какие основные типы и классификация сварочных технологий
Сварка — высокопроизводительный, экономически выгодный технологический процесс стыковки металлов, применяемый практически во всех сферах жизнедеятельности. Сказать однозначно какая бывает сварка затруднительно поскольку на сегодняшний день насчитывается более 50 разных способов, каждому из которых характерны определенные особенности и отличия.
Классификация способов сваривания
С помощью сварки создают самые разные по сложности металлоконструкции посредством соединения однородных и разнородных металлических сплавов между собой, а также с некоторыми видами неметаллических материалов, например, графитом, керамикой, стеклом, пластмассой.
Сущность процесса сваривания состоит в том, что вследствие воздействия электрической дуги расплавляется электрод, образуя при этом сварочную ванну. Расплавленный металл электрода смешивается с основным материалом, при этом на поверхность всплывают шлаки, выступая в качестве защитной пленки. После затвердевания металла образуются сварные соединения.
Учитывая сколько видов сварки существует, очень важно правильно выбрать способ, поскольку от этого зависит не только аккуратность и качество сварного соединения, но также стоимость работы.
Все виды сварки разделяются на три больших класса: термический, термомеханический, механический. В каждый из классов входят разные типы сварки, проводимые с помощью разного оборудования и образующие надежные и прочные стыки.
Термический класс
Сварочные работы этого класса выполняются посредством плавления кромок свариваемых друг с другом элементов. Сперва в месте стыковки возникает сварочная ванна и после ее отвода выполняется шовное соединение.
Виды термической сварки разделяются на несколько подклассов: газовая, термитная, электронно-лучевая, лазерная, плазменная, электрическая дуговая стыковка материалов.
Последняя разновидность считается самой распространенной. Она не требует применения специальных приспособлений и инструментария.
Дуговая сварка
Принцип электродугового метода основан на воздействии тепловой энергии, образуемой электрической дугой. Прежде чем приступать к свариванию необходимо тщательно очистить стыкуемые кромки от пыли, следов масла, ржавчины и других загрязнений.Дуговой технологический процесс считается наиболее простой и универсальной методикой. Она востребована при необходимости создать небольшие швы, а также при проведении монтажных работ, в том числе и в труднодоступных местах.
Существуют следующие виды сварки дуговым способом:
- ручная;
- электродная;
- в среде защитного газа;
- автоматическая под флюсом.
Для создания швов применяют плавящиеся и неплавящиеся электроды, переменный и постоянный ток. Для каждого металла технология подбирается индивидуально.
Газовая сварка
Это электродуговой способ, подразумевающий сваривание в защитной газовой активной или инертной среде. Различают две разновидности сварки: МИГ и МАГ, отличающиеся механическими характеристиками используемых материалов.
Свариванию материалов в газовой среде характерны следующие преимущества:
- отменное качество сварных соединений;
- возможность стыковки в разных пространственных положениях;
- легкость процесса за счет автоматизации и возможность наблюдать за образованием стыка.
В числе минусов отмечают необходимость использовать защитные меры, противостоящие тепловой и световой радиации дуги, а также вероятность нарушения газовой защиты в случаях сдувания струи.
Лучевой способ
Сварочный процесс происходит в вакууме, благодаря чему можно достичь безупречного качества соединительного шва. К заготовке передается мощный поток энергии, электроды вступают в реакцию с компонентами материала ускоряя процесс разогрева до температуры плавления.
Используются лучевые виды сварок в работе с микроэлементами, потому что здесь без осложнений можно отрегулировать луч до размеров микрона в диаметре.
Термитный способ
Уже из названия можно понять, что процесс сваривания осуществляется с применением термита — специального порошкообразного материала, основными составляющими которого являются соединения алюминия или магния, железной окалины.
Методика образует прочные швы и пользуется популярностью для стыковки рельсов, труб и для наплавки массивных деталей.
Электрошлаковая техника
В осуществлении сварочных работ относительно новый метод. Свариваемые элементы обволакиваются шлаком, предварительно разогретым до температуры, превышающей плавление проволоки и самого материала.
С помощью технологии в один проход можно заполнять большие разрывы. Образующаяся защитная ванна обеспечивает безупречное качество шва путем выдвигания на поверхность самых нестандартных металлических соединений.
Электрошлаковая методика подходит для выполнения самых сложных швов и создания крупногабаритных высокоточных деталей благодаря отсутствию трещин и пустот в соединениях.
Термомеханический класс сварки
Это комбинированные виды сварки металла, выполняемые с применением повышенной температуры и механических усилий. Как правило применяется способ для соединения малогабаритных деталей, которые стыковать обычными классическими методами невозможно.
Рабочий процесс выполняется с помощью электродов-губок, в которых одновременно крепится две части изделия. Основные виды сварки термомеханического класса — кузнечная, контактная и диффузионная.
Кузнечная техника
Выполняется с помощью ручных инструментов. Металл вначале раскаляется, потом дна на другую нахлестываются детали и сверху молотком наносятся удары.
Чтобы достичь максимально качественных соединений предварительно необходимо тщательно очистить заготовки от налетов и образовавшихся на поверхности окислений.
Данный способ подходит не для всех металлов. Весомым недостатком считается низкая производительность. Поэтому кузнечное дело активно вытесняют другие более современные и технологичные типы сварок.
Контактная сварка
Процесс сваривания выполняется следующим образом. Нагрев поверхности достигается за счет прилегания к изделию поверхности иглы. Металл подготавливается методом механического осадочного воздействия или сдавливания. Потом через инструмент с необходимым диаметром подается электрический ток.
Благодаря химическому воздействию атомов металла даже самые мелкие элементы можно сваривать с максимальной надежностью и прочностью.
Виды сварок металла контактной техникой разделяют на стыковые, роликовые и точечные. Такие способы активно применяются в машиностроении и других промышленных направлениях.
Диффузионный способ
Применяется для материалов с плохими контактирующими свойствами. Основан метод на процессе диффузии атомов при повышенном уровне вакуума. Верхний слой свариваемой поверхности нагревается до аналогичной плавлению температуры. Посредством усиленного механического воздействия осуществляется контакт и стыковка, при этом 20 Мпа должна составлять минимальная мощность сжатия.
Процесс стыковки происходит в специальной камере. Помещаемые в нее детали длительное время выдерживаются под воздействием электрического тока.
Механический класс
Классификация способов сварки включает еще одну разновидность — механическую состыковку материалов, выполняемую путем физического воздействия на них. В данном случае нет необходимости применять температуру плавления. Нагревание происходит при переходе механической энергии в кинетическую и при достижении момента плавления изделия соединяются прочными швами.
Механические классы сварки подразумевают применение нескольких эффективных технологий.
Способ трения
В большинстве случаев сваривание трением используется для стержневых конструкций и труб с небольшим диаметром. Процесс автоматизированный и происходит в специальных установках в шпиндель которых фиксируются рабочие заготовки. Движущуюся деталь машина перемещает к неподвижной, в результате элементы нагреваются и происходит оплавление.
Техника позволяет варить состоящие из разных сплавов металлы, быстро выполняет нужные задачи и отличается экономичностью.
Холодная сварка
Механическая сварка холодным видом востребована при необходимости состыковать трубы, проволоки или шины. Соединяются заготовки вследствие деформирования пластических материалов при воздействии давления от 1 до 3 Гпа. При этом температура может быть даже минусовой.
Свариваемые поверхности нужно хорошо очистить от загрязнений и ржавчины. Поскольку происходит стыковка на межатомном уровне, то соответственно поверхности элементов должны быть безупречно обработанными и идеально ровными.
Сварка взрывом
Соединение деталей этим способом происходит посредством пластической синхронной их деформации. К надежно закрепленной мишени параллельно прикладывается подвижная часть изделия. Далее выполняется максимально контролируемый взрыв.
Методика подходит для соединения разнородных металлов. В качестве взрывных веществ используются смеси аммонита, гранулотола и гексогена.
Ультразвуковая методика
Перечисляя входящие в механическую группу виды сварок металла следует также уделить внимание УЗ-технологии. В данном случае задействованы источники энергии, которые на выходе образуют ультразвуковые колебания.
Актуален способ при создании точечных и шовных соединений под механическим воздействием. Вследствие сухого трения оксидные пленки разрушаются, далее осуществляется сваривание в процессе чистого трения.
Важным плюсом здесь является то, что отпадает необходимость предварительно очищать поверхности, а это обеспечивает экономию временных затрат. К недостаткам относят высокую стоимость оборудования, а также мизерный диапазон толщины соединяемых материалов.
Особенности выбора подходящего вида и техники сварки
Классификация видов сварки настолько широка, что довольно часто специалисты (особенно начинающие) задаются вопросом — какие виды сварки существуют, с помощью которых даже непрофессионал смог бы осуществлять сваривание и получать при этом стыки безупречного качества.
Если перечислить все виды сварок не составит особых затруднений, то однозначно ответить какой из них самый лучший невозможно. Дело в том, что каждый среди тех какие виды сварки есть отличается техникой исполнения и используемым оборудованием. Также рассматривать необходимо и то, какими достоинствами и недостатками обладают конкретные виды сварок и их применение имеет четкое ограничение.
Аргоновая сварка
Сущность методики состоит в применении неплавящихся электродов. Преимуществами являются:
- идеальная фиксация тонких элементов;
- возможность контролировать глубину прогрева металла;
- намного меньше брызги от искр если сравнивать другие виды сварок, какие бывают и активно применяются;
- ровный, равномерный, красивый внешне шов, что особенно важно в случаях, где большое значение отводится эстетическим показателям готового изделия.
Недостатки:
- при ручном сваривании весьма низкая производительность;
- автоматическое соединение противопоказано для стыков с разной направленностью или слишком коротких;
- дорогостоящее оборудование.
Применяется сваривание аргоном при изготовлении металлоконструкций из алюминия, меди, титана, нержавеющей и легированной стали, сплавов цветных металлов.
Дуговая сварка
Достаточно распространенная классификация сварки, обладающая рядом положительных особенностей:
- возможность соединять детали в любых пространственных положениях;
- универсальность применения в местах с ограниченным доступом;
- рабочий процесс доступен на переменном и постоянном токе;
- невысокая стоимость.
Продолжением преимуществ выступают также и минусы:
- швы не отличаются желаемым качеством, на них присутствуют непровары и бугорки;
- весьма низкий КПД из-за высокого количества отходов;
- не подходит для состыковки тонких заготовок;
- низкие показатели производительности.
Применяют дуговую технику для изготовления лестниц, навесов, ограждений, стыковки труб, монтажа магистральных трубопроводов. Высокими эстетическими свойствами шов не отличается, но если выбирать какие виды сварки существуют для создания изделий из толстого металла, то одним из лучших способов считается дуговой.
Газопламенная техника
Сопоставляя современные виды сварки, которые подойдут для сваривания изготавливаемых из труб узлов и соединений, а также для монтажа трубопроводов среднего и малого диаметров, то здесь стоит отдать предпочтение газовому способу.
Очевидные преимущества:
- полная независимость от электропитания;
- удобность транспортировки оборудования из одного места в другое;
- отсутствие перегрева и прожогов металла;
- возможность создавать внутренние швы в трубах маленького диаметра.
Но есть у методики и некоторые недостатки. Это повышенные требования к профессионализму сварщика, достаточно большая площадь нагрева, низкие коэффициенты производительности.
Сваривание полуавтоматом
Технология аналогична дуговой, но здесь подача электрода происходит автоматически. В числе плюсов следует отметить:
- легкость и безопасность рабочего процесса;
- экономичность;
- отменная точность и хорошая производительность;
- ровность швов;
- возможность соединять детали от 2 до 30 мм толщиной.
Отрицательные моменты полуавтоматического способа:
- невозможность скорректировать стык во время рабочего процесса, поскольку увидеть его нельзя;
- если ток больше 200А, то расплавленный металл сильно разбрызгивается и необходимо удалять все окалины;
- применять полуавтомат можно только внутри помещений.
Что касается применения, то данная техника подходит для создания и монтажа металлических ограждений, лестниц, ворот, гаражей и других конструкций.
Чтобы выбрать наиболее подходящий для конкретных целей способ состыковки элементов необходимо знать какие бывают виды сварки, проводить аналогию каждого из них и только после тщательного анализа отдавать предпочтение конкретной технологии.
Интересное видео
это, их краткая характеристика, типы, давлением металлов, художественная, какие бывают, классификация способов работ – Виды сварки на Svarka.guru
Жизнь современного человека тесно связана с вещами, изготовленными с применением сварочных технологий. Речь идет не только о соединении металла, но и прочих материалов, которые можно соединить на молекулярном уровне. В статье будут рассмотрены основные виды сварки.
Понятие процесса
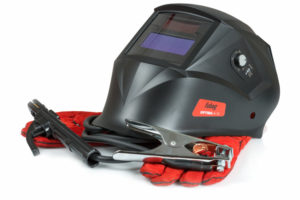
Физические признаки
Металлы отличаются высокой температурой плавления. Без дополнительных факторов площадь контактные части свариваемых изделий не будут взаимодействовать друг с другом. Для изменения агрегатного состояния металла требуется повысить его температуру. По достижению определенного уровня создаются условия, при которых появляется возможность выполнить стыковку деталей с получением крепкой межатомной связи между поверхностями.
Технологичность – главное свойство сварных работ
Применяемые типы сварки зависят от характеристик рабочих элементов, а также производственных условий. Наиболее употребительными являются следующие технологии:
Важность свойств
В процессе соединения заготовок необходимо обеспечить надежную защиту зоны температурного воздействия от агрессивного влияния кислорода в атмосфере. В противном случае в области обработки будут активно развиваться коррозионные процессы, ухудшающие качество конструкции. Основные способы предотвращения контакта расплава с воздухом:
- флюс;
- вакуум;
- защитные газы;
- пена.


Флюс можно вносить непосредственно в зону контакта, как при автоматической сварке. Дуговая технология подразумевает использование стержней с флюсовым материалом, который расплавляясь, защищает сварочную область.
Классификация
Классификацию сварки металлов осуществляют исходя из характера воздействия на плоскость:
- Термический класс. Характеризуется бесконтактным способом воздействия на поверхность – электрической дугой или пламенем газа.
- Термомеханический класс. Данный вид сварочных работ сочетает в себе бесконтактное воздействие, для достижения нужной температуры, а также механического давления для выполнения соединения.
- Механический класс. Заданные тепловые параметры получают исключительно за счет механического воздействия на соединяемые изделия.
Ниже будут рассмотрены виды сварок и их краткая характеристика, для каждого класса.
Термический класс
Сварочная дуга
Сварочная дуга – это источник тепловой энергии для расплава металла. Представляет собой электрический разряд, возникающий при разрыве цепи. В качестве питающего механизма применяются устройства, работающие на постоянном или переменном токе.
Электродуговая
Электродуговая технология – наиболее распространенный способ соединения металлических изделий. Своей популярностью обязан относительной простоте применяемого оборудования и низкой себестоимости выполнения работ. Известно несколько видов дуговой сварки.
Ручная дуговая
Работы выполняются электродами с флюсовым покрытием и аппарата для сварки. Метод получил свое название благодаря функциям, которые осуществляются сварщиком:
- Выбор направления движения стержня и его скорость.
- Длина дуги;
Под действием высокой температуры флюс расплавляется. Одни компоненты попадают в зону расплава, улучшая качественные характеристик, другие остаются на поверхности, образуя защитную пленку.
Неплавящимся электродом
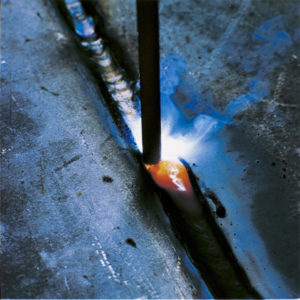
В качестве электродного материала используются тугоплавкие элементы: вольфрам или графит. Температура плавления базовой поверхности ниже, чем у электрода. Это обстоятельство увеличивает срок эксплуатации стержней. Допустимо использование присадочных металлов. Ввиду отсутствия флюса, работы ведутся в среде инертных газов.
Механизированная плавящимся электродом в среде защитного газа
Данный вид работ характеризуется применением особого присадочного материала – электродной проволоки, состав который зависит от свойств рабочей поверхности. Для подачи материала в зону сварки используют подающие механизмы. Они могут быть как одним из узлов агрегата, так и автономным оборудованием. Проволока не имеет защитного покрытия, поэтому соединение выполняют под защитой газа. При его отсутствии используют особый тип присадки – порошковую проволоку, которая содержит флюс для защиты шва. Для работы применяются аппараты, функционирующие в полуавтоматическом режиме.
Под флюсом
В этом случае на зону соединения вносят флюсовый состав, при плавлении которого возникает газовый пузырь, служащий барьером для вредных атмосферных факторов. Подчиняется требованиям ГОСТа 8713-89. На серийных производствах имеются установки, выполняющие сварку под флюсом в автоматическом режиме.
Электрошлаковая
Особенностью метода является система подачи тепловой энергии: ток проходит через флюс, нагревая его. Затем происходит плавление присадочного материала и заготовки. Способ незаменим при вертикальных соединениях с углублением, относительно основной плоскости.
Орбитальная
Метод промышленного стыкования поверхностей с круглым сечением, таких как трубы. Существует два способа реализации неразъемной связи. В первом случае заготовки вращаются вокруг своей оси. Под действие силы трения достигается рабочая температура. Во втором случае изделия зафиксированы, а вокруг них вращается подвижная головка аппарата для дуговой сварки. В этом случае используется электродная проволока.
Газопламенная
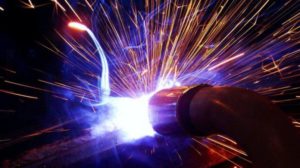
Технология характеризуется использованием тепловой энергии, образующейся при сгорании горючих газов и их смесей. В зависимости от массовой доли кислорода, определяется характер пламени. Оно может быть трех типов:
- окислительное;
- нейтральное;
- восстановительное.


Наиболее перспективным считают использование дециана. Препятствием к распространению является его токсичные свойства, однако рабочие параметры газа сопоставимы с технологией дуговой сварки, поэтому ученые активно ищут возможность устранения вредных факторов.
Плазменная
Рабочим инструментом является плазмотрон, генерирующий высокотемпературную плазменную дугу. В качестве механизма регулировки струи используют электромагнитные силы, увеличивая скорость ионов до необходимой величины. Помимо сварки, плазму используют наплавки, резки и напыления.
Электронно-лучевая
Высокотехнологичный метод, отличающийся принципом нагрева поверхности – для повышения температуры используется электронная пушка, которая создает поток электронов. Соединение элементов выполняют в условиях вакуумных камер.
Лазерная
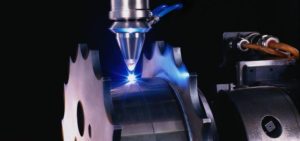
Стыковой метод соединения пластмасс оплавлением
Исходя из названия, для оплавления пластиковых изделий используется нагревательный элемент с покрытием из тефлона.
С закладными нагревателями
Еще один метод соединения полимеров. Нагрев осуществляется элементами сопротивления, которые устанавливают на соединительную муфту. После монтажа заготовки подается электрический ток, расплавляющий пластик.
Термомеханический класс сварки
Кузнечная
В качестве рабочего инструмента использовался кузнечный молот, деформирующий заготовки. Является самым старым способом выполнения соединения. В настоящее время практически не используется.
Контактная
Наиболее популярный способ данного класса. Рабочий цикл включает в себя два этапа. Первый – плавление поверхности до пластичного состояния. Второй – давление на нагретые элементы, которое может осуществляться как вручную, так и с помощью различных приводных механизмов. Подвидами контактной технологии являются.
Точечная
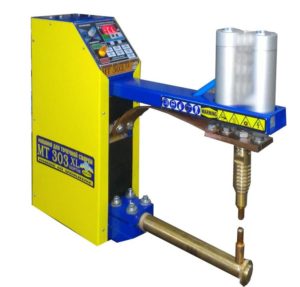
Популярная технология, которая может быть реализована в домашних условиях. Изделие помещают между двумя стержнями, выполняющими роль электродов. На них подается кратковременный импульсный заряд, нагревающий плоскость. Затем заготовка сжимается электродами, образуя межатомное соединение.
Стыковая
Основное отличие технологии заключается в ширине воздействия на поверхность. Соединение выполняется по всей плоскости касания. Существует два способа создания соединения:
- сопротивлением;
- непрерывным оплавлением.


Метод оплавления используется на промышленных предприятий. Его цель – автоматизация процесса сваривания различных металлических конструкций.
Рельефная
Метод характеризуется специфической подготовкой к свариванию. На контактные плоскости предварительно устанавливают возвышения, называемые рельефами. После выполнения стыковки по точкам на них подают электрический ток, который вызывает деформацию рельефов.
Диффузионная
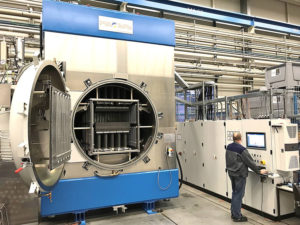
В основе технологии лежит явление диффузии – взаимного проникновения частиц друг в друга. При повышении температуры интенсивность движения атомов возрастает, создавая оптимальные условия для соединения деталей. Процесс протекает в условиях безвоздушного пространства или в среде защитных газов.
Высокочастотными токами
Металл плавится под влиянием токов высокой частоты. После кристаллизации обрабатываемой зоны образуется прочный сварной шов.


Существует способ соединения, не попадающий под классификацию способов сварки. Это соединение мягких тканей в медицинской практике, которое проводится путем воздействия высокочастотного тока на отдельные участки организма, нагревая их до 70 Сº.
Трением
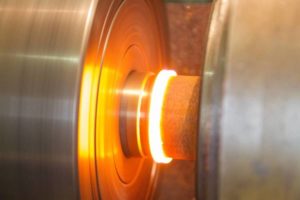
Основное преимущество данного способа сочленения – возможность работы с разнородными металлами. Согласно технологическим требованиям, одна заготовка должна быть надежно зафиксирована в специальном суппорте. Вторую раскручивают вокруг своей оси и под давлением стыкуют с первой. Тепловой энергии, которая выделяется за счет силы трения, достаточно для образования новых молекулярных связей.
Механический класс
Взрывом
Основной способ для получения биметаллических соединений. Для спекания заготовок используют тепловую энергию, которая освобождается при взрыве.
Ультразвуковая
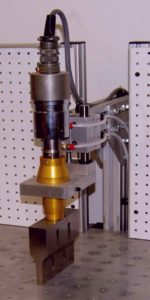
Данный способ использует ультразвуковые колебания для образования неразъемных связей между атомами. Уникальность технологии заключается в возможности сваривания различных материалов, начиная от металла, заканчивая кожей или стеклом.
Холодная
Уникальный метод сваривания материалов, который отличается низкой рабочей температурой, находящейся ниже уровня рекристаллизации структуры металла. Технологические требования заключаются в тщательной подготовки рабочей плоскости. Она должна быть очищена от чужеродных элементов. Непосредственно перед началом цикла производят обезжиривание поверхности.
Эту сварку давлением применяют для работы с материалами, чувствительными к температурным перепадам.
Международные обозначения
При выполнении работ на территории России, в строительстве и других отраслях промышленности, все сварочные процессы подчиняются требованиям ГОСТа Р ИСО 4063-2010. Это отечественный аналог международного стандарта ISO 4063:2009.
В искусстве
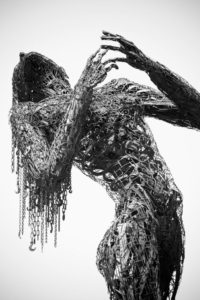
Художественная сварка – это недавно зародившееся направление в искусстве. Мастера, занимающегося созданием скульптурных композиций называют арт-сварщиком. В Москве, и других крупных городах, проходят многочисленные выставки, которые знакомят ценителей с новыми произведениями.
Можно с уверенностью утверждать, что художественной сваркой по металлу с каждым годом интересуется все больше людей.
Заключение
В статье было рассказано, какие бывают виды сварки: от электросварки до соединения ультразвуком.


Сварщик 6-го разряда Гресь Олег Станиславович Опыт работы 20 лет: «Месяц назад был на выставке сварочных композиций. Если честно, я был поражен – несмотря на то, что в описании указывалось, что работы выполнялись любителями, замысел и качество реализации были на высоте».
Основные виды сварки
Наиболее распространенными являются следующие виды сварки.
Механическая сварка.
Она же сварка взрывом. Выделение тепла происходит за счет трения между соединяемыми материалами. Трение происходит за счет взрыва, который сжимает соприкасающиеся поверхности деталей. Данный метод применяется для плакирования металлов инородным материалом. Например, сталь плакируется алюминием.
Термическая сварка.
Данный тип сварки включает в себя несколько разновидностей, которые мы сейчас и рассмотрим.
Электродуговая сварка.
Данный вид сварки наиболее часто используемый. Расплавление свариваемых материалов и/или деталей происходит за счет выделяемой электрической дугой теплоты. После застывания свариваемые поверхности образуют единое сварное соединение. Для данного типа сварки необходим сильноточный источник питания низкого напряжения. К его зажиму присоединяется сварочный электрод, к которому, в свою очередь, прикасается свариваемая деталь.
Основными «подвидами» электродуговой сварки являются: ручная дуговая сварка, сварка неплавящимся электродом, сварка плавящимся электродом, сварка под флюсом, электрошлаковая сварка.
Ручная дуговая сварка.
Является универсальным технологическим процессом. С её помощью можно производить сварочные работы в любом пространственном положении, из различных марок сталей, даже при отсутствии необходимого оборудования. Используется специальный покрытый флюсом электрод. Покрытие используется для защиты шва металла от внешних воздействий. Сварка проводится на постоянном токе прямой или обратной полярности и на переменном токе. Данный вид сварки применяется для выполнения коротких и криволинейных швов в труднодоступных местах, а также при монтажных работах.
Сварка неплавящимся электродом.
В качестве электрода используется стержень из графита или вольфрама. Температура плавления данных материалов выше температуры, при которой протекает сварочный процесс. Сварка чаще всего проводится в среде защитного газа (аргон, гелий, азот и их смесях) для защиты шва и электрода от влияния атмосферы. Сварку может проводить как без присадочного материала, так и с ним. В качестве присадочного материала используются металлические прутки, проволока, полосы.
Сварка плавящимся электродом.
В качестве электрода используется проволока (стальная, медная или алюминиевая), к которой через токопроводящий наконечник подводится ток. Электрическая дуга расплавляет проволоку, и для обеспечения её постоянной длины проволока подаётся автоматически механизмом подачи. Для защиты от атмосферы применяются защитные газы (аргон, гелий, углекислый газ и их смеси), подающиеся из сварочной головки вместе с электродной проволокой.
Сварка под флюсом.
В этом виде сварки конец электрода также представлен в виде металлической проволоки или стержня, на конец которой (-го) подается слой флюса. В качестве флюсов применяют прокаленную буру, борную кислоту, кремниевую кислоту и др. Флюсы используются в виде порошков, паст, водных растворов. Горение дуги происходит в газовом пузыре, находящемся между металлом и слоем флюса. Сама дуга при этом не видна. Благодаря этой технологии усиливается защита металла от вредного воздействия атмосферы и улучшается глубина проплавления металла.
Электрошлаковая сварка.
При электрошлаковой сварке в качестве электродов служат: электродная проволока, стержни, пластины. Источником теплоты является расплавленный шлак, через который протекает электрический ток. При этом теплота, выделяемая флюсом, расплавляет кромки свариваемых деталей и присадочную проволоку. Способ находит своё применение при сварке вертикальных швов толстостенных изделий. Электрошлаковую сварку используют в машиностроении для изготовления ковано-сварных и лито-сварных конструкций.
Плазменная сварка.
Источником теплоты является плазменная струя, получаемая при нагреве электрическим током электрода. Струя плазмы сжимается и ускоряется под действием электромагнитных сил, оказывая на свариваемое изделие как тепловое, так и газодинамическое воздействие. Теплом струи расплавляется основной металл около дуги, а также присадочный металл. Помимо сварки этот способ часто используется для наплавки, напыления и резки.
Электронно-лучевая сварка.
Источником теплоты является электронный луч. Луч получается за счёт термоэлектронной эмиссии с катода электронно-лучевой пушки. Данный вид сварки применяется в промышленных условиях в вакуумных камерах. Известна также технология сварки электронным лучом в атмосфере нормального давления, когда электронный луч покидает область вакуума непосредственно перед свариваемыми деталями. Кстати, подробный обзор этого типа сварки читайте тут.
Лазерная сварка.
Источником теплоты служит сфокусированный лазерный луч. Применяют твердотельные, газовые, жидкостные и полупроводниковые лазерные установки. Лазерный луч также используется для резки различных материалов. Основными достоинствами лазерной сварки являются: возможность вести процесс на больших скоростях, практически отсутствие деформаций изделия и узкий шов.
Газопламенная сварка.
Источником теплоты является газовый факел, образующийся при сгорании смеси кислорода и горючего газа. В качестве горючего газа могут быть использованы ацетилен, водород, пропан, бутан и их смеси. Тепло, выделяющееся при горении смеси кислорода и горючего газа, оплавляет свариваемые поверхности и присадочный материал с образованием сварочной ванны. Пламя может быть «окислительным» или «восстановительным», это регулируется количеством кислорода.
Термомеханическая сварка
Сварка происходит за счет нагревания свариваемых поверхностей. У этого вида сварки тоже имеются свои разновидности.
Контактная сварка.
При данном типе сварки изделия нагреваются и происходит их деформация, что обеспечивает их взаимное проникновение. Свариваемые детали зажимаются в сварочных клещах, и по электродам пускают ток высокого напряжения, который плавит детали. Затем ток отключают и сильно сжимают клещи, из-за чего металл кристаллизируется, образуя сварной шов.
Диффузионная сварка.
При диффузионной сварке соединяемые поверхности сдавливают и нагревают. Обычно этот процесс происходит в вакууме. В результате этого действия образуется сварочный шов. Данная технология весьма дорогостоящая и поэтому находит свое применение в основном в авиакосмической, электронной и инструментальной промышленности.
Кузнечная сварка.
Сваривание поверхностей происходит за счет ударов кованым молотом по раскаленным деталям. Данный тип сварки не надежен, малопроизводителен и пригоден для ограниченного числа сплавов. Кузнечная сварка на сегодняшний день практически нигде не используется.
Сварка высокочастотными токами.
Свариваемые изделия располагают вплотную друг к другу и разогревают за счет пропускания тока высокой частоты, затем детали сжимают. После этого полученному изделию необходимо остыть, и оно готово. Метод применяется в основном для изготовления труб и фасонных изделий из сортовой стали.
Какие виды сварки бывают писание и применение
Оглавление:
Итак, инверторная сварка,- что это? По сути, инверторная сварка является процессом, в котором используется схема, система или некий прибор, задача которого заключается в создании переменного напряжения при использовании источника постоянного тока.
Инверторная сварка
В общую схему такого сварочного аппарата включается сетевой фильтр, сетевой выпрямитель, частотный преобразователь, высокочастотный трансформатор, силовой выпрямитель и управляющая система.
Естественно, чтобы осуществлять сварку металлических конструкций, не достаточно только сварочного аппарата, потребуется пользоваться еще различными аксессуарами – маской, держателями и, естественно, электродами. Осуществление сварки без электродов просто невозможно. В процессе инверторной сварки пользуются тремя типами электродов – углеродистыми, легированными и высоколегированными.
Основные достоинства сварочных работ с использованием инверторного аппарата таковы:
- розжиг осуществляется легко и быстро, дуга горит устойчиво и обладает хорошей эластичностью;
- высокое качество сварного шва;
- невысокие энергетические затраты при работе;
- достаточно хороший КПД;
- перепады напряжения питания не сказываются на качественных параметрах сварочных соединений;
- данные аппараты легкие и мобильные.
Естественно, как и у любого процесса, у инверторной сварки имеются и свои минусы: сварочные аппараты инверторного типа, как и любые сложные электронные приборы, сильно подвержены влиянию воды, пыли и морозов. По этой причине, аппараты такого типа должны храниться в помещении, обеспечивающем требуемые параметры сухости и теплоты.
Еще одним важным моментом является уход за сварочным аппаратом, периодически будет требоваться открытие корпуса и продувка компонентов прибора при помощи сжатого воздуха.
Аргоновая сварка
Аргоновая сварка является одним из видов сварочных работ, позволяющих производить сваривание сложных и тугоплавких металлов. При помощи этого метода сварки, часто варят алюминий и другие металлы, у которых происходит процесс окисления взаимодействия с воздухом.
Аргоновую сварку чаще всего применяют в такой отрасли как автомобильная промышленность, во время ремонта различных узлов автомобиля, сделанных из алюминия. Кроме этого, аргоновую сварку используют в металлургической отрасли, к примеру, чтобы осуществлять горячую обработку титана, тантала, ниобия, бериллия, циркония, гафния, вольфрама, урана, тория и чтобы обрабатывать щелочные металлы.
Применение аргона как газа – достаточно распространенная практика, к примеру, электрические лампочки тоже его содержат.
Аргоновая сварка — это достаточно сложный процесс, для осуществления которого требуется высокая квалификация и современное оборудование. Однако, и результат данного процесса на уровне – швы получаются ровными, бывает, что почти незаметные, и в то время очень прочные.
Аргонно-дуговую сварку осуществляют, применяя для этого вольфрамовые электроды и керамическое сопло. Именно по этому соплу на место сварки и поставляется аргон, которые не дает металлу вступить в контакт с атмосферой. А это в свою очередь препятствует окислению металла и обеспечивает выполнение прочного сварного шва.
Аргоновую сварку можно разделить на два вида: на ручную сварку и автоматическую.
Так чем же хороша аргонно-дуговая резка и сварка металлических конструкций? Для начала, стоит отметить, что в связи с тем, что при данном процессе используется современное оборудование, время работы значительно уменьшается. Помимо этого, аргоновая струя в процессе сварочных работ кроме защиты металла от влияния воздуха еще и сдувает все лишнее и не нужное.
Ну и последнее, но самое главное, данный вид сварочных работ является очень экономичным. Это связано с тем, что при помощи аргона электрическая дуга сжимается и концентрируется в узкой области. По этой причине, имея сравнительно небольшие затраты электроэнергии, можно добить температуры зоны резки порядка 4000…6000°C.
Аргонно-дуговая сварка
Если вам потребовалось сварить стальную конструкцию, то вы, недолго думая, возьмете в руки сварочный аппарат и без труда справитесь с этой задачей. Но что делать, если сварочные работы требуется произвести, к примеру, для алюминиевой конструкции? Тут-то вам и поможет аргонно-дуговая сварка.
Аргонодуговая сварка является сваркой при помощи электрической дуги в инертной аргоновой среде. Для данной сварки могут использовать плавящиеся или неплавящиеся электроды. Как неплавящимся электродом, чаще всего пользуются вольфрамовым электродом.
Горение дуги происходит от свариваемого изделия до неплавящегося электрода (как уже говорилось, скорее всего, вольфрамового). Крепеж электрода производиться к горелке, по соплу которой производиться подача защитного газа. Подача присадочного материала производиться к зоне дуги из вне, в электрической цепи не включается.
Аргоновый сварку могут производить в ручном режиме, когда управление горелкой и присадочным прутком производит сварщик, и в автоматическом режиме, когда перемещение горелки и присадочной проволоки производиться без помощи рабочего.
При сварке неплавящимся электродом, в отличие от сваривания при помощи плавящегося электрода, во время розжига дуги электрод не прикасается к изделию по таким причинам. Для начала, у аргона имеется высокий потенциал ионизации, по этой причине ионизация дугового промежутка при помощи искры от электрода к изделию – это достаточно сложная задача.
Для случая с аргоновой сваркой при помощи плавящегося электрода после касания проволокой детали, зона дуги насыщается парами металла, которые обладают потенциалом ионизации почти в три раза ниже, чем имеет аргон, в результате чего разжигается дуга.
Кроме этого, если произойдет касание детали и вольфрамового электрода, будут происходить такие вещи как загрязнение и интенсивное оплавление. По этой причине во время аргоновой сварки с использованием неплавящегося электрода, чтобы разжечь дугу к сети источника питания параллельно подключают прибор, который называется «осциллятором».
При помощи осциллятора, чтобы зажечь дугу к электроду производиться подача высокочастотных высоковольтных импульсов, ионизирующих дуговое пространство и обеспечивающих розжиг дуги, когда включается сварочный ток. Если аргоновую сварку производят с переменным током, когда дуга разожжена, осциллятор начинает работать как стабилизатор, подающий импульсы к дуге, когда сменяется полярность.
Это нужно для предотвращения деионизации дугового пространства и обеспечения устойчивого горения дуги.
Во время сварки с постоянным током, анод и катод выделяют разное тепло. Когда токи меньше 300 А, анод выделяет больше тепла чем катод, 70 на 30 в процентном соотношении, по этой причине обычно используют прямую полярность, для обеспечения максимального проплавления детали и минимального разогрева электрода.
При сварке всех сталей, титана и других материалов, кроме алюминия, используется прямая полярность. При сварке алюминия используется переменный ток, чтобы улучшить разрушение оксидной пленки.
Аргон иногда смешивают с 3–5% кислорода, для уменьшения пористости. Это становиться причиной более активной защиты металла. Аргон в чистом виде производит защиту металла от таких явлений как влага или другие включения, попавшие в сварочную зону. А при помощи кислорода осуществляется выгорание вредных примесей, или их выделение наружу. А это помогает бороться с пористостью.
Сварочный полуавтомат без газа
Если вы решили купить сварочный полуавтомат без газа, то, скорее всего вы уже столкнулись с огромным множеством различных вариантов, представленных на рынке. Давайте же попробуем разобраться в том, как должен выглядеть этот прибор в общем виде.
Сварочный аппарат должен быть недорогим и мощным. Лучше всего чтобы он работал полуавтоматически, от постоянного тока с использование плавящейся проволоки. Желательно, чтобы в автомате, кроме режима работы без газа на флюсовой проволоке, была еще реализована возможность работы на газу (на углекислом газе и на аргоне).
Немаловажный фактором является и выбор компании производителя. Изготовитель выбранного вами аппарата должен находиться в числе лидеров в таких сферах как промышленное и бытовое производство оборудования для сварочных работ. Данная компания должна быть официально представлена на рынке вашей страны, и обладать всеми сертификатами качества и безопасности, а так же иметь сервисные центы обслуживания.
Подача проволоки должна регулироваться плавно. Должна быть возможность реализовать ступенчатую регулировку мощности сварочных токов от 50 до 140 А. В аппарат должна помещаться даже 5-тикилограмовая катушка проволоки. Устройство должно быть снабжено тепловой защитой и принудительным воздушным охлаждением. В автомате должна быть реализована возможность работы с питанием от слабых сетей.
Обмотка в трансформаторе аппарата должна быть выполнена из меди. Устройство должно быть многофункциональным, кроме использования в быту, аппарат должен осилить и производственные потребности (к примеру, ремонтная мастерская и СТО). Хорошо, если аппарат будет снабжаться колесиками, для удобства транспортировки.
Ну и последнее, и самое главное, при выборе сварочного полуавтомата без газа, зайдите в интернет и внимательно изучите отзывы о данном аппарате людей, которые им пользовались, и которым есть с чем сравнивать.
Виды сварок
Сварочные работы по металлу – один из самых надежных способов соединения деталей и конструкций. Как технологический процесс сварка известна практически со времен, когда человек научился выплавлять металлы из руды и соединять части самородков драгоценных металлов. Если сделать краткий экскурс в историю, то виды сварки по хронологии будет размещены так:
• соединение способом промежуточного литья;
• кузнечно-горновая сварка;
• контактная (стыковая) сварка – 1856 г., лорд Кельвин;
• ручная электродуговая сварка – 1882 г., российский изобретатель Н.Бернардос;
• электрическая дуговая сварка – 1890 г., российский ученый Н. Славянов;
• сварка флюсом – 1929 г. советский ученый Д.Дульчевский;
• остальные современные способы: порошковыми материалами, электрошлаковая, контактная, плазменная, сварка под водой – почти все были изобретены и внедрены в Институте электросварки им. Е.О.Патона.
Самые востребованные виды сварки
Компания Азмен специализируется на предоставлении услуг по обработке металла — все виды сварки на заказ. Наша компания располагает всем необходимым современным оборудованием и специалистами самой высокой квалификации в этой области. В зависимости от требований, которые выдвигаются параметрами сварочных швов и типа материалов для соединения, мы выбираем наиболее эффективный из существующих видов сварки.
Сварка электрической дугой
Это самый распространенный способ соединения металлов и применяется в двух видах: ручной режим и на сварочных автоматах. Принцип действия основан на свойствах электрической дуги с очень высокой температурой, которая возникает при прохождении электрического тока через электроды и свариваемую поверхность вследствие существующей разности потенциалов. Электрическая дуга сильно нагревает поверхность металла и соединяет его сварочным швом. При этом образуется окалина, которую и последствии обивают, а шов шлифуют.
Заказать сварку электрической дугой Вы можете в нашей компании по доступной цене.
Сферы применения: выполнение коротких и криволинейных швов различной сложности, в труднодоступных местах, например, при изготовлении металлоконструкций и каркасов для строительства и промышленности, соединение закладных деталей, сварка трубопроводов и пр.
Газовая сварка
Выполняется с использованием обогащенной кислородной смеси в среде горючих газов (ацетилен – чаще всего, водород, метан, пропан). Этот способ больше подходит для сварки деталей из цветных металлов, тонкостенных деталей и легкоплавких марок стали, так как газовая сварка позволяет легко регулировать температуру горения, а значит, и нагрева свариваемых поверхностей.
Сферы применения: чаще всего этот тип сварки применяют в бытовых нуждах, для ремонта автомобилей, резервуаров и инженерных сетей из цветных металлов и стали толщиной до 3 мм.
Электрошлаковая сварка
По сути, это один из видов электродуговой сварки, но в процессе работы металлы соединяются в образующейся сварной ванне. Это дает более широкое поле для соединения и позволяется проваривать даже толстые заготовки и детали.
Сфера применения: целесообразно применять для заготовок толщиной больше 40 мм. Этот способ — самый эффективный для деталей свыше 100 мм толщиной. Кстати, рекордная толщина свариваемых электрошлаковой сваркой изделий – 2600 мм.
Сварка под флюсом
Усовершенствованной разновидностью электрошлакового способа является сварка под флюсом, то есть, когда расплавление конца электрода и свариваемых поверхностей происходит под слоем гранулированного флюса, который от нагревания дугой образует газовый пузырь, в котором образуется сварной шов. По мере остывания флюс образует сварную корку, которая легко отделяется от шва. Сварка под флюсом бывает автоматической и полуавтоматической. В сравнении с обычной электродуговой сваркой этот вариант имеет намного большую производительность – в 5-10 раз, а благодаря повышенным температурам в области сваривания резко увеличивается глубина проплавления металла. Еще одним огромным плюсом можно назвать высокую экономичность – потери материалов уменьшаются на 5-15% (за счет полного отсутствия разбрызгивания), а экономия электроэнергии – до 30-40%.
Сфера применения: в виду того, что этот способ возможно выполнять только в цеховых условиях, его применяют в массовых производствах для соединения деталей с прямолинейными и кольцевыми швами большой длины на деталях с достаточной толщиной. Пример – сваривание труб большого диаметра, изготовление балок для кранов, в кораблестроении.
Контактная сварка
Еще ее называют точечной сваркой, осуществляется путем нагревания током металла до размягчения и далее под действием усилия осуществляется соединение частей точками. Скорость этого процесса очень высокая – до 600 точек в минуту.
Сфера применения. Используется для сваривания очень тонких деталей (от 0,01 мкм), а также, для листов стали толщиной не больше 20 мм. Находит применение в изготовлении электроники, авиационной промышленности и судостроении, машиностроении.
Сварка неплавящимся электродом
Суть этого способа соединения в том, что процесс сваривания осуществляется в среде инертного газа, который защищает неплавящийся электрод и металл от кислорода в воздухе. Инертный газ подается через специальное сопло, а его вид выбирается в зависимости от материала электрода:
• для вольфрамового электрода применяется аргон, гелий, или их смесь;
• для медных электродов и со вставками гафния или циркония берут азот;
• для графитовых электродов со вставками тугоплавких металлов также применяют аргон.
Сфера применения. Этим способом можно отлично соединять все виды стали, цветные металлы, а также, разнородные сплавы металлов. Неплавящимся электродом лучше всех других способов сваривать тонколистовой металл – швы практически незаметны.
Плазменная сварка
Такой способ – это проведение работ в среде ионизированного газа, а специальная методика сжатия электрической дуги в плазмотроне позволяет достигать очень высоких температур – до 30 тысяч градусов (против 5-7 тысяч в парах аргона, например). Благодаря этому происходит более глубокое проплавление металла. А шов получается очень тонкий и аккуратный.
Сфера применения. Соединение деталей из самых различных сплавов, в том числе очень тугоплавких, в изготовлении толстостенных деталей, габаритный конструкций.
Мы предлагаем сварочные работы всех видов на заказ в Москве.
Сохранить
Поделитесь информацией
Сварочные технологии: виды и способы сварки
Сварка — одно из важнейших ремесел для человека. С помощью сварочных технологий нам удается создавать по-настоящему удивительные вещи: от простейших бытовых приборов до космических ракет. В этой статье мы расскажем, как происходит сварка, какие существуют виды сварки и их краткая характеристика.


Содержание статьи
Общая информация
Что такое сварка? Каковы основы сварки? Эти вопросы задаю многие начинающие умельцы. По сути своей, сварка — это процесс соединения разных металлов. Соединение (его также называют швом) формируется на межатомном уровне с помощью нагрева или механической деформации.
Теория сварки металлов очень обширна и невозможно в рамках одной статьи описать все нюансы. Также как невозможно описать все способы сварки металлов, поскольку на данный момент способов около сотни. Но мы постараемся кратко классифицировать методы сварки, чтобы новички не запутались.
Итак, на данный момент возможна термическая, термомеханическая и полностью механическая сварка деталей из металла или других материалов (например, пластика или стекла). При выборе способа сварки учитывается каждый нюанс: толщина деталей, их состав, условия работы и прочее. От этого зависит технология сварки металла.


Термическая сварка — это процесс соединения деталей только с помощью высоких температур. Металл плавится, образуется надежное сварное соединение. К термическим методам относится, например, дуговая и газовая сварка (о них мы поговорим позже).
Термомеханическая сварка — это процесс соединения деталей с помощью высоких температур и механического воздействия, например, давления. К такому типу принадлежит контактная сварка. Деталь нагревается не так сильно, как в случае обычной термической сварки, а для формирования шва используется механическая нагрузка, а не плавление металла как такового.
Механическая сварка — процесс соединения деталей без применения высоких температур и вообще тепловой энергии. Здесь ключевой элемент — механическое воздействие. К такому типу относится холодная сварка, ультразвуковая сварка или соединение деталей трением.
Также существует классификация способов сварки по техническим признакам. Используя такую классификацию можно довольно кратко описать все имеющиеся типы сварки. Они делятся на:
- Сварку в защитной среде (для защиты может использоваться флюс, инертный газ, активный газ, вакуум, защита может быть комбинированной и состоять из нескольких материалов сразу).
- Сварку прерывистую и непрерывную.
- Сварку ручную, механизированную, полуавтоматическую, автоматическую, роботизированную.
Если вы ранее не сталкивались со сваркой и все перечисленное выше кажется чем-то запутанным и непонятным, то не беспокойтесь. Далее мы расскажем, какие самые популярные методы сварки используются в домашних и промышленных условиях.
Вам будем дана характеристика основных видов сварки и некоторые особенности, которые нужно учесть. Кстати, многим видам сварки мы посвящали отдельные статьи, которые вы можете прочесть, открыв рубрику «Виды и способы сварки» на нашем сайте.
Ручная дуговая сварка с применением неплавящихся электродов
Способ ручной дуговой сварки разных металлов с применением неплавящихся электродов — один из самых популярных методов как среди домашних умельцев, так и среди профессионалов своего дела. Ручная дуговая сварка — это вообще один из древнейших способов сварки. Благодаря большому выбору сварочных аппаратов для дуговой сварки такой метод стал доступен широкому кругу сварщиков.
Электрод — это стержень, выполняющий роль проводника тока. Он может быть изготовлен из различных материалов и иметь специальное покрытие.


Технология дуговой сварки неплавящимся электродом крайне проста: детали подгоняют друг к другу, затем электродом постукивают или чиркают о поверхность металла, зажигая сварочную дугу. В качестве основного оборудования используют сварочные инверторы.
Для сварки инвертором выбирают неплавящиеся электроды, сделанные из угля, вольфрама или графита. Во время сварки электрод нагревается до высокой температуры, плавя металл и образуя сварочную ванну, в которой как раз и формируется шов. Такой метод используют для сварки цветных металлов.
Ручная дуговая сварка с применением плавящихся электродов
Виды сварки плавлением металла не заканчиваются на применении неплавящихся стержней. Для работы также можно использовать плавящиеся электроды. Технология сварки металла с использованием плавящихся стержней такая же, что и при работе с неплавящимися материалами.


Отличие лишь в составе самого электрода: плавящиеся стержни обычно изготавливаются из легкоплавких металлов. Такие стержни также пригодны для сварки инвертором в домашних условиях. Здесь шов образуется не только за счет расплавленного металла детали, но и за счет расплавленного электрода.
Дуговая сварка с использованием защитного газа
Способ дуговой сварки разных металлов с использованием защитного газа выполняется с помощью плавящихся и неплавящихся электродов. Технология сварки такая же, как и при классической ручной дуговой сварке. Но здесь для дополнительной защиты сварочной ванны в зону сварки подается специальный защитный газ, поставляемый в баллонах.


Дело в том, что сварочная ванна легко подвержена негативному влиянию кислорода и под его воздействием шов может окислиться и получиться некачественным. Газ как раз и помогает избежать этих проблем. При его подаче в сварочную зону образуется плотное газовое облако, не дающее кислороду проникнуть в сварочную ванну.
Автоматическая и полуавтоматическая сварка с использованием флюса или газа
Автоматическая и полуавтоматическая сварка с применением флюса или газа — это уже более продвинутый способ соединения металлов. Здесь часть работ механизирована, например, подача электрода в сварочную зону. Это значит, что сварщик подает стержень не с помощью рук, а с помощью специального механизма.
Автоматическая сварка подразумевает механизированную подачу и дальнейшее движение электрода, а полуавтоматическая подразумевает только механизированную подачу. Дальнейшее движение электрода сварщик осуществляет вручную.


Здесь защита сварочной ванны от кислорода просто обязательна, поэтому используется газ (по аналогии с дуговой сваркой с применением газов) или специальный флюс. Флюс может быть жидким, пастообразным или кристаллическим. С помощью флюса можно значительно улучшить качество шва.
Прочие методы соединения металлов
Помимо традиционных способов сварки в современной промышленности применяются методы, позволяющие соединить уникальные металлы. Зачастую такие металлы обладают ярко выраженными химическими или тугоплавкими свойствами, отчего привычные способы сварки не подходят для их соединения. Конечно, такие металлы не используются в домашней сварке, но они широко применяются для создания ответственных деталей на крупном производстве.
Мы расскажем про виды сварки плавлением, когда суть сварки заключается в подаче большого количества тепла на маленький участок сварки. К таким методам относится лазерная сварка и плазменная сварка.
Лазерная сварка металлов выполняется с помощью автоматического и полуавтоматического оборудования. Такой процесс сварки может быть полностью роботизирован и не требует присутствия человека. Здесь деталь нагревается, а затем и плавится под воздействием тепла, исходящего от лазерного луча и направленного в определенную точку.
Тепло концентрируется строго в одной точке, позволяя сваривать очень мелкие детали размером менее одного миллиметра. Также с помощью призмы лазер можно расщепить и направиться в разные стороны, чтобы сварить несколько деталей сразу.
Плазменная сварка металлов выполняется с применением ионизированного газа, называемого плазмой. Газ струёй подается в сварочную зону, образовывая плазму. Она работает в связке с вольфрамовым электродом и газ нагревается за счет электрической дуги.
Сам ионизированный газ обладает свойством проводника тока, поэтому в случае плазменной сварки именно плазма является ключевым элементом в рабочем процессе. Также плазма активно защищает сварочную ванну от негативного влияния кислорода. Такой метод сварки используется при работе с металлами, толщиной до 9 миллиметров.
Технологический процесс сварки
Мало знать способы сварки, нужно еще понимать, какие необходимы документы на сварку и из каких этапов состоит сварочный процесс. Конечно, это справедливо только в отношении профессиональных сварщиков, выполняющих работу в цеху или на производстве. Вам это не нужно, если вы собираетесь варить забор на даче, но дополнительные знания тоже не помешают.
Итак, вот наше краткое описание технологического процесса сварки:
- Разработка чертежа
- Составление технологической карты
- Подготовка рабочего места сварщика и подготовка металла
- Непосредственно сварка
- Очистка металла
- Контроль качества
Сам по себе техпроцесс — это полное описание этапов сварки. Технический процесс разрабатывается после того, как будут готовы чертежи будущей металлоконструкции. Чертеж делают, опираясь на правила (ГОСТы, например), при этом во главу ставят качество будущей конструкции и разумную экономию.
Технологический процесс сварки оформляется на специально разработанных для этого бланках. Стандартный бланк для описания техпроцесса называется «технологическая карта». В технологической карте и описываются все этапы производства. Если производство серийное или крупномасштабное, то изложение может быть довольно подробным, с описанием каждого нюанса.


В технологическую карту заносят тип металла, из которого изготовлены детали, способы сварки металлов, используемые для соединения этих деталей, применяемое для этих целей сварочное или иное оборудование, типы присадочных материалов, электродов, газов или флюсов, используемых в работе. Также указывается последовательность формирования швов, их размеры и прочие характеристики.
Также в технологической карте указывают марку электродов, их диаметр, скорость их подачи, скорость сварки, количество слоев у шва, рекомендуемые настройки сварочного аппарата (параметр полярности и величины сварочного тока), указывают марку флюса. Перед самой сваркой детали тщательно подготавливают, очищая их от коррозии, загрязнений и масла. Поверхность металла обезжиривают с помощью растворителя. Если у детали есть значительные видимые дефекты (например, трещины), то она не допускается к сварке.
После сварки предстоит контроль сварочных швов. Этой теме мы посвятили отдельную статью, но здесь кратко расскажем об основных методах контроля. Прежде всего, применяется визуальный контроль, когда сварщик может сам определить наличие дефектов у сварочного соединения. Специалистами проводится дополнительный контроль с помощью специальных приборов (это может быть магнитный контроль, радиационный или ультразвуковой).
Конечно, не все дефекты считаются плохими. Для каждых сварочных работ составляется перечень с дефектами, которые допустимы и не сильно повлияют на качество готового изделия. Контролером может быть сварщик или отдельный специалист. Его имя обязательно указывается в документах, он является ответственным лицом на этапе контроля.
Вместо заключения
В этой статье мы рассказали самое основное. Конечно, мы не сможем перечислить и описать все виды сварочных работ в рамках одной этой статьи, но на нашем сайте вы можете найти материалы, где мы рассказываем все о сварке и объясняем основы сварки различных металлов.
Для любого мастера теория сварочных процессов имеет большое значения, но без практики она не работает. Так что не теряйте время и вслед за чтением статей применяйте знания на практике. Желаем удачи в работе!
[Всего голосов: 1 Средний: 5/5]Виды и назначение сварки
Сварка является одним из самых распространенных технологических процессов обработки металлов и служит для неразъемного соединения металлов путем нагревания сварных швов до жидкого или пластического состояния.
Сущность сварки в сближении частиц металлов на расстояние, близкое к расстоянию между молекулами, что обеспечивает большую прочность сварочного соединения. В современном обществе трудно назвать такую область обработки металла, где не применялась бы сварка. Это и кино- и радиоаппаратура, точное приборостроение, строительство каркасов зданий, морских судов, газопроводов, машиностроение, особенно актуальная в последнее время сварка металлоконструкций: металлические заборы и ворота, решетки на окна и другие элементы архитектурных форм в городе, отвечающие за благоустройство.
Сварка даёт возможность замены тяжелых и трудоемких работ на более простые и легкие. За счет чего экономится металл, сокращаются сроки работ, снижается себестоимость изготовления конструкций. Сварные соединения прочны и надежны, что имеет большое значение в производстве различных сосудов, где хранятся и перевозятся жидкости и сжиженные газы, для котлов отопления и т.п.
Огромное значение сварки обуславливается тем, что такие способы как электродуговая, контактная, электрошлаковая и другие, автоматизированы и механизированы, что позволяет получать сложные сварные конструкции при высоких техническо-экономических показателях. Достижения в технологии, удобная аппаратура плюс высокая производительность сварочных процессов обеспечивают сварке всё более широкое применение в различных областях производства, строительства и ремонта.
При выборе вида сварки необходимо учитывать способность металла к образованию прочного соединения. Хорошо свариваются металлы с высокой теплопроводностью, взаимной растворимостью, низким коэффициентом линейного расширения и небольшой усадкой.
Способы сварки
Кузнечная сварка.
Металл при этом виде сварки нагревают в кузнечном горне или в специализированной печи. Для получения прочного шва, нужно чтобы в местах соединения металл прогревался полностью.
Контактная электросварка или сварка электросопротивлением, основана на быстром нагреве зоны контакта свариваемых металлов путем пропускания через них тока большой силы и малого напряжения.
При электродуговой сварке места сварки и присадочный материал расплавляются жаром электрической дуги. Расплавленные электродный и основной материал смешиваются в сварочной ванне и при движении дуги вдоль свариваемых кромок быстро твердеет, образуя, сварочный шов.
При газовой сварке места соединения металлов и присадка плавятся за счет сгорания горючих газов, которые, смешиваясь с кислородом, дают высокую температуру пламени (около 3000 градусов по Цельсию). Обычно горючим газом служит ацетилен. Газорезку используют для разделения на части рельсов, сортового проката, материала большой толщины, а так же для вырезания из толстого листа деталей сложной конфигурации.
Газовая резка позволяет разрезать сталь толщиной свыше 2000 миллиметров. Качество сварных швов проверяется многочисленными способами. Простейшим из них, является осмотр мест сварки при помощи лупы. Он позволяет выявить поверхностные раковины, поры, шлаковые включения, пережог, мелкие трещины, неравномерность швов и другие наружные дефекты. Часто практикуется проба на изгиб. Суть её состоит в определении угла, при котором на шве появляется первая трещина. Причина возникновения дефектов в сварном шве очень разнообразны.
Как правило, дефекты возникают из-за низкого качества металла. К ним относятся расслоения плены, раковины, присутствие окалины, включения серы.
В связи с нарушением процесса сварки получаются:
1. непровары – слабое соединение основного металла с наплавленным;
2. недовары – неполномерные швы;
3. закалка околошовной зоны; неравномерность, несимметричность, неполность сварных швов;
4. наплывы и др.
Изучение сварочных процессов и достижений в области их выполнения являются непосредственной задачей сварщиков.
Автор: Кузнецов М.Ю., сотрудник Монолит-Мет — монтаж металлоконструкций
Другие статьи, публикации по ремонту, строительству: