Титановые сплавы и их свойства
Расширяющееся применение титановых сплавов в промышленности объясняется сочетанием у них ряда ценных свойств: малой плотности (4,43—4,6 г/см3), большой удельной прочности, необычайно высокой коррозионной стойкости, значительной прочности при повышенных температурах. Титановые сплавы по прочности не уступают сталям и в несколько раз прочнее алюминиевых и магниевых сплавов. Удельная прочность титановых сплавов является наивысшей среди применяемых в промышленности сплавов. Они являются особо ценными материалами в тех отраслях техники, где выигрыш в массе имеет определяющее значение, в частности в ракетостроении и авиации. Титановые сплавы в промышленном масштабе впервые были использованы в конструкциях авиационных реактивных двигателей, что позволило уменьшить их массу на 10—25%.
Благодаря высокой коррозионной стойкости ко многим химически активным средам титановые сплавы используют в химическом машиностроении, в цветной металлургии, в судостроении и медицинской промышленности.
Литейные свойства титановых сплавов определяются прежде всего двумя особенностями: малым температурным интервалом кристаллизации и исключительно высокой реакционной способностью в расплавленном состоянии по отношению к формовочным материалам, огнеупорам, газам, содержащимся в атмосфере.
Поэтому получение отливок из титановых сплавов связано со значительными технологическими трудностями.
Для фасонных отливок применяют титан и его сплавы: ВТ1Л, ВТ5Л, ВТ6Л, ВТЗ-1Л, ВТ9Л, ВТ14Л. Наиболее широко используют сплав ВТ5Л с 5% А1, отличающийся хорошими литейными свойствами, технологичностью, недефицитностью легирующих элементов, удовлетворительной пластичностью и прочностью (σв = 700 МПа и 900 МПа соответственно). Предназначены сплавы для отливок, длительно работающих при температурах до 400°С.
Сплав титана с алюминием, молибденом и хромом BT3-1Л — наиболее прочный из литейных сплавов. Его прочность (σв = 1050 МПа) приближается к прочности деформируемого сплава. Но его литейные свойства и пластичность ниже, чем у сплава ВТ5Л. Сплав отличается высокой жаропрочностью, отливки из него могут длительно работать при температуре до 450°С.
Сплав титана с алюминием, молибденом и цирконием ВТ9Л обладает повышенной жаропрочностью и предназначен для изготовления литых деталей, работающих при температурах 500—550°С.
Контрольные вопросы
1. Что такое литейные сплавы и как они классифицируются?
2. Какие требования предъявляются к свойствам литейных сплавов?
3. Что такое литейные свойства сплавов и как они влияют на качество отливок?
4. В чем особенности состава, структуры и свойств чугунов для фасонного литья?
5. Чем отличаются высокопрочные чугуны по структуре и свойствам от обычных серых?
6. Как получают ковкий чугун?
7. Как классифицируются литейные стали и каково их назначение?
8. Какие литейные сплавы относятся к цветным?
9. Назовите литейные сплавы на медной основе, получившие наиболее широкое промышленное применение.
10. Какими достоинствами обладают алюминиевые литейные сплавы?
11. Из каких компонентов состоят магниевые литейные сплавы и в каких областях техники эти сплавы нашли наибольшее применение?
12. В чем состоят особенности свойств титановых литейных сплавов, каковы их состав и свойства?
Общая характеристика структуры титановых сплавов и закономерности ее образования » Строительство и ремонт: теория и практика
В деформированных полуфабрикатах из сплавов на основе титана, в особенности двухфазных, наблюдается большое разнообразие структур, отличающихся по величине зерен, форме и внутризеренному строению и зависящих от состава сплавов, термомеханических параметров деформирования, условий нагревa и охлаждения, режимов термической обработки.
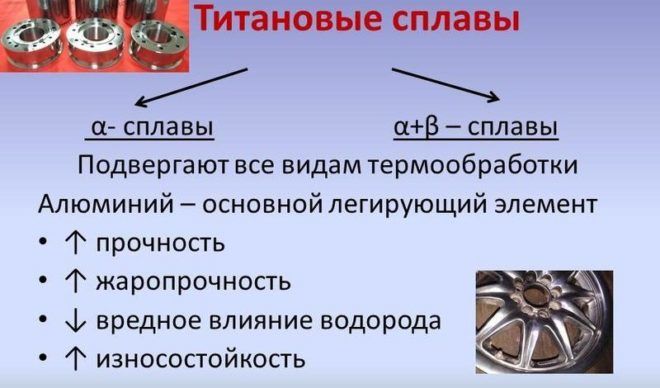
В зависимости от формы структурных составляющих все наблюдаемые в титановых сплавах разновидности структур относятся к одному из двух типов: к структуре с глобулярной формой частиц а фазы и к структуре с пластинчатой а-фазой. На практике их часто называют равноосной и игольчатой структурами.
Опыт многих исследователей показал, что наиболее реальный пуль для получения структуры с глобулярной а-фазой — пластическая деформация при температурах ниже температуры полиморфного превращения и с достаточно большими обжатиями (более 60—70%). Действительная форма кристаллов а-фазы в такой структуре может быть близка к сфероидальной (равноосной), дискообразной, волокнистой, червячнообразной, а их размеры могут изменяться от нескольких микрон до десятков микрон.
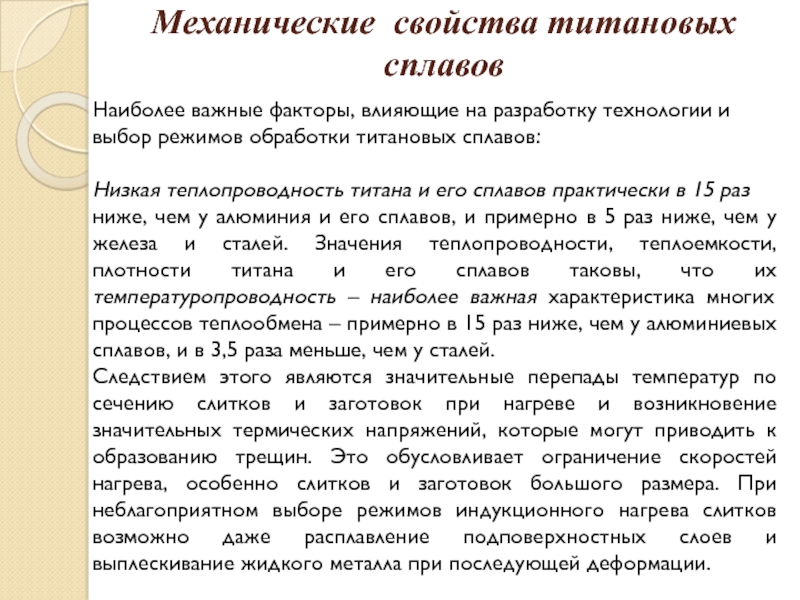
Характерной особенностью структуры пластинчатого типа в титане и его сплавах является в большинстве случаев значительный размер первичных в-зерен, который может достигать нескольких тысяч микрон. По мнению авторов работы, исключительно быстрый рост зерен в титановых сплавах при температурах в-области связан с тем, что диффузия легирующих элементов и примесей при одинаковой температуре в в-титане протекает интенсивнее, чем в а-титане. Замедленный рост в-зерен при нагреве в двухфазной области обусловлен сдерживающим влиянием пограничного каркаса а-фазы.
Внутризеренное строение пластинчатой структуры характеризуется наличием комплекса фрагментов или колоний, состоящих из чередующихся, параллельных или разориентированных пластин а-фазы и второй фазы, напоминая по своему внешнему виду структуру пластинчатого перлита в сталях.
Анализ большого количества микроструктур двухфазных титановых сплавов показал, что после мед ленного охлаждения в каждом p-зерне может быть до вольно ограниченный набор различных ориентировок а-пластин.

Другим важным условием образования пластинчатой структуры является возникновение при полиморфном превращении вдоль фронта зарождения a-фазы второй фазы представляющей собой либо а-фазу с отличающимся от матрицы составом, либо в-фазу.
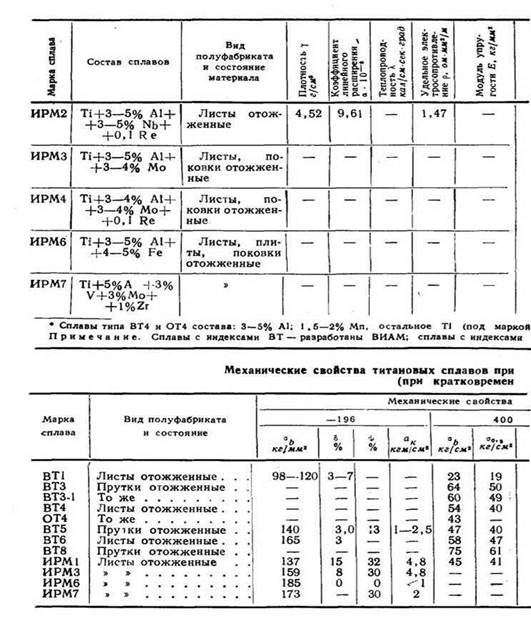
Наиболее четко пластинчатый характер в-превращенной структуры выражен в a+в титановых сплавах, имеющих повышенное количество второй фазы.
В сплавах с полиэдрической структурой вторая фаза расположена по границам a-зерен. Ее количество также тем больше, чем выше содержание в-стабилизирующих элементов Однако в небольших количествах она имеется и в сплавах, которые считаются однофазными. Таким образом, большинство а-титановых сплавов на самом деле в отожженном состоянии двухфазны.
Пластинчатая структура титановых сплавов очень устойчива Действительно, известно, что в сталях для измельчения подобной структуры и перевода пластинчатого перлита в глобулирный широко применяют циклический отжиг при температурах, близких к Ac3, длительный отжиг при температурах несколько ниже Ас3 и закалку с температур у-области с последующим рекристаллизационным отжигом.
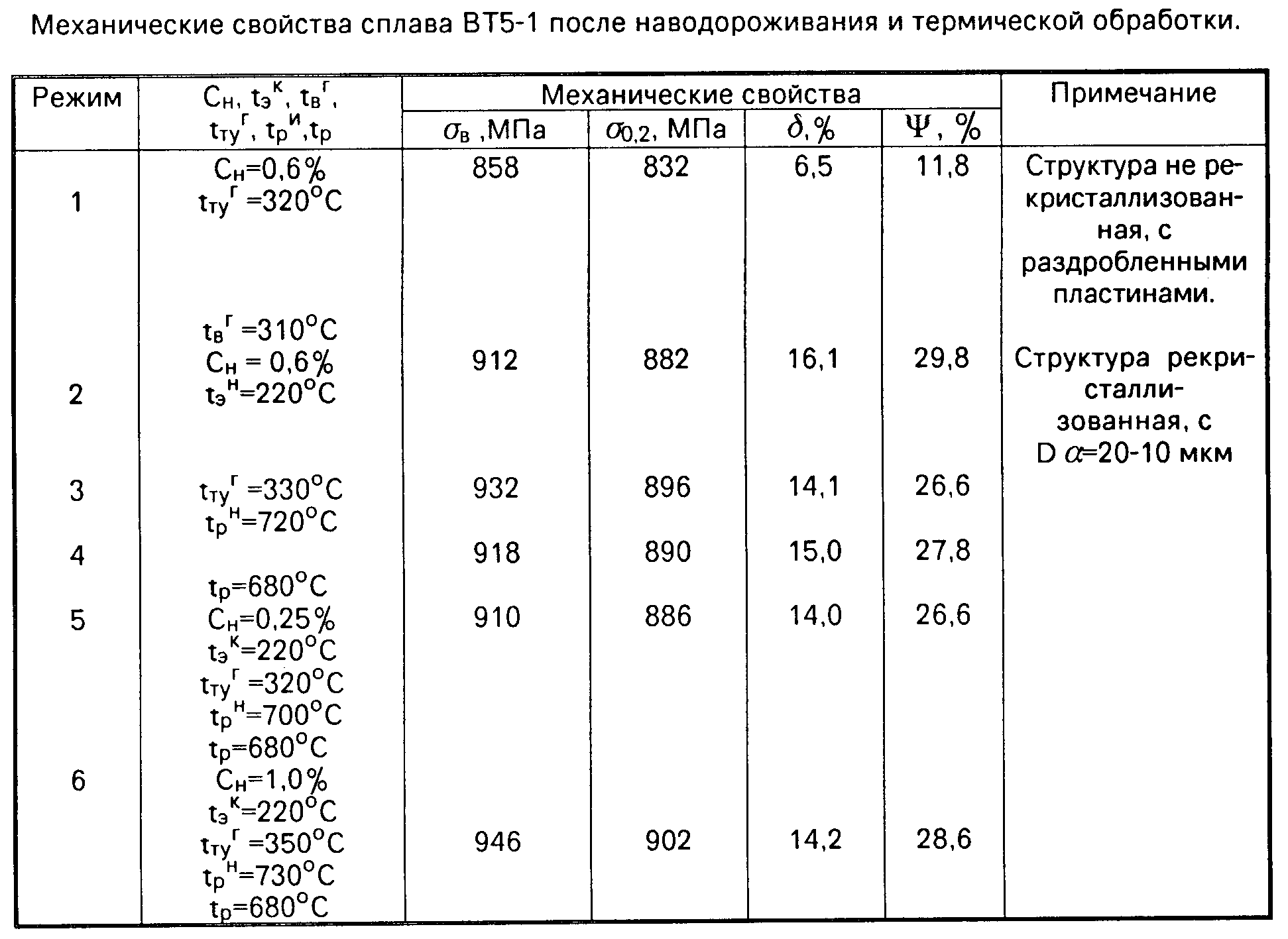
Вместе с тем наряду с работами, в которых высказываются сомнения о возможностях эффективного исправления пластинчатой структуры в титановых сплавах методами термической обработки, известны работы с более обнадеживающими результатами и более оптимистическим отношением к термической обработке как к способу воздействия на пластинчатую структуру.

Измельчение зерна в этом случае авторы объясняют внутрифазовым наклепом и термическими напряжениями, возникающими при закалке, и последующей рекристаллизацией при повторном нагреве. В работе методом автоэлектронной микроскопии обнаружено, что многократное повторение а->в — переходов и последующий высокотемпературный отжиг нелегированного титана приводят к появлению новых зерен.

Для удобства оценки структуры полуфабрикатов и контроля их качества были разработаны различные шкалы макро- и микроструктур, некоторые из которых приведены на рис. 24 и 25.
Приведенные шкалы являются обобщением производственного опыта по контролю структуры и свойств полуфабрикатов из титановых сплавов. Представленные в них эталонные типы структур отражают многие особенности структуры титановых полуфабрикатов, ее многообразие, зависимость от состава сплавов и условий деформирования.
Например, первые два — три типа микроструктур, приведенных в этих шкалах, характеризуют микроструктуру. полученную деформацией при температурах а+в-области Структуры следующих двух—трех типов, которые часто называют структурой «корзиночного плетения», образуются при деформации вблизи температуры полиморфного превращения или в тех случаях, когда деформация начинается при температурах в-области, а заканчивается при температурах a+в области. Остальные структуры соответствуют различным условиям деформации при температурах в-области.

Последующая стандартная термообработка при температурах а- или а+в-области, как правило, несколько укрупняет отдельные элементы структуры, сохраняя ту же гамму структур, что и в деформированных полуфабрикатах.
Особенностью шкал, действующих для контроля структуры титановых сплавов, в отличие, например, от шкал, принятых для сталей, является то, что принадлежность структуры, особенно пластинчатой, к тому или иному типу определяется не только размером зерен, но и внутризеренным строением. Тем не менее в связи с ограниченным количеством использованных эталонов эти шкалы далеко не охватывают всего многообразия встречающихся на практике структур. Кроме того, их деление на типы структур лишено строгой физической основы и построено на качественных, а не на количественных различиях, что вносит значительный элемент субъективности при их использовании.
Указанные недостатки исключены в методике контроля пластинчатой структуры, основанной на измерении величины первичных p-зерен, размеров a-колоний и толщины а-пластин, разработанной Г.
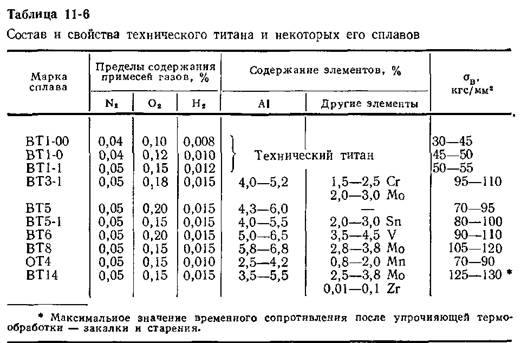
Основное достоинство методики заключается в возможности проведения количественного анализа структуры.
В исследовательских работах для анализа структуры в последние годы все более широкое применение получают различные автоматические методы с использованием компьютеров и счетных устройств.
В данном разделе изложены общие для всех полуфабрикатов представления о процессах образования пластинчатой структуры из глобулярной, о влиянии температурно-силовых параметров деформации, условий охлаждения деформированного и недеформированного материала, а также режимов термической обработки на структуру титановых сплавов, в особенности структуру пластинчатого типа, о закономерностях превращения пластинчатой структуры в глобулярную.

Вопросам образования пластинчатой структуры из глобулярной и ее роста в зависимости от температуры и времени нагрева в в-области посвящено довольно много исследований. Уже в первых выполненных работах было обращено внимание на чрезвычайно быстрый рост зерен при температурах р области. О значительной интенсивности укрупнения зерен при этих температурах, особенно по сравнению с докритическими температурами, можно судить по диаграммам рекристаллизации титана и его сплавов, приведенных в первых двух томах настоящей серии Наглядное представление об этом дают, например, кривые, приведенные на рис. 26, а.
Скорость роста p-зерен настолько велика, что микроскопическая картина этого процесса выглядит так, как если бы рост зерен происходил не путем постепенного перемещения их границ, а скачкообразно путем последовательного возникновения новых границ, не связанных со старыми.
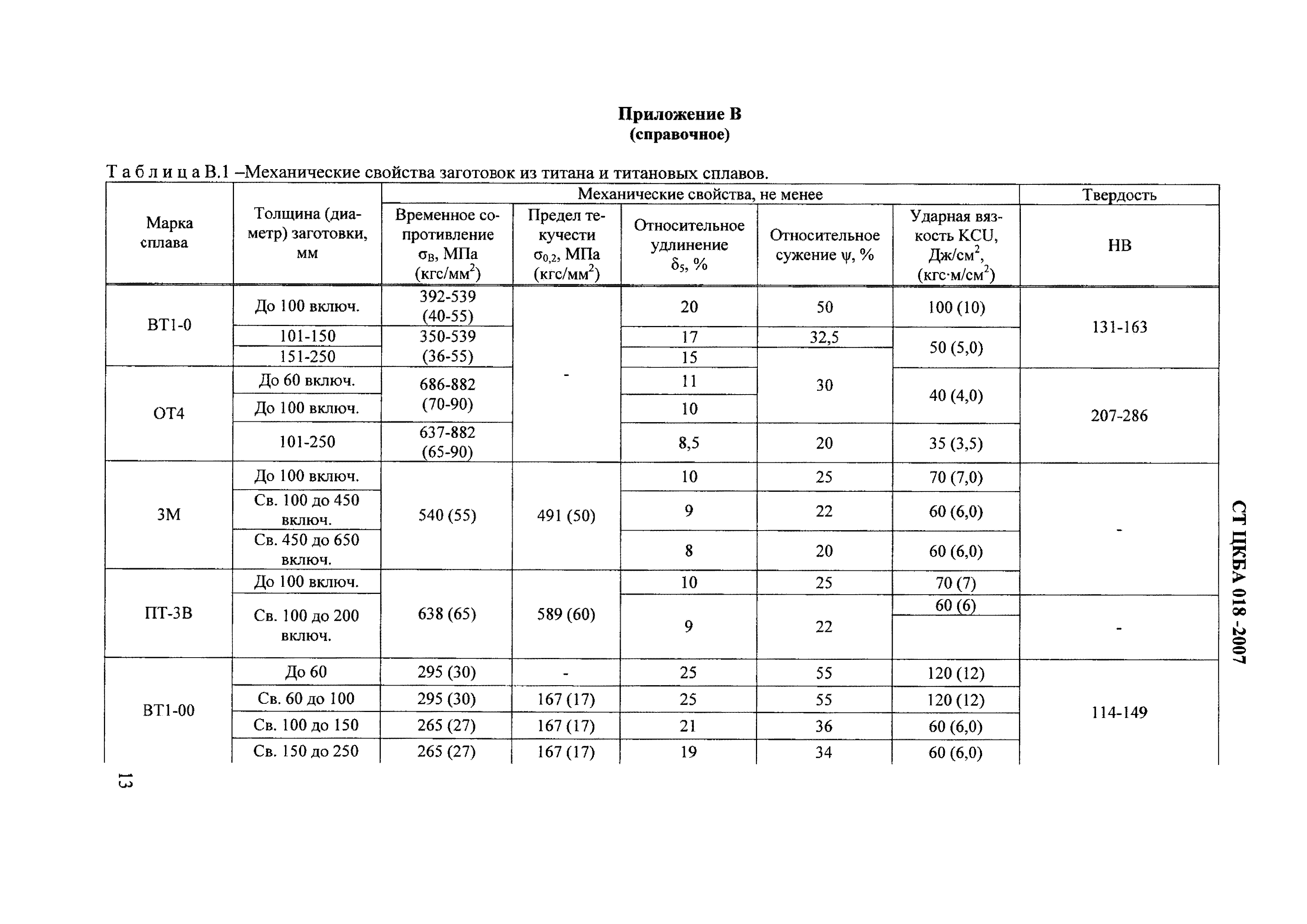
Решающее влияние на кинетику роста в-зерен оказывает температура нагрева. Чем выше температура нагрева, тем интенсивнее происходит рост зерен. По данным работы, при температурах на 50—100° C выше температуры полиморфного превращения размер р зерен увеличивается незначительно, так как его росту препятствуют примеси. При более высоких температурах влияние примесей исчезает и интенсивность роста зерна резко возрастает.

Абсолютный размер p-зерен в значительной мере зависит от состава става него предшествовавшей обработки. В работах отмечается, что величина и скорость роста зерен в структуре титановых сплавов уменьшаются при увеличении содержания легирующих элементов и некоторых примесей внедрения. Наиболее эффективно замедляют рост в-зерен бор, молибден, ванадий, хром.
Увеличение степени деформации приводит к весьма эффективному измельчению структуры. Это видно из диаграмм рекристаллизации, а также из основанных на экспериментальных данных схем, представленных на рис 27, а.
Весьма характерно, что измельчение зерен в случае в-деформации обычно более значительно, чем при а+в-деформации. Кроме того, повышение в определенном интервале температуры в-деформации нередко приводит не к увеличению, как можно было бы предполагать, а к уменьшению величины зерен (рис. 27, б). Это объясняется развитием процесса первичной рекристаллизации в деформированной в-структуре, вызывающей появление новых зерен.

Влияние степени деформации на величину зерна различно для разных сплавов. Из полученных в работе данных следует, что для менее легированных сплавов, имеющих более крупную исходную структуру, это влияние проявляется сильнее, чем для более легированных сплавов. Последующий рост зерен при собирательной рекристаллизации в малолегированных сплавах также происходит более интенсивно, чем в высоколегированных сплавах.
Наряду с легированием, температурой и степенью деформации существенное влияние на размер в-зерен оказывает скорость охлаждения после в-деформации. Как правило, при ускорении охлаждения зерно измельчается (рис. 27, в). Однако нередко наблюдаются и обратные случаи, особенно при небольших обжатиях, когда размер p-зерна при ускорении охлаждения увеличивается. Это, по видимому, происходит в тех случаях, когда время пребывания материала при высоких температурах настолько уменьшается, что не успевают пройти процессы рекристаллизации, измельчающие зерно.

Итак, несмотря на присущую титану и сплавам на его основе склонность к интенсивному росту зерен при температурах в-области, на практике могут быть созданы условия, при которых можно не опасаться чрезмерного укрупнения зерен, достаточно высокие степени деформации, правильно выбранные температурно-временные режимы нагрева или деформации, регламентированные условия охлаждения. Большие возможности для получения необходимой величины зерна в полуфабрикатах из титановых сплавов имеет скоростной нагрев, масштабы применения которого, несомненно, должны быть значительно расширены.
Изменение величины и формы в-зерен сопровождается одновременным изменением внутреннего состояния в-структуры, которое при последующем охлаждении металла ниже температуры полиморфного превращения влияет на характер образующейся внутризеренной пластинчатой структуры и ее основные параметры: размер a-колонии (d) и толщину а-пластин (b). Однако в связи с тем, что сами пластины при температурах в-области не существуют и, следовательно, не подвергаются деформации, а лишь наследуют изменения, происходящие в в-структуре, влияние температуры и степени деформации на d и b обычно меньше, чем на D.
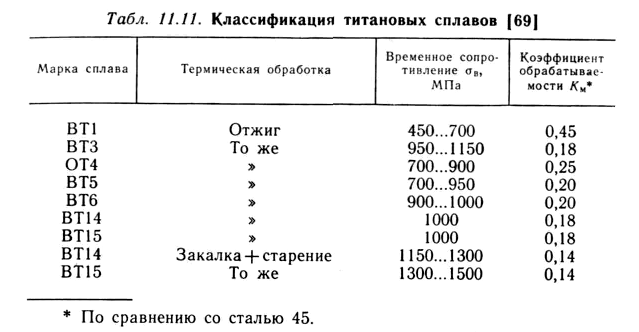
Характер этих изменений представляется следующим. Любые изменения технологического процесса, способствующие сохранению нерекристаллизованной структуры с избыточной плотностью дефектов кристаллического строения — снижение температуры деформации, увеличение до определенных пределов степени деформации, интенсификация охлаждения, как правило, приводят к уменьшению d и b, т. е. к уменьшению размеров пластин и увеличению их разориентированности. Это обусловлено тем, что образовавшиеся при деформации или возникшие при быстром охлаждении вследствие фазового наклепа дефекты способствуют зарождению а-пластин не только на границах в-зерен, но и внутри них, а также препятствуют свободному росту пластин в одном направлении.
Если сравнивать относительное влияние температуры нагрева или деформации в в-области, степени деформации и скорости охлаждения на внутризеренное строение титановых сплавов, то наиболее сильное влияние, по-видимому, оказывает скорость охлаждения. Влияние скорости охлаждения на внутризеренную структуру титановых сплавов после нагрева в в-области и при достаточно высоких температурах а+в-области определяется происходящими при охлаждении фазовыми превращениями, возникающими под влиянием деформационных, фазовых и термических напряжений искажениями структуры, а также развитием диффузионных процессов.
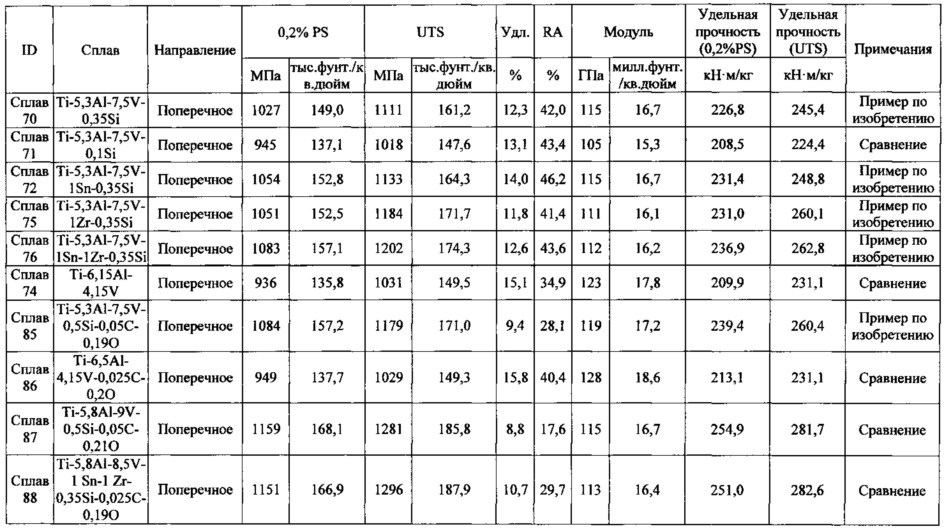
Систематические исследования по влиянию режимов охлаждения на внутризеренное строение титановых сплавов выполнены в работах. В одной из них на сплаве ВТ3-1 было установлено, что его охлаждение с температур в-области со скоростями 50—2 град/с приводит к образованию структуры мартенситного типа. После охлаждения со скоростью ниже 2 град/с образуется структура, напоминающая структуру видманштеттового типа. При такой скорости охлаждения наряду с первичной a-фазой, сохранившейся при нагреве, образуется вторичная а-фаза.
Дальнейшее уменьшение скорости охлаждения до 0,08—0,005 град/с сопровождается еще более значительными изменениями структуры. Образуется типичная в-превращенная структура, границы зерен которой окантованы оторочкой а фазы, а внутризеренное строение характеризуется наличием пластин a-фазы, имеющих одинаковую ориентировку в пределах отдельных фрагментов-колоний. Толщина а-пластин при этом тем больше, чем меньше скорость охлаждения.
Размер колоний с одинаково ориентированными а-пластинами изменяется в зависимости от скорости охлаждения аналогично изменению толщины пластин (см.

Увеличение интенсивности охлаждения вызывает их измельчение, а замедленное охлаждение приводит к укрупнению. Поэтому внутризеренная структура титановых сплавов после быстрого охлаждения выглядит более разориентированной, чем после медленного охлаждения. Причины подобного влияния условий охлаждения на размер a-колоний, как уже отмечалось, по-видимому, заключается в увеличении плотности дефектов кристаллического строения при ускорении охлаждения, препятствующих непрерывному и свободному росту а-пластин и способствующих зарождению новых а-пластин не только на границах, но и внутри в-зерен. В связи с этим наиболее значительное измельчение внутризеренной структуры титановых сплавов наблюдается в тех случаях, когда быстрому охлаждению предшествует пластическая деформация, вызывающая дополнительное существенное повышение плотности несовершенств.
Заключительной операцией при производстве полуфабрикатов из титановых сплавов является термическая обработка. Возможные при ее проведении изменения пластинчатой структуры схематически показаны на рис.

Увеличение времени нагрева при температурах а+в-области приводит к коагуляции а-пластин при уменьшении их количества и увеличении ширины в-прослоек. Механизм их коагуляции заключается, по видимому, в растворении менее устойчивых при нагреве а-кристаллитов, диффузионном переносе их массы через твердый раствор и осаждении на более устойчивых против растворения кристаллитах.
Итак, на формирование пластинчатой структуры, образующейся в процессе нагрева или деформации при температурах в-области, в большей или меньшей степени влияют все основные параметры технологического процесса. Абсолютные размеры в-зерен, a-колоний и а-пластин в значительной мере зависят также от состава сплавов и главным образом от содержания в-стабилизирующих элементов. Увеличение количества в-стабилизаторов обеспечивает уменьшение размеров всех структурных составляющих.

О характере и последовательности происходящих при в-деформации и рассмотренных выше изменениях пластинчатой структуры можно судить по схеме, представленной на рис. 28.
Из схемы видно, что процесс формирования структуры при деформации в в-области состоит из двух основных стадий: стадии, при которой происходит формирование зеренной структуры, и стадии, при которой формируется внутризеренная структура.
Изменение зеренной структуры, происходящее в области существования в-фазы, подчиняется общим закономерностям изменения структуры металлов и сплавов под влиянием деформации. При увеличении степени деформации происходит изменение размеров D и формы в-зерен, которые сплющиваются, вытягиваются вдоль направления течения металла, приобретая эллипсоидную форму, затем, как уже отмечалось, может произойти первичная рекристаллизация, приводящая к измельчению структуры из-за появления новых зерен, и собирательная рекристаллизация, вызывающая укрупнение структуры до начальных и даже больших размеров.
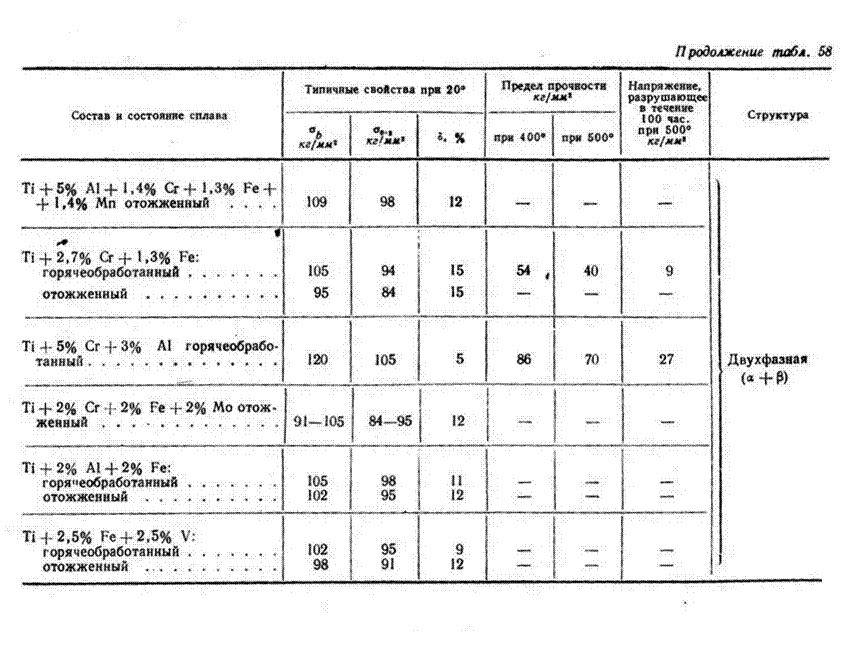
Внутризеренная структура, образующаяся при последующем охлаждении, еще более разнообразна, так как зависит не только от параметров деформации, но и от условий фазовой перекристаллизации и режимов термической обработки.
Наряду с деформацией при температурах в-области процесс деформации а+в-титановых сплавов может осуществляться в двухфазной области или начинаться в первой, а заканчиваться во второй.
На рис. 29 схематически показаны основные разновидности структур, образующихся из пластинчатой структуры при a+в-деформации. В отличие от деформации при температурах в-области в процессе деформации при температурах а+в-области происходит одновременно изменение в-зерен и а-пластин. Они сплющиваются, вытягиваются вдоль направления течения металла, дробятся. Постепенно исчезает различие между приграничной и внутризеренной a-фазой. После деформации со степенью, превышающей 60—70%, уже не остается никаких видимых следов пластинчатой структуры. При определенных температурах и степенях деформации происходит рекристаллизация, причем рекристаллизация в а-фазе опережает рекристаллизацию в в-фазе.

Если деформацию проводить при температурах, близких к температуре полного полиморфного превращения, то наряду с глобулярной a-фазой в структуре полуфабрикатов наблюдается пластинчатая a-фаза, образующаяся из в-фазы в процессе охлаждения. Ее количество тем больше, чем ближе температура металла к температуре полного полиморфного превращения В отличие от а-фазы, образующейся с температур в-области, эта а-фаза характеризуется меньшей протяженностью и большей разориентированностью пластин.
Последующая термическая обработка при температурах двухфазной области, как правило, не изменяет характер структуры, образовавшейся при а+в-деформации. Существенного видоизменения такой структуры можно добиться лишь путем нагрева почти до температуры полиморфного превращения, приводящего к изменению соотношения между количествами первичной а-фазы глобулярного типа и вторичной а-фазы пластинчатого типа.

Наряду с в и а+в деформацией, на практике нередко применяют комбинированную обработку, при которой деформация начинается при температурах в-области, а заканчивается при температурах а+в-области. Образующаяся после такой обработки микроструктура в основном зависит от степени деформации при температурах а+в-области. При достаточно больших степенях деформации (> 50—60%) она аналогична структуре, получаемой путем обычной a+в-деформации. При меньших степенях деформации структура отличается локальной неоднородностью, которая заключается в чередовании участков с пластинчатой и глобулярной а-фазой (см. рис. 30, 31).
Образование подобной неоднородности можно представить следующим образом.
При в-деформации температура металла, несмотря на разогрев в очаге деформации, снижается по ходу процесса Когда она достигает температуры полиморфного превращения, из в-фазы начинает образовываться а-фаза. Зарождение a-фазы начинается на границах первичных в-зерен, которые обогащены а-стабилизирующими элементами. Только при дальнейшем снижении температуры a-фаза выделяется внутри зерен.
В связи с более ранним образованием приграничная a-фаза претерпевает и большую деформацию при температурах а+в-области. Поэтому она прорабатывается в большей степени, чем внутризеренная a-фаза. Кроме того, в приграничных участках в-зерен раньше начинается рекристаллизация, приводящая к образованию а-частиц сферической формы. Если же рекристаллизация не успевает пройти, то структура этих участков отличается от внутризеренной структуры более мелкопластинчатым строением.
Таким образом, наблюдаемые различия в структуре полуфабрикатов, полученных деформацией при температурах а+в-области и деформацией, начинающейся при температурах в-области, а заканчивающейся при температурах а+в-области, объясняется тем, что в первом случае весь объем в-зерна претерпевает одинаковую деформацию, тогда как во втором случае разные участки в-зерна деформируются по-разному.
Заканчивая на этом рассмотрение данных о структуре деформированных полуфабрикатов из двухфазных титановых сплавов, следует отметить, что высказанные соображения о закономерностях формирования различных структур не являются исчерпывающими и необходимы дальнейшие исследования по влиянию легирования, параметров деформации и режимов термической обработки на структуру полуфабрикатов.
Титановые основания: особенности сплавов
31.07.2019Титан позволяет создавать очень прочные реставрации, но для стоматологии используются не все сплавы.
В основном для работы применяют никелид титана и пористый титан, которые обладают двумя основными характеристиками, необходимых при протезировании:
— твердость;
— пластичность.
Общие характеристики
Титан рекомендован при восстановлении зубов по ряду причин:
— пассивизация. Это качество обеспечивается за счет образования оксидной пленки на поверхности сплава, которая исключает любое взаимодействие с активными средами;
— низкая теплопроводность. За счет этого улучшается способность удерживать облицовку, так как нет значительных деформаций при перепадах температур;
— простота литья. Сплавы никеля и титана дешевы при производстве.
Наиболее востребованным участком протезирования для титана являются жевательные зубы.
Здесь постоянные методичные нагрузки (давление и истирание), с которыми металл хорошо справляется. Удельный вес сплава сравнительно небольшой, что обеспечивает приемлемую массу даже крупных элементов.
Особенности сплавов
В чистом виде титан не используется, в основном применяют сочетание со следующими элементами:
— алюминий;
— хром;
— молибден;
— олово;
— железо;
— марганец;
— кремний;
— цирконий.
Эти составные сплава разделяют на три группы в зависимости от влияния на характеристики конечного сплава:
— альфа-стабилизаторы. Компоненты стабилизируют сплав, увеличивают прочностные характеристики. При переходе между фазами состояния металла увеличиваются температурные промежутки. К этой группе относится кислород, азот, алюминий;
— нейтральные стабилизаторы. Свойства сплава не затрагиваются, за исключением повышения его прочности. В числе этих элементов цирконий, олово;
— бета-стабилизаторы. Прочность готового материала увеличивается за счет снижения температуры, при которой происходит переход между фазами состояния.
Чаще всего в стоматологии встречаются следующие сплавы титана:
— ВТ-5Л, применяется для литых изделий (коронки, базисы), мостовидных конструкций, бюгельных и шинирующих систем;
— ВТ-6, используется для создания имплантируемых опорных элементов;
— ВТ1-00, выступает сырьем для имплантатов, съемных протезов и каркасов металлокерамических структур.
За счет добавления алюминия ВТ-5Л обладает упругостью и прочностью, что делает возможным все типы обработки (ковка, литье, штамповка). ВТ-6 включает алюминий и ванадий, отличается повышенной пластичностью и наилучшей сопротивляемостью коррозии в сравнении с прочими сплавами под титановые абатменты. ВТ-1-00 содержит железо, пластичен, сфера применения зависит от процентного соотношения составных элементов.
Один из общих параметров, которому отвечают перечисленные сплавы, это безопасность для человека.
При любых воздействиях на всем периоде эксплуатации металл не выделяет вредных соединений, не провоцирует появления постороннего запаха и привкуса, потемнения участка контакта с мягкими тканями.
Сроки службы изделий составляют 15 лет и более, вероятно, что это один из вариантов протезов, которые будут служить пожизненно при должном уходе.
Оксидная пленка препятствует протеканию реакций с активными веществами, красящими компонентами пищи и напитков, поверхность монолитная, полируется до идеальной гладкости.
За счет этого так же не происходит осаждения и обрастания зубным налетом, микроорганизмам тяжелее колонизировать такую поверхность.
Титановые диски для фрезерования — методы применения Титан долгое время используется в медицине благодаря уникальному сочетанию качеств.
Единственный недостаток сплавов в том, что они полностью светонепроницаемы, потому достаточно заметны даже при создании облицовки. Металлические компоненты могут просвещаться через мягкие ткани. За счет этого сплавы часто используют именно для восстановления моляров и премоляров, где важна не эстетика, а прочностные характеристики.
Специфика обработки
Характеристики сплавов усложняют обработку, которая может варьироваться в зависимости от следующих показателей:
— фазы окисления;
— строение кристаллической решетки;
— физические свойства.
Для обработки заготовок используется фрезерный станок, в котором для работы с титаном используются специальные фрезы. От прочих их отличает крестообразная насечка из режущих кромок.
Для повышения эффективности и сокращения износа режущих элементов, применяют несколько режимов:
— интенсивность подачи снижается, что исключает перегрев фрезы, ее деформацию. Сокращаются вибрации при работе, увеличивается ресурс инструмента и станка в целом;
— подача воды. Охлаждение участка обработки позволяет избежать перегрева режущих кромок и обрабатываемой заготовки. Благодаря этому не происходит негативных изменений кристаллической решетки;
— угол подачи инструмента выбирается минимальный, что положительно сказывается на ресурсе фрезы.
Несоблюдение этих требований при обработке можно заметить во внешних изменениях металла. Обычно перегретый участок меняет цвет, поверхность может стать шероховатой, появляются трещины, кромки крошатся.
Каждый этап обработки требует соблюдения оптимальных условий изготовления конструкций. Помимо специальных фрез применяют карборундовые камни, диски, поверхность подвергается пескоструйной обработке.
Затем проводится шлифовка/полировка, для чего используются резиновые насадки совместно с полировочными пастами. За счет применения последних снижается риск повреждения поверхности при обработке мелких неровностей и тонких деталей.
Фреза должна вращаться на низких оборотах, подача осуществляется строго в одной плоскости, острые углы конструкции сглаживаются, необходимо регулярно очищать режущие кромки от металлической стружки и крошки.
Пескоструйная обработка проводится только с использованием одноразового оксида алюминия, либо песка с мелкой фракцией.
Струя по отношению к обрабатываемой поверхности располагается под прямым углом. После данного этапа нужно дать оксидной пленке снова появиться на поверхности, для чего достаточно оставить заготовку в покое на 2-5 минут. После этого конструкцию подвергают паровой очистке.
Инструменты для обработки сплавов хранят отдельно, крайне важно соблюдение чистоты. Фрезу обрабатывают специальными кисточками, поверхность очищается пескоструйкой.
Методы изготовления протезов
Титан подходит для трех методов изготовления конструкций, например, отдельные коронки и мосты изготавливаются путем литья, как одиночные реставрации, так и протяженные системы. Сначала создается оттиск челюстей, затем формируется литьевая форма, рабочая модель, полученные заготовки корректируются и подгоняются, металл облицовывается керамикой или пластиком.
Реже техники используют метод штамповки, из-за архаичности и недостатков.
В этом случае сначала создается гипсовая модель, с помощью воска моделируется реставрация и формируется штампик из металла. Гильза из сплава формуется на подготовленном штампе, предварительно ее разогревают для повышения пластичности.
Достаточно быстрой и простой методикой считается пластичная формовка. В этом случае сначала делают слепок челюсти, затем матрицу, лист металла небольшого размера формуется по матрице.
CAD/CAM является перспективной методикой, которая стремительно развивается и внедряется. В этом случае задействуется фрезерный станок, комплекс сканеров и программ, обрабатывающих собранные данные для получения компьютерной модели.
Точность максимальна, но для внедрения методики необходимо серьезное переоснащение лаборатории, которую не в силах позволить себе каждый техник.
Часто один большой фрезерный центр обслуживает множество стоматологических клиник и частных кабинетов. В этом случае сначала создается модель с помощью сканирования ротовой полости, либо создается слепок и сканируется, обрабатывается модель в программе, после чего запускается цикл обработки на станке с ЧПУ.
Объемная печать появилась не так давно, но расценивается, как перспективная, за счет экономических преимуществ.
В этом случае специальный принтер наслаивает заготовку в соответствии с разработанной моделью. Металл в этом случае имеет порошкообразную структуру, сплавление в монолитный сплав происходит под действием лазера.
Из Справочника по Металловедению: Титан
Из Справочника по Металловедению с сайта http://www.naukaspb.ru/
(В.Г. Шипша)
ТИТАН
Титан широко распространен в земной коре, где его содержится около 6 %, а по распространенности он занимает четвертое место после алю-миния, железа и магния. Однако промышленный способ его извлечения был разработан лишь в 40-х годах ХХ века. Благодаря прогрессу в области самолето- и ракетостроения производство титана и его сплавов интенсивно развивалось. Это объясняется сочетанием таких ценных свойств титана, как малая плотность, высокая удельная прочность (s в/r × g), коррозионная стойкость, технологичность при обработке давлением и свариваемость, хладостойкость, немагнитность и ряд других ценных физико-механических характеристик, приведенных ниже.
Характеристики физико-механических свойств титана (ВТ1-00)
Плотность r , кг/м3 | 4,5 × 10–3 |
Температура плавления Тпл, ° С | 1668± 4 |
Коэффициент линейного расширения a × 10–6, град–1 | 8,9 |
Теплопроводность l , Вт/(м × град) | 16,76 |
Предел прочности при растяжении s в, МПа | 300–450 |
Условный предел текучести s 0,2, МПа | 250–380 |
Удельная прочность (s в/r × g)× 10–3, км | 7–10 |
Относительное удлинение d , % | 25–30 |
Относительное сужение Y , % | 50–60 |
Модуль нормальной упругости Е´ 10–3, МПа | 110,25 |
Модуль сдвига G´ 10–3, МПа | 41 |
Коэффициент Пуассона m , | 0,32 |
Твердость НВ | 103 |
Ударная вязкость KCU, Дж/см2 | 120 |
Титан имеет две полиморфные модификации: a -титана с гексагональной плотноупакованной решеткой с периодами а = 0,296 нм, с = 0,472 нм и высокотемпературную модификацию b -титана с кубической объемно-центрированной решеткой с периодом а = 0,332 нм при 900 ° С. Температура полиморфного a « b -превращения составляет 882 ° С.
Механические свойства титана существенно зависят от содержания примесей в металле. Различают примеси внедрения — кислород, азот, углерод, водород и примеси замещения, к которым относятся железо и кремний. Хотя примеси повышают прочность, но одновременно резко снижают пластичность, причем наиболее сильное отрицательное действие оказывают примеси внедрения, особенно газы. При введении всего лишь 0,003 % Н, 0,02 % N или 0,7 % О титан полностью теряет способность к пластическому деформированию и хрупко разрушается.
Особенно вреден водород, вызывающий водородную хрупкость титановых сплавов. Водород попадает в металл при плавке и последующей обработке, в частности при травлении полуфабрикатов. Водород малорастворим в a -титане и образует пластинчатые частицы гидрида, снижающего ударную вязкость и особенно отрицательно проявляющегося в испытаниях на замедленное разрушение.
Поэтому содержание примесей, особенно газов, в титане и титановых сплавах (табл. 17.1, 17.2) строго ограничено.
Промышленный способ производства титана состоит в обогащении и хлорировании титановой руды с последующим его восстановлением из четыреххлористого титана металлическим магнием (магнийтермический метод). Полученный этим методом титан губчатый (ГОСТ 17746–79) в зависимости от химического состава и механических свойств выпускают следующих марок:
ТГ-90, ТГ-100, ТГ-110, ТГ-120, ТГ-130, ТГ-150, ТГ-ТВ (см. табл. 17.1). Цифры означают твердость по Бринеллю НВ, ТВ — твердый.
Для получения монолитного титана губка размалывается в порошок, прессуется и спекается или переплавляется в дуговых печах в вакууме или атмосфере инертных газов.
Механические свойства титана характеризуются хорошим сочетанием прочности и пластичности. Например, технически чистый титан марки ВТ1-0 имеет: s в = 375–540 МПа, s 0,2 = 295–410 МПа, d ³ 20 %, и по этим характеристикам не уступает ряду углеродистых и Cr—Ni коррозионностойких сталей.
Высокая пластичность титана по сравнению с другими металлами, имеющими ГПУ- решетку (Zn, Mg, Cd), объясняется большим количеством систем скольжения и двойникования благодаря малому сотношению с/а = 1,587. По-видимому, с этим связана высокая хладостойкость титана и его сплавов (подробнее см. гл. 13).
При повышении температуры до 250 ° С прочность титана снижается почти в 2 раза. Однако жаропрочные Ti-сплавы по удельной прочности в интервале температур 300–600 ° С не имеют себе равных; при температурах выше 600 ° С сплавы титана уступают сплавам на основе железа и никеля.
Титан имеет низкий модуль нормальной упругости (Е = 110,25 ГПа) — почти в 2 раза меньше, чем у железа и никеля, что затрудняет изготовление жестких конструкций.
Титан относится к числу химически активных металлов, однако он обладает высокой коррозионной стойкостью, так как на его поверхности образуется стойкая пассивная пленка TiO2, прочно связанная с основным металлом и исключающая его непосредственный контакт с коррозионной средой. Толщина этой пленки обычно достигает 5–6 нм.
Благодаря оксидной пленке, титан и его сплавы не корродируют в атмосфере, в пресной и морской воде, устойчивы против кавитационной коррозии и коррозии под напряжением, а также в кислотах органического происхождения.
Производство изделий из титана и его сплавов имеет ряд технологических особенностей. Из-за высокой химической активности расплавленного титана его плавку, разливку и дуговую сварку производят в вакууме или в атмосфере инертных газов.
При технологических и эксплуатационных нагревах, особенно выше 550–600 ° С, необходимо принимать меры для защиты титана от окисления и газонасыщения (альфированный слой) (см. гл. 3).
Титан хорошо обрабатывается давлением в горячем состоянии и удовлетворительно в холодном. Он легко прокатывается, куется, штампуется. Титан и его сплавы хорошо свариваются контактной и аргонодуговой сваркой, обеспечивая высокую прочность и пластичность сварного соединения. Недостатком титана является плохая обрабатываемость резанием из-за склонности к налипанию, низкой теплопроводности и плохих антифрикционных свойств.
Основной целью легирования титановых сплавов является повышение прочности, жаропрочности и коррозионной стойкости. Широкое применение нашли сплавы титана с алюминием, хромом, молибденом, ванадием, марганцем, оловом и др. элементами. Легирующие элементы оказывают большое влияние на полиморфные превращения титана.
Таблица 17.1
Марки, химический состав (%) и твердость титана губчатого (ГОСТ 17746–79)
Марка | Ti, не менее | Не более | Твердость НВ, 10/1500/30, не более | ||||||
Fe | Si | Ni | C | Cl | N | O | |||
ТГ-90 | 99,74 | 0,05 | 0,01 | 0,04 | 0,02 | 0,08 | 0,02 | 0,04 | 90 |
ТГ-100 | 99,72 | 0,06 | 0,01 | 0,04 | 0,03 | 0,08 | 0,02 | 0,04 | 100 |
ТГ-110 | 99,67 | 0,09 | 0,02 | 0,04 | 0,03 | 0,08 | 0,02 | 0,05 | 110 |
ТГ-120 | 99,64 | 0,11 | 0,02 | 0,04 | 0,03 | 0,08 | 0,02 | 0,06 | 120 |
ТГ-130 | 99,56 | 0,13 | 0,03 | 0,04 | 0,03 | 0,10 | 0,03 | 0,08 | 130 |
ТГ-150 | 99,45 | 0,2 | 0,03 | 0,04 | 0,03 | 0,12 | 0,03 | 0,10 | 150 |
ТГ-Тв | 99,75 | 1,9 | – | – | 0,10 | 0,15 | 0,10 | – | – |
Таблица 17.2
Марки и химический состав (%) деформируемых титановых сплавов (ГОСТ 19807–91)
Обозначения | Ti | Al | V | Mo | Sn | Zr | Mn | Cr | Si | Fe | O | H | N | C |
ВТ1-00 | Основа | – | – | – | – | – | – | – | 0,08 | 0,15 | 0,10 | 0,008 | 0,04 | 0,05 |
ВТ1-0 | То же | – | – | – | – | – | – | – | 0,10 | 0,25 | 0,20 | 0,010 | 0,04 | 0,07 |
ВТ1-2 | То же | – | – | – | – | – | – | – | 0,15 | 1,5 | 0,30 | 0,010 | 0,15 | 0,10 |
ОТ4-0 | То же | 0,4–1,4 | – | – | – | 0,30 | 0,5–1,3 | – | 0,12 | 0,30 | 0,15 | 0,012 | 0,05 | 0,10 |
ОТ4-1 | То же | 1,5–2,5 | – | – | – | 0,30 | 0,7–2,0 | – | 0,12 | 0,30 | 0,15 | 0,012 | 0,05 | 0,10 |
ОТ4 | То же | 3,5–5,0 | – | – | – | 0,30 | 0,8–2,0 | – | 0,12 | 0,30 | 0,15 | 0,012 | 0,05 | 0,10 |
ВТ5 | То же | 4,5–6,2 | 1,2 | 0,8 | – | 0,30 | – | – | 0,12 | 0,30 | 0,20 | 0,015 | 0,05 | 0,10 |
ВТ5-1 | То же | 4,3–6,0 | 1,0 | – | 2,0 –3,0 | 0,30 | – | – | 0,12 | 0,30 | 0,15 | 0,015 | 0,05 | 0,10 |
ВТ6 | То же | 5,3–6,8 | 3,5–5,3 | – | – | 0,30 | – | – | 0,10 | 0,60 | 0,20 | 0,015 | 0,05 | 0,10 |
ВТ6с | То же | 5,3–6,5 | 3,5–4,5 | – | – | 0,30 | – | – | 0,15 | 0,25 | 0,15 | 0,015 | 0,04 | 0,10 |
ВТ3-1 | То же | 5,5–7,0 | – | 2,0–3,0 | – | 0,50 | – | 0,8–2,0 | 0,15–0,40 | 0,2–0,7 | 0,15 | 0,015 | 0,05 | 0,10 |
ВТ8 | То же | 5,8–7,0 | – | 2,8–3,8 | – | 0,50 | – | – | 0,20–0,40 | 0,30 | 0,15 | 0,015 | 0,05 | 0,10 |
ВТ9 | То же | 5,8–7,0 | – | 2,8–3,8 | – | 1,0–2,0 | – | – | 0,20–0,35 | 0,25 | 0,15 | 0,015 | 0,05 | 0,10 |
ВТ14 | То же | 3,5–6,3 | 0,9–1,9 | 2,5–3,8 | – | 0,30 | – | – | 0,15 | 0,25 | 0,15 | 0,015 | 0,05 | 0,10 |
ВТ20 | То же | 5,5–7,0 | 0,8–2,5 | 0,5–2,0 | – | 1,5–2,5 | – | – | 0,15 | 0,25 | 0,15 | 0,015 | 0,05 | 0,10 |
ВТ22 | То же | 4,4–5,7 | 4,0–5,5 | 4,0–5,5 | – | 0,30 | – | 0,5–1,5 | 0,15 | 0,5–1,5 | 0,18 | 0,015 | 0,05 | 0,10 |
ПТ-7М | То же | 1,8–2,5 | – | – | – | 2,0–3,0 | – | – | 0,12 | 0,25 | 0,15 | 0,006 | 0,04 | 0,10 |
ПТ-3В | То же | 3,5–5,0 | 1,2–2,5 | – | – | 0,30 | – | – | 0,12 | 0,25 | 0,15 | 0,006 | 0,04 | 0,10 |
АТ3 | То же | 2,0–3,5 | – | – | – | – | – | 0,2–0,5 | 0,20–0,40 | 0,2–0,5 | 0,15 | 0,008 | 0,05 | 0,10 |
Примечание. Сумма прочих примесей во всех сплавах составляет 0,30 %, в сплаве ВТ1-00 — 0,10 %.
ФАЗОВЫЕ ПРЕВРАЩЕНИЯ В ТИТАНОВЫХ СПЛАВАХ
На формирование структуры и, следовательно, свойств титановых сплавов решающее влияние оказывают фазовые превращения, связанные с полиморфизмом титана. На рис. 17.1 представлены схемы диаграмм состояния «титан-легирующий элемент», отражающие подразделение легирующих элементов по характеру влияния на полиморфные превращения титана на четыре группы.
a -Стабилизаторы (Al, O, N), которые повышают температуру полиморфного превращения a « b и расширяют область твердых растворов на основе a -титана (рис. 17.1, а). Учитывая охрупчивающее действия азота и кислорода, практическое значение для легирования титана имеет только алюминий. Он является основным легирующим элементом во всех промышленных титановых сплавах, уменьшает их плотность и склонность к водородной хрупкости, а также повышает прочность и модуль упругости. Сплавы с устойчивой a -структурой термической обработкой не упрочняются.
Изоморфные b -стабилизаторы (Mo, V, Ni, Ta и др.), которые понижают температуру a « b -пре-вращения и расширяют область твердых растворов на основе b -титана (рис. 17.1, б).
Эвтектоидообразующие b -стабилизаторы (Cr, Mn, Cu и др.) могут образовывать с титаном интерметаллиды типа TiХ. В этом случае при охлаждении b -фаза претерпевает эвтектоидное превращение b ® a + TiХ (рис. 17.1, в). Большинство
b -стабилизаторов повышает прочность, жаропрочность и термическую стабильность титановых сплавов, несколько снижая их пластичность (рис. 17.2.). Кроме того, сплавы с (a + b ) и псевдо-b -структурой могут упрочняться термообработкой (закалка + старение).
Нейтральные элементы (Zr, Sn) не оказывают существенного влияния на температуру полиморфного превращения и не меняют фазового состава титановых сплавов (рис. 17.1, г).
Полиморфное b ® a -превращение может происходить двумя путями. При медленном охлаждении и высокой подвижности атомов оно происходит по обычному диффузионному механизму с образованием полиэдрической структуры твердого a -раствора. При быстром охлаждении — по бездиффузионному мартенситному механизму с образованием игольчатой мартенситной структуры, обозначаемой a ¢ или при большей степени легированности — a ¢ ¢ . Кристаллическая структура a , a ¢ , a ¢ ¢ практически однотипная (ГПУ), однако решетка a ¢ и a ¢ ¢ более искажена, причем степень искаженности возрастает с увеличением концентрации легирующих элементов. Есть сведения [ 1] , что решетка a ¢ ¢ -фазы скорее ромбическая, чем гексагональная. При старении из фаз a ¢ и a ¢ ¢ выделяется b -фаза или интерметаллидная фаза.
Рис. 17.1. Диаграммы состояний систем «Тi-легирующий элемент» (схемы):
а) «Тi-a -стабилизаторы»;
б) «Тi-изоморфные b -стабилизаторы»;
в) «Тi-эвтектоидообразующие b -стабилизаторы»;
г) «Тi-нейтральные элементы»
Рис. 17.2. Влияние легирующих элементов на механические свойства титана
В отличие от мартенсита углеродистых сталей, являющегося раствором внедрения и характеризующегося высокой прочностью и хрупкостью, титановый мартенсит является раствором замещения, и закалка титановых сплавов на мартенсит a ¢ приводит к небольшому упрочнению и не сопровождается резким снижением пластичности.
Фазовые превращения, происходящие при медленном и быстром охлаждении титановых сплавов с различным содержанием b -стабилизаторов, а также получаемые структуры отражены на обобщенной диаграмме (рис. 17.3). Она справедлива для изоморфных b -стабилизаторов (рис. 17.1, б) и, с некоторым приближением, для эвтектоидообразующих b -стабилизаторов (рис. 17.1, в), так как эвтектоидный распад в этих сплавах происходит очень медленно, и им можно пренебречь.
Рис. 17.3. Схема изменения фазового состава сплавов «Ti-b -стабилизатор» в зависимости от скорости
охлаждения и закалки из b -области
При медленном охлаждении в титановых сплавах, в зависимости от концентрации b -стабилизаторов, могут быть получены структуры: a , a + b или b соответственно.
При закалке в результате мартенситного превращения в интервале температур Мн–Мк (на рис. 17.3 показаны пунктиром) следует различать четыре группы сплавов.
В первую группу входят сплавы с концентрацией b -стабилизирующих элементов до С1, т. е. сплавы, которые при закалке из b -области имеют исключительно a ¢ (a ¢ ¢ )-структуру. После закалки этих сплавов с температур (a + b )-области в интервале от полиморфного превращения до Т1, их структура представляет собой смесь фаз a ¢ (a ¢ ¢ ), a и b , а после закалки с температур ниже Ткр они имеют (a + b )-структуру.
Вторую группу составляют сплавы с концентрацией легирующих элементов от С1 до Скр, у которых при закалке из b -области мартенситное превращение не происходит до конца и они имеют структуру a ¢ (a ¢ ¢ ) и b . Сплавы этой группы после закалки с температур от полиморфного превращения до Ткр имеют структуру a ¢ (a ¢ ¢ ), a и b , а с температур ниже Ткр — структуру (a + b ).
Закалка сплавов третьей группы с концентрацией b -стабилизирующих элементов от Скр до С2 с температур b -области или с температур от полиморфного превращения до Т2 сопровождается превращением части b -фазы в w -фазу, и сплавы этого типа после закалки имеют структуру (b + w ). Сплавы третьей группы после закалки с температур ниже Т2 имеют структуру (b + a ).
Сплавы четвертой группы после закалки с температур выше полиморфного превращения имеют исключительно b -структуру, а с температур ниже полиморфного превращения — (b + a ).
Необходимо отметить, что превращения b ® b + w может происходить как при закалке сплавов с концентрацией (Скр–С2), так и при старении сплавов с концентрацией более С2, имеющих метастабильную b -фазу. В любом случае, присутствие w -фазы нежелательно, так как она сильно охрупчивает титановые сплавы. Рекомендуемые режимы термообработки исключают ее присутствие в промышленных сплавах или появление в условиях эксплуатации.
Для титановых сплавов применяют следующие виды термообработки: отжиг, закалка и старение, а также химико-термическая обработка (азотирование, силицирование, оксидирование и др.).
Отжиг проводится для всех титановых сплавов с целью завершения формирования структуры, выравнивания структурной и концентрационной неоднородности, а также механических свойств. Температура отжига должна быть выше температуры рекрисаллизации, но ниже температуры перехода в b -состояние (Тпп) во избежание роста зерна. Применяют обычный отжиг, двойной или изотермический (для стабилизации структуры и свойств), неполный (для снятия внутренних напряжений).
Закалка и старение (упрочняющая термообработка) применима к титановым сплавам с (a + b )-структурой. Принцип упрочняющей термообработки заключается в получении при закалке метастабильных фаз b , a ¢ , a ¢ ¢ и последующем их распаде с выделением дисперсных частиц a — и b -фаз при искусственном старении. При этом эффект упрочнения зависит от типа, количества и состава метастабильных фаз, а также дисперсности образовавшихся после старения частиц a — и b -фаз.
Химико-термическая обработка проводится для повышения твердости и износостойкости, стойкости к «схватыванию» при работе в условиях трения, усталостной прочности, а также улучшения коррозионной стойкости, жаростойкости и жаропрочности. Практическое применение имеют азотирование, силицирование и некоторые виды диффузионной металлизации.
ПРОМЫШЛЕННЫЕ ТИТАНОВЫЕ СПЛАВЫ
Титановые сплавы по сравнению с техническим титаном имеют более высокую прочность, в том числе и при высоких температурах, сохраняя при этом достаточно высокую пластичность и коррозионную стойкость.
Марки и химический состав отечественных
сплавов (ГОСТ 19807–91) представлены в табл. 17.2.
По технологии изготовления титановые сплавы подразделяются на деформируемые и литейные; по уровню механических свойств — на сплавы невысокой прочности и повышенной пластичности, средней прочности, высокопрочные; по условиям применения — на хладостойкие, жаропрочные, коррозионностойкие. По способности упрочняться термообработкой они делятся на упрочняемые и неупрочняемые, по структуре в отожженном состоянии — на a -, псевдо-a -, (a + b )-, псевдо-b — и b -сплавы (табл. 17.3).
Отдельные группы титановых сплавов различаются по величине условного коэффициента стабилизации Кb , который показывает отношение содержания b -стабилизирующего легирующего элемента к его содержанию в сплаве критического состава скр. При содержании в сплаве нескольких b -стабилизирующих элементов их Кb суммируется.
Деформируемые титановые сплавы
Титановые сплавы невысокой прочности и повышенной пластичности
К этой группе относятся сплавы с пределом прочности s в < 700 МПа, а именно: a -сплавы марок ВТ1-00, ВТ1-0 (технический титан) и сплавы ОТ4-0, ОТ4-1 (система Ti—Al—Mn), АТ3 (система Ti—Al c небольшими добавками Cr, Fe, Si, B), относящиеся к псевдо-a -сплавам с небольшим количеством b -фазы. Характеристики прочности этих сплавов выше, чем чистого титана благодаря примесям в сплавах ВТ1-00 и ВТ1-0 и незначительному легированию a — и b -стабилизаторами в сплавах ОТ4-0, ОТ4-1, АТ3.
Эти сплавы отличаются высокой пластичностью как в горячем, так и в холодном состоянии, что позволяет получать все виды полуфабрикатов: фольгу, ленту, листы, плиты, поковки, штамповки, профили, трубы и т. п. Механические свойства полуфабрикатов из этих сплавов приведены в табл. 17.4–17.6.
Таблица 17.3
Классификация титановых сплавов по структуре
Группа сплавов | Марка сплава |
a -Сплавы | ВТ1-00, ВТ1-0, ВТ5, ВТ5-1, ПТ-7М |
Псевдо-a -сплавы | ОТ4-0, ОТ4-1, ОТ4, ВТ20, АТ3 |
(a + b )-Мартенситного класса (Кb = 0,3–0,9) | ВТ6С, ВТ6, ВТ14, ВТ8, ВТ9, ПТ-3В, ВТ3-1, АТ3 |
(a + b )-Сплавы переходного класса (Кb = 1,0–1,4) | ВТ22, ВТ30* |
Псевдо-b -сплавы (Кb = 1,5–2,4) | ВТ35*, ВТ32*, ВТ15 |
b -Сплавы (Кb = 2,5–3,0) | 4201* |
* Опытные сплавы.
Таблица 17.4
Механические свойства листов из титановых сплавов (ГОСТ 22178–76)
Марки титановых | Состояние образцов | Толщина листов, | Предел прочности, s в, МПа | Относительное удлинение, d , % |
не менее | ||||
ВТ1-00 | Отожженное | 0,3–1,8 | 295 (295–440) | 30 (30) |
Св. 1,8–6,0 | 25 (30) | |||
Св. 6,0–10,5 | 20 (20) | |||
ВТ1-0 | То же | 0,3–0,4 | 375 (375–540) | 25 (25) |
Св. 0,4–1,8 | 30 (30) | |||
Св. 1,8–6,0 | 25 (25) | |||
Св. 6,0–10,5 | 20 (20) | |||
ОТ4-0 | Отожженное | 0,3–0,4 | 470 (490–635) | 25 (25) |
0,4–1,8 | 30 (30) | |||
1,8–6,0 | 25 (25) | |||
6,0–10,5 | 20 (20) | |||
ОТ4-1 | То же | 0,3–0,7 | 590 (590–785) | 25 (25) |
Св. 0,7–1,8 | 20 (20) | |||
Св. 1,8–6,0 | 15 (15) | |||
Св. 6,0–10,5 | 13 (13) | |||
ОТ4 | То же | 0,5–1,0 | 685 (685–885) | 20 (20) |
Св.1,0–1,8 | 15 (15) | |||
Св. 1,8–6,0 | 12 (12) | |||
Св. 6,0–10,5 | 10 (12) | |||
ВТ5-1 | То же | 0,8–1,2 | 735 (735–930) | 15 (15) |
Св. 1,2–1,8 | 12 (12) | |||
Св. 1,8–6,0 | 10 (10) | |||
Св. 6,0–10,5 | 8 (8) | |||
ВТ6 | То же | 1,0–10,5 | 885 (885–1080) | 8 (8) |
ВТ14 | Отожженное | 0,8–5,0 | 885 (885–1050) | 8 (8) |
Св. 5,0–10,5 | 835 (835–1050) | 8 (8) | ||
Закаленное и | 0,8–1,5 | 1080 (1080) | 5 (5) | |
Св. 1,5–5,0 | 1180 (1180) | 6 (6) | ||
Св. 5,0–7,0 | 1080 (1080) | 4 (4) | ||
Св. 7,0–10,5 | 1100 (1100) | 4 (4) | ||
ВТ20 | Отожженное | 0,8–1,8 | 930 (930–1180) | 12 (12) |
Св. 1,8–4,0 | 10 (10) | |||
Св. 4,0–10,5 | 8 (8) | |||
Отожженное | 0,8–4,0 | 980 (980–1180) | 9 (9) | |
Св. 4,0–10,5 | 6 (6) |
Примечание. В скобках приведены данные для листов с высокой отделкой поверхности.
Таблица 17.5
Механические свойства прутков из титановых сплавов (ГОСТ 26492–85)
Марка сплава | Состояние | Диаметр прутка, мм | Предел | Относительное | Относительное % | Ударная |
не менее | ||||||
ВТ1-00 | Отожженные | 10–100 | 295 (295–440) | 20 (20) | 50 (55) | 100 (120) |
100–150 | 265 (265–440) | 40 (42) | 60 (60) | |||
ВТ1-0 | То же | 10–100 | 345 (345–540) | 15 (20) | 40 (50) | 70 (100) |
100–150 | 36 (38) | 50 (60) | ||||
ВТ1-2 | То же | 65–150 | 590–930 | 8 | 17 | 25 |
ОТ4-0 | То же | 10–100 | 440 (490–635) | 15 (20) | 35 (40) | 50 (70) |
100–150 | 13 (20) | 30 (32) | 40 (50) | |||
ОТ4-1 | То же | 10–100 | 540 (590–735) | 12 (15) | 30 (35) | 45 (45) |
100–150 | 10 (13) | 21 (24) | 40 (40) | |||
ОТ4 | То же | 10–100 | 685 (685–885) | 8 (10) | 25 (30) | 40 (40) |
100–150 | 635 (635–885) | 20 (21) | 35 (35) | |||
ВТ5 | Отожженные | 10–100 | 735 (735–930) | 8 (10) | 20 (25) | 30 (50) |
100–150 | 685 (715–930) | 6 (6) | 15 (18) | 30 (50) | ||
ВТ5-1 | То же | 10–100 | 785 (785–980) | 8 (10) | 20 (25) | 40 (40) |
100–150 | 745 (745–980) | 6 (6) | 15 (18) | 40 (45) | ||
ВТ6 | Отожженные | 10–100 | 885 (905–1050) |
Химические и механические свойства титана и его сплавов
Химические свойства
Титан, как и другие элементы, представляет собой смесь нескольких изотопов, атомный вес которых находится в диапазоне от 46 до 50. Пропорции этих изотопов были рассчитаны на основе спектрографического анализа. Математические расчеты с использованием пропорций и массовых чисел дали титану средний атомный вес 47,88.
Титан имеет большое поперечное сечение захвата, и были идентифицированы пять других изотопов титана.Титан 43 имеет период полураспада 0,58 секунды и является бета-положительным излучателем. Титан 45 имеет две формы: бета-положительный и гамма-излучатель с периодом полураспада 3,08 часа, а вторую — с периодом полураспада 21 день. Титан 51 имеет период полураспада 72 дня и является бета-отрицательным и гамма-излучателем. Существует также метастабильная форма титана 51, который имеет период полураспада 6 минут и также является гамма- и бета-отрицательным излучателем.
Валентность. Как характерно для переходных элементов, титан имеет переменную валентность и обычно находится в двух-, трех- и четырехвалентном состояниях.В литературе сообщается о валентности пять и выше, но никакого подтверждения этому никогда не было.
Газы . Химическая активность титана зависит от температуры. Взаимодействие металла с другими веществами легче происходит при повышенных температурах. Это свойство особенно подтверждается чрезвычайной реакционной способностью металла по отношению к газам атмосферы при высоких температурах.
Это требует использования инертной атмосферы для горячей обработки и защиты поверхности при высоких температурах.Быстрое сочетание титана с химически активными газами атмосферы при температуре выше 950 ° F приводит к образованию накипи на поверхности. По мере увеличения промежутков времени и повышения температуры газы диффундируют в решетку.
Металл соединяется с кислородом с образованием длинного ряда оксидов от TiO до Ti 7 O 12 , каждый из которых имеет различный оттенок, и при коротких выдержках образуется поверхностная пленка радужного цвета. Хотя это поверхностное окисление происходит при температуре 950 ° F, заметной диффузии в решетку ниже 1300 ° F не происходит.Воспламенение металла происходит на воздухе при температуре 2200 ° F, а в атмосфере чистого кислорода эта температура снижается до 1130 ° F.
Реакционная способность титана с азотом аналогична его действию с кислородом, где на поверхности образуется желто-коричневый налет в виде нитрида. Азот будет диффундировать в решетку с ограниченной глубиной проникновения. Это свойство было использовано в нитридной оболочке металла.
Самая уникальная из реакций газ-титан — это реакция между водородом и металлом.Реакция протекает при температурах немного выше комнатной, и до 400 см3 газа может быть поглощено одним граммом титана. В небольших количествах газ добавляется в виде примеси, но при более высоких концентрациях образуется гидрид TiH. Однако добавление водорода к титану стабильно только при температуре ниже 680 ° F; выше этой температуры газ выделяется и горит.
Все эти газо-титановые реакции ускоряются за счет снижения давления пара, и требуется полная защита от атмосферы.
Водяной пар и диоксид углерода разлагаются горячим металлическим титаном. При температуре выше 1500 ° F водяной пар и металл объединяются, образуя оксид и выделяя водород. При более высоких температурах чугун поглотит CO 2 и может образовать оксид и карбид.
Кислоты. Химическая реакционная способность титана по отношению к галогенидам аналогичным образом проявляется в его сочетании с их кислотами. Самая быстрая реакция — снова с фторидом. Эта реакция имеет различные применения; это один из основных агентов растворения металла и его сплавов для химического анализа; он используется в качестве общего травителя как в макро, так и в микромасштабе, в металлографических работах; и он также используется в качестве средства для удаления накипи.
Действие соляной кислоты и аналогичным образом серной кислоты протекает медленно при комнатной температуре. Однако небольшое количество тепла ускоряет атаку, что приводит к образованию низших хлоридов и моносульфата. Эти реакции используются таким же образом, что и плавиковая кислота, и, поскольку они менее токсичны и вызывают коррозию, они постепенно заменяют фтористую кислоту.
Органика. Химическая реакционная способность титана с органическими веществами используется в металлургической промышленности лишь в незначительной степени.Реакции органической кислоты с титаном приводят к образованию окрашенных пленок на поверхности металла, которые металлографы используют для травления микропрепаратов.
Твердые тела. В расплавленном состоянии титан соединяется со многими металлами, металлоидами и углеродистыми веществами с образованием систем большого значения. В оксидном состоянии он реагирует с щелочными, щелочноземельными и тяжелыми неблагородными металлами с образованием титанатов, некоторые из которых изучаются в сочетании с более дешевыми методами производства.
Реакционная способность к металлоидам, особенно к оксидам металлов, чрезвычайно беспокоила литейщика, поскольку расплавленный титан сильно разрушает большинство известных огнеупоров с образованием систем металл-металлоид. Такие тугоплавкие материалы, как диоксид кремния и оксид алюминия, подвергаются настолько сильному воздействию, что их использование опасно. Из всех металлоидов только оксид бериллия и оксид тория показали заметное сопротивление жидкому металлу.
Еще одна очень важная реакция — это углерод и титан.Металл в расплавленном состоянии имеет большое сродство к углероду, и из-за его пагубного воздействия на свойства титана необходимо проявлять особую осторожность, чтобы минимизировать его присутствие в готовых изделиях.
Электрохимия. Металл можно электроосаждать различными комплексными методами, ни один из которых не дает промышленно применимых пленок. Электролитические средства использовались для восстановления металла из его четырехвалентного состояния как в двух-, так и в трехвалентную формы с использованием кислотных электролитов и электродов из свинца, меди, платины или ртути.
Безопасность. Химическая активность титана, как правило, не представляет опасности. За исключением мелкодисперсных частиц и металла, подвергающегося воздействию дымящей азотной кислоты в течение длительного времени, он не является взрывоопасным или легковоспламеняющимся веществом.
Механические свойства
Свойства при растяжении. Нелегированный титан может иметь предел прочности на разрыв от 35000 фунтов на квадратный дюйм (250 МПа) для металла высокой чистоты, полученного в процессе восстановления йодида, до 100000 фунтов на квадратный дюйм (690 МПа) для металла, полученного из губчатого титана высокой твердости.Изделия из нелегированного титана, полученные дуговой плавкой, достаточно пластичны.Пластичность. Продукты из технически чистого титана, полученные дуговым плавлением, имеют пластичность от 20% до 40% при удлинении и от 45% до 65% уменьшения площади в зависимости от содержания внедрения. Обработка титана йодидом дает продукт с удлинением 55% при уменьшении площади на 80%.
Как и в случае со сталью, титан сплавлен с другими металлами для повышения его прочности.Такие металлические добавки, как Al , V , Cr , Fe , Mn , Sn , используются либо как бинарные добавки, либо как сложные системы. Однако результирующее увеличение прочности достигается за счет снижения пластичности.
Модуль упругости. Нелегированный титан имеет модуль около 15×10 6 psi и может быть увеличен до 18×10 6 psi путем легирования. Модуль упругости титана выгодно отличается от модуля упругости алюминия (10.4×10 6 ) и магния (6,4×10 6 ), но хуже, чем у стали (29×10 6 ).
Как и модуль упругости, модуль упругости при сдвиге, модуль жесткости титана находится между модулями алюминия и стали.
Твердость. Титан — гораздо более твердый металл, чем алюминий, и приближается к высокой твердости, присущей некоторым термообработанным легированным сталям. Титан йодидной чистоты имеет твердость 90 VHN (по Виккерсу), нелегированный технический титан имеет твердость около 160 VHN, а при легировании и термообработке титан может достигать твердости в диапазоне от 250 до 500 VHN.Можно ожидать, что типичный промышленный сплав с пределом текучести 130 000 фунтов на квадратный дюйм будет иметь твердость около 320 VHN или 34 по шкале Роквелла C.
Ударопрочность. Знания прочности на растяжение и пластичности металла недостаточны для многих инженерных приложений без знания ударной вязкости. Титан — один из немногих металлов, обладающих хорошей ударной вязкостью, высокой прочностью и пластичностью.
Титан может иметь ударную вязкость в диапазоне от более 100 фут-фунтов по Шарпи для йодидного продукта более высокой чистоты и 30 фут-фунтов для коммерческого нелегированного продукта до 1 или 2 фут-фунта для некоторых высокопрочных, но хрупких сплавов.
AMS | Недвижимость |
4900L | Лист, полоса и пластина, ХП, отожженный, предел текучести 55,0 тыс. Фунтов на кв. Дюйм (379 МПа) |
4901M | Лист, полоса и пластина, C.P. Отожженная, 70.0 тыс. Фунтов / кв. Дюйм (485 МПа) |
4902G | Лист, полоса и пластина, C.P. Отожженный, 40,0 тыс. Фунтов на квадратный дюйм (276 МПа). |
4905B | Поврежденная пластина класса 6AL — 4V, бета, отожженная |
4907F | Листы, полосы и пластины 6AL-4V, отожженные со сверхнизким межстраничным покрытием |
4908F | Лист и полоса, 8Mn, отожженные, 110000 фунтов на кв. Дюйм (760 МПа) Предел текучести |
4909F | Лист, полоса и пластина 5AL -2.5Sn, сверхнизкое межстраничное объявление, отожженное |
4910K | Лист, полосы и пластины 5AL — 2.5Sn отожженный |
4911H | Лист, полоса и пластина, 6AL — 4V, отожженный |
4914A | Холоднокатаный лист и полоса, 15V — 3AL — 3Cr — 3Sn термообработка в растворе |
4915G | Лист, полоса и пластина, 8AL — 1V — 1Mo, однократный отжиг |
4916F | Лист, полоса и пластина, 8AL — 1Mo — 1V, дуплексный отожженный |
4917E | Лист, полоса и пластина, 13.5V — 11Cr — 3.0AL, термообработка в растворе |
4918H | Лист, полоса и пластина, 6AL — 6V- 2Sn отожженный |
4919C | Лист, полоса и пластина, 6AL– 2Sn — 4Zr — 2M0 — 0,08Si, дуплексный отжиг |
4920B | Поковки, 6AL — 4V, альфа-бета- или бета-обработка, отожженные |
4921G | Проволока, поковки и кольца C.P. 70,0 ksi (438 МПа) Предел текучести |
4924D | Прутки, поковки и кольца 5AL — 2,5Sn, сверхнизкое межстраничное покрытие, отожженные |
4926J | Прутки, проволока и кольца, 5AL — 2,5Sn отожженные, предел текучести 110 тыс. Фунтов на кв. Дюйм (758 МПа) |
4928Q | Прутки, проволока, поковки, кольца и фасонные детали 6AL — 4V, отожженные |
4930E | Прутки, проволока, поковки и кольца, 6AL — 4V, отожженные со сверхмалым межузельным промежутком |
4931A | Прутки, поковки и кольца 6AL — 4V Дуплексный отжиг со сверхнизким промежутком (ELI), вязкость разрушения |
4933B | Кольца для экструзии и оплавления, 8AL — 1Mo — 1V, термообработанные и стабилизированные в растворе |
4934C | Экструзионные и оплавленные кольца 6AL — 4V Термообработка и выдержка в растворе |
4935F | Кольца для экструзии и оплавления, 6AL — 4V, отожженные, обработанные бета-версии |
4936D | Кольца, изготовленные методом экструзии и оплавления, 6AL — 6V — 2Sn, бета-прессованные, отожженные, термообработанные |
4937A | Кольца, изготовленные методом экструзии и оплавления 6AL –6V — 2Sn Beta Extruded Plus, отожженные, термообработанные |
4941C | Трубки, сварные, отожженные, предел текучести 40 000 фунтов на кв. Дюйм (275 МПа) |
4942D | Трубки, бесшовные, отожженные, предел текучести 40 000 фунтов на кв. Дюйм (275 МПа) |
4943F | Гидравлические, бесшовные трубы 3.0AL — 2,5 В отожженный |
4944F | Бесшовные гидравлические трубки 3.0AL — 2.5 В, холодная обработка, снятие напряжений |
4945B | Трубки, бесшовные, гидравлические, 3AL — 2,5 В, с регулируемой текстурой, предел текучести 105 тыс. Фунтов на кв. Дюйм (724 МПа) Холодная обработка, снятие напряжений |
4950 | Прутки, проволока, поковки и кольца 6.0AL — 4.0V Раствор, термообработанный и модифицированный после выдержки, прочность |
4951F | Сварочная проволока, C.P. Упаковка с контролем окружающей среды |
4952A | Проволока сварочная, 6AL — 2Sn — 4Zr — 2Mo |
4953C | Сварочная проволока.5АЛ — 2.5Сн |
4954F | Проволока сварочная, 6AL — 4В |
4955D | Сварочная проволока, 8AL — 1Mo — 1V |
4956C | Сварочная проволока, 6AL — 4V, сверхмалое межстраничное пространство, упаковка с контролем окружающей среды |
4957B | Круглый пруток и проволока, 3AL — 8V — 6Cr — 4Mo — 4Zr, плавящийся расходный электрод, термообработка и холодная вытяжка в растворе |
4958A | Прутки и стержни, 3AL — 8V — 6Cr — 4Mo — 4Zr, плавящийся плавящийся электрод, термообработка на твердом растворе и бесцентровая шлифовка |
4959C | Провод, 13.5V — 11Cr — 3AL, Пружина |
4963 | Прутки, проволока, поковки и кольца 6AL — отожженные на 4 В, термообработанные, с измененной прочностью |
4965G | Прутки, проволока, поковки и кольца 6AL — 4V Термообработка и выдержка в растворе |
4966L | Поковки 5АЛ — 2.5Sn отожженный, 110 тыс. Фунтов на кв. Дюйм (758 МПа) Предел текучести |
4967H | Прутки, проволока, поковки и кольца 6AL — 4V, отожженные, термообработанные |
4970F | Прутки, проволока и поковки 7AL — 4Mo, термообработанные в растворе и осаждении |
4971E | Прутки, проволока, поковки и кольца 6AL — 6V — 2Sn отожженные, термообрабатываемые |
4972D | стержни, проволока и кольца, 8AL — 1Mo — 1V, термообработанные и стабилизированные в растворе |
4973D | Поковки, 8AL — 1Mo — 1V, термообработанные и стабилизированные в растворе |
4974C | Прутки и поковки, 11Sn — 5.0Zr — 2.3AL — 1.0Mo — 0.21Si, термообработка в растворе и осаждении |
4975G | Прутки, проволока и кольца, 6.0AL — 2.0Sn — 4.0Zr — 2.oMo — 0,08Si, термообработка в растворе и осаждении |
4976E | Поковки, 6AL — 2Sn — 4Zr — 2Mo, термообработанные в растворе и осаждении |
4978C | Прутки, проволока, поковки и кольца, 6AL — 6V — 2Sn, отожженные |
4979D | Прутки, проволока, поковки и кольца 6AL — 6V — 2Sn с термообработкой в растворе и осаждении |
4981C | Прутки, проволока и поковки, 6AL– 2Sn — 4Zr — 6Mo, термообработанные в растворе и осаждении |
Обрабатываемость титановых сплавов при сверлении
1.Введение
1.1. Технология сверления
Изготовление отверстий является важным процессом в конструктивных каркасах самолета и составляет от 40 до 60% всех операций по удалению материала (Brinksmeier, 1990). Этот процесс обычно делится на сверление коротких и глубоких отверстий. Бурение коротких отверстий обычно охватывает отверстия с малым отношением глубины к диаметру, диаметром до 30 мм и глубиной не более чем в 5 раз больше диаметра. Между тем, при глубоком сверлении используются отверстия диаметром более 30 мм, а глубина обычно превышает 2.В 5 раз больше диаметра отверстия. Для сверления более глубоких отверстий с помощью обычных сверл требуется метод клевки, чтобы стружка могла легко вытекать из отверстия. Сверление глубоких отверстий сложнее, особенно когда прямолинейность отверстия является основной проблемой. Поэтому обычным методом является выполнение круглого пропила с использованием полого режущего инструмента. Этот метод позволяет просверливать отверстия большего диаметра с меньшей мощностью. Кроме того, отверстия могут быть выполнены во многих формах, включая сквозные или глухие (рис. 1).Сквозное отверстие — это отверстие, которое просверливается полностью насквозь заготовку, в то время как глухое отверстие просверливается только на определенную глубину.
Спиральное сверло состоит из 3 основных частей, как показано на рис. 2. Наиболее важными характеристиками с аналитической точки зрения являются передний угол, угол при вершине, толщина стенки, номинальный задний угол, диаметр сверла, угол наклона и кромка долота. угол. Передний угол обычно определяется как угол винтовой линии на периферии. Направление потока стружки определяется углом при вершине.Крутящий момент уменьшается с увеличением угла при вершине из-за увеличения ортогонального переднего угла в каждой точке на основных режущих кромках. Кроме того, сила тяги всегда увеличивается с увеличением угла при вершине.
На рис. 3 показаны этапы операции бурения, первая — это фаза запуска и центрирования, вторая — фаза полного бурения и, наконец, фаза прорыва (Tonshoff et al., 1994). Для обеспечения хорошего качества поверхности и точности отверстий очень важен первый этап (рис.3 (а)), чтобы избежать преждевременного износа и поломки сверла. На этом этапе крутящий момент и усилие инструмента постоянно увеличиваются. Полная фаза сверления начинается, когда основные режущие кромки полностью входят в зацепление (Рис. 3 (b)). Фаза прорыва начинается, когда острие сверла пробивает нижнюю часть заготовки, и процесс останавливается, когда корпус сверла проходит через заготовку (рис. 3 (c)).
Рис. 1.
Тип отверстия, (a) Сквозное отверстие и (b) глухое отверстие.
Рис. 2.
Геометрия сверла (Линдберг, 1990).
Рис. 3.
Фазы бурения: (а) фаза центрирования, (б) фаза полного сверления и (в) фаза прорыва.
2. Износ инструмента в процессе сверления
Выделение тепла, давление, трение и распределение напряжений являются основными факторами износа сверла. Износ сверла можно разделить на (Kanai et al., 1978): внешний угол ( w ), износ по задней поверхности ( V b ), краевой износ ( M w ), Кратерный износ ( K M ), а также два типа износа кромки долота ( C T и C M ) и сколы на режущих кромках ( P T и P M ).На рис. 4 показаны вышеупомянутые типы износа. Износ начинается с острых углов режущих кромок и распространяется по режущим кромкам до кромки долота и сверла (Schneider, 2001). Износ по задней поверхности считается одним из критериев оценки производительности сверла. Это происходит из-за трения между заготовкой и контактной площадкой на задней поверхности. Однако Kanai et al. (1978) предположили, что износ внешнего угла должен использоваться в качестве основного критерия производительности инструмента из-за относительной простоты измерения и тесной связи между этим типом износа и сроком службы сверла.
Рис. 4.
Типы износа сверла (Kanai et al., 1978).
Кратерный износ также наблюдался на передней поверхности сверла, и его можно отчетливо обнаружить вокруг внешних углов режущих кромок (Choudhury & Raju, 2000; Kaldor & Lenz, 1980). Согласно Dolinsek et al., (2001), поверхность износа за режущими кромками менее значима как индикатор износа инструмента, поскольку она зависит от угла заточки. Они предположили, что сверло будет считаться поврежденным после того, как угол сверла будет закруглен, как показано на рис.5. Однако Fujise и Ohtani (1998) и Harris et al. (2003) рассматривали износ внешнего угла в качестве критерия отказа от инструмента (рис. 6). Инструмент был забракован, когда износ внешнего угла достиг 75% от общей ширины поля. Калдор и Ленц (1980) также использовали угловой износ в качестве критерия стойкости инструмента при сверлении из-за аналогичного износа других режущих инструментов.
Рис. 5.
Расположение износа по задней поверхности сверла (Dolinsek et al., 2001).
Рисунок 6.
Метод измерения износа внешнего угла от фиксированной контрольной точки (Harris et al., 2003).
Tetsutaro & Zhao (1989) считают, что инструмент отвергается, когда максимальная ширина износа по задней поверхности V b, max достигла 0,7 мм при сверлении простой стали. Wen & Xiao (2000) использовали для измерения ширины износа на боковых поверхностях при сверлении нержавеющей стали. Линь (2002) отклонил инструмент на основании критериев отклонения инструмента, когда максимальная площадь износа по задней поверхности превышала 0.8 мм, значение шероховатости поверхности превышало 5,0 мкм, чрезмерный надрыв внешнего угла и сколы спиральных канавок. Choudhury & Raju (2000) изучали влияние подачи и скорости на кратерный износ в различных точках вдоль режущей кромки при бурении. Эзугву и Лай (Ezugwu & Lai, 1995) отвергли сверло, когда максимальный износ по задней поверхности любой из губ сверла превышал 0,38 мм, возникал скрипящий шум во время обработки и разрушение или катастрофический отказ сверла. Эти критерии использовались при исследовании бурения Inconel 901 с использованием сверл из быстрорежущей стали.
3. Титановые сплавы
Легкие материалы, такие как титановые сплавы, в настоящее время используются в конструкции современных самолетов, особенно в компонентах реактивных двигателей, которые подвергаются температурам до 1000 ° C. Титановые сплавы обладают наилучшим сочетанием физических и металлургических свойств и зарекомендовали себя как весьма привлекательные в качестве конструкционных материалов из-за их высокого отношения прочности к весу, низкой плотности, превосходной коррозионной стойкости, превосходной эрозионной стойкости и низкого модуля упругости (Brewer et al. al., 1998)
Титановые сплавы подразделяются на группы на основе легирующих элементов и образующихся преобладающих составляющих фаз при комнатной температуре. Эти группы включают α-сплав, α- β-сплав и β-сплав. Сплавы α можно разделить на два типа: технически чистые сорта титана и сплавы с добавками α-стабилизаторов, таких как Al и Sn. Сплавы α не поддаются термической обработке и обычно хорошо свариваются. Они обладают прочностью от низкой до средней, хорошей ударной вязкостью, достаточно хорошей пластичностью и обладают превосходными механическими свойствами, которые обеспечивают оптимальную стойкость к ползучести при высоких температурах и стойкость к окислению (Boyer, 1996; Ezugwu and Wang, 1997).К ним относятся такие сплавы, как Ti-3Al-2.5V, Ti-5Al-2.5Sn, Ti-8Al-1Mo-1V и Ti-6Al-2Sn-4Zr-2Mo. Широкий спектр применения α-сплавов включает кожухи газотурбинных двигателей, обшивку воздушной рамы и конструктивные элементы, а также лопатки компрессора реактивного двигателя.
Большинство титановых сплавов, используемых в промышленности, содержат альфа- и бета-стабилизаторы. Эти сплавы включают Ti-6Al-4V, Ti-6Al-6V-2Sn и Ti-6Al-2Sn-4Zr-6Mo. Они поддаются термообработке, и большинство из них пригодны для сварки, особенно с нижним β-стабилизатором. Их уровни силы от среднего до высокого.Эти сплавы обладают превосходным сочетанием прочности, ударной вязкости и коррозионной стойкости. Типичные области применения включают лопасти и диски для турбин и компрессоров реактивных двигателей, структурные компоненты самолетов и шасси, химическое технологическое оборудование, морские компоненты и хирургические имплантаты. Между тем, β-сплавы содержат небольшое количество α-стабилизирующих элементов в качестве упрочняющих и обычно свариваемых, имеют высокую коррозионную стойкость и хорошее сопротивление ползучести при промежуточных температурах. Добавки ванадия, железа и хрома в качестве стабилизирующих элементов обеспечивают превосходные характеристики горячей обработки.Ti-10V-2Fe-3Al, Ti-15V-3Cr-3Al-3Sn, Ti-15Mo-2.7Nb-3Al-0.2Si и Ti-3Al-8V-6Cr-4Mo-4Zr являются примерами этих сплавов. Типичные области применения включают компоненты планера, крепежные детали, пружины, трубы, а также коммерческие и потребительские товары.
4. Обрабатываемость титановых сплавов
Исследования обрабатываемости титановых сплавов были проведены всесторонне и тщательно проанализированы несколькими исследователями. Растущие требования к титановым сплавам с превосходными высокотемпературными, механическими и химическими свойствами затрудняют их обработку.По данным Ezugwu et al. (2003) обрабатываемость можно сформулировать как сложность обработки конкретного материала при заданном наборе параметров обработки, таких как скорость резания, скорость подачи и глубина резания. Его можно оценить с точки зрения стойкости инструмента, качества поверхности, реакции сил резания, а также стоимости обработки детали. В основном, деформационное упрочнение, низкая теплопроводность, абразивность, высокий уровень прочности и высокое тепловыделение были основными причинами сложности обработки титановых сплавов.Тепло — это самый важный фактор, о котором нужно помнить при обработке титановых сплавов. Избыточный нагрев может быстро повредить режущий инструмент. Основными источниками тепла во время обработки являются зона сдвига, трение на границе раздела инструмент-стружка и трение на границе раздела инструмент-заготовка. Однако слишком сильный нагрев — не единственная причина, связанная с поломкой инструмента. Отсутствие жесткости при удерживании державки с режущим инструментом и заготовкой также может сократить срок службы инструмента. Нежесткие установки с вибрацией или непостоянным давлением резания и прерывистым резанием часто вызывают скалывание инструмента или трещины.Продолжительная обработка также приводит к сильному выкрашиванию и разрушению кромки инструмента.
5. Оценка эффективности сверления титановых сплавов
Среди различных процессов обработки сверление может быть значительно более сложным процессом по сравнению с фрезерованием и точением. Многие исследователи в прошлом изучали обрабатываемость титановых сплавов, особенно при токарных и фрезерных операциях. Несмотря на то, что были опубликованы обширные отчеты о расследованиях, не было достигнуто значительного прогресса и не сообщалось о бурении этих сплавов.
5.1. Износ инструмента
Износ режущего инструмента при резке металла составляет значительную часть производственных затрат на компонент. Износ инструмента происходит из-за физического и химического взаимодействия между режущим инструментом и заготовкой в результате удаления мелких частиц материала инструмента с кромки режущего инструмента. Износ инструмента происходит в три этапа, как показано на рис. (Вон, 1966). Износ инструмента быстро развивался на начальном этапе, а затем равномерно увеличивался, пока не достиг своего предельного значения.На третьем этапе износ инструмента быстро развивался и приводил к выходу инструмента из строя. Обработка сверх этого предела приведет к катастрофическим отказам инструмента, и обычно этого следует избегать.
Рис. 7.
Типичные стадии износа инструмента при механической обработке (Вон, 1966).
Основная проблема при сверлении титана и его сплавов — быстрый износ режущего инструмента. Допустимые скорости съема металла низкие, несмотря на низкие усилия резания. Ингибитором обработки титановых сплавов являются высокая температура и неблагоприятное распределение температуры в режущем инструменте (Ezugwu & Wang, 1997; Vaughn, 1966).Из-за низкой теплопроводности титановых сплавов температура на передней поверхности может быть выше 900 ° C даже при умеренной скорости резания.
При сверлении титановых сплавов могут наблюдаться различные виды износа, а именно неравномерный износ по задней поверхности, чрезмерное выкрашивание и микротрещины. Эти типы износа являются преобладающими видами отказов инструмента при сверлении Ti-6Al-4V. Износ происходит по режущей кромке сверла или по боковым поверхностям. Увеличение скорости резания привело к пропорциональному увеличению ширины износа по задней поверхности.Увеличение скорости износа по задней поверхности может способствовать прилипанию материала заготовки и может привести к истиранию и, в конечном итоге, к сильному выкрашиванию.
Во время сверления Ti-48Al-2Mn-2Nb Мантл и соавторы (Mantle et al. (1995)) обнаружили, что материал заготовки прилипает к долоту и режущим кромкам. Адгезия Ti-48Al-2Mn-2Nb была меньше, чем у Ti-6Al-4V, и после проверки с помощью SEM они пришли к выводу, что прилипший материал был основной причиной отказа инструмента.Титан обладает высокой химической реактивностью и имеет тенденцию привариваться к режущему инструменту во время обработки. Вначале приклеенный материал может защитить режущие кромки от износа, как показано на рис. 8. На этом рисунке сцепление происходило в основном на режущей кромке, около периферии и на кромке долота. Однако при длительном сверлении налипший материал становится нестабильным и отрывается от инструмента, увлекая небольшое количество частиц инструмента. Эта ситуация может привести к сильному выкрашиванию режущей кромки.
Рис. 8.
Адгезия материалов заготовки наблюдается на: (а) кромке долота и (б) режущей кромке после сверления Ti-6Al-4V (Rahim, 2005).
На рис. 9 показана термическая трещина на боковой поверхности сверла (Rahim, 2005). Видно, что линия трещины распространялась перпендикулярно режущей кромке. Трещины на режущем инструменте и разрушение всей режущей кромки в основном наблюдались при обработке титановых сплавов в более высоких режимах резания (Ezugwu et al., 2000; Jawaid et al., 2000). Трещины обычно возникают в области сколов и постепенно распространяются по изношенной боковой поверхности. Выкрашивание на режущих кромках в основном связано с возникновением циклических поверхностных напряжений во время сверления, которые могут привести к циклическим нагрузкам, приводящим к образованию параллельных трещин на режущей кромке. Распространение трещин при длительной обработке приводит к выкрашиванию по режущей кромке. Выкрашивание может происходить и без образования трещин, особенно на начальных стадиях развития износа.Если трещин станет очень много, они могут соединиться и отколоть небольшие фрагменты режущей кромки.
Рис. 9.
Трещина на боковой поверхности после сверления Ti-6Al-4V в течение 1 минуты при 55 м / мин и 0,06 мм / об (Rahim, 2005).
Cantero et al. (2005) сообщили о подходе к бурению Ti-6Al-4V в сухих условиях. Используя сверло с твердосплавным покрытием диаметром 6 мм, они рекомендовали, чтобы скорость и скорость подачи для сверления Ti-6Al-4V составляли 50 м / мин и 0,07 мм / об соответственно.Истирание и диффузия были основными механизмами износа инструмента, особенно в винтовой канавке сверла. При длительном сверлении эти механизмы износа инструмента приводят к катастрофическому выходу сверла из строя. Износ при истирании — это удаление зерен или агломератов инструментального материала прилипшей стружкой или заготовкой (Dearnley and Grearson, 1986). Это могло произойти из-за прерывистого прилипания инструмента к заготовке в результате нерегулярного потока стружки и разрушения частично устойчивой наростной кромки.Когда заедание между инструментом и заготовкой нарушается, небольшие фрагменты инструмента могут быть вырваны из-за ослабления связки и транспортируемого материала через нижнюю часть стружки или заготовку. Наличие усталости во время обработки может вызвать появление трещин, а также способствовать их распространению на инструменте.
Кроме того, диффузионный износ связан с химическим сродством материала инструмента и заготовки под воздействием высокой температуры и давления во время обработки титановых сплавов (Hartung and Kramer, 1982; Kramer, 1987).Тесный контакт между поверхностью раздела инструмент-заготовка при температуре выше 800 ° C обеспечивает идеальную среду для диффузии инструментального материала через поверхность раздела инструмент-заготовка. Анализ EDAX (рис. 10) подтвердил, что элементы инструмента (C, Co и W) проникли в поверхность раздела между инструментом и заготовкой во время сверления Ti-6Al-4V (Rahim & Sharif, 2009). Диффузионный износ является значительным на границе раздела инструмент-заготовка, особенно при высокой температуре резания. Из-за высокой химической активности титановых сплавов углерод легко реагирует с титаном.Следовательно, образование карбида титана произошло на границе раздела между инструментом и рабочим материалом.
Рис. 10.
EDAX Часть изношенного инструмента, демонстрирующая прилипший материал заготовки на режущей кромке после сверления Ti-6Al-4V в течение 2 минут при 45 м / мин и 0,06 мм / об (Rahim & Sharif, 2009).
5.2. Усилие и крутящий момент
Пьезоэлектрический динамометр обычно используется для измерения силы резания в большинстве процессов обработки. Различные типы динамометра зависят от процесса обработки, такого как токарная обработка, фрезерование, сверление или шлифование.Трехкомпонентный динамометр может измерять силу резания и усилие подачи, особенно при фрезерных и токарных операциях. Между тем, двухкомпонентный динамометр обычно используется в процессе бурения для измерения силы тяги и крутящего момента.
Сравнение осевой силы в зависимости от условий охлаждающей жидкости и смазки при скорости резания 60 м / мин и скорости подачи 0,1 мм / об представлено на рис. 11 (Rahim & Sasahara, 2011). Было обнаружено, что в условиях продувки воздухом создается самая высокая сила тяги по сравнению с другими условиями охлаждающей жидкости и смазки.Напротив, MQLPO (пальмовое масло с использованием условия MQL) и условия наводнения показали сопоставимую и самую низкую силу тяги среди других испытанных условий. Как и ожидалось, в условиях затопления был продемонстрирован самый низкий крутящий момент среди других испытанных условий, как показано на рисунке 12. Путем сравнения было обнаружено, что продувка воздухом не снижает крутящий момент сверления в такой степени, как другие условия охлаждающей жидкости и смазки. Они пришли к выводу, что наибольшее значение силы тяги и крутящего момента для условий обдува можно отнести к большему трению между поверхностью раздела инструмент-стружка, следовательно, в процессе сверления выделяется больше тепла.Кроме того, Лопес и его сотрудники обнаружили, что сила резания, создаваемая методом внутреннего охлаждения под высоким давлением, была ниже по сравнению с внешним охлаждением, что положительно сказалось на деформации заготовки и качестве отверстия (Lopez et al., 2000).
Рис. 11.
Сила тяги при высокоскоростном бурении Ti-6Al-4V в различных условиях охлаждающей жидкости (Rahim & Sasahara, 2011).
Влияние параметров бурения было оценено для различных характеристик материалов и свойств титановых сплавов (Mantle et al., 1995). Результат показывает, что сила тяги и крутящий момент для Ti-48Al-2Mn-2Nb были больше, чем для Ti-6Al-4V. Как показано на фиг. 13 и 14, сила тяги уменьшается с увеличением скорости резания (Rahim et al., 2008). В то же время результаты также показали, что низкие значения крутящего момента были получены при максимальной скорости резания. Такое поведение объясняется уменьшением площади контакта между поверхностью раздела инструмент-заготовка и уменьшением удельной энергии резания. Более того, с увеличением скорости резания увеличивается температура резания, соответственно снижается твердость материала.В результате уменьшается сила тяги и крутящий момент. Между тем, значения осевой силы и крутящего момента были значительно увеличены при увеличении скорости подачи, как показано на рис. 15 (Rahim & Sasahara, 2011). Сила тяги и крутящий момент сильно коррелируют с толщиной стружки, которая связана со скоростью подачи (Liao et al., 2007). Это связано с тем, что высокая скорость подачи приводит к увеличению площади поперечного сечения недеформированной стружки и, как следствие, к увеличению осевой силы и крутящего момента.
Рис. 12.
Крутящий момент при высокоскоростном сверлении Ti-6Al-4V в различных условиях охлаждающей жидкости (Rahim & Sasahara, 2011).
Рис. 13.
Сравнение осевой силы при бурении Ti-6Al-4V с использованием твердосплавного инструмента в условиях заводнения охлаждающей жидкости (Rahim et al., 2008).
Рис. 14.
Сравнение крутящего момента при сверлении Ti-6Al-4V с использованием твердосплавного инструмента в условиях обводнения охлаждающей жидкостью (Rahim et al., 2008).
Некоторые исследователи опробовали несколько методов сверления титановых сплавов.Сверление со ступенчатой подачей или бурение с периодически замедленной подачей и вибрационное бурение были проведены соавторами Сакураи (Sakurai et al., 1992; Sakurai et al., 1996) для изучения силы резания и характеристик резания кобальтовой HSS с покрытием из TiN и обработки оксидов азотированная кобальтовая HSS при сверлении Ti-6Al-4V. Результаты их исследования показали, что бурение со ступенчатой подачей обеспечивает меньшую силу тяги и крутящий момент по сравнению с обычным непрерывным бурением. Кроме того, осевое усилие и крутящий момент у сверл из TiN ниже, чем у сверл с нитридной обработкой оксидом, как при обычном, так и при ступенчатом сверлении.Как сообщили Окамура с соавторами (Okamura et al., 2006), безвибрационное бурение показывает огромное снижение осевой силы. Однако значение имеет тенденцию уменьшаться, когда вибрация превышает 20 кГц. Считается, что собственная частота измерительных систем не превышает частоту колебаний. В другой работе Рахим и его коллеги (Rahim et al., 2008) показали, что метод долбленого бурения значительно снижает силу тяги и крутящий момент.
Рис. 15.
a) Сила тяги и (b) крутящий момент для MQLSE и MQLPO при различной скорости резания и скорости подачи (Rahim & Sasahara, 2011).
5.3. Температура
Встроенные термопары были одним из первых методов, используемых для оценки температуры в различных производственных и трибологических приложениях. Чтобы использовать этот метод, особенно при механической обработке, необходимо проделать ряд мелких глубоких отверстий в неподвижной части, а именно в заготовке или режущем инструменте, а термопары должны быть вставлены в разные места внутри детали, причем некоторые из них как можно ближе к поверхности.В процессе сверления измерение температуры с помощью проводов термопар может быть выполнено путем встраивания проводов в заготовку и режущий инструмент, как показано на рис. 16, 17, 18 и 19 соответственно. Эти методы позволяют измерять температуру заготовки и режущего инструмента, особенно при сверлении титановых сплавов.
Рис. 16.
Расположение термопар (Rahim & Sasahara, 2010a).
Рис. 17.
Система для измерения температуры детали (Zeilmann & Weingaertner, 2006).
Скорость резания и скорость подачи являются одними из факторов, влияющих на изменение температуры во время сверления титановых сплавов. Температура резания увеличивается с увеличением скорости резания. Это соответствует высокой энергии резания, скорости деформации, а также тепловому потоку (Rahim & Sasahara, 2011). Кроме того, сверление с высокой скоростью подачи увеличивает трение и напряжения, тем самым повышая температуру резания.
Применение различных методов охлаждения приводит к изменению результатов по температуре.Например, максимальные температуры, зарегистрированные для бурения с обильной эмульсией внутри инструмента, оставались в диапазоне 22–32% от значений, полученных при применении MQL с внешним соплом, как показано на рис. 20 (Zeilmann & Weingartner , 2006). Сравнивая сверление с использованием MQL с использованием внешнего сопла и сухого бурения, значения, полученные для второго условия, были примерно на 6% выше, в диапазоне от 455 до 482 ° C. Кроме того, в условиях затопления и MQL зафиксирована низкая температура детали по сравнению с условиями продувки воздухом, как показано на рис.21 (Рахим и Сасахара, 2011).
Рис. 18.
Термопара была вставлена в масляное отверстие твердосплавного сверла с внутренним подводом СОЖ (Ozcelik & Bagci, 2006).
Рис. 19.
Вид сверху и координаты наконечников термопар на боковой поверхности сверла (Li & Shih, 2007).
Рисунок 20.
Максимальная температура в детали для различных условий смазочно-охлаждающей жидкости при сверлении Ti-6Al-4V с использованием твердосплавного инструмента марки K10 (Zeilmann & Weingartner, 2006).
Рис. 21.
Максимальная температура заготовки при высокоскоростном сверлении Ti-6Al-4V в различных условиях охлаждающей жидкости (Rahim & Sasahara, 2011).
Как сообщили Пуджана и его коллеги (Pujana et al., 2009), температура резания была выше при использовании ультразвукового сверления по сравнению с бурением без вибрации. В этом случае, чем выше амплитуда колебаний, тем больше колебания температуры. Окамура и соавторы (Okamura et al., 2006) разработали низкочастотный вибрационный сверлильный станок для сверления Ti-6Al-4V.Они описали влияние низкочастотного вибрационного сверления на температуру резания. Результаты показали, что более высокая амплитуда 0,24 мм и частота 30 Гц показывают более низкую температуру резания по сравнению с сверлением без вибрации.
6. Целостность поверхности
Целостность поверхности определяется как неизменное или улучшенное состояние поверхности материала в результате воздействия контролируемого производственного процесса (Field and Kahles, 1964). Поврежденный слой и целостность поверхности обработанной поверхности существенно влияют на износостойкость, коррозионную стойкость и усталостную прочность обрабатываемых деталей.Целостность поверхности, полученная в результате операции удаления металла, можно разделить на геометрическую целостность поверхности и целостность физической поверхности. Чтобы определить влияние производственного процесса на свойства материала, необходимо учитывать эффекты обеих категорий. Аспекты целостности поверхности очень важны, особенно в аэрокосмической промышленности в отношении высокой степени безопасности. Целостность поверхности в первую очередь связана с влиянием процесса обработки на изменения поверхности и подповерхности детали, которые подразделяются на шероховатость поверхности, пластическую деформацию, остаточное напряжение и микротвердость.
6.1. Шероховатость поверхности
Шероховатость поверхности имеет три основных параметра; среднее арифметическое отклонение профиля (R a ), максимальная высота профиля (R max ) и высота неровностей профиля в десяти точках (R z ). Считается, что более высокое значение шероховатости приводит к снижению усталостной прочности обработанной поверхности. Значительное улучшение шероховатости поверхности может быть получено при использовании низкой скорости подачи и высокой скорости резания.Однако реакция шероховатости поверхности на скорость резания была менее значительной по сравнению со скоростью подачи. Sun и Guo (Sun & Guo, 2009) сообщили, что значение шероховатости поверхности увеличивается с увеличением скорости подачи и радиальной глубины резания.
Предыдущее исследование показало, что значение шероховатости поверхности ниже при высокой скорости резания при сверлении Ti-6Al-4V с использованием твердосплавных сверл (Sharif & Rahim, 2007). Во время обработки на высокой скорости резания температура резания увеличивается из-за небольшой длины контакта между поверхностями раздела инструмент-заготовка.Это может быть связано со снижением коэффициента трения, что приводит к низкому трению на границе раздела инструмент-заготовка. Эти факторы могут способствовать улучшению значений шероховатости поверхности, как показано на рис. 22 (Rahim & Sasahara, 2010b). Кроме того, по мере увеличения скорости резания выделяется больше тепла, что смягчает материал заготовки, что, в свою очередь, улучшает шероховатость поверхности. Однако низкая скорость резания может привести к образованию нароста на кромке и, следовательно, к ухудшению качества обработанной поверхности.Исследование показало, что при высокой скорости подачи шероховатость поверхности плохая, вероятно, из-за отчетливых следов подачи, полученных при высокой скорости подачи (Rahim & Sasahara, 2010).
Рис. 22.
Сравнение уровня шероховатости поверхности, полученного при сверлении Ti-6Al. -4V с использованием твердосплавного инструмента с покрытием TiAlN в соответствии с MQLSE и MQLPO (Rahim & Sasahara, 2010b).
Типы смазочно-охлаждающей жидкости также влияют на шероховатость обрабатываемой поверхности. В условиях MQL растительное масло (MQLPO: пальмовое масло) демонстрирует лучшую шероховатость поверхности, чем синтетический эфир (MQLSE), как показано на рис.22 (Рахим и Сасахара, 2010b). Можно предположить, что при использовании пальмового масла выделяется меньше тепла, что дает достаточно времени для охлаждения и смазки поверхности раздела инструмент-заготовка. Очевидно, такое уменьшение может быть связано с улучшением смазки и меньшей длиной контакта инструментальной стружки во время сверления. Более того, шероховатость поверхности, измеренная методом долбления, намного лучше, чем при обычном методе сверления (Rahim et al, 2008).
6.2. Микротвердость
Изменения микротвердости, наблюдаемые во время обработки, могут быть следствием термической, механической и химической реакции.Многие исследователи полагали, что материал заготовки подвергается механическому упрочнению и термическому разупрочнению во время обработки, особенно при высокой температуре и давлении резания (Che Haron, 2001; Ginting & Nouari, 2009). При механической обработке титановых сплавов твердость непосредственно под обработанной поверхностью оказалась более мягкой, чем твердость массивного материала из-за эффекта термического размягчения. Однако, когда глубина под обработанной поверхностью увеличивается, значение твердости начинает увеличиваться, прежде чем достигнет своего пикового значения, и, наконец, постепенно падает до твердости объемного материала, как показано на рис.23. Повышение твердости напрямую связано с эффектом наклепа. Этот эффект зависит от температуры, времени резки и механизма релаксации внутреннего напряжения (Ginting and Nouari, 2009).
Рис. 23 показывает, что микротвердость подповерхности на 0,025 мм ниже обработанной поверхности была ниже средней твердости основного материала. Это указывает на то, что обработанная поверхность испытала эффект термического размягчения или чрезмерного старения из-за локального нагрева во время процесса сверления (Rahim & Sasahara, 2010b).Испытания на токарную обработку титановых сплавов, проведенные Хароном и Джаваидом (Haron & Jawaid, 2005) и Гинтингом и Нуари (Ginting & Nouari, 2009), также показали значительное падение значения микротвердости вблизи поверхности обработанного слоя. Они указали, что наличие высокой температуры резания и высокого давления резания приводит к заметному размягчению поверхности.
Рис. 23 также показывает, что под размягченным слоем находится упрочняющий слой, твердость которого зависит от параметров резания (т.е.e скорость резания, подача, глубина резания), а также механическое и термическое взаимодействие. В области деформационного упрочнения обычно наблюдали, что микротвердость увеличивается с увеличением скорости резания и подачи. Повышение микротвердости поверхностного слоя в результате высокой скорости подачи может быть связано с высокой нагрузкой трения между инструментом и обрабатываемой поверхностью и, как следствие, эффектом наклепа.
Рис. 23.
Вариации подповерхностной твердости после сверления Ti-6Al-4V с использованием MQLSE (Rahim & Sasahara, 2010b).
В другой работе Рахима и Шарифа (Rahim & Sharif, 2006) сообщалось, что значение твердости под просверленной поверхностью было выше, чем средняя твердость массивного материала при сверлении Ti-5Al-4V-Mo / Fe ( Рис.24). Между тем, значительное изменение значений микротвердости также наблюдалось под обработанной поверхностью. Это произошло из-за превращения бета-фазы в альфа-фазу во время бурения (Cantero et al., 2005).
Рис. 24.
Изменение микротвердости под поверхностью, возникающее при сверлении Ti-5Al-4V-Mo / Fe (Rahim & Sharif, 2006).
6.3. Подповерхностная пластическая деформация
Видно, что поверхность и подповерхность обработанной поверхности подвергаются пластической деформации. Подповерхностная пластическая деформация, в частности, происходит из-за эффекта большой деформации, скорости деформации и температуры. Кроме того, свежепрорезанная поверхность может быть отполирована тупым режущим инструментом, что приводит к деформационному упрочнению обработанной поверхности. Джилани и Рамакришнан (Jeelani & Ramakrishnan, 1983) заметили, что обработанная поверхность серьезно повреждена пластическим потоком в направлении движения инструмента.Между тем, Веласкес и его сотрудники (Velasques et al., 2010) обнаружили, что сильная деформация под обработанной поверхностью связана с высокой скоростью резания. Зону подповерхностной пластической деформации можно разделить на три зоны: сильно возмущенную зону, пластически деформированный слой и неповрежденную зону. Обычно подповерхностные пластические деформации микроструктуры обработанных поверхностей исследуются под микроскопом с большим увеличением в протравленном состоянии.
В большинстве случаев пластическая деформация происходит в направлении вращения шпинделя.При сверлении титановых сплавов при более высоких скоростях резания и подаче может наблюдаться более толстая пластическая деформация. В этом состоянии температура между поверхностью раздела инструмент-чип увеличивается, в результате чего возникает область трения прилипания. Таким образом, сочетание высокой температуры резания и прилипающего трения способствовало сильной и заметной подповерхностной пластической деформации (Rahim & Sasahara, 2010).
На рис. 25 показаны признаки подповерхностной пластической деформации при сверлении Ti-5Al-4V-Mo / Fe (Rahim & Sharif, 2006).На этом рисунке обнаружена сильная деформация после длительного бурения. В этом случае не наблюдается белого слоя, особенно на верхней части обработанной поверхности. Авторы заявили, что высокая сила резания и температура являются доминирующими факторами, которые приводят к сильной пластической деформации. Кантеро и его сотрудники (Cantero et al., 2005) также обнаружили то же явление и пришли к выводу, что пластические деформации во время обработки вызваны механическими силами режущего инструмента, действующими на заготовку.Дополнительная деформация может возникать как следствие температурных градиентов из-за локального нагрева обработанной поверхности.
Рис. 25.
Увеличенный вид обработанной подповерхности при сверлении Ti-5Al-4V-Mo / Fe (Rahim & Sharif, 2006).
| Домой Свойства Использует Ювелирные изделия Кольца Часы Mokume Gane Велосипедные рамы Ракетки Химические вещества Анодирование Авиация Имплантаты Протезы Книги FUN Page | СВОЙСТВА Интересные факты о титане, объясняющие, какой металл является предпочтительным для многих применений, в спорт, медицина и ювелирные изделия. Название Устойчивость к коррозии Это пассивное оксидное покрытие, которое обеспечивает коррозионную стойкость и устойчивость к потускнению при комнатная температура. Плотность и прочность Плотность и прочность на разрыв
Характеристики титана и конструкционных металлов
Физико-химические свойства Некоторые промышленные титановые сплавы
Окраска Радиоактивный потенциал Оксид титана Приложения Сплавы В частности, титан-ванадиевые сплавы широко используются в авиации при производстве шасси, гидравлические трубы, противопожарные перегородки и т. д. Кристальная структура Элементарная ячейка β фазы Точное температура превращения сильно зависит от межузельного и замещающего элементов и поэтому зависит от чистоты металла. Кристаллическая упаковка титана помогает предсказать, как титан поддается растяжению или другим деформирующим силам, поскольку деформации будут иметь тенденцию происходить вдоль кристаллических плоскостей, которые выравнивают и определяют направление самые слабые плоскости в материале. Добыча Титан нелегко извлечь из руды. Еще в 1946 году Уильям Джастин Кролл обнаружил средства для его коммерческой добычи восстановление тетрахлорида титана магнием. Оксид превращается в хлорид посредством карбохлорирования, в результате чего газообразный хлор выделяется. пропускали через раскаленный рутил или ильменит в присутствии углерода с образованием TiCl4. Это сжато и очищают фракционной перегонкой, а затем восстанавливают расплавленным магнием при 800 ° C в аргоне. Атмосфера. Несмотря на сложность и дороговизну, процесс Kroll все еще используется сегодня. Кембриджский процесс FFC — это новый метод, пользующийся все большей популярностью. Поскольку это снижает стоимость добычи, есть надежда, что титан будет использоваться. более широко, например, в аэрокосмической промышленности. Оксид титана производится путем смешивания измельченной минеральной руды и ее смешивания с калием. карбонат и водная фтористоводородная кислота. Этот продукт химической реакции фторотитанат калия (K2TiF6) — это экстрагируют горячей водой и разлагают аммиаком с образованием гидратированного оксида аммиака.Этот в свою очередь воспламеняется в платиновом сосуде, что создает чистый диоксид титана. |
Области применения титана | Применение титана
СВЯЗАТЬСЯ С НАМИ: (805) 487-5050- TITAN Group
- TITAN Metal Fabricators, Inc.
- Обзор
- О
- Официальный сайт
- Обзор
- TITAN Metal Fabricators, Wuxi Co Ltd.
- Обзор
- О
- Официальный сайт PrivEC
- Обзор
ISEC Ltd.- TITAN Metal Fabricators, Inc.
- Обзор
- О
- Официальный сайт
- TITAN Plating & Anodizing Division
- Обзор
- О
- Официальный сайт
- О
- Официальный веб-сайт
- Обзор
- Оптимальные анодные технологии
- Обзор
- О
- Официальный сайт
- Обзор
- Титановые теплообменники
- Титановые колонны
- Титановые трубы
- Титановые резервуары под давлением
- Титановые реакторы
- Zi Ркониевые продукты
- Циркониевые теплообменники
- Циркониевые колонны
- Циркониевые трубопроводы
- Циркониевые сосуды под давлением
- Циркониевые реакторы
- TITAN Hastelloy Products
- Hastelloy
- Теплообменники Hastelloy
- Теплообменники Hastelloy 94
- Дуплексные изделия из нержавеющей стали TITAN
- Дуплексные теплообменники из нержавеющей стали
- Дуплексная нержавеющая сталь Col umns
- Трубопроводы из дуплексной нержавеющей стали
- Сосуды под давлением из дуплексной нержавеющей стали
- Реакторы из дуплексной нержавеющей стали
- Теплообменники
- Теплообменники
- Теплообменники
- Теплообменники для травления стали
- Фармацевтические теплообменники
- Нефтегазовые теплообменники
- Материалы
- Титановые теплообменники
- Танталовые теплообменники
- Циркониевые теплообменники
- Теплообменники из нержавеющей стали
- Теплообменники из нержавеющей стали
- Теплообменники
- Теплообменники
- Колонны
- Колонны
- Титановые колонны
- Танталовые колонны
- Циркониевые колонны
- Колонны из хастеллоя
- Дуплексные колонны из нержавеющей стали
- Трубопровод
- Трубопровод
- Титановый трубопровод
- Танталовый трубопровод
- Циркониевый трубопровод
- Трубопровод из хастеллоя
- Дуплексный трубопровод из нержавеющей стали
- Сосуды под давлением
Сосуды под давлением
- Трубопровод
- Колонны
- Теплообменники
- Сосуды под давлением из тантала
- Сосуды под давлением из циркония
- Сосуды под давлением из хастеллоя
- Сосуды под давлением из дуплексной нержавеющей стали
- Реакторы
- Реакторы
- Титановые 49
- Титановые49
- Реакторы Титановые 49
- Дуплексные реакторы из нержавеющей стали
- Реакторы
- Вспомогательное оборудование
- Вспомогательное оборудование
- TITAN Pla Подразделение анодирования и анодирования
- Подразделение покрытия и анодирования TITAN
- Анодные корзины
- Погружные катушки
- Вспомогательные аноды
- Резервуары, футеровки резервуаров и изготовление по индивидуальному заказу
- Области применения
- Погружная катушка 913 Для водяного охлаждения
- Для водяного отопления
- Для водяного отопления
- Подразделение покрытия и анодирования TITAN
- TITAN Pla Подразделение анодирования и анодирования
- Оптимальные анодные технологии
- Оптимальные анодные технологии
- Калькуляторы
- Расчет площади поверхности
- Катушка погружения 9 Области применения
- Для водяного охлаждения
- Для водяного отопления
- Для водяного отопления
- Расчет площади поверхности
- Химическая промышленность
- Химическая промышленность
- Химические теплообменники
- Колонны
- Трубопроводы
- Сосуды под давлением
- Реакторы
- Химическая промышленность
- Нефтегазовая промышленность
- Нефтегазовая промышленность
- Колонны 1348
- Нефтегазовые теплообменники
- Колонны
- Сосуды под давлением
- Реакторы
- Нефтегазовая промышленность
- Фармацевтическая промышленность
- Фармацевтическая промышленность
- Фармацевтические теплообменники
- Колонны
- Трубопроводы
- Сосуды под давлением 1358
- Сосуды
- Сталелитейное оборудование
- 913
- Сталелитейная промышленность
- Теплообменники травления стали
- Альтернативная энергетика
- Геотермальная энергия
- Биомасса
- Солнечная тепловая энергия
- Подразделение покрытия и анодирования TITAN 9134 7
- Отделение покрытия и анодирования TITAN
- Фармацевтическая промышленность
- Химическая промышленность
- Теплообменники
- Колонны
Обработка титана в JobShop.com
Многие характеристики материала и конструкции компонентов титана делают его дорогостоящим в обработке. Из первичных форм, таких как поковки, листы, прутки и т. Д., Необходимо удалить значительное количество материала. В некоторых случаях от 50 до 90% веса первичной формы остается в виде стружки. (Сложность некоторых готовых деталей, таких как переборка, затрудняет использование методов получения почти чистой формы, которые минимизируют стружкообразование.) Для минимизации затрат на удаление припуска требуется максимальная эффективность обработки титановых сплавов.
Исторически титан считался материалом, который трудно обрабатывать. Благодаря растущему распространению титана во многих отраслях промышленности, а также опыту, накопленному прогрессивными производителями, в настоящее время существует обширная база знаний в области обработки титана. Производители теперь знают, что при правильных процедурах титан можно производить с использованием технологий, не более сложных, чем те, которые используются для обработки нержавеющей стали 316.
Рассказы о проблемах, возникающих при обработке титана, обычно возникают в цехах, работающих с авиационными сплавами.Дело в том, что технически чистые сорта титана (ASTM B, классы 1, 2, 3 и 4) с пределом прочности на разрыв от 241 до 552 МПа (от 35 до 80 ksi) обрабатываются намного легче, чем авиационные сплавы (например, ASTM B, сорт 5). : Ти-6АЛ-4В).
При более высоком содержании сплава и повышении твердости обрабатываемость титановых сплавов традиционными методами изготовления стружки обычно снижается. (Это верно для большинства других металлов.) При уровне твердости более 38 RC (350 BHN) можно ожидать увеличения сложности таких операций, как нарезание резьбы, фрезерование и протяжка.В целом, однако, если принять во внимание особые характеристики титана, обработка титана и его сплавов не должна создавать чрезмерных проблем.
Обработка титановых сплавов требует усилий резания, лишь немного превышающих силы, необходимые для обработки сталей, но эти сплавы обладают металлургическими характеристиками, которые делают их несколько более трудными для обработки, чем стали эквивалентной твердости. Бета-сплавы — самые сложные для обработки титановые сплавы.Когда условия обработки выбраны правильно для определенного состава сплава и последовательности обработки, можно достичь разумной производительности обработки при приемлемом уровне затрат.
Необходимо проявлять осторожность, чтобы избежать потери целостности поверхности, особенно во время шлифования; в противном случае может произойти резкое ухудшение механических характеристик, например усталость. На сегодняшний день такие методы, как высокоскоростная обработка, не улучшили обрабатываемость титана. Похоже, что прорыв требует разработки новых инструментальных материалов.
Характеристики, влияющие на обрабатываемостьТот факт, что титан иногда классифицируют как труднообрабатываемый традиционными методами, частично можно объяснить физическими, химическими и механическими свойствами металла. Например:
- Титан плохо проводит тепло. Тепло, выделяемое при резке, не рассеивается быстро. Таким образом, большая часть тепла сосредоточена на режущей кромке и торце инструмента.
- Титан имеет сильную склонность к легированию или химической активности с материалами в режущих инструментах при рабочих температурах инструмента.Это вызывает истирание, сварку и смазывание, а также быстрое разрушение режущего инструмента.
- Титан имеет относительно низкий модуль упругости, благодаря чему он обладает большей «упругостью», чем сталь. Работа имеет тенденцию отходить от режущего инструмента, если не выполняются тяжелые разрезы или не используется надлежащая поддержка. Тонкие детали имеют тенденцию отклоняться под давлением инструмента, вызывая вибрацию, трение инструмента и проблемы с допусками. Следовательно, очень важна жесткость всей системы, а также использование острых режущих инструментов правильной формы.
- Усталостные свойства титана сильно зависят от склонности к повреждению поверхности при использовании определенных методов обработки. Следует проявлять осторожность, чтобы избежать потери целостности поверхности, особенно во время шлифования. (Эта характеристика описана более подробно ниже.)
- Характеристики наклепа титана таковы, что титановые сплавы демонстрируют полное отсутствие «наростов». Из-за отсутствия неподвижной массы металла (нароста) перед режущим инструментом образуется большой угол сдвига.Это приводит к тому, что тонкая стружка контактирует с относительно небольшой площадью на поверхности режущего инструмента, что приводит к высоким нагрузкам на подшипник на единицу площади. Высокая несущая сила, в сочетании с трением, разработанным микросхемой, как она устремляется по области подшипника, приводит к значительному увеличению тепла на очень локализованный участке режущего инструмента. Кроме того, сочетание высоких опорных усилий и тепла приводит к образованию трещин вблизи режущей кромки, что приводит к быстрой поломке инструмента.
Что касается усталостных свойств титана, кратко указанных в приведенном выше списке, представляют интерес следующие детали.Как указано, следует избегать потери целостности поверхности. Несоблюдение этой меры предосторожности может привести к резкой потере механических свойств (например, усталости). Даже правильная практика шлифования с использованием обычных параметров (частота вращения круга, подача вниз и т. Д.) Может привести к значительному снижению усталостной прочности из-за повреждения поверхности. Основные усталостные свойства многих титановых сплавов основаны на благоприятном сжимающем поверхностном напряжении, вызываемом действием инструмента во время обработки. Электромеханическое удаление материала с получением поверхности без напряжений может привести к отклонению от обычных расчетных характеристик усталостной прочности.(Эти результаты аналогичны, когда задействованы механические процессы, такие как шлифование, хотя причины разные.)
Традиционная обработка титанаТермин «механическая обработка» имеет широкое применение и относится ко всем типам процессов удаления металла и резки. К ним относятся токарная обработка, растачивание, фрезерование, сверление, развертывание, нарезание резьбы, пиление и газовая резка, протяжка, строгание, фрезерование зубчатых колес, профилирование, стружка и шлифование.
Технология обработки титановых сплавов в основном очень похожа на технологию обработки других сплавов.Эффективная обработка металла требует доступа к данным, связывающим параметры обработки режущего инструмента с рабочим материалом для данной операции. К важным параметрам относятся:
- Стойкость инструмента
- Сил
- Требования к питанию
- Режущие инструменты и жидкости
Данные о стойкости инструмента были получены экспериментально для широкого спектра титановых сплавов. Обычный способ представления таких данных показан на рисунке 6.1, где стойкость инструмента (как время) отложена в зависимости от скорости резания (фут / мин) для данного материала режущего инструмента при постоянной подаче и глубине относительно Ti-6Al-4V. Видно, что при высокой скорости резания стойкость инструмента чрезвычайно мала. С уменьшением скорости резания резко увеличивается стойкость инструмента.
Титановые сплавы очень чувствительны к изменениям подачи, как показано на Рисунке 6.1. В промышленности обычно используются скорости резания, обеспечивающие длительный срок службы инструмента. Подгонка кривой стойкости инструмента к подаче, скорости и другим параметрам обработки обычно выполняется с помощью компьютерных технологий.Однако в случаях, когда базы данных не существует, следует признать определенные практические правила. Например, при резке титана между заготовкой и стружкой образуется большой угол сдвига, в результате чего тонкая стружка течет с высокой скоростью по торцу инструмента. Развиваются высокие температуры, и, поскольку титан имеет низкую теплопроводность, стружка имеет тенденцию к истиранию и приваривается к режущим кромкам инструмента. Это ускоряет износ и выход инструмента из строя. При работе со станками с высокими фиксированными затратами производительность может быть намного важнее, чем срок службы режущего инструмента! Таким образом, может быть разумным поработать с инструментом на максимальной мощности, а затем заменить его, как только эффективность его резания начнет заметно снижаться, тем самым максимально поддерживая время безотказной работы.
При обработке титана в условиях, когда производственные затраты не имеют первостепенного значения, все еще нецелесообразно позволять инструментам работать до разрушения. Другая крайность, преждевременная смена инструмента, может привести к небольшому количеству деталей на шлифовку инструмента, но чем меньше износ инструмента, тем дешевле переточка.
В идеале, инструмент должен продолжать резать как можно дольше без риска повреждения инструмента или работы, но с сохранением целостности поверхности.Единственный способ найти безопасную точку остановки — это проверить несколько прогонов, подсчитав произведенные детали и проверив качество поверхности, размеры и целостность поверхности. Таким образом можно установить, сколько приемлемых деталей можно изготовить до того, как инструмент выйдет из строя.
Силы и требования к мощности
Силы при обработке можно определить с помощью динамометра. При токарной обработке динамометр инструмента обычно измеряет три компонента:
- Тангенциальная или сила резания
- Тяга или разделяющая сила
- Подача или осевое усилие
Для общих приближений, потребляемая мощность при токарной и фрезерной обработке может быть получена путем измерения мощности, потребляемой приводным двигателем станка во время операции резания, и путем вычитания из нее тары или мощности холостого хода. Хорошее приближение мощности, необходимой для большинства операций обработки, можно предсказать, исходя из требований к мощности агрегата. В таблице ниже показаны требования к мощности для титана по сравнению с другими сплавами.
Средняя потребляемая мощность для токарной обработки, сверления или фрезерования титана по сравнению с другими конкурирующими системами из сплавов
Мощность для острых инструментов (а) л.с. / дюйм. 3 / мин | ||||
СВЕРЛЕНИЕ СВЕРЛА HSS | ФРЕЗЕРОВАНИЕ ИНСТРУМЕНТЫ ИЗ HSS И КАРБИДА | |||
Стали | 35-40 R C | 1.4 | 1,4 | 1,5 |
Титан Сплавы | 250–375 | 1,2 | 1,1 | 1.1 |
Высокотемпературный Сплавы на основе никеля и кобальта | 200–360 | 2,5 | 2,0 | 2,0 |
Алюминий Сплавы | 30–150 (500 кг) | 0.25 | 0,16 | 0,32 |
(а) Требования к мощности на приводном двигателе шпинделя, исправлено до 80% КПД привода шпинделя. Скучный инструменты могут потребовать на 25% больше энергии. |
Режущие инструменты
Значительное улучшение скорости обработки деталей обычно является результатом разработки и применения новых инструментальных материалов.За последние несколько лет были достигнуты значительные успехи в разработке режущих инструментов, включая карбиды с покрытием, керамику, металлокерамику, кубический нитрид бора и поликристаллический алмаз. Они нашли полезное применение при механической обработке чугуна, стали, жаропрочных и алюминиевых сплавов.
К сожалению, ни один из этих или других новых материалов не улучшил скорость съема титановых сплавов. В исследованиях, проведенных еще в 1950 году, прямые режущие инструменты из карбида вольфрама (WC), обычно марки C-2, лучше всего работали при таких операциях, как токарная обработка и торцевое фрезерование, в то время как высококобальтовые быстрорежущие стали наиболее подходили для сверления. , нарезание резьбы и концевое фрезерование.
Сегодня ситуация примерно такая же. Карбиды C-2 широко используются в производстве двигателей и корпусов самолетов для токарных и торцевых фрезерных операций. В последние годы в Соединенных Штатах, а также в Европе твердые концевые фрезы C-2 и концевые фрезы со сменными карбидами C-2 находят применение, особенно на аэрокосмических предприятиях. Сегодня быстрорежущие стали M7, а чаще M42 и M33 рекомендуются для концевого фрезерования, сверления и нарезания резьбы по титановым сплавам.
СОЖ
Смазочно-охлаждающие жидкости, используемые при обработке титановых сплавов, требуют особого внимания, потому что ионы хлора при определенных обстоятельствах вызывают коррозионное растрескивание под напряжением при лабораторных испытаниях этих сплавов на механические свойства. Следовательно, когда-то хлор считался подозрительным элементом независимо от концентрации и конкретных условий, используемых в производственных операциях, таких как механическая обработка.
При выборе смазочно-охлаждающих жидкостей для обработки титана некоторые компании практически не имеют ограничений, кроме использования процедур контролируемой промывки на деталях после обработки.Другие производители поступают так же, за исключением того, что они не используют хлорсодержащие охлаждающие жидкости для деталей, которые подвергаются более высоким температурам в сварочных процессах или в процессе эксплуатации. Также при механической обработке узлов действуют те же ограничения из-за трудностей с хорошей очисткой после обработки. Другие организации, занимающиеся аэрокосмическим производством, не допускают активного хлора в смазочно-охлаждающих жидкостях, используемых для обработки титановых сплавов.
Была проведена программа по определению влияния экспериментальных хлорированных и сульфированных смазочно-охлаждающих жидкостей на механические свойства сплава Ti-6AL-4V (отожженный, 34 Rc).Оценка механических свойств включала:
- Многоцикловая усталость как при комнатной, так и при повышенных температурах
- Распространение усталостной трещины на двух циклических частотах
- Вязкость разрушения
- Воздействие коррозии под напряжением / поверхностного охрупчивания
В рамках программы и в пределах диапазона исследованных переменных результаты показали, что в целом не произошло ухудшения механических свойств по сравнению со свойствами нейтральных смазочно-охлаждающих жидкостей.Аналогичные результаты были получены при использовании хлорированных и сернистых жидкостей при механической обработке или при наличии этих смазочно-охлаждающих жидкостей в качестве среды во время испытаний. Использование хлорсодержащих (или галогенсодержащих) смазочно-охлаждающих жидкостей обычно не рекомендуется, несмотря на вышеупомянутые результаты, которые относятся только к одному титановому сплаву.
Существуют отличные смазочно-охлаждающие жидкости, не содержащие галогеновых соединений. Фактически, из обширных данных испытаний, собранных Лабораторией материалов ВВС, можно сделать вывод, что хлорсодержащие смазочно-охлаждающие жидкости не всегда обеспечивают лучшую стойкость инструмента.Для некоторых сплавов и операций предпочтительна сухая обработка. Обычно тяжелые хлорсодержащие жидкости отлично подходят для таких операций, как сверление, нарезание резьбы и протяжка. На рисунке 6.2 показано влияние различных смазочно-охлаждающих жидкостей на стойкость инструмента при сверлении Ti-6Al-4V.
Данные обработки: скорости и подачиСкорость резания и подача — два наиболее важных параметра для всех типов операций обработки. В результате тщательного тестирования были получены данные о сроке службы инструмента, как показано на Рисунке 6.2, для точения Ti-6Al-4V. Один производитель предлагает следующие общие рекомендации для типичных операций обработки.
Хотя основные свойства обработки металлического титана не могут быть существенно изменены, их влияние можно значительно минимизировать за счет снижения температуры, возникающей на торце инструмента и режущей кромке. Благодаря применению этих основных правил обработки титана были разработаны экономичные производственные технологии:
- Используйте низкие скорости резания.На температуру режущей кромки инструмента больше влияет скорость резания, чем любая другая переменная. Изменение с 6 до 46 метров в минуту (от 20 до 150 фут / мин) с твердосплавными инструментами приводит к изменению температуры с 427 ° C до 927 ° C (от 800 ° F до 1700 ° F).
- Поддерживайте высокую скорость подачи. На температуру влияет не столько скорость подачи, сколько скорость, поэтому следует использовать самые высокие скорости подачи, соответствующие хорошей практике обработки. Изменение с 0,05 до 0,51 мм (от 0,002 дюйма до 0,020 дюйма) за оборот приводит к повышению температуры всего на 149 ° C (300 ° F).
- Используйте большое количество смазочно-охлаждающей жидкости. Охлаждающая жидкость отводит тепло, смывает стружку и снижает усилия резания.
- Используйте острые инструменты и заменяйте их при первых признаках износа или в соответствии с соображениями производства / стоимости. Износ инструмента при резке титана не является линейным. Полный отказ инструмента происходит довольно быстро после небольшого начального износа.
- Никогда не прекращайте подачу, когда инструмент и заготовка находятся в подвижном контакте. Если позволить инструменту находиться в движущемся контакте, это вызывает деформационное упрочнение и способствует смазыванию, истиранию, заеданию и полному выходу инструмента из строя.