Таблица цветов побежалости — углеродистая сталь. ~ БЛОГ О ЗАТОЧКЕ
Иногда при заточке инструментов образуются прижоги металла — в основном на режущей кромки, где толщина металла меньше. Это говорит о неосторожности заточника и перегреве обрабатываемого участка инструмента. Такой же прижог образуется и при местном или полном нагреве металлического инструмента, заявляя о себе цветами побежалости.
По сути, цвета побежалости образуются оксидной пленкой определенной толщины и интерференции света в ней. Толщина оксидного слоя, а следовательно и его цвет при отражении света, тесно связана с температурой, когда при ее определенных значениях оксид железа образует слой, вызывающий интерференцию тонких пленок.
При увеличении температуры слой оксида железа увеличивается в толщине, меняя свой цвет от светло-соломенного до коричневого, синего и т.д. Тем самым давая очень точную информацию для измерения температуры. Поэтому образующиеся при его нагреве металла цвета побежалости, с давних пор используют для определения температуры нагрева при термообработке стали, например для ее отпуска.
Ниже приведена таблица, которая показывает температуры нагрева углеродистой стали, соответствующие различным цветам побежалости.
Таблица цветов побежалости для углеродистой стали:* | |
Ярко-жёлтый | 1100° С |
Тёмно-жёлтый | 1040° С |
Оранжево-жёлтый | 980° С |
Оранжевый | 930° С |
Красно-оранжевый | 870° С |
Ярко-красный | 820° С |
Красный | 760° С |
Тускло-красный | 650° С |
Красноватый с серым оттенком | 590° С |
Серый с красным оттенком | 540° С |
Темно-серый | 430° С |
Серо-синий | 320° С |
Светло-синий | 310° С |
Синий | 300° С |
Тёмно-фиолетовый | 280° С |
Фиолетовый | 270° С |
Коричнево-фиолетовый | 260° С |
Коричневый | 250° С |
Светло-коричневый | 240° С |
Золотисто-жёлтый | 230° С |
Светло-желтый | 220° С |
Соломенный | 210° С |
Светло-соломенный | 200° С |
* В зависимости от состава и теплопроводности стали, значения температур для отдельных цветов побежалости могут незначительно отличаться от приведенных в таблице.
Также следует помнить, что:
2. Для более стойких к окислению на воздухе легированных и нержавеющих сталей цвета побежалости начинают быть заметны при более высоких температурах.
3. Толщина оксидной пленки увеличивается с увеличением времени нагрева — это следует учитывать, если инструмент или деталь подвергаются постоянному или периодическому нагреванию. Поэтому сталь, которая длительное (при постоянном или периодическом нагревании) выдерживалась при температуре 200° С может стать коричневой или фиолетовой. Хотя при этом температура ее нагрева ни когда не превышала необходимую для получения светло-соломенного цвета побежалости.
4. Увеличение толщины оксидной пленки может привести к нарушению работы шарнирных инструментов.
На этом пока всё.
Источники: wikipedia.org, threeplanes.
P.S. Не забудьте подписаться на мой канал в YouTube…
Создана 27.09.10, посл.обновление — 25.02.20
Определение температуры нагрева стали | info.selink.ru
Температуру нагрева стали можно приблизительно определить по цвету каления стали и по цветам побежалости.
Цвета каления стали.
Темпретура градусав цельсия — цвет каления.
550-580 — Темно-коричневый
580-650 — Коричнево-красный
650-730 — Темно-красный
730-770 — Темно-вишнево-красный
770-800 — Вишнево-красный
800-830 — Светло-вишневокрасный
830 — 900 — Светло-красный
900 — 1050 — Оранжевый
1050 — 1150 — Темно-желтый
1150 — 1250 — Светло-желтый
1250 — 1300 — Ярко-желтый
Цвета побежалости углеродистой стали
Температура, С — Цвет побежалости
220 — Светло-желтый
240 — Темно-желтый
255 — Коричнево-желтый
265 — Коричнево-красный
275 — Пурпурно-красный
Цвета побежалости коррозионно-стойких сталей и жаропрочных сплавов.
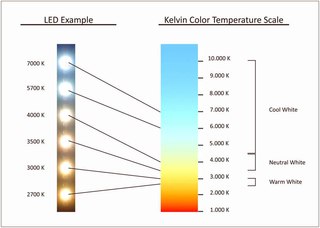
Температура С | Цвет побежалости | ||
12Х18Н9Т | ХН75МБТЮ | ХН77ТЮР | |
300 | Светло-соломенный |
|
|
400 | Соломенный | Светло-желтый |
|
500 | Красновато-коричневый | Желтый | Светло-соломенный |
600 | Фиолетово-синий | Коричневый | Фиолетовый |
700 | Синий | Синий | Синий |
800 |
| Голубой | Голубой |
Изменение свойств металла при нагреве и ковке
Справочная информация
1. Режимы нагрева металлов
Чтобы правильно вести процесс ковки, необходимо знать температуру начала и конца ковки каждого металла, каждой марки стали, т. е. знать режимы нагрева.
Режим нагрева металла — это порядок и способ нагрева металла, который обеспечивает температуру и скорость, необходимые для получения заготовок, пригодных для ковки и получения из них качественных поковок.
Температура ковки для различных марок сталей не одинакова и зависит от их химического состава. Чем больше углерода встали, тем ниже температура плавления и ковки.
Температура нагрева металла для ковки имеет очень важное значение, так как может влиять на качество деталей получаемых ковкой, поэтому за ней требуется постоянный контроль. Для этого в кузницах с нагревательными печами используют термопары и различные виды пирометров. При нагреве металла в горнах, как правило, можно приближенно определять температуру нагрева металлов на глаз по следующим цветам каления, при дневном освещении в тени:
Цвет нагретого металла | Температура…………. . °С
Темно-коричневый (заметен в темноте)…..530 … 580
Коричнево-красный…………………………….580 … 650
Темно-красный………………………………….650… 730
Темно-вишнево-красный………………………730 … 770
Вишневый………………………………………..720 … 830
Светло-вишневый………………………………780… 830
Красный…………………………………………..830… 900
Светло-красный…………………………………900 … 1050
Желтый………………………………………….1050 … 1150
Светло-желтый…………………………………1150… 1250
Белый…………………………………………….1250 … 1300
При охлаждении металла цвет каления изменяется в обратной последовательности.
Температура нагрева сталей в начале ковки должна быть ниже их температуры плавления на 150…200°С. При более высокой температуре может наступить явление пережога. Во время ковки металл остывает и ковать его становится затруднительно, а затем и невозможно. Поэтому ковку металла следует заканчивать с температурой на 20 … 30 °С выше допускаемой температуры ковки.
Время нагрева сталей зависит от размеров заготовок и Химического состава. С одной стороны, для уменьшения образования Окалины и увеличения производительности желательно уменьшать время нагрева. С другой, — заготовки больших размеров, а также из высокоуглеродистых и высоколегированных сталей следует нагревать постепенно и даже ступенчато.
2. Дефекты при нагреве и меры их предупреждения
При нагреве заготовок в них могут появиться следующие дефекты:
— окалинообразование или угар,
— обезуглероживание,
— недогрев металла,
— перегревмстальной заготовки,
— пережог металла.
Окалинообразование или угар получается в результате образования оксидов железа на поверхности заготовки яри ее нагреве. Образование окалины обычно называют угаром металла.
Окалина — это хрупкое и непрочное вещество с содержанием до 30% железа. Угар стали, в результате образования окалины, может достигать 4 … 5% от массы заготовки за один нагрев в горнах и несколько меньше (до 3%) в нагревательных печах.
Количество образующейся окалины зависит от скорости и температуры нагрева метелла, формы заготовки, химического состава стали, вида топлива, пламени и других факторов.
Обезуглероживание происходит одновременно с окислением железа и выражается в том, что при нагреве стали углерод, содержащийся в ее верхних слоях, выгорает и сталь становится более мягкой. Значит химический состав стали изменится и не будет соответствовать той марке, из которой должна быть изготовлена деталь. При уменьшении содержания углерода уменьшается прочность и твердость стали, ухудшается способность ее закаливаться. Глубина обезуглероженного слоя может достигать 2 … 4 мм, поэтому обезуглероживание опасно и для мелких поковок, имеющих небольшие припуски и для поковок, которые после механической обработки подвергаются закалке.
Процесс обезуглероживания начинается при температуре 800 … 850 °С. Интенсивность обезуглероживания зависит от содержания углерода в стали.
Чем больше углерода, тем медленнее идет обезуглероживание.
Недогрев — это такой нагрев металла, при котором заготовка нагрелась неравномерно по сечению или участкам длины. Очевидно, что такую заготовку нельзя вынимать из горна или печи и ковать. Если заготовка с одной стороны имеет белый цвет каления, а с другой еще желтый или красный, то из нее будет затруднительно получить поковку требуемой формы. Недогрев заготовок по толщине нельзя обнаружить по цвету каления. Поэтому необходимо знать расчетную или опытную нормативную величину продолжительности нагрева различных по сечению заготовок и строго ее придерживаться. Недогрев может появляться при плохом тепловом режиме.
Перегрев нельзя обнаружить по внешнему виду нагретой заготовки и даже в процессе ее ковки. Деталь, изготовленная из перегретого металла, быстро ломается, так как перегретый металл имеет крупнозернистую структуру и поэтому не прочен. Сильно перегретая заготовка иногда разрушается уже при ковке — в углах появляются трещины. Для предотвращения перегрева не следует допускать выдержки заготовки в горне или печи при высокой температуре больше, чем рекомендуется расчетами или нормативами.
Пережог является опасным дефектом нагрева металла. Явление пережога объясняется следующим образом. При температуре выше 1250 … 1300 °С зерна металла становятся очень крупными, а связь между ними настолько ослабевает, что начинает проникать кислород и сталь при действии на нее небольших сил разрушается. Пережженную сталь необходимо отправлять на переплавку.
Пережог можно обнаружить по внешнему виду нагреваемого металла. Поверхность металла при пережоге имеет ослепительно белый искрящийся цвет. При передвижении пережженной заготовки от нее отлетают ярко-белые искры.
Трещины и раскалывание поковок являются дефектами нагрева металла. Наиболее часто поковки с такими дефектами получают из легированных и инструментальных сталей вследствие несоблюдения режимов нагрева их и продолжения ковки с температурой ниже температуры окончания ковки.
3. Изменения, происходящие в металлах при нагреве и ковке
Пластичность стали увеличивается при нагреве, т. е. когда в ней начинаются внутренние превращения, состоящие в укрупнении зерен и ослаблении связей между ними. Поэтому прочность стали уменьшается, она становится мягкой и пластичной. Это позволяет с меньшими усилиями деформировать металлы.
Зернистое строение металла изменяется в зависимости от температуры и скорости деформирования его. Соответственно этим воздействием на металл изменяется и прочность его.
Износостойкость стальной заготовки. Чем быстрее будет проходить процесс деформации металла от начала ковки до конца ковки, тем металл будет прочнее, следовательно, ковку горячего металла рекомендуется проводить как можно быстрее и сильными ударами, потому что при ковке сильно нагретого металла слабыми ударами в конце ковки он получается – с крупнозернистым строением и поковка будет не прочной. Если требуется небольшая деформация металла, то перед ковкой его можно нагревать несколько ниже температуры начала ковки, имея в виду, что ковка будет закончена до наступления критической температуры (723 °С).
При продолжении ковки ниже критической температуры зерна пластически деформируются (вытягиваются) и остаются в напряженном состоянии, потому что при низкой температуре они уже не успевают переформироваться в более мелкие зерна. После этого металл утрачивает пластичность и становится более прочным, твердым и хрупким.
Упрочнение металла под действием пластической деформации называется Наклепом или Нагартовкой. Наклеп не желателен, так как при этом, кроме хрупкости, резко уменьшается свойство металла обрабатываться резанием.
Термическая и химико-термическая обработка стали
Термическая и химико-термическая обработка стали
Термическая обработка. Чтобы улучшить физические и механические свойства стали, ее подвергают термической обработке. Она заключается в нагреве металла до определенной температуры, выдержке при этой температуре и последующем охлаждении по заданному режиму.
Уже в давние времена люди подметили, что скорость охлаждения нагретой стали влияет на ее механические свойства, и применяли закалку стали при изготовлении оружия. С течением времени термическая обработка совершенствовалась, но сущность происходящих при этом процессов оставалась невыясненной. В 1868 г. выдающийся русский металлург Д. К. Чернов высказал мысль о том, что расположение атомов в кристаллической решетке железа при высоких и низких температурах неодинаково и, следовательно, можно изменять структуру и свойства стали с помощью тепловых воздействий. Д. К. Чернов открыл критические точки (точки Чернова), т. е. такие температуры, при которых происходят важные структурные изменения в стали. Это открытие послужило научной основой современных методов термической обработки стали.
Причины изменения свойств стали при термической обработке связаны в основном со способностью железа изменять строение кристаллической решетки при различной температуре, а также с неодинаковой растворимостью углерода в кристаллических решетках разного типа. Переход кристаллической решетки железа от одного типа к другому зависит от режима нагрева, изотермической выдержки и охлаждения стали. Так же неодинаково протекает и формирование основных структурных составляющих стали — феррита и цементита. Термическая обработка позволяет изменять их размеры и форму по сравнению с теми, какими они были в равновесном состоянии. Таким образом, свойства термически обработанных сталей зависят от степени искажения кристаллической решетки железа, а также от размеров, формы зерен и содержания структурных составляющих.
Термическую обработку применяют как промежуточную операцию для улучшения технологических свойств стали, например обрабатываемости давлением, резанием, а также как окончательную — для придания ей необходимых физических и механических свойств. В частности, такой обработке подвергают горячекатаную арматурную сталь периодического профиля для повышения ее прочности, анкерные устройства, рабочие поверхности инструментов и некоторых деталей машин, применяемых при арматурных и бетонных работах.
К основным видам термической обработки относятся отжиг, нормализация, закалка и отпуск.
Отжиг заключается в нагреве стали, выдержке ее при температуре нагрева и последующем медленном охлаждении. В процессе выполнения многих технологических операций (прокатки, волочения) в стали образуется неустойчивая структура. Цель отжига — получить сталь, структура которой близка к равновесному состоянию. В результате сталь становится более податливой к механической обработке, повышается ее пластичность, уменьшаются остаточные напряжения в изделиях. Из многих разновидностей этого процесса чаще применяют полный, неполный, изотермический и рекристаллизационный отжиг.
Полный отжиг состоит в нагреве стального изделия до температуры, на 20…50 °С превышающей критическую, выдержке его при этой температуре и медленном охлаждении. Критическая температура зависит от содержания в стали углерода и может находиться в пределах 727…910 °С. Для малоуглеродистых сталей критическая температура тем ниже, чем выше содержание углерода. Изделия охлаждают до 500 °С медленно (со скоростью 50…100 °С/ч), а затем— на Еоздухе до комнатной температуры’.
Неполный отжиг заключается в нагреве стали до температуры не более 768 °С и последующем медленном охлаждении. В этом случае благодаря частичной перекристаллизации структурных составляющих стали снижаются внутренние напряжения, уменьшается твердость, возрастают пластичность и вязкость, улучшается обрабатываемость резанием.
Изотермический отжиг состоит в нагреве стали до температуры 800…900 °С, выдержке при такой температуре, быстром охлаждении до температуры 600…700 °С, новой выдержке и охлаждении до‘ком-натной температуры. Изотермический отжиг требует горазДо меньше времени, чём полный.
Рекристаллизационный отжиг применяют после холодной пластической деформации изделий. Для этого нагревают низкоуглеродистую сталь до температуры 600…700 °С. В результате механические свойства изделий становятся более однородными в разных направлениях, так как отжиг устраняет деформацию зерен металла. Пластичность стали повышается, твердость и прочность уменьшаются.
Нормализация состоит в нагреве стали примерно до температуры 750…950 °С, непродолжительной выдержке и последующем охлаждении на воздухе. Скорость охлаждения стали при нормализации несколько больше, чем при отжиге. Нормализованные стали характеризуются мелкозернистой однородной структурой, их твердость и прочность несколько выше, чем при отжиге. Для некоторых сталей нормализация является окончательной термической обработкой, так как при; водит к хорошему сочетанию прочности и пластичности. В6 многих случаях эта операция предшествует закалке стали.
Закалка — процесс нагрева, а затем быстрого охлаждения стали. Используемые в строительстве конструкционные стали закаливают при температуре, на 30…50 °С превышающей температуру фазовых превращений, т. е. 727…910 °С. Так же, как и при отжиге, температура нагрева зависит от содержания в стали углерода: чем больше углерода, тем ниже температура. Во время закалки вследствие очень высокой скорости охлаждения сталь переходит в неравновесное структурное состояние, не свойственное ей при нормальной температуре. В закаленной стали появляются новые структурные составляющие, отличающиеся высокой твердостью. К их числу относится мартенсит — пересыщенный твердый раствор углерода в железе.
Необходимые свойства закаленной стали создаются только при правильно проведенных операциях нагрева н охлаждения. Если используют печи, поверхностный слой изделий ухудшается, так как часть углерода выгорает в атмосферном воздухе. Кроме того, возможно окисление этого слоя. В результате механические свойства закаленной стали несколько снижаются. Поэтому стремятся использовать более эффективные методы, нагревая металл в ваннах, наполненных расплавленными солями или свинцом. Чтобы предохранить металл от окисления, создают в печах защитную газовую атмосферу, применяя для этого оксид углерода СО, очищенный азот и другие газы. Так обрабатывают инструментальные и легированные стали.
Горячекатаную арматурную сталь закаливают и отпускают на прокатном стане, используя теплоту нагретого металла. Температура стержня после накатки на него периодического профиля составляет около 1000 °С. В процессе дальнейшего перемещения стержень резко охлаждают струями воды до температуры 300…400 °С, а затем он медленно остывает.
Температуру нагрева регистрируют термоэлектрическими преобразователями или оптическими пирометрами. В первом приближении можно оценить температуру стали по цвету изделия. При температуре выше 550 °С сталь начинает светиться. Цвета свечения называют цветами каления. Для стали характерны следующие цвета каления (температура в °С): 550— темно-коричневый; 630 — коричнево-красный; 680 — темно-красный; 740 — темно-вишневый; 770 — вишневый; 800 — ярко- или светло-вишневый; 850 — ярко-или светло-красный; 900 — ярко-красный; 950 — желто-красный; 1000 — желтый; 1100 — ярко- или светло-желтый; 1200 — жеЛто-белый; 1300 —белый.
Скорость охлаждейия стали оказывает решающее влияние на ее структуру. Чем быстрее охлаждение, тем выше твердость и прочность стали. Для регулирования этой скорости при закалке используют закалочные среды: холодную воду, растворы солей, кислот или щелочей, минеральные масла. Иногда применяют расплавленные соли или свинец, но это наиболее слабые охлаждающие среды.
Легированные стали охлаждают не так быстро, как углеродистые. Поэтому охлаждающей средой для них чаще служат минеральные масла, а не вода.
Способ закалки выбирают в зависимости от требуемых свойств стали. Обычную закалку ведут в одном охладителе. Ее применяют для обработки деталей простой формы. Изделия более сложной формы подвергают прерывистой закалке. Для этого их после нагрева охлаждают в двух различных жидких средах: сначала быстро в воде, затем более медленно в масле. Это позволяет избежать коробления изделий.
Ступенчатую закалку проводят также в две стадии. Нагретое изделие быстро переносят в ванну с температурой 270…290 °С и после некоторой выдержки завершают охлаждение в масле или на воздухе. Ступенчатую закалку применяют при обработке легированных сталей или для деталей небольших сечений из углеродистой стали.
Изотермическую закалку, как и ступенчатую, проводят с выдержкой изделия при постоянной температуре в процессе охлаждения, но длительность выдержки увеличивают. Это способствует резкому уменьшению закалочных напряжений.
В некоторых изделиях, например валах, поверхность должна быть твердой, а сердцевина вязкой. Этого добиваются с помощью поверхностной закалки. Деталь нагревают только по поверхности, используя для этого токи высокой частоты или газовые горелки, а затем закаливают.
В процессе закалки стали сильно возрастают не только ее твердость, но и хрупкость, что нежелательно. Чтобы уменьшить хрупкость и повысить пластичность закаленной стали, ее подвергают отпуску.
Отпуск представляет собой нагрев закаленной стали до некоторой температуры (не более 727 °С) с последующим охлаждением на воздухе или в воде. В результате этого процесса происходит перекристаллизация структурных составляющих, уменьшаются внутренние напряжения, снижаются твердость и хрупкость стали. В зависимости от температуры нагрева различают низкий, средний и высокий отпуск.
Низкий отпуск производят путем нагрева закаленной стали до температуры 120…250 °С. Происходящие при этом небольшие структурные изменения позволяют частично снять внутренние напряжения, увеличить вязкость и пластичность стали без заметного снижения твердости. Низкому отпуску подвергают режущий и мерительный инструменты.
Средний отпуск осуществляют нагревом закаленной стали до температуры 300…400 °С. Структура стали становится мелкодисперсной, сталь приобретает большую пластичность, но твердость и прочность ее несколько понижаются.
Имея достаточный навык, можно определять температуру изделий при низком и среднем отпуске по цветам побежалости, т. е. радужной окраске, возникающей на чистой поверхности нагретой стали в результате появления на ней слоя оксидов. От температуры нагрева зависят толщина и, следовательно, цвет оксидной пленки. Для углеродистой стали характерны следующие цвета побежалости (температура в °С): при 220 — соломенный, 230 — золотистый, 240 — коричневый, 250 — красно-коричневый, 260 — пурпурный, 280 — фиолетовый, 300 — синий (васильковый), 320 — светло-голубой, 330…350 — светло-серый.
Высокий отпуск выполняют в интервале температур 450…650 °С. Получаемая структура характерна средней зернистостью, что придает стали наилучшее сочетание прочности и пластичности. Высокому отпуску подвергают большинство ответственных деталей машин и конструкций.
Закалку в сочетании с высоким отпуском называют улучшением стали. Улучшают конструкционные стали, содержащие 0,3…0,5% углерода, в частности арматурную сталь.
Химико-термическая обработка стали. Заключается она в том, что металл нагревают в химически активной среде для изменения химического состава, структуры и свойств поверхностных слоев изделия. Различают химико-термическую обработку следующих видов: цементация (насыщение поверхностных слоев углеродом), азотирование (азотом), цианирование (углеродом и азотом), алитирование (алюминием), хромирование (хромом), силицирование (кремнием) и т. п. В результате такой обработки поверхностные слои стали упрочняются, резко возрастают их твердость, износостойкость, стойкость к коррозии. Например, цементация низкоуглеродистой стали на глубину 0,5…2 мм увеличивает содержание углерода в поверхностном слое до 0,75… 1,2%, в то время как сердцевина изделия содержит 0,2…0,3%. После закалки детали твердость поверхностного науглероженного слоя увеличивается, а сердцевина из мягкой стали не воспринимает закалки и остается вязкой. Полученная таким образом деталь обладает высокой твердостью и в то же время благодаря пластичности основного металла воспринимает ударные нагрузки.
Азотирование позволяет получать твердость в поверхностном слое, которая в 1,5…2 раза выше, чем при цементации. Цианирование повышает не только поверхностную твердость, но и износостойкость изделий. При алитировании на поверхности деталей создают пленку оксида алюминия, температура плавления которого рколо 2000 °С. Такая пленка предохраняет ос-новнЬй металл от коррозии и одновременно повышает жаростойкость изделий до 850…900 °С. Хромированная сталь стойка к образованию окалины при нагреве до температуры 800…900 °С и хорошо противостоит коррозии в морской воде и растворах кислот. Силици-рование приводит к получению износостойких изделий, одновременно повышается их сопротивляемость коррозии и кислотостойкость.
Читать далее:
Теплоизоляционные материалы
Основные свойства строительных материалов
Фиксаторы арматуры
Материалы для смазывания форм
Сборные бетонные и железобетонные конструкции
Арматурные изделия и закладные детали
Проволочная арматура
Стержневая арматура
Классификация арматуры и технические требования к сталям
Обработка давлением
Способы и режимы закалки и отпуска стали
Термическая обработка сталей – одна из самых важных операций в машиностроении, от правильного проведения которой зависит качество выпускаемой продукции. Закалка и отпуск сталей являются одними из разнообразных видов термообработки металлов.
Тепловое воздействие на металл меняет его свойства и структуру. Это позволяет повысить механические свойства материала, долговечность и надежность изделий, а также уменьшить размеры и массу механизмов и машин. Кроме того, благодаря термообработке, для изготовления различных деталей можно применять более дешевые сплавы.
Также вам не помешает знать, как правильно варить полуавтоматом.
Как закалялась сталь
Термообработка стали заключается в тепловом воздействии на металл по определенным режимам ля изменения его структуры и свойств.
К операциям термообработки относятся:
- отжиг;
- нормализация;
- старение;
- закалка стали и отпуск стали (и пр.).
Термообработка стали: закалка отпуск – зависит от следующих факторов:
- температуры нагрева;
- времени (скорости) нагрева;
- продолжительности выдержки при заданной температуре;
- скорости охлаждения.
Закалка
Закалка стали – это процесс термообработки, суть которого заключается в нагреве стали до температуры выше критической с последующим быстрым охлаждением. В результате этой операции повышаются твердость и прочность стали, а пластичность снижается.
При нагреве и охлаждении сталей происходит перестройка атомной решетки. Критические значения температур у разных марок сталей неодинаковы: они зависят от содержания углерода и легирующих примесей, а также от скорости нагрева и охлаждения.
После закалки сталь становится хрупкой и твердой. Поверхностный слой изделий при нагреве в термических печах покрывается окалиной и обезуглероживается тем более, чем выше температура нагрева и время выдержки в печи. Если детали имеют малый припуск для дальнейшей обработки, то брак этот является неисправимым. Режимы закалки закалки стали зависят от ее состава и технических требований к изделию.
Охлаждать детали при закалке следует быстро, чтобы аустенит не успел превратиться в структуры промежуточные (сорбит или троостит). Необходимая скорость охлаждения обеспечивается посредством выбора охлаждающей среды. При этом чрезмерно быстрое охлаждение приводит к появлению трещин или короблению изделия. Чтобы этого избежать, в интервале температур от 300 до 200 градусов скорость охлаждения надо замедлять, применяя для этого комбинированные методы закалки. Большое значение для уменьшения коробления изделия имеет способ погружения детали в охлаждающую среду.
Нагрев металла
Все способы закалки стали состоят из:
- нагрева стали;
- последующей выдержки для достижения сквозного прогрева изделия и завершения структурных превращений;
- охлаждения с определенной скоростью.
Изделия из углеродистой стали нагревают в камерных печах. Предварительный подогрев в этом случае не требуется, так как эти марки сталей не подвергаются растрескиванию или короблению.
Сложные изделия (например, инструмент, имеющий выступающие тонкие грани или резкие переходы) предварительно подогревают:
- в соляных ваннах путем двух-или трехкратного погружения на 2 – 4 секунды;
- в отдельных печах до температуры 400 – 500 градусов по Цельсию.
Нагрев всех частей изделия должен протекать равномерно. Если это невозможно обеспечить за один прием (крупные поковки), то делаются две выдержки для сквозного прогрева.
Если в печь помещается только одна деталь, то время нагрева сокращается. Так, например, одна дисковая фреза толщиной 24 мм нагревается в течение 13 минут, а десять таких изделий – в течение 18 минут.
Защита изделия от окалины и обезуглероживания
Для изделий, поверхности которых после термообработки не шлифуются, выгорание углерода и образование окалины недопустимо. Защищают поверхности от подобного брака применением защитных газов, подаваемых в полость электропечи. Разумеется, такой прием возможен только в специальных герметизированных печах. Источником подаваемого в зону нагрева газа служат генераторы защитного газа. Они могут работать на метане, аммиаке и других углеводородных газах.
Если защитная атмосфера отсутствует, то изделия перед нагревом упаковывают в тару и засыпают отработанным карбюризатором, чугунной стружкой (термисту следует знать, что древесный уголь не защищает инструментальные стали от обезуглероживания). Чтобы в тару не попадал воздух, ее обмазывают глиной.
Соляные ванны при нагреве не дают металлу окисляться, но от обезуглероживания не защищают. Поэтому на производстве их раскисляют не менее двух раз в смену бурой, кровяной солью или борной кислотой. Соляные ванны, работающие на температурах 760 – 1000 градусов Цельсия, весьма эффективно раскисляются древесным углем. Для этого стакан, имеющий множество отверстий по всей поверхности, наполняют просушенным углем древесным, закрывают крышкой (чтобы уголь не всплыл) и после подогрева опускают на дно соляной ванны. Сначала появляется значительное количество языков пламени, затем оно уменьшается. Если в течение смены таким способом трижды раскислять ванну, то нагреваемые изделия будут полностью защищены от обезуглероживания.
Степень раскисления соляных ванн проверяется очень просто: обычное лезвие, нагретое в ванне в течение 5 – 7 минут в качественно раскисленной ванне и закаленное в воде, будет ломаться, а не гнуться.
Охлаждающие жидкости
Основной охлаждающей жидкостью для стали является вода. Если в воду добавить небольшое количество солей или мыла, то скорость охлаждения изменится. Поэтому ни в коем случае нельзя использовать закалочный бак для посторонних целей (например, для мытья рук). Для достижения одинаковой твердости на закаленной поверхности необходимо поддерживать температуру охлаждающей жидкости 20 – 30 градусов. Не следует часто менять воду в баке. Совершенно недопустимо охлаждать изделие в проточной воде.
Недостатком водяной закалки является образование трещин и коробления. Поэтому таким методом закаливают изделия только несложной формы или цементированные.
- При закалке изделий сложной конфигурации из конструкционной стали применяется пятидесятипроцентный раствор соды каустической (холодный или подогретый до 50 – 60 градусов). Детали, нагретые в соляной ванне и закаленные в этом растворе, получаются светлыми. Нельзя допускать, чтобы температура раствора превышала 60 градусов.
Пары, образующиеся при закалке в растворе каустика, вредны для человека, поэтому закалочную ванну обязательно оборудуют вытяжной вентиляцией.
- Закалку легированной стали производят в минеральных маслах. Кстати, тонкие изделия из углеродистой стали также проводят в масле. Главное преимущество масляных ванн заключается в том, что скорость охлаждения не зависит от температуры масла: при температуре 20 градусов и 150 градусов изделие будет охлаждаться с одинаковой скоростью.
Следует остерегаться попадания воды в масляную ванну, так как это может привести к растрескиванию изделия. Что интересно: в масле, разогретом до температуры выше 100 градусов, попадание воды не приводит к появлению трещин в металле.
Недостатком масляной ванны является:
- выделение вредных газов при закалке;
- образование налета на изделии;
- склонность масла к воспламеняемости;
- постепенное ухудшение закаливающей способности.
- Стали с устойчивым аустенитом (например, Х12М) можно охлаждать воздухом, который подают компрессором или вентилятором. При этом важно не допускать попадания в воздухопровод воды: это может привести к образованию трещин на изделии.
- Ступенчатая закалка выполняется в горячем масле, расплавленных щелочах, солях легкоплавких.
- Прерывистая закалка сталей в двух охлаждающих средах применяется для обработки сложных деталей, изготовленных из углеродистых сталей. Сначала их охлаждают в воде до температуры 250 – 200 градусов, а затем в масле. Изделие выдерживается в воде не более 1 – 2 секунд на каждые 5 – 6 мм толщины. Если время выдержки в воде увеличить, то на изделии неизбежно появятся трещины. Перенос детали из воды в масло следует выполнять очень быстро.
Процесс отпуска
Отпуску подвергаются все закаленные детали. Это делается для снятия внутренних напряжений. В результате отпуска несколько снижается твердость и повышается пластичность стали.
В зависимости от требуемой температуры отпуск производится :
- в масляных ваннах;
- в селитровых ваннах;
- в печах с принудительной воздушной циркуляцией;
- в ваннах с расплавленной щелочью.
Температура отпуска зависит от марки стали и требуемой твердости изделия, например, инструмент, для которого необходима твердость HRC 59 – 60, следует отпускать при температуре 150 – 200 градусов. В этом случае внутренние напряжения уменьшаются, а твердость снижается незначительно.
Быстрорежущая сталь отпускается при температуре 540 – 580 градусов. Такой отпуск называют вторичным отвердением, так как в результате твердость изделия повышается.
Изделия можно отпускать на цвет побежалости, нагревая их на электроплитах, в печах, даже в горячем песке. Окисная пленка, которая появляется в результате нагрева, приобретает различные цвета побежалости, зависящие от температуры. Прежде чем приступать к отпуску на один из цветов побежалости, надо очистить поверхность изделия от окалины, нагара масла и т. д.
Обычно после отпуска металл охлаждают на воздухе. Но хромоникелевые стали следует охлаждать в воде или масле, так как медленное охлаждение этих марок приводит к отпускной хрупкости.
Оборудование для закалки, охлаждения и отпуска | Слесарное дело
Охлаждение стали можно вести на воздухе, в воде, водных растворах, маслах, жирах и на стальных плитах. Оборудование для охлаждения — это ванны и баки с охлаждающей жидкостью, часто проточной, баки с внутренним змеевиком для подогрева жидкости и другое оборудование (рис. 48 и 49) для измерения температуры и твердости стали.
Назвать способы определения температуры.
Определение температуры при термической обработке можно производить на основании цвета излучения нагретой стали или с использованием измерительных приборов.
Ориентировочно температуру можно определить по цвету нагретого металла:
- Изменение цвета нагретого металла в зависимости от температуры
Назвать виды измерительных приборов для измерения температур.
К измерительным приборам для измерения температур относятся различные термометры (манометрические термометры, термометры сопротивления и др.), термопары, оптические пирометры, термоэлектрические пирометры и термокарандаши (рис. 50).
- Приборы для измерения температуры
Перечислить методы определения твердости металла.
Используют следующие методы определения твердости металла: проба напильником (метод неточен), проба по цвету искры (заточка изделия на шлифовальном круге, измерение также неточное), а также определение по Бринеллю (ГОСТ 9012—59, вдавливание стального шарика в исследуемый металл), по Роквеллу (ГОСТ 9013—59, вдавливание в исследуемый металл алмазного конуса) и по Викерсу (ГОСТ 2999—75, вдавливание в исследуемый материал алмазной пирамиды), а также определение твердости по методу упругой отдачи по Шору (по высоте отскакивания шарика или бойка от обработанной поверхности).
Страницы: 1 2
Автор admin | Категория | 11 23, 2008 | Комментариев нет
Теги: вал, жидкость, закалка, измерения, мастер, металл, напильник, нефть, отпуск, стали, сталь, ток, участок, цех
Температура нагрева автомобиля в жаркий день зависит от цвета кузова: тест
Вот результаты проверки нагрева кузова в солнечный жаркий день.
Вы когда-нибудь задумывались, до какой температуры нагревается кузов вашей машины, которую вы оставили под прямыми солнечными лучами в жаркий летний день? Угадайте, до какой температуры может нагреться автомобиль красного, синего, белого, серебристого и черного цвета? Для того чтобы подтвердить свою догадку, вот вам результат блогера из Китая, который решил выяснить это на практике.
Блогер решил взять инфракрасный термометр и проверить точно, до скольких градусов нагревается поверхность кузова, окрашенная в разные цвета. Вот что вышло:
До скольких градусов нагревается автомобиль синего цвета
Да, чудес от этого цвета ждать не стоит. Красивый «синий металлик» также подвержен сильному нагреву под прямыми солнечными лучами. Во время замера цифровой градусник показал почти 75 градусов по Цельсию.
Далее блогер замерил красный автомобиль.
До скольких градусов нагревается автомобиль красного цвета
Красное лакокрасочное покрытие показало 73,2 градуса, что меньше, чем у синего автомобиля. Тем не менее результат все равно близок к тому же, что и у синего.
До скольких градусов нагревается автомобиль с цветом кузова «серебристый металлик»
Цвет «серебристый металлик» нагревается на солнце меньше, чем синий и красный. Инфракрасный градусник показал температуру в 62,6 градуса, что уже значительно ниже температур вышеуказанных окрасок кузова.
До скольких градусов нагревается автомобиль белого цвета
Далее блогер из Китая проверил уровень нагрева белого автомобиля. Результат хоть и предсказуем, но все равно удивляет. Так, градусник показал, что кузов нагрелся только до 55,4 градуса. Это, пожалуй, самый выгодный цвет кузова.
А теперь наш антипобедитель – автомобиль черного цвета, который показал самые большие температурные значения.
До скольких градусов нагревается автомобиль черного цвета
Конечно же, черный не оправдал ожиданий. Но температура в 81,2 градуса пугает. Ведь это очень много, с учетом того, что вода начинает закипать уже ближе к 100 градусам. Так что летом черный автомобиль самый нагреваемый. Естественно, это приводит к ускоренному повреждению лакокрасочного покрытия. Вот почему автомобиль черного цвета необходимо более тщательно защищать от воздействия ультрафиолета с помощью различных составов, которые необходимо наносить на кузов.
Так что если ваш автомобиль черного цвета, старайтесь не парковать его на открытом пространстве в летнее время, защищая лакокрасочное покрытие от прямых солнечных лучей.
Также стоит отметить, что, так как кузов черного автомобиля нагревается больше всего, вы будете тратить больше денег на топливо при включенном кондиционере, поскольку ему будет необходимо больше мощности, чтобы поддерживать заданную температуру в салоне.
Руководство для деревообработчика по инструментальной стали и термообработке
Справочник плотника по инструментальной стали и плавке Лечение
Вы когда-нибудь задумывались, из какой волшебной стали можно сделать твердую или твердую? мягкий? Я тоже. После закалки моего первого плоского железа я решил выяснить. Эта страница — результат моих исследований. Пока существуют десятки различных рецептур инструментальной стали, только один, с которым у меня есть опыт, это O-1 Oil. Закалочная инструментальная сталь .Я использую O-1 для следующих причины:
- Это дешево и доступно
- Имеет одну из самых низких температур затвердевания среди всех инструментальные стали, предназначенные для термообработки в домашних условиях
- Обладает хорошей устойчивостью к короблению при закалке.
- Справочник по машинному оборудованию рекомендует O-1 для «инструменты с острыми краями (ножи, бритвы)» и «инструменты для операции, в которых не требуется высокая скорость, но стабильность при термической обработке и значительной стойкости к истиранию необходимо «
В следующих обсуждениях термины «сталь», «инструмент» сталь »и« углеродистая сталь »следует понимать как относящиеся к к О-1.В то время как физические изменения и фазовые отношения в термическая обработка практически одинакова для всех инструментальных сталей, требуемые температуры (и другие физические свойства) широко варьируются в зависимости от состава. Отметим также, что другие жидкости (вода, воздух) помимо масла используются для закалки различных Инструментальные стали и процедуры отпуска также различаются.
Химический состав инструментальной стали O-1 | Физические свойства инструментальной стали О-1 | ||
---|---|---|---|
Утюг | 97.1% | Закалка (° F) | 1450–1500 |
Углерод | 0,90% | (° C) | 788–816 |
Хром | 0.50% | Темперирование (° F) | 350–550 |
Марганец | 1.00% | (° C) | 177 — 228 |
Вольфрам | 0.50% | Диапазон твердости (R c ) | 64–58 |
Определения:
Отжиг — Размягчение инструмента сталь для обработки, путем нагрева до температуры закалки и медленно остывает.Медленное охлаждение может быть достигнуто закапывать сталь в изолирующую среду, такую как известь или вермикулита и дать ему остыть до комнатной температуры.Закалка — Нагрев стали до закалки температура и внезапное охлаждение путем закалки в масле ванна.
Закалка — Повторный нагрев закаленной стали до температура отпуска для снятия напряжения, вызванного процесс закалки, и удалите часть твердости в обмен на стойкость.Незаконченная, закаленная инструментальная сталь почти такой же хрупкий, как стекло.
Что происходит при термообработке инструмента Стали?
Углерод и железо существуют вместе в нескольких различные фазы, в зависимости от процентного содержания углерода и температура. Фазовая диаграмма Fe-C показывает эти отношения. Упрощенная фаза Fe-C Схема (стальная часть) Для нашего обсуждения важны четыре этапа: Обратите внимание, что показанная диаграмма предназначена только для стальной части. системы.При содержании углерода 2-6,67% сплав чугун. Сплав с содержанием углерода более 6,67% состоит из цементит и графит.Сплав, состоящий ровно из 0,76% углерода и 99,24% Fe, имеет самую низкую температуру, при которой преобразование феррита и цементита в аустентит завершено. Эта сталь известна как эвтектоид . Увеличение количества углерода выше этого количества, а также добавление других легирующих элементов, также увеличивает температуру полного фазового превращения (т.е.е., закалка).
Полностью отожженная углеродистая сталь состоит, помимо примеси и другие легированные элементы механического смесь железа и карбида железа. Утюг берет кристаллическая форма феррита, а карбид железа принимает кристаллическая форма цементита. Общая структура состоит из полосы этих двух компонентов и известен как перлит. В этом состоянии сталь мягкая и работоспособный.
Поскольку сталь нагревается выше критической температуры, около 1335 ° F (724 ° C), он претерпевает фазовый переход, перекристаллизовывается в виде аустенита.Продолжение нагрева до температура отверждения, 1450-1500 ° F (788-843 ° C) обеспечивает полное превращение в аустенит. На данный момент сталь перестала быть магнитной и приобрела вишнево-красный цвет.
Если аустенитная сталь охлаждается медленно (процесс известный как отжиг), он вернется в перлитный состав. Однако если его резко охладить путем закалки в масляная ванна, новая кристаллическая структура, мартенсит, — это сформирован.Для мартенсита характерна угловатая игольчатая форма. структура и очень высокая твердость.
Хотя мартенситная сталь чрезвычайно твердая, она также чрезвычайно хрупкий, ломается, раскалывается и рассыпается вместе с малейшее потрясение. Кроме того, внутренние напряжения остаются в средство от внезапной закалки; это также облегчит поломка инструмента. Закалка снимает эти стрессы и вызывает частичное разложение мартенсита на феррит и цементит.Величина этого частичного изменения фазы равна контролируется температурой отпуска. Закаленная сталь не такая твердая, как чистая мартенсит, но намного прочнее.
Влияние легирующих элементов на свойства инструментальной стали:
- Углерод: Повышение содержания углерода незначительно увеличивает твердость и значительно увеличивает износостойкость.
- Марганец: Небольшие количества марганца снижают хрупкость и улучшают ковкость.Большие суммы марганца улучшают прокаливаемость, позволяют закалку в масле и уменьшают закалочную деформацию.
- Кремний: Повышает прочность, ударную вязкость и ударопрочность.
- Вольфрам: Повышает «горячую твердость» — используется в быстрорежущей инструментальной стали.
- Ванадий: Улучшает структуру карбида и ковкость, а также повышает твердость и износостойкость.
- Молибден: Повышает глубокую закалку, повышает ударную вязкость и, в больших количествах, «горячую твердость».Используется в быстрорежущей инструментальной стали, потому что она дешевле вольфрама.
- Хром: Повышает прокаливаемость, износостойкость и прочность.
- Никель: В меньшей степени повышает ударную вязкость и износостойкость.
Типы инструментальной стали, кроме О-1:
Серии A и D (A-2, D-2 и т. Д.) Содержат больше хрома и, следовательно, обладают большей износостойкостью.Серия S содержит больше кремния и, следовательно, более устойчива к ударам. Серии M и T содержат больше молибдена или вольфрама, а также быстрорежущие стали с гораздо большей жаропрочностью. Все они требуют значительно более высоких температур для затвердевания, чем O-1, и не являются действительно подходит для закаливания в домашних условиях.Зачем криогенно обрабатывать инструментальную сталь?
В некоторых легированных инструментальных сталях значительные количества аустенита не превращаются в мартенсит при закалке.Это особенно верно в отношении A-2 и D-2; эти стали выбираются для режущих инструментов из-за их более высоких износостойкость, которая снижается за счет остаточного аустенита. Поскольку аустенит нестабилен при комнатной температуре, он постепенно превращается в до мартенсита в течение определенного периода времени — но мы говорим о годах, слишком долго, чтобы быть практичным. Так переохлаждение закаленного, закаленная сталь ускоряет преобразование до нескольких часов. После криогенной обработки инструмент повторно закаляется, и исследования показывают, что в результате существенно повышается износостойкость.Поскольку мартенситное превращение более полное в O-1, криогенная обработка для этой инструментальной стали не требуется.
Цвет инструментальной стали в зависимости от температуры
2000 ° F | Ярко-желтый | 1093 ° С |
1900 ° F | Темно-желтый | 1038 ° С |
1800 ° F | Оранжево-желтый | 982 ° С |
1700 ° F | Апельсин | 927 ° С |
1600 ° F | Оранжевый красный | 871 ° С |
1500 ° F | Ярко-красный | 816 ° С |
1400 ° F | Красный | 760 ° С |
1300 ° F | Средний красный | 704 ° С |
1200 ° F | Тусклый красный | 649 ° С |
1100 ° F | Светло-красный | 593 ° С |
1000 ° F | Очень слабый красный, в основном серый | 538 ° С |
0800 ° F | Темно-серый | 427 ° С |
0575 ° F | Синий | 302 ° С |
0540 ° F | Темно-фиолетовый | 282 ° С |
0520 ° F | Фиолетовый | 271 ° С |
0500 ° F | Коричневый / фиолетовый | 260 ° С |
0480 ° F | Коричневый | 249 ° С |
0465 ° F | Темная солома | 241 ° С |
0445 ° F | Светлая солома | 229 ° С |
0390 ° F | Слабая солома | 199 ° С |
Сталь может иметь разные цвета в зависимости от температуры.Температуры выше 800 ° F (427 ° C) производят
лампы накаливания; атомы в стали так возбуждены
из-за тепла они испускают фотоны. Температура ниже
800 ° F (427 ° C) дает цвета окисления. Как
сталь нагревается, на поверхности образуется оксидный слой; это
толщина (и, следовательно, интерференционный цвет, как свет
отражено) является функцией температуры. Эти цвета могут быть
используется в закалке инструментальной стали.
Если цвета являются проблемой:
Использовать цвет для определения температуры не всегда практично.От пяти до десяти процентов мужчин население дальтоник; кроме того, на солнце гораздо труднее судить о цвете раскаленной стали, если вы делаете термообработку на открытом воздухе, что вам необходимо, если в вашем магазине нет вытяжного шкафа и дымохода. Темперирование может быть делается в духовке с помощью точного градусника. Для температуры застывания есть несколько решений:Магнетизм: Помните, что при критической температуре, когда начинается фазовый переход в аустенит, сталь будет стать немагнитным.
Пирометры: Хотя хорошие пирометры дороги, термопару типа K можно купить за несколько долларов в магазине.
цех изделий из стекла или керамики. Подключите его к цифровому мультиметру, загрузите милливольт в график температуры.
для термопары, и все готово. Я проделал это, пропустив термопару через небольшое отверстие в боковой стенке газовой кузницы,
и это кажется довольно точным. Некоторые интернет-ресурсы:
Tempilstiks: Tempilstiks — это цветные карандаши, которые гарантированно тают в пределах 1% от их номинальной температуры.Доступно в широкий диапазон температур до 2500 ° F, их можно приобрести у дилеров кузнечного / кузнечного оборудования (онлайн на Кентавр Кузница).
Руководство по закалке и отпуску инструментальной стали O-1
Старт с отожженной сталью. На этом этапе сталь мягкая Достаточно для работы с файлом. Теперь займись формированием всего. Однако, если вы делаете кромочный инструмент, пока не шлифуйте острую кромку — просто остановитесь. острого, оставив его тупым.
Маленькая газовая кузница с самовоздушной горелкой (Острый край во время жары обработка приведет к нежелательным нагрузкам на инструмент.)Используя соответствующий источника тепла (или Building the Reil Burner) нагрейте сталь до критической температуры. Как узнать, когда вы достигли критической температуры? Аустенит, кристаллическая структура железа / углерода, которая образуется выше критическая температура, немагнитна.Я держу старую Магнит, удерживаемый в тисках, удобен при закалке. Когда сталь достаточно горячая, магнит не прилипнет. В в этот момент сталь вишнево-красного цвета.
На изображении действительно видно приближающееся темно-желтое ярко-желтый; вишнево-красный можно увидеть ниже лезвие. Теперь снимите сталь с огня и немедленно закалить в масле. Подойдет любое масло; Я погасил с отработанным моторным маслом, но теперь предпочитаю дешевое растительное масло в металлическое ведро на 5 галлонов.(Я бы предпочел думать о картофеле-фри чем двигатель, работающий на масле.) Когда ты окунуть раскаленную сталь в масло вертикально — если если погрузить его под углом, он покоробится. Тщательно перемешайте его в масле, двигаясь вверх-вниз. движение; перемешивание также может вызвать коробление. Это Хотя, похоже, я вхожу под углом в картинка, клещи держат инструмент под одним углом, и фактически движение инструмента и моей руки вертикальный.важно, чтобы он продолжал двигаться, чтобы пополнить масло на поверхность из стали; иначе образуется паровой слой в результате гашение происходит медленнее, чем хотелось бы. Если тушить слишком медленно, инструмент будет недостаточно твердым. Держите сталь в масло, пока масло не перестанет пузыриться.Как только сталь достаточно остынет, протрите ее. и проверьте его твердость. Если вы все сделали правильно, файл не кусается — он просто соскользнет с края инструмента.Если это достаточно тяжело, пора закаляться; это важно закалить как можно скорее после закалки. Вы можете просто поставьте инструмент в духовку, если доверяете его настройке температуры (может быть, хороший термометр будет хорошей инвестицией), или можно закалить, как это делают кузнецы — нагревая инструмент до он достигает нужного цвета. Чтобы увидеть цвета окисления, вам придется осветлить инструмент на грубой бумаге эмори. Мы не говорим здесь о зеркальной отделке — достаточно, чтобы обнажить голый металл (возможно, до 220 грит).Теперь, используя подходящего источника тепла, осторожно нагрейте инструмент от некоммерческое преимущество. Идея состоит в том, чтобы смягчить резку край, поэтому режущая кромка будет тверже, чем другой конец инструмента. Например, лезвие ножа будет тверже. чем вдоль его спины — спина будет закалена больше, чтобы дать это гибкость. По мере того, как инструмент нагревается, вы первым окрашиваете должен увидеть бледно-соломенный цвет. Продолжайте нагреваться и позвольте этот цвет растекаться по направлению к режущей кромке.Так же, как это достигнув режущей кромки, погрузите инструмент в воду, чтобы не допускайте чрезмерного закаливания. Готово, если инструмент это рубанок или долото — все, что вам нужно сделать сейчас, это сплющить спину и заточите. Для инструмента, требующего большей прочности (меньшая хрупкость), например, холодное долото, вам следует темперамент немного повыше. Для настоящей гибкости, как пружина, идти до синего.
Зависимость твердости от температуры отпуска
Авторское право © Питер Л. Берглунд, 2006 г.Все права защищены; контент не может быть воспроизведен без разрешения автора.
Таблица штамповки и отпуска стали
Термическая обработка является важной частью процесса изготовления ножа, которая увеличивает твердость вашего лезвия и дает вашему ножу более высокую остроту. По мере прохождения этого процесса вы, кузнец, будете формировать лезвие, чтобы создать нож, который будет прочным и полезным.
Есть два важных этапа процесса термообработки: ковка ножом и отпуск.Процесс ковки включал формование ножа при критически высоком уровне нагрева (обычно 900–2000 градусов по Фаренгейту) для повышения его твердости. Когда вы закончите ковку ножа, вы можете перейти к процессу закалки, в котором вы увеличиваете гибкость и остроту ножа при более низкой температуре, обычно между 390-800 градусами по Фаренгейту.
Чтобы определить, в какой стадии находится лезвие, вы должны обратить внимание на цвет лезвия, который указывает на температуру лезвия.Следующая таблица служит руководством для вас, чтобы определить температуру вашего лезвия в зависимости от его цвета во время термической обработки.
Загрузите этот график в формате PDF …
Кузнечная сварка | Фаренгейт | Стальной цвет |
---|---|---|
Ковка | 2,000 ° | Ярко-желтый |
1,900 ° | Темно-желтый | |
1,800 ° | оранжево-желтый | |
1,700 ° | оранжевый | |
1,600 ° | Оранжевый Красный | |
1,500 ° | Ярко-красный | |
1,400 ° | Красный | |
1,300 ° | Средний красный | |
1,200 ° | Тусклый красный | |
1000 ° | Светло-красный | |
900 ° | Очень легкий красный, преимущественно серый | |
Закалка | 800 ° | Темно-серый |
575 ° | Синий | |
540 ° | Темно-фиолетовый | |
520 ° | фиолетовый | |
500 ° | коричневый / фиолетовый | |
480 ° | коричневый | |
465 ° | Темная солома | |
445 ° | Светлая солома | |
390 ° | Слабая солома |
|
|
Цветовой спектр стали с подогревом «Adafruit Industries — Создатели, хакеры, художники, дизайнеры и инженеры!
Прекратите макетирование и пайку — немедленно приступайте к изготовлению! Площадка Circuit Playground от Adafruit забита светодиодами, датчиками, кнопками, зажимами из кожи аллигатора и многим другим.Создавайте проекты с помощью Circuit Playground за несколько минут с помощью сайта программирования MakeCode с перетаскиванием, изучайте информатику с помощью класса CS Discoveries на code.org, переходите в CircuitPython, чтобы изучать Python и оборудование вместе, TinyGO или даже использовать Arduino IDE. Circuit Playground Express — это новейшая и лучшая плата Circuit Playground с поддержкой CircuitPython, MakeCode и Arduino. Он имеет мощный процессор, 10 NeoPixels, мини-динамик, инфракрасный прием и передачу, две кнопки, переключатель, 14 зажимов из кожи аллигатора и множество датчиков: емкостное прикосновение, ИК-приближение, температуру, свет, движение и звук.Вас ждет целый мир электроники и программирования, и он умещается на ладони.
Присоединяйтесь к более чем 28 000 создателей на каналах Adafruit в Discord и станьте частью сообщества! http://adafru.it/discord
Хотите поделиться замечательным проектом? Выставка Electronics Show and Tell проходит каждую среду в 19:00 по восточному времени! Чтобы присоединиться, перейдите на YouTube и посмотрите чат в прямом эфире шоу — мы разместим ссылку там.
Присоединяйтесь к нам каждую среду вечером в 20:00 по восточноевропейскому времени на «Спроси инженера»!
Подпишитесь на Adafruit в Instagram, чтобы узнать о совершенно секретных новых продуктах, о том, что происходит за кулисами, и многом другом https: // www.instagram.com/adafruit/
CircuitPython — Самый простой способ программирования микроконтроллеров — CircuitPython.org
Получайте единственную ежедневную рассылку без спама о носимых устройствах, ведении делопроизводства, электронных советах и многом другом! Подпишитесь на AdafruitDaily.com!Пока комментариев нет.
Извините, форма комментариев в настоящее время закрыта.
Почему цвет вашего стального и металлического здания влияет на внутреннюю температуру
По словам производителя красок Sherwin-Williams, наиболее популярными цветами для коммерческих зданий по-прежнему остаются нейтральные и белые, которые подчеркнуты смелыми оттенками.По словам Шервина-Уильямса, это корпоративный эквивалент оранжевой двери.
Между тем, если у вас есть металлическое здание, используемое для сельского хозяйства, самые популярные цвета — это то, что Шервин-Уильямс называет «цветами устойчивости». Мы уже знаем, что сталь является одним из наиболее перерабатываемых материалов на планете, поэтому цвета, которые дополняют преобладающие в природе, имеют смысл.
Почему цвет имеет значение
Это больше, чем просто то, что кажется на первый взгляд. Выбор цвета экстерьера, подходящего для вашего района, также может помочь вам снизить общее потребление энергии и сделать ваше сборное здание из металла и стали более экологически чистым.
Более темные цвета кузова имеют тенденцию поглощать энергию солнца, в то время как более светлые цвета имеют тенденцию отражать как свет, так и сопутствующее тепло. Если эта энергия поглощается вашим зданием, она передается внутрь.
Цвет играет важную роль, но не менее важен и выбранный вами материал. Например, стандартный металл является эффективным передатчиком температуры. Более тяжелые материалы, такие как кирпич или камень, будут блокировать передачу энергии и сохранять прохладу в жаркие летние месяцы.
Как правильный цвет экономит доллары и имеет смысл
Страховой гигант Allstate недавно изучил, насколько выбор цвета кузова может повлиять на энергоэффективность. Они поспешили указать, что их выводы согласуются с отчетом Министерства энергетики (DOE) Cooling Your Home Naturally.
Доказано, что темные тусклые цвета поглощают до 90 процентов солнечной энергии. Он переносится в ваше здание, и тогда вам нужно найти способы компенсации.Однако, если вы выберете светлый цвет кузова, чтобы отразить эту солнечную энергию, вам не придется так усердно работать, чтобы сохранять прохладу.
Хорошо, да. Белый может быть скучным.
Вот почему все больше людей выбирают строительные конструкции Miracle Truss®. Помните, что плотные строительные материалы, такие как камень или кирпич, впитывают тепло и дольше удерживают его, не передавая его внутрь. Это также может помочь сохранить тепло в вашем доме зимой, потому что энергия улавливается и удерживается кирпичом или камнем.
Наши варианты дизайна позволяют вам делать заказы только на фермы, которые позволят вам отделать экстерьер любым материалом по вашему выбору. Легко использовать внешние боковые стены из кирпича или даже винила.
Узнайте, насколько доступными могут быть наши здания. Запросите бесплатное предложение.
Температура отпуска — обзор
Отпуск — это термин, исторически связанный с термической обработкой мартенсита в сталях для изменения микроструктуры и механических свойств путем изотермической выдержки стального компонента при температуре, ниже которой аустенит не может образоваться.После закалки стали закаленный мартенсит не только очень твердый, но и имеет низкую вязкость. Отпуск, также известный как «вытяжка», представляет собой термическую обработку закаленных и нормализованных сталей для получения улучшенной ударной вязкости и пластичности, более низкой твердости и улучшенной стабильности размеров. Во время отпуска происходят твердотельные реакции, и закаленный мартенсит превращается в отпущенный мартенсит, который при более высоких температурах отпуска состоит из высокодисперсных сфероидов цементита (карбидов), диспергированных в мягкой матрице феррита, что приводит к пониженной твердости. и повышенная прочность.Цель состоит в том, чтобы позволить твердости снизиться до желаемого уровня, а затем остановить твердофазные реакции в виде последовательности выделения карбида при охлаждении. Степень эффекта отпуска определяется температурой и временем процесса ( 56 ).
Обычно время отпуска составляет минимум около 1 часа. Телнинг сообщил о «практическом правиле»: 1–2 часа на дюйм. –1 толщины сечения после того, как нагрузка достигнет заданной температуры ( 60 ). После нагрева сталь охлаждается до комнатной температуры на неподвижном воздухе.Рекомендуемые условия отпуска, в дополнение к рекомендуемым циклам термообработки, для широкого диапазона углеродистых и легированных сталей приведены в SAE AMS 2759. В некоторых производственных условиях после отпуска могут применяться процессы быстрого охлаждения для получения остаточного состояния тангенциального сжатия. напряжений на поверхности детали с допустимой деформацией.
Время отпуска и температуры также могут быть рассчитаны различными методами. Один из наиболее распространенных методов — использовать уравнение Ларсена – Миллера.Уравнение Ларсена – Миллера, хотя изначально было разработано для прогнозирования данных о ползучести, успешно использовалось для прогнозирования эффекта отпуска средне / высоколегированных сталей ( 61 ).
Это уравнение действительно для 490 ° C < T t <610 ° C и для времени отпуска 1 час.
Это уравнение действительно для времени отпуска 2 часа.
12.02.7.1 Реакции отпуска
Закалка — это процесс, при котором микроструктура приближается к равновесию при термической активации.Отсюда следует, что склонность к отпуску зависит от того, насколько исходная микроструктура отклоняется от равновесия ( 63 ).
Во время отпуска мартенситная структура подвергается последовательности твердофазных реакций, часто накладываемых друг на друга, определяемых как стадии отпуска ( 32 , 59 , 63 ). Эти процессы включают сегрегацию углерода, выделение карбида, разложение остаточного аустенита и перекристаллизацию мартенситной структуры.
Стадия 1 — В высокоуглеродистых сталях выделение избыточного углерода начинается с образования переходного карбида, такого как ε-карбид (Fe 2.4 C) или η-карбид (Fe 2 C), которые могут расти при температурах до 50 ° C. Эта стадия начинается при комнатной температуре до 250 ° C. Соотношение между ε-карбидами и структурой железа обусловлено эффектом дисперсионного упрочнения мартенсита в стали с высоким содержанием углерода, отпускаемых при температуре от 50 до 100 ° C.
Этап 2 — отпуск при более высоких температурах в диапазоне 200–300 ° C в течение 1 часа вызывает разложение остаточного аустенита на смесь цементита и феррита.Когда аустенит присутствует в виде пленки, цементит также выделяется в виде непрерывного массива частиц, которые имеют вид пленки ( 32 , 59 , 63 ). Мартенсит сталей с содержанием углерода менее 0,5% содержит остаточный аустенит в диапазоне от менее 2% до 6% для сталей с содержанием углерода 0,8%. Есть некоторые признаки того, что аустенит разлагается на феррит и цементит, но в настоящее время нет единого мнения, можно ли соотнести эту структуру с нижним бейнитом, обычно присутствующим в результате изотермического разложения аустенита в диапазоне температур 230–300 ° C.
Этап 3 — Отпуск при еще более высоких температурах приводит к укрупнению частиц цементита, при этом частицы, расположенные на границах пластин, растут за счет частиц внутри пластин. Это выделение отвечает за явление охрупчивания, наблюдаемое между температурами от 250 до 400 ° C, и его можно избежать, добавляя Si, потому что это элемент, нерастворимый в цементите, просто позволяя образование цементита при температурах, при которых происходит диффузия Si.Это считается медленным процессом, потому что этот элемент сплава является замещающим. Si, накопленный в матрице железа рядом с карбидом Fe 3 C в процессе выращивания, увеличивает активность C в этой области за счет уменьшения потока C к растущей частице и, следовательно, снижения скорости ее роста ( 33 , 64 , 65 ). Эта реакция начинается при температурах порядка 100 ° C, что указывает на промежуточное состояние между стадиями отпуска. Можно предположить, что при температурах от 260 до 360 ° C кинетические реакции выше.
Цементит может также наблюдаться во время закалки, когда температура M s повышена, как в случае стали с низким содержанием C, в основном в мартенсите, образовавшемся непосредственно ниже температуры M s . Это явление известно как самоотпуск ( 32 ). В углеродистых сталях Стадия 3 отмечает окончание процесса отпуска, если сталь не подвергается отпуску в течение длительного времени или если она не подвергается чрезмерно высокой температуре отпуска. Когда это происходит, рост цементита соответствует коалесценции этого карбида и иногда называется Стадия 4 отпуска ( 6 ).
В общем случае точка перегиба кривой, связывающей твердость со временем отпуска, является показателем того, что начинается новый металлургический процесс. Влияние температуры отпуска для сталей с повышенным содержанием углерода можно увидеть на Рисунке 48.
Рисунок 48. Твердость как функция температуры отпуска для простых углеродистых сталей.
Воспроизведено из Speich, G. R .; Лесли, У. С. Закалка стали. Металл. Пер. Май 1972 г. , 3 (5), 1043–1054.В низкоуглеродистом мартенсите эпсилон-карбид появляется только во время реакции отпуска, когда содержание углерода превышает 0,2%. Высокая плотность дислокаций реечного мартенсита потребляет не менее 0,2% углерода из-за сегрегации по линиям дислокации ( 36 ).
Легированные стали могут иметь другую стадию, на которой осаждение карбидов сплава, включая M 2 C (с высоким содержанием Mo), M 7 C 3 , M 6 C, M 23 C 6 (Cr -rich), V 4 C 3 , а также TiC и т. д., где M обозначает комбинацию атомов металла. Однако все эти карбиды требуют диффузии атомов замещения на большие расстояния. Они могут выпадать в осадок только тогда, когда комбинация времени и температуры достаточна для такой диффузии. Карбиды сплавов растут за счет менее стабильного цементита. Если концентрация сильных карбидообразующих элементов, таких как Mo, Cr, Ti, V и Nb, велика, то весь углерод может быть размещен в карбиде сплава, тем самым полностью исключая цементит.На рисунке 49 показано влияние легирующих элементов на твердость в зависимости от температуры отпуска углеродистых сталей ( 36 ).
Рис. 49. Влияние Ti, V, Cr и Mo на твердость при отпуске.
Воспроизведено из Speich, G. R .; Лесли, У. С. Закалка стали. Металл. Пер. Май 1972 г. , 3 (5), 1043–1054.Твердость, повышенная с добавками Ti, V, Mo и Cr, связана с выделением карбида сплава. Это явление характерно для инструментальных сталей и может повлиять на их ударную вязкость.Однако добавки Nb не дают такого же эффекта. Отсутствие эффекта Nb связано с его низкой растворимостью в аустените, а основным эффектом является выделение стабильных первичных карбидов, форма которых зависит от добавления других элементов, таких как титан. Добавляются легирующие элементы, чтобы обеспечить улучшенные характеристики различных марок сталей, особенно инструментальных сталей. При рассмотрении конструкции сплава необходимо учитывать такие эффекты, как эффекты дисперсионного твердения, растворимость твердых веществ при различных температурах, характеристики прокаливаемости, расход углерода во время формования и его характеристики во время затвердевания.Следует учитывать концепцию стальной матрицы, если разработка сплава основана на существующей марке стали. Следует учитывать даже состав матрицы, поскольку он напрямую связан с температурой аустенизации. При повышении температуры аустенизации различные карбиды, даже более стабильные, начинают растворяться, что приводит к расходу части матричного состава. Ниобий, который может быть полезен для повышения износостойкости, например, образует твердый карбид, так как его растворимость в матрице железа незначительна даже при высоких температурах аустенизации, при низком влиянии на другие твердофазные реакции, что указывает на низкую удар в обычных маршрутах термообработки.Что касается простой углеродистой стали, твердость уменьшается с повышением температуры отпуска. Следовательно, также снижаются предел текучести и предел прочности. Однако также увеличивается удлинение при разрыве и пластичность.
Как нагрев металла влияет на его свойства | Металлические супермаркеты
Электрические, магнитные и структурные свойства металлов могут изменяться под воздействием тепла. Поскольку области применения металла различны, в разных средах важны разные качества. Например, в инженерных приложениях желательна ударная вязкость; в электрических приложениях важно низкое удельное сопротивление.
Есть несколько способов нагрева металла, которые обычно используются для изменения этих свойств. Температура, до которой нагревается металл, и скорость охлаждения тщательно контролируются для достижения желаемого результата.
Воздействие тепла на металл
Наиболее важные способы преобразования металлов под действием тепла:
- Электрическое сопротивление
- Тепловое расширение
- Строение
- Магнетизм
Электрическое сопротивление
Электрическое сопротивление — это мера того, насколько сильно металл препятствует прохождению электрического тока.Проходя через металл, электроны рассеиваются при столкновении с металлической структурой. Когда металл нагревается, электроны поглощают больше энергии и движутся быстрее. Это приводит к большему рассеянию, тем самым увеличивая сопротивление. Термометры фактически используют изменение электрического сопротивления в куске проволоки для измерения температуры.
Тепловое расширение
Металл расширяется при нагревании. Длина, площадь поверхности и объем увеличиваются с повышением температуры. Научный термин для этого — тепловое расширение.Степень теплового расширения варьируется в зависимости от типа металла. Тепловое расширение происходит из-за того, что тепло увеличивает колебания атомов в металле. Учет теплового расширения важен при проектировании металлических конструкций. Обычным примером может служить конструкция бытовых труб, которая должна учитывать расширение и сжатие в зависимости от сезона.
Структура
Металлы состоят из симметричной структуры атомов, известной как аллотроп. Нагревание металла приведет к смещению атомов с их позиций, и смещенные атомы образуют новую структуру.Этот процесс известен как аллотропное фазовое превращение. Аллотропное фазовое превращение изменяет твердость, прочность и пластичность металла. Наиболее важное аллотропное фазовое превращение претерпевает железо. Когда железо нагревается до температуры выше 1674 градусов по Фаренгейту, оно способно поглощать больше углерода, который является ингредиентом, повышающим твердость любого стального изделия. Этот желаемый эффект используется в нескольких типах высокоуглеродистой (углеродистой более 0,50) стали — Пример: инструментальная сталь
.Магнетизм
Есть три металла с магнитными свойствами: железо, никель и кобальт.Они известны как ферромагнитные металлы. Нагревание этих металлов снизит их намагниченность до такой степени, что магнетизм полностью исчезнет. Температура, при которой это происходит, называется температурой Кюри. Для никеля эта температура составляет 626 градусов по Фаренгейту; для кобальта — 2 012 градусов по Фаренгейту; а для железа это 1418 градусов по Фаренгейту.
Термическая обработка
Термическая обработка — это процесс, предназначенный для изменения свойств металла в соответствии с его назначением.Основные виды термической обработки:
Отжиг
Отжиг часто используется для смягчения металлов, включая железо, сталь, медь, латунь и серебро. Процесс включает нагрев металла до определенной температуры, а затем позволяет ему медленно остыть с контролируемой скоростью. Отжиг изменяет физические и химические свойства металла, увеличивая пластичность и снижая твердость. Это облегчает процессы формовки, штамповки или формовки и позволяет легче резать металл.Отжиг также увеличивает электрическую проводимость.
Нормализация
Нормализация (обычно называемая нормализованной) применяется к сплавам для обеспечения однородности по размеру зерна и составу. Металл нагревается до заданной температуры, а затем охлаждается воздухом. Полученный металл не содержит нежелательных примесей и обладает большей прочностью и твердостью. Нормализация часто используется для получения более твердой и прочной стали, хотя и менее пластичной, чем сталь, полученная отжигом.Обычно процесс нормализации выполняется на материалах, которые будут подвергаться механической обработке, потому что процесс улучшил этот атрибут.
Закалка
Закалка применяется к стали и другим сплавам для улучшения их механических свойств. Во время закалки металл нагревается до высокой температуры, и эта температура поддерживается до тех пор, пока часть углерода не растворится. Затем металл закаливают, что включает его быстрое охлаждение в масле или воде. При закалке образуется сплав, обладающий высокой прочностью и износостойкостью.Однако упрочнение также увеличивает хрупкость и не подходит для инженерных применений. Если необходимо, чтобы поверхность детали была достаточно твердой, чтобы противостоять износу и эрозии, при сохранении пластичности и прочности, чтобы выдерживать удары и ударные нагрузки, следует использовать поверхностное упрочнение.
Закалка
Закалка применяется к стали, где требуется пластичность. Незакаленная сталь очень твердая, но слишком хрупкая для большинства практических применений. Отпуск — это процесс низкотемпературной термообработки, обычно выполняемый после закалки (нейтральная закалка, двойная закалка, науглероживание при атмосферном давлении, нитроцементация или индукционная закалка) для достижения желаемого соотношения твердость / вязкость.Процесс включает нагрев стали до более низкой температуры, чтобы уменьшить часть избыточной твердости. Затем металлу дают остыть на неподвижном воздухе, что приводит к более жесткой и менее хрупкой стали.
Metal Supermarkets — крупнейший в мире поставщик мелкосерийного металла с более чем 85 обычными магазинами в США, Канаде и Великобритании. Мы являемся экспертами по металлу и обеспечиваем качественное обслуживание клиентов и продукцию с 1985 года.
В Metal Supermarkets мы поставляем широкий ассортимент металлов для различных областей применения.