Механические свойства титана
Главная \ СТАТЬИ О ТИТАНЕ \ Механические свойства титана
Механические свойства титана
Прочность титана при растяжении. Нелегированный титан может обладать прочностью при растяжении от 24,5 кг/мм2 для металла высокой степени чистоты, получаемого методами термического разложения иодида титана, до 70 кг/мм2 для металла повышенной вердости, получаемого из губки. Фирма Рем-Крю выпускает технически чистый металл двух марок (RC-A-55 и RC-A-70) с номинальным пределом текучести 38,5 и 49 кг/мм2.
Фирма Рипаблик стил подобным же образом производит титан марок RS 40, RS 55 и RS 70, а Тайтениум металз — Ti 75A и Ti 100A с номинальным пределом прочности при растяжении 56 и 70 кг/мм2. Фирма Мэллори-Шарон выпускает нелегированный переплавленный в дуговых печах титан 3-го сорта с номинальным пределом прочности 52,5 кг/мм2 и пределом текучести 35 кг/мм2. Нелегированный титан этой фирмы, переплавленный в индукционных печах (4-го сорта), имеет предел прочности при растяжении 70 кг/мм2 и предел текучести 60 кг/мм2.
Пластичность. Пластичность можно определить как способность материала деформироваться без разрушения. Пластичный материал легко поддается таким видам холодной обработки, как гибка, глубокая вытяжка и выдавка.
Технически чистый титан, переплавленный в дуговых печах, обладает в зависимости от содержания примесей следующими показателями пластичности: относительным удлинением 20-40% и поперечным сужением 45-65%. Иодидный титан обладает относительным удлинением до 55% и сужением поперечного сечения до 80%.
Как и в случае стали, титан в целях упрочнения легируют другими металлами. Добавки алюминия, ванадия, хрома, железа, марганца и олова вводятся отдельно и в сочетании друг с другом.
Однако в этом случае повышение прочности достигается за счет снижения пластичности. О легировании титана подробнее говорится далее, здесь же достаточно ограничиться указанием на то, что созданы титановые сплавы с пределом прочности свыше 140 кг/мм2, обладающие удовлетворительной пластичностью (относительное удлинение до 15%).
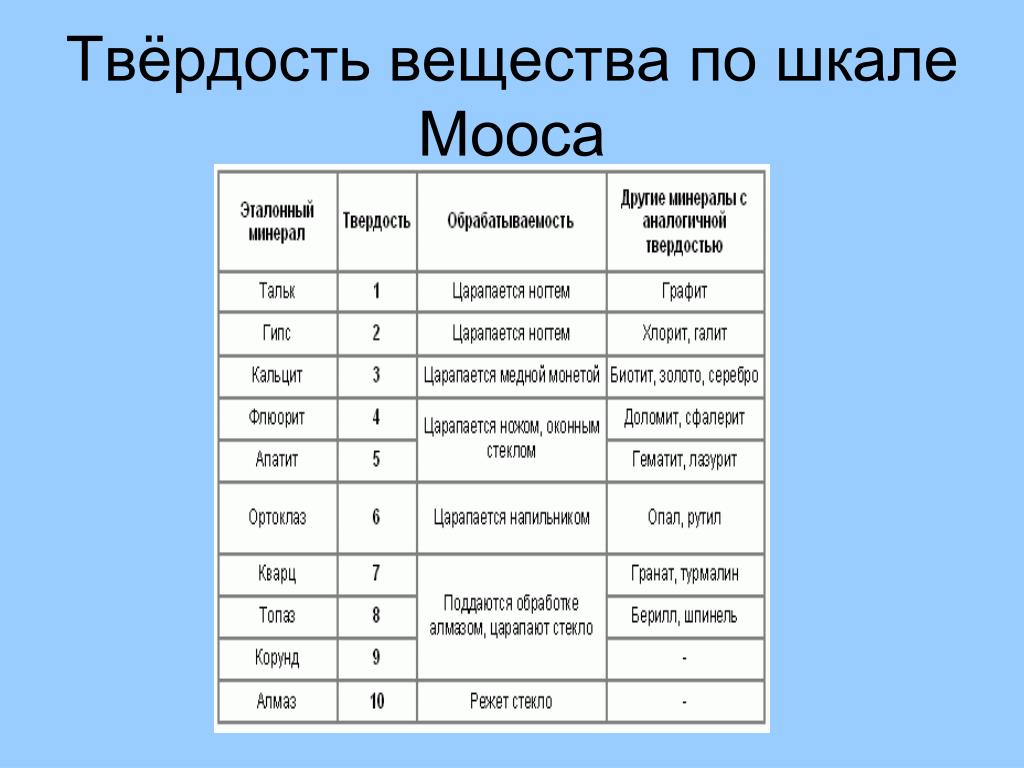
Прочность промышленных сплавов титана колеблется от 70 до 105 кг/мм2. Эти сплавы выплавляются в дуговых печах и обладают удовлетворительной пластичностью (10-20%). Сплавы, выплавленные в индукционных печах, обладают гораздо более высокой прочностью, но их пониженная пластичность делает их пригодными для использования только в ограниченных целях.
Твердость. Титан значительно тверже алюминия и по твердости приближается к некоторым термически обработанным легированным сталям. Иодидный титан имеет твердость 90, тогда как твердость нелегированного технического титана составляет около 160 единиц, а для сплавов после термообработки 250-500 единиц по Hv. Типичный промышленный сплав с пределом текучести около 90 кг/мм2 может иметь твердость до 320 единиц по Hv.
Сопротивление удару. Для многих случаев применения металлов мало знать только их прочность и пластичность. Часто бывают нужны сведения и об их вязкости. Титан принадлежит к числу немногих металлов, которые наряду с высокой прочностью и пластичностью обладают еще хорошей вязкостью.
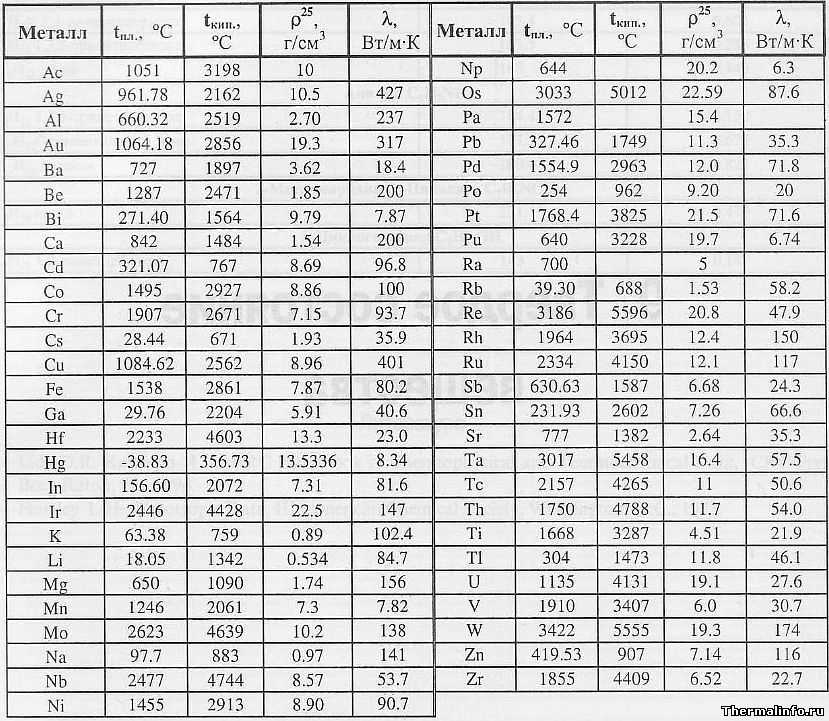
Наиболее распространенными методами определения ударной вязкости является испытание надрезанных стандартных образцов Шарпи и Изода с их разрушением при изгибе. Работа разрушения образцов Шарпи из иодидного титана высокой степени чистоты может достигать 14 кгм, составляя около 4 кгм для образцов из нелегированного титана и всего 0,15-0,30 кгм для образцов из некоторых высокопрочных, но хрупких сплавов титана. Сейчас в промышленных масштабах выпускаются сплавы с пределом текучести 91 кг/мм2 и ударной вязкостью по Шарпи до 3,5 кгм.
В результате проводимой экспериментальной работы, видимо, скоро начнется производство еще более вязких и прочных технических сплавов титана.
Предел выносливости. Данных о пределе выносливости титана опубликовано мало, да к тому же они в значительной степени противоречивы. Однако можно утверждать, что титан обладает отличной выносливостью. Испытания показывают, что предел выносливости составляет 60% предела прочности, но для образцов из нелегированного титана с острым надрезом эта цифра снижается до 32%.

Ползучесть. Если материал подвергнуть действию постоянной нагрузки, то он с течением времени пластически деформируется. Удлинение материала под постоянной нагрузкой называется ползучестью, причем предел ползучести определяется как прочность, необходимая для того, чтобы получить определенное удлинение за установленное время.
Влияние температуры и наклепа на механические свойства. С повышением температуры уменьшается не только предел ползучести, но и пределы прочности, текучести, усталости, а также твердость. Повышение температуры мало сказывается на величине модуля упругости, но сопровождается улучшением вязкости и пластичности.

Наклеп титановых сплавов сопровождается их упрочнением. С повышением температуры прочность алюминия быстро снижается, тогда как температурное разупрочнение титана происходит медленнее, так что при температурах выше 200° С величина отношения прочность: удельный вес получается для титана больше, чем для алюминия.
Однако это превосходство титана сохраняется приблизительно до 425° С, после чего определяющим фактором становится чрезвычайная активность титана, о чем уже говорилось выше.
Твердость титана по роквеллу — О металле
Твердость титана по роквеллу — Справочник металлиста
Понятие твердости металлов раньше было известно только выпускникам технических вузов, рабочим машиностроительных заводов и мастерам кузнечного дела. В обиход современного ножемана этот термин вошел вместе с принятием закона об оружии и ГОСТов, которые приводят признаки, на основании которых нож может быть отнесен к холодному оружию.
Одним из обязательных признаков, по которым то или иное изделие относится к холодному оружию является твердость стали из которой выполнен клинок ножа (или как это называется в ГОСТе — боевая часть холодного оружия).
И начиная с этого момента, найфоманы в России начали потихоньку почитывать справочники в которых приводятся характеристики разных сталей, пояснения в различии порошковых и ламинированных сталей, ну и конечно показатели твердости стали, те самые заметные HRC.
Если один автолюбитель сможет спросить другого о том, сколько «кубиков в движке», то продвинутый найфоман, посмотрев на характеристики полевого ножа в которых указано «57-59 HRC» может на полном серьезе определить, что это модель хлипковата для бушкрафта и ей место на кухне.
Данная статья в простой и понятной форме расскажет о том, что же за зверь такой HRC, откуда от взялся и зачем он вообще нужен.
Интересный факт: На американских и европейских сайтах в числе параметров, которые указывают продавцы или производители крайне редко встречается такой параметр, как твердость стали. Законодательно этот вопрос никак не регулируется, вот и не нужен этот параметр обычному неискушенному покупателю.
Итак, что же нам нужно знать о твердости металлов?
Человек издревле столкнулся с понятием твердости материалов. А также достаточно быстро понял, что различные материалы отличаются друг от друга по твердости и прочности.
Если ударить палкой по камню, то палка либо сломается, либо отскочит. Если ударить камнем по палке, то палка сломается. Если кокос упадет с дерева на галечный пляж, то разобьется.
А если долго и старательно бить кремнем по более мягкому камню, то вполне себе можно изготовить голову для каменного топора.
Постепенно, в процессе эволюции наши с вами предки поняли, что различные материалы имеют различную твердость, и в зависимости от этой твердости обладают или не обладают нужными свойствами. Так родился способ определения твердости материла, посредством сравнения его с неким эталоном.
Так, хороший плотник может определить степень усушки бревна постукивая по нему киянкой, выполненной из дерева более твердой породы. Гончар с помощью специального молоточка может определить степень готовности глиняной посуды. Вольно или невольно, каждый из нас хоть раз в жизни прибегал к аналогичному способу определения твердости предмета.
Однако, самым распространенным методом определения твердости материала до недавнего времени был склерометрический метод. Склерометрия представляет собой физический процесс, когда проверяемый материал царапает (или царапается) некий эталонный образец. Если проверяемый материла царапает эталон — значит проверяемый материал тверже.
Если проверяемый материал не может оставить следа на эталоне и при этом сам легко царапается эталоном — значит проверяемый материал имеет твердость меньше чем у эталона.
Сейчас такая процедура кажется нам смешной, но до недавнего времени, это был единственный способ определить твердость материала.
А как еще древние шумеры могли определить, что можно наносить надписи острой палочкой на почти засохшую глину?
Вопрос с определением твердости материалов (особенно камней и металлов) остро встал в конце XVIII и начале XIX веков, с развитием геологии и началом расцвета машиностроения.
Именно к этому времени относится появление известной всем физикам и археологам «шкалы Мооса». Однако, первым кто предложил измерять твердость металлов посредством их сравнения с эталоном был французский естествоиспытатель середины XVIII века Рене Антуан Реомюр.
Реомюр активно проводил эксперименты, связанные с плавлением и обработкой металлов и поэтому перед ним остро стоял вопрос определения различных характеристик тех сплавов, которые он получал в процессе своих изысканий.
Его идеи подхватил и развил немецкий естествоиспытатель и геолог Карл Фридрих Христиан Моос. В 1811-м году он придумал систему эталонного сравнения минералов, которая теперь носит его имя. Примерно до середины XX века это шкалой активно пользовались разведывательные геологические партии по всему миру.
Шкала Мооса представляет собой сравнительную таблицу в которой указаны различные по твердости известные минералы и указана их твердость измеряемая в критериях:
- Царапается ногтем;
- Царапается медью;
- Царапается стеклом;
- Царапает стекло;
- Обрабатывается только алмазом.
К самому мягкому эталонному минералу относится тальк, к самому твердому минералу отнесен алмаз. Твердость талька по шкале Мооса составляет «1», твердость алмаза составляет «10».
Между тальком и алмазом по мере возрастания твердости расположены: гипс (твердость 2), кальцит (твердость 3), флюорит (твердость 4), апатит (твердость 5), ортоклаз (твердость 6), кварц (твердость 7), топаз (твердость 8), корунд (твердость 9).
Такой простой способ определения твердости минералов оказался незаменим в полевых условиях.
Помимо шкалы Мооса, существуют другие способы определения твердости материалов, которые получили активное развитие в конце XIX и в начале XX века. Обычно выделяют четыре самых известных способа определения твердости металлов:
- Метод Бринелля;
- Метод Виккерса;
- Метод Шора;
- Метод Роквелла.
Забегая вперед, заметим: все эти методы похожи между собой, так как основаны на вдавливании эталонного образца в поверхность металла. Различаются только форма эталона, сила давления, формула расчета величины.
Элемент, который вдавливается в поверхность металла, называется «индентор». В качестве индентора могут использоваться стальной шарик (метод Бринелля), алмазный конус (метод Роквелла), алмазная пирамидка (методы Виккерса и Шора).
Востребованность указанных методов измерения твердости металла объясняется их следующими особенностями:
- все описанные методы позволяют производить измерения каждого готового образца в отдельности, что, несомненно, повышает качество серийной продукции;
- не происходит разрушения готового изделия (например, ножа) и в дальнейшем его можно использовать по назначению;
- высокая скорость измерений, а значит большая производительность метода.
Важно: Результаты испытаний с помощью различных методов несопоставимы между собой.
Рассмотрим каждый метод в отдельности, уделив особое внимание методу Роквелла.
Метод Бринелля
Этот метод был предложен шведом Юханом Августом Бринеллем начале 20-го века. На тот момент, это был самый точный способ определения твердости металлов. В качестве индентора используются стальные шарики различного диаметра (от 1,2 до 10 миллиметров). Диаметр шарика выбирается в зависимости от предполагаемой твердости металла.
Бринелль разделил металлы на несколько групп, объединив их по твердости. В группу с минимальной твердостью попали олова, свинец и их сплавы. В группу с самой высокой твердостью вошли титан, никель и стальные сплавы. Для металлов с минимальной твердостью используется шарик самого малого диаметра, для металлов высокой твердости используется шарик самого большого диаметра.
Измерения происходят по следующему алгоритму: проверяемый образец помещают на специальный стол, сверху в образец происходит вдавливание индентора с постепенно увеличивающейся нагрузкой.
Это происходит в течение короткого промежутка времени от 2-х до 8-ми секунд. После достижения максимального уровня динамической нагрузки, нагрузка поддерживается в статическом состоянии, примерно в течение 10-ти секунд.
После завершения процедуры, на проверяемом образце замеряют диаметр отпечатка.
Расчет твердости происходит по формуле, где учитываются приложенная нагрузка, диаметр индентора и диаметр отпечатка. Твердость указывается в формате кгс/мм2, формат отображения HBW.
Метод Виккерса
При измерении твердости по методу Виккерса в качестве индентора используется наконечник в форме пирамиды, грани которой сходятся между собой под углом в 136 градусов. Для обеспечения точности испытания важно соблюсти несколько моментов:
- нагрузка должна приходиться строго в центр алмазного наконечника;
- вектор приложения нагрузки должен быть строго перпендикулярен поверхности испытуемого образца.
Измерения происходят по следующему алгоритму: проверяемый образец помещают на специальный стол, сверху в образец происходит вдавливание индентора сразу с необходимым уровнем нагрузки (максимальное возможное значение до 100 кгс). Далее происходит удержание индентора под нагрузкой в течение 10-15 секунд. После снятия индентора происходит измерение глубины вдавливания и диагонали отпечатка.
Далее происходит расчет по форму, где учитывается соотношение приложенной нагрузки к диагонали отпечатка и времени в течение которого происходило испытание. Твердость указывается в формате кгс/мм2, формат отображения HV. Метод Виккерса за счет использования алмазного наконечника позволяет делать более точные измерения, чем метод Бринелля.
Метод Шора
Этот метод является продолжением всем хорошо известного метода «постукивания», когда постукивая по детали или заготовке, мастер пытается определить ее твердость. Метод предложен американский инженером Альбертом Шором в начале XX века. Суть метода заключается в том, что твердость металла определяется по высоте отскока индентора.
Прибор для измерения твердости состоит из полой трубки, на которой по всей длине сделан пропил с нанесенными делениями. Трубка устанавливается на поверхность измеряемого образца и в нее сбрасывается боек с алмазным наконечником. Твердость металла определяется визуально по высоте отскока бойка. По сути, этот прибор является «склерометром».
Формат отображения твердости по Шору HSD(или HSC, в зависимости от используемой шкалы).
Метод Роквелла
В последнее время этот метод получил большое распространение, благодаря своей простоте и универсальности. Метод Роквелла не требует проведения дополнительных вычислений и значение измерения сразу выводится на шкалу прибора.
Этот метод придумали два однофамильца, которые носили одну фамилию Роквелл. Звали их Хью и Стенли.
Оба они работали в металлургическом холдинге в штате Коннектикут, где в то время остро встал вопрос оперативного измерения твердости элементов подшипников.
Существующий метод Бринелля не позволял производить измерения с высокой точностью, а также не позволял производить испытание на каждом готовом экземпляре.
Твердость титана по роквеллу
· 09.09.2019
Титан широко распространен в земной коре, где его содержится около 6 %, а по распространенности он занимает четвертое место после алю-миния, железа и магния. Однако промышленный способ его извлечения был разработан лишь в 40-х годах ХХ века.
Благодаря прогрессу в области самолето- и ракетостроения производство титана и его сплавов интенсивно развивалось.
Это объясняется сочетанием таких ценных свойств титана, как малая плотность, высокая удельная прочность (s в/r × g), коррозионная стойкость, технологичность при обработке давлением и свариваемость, хладостойкость, немагнитность и ряд других ценных физико-механических характеристик.
Основные сведения о титане
Титан — химический элемент с порядковым номером 22, атомный вес 47,88, легкий серебристо-белый металл. Плотность 4,51 г/см3, Tпл=1668+(-)5 °С, Tкип=3260 °С. Титан и титановые сплавы сочетают легкость, прочность, высокую коррозионную стойкость, низкий коэффициент теплового расширения, возможность работы в широком диапазоне температур.
История открытия титана
Оксид титана TiO2 впервые был обнаружен в 1789 году английским ученым, специалистом в области минералогии У. Грегором, который при исследовании магнитного железистого песка выделил окись неизвестного металла, назвав ее менакеновой. Первый образец металлического титана получил в 1825 году шведский химик и минераловед Й. Я. Берцелиус.
Свойства титана
В периодической системе элементов Д. И. Менделеева титан расположен в IV группе 4-го периода под номером 22. В важнейших и наиболее устойчивых соединениях металл четырехвалентен.
По внешнему виду похож на сталь. Титан относится к переходным элементам.
Данный металл плавится при довольно высокой температуре (1668±4 °С) и кипит при 3300 °С, скрытая теплота плавления и испарения титана почти в два раза больше, чем у железа.
Известны две аллотропические модификации титана (две разновидности титана, имеющие одинаковый химический состав, но различное строение и свойства). Низкотемпературная альфа-модификация, существующая до 882,5 °С и высокотемпературная бетта-модификация, устойчивая от 882,5 °С и до температуры плавления.
По плотности и удельной теплоемкости титан занимает промежуточное место между двумя основными конструкционными металлами: алюминием и железом.
Стоит также отметить, что его механическая прочность примерно вдвое больше, чем чистого железа, и почти в шесть раз выше, чем алюминия.
Но титан может активно поглощать кислород, азот и водород, которые резко снижают пластические свойства металла. С углеродом титан образует тугоплавкие карбиды, обладающие высокой твердостью.
Титан обладает низкой теплопроводностью, которая в 13 раз меньше теплопроводности алюминия и в 4 раза — железа. Коэффициент термического расширения при комнатной температуре сравнительно мал, с повышением температуры он возрастает.
Модули упругости титана невелики и обнаруживают существенную анизотропию. Модули упругости характеризуют способность материала упруго деформироваться при приложении к нему силы. Анизотропия заключается в различии свойств упругости в зависимости от направления действия силы.
С повышением температуры до 350 °С модули упругости уменьшаются почти по линейному закону. Небольшое значение модулей упругости титана — существенный его недостаток, т.к.
в некоторых случаях для получения достаточно жестких конструкций приходится применять большие сечения изделий по сравнению с теми, которые следуют из условий прочности.
Титан имеет довольно высокое удельное электросопротивление, которое в зависимости от содержания примесей колеблется в пределах от 42·10-8до 80·10-6 Ом·см. При температурах ниже 0,45 К он становится сверхпроводником.
Титан — парамагнитный металл. Обычно у парамагнитных веществ магнитная восприимчивость при нагревании уменьшается. Магнитная восприимчивость характеризует связь между намагниченностью вещества и магнитным полем в этом веществе. Титан составляет исключение из этого правила — его восприимчивость существенно увеличивается с температурой.
Характеристики физико-механических свойств титана (ВТ1-00)
4,5 × 10 –3 |
1668± 4 |
8,9 |
16,76 |
300–450 |
250–380 |
7–10 |
25–30 |
50–60 |
110,25 |
41 |
0,32 |
103 |
120 |
Титан имеет две полиморфные модификации: a -титана с гексагональной плотноупакованной решеткой с периодами а = 0,296 нм, с = 0,472 нм и высокотемпературную модификацию b -титана с кубической объемно-центрированной решеткой с периодом а = 0,332 нм при 900 ° С. Температура полиморфного a « b -превращения составляет 882 ° С.
Механические свойства титана существенно зависят от содержания примесей в металле. Различают примеси внедрения — кислород, азот, углерод, водород и примеси замещения, к которым относятся железо и кремний.
Хотя примеси повышают прочность, но одновременно резко снижают пластичность, причем наиболее сильное отрицательное действие оказывают примеси внедрения, особенно газы.
При введении всего лишь 0,003 % Н, 0,02 % N или 0,7 % О титан полностью теряет способность к пластическому деформированию и хрупко разрушается.
Особенно вреден водород, вызывающий водородную хрупкость титановых сплавов. Водород попадает в металл при плавке и последующей обработке, в частности при травлении полуфабрикатов. Водород малорастворим в a -титане и образует пластинчатые частицы гидрида, снижающего ударную вязкость и особенно отрицательно проявляющегося в испытаниях на замедленное разрушение.
Поэтому содержание примесей, особенно газов, в титане и титановых сплавах (табл. 17.1, 17.2) строго ограничено.
Промышленный способ производства титана состоит в обогащении и хлорировании титановой руды с последующим его восстановлением из четыреххлористого титана металлическим магнием (магнийтермический метод).
Полученный этим методом титан губчатый (ГОСТ 17746–79) в зависимости от химического состава и механических свойств выпускают следующих марок:
ТГ-90, ТГ-100, ТГ-110, ТГ-120, ТГ-130, ТГ-150, ТГ-ТВ (см. табл. 17.1).
Цифры означают твердость по Бринеллю НВ, ТВ — твердый.
Для получения монолитного титана губка размалывается в порошок, прессуется и спекается или переплавляется в дуговых печах в вакууме или атмосфере инертных газов.
Твердость металлов.

Для того чтобы детали и механизмы служили длительно и надежно, материалы, из которых они изготовлены, должны соответствовать необходимым условиям работы.
Именно поэтому важно контролировать допустимые значения их основных механических показателей. К механическим свойствам относятся твердость, прочность, ударная вязкость, пластичность.
Твердость металлов — первичная конструкционная характеристика.
Понятие
Твердость металлов и сплавов — это свойство материала создавать сопротивление при проникновении в его поверхностные слои иного тела, которое не деформируется и не разрушается при сопутствующих нагрузках (индентора). Определяют с целью:
- получения информации о допустимых конструкционных особенностях и о возможностях эксплуатации;
- анализа состояния под действием времени;
- контроля результатов температурной обработки.
От этого показателя частично зависят прочность и устойчивость поверхности к старению. Исследуют как исходный материал, так и уже готовые детали.
Варианты исследования
Показателем является величина, которая называется числом твердости. Существуют различные методы измерения твердости металлов. Наиболее точные исследования заключаются в использовании различных видов вычисления, инденторов и соответствующих твердомеров:
- Бринелля: суть работы аппарата – вдавливание шарика в исследуемый металл или сплав, вычисление диаметра отпечатка и последующее математическое вычисление механического параметра.
- Роквелла: используются шарик или алмазный конусный наконечник. Значение отображается на шкале или определяется расчётно.
- Виккерса: наиболее точное измерение твердости металла с применением алмазного пирамидального наконечника.
Для определения параметрических соответствий между показателями разных способов измерения для одного и того же материала существуют специальные формулы и таблицы.
Факторы, определяющие вариант измерения
В лабораторных условиях, при наличии необходимого ассортимента оборудования, выбор способа исследования осуществляется в зависимости от определенных характеристик заготовки.
- Ориентировочное значение механического параметра. Для конструкционных сталей и материалов с небольшой твердостью до 450-650 НВ применяют метод Бринелля; для инструментальных, легированных сталей и других сплавов – Роквелла; для твердосплавов – Виккерса.
- Размеры испытуемого образца. Особо маленькие и тонкие детали обследуются с помощью твердомера Виккерса.
- Толщина металла в месте замера, в частности, цементированного или азотированного слоя.
Все требования и соответствия задокументированы ГОСТом.
Особенности методики Бринелля
Испытания на твердость металлов и сплавов с помощью твердомера Бринелля проводятся со следующими особенностями:
- Индентор – шарик из легированной стали или из карбидо-вольфрамового сплава диаметром 1, 2, 2,5, 5 или 10 мм (гост 3722-81).
- Продолжительность статического вдавливания: для чугуна и стали – 10-15 с., для цветных сплавов – 30, также возможна длительность в 60 с., а в некоторых случаях – 120 и 180 с.
- Граничное значение механического параметра: 450 НВ при измерении стальным шариком; 650 НВ при использовании твердосплава.
- Возможные нагрузки. С помощью входящих в комплект грузов корректируется фактическая сила деформации на испытуемый образец. Их минимальные допустимые значения: 153,2, 187,5, 250 Н; максимальные – 9807, 14710, 29420 Н (гост 23677-79).
С помощью формул, в зависимости от диаметра выбранного шарика и от испытуемого материала, можно вычислить соответствующее допустимое усилие вдавливания.
Тип сплава | Математическое вычисление нагрузки |
Сталь, сплавы никеля и титана | 30D2 |
Чугун | 10D2, 30D2 |
Медь и медные сплавы | 5D2, 10D2, 30D2 |
Легкие металлы и сплавы | 2,5D2, 5D2, 10D2, 15D2 |
Свинец, олово | 1D2 |
Пример обозначения:
400HB10/1500/20, где 400HB – твердость металла по Бринеллю; 10 – диаметр шарика, 10 мм; 1500 – статическая нагрузка, 1500 кгс; 20 – период осуществления вдавливания, 20 с.
Для установления точных цифр рационально исследовать один и тот же образец в нескольких местах, а общий результат определять путем нахождения среднего значения из полученных.
Определение твердости по методу Бринелля
Процесс исследования протекает в следующей последовательности:
- Проверка детали на соответствие требованиям (ГОСТ 9012-59, гост 2789).
- Проверка исправности аппарата.
- Выбор необходимого шарика, определение возможного усилия, установка грузов для его формирования, периода вдавливания.
- Запуск твердомера и деформация образца.
- Измерение диаметра углубления.
- Эмпирическое вычисление.
НВ=F/A,
где F – нагрузка, кгс или Н; A – площадь отпечатка, мм2.
НВ=(0,102*F)/(π*D*h),
где D – диаметр шарика, мм; h – глубина отпечатка, мм.
Твердость металлов, измеренная этим способом, имеет эмпирическую связь с вычислением параметров прочности. Метод точен, особенно для мягких сплавов. Является основополагающим в системах определения значений этого механического свойства.
Особенности методики Роквелла
Этот способ измерения был изобретен в 20-х годах XX века, более автоматизирован, чем предыдущий. Применяется для более твердых материалов. Основные его характеристики (ГОСТ 9013-59; гост 23677-79):
- Наличие первичной нагрузки в 10 кгс.
- Период выдержки: 10-60 с.
- Граничные значения возможных показателей: HRA: 20-88; HRB: 20-100; HRC: 20-70.
- Число визуализируется на циферблате твердомера, также может рассчитываться арифметически.
- Шкалы и инденторы. Известно 11 различных шкал в зависимости от типа индентора и предельно-допустимой статической нагрузки. Наиболее распространённые в использовании: А, В и С.
А: алмазный конусный наконечник, угол при вершине 120˚, общая допустимая сила статического влияния – 60 кгс, HRA; исследуются тонкие изделия, в основном прокат.
С: также алмазный конус, рассчитанный на максимальное усилие 150 кгс, HRC, применим для твердых и закаленных материалов.
В: шарик размером 1,588 мм, изготовленный из закаленной стали или из твердого карбидо-вольфрамового сплава, нагрузка – 100 кгс, HRB, используется для оценки твердости отожжённых изделий.
Шарикообразный наконечник (1,588 мм) применим для шкал Роквелла B, F, G. Также существуют шкалы E, H, K, для которых используется шарик диаметром 3,175 мм (ГОСТ 9013-59).
Количество проб, проделанных с помощью твердомера Роквелла на одной площади, ограничивается размером детали. Допускается повторная проба на расстоянии 3-4 диаметра от предыдущего места деформации. Толщина испытуемого изделия также регламентируется. Она должна быть не меньше увеличенной в 10 раз глубины внедрения наконечника.
Пример обозначения:
50HRC – твердость металла по Роквеллу, измерена с помощью алмазного наконечника, ее число равно 50.
План исследования по методу Роквелла
Измерение твердости металла более упрощено, нежели для способа Бринелля.
- Оценка размеров и характеристик поверхности детали.
- Проверка исправности аппарата.
- Определение типа наконечника и допустимой нагрузки.
- Установка образца.
- Осуществление первичного усилия на материал, величиной в 10 кгс.
- Осуществление полного соответствующего усилия.
- Чтение полученного числа на шкале циферблата.
Также возможен математический расчет с целью точного определения механического параметра.
При условии использования алмазного конуса с нагрузкой 60 или 150 кгс:
HR=100-((H-h)/0,002;
при совершении испытания с помощью шарика под усилием 100 кгс:
HR=130-((H-h)/0,002,
где h – глубина внедрения индентора при первичном усилии 10 кгс; H – глубина внедрения индентора при полной нагрузке; 0,002 – коэффициент, регламентирующий величину перемещения наконечника при изменении числа твердости на 1 единицу.
Метод Роквелла является простым, но недостаточно точным. В то же время он позволяет измерять показатели механического свойства для твердых металлов и сплавов.
Характеристики методики Виккерса
Определение твердости металлов по данному способу наиболее просто и точно. Работа твердомера основана на вдавливании в образец алмазного пирамидального наконечника.
Основные особенности:
- Индентор: алмазная пирамида с углом при вершине 136°.
- Предельно допустимая нагрузка: для легированного чугуна и стали — 5-100 кгс; для медных сплавов — 2,5-50 кгс; для алюминия и сплавов на его основе — 1-100 кгс.
- Период выдержки статической нагрузки: от 10 до 15 с.
- Испытуемые материалы: сталь и цветные металлы с твердостью более 450-500 НВ, в том числе изделия после химико-термической обработки.
Пример обозначения:
700HV20/15,
где 700HV – число твердости по Виккерсу; 20 – нагрузка, 20 кгс; 15 – период статического усилия, 15 с.
Последовательность исследования Виккерса
Порядок действий предельно упрощен.
- Проверка образца и аппаратуры. Особое внимание уделяется поверхности детали.
- Выбор допустимого усилия.
- Установка испытуемого материала.
- Запуск твердомера в работу.
- Чтение результата на циферблате.
Математический расчет по этому способу выглядит следующим образом:
HV=1,8544*(F/d2),
где F – нагрузка, кгс; d – среднее значение длин диагоналей отпечатка, мм.
Он позволяет измерять высокую твердость металлов, тонких и небольших деталей, при этом предоставляя высокую точность результата.
Способы перехода между шкалами
Определив диаметр отпечатка с помощью специального оборудования, можно с помощью таблиц определить твердость. Таблица твердости металлов – проверенный помощник в вычислении данного механического параметра. Так, если известно значение по Бринеллю, можно легко определить соответствующее число Виккерса или Роквелла.
Пример некоторых значений соответствия:
Диаметр отпечатка,мм | Метод исследования | ||||
Бринелля | Роквелла | Виккерса | |||
A | C | B | |||
3,90 | 241 | 62,8 | 24,0 | 99,8 | 242 |
4,09 | 218 | 60,8 | 20,3 | 96,7 | 218 |
4,20 | 206 | 59,6 | 17,9 | 94,6 | 206 |
4,99 | 143 | 49,8 | — | 77,6 | 143 |
Таблица твердости металлов составлена на основе экспериментальных данных и имеет высокую точность. Также существуют графические зависимости твердости по Бринеллю от содержания углерода в железоуглеродистом сплаве. Так, в соответствии с такими зависимостями, для стали с количеством карбона в составе равному 0,2% она составляет 130 НВ.
Требования к образцу
В соответствии с требованиями ГОСТов, испытуемые детали должны соответствовать следующим характеристикам:
- Заготовка должна быть ровная, твердо лежать на столе твердомера, ее края должны быть гладкими или тщательно обработаны.
- Поверхность должна иметь минимальную шероховатость. Должна быть отшлифована и очищена, в том числе с помощью химических составов. Одновременно, во время процессов механической обработки, важно предупредить образование наклепа и повышения температуры обрабатываемого слоя.
- Деталь должна соответствовать выбранному методу определения твердости по параметрическим свойствам.
Выполнение первичных требований – обязательное условие точности измерений.
Твердость металлов — важное основополагающее механическое свойство, определяющее их некоторые остальные механические и технологические особенности, результаты предыдущих процессов обработки, влияние временных факторов, возможные условия эксплуатации. Выбор методики исследования зависит от ориентировочных характеристик образца, его параметров и химического состава.
Твердость – главный показатель качества инструмента
Выбирая инструмент для работы, мы сталкиваемся с такой его характеристикой как твердость, которая характеризует его качество.
Чем выше этот показатель, тем выше его способность сопротивляться пластической деформации и износу при воздействии на обрабатываемый материал.
Именно этот показатель определяет, согнется ли зуб пилы при распиловке заготовок, или какую проволоку смогут перекусить кусачки.
Метод Роквелла
Среди всех существующих методов определения твердости сталей и цветных металлов самым распространенным и наиболее точным является метод Роквелла.
Проведение измерений и определение числа твердости по Роквеллу регламентируется соответствующими документами ГОСТа 9013-59.
Этот метод реализуется путем вдавливания в тестируемый материал инденторов – алмазного конуса или твердосплавного шарика.
Алмазные инденторы используются для тестирования закаленных сталей и твердых сплавов, а твердосплавные шарики – для менее твердых и относительно мягких металлов. Измерения проводят на механических или электронных твердомерах.
Методом Роквелла предусматривается возможность применения целого ряда шкал твердости A, B, C, D, E, F, G, H (всего – 54), каждая из которых обеспечивает наибольшую точность только в своем, относительно узком диапазоне измерений.
Для измерения высоких значений твердости алмазным конусом чаще всего используются шкалы «А», «С». По ним тестируют образцы из закаленных инструментальных сталей и других твердых стальных сплавов. А сравнительно более мягкие материалы, такие как алюминий, медь, латунь, отожженные стали испытываются шариковыми инденторами по шкале «В».
Пример обозначения твердости по Роквеллу: 58 HRC или 42 HRB.
Впереди стоящие цифры обозначают число или условную единицу измерения. Две буквы после них – символ твердости по Роквеллу, третья буква – шкала, по которой проводились испытания.
(!) Два одинаковых значения от разных шкал – это не одно и то же, например, 58 HRC ≠ 58 HRA. Сопоставлять числовые значения по Роквеллу можно только в том случае, если они относятся к одной шкале.
Диапазоны шкал Роквелла по ГОСТ 8.064-94:
A | 70-93 HR |
B | 25-100 HR |
C | 20-67 HR |
Инструменты для ручной обработки металлов (рубка, резка, опиливание, клеймение, пробивка, разметка) изготавливают из углеродистых и легированных инструментальных сталей. Их рабочие части подвергают закаливанию до определенной твердости, которая должна находиться в пределах:
Ножовочные полотна, напильники | 58 – 64 HRC |
Зубила, крейцмессели, бородки, кернеры, чертилки | 54 – 60 HRC |
Молотки (боек, носок) | 50 – 57 HRC |
Сюда относятся различные гаечные ключи, отвертки, шарнирно-губцевый инструмент. Норму твердости для их рабочих частей устанавливают действующие стандарты. Это очень важный показатель, от которого зависит, насколько инструмент износостоек и способен сопротивляться смятию. Достаточные значения для некоторых инструментов приведены ниже:
Гаечные ключи с размером зева до 36 мм | 45,5 – 51,5 HRC |
Гаечные ключи с размером зева от 36 мм | 40,5 – 46,5 HRC |
Отвертки крестовые, шлицевые | 47 – 52 HRC |
Плоскогубцы, пассатижи, утконосы | 44 – 50 HRC |
Кусачки, бокорезы, ножницы по металлу | 56 – 61 HRC |
В эту категорию входит расходная оснастка для обработки металла резанием, используемая на станках или с ручными инструментами. Для ее изготовления используются быстрорежущие стали или твердые сплавы, которые сохраняют твердость в холодном и перегретом состоянии.
Метчики, плашки | 61 – 64 HRC |
Зенкеры, зенковки, цековки | 61 – 65 HRC |
Сверла по металлу | 63 – 69 HRC |
Сверла с покрытием нитрид-титана | до 80 HRC |
Фрезы из HSS | 62 – 66 HRC |
Примечание: Некоторые производители фрез указывают в маркировке твердость не самой фрезы, а материала, который она может обрабатывать.
Существует взаимосвязь между классом прочности крепежа и его твердостью. Для высокопрочных болтов, винтов, гаек эта взаимосвязь отражена в таблице:
Болты и винты | Гайки | Шайбы | |||||||||
Классы прочности | 8.8 | 10.9 | 12.9 | 8 | 10 | 12 | Ст. | Зак.ст. | |||
d16 мм | d16 мм | ||||||||||
Твердость по Роквеллу, HRC | min | 23 | 23 | 32 | 39 | 11 | 19 | 26 | 29.2 | 20.3 | 28.5 |
max | 34 | 34 | 39 | 44 | 30 | 36 | 36 | 36 | 23.1 | 40.8 |
Если для болтов и гаек главной механической характеристикой является класс прочности, то для таких крепежных изделий как стопорные гайки, шайбы, установочные винты, твердость не менее важна.
Стандартами установлены следующие минимальные / максимальные значения по Роквеллу:
Стопорные кольца до Ø 38 мм | 47 – 52 HRC |
Стопорные кольца Ø 38 -200 мм | 44 – 49 HRC |
Стопорные кольца от Ø 200 мм | 41 – 46 HRC |
Стопорные зубчатые шайбы | 43.5 – 47.5 HRB |
Шайбы пружинные стальные (гровер) | 41.5 – 51 HRC |
Шайбы пружинные бронзовые (гровер) | 90 HRB |
Установочные винты класса прочности 14Н и 22Н | 75 – 105 HRB |
Установочные винты класса прочности 33Н и 45Н | 33 – 53 HRC |
Относительное измерение твердости при помощи напильников
Стоимость стационарных и портативных твердомеров довольно высока, поэтому их приобретение оправдано только необходимостью частой эксплуатации. Многие мастеровые по мере надобности практикуют измерять твердость металлов и сплавов относительно, при помощи подручных средств.
Опиливание образца напильником – один из самых доступных, однако далеко не самый объективный способ проверки твердости стальных деталей, инструмента, оснастки.
Напильник должен иметь не затупленную двойную насечку средней величины №3 или №4.
Сопротивление опиливанию и сопровождающий его скрежет позволяет даже при небольшом навыке отличить незакаленную сталь от умеренно (40 HRC) или твердо закаленной (55 HRC).
Для тестирования с большей точностью существуют наборы тарированных напильников, именуемые также царапающий твердомер. Они применяются для испытания зубьев пил, фрез, шестерен. Каждый такой напильник является носителем определенного значения по шкале Роквелла.
Твердость измеряется коротким царапанием металлической поверхности поочередно напильниками из набора. Затем выбираются два близко стоящие – более твердый, который оставил царапину и менее твердый, который не смог поцарапать поверхность.
Твердость тестируемого металла будет находиться между значениями твердости этих двух напильников.
Переводная таблица твердости
Для сопоставления чисел твердости Роквелла, Бринелля, Виккерса, а также для перевода показателей одного метода в другой существует справочная таблица:
Виккерс, HV | Бринелль, HB | Роквелл, HRB |
100 | 100 | 52.4 |
105 | 105 | 57.5 |
110 | 110 | 60.9 |
115 | 115 | 64.1 |
120 | 120 | 67.0 |
125 | 125 | 69.8 |
130 | 130 | 72.4 |
135 | 135 | 74.7 |
140 | 140 | 76.6 |
145 | 145 | 78.![]() |
150 | 150 | 79.9 |
155 | 155 | 81.4 |
160 | 160 | 82.8 |
165 | 165 | 84.2 |
170 | 170 | 85.6 |
175 | 175 | 87.0 |
180 | 180 | 88.3 |
185 | 185 | 89.5 |
190 | 190 | 90.6 |
195 | 195 | 91.7 |
200 | 200 | 92.8 |
205 | 205 | 93.8 |
210 | 210 | 94.8 |
215 | 215 | 95.7 |
220 | 220 | 96.6 |
225 | 225 | 97.5 |
230 | 230 | 98.4 |
235 | 235 | 99.2 |
240 | 240 | 100 |
Виккерс, HV | Бринелль, HB | Роквелл, HRC |
245 | 245 | 21.![]() |
250 | 250 | 22.1 |
255 | 255 | 23.0 |
260 | 260 | 23.9 |
265 | 265 | 24.8 |
270 | 270 | 25.6 |
275 | 275 | 26.4 |
280 | 280 | 27.2 |
285 | 285 | 28.0 |
290 | 290 | 28.8 |
295 | 295 | 29.5 |
300 | 300 | 30.2 |
310 | 310 | 31.6 |
320 | 319 | 33.0 |
330 | 328 | 34.2 |
340 | 336 | 35.3 |
350 | 344 | 36.3 |
360 | 352 | 37.2 |
370 | 360 | 38.1 |
380 | 368 | 38.9 |
390 | 376 | 39.![]() |
400 | 384 | 40.5 |
410 | 392 | 41.3 |
420 | 400 | 42.1 |
430 | 408 | 42.9 |
440 | 416 | 43.7 |
450 | 425 | 44.5 |
460 | 434 | 45.3 |
470 | 443 | 46.1 |
490 | — | 47.5 |
500 | — | 48.2 |
520 | — | 49.6 |
540 | — | 50.8 |
560 | — | 52.0 |
580 | — | 53.1 |
600 | — | 54.2 |
620 | — | 55.4 |
640 | — | 56.5 |
660 | — | 57.5 |
680 | — | 58.4 |
700 | — | 59.![]() |
720 | — | 60.2 |
740 | — | 61.1 |
760 | — | 62.0 |
780 | — | 62.8 |
800 | — | 63.6 |
820 | — | 64.3 |
840 | — | 65.1 |
860 | — | 65.8 |
880 | — | 66.4 |
900 | — | 67.0 |
1114 | — | 69.0 |
1120 | — | 72.0 |
Примечание: В таблице приведены приближенные соотношения чисел, полученные разными методами. Погрешность перевода значений HV в HB составляет ±20 единиц, а перевода HV в HR (шкала C и B) до ±3 единиц.
При выборе инструмента желательно предпочесть модели известных производителей. Это дает уверенность в том, что приобретаемый продукт изготовлен с соблюдением технологий, а его твердость отвечает заявленным значениям.
Статьи о продукции 23.09.2019 16:32:41
Самые прочные металлы на Земле
Первое качество, с которым ассоциируется у нас металл, это прочность. На самом деле прочность определяется несколькими свойствами, учитывая которые именно сталь и ее сплавы находятся в списке самых прочных металлов.
Что же такое прочность? Это способность материала выдерживать внешние нагрузки, при этом не разрушаясь. При оценке прочности металла учитывается много параметров и качеств: насколько хорошо металл сопротивляется разрыву, как он противостоит сжатию, каков порог перехода от упругого к пластическому состоянию, когда деформация материала становится необратимой, какова способность материала сопротивляться распространению трещин и т.п.
Прочные сплавы и природные металлы
Сплавы представляют собой комбинации разных металлов. Потребность получить самые разные качественные характеристики металлов, среди которых и прочность, привела к появлению различных сплавов. Одним из важных в этом смысле сплавов является сталь, которая представляет собой комбинацию железа и углерода. Итак, какие же металлы принято считать самыми прочными на Земле?
Поскольку для определения прочности металла необходимо учесть очень много факторов, трудно однозначным образом упорядочить металлы от самого «крепкого» до самого «слабого». В зависимости от того, какое свойство считается наиболее важным в каждом конкретном случае, и будет складываться расстановка сил прочности среди металлов.
Сталь и ее сплавы
Сталь — это прочный сплав железа и углерода, с добавками других элементов, таких как кремний, марганец, ванадий, ниобий и пр. Благодаря различным системам легирования стали можно получать совершенно разный комплекс свойств новых сплавов.
Так, высокоуглеродистая сталь — это сплав железа с высоким содержанием углерода — получается прочной, относительно дешевой, долговечной, она хорошо поддается обработке. Из недостатков стоит отметить низкую прокаливаемость и низкую теплостойкость, что делает углеродистую сталь уязвимой в агрессивной среде.
Сферы применения: из углеродистой стали изготавливают различные инструменты, детали машин и сложных механизмов, элементы металлоконструкций. Важным условием применения таких изделий является неагрессивная среда.
Сплав стали, железа и никеля – один из наиболее прочных сплавов. Существует несколько его разновидностей, но в целом легирование углеродистой стали никелем увеличивает предел текучести до 1420 МПа и при этом показатель предела прочности на разрыв доходит до 1460 МПа.
Сферы применения: сплавы на никелевой основе используют в конструкциях некоторых типов мощных атомных реакторов в качестве защитных высокотемпературных оболочек для предохранения от коррозии урановых стержней.
Нержавеющая сталь – коррозионностойкий сплав стали, хрома и марганца с пределом текучести до 1560 МПа и пределом прочности на разрыв до 1600 МПа. Как и все виды стали, этот сплав обладает высокой ударопрочностью и имеет средний балл по шкале Мооса.
Сферы применения: благодаря своим антикоррозийным свойствам нержавеющую сталь широко применяют в самых разных областях – нефтехимической промышленности, машиностроении, строительстве, электроэнергетике, кораблестроении, пищевой промышленности и для изготовления бытовых приборов.
Особо твердые сплавы
Сплавы на основе карбидов вольфрама, титана, тантала обладают твердостью, которой позавидует любой молот Тора.
Титан – это наиболее растиражированный в средствах массовой информации и кинематографе природный металл, который принято ассоциировать с суперпрочностью. Его удельная прочность почти вдвое выше, чем аналогичная характеристика легированных сталей. Он обладает самым высоким отношением прочности на разрыв к плотности из всех металлов. По этому показателю он обошел вольфрам, вот только по шкале твердости Мооса титан ему уступает. Тем не менее, титановые сплавы прочны и легки.
Сферы применения:
Вольфрам с его самой высокой прочностью на растяжение среди всех встречающихся в природе металлов часто комбинируют со сталью и другими металлами для создания еще более прочных сплавов. К недостаткам вольфрама можно отнести его хрупкость и способность к разрушению при ударе.
Сферы применения: вольфрам применяют в металлургии для производства легированных сталей и различных сплавов, в электротехнической индустрии для изготовления элементов осветительных приборов, в машино- и авиастроении, в космической отрасли и химпроме. Сплав вольфрама и углерода (карбид вольфрама) используют для производства инструментов с режущими краями, таких как ножи и дисковые пилы, а также износостойких рабочих элементов горношахтного оборудования и прокатных валков.
Тантал обладает сразу тремя достоинствами – прочностью, плотностью и устойчивостью к коррозии. Он состоит в группе тугоплавких металлов, как и выше описанный вольфрам.
Сферы применения: тантал используется в производстве электроники и сверхмощных конденсаторов для персональных компьютеров, смартфонов, камер и для электронных устройств в автомобилях.
Инновационные сплавы
Существует ряд сплавов, которые появились совсем недавно, но уже успели завоевать признание благодаря своим «сверхкачествам» и активно используются в аэрокосмической сфере и медицине.
Алюминид титана – сплав титана и алюминия, который выдерживает высокие температуры и обладает антикоррозийными свойствами, но при этом он довольно хрупкий и недостаточно пластичный. Тем не менее, он нашел свое применение в производстве специальных защитных покрытий.
Сплав титана с золотом – еще один уникальный материал, который был разработан несколько лет назад группой ученых из университетов США. Основная задача, которая стояла перед учеными, создать материал крепче титана, который можно было бы применять в медицине для производства протезов, совместимых с биотканью. Дело в том, что титановые протезы, несмотря на свою прочность, изнашиваются относительно быстро, их приходится менять каждые 10 лет. А вот сплав титана с золотом оказался вчетверо более прочным, чем те сплавы, что сейчас используются в производстве протезов.
методы измерения, шкалы HB, HRC, HV
Понятие твердости
Твердость материала – это стойкость к разрушению при внедрении во внешний слой более твердого материала. Другими словами, способность к сопротивлению деформирующим усилиям (упругой или пластической деформации).
Определение твердости металлов производится посредством внедрения в образец твердого тела, именуемого индентором. Роль индентора выполняет: металлически шарик высокой твердости; алмазный конус или пирамида.
После воздействия индентора на поверхности испытуемого образца или детали остается отпечаток, по размеру которого определяется твердость. На практике используются кинематические, динамические, статические способы измерения твердости.
В основе кинематического метода лежит составление диаграммы на основе постоянно регистрирующихся показаний, которые изменяются по мере вдавливания инструмента в образец. Здесь прослеживается кинематика всего процесса, а не только конечного результата.
Динамический метод заключается в следующем. Измерительный инструмент воздействует на деталь. Обратная реакция позволяет рассчитать затраченную кинетическую энергию. Данный метод позволяет проводить испытание на твердость не только поверхности, но и некоторого объема металла.
Статические методы – это неразрушающие способы, позволяющие определить свойства металлов. Методы основаны на плавном вдавливании и последующей выдержке в течение некоторого времени. Параметры регламентируются методиками и стандартами.
Прилагаемая нагрузка может прилагаться:
- вдавливанием;
- царапанием;
- резанием;
- отскоком.
Машиностроительные предприятия на данный момент для определения твердости материалов используют методы Бринелля, Роквелла, Виккерса, а также метод микротвердости.
На основе проводимых испытаний составляется таблица, в которой указываются материалы, прилагаемые нагрузки и полученные результаты.
Как проверить твердость металла – главные секреты
Когда речь заходит о металлах, имеет значение важный показатель как его твердость. Фактор такого плана играет значимую роль в выборе, использовать или нет тот или иной металл в производстве для изготовления изделий определенного предназначения. Стоит разобраться подробнее в этом вопросе, для чего требуется проверка твердости металла в производственной линии разных отраслей деятельности.
Что такое твердость металла
Под данным понятием подразумевают характеристику, тесно связанную с металлами и их сплавами. Это способность не поддаваться разрушениям при синхронизации верхнего слоя с более твердым металлом. На основе этих знаний изготавливают различное оборудование, детали, играющие роль в долговечности эксплуатации предметов, конструкций, машин, инструментов. Проще говоря, устойчивость к деформации. Проверять этот параметр можно разными способами.
Методы проверки твердости металлов
Эксперты различают несколько вариантов проверок характеристики:
- Согласно методу Бриннеля, в процессе проверки принимает участие стальной шарик. Его под большим давлением вдавливают в металлическую поверхность. Затем специальная лупа вступает в действие, и с ее помощью специалист замеряет диаметр лунки. Твердость определяется по табличным данным. Этот способ – первый метод определения характера металла. Так измеряются мягкие сплавы.
- Методика Роквелла предполагает воздействие на металлическую поверхность с помощью алмазного конуса. В деле измерения твердости мягких, цветных, тонких Ме применяют специальный пресс. Его не относят к очень точным, хотя успешно он участвует для исследования твердых сплавов.
- Аналогичные действия с предыдущим заложены в метод Викксера, предполагающий обращение к алмазной пирамиде, только угол вершины не 120, а 136 градусов. Нагрузка осуществляется в строго перпендикулярном виде к металлу и медленно увеличивается. Относится к высокоточным способам.
- Способ Шора подразумевает наличие бойка с наконечником из алмазного напыления. Он падает с конкретной высоты на поверхность испытуемого материала. Твердость измеряется по высоте отскока бойка. Отличается эта методология большим разбросом показаний, по большей части применяется для измерения криволинейных предметов, крупногабаритных деталей.
В домашних условиях показатель также измеряется, но ожидать высокой точности не стоит. При обращении к профессионалам можно получить высокоточный результат, и это ответственный момент. Некоторые проводят домашний ликбез по определению этой величины, используя обычную бутылку и царапая по ней металлическим предметом, например, лезвием ножа. Металл в 62 единицы легко царапает стекло, чего не сказать о 56 единицах.
О чем говорит твердость металла, что это дает
Возникает вопрос, зачем вообще нужно замерять данный параметр. Характеристики металлов имеют значение для специалистов, занятых в отрасли термообработки сталей. Вывод о механических свойствах сварочного шва получают также при исследовании околошовной поверхности.
Целесообразность проводимых исследований также предопределена намерением производителей получить высокопрочные изделия, чтобы они могли выдержать разные условия эксплуатации, температурные перепады, обеспечить надежность. Твердость металлоизделия относится к первичной конструкционной характеристике.
Исследования производятся, ставя следующие цели.
- Проанализировать состояние материала под действием времени.
- Получить сведения о вероятных деструктивных последствиях для улучшения эксплуатационных возможностей.
- Осуществить контроль полученных итогов в рамках температурной обработки.
По сведениям, приобретенным в ходе экспериментов, удается выяснить устойчивость к истиранию, износу исходного материала.
Заключение
Для проведения анализа выдвигаются определенные условия к испытываемому материалу. В частности заготовку подбирают ровную. Она должна плотно прилегать к твердомеру, с тщательно обработанными краями. В результате добиваются основополагающего механического качества, играющего роль в производстве добротных изделий.
Специалисты используют результаты, полученные в ходе исследования, сверяют их с ранее известным анализом, и это большая работа, помогающая определиться с методикой производства. Информация необходима для машиностроительных, металлообрабатывающих, металлургических предприятий. Понятие «твердость» связано с упругостью, пластичностью, прочностью, хотя прямой связи между механическими качествами нет.
Важно обращаться к профессионалам для выполнения подобных работ, домашняя методика годится только для задач по закаливанию ножей.
Источник: https://rosgranitsa.ru/stroitelstvo/raznoe-2/kak-proverit-tverdost-metalla-glavnye-sekrety/
Единицы измерения твердости
Каждый способов измерения сопротивления металла к пластической деформации имеет свою методику его проведения, а также единицы измерения.
Измерение твердости мягких металлов производится методом Бринелля. Данному способу подвергаются цветные металлы (медь, алюминий, магний, свинец, олово) и сплавы на их основе, чугуны (за исключением белого) и отожженные стали.
Твердость по Бринеллю определяется вдавливанием закаленного, отполированного шарика из шарикоподшипниковой стали ШХ15. Окружность шарика зависит от испытуемого материала. Для твердых материалов – все виды сталей и чугунов – 10 мм, для более мягких – 1 – 2 — 2,5 — 5 мм. Необходимая нагрузка, прилагаемая к шарику:
- сплавы железа – 30 кгс/мм2;
- медь и никель – 10 кгс/мм2;
- алюминий и магний – 5 кгс/мм2.
Единица измерения твердости – это числовое значение и следующий за ними числовой индекс HB. Например, 200 НВ.
Твердость по Роквеллу определяется посредством разницы приложенных нагрузок к детали. Вначале прикладывается предварительная нагрузка, а затем общая, при которой происходит внедрение индентора в образец и выдержка.
В испытуемый образец внедряется пирамида (конус) из алмаза или шарик из карбида вольфрама (каленой стали). После снятия нагрузки производится замер глубины отпечатка.
Единица измерения твердости – это условные единицы. Принято считать, что единица — это величина осевого перемещения конуса, равная 2 мкм. Обозначение твердости маркируется тремя буквами HR (А, В, С) и числовым значением. Третья буква в маркировке обозначает шкалу.
Методика отображает тип индентора и прилагаемую к нему нагрузку.
Тип шкалы | Инструмент | Прилагаемая нагрузка, кгс |
А | Конус из алмаза, угол вершины которого 120° | 50-60 |
В | Шарик 1/16 дюйма | 90-100 |
С | Конус из алмаза, угол вершины которого 120° | 140-150 |
В основном, используются шкалы измерения А и С. Например, твердость стали HRC 26…32, HRB 25…29, HRA 70…75.
Измерению твердости по Виккерсу подвергаются изделия небольшой толщины или детали, имеющие тонкий, твердый поверхностный слой. В качестве клинка используется правильная четырехгранная пирамида угол при вершине, которой составляет 136°. Отображение значений твердости выглядит следующим образом: 220 HV.
Измерение твердости по методу Шора производится путем замера высоты отскока упавшего бойка. Обозначается цифрами и буквами, например, 90 HSD.
К определению микротвердости прибегают, когда необходимо получить значения мелких деталей, тонкого покрытия или отдельной структуры сплава. Измерение производят путем измерения отпечатка наконечника определенной формы. Обозначение значения выглядит следующим образом:
Н□ 0,195 = 2800, где
□ — форма наконечника;
0,196 — нагрузка на наконечник, Н;
2800 – численное значение твердости, Н/мм2.
Титан и его сплавы
Титан по распространенности в земной коре занимает среди конструкционных металлов четвертое место, уступая лишь алюминию, железу и магнию (рис. 1). Титан обладает удельным весом порядка 4500 кг/м3 и довольно высокой температурой плавления, ~1665± 5оС. Титан – парамагнитный металл.
а б
Рис. 1. Титанит – потенциальный источник титана (а), брусок кристаллического титана (б)
Титан – твердый металл: он в 12 раз твёрже алюминия, в 4 раза — железа и меди. Титан химически стоек. На поверхности титана легко образуется стойкая оксидная пленка TiO2, вследствие чего он обладает высокой сопротивляемостью коррозии в пресной и морской воде и в некоторых кислотах, устойчив против коррозии под напряжением. Во влажном воздухе, в морской воде и азотной кислоте он противостоит коррозии не хуже нержавеющей стали, а в соляной кислоте во много раз лучше ее. При температурах выше 500°С титан и его сплавы легко окисляются и поглощают водород, который вызывает охрупчивание (водородная хрупкость).
Титан имеет две полиморфные модификации (рис. 2):
- низкотемпературную модификацию α – Ti, устойчивую до 882°С, (ГП – решетка, а = 0,296 нм, с = 0,472 нм)
- высокотемпературную β – Ti, устойчивую выше 882оС (ОЦК – решетка, а= 0,332 нм).
Рис. 2. Две полиморфные модификации титана: а – αТi (гексагональная плотноупакованная решётка), б – β-Тi (объёмноцентрированная кристаллическая решётка)
Механические свойства титана.
Примечание. В отличие от мартенсита углеродистых сталей, являющегося раствором внедрения и характеризующегося высокой прочностью и хрупкостью, титановый мартенсит является раствором замещения, и закалка титановых сплавов на мартенсит приводит к небольшому упрочнению и не сопровождается резким снижением пластичности.
Значительное влияние на механические свойства титана оказывают примеси кислорода, водорода, углерода и азота, которые образуют с титаном твердые растворы внедрения и промежуточные фазы: оксиды, гидриды, карбиды и нитриды, повышая его характеристики прочности при одновременном снижении пластичности. Поэтому содержание этих примесей в титане ограничено сотыми и даже тысячными долями процента. Опасность водородной хрупкости, особенно в напряженных сварных конструкциях ограничивает содержание водорода. В техническом титане оно находится в пределах 0,008 — 0,012%.
Титан обладает высокой прочностью и удельной прочностью и в условиях глубокого холода, сохраняя при этом достаточную пластичность.
ТоС | +20 | -70 | -196 | |
δ, % | 20-30 | 10-5 | 3-10 | |
σв, МПа | 600-700 | 800…900 | 1000…1200 |
Высокая пластичность титана по сравнению с другими металлами, имеющими ГПУ— решетку (Zn, Mg, Cd), объясняется большим количеством систем скольжения и двойникования (рис. 3) благодаря малому соотношению с/а = 1,587. По-видимому, с этим связана высокая хладостойкость титана и его сплавов.
Рис. 3. Схемы систем скольжения и двойникования
Промышленный способ производства титана состоит в обогащении и хлорировании титановой руды с последующим его восстановлением из четыреххлористого титана металлическим магнием (магнийтермический метод). Полученный этим методом титан губчатый (ГОСТ 17746–79) в зависимости от химического состава и механических свойств выпускают следующих марок: ТГ-90, ТГ-100, ТГ-110, ТГ-120, ТГ-130, ТГ-150, ТГ-ТВ(см. табл.1).
Цифры означают твердость по Бринеллю НВ, ТВ — твердый.
Таблица 1. Марки, химический состав (%) и твердость титана губчатого (ГОСТ 17746–79)
Марка | Ti, не менее | Не более | Твердость НВ, 10/1500/30, не более | ||||||
Fe | Si | Ni | C | Cl | N | O | |||
ТГ-90 | 99,74 | 0,05 | 0,01 | 0,04 | 0,02 | 0,08 | 0,02 | 0,04 | 90 |
ТГ-100 | 99,72 | 0,06 | 0,01 | 0,04 | 0,03 | 0,08 | 0,02 | 0,04 | 100 |
ТГ110 | 99,67 | 0,09 | 0,02 | 0,04 | 0,03 | 0,08 | 0,02 | 0,05 | 110 |
ТГ-120 | 99,64 | 0,11 | 0,02 | 0,04 | 0,03 | 0,08 | 0,02 | 0,06 | 120 |
ТГ-130 | 99,56 | 0,13 | 0,03 | 0,04 | 0,03 | 0,10 | 0,03 | 0,08 | 130 |
ТГ-150 | 99,45 | 0,2 | 0,03 | 0,04 | 0,03 | 0,12 | 0,03 | 0,10 | 150 |
ТГ-Тв | 99,75 | 1,9 | – | – | 0,10 | 0,15 | 0,10 | – | – |
Для получения монолитного титана губка размалывается в порошок, прессуется и спекается или переплавляется в дуговых печах в вакууме или атмосфере инертных газов.
Механические свойства титана характеризуются хорошим сочетанием прочности и пластичности. Например, технически чистый титан марки ВТ1-0 имеет: σв = 375–540 МПа, σ0,2 = 295–410 МПа, δ = 20 %, и по этим характеристикам не уступает ряду углеродистых и Cr—Ni коррозионностойких сталей.
Титан хорошо обрабатывается давлением в горячем состоянии и удовлетворительно в холодном. Он легко прокатывается, куется, штампуется (рис. 4). Титан и его сплавы хорошо свариваются контактной и аргонодуговой сваркой, обеспечивая высокую прочность и пластичность сварного соединения (рис. 5). Недостатком титана является плохая обрабатываемость резанием из-за склонности к налипанию, низкой теплопроводности и плохих антифрикционных свойств.
Рис. 4. Заготовка титанового шпангоута истребителя до и после прессования на штамповочном прессе
Рис. 5. Аргонная сварка титана
Примечание. При сварке титана и его сплавов требуется уделить особое внимание чистоте рабочего места. Для сварочных цехов, где производятся работы с различными металлами, необходимо выделить специальную область, которая будет использоваться специально для сварки титана. Место, отведенное для этого, должно быть защищено от потоков воздуха, влаги, пыли, жира и других загрязнений, которые могут препятствовать качественной сварке. Это место должно быть защищено от воздействия таких процессов, как зачистка, резка и окраска. Кроме того, должна быть под контролем и влажность воздуха.
Фазовые превращения в титановых сплавах
На формирование структуры и, следовательно, свойств титановых сплавов решающее влияние оказывают фазовые превращения, связанные с полиморфизмом титана. В табл.2 представлены схемы диаграмм состояния «титан – легирующий элемент», отражающие подразделение легирующих элементов по характеру влияния на полиморфные превращения титана на четыре группы.
- α – Стабилизаторы (Al, O, N), которые повышают температуру полиморфного превращения α↔β и расширяют область твердых растворов на основе α –титана.
Учитывая охрупчивающее действия азота и кислорода, практическое значение для легирования титана имеет только алюминий. Он является основным легирующим элементом во всех промышленных титановых сплавах, уменьшает их плотность и склонность к водородной хрупкости, а также повышает прочность и модуль упругости. Сплавы с устойчивой α – структурой термической обработкой не упрочняются.
- Изоморфные β – стабилизаторы (Mo, V, Ni, Ta и др.), которые понижают температуру α↔β превращения и расширяют область твердых растворов на основе β – титана.
- Эвтектоидообразующие β – стабилизаторы (Cr, Mn, Cu и др.) могут образовывать с титаном интерметаллиды типа TiХ. В этом случае при охлаждении β – фаза претерпевает эвтектойдное превращение β + TiХ. Большинство β – стабилизаторов повышает прочность, жаропрочность и термическую стабильность титановых сплавов, несколько снижая их пластичность.
Кроме того, сплавы с (α + β) и псевдо – β – структурой могут упрочняться термообработкой (закалка + старение).
- Нейтральные элементы (Zr, Sn) не оказывают существенного влияния на температуру полиморфного превращения и не меняют фазового состава титановых сплавов.
Основной целью легирования титановых сплавов является повышение прочности, жаропрочности и коррозионной стойкости. Широкое применение нашли сплавы титана с алюминием, хромом, молибденом, ванадием, марганцем, оловом и др. элементами. Легирующие элементы оказывают большое влияние на полиморфные превращения титана.
Для титановых сплавов применяют следующие виды термообработки: отжиг, закалка и старение, а также химико-термическая обработка (азотирование, силицирование, оксидирование и др.).
Отжиг проводится для всех титановых сплавов с целью завершения формирования структуры, выравнивания структурной и концентрационной неоднородности, а также механических свойств. Температура отжига должна быть выше температуры рекристаллизации, но ниже температуры перехода в β – состояние во избежание роста зерна. Применяют обычный отжиг, двойной или изотермический (для стабилизации структуры и свойств), неполный (для снятия внутренних напряжений).
Закалка и старение (упрочняющая термообработка) применима к титановым сплавам с (α + β) – структурой. Принцип упрочняющей термообработки заключается в получении при закалке метастабильных фаз β и α с последующем их распаде с выделением дисперсных частиц α и β – фаз при искусственном старении. При этом эффект упрочнения зависит от типа, количества и состава метастабильных фаз, а также дисперсности образовавшихся после старения частиц α и β – фаз.
Химико-термическая обработка проводится для повышения твердости и износостойкости, стойкости к «схватыванию» при работе в условиях трения, усталостной прочности, а также улучшения коррозионной стойкости, жаростойкости и жаропрочности. Практическое применение имеют азотирование, силицирование и некоторые виды диффузионной металлизации.
Таблица 2
Промышленные титановые сплавы.
Титановые сплавы по сравнению с техническим титаном имеют более высокую прочность, в том числе и при высоких температурах, сохраняя при этом достаточно высокую пластичность и коррозионную стойкость.
По технологии изготовления титановые сплавы подразделяются на деформируемые и литейные; по уровню механических свойств — на сплавы невысокой прочности и повышенной пластичности, средней прочности, высокопрочные; по условиям применения — на хладостойкие, жаропрочные, коррозионностойкие. По способности упрочняться термообработкой они делятся на упрочняемые и не упрочняемые, по структуре в отожженном состоянии — на α, псевдо-α, (α + β), псевдо-β и β –сплавы (табл.3).
Таблица 3
Дефармируемые титановые сплавы
Титановые сплавы невысокой прочности и повышенной пластичности
К этой группе относятся сплавы с пределом прочности σ ≥ 700 МПа, а именно: α – сплавы марок ВТ1-00, ВТ1-0 (технический титан) и сплавы ОТ4- 0, ОТ4-1 (система Ti—Al—Mn), АТ3 (система Ti—Al c небольшими добавками Cr, Fe, Si, B), относящиеся к псевдо – α-сплавам с небольшим количеством β-фазы. Характеристики прочности этих сплавов выше, чем чистого титана благодаря примесям в сплавах ВТ1-00 и ВТ1-0 и незначительному легированию α – и β – стабилизаторами в сплавах ОТ4-0, ОТ4-1, АТ3.
Эти сплавы отличаются высокой пластичностью как в горячем, так и в холодном состоянии, что позволяет получать все виды полуфабрикатов: фольгу, ленту, листы, плиты, поковки, штамповки, профили, трубы и т. п. (рис. 6).
Рис. 6. Изделия из титановых сплавов
Ковка, объемная и листовая штамповка, прокатка, прессование производятся в горячем состоянии. Окончательная прокатка, листовая штамповка, волочение и другие операции производятся в холодном состоянии.
Для снятия внутренних напряжений, образовавшихся в результате механической обработки, листовой штамповки, сварки и др., применяется неполный отжиг.
Указанные сплавы хорошо свариваются сваркой плавлением (аргонодуговая, под флюсом, электрошлаковая) и контактной (точечная, роликовая). При сварке плавлением прочность и пластичность сварного соединения практически аналогичные основному металлу.
Коррозионная стойкость данных сплавов высокая во многих средах (морская вода, хлориды, щелочи, органические кислоты и т. п.), кроме растворов HF, h3SO4, HCl и некоторых других.
Применение. Эти сплавы широко применяются как конструкционные материалы для изготовления практически всех видов полуфабрикатов, деталей и конструкций, включая сварные. Наиболее эффективно их применение в
авиационно-космической технике (рис. 7), в химическом машиностроении, криогенной технике (высокая ударная вязкость сохраняется до –253oС), (табл. 4), а также в узлах и конструкциях, работающих при температурах до 300–350 ° С.
Рис. 7. Применение титановых сплавов в авиационно-космической технике
Таблица 4 Механические характеристики титановых сплавов при низких температурах
Сплав | σв (МПа) при температуре, ° С | δ (%) при температуре, ° С | КСU, Дж/см2 при температуре, ° С | |||||
–196 | –253 | –269 | –196 | –253 | –269 | –196 | –253 | |
ВТ1-0 | 920 | 1310 | – | 48 | 24 | – | 220 | 130 |
ВТ5-1 | 1200– 1350 | 1350– 1600 | 1710 | 15 | 8–10 | 9,3 | 40 | 30 |
ОТ4 | 1430 | 1560 | – | 13 | 16 | – | 50 | 40 |
ОТ4-1 | 1080 | 1390 | – | 19,4 | 17,5 | – | 23 | 30 |
ВТ3-1 | 1650 | 2060 | 2020 | 6,5 | 7,5 | 3 | 30 | 60 |
ВТ6 | 1640 | 1820 | – | 17,8 | 3,5 | – | 39 | 40 |
ВТ6С | 1310 | 1580 | – | 7–10 | 3–6 | – | 40 | 25 |
ВТ14 | 1650 | – | – | 10 | – | – | 40 | – |
Титановые сплавы средней прочности
К этой группе относятся сплавы с пределом прочности σв = 750–1000 МПа, а именно: α – сплавы марок ВТ5 и ВТ5-1; псевдо – α – сплавы марок ОТ4, ВТ20; (α + β) – сплавы марок ПТ3В, а также ВТ6, ВТ6С, ВТ14 в отожженном состоянии. Классификация и химический состав этих сплавов смотри табл. 5.
Сплавы ВТ5, ВТ5-1, ОТ4, ВТ20, ПТ3В, ВТ6С, содержащие небольшое количество β – фазы (2–7 % β – фазы в равновесном состоянии), упрочняющей термообработке не подвергаются и используются в отожженном состоянии. Сплав ВТ6С иногда применяют в термически упрочненном состоянии. Сплавы ВТ6 и ВТ14 используют как в отожженном, так и в термически упрочненном состоянии. В последнем случае их прочность становится выше 1000 МПа, и они будут рассмотрены в разделе, посвященном высокопрочным сплавам.
Рассматриваемые сплавы, наряду с повышенной прочностью, сохраняют удовлетворительную пластичность в холодном состоянии и хорошую пластичность в горячем состоянии, что позволяет получать из них все виды полуфабрикатов: листы, ленту, профили, поковки, штамповки, трубы и др. Исключение составляет сплав ВТ5, из которого листы и плиты не изготавливают из-за невысокой технологической пластичности.
На эту категорию сплавов приходится основной объем производства полуфабрикатов, применяемых в машиностроении.
Все среднепрочные сплавы хорошо свариваются всеми видами сварки, применяемыми для титана. Прочность и пластичность сварного соединения, выполненного сваркой плавлением, близка к прочности и пластичности основного металла (для сплавов ВТ20 и ВТ6С это соотношение составляет 0,9– 0,95). После сварки рекомендован неполный отжиг для снятия внутренних сварочных напряжений.
Таблица 5
Обрабатываемость резанием этих сплавов хорошая. Коррозионная стойкость в большинстве агрессивных сред аналогична техническому титану ВТ1-0.
Применение. Данные сплавы рекомендуется применять для изготовления изделий листовой штамповкой (ОТ4, ВТ20), для сварных деталей и узлов, для штампосварных деталей (ВТ5, ВТ5-1, ВТ6С, ВТ20) и др. Сплав ВТ6С широко применяется для изготовления сосудов и ёмкостей высокого давления (рис. 8). Детали и узлы из сплавов ОТ4, ВТ5 могут длительно работать при температурах до 400 ° С и кратковременно — до 750 ° С; из сплавов ВТ5-1, ВТ20 — длительно при температурах до 450–500 ° С и кратковременно — до 800–850 ° С. Сплавы ВТ5-1, ОТ4, ВТ6С также рекомендуются для применения в холодильной и криогенной технике.
Рис. 8. Изделия из титановых сплавов ВТ6С Высокопрочные титановые сплавы
К этой группе относятся сплавы с пределом прочности σв ≥ 1000 МПа, а именно (α + β) – сплавы марок ВТ6, ВТ14, ВТ3-1, ВТ22. Высокая прочность в этих сплавах достигается упрочняющей термообработкой (закалка + старение). Исключение составляет высоколегированный сплав ВТ22, который даже в отожженном состоянии имеет σв > 1000 МПа.
Указанные сплавы наряду с высокой прочностью сохраняют хорошую (ВТ6) и удовлетворительную (ВТ14, ВТ3-1, ВТ22) технологическую пластичность в горячем состоянии, что позволяет получать из них различные полуфабрикаты: листы (кроме ВТ3-1), прутки, плиты, поковки, штамповки, профили и др. Сплавы ВТ6 и ВТ14 в отожженном состоянии (σв ≥ 850 МПа) могут подвергаться холодной листовой штамповке с малыми деформациями.
Несмотря на гетерофазность структуры, рассматриваемые сплавы обладают удовлетворительной свариваемостью всеми видами сварки, применяемыми для титана. Для обеспечения требуемого уровня прочности и пластичности обязательно проводят полный отжиг, а для сплава ВТ14 (при толщине свариваемых деталей 10–18 мм) рекомендуется проводить закалку с последующим старением. При этом прочность сварного соединения (сварка плавлением) составляет не менее 0,9 от прочности основного металла. Пластичность сварного соединения близка к пластичности основного металла.
Обрабатываемость резанием удовлетворительная. Обработку резанием сплавов можно проводить как в отожженном, так и в термически упрочненном состоянии.
Данные сплавы обладают высокой коррозионной стойкостью в отожженном и термически упрочненном состояниях во влажной атмосфере, морской воде, во многих других агрессивных средах, как и технический титан.
Термическая обработка. Сплавы ВТ3-1, ВТ6, ВТ6С, ВТ14, ВТ22 подвергаются закалке и старению. Рекомендуемые режимы нагрева под закалку и старение для монолитных изделий, полуфабрикатов и сварных деталей приведены в табл. 6.6.
Охлаждение при закалке производится в воде, а после старения — на воздухе. Полная прокаливаемость обеспечивается для деталей из сплавов ВТ6, ВТ6С с максимальным сечением до 40 – 45 мм, а из сплавов ВТ3-1, ВТ14, ВТ22 — до 60 мм.
Для обеспечения удовлетворительного сочетания прочности и пластичности сплавов с (α + β) – структурой после закалки и старения необходимо, чтобы их структура перед упрочняющей термической обработкой была равноосной или «корзиночного плетения». Примеры исходных микроструктур, обеспечивающие удовлетворительные свойства, приведены на рис. 9.
Таблица 6. Режимы упрочняющей термической обработки титановых сплавов
Марка сплава | Температура полиморфного превращения Тпп, ° С | Температура нагрева под закалку, ° С | Температура старения, ° С | Продолжительность старения, ч |
ВТ3-1 | 960–1000 | 860–900 | 500–620 | 1–6 |
ВТ6 | 980–1010 | 900–950 | 450–550 | 2–4 |
ВТ6С | 950–990 | 880–930 | 450–500 | 2–4 |
ВТ8, ВТ9 | 980–1020 | 920–940 | 500–600 | 1–6 |
ВТ14 | 920–960 | 870–910 | 480–560 | 8–16 |
ВТ22 | 840–880 | 690–750 | 480–540 | 8–16 |
Рис. 9. Структура ВТ14 сплава перед упрочняющей термообработки
Применение. Высокопрочные титановые сплавы применяются для изготовления деталей и узлов ответственного назначения: сварные конструкции (ВТ6, ВТ14) рис. 10, турбины (ВТ3-1), штампосварные узлы (ВТ14), высоконагруженные детали и штампованные конструкции (ВТ22). Эти сплавы могут длительно работать при температурах до 400 ° С и кратковременно до 750 ° С.
Особенность высокопрочных титановых сплавов как конструкционного материала — их повышенная чувствительность к концентраторам напряжения. Поэтому при конструировании деталей из этих сплавов необходимо учитывать ряд требований (повышенное качество поверхности, увеличение радиусов перехода от одних сечений к другим и т. п.), аналогичных тем, которые существуют при применении высокопрочных сталей.
Рис. 10. Сварная конструкция из ВТ14 сплава
Литейные титановые сплавы
Титановые литейные сплавы подразделяется на 5 групп в зависимости от микроструктуры (α – сплавы, псевдо α – сплавы, α + β сплавы, псевдо β – сплавы, β – сплавы).
В состав титановых сплавов входят алюминий, ванадий, молибден, кремний, хром, цирконий и др. Эти сплавы обладают свойствами, выгодно выделяющих их из остальных сплавов: по прочности они не уступают сталям, имеют достаточно низкую плотность (~4,5 г/мм3), высокую химическую стойкость при температуре до 500 °С, высокую коррозионную стойкость во влажном воздухе, морской воде, азотной и соляной кислоте. Благодаря этим свойствам титановые сплавы интенсивно внедряются в авиа-, ракета- и кораблестроении.
В справочной литературе приводятся химический состав и механические свойства восьми литейных титановых сплавов – ВТ1Л, ВТ5Л, ВТ20Л, ВТ3-1Л, ВТ6Л, ВТ9Л, ВТ14Л, ВТ22Л, где буква В означает наименование организации-разработчика (ВИАМ), Т – титановый сплав, Л – литейный, цифра – номер сплава. Упоминается и новый сплав ВТ35Л.
Титановые сплавы обладают хорошей жидкотекучестью (460–520 мм), небольшой линейной (0,8–1,2 %) и объемной (2,4–3,2%) усадкой.
Сплав ВТ3-1Л относится к числу наиболее освоенных в производстве (рис. 11).
Прочность титановых сплавов σв = 34…93 кг/мм2, пластичность δ = 4–10%.
Главный недостаток титановых литейных сплавов – высокая температура плавления (до 1665 °С) и активное взаимодействие (при плавке) со всеми газами и огнеупорными материалами. Отсюда – проблема плавки (вакуумная, в атмосфере нейтральных газов) и материалов для литейных форм, что резко удорожает технологические процессы литья.
Рис. 11. Детали из титана марки ВТ3-1Л
599
Твердость основных металлов и сплавов
Измерение значения твердости проводится на готовых деталях, отправляющихся на сборку. Контроль производится на соответствие чертежу и технологическому процессу. На все основные материалы уже составлены таблицы значений твердости как в исходном состоянии, так и после термической обработки.
Цветные металлы
Твердость меди по Бринеллю составляет 35 НВ, значения латуни равны 42-60 НВ единиц в зависимости от ее марки. У алюминия твердость находится в диапазоне 15-20 НВ, а у дюралюминия уже 70НВ.
Черные металлы
Твердость по Роквеллу чугуна СЧ20 HRC 22, что соответствует 220 НВ. Сталь: инструментальная – 640-700 НВ, нержавеющая – 250НВ.
Для перевода из одной системы измерения в другую пользуются таблицами. Значения в них не являются истинными, потому что выведены империческим путем. Не полный объем представлен в таблице.
HB | HV | HRC | HRA | HSD |
228 | 240 | 20 | 60.7 | 36 |
260 | 275 | 24 | 62.5 | 40 |
280 | 295 | 29 | 65 | 44 |
320 | 340 | 34.5 | 67.5 | 49 |
360 | 380 | 39 | 70 | 54 |
415 | 440 | 44.5 | 73 | 61 |
450 | 480 | 47 | 74.5 | 64 |
480 | 520 | 50 | 76 | 68 |
500 | 540 | 52 | 77 | 73 |
535 | 580 | 54 | 78 | 78 |
Значения твердости, даже если они производятся одним и тем же методом, зависят от прилагаемой нагрузки. Чем меньше нагрузка, тем выше показания.
Таблица соотношений между числами твердости по Бринеллю, Роквеллу, Виккерсу, Шору
Указанные значения твердости по Роквеллу, Виккерсу и Шору соответствуют значениям твердости по Бринеллю, определенным с помощью шарика диаметром 10 мм.
По Роквеллу | По Бринеллю | По Виккерсу (HV) | По Шору | |||
HRC | HRA | HRB | Диаметр отпечатка | HB | ||
65 | 84,5 | – | 2,34 | 688 | 940 | 96 |
64 | 83,5 | – | 2,37 | 670 | 912 | 94 |
63 | 83 | – | 2,39 | 659 | 867 | 93 |
62 | 82,5 | – | 2,42 | 643 | 846 | 92 |
61 | 82 | – | 2,45 | 627 | 818 | 91 |
60 | 81,5 | – | 2,47 | 616 | – | – |
59 | 81 | – | 2,5 | 601 | 756 | 86 |
58 | 80,5 | – | 2,54 | 582 | 704 | 83 |
57 | 80 | – | 2,56 | 573 | 693 | – |
56 | 79 | – | 2,6 | 555 | 653 | 79,5 |
55 | 79 | – | 2,61 | 551 | 644 | – |
54 | 78,5 | – | 2,65 | 534 | 618 | 76,5 |
53 | 78 | – | 2,68 | 522 | 594 | – |
52 | 77,5 | – | 2,71 | 510 | 578 | – |
51 | 76 | – | 2,75 | 495 | 56 | 71 |
50 | 76 | – | 2,76 | 492 | 549 | – |
49 | 76 | – | 2,81 | 474 | 528 | – |
48 | 75 | – | 2,85 | 461 | 509 | 65,5 |
47 | 74 | – | 2,9 | 444 | 484 | 63,5 |
46 | 73,5 | – | 2,93 | 435 | 469 | – |
45 | 73 | – | 2,95 | 429 | 461 | 61,5 |
44 | 73 | – | 3 | 415 | 442 | 59,5 |
42 | 72 | – | 3,06 | 398 | 419 | – |
40 | 71 | – | 3,14 | 378 | 395 | 54 |
38 | 69 | – | 3,24 | 354 | 366 | 50 |
36 | 68 | – | 3,34 | 333 | 342 | – |
34 | 67 | – | 3,44 | 313 | 319 | 44 |
32 | 67 | – | 3,52 | 298 | 302 | – |
30 | 66 | – | 3,6 | 285 | 288 | 40,5 |
28 | 65 | – | 3,7 | 269 | 271 | 38,5 |
26 | 64 | – | 3,8 | 255 | 256 | 36,5 |
24 | 63 | 100 | 3,9 | 241 | 242 | 34,5 |
22 | 62 | 98 | 4 | 229 | 229 | 32,5 |
20 | 61 | 97 | 4,1 | 217 | 217 | 31 |
18 | 60 | 95 | 4,2 | 207 | 206 | 29,5 |
– | 59 | 93 | 4,26 | 200 | 199 | – |
– | 58 | – | 4,34 | 193 | 192 | 27,5 |
– | 57 | 91 | 4,4 | 187 | 186 | 27 |
– | 56 | 89 | 4,48 | 180 | 179 | 25 |
Читать также: Момент затяжки динамометрическим ключом таблица
Отверстия под резьбу
Таблица сверл для отверстий под нарезание трубной цилиндрической резьбы.
Размеры гаек под ключ
Основные размеры под ключ для шестигранных головок болтов и шестигранных гаек.
G и M коды
Примеры, описание и расшифровка Ж и М кодов для создания управляющих программ на фрезерных и токарных станках с ЧПУ.
Типы резьб
Типы и характеристики метрической, трубной, упорной, трапецеидальной и круглой резьбы.
Масштабы чертежей
Стандартные масштабы изображений деталей на машиностроительных и строительных чертежах.
Режимы резания
Онлайн калькулятор для расчета режимов резания при точении.
Отверстия под резьбу
Таблица сверл и отверстий для нарезания метрической резьбы c крупным (основным) шагом.
Станки с ЧПУ
Классификация станков с ЧПУ, станки с ЧПУ по металлу для точения, фрезерования, сверления, расточки, нарезания резьбы, развёртывания, зенкерования.
Режимы резания
Онлайн калькулятор для расчета режимов резания при фрезеровании.
Форматы чертежей
Таблица размеров сторон основных и дополнительных форматов листов чертежей.
CAD/CAM/CAE системы
Системы автоматизированного проектирования САПР, 3D программы для проектирования, моделирования и создания 3d моделей.
Чтение чертежей
Техническое черчение, правила выполнения чертежей деталей и сборочных чертежей.
Источник: ОСТ 3-1279-86
Таблица 1
Таблица 2
К оглавлению
Следите за нами:
Главконструктор работает с компаниями в городах:
Санкт-Петербург, Москва, Севастополь, Воронеж, вся Россия.
Химические и физические свойства хрома
Температура плавления и кипения
Физические характеристики металла зависят от примесей до такой степени, что сложным оказалось установить даже температуру плавления.
- Согласно современным измерениям температура плавления считается величина в 1907 С. Металл относится к тугоплавким веществам.
- Температура кипения равна 2671 С.
Ниже будет дана общая характеристика физических и магнитных свойств металла хром.
Общие свойства и характеристики хрома
Физические особенности
Хром относится к наиболее устойчивым из всех тугоплавких металлов.
- Плотность в нормальных условиях составляет 7200 кг/куб. м, это меньше чем у железа.
- Твердость по шкале Мооса составляет 5, по шкале Бринелля 7–9 Мн/м2. Хром является самым твердым металлом из известных, уступает только урану, иридию, вольфраму и бериллию.
- Модуль упругости при 20 С составляет 294 ГПа. Это довольно умеренный показатель.
Благодаря строению – объемно-центрированная решетка, хром обладает такой характеристикой, как температура хрупко-вязкого периода. Вот только когда речь идет об этом металле, эта величина оказывается сильно зависящей от степени чистоты и колеблется от -50 до +350 С. На практике раскристаллизированный хром никакой пластичностью не обладает, но после мягкого отжига и формовки становится ковким.
Прочность металла также растет при холодной обработке. Легирующие добавки тоже заметно усиливают это качество.
Далее представлена краткая характеристика теплофизических свойств хрома.
Теплофизические характеристики
Как правило, тугоплавкие металлы имеют высокий уровень теплопроводности и, соответственно, низкий коэффициент теплового расширения. Однако хром заметно отличается по своим качествам.
В точке Нееля коэффициент теплового расширения совершает резкий скачок, а затем с увеличением температуры продолжает заметно расти. При 29 С (до скачка) величина коэффициента составляет 6.2 · 10-6 м/(м•K).
Теплопроводность подчиняется этой же закономерности: в точке Нееля она падает, хотя и не столь резко и уменьшается с возрастанием температуры.
- В нормальных условиях теплопроводность вещества равна 93.7 Вт/(м•K).
- Удельная теплоемкость в тех же условиях – 0.45 Дж/(г•K).
Электрические свойства
Несмотря на нетипичное «поведение» теплопроводности хром является одним из лучших проводников тока, уступая по этому параметру только серебру, меди и золоту.
- При нормальной температуре электропроводность металла составит 7.9 · 106 1/(Ом•м).
- Удельное электрическое сопротивление – 0.127 (Ом•мм2)/м.
До точки Нееля – 38 С, вещество является антиферромагнетиком, то есть, под действием магнитного поля и при его отсутствии никаких магнитных свойств не проявляется. Выше 38 С хром становится парамагнетиком: проявляет магнитные свойства под действием внешнего магнитного поля.
Какие методы измерения твердости металлов используются сегодня?
Твердость металлов является основным показателем, который важно учитывать при работе с ними. Для этого существуют методы научных исследователей, а также современные принципы с использованием высокотехнологического оборудования. Однако как выглядят все способы, и как на практике они работают?
В этой статье будут рассмотрены все прямые и косвенные методы проверки.
Твердость металлов — это показатель, который означает устойчивость стали к механическому воздействию других более твердых материалов. Оцениваются показатели в единицах твердости, на основе которых делается вывод о состоянии материала.
Твердость металлов важно учитывать в большинстве видов работы с ними. Например, когда на производстве изготавливаются объемные конструкции с большим весом, где применяются несколько типов металлов, важно знать, что они будут оптимально взаимодействовать и успешно выдерживать большую нагрузку.
Особо важно учитывать показатель твердости металла в следующих сферах:
- Кораблестроительство;
- Изготовление автомобилей;
- Сборка самолетов;
- Изготовление строительных материалов на основе металла и расходников.
В любой из этих областей устойчивость к механическому воздействию определяет безопасность человека, возможность выполнить поставленную задачу и эксплуатационный срок.
Для определения твердости в металл вдавливается индентор — тело, изготовленное из твердого сплава или алмаза, которое обладает наилучшим показателем сопротивления к механическим воздействиям. Чем большую силу вдавливания выдерживает металл, тем его твердость больше.
Прямые методы
Классические способы измерения твердости представляют собой принципы, которые изобретались известными ученными и успешно проявляли себя в исследованиях на протяжении многих лет. Благодаря ним человечество сегодня имеет возможность пользоваться ископаемыми и успешно внедрять их в жизнь.
В измерении принимают участие специальное оборудование, которое устанавливается стационарно и дает большую нагрузку на материал с помощью индентора.
Способ Бринелля
Твердость металла на основе этого принципа измеряется с помощью специального твердомера. К его оправке крепится индентор из алмаза или прочного сплава в форме шарика определенного диаметра. Под заданной нагрузкой шар воздействует на металл в течение установленного времени.
После манипуляций на поверхности материала остается отпечаток индентора. На основе измерения его диаметра и площади выносится результат исследования и металлу присваивается определенный результат. Далее эта информация позволит успешно использовать материал или наоборот, убрать его из производства.
Единственный недостаток такого метода — отсутствие мобильности оборудования для измерения. Исследования можно проводить только на месте. При установке учитывается уровень поверхности пола и другие показатели, которые могу влиять на результат эксперимента.
Метод Роквелла
Основа принципа проверки заключается на твердости, которая определяется различием между глубиной углубления индентора, а также остаточным показателем проникновения под установленной нагрузкой. При этом показатели измеряются при сохранении предварительной нагрузки.
В методе исследования используется закаленный шарик или алмазный конус в качестве индентора. В отличие от предыдущего принципа, твердость исследуется на основе глубины лунки, а не ее площади.
Показатель измеряется в результате вдавливания, что позволяет получить максимально точный результат. Нагрузка дается поэтапно, согласно государственным стандартам. Сначала дается небольшое воздействие, после чего основное усилие. Современные твердомеры измеряют различие между глубиной лунок, которые получаются после вдавливания наконечника под предварительным и основным усилием.
Важно! При применении этого способа важно, чтобы на поверхности исследуемого материала не было трещин, окалин, выбоин и прочих повреждений, которые могут повлиять на правильность результата.
Следует следить за перпендикулярностью нагрузки, а также устойчивостью металла на рабочей поверхности.
Важно знать: Виды термической обработки
Динамическое вдавливание
Бывают случаи, когда необходимо проверить показатели металла, который используется в конструкции, а переносимого образца под рукой нет. Стационарные установки для этого не подходят, поэтому предыдущие методы отходят на второй план. На помощь приходит мобильный прибор, который изготовлен на основе государственного образца.
Он представляет собой специальный молоточек и инструмент с шариком на конце. При ударе по прибору он оставляет следы на исследуемом материале. Также, следует провести аналогичные действия на эталонном образце, твердость которого уже известна.
Далее проводится сравнение отпечатков, их глубины и площади, после чего выносится результат исследования. Однако специалисты рекомендуют проверять твердость металла перед тем, как использовать его в каких-либо конструкциях важного назначения.
Принцип упругой отдачи
Помимо проблем со стационарностью оборудования, возникают ситуации, когда необходимо проверить показатели металла без нанесения ему повреждений. Для этого применяется принцип упругой отдачи, с помощью которого измеряют твердость без вдавливания и других механических воздействий.
На специальном приборе закрепляется шарик фиксированного веса на постоянной высоте. Далее он падает с нее на металл и отскакивает. Высота отскока прямо говорит о твердости. Чем больше отскок, не больше твердость металла. Производительность этого принципа является очень высокой, поэтому можно проводить около 100 измерений за один час.
Однако рекомендуется применять метод только для сравнения твердости изделий из одного материала (металла), ведь показатели упругости также могут влиять на результат исследования и должны быть одинаковыми.
Косвенные методы
Измерение показателя с помощью косвенных методов производится с помощью двух видов измерения — динамический и ультразвуковой. Они не исследуют твердость напрямую, а лишь сравнивают показатели металла и другие физические свойства.
Измерение твердости с применением ультразвука заключается в уровне изменения частоты колебаний металла с установленным на краю индентором. Чем больше глубина проникновения, тем мягче металл.
Соответственно, чем больше площадь контакта, тем выше уровень затухания частоты.
Принцип не имеет каких-либо ограничений по размерам и массе исследуемых металлов, поэтому широко используется на производствах.
Динамический способ исследует зависимость скорости отскока индентора от поверхности металла. Он похож на один из классических способов, но, помимо высоты отскока, измеряется его скорость и глубина отпечатка после ударения.
Преимущества метода заключаются в том, что он менее требователен к состоянию поверхности металла, а также позволяет увеличить количество исследований за определенное количество времени. Именно поэтому он часто используется во многих сферах производства.
в чем различия? (Окончательное сравнение)
Сталь и титан часто первые материалы, которые приходят на ум, когда дизайнеры думают о прочности и долговечности в своих проектах. Эти два металла входят в состав самых разных сплавов и используются для различных целей. Разницу между сталью и титаном будет нелегко распознать, если вы не углубитесь в их химические и структурные свойства. Если вам интересно, как сравнить эти два металла, вы находитесь в нужном месте. Эта статья рассматривает сталь и титан и исследует различия между ними, чтобы помочь вам понять основы каждого металла. Этот пост поможет вам выбрать подходящий материал для вашего проекта путем сравнения титана и стали на основе изучения механических, физических и рабочих свойств. Но прежде чем мы перейдем к сравнению, давайте сначала рассмотрим каждый металл.
Contents [show]
- 1 Что такое сталь?
- 2 Что такое титан?
- 3 Сравнение титана и стали
- 3.1 Сталь против. Титан: плотность
- 3.2 Сталь против. Титан: эластичность
- 3.3 Сталь против. Титан: прочность на разрыв
- 3.4 Сталь против. Титан: удлинение при разрыве
- 3.
5 Сталь против. Титан: твердость
- 4 В нижней строке
Сталь создается путем добавления углерода к элементарному железу. Этот процесс увеличивает твердость, прочность и устойчивость к ударам, коррозии и температуре. Сталь имеет широкий спектр сплавов, в состав которых входят легирующие элементы, такие как цинк, хром, молибден и кремний. Эти элементы улучшают способность стали противостоять коррозии, поэтому ее чаще всего называют нержавеющей сталью. Количество хрома, добавленного в сталь, определяет ее устойчивость к коррозии. Трудно обобщить свойства стали, поскольку она существует во многих типах и калибрах.
В частности, большинство сплавов стали плотные и твердые, но их все же можно обрабатывать. Сталь также поддается термической обработке, что придает ей разные свойства в зависимости от процесса и типа стали. Кроме того, сталь является отличным проводником как тепла, так и электричества. Некоторые образцы стали подвержены ржавчине из-за наличия железа. Однако эта проблема решается добавлением хрома для изготовления нержавеющей стали.
Титан — четвертый по распространенности металл на Земле. Однако титан в элементарной форме или в высокой концентрации встречается нечасто. Кроме того, титан очень трудно очистить, что делает его более дорогим.
Титан имеет плотность 4.51 г / см.3, что означает, что он легкий по сравнению с другими металлами. Кроме того, чистая форма бывает серебристо-серого цвета. Важно отметить, что титан не магнитный. Как и многие металлы, титан может присутствовать в элементарной форме или в различных сплавах. Эти сплавы часто упрочняются и более устойчивы к коррозии. Большинство сплавов титана используются в аэрокосмической, конструкционной и других областях, где требуется устойчивость к высоким температурам. Элементарный титан часто используется в качестве легирующего элемента.
Сравнение титана и СтальВыбор между сталью и титаном зависит от конкретной области применения. В этом разделе сравниваются механические характеристики стали и титана, что помогает определить, как можно специфицировать каждый металл. Однако лучшее сравнение этих металлов основано на разных типах сплавов, а не на обобщенных данных.
Плотность можно использовать для определения веса каждого металла. Как отмечалось ранее, титан легче стали и весит почти вдвое меньше стали. Это свойство делает титан подходящим для применений, требующих прочности и легкости, например, в аэрокосмической промышленности. С другой стороны, плотность стали выгодна при использовании в таких местах, как шасси транспортных средств.
Сталь против. Титан: эластичностьЭластичность материала характеризует его гибкость. Эту меру иногда называют модусом Юнга. Это свойство важно для понимания того, как материал реагирует на удар, изгибается он или деформируется, не достигая пластической деформации или нет.
В этом отношении титан имеет низкую эластичность, что означает, что материал изгибается и деформируется под давлением. Эта особенность также затрудняет обработку титана. С другой стороны, сталь имеет более высокий модуль упругости и ее можно обрабатывать с меньшими трудностями. Это свойство делает сталь пригодной для изготовления режущих кромок, поскольку она может ломаться, не сгибаясь под нагрузкой.
Сталь против. Титан: прочность на разрывС точки зрения прочности на разрыв сталь намного прочнее титана, в отличие от большинства людей, которые считают, что титан более мощный, чем большинство металлов. Эта особенность делает сталь более широко используемым металлом по сравнению с титаном. Однако титан столь же прочнее, как сталь, и весит почти вдвое меньше стали. Это делает титан более прочным на единицу массы по сравнению со сталью.
В приложениях, требующих общей прочности, сталь является наиболее предпочтительной, поскольку большинство ее сплавов имеют более высокий предел текучести по сравнению с другими металлами. Если вы ищете исключительно прочность, тогда сталь должна быть вашим металлом. Однако, если проект требует прочности на единицу массы, вы выбираете титан.
Сталь против. Титан: удлинение при разрывеЭта функция является мерой того, насколько материал растягивается до разрыва. Более высокое удлинение при разрыве означает, что материал растягивается больше, прежде чем окончательно разорвется. Другими словами, если металл имеет большее удлинение при разрыве, то он более ковкий. Титан очень пластичен и перед разрушением растягивается почти на половину своей длины. Эта особенность затрудняет обработку титана. С другой стороны, сталь имеет широкий спектр сплавов с низким удлинением при разрыве, что означает, что она более твердая и хрупкая.
Твердость считается относительной величиной, которая относится к тому, как материал реагирует на царапины, вмятины, травления и другие удары, наносимые на его поверхность. Твердость металла измеряется с помощью индентора. Титан тверд, но не достигает уровня стали. Это не означает, что титан легко деформируется. Напротив, титан образует твердый слой диоксида, который защищает металл от царапин. Сталь твердая и не царапается. Это делает его подходящим для применений, требующих воздействия суровых условий.
В нижней строкеСравнение стали с титаном — лучший способ определить лучший материал для проекта. Однако важно понимать, что выбор материала между сталью и титаном зависит от конкретной области применения.
Различия между титаном и сталью можно объяснить различными аспектами, такими как механические свойства. Эти различия позволяют лучше понять каждый металл.
Ссылки на связанные источники:
Нержавеющая сталь 18/10 VS Нержавеющая сталь 18/8: в чем различия
Алюминий против нержавеющей стали: в чем разница?
Углеродистая сталь и нержавеющая сталь: в чем разница?
Нержавеющая сталь 304 и 316: в чем разница?
Нержавеющая сталь 420 и нержавеющая сталь 430: в чем разница?
Хирургическая сталь и нержавеющая сталь: в чем разница?
Рошиндустри специализируется на высоком качестве Быстрое прототипирование, быстрый мелкосерийное производство и крупносерийное производство. Услуги быстрого прототипа, которые мы предоставляем, — это профессиональный инжиниринг, Обработка CNC включая фрезерные и токарные станки с ЧПУ, Изготовление листового металла или прототипирование листового металла, Умрите литье, металлическое тиснение, Вакуумное литье, 3D печать, SLA, Изготовление прототипов методом экструзии пластика и алюминия, Быстрая оснастка, Быстрое литье под давлением, Обработка поверхности закончить услуги и другие услуги быстрого прототипирования Китая, пожалуйста свяжитесь с нами прямо сейчас.
Рейтинг самых твердых металлов на планете
Оглавление
Просмотров: 172
В мире существует большое разнообразие металлов, которые обладают своими отличительными особенностями и уникальными характеристиками. Некоторые из них отличаются низким или высоким коэффициентом сопротивления, другие являются ковкими, третьи – пластичными.
Титан металл фотоСуществуют металлы, которые отличаются своей невероятной твердостью. Самым известным из них является титан. Однако и у него есть достойные конкуренты.
Характеристика титана
Данный химический элемент в чистом виде был выделен в 1825 году. Удалось это шведскому химику Берцелиусу. Титан – это металл, который имеет серебристо-белый цвет и отличается небольшим весом. Элемент имеет малую молекулярную массу, которая составляет всего 22. Для титана характерны следующие свойства:
1. Плотность твердого титана составляет 4,51 грамм на кубический сантиметр. В жидком состоянии плотность металла снижается до 4,12 грамм на сантиметр кубический.
2. Температура плавления – 1668 градусов Цельсия.
3. Температура закипания – 3227 градусов Цельсия.
4. Твердость НВ – 103. Данный показатель может изменяться в зависимости от наличия и количества примесей.
5. Упругость у титана не самая высокая, что является весомым недостатком материала.
6. При обычных условиях металл не корродирует.
7. Титан – это инертный материал, благодаря этому его широко используют в медицинских целях. Однако инертность снижается под влиянием высоких температур. Таким образом, при ее повышении до 200 градусов, титан начинает активно поглощать водород, меняя свои характеристики.
8. Плохо проводит электрический ток.
По шкале МООСА твердость титана составляет 4,5. Из этого можно сделать вывод, что он не является самым твердым металлом. Тем не менее, из других твердых он получил наибольшее распространение.
Использование титана
Использование титана в промышленностиТитан применяется практически в каждой области промышленности, притом довольно широко его распространение.
Сегодня материал используется в таких сферах человеческой деятельности:
• Авиастроение. Некоторые элементы самолетов испытывают воздействие высоких температур, а также подвергаются действию деформационных сил. Поэтому в воздушном судне многие детали (элементы шасси, заклепки, некоторые части корпуса) сделаны из титана.
Использование титана в авиастроении• Космические аппараты. Данная техника испытывает еще большие нагрузки чем самолеты, поэтому здесь также используется титан. В больших количествах материал применяется для обшивки.
Использование титана космических аппаратах• Судостроение.
Использование титана судостроении• Добыча нефти и газа. Титановые компоненты в основном встречаются в бурящих трубах и насосах, работающих под большим давлением.
Использование титана добыче нефти и газа• Строительство. Титан, который обладает высокой твердостью, необходим для создания особенно важных элементов конструкций.
Использование титана в строительстве• Медицинская промышленность. Многие протезы и инструменты изготавливаются из данного металла.
• Спорт. Из титана делаются некоторые велосипедные детали, турники и другой спортивный инвентарь.
Использование титана в спорте• Химическая промышленность. Титан является незаменимым, когда необходимо получить твердое вещество устойчивое к кислотам. В химической промышленности без данного металла невозможно обойтись при изготовлении различных обменников, труб и других различных конструкций.
Использование титана в химической промышленностиНесмотря на свою высокую твердость, титан достаточно легкий металл. Данный факт также влияет на широкое распространение использование титана в разных сферах промышленности. Изделия из него отличаются долговечностью.
Особенности титана и его примесей
Данный металл обладает еще одним примечательным свойством – парамагнитность. Это означает, что титан не притягивается под действием магнитного поля, вместе с тем он и не может выталкиваться магнитного поля. В процессе производства пытаются получить максимально чистый металл, где будет минимальное количество примесей. Это необходимо, чтоб получить максимальную твердость вещества.
Если в титане присутствуют неметаллические примеси, то такое вещество получается не таким твердым и более ломким. При этом примеси других металлов сделают материал менее жаропрочным. Если в титане присутствует какая-либо примесь (даже в минимальном количестве), то металл считается техническим. Зачастую данная разновидность проявляет наибольшую противокоррозионную стойкость.
Важно! Необычным свойствам титана является тот факт, что даже минимальное попадание в него другого вещества, в значительной степени влияет на первоначальные характеристики металла.
В сравнении с другими металлами, которые часто используются в хозяйственной деятельности человечества, то титан вдвое прочнее железа и в шесть раз крепче алюминия. Данный материал практически не подвержен коррозии. По данной характеристике он ушел далеко вперед от нержавеющей стали и алюминия.
Получение материала
По распространенности титан занимает 10 место на планете. Зачастую рассматриваемое вещество в природе встречается в виде титановой кислоты, находящейся в минералах. В частности бывают такие титановые руды:
• Анатаз;
• Брукит;
• Первоксит;
• Рутил.
Запасы данных веществ в большом количестве присутствуют в Бельгии, Великобритании, Испании, РФ, США, Франции и Японии.
На данный момент используется несколько вариантов получения титана:
1. Электролиз. Через титановую руду пропускают сильный ток, в результате материал распадается на компоненты.
2. Магниетермия. В первую очередь добывают диоксид титана. Далее вещество хлорируют с добавлением специального катализатора, ведь в естественных условиях процесс будет протекать очень медленно и долго. Вырабатывается газ, который восстанавливается при помощи натрия и магния. Далее смесь нагревается и из нее выплавляется титан.
3. Рафинирование. В данном случае диоксид титана обрабатывают при помощи паров йода. Таким образом получают йодид титана. Полученное вещество нагревается до высоких температур, а также подвергается воздействию тока. На выходе получается йод и титан.
4. Гидридно-кальциевый метод. Для начала добывают гидрид натрия. Далее происходит разделение смеси на составляющие.
На масштабных производствах зачастую используется два метода: магниетермический и гидридно-кальциевый. Это связано с тем, что данные способы позволяют получить чистый титан при самых низких затратах.
Иные металлы с высокой твердостью
Как уже было сказано, титан – это не самый твердый металл на Земле. Он имеет достаточно много конкурентов (если в расчет брать исключительно прочностные характеристики). Кроме титана в мире существуют такие твердые металлы:
• Иридий. На самом деле именно этот материал занимает первое место по твердости. Однако это является также и его минусом: его очень трудно обрабатывать, поэтому его используют крайне редко. Его применяют для изготовления некоторых компонентов в ракетостроении, кроме того, он используется в машиностроении и в производстве шариков для ручек. Иридий плавиться при температуре 2466 градусов Цельсия, имеет светло-серебристый цвет. В природе встречается очень редко, зачастую имеет метеоритное происхождение.
• Рутений. Также очень редкий металл, по подсчетам его на Земле всего около 5 000 тонн. Добыча рутения составляет порядка 18 тонн в год. В связи с тем, что вещества крайне мало, оно используется только как катализатор химически процессов. Кроме того, рутений добавляют к титану, чтоб получить более устойчивый к ржавчине материал.
Рутений металл• Хром. Материал был открыт в середине 18 века. Он имеет голубовато-белый цвет. Нашел применение в металлургии, машиностроении и в науке. В природе имеется достаточно ограниченное количество вещества.
Хром металл• Бериллий. Данный материал получил распространение в атомной энергетике, кроме того, его используют в производстве рентгеновских аппаратов, громкоговорителей высоких частот, огнеупорных материалов. Бериллий очень сложно обрабатывать, ведь он не только твердый, но еще и очень хрупкий.
• Осмий. По характеристикам очень похож на иридий. Данный материал является тугоплавким, невероятно твердым и сложным в обработке. Зачастую встречается в медицинской промышленности. В частности, его используют практически во всех кардиостимуляторах.
Осмий металл фото. Самый тяжелый металл в мире• Вольфрам. Самый тугоплавкий металл на планете, он имеет серебристо-серый оттенок. Благодаря своему свойству используется в элементах накаливания. Довольно часто из него делают тару для хранения радиоактивных веществ. Также из вольфрама делают хирургический инструмент, используется в военной промышленности.
Вольфрам металл фото• Уран. Достаточно распространенный твердый металл. Характерной особенностью являются радиоактивные свойства.
Уран металл фотоЗаключение
Твердые материалы нужны во многих областях промышленности. В частности для производства продукции, которая в последствие будет подвергаться сильному силовому влиянию. Такие металлы нужны для постройки космических кораблей, морских и воздушных судов – для всего этого требуется твердый и тугоплавкий материал, который не подвержен коррозии.
В природе существует несколько твердых металлов, однако большинство из них достаточно редкие. Самым популярным стал титан. Для его получения используют несколько методов. В природе он встречается в виде нескольких минералов.
Также в промышленности используют и сплавы титана, ведь примеси в значительной степени могут изменить свойства металла.
Система комментирования SigComments
Titanium Product Guide — Alcobra Metals
Как и другие металлы, используемые в промышленности, титан имеет множество различных марок. Класс 2 чаще всего используется для чистого титана, а класс 5 (6AL-4V) чаще всего используется для сплава титана, оба считаются «рабочими лошадками» в мире титана. Титан широко используется из-за его высокой коррозионной стойкости и высокого отношения прочности к весу. Типичные приложения: аэрокосмическая, автомобильная, медицинская, промышленная, химическая, нефтяная и другие отрасли промышленности.
Покупка изделий из титана
Класс 1
Титан класса 1 представляет собой относительно низкую прочность с высокой пластичностью. Это самый мягкий и пластичный из различных сортов титана. Из-за этих качеств класс 1 обычно используется из-за его формуемости.
Общие области применения:
- Химическая промышленность
- Архитектура
- Медицина
- Судостроение
- Автомобилестроение
- Воздушное судно
Титан класса 1 | ||
---|---|---|
Минимальные свойства | Предел прочности при растяжении, psi | 34800 |
Предел текучести, psi | 24700-45000 | |
Твердость по Бринеллю | 120 | |
Твердость по Роквеллу B | 70 | |
Химия | C | Макс.![]() |
Fe | Макс. 2 | |
В | Макс. 0,015 | |
N | Макс. 0,03 | |
O | Макс. 18 | |
Ти | 99,5 |
Класс 2
Класс 2 Титан имеет наилучшее сочетание прочности, пластичности и свариваемости. Широко известный как «рабочая лошадка» в титановой промышленности, класс 2 более удобен и доступен.
Common Applications:
- Architecture
- Medical
- Marine
- Exhaust
- Air Craft
- Chemical
- Automotive
Grade 2 Titanium | ||
---|---|---|
Минимальные свойства | Предел прочности при растяжении, psi | 62400 |
Предел текучести, psi | 24700-45000 | |
Твердость по Бринеллю | 200 | |
Твердость по Роквеллу B | 98 | |
Химия | C | Макс.![]() |
Fe | Макс.3 | |
В | Макс. 0,015 | |
N | Макс. 0,03 | |
O | Макс. 25 | |
Ти | 99,2 |
Grade 3
Титан Grade 3 является одним из наименее используемых сортов технически чистого титана. Класс 3 прочнее, чем класс 1 и 2, но похож по пластичности и меньшей формуемости. Марка 3 имеет более высокие механические свойства, что позволяет использовать ее в приложениях, требующих умеренной прочности и более высокой коррозионной стойкости.
Общие области применения:
- Аэрокосмическая промышленность
- Химическая промышленность
- Медицина
- Морской
Титан класса 3 | ||
---|---|---|
Минимальные свойства | Предел прочности при растяжении, psi | 75400 |
Предел текучести, psi | 65300 | |
Твердость по Бринеллю | 266 | |
Твердость по Роквеллу B | 26 | |
Химия | С | Макс.![]() |
Fe | Макс.3 | |
В | Макс. 0,015 | |
N | Макс. 0,05 | |
O | Макс. 35 | |
Ти | 99,1 |
Класс 4
Класс 4 Титан хорошо известен своей высокой прочностью, коррозионной стойкостью и хорошей формуемостью. Класс 4 также наиболее широко используется в медицинской промышленности.
Общие применения:
- Medical
- Криогенный
- Хирургическое оборудование
- Теплообмен
4 класс. | ||
---|---|---|
Минимальные свойства | Предел прочности при растяжении, psi | 95700 |
Предел текучести, psi | 85600 | |
Твердость по Бринеллю | 265 | |
Твердость по Роквеллу B | 23 | |
Химия | C | Макс.![]() |
Fe | Макс. 5 | |
В | Макс. 0,015 | |
N | Макс. 0,05 | |
O | Макс. 4 | |
Ти | 99 |
Класс 5 (6АЛ-4В)
Марка 5, также известная как 6АЛ-4В, считается «рабочей лошадкой» для титанового сплава. Чаще всего используется из-за высокого отношения прочности к весу и коррозионной стойкости. Марка 5 также может подвергаться термообработке для повышения прочности.
Общие применения:
- Aerospace
- Automotive
- Высокоэффективность
- Marine
- Спортивное оборудование
Стал 5 TITAT0032 | ||
---|---|---|
Минимальные свойства | Предел прочности при растяжении, psi | 138000 |
Предел текучести, psi | 128000 | |
Твердость по Бринеллю | 334 | |
Твердость по Роквеллу B | 36 | |
Химия | Ал | 6 |
Fe | Макс.![]() | |
О | Макс. .25 | |
Ти | 90 | |
В | 4 |
Alcobra Metals заявляет, что все технические данные предназначены только для целей сравнения и НЕ ПРЕДНАЗНАЧЕНЫ ДЛЯ ПРОЕКТИРОВАНИЯ. Он был составлен из источников, которые мы считаем точными, но не можем гарантировать. Пожалуйста, проконсультируйтесь с инженером.
Сталь и титан: прочность, свойства и применение
Когда дизайнерам требуются прочные и прочные материалы для своих проектов, первыми на ум приходят сталь и титан. Эти металлы входят в широкий ассортимент сплавов — неблагородные металлы, пропитанные другими металлическими элементами, которые в сумме производят больше, чем его части. Существуют десятки титановых сплавов и еще сотни стальных сплавов, поэтому часто бывает сложно решить, с чего начать при рассмотрении этих двух металлов. Эта статья, посредством изучения физических, механических и рабочих свойств стали и титана, может помочь разработчикам выбрать, какой материал подходит для их работы. Каждый металл будет кратко изучен, а затем последует сравнение их различий, чтобы показать, когда лучше выбрать один, а не другой.
Сталь
Усовершенствованная в начале 20-го века сталь быстро стала самым полезным и разнообразным металлом на Земле. Он создается путем обогащения элементарного железа углеродом, что увеличивает его твердость, прочность и сопротивление. Во многих так называемых легированных сталях также используются такие элементы, как цинк, хром, марганец, молибден, кремний и даже титан, для повышения их устойчивости к коррозии, деформации, высоким температурам и многому другому. Например, сталь с высоким содержанием хрома относится к нержавеющим сталям или тем, которые менее подвержены коррозии, чем другие сплавы. Поскольку существует много видов стали, трудно обобщить ее конкретные свойства, но наша статья о типах стали дает хорошее представление о различных классах.
Вообще говоря, сталь — это плотный, твердый, но пригодный для обработки металл. Он реагирует на процесс упрочнения термической обработкой, который позволяет даже самым простым сталям иметь переменные свойства в зависимости от того, как они были нагреты/охлаждены. Он магнитен и может легко проводить как тепло, так и электричество. Большинство сталей подвержены коррозии из-за своего состава железа, хотя нержавеющие стали в некоторой степени успешно устраняют эту слабость. Сталь имеет высокий уровень прочности, но эта прочность обратно пропорциональна ее ударной вязкости, или мере устойчивости к деформации без разрушения. Несмотря на то, что доступны стали для механической обработки, есть и другие стали, которые трудно, если вообще возможно, обрабатывать из-за их рабочих свойств.
Должно быть ясно, что сталь может выполнять множество различных задач: она может быть твердой, жесткой, прочной, термостойкой или коррозионностойкой; беда в том, что это не может быть все это сразу, без жертвы одним свойством над другим. Однако это не является большой проблемой, так как большинство марок стали недороги и позволяют разработчикам комбинировать различные стали в своих проектах, чтобы получить преимущества смешивания. В результате сталь находит применение практически во всех отраслях промышленности: в автомобильной, аэрокосмической, конструкционной, архитектурной, производственной, электронной, инфраструктурной и десятках других применений.
Титан
Титан был впервые очищен до металлической формы в начале 1900-х годов и не так редок, как думает большинство людей. На самом деле это четвертый по распространенности металл на Земле, но его трудно найти в высоких концентрациях или в элементарной форме. Его также трудно очистить, что делает его более дорогим в производстве, чем в источнике.
Элементарный титан представляет собой серебристо-серый немагнитный металл с плотностью 4,51 г/см 3 , что делает его почти вдвое менее плотным, чем сталь, и относит его к категории «легкий металл». Современный титан выпускается либо в виде элементарного титана, либо в виде различных титановых сплавов, и все они сделаны для повышения как прочности, так и коррозионной стойкости базового титана. Эти сплавы обладают необходимой прочностью для использования в качестве аэрокосмических, конструкционных, биомедицинских и высокотемпературных материалов, в то время как элементарный титан обычно используется в качестве легирующего агента для других металлов.
Титан трудно сваривать, обрабатывать или формовать, но его можно подвергнуть термической обработке для повышения прочности. Его уникальное преимущество заключается в том, что он биосовместим, то есть титан внутри тела остается инертным, что делает его незаменимым для технологии медицинских имплантатов. Он имеет отличное соотношение прочности к весу, обеспечивая такую же прочность, как сталь при 40% его веса, и устойчив к коррозии благодаря тонкому оксидному слою, образующемуся на его поверхности в присутствии воздуха или воды. Он также устойчив к кавитации и эрозии, что предрасполагает его к применению в условиях высоких нагрузок, таких как авиация и военные технологии. Титан жизненно важен для проектов, где вес минимален, а прочность максимальна, а его отличная коррозионная стойкость и биосовместимость позволяют использовать его в некоторых уникальных отраслях, не охватываемых более традиционными металлами.
Сравнение стали и титана
Выбор одного из этих металлов над другим зависит от конкретного применения. В этом разделе сравниваются некоторые механические свойства, общие для стали и титана, чтобы показать, где следует указать каждый металл (представлены в таблице 1 ниже). Обратите внимание, что значения как для стали, так и для титана в таблице 1 взяты из обобщенных таблиц, поскольку каждый металл сильно различается по характеристикам в зависимости от типа сплава, процесса термообработки и состава.
Таблица 1: Сравнение свойств материалов стали и титана
Свойства материалов | Сталь | Титан | |||
шт. | Метрическая система | Английский | Метрическая система | Английский | |
Плотность | 7,8–8 г/см 3 | 0,282–0,289 фунт/дюйм 3 | 4,51 г/см 3 | 0,163 фунта/дюйм 3 | |
Модуль упругости | 200 ГПа | 29000 тысяч фунтов на квадратный дюйм | 116 ГПа | 16800 тысяч фунтов на квадратный дюйм | |
Предел текучести при растяжении | 350 МПа* | 50800 фунтов на кв. | 140 МПа* | 20300 фунтов на кв. дюйм* | |
Удлинение при разрыве | 15%* | 54% | |||
Твердость (по Бринеллю) | 121* | 70 |
Первое бросающееся в глаза различие между титаном и сталью заключается в их плотности; как обсуждалось ранее, плотность титана примерно вдвое меньше плотности стали, что делает его значительно легче. Это подходит для применения титана в приложениях, где требуется прочность стали в более легком корпусе, и позволяет использовать титан в деталях самолетов и других приложениях, зависящих от веса. Плотность стали может быть преимуществом в определенных приложениях, например, в шасси автомобиля, но в большинстве случаев снижение веса часто вызывает беспокойство.
Модуль упругости, иногда называемый модулем Юнга, является мерой гибкости материала. Он описывает, насколько легко согнуть или деформировать материал без пластической деформации, и часто является хорошей мерой общей упругой реакции материала. Модуль упругости титана довольно низкий, что говорит о том, что он легко изгибается и деформируется. Отчасти поэтому титан трудно поддается механической обработке, так как он склеивает фрезы и предпочитает возвращаться к своей первоначальной форме. С другой стороны, сталь имеет гораздо более высокий модуль упругости, что позволяет легко обрабатывать ее и использовать в таких приложениях, как лезвия ножей, поскольку она ломается и не изгибается под нагрузкой.
При сравнении пределов текучести при растяжении титана и стали обнаруживается интересный факт; сталь в целом прочнее титана. Это противоречит распространенному заблуждению о том, что титан прочнее большинства других металлов, и показывает преимущество стали перед титаном. В то время как титан только на одном уровне со сталью с точки зрения прочности, он весит вдвое меньше, что делает его одним из самых прочных металлов на единицу массы. Тем не менее, сталь является предпочтительным материалом, когда речь идет об общей прочности, поскольку некоторые из ее сплавов превосходят все другие металлы с точки зрения пределов текучести. Конструкторы, стремящиеся исключительно к прочности, должны выбирать сталь, а дизайнеры, заинтересованные в прочности на единицу массы, должны выбирать титан.
Удлинение при разрыве — это мера начальной длины образца для испытаний, деленная на его длину непосредственно перед разрушением при испытании на растяжение, умноженная на 100 для получения процента. Большое удлинение при разрыве говорит о том, что материал больше «растягивается»; другими словами, он более склонен к повышенной пластичности перед разрушением. Титан — это такой материал, что он растягивается почти на половину своей длины, прежде чем сломаться. Это еще одна причина, по которой титан так трудно обрабатывать, поскольку он растягивается и деформируется, а не откалывается. Сталь бывает разных видов, но, как правило, имеет низкое удлинение при разрыве, что делает ее более твердой и более склонной к хрупкому разрушению при растяжении.
Твердость — это сравнительная величина, которая описывает реакцию материала на царапание, травление, вдавливание или деформацию его поверхности. Он измеряется с помощью инденторных машин, которые бывают разных видов в зависимости от материала. Для высокопрочных металлов часто указывается критерий твердости по Бринеллю, который приведен в таблице 1. Несмотря на то, что твердость стали по Бринеллю сильно различается в зависимости от термической обработки и состава сплава, в большинстве случаев она всегда тверже титана. Это не означает, что титан легко деформируется при царапинах или вмятинах; напротив, слой диоксида титана, образующийся на поверхности, исключительно твердый и противостоит большинству проникающих сил. Они оба являются стойкими материалами, которые отлично работают в суровых условиях, исключая любые дополнительные химические воздействия.
Резюме
В этой статье представлено краткое сравнение свойств, прочности и областей применения стали и титана. Для получения информации о других продуктах обратитесь к нашим дополнительным руководствам или посетите платформу поиска поставщиков Thomas, чтобы найти потенциальные источники поставок или просмотреть подробную информацию о конкретных продуктах.
Источники:
- https://books.google.com/books?hl=en&lr=&id=68mQLz7yJ8UC&oi=fnd&pg=PR5&dq=introduction+to+titanium+alloys&ots=lhsHnla-iW&sig=iwc5SZXiHIpScg7X5sjjHGOFi5E#v=onepage&q=introduction0%ti%20tiumto2tanium 20 сплавов&f=ложь
- https://crosstraxx.com/pages/a-look-at-the-differences-between-titanium-and-stainless-steel
- http://www.matweb.com/search/datasheet.aspx?bassnum=MS0001&ckck=1
- http://www.matweb.com/search/DataSheet.
aspx?MatGUID=66a15d609a3f4c829cb6ad08f0dafc01
- http://web.mit.edu/ruddman/www/iap/materialsselection.pdf
Прочие стальные изделия
- Типы профилей из конструкционной стали
- Ведущие производители и поставщики арматуры
- Типы арматуры
- Типы стали
- Типы нержавеющей стали
- Ведущие сталелитейные компании США и производители стали в мире
- Все о стали 5160 (свойства, прочность, применение)
- Все о стали 440 (свойства, прочность, применение)
- Все о стали 430 (свойства, прочность, применение)
- Все о стали 304 (свойства, прочность, применение)
- Все о 52100 Сталь
- Свойства, составы и применение стандартных сталей
- Поверхностная закалка стали (цементация)
- Все о стали 9260 (свойства, прочность, применение)
- Все о стали 4130 (свойства, прочность, применение)
Больше из Металлы и изделия из металла
Титан — Прочность — Твердость — Эластичность
О Титане
Титан — блестящий переходный металл серебристого цвета, низкой плотности и высокой прочности. Титан устойчив к коррозии в морской воде, царской водке и хлоре. Титан можно использовать в поверхностных конденсаторах. В этих конденсаторах используются трубки, которые обычно изготавливаются из нержавеющей стали, медных сплавов или титана в зависимости от нескольких критериев выбора (таких как теплопроводность или коррозионная стойкость). Титановые трубки конденсатора обычно являются лучшим техническим выбором, однако титан является очень дорогим материалом, и использование титановых трубок конденсатора связано с очень высокими первоначальными затратами.
Прочность титана
В механике материалов прочность материала — это его способность выдерживать приложенную нагрузку без разрушения или пластической деформации. Прочность материалов в основном рассматривает взаимосвязь между внешними нагрузками , приложенными к материалу, и результирующей деформацией или изменением размеров материала. При проектировании конструкций и машин важно учитывать эти факторы, чтобы выбранный материал имел достаточную прочность, чтобы противостоять приложенным нагрузкам или силам и сохранять свою первоначальную форму. Прочность материала — это его способность выдерживать приложенную нагрузку без разрушения или пластической деформации.
При растяжении способность материала или конструкции выдерживать нагрузки, имеющие тенденцию к удлинению, известна как предел прочности при растяжении (UTS). Предел текучести или предел текучести — это свойство материала, определяемое как напряжение, при котором материал начинает пластически деформироваться, тогда как предел текучести — это точка, в которой начинается нелинейная (упругая + пластическая) деформация.
Предел прочности при растяжении титана
Предел прочности при растяжении титана составляет 434 МПа, 293 МПа (чистый).
Предел текучести титана
Предел текучести титана составляет 380 МПа.
Модуль упругости титана
Модуль упругости Юнга титана 380 МПа.
Модуль упругости при сдвиге титана 44 ГПа.
Объемный модуль упругости титана составляет 110 ГПа.
Твердость титана
В материаловедении твердость – это способность выдерживать вдавливание поверхности ( локализованная пластическая деформация ) и царапание . Испытание на твердость по Бринеллю В испытаниях по Бринеллю твердый сферический индентор вдавливается под определенной нагрузкой в поверхность испытуемого металла.
Твердость титана по Бринеллю составляет приблизительно 700 – 2700 МПа.
Метод измерения твердости по Виккерсу был разработан Робертом Л. Смитом и Джорджем Э. Сандландом из Vickers Ltd в качестве альтернативы методу Бринелля для измерения твердости материалов. Метод определения твердости по Виккерсу можно также использовать в качестве метода определения микротвердости , который в основном используется для небольших деталей, тонких срезов или обработки глубины корпуса.
Твердость титана по Виккерсу составляет приблизительно 800 – 3400 МПа.
Твердость к царапанью является мерой устойчивости образца к остаточной пластической деформации из-за трения об острый предмет. Наиболее распространенная шкала для этого качественного теста — 9.Шкала Мооса 0580 , которая используется в минералогии. Шкала твердости минералов Мооса основана на способности одного природного образца минерала заметно царапать другой минерал.
Титан имеет твердость приблизительно 6.
Титан – кристаллическая структура
Возможная кристаллическая структура титана представляет собой гексагональную плотноупакованную структуру .
В металлах и во многих других твердых телах атомы расположены в виде правильных рядов, называемых кристаллами. Кристаллическая решетка — это повторяющийся узор из математических точек, простирающийся по всему пространству. Силы химической связи вызывают это повторение. Именно этот повторяющийся узор определяет такие свойства, как прочность, пластичность, плотность, проводимость (свойство проводить или передавать тепло, электричество и т. д.) и форму. Существует 14 основных типов таких паттернов, известных как решетки Браве.
Кристаллическая структура титана
Прочность элементов
Эластичность элементов
Т. способность выдерживать приложенную нагрузку без разрушения или пластической деформации.
Сопротивление материалов в основном учитывает взаимосвязь между внешними нагрузками применяется к материалу и в результате деформация или изменение размеров материала. При проектировании конструкций и машин важно учитывать эти факторы, чтобы выбранный материал имел достаточную прочность, чтобы противостоять приложенным нагрузкам или силам и сохранять свою первоначальную форму. Прочность материала – это его способность выдерживать приложенную нагрузку без разрушения или пластической деформации. Схематическая диаграмма кривой напряжения-деформации из низкоуглеродистой стали при комнатной температуре показан на рисунке. Есть несколько стадий, демонстрирующих различное поведение, что предполагает разные механические свойства. Чтобы уточнить, материалы могут пропускать одну или несколько стадий, показанных на рисунке, или иметь совершенно разные стадии. В этом случае приходится различать напряженно-деформированные характеристики пластичных и хрупких материалов. Следующие пункты описывают различные области кривой напряжения-деформации и важность нескольких конкретных мест.
- Предел пропорциональности . Пропорциональный предел соответствует расположению напряжения в конце линейной области , поэтому график напряжения-деформации представляет собой прямую линию, а градиент будет равен модулю упругости материала. Для напряжения растяжения и сжатия наклон участка кривой, на котором напряжение пропорционально деформации, называется модулем Юнга , а применяется закон Гука . Между пределом пропорциональности и пределом текучести закон Гука становится сомнительным, и деформация возрастает быстрее.
- Предел текучести . Предел текучести — это точка на кривой напряжения-деформации, которая указывает предел упругого поведения и начало пластического поведения. Предел текучести или предел текучести — это свойство материала, определяемое как напряжение, при котором материал начинает пластически деформироваться, тогда как предел текучести — это точка, в которой начинается нелинейная (упругая + пластическая) деформация. До предела текучести материал будет упруго деформироваться и вернется к своей первоначальной форме, когда приложенное напряжение будет снято. Как только предел текучести пройден, некоторая часть деформации будет постоянной и необратимой. Некоторые стали и другие материалы демонстрируют явление, называемое явлением предела текучести. Пределы текучести варьируются от 35 МПа для низкопрочного алюминия до более 1400 МПа для очень высокопрочных сталей.
- Предел прочности при растяжении . Предел прочности при растяжении является максимальным на инженерной кривой напряжения-деформации.
Это соответствует максимальному напряжению , которое может выдержать конструкция при растяжении. Предельная прочность на растяжение часто сокращается до «предельной прочности» или даже до «предельной». Если это напряжение применяется и поддерживается, произойдет разрушение. Часто это значение значительно превышает предел текучести (на 50–60 % превышает предел текучести для некоторых типов металлов). Когда пластичный материал достигает предела прочности, он испытывает сужение, когда площадь поперечного сечения локально уменьшается. Кривая напряжение-деформация не содержит более высокого напряжения, чем предел прочности. Несмотря на то, что деформации могут продолжать увеличиваться, напряжение обычно уменьшается после достижения предела прочности. Это интенсивное свойство; поэтому его значение не зависит от размера испытуемого образца. Однако это зависит от других факторов, таких как подготовка образца, наличие или отсутствие поверхностных дефектов, температура тестовой среды и материала.
Предел прочности при растяжении варьируется от 50 МПа для алюминия до 3000 МПа для очень высокопрочных сталей.
- Точка разрушения : Точка разрушения — это точка деформации, в которой материал физически разделяется. В этот момент деформация достигает своего максимального значения, и материал фактически разрушается, хотя соответствующее напряжение может быть меньше предела прочности в этот момент. Пластичные материалы имеют предел прочности при разрушении ниже, чем предел прочности при растяжении (UTS), тогда как в хрупких материалах предел прочности эквивалентен пределу прочности при растяжении (UTS). Если пластичный материал достигает своего предела прочности при растяжении в ситуации с регулируемой нагрузкой, он будет продолжать деформироваться без приложения дополнительной нагрузки, пока не разорвется. Однако, если нагрузка контролируется по смещению, деформация материала может уменьшить нагрузку, предотвращая разрыв.
О модуле упругости
При растяжении однородного стержня (кривая напряжения-деформации) Закон Гука описывает поведение стержня в упругой области. В этой области удлинение стержня прямо пропорционально силе растяжения и длине стержня и обратно пропорционально площади поперечного сечения и модулю упругости . Вплоть до предельного напряжения тело сможет восстановить свои размеры при снятии нагрузки. Приложенные напряжения заставляют атомы в кристалле перемещаться из своего положения равновесия. Все атомы смещены на одинаковую величину и сохраняют свою относительную геометрию. Когда напряжения снимаются, все атомы возвращаются в исходное положение, и остаточная деформация не возникает. Согласно Закон Гука, напряжение пропорционально деформации (в области упругости), а наклон равен модулю Юнга .
Мы можем расширить ту же идею связи напряжения с деформацией с приложениями сдвига в линейной области, связав напряжение сдвига с деформацией сдвига, чтобы создать Закон Гука для напряжения сдвига :
Для изотропных материалов в области упругости вы можно связать коэффициент Пуассона (ν), модуль упругости Юнга (E) и модуль упругости сдвига (G):
Модули упругости, относящиеся к поликристаллическим материалам:
- Модуль упругости Юнга.
Модуль упругости Юнга представляет собой модуль упругости при растяжении и сжатии в режиме линейной упругости при одноосной деформации и обычно оценивается испытаниями на растяжение.
- Модуль упругости при сдвиге. Модуль сдвига или модуль жесткости получают при кручении цилиндрического образца. Он описывает реакцию материала на напряжение сдвига. Его символ — G. Модуль сдвига — одна из нескольких величин для измерения жесткости материалов, возникающая в обобщенном законе Гука.
- Объемный модуль упругости. Объемный модуль упругости описывает объемную упругость или тенденцию объекта деформироваться во всех направлениях при равномерной нагрузке во всех направлениях. Например, он описывает упругую реакцию на гидростатическое давление и равностороннее растяжение (как давление на дне океана или в глубоком бассейне). Это также свойство материала, определяющее упругую реакцию на приложение напряжения. Для жидкости имеет значение только объемный модуль.
О твердости
В материаловедении твердость — это способность выдерживать вдавливание поверхности ( локализованная пластическая деформация ) и царапание . Твердость , вероятно, является наиболее плохо определенным свойством материала, поскольку она может указывать на стойкость к царапанию, стойкость к истиранию, стойкость к вдавливанию или даже стойкость к формованию или локализованной пластической деформации. Твердость важна с инженерной точки зрения, потому что сопротивление износу при трении или эрозии паром, маслом и водой обычно увеличивается с увеличением твердости.
Существует три основных типа измерений твердости :
- Твердость при царапании . Твердость к царапанию — это мера устойчивости образца к остаточной пластической деформации из-за трения об острый предмет. Наиболее распространенной шкалой для этого качественного теста является шкала Мооса , которая используется в минералогии.
Шкала твердости минералов Мооса основана на способности одного природного образца минерала заметно царапать другой минерал. Твердость материала измеряется по шкале путем нахождения самого твердого материала, который данный материал может поцарапать, или самого мягкого материала, который может поцарапать данный материал. Например, если какой-то материал царапается топазом, а не кварцем, его твердость по шкале Мооса будет находиться между 7 и 8.
- Твердость при вдавливании . Твердость при вдавливании измеряет способность выдерживать поверхностное вдавливание (локальная пластическая деформация) и сопротивление образца деформации материала из-за постоянной сжимающей нагрузки от острого предмета. Испытания на твердость при вдавливании в основном используются в машиностроении и металлургии. Традиционные методы основаны на четко определенных испытаниях на физическую твердость при вдавливании. Очень твердые инденторы определенной геометрии и размеров непрерывно вдавливаются в материал с определенной силой.
Параметры деформации, такие как глубина вдавливания по методу Роквелла, записываются для измерения твердости. Общая шкала твердости при вдавливании равна 9.0580 Бринелль , Роквелл и Виккерс .
- Твердость по отскоку . Твердость отскока, также известная как динамическая твердость, измеряет высоту «отскока» молотка с алмазным наконечником, падающего с фиксированной высоты на материал. Одно из устройств, используемых для этого измерения, известно как склероскоп . Он состоит из стального шара, сброшенного с фиксированной высоты. Этот тип твердости связан с эластичностью.
О кристаллической структуре
Три наиболее распространенных основных кристаллических узора:
- bcc. В ОЦК (ОЦК) расположении атомов элементарная ячейка состоит из восьми атомов в углах куба и одного атома в центре тела куба. В ОЦК элементарная ячейка содержит (8 угловых атомов × ⅛) + (1 центральный атом × 1) = 2 атома.
Упаковка более эффективна (68%), чем простая кубическая, а структура обычная для щелочных металлов и ранних переходных металлов. Металлы, содержащие структуры ОЦК, включают феррит, хром, ванадий, молибден и вольфрам. Эти металлы обладают высокой прочностью и низкой пластичностью.
- ФЦК. В ГЦК (ГЦК) расположении атомов элементарная ячейка состоит из восьми атомов в углах куба и одного атома в центре каждой из граней куба. В ГЦК-системе элементарная ячейка содержит (8 угловых атомов × ⅛) + (6 атомов на гранях × ½) = 4 атома. Эта структура, наряду со своим гексагональным родственником (ГПУ), имеет наиболее эффективную упаковку (74%). Металлы, содержащие структуры FCC, включают аустенит, алюминий, медь, свинец, серебро, золото, никель, платину и торий. Эти металлы обладают низкой прочностью и высокой пластичностью.
- л.с. В ГПУ (ГПУ) расположении атомов элементарная ячейка состоит из трех слоев атомов. Верхний и нижний слои содержат по шесть атомов в углах шестиугольника и по одному атому в центре каждого шестиугольника.
Средний слой содержит три атома, расположенные между атомами верхнего и нижнего слоев, отсюда и название плотная упаковка. Гексагональная плотная упаковка (ГПУ) — это один из двух простых типов атомной упаковки с самой высокой плотностью, второй — гранецентрированная кубическая (ГЦК). Однако, в отличие от ГЦК, это не решетка Браве, поскольку есть два неэквивалентных набора точек решетки. Металлы, содержащие структуры ГПУ, включают бериллий, магний, цинк, кадмий, кобальт, таллий и цирконий. Металлы HCP не такие пластичные, как металлы FCC.
Сводка
Элемент | Титан |
Предел прочности при растяжении | 434 МПа, 293 МПа (чистый) |
Предел текучести | 380 МПа |
Модуль упругости Юнга | 116 ГПа |
Модуль упругости при сдвиге | 44 ГПа |
Объемный модуль упругости | 110 ГПа |
Шкала Мооса | 6 |
Твердость по Бринеллю | 700 – 2700 МПа |
Твердость по Виккерсу | 800 – 3400 МПа |
Источник: www. luciteria.com
Свойства других элементов
Другие свойства титана
Свойства титана класса 5 (Ti6Al4V или Ti 6-4)
от Alex Sparr | 11 декабря 2019 г. | Блог | 0 комментариев
Титан класса 5 является одним из самых популярных сплавов в титановой промышленности и составляет почти половину титана, используемого в мире. Обычно обозначаемый как Ti-6AL-4V (или Ti 6-4), это обозначение относится к его химическому составу, состоящему почти из 90% титана, 6% алюминия, 4% ванадия, 0,25% (макс.) железа и 0,2% (макс.) кислород. Обладает отличной прочностью, низким модулем упругости, высокой коррозионной стойкостью, хорошей свариваемостью и поддается термообработке. Добавление алюминия и ванадия повышает твердость материала в матрице сплава, улучшая его физико-механические свойства.
- Высокая прочность на растяжение — прочность Ti 6Al-4V приближается к
прочности нержавеющей стали, что требует высокого усилия резания
. - Низкая теплопроводность — тепло
не передается легко в стружку, а скорее поступает в режущий инструмент
, что делает режущую
кромку очень горячей во время процесса обработки.
- Высокий модуль упругости — титан очень
«пружинист». При заданной силе он отклонится на
больше, чем сталь, что приводит к более высокой вероятности
вибрация, стук и плохое стружкообразование. - Срезной механизм — для титана требуется острая режущая кромка
, чтобы резать материал и избегать разрывов
и размазывания, что быстро приведет к выходу из строя инструмента
Механические свойства | Метрическая система | Английский |
Твердость по Бринеллю | 379 | 379 |
Твердость по Кнупу | 414 | 414 |
Твердость по Роквеллу C | 41 | 41 |
Твердость по Виккерсу | 396 | 396 |
Прочность на растяжение, максимальная | 1170 МПа | 170000 фунтов на квадратный дюйм |
Прочность на растяжение, предел текучести | 1100 МПа | 160000 фунтов на квадратный дюйм |
Удлинение при разрыве | 10 % | 10 % |
Модуль упругости | 114 ГПа | 16500 тыс.![]() |
Предел текучести при сжатии | 1070 МПа | 155000 фунтов на квадратный дюйм |
Прочность на растяжение с надрезом | 1550 МПа | 225000 фунтов на квадратный дюйм |
Предельная несущая способность | 2140 МПа | 310000 фунтов на квадратный дюйм |
Предел текучести подшипника | 1790 МПа | 260000 фунтов на квадратный дюйм |
Коэффициент Пуассона | 0,33 | 0,33 |
Удар по Шарпи | 23 Дж | 17 фут-фунт |
Усталостная прочность мин | 160 МПа | 23200 фунтов на квадратный дюйм |
Усталостная прочность макс.![]() | 700 МПа | 102000 psi |
Прочность на излом | 43 МПа-м½ | 39,1 тыс.фунтов на кв. дюйм½ |
Модуль сдвига | 44 ГПа | 6380 тысяч фунтов на квадратный дюйм |
Прочность на сдвиг | 760 МПа | 110000 фунтов на квадратный дюйм |
Электрические свойства | Метрическая система | Английский |
Удельное электрическое сопротивление | 0,000178 Ом-см | 0,000178 Ом-см |
Магнитная проницаемость | 1.![]() | 1.00005 |
Магнитная восприимчивость | 3.3e-006 | 3.3e-006 |
Тепловые свойства | Метрическая система | Английский |
КТР, линейный, 20°C | 8,6 мкм/м-°C | 4,78 мкдюйм/дюйм-°F |
КТР, линейный, 250°C | 9,2 мкм/м-°C | 5,11 мкдюйм/дюйм-°F |
КТР, линейный, 500°C | 90,7 мкм/м-°C | 5,39 мкдюйм/дюйм-°F |
Удельная теплоемкость | 0,5263 Дж/г-°C | 0,126 БТЕ/фунт-°F |
Теплопроводность | 6,7 Вт/м-К | 46,5 БТЕ-дюйм/ч-фут²-°F |
Точка плавления | 1604 – 1660 °С | 2920 – 3020 °F |
Солидус | 1604 °С | 2920 °F |
Ликвидус | 1660 °С | 3020 °F |
Бета Трансус | 980 °С | 1800 °F |
Титан или сталь: что лучше выбрать для вашего проекта
Подумайте о самых прочных и универсальных металлах, используемых сегодня в промышленности. Конечно, ваш выбор включает титан и сталь. Оба эти металла являются отличным выбором для различных применений из-за их превосходных химических и физических свойств.
Титан против стали, безусловно, важная дискуссия. Хотя оба металла предлагают широкий спектр сплавов и областей применения, они различаются многими ключевыми характеристиками, а также ценой, ударной вязкостью и прочностью.
Иногда даже самые опытные профессионалы не могут сделать правильный выбор. Для достижения наилучших результатов важно понимать основные различия между двумя металлами.
Титан и сталь: обзор
И титан, и сталь обладают различными преимуществами. Прежде чем углубляться в технические детали, давайте взглянем на краткий обзор обоих металлов, обсудив их основные свойства, доступность, цены и общие области применения.
Титан
Титан — это элемент земли. В основном вы найдете его в высокопроизводительных отраслях из-за его высокой стоимости. Из-за ценника многие люди считают титан редким металлом. На самом деле, его высокая цена на самом деле связана со сложными требованиями к обработке.
Естественно, титан имеет чрезвычайно высокую температуру плавления. Это делает его очень трудным для механической обработки или обработки титана по сравнению со сталью. Этот металл имеет несколько сплавов с железом, алюминием и другими металлами.
Сегодня титан является важным выбором для ряда высокопроизводительных приложений, таких как аэрокосмическая промышленность, автомобильные двигатели, морское оборудование премиум-класса и промышленные машины. Кроме того, вы даже найдете титан в некоторых потребительских товарах. Однако такое использование встречается довольно редко и предназначено только для продуктов премиум-класса.
Превосходная коррозионная стойкость титана, способность поглощать удары, отношение прочности к весу и многие другие свойства делают его лучшим выбором, обеспечивающим превосходные характеристики практически в любых условиях.
Сталь
В отличие от титана, сталь не встречается в природе и требует определенных процессов, прежде чем она будет готова. Сталь – это прежде всего сплав железа и углерода. Он доступен в различных комбинациях с различными количествами других металлов, таких как титан, хром, цинк или другие металлы, для улучшения какого-либо конкретного свойства.
Как правило, сталь известна своей прочностью, термостойкостью, пределом прочности при растяжении, высокой обрабатываемостью и другими превосходными физическими свойствами. Более низкая стоимость и рабочие характеристики делают сталь популярным выбором во многих отраслях промышленности, включая строительство, автомобилестроение, инфраструктуру, промышленное оборудование и многое другое.
Сталь против титана: 8 основных различий между двумя популярными металлами
И сталь, и титан являются прочными материалами, широко используемыми в различных областях. Вопрос в том, что в матче между сталью и титаном что окажется лучше, сталь или титан?
Правильный ответ зависит от области применения и ограничений вашего проекта. Иногда сталь была бы лучшим выбором из-за функциональных требований или доступного бюджета. Тем не менее, превосходные физические свойства титана также могут быть тем, что вам нужно в различных приложениях.
Вот 8 наиболее важных различий, которые вы можете учитывать при сравнении титана и стали для вашего применения.
1 – Элементный состав
Элементный состав является первым важным отличием в сопоставлении титана со сталью. Как указывалось ранее, титан является природным элементом и доступен как в чистом виде, так и в виде сплава. В большинстве случаев Ti 6-4 — сплав, содержащий алюминий и ванадий — является наиболее распространенным титановым сплавом, который вы найдете.
Сталь, напротив, не встречается в природе. В первую очередь это комбинация железа и углерода с различным количеством других элементов, добавленных для настройки свойств в зависимости от применения. Вот почему вы нигде не найдете технических свойств стали. Для получения подробной информации вам нужно будет указать сплав, например нержавеющую сталь (даже у которой есть много типов), высокоуглеродистую сталь или определенные сплавы, такие как 4130, 4140 или A36.
2 – Вес
Определяющими характеристиками титана являются его низкая плотность и высокое отношение прочности к весу. Вот почему этот металл является предпочтительным материалом для станков с ЧПУ в аэрокосмической промышленности и других подобных областях, где вам необходимо уменьшить вес без ущерба для прочности.
Напротив, стальные сплавы, как правило, долговечны и обладают большой прочностью, но проигрывают в весе. Они являются идеальным выбором для приложений, где вес не является одним из основных конструктивных ограничений.
3 – Твердость
Твердость является одной из областей, в которых сталь превосходит титан. Низкое число Бринелля — одна из причин, почему титан так трудно поддается механической обработке. Титановые сплавы часто используются в промышленности, поскольку следовые количества других металлов компенсируют низкую твердость титана.
4 – Эластичность
Это еще одна область, в которой сталь превосходит титан, поскольку большинство его сплавов более эластичны. Опять же, большая эластичность облегчает обработку стали и создание нестандартных деталей, что является чрезвычайно важной характеристикой, поскольку напрямую влияет на стоимость обработки.
Споры о стали и титане никогда не дадут однозначного ответа. Во всех случаях ваш проект, условия и доступный бюджет определят, какой из них является лучшим выбором.
5 – Долговечность
Долговечность – это многогранный параметр с несколькими аспектами, зависящими от области применения. С точки зрения прочности и долговечности многие стальные сплавы имеют такие же (иногда даже лучшие) характеристики, как и титан. Однако титан выделяется своей предельной коррозионной стойкостью и способностью выдерживать экстремальные температуры.
В то время как стальные сплавы, как правило, работают достаточно хорошо во многих условиях, присутствие железа означает, что они со временем подвергаются коррозии. Титан, с другой стороны, работает значительно лучше и, следовательно, используется во многих суровых условиях, где ожидается постоянное воздействие влаги, химикатов и других элементов.
6 – Предел текучести при растяжении
При любом сравнении титана со сталью вы увидите, что титан обладает большей прочностью на единицу массы. Тем не менее, сталь по-прежнему является лучшим выбором, когда речь идет об общей прочности, и этот факт становится очевидным, когда вы сравниваете их предел текучести при растяжении.
Если прочность выбранного вами металла является единственной задачей, тогда сталь является естественным выбором. Титан идеально подходит для ситуаций, когда вас беспокоит прочность наряду с весом. Вот почему строительство и промышленность полагаются на сталь, а в автомобильной и аэрокосмической промышленности — на титан.
7 – Общие области применения
Титан обычно используется для высокопроизводительных применений, где требуются отличные тепловые свойства, коррозионная стойкость и высокое отношение прочности к весу. Некоторые из наиболее распространенных применений титана:
- Хирургические инструменты и приложения
- Протезы
- Аэрокосмическая промышленность
- Теннисные ракетки
- Автоспорт .
От производства металлических деталей до простого строительства и разработки машин. Вы найдете его повсюду. Вот некоторые из его наиболее распространенных применений:
- Строительство
- Электроприборы
- Производство труб
- Поезда и автомобили
- Различные типы обычных инструментов
отделение. Как указывалось ранее, титан довольно распространен, но его высокая температура плавления и требования к обработке делают его очистку и обработку значительно дороже. Во многих случаях использование чего-то столь дорогого, как титан, просто не имеет смысла для бизнеса.
В отличие от титана, сталь является чрезвычайно экономичным вариантом. Его легче производить, так как в мире нет недостатка в железе и углероде. Кроме того, сталь не имеет каких-либо сложных требований к обработке. Однако цены на сталь сильно различаются из-за огромного количества ее вариантов. Сплав, содержащий только углерод и железо, будет самым дешевым, в то время как сплав, обогащенный хромом, цинком или даже титаном, потребует больше капитала.
Теперь вы можете лучше понять разницу между титаном и сталью, чтобы знать, как выбрать лучший материал для вашего проекта. Если вы проектируете металлическую деталь и ищете услуги по быстрому прототипированию, RapidDirect — ваш выбор. RapidDirect славится производством деталей и прототипов по конкурентоспособным ценам и в кратчайшие сроки. Начать сейчас!
Хотите получить быстрый ответ? Вот краткая таблица, чтобы дать вам краткий обзор сравнения стали и титана.Characteristic Titanium Steel Elemental composition It’s a naturally occurring element that you can find in its pure form and as an alloy as well. Сталь в основном представляет собой сплав железа и углерода и должна подвергаться многочисленным процессам. Его свойства можно настроить с помощью других элементов, в зависимости от ваших требований. Вес Титан намного легче по сравнению с некоторыми его альтернативами и предлагает лучшее соотношение веса и прочности. Это потери в отделе веса. Сталь идеально подходит для приложений, где вес не имеет значения. Твердость Титан плохо поддается механической обработке, так как имеет низкую твердость Сталь намного лучше титана в этом отношении и обычно имеет высокое число Бринелля. Эластичность Эластичность титана низкая, что затрудняет его обработку, так как он легко деформируется. Имея гораздо более высокую эластичность, сталь легче поддается обработке. Долговечность Как правило, титан обладает лучшей устойчивостью к коррозии и температуре. Сталь в идеальных условиях может работать лучше, чем титан, но она подвержена коррозии. Предел текучести при растяжении Несмотря на большую прочность на единицу, титан имеет более низкий предел текучести при растяжении по сравнению со сталью. Сталь обладает высоким пределом текучести, что делает ее предпочтительным выбором для конструкторов, которые уделяют основное внимание только прочности. Применение Высокопроизводительные изделия, такие как аэрокосмическая промышленность, автоспорт, судовые двигатели и т. д. Цена Как правило, дороже из-за высоких требований к извлечению и обработке. Более экономичный выбор из-за простых требований к производству и обработке. Титан по сравнению со сталью – плюсы и минусы каждого металла
Оба эти материала обладают уникальным набором свойств, которые делают тот или иной материал более подходящим для ваших конкретных требований. Итак, титан для вас лучше нержавеющей стали? Следующий углубленный анализ их преимуществ и недостатков может помочь прояснить часть этой путаницы.
Преимущества титана
Коррозионная стойкостьСамое лучшее в использовании титана — его невероятная коррозионная стойкость.
Необычно высокая температура плавленияТитан образует тонкий непроницаемый слой оксида на своей поверхности при контакте с воздухом. Кроме того, оксидный слой обладает естественной прочностью и устойчив почти ко всем распространенным источникам коррозии, что делает титан идеальным выбором для любого наружного применения.
Титан также демонстрирует высокую температуру плавления. Благодаря температуре плавления около 1668 °C титан идеально подходит для высокотемпературных применений, таких как газотурбинные реактивные двигатели и т. д.
Нетоксичный элементВ отличие от большинства материалов титан не токсичен для людей и животных. Вот почему вы увидите широкое использование титана в медицинской промышленности. От укрепления костей до зубных брекетов титан является основным выбором для медицинских работников.
Способность выдерживать экстремальные температурыМногие свойства титана позволяют ему демонстрировать высокую устойчивость к экстремальным температурам.
Высокая прочностьТитан не сжимается и не расширяется, что делает его важным компонентом для поддержания структурной целостности.
Наконец, титан — один из самых прочных материалов, которые только можно найти. Несмотря на легкий вес, титан предлагает отличное соотношение прочности и веса.
Преимущества стали
Низкая стоимостьСталь является одним из наиболее часто используемых и широко доступных материалов в мире. Это также относительно недорого и дешево приобрести.
Высокая прочностьНикогда еще сталь не славилась своей прочностью и долговечностью. Сталь также может выжить и сохранить структурную целостность в суровых условиях, таких как торнадо, ураганы и т. д.
ЭкологичностьСамое лучшее в стали то, что ее всегда можно использовать повторно с минимальной обработкой, не теряя своей первоначальной прочности или универсальности.
МодифицируемыйСталь как компонент обеспечивает дизайнерам большую гибкость и возможности настройки по сравнению с другими альтернативами. Используя различные другие элементы, свойства стали можно изменить в соответствии с вашими потребностями.
Предсказуемые реакцииВы никогда не узнаете, как тот или иной материал поведет себя в неконтролируемых условиях, но обычно это не относится к стали, поскольку ее реакцию легко предсказать.
Недостатки титана
Высокая стоимостьМногие преимущества титана могут быть компенсированы его высокой стоимостью. Без надлежащего рассмотрения вы можете легко исчерпать свой бюджет.
ДеформацияТитан имеет низкий модуль упругости и легко деформируется. Низкое отношение напряжения к деформации титана затрудняет его обработку.
Сложности с литьемЕсли вы планируете использовать титан для литья, вам следует остановиться и поискать другие альтернативы.
Сложная обработкаНеотъемлемые свойства титана, такие как его высокая температура плавления и прочность, усложняют процесс литья.
Говоря простым языком, это свойство титана должно управляться по-разному на всех этапах производства, что делает его дорогим и сложным в обработке.
Трудно извлечьИзвлечь титан также сложно. Компоненты, необходимые для экстракции, не только дороги, но и опасны в обращении. Кроме того, процесс добычи также приводит к эрозии почвы и другим экологическим проблемам.
Недостатки стали
Высокий уровень обслуживанияЕсли за сталью не ухаживать должным образом, она может ежегодно терять до 1,5 мм своей толщины и, следовательно, своей прочности.
Низкая прочность при высоких температурахСталь также требует надежной защиты от высоких температур. Хотя вам никогда не будет угрожать возгорание, сталь может деформироваться при высоких температурах и даже привести к обрушению всей конструкции.
Потеря устойчивостиОбычно стальные профили изготавливаются из тонких стальных листов. Если на эти пластины оказывается дополнительная нагрузка, это может привести к деформации стали.
ЭстетикаДля большинства предметов сталь не считается приятной на вид. Вот почему стальные изделия обычно нуждаются в отделке поверхности или облицовке, чтобы сделать их более привлекательными с эстетической точки зрения.
КоррозияСталь очень восприимчива к коррозии и требует регулярного обслуживания и защиты от ржавчины. Одним из наиболее распространенных способов защиты стальных конструкций является их покрытие краской и ограничение их контакта с воздухом.
Выберите лучшего партнера
Все еще не знаете, что лучше использовать: титан или сталь? Или вам нужен партнер, который поможет вам извлечь максимальную пользу из обоих этих материалов и поставлять продукцию высочайшего качества по самой низкой цене? Если это так, RapidDirect — это именно то, что вам нужно.
Компания RapidDirect имеет опыт работы с титаном и сталью и может предоставить услуги по изготовлению и изготовлению на заказ. Мы также обеспечиваем конкурентоспособное прототипирование и производство для мелкосерийного производства. Вы можете связаться с нами как для руководства, так и для профессионального совета относительно изготовления вашего дизайна и использования материалов. Просто загрузите файл САПР и получите мгновенное предложение.
Не стесняйтесь загружать файл дизайна здесь
Титан против стали: Заключение
Есть причина, по которой выбор между использованием стали и титана не так прост, как кажется. В зависимости от уникальных требований вашего дизайна вы предпочтете тот или иной вариант. Прежде чем сделать окончательный выбор, лучше всего понять основные свойства обоих материалов.
Углерододефицитный карбид титана с повышенной твердостью
Введение
Разработка многофункциональных сверхтвердых материалов для замены существующих сверхтвердых материалов на основе B-C-N остается сложной задачей и требует учета научных, технологических и инфраструктурных аспектов [1–5].
]. Карбиды, бориды и нитриды переходных металлов обладают высокой твердостью, что объясняется прочной ковалентной связью между углеродом и переходным металлом, а также связями легких элементов [1, 5–7]. Кроме того, соединения легких элементов переходных металлов (TMLE) обладают электропроводностью, сверхпроводимостью и ферромагнитными, а также каталитическими свойствами, которые полезны в областях, где очень желательны многофункциональные свойства. Согласно недавним сообщениям, существует много общих подходов к разработке материалов с более высокой твердостью, таких как (а) наличие высокой плотности валентных электронов, (б) использование высокого содержания легкого элемента и (в) использование изоляционных или полупроводниковых материалов. 8, 9]. Обычно считается, что более высокое содержание легких элементов приведет к получению сверхтвердых материалов из-за высокого процента ковалентных связей. Используя упомянутые выше подходы к проектированию, были разработаны и синтезированы многие ТМЛЭ высокой твердости, в том числе FeB 4 , WB 4 , MnB 4 , MoB 4 , ZrB 12 [10–14].
Хотя эти синтезированные соединения обладают очень высокой твердостью, их значения твердости все же ниже порога сверхтвердости. Следовательно, есть некоторые сомнения в том, могут ли соединения переходных металлов с легкими элементами быть кандидатами на сверхтвердость, или имеет место гибридизация между ТМ и ЛЭ [15]. Однако недавнее исследование показывает, что некоторые аналоги, богатые переходными металлами, такие как W 0,5 Ta 0,5 B, обладают чрезвычайно высокой твердостью [16]. Это говорит о том, что между переходными металлами и легкими элементами p-блока может иметь место сильная гибридизация, и будут другие новые механизмы повышения твердости.
В большинстве соединений переходных металлов с легкими элементами в кристаллической структуре сосуществуют связи TM-TM, TM-LE и LEs-LEs [9, 17]. Трудно определить влияние связей TM-LE на твердость. К счастью, структура каменной соли, характерная для монокарбидов, боридов и нитридов переходных металлов, содержит только связи TM-LE.
Это идеальная система для исследования гибридизации связей TM-LE в TMLE. Если в этих структурах можно реализовать более высокую твердость, можно продемонстрировать существование сильной гибридизации. Бинарные карбиды переходных металлов склонны к кубической кристаллической структуре, если правило Хэгга (R C /R TM <0,59), где R C относится к атомному радиусу углерода, а R TM обозначает атомный радиус атома переходного металла. Отношение атомного радиуса углерода к атомному радиусу титана составляет 0,38. Согласно предыдущему отчету [18, 19], карбид титана обычно обладает превосходными механическими свойствами и широко используется для резки и защиты. Таким образом, структура каменной соли TiC является идеальной системой для исследования гибридизации между орбиталями переходного металла-d и C-2p-орбиталями. Кроме того, использование других внешних упрочняющих эффектов может дополнительно повысить твердость карбида титана.
В данной работе синтез высококристаллического поликристаллического образца TiC проводился в условиях высокого давления и высокой температуры.
Концентрация углерода в этой структуре исследована методами рентгеновской дифракции, энергодисперсионной спектроскопии и рентгеновской фотоэлектронной спектроскопии. Кристаллическая структура, твердость по Виккерсу и электронная структура были охарактеризованы для определения механических свойств. Чтобы определить причину его высокой твердости, особенности связей TiC были тщательно исследованы как экспериментально, так и расчетом из первых принципов. Высокая твердость образца TiC объясняется сильной орбитальной гибридизацией между орбиталями Ti-3d и C-2p, а также его углеродными вакансиями. Наши результаты показывают, что более высокое содержание легкого элемента не является критическим фактором для высокой твердости, а углеродные вакансии также являются эффективным способом повышения твердости.
Эксперимент
Кубический поликристаллический TiC 1-x был приготовлен из порошка металлического титана (чистота 99,9%) и порошка графита (чистота 99,99%). Порошки-сырцы смешивали в соотношении Ti:C = 1:1-x, где x = 0,5, 0,4, 0,3, 0,2, 0,1, 0.
Для получения однородных смесей использовали агатовую ступку и пестик. Для каждой смеси сырье подвергали холодному прессованию в цилиндрические таблетки (4 мм в диаметре, 2,5 мм в высоту) и запечатывали в шестиугольную капсулу из BN, используемую для предотвращения реакции образца с графитовым нагревателем. Эксперименты по синтезу при высоких давлениях и температурах проводились на кубическом прессе с несколькими упорами SPD 6 × 600 Тл. Порошковую смесь нагревали до заданной температуры (1400–2300 К) и выдерживали в течение 15 мин при повышенном давлении 5,0 ГПа. Затем образец охлаждали до комнатной температуры (300 К), отключив электропитание перед декомпрессией.
Поликристаллические образцы после синтеза были измельчены в порошок, и их структура была охарактеризована с помощью рентгеновской дифракции с монохроматическим излучением Cu K α (длина волны 1,5418, напряжение и ток 40 кВ и 30 мА соответственно). Микроморфологию и элементный состав полученных поликристаллических образцов исследовали с помощью сканирующего электронного микроскопа (Magellan 400 SEM) с энергодисперсионным спектром (ЭДС).
Кристаллическая структура TiC 1-x исследовали с помощью дифракции электронов на выбранных участках (SAED) и переходной электронной микроскопии высокого разрешения (HRTEM) на просвечивающем электронном микроскопе JEM-2200FS. Свежеприготовленные поликристаллические образцы сначала полировали карбидокремниевой бумагой, а затем алмазным порошком до получения зеркальной поверхности. Затем для получения средней твердости по Виккерсу на полированной поверхности образца делали не менее пяти отпечатков при различных приложенных нагрузках с выдержкой 15 с. Перед измерением энергии связи титана и углерода поверхности поликристаллических образцов бомбардировали Ar + ионов за 600 с. Измерения XPS проводились с источником рентгеновского излучения, оснащенным Mg-анодом (hν = 1253,6 эВ) при базовом давлении 10 -10 мбар, достигаемом с использованием камеры сверхвысокого вакуума (СВВ).
Чтобы исследовать электронную структуру TiC, мы выполнили расчет из первых принципов с использованием пакета моделирования Vienna ab initio (VASP) [20].
Обменно-корреляционная зависимость Пердью-Берка-Эрнзергофа (PBE) использовалась в обобщенном градиентном приближении GGA [21]. Энергетическая отсечка 500,0 эВ и плотная сетка пакетов Монкхорста были выбраны, чтобы гарантировать, что разница энергий будет <1,0 мэВ/атом. Механические свойства были рассчитаны на основе кода CASTEP с суперячейкой 2 × 2 × 2, в которой 300,0 эВ и 2π × 0,03 −1 были выбраны в качестве значения энергии отсечки и значения k-сетки соответственно [20, 22, 23].
Результаты и обсуждение
Поликристаллические образцы TiC 1-x были синтезированы при высоком давлении 5,0 ГПа и температуре от 1900 до 2300 К с выдержкой 15 мин. Порошки металлического титана начинают реагировать с графитовым порошком при температуре выше 1600 К, а чистый кубический поликристаллический TiC 1−x был синтезирован при температуре выше 1,900 K. Профили дифракции рентгеновских лучей при комнатной температуре для различных закаленных поликристаллических образцов TiC 1-x показаны на рисунке 1a.
Основные пики рентгеновской дифракции TiC 0,7 хорошо характеризуются кубической структурой каменной соли с параметрами a = b = c = 4,3254 , что достаточно хорошо согласуется с предыдущим сообщением [ 18]. Рентгеновская дифракция (XRD) показывает крошечный пик при 26,8°, который соответствует графитовой фазе, и это можно обнаружить на расширенных профилях XRD. Крошечный пик графита предполагает, что определенное количество графита исключено из решетки TiC. Поэтому вполне вероятно, что в TiC 9 присутствуют углеродные вакансии.1857 1−x структура. Поскольку крошечные пики графита не давали подробной структурной информации для TiC 1-x , мы не могли подтвердить относительное количество атомов углерода, которые были исключены из кубической структуры TiC. Чтобы исследовать исключение атомов углерода, мы сравнили образцы с различным соотношением исходных материалов Ti:C = 1:1-x. На рис. 1b показано изменение дифракционных пиков при увеличении разрешения x .
Сначала они смещаются влево, что свидетельствует об уменьшении параметров решетки. Когда x достигает 0,3, трудно увидеть какие-либо графитовые дифракционные пики, и мы предварительно определяем количество углеродных вакансий как ~30%. Хотя смеси исходных материалов были стехиометрическими, а соединения были синтезированы при высоком давлении и высокой температуре, появление пиков дифракции графита указывает на то, что углеродные вакансии чрезвычайно устойчивы. Когда x больше 0,5, рентгеновская дифракция показывает дополнительные пики другой фазы. Появление других фаз, вероятно, свидетельствует о том, что предел x для синтеза TiC 1−x равно 0,5.
Рис. 1. (a) Профили дифракции рентгеновских лучей образцов TiC 1−x ( x = 0, 0,1, 0,2, 0,3, 0,4, 0,5), синтезированных при 2000 K, 5,0 ГПа, 15 мин. . (b) Увеличенное положение пика рентгеновской дифракции плоскости (200) при уменьшении содержания углерода.
(c, d) Типичные фотографии TiC 0,7 на сканирующем электронном микроскопе (SEM) в различных областях. (e) Светлопольные изображения синтезированного образца. На вставке приведены выбранные картины дифракции электронов. (f) ПЭМ-изображение полученного образца с высоким разрешением.
Дальнейшие наблюдения с помощью СЭМ показали, что синтезированные образцы TiC 0,7 не имели видимых микротрещин и пор и имели высокую относительную плотность ~97%. На рисунках 1c, d показаны типичные изображения сканирующего электронного микроскопа в полевых условиях сечения трещины в различных произвольных местах. Из рисунка 1с видно, что образцы после синтеза имеют высококристаллические зерна. Размер зерна определен как 20–40 мкм. Кроме того, на рисунке 1d также можно увидеть ламинарную морфологию, которая возникает из-за трещины в образце. Элементный состав и соотношение в синтезированном образце, подтвержденные ЭДС, составляют около TiC 0,7 , что свидетельствует о нестехиометричности синтезированного образца.
Это согласуется с ab initio составом этого образца. Картины SAED показали, что дифракционные пятна находятся в хорошем порядке и определяют, что это кубическая структура, как показано на рисунке 1e. Вокруг основных пятен трудно обнаружить сателлитные пятна, что исключает возможность образования углеродными вакансиями сверхструктуры в основной решетке [24]. Образец также был изучен с помощью просвечивающего электронного микроскопа высокого разрешения (HRTEM). Как видно из рисунка 1f, межплоскостное расстояние оказалось равным 2,58, что соответствует грани (111) TiC. Несмотря на то, что углеродная вакансия составляет 30%, образец по-прежнему демонстрирует сильно кристаллическую природу, как видно из изображений HRTEM.
Принимая во внимание, что количество углеродных вакансий существенно не изменяется при изменении исходного состава, когда x больше 0,3, мы пришли к выводу, что влияние остаточного предшественника графита на твердость для TiC 0,7 можно не учитывать.
Если образец демонстрирует высокую твердость, будет иметь место сильная орбитальная гибридизация между орбиталью переходного металла-d и орбиталью C-2p, которая, как предполагается, полезна для высокой твердости. Измерение твердости TiC 9Образец 1857 0,7 проведен по полированной поверхности зеркала по шкале твердости по Виккерсу пирамидальным алмазным индентором. Сила нагрузки, действующая на образцы, варьировалась от 25 до 1000 г до достижения конвергентной твердости по Виккерсу. Значение микротвердости по Виккерсу было подтверждено в соответствии с уравнением (1):
Hv=1,8544pd2 (1)
, где d — длина двух диагоналей отпечатков, а P — приложенная сила с продолжительность 15 с. На поверхности образца было сделано не менее пяти отпечатков для получения точных данных о твердости. Среднее значение твердости по Виккерсу поликристаллического TiC 9Образец 1857 0,7 при различных усилиях нагружения приведен на вставке рисунка 2А.
Твердость уменьшается с увеличением силы нагрузки. С увеличением силы нагрузки твердость по Виккерсу постепенно приближалась к асимптотическому значению твердости по Виккерсу 27,1 ГПа. По сравнению с предыдущими результатами 24,7 ГПа измеренная асимптотическая твердость по Виккерсу образцов, изготовленных в условиях HPHT, несколько выше. Образец с более высокой твердостью по Виккерсу, полученный синтезом HPHT, не является неожиданностью, поскольку измеренная твердость тесно связана с качеством образца. Поскольку эффект заполнения пор будет влиять на размер отпечатка твердости, более высокая относительная плотность образца предполагает, что полученное значение твердости будет ближе к значению определенного материала. Показано, что метод HPHT эффективен при подготовке образцов с высокой относительной плотностью.
Рис. 2. (A) Значение твердости по Виккерсу, полученное как функция приложенной нагрузки TiC 0,7 . Соответствующие изображения вдавливания при различных приложенных нагрузках представлены над каждой точкой данных.
(B) Значения твердости по Виккерсу боридов переходных металлов с высокой концентрацией бора и карбида титана.
На рис. 2B показаны значения твердости по Виккерсу для различных боридов переходных металлов с высокой концентрацией бора, широко используемых карбидов переходных металлов и нашего образца карбида титана. Мы видим, что асимптотическая жесткость по Виккерсу даже больше, чем у ReB 2 , WB 3 , ReB 2 , MnB 4 , ZrB 12 и даже FeB 4 , который ранее считался сверхтвердым [2, 11, 1]. По сравнению с другими широко используемыми карбидами переходных металлов (WC, WC-8%Co, TaC и Mo 3 C 2 ), TiC x демонстрирует более высокую твердость. Низкое содержание легких элементов также вызывает более высокую твердость TiC [26–29]. Этот факт указывает на то, что высокое содержание легких элементов или высокоразмерные каркасы из легких элементов не могут быть критическим критерием для создания сверхтвердых материалов.
Объемный модуль (В) обозначает способность материала сопротивляться изменению объема под действием гидростатического давления. Сверхтвердые материалы обычно обладают высоким значением объемного модуля, хотя обратное не всегда верно [30]. Элементарная ячейка TiC кристаллизуется в кубическую структуру с параметром решетки a = 4,32 Å, что дает объем элементарной ячейки 80,62 Å 3 . Таким образом, молекулярный объем равен 20,16 Å 3 . Состав валентной электронной оболочки Ti: 3d 2 4s 2 или Z = 4, а C равно 2s 2 p 2 с Z из 4. Таким образом, общее число валентных электронов в одной элементарной ячейке равно восьми, а плотность валентных электронов ( ВЭД) составляет 0,4 электрона/Å 3 . Сообщается, что алмаз имеет самый высокий объемный модуль 442,0 ГПа и ВЭД 0,7 электрон/Å 3 , а наиболее несжимаемый металл Os имеет объемный модуль 411,0 ГПа и ВЭД 0,57 электрон/Å 3 .
[8]. Относительно низкий VED не может гарантировать структуру TiC с исключительно высоким объемным модулем. Следовательно, рассчитанный объемный модуль TiC на основе расчетов из первых принципов составляет всего 252,4 ГПа, что намного ниже, чем у алмаза, Os и диборидов осмия. Однако, согласно недавним сообщениям S.H. Jhi и YC Liang, число валентных электронов, равное восьми, приводит к наиболее приемлемой электронной структуре и, следовательно, к более высокой твердости [31–34]. Валентный электрон TiC составляет около восьми электронов, и это может быть одной из причин его исключительно высокой твердости.
Недавние исследования на микроскопическом уровне показали, что твердость твердого тела зависит от плотности связи, длины связи, прочности связи и электроотрицательности связи. Согласно предыдущим результатам, преобладающей связью в структуре каменной соли монокарбидов переходных металлов являются связи TM-C, образованные гибридизацией между орбиталями переходного металла-d и C-2p-орбиталями.
Необходимо изучить эту характеристику связи и электронные конфигурации TiC, потому что характеристика химических связей имеет решающее значение для механических свойств. Одним из наиболее многообещающих средств для этого было бы сочетание взаимосвязей между расчетом из первых принципов и измерениями энергии связи. На рисунке 3B показан XPS-спектр C-1 с энергией связи от 283,0 до 29.2,0 эВ. Как видно из спектра, имеются два пика при энергии связи 284,7 и 287,5 эВ. Энергия связи пика графита 1s обычно находится на уровне 284,5 эВ. Следовательно, пик при энергии связи 284,7 эВ принадлежит остаточному графиту, извлеченному из основной матрицы TiC. Появление графитового пика подтверждает наличие углеродных вакансий в синтезированных поликристаллических образцах. Другой пик с более высокой энергией связи 287,5 эВ можно отнести к TiC. Тот факт, что энергия связи выше, чем у графита, предполагает перенос электрона от титана к атомам углерода. На рис. 3А представлен Ti-2p 9.0560 3/2 и 2p 1/2 спектры от энергии связи 455 до 468 эВ.
В спектрах РФЭС Ti 2p присутствуют две пары пиков энергии связи. Два основных пика при 457,7 и 463,7 эВ относятся к высококристаллическому TiC, а пара небольших пиков при 458,7 и 464,6 эВ – к дефектной структуре. Сравнивая площадь пика двух парных пиков TiC, можно подтвердить, что углеродные вакансии x составляют примерно от 0,37 до 0,38, что примерно соответствует предыдущему результату EDS для TiC 9.1857 0,7 . Энергия связи C-1s у TiC выше, чем у графита, а это означает, что некоторые электроны трансформируются из атомов титана в атомы углерода. Преобразование заряда между углеродом и титаном предполагает, что в связи Ti-C есть некоторая ионная характеристика.
Рисунок 3 . Получены XPS-спектры высокого разрешения карбида титана TiC 0,7 , синтезированного при высоком давлении и высокой температуре и предварительно подвергнутого бомбардировке распылением Ar + в течение 600 с. (A) Спектр Ti-2p 3/2 и 2p 1/2 и спектр (B) C-1s.
Твердость TiC также была рассчитана с помощью модели Чена по следующему уравнению:
Hv=2(k2G)0,585 -3 (2)
[35]. Расчетные объемный модуль и модуль сдвига составляют 252,4 и 176,1 ГПа соответственно. Основываясь на приведенном выше теоретическом модуле, смоделированная твердость по Виккерсу составляет около 24,0 ГПа, что согласуется с экспериментальным значением асимптотической твердости. Для дальнейшего изучения электронных свойств и характеристик связи TiC были выполнены расчеты из первых принципов с использованием кода CASTEP. В соответствии с кристаллической структурой и функцией локации электронов (ELF) каменной соли TiC, как показано на рисунке 4A, B. , в структуре TiC существует только один тип связи Ti-C. На рисунке 4C представлена полная и парциальная плотность состояний TiC. По плотности состояний можно наблюдать своеобразную конфигурацию связи, указывающую на высокую степень соответствия между орбиталями Ti-3d и орбиталями C-2p от -3 до -1 эВ.
Совпадение парциальной плотности состояний (PDOS) предполагает, что связь Ti-C в кристаллической решетке также имеет некоторые сильные ковалентные свойства. Ненулевая плотность электронов на уровне Ферми указывает на металлическую особенность кристаллической структуры TiC, что согласуется с удельным электропроводным сопротивлением 3,56 × 10 −7 Ом·м. Для дальнейшего количественного описания характера связывания TiC мы провели анализ популяции Малликена. Высокое перекрытие между электронной конфигурацией или более высокой заселенностью по Малликену соответствует сильной ковалентной связи, тогда как значение, близкое к нулю, указывает на слабое взаимодействие между двумя атомами. Результаты расчетов подтвердили наше предыдущее предположение о связи. По сравнению с заселенностью Малликена связями CC в алмазе Pv = 0,75, Re-B в ReB 2 , Pv = 0,73 и B1-B1 в WB 4 , можно сделать вывод, что связь Ti-C, Pv = 0,81, имеет характеристику ковалентной связи [36].
Более того, расчет населенности Малликена также показывает, что определенно происходит перенос заряда между атомами Ti и C в связи Ti-C. Средние атомные заряды Малликена составляют 0,84 и -0,84 для C и Ti. Перенос электрона от атомов титана к атомам углерода не согласуется с заключением РФЭС. Результаты анализа заселенности Малликена также подтвердили, что связь Ti-C одновременно обладает ионными характеристиками. Это согласуется с результатами XPS. Таким образом, связи TiC имеют сочетание ковалентных металлических и ионных характеристик. Однако, согласно предыдущим отчетам, ионные и металлические связи ухудшают твердость. Следовательно, при синтезе сверхтвердых материалов целесообразно избегать металлических и ионных связей в карбиде переходного металла. Однако по сравнению с образцами TiC, полученными другими методами, синтезированный TiC 9Образец 1857 1−x показал более высокое значение твердости. Предположительно это связано с внешним фактором. Поскольку дефекты действуют как центры закрепления, дефекты могут препятствовать движению дислокаций и тем самым повышать механическую прочность.
Кроме того, появление углеродных вакансий изменяет электронный номер в кристаллической структуре и приводит к оптимизации электронной структуры [33, 34]. Следовательно, образцы TiC 1−x обладают чрезвычайно высокой твердостью по сравнению с другими методами изготовления.
Рис. 4. (A,B) Срезы ELF и CDD плоскости (110) TiC. (C) Расчетная плотность состояний TiC. Энергетический уровень Ферми (E F ) показан вертикальной пунктирной линией.
Выводы
Таким образом, образцы TiC 1−x с дефицитом углерода были синтезированы в условиях высокой температуры и высокого давления. Синтезированные образцы обладают относительно высокой твердостью, превышающей многие соединения с высоким содержанием бора. Основываясь на результатах расчета из первых принципов, мы пришли к выводу, что более высокая твердость TiC может быть связана с сильными связями Ti-C и оптимизированной электронной структурой. Кроме того, углеродные вакансии также играют важную роль в повышении твердости методом внешнего упрочнения.
Хотя углеродная вакансия хороша для высокой твердости, углеродные вакансии в этих образцах имеют тенденцию быть устойчивыми даже в условиях синтеза HPHT. Может потребоваться дальнейшее исследование критических условий синтеза, чтобы решить проблему углеродных вакансий и добиться более высокой твердости, ожидаемой для стехиометрического TiC.
Заявление о доступности данных
Необработанные данные, подтверждающие выводы этой статьи, будут предоставлены авторами без неоправданных оговорок.
Вклад авторов
LC и ZY внесли вклад в разработку концепции и дизайна исследования. З.Ы. организовал литературу. HL и SM выполнили дизайн рисунков и написали первый набросок рукописи. Все авторы внесли свой вклад в доработку рукописи, прочитали и одобрили представленную версию.
Финансирование
Это исследование было поддержано Фондом естественных наук Гуанси в рамках гранта № 2018GXNSFBA050034 и 2019GXNSFBA185001, проекта повышения базовых способностей учителей молодого и среднего возраста Департамента образования Гуанси, № 2020KY04022.
Конфликт интересов
Авторы заявляют, что исследование проводилось при отсутствии каких-либо коммерческих или финансовых отношений, которые могли бы быть истолкованы как потенциальный конфликт интересов.
Каталожные номера
1. Кнаппшнайдер А., Литтершайд С., Курцман Дж., Сешадри Р., Альберт Б. Уточнение кристаллической структуры и схемы связывания crB 4 : борид с высоким содержанием бора с каркасом из тетраэдрически координированных атомов B. Неорг. хим. (2011) 50:10540–2. doi: 10.1021/ic2018083
PubMed Abstract | Полный текст перекрестной ссылки | Google Scholar
2. Qin J, He D, Wang J, Fang L, Lei L, Li Y, et al. Является ли диборид рения сверхтвердым материалом? Adv Mater. (2008) 20:4780–3. doi: 10.1002/adma.200801471
Полнотекстовая перекрестная ссылка | Google Scholar
3. Канер Р.Б., Гилман Дж.Дж., Толберт С.Х. Создание сверхтвердых материалов. Наука . (2005) 308:1268–9. doi: 10.
1126/science.1109830
PubMed Abstract | Полный текст перекрестной ссылки | Google Scholar
4. Gu Q, Krauss G, Steurer W. Бориды переходных металлов: сверхтвердые и сверхнесжимаемые. Adv Mater. (2008) 20:3620–6. doi: 10.1002/adma.200703025
Полный текст CrossRef | Академия Google
5. Mohammadi R, Lech AT, Xie M, Weaver BE, Yeung MT, Tolbert SH, et al. Тетраборид вольфрама, недорогой сверхтвердый материал. ПНАС . (2011) 108:10958–62. doi: 10.1073/pnas.1102636108
PubMed Abstract | Полный текст перекрестной ссылки | Google Scholar
6. Ma S, Bao K, Tao Q, Zhu P, Ma T, Liu B, et al. Моноборид марганца, недорогой твердый ферромагнитный материал при комнатной температуре. Научный представитель (2017) 7:43759. doi: 10.1038/srep43759
PubMed Abstract | Полный текст перекрестной ссылки | Академия Google
7. Li H, Wen P, Li Q, Dun C, Xing J, Lu C, et al. Земнообильные наночастицы диборида железа (FeB 2 ) в качестве высокоактивных бифункциональных электрокатализаторов для общего расщепления воды.
Adv Energy Mater. (2017) 7:1700513. doi: 10.1002/aenm.201700513
Полный текст CrossRef | Google Scholar
8. Gilman JJ, Cumberland RW, Kaner RB. Дизайн твердых кристаллов. Int J Refractory Metals Hard Mater. (2006) 24:1–5. doi: 10.1016/j.ijrmhm.2005.05.015
Полнотекстовая перекрестная ссылка | Google Scholar
9. Guo X, Li L, Liu Z, Yu D, He J, Liu R, et al.-Wang T. Твердость ковалентных соединений: роль металлического компонента и D валентных электронов. J Appl Phys. (2008) 104:023503. doi: 10.1063/1.2956594
Полный текст CrossRef | Google Scholar
10. Wang Q, He J, Hu W, Zhao Z, Zhang C, Luo K, et al. Является ли орторомбический тетраборид железа сверхтвердым? J Материал. (2015) 1:45–51. doi: 10.1016/j.jmat.2015.03.004
Полнотекстовая перекрестная ссылка | Google Scholar
11. Tao Q, Zheng D, Zhao X, Chen Y, Zhu P. Изучение твердости и искаженной sp2-гибридизации связей b–B в wB 3 .
Хим. (2014) 26:5297–302. doi: 10.1021/cm5021806
Полный текст CrossRef | Google Scholar
12. Ma S, Bao K, Tao Q, Huang Y, Xu C, Li L, et al. Исследование происхождения и механических свойств необычных жестких алмазоподобных сетчатых аналогов в тетрабориде марганца. Int J Refractory Metals Hard Mater. (2019) 85:104845. doi: 10.1016/j.ijrmhm.2018.12.010
CrossRef Полный текст | Google Scholar
13. Tang H, Gao X, Zhang J, Gao B, Gou H. Богатый бором борид молибдена с необычным ближним упорядочением вакансий, анизотропной твердостью и сверхпроводимостью. Хим. (2019) 32:459–67. doi: 10.1021/acs.chemmater.9b04052
Полный текст CrossRef | Google Scholar
14. Ma T, Li H, Zheng X, Wang S, Wang X, Zhao H. Сверхпрочные каркасы бора в zrB 12 : Шоссе для электронной проводимости. Adv Mater. (2016) 29:1604003. doi: 10.1002/adma.201604003
PubMed Abstract | Полный текст перекрестной ссылки | Google Scholar
15.
Ван С., Тао К., Ма С., Цуй Т., Ван С., Донг С. и др. WB 2 : не сверхтвердый материал для сильного поляризационного характера межслойной связи w-B. Phys Chem Chem Phys. (2017) 19:8919–24. doi: 10.1039/C6CP04287B
PubMed Abstract | Полный текст перекрестной ссылки | Академия Google
16. Юнг М.Т., Акопов Г., С.-Лин В., Кинг Д.Дж., Ли Р.Л., Собелл З.К. и соавт. Сверхтвердые w 0,5 Ta 0,5 B нанопроволоки, приготовленные при атмосферном давлении. Appl Phys Lett. (2016) 109:203107. doi: 10.1063/1.4967447
Полный текст CrossRef | Google Scholar
17. Li Q, Zhou D, Zheng W, Ma Y, Chen C. Аномальная реакция сверхтвердых соединений wBn на стресс. Phys Rev Lett. (2015) 115:185502. doi: 10.1103/PhysRevLett.115.185502
PubMed Abstract | Полный текст перекрестной ссылки | Академия Google
18. Рагурам Буншах КАРФ. Влияние температуры подложки на структуру карбида титана, осажденного методом активированного реактивного испарения.
J Vacuum Sci Technol. (1972) 9:1389–94. doi: 10.1116/1.1317046
Полный текст CrossRef | Google Scholar
19. Kumashiro Y, Itoh A, Kinoshita T, Sobajima M. Микротвердость монокристаллов TiC по Виккерсу при температуре до 1500°C. J Mater. (1977) 12: 595–601. doi: 10.1007/BF00540285
Полный текст CrossRef | Академия Google
20. Кресс Г. Эффективные итерационные схемы для неэмпирических расчетов полной энергии с использованием базисного набора плоских волн. Phys Rev B. (1996) 54:11169–86. doi: 10.1103/PhysRevB.54.11169
PubMed Abstract | Полный текст перекрестной ссылки | Google Scholar
21. Пердью Дж. П., Берк К., Эрнцерхоф М. Упрощение обобщенной градиентной аппроксимации. Phys Rev Lett. (1996) 77:3865–8. doi: 10.1103/PhysRevLett.77.3865
PubMed Abstract | Полный текст перекрестной ссылки | Академия Google
22. Segall MD, Lindan PJD, Probert MJ, Pickard CJ, Hasnip PJ, Clark SJ, et al. Моделирование первых принципов: идеи, иллюстрации и код CASTEP.
J Phys Конденсирует Материю. (2002) 14:2717–44. doi: 10.1088/0953-8984/14/11/301
CrossRef Full Text | Google Scholar
23. Segall MD, Shah R, Pickard CJ, Payne MC. Популяционный анализ плосковолновых расчетов электронной структуры объемных материалов. Phys Rev B. (1996) 54:16317–20. doi: 10.1103/PhysRevB.54.16317
Реферат PubMed | Полный текст перекрестной ссылки | Google Scholar
24. Sathish CI, Guo Y, Wang X, Tsujimoto Y, Li J, Zhang S, et al. Сверхпроводящие и структурные свойства кубической фазы карбида молибдена d-MoC0,681. J Химия твердого тела. (2012) 196:579–85. doi: 10.1016/j.jssc.2012.07.037
Полный текст CrossRef | Google Scholar
25. Wang S, Yu X, Zhang J, Zhang Y, Wang L, Leinenweber K, et al. Кристаллическая структура, упругие свойства и твердость синтезированного под высоким давлением crB 2 и crB 4 . J Сверхтвердый материал. (2014) 36: 279–87. doi: 10.3103/S1063457614040066
Полный текст CrossRef | Google Scholar
26.
Chen Y, He D, Qin J, Kou Z, Bi Y. Ультразвуковые измерения и измерения твердости для керамики wB, изготовленной сверхвысоким давлением. Int J Refractory Metals Hard Mater. (2011) 29:329–31. doi: 10.1016/j.ijrmhm.2010.12.006
CrossRef Полный текст | Google Scholar
27. Sun W, Kuang X, Liang H, Xia X, Zhang Z, Lu C и другие. Механические свойства карбида тантала из синтеза при высоком давлении/высокой температуре и основные расчеты. г. Phys Chem Chem Phys. (2020) 22:1–6. doi: 10.1039/C9CP06819H
PubMed Abstract | Полный текст перекрестной ссылки | Google Scholar
28. Ge Y, Ma S, Kuo B, Tao Q, Zhao X, Feng X и др. Сверхпроводимость с высокой твердостью в Mo 3 C 2 . Неорган Хим Фронт. (2019) 6:1282–8. doi: 10.1039/C9QI00182D
CrossRef Полный текст | Google Scholar
29. Zou Y, Wang X, Chen T, Li X, Qi X, Welch D, et al. ε-NbN с гексагональной структурой: сверхнесжимаемость, высокая жесткость при сдвиге и, возможно, твердый сверхпроводящий материал.
г. Научный представитель (2015) 5:10811. doi: 10.1038/srep10811
PubMed Abstract | Полный текст перекрестной ссылки | Google Scholar
30. Камберленд Р.В., Вайнбергер М.Б., Гилман Дж.Дж., Кларк С.М., Толберт С.Х., Канер Р.Б. Диборид осмия, сверхнесжимаемый, твердый материал. J Am Chem Soc. (2005) 127:7264–5. doi: 10.1021/ja043806y
PubMed Abstract | Полный текст перекрестной ссылки | Google Scholar
31. Liang Y, Gao Z, Qin P, Gao L, Tang C. Механизм аномального упрочнения моноборидов переходных металлов. Наношкала. (2017) 9:9112–8. doi: 10.1039/C7NR02377D
PubMed Abstract | Полный текст перекрестной ссылки | Google Scholar
32. Liang Y, Qin P, Jiang H, Zhang L, Zhang J, Tang C. Проектирование сверхтвердых металлов: случай низких боридов. AIP Adv. (2018) 8:045305. doi: 10.1063/1.5023830
Полный текст CrossRef | Google Scholar
33. Jhi SH, Ihm J, Louie SG, Cohen ML. Электронный механизм повышения твердости карбонитридов переходных металлов.