Стыковые сварные соединения
Подготовка кромок листов и стенок профилей под сварку. Разделка кромок под сварку должна производиться в соответствии с ГОСТами, отраслевыми стандартами или чертежами, одобренными Регистром.
Кромки листовых и профильных деталей должны быть обработаны под сварку встык газовой резкой или механическим способом. На кромках при этом допускаются штрихи глубиной не более 0,3 мм и выхваты глубиной не более 2 мм на длине до 6 мм (не более одного на 1 пог. м кромки).
Листы корпусной стали и профили с толщиной стенки менее 5 мм (в некоторых случаях допускается при толщине 6 мм) должны свариваться двусторонним швом без разделки кромок.
Разделку кромок швов стыковых соединений при ручной электродуговой сварке следует производить:
V-образной — для листов (стенок профилей) толщиной от 5 до 12 мм (допускается до 16 мм). Угол разделки а=60°, зазор от 2,0 до 5,0 мм (допускается сварка без зазора при V-образной разделке), притупление от 2 до 3 мм;
V-образной, Х-образной симметричной или 2/3 Х-образной несимметричной (глубина большего раскрытия равна 2/з толщины листа)“—для листов толщиной более 12 мм;
U-образной с углом разделки каждой кромки 10°, зазором 2 мм и притуплением 3 мм — для больших толщин.
Контроль качества подготовки кромок под сварку. От качества подготовки кромок под сварку непосредственно зависит качество сварного стыкового соединения в целом. Поэтому сборочные работы должны быть выполнены аккуратно, все соединения должны быть тщательно подогнаны, без применения чрезмерных усилий для правки и подгонки, создающих напряжения в конструкции.
При контроле качества подготовки кромок под сварку необходимо проверять углы разделки кромок, смещения кромок, величины притупления и зазоров межстыкуемыми элементами при помощи шаблонов и контрольно-измерительных инструментов.
Допускаемое при сборке стыковых соединении смещение кромок листов составляет 0,1 толщины меньшего из стыкуемых листов, но не более 3 мм.
Отклонения размеров подготовленных под сварку кромок не должны превышать допусков, регламентированных ГОСТами, отраслевыми стандартами и другой технической документацией по сварке. В общем случае зазор между кромками стыкуемых соединений ни в каком месте не должен превышать удвоенного номинального зазора, предписанного стандартом.
Зазоры, превышающие допустимые значения, по согласованию с инспектором регистра могут быть исправлены наплавкой кромки (кромок), если отклонение от нормы не превосходит толщины меньшего из стыкуемых листов или 10 мм, в зависимости от того, что меньше.
Излишек основного металла в подготовленном под сварку встык соединении (недопустимо большое притупление и малый зазор, а также малый угол разделки) должен удаляться любым из разрешенных для данной марки стали способом.
Зачистка кромок перед сваркой. Стыкуемые кромки, обработанные тепловой резкой или механическим способом, должны быть очищены от влаги, ржавчины, окалины, масла или краски. Загрязнения должны удаляться перед сборкой. Зачистка кромок стыкуемых соединений должна производиться непосредственно перед сваркой, в том числе прилегающих поверхностей листов на ширине 20— 30 мм. Если разделка кромок производилась воздушно-дуговой строжкой, необходимо дополнительно обработать кромки наждачным кругом с последующей их зачисткой перед сваркой стальными щетками. Важно выполнить это требование при сварке сталей повышенной прочности с целью свести до минимума возможность насыщения углеродом поверхностного слоя кромок свариваемых листов.
Стыковое соединение листов разных толщин. Для плавного перехода при соединении всгык необходимо скашивать кромки толстого листа до толщины тонкого в соответствии с действующим стандартом. Если разница в толщине стыкуемых элементов превышает 30% толщины более толстого из них либо 5 мм (в зависимости от того, что меньше), скашивать кромку толстого листа надо на длине, составляющей не менее трехкратной разности между толщинами листов. Высота усиления стыкового сварного шва не должна превышать 10% толщины листа.
Для ответственных соединений листов разных толщин, например стыков усиленных листов наружной обшивки и расчетной палубы у концов надстроек, в углах вырезов грузовых люков и больших лацпортов, кромка более толстого листа должна быть скошена, если разница толщин превышает 25% толщины более тонкого из соединяемых листов или более 3 мм, в зависимости от того, что меньше.
Выбор положения V-образной разделки. Все стыковые швы листов и профилей должны, как правило, выполняться с подваркой корня шва. Ручную сварку и полуавтоматическую сварку в углекислом газе следует начинать со стороны, трудно доступной для удаления (строжки, подрубки)» корня шва. Наложение шва с другой стороны (подварка корня) надо выполнять после удаления корня шва до чистого металла.
Для стыковых соединений листов пастила палуб, платформ, второго дна и днищевой обшивки, а также горизонтальных элементов продольного набора раскрытие V-образной и 2/з Х-образной разделки должно быть достаточным для выполнения основного шва в нижнем положении.
В отдельных случаях допускается по согласованию с инспектором Регистра выполнение односторонних стыковых швов на остающейся стальной подкладке. В этом случае разделка кромок должна быть V-образной, но с увеличенным зазором: примерно от 4 До 8 мм в зависимости от толщины свариваемых листов.
Рис. 1. Односторонняя сварка на остающейся подкладке стальных листов (а) и стальной отливки с листом (б)
Сварка швов стыковых соединений. Ручная электродуговая сварка и полуавтоматическая сварка в углекислом газе должны производиться: симметрично от середины конструкции к ее краям при длине сварного шва более 2 м; «напроход» при длине сварного шва до 2 м.
При вертикальном положении конструкции (бортовая обшивка, переборки, вертикальный набор и т. п.) сварку следует вести «снизу вверх». Если от середины конструкции направление сварки идет «вниз», то сварка должна вестись обратноступенчатым способом, если же «вверх», то сварку следует производить «напроход».
Стыковые швы должны выполняться с полным проваром или под-варкой корня шва, удаленного до чистого металла.
Сварка мест пересечения стыков и пазов должна производиться особенно тщательно. Для обеспечения полного провара .и исключения возможного концентратора напряжений в стыковом шве (т. е. дефектов сварки) сварку следует выполнять в следующей последовательности:
1) при заварке паза оставить недоваренными примыкающие к стыку участки длиной 300—400 мм;
2) полностью заварить стыковой шов, пересекающий паз;
3) удалить наплавленный металл стыкового шва в месте пересечения до получения заданной формы разделки кромок паза;
4) произвести окончательную разделку кромок и заварку недоваренных участков паза.
Если стенка набора пересекает уже выполненный стыковой шов обшивки, последний должен быть зачищен заподлицо с поверхностью листов в месте пересечения швов. Если листы обшивки свариваются после установки и приварки набора, в стенке набора необходимо предусматривать полукруглые отверстия радиусом 30 мм.
Стыковые соединения балок набора. Согласно требованиям Правил Регистра соединения балок набора должны выполняться встык. Для продольного набора, особенно в районе 0,6L в средней части судна, важным условием является обеспечение непрерывности балок по длине судна.
Расположение стыковых соединений. Стыки балок продольного набора полособульбового профиля, а также из полосового проката должны, как правило, располагаться у опорных сечений и перекрываться кницами или бракетами.
Рис. 2. Расположение стыка продольной балки днища у опорного сечения (а) и стыки пояска, стенки сварной тавровой балки и стык листа обшивки, разнесенные на расстояние не менее половины высоты стенки балки (б)
Рис. 3. Наименьшая длина заменяемого участка продольной балки 4h, но не менее 500 мм
Рис. 4. Стыковое соединение бортовых шпангоутов полособульбового профиля
Стыки элементов тавровых балок должны, как правило, располагаться в районе опорных книц (аналогично стыкам полособульбового профиля) либо вне книц на расстоянии не менее половины высоты стенки балки от конца кницы.
В основном следует стремиться к ограничению числа стыковых соединений балок продольного набора. При секционном ремонте рекомендуется назначать максимально допустимую из производственных возможностей длину балок набора. Вместе с тем допускается замена отдельных участков продольных балок на длине не менее четырех высот h профиля (высоты стенки балки) или 500 мм в зависимости от того, что больше.
Стыковые швы поперечного набора (шпангоуты, бимсы) допускается выполнять при ремонте корпуса как перпендикулярно обшивке, так и под углом до 45°. Не допускается располагать стыки бортовых шпангоутов в районе ледового пояса, а также в других районах корпуса, воспринимающих значительные сосредоточенные усилия, в том числе динамического характера, например бортовые перекрытия судов, швартующихся в открытом море, и т. п.
При необходимости балки набора в районе стыковых соединений могут быть подкреплены накладной полосой или полосой, приваренной перпендикулярно стенке набора.
Стыковые соединения поясков пересекающихся балок таврового профиля (карлингсов с рамными бимсами, рамных шпангоутов с бортовыми стрингерами, флоров с вертикальным килем и днищевыми стрингерами на судах без второго дна и т. п.) в районе 0,6L в средней части, а также в районах интенсивной вибрации и больших динамических нагрузок должны выполняться с применением крестовин, уменьшающих концентрацию напряжений.
Усталостная прочность такого соединения в 2—3 раза выше, чем непосредственного соединения поясков встык. Практика эксплуатации показала возможность возникновения усталостных трещин в поясках продольных балок, распространяющихся затем на стенки балок и в конечном итоге на обшивку или настил палубы (рис. 4-25,6). Как временная мера при ремонте может быть рекомендована установка скругленных книц (рис. 4-25, е).
Рис. 5. Стыковое соединение продольной подпалубной балки углового профиля с подкреплением места стыка накладной полосой (подварка корня шва затруднена)
Рис. 6. Стыковое соединение стойки водонепроницаемой переборки в междупалубном помещении. Стойка в месте стыка подкреплена приваренным ребром из полосы 40×10 мм, концы полосы срезаны «на ус» под углом 45°
Стыки стенок балок набора в местах излома оси могут быть выполнены без ограничений как для подпалубного, так и бортового набора. Для балок таврового профиля рекомендуется разносить стыки поясков от места излома на 200 мм, а поясок приварить к стенке усиленным в 1,5 раза угловым швом или с разделкой кромок стенки на длине, равной высоте профиля.
Бортовые шпангоуты в районе стыка на изломе оси рекомендуется подкрепить кницей.
Часто при ремонте приходится заменять существующий профиль набора другим, имеющимся в наличии либо изготовленным. Варианты стыковых сварных соединений различных профилей набора между собой приведены на рис. 4-26.
Рис. 7. Стыковое соединение поясков пересекающихся балок набора:
а — обеспечение плавного перехода в соединении поясков при помощи крестовины; б — трещины в соединении поясков рамного шпангоута 2 и бортового стрингера 3\ в — устранение повреждений узла (трещины в поясках и стенках балок) постановкой скругленных книц
Рис. 8. Стыковое соединение различных профилей:
а — полособульбового профиля с тавром: б — углового профиля с тавром
Рис. 9. Разделка полособульбового профиля под сварку:
а — для номеров 5—9; б — для номеров 10—24
Рис. 10. Стыковое соединение полособульбового профиля разной высоты:
а — для номеров 6—9; б — для номеров 10—24
Если невозможна подварка стыкового шва набора, допускается сварка полособульбового профиля на остающейся стальной подкладке, а углового профиля — с подкреплением места стыка накладной полосой.
7.Стыковые сварные соединения. Расчет и конструирование.
Стыковые —
соединяются торцами (а). Имеют наименьшую
концентрацию напряжений при передаче
усилий, экономичны. Толщина элементов
не ограничена. Соединение = прямым или
косым швом.
Усиливают накладками – комбинир. (б).
Стыковые наиболее рациональны, но требуют дополнительной разделки кромок.
Работа и расчет стыковых швов
Прочность при растяжении или сжатии зависит от характеристик металла и шва.
При действии N распределение напряжений по длине шва принимается равномерным, рабочая толщина шва = меньшей из толщин элементов. Напряжение в шве (а) Rсв — расчетное сопротивление сварного стыкового соединения сжатию или растяжению, у — коэффициент условий работы элемента.
Расчетное сопротивление стыкового соединения при сжатии соединения Rсв=R.
При Rсв ≤ Rосновного металла то шов делают косым (с проверкой) (б). Рассчёт косых швов: перпендикулярно шву
вдоль шва
а и б — на продольную силу; в — на изгиб
При действии изгибающего момента (в)
где
— момент сопротивления шва.
Соединения встык, работающие на нормальные напряжения и срез, проверяют
8.Сварные соединения с угловыми швами. Расчет и конструирование.
Угловые — элементы расположены под углом (г).
Валиковые швы — элементы, расположенны в разных плоскостях.
Фланговые — параллельно осевому усилию.
Лобовые — перпендикулярно усилию (рассчитывают условно).
Работа и расчет соединений, выполненных угловыми швами
— соединения внахлестку.
Фланговые работают на срез и изгиб. Разрушение может происходить по металлу шва, по осн. металлу на границе его сплавления с металлом шва.
Велики напряжения в корне шва.
Рассматриваем возможность разрушения шва от условного среза:
По металлу шва
По границе сплавления с металлом шва
βш
и βс — коэфф. глубины проплавления — в зависимости
от вида сварки
Lш =L-10мм, RВш—расчетное сопротивление срезу металла шва;
Rувс—расчетное сопротивление срезу (условному) металла границы сплавления.
Удобнее определять необходимую длину швов, задаваясь их толщиной kш: kш = меньшей из толщин элементов,
Толщина шва исходя из его возможной расчетной длины:
Напряжения от силы сдвига и момента:
По металлу шва
По металлу границы сплавления
Площади швов должны быть распределены обратно пропорционально расстояниям от шва до оси элемента.
при общей требуемой площади швов —
Площадь большего шва на «обушке» уголка
Площадь меньшего шва на «пере» уголка
9.Достоинства и недостатки болтовых соединений. Виды болтов, применяемые в строительных мк.

Болтовые = раньше сварных. Простота и надежность в работе.
Они более металлоемки, имеют накладки, ослабляют отверстиями.
Болты грубой и нормальной точности — отклонения диаметра 1 мм и 0,52 мм (для болтов d≤30 мм). Они = из углеродистой стали. Класс прочности болтов (5.6). Первое число = 50 = временное сопротивление (σв кгс/мм2), а 5*6=30 — предел текучести материала (σ т кгс/мм2).
Отверстия на 2—3 мм больше диаметра болта — облегчает посадку болтов (преимущество). Но это повышает деформативность соединения при работе на сдвиг. Эти болты = крепежные.
Болты повышенной точности — из углеродистой стали. d отверстия = +0,3 мм от диаметра болта.
Болты сидят плотно и хорошо воспринимают сдвигающие силы. Сложность изготовления и постановки болтов = применяются редко.
Высокопрочные
болты — из
легированной стали, термически
обрабатывают. Они = нормальной точности,
отверстия большего диаметра, но гайки
затягивают спец-ключом. Силы трения
препятствуют сдвигу элементов
относительно друг друга. Высокопрочный
болт работает на осевое растяжение.
Необходима одинаковая толщина элементов, а то несущая способность болта резко уменьшается.
Применяют клееболтовое. Преимущества — простота устройства; По качеству — не уступают сварке, но уступают ей по расходу металла.
Самонарезающие болты — наличие резьбы. Материал — сталь термоупрочненная. d=6 мм для прикрепления профилированного настила к прогонам и элементам фахверка. Преимущество — доступ к конструкции только с одной стороны.
Фундаментные (анкерные) болты — передачи растягивающих усилий с колонн на фундамент. Материал — стали марок ВСтЗкп2, 09Г2С и 10Г2С1.
Стыковой шов | Сварка металлов
Соединения без скоса
Односторонние стыковые швы без скоса кромок выполняют покрытыми электродами диаметром, равным толщине свариваемых листов, если она не превышает 4 мм. Ток подбирают в зависимости от диаметра электрода, вида и толщины покрытия (табл. 6). Листы без скоса кромок толщиной от 2 до 8 мм сваривают двусторонним швом. Положение и поперечные движения электрода при сварке приведены на рис. 29.
Соединение со скосом
Стыковые соединения со скосом двух кромок в зависимости от толщины металла выполняют однослойными, многослойными или многопроходными швами.
Рис. 29. Положение (я) и движения электрода (б) при выполнении стыковых швов со скосом кромок
Однослойный шов
Металл толщиной от 1 до 6 мм без скоса кромок сваривается однослойным (однопроходным) швом.
Однослойные швы со скосом двух кромок выполняют поперечными колебательными движениями электрода в виде треугольников без задержки в корне шва (листы толщиной 1-4 мм) и с задержкой в корне шва (толщиной 4 — 6 мм).
Листы толщиной 12 мм и более соединяются встык с двумя несимметричными скосами двух кромок многослойным или многопроходным швом.
Таблица 6. Ориентировочные режимы сварки стыковых соединений без скоса кромок
Толщина металла, мм | Шов | Зазор, мм | Диаметр электрода, мм | Среднее значение тока, А | |
нижнее положение шва | вертикальное и потолочное положение шва | ||||
3-4 | Односторонний | 1,0 | 3-4 | 180 | 160 |
5-6 | Двусторонний | 1,0- 1,5 | 4-5 | 180-260 | 160-230 |
7-8 | » | 1,5-2,0 | 5 | 260 | 230 |
10 | » | 2,0 | 6 | 330 | 290 |
Примечание. Максимальные значения тока должны уточняться по данным паспорта электродов.
Многослойный шов
Многослойный шов выполняется быстрее многопроходного. Выбор многослойного или многопроходного шва зависит от химического состава и толщины свариваемой стали и от установленной технологии на сварку.
Каждый слой многослойного шва имеет увеличенное в несколько раз сечение по сравнению с сечением каждого валика при многопроходной сварке. Режимы дуговой сварки покрытыми электродами нижних стыковых многослойных швов даны в табл. 7.
Таблица 7. Ориентировочные режимы сварки стальных листов со скосом двух кромок встык
Толщина металла, мм | Зазор, мм | Число слоев, кроме подварочного и декоративного | Диаметр электрода, мм, при наплавке | Среднее значение тока, А (нижнее положение шва) | |
первого | Последующего | ||||
10 | 1,5-2,0 | 2 | 4 | 5 | 180-260 |
12 | 2,0-2,5 | 3 | 4 | 5 | 180-260 |
14 | 2,5-3. | 4 | 4 | 5 | 180-260 |
16 | 3,0-3,5 | 5 | 4 | 5 | 180-260 |
18 | 3,5-4,0 | 6 | 5 | 6 | 220-320 |
Примечание. Максимальные значения тока должны уточняться по данным паспорта электродов.
Многопроходный шов
Многопроходной шов выполняется тонкими и узкими валиками, без поперечных колебательных движений электрода. Сварку рекомендуется выполнять электродами, предназначенными для опирания. В этом случае применяют электроды диаметром от 1,6 до 3 мм (редко 4 мм). Весь многопроходной шов может выполняться электродами одного и того же диаметра.
Иногда для обеспечения провара по всей толщине металла сварка ведется на медной подкладке толщиной 4-6 мм. В этом случае сварочный ток можно повысить на 20 — 30%. Если конструкция и назначение сварного изделия допускают сквозное проплавление, сварка может вестись на остающейся стальной подкладке.
В особо ответственных конструкциях перед подваркой шва его (с обратной стороны) предварительно зачищают резаком для поверхностной резки или резцом для удаления возможных дефектов (непровара, трещин, газовых и шлаковых включений).
Угол раскрытия шва
Оптимальный угол раскрытия шва определяется следующими соображениями. Большой угол разделки (80° — 90°) обеспечивает большие удобства сварщику, уменьшает опасность непровара корня шва, но увеличивает объем наплавленною металла, следовательно, уменьшает производительность и увеличивает деформации изделия. Для нормального процесса ручной дуговой сварки принят угол разделки (50 ± 4)° (сварное соединение типа С17).
Зазор между стыкуемыми элементами и притупление кромок составляет от 1,5 до 4,0 мм в зависимости от толщины листов, режима сварки и характера свариваемой конструкции.
Провар корня шва
Наиболее трудным при сварке является получение полного (надежного) провара корня шва. Здесь чаше всего бывают дефекты, например непровар, газовые и шлаковые включения. Поэтому (если это возможно) следует подваривать корень шва с обратной стороны.
Виды сварных соединений
По конструкции различают следующие сварные соединения: стыковые, нахлесточные, тавровые, угловые, комбинированные (табл. 10.8).
Стыковыми называются соединения, в которых элементы соединяются торцами или кромками и один элемент является продолжением другого. Место их соединения (зазор) заполняется сварным швом. Стыковые соединения наиболее рациональны и надежны, так как имеют наименьшую концентрацию напряжений при передаче усилий, отличаются экономичностью и удобны для контроля.
Толщина свариваемых элементов в соединениях такого вида почти не ограничена. Стыковое соединение листового металла может быть сделано
Таблица 1.8
Виды сварных соединений
Стыковые |
Нахлесточные |
Комбинирован- ные |
Тавровые |
Угловые |
||
угловыми швами |
точечной сваркой |
|||||
без накладок Внимание! Если вам нужна помощь в написании работы, то рекомендуем обратиться к
профессионалам. Расчет стоимостиГарантииОтзывы |
с накладками |
|||||
прямым или косым швом. Стыковые соединения профильного металла применяются реже, так как затруднена обработка их кромок под сварку.
Сварные стыковые соединения листовых деталей, как правило, проектируют прямыми с полным проваром и с применением выводных планок. В монтажных условиях допускается односторонняя сварка с подваркой корня и сварка на остающейся стальной подкладке.
При соединении стальных листов различной толщины (или ширины) их размеры в месте стыка должны быть одинаковыми во избежание резкого изменения сечения. Для этого в более толстом (или широком) элементе устраивается скос с уклоном 1:5 с одной или двух сторон до толщины тонкой детали (рис. 10.19).
Рис. 10.19. Соединение элементов:
а – при разной толщине; б – при разной ширине
Длиной скоса листа регулируют плавный переход от толстой свариваемой детали к более тонкой, кроме того, длиной скоса устраняют концентраторы напряжений в сварных конструкциях. Стыки без скосов по толщине допускаются в деталях из углеродистой или низколегированной сталей с пределом текучести до 400 МПа при разнице толщин = (t2 – t1), не превышающей значений, указанных в табл. 10.9.
Нахлесточные соединениями
называются такие, в которых поверхности свариваемых элементов частично находят друг на друга. Разновидностью соединений внахлестку являются соединения с накладками. Их применяют с одной или двумя накладками. Накладки служат для соединения частей изделия. Соединения внахлестку выполняются угловыми швами. Они отличаются
Таблица 10.9
Допустимая наибольшая разность толщин деталей,
свариваемых встык без скоса кромок
Толщина тонкой детали t1, мм |
Разность толщин деталей , мм |
1…4 5…20 21…30 Св. 30 |
1 2 3 4 |
простотой обработки элементов под сварку, обеспечивают возможность подгонки размеров за счет регулирования величины нахлестки, но по расходу металла менее экономичны, чем стыковые. Недостатками нахлесточных соединений являются изменение направления силового потока и возможность образования щели между элементами. Неравномерное распределение силового потока вызывает концентрацию напряжений, такие соединения не рекомендуется применять в конструкциях, воспринимающих переменные или динамические нагрузки; проникновение влаги в щель между соединяемыми элементами может привести к щелевой коррозии и разрушению сварных швов за счет распирающего воздействия продуктов коррозии.
К нахлесточным также относятся соединения, выполненные контактной точечной сваркой.
Комбинированными
называются соединения, в которых имеется несколько разных видов сварных швов. К таким соединениям можно отнести соединения, выполненные сварными швами различной ориентации относительно линии действия внешнего усилия (лобовыми и фланговыми). Другой тип комбинированного соединения представляет собой стыковой шов, дополнительно усиленный накладками. Необходимость выполнения такого соединения может появиться для обеспечения равнопрочности стыка и соединяемых элементов при недостаточной прочности стыкового шва и невозможности применить физические методы контроля качества сварного шва.
Тавровое соединение представляет собой крепление торца одного элемента к поверхности другого, как правило, под прямым углом. При угловом соединении впритык крепятся торцы элементов, находящихся во взаимно перпендикулярных плоскостях. Тавровые и угловые соединения отличаются простотой выполнения, высокой прочностью и экономичностью. При воздействии статических нагрузок тавровые соединения выполняют, как правило, с предусмотренным конструктивным непроваром. Обеспечение полного проплавления тавровых соединений усложняет процесс сварки, удорожает изготовление конструкции, поэтому может применяться только в обоснованных случаях, например, при проектировании поясных швов балок под подвижную нагрузку, так как непровар в корне шва приводит к заметному снижению усталостной прочности.
Соединения впритык применяются при изготовлении сварных стержней (двутавров, швеллеров) и других конструктивных элементов.
По месту выполнения соединения разделяются на заводские и монтажные. К заводским относятся соединения, выполняемые при изготовлении металлоконструкций на специализированных заводах, к монтажным – соединения, выполняемые при монтажной сборке металлоконструкций на местах строительства зданий и сооружений.
Поможем написать любую работу на аналогичную тему
Реферат
Виды сварных соединений
От 250 руб
Контрольная работа
Виды сварных соединений
От 250 руб
Курсовая работа
Виды сварных соединений
От 700 руб
Получить выполненную работу или консультацию специалиста по вашему учебному проекту
Узнать стоимость
Сварка стыковых соединений в нижнем положении
Сеть профессиональных контактов специалистов сварки
Сварка стыковых соединений в нижнем положении с разделкой кромок и угловых швов затруднена тем, что сварка ведется в стесненных условиях.
Отличительная особенность сварки стыковых соединений в нижнем положении заключается в следующем:
- жидкому шлаку стекать по краям валика не позволяют кромки разделки;
- шлака на единицу площади поверхности металла шва больше, чем при сварке валика на открытой поверхности;
- из-за большого количества жидкого шлака происходит накат его на сварочную дугу;
- шлак, идущий впереди, стекает вниз разделки и мешает сварочному процессу, что приводит к непровару и зашлаковке, В этом случае сварку необходимо производить «углом назад». При сварке ответственных изделий, подлежащих всем видам контроля, к стыковым швам предъявляются особые требования при выполнении всех операций.
Корень шва.
Особое требование предъявляется к сварке корня шва, который состоит из первого валика — «сварка в зазор» и второго — «сварка с обратной стороны».
Качество корневого шва зависит:
- От качества сформированного первого корневого валика.
- От качественной подготовки обратной стороны корня шва под сварку второго валика.
- От качественной сварки второго корневого валика (валика с обратной стороны).
Сварка первого корневого валика в стыковом соединении.
Сварка первого корневого валика в стыковом соединении самая сложная и требует от сварщика особых навыков и большой тренировки.
Рисунок 1.
Выполненный валик должен быть «нормальным» или «вогнутым», с проплавлением обоих кромок, без подрезов, с хорошим формированием с обратной стороны. Все это достигается при определенной совокупности подбора сварочного тока, скорости сварки, длины дуги, наклона и манипулирования электродом.
При сварке первого корневого валика в зазор с V-образной разделкой кромок (рис. 1а) применяется электрод диаметром 3 мм, сварочный ток в диапазоне 85 ± 5 ампер в зависимости от толщины металла, зазора и притупления.
При сварке V-образной (рис. 1б) и Х-образной разделке (рис. 1в) применяются электроды диаметром 3-4 мм (рекомендуется применять электрод диаметром 4 мм). Протяженность валика одного электрода диаметром 4 мм в 2-3 раза превышает длину валика, сваренного электродом диаметром 3 мм. Сокращается количество стыковок электрода (начало и конец сварки), что уменьшает возможность дефектов и резко увеличивает производительность. Сварочный ток для электрода диаметром 3 мм — 90 А ± 5 А, 4мм — 140 А±5 А.
Подобрав диаметр электрода и сварочный ток в зависимости от сборки и вышеперечисленных условий, сварку в зазор первого валика рекомендуется производить тремя способами:
1-й способ — без манипулирований (рис. 2), Этот способ возможен при совокупности минимального рекомендуемого тока в V-образной и минимально го или среднего в Х-образной разделке, средней длины дуги при определенном зазоре и притуплении кромок и толщине металла. Наблюдая за оплавлением обеих кромок и притупления сварочной дугой и заполнением зазора жидким электродным металлом, необходимо производить поступательное движение с определенной скоростью, не позволяющей делать пропуски в соединении кромок при большой скорости и прожоги при маленькой скорости.
Рисунок 2. Сварка стыковых соединений в нижнем положении: сварка первого валика без манипулирования.
Угол наклона электрода по отношению к направлению сварки выдерживать 90 ± 10°. Сварка под «прямым углом» и «углом вперед» в разделке возможна только при сварке первого валика в зазор, т.к. часть жидкого шлака, идущего впереди, стекает в зазор и защищает жидкий металл шва с обратной стороны изделия.
В случае недостаточного зазора (при сборке) или же стяжки кромок и др. причин в процессе сварки шлак, идущий впереди, не успевает стекать в зазор и происходит его излишнее накопление впереди электрода, что может привести к непровару корня шва.
В этом случае необходимо сварку производить «углом назад».
В том случае, когда зазор в сочетании с другими параметрами оказался большой и происходит чрезмерный проплав или сварка на грани прожога, необходимо применять сварку «углом вперед». В этом случае воздействие на притупление и зазор происходит не прямой («открытой дугой»), с максимальным проплавлением, а через жидкий металл, идущий чуть впереди. При этом внимательно наблюдать, чтобы жидкий металл, идущий впереди электрода (получается как бы поступательным движением электрода мы «катим» впереди жидкий металл), оплавлял обе кромки притупления, соединяя их электродным металлом. Это возможно при определенной скорости сварки, которую должен определить сварщик.
2-й способ — с манипулированием электродом — «вперед назад». Не меняя наклона электрода, для избежания прожога, действуя «открытой дугой» на кромки в зазоре, производить возвратно-поступательные движения. При возврате на кристаллизующийся валик (8-12 мм) место перехода кратера в зазор подстывает. Затем снова выполнить движение вперед, проплавляя открытой дугой край кратера и кромки притупления в зазоре.
Расстояние прохода открытой дугой над зазором зависит от всех перечисленных выше условий. Поэтому сварщик сам должен ориентироваться и выбирать оптимальный вариант.
Рисунок 3.
с манипулированием электродом.
3-й способ — с манипулированием электродом (рис. 3) — «лестница», том случае, когда происходит чрезмерное проплавление, рекомендуете, производить поперечные колебательные движения от одной кромки к дру гой. Очень важен переход над зазором. Если кромки притупления не оплавляются — значит, слишком быстрый переход и высокая длина дуги. Необходимо при переходе над зазором уменьшить длину дуги, а при подходе к кромке разделки чуть подняться по ней вверх и в месте задержки сделать короткую дугу (как бы прижаться электродом к изделию). Задержка необходима для отвода тепла от зазора, для прогрева кромки и для наполнения кратера электродным металлом. Переход к другой кромке осуществлять (без суеты) спокойно (для избежания подреза на кромке). В зависимости от проплавления кромок притупления проходить либо через зазор (как бы спускаясь), либо над зазором, выдерживая выбранную высоту валика от зазора. Наклон электрода по отношению направления сварки 90° ±10°
Большое значение на качество корневого валика имеет начало и коне сварки (при замене электрода).
При недостаточной квалификации сварщика при сварке первого корневого валика (в зазор) в местах стыковки электродов при формировании корня шва с обратной стороны образуются «ямочки», т.е. углубленные несплавления (рис. 4). Приходится проводить глубокую механическую выборку обратной стороны корневого шва, даже при наличии хорошо сформированного обратного валика.
Рисунок 4.
Для того, чтобы избежать выборки, необходимо, чтобы:
1. Высота корневого валика не превышала диаметра электрода.
2. Кратер при окончании электрода оставался пологим.
3. Перед зажиганием нового электрода тщательно очистить кратер и особенно окончание кратера, переходящего в зазор, и сам зазор от застывшего шлака. При необходимости зачистить механическим способом кратер с плавным переходом в зазор.
4. Зажигание нового электрода производить на вершине кратера, соединив первую чешуйку с последней чешуйкой застывшего валика (рис. 5).
Рисунок 5.
Спускаясь по кратеру с положения (1) к зазору, необходимо не допускать подтекания жидкого шлака под дугу в зазор (путем правильного выбора угла наклона электрода и скорости продвижения). Не доходя до окончания кратера, из положения 2, быстро перевести электрод (при этом выровнять наклон электрода до 90° к направлению сварки) в положение 3 и, действуя открытой дугой, произвести задержку центром дуги в месте перехода кратера в зазор при короткой длине дуги. Время задержки определяется следующим образом. В начале горение большей части дуги происходит по другую сторону зазора, т.е. с обратной стороны, что и позволяет проплавить перемычку с обеих сторон. И после того, как электродный металл заполнит зазор в месте задержки и дуга в основном будет гореть со стороны сварки, начать поступательное движение одним из способов, выбранным сварщиком. Все это позволит сформировать корень шва с обратной стороны с минимальными перепадами в местах замены электродов и избежать глубоких «ямочек». При хорошо сформированном обратном валике не требуется выборки, что уменьшает расход материалов и увеличивает производительность труда.
Примечание. Можно, не обивая шлака, начинать новый электрод. Это идеальный вариант для качественной стыковки окончания и начала сварки, но требует высокого мастерства, сноровки в быстрой замене электрода (не при каждом держателе есть такая возможность) и ряде других факторов, когда не успевает застыть кратер и шлак еще жидкий (полужидкий) и красный, все это дает возможность легкого зажигания электрода и хорошего проплавления в стыковке. Такое зажигание исключает образование стартовых пор. Это возможно, повторяем, только при незастывшем кратере.
Таким способом можно варить корень шва двумя сварщиками в «перехват».
Перед подготовкой к сварке обратной стороны разделки необходимо на первый корневой валик проложить еще 1-2 валика (в зависимости от толщины металла) для увеличения сечения шва по высоте. Это требуется для того, чтобы в случае выборки обратной стороны не осталось тонкое сечение первого корневого валика. Если позволяет ширина предыдущего валика, перейти на больший диаметр электрода. Сварочный ток — средний или максимальный. Сварку производить «углом назад». Угол наклона электрода в зависимости от расположения шлака. Скорость сварки выдерживать такую, чтобы валики были без усиления, без подрезов по краям шва Манипулирование электродом производить в зависимости от ширины предыдущего и выполняемого валиков, с обязательной задержкой на кромка разделки. Задержка необходима для прогревания кромок, что способствует лучшему формированию валика и исключению подрезов по краям шва
II. Подготовка обратной стороны корня шва.
В зависимости от форм разделки и качества сформированного первого валика с обратной стороны произвести выборку обратной стороны до чистого металла таким образом, чтобы торец электрода с покрытием по всей длине выборки касался «дна» выборки. Ширина (S) выборки зависит от глубины выборки. Глубина (h) выборки зависит от качества сформированного обратного валика.
Рисунок 6.
Рис. 6а — при V-образной разделке выборку рекомендуется подготовить под электрод диаметром 4 мм.
Сварку выполнять в один-два слоя электродом диаметром 4-5 мм.
Рис. 6б — при h < 2 мм произвести выборку на ширину 3-4 мм. Сварку выполнить в один проход электродом диаметром 4-5 мм.
Рис. 6в — выборка на глубину 3 мм и более, a S менее диаметра электрода с покрытием может привести к непровару и зашлаковке. Не рекомендуется.
Рис. 6г — Х-образная разделка. При качественно сформированном корне шва с обратной стороны, когда ширина S по всей длине разделки равна или более диаметра электрода с покрытием, выборка не требуется. Это самый оптимальный и производительный случай.
В том случае, когда необходима выборка, произвести ее как показано на рис. 6д, очень важно — места 1 и 2 раздать (срезать).
Рис. 6е — если выборка глубокая и места 1, 2 не срезаны, получаются параллельные кромки. И если даже электрод с покрытием входит в такую разделку, то горение сварочной дуги происходит в сжатых условиях, что приводит к непроварам и зашлаковке в местах «3» и нестабильному сварочному процессу.
Рекомендуется выборку делать отрезным камнем толщиной в 6 мм, что позволит применять электрод диаметром 4 мм, о преимуществе которого говорилось ранее.
III. Сварка второго корневого валика.
Корневой валик с обратной стороны является завершением сварки корня шва в Х-образной разделке и в V-образной (с подваркой корня с обратной стороны). Чаще всего дефекты в корне шва бывают не при сварке первого валика, а при сварке корневого валика с обратной стороны, т.е. между первым и обратным корневым валиках. Рекомендуемые ниже советы помогут избежать дефектов в основе шва.
После подготовки обратной стороны корневого валика сварщик должен убедиться в качестве выборки (подготовки) обратной стороны путем промера S разделки выбранным диаметром электрода (рис. 7а).
Сварочный ток подобрать согласно диаметру электрода от среднего до максимального значения в зависимости от конкретного случая. Подобрав сварочный ток, большое значение на качество сварки 1-го валика с обратной стороны оказывает угол наклона электрода. Сварка ведется в самом узком месте. И если при сварке в зазор идущий впереди жидкий шлак частично стекает в зазор, то в данном случае ему некуда стекать, как только под электрод. Кроме того, избыточное его количество на единицу площади металла шва напирает на сварочную дугу. Происходит зашлаковка и непровар между первым корневым и вторым свариваемым валиком. Чтобы избежать зашлаковки и добиться максимального переплавления с первым корневым валиком, необходимо сварку производить «углом назад», чтобы силой дуги оттеснять жидкий шлак. Иногда, чтобы добиться качественного валика, необходимо наклонять электрод под очень малым углом к изделию, чуть ли не «лежа».
Рисунок 7.
В случаях, когда все же жидкий шлак начинает появляться впереди электрода, — необходимо увеличить: наклон электрода, скорость сварки, длину дуги и произвести короткую пробежку электрода чуть вперед на 5-12 мм. В этом случае дуга отгоняет жидкий шлак назад. Затем небольшой возврат (для выравнивания валика), после чего продолжать поступательное движение с определенной скоростью и определенным углом наклона электрода.
Скорость сварки значительно влияет на расположение жидкого шлака. Необходимо поступательное движение электрода выбрать таким, чтобы высота валика была минимальной, а ширина достаточной для соединения обеих кромок разделки (выборки). Валик должен быть «нормальным» или «вогнутым» (рис. 7б). При оптимально выбранных скорости и наклоне электрода происходит прямое воздействие на «дно» разделки открытой дугой, что способствует максимальному сплавлению второго валика с первым. При выполнении «горбатого» валика возможны непровары, зашлаковки по краям шва. В таком случае требуется выборка — зачистка усиления, что влечет за собой излишний расход материалов, электродов и времени.
Длину дуги при сварке первого корневого валика с обратной стороны корня шва рекомендуется выдерживать средней или между средней и короткой. При средней длине дуги ванна шире и захватывает обе кромки, меньше скапливается жидкого шлака впереди электрода.
Заполнение разделки.
Рисунок 8.
Рисунок 9/
.
Заполнение разделки — 2 этап сварки стыковых и угловых соединений. После сварки корня шва перейти на больший диаметр электрода, если позволяет ширина корневого валика. Последующие 3-й и 4-й валики с обеих сторон в Х-образной разделке и 2-й и 3-й в V-образной разделке, а также при сварке «в лодочку» в угловых соединениях, рекомендуется варить на максимальном или близко к максимальному сварочном токе (рис. 8). Валики, выполненные во всю ширину разделки, должны быть «нормальными». С увеличением ширины разделки переходить на сварку с манипулированием, как показан 5-й валик. Выполнить «нормальные» валики без подрезов с плавным переходом на кромки позволит задержка на каждой кромке. При подходе к стенке разделки краем электрода (обмазки) плотно прижаться к кромке. Сделав задержку, мы прогреваем ее и, уходя электродом к другой стенке, жидкий металл хорошо формируется у прогретой стенки. Переход от одной стенки к другой осуществлять после заполнения электродным металлом кратера плавно, не допуская подреза.
Многопроходная, многослойная сварка сравнима с наплавкой. При заполнении разделки больших толщин, когда ширина валика превышает 3 диаметра электрода (с покрытием), необходимо переходить на сварку последующих слоев в несколько проходов. При переходе в два валика, первый валик (6-ой по рис. 9) рекомендуется прокладывать с неудобной для сварщика стороны, оставляя место для второго валика не менее диаметра электрода с покрытием. Сварочный ток — в максимальном диапазоне. Валик должен быть с усилением, как при обычной наплавке, но с плавным переходом к кромке и нижнему валику Для второго валика получается форма как при сварке «в лодочку». Его высоту можно выполнить наравне с 6-м валиком, чуть ниже или выше. Последующие слои — обычная наплавка (не забывая оставлять между предпоследним валиком каждого слоя и кромкой расстояние не менее диаметра электрода с покрытием).
При Х-образной разделке необходимо чередовать сварку с обеих сторон. Чем чаще чередовать, тем меньше поводки изделия. Минимальное количество кантовок — 3 раза:
1) 1/3 разделки с корня шва с одной стороны — 1-я кантовка.
2) 1/2 разделки с другой стороны корня шва — 2-я кантовка.
3) Окончательное заполнение разделки с начальной стороны — 3-я кантовка.
4) Окончательное заполнение второй стороны.
Сварка лицевого валика (слоя).
Для завершения всего шва правильной формы или по заданному техпроцессу необходимо предпоследний валик (4-й, рис. 10а и 11…13 валики, рис. 10б) закончить так, чтобы оставить незаполненную разделку от 2 мм до -0,5 мм. Это необходимо для качественного формирования лицевого слоя.
Рисунок 10. Сварка стыковых соединений в нижнем положении : сварка лицевого слоя.
Если предпоследний слой выполнен в ноль с поверхностью, то лицевой слой по краям проложить трудно (нет ориентира по кромке) и шов может быть неровный по краям и не выдержан по высоте.
Если оставить незаполненную разделку глубже 2-х мм, то по краям могут быть подрезы и непровары, а сам лицевой шов может быть занижен. Лицевой слой выполняется в зависимости от размеров разделки и может быть выполнен в один или несколько проходов. Край разделки необходимо захватить сварочной дугой на расстоянии не более чем в пол-электрода. Последним валиком (16-м) в многопроходном слое соединить вершины боковых валиков.
Copyright. При любом цитировании материалов Cайта, включая сообщения из форумов, прямая активная ссылка на портал weldzone.info обязательна.
Основные сварочные соединения
Подготовка металла под сварку
Подготовка поверхности металла под сварку необходима для того чтобы обеспечить более высокое качество сварного шва, для этого металл подвергается правке, разметке, обработке кромок под сварку, холодной или горячей гибки. Материал выравнивают на листоправильных вальцах или с помощью ручного винтового пресса, дальше идет, операция разметка будущей детали. Для прямолинейного реза используется лазерная резка, газокислородной и плазменно-дуговой, режут углеродистые стали, для резки легированных и цветных металлов используется лазерная или плазменно –дуговая.
Обработка кромок, подлежащих сварке, производится в соответствии с чертежами и согласно требованиям ГОСТов на основные типы и конструктивные элементы швов сварных соединений. Кромки соединений под сварку обрабатывают на кромкострогальных или фрезерных станках, а также путем лазерной и плазменной резки на специальных станках. Размеры элементов кромок должны соответствовать требованиям ГОСТ. Подготовка кромок металла под сварку производится с целью обеспечения полного провара металла по всей его толщине и получения: доброкачественного сварного соединения.
Скос кромок делается для металла толщиной свыше 5 мм. Угол скоса 70—90° выбирают из расчета возможности свободного доступа к вершине шва и ее проварки. Следует уделять большое внимание чистоте кромок, так как загрязненная поверхность кромок металла приводит к плохому провару и образованию в сварном шве неметаллических включений. Поэтому перед сваркой кромки, а также соседние с каждой кромкой участки на ширину 20—30 мм должны очищаться до металлического блеска от окалины, ржавчины, масла, краски и других загрязнений. Очистка от окалины, краски и масла может осуществляться непосредственно пламенем сварочной горелки. При этом окалина отстает от металла, а масло и краска сгорают. После нагрева пламенем поверхность зачищается стальной щеткой.
Основные типы сварочных соединений
Термины и определения основных понятий по сварке металлов устанавливает ГОСТ. Сварные соединения подразделяются на несколько типов, определяемых взаимным расположением свариваемых деталей. Основными из них являются:
— стыковые;
— угловые;
— тавровые;
— нахлесточные;
— торцовые.
Для образования этих соединений и обеспечения требуемого качества должны быть заранее подготовлены кромки элементов конструкций, соединяемых сваркой.
Стыковым соединением называют соединение двух элементов, примыкающих друг к другу торцевыми поверхностями.
При большой толщине металла ручной сваркой невозможно обеспечить проплавление кромок на всю толщину, поэтому делают разделку кромок, т.е. скос их с двух или одной стороны. Кромки скашивает строгальный станок или термической резкой (плазменной, газокислородной). Общий угол скоса (50±4)°, такая подготовка называется односторонней со скосом двух кромок. При этом должна быть выдержана величина притупления (нескошенной части) и зазор, величины которых установлены стандартом в зависимости от толщины металла. Шов стыкового соединения называют стыковым швом, а подварочный шов – это меньшая часть двустороннего шва, выполняемая предварительно для предотвращения прожогов при последующей сварке основного шва или накладываемая в последнюю очередь, после его выполнения. При подготовке кромок стали толщиной 8–120 мм. Обе кромки свариваемых элементов скашивают с двух сторон на угол (25±2)° каждую, при этом общий угол скоса составляет (50 ± ±4)°, притупление и зазор устанавливаются стандартом в зависимости от толщины стали. Такая подготовка называется двусторонней со скосом двух кромок. При этой подготовке усложняется обработка кромок, но зато резко уменьшается объем наплавленного металла по сравнению с односторонней подготовкой.
Стандартом предусмотрено несколько вариантов двусторонней подготовки кромок: подготовка только одной верхней кромки, применяемая при вертикальном расположении деталей, подготовка с неравномерным пс толщине скосом кромок и др.
Угловым соединением называют соединение двух элементов, расположенных под углом и сваренных в месте примыкания их краев. Таких соединений насчитывается 10: от У1 до У10.
Для толщины металла 3 – 60 мм кромку примыкающего элемента скашивают под углом (45±2) 1°, сварной шов основной и под-варочный. При этой же толщине и сквозном проваре можно обойтись без подварочного шва. Часто применяют угловое соединение со стальной подкладкой, которая обеспечивает надежный провар элементов по всему сечению. При толщине металла 8–100 мм применяют двустороннюю разделку примыкающего элемента под углом (45±2)°.
Тавровым соединением называют сварное соединение, в котором торец одного элемента примыкает под углом и приварен угловыми швами к боковой поверхности другого элемента. Стандартом предусмотрено несколько типов таких соединений: с Т1 по Т9. Распространенным является соединение, для металла толщиной 2–40 мм. Для такого соединения никакого скоса кромок не делают, а обеспечивают ровную обрезку примыкающего элемента и ровную поверхность другого элемента.
При толщине металла 3–60 мм и необходимости сплошного шва между элементами, что предусматривается проектом конструкции, в примыкающем элементе делают разделку кромок под углом (45±2)°. На практике часто применяют тавровое соединение с подкладкой при толщине стали 8–30 мм, а также соединение с двусторонним скосом кромок примыкающего элемента при толщине стали 8–40 мм. Все эти соединения со скосом кромок примыкающего элемента обеспечивают получение сплошного шва и наилучшие условия работы конструкций.
Нахлесточным соединением называют сварное соединение, в котором сваренные угловыми швами элементы расположены параллельно и частично перекрывают друг друга. Стандартом предусмотрено два таких соединения: HI и Н2. Применяют иногда разновидности нахлесточного соединения: с накладкой и с точечными швами, соединяющими части элементов конструкции.
Из перечисленных сварных соединений наиболее надежными и экономичными являются стыковые соединения, в которых действующие нагрузки и усилия воспринимаются так же, как в целых элементах, не подвергавшихся сварке, т.е. они практически равноценны основному металлу, конечно, при соответствующем качестве таких работ, как сварочные работы. Однако надо иметь в виду, что обработка кромок стыковых соединений и их подгонка под сварку достаточно сложны, кроме того, применение их бывает ограничено особенностями формы конструкций. Угловые и тавровые соединения также распространены в конструкциях. Нахлесточные соединения наиболее просты в работе, так как не нуждаются в предварительной разделке кромок, и подготовка их к сварке проще, чем стыковых и угловых соединений. Вследствие этого, а также из-за конструктивной форме некоторых сооружений они получили распространение для соединения элементов небольшой толщины, но допускаются для элементов толщиной до 60 мм. Недостатком нахлесточных соединений является их неэкономичность, вызванная перерасходом основного и наплавленного металла. Кроме того, из-за смещения линии действия усилий при переходе с одной детали на другую и возникновения концентрации напряжений снижается несущая способность таких соединений.
Сварка стыковых соединений – CarTechBooks
Джерри Уттрахи
Первое сварное соединение, которое вы должны изучить, это стыковое соединение. В то время как основной квадратный стык довольно легко освоить при должном количестве практики, есть много других стыков, которые вам нужно иметь в своем репертуаре. К ним относятся проходной квадратный стык, стыковое соединение, одиночный V-образный стык, одиночный V-образный сварной шов с подложкой, сварной шов внахлестку и многие другие.
Простые квадратные стыковые сварные швы часто используются при автомобильной сварке. Вариации могут быть полезны для обеспечения повышенной прочности. Сварка только с одной стороны может оставить часть корневой зоны несваренной. Это оставляет концентрацию напряжения, которая может вызвать образование трещины в сварном шве. Там, где требуется максимальная прочность, следует использовать сварной шов с полным проплавлением. TIG может производить сварку шва с полным проплавлением с одной стороны, но вам необходимо тщательно контролировать проплавление и убедиться, что шов полностью расплавлен.
Рис. 2.1. В сварных конструкциях используются сотни типов соединений. Ряд более сложных конструкций соединений относится к сварке толстых профилей, где J-образные канавки и U-образные канавки используются для уменьшения количества необходимого сварочного металла. Также существует множество соединений, предназначенных для использования в листовом металле, например, в воздуховодах, которые можно использовать в уличных стержнях.
Рис. 2.2. Изготовители разработали множество конструкций сварных соединений в качестве эффективных методов достижения подгонки, необходимой для получения сварных швов стабильного качества. Ряд отраслей, использующих трубчатые структурные компоненты, разработали критерии проектирования и процедуры сварки, которые могут быть адаптированы для изготовления гоночных автомобилей и уличных удилищ.
Когда вы можете сваривать с обеих сторон соединения, сварку с полным проплавлением выполнить легче. Для тонкого материала края могут быть соединены встык, сварной шов выполнен с одной стороны, а сварной шов выполнен с обратной стороны, которая полностью проникает в первую.
Рис. 2.3. Для достижения максимальной прочности следует использовать сварной шов с полным проплавлением. На нижней левой панели показано соединение, которое очень полезно для несколько более толстого материала. Сначала выполняется сварка в одном V-образном соединении для достижения хорошего провара. Затем задняя сторона выдалбливается или шлифуется до прочного металла сварного шва, образуя U-образную канавку. Затем в U-образной канавке делается второй сварной шов, чтобы полностью проникнуть в первый наплавленный металл.
Одиночная V-образная подготовка стыковых соединений является проверенным методом, принятым для ряда проектных спецификаций, и может обеспечить получение сварного шва с полным проплавлением. V-образная подготовка, используемая для соединения с полным проваром, особенно полезна для более толстых материалов, таких как пластины толщиной 3/16 и 1/4 дюйма. Если сначала использовать одну V-образную препаровку, оставив половину толщины пластины в качестве площадки, то можно достичь двух целей. Он обеспечивает хорошее проплавление первого сварного шва и оставляет площадку под V-образным швом, что предотвращает чрезмерное проплавление там, где посадка не является идеально плотной.
V часто можно сделать с помощью шлифовального станка, но вы должны быть осторожны, чтобы половина поверхности оставалась землей. Первый сварной шов размещается в V-образной канавке. Это должно быть сделано с достаточным током и скоростью, чтобы проникнуть примерно на три четверти толщины пластины.
Затем задняя сторона выдалбливается или шлифуется до прочного металла сварного шва с помощью шлифовальной машины, удерживаемой на боку, или пневматической рубительной машины с соответствующей канавкой, которая должна быть достаточно глубокой, чтобы нижняя часть достигала бездефектного металла сварного шва в первую очередь. боковой сварной шов, и в результате должно получиться U-образное соединение.
Затем в U-образную канавку помещают второй сварной шов с достаточным током, чтобы он сплавился с канавкой при первом проходе. Полученный сварной шов должен перекрывать около 20 процентов толщины шва. Это перекрытие устраняет любые корневые дефекты, которые могли быть созданы в первом сварном шве.
J-образная канавка представляет собой половину U-образной канавки и может использоваться там, где край толстой пластины упирается в вертикальный элемент, как это может быть при креплении поперечной распорки к боковой балке рамы. Как и U-образная канавка, J-образная канавка сводит к минимуму количество сварочного металла и тепла сварки, при этом обеспечивая адекватное проплавление.
Квадратные стыковые сварные швы из листового металла требуют очень плотной посадки. Для облегчения сварки этих соединений используется несколько методов. Одним из подходов является изготовление уступа или фланцевого соединения, используемого для изготовления баллонов с пропаном, огнетушителей и других сварных швов торцевых крышек сосудов из тонкого листового металла. При таком подходе один край соединения формируется так, что соединительная пластина надевается на изогнутую область. Это обеспечивает заднюю поддержку сварного шва и более терпимо к небольшим отклонениям при подгонке.
Соединение внахлест со смещением — это официальное кодовое название AWS Sheet Metal для этого типа соединения. Сам сварной шов называется сварным швом с развальцовкой. Как ни назови, это отличный стык при сварке патч-панели из листового металла. Доступны простые плоскогубцы с матрицами, приваренными к поверхностям захвата, от таких компаний, как Eastwood, которые могут постепенно формировать края, обеспечивая основу для последующего сварного шва. Есть пневматические устройства, которые обеспечивают такой же прогрессивный обжим и ускоряют задачу подготовки панели.
Рис. 2.4. Эти соединения подходят для сварки листового металла. Верхнее левое соединение обычно называют шарнирным соединением или фланцевым соединением. Официальное название AWS Sheet Metal Code — соединение внахлест со смещением. Как бы это не называлось, это отличный стык при сварке патч-панели. Доступны простые плоскогубцы с замком, которые могут постепенно формировать края, обеспечивая основу для последующего сварного шва.
В ряде отраслей промышленности изготавливаются детали из листового металла, такие как воздуховоды и кабины тракторов. Ряд соединений был разработан для облегчения сварки определенных типов профилей. Некоторые из этих конструкций, которые включают фланцевые соединения, могут быть полезны для конкретных применений уличных стержней. Эти фланцевые соединения, как их называют, облегчают сварку и могут потребовать меньшего подвода тепла. Оплавление кромок фланцевого стыкового шва, как показано на рис. 2.5, проще, чем изготовление квадратного стыкового шва из листового металла. Кроме того, кромки можно легко соединить зажимами и выполнить прихватку перед окончательной сваркой шва.
Те же преимущества при подгонке и сварке существуют для углового сварного шва полки. Подкладка сварного шва другой деталью, например, в угловом сварном шве, повышает прочность и более терпима к неточной подгонке.
Рис. 2.5. Изготовители, в том числе изготавливающие воздуховоды и кабины тракторов, сваривают листовой металл. Они разработали ряд соединений, упрощающих сварку определенных секций. Некоторые из них полезны для конкретных автомобильных приложений. Фланцевые соединения облегчают сварку и могут потребовать меньшего подвода тепла. Подложка сварного шва, как показанный угловой сварной шов, добавляет прочности и позволяет менее точную подгонку.
Типы сварных соединений | Геометрия стыкового шва | Расположение элементов обозначения сварки
«Сварочный шов — это точка или кромка, в которой соединяются вместе два или более куска металла или пластика. Они образуются путем сварки двух или более заготовок (металла или пластика) по определенной геометрии. Пять типов соединений, на которые ссылается Американское общество сварщиков: стыковые, угловые, кромочные, внахлестку и тройники. Эти конфигурации могут иметь различные конфигурации в месте соединения, где может происходить фактическая сварка». [Сварное соединение. Википедия]
Пример инженерного чертежа «Типы сварных соединений» был создан с использованием программного обеспечения для построения диаграмм и векторной графики ConceptDraw PRO, расширенного с помощью решения «Машиностроение» из области «Инженерное дело» ConceptDraw Solution Park.
Сварные швы
Используемые растворы
Инжиниринг >
Машиностроение
На этом техническом чертеже показаны различные типы геометрии стыковых сварных швов.
«Сварные швы могут быть геометрически подготовлены различными способами. Пять основных типов сварных соединений — это стыковое соединение, соединение внахлестку, угловое соединение, краевое соединение и Т-образное соединение (разновидностью последнего является крестообразное соединение). Другое также существуют вариации — например, разделочные швы двойной V характеризуются двумя кусками материала, каждый из которых сужается к единой центральной точке на половине их высоты. Имея прямые края, такие как одинарные V-образные и двойные V-образные подготовительные швы, они изогнуты, образуя форму буквы U. Соединения внахлест также обычно имеют толщину более двух частей — в зависимости от используемого процесса и толщины материала, многие детали могут быть сварены вместе в геометрии соединения внахлест». [Сварка. Википедия]
Этот пример инженерного чертежа был переработан с использованием программного обеспечения для построения диаграмм и векторной графики ConceptDraw PRO из файла Wikimedia Commons: Butt Weld Geometry.GIF.
[commons.wikimedia.org/ wiki/ File:Butt_ Weld_ Geometry.GIF]
Пример инженерного чертежа «Геометрия стыкового сварного шва» включен в решение «Машиностроение» из области «Инженерное дело» в парке решений ConceptDraw.
Схема сварного соединения
Используемые растворы
Инжиниринг >
Машиностроение
«Символы и условные обозначения, используемые в документации по сварке, указаны в национальных и международных стандартах, таких как ISO 2553 Сварные и паяные соединения. Символическое изображение на чертежах и ISO 4063 Сварка и родственные процессы. Номенклатура процессов и ссылки Стандартные символы США определены Американским национальным институтом стандартов и Американским обществом сварщиков и отмечены как «ANSI/AWS».
На технических чертежах каждый сварной шов обычно обозначается стрелкой, указывающей на свариваемое соединение. Стрелка снабжена буквами, цифрами и символами, которые указывают точную спецификацию сварного шва. В сложных приложениях, таких как сплавы, отличные от низкоуглеродистой стали, может потребоваться больше информации, чем можно указать с помощью одних только символов. В этих случаях используются аннотации». [Символы и условные обозначения, используемые в документации по сварке. Википедия]
Пример диаграммы «Элементы символа сварки» переработан с использованием программного обеспечения для построения диаграмм и векторного рисования ConceptDraw PRO из файла Википедии: Элементы символа сварки.PNG.
[en.wikipedia.org/ wiki/ File:Elements_ of_ a_ welding_ symbol.PNG]
Пример диаграммы «Расположение элементов символа сварки» содержится в решении «Машиностроение» из области «Инженерное дело» в парке решений ConceptDraw.
Таблица символов сварных соединений
Используемые решения
Инжиниринг >
Машиностроение
Библиотека векторных трафаретов «Сварка» содержит 38 обозначений сварных соединений для обозначения галтелей, контуров, контактных швов, пазов, наплавок и подкладок.
Используется для обозначения сварочных операций на рабочих чертежах.
«Сварка — это производственный или скульптурный процесс, который соединяет материалы, обычно металлы или термопласты, вызывая коалесценцию. Это часто делается путем плавления заготовок и добавления наполнителя для формирования ванны расплавленного материала (сварочная ванна), которая охлаждается до стать прочным соединением, при котором давление иногда используется в сочетании с теплом или само по себе для создания сварного шва, в отличие от пайки и пайки твердым припоем, которые включают расплавление материала с более низкой температурой плавления между заготовками для образования связи между ними. их, не расплавляя заготовки.
Для сварки можно использовать множество различных источников энергии, включая газовое пламя, электрическую дугу, лазер, электронный луч, трение и ультразвук.
Сварные швы могут быть геометрически подготовлены различными способами. Пять основных типов сварных соединений — это стыковое соединение, соединение внахлестку, угловое соединение, краевое соединение и Т-образное соединение (вариантом последнего является крестообразное соединение). Существуют и другие варианты — например, двойные V-образные подготовительные швы характеризуются двумя кусками материала, каждый из которых сужается к одной центральной точке на половине своей высоты. Одиночные U-образные и двойные U-образные подготовительные швы также довольно распространены — вместо того, чтобы иметь прямые края, как у одинарных V-образных и двойных V-образных подготовительных швов, они изогнуты, образуя форму U. Соединения внахлест также обычно имеют более двух толстые детали — в зависимости от используемого процесса и толщины материала многие детали могут быть сварены вместе в геометрии соединения внахлест.» [Сварка. Википедия]
Пример формы «Элементы дизайна — сварка» был создан с использованием программного обеспечения для построения диаграмм и векторной графики ConceptDraw PRO, расширенного с помощью решения «Машиностроение» из области «Инженерное дело» ConceptDraw Solution Park.
Символы сварных соединений
Используемые решения
Инжиниринг >
Машиностроение
«Сварочное соединение представляет собой точку или кромку, в которой два или более куска металла или пластика соединяются вместе. Они образуются путем сварки двух или более заготовок (металла или пластика) в соответствии с определенной геометрией. Пять типов соединений, упомянутых Американским обществом сварщиков: встык, угол, кромка, внахлест и тройник. Эти конфигурации могут иметь различные конфигурации в стыке, где может происходить фактическая сварка ». [Сварное соединение. Википедия]
Этот пример инженерного чертежа был переработан с использованием программы для построения диаграмм и векторной графики ConceptDraw PRO из файла Wikimedia Commons: Common Joint Types.png.
[commons.wikimedia.org/ wiki/ File:Common_joint_types.png]
Этот файл находится под лицензией Creative Commons Attribution-Share Alike 3.0 Unported.
[creativecommons.org/licenses/by-sa/3.0/deed.en]
Пример технического чертежа «Обычные типы соединений» включен в решение «Машиностроение» из области «Инженерное дело» в парке решений ConceptDraw.
Типы сварных соединений
Используемые растворы
Инжиниринг >
Машиностроение
На этом техническом чертеже представлены обозначения типов сварных швов и обозначения угловых сварных швов.
Символ типа сварного шва обычно размещается выше или ниже центра контрольной линии, в зависимости от того, на какой стороне соединения он находится. Символ интерпретируется как упрощенное поперечное сечение сварного шва.
«Угловая сварка относится к процессу соединения двух кусков металла вместе, независимо от того, расположены ли они перпендикулярно или под углом. Эти сварные швы обычно называются тройниковыми соединениями, которые представляют собой два куска металла, перпендикулярные друг другу, или соединениями внахлестку, которые состоят из двух частей. из металла, которые перекрываются и свариваются по краям.Шов имеет эстетически треугольную форму и может иметь вогнутую, плоскую или выпуклую поверхность в зависимости от техники сварщика.Сварщики используют угловые швы при соединении фланцев с трубами, сварке поперечных профилей инфраструктуры, и при недостаточно прочном креплении металла болтами». [Угловой шов. Википедия]
Пример инженерного чертежа Символы сварки включены в решение «Машиностроение» из области «Инженерное дело» в парке решений ConceptDraw.
Символы сварных соединений
Используемые решения
Инжиниринг >
Машиностроение
Библиотека векторных трафаретов «Сварка» содержит 38 обозначений сварных соединений для обозначения галтелей, контуров, контактных швов, пазов, наплавок и подкладок.
Используйте его для обозначения сварочных операций на рабочих чертежах в программном обеспечении для построения диаграмм и векторной графики ConceptDraw PRO, дополненном решением для машиностроения из области проектирования в парке решений ConceptDraw.
www.conceptdraw.com/solution-park/ engineering-mechanical
Дополнительная стрелка
Текстовый блок
Скругление
Прорезь/заглушка
Шпилька
Противостоящий шов
09002 Основа02 Уголок фланца
Край фланца
квадратная канавка
V-Grove
Bevel Groove
U-Grow Монтажная сварка
Основа/прокладка
Вставка
Стрела с изгибом
Стрела с изгибом, хвост
Стрела с изгибом, круг
Стрела с изгибом, круг, хвост
Стрела
стрелка, хвост
стрелка, круг
стрелка, круг, хвост
Spot
Проекционная сварка
Contour, Congave
Contour, Congex
Contour, Flush
Contour Angled, Concave
Contour.
Контур угловой, заподлицо
Квадратный стык
Закрытый квадратный стык
Стык с одинарным скосом
Стык с двойным скосом
Стык с V-образным вырезом
Двойной V-образный стык
Двойной J-образный стык
Двойной J-образный стык
Двойной U-образный стык
Двойной U-образный стык
Фланец встык
Square Butt Saint
Single V-подготовка для подготовки
LAP SAINT
T-Joint
Butt Weld
Butt Weld, Single-V
Двусторонний WALD WELD
TEE WELD
Угловой WELD
Механический швара
0005
Используемые растворы
Инжиниринг >
Машиностроение
Это решение расширяет программное обеспечение для черчения ConceptDraw DIAGRAM.9 (или более позднюю версию) образцами символов для механических чертежей, шаблонами и библиотеками элементов дизайна для помощи при составлении чертежей машиностроения или деталей, сборки, пневматики,
Решение для машиностроения — доступны 8 библиотек с 602 часто используемыми символами для чертежей в машиностроении, включая библиотеки под названием «Подшипники» с 59 элементами роликовых и шарикоподшипников, валов, шестерен, крюков, пружин, шпинделей и шпонок; Определение размеров и допусков с 45 элементами; Гидроэнергетическое оборудование, содержащее 113 элементов двигателей, насосов, воздушных компрессоров, счетчиков, цилиндров, приводов и датчиков; Гидравлические силовые клапаны, содержащие 93 элемента пневматических и гидравлических клапанов (распределители, клапаны управления потоком, клапаны регулирования давления) и клапаны электрогидравлические и электропневматические; а также многие другие сложные символы и шаблоны для вашего использования.
Библиотека векторных трафаретов «Арматура и фитинги» содержит 104 условных обозначения компонентов арматуры.
Используйте эти значки для рисования промышленных трубопроводных систем; технологические, вакуумные и жидкостные трубопроводы; трубопроводы гидравлики; воздуховоды и газопроводы; распространение материалов; и системы перекачки жидкости в программном обеспечении ConceptDraw PRO, дополненном решением для химической и технологической инженерии из области химической и технологической инженерии в ConceptDraw Solution Park.
www.conceptdraw.com/ Solution-park/ Engineering-Chemical-Process
Электрически связанный
Разрывной диск
Flame Arrester
Seperator
Гидюшн
ROOT
Выхлоп
Гидюшн
Bell
5955Bell Rooth
Дренажный глушитель
Жидкостное уплотнение открытое/закрытое
Y-образный сетчатый фильтр
Задвижка
Запорный клапан
Запорный клапан 2
Запорный клапан 3
СВИНТ-ВАЛАПАН КЛАПАН
Клапан с блокировкой
Клапан катушки
Проверка клапана
Проверка клапана 2
Проверка клапана 3
Проверьте клапан.
Мембранный клапан 3
Клапан с приводом
Клапан с приводом 2
Клапан с приводом 3
Игольчатый клапан
Игольчатый клапан 2
Игольчатый клапан 3
5 900 Предохранительный клапан0005
Свободный клапан 2
Свободный клапан 3
Угловой клапан
Угловой клапан 2
Угловой клапан 3
Угловой клапан 4
Флот. Поворотный затвор 2
Задвижка клиновая
Задвижка параллельная
Шаровой кран
Шаровой кран 2
Шаровой кран 3
Предохранительный угловой вакуумный клапан
Давление на угловом клапане рельефа
Редоверенный клапан
РЕЗУМИТЕЛЬНЫЙ КЛАПАН 2
Клапан подключения 3 WATE
Клапан подключения L Точка
Подключаемый клапан 2
Клапан подключения
Прямой клапан
T -Tope Tope
3 3 30002.
3-ходовой плунжерный клапан 2
3-ходовой плунжерный клапан 3
Смесительный клапан
Клапанный блок
Портовой клапан с характеристическими характеристиками
Редуктор
Редуктор 2
Общий сустав
Butt Weld
Butt Weld 2
Butt Weld 3
Butt Weld 4
фланцевой / болт -болтов Резьбовое соединение 3
Муфта и цапфа
Муфта и цапфа 2
Муфта и цапфа 3
Муфта
Муфта 2
Резьбовая муфта
Резьбовая муфта 20005
Socket Weld
Socket Weld 2
Смотанный соединительный соединение
Поворотный сустав 2
Своинный соединительный соединение 3
Конечная колпачка
Конечная крышка сварки
Конечная крышка наполненной
сварная
Торцевая крышка с резьбой и пробкой
Торцевая крышка быстросъемная
Торцевая крышка фланцевая и болтовая
Торцевая крышка фланцевая и болтовая 2
Электроизолированная
Промковш
Сифонный дренаж
Открытый клапан
Используемые растворы
Инжиниринг >
Химическая и технологическая инженерия
Библиотека векторных трафаретов «Трубы 1» содержит 28 символов труб. Используйте его для рисования планов зданий сантехники и трубопроводов, схематических диаграмм, чертежей или технических чертежей систем удаления сточных вод, систем горячего и холодного водоснабжения в программном обеспечении для построения диаграмм и векторной графики ConceptDraw PRO, дополненном решением Plumbing and Piping Plans от Building. Планы территории ConceptDraw Solution Park.
General joint
Butt weld
Soldered / solvent
Screwed joint
Socket and spigot
Sleeve joint
Socket weld
Flanged / bolted
Swivel joint
Electrically bonded
Electrically insulated
End заглушки 1
Заглушки 2
Заглушки 3
Фильтр
Сепаратор
Глушитель выхлопа
Глушитель дренажа
Открытое вентиляционное отверстие
Siphon Drain
Gudrant
Tundish
Bell Mouth
Выхлопная головка
Разрывной диск
Arrester Flame
Y Litger
Liquid Seare Open
. Строительные планы
>
Схемы сантехники и трубопроводов
«Сварочное соединение представляет собой точку или кромку, в которой два или более куска металла или пластика соединяются вместе. Они образуются путем сварки двух или более заготовок (металла или пластика) в соответствии с определенной геометрией. Пять типов соединений, упомянутых Американским обществом сварщиков: встык, угол, кромка, внахлест и тройник. Эти конфигурации могут иметь различные конфигурации в стыке, где может происходить фактическая сварка ». [Сварное соединение. Википедия]
Пример инженерного чертежа «Типы сварных соединений» был создан с использованием программного обеспечения для построения диаграмм и векторной графики ConceptDraw PRO, расширенного с помощью решения «Машиностроение» из области «Инженерное дело» ConceptDraw Solution Park.
Сварные швы
Используемые растворы
Инжиниринг >
Машиностроение
На этом техническом чертеже представлены обозначения типов сварных швов и обозначения угловых сварных швов.
Символ типа сварного шва обычно размещается выше или ниже центра контрольной линии, в зависимости от того, на какой стороне соединения он находится. Символ интерпретируется как упрощенное поперечное сечение сварного шва.
«Угловая сварка относится к процессу соединения двух металлических частей вместе, независимо от того, расположены ли они перпендикулярно или под углом. Эти сварные швы обычно называются тройниковыми соединениями, которые представляют собой два куска металла, перпендикулярные друг другу, или соединениями внахлестку, которые состоят из двух частей. из металла, которые перекрываются и свариваются по краям.Шов имеет эстетически треугольную форму и может иметь вогнутую, плоскую или выпуклую поверхность в зависимости от техники сварщика.Сварщики используют угловые швы при соединении фланцев с трубами, сварке поперечных профилей инфраструктуры, и при недостаточно прочном креплении металла болтами». [Угловой шов. Википедия]
Пример инженерного чертежа Символы сварки включены в решение «Машиностроение» из области «Инженерное дело» в парке решений ConceptDraw.
Символы сварных соединений
Используемые решения
Инжиниринг >
Машиностроение
Библиотека векторных трафаретов «Трубы 2» содержит 48 условных обозначений труб. Используйте его для рисования планов зданий сантехники и трубопроводов, схематических диаграмм, чертежей или технических чертежей систем удаления сточных вод, систем горячего и холодного водоснабжения в программном обеспечении для построения диаграмм и векторной графики ConceptDraw PRO, дополненном решением Plumbing and Piping Plans от Building. Планы территории ConceptDraw Solution Park.
пересечение
Junction
Основная поддержка
Руководство 1
Руководство 2
Руководство 3
Stopper
Anchor
Опочка / Анкер
Hunger
Double Branked
9000Double Brankved
.
Муфтовое соединение
Компенсационное муфтовое соединение
С лагами
Сильфон
Индикатор потока
Индикатор потока 2
Переходник
Reducer,arrow
Pipe bore change
Flexibility provision
Sleeve extension
Flow restrictor
Elbow 45
Elbow 90
Heated or cooled
Pneumatic line
Signal line
Electric line
Hydraulic line
Капиллярная линия
Внутреннее соединение
Трассовое излучение
Механическая связь
Электрическое устройство
Вибрационное устройство
Весовое устройство
Spray Device
Роторное движение
помешивание / вентилятор
Точки доступа
TRAP
Lop Lo Строительные планы >
Схемы сантехники и трубопроводов
Библиотека векторных трафаретов «Арматура и фитинги» содержит 104 условных обозначения компонентов арматуры.
Используйте эти значки для рисования промышленных трубопроводных систем; технологические, вакуумные и жидкостные трубопроводы; трубопроводы гидравлики; воздуховоды и газопроводы; распространение материалов; и системы перекачки жидкости.
«Клапан — это устройство, которое регулирует, направляет или регулирует поток жидкости (газов, жидкостей, псевдоожиженных твердых веществ или взвесей) путем открытия, закрытия или частичного перекрытия различных проходов. Клапаны технически представляют собой фитинги клапанов, но обычно обсуждаются в отдельную категорию В открытом клапане жидкость течет в направлении от более высокого давления к более низкому давлению.
Простейший и очень древний клапан представляет собой просто свободно откидывающуюся створку, которая опускается, препятствуя потоку жидкости (газа или жидкости) в одном направлении, но открывается потоком в противоположном направлении. Это называется обратным клапаном, так как он предотвращает или «контролирует» поток в одном направлении. …
Клапаны
используются практически во всех промышленных процессах, включая водоснабжение и очистку сточных вод, горнодобывающую промышленность, производство электроэнергии, переработку нефти, газа и нефти, производство продуктов питания, химическое производство и производство пластмасс и многие другие области. …
Клапаны могут управляться вручную с помощью рукоятки, рычага, педали или колеса. Клапаны также могут быть автоматическими, приводимыми в действие изменениями давления, температуры или расхода. Эти изменения могут воздействовать на диафрагму или поршень, который, в свою очередь, активирует клапан. Примерами такого типа клапана обычно являются предохранительные клапаны, устанавливаемые на системы горячего водоснабжения или бойлеры.
Для более сложных систем управления, использующих клапаны, требующих автоматического управления на основе внешнего входа (т. е. регулирования расхода через трубу в соответствии с изменением заданного значения), требуется привод. Привод будет перемещать клапан в зависимости от его входного сигнала и настройки, позволяя точно позиционировать клапан и позволяя контролировать различные требования». [Клапан. Википедия]
Пример «Элементы дизайна — Клапаны и фитинги» был создан с использованием программного обеспечения для построения диаграмм и векторной графики ConceptDraw PRO, дополненного решением Chemical and Process Engineering из области Engineering в ConceptDraw Solution Park.
Символы клапанов и фитингов
Используемые решения
Инжиниринг >
Химическая и технологическая инженерия
Библиотеки векторных трафаретов «Трубы 1» и «Трубы 2» содержат 28 и 48 символов труб, труб и фитингов соответственно.
«Фитинги используются в водопроводно-канализационных системах для соединения прямых секций труб или труб, для адаптации к разным размерам или формам, а также для других целей, таких как регулирование или измерение потока жидкости. Термин «сантехника» обычно используется для описания подачи воды. , газ или жидкие отходы в обычных бытовых или коммерческих условиях, тогда как трубопровод часто используется для описания высокопроизводительной (например, высокого давления, высокого расхода, высокой температуры, опасных материалов) транспортировки жидкостей в специализированных приложениях. для более легких труб, особенно таких, которые достаточно гибкие, чтобы их можно было поставлять в бухтах.
Фитинги (особенно необычные типы) требуют денег, времени, материалов и инструментов для установки, поэтому они являются нетривиальной частью трубопроводных и сантехнических систем.
Используйте библиотеки элементов дизайна «Трубы 1» и «Трубы 2» для рисования планов зданий сантехники и трубопроводов, принципиальных схем, чертежей или технических чертежей систем водоотведения, систем горячего и холодного водоснабжения с использованием диаграмм и векторов ConceptDraw PRO. ПО для рисования.
Библиотеки форм «Трубы 1» и «Трубы 2» содержатся в решении Plumbing and Piping Plans из области Building Plans в ConceptDraw Solution Park.
Символы трубопроводов
Используемые решения
Строительные планы >
Схемы сантехники и трубопроводов
Библиотека векторных трафаретов «Клеммы и разъемы» содержит 43 обозначения элементов клемм, разъемов, вилок, поляризованных разъемов, разъемов, коаксиальных кабелей и проводников.
Используйте его для рисования электрических схем, электрических схем, электронных схем и принципиальных схем.
«Электрический соединитель — это электромеханическое устройство для соединения электрических цепей в качестве интерфейса с использованием механического узла. Соединители состоят из вилок (штыревых) и гнезд (гнездовых). Соединение может быть временным, как для переносного оборудования , требуют инструмента для сборки и снятия или служат постоянным электрическим соединением между двумя проводами или устройствами.Адаптер можно использовать для эффективного соединения разнородных разъемов.
Существуют сотни типов электрических разъемов. Соединители могут соединять два отрезка гибкого медного провода или кабеля или соединять провод, кабель или оптический интерфейс с электрическим терминалом.
В вычислительной технике электрический разъем также может быть известен как физический интерфейс… Кабельные вводы, известные в США как кабельные разъемы, соединяют провода с устройствами механически, а не электрически, и отличаются от быстроразъемных соединений, выполняющих последнее.» [ Электрический разъем.Википедия]
«Вывод — это точка, в которой заканчивается проводник электрического компонента, устройства или сети и обеспечивает точку подключения к внешним цепям. Вывод может быть просто концом провода или может быть снабжен соединитель или застежка. В сетевом анализе терминал означает точку, в которой теоретически могут быть установлены соединения с сетью, и не обязательно относится к какому-либо реальному физическому объекту. В этом контексте, особенно в старых документах, его иногда называют «полюсом». «.
Соединение может быть временным, как в портативном оборудовании, может требовать инструмента для сборки и удаления, или может быть постоянным электрическим соединением между двумя проводами или устройствами.
Все электроэлементы имеют две клеммы. Первая клемма положительная, а вторая отрицательная. Положительная клемма выглядит как металлический колпачок, а отрицательная клемма выглядит как металлический диск. Ток течет от положительной клеммы и выходит через отрицательную клемму, повторяя ток (от положительного (+) к отрицательному (-) потоку)». [Терминал (электроника). Википедия]
Пример формы «Элементы дизайна — Клеммы и соединители» был нарисован с использованием программного обеспечения для построения диаграмм и векторной графики ConceptDraw PRO, расширенного с помощью решения «Электротехника» из области «Инженерия» в парке решений ConceptDraw.
Символы клемм и разъемов
Используемые решения
Инжиниринг >
Электротехника
Библиотека векторных трафаретов «Сварка» содержит 38 обозначений сварных соединений для обозначения галтелей, контуров, контактных швов, канавок, наплавок и подкладок.
Используйте его для обозначения сварочных операций на рабочих чертежах в программном обеспечении для построения диаграмм и векторной графики ConceptDraw PRO, дополненном решением для машиностроения из области проектирования в ConceptDraw Solution Park.
www.conceptdraw.com/solution-park/ engineering-mechanical
Дополнительная стрелка
Текстовый блок
Филлет
Слот / Плакатель
СТУД
Устойчивый швы
ОБСЛУЖИВАНИЕ
КВАРФАНТА
Угловой
BEVELANGE
Квадрат
V-GROEV канавка
J-образная канавка
Развальцовка V-образная канавка
Развальцовка скошенная канавка
Скос
Сварной шов проплавлением
Монтажная сварка
Основа/прокладка
Вставка
Стрела с изгибом
Стрела с изгибом, хвост
Стрела с изгибом, круг
Стрела с изгибом, круг, хвост
Стрела
Стрела, хвост
Стрела, хвост
Стрела, круг 9005 Стрела, хвост 9002
Точечный
Выступающий сварной шов
Контур, вогнутый
Контур, выпуклый
Контур, заподлицо
Контур, изогнутый, вогнутый
Контур, угловой, выпуклый 9000 0d0005
Квадратный стык
Закрытый квадратный стык
Стык с одинарным скосом
Стык с двойным скосом
Стык с одинарным V
Стык с двойным V
Стык с двойным J05 0 9 Сварка встык J
Сварка встык одинарной U-образной формы
Сварка встык двойной U-образной формы
Сварка встык с фланцем
Сварка встык с тройником
Сварка встык с развальцовкой
Квадратное стыковое соединение
Соединение внахлест 9 Подготовка
05
Тройник
Сварка встык
Сварка встык, одиночный V
Двусторонний шов внахлест
Тройник
Угловой шов
Механическая сварка
Используемые решения Инжиниринг >
Машиностроение
Библиотека векторных трафаретов «Кабельное телевидение» содержит 64 символа сетевого оборудования кабельного телевидения.
Используйте эти формы для рисования планов этажей проекта системы кабельного телевидения, схем топологии сети, схем проводки и схем разводки кабелей в программном обеспечении ConceptDraw PRO для построения диаграмм и векторного рисования.
Библиотека векторных шаблонов «Кабельное телевидение» включена в решение «Планы электроснабжения и телекоммуникаций» из области «Планы зданий» в ConceptDraw Solution Park.
Ответвитель направления вывода 1
Ответвитель направления вывода 2
Ответвитель направления вывода 3
Ответвитель направления вывода 4
Выходная направленная нажатие 5
2-way Splitter
3-hip Splitter
4. Нижняя оттяжка с анкером
Межполюсная оттяжка
Тротуарная нижняя оттяжка с анкером
Тротуарная нижняя оттяжка
Провисающий трос
Натянутый несущий трос без троса
Натянутый несущий трос
Заземление
Совместное использование (силовая и телефонная опора)
Соединение опоры Usgae с трансформатором
Распорка
Растяжка с анкером
Толкающая скоба (меньшая опора в фактическом относительном положении)
2 Встроенная опора CATV2
Предлагаемая опора кабельного телевидения
Направленный ответвитель 1
Направленный ответвитель 2
Люк
Телефонная опора
Подъемная стойка
Портативное хранилище Vault
Фиксированный эквалайзер0005Фиксированные плоские аттенюаторы
Другие вспомогательные конструкции
Пьедестал-подземная маршрутизация
Power Pole
Прямая похороненная подземная маршрутизация
Линия Duct Line Under Ground
3-way Lecination Место соединения
Место соединения четырехканального оптического кабеля
> Место соединения четырехжильного оптического кабеля
Оптический усилитель
Кабельный объединитель мощности переменного тока
Оптическое волоконно -кабельное кабель
Оптический разъем
Демольтиплекзер
. Концентратор
Коаксиальный соединитель
Блок питания
Переменный эквалайзер
Используемые решения
Строительные планы >
Электрические и телекоммуникационные планы
Сверхвысокая частота (UHF) — это обозначение ITU для радиочастот в диапазоне от 300 МГц до 3 ГГц, также известном как дециметровый диапазон, поскольку длина волны находится в диапазоне от одного метра до одного дециметра. Радиоволны с частотами выше диапазона УВЧ попадают в СВЧ (сверхвысокую частоту) или микроволновый диапазон частот. Сигналы более низкой частоты попадают в VHF (очень высокие частоты) или в более низкие диапазоны. Радиоволны УВЧ распространяются в основном по линии прямой видимости; они заблокированы холмами и большими зданиями, хотя передача через стены зданий достаточно сильна для приема внутри помещений. Они используются для телевизионного вещания, сотовых телефонов, спутниковой связи, включая GPS, персональных радиослужб, включая Wi-Fi и Bluetooth, раций, беспроводных телефонов и многих других приложений.
26 библиотек электротехнического решения ConceptDraw DIAGRAM делают ваши электрические схемы простыми, эффективными и действенными. Вы можете просто и быстро перетаскивать готовые к использованию объекты из библиотек в свой документ для создания электрической схемы.
Что, схема, символ, процесс, машина, прочность и несколько фактов – Lambda Geeks
Стыковая сварка часто используется в сварочной промышленности, как автоматические, так и ручные методы стыковой сварки очень популярны уже несколько десятилетий.
Стыковой сварной шов соединяет две металлические поверхности, лежащие кромкой к кромке в одной плоскости относительно друг друга. В случае зазора между пластинами максимально допустимый зазор составляет 1/16 дюйма, и, наконец, этот зазор заполняется сварочным стержнем в процессе сварки.
В основном стыковые и угловые швы представляют собой два типа непрерывных швов, все остальные соединения являются модификациями этих двух типов.
Одинарная V-образная сварка встык; Изображение предоставлено: wikipedia Что такое сварка встык?Сварка встык — наиболее известная, простая и универсальная форма соединения, используемая в производственных отраслях и трубопроводах.
При сварке встык два элемента не перекрывают друг друга, а их края почти параллельны друг другу. Стыковое сварное соединение выполняется простым размещением двух металлических пластин или компонентов рядом друг с другом в одной плоскости, при этом металл сварного шва остается вдоль стыка в пределах плоскостей поверхностей.
Этот метод сварки очень распространен в таких отраслях, как трубопроводная, автомобильная, энергетическая, энергетическая и т. д.
Схема стыкового соединения Стыковые соединения широко используются в производстве и трубопроводах. Расплавленный металл наносится по внешней окружности соединения.
Различные типы стыковых сварных швов подготавливаются в зависимости от толщины металлических листов, перед сваркой необходима подготовка разделки и кромки. На рисунке ниже показаны различные типы стыковых сварных швов, которые дадут четкое представление.
Геометрия стыкового соединения; Кредит изображения: Википедия Символ стыкового сварного шваСтандартные символы используются на чертеже для руководства сварщиками, что, в свою очередь, помогает лучше контролировать внешний вид и механические свойства сварных швов.
Стандартные символы США определены Американским национальным институтом стандартов и Американским обществом сварщиков и отмечены как «ANSI/AWS». Символы сварки наиболее широко используются в чертежах металлоконструкций.
Символы сварки наиболее широко используются в чертежах металлоконструкций.
Стыковой сварной шов может быть обозначен с помощью
1. Линия со стрелкой
2. Базовая линия
3. Пунктирная линия
4. Символ
Технические чертежи сварных швов состоят из стрелки, острие стрелки всегда указывает на свариваемое соединение. Эта стрелка состоит из букв, определенных символов и цифр, которые указывают на конструкцию или схему сварного соединения.
Символическое изображение V-образного сварного шва пластин с фаской на техническом чертеже; Кредит изображения: Википедия Процесс стыковой сваркиКак правило, стыковые соединения привариваются с использованием таких методов, как дуговая сварка, контактная сварка, высокоэнергетическая лучевая сварка и даже пайка медных деталей.
MIG или TIG в основном применяются для сварки встык, поскольку они могут естественным образом соединять два куска металла вместе, для улучшения таких свойств, как коррозионная стойкость и прочность, используются различные типы сварочных электродов.
Область, которая оплавляется в процессе сварки, называется поверхностью стыка. Для повышения прочности сварного шва поверхность стыка должна быть сформирована, что широко известно как подготовка кромок. Подготовка кромок является обязательной для большинства конструкций стыковых соединений.
Подготовка кромок может быть одинаковой или различной для обоих элементов стыкового соединения.
Применение встыкПростой, прочный, долговечный, с широким спектром охвата материалов, гладкой поверхностью и т. д. — преимущества, делающие стыковой шов более универсальным.
Один из наиболее распространенных типов сварных соединений, применяемых при изготовлении трубопроводов и трубопроводов в промышленности. Стыковые соединения также используются в автомобильной промышленности, при ручной дуговой сварке, в энергетике.
Преимущества стыкового соединения Сварка встык предпочтительнее других типов сварки, так как она создает прочный шов и может применяться в различных ситуациях.
Преимущества стыковой сварки:
- Стыковая сварка может выполняться на широком спектре материалов, таких как алюминий, сталь, нержавеющая сталь, никелевые сплавы, титан и т. д.
- прочный и постоянно герметичный шов с полным сплавлением.
- Мы можем получить недорогие фитинги с этими сварными швами.
- Сварные швы имеют гладкую поверхность, так как присадочный металл помещается в канавку.
- Занять небольшое место в здании.
- Можно создать несколько сварных швов различной формы и размера в области стыка.
- Проверка стыковых сварных швов очень проста.
- Обработка проста и
- Обеспечивает контроль искажений.
- Менее подвержен загрязнениям.
Преимущества, связанные со стыковым соединением, следующие:
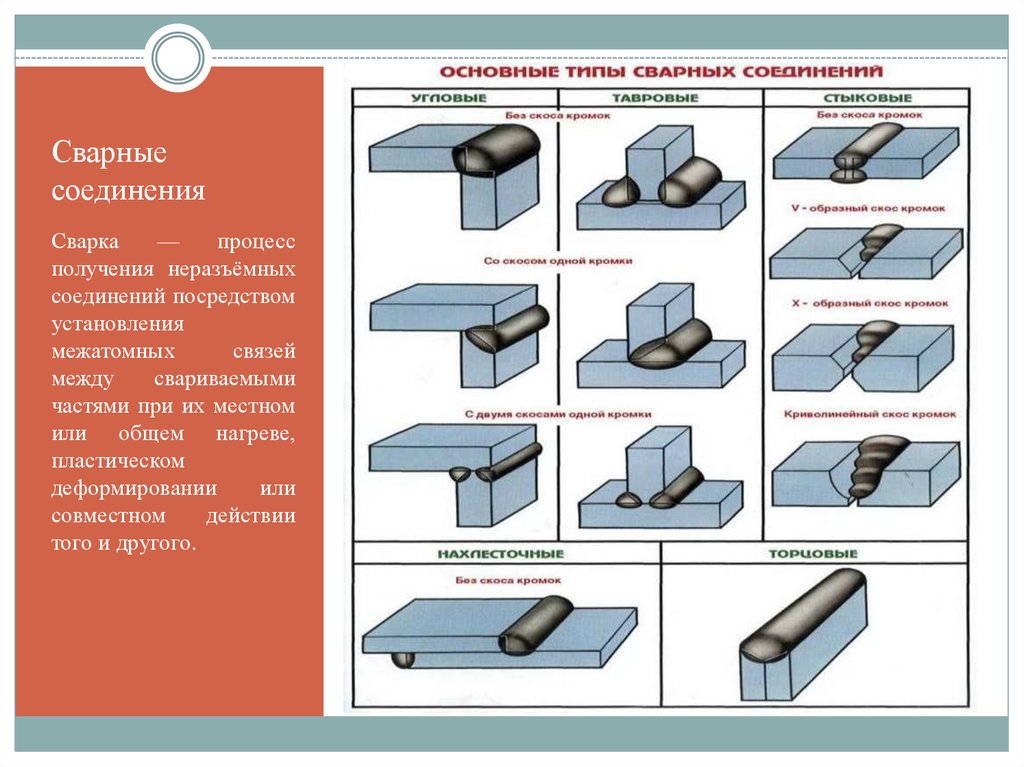
Стыковые соединения изготавливаются в различных исполнениях в зависимости от ширины зазора, толщины пластин и используются для разных целей.
Certain typical examples of Butt Joints are listed below:
- Square butt weld
- Single and double Bevel Butt Weld
- Single and Double V but t weld
- Single и двойной U-образный стыковой шов
- Одинарный и двойной J-образный стыковой шов
Это простейшая конструкция соединения, толщина соединяемых металлических деталей составляет 3/16 дюйма или меньше. чем это. На тонких металлических деталях возможно полное проплавление сварных швов с использованием квадратных стыковых сварных швов.
Хотя квадратные стыковые швы довольно прочные, они не подходят для постоянных усталостных нагрузок. Края двух частей не требуют каких-либо модификаций, таких как скашивание или снятие фасок.
Одинарная и двойная стыковая сварка со скосомВ случае толстых металлических деталей сложно получить 100% проплавление при стыковой сварке, для этого требуется определенный тип подготовки разделки.
В конструкции с одним скосом одна часть остается квадратной, а другая часть скошена под заданным углом.
Одинарная и двойная V-образная стыковая сварка V-образные сварные швы требуют больше затрат на подготовку, чем квадратные стыковые сварные швы, а также требуют больше присадочного материала. С помощью резака или станка для снятия фаски подготавливается V-образный паз. Основное преимущество заключается в том, что V-образные швы прочнее, чем квадратные стыковые швы.
Время подготовки для двойного V-образного шва больше по сравнению с одинарным V-образным швом. Но использование присадочного металла меньше, поскольку двойной V-образный шов дает более узкое пространство.
Одинарная и двойная U-образная стыковая сваркаСтоимость подготовки и сварки U-образного соединения самая высокая. Два куска выполнены в виде J-образной канавки, и когда они соединяются, получается форма в форме буквы U.
В двойном U-образном соединении U-образная канавка существует как в верхней, так и в нижней части соединения, обычно наносится на толстое основание. металлы.
Одинарная и двойная J-образная сварка встык Подготовка J-образной канавки сложнее и дороже, чем V-образная, подготовка канавки выполняется с помощью специального оборудования или шлифования. Здесь один элемент имеет форму буквы J, а другой — квадратную форму.
В двойном J одна часть имеет J-образную форму с обоих концов, а другая – квадратную.
Стыковое соединение под угломКлассический пример стыкового соединения под углом — это рамка для картины, состоящая из четырех стыковых соединений в каждом углу, все четыре конца которых срезаны под углом 45 градусов.
Стыковое соединение под углом
– это соединение между двумя деталями, срезанными под углом 45 градусов в углу и расположенными рядом друг с другом , обычно образующими угол 90 градусов. Он может изменяться и действительно изменяется под любым углом, превышающим 0 градусов, и соединение встречается в острой точке. Рамка для картины, лепнина и трубы являются общими примерами. Угловое соединение двух труб; Кредит изображения: Википедия. Это разновидность простого соединения по дереву, которое обычно придает красивый вид рамам для картин и картин. Они недостаточно прочны, так как не имеют замковых элементов и зависят только от столярного клея.
Стыковая сварка с осадкой или сопротивлением в основном используется для цветных металлов с меньшим поперечным сечением, таких как стержни, стержни, трубы, проволока и т. д. за счет тепла, выделяемого электрическим сопротивлением через область, где поверхности соприкасаются. Приложение давления является обязательным, применение тепла начинается до нагрева и продолжается на протяжении всего процесса.
Сварка внахлестку также наблюдается в стальных рельсах, закрытии капсул, небольших контейнеров и т.д. или меньше этого.
Хотя квадратные стыковые швы довольно прочные, они не подходят для постоянных усталостных нагрузок. Края двух частей не требуют каких-либо модификаций, таких как скашивание или снятие фасок. На тонком металлическом листе возможны сварные швы с полным проплавлением, используя квадратные стыковые сварные швы.
Оба они являются наиболее распространенными непрерывными швами.
Различают стыковые и угловые сварные швы, как указано ниже:

Сварка внахлест и встык довольно популярны.
Мы можем дифференцировать сварные швы с прикладом и сокетами, как упомянуто ниже:
Butt | Сокет |
. | При сварке внахлест используются две трубы разного диаметра, и меньшая вставляется в большую. |
Для лучшего проникновения требуется снятие фаски. | Оба конца имеют прямоугольную форму и не требуют снятия фаски или какой-либо подготовки, кроме очистки поверхности. |
Обычно используется для труб большого диаметра. | В основном применяется для труб малого диаметра. |
Трубы соединяются сваркой встык. | Дает угловой шов.![]() |
Метод рентгеновского контроля принят для испытаний. | Приняты неразрушающие методы испытаний, такие как испытание магнитным порошком (MT) или испытание на проникновение (PT) . |
Высокая устойчивость к коррозии. | Менее устойчивый к коррозии. |
Если мы рассматриваем трубы малого диаметра, стоимость фитингов для сварки враструб выше, чем фитингов для сварки встык, но сварка встык дороже, если учитывать проектирование, испытания, установку и техническое обслуживание. Раструбные соединения довольно просты с точки зрения сборки, обслуживания и установки, что делает их менее дорогими, чем сварные швы.
При определенных условиях сварка встык почти в два раза прочнее, чем сварка враструб.
.
Стыковая сварка Машина Эффективная машина для стыковой сварки должна обеспечивать точное давление сварки, а также высокую прочность сварки.
А Машина для стыковой сварки должна иметь корпус с зажимами, триммером, нагревателем, съемным электронарезчиком, блоком управления, коробом корпуса машины и набором вставок для подгонки под разные диаметры труб.
Цена сварочного аппарата варьируется в зависимости от диаметра свариваемого изделия, для большого диаметра сварного шва стоимость сварочного аппарата также высока.
Размеры этих машин варьируются от W160 (мощность 220 В — 0,55 кВт) до W2800 (мощность 380 В — 4 кВт).
Заключение:
В завершение нашего поста мы можем сказать, что стыковая сварка является одним из наиболее широко используемых сварочных процессов, который приводит к различным типам стыковых сварных швов с различными особенностями, и их необходимо тщательно выбирать в соответствии с нашими требованиями и бюджет.
Что такое сварка встык
Материалы
Дипломированный инженер
Что такое сварка встыкСварка встык — один из самых простых и универсальных видов сварных соединений. Сварка встык выполняется путем размещения двух кусков металла встык и их сварки вдоль стыка.
Важнейшим аспектом стыковой сварки является то, что два куска металла, соединенные вместе, находятся в одной плоскости, а сварной шов остается в плоскости поверхностей. В результате два металла расположены или почти параллельны друг другу без перекрывающихся аспектов.
Теплопроницаемость важна для стыкового сварного шва, который не представляет сложности при соединении тонких металлических деталей. Однако с более толстыми заготовками это сложнее.
При стыковой сварке более толстых заготовок требуется подготовка поверхности, чтобы сохранить проникновение тепла. Подготовка поверхности включает создание различных форм клина между двумя соединяемыми материалами.
Созданы различные формы клина, включая U-образный, J-образный, V-образный клин и многие другие (см. ниже)
Различные геометрии клина для стыкового шва Источник: здесьВ зависимости от требуемой степени проникновения тепла, определяемой толщиной материала, требуются различные клинья. Приоритетным соображением является минимизация объема сварного шва, необходимого для заполнения шва.
Стыковые сварные швы, как и все остальные сварные швы, обладают наибольшей прочностью при наименьшем количестве дефектов. Следовательно, минимизация требуемого объема сварного шва сводит к минимуму вероятность возникновения дефектов.
Лучшим методом стыковой сварки является сварка MIG или TIG, которые являются типами дуговой сварки. Сварка выполняется вручную или автоматически.
Сварка встык обычно выполняется на стальных деталях из-за популярности стали в сварных конструкциях.
Типы стыковой сварки Существует ряд других способов выполнения стыковой сварки помимо сварки MIG и TIG. Двумя альтернативными методами являются сварка оплавлением и сварка сопротивлением.
Сварка оплавлением представляет собой разновидность контактной сварки и представляет собой процесс, не требующий присадочного материала. В зависимости от ряда факторов, таких как толщина материала, желаемые свойства сварного шва и состав материала, два сопрягаемых материала располагаются на заданном расстоянии друг от друга.
После установки на металл подается ток, что приводит к образованию сопротивления между двумя сопрягаемыми частями. Сопротивление между двумя частями помогает создать дугу, плавя металлы и образуя сварной шов.
Заготовки прижимаются друг к другу после достижения нужной температуры, что способствует укреплению сварного соединения.
Операция при сварке оплавлением. Предоставлено: Bigchrisrogers Лицензия: CC BY-SA 3.0 Сварка сопротивлением Сварка сопротивлением состоит из двух заготовок, удерживаемых вместе с заданной силой. Два сварочных наконечника фиксируют детали на месте.
Через наконечники проходит ток, который проходит через две части, соединенные вместе. Из-за высокого сопротивления на поверхности поверхности детали выделяется тепло, которое инициирует плавление заготовок и создает сварной шов.
Наконечники для сварки имеют внутренний механизм охлаждения, предотвращающий выделение избыточного тепла на поверхности и локализующий его на границе раздела деталей.
Схема контактной сварки. Источник: Сварка алюминия и его сплавов Типы стыковых сварных соединенийСварщики могут использовать множество различных типов стыковых сварных соединений. Они следуют основной номенклатуре, названной в честь формы клиньев, созданных в результате подготовки поверхности.
Одинарная V-образная стыковая сварка. Предоставлено: Натаниэль С. Шитц. Лицензия: CC BY-SA 3.0 Эти различные типы включают V-образное соединение, коническое соединение, U-образное соединение, J-соединение и многие другие. Для большинства типов суставов характерно наличие «двойного» аналога. Например, двойной V-образный шарнир, двойной J-образный шарнир и т. д.
Самый простой тип стыкового сварного соединения – квадратное стыковое сварное соединение. Основной причиной этого является выравнивание соединения перед сваркой.
Преимущества сварки встыкИспользование сварки встык имеет множество преимуществ:
- Простота контроля качества
- Высокая прочность при полном проплавлении
- Простота выполнения послесварочных работ, таких как шлифовка
5
5 Недостатки стыковых сварных швов
Хотя стыковой шов является универсальным сварным соединением, он также имеет некоторые недостатки:
- Может потребоваться крепление
- Геометрия сварного шва может ограничивать область применения
- Чувствительность к определенным поверхностным условиям
- Похожие сообщения:
- Что такое сварка и дуговая сварка?
- Что такое пористость сварных швов
Социальные сети: LinkedIn, Facebook, Twitter
Сварка трением с перемешиванием: сравнение встык и внахлестку
Квадратное стыковое соединение
Торцевое стыковое соединение
Т-образное стыковое соединение
На следующем поперечном сечении мы можем увидеть, как стыковый шов выполняется внутри сварного шва толщиной 2 мм:
Поперечное сечение стыкового шва FSW сварка
Хорошим примером применения стыковой сварки является изготовление радиаторов :
Водяной радиатор, сваренный СТП, для электромобилей
Например, в этом водяном радиаторе для e-mobile, на корпус надевается крышка, через которую циркулирует холодная вода.
Он приварен к радиатору методом СТП, в частности, сваркой встык.
Другой пример стыковой сварки можно увидеть в этих двух сварных реолитых деталях (СТП более сложных компонентов, которые ранее не подвергались литью):
СТП двух реолитых деталей
СВАРКА В НАХОДКУ 02 90,0578 Альтернативно сварка внахлест, детали располагаются друг над другом:
Опять же, есть три положения, которые могут быть выбраны для выполнения сварки внахлест посредством сварки трением с перемешиванием: соединение внахлестку, соединение внахлестку и Т-образное соединение внахлестку.
Решение о выборе типа сварки встык или внахлест зависит от области применения, для которой предназначена сварка трением с перемешиванием. Однако выбор типа сварки влияет на 5 пунктов:
• Типичные дефекты СТП в зависимости от типа сварного шва
• Стойкость СТП в зависимости от сварки внахлест/встык
• Скорость сварки СТП в зависимости от сварки встык или внахлестку
• Подготовка поверхности СТП в зависимости от типа сварки
• Система зажима СТП, предназначенная для сварка встык или внахлестВажно знать об этих различиях, чтобы выбрать наиболее эффективный способ сварки.
Поэтому мы объясним каждый из них по пунктам ниже.
Продолжайте читать и не упустите ни одной детали!
FSW Типичные дефекты, связанные с типом сварки
Коммунальные дефекты FSW к сварке приклада и сварки на коленяхКогда процесс сварки фрикционных перевозки может возникнуть. Особое внимание следует уделить тому, чтобы избежать их, чтобы добиться высокого качества сварного шва. Некоторые из них могут возникать независимо от положения деталей при сварке, то есть могут возникать вне зависимости от того, стыковая это сварка или сварка внахлестку.
Например, типы дефектов, которые могут появиться независимо от того, является ли это сваркой встык или внахлестку: заусенец и червоточина (оба видны невооруженным глазом):
червоточина
Однако существуют являются другими типами дефектов СТП, которые специально связаны со сваркой встык или внахлестку.
ЧАСТЫЕ ДЕФЕКТЫ СТП ПРИ СТЫКОВОЙ СВАРКЕ0012 отсутствие проникновения происходит.
Этот дефект возникает, когда инструмент СТП не проходит полностью через детали, оставляя часть их несваренными. Этот дефект нельзя увидеть невооруженным глазом, так как это внутренний дефект.
Непровар
При осмотре дефекта изнутри видно, что детали не сварены, а просто склеены. На следующих изображениях мы можем видеть линию, которая разделяет обе части и показывает, что они не сварены (поскольку части не были удалены, создавая единое целое):
Тем не менее, мы не должны слишком беспокоиться об этом дефекте, так как его легко избежать. Поэтому выполнять стыковую сварку проще, чем сварку внахлестку, если ориентироваться на этот момент.
ЧАСТЫЕ ДЕФЕКТЫ СТП ПРИ СВАРКЕ В НАХОДКУГоворя о дефектах, которые могут возникнуть при выполнении сварки внахлестку, необходимо учитывать зацепление и поцелуй :
С одной стороны, сцепление поцелуев происходит, когда поверхность раздела между двумя соединяемыми металлами недостаточно нагрета и перемешана, что приводит к образованию остаточного оксидного слоя.
На границе раздела связь может быть незначительной или вообще отсутствовать, что увеличивает местное напряжение в сварном шве во время механического воздействия. В случае сварки внахлест разрушение оксида на границе раздела листов затруднено, чем при сварке встык, из-за ориентации границы раздела по отношению к инструменту СТП.
С другой стороны, дефект зацепления образуется, когда поверхность раздела между двумя соединяемыми листами встряхивается в верхний лист, что эффективно уменьшает площадь поперечного сечения верхнего листа. Дефект зацепления возникает в TMAZ AS (TMAZ = зона термомеханического воздействия). Более того, форма и вертикальное направление надреза могут снижать механические свойства, выступая в качестве места зарождения трещины при поперечном нагружении. Наконец, с обеих сторон наблюдается истончение верхнего листа. В качестве дефекта зацепления это утончение происходит из-за втягивания границы раздела в верхний лист, тем самым уменьшая его поперечное сечение.
Зацепление
На следующем изображении мы можем видеть, как оба дефекта были получены в одном и том же сварном шве внахлестку:
В отличие от отсутствия проникновения, гораздо труднее предотвратить появление дефектов зацепления и поцелуев. Для этого необходимо полагаться на специалистов, которые выполняют сварку с соответствующими параметрами, и использовать правильный инструмент СТП. Но не волнуйтесь, Stirweld может вам помочь.
СТОЙКОСТЬ К СВАРКЕ ТРЕНИЕМ С ПЕРЕМЕШИВАНИЕМ В СООТВЕТСТВИИ С СВАРКОЙ В НАХОД/СТЫК
Ранее заявленные дефекты оказывают сильное влияние на механическую стойкость при сварке трением с перемешиванием.
Дефект зацепления приводит к зарождению трещин и, следовательно, снижает сопротивление усталости. Этот дефект не приводит к прямому разрыву сварной детали, но со временем, поскольку две части не полностью сварены, а просто соединены вместе, обе части могут в конечном итоге разъединиться:
Визуализация соединения в поперечном сечении.
Очень серьезный дефект из-за сил, приложенных к верхней пластине в направлении, которое мы видим выше.
Переходя к разговору конкретно о дефекте поцелуев, так как это не перемешиваемая зона, мы уменьшаем сечение сварного шва. То есть мы уменьшаем механическое сопротивление сварного шва за счет того, что шов меньше.
Эти дефекты (зацепление и поцелуй) непосредственно влияют на сопротивление сварного шва, и оба они могут быть обнаружены при сварке внахлестку. Таким образом, сварка внахлест обычно имеет более низкое сопротивление, чем сварка встык 9.0013 .
СКОРОСТЬ СВАРКИ СТП
Как мы уже упоминали, зацепление и сцепление возникают из-за плохого перемешивания. Поэтому для предотвращения возникновения этих дефектов необходимо усилить эффект перемешивания, что достигается за счет снижения скорости сварки СТП.
Таким образом, при сравнении сварки встык и внахлестку необходимо учитывать, что сварка внахлестку (имеющая возможность образования зацепления и соединения внахлест) должна выполняться на более низкой скорости.
В частности, сварка внахлест обычно выполняется со скоростью 2,0 метра в минуту, а сварка встык выполняется со скоростью 3,0 метра в минуту.
ПОДГОТОВКА ПОВЕРХНОСТИ СТП
При сварке трением с перемешиванием материал не подается в сварной шов. Тогда FSW не сможет выдержать значительный зазор между двумя свариваемыми компонентами. При стыковой сварке максимально допустимый зазор составляет 10 % от толщины (до 10 миллиметров). Если зазор выше этого процента, в сварном шве возникает сквозной дефект. Вот почему перед выполнением стыковой сварки важно выполнить точную подготовку кромок. Существует несколько способов выполнения этого процесса: лазерная резка, резка водой или механическая обработка. Однако это не может быть осуществлено стрижкой.
Для сварки СТП внахлестку подготовка кромок не требуется, так как свариваемые детали располагаются друг над другом. Кроме того, не требуется дополнительная подготовка поверхности (без обезжиривания, без обработки кистью).
СВАРКА ТРЕНИЕМ С ПЕРЕМЕШИВАНИЕМ: ЗАЖИМНАЯ СИСТЕМА
Тот же принцип применим к системе зажима. Поскольку при выполнении стыкового шва невозможно получить зазор более 10% от толщины свариваемых деталей, крайне важно иметь правильную систему зажима. Это должно быть достаточно точным, чтобы предотвратить появление большего разрыва.
Этот процесс упрощается за счет сварки трением с перемешиванием внахлестку. Почему? Инструмент нажимает одну деталь на другую с силой, ограничивающей зазор между компонентами.
Кроме того, при выполнении стыковой сварки обязательно, чтобы инструмент следовал за проходом стыка. Причина этого в том, что если инструмент FSW находится вдали от этой линии стыка, у нас могут быть такие дефекты, как непровар. Поэтому важно, чтобы система зажима всегда обеспечивала правильное положение инструмента во время сварки трением с перемешиванием. Однако при выполнении сварки СТП внахлест нет необходимости следовать какой-либо линии стыка, поэтому система зажима может быть менее точной.
Автоматический шаблон для стыковой сварки
СТП КАЧЕСТВО ЗАПЕЧИВАНИЯ
Наконец, следует отметить, что в обоих случаях (стыковая и нахлесточная сварка) мы получаем водонепроницаемые и герметичные швы. Таким образом, невозможно найти различия между двумя типами сварки СТП по этой характеристике.
Несущая способность стыковых сварных соединений высокопрочных сталей | Дж. Инж. Матер. Технол.
Пропустить пункт назначения навигации
Научная статья
М. Хуршид,
З. Барсум,
И. Барсум
Информация об авторе и статье
1Ответственный автор.
Предоставлено Отделом материалов ASME для публикации в JOURNAL OF ENGINEERING MATERIALS AND TECHNOLOGY.
Рукопись получена 17 октября 2014 г.; окончательный вариант рукописи получен 21 мая 2015 г.; опубликовано онлайн 15 июня 2015 г. Доц. Редактор: Вадим В. Зильбершмидт.
Дж. Инж. Матер. Технол . Октябрь 2015 г., 137(4): 041003 (9 страниц)
Номер статьи: МАТС-14-1198 https://doi.org/10.1115/1.4030687
Опубликовано в Интернете: 1 октября 2015 г.
История статьи
Получено:
17 октября 2014 г.
Пересмотр получено:
21 мая 2015 г.
Онлайн:
15 июня 2015 г.
- 1162
Просмотры
- Содержание артикула
- Рисунки и таблицы
- Видео
- Аудио
- Дополнительные данные
- Экспертная оценка
- Делиться
- MailTo
- Твиттер
Иконка Цитировать Цитировать
Разрешения
- Поиск по сайту
Цитирование
Хуршид М. , Барсум З. и Барсум И. (1 октября 2015 г.). «Несущая способность стыковых сварных соединений высокопрочных сталей». КАК Я. Дж. Инж. Матер. Технол . октябрь 2015 г.; 137(4): 041003. https://doi.org/10.1115/1.4030687
Скачать файл цитаты:
- Рис (Зотеро)
- Менеджер ссылок
- EasyBib
- Подставки для книг
- Менделей
- Бумаги
- КонецПримечание
- RefWorks
- Бибтекс
- ProCite
- Медларс
Расширенный поиск
Целью данного исследования является исследование влияния предела текучести присадочного материала и проплавления металла шва на несущую способность стыковых сварных соединений высокопрочных сталей (HSS) (т. е. марок S700 и S9).60). Эти соединения изготавливаются с использованием трех различных присадочных материалов (недостаточная, стыковочная и избыточная стыковка) с полным и частичным проплавлением металла шва. Несущая способность этих упомянутых соединений оценивается с помощью экспериментов и сравнивается с оценками методом конечных элементов (FEA) и правилами проектирования в Eurocode3 и AWS D1.1 Американского общества сварщиков. Результаты показывают, что оценки несущей способности с помощью FEA, Eurocode3 и AWS D1.1 хорошо согласуются с экспериментами. Отмечено, что общая несущая способность и пластичность соединений зависят от проникновения металла шва и предела текучести основного и присадочного материалов. Это влияние более выражено в суставах в S9.Сталь 60, сваренная с недостаточно подобранным присадочным материалом. Кроме того, прочность материала базовой пластины может быть использована в сварных стыковых соединениях с недостаточным согласованием при условии обеспечения соответствующего проплавления металла шва и его ширины. Кроме того, также установлено, что правила проектирования Еврокода 3 (действительные для расчета сварных соединений сталей до S700) могут быть распространены на проектирование сварных швов сталей S960 с использованием коэффициента корреляции, равного единице.
Раздел выпуска:
Исследовательские работы
Ключевые слова:
Соединение, механическое поведение, Пластическое поведение
Темы:
Дизайн, Наполнители (Материалы), Анализ методом конечных элементов, Грузоподъемность, Металлы, стресс, Сварные соединения, Предел текучести, Сварка, Пластичность, деформация, Сталь
1.
CEN, 2004 г., «Еврокод 3: Проектирование стальных конструкций — Часть 1–8: Проектирование соединений», Европейский комитет по стандартизации, Брюссель.
2.
Комитет AWS по сварке конструкций, 2000 г., «AWS D1.1-Кодекс сварки конструкций – сталь», Американское общество сварщиков, Майами, Флорида.
3.
CEN, 2005, «Еврокод 3-Часть 1-12-Дополнительные правила для расширения EN 1993-1-8 до классов S700», Европейский комитет по стандартизации, Брюссель.
4.
Björk
,
T.
,
Toivonen
,
J.
, and
Nykänen
,
T.
,
2012
, “
Capacity угловых сварных соединений из сверхвысокопрочной стали
»,
Сварка. Мир.
,
56
(
3–4
), стр.
71
–
84
. 10.1007/BF03321337
5.
Collin
,
P.
и
Johansson
,
B.
,
2005
,B.
,
9005
,
,
9000 20059,,
,
,
. Прочность стали
»,
4-я Европейская конференция по стальным и композитным конструкциям
, Маастрихт, Нидерланды, 8-10 июня, Vol. С, стр.
4.10-89
–
4.10-98
.
6.
RASCHE
,
C.
и
Kuhlmann
,
U.
,
2009
, «
Heartidt Detet Lapdet Stiledet Lapdet Detet Lapdetet Lapdetet Lapdetet Sweldet Lapdetet Lapdetet Lapdetet Detet Lapdetet Lapdetet Lapdetet Lapdetet Lapdetet Lapdetet Lapdetet Lapdetet Lapdetet Lapdetet Lapdetet Lapdetet Lapdetet Lapdetet Lapdetet Lapdetet Lapdet Detet LAPDETTET
»,
Nordic Steel Construction Conference
, (
NSCC2009
), Мальмё, Швеция, 2–4 сентября, стр. 462–469.http://www.nordicsteel2009.se/pdf/20. pdf
7.
Хуршид
,
M.
,
Barsoum
,
Z.
и
Mumtaz
,
N. A.
,
20126666. «
,
2012
99666,«,
20126666 ». для угловых сварных швов высокопрочных сталей
»,
Материал. Дес.
,
40
, с.0005
8.
Picón
,
R.
, и
Cañas
,
J.
,
2009
, «
на прочти.
Междунар. Дж. Мех. науч.
,
51
(
8
), pp.
609
–
618
.10.1016/j.ijmecsci.2009.06.003
9.
Mellor
,
B. G.
,
Rainey
,
R. C. T.
, и
Kirik
,
N. E.
,
9999999.,
,
9999999.,
. Соединения угловым сварным швом
”,
Материал. Дес.
,
20
(
4
), стр.
193
—
205
.10.1016/S0261-3069(99) 00027-8
10.
Collin
,
P.
,
Möller
,
M.
,
Nilsson
,
,
Nilsson
.
Törnblom
,
S.
,
2009
, «
Internatching Butt Welds в высокопрочной стали
»,
Международная ассоциация для мостового и конструктивного инженерия
»
.0005
, Бангкок, Таиланд, 9-11, с. 96–106.10.2749/222137809796078829
11.
и
,
D. P.
, и
,
D. P.
, и
,
D. P.
, и
,
D. P.
, и
,
D. P.
, и
,
D. P.
, и
,
D. P.
, и
.
,
1989
, «
Поведение и предел прочности при растяжении сварных швов с частичным проплавлением
»,
Can. Дж. Гражданский инж.
,
16
(
3
), стр.
384
—
399
. 10.1139/L89-062
12.
Lesik
,
D. F.
и
,
D. F.
и
,
D. F.
, и
,
D. F.
, и
.
,
1990
, «
Предел прочности угловых сварных соединений под нагрузкой в плоскости
»,
Can. Дж. Гражданский инж.
,
17
(
1
), стр.
55
–
67
.10.1139/l90-008
13.
Satoh
,
K.
, and
Toyoda
,
M.
,
1975
, «
Прочность суставов тяжелых пластин с более низкой прочностью сварного шва металла
»,
Приложение для исследования сварки
, с.
311
—
319
.org/wj/дополнение/WJ_1975_09_s311.pdf
14.
Rodrigues
,
D. M.
,
Menezes
,
L. F.
,
Loureiro
,
A.
, and
Fernandes
,
J. V.
,
2004
, «
Численное исследование пластического поведения при растяжении сварных швов высокопрочных сталей
»,
.Int Дж. Пласт.
,
20
(
1
), pp.
1
–
18
.10.1016/S0749-6419(02)00112-2
15.
Loureiro
,
A. J. R.
,
2002
, «
Влияние тепловложения на пластическую деформацию несоответствующих сварных швов
»,
J. Mater. Процесс. Технол.
,
128
(
1–3
), pp.
240
–
249
.10.1016/S0924-0136(02)00457-0
16.
Mochizuki
,
M.
,
Shintomi
,
T.
,
Hashimoto
,
Y.
и
Toyoda
,
M.
,
2004 9005 9006, «
,
2004
»
,
20046, «
». Прочность сварных соединений мелкозернистых сталей, умягченных ЗТВ
»,
Сварка. World
,
48
(
9–10
), pp.
2
–
12
.10.1007/BF03263396
17.
Hochhauser
,
F.
,
ERNST
,
W.
,
RAUCH
,
R.
,
Vallant
,
R.
, и
,
.0005
Enzinger
,
N.
,
2012
, «
Влияние мягкой зоны на силу сварных современных HSLA -сталей
»,
Weld. World
,
56
(
5–6
), pp.
77
–
85
.10.1007/BF03321352
18.
Vuik
,
J.
,
Ван Вортель
,
J. C.
и
Van Seenhoven
,
C.
,
1994
, «
Применение очень низких потреблений прочности в корневом проходе сварки, чтобы избежать предварительного управления
66666666666666666666666666666666666616 гг. »,
Сварка. Мир
,
33
(
5
), стр.
362
–
369
5 9.
19.
Панда
,
S. K.
,
Sreenivasan
,
N.
,
Kuntz
,
M. L.
, and
Zhou
,
Y.
,
2008
, «
Численное моделирование и экспериментальные результаты испытаний на растяжение поведения сталей DP980, сваренных встык лазером
»,
ASME J. Eng. Матер. Технол.
,
130
(
4
), с.
041003
.10.1115/1,2969256
20.
SSAB
,
2009
,
Helding Handbook
, 1st Ed. , SSAB, xelösund AB, SWEDMHEN.
21.
SSI
,
2011
, «
Разрушающие испытания сварных швов металлических материалов — Испытание на поперечное растяжение
, Швеция. 1 Стокгольм, SS-EN № 3, Институт стандартов Швеции.
22.
Шведский институт стандартов, 2011
, «
Разрушающие испытания сварных швов металлических материалов — определение твердости
», Шведский институт стандартов, Стокгольм, Швеция, стандарт № SS-EN ISO 9015-1.
23.
SSI, 2006
, «
Металлические материалы — испытание на твердость по Виккерсу
», Шведский институт стандартов, Стокгольм, Швеция, стандарт № SS-EN ISO 6507-1.
24.
Декстер
,
R. J.
,
1997
,
–
73
.
25.
Стошка
,
М.
,
Лейтнер
,
М.
,
POSCH
,
G.
и
EICHLSEDER
,
W.
,
2013
, «
Эффект высокой начинки на наполнителе Metals Metals Metals Metals Metals Metals Metals Metals Metals Metals Metals Metals Metals. Стыковые соединения
»,
Сварка. World
,
57
(
1
), стр.
85
—
96
.10.1007/S40194-012-0010-6 9005
6.1007/S40194-012-0010-6 9005
6.9.997/S40194-012-0010-6
9000 26.9. 9007/S40194-012-0010-6
.0005
Hobbacher
,
A.
,
2007
, «
Рекомендация для усталости сварных суставов и компонентов
», Международный институт сварки, Villepinte, France, IIW Document XII-21515151515151516. 07/XV-1254-07.
27.
Fricke
,
W.
,
2008
, “
Руководство по оценке усталостных конструкций сварных швов с надрезом
»,
Гамбургский технологический университет Проектирование и анализ конструкций судов
,
Гамбург, Германия
, IIW-Doc. XIII-2240р1-08/XV-1289р1-08.
28.
Cahhon
,
J. R.
,
1972
, «
Улучшенное уравнение, связанное с твердостью до предела прочности
,»
Metall. Транс.
,
3
(
11
), с.
3040
.10.1007/BF02652880
29.
Pavlina
,
E. J.
, and
Van Tyne
,
C. J.
,
2008
, “
Correlation of Предел текучести и предел прочности при растяжении с твердостью для сталей
»,
J. Mater. англ. Выполнять.
,
17
(
6
), стр.
888
—
893
.10.1007/S11665-008-9225-5
30.
Barsoum
,
I.
,
,
,
,
,
,
. и
Barsoum
,
Z.
,
2014
, «
Анализ прочности на кручение закаленных шлицевых валов», 9,00005
65 90 Дес.
,
54
, стр.
130
—
136
.10.1016/j.matdes.2013.08.020
31.
Koçak
,
M.
,
016
6,
M.
,
05966,
M.
,
059916,M.
,
9005 6,M.
,
. Сварные конструкции: взаимосвязь процесс-свойства-производительность (3P)
»,
63-я ежегодная ассамблея и международная конференция Международного института сварки
, Стамбул, Турция, 11–16 июля, стр.
11
–
17
.
32.
Ananthan
,
V. S.
, and
Hall
,
E. O.
,
1991
, “
Macroscopic Aspects of Lüders Band Deformation in Mild Steel
,
Акта Металл. Матер.
,
39
(
12
), стр.
3153
–
3160
.10.1016/0956-7151(91)
-7
33.
Pisarski
,
H. G.
, and
Dolby
,
R. E.
,
2003
, “
Значение размягченных ЗТВ в высокопрочных конструкционных сталях
»,
Сварка. Мир
,
47
(
5–6
), стр.
32
–
40
.10.1007/BF03266387
34.
Maurer
,
W.
,
Ernst
,
W.
,
Rauch
,
R.
,
KAPL
,
S.
,
POHL
,
A.
,
Krüssel
,
T.
,
Vallant
T.