Круг, проволока Лист, Плита, Лента (полоса), Шина Шестигранник Квадрат Труба круглая, втулка Труба профильная Уголок Швеллер Тавр Двутавр | -Выберите-АлюминийМедьЛатуньБронзаОловоСвинецЦинкНикелевые сплавыМедно-никелевые сплавыНихромНержавеющие сталиСталь А5, А5Е, А6, А7, АД0, АД00 Д16 АМц, АМцС, ММ АД31 АД1 АМг6 АМг5 АМг3 АМг2 М1, М2, М3 Л90 Л85 Л80 Л70 ЛС59-1 Л68 Л63 БрОФ7-0,2 БрОФ6,5-0,15 БрАЖН10-4-4 БрХ1 БрБ2БрКМц3-1 БрАМц9-2 БрАЖМц10-3-1,5 БрОЦС5-5-5 БрАЖ9-4 С0, С1, С2 Ц0, Ц1 НМц2,5 НМц5 НК0,2 Алюмель НМцАК2-2-1 Монель НМЖМц28-2,5-1,5 Хромель Т НХ9,5 Куниаль Б МНА6-1,5 Нейзильбер МНЦ15-20 Куниаль А МНА6-1,5 Константан МНМц40-1,5 Копель МНМц43-0,5 Мельхиор МН19 Манганин МНМц3-12 МНЖ5-1 Х15Н60 Х20Н80 12Х18Н10Т, 12Х18Н12Т, 12Х18Н9 04Х18Н10Т, 08Х18Н12Б 08Х13, 08Х17Т, 08Х20Н14С2 08Х22Н6Т, 15Х25Т 08Х18Н10, 08Х18Н10Т 08Х18Н12Т 10Х17Н13М2Т 10Х23Н18 12Х13, 12Х17 Ст3, Ст5, Ст10, Ст20 | Длина (м) b — Диаметр (мм) Длина (м) b — Ширина (мм) c — Толщина (мм) Длина (м) b — Сечение (мм) Длина (м) b — Сечение (мм) Длина (м) b — Толщина стенки (мм) c — Диаметр (мм) Длина (м) b — Толщина стенки (мм) c — Ширина (мм) d — Высота (мм) Длина (м) b — Толщина стенки (мм) c — Высота полки1 (мм) d — Высота полки2 (мм) Длина (м) b — Толщина стенки (мм) c — Ширина (мм) d — Высота (мм) Длина (м) b — Толщина стенки (мм) c — Ширина (мм) d — Высота (мм) e — Толщина перемычки (мм) Длина (м) b — Толщина стенки (мм) c — Ширина (мм) d — Высота (мм) e — Толщина перемычки (мм) |
Алюминий с «титановой» прочностью | Наука НИТУ «МИСиС»
В НИТУ «МИСиС» разработали упрочняющие модификаторы для 3D-печати изделий из алюминиевых композитов для аэрокосмической промышленности. Ученые НИТУ «МИСиС» предложили технологию, позволяющую в 2 раза увеличить прочность композитов, полученных с помощью 3D печати из алюминиевого порошка и приблизить характеристики полученных изделий к качеству титановых сплавов: прочность титана примерно в 6 раз выше, чем у алюминия, но и плотность титана в 1,7 раз выше (самолет или космический корабль из алюминия был бы значительно легче).
Ученые НИТУ «МИСиС» разработали упрочняющие модификаторы для 3D-печати изделий из алюминиевых композитов для аэрокосмической промышленности. Предложенная технология позволяет в 2 раза увеличить прочность композитов, полученных с помощью 3D-печати из алюминиевого порошка и приблизить характеристики полученных изделий к качеству титановых сплавов: прочность титана примерно в 6 раз выше, чем у алюминия, но и плотность титана в 1,7 раз выше. Основой нового композита стали разработанные модификаторы-прекурсоры на основе нитридов и оксидов алюминия, полученные сжиганием. Результаты работы опубликованы в высокорейтинговом научном журнале Sustainable Materials and Technologies.
Еще два десятилетия назад литьё в формы рассматривалось как единственный рентабельный способ изготовления объемных изделий. Прошли годы, прежде чем появился 3D-принтер по металлу, способный составить достойную конкуренцию металлургическим способам производства. Преимущество изготовления изделий сложной формы с помощью аддитивных технологий в получении более сложных конструкций получаемых изделий, низкая себестоимость и теоретически любая комбинация получаемых материалов.
В настоящее время существует несколько технологий, которые используются для печати металлом, основными из которых являются селективное лазерное плавление (Selective Laser Melting, SLM) и селективное лазерное спекание (Selective Laser Sintering, SLS). Обе они подразумевают постепенное наслаивание металлических порошковых «чернил» слой за слоем для построения заданной объемной фигуры. SLS или SLM — технологии аддитивного производства, основанные на послойном спекании порошковых материалов с помощью луча мощного (до 500 Ватт) лазера.
Один из оптимальных по характеристикам металлов для изготовления изделий для аэрокосмической промышленности— это титан, однако в 3D-печати он неприменим по причине пожаро- и взрывоопасности порошков. Альтернативой выступает алюминий, легкий (плотность 2700 кг/м3) — одно из главных требований отрасли, пластичный, обладающий модулем упругости ~70 МПа, пригодный для 3D-печати, однако недостаточно прочный и твердый: предел прочности даже для сплава Дюраль до 500 МПа, твердость по Бринелю НВ на уровне 20 кгс/мм2.
Решение задачи упрочения алюминиевой 3D-печати предложил научный коллектив кафедры цветных металлов и золота НИТУ «МИСиС» под руководством приглашенного профессора Александра Громова.
«Мы разработали технологию упрочения алюмоматричных композитов, полученных методом 3D-печати, получив инновационные прекурсоры — модификаторы, полученные сжиганием порошков алюминия. Продукты горения — нитриды и оксиды алюминия — обладают специфически подготовленной для спекания, разветвленной поверхностью со сформированными переходными нанослоями между частицами. Именно особые свойства и структура поверхности позволяет частицам прочно прикрепляться к алюминиевой матрице и в итоге повышает прочность полученных композитов в 2 раза», — рассказал руководитель исследовательской группы Александр Громов.
В настоящее время коллектив разработчиков тестирует полученные с помощью новой технологии прототипы изделий.
Титановые сплавы в медицине TI-4 и TI-6 Ti-4 Ti-6 (Ti6Al4V)
Титановые сплавы TI6AL4V и Ti6Al4V ELI в медицине
Титановые сплавы TI6AL4V и Ti6Al4V ELI в медицине
В 1951 году Levanthal G.C. в своей работе “Titanium: a metalforsurgery” [2] выделил титановый сплав Ti-4 Ti-6 (Ti6Al4V), как прекрасный металл для целей и задач восстановительной хирургии и ортопедии. Он считал, что у основанных на титане сплавов есть превосходные свойства для естественной биологической фиксации протезов. У данного титанового сплава, наряду с высоким уровнем биологической совместимости и отсутствием коррозии, показатель модуля эластичности близок к модулю эластичности костной ткани человека. Но из-за недостаточной прочности изделий из чистого титана были разработаны титановые сплавы с использованием легирующих добавок, повышающих модуль упругости конечного изделия, использующегося в медицине.
Титановые сплавы TI6AL4V и Ti6Al4V ELI (ExtraLowInterstitial — супер чистый) это сплавы, сделанные с добавлением 6% алюминия и 4% ванадия. Они являются наиболее распространенными типами титана, используемого в медицине. Из-за высокой биосовместимости с человеческим телом эти сплавы титана обычно используются в медицинских процедурах, а также при пирсинге. Также TI6AL4V и Ti6Al4V ELI, известные как Grade 5 и Grade 23, являются самыми часто используемыми в медицинских целях типами титановых сплавов в США. Эти титановые сплавы за счёт своей более высокой прочности относительно других титановых сплавов типа Grade 1,2,3 и 4 обладают лучшими характеристиками и отличаются большим сопротивлением к перелому. Это обуславливает их использование в качестве основы зубных (стоматологических или дентальных) имплантатов.[3]
Титановый сплав Ti6Al4V ELI (ExtraLowInterstitial — супер чистый) усиленная и более чистая версия сплава TI6AL4V. Это идеальный вариант, когда от титанового сплава нужно получить высокую прочность, отсутствие коррозии, прекрасную биосовместимость и небольшой вес. Он значительно более устойчив к такому явлению, как усталость металла, в сравнении с другими титановыми сплавами. Совокупность данных качеств сделали сплав Ti6Al4V ELI (Grade 23) одним из наиболее востребованных сплавов в медицине и стоматологии, в том числе и дентальной имплантологии.
В настоящее время титановые сплавы являются наиболее часто используемыми металлическими материалами в биомедицинских процедурах. Как правило, их используют для имплантации в целях замещения или восстановления утраченных твердых тканей. Титановый сплав TI6AL4V долгое время является основным медицинским сплавом для производства таких изделий, как искусственные коленные суставы, суставные головки, костные пластины, винты для фиксации костных тканей, протезы сердечного клапана и кардио-стимуляторы.
Механические свойства титановых сплавов
Свойство | TiGrade 4 | Ti 6Al4V (Grade 5) | Ti 6Al4V ELI (Grade 23) |
Предел прочности на растяжение (МПа) | 550 | 860 | 860 |
Деформация, растяжение(%) | 15 | 10 | 10 |
Модуль упругости (ГПа) | 103-107 | 114-120 | 115-120 |
Список использованной литературы:
- ASTM F136 «Standard Specification for Wrought Titanium 6AL-4VELi Alloy for Surgical Implant».
- Levanthal GC. Titanium: a metal for surgery. J BoneJointSurg. 1951. 33:473.
- Craig Schank . Titanium: The medical metal of choice. November 2012. 2.
- Arturo Corces, MD; Metallic Alloys. March 2015.
Повышение прочностных характеристик титановых сплавов
Библиографическое описание:Яшкова, С. С. Повышение прочностных характеристик титановых сплавов / С. С. Яшкова, Н. В. Бобков. — Текст : непосредственный // Молодой ученый. — 2016. — № 28 (132). — С. 215-217. — URL: https://moluch.ru/archive/132/36752/ (дата обращения: 13.04.2021).
Современное машиностроение трудно представить без термической обработки. С её помощью можно повысить прочностные характеристики любого металла (Рис. 1). В нашей статье речь пойдет о термической обработке титановых сплавов. В зависимости от состава и назначения их можно подвергать таким видам термической обработки как: отжиг, закалка, старение и химико-термическая обработка.
Рис. 1. термическая обработка металла
Изделия из титана чаще всего применяются в авиа и ракетостроении. Например, наиболее трудоемким является производство моноколеса (Рис. 2), представляющего собой диск с лопатками для забора воздуха. Всем известно, что остаточные напряжения после проточки лопастей, могут согнуть лопатки, приведя изделие в негодность. А так как титан металл не из дешевых, то такой брак, нанесет серьёзный ущерб предприятию. Для снятия остаточных напряжений применяется термическая обработка готовых изделий.
Рис. 2. Моноколесо
Чаще всего изделия из титана подвергают отжигу. Нагрев до 870–980град и далее выдержка при 530–660град. Широко применяется вакуумный отжиг, который позволяет уменьшить содержание водорода в титановых сплавах, что приводит к уменьшению склонности к замедленному разрушению и коррозийному растрескиванию. Для снятия небольших внутренних напряжений применяют неполный отжиг при 550–650 град. Титановые сплавы имеют низкое сопротивление износу и при использовании в узлах трения подвергаются химико-термической обработке. Для повышения износостойкости титан азотируют при 850–950 град в течение 30–60 часов в атмосфере азота (слой 0,05–0,15 мм). ВТ5 хорошо обрабатывается давлением и сваривается. ВТ6 обладает хорошими механическими и технологическими свойствами и упрочняется термической обработкой. ВТ14 применяют для изготовления тяжелонагруженных деталей. Сплав упрочняется закалкой (Рис. 3) при 850–880град в воде с последующим старением при 480–500град 12–16 часов. ВТ8 применяют после изотермического отжига. Для фасонного литья применяют сплавы ВТ5Л, ВТ6Л, ВТ14Л, которые обладают достаточно хорошими литейными и механическими свойствами.
Рис. 3 Термическая обработка в печи
Рассмотрено влияние интенсивной пластической деформации и режимов обработки на структуру и механические свойстватитанового сплава ВТ6. Показано, что применение всесторонней изотермической ковки (ВИК) и оптимальных режимов последующей термической и термомеханической обработки позволяет получить в сплаве повышенные прочностные свойства. Так, после ВИК и последующей закалки с температуры 960 °С с последующим старением при температуре 480 °С достигаются предел прочности σ = 1540 МПа и условный предел текучести ψ = 1485 МПа при удовлетворительном уровне относительного удлинения σ = 7 % и относительном сужении ψ = 34 %. Повышенныемеханические свойстваявляются результатом формирования мелкозернистой глобулярной микроструктуры в ходе ВИК, а также наследования дислокационной структуры деформации, которые позволяют при старении получить высокодисперсные продукты распада, обеспечивающие высокие прочностные характеристики.
Принципы выбора режимов отжига титана и его сплавов.
Отжиг первого рода, включающий рекристаллизационный, дорекристаллизационный отжиг и отжиг для уменьшения остаточных напряжений, в чистом виде применим лишь для α-сплавов и β-сплавов с термодинамически устойчивой β-фазой. В псевдо-α-, типичных α+β-и β-сплавах с термодинамически неустойчивой β-фазой на рекристаллизационные процессы могут накладываться фазовые превращения. Вклад фазовых превращении в формирование структуры и свойств сплавов наибольший при рекристаллизационном и дорекристаллизационном отжиге и наименьший при отжиге с целью снятия остаточных напряжений [1]. Если температура отжига для уменьшения остаточных напряжений достаточно низка, то фазовые превращения могут не развиваться и не влиять на структуру и свойства псевдо-α, α+β- и β-сплавов (с термодинамически неустойчивой β-фазой). Гомогенизационный отжиг для титановых сплавов не применяют из-за его малой эффективности.
Дорекристаллизационный отжиг основан на явлениях возврата I рода (отдыха) и II рода (полигонизации). Его проводят с целью, если не для полного, то хотя бы частичного снятия нагартовки, внесенной в металл предшествующей пластической деформацией. В титане и малолегированных сплавах на его основе при дорекристаллизационном отжиге нагартованный металл существенно разупрочняется, что связано с довольно большой в них энергией дефектов упаковки. Вследствие этого легко развивается полигонизация, в ходе которой существенно снижается средняя плотность дислокаций.
В термически упрочняемых сплавах, в частности в β-сплавах, полигонизация развивается при тех же температурах, при которых распадается метастабильная β-фаза. В тех случаях, когда температура деформации и скорости охлаждения после деформации были достаточно высокими, в деформированных полуфабрикатах фиксируется термодинамически нестабильная β-фаза. При нагреве деформированных полуфабрикатов до 500–700° С в них происходят не только процессы возврата и полигонизации, но и распад метастабильной β-фазы. Свойства отожженных титановых сплавов существенно зависят от того, что произойдет раньше — полигонизация или распад β-фазы.
В неполигонизованных титановых β-сплавах распад β-фазы при старении обычно протекает очень неоднородно по объему зерна, что приводит к низким пластическим характеристикам. После полигонизации метастабильная β-фаза распадается равномерно, что обусловливает повышенный комплекс механических свойств сплава и большую их однородность [2].
Выводы.
На данном этапе понятно, что термическая обработка заметно улучшает характеристики титановых сплавов, дальнейшей целью наших исследований стоит определение наилучших параметров для обработки титанового сплава ВТ6 и исследование прочностных характеристик для каждого из режимов, подобранных экспериментальным путем.
Литература:
- Gao P. F., Fan X. G. & Yang, H. (2017). Role of processing parameters in the development of tri-modal microstructure during isothermal local loading forming of TA15 titanium alloy. Journal of Materials Processing Technology, 239, 160–171. http://doi.org/10.1016/j.jmatprotec.2016.
08.015
- Wang, Z., Wang, X. & Zhu, Z. (2017). Characterization of high-temperature deformation behavior and processing map of TB17 titanium alloy. Journal of Alloys and Compounds, 692, 149–154. http://doi.org/10.1016/j.jallcom.2016.09.012
Основные термины (генерируются автоматически): термическая обработка, сплав, отжиг, напряжение, последующее старение, свойство, титан, химико-термическая обработка.
Высокопрочные коррозионно-стойкие титановые сплавы для атомного машиностроения и ядерной энергетики
Руководители проекта:
Копылов Владимир Ильич, к.т.н., ведущий научный сотрудник НИФТИ ННГУ, ведущий научный сотрудник ФТИ НАН Беларуси – ведущий мировой специалист в области методов получения наноструктурированных и ультрамелкозернистых металлов и сплавов, разработчик (совместно с В.М. Сегалом) технологии равноканального углового прессования.
Чувильдеев Владимир Николаевич, д.ф.-м.н., профессор, директор НИФТИ ННГУ, заведующий кафедрой физического материаловедения ННГУ.
Структурные подразделения ННГУ – исполнители проекта:
Описание проекта
Научной целью проекта является разработка новых принципов нано- и микродизайна структуры радиационно-стойких конструкционных материалов (в первую очередь – титановых сплавов, а также аустенитных сталей), широко применяемых в атомном машиностроении и в ядерной энергетике. Разрабатываемые методы управления структурно-фазовым состоянием должны обеспечить решение задачи одновременного повышения их физико-механических свойств и эксплуатационных характеристик (в первую очередь – коррозионной стойкости и коррозионно-усталостной прочности).
Практической целью проекта является разработка технологических процессов получения изделий из нано- и микроструктурированных высокопрочных коррозионно-стойких титановых сплавов, которые могут успешно эксплуатироваться в течение длительного времени в экстремальных условиях одновременного воздействия повышенных нагрузок, температур, вибраций, радиационного воздействия. С практической точки зрения разрабатываемые методы дизайна базируются, в первую очередь, на современных технологиях интенсивного пластического деформирования (равноканально-угловое прессование, ротационная ковка), позволяющих формировать однородную нано- и микрокристаллическую структуру в металлических образцах, а также на теоретических подходах к описанию неравновесного состояния границ зерен, активно развиваемых в НИФТИ ННГУ и на кафедре физического материаловедения ННГУ.
Структура титанового сплава ПТ3В: исходное состояние (справа) и УМЗ состояние после равноканального углового прессования (слева)
В течение последних 3 лет коллективами НИФТИ ННГУ и АО “ОКБМ Африкантов” в рамках гранта РНФ №16-13-00066 был проведен большой цикл прикладных и фундаментальных исследований по разработке новых перспективных α- и псевдо-α титановых сплавов (Ti-5Al-2V, Ti-2.5Al-2.6Zr, Ti-0.5Al, Ti-0.16Pd и др.).
В ходе реализации данного блока работ были получены следующие результаты:
1. Изучена физико-химическая природа процессов горячей солевой коррозии в нано- и микроструктурированных титановых сплавах. Показано, что в α-титановых сплавах (Ti-5Al-2V) межкристаллитный характер горячей солевой коррозии обусловлен присутствием на границах зерен повышенной концентрации атомов ванадия, образующих микрогальваническую пару с кристаллической решеткой α-Ti. Установлено, что склонность псевдо-α титановых сплавах (Ti-2.5Al-2.6Zr) к горячей солевой коррозии определяется конкурирующим влиянием зернограничных сегрегаций и частиц β-фазы, располагающихся по границам зерен α- и α′-фаз.
2. Показано, что формирование ультрамелкозернистой структуры в α-титановом сплаве Ti-5Al-2V с использованием технологии равноканально-углового прессования позволяет обеспечить одновременное повышение прочности и стойкости к горячей солевой коррозии. Установлено, что повышенная коррозионная стойкость ультрамелкозернистого α-титанового сплава обусловлена эффектом уменьшения локальной концентрации атомов примесей (в первую очередь – ванадия) на границах зерен α-Ti и, соответственно, уменьшением разницы в концентрациях атомов алюминия и ванадия между объемом кристаллической решетки и границей зерен.
Общий вид образцов титанового сплава до испытаний (слева) и после испытаний на горячую солевую коррозию (справа). На поверхности испытанных образцов – пористые солевые отложения и оксиды титана (рутил, анатаз)
Сравнение характера коррозионного разрушения крупнозернистого (слева) и УМЗ сплава ПТ3В (справа). Глубина коррозии в УМЗ сплаве оказывается намного меньше, чем в крупнозернистом сплаве
Выделение частиц циркония (слева) и α”-фазы (справа) в УМЗ титановом сплаве ПТ7М при отжиге. Просвечивающая электронная микроскопия
3. Впервые изучен эффект деформационно-стимулированной пассивности наноструктурированного титанового сплава Ti-0.5Al в кислотных средах. Показано, что формирование методом ротационной ковки наноструктурированного состояния с высоким уровнем внутренних напряжений в сплаве Ti-0.5Al позволяет обеспечить пассивацию поверхности УМЗ титанового сплава и существенно снизить скорость электрохимической коррозии.
4. Установлено, что формирование наноструктурированного состояния в сплаве Ti-2.5Al-2.6Zr с использованием технологии ротационной ковки позволяет обеспечить одновременное повышение прочности и стойкости против коррозионно-усталостного разрушения.
Результаты фрактографического анализа различных участков излома образца сплава ПТ7М после коррозионно-усталостных испытаний. Растровая электронная микроскопия
В настоящее время исследования сконцентрированы вокруг решения задачи разработки новых рентгеновских методик исследований особенностей структурно-фазовых превращений в титановых сплавах при их горячей солевой коррозии и водородного охрупчивания (данные работы проводятся совместно с кафедрой кристаллографии и экспериментальной физики ННГУ), исследований особенностей зарождения и распространения коррозионно-усталостных трещин в титановых сплавах, а также на разработке основ новой технологии высокоскоростной диффузионной сварки УМЗ титановых сплавов, позволяющей сохранить однородную мелкозернистую структуру в сварном соединении и, как следствие, высокую прочность и коррозионную стойкость конструкции.
Микроструктура сварного шва в титановом сплаве ПТ3В, полученного методами аргоно-дуговой сварки (слева, сверху), электронно-лучевой сварки (слева, снизу) и высокоскоростной диффузионной сварки (справа)
Финансирование проекта
- Договора с АО “ОКБМ Африкантов” на выполнение прикладных НИОКР по разработке технологических процессов получения и обработки высокопрочных коррозионно-стойких титановых и циркониевых сплавов.
- Госконтракт №П2543 на выполнение НИР “Физические методы наномодифицирования структуры металлов и сплавов для создания новых материалов для радиационно-стойких элементов и конструкций атомной техники” в рамках ФЦП «Научные и научно-педагогические кадры инновационной России» на 2009-2013 годы.
- Госконтракт №П2340 на выполнение НИР “Разработка и исследование наноструктурированного технически чистого титана, обладающего уникальными физико-механическими свойствами” ФЦП «Научные и научно-педагогические кадры инновационной России» на 2009-2013 годы.
- Грант №14.В37.21.0761 на выполнение НИР “Разработка и исследование субмикрокристаллических циркониевых сплавов с повышенной прочностью и стойкостью к особым видам коррозии для тепловыделяющих элементов и других высокоответственных элементов конструкций и узлов активной зоны перспективных ядерно-энергетических установок” в рамках ФЦП «Научные и научно-педагогические кадры инновационной России» на 2009-2013 годы.
- Грант №14.740.11.1367 на выполнение НИР “Разработка новых наноструктурированных и субмикрокристаллических сталей с повышенными физико-механическими свойствами и коррозионной стойкостью для современных транспортных ядерно-энергетических установок и других приложений в машиностроении” в рамках ФЦП «Научные и научно-педагогические кадры инновационной России» на 2009-2013 годы.
- Госконтракт №16.516.11.6088 на выполнение НИОКР “Разработка новых субмикрокристаллических титановых сплавов с одновременно повышенной прочностью и коррозионной стойкостью” в рамках ФЦП «Исследования и разработки по приоритетным направлениям развития научно-технического комплекса России на 2007-2013 годы».
- Грант РФФИ №12-08-90003-Бел_а “Разработка и исследование термостабильных наноструктурированных и субмикрокристаллических титановых сплавов для ядерной энергетики и атомного машиностроения”.
- Грант РФФИ №12-08-33080-мол_вед_а “Высокопрочные коррозионно-стойкие субмикрокристаллические конструкционные материалы для перспективных приложений в машиностроении: разработка и исследование”.
- Грант РФФИ №13-03-97109-р_поволжье_а “Исследования свариваемости высокопрочных коррозионно-стойких субмикрокристаллических металлов и сплавов в условиях высокоскоростного нагрева”.
- Грант РНФ №16-13-00066 “Коррозионно-механическое разрушение и межкристаллитная коррозия высокопрочных мелкозернистых титановых сплавов: эксперимент, моделирование и методики”.
- Грант РНФ №19-73-00295 «Исследование структурно-фазовых особенностей перспективных титановых сплавов с повышенной коррозионной стойкостью».
- Грант СП-1671.2019.2 “Исследование механизмов коррозионно-усталостного разрушения перспективных мелкозернистых титановых сплавов” (стипендия Президента РФ для молодых ученых и аспирантов, осуществляющих перспективные исследования и разработки по приоритетным направлениям модернизации российской экономики).
Партнеры проекта
- АО “ОКБМ Африкантова” (г. Нижний Новгород) – ведущий отечественный разработчик ядерных ректоров, входящий в состав ГК “Росатом”.
- ФТИ НАН Беларуси (г. Минск, Беларусь) – совместные исследования в области новых способов формирования нано- и ультрамелкозернистых структур в титановых сплавах.
- НИТУ “МИСИС” (г. Москва) – совместные исследования титановых нано- и ультрамелкозернистых сплавов методами высокоразрешающей просвечивающей электронной микроскопии.
Основные публикации проекта (за последние 5 лет)
- Чувильдеев В.Н., Копылов В.И., Бахметьев А.М., Сандлер Н.Г., Нохрин А.В., Тряев П.В., Лопатин Ю.Г., Козлова Н.А., Пискунов А.В., Мелехин Н.В. Эффект одновременного повышения прочности и коррозионной стойкости микрокристаллических титановых сплавов // Доклады академии наук, 2012, т.
442, №3, с.329-331.
- Чувильдеев В.Н., Копылов В.И., Нохрин А.В., Лопатин Ю.Г., Козлова Н.А., Табачкова Н.Ю., Семенычева А.В., Смирнова Е.С., Грязнов М.Ю., Пирожникова О.Э. Влияние состояния границ зерен на термическую стабильность структуры субмикрокристаллического титанового сплава // Письма в ЖТФ, 2015, т.41, вып.11, с.1-9.
- Чувильдеев В.Н., Копылов В.И., Нохрин А.В., Бахметьев А.М., Сандлер Н.Г., Тряев П.В., Козлова Н.А., Табачкова Н.Ю., Михайлов А.С., Чегуров М.К., Смирнова Е.С. Влияние локального химического состава границ зерен на коррозионную стойкость титанового сплава // Письма в ЖТФ, 2016, т.42, №24, с.24-32.
- Chuvil’deev V.N., Kopylov V.I., Nokhrin A.V., Tryaev P.V., Kozlova N.A., Tabachkova N.Yu., Lopatin Yu.G., Ershova A.V., Mikhaylov A.S., Gryaznov M.Yu., Chegurov M.K. Study of mechanical properties and corrosive resistance of ultrafine-grained a-titanium alloy Ti-5Al-2V // Journal of Alloys and Compounds, 2017, v.723, p.354-367.
- Чувильдеев В.Н., Копылов В.И., Нохрин А.В., Бахметьев А.М., Сандлер Н.Г., Козлова Н.А., Тряев П.В., Табачкова Н.Ю., Михайлов А.С., Ершова А.В., Грязнов М.Ю., Чегуров М.К., Сысоев А.Н., Смирнова Е.С. Эффект одновременного повышения прочности, пластичности и коррозионной стойкости ультрамелкозернистого псевдо-альфа титанового сплава Ti-4Al-2V // Письма в ЖТФ, 2017, т.43, №10, с.25-33.
- Nokhrin A.V., Chuvil’deev V.N., Boldin М.S., Piskunov A.V., Kozlova N.A., Chegurov M.K., Popov A.A., Lantcev E.A., Kopylov V.I. and N Yu Tabachkova. The use of Spark Plasma Sintering method for high-rate diffusion welding of high-strength UFG titanium alloys // IOP Conference Series: Materials Science and Engineering, 218 (2017) 012013. doi: 10.1088/1757-899X/218/1/012013
- Ozerov M., Klimova M., Sokolovsky V., Stepanov N., Popov A., Boldin M., Zherebtsov S. Evolution of microstructure and mechanical properties of Ti/TiB metal-matrix composite during isothermal multiaxial forging // Journal of Alloys and Compounds, 2019, v.
770, p. 840-848.
- Chuvil’deev V.N., Kopylov V.I., Nokhrin A.V., Tryaev P.V., Tabachkova N.Y., Chegurov M.K., Kozlova N.A., Mikhaylov A.S., Ershova A.V., Gryaznov M.Yu., Shadrina Y.S., Likhnitskii C.V. Effect of severe plastic deformation realized by rotary swaging on the mechanical properties and corrosion resistance of near-α-titanium alloy Ti-2.5Al-2.6Zr // Journal of Alloys and Compounds, 2019, v.785, p.1233-1244.
- Nokhrin A.V., Boldin M.S., Piskunov A.V., Kozlova N.A., Chegurov M.K., Tabachkova N.Yu., Chuvil’deev V.N., Tryaev P.V. The Use of SPS for High-Rate Diffusion Welding of High-Strength Ultrafine-Grained α-Titanium Alloy Ti-5Al-2V. Chapter 24 in book ‘Spark Plasma Sintering of Materials’. Ed. Cavaliere P. (ISBN 978-3-030-05326-0, DOI 10.1007/978-3-030-05327-7), 2019, Springer Nature. (doi: 10.1007/978-3-030-05327-7_24).
- Chuvil’deev V.N., Kopylov V.I., Berendeev N.N., Murashov A.A., Nokhrin A.V., Gryaznov M.Yu., Shadrina I.S., Tabachkova N.Yu., Likhnitskii C.V., Kotkov D.N., Tryaev P.V. Corrosion fatigue crack initiation if ultrafine-grained near-α titanium alloy PT7M prepared by Rotary Swaging // Journal of Alloys and Compounds, 2019, v.790, p.347-362.
- Chuvil’deev V.N., Nokhrin A.V., Kopylov V.I., Boldin M.S., Vostokov M.M., Gryaznov M.Yu., Tabachkova N.Yu., Tryaev P. Spark plasma sintering for high-speed diffusion bonding of the ultrafine-grained near-α Ti–5Al–2V alloy with high strength and corrosion resistance for nuclear engineering // Journal of Materials Science, 2019, v.54, iss.24, p.14926-14949.
- Андреев П.В., Сметанина К.Е., Гудзь Д.А., Табачкова Н.Ю., Шадрина Я.С. Рентгенодифракционные исследования фазового состава α- и псевдо-α-титановых сплавов // Заводская лаборатория. Диагностика материалов, 2020, т.86, №9, с.45-51.
- Чувильдеев В.Н., Берендеев Н.Н., Мурашов А.А., Копылов В.И., Нохрин А.В., Грязнов М.Ю., Лихницкий К.В., Табачкова Н.Ю., Галаева Е.А., Котков Д.Н., Бахметьев А.М., Тряев П.В., Мышляев М.
М. Изучение особенностей коррозионно-усталостного разрушения мелкозернистого титанового сплава ПТ-7М, полученного методом ротационной ковки // Металлы, 2020, №4,с.64-76.
СМИ о проекте:
- Нижегородские ученые повысили прочность титановых сплавов для атомного машиностроения (источник – сайт ННГУ).
- Титановые сплавы для атомных реакторов можно сделать гораздо прочнее и лучше без легирования платиновыми или другими редкими металлами (источник – сайт Индикатор.ру).
К участию в проекте, выполнению курсовых и дипломных работ по тематике проекта, приглашаются бакалавры, магистры и аспиранты физического факультета ННГУ, в первую очередь — студенты и аспиранты кафедры физического материаловедения и кафедры кристаллографии и экспериментальной физики ННГУ.
Контактная информация для студентов: Нохрин А.В., e-mail: [email protected]
Состав и свойства титановых сплавов » Все о металлургии
23.04.2015
Титан относят к группе тугоплавких элементов, обладающих высокой химической активностью в расплавленном состоянии. Температура плавления его 1680 °С, плотность 4,5 г/см3; он имеет в 18 раз меньшую, чем алюминий, и в 4 раза меньшую, чем железо, теплопроводность, высокое электрическое сопротивление и достаточно химически стоек в ряде агрессивных сред. До 882 °C устойчива α-модификация титана с гексагональной кристаллической решеткой, выше этой температуры устойчива β-модификация с кубической пространственно-центрированной кристаллической решеткой. При нормальной температуре титан имеет резко выраженную анизотропию свойств.
Фасонные отливки изготовляют из сплавов, состав которых приведен в табл. 29. В качестве основного литейного сплава в России принят сплав ВТ5Л, сочетающий высокую прочность и хорошие литейные свойства.
Чистый титан и его сплавы обладают ценным комплексом физико-химических и механических свойств: высокой удельной прочностью, удовлетворительной пластичностью при комнатной, повышенной и минусовой температурах, хорошей свариваемостью, малым коэффициентом линейного расширения, высокой коррозионной стойкостью в ряде агрессивных сред и др.
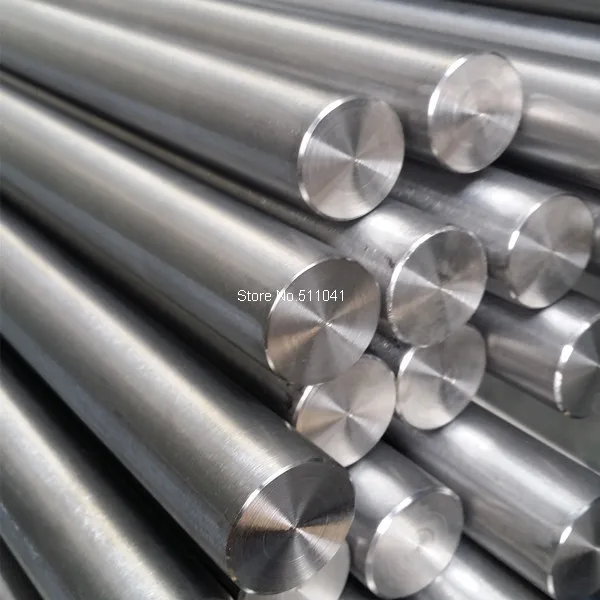
Интервал кристаллизации у большинства литейных сплавов не превышает 50 70 °С, поэтому они мало предрасположены к образованию рассеянной усадочной пористости. Титан и сплавы на его основе имеют хорошую жидкотекучесть. Линейная усадка их составляет 1,5 % при литье в керамические формы и 2—2,3 % при заливке в металлические формы. Объемная усадка при кристаллизации не превышает 3 %. Титановые сплавы имеют малую склонность к образованию усадочных трещин.
Прочностные свойства (σв, σ0,2, Е) литейных титановых сплавов близки к свойствам сплавов, прошедших горячую пластическую обработку. В то же время значения относительного удлинения, относительного сужения, ударной вязкости и характеристики усталости ниже, чем у деформируемых сплавов.
Деформируемые сплавы по составу мало отличаются от литейных. В зависимости от назначения титановые сплавы делят на четыре группы: 1) свариваемые конструкционные; 2) высокопрочные; 3) жаропрочные; 4) сплавы со специальными свойствами (коррозионностойкие, для криогенных температур).
К первой группе относят нелегированный титан (ВТ 1-0), сплавы тройной системы Ti—Al—Mn (ОТ4) с гарантированной прочностью 500, 600 и 700 МПа, сплавы ВТ5-1 (5 % Al; 2,5 % Sn) и ВТ20 (6 % Al; 2 % Zr; 1 % V; 1 % Mo) с гарантированной прочностью 750 и 950 МПа соответственно.
Ко второй группе относят сплавы с пределом прочности при комнатной температуре более 1000 МПа: ВТ6, ВТ14, BT16, ВТ22. Все они, кроме алюминия, содержат в своем составе ванадий или молибден и ванадий.
К третьей группе относят сплавы, легированные алюминием, молибденом и цирконием (или хромом): ВТЗ-1, ВТ9.
В четвертую группу входят сплавы с молибденом и палладием и сплавы ВТ5-1 и ВТ6 повышенной чистоты.
Медицина
Соответствие титана целям имплантации
Порядка 4000 тонн титановых приспособлений различных наименований и назначения имплантируются каждый год по всему миру. Потребности в замене суставов продолжают расти, т.к. продолжительность жизни увеличивается, люди все чаще получают повреждения в результате занятия тяжелыми видами спорта или бега, они получают серьезные травмы в автомобильных авариях и других происшествиях. Легкий, прочный и полностью биосовместимый, титан является одним из немногих материалов, которые по природе своей отвечают требованиям имплантации в человеческое тело. Соотношение прочности и веса титановых сплавов медицинского качества значительно выше по сравнению с нержавеющей сталью. Разнообразие существующих титановых сплавов позволяет специалистам и разработчикам в области медицины выбирать материалы и формы, которые приспособлены к нуждам данной области применения.
Характеристики титана в медицине
«Сделай и забудь» составляет основное требование там, где оборудование критического назначения, будучи установленным, уже не подлежит периодическому ремонту или замене. В данном отношении нет ничего более требовательного, чем имплантанты в человеческом теле. Титан считается абсолютно неактивным и устойчивым к коррозии в результате воздействия жидкостей и тканей организма, а потому полностью биосовместимым.
Замена костей и суставов
Более двух миллионов пациентов по всему миру ежегодно проходят лечение с целью замены бедренных и коленных суставов. Выпускаются протезы различных форм и размеров. Бедренные суставы обычно имеют металлический бедренный стержень и головку, которая помещается в углубление из полиэтилена низкого трения с чрезвычайно высоким молекулярным весом, обе части фиксируются при помощи костного цемента полиметилметакрилата. В некоторых разработках, в том числе в суставах без цемента, используются биоактивные поверхности с шероховатостью (включая гидроксиапатит), которые способствуют интеграции с костной тканью, ограничивают резорбцию, и таком образом, повышают срок службы имплантантов для молодых реципиентов. Внутренняя и внешняя фиксация костных переломов еще расширяет круг возможных способов применения титана, например, в качестве приспособлений для укрепления позвоночника, штифтов, костных пластин, винтов, внутримозговых стержней и наружных фиксаторов.
Зубные имплантанты
Значительные перемены в стоматологической восстановительной практике оказались возможными благодаря применению титановых имплантантов. Титановый «корень» вживляется в челюстную кость на время, необходимое для интеграции с костной тканью. Затем на имплантант наращивается верхняя часть зуба, что обеспечивает эффективное замещение.
Лечение челюстно-лицевой и черепно-лицевой области
Хирургические операции по исправлению повреждений лица с применением собственных тканей пациента не всегда приводят к желаемым результатам. Искусственные элементы могут потребоваться для восстановления способности говорить или есть, а также для пластических операций по изменению черт лица после повреждения или болезни. Титановые имплантанты, которые интегрируются с костной тканью и отвечают всем требованиям биосовместимости и прочности, сделали возможными беспрецедентные достижения в области хирургии для успешного лечения пациентов со значительными дефектами и тех, кто до сих пор находился в чрезвычайно тяжелом состоянии.
Сердечно-сосудистые приспособления
Титан обычно используется для корпусов электронных стимуляторов сердца и дефибрилляторов в качестве несущего приспособления для замены сердечных клапанов и для внутрисосудистых стентов.
Наружные протезы
Титан подходит как для временных, так и для используемых долгое время наружных фиксаторов и приспособлений, а также для металлических шин в биопротезировании и искусственных конечностей, в обоих случаях титан широко используется благодаря его легкости, вязкости и устойчивости к коррозии.
Хирургические инструменты
Широкий ассортимент хирургических инструментов изготавливается из титана. Легкость металла положительно сказывается на снижении усталости хирурга. Часто инструменты подвергаются анодированию с целью создания неотражающей поверхности, которая приобретает особое значение в микрохирургии, например, в глазной хирургии. Титановые инструменты выдерживают повторную стерилизацию без ущерба качеству лезвия или поверхности, устойчивости к коррозии или прочности. Титан не намагничивается, и поэтому не представляет угрозы для небольших и чувствительных вживленных электронных устройств.
Сердечные клапана
марок титана — Continental Steel & Tube Company
Титан CP4 — сорт 1
Коммерчески чистый титан Grade 1 — самый мягкий титан с самой высокой пластичностью. Он обладает хорошими характеристиками холодной штамповки и обеспечивает отличную коррозионную стойкость. Он также обладает отличными сварочными свойствами и высокой ударной вязкостью.
Архитектура, Автомобильное опреснение, Габаритные стабильные аноды, Медицинский, Морской, Обработка и производство хлоратов
ASME SB-363, ASME SB-381, ASME SB-337, ASME SB-338, ASME SB-348, ASTM F-67, ASME SB-265, ASME SB-337, ASME SB-338
Штанга, Фланцы, Поковки, Простынь, Сварочная проволока
Титан CP3 — марка 2
Технически чистый титан марки 2 обладает средней прочностью и отличными характеристиками холодной штамповки.Он обеспечивает отличные сварочные свойства и обладает отличной стойкостью к окислению и коррозии.
Аэрокосмическая промышленность, Автомобильная промышленность, Химическая обработка и производство хлоратов, Опреснение, Архитектура, Обработка углеводородов, Морской, Медицинский, Энергетика
ASME SB-363, ASME SB-381, ASME SB-337, ASME SB-338, ASME SB-348, ASTM F-67, AMS 4921, г. ASME SB-265, AMS 4902, ASME SB-337, ASME SB-338, AMS 4942
Бар, Фитинги, Фланцы, Поковки, Труба, плита, Простынь, Трубка, Сварочная проволока, Проволока
Титан CP2 — марка 3
Технически чистый титан 3-й степени прочнее и менее пластичен, чем титан 1 и 2 марки.Он используется в аэрокосмической и промышленной сферах, где требуется умеренная прочность. Титан класса 3 обладает отличной коррозионной стойкостью.
Аэрокосмическая промышленность, Архитектура, Автомобильная промышленность, Химическая обработка и производство хлоратов, Опреснение, Обработка углеводородов, Морской, Медицинский, Энергетика,
ASME SB-363, ASME SB-381, ASME SB-337, ASME SB-338, ASME SB-348, ASTM F-67, AMS 4921, г. ASME SB-265, AMS 4902, ASME SB-337, ASME SB-338, AMS 4942
Бар, Фитинги, Фланцы, Поковки, Труба, плита, Простынь, Трубка, Сварочная проволока, Проволока
Титан CP1 — марка 4
Коммерчески чистый титан марки 4 прочнее, чем CP марок 2 и 3 — он может быть подвергнут холодной деформации, но имеет более низкую пластичность.Обладает отличной коррозионной стойкостью в самых разных средах. Титан класса 4 обычно используется в аэрокосмической, промышленной и медицинской областях, где требуется высокая прочность.
Аэрокосмическая промышленность, Химический процесс, Промышленное, Морской, Медицинский
ASME SB-363, ASME SB-381, ASME SB-337, ASME SB-348, ASTM F-67, AMS 4921, г. ASME SB-265, AMS 4901, г. ASME SB-338
Штанга, Поковки, Простынь, Сварочная проволока, Проволока
Титан Grade 7
Титан Grade 7 имеет физические и механические свойства, эквивалентные титану CP3 или Grade 2.Он имеет отличные сварочные и технологические свойства и чрезвычайно устойчив к коррозии, особенно от восстанавливающих кислот.
Химическая обработка, Опреснение, Электроэнергетика
ASME SB-363, ASME SB-381, ASME SB-337, ASME SB-338, ASME SB-348, ASME SB-265, ASME SB-337, ASME SB-338,
Бар, Поковки, Пластина, Простынь, Трубка, Сварочная проволока, Проволока
Титан Grade 11 — CP Ti-0.15Pd
Титан Grade 11 обладает высокой устойчивостью к коррозии, имеет физические и механические свойства, аналогичные титану CP Grade 2.
Химическая обработка, Опреснение Энергетика, Промышленные
Сплавы на основе титана
Титан Grade 5 — Титан 6Al-4V
Титановый сплав Grade 5 является наиболее коммерчески доступным из всех титановых сплавов. Он предлагает отличное сочетание высокой прочности и жесткости. Титан 5-го класса обладает хорошими сварочно-технологическими характеристиками.
Аэрокосмическая промышленность, Химическая обработка, Морской, Медицинский
ASME SB-265, AMS 4911, г. ASME SB-348, AMS 4928, г. AMS 4965, AMS 4967
Титан Grade 6 — Титан 5Al-2.5Sn
Титановый сплав Grade 6 обеспечивает хорошую свариваемость, стабильность и прочность при повышенных температурах.
ASME SB-381, AMS 4966, МИЛ-Т-9046, МИЛ-Т-9047, ASME SB-348, AMS 4976, г. AMS 4956, г. ASME SB-265, AMS 4910, г. AMS 4926
Бар, Поковки плита, Простынь, Проволока
Титан Grade 9 — Титан 3Al-2.5V
Титан Grade 9 имеет среднюю прочность, которая находится между Grade 4 и Grade 5. Он обладает превосходной коррозионной стойкостью и используется в аэрокосмической и промышленной сферах.Титан марки 9 можно использовать при более высоких температурах, чем титан марок 1–4. Титан марки 9 обладает хорошими свойствами холодной прокатки.
Аэрокосмическая промышленность, Автомобильная промышленность, Химическая обработка, Потребительские приложения, Морской, Медицинский, Транспорт
AMS 4943, AMS 4944, г. ASME SB-338
Штанга, Поковки плита, Простынь, Проволока
Титан Grade 12 — Ti-0.3-Mo-0.8Ni
Этот сплав титана марки 12 аналогичен титану марок 2 и 3, за исключением того, что титан марки 12 имеет значение 0.3% молибдена и 0,8% никеля. Это обеспечивает повышенную коррозионную стойкость.
Химическая обработка, Опреснение, Выработка энергии, Промышленный
Титан Grade 19 — Titanium Beta C
Титан марки 19 обладает очень высокой прочностью и может подвергаться термообработке. Обладает хорошей устойчивостью к нагрузкам и коррозии.
МИЛ-Т-9046, МИЛ-Т-9047, ASME SB-348, AMS 4957, г. AMS 4958, ASME SB-265
Титан, класс 23 — Титан 6Al-4V ELI
Титан Grade 23 аналогичен Grade 5, но содержит меньше кислорода, азота и железа. У него лучшая пластичность и вязкость разрушения, чем у титана марки 5.
Аэрокосмическая промышленность, Химическая обработка, Морской, Медицинский
АМС 4911, AMS 4928, AMS 4930, AMS 4931, AMS 4935, г. AMS 4965, AMS 4967, AMS 4985, AMS 4991, г. MIL-T-9046, MIL-T-9047, БСТА 10,11,12, БСТА 28,56,59, DIN 3.7165, AMS 4907 ELI, AMS 4930 ELI, AMS 4956 ELI, ASTM F136 ELI, UNS R56407
Бар, Поковки, Пластина, Простынь, Сварочная проволока, Проволока
Титан 6Al-6V-2Sn — Титан 6-6-2
Титан 6-2-4-2 обладает превосходной прочностью, стабильностью и сопротивлением ползучести при температурах до 550 ° C.
Газ, Форсажная камера двигателя компрессора турбины, Aerospace
AMS 4919, г. AMS 4952, AMS 4975, DIN 3.7164, GE B50 TF22, GE B50TF21, GE B50TF22, GE C50TF7, MIL F-83142, МИЛ Т-9046, МИЛ Т-9047, PWA 1220, UNS R54620
Титан 6Al-2Sn-4Zr-2Mo — Титан 6-2-4-2
Титан 6Al-6V-2Sn представляет собой двухфазный альфа-бета-сплав. Обычно он используется в отожженных или обработанных на твердый раствор и выдержанных условиях.Это термически обрабатываемый высокопрочный сплав с более низкой вязкостью и пластичностью, чем у титана марки 5 (6Al-4V), и его трудно сваривать. Холодная штамповка титана 6Al-6V-2Sn затруднена из-за его высокой прочности и большого количества возникающих в результате упругого возврата. Этот сплав можно сваривать с помощью процесса сварки плавлением в среде защитного инертного газа, но зона термического воздействия будет иметь меньшую пластичность и вязкость, чем основной материал. Твердость титана 6-6-2 приблизительно равна C 36-38 по Роквеллу. Этот сорт в основном используется для деталей планера и реактивного двигателя, корпусов ракетных двигателей и компонентов боеприпасов.Позвоните нам, чтобы определить минимальное количество товара.
Компоненты планера, Детали реактивного двигателя, Компоненты постановления, Корпуса ракетных двигателей
Бар, Проволочный лист, Пластина, Поковки, Фитинги, Фланцы, Бесшовная труба, Бесшовная труба, Сварная труба, Труба сварная
Титан 6Al-2Sn-4Zr-6Mo — Титан 6-2-4-6
Титан 6Al-2Sn-4Zr-6Mo — это сплав альфа-бета, который обычно считается основным сплавом титановой промышленности. Сплав полностью поддается термообработке с размером сечения до одного дюйма и используется при температуре примерно до 400 ° C (750 ° F). Так как это один из наиболее часто используемых сплавов (более 70% всех расплавленных марок сплавов — это субсорт Ti-6-4), его применение охватывает многие компоненты аэрокосмических двигателей и планера. Титан 6Al-2Sn-4Zr-6Mo также используется во многих неавиационно-космических приложениях, таких как судостроение, шельфовая промышленность и электроэнергетика. Этот альфа-бета-сплав сочетает в себе хорошую коррозионную стойкость и прочность, свариваемость и технологичность.Сплав обычно доступен в форме стержня и обычно используется в глубоких кислых скважинах. Этот сплав может быть горячего или холодного формования. Позвоните нам, чтобы определить минимальное количество товара.
Аэрокосмические двигатели, Компоненты планера, Морские приложения, Офшорные приложения, Применение в электроэнергетике
Титан 8Al-1Mo-1V — Титан 8-1-1
Титан 8Al-1Mo-1V — это почти альфа-сплав, который в первую очередь был разработан для использования при повышенных температурах — до 455 градусов по Цельсию.Он предлагает самый высокий модуль и самую низкую плотность среди всех титановых сплавов. Он обладает хорошим сопротивлением ползучести и поддается сварке методами плавления в инертном газе и контактной сварки. Титан 8Al-1Mo-1V используется в отожженном состоянии для таких применений, как детали планера и реактивного двигателя, которые требуют высокой прочности, превосходного сопротивления ползучести и хорошего отношения жесткости к плотности. Обрабатываемость этой марки аналогична титану 6Al-4V. Позвоните нам, чтобы определить минимальное количество товара.
Детали планера, Детали реактивного двигателя
MIL-T-9046, МИЛ-Т-9047, AMS 4972, AMS 4915, г. AMS 4973, г. AMS 4955, AMS 4916
Поковки, Бар, Простынь, Пластина, Полоска, Экструзии, Проволока
Титан 10В-2Fe-3Al
Титан 10V-2Fe-3Al — это титановый бета-сплав. Он тверже и прочнее многих титановых сплавов. Этот титан — термообрабатываемый сплав, свариваемый и легко формующийся. Титан 10V-2Fe-3Al является полностью бета-сплавом и его труднее обрабатывать, чем большинство титановых сплавов.Основные проблемы включают износ по задней поверхности, пружинение и контроль стружки. Благодаря этим характеристикам предпочтительными являются канавки для стружки с положительным передним выступом в сочетании со светлыми точками на режущей кромке. Позвоните нам, чтобы определить минимальное количество товара.
Компоненты планера, Лопатки, диски, колеса и проставки компрессора
AMS 4983, AMS 4984, г. AMS 4986, г. AMS 4987
Бар, Поковки, Пластина, Простынь, Бесшовная труба, Бесшовная труба, Сварная труба, Сварная труба, Проволока
Титан 15В-3Cr-3Sn-3Al
Этот метастабильный бета-сплав используется в основном в виде листового металла.Он устойчив к старению и хорошо деформируется в холодном состоянии. Титан 15В-3-3-3 часто используется для замены горячеформованного листа титана Grade 5 (6Al-4V). Он также может производиться в виде фольги и является отличным сплавом для отливок. Для аэрокосмических приложений этот сорт часто указывается как AMS 4914. Пожалуйста, позвоните, чтобы определить минимальное количество товара.
Применение в аэрокосмических резервуарах, Приложения для планера, Отливки, Крепеж Высокопрочные гидравлические трубки
Титановые альфа-сплавы
Технически чистый титан и альфа-сплавы титана не подлежат термической обработке и обладают очень хорошими сварочными характеристиками.
Криогенные приложения, Детали самолетов, Химико-технологическое оборудование
AMS 4973, AMS 4976, г. AMS 4924, г. AMS 4972, МИЛ-Т-9047, AMS 4910, г. ASTM B265, GR-6 MIL-T9046, AMS 4909, г. AMS 4915/4916, AMS 4966, AMS 4924, г. AMS 4973, г. AMS 4933, г. MIL-T-81556A A-1, MIL-T-81556A A-2, MIL-T-81556A A-4
Бар, Поковки, Пластина, Листовые экструзии
Бета-сплавы титана
Титановые бета-сплавы или сплавы, близкие к бета:
- Полностью поддается термообработке Обычно сваривается
- Обладает высокой прочностью Обладает хорошей стойкостью к ползучести до промежуточных температур
- В состоянии, обработанном раствором, от Beta Alloys можно ожидать отличной формуемости.
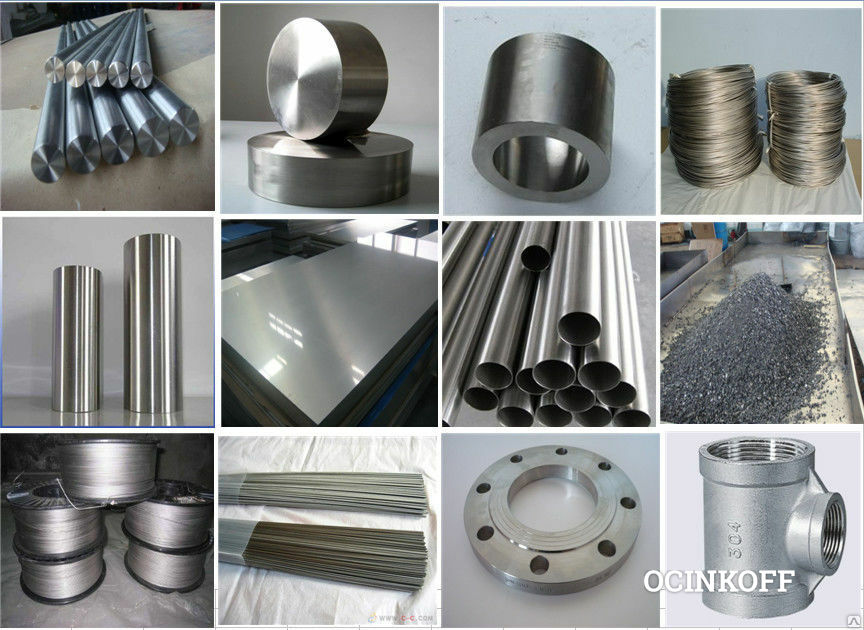
Бета-титановые сплавы идеально подходят для спортинга.Распространенные титановые бета-сплавы включают:
Ti3Al8V6Cr4Mo4Zr
ASTM Grade 19
Ti-3Al-8V-6Cr-4Mo-4Zr
AMS 4983, 4984, 4987
Ti-10V-2Fe-3Al
ASTM Grade 21
Ti-15Mo-3Nb-3Al-2Si
AMS 4914
Ti-15V-3Cr-3Sn-3Al
Метастабильные бета-сплавы титана поддаются термообработке путем обработки на твердый раствор и старения. Полностью стабильные бета-сплавы можно только отжигать.
AMS 4914, г. AMS 4983, г. AMS 4984, г. AMS 4987, г. ASTM класс 19, ASTM Grade 21
Титановые альфа-бета-сплавы
Титановые сплавы Alpha Beta поддаются термообработке, и большинство из них также поддаются сварке.Типичные свойства титановых альфа-бета-сплавов:
- От среднего до высокого уровня прочности;
- Сопротивление ползучести при высоких температурах не меньше, чем у большинства альфа-сплавов;
- Холодная штамповка ограничена, но качество горячей штамповки обычно хорошее;
Наиболее часто используемым титановым альфа-бета-сплавом является Ti 6Al-4V. Титан 6Al-4V был разработан во многих вариациях основного состава для множества и самых разных применений.
Другие титановые альфа-бета-сплавы включают: 6Al-4V-ELI 6Al-6V-2Sn 6Al-2Sn-4Zr-2Mo 3Al-2.5В 8Мн
Детали авиационных и авиационных турбин, Химико-технологическое оборудование, Морское оборудование, Протезы
ASME SB-265, AMS 4911, г. ASME SB-348, AMS 4928, г. AMS 4965, AMS 4967, г. AMS 4981, г. МИЛ-Т-9047, AMS 4930, AMS 4971, г. AMS 4907, г. ASTM F 136, МИЛ-Т-9046, AMS 4918, г. DMS1879 / 2237, AMS 4908, г. AMS 4943, г. ASTM B348, AMS 4975, MIL-T-9047 G, AMS 4928, г. БМС 7-348, DMS 1570, AMS 4976, г. AMS 4920, AMS 4934
Бар, Фитинги, Фланцы, Поковки, Трубка, Пластина, Простынь, Трубка, Проволока
Пластичность и хрупкость перехода титановых сплавов при сверхточной обработке
Стружкообразование
Морфология стружки и сегментация играют решающую роль в наблюдении обрабатываемости и механизма обработки титановых сплавов. Образования стружки, образовавшиеся на разной глубине резания, показаны на рис. 2 (a – f). Cook 27 объяснил взаимосвязь между морфологией стружки и температурой резания в процессе резания титановых сплавов; когда эффект термического разупрочнения в зоне первичной деформации преобладал над эффектом деформационного упрочнения, стружка имела бы зубчатую форму. Согласно рис. 2 (а), для стружкообразования, образовавшегося на глубине резания 2 мкм, длина зуба пилы была наибольшей по сравнению с длиной зуба пилы, образовавшейся на другой глубине резания, это объясняет, что эффект термического разупрочнения был сильнее при относительно небольшая глубина резания.Эффект интенсивного термического размягчения на границе раздела инструмент / заготовка дополнительно способствовал пластической деформации в зоне резания, поэтому длина зуба пилы уменьшалась с увеличением глубины резания, а степень пластической деформации уменьшалась с увеличением толщины резания.
( a — f ). Стружкообразование с указанием участков хрупкой и пластичной деформации на глубине резания 2–7 мкм. Буквы B и D обозначают зону хрупкой деформации и зону пластической деформации соответственно.
Кромка стружки показывала пилообразную форму в условиях резания с глубиной резания 2–4 мкм, кромка пилообразной формы постепенно исчезала при увеличении глубины резания до 5 мкм и более. Кроме того, согласно рис. 2 (а – в), зарождение пустот наблюдалось около кромки стружки на глубине реза 2–4 мкм; образование пустот внутри стружки свидетельствует о пластическом разрушении в процессе резания 28,29,30 , что свидетельствует о наличии пластичной деформации на такой глубине резания.Для образований стружки, образовавшихся при большей глубине резания 5–7 мкм, как показано на рис. 2 (d – f), формы этих стружек были цельными, без пустот, что означает, что хрупкая деформация преобладала на всем резании. процесс без использования пластичного режима резки. Приведенные выше экспериментальные результаты объясняют, что толщина резки определяет пластичную и хрупкую деформацию UPM титановых сплавов.
С другой стороны, на кромке стружки на глубине резания 2–4 мкм наблюдался периодический зубчатый зуб, при этом длина зуба пилы на кромке стружки была неоднородной в одной единственной стружке.Части кромки стружки отображали более длинный зуб с пилой, в то время как другие части отображали более короткий зуб пилы. Этот вывод согласуется с отчетом Sun. S и др. . 31 , в котором они заметили, что периодическая кромка стружки появлялась в поперечном сечении стружки при токарной обработке титановых сплавов. Периодическая структура стружки исчезла при увеличении глубины резания до 5–7 мкм. Образование неоднородной кромки стружки на глубине резания 2–4 мкм указывает на то, что хрупкая и пластичная деформация происходила одновременно за один проход при относительно небольшой глубине резания, аналогично формирование однородной кромки стружки на глубине резания 5 мкм– 7 мкм означало, что хрупкая деформация была единственным механизмом деформации при относительно большой глубине резания.Соответствующие области хрупких и пластичных деформаций на кромке стружки обозначены буквами «B» и «D» соответственно на рис. 2 (a – f).
Профиль резания и качество поверхности
Профили резания обработанной канавки на глубине резания 2–7 мкм показаны на рис. 3. Согласно рис. 3 профили резания каждой отдельной обработанной канавки (2–7 мкм) мкм) показали разную глубину при постоянной глубине резания, что было вызвано эффектом набухания материала. Фактически, эффект набухания материала обычно возникает в UPM.При непрерывном резании расплавленные материалы становятся вязкой жидкостью, и текучая среда располагается на двух сторонах и на дне кромки инструмента. Металлическая жидкость затвердевает и расширяется при снижении температуры обработанной поверхности 32,33 , в результате обрабатываемая поверхность набухает и на обработанной поверхности остаются видимые следы инструмента, что приводит к отклонению фактической глубины резания от заданной. Были сняты микроскопы трех областей каждой обработанной канавки, они обозначены как X, Y и Z, как показано на рисунках.Буквы X, Y и Z с индексом глубины резания обозначают обработанные области с «более низким уровнем набухания материала», «точкой перехода от более низкого набухания материала к более высокому набуханию материала» и «более высокого уровня набухания материала. » соответственно. Различия глубины между отдельными обработанными канавками отличались друг от друга и сильно зависели от глубины резания. Согласно рис. 3, при глубине резания 2–4 мкм глубина обработанной канавки изменялась вдоль обрабатываемой поверхности, глубина обработанной канавки сначала уменьшалась, а затем достигала минимального значения, глубина снова увеличивалась при следующем резании. расстояние, демонстрирующее разную степень набухания материала за один проход.Для обработанной канавки, сформированной при глубине резания 5–7 мкм, их режущие профили выглядели отчетливо, скорость уменьшения / увеличения глубины в профиле резания была меньше. Приведенные выше результаты предполагают, что скорость набухания материала изменяется при изменении глубины резания, и, следовательно, режущий механизм изменяется при изменении глубины резания.
Профили канавок и поверхности канавок, образующиеся при глубине резания 2–7 мкм. Буквы X, Y и Z обозначают область с «более низким уровнем набухания материала», «точкой перехода от более низкого набухания материала к более высокому набуханию материала» и «более высокого уровня набухания материала».
Области X всех обработанных канавок отображаются иначе, чем области Y и Z; области X имели более гладкую и тонкую поверхность по сравнению с областями Y и X, сформированными на всей глубине резания, на поверхности и краю поверхности на участках X не было разрывов. Для областей Y была четкая трещина на кромка канавки (показана красными кружками на рис. 3), она стала важным индикатором для точки перехода от области более низкого набухания материала к области более высокого набухания материала и начала перехода из пластичного в хрупкое состояние, трещина была определена как переход точка от пластичной до хрупкой области. Обработанные поверхности областей Z имели шероховатость, слева от кромки канавки в областях Z были трещины (показаны синим кружком на рис. 3), и они были следами неразрезанных материалов, которые образовались в результате хрупкой деформации в режиме хрупкого разрушения.
Шероховатость поверхности участков X, Y и Z на глубине резания 2–7 мкм показана на рис. 4. Результаты согласуются с профилями резания, показанными на рис. 3, из-за хрупкой деформации и разрушения трещин. стружки в областях Z было видно, что чистовая обработка поверхности, полученная в областях X, была лучше, чем у областей Z, где шероховатость поверхности областей X всегда была меньше, чем шероховатость поверхности областей Z.Особенно для поверхности, образованной на глубине реза 3 мкм и 4 мкм, разница в шероховатости поверхности между этими двумя областями была очень большой, это большое отклонение снова учитывалось различными режимами деформации в области X (пластичный) и области Z (хрупкий). Для областей Y на всей глубине резания шероховатость поверхности была самой высокой среди других областей; основной причиной было образование трещины в точке перехода из пластичного в хрупкое состояние, следовательно, рваная поверхность стала причиной худшего качества поверхности.
Рисунок 4Шероховатость поверхности участков X, Y и Z, образовавшаяся при глубине резания 2–7 мкм.
Расстояние резания между областями X и Y выражается как d, это объясняет минимальное / критическое расстояние резания при деформации хрупкого разрушения и начало появления огрубевшей поверхности. График зависимости d от глубины резания показан на рис. 5. Минимальное / критическое расстояние резания увеличивается с увеличением глубины резания.
Рисунок 5График зависимости d от разной глубины резания.d — минимальное / критическое расстояние резания для начала деформации хрупкого разрушения.
На рис. 6 показан процент глубокого набухания материала областей X и Z после алмазной резки, который был определен разницей между заданной и фактической глубиной резания на дне обработанной поверхности. Глубокое набухание материала вызывается расширенными материалами после затвердевания расплавленной металлической жидкости при резке. Согласно рис.6, эффект набухания материала был серьезным для титановых сплавов в UPM, процент набухания материала был более 40% для обеих областей X и Z, независимо от значения глубины резания, это одна из важных характеристик обработки. титановых сплавов, материалов с низким модулем упругости.
Процент восстановления материала областей X и Z.
Анализ силы резания
На рисунке 7 показано усилие осевого усилия обработанной канавки, возникающее при глубине резания 2–7 мкм. Сила тяги использовалась для определения уровня глубокого набухания материала в нижней части обработанной поверхности 9,10,11 . Более высокое значение силы тяги означает более высокий уровень глубокого разбухания материала на обрабатываемой поверхности и сквозных отверстиях. Согласно рис.7, сила тяги изменялась за один проход, это означало, что уровень набухания материала изменялся только на одну машинную канавку, и это соответствовало различным значениям глубины резания на отдельной обработанной канавке, как показано на рис.3. Вариация силы тяги уменьшалась с увеличением глубины резания. Усилия осевого напора в значительной степени колебались на глубине реза 2–4 мкм, а на глубине реза 5–7 мкм он становился более плоским и стабильным. В общем, влияние моделей осевой силы на рис. 7 было согласовано с профилями резания, показанными на рис. 3.
Рис. 7Осевые силы обработанных канавок, возникающие на глубине резания 2–7 мкм.
Как показано на рис. 7, тенденции увеличения / уменьшения осевой силы при глубине резания 2–4 мкм отличались от таковой при глубине резания 5–7 мкм.Для осевых сил, возникающих на глубине реза 2–4 мкм, осевые силы сначала уменьшались, а затем, с тенденцией к увеличению, наблюдались самые низкие острые точки в точках перехода. Напротив, для сил осевого напора на глубине реза 5–7 мкм картины осевого усилия отображались по-разному, они были относительно плоскими по сравнению с таковой при меньшей глубине реза 2–4 мкм, которая показывала сравнительно меньшее увеличение / скорость убывания, и наиболее высокие точки резкого перехода были продемонстрированы в сигналах силы тяги.Фактически, увеличение и уменьшение осевых сил при постоянной глубине резания означало, что в одном резе использовались два режущих механизма. Демонстрация относительно плоских структур осевого усилия на глубине резания 5–7 мкм объясняет только один механизм резания на протяжении всего процесса резания; с учетом информации о стружкообразовании и профиле резания, обсужденных выше, можно сделать вывод, что все процессы резания, проводимые на глубине резания 5–7 мкм, описываются как хрупкая обработка без процесса удаления пластичного материала.
(PDF) Атрибуты, характеристики и применение титана и его сплавов
Vol. 62 № 5 • JOM 31
www.tms.org/jom.html
УНИКАЛЬНЫЕ СВОЙСТВА
ТИТАНА
Общая коррозионная стойкость уже обсуждена. Что касается коррозионного растрескивания под напряжением (SCC)
, чистая часть
и большинство титановых сплавов
практически неуязвимы, если только
не является свежей острой трещиной в присутствии
напряжения.Если титан растрескивается в воздухе
, защитный оксид немедленно переформируется, и SCC может не возникнуть.
Если трещина возникла в морской воде, для случая
, то SCC может произойти на некоторых высокопрочных сплавах с высоким содержанием кислорода
марок технически чистого титана.
Даже здесь SCC может быть уменьшен
, если часть не загружается немедленно.
Доусон и Пеллух4 показали, что рост трещин на Ti-6Al-6V-2Sn
может быть уменьшен при испытании на низкой частоте
до тех пор, пока интенсивность напряжения
ниже, чем у Ti-6Al-6V-2Sn
. коррозия под напряжением
порог.Это объясняется повторным прохождением
сивации (повторного образования оксида) в морской воде
на более низкой частоте
, тогда как для
этого недостаточно времени, чтобы это происходило на более высоких частотах.
Модуль β-сплавов может быть значительно изменен. Ti-15V-3Cr-3Al-3Sn
при 60% холодной обработки имел прочность на растяжение
~ 1070 МПа с модулем
~ 76–83 ГПа. При старении при 480 ° C
прочность и модуль были ~ 1,515
МПа и 103 ГПа соответственно.Tita-
Сплавыниия, содержащие Nb, Zr и Ta,
, называемые металлической камедью, разработанные для
медицинской промышленности, имеют упругий мод
uli до 40-50 ГПа в зависимости от ориентации
и обработка. Эти модели
близки к моделям костей, что делает их идеальными для протезирования. Холодная
работа снижает модуль, а
увеличивает прочность. разные направления.
Ларсон6 смоделировал модуль гексагонального кристалла технически чистого титана
мкм и определил, что при напряжении
вдоль базального полюса модуль составляет
~ 144 ГПа, а при напряжении ортогонально
онал. до базального полюса ~ 96 ГПа.
Различия в пределе прочности на растяжение,
, которые также являются индикатором логографической текстуры кристалла
, между продольным
и поперечным направлением около
205 МПа недавно наблюдались
для катаной полосы, с непрерывная прокатка
в одном направлении, что может привести к сильной текстуре
.
Эффект Баушингера, хотя и не
обязательно уникален, кажется, имеет на
более сильный эффект в титановых сплавах, чем
в других системах сплавов. Это связано с
ограниченным количеством систем скольжения в
гексагональной плотноупакованной (ГПУ) низкой
температурной α-фазе. Если образец на растяжение
человек растягивается при растяжении и испытание останавливается до разрушения, а образец на сжатие
берется из калибра
длины образца на растяжение, то появляется знак
. Невозможность падения предела текучести составляет
обслуж.Деформация растяжения 0,5% при комнатной температуре
может снизить выход при сжатии
на 30%. Это связано с
дислокациями в материале, движущимися в
обратном направлении по тому же пути скольжения
, что означает, что дислокационные барьеры
не нужно преодолевать на ранних стадиях деформации
. Тот же самый термин phe-
наблюдается, если растягивать образец сжатия
, а затем растягивать
на его измерительной длине.Этот эффект
может быть устранен или уменьшен путем формовки
при повышенной температуре или последующего отжига
. Следовательно,
, по крайней мере, в аэрокосмической промышленности, когда
формируется титановая деталь, ее затем подвергают постоянному отжигу, чтобы избежать этого большого снижения выхода
. Не влияет на прочность на разрыв ulti-
mate.
Охрупчивание твердых металлов было
проблемой титана и его сплавов,
наиболее ярким примером является
кадмий.Для этого требуются плотный контакт (
титана в кадмий или наоборот
) и высокие растягивающие напряжения.
ВЫСОКАЯ СТОИМОСТЬ ТИТАНА
Как известно многим, основным фактором, ограничивающим более широкое использование титана
, является его стоимость. Поскольку стоимость на
значительно выше, чем у алюминия и стальных сплавов
, использование титана должно быть на
оправданным для каждого применения.Есть несколько факторов, способствующих этому.
Для отделения
металла от руды требуется большая энергия. Плавка слитков
также энергоемка; кроме того, его высокая реакционная способность
требует плавления в инертной атмосфере
с использованием водоохлаждаемой медной реторты или пода
, в зависимости от технологии плавки
. Обработка
также очень высокая стоимость, порядка
10–100 раз медленнее, чем обработка алюминиевых сплавов. Недавно Froes7 указал на
, что килограмм
алюминиевого листа можно купить
по более низкой цене, чем килограмм
титановой губки, исходный материал —
риала. Эта губка по-прежнему должна быть многократно:
плавленая с добавлением лигатуры,
кованая или кованая и прокатана до размера примерно
, предназначенного для листового проката, помещается в упаковку
с несколькими листовыми стержнями, прокатывается до
соответствующей толщины и протравливание и
Рисунок 3.Титановые аппликации —
на боевой машине пехоты M2 Bradley
.2
Рис. 4. Компонент, сваренный лазером. Деталь
изначально была изготовлена из листа
с соотношением закупки и выпуска 30: 1. Показанная сварная деталь, сваренная лазером
, имела отношение закупки к годности
3: 1.
Металлы | Бесплатный полнотекстовый | Обзор метастабильных бета-титановых сплавов
Высокая стоимость производства традиционных титановых сплавов подтолкнула к проведению новых исследований по обработке титановых сплавов, близких к конечной, с помощью твердотельной порошковой обработки [100].Недавно были разработаны процессы производства порошков, которые обеспечивают экономию затрат по сравнению с процессом Kroll. В рамках различных способов обработки порошка бета-титановых сплавов порошковый процесс TiH 2 продемонстрировал потенциал для производства больших деталей из бета-титановых сплавов с хорошими композиционными и микроструктурными качествами [101,102]. Порошок TiH 2 получают путем охлаждения металлотермическим восстановлением TiCl 4 в атмосфере водорода. Порошок TiH 2 смешивается с порошками различных сплавов и подвергается холодному прессованию и спеканию в вакууме при температуре выше 400 ° C, что приводит к выделению водорода, восстановлению любых оксидов и образованию стержней из сплава.Хрупкий порошок TiH 2 легко измельчается, в отличие от титановой губки, производимой традиционными методами, что снижает затраты и снижает потребление энергии.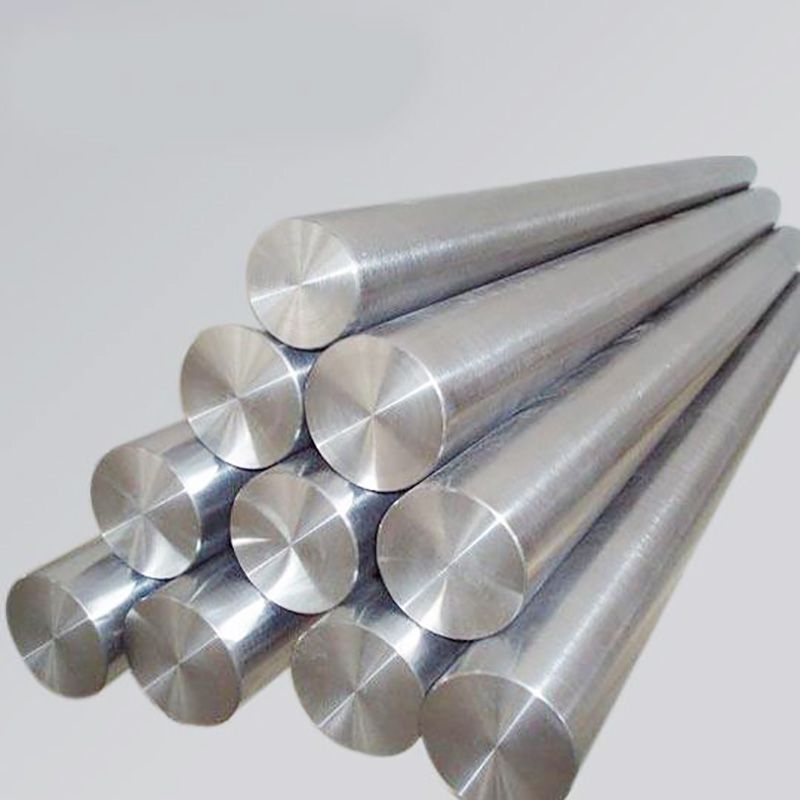
против титана — прочность, свойства и области применения
Когда проектировщикам требуются прочные, прочные материалы для своих проектов, сталь и титан — это первые варианты, которые приходят на ум. Эти металлы входят в широкий ассортимент сплавов — неблагородные металлы, пропитанные другими металлическими элементами, которые производят в сумме больше, чем его части.Существуют десятки титановых сплавов и сотни других стальных сплавов, поэтому часто бывает сложно решить, с чего начать при рассмотрении этих двух металлов. Эта статья, посвященная изучению физических, механических и рабочих свойств стали и титана, может помочь дизайнерам выбрать, какой материал подходит для их работы. Каждый металл будет кратко исследован, а затем последует сравнение их различий, чтобы показать, когда лучше выбрать один из них.
Сталь
Сталь, усовершенствованная в начале 20 века, быстро стала самым полезным и разнообразным металлом на Земле.Он создается путем обогащения элементарного железа углеродом, который увеличивает его твердость, прочность и стойкость. Во многих так называемых легированных сталях также используются такие элементы, как цинк, хром, марганец, молибден, кремний и даже титан, для повышения их устойчивости к коррозии, деформации, высоким температурам и т. Д. Например, сталь с высоким содержанием хрома относится к нержавеющим сталям или к тем сталям, которые менее подвержены коррозии, чем другие сплавы. Поскольку существует много видов стали, трудно обобщить ее конкретные свойства, но наша статья о типах стали дает хорошее представление о различных классах.
В общем, сталь — это плотный, твердый, но работоспособный металл. Он реагирует на процесс упрочнения при термообработке, что позволяет даже самой простой стали иметь переменные свойства в зависимости от того, как она была нагрета / охлаждена. Он магнитный и может легко проводить как тепло, так и электричество. Большинство сталей подвержены коррозии из-за состава железа, хотя нержавеющие стали в некоторой степени успешно устраняют этот недостаток. Сталь имеет высокий уровень прочности, но эта прочность обратно пропорциональна ее ударной вязкости или показателю устойчивости к деформации без разрушения. Хотя существуют стали для механической обработки, существуют и другие стали, которые трудно, если вообще возможно, обрабатывать из-за их рабочих свойств.
Должно быть ясно, что сталь может использоваться для множества различных работ: она может быть твердой, жесткой, прочной, устойчивой к температурам или коррозии; Беда в том, что невозможно сделать все это сразу, не жертвуя одним свойством над другим. Тем не менее, это не большая проблема, поскольку большинство марок стали недорогие и позволяют конструкторам комбинировать различные стали в своих проектах для получения дополнительных преимуществ.В результате сталь находит свое применение почти во всех отраслях промышленности: в автомобильной, аэрокосмической, строительной, архитектурной, производственной, электронной, инфраструктурной и десятках других сферах.
Титан
Титан был впервые очищен до металлических форм в начале 1900-х годов, и он не так редок, как думает большинство людей. Фактически, это четвертый по распространенности металл на Земле, но его трудно найти в высоких концентрациях или в элементарной форме. Кроме того, его трудно очистить, что делает его более дорогим в производстве, чем в источниках.
Элементарный титан — серебристо-серый немагнитный металл с плотностью 4,51 г / см. 3 , что делает его почти вдвое меньше стали и помещает его в категорию «легких металлов». Современный титан выпускается либо в виде элементарного титана, либо в виде различных титановых сплавов, и все они созданы для повышения прочности и коррозионной стойкости основного титана. Эти сплавы обладают необходимой прочностью для использования в качестве материалов для аэрокосмической, конструкционной, биомедицинской и высокотемпературной областей, тогда как элементарный титан обычно используется в качестве легирующего агента для других металлов.
Титан трудно сваривать, обрабатывать или формировать, но его можно подвергать термообработке для повышения его прочности. Он обладает уникальным преимуществом биосовместимости, то есть титан внутри тела остается инертным, что делает его незаменимым для технологии медицинских имплантатов. Он имеет отличное соотношение прочности и веса, обеспечивая такую же прочность, как сталь при 40% ее веса, и устойчив к коррозии благодаря тонкому слою оксида, образующемуся на его поверхности в присутствии воздуха или воды.Он также противостоит кавитации и эрозии, что предрасполагает его к приложениям с высокими напряжениями, таким как авиация и военные технологии. Титан жизненно важен для проектов, где вес сведен к минимуму, но прочность максимальна, а его высокая коррозионная стойкость и биосовместимость позволяют использовать его в некоторых уникальных отраслях промышленности, не охватываемых более традиционными металлами.
Сравнение стали и титана
Выбор одного из этих металлов зависит от конкретного применения. В этом разделе будут сравниваться некоторые механические свойства, общие для стали и титана, чтобы показать, где должен быть указан каждый металл (представлен в Таблице 1 ниже).Обратите внимание, что значения для стали и титана в таблице 1 взяты из обобщенных таблиц, так как каждый металл сильно различается по характеристикам в зависимости от типа сплава, процесса термообработки и состава.
Таблица 1: Сравнение свойств материалов стали и титана
Свойства материала | Сталь | Титан | |||
Шт. | Метрическая система | Английский | Метрическая система | Английский | |
Плотность | 7. | 0,282-0,289 фунта / дюйм 3 | 4,51 г / см 3 | 0,163 фунта / дюйм 3 | |
Модуль упругости | 200 ГПа | 29000 тысяч фунтов / кв. Дюйм | 116 ГПа | 16800 тысяч фунтов / кв. Дюйм | |
Предел текучести при растяжении | 350 МПа * | 50800 фунтов на кв. Дюйм * | 140 МПа * | 20300 фунтов на кв. Дюйм * | |
Удлинение при разрыве | 15% * | 54% | |||
Твердость (по Бринеллю) | 121 * | 70 |
Первое поразительное различие между титаном и сталью — это их плотность; как обсуждалось ранее, титан примерно вдвое меньше стали, что делает его значительно легче.Это подходит для применения титана в областях, где требуется прочность стали в более легком корпусе, и дает возможность использовать титан в деталях самолетов и других приложениях, зависящих от веса. Плотность стали может быть преимуществом в определенных областях применения, например, в шасси транспортных средств, но в большинстве случаев снижение веса часто вызывает беспокойство.
Модуль упругости, иногда называемый модулем Юнга, является мерой гибкости материала. Он описывает, насколько легко согнуть или деформировать материал без пластической деформации, и часто является хорошей мерой общей упругой реакции материала.Модуль упругости титана довольно низкий, что говорит о том, что он легко сгибается и деформируется. Отчасти поэтому титан трудно обрабатывать, поскольку он склеивает мельницы и предпочитает возвращаться к своей первоначальной форме. Сталь, с другой стороны, имеет гораздо более высокий модуль упругости, что позволяет легко обрабатывать ее и позволяет использовать ее в таких областях, как режущие кромки, поскольку она ломается и не сгибается под нагрузкой.
При сравнении пределов текучести титана и стали при растяжении возникает интересный факт; сталь в целом прочнее титана.Это противоречит распространенному заблуждению о том, что титан прочнее большинства других металлов, и показывает преимущество стали перед титаном. Хотя титан по прочности не уступает стали, он весит вдвое меньше, что делает его одним из самых прочных металлов на единицу массы. Однако сталь является основным материалом, когда важна общая прочность, поскольку некоторые из ее сплавов превосходят все другие металлы с точки зрения предела текучести. Дизайнеры, стремящиеся исключительно к прочности, должны выбирать сталь, но дизайнеры, озабоченные прочностью на единицу массы, должны выбирать титан.
Относительное удлинение при разрыве — это мера начальной длины испытуемого образца, деленная на его длину непосредственно перед разрушением в испытании на растяжение, умноженная на 100 для получения процента. Большое удлинение при разрыве предполагает, что материал «растягивается» больше; Другими словами, он более склонен к повышенной пластичности перед разрушением. Титан является таким материалом, где он растягивается почти на половину своей длины перед разрушением. Это еще одна причина того, почему титан так трудно обрабатывать, поскольку он тянется и деформируется, а не скалывается.Сталь бывает многих разновидностей, но обычно имеет низкое удлинение при разрыве, что делает ее более твердой и более склонной к хрупкому разрушению при растяжении.
Твердость — это сравнительное значение, которое описывает реакцию материала на царапины, травления, вмятины или деформации на его поверхности. Он измеряется с помощью инденторов, которые бывают разных видов в зависимости от материала. Для высокопрочных металлов часто указывается тест на твердость по Бринеллю, который представлен в таблице 1. Несмотря на то, что твердость стали по Бринеллю сильно варьируется в зависимости от термообработки и состава сплава, в большинстве случаев она всегда тверже, чем титан.Это не означает, что титан легко деформируется при появлении царапин или вмятин; Напротив, слой диоксида титана, образующийся на поверхности, исключительно твердый и выдерживает большинство сил проникновения. Оба они являются стойкими материалами, которые отлично работают в суровых условиях, исключая любые дополнительные химические воздействия.
Сводка
В этой статье представлено краткое сравнение свойств, прочности и областей применения стали и титана. Для получения информации о других продуктах обратитесь к нашим дополнительным руководствам или посетите платформу Thomas Supplier Discovery Platform, чтобы найти потенциальные источники поставок или просмотреть подробную информацию о конкретных продуктах.
Источники:
- https://books.google.com/books?hl=en&lr=&id=68mQLz7yJ8UC&oi=fnd&pg=PR5&dq=introduction+to+titanium+alloys&ots=lhsHnla-iW&sig=iwFic5SZXiHIp=GoiTanium+alloys&ots=lhsHnla-iW&sig=iwFic5SZXiHIp=GoToS5 20 сплавов & f = false
- https://crosstraxx.com/pages/a-look-at-the-differences-between-titanium-and-stronic-steel
- http://www.matweb.com/search/datasheet.aspx?bassnum=MS0001&ckck=1
- http: // www.matweb.com/search/DataSheet.aspx?MatGUID=66a15d609a3f4c829cb6ad08f0dafc01
- http://web.mit.edu/ruddman/www/iap/materialsselection.pdf
Прочие изделия из стали
- Типы профилей из конструкционной стали
- Ведущие производители и поставщики арматуры
- Типы арматуры
- Виды стали
- Типы нержавеющей стали
- Ведущие сталелитейные компании и производители стали США в мире
- Все о стали 5160 (свойства, прочность, применение)
- Все о стали 440 (свойства, прочность, применение)
- Все о стали 430 (свойства, прочность, применение)
- Все о стали 304 (свойства, прочность, применение)
- Все о 52100 Сталь
- Свойства, состав и применение стандартных сталей
- Обработка стали поверхностным упрочнением (цементирование)
- Все о стали 9260 (свойства, прочность, применение)
- Все о стали 4130 (свойства, прочность, применение)
Больше от Metals & Metal Products
ТИТАНОВЫЕ СПЛАВЫ: ВВЕДЕНИЕ, ХАРАКТЕРИСТИКИ И ПРИМЕНЕНИЕ
ТИТАН ЯВЛЯЕТСЯ ДЕВЯТЫМ ЭЛЕМЕНТОМ И ЧЕТВЕРТЫМ НАИБОЛЕЕ ЧЕТВЕРТЫМ МЕТАЛЛОМ НА ЗЕМНОЙ КОРЕ (ПОСЛЕ ЖЕЛЕЗА, АЛЮМИНИЯ И МАГНИЯ): ДАВАЙТЕ УЗНАТЬ БОЛЬШЕ О ЕГО ИСТОРИИ И ХАРАКТЕРИСТИКАХ.
Это было еще в 1791 году в Корнуолле, когда приходской священник Уильям Грегор, выпускник Кембриджа и химик-любитель, исследуя песок местной реки Херфорд, идентифицировал элемент, который до того времени не был известен, и который, как мы теперь знаем, был ильменитом. , смешанный оксид железа и титана (FeTiO 3 ) , который содержит около 20% титана. Четыре года спустя немецкий химик Мартин Х. Клапрот также выделил ранее неизвестное вещество, ныне известное как рутил (TiO 2 ).Он продемонстрировал, что ильменит приходского священника Грегора и обнаруженный им рутил были минералами (оксидами) того же металла, который он назвал титаном. При выборе имени он был вдохновлен Титанами, шестью сыновьями Урана (Небо) и Геа (Земля), которые в греческой мифологии были побеждены Зевсом и брошены в Тартар.
Однако открытие тонкой настройки процесса производства чистого титана заняло более века: процесс производства на самом деле оказался очень сложным из-за тенденции этого металла реагировать с атмосферным газы и особенно кислород.
Только в 1910 году Мэтью А. Хантер произвел достаточно существенное и чистое количество, чтобы начать исследования свойств этого нового металла. Процесс заключался в восстановлении тетрахлорида титана натрием.
Позже Уильям Дж. Кролл усовершенствовал процесс, в котором он заменил натрий магнием, и в 1937 году в Санкт-Петербурге были произведены первые две тонны титана. Процесс Кролла, несмотря на его высокую стоимость, по-прежнему остается наиболее часто используемым методом промышленного производства титана. Следует отметить, что это производственный процесс , который намного менее эффективен, чем производство стали в доменной печи, , который может легко объяснить причины высокой стоимости титановых компонентов, особенно по сравнению со стальными деталями. .
Фактическое промышленное развитие титана, однако, происходит благодаря промышленности армии США в начале 1940-х годов, а позже, в середине холодной войны, благодаря русским (начиная с начала 1950-х годов).Фактически, в течение нескольких десятилетий титан классифицировался как стратегический металл для производства вооружений и исключался из какого-либо значительного распределения на гражданском уровне .
Наиболее ярким примером этого доказательства является разведывательный самолет Lockheed SR-71, более известный исторически как «Блэкберд», , сделанный из титанового сплава на 93% своего веса, который побил ряд рекордов, таких как Максимальная скорость , когда-либо достигнутая пилотируемым самолетом, 3 530 км / ч, а максимальная высота составляет почти 26 000 м.Чтобы быть более точным, три различных титановых сплава были использованы для этого самолета: Ti-6Al-4V, Ti-5Al-2,5Sn и Ti-13V-11Cr-3Al (также известный как B120VCA).
Диаг. 1: Lockheed SR-71 или «Блэкберд»Более того, в течение как минимум трех десятилетий (с середины 1950-х до конца 1980-х) титан считался ведущим материалом для американской аэрокосмической промышленности.
В конце 1980-х, с окончанием холодной войны, военные ограничения, наложенные на титан до этого момента, были постепенно сняты, что позволило развивать многие другие области применения, включая биомедицинскую, архитектурную, химическую, ювелирную и др. инфраструктура и досуговое оборудование (теннисные ракетки, клюшки, велосипедные рамы).Также автомобильный сектор и, в частности, сектор гоночных автомобилей , играл и продолжает играть ведущую роль в разработке титановых сплавов для различных компонентов.
ФИЗИКО-МЕХАНИЧЕСКИЕ СВОЙСТВА ТИТАНАТитан имеет плотность около 4,5 г / см. 3 , выше, чем , чем другие легкие металлы, представляющие структурный интерес, такие как алюминий или магний, но почти наполовину по сравнению со сталями. Титан также обладает превосходной механической стойкостью к деформации и разрушению, модулем упругости около 115 ГПа и отличной стойкостью к различным формам коррозии.
Титан также может похвастаться очень низкими коэффициентами теплопроводности и теплового расширения , около 22 Вт / мК и 8,410 -6 C -1 соответственно, что составляет почти один порядок и 1/3 соответственно. те из алюминия.
Что касается аспекта кристаллической структуры, титан допускает аллотропное превращение, при котором кристаллическая решетка переходит от компактной гексагональной (CH) при комнатной температуре к объемно-центрированной кубической (BCC) структуре при температурах, которые сильно зависят от специфический химический состав сплава. Как правило, в случае чистого титана компактная гексагональная кристаллографическая структура (или фаза α) сохраняется до 882 ° C, температуры, которой принято называть β-transus (рис. 2). При более высокой температуре стабильная структура представляет собой объемно-центрированную кубическую (фазу β) структуру, которая сохраняется до 1670 ° C, значения, которое соответствует температуре плавления чистого титана.
Диаг. 2: Аллотропное превращение в технически чистом титане ДОБАВЛЕНИЕ ЭЛЕМЕНТОВ И ФОРМИРОВАНИЕ СПЛАВОВЭлементы сплава классифицируются как α- или β-стабилизаторы на основании относительного влияния на температуру перехода α-β или на различную растворимость в двух разных фазах.Следует подчеркнуть, что в бинарных сплавах, в отличие от чистого титана, переход из фазы α в β происходит не точно при точной температуре (например, 882 ° C), а в диапазоне температур: в данном случае β -температура перехода сплава обычно определяется как температура, за пределами которой микроструктура материала полностью состоит из фазы β.
Заместительный элемент Al и промежуточные элементы O, C и N являются мощными α-стабилизаторами и повышают температуру β-перехода, как показано на схеме состояний на рис.3. β-стабилизирующие элементы, напротив, понижают температуру перехода. Последние подразделяются на β-изоморфы (V, Mo, Nb, Ta) и β-эветтоиды (Mn, Fe, Cr, Co, Ni, Si, H) в зависимости от формы диаграммы бинарных состояний титана. . Наконец, другие элементы, такие как Sn и Zr, ведут себя в основном нейтрально, , определяя лишь небольшое понижение температуры β-перехода.
Диаг. 3: Примеры различных типов бинарных диаграмм состояния, подчеркивающие влияние основных элементов сплава на температуру β-перехода и на стабильность фаз α и β.Из того, что было только что проиллюстрировано, легко заметить, что , должным образом изменяя тип и содержание легирующих элементов, можно получить сплавы при температуре окружающей среды со структурой, полностью состоящей из фазы α, или двухфазные сплавы с одновременное присутствие фаз α и β или, наконец, полностью фазовых β сплавов.
Титановые сплавы могут достигать механической прочности на растяжение, которая даже превышает 1200 МПа, с модулем упругости, который, в зависимости от структуры и относительных фаз, может варьироваться от 80 до 145 ГПа.В связи с этим на рис. 4 показаны характеристики удельного сопротивления (рассчитанного как предел текучести по отношению к плотности) в зависимости от температуры для различных типов металлических сплавов.
Диаг. 4: Удельное сопротивление, основанное на рабочей температуре титановых сплавов по сравнению с другими типами металлических материалов, обычно используемых в промышленной деятельности.Основные свойства коммерческих титановых сплавов можно резюмировать следующим образом:
- Модуль упругости, который увеличивается с содержанием промежуточных элементов (C, N, O и H) и алюминия, но также может уменьшаться после добавления β-стабилизаторов.
- Высокая твердость, которая обычно увеличивается при добавлении β-стабилизирующих элементов (некоторые сплавы, как будет более подробно объяснено ниже, могут быть упрочнены посредством термической обработки солюбилизацией с последующим старением).
- Высокое сопротивление ползучести до 0,6T f (T f — это температура плавления , выраженная в градусах Кельвина).
- Высокая стойкость к удельной механической усталости (предел усталости по сравнению с плотностью), что составляет сильную сторону титановых сплавов, поскольку он превосходит любой другой металлический сплав с такой же механической прочностью.
Подождите следующего выпуска, чтобы узнать больше о характеристиках и свойствах различных титановых сплавов!
Влияние скорости деформации, температуры, термомеханической обработки и состава никеля на память формы и сверхупругие характеристики
AbstractПочти четыре десятилетия академических исследований и промышленного интереса к нитинолу в основном были сосредоточены на сверхупругих приложениях в биомедицинском секторе и в других отраслях промышленности. разработка « умных » датчиков на основе памяти формы с низкой скоростью деформации (̃0.001 / с) отклик NiTi. Лишь в течение последнего десятилетия наблюдается рост интереса к использованию нитинола в приложениях с высокой скоростью деформации, таких как сейсмическое демпфирование, смягчение последствий взрывов или поглощение энергии. Однако систематического исследования влияния высокой скорости деформации и температуры на характеристики памяти формы NiTi крайне не хватает. В текущей исследовательской программе представлены результаты по: (1) механизмам фазового превращения в сплавах Ni-Ti с высоким содержанием никеля.К ним относятся (а) бездиффузионные многоступенчатые мартенситные превращения и (б) фазовые превращения на основе диффузии, которые определяют реакции выделения в сплавах с высоким содержанием никеля и общие кривые время-температура-превращение (TTT). (2) Систематическое изучение реакции высокоскоростной деформации NiTi-сплавов с высоким содержанием никеля в зависимости от температуры (от -196 ° C до 400 ° C) и термомеханической обработки, а именно условий полного отжига, деформационного упрочнения и дисперсионного твердения. Два никелевых сплава нитинола, товарный знак 50.Для исследования были выбраны 8-NiTi (ат.%) И новый 55-NiTi (ат.%), Поскольку состав Ni определяет процессы выделения и, что особенно важно, температуры превращения в сплавах NiTi. Было замечено, что наличие дислокаций (из-за деформационного упрочнения) и наличие выделений с высоким содержанием Ni (из-за старения) способствует более сложным двухстадийным или многоступенчатым превращениям, а также улучшает общую прочность NiTi. сплав. На основе микроструктурных изменений, таких как восстановление, перекристаллизация и образование осадков в 50.8-NiTi сплавы, текущая работа однозначно обеспечивает единое и общее понимание различных многоступенчатых преобразований, описанных в литературе, в частности, обеспечивая переход между двумя основными механизмами последовательности преобразований, рационализированных на основе исследований методом частичной дифференциальной сканирующей калориметрии (ДСК). . Кроме того, работа также выявила необычные многоступенчатые превращения в 55-NiTi. Старение в обогащенном никелем 55NiTi вызывало реакции осаждения с последовательным образованием Ti₃Ni₄, Ti₂Ni₃ и TiNi₃.Была построена диаграмма времени-температуры-превращения для 55NiTi, а также был оценен верхний температурный предел образования нескольких выделений для системы сплавов NiTi с высоким содержанием никеля в зависимости от концентрации Ni между 50,6-56 ат.%. Характеристики сверхэластичности и памяти формы в Ni-Rich 55NiTi, которые считались невозможными, были успешно продемонстрированы с восстанавливаемыми деформациями до ~ 4-6%
Основное содержаниеЗагрузить PDF для просмотраПросмотреть больше
Больше информации Меньше информации
Закрывать
Введите пароль, чтобы открыть этот PDF-файл:
Отмена ОК
Подготовка документа к печати…
Отмена
.