Оборудование сварочного поста для ручной дуговой сварки
Сварочные работы: Практическое пособие для электрогазосварщика
Рабочее место сварщика — это сварочный пост (рис. 20), который оснащен необходимым инструментом и оборудованием для выполнения работ. Сварочные посты могут быть оборудованы как в производственном помещении, так и на открытой производственной площадке (строительно-монтажные условия работы). В зависимости от условий работы сварочные посты могут быть стационарными или передвижными. Сварочные посты необходимо размещать в специальных сварочных кабинах. В кабинах в качестве источников питания размещаются наиболее распространенные однопостовые сварочные трансформаторы типа ТДМ для сварки на переменном токе, или сварочные выпрямители типа ВД или ВДУ для сварки на постоянном токе. Применяются также и многопостовые источники питания на несколько независимых постов.
Рис. 20. Сварочный пост для ручной сварки: 1 — сеть
электрического питания; 2 — рубильник или магнитный пускатель; 3 — источник питания; 4 — сварочные провода; 5 — электрододержатель; 6 — зонд местной вытяжки воздуха
Кабина сварочного поста должна иметь размеры: 2(1,5) или 2(2) м и высоту не менее 2 м. В кабине устанавливается металлический стол, к верхней части кабины подводится зонд местной вытяжки воздуха от вентиляционной системы. В столе предусматриваются выдвижные ящики для хранения необходимого инструмента и приспособлений. Сварочный пост комплектуется источником питания, электрододержателем, сварочными проводами, зажимами для токонепроводящего провода,
сварочным щитком с защитными светофильтрами, различными
зачистными и мерительными инструментами. Сварщики обеспечиваются средствами личной защиты, спецодеждой. Электрододержатель — приспособление для закрепления электрода и подвода к нему тока (рис. 21). Среди всего многообразия применяемых электрододержателей наиболее безопасными являются пружинные, изготовляемые в
соответствии с существующими стандартами: I типа — для тока до 125 А; II типа — для тока 125—315 A; III типа — для тока 315- 500 А. Эти электрододержатели выдерживают без ремонта 8 000—10 000 зажимов. Время замены электрода не превышает 3—4 с. По конструкции различаются винтовые, пластинчатые, вилочные и пружинные
электрододержатели.
Рис. 21. Типы электрододержателей: а — вилочный; б — 111игатовый; в — завода «Электрик»; г — с пружинящим кольцом |
Щитки сварочные изготавливаются двух типов: ручные и головные из легких негорючих материалов. Масса щитка не должна превышать 0,50 кг. Защитные светофильтры (затемненные стекла), предназначенные для защиты глаз от излучения дуги, брызг металла и шлака, изготавливаются 13 классов или номеров. Номер светофильтра
подбирается в первую очередь в зависимости от индивидуальных особенностей зрения сварщика. Однако следует учитывать некоторые объективные факторы: величину сварочного тока, состав свариваемого металла, вид дуговой сварки, защиту сварочной ванны от воздействия газов воздуха. Размер светофильтра 52×102 мм. При сварке покрытыми электродами следует ориентироваться на применение светофильтров различных номеров в зависимости от величины сварочного тока: 100 А — №С5; 200 А-№С6; 300 А-№С7; 400 А-№С8; 500 А -№С9 ит. д. При сварке плавящимся электродом тяжелых металлов в инертном газе следует пользоваться светофильтром на номер меньше, а легких металлов — на номер больше по сравнению со светофильтром при сварке покрытыми электродами. При сварке в среде С02 применяют следующие светофильтры: до 100 А-№С1; 100-150 А-№С2; 150-250 А — № СЗ; 250—300 А -№С4; 300—400 А-№С5 ит. д. Светофильтры вставляются в рамку щитка, а снаружи светофильтр защищают обычным стеклом от брызг металла и шлака. Прозрачное стекло периодически заменяют. Кабели и сварочные провода необходимы для подвода тока от источника питания к электрододержателю и изделию. Кабели изготавливают многожильными (гибкими) по установленным нормативам для электротехнических установок согласно ПУЭ (Правила устройства и эксплуатации электроустановок) из расчета плотности тока до 5 А/мм2 при токах до 300 А. Электрододержатели присоединяются к гибкому (многожильному) медному кабелю марки ПРГД или ПРГДО. Кабель сплетен из большого числа отожженных медных проволочек диаметром 0,18— 0,20 мм. Применять провод длиной более 30 м не рекомендуется, так как это вызывает значительное падение напряжения в сварочной цепи. Рекомендуемые сечения сварочных проводов для подвода тока от сварочной машины или источника питания к электрододержателю и свариваемому изделию приведены в (табл. 2).
Сндз тока, А | Плріендь сечения провода, мм, | |
одинарного | ДВОЙНОГО | |
125 | 25 | — |
315 | 50 | 2×16 |
500 | 70 | 2ч25 |
Токоподводящий провод соединяется с изделием через специальные зажимы. В сварочном поворотном приспособлении должны быть предусмотрены специальные клеммы. Закрепление провода должно быть надежным. Самодельные удлинители токоподводящего провода в виде кусков или обрезков металла не допускаются. Некоторые виды зажимов приведены на рис 22.
Рис. 22. Токопроводящие зажимы: а- быстродействующий с
пружинным зажимом; б — с винтовым зажимом; в — с винтовой струбциной
Одежда сварщика изготовляется из различных тканей, которые должны удовлетворять двум основным требованиям: наружная
поверхность одежды должна быть огнестойкой и термостойкой; внутренняя (изнаночная) поверхность одежды должна быть влагопоглощающей. Исходя из этих требований одежду для сварщиков — куртку и брюки — шьют из брезента, сукна, замши; иногда комбинируют ткани. Ассортимент тканей и самой спецодежды постоянно расширяется.
Зарубежные и отечественные фирмы изготавливают универсальную спецодежду, применяемую сварщиками, автогонщиками, работниками аварийно-спасательной службы. Наиболее совершенные костюмы для сварщиков изготавливает отечественная фирма «Авто-химэкс». Куртка и брюки изготовлены из двухлицевой ткани, у которой внешняя сторона — из нити типа кевлар, а внутренняя — из хлопчатобумажной пряжи. Ткань обладает повышенной прочностью, малым удлинением, что обеспечивает сохранение формы костюма (куртка, полукомбинезон или комбинезон). Температура, при которой рабочий чувствует себя комфортно длительное время, составляет 200—250 °С. Все сварщики должны пользоваться защитными рукавицами. При выполнении сварочных работ внутри котлов, емкостей, резервуаров и т. д. сварщики должны обеспечиваться резиновыми ковриками, ботами, галошами, особыми наколенниками и подлокотниками, деревянными подложками и др. При выполнении сварочных работ сварщик пользуется традиционным инструментом: металлической щеткой для зачистки кромок перед
сваркой и удаления остатков шлака после сварки; молотком — шлакоотделителем для удаления шлаковой корки; зубилом, шаблонами для проверки размеров швов, личным клеймом, рулеткой металлической, угольником, чертилкой и т. д. (рис. 23).
Рис. 23. Инструмент для зачистки сварного шва и свариваемых кромок: а — металлическая щетка; б — молоток-шлакоотделитель
В данной главе рассмотрены сварочные аппараты для механизированной и автоматической дуговой сварки и их отдельные узлы: подающие механизмы, сварочные горелки, флюсовая и газовая аппаратура. Аппарат для механизированной дуговой сварки, включающий …
Освоение производства источников питания со звеном повышенной частоты является перспективным и интенсивным направлением совершенствования оборудования для дуговой сварки. Ниже приводятся сведения об инверторных источниках тока ВДУЧ-301 и ВДЧИ-251 (табл. 9). …
Отечественные сварочные выпрямители имеют, как правило, трехфазное питание, выполняются как на диодах, так и на тиристорах. В выпрямителях используются трехфазная мостовая, двойная трехфазная схема с уравнительным дросселем и кольцевая схема …
устройство стационарного и передвижного поста
Автор admin На чтение 3 мин. Просмотров 231 Опубликовано
От того, насколько рационально и удобно обустроено рабочее место сварщика, зависит производительность его работы и качество получаемых сварных соединений. Рабочее место, на котором сварщик выполняет всю свою работу, называется сварочным постом.
Сварочный пост для ручной дуговой сварки по своему обустройству заметно отличается от рабочего места сварщика, проводящего автоматическую сварку. Об особенностях размещения необходимых инструментов и оборудования пойдет речь далее.
Устройство поста для ручной дуговой сварки
В обязательном порядке на каждом сварочном посту должны находиться все необходимые материалы, инструменты и сварочное оборудование. Короче, все то, что необходимо сварщику для работы. Это сварочный аппарат нужного типа, электроды и держатели для них, средства заземления, источник питания, а также минимальный комплект металлической мебели.
Сварочный пост может быть стационарным или передвижным, в зависимости от своего назначения и места нахождения.
Стационарный сварочный пост для ручной сварки
Это рабочее место, которое обустроено на постоянной основе. Его габариты зависят от размеров свариваемых изделий. Как правило, сюда входят металлический стол и стул, который регулируется по высоте. Питание подводится непосредственно к столу, а сварщик работает, не вставая из-за стола. Все изделия подаются к нему на рабочее место. Вместо стола часто используется специальный кантователь, позволяющий легко перемещать и поворачивать детали так, как это нужно сварщику.
Если приходится варить крупногабаритное изделие, то сварщик может вставать из-за стола и передвигаться на расстояние, равное длине сварочного кабеля. Перемещение осуществляется в разумных пределах, так как увеличение длины кабеля приводит к изменению напряжения на электроде в меньшую сторону.
Для стационарного поста обычно изготавливают металлический бокс, стены которого имеют высоту не менее 2 м.
Очень важно делать подобные боксы не глухими, а вентилируемыми. Для этого их стены приподнимают над уровнем пола на высоту около 50 см.
В качестве материалов для стен также могут использоваться любые негорючие материалы, например, листы асбестоцемента. Вход в каждый бокс завешивается брезентовыми шторками, которые пропитаны огнезащитным составом.
Также огнезащитными свойствами должен обладать и пол стационарного поста.
Передвижной пост для ручной сварки
Пост, который способен перемещаться в пределах какого-то объекта, называется передвижным постом. Такое рабочее место популярно на различных стройках, когда сварщику приходится перемещаться на определенные расстояния, выполняя работу по сварке габаритных изделий или изделий, которые невозможно доставить к стационарному посту.
Передвижной пост изготавливается из тонких стальных листов, закрепленных на металлическом каркасе. В такой кабинке также находится все необходимое сварочное оборудование. Такие передвижные кабинки можно перемещать по стройплощадке краном или по рельсам.
В некоторых случаях оборудуются мобильные сварочные места, которые не имеют металлических стенок. Обязательным условием их использования является расположение их под навесами. В случае если сварочный пост находится на высоте более 2 м, обязательным является наличие вокруг него лестниц и заграждений.
Практическая работа №7 по МДК.01.01. Сварочный пост для ручной сварки
Практическая работа №7
Тема: Сварочный пост для ручной сварки.
Цель работы: Приобрести практические навыки при изучении устройства сварочных постов.
Ход выполнения работы:
Ознакомление с теоретическими сведениями
Вычертить схему стационарного сварочного постов
По результатам выполнения работы необходимо сформулировать выводы
Ответить на контрольные вопросы
Ответь на контрольные вопросы. теста.
Теоретические сведения
Сварочным постом называют рабочее место сварщика, оборудованное всем необходимым для проведения сварочных работ.
Устройство поста для ручной дуговой сварки.
На заводах, как правило, сварочные посты располагаются в специальных кабинах площадью не менее 2×3м2 каждая. Кабину отгораживают перегородками, а вход закрывают занавесками, пропитанными огнестойким составом. При сварке громоздких деталей и крупногабаритных сварных конструкций сварочные посты развертывают открыто в цехе, на монтажно-строительной площадке, на магистральной трассе. При этом рабочее место по возможности огораживают защитными щитами или ширмами.
Рис. Общий вид сварочного поста
Сварочные посты бывают как стационарными, так и передвижными (то есть такими которые можно перевозить на разные площадки).
Стационарный сварочный пост для ручной сварки — это рабочее место, которое обустроено на постоянной основе. Его габариты зависят от размеров свариваемых изделий. Как правило, сюда входят металлический стол и стул, который регулируется по высоте. Питание подводится непосредственно к столу, а сварщик работает, не вставая из-за стола. Все изделия подаются к нему на рабочее место. Вместо стола часто используется специальный кантователь, позволяющий легко перемещать и поворачивать детали так, как это нужно сварщику. Особенность работы на стационарном посту заключается в том, что к рабочему месту сварщика подаются конструкции, которые необходимо сварить. Сварщик, выполняя работы, перемещается от шва ко шву, при этом вся аппаратура находится на одном месте.
Стационарный сварочный пост Схема постов от многопостовых источников
для ручной сварки.
Размеры сварочного поста зависят от объемов работ, которые выполняет сварщик. Так, если он обычно работает с металлоизделиями небольших размеров, то и сварочный пост имеет соответствующие габариты. Кроме того, эти факторы также влияют и на то, как правильно обустроить сварочный пост.
Обычно для таких постов изготовляют металлическую кабину с высотой стен не меньше двух метров. Вообще, кабина выполняется из любых материалов, которые не подвержены возгоранию – это листы стали, плиты, изготовленные из асбестоцемента и прочее.
Кабина имеет вход, который закрывается специальной брезентовой шторкой. Предварительно брезент поддают обработке пропиткой, имеющей огнестойкие свойства. Из стойких к огню материалов выполняется и пол кабины.
Такая кабина имеет и вентиляцию – для этого стены ее поднимают над полом на полметра. Внутри кабины устанавливается стол из металла для работы стоя или сидя. Заметим, что часто устанавливают не стол, а специальный кантователь либо другое устройство, которое позволяет поворачивать металлоизделие без особых усилий.
Также кабина оснащается стулом, сиденье которого при необходимости можно поднять. Имеются в кабине карманы либо ящики для отходов, инструментов и необходимых для сварки материалов.
Сварочная аппаратура может находиться как внутри кабины, так и за ее пределами. Находиться аппарат для ручной сварки может не дальше, чем за 15 метров от кабины.
Передвижение сварщика может быть в пределах длины сварочного кабеля — не более 30—40 м; при большей длине растет падение напряжения в сварочной цепи, что препятствует нормальному процессу сварки.
При сварке небольших изделий сварочный пост оборудуют в кабине (12.2) размерами в плане 2х1 ; 2х2; 2×3 м и высотой не менее 2 м, которую изготавливают из любых несгораемых материалоз (тонкие стальные листы, асбестоцементные плиты и т. п.). Вход в кабину делают в виде штор из брезента с огнестойкой пропиткой, а пол — из огнестойких материалов. Между стенками кабины и полом должен быть зазор не менее 50 мм для вентиляции. В кабине устанавливают металлический сварочный стол высотой 0,5—0,6 м для работы сидя или 0,9 м для работы стоя.
К столу прикрепляют «карманы» для электродов и огарков или устанавливают металлические ящики около кантователя. Для работы сидя ставят стул с подъемным сиденьем. Сварочный аппарат и пусковую аппаратуру, как правило, устанавливают в кабине, однако они могут быть вынесены за ее пределы. В этом случае сварочные аппараты располагают на расстоянии не более 15 м от кабины или места сварки в свободных от конструкций промежутках между колоннами по продольной оси цеха. Кабину, как правило, оборудуют вентиляцией и консольным краном для подачи изделий под сварку. Питание постов сварочным током может быть централизованным.
В цехе устраивают центральный машинный зал, оснащенный мощными сварочными аппаратами, от которых проводят медные шины вдоль колонн для подачи сварочного тока к 20—30 постам. Посты оборудуют распределительной пусковой аппаратурой, подсоединяемой4 к шине, и балластным реостатом для регулирования сварочного тока.
Передвижной пост для ручной сварки.
На разнообразных стройках обычно используются сварочные посты передвижного типа. Передвижной сварочный пост создают непосредственно на стройплощадке. Обычно оборудование сварочного поста для ручной дуговой сварки размещается в передвижных машинных залах, которые делаются из стали (каркас) и тонких железных листов (обшивка). В таком машинном зале может быть от одного до трех сварочных аппаратов. Здесь также находятся аппаратура для пуска, шкаф, где хранятся инструменты, кабеля и пр., печь, предназначенная для прокалки электродов.
Заметим, что такие машинные залы комплектуются полозьями и проушинами, чтобы их можно было перемещать на небольшое расстояние по горизонтальной поверхности, и с помощью кранов поднимать их.
При маленьких объемах работ, сварочный пост можно организовать и на строительной площадке. Его ставят исключительно под навесом так, чтобы аппаратура находилась не далеко от места, где требуется произвести сварочные работы. Если пост находится на площадках, расположенных на высоте от двух метров, пост обязательно оборудуют ограждениями, лестницами.
Правильная организация рабочего места сварщика способствует не только повышению производительности труда и качества сварки, но и обеспечению безопасных условий работы, снижению травматизма и несчастных случаев.
В зависимости от габаритов свариваемых изделий и характера производства рабочее место сварщика может быть расположено либо в специальной кабине, либо в цехе или непосредственно на сборочном объекте. Размеры кабины должны быть не менее 2×2 м2. Стены кабины делают высотой 1,8-2 м. Для лучшей вентиляции между полом к нижним обрезом стенки оставляют просвет 150-200 мм. В качестве материала для стен кабины можно использовать тонкое железо, а также фанеру, брезент, прочитанные огнестойким составом, или другие огнестойкие материалы. Каркас кабины делают из металлических труб или уголковой стали. Дверной проем кабины обычно закрывают брезентовым занавесом, укрепленным на кольцах.
Для окраски стен кабины рекомендуется применять цинковые белила, желтый крон, титановые белила, которые хорошо поглощают ультрафиолетовые лучи. Окраска сварочных цехов и кабин в темные цвета не рекомендуется, так как при этом ухудшается общая освещенность места сварки. В тех случаях, когда сварочные работы приходится выполнять на открытых участках цеха, места сварки со всех сторон надо огораживать щитами или ширмами. Наружные стороны таких оградительных устройств рекомендуется окрашивать в яркие цвете (лучше в виде «зебры»), чтобы они лучше просматривались. Чтобы предупредить посторонних лиц об опасности, на таких щитах надо делать крупными буквами надписи: «Осторожно, идет сварка»!
В организации сварочных работ важное значение имеет правильное размещение оборудования. Многопостовые агрегаты и установки, состоящие из нескольких сварочных агрегатов, располагают в отдельном помещении или на площади общего производственного помещения, огражденной постоянными перегородками высотой не менее 1,7 м. Сварочные преобразователи при работу создают шум, оказывающий вредное действие на нервную систему человека, вызывая понижение внимания и снижение работоспособности. По этой причине все сварочные преобразователи надо изолировать в помещение цеха или вынести их за пределы производственного помещения, огородив со всех сторон и укрыв от атмосферных осадков.
В стационарных многопостовых сварочных установках присоединение сварочных постов к электросварочному агрегату осуществляют через общий щит, на котором должны находиться необходимые измерительные приборы, защитные средства, сигнальные лампочки, рубильники и зажимы для присоединения сварочных постов. При однопостовой сварке должны быть предусмотрены индивидуальные щиты, оборудованные вольтметром и сигнальной лампочкой, указывающей сварщику на наличие пли отсутствие напряжения в сварочной цепи.
Проходы между многопостовыми сварочными агрегатами и между установками автоматической сварки должны быть не менее 1,5 м; проходы между однопостовыми сварочными трансформаторами или между сварочными генераторами, а также проходы с каждой стороны стеллажа или стола для выполнения ручных сварочных работ — не менее 1 м. Расстояние между стационарным сварочным агрегатом и стеной или колонной должно составлять не менее 0,5 м, а расстояние между стеной или колонной и сварочным автоматом — не менее 1 м. Проходы между машинами точечной и шовной (роликовой) сварки с расположением рабочих мест напротив друг друга должны быть не менее 2 м, а между машинами стыковой сварки — не менее 3 м. Мри расположении перечисленных выше машин тыльными сторонами друг к другу ширина проходов должна быть не менее 1 м, а при расположении передними и тыльными сторонами друг к другу — не менее 1,5 м.
Инструменты и принадлежности сварщика
К инструменту сварщика относятся:
Электрододержатель служит для зажима электрода и подвода к нему сварочного тока. Он должен прочно удерживать электрод, обеспечивать удобное и прочное закрепление сварочного кабеля, а также быстрое удаление огарков и закладку нового электрода. Электрододержатели изготовляют трех типов по ГОСТ 14651-78: для тока 125 А и провода сечением 25 мм2, для тока 315 А и провода сечением 50 мм, для тока 500 А и провода сечением 70 мм2. Они должны выдерживать 8000 зажимов электродов, затрачивая на каждую замену электрода не более 4 с. Применяют электрододержатели с различными способами закрепления электродов.
Рис. Виды электрододержателей
Щиток или маска применяется для предохранения глаз и кожи лица сварщика от вредного влияния инфракрасного излучения и брызг металла.
В них имеется смотровое отверстие, в которое вставляют специальное стекло – светофильтр, задерживающий инфракрасные и ультрафиолетовые лучи и снижающий яркость световых лучей дуги. Снаружи светофильтр защищен от брызг металла простым прозрачным стеклом.
Рис. Защитные средства глаз и лица сварщика
Сварочные провода по которым ток от силовой сети подводится к сварочному аппарату (марки КРПТ) от сварочных аппаратов к местам работы, сварочный ток поступает по гибкому проводу марки ПРГ, АПР, или ПРГД с резиновой изоляцией.
К принадлежностям сварщика относятся;
Стальная щётка, применяемая для зачистки металла от грязи, ржавчины перед сваркой и шлака после сварки.
Молоток с заострённым концом для отбивки шлака со сварочных швов и для поставки личного клейма.
Зубило для вырубки дефектных мест сварного шва.
Шаблоны — для замера геометрического размеров швов.
Измерительные инструменты (линейка, рулетка).
Угольник для проверки углов используется.
Контрольные вопросы:
Чем отличается стационарный сварочный пост от передвижного?
Требования к устройству сварочных постов?
Перечислить инструменты и принадлежности электросварщика.
Какой инструмент предназначен для удаления шлаковой корки?
Тест:
Для каких номинальных токов выпускают электрододержатели?
менее 125 А
220 А
380 А
125 А; 200 А; 250 А; 220 А; 315 А; 400 А; 500 А;
Масса электрододержателя может составлять:
0,35-0,75 кг
до 0,35кг
свыше 0,75 кг
100 г
Электрододержатели должны обеспечивать смену электрода за время не более:
1 с
4 с
10 с
4 0с
Длина сварочного кабеля не должна превышать:
10 м
40 м
100 м
400 м
Площадь сечения сварочного кабеля выбирают в зависимости от сварочного тока и допустимых нагрузок из расчетов:
1-4 А/м2
5-7 А/м2
8-14 А/м2
15-20 А/м2
Площадь сечения оножилого кабеля для силы сварочного тока 200 А должна составлять:
10 м 2
40 м 2
100 м 2
400 м 2
При продолжительной непрерывной работе кабель и электрододержатель перегреваются, поэтому сечение кабеля выбирают с учетом возможности его нагрева при работе до:
30С
40 С
80С
100С
Выпускают 13 классов светофильтров и выбирают их в зависимости от:
возраста сварщика
скорости сварки
напряжении на дуге
силы сварочного тока
Какой цвет имеют светофильтры сварщика?
красный
желтый
зеленый
синий
Защита светофильтра от брызг металла при сварке обеспечивается пластинками из оргстекла, которые по мере повреждения заменяются новыми 1-2 раза в:
1 час
смену
месяц
год
Ответы теста
Вопрос1
2
3
4
5
6
7
8
9
10
Ответ
Оборудование Сварочного Поста Для Ручной Дуговой Сварки — КиберПедия
Рабочее место сварщика – это сварочный пост (рис. 20), который оснащен необходимым инструментом и оборудованием для выполнения работ. Сварочные посты могут быть оборудованы как в производственном помещении, так и на открытой производственной площадке (строительно-монтажные условия работы). В зависимости от условий работы сварочные посты могут быть стационарными или передвижными.
Сварочные посты необходимо размещать в специальных сварочных кабинах.
В кабинах в качестве источников питания размещаются наиболее распространенные однопостовые сварочные трансформаторы типа ТДМ для сварки на переменном токе, или сварочные выпрямители типа ВД или ВДУ для сварки на постоянном токе.
Применяются также и многопостовые источники питания на несколько независимых постов.
Рис. 20. Сварочный пост для ручной сварки:
1 – сеть электрического питания;
2 – рубильник или магнитный пускатель; 3 – источник питания; 4 – сварочные провода; 5 –электрододержатель; 6 – зонд местной вытяжки воздуха
Кабина сварочного поста должна иметь размеры: 2(1,5) или 2(2) м и высоту не менее 2 м. В кабине устанавливается металлический стол, к верхней части кабины подводится зонд местной вытяжки воздуха от вентиляционной системы. В столе предусматриваются выдвижные ящики для хранения необходимого инструмента и приспособлений.
Сварочный пост комплектуется источником питания, электрододержателем, сварочными проводами, зажимами для токонепроводящего провода, сварочным щитком с защитными светофильтрами, различными зачистными и мерительными инструментами.
Сварщики обеспечиваются средствами личной защиты, спецодеждой.
Электрододержатель – приспособление для закрепления электрода и подвода к нему тока (рис. 21). Среди всего многообразия применяемых электрододержателей наиболее безопасными являются пружинные, изготовляемые в соответствии с существующими стандартами: I типа – для тока до 125 А; II типа – для тока 125—315 A; III типа – для тока 315– 500 А. Эти электрододержатели выдерживают без ремонта 8 000—10 000 зажимов. Время замены электрода не превышает 3—4 с. По конструкции различаются винтовые, пластинчатые, вилочные и пружинные электрододержатели.
Рис. 21. Типы электрододержателей: а – вилочный; б – 111игатовый; в – завода «Электрик»; г – с пружинящим кольцом
Щитки сварочные изготавливаются двух типов: ручные и головные из легких негорючих материалов. Масса щитка не должна превышать 0,50 кг.
Защитные светофильтры (затемненные стекла), предназначенные для защиты глаз от излучения дуги, брызг металла и шлака, изготавливаются 13 классов или номеров. Номер светофильтра подбирается в первую очередь в зависимости от индивидуальных особенностей зрения сварщика. Однако следует учитывать некоторые объективные факторы: величину сварочного тока, состав свариваемого металла, вид дуговой сварки, защиту сварочной ванны от воздействия газов воздуха. Размер светофильтра 52×102 мм. При сварке покрытыми электродами следует ориентироваться на применение светофильтров различных номеров в зависимости от величины сварочного тока: 100 А – № С5; 200 А – № С6; 300 А – № С7; 400 А – № С8; 500 А – № С9 и т. д.
При сварке плавящимся электродом тяжелых металлов в инертном газе следует пользоваться светофильтром на номер меньше, а легких металлов – на номер больше по сравнению со светофильтром при сварке покрытыми электродами.
При сварке в среде С02 применяют следующие светофильтры: до 100 А – № С1; 100—150 А – № С2; 150—250 А – № СЗ; 250—300 А – № С4; 300—400 А – № С5 и т. д. Светофильтры вставляются в рамку щитка, а снаружи светофильтр защищают обычным стеклом от брызг металла и шлака. Прозрачное стекло периодически заменяют.
Кабели и сварочные провода необходимы для подвода тока от источника питания к электрододержателю и изделию. Кабели изготавливают многожильными (гибкими) по установленным нормативам для электротехнических установок согласно ПУЭ (Правила устройства и эксплуатации электроустановок) из расчета плотности тока до 5 А/мм2 при токах до 300 А. Электрододержатели присоединяются к гибкому (многожильному) медному кабелю марки ПРГД или ПРГДО. Кабель сплетен из большого числа отожженных медных проволочек диаметром 0,18—0,20 мм. Применять провод длиной более 30 м не рекомендуется, так как это вызывает значительное падение напряжения в сварочной цепи. Рекомендуемые сечения сварочных проводов для подвода тока от сварочной машины или источника питания к электрододержателю и свариваемому изделию приведены в (табл. 2).
Таблица 2
Площадь поперечного сечения сварочных проводов
Токоподводящий провод соединяется с изделием через специальные зажимы. В сварочном поворотном приспособлении должны быть предусмотрены специальные клеммы. Закрепление провода должно быть надежным. Самодельные удлинители токоподводящего провода в виде кусков или обрезков металла не допускаются. Некоторые виды зажимов приведены на рис 22.
Рис. 22. Токопроводящие зажимы:
а – быстродействующий с пружинным зажимом; б – с винтовым зажимом; в – с винтовой струбциной
Одежда сварщика изготовляется из различных тканей, которые должны удовлетворять двум основным требованиям:
наружная поверхность одежды должна быть огнестойкой и термостойкой;
внутренняя (изнаночная) поверхность одежды должна быть влаго-поглощающей.
Исходя из этих требований одежду для сварщиков – куртку и брюки – шьют из брезента, сукна, замши; иногда комбинируют ткани.
Ассортимент тканей и самой спецодежды постоянно расширяется. Зарубежные и отечественные фирмы изготавливают универсальную спецодежду, применяемую сварщиками, автогонщиками, работниками аварийно-спасательной службы. Наиболее совершенные костюмы для сварщиков изготавливает отечественная фирма «Авто-химэкс». Куртка и брюки изготовлены из двухлицевой ткани, у которой внешняя сторона – из нити типа кевлар, а внутренняя – из хлопчатобумажной пряжи. Ткань обладает повышенной прочностью, малым удлинением, что обеспечивает сохранение формы костюма (куртка, полукомбинезон или комбинезон). Температура, при которой рабочий чувствует себя комфортно длительное время, составляет 200—250 °С.
Все сварщики должны пользоваться защитными рукавицами. При выполнении сварочных работ внутри котлов, емкостей, резервуаров и т. д. сварщики должны обеспечиваться резиновыми ковриками, ботами, галошами, особыми наколенниками и подлокотниками, деревянными подложками и др.
При выполнении сварочных работ сварщик пользуется традиционным инструментом: металлической щеткой для зачистки кромок перед сваркой и удаления остатков шлака после сварки; молотком-шлакоотделителем для удаления шлаковой корки; зубилом, шаблонами для проверки размеров швов, личным клеймом, рулеткой металлической, угольником, чертилкой и т. д. (рис. 23).
Рис. 23. Инструмент для зачистки сварного шва и свариваемых кромок: а – металлическая щетка; б – молоток-шлакоотделитель
Контрольные вопросы:
1. Что называется сварочным постом, где могут быть оборудованы сварочные посты в зависимости от условий работы?
2. Какие источники питания применяются для оснащения сварочного поста?
3. Что вы знаете об устройстве кабины для сварочного поста и ее оснащении?
4. Что представляет собой электрододержатель?
5. Расскажите о назначении сварочных щитков и применяемых светофильтров.
6. Какие кабели и сварочные провода применяются при оснащении сварочных постов?
7. Для чего применяются токоподводящие зажимы?
8. Какие основные требования предъявляются к одежде сварщика?
9. Какими инструментами пользуется сварщик при выполнении сварочных работ?
Основные Требования Безопасности Труда При Ручной Дуговой Сварке
При выполнении сварочных работ существуют опасности для здоровья рабочего:
поражение электрическим током;
поражение глаз и открытых поверхностей кожи лучами дуги; отравление вредными газами и пылью;
ожоги от разбрызгивания электродного расплавленного металла и шлака;
ушибы и порезы в процессе подготовки изделий под сварку и во время сварки.
Поэтому, прежде чем приступить к сварочным работам, необходимо изучить на рабочем месте инструкцию по безопасным приемам обращения со сварочным оборудованием и расписаться в регистрационном журнале.
После этого необходимо ознакомиться с порядком включения и выключения питающей сети высокого напряжения, убедиться в наличии актов обязательной ежегодной проверки заземления и сопротивления изоляции коммутационных проводов и электрододержателей.
Во время сварки необходимо работать только в спецодежде. Куртка должна быть надета поверх брюк и застегнута, брюки должны закрывать обувь.
Запрещается пользоваться неисправными сварочными щитками, разбитыми защитными светофильтрами. Нельзя производить сварочные работы при отключенной или неисправной системе вентиляции.
После окончания работы электрододержатель должен находиться в таком положении, при котором исключался бы его контакт с токоведущими частями сварочного поста. Сварочное оборудование в процессе эксплуатации требует внимательного ухода и обслуживания. Сварщику необходимо принимать следующие меры:
перед включением источника питания очистить его от пыли, грязи, случайно попавших огарков электродов или кусков сварочной проволоки;
проверить надежность изоляции сварочных проводов и их соединения, при необходимости подтянуть крепление, изолировать место повреждения сварочного кабеля;
убедиться в наличии заземления.
Эти меры гарантируют длительную, надежную и безопасную работу источника питания.
При включении источника питания могут быть обнаружены его дефекты или неисправности. В этом случае необходимо отключить источник питания и сообщить об этом мастеру, наладчику или электромонтеру для устранения неисправностей источника питания.
Контрольные вопросы:
1. Расскажите об обязанностях обучающихся перед проведением сварочных работ.
2. Каковы правила пользования спецодеждой и сварочными щитками? Расскажите об обязанностях сварщиков по обслуживанию сварочного оборудования.
«Сварочный пост для ручной дуговой сварки» — Студопедия.Нет
Nbsp; ВИДЫ И ОБОРУДОВАНИЕ СВАРОЧНЫХ ПОСТОВ Сварочным постом называется рабочее место сварщика, оборудованное всем необходимым для производства сварочных работ. Сварочные посты подразделяются: 1. По роду тока при сварке на: а) пост переменного тока б) пост постоянного тока Принципиальной разницы в оборудовании постов обоих видов нет. Отличие только в источниках питания сварочной дуги. при сварке на переменном токе используется сварочный трансформатор. При сварке на постоянном токе – сварочный генератор (преобразователь или агрегат) или выпрямитель. Различают высокую и низкую сторону источника питания. Высокую сторону подключают к 3-х фазной сети переменного тока напряжением 380 В. Подключение к ней должно производится лицом электротехнического персонала (квалификационная группа по электробезопасности не ниже третьей). Для этого используются провода электротехнического назначения (до 8 м), достаточного сечения. В высокую сторону включается рубильник с плавкими предохранителями или термореле (автомат). К зажимам низкой стороны источника питания подключаются специальные сварочные провода. Один из них называется прямым, к нему подключается электрододержатель с электродом. Другой провод называется обратным, он подключается к сварочному столу или свариваемому металлу. Источник переменного тока (трансформатор) полярности зажимом низкой стороны не имеет и все равно к какому из них может быть подключен прямой и обратный провод. Зажимы источника постоянного тока обозначены (+) и (-) и возможно два варианта подключения прямого и обратного провода. Если прямой провод подключен к зажиму (-), а обратный к зажиму (+), то полярность при сварке считается прямой. Если прямой провод подключен зажиму (+), а обратный к зажиму (-), то полярность при сварке считается обратной. Полярность при сварке на постоянном токе имеет значение, о чем будет говориться в последующих темах. Основной опасностью в работе электросварщика является поражение электрическим током, поэтому необходимо соблюдать электробезопасность. Одним из мероприятий является заземление определенных мест сварочного поста, которые могут оказаться под напряжением. Должны быть заземлены: — металлический кожух рубильника; — корпус источника питания; — сварочный стол; — у сварочного трансформатора, один из зажимом низкой стороны (вторичной обмотки), тот к которому подключен обратный провод. Заземление производится медным многожильным проводом без изоляции к контуру заземления, стальной полосе закрепленной на стене в 1 м от пола, по периметру производственного помещения. Устанавливается заземления от места заземления к контуру, а снимается – наоборот. 2. сварочные посты различают с питанием от: — однопостового источника, рассчитанного на работу одного сварщика; — многопостового источника, рассчитанного на работу нескольких сварщиков. 3. Сварочные посты могут быть: а) стационарными, когда рабочее место сварщика длительно не меняется; б) передвижные, характерные при ремонтных, монтажных работах, когда рабочее место систематически меняется. При этом приходится перемещать сварочный аппарат и остальные принадлежности. Стационарный сварочный пост представляет собой кабину, огражденную с трех сторон стенкой из светонепроницаемого, несгораемого материала (кирпича, железа, асбестоцементовых листов и т.п.). Между стенкой и полом оставляется зазор не менее 200 мм для естественной вентиляции кабины. С четвертой стороны преградой выхода излучений дуги за пределы кабины служит брезентовая ширма. Площадь кабины 3 -4 кв.м. В кабине устанавливается следующее оборудование: — сварочный стол, площадью не менее 1кв.м, который должен быть заземлен; — стул винтовой со спинкой; — сварочный аппарат: трансформатор или выпрямитель. Преобразователь обычно располагают за пределами кабины, т.к. он издает много шума. — сварочный стол оборудуется отсосом (зонтом) вытяжной вентиляции, который располагают сбоку. Пеналом для хранения электродов. Ящиком для огарков электродов и подставкой под электрододержатель, чтобы он не замыкал на стол. Устройствотиповогосварочноготрансформатора Сварочный трансформатор служит для преобразования напряжения сети переменного тока 220В, 380В, в напряжение необходимое для зажигания дуги 60–70 В. Наибольшее распространение получили сварочные трансформаторы с подвижной вторичной обмоткой марки ТС, который назовем типовым. Он состоит из: 1. Сердечника или магнитопровода, который набирается из пластин специальной электротехнической стали толщиной 0,5 – 1 мм. Пластины изолируют между собой слоем лака или окалины. Такая конструкция позволяет избежать значительного его нагрева возникающими вихревыми токами и уменьшить потери электроэнергии. Для того, чтобы избежать шума при работе трансформатора, пластины плотно между собой стягиваются шпильками. Сердечник замкнутого типа имеет прямоугольную форму. 2. Первичной обмотки, закрепленной в нижней части сердечника и подключаемой к сети переменного тока. Она состоит из двух параллельно соединенных между собой катушек, выполненных из более тонкого провода с большим числом витков, чем вторичная обмотка. Первичная обмотка входит в состав высокой стороны сварочного поста. 3. Вторичной обмотки, находящейся в верхней части сердечника и входящей в состав низкой стороны сварочного поста. Она так же состоит из двух параллельно соединенных между собой катушек, но выполненных из более толстого провода с меньшим числом витков. Вторичная обмотка является подвижной, что дает возможность плавно регулировать силу сварочного тока. При перемещении ее вверх, увеличивая расстояние между первичной и вторичной обмотками, сила тока уменьшается. При перемещении ее вниз, при сближении обмоток, сила тока повышается. 4. Винтового механизма для перемещения вторичной обмотки, состоящего из винта и гайки, закрепленной на траверсе катушек вторичной обмотки. При вращении винта гайка поступательно перемещается по винту, давая возможность перемещать и вторичную обмотку. Рукоятка вращения винта выведена на лицевую панель трансформатора. Там же имеется шкала для отсчета силы сварочного тока. 5. Зажимов высокой стороны, к которым подключается сеть переменного тока. 6. Зажимов низкой стороны, к которым подключаются сварочные провода, прямой и обратный, имеющие большее сечения (диаметр) и часто изготавливаемые из меди. Это объясняется значительно большей плотностью тока в сварочной цепи. Малое сечение может привести к их сильному нагреву. Принцип работы трансформатора основан на электромагнитной индукции и заключается в следующем. Когда по первичной обмотке проходит переменный ток, ею возбуждается переменный магнитный поток в сердечнике (магнитопроводе). Магнитный поток, пронизывая витки вторичной обмотки, индуктирует в них Э.Д.С. электромагнитной индукции. Но Э.Д.С. это напряжение на выходных зажимах, без подключенной нагрузки (сварочной дуги). Во время же сварки, при горении дуги, в сварочной цепи будет проходить индукционный ток. Устройствотиповогосварочногопреобразователя Сварочным преобразователем называется машина, служащая для преобразования переменного тока в постоянный, и преобразования напряжения сети 220В, 380В в напряжение необходимое для зажигания дуги 60 – 70В. Под машиной понимается преобразователь энергии из одного вида в другой, поэтому он состоит из двух частей: — 3 — фазного асинхронного двигателя, преобразующего электрическую энергию в механическую; — сварочного генератора, преобразующего механическую энергию в электрическую. Генератор имеет: 1. Статор с полюсами, представляющие собой электромагниты, имеющие обмотки возбуждения магнитного поля расположенные на сердечниках, оканчивающиеся полюсными наконечниками. Обмотки возбуждения могут питаться либо от независимого источника, например сети, либо от третей дополнительной щетки генератора. Число полюсов генератора четное и они обычно чередуются N – S – N – S. Наиболее распространены 6 –ти полюсные генераторы. Из них 4 полюса главных, которые возбуждают магнитный поток, и 2 полюса дополнительных, препятствующих искрению между щетками и коллектором. 2. Якорь, имеющий цилиндрическую форму, находящийся между полюсами, на небольшом расстоянии от них. На его поверхности выполнены продольные пазы, в которых прочно закреплены обмотки якоря, концы которых присоединены к соответствующим пластинам коллектора. 3. Коллектора, являющегося продолжением якоря, но несколько меньшего диаметра и на поверхности имеющего большое число изолированных друг от друга и от вала медных пластин. Их число равно числу концов обмоток якоря. Пластины соединены с обмотками якоря. 4. Токосъемника, состоящего из графитовых щеток, закрепленных в щеткодержателях на траверсах и прижатых к поверхности коллектора пружинным механизмом. Щетки установлены так, что каждая из них снимает ток только одной полярности, который затем поступает на выходные зажимы. Вал машины общий, как для двигателя, так и для генератора, что позволяет избежать вибраций и шума. Концы вала установлены в подшипниковые гнезда, находящиеся в боковых щеках машины. Между двигателем и генератором установлена на валу крыльчатка, которая создает при вращении воздушное охлаждение. Все вышеперечисленное заключено в чугунный литой корпус, установленный на 3-х колесную тележку. На внешней стороне корпуса установлена пуска – регулирующая аппаратура (пускатель двигателя и регулятор тока), а так же имеются входные (меньшего сечения) и выходные (большого сечения) зажимы. Если на выходных клеммах имеется перемычка, то она позволяет ступенчато регулировать силу сварочного тока, т.е. сварку вести на малом или большом диапазоне тока. Обмотки статора 3-х фазного асинхронного двигателя, устройство и принцип работы которого рассматривается в электротехнике, можно включить по схеме «звезда» при напряжении сети 380 В или в «треугольник» — при напряжении в 220 В. Принцип работы генератора основан на электромагнитной индукции. Когда по обмоткам возбуждения, находящимися на полюсах, проходит постоянный ток, то возбуждается магнитное поле, в котором вращается якорь, с расположенными на нем обмотками. Активные, горизонтальные участки обмоток пересекают магнитный поток, и в них индуктируется Э.Д.С. электромагнитной индукции, которая затем поступает на выходные зажимы. Если к выходным зажимам подключена нагрузка (сварочная дуга), то в сварочной цепи будет проходить индукционный ток. Устройствотиповогосварочноговыпрямителя Сварочный выпрямитель служит для преобразования переменного тока в постоянный и, преобразования напряжения сети 220В; 380В в напряжение, необходимое для зажигания дуги 60 – 70В. Для преобразования напряжения, в устройство выпрямителя входит сварочный трансформатор СТ любой конструкции. Устройство сварочного трансформатора рассматривалось в предыдущем вопросе. Для преобразования переменного тока в постоянный служит выпрямительный блок ВБ, состоящий из полупроводниковых кремниевых, селеновых или германиевых вентилей, устройств, способных пропускать ток только в одном направлении. Селеновые вентили получили наибольшее распространение, т.к. они менее чувствительны к перегрузке, их К.П.Д. около 75%. Сварочные выпрямители изготавливают по одной из двух распространенных схем: — однофазной мостовой, 2-х полупериодного выпрямления; — 3 –х фазной мостовой. Более распространена 3 –х фазная мостовая схема обеспечивающая: — большую устойчивость горения дуги; — более равномерную загрузку фаз питающей сети; — лучшее использование трансформатора выпрямителя. Принцип выпрямления по этим схемам рассматривается в электротехнике. Но полупроводниковые материалы, по сравнению с проводниками, имеют большее электрическое сопротивление и при прохождении по вентилям больших сварочных токов, они могут перегреться и выйти из строя. Поэтому в конструкциях выпрямителей предусматривается электрический вентилятор, создающий воздушное охлаждение. Так же в электрической схеме выпрямителя предусматривается пускорегулирующая и стабилизирующая аппаратура. Срочные выпрямители, по сравнению с преобразователями имеют следующие преимущества: 1. Более высокий К.П.Д., так как нет значительных затрат энергии для вращения массивных частей. 2. Проще в эксплуатации и обслуживании, так как нет коллектора, токосъемника, подшипников, за которыми требуется следить при эксплуатации преобразователей. 3. Меньшие габариты и масса при той же мощности. 4. Выпрямитель создает гораздо меньше шума, что улучшает санитарно — гигиенические условия труда. Поэтому выпрямители, в последние десятилетия, получили большее распространение, как источники постоянного тока при сварке. Инструменты,Принадлежностииспецодеждасварщика К инструментам и принадлежностям сварщика относятся: 1. Электрододержатель служит для фиксации электрода и подвода к его стержню сварочного тока. По конструкции или способу фиксации электрода различают электрододержатели: — вилочные; — пластинчатые; -пружинные; -винтовые -безогарковые, которые используются при применении безогарковых электродов, с полностью нанесенным на стержень покрытием, а фиксация происходит посредством приварки стержня электрода к держателю. К электрододержателям предъявляются следующие требования: I.В отношение электробезопасности: 1) Должна быть надежная электроизоляция рукоятки, так как по электрододержателю проходит ток большой силы. 2) Должна быть обеспечена теплоизоляция рукоятки, так как электрододержатель нагревается теплом дуги и за счет сопротивления материала. 3) Должен быть надежный и плотный контакт сварочного провода с рукояткой держателя, который при изготовлении самодельного держателя можно осуществить: а) с помощью винта, приваренного к рукоятке и гайки; б) с помощью тонкостенной стальной трубки, приваренной к держателю, и после установки в нее зачищенного конца сварочного провода обжатой в тисках; в) пайкой латунью; г) сваркой, но это менее надежный способ, т.к. сталь с медью свариваются плохо. 4) Электрическое сопротивление материала, из которого изготовлен держатель, не должно быть высоким. Среди большого разнообразия держателей наиболее безопасными являются пружинные (пассатижные) изготавливаемые промышленностью по ГОСТ 14651-78Е: I типа для тока до 125 А; II типа для тока 125-315 А; III типа для тока 315-500 А, выдерживающих без ремонта 8-10 тысяч зажатий. II.В отношении удобства работы: 1) Должен быть легким, массой не более 500г; 2) конструкция электрододержателя должна предусматривать быструю смену электрода в течение 2-3 с. 3) Так же конструкция должна предусматривать как можно больший вариант углов фиксации электрода, т.к. иногда приходится менять его положение при сварке в трудно доступных местах. 2. Сварочные провода служат для подвода сварочного тока к электрододержателю и сварочному металлу или столу. Для этого используют специальные сварочные провода, которые должны быть гибкими и не затруднять движение сварщику. Изоляция должна быть трудносгораемая, износостойкая и сопротивляться ударам, не разрушаясь. Наиболее полно удовлетворяют этим требованиям провода марок ПРГД; ПРГДО (медные многожильные), АПРГД (алюминиевый многожильный). Более жесткие сварочные провода марок КРПТ; КРПТН. Рекомендуемая максимальная длина сварочных проводов 25 м. Возможно и более длинные провода, но надо иметь ввиду, что провода хоть и медные и большого сечения, они включаются с дугой последовательно и на них происходит падение напряжения U=I•R и дуга может плохо возбуждаться, и гореть менее устойчиво. Минимальная длина сварочного провода 2 -3 м, так как меньшая длина сковывает движения сварщику. Сечение сварочного провода выбирают таким, чтобы плотность тока была в пределах 5 -6 А/мм2. Большая плотность тока может привести к нагреву и перегреву провода, к старению и разрушению изоляции. При меньшей плотности тока, приходится держать на весу большую массу провода, что приводит к большому утомлению. Сварочные провода выпускаются сечением 25; 50; 70 кв.мм. В последнее время стали выпускаться сварочные провода под марками КГ-25; КГ-50 и т.п., где КГ означает – кабель гибкий, а цифры — его сечение в кв.мм. 3. Щиток или маска служит для защиты лица и глаз сварщика от излучения дуги и брызг расплавленного металла. Щиток от маски отличается тем, что имеет рукоятку, а маска с помощью наголовника одевается на голову. Изготавливается щиток (маска) из светонепроницаемого, трудносгораемого, диэлектрического материала – фанеры толщиной 2 мм, фибры (прессованного картона пропитанного огнестойким составом), пластмассы. В лицевой части щитка (маски) имеется прямоугольное отверстие с рамкой, в которую устанавливается с внешней стороны защитное, прозрачное, оконное стекло толщиной 2 мм и размерами 52х102 мм. С внутренней стороны такого же размера и толщины светофильтр. Между ними устанавливается картонная прокладка толщиной 0.5 мм. Стекло служит для защиты светофильтра от копоти и брызг расплавленного металла и по мере загрязнения меняется. Выпускаются светофильтры: -черного типа (дуга горит на оранжевом фоне) марок: Э1 до 75 А; Э2 (75 -200) А; Э3 (200 -400) А; Э4 (400 -500) А; Э5 свыше 500 А. — зеленого типа (дуга горит на зеленом фоне) марок от С1 до С13, так же выбираемые в зависимости от силы сварочного тока: С5 (30 – 50) А; С6 (50 – 100) А; С7 (100 -175) А; С8 (175 – 300) А; С9 (300 -350) А; С10 (350- 500) А. Щитки (маски) выпускаются по ГОСТ 12.4.035 -75. Маска щитка не должна превышать 0,5 кг, маски 0,6 кг. В комплект инструментов и принадлежностей входят так же: 4.Стальная щетка для зачистки кромок от грязи, окалины и ржавчины. 5.Молоток с острым концом для отбивки шлака. 6.Зубило для вырубки дефектов шва. 7.Шаблоны для контроля катета угловых швов; ширины шва и высоты усиления при контроле стыковых швов. Спецодежда служит для защиты тела сварщика от излучения дуги и брызг металла. В комплект спецодежды входят: куртка, брюки, рукавицы, изготовленные из плотного трудно сгораемого материала (брезента, замши, спилка). Ботинки или сапоги обеспечивают защиту ног от брызг расплавленного металла. Спецодежда должна быть исправной, сухой, и эксплуатироваться так, чтобы излучение дуги, брызги расплавленного металла не попадали на тело, во избежание ожогов.
ЗАДАНИЕ S 4.1
ТЕМА: «Сварочный пост для ручной дуговой сварки»
Презентация по сварочному производству «Оборудование , приспособления и инструмент сварочного поста сварщика ручной дуговой сварки»
Инфоурок › Технология ›Презентации›Презентация по сварочному производству «Оборудование , приспособления и инструмент сварочного поста сварщика ручной дуговой сварки»Описание презентации по отдельным слайдам:
1 слайд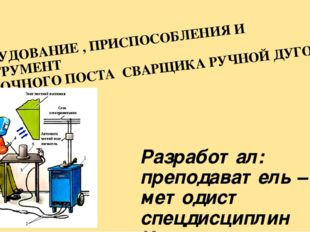
ОБОРУДОВАНИЕ , ПРИСПОСОБЛЕНИЯ И ИНСТРУМЕНТ СВАРОЧНОГО ПОСТА СВАРЩИКА РУЧНОЙ ДУГОВОЙ СВАРКИ Разработал: преподаватель – методист спецдисциплин Краматорского центра ПТО «Заслуженный учитель Украины» Онищенко Сергей Яковлевич
2 слайд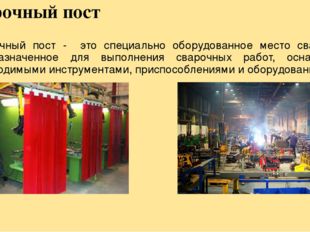
Сварочный пост Сварочный пост — это специально оборудованное место сварщика, предназначенное для выполнения сварочных работ, оснащенное необходимыми инструментами, приспособлениями и оборудованием. Различают сварочные посты: СТАЦИОНАРНЫЕ ПЕРЕДВИЖНЫЕ
3 слайд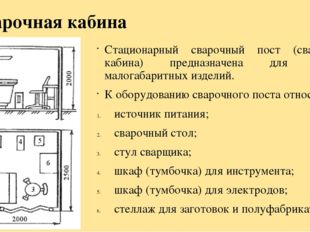
Сварочная кабина Стационарный сварочный пост (сварочная кабина) предназначена для сварки малогабаритных изделий. К оборудованию сварочного поста относятся: источник питания; сварочный стол; стул сварщика; шкаф (тумбочка) для инструмента; шкаф (тумбочка) для электродов; стеллаж для заготовок и полуфабрикатов.
4 слайд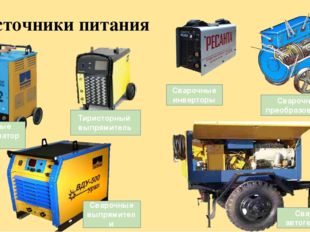
Источники питания Тиристорный выпрямитель Сварочные инверторы Сварочные трансформаторы Сварочные выпрямители Сварочные преобразователи Сварочные автогенераторы
5 слайд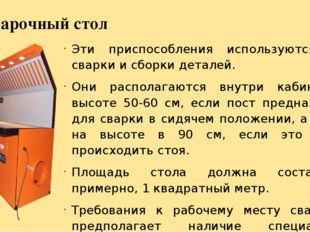
Сварочный стол Эти приспособления используются для сварки и сборки деталей. Они располагаются внутри кабины на высоте 50-60 см, если пост предназначен для сварки в сидячем положении, а также на высоте в 90 см, если это будет происходить стоя. Площадь стола должна составлять, примерно, 1 квадратный метр. Требования к рабочему месту сварщика предполагает наличие специальных болтов, к которым крепятся токопроводящие провода от сварочного аппарата. На столе должны быть гнезда для электродов. Если имеется выдвижной ящик, то там можно хранить документы и инструменты.
6 слайд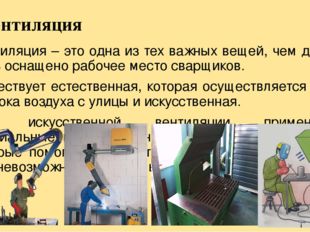
Вентиляция Вентиляция – это одна из тех важных вещей, чем должно быть оснащено рабочее место сварщиков. Существует естественная, которая осуществляется путем притока воздуха с улицы и искусственная. Для искусственной вентиляции применяются специальные вытяжки, вентиляторы и прочие средства, которые помогают осуществить циркуляция воздуха, где оно невозможно сделать обыкновенным путем.
7 слайд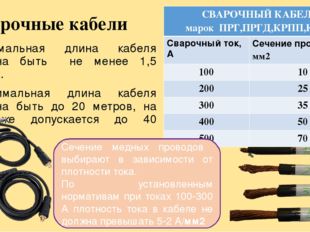
Сварочные кабели Минимальная длина кабеля должна быть не менее 1,5 метра. Максимальная длина кабеля должна быть до 20 метров, на монтаже допускается до 40 метров. Сечение медных проводов выбирают в зависимости от плотности тока. По установленным нормативам при токах 100-300 А плотность тока в кабеле не должна превышать 5-2 А/мм2 СВАРОЧНЫЙ КАБЕЛЬ марок ПРГ,ПРГД,КРПП,КРПГ Сварочный ток, А Сечение провода,мм2 100 10 200 25 300 35 400 50 500 70
8 слайд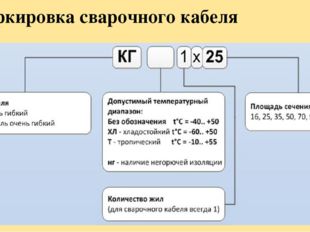
Маркировка сварочного кабеля
9 слайд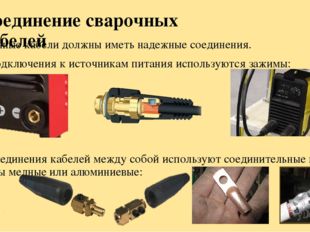
Соединение сварочных кабелей Сварочные кабели должны иметь надежные соединения. Для подключения к источникам питания используются зажимы: Для соединения кабелей между собой используют соединительные муфты и клеммы медные или алюминиевые:
10 слайд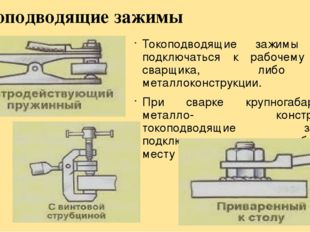
Токоподводящие зажимы Токоподводящие зажимы могут подключаться к рабочему столу сварщика, либо к металлоконструкции. При сварке крупногабаритных металло- конструкций, токоподводящие зажимы подключаются, как можно ближе к месту сварки.
11 слайд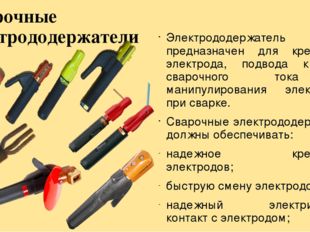
Сварочные электрододержатели Электрододержатель предназначен для крепления электрода, подвода к нему сварочного тока и манипулирования электродом при сварке. Сварочные электрододержатели должны обеспечивать: надежное крепление электродов; быструю смену электродов; надежный электрический контакт с электродом; должен выдержать цикл в 6000 установок и извлечений электродов; возможность, крепления электрода не менее чем в двух положениях; под углами 90 и 115° к его оси.
12 слайд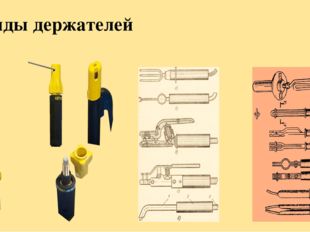
Виды держателей
13 слайд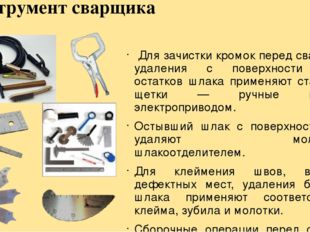
Инструмент сварщика Для зачистки кромок перед сваркой и удаления с поверхности швов остатков шлака применяют стальные щетки — ручные и с электроприводом. Остывший шлак с поверхности шва удаляют молотком-шлакоотделителем. Для клеймения швов, вырубки дефектных мест, удаления брызг я шлака применяют соответственно клейма, зубила и молотки. Сборочные операции перед сваркой выполняют с помощью шаблонов, отвесов, линеек, угольников, чертилок и специальных приспособлений.
14 слайд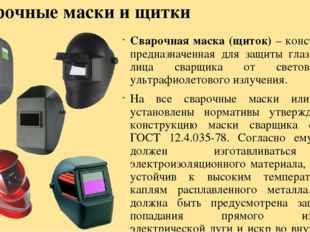
Сварочные маски и щитки Сварочная маска (щиток) – конструкция, предназначенная для защиты глаз и кожи лица сварщика от светового и ультрафиолетового излучения. На все сварочные маски или щитки установлены нормативы утверждающими конструкцию маски сварщика согласно ГОСТ 12.4.035-78. Согласно ему щиток должен изготавливаться из электроизоляционного материала, который устойчив к высоким температурам и каплям расплавленного металла. Также должна быть предусмотрена защита от попадания прямого излучения электрической дуги и искр во внутреннюю часть маски. Самый популярный материал для изготовления подобного средства защиты сварщика – это пластик или электрокартон. Масса сварочного щитка не должна превышать 0,48 кг, а сварочной маски – 0,50 кг.
15 слайд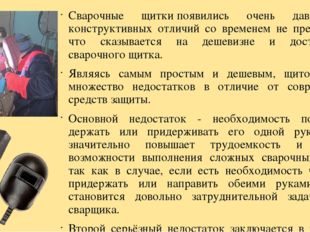
Сварочные щитки появились очень давно, но конструктивных отличий со временем не претерпели, что сказывается на дешевизне и доступности сварочного щитка. Являясь самым простым и дешевым, щиток имеет множество недостатков в отличие от современных средств защиты. Основной недостаток — необходимость постоянно держать или придерживать его одной рукой, что значительно повышает трудоемкость и лишает возможности выполнения сложных сварочных работ, так как в случае, если есть необходимость что-либо придержать или направить обеими руками — это становится довольно затруднительной задачей для сварщика. Второй серьёзный недостаток заключается в том, что фильтром в подобном щитке выступает обычное стекло, затемненное под определенный вид сварки. При неосторожном обращении это стекло может легко разбиться. Таким образом, сварочный щиток удобен разве что для прихваток.
16 слайд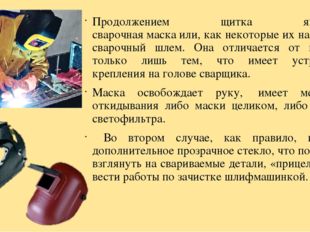
Продолжением щитка является сварочная маска или, как некоторые их называют, сварочный шлем. Она отличается от первого только лишь тем, что имеет устройства крепления на голове сварщика. Маска освобождает руку, имеет механизм откидывания либо маски целиком, либо только светофильтра. Во втором случае, как правило, имеется дополнительное прозрачное стекло, что позволяет взглянуть на свариваемые детали, «прицелиться», вести работы по зачистке шлифмашинкой.
17 слайд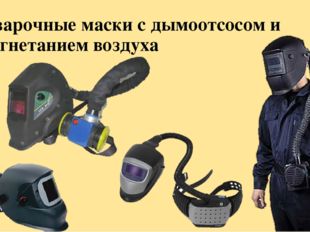
Сварочные маски с дымоотсосом и нагнетанием воздуха
18 слайд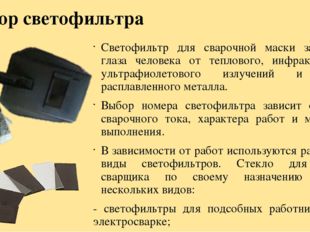
Выбор светофильтра Светофильтр для сварочной маски защищает глаза человека от теплового, инфракрасного, ультрафиолетового излучений и брызг расплавленного металла. Выбор номера светофильтра зависит от силы сварочного тока, характера работ и места их выполнения. В зависимости от работ используются различные виды светофильтров. Стекло для маски сварщика по своему назначению бывает нескольких видов: — светофильтры для подсобных работников при электросварке; для работы с газосварочным и резочным оборудованием; светофильтры для электросварщиков.
19 слайд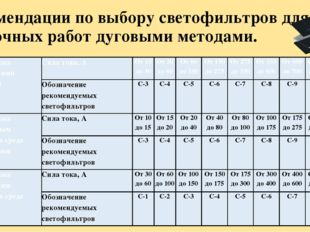
Рекомендации по выбору светофильтров для сварочных работ дуговыми методами. Дуговая сварка металлическими электродами Сила тока, А От 15 до 30 От 30 до 60 От 60 до 150 От 150 до 275 От 275 до 350 От 350 до 600 От 600 до 700 От 700 до 900 Свыше 900 Обозначение рекомендуемых светофильтров С-3 С-4 С-5 С-6 С-7 С-8 С-9 С-10 С11 Дуговая сварка вольфрамовым электродом в среде инертных газов Сила тока, А От 10 до 15 От 15 до 20 От 20 до 40 От 40 до 80 От 80 до 100 От 100 до 175 От 175 до 275 От 275 до 300 От 300 до 400 Обозначение рекомендуемых светофильтров С-3 С-4 С-5 С-6 С-7 С-8 С-9 С-10 С-11 Дуговая сварка металлическим электродом всреде СО2 Сила тока, А От 30 до 60 От 60 до 100 От 100 до 150 От 150 до 175 От 175 до 300 От 300 до 400 От 400 до 600 От 600 до 700 От 700 до 900 Обозначение рекомендуемых светофильтров С-1 С-2 С-3 С-4 С-5 С-6 С-7 С-8 С-9
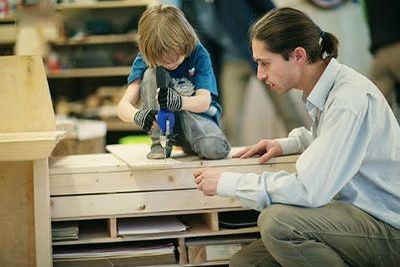
Курс профессиональной переподготовки
Учитель, преподаватель технологии
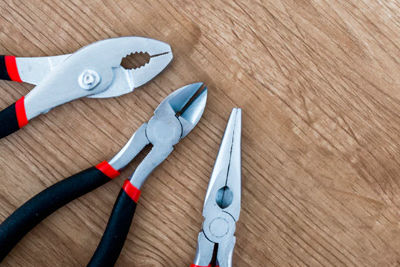
Курс повышения квалификации
Найдите материал к любому уроку,
указав свой предмет (категорию), класс, учебник и тему:
Выберите категорию: Все категорииАлгебраАнглийский языкАстрономияБиологияВсеобщая историяГеографияГеометрияДиректору, завучуДоп. образованиеДошкольное образованиеЕстествознаниеИЗО, МХКИностранные языкиИнформатикаИстория РоссииКлассному руководителюКоррекционное обучениеЛитератураЛитературное чтениеЛогопедия, ДефектологияМатематикаМузыкаНачальные классыНемецкий языкОБЖОбществознаниеОкружающий мирПриродоведениеРелигиоведениеРодная литератураРодной языкРусский языкСоциальному педагогуТехнологияУкраинский языкФизикаФизическая культураФилософияФранцузский языкХимияЧерчениеШкольному психологуЭкологияДругое
Выберите класс: Все классыДошкольники1 класс2 класс3 класс4 класс5 класс6 класс7 класс8 класс9 класс10 класс11 класс
Выберите учебник: Все учебники
Выберите тему: Все темы
также Вы можете выбрать тип материала:

Общая информация
Номер материала: ДБ-715865
Похожие материалы
Вам будут интересны эти курсы:
Оставьте свой комментарийСВАРОЧНЫЙ ПОСТ ДЛЯ РУЧНОЙ ДУГОВОЙ СВАРКИ — КиберПедия
Сварочным постом называют специально оборудованное рабочее место для сварки. Сварочный пост состоит из сварочного аппарата -источника питания дуги электрическим током – пусковой аппаратуры, комплекта сварочных проводов, электрододержателя и самого рабочего места, на котором работает сварщик. При постоянном расположении сварочный пост называют стационарным, при переменном – передвижным.
Передвижные сварочные посты применяют при строительстве различных зданий и сооружений непосредственно на строительной площадке.
Основным оборудованием сварочного поста являются источники питания. Наиболее распространены источники питания переменного тока – сварочные трансформаторы. Обычно применяют трансформаторы типа ТД и ТДМ. Для ответственных и сложных сварочных работ посты укомплектовываются источниками постоянного тока – преобразователями ПД-502, или ПСО, а также однопостовыми выпрямителями ВД-401, ВД-501 и др.
В условиях цеха или на крупных металлоёмких объектах может быть использован многопостовой источник питания – преобразователь ПСМ-1001, выпрямитель ВДМ-1001 и др. В этом случае пост оборудуют балластным реостатом РБ-300 или РБ-500, подсоединяемым к сварочной шине (или проводу), идущей от многопостового источника.
На рис. 82 изображена схема поста для сварки переменным током.
Рисунок 82 — Сварочный пост для ручной дуговой сварки:
1 – трансформатор; 2 – провода; 3 – рабочий стол; 4 – электрододержатель; 5 – свариваемая деталь
Переменный ток от сети по проводам подводится к сварочному трансформатору 1, который понижает напряжение подводимого от сети переменного тока с 220 или 380 В до 69…65 В, требуемого для возбуждения дуги при сварке.
Основным рабочим инструментом электросварщика является электрододержатель, служащий для удержания электрода, подвода к нему сварочного тока и манипулирования электродом в процессе сварки.
Электрододержатели должны допускать возможность захвата электрода не менее чем в двух положениях: перпендикулярно и под углом не менее 115° к оси электрододержателя. Конструкция электрододержателя должна обеспечить время на смену электрода не более 4 с. Токоведущие части электрододержателей должны быть надежно изолированы от случайного соприкосновения со свариваемым изделием или руками сварщика.
Электрододержатели должны обладать достаточной, механической прочностью. Наиболее распространенные конструкции электрододержателей показаны на рис. 83.
а
б
Рисунок 83 — Электродержатели:
а – открытого типа с зажимом; б – винтового типа.
Щитки и шлемы (маски) применяют для защиты лица сварщика от вредного действия лучей сварочной дуги и брызг расплавленного металла. Их изготовляют по ГОСТ 1361–69 из фибры черного матового цвета или специально обработанной фанеры. Щитки и шлемы должны иметь массу не более 0,6 кг. В щиток или шлем вставляют специальный светофильтр, удерживаемый рамкой размером 120× 60 мм. Нельзя пользоваться случайными цветными стеклами, так как они не могут надежно защищать глаза от лучей сварочной дуги, вызывающих хроническое заболевание глаз.
Защитные светофильтры имеют различную плотность. Наиболее темное стекло имеет марку ЭС-500 и применяется при сварке током до 500 А, среднее ЭС-300 — для сварки током до 300 А, более светлое стекло ЭС-100 — для сварки током 100 А и менее. Снаружи светофильтр защищают от брызг расплавленного металла обычным прозрачным стеклом, которое нужно 2-3 раза в месяц заменять новым.
Для зачистки швов и удаления шлака применяют проволочные щетки — ручные и с электроприводом.
Для клеймения швов, вырубки дефектных мест, удаления брызг и шлака служат клейма, зубила и молотки.
3.9 КОНТРОЛЬ КАЧЕСТВА СВАРКИ
В процессе образования сварного соединения в металле шва и зоне термического влияния могут возникать дефекты (рис.84) т.е отклонения от установленных норм и требований, приводящие к снижению прочности, надежности, точности, а также ухудшению внешнего вида изделия.
Дефекты по расположению в сварном соединении разделяют на внешние и внутренние. К внешним дефектам относятся: неравномерная форма шва, непровар, подрез зоны сплавления, прожог, наплыв, поверхностные поры, незаваренные кратеры и трещины на поверхности шва. К внутренним дефектам относятся следующие: непровары и внутренние трещины, внутренние поры, шлаковые включения, не выходящие на поверхность, пережог металла.
Нарушение формы шва являются результатом низкой квалификации сварщика, неустойчивого режима сварки и неточного направления электрода.
Трещины могут быть в металле шва или околошовной зоне. Они подразделяются на горячие и холодные. Возникновение трещин связано с химическим составом, характером и скоростью нагрева и охлаждения металла, жесткостью конструкций. Трещины резко снижают пластические свойства и являются очагами разрушения сварных соединений.
Подрезы – это углубления на основном металле у края шва. Подрезы возникают при сварке на повышенном токе и напряжении, неправильном угле наклона электрода, несоответствии диаметра электрода. Подрезы являются концентраторами напряжений, уменьшают поперечное сечение сварочного шва.
Непровары – это местные несплавления в сварном соединении вследствие неполного расплавления кромок или поверхностей ранее выполненных валиков. Причинам непроваров могут быть также неправильное ведение процесса сварки, плохая подготовка кромок, малый зазор между ними, загрязнение поверхности металла, недостаточный сварочный ток; завышенная скорость сварки и др. Непровары снижают прочность соединений.
Поры и раковины образуются в результате перенасыщения расплавленного металла шва газами. Поры могут быть поверхностными, внутренними или располагаться в цепочку. Поры возникают из-за недостаточной защиты расплавленного металла от воздуха, попадания влаги в зону сварки и плохой очистки свариваемых поверхностей от масла, ржавчины, большой скорости сварки и охлаждения металла. Поры нарушают прочность, нарушают герметичность изделия.
Наплывы – результат натекания наплавленного металла шва на непрогретую поверхность основного металла или ранее выполненного валика без сплавления с ним. Наплывы образуются при неправильном режиме сварки и положении электрода. Наплывы являются концентраторами напряжений, снижают прочность соединения.
Кратеры (незаплавленные углубления) – возникают при низкой квалификации сварщика.
Прожог – сквозное отверстие в сварном шве. Основные причины прожога: большой ток при малой скорости сварки; большой зазор между кромками; малая толщина металла.
Включение шлака возникают из-за большой скорости сварки, плохой очистки свариваемых поверхностей от грязи. Шлаковые включения вызывают концентрацию напряжений, снижают прочность.
а б в
г д е
ж з и
Рисунок 84 — Дефекты сварных швов:
а — неравномерная форма шва; б – трещины; в – подрезы; г – непровары; д – поры и раковины; е – наплывы; ж – кратеры; з – прожог; и – включения шлака
В качестве основного метода контроля сварных соединений применяют внешний осмотр. При осмотре выявляют наличие трещин, подрезов, прожогов, наплывов, кратеров, пористости, непроваров, определяют дефекты формы шва. Некоторые из указанных дефектов недопустимы и подлежат вырубке и повторной заварке.
В ряде случаев для оценки качества сварного соединения применяют методы разрушающего и неразрушающего контроля.
Разрушающие испытания проводят на образцах или на моделях, которые сваривают из того же материала и по той же технологии, что и основное изделие. Механические испытания соединений проводят на растяжение, изгиб, ударную вязкость.
Для исследования структуры и дефектов сварных швов используют методы металлографического анализа. Для анализа изготавливают микрошлифы и затем изучают на металлографических микроскопах при увеличении в 100…1500 раз. При этом обнаруживают микротрещины, перегрев или пережог металла, изучают строение и структуру металла шва и основного металла.
При неразрушающих испытаниях, проводимых обычно на самих изделиях, оценивают те или иные физические свойства, косвенно характеризующие качество, прочность или надежность соединения. Основными методами неразрушающего контроля являются: радиационные (определяют объемные внутренние и поверхностные несплошности в любых материалах), ультразвуковой (внутренние и поверхностные несплошности в любых материалах, кроме крупнозернистых), магнитный (поверхностные и подповерхностные несплошности в ферромагнитных материалах), люминисцентный и капиллярный (поверхностные несплошности в любых материалах) и на герметичность жидкостями (керосином, водой) и газами (гелием, аммиаком, сжатым воздухом).
Радиационные методы контроля являются надежными и широко распространенными методами контроля, основанными на способности рентгеновского и гамма-излучения проникать через металл. Выявление дефектов при радиационных методах основано на разном поглощении рентгеновского или гамма-излучения участками металла с дефектами и без них. Сварные соединения просвечивают специальными аппаратами. С одной стороны шва на некотором расстоянии от него помещают источник излучения, с противоположной стороны плотно прижимают кассету с чувствительной фотопленкой (рис. 85). При просвечивании лучи проходят через сварное соединение и облучают пленку. В местах, где имеются поры, шлаковые включения, непровары, крупные трещины, на пленке образуются темные пятна. Источниками рентгеновского излучения служат специальные аппараты (РУП-150-1, РУП-120-5-1 и др.). Рентгенопросвечиванием целесообразно выявлять дефекты в деталях толщиной до 60 мм. Наряду с рентгенографированием (экспозицией на пленку) применяют и рентгеноскопию. Имеющиеся дефекты в этом случае рассматривают на экране. Такой способ можно сочетать с телевизионными устройствами и контроль вести на расстоянии. При просвечивании сварных соединений гамма-излучением источником излучения служат радиоактивные изотопы: кобальт-60, тулий-170, иридий-192 и др. Ампула с радиоактивным изотопом помещается в свинцовый контейнер. Технология выполнения просвечивания подобна рентгеновскому просвечиванию. Гамма-излучение отличается от рентгеновского большей жесткостью и меньшей длиной волны, поэтому оно может проникать в металл на большую глубину. Оно позволяет просвечивать металл толщиной до 300 мм. Недостатками просвечивания гамма-излучением по сравнению с рентгеновским являются меньшая чувствительность при просвечивании тонкого металла (менее 50 мм), невозможность регулирования интенсивности излучения, большая опасность гамма-излучения при неосторожном обращении с гамма-аппаратами.
Рисунок 85 — Схема радиационного просвечивания швов:
а – рентгеновское, б – гамма-излучением; 1 – источник излучения, 2 – изделие, 3 – чувствительная пленка
Ультразвуковой контроль основан на способности ультразвуковых волн, проникать в металл на большую глубину и отражаться от находящихся в нем дефектных участков.
На рисунке 86 приведена принципиальная схема импульсного ультразвукового дефектоскопа. Генератор ультразвуковых волн 3 возбуждает, пьезопластину передающей искательной головки 1. Ультразвуковые колебания распространяются в контролируемой детали, отражаются от ее противоположной стенки («донный сигнал») и попадают на пьезопластину приемной искательной головки 2. Эти колебания после их усиления подаются на экран 5 электронно-лучевой трубки дефектоскопа, которые свидетельствуют о наличии дефектов. На экране различают сигнал начального (зондирующего) импульса I, сигнал от дефекта II и донный сигнал III. При отсутствии дефекта в контролируемом участке детали на экране осциллографа импульс II будет отсутствовать.
Рисунок 86 — Схема ультразвукового дефектоскопа:
1 – передающая искательная головка; 2 – приемная искательная головка; 3 – усилитель; 4 – генератор УЗК; 5 – экран; 6 – развертывающее устройство
Перемещая передающую и приемную искательные головки по поверхности сварочного шва, обнаруживают дефекты и определяют их местоположение. В некоторых конструкциях ультразвуковых дефектоскопов имеется только одна совмещенная искательная головка, которая используется как для передачи, так и для приема ультразвуковых колебаний. Места прилегания искательных головок к контролируемой детали смазывается тонким слоем трансформаторного масла или вазелина для обеспечения непрерывного акустического контакта искательных головок с поверхностью контролируемого изделия.
Ультразвуковой контроль можно проводить при одностороннем доступе к сварному шву без снятия усиления и предварительной обработки поверхности шва. Ультразвуковой контроль имеет следующие преимущества: высокая чувствительность (1…2 %), позволяющая обнаруживать, измерять и определять местонахождение дефектов площадью 1…2 мм2; большая проникающая способность ультразвуковых волн, позволяющая контролировать детали большой толщины; возможность контроля сварных соединений с односторонним подходом; высокая производительность и отсутствие громоздкого оборудования. Существенным недостатком ультразвукового контроля является сложность установления вида дефекта. Этот метод применяют и как основной вид контроля, и как предварительный с последующим просвечиванием сварных соединений рентгеновским или гамма-излучением.
Люминесцентный контроль и контроль капиллярной дефектоскопией, проводят с помощью специальных жидкостей, которые наносят на контролируемую поверхность изделия. Эти жидкости, обладающие большой смачивающей способностью, проникают в мельчайшие поверхностные дефекты – трещины, поры, непровары.
Люминесцентный контроль основан на свойстве некоторых веществ светиться под действием ультрафиолетового облучения. Перед контролем поверхности шва и околошовной зоны очищают от шлака и загрязнений, на них наносят слой проникающей жидкости, которая затем удаляется, а изделие просушивается. Для обнаружения дефектов поверхность облучают ультрафиолетовым излучением – в местах дефектов следы жидкости обнаруживаются по свечению.
Контроль капиллярной дефектоскопией заключается в том, что на очищенную поверхность сварного соединения наносится смачивающая жидкость, которая под действием капиллярных сил проникает в полость дефектов. После ее удаления на поверхность шва наносится белая краска. Выступающие следы жидкости окрашивают места расположения дефектов.
Магнитные методы контроля основаны на обнаружении полей магнитного рассеяния, образующихся в местах дефектов при намагничивании контролируемых изделий. В зависимости от способа обнаружения потоков рассеяния различают следующие методы магнитного контроля: метод магнитного порошка, индукционный и магнитографический. При методе магнитного порошка на поверхность намагниченного соединения наносят магнитный порошок (окалина, железные опилки) в сухом виде (сухой способ) или суспензию магнитного порошка в жидкости (мокрый способ). Над местом расположения дефекта образуются скопления порошка. Для облегчения подвижности порошка изделие слегка обстукивают. С помощью магнитного порошка выявляют трещины, невидимые невооруженным глазом, внутренние трещины на глубине не более 15 мм, расслоение металла, а также крупные поры, раковины и шлаковые включения на глубине не более 3…5 мм. При индукционном методе дефекты обнаруживают с помощью искателя, в катушке которого под воздействием поля рассеяния индуцируется э.д.с., вызывающая оптический или звуковой сигнал на индикаторе. При магнитографическом методе поле рассеяния фиксируется на эластичной магнитной ленте, плотно прижатой к поверхности соединения. Запись воспроизводится на магнитографическом дефектоскопе. В результате сравнения контролируемого соединения с эталоном делается вывод о качестве соединения.
Сварные швы и соединения ряда изделий и сооружений должны отвечать требованиям непроницаемости (герметичности) для различных жидкостей и газов. Учитывая это, во многих сварных конструкциях (емкости, трубопроводы, химическая аппаратура и т.д.) сварные швы подвергают контролю на плотность. Этот вид контроля производится после окончания монтажа или изготовления конструкции. Дефекты, выявленные внешним осмотром, устраняются до начала испытаний.
Существуют несколько методов испытания: гидравлическое, пневматическое, аммиаком, вакуумом, керосином.
Гидравлическое испытание. При этом методе испытания в сосуде после наполнения его водой с помощью насоса или гидравлического пресса создают избыточное давление. Давление при испытании обычно берут в 1,5-—2 раза больше рабочего. Величину давления определяют по проверенному и опломбированному манометру. Испытуемый сосуд под давлением выдерживают в течение 5—10 мин. В это время швы осматривают на отсутствие течи, капель и отпотевания. Для гидравлического испытания применяют не только воду, но и авиационное масло, или дизельное топливо (при контроле плотности швов в масляных и топливных баках, трубопроводах).
Пневматическое испытание. При пневматическом испытании сжатый газ (воздух, азот, инертные газы) или пар подают в испытываемый сосуд. Сосуды небольшого объема погружают в ванну с водой, где по выходящим через не плотности в швах пузырькам газа обнаруживают дефектные места. Более крупные сварные резервуары и трубопроводы испытывают путем смазывания сварных швов пенным индикатором, который пузырится в местах неплотностей. Самым простым пенным индикатором является водный раствор мыла. Для испытания при отрицательных температурах пригодны смесь мыльного растворе с глицерином, льняное масло и др.
Испытание аммиаком. Сущность этого метода заключается в том, что испытуемые швы покрывают бумажной лентой или марлей (pис. 87), которая пропитана 5%-ным водным раствором азотнокислой ртути или фенолфталеином. В изделие нагнетается воздух до определенного давления и одновременно подают некоторое количество газа (аммиака), Проходя через поры шва, аммиак оставляет на бумаге черные (бумага пропитана раствором азотнокислой ртути) или красные (фенолфталеиновая бумага) пятна.
Рисунок 87 — Схема испытания плотности швов аммиаком
Вакуумному контролю подвергают сварные швы, которые невозможно испытать керосином, воздухом или водой, доступ к которым возможен только с одной стороны. Участок шва, проверяемым на плотность, смачивают водным раствором мыла. На шов устанавливают вакуум — камеру, представляющую собой коробку с открытым дном и прозрачной верхней крышкой из плексигласа. По контуру открытого дна вакуум — камера имеет резиновое уплотнение. Из камеры выкачивают воздух до определенного разрежения. По вспениванию мыльного раствора, которое наблюдают через крышку, обнаруживают расположение дефектов. Этот метод нашел применение при контроле стыковых швов днищ, резервуаров.
Испытание керосином. Этот метод испытания основан на явлении капиллярности, которое заключается в способности многих жидкостей, в том числе и керосина, подниматься по капиллярным трубкам (трубкам малого поперечного сечения). Такими капиллярными являются сквозные поры и трещины в металле сварного шва. Одну сторону стыкового шва покрывают водным раствором мела, после высыхания которого, другую сторону смачивают керосином. Время выдержки изделия после смачивания керосином зависит от толщины свариваемых деталей: чем больше толщина и чем ниже температура воздуха, тем больше время выдержки.
Испытания с помощью течеискателей. При этом методе испытания применяют гелиевые или галоидные течеискатели. При применении гелиевых течеискателей внутри испытуемого сосуда создают вакуум, а снаружи сварные швы обдувают смесью воздуха с гелием. При наличии не плотностей гелий проникает внутрь, сосуда, а затем поступает в течеискатель, где имеется специальная аппаратура для его обнаружения.
В случае применения галоидных течеискателей внутри испытуемого сосуда создают избыточное давление и вводят небольшое количество голоидного газа. Газ проникает через не плотности шва, отсасывается снаружи сосуда и поступает в специальную аппаратуру. По наличию галоидного газа определяют неплотность шва. Этот метод обладает высокой чувствительностью и применяется для контроля ответственных сварных изделий.
СОДЕРЖАНИЕ СВАРОЧНОЙ ПРАКТИКИ
Цель:ознакомится с оборудованием для ручной дуговой сварки и требованиями, предъявляемыми к источникам питания; ознакомится с маркировкой и назначением электродов для ручной дуговой сварки; изучить основы выбора режима и технологии ручной дуговой сварки; изучить особенности сварочного процессов, строение и дефекты сварных соединений, а также методы контроля сварных соединений.
Оборудование и оснащение рабочих мест: стол сварочный – ССН-101 СВАГА; комплект сварочных проводов; электрододержатели; сварочные маски; сварочные выпрямители – ВДМ-6303С, ВД 301У3; реостат балластный – РБ-302У2; сварочный полуавтомат – А-1230М; сварочный аппарат в среде защитных газов – УДГУ 301УХЛ4; верстаки слесарные 1- и 2-тумбовые; тумбочки инструментальные; шкафы металлические; ящики для инструментов.