Сваркой называется процесс получения неразъемных соединений посредством установления межатомных связей между свариваемыми частями при их местном или общем нагреве, или пластическом деформировании, или совместным действием того и другого. Определение сварки относится к металлам и неметаллическим материалам (пластмассы, стекло, резина и т. д.). Свойства материала определяются его внутренним строением — структурой атомов. Все металлы в твердом состоянии являются телами с кристаллической структурой. Аморфные тела (стекло и др.) имеют хаотическое расположение атомов. Для соединения свариваемых частей в одно целое нужно их элементарные частицы (ионы, атомы) сблизить настолько, чтобы между ними начали действовать межатомные связи, что и достигается местным или общим нагревом или пластическим деформированием или тем и другим. В зависимости от условий, при которых осуществляется сваривание (образование межатомных связей) частиц металла, различают сварку плавлением и сварку давлением. Сущность сварки плавлением (рис. 1) состоит в том, что металл по кромкам свариваемых деталей 1 и 2 подвергается плавлению от нагрева сильным концентрированным источником тепла: электрической дугой, газовым пламенем, химической реакцией, расплавленным шлаком, энергией электронного луча, плазмой, энергией лазерного луча. Во всех этих случаях образующийся от нагрева жидкий металл одной кромки самопроизвольно соединяется с жидким металлом другой кромки. Создается общий объем жидкого металла, который называется сварочной ванной. После застывания металла сварочной ванны получается металл шва 4. Металл шва может образоваться только за счет переплавления металла по кромкам 3 или дополнительного присадочного металла, введенного в сварочную ванну. Рис. 1. Схема соединения деталей сваркой плавлением: а — детали перед сваркой, б — детали после сварки Зона частично оплавившихся зерен металла на границе кромки свариваемой детали и шва называется зоной плавления, в этой зоне достигается межатомная связь. Сущность сварки давлением (рис. 2) состоит в пластическом деформировании металла в месте соединения под действием силы P. Находящиеся на соединяемых поверхностях различные загрязнения вытесняются наружу, а поверхности свариваемых частей будут чистыми, ровными и сближенными по всему сечению на расстояние атомного сцепления. Зона, в которой установилась межатомная связь, называется зоной соединения. Ширина зоны соединения измеряется десятками микрон. Рис. 2. Схема соединения деталей сваркой давлением: а — стыковая контактная сварка, б — точечная контактная сварка; 1 и 2 — свариваемые детали, 3 — медные электроды, 4 — место сварки, 5 — сварочный трансформатор, P — сжимающее усилие Пластическую деформацию кромок деталей осуществить легче, если нагревать место соединения. Источником тепла (при сварке с местным нагревом) служит электрический ток, газовое пламя, химическая реакция, механическое трение; при сварке, с общим нагревом — кузнечный горн, нагревательная печь. Процесс сварки делят на три класса (ГОСТ 19521 — 74): термический, термомеханический и механический. Термический класс объединяет виды сварки, осуществляемые плавлением металла. Термомеханический класс включает виды сварки, осуществляемые давлением с использованием тепловой энергии. К механическому классу относятся виды сварки, выполняемые давлением с дополнительной механической энергией. Сварка по виду применяемой энергии подразделяется на следующие основные виды: давлением с общим нагревом: кузнечная, прокаткой, выдавливанием; давлением с местным нагревом: контактная, индукционно-прессовая, термитно-прессовая, газопрессовая, диффузионная, дуго-прессовая; давлением без нагрева металла внешним источником тепла; ультразвуковая, холодная, трением, взрывом, магнитноимпульсная; плавлением: дуговая, газовая, термитная, электрошлаковая, электронно-лучевая, лазерным лучом, плазменная. |
Физическая сущность и классификация видов сварки
Сварка — технологический процесс получения неразъёмных соединений посредством установления межатомных связей между соединяемыми деталями любой конструкции при внесении энергии извне в форме теплоты или работы механического сжатия.
Сварное соединение — это часть конструкции в месте, где выполнена сварка деталей.
Сварной шов — часть сварочного соединения, где достигнуто взаимодействие межатомных сил сцепления в результате кристаллизации расплавленного металла, пластического деформирования при сжатии деталей, или сочетания кристаллиза¬ции и деформирования. По сравнению с соединениями, полученными другими способами, сварные соединения обладают монолитностью, непроницаемостью, герметичностью, меньшей массой, более рациональным использованием материалов, меньшими затратами труда, возможностью механизации и автоматизации процесса их получения.
При образовании сварных швов происходит сближение атомов кристаллических решёток двух (или более) твёрдых тел до расстояния, соизмеримого с атомным радиусом ra (см. рис. 1.2), при котором силы притяжения атомов (как частиц масс) начинают преобладать над силами отталкивания их (как одноимённо заряженных частиц). Суммирование этих сил изображено пунктирной кривой.
Установление межатомных связей на границах раздела соединяемых деталей может быть достигнуто различными технологическими приёмами, определяющими все существующие виды и разновидности сварки. Эти приёмы отличаются формой вносимой извне энергии, способами и средствами защиты сварочной ванны и металла шва, уровнем механизации и другими признаками. Полученная в результате сварки система в термодинамическом смысле представляет собой устойчивую систему, в которой в процессе сварки произошло уменьшение энергии. Однако самопроизвольный процесс образования сварного соединения невозможен, так как реальные свариваемые детали не имеют идеально чистых и гладких поверхностей.
Поэтому в случае сближения атомов до расстояния, соизмеримого с параметром кристаллической решётки, за счёт сжатия (рис. 1.3, а)
(сварка давлением — механический класс сварки) необходимо обязательно взаимно деформировать поверхности соединяемых деталей для смятия неровностей и обеспечения надёжного физического контакта, а также активизировать их, сообщив поверхностным атомам некоторую энергию активации.
При этом внешние орбиты атомов должны перекрыть друг друга таким образом, чтобы электроны могли свободно перемещаться с одной орбиты на другую. Это является условием образования в соединении сквозной металлической связи. Усилия сжатия можно уменьшить, если одновременно нагревать свариваемые поверхности (термомеханический класс сварки).
Образование соединений металлических деталей возможно и без применения усилий сжатия (автогенно) за счёт временного местного расплавления кромок для образования общей сварочной ванны (сварка плавлением термический класс сварки). В жидком металле и на образовавшихся межфазовых границах (рис. 1.3, 6) связи между атомами сохраняются. Сквозная межатомная связь в соединении образуется в результате кристаллизации жидкой сварочной ванны, а также развития диффузионных процессов с массопереносом через границу шва.
Таким образом, основной процесс сварки (образование сварного шва) включает установление физического контакта между поверхностями деталей или через жидкий металл сварочной ванны, образования прочных межатомных связей и развития диффузии.
Качество сварных соединений, характеризуемое прочностью, коррозионной стойкостью, отсутствием внутренних дефектов, зависит не только от основного, но и от сопутствующих процессов. Так как при сварке плавлением в сварном соединении появляется зона термического влияния (ЗТВ), то сопутствующими процессами здесь являются:
- изменение структуры и свойств металла в ЗТВ;
- металлургические процессы в сварочной ванне;
- процессы кристаллизации сварного шва;
- возникновение сварочных напряжений и деформаций.
Влияние основных и сопутствующих процессов на качество сварных соединений зависит от состава и свойств свариваемых и присадочных металлов, а также от технологических факторов: режима сварки, средств защиты сварочной ванны и др.
В процессе сварки технологическими факторами можно активно управлять. Состав и свойства свариваемого металла остаются неизменными. Для оценки степени влияния состава и свойств свариваемого металла на протекание основного и сопутствующего процессов введено понятие о свариваемости металлов как способности образовывать неразъёмное соединение с заданными свойствами в условиях принятого технологического процесса. Поскольку эти условия в производстве могут варьироваться, то и оценка свариваемости может быть неоднозначной.
В соответствии с действующими стандартами сварку классифицируют по трём признакам: физическим, техническим и технологическим (рис. 1.4).
По физическим признакам, в зависимости от формы энергии, используемой для образования сварного соединения, различают три класса сварки: термический, термомеханический и механический. В зависимости от источников энергии, используемых для образования сварного соединения, по каждому классу выделено несколько видов сварки.
По техническим признакам сварку классифицируют в зависимости от способа защиты расплавленного металла от воздуха, типа защитною газа и степени механизации.
По технологическим признакам сварку классифицируют по виду электрода, по роду тока, по виду и характеру дуги, по воздействию на жидкий металл.
Литература
Основы сварки и газотермических процессов в судостроении и судоремонте — Бурмистров Е. Г. [2017]
Сущность процесса сварки в углекислом газе — FINDOUT.SU
Поможем в ✍️ написании учебной работы
Имя
Поможем с курсовой, контрольной, дипломной, рефератом, отчетом по практике, научно-исследовательской и любой другой работой
Выберите тип работыЧасть дипломаДипломная работаКурсовая работаКонтрольная работаРешение задачРефератНаучно — исследовательская работаОтчет по практикеОтветы на билетыТест/экзамен onlineМонографияЭссеДокладКомпьютерный набор текстаКомпьютерный чертежРецензияПереводРепетиторБизнес-планКонспектыПроверка качестваЭкзамен на сайтеАспирантский рефератМагистерская работаНаучная статьяНаучный трудТехническая редакция текстаЧертеж от рукиДиаграммы, таблицыПрезентация к защитеТезисный планРечь к дипломуДоработка заказа клиентаОтзыв на дипломПубликация статьи в ВАКПубликация статьи в ScopusДипломная работа MBAПовышение оригинальностиКопирайтингДругое
Нажимая кнопку «Продолжить», я принимаю политику конфиденциальности
Сварки в углекислом газе осуществляется плавящимся электродом. Дуга, металл сварочной ванны, плавящийся электрод и кристаллизующийся шов защищены от воздействия воздуха углекислым газом, подаваемым в зону сварки горелкой.
Рис. 6.1. Схема сварки в углекислом газе
Под действием теплоты сварочной дуги углекислый газ диссоциирует с образованием атомарного кислорода по реакции:
СО2↔СО+О; СО↔С+О
Атомарный кислород окисляет железо и легирующие элементы, содержащиеся в стали
Fe(Me)+O→FeO (МеmОn)
В результате этого металл сварочной ванны насыщается кислородом, а его свойства ухудшаются. При охлаждении расплавленного металла углерод, содержащийся в стали, окисляясь, способствует образованию окиси углерода по реакциям:
С+О→СО; FeO+C→Fe+CO
Образующийся при кристаллизации металла шва углекислый газ выделяется в виде пузырьков, часть из которых, не успевая покинуть металл сварочной ванны, остается в металле шва, образуя поры.
В том случае, если сварочная проволока легирована кремнием и марганцем, окислы железа раскисляются не за счет углерода, а в основном за счет этих элементов, в результате чего предотвращается образование окиси углерода и образование пор.
[FeO]+[Si; Mn]→[Fe]+[SiO2; MnO]
Окислы SiO2 и MnO в виде шлака скапливаются на поверхности сварочной ванны, а после её кристаллизации — на поверхности металла шва.
Кромки свариваемого изделия расплавляются дугой, горящей между изделием и плавящейся электродной проволокой, непрерывно поступающей
в дугу и служащей одновременно присадочным материалом. Дуга расплавляет проволоку и кромки изделия, образуя сварочную ванну. Дуга,
металл сварочной ванны, плавящийся электрод и кристаллизующийся шов защищены от воздействия воздуха газом, подаваемым в зону сварки горелкой. По мере перемещения дуги сварочная ванна кристаллизуется, образуя сварной шов .
Изменение состава защитного газа в зоне сварки в результате термической диссоциации углекислого газа:
СО2 ↔ СО + 0,5О2
без учета его разбавления парами и газами, выделяющимися из металла, приведено на рисунке 3. 2.
Рис.6.2. Изменение состава газа в реакционной зоне в результате диссоциации углекислого газа
6.2. Выбор параметров режима сварки Основными параметрами режимов механизированных процессов дуговой сварки в защитных газах являются:
— диаметр электродной проволоки – dэ;
— вылет электродной проволоки -lэ;
— скорость подачи электродной проволоки — Vп.п;
— сила тока – Iсв;
— напряжение дуги – Uд;
— скорость сварки – Vсв;
— удельный расход СО2.
Сварку обычно выполняют на постоянном токе обратной полярности. Иногда возможна сварка на переменном токе. При прямой полярности скорость расплавления в 1,4-1,6 раза выше, чем при обратной, однако дуга горит менее стабильно, с интенсивным разбрызгиванием. Диаметр сварочной проволоки d 3 выбирается в зависимости от толщины свариваемых заготовок d :
d ,мм……0,5-1,0 | 1,0-2,0 | 2,0-4,0 | 5,0-8,0 | 8,0-1,2 | 12-18 |
d э , мм……0,5-0,8 | 0,8-1,0 | 1,0-1,2 | 1,6-2,0 | 2,0 | 2,0-2,5 |
Увеличение диаметра электродной проволоки (при равных условиях) сопровождается существенным уменьшением коэффициента наплавки, некоторым увеличением ширины шва и уменьшением глубины проплавления основного металла. Больший диаметр проволоки ( Dпров ,мм) требует увеличения сварочного тока (рис.3.3).
Рис.6.3. Зависимость необходимого сварочного тока от диаметра проволоки при сварке в углекислом газе
Сварочный ток оказывает большое влияние на процесс сварки. Повышение силы тока вызывает увеличение глубины проплавления (рис. 3.4). При этом количество наплавленного металла возрастает медленнее, чем проплавление. Следовательно, и доля электродного металла в металле шва существенно уменьшается, что значительно увеличивает возможность появления горячих трещин в металле швов, выполненных на сталях с повышенным содержанием углерода. Ширина шва с повышением силы тока сначала увеличивается, а затем несколько уменьшается. Оптимальные режимы сварки соответствуют максимальной ширине шва. Ток регулируют скоростью подачи сварочной проволоки.
Рис.6.4. Влияние сварочного тока 100 А (а) и 200А (б) на глубину проплавления
С ростом напряжения на дуге глубина проплавления уменьшается, а ширина шва и разбрызгивание металла увеличиваются (рис. 3.5). Ухудшается газовая защита, образуются поры. Напряжение на дуге устанавливают в зависимости от выбранного сварочного тока и регулируют положением вольтамперной характеристики, изменяя напряжение холостого хода источника питания.
Рис. 6.5. Влияние наряжения на дуге 16 В (а) и 40 В (б) на процесс сварки
Скорость подачи электродной проволоки связана со сварочным током.Электродную проволоку устанавливают так, чтобы процесс сварки происходил стабильно, без коротких замыканий и обрывов дуги.
Скорость сварки налаживают в зависимости от толщины свариваемого металла с учётом качественного формирования шва. Металл большой толщины сваривают узкими швами с высокой скоростью.
Медленная сварка способствует разрастанию сварочной ванны и повышает вероятность образования пор в металле шва. При чрезмерной скорости сварки могут окислиться конец проволоки и металл шва.
Качество сварных швов зависит от чистоты СО2, его расхода и характера истечения из сопла инструмента. Защитный газ должен истекать из сопла под небольшим давлением (0,01-0,03 МПа), обеспечивающим ламинарный (спокойный) характер истечения. Такое важное требование выполняется, если расход газа составляет ~ 8-12 л/мин при диаметре электродной проволоки 0,8-1,2 мм. Турбулентный характер истечения газового потока ухудшает качество защиты сварочной зоны вследствие возможного подсоса воздуха в эту зону.
Вылет электрода -это расстояние от точки токоподвода до торца сварочной проволоки (рис.3. 6).
С увеличением вылета ухудшаются устойчивость горения дуги и формирование шва, интенсивнее разбрызгивается металл. Малый вылет затрудняет процесс сварки, вызывает подгорание газового сопла и токоподводящего наконечника.
Рис. 6.6. Схема сварочной горелки
В таблице 3.1. показана зависимость вылета электрода от его диаметра:
Таблица 3.1 — Зависимость вылета электрода от его диаметра
Диаметр проволоки, мм…….![]() | 1-1,4 | 1,6-2 | 2,5-3 |
Вылет электрода, мм…………7-10 | 8-15 | 15-25 | 18-30 |
Расход газа, л/мин……………5-8 | 8-16 | 15-20 | 20-30 |
Металл толщиной от 0,8 до 4 мм рекомендуется сваривать без разделки кромок в сборочно-сварочных приспособлениях на съѐмных медных или нержавеющих подкладках, либо остающихся подкладках.
При сварке в углекислом газе для предупреждения появления дефектов в виде небольших несплавлений не рекомендуется перемещать конец электрода «змейкой». Повышенная склонность к локальным несплавлениям при полуавтоматической сварке в углекислом газе по сравнению с ручной сваркой и сваркой в аргоне объясняется меньшими при сварке в углекислом газе размерами столба дуги и электродных пятен, что может приводить к натеканию жидкого металла на твѐрдый металл без предварительной обработки последнего сварочной дугой.
Заглавная страница
КАТЕГОРИИ: Археология ТОП 10 на сайте Приготовление дезинфицирующих растворов различной концентрации Техника нижней прямой подачи мяча. Франко-прусская война (причины и последствия) Организация работы процедурного кабинета Смысловое и механическое запоминание, их место и роль в усвоении знаний Коммуникативные барьеры и пути их преодоления Обработка изделий медицинского назначения многократного применения Образцы текста публицистического стиля Четыре типа изменения баланса Задачи с ответами для Всероссийской олимпиады по праву Мы поможем в написании ваших работ! ЗНАЕТЕ ЛИ ВЫ? Влияние общества на человека Приготовление дезинфицирующих растворов различной концентрации Практические работы по географии для 6 класса Организация работы процедурного кабинета Изменения в неживой природе осенью Уборка процедурного кабинета Сольфеджио. Балочные системы. Определение реакций опор и моментов защемления |
⇐ ПредыдущаяСтр 4 из 7Следующая ⇒ Полное наименование этого процесса сварки таково: Ручная дуговая сварка в инертном газе вольфрамовым электродом (ДСТУ 3761.3-98 «Сварка и родственные процессы. Часть 3 Сварка металлов: соединения и швы, технология, материалы и оборудование. Термины и определения»). Схема и сущность процесса сварки ТИГ показана на рисунке ниже. Кромки свариваемого изделия и присадочный металл расплавляются дугой, горящей между неплавящимся вольфрамовым электродом и изделием. При этом используется электрод либо из чистого, либо из активированного вольфрама. При необходимости в сварочную ванну добавляется присадочный металл. По мере перемещения дуги расплавленный (жидкий) металл сварочной ванны затвердевает (то есть кристаллизируется), образуя сварной шов, соединяющий кромки деталей. Область применения сварки ТИГ Этот способ сварки широко применяется в химической, теплоэнергетической, нефтеперерабатывающей, авиационно-космической, пищевой, автомобилестроительной и других отраслях промышленности для сварки практически всех металлов и сплавов: углеродистых, конструкционных и нержавеющих сталей, алюминия и его сплавов, титана, никеля, меди, латуней, кремнистых бронз, а так же разнородных металлов и сплавов; наплавка одних металлов на другие. Сварочный источник питания Сварочный источник питания обеспечивает сварочную дугу электрической энергией. В качестве источника питания при сварке ТИГ используются: — сварочные трансформаторы – при сварке на переменном токе; Источники питания для сварки ТИГ должны иметь крутопадающую внешнюю вольт-амперную характеристику (Источники питания для дуговой сварки). Такая характеристика обеспечивает постоянство заданного значения тока сварки при нарушениях длины дуги, например, из-за колебаний руки сварщика. Сварочная горелка Основным назначением горелки для дуговой сварки ТИГ является жесткое фиксирование вольфрамового электрода (W-электрода) в требуемом положении, подвода к нему электрического тока и равномерного распределения потока защитного газа вокруг сварочной ванны. Горелки для сварки ТИГ разработаны самых разных конструкций и размеров в зависимости от максимального требуемого тока, а также от условий ее применения. Размер горелки также влияет на то, как горелка будет нагреваться и охлаждаться при сварке. Конструкция некоторых горелок предполагает их охлаждение потоком защитного газа (это так называемые, горелки воздушного охлаждения). Горелки также отводят тепло в окружающее пространство. Газовое сопло. Функцией газового сопла является направлять защитный газ в зону сварки с тем, чтобы он замещал окружающий воздух. Газовое сопло крепится к горелке ТИГ на резьбе, что, в случае необходимости, облегчает его замену. Они обычно изготавливаются из керамического материала для того, чтобы противостоять интенсивному нагреву. Газовые линзы. Другим типом сопел являются сопла со встроенными газовыми линзами, в которых поток газа проходит через металлическую решетку, что придает ему большую ламинарность, обеспечивающую более надежную защиту, так как такой поток более устойчив к воздействиям поперечных воздушных потоков и действует на большее расстояние. Преимуществом сопла, обеспечивающего ламинарный поток газа, заключается в том, что можно устанавливать больший вылет электрода, что дает сварщику лучший обзор сварочной ванны. Обычное сопло (слева) и сопло с газовой линзой (справа) Форма потока защитного газа от обычного сопла Форма потока защитного газа от сопла с газовой линзой ⇐ Предыдущая1234567Следующая ⇒ Читайте также: Коммуникативные барьеры и пути их преодоления Рынок недвижимости. Сущность недвижимости Решение задач с использованием генеалогического метода История происхождения и развития детской игры |
Последнее изменение этой страницы: 2016-07-16; просмотров: 178; Нарушение авторского права страницы; Мы поможем в написании вашей работы! infopedia. |
Сварка. Понятие, сущность процесса — Студопедия
Поделись
Понятие о свариваемости.
К любым материалам рекомендуемым для изготовления сварных конструкций предъявляются требования свариваемости. Под свариваемостью понимают: технологическое свойство металлов (или их сочетаний) образовывать в процессе сварки соединения отвечающие конструктивным и эксплуатационным требованиям к ним. Свариваемость бывает:
— Хорошая, (без подогрева и термообработки).
— Удовлетворительная, (с подогревом).
— Ограниченная, (требуется подогрев + термообработка после сварки).
— Неудовлетворительная.
Кроме того, свариваемость разделяют на:
Металлургическую (влияние химического состава металла на характер химического взаимодействия элементов в металле шва и околошовной зоне).
Тепловую (влияние на свариваемость металла — термодеформационного цикла сварки).
Конструктивную (в зависимости от взаимного расположения свариваемых деталей возникновение дефектов).
Технологическую (способность металла сварного соединения выдерживать различного рода повреждения (разрушения) весь технологический процесс сварки).
Принципиальную (способность к получению принципиальных (атомных) связей).
Достаточную (относительно основного металла).
Недостаточную (относительно основного металла).
В связи с тем, что свариваемость определяется совокупностью свойств единой методики, однозначно определяющих свариваемость — не существует. Для оценки свариваемости проводят ряд испытаний, каждое из которых характеризует те или иные свойства.
Сварка представляет собой процесс получения неразъемного соединения посредством установления непрерывных межатомных связей между соединяемыми деталями при их нагревании и (или) пластическом деформировании.
Всего существует около 200 способов.
Все существующие способы сварки, можно разделить на две основные группы: сварку давлением (контактная, газопрессовая, трением, холодная, ультразвуком) и сварку плавлением (газовая, термитная, электродуговая, электрошлаковая, электронно-лучевая, лазерная).
Самое широкое распространение получили различные способы электрической сварки плавлением, а ведущее место занимает дуговая сварка, при которой источником теплоты служит электрическая дуга.
Наибольший объём среди других видов сварки занимает ручная дуговая сварка — сварка плавлением штучными электродами, при которой подача электрода и перемещение дуги вдоль свариваемых кромок производится вручную.
Электрическую сварку плавлением в зависимости от характера источников нагрева и расплавления свариваемых кромок можно разделить на следующие основные виды сварки:
1. электрическая дуговая, где источником тепла является электрическая дуга;
2. электрошлаковая, где основным источником теплоты является расплавленный шлак, через
который протекает электрический ток;
3. электронно-лучевая, при которой нагрев и расплавление кромок соединяемых деталей производят направленным потоком электронов, излучаемых раскалённым катодом;
4. лазерная, при которой нагрев и расплавление кромок соединяемых деталей производят направленным сфокусированным мощным световым лучом микрочастиц — фотонов.
При электрической дуговой сварке основная часть теплоты, необходимая для нагрева у плавления металла, получается за счет дугового разряда, возникающего между свариваемым металлом и электродом. Под действием теплоты дуги кромки свариваемых деталей и тори плавящегося электрода расплавляются, образуя сварочную ванну, которая некоторое время находится в расплавленном состоянии. При затвердевании металла образуется сварное соединение. Энергия, необходимая для образования и поддержания дугового разряда, получаете; от источников питания дуги постоянного или переменного тока. Классификация дуговой сварю производится в зависимости от степени механизации процесса сварки, рода тока и полярности типа дуги, свойств электрода, вида защиты зоны сварки от атмосферного воздуха и др.
По степени механизации различают ручную, полуавтоматическую и автоматическую сварку. Отнесение процессов к тому или иному способу зависит от того, как выполняются зажигание и поддержание определенной длины дуги, манипуляция электродом для придания шву нужной формы, перемещение электрода по линии наложения шва и прекращения процесса сварки.
По роду защиты зоны сварки от окружающего воздуха различают следующие способы сварки: без защиты (голым электродом, электродом со стабилизирующим покрытием), со шлаковой защитой (толстопокрытыми электродами, под флюсом), шлакогазовой (толстопокрытыми электродами), газовой защитой (в среде защитных газов – аргон, азот, углекислый газ и др.), с комбинированной зашитой (газовая среда и покрытие или флюс). Стабилизирующие покрытия представляют co6oй материалы, содержащие элементы, легко ионизирующие сварочную дугу. Наносятся тонким слоем на стержни электродов (тонкопокрытые электроды), предназначенных для ручной дуговой сварки. Защитные покрытия представляют собой механическую смесь различных материалов предназначенных ограждать расплавленный металл от воздействия воздуха, стабилизировать горение дуги, легировать и рафинировать металл шва.
Наибольшее применение имеют средне — и толстопокрытые электроды, предназначенные для ручной дуговой сварки и наплавки, изготовляемые в специальных цехах или на заводах.
Применяются также магнитные покрытия, которые наносятся на проволоку в процесс сварки за счёт электромагнитных сил, возникающих между находящейся под током электродной проволокой и ферромагнитным порошком, находящемся в бункере, через который проходи электродная проволока при полуавтоматической или автоматической сварке. Иногда это ещё сопровождается дополнительной подачей защитного газа.
При ручной сварке указанные операции, необходимые для образования шва, выполняются рабочим-сварщиком вручную без применения механизмов.
При полуавтоматической сварке плавящимся электродом механизируются операции п подаче электродной проволоки в сварочную зону, а остальные операции процесса сварки осуществляются вручную.
При автоматической сварке под флюсом механизируются операции по возбуждению дуги, поддержанию определённой длины дуги, перемещению дуги по линии наложения шва. Автоматическая сварка плавящимся электродом ведётся сварочной проволокой диаметром 1-6 мм, при этом режим сварки (ток, напряжение, скорость перемещения дуги и др.) более стабилен, что обеспечивает однородность качества шва по его длине, в то же время требуется большая точность в подготовке и сборке деталей под сварку.
Сущность способа сварки порошковой проволокой
Сущность способа сварки порошковой проволокой
Порошковая проволока представляет собой непрерывный электрод трубчатой или другой, более сложной конструкции с порошкообразным наполнителем — сердечником. Сердечник состоит из смеси минералов, руд, ферросплавов металлических порошков, химикатов и других материалов. Назначение различных составляющих сердечника подобно назначению электродных покрытий — защита расплавленного металла от вредного влияния воздуха, раскисление, легирование металла, связывание азота в стойкие нитриды, стабилизация дугового разряда и др. Составляющие сердечника должны, кроме того, удовлетворять общепринятым требованиям, предъявляемым ко всем сварочным материалам: обеспечивать хорошее формирование швов, легкую отделимость шлаковой корки, провар основного металла, минимальное разбрызгивание металла, отсутствие пор, трещин, шлаковых включений и других дефектов, определенные механические свойства швов и сварных соединений и т. д.
Порошковые проволоки используются для сварки без дополнительной защиты зоны сварки, а также для сварки в защитных газах, под флюсом, электрошлаковой. Проволоки, используемые для сварки без дополнительной защиты, называются самозащитными. Входящие в состав сердечника таких проволок материалы при нагреве и расплавлении в дуге создают необходимую шлаковую и газовую защиту расплавленного металла. В настоящее время наибольшее распространение получили порошковые проволоки для сварки в углекислом газе и самозащитные порошковые проволоки.
В зависимости от диаметра и состава порошковой проволоки сварка может осуществляться во всех трех пространственных положениях.
Схема процесса сварки самозащитной порошковой проволокой со свободным формированием шва приведена на рис. 1.
Рис. 1. Схема процесса сварки самозащитной порошковой проволокой.
Электрическая дуга возбуждается между оболочкой 1 порошковой проволоки и основным металлом 10 . За счет тепла, выделяемого в дуге, плавятся оболочка и сердечник 2 проволоки. Расплавившийся металл оболочки и сердечника образует на торце проволоки капли 3, которые растут и переносятся в сварочную ванну 5. При расплавлении минералов, руд и химикатов, входящих в состав сердечника, образуется шлак 6, покрывающий тонким слоем капли и сварочную ванну. Дуга 4 горит между каплей или оболочкой и сварочной ванной. При разложении карбонатов и органических материалов сердечника выделяются газы 9, которые защищают расплавленный металл от воздуха. Проволока по мере оплавления автоматически подается в зону сварки. При удалении дуги жидкий металл сварочной ванны кристаллизуется, образуя сварной шов 7, покрытый слоем затвердевшего шлака 8.
Схема процесса сварки порошковой проволокой в защитном газе приведена на рис. 2.
Рис. 2. Схема процесса сварки порошковой проволокой в углекислом газе: 1 — проволока; 2 — токоподвод; 3 — сопло; 4 — углекислый газ.
Порошковая проволока может использоваться также для сварки с принудительным формированием (рис. 3).
Рис. 3. Схема электродугового процесса сварки с принудительным формирование порошковой проволокой: а — в углекислом газе; б- открытой дугой. 1 — порошковая проволока; 2 — свариваемый металл; 3- шлак; 4 — ползун 5 — сварочная ванна, 6 — шов.
Классификация сварочных порошковых проволок
Порошковые проволоки могут быть классифицированы по назначению, способу защиты металла от влияния воздуха, типу сердечника, механическим свойствам металла шва.
Назначение проволоки определяется классом свариваемого металла. Порошковые проволоки применяются для сварки малоуглеродистых и низколегированных конструкционных сталей, легированных сталей, чугуна, цветных металлов и сплавов. Наиболее широкое распространение получили проволоки для сварки малоуглеродистых и низколегированных сталей. Рассмотрению свойств этих проволок и особенностей сварки посвящена, в основном, настоящая монография.
По способу защиты порошковые проволоки делятся на два вида: 1) самозащитные; 2) для сварки с дополнительной защитой газом или флюсом.
В зависимости от состава сердечника проволоки, применяющиеся в нашей стране, можно разделить на пять типов — рутил-органические, рутиловые, карбонатно-флюоритные, рутил-флюоритные, флюоритные.
Сердечник проволоки рутил-органического типа состоит в основном из рутилового концентрата и алюмосиликатов (полевой шпат, слюда, гранит и др.). В качестве раскислителей используется ферромарганец, а газообразующими материалами служат крахмал или целлюлоза. Проволоки с сердечником рутил-органического типа используются как самозащитные.
В состав сердечника проволок рутилового типа входят в основном рутиловый концентрат, алюмосиликаты и руды. Раскислителями служат ферромарганец, ферросилиций, ферротитан, ферроалюминий. Проволоки с сердечником рутилового типа используются с дополнительной защитой углекислым газом.
В сердечник проволоки карбонатно-флюоритного типа вводят в качестве газообразующих материалов карбонаты кальция, магния, натрия. В качестве шлакообразующих материалов используют рутиловый концентрат, алюмосиликаты, окислы щелочноземельных металлов, флюоритовый концентрат. Раскисляют металл ферромарганцем, ферросилицием. Для дополнительного раскисления металла и связывания азота в нитриды в сердечник проволок этого типа иногда вводят титан и алюминий. Проволоки с сердечником карбонатно-флюоритного типа чаще всего используют как самозащитные, но применяют и в сочетании с дополнительной защитой углекислым газом.
В состав сердечника проволок рутил-флюоритного типа входят в основном рутиловый и флюоритовый концентраты, в качестве шлакообразующих иногда вводят окислы щелочноземельных металлов, алюмосиликаты. Раскислителями служат ферромарганец и ферросилиций. Проволоки с сердечником этого типа применяются, как правило, с дополнительной защитой углекислым газом.
Сердечник проволок флюоритного типа в основном состоит из флюоритового концентрата, в небольших количествах вводят окислы щелочноземельных металлов. Для раскисления металла применяют ферромарганец, алюминий, магний. Алюминий также связывает азот металла сварочной ванны в нитриды. Проволоки с сердечником флюоритного типа используются как самозащитные.
В сердечники проволок всех типов с целью увеличения производительности сварки и придания благоприятных сварочно-технологических свойств вводят железный порошок.
Классификация проволок по механическим свойствам наплавленного металла пока еще не утверждена. Обычно по этому признаку свойства швов, выполненных порошковыми проволоками, сравнивают со свойствами шпон, выполненных электродами различных типов, регламентированных ГОСТом 9467—60.
Конструкции порошковых проволок.

Из применяющихся конструкции порошковых проволок (рис. 4) наиболее распространены проволоки трубчатой конструкции (а, б, в ). Введение части оболочки внутрь сердечника (г, д, е, ж, з ) обеспечивает более равномерное плавление его и более эффективную защиту металла от воздуха.
Рис. 4. Конструкции порошковой проволоки
Влияние конструкции проволоки на особенности ее плавления и свойства швов рассматривается ниже.
Коэффициент заполнения.
Количество материала в сердечнике порошковой проволоки принято оценивать коэффициентом: заполнения Кз:
где Gпор— масса порошкового наполнителя; Gпров — общая масса проволоки.
В зависимости от назначения проволоки Кз колеблется в широких пределах (10—40%). От величины Кз в значительной мере зависит эффективность защиты расплавленного металла. Стабильность коэффициента заполнения определяет качество изготовления проволоки.
Характеристики расплавления
Коэффициент расплавления (αр) представляет удельную (отнесенную к одному амперу сварочного тока) производительность процесса расплавления оболочки проволоки и определяется из выражения:
где Iсв — сила тока, τ- время расплавления проволоки.
Коэффициентом наплавки αН характеризуется удельная производительность процесса наплавки;
где GН — масса металла, наплавленного за время τ .
Потери электродного металла (без учета потерь на угар и испарение) учитываются коэффициентом набрызгивания αнб
где αнб — потери электродного металла на разбрызгивание; Gбр — масса брызг; GН — масса наплавленного металла.
Производительность процесса Gпр часто определяют массой металла, наплавленного в единицу времени:
Что такое рабочий цикл в сварке? (с таблицей)
Рабочий цикл сварки представляет собой процентную долю 10-минутного интервала, в течение которого источник сварочного тока может непрерывно выдавать номинальную силу тока. Рабочий цикл сварочного аппарата определяет, как долго сварочный аппарат может выдавать номинальную силу тока, прежде чем ему потребуется охлаждение.
Например, сварщик с номинальным рабочим циклом 200 А при нагрузке 60 % может выдавать 200 А в течение шести минут, прежде чем ему потребуется отдохнуть в течение оставшихся четырех минут 10-минутного интервала.
Вот хорошее видео, объясняющее суть:
Важность ПВ при сварке
Сварочные аппараты переходят в режим тепловой перегрузки при превышении предела ПВ во время сварки. Мощность дуги отключается, а охлаждающий вентилятор продолжает работать, помогая отводить тепло от чувствительных частей внутри сварочного аппарата.
Внутренние компоненты сварочных аппаратов, такие как IGBT-транзисторы, трансформаторы, выпрямители, конденсаторы и резисторы, во время сварки нагреваются. Чем выше выходной ток, тем больше выделяется тепла. Любая из этих частей может выйти из строя, если машина перегружена. Поэтому производители разрабатывают и тестируют свои сварочные аппараты, чтобы определить оптимальный рабочий цикл для безопасной работы.
Рабочий цикл является важным показателем, поскольку он дает общее представление о том, с какими работами может справиться сварщик. Например, сварочные аппараты-любители обычно имеют более короткие рабочие циклы, а профессиональные — гораздо более длительные.
Всегда ли рабочий цикл проверяется одинаково?
Рабочий цикл не всегда проверяется одинаково. Это создает путаницу и несправедливое «преимущество» среди производителей сварочных аппаратов.
10-минутный период рабочего цикла является золотым стандартом в отрасли, и его используют большинство производителей в США, ЕС и Австралии. Тем не менее, ничто не мешает бренду оценивать своих сварщиков, используя 5-минутный период времени, что позволяет им заявлять о гораздо более длительном рабочем цикле. В этом примере до 50% дольше.
Однако, если производитель отклоняется от 10-минутного рейтинга, он не может утверждать, что соответствует европейскому стандарту EN60974-1 или австралийскому стандарту AS60974-1 (на основе стандарта ЕС).
Кроме того, в том же стандарте AS/EN60974-1 указано, что испытания должны проводиться при температуре окружающей среды 40°C после как минимум двух тепловых перегрузок. Таким образом, если бренд тестирует свои сварочные аппараты при температуре 20°C или не перегружает аппарат дважды во время предварительного тестирования, он может заявить завышенное значение.
Как вы понимаете, испытание аппарата для холодной сварки при низкой температуре окружающей среды приводит к более высокому рейтингу. Но такие тесты не являются подлинными. В реальном мире машина должна достичь своего номинального рабочего цикла даже после нескольких последовательных тепловых перегрузок.
Убедитесь, что сварочный аппарат, который вы покупаете, соответствует стандарту AS/EN60974-1. У многих сварочных аппаратов этот стандарт указан на табличке с техническими характеристиками сзади. Прочтите руководство пользователя или обратитесь в службу поддержки бренда, если его там нет.
И последнее замечание: невозможно сравнивать два сварочных аппарата, если рабочие циклы тестировались по-разному. Стандарт AS/EN60974-1 широко распространен, и бренды, заявляющие о высоких рабочих циклах без использования этого стандарта, скорее всего, преувеличивают свои цифры. Будьте осторожны с такими маркетинговыми уловками.
Изображение задней панели инверторного сварочного аппарата переменного/постоянного тока TIG-250P компании YesWelder, на котором показан печатный стандарт IEC 60974-1. IEC — сокращение от Международной электротехнической комиссии.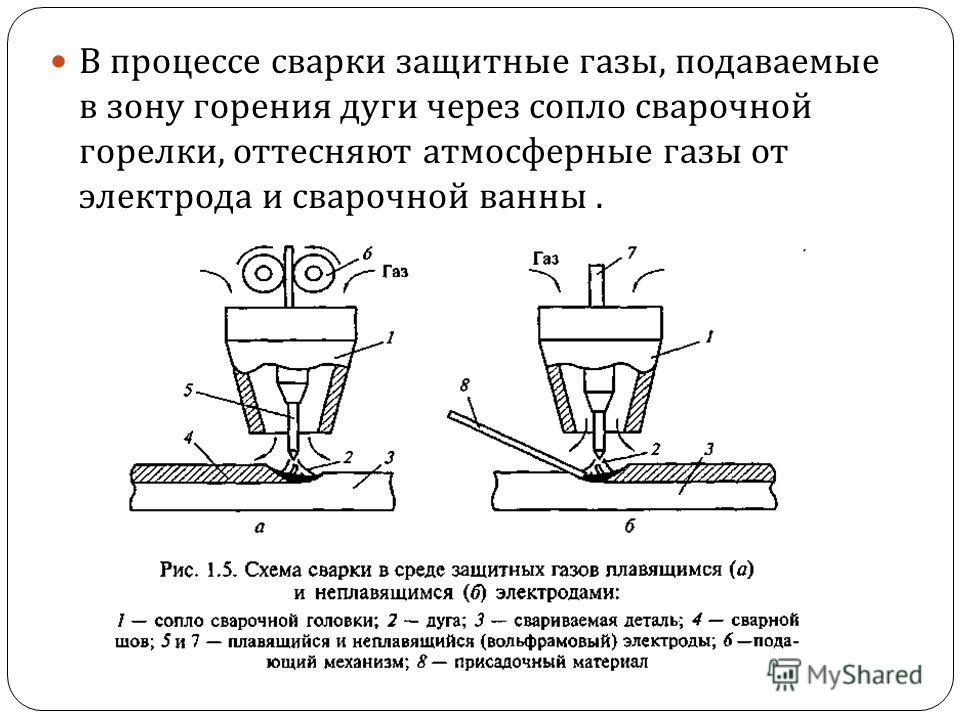
Стандарт AS/EN60974-1 также требует, чтобы защита сварщика от тепловой перегрузки выдерживала 100 последовательных перегрузок для устройств с рабочим циклом 35 % или выше. Машины с рабочим циклом ниже 35% должны выдерживать 200 перегрузок. Таким образом, если сварочный аппарат не соответствует этому стандарту, его внутренние компоненты могут быть некачественными.
Изображение абзаца из стандарта IEC EN60974-1Является ли рабочий цикл лучшим способом оценки сварщика?
Рабочий цикл — не единственный лучший способ оценки сварщика. Существует множество других факторов, которые следует учитывать при выборе машины. Тем не менее, рабочий цикл является одной из важнейших характеристик, которые следует учитывать.
Пример диаграммы рабочего цикла для сварочного аппарата с двойным напряжением (120 В и 240 В) Сварочный аппарат с коротким рабочим циклом будет постоянно перегреваться, если вы планируете выполнять сварку в больших объемах при высокой выходной силе тока. Точно так же покупка высококачественного сварочного аппарата — пустая трата денег, если вы любитель или вам нужен сварочный аппарат для легкой сварки в цеху.
Помимо рабочего цикла, вы должны учитывать диапазон выходной силы тока сварочного аппарата, включенные функции, портативность, качество сборки и, самое главное, гарантию. Если сварочный аппарат имеет большой рабочий цикл, но на него распространяется гарантия менее года, он, скорее всего, выйдет из строя быстрее, чем вам хотелось бы.
Кроме того, учтите, что вы вряд ли сможете сваривать при температуре окружающей среды 40°C после двух последовательных тепловых перегрузок. Таким образом, какую бы машину вы ни купили, у вас, вероятно, будет более длительный рабочий цикл, чем тот, который указан на этикетке, если производитель соблюдает стандарт AS/EN60974-1.
Взгляните на сравнение рабочего цикла в видео ниже. Все четыре марки превзошли свои номинальные рабочие циклы при испытаниях в реальном сварочном цехе. Наиболее вероятные причины: температура окружающей среды была ниже 40°C, а сварщики были холодными в начале испытаний.
Рабочий цикл, техническое обслуживание и влажность
Помимо температуры окружающей среды, на рабочий цикл вашего сварочного аппарата могут влиять пыль и другой мусор. Если вентиляционные отверстия забиты мусором, ваша машина будет перегреваться быстрее. Кроме того, если пыль «изолирует» чувствительные компоненты внутри сварочного аппарата, тепло будет труднее рассеиваться. Слой пыли действует как одеяло. Поэтому убедитесь, что охлаждающие вентиляторы не заблокированы, и регулярно выполняйте техническое обслуживание сварочного аппарата.
Кроме того, влажность может влиять на рассеивание тепла и сокращать рабочий цикл. Окружающий воздух с высокой относительной влажностью имеет более низкую теплопроводность, что замедляет передачу тепла от нагретых элементов внутри сварочного аппарата в атмосферу. Если вы работаете в условиях повышенной влажности, рабочий цикл может сократиться.
Рабочие циклы для различных сварочных процессов
Такие процессы дуговой сварки, как MIG, TIG и SMAW, предъявляют к сварщику разные требования. В результате они имеют присущие им различия, которые напрямую влияют на потребности рабочего цикла.
Рабочий цикл сварки МИГ
В процессе сварки МИГ используется автоматическая подача проволоки и обеспечивается непрерывная сварка. Поскольку процесс не требует частых пауз, сварочные аппараты MIG часто имеют длительные рабочие циклы.
Конечно, если вы выполняете сварку только легкого листового металла, вам подойдет сварочный аппарат MIG с коротким рабочим циклом. Но, если вы планируете сваривать толстые секции с помощью сварочного аппарата MIG, вам следует приобрести аппарат с высоким рабочим циклом.
Вы должны учитывать толщину, которую вы хотите сварить, и силу тока, необходимую для этого. Затем купите сварочный аппарат с рабочим циклом не менее 60% при требуемой силе тока.
Рабочий цикл сварки ВИГ
Процесс сварки ВИГ медленный и не требует частых остановок. Возможно, вам придется приостановить сварку, чтобы получить еще один стержень из присадочного металла, но это короткий перерыв, который не приведет к значительному охлаждению машины. Итак, если вы свариваете толстые секции, приобретите сварочный аппарат с высоким рабочим циклом.
Однако для большинства сварок TIG требуется менее 100–130 А. Многие сварочные аппараты могут работать со 100% рабочим циклом при таких низких нагрузках. Таким образом, если вы выполняете прецизионную работу с более тонкими материалами, вам не придется сильно беспокоиться о рабочем цикле.
Кроме того, сварочные аппараты не рассчитаны на импульсный выходной ток. Профессиональное оборудование TIG позволяет выполнять импульсную сварку с чередующейся высокой и низкой выходной силой тока. Это приводит к более длительному рабочему циклу, поскольку электрические компоненты машины подвергаются меньшей нагрузке. Кроме того, даже если аппарат для сварки TIG не имеет импульсной функции, использование ножной педали TIG для уменьшения выходной силы тока при сварке также увеличивает продолжительность рабочего цикла, поскольку средняя непрерывная нагрузка ниже.
Рабочий цикл сварки электродом
Процесс сварки электродом допускает частые прерывистые паузы при перемещении по стыку. Замена стержневого сварочного электрода, удаление шлака, очистка сажи и удаление мелких частиц шлака, а также наклеп в сварных швах позволяют сварочному аппарату остыть. В результате вы можете использовать машину с более коротким рабочим циклом и выполнять большую часть работы.
Длительные паузы при сварке электродами являются одной из причин того, что многопроцессорные сварочные аппараты обеспечивают кратчайший рабочий цикл для процесса сварки электродами.
Большинство работ можно выполнить с помощью сварочного аппарата на 150 А с рабочим циклом 40 %. Сварка стержнем обеспечивает более глубокое проплавление, чем другие процессы дуговой сварки. Таким образом, с некоторой подготовкой шва и мощностью не менее 150 А вы можете сваривать любую сталь толщиной менее 1/2 дюйма. При рабочем цикле 40% вы сможете сваривать около четырех минут. Скорее всего, вы израсходуете стержневой электрод быстрее, и машина остынет, пока вы очищаете шлак и готовите соединение для следующего электрода.
Что происходит, когда рабочий цикл превышен?
При превышении рабочего цикла сварочного аппарата сварщик активирует функцию защиты от тепловой перегрузки. У большинства сварщиков есть эта мера безопасности. Тем не менее, некоторые сварочные аппараты этого не делают, и они могут загореться, или некоторые из их чувствительных частей могут загореться.
Большинство сварочных аппаратов имеют внутри термопары для контроля температуры внутренних компонентов. Как только достигается критическая температура, термопара посылает сигнал на схему защиты от тепловой перегрузки, которая отключает питание.
Не тяните за вилку сварочного аппарата, если активирован режим тепловой перегрузки. Это выключит охлаждающие вентиляторы, которые должны продолжать работать, чтобы способствовать отводу избыточного тепла.
Если постоянно нарушать рабочий цикл, срок службы сварочного аппарата сократится, независимо от того, что заявляет производитель. Внутренние компоненты и их изоляция начинают разрушаться при высоких температурах, что в итоге приводит к выходу оборудования из строя.
Таким образом, вам следует избегать постоянного превышения пределов рабочего цикла. Современные сварщики используют сотни крошечных компонентов на своих печатных платах, и один резистор, конденсатор или IGBT-транзистор могут сгореть, если вы толкнете машину. Кроме того, многие из этих компонентов основаны на крошечных соединениях толщиной с человеческий волос. Они чувствительны, и постоянный перегрев приведет к повреждению.
Обмотка
Не всегда возможно напрямую сравнить рабочие циклы двух сварочных аппаратов. Производители могут варьировать свои методы тестирования. Таким образом, сравнение не имеет большого значения, если вы не сравниваете бренды, которые следуют одному и тому же стандарту тестирования.
Приобретите сварочный аппарат с увеличенным рабочим циклом, если позволяет бюджет. Лучше перестраховаться, чем сожалеть.
Однако, если вы не планируете часто сваривать или делать длинные швы, можно сэкономить деньги и приобрести менее дорогой станок. Вы должны отдавать предпочтение гарантии, а не рабочему циклу, особенно когда бренд заявляет о высоком рабочем цикле, но предоставляет короткую гарантию.
Наконец, при покупке сварочного аппарата следует учитывать не только рабочий цикл. Убедитесь, что мощность машины соответствует толщине, которую вы собираетесь сваривать, и характеристикам, необходимым для материалов, которые вы хотите соединить.
Например, если вы хотите сваривать алюминий, сварочный аппарат MIG должен поддерживать шпульный пистолет, а сварочный аппарат TIG должен работать на переменном токе. Итак, сначала убедитесь, что машина может достичь того, что вам нужно, а затем учитывайте рабочий цикл.
Сварка труб высокой чистоты: сварка труб высокой и сверхчистой чистоты
Сварной шов высокой чистоты — это любой сварной шов, который содержит менее десяти частей на миллион (частей на миллион) загрязняющих веществ, таких как кислород, водород и углерод. Сварка сверхвысокой чистоты удерживает эти загрязняющие вещества ниже одной части на миллион. Сварка труб высокой и сверхвысокой чистоты используется в процессах, где чистота продукта имеет первостепенное значение, например, в производстве полупроводниковых или биофармацевтических технологических трубопроводов. Он также используется там, где требования к прочности и надежности сварного шва выше, чем обычно можно получить — аэрокосмические приложения являются одним из примеров такого типа использования. Сварка труб высокой чистоты также используется, когда требуется как чистота, так и прочность, например, в сосудах высокого давления электростанций и теплообменниках.
Уровень загрязнения менее десяти частей на миллион значительно ниже того, что обычно можно получить при сварке в обычной атмосферной среде. Это означает, что высокочистые сварные швы любого типа выполняются либо в вакуумной камере, погруженной в защитную среду, либо под защитой инертного газа. Обычно используется последний из них — защита инертным газом. Широко используются два процесса дуговой сварки в среде защитных газов: дуговая сварка металлическим электродом с подачей проволоки (GMAW) и дуговая сварка вольфрамовым электродом в среде защитного газа (GTAW). GTAW, также известная как сварка вольфрамовым электродом в среде инертного газа (TIG), является выбранным процессом сварки для сварки труб высокой и сверхвысокой чистоты благодаря сочетанию чистоты сварного шва и контроля дуги, которое обеспечивает этот процесс.
Одним из больших преимуществ GTAW является чистота сварных швов благодаря использованию защитного газа. Во-вторых, использование в процессе нерасходуемых вольфрамовых электродов позволяет невероятно точно контролировать дугу. Выбор угла заточки вольфрама для этого электрода позволяет пользователю в значительной степени контролировать геометрию дуги и то, как ее тепло рассеивается по стыку и через него во время сварки. Это позволяет сварщику контролировать проплавление и ширину зоны термического влияния. Эти факторы способствуют получению сварных швов не только чистыми, но также точными и прочными.
Однако чистота и уровень контроля, которые предлагает GTAW, также являются источником его основных недостатков:
- GTAW — сложный процесс. Сварщик должен активно контролировать все параметры сварки в процессе сварки. Это требует особого внимания, опыта и навыков, и даже небольшие ошибки могут привести к загрязнению сварного шва.
- Квалифицированных сварщиков GTAW найти сложно. Общеизвестно, что сварке GTAW трудно научиться, и квалифицированных, опытных сварщиков GTAW относительно немного.
- GTAW требует места для маневра сварщика. Сварка в недоступных или труднодоступных местах затруднена даже для тех, кто освоил GTAW, и значительно увеличивает вероятность загрязнения сварного шва.
Орбитальная сварка GTAW была разработана специально для решения этих проблем. Этот процесс хорошо подходит для высокочистой сварки труб, поскольку он держит под контролем многие элементы сварки GTAW, позволяя сварщику сосредоточиться на внесении небольших корректировок с помощью пульта дистанционного управления сваркой, чтобы обеспечить правильное выполнение сварки. Он также позволяет сваривать трубу или трубу методом TIG без необходимости останавливаться и менять положение для сварки по всей окружности, как при ручной сварке. Поскольку головка для орбитальной сварки прижимается непосредственно к трубе, орбитальная сварка GTAW может использоваться в закрытых и недоступных пространствах, где выполняется большая часть высокочистой сварки труб.
В большинстве случаев сварка труб высокой чистоты связана с технологическими трубопроводами из нержавеющей стали для пищевой, фармацевтической и полупроводниковой промышленности. Этот трубопровод обычно подвергается электрополировке либо до, либо после сварки, а иногда и того, и другого. В этих отраслях процесс электрополировки включает погружение деталей в электрически заряженную ванну, которая удаляет железо с поверхности детали из нержавеющей стали, оставляя более устойчивые к коррозии хром и никель на поверхности нержавеющей стали. Внутреннюю часть трубы можно подвергнуть электрополировке после сварки, заполнив внутренний объем трубы раствором для электрополировки. Эта и другие подготовительные работы играют ключевую роль в высокочистой сварке труб.
Как минимум, высокочистая сварка труб должна включать следующую подготовку:
- Рабочая зона должна быть чистой. В рабочей среде не должно быть чрезмерного количества пыли, грязи, нефтепродуктов или разливов.
- Средства индивидуальной защиты должны быть безупречно чистыми. Перчатки, фартук, одежда и даже кожа сварщика должны быть очищены от грязи и старых масляных пятен.
- На заготовке не должно быть грязи, пыли, углеводородов или растворителей.
Если заготовку необходимо очистить, ее следует тщательно протереть изопропиловым спиртом и дать высохнуть перед началом сварки.
Сварные швы труб высокой чистоты должны быть чистыми снаружи и внутри трубы. Это означает, что объем трубы должен быть заполнен инертным продувочным газом, таким как аргон, для вытеснения богатой кислородом атмосферы. Новая технология сварочного аппарата, такая как кислородный датчик, может помочь обеспечить полную замену внутренней атмосферы защитным газом до начала сварки. Внутренний объем должен достигать заданного давления и быть в состоянии поддерживать это давление на протяжении всего процесса.
По сути, высокочистая сварка труб — это искусство снижения потенциального воздействия загрязняющих веществ на сварной шов.
Фактический процесс сварки высокочистых труб будет отличаться, поскольку параметры сварки зависят от точных характеристик свариваемого металла и типа выполняемого сварного шва. Однако, как правило, длина дуги должна быть короткой, чтобы уменьшить воздействие потенциальных загрязняющих веществ. Размер сварного шва также должен быть небольшим по тем же причинам.
По сути, высокочистая сварка труб — это искусство снижения потенциального воздействия загрязняющих веществ на сварной шов. Поддержание рабочей зоны и заготовки в чистоте является важной частью снижения воздействия загрязняющих веществ. Правильная подготовка шва также помогает обеспечить чистоту сварного шва. Во время фактического процесса сварки использование орбитальной GTAW ограничивает возможность загрязнения расплавленного сварного шва и создает прочный, надежный и точный сварной шов, что делает его подходящим для приложений с высокой степенью чистоты.
Компания Arc Machines, Inc. является давним лидером в производстве надежных головок для орбитальной сварки и источников питания. Контакт [email protected] . По вопросам обслуживания обращайтесь по телефону [email protected] . Arc Machines приветствует возможность обсудить ваши конкретные потребности. Свяжитесь с нами , чтобы узнать больше.
Возрождение сварки сопротивлением — Повышение производительности сварки
В сущности, физика сварки сопротивлением существует уже несколько тысячелетий. Все началось с грубой техники ковки – нагревания металла и придания ему формы. Со стороны современная контактная сварка может показаться довольно сложной, учитывая компьютеры и хитроумные приспособления, составляющие процессы контактной сварки, но, в принципе, физика недалеко ушла от того, как самураи ковали свои впечатляющие мечи сотни лет назад. Однако с термоэлектрическим процессом, который является основным в современной сварке сопротивлением, произошел ряд изменений с момента его появления в начале 19 века. 00с.
Джефф Морган проработал в автомобильной промышленности четыре десятилетия, дослужившись до старшего инженера-сварщика, прежде чем занять нынешнюю должность в отделе продаж T.J. Snow Co., компания из Теннесси, признанная лидером в области контактной сварки с полным спектром услуг. Морган пришел в отрасль в то время, когда в контактной сварке использовались игнитронные лампы и тиратронные вакуумные лампы для управления процессом синхронизации. Сегодня, по его словам, твердое тело взяло верх. Но более значительные изменения в процессе контактной сварки произошли и продолжают происходить за счет новых, более легких и сложных для сварки материалов.
Рэй Мишелена, технический специалист и пилот T.J. Сноу устанавливает отремонтированный сварочный аппарат для точечной сварки с двумя пистолетами. Морган и другие представители отрасли называют их «экзотическими» материалами. Однако даже алюминий может создавать проблемы с энергоресурсами для контактной сварки. Морган говорит, что «оболочка свариваемости» становится более сложной.
«Проблема в том, — начинает Морган, — что люди в мире дизайна хотят более легкие и прочные материалы. Поэтому, поскольку мы придумываем более легкие и прочные материалы, такие как алюминий, передовые высокопрочные стали, HSLA и многие другие материалы, они усложняют процесс».
Рэй Микелена, у которого есть ряд титулов с T.J. Сноу, включая директора по технике безопасности, инструктора семинаров и старшего пилота, говорит, что существует спрос на качество контактной сварки, что не так давно означало, что если клиент знал, что в детали задействовано 12 сварных швов, он хотел, чтобы их было как минимум 10. быть хорошим.
«В современном мире, — говорит Микелена, — клиенты хотят, чтобы эти 12 сварных швов были идеальными. Итак, в этом аспекте я вижу, что контактная сварка стала более сложной».
Стоимость качества У каждого метода сварки есть свои тонкости, и контактная сварка ничем не отличается. Однако эти сложности могут стать проблемой для сварщиков, не привыкших к этому процессу. Например, Морган говорит, что проблема, которую необходимо решить, заключается в том, чтобы убедиться, что нужные люди на производственном предприятии понимают, как обслуживать задействованное оборудование.
«При контактной сварке цена качества заключается в поддержании компонентов, которые выполняют сварку», — говорит он. «Обслуживание электродов, шунтов и электрических соединений внутри пистолета — обслуживание всего процесса становится реальной проблемой».
Частично проблема заключается в том, что больше не существует фундаментальных указаний о том, кто должен отвечать за техническое обслуживание оборудования для контактной сварки. Морган говорит, что когда он начинал свою карьеру в Ford Motor Co., монтажники труб отвечали за техническое обслуживание сварочных наконечников, в то время как на других заводах этим занимались электрики.
Т.Дж. Сварочные аппараты сопротивления снегу, такие как сварочные аппараты SlimLine на пьедестале, сконструированы так, чтобы занимать небольшую площадь.
«Количество людей, участвующих в обслуживании процесса, выросло в геометрической прогрессии, — объясняет Морган. «Очень важно, чтобы эти люди были обучены, и я думаю, что это, вероятно, одна из самых больших проблем — заставить их понять, почему они должны менять наконечники, когда приспособление для наконечников работает правильно или нет, и правильно ли установлен пистолет. ”
Эти кажущиеся незначительными аспекты процесса могут привести к проблемам. Как объясняет Микелена, эти маленькие проблемы «подобны снежинке, и каждый раз, когда эти снежинки собираются вместе, возникает метель». И, к сожалению, некоторые работники, которые выполняли процесс определенным образом в течение многих лет, не хотят меняться.
«Много раз люди не понимали переменных, за которыми нужно следить, — отмечает Микелена, — они позволяли машине выходить из строя. Они не понимают, что им нужно делать, чтобы процесс и машина работали правильно».
«Грязные навыки» Морган говорит, что большему количеству работников необходимо «выучить грязные навыки». Тем не менее, сегодняшние новейшие сварщики не так заинтересованы в том, чтобы пачкать руки, чтобы работать с частями оборудования, которое может «потребовать от них время от времени чистить ногти». Скорее, они полагаются на компьютерные процессы.
«Дело в том, — утверждает Морган, — что не так уж много людей хотят этим заниматься. Людей с механическими способностями, которые когда-то были в отрасли, не так много. Так что это, безусловно, фактор».
Микелена соглашается и говорит, что проблема возникла из-за индустрии.
«Клиенты хотят нанимать людей с улицы как можно дешевле», — говорит Микелена, добавляя, что их ставят перед автоматизированными машинами, для работы с которыми практически не требуются навыки. «Это был уровень ожиданий производителя от сотрудника. Проблема, с которой мы сталкиваемся здесь, в Соединенных Штатах, заключается в таком менталитете — у нас нет людей, которые хотят взять на себя понимание этого процесса. Мы создали его сами, и теперь мы живем с последствиями».
По словам Моргана, проблема также связана с непониманием управленческой командой производителя процесса. Например, руководство должно знать, что если они собираются использовать алюминий для сварки сопротивлением, им необходимо знать, почему они зачищают наконечники, и понимать, что наконечник должен быть холодным во время сварки. Поверхность электрода должна быть подогнана к детали — мелкие детали, которые, опять же, приводят к неэффективности при неправильном выполнении.
Переменный ток по сравнению с MFDC Постоянный ток средней частоты (MFDC) может быть более дорогим для внедрения в условиях цеха, но, по словам Моргана, когда предпочтение отдается контактной сварке, у MFDC есть преимущества. Он говорит, что не рекомендует использовать старые установки без планов по внедрению экзотических металлов для внедрения MFDC из-за связанных с этим затрат, но есть определенные преимущества, о которых следует говорить для тех, кто это делает.
«Если я строю совершенно новый объект, я бы определенно предложил MFDC», — объясняет Морган. «Это снизит энергопотребление в здании; поток энергии к сварному шву более постоянный».
Сверхвысокопрочные и высокопрочные материалы лучше преформируются с MFDC, говорит он, потому что «время подъема тепла» меньше.
«Мы также узнали, что MFDC очень хорошо работает с рельефной сваркой, — говорит Морган. «Мы обнаружили, что с MFDC время нарастания, то есть время от нуля до максимальной энергии, очень быстрое».
Микелена говорит, что преимущества MFDC также включают в себя тот факт, что это трехфазная система, а это означает, что сварщик может получать питание от трех ветвей вместо двух, что помогает экономить энергопотребление. Кроме того, он говорит, что размер трансформатора, используемого в процессах MFDC, меньше, а его вес примерно на две трети меньше, чем требуется для систем переменного тока.
«В системе MFDC у вас больше возможностей для выбора типов материалов, — добавляет Микелена, — тогда как система переменного тока в основном предназначена для холоднокатаной стали и нержавеющей стали. Вы можете попробовать работать с переменным током на более продвинутых материалах, но у MFDC определенно есть преимущества».
MFDC также позволяет производителям выбрать размер роботов, используемых в цехе.
«Во многих случаях, — говорит Морган, — вы можете использовать робота меньшего размера. На самом деле иногда это может окупить обращение к MFDC, если вы добавляете новую линию или новый процесс. Если вы покупаете меньшего и более дешевого робота, вы действительно можете позволить себе заплатить за компоненты для контактной сварки MFDC».
Сертификация контактной сварки Микелена входит в состав Комитета по контактной сварке Американского общества сварщиков (AWS), а также в подкомитет по сертификации персонала контактной сварки. Он говорит, что AWS работает над тем, чтобы привлечь больше внимания к контактной сварке, как и к большинству других методов сварки.
Несмотря на то, что сварщики могут пройти тест на контактную сварку, чтобы получить статус сертифицированного специалиста по контактной сварке (CRWT), в настоящее время нет официального курса по этому вопросу, а это означает, что сварщики должны потратить годы на контактную сварку, чтобы получить пройти тест из 100 вопросов (70 вопросов, на которые они должны ответить правильно, чтобы получить обозначение).
Джефф Морган, менеджер по продажам компании T. J. Snow, позирует перед сварочным аппаратом с несколькими пистолетами, предназначенными для сварки двух выдвижных ящиков.«Мы должны признать, что контактная сварка — очень важный процесс, — говорит Микелена. «CRWT поможет установить эту важность. Проблема в том, что у AWS пока нет обучающего курса для этого».
Микелена говорит, что настаивает на том, чтобы AWS разработала курс, который поможет сварщикам пройти сертификацию. Он говорит, что на создание таких программ уходят месяцы, если не годы. Однако он и несколько других сотрудников T. J. Snow проводит ежемесячные региональные семинары по основам контактной сварки, а также предлагает шестичасовые учебные курсы на заводах клиентов, которые включают два-три часа практической работы с оборудованием для контактной сварки.
«Это услуга», — объясняет Микелена. «Чем больше мы сможем представить сварку сопротивлением в хорошем свете, тем лучше люди поймут этот процесс и станут более успешными в сварке сопротивлением».
Т.Дж. Snow Co.
Оптимизация процесса сварки с помощью интегрированных данных
Меню
Будущий блог Люди Машинного Зрения
Оптимизация процесса сварки с помощью интегрированных данных
Возможны ли самооптимизирующиеся сварочные линии?
Читать статью
Ни один дефектный сварной шов не должен покидать производство: это один из непреложных законов серийного производства деталей транспортных средств, важных для безопасности.
Но полный визуальный осмотр — это только последний шаг: лучший вариант — предотвратить дефекты сварных швов и брак с самого начала. Как для этого оптимизировать процесс сварки – без длительных простоев и с минимальным количеством ручных вмешательств?
Прочитать сводку
Без автоматической проверки не получится
Для оптимизации процессов вам нужны данные. Как следует из термина Big Data: чем больше, тем лучше. Сегодня тестирование и оптимизация по-прежнему часто основываются на эмпирических значениях, которые представляют собой не что иное, как «данные, собранные в голове». Однако их трудно оценить, и они зависят от отдельных инспекторов и инженеров.
Здесь ручная визуальная проверка сварных швов достигает своих пределов: обученные инспекторы-люди могут быть такими же точными или даже более точными в определенных точках, чем автоматический контроль с использованием промышленной обработки изображений. Но только последний измеряет и документирует все данные каждого сварного шва без зазоров, такие как размеры или объем, и прежде всего несоответствия, т. е. дефекты.
Для каждого сварного шва фиксируются десятки записей данных, которые теперь можно использовать для оптимизации.
Соединение данных испытаний и данных процесса
Однако одних только данных проверки недостаточно: они не показывают, что вызвало дефекты . Только обладая этими знаниями, вы сможете оптимизировать процесс сварки и устранить источники ошибок.
Для этого необходимо сравнить данные контроля (обработки изображения) с данными процесса (процесса сварки) производственной детали. Сравнивая два набора данных, вы можете выяснить причину примерно 60 процентов всех дефектов сварки.
Это результат проверки почти 1000 проверок сварных швов, которые вы можете увидеть на этом графике:
Однако это не очень помогает, если у вас есть эти данные в отдельных системах. Вам пришлось бы вручную сравнивать тысячи данных и анализировать измеренные значения по отдельности: задача, которая едва ли выполнима.
Только за счет интеграции всех данных можно значительно ускорить устранение неполадок и оптимизацию процессов — и даже автоматизировать их. Как это работает?
Сначала программа анализирует наиболее частые ошибки и их корреляцию с данными процесса и геометрическими данными сварного шва. В будущем искусственный интеллект (ИИ) будет анализировать полные собранные данные для выявления закономерностей.
На следующем рисунке показано, как программное обеспечение отображает корреляции между данными оптического изображения, измеренными данными контроля и данными процесса. Таким образом, неисправный угол соединения можно легко проследить до падения напряжения:
Этот тип анализа работает не только для отдельных производственных деталей. Точно так же вы можете собирать и анализировать данные с течением времени, чтобы найти причины распространенных дефектов.
Потенциал оптимизации вашего сварочного процесса
Как вы оптимизируете свою сварочную линию, связывая эти данные? Вы можете получить три результата:
- Как уже было показано, вы можете сразу распознать большую часть причин ошибок и сразу же провести оптимизацию.
- Вы можете оптимизировать точность самой проверки и, прежде всего, свести к минимуму псевдодефекты (ложноотрицательные проверки). В дополнение к данным изображения блок контроля имеет данные процесса, доступные для анализа. На основе этих данных можно решить, например, следует ли оценивать сварной шов как все еще «в пределах допуска» или сообщать о дефекте.
- Если несоответствия в процессе часто приводят к ошибкам, их можно исправить с помощью процесса обратной связи уже во время сварки.
В результате вы получаете более стабильные сварочные процессы, сокращаете время простоя и меньше брака.
Самооптимизирующаяся сварочная линия – вопрос времени
Можно ли автоматизировать процесс оптимизации – точно так же, как само серийное производство во многих местах уже работает без ручного вмешательства?
Еще нет. Однако это лишь вопрос времени. Искусственный интеллект обучается с каждым дополнительным набором данных и каждой обнаруженной ошибкой. Они могут все лучше и лучше распознавать закономерности и корреляции и делать выводы: в этом суть так называемого машинного обучения.
Если, например, определенное падение напряжения уже вызвало дефект сварки 1000 раз, весьма вероятно, что это произойдет и в 1001-й раз. Тогда ИИ мог бы вмешаться и, скорее всего, был бы прав.
Замкнутый цикл с интеграцией данных с разных этапов процесса приводит к повышению производительности процесса сварки и повышению безопасности при автоматизированном контроле качества. В будущем определенные усовершенствования процессов и превентивные вмешательства станут возможными без вмешательства человека.
Андреас Ньеуэс Разработчик VIRO WSI, VITRONIC
Таким образом, сварочная линия становится замкнутой системой, которая непрерывно собирает и оценивает данные, оптимизируется и, в идеале, вмешивается до возникновения ошибок.
Важно! Вы сами решаете, какие действия вы хотите разрешить программному обеспечению, а какие требуют одобрения человека. Как человек, ответственный за процесс сварки, вы сохраняете суверенитет над оптимизацией — система поддерживает вас в этом.
Сводка
Коротко
- Вы должны как можно полнее записывать данные в каждой точке вдоль линии сварки.
- Связав данные контроля и процесса, можно сразу определить причину примерно 60 % всех дефектов сварки.
- Данные позволяют оптимизировать как процесс сварки, так и контроль.
Заключение
Интеграция данных контроля и технологических данных со сварочных линий позволяет немедленно выявлять, устранять и даже предотвращать причины неисправностей.
Доктор Питер Даниэль
Менеджер по продукту
- Телефон
- +49 611 7152 307
- Электронная почта
- [email protected]
Следуй за мной
Подписаться на рассылку новостей
Адрес электронной почты
Люди с машинным зрением
Будь то автоматизация или организация дорожного движения: с нашими системами наши клиенты видят больше. Сочетание аппаратного обеспечения, данных и интеллектуальной оценки делает возможными приложения и анализы, которые до недавнего времени были немыслимы. Ранее скрытый мир становится видимым и доступным для использования.
Предложения по
- Кандидаты
- Журналисты
- Поставщики
Промышленность
- 3D сканирование тела
- Автомобильный
- Здравоохранение
- Логистика
- Фотовольтаика
- Технология трафика
Сервис и поддержка
- +49 611 7152 7777
- Запрос запасных частей
- Тренинги
Актуальные темы
- 35 лет ВИТРОНИК
- Визионер — Блог о будущем
Огневая сварка
Огневая сваркаПроблема | ||||||||
Огневая сварка; также называемый молотковая сварка , кузнечная сварка , сварка давлением или контактная
сварка, является наиболее важной технологией в обработке железа и стали до тех пор, пока
вы не можете расплавить материал.![]() Я дал вам уже целый модуль о «Сварке с помощью молота и огня». Я думаю, там довольно ясно описано, что происходит. Так почему у меня проблемы огневой или молотковой сваркой теперь , маркировка на нем уже здесь или там? Моя нынешняя проблема, или «проблема», довольно проста: слишком много вопросы возникают, как только кто-то более внимательно смотрит на огневую сварку. В суть, все они касаются того, как избавиться от окислов, покрывающих поверхности быть сварены. ![]() Я допускаю, что некоторое количество оставшегося оксида может не быть большой проблемой, поскольку удары молотком разобьют его на мелкие части. Но эти маленькие частицы будут обнаружены в районе сварного шва, и вы не сможете иметь слишком много без ущерба для качества продукта. Учитывая, что сварка огнем происходила все время в железе и стали технологии, очевидно, это не так уж сложно сделать. Шлак, оксид и Частицы «флюса» действительно обнаруживаются в сварных швах довольно часто. можно было ожидать. Так в чем проблема? Проблема в том, что слишком много вопросов, не имеющих четкого и убедительные ответы. ![]() | ||||||||
| ||||||||
| ||||||||
На снимке современная огневая сварка восьми
большие плоские простыни с плотным прилеганием.![]() Также весьма маловероятно, что заготовка имеет температуру 1200 или С. температура. В то время как нужно быть осторожным с воспроизведением цветов на экраны, он конечно не полностью белый как требуется при такой температуре. Там также не является восстановительной атмосферой, конечно. Тем не менее — процесс работает. | ||||||||
Чем мы занимаемся Знать? | ||
Давайте копнем немного глубже, взглянув на
кое-что из того, что было написано о огневой сварке в контексте
вопросы выше.![]() | ||
Ван Бухвальд посвящает несколько страниц
своей книги «Искусство молотковой сварки». Он по существу следует
логика, изложенная выше, но с небольшими противоречиями: сварка молотком требует
температуры при «1100 — 1250 o С» или требует «нагрева
примерно до 1100 o C в восстановительной атмосфере». Образование оксида
о горячем железе обсуждается довольно подробно, и Бухвальд указывает, что
«они (оксиды)
легко достичь толщины 0,2 мм за считанные минуты при высокой
температур». Похоже, Бухвальд полагает, что некоторые
вюстит неизбежен и что все сварные швы должны содержать некоторые
вещи. Несколько изображений иллюстрируют это, показывая сварные швы с включениями.
оксида (вюстит, FeO) или даже SiO 2 зерен иногда.
Тем не менее, в других местах есть много фотографий, на которых виден идеально чистый сварной шов.![]() | ||
На более детальном уровне Бухвальд утверждает, что
Процесс окисления приведет к обезуглероживанию углерода и обогащению фосфором.
поверхностном слое и, следовательно, в сварном шве с различной концентрацией примесей.
от массы. Возможно, так и было, и это наблюдалось, но
это не обязательно следует из приведенных аргументов. Действие «флюса» SiO 2 двоякое. Во-первых, фаялитовый «шлак», образующийся в результате реакции с оксидом, защищает железо /steel от кислорода воздуха и, таким образом, препятствует дальнейшему окислению. Второй, разжиженное вещество можно «выдавить» или заставить убежать постукивание по заготовке, обеспечение чистоты поверхностей. Бухвальд упоминает, что бура также работает как «флюс», но не говорит как. | ||
Он также добавляет новый пункт: «любопытно,
песок/кварц не вступает в реакцию с поверхностными оксидами на горячекованом железе , если только железо не окружено восстановительной атмосферой, так что
поверхностный оксид FeO».![]() |
Все, что пишет Бухвальд, делает смысле — но на самом деле не отвечает на мои вопросы сверху. Итак, давайте посмотрим, как современные практики описывают процесс огневой сварки. | ||
Проверил несколько «мануалов» на предмет
начинающие кузнецы о том, как сварить огнем. Они все согласились, что вы должны положить
некоторый «флюс» на свариваемых поверхностях: «Когда полосы становятся ярко-оранжевыми, с полосами
оставшись в огне, возьмите свои грабли и сделайте отверстие в огне над
шарфы (детали для сварки), поэтому флюс может быть
сыпали на лицо платки».![]() Также рекомендуется две соединяемые поверхности делать слегка выпуклыми. Тогда они соприкасаются только в центре, и вы можете сваривать их молотком с центр наружу, позволяя жидкому шлаку / флюсу отходить по мере того, как вы продолжить. | ||
Существует также общее соглашение о
следующие пункты:
| ||
Все нормально и рецепты учитывая явно работу. Но я придерживаюсь своего мнения и утверждаю, что большая часть моего вопроса выше толком не ответили. И не забывайте, что ситуация сейчас отличается от того, что было 2000 лет назад. Современный кузнец может легко дойти до 1200 o C, возможно, даже в редуцирующей части его огня, просто провернув увеличьте мощность своего воздушного (или, возможно, кислородного) вентилятора. Древний кузнец бы у него было гораздо больше проблем при этом, если он вообще мог это сделать. | ||
До пункта 10
касается моего списка вопросов, я просто отсылаю вас к некоторым современным писаниям
— по этой ссылке.![]() | ||
Давайте остановимся здесь. Есть много
возможные комментарии и пояснения к моим вопросам сверху. я мог бы продолжить
в течение довольно долгого времени, но мы просто никуда не доберемся. Факты таковы, что огневая сварка довольно сложна и ее нелегко выполнить новички в кузнечном деле. ![]() | ||
1) | Г. Беккер: «Нидриг schmelzende Eisen-Arsen-Legirungen als Hilfsmittel für den Verbund römischer Schwertklingen». Arch. Eisenhüttenwes. 32, (1961), стр. 661 — 665. |
С рамкой
Глоссарий
Книги и другие основные источники
11.2.2 Металлургия кельтских мечей
Критический путеводитель по музею: Метрополитен-музей, Нью-Йорк
.
Местонахождения раннего железа: Хаттуса
Античные тексты о железе
11.3 Шаблонная сварка 11.3.1 Общие сведения о шаблонной сварке
Большие изображения 1
пидор
Места для меча: Луристан
6.2.3 Сварка огнём или молотом
Большие изображения глава 11.4
Крупные изображения 2 — Глава 11.3
11.6.4 Металлургия японского меча
Рукоять кельтского антропоидного меча
Моравские мечи 9 века
Крупные изображения — Глава 11.2
Кельты
Крупные изображения — Глава 11.1
Уловки кузнецов
Клепка, пайка, жидкостная сварка плюс склеивание и завинчивание
Разногласия по исследованию истории железных технологий
Металлография мечей и саксофонов 8-9 веков
Анализ ковки меча «Викинг»
11.3.4 Металлография шаблонных сварных мечей
11.6.2 Изготовление японского меча — часть 1
Англо-саксонское кладбище в Довер-Бакленде, Кент, Великобритания, и технологии
некоторых изделий из железа.
Большие изображения 3
© H. Föll (сценарий «Железо, сталь и мечи»)
Услуги по сварке трением алюминия и других материалов
СВАРКА ТРЕНИЕМ
Сварка трением относится к методу сварки с использованием тепла, выделяемого при трении контактной поверхности заготовки, как источник тепла, вызывающий пластическую деформацию заготовки под давлением.
Под действием давления, под действием постоянного или ступенчатого давления и крутящего момента относительное перемещение между торцами привариваемого контакта создает теплоту трения и теплоту пластической деформации на поверхности трения и вблизи нее, так что температура ее В области температур, близких к температуре плавления, но, как правило, ниже, сопротивление деформации материала снижается, пластичность улучшается, а оксидная пленка на границе раздела разрушается. Под действием осадочного давления пластическая деформация и течение материала сопровождаются молекулярной диффузией и рекристаллизацией на границе раздела. Твердофазный метод сварки для осуществления сварки.
Minghe предлагает комплексные решения для сварки трением для широкого спектра задач литья под давлением — с большим портфелем машин и дополнительной поддержкой, начиная от проектирования и заканчивая обслуживанием. Являясь мировым лидером в производстве литья по выплавляемым моделям, мы гордимся тем, что предлагаем только лучшие услуги на рынке. Наша страсть к превосходному обслуживанию клиентов ведет нас к совершенству. Чтобы узнать больше о наших услугах или обсудить варианты вашего следующего проекта, свяжитесь с командой сегодня.
Сущность сварки трением
Металлические поверхности механических деталей обычно склеиваются и свариваются из-за трения. В процессе резки металла и высокоскоростного вращения станка часто обнаруживается, что поверхности двух металлических деталей свариваются между собой за счет трения и нагрева. Например: при точении на токарном инструменте образуется нарост; во время сверления сверло и заготовка часто склеиваются между собой; подшипник скольжения заедает из-за обгорания вала. Конечно, эти ситуации всегда были случайностями, которых люди старались избегать. Анализируя явление сварки, их процесс не идеален, а качество сварки не идеально.
Тем не менее, посредством анализа этих явлений соединения и сварки полезно понять суть сварки трением.
Трение разрушает оксидную пленку на поверхности металла. Выделение теплоты трения снижает прочность металла, но повышает его пластичность. Металл поверхности трения вызывает пластическую деформацию и течение, что препятствует окислению металла, способствует взаимной диффузии атомов металла шва и формирует прочное сварное соединение. В этом суть сварки трением.
Особенности сварки трением
Почему сварка трением развивается очень быстро в стране и за рубежом, и ее применение очень широко, это потому, что она имеет ряд преимуществ. Эти преимущества включают следующие аспекты:
1. Качество сварки соединения хорошее и стабильное
Доля брака переходных соединений алюминий-медь, полученных низкотемпературной сваркой трением в моей стране, составляет менее 0,01%; котельный завод использует сварку трением вместо сварки оплавлением для производства змеевиков экономайзера, а доля сварочного брака снижается с 10% до 0,001%. Западная Германия использует сварку трением вместо сварки оплавлением для производства выпускных клапанов автомобилей, и процент брака при сварке снизился с 1,4% до 0,04~0,01%. Из приведенных выше примеров видно, что процент брака при сварке трением очень низок, около 1% от общего метода сварки.
2. Подходит для сварки разнородных сталей и разнородных металлов.
Сварка трением позволяет сваривать не только обычные разнородные стали, но также разнородные стали и разнородные металлы с очень разными механическими и физическими свойствами при комнатной и высокой температуре, например углеродистую конструкционную сталь — быстрорежущую инструментальную сталь; медь-нержавеющая сталь. Кроме того, он также может сваривать разнородные металлы, образующие хрупкие сплавы, такие как алюминий-медь, алюминий-сталь и т. д.
3. Высокая точность размера сварного шва
Для предкамеры сгорания дизельного двигателя, изготовленной сваркой трением, максимальная погрешность общей длины составляет ±0,1 мм.