2. Основные виды и особенности сварки пластмасс. Сварка пластмасс
Сварка пластмасс
реферат
Сварка пластмасс — это процесс неразъёмного соединения термопластов и реактопластов, в результате которого исчезает граница раздела между соединяемыми деталями.
Соединение реактопластов осуществляют способом, основанным на химическом взаимодействии между поверхностями непосредственно или с участием присадочного материала (т. н. химическая сварка). Осуществление этого способа требует интенсивного прогрева поверхностей и интенсификации колебаний звеньев молекул полимера током или ультразвуком.
Далее в работе будет говориться о сварке термопластов.
Сварку термопластов производят с использованием тепла. В зависимости от того, используются ли непосредственно источники теплоты или применяется преобразование различных видов энергии в тепловую, способы сварки термопластов подразделяют на две группы.
К первому виду сварок относятся сварка нагретым элементом, сварка горячим воздухом (газом), экструзионная и инжекционная сварка. Ко второму — электрическое соединение, ультразвуковая и высокочастотная сварка, сварка трением и др. Отличительной особенностью сварки пластмасс является то, что процесс соединения происходит при температуре выше температуры размягчения, но ниже температуры разложения при вязко-текучем состоянии полимера под давлением.
1. Сварка нагретым элементом
При контактно-тепловой сварке термопластов, относящейся к первому типу сварок, образование соединения происходит за счет нагрева соединяемых поверхностей нагревательным инструментом и приложения давления. Существует два основных способа контактно-тепловой сварки: сварка оплавлением и проплавлением.
Рисунок 2. Сварка нагретым элементом. 1 — свариваемые заготовки; 2 — лента из фторопласта; 3 — прижимной ролик; 4 — нагретый элемент.
При сварке оплавлением нагреватель плотно прилегает непосредственно к поверхностям, подлежащим сварке, и оплавляет их. Затем нагревательный элемент удаляют из зоны сварки, детали соединяют, прикладывают давление и выдерживают некоторое время до остывания сварного шва.
Прочность изделий из пластмасс определяется также конструкцией соединения. Типы сварных соединений, выполняемых сваркой оплавлением, представлены на рисунке 3.
Рисунок 3. Типы сварных соединений, выполняемые контактно-тепловой сваркой оплавлением
Оплавление кромок фигурным нагревателем приводит к повышению прочности сварного соединения за счет увеличения поверхности соединения.
Сварку оплавлением применяют для соединения листов, сварки пластиковых труб, пластин и блоков с подготовкой кромок механической резкой.
При контактной сварке проплавлением нагревательный элемент контактирует с внешними поверхностями деталей, и теплота передается к свариваемым поверхностям за счет теплопроводности сквозь их толщу. Нагрев деталей осуществляется с одной или двух сторон. Двусторонний нагрев материала облегчает условия сварки, позволяет быстрее нагреть материал до требуемой температуры. Можно соединять изделие по всей длине или проводить шаговую сварку. Для получения непрерывных швов использую роликовые и ленточные аппараты.
В зависимости от свойств свариваемого материала, толщины прокладок, температуры инструмента продолжительность сварки составляет 3-5 с. Для предупреждения коробления детали охлаждают под давлением.
Контактно-тепловой сваркой проплавлением соединяют листы и пленки толщиной до 2-3 мм в нахлестку. Изменяя величину нахлестки, можно изменять прочность сварного шва в широких пределах. Конструкция сварных соединений представлена на рисунке 4.
пластмасса полимерный сварка контактный
Рисунок 4. Конструкция сварных соединений пленок: а — нахлесточное; б, в — с накладками
2. Сварка горячим воздухом (газом)
При этом типе сварки используется горячий воздух (газ) для нагревания поверхности пластмассы. Окисление пластмассы может ослабить сварное соединение. При возникновении данной проблемы горячий воздух заменяют горячим газом (например, азот), поскольку содержащаяся в воздухе влажность может усиливать окисление. Что касается устойчивости температуры, у сварочных установок с горячим газом имеется преимущество перед сварочными установками с горячим воздухом.
Рисунок 5. Сварка горячим газом. 1 — присадочный пруток; 2 — ролик; 3 — горелка; 4 — сварной шов; 5 -свариваемые заготовки; 6 — направление сварки
3. Экструзионная сварка
В данном виде сварки используется шнековый механизм (винтовой транспортер), который перемещает стержень или гранулы (в зависимости от размера электрода) через цилиндр. Внутри цилиндра происходит смешивание пластмасс, их сжатие и расплавление. Винтовой транспортер толкает расплавленную пластмассу через сварочную установку сквозь «ползун», создавая наплавленный валик. Экструзионная сварочная установка осуществляет предварительное нагревание сварной области с помощью горячего воздуха или газа.[2]
4. Инжекционная сварка
Эта система сварки использует сочетание разогретого наконечника и давления инжекции для формования сварных соединений. Горячий (заменяемый) наконечник разогревает поверхность пластмассы и создает зону сварного соединения, в которую впрыскивается расплавленная пластмасса. При этом не происходит реального физического смешивания сварного шва и пластмассы. В охлажденном состоянии это сварное соединение самое прочное из тех, что можно получить с помощью данной группы технологий. Поскольку наконечник вызывает растрескивание поверхности пластмассы, нет необходимости осуществлять подготовку поверхности, если только нет сильного загрязнения. Это позволяет сэкономить время при производстве сварочных работ.
Далее представлены виды сварочных технологий, относящиеся ко второму типу:
5. Электрическое цокольное соединение
В этой технологии используется электрический патрон для сварки пластмассовых деталей (таких как полиэтиленовые трубы). Электрическая энергия нагревает медную проволоку внутри патрона, пластмасса плавится и расширяется, давление расширения соединяет детали.
6. Ультразвуковая сварка
При ультразвуковой сварке используется акустический инструмент для передачи энергии вибрации через пластмассовые детали в область сварки. Трение вибрирующих молекул создает тепло, которое расплавляет и сваривает пластмассу. Когда пластмасса достигает состояния расплава, вибрация прекращается. Давление применяется по мере отверждения расплавленной пластмассы. Такая система используется для сваривания мелких деталей.
Рисунок 6. Придаточная ультразвуковая сварка. 1 — инструмент-волновод; 2 — свариваемые детали
Рисунок 7. Контактная ультразвуковая сварка: а — прессовая; б — шовная; в — возможные формы конца волновода. 1 — инструмент-волновод; 2 — свариваемые детали; 3 — опора
7. Высокочастотная сварка
Высокочастотная сварка в отличие от ультразвуковой, соединения которой похожи на штамповку, позволяет достичь непрерывности сварных соединений. Типичным применением данного типа сварки является сваривание тонких материалов.
Рисунок 8. Сварка труб токами высокой частоты.
8. Сварка трением
Сваркой трением соединяют круглые пластмассовые детали с помощью их прижимания друг к другу в процессе кругового вращательного движения. При этом одну деталь держат неподвижно, а вторую вращают. Трение между двумя деталями вырабатывает тепло, которое в свою очередь вызывает расплавление и слияние (при охлаждении).
Рисунок 9. Сварка трением
9. Вибрационная сварка
При данном типе сварки поверхности свариваемых деталей нагреваются за счет вибрации, что вызывает их расплавление и создание сварного соединения.
Рисунок 10. Схема вибрационной сварки
10. Лазерная сварка
Лазерная сварка бывает трех видов: сварка по контуру, синхронная и квазисинхронная сварка. При сварке по контуру слои соединяются лазерным лучом, который передвигается и расплавляет пластмассы по шву, или же прижатые друг к другу слои перемещаются вдоль зафиксированного лазерного луча.
При синхронной сварке лазерные лучи от нескольких диодов направлены на линию контура шва, вызывая одновременное плавление и сваривание всего профиля.
Квазисинхронная сварка представляет собой сочетание сварки по контуру и синхронной сварки. Зеркала направляют лазерный луч на больших скоростях вдоль свариваемой детали, в результате чего весь контур постепенно нагревается и расплавляется.
Рисунок 11. Лазерная сварка. Слева направо: сварка по контуру, синхронная сварка, квазисинхронная сварка.
Для всех перечисленных видов сварки характерны следующие основные параметры: температура сварки, время нагрева (оплавления), величина давления при нагреве и осадке, время осадки и выдержки под давлением, величина и скорость осадки, глубина проплавления.
Температура нагрева при сварке с помощью сварочных аппаратов стыковой сварки и последующее охлаждение определяются кинетикой тепловых процессов, структурными превращениями в шве и околошовной зоне. При этом не должно происходить разложение полимера, иначе качество сварного шва снизится. Температуру нагревательного элемента обычно устанавливают на 100-120 0С выше температуры плавления термопласта.
Нужно также избегать резкого охлаждения сварного шва (водой или холодным воздухом), так как это может привести к возрастанию внутренних напряжений в нем.
Величина давления и скорость осадки при сварке должны обеспечить удаление прослоек (газовая и окисленный слой). Давление позволяет молекулам пластмасс смешиваться. При сварке пластмасс наилучшее соединение получается тогда, когда не происходит реального физического смешивания пластмассовых материалов. Если давление слишком низкое или слишком высокое, качество сварного шва ухудшается.
Прочность сварных соединений увеличивается с повышением длительности сварки и температуры торцов оплавляемых деталей только до определенного предела, до температуры активного разложения полимера. С увеличением давления при осадке прочность сварных соединений возрастает.
Прочность по сечению шва имеет максимальное значение в середине стыка. Это объясняется течением расплава в процессе формирования и остывания шва. Течение расплава особенно интенсивно в периферийной зоне.
При производстве сварочных работ нужно помнить следующее. Во-первых, нельзя сваривать вместе различные виды пластмасс, так как у каждой пластмассы своя молекулярная структура и температура сварки. Во-вторых, для сварки с использованием большинства сварочных систем необходимо провести подготовку поверхности пластмассы, что необходимо для получения качественного сварного соединения. Подготовка поверхности уменьшает окисление и удаляет прочие загрязняющие вещества, такие как жир, пыль, устраняет поверхностные повреждения.
Также нужно помнить и то, что не существует универсального способа сварки. Вид сварки выбирается в зависимости от молекулярной структуры и свойств свариваемой пластмассы, а также от размеров изделия.
Общий экзамен Уровень 3 (Сварка пластмасс)
Какие факторы вызывают старение полимеров?
тепло, кислород, озон
Наличие сварных соединений
Контакт с грунтом
Для замедления старения в полимеры добавляют
Стабилизаторы
Ионизаторы
Консерванты
В полиэтилен в качестве стабилизатора добавляют:
Сажу .
Кварцевый песок
Алюминиевую пудру
Являются ли пластмассы диэлектриками?
Да
Нет
Зависит от их состава
На какие основные группы делятся пластмассы?
Термопласты и реактопласты
Жидкие и твердые
Ковкие и хрупкие
Более пластичны в твердом состоянии:
Термопласты
Реактопласты
Пластичность всех полимеров одинакова
Свариваемость пластмасс повышают;
Стабилизаторы
Красители
Пластификаторы
Какие пластмассы могут многократно плавиться?
Только термопласты
Только реактопласты
Все
Сколько раз можно плавить термопласты?
Один
Два
Несколько
Температура воспламенения полиэтилена:
180 градусов Цельсия
220 градусов Цельсия
365 градусов Цельсия
Гарантийный срок хранения полиэтиленовых труб:
6 мес
1 год
2 года
Гарантийный срок хранения соединительных деталей из полиэтилена определяется:
СНиПом
ГОСТом
Документом на продукцию
Свариваемость полимеров зависит от:
Текучести расплава полимера
Плотности полимера
Относительного удлинения полимера
Полиэтиленовые трубы производят в основном:
Литьем под давлением
Прессованием
Непрерывной шнековой экструзией
Соединительные детали производят в основном:
Литьем под давлением
Прессованием
Непрерывной шнековой экструзией
Как влияет солнечный свет на полиэтиленовые трубы?
Вызывает разрушение
Вызывает старение
Положительно
SDR обозначает:
Отношение номинального наружного диаметра трубы к номинальной толщине стенки
Сокращённое наименование материала
Предел текучести материала
Для изготовления газопроводных труб применяют;
ПЭ63 и ПЭ80
ПЭбЗ И ПЭ100
ПЭ80 и ПЭ100
Можно ли использовать вторичный полиэтилен для производства газопроводных труб и
соединительных деталей?
Да
Нет.
Да, только для соединительных деталей
Какой из полимеров нельзя сваривать токами высокой частоты:
Полиэтилен «
Поливинилхлорид
Полиамид
Сварка нагретым инструментом основана на:
Плавлении
Склеивании
Химической реакции
Сварка полимеров плавлением основана на:
Прочностных свойствах полимера
Свойствах полимера иметь трехмерные макроструктуры
Вэаимодиффузии макромолекул полимера в вязко-текучем состоянии
Основные параметры сварки встык полимеров:
Температура и время нагрева поверхностей, давление при сварке и время его воздействия г
Сила тока и напряжение на режущем устройстве
Напряжение питания сварочного аппарата
Режимы сварки пластмасс нагретым инструментом задают в интервале:
Ниже температуры текучести, но выше температуры деструкции
Выше температуры текучести, но ниже температуры деструкции •
Ниже температуры текучести
К какому классу относятся такие виды сварки, как экструзионная, расплавом, нагретым газом?
Механическому
Термическому
Электромагнитному
При сварке нагретым газом присадочный материал:
Используется
Не используется
Оба варианта верны
При сварке нагретым газом присадочный материал подается в зону сварки в виде:
Порошка
Прутка
Жидкости
Какой теплоноситель обычно используют при сварке нагретым газом неответственных конструкций?
Кислород
Воздух
Азот
Какова прочность сварного соединения полиэтилена, выполненного сваркой нагретым газом?
30-60% от прочности основного материала.
Достигается равнопрочность
110% от прочности основного материала
Сварка расплавленной присадкой заключается в подаче на свариваемые поверхности термопласта:
Находящегося в вязко-текучем состоянии
Нагретого горячим газом
Нагретого горелкой инфракрасного излучения
Экструзионная сварка заключается в том, что:
Расплавленный материал, выходящий из экструдера, нагревает поверхности до температуры
сварки и сплавляется с ней
Экструдируемой присадка распыляется
Экструдируемая присадка склеивает соединяемые поверхности
Какова прочность сварного соединения полиэтилена, выполненного эксгрузионной сваркой?
Достигается равнопрочность
120% от прочности основного материала
65-75% прочности основного материала
Каковы основные технологические параметры сварки литьем под давлением?
Температура и давление впрыскивания присадочного расплава
Температура присадочного расплава и время сварки
Давление впрыскивания присадочного расплава и время остывания
Сварка трением основана на:
Превращении энергии звуковых колебаний в тепловую энергию
Введении третьего компонента
Превращении механической энергии трения свариваемых поверхностей в тепловую энергию ,
Можно ли сваривать трением разнородные пластмассы?
Да
Нет
Только ПВХ с полиамидом ПА-6
Раструбная сварка пластмассовых груб относится к сварке:
Нагретым газом
Нагретым инструментом
Эксгрузионной
Сварка с помощью инфракрасного излучения основана на превращении энергии:
Нагретого излучением газа в тепловую энергию
Источника ИК- излучения в тепловую энергию
Тока высокой частоты в тепловую энергию
Основные технологические параметры сварки излучением:
Глубина проплавления, усилие и скорость осадки г
Глубина проплавления и технологическая пауза
Время проплавления и время осадки
К какому виду сварки относится сварка токами высокой частоты?
Электромеханический
Механический
Электрический
В каком электромагнитном поле производится сварка ТВЧ пластмасс?
Постоянном
Вихревом
Переменном
Полиэтиленовые трубы, как правило, сваривают:
ТВЧ, лазером
Химическим способом
Нагретым инструментом, экструзией, трением
Соединительные детали из полиэтилена для трубопроводов, как правило, сваривают:
Нагретым инструментом, трением
ТВЧ,. излучением, экструзией
Химическим способом
Пленочные упаковки, покрытия из полимеров сваривают:
ТВЧ,нагретым инструментом, ультразвуком, излучением
Лазером, экструзией
Трением, нейтронной сваркой
Интервал вязко-текучего состояния полиэтилена:
30 градусов Цельсия
40 градусов Цельсия
70-100 градусов Цельсия
Контактной сваркой проплавлением соединяют, как правило:
Трубы
Пленки
Листовой полиэтилен
Технологическая пауза при сварке встык, это:
Время между выходом первичного грата и соединением свариваемых поверхностей
Время между окончанием нагрева и соединением свариваемых поверхностей
Время между соединением свариваемых поверхностей и охлаждением стыка
Почему технологическая пауза при сварке встык должна быть минимальной?
Из — за охлаждения вследствие контакта с воздухом
Из-за возможной деформации деталей
Из — за возможного контакта с инородными телами
К чему приводит перегрев нагревателя при сварке встык?
Деструкции полимера
Улучшению качества сварного соединения
Отвердению полимера
Что способствует деструкции полимера при сварке встык?
Певышение значений давления и технологической паузы
Певышение значений давления и времени торцевания
Певышение заданной температуры нагревателя и времени нагрева
На чем основано образование сварного соединения полиэтиленовых труб?
Взаимодиффузии макромолекул на соединяемых поверхностях
Изменении химического состава соединяемых поверхностей
Электромагнитном взаимодействии
Чем нагревают зеркало нагревательного инструмента при сварке встык?
Электрическим током или газовой горелкой
Токами высокой частоты
В электрической муфельной печи
Чем определяются требования к режимам сварки встык?
Техническими условиями на свариваемые трубы
Нормативными документами по строительству
Инструкциями на сварочные аппараты
В чем заключается сварка встык?
В сильном сдавливании торцов полимерных труб с одновременным нагревом
В нагреве торцов полимерных труб или деталей до вязко-текучего состояния при контакте с нагревателем и соединении под давлением после удаления нагревателя
В обжатии нагревателями полимерных труб до вязко-текучего состояния с последующим охлаждением
Что используют для защиты полиэтиленовой трубы от повреждения о стенки стального
футляра после протяжки?
Редукционные вкладыши
Пластиковые втулки, раструбы
Асбоцементные полукольца
Привод зажимов центратора в аппаратах для сварки встык бывает:
Ручным
Гидравлическим
Гидравлическим, ручным, электрическим
Аппараты для сварки встык по степени автоматизации бывают:
Высокой степени, средней степени, с ручным управлением
Автоматизированные и механизированные
С низкой и высокой степенью автоматизации
Аппараты для сварки деталями с закладным нагревателем с тремя и более способами ввода
технологических параметров относятся к:
Многоцелевым
Универсальным
Таких аппаратов не существует
При разматывании длинномерных полиэтиленовых труб с барабана стяжки следует обрезать:
Все сразу
По мере разматывания, не допуская перехлеста витков
Обрезка не допускается, стяжки должны лопнуть сами
При сооружении полиэтиленовых газопроводов допускается использование соединительных деталей:
С закладным нагревателем
Без закладного нагревателя (гладких)
Оба варианта верны
Электропитание аппарата для сварки деталями с закладным нагревателем может осуществляться:
От электрогенератора, напряжением 220 В, 48 В
От аккумулятора
Оба варианта верны
Какова максимальная сменная производительность при стыковой сварке лояйзтиленовых труб О 110 мм?
Около 10 стыков
Около 30 стыков
Около 40 стыков
Максимальное рабочее давление полиэтиленового газопровода зависит от:
Вида поставки труб и вида используемых соединительных деталей
Способа сварки труб, квалификации сварщиков
Марки полиэтилена и SDR-труб, коэффициента запаса прочности
Разрешено ли возобновлять прерванную аппаратом сварку полиэтиленовых труб деталями с
закладным нагревателем?
Зависит от SDR труб
Нет
Да, после полного остывания соединения
Для сварки встык труб с диаметром, отличным от максимального для используемого
аппарата, следует использовать:
Опорные ролики
Специальные струбцины
Редукционные вкладыши
Общая потребляемая аппаратом для стыковой сварки мощность обычно составляет:
От 1 до 2 кВт
Не менее 3,5 кВт
Не более 1 кВт
Для обеспечения надежной работы сварочных аппаратов наиболее важными параметрами автономных источников электропитания являются:
Вид привода и вид используемого топлива
Цена, простота обслуживания
Величина и стабильность напряжения и силы тока, вырабатываемого генератором, мощность, надежность
При работе на аппарате для сварки встык возможны следующие виды травм персонала
Поражение электрическим током
Ожог нагревателем, защемление движущимися зажимами
Оба варианта верны
При работе на аппарате для сварки деталями с закладным нагревателем возможны следующие виды травм персонала:
Поражение электрическим током
Ожог нагревателем
Оба варианта верны
Возможно ли последовательное включение в заземляющий проводник нескольких сварочных
аппаратов?
Да
Нет
Оба варианта верны
Какой источник электропитания аппаратов для сварки полиэтиленовых труб редпочтительней?
САК
Автономный электрогенератор переменного тока
Электрическая сеть ближайшего к месту сварки здания
По окончании работе электрооборудованием сварщик должен:
Выключить сетевой рубильник
Отсоединить клеммы сетевого кабеля
Отсоединить сварочные кабели
Электрическое сопротивление закладного нагревателя в соединительной детали обычно составляет:
1 — 100 кОм
До нескольких десятков Ом
0,1 — 1 МОм
Редукционные вкладыши используют для изменения диаметра труб:
Закрепляемых в зажимах центратора, позиционера
Монтируемого трубопровода, согласно проекту
Оба варианта верны
Устройство постели под основание полиэтиленового газопровода должно проводиться:
Перед началом сварки тру
После завершения монтажа и опрессовкb
Оба варианта верны
Для перекрытия потока газа в полиэтиленовом газопроводе можно использовать:
Задвижку
Механический или гидравлический передавливатель
Оба варианта верны
При нехватке рабочего времени для сварки очередного стыка полиэтиленовых труб можно:
Не проводить механическую обработку труб
Сократить время остывания сварного соединения
Перенести сварку на другой день
Для фиксации длинномерных полиэтиленовых труб при сварке тройникового соединения с
закладным нагревателем О 160 мм следует использовать:
Центратор
Ломы, тросы, клинья
Позиционер
Допускается ли принудительное охлаждение сварного соединения?
Да, при слишком высокой температуре воздуха
Нет
Да, с разрешения инспектора ФАТН
Какое оборудование можно использовать для выравнивания овальности труб?
Передавливатели
Калибрующие зажимы — струбцины,
Позиционеры
При протяжке полиэтиленовых труб в футлярах тяговое усилие на тросе лебедки
ограничивают во избежание:
Выхода лебедки из строя
Повреждения протягиваемой трубы
Обрыва троса
Допускается ли применение электрических кабелей и проводов с поврежденной оплеткой и золяцией?
Да, при разрешении инженера по технике безопасности
Да, если длина поврежденного участка менее 20 мм
Нет
Тяжесть поражения человека электрическим током зависит от:
Силы электрического тока
Пути протекания электрического тока по его организму
Оба варианта верны
Минимальная сила тока, которая может оказаться смертельной для человека:
1 мА~
10 мА
100 мА
Какие вредные вещества выделяются при плавлении полиэтилена?
Пары металла
Сернистые соединения, перекись водорода
Пары формальдегида, ацетальдегида, окись углерода
Какие вредные, вещества выделяются при нагревании поливинилхлорида?
Фтористые соединения
Углеродистые соединения
Хлористые соединения
Какие вредные вещества выделяются при нагревании фторопластов?
Фтористые соединения
Углеродистые соединения
Хлористые соединения
Чем заземляют поверхность полиэтиленовых труб при выполнении ремонтных операций?
Медным многожильным проводом
Прядью хлопчатобумажного волокна, пропитанного водой. Необходимо также обильно смочить поверхность трубы и почву возле заземляющего пикета
Оба варианта верны
Допускается ли совместное хранение горюче-смазочных материалов с полиэтиленовыми трубами и
деталями?
Нет
Да
Нормативными документами не регламентируется
Постоянное давление при расходе газа поддерживает:
Ротаметр
Резистор
Редуктор
Постоянный расход газа поддерживает:
Ротаметр
Резистор
Редуктор
Давление газа измеряют
Ротаметром
Манометром
Тонометром
Расход газа измеряют:
Ротаметром
Резистором
Редуктором
Определение дефекта сварного соединения:
Нормированное отклонение, указанное в нормативно-технической документации
Отдельное несоответствие требованиям, установленным нормативной документацией
Отклонение от требований конструкторской документации
Дефекты в сварном шве подразделяются на:
Внешние и внутренние
Краевые и боковые
Местные и общие
Пора — это дефект сварного шва в виде:
Округлой полости, заполненной расплавом
Округлой полости, заполненной газом
Полости, заполненной продуктами деструкции
Основная причина образования пор, это:
Наличие сквозняков и ветра
Наличие воздуха между свариваемыми поверхностями
Длительный контакт с воздухом оплавленных поверхностей перед осадкой
Несплавление — это дефект в виде:
Отсутствия сплавления в сварном шве между свариваемыми кромками или между кромками и материалом шва
Отсутствия сквозного проплавления по всей ширине детали
Сквозного отверстия в шве
Основные причины образования несплавления, это:
Превышение допустимых зазоров, неплотный контакт сплавляемых поверхностей
Превышение технологической паузы, недостаточное давление осадки
Оба варианта верны
Основная причина образования трещин, это:
Низкая квалификация сварщика
Неравномерность и повышенная скорость охлаждения сварного шва, вызывающие повышенный уровень усадочных напряжений
Низкое давление и недостаточная длительность осадки
Основная причина образования непровара, это:
Низкая квалификация сварщика
Длительный контакт с воздухом оплавленных поверхностей перед их осадкой
Низкое давление и недостаточная длительность осадки, нарушение параметров сварки
Дефектами сварных соединений называют:
Структурные микро- и макро- неоднородности, возникающие в сварном шве вследствие нарушений технологии подготовки свариваемых конструкций, их сборки и сварки
Отклонения от требований конструкторской документации
Нормированные отклонения, указанные в нормативно-технической документации
Непровар — это дефект в виде:
Отсутствия наплавленного материала на участке сварного шва
Несплавления в сварном соединении вследствие неполного расплавления кромок основного материала или поверхностей или наплавного материала с основной поверхностью
Неровностей поверхностей основного или наплавного материала
Какие бывают трещины по расположению и внешнему виду?
Внутренние; продольные, сквозные, глухие
Наружные; кратерные, продольные, поперечные
Наружные и внутренние, продольные, поперечные, разветвленные, радиальные и кратерные
Какие виды контроля применяют при изготовлении (монтаже, ремонте) сварных соединений?
Предварительный, операционный контроль и контроль качества готового сварного соединения
Контроль сборки под сварку, контроль качества сварного соединения
Контроль материалов: основных и сварочных
На какие две основные группы делятся методы контроля по воздействию на материал сварного соединения?
Разрушающие и щадящие
Механические и электрические
Разрушающие и неразрушающие
Чем выявляют дефекты формы шва и его размеры?
Специальными шаблонами и измерительными инструментам 1
Металлографическими исследованиями
Ультразвуковым или рентгенографическим методами
Контроль качества готовых сварных соединений
Формы, размеров, сплошности шва и свойств материала
Формы и размеров шва
Свойств материала в различных зонах
Каким должен быть характер разрушения при испытании образцов контрольных стыков газопровода?
Пластичным
Низкопластичным
Хрупким
По каким признакам способы сварки пластмасс делятся на классы?
По видам энергии, используемой для сварки
По давлению осадки
По температуре нагревателя
К чему приводит превышение установленной температуры нагретого инструмента при сварке полиэтиленовых труб встык?
К расплавлению полиэтилена
К деструкции полиэтилена
К переходу пластмассы в стеклообразное состояние
На чем основан механизм сварки ультразвуком?
Превращении электрической энергии в тепловую
Превращении электрических колебаний ультразвуковой частоты в механическую, а затем в тепловую энергию в условиях статического давления рабочего торца волновода
Превращении тепловой энергии в электрическую
С какой целью при сварке полиэтиленовых труб нагретым инструментом встык необходимо
прикладывать давление к торцам труб на этапе осадки (Рн = Роп):
Для обеспечения плотного контакта свариваемых поверхностей с нагревательным инструментом
Для обеспечения течения расплава в зоне сварки и сближения макромолекул на
расстояния, соизмеримые с радиусом действия сил межмолекулярного взаимодействия
Для продвижения теплового потока вглубь свариваемых деталей и получения необходимой глубины расплавленного материала
Для уменьшения упругих напряжений, возникающих в расплаве материала
Какой способностью должен обладать полимерный материал, чтобы детали из него могли соединяться
сваркой плавлением:
Способностью сохранять при нагреве высокую вязкость расплава
Способностью переходить в вязкотекучее состояние
Способностью образовывать при нагреве новые физические и химические связи
Укажите физико-механическую характеристику полимера, которая в наибольшей степени
характеризует его свариваемость:
Относительное удлинение при растяжении
Предел текучести при растяжении
Плотность
Показатель текучести расплава
Для изготовления каких труб предназначен полиэтилен желтого цвета?
Напорных для водоснабжения
Напорных для газопроводов
Безнапорных для канализации
С какой целью полиэтилен средней плотности контролируется на стойкость к постоянному
внутреннему давлению при 800С?
Для уточнения прочностных свойств
Для подтверждения 50-летнего срока службы труб и фитингов, изготовленных из него
Для определения массовой доли летучих веществ
В чем проявляется «старение» полимеров?
В повышении молекулярной массы
В изменении структуры, сопровождающейся изменением механических характеристик
В повышении плотности
К какому виду пластмасс относятся трубы и соединительные детали из полиэтилена?
Реактопластам
Термопластам
Пенопластам
Почему для транспорта газа используются трубы из полиэтилена средней и высокой плотности?
Имеют низкую газопроницаемость в виду высокой плотности материала и высокую стойкость к трещинообразованию
Полиэтилен хорошо сваривается
Срок службы труб-50 лет
В чем основное различие полиэтилена ПЭ80 и ПЭ100?
В значении относительного удлинения при разрыве и плотности материала
В значении минимальной длительной прочности
В термостабильности
Какова длительная прочность ПЭ80 и ПЭ100?
8,0 и 10,0 МПа, соответственно
80 и 100 МПа, соответственно
0,8 и 1,0 МПа, соответственно
В каком физическом состоянии находится полиэтилен при изготовлении и сварке труб из него?
Вязкотекучем
Стеклообразном
Высокоэластичном
Как оцениваются прочностные характеристики сварных соединений пластмасс?
По применимости способа сварки
Сопоставлением характеристик сварного соединения с аналогичными характеристиками основного материала или с их заданными значениями
По температуре текучести
Из каких материалов изготавливается закладной нагревательный элемент, используемый в деталях с
закладным электронагревателем?
Из любого токопроводящего материала
Из металлической проволоки с низким электрическим сопротивлением
Из металлической проволоки с высоким электрическим
Каким путем должна обеспечиваться безопасность обслуживающего персонала и посторонних лиц при
работе на электрифицированном оборудовании:
Применения надлежащей изоляции, а в отдельных случаях — повышенной; применением двойной изоляции;
соблюдения соответствующих расстояний до токоведущих частей или путем закрытия, ограждения токоведущих частей; применения блокировки аппаратов и ограждающих устройств для предотвращения ошибочных операций и доступа к токоведущим частям
Надежного и быстродействующего автоматического отключения частей электрооборудования, случае оказавшихся под напряжением, и поврежденных участков сети, в том числе защитного отключения
Заземления или зануления корпусов электрооборудования и элементов электроустановок, которые могут
оказаться под напряжением вследствие повреждения изоляции; выравнивания потенциалов; применения
разделительных трансформаторов; применения напряжений 42 В и ниже переменного тока частотой 50 Гц
и 110 В и ниже постоянного тока;применения предупреждающей сигнализации надписей и плакатов;
применения устройств, снижающих напряженность электрических полей; использование средств защиты
и приспособлений, в том числе для защиты от воздействия электрического поля в электроустановках, в которых его напряженность превышает допустимые нормы
Все ответы правильные
Какие установки до 1кВ должны проверяться по режиму короткого замыкания:
Трансформаторы тока
Распределительные щиты, токопроводы, силовые щиты
Правильные ответы 1 и 2
Что называют заземлителем:
Случайное соединение находящихся под напряжением частей электроустановки
Проводник или их совокупность металлически соединенных между собой проводников, находящихся в соприкосновении с землей
Зона земли, находящаяся за пределами зоны растекания электрического тока
Что называют естественным заземлителем при реализации защитных мер электробезопасности
Случайное соединение находящихся под напряжением частей электроустановки с конструктивными частями, не изолированными от земли или непосредственно с землей
Заземлитель, специально выполняемый для целей заземления
Находящиеся в соприкосновении с землей электропроводящие части коммуникаций, зданий и сооружений производственного или иного назначения, используемые для целей заземления
Что называют искуственным заземлителем при реализации защитных мер электробезопасности
Случайное соединение находящихся под напряжением частей электроустановки с конструктивными частями, не изолированными от земли или непосредственно с землей
Заземлитель, специально выполняемый для целей заземления
Находящиеся в соприкосновении с землей электропроводящие части коммуникаций, зданий и сооружений производственного или иного назначения, испольэуемыек для целей заземления
Дайте определение термину «напряжение шага»
Напряжение между двумя точками земли, обусловленное растеканием тока замыкания на землю, при одновременном касании их ногами человека
Напряжение между двумя точками цепи тока замыкания на землю (на корпус) при одновременном прикосновении к ним человека
Область земли при стекании тока на землю
Что называется защитным отключением в электроустановках напряжением до 1кВ:
Автоматическое отключение всех фаз (полюсов) участка сети
Автоматическое отключение одной из фаз участка сети
Автоматическое отключение нулевых проводников участка сети
Какая из следующих защитных мер должна быть применена по крайней мере для защиты людей
поражения электрическим током при повреждении изоляции:
Малое напряжение, двойная изоляция, дублирующая проводка
Заземление, зануление, защитное отключение, разделительный трансформатор, малое напряжем двойная изоляция, выравнивание потенциалов
Выполнение защитных ограждений, специальные защитные костюмы
При каких номинальных напряжениях не требуется заземление или зануление электроустановок:
До 36 В переменного тока и до 120 В постоянного тока
До 42 В переменного тока и до 110 В постоянного тока
До 24 В переменного тока и до 140 В постоянного тока
Могут ли в целях защиты людей от поражения электрическим током использоваться естественные заземлители (проложенные в земле металлические водопроводы, обсадные трубы скважин и т. п.) для заземления электроустановок:
Нет, могут использоваться только искусственные горизонтальные и вертикальные заземлители
Могут только в случае/если использование искусственных заземлителей вызывает трудности
Могут преимущественно использоваться естественные заземлители
В каких случаях рекомендуется применять для заземления электроустановок одно
заземляющее устройство:
Если электроустановки имеют одинаковое напряжение питания
Если электроустановки имеют одинаковое назначение
Если электроустановки территориально приближены друг к другу
Все варианты ответов правильные
В электроустановках до 1 кВ, в местах, где в качестве защитной меры применяются разделительные
или понижающие трансформаторы, вторичное напряжение трансформаторов должно быть:
Для разделительных трансформаторов — не более 380 В, для понижающих трансформаторов не более 42\ В
Для разделительных трансформаторов — не более 220 В, для понижающих трансформаторов — не более 42 В
Для разделительных трансформаторов — не более 360 В, для понижающих трансформаторов — не более 24 В
Какие стальные электроды могут быть использованы в качестве искусственных заземлителей:
Имеющие окраску
Не имеющие окраску
Покрытые специальным битумным раствором для защиты от коррозии
Какие проводники должны использоваться в качестве нулевых защитных проводников, идущих к
переносным электроприемникам?
Нулевые рабочие проводники, присоединяемые к корпусу электроприемника
Отдельный проводник, присоединяемый к специальному контакту вилки втычного соединения и к корпусу электроприемника
Все ответы правильные
С каким напряжением следует предусматривать питание переносных электроприемников от сети
Не выше 127 В
Не выше 220 В
Не выше 380/220 В
Каким должно быть сечение заземляющей или зануляющей жилы переносных электроприемников:
Должно быть равным сечению фазных проводников
Должно быть не менее 75% сечения фазных проводников
Должно превышать сечение фазных проводников на не менее чем 25%
Как должны быть подведены электрические проводники во втычных соединениях переносных электроприемников?
К розетке подведены проводники со стороны питания, а к вилке — со стороны электроприемников
К розетке подведены проводники со стороны электроприемников, а к вилке-со стороны питания Подвод проводников может быть выбран произвольно, исходя из удобства в работе
Какой цвет должны иметь провода электропроводки по всей длине:
Иметь разный цвет, при этом цвет должен обозначать назначение проводника
Иметь разный цвет, при этом комбинация цветов не имеет значения
Быть одного цвета: черного или белого
243ПУЭ Какие кабели следует использовать для питания переносных и передвижных электроприемников:
Специальные шнуры и гибкие кабели с медными жилами
Специальные шнуры и гибкие кабели с алюминиевыми жилами
Любые провода и кабели, сечение которых соответствует мощности электроприемника
Где должны быть установлены предохранители, предназначенные для защиты электрических сетей
На всех нормально незаземленных полюсах или фазах
На всех заземленных фазах сети и в нулевом рабочем проводнике
В нулевом рабочем проводнике
Какими следует выбирать номинальные токи плавких вставок предохранителей и токи установок автоматических выключателей, служащих для защиты отдельных участков сети
Наименьшими по расчетным токам этих участков
Наибольшими по расчетным токам этих участков
Равными по расчетным токам этих участков
Где должны быть нанесены надпись на каждом аппарате защиты, указывающие значение
номинального тока аппарата, уставки расцепителя:
хеме, расположенной вблизи места установки
аппаратов защиты
Надписи наносятся на электрических проводника
Надписи наносятся только на аппарате
Как следует предусматривать присоединения к электрическим сетям переносных и передвижных
электросварочных установок (кроме автономных):
Непосредственно кабелем или кабелем через троллеи (тяговое устройство). Длина троллейных проводников не нормируется, их сечение должно быть выбрано с учетом мощности источника сварочного тока •
Непосредственно кабелем или кабелем через троллеи. Длина троллейных проводников нормируется и не должна превышать 10 м
Непосредственно кабелем, без применения троллейных проводников
Допускается для постоянных работ, выполняемых с соблюдением требований, изложенных в действующих положениях и инструкциях, согласованных и утвержденных пожарными службами
Не допускается
Допускается для временных работ, выполняемых с соблюдением требований, изложенных в действующих! положениях и инструкциях, согласованных с пожарными службами и утвержденных Ростехнадзором (Госгортехнадзором) России
Возможно ли выполнение сварочных работ в зонах постоянно действующих и потенциально опасных производственных факторов, не связанных с характером выполнения сварочных работ:
Возможно при оформлении наряда-допуска на опасные виды работ %
Возможно в течение не более 4 часов в день
Сварочные работы в опасных зонах проводить запрещается
Какие зоны, вне пределов которых должны располагаться места размещения сварочного
борудования, относятся к зонам постоянно действующих и потенциально опасных производственных
факторов?
Места вблизи от неизолированных токоведущих частей установок, места, где возможно превышение предельных концентраций вредных веществ в воздухе
Места вблизи от неогражденных перепадов по высоте более 1,3 м
Зоны перемещения машин, оборудования их рабочих органов, места, над которыми происходит перемещения грузов кранами
Правильные ответы 1,2 и 3 —
Какое напряжение применяется для светильников местного освещения в помещениях с повышенной
опасностью?
Для стационарно установленных на более 42 В, а для переносных светильников — 12 В.
Для стационарно установленных на более 42 В, а для переносных светильников — 36 В.
Для стационарно установленных на более 220 В, а для перекосных светильников — 12 В.
На какой минимальной высоте над рабочим местом разрешается подвешивать временную
электропроводку?
2,5 м
3,5 м
6 м
На какой минимальной высоте над проходами разрешается подвешивать
временную электропроводку?
2,5 м
3,5 м «
6 м
На какой минимальной высоте над проездами разрешается подвешивать
временную электропроводку?
2,5 м
3,5 м
6 м.
В каких случаях ручные электроинструменты (входящие в комплект сварочного оборудования)
должны быть выключены и отсоединены от электрической сети:
При перерывах в работе и по окончанию работы
При смазке и очистке
При смене рабочего инструмента (ножей и
Правильные ответы 1,2 и3
Какую группу по электробезопасносги должны иметь лица, допускаемые к управлению ручными
электрическими машинами на площадках (в помещениях), не отнесенных к повышенной опасности
I группу по электробезопасности, подтверждаемую ежегодно
группу по электробезопасности, подтверждаемую ежемесячно
II группу по электробезопасности, подтверждаемую ежего*
В какие сроки должен осматриваться инструмент, применяемый в строительстве, на предмет его исправности:
Не реже одного раза в день
Не реже одного раза в 10 дней, а также непосредственно перед применением
Не реже одного раза в месяц, а также непосредственно перед применением
При получении инструмента со склада организации
На каком расстоянии должны находиться сварочные кабели от баллонов с
кислородом?
Не менее 5 м.
Не менее 0,5 м.
Не менее 8,5 м.
Письменное разрешение какого руководителя или специалиста в организации
требуется получить при производстве сварочных работ вне постоянных сварочных постов:
Руководителя или специалиста, отвечающего за пожарную безопасность
Руководителя или специалиста, аттестованного в качестве специалиста не ниже III уровня
Руководителя или специалиста, имеющего право руководства газоопасными работами
Мастера (прораба) строительного участка
Суть и особенности ультразвуковой сварки пластмасс
Сваривание пластмасс ультразвуком — это распространенный метод сварки полимеров, например, изделий из полипропилена. Ультразвуковая сварка пластмасс прочно заняла свое положение в промышленности, поскольку позволяет сократить расходы, при этом увеличить эффективность и качество сварочных работ.
В этой статье мы подробно разберем, что такое ультразвуковая сварка, какое оборудование необходимо для сварки пластмасс ультразвуком и какие есть преимущества у этого метода.
Принцип действия ультразвуковой сварки
Итак, что из себя представляет ультразвуковой метод сварки? Говоря простыми словами, ультразвуковое оборудование генерирует механические колебания, которые затем преобразовывает в тепловую энергию, которая как раз и используется для выполнения соединений. Этот процесс также называется «использование энергии преобразования», в нашем случае преобразования механической энергии в тепловую.
Сам процесс условно состоит из двух этапов. На первом этапе тепловая энергия, полученная в результате преобразования механических колебаний, и точечно направленная на место сварки увеличивает диффузию молекул у пластмассовых деталей. После этого границы свариваемых деталей начинают плавиться и скрепляться между собой. На втором этапе границы свариваемых деталей остывают и образуют прочный шов. Это примерное описание принципа действия ультразвуковой сварки. Далее мы более подробно разберем, как получаются такие соединения.
youtube.com/embed/Wy5KefNhAO8?feature=oembed» frameborder=»0″ allow=»accelerometer; autoplay; clipboard-write; encrypted-media; gyroscope; picture-in-picture» allowfullscreen=»»>Как это работает?
Что такое ультразвуковая сварка пластмасс? Если по-простому, это процесс, в котором происходит превращение механических колебаний, созданных специальным оборудованием, в тепло, энергия которого образует сварочный шов.
Иными словами, происходит трансформация энергии (механическая переходит в тепловую), поэтому подобный процесс можно назвать «использованием энергии преобразования».
В процессе ультразвукового сваривания пластмасс можно выделить 2 этапа: соединения деталей и образования шва.
Первый этап представляет собой воздействие на детали на молекулярном уровне: тепло, сформировавшееся в результате трансформации механической энергии, точечно фокусируется в месте будущего скрепления материалов.
Происходит увеличение показателя движения молекул пластмассы. Из-за этого начинается оплавление и соединение элементов конструкции. Второй этап представляет собой остывание мест сварки пластмассы и формирование крепкого шва.
Так вкратце можно описать принцип работы этого метода. Подробнее этот материал приводится в следующем разделе.
Суть получения швов ультразвуком
Классическая ультразвуковая сварка существенно отличается от привычной для многих сварки металла. Для сварки металла требуется крайне высокая температура плавления, но в случае с ультразвуком необходима лишь энергия, исходящая от ультразвуковой волны, и одновременное механическое воздействие на предполагаемое место будущего шва. Поэтому нет необходимости использовать дополнительные расходники, вроде электродов или проволоки.
Сварщик подключает к ультразвуковому сварочную оборудованию генератор, благодаря которому образуются ультразвуковые колебания. Эти колебания преобразовываются в механические, происходит это с помощью специального преобразователя. Затем подключается волновод, который колеблется перпендикулярно сварному шву. За счет этого преобразованные колебания напрямую попадают в предполагаемое место будущего сварного соединения, также образуется статическое и динамическое давление. Статическое и динамическое давление направлено перпендикулярно деталям, при этом каждое из типов давлений выполняет свою функцию. Динамическое давление позволяет достичь необходимой температуры плавления для того или иного вида пластмассы, а статическое способствует формированию прочного соединения.
Благодаря всем этим особенностям с помощью ультразвуковой сварки можно соединить даже металл и пластмассу, хотя их температура плавления существенно отличается. Также пластмассу можно соединить с любым другим материалом, способным выдержать ультразвуковую сварку.
Как образуется шов?
Работа с металлом не похожа на сварку ультразвуком. Для второй не понадобятся привычные по работе с металлом расходные материалы (проволока, стержни электродов и пр.) и высокое температурное воздействие.
Зато потребуются механическое влияние на место формирования шва и энергия ультразвуковых колебаний.
Образование колебаний начинается с подсоединения генератора к ультразвуковому сварочному аппарату для пластмассы. Преобразователь трансформирует колебания одного вида в другие (ультразвуковые в механические).
Следом происходит подключение колеблющегося параллельно будущем шву волновода.
Он позволяет локально сфокусировать энергию в конкретной точке и создаёт два типа давлений: статическое и динамическое. Они приложены к детали под углом в 90°, и у каждого из них своя роль.
Первое отвечает за получение прочного шва, а второе — за достижение уровня температуры, оптимальной для работы с разными типами пластика и пластмасс.
Технически, возможности этого метода позволяют скреплять пластмассу с деталями различного состава, главное условие — чтобы материал выдерживал воздействие ультразвука.
В теории возможно соединение пластмассы с металлом, несмотря на разницу их температур плавления.
Какие есть параметры у ультразвукового сварочного оборудования
Для работы с ультразвуковым оборудованием следует ознакомиться с основными параметрами, которые можно отрегулировать в зависимости от вашей работы. Итак, вы можете регулировать:
- Амплитуду колебаний торца волновода (этот параметр позволяет настроить время сварки и прочность готового шва)
- Частоту электрических колебаний и силу давления волновода на пластмассу.
- Продолжительность импульса (этот параметр регулирует скорость сварки).
- Статистическое (сварочное) давление (этот параметр зависит от амплитуды колебаний и влияет на качество готового шва).
Также существуют дополнительные параметры. К примеру: температура предварительного разогрева детали, параметры, учитывающие размер и форму деталей, и многие другие.
Для каждого отдельного типа пластмассы и шва, который необходимо получить, устанавливаются свои индивидуальные параметры. Их совокупность называется режимом сварки. Оптимальный режим сварки для тех или иных деталей в промышленных условиях выбирается только после проведенных исследований. Специалисты в лаборатории выполняют соединения с различными режимами и тестируют швы на герметичность, надежность и прочие качества. Конечно, если вы планируете использовать ультразвуковое сварочное оборудование для личных целей, вы не будете проводить исследования. Но мы рекомендуем все же потренироваться на небольших образцах. Лишь пройдя путь проб и ошибок вы сможете найти оптимальные параметры для каждого типа сварки.
Подробное описание реализации различных способов сварки ультразвуком:
- Отчет о результатах исследования сварки компасов ультразвуком
- Рекомендации по выбору технологических режимов и параметров для ультразвуковой сварки изделий из полимерных материалов
- Сварка заклепок ультразвуком
- Ультразвуковая сварка полимерных пленок
- Формирование кольцевого сварного шва большого диаметра ультразвуковой сваркой
Наша компания предлагает широкий спектр ультразвуковых аппаратов и принадлежностей к ним для сварки различных изделий из термопластичных полимеров:
1) Аппараты серии «ГИМИНЕЙ-УЛЬТРА», различных моделей для соединения конструкционных изделий и листовых материалов методом непрерывной или пошаговой ультразвуковой сварки.![]() | |||
АУС-0,1/27-ОМА (вариант исполнения №2) | АУС-0,4/22-ОМ | АУС-0,4/22-ОМЛн (вариант исполнения №2) | АУС-1/22-ОМ |
2) Аппараты серии «ГИМИНЕЙ-К», различных моделей для формирования методом ультразвуковой сварки герметичного сварного соединения кольцевой формы. | |||
АУС-0,63/22-ОК-25 | АУС-1/22-ОК-40 | АУС-1/22-ОК-50 (вариант исполнения №2) | АУС-3/22-ОК-100 |
3) Аппараты серии «ГИМИНЕЙ-Ш», различных моделей для формирования сварных швов методом непрерывной или пошаговой (длина от 50-360 мм, ширина до 12 мм) низкотемпературной ультразвуковой сварки. | |||
АУС-1/22-ОШ-75 (вариант исполнения №2) | АУС-3/22-ОШ-220 | АУС-3/22-ОШ-270 | АУС-3/18-ОШ-360 |
Подробная классификация
Мы классифицировали ультразвуковой метод сварки на несколько категорий, которые в свою очередь имеют свои подвиды. Итак, ультразвуковая сварка пластмасс подразделяется по:
- Принципу перемещения вдоль шва.
Может быть ручным, когда сварщик сам направляет сварочный инструмент, или механическим, когда сварка происходит с использованием автоматического оборудованию по заранее заданным параметрам. Механический способ точнее, чем ручной, но при этом нет возможности оперативно изменить направление шва, если это необходимо.
- Принципу подачи энергии. Может быть двусторонней или односторонней. Односторонняя больше предназначена для сваривания толстых деталей и, а двусторонняя — для тонких. Но для двусторонней необходимо дополнительное охлаждение.
- Принципу перемещения волновода. Может быть непрерывным, когда волновод перемещается с постоянной скоростью, а может быть прерывным, совершая одно короткое движение с заданными промежутками.
Более глобально ультразвуковую сварку разделяют на контактную и передаточную. Контактная сварка нужна для соединения тонких пластмассовых деталей (до 2 мм). Для выполнения шва детали укладывают друг на друга с небольшим нахлестом и по уже по нему выполняется шов.
Передаточная сварка используется во всех остальных случаях, а еще в те моменты, когда свариваемые пластмассы обладают высокими акустическими свойствами. Суть передаточной сварки заключается во введении механических колебаний в определенные точки. При этом энергия выделяется в том количестве, которое необходимо, чтобы ультразвуковая волна могла сама равномерно распространиться. В таком случае шов получается надежным и качественным. Передаточная сварка часто применяется при сварке мягкой пластмассы (ее необходимо предварительно заморозить) или для стыковых швов у полистирольных, полиамидных и поликарбонатовых деталей.
Категории сварки
Известно несколько вариантов классификаций сварки пластмасс ультразвуком. Каждая из них включает несколько пунктов. Ниже приведены наиболее популярные.
- Классификация по подаче энергии:
- Односторонняя (применяется для соединения толстостенных конструкций).
- Двусторонняя (оптимальна для тонкостенных деталей, но требует добавочного охлаждения).
- Классификация по передвижению волновода:
- Непрерывное (скорость движения волновода не изменяется со временем).
- Прерывное (движения с заранее известными временными промежутками).
- Классификация по движению вдоль шва:
- Ручное (сила, направляющая аппарат, сосредоточена в руках мастера).
- Механическое (сварочный аппарат перемещается вдоль шва автоматически, по ранее сформированным параметрам. Менее сфокусированный, чем ручной, но даёт возможность поменять направление сварного соединения).
- Классификация по типу сварки:
- Контактная (шов формируется по уложенным внахлёст конструкциям. Подходит для деталей толщиной 2 миллиметра и меньше).
- Передаточная (формирование механических колебаний проводится в установленные точки на деталях в таких количествах, чтобы гарантировать равномерное распространение волны ультразвука и, как следствие, прочность и качество соединения. Используется при сварке деталей толще 2 миллиметров, пластмасс с акустическими свойствами, мягких пластмасс, которые предварительно замораживаются, а также для выполнения стыковых швов у изделий из поликарбоната, полистирола и полиамида).
Преимущества и недостатки ультразвуковой сварки
У этого метода сварки есть масса преимуществ, благодаря чему он и стал настолько популярен в промышленности и не только. Вот некоторые из них:
- Обеспечивает высокую производительность при относительно небольших затратах.
- Позволяет получить на деталях любой толщины качественные герметичные швы, устойчивые к механическому воздействию.
- Дает возможность проводить сварочные работы с деталями в любом состоянии, поверхность не нужно предварительно очищать.
- Тепло выделяется только в одной конкретной точке, поэтому отсутствует вероятность перегрева сварного шва.
- Напряжение не подводится к поверхности свариваемых деталей, из-за чего исключено формирование радиопомех.
- Можно выполнять различные швы: от точечного ремонта до непрерывного соединения деталей в промышленных масштабах. При этом не нужно соблюдать особые условия, сварку ультразвуком можно проводить в любом месте, где есть электроэнергия.
- Этот метод позволяет комбинировать сразу несколько задач. Например, можно сваривать пластмассу и одновременно наносить какое-либо полимерное напыление или осуществлять резку.
- Можно сварить друг с другом любые пластмассы.
- Если точно выбрать режим сварки, то можно добиться практически незаметного шва.
- Не нужно использовать в работе расходники, а также клей или растворитель, который может оказать пагубное влияние на организм.
Но, как и у любого метода сварки, здесь не обошлось без недостатков:
- Частная необходимость применения двусторонней подачи энергии из-за маленькой мощности процесса сварки.
- Не существует единого способа контроля качества свариваемого соединения, из-за этого работа может получиться некачественной.
Как видите, недостатков мало. Но учтите, что все достоинства сварки ультразвуком доступны лишь в случае, если вы правильно настроите режим. Если вы начинающий, то мы рекомендуем выбрать оборудование с автоматическим определением оптимального режима сварки.
Если вы намерены выбирать режим вручную, то воспользуйтесь таблицей, приведенной ниже (здесь в качестве примера параметры для сварки пластиковых труб). В ней указаны рекомендуемые параметры. Со временем вы получите больше опыта и сможете самостоятельно выбирать оптимальный режим.
Сварка жестких пластмасс
Сварка полистирола, сополимеров стирола, полиметилметакрилата, капролона, поликарбоната и других полимеров, имеющих высокий модуль упругости и низкий коэффициент затухания, широко применяется при изготовлении различных объемных деталей и конструкций: от контейнеров и сосудов до товаров народного потребления (спортивных изделий и игрушек). В этом случае ультразвуковая сварка позволяет значительно снизить трудоемкость процесса, увеличить производительность труда, повысить культуру производства и освободиться от применения токсичных клеев, вредных для здоровья человека.
В зависимости от формы изделия и материала может применяться контактная и передаточная сварка или комбинация этих способов. При передаточной сварке нет необходимости разогревать весь объем материала. Сварной шов получается в результате расплавления полимера в зоне контакта деталей. Ясно, что в процессе сварки следует стремиться к концентрации энергии ультразвуковых колебаний непосредственно на стыкуемых поверхностях. Изменением геометрии свариваемых деталей можно концентрировать энергию ультразвуковых колебаний в том или ином сочетании, что позволяет ускорить процесс сварки.
Рекомендуются разнообразные формы и размеры стыков деталей под ультразвуковую сварку в зависимости от конкретных изделий и материалов, но наиболее распространенной является V — образная разделка кромок, которая проста в изготовлении и дает хорошие показатели прочности сварных соединений. Наиболее эффективным углом при вершине V — образного выступа является угол 90°, при котором обеспечивается минимальная площадь контакта деталей перед сваркой.
Малогабаритные детали несложной формы свариваются за один контакт волновода с изделием, причем волновод устанавливается перпендикулярно к свариваемым поверхностям, по оси симметрии. если деталь сложная и длина сварного шва значительная, то количество точек и место введения ультразвуковых колебаний определяется экспериментально. В зависимости от формы литьевого изделия для сварки могут быть использованы волноводы с плоской или фигурной рабочей поверхностью. В последнем случае рабочий торец волновода прилегает к поверхности свариваемых деталей, копируя ее форму. Это необходимо в том случае, когда нужно получить герметичный шов.
Для фиксации деталей могут применяться различные удерживающие устройства: опоры гнездообразные, сферические и т.д. Оптимальный режим сварки: время 3 с; амплитуда 40-40 мкм; усилие сжатия 50-150 Н; частота 22 кГц.
Оборудование для сварки ультразвуком
Комплект ультразвукового оборудования состоит из ультразвукового генератора, пресса, опоры, преобразователя, волновода и сварочного инструмента. При этом выделяют несколько основных узлов, играющих первостепенную роль. К ним относятся:
- Ультразвуковой генератор
Генератор вырабатывает ультразвуковые колебания, а затем преобразовывает их в механические, при этом сохраняя ту же частоту. Также с помощью генератора можно регулировать скорость колебаний и определять способ передачи ультразвуковой энергии.
- Преобразователь
Преобразователь (чаще всего пьезокерамический или магнитострикционный) в связке с генератором отвечает за преобразование электрической энергии в механическую и используется в аппаратах с двусторонним подводом энергии. При этом важно учесть, что такому оборудованию необходимо постоянное охлаждение, например, водное или воздушное.
- Трансформатор упругих колебаний
Трансформатор упругих колебаний согласовывает между собой работу преобразователя и волновода, по сути являясь связующих звеном. Также он способен повысить амплитуду колебаний с торца волновода.
- Волновод
Волновод передает механическую энергию и создает давление в определенных местах. Роль волновода может выполнять акустический трансформатор.
- Опора
Опора необходима для надежного фиксирования деталей. В некоторых случаях она напрямую используется для сварки в качестве дополнительного волновода.
Дополнительно оборудование может быть оснащено функцией автоматического или ручного контроля параметров работы. Мы рекомендуем использовать именно такое оборудование, поскольку оно позволяет выполнить работу по-настоящему качественно. Лишь в таком случае можно достигнуть максимальной прочности сварных швов.
Ультразвуковая сварка пластмасс и полимерных материалов
Ультразвуковая сварка изделий из термопластичных полимеров и пластмасс не имеет альтернативы при упаковке жидких, пастообразных, порошкообразных, сыпучих и пылящих материалов, производимых химической и смежными отраслями промышленности. Ультразвуковая сварка сегодня повсеместно заменяет склеивание и термические (газотермический нагрев, ТВЧ, фрикционный) методы соединения изделий из полимеров на основе полистирола, лавсана, капрона, поливинилхлорида и аналогичных термопластичных материалов. Ультразвуковая сварка решает проблемы изготовления изделий пищевой и легкой промышленности, парфюмерии, радиоэлектроники и электротехники, товаров широкого потребления начиная от детских игрушек до укрепления дорожных покрытий. Аппараты ультразвуковой сварки используется для запрессовки втулок, манжет, выводных зажимов, шарниров, крепежных деталей, рукояток, установочных штифтов, клемм, декоративных деталей металлической арматуры в изделия из полимеров и пластиков. Ультразвуковая сварка — это соединение с прочностью, близкой к прочности основного материала, при температуре, ниже температуры плавления материала, по поверхностям, загрязненным различными продуктами, на большом удалении от места подвода энергии, в труднодоступных местах.
Ультразвуковая сварка — это возможность упаковки жидкостей без доступа кислорода, горючих и взрывоопасных материалов
Вопросам ультразвуковой сварки посвящена монография «Ультразвуковая сварка термопластичных материалов» В.Н. Хмелев, А.Н. Сливин, А.Д. Абрамов, С.С. Хмелев
Используемое оборудование
Учитывая высокую стоимость аппарата УЗ-сварки, многие домашние мастера подумывают о самостоятельном изготовлении установки. К сожалению, это не сварочный трансформатор и даже не выпрямитель, и для проектирования и создания аппарата потребуются серьезные знания и навыки в области акустики и электроники. Кроме того, для изготовления деталей излучателя и волновода нужны станки высокого класса точности, недоступные в домашних условиях.
Пресс для ультразвуковой сварки
Оборудование для ультразвуковой сварки разделяют на три категории:
- точеное;
- шовное;
- шовно–шаговое.
Диапазон мощности — 50 ватт до 2 киловатт, рабочая частота в районе 20-22 килогерц
Основной узел установки ультразвуковой сварки — генератор колебаний и преобразователь электрических колебаний в механические той же частоты.
Механические колебания ультразвукового генератора преобразуются магнитострикционным преобразователем. Для отведения излишнего тепла используется водяная система охлаждения
Волновой трансформатор согласует параметры взаимодействия преобразователя и волновода. Он повышает частоту колебаний на выходе волновода.
Волновод транспортирует энергетический поток к месту сваривания. На его рабочем окончании смонтирована сменная сварочная головка. Ее геометрические параметры выбирают, исходя из материала заготовки, его толщины и вида шва. Так, для приваривания выводов микросхем берут головку, заканчивающуюся тонким жалом.
Волновод
Опорная рама служит для размещения всех узлов и деталей. На ней также монтируется механизм перемещения заготовки или головки волновода.
Работа с металлическими деталями
Высокой эффективностью отличается применение ультразвуковой сварки к деталям небольших размеров. Особенно удачно применяют метод в микроэлектронике и приборостроении.
Читать также: Термическая обработка титановых сплавов
Соединение металлов проходит при существенно более низких температурах, чем при использовании «горячих» сварочных технологий, таких, так электродуговая или газовая сварка. Это открывает широкие возможности для быстрого и надежного соединения компонентов, чувствительных к перегреву.
Кроме того, метод способен сварить пары металлов, с трудом соединяемые другими способами: Cu+Al, Al+ Ni и т.д.
Прочностные характеристики шва достигают 70% от значений для исходного сплава.
Метод также позволяет сваривать металл, пластик, керамику, композиты, стекло в любых комбинациях. Применим он и к тугоплавким сплавам.
Ограничения
Основное ограничение, накладываемое на применимость технологии – это размер свариваемых заготовок. Он ограничен 25-30 см. Это обуславливается малой мощностью генератора и высоким затуханием и рассеянием ультразвуковых колебаний в твердой среде. При прямом увеличении мощности и амплитуды колебаний потребуется непропорциональное увеличение размеров установки и потребляемой мощности. Это сведет на нет все экономические преимущества метода.
Кроме того, материалы, свариваемые ультразвуком, должны иметь минимальную влажность, причем ка на поверхности, таки по всему объему. Если этого невозможно добиться, то следует использовать другие технологии.
Процесс ультразвуковой сварки металла
Использование сваривания ультразвуком не имеет экономического смысла и для толстостенных изделий.
Если вы нашли ошибку, пожалуйста, выделите фрагмент текста и нажмите Ctrl+Enter.
Сварка пластмасс ультразвуком является промышленным методом соединения полимерных материалов и уже давно заняла позиции экономически обоснованного способа сварки. Ультразвуковая сварка пластмасс основывается на искусственно созданных механических колебаниях, которые прикладываются к зоне контакта и преобразовываются в тепловую энергию. В результате таких процессов происходит увеличение диффузии молекул и стирание границ между свариваемыми деталями.
Сварка пластмасс
Подробности
- Подробности
-
Опубликовано 25.
05.2012 15:45
- Просмотров: 21925
В настоящее время широко используются различные пластмассы. Обладая целым рядом ценных свойств (достаточная прочность, антикоррозионность, стойкость против химически агрессивных сред, теплостойкость и др.), пластмассы получают большое применение в самых различных отраслях народного хозяйства не только как заменители дефицитных материалов, но и как основные конструкционные материалы.
Основные виды пластмасс, применяемые в технике, следующие:
Фенопласты — пластические материалы на основе фенолоальдегидных смол. В зависимости от соотношения фенола и альдегида, а также технологии изготовления получают либо термореактивные (резольные смолы), либо термопластические (новолачные смолы) материалы. Важной особенностью фенолоальдегидных смол является их способность в сочетании с различными наполнителями образовывать пластмассы с повышенными прочностными, диэлектрическими, антикоррозионными и другими свойствами.
Из материалов с волокнистым наполнителем большое применение получили волокниты, текстолит-крошка и стекловолокнит. Они применяются для изготовления деталей, работающих на изгиб и кручение и требующих хороших механических и антифрикционных свойств (шестерни, втулки, ролики, кулачки, вкладыши подшипников и др.). Из слоистых пластиков в промышленности большое распространение получили текстолит (наполнителем служит хлопчатобумажная ткань), древесные слоистые пластики ДСП (наполнитель-древесный шпон) и гетинакс (наполнитель — сульфатная бумага). Эти пластмассы обладают большей прочностью, чем волокнистые.
ДСП используют в машиностроении как конструкционный и антифрикционный материал.
Гетинакс используют в качестве электроизоляционного материала для деталей электрооборудования.
Аминопласты — термореактивные пластические материалы на основе карбамидно-формальдегидных или меламино-формальдегидных смол. Они бесцветны, прозрачны и могут быть окрашены в любые (особенно светлые) тона с помощью красителей. В качестве наполнителей применяют сульфидную целлюлозу (аминопласт, меланит), хлопковую целлюлозу (мелаволокнит), асбест, тальк и др.
Изделия из аминопластов получают методами горячего и холодного прессования при различных режимах.
Например, при изготовлении деталей из аминопласта температура прессования 135… 145° С, давление 10,5 … 42 МПа (105 … 420 кгс/см2), время выдержки 1 мин на 1 мм толщины изделия.
Полиэтилен — высокомолекулярный продукт полимеризации этилена. Он является кристаллическим полимером со степенью кристаллизации от 55 до 92% (в зависимости от метода получения). Полиэтилен-термопластичный материал. Изделия из него могут быть изготовлены методом литья (под давлением, центробежным литьем), штамповкой (при температуре 120 . .. 135° С) и прессованием. Он обладает высокой химической стойкостью к агрессивным средам и является хорошим диэлектриком. Применяется при изготовлении подводных, силовых и радиочастотных кабелей в качестве изоляции. Большое применение получил полиэтилен при изготовлении различного оборудования химической промышленности методом прессования и сварки (трубы, цистерны, плиты, фитинги, профили, тонкостенные детали и др.)
Винипласт — жесткий материал, получаемый путем обработки непластифицированного поливинилхлорида со стабилизаторами и смазывающими веществами при температуре 160 … 180° С. Он обладает большой прочностью, твердостью, хорошими диэлектрическими свойствами и высокой химической стойкостью. Винипласт легко подвергается различной механической обработке, сварке, склеиванию. Винипласт получил большое применение в различных отраслях народного хозяства, особенно в химической промышленности. Из винипласта изготовляют трубы, вентили, краны, фитинги.
Винипластовые пленки применяют для футеровки металлической аппаратуры, электролизных ванн, изготовления различного химического и лабораторного оборудования.
Полистирол — продукт полимеризации стирола. Легко перерабатывается в изделия, как и обычные термопласты. Он отличается очень хорошими диэлектрическими свойствами, прозрачен, водостоек, морозостоек. Недостатками полистирола являются низкая теплостойкость, горючесть и хрупкость. Полистирол служит материалом для изготовления радио-и электроаппаратуры, высокочастотных приборов и химической аппаратуры. Его применяют также для изготовления электроизоляционных пленок, нитей и упаковочной пленки. Полиакрилаты — группа полимеров на основе производных акриловой и метакриловой кислот. Они производятся путем полимеризации мономерных эфиров. Наибольшее применение получили листовые акриловые материалы (органическое стекло различных марок). Кроме того, выпускают заготовки в виде стержней, труб, листов и материалов для изготовления деталей прессованием или литьем под давлением.
Органическое стекло ПММА — полиметилметакрилат — отличается высокой светопроницаемостью, удовлетворительными прочностью и твердостью. Важной особенностью органического стекла является его способность почти полностью пропускать ультрафиолетовые лучи. Следует также отметить хорошие технологические свойства: обрабатываемость сверлением, фрезерованием, штамповкой, сваркой. Некоторые марки органического стекла перерабатывают в изделия литьем под давлением. Применяют органическое стекло для остекления, изготовления изделий технического назначения в приборостроении, машиностроении и других отраслях промышленности. Полихлорвиниловый пластикат получают из поливинилхлорида, наполнителей и красителей. Наполнители повышают механическую прочность пластиката и снижают его стоимость.
Пластикат используют как футеровочный и электроизоляционный материалы, а также для изготовления труб с толщиной стенки 0,3 .
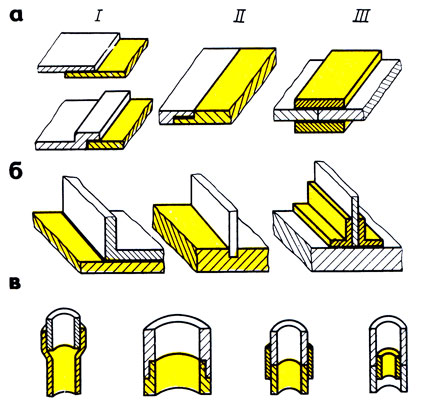
Способы сварки пластмасс
Сварка пластмасс заключается в нагреве свариваемых кромок до пластического вязко-текучего состояния и соединения их под некоторым давлением.
Применяются следующие способы сварки пластмасс:
Сварка нагретым газом
Свариваемые кромки детали и присадочный материал нагревают до температуры сварки струей горячего воздуха или газа. Для нагрева воздуха (газа) используют специальные электронагреватели или газовые горелки. На рисунке представлена схема сварки этим способом стыкового соединения с присадочным прутком. Свариваемые кромки детали и присадочный пруток с помощью горелки нагревают до получения тонкого вязко-текучего поверхностного слоя. Присадочный пруток вдавливается в разделку шва, нагретые слои материала слипаются и присадочный пруток образует сварной шов. При сварке толстого материала в разделку шва последовательно укладывают несколько нагретых присадочных прутков, как показано на рисунке. Подготовка кромок к сварке заключается в скашивании их под углом 60° при сварке стыковых и нахлесточных соединений. Для получения полного провара необходимо у вершины шва оставить зазор 0,4… 0,5 мм. Сварку без скоса кромок применяют для соединения листов толщиной менее 4 мм. При большой толщине применяют V-образные и Х-образные разделки кромок шва. При этом Х-образные формы более прочны. В процессе сварки по мере размягчения поверхностей свариваемых кромок и присадочного прутка необходимо непрерывно вжимать пруток в основание разделки под небольшим, но постоянным давлением.
При сварке мягких термопластов (полиэтилен и др.) присадочный пруток вводят под тупым углом, чтобы обеспечить достаточное давление на свариваемые кромки. При сварке жестких термопластов (винипласт, органическое стекло и др.) пруток вводят в разделку шва почти под углом 90° к шву. Полиэтилен и полистирол при сварке нагревают горячим газом или воздухом до температуры не выше 160 … 180°С. Органическое стекло рекомендуют сваривать струей воздуха, нагретого до 200 …220° С. Присадочным материалом служат прутки площадью сечения от 7 до 12 мм2. Допускается использование сварочных прутков из винипласта (диаметром от 3,0 до 5,0 мм). Винипласт сваривают в размягченном (вязко-текучем) состоянии при температуре 220… 240° С. Присадочным материалом служат сварочные прутки диаметром до 5 мм из пластифицированного винипласта. Процесс сварки осуществляется путем размягчения прутков и сцепления их с основным материалом.
Для сварки пластмасс толщиной от 2 до 25 мм этим способом применяют горелки ГГП-1-66. Теплоносителем является воздух в смеси с продуктами сгорания пропан бутановой смеси. Масса горелки 0,6 кг. Горелка ГЭП-1А-67 работает на основе электроподогрева теплоносителя — газа (воздух, азот и др.). Для этого на пути движения газа в корпусе горелки установлена электроспираль. Масса горелки 0,68 кг. Этим способом можно сваривать детали любых размеров и различной конфигурации. Простота оборудования и технологии сварки позволяют применять этот способ при самых различных строительно-монтажных работах. При сварке следует учесть, что пластмассы имеют высокий коэффициент температурного расширения (в 4 … 6 раз больше металлов). Это вызывает опасность возникновения относительно больших внутренних напряжений в сварном шве, ослабляющих сварное соединение и вызывающих коробление свариваемых деталей. Для получения хорошего сварного шва рекомендуется применять небольшие площади сечения струи нагретого газа (диаметр струи 3 … 5 мм), а также различные фиксирующие приспособления.
Сварка контактным нагревом
При этом способе нагрев свариваемых поверхностей производят при помощи электронагревательных элементов. Нагретый элемент устанавливают между свариваемыми поверхностями и доводят их до вязко-текучего состояния. Затем нагревательный элемент удаляют, а свариваемые поверхности соединяют сдавливанием. При сварке пленочных пластмасс нагревательным элементом может служить устройство в виде электроутюга, нагревательного ролика или валика. Пленки соединяют внахлестку и разогревают до определенной температуры. Этим способом сваривают пленки толщиной не более 2 мм, так как низкая теплопроводность затрудняет нагрев пластмасс до нужной температуры. Этот способ сварки годен как для мягких, так и для жестких полимеров. Однако он требует большего времени на нагрев элемента, регулировку температуры и охлаждения шва (под давлением) после сварки.
Сварка токами высокой частоты
Нагрев свариваемых деталей производят в высокочастотном электрическом поле. После разогрева кромок до пластического состояния их сдавливают для получения прочного соединения. Этот способ очень экономичен и широко распространен в промышленности. Наибольшее применение получила сварка высокочастотным током изделий из поливинилхлоридных пластиков. Например, для сварки винипласта применяют токи частотой 60 . .. 75 МГц. Толщина свариваемого материала от 0,5 до 2 мм. При меньшей толщине большая часть теплоты расходуется непроизводительно на нагрев прижимающих электродов. Производительность сварки в 5 … 10 раз выше рассмотренных ранее способов. Для шовной сварки пластмассовых пленок и лент применяют специальные сварочные машины ЛГС-02, МСТ-ЗМ и др. Свариваемый материал прокатывают между двумя вращающимися роликами-электродами, к которым подключен высокочастотный ток. Сварка обеспечивает получение непрерывного, прочного и герметичного шва. Нахлесточные соединения можно сваривать без скоса и со скосом кромок под углом 45°. Ширину шва выбирают в пределах 2 … 4 мм, скорость сварки достигает 3 м/мин.
Сварка трением
Осуществляется путем нагрева свариваемых кромок деталей до пластического состояния теплотой, выделяющейся при трении поверхностей этих кромок друг о друга. Для сварки одну часть детали закрепляют в патроне токарного или сверлильного станка и после вращения прижимают ко второй части детали, закрепленной неподвижно в специальном приспособлении. Поскольку термопласты имеют плохую теплопроводность трущиеся поверхности быстро нагреваются. Давление сжатия в зависимости от материала составляет 0,2 … 1 МПа (2 … 10 кгс/см2). Такой способ сварки не требует подготовки поверхности, так как пленка и грязь вытесняются при сварке.
Преимуществом этого способа является быстрота сварки. В зоне трения температура быстро повышается, обеспечивая моментальную сварку, в то время как температура материала около зоны соединения почти не изменяется. Однако этим способом можно сваривать только тела вращения. Кроме того, необходимость обеспечения давления для сварки делает этот способ применимым для жестких термопластов. На рисунке представлена принципиальная схема установки и способы получения сварных соединений из сплошного и полого материалов.
Сварка ультразвуком
Производится посредством нагрева свариваемых кромок под действием ультразвуковых колебаний. Ультразвуковая сварка является более универсальным способом даже по сравнению с высокочастотной электросваркой. Ее применяют для соединения большого количества разнообразных пластических материалов. Однако If в настоящее время этот способ находится в стадии исследования. Уже разработана ультразвуковая сварка ряда пластиков толщиной более 0,1 мм. Следует ожидать, что в ближайшие годы сварка ультразвуком станет одним из основных способов сварки термопластиков.
Читайте также
Добавить комментарий
Сварка в автомобилестроении
Сварка в автомобилестроении
Сваркой получают неразъемные соединения деталей из однородного полимера за счет взаимного проникновения (диффузии) частиц поверхностных слоев в расплавленном состоянии при определенном давлении прижима. Существующие различные методы сварки пластмасс можно условно разделить на 3 группы: сварка с помощью внешних источников теплоты (нагретые газ, инструмент, присадочный материал, трение), сварка с помощью внутренних источников теплоты (токи высокой частоты, ультразвук) и так называемая химическая сварка.
Первые две группы используют для соединения термопластичных материалов. Химическая сварка является одним из перспективных методов сварки термореактивных пластмасс на основе фенолоформальдегидных, кремнийорганических, эпоксидных и ненасыщенных полиэфирных смол.
Промышленное применение получили следующие способы сварки: горячим газом, контактным нагревом, трением, высокочастотная и ультразвуковая. Выбор способа сварки обусловливается природой материала, конструкцией соединяемых деталей, требованиями к сварному соединению, условиями работы изделия, а также необходимой производительностью. В табл. 3.20 приведена способность к сварке различными способами основных термопластов и температурный режим сварки.
Рекламные предложения на основе ваших интересов:
Дополнительные материалы по теме:
Сварка горячим газом производится специальными горелками с помощью присадочного прутка и без него. Сущность способа заключается в том, что поверхность свариваемого термопласта и присадочный пруток нагреваются горячим газом (воздухом, азотом, аргоном) и размягчаются настолько, что при небольшом давлении происходит соединение свариваемых элементов.
При сварке непленочного материала газовыми теплоносителями с применением присадочного материала наиболее рациональны стыковые соединения всех видов — угловые, тавровые, торцовые и швы внахлестку. При сварке встык листов толщиной 2—6 мм выполняют V- и Х-образ-ную разделку кромок. Угол разделки кромок 55—60°. При больших толщинах рекомендуется увеличение его до 70—90°.
Швы внахлестку при сварке нагретым газом применяются редко, так как прочность таких соединений при растягивающих и изгибающих нагрузках почти в 5 раз меньше прочности стыковых. Сварка изделий с присадочным прутком при нагреве газовыми теплоносителями имеет ряд недостатков, главными из которых являются низкие прочность и пластичность сварного шва. Этот метод часто применяют при изготовлении футе-ровок электролизных и травильных ванн и др.
Сварка горячим газом без присадочного материала дает возможность значительно повысить прочность соединения по сравнению с прочностью, достигаемой при сварке с присадочным материалом.
Для того чтобы изделие имело одинаковую толщину во всех сечениях, кромки листов перед сваркой срезают под углом 20°, затем складывают по кромкам, которые равномерно нагревают подогретым воздухом. Угол наклона наконечника горелки к поверхности сварного шва выбирают в зависимости от толщины материала. При толщине листа до 5 мм он равен 20—25°, а для сварки листов толщиной 10—20 мм — 30—45°.
Сварка нагретым инструментом — наиболее универсальный метод соединения изделий из полимерных материалов. Метод заключается в том, что свариваемое изделие, соприкасаясь со специальным нагретым инструментом, разогревается в местах соединения и спрессовывается чаще всего под давлением того же инструмента.
При сварке трением для нагрева материала используют теплоту, получаемую в процессе трения свариваемых поверхностей при приложении давления. Режим процесса подбирают так, чтобы в течение нескольких секунд концы деталей нагрелись до температуры перехода полимера в вязкотекучее состояние, при котором возможно сваривание. В этот момент движение деталей прекращается и под действием осевого давления они прочно соединяются. Процесс сварки заканчивается естественным охлаждением изделия, сжатого осевым усилием. Этим методом в производстве можно приваривать горловину к емкостям из термопластов. Недостатком метода является ограниченность конфигурации свариваемых изделий.
При сварке токами высокой частоты детали нагреваются в высокочастотном электрическом поле до пластического состояния с одновременным сдавливанием. Нагрев происходит равномерно по всей массе материала, помещенного между электродами, и основан на принципе преобразования электроэнергии, полученной от высокочастотного генератора, в тепловую. Этим методом в настоящее время свариваются материалы толщиной до 5 мм.
Ультразвуковая сварка относится к наиболее перспективным способам соединения пластмасс в автомобилестроении. Под влиянием ультразвуковых колебаний более 20 кГц в свариваемых деталях возникают механические высокочастотные колебания, которые преобразуются в тепловую энергию, идущую на создание шва между свариваемыми поверхностями. Толщина материалов, свариваемых ультразвуком,— от 0,1 до 10 .л. Можно применять этот метод и при сварке эластичных полимеров небольшой толщины «0,05—1,5 мм.
Химическая сварка применяется для термореактив! >ix полимерных материалов, как правило, с наполнителем в виде пороил зв или стеклянных волокон. Этот метод основан на том, что поверхность пленки термореактивной смолы имеет химически активные функциональные группы, которые могут вступать в реакцию и образовывать химические связи. До осуществления сварки необходим тесный контакт между соединяемыми поверхностями. Иногда для ускорения процесса и повышения надежности соединения на поверхность наносят присадки: при сварке фенольных стеклопластиков типа АГ-У, ДСВ применяют пленку на основе связующего БФ-4, при сварке препрегов на основе полиэфирных смол — раствор гликольмалеинатной смолы в стироле (смола ПН-1, ПН-3 и т. д.) с добавкой органических перекисей или гидроперекисей. Удельное давление сварки для фенольных стеклопластиков 4—5 МПа, а для изделий из препрегов 2,5—3,0 МПа.
Если в настоящее время сварка пластмасс как технологический процесс применяется для соединений автомобильных узлов еше мало, то при создании крупногабаритных конструкций из полимеров, таких как панели приборов, топливные баки, она получит широкое распространение.
ПРЕДИСЛОВИЕ |
Соединение пластика | Конструкция машины
Существует несколько способов соединения пластиковых деталей. Стоимость оборудования и трудозатраты для каждого метода значительно различаются. Большинство методов имеют ограничения на размеры и типы пластика, которые можно соединять.
Механическое крепление: Самый простой способ соединения пластиковых деталей – это встраивание в детали крепежного элемента (шарнира, защелки, фиксатора). Для этого метода подходят только более прочные пластмассы, поскольку соединение должно выдерживать деформации при сборке, эксплуатационные нагрузки и возможное многократное использование. Эта форма крепления подходит только для слабонагруженных нежестких узлов, где точность не имеет решающего значения.
Скачать эту статью в формате .PDF Этот тип файла включает в себя графику и схемы высокого разрешения, если это применимо. |
Механический крепеж (винты, заклепки, штифты, гайки из листового металла) является наиболее распространенным методом соединения. Для них требуется пластик, способный выдерживать нагрузку при вставке застежки и последующую высокую нагрузку на застежку. Обычные крепежные винты используются редко, за исключением чрезвычайно прочного пластика.
Существует ряд застежек, предназначенных для использования с пластмассами. Резьбовые крепления лучше всего подходят для толстых секций. Для более мягких материалов предпочтительны резьбонарезные винты, а для более твердых пластиков лучше всего подходят нарезные винты. Нажимные контргайки и зажимы могут быть лучше для более тонких секций. Если застежку приходится снимать несколько раз, рекомендуются металлические вставки. Они могут быть отформованы на месте, спрессованы, приклеены или расширены в отверстия или вставлены с помощью ультразвука.
Сварка плавлением: Пластмассовые детали, слишком сложные или большие для изготовления на доступном формовочном оборудовании, иногда изготавливаются в виде подкомпонентов и свариваются вместе с помощью сварки плавлением. Удерживающие приспособления обеспечивают точное сопряжение и соосность соединяемых деталей.
Для пластификации кромок деталей приспособления прижимают детали к нагревательной плите. По мере того как валик плавит поверхность детали, пластик смещается, в то время как приспособление поддерживает частичное давление на валик. Это начальное сплавление создает гладкую поверхность за счет удаления дефектов поверхности, деформации или небольших раковин. Расплавленный материал продолжает перемещаться до тех пор, пока «остановки расплава» на плите не коснутся удерживающих приспособлений. После этого материал больше не смещается, а детали удерживаются на плите до тех пор, пока каждый край детали не пластифицируется на заданную глубину. Глубина расплава регулируется временем контакта, которое обычно составляет от 3 до 6 с.
После пластификации краев детали фиксаторы открываются и плита вынимается. Затем приспособления снова закрываются, сжимая детали вместе до тех пор, пока «уплотняющие упоры» на приспособлениях не соприкоснутся. Детали удерживаются вместе под давлением по мере того, как расплавленный материал остывает, связывая их вместе.
Обычно склеивание плавлением соединяет термопласты, такие как полиэтилен, полипропилен и АБС. Однако с небольшими изменениями этот процесс можно использовать для соединения как наполненного, так и ненаполненного нейлона.
Для сплавления нейлона без наполнителя тонкое никель-хромовое лезвие, а не плита, нагревается примерно до 1100°F. Нагретое лезвие приближается к материалу на расстояние 0,0005 дюйма за короткий цикл нагрева. Затем лезвие удаляется, а деталь закрепляется обычным образом. Стеклонаполненный нейлон можно смягчить прямым нагревом, если между каждым циклом очищать лезвие или плиту стальной щеткой.
Время охлаждения обычно такое же, как и время расплавления — от 3 до 6 сек. По завершении охлаждения механизм захвата в одном из удерживающих приспособлений освобождает деталь, приспособления открываются, и готовая деталь удаляется вручную или автоматически. Общее машинное время от начала до конца обычно составляет около 15 секунд, что вполне соответствует диапазону систем литья под давлением, часто используемых в сочетании со сваркой.
Сварка горячим газом: Это низкоскоростной процесс изготовления крупных конструкционных деталей из листового материала. Стержень из термопласта нагревают вместе с соединяемыми деталями до тех пор, пока они не размягчатся и их можно будет соединить. Источником тепла обычно является инертный газ. Максимальная скорость на длинных прямых сварных швах составляет около 40 дюймов/мин. Сложные детали требуют больше времени. Навыки оператора имеют решающее значение как для прочности сварного шва, так и для внешнего вида.
Вибрационная сварка: Вибрационная сварка обеспечивает герметичное соединение деталей круглой, прямоугольной или неправильной формы, изготовленных практически из любого термопластичного материала, даже из разнородных материалов, имеющих разброс температур расплава до 100°F. Этот процесс особенно подходит для полых компонентов контейнерного типа, имеющих сварной шов в одной плоскости.
Детали нагреты трением путем прижатия их друг к другу и вибрации одной из частей с частотой от 120 до 240 Гц в плоскости соединения.
Через 2-3 секунды вибрация прекращается в точном требуемом взаимном положении двух частей. Давление поддерживается кратковременно, пока размягченный пластик охлаждается. Прочность соединения очень близка к прочности основного материала. Время цикла, включая ручную загрузку и разгрузку, для большинства деталей составляет от 5 до 8 секунд. Процесс адаптируется к полностью автоматизированным системам.
Вибрационная сварка подходит для крупных деталей, сварка которых другими методами невозможна или нецелесообразна. Детали могут быть прямоугольными или неправильными, если сварной шов находится в одной плоскости и возможно небольшое перемещение (не менее 0,12 дюйма) в этой плоскости. Компоненты с поверхностями сварки длиной до 20 дюймов были успешно соединены.
Склеивание растворителем: Пластмассы размягчаются путем покрытия их растворителем, затем зажимаются или прессуются. Молекулы пластика смешиваются друг с другом, и детали соединяются при испарении растворителя. Этот процесс ограничен термопластами. Время плавления зависит от скорости испарения растворителя и может быть сокращено путем нагревания.
Чистые растворители обеспечивают самое простое и дешевое соединение. Легированные растворители, которые стоят дороже, содержат растворы пластика, склеиваемого для заполнения зазоров в плохо подогнанных деталях. Следующими по сложности и стоимости идут мономеры и растворители для полимеризации. Эти материалы содержат катализаторы и промоторы, добавленные к легированным растворителям для проведения полимеризации при комнатной температуре или температуре ниже точки размягчения термопласта.
Склеенные растворителем детали должны быть прижаты друг к другу на 10–30 секунд, прежде чем с ними можно будет работать. Давление имеет решающее значение, так как слишком большое давление приводит к деформации деталей. Для отверждения бонда может потребоваться день или более при комнатной температуре или несколько часов при повышенной температуре.
Ультразвуковая сварка: Импульсы передаются детали с помощью резонансного вибрационного инструмента, называемого рогом, заставляющего два пластиковых материала вибрировать друг относительно друга. Вибрация нагревает и сплавляет детали. Пластмассовые изделия, включая смеси или сплавы различных семейств смол, можно соединять с помощью ультразвуковой сварки. Такие разнородные детали должны быть тщательно спроектированы, и поставщики смолы и оборудования должны быть привлечены заранее, чтобы гарантировать, что ультразвуковые методы могут обеспечить подходящее соединение.
Ультразвуковая сборка часто выполняется на частоте 20 кГц для достижения амплитуды и мощности колебаний, необходимых для плавления термопластов. Однако более высокие частоты, вызывающие меньшую вибрацию, также могут соединяться с термопластами, особенно с конструкционными термопластами, такими как армированные полимеры. Для некоторых применений использование частоты 40 кГц означает меньшую деградацию материала. Инструменты, используемые для сварки на частоте 40 кГц, меньше, чем инструменты, используемые для сварки на частоте 20 кГц; поэтому сварные швы, выполненные на частоте 40 кГц, обычно меньше.
Критическое давление. Слишком много заставляет детали вибрировать как единая конструкция без нагрева. Слишком малое количество не обеспечивает достаточного контактного трения или нагрева.
Ультразвуковая сварка выполняется быстро. На одной станции возможна скорость сборки более 25 деталей в минуту. Нет никаких вторичных операций, таких как покрытие, вставка или очистка. Процесс требует довольно жестких материалов. Звуковая сварка разнородных материалов может быть выполнена, но температуры плавления обоих материалов должны быть довольно близкими, иначе размягчится только материал с более низкой температурой плавления, и связь не образуется.
Ультразвук также можно использовать для вставки металлических компонентов в пластик, соединения металлических и пластиковых деталей или точечной сварки пластиковых секций.
Индукционная сварка: Индукционная сварка может быть выполнена путем сжатия двух кусков пластика вокруг металлической вставки. При прохождении через магнитное поле металл в оболочке нагревается, и при сжатии образуется сварной шов. Металл остается запечатанным внутри детали.
Термопластичные связующие, наполненные электромагнитными или ферритовыми материалами, также могут использоваться при индукционной сварке. Материал в виде предварительно сформированного кольца или полосы или, например, в виде горячего расплава вводится между сопрягаемыми деталями перед индукционным нагревом. Если используются металлические частицы, переменное магнитное поле индуцирует ток внутри частиц, выделяя тепло. При использовании феррита ток не вырабатывается. Вместо этого тепло вырабатывается молекулярным трением, поскольку частицы пытаются сохранить свой магнитный заряд, когда поля меняются местами.
Чтобы исключить необходимость добавления металла в соединение, металлический порошок можно добавить в исходную пластиковую форму, но требуется гораздо более высокая частота.
Индукционная сварка является дорогостоящим методом и подходит для трудносвариваемых пластиков, таких как полипропилен, а также для форм, которые не подходят для ультразвуковой сварочной машины. Этот процесс лучше всего подходит для склеивания большинства видов полипропилена, полиэтилена, стирола, АБС-пластика, полиэстера и нейлона в ходе крупномасштабных высокоавтоматизированных операций соединения.
Термостойкие полипропилены, которые нельзя соединить с помощью клея или других методов сварки, можно успешно соединить с помощью индукционной сварки. Связующие вещества, нагретые индукционным способом, достигают температуры 300°F за 0,1 секунды, чтобы сплавиться с термостойкими веществами.
Диэлектрическая сварка: Диэлектрическая сварка используется на пленках и тонких листах толщиной до 60 мил, в основном в упаковке. В этом методе используется пробой пластика под действием высоких напряжений и частот (от 13 до 120 МГц) для диэлектрического нагрева и плавления пластика. Скорость сварки зависит от коэффициента диэлектрических потерь, толщины материала и площади, на которую действует напряжение. Диэлектрическая сварка идеально подходит для материалов из ПВХ.
404 — Seite nicht gefunden
404 — Seite nicht gefunden — WHMПродукт-Суче
CAD-инструмент
УРА! 404
Похоже, ты заблудился! Попробуйте поискать здесь
Датеншутцеинстеллунген
Не используйте файлы cookie на веб-сайте. Einige von ihnen sind essenziell, während andere uns helfen, diese Website und Ihre Erfahrung zu verbessern.
- Файлы cookie Technisch notwendige
- Экстерн Медиен
Все активы
Шпайхерн
Individuelle Datenschutzeinstellungen
Информация о файлах cookie Datenschutzerklärung Импрессум
Datenschutzeinstellungen
Он нашел Sie eine Übersicht über alle verwendeten Cookies. Sie können Ihre Einwilligung zu ganzen Kategorien geben oder sich weitere Informationen anzeigen lassen und so nur bestimmte Cookies auswählen.
Все активы Шпайхерн
Цурюк
Печенье Technisch notwendige (1)
Technisch notwendige Cookies ermöglichen grundlegende Funktionen und sind für die einwandfreie Funktion der Website erforderlich.
Информация о файлах cookie Информация о файлах cookie изменена
Имя | Веб-сайт-Cookie |
---|---|
Анбитер | Вильгельм Херм.![]() |
Цвек | Speichert die Einstellungen der Besucher, die in der Cookie Box от Borlabs Cookie ausgewählt wurden. |
Имя файла cookie | стартовый файл cookie |
Печенье Laufzeit | 1 Яр |
Экстерн Медиен (4)
Inhalte von Videoplattformen und Social-Media-Plattformen werden standardmäßig blockiert. Wenn Cookies von externen Medien akzeptiert werden, bedarf der Zugriff auf diese Inhalte keiner manuellen Einwilligung mehr.
Информация о файлах cookie Информация о файлах cookie изменена
Акзептирен | |
---|---|
Имя | Фейсбук |
Анбитер | Фейсбук |
Цвек | Wird verwendet, um Facebook-Inhalte zu entsperren.![]() |
Датеншуцерклерунг | https://www.facebook.com/privacy/explanation |
Хост(ы) | .facebook.com |
Акзептирен | |
---|---|
Имя | Карты Гугл |
Анбитер | Гугл |
Цвек | Wird zum Entsperren от Google Maps-Inhalten verwendet.![]() |
Датеншуцерклерунг | https://policies.google.com/privacy |
Хост(ы) | .google.com |
Имя файла cookie | НИД |
Печенье Laufzeit | 6 Монат |
Акзептирен | |
---|---|
Имя | Инстаграм |
Анбитер | Фейсбук |
Цвек | Wird verwendet, um Instagram-Inhalte zu entsperren.![]() |
Датеншуцерклерунг | https://www.instagram.com/legal/privacy/ |
Хост(ы) | .instagram.com |
Имя файла cookie | голубь_состояние |
Печенье Laufzeit | Сицунг |
Акзептирен | |
---|---|
Имя | YouTube |
Анбитер | Ютуб |
Цвек | Wird verwendet, um YouTube-Inhalte zu entsperren.![]() |
Датеншуцерклерунг | https://policies.google.com/privacy |
Хост(ы) | google.com |
Имя файла cookie | НИД |
Печенье Laufzeit | 6 Монате |
на базе Borlabs Cookie
Datenschutzerklärung Импрессум
Сварка пластика — Weld World
Соглашение
Сварка пластика ПРЕДИСЛОВИЯ . строгий поиск материалов-заменителей в 1933 г. из-за нехватки цветных металлов.
Два года спустя, в 1935 поливинилхлорид стал доступен в промышленных масштабах. Вскоре после этого было обнаружено, что пластифицированный ПВХ можно формовать, экструдировать и подвергать термоформованию при условии, что он надлежащим образом стабилизирован.
Последующие исследования (США, 1937 г., Германия, 1938 г. и Великобритания, 1939 г.) выявили тот факт, что ПВХ можно сваривать при одновременном воздействии тепла и давления.
Первые патенты на сварку пластмасс были выданы Dow Chemical Company 5 ноября 1940 в США и IG Farbenindustekt 19 августа в Германии.
Газовая сварка пластмасс широко практиковалась в Германии во время Второй мировой войны, когда немцы представили ее некоторым фирмам в Австрии, Бельгии, Франции, Дании, Голландии, Италии и Норвегии.
Первоначальная работа по сварке пластмасс в основном невольно сосредоточивалась на ПВХ.
В настоящее время сварка является важной технологией изготовления, при этом большое внимание уделяется жесткому ПВХ и, в меньшей степени, полиэтилену. Без технологии сварки многие изделия, связанные с пластиковыми изделиями, никогда не могут быть изготовлены.
Любой процесс сварки пластика включает использование энергии, в основном в виде тепла, для сплавления листового материала.
Типы пластика :Пластик можно сгруппировать следующим образом:
1-Термопластик
| 2-термореактивные пластмассы
|
1- поливинилхлорид (ПВХ)
2-Полипропилен (ПП) | 6-полиацеталь 7-полиамид (нейлон) 8-поливинилдихлорид (ПВДХ) 9-акрил 10-фторуглерод |
Конструкции соединений, аналогичные листовому металлу, используются для сварки пластмасс,
Обычно все виды сварных швов, известные для сварки металлов, могут быть использованы для сварки термопластов. например:
Стыковые швы, угловые швы, швы внахлестку, угловые швы, кромочные швы, полосовые швы и т. д.
Снятие фаски с соединенияСнятие фаски очень важно для получения качественных сварных швов. Однако квадратные стыковые, тавровые и угловые сварные швы (поверх) не требуют снятия фаски.
Присадочные материалы При необходимости в сварной шов может быть добавлен дополнительный пластик, для этого используется круглый стержень, овальный стержень, треугольный стержень или плоский стержень.
Гибкая плоская пластиковая полоса используется для сварки или ремонта футеровки резервуара.
Следуя базовому процессу сварки используется для соединения термопластиков
1-го придуванной сварки для инструментов 2-hot Газовая сварка
3-H-H-HED SWIND 4-OULTRASONIAL GELDVIND
9000 5-FRIC 3-H-HARDSINGE 4-OULTRASONICE WELRID 5-FRIC 3-H-HI-HID. — Индукционная сварка
В этом процессе тепло передается на поверхности, которые соединяются или находятся в контакте с источником тепла, например, удлинителем
нагреватель, электроплитка, паяльник и т. д. При этом после размягчения пластика источник тепла удаляется, и компоненты быстро свариваются встык или свариваются вместе под небольшим давлением и удерживаются до тех пор, пока соединение не остынет.
Важным фактором при сварке нагретым инструментом является интервал между снятием компонентов с горячего инструмента и приложением давления.
Эта продолжительность должна быть как можно короче, поскольку задержка в этот момент приведет к ухудшению качества сварки.
Применение сварки с подогревом Сварка с подогревом может применяться для широкого спектра термопластов и в основном используется для полиэтилена низкой и высокой плотности, пластифицированного ПВХ, полипропилена и, в меньшей степени, акрила.
Жесткий ПВХ обычно не подходит для сварки нагретым инструментом, так как материал имеет тенденцию к термической деструкции при контакте с горячими металлическими поверхностями.
Сварка нагретым инструментом подходит для изготовления листов из полиэтилена и широко используется при сварке труб и труб большого диаметра.
Сварка пластмассы горячим газомВ технике сварки горячим газом используется поток горячего газа для размягчения основного металла и присадочных материалов.
Обычно при сварке пластмасс используются два типа сварочных горелок: (а) с электрическим нагревом и (б) с газовым нагревом.
Продолжение следует
Как сваривать пластмассы. Руководство для начинающих
Сварка пластмасс – это сварка полуфабрикатов пластмасс. Это процесс соединения размягченных поверхностей материалов, как правило, при нагревании (кроме сварки растворителем). Для соединения пластмасс разработаны многочисленные методы сварки. В зависимости от механизма тепловыделения на границе сварки методы сварки можно разделить на методы внешнего и внутреннего нагрева. Хорошее качество сварного шва зависит от методов сварки и свариваемости основных материалов. В этой статье объясняется, как сваривать пластмассы, путем рассмотрения различных методов сварки и различных пластмасс, которые можно сваривать.
Изображение предоставлено Shutterstock.com/drasa
Различные методы сварки
Для сварки изделий из термопластов используется множество различных технологий.
Сварка горячим газом
Сварка горячим газом также известна как сварка горячим воздухом. Это метод сварки пластика с использованием тепла. Тепловая пушка специальной конструкции направляет горячий воздух для смягчения обеих соединяемых деталей вместе с пластиковым наполнителем, все из которых должны быть из одного или очень похожего пластика. Сварка горячим газом является распространенным методом изготовления небольших химических, водяных, теплообменников и водопроводной арматуры.
Сварочная проволока
Пластмассовый сварочный стержень, также называемый термопластичным сварочным стержнем, имеет круглое или треугольное поперечное сечение, которое используется для соединения двух кусков пластика. Стержни доступны в разных цветах, чтобы соответствовать цвету основного пластика. Намотанный на катушку пластиковый сварочный стержень известен как «сплайн».
Термосварка
Термосваривание использует тепло и давление. В методе термосваривания с прямым контактом используется постоянно нагретая матрица или запаивающий стержень для подачи тепла на определенную контактную область или путь для сварки термопластов вместе. Он используется для многих применений, таких как соединители с термосваркой, термически активируемые клеи и запечатывание пленкой или фольгой.
Сварочный наконечник Speed
При скоростной сварке сварочный аппарат для пластмасс, похожий на паяльник, имеет подающую трубку для пластикового сварочного стержня. Пластмассовый сварочный аппарат нагревает стержень и подложку, одновременно прижимая расплавленный сварочный стержень к нужному месту. В стык помещается валик из размягченного пластика, и детали и сварочный стержень сплавляются. Метод быстрой сварки наконечником является гораздо более быстрой техникой сварки и может использоваться в крутых углах с практикой. Вариант «пистолета» со скоростным наконечником представляет собой паяльник с широким плоским наконечником, который может расплавить сварной шов и присадочный материал для создания соединения.
Свободная сварка
При ручной сварке струя горячего воздуха от сварочного аппарата направляется одновременно на область сварки и на кончик сварочного стержня. Когда пластиковый стержень размягчается, он вдавливается в сустав и сплавляется. Этот процесс медленнее, чем некоторые другие, описанные здесь, но его можно использовать практически в любой ситуации.
Экструзионная сварка
Экструзионная сварка позволяет выполнять больше сварных швов за один проход. Это идеальный метод для соединения материалов толщиной более шести мм. Сварочный стержень втягивается в крошечный ручной пластиковый экструдер, пластифицируется и выталкивается из экструдера к соединенным частям, которые размягчаются струей горячего воздуха для обеспечения соединения.
Контактная сварка
В этом методе используется тепло, подаваемое за счет теплопроводности наконечников щипцов вместо электропроводности, используемой при точечной сварке. Две части скрепляются нагретыми наконечниками, которые плавятся и соединяются.
Сварка горячей пластиной
Этот метод аналогичен контактной сварке и используется для сварки крупных деталей или деталей со сложной геометрией сварного шва. Две свариваемые детали помещаются в оснастку, прикрепленную к двум противоположным плитам пресса. Затем горячая пластина, форма которой соответствует геометрии сварного шва свариваемых деталей, перемещается в положение между двумя деталями. Две противоположные пластины перемещают детали в контакте с горячей пластиной до тех пор, пока тепло не размягчит поверхности до точки плавления пластика. Когда это условие достигнуто, горячая пластина удаляется, а детали прижимаются друг к другу и удерживаются до тех пор, пока сварной шов не остынет и не затвердеет, чтобы создать прочную связь.
Сварочное оборудование с горячей пластиной обычно управляется пневматически, гидравлически или электрически с помощью серводвигателей.
Высокочастотная сварка
Высокочастотная сварка также известна как диэлектрическая герметизация или радиочастотная сварка (РЧ). Высокочастотные электромагнитные волны в диапазоне радиочастот могут нагревать полимеры, чтобы смягчить пластмассы для соединения. Быстрая переориентация некоторых химических диполей полимера приводит к выделению тепла, что означает локализацию тепла, и процесс может быть непрерывным.
Настольный пресс оказывает давление на поверхности двух кусков материала. Плашки руководят процессом сварки. Когда пресс смыкается, высокочастотные волны проходят через небольшой участок между матрицей и столом, где происходит сварка. Эта высокая частота нагревает пластик, который сваривается под давлением и принимает форму штампа.
Ультразвуковая сварка
При ультразвуковой сварке высокочастотная вибрация с низкой амплитудой создает тепло за счет трения. Граница двух частей специально разработана для концентрации энергии для максимальной прочности сварного шва. Ультразвуковая сварка может использоваться практически для всех пластиков. Это самая быстрая технология сварки пластмасс.
Лазерная сварка
Для этого метода требуется, чтобы одна часть пропускала лазерный луч. Другая часть должна быть абсорбирующей или иметь абсорбирующее покрытие на границе раздела. Давление прикладывается к двум частям, в то время как лазерный луч перемещается вдоль линии соединения. Луч проходит через первую пластиковую часть и поглощается другой, чтобы произвести достаточно тепла, чтобы смягчить поверхность раздела и создать прочный сварной шов.
Применения лазерной сварки включают в себя герметизацию пакетов катетеров, медицинских контейнеров, автомобильных ключей дистанционного управления, соединений с защитой от вскрытия шприцев, корпусов кардиостимуляторов, узлов фар или задних фонарей, корпусов насосов и деталей сотовых телефонов.
Сварка растворителем
При сварке растворителем растворитель применяется для временного растворения полимера при комнатной температуре. Когда это происходит, полимерные цепи могут свободно перемещаться в жидкости и смешиваться с другими столь же растворенными цепями в другом компоненте. Со временем растворитель проникает в полимер так, что цепи теряют свою подвижность. Остается твердая масса перепутанных полимерных цепей, которая создает сварной шов. Этот метод часто используется для соединения труб из ПВХ и АБС, используемых в бытовой сантехнике.
Типы сварки пластмасс
Пластмассы можно разделить на два типа: термореактивные и термопластичные. Термореактивные материалы можно формовать только один раз. После первого плавления они затвердевают навсегда. Термопластик можно плавить много раз, и форма пластика может меняться. Сваривать можно только термопласты.
Разница между двумя типами пластика заключается в том, как макромолекулы связываются друг с другом на атомном уровне. Молекулы термореактивных материалов запускаются под действием тепла, чтобы вступить в химическую реакцию и соединиться. Молекулы термопластов химически не связаны.
Наиболее распространенными термопластичными материалами, пригодными для сварки, являются HPDE (полиэтилен высокой плотности), PP (полипропилен), CPVC (хлорированный поливинилхлорид), PVC (поливинилхлорид), PVDF (поливинилфторид) и ABS (акрилонитрилбутадиен-стирол).
Выводы
Выше мы объяснили, как работает сварка пластика, а также различные методы и используемые пластики. Мы надеемся, что эта информация была вам полезна. Чтобы узнать больше о других промышленных процессах, найти поставщиков или составить собственный список поставщиков, посетите сайт Thomas Supplier Discovery, где есть информация о других аналогичных продуктах.
Источники
- https://waterwelders.com/how-to-weld-plastics/
- https://accendoreliability.com/heat-welding-plastics/
- https://thermoweld.
co.za/welding-joining/
Связанные статьи
- Сварка трением с перемешиванием: параметры сварки
- Процесс экструзии пластмасс
- Стандартные пластиковые профили
- Термическая сварка с перемешиванием
- Сварка против пайки
- Типы пластиковых шнеков для экструзии
- Сравнение термореактивных и термопластичных материалов
- ПЭТ-пластик: экономия денег и энергии благодаря вторичному пластику
- Коэкструзия пластика
- Машина для экструзии пластмасс – процесс и методы
- Стать сварщиком — руководство
- Ведущие компании по литью под давлением в США
- Производство пластиковых преформ
- Технологии и методы изготовления пластмасс
- Основы сварки трением с перемешиванием
- Как металлизировать пластик
- О сварочных услугах
- Об услугах по электронно-лучевой (ЭЛ) сварке
- О лазерной сварке
- О пластиковых вставках
Больше из Изготовление и изготовление на заказ
Сборка пластмасс в медицинских устройствах
Сборка пластмасс может производиться различными способами: с помощью механических средств, посредством сварки и склеивания. Здесь мы поговорим об этих методах и приведем примеры каждого.
Механическое соединение деталей включает запрессовку, защелку и механическое крепление. При запрессовке деталь вставляется в отверстие несколько меньших размеров, в результате чего возникают сжимающие усилия во вставляемой детали и растягивающие усилия в сопрягаемой детали. Шестерни и колеса обычно устанавливаются на валах с помощью прессовой посадки.
Соединения с защелкой включают элементы, отлитые непосредственно в детали, такие как карабины или балки, кольцевые или кольцевые защелки, шаровые защелки и защелки или торсионные защелки. Здесь рассматриваются вопросы проектирования некоторых защелкивающихся соединений. Защелкивающиеся соединения могут быть разъемными и неразъемными. Разъемные соединения используются, когда продукт должен быть разобран в какой-то момент в течение его срока службы, например, крышка аккумуляторного отсека. Неразъемные соединения используются, когда нет необходимости разбирать продукт или когда это опасно из-за возможности поражения электрическим током, например, с электроприбором.
Механические застежки используются, когда соединения с защелкой невозможны или неуместны, и включают в себя винты, металлические вставки, вставные застежки, зажимы и гайки, заклепки, шпильки, скобы и петли. Типы винтов включают крепежные винты/гайки/шайбы и саморезы. Вставные застежки имеют зазубрины, которые позволяют вставлять застежку, но не дают ей вывернуться. Скоростные зажимы и гайки нажимаются, но не снимаются. Одним из потенциальных недостатков механического крепления является использование отверстий или точечных мест приложения усилий, которые приводят к возникновению областей концентрации напряжений в пластике.
Сварные соединенияСварка пластиковых деталей приводит к неразъемным соединениям. Типы сварки включают ультразвуковую, вибрационную, вращательную, сварку горячим инструментом, индукционную, контактную, сварку горячим газом и экструзионную сварку.
Ультразвуковая сварка широко используется в автомобильной, бытовой, медицинской и игрушечной промышленности. Низкоамплитудная (0,025-0,125 мм), высокочастотная (15-40 кГц) вибрационная энергия создает межмолекулярное трение и тепло для расплавления деталей. Направляющие энергии отлиты непосредственно в сопрягаемую поверхность детали, контактирующей с рупором сварщика США, чтобы помочь сфокусировать энергию и создать локальное соединение. Чтобы узнать больше об ультразвуковой сварке, перейдите сюда, а хорошее объяснение ультразвуковой и вибрационной сварки — здесь.
Вибрационная сварка используется для деталей среднего и большого размера, а также деталей с большими зазорами в направлении вибрации. Детали притирают друг к другу с низкой частотой (120-240 Гц) и большой амплитудой (0,4-4 мм) под давлением до расплавления соприкасающихся поверхностей, затем детали выдерживают под давлением до затвердевания и остывания шва. Подробнее о вибрационной сварке можно узнать здесь.
Сварка вращением/вращением используется для соединения круглых деталей, малых и больших (диаметром до 24 дюймов). Одна часть удерживается неподвижно, в то время как сопрягаемая часть вращается под давлением относительно неподвижной части. Соприкасающиеся поверхности плавятся под действием возникающей силы трения, а детали удерживаются вместе под давлением, в то время как сварной шов остывает и затвердевает. Подробнее о спиновой сварке можно прочитать здесь.
Сварка горячим инструментом включает в себя использование нагретого инструмента для плавления поверхностей, которые должны быть соединены, а затем приложение давления к двум соединяемым частям, в то время как сварной шов остывает и затвердевает. Подробнее о сварке горячим инструментом или горячей пластиной можно узнать здесь.
Индукционная/электромагнитная сварка предполагает использование электромагнитной энергии для расплавления прокладки или предварительно отформованного магнитного материала между соединяемыми частями. Магнитный материал состоит из базового полимера, совместимого с полимером соединяемых деталей, и мелкодисперсных микронных частиц железа, оксида железа, нержавеющей стали или других магнитных материалов. Подробнее об индукционной сварке можно прочитать здесь.
Сварка сопротивлением использует тепло, выделяемое электрическим током, проходящим через проволоку, для нагрева и плавления соединяемых поверхностей. После соединения поверхностей к двум компонентам прикладывается давление, пока сварной шов остывает и затвердевает. Для получения дополнительной информации о контактной сварке в целом перейдите сюда.
Сварка горячим газом использует нагретый воздух или азот для расплавления свариваемых поверхностей, а также пластиковый сварочный стержень, который вставляется в соединение, которое имеет канавку или v-образную форму для размещения расплавленного сварочного материала. Затем к сварному шву прикладывается давление по мере его охлаждения и затвердевания. Подробнее о сварке горячим газом можно прочитать здесь.
Экструзионная сварка аналогична сварке горячим газом, за исключением того, что наполнитель сварного шва размягчается посредством экструзии. После того, как заполняющий материал нанесен в канавку или «V» соединения, к сварному шву прикладывается давление до тех пор, пока он не остынет и не затвердеет.
Склеивание пластиковых деталей с помощью клеев означает создание межмолекулярных связей между пластмассовыми деталями и клеящим веществом или между самими пластмассовыми деталями. Таким образом можно склеивать разнородные материалы, а склеенные детали, как правило, неразделимы. Одним из преимуществ склеенных деталей является то, что может быть образована водонепроницаемая герметизация.
Склеивание жидким клеем включает дозирование жидкого клея между деталями и его отверждение со временем. Время отверждения варьируется от минут до часов.
УФ-склейка включает дозирование жидкого клея между деталями и полимеризацию клея с помощью УФ-излучения. Детали должны быть прозрачными для прохождения УФ-излучения, а время отверждения короткое, от 1 до 5 секунд.
Склеивание растворителем включает дозирование жидкого растворителя между деталями, фиксацию их вместе, чтобы они не могли двигаться, и предоставление растворителю возможности испариться. Растворитель вступает в химическую реакцию с поверхностью каждой детали, создавая межмолекулярную связь между поверхностями. Время отверждения обычно находится в диапазоне от минут до часов.
Эта ссылка обеспечивает отличный подход к выбору метода сборки пластмасс.
Пожалуйста, свяжитесь с нами для помощи с вашим текущим пластиковым дизайном!
Выбор наилучшего процесса соединения пластмасс для конкретного применения » Декорирование пластмасс
Билл Хезервик, Branson Ultrasonics Corporation
Эта статья поможет дизайнеру решить тайну выбора наилучшей технологии соединения пластмасс для каждого применения. С некоторыми практическими рекомендациями можно сделать оптимальный выбор процесса из множества доступных технологий соединения. Выбор процесса не является абсолютной наукой, и может подходить более одного процесса. «Лучший» процесс в конечном итоге зависит от конкретных потребностей, материала, размера, геометрии и функциональных требований.
Методы сборки
Детали можно собирать различными способами, включая механическое, химическое и термическое соединение. Это три отдельные категории, на которые обычно ссылаются при выборе метода сборки. И механический, и химический методы часто требуют третьего «расходного» компонента для создания сборки.
Существует два типа методов механической сборки: крепеж и другие механические средства. Механическая сборка обычно используется для соединения двух разнородных материалов. Первым и наиболее распространенным методом является крепеж, который включает в себя винты, болты и зажимы. Другие механические средства включают формованные элементы, такие как защелки, прессовые посадки и выступ для распорки, и это лишь некоторые из них.
Химические связи создаются с помощью клеев или растворителей. В этой статье будут обсуждаться технологии соединения пластиков, которые основаны на тепловом источнике тепла для соединения. Дальнейшее обсуждение будет ограничено совместимыми термопластичными полимерными материалами.
Соединение пластмасс Требования к применению и выбор материала
При определении метода соединения, который будет использоваться для приложения, важно четко определить потребности, для которых предназначено приложение. Это часто будет определять тип выбранного полимера. Тип материала можно разделить на два типа: аморфный или полукристаллический. Цель состоит не в том, чтобы помочь дизайнеру определить тип пластика, который будет использоваться, а в том, чтобы определить лучший метод их соединения после того, как материал выбран.
При определении метода соединения двух или более деталей необходимо сначала определить совместимость материалов для соединения нескольких деталей. Было проведено много исследований с различными производителями смол, университетами и поставщиками соединительного оборудования для определения совместимости термопластичных материалов.
Успех процесса соединения в значительной степени зависит от совместимости используемых термопластичных материалов. Полимерные цепи двух расплавленных материалов соединяются вместе, образуя полимерную связь или соединение. (Рис. 1) Все технологии термического соединения основаны на каком-либо источнике тепла, который приводит к такому типу соединения. Доступно множество вариантов. Один из методов заключается в использовании трения, как в технологиях ультразвуковой, вибрационной и спиновой сварки. Существуют также методы, в которых используется проводящий источник тепла, такой как горячая плита, инфракрасная и лазерная сварка.
Как правило, большинство материалов, изготовленных из одной и той же базовой смолы, совместимы друг с другом. Для справки прилагается таблица совместимости (рис. 2).
Из таблицы видно, что аморфная смола категории имеет повышенную совместимость. Это в значительной степени связано с аналогичными базовыми смолами и сополимерами, из которых состоят эти смолы. Кроме того, важно отметить, что эти смолы обладают характеристикой плавления, обозначаемой как 9. 0006 температура стеклования (Tg). Это точка или переход, в котором смола переходит из твердого состояния в жидкое или расплавленное состояние. Этот переход является постепенным и позволяет другим аморфным смолам связываться друг с другом. Кроме того, из таблицы видно, что большинство полукристаллических смол совместимы только друг с другом. Это связано с тем, что характеристики расплава полукристаллической смолы при переходе из твердого состояния в жидкое или расплавленное и обратно в твердое создают очень резкий переход (рис. 3).
Понимание совместимости материалов является первым шагом в определении того, какой процесс можно рассматривать для применения. Если требуется, чтобы приложение было выполнено из разнородных материалов или материалов, несовместимых с термическим соединением, то варианты могут быть ограничены использованием механических креплений или клея для сборки. Несколько других ключевых существенных факторов могут помочь в объединении соображений. Это температура плавления материала , модуль упругости, и индекс текучести расплава . Эту информацию можно легко найти в технических описаниях различных производителей смол.
- Температура расплава Более высокие температуры расплава требуют больше энергии. При сварке разнородных смол требуются одинаковые температуры расплава. Разницы в 40 градусов по Фаренгейту достаточно, чтобы помешать совместимости.
- Модуль упругости Как правило, чем жестче материал, тем лучше способность передачи энергии для процессов сварки трением, таких как ультразвуковая, вибрационная и спиновая сварка.
- Течение расплава (индекс) Скорость потока разнородных материалов должна быть достаточно близкой для достижения совместимости (т. е. от 8 до 10).
Наиболее часто задаваемый вопрос: насколько прочной будет связь? Это сложный вопрос, состоящий из многих частей. Прежде всего, исходная прочность или «чистая прочность» должна рассматриваться как основа для определения прочности сварного шва. В большинстве случаев можно с уверенностью сказать, что большинство имеющихся на рынке процессов термического соединения позволяют получить от 70 до 80 процентов исходного материала.
Если используются наполнители, они часто приводят к снижению прочности сварного шва почти на тот же процент, что и содержание наполнителя. Наполнители — это материалы, которые занимают место по объему и не добавляют прочности предполагаемому стыку. Только в редких случаях, например, в лабораториях, присадочный материал мигрировал или пересекал линию сварки. В обычных случаях они снижают прочность сварного шва. Например, если используется нейлоновый материал, наполненный стекловолокном на 30%, то прочность соединения должна составлять 40-50% исходного материала, при использовании 70% в качестве базового уровня или в лучшем случае.
Большинство методов соединения позволяют сваривать большую площадь, обеспечивая требуемую прочность соединения. Предлагается консультироваться с поставщиком материала во время разработки вместе с присоединяющимся поставщиком, чтобы помочь в принятии этих решений. Можно выполнить простые испытания сварки, которые могут помочь определить исходную прочность материала.
Понимание рабочих характеристик приложения также важно при выборе надлежащей технологии соединения для окончательной сборки. Элементы, которые необходимо учитывать, — это скорость утечки, прочность на растяжение и общий внешний вид детали, и это лишь некоторые из них. Должен ли сварной шов быть пламенным и свободным от твердых частиц, или в конструкции могут быть предусмотрены пламегасители, которые могут скрыть это условие?
Описание процесса соединения
Ультразвуковая сварка является наиболее широко используемым методом сварки. Система преобразует поступающую электрическую мощность с частотой 50/60 Гц в определенную выходную механическую частоту. В настоящее время наиболее распространенными частотами являются 20 кГц и 40 кГц; тем не менее, 15 кГц и 30 кГц получают признание в отрасли, поскольку приложения и использование этой технологии продолжают расти. Сетевое напряжение преобразуется через источник питания. Затем выходное напряжение преобразуется в механическую вибрацию или амплитуду через преобразователь, устройство преобразователя с компонентами, которые механически вибрируют с той же частотой, что и электрический вход. Эта вибрация передается через механический усилитель, называемый «усилителем», который может увеличивать или уменьшать механическую вибрацию, исходящую от преобразователя. «Рог» — это акустический инструмент, передающий вибрационную энергию на соединяемую деталь (рис. 5).
Энергия вибрации, необходимая для сварки, называется амплитудой. В большинстве случаев для полукристаллических или инженерных смол требуется большая амплитуда (в диапазоне 80–120 микрон от пика до пика) по сравнению с аморфными смолами (обычно 40–80 микрон от пика до пика). Существуют некоторые основные ограничения ультразвуковой сварки в зависимости от формы и длины сварного шва:
- Изменение высоты плоскости сварного шва составляет 0,4 дюйма/10,2 мм
- Максимальный диаметр круглого сварного шва 12″/304,8 мм
- Максимальные размеры сварного шва 14″ x 3″ или 355,6 мм x 76,2 мм
Типы конструкций сварных соединений включают направление энергии, соединение сдвигом и точечную сварку. Доступно множество вариантов дизайна для удовлетворения требований приложения. В тех случаях, когда требуется, чтобы сварной шов был больше максимального, можно использовать сегментированный или прерывистый сварной шов. Другая возможность заключается в использовании локальной сварки, которая может быть осуществлена за счет использования нескольких сварочных аппаратов.
Вибрационная сварка – это технология соединения, при которой необходимая температура плавления создается трением в зоне сварки. Как правило, одна из двух соединяемых частей остается неподвижной, а другая совершает возвратно-поступательное движение относительно нее с заданным смещением, частотой и силой. По завершении расплавления детали повторно выравниваются и дают затвердеть, образуя связь. Этот процесс позволяет производить непрерывные сварные швы. Однако сварной шов должен быть рассчитан на правильное перемещение деталей во время сварки.
В случае высокочастотной вибрационной сварки (240 Гц) требуется 1,8 мм смещения от пика к пику, а при низкочастотной сварке (100 Гц) — 4 мм от пика к пику. Если детали правильно спроектированы, можно без проблем сваривать с наклоном до 10 градусов в направлении вибрации. Возможны также горизонтальные и вертикальные плоскости сварки, если они расположены в направлении вибрации. (Это обычно называют плоскостью скольжения.) Две части должны иметь свободу движения, чтобы их можно было успешно соединить. Сегодня существуют сварочные аппараты различных размеров и конфигураций, которые могут сваривать небольшие детали с площадью сварного шва 5 см2 с большими деталями с площадью сварного шва 750 см2.
Сварка горячей пластиной – это технология соединения, при которой тепло передается непосредственно на свариваемую поверхность. Как правило, обе соединяемые детали прижимаются к нагревательной плите при заданной температуре в течение определенного периода времени и/или смещения расплава. Это смещение контролируется инструментальной оснасткой (ограничителями расплава). Детали снимаются с нагревательной плиты, а затем плита удаляется. Детали под действием силы сводятся к неподвижным упорам (упорам-уплотнителям).
Затем детали соединяются вместе и дают им затвердеть, образуя связь. Обычно существует два типа сварки горячей пластиной: высокотемпературная и низкотемпературная. Температура расплава пластика определяет выбор типа. Граница между высокой и низкой температурой составляет 650 градусов по Фаренгейту.
Инфракрасная сварка представляет собой «бесконтактную» технологию соединения, при которой тепло передается непосредственно на свариваемую поверхность посредством излучения или конвекционного нагрева. Как правило, обе соединяемые детали помещаются в непосредственной близости (0,2–0,5 мм) от плиты инфракрасного нагрева на определенное время. Время нагрева будет зависеть от интенсивности излучателя и скорости поглощения для данного термопластика. Это расстояние контролируется упорами инструмента. Детали снимаются с инфракрасной плиты, а затем плита удаляется. Детали под действием силы сводятся к неподвижным упорам (упорам-уплотнителям). Затем части соединяются вместе и дают затвердеть, образуя связь. Сегодня в производстве широко используются различные типы ИК-излучателей, включая металлическую фольгу или стеклянную колбу. Эти излучатели обычно относятся к среднему диапазону волн, поскольку большинство смол лучше всего поглощают волны в диапазоне 2–4 мкм. Это отличный процесс для использования с полукристаллическими материалами, которые склонны прилипать к нагретой плите. Этот процесс также обычно на 40-50 процентов быстрее, чем стандартная сварка горячей пластиной.
Лазерная сварка — это процесс, при котором лазерная энергия генерируется с помощью мощных диодов в диапазоне 780–980 нм. Это часто упоминается как Инфракрасная сварка сквозным пропусканием (TTIr) . Свариваемые детали скрепляются вместе, в то время как лазерная энергия проходит через одну деталь; эта энергия поглощается вторым куском. Поглощенная энергия создает тепло, которое позволяет суставу размягчиться и сформировать связь. Сегодня на рынке существует множество технологий, включая Одновременная инфракрасная сварка со сквозным пропусканием (STTIr), сварка трассировки и Сканирование широким лучом , и это лишь некоторые из них. Этот процесс сварки часто ассоциируется с приложениями, требующими сборки без облоя или твердых частиц.
Другим важным требованием является то, что детали должны быть отлиты с жесткими допусками. Когда детали собраны и есть небольшие зазоры или места, где детали не соприкасаются, это влияет на способность лазера проходить через этот воздушный зазор. Это можно компенсировать с помощью STTIr, который позволяет перемещать или расплавлять материал.
При сварке вращением необходимая температура плавления создается трением в зоне сварки. Как правило, одна из двух соединяемых частей остается неподвижной, в то время как другая перемещается относительно нее круговыми или вращательными движениями с заданной скоростью или числом оборотов в минуту (об/мин), скоростью опускания и давлением.
После завершения плавки детали затвердевают, образуя соединение. В настоящее время на рынке доступны, как правило, два типа сварочных систем – неориентирующие и ориентирующие технологии. Неориентирование обычно приводится в действие пневматическим «воздушным» двигателем. Это зависит от веса инструмента, чтобы выдерживать обороты, необходимые для выполнения сварки. Альтернативой являются системы с электроприводом или сервоприводом, которые позволяют выполнять окончательную ориентацию детали. Как правило, по мере уменьшения диаметра детали сварку необходимо выполнять с более высокой скоростью или числом оборотов в минуту. И наоборот, по мере увеличения диаметра детали требуется меньшая скорость, но больший крутящий момент. Изготовлены специальные системы для сварки крупных деталей диаметром 1100 мм. Технология основана на деталях, имеющих круглую геометрию в месте сварного соединения. Наиболее важным размером является концентричность или округлость деталей. Кажется, это самый важный фактор, влияющий на успешное внедрение этой технологии соединения.
Понятно, что существует множество различных технологий сварки, которые могут предоставить конечному пользователю узел, отвечающий конкретным потребностям; и преимущества и ограничения существуют для каждой технологии соединения. Использование их в качестве основного руководства или отправной точки поможет вам выбрать наилучший процесс, основанный на материале и требованиях для конкретного применения. Следует связаться с отдельными поставщиками соединений для получения помощи в оценке потребностей и требований для дальнейшей помощи в процессе выбора пластиковых соединений.
Билл Хезервик (Bill Heatherwick) — менеджер по рыночным сегментам корпорации Branson Ultrasonics. Основана в 1946 году (дочерняя компания Emerson Co.), Сент-Луис, штат Миссури, как часть подразделения промышленной автоматизации. Наряду с более чем 60-летним опытом объединения технологий, инноваций и глобального лидерства во многих сегментах рынка, которые он обслуживает, Branson стремится предоставлять своим клиентам лучшие решения для их конкретного применения. Для получения дополнительной информации звоните по телефону (248) 299-0400 x.108, пишите по электронной почте [email protected] или посетите сайт www.bransonplasticsjoining.