Методы и виды контроля качества сварных соединений
Методы и виды контроля качества сварных соединений
По своей сути, методы контроля качества сварных соединений можно разделить на две группы: методы разрушающего контроля и методы неразрушающего контроля сварных соединений.
Если виды контроля качества сварных соединений, называемые разрушающими, применяются только к контрольным образцам, для выяснения общих механических свойств, то неразрушающие методы контроля качества сварных соединений служат для массового контроля качества продукции. Так, пооперационный контроль качества сварных соединений производится в большинстве случаев только неразрушающими способами контроля качества соединений, а объем контроля сварных соединений визуально-измерительным методом составляет 100%.
Рассмотрим некоторые неразрушающие методы контроля сварных соединений. Все методы контроля сварных швов можно найти в ГОСТ 18353-79 «Контроль неразрушающий. Классификация видов и методов».
Контроль качества сварных швов и соединений начинается с визуально-измерительного метода. РД 03-606-03(статус: действующий) регламентирует порядок проведения контроля сварных швов. Контроль качества сварного шва ВИК обязателен, так как позволяет менее затратным способом выявить дефекты.
Магнитографический контроль сварных соединений основан на обнаружении полей рассеивания, образующихся в местах расположения дефектов при намагничивании контролируемых сварных соединений. Поля рассеивания фиксируются на эластичной магнитной ленте, плотно прижатой к поверхности шва. Запись производят на дефектоскопе. Дефектоскопия сварных швов магнитнопорошковым методом применяется только для проверки сварных соединений металлов и сплавов небольшой толщины, обладающих ферромагнитными свойствами.
К радиационной дефектоскопии относятся рентгенографический контроль сварных соединений и гаммаграфический контроль сварных соединений. Эти методы заключаются в получении на рентгеновской пленке или экране изображения сварного соединения, просвечиваемого рентгеновским или гамма-излучением.
Ультразвуковой контроль основан на способности ультразвуковых колебаний отражаться от поверхности, разделяющей среды с разными акустическими свойствами. УЗ контроль сварных швов относится к акустическим методам неразрушающего контроля. Ультразвуковая толщинометрия — одним из акустических методов, для определения технического состояния технологического оборудования. Приборы толщинометрии весьма разнообразны и подбираются индивидуально.
Капиллярная дефектоскопия сварных швов предназначена для выявления невидимых или слабо видимых дефектов. Основой для этого метода дефектоскопии сварных швов послужила способность жидкостей втягиваться и заполнять даже мельчайшие каналы.
Виды контроля качества сварных соединений
Контроль качества сварных соединений является определяющим показателем дальнейшего поведения данного соединения конструкции.
Вне зависимости от выбранного способа проведения сварочных работ, контроль качества сварных соединений является определяющим показателем дальнейшего поведения данного соединения конструкции. Наличие различных дефектов в сварных соединениях, скрытых при простом визуальном осмотре, может приводить не только к потере его прочности или герметичности, но и к возможности аварийного разрушения во время эксплуатации.
Зачем необходим контроль
После проведения сварочных работ на ответственных конструкциях и изделиях необходимо проводить контроль качества выполненных работ на предмет обнаружения различных дефектов. Если наличие крупных наружных трещин и воздушных пор можно выявить при простом визуальном осмотре, то непровары, внутренние поры и вкрапления шлака уже невозможно обнаружить невооруженным глазом, так как большая их часть скрыта под поверхность металла, имея при этом довольно малые размеры.
Поэтому контроль качества сварных швов подразумевает применение различных методик, специальных приборов и реагентов для того, чтобы: своевременно выявлять и устранять все виды дефектов; получать сварные высококачественные соединения; определять точность выполнения технологического процесса сварочных работ; готовое изделие могло соответствовать предъявляемым заказчиком требованиям.
Контролирующие органы
Контроль качества сварных швов осуществляется специально подготовленными контролерами, имеющими аттестационные удостоверения, которые дают им право на проведение визуально-измерительного контроля сварных соединений, но только определенным способом или методикой.
Для этого из числа ИТР назначаются наиболее ответственные работники, которые проходят по специальной программе теоретическое и практическое обучение. После прохождения курса обучения и сдав аттестационные экзамены, контролеры допускаются отделениями Госгортехнадзора России к контролю качества сварных соединений. Обучения контролеров осуществляется только специальными учебными заведениями, имеющими соответствующие лицензии на право подготовки таких специалистов.
Обучение контролеров проводится по программам теоретической и практической подготовки, строго по специализациям в зависимости от методики проведения контроля качества или вида сварных соединений. Специализация контролеров должна быть указана в их аттестационных удостоверениях, к примеру: вид радиографирования или ультразвуковая дефектоскопия.
Существующие методы контроля
На практике существуют два способа проведения проверки качества для сварных соединений: разрушающий метод контроля, неразрушающий метод контроля.
К разрушающим методикам проверки качества можно отнести: все механические испытания готовых образцов; различные химические и физические исследования; металлографическое обследование; мероприятия по контролю исходного материала.
Неразрушающий контроль сварных соединений включает: квалификационную проверку производственного персонала; проверку сварочного оборудования и режима сварки; визуальный осмотр внешнего вида сварного шва; различные методики проведения непосредственного выявления дефектов.
К неразрушающим методикам выявления дефектов относятся: метод тепловой томографии; капиллярный метод контроля; методом истечения или испытания избыточным давлением; акустический или ультразвуковой метод контроля; электромагнитная дефектоскопия; различные радиографические методы; рентгенографический метод.
При этом, вне зависимости от конечного способа контроля качества полученного соединения сварного шва, проверка обязательно должна включать и учитывать всю совокупность подготовительных, технологических и организационных мероприятий, начиная от качества подготовки поверхности заготовки, вида используемого оборудования и материалов, а также квалификации сварщика, заканчивая непосредственной технологией выполнения сварочных работ.
Технология применения
К наиболее технологически простым и наименее затратным можно отнести или выделить визуально-измерительные методы неразрушающего контроля сварных соединений, а именно: тепловой томографии; капиллярную методику; методом истечения или испытания давлением.
Метод тепловой томографии сварных соединений, в свою очередь, делится на: пассивный, когда не требуется внешнее тепловое поле; активный, когда исследуемый образец нагревают за счет внешнего источника тепла. Данная тепловая методика основывается на том, что все обнаруженные дефекты нарушений однородности в виде раковин, воздушных пор, трещин и тому подобных отклонений представляют собой локальные цветовые отклонения при отражении температурного поля на поверхности экрана тепловизора.
Отсутствие необходимости в дополнительных материалах и мероприятиях является главным достоинством такой методики. А вот обязательное наличие дорогостоящего тепловизора, а также невозможность выявить глубину обнаруженных дефектов можно отнести к недостаткам этого метода.
Капиллярная методика контроля основывается на физических свойствах различных активных жидкостей, которые заключаются в способности заполнять мельчайшие воздушные поры и каналы, которые могут образоваться в структуре сварного шва металла. Главным условиями работы такой методики являются наличие высокой текучести применяемой жидкости, а также и величина радиуса воздушного канала, причем чем выше текучесть и больше размер капиллярного отверстия, тем больше вероятность визуального выявления дефекта.
Методика, основанная на капиллярном эффекте, позволяет проверять сварные швы любых металлов как черных, обладающих ферромагнитными свойствами, так и цветных. Данную методику в основном применяют для обнаружения не только поверхностных неоднородностей, но и для выявления сквозных дефектов на открытых поверхностях, например таких, как сварные швы трубопроводов и различных наливных емкостей. Для получения нужного эффекта жидкостью смачивают сварной шов, после чего, спустя некоторое время, ее вытирают с поверхности. Путем подсвечивания ультрафиолетом все дефекты в виде капилляров начинают светиться. Для данного метода используют смесь керосина с мелом или пенетранты. Это специальные жидкости, которые обладают высокой текучестью и большой световой и цветовой контрастность, что позволяет с легкостью обнаруживать дефекты, за счет их особой окраски из-за заполнения пенетрантами. Основным достоинством капиллярной методики контроля является быстрота и небольшая стоимость проведения работ. А вот невозможность выявить глубину и характер обнаруженных дефектов можно отнести к довольно существенным недостаткам данной методики.
Метод истечения или испытания давлением является одним из наиболее широко применяемых способов обнаружения дефектов в целостности сварных швов. Как правило, метод истечения применяется для закрытых трубопроводных систем или различных емкостей и сосудов. Сущность метода заключается в нагнетании давления пневматическим или гидравлическим способом в закрытой системе.
Ультразвуковая и электромагнитная дефектоскопия является относительно несложными методиками и позволяют по ряду визуальных признаков, отображенных на экране приборов, определять количество, вид и глубину дефектов, но при этом никак не получиться установить точный характер имеющегося отклонения в структуре металла.
Стопроцентную визуализацию структуры выполненного сварного соединения позволяют получить только рентгеновский и радиографический контроль сварных соединений. Данные методики технологически очень сложны, поэтому их применяют для проверки сварочных соединений для особо ответственных конструкций и изделий в следующих отраслях: в нефтегазовой промышленности при строительстве магистральных трубопроводов; в точном и среднем машиностроении; в авиационной и космической промышленности.
Самым достоверным способом проверки целостности основного металла и состояния сварных соединений является просвечивание с помощью рентгеновского излучения. Этот способ широко применяют для проверки качества сварных швов магистральных трубопроводов, технологических конструкций кранового оборудования, композитных соединений материалов в авиационной и космической промышленности.
Рентгенографическая дефектоскопия основывается на физическом явлении, которое заключается в прохождении рентгеновского излучения практически через любой существующий материал. А точнее, используется интенсивность его прохождения, которая во многом зависит от физико-химических свойств испытуемого материала и его плотности. Отсюда, рентгеновские лучи, проходя через среду, позволяют показать на экране прибора или на фотопластине любые дефекты в масштабе, которые их ослабляют в зависимости от своей плотности.
Главным достоинством рентгенографии является возможность по отражению контрастности на детекторе не только визуально определять количество и расположение, но и размеры дефектов, а также их структуру в испытуемом материале.
Недостатками рентгенографии дефектоскопии можно считать: громоздкость оборудования; жесткое электромагнитное излучение, опасное для жизни человека; существенные энергозатраты; высокая стоимость исследований.
К более специфичным методикам контроля сварных соединений можно отнести различные радиографические способы. К ним можно отнести: ксерорадиографию, использующую рентгеновское или Y-излучение, как ионизационное облучение для ионизации красящегося порошка в местах обнаружения дефектов; флюорографию, позволяющего отразить структуру исследуемого материала со всеми дефектами на фотобумаге или фотопленке, за счет просвечивания его рентгеновским или Y-излучением; цветовую радиографию, при которой можно получать дополнительно цветное изображение на обычном черно-белом рентгеновском снимке; нейтронную радиографию, использующую облучение материала пучком нейтронов для показа его структуры на детекторе излучения; протонную радиографию, где для просвечивания материала используются особенности прохождения различных веществ потоком протонов или α-чaстиц.
Все эти методики дефекторадиографии позволяют получать самую достоверную и высокоточную информацию при контроле качества сварных соединений, но они имеют один существенный недостаток, который заключается в необходимости использования жесткого электромагнитного излучения, которое, в свою очередь, сильно усложняет применение данной методике на практике.
Контроль качества сварки стальных труб
Контроль качества сварных швов осуществляет строительномонтажная организация в течение всего периода сварочных работ. Проверке подлежат: качество применяемых материалов, техническое состояние сварочного оборудования и инструмента, а также квалификация сварщиков; качество работ по операциям при сборке, прихватке и положении швов; сварные швы (внешний осмотр). Контроль также включает проверку физическими методами сплошности швов, механические испытания образцов, вырезанных из контрольных стыков, и пневматические или гидравлические испытания законченного строительством теплопровода при обеспечении безопасности работ.
Сварочные материалы проверяют сравниванием характеристик, указанных в сертификатах, с требованиями соответствующих ГОСТов и технических условий, а также тщательным внешним осмотром. Техническое состояние сварочного оборудования и инструмента проверяют до начала ведения работ, а также по документам и при необходимости — по пробному стыку. Пооперационный контроль ведут в процессе сборки и сварки стыков трубопроводов. При этом проверяют правильность центровки труб, совпадение кромок, величину зазора, скос кромок, притупление и зачистку кромок, расположение и качество прихваток. Проверяют также технологию и режим сварки, порядок наложения отдельных слоев шва, форму слоев шва, зачистку шлака, отсутствие подрезов, пор, трещин и других внешних дефектов шва. Устанавливают соответствие с технологическими инструкциями. При проведении внешнего осмотра всех стыков к ним предъявляют следующие требования: поверхность наплавленного металла по всему периметру дожна быть слегка выпуклой с плавным переходом наплавленного металла к основному без подрезов, на шве не должно быть незаваренных кратеров; высота усиления шва должна быть ровной; ширина сварного шва должна быть равномерной, не допуская наличия в шве трещин любых размеров, пор, наплывов, кратеров и грубой чешуйчатости. Стыки, не удовлетворяющие по внешнему виду изложенным выше требованиям, бракуют и немедленно исправляют
Проверке сплошности неразрушающими методами контроля подвергаются следующие сварные соединения: трубопроводы, на которые распространяются требования Правил Госгортехнадзора России, наружным диаметром до 465 мм — в объеме предусмотренном этими Правилами, диаметром свыше 465 до 900 мм — в объеме не менее 10% (но не менее четырех стыков), диаметром свыше 900 мм — в объеме не менее 15% (но не менее четырех стыков) общего числа однотипных стыков, выполненных каждым сварщиком. В случае проверки сплошности сварных соединений с помощью магнитографического контроля 10% общего числа стыков, подвергнутых контролю, должно быть проверено, кроме того, радиографическим методом.
При прокладке теплопроводов под железнодорожными и трамвайными путями, автомобильными дорогами, городскими проездами и при устройстве подводных, а также подземных переходов через указанные препятствия, при прокладке в коллекторах и технических коридорах физическим методам контроля подвергаются 100% сварных стыков на данном участке.
Сварные стыки теплопроводов бракуют, если при проверке неразрушающими методами контроля обнаруживают трещины, не- заваренные кратеры, прожоги, а также непровары в корне шва, выполненного на подкладном кольце.
При выявлении неразрушающими методами контроля недопустимых дефектов в сварных швах трубопроводов, на которые распространяются требования Правил Госгортехнадзора России, производят повторный контроль качества швов, установленных этими Правилами, а в сварных швах трубопроводов, на которые не распространяются требования Правил,— с удвоенным числом стыков по сравнению с указанным выше.
При обнаружении при повторной проверке недопустимых дефектов проверяют все стыки, выполненные данным сварщиком. Испытания сварных стыков на растяжение и изгиб механическим способом производят на образцах, вырезанных из контрольных стыков.
Контрольные стыки сваривают в условиях, тождественных условиям сварки рабочих трубопроводов, с применением тех же основных и присадочных материалов и в том же положении, в котором производилась сварка производственных стыков.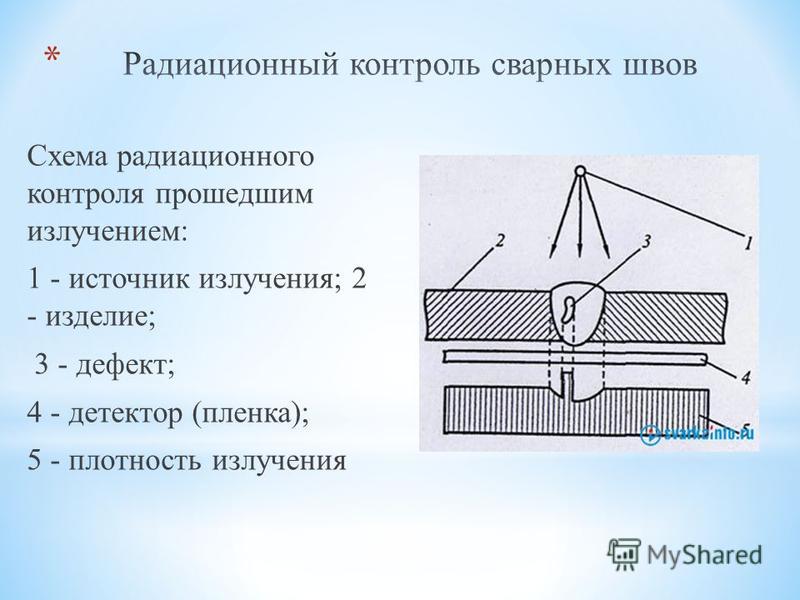
Контроль качества сварочных работ
Контроль качества сварочных работ включает: предварительный контроль, контроль в процессе выполнения сварки (текущий контроль), контроль качества сварных соединений и конструкций.
Цель первых двух видов контроля — предупредить образование дефектов. С помощью третьего вида контроля устанавливают дефекты, определяют необходимые характеристики и свойства сварных соединений и конструкций.
Предварительный контроль. Целью предварительного контроля является ознакомление с технической документацией на изделия, проверка качества состояния средств механизации сборки и сварочного оборудования, электроизмерительных приборов, квалификации сборщиков и сварщиков.
Качество каждой партии металла определяют по маркировке и сертификату, поступившему с завода-поставщика.
В сертификате указываются номер плавки, химический состав и механические свойства металла. Данные сертификата должны отвечать требованиям ГОСТа и ТУ. Металл без сертификата необходимо подвергать химическому анализу, механическим и технологическим испытаниям.
При проверке электродной проволоки и флюса устанавливают, соответствуют ли данные сертификатов требованиям ГОСТа и ТУ. В сертификате на каждую партию проволоки указывается: завод- изготовитель, диаметр, марка, масса проволоки и номер плавки, результаты химического анализа и ГОСТ. Аустенитные нержавеющие проволоки проверяют на горячие трещины по специальным инструкциям.
На каждой бухте электродной проволоки и таре флюса должны быть бирки.
Рекомендуется проводить испытания флюса, при которых определяют, как данный флюс влияет на формирование шва, устойчивость процесса сварки, стойкость металла шва против появления горячих трещин и пор.
Устойчивость процесса сварки и качество формирования шва определяется путем наплавок под испытуемым флюсом на различных режимах. Об устойчивости процесса сварки судят по показаниям приборов, а качество формирования швов определяют визуальным контролем наплавок. При наличии трещин в шве флюс должен быть подвергнут полному химическому анализу.
Влияние флюса на пористость шва проверяют в производственных условиях при сварке типичных для данного производства швов на металле обычной загрязненности. Сравнивается пористость швов, выполненных в равных условиях под испытуемым и эталонным флюсами.
В случае образования в швах чрезмерной пористости флюс подвергают полному химическому анализу. Если химический состав флюса не соответствует требованиям ГОСТа или ТУ, его бракуют.
Проверять качество заготовок внешним осмотром и замерами следует до начала сборки. Размеры заготовок и углы скоса кромок должны соответствовать требованиям чертежа. Протяженность зарезов и выхватов на кромках после газовой резки не должна превышать 10% длины кромки при глубине зареза <1,5—2 мм.
Качество сборки проверяют внешним осмотром и замерами. При этом определяют перекосы, несовмещения кромок, величину и постоянство зазора между деталями, правильность взаимного расположения деталей, размеры и места расположения прихваток, габаритные размеры собранного узла или конструкции.
Проверка приспособлений для сборки (стеллажей, кондукторов, кантователей, манипуляторов и др.) заключается в определении горизонтальности и шероховатости поверхностей, контроле базовых размеров, состояния упоров, фиксаторов и крепежных деталей люфтов, состояния приводных механизмов и надежности их действия, Чтобы сборочные приспособления были в исправном состоянии, необходимо проводить профилактические и восстановительные ремонты.
Измерительный и вспомогательный инструменты сборщиков и сварщиков должны быть в образцовом состоянии.
Контроль состояния сварочного оборудования заключается в проверке действия механической и электрической частей, чистоты и плотности прилегания электрических контактов, возможности получения необходимого режима сварки и установления его стабильности, а также в определении точности и правильности регулировки параметров режима. На таких приборах, как амперметры и вольтметры, должны быть пломбы, эти приборы необходимо систематически проверять у Госповерителя.
В конце каждой смены следует тщательно очищать сборочное и сварочное оборудование от пыли и других загрязнений, а также систематически заменять изношенные детали.
К выполнению работ по сборке и сварке допускаются рабочие, сдавшие специальные теоретические и практические испытания.
Сборщикам и сварщикам, сдавшим испытания, выдаются удостоверения.
2.6 Контроль качества сварных соединений. Совершенствование технологического процесса изготовления конструкции металлургической промышленности на ОАО «ЗСМК»
Похожие главы из других работ:
Возникновение и развитие сварки
Контроль сварных соединений.
Сварку деталей необходимо производить в стационарных или универсальных приспособлениях, предусмотренных технологическим процессом данного предприятия. Качественный сварной шов при любом виде сварки должен иметь ровную. ..
Испытания смонтированного оборудования трубопроводов
Методы неразрушающего контроля качества сварных соединений.
Рентгеновский контроль. Рентгеновские лучи обладают свойством проникать через непрозрачные тела. Пронизывая сварной шов и встречая на своём пути дефекты, они изменяют интенсивность, что фиксируется на рентгеновской плёнке…
Капитальный ремонт магистрального нефтепровода
2.15 Контроль сварных соединений
Контроль сварных стыков трубопровода производится: — систематическим операционным контролем…
Методы контроля сварных соединений
1.Дефекты и контроль качества сварных соединений. Общие сведения и организация контроля
По ГОСТ 15467-79 качество продукции есть совокупность свойств продукции, обусловливающих ее пригодность удовлетворять определенные потребности в соответствии с ее назначением…
Разработка технологии сооружения поселковых газопроводов из полиэтиленовых труб на давление p = 0,003 МПа, диаметр 110 мм, глубина заложения 1,5 м, трубопроводы подвода газа к дому диметром 25 мм (28 домов)
3.
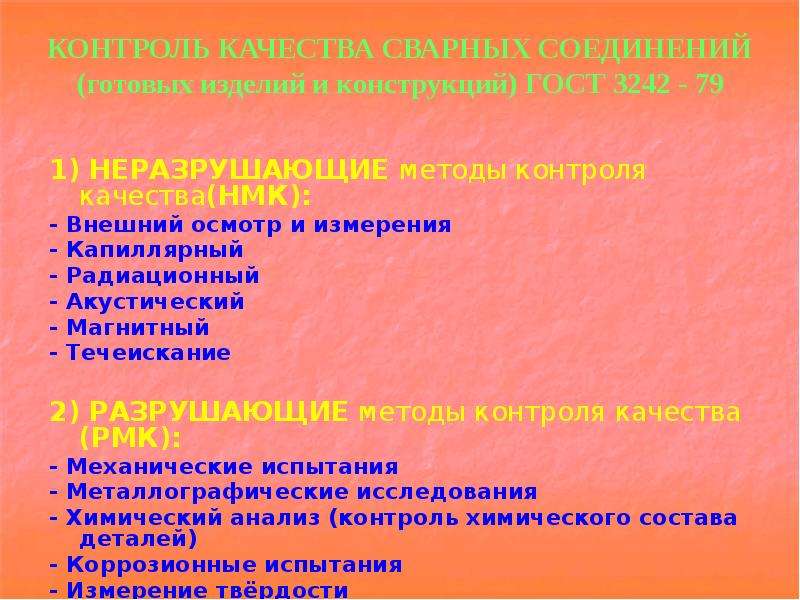
При строительстве полиэтиленовых газопроводов для обеспечения требуемого уровня качества сварных стыков выполняют следующие операции: 1. проверку квалификации сварщиков; 2…
Расчет и проектирование сварной балки двутаврового сечения
2.1 Выбор способа сварки и методов контроля качества сварных соединений
Для изготовления балки выбираем механизированный способ сварки в углекислом газе и применяем проволоку Св08Г2С. Так как данная проволока является универсальной и гарантирует высокие сварочно-технологические свойства…
Сварочно-монтажные работы при сооружении линейной части трубопровода
11. Контроль качества сварных стыков
Для обеспечения требуемого уровня качества сварных соединений необходимо выполнять: А) Пооперационный контроль, производитель работ выполняет непосредственно и непрерывно в процессе проведения операций по сборке и сварке…
Совершенствование технологического процесса изготовления конструкции металлургической промышленности на ОАО «ЗСМК»
2.
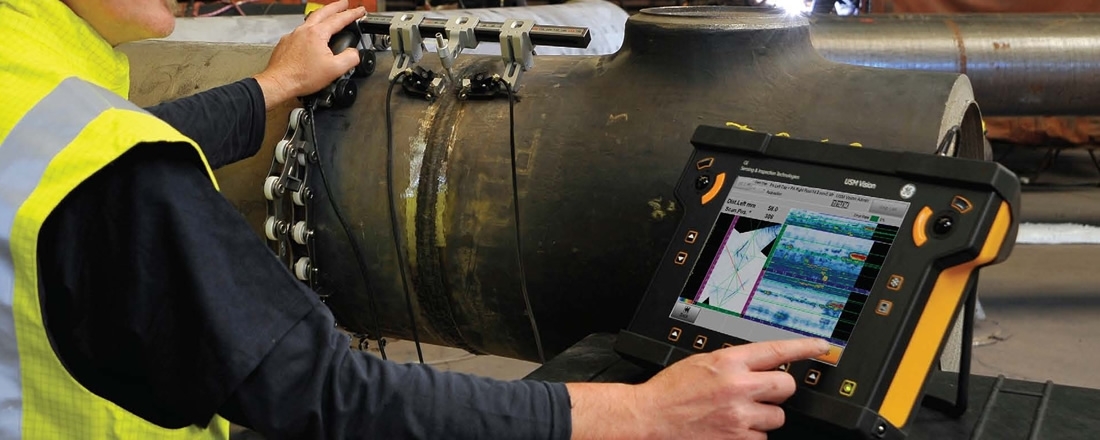
…
Совершенствование технологического процесса изготовления конструкции металлургической промышленности на ОАО «ЗСМК»
2.6.1 Металлографический анализ качества сварных соединений
…
Технологический процесс изготовления корпуса аппарата
8. Контроль качества сварных соединений
Качество сварных соединений в значительной мере определяет эксплуатационную надежность и экономичность конструкций. Наличие в сварных соединениях дефектов — отклонений от заданных свойств, формы и сплошности шва…
Технологический процесс изготовления ригеля сварного
1.9 Контроль качества сварных соединений
…
Технологический процесс изготовления ригеля сварного
1.9.1 Металловедческий анализ качества сварных соединений
Сталь 09Г2С обладает хорошей свариваемостью. Важное требование при сварке — обеспечение равнопрочности сварного соединения с основным металлом и отсутствие дефектов в сварном шве. ..
Технология сборки и сварки подпятника
КОНТРОЛЬ КАЧЕСТВА СВАРНЫХ СОЕДИНЕНИЙ
Работоспособность сварных соединений и конструкций во многом определяется качеством сварных швов. При обработке материалов, в том числе и при сварке, практически всегда образуются различные дефекты…
Ультразвуковой контроль сварных соединений на примере стыкового сварного соединения
3. Ультразвуковой контроль сварных соединений
Для изучения ультразвукового контроля сварных соединений необходимо ввести ключевые определения: Сварное соединение — неразъемное соединение деталей, выполненное сваркой и включающее в себя шов и зону термического влияния…
Эксплуатация газонефтехранилищ
3. Дефекты сварных швов и способы контроля качества швов и сварных соединений
Учитывая особенности работы, к листовым конструкциям предъявляются определенные требования: швы должны быть прочными и плотными. Дефектами сварных швов называют различные отклонения от установленных норм и технических требований. ..
Как организовать контроль качества сварных швов и соединений
1980 год. Северное море, Норвегия. Разлом буровой платформы.
2004 год. CША, Хьюстон. Взрыв и сильный пожар на нефтехимическом заводе.
2016 год. Канада. Разлив 63,6 тыс. литров нефти из-за утечки в нефтепроводе.
Причиной всех этих аварий стала некачественная сварка. Там не доглядели, там упустили, там понадеялись на авось. Жертвы, разрушения, убытки.
Предотвратить подобные инциденты призван своевременный и профессиональный контроль качества сварных швов и соединений.
Кто уполномочен проводить контроль качества сварных швов и соединений?
Контроль осуществляет аттестованный специалист. В РФ аттестацию специалистов сварочных технологий проводит Национальное Агентство Контроля Сварки (НАКС), которое ведет соответствующий реестр аттестованного персонала. Кроме того, для целей контроля качества сварных швов необходимо пройти аттестацию по неразрушающему контролю.
Аттестации в НАКС подлежат также оборудование, приборы и инструменты, применяемые при контроле. Сертификаты выдаются сроком на один год. Без этого пакета документов использование сварочного оборудования и приборов для контроля качества сварки запрещено.
Что подлежит контролю?
Сварка бывает ручная, полуавтоматическая и автоматическая.
- Ручная сварка — это процесс создания соединения при помощи электрической дуги. Дуга между поверхностью металла и электродом зажигается и стабильно горит, формируя практически ровный шов. В работе применяются электроды не длиннее 45 см.
- Полуавтоматическая — сварочный процесс, при котором электрод подается в зону сварки с переменной или постоянной скоростью, куда одновременно поступает инертный или активный газ. Это могут быть и смеси, которые защищают нагретые элементы от воздействия окружающей среды. Такая сварка обеспечивает высококачественный шов и удобство работы.
- Автоматическая — это механизированный вид сварки.
Направление и скорость движения электрода выполняется автоматическим способом. Для данного метода требуются ровные поверхности свариваемых элементов.
Как правило, к контролю предъявляется ручная сварка. При ручной сварке в металле и сварных швах часто образуются дефекты, которые влияют на качество изделия. Серьезные изъяны могут привести к непоправимым последствиям — разрыву трубопровода, разрушению металлоконструкций или обрушению из-за некачественно сваренной арматуры.
Где и когда проводится контроль сварных швов и соединений?
Для проведения проверки инспектор выезжает
- на место производства сварочных работ при изготовлении изделия,
- на объект, где сварные изделия будут свариваться между собой, монтироваться и применяться.
Рассмотрим в качестве примера трубы.
- На заводе-изготовителе материал проходит через ультразвуковой автоматический прибор, который способен находить в металле дефекты, возникающие при прокатке, и они устраняются.
- Дальше трубы поступают на сварку. Технологический процесс примерно выглядит так: лист металла сворачивается и делается продольный сварочный шов. Вот в этот момент инспекторы SGS приезжают на производство и смотрят, не нарушается ли технология. Преимущество проведения инспекции на заводе-изготовителей в том, что бракованное изделие не будет отгружено, т.е. заказчик сэкономит время на транспортировку и отбраковку конструкций с дефектом.
- Входной контроль на объекте применения сварных изделий также эффективен, поскольку позволяет не допустить в производство строительных работ дефектные изделия.
- После передачи качественных труб и других материалов в производство сварочно-монтажных работ, производится сборка этих материалов и их сварка в единый технологический или магистральный трубопровод. Контроль качества сварки на этом этапе не менее важен.
Наибольшего эффекта можно добиться, используя комбинацию этих инспекций, то есть проводя как контроль производства трубной продукции, так и её входной контроль на объекте.
О методах и порядке проведения контроля сварных швов читайте в нашей следующей статье.
Группа SGS является мировым лидером на рынке контроля, экспертизы, испытаний и сертификации. Основанная в 1878 году, сегодня SGS признана эталоном качества и деловой этики. Более 94,000 сотрудников работает в сети SGS, насчитывающей свыше 2,600 офисов и лабораторий по всему миру со штаб-квартирой в Женеве, Швейцария.
svarka (Контроль качества сварных соединений) — документ, страница 3
Технологический контроль является основой создания технически современных и экономически целесообразных (т.е. технологичных) сварных изделий в процессе их изготовления и эксплуатации. Создание технологичных сварных изделий обеспечивают путем контроля конструкторской документации на технологичность.
Технологичность изделия отражает совокупность его свойств, которые проявляются в возможности минимизации затрат труда, средств, материалов и времени при производстве и эксплуатации. На стадии проектирования сварных изделий уровень технологичности должен оцениваться по всей совокупности ее показателей, охватывающих заготовительную, обрабатывающую, сборочно-сварочную и послесварочную стадии производства, а также эксплуатацию. Технологичность конструкции, таким образом, включает понятия производственной и эксплуатационной технологичности. Производственная технологичность определяется применительно к изготовлению, а эксплуатационная технологичность – применительно к выполнению технического обслуживания и ремонта изделий в процессе их эксплуатации.
И в том, и другом случае проблема технологичности по своему содержанию теснейшим образом связана с проблемой обеспечения рационального использования трудовых и материальных ресурсов и оборудования.
При контроле и отработке изделий на производственную технологичность обращают внимание на следующие факторы:
1) Выбор материала и анализ его физико-химических свойств;
2) Использование исходных заготовок и деталей простой формы, выполненных из листового и фасонного проката, гнутых и штампованных элементов;
3) Схема расчленения сварных конструкций на узлы, определение минимального числа соединений, обеспечение доступа инструмента к зоне сварки, схема собираемости;
4) Выбор типа и размеров сварных соединений;
5) Выбор способов сварки, исходя из анализа их технических возможностей и технологических особенностей;
6) Обеспечение точности изготовления сварных конструкций (разработка технологических мер, обеспечивающих минимальные напряжения и деформации).
Основными количественными показателями, характеризующими уровень технологичности изделий, являются:
Под трудоёмкостью понимают затраты труда на изготовление данного изделия.
Под материалоёмкостью понимают не только затраты на материал, необходимые для изготовления единицы изделия, но и массу отходов при изготовлении продукции. При этом вводится коэффициент использования материалов (КИМ).
КИМ = (масса изделия) / (масса всего затраченного материала)
Под себестоимостью понимают сумму материальных затрат на производство изделий по всем расходным статьям изготовления продукции.
Перечисленные показатели рассчитываются и сравниваются с нормативными (базовыми) показателями.
После передачи конструкторской документации в производство, ответственность за соответствие фактических показателей технологичности расчётным, несёт технологическая служба предприятия – изготовителя продукции.
Применительно к сварочному производству сварное изделие считается технологичным, если оно сконструировано из такого числа элементов, с приданием им таких размеров и форм, с применением таких марок материалов, технологии, типов оборудования и технологической оснастки, методов организации и управления производством, которые при заданной программе выпуска и полном соблюдении эксплуатационных характеристик изделия обеспечивают его простое и экономичное изготовление.
При отработке сварных изделий на технологичность необходимо учитывать ряд общих условий:
технологичность изделий в значительной степени зависит от программы выпуска, типа сварочного производства (единичное, серийное, крупносерийное и массовое) и специфики предприятия-изготовителя;
технологичность отдельных элементов или узлов конструкции должна рассматриваться с технологичностью изделия в целом;
отработку технологичности конструкции необходимо рассматривать как комплексную задачу, учитывающую требования ко всем стадиям производственного процесса, начиная от заготовок и кончая испытанием готовых изделий, а также к стадии их эксплуатации;
при отработке технологичности изделий необходимо исходить из учета передового опыта и показателей наиболее высокого технологического уровня, достигнутого в сварочном производстве.
контроль технической документации и отработка изделий на технологичность должны быть непрерывным процессом, начинающимся с момента разработки эскизного проекта и продолжающимся на всех стадиях проектирования и изготовления опытных образцов и установочных серий изделий.
Составной частью анализа конструкции на технологичность является оценка ее контролепригодности.
Контролепригодность – совокупность свойств изделий, обеспечивающих возможность контроля сварных соединений одним или несколькими методами неразрушающего контроля и инструментальную доступность к контролируемым зонам сварных соединений.
Конструктор разрабатывает техническую документацию на контроль, включающую определение и составление перечня контролируемых сварных соединений, рекомендуемые методы и средства контроля, критерии браковки изделий.
Работы по обеспечению контролепригодности и созданию технической документации на контроль конструктор выполняет совместно с технологами, специалистами-дефектоскопистами и эксплуатационниками. На основе анализа расчетных напряжений, результатов испытаний опытных образцов, а также учета статистики отказов при эксплуатации изделий конструктор определяет высоконагруженные детали и узлы, зоны концентраторов напряжений и возможных разрушений, методы контроля изделий при эксплуатации. При этом ставка делается не только на выявление дефектов готовых изделий, но и на профилактику (предотвращение) отказов сварных изделий при эксплуатации.
При контроле технической документации контролируют установленные нормы допустимых дефектов на конкретные виды продукции. Нормы устанавливают в зависимости от степени ответственности (категории) сварных соединений.
В различных отраслях промышленности, как правило, существует три категории ответственности сварных изделий.
1 (первая) – самая высокая. Для первой категории ответственности сварных соединений устанавливаются самые жесткие нормы дефектности, так как соединения работают в самых сложных эксплуатационных условиях.
Изделия 2 (второй) и 3 (третьей) категорий ответственности работают в менее напряженных условиях и поэтому нормы дефектности снижаются.
Тема 7. МЕТРОЛОГИЧЕСКАЯ ЭКСПЕРТИЗА И НОРМОКОНТРОЛЬ ТЕХНИЧЕСКОЙ ДОКУМЕНТАЦИИ.
Основной целью метрологической экспертизы является анализ и оценка технических решений по выбору параметров, подлежащих измерению, установлению норм точности и обеспечению методами и средствами измерений технологического процесса изготовления продукции, подлежащей выпуску.
В задачи метрологической экспертизы технической документации входят:
Для метрологической экспертизы технической документации должны быть разработаны нормативно-технические документы, определяющие метрологические правила и нормы, оформленные в виде стандартов.
В производстве сварных изделий номенклатуру контролируемых параметров можно объединить в четыре группы:
Параметры, характеризующие качество продукции на всех стадиях технологического процесса, начиная от исходного материала и кончая готовой продукцией;
Параметры, характеризующие метрологические характеристики используемого технологического оборудования. От точности характеристик технологического оборудования зависит точность размеров изготавливаемых изделий.
Параметры, характеризующие режим работы технологического оборудования. От стабильности поддержания заданных режимов зависит качество продукции.
Параметры, характеризующие условия выполнения технологических процессов, нормы безопасности труда и охраны окружающей среды (влажность, температура и др.
).
Метрологическую экспертизу проводит эксперт-метролог на основании перечня технических документов, подлежащих экспертизе и утвержденных руководителем предприятия-разработчика технической документации. Экспертиза проводится по мере разработки технических документов. Эксперт должен располагать необходимой информацией и рекомендациями по проведению этого контроля.
Нормоконтроль (стандартизационный контроль) – контроль технической документации на соблюдение в ней норм и правил, установленных комплексами государственных стандартов (ЕСКД, ЕСТД, ЕСТПП).
ЕСКД устанавливает виды конструкторских документов (сборочные чертежи, чертежи деталей, спецификации), стадии их разработки (эскизное проектирование, техническое проектирование, рабочее проектирование), общие правила их оформления и выполнения, а также хранения, размножения и учета
ЕСТД устанавливает виды (маршрутная карта, директивная карта, операционная карта).
и формы технологических документов, правила их оформления, термины и определения, правила хранения, размножения и учета.
ЕСТПП устанавливает единые правила по организации и технологической подготовке производства, предусматривающей применение типовых технологических процессов, стандартной технологической оснастки, средств механизации, автоматизации и др.
Контроль технической документации на соответствия ЕСКД, ЕСТД, ЕСТПП позволяет повысить уровень типизации технологического процесса и использования унифицированных технологических документов, а также позволяет обеспечить подготовку производства к серийному выпуску продукции в минимальные сроки, при минимальных затратах и обеспечении качества выпускаемой продукции.
Под унификацией понимают приведение изделий и документов к единообразию на основе установления рационального числа их разновидностей. Унификация является одним из эффективных средств снижения затрат времени и ресурсов при разработке конструкторской и технологической документации, потребных для изготовления изделия, за счет сокращения ее количества. Унификация также снижает потребное количество технологической оснастки, повышает серийность деталей и сборочных единиц и обеспечивает снижение трудоемкости и себестоимости изготовления.
Типизация – метод унификации, состоящий в разработке типовых решений для применения их при создании новых изделий, процессов или проведении соответствующих работ.
Как правило, нормоконтроль технической документации осуществляется нормоконтролерами службы стандартизации предприятия. Нормоконтроль является завершающим этапом разработки технической документации.
Все виды контроля технической документации рекомендуется проводить на рабочих местах контролеров-исполнителей. В процессе разработки технических документов консультации контролеров-исполнителей, соответствующих видов контроля, могут проводиться и на рабочих местах разработчиков документации.
В случае несоответствии результатов каждого из видов контроля технической документации установленным требованиям оформляются экспертные заключения и протоколы согласования, куда вносятся все замечания и предложения о необходимости внесения изменений в техническую документацию.
После доработки технических документов и выполнения мероприятий по устранению замечаний производится повторный их контроль и дается общее заключение по контролю. При отсутствии замечаний техническая документация подписывается исполнителями всех видов контроля, утверждается руководством предприятия-разработчика и передается предприятию изготовителю.
Тема 8. СИСТЕМА ТЕХНИЧЕСКОГО КОНТРОЛЯ В СВАРОЧНОМ ПРОИЗВОДСТВЕ.
Важнейшей функцией системы организации производства продукции предприятием-изготовителем является ее технический контроль, под которым понимают проверку соответствия объекта контроля установленным техническим требованиям.
Система технического контроля предусматривает организацию на предприятии службы технического контроля, которая наряду с технологическими службами должна обеспечивать высокое качество выпускаемой продукции.
Система технического контроля включает следующие основные элементы:
Под объектом контроля понимают продукцию на той или иной стадии технологического процесса, средства производства и технологические процессы.
Метод контроля – это совокупность определенных принципов и правил выполнения контроля.
К средствам контроля относят контрольно-измерительные приборы, инструменты, аппаратуру, материалы, применяемые при контроле (например, рентгеновская пленка).
Под исполнителями контроля понимают специалистов отдела технического контроля (ОТК) и работников центральной заводской лаборатории (ЦЗЛ), занимающейся поверкой и ремонтом средств измерения.
При техническом контроле выявляют отклонения объекта контроля от установленных требований НТД (нормативно-технической документации).
Технический контроль проводится в соответствии с технической документации и организуется по правилам, установленным стандартом предприятия. Алгоритм выполнения операции контроля представлен на схеме.
Подготовка объекта контроля
Подготовка средств контроля
Техническая документация на контроль
Контроль и обеспечение качества при изготовлении сварных конструкций, подверженных усталостным нагрузкам
Сталь является основным материалом для многих типов несущих конструкций и компонентов строительной техники, кранов-манипуляторов, лесозаготовительных машин, горнодобывающего оборудования, транспортных средств и сельскохозяйственного оборудования. Обычно 60–80% веса автомобиля составляют стальные листы и стальные отливки толщиной 6–70 мм с использованием сварки в качестве основной технологии соединения. Конструкционные детали грузовиков, автобусов и поездов также часто изготавливаются с использованием различных технологий сварки.Таким образом, большая часть продукции, используемой в глобальной транспортной системе, часто состоит из тяжелых стальных конструкций, в которых сварка является доминирующей технологией соединения. Конструкционные детали и компоненты многих из этих продуктов постоянно подвергаются переменным нагрузкам во время работы. Обычно диапазон нагрузок для многих типов транспортных средств и механизмов составляет 1000–20 000 циклов в час. Это означает, что в течение срока службы 10 000–25 000 часов работы компоненты выдержат 10–500 миллионов диапазонов нагрузок.Таким образом, усталостная нагрузка является наиболее частым видом отказа для вышеупомянутых изделий.
Материалы и технологии изготовления сварных конструкций постоянно развиваются. Конечные пользователи также продолжают расширять границы конструкций, используемых в автомобильной, строительной, морской, энергетической и многих других областях. Попытки снизить вес и стоимость, повысить энергоэффективность, улучшить характеристики и уменьшить воздействие на окружающую среду по-прежнему создают проблемы при расчетах на усталость сварных конструкций.Конструкции, в которых используется сварка высокопрочных материалов, также требуют фундаментального понимания возможных режимов и механизмов разрушения. Чтобы сделать возможным производство более легких конструкций, использование высокопрочных материалов быстро увеличивается. Однако при проектировании сварной конструкции из высокопрочной стали проектировщику необходимо учитывать несколько важных факторов, чтобы учесть потенциал облегчения, т. Е. Уменьшить разброс качества при производстве и в то же время повысить качество сварного шва.
Усталостные разрушения сварных конструкций часто начинаются в сварном шве, где усталостная прочность обычно ниже по сравнению с основным материалом и компонентами с надрезами, см. Рис. 1а. Усталостная долговечность основного материала и компонентов с надрезом определяется фазой зарождения трещины; однако в сварных конструкциях большая часть фазы распространения расходуется из-за дефектов и дефектов, возникающих в процессе сварки. Существует большой разброс значений усталостной долговечности сварных соединений, который в основном связан с изменением локальной геометрии сварного шва, его размеров и расположения дефектов и остаточных напряжений, возникающих в процессе сварки.Это подтверждено многочисленными исследованиями и включено в стандарты качества сварных швов и рекомендации по расчету на усталость сварных соединений [1, 2]. Поскольку дефекты, дефекты и другие виды неровностей являются обычным явлением в сварных швах, становится важным иметь для них правила и критерии приемки. Эти дефекты сварного шва определяют усталостную долговечность, что подтверждается диаграммой Китагавы, рис. 1b, которая показывает зависимость усталостной прочности от размера дефекта в различных местах сварного соединения [6].
Система классов сварных швов описывает многие виды дефектов и устанавливает допустимые пределы для различных уровней качества, например, ISO 5817 [3], имеющий классы D, C и B, где B имеет наивысшее качество сварки, а D — самое низкое. Однако действующие правила, приведенные в этой системе, показывают недельную связь с утомлением, что было доказано в нескольких исследованиях [4, 5]. Следовательно, если конструкторы используют эту систему для уменьшения веса несущей конструкции и оптимизации толщины листа наряду с геометрией сварного шва с учетом усталости, они сталкиваются с проблемой определения надлежащего качества, выраженного как уровень качества сварного шва.
a Схематическое изображение усталостной прочности основного материала, а также деталей с надрезом и сваркой. b Диаграмма Китагавы, зависимость усталостной прочности от размера дефекта, с указанными положениями сварных швов [6]
Проектирование и изготовление сварных конструкций — важные задачи, требующие точности, особенно при роботизированной сварке в серийном производстве. Однако для легких сварных конструкций, где используются более тонкие и высокопрочные стали, повышенные уровни номинальных напряжений требуют учета других аспектов проектирования, таких как изгиб, пластическое смятие и усталостная прочность.Высокопрочные стали страдают повышенной чувствительностью к зазубринам и дефектам по сравнению с мягкими сталями. Для сварных компонентов усталостная прочность будет одинаковой для высокопрочной и низкоуглеродистой стали, если не будет достигнуто улучшение качества сварки [6]. Таким образом, улучшение конструкции сварной конструкции за счет использования высокопрочной стали требует улучшенного качества сварки, что, в свою очередь, требует улучшенного обеспечения качества. Сегодня большая часть контроля качества сварных компонентов осуществляется в процессе аудита, отдельно от производственной линии, с использованием стандартных портативных измерительных приборов.Хаммерсберг и Олссон [7] пришли к выводу, что основные стандартные калибры и методы обеспечения качества сварных швов устарели, если не будут приняты меры для исследования и улучшения используемых систем измерения относительно реальных изменений, происходящих в процессе производства.
Таким образом, для полного достижения облегчения конструкции сварных конструкций компании-производители, использующие серийное производство, столкнутся с проблемами в обеспечении качества при использовании высокопрочной стали в своей продукции. Другими методами и инструментами, которые могут использоваться для оценки геометрии поверхности сварного шва, являются лазерные профильные датчики или системы технического зрения, в которых сканирующее устройство используется для измерения поверхности, а затем алгоритм вычисляет определенные характеристики поверхности измеряемого сварного соединения [8, 9,10].
В данном исследовании дается краткое описание того, как определять качество сварного шва, различные системы качества сварки для контроля качества сварных швов и гарантии для сварных конструкций, подверженных усталостным нагрузкам. Кроме того, он проливает свет на аспекты, которые важны для обеспечения качества сварных конструкций, а также на то, как сварные швы могут быть спроектированы и изготовлены для определенной цели. Наконец, представлен новый онлайн-метод объективного контроля качества геометрических сварных швов, который успешно подтверждается испытаниями.Основное внимание в этом исследовании уделяется аспектам внешней формы геометрии сварного шва; следовательно, внутренние аспекты, такие как проникновение и отсутствие плавления, не рассматриваются.
Проектирование и изготовление сварных конструкций — важные задачи, требующие точности, особенно при роботизированной сварке в серийном производстве. Однако для легких сварных конструкций, где используются более тонкие и высокопрочные стали, повышенные уровни номинальных напряжений требуют учета других аспектов проектирования, таких как изгиб, пластическое смятие и усталостная прочность.Высокопрочные стали страдают повышенной чувствительностью к зазубринам и дефектам по сравнению с мягкими сталями. Для сварных компонентов усталостная прочность будет одинаковой для высокопрочной и низкоуглеродистой стали, если не будет достигнуто улучшение качества сварки [6]. Таким образом, улучшение конструкции сварной конструкции за счет использования высокопрочной стали требует улучшенного качества сварного шва, что, в свою очередь, требует улучшенного обеспечения качества. Сегодня большая часть контроля качества сварных компонентов осуществляется в процессе аудита отдельно от производственной линии с использованием стандартных калибров.Хаммерсберг и Олссон [7] пришли к выводу, что основные стандартные приборы и методы для обеспечения качества сварных швов устарели, если не будут приняты меры для исследования и улучшения используемых систем измерения относительно реальных изменений, происходящих в процессе производства. Таким образом, для полного достижения облегчения конструкции сварных конструкций компании-производители, использующие серийное производство, столкнутся с проблемами в обеспечении качества при использовании высокопрочной стали в своей продукции.
В данном исследовании дается краткое описание различных систем качества сварки для контроля и обеспечения качества сварных конструкций, подвергающихся усталостным нагрузкам. Кроме того, он проливает свет на аспекты, которые важны для обеспечения качества сварных конструкций, а также на то, как сварные швы могут быть спроектированы и изготовлены для определенной цели. Наконец, представлен новый онлайн-метод объективного контроля качества геометрических сварных швов, который успешно подтверждается испытаниями и внедрением в среду производства сварных швов.
(PDF) Контроль и обеспечение качества при изготовлении сварных конструкций, подверженных усталостным нагрузкам
конструкции, однако при использовании более тонких и высокопрочных сталей
повышенные уровни номинальных напряжений требуют учета других аспектов проектирования. такие как изгиб, пластмассовый износ цв.
и усталостная прочность.Высокопрочные стали
страдают повышенной чувствительностью к зазубринам и дефектам по сравнению с мягкими сталями
. Для сварных компонентов усталостная прочность
будет одинаковой для высокопрочной и низкоуглеродистой стали, если не будет достигнуто качество сварного шва, подтвержденное im-
[6]. Таким образом, улучшение знака de-
сварной конструкции за счет использования высокопрочной стали re-
требует улучшения качества сварного шва, что, в свою очередь, требует подтвержденного контроля качества.Сегодня большая часть обеспечения качества
для сварных компонентов осуществляется в процессе аудита,
отдельно от производственной линии, с использованием стандартных калибров.
Хаммерсберг и Олссон [7] пришли к выводу, что базовый стандартный калибр
и методы обеспечения качества сварных швов устарели, если
не будут приняты меры для исследования и улучшения используемых систем измерения —
измерительных систем относительно реальных изменений, происходящих в
.производства. Таким образом, для полного достижения облегченной конструкции сварных конструкций
производственные компании, использующие продукцию SE-
rial, столкнутся с проблемами в обеспечении качества, когда
будет внедрять в свою продукцию высокопрочную сталь.
В данном исследовании дается краткое описание различных
систем качества сварных швов для контроля и обеспечения качества
сварных конструкций, подверженных усталостным нагрузкам.
Кроме того, он проливает свет на аспекты, важные
для обеспечения качества сварных конструкций, а также то, как сварные швы
могут быть спроектированы и изготовлены для определенных целей. Наконец, представлен новый онлайн-метод
для обеспечения объективного геометрического сварного шва
, который успешно подтвержден испытаниями
и внедрением в производственной среде.
2 Стандарты качества сварного шва
Качество сварного шва количественно определяет способность сварных соединений соответствовать функциональным требованиям сварного шва в течение срока службы конструкции. Это может быть либо долговечность при статической и / или динамической нагрузке
,, устойчивость к коррозии, внешний вид, либо любая другая механическая функция. Недостаточное качество
следует избегать из-за серьезных последствий для безопасности и стоимости
, т.е.Т. е. выход из строя происходит на ранней стадии. Чрезмерное качество
, с другой стороны, может привести к увеличению стоимости изготовления, что не увеличивает потребительскую ценность продукта. Также как инженеру-проектировщику необходимо указать
достаточного качества
в соответствующих местах конструкции, поскольку различные участки
в конструкции могут испытывать повышенную нагрузку из-за локальных концентраторов напряжений
, таких как ребра жесткости, отверстия и т. Д. и насечки [6].Геометрия сварного шва
зависит от нескольких факторов, таких как присадочный материал
шва, ориентация заготовки во время сварки,
и параметры процесса [11–13]. Кроме того, различная шероховатость сварного шва
и геометрические дефекты по-разному влияют на усталостную долговечность
сварного соединения. Эффективное производство сварных конструкций
требует наличия системы качества.
Это должно поддерживать передовой опыт и давать прогнозируемые усталостные
долговечные свойства конструкций.Требования к сварке — это
наиболее важных факторов в системе качества, которые определяют
как стоимость изготовления, так и усталостную долговечность.
При сравнении шести международных и национальных стандартов
для критериев качества сварки, требования, как правило, основаны на качестве изготовления
, а не на усталостных свойствах. Один стандарт ap-
соответствует назначению, но этот стандарт используется для ядерных энергетических установок
ar и не получил широкого распространения [14].
2.1 Международный стандарт SS-EN ISO 5817
SS-EN ISO 5817 — это европейский стандарт для сварных соединений плавлением
из стали, никеля, титана и их сплавов с уровнями качества и дефектами
[3]. Качество сварного шва определяется уровнями качества
(B, C или D), где B — наивысшее, а D — самое низкое качество сварного шва
, соответственно. Буквы обозначают различные уровни качества
с допустимыми пределами, определенными для каждого дефекта сварного шва и дефекта
.Многим требованиям не хватает
связи с усталостью и нет необходимости, например,
перекрытия и избыточного металла сварного шва. Другие требования слишком общие, например, неполное заполнение канавки или линейное несоосность
, и их наличие может снизить усталостную долговечность. В идеальном стандарте сварки
должно быть четкое и последовательное соединение; обеспечение того, чтобы определенный уровень качества сварки всегда приводил к определенной усталостной долговечности сварного соединения
.
Карлссон и Ленандер [5] провели всестороннее исследование
связи между допустимыми пределами в пределах
ISO 5817 и полученной усталостной долговечностью с использованием механики разрушения. Было показано, что для некоторых недостатков существует прямая зависимость
между допустимым пределом и результирующим усталостным ресурсом
, то есть более высокий уровень качества должен приводить к увеличению усталостной долговечности
по сравнению с более низким уровнем качества.
Однако это не было единообразным для всех несплошностей, где
несколько показывает незначительную связь между уровнем качества
и усталостной долговечностью или не имеет никакой связи. На рисунке 3 приведены примеры неравномерности
, которые имеют плохую корреляцию между качеством сварного шва
и усталостной долговечностью (чрезмерная выпуклость 1,10 и неравная длина ветви
1,16) и хорошей корреляцией (корневая вогнутость 1,17 и угловая несоосность 3,2
) соответственно. Одной из наиболее важных характеристик локальной геометрии сварного шва
является радиус захождения шва [13,15,16]
, который нечетко регулируется допустимыми пределами с простым требованием
плавного перехода.Одна из причин заключается в том, что
до настоящего времени было трудно точно и надежно количественно определить радиус сварного шва
. Вместо этого ISO 5817 дает уровень допуска
для угла захождения сварного шва.
В текущем состоянии у конструкторов нет другого выбора, кроме
, чтобы принять среднюю усталостную прочность из-за отсутствия руководящих указаний
Wel d World
% PDF-1.4
%
334 0 объект
>
эндобдж
xref
334 758
0000000016 00000 н.
0000017037 00000 п.
0000017247 00000 п.
0000017291 00000 п.
0000017327 00000 п.
0000026903 00000 п.
0000027076 00000 п.
0000027226 00000 п.
0000027381 00000 п.
0000027528 00000 п.
0000027743 00000 п.
0000027891 00000 п.
0000028655 00000 п.
0000029348 00000 п.
0000029636 00000 п.
0000029803 00000 п.
0000030217 00000 п.
0000030405 00000 п.
0000030442 00000 п.
0000030545 00000 п.
0000030749 00000 п.
0000030939 00000 п.
0000031133 00000 п.
0000031314 00000 п.
0000044344 00000 п.
0000055023 00000 п.
0000063751 00000 п.
0000070673 00000 п.
0000078108 00000 п.
0000084827 00000 н.
0000085368 00000 п.
0000085497 00000 п.
0000092206 00000 п.
0000100922 00000 н.
0000103615 00000 н.
0000114783 00000 н. 0000115220 00000 н.
0000123756 00000 н.
0000124153 00000 н.
0000125076 00000 н.
0000125255 00000 н.
0000125599 00000 н.
0000125783 00000 н.
0000126331 00000 п.
0000126465 00000 н.
0000148743 00000 н.
0000148782 00000 н.
0000149311 00000 п.
0000149425 00000 н.
0000152417 00000 н.
0000152456 00000 н.
0000153134 00000 н.
0000153287 00000 н.
0000153574 00000 н.
0000153722 00000 н.
0000154333 00000 н.
0000154484 00000 н.
0000154635 00000 н.
0000155233 00000 н.
0000155386 00000 н.
0000155989 00000 н.
0000156141 00000 н.
0000156294 00000 н.
0000156447 00000 н.
0000156600 00000 н.
0000156752 00000 н.
0000156905 00000 н.
0000157056 00000 н.
0000157209 00000 н.
0000157362 00000 н.
0000157514 00000 н.
0000157667 00000 н.
0000157819 00000 п.
0000157972 00000 н.
0000158125 00000 н.
0000158278 00000 н.
0000158431 00000 н.
0000158584 00000 н.
0000158735 00000 н.
0000158887 00000 н.
0000159040 00000 н.
0000159192 00000 н.
0000159344 00000 н.
0000159497 00000 н.
0000159650 00000 н.
0000159803 00000 н.
0000159956 00000 н.
0000160109 00000 н.
0000160262 00000 н.
0000160414 00000 н.
0000160567 00000 н.
0000160720 00000 н.
0000160872 00000 н.
0000161025 00000 н.
0000161177 00000 н.
0000161330 00000 н.
0000161482 00000 н.
0000161635 00000 н.
0000161788 00000 н.
0000161940 00000 н.
0000162092 00000 н.
0000162245 00000 н.
0000162397 00000 н.
0000162549 00000 н.
0000162702 00000 н.
0000162856 00000 н.
0000163009 00000 н.
0000163163 00000 н.
0000163318 00000 н.
0000163471 00000 н.
0000163625 00000 н.
0000163780 00000 н.
0000164377 00000 н.
0000164531 00000 н.
0000164684 00000 н.
0000165261 00000 н.
0000165414 00000 н.
0000166000 00000 н.
0000166154 00000 н.
0000166720 00000 н.
0000166874 00000 н.
0000167028 00000 н.
0000167182 00000 н.
0000167334 00000 н.
0000167488 00000 н.
0000167640 00000 н.
0000167794 00000 н.
0000167948 00000 н.
0000168101 00000 н.
0000168255 00000 н.
0000168406 00000 н.
0000168559 00000 н.
0000168713 00000 н.
0000168864 00000 н.
0000169017 00000 н.
0000169171 00000 н.
0000169325 00000 н.
0000169479 00000 н.
0000169633 00000 н.
0000169786 00000 н.
0000169940 00000 н.
0000170093 00000 н.
0000170245 00000 н.
0000170398 00000 н.
0000170552 00000 н.
0000170706 00000 н.
0000170859 00000 п.
0000171012 00000 н.
0000171165 00000 н.
0000171319 00000 н.
0000171472 00000 н.
0000171625 00000 н.
0000171779 00000 н.
0000171933 00000 н.
0000172086 00000 н.
0000172240 00000 н.
0000172393 00000 н.
0000172546 00000 н.
0000172699 00000 н.
0000172852 00000 н.
0000173006 00000 н.
0000173158 00000 н.
0000173312 00000 н.
0000173466 00000 н.
0000173620 00000 н.
0000173774 00000 н.
0000173928 00000 н.
0000174082 00000 н.
0000174236 00000 п.
0000174390 00000 н.
0000174543 00000 н.
0000174697 00000 н.
0000175316 00000 н.
0000175469 00000 н.
0000175621 00000 н.
0000175773 00000 н.
0000175926 00000 н.
0000176077 00000 н.
0000176231 00000 п.
0000176384 00000 н.
0000176537 00000 н.
0000176691 00000 н.
0000176844 00000 н.
0000176997 00000 н.
0000177150 00000 н.
0000177303 00000 н.
0000177457 00000 н.
0000177611 00000 н.
0000177763 00000 н.
0000177916 00000 н.
0000178070 00000 н.
0000178224 00000 н.
0000178378 00000 н.
0000178532 00000 н.
0000178686 00000 н.
0000178840 00000 н.
0000178993 00000 н.
0000179147 00000 н.
0000179300 00000 н.
0000179454 00000 н.
0000179607 00000 н.
0000179761 00000 н.
0000179914 00000 н.
0000180068 00000 н.
0000180222 00000 п.
0000180376 00000 н.
0000180529 00000 н.
0000180682 00000 н.
0000180836 00000 н.
0000181420 00000 н.
0000181572 00000 н.
0000182141 00000 н.
0000182293 00000 н.
0000182863 00000 н.
0000183015 00000 н.
0000183167 00000 н.
0000183729 00000 н.
0000183881 00000 н.
0000184032 00000 н.
0000184184 00000 н.
0000184335 00000 н.
0000184487 00000 н.
0000184640 00000 н.
0000184792 00000 н.
0000184941 00000 н.
0000185092 00000 н.
0000185243 00000 н.
0000185394 00000 н.
0000185546 00000 н.
0000185698 00000 н.
0000185850 00000 н.
0000186000 00000 н.
0000186152 00000 н.
0000186305 00000 н.
0000186455 00000 н.
0000186607 00000 н.
0000186758 00000 н.
0000186909 00000 н.
0000187060 00000 п.
0000187210 00000 н.
0000187362 00000 н.
0000187513 00000 н.
0000187665 00000 н.
0000187817 00000 н.
0000187969 00000 н.
0000188121 00000 н.
0000188272 00000 н.
0000188424 00000 н.
0000188576 00000 н.
0000188727 00000 н.
0000188878 00000 н.
0000189030 00000 н.
0000189182 00000 н.
0000189334 00000 н.
0000189486 00000 н.
0000189639 00000 н.
0000189791 00000 н.
0000189943 00000 н.
00001
00000 н. 00001
00000 н. 0000190703 00000 н. 0000190854 00000 н. 0000191006 00000 н. 0000191156 00000 н. 0000191309 00000 н. 0000191461 00000 н. 0000191613 00000 н. 0000191764 00000 н. 0000191916 00000 н. 0000192067 00000 н. 0000192217 00000 н. 0000192368 00000 н. 0000192520 00000 н. 0000192672 00000 н.



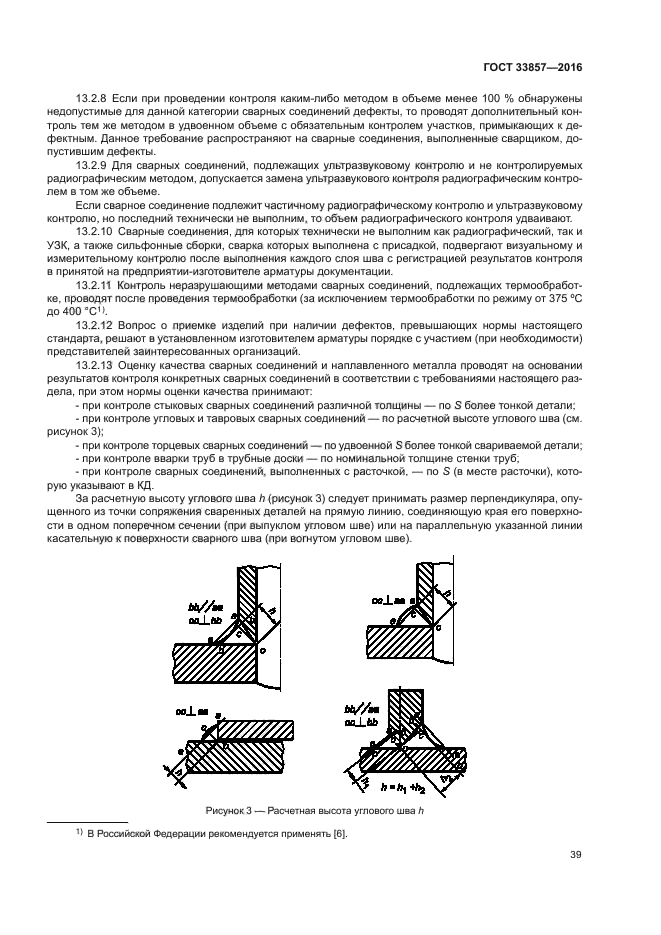


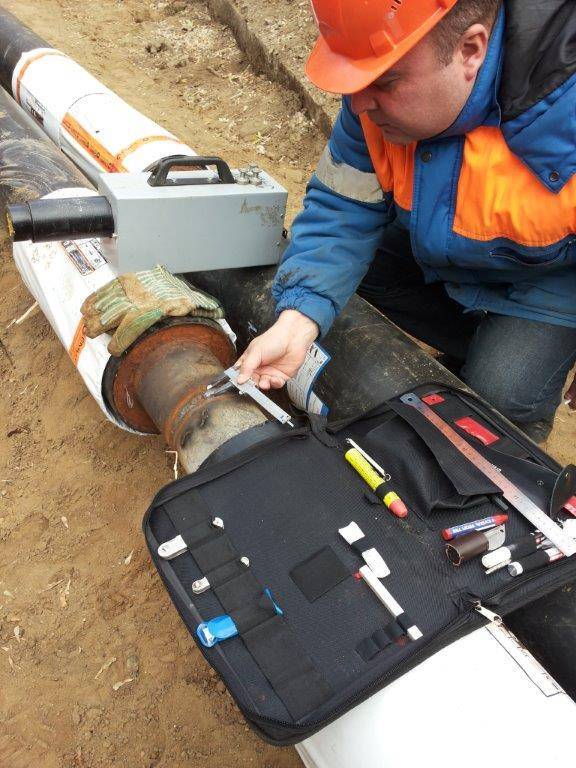
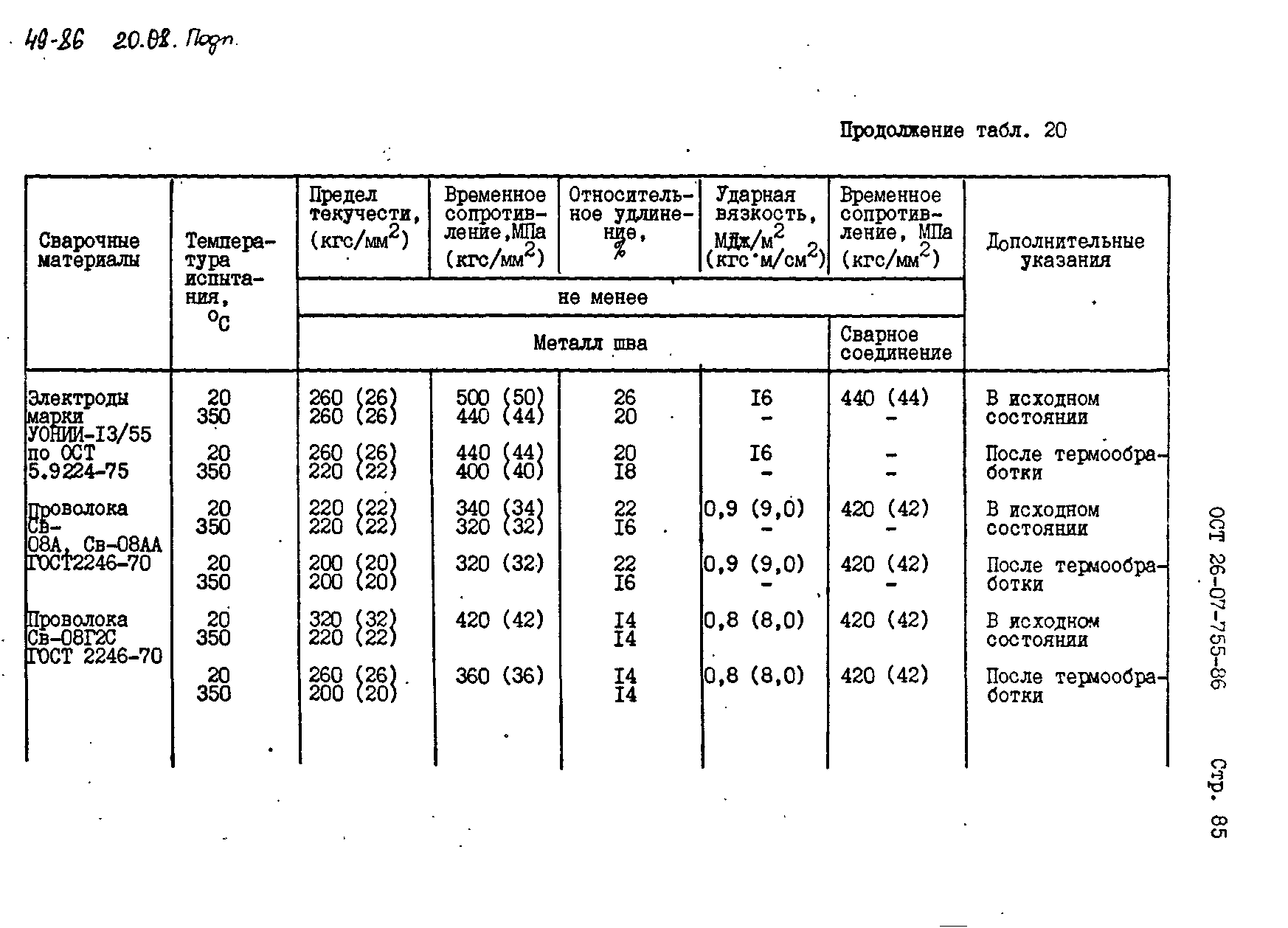



05: Контроль, проверка и испытания качества сварки
Продолжительность: ± 4 недели | Код курса: TW ~ 005 | Стоимость от: 5 500 рандов (300 долларов США) на человека
Этот курс специально предназначен для инспекторов по сварке и персонала по контролю качества, но также чрезвычайно полезен для руководителей мастерских, менеджеров и лаборантов.
Понимание процесса сварки необходимо для контроля качества и прочности сварных швов.Инспекция и испытания являются неотъемлемой частью процесса сварки на любом производственном предприятии, цехе или площадке. Более рентабельно тратить время на проверку и испытание сварных швов с помощью структурированной системы контроля качества, чем на ремонт дефектных сварных швов после происшествия.
Эти модули также являются частью обучения сварщиков для конкретных сварочных процессов, поскольку квалифицированным сварщикам необходимо знать и понимать Требования к качеству сварных соединений, а также то, как они контролируются, контролируются и тестируются.
Этот курс состоит из 13 модулей по следующим темам и предметам:
Сварка- Подготовка сварного шва
- Сварочные позиции
- Простая сварка в металлургии
- Дефекты сварных швов
- Визуальный осмотр
- Неразрушающий контроль
- Разрушающее испытание
- Сварочные символы на чертежах
- Термическая обработка перед нагревом и после сварки
- Контроль качества
Этим вышеупомянутым модулям следует последовательно следовать и, по возможности, изучать и сравнивать практические примеры.
Для просмотра видео нажмите кнопку воспроизведения, а затем при необходимости можно будет развернуть экран в полноэкранном режиме
(При просмотре видеотрейлеров лучше всего запустить видео , а затем сразу приостановить его, , затем подождать несколько минут, чтобы разрешить потоковую передачу, прежде чем начать воспроизвести снова.)
Качество сварного шва — обзор
6.06.3.1.2 Механические свойства сварного шва
Применение факторного метода для прогнозирования качества сварного шва для процесса наплавки с плазменной дугой (PTA) на низкоуглеродистой стали было исследовано Харрисом и Смит ( 36 ).В качестве переменных процесса учитывались ток, скорость подачи порошка, скорость перемещения резака, ширина колебаний и расстояние от резака. Были измерены четыре характеристики качества наплавки, а именно: высота, ширина, твердость и разбавление наплавки. Было подтверждено, что все параметры процесса действовали как основные параметры процесса при контроле качества отложений. Также сообщалось, что процесс PTA является отличным выбором для нанесения высококачественных твердых покрытий при низком контролируемом разбавлении.
Оптимизация сварки трением разнородных материалов с использованием факторного расчета была изучена Мурти и Сундаресан ( 37 ).Они изучили сварку трением трех разнородных материалов, используемых в промышленности: низколегированной стали с аустенитной нержавеющей сталью, среднеуглеродистой стали с быстрорежущей сталью и алюминия с нержавеющей сталью. Основная цель заключалась в определении металлургических и механических характеристик сварных соединений трением, полученных при оптимальных режимах сварки. Были разработаны три математические модели для связи прочности на разрыв с надрезом (NTS) и энергии сдвига с параметрами процесса, а именно: давление трения, время трения и давление ковки с разными уровнями в зависимости от двух материалов, из которых образовано соединение.Сообщалось, что статистический экспериментальный план был полезен для сокращения количества испытаний, необходимых для оптимизации условий сварки трением. Кроме того, прочность соединения, которое было произведено с использованием оптимизированных условий, удовлетворительно соответствовала прогнозируемым результатам. Более того, во всех случаях прочность соединения была по крайней мере такой же высокой, как у более мягкого из двух материалов, из которых образовывалось соединение.
Контроль искажений в роботизированной системе FCAW, экранированной CO 2 , исследовали Арья и Пармар ( 38 ).Метод трехуровневого дробного факторного анализа был использован для разработки математических моделей для прогнозирования угловой деформации в низкоуглеродистой стали толщиной 10 мм. Было исследовано влияние напряжения дуги, скорости подачи проволоки, скорости сварки и угла канавки на угловую деформацию в одинарных V-образных стыковых сварных швах с запечатыванием и без него. Был сделан вывод, что разработанные модели были достаточно точными и могут быть с успехом использованы для контроля угловой деформации в автоматических сварочных линиях с использованием процесса FCAW.
Zhou et al. ( 39 ) использовали факторные эксперименты для исследования влияния параметров соединения (скорости вращения, времени трения и давления) на NTS фрикционных соединений из разнородных композиционных материалов на основе алюминия и нержавеющей стали MMC / AISI304. Было замечено, что давление трения и скорость вращения имеют статистически значимое влияние на значения NTS. Более того, они сообщили, что самый высокий НТС наблюдается в соединениях, изготовленных при высоком давлении трения 120 МПа.
Усталостная выносливость крестообразных соединений FCAW, содержащих непровар, с использованием схемы эксперимента была изучена Баласубраманианом и Гуха ( 40 ). Целью было оптимизировать некоторые размерные факторы, влияющие на усталостную долговечность крестообразных соединений, изготовленных из закаленной и отпущенной стали (класс ASTM 517 F). Было упомянуто, что методы, описанные в этой работе, были довольно простыми и экономичными для оптимизации длительных испытаний на усталость. Также сообщалось, что некоторые факторы, влияющие на усталостную выносливость, были оптимизированы для достижения максимальной усталостной долговечности, но валидность процедуры ограничена областью факторов, рассматриваемой для исследования.Было отмечено, что метод дисперсионного анализа (ANOVA) является наиболее удобным для определения значимости основных эффектов и эффектов взаимодействия совместных размеров. Те же авторы ( 41 ) продолжили свои исследования, разработав математические модели с использованием плана эксперимента для прогнозирования усталостной долговечности дуговой сварки экранированным металлом (SMAW) и крестообразных соединений FCAW, выходящих из строя в области корня и пальца ноги. Используя разработанные модели, усталостную долговечность крестообразного соединения SMAW и FCAW можно спрогнозировать с доверительной вероятностью 95%, однако достоверность моделей ограничена областью факторов.Было обнаружено, что метод факторного экспериментирования при планировании эксперимента более экономичен для прогнозирования влияния различных факторов на усталостную долговечность за счет проведения минимального количества экспериментов.
Коганти и др. ( 42 ) использовали полный факторный расчет для определения оптимальных параметров процесса сварки MIG для необработанных алюминиевых сплавов 5754. Исследовано влияние параметров процесса сварки на разрушающую нагрузку соединения внахлест (предел прочности на разрыв) и проплавление шва.Параметры процесса: потребляемая мощность, скорость горелки, напряжение, ток, скорость подачи проволоки, частота импульсов и расход газа. Прочность соединений и проплавление шва были измерены для различных рабочих диапазонов факторов сварного шва. Было указано, что потребляемая мощность и расход газа были двумя важными факторами, основанными на данных о нагрузке на сдвиг до разрушения и проплавлении сварного шва. Сообщалось также, что чем ниже потребляемая мощность, тем ниже нагрузка сдвига до разрушения и глубина проникновения, и наоборот.Оптимальными настройками коэффициента для более высокой прочности соединения были высокая потребляемая мощность и высокий расход газа.
Sampath ( 43 ) представил инновационный подход на основе ограничений, который оказался весьма эффективным при разработке спецификации расходных сплошных проволочных электродов для GMAW из сталей HSLA-80 и HSLA-100, которые соответствуют или превосходят требования ВМС США. Первоначально он преобразовал требования ВМС США в набор ограничений, которые связывали химический состав сталей с определенными металлургическими характеристиками.Впоследствии факторный план 2 3 был использован для разработки партии сварочных электродов с целью оценки их характеристик. Было показано, что среди восьми использованных электродов два электрода соответствовали требованиям ER-100 или превосходили их, а один электрод соответствовал требованиям ER-120 или превосходил их. Был сделан вывод, что использование этого подхода значительно снижает риск, связанный с разработкой технических характеристик электродов.
Pine et al. ( 44 ) представили экспериментальное и численное исследование для определения жесткости на кручение, предела упругости и предела прочности сваренных точечной сваркой, клеевых и сварных коробчатых секций.Они исследовали множество факторов, а именно: технику соединения, толщину листа, прочность стали, площадь сечения, конструкцию сечения и торцевой сварной шов, используя методы факторного проектирования, чтобы определить их влияние на крутильные свойства коробчатых сечений. Авторы пришли к выводу, что технология соединения, площадь сечения и толщина сечения были основными факторами, которые имеют наибольшее влияние на жесткость коробчатых сечений на кручение. Было обнаружено, что жесткость на кручение можно улучшить без существенного увеличения веса, изменив технику соединения с точечной сварки с шагом 50 мм на клеевое соединение, увеличив площадь сечения и, в меньшей степени, изменив конструкцию сечения.Кроме того, прочность стали была наиболее важным фактором при определении предела упругости и предела прочности.
Хан и др. ( 45 ) использовали полное факторное проектирование для оптимизации процесса лазерной сварки, чтобы получить наиболее желаемое качество сварки с точки зрения геометрии сварного шва и механической прочности, а также определить соответствующие оптимальные настройки параметров сварки. Мощность лазера и скорость сварки были указаны как наиболее важные факторы, влияющие на геометрию сварного шва, а также на силу сдвига сварного шва. Максимально достижимая длина сопротивления сварного шва и, следовательно, усилие сдвига сварного шва были ограничены по энергии в зависимости от условий сварки, конфигурации соединения и используемых материалов. Оптимальные результаты были представлены в числовом и графическом виде, что позволяет быстрее найти оптимальные настройки для лазерной сварки.
Контроль качества сварки
Главная »Контроль качества сваркиКонтроль качества ( QC ) — это процесс подтверждения того, что продукт соответствует спецификациям.При сварке , QA / QC играет жизненно важную роль в обеспечении качественных и надежных сварных швов и минимизации переделок.
Обеспечение качества
Обеспечение качества (QA) — это набор определенных процессов для систематического мониторинга и оценки для обеспечения качества продукции.
Контроль качества
Контроль качества (QC) — это процесс подтверждения того, что продукт соответствует спецификациям. Он включает в себя проверку и тестирование производственных процессов, а также готовой продукции.Результаты этих испытаний сравниваются с набором определенных критериев приемлемости. Проведение контроля качества во время производства позволяет своевременно выявлять дефекты, что позволяет исправить дефект продукта и, при необходимости, внести коррективы в производственный процесс, чтобы предотвратить дальнейшее появление дефектов на выходе.
При сварке контроль качества / контроля качества играет жизненно важную роль в обеспечении прочных и надежных сварных швов и в минимизации переделок.
Что может произойти, если не соблюдаются процедуры обеспечения и контроля качества?
Отсутствие надлежащего контроля качества во время изготовления может привести к различному качеству сварных швов.При обнаружении дефектов сварного шва потребуется их устранение, что может задержать доставку продукта заказчику. Это также может привести к потере репутации изготовителя. Если договорное соглашение с заказчиком требует соблюдения стандартов, а применимые требования QA / QC не были соблюдены, это может привести к договорным вопросам и юридическим штрафам. Этот сценарий более вероятен, если после завершения изготовления обнаруживаются проблемы с качеством, ведущие к задержкам и, что еще хуже, к выходу продукта из строя во время использования.
После составления WPS сам WPS и сварщик должны пройти квалификацию.
Квалификация сварщика
Квалификация сварщика должна быть проведена для подтверждения способности сварщика наплавить качественный сварной металл для определенного типа сварного шва, материала и положения сварного шва.
Квалификация WPS
АттестацияWPS служит для определения того, способны ли сварные швы обеспечивать требуемые характеристики для их применения.
Объем испытаний, необходимых для аттестации WPS, будет зависеть от того, используются ли предварительно квалифицированная подготовка к сварке и расходные материалы. В некоторых случаях (например, при использовании стандартных предварительно аттестованных сварных швов) может потребоваться минимальное тестирование или его отсутствие. Если требуется квалификация WPS, образцы для испытаний сварных швов (также называемые сварочными купонами) изготавливаются в соответствии с WPS и стандартом соответствия. Неразрушающий контроль (NDT) и Разрушающий контроль (DT) затем проводится на испытательных образцах для проверки дефектов сварных швов и свойств соединения.A Процедура Протокол аттестации (PQR) или Протокол аттестации процедуры сварки (WPQR) используется для документирования аттестации сварного шва.
Аттестацию сварщика необходимо выполнить, чтобы подтвердить способность сварщика наплавлять прочный металл сварного шва для определенного типа сварного шва, материала и положения сварного шва. Квалификация сварщика действительна для различных материалов, толщин, положений и типов сварных швов, в зависимости от квалификационного стандарта. Это задокументировано в Свидетельстве о квалификационном испытании сварщика и квалификационном аттестации сварщика .
Процедура проверки и испытаний (ITP) , Листы проверок и испытаний — Эти документы созданы на основе WPS и проектной документации. Они заполняются по мере проведения проверок / тестов QC для записи.
Контроль качества перед сваркой
Контроль качества перед фактической сваркой обычно включает следующее:
- Подтверждение материала для обеспечения того, чтобы химический состав и механические свойства соответствовали проектным спецификациям — обычно делается путем просмотра сертификатов на материалы.В определенных обстоятельствах также может потребоваться некоторое тестирование, например на толстых пластинах UT, чтобы исключить ламинарный разрыв во время / после сварки.
- Подготовка шва для обеспечения соответствия подготовки проектной спецификации и / или установленному стандарту сварки.
Сюда входят проверки размеров и чистоты.
- Подгонка швов проверок — корневое отверстие, прихватки и подкладочный материал (и т. Д.) Соответствуют WPS и стандартам соответствия.
- Сварщик Квалификация — убедитесь, что сварщик имеет квалификацию для выполнения сварки.
Контроль качества во время сварки
- Проверить температуры предварительного нагрева и промежуточного прохода находятся в пределах, указанных в WPS
- Подтвердите, что присадочный материал соответствует спецификации WPS
- Прочие проверки: очистка между проходами, внешний вид сварного шва, задняя строжка, если указано
- Подтвердите, что WPS соблюдается
- Неразрушающий контроль в соответствии с требованиями
Контроль качества после сварки
Масштаб контроля качества будет зависеть от стандарта соответствия сварки, класса сварного шва и договоренности с заказчиком. Тестирование может быть DT или NDT .
Визуальный контроль сварных соединений
Визуальный контроль сварных соединений
Визуальный осмотр, вероятно, является наиболее недооцененным и часто неправильно используемым методом контроля сварки. Из-за простоты и отсутствия сложного оборудования возможности этого метода контроля часто недооцениваются. Визуальный осмотр сварки часто бывает самым простым и обычно наименее дорогостоящим.При правильном проведении такой контроль часто может быть чрезвычайно эффективным методом поддержания приемлемого качества сварки и предотвращения проблем при сварке. В сварочных операциях есть много областей, которые можно проверить и оценить с помощью этого метода контроля.
При разработке плана проверки нам необходимо определить наиболее подходящие области для применения нашей проверки. Нам нужно рассмотреть возможность предотвращения проблем, связанных со сваркой, а не обнаруживать проблемы, которые могли уже возникнуть. Неразрушающий контроль (NDT), который обычно используется для проверки завершенных сварных швов, обычно разрабатывается и проводится для выявления проблем со сваркой постфактум, когда сварка завершена. Визуальный осмотр часто используется для предотвращения возникновения проблем со сваркой. Функция контроля сварки часто делится на три области. Первым и часто наименее используемым является осмотр перед сваркой. Этот тип проверки часто может дать нам возможность обнаружить и исправить неприемлемые условия до того, как они перерастут в настоящие проблемы сварки.Во-вторых, проверка во время операции сварки часто может предотвратить проблемы в готовом сварном шве путем проверки условий сварки и процедурных требований. В-третьих, визуальный контроль после сварки — это относительно простой метод проведения оценки качества сварного шва. Рассмотрим подробнее каждый из этих этапов проверки.
Осмотр перед сваркой
Эта проверка проводится перед началом сварочных работ. Этот тип проверки обычно связан с проверкой подготовки сварного шва и проверкой параметров, которые было бы трудно или невозможно подтвердить во время или после сварки. Это область проверки, где мы можем лучше всего внедрить средства контроля, которые могут предотвратить дефектную сварку. Некоторыми областями предварительного контроля сварного шва являются контроль подготовки стыка / предварительная подготовка сварного шва. Это может включать в себя проверку размеров корневых отверстий. Слишком плотные корневые отверстия могут привести к недостаточному проникновению корней. Слишком большие корневые отверстия могут вызвать чрезмерное проникновение. Если угол наклона сварного шва слишком мал, он может вызвать неплавление, а если он слишком большой, то может привести к деформации сварного соединения из-за перегрева и чрезмерного напряжения усадки.Выравнивание стыка (перекос сварного стыка) может привести к затруднениям в получении прочного сварного шва и концентрации напряжений в месте его расположения, что приведет к снижению усталостной долговечности. Состояние и чистота поверхности листа, предварительная очистка перед сваркой часто могут иметь огромное значение.
Неправильная или недостаточная очистка может привести к недопустимому уровню пористости в готовом сварном шве. Другие проверки перед сваркой могут включать проверку предварительного нагрева, температуру и метод нагрева, наличие и расположение устройств контроля термообработки, а также тип и эффективность продувки газом, если применимо.
Осмотр перед сваркой может также включать оценку и проверку документации, сертификацию материалов, сертификацию присадочных сплавов, квалификацию сварщика, квалификацию процедуры сварки, а также идентификацию сварщика и сварщика для прослеживаемости, если это применимо.
Контроль во время сварки
Это проверка, которая проводится во время операции сварки и связана, в основном, с требованиями спецификации процедуры сварки (WPS).Эта проверка включает в себя такие элементы, как методы очистки между проходами, контроль температуры между проходами, настройки сварочного тока, скорость хода сварки, тип защитного газа, расход газа и последовательность сварки, если применимо. Кроме того, любые условия окружающей среды, которые могут повлиять на качество сварного шва, такие как дождь, ветер и экстремальные температуры.
Контроль после сварки
Эта проверка обычно проводится для проверки целостности сварного шва. Многие методы неразрушающего контроля (NDT) используются для контроля после сварки.Однако, даже если сварной шов будет подвергаться неразрушающему контролю, обычно целесообразно сначала провести визуальный осмотр. Одна из причин этого заключается в том, что неоднородности поверхности, которые можно обнаружить при визуальном осмотре, иногда могут вызывать неправильную интерпретацию результатов неразрушающего контроля или скрывать другие неоднородности в теле сварного шва. Наиболее частыми нарушениями сплошности сварки, обнаруживаемыми при визуальном осмотре, являются такие условия, как сварные швы меньшего размера, подрез, перекрытие, растрескивание поверхности, пористость поверхности, недостаточное заполнение, неполное проникновение корня, чрезмерное проникновение корня, прожог и чрезмерное армирование.
Заключение
Хороший план проверки перед сваркой может предоставить нам прекрасную возможность предотвратить проблемы при сварке до их начала путем обнаружения и исправления ситуаций, которые могут вызвать проблемы при сварке или прерывания сварки.
Проверка, проводимая во время операции сварки, часто позволяет выявить проблемы до того, как они усилятся, а также помогает обеспечить уверенность в конечном свариваемом продукте.
Контроль после сварки часто может обеспечить экономичный метод определения приемлемости сварного шва с учетом многих неоднородностей поверхности.
.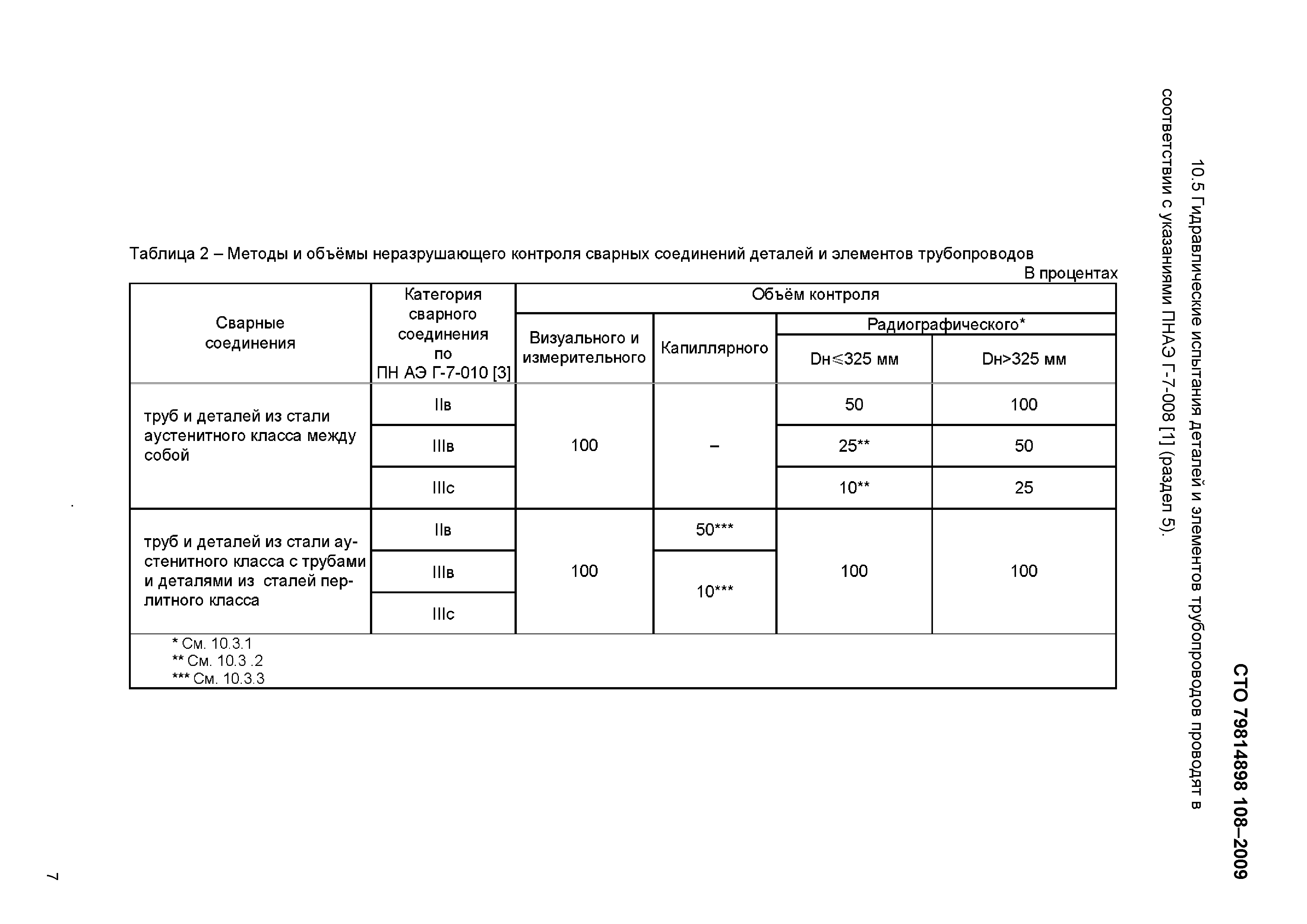