Технология ручной дуговой наплавки стали
Для электродуговой наплавки специальными электродами используют большое количество марок покрытых электродов различного назначения. ГОСТ 10051—75* предусматривает 44 типа таких электродов. Основными характеристиками электрода каждого типа, согласно ГОСТ, являются химический состав наплавленного металла и твердость в рабочем состоянии. Кроме того, электроды разделяются по их назначению, например наплавку изношенных деталей машин (осей и валов), работающих на смятие и интенсивные ударные нагрузки, производят электродами Э15Г5 марки ОЗН-400У. Наплавленный металл, как видно из наименования типа электрода, обеспечивает содержание в среднем 0,15% (0,12—0,18) углерода, 5% (4,1—5,2) марганца и твердость по Роквеллу (HRC) 40—44 Подвергаемые износу, смятию и интенсивным ударным нагрузкам, концы рельсов, оси, автотранспортные и другие детали наплавляют электродами Э11ГЗ марки ОЗН-ЗООУ с содержанием 0,11 % (0,08— 0,13) углерода, 3 % (2,8—4) марганца и твердость по Роквеллу 28—35.
ножей дорожных машин и т. д. Ручная дуговая наплавка покрытыми электродами на поверхности деталей широко распространена, так как ее можно применять при различных конфигурациях деталей и типовом сварочном оборудовании — нужны только наплавочные электроды и навыки сварщика.
Для наплавочных электродов используют специальную электродную проволоку, изготовляемую в соответствии с ГОСТ 10543—82*. Из различных марок этой проволоки изготовляют стержни и наносят на них специально подобранное покрытие. Отдельные марки электродной проволоки используют при аргонодуговой наплавке вольфрамовым электродом. Для наплавки твердых сплавов применяют литые стержни, так называемые стеллиты марок В2К, ВЗК и их заменители стеллитоподобиые сплавы сормайт-1 и сормайт-2.
Для уменьшения доли основного металла в наплавке применяют пониженный сварочный ток, обеспечивающий устойчивое горение дуги. При однослойной наплавке использование таких режимов уменьшает долю основного металла до 0,3—0,45. При поперечном колебании электрода эта доля может быть уменьшена до 0,25. Для дальнейшего уменьшения присутствия основного металла в наплавке ее следует вести в 2—3 слоя. В случаях, когда металл наплавки и зоны термического влияния склонны к закалке и образованию трещин, необходимо применять предварительный и сопутствующий подогрев — при наплавке твердых спла-
Рис. 21.1. Наплавка порошкообразной смеси угольным электродом
вов до температуры 300—600 °С в зависимости от состава металла. Необходимо отметить, что электро — дуговая ручная наплавка покрытыми электродами — трудоемкий и низкопроизводительный процесс в связи с пониженными режимами и работой вручную. Производительность такой наплавки 0,8—3 кг/ч, а при автоматической наплавке под флюсом 2—15 кг/ч и элект — рошлаковой — до 150 кг/ч. Однако ручную наплавку продолжают широко применять благодаря простоте и доступности процесса.
Для наплавки твердых сплавов применяют порошкообразные зернистые материалы, например сталинит, который приготовляют перемешиванием порошков ферромарганца, углеродистого феррохрома, чугунной стружки и нефтяного кокса. Этот материал используют для наплавки ножей бульдозеров, деталей ковшей экскаваторов и т. д. Твердость наплавки по Роквеллу HRC 52. Для наплавки бурильного инструмента применяют смесь вольфрама и углерода — Вокар. В промышленности применяют и другие смеси.
Для наплавки порошкообразной смеси подготавливают плоскость наплавляемой детали, очищая ее от ржавчины, масла и грязи. Затем на подготовленную поверхность насыпают тонкий слой (0,2—0,3 мм) прокаленной буры (флюса) и на него слой порошкообразной смеси высотой 2—7 мм, который разравнивают и уплотняют гладилкой. Наплавку производят угольной или графитизированной дугой прямой полярности либо переменным током с осциллятором, совершая
плавные движения электрода поперек полосы на 40— 50 мм с постепенным продвижением вдоль нее (рис. 21.1). После расплавления порошка высота его уменьшается в 2—4 раза. Возможна многослойная наплавка, но общая толщина наплавленного слоя для разных смесей ограничена: например для сталинита — 5—6 мм, вокара — 3—4 мм. Рекомендуются предварительный подогрев до 500 °С и медленное охлаждение в горячем песке, закрытом асбестом.
Некоторое применение нашла аргонодуговая наплавка неплавяшимся (вольфрамовым) электродом высоколегированных сталей и сплавов. Для наплавки используют высоколегированную наплавочную проволоку и литые стержни.
Ручная дуговая, электродуговая наплавка – как защищают металл? + Видео
Электродуговая наплавка используется для создания на поверхности деталей добавочного металлического слоя, характеризуемого высокой жаро-, коррозионо- и износостойкостью, а также с целью восстановления исходных параметров изношенных изделий.
1 Ручная дуговая наплавка под флюсом
Технология такого процесса предусматривает нагрев основного металла и его расплавление теплом горящей сварочной дуги, расположенной под слоем флюса между обрабатываемой деталью и электродом плавящегося типа.
Данный вид наплавки используется очень часто, он считается самым популярным вариантом выполнения механизированной наплавки.
При обработке металлов дуговой наплавкой под флюсом наплавленная поверхность имеет очень качественный внешний вид:
- переходы между наплавленными валиками отличаются плавностью;
- слой металла получается безупречно ровным.
Кроме того, данный способ наплавки металлов характеризуется следующими положительными факторами:
- нет открытого излучения электродуги;
- электродный материал теряется несущественно;
- процесс признается высокопроизводительным за счет своей несложности и непрерывности выполнения операций.
Наплавленный материал при его обработке под флюсом допускается легировать по четырем разным методикам:
- Использование стандартных плавленых смесей с порошковой лентой либо проволокой. Указанная проволока или лента (их конкретная марка подбирается от необходимой твердости и непосредственно вида наплавленного металла) при нагреве в дуге формируют жидкий состав с высокой степенью однородности.
- Использование флюсов в сочетании с легированной лентой (проволокой).
Обычно при таком способе применяют флюсы марки АН (26 или 20), спеченные и обычные сварочные ленты, специальные и легированные проволоки.
- Использование керамических смесей марки АНК в комбинации с лентой либо проволокой с малым содержанием углерода. Флюсы АНК гарантируют беспроблемное удаление корки шлака, качественное образование защитного слоя и его отличную стойкость против появления трещин и пор.
- Использование обычных флюсов и низкоуглеродистых лент (проволок) с обязательным размещением элементов с легирующими возможностями на верхнюю часть деталей, которые планируется наплавлять.
Рассматриваемая технология при нанесении нескольких защитных слоев предусматривает необходимость удаления корки шлака перед наплавлением следующего слоя во избежание формирования непроваров и включений шлаков. Изделия из легированных сталей обычно обрабатывают под флюсами с малым содержанием кремния (АН-26 или 22), из низколегированных и углеродистых – под АН-348-А либо ОСЦ-45, из хромоникелевых с высоким уровнем легирования – под АНФ (1 и 5), которые содержат много фтора.
Наплавка металлов под флюсом производится с помощью агрегатов для электродуговой сварки, а также специальных приспособлений, когда речь идет об обработке цилиндрических тел.
2 Электродуговая наплавка проволоками порошкового типа
При такой методике флюсы не нужны. Ее особенность заключается в том, что в наплавочной проволоке (в ее сердечнике) имеются не только легирующие элементы, но еще и добавочные газо- и шлакоформирующие компоненты. При выполнении операции они предохраняют зону наплавки от кислорода, находящегося в воздухе, и от азота. А легирующие добавки при этом легко проникают в получаемый шов и придают поверхности деталей требуемые характеристики.
При использовании порошковых проволок на изделие можно наносить несколько слоев, не удаляя образующуюся шлаковую корку (она очень тонкая и существенного влияния на показатели покрытия не имеет).
- малую себестоимость операции;
- высокую производительность наплавки;
- возможность проведения наплавочных мероприятий вне помещений;
- простоту используемых приспособлений.
Немаловажными технологическими преимуществами описываемого способа наплавки признается то, что человек, выполняющий операцию, четко контролирует все ее стадии, может постоянно следить за образованием защитной поверхности и перемещать сварочный стержень в нужном направлении.
Для выполнения операции применяются проволоки (порошковые) с самозащитными возможностями:
- ПП-АН3 – для наплавки низкоуглеродистых металлов;
- ПП-У15Х12М-О – для обработки деталей, которым требуется придать такие свойства, которые будут противостоять их активному абразивному износу;
- ПП-3ХВ3Ф-О – для изделий, функционирующих при высоких показателях температуры и рабочего давления.
youtube.com/embed/iMvuvvgJdew?rel=0″ frameborder=»0″ allowfullscreen=»»/>
3 Технология и особенности наплавки металлов в защитных газах
Данная методика оптимальна для восстановления и придания особых свойств поверхностям деталей сложных конфигураций, отверстиям с большой глубиной. Она выполняется в разных положениях (пространственных) обрабатываемых изделий, позволяет автоматизировать и механизировать наплавку, используя серийные аппараты для сварки, а главное состоит в том, что специалист четко видит весь процесс и может внести в него необходимые корректировки.
Технология наплавки с применением флюсов и с использованием защитных газов по своей сути одна и та же. Но вторую методику разумнее реализовывать в тех случаях, когда по условиям выполнения операции сложно удалять корку шлака либо подавать в зону наплавки флюс. Осуществляется она в атмосфере одного из четырех газов (гелий, углекислый, азот, аргон).
Легированные и углеродистые металлы наплавляют в углекислом газе, который имеет малую стоимость, медные сплавы – в нейтральном по отношению к меди азоте, магниевых и алюминиевых сплавов, а также высоколегированных сталей – в гелии и аргоне. Причем в последнем случае чаще всего используются вольфрамовые неплавящиеся сварочные стержни, а в остальных – плавящиеся (процесс ведется на обратной полярности постоянного тока).
Недостатком описываемого вида наплавки признается то, что на открытом воздухе выполнять наплавочные мероприятия не рекомендуется, так как есть реальная опасность задувания ветром струи газа. Кроме того, жидкий металл при обработке металлов весьма активно разбрызгивается, засоряя тем самым горелку (ее сопло) и мундштук.
Некоторые особенности наплавки в защитных газах:
- для обработки внутренних поверхностей конической и цилиндрической формы рекомендуется использовать специальные мундштуки большой длины;
- операция выполняется на максимально возможной короткой электродуге, что обеспечивает минимальное разбрызгивание материала;
- изделия цилиндрической формы допускается восстанавливать по винтовой линии, применяя способ поперечного передвижения сварочного стержня либо методику непрерывного валика;
- плоские поверхности желательно наплавлять небольшими «разбросанными» участками, чтобы изделие не коробилось;
- когда используется углекислый газ, в проволоке для наплавки должен присутствовать кремний, марганец или иной раскисляющий компонент;
- допускается вести процесс порошковыми проволоками в тех ситуациях, когда наплавленная поверхность должна иметь после операции какие-либо специальные характеристики.
Сварочные и наплавочные проволоки вводят в процесс наплавки и при восстановлении деталей из низколегированных и углеродистых сплавов. Часто используются проволоки Нп (30ХГСА, 50, 40) и Св (12ГС, 08Г2С, 08ГС). Отметим, что они могут быть и порошковыми, и сплошными по сечению.
Ручная наплавка
Для ручной наплавки поверхностных слоев детали изготавливаются наплавочные электроды двух групп. Первая группа электродов обеспечивает повышение твердости металла. Заданную твердость наплавленного слоя получают путем использования электродной проволоки из малоуглеродистой стали и легирования слоя через обмазку (электроды типа ЦМ-1М, ЭНг-50, ОЗН и др.) или электродной проволоки из легированной стали с дополнительнымлегированием через обмазку (электроды типа ЦС-1, ЦН-2, ЦН-3 и др.).
Электроды второй группы применяются для легирования наплавленного слоя
хромом, бором, марганцем и другими элементами (до 25 — 30%) через обмазку и
дополнительно за счет металла стержня электрода.
Для наплавки режущего инструмента (резцы для токарных, револьверных, долбежных, строгальных станков, фрезы, плашки, резьбовые гребенки, сверла и др.) используются также специальные электроды (ЦИ-IV; ЦИ-1Л и др.), дающие наплавленный слой, соответствующий по составу быстрорежущей стали РФ-1, и электроды (РК-2), легирующие наплавленный металл через обмазку углеродом, хромом, бором и молибденом. Наплавка штампов производится также специальными электродами (Т-540 и др.).
Ручная дуговая наплавка покрытым электродом благодаря
простоте, возможности наплавки на поверхности любой формы широко применяется в
промышленности. Доля участия основного металла в образовании слоя при
использовании режимов, обеспечивающих устойчивое горение дуги, составляет m =
0,3÷0,45. Использование поперечных колебаний позволяет снизить долю участия
основного металла до m = 0,25. Однако дальнейшее снижение m увеличивает
вероятность образования непровара. В зависимости от требований, предъявляемых к
наплавленному слою, используют или обычные покрытые электроды для дуговой сварки
различных сталей, металлов и сплавов, или специальные покрытые электроды для
ручной дуговой наплавки поверхностных слоев с особыми свойствами по ГОСТ
10051—75 (например, электроды марки ОЗШ-4 типа Э-10М9Н8К8Х2СФ по ГОСТ 10051—75,
предназначенные для наплавки штампов холодной штамповки).
Основные недостатки способа — низкая производительность, тяжелые условия труда, непостоянство химического состава наплавленного металла из-за неизбежных колебаний проплавления. Это особенно проявляется при однослойной наплавке.
Ручная дуговая наплавка угольным электродом в основном используется для наплавки порошковых наплавочных смесей. В частности, для создания износостойких слоев на деталях, работающих в условиях интенсивного абразивного изнашивания. Например, для наплавки ножей грейдеров, бульдозеров используют наплавочные смеси С-2М, БХ, КБХ по ГОСТ 11546—75.
Наплавку рекомендуется выполнять в один слой, графитовым электродом, на
постоянном токе прямой полярности. Для получения наплавленного слоя толщиной 2—3
мм толщина слоя порошкообразной смеси должна быть 6—8 мм. Наплавку ведут с
использованием флюса. Обычно используют буру в количестве 2—5 % массы шихты.
Следует отметить, что использование только шлаков не обеспечивает достаточной
защиты. По этой причине наблюдается некоторое окисление легирующих элементов и
образование в наплавленном металле дефектов: пор, неметаллических
включений.
Ручная дуговая наплавка металла — презентация онлайн
1. Письменная экзаменационная работа на тему:
Ручная дуговая наплавкаметалла
Обучающегося группы 31
Тарбаева Владимира Анатольевича
2. Актуальность
Ручная дуговая наплавка является универсальнымспособом и находит широкое применение в
ремонтных работах. Этот способ обладает большой
маневренностью: можно выполнять наплавку в любом
пространственном положении, быстро изменять
направление и место наплавки и тем регулировать
возможность деформации детали, изменять состав
наплавляемого металла в широких пределах за счет
применения различных электродов.
3. Цель работы:
проанализировать способы наплавкиразличных металлов
4. Объект работы:
ручная дуговая наплавка5. Задачи:
1.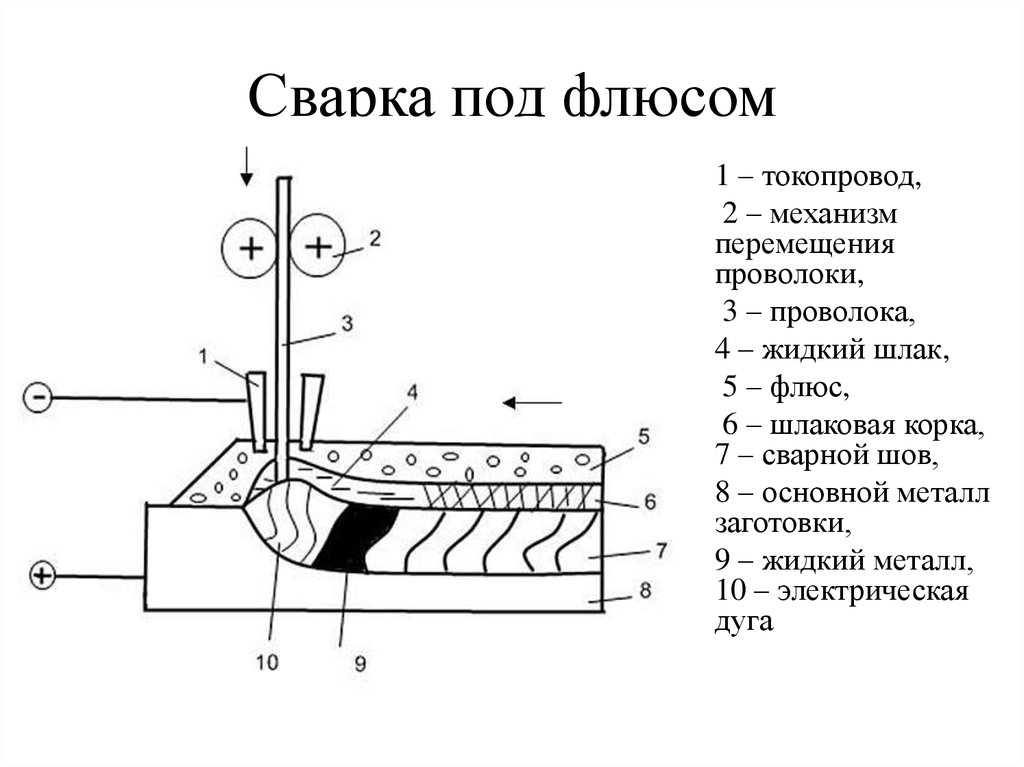
2. Представить основное оборудование, материалы и
технику ручной дуговой наплавки.
3. Обосновать основные положения и требования
охраны труда, меры безопасности при
электросварочных и наплавочных работах.
6. 1 Основы дуговой наплавки
1.1 Общие сведения о Наплавка предусматривает нанесениенаплавке
расплавленного металла на
оплавленную металлическую
поверхность с последующей его
кристаллизацией для создания слоя с
заданными свойствами и
геометрическими параметрами.
Наплавку применяют для восстановления изношенных деталей, а
также при изготовлении новых
деталей с целью получения
поверхностных слоев, обладающих
повышенными твердостью,
износостойкостью, жаропрочностью,
кислотостойкостью или другими
свойствами.
7. 1.2 Материалы для наплавки
Для ручной наплавкииспользуют сварочные
электроды.
ГОСТ 10543-98
устанавливает 44 типа
покрытых металлических
электродов для ручной
дуговой наплавки.

8. 1.3 Оборудование для ручной наплавки
Ручная наплавка, какправило, производится в
стационарных условиях. В
комплект оборудования
поста для ручной
электродуговой наплавки
входит: источник питания,
стол или манипулятор
изделия,
электрододержатель,
сварочные провода,
защитные приспособления,
вспомогательный
инструмент. Рабочее место
наплавщика оборудуется
приточно-вытяжной
вентиляцией.
9. Сварочный трансформатор
Сварочный трансформаторпредназначен для питания дуги
переменным током. Трансформатор
разделяет силовую сеть и сварочную
цепь, понижает напряжение сети до
напряжения, необходимого для сварки,
обеспечивает самостоятельно или в
комплекте с дополнительными
устройствами начальное и повторное
возбуждение и стабильное горение
дуги, формирование требуемых
внешних характеристик и
регулирование силы сварочного тока
или напряжения на дуге.

10. Сварочные выпрямители
Сварочные выпрямители — это устройства,преобразующие с помощью
полупроводниковых элементов — вентилей —
переменный ток в постоянный и
предназначенные для питания сварочной дуги.
Наиболее распространенные выпрямители для
ручной дуговой наплавкии: серии ВД (ВД-101,
ВД-102, ВД-201, ВД-301, ВД-302, ВД-303, ВД506Д, ВД-401), типов ВСС-120-4, ВСС-300-3.
Весьма популярны и универсальные
сварочные выпрямители, формирующие как
падающие, так и жесткие характеристики.
Наиболее известные типы: — серии ВСК (ВСК150, ВСК-300, ВСК-500) и серий ВСУ (ВСУ300, ВСУ-500) и ВДУ (ВДУ-504, ВДУ-305,
ВДУ-1201, ВДУ-1601)
11. Сварочные электромашинные генераторы и преобразователи
Сварочные генераторы,преобразуют
механическую энергию в
электрическую.
Инвертор, преобразует
постоянный ток в
переменный высокой
частоты.
12. 2 Технология ручной дуговой наплавки
2.1 Основныевиды ручной
наплавки
Ручная дуговая наплавка
осуществляется неплавящимися
угольными, графитовыми или
вольфрамовыми и плавящимися
металлическими электродами.
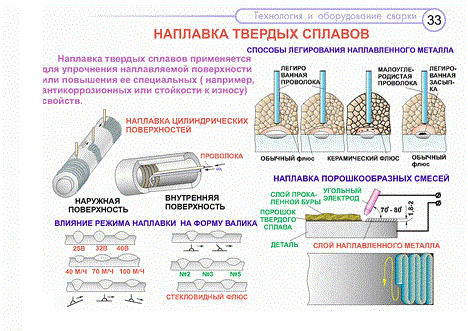
Для повышения производительности
труда и снижения расхода
электроэнергии в ремонтном
производстве применяются
высокопроизводительные методы
ручной дуговой наплавки пучком
электродов и трехфазной дугой.
2.2 Технологический
наплавки металла
процесс
ручной
Процесс наплавки металла
состоит из трех этапов:
подготовки деталей,
наплавки, зачистки.
14. Технологический процесс ручной наплавки металла
При ручной дуговой наплавке к параметрамрежима сварки относятся сила сварочного тока,
напряжение, скорость перемещения электрода
вдоль шва (скорость сварки), род тока, полярность
и др. Дуговую наплавку производят электродами
диаметром стержня 4…5 мм. Сварочный ток
составляет 160…250 А. Напряжение дуги —
22…26 В.
Наплавку производят короткой дугой постоянным
током обратной полярности. При наплавке
(особенно электродами ОЗН) перегрев
наплавленного слоя не допускается.

слой наплавляют отдельными валиками с полным
последовательным охлаждением каждого валика.
15. Техника наплавки
При наложении валика электрод следуетдержать наклонно, под некоторым углом к
вертикальной линии, чтобы капли металла,
перемещающиеся при расплавлении конца
электрода в направлении его оси, попадали в
расплавленный металл ванны. Электрод
должен быть наклонен в сторону направления
сварки. При этом глубина проплавления
основного металла получается больше. Угол
наклона а покрытого электрода к вертикали
должен составлять 15—20°. Изменяя наклон
электрода, сварщик может регулировать
глубину расплавления металла, способствовать
лучшему формированию валика шва и влиять
на скорость охлаждения ванны.
Чем медленнее сварщик перемещает электрод
вдоль шва, тем шире получается валик.
16. Наплавка плоских поверхностей
Плоские поверхности наплавляют двумяспособами. Первый способ — наплавка валиков с
перекрытием друг друга по ширине.

качество наплавки получается при ширине
валика, равной 2,5 диаметра электрода.
Для этого амплитуда поперечного
колебательного перемещения электрода должна
быть равна 1,5-2 диаметрам электрода. Валики
следует накладывать так, чтобы каждый
последующий перекрывал предыдущий на 1/21/3 своей ширины.
Второй способ — укладка узких валиков на
некотором расстоянии один от другого. При
этом шлак удаляют после наложения
нескольких валиков. После этого валики
наплавляются и в промежутках.
17. Наплавка криволинейных поверхностей
Наплавку криволинейныхповерхностей тел вращения
выполняют тремя способами:
наплавкой валиков вдоль образующей
тела вращения, по окружностям и по
винтовой линии. Наплавку по
образующей выполняют отдельными
валиками так же, как при наплавке
плоских поверхностей. Наплавка по
окружностям также выполняется
отдельными валиками до полного
замыкания начального и конечного
участков их со смещением на
определенный шаг вдоль образующей.

18. Винтовая наплавка
При винтовой наплавке деталь вращаетсянепрерывно, при этом источник нагрева
перемещается вдоль оси тела со
скоростью, при которой одному обороту
детали соответствует смещение источника
нагрева, равное шагу наплавки. При
наплавке тел вращения необходимо
учитывать возможность стекания
расплавленного металла в направлении
вращения детали. В этом случае
целесообразно источник нагрева смещать
в сторону, противоположную
направлению вращения, учитывая при
этом длину сварочной ванны и диаметр
изделия.
19. 3 Охрана труда
3.1. Общие требования К сварочным работам допускаетсяохраны труда
персонал не моложе 18 лет, прошедший
специальную подготовку, имеющий
удостоверение на право работы и не
имеющий противопоказаний по
состоянию здоровья. Перед началом
сварочных работ электросварщик обязан
проверить защитные приспособления,
шлем, щиток, диэлектрический коврик
или диэлектрические боты, надеть
спецодежду — брезентовый костюм с
огнестойкой пропиткой, ботинки,
головной убор, диэлектрические перчатки
или брезентовые рукавицы.

20. 3.2 Меры безопасности при электросварочных и наплавочных работах
3.2 Меры безопасности приэлектросварочных и наплавочных работах
— работать только в
специальной одежде и
защитных масках и др.;
— соблюдать ТБ при работе с
оборудованием;
— соблюдать правила
пожарной безопасности.
21. Вывод
Ручная дуговая наплавка в промышленностииспользуют для восстановления исходных размеров
детали и для придания поверхностному слою детали
определенных свойств. Она обладает большой
маневренностью, может проводиться в любом
пространственном положении. Современный сварщик
должен обладать достаточными знаниями для
качественного проведения наплавки.
22. ЛИТЕРАТУРА
1. Виноградов В.С. Электрическая дуговая сварка: учебник для нач. проф. образования– М.: Издательский центр «Академия», 2009- 320с.
2. Думов С. И. Технология электрической сварки плавлением — Л 3. Машиностроение,
2000 —468 с.
3. Казаков Ю.В Сварка и резка материалов учеб. пособие для нач. проф.образования –
М.: Издательский центр «Академия», 2010- 400 с.
4. Куликов О.Н. Ролин Е.И Охрана труда при производстве сварочных работ учеб.
пособие для нач.проф. образования – М.: Издательский центр «Академия», 2010- 176 с..
5. Маслов В.И Сварочные работы: учеб. пособие для нач. проф. образования – М.:
Издательский центр «Академия», 2010- 240 с.
6. Овчинников В.В Технология электросварочных и газосварочных работ: учебник для
нач. проф. образования – М.: Издательский центр «Академия», 2010- 272 с.
7. Рыбаков В. М, Дуговая и газовая сварка — М.; Высшая школа, 2010 -420 c.
8. Чернышов Г.Г Сварочное дело: Сварка и резка металлов: учебник для нач проф.
образования. – М.: Издательский центр «Академия», 2010.- 496 с.
Наплавка ручная дуговая — Энциклопедия по машиностроению XXL
В промышленности широко используются следующие способы наплавки ручная дуговая наплавка плавящимся электродом, дуговая наплавка под флюсом, дуговая наплавка в защитных газах неплавящимся и плавящимся электродами. [c.103]Несмотря на внедрение высокопроизводительных методов наплавки, ручная дуговая сварка необходима главным образом для заварки трещин, допускаемых правилами ремонта, и для наплавки небольших или труднодоступных поверхностей деталей. Перед заваркой трещину разделывают на полную глубину при помощи ручного или пневматического зубила допускается также разделка газовой резкой или электрорезка электродами типа Э-42. Нельзя с этой целью применять угольный электрод. [c.151]
Существуют следующие способы наплавки ручная дуговая наплавка плавящимся и неплавящимся электродом, полуавтоматическая и автоматическая под флюсом. [c.357]
Газовая наплавка. ……. Ручная дуговая наплавка с ме- 2—4 2—20 3 0.15—0,3 [c.69]
Ручная дуговая наплавка металлическими электродами — самый простой способ. Наплавку выполняют короткой дугой ка минимальном токе. Для повышения производительности применяют наплавку пучком электродов и трехфазной дугой. [c.227]
При ручной дуговой сварке покрытым электродом доля основного металла в шве составляет 0,15—0,40 — при наплавке валиков, 0,25—0,50 — при сварке корневых швов, 0,25—0,60 — при сварке под флюсом. [c.25]
Электроды для ручной дуговой сварки и наплавки [c.49]
Ручную дуговую наплавку применяют при восстановлении изношенных поверхностей, восстановлении брака литья и для наплавки поверхностей со специальными свойствами. [c.90]
Ручную дуговую наплавку выполняют покрытым плавящимся и неплавящимся электродами. Перед наплавкой плавящимся элект- [c.90]
В чем сущность ручной дуговой наплавки [c.93]
Для сталей, имеющих ограничения по скоростям охлаждения (то есть склонных либо к закалке, либо к перегреву в зоне термического влияния — низколегированные, среднелегированные и другие стали), для определения скорости сварки v ется использовать пункты 5 — 8 расчета режимов ручной дуговой сварки (РДС), так как подход аналогичен. Однако в определении коэффициента наплавки а (согласно выражению [c.44]
Электроды покрытые металлические для ручной дуговой наплавки поверхностных слоев с особыми свойствами (по ГОСТ 10051—75) [c.24]
Электроды покрытые металлические для ручной дуговой сварки и наплавки. В соответствии с ГОСТ 9466—75 электроды подразделяют по назначению (буквами дано условное обозначение) [c.330]
При выполнении указанных режимов толщина однослойной наплавки составляет около 4 мм, наплавленная поверхность получается ровной с минимальным объемом последующей обработки. При необходимости, наплавки большего объема металла производить это следует в несколько слоев, подобно тому, как это делается при ручной дуговой наплавке штучными электродами. [c.77]
Применение этого способа восстановительной наплавки по сравнению с ручной дуговой штучными электродами дает возможность повысить производительность труда примерно в 2—2,5 раза. Кроме того, значительно сокращается трудоемкость последующей обработки наплавленных поверхностей, улучшается оличество наплавленного металла (отсутствуют шлаковые включения и другие дефекты). [c.78]
Кроме ручной дуговой наплавки, может быть применена наплавка в углекислом газе хромоникелевой проволокой диаметром 1,2 мм с соблюдением указанных требований. Во всех случаях обязательным условием является наложение не менее двух слоев наплавленного металла. Если глубина эрозионных разрушений незначительна (2—3 мм), второй (отжигающий) слой может быть полностью удален при обработке. [c.102]
Наплавочные материалы. Износостойкие материалы высокой твердости часто применяют в виде толстых слоев (единицы и десятки миллиметров), наплавляемых на поверхности деталей различными методами. Применяемые для этой цели материалы (электроды, проволоки, порошки) получили название наплавочных. Используются они для восстановления изношенных деталей (восстановительная наплавка) и для повышения надежности деталей (износостойкая и антикоррозионная наплавка). Наиболее распространенный вид наплавочных материалов — покрытые металлические электроды, применяемые для ручной дуговой наплавки. Восстановительную и антикоррозионную наплавку осуществляют сварочными электродами, износостойкую — наплавочными электродами. [c.146]
Размеры и общие технические требования на покрытые металлические электроды для ручной дуговой сварки сталей и наплавки поверхностных слоев из сталей и сплавов приведены в ГОСТ 9466-75. [c.24]
Какими приемами можно снизить долю участия основного металла в формировании шва при ручной дуговой наплавке [c.136]
В группу электродов для наплавки входят электроды, предназначенные для ручной дуговой наплавки поверхностных слоев с особыми свойствами. Электроды изготовляют и поставляют в соответствии с требованиями ГОСТ 9466-75 и 1005-75. Для наплавочных работ в некоторых случаях также используют сварочные электроды, например электроды, предназначенные для сварки высоколегированных коррозионно-стойких, жаростойких и жаропрочных сталей. [c.178]
Для восстановления изношенных поверхностей деталей применяют различные способы механизированной и ручной наплавки. Ручную дуговую наплавку выполняют электродами двух видов обычными покрытыми (ГОСТ 10051—62) и трубчатыми, у которых вместо стержня металлическая трубка, наполненная порош(кообразной шихтой. Обычные покрытые электроды для наплавки можно разделить на три группы электроды, обеспечивающие наплавку (Металла средней твердости электроды, обеспечивающие наплавку металла высокой твердости, и электроды, предназначенные для из- [c.217]
Основы технологии. В практике применяются следующие виды наплавки ручная дуговая, металлическим электродом, ручная дуговая угольным или графитовым электродом с расплавлением зернистых сплавов или литых стержней полуавтоматическая дуговая без защиты дуги специальными напла-. вочными проволоками, или порощковой проволокой, или механической присадочной проволокой с защитой дуги газом , полуавтоматическая дуговая под керамическими и плавлеными флюсами автоматическая дуговая в тех же вариантах, что и полуавтоматическая электрощлаковая вибродуговая газовая ручная ацетилено-кислородная и на газах-заменителях газовая автоматическая с индукционным нагревом. [c.162]
При ручной дуговой наплавке покрытыми электродами, а особенно при механизированной наплавке плавящейся электродной проволокой в среде защитных газов или под флюсом, доля основного металла в наплавленнол слое Уо, 1[c.397]
Козк )фициенты ар, а , ф зависят от вида, способа и параметров режима сварки. При малых плотностях тока (ручная дуговая сварка) значение коэффициентов расплавления и наплавки не превышает 7-Ь 10 г/(А ч). С увеличением плотности тока значение коэффициентов возрастает до 17 г/(А-ч) и более. Коэффициент потерь для различных способов сварки составляет 1—15%. [c.22]
Классификация стальн.ых покрытых элек-т р о д о в. Металлические электроды для дуговой сварки сталей и наплавки изготовляют в соответствии с ГОСТ 9466-75 Электроды покрытые металлические для ручной дуговой сварки сталей и наплавки. Классификация, размеры и общие технические требования . Стальные покрытые электроды для ручной дуговой сварки и наплавки подразделяются по назначению (ГОСТ 9467-75) [c.50]
ГОСТ 9466. Электроды покрытые металлические для ручной дуговой сварки сталей и наплавки. ЬСлассификация и общие технические условия. [c.57]
Электрода покрытые металлические для ручной дуговой наплавки новерхиостных слоев с особыми свойствами 24 —для ручной дуговр сварки конструкционных п теплоустойчивых сталей — Назначение 25, 26 — Титл 23, 24 [c.557]
Наплавку отверстий рекомендуется производить одним из способов — автоматическим, под слоем флюса с поперечными колебаниями электрода или ручной дуговой сваркой поперечными валиками на всю толщину стенки. Эти способы позволяют свести действие факторов, способствующих образованию усов и шлаковых включений в зонах, примыкающих к зазорам, до минимума. Автоматический метод применяется для наплавки поверхности отверстий диаметром более 200 мм, выполненных в виде цилиндра или усеченного конуса. При меньших диаметрах и Х-образной разделке используется ручная дуговая сварка электродами диаметром 5 мм с применением повышенных режимов. Для автоматической наплавки ИркутскНИИхиммашеи разработан специализированный наплавочный автомат, позволяющий производить за один проход наплавку шириной до 250 мм. [c.77]
В сосудах энергетического машиностроения часто для создания внутреннего коррозионноустойчивого слоя применяют автоматическую наплавку проволокой или лентой под слоем флюса. Используют также наплавку ручной электро-дуговой сваркой. Наплавка обеспечивает прочное и плотног сцепление слоев. [c.116]
Сварочные работы, в том числе прихватки и наплавка, рекомендуется выполнять ручной дуговой сваркой с использованием электродов типа Э42А марки УОНИ 13/45 диаметром 3—5 мм. [c.378]
Заварку трещин или наплавки на обечайках и днищах корпусов, а также на коллекторах и распределительных трубах ручной дуговой сваркой производят электродами Э50А (ГОСТ 9467—75), заварки или наплавки на остальных частях производят электродами Э42А (ГОСТ 9467—75). [c.381]
Этот способ наплавки имеет ряд преимуществ перед ручной дуговой штучными электродами. Производительность наялаоии в среде углекислого газа выше, чем при ручной дуговой наплавке. Кроме того, при ручной дуговой наплавке необходима тщательная очистка от шлака поверхности каждого предыдущего валика перед наложением последующего, наплавленная поверхность имеет грубую чешуйчатость, неравномерные по высоте усиления швов, которые подлежат выравниванию и снятию при обработке. Все это значительно увеличивает трудоемкость процесса и длительность ремонтных работ. [c.70]
Выбрать способ наплавки. В ремонтных условиях возможно применять либо ручную дуговую, либо полуавтоматическую наплавку в среде углекислого газа. При малом объеме работ наплавку можно производить штуч- [c.86]
Наплавка камеры производилась проволокой марки Х18Н10Т диаметорм 1,2 мм в один слой полуавтоматом А-547Р с источником питания ПГС-500. Для наплавки поверхность камеры была разбита на 4 участка по количеству одновременно работающих сварщиков. В свою очередь каждый сварщик свой участок разбивал на узкие полосы щириной 100—140 мм, наплавку которых производил Горизонтальными валиками без отрыва дуги, перемещаясь снизу вверх. После наплавки одной полосы на всю высоту (il,8 м) сварщик переходил на соседнюю полосу и наплавлял ее тем же способом. За 6-часовой рабочий день сварщик наплавлял 0,30—0,35 против 0,12—0,15 при ручной дуговой наплавке электродами ЦЛ-9. После наплавки производилась обработка поверхности наждачными кругами, контроль профиля по шаблону и окончательная полировка поверхности войлочными кругами. При осмотре наплавленной камеры после 12 тыс. ч эксплуатации никаких признаков кавитационной эрозии не обнаружено. Поверхность камеры чистая, блестящая. [c.96]
Расход сварочных материалов может быть также определен по Временным нормам расхода материалов на сварочные работы при ремонте энергетического оборудования тепловых электростанций (Союзтех-нерго, 1979), в которых приведены нормы расхода сварочных материалов (электродов, порошковых проволок, защитных газов) йри различных способах сварки (ручной дуговой, комбинированной и полуавтоматической в среде углекислого газа), нормы расхода порошковых проволок и электродов для наплавки и заварки дефектов на деталях энергетического оборудования, а также нормы расхода материалов (э.лектродов, аргона и труб) на обучение и проверку электросварщиков. [c.135]
Защиту и восстановление изношенных деталей осуществляют ручной, дуговой, автоматической дуговой под слоем флюса, вибродуго-вой, электрошлаковой дуговой, электроискровой и ацетилено-кислород-ной наплавкой, а также напеканием порошковой наплавочной смеси. [c.131]
Наплавка деталей ручной дуговой сваркой производится с целью придания поверхности детали особых свойств или восстановления изношенной поверхности, работавшей в сложных условиях. Традиционно подвергают наплавке детали, работающие в условиях ударных нагрузок, абразивного износа, в агрессивных средах. Наилучшим образом работают детали, имеющие достаточно пластичное основание и поверхность высокой твердости и износостойкости. К числу таких деталей относятся, например, элементы штамповой оснастки, иногда целиком вся поверхность штампа может предварительно наплавляться. Рабочие поверхности насосов для перекачки бетонопесчаных смесей должны иметь твердость выше HR 40…50 на глубину до [c.130]
1
Первый слайд презентации: ДИПЛОМНАЯ РАБОТА НА ТЕмУ : “ Технология дуговой наплавки ”
Г. КРАМАТОРСК-2017 Учащегося группы ОМП 14-4 Касимова Станислава КРАМАТОРСКОЕ ВЫСШЕЕ ПРОФЕССИОНАЛЬНОЕ УЧИЛИЩЕ
Изображение слайда
2
Слайд 2
Наплавка предусматривает нанесение расплавленного металла на оплавленную металлическую поверхность с последующей его кристаллизацией для создания слоя с заданными свойствами и геометрическими параметрами. Наплавку применяют для восстановления изношенных деталей, а также при изготовлении новых деталей с целью получения поверхностных слоев, обладающих повышенными твердостью, износостойкостью, жаропрочностью, кислотостойкостью или другими свойствами.
Изображение слайда
3
Слайд 3: Основные способы наплавки
Ручная дуговая наплавка электродами Дуговая наплавка под флюсом Дуговая наплавка в защитных газах Дуговая наплавка порошковыми проволоками Плазменная наплавка Электрошлаковая наплавка Вибродуговая наплавка
Изображение слайда
4
Слайд 4: Общие требования к наплавке
При наплавке должен выполняться ряд технологических требований. В первую очередь таким требованием является минимальное разбавление направленного слоя основным металлом, расплавляемым при наложении валиков. Поэтому в процессе наплавки необходимо получение наплавленного слоя с минимальным проплавлением основного металла, так как в противном случае возрастает доля основного металла в формировании наплавленного слоя. Далее при наплавке необходимо обеспечение минимальной зоны термического влияния и минимальных напряжений и деформации.
Изображение слайда
5
Слайд 5: Наплавка плоских и фасонных поверхностей
Перед наплавкой поверхность тщательно очищают от масла, краски, окалины и других загрязнений. Поверхностные дефекты, в том числе и ранее наклепанный слой, удаляют механическим путем или резаком для поверхностной кислородной резки. С целью снижения сварочных напряжений необходимо добиваться равномерной толщины наплавленного слоя. Поверхность, имеющую неравномерную выработку с большими колебаниями по высоте, выравнивают механическим путем на металлорежущем оборудовании.
Изображение слайда
6
Слайд 6: Подготовка поверхностей под наплавку
Правильная (П) и неправильная (Н) подготовка поверхностей под наплавку; 1…6 — последовательность наложения валиков
Изображение слайда
7
Слайд 7: Защита наплавленного металла
В процессе наплавки в изделии появляются значительные внутренние напряжения, которые приводят к его короблению, а иногда и к разрушению. К мерам, принимаемым для предотвращения возникновения напряжений или снятия их с целью уменьшения деформации изделия, относятся следующие: предварительный подогрев до 200…400 °С; ведение наплавки с погружением изделия в воду без смачивания наплавляемой поверхности; ведение процесса при жестком закреплении изделия в приспособлении; предварительный изгиб изделия в направлении, обратном ожидаемому изгибу; высокотемпературный отпуск после наплавки с нагревом до 650…680 °С.
Изображение слайда
8
Слайд 8: Рисунок нанесения валиков
При износостойкой наплавке применяют способы, различающиеся по рисунку нанесения валиков: Сплошная наплавка – имеет наибольшее распространение как при восстановлении изношенных деталей, так и при изготовлении новых с заданными свойствами поверхностных слоев; Линейчатая наплавка — сочетание разнообразных наплавочных материалов (твердых сплавов, коррозионно-стойкой, перлитной стали и др.) предотвращает образование трещин и отрыва наплавленного металла от основного ;
Изображение слайда
9
Слайд 9: Рисунок нанесения валиков
Сетчатая наплавка — способствует снижению погонной энергии и чувствительности к трещинам; при попадании грунта в узлы сетки повышается стойкость к абразивному изнашиванию; Полосчатая наплавка – равноценна сетчатой наплавке; Точечная наплавка — снижает вредное влияние на основной металл, сокращает потребление наплавочных материалов и повышает износостойкость покрытий; отличается трудоемкостью, поскольку наплавка не является непрерывной.
Изображение слайда
10
Слайд 10: Наплавка криволинейных поверхностей
Наплавку криволинейных поверхностей тел вращения выполняют тремя способами: А) наплавкой валиков вдоль образующей тела вращения. Б) наплавка по окружностям также выполняется отдельными валиками до полного замыкания начального и конечного участков. В) При винтовой наплавке деталь вращается непрерывно, при этом источник нагрева перемещается вдоль оси тела со скоростью, при которой одному обороту детали соответствует смещение источника нагрева, равное шагу наплавки.
Изображение слайда
11
Слайд 11: Смещение электрода при наплавке тел вращения
При наплавке тел вращения необходимо учитывать возможность стекания расплавленного металла в направлении вращения детали. В этом случае целесообразно источник нагрева смещать в сторону, противоположную направлению вращения, учитывая при этом длину сварочной ванны и диаметр изделия.
Изображение слайда
12
Слайд 12: Основные Способы дуговой наплавки
Изображение слайда
13
Слайд 13: Ручная дуговая наплавка покрытыми электродами
Эта технология наплавки при меняется наиболее часто благодаря свой универсальности: детали могут быть практически любой формы, находиться в любом пространственном положении. Простота применяемого оборудования (обычное сварочное), возможность получения наплавки практически любой системы легирования делают способ весьма распространенным.
Изображение слайда
14
Слайд 14: Дуговая наплавка под флюсом
Изображение слайда
15
Слайд 15: Дуговая наплавка в защитных газах
Изображение слайда
16
Слайд 16: Дуговая наплавка порошковыми проволоками
Изображение слайда
17
Слайд 17: Плазменная наплавка
Изображение слайда
18
Слайд 18: Электрошлаковая наплавка
При электрошлаковой наплавке для оплавления основного и присадочного металла служит шлаковая ванна, разогреваемая проходящим через нее электрическим током. Этот способ наплавки, как правило, сочетается с принудительным формированием наплавляемого слоя.
Изображение слайда
19
Слайд 19: Вибродуговая наплавка
Изображение слайда
20
Последний слайд презентации: ДИПЛОМНАЯ РАБОТА НА ТЕмУ : “ Технология дуговой наплавки ”: СПАСИБО ЗА ВНИМАНИЕ
Изображение слайда
Наплавка
(обзор страниц по теме »
Наплавка
«)
Сварщики, аттестованные в НАКС на вид деятельности:
Специалисты по технологиям:
«Наплавка» в разделе «Технология»:
1. Технология наплавки. Рассматриваются одиннадцать применяемые технологий наплавки : ручная дуговая покрытыми электродами, под флюсом, плазменная, электрошлаковая, лазерная, электронно-лучевая, газовая, индукционная, электроконтактная, трением, плакирование энергией взрыва поверхности листов.
2. Вибродуговая наплавка. Обобщенное описание процесса.
3. Наплавка под слоем флюса. Схема процесса. Причины производительности этого вида наплавки.
4. Плазменная сварка и наплавка. Схема плазменного наплавления порошка. 5 достоинств плазменной наплавки.
5. Электрошлаковая наплавка. Общая схема процесса наплавки. Область применения.
6. Восстановление деталей наплавкой. Особенности процесса для различных материалов : низкоуглеродистых сталей, хромовольфрамовых, хромомолибденовых и др. инструментальных теплостойких сталей, штамповых инструментальных, быстрорежущих, низко- и высокоуглеродистых хромистых сталей, ледебуритных хромистых, коррозионно-стойких и т.д.
7. Влияние легирующих элементов на склонность наплавленного металла к трещинообразованию. Влияние Cr, W, Mn, Si, Ti на стойкость к образованию трещин.
«Наплавка» в разделе «Оборудование»:
1. Горелки для наплавки. Рассмотрены характеристики горелок ГН-4, ГН-3, ГН-2, ГН-1.
2. Установки для плазменной наплавки. Несколько примеров установой с приведением их технических характеристик, с кратким описанием.
«Наплавка» в разделе «Сварочные материалы»:
1. Наплавочные материалы. Рассматриваются возможные варианты химического состава материалов и какими свойствами обладает наплавленный материал исходя из этого химсостава. Рассмотрены перлитные, мартенситные, высокомарганцовистые и аустенитные, высокохромистые, коррозионно-стойкие материалы.
2. Порошковая проволока для наплавки чугуна. Назначение проволоки ПП-АНЧ-3, ПП-АНЧ-2, ПП-АНЧ-1, химический состав металла шва. Направления использования порошковой проволоки. Повышение производительности наплавки.
3. Электродные ленты, применяемые для наплавки.
4. Проволоки для наплавки. Перечисление отечественных марок порошковой проволоки и проволоки сплаошного сечения, применяемых для наплавки.
5. Порошковая проволока OK Tubrodur 14.71, OK Tubrodur 14.70, OK Tubrodur 15.42, OK Tubrodur 15.40 для наплавки и ремонта.
6. Порошковая проволока OK Tubrodur 15.43, OK Tubrodur 15.52, OK Tubrodur 15.60, OK Tubrodur 15.72S для наплавки и ремонта деталей.
7. Порошковая проволока OK Tubrodur 15.80, OK Tubrodur 15.73, OK Tubrodur 15.84, OK Tubrodur 15.91S, OK Tubrodur 15.86, для наплавки и ремонта.
8. Проволока OK Autrod 13.90, OK Autrod 13.89, OK Autrod 13.91 для наплавки и ремонта.
9. Марки электродов. Перечислены марки электродов, в т.ч. наплавочных, технические характеристики которых есть на сайте и даны ссылки на страницы с характеристиками каждой марки.
10. Электроды для наплавки ВСН-6.
11. Электроды наплавочные ОЗИ-3.
12. Электроды наплавочные ОЗИ-5.
13. Электроды ОЗИ-6.
14. Электроды OЗИ-6СЭ.
15. Электроды OЗИ-7СЭ.
16. Электроды ОЗН-6.
17. Электроды ОЗН-7.
18. Электроды ОЗН-7М,.
19. Электроды ОЗН-300М.
20. Электроды ОЗН-300СЭ.
21. Электроды ОЗН-400М.
22. Электроды ОЗН-400СЭ.
23. Электроды ОЗН/ВСН-9.
24. Электроды ОЗШ-2.
25. Электроды ОЗШ-3.
26. Электроды ОЗШ-6.
27. Электроды ОЗШ-7.
28. Электроды ОЗШ-8.
29. Электроды ОМГ-Н.
30. Электроды Т-590.
31. Электроды Т-620.
32. Электроды УОНИ-13/НЖ/20Х13.
33. Электроды ЦН-6Л.
34. Электроды ЦН-12М.
35. Электроды ЦНИИН-4.
36. Электроды ЭН-60М.
37. Электроды ЭНУ-2.
38. Электроды для сварки и наплавки чугуна. Спосок марок электродов с кратким описанием назначения, положений сварки, выпускаемых диаметров.
39. Электроды для сварки и наплавки алюминия, меди, никеля, их сплавов.
40. Электроды для наплавки — классификация на шесть групп, краткое описание каждой марки, её назначения.
41. Электроды для наплавки поверхностных слоев с особыми свойствами — кодирование по ГОСТ 10051–75 ГОСТ 9466–75.
42. Области применения наплавочных проволок. Отечественные марки проволоки, подходящие для определенных условий работы.
43. Проволока стальная сварочная сплошного сечения, рекомендуемая для наплавки (ГОСТ 2246-70).
«Наплавка» в разделе «Нормативная база»:
1. ГОСТ 26101-84 Проволока порошковая наплавочная.
2. ГОСТ 10051-75 Электроды покрытые металлические для ручной дуговой наплавки поверхностных слоев с особыми свойствами Типы.
Наплавка и всё для неё в Сварочном каталоге:
1. Работы / услуги | Сварка стали, восстановление деталей наплавкой
2. Работы / услуги | Сварка и наплавка алюминия
3. Работы / услуги | Сварка и наплавка чугуна
4. Электроды для наплавки (предложения участников о продаже)
5. Газы для сварки, резки, наплавки, пайки
6. Проволока для наплавки
7. Порошковая проволока для сварки и наплавки
- < Технология наплавки
- Вибродуговая наплавка >
(PDF) Инновации в дуговой сварке
-15-
3. СВАРКА TIG
Обычная сварка TIG (вольфрамовым инертным газом) — это очень управляемый и точный процесс сварки
, который использовался с начала Второй мировой войны Война. Можно производить
высококачественных сварных соединений из широкого диапазона основных материалов (например, углеродистых сталей, нержавеющих сталей
, сплавов Ni, Ti, Cu или Mg) при отсутствии дефектов, деформации, дыма и низкого качества
Требуетсяуровня водорода.Для более тонких листов (≤ 3 мм) ручная сварка TIG обычно выполняется
в ручном варианте, где сварочные токи ниже. Однако требуются квалифицированные операторы
. Самый главный недостаток процесса — сварка более толстых секций (> 3 мм).
В этих случаях требуются сварные канавки «V» или «X» и присадочный металл, однако связанная с этим более низкая скорость наплавки
(менее 0,5 кг · ч
-1
) является основным недостатком в отношении
.производительность сварки.Связанное с этим несколько проходов и термические циклы (пропорциональные толщине
) также приведут к искажению и более высокому уровню загрязнения.
MIG / MAG (металлический инертный газ / металлический активный газ), PAW (плазменно-дуговая сварка), LBW (лазерная
-лучевая сварка) или EBW (электронно-лучевая сварка) — подходящие процессы для сварки более толстых
секций, тем не менее, MIG / Качество сварки MAG хуже в режиме короткого замыкания,
, особенно при корневых проходах.Все остальные сварочные процессы требуют более высоких начальных капиталовложений,
— это процесс PAW, чувствительный к изменению параметров процесса с более высокой сложностью конструкции горелки
и обычно требующий большого обслуживания.
Для увеличения скорости обычной сварки TIG с увеличением скорости потока в последние годы
были разработаны другие варианты сварки TIG. «Горячая проволока», «узкий зазор», «сильноточная сварка» — это примеры
входящих технологий, нацеленных на повышение скорости наплавки, что является основным недостатком
традиционной сварки TIG.Хотя вариант с «горячей» проволокой пропускает горячую проволоку через задний кожух
и обеспечивает его достаточную экранирующую защиту, это может вызвать дополнительные проблемы. С другой стороны, при использовании варианта «узкая канавка»
трудно контролировать сварку боковых стенок и обеспечивать
правильное позиционирование резака для доступа к нижним частям канавки. Вариант «сильноточного» плавления в
(«скрытая дуга» или «погруженная дуга») обычно автоматизирован и использует силу удара электромагнитной дуги
(> 300 А), которая вызовет значительное смещение
сварочная ванна приводит к более глубокому проплавлению.
Эта относительно глубокая сварочная ванна образуется за счет комбинированного действия теплопроводности и конвекции
в жидком металле, а также разрежения поверхности ванны давлением дуги. В расплаве-
в рабочем режиме (не полностью проникающем) процесс может стать трудноуправляемым, особенно в том, что касается
степени проникновения. При токах свыше 350 А обычно встречаются дефекты (полый валик)
, а при токах более 500 А сварной валик становится очень нестабильным.Высокое давление дуги
вызовет полость под дугой, однако поверхностное натяжение будет сопротивляться деформации
, что делает бассейн довольно нестабильным.
3.1. TIG Keyhole
Режим TIG keyhole (K-TIG) (Jarvis, 2000; CSIRO) был впервые разработан австралийской промышленностью
в конце 1997 года в отношении стабильности сварных швов, профилей глубинной сварки и значительного увеличения производства на
. Процесс сварки был совместно разработан CSIRO
(Организация научных и промышленных исследований Содружества) и CRC-WS (Оперативный исследовательский центр сварных конструкций Co-
), которые представили уникальное и замечательное решение
с высоким потенциалом производительности для стыковые сплавы черных, никелевых и титановых
(листы и трубчатые изделия) толщиной от 3 до 12 мм.Сварка K-TIG — это автоматизированный процесс сварки
, который работает при более высоких токах, чем обычный TIG, чтобы проколоть небольшой
Технология сварки с наложением и восстановление осевой трубы
Анализ металлографической структуры
Зона плавления является слабым местом сварного соединения, которое отличается неоднородностью химического состава и большим количеством дефектов микроструктуры, таких как холодное растрескивание, растрескивание при повторном нагреве и хрупкая фаза [8].
На рис. 5 показана микроскопическая структура основного металла 40Mn.Серая массивная микроструктура — это феррит, который является основной микроструктурой основного металла. Черная микроструктура — перлит.
Рис.5Микроскопическая структура основного металла
Микроструктура зоны плавления при электродуговой сварке, которая близка к основному металлу, представляет собой однородный феррит и перлит, как показано на рис. 6. Микроструктура сильно отличается от основного металла 40Mn, что может быть вызвано высокой температурой сварки. изменяет микроструктуру основного металла на аустенит, сопровождаясь меньшим размером.Тогда мы можем получить однородный феррит и перлит при охлаждении на воздухе. Микроструктура зоны плавления, близкой к наплавке, представляет собой черный агломерированный мартенсит и белый остаточный аустенит. Это связано с тем, что температура зоны плавления, закрытой для наплавки, очень высока. Наконец, достигается высокая степень переохлаждения. Это способствует образованию мартенсита, который препятствует фазовому превращению аустенита, и в зоне плавления появляется остаточная организация аустенита.
Рис.6Микроскопическая структура зоны плавления при электродуговой сварке
На рис. 7 показана микроскопическая структура зоны плавления при сварке в среде защитной дуги CO 2 . Микроструктура зоны плавления, близкая к основному металлу, представлена серым массивным ферритом и черным перлитом. Превращение перлита и части феррита в аутенит происходит при пайке, а остальные сохраняются. После охлаждения продуктом аустенитного рекристалла являются феррит и перлит, а сохранившийся феррит нарастает, что отличается от микроструктуры электродуговой сварки.Микроструктура зоны плавления, которая близка к наплавке, представляет собой черный агломерированный мартенсит и белый остаточный аустенит. Причины его образования те же, что и при электродуговой сварке.
Рис.7Микроскопическая структура зоны плавления СО 2 дуговая сварка в защитных оболочках
Микроструктура зоны плавления при дуговой сварке в среде аргона представлена на рис. 8. Микроструктура зоны плавления, которая близка к основному металлу, представляет собой однородный феррит и перлит.Причины его образования также те же, что и при электродуговой сварке. Микроструктура зоны плавления, близкой к наплавке, представляет собой черный реечный мартенсит и белый остаточный аустенит. Пластинчатый мартенсит отличается от агломерированного мартенсита, полученного при сварке в среде защитной дуги CO 2 . Основная причина может заключаться в том, что степень разбавления при сварке в среде защитной дуги CO 2 выше, чем при сварке в среде защитного аргона. Это приводит к тому, что содержание углерода при сварке в среде защитной дуги CO 2 становится выше, чем при сварке в среде защитного аргона.Это способствует образованию мартенсита.
Рис.8Микроскопическая структура зоны плавления при дуговой сварке в среде аргона
В заключение, микроструктура зоны плавления при дуговой сварке в среде аргона более тщательная и однородная, чем при электродуговой сварке и сварке в среде защитной дуги CO 2 .
Чтобы проанализировать связь между остаточным напряжением и микроскопической структурой, определяется микроскопическая структура внешнего слоя наплавки (см. Рис.9–11).
Рис.9Микроскопическая структура внешнего слоя электродуговой сварки
Рис. 10Микроскопическая структура внешнего слоя CO 2 дуговая сварка в защитных оболочках
Рис. 11Микроскопическая структура внешнего слоя при дуговой сварке в среде аргона
Анализ остаточного напряжения
Поперечные и продольные остаточные напряжения трех методов сварки перечислены в таблицах 2–7 соответственно.В таблице 8 показано среднее значение остаточного напряжения для трех методов сварки. Знак минус обозначает напряжение давления.
Таблица 2 Поперечные остаточные напряжения поверхности шва при ручной электродуговой сварке Таблица 3 Продольные остаточные напряжения поверхности шва ручной электродуговой сварки Таблица 4 Поперечные остаточные напряжения поверхности шва СО 2 дуговая сварка в защитных оболочках Таблица 5 Продольные остаточные напряжения поверхности шва СО 2 дуговая сварка в защитных оболочках Таблица 6 Поперечные остаточные напряжения поверхности шва при дуговой сварке в среде аргона Таблица 7 Продольные остаточные напряжения поверхности шва при дуговой сварке в среде аргона Таблица 8 Среднее значение остаточного напряжения трех методовБезопасность, надежность и технологичность сварочной конструкции, остаточные сварочные напряжения являются важными факторами, вызывающими трещины сварного шва и усталостное разрушение [9].
Распределение остаточных напряжений трех методов сварки показано на рис. 12. Из рис. 12 видно, что все остаточные напряжения трех методов сварки представляют собой сжимающие напряжения. Поперечные остаточные напряжения в основном такие же. Продольное остаточное напряжение (абсолютное значение) при электродуговой сварке ниже, чем у двух других методов, а продольное напряжение (абсолютное значение) при дуговой сварке в среде аргона немного больше, чем при сварке в среде защитной дуги CO 2 .Хорошо известно, что напряжение сжатия препятствует распространению трещин и может улучшить усталостную прочность и ударную вязкость. С точки зрения напряжения, перекрывающиеся свойства дуговой сварки в среде аргона превосходят свойства дуговой сварки и сварки в среде защитного газа CO 2 .
Рис.12Распределение поперечных и продольных напряжений
Напряжение сжатия наплавленного металла можно объяснить с точки зрения металлографической структуры.Превращение аустенита в мартенсит происходит при низкой температуре, что указывает на то, что материал находится в упругопластическом или упругом состоянии. Объемное расширение металлического фазового превращения ограничено, и возникает напряжение фазового превращения. Напряжение уменьшит остаточное напряжение, вызванное сварочным тепловым полем, и вызовет остаточное напряжение сжатия [10]. Из таблицы 1 видно, что содержание марганца составляет 0,70% –1,00%, 0,31% и 1,40–1,85% в основном металле, электроде и припойной проволоке соответственно.Хорошо известно, что марганец может снижать температуру аустенитного превращения. Микроскопическая структура (см. Рис. 9–11) внешнего наплавочного слоя подтверждает организацию низкотемпературного фазового перехода, указывая на то, что возможно, что низкотемпературный фазовый переход происходит во время процесса наплавки, и сжимающее напряжение возникает в самой внешней наплавке. слой. Из таблицы 1 видно, что содержание марганца в припойной проволоке намного больше, чем в электроде.Если низкотемпературный фазовый переход действительно происходит, температура аустенитного фазового перехода при двух видах газозащитной сварки будет ниже, чем при электродуговой сварке, и эффект того, что напряжение фазового перехода снижает термическое напряжение сварки, будет более очевидным. Основной металл и припойная проволока для двух видов газозащитной сварки одинаковы, и содержание в них легирующего элемента одинаково, поэтому их фазовое превращение и конечное остаточное напряжение в основном одинаковы.
Анализ твердости
Твердость — это общая характеристика эластичности, пластичности, прочности и ударной вязкости. На рисунках 13–15 показана твердость трех способов сварки, при которых твердость наплавленного металла находится слева от пунктирной линии, а твердость основного металла — с другой стороны. Слои для определения твердости распределяются равномерно от внешнего слоя сварки до основного металла, и каждый слой обнаружения размещается на расстоянии 0,5 мм.
Фиг.13Твердость электродуговой сварки
Фиг.14Твердость CO 2 дуговая сварка в защитных оболочках
Рис.15Сварка в среде защитного аргона
Из рис. 13–15, можно заметить, что значения твердости основного металла составляют около 240–250 HV, что согласуется с твердостью 40Mn. При сравнении изменения твердости трех видов зон термического влияния значения твердости при электродуговой сварке и сварке в среде защитной дуги CO 2 резко снижаются, а при сварке в среде защитного аргона — медленно.Известно, что микроструктура металла является важным элементом твердости [11]. Из фиг. 6–8, морфология структуры электродуговой сварки и сварки в среде защитного газа CO 2 имеет очевидное различие, а морфология структуры дуговой сварки в среде аргона — меньше. Различная морфология микроструктуры способствует различному изменению твердости. На рисунках 13–15 также показано, что твердость крайних слоев при электродуговой сварке и сварке в среде защитного аргона составляет около 180 HV, а твердость при сварке в среде защитной дуги CO 2 — около 155 HV.Разницу также можно объяснить морфологией структуры. Наружные слои при электродуговой сварке и дуговой сварке в среде аргона имеют гораздо больше пластинчатого мартенсита, в то время как при сварке в среде защитной дуги CO 2 гораздо больше пластинчатого мартенсита и аустенита, как видно из рис. 9–11. Известно, что твердость пластинчатого мартенсита выше, чем реечного мартенсита, а твердость аустенита невысока. Следовательно, твердость электродуговой сварки и дуговой сварки в среде аргона выше, чем у сварки в среде защитного газа CO 2 .
Кроме того, известно, что твердость сварочного материала обычно слишком высока для токарной обработки. Поэтому в этом эксперименте материал с низкой твердостью выбран на основе свариваемости. Недостаток теста состоит в том, что все значения твердости наплавленного металла ниже, чем у основного металла. Это увеличивает риск выхода из строя винта, хотя это выгодно для токарного станка. Чтобы решить эту проблему и сделать твердость равной или немного превышающей твердость основного металла, хорошим выбором будет соответствующая местная термообработка или более подходящий сварочный материал.
Сварка дуговой сваркой — Контрольный список безопасности | NIOSH
Октябрь 2003
DHHS (NIOSH) Номер публикации 2004-101
Контрольный список для самопроверки
Руководящие принципы
В этот контрольный список включены правила, изданные Министерством труда, охраны труда и здоровья США (OSHA) в соответствии с общими отраслевыми стандартами 29 CFR 1910.254 и 1910.306, а также строительными стандартами 1926 года.351 и 1926. 353. Это касается использования оборудования для дуговой сварки и резки. Этот контрольный список необходимо использовать с контрольным списком «Сварка, резка и пайка — Общие требования». Указанные правила применяются только к частным работодателям и их работникам, если они не приняты государственным агентством и не применяются к другим группам, таким как государственные служащие. Ответ «да» на вопрос означает, что эта часть проверки соответствует стандарту OSHA или Агентства по охране окружающей среды США (EPA) или рекомендациям, не относящимся к нормативным актам.
Вопросы, отмеченные этим символом, могут потребовать помощи стороннего эксперта.
Общий
- Имеют ли сотрудники и студенты надлежащие инструкции и квалификацию для работы с оборудованием для дуговой сварки? [29 CFR 1910.254 (a) (3) и 1926.351 (d)]
Применение оборудования для дуговой сварки
- Соответствует ли оборудование для дуговой сварки требованиям к аппаратам для электродуговой сварки (NEMA EW-1-1962, Национальная ассоциация производителей электрооборудования) или Стандарту безопасности для машин для дуговой сварки трансформаторного типа (ANSI C33-2-1956, Underwriters Laboratories)? [29 CFR 1910.254 (b) (1)]
- Спроектированы и сконструированы ли аппараты для дуговой сварки для работы в ожидаемых условиях окружающей среды, включая необычную высоту, температуру, агрессивные химические вещества, пар, влажность, пары масла, легковоспламеняющиеся жидкости, вибрацию / удары, пыль или погодные условия? [29 Свода федеральных правил 1910.254 (b) (2)]
- Ограничены ли устройства ручной дуговой сварки и резки на переменном токе напряжением 80 вольт? [29 Свода федеральных правил 1910.254 (b) (3) (i) (A)]
- Ограничены ли устройства автоматической дуговой сварки и резки на переменном токе напряжением 100 вольт? [29 CFR 1910.254 (b) (3) (i) (B)]
- Ограничены ли устройства ручной или автоматической дуговой сварки и резки постоянным током напряжением 100 вольт? [29 Свода федеральных правил 1910.254 (b) (3) (ii) (A)]
- Защищены ли клеммы для сварочных проводов от прикосновения? [29 Свода федеральных правил 1910.254 (b) (4) (iv)]
- Предназначены ли ручные держатели электродов специально для дуговой сварки и резки? [29 Свода федеральных правил 1926.351 (a) (1)]
- Способны ли ручные электрододержатели достаточной емкости безопасно выдерживать максимальный номинальный ток, необходимый для электродов? [29 CFR 1926 г.351 (а) (1)]
- Полностью ли изолированы внешние поверхности губок держателя и все токоведущие части, проходящие через ту часть держателя, которую захватывает аппарат для дуговой сварки или резак, от максимального напряжения относительно земли? [29 Свода федеральных правил 1926.351 (а) (2)]
- Являются ли кабели для дуговой сварки и резки полностью изолированными, гибкими и способными выдерживать максимальный ток, необходимый для выполняемых работ? [29 CFR 1926.351 (b) (1)]
Установка оборудования для дуговой сварки
- Заземлены ли корпуса или корпуса аппарата дуговой сварки? [29 CFR 1910.254 (c) (2) (i)]
- Имеет ли цепь между землей и заземленным проводом питания достаточно низкое сопротивление, чтобы пропустить достаточный ток, чтобы предохранитель или автоматический выключатель прервали ток? [29 Свода федеральных правил 1926.351 (c) (5)]
- Имеют ли кабели заземления безопасная пропускная способность по току, равная или превышающая максимальную выходную мощность блока дуговой сварки или резки, которое они обслуживают? [29 Свода федеральных правил 1926.351 (c) (1)]
- Запрещается ли использование цепей, тросов, кранов, подъемников, лифтов и трубопроводов, содержащих электрические проводники, для замыкания цепей рабочих выводов? [29 CFR 1910.254 (c) (2) (ii) и (iii) и 1926. 351 (c) (2)]
- Если трубопроводы временно используются для завершения контуров рабочего кабеля, не имеют ли они резьбовых соединений, фланцевых болтовых соединений или герметичных соединений? [29 CFR 1910.254 (c) (2) (ii)] Примечание. Необходимо также принять особые меры предосторожности, чтобы избежать искрения при подключении тока рабочего кабеля.
- Если конструкция или трубопровод используются в качестве цепи заземления, проводятся ли периодические проверки для определения наличия необходимого электрического контакта на всех стыках? [29 CFR 1926 г.351 (c) (3)] Примечание. Возникновение дуги, искр или тепла в любой точке должно вызывать отказ от конструкций в качестве цепи заземления. Если конструкция или трубопроводы используются постоянно, все стыки должны быть скреплены, а периодические проверки должны проводиться, чтобы гарантировать отсутствие электролиза или опасности возникновения пожара из-за такого использования.
- Все заземляющие соединения проверены, чтобы определить, являются ли они механически прочными и электрически адекватными для требуемого тока? [29 CFR 1910.254 (c) (2) (v) и 1926.351 (c) (6)]
- Находится ли выключатель с максимальной токовой защитой на каждом сварочном аппарате или рядом с ним, у которого нет такого выключателя? [29 CFR 1910.254 (c) (3) (i) и 29 CFR 1910.306 (d) (1)]
- Предусмотрен ли выключатель с максимальной токовой защитой для каждой розетки, предназначенной для подключения к переносному сварочному аппарату? [29 Свода федеральных правил 1910.254 (c) (3) (i)]
- Для отдельных сварочных аппаратов: номинальная допустимая токовая нагрузка питающих проводов не меньше номинального первичного тока сварочного аппарата? [29 CFR 1910.254 (c) (3) (ii)]
- Все ли аппараты для дуговой сварки постоянным током подключены с одинаковой полярностью? [29 Свода федеральных правил 1910.254 (c) (3) (iv) (A)]
- Все ли аппараты для дуговой сварки переменным током подключены к одной и той же фазе цепи питания и с одинаковой мгновенной полярностью? [29 CFR 1910.254 (c) (3) (iv) (B)]
Эксплуатация и техническое обслуживание
- Ознакомлены ли сотрудники и студенты, которым поручено работать или обслуживать оборудование для дуговой сварки, с требованиями 29 CFR 1910.252 и 1910.254? [29 CFR 1910.254 (d) (1)]
- Знакомы ли сотрудники и студенты, занимающиеся дуговой сваркой в среде защитного газа, с Рекомендуемыми методами безопасности при дуговой сварке в среде защитного газа (A6.1-1966, Американское общество сварки)? [29 Свода федеральных правил 1910.254 (d) (1)]
- Проверяются ли подключения аппарата дуговой сварки перед началом работы? [29 Свода федеральных правил 1910.254 (d) (2)]
- Разложен ли спиральный сварочный кабель перед использованием, чтобы избежать серьезного перегрева и повреждения изоляции? [29 Свода федеральных правил 1910.254 (d) (2)]
- Проверяется ли заземление рамы сварочного аппарата перед началом работы? [29 CFR 1910.254 (d) (3)]
- Проверяются ли аппараты для дуговой сварки на предмет утечки охлаждающей воды, защитного газа или моторного топлива перед началом работы? [29 Свода федеральных правил 1910.254 (d) (4)]
- Имеется ли соответствующее коммутационное оборудование для выключения машины? [29 CFR 1910.254 (d) (5)]
- Строго соблюдаются ли напечатанные производителем правила и инструкции по эксплуатации поставляемого оборудования? [29 Свода федеральных правил 1910.254 (d) (6)]
- Когда не используются в течение длительного периода времени (например, во время обеденного перерыва или в ночное время): (а) электроды вынимаются из держателей; (b) держатели надежно размещены так, чтобы они не могли контактировать с людьми, токопроводящими предметами, топливными баками или резервуарами для сжатого газа; и (c) машины отключены от источника питания? [29 CFR 1910.254 (d) (7) и 1926.351 (d) (1) и (d) (3)]
- На кабелях электродов нет стыков в пределах 10 футов от держателей? [29 CFR 1910.254 (d) (8) и 1926.351 (b) (1)] Примечание: Общий отраслевой стандарт 1910.254 (d) (9) (iii) и строительный стандарт 1926.351 (b) (1) разрешают соединять отрезки длиной кабель стандартными изолированными разъемами, специально разработанными для этой цели. Строительный стандарт, однако, также допускает сращивания с изоляцией, как и оригинальный кабель.
- Обязан ли оператор сообщать о любых дефектах оборудования или угрозах безопасности и прекращать использование до тех пор, пока безопасность не будет обеспечена? [29 CFR 1910.254 (d) (9) (i) и 1926.351 (d) (4)]
- Ремонт аппаратов для дуговой сварки только квалифицированным персоналом? [29 Свода федеральных правил 1910.254 (d) (9) (i)]
- Если аппараты для дуговой сварки намокнут, тщательно ли они высушены и проверены перед использованием? [29 Свода федеральных правил 1910.254 (d) (9) (ii)]
- Запрещено ли погружать держатели горячих электродов в воду? [29 Свода федеральных правил 1926.351 (d) (2)]
- Заменяются ли кабели с поврежденной изоляцией или оголенными проводниками? [29 CFR 1910.254 (d) (9) (iii)] Примечание: Строительный стандарт 1926 года.351 (b) (4) разрешает ремонт кабелей с помощью резины и фрикционной ленты или других эквивалентных средств при условии, что участки защищены достаточной изоляцией.
- При дуговой сварке в среде инертного газа принимаются ли особые меры предосторожности в отношении опасностей, связанных с хлорсодержащими растворителями? [29 CFR 1926.353 (d) (1) (i)] Примечание: дуговая сварка в среде инертного газа дает в 5–30 раз больше ультрафиолетового излучения, чем дуговая сварка в среде защитного газа. Ультрафиолетовые лучи вызывают разложение хлорированных растворителей с выделением токсичных паров и газов.При использовании хлорированные растворители должны находиться на расстоянии не менее 200 футов от открытой дуги (если они не экранированы), а поверхности, подготовленные с помощью хлорированных растворителей, должны быть полностью высушены перед тем, как разрешить сварку. Кроме того, необходимо увеличить плотность затенения фильтровальных линз. Вся кожа должна быть закрыта для защиты от вспышек и лучистой энергии.
Учебник по дуговой сварке
Содержание
Глава 1. Дуговая сварка экранированного металла
Темы: Сварочный ток; Длина дуги; Сварочные аппараты; Полярность; Инструменты и аксессуары; Электроды; Настройка и работа; Персональная защита
Задачи обучения:
- Объяснить, как работает процесс дуговой сварки экранированным металлом.
- Расскажите, что обеспечивает защиту при дуговой сварке экранированным металлом.
- Определите длину дуги и объясните ее важность.
- Перечислите факторы, которые следует учитывать при выборе электрода.
- Опишите средства индивидуальной защиты, необходимые для сварки.
Глава 2: Выбор электродов для SMAW
Темы: Идентификация электродов; Текущие диапазоны; Электродные покрытия; Обращение, хранение и консервация электродов
Цели обучения:
- Объясните факторы, влияющие на выбор электродов SMAW.
- Объясните, как определять разные сварочные электроды.
- Приведите примеры нескольких видов электродных покрытий и расскажите, когда каждый из них используется.
- Опишите правильные процедуры обращения, хранения и консервации электродов.
Глава 3. Дуговая сварка металла в газовой среде
Темы: Сравнение GMAW и SMAW; Методы переноса металла; Защитные газы; Электродная проволока; Оборудование и аксессуары; Работа пистолета; Безопасность
Цели обучения:
- Назовите и опишите три основных типа переноса металла для GMAW.
- Назовите наиболее распространенные защитные газы, используемые при GMAW, и расскажите, какие факторы влияют на их выбор.
- Перечислите факторы, влияющие на выбор электрода для GMAW.
- Опишите работу пистолета GMAW.
Глава 4: Дуговая сварка вольфрамовым газом
Темы: Процесс GTAW, оборудование, ток, горелки и электроды; Защитные газы; Присадочные металлы; Добавление присадочного металла; Точечная сварка; Безопасность
Цели обучения:
- Перечислите преимущества GTAW по сравнению с другими сварочными процессами.
- Опишите оборудование и материалы, необходимые для GTAW.
- Объясните назначение электрода для GTAW и расскажите, чем он отличается от других видов сварки.
- Правильно выберите защитные газы и присадочные материалы для GTAW.
- Опишите, как использовать GTAW для сварки обычных металлов.
Глава 5: Другие сварочные процессы
Темы: Сопротивление, вспышка, удар, порошковая дуга, дуга под флюсом, плазменная дуга, шпилька, электронный луч, лазерный луч, трение и ультразвуковая сварка
Цели обучения:
- Опишите контактную точечную сварку и контактную сварку швом.
- Определите сварку оплавлением, сварку с высадкой и ударную сварку и расскажите, чем они отличаются.
- Объясните, чем сварка под флюсом и плазменная сварка отличаются от других методов дуговой сварки.
- Опишите три формы сварки трением.
- Опишите два преимущества ультразвуковой сварки.
Глава 6: Предварительный и последующий нагрев
Темы: Напряжение; Изменения в свойствах; Когда разогревать и разогревать; Оборудование и методы предварительного нагрева; Точечный предварительный нагрев; Методы последующего нагрева
Цели обучения:
- Описать влияние неравномерного или быстрого нагрева и охлаждения на основные металлы и сварные швы.
- Определите зону термического влияния и сообщите, какие изменения могут произойти в ней во время сварки.
- Объясните преимущества предварительного нагрева и объясните, когда его следует использовать.
- Перечислите несколько факторов при сварочных работах, по которым рекомендуется последующий нагрев.
- Опишите методы и материалы для предварительного и последующего нагрева.
Глава 7. Сварка черных металлов
Темы: Идентификация черных металлов; Подготовка кромки; Сварка чугуна, углеродистой и легированной стали
Цели обучения:
- Дать определение черным металлам и описать их характеристики, включая свариваемость.
- Объясняет необходимость очистки и подготовки кромок перед сваркой черных металлов.
- Назовите процессы и методы сварки, которые используются для различных типов и толщин черных металлов.
- Перечислите несколько различных типов электродов и их преимущества для сварки черных металлов.
- Объясните конкретные процедуры, которые следует использовать при сварке легированных сталей.
Глава 8. Сварка цветных металлов
Темы: Идентификация цветных металлов; Подготовка кромки; Уборка; Сварка алюминия, нержавеющей стали, никеля и меди
Цели обучения:
- Назовите особые свойства нескольких цветных металлов и объясните, как эти свойства влияют на подготовку и процедуры сварки.
- Опишите некоторые методы идентификации различных цветных металлов.
- Сравните семь процессов дуговой резки, используемых для обработки кромок цветных металлов.
- Объясните правильные методы очистки цветных металлов перед сваркой.
- Укажите способы сварки, подходящие для цветных металлов.
Глава 9. Сварка труб
Темы: Трубопроводные системы и соединения; Коды; Трубные материалы; Безопасность ремонта; Процессы дуговой, кислородно-топливной сварки; Виды сварных соединений; Подготовка и подгонка кромок
Цели обучения:
- Сравнить преимущества сварных соединений труб с болтовыми или винтовыми соединениями.
- Обсудите правила сварки труб и их охват.
- Перечислите сварочные процессы, используемые для соединения труб, а также их преимущества и недостатки.
- Укажите некоторые специальные методы и принадлежности, которые используются при сварке труб в отличие от сварки плоских поверхностей.
- Приведите примеры использования предварительного и последующего нагрева при сварке труб.
Глава 10: Наплавка и восстановление
Темы: Сплавы для наплавки; Недрагоценные металлы; Предварительный нагрев; Склеивание поверхностей; Кислородно-ацетиленовая, ручная дуговая и автоматическая наплавка; Термическое напыление
Цели обучения:
- Перечислите несколько целей наплавки и восстановления.
- Укажите различные типы сплавов для наплавки и их конкретные применения.
- Опишите эффективную перекрестную проверку и объясните, почему она желательна.
- Объясните специальные методы, используемые при наплавке, и объясните, почему они необходимы.
- Назовите сварочные процессы, используемые при наплавке, и объясните, почему они адаптированы для этой работы.
RussianGost | Официальная нормативная библиотека — ГОСТ 9466-75
Товар содержится в следующих классификаторах:
Конструкция (макс.) » Стандарты » Прочие государственные стандарты, применяемые в строительстве » 25 Машиностроение »
Правила сварки » Сварочные работы »
Правила сварки » Дефекты »
Правила сварки » Сварочные работы » Механизированная сварка »
Правила сварки » Сварочные работы » Наплавка »
Правила сварки » Сварочные работы » Удаление пыли »
Стандарты на трубопроводную арматуру (ТПА) » 10.Производство » 10.4 Наплавка »
Стандарты на трубопроводную арматуру (ТПА) » 10. Производство » 10.3 Сварка »
ПромЭксперт » РАЗДЕЛ I. ТЕХНИЧЕСКИЙ РЕГЛАМЕНТ » V Тестирование и контроль » 4 Тестирование и контроль продукции » 4.13 Испытания и контроль продукции машиностроения » 4.13.2 Машины и оборудование специального назначения » 4.13.2.12 Оборудование для производства электротехнических изделий и материалов и электрофизической обработки материалов »
ПромЭксперт » РАЗДЕЛ I. ТЕХНИЧЕСКИЙ РЕГЛАМЕНТ » V Тестирование и контроль » 4 Тестирование и контроль продукции » 4.12 Испытания и контроль продукции металлургической промышленности » 4.12.6 Металлические изделия »
Классификатор ISO » 25 МАШИНОСТРОЕНИЕ » 25.160 Сварка, пайка твердым припоем » 25.160.20 Сварочные материалы »
Национальные стандарты » 25 МАШИНОСТРОЕНИЕ » 25.160 Сварка, пайка твердым припоем » 25.160.20 Сварочные материалы »
Национальные стандарты для сомов » Последнее издание » V Металлы и изделия из них » V0 Общие правила и положения по металлургии » V05 Сварка и резка металлов.Пайка, клепка »
В качестве замены:
ГОСТ 9466-60 — Электроды металлические для дуговой сварки сталей и наплавки. Размеры и общие характеристики
Ссылки на документы:
ГОСТ 10051-75 — Электроды покрытые металлом для ручной дуговой наплавки верхних слоев с особыми свойствами типа
.ГОСТ 10052-75 — Электроды с металлическим покрытием для ручной дуговой сварки высоколегированных сталей с особыми свойствами.Типы
ГОСТ 10198-91 — Ящики деревянные для гирь массой от 200 до 20000 кг. Общие технические условия
ГОСТ 10354-82 — Пленка полиэтиленовая. Технические условия
.ГОСТ 1050-88 — Прокат калиброванный из углеродистой конструкционной качественной стали со специальной обработкой поверхности. Общие технические условия
ГОСТ 11878-66 — Прокат из аустенитной стали. Методы определения ферритной фазы
ГОСТ 12344-2003 — Стали легированные и высоколегированные. Методы определения углерода
ГОСТ 12345-2001 — Стали легированные и высоколегированные.Методы определения серы
ГОСТ 12347-77 — Стали легированные и высоколегированные. Методы определения фосфора
ГОСТ 12348-78 — Стали легированные и высоколегированные. Методы определения марганца
ГОСТ 12349-83 — Стали легированные и высоколегированные. Методы определения вольфрама
ГОСТ 12350-78 — Стали легированные и высоколегированные. Методы определения хрома
ГОСТ 12351-2003 — Стали легированные и высоколегированные.Методы определения ванадия
ГОСТ 12352-81 — Стали легированные и высоколегированные. Методы определения никеля
ГОСТ 12353-78 — Стали легированные и высоколегированные. Методы определения кобальта
ГОСТ 12354-81 — Стали легированные и высоколегированные. Методы определения молибдена
ГОСТ 12355-78 — Стали легированные и высоколегированные. Методы определения меди
ГОСТ 12356-81 — Стали легированные и высоколегированные.Методы определения титана
ГОСТ 12357-84 — Стали легированные и высоколегированные. Методы определения алюминия
ГОСТ 12358-2002 — Стали легированные и высоколегированные. Методы определения мышьяка
ГОСТ 12359-99 — Стали углеродистые, легированные и высоколегированные. Методы определения азота
ГОСТ 12360-82 — Стали легированные и высоколегированные. Методы определения бора
ГОСТ 12361-2002 — Стали легированные и высоколегированные.Методы определения ниобия
ГОСТ 12362-79 — Стали легированные и высоколегированные. Методы определения сурьмы, свинца, олова, цинка и кадмия
ГОСТ 12363-79 — Стали легированные и высоколегированные. Методы определения селена
ГОСТ 12364-84 — Стали легированные и высоколегированные. Методы определения цетиума
ГОСТ 12365-84 — Стали легированные и высоколегированные. Методы определения циркония
ГОСТ 14192-96 — Маркировка грузов
.ГОСТ 15623-84 — Ящики деревянные для инструментов и принадлежностей.Технические характеристики
ГОСТ 15846-2002 — Продукция для транспортировки в районы Крайнего Севера и приравненных к ним регионов. Упаковка, маркировка, транспортировка и хранение
ГОСТ 18617-83 — Ящики деревянные для метизов. Технические характеристики
ГОСТ 18895-97 — Сталь. Метод фотоэлектрического спектрального анализа
ГОСТ 2228-81 — Бумага пакетная
.ГОСТ 2246-70 — Проволока стальная сварочная. Технические характеристики
ГОСТ 22536.0-87 — Сталь углеродистая и чугун нелегированный.Общие требования к методам анализа
ГОСТ 22536.10-88 — Сталь углеродистая и чугун нелегированный. Методы определения алюминия
ГОСТ 22536.11-87 — Сталь углеродистая и чугун нелегированный. Методы определения титана
ГОСТ 22536.12-88 — Сталь углеродистая и чугун нелегированный. Методы определения ванадия
ГОСТ 22536.1-88 — Сталь углеродистая и чугун нелегированный. Методы определения общего углерода и графита
ГОСТ 22536.2-87: Углеродистая сталь и нелегированный чугун. Методы определения серы
ГОСТ 22536.3-88 — Сталь углеродистая и чугун нелегированный. Методы определения фосфора
ГОСТ 22536.4-88 — Сталь углеродистая и чугун нелегированный. Методы определения кремния
ГОСТ 22536.5-87 — Сталь углеродистая и чугун нелегированный. Методы определения марганца
ГОСТ 22536.6-88 — Сталь углеродистая и чугун нелегированный. Методы определения мышьяка
ГОСТ 22536.7-88: Углеродистая сталь и нелегированный чугун. Методы определения хрома
ГОСТ 22536.8-87 — Сталь углеродистая и чугун нелегированный. Методы определения меди
ГОСТ 22536.9-88 — Сталь углеродистая и чугун нелегированный. Методы определения никеля
ГОСТ 25591-83 — Мастики кровельные и гидроизоляционные. Классификация и общие требования
ГОСТ 25951-83 — Пленка полиэтиленовая термоусадочная. Технические характеристики
ГОСТ 26381-84 — Поддоны плоские одноразовые. Общие технические условия
.ГОСТ 26663-85 — Пакеты транспортные.Формирование упаковочными средствами. Общие технические требования
ГОСТ 2789-73 — Шероховатость поверхности. Параметры и характеристики
ГОСТ 28473-90 — Железо, сталь, ферросплавы, металлический хром и металлический марганец. Общие требования к методам анализа
ГОСТ 380-94 — Сталь углеродистая нормального качества
.ГОСТ 4598-86 — Плиты древесноволокнистые. Технические характеристики
ГОСТ 5632-72 — Стали высоколегированные и сплавы нержавеющие, жаропрочные и термически обработанные.Оценки
ГОСТ 6032-2003 — Стали и сплавы коррозионно-стойкие. Методы испытаний на стойкость к межкристаллитной коррозии
ГОСТ 6996-66 — Соединения сварные. Методы определения механических свойств
ГОСТ 7376-89 — Картон гофрированный
.ГОСТ 7512-82 — Контроль неразрушающий. Сварные соединения. Рентгенологический метод
ГОСТ 7933-89 — Картон для розничной тары
.ГОСТ 8273-75 — Бумага упаковочная
.ГОСТ 8828-89 — Бумага-основа и бумага упаковочная влагостойкая двухслойная
.ГОСТ 9421-80 — Картон плоская тара
.ГОСТ 9466-60 — Электроды металлические для дуговой сварки сталей и наплавки.Размеры и общие характеристики
ГОСТ 9467-75 — Электроды с металлическим покрытием для ручной дуговой сварки конструкционных и жаропрочных сталей. Типы
ГОСТ 12346-78 — Стали легированные и высоколегированные. Методы определения кремния
Ссылка на документ:
ГОСТ 10051-75 — Электроды покрытые металлом для ручной дуговой наплавки верхних слоев с особыми свойствами типа
.ГОСТ 10052-75 — Электроды с металлическим покрытием для ручной дуговой сварки высоколегированных сталей с особыми свойствами.Типы
ГОСТ 11435-75 — Инструмент ручной и молотковый кузнечный. Технические требования
ГОСТ 12.4.035-78 — Маски защитные лицевые
.ГОСТ 12367-85 — Мельницы трубные мелющие. Общие технические условия
ГОСТ 14110-97 — Стропы полужесткие многоразовые
.ГОСТ 15846-2002 — Продукция для транспортировки в районы Крайнего Севера и приравненных к ним регионов. Упаковка, маркировка, транспортировка и хранение
ГОСТ 15846-79 — Продукция для транспортировки в районы Крайнего Севера и отдаленные районы
.ГОСТ 19191-73 — Винты такелажные с автоматической остановкой.Технические характеристики
ГОСТ 22956-83 — Стропы цепные механизированные для крепления грузов на автотранспортных средствах. Спецификация
ГОСТ 24663-81 — Котлы паровые и водогрейные. Требования к сварке стали
ГОСТ 26155-84 — Бочки из коррозионно-стойкой стали
.ГОСТ 26271-84 — Порошковая проволока для сварки углеродистых и низколегированных сталей. Общие технические условия
ГОСТ 30430-96 — Дуговая сварка конструкционных чугунов. Требования к технологическому процессу
ГОСТ 31832-2012 — Приводы штанговых насосов.Общие технические требования
ГОСТ 31841-2012 — Нефтяная и газовая промышленность. Оборудование для обслуживания скважин. Общие технические требования
ГОСТ 31846-2012 — Подвижной состав специальный. Требования к прочности несущей конструкции и динамическим свойствам
ГОСТ 32569-2013 — Технология стальных труб. Требования к устройству и эксплуатации взрывоопасного и химически опасного производства
ГОСТ 33119-2014 — Конструкции мостов из полимерных композитов.Технические характеристики
ГОСТ 33260-2015 — Арматура трубопроводная. Металлы, используемые в производстве трубопроводной арматуры. Основные требования к выбору материалов
ГОСТ 33796-2016 — Агрегаты железнодорожные. Требования к прочности и динамике
ГОСТ 33857-2016 — Арматура трубопроводная. Сварка и контроль качества сварных соединений. Технические требования
ГОСТ 33976-2016 — Соединения сварные стальных конструкций железнодорожного подвижного состава. Требования к проектированию, внедрению и контролю качества
ГОСТ 9467-75 — Электроды с металлическим покрытием для ручной дуговой сварки конструкционных и жаропрочных сталей.Типы
ГОСТ 95-77 — Трансформаторы однофазные однофазные для ручной дуговой сварки. Общие технические условия
ГОСТ Р 51365-2009 — Нефтяная и газовая промышленность. Буровое и производственное оборудование. Устьевое и елочное оборудование. Общие технические условия
ГОСТ Р 51365-99 — Оборудование нефтепромысловое управляющее головное. Общие технические условия
ГОСТ Р 51763-2001 — Приводы штанговых насосов. Общие технические требования
ГОСТ Р 52277-2004 — Подбиватели балластных трамбовок для выравнивания и облицовки железнодорожных путей.Технические характеристики
ГОСТ Р 52630-2006 — Сосуды и аппараты стальные сварные. Общие технические условия
ГОСТ Р 52630-2012 — Сосуды и аппараты стальные сварные. Основные Характеристики.
ГОСТ Р 52664-2010 — Сваи трубные шпунтовые сварные. Технические характеристики
ГОСТ Р 53192-2008 — Конструкции стальные сварные грузовых вагонов. Технические требования
ГОСТ Р 53192-2014 — Соединения сварные стальных конструкций железнодорожного подвижного состава. Требования к проектированию, производству и контролю качества
ГОСТ Р 53337-2009 — Подвижной состав специальный.Требования к прочности несущей конструкции и динамическим свойствам
ГОСТ Р 53629-2009 — Сваи шпунтовые из стальных холодногнутых профилей. Технические характеристики
ГОСТ Р 53680-2009 — Нефтяная и газовая промышленность. Оборудование для обслуживания скважин. Общие технические требования
ГОСТ Р 53686-2009 — Сварка. Определение ферритного числа (FN) в наплавленном металле
аустенитной и дуплексной ферритно-аустенитной хромоникелевой нержавеющей сталиГОСТ Р 54803-2011 — Сосуды стальные сварные под высоким давлением.Общие технические требования
ГОСТ Р 54889-2012 — Стропы полужесткие многоразовые. Технические характеристики
ГОСТ Р 54892-2012 — Монтаж воздухоразделительных установок и другого криогенного оборудования. Общие положения
ГОСТ Р 55495-2013 — Агрегаты железнодорожные. Требования к прочности и динамике
ГОСТ Р 55509-2013 — Арматура трубопроводная. Металлы, используемые в производстве трубопроводной арматуры. Основные требования к выбору материалов
ГОСТ Р 55513-2013 — Локомотивы.Требования к прочностным и динамическим свойствам
ГОСТ Р 56001-2014 — Арматура трубопроводная для объектов газовой промышленности. Общие технические условия
ГОСТ Р 57054-2016 — Оборудование горное. НКТ чугунные. Комплекты колец для НКТ. Общие технические условия
ГОСТ Р 58018-2017 — Опоры промежуточные композитные полимерные для воздушных линий электропередачи напряжением 35-220 кВ. Общие технические условия
ГОСТ Р 58021-2017 — Опоры композитные полимерные для воздушных линий электропередачи напряжением 6-20 кВ.Общие технические условия
ГОСТ Р 58095.1-2018 — Системы газораспределения. Требования к сетям газопотребления. Часть 1. Газопроводы стальные
Руководство: Руководство для импульсных систем пожаротушения с низким потреблением энергии
МДС 12-23.2006: Временные рекомендации по технологии и организации строительства многофункциональных высотных зданий и строительных комплексов в Москве
MRDS 02-08: Руководство по научно-техническому обеспечению и мониторингу строящихся зданий и сооружений, в том числе большепролетных, высотных и уникальных
ОСТ 108.004.10-86: Программа контроля качества продукции атомной энергетики.
ОСТ 24.030.10 — Сосуды и аппараты для водоочистных сооружений. Общие технические условия
ОСТ 24.125.170-01 — Детали и сборные узлы опор, подвесов, стяжек линзовых компенсаторов и приводов для дистанционного управления трубопроводной арматурой тепловых и атомных электростанций. Основные Характеристики.
ОСТ 24.191.08-81 — Подвески крановые крюковые. Дизайн и размеры.
ОСТ 24.200.02-91: Монтаж узлов стальных трубопроводов на номинальное давление
.ОСТ 24.201.03-90 — Сосуды и аппараты стальные высокого давления. Общие технические требования.
ОСТ 26.260.01-2001 — Сосуды и аппараты стальные эмалевые. Общие технические характеристики.
ОСТ 26.260.18-2004 — Модули технологические для нефтегазовой отрасли. Общие технические условия
ОСТ 26.260.480-2003 — Сосуды и аппараты стальные двухслойные. Сварка и наплавка.
ОСТ 26-01-151-82 — Сосуды и аппараты стальные сварные для низкотемпературной сепарации газов.Технические требования, правила приемки и методы испытаний.
ОСТ 26-04-1036-74 — Сборочные узлы и детали крепления теплых трубопроводов диаметром от 100 до 1020 мм. Дизайн и размеры.
ОСТ 26-04-1038-74 — Сборочные узлы и детали крепления труб диаметром от 6 до 10 мм. Дизайн и размеры.
ОСТ 26-04-1039-74 — Детали для монтажа труб диаметром от 6 до 95 мм. Дизайн и габариты
ОСТ 26-04-1040-74 — Опоры для трубопроводов теплого воздуха диаметром от 100 до 325 мм.Дизайн и размеры.
ОСТ 26-04-1041-74 — Опоры для трубопроводов теплого воздуха диаметром от 325 до 1020 мм. Дизайн и размеры.
ОСТ 26-04-1042-74 — Сталь подшипниковая углеродистая для холодных труб диаметром от 250 до 1020 мм. Конструкция и размеры ..
ОСТ 26-04-1043-74 — Опора из высоколегированной стали для холодных труб. Дизайн и размеры.
ОСТ 26-04-1334-75 — Отводы прямые сварные из углеродистой стали. Дизайн и размеры.
ОСТ 26-04-1336-75 — Тройники сварные прямые из углеродистой стали.Дизайн и размеры.
ОСТ 26-04-1338-75 — Крестовины стальные четырехсторонние приварные прямые углеродистые. Дизайн и размеры.
ОСТ 26-04-2386-79 — Заглушки транспортировочные проушинные для рабочих Р 0 МПа (0 кг / см2). Дизайн и размеры.
ОСТ 26-04-2387-79 — Заглушки стальные к сосудам и аппаратам для испытаний на Ру 0,1 МПа (1 кг / см2), Ру 0,6 МПа (6 кг / см2). Дизайн и размеры.
ОСТ 26-07-2028-81 — Наплавка уплотнительных поверхностей труб электродами типа Э-20Х13. Технические требования.
ОСТ 26-18-5-88 — Агрегаты технологические газовой и нефтяной промышленности. Общие технические требования.
ОСТ 26-291-94 — Сосуды и аппараты стальные сварные. Общие технические требования.
ОСТ 26-3-87 — Сварка в химическом машиностроении. Основные положения.
ОСТ 34-42-816-85 — Сварка трубопроводов из перлитных и аустенитных сталей на атомных электростанциях. Основные положения.
ОСТ 36-39-80 — Трубопроводы стальные технологические из углеродистых и легированных сталей на давление Ру до 9.81 МПа (100 кгс / см2). Экранированная ручная дуговая сварка металлом. Типовой технологический процесс.
ОСТ 36-58-81 — Конструкции строительные стальные. Сварка. Базовые требования.
ОСТ 36-60-81 — Сварка при монтаже металлических строительных конструкций. Основные положения.
ОСТ 36-62-81 — Оборудование подъемное. Общие технические требования.
ОСТ 5 9137-83 — Сварка дефектов отливок стали и чугуна. Технические требования
ОСТ 95 10575-2002 — Оборудование и трубопроводы сепарационных установок.Сварные соединения и наплавки. Правила контроля
ПБ 03-108-96 — Правила устройства и безопасной эксплуатации технологических трубопроводов
ПБ 03-278-99 — Правила проведения квалификационных испытаний сварщиков и специалистов сварочного производства
ПБ 03-384-00 — Правила проектирования, изготовления и приемки сосудов и аппаратов стальных сварных
ПБ 03-576-03 — Правила устройства и безопасной эксплуатации сосудов под давлением
.ПБ 03-75-94 — Правила устройства и безопасной эксплуатации трубопроводов пара и горячей воды
.ПБ 08-258-98 — Правила устройства и безопасной эксплуатации магистрального трубопровода для транспортировки жидкого аммиака
ПБ 10-05-92 — Требования к установке и безопасной эксплуатации электродных котлов и котельных
ПБ 10-115-96 — Правила устройства и безопасной эксплуатации сосудов под давлением
.ПБ 10-11-92 — Требования к установке и безопасной эксплуатации подъемников (подъемных опор)
ПБ 10-157-97 — Требования к монтажу и безопасной эксплуатации трубоукладочных машин Безопасность
ПБ 10-256-98 — Положение по устройству и безопасной эксплуатации подъемников (вышек)
.ПБ 10-573-03: Серия 17.Документы по надзору в электроэнергетике. Выпуск 46. Правила устройства и безопасной эксплуатации трубопроводов пара и горячей воды.
ПНАЭ Г-10-031-92: Основные положения по локализации сварки элементов системы безопасности на атомных станциях
ПНАЭ Г-10-032-92: Требования к приварке элементов уплотнения ограничивающих систем безопасности АЭС
ПНАЭ Г-7-009-89: Оборудование и трубопроводы ядерных энергетических установок. Сварка и наплавка, общие положения
РД 01-001-06: Сварка стальных газопроводов и газового оборудования в городском коммунальном хозяйстве и энергоустановках.
РД 03-495-02 — Порядок проведения квалификационных испытаний сварщиков и специалистов сварочных работ
РД 10-69-94 — Типовой технологический процесс монтажа электрооборудования. Основные положения.
РД 108.021.112-88 — Устранение дефектов литых корпусных деталей паровых турбин и арматуры сваркой без термической обработки
РД 153-34.1-003-01 — Сварка, термообработка и контроль медных трубопроводных систем и трубопроводов при монтаже и ремонте энергетического оборудования.
РД 153-39.4-044-99 — Правила капитального ремонта магистральных нефтепродуктопроводов, прокладываемых в городах, поселках и въездах на территорию нефтебаз и насосных станций
РД 153-39.4-075-01 — Правила текущего ремонта магистрального нефтепровода на водных, железнодорожных и автомобильных переходах I-IV категорий.
РД 24.090.52-90 — Машины подъемно-транспортные. Материалы для сварных металлоконструкций.
РД 24.200.04-90 — Швы сварные. Металлографический метод контроля основного металла и сварных соединений нефтехимического оборудования
РД 26.260.12-99 — Продление срока службы сосудов с жидкой углекислотой. Учебное руководство.
РД 26-02-80-2004 — Ведущий документ. Сварные змеевики для трубчатых печей. Требования к проектированию, изготовлению и доставке.
РД 26-07-264-86 — Наплавка антикоррозийных соединений уплотнительных поверхностей трубопроводной арматуры.
РД 26-11-08-86 — Соединения сварные. Механические испытания
РД 26-17-049-85 — Организация хранения, подготовки и контроля сварочных материалов
РД 26-3-86 — Методические указания по продлению срока службы резервуаров для жидкой двуокиси углерода
РД 2730.300.06-98: Светильники для атомных станций и тепловых станций. Плакировка уплотнительных поверхностей. Технические характеристики
РД 31.1.02-04: Правила технической эксплуатации подъемно-транспортного оборудования морских торговых портов
РД 31.44.01-97: Правила технической эксплуатации подъемно-транспортного оборудования морских торговых портов
РД 34 02.028-2007 — Технические правила. Механическое оборудование и специальные металлоконструкции для гидротехнических сооружений. Изготовление, установка и приемка.
РД 34.10.124-94 — Инструкция по подготовке и хранению сварочных материалов
РД 34.10.306-88 — Материальные пособия на ремонт. Стационарные паровые котлы.
РД 34.15.027-93 — Сварка, термическая обработка и испытание систем котельных и трубопроводов при монтаже и ремонте оборудования станций электроснабжения (РТМ-1с-93)
РД 34.46.605 — Трансформаторы на напряжение 110-1150 кВ, мощностью 80 МВ · А и выше
РД 34-10.030-89: Правила контроля качества сварных соединений трубопроводов АЭС
РД 36-62-00 — Оборудование подъемное. Общие технические требования.
РД 3689-002-00220302 / 31-2008 — Сварка радиационных труб и их элементов для реакционных трубчатых печей. Основные положения
РД 38.13.004-86 — Эксплуатация и ремонт технологических трубопроводов, работающих под давлением до 10,0 МПа (100 кгс / см2)
РД 39-0147014-535-87 — Инструкция по сварке при монтаже и ремонте трубопроводов и ответственных металлоконструкций в организациях и на предприятиях Министерства нефтегазовой промышленности.
РД 39-0147103-330-86 — Методические указания по приварке заплат и муфт к стенкам нефтепроводов, работающих под давлением до 2,0 МПа
РД 39-0147103-360-89 — Инструкция по безопасному ведению сварки при ремонте нефтепродуктопроводов и нефтепродуктопроводов под давлением
РД 39-132-94 — Правила эксплуатации, обследования, ремонта и утилизации промысловых трубопроводов 1994
РД РТМ 26-07-246-80 — Правила проектирования, изготовления и контроля сварных соединений стальной трубопроводной арматуры.
РД РТМ 26-362-80 — Ускоренные и маркировочные методы химического и спектрального анализа основных и сварочных материалов в химическом и нефтяном машиностроении. Методы химического анализа чугуна и стали
РМ 4-249-91 — Системы автоматизации производственных процессов. Устройство заземляющих сетей. Пособие по БЧ 205-84 / ММСС СССР
РТМ 393-94 — Технические руководства по сварке и контролю качества соединений арматуры и закладных элементов железобетонных элементов
Правила выбора сосудов под давлением и оборудования: Инструкция по выбору сосудов под давлением и устройств, работающих под давлением 100 кгс / см2 и защиты от избыточного давления, Министерство нефтяной энергетики
СА 03-005-07: Промышленные трубопроводы нефтеперерабатывающей, нефтехимической и химической промышленности.Требования к настройке и эксплуатации
СН 393-78 — Инструкция по сварке стыков арматуры и закладных частей железобетонных конструкций
.СНиП 3.05.03-85: Тепловые сети
СНиП II-45-75: Магистральные трубопроводы
СП 105-34-96 — Свод правил строительства магистральных газопроводов. Сварочные работы и контроль качества сварных соединений
СП 34-116-97 — Инструкция по проектированию, строительству и реконструкции промысловых нефтегазопроводов
СП 36.13330.2012: Магистральные трубопроводы
.СП 42-102-2004 — Проектирование и строительство газопроводов из металлических труб. Заменить СП 42-102-96
СП 86.13330.2014 — Трубопроводы магистральные (магистральные)
.СТ РК 1358-2005 — Сосуды под давлением. Требования к сварке сталей
СТ ЦКБА 005.1-2003 — Арматура трубопроводная. Металлы, используемые в арматурной промышленности. Часть 1. Основные требования к выбору материалов
СТ ЦКБА 015-2005 — Арматура трубопроводная. Программа контроля качества арматуры АЭС
СТ ЦКБА 025-2006 — Арматура трубопроводная.Сварка и контроль качества сварных соединений. Технические требования
СТ ЦКБА 089-2010 — Арматура трубопроводная. Дефекты сварки отливок. Технические требования
СТО 95 12005-2017: Объекты использования атомной энергии. Бетонные работы при сооружении защитной оболочки реакторной установки АЭС. Основные требования и организация контроля качества
ТР 182-08: Технические рекомендации по научно-техническому сопровождению и мониторингу строительства большепролетных, высотных и других уникальных зданий и сооружений
ТР 50-180-06 — Технические рекомендации по проектированию и устройству свайных фундаментов по разрядно-импульсной технологии для высотных зданий
ТУ 102-107-76 — Ящики унифицированные с навесными панелями типа БНП (строительная часть блок-боксов)
ТУ 24.08.1702-91: Электроды марки ОЗС-4
ВСН 005-88: Строительство промысловых стальных трубопроводов Технология и устройство
ВСН 006-89: Строительство магистральных и промысловых трубопроводов Сварка
ВСН 110-64: Технические рекомендации по проектированию и устройству фундаментов и опор из сборных железобетонных оболочек
ВСН 169-80: Руководство по использованию ручной и автоматизированной сварки при заводском изготовлении элементов конструкционной стали для мостов
ВСН 170-80: Руководство по возведению 16-этажных крупнопанельных жилых домов из стандартизированных изделий, перечисленных в едином каталоге серии P44 / 16, возводимых ДСК-1
ВСН 200-83: Методика выполнения работ по устройству подконструкции многоэтажных жилых домов
ВСН 202-90: Методические указания по возведению 22-этажных крупнопанельных жилых домов из сборно-модульных элементов (КОПЭ-85), возводимых ДСК-2
ВСН 349-87 — Сварка стальных оцинкованных ребристых кровельных настилов для облегченных кровель
ВСН 433-82: Методические указания по полуавтоматической сварке проволокой с сердечником сборочных соединений стальных конструкций производственных и производственных зданий и сооружений
ВСН 464-85: Общие нормативные квоты на строительные материалы.Справочник 20: Установка промышленных вентиляционных систем
ВСН 70-79: Руководство по монтажу и испытаниям трубопроводов с условным проходом до 400 мм (включительно) в диаметре, работающих при давлениях от 9,8 МПа до 245 МПа (от 100 кгс на кв.м до 2500 кгс на кв. м)
ГОСТ 23858-2019 — Соединения сварные стыковые железобетонных конструкций. Ультразвуковые методы контроля качества. Правила приема
ODM 218.2.058-2019: Рекомендации по применению композитных материалов при строительстве мостовых сооружений и пешеходных мостов
ODM 218.2.076-2019: Рекомендации по применению композитных конструкций для участков с экстремальным температурным режимом (ниже минус 40 градусов Цельсия и выше плюс 40 градусов Цельсия)
ОТТ 1.5.2.01.999.0157-2013: Несущие конструкции элементов атомных станций с водо-водяными энергетическими реакторами. Общие технические требования
ОТУ 3-01 — Сосуды и аппараты. Общие технические условия на ремонт корпуса
РД 22-16-2005 *: Руководящий нормативный материал.Подъемные машины. Подбор материалов для изготовления, ремонта и реконструкции сварных металлоконструкций
РД 24.090.120-07: Проектирование и расчет транспортно-технологических подъемных кранов для обслуживающих предприятий металлургической отрасли. Справочник
РД 31.44.06-89 — Полуприцепы низкорамные платформы. Характеристики ремонта
РД 31.52.23-89 — Двигатели судовые. Восстановление крышек цилиндров с помощью сварки. Типовые процессы
РД 31.55.03.07-86: Восстановление наплавки поршней чугунных дизелей Д100. Типовые процессы
РД 32 ЦВ-056-97 — Вагоны железнодорожные колеи 1520 мм. Краткое руководство
РД 34.10.354-88 — Трансформаторы Расход материалов на ремонт
РД 34.15.132-96 — Сварка и контроль качества сварных соединений металлических конструкций зданий при строительстве промышленных объектов
РСН 342-86 — Технология усиления строительных конструкций реконструируемых предприятий
ТУ 24-09.411-82: Краны мостовые электрические специальные
.ТУ 3680-001-04698606-04 — Опора трубная
ВСН 2-120-80 / Миннефтегазстрой: Инструкция по технологии сварки трубопроводов и технологического оборудования при монтаже компрессорных и насосных станций
Клиентов, которые просматривали этот товар, также просматривали:
|
ВАШ ЗАКАЗ ПРОСТО!
RussianGost.com — ведущая в отрасли компания со строгими стандартами контроля качества, и наша приверженность точности, надежности и точности — одна из причин, по которым некоторые из крупнейших мировых компаний доверяют нам разработку своей национальной нормативно-правовой базы и перевод критически важных сложная и конфиденциальная информация.
Наша нишевая специализация — локализация национальных нормативных баз данных, включающих: технические нормы, стандарты и правила; государственные законы, кодексы и постановления; а также кодексы, требования и инструкции агентств РФ.
У нас есть база данных, содержащая более 220 000 нормативных документов на английском и других языках для следующих 12 стран: Армения, Азербайджан, Беларусь, Казахстан, Кыргызстан, Молдова, Монголия, Россия, Таджикистан, Туркменистан, Украина и Узбекистан.
Размещение заказа
Выберите выбранный вами документ, перейдите на «страницу оформления заказа» и выберите желаемую форму оплаты. Мы принимаем все основные кредитные карты и банковские переводы. Мы также принимаем PayPal и Google Checkout для вашего удобства. Пожалуйста, свяжитесь с нами для любых дополнительных договоренностей (договорные соглашения, заказ на поставку и т. Д.).
После размещения заказа он будет проверен и обработан в течение нескольких часов, но в редких случаях — максимум 24 часа.
Для товаров, имеющихся на складе, вам будет отправлено электронное письмо по ссылке на документ / веб-сайт, чтобы вы могли загрузить и сохранить ее для своих записей.
Если товары отсутствуют на складе (поставка сторонних поставщиков), вы будете уведомлены о том, для каких товаров потребуется дополнительное время. Обычно мы поставляем такие товары менее чем за три дня.
Как только заказ будет размещен, вы получите квитанцию / счет, который можно будет заполнить для отчетности и бухгалтерского учета. Эту квитанцию можно легко сохранить и распечатать для ваших записей.
Гарантия лучшего качества и подлинности вашего заказа
Ваш заказ предоставляется в электронном формате (обычно это Adobe Acrobat или MS Word).
Мы всегда гарантируем лучшее качество всей нашей продукции. Если по какой-либо причине вы не удовлетворены, мы можем провести совершенно БЕСПЛАТНУЮ ревизию и редактирование приобретенных вами продуктов. Кроме того, мы предоставляем БЕСПЛАТНЫЕ обновления нормативных требований, если, например, документ имеет более новую версию на дату покупки.
Гарантируем подлинность. Каждый документ на английском языке сверяется с оригинальной и официальной версией. Мы используем только официальные нормативные источники, чтобы убедиться, что у вас самая последняя версия документа, причем все из надежных официальных источников.
А как насчет дуговой сварки под флюсом?
Лазерное отслеживание шва генерирует, анализирует и передает трехмерные профили области сварного шва.
Ваша компания все активнее занимается сваркой профильных конструкций или сосудов под давлением для тяжелой промышленности.Скорее всего, вы хотите депонировать металл со скоростью, которую невозможно сделать вручную — в диапазоне 20, 30 или даже 40 фунтов. в час.
Дуговая сварка под флюсом (SAW) справится со сваркой, но контроль того, где и как вы сваривать, может быть не менее важным, чем то, что плавит проволоку.
Покупка системы SAW без вспомогательного оборудования, такого как манипулятор или портал, подобна покупке двигателя без остальной части автомобиля. Вы можете включить его, и он будет дымить, но он не доставит вас туда, куда вам нужно.
Знание ваших областей применения поможет вам определить, какое дополнительное оборудование вам потребуется для манипулирования сварочной головкой и достижения желаемой производительности.
Опишите соединение
Одна из первых вещей, которую необходимо определить при выборе вспомогательного оборудования для ПАВ, — это тип и разнообразие соединений, которые вы будете сваривать. Будет:
- Большие соединения с V-образной канавкой и достаточно места для большой сварочной горелки?
- Узкие глубокие канавки для минимизации количества наплавленного материала?
- Многопроходные сварные швы, и если да, то сколько проходов?
- Угловые швы?
- Применения для облицовки, в которых необходимо последовательно выполнить несколько проходов?
- Прямые и однородные или волнистые и непоследовательные швы?
Определите типовой проект
Свариваемая деталь также поможет определить требования к дополнительному оборудованию.Следующие хорошие вопросы можно задать:
- Соединения выполнены из длинных, прямых или круглых материалов?
- Они вертикальные?
- Насколько велика деталь, и нужно ли ее позиционировать или поворачивать, чтобы получить доступ ко всем точкам сварки?
При сварке большой детали время, необходимое для ее позиционирования, может существенно повлиять на производительность. Переворачивание большой заготовки для достижения сварного шва требует времени и может быть опасно для операторов.
Манипулятор со стрелой и колонной, вероятно, является наиболее экономичным и универсальным способом удерживания сварочной головки над заготовкой. Если соединение длинное и прямое, может быть эффективен манипулятор со стрелой и колонной на рельсах с ходовой тележкой. Важно убедиться, что скорость машины подходит как для ускоренного хода, так и для обычных скоростей сварки.
Если заготовка круглая, например, ветряная мачта или сосуд высокого давления, ее нужно будет повернуть под горелкой.Для этого обычно используются токарные валки и сварочные позиционеры. Валки вращают длинные и часто очень тяжелые цилиндрические заготовки, центр масс которых находится примерно на средней линии заготовки. Позиционеры вращают заготовки с центром масс, который не находится на оси вращения или рядом с ней.
Количество наплавленной сварочной проволоки и толщина основного металла определяют другие требования к оборудованию. Например, для предварительного нагрева толстого материала может потребоваться обычное оборудование для пламенного или индукционного нагрева.
Размещение камеры на месте сварки позволяет оператору наблюдать за процессом и качеством сварки из удобного и безопасного места.
Ответы на два вопроса о процессе могут определить, какое дополнительное оборудование необходимо:
- Какой ток нужен?
- Как долго мне нужно сваривать?
Если вы будете проводить сварку на большом токе в течение продолжительных периодов времени, совершенно необходимо правильно подобрать сварочную цепь.Если ваши кабели недостаточно велики по обе стороны от дуги, вы рискуете расплавить что-то, кроме электрода.
Еще одно важное соображение — теплопередача. Когда ток проходит через сварочные кабели, они нагреваются и могут расплавиться. Вокруг кабелей должно быть достаточно воздуха, чтобы они оставались прохладными.
Найдите свою автоматизацию Рентабельность инвестиций
В некоторых случаях автоматизация SAW требует длительного времени окупаемости. В других случаях стоимость быстро оправдывается.
С одной стороны, многопроходные сварные швы часто трудно автоматизировать, потому что размещение последовательных валиков может быть очень важным.Трудно превзойти хорошо обученного оператора пилы.
С другой стороны, облицовка, структурные профили, толстостенные сосуды высокого давления и другие процессы, требующие высоких скоростей наплавки, являются основными кандидатами на автоматизацию. Полагаться на человека-оператора, который точно наносит сотни фунтов сварочного металла в последовательные валики в течение нескольких часов за раз, обычно не экономично, практично или даже невозможно.
Для подобных применений типичный процесс сварки под флюсом с однопроволочной дугой позволяет легко нагружать 15 или 20 фунтов.в час, а процесс с двойной или тандемной двухпроводной сваркой под флюсом может дать до 40 фунтов. в час, обеспечивая до 10 раз или 1000 процентов более высокую скорость наплавки, чем при обычной ручной дуговой сварке металлическим электродом в защитных оболочках или газовой дуговой сварке.
Выберите отслеживание шва
Отслеживание шва может облегчить сварку неровной траектории волнистых стыков. Датчик или обратная связь от сварного шва используются для регулировки положения сварочной головки таким образом, чтобы она оставалась в заданном месте на стыке.Это может повысить производительность во многих областях применения и помочь менее опытным операторам выполнять качественные сварные швы.
Наиболее распространенными методами отслеживания являются тактильное, лазерное и сквозное.
Тактильное отслеживание швов экономично. Механический датчик перемещается по суставу и посылает сигналы на поперечные направляющие с приводом, чтобы проследить линию движения. Он требует четко определенного стыка и поэтому не подходит для стыковых швов или очень мелких стыковых профилей.
Процессы, требующие высокой производительности наплавки, являются хорошими кандидатами для автоматической сварки под флюсом.
Лазерное отслеживание шва проецирует лазерный луч на заготовку и использует алгоритмы обработки изображений для распознавания профиля сварного шва. Профиль используется для точного позиционирования сварочной головки. Поскольку между датчиком и заготовкой нет физического контакта, лазерные датчики отслеживания шва не подвержены заклиниванию или поломке. Их можно использовать для автоматизации многопроходных сварных швов; однако расширенная функциональность обходится дороже.
Отслеживание шва через дугу требует колебания сварочной головки и использует показания напряжения и тока в реальном времени для определения краев стыка.Обычно это используется с системами GMAW, но может использоваться и с системами SAW. Сочетание ваших технических требований, бюджетных ассигнований и поставщика или системного интегратора поможет выбрать правильную систему для отслеживания ваших сварных швов.
Восстановить неиспользованный флюс
Для больших V-образных канавок и многопроходных сварных швов обычно требуются большие катушки или барабаны сварочной проволоки и системы подачи и восстановления флюса подходящего размера. Как правило, 2 фунта. флюса необходимы на каждый фунт израсходованной проволоки.Емкость флюса может быть увеличена за счет использования системы восстановления флюса: в основном это вакуум, который всасывает флюс, который не превратился в шлак, чтобы его можно было повторно использовать. Использование системы восстановления флюса может снизить отношение флюса к проволоке. Одна только экономия на рекуперированном флюсе может компенсировать стоимость системы надлежащего размера.
ЕмкостьFlux может сопровождаться собственными скрытыми затратами. Бункер с гравитационной подачей должен располагаться над сварочной головкой, а это означает, что необходимо поддерживать вес бункера, сварочной головки и катушки с проволокой.Вообще говоря, чем тяжелее сварочная головка, тем дороже оборудование, необходимое для ее поддержки над заготовкой.
Монитор качества сварки
Контроль и наблюдение за процессом сварки также важны. Есть несколько подходов к размещению оператора для наблюдения за сваркой на больших заготовках: поставьте сиденье оператора рядом со сварочной головкой; добавить строительные леса или лестницу, чтобы оператор мог стоять рядом с сварочной головкой; или поместите камеру на сварочную головку.
Добавление сиденья оператора эффективно превращает манипулятор или портал в лифт, а дополнительные требования могут значительно увеличить стоимость системы.Лестницы и строительные леса могут быть громоздкими и способствовать повторяющимся травмам от напряжения и напряжения, если оператор длительное время находится в неудобном положении. Сварочная камера может удерживать оператора в безопасном положении, обеспечивая четкий обзор процесса сварки.
Посмотрите на картинку целиком
Сварка под флюсом в значительной степени зависит от вспомогательного оборудования, такого как манипуляторы или порталы, системы отслеживания шва, камеры и системы управления потоком для создания прочных сварных швов.