Травление швов и средство для сварки
Раствор, паста для травления стали и обезжиривание перед сваркой
Предлагаем средство для обезжиривания перед сваркой и травильный состав для пассивации стали и сварных швов. Эти препараты получили высокую оценку у потребителей и специалистов.
Для травления стали, химической пассивации нержавеющей стали Дезоксил-1 и пасту для травления стали Дезоксил-1 Гель. Для удаления травильного шлама, мы не могли позаботиться об очистителе и обезжиривании для сварки. Этот раствор получил название КФ-22.
Химическая пассивация нержавеющей сталиС помощью травильного состава Дезоксил-1 Гель можно провести качественное химическое травление и пассивацию нержавеющей стали и других металлов. Раствор не имеет аналогов в стране и признан лучшей разработкой 2012 года. До этого при химическом травлении стали мастера вынуждены были пользоваться зарубежными препаратами. Наша новая разработка в корне изменила ситуацию. Гель – паста для травления стали Дезоксил-1 по своим рабочим качествам не только не уступает лучшим зарубежным аналогам, а превосходит их по многим параметрам. Применяется он для пассивации и травления нержавеющей стали и сварных швов. Эффективно удаляют слой, прилегающий к шву, с пониженным содержанием хрома, и другой травильный шлам. Химическая пассивация и травление стали гелем обеспечивают высокую чистоту шва, хороший внешний вид и коррозионную стойкость сварного соединения.
Обезжириватель и очиститель для сварки
Для обработки металла перед сваркой предлагаем концентрированное пенное средство на основе ортофосфорной кислоты КФ-22. С его помощью можно проводить не только очищение и обезжиривание для сварки, но и аморфное фосфатирование алюминиевых и стальных поверхностей. Одновременно с обезжиривание и очисткой от загрязнений, удалением коррозии, на металле образуется цинко-фосфатное аморфное покрытие массой 0,2-1,0 г/м2. Производители составов для удаления травильного шлама и обезжиривания для сварки будут рады сотрудничеству с вами.
Сварка нержавеющей стали
Методы сварки
Нержавеющая сталь может свариваться с помощью различных методов дуговой сварки, таких как ручная дуговая сварка MMA, аргонодуговая сварка вольфрамовым электродом TIG и полуавтоматическая сварка MIG/MAG. Наиболее предпочтительна дуговая сварка неплавящимся электродом в инертном газе (TIG). Аргонодуговая сварка TIG широко используется для сварки тонких листов из нержавеющей стали. В качестве защитного сварочного газа наиболее часто используется 100% аргон. Для автоматической сварки иногда применяют аргонно-гелиевую смесь. Аргонодуговая сварка может быть без подачи присадочной проволоки (для сварки тонкого металла), так и с подачей, вручную или автоматической. Аустенитные стали обладают пониженной температурой плавления, более низкой теплопроводностью и высоким коэффициентом линейного расширения, чем углеродистые стали. Поэтому при сварке этих нержавеющих сталей расплавление идет быстрее с большим перепадом температуры от сварного шва к остальному металлу.
Обработка сварных швов
На поверхности сваренного соединения в районе сварного шва, образуется пористый оксидный слой, содержащий в основном хром. Этот слой значительно ослабляет стойкость соединения к коррозии, т.к. под ним образуется зона со сниженным содержанием хрома. Если необходимо добиться такой же высокой стойкости сварного соединения к коррозии, как и у основного материала, оксидный слой и зону со сниженным содержанием хрома следует удалить, т.е. сварное соединение должно пройти последующую обработку травлением.
Травление является наиболее эффективным методом обработки сварных швов. При правильном выполнении, травление позволяет устранить вредный оксидный слой и зону со сниженным содержанием хрома.
Травление выполняется путем погружения, поверхностного нанесения травильного раствора или покрытия сварных швов травильными пастами. Еще больше увеличит стойкость к коррозии доведение степени шероховатости сварного шва до соответствующего показателя основного листа путем шлифования или полирования после травления.
Для механической обработки нержавеющей стали используют шлифовальные ленты, круги, щетки и т.п. специально предназначенные для обработки нержавеющего проката.
Используемые методы сварки нержавеющей стали
На сегодняшний день применяются следующие методы сварки нержавеющей стали:
- если толщина материала превышает 1,5 мм — дуговая ручная сварка;
- для сварки листов и труб малой толщины применяется метод дуговой сварки в инертном газе вольфрамовым электродом, эта технология сварки отличается повышенной производительностью;
- для листов стали, толщина которых составляет 0,8 мм, используется дуговая импульсивная сварка в инертном газе с плавящимся электродом;
- листы, имеющие толщину от 0,8 мм до 3 мм, обрабатываются дуговой сваркой со струйным переносом;
- плазменная сварка используется для листов очень разной толщины и сегодня является очень распространённой технологией сварки нержавеющей стали;
- для листов толщиной свыше 10 мм используется дуговая сварка под флюсом.
Известны также следующие технологии сварки: роликовая, точечная, высокочастотная, лазерная, сварка сопротивления.
Следующим после сварки этапом является обработка сварных швов. Поверхность соединения, образующегося после сварки нержавеющей стали, состоит из оксидного пористого слоя, содержащего хром. Данный слой сильно уменьшает устойчивость к коррозии. Поверхность этого слоя формируется из стали, затем под оксидным слоем образуется следующий слой, содержащий хром. При возникновении необходимости в повышении устойчивости сварного соединения к действию коррозии требуется удаление оксидного слоя и слоя, характеризующегося низким содержанием хрома. Этот процесс проводится с использованием термообработки, в данном случае вызывающей растворение в стальной конструкции, которое сглаживает все потенциальные отличия присадочных материалов друг от друга. При этом допустимо применение только тех инструментов, которые специально предназначены для обработки нержавеющей стали: шлифовальных кругов и лент, щёток для обработки проката из нержавеющей стали, дроби из нержавейки.
Эффективный способ обработки сварных швов — травление. При его правильном выполнении качественно устраняется оксидный слой, а также зона низкого содержания хрома. Обработка данным способом выполняется посредством погружения, покрытия либо наружного нанесения пасты в зависимости от конкретных условий. Преимущественно при травлении применяется смесь кислот (плавиковая и азотная) в соотношении 0,5-5% плавиковой кислоты и 8-20% азотной кислоты с добавлением воды. Время травления определяется концентрацией кислот, сортом проката, температурой и толщиной окалины (для кислотоупорного проката требуется более длительная обработка).
Травильная паста Avesta RedOne Pickling Paste 140 (Красная) — Сваркатверь
Описание товара
Травильная паста Avesta RedOne Pickling Paste 140 (Красная)
Применение травильных средств:
Травильные средства используются для травления поверхностей металла после формовки, резки, для удаления образующихся при сварке металлов оксидов и, находящихся под ними слоев металла, обедненных хромом. Они удаляют также шлаковые микрочастицы и другие загрязнения, которые могут привести к образованию локальной коррозии. С целью усиления, в ряде случаев травление может осуществляться одновременно с механической обработкой, например, с очисткой щетками. Травильные растворы (в виде паст, гелей и аэрозолей) обычно представляют собой смеси азотной (HNO ) и фтористоводородной кислот (HF), (ортофосфорная кислота может использоваться для легкого травления) с загустителями и поверхностно активными веществами для получения надлежащей фиксотропии и хорошей вязкости. Паста и гель рекомендуются для травления ограниченных участков поверхности, например, зон, подвергшихся воздействию сварки и небольших поверхностей. Растворы в виде аэрозолей подходят для травления больших поверхностей, например, когда требуется также удаление железных загрязнений.
Характеристики пасты:
Паста Avesta RedOne Pickling Paste 140 (Красная)
Предназначена для интенсивного травления швов после сварки электродами или флюсовой (порошковой) проволокой и грубых горячекатаных поверхностей материалов из высоколегированных нержавеющих сталей. Выделения оксидов азота снижены на 50%. Обеспечивает быстрое травление даже при температурах ниже +5°С.. Рекомендуется для обработки больших поверхностей. Не высыхает продолжительное время, что позволяет вести обработку с большими перерывами. Уровень кислотности рН 0. Неогнеопасна. Поставляется в полиэтиленовых контейнерах весом 2,4 и 20 кг, одобренных ООН для хранения опасных товаров.
Инструкция по использованию:
1. Поверхность для травления должна быть очищена от органических загрязнений.
2. Размешайте или взболтайте пасту/гель перед использованием.
3. Наложите пасту/гель с помощью прилагаемой кисточки.
4. Оставьте пасту/гель на время. Длительность реакции варьируется в пределах от 30 минут до 4 часов, в зависимости от марки нержавеющей стали, температуры, вида загрязнений и используемой пасты/геля.
Эффективность кислот сильно увеличивается с увеличением температуры. Это означает, что, например, степень травления, может быть значительно увеличена при повышении температуры. Однако существуют верхние температурные пределы, которые следует принимать во внимание. Больший риск возникает при высыхании пасты из-за образующихся паров, которое отражается на уменьшении эффективности травления и последующей промывки.
Хранение:
Пасты/гели для травления следует хранить при комнатной температуре в помещении. Контейнеры должны быть тщательно закрыты и, находиться в вертикальном положении в недоступном для неквалифицированных лиц месте. Пасты/гели являются скоропортящимися, поэтому не стоит хранить их дольше, чем это необходимо. Максимальный срок хранения при комнатной температуре – 1 год. При хранении при более высоких температурах срок годности может сократиться.
Паста Авеста 140
Травильная паста в компании «РУСЕВРОСТАЛЬ»
РУСЕВРОСТАЛЬ поставляет травильную пасту от ведущих мировых производителей. В зависимости от Ваших задач, предлагаем Вам купить травильную пасту производства Австрии и Швеции. Каждый производитель использует свои разработки и технологии для производства травильной пасты для нержавеющей стали, делая упор на качество травления и расход пасты во время проведения сварочных работ.Для проведения сварочных работ по нержавеющей стали очень важно правильно подобрать тип травильной пасты. Ниже указаны три вида травильных паст для разных марок и поверхностей нержавеющей стали на примере травильной пасты Avesta.
Травильная паста Авеста из наличия со склада в Москве и под заказ
Упаковка: полиэтиленовая банка: 0,1 кг; 2,4 кг; 20 кг
Минимальный заказ от 1 банки
Производитель: AVESTA (Швеция)
AVESTA GreenOne 120 Данная паста предназначена для легкого травления низколегированных сплавов нержавеющей стали: AISI 304/304L. Рекомендуемая температура при травлении: от +10°C до +30°C. Особенности: бережное травление шлифованной и полированной поверхности, снятие верхнего слоя окисления после сварки. |
|
AVESTA BlueOne 130 Данная паста применяется для холоднокатаного металла: AISI 304/ 304L, AISI 316/316L, AISI 321. Рекомендуемая температура при травлении: от +10°C до +30°C. ![]() |
|
AVESTA RedOne 140 Данная паста применяется для высоколегированных марок нержавеющей стали AISI 904L. Рекомендуемая температура при травлении: от +5°C и ниже. Особенности: подходит для травления горячекатаной поверхности, грубых швов после сварки электродами либо проволокой. Быстрый процесс травления. |
Инструкция по применению травильной пасты
11 советов по сварке алюминия в отрасли судостроения
11 советов по сварке алюминия в отрасли судостроения
Автор: Фрэнк Г. Армао (Frank G. Armao), директор по технологиям сварки алюминия
Компания Lincoln Electric
Алюминиевые сплавы отличаются низким весом и коррозионной устойчивостью в морской среде, и благодаря этому они получили широкое распространение в отрасли судостроения.
Есть две особенности, которые отличают сварку судостроительного алюминия от сварки стали, и обе они связаны с тем, что в большинстве случаев она происходит под открытым небом:
- во избежание окисления алюминиевых пластин и прессованных профилей важно обеспечить их правильное хранение;
- особенно внимательно нужно следить за тем, чтобы на сварочном участке не было ветра.
Ниже мы обсудим эти особенности более подробно.
Вы должны знать, что за алюминий вы свариваете
Недостаточно знать, что это алюминий. Профессиональные сварщики всегда учитывают, с каким именно сплавом алюминия они работают, и выбирают для этого подходящие присадочные материалы. Чаще всего в судостроении используются листовой алюминий из сплавов Al-Mg 5XXX и сплавы для прессования Al-Mg-Si 6XXX, во многом благодаря их отличной коррозионной устойчивости.
Большинство сплавов алюминия легко поддаются дуговой сварке. Практически все сплавы серий 1XXX, 3XXX, 4XXX, 5XXX и 6XXX пригодны для сварки в режимах TIG и MIG/MAG. Однако большинство сплавов серий 2XXX и 7XXX дуговой сварке не поддаются. Единственные исключения из этого правила в серии 2XXX — это сплавы 2219 и 2519. Практически все остальные сплавы 2XXX во время сварки подвержены сильному трещинообразованию. Аналогичным образом в семействе 7XXX для сварки пригодны только сплавы 7003, 7004, 7005 и 7039.
Особенно остерегайтесь сплавов 2024 и 7075. Они имеют высокие механические характеристики и широко распространены, поэтому часто возникает соблазн использовать эти сплавы для ремонтных работ. Тем не менее, при дуговой сварке они очень склонны к образованию трещин.
Сварка «несвариваемых сплавов» или использование неподходящих присадочных прутков могут привести к немедленному растрескиванию или преждевременной поломке во время эксплуатации.
Зачем нужен предварительный подогрев?
Многие считают, что для сварки алюминия, как в режиме TIG, так и MIG/MAG, обязательно требуется предварительный подогрев. Это не всегда так. Более того, при использовании подходящего оборудования предварительный подогрев требуется достаточно редко.
Ненужный предварительный подогрев даже может привести к падению механических характеристик. Последний этап термообработки алюминия — это старение, которое проводится при температурах от 160 до 200°C. Если температура предварительного подогрева достигнет или превысит температуру старения, вы испортите механические характеристики металла.
Конечно, нельзя сказать, что предварительный подогрев — это обязательно плохо. Например, при высокой температуре и влажности окружающей среды для удаления влаги допускается предварительный подогрев до 90°C. Но не увлекайтесь.
Хранение алюминиевых листов, пластин и прессованных деталей
В большинстве случаев алюминий перед использованием рекомендуют хранить в помещении. Хотя это действительно хороший совет, в судостроительной отрасли это малореализуемо, потому что сварка обычно проводится под открытым небом. Поэтому в судостроении предъявляются более реалистичные требования к хранению.
Во-первых, по возможности алюминиевые пластины не нужно укладывать горизонтальными штабелями прямо на земле. Так между штабелями будет скапливаться влага, которая приведет к усилению коррозии. Вместо этого складывайте пластины диагонально на края друг друга, чтобы с них могла стекать вода. Если их все же нужно сложить горизонтально, снимите всю прокладочную бумагу и упаковку между пластинами. Если ее оставить, она будет впитывать и накапливать влагу между пластинами. Если листы укладываются горизонтально, старайтесь не располагать их прямо один на другой. Вместо этого вставьте между листами деревянные или алюминиевые «закладки», которые дали бы воде стекать.
Все эти меры призваны снизить интенсивность коррозии, т. е. образование слоя оксида между хранящимися листами. Если толщина слоя оксида станет слишком большой, перед сваркой его придется удалить механическими средствами.
Перед сваркой обязательно произведите зачистку деталей
Предсварочная зачистка алюминия состоит из двух отдельных операций. Сначала удаляются остатки масел, смазки, охлаждающей жидкости и других углеводородов, которые могли использоваться на производстве. Оставшиеся на поверхности углеводороды попадут в сварочную дугу и выделят газообразный водород, который вызывает пористость в наплавленном металле.
Углеводороды удаляются одним из двух способов. Чаще всего поверхность протирают чистой тканью, пропитанной хорошим обезжиривающим растворителем, например, ацетоном, толуолом, метилэтилкетоном или очистителем для карбюраторов. Спирты не относятся к хорошим очистителям и не должны использоваться для чистки алюминия. Менее распространен способ с погружением алюминия в резервуар с умеренным щелочным раствором с последующим ополаскиванием и сушкой.
Во-вторых, перед сваркой с алюминия следует удалить все тяжелые оксиды. Обычно это делают вручную или механически с помощью щетки из нержавеющей стали. Если материалы хранились снаружи и на них появился слой серого оксида большой толщины, его может понадобиться удалить пескоструйной обработкой или шлифовальным диском.
Используйте подходящее оборудование
Перед каждой сменой нужно проверять, что сварочное оборудование настроено именно для сварки алюминия. Это особенно важно, если этим оборудованием поочередно пользуются для сварки разных материалов.
Особенно в режиме MIG/MAG:
- Проверьте, что тормозной механизм кассеты отрегулирован не слишком туго. Слишком сильное натяжение может затруднить подачу проволоки. Усилия тормозного механизма просто должно быть достаточно, чтобы предотвратить прокручивание кассеты при остановке проволоки.
- Также проверьте, что ролики механизма привода предназначены для алюминиевой проволоки и имеют подходящий диаметр. Ролики с V-образными канавками для стальной проволоки могут деформировать алюминиевую и вызвать перебои с подачей проволоки.
- Натяжение роликов должно быть отрегулировано так, чтобы его едва хватало для того, чтобы проволока не проскальзывала на роликах. Слишком сильное натяжение приведет к деформациям проволоки.
- Убедитесь в наличии входных и выходных пластиковых направляющих втулок подходящего типа. Стальные детали, которые используются для подачи стальной проволоки, также могут вызвать перебои в подаче проволоки.
- Убедитесь, что гусак горелки изготовлен из подходящего пластика для подачи алюминиевой проволоки. Спиральные гусаки горелки, которые часто используются для подачи стальной проволоки, будут соскребать стружку с мягкой алюминиевой проволоки, что может привести к засору.
- Также убедитесь, что используете контактный наконечник подходящего размера для проволоки данного диаметра. Многие считают, что лучше использовать контактные наконечники большего размера — например, наконечник 1,6 мм для проволоки 1,2 мм. НЕ ДЕЛАЙТЕ ЭТОГО. Наконечник должен быть достаточного размера для того, чтобы через него свободно проходила проволока, но при этом достаточно узким, чтобы обеспечить равномерный электрический контакт между контактным наконечником и проволокой. Слишком большой контактный наконечник не обеспечит равномерный перенос тока, что приведет к частому прожиганию материала.
Правильный расход защитного газа
Расход аргона должен составлять минимум 16,5 л/мин. для MIG/MAG и 11,8 л/мин. для TIG-сварки. В обоих режимах при использовании сопла большого диаметра расход защитного газа следует увеличить. Если сварка проводится под открытым небом, расход защитного газа должен быть еще выше — мин. 21,2 л/мин. для MIG/MAG и 16,5 л/мин. для TIG — потому что аргон легче воздуха и более подвержен воздействию ветра и сквозняков. Недостаточная газовая защита сварочной ванны приведет к появлению пористости. Если в качестве защитного газа используется смесь аргона и гелия, расход следует увеличить примерно на 25%, потому для гелия характерно низкое очищающее воздействие.
После чистки зоны сварки она должна оставаться чистой
После зачистки и подгонки деталей нужно постараться как можно быстрее провести сварку. Это вызвано даже не тем, что детали могут окислиться — при комнатной температуре в сухих условиях алюминий окисляется достаточно медленно. Главная проблема заключается в том, что в цеховых условиях очищенный материал может оказаться покрыт грязью, маслом, водными парами и т. д. После зачистки, подгонки и сборки не оставляйте открытые детали на ночь или выходные. Если до сварки все же должно пройти некоторое время, накройте соединение крафт-бумагой и закрепите ее скотчем.
Правильное хранение сварочной проволоки
Алюминиевую сварочную проволоку следует хранить в чистом, сухом помещении, желательно в исходной упаковке. В таких условиях проволока может храниться несколько лет.
Хотя для хранения проволоки необязательно требуется вентиляция, будет полезно обеспечить низкую относительную влажность. Не допускайте отсыревания проволоки.
Самый простой способ сделать это — хранить проволоку в исходной упаковке в закрытых металлических шкафах с включенной 60-ваттной лампочкой. Тепло от лампочки повысит температуру внутри шкафа примерно на 10°C и снизит относительную влажность.
Частично израсходованные кассеты проволоки нельзя оставлять на ночь в сварочном аппарате. Их следует вернуть в исходную упаковку. В противном случае можно воспользоваться пластиковыми крышками для кассет, которые совместимы с большинством подающих механизмов. Кассету проволоки можно оставить в подающем механизме
до полного израсходования.
Хранение проволоки в кондиционируемом помещении также может быть связано со сложностями. Если в горячий, влажный день относительно холодную проволоку занести в цех и сразу вскрыть упаковку, из-за влажного воздуха на проволоке может образоваться конденсат. Если проволока хранилась в кондиционируемом помещении, выдержите ее некоторое время в цеху перед вскрытием упаковки, чтобы она согрелась. Более того, хранение в комнате с низкой влажностью будет более полезно, чем в кондиционируемой. Тем не менее, при правильных условиях хранения ни то, ни другое не обязательно.
Продольные и поперечные колебания
В то время как все сходятся на мнении, что поперечные колебания горелкой приводят к чрезмерному увеличению тепловложения, в некоторых отраслях сварщики прибегают к продольным колебаниям, или «копательным» движениям горелки. Задача такой техники сварки — добиться равномерного образования валиков при небольшой ширине соединения. Главное преимущество этого метода — очень равномерная «рябь» из валиков, похожая на внешний вид швов от аргонодуговой сварки. Однако такая техника никак не влияет на глубину проплавления или очищающее воздействие дуги. Она имеет чисто косметический эффект.
Сварка с «копательными» движениями электрода вполне допустима, но при этом нужно контролировать амплитуду колебаний. Она должна составлять около 3-5 мм. При большей амплитуде между валиками могут оказаться промежутки. Это может привести к уменьшению глубины проплавления и не является допустимым.
Используйте подходящую сварочную проволоку
Сварка в области судостроения чаще всего подразумевает соединение листов и пластин серии 5XXX Al-Mg, например, 5052, 5154, 5454 или 5083, между собой или с прессованными деталями 6XXX.
Для сварки сплавов серии 5ХХХ между собой для 5154 и 5454 в качестве присадочного материала используется сплав 5554. Для 5052 используется сплав 5356. Для сварки 5083, который имеет более высокие механические характеристики, рекомендуются сплавы 5556 или 5183, потому что 5356 не способен обеспечить механические характеристики, равные 5083. 4043 нельзя использовать в качестве присадочного металла при сварке сплавов 5ХХХ за исключением 5052, который имеет низкое содержание Mg.
Для соединения листов или пластин серии 5ХХХ с прессованными деталями серии 6ХХХ, например, 6061-T6, в качестве присадочного металла рекомендуются сплавы 5356 или 5554. 4043 используется как присадочный металл в области судостроения довольно редко из-за своей подверженности коррозии. В этой области использование высокопрочных сплавов 5183 или 5556 в качестве присадочного материала не дает никакой дополнительной пользы. Некоторые поставщики стараются продать именно эти более дорогостоящие сплавы, но они себя не оправдывают.
Итак, в этой небольшой статье мы попробовали дать рекомендации, которые были бы полезны сварщикам, работающим в области судостроения. Мы надеемся, что вы сможете почерпнуть из нее новые идеи и улучшить свои навыки по сварке судостроительного алюминия.
Оригинал статьи
Сварочные работы — CNC POWER
Мы произодим сварочные работы с использованием полуавтоматической сварки, сварки штучным электродом (ручная дуговая сварка) и аргоннодуговой сварки.
Аргоннодуговая сварка является основным профилем нашей компании.
Она обеспечивает минимальное тепловложение, как следствие минимальное коробление свариваемых деталей, эстетичный внешний вид шва (чаще всего даже не требующий дальнейшей механической обработки).
Т.к. сварка производится в среде инертного газа, то минмизируется взаимодействие расплавленного металла с воздухом, что позволяет практически полностью избежать выгорание легирующих элементов, что важно при сварке конструкций из нержавеющих сталей.
Только с использованием аргоннодуговой сварки на переменом токе можно по настоящему качественно сваривать конструкции из алюминиевых сплавов.
В работе мы используем сварочный инвертор для аргоннодуговой сварки на постоянном и переменном токах FoxWeld TIG 203 AC/DC Pulse.
Сварочные материалы (электроды, присадки и т.д.) применяются только ведущих европейских фирм.
Сварка ответственных, в геометрическом плане, конструкций осуществляется на монтажной плите, обеспечивающей хорошую плоскостность получаемых изделий.
По желанию клиента, сваренные конструкции могут быть окрашены порошковыми красками с предварительной пекоструйной или дробеструйной обработкой.
Также мы можем предложить ручную покраску при помощи краскопульта.
Обработка сварных изделий из нержавеющих сталей может включать в себя:
- травление сварных швов травильными пастами (убирает цвета побежалости и восстановливает коррозионные свойства в околошовной зоне)
- шлифовку сварных швов и снятие усилений сварных швов
- полировка и окончательная доводка внешнего вида изделия
- в качестве альтернативы механической полировке можем предложить химическую полировку
- пескоструйная обработка. Производится с использованием микростеклосфер, что позволяет получить равномерную матовую и при этом не маркую поверхноть.
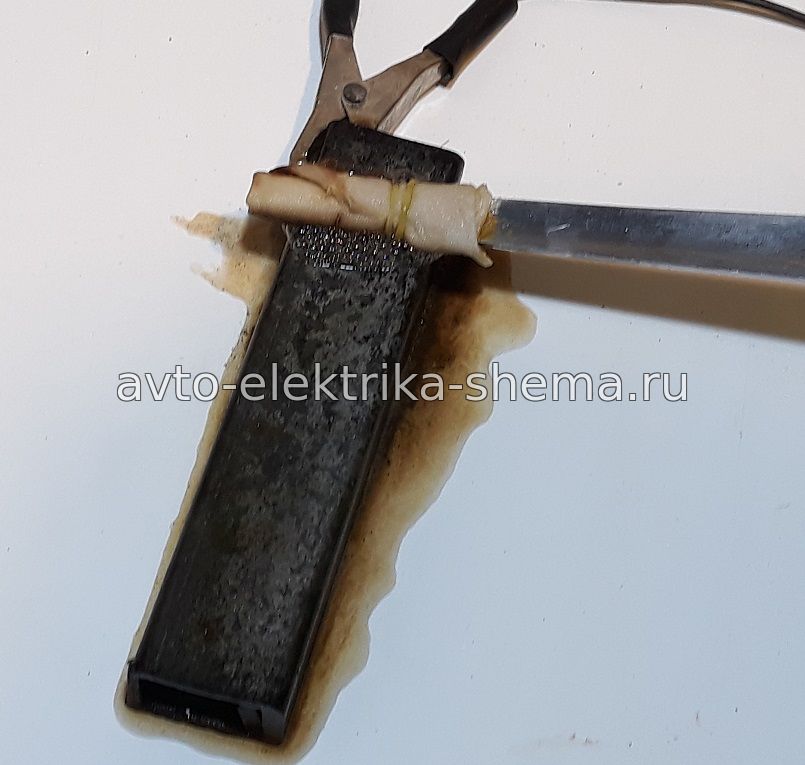
Статьи на тему:
ИНСПЕКЦИОННЫЕ ТРАВИТЕЛИ ДЛЯ СВАРКИ | Магазин Etchant
Наши кислоты для макротравления разработаны металлургами, чтобы выявить самородок сварного шва во время испытания на проплавление. Эти химические вещества эффективны для нержавеющей стали, мягкой стали, алюминия и т. Д. Все они предварительно смешаны, готовы к использованию и могут храниться при комнатной температуре до одного года.
Процедура макротравмирования сварных деталей обычно начинается с удаления следов порезов с использованием наждачной бумаги разного размера от крупной до мелкой.Для шлифования мы используем зерно 180, 320 и 600. Перед травлением поверхность поперечного сечения будет иметь однородную зернистость 600. Если возможно, отполируйте поверхность зеркалом. Чем мельче отделка, тем лучше подействует химикат для травления и тем больше деталей вы увидите. Промойте и высушите поверхность, затем нанесите протравку ватными тампонами. Дайте ему постоять от нескольких секунд до минут. Когда сварной шов станет виден, промойте его водой, чтобы остановить реакцию.
Если вам нужна помощь со специальным сплавом, пришлите нам небольшой образец.Мы порекомендуем подходящий продукт на основании результатов теста.
Сварные швы из углеродистой стали:- Nital Etch, 5%: Традиционный выбор для сварки углеродистой стали. AKA Nitol или Nytal. Он содержит азотную кислоту и более эффективен, чем гель для удаления ржавчины.
- Реагент Фрая: (опционально, 2-я ступень) Для выделения сварных швов низкоуглеродистой / мягкой стали. Используйте после протравливания Nital. Это приведет к появлению пятен на сварке, сделает сварной шов более темным и более заметным.
Изображение: Низкоуглеродистая сталь A36
Сварные швы из нержавеющей стали:- Травление сварного шва для нержавеющей стали: Наше средство для травления нержавеющей стали общего назначения.
В отличие от Lepito’s Etch или Aqua Regia, смешивание или нагревание не требуется. Плюс его можно хранить.
Изображения: 304, 308, 316, 409, 439, 2205 дуплекс, 17-7 PH
Алюминиевые сварные швы:- AWS D1.2 Basic Etchant: Внесено в сварочный код D1.2. Быстро и эффективно.
Фотографии: 3003, 5052, 5085, 5456, 6061, 6063
- Реагент Келлера: Только для опытных пользователей. Он содержит фтористоводородную кислоту! Пожалуйста, обращаться осторожно.
- Травитель с хлоридом железа: Травление общего назначения для сварных швов на основе меди. Предварительно смешанный, готовый к использованию.
- AWS D1.9 Титановый сварной шов: Внесен в код сварки D1.9. Он содержит фтористоводородную кислоту! Пожалуйста, обращаться осторожно.
- Отшлифуйте поверхность шва до однородной шероховатости зернистостью 600. Быстро промойте и высушите поверхность, а затем немедленно протравите ее с помощью реагента Adler’s Reagent . В противном случае Inco 625 будет реагировать с воздухом и пассивироваться.
Изображение: Сварка Inco 625
Кислотное травлениепри испытаниях сварки: что это такое?
20 августа 2019 г. Для инспекторов по сварке комплекты кислотного травления — это просто еще один инструмент.Эта коробка с мягкими пузырьками отлично сочетается с обширным набором инструментов для совместного обследования. Правда, эти вещества намного энергетичнее, чем краситель-пенетрант. В конце концов, кислоты предназначены для коррозии. Но это не старые летучие химические вещества. Напротив, они специально разработаны таким образом, чтобы растворять граничные, закрывающие шлаковые включения.
Это механизм устранения дефектов
Исследования кислотным травлением растворяют шлак сварного шва. Испытание подчеркивает границы между сварными швами и краями основного металла.Другими словами, тест подчеркивает топографическую анатомию сварного шва. В противном случае предполагаемые демаркационные зоны вокруг каждого участка сварного шва было бы невозможно различить. В отличие от колец, обозначающих возраст внутри срубленного дерева, эти граничные линии не распознаются мгновенно, если только сварной шов не обработан раствором кислотного травления. Однако, как и это дерево, эту внутреннюю перспективу нельзя увидеть, пока не будет сделано поперечное сечение сварного шва. Отполированный и протравленный кислотой, срезанный поперечный разрез подготовлен так, чтобы он раскрыл свои секреты.
Испытание на разрушающую и коррозионную сварку сварных швов
Без сомнения, экзамен можно назвать только тяжелым испытанием. После открытия смотрового бокса инспектора осторожно наносят раствор соляной или азотной кислоты. Образец поперечного сечения для испытаний был отрезан от подозрительного сварного шва, и теперь он находится в посуде, полной кислоты. Коррозийное соединение проникает в образец. Вскоре после этого происходит очень показательное химическое действие.Границы между сварным швом и основным металлом выделяются, отложения шлаковых включений растворяются, открываются скрытые газовые карманы, и все, когда-то замаскированные дефекты сварного шва, становится намного легче распознать.
Используется как устройство для определения прочности
Целостность сварного шва подвергается серьезным испытаниям с помощью этого режима разрушающих совместных пыток. При расплавлении шлаковых включений обнажаются дефекты сварного шва. Если таким образом можно выделить границу сварного шва, подумайте, как будут обнаруживаться трещины. Проблемы с пористостью, плохие сплавы, трещины на волосах и все другие формы деградации сплавов — они не могут укрыться от химического воздействия, которое разработано для растворения всего случайного маскирующего дефекты сварочного детрита.
Если дефект сварного шва находится глубоко внутри остывшего металла, его практически невозможно обнаружить. Даже красители и микроскопы могут пропустить крошечные дефекты пористости и другие дефекты, нанесенные сварщиком или оборудованием. После пропуска дефекты со временем усугубляются, сварной шов вызывает дефект конструкции, и конструкция страдает. Инспекторы по сварке не могут мириться с такими вопросами, влияющими на качество и безопасность, поэтому так важны испытания на кислотное травление. Коррозионное вещество, используемое для разрушения скрытых дефектов стыков, обнажает мельчайшие неровности сварного шва для всеобщего обозрения.
Оптимизировано: Netwizard SEO
509 Превышен предел пропускной способности
509 Превышен предел пропускной способности Сервер временно не может обслуживать ваш запрос из-за того, что владелец сайта достиг своего ограничение пропускной способности.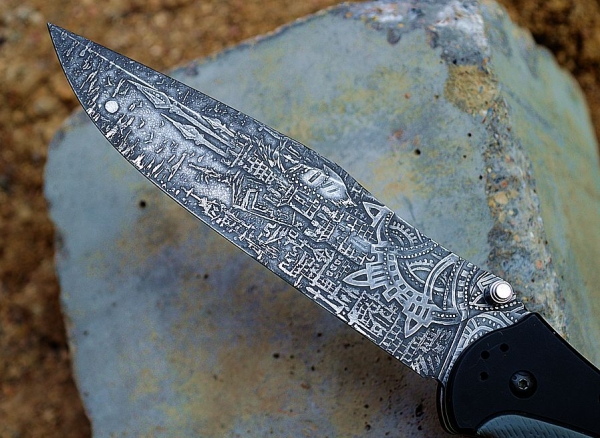
Рисунок травления сварной стали (Дамаск)
Травление сварной стали по шаблону (иногда называемой дамасской) было довольно сложным процессом. В первый раз, когда я попробовал это, потребовалось 5 попыток, прежде чем я был доволен результатами. Я только что закончил еще 2 дамасковых самолета и почти уверен, что знаю, что делаю сейчас.
На фото выше показана установка.
A) Ацетон
B) Хлорид железа (травящая кислота)
C) Ведро для ополаскивания горячей водой
D) Ведро с нейтрализующим раствором
E) Пищевая сода
F) мерный стакан
G) щетки
H) стекло 9 «x9» Форма для выпечки
Стальные стороны рубанка отшлифованы до зернистости 600.Это намного мельче, чем я обычно использую, но если поверхность не совсем гладкая, будут видны зазубрины на стали, оставленные более грубой бумагой — даже после травления (узнал об этом после первого раунда 🙂
Проблема с травлением Плоскость — это тот факт, что у вас есть заполняющий материал (в данном случае Ebony), касающийся стали, подлежащей травлению. Обычно лезвие ножа можно погрузить в различные растворы, что происходит очень быстро и, что более важно, покрытие остается постоянным.На плоскости необходимо нанести кистью различные растворы, что затрудняет получение равномерного травления. По мере того, как раствор стекает по сторонам плоскости, скорость травления изменяется соответственно. Я не мог придумать способ прикрыть бронзовую крышку рычага или защитить Ebony достаточно, чтобы погрузить самолет.
Вот процесс.
Используйте ацетон для очистки стальной поверхности от воска, масла или отпечатков пальцев. Это очень важно, так как что-либо на поверхности стали будет замедлять процесс травления, и это будет видно!
Я смешиваю хлорид железа с дистиллированной водой — 50/50 — по одной полной мерной чашке каждого.Я выливаю это в стеклянный поддон.
Я вскипячу чайник воды и наливаю половину воды в ведро для полоскания, а остальную часть — в ведро для нейтрализующего полоскания — вместе со связкой пищевой соды. Я не могу измерить, сколько … просто небольшая кучка на дне ведра.
На трех фотографиях выше показан процесс травления. Это заняло около 20 минут, чтобы сделать каждый самолет. Я наносил раствор хлорида железа по бокам, стараясь не попасть слишком много на синюю ленту или бронзовую крышку рычага.Я не беспокоился о том, что они попадут на подошву, так как они вылезут после подпиливания рта. Инструментальная сталь 01 (подошва и поперечные штифты) также подвержена травлению, но они приобретают приятный тускло-серый цвет. Примерно через 10 минут постоянного мытья сторон в протравке, я беру кусок влажной / сухой бумаги зернистостью 2000 и шлифую влажным способом поверхность сторон. Это удалит черную грязь (мое научное название для нее) и обнажит свежую сталь для травления. Вы должны быть очень осторожны, чтобы шлифовать равномерно — вплоть до края ленты — иначе травление не будет однородным.Затем повторно нанесите травитель еще на 10 минут или около того, пока он не станет похожим на то, что вам нужно.
На этом этапе вы почувствуете себя героем, потому что стороны будут выглядеть потрясающе. На следующем этапе колеса часто падают, и вам нужно выбросить самолет в окно.
Как только вы будете довольны количеством травления, вы должны смыть столько травителя, сколько сможете, а затем нейтрализовать его. И быстро. Я использую вторую чистую кисть и теплую / горячую воду, чтобы смыть травитель, а затем сразу же промываю его раствором пищевой соды.Звучит легко, но по мере того, как вода отступает по бокам, обычно появляется ржавчина. Лучшее решение, которое я нашел, чтобы держать это в страхе, — это использовать фен (не тот, который использовался для ленточной пилы) и как можно быстрее удалить воду.
ПРИМЕЧАНИЕ. Если вы не смываете травитель предварительно, между ним и раствором пищевой соды будет довольно пенная реакция.
Вот снимок обезвреженного и сухого самолета. Обратите внимание, насколько все серо. Он потемнеет, как только вы положите что-нибудь на сталь, чтобы защитить ее от ржавчины. Я использовал WD40, а затем слой пасты.
Готовый XSNo.4D
Готовый SNo.4D и несколько снимков пары.
Мне нужно еще раз поблагодарить моего друга Брайана Бакнера, который мне очень помог в прошлый раз, когда я это сделал. У меня с собой была распечатка его инструкций по электронной почте, которые снова мне очень помогли. И если у кого-то еще есть предложения о том, как я могу улучшить этот процесс — я хотел бы услышать от вас.
Услуги по сварке с макротравлением, Услуги по лазерной сварке — Kerri Engineering Works, Висакхапатнам
Услуги по сварке с макротравлением, Услуги по лазерной сварке — Kerri Engineering Works, Висакхапатнам | ID: 10964054462Уведомление : преобразование массива в строку в / home / indiamart / public_html / prod-fcp / cgi / view / product_details.php на линии 290
Описание продукта
Характеристики:- Прочная конструкция
- Превосходная производительность
- Высочайшая эффективность
Заинтересовал этот товар? Получите последнюю цену у продавца
Связаться с продавцом
Изображение продукта
О компании
Год основания 2000
Юридический статус Фирмы Физическое лицо — Собственник
Характер бизнеса Производитель
Количество сотрудников от 26 до 50 человек
Годовой оборот5–10 крор
Участник IndiaMART с августа 2011 г.
GST37ADJPC2804Q1ZC
Компания Kerri Engineering Works была основана в 2000 году. Мы являемся ведущим производителем и поставщиком услуг по сварке сварных швов для макротравливания, пневматической системы транспортировки проб и т. Д. Мы входим в число ведущих производителей и предлагаем широкий ассортимент пневматических конвейерных систем и заняли свою нишу. в этой товарной категории. Мы предоставляем нашим клиентам высокоэффективную транспортную систему.Мы предлагаем множество вариантов пневматических конвейерных систем, включая вакуумные системы с разреженной фазой или системы давления для муки, сахара или химикатов, а также вакуумные системы с плотной фазой или системы давления для работы с различными материалами.
Вернуться к началу 1
Есть потребность?
Получите лучшую цену
Есть потребность?
Получите лучшую цену
Лазерное травление: все, что вам нужно знать
Из-за скорости и надежности лазерное травление — это процесс, который мы рекомендуем для большинства маркировочных работ.
На протяжении многих лет нам задавали всевозможные вопросы по этому поводу. Если вы хотите узнать, как это работает, чем он отличается от других процессов лазерной маркировки или сколько это стоит, мы уверены, что вы найдете все, что вам нужно знать, в этой статье.
Что такое лазерное травление?
Лазерное травление — это процесс, при котором на деталях и изделиях остаются следы путем плавления их поверхности. Это часть более широкой категории, называемой лазерной маркировкой, которая также включает лазерную гравировку и лазерный отжиг.Очень универсальный, он может использоваться с большинством металлов.
Для создания выпуклой метки лазерный луч передает большое количество энергии на небольшую площадь. В результате поверхность материала плавится и расширяется. Это может окрасить материал в черный, белый или серый цвет.
Чаще всего травление используется для нанесения стойкой маркировки, такой как коды матрицы данных, серийные номера, штрих-коды и логотипы.
Когда было изобретено лазерное травление?
Дата изобретения лазерного травления неизвестна, но мы знаем, что лазерная гравировка была впервые использована в 1978 году.Поскольку эти два процесса очень похожи (лазерная гравировка включает в себя некоторый уровень плавления), происхождение лазерного травления, возможно, такое же, как и при лазерной гравировке.
Вот некоторые из ключевых событий, которые привели к изобретению лазерного травления, каким мы его знаем сегодня:
- 1917 — Альберт Эйнштейн теоретизирует, что электроны можно заставить излучать свет определенной длины волны в своей статье «Квантовая теория излучения».
- 1951 — Чарльз Хард Таунс создает мазер (усиление микроволнового излучения за счет вынужденного излучения), предшественника лазера (усиление света за счет вынужденного излучения).В 1954 году он демонстрирует, что мазер работает с устройством, излучающим длину волны ≈1 см.
- 1957 — Гордон Гулд теоретизирует о лазере. Почти в то же время, в 1958 году, Таунс публикует статью, в которой показано, что мазеры могут работать в оптическом и инфракрасном спектрах. Это приводит к длительным патентным спорам, при этом Гулд получает патенты только в 1977 и 1979 годах. В 1988 году он получает гонорары впервые после 30 лет споров.
- 1960 — Создан первый лазер.
Он использует синтетический кристалл рубина (его усиливающая среда) для усиления света.
- 1960 — Генерируется первый непрерывный лазерный луч. Сегодня этот метод используется в таких областях, как лазерная сварка и лазерная резка.
- 1962 — Изобретена модуляция добротности — метод получения импульсных лазерных лучей. Импульсные лучи достигают более высоких пиковых мощностей, чем непрерывные лучи, и сегодня используются для лазерного травления, лазерной гравировки, а также во многих других промышленных приложениях.
- 1964 — Изобретение Nd: YAG-лазера. В современном производстве варианты этого лазера используются для лазерного травления, лазерной резки и лазерной сварки.
- 1964 — Изобретение СО2-лазера. Сегодня он используется для лазерной маркировки и лазерной резки.
- 1978 — Приобретен первый лазерный гравер, хотя и в примитивном виде. Его используют для создания произведений искусства по дереву.
- 1996 — Создано первое программное обеспечение, разработанное специально для лазеров.Со временем компьютеры интегрируются непосредственно в лазерные гравировальные станки.
С этого момента лазерное травление и лазерная гравировка стали более широко использоваться для гравировки личных вещей и обеспечения современной прослеживаемости на производственных линиях.
Как работает лазерное травление?
Все методы лазерной маркировки имеют одну общую черту: лазерный луч является импульсным, испускающим внезапные всплески энергии через определенные промежутки времени. За 1 секунду импульсный лазер мощностью 100 Вт может испустить 100 000 импульсов.Каждый импульс содержит 1 миллиджоуль энергии и может достигать 10 000 Вт пиковой мощности.
Поскольку лазерное травление металла требует меньше энергии на единицу площади, чем его гравировка, импульсы более удалены друг от друга, как показано ниже.
Процесс лазерного травления | Процесс лазерной гравировки |
Когда луч попадает на поверхность, материал поглощает его энергию, превращая ее в тепло.Хотя поверхность материала отражает большую часть энергии луча, она также поглощает и преобразует часть этой энергии в тепло. Чтобы произошло лазерное травление, материал должен поглотить достаточно энергии, чтобы расплавить его микроповерхность и заставить ее расшириться.
Когда энергия луча преобразуется в тепло, температура материала увеличивается. При таком сильном нагреве поверхность становится податливой, что позволяет изменять ее форму.
Материал | Точка плавления |
---|---|
Алюминий 6061 | 585 ° С |
Алюминий 380 | 566 ° С |
Углеродистая сталь | 1425—1540 ° С |
Свинец | 327.5 ° С |
Магний | 650 ° С |
Нержавеющая сталь марки 304 | 1400—1450 ° С |
Нержавеющая сталь марки 316 | 1375—1400 ° С |
По мере того, как материал плавится и остывает за миллисекунды, на поверхности происходят локальные изменения. Изменяется шероховатость поверхности, образуя стойкую маркировку.
Как выглядят изменения шероховатости? Давайте посмотрим на увеличенные изображения, сделанные с помощью электронного микроскопа.
Перед процессом лазерного травления | После процесса лазерного травления |
Как видите, шероховатость поверхности постоянно изменяется. Изменения цвета появляются в результате появления на поверхности различных рисунков. Для качественной маркировки лучше всего контрастируют черный и белый цвета.
Конечно, процесс оптимизирован для каждого приложения и поэтому немного отличается.Если у вас есть особые требования, лучший способ узнать, как процесс травления работает для вашего приложения, — это спросить эксперта по лазерам.
Если вы хотите глубже изучить физику, лежащую в основе лазерных технологий, вы также можете посмотреть бесплатные обучающие видеоролики, созданные Массачусетским технологическим институтом.
В чем разница между лазерным травлением и лазерной гравировкой?
Лазерное травление | Лазерная гравировка |
Лазерное травление выполняется быстрее, но лазерная гравировка более долговечна.Это связано с тем, что для достижения точки плавления материала (лазерное травление) требуется меньше энергии, чем для его испарения (лазерная гравировка). Для глубокой лазерной гравировки может потребоваться даже несколько проходов лазера и неизбежно даже больше времени.
С другой стороны, отверстия, вырытые с помощью гравировки, имеют лучшую защиту от истирания, чем приподнятые метки, образованные травлением. Фактически, высота лазерного травления может достигать 80 микрон, тогда как глубина лазерной гравировки может достигать 500 микрон.
Лазерное травление выделяется, когда дело доходит до создания высококонтрастной маркировки.В то время как лазерная гравировка создает только черные метки, лазерное травление можно использовать для создания как черных, так и белых меток. По этой причине лазерная гравировка обычно используется в сочетании с лазерным травлением для создания высококонтрастных гравюр.
Обычно травление лучше гравировки, если вам не нужна высокая устойчивость к истиранию. Если вы все еще не можете решить, что лучше для вас, мы подготовили статью, которая поможет вам выбрать между травлением и гравировкой. Или вы можете спросить у специалиста по лазерам.
Посмотрите это видео, чтобы увидеть как лазерную гравировку (темные отметки), так и лазерное травление (бледные отметки).
Является ли лазерное травление постоянным?
Да, лазерное травление необратимо. Лазерная маркировка останется читаемой в течение всего срока службы детали с лучшей читаемостью, чем другие технологии прямой маркировки детали. Фактически, лазерное травление может выдерживать неабразивную обработку, включая электронное покрытие, порошковое покрытие и термообработку.
Но знайте, что у лазерного травления есть свои ограничения. Абразивные процедуры, такие как дробеструйная обработка и пескоструйная обработка, обычно удаляют следы лазерного травления.Чтобы сохранить читаемость после абразивной обработки, вам необходимо маркировать детали с помощью ударопрочной лазерной гравировки.
Какие материалы можно травить лазером?
Лазерное травление — это универсальный процесс, который можно использовать практически с любым металлом. Следующий список не является исчерпывающим:
Для получения информации о маркировке различных материалов обратитесь к специалисту по лазерам.
Какие цвета можно травить лазером?
Лазерное травление позволяет получать черный, белый и оттенки серого.Для высококачественной маркировки и отслеживания деталей черный и белый обеспечивают наилучший контраст. Вот как лазерное травление создает эти цвета:
Рассеянное отражение создает белый цвет | Абсорбция создает черный |
Если шероховатость поверхности заставляет световые лучи отражаться под разными углами (т. | Там, где шероховатость поверхности приводит к улавливанию световых лучей (т.е.е., впитывается) поверхность кажется черной. |
Лазерный отжиг, другой процесс маркировки, позволяет создавать более широкий диапазон цветов на стали и нержавеющей стали. Модулируя параметры лазера, можно создавать разные цвета, как показано на следующих рисунках.
Насколько быстро выполняется лазерное травление?
Лазерное травление более чем в два раза быстрее гравировки и отжига, что делает его самым быстрым процессом лазерной маркировки.Для увеличения скорости травления можно использовать системы с большей мощностью лазера. Для большинства маркировочных работ максимальная мощность лазера, которая вам понадобится, составляет 100 Вт. При необходимости также доступны более мощные лазеры.
Система равной мощности может травить быстрее, чем другая, если она построена с лучшими оптическими компонентами и оптимизированы параметры лазера. Наша серия LXQ является типичным примером этого. Тесты скорости показали, что это самый быстрый лазерный маркер для металлов.
Кроме этого, скорость маркировки также зависит от типа материала, размера идентификатора и его цветов (вытравливание белых меток выполняется быстрее, чем черных меток).Следующие ресурсы предоставляют вам примеры скорости маркировки:
Какие типы лазеров подходят для лазерного травления?
Для лазерного травления можно использовать только волоконные лазеры. Это связано с тем, что травление — это процесс, используемый для металлов, которые лучше реагируют на волоконный лазер. На самом деле, какой лазер вам нужен, зависит от типа материала, который вы хотите травить, а не от вашего процесса маркировки.
Но зачем вам волоконные лазеры для травления металлов? Потерпите, ответ технический.
Лазеры выделяют энергию, испуская лазерные лучи определенной длины волны.Когда луч падает на поверхность, материал отражает большую часть своей энергии. Оставшаяся энергия поглощается и превращается в тепло. Для лазерного травления материал должен поглощать достаточно энергии, чтобы расплавиться.
Теперь волоконные и СО2-лазеры генерируют волны разной длины, и каждый материал по-разному поглощает / отражает эти длины волн. Чтобы максимизировать передачу энергии от лазерного луча к материалу, вам нужна правильная длина волны.
Как видно на следующем графике, металлы поглощают длину волны волоконного лазера (1064 нм) более эффективно, чем лазер CO2 (10.6 мкм). По этой причине волоконный лазер (разновидность твердотельного лазера) является лучшим выбором для маркировки металлов.
Оригинальная работа, опубликованная в Laser Focus World, перепечатана с разрешения Endeavour Business Media, LLC.
Сколько стоит станок для лазерного травления?
Трудно назвать цену, которая покрывала бы все решения для лазерного травления, особенно потому, что цена сильно варьируется от одной компании к другой. Но мы можем дать вам представление о связанных с этим расходах.
Сама лазерная система не такая уж и дорогая, с более высокими ценами для производственных приложений и более низкими ценами для менее серьезных приложений. Цена, которую вы платите, также зависит от необходимого вам уровня автоматизации.
- Настольные лазеры или настольные лазеры — наименее дорогие решения. Они предназначены для местных магазинов, которые хотят выгравировать личные вещи, такие как украшения, трофеи и оружие. Поскольку маркировка не выполняется внутри корпуса, необходимо надевать очки для защиты от лазера.
- Рабочие места с ручным управлением дороже настольных лазеров, потому что они включают корпус лазера класса 1, который обеспечивает 100% безопасность оператора. Этот тип лазера идеально подходит для маркировки партий.
- Полуавтоматические рабочие места оснащены поворотным столом, который поддерживает оператора, что позволяет выполнять операцию маркировки в скрытое время. Этот тип рабочей станции используется для встроенной лазерной маркировки (оператор должен следить за производственным процессом). Он также используется для маркировки партий.
- Полностью автоматизированные лазерные станки — самые дорогие решения. Они предназначены для интеграции в крупносерийные производственные линии, в которых используются роботы или конвейерные системы, такие как те, которые используются на плавильных заводах, литейных заводах и сборочных линиях.
Что делает некоторые лазеры более дорогими?
Приведенные ниже примеры помогут вам понять разницу в цене между лазерами от разных компаний.
- Некоторые лазерные машины не обеспечивают защиты окружающей среды, в то время как другие имеют степень защиты IP, предлагая защиту от пыли, воды и других загрязнений, которые со временем могут сломать вашу систему.
- Некоторые лазерные системы сделаны из дешевых оптических компонентов, которые создают некачественную маркировку. В других лазерах используются компоненты более высокого качества, которые улучшают долговечность, скорость, контрастность и точность.
- Некоторые лазеры заключены в пластиковые корпуса, которые легко сломаются. Другие заключены в прочный металлический каркас, который выдерживает прямые удары и защищает внутренние компоненты.
Перед покупкой лазера необходимо:
- Обсудите ваше приложение со специалистом по лазерам, который может вам посоветовать.
- Спросите, чем продукт отличается от продуктов конкурентов.
- Запросить образец маркировки.
Как осуществить лазерное травление?
Для реализации лазерного травления внутри и вне производственных линий Laserax предлагает машины для лазерной маркировки (для стандартных решений) и лазерные маркеры OEM (для индивидуальных решений с системными интеграторами).
Мы знаем, что к каждому проекту предъявляются особые требования. Если у вас есть вопросы о том, как реализовано лазерное травление, мы можем вам помочь.Все, что вам нужно сделать, это спросить наших специалистов.
Расскажите о своей заявке
Идентификация фаз в нержавеющих сталях травлением
Реферат
Для селективного выявления фаз матрицы и компонентов второй фазы в ферритных, мартенситных, ферритно-мартенситных, аустенитных, феррито-аустенитных (дуплексных) и дисперсионно-твердеющих нержавеющих сталях использовались многочисленные травители. Описаны процедуры идентификации вторых фаз, таких как карбиды, сигма и хи, а также дельта-феррит в аустенитных или дисперсионно-твердеющих нержавеющих сталях с использованием селективных травителей.
Введение
Микроструктура нержавеющей стали довольно сложна, и воздействие высоких рабочих температур усложняет ее, поскольку можно наблюдать множество фаз. Помимо матричных фаз феррита, аустенита и мартенсита, а также дуплексного аустенитно-ферритного и (реже) феррит-мартенсита, существует множество возможных второстепенных составляющих. В семействе карбидов наиболее распространены карбиды M 23 C 6 (гранецентрированный кубический) и M 7 C 3 (шестиугольный), но M 6 C (гранецентрированный кубический) и Карбиды MC (гранецентрированные кубические) также наблюдаются в некоторых сплавах.Определенные нитриды могут наблюдаться и в интерметаллических фазах, сигма, σ (тетрагональная), chi, χ (объемно-центрированная кубическая) и Laves, η (гексагональная). Много было опубликовано относительно методов селективного травления для отличия сигма от феррита или дельта-феррита, а также для различных карбидов, но мало было опубликовано относительно chi и Laves. Эти две составляющие наблюдаются только в некоторых сплавах и при определенных условиях.
Несмотря на то, что некоторые из этих составляющих имеют некубические кристаллические структуры, они плохо реагируют на поляризованный свет, и этот режим наблюдения бесполезен для целей распознавания.ДВС Номарского может быть полезен, чтобы увидеть, какие составляющие сложнее матрицы, но это, в лучшем случае, дает ограниченную помощь. Лучшими методами для идентификации фаз и составляющих являются дифракция, либо дифракция рентгеновских лучей извлеченных остатков, либо дифракция электронов на сходящемся пучке с использованием реплик экстракции или тонкой фольги. Оба метода медленные и требуют дорогостоящего оборудования. Анализ WDS или EDS может быть очень полезным, если эти методы используются на хорошо изученных образцах (ранее исследованных дифракционными методами), но они также требуют дорогостоящего оборудования.Следовательно, существует долгая история интереса к идентификации этих фаз и компонентов с помощью светового микроскопа.
Экспериментальная программа
Для исследования были получены образцы из аустенитной нержавеющей стали типа 316, сваренные сварочным прутом типа 312, предназначенным для образования дельта-феррита в сварном изделии примерно 12-15%. Пластину приваривали с каждой стороны за четыре прохода. Срез выдерживали при 816 ºC (1500 ºF) в течение 160 часов (и медленно охлаждали до температуры окружающей среды) для преобразования дельта-феррита в сигма, а также для повышения чувствительности образца путем осаждения карбида на границах зерен.
Образцы смонтированы и подготовлены металлографическим способом. Каждый был протравлен реагентами, описанными ниже. Они были повторно подготовлены между травлениями. Использовались следующие травители.
- Реагент Вилеллы (1 г пикриновой кислоты, 4 мл HCl, 96 мл этанола), использовали тампоном в течение 10-20 с. Это обозначило дельту и сигму и выявило карбиды на границах аустенитных зерен основного металла и в сварной детали. Сигма-фаза была более резко очерчена, чем дельта-феррит.
Границы зерен аустенита не обнаружены.
- Реагент Мураками (10 г КОН или NaOH, 10 г феррицианида калия, 100 мл воды), используемый при комнатной температуре или от 80 до 100 ºC. При комнатной температуре карбиды могут обнаруживаться на границах аустенитных зерен и внутри сварного шва. При использовании при температуре кипения или около нее обнаруживаются как дельта, так и сигма. Дельта проявляется не так отчетливо, как сигма. С КОН сигма окрасилась в оранжево-коричневый цвет за 30 с, но еще через 30 с почти весь цвет исчез.При использовании NaOH сигма окрашивалась в оранжево-коричневый цвет через 60 с. Дельта-феррит был окрашен лучше при использовании NaOH, чем при использовании КОН (очень слабый).
- 20% NaOH в воде при 3 В постоянного тока, 10 с, используется для окраски как дельта-феррита (желто-коричневый / синий), так и сигма (оранжево-коричневый). Карбиды были видны, но не сильно выявлены.
- Для окрашивания карбидов использовали 10% персульфат аммония в воде при постоянном напряжении 6 В, 10 с. Контрастность была немного лучше, чем у Вилеллы, но оба отлично показали карбиды. Этим травлением были выделены как дельта-феррит, так и сигма-фаза.Опять же, резкость фазовых границ была превосходной для сигма и неоднородной для дельта-феррита.
- Концентрированный гидроксид аммония при 1,5 В постоянного тока и 6 В постоянного тока в течение 60 с, был использован для выявления структуры. При постоянном напряжении 1,5 В карбиды проявлялись слабо через 60 с. При 6 В постоянного тока карбиды были видны через 60 с, но не с контрастом, создаваемым Вилеллой или персульфатом аммония. Сигма не была раскрашена. Катод из нержавеющей стали использовался для всего электролитического травления.
Микроструктуры
Образец после сварки не был сенсибилизирован, и карбид в основном металле не наблюдался. Однако в основном металле типа 316 наблюдались небольшие удлиненные частицы дельта-феррита. Это показано на Рисунке 1 после травления реактивом Вилеллы. В сварном шве присутствовало некоторое количество карбида. На рис. 2 показан карбид плюс некоторые включения шлака (обратите внимание на показанное очень большое) после травления при комнатной температуре в течение 60 с реактивом Мураками.
Рис. 1. Стрингеры из дельта-феррита (стрелки) в основном металле 316, образец сразу после сварки, после травления реактивом Вилеллы. | Рис. 2. Мелкая дисперсия карбидов, связанных с (слабо видимым) дельта-ферритом в металле сварного шва 312, в состоянии после сварки (Murakami’s, 60 с при 20 ºC). |
Дельта-феррит показан на рисунках 3 a, b, c и d после травления реагентом Вилеллы, реагентом Мураками (кипячение, 3 мин), 20% NaOH (3 В постоянного тока, 10 с) и 10% аммония. персульфат (6 В постоянного тока, 10 с) соответственно.Обратите внимание, что последнее травление только очерчивало дельта-феррит, и это было немного неравномерно. Электролитический гидроксид натрия дает наиболее однородные результаты с наилучшей резкостью и контрастом и настоятельно рекомендуется для этой цели.
Рисунок 3 а. Дельта-феррит в образце после сварки, выявленный с помощью реактива Вилеллы. | Рисунок 3 б. Дельта-феррит в образце после сварки, выявленный с помощью реактива Мураками (3 мин при 90-100 ºC). |
Рисунок 3c. Дельта-феррит в образце после сварки, обнаруженный с помощью 20% NaOH (3 В постоянного тока, 10 с). | Рисунок 3d. |
Микроструктура состаренного образца немного сложнее, поскольку сварная деталь содержит сигма и карбид, а основной металл был сенсибилизирован и имеет карбид M23C6 на границах зерен и двойников.Несколько травителей хорошо выявили карбиды. Реагент Вилеллы выявил карбиды очень четко и с хорошим контрастом, а также очень четко обозначил сигма-фазу. Четкость и однородность очертания были намного лучше, чем у дельта-феррита. Небольшие участки дельта-феррита, которые наблюдались в основном металле 316, были преобразованы в сигма при обработке старением, и теперь они выглядят совсем иначе при травлении с помощью Vilella’s, рисунок 4 (сравните с рисунком 1). Один стрингер находится в правом верхнем углу изображения.Остальные крупные осадки представляют собой включения сульфидов. Границы зерен и двойников почти полностью покрыты карбидом, выделившимся при термообработке после сварки. Помимо межкристаллитного карбида есть внутризеренный карбид. Реагент Вилеллы очертил сигму в сварной конструкции, рис. 5, а границы фаз более резкие, чем для дельта-феррита, рис. 3а. Большие черные круглые частицы на рисунке 5 — это частицы шлака. Более мелкие темные частицы в аустенитной матрице представляют собой карбиды.
Рис. 4. Сенсибилизация границ зерен у старых образцов, выявленная Вилеллой. | Рис. 5. Дельта-феррит в состаренном образце, выявленный с помощью реактива Вилеллы. |
20% гидроксид натрия в воде при 3 В постоянного тока, 10 с, отлично подходит для выявления сигма-фазы в состаренном образце, но дает несколько более слабый контраст для карбидов границ зерен. На рис. 6 показан основной металл 316, и на нем отчетливо видны небольшие дельта-ферритовые стрингеры в основном металле. Карбиды на границах зерен видны, но не так сильно, как у Vilella. На рис. 7 показана ярко выраженная сигма-фаза сварного шва 312, окрашенная в оранжево-коричневый цвет.
Реагент Мураками при комнатной температуре выявил карбиды как в состаренном основном металле, так и в сварной детали, но не на сигме. На рисунке 8 показан основной металл. Обратите внимание на отмеченные стрелками области, которые содержат несколько более крупных карбидов. Поскольку ни сигма-феррит, ни дельта-феррит не были обнаружены в образцах после сварки или состаренных при старении при комнатной температуре, предполагается, что эти частицы являются карбидами.На рис. 9 показаны карбиды, обнаруженные в сварной детали. Это полезно, поскольку многие другие травители также обнаруживают сигму, что затрудняет просмотр карбидов в сварной детали.
Рис. 6. Карбиды и сигма-стрингеры в состаренном основном металле 316, выявленные с помощью электролитического гидроксида натрия. | Рис. 7. Сигма-фаза в состаренном металле сварного шва 312, выявленная с помощью электролитического гидроксида натрия. |
Рис. 8. Сенсибилизация состаренного основного металла 316, выявленная реактивом Мураками (60 с при 20 ºC). | Рис. 9. Осаждение карбида в состаренном металле сварного шва 312, обнаруженное реактивом Мураками (60 с при 20 ºC). |
Прибор Мураками, использованный при 80-100 ºC, показал сигма-фазу оранжево-коричневого цвета. На рисунке 10 показана сигма с использованием NaOH в составе.Когда использовался КОН, сигма окрашивалась аналогичным образом через 30 с, но с дополнительным 30-секундным травлением окраска была в значительной степени удалена. Использование NaOH по сравнению с KOH у Мураками требует дальнейшего изучения. Обычно они считаются эквивалентными. В будущих работах будут также рассмотрены версии 20/20/100 и 30/30/100 Мураками.
10% персульфат аммония при 6 В постоянного тока, 10 с, является отличным травителем для выявления сенсибилизации, и он снова оказался весьма полезным для этой цели, как показано на рисунке 11.Это показывает хорошо заметные карбиды в состаренном основном металле 316. На рисунке 12 показано, что персульфат аммония довольно хорошо обрисовывает сигму, но не окрашивает ее. Обратите внимание, что очертания намного четче и однороднее, чем у дельта-феррита (рис. 3d).
Рис. 10. Сигма очень хорошо проявляется в состаренном металле сварного шва 312 с использованием реактива Мураками (80-100 ºC в течение 60 с). | Рисунок 11.Электролитический 10% персульфат аммония отлично подходит для выявления сенсибилизации границ зерен. |
Последний пример — использование концентрированного гидроксида аммония электролитическим способом. Результаты были не лучше, чем для других более легко используемых реагентов, и из-за сильного резкого запаха гидроксида аммония и раздражения рук, глаз, носа и горла его использование не рекомендуется. Он действительно выявил карбиды в сенсибилизированном основном металле 316, но не так хорошо, как у Вилеллы или персульфата аммония.При этом использовании сигма не была обнаружена, хотя при предыдущем использовании она была (другой экземпляр).
Выводы
Исследование показало, что для выявления составляющих в нержавеющих сталях можно использовать различные реагенты. Реагент Вилеллы и другие аналогичные реагенты общего назначения выявят карбиды, но только очертят дельта-феррит и сигму. Они бесполезны для идентификации. Электролитический 20% NaOH превосходно подходит для выявления и различения дельта-феррита и сигма, поскольку он окрашивает дельта-феррит в коричневый, синий и сигма-оранжевый цвета.Мураками работает хорошо, но дает неустойчивые результаты. При комнатной температуре он выявляет только карбид, но не так отчетливо, как у Вилеллы или персульфата аммония. При температурах, близких к температуре кипения, стандартный состав окрашивал дельта-феррит неравномерно и сигма-однородно. Но разницы в цвете не было. Персульфат аммония отлично подходит для обнаружения сенсибилизации, поскольку он очень четко выявляет карбиды. Он выделил как дельта-феррит, так и сигму. Опять же, дельта-феррит не был четко очерчен, но сигма была.Гидроксид аммония не рекомендуется использовать, так как он действует не лучше, чем любой другой травитель, и его использование очень раздражает. В будущем необходимо изучить возможность использования КОН по сравнению с NaOH в стандартном травлении Мураками и опробовать варианты с более высокой концентрацией.
Рис. 12. Сигма в состаренном металле сварного шва 312, выделенном персульфатом аммония. | Рис. 13. Карбиды в состаренном основном металле 316, выявленные с помощью гидроксида аммония. |
Микроструктурная структура нержавеющих сталей довольно сложна, и воздействие высоких рабочих температур усложняет процесс, поскольку может возникнуть множество фаз. В дополнение к матричным фазам феррита, аустенита и мартенсита, а также дуплекса аустенит-феррит и (реже) феррит-мартенсит, существует множество возможных второстепенных составляющих. В семействе карбидов наиболее распространены карбиды M 23 C6 (гранецентрированный кубический) и M 7 C 3 (шестиугольный), но M 6 C (гранецентрированный кубический) и MC (гранецентрированный кубический). -центрированные кубические) карбиды также наблюдаются в некоторых сплавах.Нитриды можно наблюдать в интерметаллических фазах: сигма (σ — тетрагональная), хи (χ — объемно-центрированная кубическая) и Лавеса (η — гексагональная). Много было опубликовано о методах селективного травления для дифференциации сигма от феррита или дельта-феррита, а также для различных карбидов, но мало опубликовано о ци и Лавесе. Эти две составляющие наблюдаются только в некоторых сплавах и при определенных условиях.
Фиг.1. Состаренный металл сварного шва из нержавеющей стали 312, в котором сигма-фаза была окрашена травлением реагентом Мураками при 80 ° C. Линия увеличения имеет длину 20 мкм |
Хотя некоторые из этих компонентов имеют некубические кристаллические структуры, они плохо реагируют на поляризованный свет, и этот режим наблюдения не полезен для целей распознавания. ДВС Номарского может быть полезен для определения того, какие компоненты тверже или мягче матрицы, но это мало помогает.Лучшими методами для идентификации фаз и компонентов является дифракция — либо дифракция рентгеновских лучей извлеченных остатков, либо дифракция электронов на сходящемся пучке с использованием реплик экстракции или тонкой фольги. Оба метода медленные и требуют дорогостоящего оборудования. Анализ WDS или EDS может быть очень полезным, если эти методы используются на хорошо изученных образцах. Дифракция обратного рассеяния электронов (EBSD) также может использоваться для идентификации фаз. Но для анализа WDS, EDS и EBSD требуются частицы больше диаметра луча (> ~ 2 мкм).Следовательно, существует долгая история интереса к идентификации этих фаз и компонентов с помощью светового микроскопа.
Образцы из аустенитной нержавеющей стали типа 316 были сварены сварочным прутом типа 312, рассчитанным на образование дельта-феррита примерно 12-15% в сварном стержне. Пластину приваривали с каждой стороны за четыре прохода. Срез выдерживали при 816 ° C (1500 ° F) в течение 160 часов (и медленно охлаждали до температуры окружающей среды) для преобразования дельта-феррита в сигма, а также для повышения чувствительности образца путем осаждения карбида на границах зерен.
Образцы смонтированы и подготовлены металлографическим способом. Каждый был протравлен реагентами, описанными ниже. Они были повторно подготовлены между травлениями. Использовались следующие травители.
1. Реагент Вилеллы (1 г пикриновой кислоты, 4 мл HCl, 96 мл этанола), использовали тампоном в течение 10-20 с. Это обозначило дельту и сигму и выявило карбиды на границах аустенитных зерен основного металла и в сварном шве. Сигма-фаза была более резко очерчена, чем дельта-феррит.Зерно аустенита и двойниковые границы не обнаружены.
2. Реагент Мураками (10 г КОН или NaOH, 10 г феррицианида калия, 100 мл воды), используемый при комнатной температуре или 80–100 ° F. При комнатной температуре карбиды могут обнаруживаться на границах аустенитных зерен и внутри сварного шва. При использовании при температуре кипения или около нее обнаруживаются как дельта, так и сигма. Дельта проявляется не так отчетливо, как сигма. С КОН сигма окрасилась в оранжево-коричневый цвет за 30 с, но еще через 30 с почти весь цвет исчез.При использовании NaOH сигма окрашивалась в оранжево-коричневый цвет через 60 с. Дельта-феррит был окрашен лучше при использовании NaOH, чем при использовании КОН (очень слабый).
Рис. 2. Электролитическое травление с использованием 10% водного персульфата аммония отлично показывает карбиды, как в этом примере сенсибилизированного основного металла нержавеющей стали 316 с карбидами M23C6 на границах зерен в зоне термического влияния |
3. 20% NaOH в воде при 3 В постоянного тока, 10 с, используется для окраски как дельта-феррита (желто-коричневый / синий), так и сигма (оранжево-коричневый). Карбиды были видны, но не сильно выявлены.
4. 10% персульфат аммония в воде при постоянном напряжении 6 В, 10 с использовался для окрашивания карбидов. Контрастность была немного лучше, чем у Вилеллы, но оба отлично показали карбиды. Этим травлением были выделены как дельта-феррит, так и сигма-фаза. Опять же, резкость фазовых границ была превосходной для сигма и неоднородной для дельта-феррита.
5. Концентрированный гидроксид аммония при 1.5 В постоянного тока и 6 В постоянного тока в течение 60 с, были использованы для выявления структуры. При постоянном напряжении 1,5 В карбиды проявлялись слабо через 60 с. При 6 В постоянного тока карбиды были видны через 60 с, но не с контрастом, создаваемым Вилеллой или персульфатом аммония. Сигма не была раскрашена. Катод из нержавеющей стали использовался для всего электролитического травления.
Исследование показало, что для выявления компонентов в нержавеющих сталях можно использовать различные реагенты. Реагент Вилеллы и другие подобные реагенты общего назначения выявят карбиды, но только очертят дельта-феррит и сигму.Они бесполезны для идентификации. Электролитический 20% NaOH превосходно подходит для выявления и различения дельта-феррита и сигма, поскольку он окрашивает дельта-феррит в коричневый, синий и сигма-оранжевый цвета. Мураками работает хорошо, но дает неустойчивые результаты. При комнатной температуре он показывает только карбид, но не так отчетливо, как персульфат аммония или Вилелла. При температурах, близких к температуре кипения, стандартный состав окрашивал дельта-феррит неравномерно, но однородно окрашивал сигму.Но разницы в цвете не было. Персульфат аммония отлично подходит для обнаружения сенсибилизации, поскольку он очень четко выявляет карбиды. Он выделил как дельта-феррит, так и сигму. Опять же, дельта-феррит не был четко очерчен, но сигма была. Гидроксид аммония не рекомендуется использовать, так как он действует не лучше, чем любой другой травитель, и его использование очень раздражает.