Эти ремни охватывают стык, и Clecos (или винты для листового металла) продеваются через отверстия, входящие в удерживаемые панели.Это работает достаточно хорошо, но не позволяет менять положение соединения после просверливания отверстий. Кроме того, усилие зажима ограничено, поэтому, если панелям требуется большая поддержка для поддержания надлежащего выравнивания, трудно получить идеальную посадку заподлицо. Еще одним недостатком является то, что этот процесс оставляет вам множество дополнительных дыр, которые нужно заполнить.
Я встретил в Австралии производителя автомобилей (имя которого ускользает от меня), который сделал несколько очень простых, но оригинальных зажимов для выравнивания панелей. Каждый зажим состоит из трех частей.Одна часть представляет собой небольшой прямоугольник из листового металла размером около 1х2 дюйма с отверстием в центре. Вторая часть представляет собой кусок круглого прутка 5/16 с загибом на одном конце. Последняя часть представляет собой подобный кусок круглого бруса с конической шлифовкой с одной стороны.
Для использования зажима прямоугольник листового металла проходит через стык, а один кусок круглого стержня проходит через отверстие на внутренней стороне панелей. Последним шагом является установка конической детали через отверстие в полосе листового металла на внешней стороне панели.Эти простые зажимы обладают очень хорошей удерживающей способностью и могут быть затянуты или ослаблены ударом молотка по изогнутому концу конического круглого стержня. На панелях с большой кривизной это помогает изгибать внутренний стержень.
Как видите, эти зажимы достаточно просты, чтобы их можно было сделать несколько десятков за час или два, и они должны прослужить всю жизнь! Иногда самые простые инструменты оказываются лучшими.
Q.
Листовой металл какой толщины следует использовать для изготовления патч-панелей?
Lee Torode
Через Интернет
A.
При изготовлении патч-панелей я всегда стараюсь ТОЧНО подбирать оригинальную толщину. Автомобили 30-х годов обычно были 19-го калибра (0,039 дюйма). После Второй мировой войны большинство производителей перешли на сталь 20-го калибра (0,033 дюйма). Новые автомобили изготавливаются из сверхтонкой стали (часто из высокопрочного сплава), толщина которой может достигать 23-го калибра (0,028 дюйма). Вот почему ремонт после столкновения на новых автомобилях обычно включает замену панели, а не выпрямление или исправление, поскольку тонкие и прочные панели имеют крайне ограниченную обрабатываемость!
Вы можете отправить свои вопросы профессору Хаммеру по электронной почте (covell @ cruzio.com) или отправьте письмо по адресу Covell Creative Metalworking, 106 Airport Blvd., Suite 105, Freedom CA 95019. Вы получите личный ответ. Рон Ковелл снял множество видеороликов по металлообработке, и теперь их можно транслировать или загружать с его веб-сайта. Посмотрите их на covell.biz, а также на серию его текущих семинаров, проводимых по всей стране, или позвоните, чтобы узнать расписание семинаров и бесплатный каталог DVD-дисков. Телефон (831) 768-0705. Также посетите канал Рона на YouTube: www.youtube.com/user/covellron.
Просмотреть все 1 фотоПочему у сварочных столов есть отверстия? >> Полезные советы и хитрости
Скоро вы узнаете, что вам нужно рабочее место для сварки. Работа с горячим металлом, электрическими дугами и брызгами сварочного шва требует чего-то более прочного, чем большинство деревянных верстаков. Сварочный стол, специально созданный для этой работы, может быть долгожданным дополнением, особенно когда сложный проект только начинается, и вы начинаете понимать, почему у сварочных столов есть отверстия.
Почему у сварочных столов есть отверстия? Сварочные столы имеют отверстия, чтобы дать сварщику больше контроля и возможностей при настройке сварочного задания, разрешив
- Полное использование столешницы для зажима
- Простое размещение зажимных приспособлений, упоров и зажимов
- Идеальное совмещение деталей и деталей
Сварочные столы доступны практически в любом стиле и размере. представить. У некоторых есть регулируемые ножки для изменения рабочей высоты.Даже отверстия бывают разных размеров.
Доступны резьбовые отверстия для использования со специальными зажимами и зажимами. На некоторых столах имеются прорези, позволяющие сварщику более легко размещать зажимы и приспособления. Выбор сварочного стола может вызвать недоумение. Вот руководство, которое упростит выбор.
В поисках идеального сварочного стола
Прежде чем отправиться в магазин сварочных материалов и купить сварочный стол, уделите несколько минут и подумайте о необходимых вам функциях, типах запланированных проектов и вашем бюджете.Предварительно важно провести небольшое исследование и планирование, чтобы убедиться, что у вас есть функции и опции, соответствующие вашим требованиям.
Есть несколько функций, которые следует учитывать.
- Ваши проекты — Какие проекты вы строите? Насколько они большие? Какой вес вы ожидаете положить на сварочный стол? Какие материалы вы обычно свариваете? Все эти вопросы влияют на принятие решения о следующих нескольких функциях, о которых вам следует подумать.
- Качество — Качество конструкции вашего сварочного стола является ключом к нескольким факторам. Прочность одна. Столы более высокого качества прослужат дольше в магазине. Таблицы более высокого качества также более точны и квадратны. Если вы выберете переносной сварочный стол, удачный дизайн сделает его удобным в использовании и хранении.
Подробнее о безопасности при сварке — Здесь вы можете найти статью с нашего веб-сайта о : Средства индивидуальной защиты для сварщиков — СИЗ | Список и требования
- Размер и вес — Эти два элемента сочетаются друг с другом, как хлеб с маслом.Если ваши проекты требуют, чтобы вы отправлялись на место работы, а не приносили работу в магазин, размер и вес быстро вступают в игру. Если вы создаете большие и тяжелые проекты, может потребоваться стол побольше и тяжелее. Постарайтесь подогнать размер и вес сварочного стола к требованиям вашей работы.
- Высота — Если возможно, купите сварочный стол с регулируемыми ножками. Возможность регулировать высоту рабочей зоны может сделать вашу жизнь намного приятнее. Настроить рабочее пространство в соответствии с вашими требованиями гораздо эргономичнее , чем пытаться приспособить свое положение к рабочему пространству. Это может привести к усталости и другим физическим проблемам.
- Точность — Качественный сварочный стол будет точным, квадратным и плоским. Отверстия и пазы будут точно фрезерованы или просверлены. Края стола будут квадратными , как и углы. Верхняя поверхность должна быть плоской и ровной.
- Бюджет — Мы все должны учитывать бюджет. Задача всегда состоит в том, чтобы найти лучший компромисс между функциями, качеством и бюджетными ограничениями. Мы советуем по возможности увеличить бюджет. . Чем качественнее сварочный стол вы можете купить, тем лучше он будет работать в долгосрочной перспективе.
Отверстия и прорези
Большинство имеющихся в продаже сварочных столов имеют отверстия и прорези в поверхности сварочного стола, чтобы упростить использование зажимных приспособлений, ограничителей и зажимов.Вы должны понимать некоторые проблемы с добавлением отверстий и пазов на сварочном столе.
- Пазы могут деформироваться при нагревании поверхности стола. — Сварка выделяет много тепла. Так работает вся система. Это означает, что ваш сварочный стол также будет поглощать много тепла. Длинные прорези могут деформироваться и смещаться во время повторяющихся циклов нагрева и охлаждения.
- Проблема с отверстиями в целом — Столы со щелями и отверстиями имеют тенденцию пропускать предметы.У мыльного камня есть раздражающая привычка проваливаться через щели каждый раз, когда он кладется на стол. Шлак, стружка и искры могут попадать в отверстия в сварочном столе, что делает нижнюю часть практически бесполезной для хранения чего-либо.
- Ситуация с подгонкой принадлежностей — Если на поверхности сварочного стола предварительно просверлены отверстия и прорезаны пазы, а отверстия имеют нарезку и резьбу, вы вынуждены использовать только те зажимы и аксессуары, которые подходят к этим отверстиям, прорезям и рисункам резьбы.Существуют некоторые отраслевые стандарты, и мы предлагаем вам найти стол с наиболее широким выбором аксессуаров.
О принадлежностях
Покупка сварочного стола — это только начало. Вскоре вам понадобятся всевозможные аксессуары для сварочного стола. Со временем вы, возможно, даже станете обрабатывать и строить собственные упоры и приспособления для своего сварочного стола. Доступные аксессуары и инструменты, облегчающие сварочные работы, включают:
- Зажимы — Зажимы бывают любого вообразимого стиля, формы и дизайна.Вы можете найти решение для ваших требований по зажиму с помощью быстрого поиска в Интернете. Основные типы зажимов для сварочного стола, которые вы можете приобрести:
- Упоры — Упоры бывают разной длины. Эти удобные аксессуары могут быть круглого или квадратного фасона. Упоры полезны для выравнивания деталей и удержания их на месте при выполнении начальных сварных швов, обеспечивая квадратное соединение.
- Прямоугольные и регулируемые угловые направляющие — Эти универсальные зажимы позволяют выполнять работу с нестандартными углами, которые останутся на месте до тех пор, пока вы не завершите сварку.
- Тиски — Доступны различные типы тисков, которые используют отверстия и прорези в сварочном столе для быстрого монтажа и демонтажа по мере необходимости. Тиски могут занимать много места на рабочем столе. Возможность иметь при необходимости тиски может быть большим плюсом.
- Другое — Есть и другие вещи, которые нужно искать в составе принадлежностей сварочного стола. Многим сварщикам нравится, когда на них можно повесить сварочный пистолет или горелку.Корзины и стеллажи для принадлежностей, инструментов и мелких деталей также пригодятся.
Вариант «Сделай сам»
Всегда есть возможность построить свой собственный сварочный стол. Сварочные столы по своей природе являются металлическими проектами, а мы сварщики. Создание собственного стола в соответствии с вашими требованиями — это первый крупный проект, за который берутся многие сварщики.
Разработка и изготовление собственного сварочного стола позволяет вам идеально адаптировать его к вашим потребностям и требованиям работы.При создании сварочного стола есть несколько проблем.
- Столешница — Подготовить верхнюю часть и убедиться, что кусок металла имеет квадратную форму, углы правильные, а края перпендикулярны верху, может быть сложной задачей.
- Рама — Вы должны убедиться, что рама идеально квадратная и правильная. Он также должен быть достаточно жестким, чтобы удерживать стол, не позволяя изгибаться или сгибаться, когда на него кладется вес.
- Отверстия и пазы — Сверление или обработка отверстий и пазов в вашем столе требует точной обработки. Могут потребоваться специализированные инструменты. Перед тем, как начать процесс, убедитесь, что у вас есть доступ к этим инструментам.
Сервировка стола
Хороший сварочный стол может сделать работу по сборке и сварке проекта быстрее и проще. Найти стол, который наилучшим образом соответствует вашим потребностям и требованиям работы, может быть непросто. .Мы надеемся, что информация в этой статье немного упростит процесс и помогла вам понять, что искать в хорошем сварочном столе.
Рекомендуемая литература
Какие газы используют сварочные аппараты MIG >> Сварочный защитный газ | Полное руководство
Можно ли сваривать MIG под дождем или во влажной среде?
Как построить сварочный стол >> Обучающее видео
Как построить сварочный стол
ОБНОВЛЕНИЕ ОТ JOHN P !: Как вы увидите ниже, создание собственного сварочного стола — это большая работа! Поэтому теперь я предлагаю готовые сварочные столы по цене меньше, чем вы можете купить даже в разобранном виде! Доступно несколько размеров, включая:
— 40 ″ x 40 ″
— 50 ″ x 50 ″
— 40 ″ x 80 ″
— 50 ″ x 100 ″
Проверьте их!
Сегодня мы получили необычный взгляд на супер-сладкую деталь НИЗКОГО технического снаряжения, для сборки которого требуется немного знаний.А именно, новый сварочный стол от ребят с WeldTables.com. Если вы следите за моим видео о том, как сваривать, это должно быть все, что вам нужно знать, чтобы выбрать один из этих комплектов и построить свой собственный сварочный стол для плохой работы!
Как построить сварочный стол — видео
Советы и методы
- Помните, самое главное — не сваривайте этот стол ПЕРЕСЕЧЕНИЕМ. Точек сварки так много, что для каждого выступа и паза не требуется больше, чем небольшой валик.А слишком сильная сварка приведет к смещению и деформации вашей суперплоской поверхности.
- Сделайте то же самое, чтобы сварные швы были короткими и холодными. Во время сварки перемещайтесь по столу, чтобы тепло рассеивалось, и постарайтесь сохранить все даже во избежание деформации.
- Этот стол довольно тяжелый, поэтому будьте готовы с напарником или каким-нибудь инструментом, который поможет вам поднять его. Примите дополнительные меры предосторожности, потому что уронить эту вещь на себя может быть катастрофой.
Принадлежности для вашего нового стола
Некоторые инструменты, которые хорошо работают с этим типом поверхности (не входят в комплект поставки стола):
Прецизионная сварка на вашем новом столе
Одно дело — иметь суперплоский стол, и возможность зажимать его — это фантастика, но иногда вам также нужна возможность выровнять детали с помощью приспособлений и приспособлений.Итак, вот несколько моих любимых. Вы можете найти полный список здесь.
Угловые приспособления для сварщика
Перечисленные выше зажимы полезны в условиях высокой мобильности, но для более тяжелых условий эксплуатации или ситуаций с более высокой точностью лучше инвестировать в сварочные приспособления, которые ускорят рабочий процесс и прослужат намного дольше.
Northern Industrial Welders Зажим для сварки под углом 90 градусов — 55 долларов на Amazon
Этот угловой зажим на 90 градусов Northern Industrial изготовлен из литой стали с прорезями для крепления в основании и винтами с медным покрытием, которые помогают выдерживать сварочные брызги.
Шаблон должен выдерживать материалы размером до 2 3/8 дюйма. Одним из недостатков базового зажимного приспособления, подобного этому, является то, что в нем отсутствует механизм быстрой регулировки для быстрого зажима материала, подобный тому, который можно найти на зажимном приспособлении Strong Hands, перечисленном ниже.
Bessey WSM-9 7-дюймовый угловой зажим для сварщика под углом 90 градусов — 116 долларов на Amazon
У этого зажимного приспособления Bessey чугунная основа, отжимной винт с медным покрытием, устойчивый к загрязнению шлаком и брызгами, а также встроенные отверстия для смазки шарнирных точек и винта.
Это одноручное самоцентрирующееся приспособление и зажим, способный удерживать материал 2,5 дюйма для Т-образных соединений и 3,5 дюйма для угловых соединений. Как правило, смазочные отверстия и прецизионная конструкция делают этот зажим превосходным, но не все готовы платить больше, чем за вариант Northern Tool.
Bessey WSM-12 9-1 / 2-дюймовый угловой зажим для сварочных аппаратов — 150 долларов на Amazon
Bessey WSM-12 является старшим братом WSM-9 с большей емкостью материала, которая позволяет использовать до 4 дюймов материала для Т-образных соединений и 4 дюйма.75 ″ стыков под углом с каждой стороны.
Этот зажим стоит месяца хотя бы по той причине, что просто большая емкость. В конечном итоге вы захотите приобрести как можно больше инструментов, чтобы выполнять как можно больше работ.
Угловые приспособления для многоосевой сварки
Strong Hand Tools Угловой зажим для многоосевого сварщика с зажимными тисками — 3 оси, модель # WAC35-SW — 223 доллара на Amazon
Это мой личный выбор, но он полезен для просмотра всех вариантов в широком диапазоне цен.Лично я купил 4 хлопка для многоосевой сварки Strong Hand Multi Axis Welder. Эти приспособления подходят для квадратного или круглого материала размером до 3,75 дюйма под углом 90 градусов для надежной фиксации во время сварки.
Это сверхмощные приспособления, которые прослужат всю жизнь (а то и немного). Прецизионные фрезерованные поверхности на платформе из литой стали обеспечивают чрезвычайно ровные и повторяемые соединения, а кнопки быстрой регулировки на зажимах позволяют очень быстро устанавливать и зажимать материал без необходимости ввинчивать винты внутрь и наружу по всей длине винта.
Эти зажимы можно использовать для простых двухсторонних сварных швов под углом 90 градусов или для создания полного угла 90 градусов. И я использовал свой много-много раз. Они снимают все беспокойства, создавая что-то с идеальными углами. Я знаю, что это вложение, но набор из них заменит все остальные зажимы в этом списке. И, честно говоря, если вы можете сузить его до одного набора инструментов для каждой возможной работы, за которую мне стоит заплатить дополнительные деньги.
Хорошо, вот и все! Если у вас есть какие-либо вопросы или комментарии, напишите их ниже или напишите мне в Твиттере @JohnPoz, и я сразу отвечу.
Зажимы для сварочного стола Harbor Freight
Набор зажимов для сварки и листового металла 2 шт.Зажимы сварочного стола портовые грузовые .
В корзину добавить в мой список. Регулируемый стальной сварочный стол 69 99. Инструменты для портовых грузовых перевозок позволяют сварщикам удовлетворить любые потребности и любой уровень опыта. Harbour Cargo закупает свои высококачественные инструменты на тех же заводах, что и наши конкуренты.В корзину добавить в мой список. Harbour Cargo закупает свои высококачественные инструменты на тех же заводах, что и наши конкуренты. Мы исключаем посредников и передаем вам экономию. Harbour Cargo закупает свои высококачественные инструменты на тех же заводах, что и наши конкуренты. Мы исключаем посредников и передаем вам экономию. Стальная поверхность этого регулируемого сварочного стола обеспечивает устойчивую огнестойкую поверхность для сварки деталей и компонентов.Держатели сварочных хомутов 16 шт. В корзину добавить в мой список. Harbour Cargo имеет полную линейку высококачественных сварочных аппаратов для сварки мигр-флюсом и стержневых сварочных аппаратов. Мы исключаем посредников и передаем вам экономию. Регулируемый стальной сварочный стол 69 99. Результаты поиска по зажимам для сварки 18 позиций. Предназначен для обеспечения электропроводности. Подключите сварочный зажим непосредственно к сварочному столу, чтобы не допустить попадания шлака и брызг.Сварочный зажим типа F 21 99. Сильный ручной инструмент ts3020 at 139 99. Harbour Cargo закупает свои высококачественные инструменты на тех же заводах, что и наши конкуренты. Мы исключаем посредников и передаем вам экономию. Я получил эту идею с потрясающего форума. Регулируемый угол наклона и упор дают вам множество вариантов сварки. В этом видео мы быстро и легко создаем зажимы для нового сварочного стола.Harbour Cargo закупает свои высококачественные инструменты на тех же заводах, что и наши конкуренты. Регулируемый стальной сварочный стол. Регулируемый стальной сварочный стол. От ремонта автомобилей до строительства — вы найдете подходящее сварочное оборудование и аксессуары для вашего проекта. Сильный ручной инструмент ts3020 at 139 99. В корзину добавить в мой список.Сильный ручной инструмент um125 c3 на 79 99. Набор для сварки и зажима листового металла 2 шт.Хомуты самодельные сварочные. Сварочное оборудование
Для выполнения основных и вспомогательных операций сварочного процесса помимо сварочного аппарата, источника питания дуги и аппаратуры управления необходимы дополнительные устройства и механизмы, образующие вместе с вышеуказанным оборудованием пост или установку для ручного, автоматического или ручного управления. полуавтоматическая сварка.Эти устройства и механизмы сильно различаются в зависимости от формы и размеров изделия, характера производства и т. Д.
Их можно разделить на следующие группы:
— сварочные и сборочно-сварочные технологические устройства;
— устройства для штабелирования и наклона сварных изделий;
— несущие металлоконструкции и тележки для рабочего и крейсерского движения сварочных аппаратов;
— металлоконструкции и механизмы для обслуживания зоны сварки;
— транспортные устройства и др.
Устройства технологические для сварки
Использование сборочно-сварочных устройств снижает трудоемкость монтажных работ, снижает остаточные деформации, улучшает качество конструкций, упрощает осмотр и приемку собранных конструкций. Правильно спроектированное и изготовленное приспособление должно соответствовать следующим требованиям:
— быть удобным в эксплуатации, обеспечивать проектные размеры изделия,
— быстро устанавливать элементы и снимать собранное или сваренное изделие,
— иметь невысокую стоимость. и соблюдать требования безопасности при выполнении монтажных и сварочных работ.
Тип светильника определяется серийностью производства и степенью сложности конструкции.
В единичном производстве обычно используются универсальные устройства. В массовом производстве в зависимости от количества выпускаемых однотипных изделий используются как универсальные, так и специализированные устройства. В массовом производстве распространены устройства разных типов, от простых до сложных, быстродействующих, с элементами автоматики.
Универсальные фитинги для сборки под сварку
Сборочные инструменты общего назначения обычно просты и портативны.Они не всегда обеспечивают требуемую точность и предназначены для проверки правильности сборочных и установочных размеров.
Зажимы переносные предназначены для фиксации взаимного расположения свариваемых деталей (рис. 1). Прижимные устройства могут применяться при сварке определенных деталей, а также при изготовлении узлов и конструкций. В этом случае они оснащаются подставками, стеллажами и другим вспомогательным оборудованием. Они выполнены в виде струбцин и болтовых зажимов, что позволяет собирать детали любого профиля.
Клиновые и зажимные хомуты используются для сборки изделий из листового металла (рис. 2). Пружинные зажимы используются для крепления тонких листов и коротких деталей из профильного проката.
Рис. 2
Захваты используются в основном для монтажа крупных конструкций (рис. 3). Отдельные элементы зажимов временно привариваются к собранным деталям, а после сварки снимаются. Зажимы жесткие и регулируемые.
Рис. 3
Стяжки используются для приближения кромок свариваемых деталей к заданным размерам.Наиболее распространены винтовые стяжки (рис. 4).
Рис. 4
Стяжка с болтом и приварными коленами для сварки крупногабаритных конструкций из листового металла.
Зажимное приспособление с приварными временными коленами для сборки труб. Он используется в ограниченном объеме и только на трубах из углеродистой стали.
Стяжка винтовая для сборки конструкций и деталей из листового, полосового и профильного проката.
Муфта рычажно-винтовая. Для сборки стыков труб чаще всего используются зажимные винтовые устройства зажимного типа, не создающие жесткого крепления стыкуемых элементов.
Распорки и домкраты предназначены для крепления изделий с замкнутым профилем изнутри, для выравнивания краев цилиндрических изделий, для удаления вмятин и т. Д. (Рис. 8). При сварке цилиндрических изделий используются проставки в сочетании с зажимными кольцами. Если диаметр обечайки небольшой, используются распорные кольца, а при больших диаметрах — винтовые распорки или домкраты (рис. 9).
Рис. 8
Усилия в стойках и домкратах создаются механическими, гидравлическими или пневматическими приводами.
Рис. 9
Центраторы предназначены для крепления отдельных труб или аналогичных изделий, так что они не имеют смещения и поворота в направлениях трех осей координат (рис. 10). Они позволяют совмещать цилиндрические поверхности стыкуемых изделий (труб, участков труб и т. Д.) Под сварку. В зависимости от положения центраторов относительно монтажных поверхностей центраторы подразделяются на внешние (захватные) и внутренние (распорные).
Наружные центраторы применяются при сборке труб в секциях под сварку на глухих основаниях или в районе строительных площадок.
Рис. 10
Хотя конструкция внешних центраторов различается, они выполняют одну и ту же операцию для обеспечения совмещения и совмещения торцевых кромок труб.
Примеры внешних центровочных устройств для сборки труб.
Широкое распространение получили наружные многорычажные центраторы типа ЦНУ (рис.11).
Состоят из двухрядной пластинчатой цепи, два крайних звена которой выполнены в виде крючков, закрепленных на цапфах гаек стяжных болтов. Зажимной винт имеет правую и левую резьбу. На концах винта имеются шестигранные проушины для ключа с трещоткой. Для центрирования труб при сборке центратор устанавливается на стык и закрепляется на трубах путем вращения винта. Универсальность конструкции при переходе с одного диаметра трубы на другой достигается за счет изменения количества звеньев.
Рис. 11
Центраторы для сборки труб диаметром 426 … 1220 мм могут комплектоваться вместо зажимного винта гидроцилиндром (рис. 12). Внешний гидравлический центратор представляет собой двухрядную пластинчатую цепь, стянутую на концах соединяемых труб домкратом, размещенным внутри кронштейна. Домкрат приводится в движение гидронасосной станцией.
Рис. 12
Внутренние центраторы обеспечивают высочайшее качество сборки труб за счет более точного совмещения их кромок.При центровке стык снаружи открыт, что обеспечивает свободный доступ к месту сварки. Использование внутренних центраторов позволяет повысить производительность и степень механизации сборки для сварки как поворотных, так и неповоротных стыков труб. Внутренние центраторы по конструкции механизма центрирующего устройства можно разделить на четыре группы: с механическими, гидравлическими, электромеханическими, пневматическими приводами разжима. Выбор центровочных приспособлений зависит от диаметра трубы и системы электроснабжения.
Сварочные приспособления незаменимы в работе. Сама сварка требует гораздо меньше времени и усилий, чем подготовка к этой работе. Основная часть подготовки — это сборка сварочного аппарата с закреплением всех компонентов в необходимом положении. Этот процесс требует особого внимания, ведь от него будет зависеть качество готового продукта.
Существует множество оборудования и огромное количество разнообразных устройств, предназначенных для сварки.Для бытовых целей подходят аппараты для механической сварки, позволяющие быстро собрать инструмент, хорошо зафиксировать все компоненты в нужном положении и получить минимальную деформацию детали.
Какие бывают устройства?
Аппараты сварочные могут быть следующими:
- Зажим. Это инструмент, который пригодится при любых металлических работах. Она может иметь самые разные формы и размеры.
- Зажимы сварочные. Их проще использовать, чем зажимы.Элемент фиксируется сжатием ручки зажима.
- Магнитные квадраты. Бывают разной формы, разные застежки, есть возможность менять угол наклона. С их помощью можно без особых усилий соединить листы и рамы под нужным углом.
- Стенды сварочные. Это устройство, имеющее 1 фиксированную основную поверхность с застежками. Они нужны для сварки продольных сварных швов на плоских изделиях.
- Кантователи. Это статические устройства, позволяющие закрепить свариваемый элемент и повернуть его в нужное положение для выполнения сварки.Их часто используют для сварки крупных элементов, имеющих разную форму и швы с разных сторон.
- Манипуляторы. Это устройства, которые необходимы для поворота элемента вокруг оси и наклона его на необходимый угол. Их используют для всех видов сварки, а также для контактной. К ним прикрепляются элементы различной формы.
- Остановок. С их помощью детали крепятся к основным поверхностям. Упоры бывают постоянные, съемные и откидные. Константы имеют вид пластин, приваренных к основанию.Складные и съемные используются, когда они в готовом изделии недопустимы.
- Зажимы. Эти устройства могут быть клиновыми, винтовыми, пружинными, эксцентриковыми, рычажными. Самыми известными являются винтовые зажимы. Такой хомут представляет собой болт с гайкой, нарезанный на 2 пластины. Благодаря им можно зажимать элементы. Зажим аналогичен листу с канавкой клиновидной формы. Эксцентриковые зажимы нужны для зажима элемента с кулачком, который установлен на рычаге.
- Стяжки. Их используют при сварке крупногабаритных элементов.Завязки приближают края элементов на необходимое расстояние.
- Распорки. Благодаря распоркам можно выровнять элементы, придать им желаемую форму и исправить дефекты.
Как сделать струбцину?
Зажим является фиксирующим устройством. Для его постройки вам потребуются следующие материалы:
- лист стальной толщиной 1 см;
- 3 гайки;
- ряд шайб большого диаметра;
- трубка с наружной резьбой по размеру гаек.
Чтобы сделать прибор своими руками, сначала из листа стали вырезают полосу. Его длина должна быть 500 мм, ширина 40 мм. Далее нарезаются 2 полоски. Вам также понадобится подвижный стержень 100 мм, 2 прямоугольника по 50 мм каждый для усиления подвижных элементов, небольшая часть для поддержки основной части зажима.
К этой детали приваривается дополнительная деталь, делая между ними букву G. На короткой части нужно приварить деталь для опоры. 3 гайки подходят друг к другу, шайбы тоже.Гайки ставятся ребром к подвижной части, они привариваются. К штанге можно прикрепить деревянную ручку, которая закреплена вверху гайкой.
Все элементы приварены снаружи к деталям. Между ними вставляется полоска зажима. Когда элементы свариваются, к ним крепится подвижная планка. К концу металлического стержня приварены большие шайбы.
Изготовление приспособлений для сварки под углом 90 °
Ручная дуговая сварка: 1-электродная; 2-х электродное покрытие; 3-газовая защита.
Сварочные магниты, удерживающие соединяемые трубы под прямым углом, необходимы для облегчения сварки. Вам потребуются следующие материалы:
- лист металла квадратной формы, стороны которого 20-25 см;
- труба квадратного сечения;
- 3 гайки и 3 болта;
- болт (диаметр 4 см) и гайка 3,5 см; Стальной цилиндр
- диаметром 5 мм;
- дрель, дрель.
К металлическому угольнику своими руками нужно приварить 2 куска трубы длиной 200 и 150 мм.Затем из этих труб делают 2 дополнительные детали. Первый — П-про разные формы из отрезков 100 мм. Второй — трапеция размером 11,5 и 5,4 см.
Хомуты с магнитами должны быть собраны путем последовательного соединения компонентов.
Они будут хорошо сваривать магниты.
Теперь вы ознакомились со сварочными приспособлениями и их конструкцией. Желаем вам удачи в сварке и правильном применении необходимых устройств для выполнения различных соединений, будь то угловые или Т-образные.
Все сварочные аппараты делятся на две группы: крепежные и установочные. Также существуют универсальные устройства, выполняющие обе функции.
Монтажные элементы
К установочным устройствам относятся устройства, предназначенные для фиксации деталей в определенном месте так, как это должно выглядеть в конце сварки.
Монтажные элементы отличаются друг от друга конструктивными и функциональными особенностями. К ним относятся:
- квадрат; Шаблон
- ;
- упор; Призма
- .
Шаблон — это инструмент, который помогает без дополнительной разметки собрать соединяемые элементы и закрепить их без использования зажимов.
Упор предназначен для фиксации привариваемых деталей к основанию. Есть несколько типов устройств: откидные, съемные, стационарные. Постоянные части чаще всего представляют собой стержни или пластины. Если необходимо поставить временный упор, то в этом случае используются съемные или откидные конструкции.
Угольник — незаменимый прибор, когда возникает необходимость установить детали под углом.Наиболее функциональными считаются поворотные устройства.
Сварка цилиндрических элементов редко обходится без призмы, фиксирующей детали в нужном положении.
Крепежные детали
Крепежные устройства — устройства, служащие для надежной фиксации деталей, в которых исключены смещения, деформация и охлаждение элементов при сварке. К ним относятся:
- зажим;
- зажим;
- зажим;
- распорка; Стяжка
- .
Быстрозажимной зажим — один из самых распространенных крепежных элементов при работе с металлом.Деталь имеет различные формы и размеры. Размер зажима может быть регулируемым или фиксированным.
С помощью сварочного зажима деталь легко и надежно фиксируется в определенном положении. Преимущество — простота процесса: крепление элементов осуществляется с помощью ручек, которыми оснащен зажим.
Существует несколько типов зажимных устройств: рычажные, эксцентриковые, клиновые, пружинные, винтовые. Последняя модель наиболее востребована при проведении сварочных работ.
Стяжка предназначена для соединения и фиксации крупногабаритных изделий. Есть несколько способов завязать галстук.
Распорка служит для выравнивания всех стыков, придания им необходимой формы и исправления дефектов.
Наиболее удобными для сварочных работ являются универсальные аппараты с функциями крепления и крепления. Принцип работы таких устройств прост и прост: в изделие вставляется нужная деталь, после чего эксцентрики и винты плотно затягиваются.
Основным недостатком вспомогательных устройств является то, что они быстро изнашиваются и часто ломаются. Чтобы снизить затраты, связанные с покупкой приспособлений, можно попробовать изготовить сварочные приспособления своими руками. Тем более, что это сделать несложно.
Зажим производительный
Зажим — фиксирующее устройство, применяемое при сварке, применяется также в слесарных, столярных, токарных работах. Для этого требуется разная прочность крепежа. Например, для соединения металлических труб нужны хомуты, выдерживающие большие нагрузки.Магазинные приспособления недостаточно надежны, поэтому сварщики часто используют самодельные приспособления для сварки.
Хомут сделать несложно, понадобится:
- лист стальной, толщина которого около 10 мм;
- гайка — 3 шт .;
- шайба большого диаметра — 4-5 шт .; Труба
- снабжена внешней резьбой, соответствующей размеру гаек.
При изготовлении устройства необходимо придерживаться определенного алгоритма. Схема устройства значительно облегчит его сборку:
Полосы вырезаются из стального листа, ширина которого 40 мм, а длина имеет разные значения:
- длиной 500 мм для основания;
- длиной 250 мм для статической фиксации внизу конструкции;
- длиной 100 мм для создания скользящей планки.
Далее следует вырезать два прямоугольника по 50 мм (A), которые служат для крепления подвижного элемента, и часть (B), которая обеспечивает упор в неподвижной части изделия. Далее к основанию зажима следует приварить вспомогательное приспособление, получив Г-образную форму. Присоедините деталь B к короткому краю. Свариваются три гайки. Шайбы также свариваются.
Затем поместите гайки краем на подвижный элемент и приварите так, чтобы стержень, который будет ввинчиваться, был параллелен основной части хомута.Штангу можно взять из купленного ранее приспособления. К нему при необходимости добавляются деревянные ручки, закрепленные гайкой.
Сварка выполняется по внешнему краю компонентов A, между которыми вставляется зажимная планка. Далее к внутренним краям деталей А прикрепляется подвижный элемент и выполняется сварка. Наконец, к краю металлической планки привариваются плоские шайбы.
Полученное изделие позволит удерживать достаточно крупную конструкцию из металлических труб без сдвигов, разрывов и перекосов.
Сварка под углом 90 °
Схема установки магнита:
Сварочные магниты, удерживающие соединяемые трубы под углом 90 °, упрощают сварочные работы. Но как сделать аккуратный шов, если такого приспособления под рукой не оказалось? Для этого нужно взять:
- лист металлический квадратный со стороной 20-25 см;
- отрезок трубы квадратного сечения;
- болтов с гайками — 3 шт .;
- болт диаметром 4 см, гайка к нему — 3.5 см;
- стальной цилиндр диаметром около 5 мм;
- сварочный аппарат, дрель, дрель.
Два отрезка трубы длиной 20 см и 15 см привариваются к металлическому угольнику (по углам, с противоположных сторон). Далее из этих труб нужно сделать пару вспомогательных элементов: П — образный, из отрезков длиной 10 см; и равнобедренная трапеция (основание 11,5 и 5,4 см).
Все расчеты должны выполняться с максимальной точностью.
Хомуты с постоянными магнитами собираются согласно последовательности соединения элементов.Они отлично выполняют функции сварных магнитов, которые для бытового использования являются довольно дорогостоящими изделиями.
Самодельный электрододержатель — довольно распространенное изделие, которое имеет множество форм и размеров в зависимости от вида работ: сварка негабаритных труб или пайка витой проволоки.
Простой электрододержатель из трубки диаметром d¾ ”:
Специалисты рекомендуют для изготовления прочного и надежного держателя для сварки труб предварительно составить схему, учитывающую все особенности изделия.Сэкономить на оборудовании можно, обратившись в школьную мастерскую, которая обычно оснащена станками для нарезания резьбы и сверления. Для бытового сварочного аппарата желательно сделать стеллаж, где будут храниться мелочи, необходимые для сварки.
Сварочное оборудование
К Категория:
Сварные соединения
Сварочное оборудование
Аппараты для сварки, кроме элементов крепления и крепления агрегата, имеют специальные дополнительные приспособления для сварки тем или иным способом (сварочные площадки и их крепления, приводы и т. Д.).).
Обычно в сварочном аппарате агрегат устанавливается в собранном и прихваточном состоянии, поэтому он должен обеспечивать возможность фиксации агрегата в положении, необходимом для сварки того или иного стыка, минимальные деформации и возможность свободного снятия готового Блок.
В сварочной практике очень распространено использование комбинированных сборочно-сварочных устройств, что позволяет выполнять сборку и сварку в одном приспособлении без прихватывания.
По типу продукции (конструкции, габаритам, весу), способу сварки и требованиям можно выделить ряд основных типов комбинированных сварочных и сборочно-сварочных аппаратов.
Сварочные стенды — это стационарные аппараты с одной неподвижной (чаще всего горизонтальной) базовой поверхностью с элементами крепления. Обычно на таких стендах продольные швы сваривают автоматической сваркой плавлением на плоских изделиях или на различных типах обечаек и т. Д. Сварка выполняется в основном на прокладках; кромки прижимаются к футеровке разными способами: механическим, пневматическим, магнитным и т. д.
Рисунок: 1. Пневматический сброс для сварки продольных швов: 1 — стойка, 2 — верхний зажим, 3 — приварная накладка, 4 — зажимной кронштейн, 5 — пневмоцилиндры, 6 — консоль
На рис.1 представлена схема стенда консольного типа с пневматическим зажимом футеровки для сварки продольных швов обечаек. На стойке консольно закреплена двутавровая балка с установленными на ней пневмоцилиндрами для прижима сварочной площадки. Свариваемую оболочку надевают на консоль и прижимают к верхним массивным фиксированным зажимам.
Верхние зажимы с консольной балкой скрепляются стяжным кронштейном. После сварки скобу отбрасывают назад, опускают сварочную площадку в нижнее положение и снимают оболочку.Консоль со сварочной подушкой и пневматическим зажимом может вращаться вокруг вертикальной оси на центральной стойке.
На рис. 2 представлена схема сварочного стенда с верхними пневмокабелями ключевого типа для сварки продольных швов на листах и оболочках из материалов малой толщины. Для сваривания изделий из более толстого материала клавиши могут нажиматься не пневмотрубным устройством, а пневмокамерами.
Рисунок: 2. Пневматическая гантель для сварки продольных швов
Кантователи — довольно распространенный вид устройств.Обычно это стационарные устройства, позволяющие закрепить свариваемую деталь и повернуть ее в нужное положение для сварки. Такие устройства чаще всего используются для сварки объемных изделий самых разнообразных форм, у которых швы расположены на противоположных сторонах.
Рисунок: 3. Схема кантователя цапфы
При производстве самолетов такие устройства используются для сварки различных силовых агрегатов, таких как балки, лонжероны и др.
Вращение продукта в приспособлении может быть ручным или механическим.Чаще всего используются вращатели цапфового типа. Собранное и прихватываемое изделие закрепляется в специальных зажимах, каждый из которых фиксируется на шкворне. Цепные опоры могут быть соединены общим основанием или быть независимыми друг от друга.
Аппараты для кольцевой сваркипозволяют устанавливать изделия в фиксированном положении и вращать их во время сварки с необходимой скоростью.
В зависимости от габаритов изделия, устройства этого типа чаще всего изготавливают с использованием концевых вращателей, роликовых опор или комбинированных.
Для изделий малых и средних габаритов обычно используются устройства с торцевыми вращателями, выполненные в виде двух опорных цапф-вращателей, один из которых, реже оба, приводные.
Рабочая часть ротатора (планшайба) выполняется съемной или специализированной для данного агрегата или группы агрегатов. На ротаторе установлены специальные приспособления для фиксации и крепления. Привод часто осуществляется от электродвигателя через редуктор с регулируемой скоростью вращения при сварке.Основание устройства сварено из профилированного проката; все элементы (передняя бабка, двигатель, привод и т. д.) прикручены к основанию на своих посадочных местах.
Рисунок: 4. Схемы устройств для сварки кольцевых швов
Для крупногабаритных изделий конического типа, изделий с малой продольной жесткостью или большим весом применяются устройства, в которых совмещены концевые вращатели и роликовые опоры.
Роликовые опоры делаются, как правило, регулируемыми по высоте или плавающими.
К поворотным устройствам также относятся устройства для сварки круговых швов на горизонтальной или наклонной плоскости … Обычно они выполняются в виде концевого вращателя с вертикальной или наклонной осью вращения.
Манипуляторы — это устройства, предназначенные для вращения продукта вокруг вертикальной или горизонтальной оси и наклона его под определенным углом, необходимым для работы.
Такие аппараты используются для ручной, полуавтоматической и автоматической сварки плавлением, а также для контактной сварки.
На манипуляторе можно закрепить изделия различной формы.В зависимости от грузоподъемности стол манипулятора вращается вручную, механически или пневматически.
Аппараты с копировальными аппаратами предназначены для автоматической сварки плавлением изделий с криволинейными швами. В зависимости от формы шва, типа изделия и способа сварки используются устройства с перемещением сварочной головки по копии, перемещением детали по копии с неподвижной головкой, перемещением как детали, так и головки по копии. ; в этом случае чаще всего сварочная головка устанавливается на плавающем подвесе.При использовании аппаратов последнего типа со сложным перемещением в процессе работы скорость сварки может изменяться, что влияет на формирование шва, поэтому при разработке такого устройства необходимо анализировать скорости в различных точках сварной контур. Отклонения от скорости сварки не должны быть более 4-5% от расчетной.
На рис. 5 представлена схема устройства для приварки фланцев, горловин, насадок к цилиндрическим оболочкам. В этом случае сварочная головка перемещается по трассеру на опорных роликах.Вращаясь, ролики катятся по поверхности копировального аппарата и поднимают или опускают стержень с подвешенной на нем сварочной головкой.
При сварке продольного шва криволинейного контура копировальный аппарат, выполненный в виде стыка, закрепляется на самом изделии (рис. 109). Изделие закреплено в приспособлении на шарнирах. При продольном перемещении сварочной тележки изделие поворачивается через стержень и копировальный аппарат в положение, заданное копировальным аппаратом.
Оборудование для автоматических методов сварки плавлением — это специальная сварочная установка, которая, помимо элементов для фиксации и манипулирования изделием, также приспособления для крепления, перемещения сварочного оборудования (сварочная головка, трактор и др.)) и управляя им. Дизайн этих устройств определяется типом продукта, количеством и характером. сварные швы и др.
Наиболее распространены устройства портального типа, консольного типа, устройства со смещенными направляющими, с установкой сварочного оборудования на прижимные элементы самого устройства и др.
Рисунок: 4. Сварочные манипуляторы: а — для сварки плавлением, б — для контактной сварки
Крепежные устройства могут быть выполнены отдельно от устройства или конструктивно связаны с ним.Обычно для относительно небольших изделий они выполняются в виде единой конструкции, для крупногабаритных изделий — раздельно. Устройства для фиксации оборудования могут быть подвижными и стационарными, с жестким креплением сварочной головки или с ее перемещением по фиксирующему устройству. Обычно такие устройства изготавливаются сварными из проката стандартной толщины или труб. Главное требование к ним — обеспечение необходимой жесткости и прочности в эксплуатации и возможность удобного манипулирования изделием и сварочным оборудованием в требуемых пределах.
Рисунок: 5. Схема установки для приварки арматуры на копировальном аппарате: 1 — копир, 2 — цапфа, 3 — деталь, 4 — сварочная головка, 5 — тяга, 6 — копировальный ролик
№Рисунок: 6. Установка для сварки по копии продольного криволинейного шва: 1 — сварочная головка. 2 — штанга, 3 — привод, 4 — копировальный аппарат, 5 — опорные копировальные ролики
Рисунок: 7. Типы сварочных установок для автоматической сварки плавлением: а — портального типа, б — консольного типа, в — со смещенными направляющими, г — с направляющими на пневматическом упоре
При контактной точечной и роликовой сварке специальные приспособления в основном используются для позиционирования, поддержки и выравнивания продукта во время процесса сварки.
Для сварки кольцевых швов в зависимости от габаритов изделия используются опорные устройства в виде опорной стойки с роликом, концевого вращателя или роликовых опор. Монтаж опорных элементов необходимо регулировать по высоте.
Устройства поддержки точечной сварки часто оснащены специальными шаговыми приводами для автоматов
.
Рисунок: 8. Устройство для точечной сварки обечаек с механизированным вращением изделия по этапу сварки: 1 — тележка, 2 — механизм поворота, 3 — торцевой вращатель, 4 — корпус, 5 — опорный ролик
перемещение продукта на шаг пунктов.В этом случае необходимо, чтобы при перемещении изделие не касалось внутренней поверхности нижнего электрода сварочного аппарата. Для этого, например, при сварке тонколистовых крупногабаритных деталей между ними и нижним электродом в свободном состоянии устанавливают зазор 1 — 3 мм.
При сварке жестких узлов для этой цели необходимо предусмотреть специальные демпфирующие устройства, которые в момент движения детали обеспечивают необходимый зазор.
Для небольших изделий опора часто прикрепляется непосредственно к сварочному аппарату.
На рис. 9 представлена схема устройства для сборки и прихватывания, закрепляемого зажимом 2 на нижней консоли сварочного аппарата. Свариваемый агрегат закреплен в приспособлении и может вращаться вокруг своей оси в подшипнике опорного диска. В свою очередь, опорный диск крепится к машине с помощью пружинно-рычажной подвески.
Для сварки крупногабаритных изделий плоской формы или небольшой кривизны (например, панелей) опорные устройства выполняются в виде подвесов или опор, например рольгангов.
Для точечной сварки в последние годы промышленность начала использовать специализированные установки с автоматическими и полуавтоматическими рабочими циклами.
На рис. 12 показан общий вид полуавтоматического манипулятора для точечной сварки крупных одиночных панелей
.
Рисунок: 9. Устройство для точечной сварки крупногабаритных изделий: 1 — указатель поворота, 2 — лента поворотно-шагового механизма. 3 — опорные ролики
или двойной кривизны. На этой установке возможно автоматическое выравнивание поверхности свариваемой панели по нормали относительно оси электродов.Устройство выполнено в двух вариантах: с механическим перемещением панели на сварочный шаг (команда дает оператор) и автоматическим. Для удобства наблюдения за местом сварки установка оснащена телеаппаратурой.
На рис. 13 изображена установка для точечной сварки полужесток панелей крылового отсека. Для сварки используются специальные плоскогубцы, которые входят во внутренние пространства отсека. Движение клещей к этапу сварки задается специальным шаговым приводным механизмом, с помощью которого подвижная каретка вместе с установленными на ней плоскогубцами перемещается по направляющим станины сварочного аппарата.
Рисунок: 10. Устройство для сварки конических секций, установленное на консоли сварочного аппарата: 1 — нижний ствол, 2 — зажим, 5 — пружина, 4 — рычаг; 6, 7 — опорные диски, 6 — шайба опорная, 8 — установочно-прихватывающее устройство, 9 — направляющее кольцо; 10 — съемный диск, 11 — деталь, 12 — зажимы, 13 — верхняя головка
Рисунок: 11. Установка. Для сварки панелей одинарной и двойной кривизны
Рисунок: 12. Автоматизированная установка для точечной сварки полуребер панелей крыла 1 — панель, 2 — рубильник, 3 — подвижный стол, 4 — сварочные клещи, 5 — сварочный аппарат, 6 — направляющие стола
Движение плоскогубцев по шву, сварка, обратное движение плоскогубцев и движение подвижного стола после завершения сварки очередного шва выполняются автоматически по специальной программе.После завершения сварки каждого ребра электроды очищают, а клещи возвращают в исходное положение.
При роликовой сварке в основном используются устройства, аналогичные разобранным. Однако в связи с тем, что при роликовой сварке детали перемещаются самим сварочным аппаратом и без подъема электродов, нет необходимости предусматривать в аппаратах специальные механизмы для принудительного перемещения и демпфирования, а они есть. вообще проще, чем точечные сварочные аппараты.
При роликовой сварке кольцевых или кольцевых швов чаще всего используются приспособления в виде различных регулируемых по высоте стоек с опорным роликом.Подобные устройства универсальны и просты. В некоторых случаях роликовую платформу можно заменить подвижной кареткой с опорными роликами. При этом передняя пара катков устанавливается чуть ниже задней. При сварке узел опирается на сварочный ролик и заднюю пару опорных роликов тележки.
Рисунок: 13. Опорное приспособление для роликовой сварки кольцевых швов обечаек
Рисунок: 14. Устройство подвесного типа для роликовой конической сварки
При сварке некоторых конструкций используются подвесные приспособления.На рис. 14 показан сварной роликовым сварным швом конус с использованием подвесного приспособления, в котором вершина конуса шарнирно подвешена на регулируемой по высоте опоре.
При сварке кожухов большого диаметра (более 1,5 — 2 м) иногда приходится поднимать сварочный аппарат или делать выемку ниже уровня пола, чтобы подвести сварочные ролики к стыкам. В этом случае иногда удобнее приваривать нижнюю часть оболочки, располагая ее над сварочными электродами.
При роликовой сварке швов на оболочке малого диаметра (меньше диаметра нижней консоли и станочного ролика) используются приспособления с внутренней токопроводящей оправкой.Оправка вставляется в оболочку и прокатывается с ней между сварочными роликами.
Для сварки плоских швов на панельных изделиях применяют аппараты, как при точечной сварке, в виде рольгангов или тележки с прикрепленным к ней изделием, перемещающейся по направляющим.
Рисунок: 5. Подвижная роликовая опора для сварки крупногабаритных корпусов
Опытные мастера и простые люди, выполняющие сварочные работы, знают, что подготовительный этап занимает не больше времени, чем сам процесс сварки.Значительная часть времени уходит на сборку сварочной конструкции и установку всех элементов в нужном месте.
Зная, насколько важны устройства для сварки фасонных труб, и зная, как правильно ими пользоваться, сварщик может быстро и эффективно выполнять поставленные перед ним задачи.
В быту используют большое количество механизмов и конструкций для сварки труб. Эти вспомогательные устройства обычно портативны и универсальны.
Они помогают быстро собрать конструкцию с надежно закрепленными деталями, а также позволяют выполнять работу практически без деформации.
Они делятся на следующие типы:
Установочные механизмы
Эти устройства позволяют установить профильные трубы в нужном положении.
Именно так они и будут располагаться в итоге. По функциональному и конструктивному решению они делятся на:
- Остановок.
- квадратов.
- Шаблоны.
- Призмы.
Постоянный … Они фиксируют заготовки на основной поверхности, могут использоваться постоянно, сниматься, есть откидные (служат для снятия и вращения).
Постоянные приспособления — это пластины, приваренные к основанию.
А съемные устройства используются в ситуациях, когда нельзя использовать устройство с постоянной установкой.
Уголок … С их помощью профильные трубы устанавливаются под заданным углом.
Призмы … Фиксируют заготовки цилиндрической формы в нужном положении.В качестве этого устройства используются очень простые конструкции, которые готовятся с углов.
Этот механизм помогает установить профильные трубы в нужном положении по отношению к уже стоящим частям будущей конструкции.
Крепеж
Такие приспособления для установки профильных труб под сварку позволяют надежно зафиксировать деталь и защитить ее от случайного смещения после остывания. К ним относятся:
- Зажимы.
- Прижимная.
- Стяжки.
- Распорки.
Зажим … Это универсальное устройство, которое можно использовать для всех видов работ с металлическими изделиями.
Мастера называют их самыми важными по значимости и говорят, что без них практически невозможно обойтись.
Зажим может быть разной формы и размера. Глотка аппарата может иметь стабильный объем, и его можно регулировать.
Особенно удобны быстрозажимные устройства, в которых кулачковый механизм выполняет зажимную функцию.
Зажимы. Если сравнить эти механизмы с фиксаторами, то они более удобны и более приспособлены к данному виду работ. Требуемый размер горловины устанавливается винтом в зажимной рукоятке и перемещением штифта.
Зажимы. Это самый распространенный. Это: клин, винт, пружина, рычаг.
Самая простая форма такого устройства — самый обычный болт и гайка, удерживающие две пластины, зажимающие заготовку.
Стяжки. Используются для объединения элементов, имеющих габаритные размеры. Длина и манера такой конструкции зависят от задач, которые она должна выполнять.
Распорка … Этот механизм дает возможность выровнять края собранных заготовок, придать им нужную форму и исправить мелкие дефекты.
Установщик и крепеж
Самые удобные конструкции, выполняющие несколько функций.При работе нужно только вставить детали и затянуть эксцентрики и винты. Все детали без дополнительных усилий помещаются в нужное место.
Большинству из нас очень часто приходится выполнять такую работу, как сварка фасонных труб. Поэтому для этого процесса было разработано большое количество различных устройств.
Центраторы. Благодаря им сохраняется ровность свариваемых деталей, а также совмещение краев на концах.Они делятся на внутренние и наружные.
Гораздо чаще используются внешние механизмы. Этот механизм состоит из нескольких звеньев, шарнирно соединенных между собой. Между собой они создают замкнутый контур.
Кроме того, соосность заготовок хорошо обеспечивают самодельные конструкции, которые изготавливаются из уголка и приваренных к нему зажимов.
Механизмы с магнитами
Эти приспособления для сварочных работ используются очень широко, они бывают самых разных форм.Соединяют листовые заготовки, каркасные конструкции и так далее в нужном месте.
Применяются такие устройства не только в форме квадрата, но и другого типа. Сила магнита в них позволяет надежно установить часть конструкции профиля в нужном месте, а в процессе сварки детали остаются неподвижными.
Сварочные приспособления своими руками: зажим
Сделать сварочные аппараты своими руками несложно.Многие мастера отдают предпочтение самодельным приспособлениям для работы, так как магазинные варианты недостаточно надежны.
Вам необходимо подготовить:
- Лист стальной толщиной от 9 до 11 мм.
- Три гайки.
- Шайба. Он нужен с большим диаметром.
- Трубная заготовка с наружной резьбой, соответствующей резьбе на гайке.
Процесс изготовления своими руками
Из стального листа вырезаются три полосы шириной 4 см и длиной 50 см, 25 см и 10 см.Затем готовятся еще две прямоугольные пластины для крепления подвижного элемента и для упора в неподвижную часть устройства.
Видео: фильм «Сделай сам» 1
Затем к основанию зажима приваривается вспомогательная. Все это вместе создает L-образную форму. Второй прямоугольный лист приваривается к меньшей стороне конструкции. Шайбы также свариваются.
Гайки размещаются «на краю» подвижной части таким образом, чтобы скрученный стержень был параллелен основанию зажима.
Видео: фильм «Сделай сам» 2
Сварка выполняется на внешней стороне первого прямоугольного листа. К его внутренним краям прикреплено подвижное устройство. В конце к краю стержня привариваются шайбы, ставятся плашмя.
Зажимы для шлангов Perfect Wire с простым инструментом DIY
Хомуты используются с тех пор, как мы используем гибкие шланги. Обычно хомут состоит из металлической планки с прорезями и винта для затяжки. Большинство из нас знает, как быстро они скользят, когда вы хотите добавить немного больше крутящего момента или разочарование из-за того, что у них нет нужного размера.К счастью [Макс Егоров] напомнил нам о зажимах для проволоки своими руками (видео после разрыва), отличной альтернативе, которая очень эффективна, охватывает бесконечный диапазон размеров и легко изготавливается с помощью простого инструмента.
Зажим для проволоки представляет собой сцепное устройство с двойным кольцом, которое плотно затягивается с загнутыми концами для сохранения натяжения. [Макс] показывает, как легко сделать свой собственный зажимной инструмент, используя основные инструменты и несколько кусочков стали. Делать его таким же богатым, как его, определенно не требуется. Вы также можете купить коммерческий инструмент, который продается под названием ClampTite, в котором используется конструкция с ходовым винтом.
Для достижения плотного уплотнения с помощью хомута для шланга главное требование — постоянное давление по всей его окружности. Эти проволочные зажимы очень хорошо справляются с этой задачей и популярны среди авиамехаников, поскольку полет на самолете с негерметичной охлаждающей жидкостью или топливным шлангом может немного сократить продолжительность вашей жизни. [Макс] также демонстрирует множество других способов их использования, включая фиксацию ручек инструментов и даже строительство лестницы.
Нам нравятся такие простые, но эффективные инструменты, и мы обязательно добавим их в наш набор инструментов.Вы использовали это раньше? Дайте нам знать об этом в комментариях!
(почти) никогда не бывает слишком много инструментов, и создание собственного очень приятно. Мы видели, как люди строили целую столярную мастерскую из фанеры и изготавливали листогибочный пресс без сварки.
Спасибо [Keith O] за подсказку!
Самодельные инструменты и приспособления | Блог пользователя jtbmetaldesigns
Большой легкий сварочный стол на дешевом
Если вам нужен сварочный стол хорошего размера, но вас не интересует вес или стоимость традиционного сверхмощного стола, тогда этот блог для вас.После того, как я прочитал хаб о сборке сварочного стола из каркасов кроватей и арматуры, у меня были каркасы кроватей, подаренные мне другом, несколько квадратных трубок, оставшихся от другого проекта стола, и я купил 20 футов 1/2 дюйма арматура в Home Depot. Я выбрал стол примерно 40 дюймов в высоту, 48 дюймов в длину и 28 дюймов в ширину.
Хорошо, поэтому я обрезал по размеру и разложил материалы, чтобы построить верх. Поскольку мне нужен был сварочный стол, было довольно сложно получить все идеально квадратные.Я сделал несколько ошибок, но все заработало.
Как видите, я мог бы попросить еще несколько ребер. Но пока это сработает. На фото выше я привариваю ножки. Я сделал все, что мог, чтобы они были квадратными, но несколько из них были расположены под углом примерно на полтора дюйма. Тем не менее, таблица функциональна и стабильна. Кроме того, я всегда могу внести изменения и дополнения позже.
Здесь вы можете видеть, что поверхность арматурного стержня имеет свои преимущества по сравнению с поверхностью твердого стального листа.Очевидная причина — вес. Такая конфигурация позволяет несколько переносить эту таблицу. Во-вторых, стержни могут служить местом для крепления сварочных зажимов и других инструментов, которые могут вам понадобиться. И последнее, но не менее важное: промежутки между арматурой можно использовать для закрепления заготовок для более надежного зажима при работе под труднодоступными углами. Если вы будете работать с более мелкими деталями, которые могут провалиться через арматуру, вы всегда можете положить более мелкие куски стальной пластины для поддержки.
Одна из моих любимых причин для этого конкретного дизайна — возможности хранения.При высоте 40 дюймов я могу разместить под столом множество аксессуаров, чтобы сделать хранение вещей в моем тесном сарае намного более эффективным.