Углекислый газ
Общие сведения об углекислом газе
Углекислый газ поставляется по ГОСТ 8050—76. Для сварки используют сварочную углекислоту сортов I и II, которые отличаются лишь содержанием паров воды (соответственно 0,178 и 0,515 Н2О в 1 м3 СО2). Применяют иногда и пищевую углекислоту, имеющую в баллоне в виде примеси свободную воду, в связи с чем требуется особенно тщательное осушение газа. Углекислоту транспортируют и хранят в стальных баллонах или цистернах большой емкости в жидком состоянии с последующей газификацией на заводе, с централизованным снабжением сварочных постов через рамны. В баллоне емкостью 40 л содержится 25 кг СО2, дающего при испарении 12,5 м3 газа при давлении 760 мм рт. ст. Балдон окрашен в черный цвет, надписи желтого цвета.
Применение углекислого газа
При применении углекислого газа вследствие большого количества свободного кислорода в газовой фазе сварочная проволока должна содержать дополнительное количество легирующих элементов с большим сродством к кислороду, чаще всего Si и Mn (сверх того количества, которое требуется для легирования металла шва).
Стремление уменьшить повышенное разбрызгивание металла и улучшить формирование шва при сварке в углекислом газе дало толчок к применению смесей углекислого газа с кислородом (2—5%). В этом случае изменяется характер переноса металла; он переходит в мелкокапельный; потери металла на разбрызгивание уменьшаются на 30—40%.
При сварке сталей по узкому зазору с целью стабилизации процесса сварки и уменьшения расхода дорогого и дефицитного аргона вполне целесообразно применение двойных смесей (75% Ar + 25% СО3) и тройных смесей (аргона, углекислого газа и кислорода). Для алюминиевых сплавов весьма эффективно с точки зрения производительности применение смеси, состоящей из 70% Не и 30% Аг. В этом случае значительно увеличивается толщина металла, свариваемого за один проход, и улучшается формирование шва.
см. также:
Аргон в сварке
Гелий в сварке
Газовые смеси
углекислота в баллонах и сварочные аппараты, редуктор для сварки в углекислотной среде, расход
Сварочный процесс с применением углекислого газа относят к разновидности сварки, выполняемой под защитой флюса. Такой тип работ чаще всего осуществляют плавящимися электродами, и этот метод нашёл применение в сфере проведения различного типа монтажных работ, а также используется при ремонте или для восстановления деталей с тонкими стенками.
Особенности
Согласно требованиям ГОСТ, сварка в углекислом газе выполняется автоматическими или полуавтоматическими сварочными устройствами, которые оснащены горелками, выделяющими углекислотную смесь из сопла. При проведении сварки в углекислой среде важно учитывать, что любые нестандартные держатели должны выдерживать радиальное истечение газа по отношению к оси электрода.
Сущность процесса сварки состоит в том, что работы ведутся под защитой углекислого газа.
Перед проведением работ и пропусканием сварочной проволоки в дюритовый шланг, конец прутка требуется завальцовывать, а сам шланг обязательно проверяют на отсутствие утечек и перегибов, так как в системе должно быть давление для равномерной подачи газа. Такие требования ГОСТ должны соблюдаться неукоснительно. Если не придерживаться установленного режима, то оборудование быстро выйдет из строя, а качество сварки будет неудовлетворительным.

В процессе сварки устойчивость электродуги, стойкость её защиты от окисляющего действия кислорода, а также быстрота остывания металла и форма сварочного шва напрямую зависят от правильного перемещения и наклона горелки аппарата относительно рабочей поверхности заготовок.
При сварке с применением углекислой среды улучшается качество сварного шва, снижается напряжение металла после выполнения работ, а также гарантируется прочность соединения между собой заготовок.
Применение углекислоты позволяет следить за сварочным процессом, снижает степень загрязнения рабочей поверхности брызгами расплавленного металла, а также сводит к нулю появление дефектов в сварочных швах.
Способы
Автоматическое и полуавтоматическое оборудование для выполнения газоэлектросварки с применением углекислого газа может работать с неплавящимся (вольфрамовым) или плавящимся электродом.
Для защиты сварочного шва в процессе работы могут быть применены инертные, активные и смешанные газы. Углекислый газ относят к группе активных газообразных веществ. Выбор газа напрямую зависит от физико-химического состава заготовок, а также исходя из требований, которые будут предъявлены к качествам сварного шва. Кроме того, газ для сварки выбирают исходя из экономической целесообразности.
Углекислый газ в этом случае является одним из наиболее выгодных с экономической точки зрения из-за низкой себестоимости.
Иногда активный углекислый газ смешивают с другими типами газа. Делают это для более высокой степени устойчивости сварочной дуги, а также для увеличения глубины проникновения в металл в процессе его плавления. Смесь газов с углекислотой увеличивает производительность сварочного процесса, а также усиливает степень перехода металла из сварочного электрода в стыковочный шов.
Рассмотрим наиболее распространенные способы применения углекислого газа для различных вариаций сварки.
- Сочетание аргона и 25% углекислой смеси. Такой состав используют для работы с плавящимися электродами. Добавление к аргону углекислоты позволяет работать с высокоуглеродистыми металлами без образования внутри шва пористой структуры. Кроме того, углекислый газ усиливает стабильность электродуги, повышает эффективность сварки на ветру, улучшает качество шва при работе с тонкостенными заготовками.
- Сочетание аргона с 20% углекислоты и 5% кислорода. Такой газ применяют для работы с плавящимися электродами при сварке легированной или углеродистой стали. Газовая смесь повышает стабильное состояние электродуги, улучшает форму и качество шва и исключает появление пористости.
- Сочетание углекислой смеси и 20% кислорода. Этот состав применяют для сварки плавящимся электродом при соединении заготовок из углеродистой стали. Газовая смесь обладает хорошей оксидной способностью, стимулирует глубокое проникновение электродуги вглубь металла, создает шов хорошей формы и исключает появление пористости.
Для выполнения сварочных работ защитная углекислая смесь в область сварки может поступать центрально или сбоку, если скорость сварки достаточно высокая.
Чтобы сэкономить расход дорогих инертных газов, их потоки разделяют, причём внутренний поток – это инертный газ, а более широкий наружный – это всегда более дешёвый углекислый газ.
Применяемые материалы и оборудование
Углекислый газ
В составе газа – углекислота, газообразное вещество, не обладает цветом, запахом и нетоксично. Для сварочного процесса используют баллоны чёрного цвета, срок годности такой ёмкости с момента проведения её первой аттестации составляет 20 лет. Баллоны имеют рабочее давление, равное 70 кгс/ см², а их объём равен 40 л, что соответствует 25 кг жидкого углекислого вещества. Примерно 80-99% баллона занимает углекислота, а остальная часть приходится на долю углекислого газа.
Для маркировки на чёрном фоне баллона делают надпись жёлтого цвета «Углекислота».
Для выполнения высококачественных сварочных работ применяют концентрацию углекислоты не менее 98%, а для наиболее ответственных участков берут 99%-ный состав. Чем выше содержание углекислоты в газе, тем больше разбрызгивается жидкий металл в процессе сварки. Для устранения этого побочного эффекта применяют специальные осушители, выполненные из силикагеля, алюминия либо купороса, которые удаляют избыток влаги.
Сварочная проволока
Следующим важным материалом, необходимым для сварки, является электрод. Для работы в среде углекислого газа применяются специальные виды электродов. Дело в том, что сварочная проволока, которая используется для работ под прикрытием флюса, не может быть применима в процессе сварки в углекислой среде. Для выполнения сварки с двуокисью углерода применяют электроды, в которых имеется повышенное содержание кремния и марганца. Эти металлы легируют сварочную проволоку, делая её более прочной. Толщина электрода зависит от типа аппарата, которым будет выполняться сварка, а также от толщины стыкуемых заготовок.
Выбирая электроды, нужно обратить внимание на то, чтобы их поверхность была чистой, не имела следов коррозии и окалины.
Если в электроде будут посторонние включения, то это отразится на качестве шва, ослабляя его возникновением пористости. Кроме того, электроды с примесями будут способствовать разбрызгиванию жидкого металла. Если требуется очистить электроды перед работой, их можно протравить в растворе серной кислоты 20% концентрации. После травления проволоку нужно прокалить в печи.
Другие
Для выполнения сварки нужны и другие комплектующие. Перечень их выглядит примерно так:
- сварочный аппарат;
- трансформатор или инвертор в качестве источника переменного тока;
- газовый баллон и кислородный редуктор;
- подающее газ устройство, куда установлен газовый клапан;
- осушитель (подогреватель) углекислого газа – используется как промежуточное приспособление, соединяющее баллон с горелкой;
- газовая горелка, укомплектованная комплектом кабелей и дюритовыми шлангами.
Чтобы качественно выполнить сварочные работы, необходимо заранее подготовить все необходимые расходные материалы и проверить исправность рабочего оборудования.
Расход
В газовом баллоне содержится объём углекислой смеси, которого хватает на 16-20 часов непрерывной работы. Расход углекислого газа напрямую зависит от интенсивности его подачи и объёма сварочных работ.
Перед тем как начать сварочные работы, баллон с газом требуется поставить вертикально и выждать время, чтобы избыток влаги естественным путем мог опуститься на дно ёмкости.
До работы и в процессе её выполнения нужно следить за тем, чтобы давление внутри ёмкости не падало ниже показателя, равного 4-5 кгс/см². Если показатели упадут ниже этих цифр, работу придётся остановить, так как в газовой смеси будет содержаться большое количество влаги, что снизит качество сварочного шва.
Для контроля за расходом углекислой смеси и уровнем её давления на баллоне устанавливают специальный редуктор-расходомер. Наиболее распространены в настоящее время редукторы марок АР-150 и АР-40. Расход углекислого газа регулируют понижающим действием редуктора – это приспособление при необходимости снижает внутреннее давление в баллоне до 0,5 атм, что позволяет экономно расходовать углекислый газ при выполнении сварочных работ.
Газ, выходя из баллона, быстро охлаждается, в результате чего происходит испарение углекислоты, которая со временем закупоривает отверстие редуктора. Чтобы этого не происходило, влаге не дают быстро испаряться, применяя обогреватель.
Технология
Для того чтобы правильно варить заготовки в домашних условиях, важно соблюдать основные параметры режима сварки и действовать по схеме. Для начинающих сварщиков может оказаться полезной следующая пошаговая инструкция выполнения работ:
- определить полноту заправки баллона с углекислым газом, чтобы рассчитать время работы;
- поместить присадочный припой в подающий механизм;
- проверить исправность роликов, которые нужно подобрать исходя из размеров сварочной проволоки;
- разложить механизм подачи проволоки путём нажатия кнопки управления;
- дождаться выхода проволоки из открытого конца горелки;
- подсоединить баллон с газом с помощью шлангов, места соединений затянуть хомутами;
- зачистить рабочую поверхность заготовок от загрязнений, снять небольшую краевую фаску материала;
- выполнить на отходах металлической стружки пробный вар для настройки параметров аппарата;
- установить горелку под углом 85° относительно заготовки;
- сформировать электродугу и вести её так же, как и при ручной сварке – во время подачи газа металл перестанет брызгать;
- закончив формирование шва, отключить подачу электротока на аппарате;
- остановить подачу сварочной проволоки;
- после начала кристаллизации поверхности сварочного шва перекрыть подачу газа.
Сварка заготовок с применением углекислого газа является одной из наиболее востребованных.
Технология выполнения этой операции зависит от выбранного режима работы сварочного аппарата и его параметров. Результатом выполнения работ будет качественный, ровный и прочный шов, имеющий защиту от коррозии металла.
О сварке электродом в углекислом газе смотрите далее.
Углекислый газ аргон кислород | Технологические газы
При сварке сталей в среде защитных газов применяют инертные и активные газы и их смеси. Основным защитным газом для полуавтоматической и автоматической сварки плавящимся электродом является углекислый газ.
Углекислый газ поставляется по ГОСТ 8050—85. Он бывает сварочный, пищевой и технический.
Сварочный углекислый газ 1-го сорта содержит не менее 99,5 % двуокиси углерода и около 0,178 г/м3 водяных паров при нормальных условиях (давление 760 мм рт. ст. и температура 20 °С).
Сварочный углекислый газ 2-го сорта содержит около 99 % двуокиси углерода и не более 0,515 г/м3 водяных паров.
Пищевой углекислый газ содержит 98,5 % двуокиси углерода и около 0,1 % воды в баллоне по массе.
Технический углекислый газ содержит не менее 98 % двуокиси углерода, до 0,05 % окиси углерода и не более 0,1 % воды в баллоне по массе.
Получают углекислый газ из кокса, известняка и антрацита путем обжига в специальных печах, из газов брожения в гидролизной промышленности и из дымовых газов котельных установок.
При охлаждении под давлением углекислый газ превращается в бесцветную жидкость, а при охлаждении без давления — в твердое тело.
Жидкую углекислоту заливают в стандартные баллоны объемом 40 литров на 60—80 % объема (до 25 кг). Давление углекислоты в баллоне может составить 6—7,5 МПа (60—75 кг/см2). При испарении 25 кг жидкой углекислоты образуется 12,6 м3 газообразной, т. е. из одного килограмма жидкой углекислоты образуется около 0,505 м3 газа.
Для хранения и транспортировки больших объемов технологических газов, в том числе и углекислоты, применяют специальные изотермические цистерны и сосуды.
Углекислый газ для сварки можно получать не только из жидкой углекислоты, но и из сухого льда. Основным преимуществом использования сухого льда для сварки является высокая чистота углекислого газа и удобство транспортировки. Брикеты сухого льда к потребителю доставляются в контейнерах. Газификация его производится в герметичных сосудах — газификаторах, обогреваемых электронагревателями или теплой водой.
Аргон для сварки поставляется по ГОСТ 10157—79. Это инертный газ. По чистоте он делится на три сорта. Аргон высшего сорта (99,99 % аргона) предназначен для сварки особо активных металлов и сплавов типа титана, циркония, ниобия.
Аргон 1-го сорта (99,98 % аргона) используется для сварки алюминия, магния, их сплавов и других активных металлов.
Аргон 2-го сорта (99,95 % аргона) применяют для сварки высоколегированных сталей и сплавов.
Для промышленных целей аргон получают в качестве побочного продукта при производстве кислорода и азота из воздуха.
Кислород — бесцветный газ, без вкуса и запаха. При температуре минус 118,8°С и давлении 5,1 МПа (51,35 кг/см2) кислород сжижается, а при температуре минус 182,96 °С и атмосферном давлении он может превращаться в жидкость.
Масса одного литра жидкого кислорода при атмосферном давлении составляет 1,14 кг. Нормальная плотность кислорода в нормальных условиях равняется 1,33 кг/ма.
Для газоплазменной обработки металлов применяют технический кислород по ГОСТ 5583—78 трех сортов: 1-й сорт с чистотой не ниже 99,7 %, 2-й сорт с чистотой не ниже 99,5 % и 3-й сорт с чистотой 99,2 %.
Кислород получают химическим методом, методом электролиза воды и разделением атмосферного воздуха методом глубокого охлаждения.
Химические способы основаны на свойстве ряда химических соединений в определенных условиях выделять кислород. Эти способы малопроизводительные, требуют применения дефицитных химикатов, дают слишком дорогой кислород.
В качестве горючих газов при сварке и термической резке используется ацетилен, пропан-бутан, природный газ, пары бензина или керосина.
Источником тепла служит пламя от сгорания смеси горючих газов с кислородом.
Наибольшую температуру пламени при сгорании в кислороде (около 3100 С) создает ацетилен (см. рис. 2, а).
Подогреватель углекислого газа.

Подогреватель углекислого газа
Вопрос: что если подогреватель углекислоты ПЭГ-3 использовать для аргона?
Углекислый газ, проходящий через регулятор давления во время сварки, приводит к сильному его переохлаждению. Происходит это потому, что сжиженный газ охлаждается при понижении давления. Как результат – клапан редуктора закупоривается льдом.
Наиболее сильное охлаждение происходит при расходе более 20дм3/ мин, а минимальная отметка, которую можно достичь -78 оС. В итоге, редуктор промерзает и выходит из строя. Во избежание таких негативных последствий, газ перед ним подогревают.
Так как аргон не сжиженный, а сжатый газ, то он и не охлаждается, поэтому применять подогреватель для него не нужно. Но если необходимо защитить оборудование от промерзания в зимнее время, нередки случаи использования «грелок».
Основное предназначение ПЭГ-3 — подогрев газа при полуавтоматической mig/mag и автоматической сварке. Используется с любыми регуляторами, их конструктивные особенности и завод-изготовитель значения не имеют. Соответствует ТУ, и ГОСТам. Температура эксплуатации устройства -20…+50 градусов Цельсия.
Это интересно знать…
ПЭГ-3 при разовых работах в домашних условиях – прибор абсолютно бессмысленный. Есть рациональное зерно в его применении только при большом объеме работ в заводских условиях, когда устанавливаются большие токи и высокие режимы расхода углекислоты – только в таком случае возникают недоразумения с обмерзанием.
Но обмерзание может произойти и если вы работаете дома при использовании баллонов малого объема до десяти литров. . Диоксид углерода не успевает достичь «нормальной» температуры внутри баллона из-за его малых размеров, что не характерно для больших сорокалитровых емкостей. В таком случае без ПЭГ-3 тоже не обойтись.
Проблема особенно актуальна, если принимать во внимание то обстоятельство, что все сварщики — обычно большие кулибины. И практически у каждого под рукой оказывается углекислотный огнетушитель! Почему-бы его не использовать для сварки?
Вот таким огнетушителем (см. фото) с устройством понижения/регулирования давления и «грелкой» можно варить. Особенно такой девайс полезен, если требуется мобильность. Можно пойти и другим путем: из огнетушителя вынуть трубку — в таком случае жидкая фаза не будет испаряться в раструбе. Родной рычажный кран долго не продержится, поэтому его меняют на кран с маховиком.
Особенности и преимущества сварки с применением кислорода и углекислого газа
В сварочном производстве кислород является едва ли не самым важным газом. Газообразный, поступающий из баллоновтехнический кислород применяют в процессе сварки или резки. По ГОСТу 5583-78 он может быть 1-го или 2-го сорта. Догадаться, что перед вами именно кислород, а не что-либо еще просто: баллон с ним голубой и имеет подтверждающую надпись черным – «кислород».
Преимущества кислорода и углекислого газа в процессе сварки
В основе сварочной смеси – углекислый газ и кислород. Последний необходим, чтобы улучшить окислительный процесс и повысить температурные показатели.
Углекислый газ в сварочном процессе существенно повышает процент разбрызгивания расплавленного металла. В последующем происходит приваривание брызг к объекту сварки, тщательная и продолжительная зачистка.
Применение кислорода:- способствует тому, что металл меньше подвержен разбрызгиванию;
- снижает вероятность, что брызги будут приварены к главному металлу;
- влияет на стабилизацию устойчивого горения дуги;
- оказывает воздействие на образование ровного шва без бугров.
Установлено, что наиболее грамотным соотношением смеси углекислого газа и кислорода будет 70-80/30-20%. Такое соотношение дает возможность сохранить ровность и гладкость шва, улучшить показатели его плотности за счет того, что сталь проплавляется достаточно глубоком уровне. В результате поверхность сварочного шва покрывается тонкой шлаковой коркой. Она легко удаляется, открывая серебристый цвет шва.
Особенности сварки углекислотой и кислородом
Если вы выбираете углекислый газ для сварки и кислород, то у вас есть возможность делать это вне зависимости от пространственного положения. Промышленный выпуск смеси углекислоты и кислорода не осуществляется – газы смешиваются непосредственно перед началом сварочного процесса.
Есть несколько технологий сварки: тот или иной вариант при сварке с помощью баллонного кислорода выбирается исходя из варианта стали и условий, предъявляемых к изделию.
До начала работ убедитесь, что баллон установлен далеко от прямого воздействия ультрафиолета. Не спешите соединять кислородный баллон и редуктор. Проверьте, исправен ли входной штуцер и накидная гайка редуктора. Если они покрыты загрязнениями (жир, масло, пыль, песок и др.), произведите очистку.
Проследите, чтобы уплотняющая прокладка из фибры отлично работала, а на штуцере редуктора находился фильтр. Сварка должна осуществляться таким образом, чтобы баллон находился в 5 м. от теплового источника.
Снимать колпак предохранителя с баллона нужно аккуратно, исключая какое-либо механическое воздействие, способное вызвать искры. Резкое открытие и закрытие вентиля баллона может привести к самовоспламенению – делайте это плавно.
Не допускается транспортировка кислородных баллонов в руке или на плечах, их падение. Когда сварка окончена, проследите за отсоединением редуктора от баллона, плотным закручиванием вентиля и навинчиванием колпака предохранителя.
Влияние смеси газов на формирование сварного шва
Влияние смеси газов на формирование сварного шва
Основным видом сварки в защитных газах применяемой в промышленности является сварка в углекислом газе. Это связано с преимуществами данного вида, такими как: низкая стоимость по сравнению с использованием других газов, например инертных, довольно высокая производительность, легкость механизации, и автоматизации. Однако, такой недостаток как повышенное разбрызгивание электродного металла, характеризующее его потери, перечеркивает все вышеперечисленные преимущества.
Сварка в атмосфере азота не нашла применения при изготовлении конструкций из стаж из-за образования пор.
Многие исследователи изучали сварку в различных смесях газов с целью получения результатов, влияющих на качественные изменения процесса, уменьшающих себестоимость и повышающих их производительность. Одно из таких направлений является сварка в смеси углекислого газа и кислорода/1-8/.
Физическими и технологическими параметрами сварочной дуги можно управлять за счет изменения состава защитной среды /9/. Одним из основных таких параметров является перенос электродного металла. Именно от переноса зависят такие характеристики как разбрызгивание и плохое формирование шва.
Наиболее благоприятным с точки зрения сварки является струйный перенос электродного металла.
При дуговой сварке в защитных газах возможно существование следующих видов переноса: крупнокапельный, мелкокапельный и струйный. Существование того или иного вида переноса зависит от критической силы тока. Так например, в работе /10-15/ величина Iкр при сварке в гелии проволокой Св-08Г2С, диаметром 2мм. составляет 560 А. Капельный и струйный перенос наблюдается в диапазоне токов меньших I кр. Из-за высокой теплопроводности и тепловой мощности гелиевой плазмы /9/ швы получаются довольно широкими и с глубоким проплавлением, а также хорошего качества Несмотря на эти преимущества сварка в гелии не нашла широкого применения при изготовлении конструкций из низкоуглеродистой и низколегированной стали из-за высокой стоимости самого процесса сварки.
Те же виды переносов, что и при сварке в Не, в зависимости от величины силы сварочного тока и импульса, можно получить и в аргоне. Однако, величина I кр в данном случае меньше (I кр — 420 А при d эл = 2 мм проволока Св-08Г2С /15/). Дуга в Аг характеризуется большей концентричностью, т.е. наличием высокотемпературного центрального канала. Поэтому швы при сварке в Аг имеют большую глубину проплавления, чем в Не.
Авторы статьи /1/ утверждают, что по сравнению со сваркой в С02, добавка до 50 % кислорода дает следующие преимущества:
- брызги легче отделяются от металла;
- формирование шва улучшается, он гладкий и менее выпуклый, форма про пара практически такая же;
- образующаяся шлаковая корка небольшой толщины и легко удаляется;
- при сварке металла с ржавчиной склонность его и образованию пор меньше, снижается количество диффузионного водорода;
- расход смеси такой же и поэтому она дешевле;
- размер неметаллических включений (окислов) одинаков.
Авторы изучали также особенности сварки в смеси (С02 + 02) с различным содержанием кислорода. Отмечены те же преимущества, а так же влияние на некоторые характеристики металла шва. Авторы предлагают оптимальный состав снеси, в которой кислорода 15 — 20 %. А при дальнейшем увеличении 02 в смеси снижаются механические свойства шва.
Что касается переноса электродного металла, то он не изменяется, т. е. остается крупнокапельным без коротких замыканий дугового промежутка, при сварке длинной дугой и с короткими замыканиями, если размеры дугового промежутка меньше или равны размерам капли, сформировавшейся на торце электрода/9,14/.
Таким образом, добавка кислорода к углекислому, газу не изменяет вид переноса и лишь при сварке порошковой проволокой процесс сварки в С02 может производится каплями среднего размера Однако, при использовании смеси (С02+ 02) может быть несколько повышена производительность и улучшены некоторые характеристики процесса.
Другие авторы предлагают использовать сварку в смеси С02 и 02 с увеличенным вылетом электрода. При этом они отмечают, что кроме технологических особенностей такой вариант сварки характеризуется меньшей температурой металла электродных капель, что должно уменьшить окисление металла защитным газом и -несколько снизить чувствительность к образованию пор азота и водорода в металле.
С точки зрения хорошего качества ведение процесса и формирования швов в сварке применяется смесь аргона с гелием. При этом наиболее применимы следующие их соотношения: 50 % Аг и 50 % Не; и 40 % Аг и 60 % Не. Характер течения процесса близок к характеру течения процессов в чистом Не, но формирование шва лучше, а разбрызгивание меньше. При этом граница значения критического тока перехода к струйному переносу смешается в сторону аргона
Однако, эта смесь, при сварке низкоуглеродистых и низколегированных сталей не нашла применения, из-за высокой стоимости. Много работ посвящено исследованию процессов сварки в смесях аргона с такими газами как кислород, углекислый газ, углекислый газ и кислород, азот. С точки зрения влияния добавок к аргону представляется интересным изучение статьи /15/. Авторы данной статьи пытаются объяснить возникновение струйного переноса при сварке в смесях газов.
Сравнивая теплопроводности таких газов как С02, Не, N2, Н2 и Аг, при высоких температурах, они делают вывод, что теплопроводность газа не является определяющим физическим свойством, от величины которого зависит вид переноса металла электрода при сварке. Изучая влияние различных добавок газов к Аг на температуру дуги, которая влияет на температуру капель, изменяя их поверхностное натяжение, авторы показывают, что этот фактор также не гжячктияет решающего влияния на перенос электродного металла. В частности максимальную температуру имеет дуга, горящая в смеси (Аг*-Н2), однако, согласно эксперименту, струйного переноса при этом не наблюдается.
Пытаясь объяснить, почему присутствие небольших добавок 02 и СО2 в смеси с Аг приводит к уменьшению критического тока, необходимого для достижения струйного переноса, они отмечают, что нельзя однозначно судить, что этот фактор связан только с действием кислорода, снижающего поверхностное натяжение жидкого металла.
Оказалось, что лишь 3 газа — 02 , N0, N02 парамагнитны и имеют положительную магнитную восприимчивость, тогда как все остальные -диамагнитны и имеют отрицательную магнитную восприимчивость X, (таблица 1.1).
Наиболее вероятной причиной, определяющей вид переноса и уменьшающей критический ток при сварке в смесях Аг с 02 и с С02 является, по-видимому, совместное действие таких факторов как магнитные свойства кислорода и снижение поверхностного натяжения расплавленного металла под воздействием растворенного кислорода. По-видимому, присутствие парамагнитного газа, окружающего столб дуги, усиливает действие электродинамической силы, что приводит к уменьшению критического тока перехода к струйному переносу. Кроме того, под воздействием магнитного поля сварочного тока, возможны сепарация компонентов газовой смеси и концентрация кислорода вблизи поверхности расплавленной капли, что должно усилить его поглощение и снизить поверхностное натяжение расплавленного металла.
Таблица 1.1. Магнитная восприимчивость газов
Газ |
Х-106 |
Газ |
Х-106 |
С02 |
-0,525 |
СО |
-11,80 |
Аг |
-0,490 |
Кг |
-ОД50 |
02 |
+107,8 |
Н2 |
-1,990 |
N0 |
+ 48,70 |
Н |
-2^30 |
N02 |
+ 3,800 |
Н2 |
-0,430 |
Не |
-0,470 |
|
|
Наиболее часто используют смесь (Аг + Оз), содержащую кислород 3 -5 %. Причем процесс сварки практически такой же, как и в чистом аргоне. Величина /*р при этом немного уменьшается. Для струйного переноса в смеси (Аг + 02) характерно несколько большее разбрызгивание, чем при сварке в чистом Аг /14/. Также в промышленности нашли применение газовые смеси следующего состава:
(75 — 80) %Аг + (20 — 25) %С02; (70 — 75) %Аг + (20 — 25) %С02 + (3 — 5) %О2. Авторы работы 7 исследуют зависимость переноса электродного металла от изменения количества Аг в газовой смеси (Аг + С02). В частности, они отмечают, что при введении в С02 (10…80) %Аг размер капель электродного металла уменьшается, а частота их переноса возрастает. При этом разбрызгивание уменьшается. Это авторы связывают с тем, что капли не выходят за пределы столба дуги. Они указывают, что при 80 %Аг в смеси наблюдается максимальная стабилизация переноса, незначительное разбрызгивание и оптимальная форма проплавления.
Кроме вышеперечисленных газовых смесей в литературных источниках упоминается использование смесей с добавками азота. Так, например, добавка до 20 % N2 к аргону не влияет на процесс сварки, т.е. он практически такой же как и в чистом Аг /14/. Процесс приближается к сварке в чистом азоте при содержании азота в смеси более 33 %.
Источник: http:// svarschik . by
Сравниваем углекислоту или сварочную смесь
Обновлено: 23.04.2021 12:51:21Защитные газы, подаваемые к месту формирования сварочного шва, служат для защиты сварочной ванны и дуги от атмосферных газов, что способствует повышению качества соединения. Кроме того сами защитные газы влияют на состав шва, повышая его плотность, глубину провара, улучшая микроструктуру металла.
В практике сварочных работ используется два вида газов: смеси и чистый углекислый газ без примесей.
Наши эксперты рассмотрели свойства и особенности использования каждого вида защитных газов, их достоинства и недостатки, что поможет вам сделать правильный выбор, так как каждая разновидность имеет свою область применения.
Сварочные смеси
Основным компонентом сварочных смесей является инертный газ аргон, который может смешиваться не только с другими инертными, но и с активными газами. Помимо этого и активные разновидности тоже могут смешиваться между собой. Используются следующие сварочные смеси:
-
Аргон с углекислотой – применяется при сварке изделий из углеродистых и низколегированных сталей. Смесь способствует более ровному и пластичному формированию шва, снижает порообразование, облегчает перенос материала электрода;
-
Аргон с кислородом (не более 5 %) – применяется при работах с изделиями из легированных и низколегированных сталей. Повышает плотность шва за счет уменьшения пористости металла, облегчает процесс струйного переноса материала электрода. Позволяет использовать более широкий ассортимент присадочной проволоки;
-
Аргон с водородом – используется для соединения деталей из нержавеющей стали и никелевых сплавов;
-
Аргон и гелий – создает абсолютно инертную среду, применяется для соединения элементов из алюминия, меди и титана, а также хромоникелевой стали;
-
Углекислота и кислород – используется при сварке из углеродистых и низколегированных сталей.
Позволяет формировать более ровный шов за счет предотвращения разбрызгивания металла, увеличивает производительность работ из-за значительного повышения температуры в зоне сварки. К минусам можно отнести повышенное окисление материала, что снижает прочностные качества соединения.
Углекислота
Углекислота или двуокись углерода в чистом виде используется для сварочных работ. Применяется для деталей из углеродистых и низколегированных сталей, а также никелевых и железоникелевых сплавов, в том числе изделий большой толщины.
Чистая двуокись углерода обладает более высокой плотностью, чем воздух, поэтому при подаче в зону сварки она вытесняет воздух, обеспечивая защитную среду. Углекислота бесцветна и не имеет запаха, хранится в стальных баллонах в виде жидкой субстанции под давлением, подается в зону работ с помощью специального редуктора. Может использоваться при любых видах сварки – ручной, полуавтоматической или автоматической. Самое широкое применение углекислота имеет при полуавтоматической сварке.
Железо и углерод, входящие в состав свариваемых деталей, при сварке в среде углекислого газа и под его воздействием окисляются. Поэтому для образования шва используется специальная присадочная проволока, в состав которой входят кремний и марганец, что предотвращает окисление металла. Расход двуокиси углерода зависит от нескольких факторов: толщины металла соединяемых заготовок, диаметра присадочной проволоки и параметров тока, подаваемого на электрод.
Таблица достоинств и недостатков
Наименование |
Достоинства |
Недостатки |
Сварочные смеси |
+ увеличение производительности за счет повышения массы наплавляемого металла в единицу времени; + снижение лишнего расхода присадочного материала за счет уменьшения количества брызг; + повышение пластичности шва, плотности за счет меньшего порообразования и, соответственно, значительное повышение прочности соединения; + снижение количества вредных аэрозолей и дымов на рабочем месте, что улучшает гигиенические условия труда;
+ стабильность процесса даже при неравномерной подаче присадочной проволоки.
|
— для смеси аргона с кислородом повышенное окисление металлов, что снижает прочность швов, также образование вредного для здоровья угарного газа; — смесь аргона с углекислым газом взрывоопасна, что требует особых предосторожностей при ведении работ; — при работах со смесью аргона с углекислотой также образуется угарный газ вследствие взаимодействия углекислоты с кислородом воздуха, поэтому оператор должен работать в специальной маске.
|
Углекислый газ |
+ возможность сваривать тонкие металлические листы, которые не деформируются, а также относительно толстых заготовок в любых пространственных положениях, то есть делать горизонтальные, вертикальные и потолочные швы; + образование хорошей дуги, что удобно для сварщиков с небольшим опытом работ; + низкая стоимость способа сварки и самой углекислоты; + безопасность в работе; + возможность сварки металлов с разными характеристиками; + несложность и доступность оборудования для сварки; + высокое качество получаемых швов;
+ при соединении деталей с большой толщиной металла углекислый газ выделяет много теплоты, что повышает производительность. |
— повышенное брызгообразование, что вызывает необходимость очистки сварных швов после сварки; — прочностные характеристики швов более низкие, чем при способах сварки под флюсом или электродами с покрытием, поэтому не рекомендуется использовать этот метод для деталей, которые будут работать в условиях низких температур или ударных нагрузок.
|
Основные отличия
Основные отличия углекислоты и сварочных смесей заключаются в следующем:
-
углекислота может использоваться только для сварки определенных видов металлов – углеродистых и низколегированных, сварочные смеси же имеют более широкую область применения – с их помощью можно сваривать детали из цветных металлов и различных сплавов;
-
углекислый газ однороден, а сварочные смеси состоят из разных газов, которые нужно смешивать с помощью специального оборудования в строго установленных пропорциях;
-
производительность сварки в среде сварочных смесей почти вдвое выше, чем производительность сварки в среде углекислого газа.
Чем похожи материалы
Сварочные смеси и углекислый газ имеют одно общее свойство – используются для создания среды, которая улучшает качество и производительность сварочных работ.
Выводы: Подводя итог, можно сделать вывод, что сварочные смеси имеют преимущество перед углекислым газом за счет более широких возможностей работы с разными материалами, более высокой производительности и получения более качественных и прочных соединений. При этом нужно заметить, что работа с углекислым газом может быть предпочтительнее в узконаправленной сфере работы с определенными материалами и при полуавтоматической сварке.
Оцените статью | |
Всего голосов: 1, рейтинг: 5 |
Сварочные газы MIG — выбор и опции для большинства металлов
Выбор газа для сварки MIG различных металлов
Газ для сварки MIG — это то, что делает сварку MIG возможной. Об этом нам сообщает название: «Сварка металлов в среде инертного газа». Инертные газы, используемые для сварки MIG, — это аргон и гелий. Термин «инертные» означает, что они не реагируют ни на что, в отличие от неинертных газов, таких как кислород, который вызывает ржавчину металла. Используемые газы защищают сварной шов от воздуха, вызывающего такие дефекты сварки, как пористость.
Когда в смесь добавляется углекислый газ или кислород, сварка MIG технически больше не является сваркой MIG. Это связано с тем, что и углекислый газ, и кислород не являются инертными газами. Затем процесс становится GMAW или дуговой сваркой металлическим газом.
Углекислый газ Неинертный газТип используемого газа также определяет:
- Насколько глубоко сварной шов проникает в свариваемый металл.
- Характеристики сварочной дуги.
- Механические свойства сварного шва.
При выборе типа используемого газа лучше всего обратиться за информацией в магазин сварочных материалов. Магазин порекомендует правильный газ, соответствующий используемой сварочной проволоке. Другой вариант — использовать рекомендации производителя сварочной проволоки. Как правило, производитель сварочной проволоки предоставляет несколько вариантов, начиная от наилучшего и заканчивая тем, что обеспечивает минимально приемлемые результаты. Наконец, на внутренней панели некоторых сварочных аппаратов MIG есть рекомендации по сварочным электродам и газам, которые дают вам варианты, как показано на рисунке ниже.В большинстве случаев окончательный выбор типа газа зависит от стоимости.
Характеристики газов для сварки MIG
Различные газы обеспечивают разные типы проплавления сварного шва и характеристики дуги. Вот основы:
- Газ аргон имеет неглубокое широкое проникновение и имеет очень гладкую жидкость, как дуга.
- Гелий обеспечивает очень горячую сварку с хорошей производительностью сварки и мягким проплавлением с помощью жидкостной дуги.
- Углекислый газ обеспечивает глубокое узкое проплавление с жесткой жесткой дугой, которая хорошо работает при сварке в неудобных положениях.
- Добавление двуокиси углерода к аргону или гелию углубляет проплавление и делает дугу более жесткой, улучшая качество сварки в нерабочем положении.
- Кислород, добавленный к гелию или аргону в небольших количествах, углубляет провар и делает дугу более жесткой.
- Добавление гелия в любую смесь делает дугу более горячей.
Влияние сварочного газа MIG на тип переноса дуги
Выбор защитного газа также влияет на тип переноса сварки. Вот основные типы переноса, связанные с газами:
- Для переноса короткого замыкания требуется либо чистый углекислый газ, либо высокий процент углекислого газа.
- Шариковый перенос лучше всего работает с 75% или более аргона в смеси.
- Спрей-перенос в зависимости от материала также содержит 75% аргона вплоть до чистого аргона для таких металлов, как алюминий.
Наиболее распространенные газы, используемые для сварки MIG
Четыре наиболее часто используемых газа:
- Аргон
- CO2 / двуокись углерода
- O2 / кислород
- Гелий (наименее распространенный)
В большинстве случаев эти газы используются в виде смеси, обычно состоящей из двуокиси углерода и аргона или кислорода.Кислород является причиной большинства дефектов сварки, однако в небольших количествах, смешанных с другими газами, он улучшает характеристики дуги. Аргон и углекислый газ можно использовать сами по себе. В некоторых случаях используется трехкомпонентный защитный газ, содержащий аргон, двуокись углерода и гелий или аргон, двуокись углерода и кислород. Я недавно использовал эту последнюю смесь, когда проходил сертификацию сварщика 3G MIG.
Наиболее распространены смеси и газы.
- C2 или 2 % углекислого газа и 98 % аргона
- C25 или 25 % углекислого газа и 95 % аргона
- 100 % углекислого газа
- 100 % аргона
Сварочный газ MIG для сварки углеродистой стали
Сварка углеродистой стали может выполняться только с использованием углекислого газа, и он обеспечивает самое глубокое проникновение, наибольшее количество дыма и самый грубый сварной шов. Наиболее широко используемая смесь называется C25 и состоит из 25% углекислого газа и 75% аргона. Существуют и другие смеси, которые хорошо работают в зависимости от типа сварки, которая будет выполняться. Большинство из них спроектировано магазинами и сетями газоснабжения сварочного производства. Обычная смесь представляет собой комбинацию аргона, углекислого газа и кислорода. Сварка MIG углеродистой стали
Сварочный газ MIG для сварки нержавеющей стали
Сварка нержавеющей стали обычно выполняется с использованием C2 или 2% углекислого газа и 98% аргона.В некоторых случаях используется трехкомпонентный защитный газ, содержащий 90 % гелия, 7,5 % аргона и 2,5 % углекислого газа. Опять же, во многих магазинах сварочных материалов есть свои собственные смеси, которые могут улучшить качество сварки и облегчить сварку нержавеющей стали. Сварка MIG из нержавеющей стали
с использованием газа C2.Сварочный газ MIG для сварки алюминия
Сварка алюминия обычно выполняется только с использованием аргона, за одним исключением. Если свариваемый алюминий толще ½ дюйма, в смесь может быть добавлен гелий.
аргон. ]]>
14 Аргон-гелий-углекислый газ Гелий и CO 2 добавление аргона увеличивает подвод тепла к сварному шву и улучшает стабильность дуги.Лучшее смачивание и профиль борта достигается. При сварке углеродистых и низколегированных сталей гелием используются дополнения для увеличения тепловложения и улучшения текучести лужи почти таким же образом что кислород используется, кроме что гелий инертен и окисление металла шва и потеря сплава не являются проблема. При сварке низких легированный материал, механические свойства могут быть достигнуты и сохранены более легко. Аргон — 10-30% He — 5-15% CO 2 – Смеси в этом диапазоне были разработаны и продается для импульсного спрея дуговая сварка как углеродистой, так и низколегированной стали.


Чем опасны газы при сварке и резке?
Введение
При сварке и резке могут образовываться газы, опасные для здоровья. Образующийся газ или газы и их концентрации зависят от используемого процесса и механизмов образования газа. Газы, некоторые из которых могут быть опасными, присущи некоторым процессам либо в качестве защитного газа для защиты расплавленной сварочной ванны от атмосферного загрязнения, либо в пламенных процессах в качестве расходуемого материала, который сгорает.
Многие газы подпадают под действие Правил контроля за опасными для здоровья веществами (COSHH) 2002 г. (поправка) 2004 г., которые требуют, чтобы их воздействие не превышало концентраций, известных как пределы воздействия на рабочем месте (WEL). Значения WEL приведены в Руководстве Eh50 Управления по охране труда и технике безопасности (HSE), которое обычно обновляется ежегодно.
Воздействие газов может быть измерено в соответствии с методологией, определенной в BS EN ISO 10882-2: 2000. Здоровье и безопасность при сварке и родственных процессах. Отбор проб частиц и газов в воздухе в зоне дыхания оператора. Часть 2. Отбор проб газов.Измерение воздействия может использоваться для проверки соблюдения правил, определения необходимости контроля воздействия или выявления неисправностей в существующих системах контроля.
В этом документе приводится информация об образующихся газах, их происхождении, воздействии на здоровье и их ожидаемых концентрациях относительно пределов воздействия.
Рекомендации по образующимся газам и их ожидаемым концентрациям относительно пределов воздействия приведены в Руководящей записке EH54 Управления по охране труда и технике безопасности «Оценка воздействия дыма при сварке и родственных процессах».Более подробная информация представлена в этом документе.
Опасности, последствия для здоровья и риски
Защитные газы
Для процессов сварки в защитных газах, таких как TIG, MIG/MAG, FCAW, защитными газами могут быть инертные газы, такие как аргон, гелий и азот, или смеси на основе аргона, содержащие двуокись углерода, кислород или и то, и другое. Гелий может быть добавлен к смесям аргона/двуокиси углерода для повышения производительности. Углекислый газ (CO 2 ) может использоваться сам по себе в MAG и FCAW. За исключением CO 2 , эти газы не считаются опасными для здоровья в соответствии с Правилами COSHH, но они являются удушающими.CO 2 имеет предел долгосрочного воздействия 5000 частей на миллион (8-часовой базовый период) и предел кратковременного воздействия 15000 частей на миллион (15-минутный базовый период). Ни один из газов не виден и не имеет запаха, поэтому их присутствие в опасных концентрациях трудно обнаружить без предварительных знаний или измерительного оборудования.
Основной опасностью, возникающей при воздействии защитных газов, является удушье, обычно возникающее в результате скопления газов в замкнутом пространстве. Защитные газы подаются со скоростью около 15 л/мин в процессах сварки в среде защитных газов, и газы могут вытекать из соединений на линиях подачи газа, если они не затянуты должным образом.Аргон тяжелее воздуха, поэтому аргон и газы, состоящие в основном из аргона, имеют тенденцию скапливаться в низких местах, таких как ямы. Вдыхание газа, такого как чистый аргон, который не содержит кислорода, может привести к потере сознания за считанные секунды. Рабочие не должны входить в атмосферу, содержащую менее 18% кислорода.
Газы, образующиеся в процессе
Окись углерода и двуокись углерода
Окись углерода (CO) и CO 2 могут образовываться в процессах сварки под флюсом при воздействии тепла на флюсовые материалы, такие как карбонаты и целлюлоза. При сварке MAG они оба могут образовываться из CO 2 в защитном газе, при этом CO 2 подвергается реакции вблизи дуги с образованием CO. Пламенные процессы также генерируют CO и CO 2 . Относительные количества зависят от того, является ли пламя окислительным или восстановительным, при этом CO присутствует в более высоких концентрациях, когда пламя восстанавливается.
CO гораздо более опасен из двух газов. Это может привести к снижению кислородной емкости крови, что может привести к летальному исходу.В более низких концентрациях вызывает головную боль и головокружение, тошноту и слабость. CO 2 действует в основном как удушающее средство, как указано выше. CO имеет краткосрочный предел воздействия (15-минутный базовый период) 200 частей на миллион и долгосрочный предел (8-часовой базовый период) 30 частей на миллион. Сверху значения для CO 2 составляют 15000 и 5000 ppm для краткосрочного и долгосрочного базисных периодов соответственно.
Количества CO и CO 2 , образующиеся в процессах с флюсами, невелики и, как правило, не представляют проблемы воздействия.Количество CO и CO 2 , образующихся в пламенных процессах, также невелико, поэтому риск чрезмерного воздействия обычно невелик. В особых случаях, таких как высокоскоростная кислородно-топливная резка, когда большое количество газа потребляется за короткий период времени, риск чрезмерного воздействия CO может быть проблемой.
Сварка MAG с защитным газом из диоксида углерода или защитными газами с высоким содержанием диоксида углерода, напр. 80%Ar/20%CO 2 обычно не представляет проблемы воздействия CO или любого CO 2 , образующегося в процессе.Однако, как указано выше, может возникнуть проблема удушья CO 2 . Аналогичный комментарий можно сделать и по поводу FCAW в среде защитного газа.
Монооксид азота и диоксид азота
Оксид азота (NO) и диоксид азота (NO 2 ) вместе известны как азотистые газы (NO x ). Они могут быть получены путем окисления азота в воздухе теплом от дуги или пламени. Предупреждения о химической опасности (CHAN) были выпущены в Великобритании в 2003 году, в которых были отменены пределы воздействия NO и NO 2 , поскольку они не считались достаточными для защиты гигиены труда.Для каждого газа были рекомендованы новые пределы воздействия 1 ppm за 8-часовой TWA.
Оксид азота является сильным раздражителем глаз, кожи и слизистых оболочек. Двуокись азота является высокотоксичным раздражающим газом. После вдыхания азотистые газы больше действуют на более глубокие, чем на верхние (нос, трахею, крупные бронхи) дыхательные пути. На первичную стадию отравления нитрозными газами указывают следующие симптомы:
- Раздражение глаз, носа и трахеи
- Интенсивный кашель
- Затрудненное дыхание
- Головокружение и головная боль
- Болезнь и усталость
Симптомы чрезмерного воздействия могут не проявляться в течение нескольких часов после прекращения резки. Сильное чрезмерное воздействие может привести к накоплению воды в легких, что ухудшает поступление кислорода в кровь и может привести к смерти.
При сварке выделяется лишь небольшое количество азотистых газов, поэтому воздействие азотистых газов во время сварки не представляет проблемы. Проблемы с воздействием могут возникнуть во время резки, особенно если резка выполняется вручную, так как это приближает оператора к выбросам. Более горячее пламя генерирует более высокие концентрации азотистых газов, поэтому при использовании ацетилена образуется больше азотистых газов, чем при использовании пропана или природного газа.
Риск чрезмерного воздействия азотистых газов считается низким при газокислородной резке, за исключением случаев, когда условия работы неблагоприятны, т.е. ручная резка в ограниченном пространстве с высокой нагрузкой.
При плазменной резке воздухом или азотом выделяется больше азотистых газов, чем при газокислородной резке, и существует значительный риск чрезмерного воздействия.
Пламя свободного горения создает самые высокие концентрации NO и NO2, а также самый высокий риск чрезмерного воздействия.Следует соблюдать осторожность во время таких операций, как нагрев пламенем, правка пламенем, пайка пламенем, напыление пламенем и т. д., особенно потому, что выбросы от этих процессов трудно контролировать. Пламя должно быть погашено, когда оно не используется.
Озон
Озон может образовываться в результате реакции между УФ-излучением дуги и кислородом воздуха. Предел воздействия озона составляет 0,2 промилле в течение 15-минутного контрольного периода.
При уровнях воздействия озона, обнаруженных при сварке, основной проблемой является раздражение верхних дыхательных путей, характеризующееся кашлем и стеснением в груди, но неконтролируемое воздействие может привести к более серьезным последствиям, включая повреждение легких.
Сварка MIG алюминиевых сплавов с алюминиево-кремниевой присадочной проволокой приводит к образованию самых высоких концентраций озона. При использовании алюминиевой присадочной проволоки образуется значительно меньше озона, а при использовании алюминиево-магниевой присадочной проволоки выделяется меньше всего озона при сварке MIG алюминиевых сплавов. Другими комбинациями процесса/материала, которые могут создавать гигиенически значимые концентрации озона, являются MAG/мягкая сталь, MAG/нержавеющая сталь и TIG/нержавеющая сталь.
Озон образуется только во время дугового разряда и быстро распадается при гашении дуги.Следовательно, воздействие озона очень зависит от используемого рабочего цикла. Хотя исследования в лаборатории показали, что концентрации озона в точках вокруг сварочной дуги могут превышать 0,2 ppm, редко можно обнаружить, что среднее воздействие озона в реальной рабочей ситуации превышает предел воздействия озона. Исключением из этого утверждения является воздействие озона во время сварки MIG с использованием расходных материалов из алюминия/кремния.
Органические газы
Становится все более распространенным, особенно при контактной сварке в автомобильной и бытовой промышленности, сварка через или рядом с органическими материалами, такими как заводские грунтовки, органические покрытия, клеи, герметики, масла и т. д.Вывод установки из эксплуатации может включать резку многих материалов покрытия, включая краску.
В процессе сварки или резки может образовываться широкий спектр продуктов разложения, состав которых трудно предсказать даже при знании состава свариваемого или разрезаемого продукта. Кроме того, редко можно найти информацию о продуктах разложения в паспортах безопасности материалов. Исследования показали, что может образовываться широкий спектр токсичных продуктов разложения, но их концентрации обычно низки.Для многих продуктов разложения не установлены пределы воздействия, но это не означает, что они безопасны. Должен осуществляться контроль до уровней, допускающих воздействие без вреда для здоровья.
Обезжиривающие газы-растворители
Хлорированные углеводороды, такие как трихлорэтилен, могут использоваться для обезжиривания. Излучение сварочной дуги вызывает разложение паров трихлорэтилена на продукты, которые легко обнаруживаются по запаху. Первичными продуктами разложения являются дихлорацетилхлорид и хлористый водород, а также фосген, который имеет очень низкие пределы воздействия (долговременный предел 0.02ppm, краткосрочный предел 0,06ppm). К счастью, запаха и слезоточивости первоначальных продуктов распада достаточно, чтобы предупредить сварщика о проблеме, и сварка, скорее всего, будет остановлена до того, как будет достигнут опасный уровень любого продукта.
Скорость образования окиси углерода при дуговой сварке CO2
Цели: Отравление угарным газом представляет собой серьезную производственную опасность на рабочих местах в Японии.Хотя неполное сгорание является основной причиной образования угарного газа, существует риск отравления угарным газом во время некоторых сварочных операций. Цель настоящего исследования состояла в том, чтобы оценить скорость образования CO при дуговой сварке CO2 в контролируемых лабораторных условиях и оценить требования к вентиляции для предотвращения отравления CO.
Методы: Наварка валика на пластину выполнялась с помощью автоматического сварочного робота на основном металле стального проката в нескольких условиях.Концентрация CO, выделяемого при сварке, измерялась монитором CO в режиме реального времени в хорошо проветриваемой лаборатории, свободной от окружающего загрязнения CO. Скорость образования CO была получена из трех измерений: скорости потока сварочного отходящего газа, концентрации CO в отходящем газе и времени горения дуги. Затем рассчитывали потребность в вентиляции для предотвращения отравления угарным газом.
Результаты: Скорость образования СО составила 386-883 мл/мин для сплошной проволоки и 331-1293 мл/мин для порошковой проволоки соответственно.Было обнаружено, что концентрация CO в помещении теоретически будет поддерживаться ниже ПДК OSHA (50 частей на миллион) при условии, что скорость вентиляции в помещении составляет 6,6–25,9 м3/мин. Фактическая потребность в вентиляции была оценена в 6,6-259 м3/мин с учетом неполного перемешивания.
Выводы: Чтобы предотвратить отравление угарным газом, необходимо срочно принять некоторые контрмеры против газообразных выбросов, а также сварочного дыма.
КАКОЙ ЗАЩИТНЫЙ ГАЗ ЛУЧШИЙ ДЛЯ СВАРКИ MIG?
КАКОЙ ЗАЩИТНЫЙ ГАЗ НАИБОЛЕЕ ЛУЧШИЙ ДЛЯ СВАРКИ MIG?
Сварка МИГ с защитный газ и сплошной проволочный электрод обеспечивают чистый шов без шлака без необходимости постоянно останавливать сварку для замены электрода, как в палке сварка.
Повышение производительности
и уменьшенная очистка — это лишь два из возможных преимуществ этого процесса.Основная цель защитного газа – предотвратить обнажение расплавленного сварного шва.
бассейн с кислородом, азотом и водородом, содержащимся в атмосфере. Реакция
этих элементов со сварочной ванной может создать множество проблем,
включая пористость (отверстия в сварном шве) и чрезмерное разбрызгивание.
Различные защитные газы также играют важную роль в определении сварного шва.
профили проплавления, стабильность дуги, механические свойства готового
сварка, используемый вами процесс переноса и многое другое.
Выбор правильного газа.
Многие сварки MIG позволяют использовать различные варианты защитного газа, и вы необходимо оценить свои сварочные цели, чтобы выбрать правильный для вашего конкретное приложение. Стоимость газа, свойства готового шва, подготовка, очистка после сварки, основной материал, процесс переноса сварки и все ваши цели производительности должны быть приняты во внимание при выборе экранирования газ.
Аргон, гелий, углерод
Диоксид и кислород являются четырьмя наиболее распространенными защитными газами, используемыми в MIG.
сварка, каждая из которых имеет уникальные преимущества и недостатки в каждом отдельном случае. применение.
Защитные газы для сварки MIG/GMAW
Металл Сварка в среде инертного газа иногда называется газовой дуговой сваркой металлом. Основным газом для сварки MIG/MAG является аргон (Ar). Гелий (He) может быть добавлен для увеличения проплавления и текучести сварочной ванны. Аргон или смеси аргона и гелия можно использовать для сварки всех марок стали.Однако небольшие добавки кислорода (O2) или углекислого газа (CO2) обычно необходимы для стабилизации дуги, повышения текучести и улучшения качества наплавленного металла. Для нержавеющих сталей также доступны газы, содержащие небольшое количество водорода (h3).
Защитные газы для сварки TIG/GTAW
Обычным газом для сварки TIG является аргон (Ar). Гелий (He) может быть добавлен для увеличения проплавления и текучести сварочной ванны. Аргон или смеси аргона и гелия можно использовать для сварки всех марок стали.В некоторых случаях для достижения особых свойств можно добавлять азот (N2) и/или водород (h3). Например, добавление водорода дает такой же, но гораздо более сильный эффект, как добавление гелия. Однако добавки водорода не следует использовать для сварки мартенситных, ферритных или дуплексных марок стали.
В качестве альтернативы, если добавить азот, можно улучшить свойства наплавленного металла, легированного азотом. Окислительные добавки не используются, поскольку они разрушают вольфрамовый электрод.
Рекомендации по защитным газам, используемым при сварке ВИГ различных нержавеющих сталей, приведены в таблице.Для плазменно-дуговой сварки в качестве плазмообразующего газа в основном используются типы газа с добавками водорода, указанные в таблице, а в качестве защитного газа – чистый аргон.
Газы для сварки
Углекислый газ (CO2): Наиболее распространенный из реактивных
газы, используемые при сварке MIG, особенно в Нигерии, и единственные, которые можно использовать в чистом виде.
без добавления инертного газа. CO2 также является наименее дорогим из
общие защитные газы, что делает привлекательный выбор, когда материальные затраты являются
главный приоритет.Чистый CO2 обеспечивает очень глубокое проплавление сварного шва, что полезно
для сварки толстого материала; однако он также дает менее стабильную дугу и
разбрызгивается больше, чем при смешивании с другими газами. Он также ограничен
только процесс короткого замыкания. Для многих компаний, в том числе тех, которые размещают
акцент на качество сварного шва, внешний вид и снижение очистки после сварки,
смесь от 75% до 95% аргона и от 5% до 25% CO2 обеспечит более
желательное сочетание стабильности дуги, контроля над сварочной ванной и меньшего разбрызгивания, чем
чистый СО2.Эта смесь также позволяет использовать процесс переноса распылением, который
может обеспечить более высокую производительность и более привлекательный внешний вид сварных швов.
Аргон: Также производит более узкую
профиль провара, который полезен для угловых и стыковых швов. Если ты
сварка цветного металла; алюминий, магний или титан, вам потребуется
используйте 100% аргон.
Кислород : Это также реактивный газ. Обычно это используется в соотношении девять процентов или менее для улучшения текучести сварочной ванны, проплавление и стабильность дуги в мягкой углеродистой, низколегированной и нержавеющей стали.Однако это вызывает окисление металла шва, поэтому не рекомендуется для использования с алюминием, магнием, медью или другими экзотическими металлами.
Гелий : В отличие от чистого аргона, обычно используется с
цветные металлы, но и нержавеющие стали. Поскольку он производит широкое,
профиль глубокого проникновения, гелий хорошо работает с толстыми материалами и обычно
используется в соотношении от 25% до 75% гелия и от 75% до 25% аргона. Настройка этих
коэффициенты изменяют проникновение, профиль борта и скорость перемещения.гелий
создает «более горячую» дугу, что позволяет увеличить скорость движения и повысить
показатели продуктивности.
Однако газообразный гелий дороже и требует более высокая скорость потока, чем у аргона, поэтому вам необходимо рассчитать значение увеличение производительности на фоне увеличения стоимости газа. С нержавеющей стали, гелий обычно используется в трехкомпонентной смеси аргона и CO2.
Когда двуокись углерода или В смесь добавляется кислород, MIG-сварка технически не является MIG-сваркой. больше.Это связано с тем, что и углекислый газ, и кислород не инертные газы. Затем процесс становится GMAW или дуговой сваркой металлическим газом.
Характеристики MIG Сварочные газыРазличные газы производят различные типы проплавления сварного шва и характеристики дуги.
- Газ аргон имеет неглубокое широкое проникновение и очень гладкая флюидная дуга.
- Гелий дает очень горячий сварной шов с хорошим сварным швом производительность и мягкое проплавление плавной дугой.
- Двуокись углерода производит глубокое узкое
проплавление жесткой резкой дугой, которая хорошо работает при сварке в любом положении.
- Добавление диоксида углерода к аргону или гелию углубляет проплавление и делает дугу более жесткой, улучшая сварку в нерабочем положении.
- Кислород, добавляемый к гелию или аргону в небольших увеличивает глубину проплавления сварного шва и делает дугу более жесткой.
- Добавление гелия в любую смесь делает дугу более горячей.
Для получения дополнительной информации чтобы узнать о нашем ассортименте продукции, пожалуйста, свяжитесь с GZ Industrial Supplies или напишите нам по адресу info@gz-ind.ком.
20 января 2020 г. Огочукву Агина
Сварочный газ MIG | Выбор защитного газа
Сварка MIGс защитным газом помогает производить высококачественные сварные швы, поскольку вы предотвращаете воздействие на сварочную ванну элементов в атмосфере, которые загрязняют сварной шов и вызывают дефекты сварки, включая пористость и брызги.
Существуют различные типы сварочного газа MIG, подходящие для различных требований. В этом руководстве объясняется, как подобрать правильную смесь защитного газа, объясняя доступные газы и их свойства.
Какой газ используется для сварки MIG?
Наиболее распространенными газами, используемыми при сварке MIG, являются углекислый газ, аргон, кислород и гелий, они часто используются в виде смеси двух газов в одном газовом баллоне. Наиболее распространенными для стали являются чистый CO2 и смесь 75% аргона и 25% CO2. Чистый CO2 является более дешевым вариантом, но дает более низкое качество сварных швов.
Различные газы соответствуют различным требованиям, поэтому вам необходимо оценить, какая газовая смесь лучше всего подходит для ваших нужд.Стоимость газа и качество сварки являются двумя основными факторами, которые следует учитывать при выборе защитного газа для сварки MIG. Ниже мы объяснили различные типы газов и области применения MIG, для которых они наиболее подходят.
Чистый углекислый газ (CO2)
CO2 является самым дешевым защитным газом, что делает его популярным выбором сварочного газа MIG, где существенным фактором является низкая стоимость материалов. Основная проблема с CO2 заключается в том, что дуга менее стабильна, чем другие газовые смеси, и дает много брызг.Поэтому, если вам нужно потратить время на очистку сварных швов, вы можете увеличить расходы, но если эстетика не важна, то это хороший выбор. CO2 горячий и обеспечивает глубокое проплавление, что делает его хорошим выбором для более толстых металлов или если вы хотите получить максимальное проплавление от сварочного аппарата MIG 115 В, но держитесь подальше, если вы свариваете тонкий листовой металл кузова. Если вы хотите получить более качественные сварные швы с CO2, вы можете купить смесь аргона и CO2 для более качественных сварных швов.
Сводка:
- Дешево
- Глубокое проникновение
- Много брызг
- Не подходит для тонкого металла
Смесь аргона и двуокиси углерода (CO2)
Смесь газов аргона и CO2 является популярной смесью защитного газа, которая обеспечивает более высокое качество сварки и меньшее разбрызгивание, чем чистый CO2. Присутствие аргона помогает сузить проплавление, обеспечить гораздо большую стабильность дуги и уменьшить разбрызгивание, обеспечивая плавный перенос струйной дуги. Смесь аргона и CO2 будет содержать от 75% до 95% аргона и от 5% до 25% CO2. Смеси с более высоким содержанием CO2 будут давать больше брызг, однако смеси с содержанием аргона более 80% могут иметь дугу, которая становится слишком жидкой и трудно контролируемой, что особенно проблематично, если вы выполняете сварку в нерабочем положении. Смесь аргона с CO2 дороже, чем чистый CO2, поэтому, если качество сварки и внешний вид не так важны, как снижение затрат на материалы, обратите внимание на чистый CO2.Смесь аргона с CO2 отлично подходит, если вы хотите сократить время очистки после сварки.
Сводка:
- Меньше брызг
- Сокращение времени очистки
- Дорогой
- Высокое качество сварки
Чистый аргон
Газ Pure Argon можно использовать для сварки MIG, но только если вы свариваете цветные металлы, такие как алюминий, магний или титан. Чистый аргон не рекомендуется для сварки стали и не обеспечивает достаточную теплопроводность для сварки черных металлов методом MIG.Если вы попытаетесь сварить сталь MIG со 100% аргоном, вы не получите достаточного проплавления или плавления, и сварной шов будет слабым. Цветные металлы, такие как алюминий, будут использовать 100% защитный газ аргон для сварки наилучшего качества. Аргон и гелий — вторая по распространенности смесь для цветных металлов, за которой следует чистый гелий.
Сводка:
- Лучший для цветных металлов
- Не подходит для стали
Аргон и гелий
Гелий в основном используется при сварке MIG цветных металлов для повышения температуры.Гелий обеспечивает очень широкое проплавление и имеет более высокую скорость потока, чем аргон, поэтому скорость сварки может быть выше, чем у чистого аргона. Гелий дороже, но вы можете компенсировать материальные затраты за счет повышения производительности и снижения трудозатрат. Процент используемого гелия может варьироваться от 25% до 75%, при этом большее количество гелия обеспечивает более широкое проникновение и скорость перемещения. Как правило, для более толстого основного металла требуется более высокий процент гелия. 75% гелия действительно можно использовать только для сварки алюминия толщиной 1 дюйм и выше в плоском положении.
Сводка:
- Лучший для цветных металлов
- Широкое проникновение
- Высокая скорость сварки
Чистый гелий
Гелийможно использовать отдельно для сварки MIG цветных металлов, однако он лучше подходит для сварки TIG с отрицательным электродом. Высокое содержание гелия лучше всего использовать для сварки MIG на более толстых материалах. Скорость сварки можно увеличить до высокой для повышения производительности, однако это дорого и используется очень редко по сравнению со смесями аргона и аргона с гелием.
Сводка:
- Лучший для цветных металлов
- Подходит для толстого основного металла
- Редко используется
Аргон и кислород
Кислород никогда не используется в качестве базового газа, но его можно смешивать в количествах обычно от 1% до 5%. Небольшие количества кислорода можно смешивать с аргоном и CO2, поскольку это помогает стабилизировать дугу, улучшить текучесть сварочной ванны и улучшить качество сварного шва и провара. Недостатком кислорода является то, что он вызывает окисление металла, поэтому его нельзя использовать при сварке алюминия, магния или меди.Кислород и аргон обычно используются для переноса распылением на нержавеющую сталь, чтобы помочь получить стабильную дугу, однако повышенная текучесть сварочной ванны может сделать сварку вне положения проблематичной.
Сводка:
- Может вызывать окисление алюминия, магния и меди
- Помогает стабилизировать дугу
Баллон с CO2 10 литров / 6,35 кг Сварочный газ
- Емкость для воды — 10 л
- Прибл. Высота — 910мм
- Прибл.Диаметр — 140мм
- Прибл. Вес брутто — 25 кг
- Прибл. Номинальное содержимое — 6,35 кг
- Прибл. Давление наполнения — 55 бар — 725 фунтов на кв.
дюйм
- Выпускной клапан — BS №8 0,860 RH EXT
- Класс доставки — 2.2 (UN1013)
Баллон CO2 Размеры и вес 10 литров являются приблизительными и могут варьироваться.
£50.00 Депозит требуется для всех 10-литровых баллонов, который полностью возвращается по телефону в любое время , полная сумма, которую вы заплатили, без вычетов!
Помните, что все наши баллоны поставляются в БЕСПЛАТНУЮ АРЕНДУ с БЕСПЛАТНОЙ ДОСТАВКОЙ ПО МЕСТНЫМ МЕСТАМ. Без доставки, сбора, транзакций, экологических или любых других скрытых платежей, и вы не можете получить более выгодную сделку!
Доступная поставка
- Нажмите и заберите с нашего склада (Ланкашир) — БЕСПЛАТНО
- Бесплатная местная доставка (пн-сб) — БЕСПЛАТНО
Местные поставки
Chorley Bottle Gas Ltd предлагает бесплатную местную доставку всех наших крупных товаров, таких как газ в баллонах, красное дизельное топливо, Paraffin Extra и Campingaz
.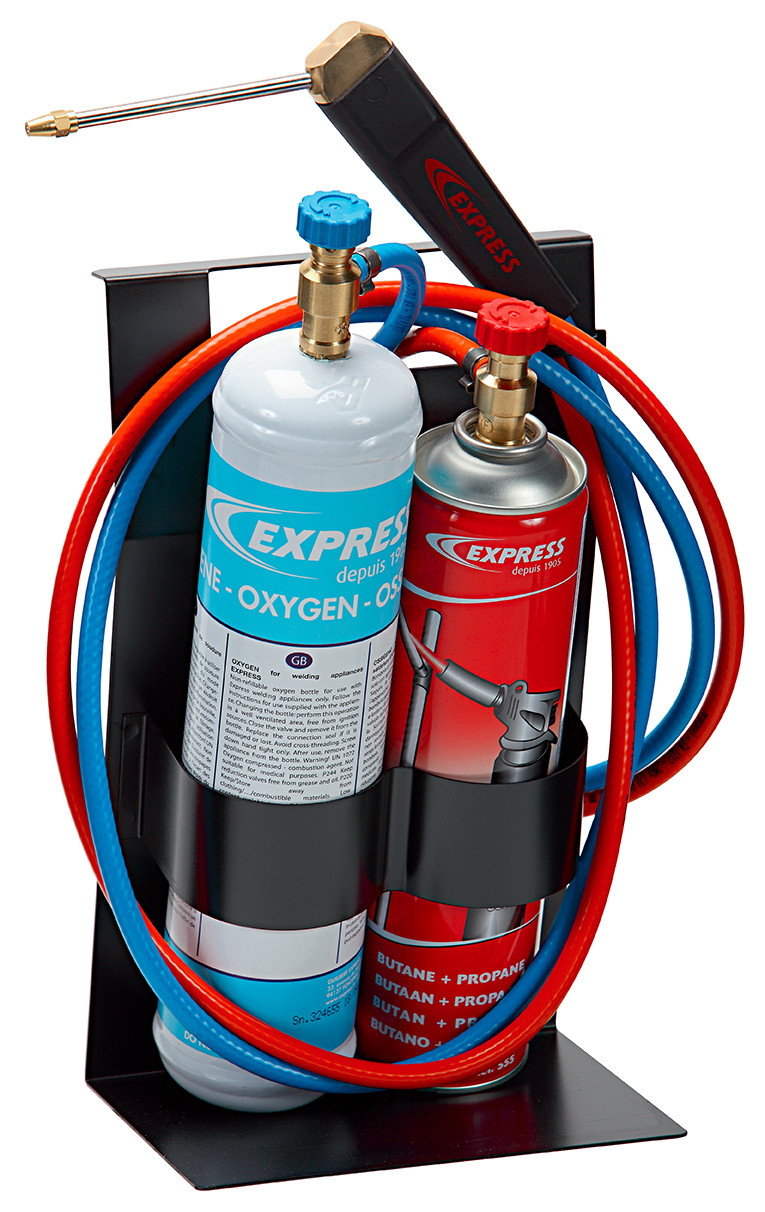
Мы доставляем в следующие районы каждый рабочий день:
- Адлингтон
- Аспулл
- Белмонт
- Блэкрод
- Болтон
- Чорли
- Фарнворт
- Хорвич
- Лейланд
- Престон (см. ниже)
- Уэстхотон
- Уиган (см. ниже)
И следующие почтовые индексы каждый день:
BL1, BL2, BL3, BL4, BL5, BL6, BL7
PR1, PR5, PR6, PR7, PR25, PR26
WN1, WN2, WN6.
Мы также доставляем на следующие почтовые индексы только по вторникам; ПН3, ПН4, ПН5.
Мы также осуществляем доставку на следующие почтовые индексы PR4: PR4 0, PR4 4, PR4 5, PR4 6 только по четвергам.
Мы осуществляем доставку шесть дней в неделю, с понедельника по пятницу, и ограниченные поставки по субботам.
Заказы на местную доставку, размещенные онлайн в пятницу вечером и в субботу утром, могут быть обработаны только в понедельник утром. Если вам требуется местная доставка в субботу утром, вам рекомендуется позвонить в офис, чтобы оформить заказ, а не размещать его через веб-сайт.