Описание технологии сварки цветных металлов и сплавов на их основе
Алюминий и его сплавы
Для алюминия и его сплавов используют все виды сварки плавлением. Наибольшее применение нашли автоматическая и полуавтоматическая дуговая сварка неплавящимся и плавящимся электродом в среде инертных защитных газов, автоматическая дуговая сварка с использованием флюса (открытой и закрытой дугой), электрошлаковая сварка, ручная дуговая сварка плавящимся электродом, электронно-лучевая сварка.
Дуговую сварку в среде инертных газов осуществляют неплавящимися (вольфрамовыми чистыми, лантанированными и иттрированными) и плавящимися электродами. Используемые инертные газы: аргон высшего и первого сорта по ГОСТ 10157-79, гелий повышенной чистоты, смесь аргона с гелием. Выбор конкретного способа сварки определяется конструкцией изделия и условиями производства.
Сварка неплавящимся электродом диаметром 2 … 6 мм используется для узлов с толщиной стенки до 12 мм.
Ручную дуговую сварку вольфрамовым электродом ведут на специально для этого разработанных установках типа УДГ. При других условиях питание дуги при сварке неплавящимся электродом может осуществляться от других источников переменного тока. Использование источников переменного тока связано с тем, что при сварке постоянным током обратной полярности допустим сварочный ток небольшой величины из-за возможного расплавления электрода, а при сварке постоянным током прямой полярности не происходит удаления окисной пленки с поверхности алюминия.
Табл. 1 Рекомендуемые режимы сварки вольфрамовым электродом
При выполнении швов на алюминии вручную особое внимание уделяется технике сварки. Угол между присадочной проволокой и электродом должен быть примерно 90°. Присадка подается короткими возвратно-поступательными движениями. Недопустимы поперечные колебания вольфрамового электрода. Длина дуги 1,5 … 2,5 мм. Вылет электрода от торца наконечника горелки 1 … 1,5 мм. Сварку ведут обычно справа налево («левый» способ), чтобы снизить перегрев свариваемого металла. При автоматической сварке вольфрамовым электродом качество и свойства шва по его длине более стабильны, чем при ручной сварке.
Производительность сварки вольфрамовым электродом можно повысить в 3 . .. 5 раз, если использовать трехфазную дугу (рис. 1). Благодаря более интенсивному прогреву за один проход на подкладке сваривают листы толщиной до 30 мм. Сварку осуществляют как ручным, так и механизированным способом (табл. 2).
Сварку плавящимся электродом выполняют полуавтоматом или автоматом в чистом аргоне либо в смеси из аргона и гелия (до 70 % Не) на постоянном токе обратной полярности проволокой диаметром 1,5 … 2,5 мм. Режимы сварки плавящимся электродом сплавов типа АМг приведены в табл. 3.
При использовании газовой смеси (30 % Аr и 70 % Не) увеличиваются ширина и глубина провара и улучшается форма шва.
Рис. 1 Схема сварки трехфазной дугой (a) и поперечное сечение сварного шва (б): 1 — сопло; 2,3 — электроды; 4 — изделие
Для обеспечения большей устойчивости процесса переноса капель с плавящегося электрода, особенно при сварке в различных пространственных положениях, используют наложение на основной сварочный ток импульсов тока заданных параметров с частотой 50 . .. 100 Гц.
Табл. 2 Ориентировочные режимы аргонодуговой сварки алюминия трехфазной дугой
Табл. 3 Рекомендуемые режимы сварки плавящимся электродом в защитных газах алюминиевых сплавов типа АМг
При сварке листов малых толщин хорошие результаты по формированию сварного соединения получают при микроплазменной сварке. При этом аргон является плазмообразующим газом, а гелий — защитным. Гелий выполняет две функции: охлаждает периферийные слои плазмы и защищает жидкий металл сварочной ванны от воздействия воздуха.
Автоматическая сварка алюминия и его ставов с применением флюсов реализуется в двух вариантах: сварка по флюсу полуоткрытой дугой и сварка под флюсом закрытой дугой.
Сварку по флюсу применяют при производстве сосудов из алюминия и сплавов типа АМц с использованием фторидно-хлоридных флюсов. Сварка по флюсу ведется вследствие высокой электропроводности данных флюсов даже в нерасплавленном состоянии, а поэтому возможно шунтирование дуги и нарушение стабильности ее горения. Благодаря высокой концентрации энергии при сварке алюминия по флюсу достигается глубокое проплавление основного металла.
При равных токах глубина проплавления алюминия в 2 … 3 раза выше, чем стали. Для технического алюминия применяют флюс АН-А1, а для сплавов — другие флюсы, не содержащие NaCl, так как в случае загрязнения металла шва восстановленным натрием ухудшается его пластичность. Толщина слоя насыпанного флюса обычно составляет 7 … 16 мм, а ширина 25 … 45 мм в зависимости от толщины свариваемого металла. Сварка ведется на постоянном токе обратной полярности одинарным (табл. 4) или сдвоенным (расщепленным) электродом на стальной формирующей подкладке.
Табл. 4 Режимы однопроходной сварки по слою флюса одиночным электродом на формирующей подкладке
Сварочные алюминиевые проволоки обладают небольшой жесткостью и вследствие значительных колебаний конца проволоки при сварке могут возникнуть непровары. Использование сдвоенных проволок позволяет увеличить размеры сварочной ванны, время пребывания в жидком состоянии, улучшить условия для дегазации сварочной ванны и уменьшить пористость.
В конструкцию тракторов для автоматической сварки по флюсу вносят специальные бункеры с дозаторами флюса, подающие механизмы тянущего типа, специальные водоохлаждаемые мундштуки, газоотсасывающее устройство. Основные преимущества сварки по флюсу: высокие производительность и экономичность по сравнению с другими способами, меньшее коробление конструкции. Недостаток — необходимость удаления шлака после сварки.
Автоматическую сварку под флюсом ведут на больших плотностях тока расщепленным электродом переменным или постоянным обратной полярности током. Применяют керамические флюсы ЖА-64 и ЖА-64А. При этом предъявляются повышенные требования к вентиляционным системам для удаления паров флюса.
Электрошлаковую сварку алюминия и его сплавов осуществляют для толщин металла 50 … 250 мм. Сварку ведут на переменном токе пластинчатыми электродами или плавящимися мундштуками. Применяют флюсы АН-301, АН-302 на основе галогенидов щелочных и щелочноземельных металлов.
Ручная дуговая сварка покрытыми электродами выполняется для изделий из технического алюминия, алюминиево-марганцевых и алюминиево-магниевых (с содержанием магния до 5 %) сплавов, силуминов при толщине металла более 4 мм. Можно сваривать металл толщиной до 20 мм без разделки кромок, но рекомендуется производить разделку с толщин 10 мм.
Наиболее применяемый тип соединения — стыковое. Соединения внахлестку и тавровые не рекомендуют, так как возможно затекание шлака в зазоры, откуда его сложно удалить при промывке. Остатки шлака могут вызвать коррозию.
При сварке необходим подогрев до 100 . .. 400 °С в зависимости от толщины деталей. Диаметр электродов d = 4 … 8 мм. Стержень электрода изготовляют из проволок состава, близкого к составу основного металла. Для сплавов типа АМг берут проволоку с увеличенным на 2 % содержанием магния для компенсации его угара при сварке.
Основу покрытия составляют криолит, хлористые и фтористые соли натрия и калия. Ток постоянный обратной полярности. При сварке алюминиевый электрод расплавляется в 2 … 3 раза быстрее стального. Покрытия электродов имеют значительное электрическое сопротивление. При обрывах дуги кратер и конец электрода покрываются пленкой шлака, препятствующей ее повторному зажиганию. Поэтому сварку рекомендуют выполнять на высоких скоростях, без колебания конца электрода, непрерывно в пределах одного электрода.
При выполнении многослойных швов перед наложением каждого слоя требуется тщательная зачистка от шлака и окислов. Получаемые сварные соединения обладают удовлетворительными механическими свойствами.
Ручная дуговая сварка угольными электродами производится только для неответственных конструкций из алюминия. Сварку производят постоянным током прямой полярности. Диаметр угольного электрода dэ = 10 … 20 мм. Конец угольного электрода затачивают на конус под углом 60°. Металл толщиной до 2,5 мм сваривают без разделки кромок, а свыше — с разделкой (угол разделки 70 … 90°). Используют присадочный пруток диаметром 2 … 5 мм. Предварительно на присадочный пруток наносят слой флюса многократным окунанием в водный раствор флюса (смеси фторидно-хлоридных солей) или флюс наносят в виде пасты на свариваемые кромки.
Газовая сварка алюминия ведется с использованием ацетилена и реже с использованием пропан-бутановой смеси и метана. Сварка ведется нормальным пламенем при незначительном избытке ацетилена. При выборе горелки исходят из расхода примерно 100 л/ч ацетилена на 1 мм толщины основного металла. Номер наконечника выбирают в зависимости от толщины свариваемых заготовок. Диаметр присадочного прутка 1,5 … 5,5 мм в зависимости от толщины свариваемых заготовок.
Наиболее распространенный флюс АФ-4А наносится на присадочный пруток или свариваемые кромки. При толщине заготовок до 4 мм разделку кромок не выполняют, а свыше 4 мм — рекомендуется выполнять. При толщине листов более 8 мм производят общий или местный подогрев. Сварку выполняют «левым» способом. После сварки швы промывают для удаления флюсов теплой или подкисленной (2 %-ный раствор хромовой кислоты) водой.
Электронно-лучевая сварка (ЭЛС) является эффективным способом соединения заготовок из алюминиевых сплавов. По сравнению с другими способами этот способ позволяет производить сварку при высокой плотности теплового потока, минимальных тепловложениях, высоких скоростях и получать минимальное разупрочнение металла в зоне термического влияния, плотные качественные швы, минимальные деформации конструкций.
Разрушение окисной пленки при электронно-лучевой сварке идет за счет воздействия на пленку паров металла и за счет разложения окиси алюминия в вакууме с образованием газообразной субокиси алюминия А1О. Вакуум способствует удалению водорода из шва.
Магний и его сплавы
Сварку магниевых сплавов в основном осуществляют вольфрамовым лантанированным или иттрированным электродом в аргоне (иногда в гелии) на переменном токе. Инертный газ аргон обеспечивает хорошую защиту сварочной ванны от окружающей атмосферы, а переменный ток способствует разрушению окисной пленки в периоды обратной полярности вследствие катодного распыления. Для предотвращения попадания в металл окисной пленки с корня шва сварку ведут с полным проплавлением кромок на подкладках из металлов с малой теплопроводностью (аустенитные стали). С этой позиции менее технологичны нахлесточные, тавровые и угловые соединения. Наилучшие защита зоны сварки и эффект катодного распыления обеспечиваются при малой длине дуги (1 … 1,5 мм). Ориентировочные режимы сварки вольфрамовым электродом приведены в табл. 5.
Для сварки металлов толщиной более 5 мм может быть использована сварка плавящимся электродом со струйным переносом электродного металла на повышенных токах. Сварку плавящимся электродом осуществляют от источников постоянного тока на обратной полярности. Сварка магниевых сплавов плавящимся электродом осуществляется за один проход при толщинах до 5 мм без разделки кромок, толщинах 10 … 20 мм -с V-образной разделкой с углом раскрытия 50 … 60° и притуплением 2 … 6 мм, при толщинах больше 20 мм — Х-образной разделкой.
Табл. 5 Ориентировочные режимы аргонодуговой сварки вольфрамовым электродом магниевых сплавов
Медь и ее сплавы
Для сварки меди и ее сплавов могут быть применены все основные способы сварки плавлением. Наибольшее применение нашли дуговая сварка в защитных газах, Ручная дуговая сварка покрытыми электродами, механизированная дуговая сварка под флюсом, газовая сварка, электронно-лучевая сварка.
Сварка в защитных газах позволяет получить сварные соединения с наиболее высокими механическими и коррозионными свойствами благодаря минимальному содержанию примесей. В качестве защитных газов используют азот особой чистоты, аргон высшего сорта, гелий высшей категории качества, а также их смеси (например, (70 …. 80) % Аr + (20 … 30) % N2 для экономии аргона и увеличения глубины проплавления). При сварке в среде азота эффективный и термический КПД дуги выше, чем при сварке в среде аргона и гелия, но ниже устойчивость горения дуги.
Табл. 6 Выбор диаметра вольфрамового электрода и присадки
При сварке в защитных газах в качестве неплавящегося электрода используют лантанированные или иттрированные вольфрамовые электроды диаметром до 6 мм. В качестве присадочного материала используют проволоку из меди и ее сплавов, по составу близкую к основному металлу, но с повышенным содержанием раскислителей (МРЗТЦрБ 0,1-0,1-0,1-0,1; БрХНТ; БрКМц 3-1; БрХ 0,7). При сварке в азоте для улучшения качества сварного шва дополнительно применяют флюс на борной основе, который наносят на присадочную проволоку или в канавку подкладки. Выбор диаметров электрода и присадки зависит от толщины свариваемых заготовок (табл. 6).
Сварку вольфрамовым электродом ведут на постоянном токе прямой полярности. При сварке в среде азота или в смеси азота с гелием сварочный ток уменьшают, а напряжение повышают (табл. 7). При толщинах более 4 … 5 мм рекомендуется подогрев до 300 … 600 °С.
Табл. 7 Рекомендуемые режимы сварки меди вольфрамовым электродом (стыковые соединения на медной водоохлаждаемой подкладке или флюсовой подушке)
При сварке плавящимся электродом используют постоянный ток обратной полярности. Широкое распространение для меди при толщинах более 4 мм получила многослойная полуавтоматическая сварка проволокой малого диаметра (1 … 2 мм). Режимы сварки: сварочный ток 150 … 200 А для проволоки диаметром 1 мм и 300 … 450 А для проволоки диаметром 2 мм, напряжение дуги 22 … 26 В, скорость сварки зависит от сечения шва. Температура подогрева 200 … 300 °С.
Для латуней, бронз и медно-никелевых сплавов предпочтительнее сварка неплавящимся электродом, так как в этом случае меньше испарение цинка, олова и других элементов. Предварительный подогрев для медных сплавов требуется при толщинах более 12 мм.
Ручная дуговая сварка меди и ее сплавов покрытыми электродами выполняется на постоянном токе обратной полярности (табл. 8). Медные листы толщиной до 4 мм сваривают без разделки кромок, до 10 мм с односторонней разделкой при угле скоса 60 … 70° и притуплении 1,5 … 3 мм, более 10 мм — с Х-образной разделкой кромок. Для сварки меди используют электроды с покрытием «Комсомолец-100», АНЦ/ОЗМ-2, АНЦ/ОЗМ-3, ЗТ, АНЦ-3.
Сварку ведут короткой дугой с возвратно-поступательным движением электродов без поперечных колебаний. Удлинение дуги ухудшает формирование шва, увеличивает разбрызгивание, снижает механические свойства сварного соединения. Предварительный подогрев делают при толщине 5 . .. 8 мм до 200 … 300 °С, а при толщине 24 мм — до 800 °С. Теплопроводность и электропроводность металла шва резко снижаются при сохранении высоких механических свойств. Для сварки латуней, бронз и медно-никелевых сплавов применяют электроды ММЗ-2, Бр1/ЛИВТ, ЦБ-1, МН-4 и др.
Табл. 8 Ориентировочные режимы ручной однопроходной сварки меди покрытыми электродами
Рис. 2 Схема механизированной сварки меди угольным электродом под флюсом
Механизированную дуговую сварку под флюсом осуществляют угольным (графитовым) электродом (рис. 2) и плавящимся электродом. Сварка угольным электродом выполняется на постоянном токе прямой полярности с использованием стандартных флюсов АН-348А, ОСЦ-45, АН-20. При сварке угольным электродом кромки 1 собирают на графитовой подкладке 2, поверх стыка накладывают полоску латуни 3, которая служит присадочным металлом. Дуга горит между угольным электродом 4, заточенным в виде плоской лопаточки, и изделием под слоем флюса 5. Способ пригоден для сварки толщин до 10 мм. Диаметр электрода до 18 мм, сила тока до 1000 А, напряжение дуги 18 … 21 В, скорость сварки 6 … 25 м/ч.
Механизированная сварка плавящимся электродом под плавлеными флюсами (АН-200, АН-348А, ОСЦ-45, АН-M1) выполняется на постоянном токе обратной полярности, а под керамическим флюсом ЖМ-1 и на переменном токе. Основным преимуществом этого способа сварки является возможность получения высоких механических свойств сварного соединения без предварительного подогрева. При сварке меди используют сварочную проволоку диаметром 1,4 … 5 мм из меди МБ, M1, бронзы БрКМц 3-1, БрОЦ 4-3 и т.д. За один проход можно сваривать без разделки кромок толщины до 15 … 20 мм, а при использовании сдвоенного (расщепленного) электрода — до 30 мм. При толщинах кромок более 15 мм рекомендуют делать V-образную разделку с углом раскрытия 90°, притуплением 2 … 5 мм, без зазора. Флюс и графитовые подкладки перед сваркой должны быть прокалены. Для возбуждения дуги при сварке под флюсом проволоку закорачивают на изделие через медную обезжиренную стружку или пружину из медной проволоки диаметром 0,5 . .. 0,8 мм. Начало и конец шва должны быть выведены на технологические планки. Режимы сварки приведены в табл. 9.
При сварке латуней применяют флюсы АН-20, ФЦ-10, МАТИ-53 и бронзовые БрКМцЗ-1, БрОЦ4-3 и латунные ЛК80-3 проволоки. Сварка ведется на низких значениях сварочного тока и напряжения для снижения интенсивности испарения цинка. Бронзы под флюсом свариваются хорошо.
Табл. 9 Ориентировочные режимы автоматической сварки меди под флюсом (стыковое соединение, диаметр электродной проволоки 5 мм)
Газовая сварка меди используется в ремонтных работах. Рекомендуют использовать ацетиленокислородную сварку, обеспечивающую наибольшую температуру ядра пламени. Для сварки меди и бронз используют нормальное пламя, а для сварки латуней — окислительное (с целью уменьшения выгорания цинка). Сварочные флюсы для газовой сварки меди содержат соединения бора (борная кислота, бура, борный ангидрид), которые с закисью меди образуют легкоплавкую эвтектику и выводят ее в шлак. Флюсы наносят на обезжиренные сварочные кромки по 10 … 12 мм на сторону и на присадочный металл. При сварке алюминиевых бронз надо вводить фториды и хлориды, растворяющие Аl2О3. При сварке меди используют присадочную проволоку из меди марок M1 и М2, а при сварке медных сплавов — сварочную проволоку такого же химического состава. При сварке латуней рекомендуют использовать проволоку из кремнистой латуни ЛК80-3. После сварки осуществляют проковку при подогреве до 300 … 400 °С с последующим отжигом для получения мелкозернистой структуры и высоких пластических свойств.
При электрошлаковой сварке меди применяют легкоплавкие флюсы системы NaF-LiF-CaF2 (AHM-10). Режим электрошлаковой сварки: сварочный ток Iсв = 1800 … 1000 А, напряжение U = 40 … 50 В, скорость подачи пластинчатого электрода 12 … 15 м/ч. Механические свойства шва мало отличаются от свойств основного металла.
Электронно-лучевая сварка меди эффективна при изготовлении электровакуумных приборов. Она обеспечивает сохранение высокой чистоты меди от примесей и получение мелкозернистой структуры.
При соединении элементов из меди и ее сплавов больших толщин хорошие результаты дает плазменная сварка. Возможно производить сварку элементов толщиной до 60 мм за один проход. Применяют плазмотроны прямого действия. Для обеспечения хорошей защиты от атмосферного воздуха плазменную сварку иногда выполняют по слою флюса, а для создания мелкозернистой структуры используют порошковую проволоку. Для сварки малых толщин до 0,5 мм эффективно используют микроплазменную сварку.
Никель и его сплавы
Основным способом сварки никеля и его сплавов является дуговая сварка в среде защитных газов. Используются также способы сварки плавлением: ручная дуговая покрытыми электродами, автоматическая дуговая под слоем флюса, угольным электродом, газовая, электрошлаковая, электронно-лучевая, лазерная.
Сварка в среде защитных газов никеля и его сплавов обеспечивает высокое качество сварных соединений, отвечающих эксплуатационным требованиям. Дуговую сварку вольфрамовым электродом выполняют на прямой полярности с применением аргона первого сорта и без присадочного или с присадочным (чаще всего проволока НМц 2,5) металлом. Сварку рекомендуют проводить на медной подкладке или с защитой корня шва аргоном, с соплами горелок, как при сварке титана. Сварку никеля осуществляют при минимально возможной длине дуги, повышенных силе тока и скорости сварки.
При ручной сварке применяют «левый» способ. Наклон горелки к оси шва должен быть 45 … 60° вылет вольфрамового электрода 12 … 15 мм. Присадочный металл подают под углом 20 … 30° к оси шва. При многопроходной сварке последующие швы необходимо накладывать после полного охлаждения, зачистки и обезжиривания предыдущих слоев. Швы, обращенные к агрессивной среде, выполняются в последнюю очередь. Начинать и заканчивать сварные швы необходимо на технологических планках. Для предотвращения образования трещин в кратере заканчивают сварку с уменьшением сварочного тока. Режимы сварки никеля приведены в табл. 10.
Табл. 10 Ориентировочные режимы ручной аргонодуговой сварки вольфрамовым электродом в среде аргона стыковых соединений никеля
Ручную дуговую сварку покрытыми электродами для листов толщиной более 1,5 мм осуществляют на постоянном токе обратной полярности. Для сварки никеля используют электроды «Прогресс-50» со стержнем из проволоки НШ и ОЗЛ-22 со стержнем НМцАТК 1-1,5-2,5-0,15. Толщины до 4 мм сваривают без разделки, а больше 4 мм с разделкой кромок (табл. 11). Рекомендуется по возможности вести сварку за 1 проход, а длинные швы выполнять отдельными участками.
Для предупреждения перегрева электрода и получения меньших остаточных напряжений при сварке используют ток, пониженный по сравнению с током при сварке сталей и пониженную скорость сварки (табл. 12).
Сварку рекомендуют вести в нижнем положении короткой дугой для уменьшения угара стабилизирующих и раскисляющих элементов, содержащихся в электродной проволоке. Продольные колебания конца электрода способствуют газоудалению и получению более плотных швов.
Ручная дуговая сварка покрытыми электродами MMA: технология
В наше время существует большое количество разнообразных способов соединения металла с помощью сварки. Было разработано множество методик, но одна из самых первых и простых по-прежнему является самой распространенной. Ручная дуговая сварка покрытыми электродами проводится при помощи сварочного трансформатора или инвертора. Существует масса моделей этой техники, а также марок покрытых электродов, которые могут быть задействованы в данном процессе. Каждая из них обладает своими особенностями, так как выпускаются под определенные марки металла.
Ручная дуговая сварка покрытыми электродами
Область применения
MMA сварка может использоваться практически в любой сфере. В основном ее применяют для соединения низкоуглеродистых сталей. Это чаще всего применяется в частной сфере, на мелких строительных работах, при ремонте различных деталей, а также на производстве. Существуют электроды, которые рассчитаны на применение в судостроительной области, металлургии, работе в химической промышленности и так далее. Для особенно ответственных мест ее стараются не использовать, так как она уступает многим другим разновидностям, таким как TIG сварка.
Преимущества
К основным преимуществам данной технологии можно отнести следующие факторы:
- Относительно низкая себестоимость получаемых швов;
- Не требуется длительный процесс настройки и подготовки сварочного оборудования и материалов;
- Здесь не возникает большой опасности взрыва, как при работе с газом;
- Сварка может проводиться как с тонкими, так и с толстыми деталями;
- Техника для проведения работ компактна и мобильна;
- Инверторы без проблем работают от обыкновенной бытовой розетки;
- Имеется широкий выбор сварочных трансформаторов и инверторов любой ценовой категории и различных параметров;
- Все материалы являются широкодоступными.
Недостатки
Но здесь имеется и ряд недостатков, среди которых следует отметить следующие:
- Покрытие электрода обеспечивает низкий уровень защиты, если сравнивать с другими технологиями, так что шов уступает по качеству им;
- Покрытие электрода может отсыреть, что приведет к попаданию внутрь ванны водорода;
- Скорость сварки является быстрой, так что неопытные сварщики могут допускать много ошибок по неосторожности;
- Цветные металлы, их сплавы, нержавейка и другие сорта, которые плохо свариваются, оказываются очень проблемными при обработке данным способом;
- Вероятность появления брака сильно зависит от внешних условий;
- Чтобы создать приемлемый уровень качества сварки нужно применять множество дополнительных материалов и видов обработки, таких как флюсы и прочее.
Режимы сварки
Для каждого конкретного случая соединения заготовок требуется подбирать свой режим. Здесь существует огромное количество факторов, которые влияют на параметры техники. Для многих случаев уже заранее подобраны параметры, которые основаны на опыте профессионалов. Но существуют и такие ситуации, когда режим нужно выставлять самостоятельно. На параметры режима оказывают влияние следующие факторы:
- Род используемого электричества;
- Полярность тока;
- Диаметр расходного материала;
- Скорость проведения сварочных работ;
- Сила напряжения;
- Сила тока;
- Пространственное положение шва.
Принцип работы
Принцип работы ручной дуговой сварки достаточно прост. Сварочный аппарат выполняет роль преобразователя электричества из сети под заданные параметры. Из него выходит два вывод – земля и держатель электрода. Каждый из них может быть как плюсом, так и минусом. Держатель проводит ток, который передается электрода, так что основной контакт образуется между ним и основным металлом.
После подачи питания электричество проходит через трансформатор и выводится на плюс и минус.
«Важно!
Сварщик создает электрическую дугу, не замыкая цепь полностью, иначе было бы короткое замыкание, а держа ее в постоянно размыкающемся состоянии, что обеспечивает появление электрической дуги.»
В этом месте температура горения достигает такого уровня, что расплавляет основной металл и электрод, из которого берется основной металл для шва.
Технология сварки
Технологи ручной дуговой сварки покрытыми электродами включает в себя не только выбор правильного режима, но и в правильном порядке действий. Сначала заполняется ванна с расплавленным металлом в достаточном объеме, чтобы можно было сформировать валик нужной формы. Шов может быть беспрерывным, если деталь обладает достаточной толщиной, чтобы противостоять деформации. В ином случае может быть коробление от высокой температуры. Чтобы его не былою нужно делать шов короткими участками.
Схема ручной дуговой сварки покрытыми электродами
Сварочные материалы
Здесь используется два основных вида сварочных материалов:
- Покрытые электроды, благодаря которым данная технология и получила свое название. В основном они разделяются по составу, так как он должен быть максимально похож на основной металл. Также есть различные типы покрытия, в зависимости от сферы применения данных материалов.
- Флюс, служащий для улучшений характеристик процесса сварки. Выделяют твердые и жидкие виды, причем некоторые из них могут содержать металлические частицы.
Техника безопасности
Во время работы нужно использовать средства индивидуальной защиты и рабочую огнеупорную одежду. Не допускается нахождение поблизости легко воспламеняемых предметов. Нужно следить за целостностью токоведущих частей и заземлением. Перед свариванием нужно очистить рабочее место от лишних предметов.
Заключение
Для ручной дуговой сварки использование покрытых электродов является наиболее распространенным вариантом. Электроды являются относительно недорогими и для простых процедур дают неплохую защиту от внешних факторов. Главное перед использованием их правильно просушить, а если потребуется, то и прокалить, чтобы не возникало проблем с применением.
Лабораторная работа № 5 Технология ручной дуговой сварки покрытыми электродами
Цель работы
Ознакомиться с технологией ручной дуговой сварки покрытыми электродами.
Задание
1. Ознакомиться с оборудованием и технологией ручной дуговой сварки.
2. Изучить влияние наклона электрода при ручной дуговой сварке на форму и параметры сварного шва.
3. Результаты испытания оформить в виде таблицы результатов.
4. Написать отчет по работе.
Технология ручной дуговой сварки
покрытыми электродами.
Рис. 1. Ручная дуговая сварка металлическим электродом с покрытием (стрелкой указано направление сварки): 1 — металлический стержень; 2 — покрытие электрода, 3 — газовая атмосфера дуги; 4 — сварочная ванна, 5 — затвердевший шлак; 6 — закристаллизовавшийся металл шва, 7 — основной металл (изделие), 8 — капли расплавленного электродного металла, 9 — глубина проплавления.
Схема ручной дуговой сварки
представлена на рис 1. Перед
зажиганием (возбуждением) дуги следует
установить необходимую силу сварочного
тока, которая зависит от марки электрода,
пространственного положения сварки,
типа сварного соединения и др. Зажигать
дугу можно двумя способами. При одном
способе электрод приближают вертикально
к поверхности изделия до касания металла
и быстро отводят вверх на необходимую
длину дуги. При другом — электродом
вскользь «чиркают» по поверхности
металла. Применение того или иного
способа зажигания дуги зависит от
условий сварки и от навыка сварщика.
Длина дуги зависит от марки и диаметра электрода, пространственного положения сварки, разделки свариваемых кромок и т. п. Нормальная длина дуги считается в пределах LД == (0,5 — 1,1) dЭЛ (dЭЛ — диаметр электрода). Увеличение длины дуги снижает качество наплавленного металла шва ввиду его интенсивного окисления и азотирования, увеличивает потери металла на угар и разбрызгивание, уменьшает глубину проплавления основного металла. Также ухудшается внешний вид шва.
Во время ведения процесса
сварщик обычно перемещает электрод не
менее чем в двух направлениях. Во-первых,
он подает электрод вдоль его оси в дугу,
поддерживая необходимую в зависимости
от скорости плавления электрода длину
дуги. Во-вторых, перемещает электрод в
направлении наплавки или сварки для
образования шва. В этом случае образуется
узкий валик, ширина которого при наплавке
равна примерно (0,8 — 1,5)dЭЛ и зависит от силы сварочного тока и
скорости перемещения дуги по поверхности
изделия. Узкие валики обычно накладывают
при проваре корня шва, сварке тонких
листов и тому подобных случаях.
При правильно выбранном диаметре электрода и силе сварочного тока скорость перемещения дуги имеет большое значение для качества шва. При повышенной скорости дуга расплавляет основной металл на малую глубину и возможно образование непроваров. При малой скорости вследствие чрезмерно большого ввода теплоты дуги в основной металл часто образуется прожог, и расплавленный металл вытекает из сварочной ванны. В некоторых случаях, например при сварке на спуск, образование под дугой жидкой прослойки из расплавленного электродного металла повышенной толщины, наоборот, может привести к образованию непроваров.
Иногда сварщику приходится
перемещать электрод поперек шва,
регулируя тем самым распределение
теплоты дуги поперек шва для получения
требуемых глубины проплавления основного
металла и ширины шва. Глубина проплавления
основного металла и формирование шва
главным образом зависят от вида поперечных
колебаний электрода, которые обычно
совершают с постоянными частотой и
амплитудой относительно оси шва (рис. 12). Траектория движения конца электрода
зависит от пространственного положения
сварки, разделки кромок и навыков
сварщика. При сварке с поперечными
колебаниями получают уширенный валик,
ширина которого обычно составляет (2 —
4)dЭЛ а форма проплавления зависит от траектории
поперечных колебаний конца электрода,
т. е. от условий ввода теплоты дуги в
основной металл.
При окончании сварки — обрыве дуги
следует правильно заварить кратер.
Кратер является зоной с наибольшим
количеством вредных примесей ввиду
повышенной скорости кристаллизации
металла, поэтому в нем наиболее вероятно
образование трещин. По окончании сварки
не следует обрывать дугу, резко отводя
электрод от изделия. Необходимо прекратить
все перемещения электрода и медленно
удлинять дугу до обрыва; расплавляющийся
при этом электродный металл заполнит
кратер. При сварке низкоуглеродистой
стали кратер иногда выводят в сторону
от шва — на основной металл. При случайных
обрывах дуги или при смене электродов
дугу возбуждают на еще не расплавленном
основном металле перед кратером и затем
проплавляют металл в кратере.
Положение электрода относительно поверхности изделия и пространственное положение сварки оказывают большое влияние
на форму шва и проплавление основного металла (рис. 2). При сварке углом назад улучшаются условия оттеснения из-под дуги жидкого металла, толщина прослойки которого уменьшается. При этом улучшаются условия теплопередачи от дуги к основному металлу и растет глубина его проплавления. То же наблюдается при сварке шва на подъем на наклонной или вертикальной плоскости. При сварке углом вперед или на спуск расплавленный металл сварочной ванны, подтекая под дугу, ухудшает теплопередачу от нее к основному металлу — глубина проплавления уменьшается, а ширина шва возрастает (сечения швов на рис 2).
Рис 2. Способы выполнения сварки: а — угол назад; б — углом вперед; в — на подъем; г — на спуск.
При прочих равных условиях количество
расплавляемого электродного металла,
приходящегося на единицу длины шва,
остается постоянным, но распределяется
на большую ширину шва и поэтому высота
его усиления уменьшается. При наплавке
или сварке тонколистового металла
(толщина до 3 мм) для уменьшения глубины
провара и предупреждения прожогов
рекомендуется сварку выполнять на
спуск (наклон до 15°) или углом вперед
без поперечных колебаний электрода.
Для сборки изделия под сварку (обеспечения заданного зазора в стыке, положения изделий и др.) можно применять специальные приспособления или короткие швы — прихватки. Длина прихваток обычно составляет 20 — 120 мм (больше при более толстом металле) и расстояние между ними 200 — 1200 мм (меньше при большей толщине металла для увеличения жесткости). Сечение прихваток не должно превышать 1/3 сечения швов. При сварке прихватки необходимо полностью переплавлять.
Оборудование сварочного поста
Сварочным постом называется рабочее
место электросварщика, оборудованное
комплектом соответствующей аппаратуры
и приспособлений. От правильной
организации рабочего места в значительной
мере зависят как обеспечение высокой
производительности труда сварщиков,
так и надежное качество сварных швов и
соединений (требования к организации
рабочих мест электросварщиков
регламентированы ГОСТ 12. 3.003). Рабочие
места сварщиков в зависимости от
выполняемой работы и габаритов свариваемых
изделий могут быть: стационарными,
расположенными в специальных сварочных
кабинах и передвижными, расположенными
непосредственно у этих, крупногабаритных
изделий.
Передвижные сварочные посты, как
правило, применяются при монтаже и
ремонтных работах. При этом часто
используют переносные сварочные
трансформаторы, сварочные агрегаты и
выпрямители, устанавливаемые на
специальные прицепы или закрытые
автомобили. Такие прицепы и автомобили
оборудованы специальными рубильниками,
к которым подключены установки. При
работе на различной высоте электроды
и необходимый инструмент сварщика
находятся в брезентовых сумках,
подвешиваемых к поясу сварщика, либо
в специальных пеналах или ящиках. Для
обеспечения удобства и безопасности
работы делают подмости с перилами
(инвентарные леса) или подвешивают
люльки. При работе на высоте и значительном
удалении от источника питания
применяют дистанционные регуляторы
сварочного тока. А при сварке в сосудах
закрытого типа для обеспечения безопасных
условий труда используют отключатели
(ограничители) холостого хода.
В зависимости от технологического процесса (марки свариваемого материала и типа покрытия электрода) сварочные работы выполняют либо на переменном, либо на постоянном токе. Постоянный ток, по-сравнению с переменным, имеет то преимущество, что дуга горит стабильнее, а, следовательно, процесс сварки вести легче, особенно на малых токах.
Питание сварочных постов переменным
током осуществляют от специальных
трансформаторов, а постоянным током —
от преобразователей и выпрямителей. На
рис.3,а показана принципиальная
электрическая схема поста для ручной
дуговой сварки переменным током (от
трансформатора типа ТС), а на рис. 3,б —
общий вид такого поста. От сети 1 переменный
ток напряжением 220 или 380 В через рубильник
2 и предохранители 3 подается к источнику
питания – сварочному трансформатору
(преобразователю) 4 а, б (в, г), где ток
трансформируется до напряжения 60—75
В, необходимого для возбуждения дуга,
и по сварочным приводам 5 через зажим 6
и электрододержатель 7 подводится — к
изделию 8.
На рис. 3,в, показана принципиальная электрическая схема песта для ручной дуговой сварки постоянным током, а на рис. 3,г — общий вид поста.
Рис. 3. Принципиальные электрические и монтажные схемы поста для ручной дуговой сварки: а, б — переменным током (l — переменная величина расстояния между катушками), а, г — постоянным током.
Балластные реостаты (см. рис. 4). Назначение балластного реостата — создание падающей характеристики на каждом посту и регулирование сварочного тока. Реостатом производится ступенчатая регулировка сварочного тока в достаточно широких пределах (20 ступеней). Реостат состоит из пяти ступеней сопротивления, которые при помощи пяти рубильников могут включаться в цепь сварочной дуги. Каждая ступень включает в себя несколько элементов сопротивлений, выполненных из проволоки или ленты с большим удельным сопротивлением.
Из рис. 4 видно, что минимальный сварочный
ток будет при включении рубильника I,
а максимальный — при включении всех
пяти рубильников. Выпускаются балластные
реостаты РБ-201, РБ-301 и РБ-501. Реостат
РБ-201 дает возможность регулировать
сварочный ток от 10 до 200 А через каждые
10 А; РБ-301-от 15 до 300 А через каждые 15 А;
РБ-501-от 25 до 500 А через каждые 25 А.
Рис. 4. Балластный реостат типа РБ: а — внешний вид, б — принципиальная схема, 1-22-сооротивления, I -V-рубильники.
Порядок выполнения работы
1. Зачистить пластину.
2. Под руководством преподавателя наплавить на размеченную пластину два валика: один – углом вперед, другой – углом назад.
3. зачистить наплавленные валики.
4. Произвести измерение ширины и высоты сварного шва.
5. Данные занести в таблицу результатов измерений.
Содержание отчета.
1. Тема лабораторной работы.
2. Цель занятия.
3. Рисунок схемы сварки покрытыми
электродами.
4. Таблица результатов измерений.
5. Выводы.
Таблица результатов измерений
1-е измерение мм | 1-е измерение мм | 1-е измерение мм | Среднее значения мм | |
углом вперед | 5,6 | 5,8 | 5,5 | |
углом назад | 4,2 | 4,1 | 4,3 |
Литература.
1. Фоминых В. П., Яковлев А. П.
Ручная дуговая сварка: Учеб. пособие для техн. училищ. — б-е изд., испр. и доп. — М.: Высш. школа, 1981. —256 с., ил.
2. СтекловО. И.
Основы сварочного производства: Учеб, для сред. ПТУ.—2-е изд., перераб. и доп.—М.: Высш. шк., 1986.—224 с., ил.
3. Справочник сварщика/Под ред. В. В. Степанова.— 4-е изд., перераб. и доп. — М.: Машиностроение, 1982.— 560 с., ил.
Техника и технология ручной дуговой сварки (наплавки, резки) покрытыми электродами
1. Приложение 4.2.10 МДК 02.01. Техника и технология ручной дуговой сварки (наплавки, резки) покрытыми электродами
ПРИЛОЖЕНИЕ 4.2.10МДК 02.01. ТЕХНИКА И
ТЕХНОЛОГИЯ РУЧНОЙ
ДУГОВОЙ СВАРКИ
(НАПЛАВКИ, РЕЗКИ)
ПОКРЫТЫМИ ЭЛЕКТРОДАМИ
ТЕХНОЛОГИЯ РУЧНОЙ ДУГОВОЙ
СВАРКИ
ЦЕЛЬ: В РЕЗУЛЬТАТЕ ОБУЧЕНИЯ ПО
ДАННОЙ ТЕМЕ ОБУЧАЮЩИЕСЯ
ПОЛУЧАТ ЗНАНИЯ О ТЕХНИКЕ И
ТЕХНОЛОГИИ ВЫПОЛНЕНИЯ ШВОВ
ПРИ РУЧНОЙ ДУГОВОЙ СВАРКЕ.
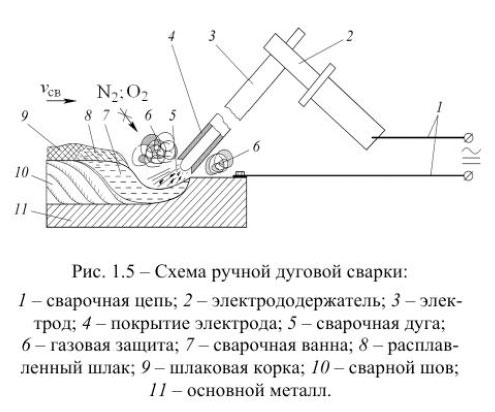
МЕСТО ПРОВЕДЕНИЯ: КАБИНЕТ
ТЕОРЕТИЧЕСКИХ ОСНОВ СВАРКИ И
РЕЗКИ МЕТАЛЛОВ
ФОРМА УРОКА : ЛЕКЦИЯ
3. Цель: В результате обучения по данной теме обучающиеся получат знания о технике и технологии выполнения швов при ручной дуговой
ДЛИНА ДУГИТехнология ручной дуговой сварки
предусматривает выполнение следующих
операций: возбуждение дуги, перемещение
электрода в процессе сварки, порядок наложения
швов в зависимости от особенностей сварных
соединений.
В процессе сварки необходимо поддерживать
постоянную длину дуги, которая зависит от марки
и диаметра электрода.
Ориентировочно нормальная длина дуги, мм: LД
= (0,5 …1,1)d.
где d — диаметр электрода, мм.
4. Длина дуги
• Умение поддерживать дугу постоянной длиныхарактеризует квалификацию сварщика.
• Длина дуги существенно влияет на качество сварного шва
и его геометрическую форму. Длинная дуга способствует
более интенсивному окислению и азотированию
расплавляемого металла, увеличивает разбрызгивание, а
при сварке покрытыми электродами основного типа
приводит к пористости металла.

ПОЛОЖЕНИЕ ЭЛЕКТРОДА
Наклон электрода при сварке
зависит от выполнения шва в
пространстве, толщины и состава
основного металла, а также
диаметра электрода, вида и
толщины его покрытия
Сварку можно вести слева
направо, справа налево,
от себя и к себе. Независимо от
направления сварки электрод
должен быть наклонен к оси шва
так, чтобы основной металл
проплавлялся на наибольшую
глубину и правильно
формировался шов
6. Положение электрода
ДВИЖЕНИЯ ЭЛЕКТРОДА• В процессе сварки электроду сообщается движение в трех
направлениях.
• Первое движение — поступательное, направлено по оси
электрода. Этим движением поддерживается постоянная
длина дуги в зависимости от скорости плавления
электрода.
8. Движения электрода
• Второе движение — перемещение электродавдоль оси валика для образования шва
• Скорость этого движения устанавливается в
зависимости от силы тока, диаметра электрода,
скорости его плавления, вида шва и других
факторов
• При отсутствии поперечных движений электрода
получается узкий шов (ниточный валик) шириной
примерно 1,5 диаметра электрода
• Такие швы применяют при сварке тонких листов,
наложении первого (корневого) слоя
многослойного шва, сварке по способу опирания
и в других случаях
Третье движение — перемещение электрода поперек шва
для получения требуемых ширины шва и глубины
проплавления
Поперечные колебательные движения конца электрода
определяются формой разделки, размерами и положением
шва, свойствами свариваемого материала, навыком
сварщика
Ширина швов, получаемых с поперечными колебаниями,
обычно составляет 1,5—5 диаметров электрода
СПОСОБЫ ЗАПОЛНЕНИЯ ШВА ПО
ДЛИНЕ И СЕЧЕНИЮ
• Порядок заполнения швов имеет большое
значение для обеспечения работоспособности
сварной конструкции,
уменьшения внутренних напряжений и
деформаций.
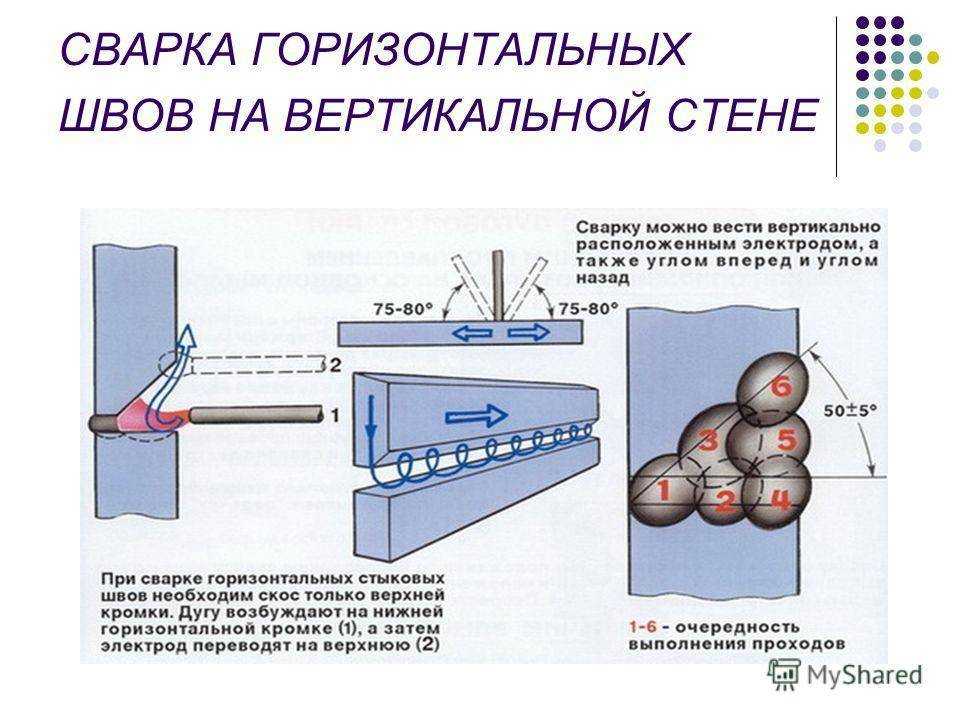
Под порядком заполнения шва понимают как
последовательность заполнения разделки шва по
поперечному сечению, так и последовательность
сварки по длине шва.
• В зависимости от количества слоев (проходов),
необходимых для заполнения сечения шва,
различают однослойные, многослойные и
многослойные многопроходные швы
• Если число слоев равно числу проходов дугой, то
шов называют многослойным.
В случае, если некоторые из слоев выполняются
за несколько проходов, такой шов называют
многопроходным
• Многослойные швы чаще применяют в стыковых
соединениях, многопроходные — в угловых и
тавровых
12. Способы заполнения шва по длине и сечению
• По протяженности все швы условно можно разделить натри группы: короткие — до 300 мм, средние — 300—
1000, длинные — свыше 1000 мм.
• В зависимости от протяженности шва, свойств
свариваемого материала, требований к точности и
качеству сварных соединений сварка швов может
выполняться различными способами.

• Короткие швы выполняют напроход — от начала шва до
его конца
• Швы средней длины сваривают от середины к концам, т.
е. обратноступенчатым способом
• Швы большой длины выполняют двумя способами: от
середины к концам (обратноступенчатым способом) и
вразброс
• При обратноступенчатом способе весь шов
разбивается на небольшие участки длиной 150—
200 мм. На каждом участке сварку ведут в
направлении, обратном общему направлению
сварки
• Горкой или каскадом выполняют швы соединений
ответственных конструкций большой толщины
(свыше 20—25 мм), когда появляются объемные
напряжения и
возрастает опасность образования трещин
• При сварке горкой сначала в разделку кромок
наплавляют первый слой небольшой длины (200
—300 мм), затем второй слой, перекрывающий
первый и имеющий в два раза большую длину.
Третий слой перекрывает второй на 200—300 мм.
Так наплавляют слои до тех пор, пока на
небольшом участке над первым слоем разделка не
будет заполнена.
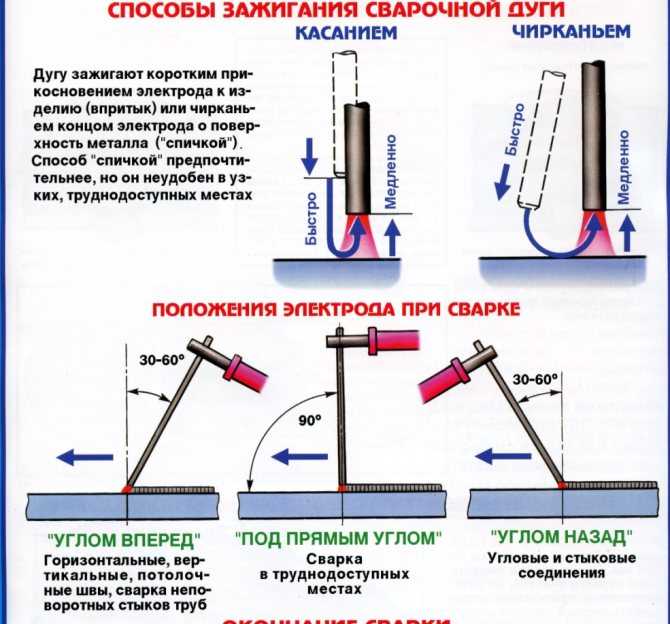
в разные стороны короткими швами тем же
способом. Таким образом, зона сварки все время
находится в горячем состоянии, что
предупреждает появление трещин.
• Сварка каскадом является разновидностью сварки
горкой.
ВЫБОР ЧИСЛА ПРОХОДОВ ПРИ
СВАРКЕ СТЫКОВЫХ И
УГЛОВЫХ СОЕДИНЕНИЙ
Стыковое соединение
Угловое соединение
Толщина
кромок, мм
Число проходов
без подварки
Катет шва, мм
Число проходов
2
4
6
8
10
12
14
16
18
20
1
1
1…2
2…3
2…3
3…4
3…5
4…6
5…6
5…7
2
6
8
10
12
14
16
18
20
22
1
1
1
1…2
3
3…4
4…5
5…6
5…6
6…7
ОКОНЧАНИЕ ШВА
• При окончании сварки — обрыве дуги в конце шва —
следует правильно заваривать кратер.
• Кратер является зоной с наибольшим количеством
вредных примесей, поэтому в нем наиболее вероятно
образование трещин.
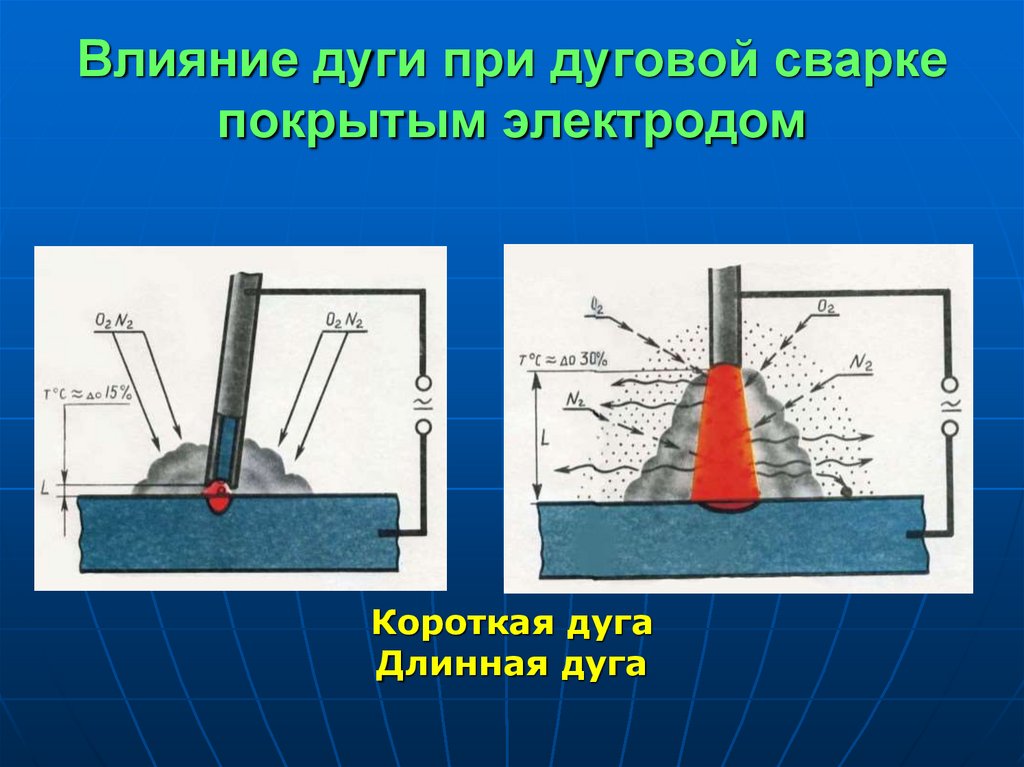
• По окончании сварки не следует обрывать дугу, резко
отводя электрод от изделия. Необходимо прекратить все
перемещения электрода и медленно удлинять дугу до
обрыва; расплавляющийся при этом электродный металл
заполнит кратер.
20. Выбор числа проходов при сварке стыковых и угловых соединений
• При сварке низкоуглеродистой стали кратериногда выводят в сторону от шва — на основной
металл
• Если сваривают сталь, склонную к образованию
закалочных структур, вывод кратера в сторону
недопустим ввиду возможности образования
трещин
• При случайных обрывах дуги или смене
электродов дугу возбуждают на еще не
расплавленном основном металле перед кратером
и затем проплавляют металл в кратере
21. Окончание шва
ТЕХНОЛОГИЯ СВАРКИВЫБОР РЕЖИМА РУЧНОЙ
ДУГОВОЙ СВАРКИ
Под режимом сварки понимают группу контролируемых
параметров, определяющих ее условия. Параметры
режима сварки подразделяют на основные и
дополнительные.

К основным параметрам режима ручной сварки
относят величину, род и полярность тока, напряжение на
дуге, скорость сварки и диаметр электрода.
Дополнительными параметрами являются
величина вылета электрода, состав и толщина покрытий
электрода, положение электрода и положение изделия при
сварке.
23. Технология сварки
ДИАМЕТР ЭЛЕКТРОДОВ• Определение режима сварки начинают с выбора диаметра электрода в
зависимости от толщины свариваемого металла и вида соединения.
• Диаметр электродов выбирают в зависимости от толщины металла,
катета шва, положения шва в пространстве. Примерное соотношение
между толщиной металла S и диаметром электрода при сварке шва в
нижнем положении приведено в таблице.
• Вертикальные, горизонтальные и потолочные швы независимо от
толщины свариваемого металла выполняют электродами
небольшого диаметра (до 4 мм), так как при этом меньше стекание
жидкого металла и шлака из сварочной ванны.
• При сварке многослойных швов для лучшего провара корня шва
первый шов сваривают электродом диаметром 3.

последующие — электродами большего диаметра.
S,мм
d,мм
1…2
2…3
3…5
3…4
4…10
4…5
12…24 30…60
5…6
6и
более
24. Выбор режима ручной дуговой сварки
Рекомендуемый
диаметр
электрода,
мм
Угловое и
тавровое
соед.. Катет
шва ,мм
Стыковое
соед..
Толщина
кромок, мм
1,63,0
2,0
—
3,0
4,0
4,0-5,0
5,0
5,0-6,0
6,08,0
4,0-5,0
—
6,0-8,0
—
—
13,015,0
16,020,0
20,0
1,53,0
2,0
4,0-8,0 9,0-12,0
25. Диаметр электродов
СИЛА СВАРОЧНОГО ТОКА• обычно устанавливают в зависимости от
выбранного диаметра электрода. При сварке швов
в нижнем положении силу тока подсчитывают,
пользуясь эмпирическими формулами.
Iсв=Kdэ.
или
I cв = (20 + 6dэ)dЭ,
• где К — коэффициент, зависящий от диаметра
электрода; dэ диаметр электрода, мм.
РЕЖИМЫ РУЧНОЙ ДУГОВОЙ СВАРКИ СТЫКОВЫХ
СОЕДИНЕНИЙ (В НИЖНЕМ ПОЛОЖЕНИИ)
ЛИСТОВОЙ СТАЛИ
Диаметр
Толщина
электрода
листа, мм
, мм
Сила
свар.
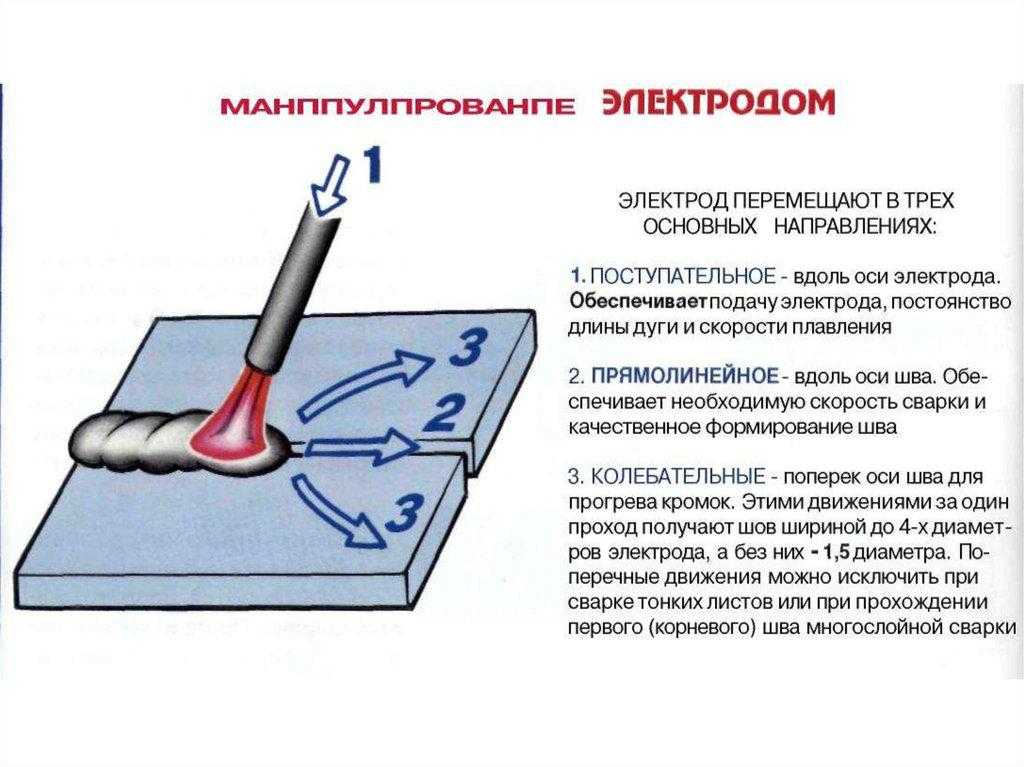
тока, А
1-4
1,5
2
25-40
60-70
3
3
100-140
4-5
3
4
100-140
160-200
Диаметр
Толщина
электрода
листа, мм
, мм
Сила
свар.
тока, А
6-12
4
5
160-200
220-280
13 и
более
5
6
7
220-280
280-340
350-400
При сварке на вертикальной плоскости силу тока
уменьшают нa 10… 15 %, а в потолочном положении — на
15 …20 % по сравнению со значением, выбранным для
нижнего положения.
27. Сила сварочного тока
РОД И ПОЛЯРНОСТЬ ТОКАВлияют на форму и размеры шва.
• При сварке постоянным током обратной
полярности глубина провара на 40—50 % больше,
чем постоянным током прямой полярности, что
объясняется различным количеством теплоты,
выделяющейся на аноде и катоде.
• При сварке переменным током глубина
провара на 15—20 % меньше, чем при сварке
постоянным током обратной полярности.
28. Режимы ручной дуговой сварки стыковых соединений (в нижнем положении) листовой стали
НАПРЯЖЕНИЕНапряжение оказывает на глубину провара
незначительное влияние, от него зависит ширина шва.

Напряжение на дуге зависит от характеристик источника
питания, материала электрода и изделия. Изменять его
можно, меняя длину дуги. Обычно напряжение дуги
составляет 20…30 В.
Повышение напряжения дуги за счет увеличения ее длины
приводит к снижению силы тока и глубины провара,
увеличивает ширину шва.
При увеличении напряжения ширина шва увеличивается
независимо от полярности.
С увеличением скорости сварки глубина провара и
ширина шва понижаются.
29. Род и полярность тока
СКОРОСТЬ РУЧНОЙ ДУГОВОЙСВАРКИ
• Скорость ручной дуговой сварки зависит от квалификации
сварщика и обычно выбирается в диапазоне 4…8 м/ч.
• С увеличением скорости сварки снижаются глубина
провара и ширина шва. Влияние скорости компенсируют
увеличением силы тока.
Ручная дуговая сварка металлическим электродом (ММА) — OpenLearn
Обновлено вторник, 6 марта 2018 г.
Сварка начинается с возбуждения электрической дуги между электродом с флюсовым покрытием и соединяемой металлической заготовкой. Комбинация расплавленного основного металла и расплавленной проволоки электрода образует сварное соединение. Сварочные материалы защищены от загрязняющих веществ в атмосфере газами, выделяемыми флюсовым покрытием.
Сварка ММА (электрод с флюсовым покрытием)
Электрическая дуга возникает между металлическим электродом, по которому течет сильный ток, и соединяемой деталью. Под интенсивным нагревом дуговой температуры (2700–5500°С) небольшой участок основного металла доводится до точки плавления. При этом конец электрода оплавляется и капли расплавленного металла проходят через дугу к основному металлу. Флюсовое покрытие на электроде обеспечивает газообразную защиту от окисления.
Производитель:
- Для сварки ММА используется переменный (ac) или постоянный (d.c.) ток. Когда переменный ток используется, дуга должна повторно зажигаться в каждом полупериоде, так как полярность меняется на противоположную.
Это вызывает некоторую нестабильность дуги, которую можно уменьшить, используя стабилизаторы дуги во флюсовом покрытии. Когда постоянный ток используется, есть выбор полярности – положительный полюс дуги самый горячий.
- Напряжение дуги поддерживается в пределах от 14 до 45 В, а напряжение холостого хода составляет 50–100 В. Источники питания варьируются от 30 до 500 А переменного тока. или постоянный ток
- Электроды с покрытием содержат шлакообразующие ингредиенты (которые создают жидкое покрытие на сварном шве при его охлаждении) и газообразующие ингредиенты (которые создают атмосферу CO 2 , CO или H 2 вокруг дуги). Основные материалы, используемые в покрытиях электродов, включают:
- Углеродистый материал типа целлюлозы (C6 h20 O5 ) n – производит защитный газ (CO).
- Кремнезем (SiO 2 ) – соединяется с оксидами металлов с образованием шлака.
- Оксид титана (TiO 2 ) – для стабилизации дуги.
- Карбонат кальция (CaCO 3 ) – разлагается с образованием CaO и, следовательно, основного шлака.
- Фторид кальция (CaF 2 ) – повышает текучесть шлака.
- Оксид натрия (Na 2 O) – действует как связующее для покрытия и способствует текучести шлака.
- Ферросилиций — действует как раскислитель.
- Железный порошок — увеличивает скорость осаждения.
- Размеры сварочных аппаратов определяются в соответствии с их выходной мощностью, которая может составлять от 150 до 1000 ампер.
- Скорость осаждения в диапазоне 2–5 кг ч -1 .
Материалы:
- Большинство технических металлов и сплавов можно сваривать методом сварки MMA (очень универсальный процесс).
- При сварке углеродистых и низколегированных сталей электроды с покрытием обычно изготавливаются из низкоуглеродистой стали. Для легированных сталей, склонных к образованию твердого и хрупкого мартенсита при охлаждении, применяют электроды из низколегированной стали.
Кроме того, эти стали склонны к водородному охрупчиванию, а покрытия не должны содержать водородообразующую целлюлозу. Вместо этого TiO 2 и CaCO 3 добавлены в покрытие. Аустенитные составы (до 25% хрома и 20% никеля) также полезны для предотвращения образования мартенсита.
- Чугуны сваривают электродами с высоким содержанием никеля или монеля (Ni-Cu).
- Большинство цветных металлов и сплавов сваривают электродами, состав которых аналогичен свариваемому металлу. Электроды из алюминиевого сплава покрывают флюсами, состоящими из смесей фторидов и хлоридов, для растворения оксида алюминия Al 2 O 3 поверхностный слой. Дисперсионно-твердеющие сплавы Al-Mg-Si теперь свариваются с помощью процессов TIG и MIG. Медные, медно-оловянные (бронзы) и медно-цинковые (латуни) сплавы имеют большие коэффициенты теплопроводности, поэтому требуют большего количества тепла и нуждаются в предварительном подогреве перед сваркой ММА (до 250–450°С).
Никелевые сплавы можно сваривать подогретыми электродами.
Исполнение:
- Существует пять основных типов сварных соединений: стыковые, угловые (угловые), кромочные, угловые (или тавровые) и внахлестку.
- Стыковые соединения с квадратными концами могут выполняться из металла толщиной до 5 мм. Одиночные V-образные стыковые сварные швы выполняются на металлическом листе толщиной от 5 до 25 мм. Минимальный прилежащий угол (α) составляет 60° с раскрытием корня 0–3 мм и поверхностью корня 0–3 мм.
- Угловые сварные швы используются для заполнения углов и являются наиболее распространенными сварными швами в строительных конструкциях (тавровые соединения).
См. также: Дуговая сварка в среде защитного газа (TIG/MIG/MAG), плазменно-дуговая сварка, электронно-лучевая сварка и лазерная сварка.
Эта статья является частью Manupedia – сборника информации о некоторых процессах, используемых для преобразования материалов в полезные предметы.
Разница между SMAW и SAW
Пинту Присоединение
Процессы дуговой сварки представляют собой подгруппу сварки плавлением, поскольку электрическая дуга, возникающая между электродом и опорными плитами, используется для подачи тепла для плавления сопрягаемых поверхностей для образования коалесценции во время сварки. Электрод иногда является расходуемым, в то время как в других процессах дуговой сварки он не является расходуемым. Помимо помощи в образовании дуги, расходуемый электрод плавится благодаря нагреву дуги, а затем осаждается на валике сварного шва в качестве присадочного металла. Некоторыми процессами дуговой сварки, в которых используется плавящийся электрод, являются SMAW, GMAW, SAW, FCAW и т. д. С другой стороны, неплавящийся электрод остается неповрежденным во время сварки и только способствует образованию дуги. Присадочный металл, если требуется, требуется поставлять отдельно. Примеры включают CAW, TIG, AHW и т. д. Независимо от типа электрода зона сварки должна быть защищена от окисления, вызванного атмосферным воздухом. Для такой защиты обычно обеспечивается защита (либо защитным газом, либо флюсом) вокруг зоны сварки. Флюс для экранирования может подаваться либо через электрод (SAMW и FCAW), либо через специальную систему подачи флюса (SAW). Некоторые процессы дуговой сварки подходят для ручной сварки, в то время как многие другие предпочтительны для автоматической или полуавтоматической сварки.
Дуговая сварка металлическим электродом в среде защитного газа (SMAW) — это один из способов сварки плавлением, при котором тепло (тепловая энергия), необходимое для плавления сопрягаемых поверхностей базовых пластин, подается с помощью электрической дуги. Дуга устанавливается между расходуемым электродом и опорными пластинами. Поскольку электрод SMAW является расходуемым, он плавится из-за тепла дуги и впоследствии осаждается на валике сварного шва в качестве присадочного металла. Такой электрод имеет форму короткой палочки, поэтому SMAW неофициально называют 9.0113 Ручная сварка . Материал электрода в основном аналогичен химическому составу базовых пластин (гомогенная сварка). Электроды также покрыты толстым слоем флюса. По мере постепенного плавления электрода флюс распадается, образуя оболочку из инертных газов для защиты зоны сварки. Отдельная подача защитных газов не требуется. Эта сварка в основном выполняется вручную опытными сварщиками, поэтому она также известна как Ручная дуговая сварка металлическим электродом (MMAW) . SAMW обычно обеспечивает глубину проникновения 3–3,5 мм за один проход. Таким образом, подготовка кромок требуется всякий раз, когда толщина компонента превышает 3,5 мм.
SMAW — это универсальный и гибкий процесс сварки, который можно применять в самых разных сферах гражданского строительства. Одним из существенных недостатков процесса SMAW является короткая длина электрода. Каждый расходуемый электрод можно использовать в течение небольшого промежутка времени, поэтому желательна частая замена электрода. Это снижает производительность, а также увеличивает вероятность возникновения дефектов в месте возобновления сварки новым электродом. Низкая скорость осаждения присадочного металла также делает процесс SMAW относительно дорогостоящим для крупномасштабных применений. А вот и Дуговая сварка под флюсом (SAW) , обеспечивающая очень высокую скорость осаждения присадочного металла. SAW также является одним из процессов дуговой сварки, при котором дуга устанавливается между плавящимся электродом и опорными пластинами. SAW использует проволочный электрод, который непрерывно подается с катушки. Благодаря очень большой длине один и тот же электрод можно использовать непрерывно в течение более длительного времени, не прерывая процесс. Это помогает повысить производительность и избежать дефектов несплошности сварного шва.
В отличие от электрода SAMW, электроды SAW не имеют покрытия (без флюсового покрытия). В SAW также не подается защитный газ. Таким образом, сварной шов защищен гранулированным флюсом, который подается отдельно из бункера перед горелкой на ПАВ. Гранулированный флюс обычно подается в больших количествах, и вся зона сварки, включая дугу, остается погруженной в этот флюс. Гранулированный флюс плавится под действием тепла дуги и смешивается с оксидами расплавленного металла, образуя жидкий шлак. Этот шлак плавает над расплавленным металлом и создает барьер, препятствующий контакту воздуха с горячим валиком сварного шва. Процесс SAW особенно предпочтителен для заполнения широких и глубоких зазоров путем нанесения наполнителя. Он обеспечивает более глубокое проникновение, даже до 10 мм. Еще одним важным отличием SAW от SMAW является способ поддержания дуги. Дуга SMAW формируется и поддерживается в газовой среде и остается открытой и не скрытой. Напротив, дуга на ПАВ поддерживается в жидкой среде (расплавленном шлаке) и остается скрытой под толстыми слоями гранулированного флюса и шлака. Различные сходства и различия между SMAW и SAW приведены ниже в виде таблицы.
- Как SMAW, так и SAW представляют собой процессы сварки плавлением, поскольку соприкасающиеся поверхности базовых пластин оплавляются для образования коалесценции во время сварки.
- Оба являются процессами дуговой сварки, поскольку тепло, необходимое для плавления базовых пластин, обеспечивается электрической дугой, застрявшей между базовыми пластинами и электродом.
- В обоих случаях используется расходуемый электрод, поскольку сам электрод плавится и осаждается на сварном шве, образуя присадочный металл. Таким образом, присадочный металл не требуется поставлять отдельно.
- Оба процесса основаны на защите на основе флюса. Однако механизм первичного экранирования у этих двух процессов несколько отличается. В SMAW флюсовое покрытие распадается с образованием дыма, окружающего зону сварки. Таким образом, этот процесс в основном основан на газовой защите. Наоборот, флюс в процессе SAW плавится с образованием жидкого шлака.
Этот шлак плавает над расплавленным металлом сварного шва, чтобы ограничить контакт с атмосферным воздухом.
- Ни в одном из этих двух процессов защитный газ не подается.
- Автогенная сварка (т. е. соединение без применения какого-либо присадочного металла) невозможна ни с одним из этих двух процессов.
SMAW | SAW |
---|---|
SMAW использует электрод с покрытием (покрытый толстым слоем флюса). | SAW использует неизолированный электрод (может быть нанесено тонкое медное покрытие, чтобы избежать коррозии). |
Флюс не требуется поставлять отдельно. Доступен с электродом (в виде покрытия). | Флюс требуется для подачи из внешнего бункера. |
Флюс не гранулированный. Он представляет собой толстое мягкое покрытие на электроде. | Флюс имеет гранулированную форму. |
Дуга остается открытой и видимой сварщику во время сварки.![]() | Дуга остается погруженной под толстые слои флюса и шлака. Дуга остается незаметной для сварщика снаружи. |
Дуга SMAW поддерживается в газовой среде. | Дуга SAW поддерживается в жидкой среде (расплавленный шлак). |
Электрод SMAW стержневого типа, короткой длины. | SAW использует очень длинный непрерывный проволочный электрод. |
Благодаря малой длине каждый электрод можно использовать для небольшой продолжительности сварки. Поэтому требуется частая замена электрода. | Благодаря непрерывному электроду сварку под флюсом можно выполнять непрерывно в течение более длительного периода времени без замены электрода. |
Скорость осаждения присадочного металла относительно низкая. | Обеспечивает очень высокую скорость осаждения присадочного металла. |
SMAW обычно выполняется вручную (поэтому ее также называют ручной дуговой сваркой металлическим электродом, MMAW).![]() | SAW — это полуавтоматический (иногда полностью автоматический) процесс, поскольку движение резака механизировано. |
Длину дуги необходимо регулировать вручную. | Длина дуги регулируется автоматически. |
Процесс менее производительный и менее экономичный из-за (i) частых перерывов для смены электрода, (ii) низкого провара и (iii) ручной сварки. | Это продуктивный и экономичный процесс. |
В нем меньше оборудования и аксессуаров. Таким образом, установка легко переносима. | Установка неудобна для переноски из-за тяжелого и громоздкого оборудования. |
Над металлом сварного шва образуется очень тонкий слой шлака. | Над металлом шва образуется относительно толстый слой шлака. |
После завершения сварки не остается неиспользованного флюса. | Большая часть (50 – 90%) подаваемого флюса остается неиспользованной. Такой неиспользованный флюс можно восстановить и использовать повторно после завершения сварки.![]() |
Интенсивность дуги и плотность тепла сравнительно низкие. Соответственно, он обеспечивает ограниченное проникновение (обычно ограничивается 3,5 мм). | Интенсивность дуги и плотность тепла намного выше. Он может обеспечить более глубокое проникновение, обычно до 12 мм. |
Подготовка кромок обязательна, если толщина детали превышает 3,0 мм. | При толщине детали до 10 мм подготовка кромок не требуется. |
Сварочные брызги характерны для процесса SMAW. Разбрызгивание приводит к потере дорогостоящего присадочного металла. | SAW не образует брызг. |
Неиспользованный конец (40 – 50 мм) каждого электрода выбрасывается. Таким образом, происходит чрезмерный расход дорогостоящего электродного металла. | Благодаря сплошному электроду здесь таких потерь не бывает. |
Может применяться для самых разных мест сварки и конфигураций. | Подходит только для горизонтального положения вниз.![]() |
Во избежание травм и других опасностей для здоровья требуются строгие меры личной защиты. | Требования к защите относительно менее строгие, поскольку дуга остается скрытой. |
- Учебник по технологии сварки О. П. Кханна (Dhanpat Rai Publications).
- Технология производства: литейное производство, формовка и сварка П. Н. Рао (Tata McGraw Hill Education Private Limited).
- Комплексная технология семинара (производственные процессы) С. К. Гарг (Laxmi Publications Private Limited).
Tagged Дуга, Нагрев, Соединение, Плавление, Экранирование, SMAW, Сварка
Дуговая сварка — Технология сварки
Дуговая сварка металлическим электродом в среде защитного газа :- Дуговая сварка металлическим электродом в среде защитного газа (SMAW), также известная как ручная дуговая сварка металлическим электродом (MMA), дуговая сварка в среде защитного флюса или, неофициально, сварка стержнем, представляет собой процесс ручной дуговой сварки, который использует расходуемый электрод, покрытый флюсом, для прокладки сварного шва.
Электрический ток в виде переменного или постоянного тока от сварочного источника питания используется для образования электрической дуги между электродом и соединяемыми металлами. По мере наложения шва флюсовое покрытие электрода распадается, выделяя пары, которые служат защитным газом, и образуя слой шлака, которые защищают зону сварки от атмосферного загрязнения.
Из-за универсальности процесса и простоты его оборудования и эксплуатации дуговая сварка защищенным металлом является одним из самых популярных сварочных процессов в мире. Он доминирует над другими сварочными процессами в сфере технического обслуживания и ремонта, и, хотя популярность дуговой сварки с флюсовой проволокой растет, SMAW продолжает широко использоваться в строительстве стальных конструкций и в промышленном производстве
История процесса SMAW .
Процесс используется в основном для сварки железа
и стали (включая нержавеющую сталь), но сплавы алюминия, никеля и меди
также можно сваривать этим методом. .
После Открытие электрической дуги в 1800 году Гемфри Дэви не имело большого значения. развития электросварки до тех пор, пока Огюст де Меритенс не разработал углеродный дуговая горелка, запатентованная в 1881 году. Николай Бенардос разработал угольную дуговую сварку, получив патенты 1887 года, показывающие рудиментарный держатель электрода. В 1888 году расходный материал металлический электрод изобрел Николай Славянов. Позже, в 1890 г., К.Л. Коффин получил патент США 428 459 на свой метод дуговой сварки, в котором использовался металл. электрод. Этот процесс, как и SMAW, заключается в осаждении расплавленного электродного металла в сварка в качестве наполнителя.
Около 1900 г. А.П.
Строменгер и Оскар Кьельберг выпустили первые покрытые электроды.
Строменгер использовал покрытие из глины и извести для стабилизации дуги, а Кьельберг
окунули железную проволоку в смеси карбонатов и силикатов, чтобы покрыть
Электрод. В 1912 году Строменгер выпустил электрод с толстым покрытием, но с высокой стоимостью. и сложные методы производства не позволили этим ранним электродам получить
популярность. В 1927 году разработка процесса экструзии снизила стоимость
электроды для покрытия, позволяя производителям производить более сложное покрытие
смеси, предназначенные для конкретных целей. В 19производители 50-х
в флюсовое покрытие ввели железный порошок, что позволило увеличить
скорость сварки.
В 1938 г. К. К. Мэдсен описал автоматизированный вариант SMAW, теперь известный как гравитационный. сварка. Он ненадолго приобрел популярность в 1960-х годах после того, как получил огласку. для его использования на японских верфях, хотя сегодня его применение ограничено. Другой малоиспользуемый вариант процесса, известный как сварка фейерверков, был разработан примерно в то же время Джорджем Хафергутом в Австрии.
Процесс SMAW :-
Чтобы зажечь электрическую дугу, электрод приводится в контакт с заготовкой путем очень легкого прикосновения электродом к основному металлу, а затем слегка отводится назад. Это инициирует дугу и, таким образом, плавление заготовки и расходуемого электрода, а также вызывает попадание капель электрода с электрода в сварочную ванну.
По мере плавления электрода флюсовое покрытие распадается, выделяя защитные газы, защищающие зону сварки от кислорода и других атмосферных газов. Кроме того, флюс образует расплавленный шлак, который покрывает присадочный металл по мере его продвижения от электрода к сварочной ванне. Попав в сварочную ванну, шлак всплывает на поверхность и защищает сварной шов от загрязнения по мере затвердевания. После затвердевания его необходимо сколоть, чтобы обнажить готовый шов.
Фактический используемый метод сварки зависит от электрода, состава заготовки и положения свариваемого соединения. Выбор электрода и положения при сварке также определяют скорость сварки. Плоские сварные швы требуют наименьших навыков оператора и могут выполняться с помощью электродов, которые быстро плавятся, но медленно затвердевают.
Преимущества процесса SMAW:
- Простое, портативное и недорогое оборудование
- С помощью этого процесса можно сваривать широкий спектр металлов и сплавов.
- Подходит для наружного применения
- Сварку можно выполнять в любом положении с хорошим качеством сварки.
- Этот процесс можно использовать для твердосплавной наплавки.
- Вспомогательная газовая защита не требуется.
- Процесс SMAW находит бесчисленное множество применений благодаря наличию большого разнообразия электродов.
Недостатки процесса SMAW:
- Если нам приходится сваривать длинные соединения, то потери времени увеличиваются.
- Процесс прерывистый из-за ограниченной длины электродов.
- Частые остановки/начала смены электрода.
- Относительно высокие потери металла (заглушки электродов).
- Пределы тока ниже, чем для непрерывных или автоматических процессов (снижает скорость осаждения).
- Сварной шов может содержать шлаковые включения.
- Пары затрудняют управление технологическим процессом.
- Не такая производительная, как непрерывная проволока.
- Концы электродов (концы) впустую.
- Высокий
уровень квалификации, необходимый для получения качественных сварных швов.
- Дуговой разряд может возникнуть при постоянном токе. (Дуга идет везде, КРОМЕ того, где вы хотите.)
Полевая сварка электродами с известковым и целлюлозным покрытием (Журнальная статья)
Полевая сварка электродами с известковым и целлюлозным покрытием (Журнальная статья) | ОСТИ.GOVперейти к основному содержанию
- Полная запись
- Другое связанное исследование
Современные трубопроводы изготавливаются преимущественно из высокопрочной термомеханически обработанной стали марок API 5LX-65 и во все большей степени API 5LX-70. Использование этих сталей с повышенным уровнем прочности отрицательно сказалось на свариваемости при ручной дуговой сварке. Были разработаны низкоуглеродистые стали с пониженным содержанием феррита или вообще без феррита, которые обязаны своей повышенной прочностью добавкам различных легирующих элементов, главным образом ниобия и ванадия, выделяющихся при термомеханической обработке. Марка стали, наиболее представительная в этой группе и обладающая наибольшей прочностью, — 5LX-70 с минимальным пределом прочности при растяжении 480 Н/мм2. Показаны различия в химическом составе и, соответственно, склонности к твердению между трубой 5LX-70 с пониженным содержанием перлита и нормализованной трубой 5LX-60. Применение электродов с целлюлозным и известковым покрытием в строительстве трубопроводов характеризуется рядом особенностей технологии сварки и материала. С металлургической точки зрения два типа электродов демонстрируют различное поведение при плавлении, которое влияет на вес металла, наплавляемого в единицу времени.
- Авторов:
- Кенигсхофер, Х; Пертенедер, Э.
- Дата публикации:
- Идентификатор ОСТИ:
- 5765434
- Тип ресурса:
- Журнальная статья
- Название журнала:
- Трубопровод Инд.; (США)
- Дополнительная информация журнала:
- Объем журнала: 58:5
- Страна публикации:
- США
- Язык:
- Английский
- Тема:
- 02 НЕФТЬ; 03 ПРИРОДНЫЙ ГАЗ; 36 МАТЕРИАЛОВЕДЕНИЕ; УГЛЕРОДИСТЫЕ СТАЛИ; ДУГОВАЯ СВАРКА; ТРУБОПРОВОДЫ; ЦЕЛЛЮЛОЗА; НИОБИЙ; ПЕРЛИТ; СВАРНЫЕ СОЕДИНЕНИЯ; СВАРОЧНЫЕ ЭЛЕКТРОДЫ; СПЛАВЫ; УГЛЕВОДЫ; ЭЛЕМЕНТЫ; ИЗГОТОВЛЕНИЕ; ЖЕЛЕЗНЫЕ СПЛАВЫ; ЖЕЛЕЗНЫЕ СПЛАВЫ; ПРИСОЕДИНЕНИЕ; СУСТАВЫ; МЕТАЛЛЫ; ОРГАНИЧЕСКИЕ СОЕДИНЕНИЯ; ПОЛИСАХАРИДЫ; САХАРИДЫ; СТАЛИ; ПЕРЕХОДНЫЕ ЭЛЕМЕНТЫ; СВАРКА; 022000* — Нефть – транспортировка, обработка и хранение; 032000 — Природный газ — транспортировка, обработка и хранение; 360101 — Металлы и сплавы — Подготовка и изготовление
Форматы цитирования
- MLA
- АПА
- Чикаго
- БибТекс
Konigshofer, H, and Perteneder, E.
Сварка в полевых условиях электродами с известковым и целлюлозным покрытием . США: Н. П., 1983.
Веб.
Копировать в буфер обмена
Konigshofer, H, & Perteneder, E. Сварка в полевых условиях электродами с известковым и целлюлозным покрытием . Соединенные Штаты.
Копировать в буфер обмена
Кенигсхофер, Х., и Пертенедер, Э. 1983.
«Полевая сварка электродами с известковым и целлюлозным покрытием». Соединенные Штаты.
Копировать в буфер обмена
@статья{osti_5765434,
title = {Полевая сварка электродами с известково-целлюлозным покрытием},
автор = {Konigshofer, H и Perteneder, E},
abstractNote = {Современные трубопроводы изготавливаются преимущественно из высокопрочной, термомеханически обработанной стали марок API 5LX-65 и, во все большей степени, API 5LX-70. Использование этих сталей с повышенным уровнем прочности отрицательно сказалось на свариваемости при ручной дуговой сварке. Были разработаны низкоуглеродистые стали с пониженным содержанием феррита или вообще без феррита, которые обязаны своей повышенной прочностью добавкам различных легирующих элементов, главным образом ниобия и ванадия, выделяющихся при термомеханической обработке. Марка стали, наиболее представительная в этой группе и обладающая наибольшей прочностью, — 5LX-70 с минимальным пределом прочности при растяжении 480 Н/мм2. Показаны различия в химическом составе и, соответственно, склонности к твердению между трубой 5LX-70 с пониженным содержанием перлита и нормализованной трубой 5LX-60. Применение электродов с целлюлозным и известковым покрытием в строительстве трубопроводов характеризуется рядом особенностей технологии сварки и материала. С металлургической точки зрения два типа электродов демонстрируют различное поведение при плавлении, что влияет на массу металла, наплавляемого в единицу времени.
},
дои = {},
URL-адрес = {https://www.osti.gov/biblio/5765434},
журнал = {индикатор трубопровода; (США)},
номер = ,
громкость = 58:5,
место = {США},
год = {1983},
месяц = {5}
}
Копировать в буфер обмена
Найдите в Google Scholar
Найдите в WorldCat библиотеки, в которых может храниться этот журнал
Экспорт метаданных
Сохранить в моей библиотеке
Вы должны войти в систему или создать учетную запись, чтобы сохранять документы в своей библиотеке.
Аналогичных записей в сборниках OSTI.GOV:
- Аналогичные записи
Разница между процессами сварки MMAW и GMAW
Сварка, наряду с креплением, широко используется в различных промышленных и бытовых сборочных целях. Сварка — это один из видов процесса соединения, при котором два или более твердых компонента могут быть соединены на постоянной основе путем образования коалесценции с применением или без применения присадочного металла, тепла и давления. С развитием технологии сварки в настоящее время она в основном вытеснила другие методы постоянного соединения, включая клепку. Сварку можно применять для эффективного и экономичного соединения металлов, пластмасс, керамики и композитов. При правильном выполнении с оптимальным набором параметров можно получить прочные и надежные соединения с прочностью, аналогичной прочности исходных компонентов. Существует большое количество сварочных процессов, которые в целом можно разделить на сварку плавлением и сварку в твердом состоянии.
Процессы сварки плавлением — это процессы, при которых соприкасающиеся поверхности основного металла сплавляются путем нагревания с образованием коалесценции для осуществления соединения; в то время как в процессах сварки в твердом состоянии такого плавления не происходит. Все процессы дуговой сварки, газовой сварки, контактной сварки и сварки с интенсивным потреблением энергии в основном являются процессами плавления. В дуговой сварке электрическая дуга образуется между исходными компонентами и электродом за счет обеспечения достаточной разности потенциалов между ними. Эта дуга является основным источником тепла (тепловой энергии) для расплавления базовых пластин и наполнителя. Опять же, существуют различные процессы дуговой сварки; например, MMAW или SMAW, GMAW (MIG и MAG), GTAW или TIG, SAW, FCAW, ESW и т. д. Каждый из них имеет определенные преимущества по сравнению с другими.
Ручная дуговая сварка металлическим электродом (MMAW) , также называемая дуговая сварка металлическим электродом в среде защитного газа (SMAW) , представляет собой процесс сварки плавлением, при котором электрическая дуга возникает между электродом и опорными пластинами. Эта сварка в основном выполняется вручную, отсюда и название. Расходуемый электрод покрывается подходящим флюсом, который распадается во время сварки с образованием защитного газа и слоя шлака, которые помогают защитить дугу и ванну расплавленного металла от окисления или загрязнения. Таким образом, не требуется отдельного применения защитного газа. Дуговая сварка металлическим газом (GMAW) также является одним из процессов сварки плавлением, при котором дуга образуется между плавящимся электродом и исходными компонентами. Электрод в виде проволоки непрерывно подается в зону сварки с катушки с проволокой с помощью механизированной системы, и в то же время из внешнего источника подается соответствующий защитный газ для защиты дуги и окружающих областей. GMAW — это очень быстрый процесс с высокой скоростью осаждения наполнителя. Различные различия между ручной дуговой сваркой металлическим электродом (MMAW) и дуговой сваркой металлическим электродом в среде защитного газа (GMAW) приведены ниже в виде таблицы.
Ручная дуговая сварка металлом | Газовая дуговая сварка |
---|---|
MMAW использует расходуемый электрод в виде короткого стержня малого диаметра.![]() | В GMAWиспользуется расходуемый электрод, который непрерывно подается с катушки с проволокой. Таким образом, не требуется прерывистой паузы для замены электрода. |
В MMAW используется электрод с флюсовым покрытием, в котором покрытие разрушается с образованием защитного газа. В целях защиты дополнительный газ не применяется. | При GMAW в зону сварки подается инертный или активный защитный газ. Электрод не содержит флюса для получения газа. |
Флюс (покрытие электрода) образует шлак на сварном шве. Этот шлак может привести к дефектам или ухудшить внешний вид. Постобработка необходима для удаления шлака. | С этим процессом не связан поток. Поэтому отложений шлака не наблюдается. Таким образом, это устраняет необходимость постобработки. |
Процесс MMAW отличается высокой гибкостью и может применяться в большинстве мест, во всех положениях и для большинства материалов.![]() | GMAW использует больше аксессуаров и поэтому не подходит для наружного применения. Его также нельзя выполнять в положении над головой. |
Обычно выполняется человеком-оператором. Так что качество соединения зависит от мастерства сварщика. | Его можно автоматизировать, требуя минимального вмешательства оператора. Таким образом, у него меньше склонности к человеческим ошибкам. |
Прерывистый и непрерывный процесс: Пруток малого диаметра (0,5–2,0 мм) длиной 30–50 см, покрытый подходящим флюсом, используется в качестве электрода при ручной дуговой сварке металлическим электродом. Поскольку этот электрод является плавящимся, его длина сокращается со временем сварки из-за его отложения на валике сварного шва. Таким образом, по истечении определенного промежутка времени (когда закончилась часть, покрытая флюсом) для проведения сварки требуется замена электрода на новый. Таким образом, MMAW требует частых остановок и является одним прерывистым процессом. Напротив, плавящийся электрод (в виде проволоки) непрерывно подается из проволочной ванны при дуговой сварке металлическим электродом в среде защитного газа. Этот пул проволоки может хранить достаточную длину проволоки (обычно она измеряется по ее весу). Таким образом, GMAW можно проводить в течение более длительного времени без перерыва на замену электрода.
Источники защитного газа: Защитный газ незаменим в процессах дуговой сварки для защиты дуги и ванны расплавленного металла от окисления или других загрязнений. Во время дуговой сварки толстый слой защитного газа окружает всю зону сварки и ограничивает контакт атмосферного воздуха с валиком сварного шва и окружающими горячими зонами. В процессе MMAW электрод покрывается флюсом, который распадается под действием тепла сварки и производит достаточно защитного газа, чтобы покрыть нагретые участки. Поэтому не требуется дополнительной подачи защитного газа. Но в GMAW на электроде нет такого флюсового покрытия. Таким образом, защитный газ подается из дополнительных источников (например, газового баллона) с использованием соответствующего нагнетательного трубопровода и форсунки.
Отложение шлака и его удаление: MMAW использует электрод с флюсовым покрытием, и этот флюс фактически выделяет защитный газ во время сварки. Флюс также образует шлак, который откладывается на верхней поверхности сварного шва и защищает его от загрязнения. Но этот шлаковый слой требуется удалить после окончания сварки, чтобы улучшить внешний вид. Обычно для такого удаления применяется шлифовка. Однако, если шлак остается внутри наплавленного валика и не всплывает на поверхность, тогда наблюдаются такие дефекты, как шлаковые включения. Такие дефекты могут снизить несущую способность, прочность соединения и сделать его уязвимым к коррозии — все это в конечном итоге снижает срок службы. GMAW не содержит шлака, так как не используется электрод с флюсовым покрытием. Таким образом устраняются дефекты, связанные со шлаком, а также необходимость последующей обработки для удаления шлака.
Производительность: MMAW не отличается высокой производительностью. При многопроходной сварке шлак, отложившийся на валике сварного шва, необходимо полностью удалять после каждого прохода, чтобы избежать образования дефектов шлакового включения. Кроме того, электрод требуется часто менять. Поэтому он не подходит, если требуется отложение большого количества расплавленного металла на валике сварного шва. Таким образом, он не является производительным для многопроходной сварки. GMAW не содержит шлака и не требует замены электрода. Таким образом, он может вносить большой объем наполнителя за короткий период времени. Таким образом, это идеальный выбор, когда корневой зазор больше, кромка имеет U- или V-образную форму и/или толщина листа больше. Кроме того, диаметр электрода GMAW меньше, чем у электрода MMAW, что увеличивает плотность тока дуги и, следовательно, скорость осаждения наполнителя.
Гибкость сварки: Гибкость указывает на способность процесса сварки использовать различные формы для соединения различными способами в различных условиях. Косвенно это относится к возможности и осуществимости применения конкретного процесса в определенных условиях. Для GMAW требуются баллоны с защитным газом, трубопроводы и аксессуары для его контролируемой подачи. Таким образом, он не подходит для наружного применения в небольших масштабах. MMAW можно применять практически в любом месте во всех положениях в пределах досягаемости электрода; однако его производительность может быть не на одном уровне во всех сценариях. Несмотря на то, что MMAW непроизводителен, он очень гибок и имеет множество применений.
Качество сварки и зависимость от сварщика: Как следует из названия, ручная дуговая сварка металлом в основном выполняется людьми. Таким образом, качество сварки зависит от навыков и опыта сварщика. Он также подвержен человеческим ошибкам, включая случайные и случайные ошибки. В отличие от этого, GMAW может быть автоматизирован и требует минимального вмешательства сварщика. Таким образом, он может обеспечить более качественные соединения, если используются соответствующие параметры.