Для чего нужны угольные электроды
Для чего нужны угольные электроды? Они нужны для того чтобы осуществлять воздушно-духовую резку металлов. Также они применяются для сварки металлов, удаления дефектов металлических листов, среза заклепок и другие. Материалов изготовления служит аморфный электротехнический уголь в виде круглых стержней с сечением от 6 до 18 миллиметров. Их длина составляет 250-700 мм. Угольные электроды имеют листово-черную поверхность.
Для резки металлов один конец электрода затачивается под углом примерно 65 градусов. Для сварки цветных металлов, а также для наплавки твердых сплавов электрод затачивают под углом 20-30 градусов.
Угольные электроды изготавливаются способом декструзии или термообработки и формования композиции. В основном составе состоит уголь или кокс, а также обязательно добавляются другие связующие вещества, например смола, деготь и другие. Иногда в электроды добавляются металлическая стружка или порошок. Угольные электроды нашли очень широкое применение.
Сварка угольными электродами уже давно себя хорошо зарекомендовала как качественная, которая имеет множество преимуществ перед самыми распространенными на сегодняшний день методами резки. При резке угольными электродами используется сжатый воздух, углерод и электроток, который позволяет получить хорошую резку металла с удалением. Резка осуществляется при взаимодействии сжатого воздуха и электрической дуги, которая расплавляет металл, а потом и сама удаляется струей воздуха.
Однако у этого способа соединения металлов есть свои особенности, например, работа может производится только постоянным током, длина дуги должна быть не менее 6 и не более 15 миллиметров.
Однако дуга, которая появляется при сваривании угольными электродами, очень чувствительна к погодным условиям, например ветер, дождь, поток газов и магнитное дутье. Также немаловажным фактором является меньшее КПД дуги при использовании угольных электродов, нежели при сварке обычными металлическими электродами. Но все-таки ценность угольных электродов очень велика: ими можно сваривать тонколистовой металл, цветной металл, наплавка твердых сплавов и электроприхватки при силе тока около 1000 А.
Все виды электродов используются для ручной дуговой сварки. Они, образно говоря, являются ручными резаками, которыми можно поправить дефекты металла или подготовить кромки для сварки. Также ими можно производить разные виды сварки и все это возможно при невысокой цене.
Производство угольных электродов — Энциклопедия по машиностроению XXL
ПРОИЗВОДСТВО УГОЛЬНЫХ ЭЛЕКТРОДОВ [c.
Монациты — единственные из редкоземельных минералов, используемые в настоящее время. Некоторые редкие земли — церий, лантан, неодим и празеодим — находят применение в промышленности, другие — самарий, европий, тербий и эрбий — служат лишь для научно-исследовательских целей. Редкие земли используются в производстве угольных электродов для вольтовых дуг. Их окислы могут применяться для полировки оптических стекол. Лантан используется для производства некоторых специальных видов стекла и светофильтров для аэрофотосъемки. [c.175]
ПОНЯТИЕ О ПРОИЗВОДСТВЕ УГОЛЬНЫХ ЭЛЕКТРОДОВ И АНОДНОЙ МАССЫ [c.408]
В 1846 г. был запатентован процесс производства угольных электродов из порошкового кокса и сахара. Обожженные электроды подвергались дальнейшей пропитке концентрированным раствором сахара и повторному обжигу. Сто лет спустя этот режим был повторен для получения высокоплотных углеграфитовых материалов.
[c.5]
Порошок оловянный (ГОСТ 9723-73), изготовляемый из олова марок 01 и 02 способом распыления и предназначенный для производства угольных электродов изделий и других металлокерамических композиций в различных отраслях промышленности, в зависимости от химического и гранулометрического состава производят следующих марок ПОЭ (олова не менее 99,0 %), П01 (99,1 %), П02 (99,0%), ПОЗ (99,0%), П04 (98,1%). Допускается использование и других марок олова. [c.713]
Угольные электроды применяют для дуговой сварки, спектрального анализа, в производстве гальванических элементов (источников тока одноразового действия), для электролиза и работы в самых разнообразных условиях. [c.378]
В производстве первичного алюминия путем электролиза расходуемые угольные электроды используют для передачи электрического тока криолитовой ванне. Эти аноды прикрепляют к стальным кронштейнам, которые, в свою очередь, соединяются болтами с алюминиевым стержнем. Механическое соединение между алюминием и сталью оказалось неудовлетворительным вследствие разницы электрического сопротивления и тенденции к быстрому ухудшению свойств в результате коррозии или искрения. Это полон ение было исправлено путем использования переходных соединений алюминий — сталь. Тогда алюминиевый стер-
[c.82]
Пайку на контактных сварочных машинах, когда вследствие высокой скорости нагрева припой, зажатый между паяемыми поверхностями, не успевает окислиться, можно проводить без использования флюса. В массовом производстве паяных изделий машины для контактной точечной сварки комплектуются специальными электродами для пайки электросопротивлением. В зависимости от свойств паяемых материалов и размеров соединяемых элементов подбирают соответствующие электроды. Наибольшее распространение получили угольные электроды марок ЭГ-2, ЭГ-8, а также электроды из вольфрама и жаростойких сплавов. [c.447]
Общие сведения. При производстве электросварочных работ применяют угольные и металлические электроды. К угольным электродам предъявляются следующие требования механическая прочность при обычной и высокой температурах, возможно более высокая электропроводность и медленное и равномерное сгорание. Угольные электроды выпускаются в виде стержней диаметром от 6 до 30 мм и длиной до 300 мм. Металлические электроды при ручной сварке применяют в виде стержней диаметром до 12 мм и длиной 450 мм. В случае выполнения сварки на автоматах в качестве электродов применяют проволоку в мотках весом до 80 /сг.
При производстве электросварочных работ применяют угольные и металлические электроды. Угольные электроды выпускают в виде стержней диаметром от 6 до 30 мм и длиной до 300 мм. Металлические электроды при ручной сварке применяют в виде стержней диаметром АО 2 мм я длиной 450 мм. В случае выполнения сварки на автоматах в качестве электродов применяют проволоку в мотках весом до 80 кг. [c.

Угольные электроды применяют при выплавке кристаллического кремния, а графитированные — при производстве безуглеродистого феррохрома, металлического хрома, металлического марганца и т.п. [c.346]
Начало развития сварочной техники совпадает с рубежом XIX и XX столетий. Первое время преимущественное значение имела газовая сварка, которая начала внедряться в производство еще в XIX веке, когда были разработаны методы промышленного получения кислорода и ацетилена, найдены способы их хранения и транспортировки, создано надежное и безопасное сварочное оборудование. В 1882 г. русский изобретатель Н. Н. Бенардос впервые предложил способ электрической сварки плавлением, использовав для расплавления кромок соединяемых деталей электрическую дугу с угольным электродом. В 1888—1890 гг. русский инженер Н. Г. Славянов использовал для дуговой электрической сварки металлический электрод, служивший, одновременно присадочным металлом, и разработал технологические и металлургические основы электродуговой сварки.
Глава XVI ПРОИЗВОДСТВО ФТОРИСТЫХ СОЛЕИ И УГОЛЬНЫХ ЭЛЕКТРОДОВ [c.406]
Применение твердого углерода для промышленных целей началось у истоков человеческой цивилизации. Можно с уверенностью утверждать, что все основные этапы развития цивилизации связаны с производством углерода. Так, анализ чернил, использовавшихся в Египте в XVI в. до нашей эры, показал, что они изготовлены с применением ламповой сажи. Изобретение пороха в Китае также связано с применением сажи. Начавшееся 200 лет назад широкое использование твердого топлива как энергетического сырья явилось одной из основ промышленной революции того времени. Последовавшее далее бурное развитие металлургических процессов неизменно связано с применением углерода как восстановителя окислов железа и одного из важнейших компонентов чугуна и стали. Развитие электротехники также потребовало создания материалов из углерода.
Антрацит, главным образом после термической обработки при 1100—1350°С (в виде термоантрацита), используется в качестве одного из компонентов в производстве электродов для алюминиевых ванн, для набивных электродов ферросплавных и карбидных печен, угольных электродов больших диаметров, микрофонного порошка и в ряде других случаев. [c.62]
Ручная дуговая наплавка Чугунные электроды ОМЧ-1, ЦЧ-4, ЦЧ-3 и др. со специальными покрытиями. Наплавка по флюсу угольными электродами Различные чугунные детали массового или индивидуального производства [c.9]
Так называемые неплавящиеся электроды применяются при различных дуговых процессах. В сварочном производстве они используются при сварке угольным электродом по способу
188]
При использовании ВДР в литейном производстве в связи с широкой номенклатурой обрабатываемых отливок с большим разнообразием литейных элементов, подлежащих удалению, их нестабильности по линейным размерам, объему и местоположению, целесообразно использование манипуляторов с ручным дистанционным управлением. Для ограничения изгибающего усилия на угольный или графитированный электрод применяют манипуляторы повышенной чувствительности обратной связи усилие, испытываемое электродом, не должно превышать 5… 10 Н. [c.404]
Термоантрацит электродный (ГОСТ 4794—75). Вырабатывается из антрацитов Донецкого бассейна. Предназначен для производства угольных электродов, углеродистых блоков для доменных печей и футеровочных материалов для алюлгинпевой и химической промышленпости. Зольность не более 5%, содержание влаги 1,5%. «Удельное электрическое сопротивленце не более 1000 0. г- inf /м. [c.395]
Электродуговые печи, созданные Эру, Жиро и рядом других конструкторов, получили название печей с прямым нагревом.
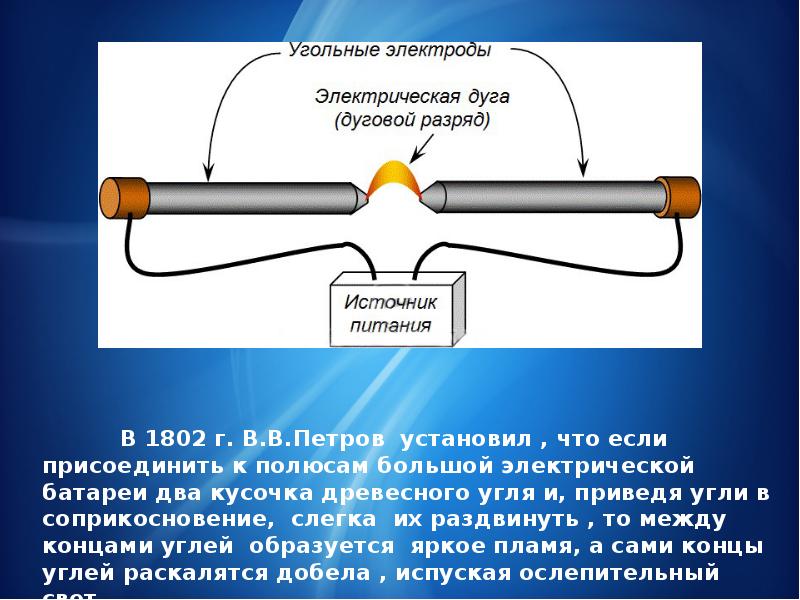
Производство чернового алюминия. AljOa растворяется в криолите (Маз[А1Рб]), который подвергается электролизу с угольными электродами. [c.378]
Впервые сварка металлов была осуществлена в России в конце прошлого столетия. В 1882 г. русский инженер Н. Н. Бенардос использовал электрическую дугу, открытую в 1802 г. академиком В. В. Петровым, для сварки металла угольным электродом. В 1886 г. другой русский инженер Н. Г. Ставянов разработал способ дуговой сварки металлическим электродом. Промышленное применение в нашей стране сварка получила после Октябрьской революции в годы первой пятилетки. Несмотря на то что в те годы сварка выполнялась только ручным способом, ее применение привело к значительной экономии металла, снижению трудоемкости производства металлоконструкций и улучшению условий труда.
[c.297]
Сложное производство алюминия требует мощных источников дещевой электроэнергии. Из схемы современного способа производства алюминия (рис. 141) следует, что, кроме большого количества электроэнергии, нужны чистые глинозем и криолит, а также беззольные угольные электроды. Все три продукта приходится изготовлять довольно сложными путями. Современная алюминиевая промышленность состоит из четырех различных производств глинозема, криолита, электродов и, наконец, производства алюминия из глинозема. [c.374]
Наиболее качественные многократно легированные стали получают в специальных электрических печах (рис. 6). Максимальная температура около 2200 °С достигается с помощью электродуги, возникающей между двумя угольными электродами. Достоинство способа в том, что на расплавленный металл не попадают вредные элементы из воздуха и газа, как это имеет место в первых двух способах. Сталь, полученная любым методом, отливается в специальные формы и отправляется в таком виде для дальнейшей обработки по производству проката, литья и других изделий.
[c.16]
После Великой Октябрьской социалистической революции развитие производства углеграфитовых изделий обусловливалось потребностями индустриализации страны. В годы, предшествовавшие Великой Отечественной войне, были построены новые заводы по производству угольных блоков и электродных масс для алюминиевой промышленности, угольных и графитированных электродов различного назначения. Было освоено массовое производство электрографитированных электрощеток и металлографитных изделий. [c.6]
Во время Великой Отечественной войны были организованы новые производства углеграфитовых изделий, обеспечивавшие потребности фронта и тыла в жизненно важной продукции — в графитированных и угольных электродах и массах для производства качественных сталей и алюминия, электрощетках для танковых генераторов и двигателей, уплотнительных материа. тах.
[c.6]
Сажа используется в производстве кино- н прожекторных углей, угольных электродов для гальванических батарей. Известно также применение хорошо графитирующихся термических саж в производстве графитнрован-ных материалов для адсорбционных колонок, а также термической сажи для высокотемпературной теплоизоляции различных объектов. [c.70]
Основными потребителями П. ш. являются металлургич., химич. и силикатная промышленности. В металлургич. промышленности П. ш. применяется в качестве флюса. В химич. промышленности вырабатывается гл. обр. фтористый натр, применяемый как антисептик в деле предохранения дерева, особенно ж.-д. шпал, от гниения и поражения грибками затем П. ш. применяется в производстве искусственного криолита, входящего в состав различных эмалей, при изготовлении матовых стекол, цианамида й др. В керамике П. ш. применяется при изготовлении эмали для железных изделий глазурованных изразцов, клинкера и др. В качестве цементирующего вещества П. ш применяется при изготовлении угольных электродов и абразивных кругов. Совершенно прозрачные кристаллы П. ш. имеют применение при изготовлении апохроматич. линз, пластинок и призм, находящих применение в оптике при использовании инфракрасных лучей. Из красиво окрашенных разностей П. ш. изготовляют чаши, вазы и другие изделия.
[c.256]
При ручной дуговой сварке металли1 еским или угольным электродом в крупносерийном или массовом производстве……………= 0,6 ч- 0,8 [c.329]
В СНГ уже построено и строятся несколько мощных солнечных печей — в Ташкенте, Ереване, Крыму и других местах. В них можно получить рабочие температуры от 2500 до 4000°С. Применение солнечных печей может очень многое дать науке и технике. Сегодня мы вправе говорить о рождении новых областей — гелиохимии и гелиометаллургии. Дело в том, что по сравнению с «классическими» печами солнечные печи обладают рядом существенных преимуществ. Прежде всего они дают возможность получить резкий скачок температуры. Скорость «теплового удара» в них превышает тысячу градусов в секунду. Во-вторых, расплавленное вещество не соприкасается ни с топливом, ни с угольными электродами, которые обычно являются источниками загрязнения продуктов плавки. Проникновению примесей из формы, неизбежному при любых иньи способах плавки, препятствует то, что сконцентрированный солнечный луч может плавить вещество в узкой зоне — как бы в форме из того же вещества. Можно вести плавку в окислительной или восстановительной атмосфере. Все это важно для получения особо чистых металлов и сплавов, для производства редкоземельных металлов, например скандия, иттрия, лантана, которые удается выделить из их окислов только при температуре более 2000 С и при условии, что источник энергии не выделяет загряз-
[c.127]
В качестве сырья для производства электроугольиых изделий можно использовать сажу, графит или антрацит. Для получения стержневых электродов измельченная масса со связующим, в качестве которого используется каменноупэльная смола, а иногда и жидкое стекло, продавливается сквозь мундштук.

Ручная электросварка с открытой дугой, применяемая преимущественно при единичном и мелкосерийном производстве сварочных работ, отличается высокой универсальностью, так как применима для сварки деталей разнообразной формы и величины. Ее недостатками являются малая производительность и пониженное качество швов сравнительно со щвами, выполняемыми автоматической или полуавтоматической сваркой. Она может осуществляться как плавящимися металлическими электродами, так и неплавящимися угольными. Выбор электрода определяется материалом свариваемых элементов, их толщиной и видом сварного соединения. [c.41]
Углеродотермический способ. Силикокальций углеродотермическим процессом выплавляют в трехфазных печах с угольной футеровкой мощностью Ю—15 MBA при линейном напряжении низкой стороны — 135 В и токе на электродах —58 кА. Технологическая схема производства приведена на рис. 20. При выплавке сплава марок СКЮ и СК15 в шихту дополнительно вводят железную стружку. Напряжение дуги в среднем составляет 30 В, полезное напряжение — 55 В, что определено необходимостью иметь глубокую и устойчивую посадку электродов в шихте, нормально составляющую >700 мм. За рубежом используют
[c.115]
Высвкоуглеродистый ферромарганец. Для выплавки высокоуглеродистого ферромарганца используют открытые и все чаще закрытые электрические печи мощностью до 85 MBA. Поперечный разрез цеха для выплавки углеродистого ферромарганца в закрытых печах приведен на рис. 26. Печи выполняют открытыми, закрытыми и герметичными, как круглыми, так и прямоугольными, в том числе шестиэлектродными, иногда с вращением ванны с частотой около одного оборота за 100 ч. Новые печи оборудованы счетнорешающим устройством, которое регулирует массу, состав и подачу шихты из бункера, а также автоматизированной системой подготовки шихты. Футеровка печей угольная. Используют набивные самообжигающиеся электроды. Плавку ферромарганца ведут при напряжении на электродах ПО—220 В. Зависимость показателей производства углеродистого ферромарганца флюсовым методом от вторичного фазового напряжения приведена на рис. 27. Уменьшение извлечения марганца и увеличение удельного рас-
[c.145]
Платина применяется в качестве анода при производстве над-х кислот, а также их солей, причем при производстве надсерной кислоты она используется в виде листов или как биметалл на меди или серебре. При производстве солей хлорной кислоты процесс подразделяется на две стадии. Окисление до хлората проводится с применением угольных или графитовых электродов, а дальнейшее окисление и очистка — с применением платиновых электродов. Платиновые аноды применяют также при получении гидроокиси натрия высшей чистоты.
[c.501]
В качестве сырья для производства электроугольных изделий используют сажу, графит или антрацит. Для получения стержневых электродов измельченную массу со связкой, в качестве которой используют каменноугольную смолу, а иногда и жидкое стекло, продавливают через мундштук. Изделия более сложной формы изготовляют в соответствующих пресс-формах. Угольные заготовки проходят процесс обжига. От режима обжига зависит форма, в которой углерод находится в изделии. При высоких температурах обжига (до 2200° С) углерод искусственно переводится в форму графита, вследствие чего такой процесс называют графитированием. [c.43]
В 1961 г. был разработан технологический процесс производства монокорунда на выпуск в печах мощностью 7500—10 500 ква. Плавка на выпуск ведется в дуговой низкошахтной электропечи. Шахта печи изнутри футеруется угольными блоками и имеет три летки — две для выпуска шлака и одну (на уровне пода) для выпуска ферросплава. Шлаковые летки футеруются графитовыми блоками и имеют наклон 30°, а ферросплавная летка футеруется угольными блоками. Электроды располагаются по углам равностороннего треугольника, против леток.
[c.90]
Неплавящиеся электроды для дуговой сварки и резки
Темы: Аргонодуговая сварка (TIG), Сварочные электроды, Резка металла.
Другие страницы по теме
Неплавящиеся электроды для дуговой сварки и резки
:
Для дуговой сварки и резки используют угольные, графитовые и вольфрамовые неплавящиеся электроды. Они имеют высокую температуру плавления и служат только для поддержания горения дуги, не участвуя в формировании металла шва.
Угольные электроды изготовляют прессованием из порошка кокса с последующим отжигом при температуре ≈1400°С. Различают два вида этих электродов — омедненные и неомедненные. Применяют их для сварки металлов, воздушно-дуговой резки, удаления прибылей отливок в других работ, Угольные электроды выпускают трех марок: ВДК — воздушно-дуговые круглые; ВДП — воздушно-дуговые плоские; СК — сварочные круглые.
Электроды марки ВДК изготовляют номинальными диаметрами 6, 8, 10 и 12 мм и длиной 300±10 мм, марки ВДП — номинальным сечением 12×5 и 18×5 и длиной (350±10) мм, марки СК — номинальными диаметрами 4, 6, 8, 10, 15 и 18 мм и длиной (250±10) мм.
Изготовление графитовых электродов, предназначенных для дуговой сварки или резки, стандартом не прудусмотрено. Их можно изготовить из остатков или отходов элуктродов плавильных печей разрезкой с последующим обтачиванием. Сопротивление графита в 4 раза меньше, чем сопротивление угля, — это позволяет использовать графитовые электроды при больших плотностях тока.
Вольфрамовые электроды изготовляют метода порошковой металлургии либо из чистого порошка вольфрама, либо с присадками (до 2 %) оксидов лантана, иттрия или тория. Введение оксидов этих металлов облегчает зажигание дуги и повышает устойчивость ее горения. Для уменьшения расхода электродов зажигать дугу следует на вспомогательной графитовой пластине.
При сварке коррозионно-стойких и жаропрочных сталей, алюминиевых и магниевых сплавов толщиной до 4 мм диаметр электрода назначают примерно равным толщине менее тонкой заготовки.
Перед началом сварки электроды затачивают; угол заточки угольных и графитовых электродов — 60…70°, вольфрамовых — 10…30°.
- < Электроды для резки АНР–2М
- Электроды для резки ОЗР-1 >
Где рождаются угольные электроды — ZAVODFOTO.RU
Продолжая рассказывать про самые передовые и смелые предприятия (которые не бояться блогеров и чувствуют тренды) в нашей стране, никак нельзя пропустить крупнейший в России электродный завод, причём он же и самый молодой в отрасли, я про Новосибирский электродный завод хочу рассказать сегодня. Он находится в посёлке Линёво в Искитимском районе Новосибирской области, а это в 79 км к югу от Новосибирска. Предприятие специализируется на выпуске графитированных электродов марок ЭГСП, ЭГП и ЭГ, угольных электродов, катодных блоков, кокса нефтяного прокаленного и электродной массы.
Осенью 1963 года к юго-востоку от станции Евсино, в степи, вешками было обозначено начало строительства Новосибирского электродного завода. Изначально предлагалось две площадки, где появится этот гигант – одна в районе Бердска, другая, как раз в районе станции Евсино. Почему именно здесь? Тут всё просто. Дело в том, что сырьём для угольных электродов служит антрацит, а его здесь было очень много, поблизости находится Горловское месторождение, а оно входит в тройку лучших в мире. И вот 3 августа 1965 года стройке был объявлен зелёный свет. В 1966 году на стройку из Новочеркасского электродного завода приехал главный инженер Алексей Обудовский. Это был первый специалист электродщик в этих местах.
2. Склад антрацита
В качестве сырья для изготовления угольных электродов используются антрацит, нефтяной кокс и искусственный графит собственного производства. Сырье на Новосибирском электродном заводе хранится на закрытых складах раздельно по типам и маркам.
3. Склад №1 хранения нефтяного кокса
Параллельно с заводом, рос и рабочий посёлок для будущих работников завода. В 1968 году здесь ввели в строй первые значительные объекты: два жилых дома и скважину, которая давала воду, медпункт, школу, котельную, детский сад и столовую. Матушка природа периодически испытывала строителей, так, например, зимы 1968 и 1969 года отличились температурами под — 55°, но в итоге слабаков тут не оказалось… В 1972 году состоялся частичный ввод мощностей нового электродного завода.
4. А здесь довольно мило, теперь понимаю, почему меня сюда так долго не пускали, боялись, что я все яблоки у них съем :).
5. Далее мы попадаем в прокалочный цех.
Прежде чем приступить к производству угольных электродов, сырьё (антрацит и нефтяной кокс) вначале подвергают кальцинации, т.е. прокаливанию при высокой температуре. Прокаливание необходимо для того, чтобы удалить влагу и другие ненужные вещества, а также предать необходимую прочность и электропроводность. Вот в таких прокалочных печах всё и происходит, а там, между прочим, ой, как горячо, примерно 1300 °С.
6.
Вращающая прокалочная печь из себя представляет стальной барабан, внутри футерованный, т.е. специально отделанный огнеупорным кирпичом и установленным под углом 3,5 градусов к горизонту. В нижнем торце барабана («горячая головка») установлена газовая гарелка, а также через него производится и выгрузка прокаленного материала. Через верхний же торец барабана («холодная головка») производится загрузка прокаленного материала и отводятся отходящие газы. Сам барабан печи установлен на специальных роликоопорах и приводится во вращение электродвигателем через венцовую шестерню. Именно за счёт этого вращения и наклонного расположения печи и происходит перемещение прокаливаемого материала вдоль печи. Прокалочная печь имеет четыре скорости вращения от 0,7 до 2,1 оборота в минуту. Это позволяет регулировать время нахождения материала в печи и соответственно степень прокаливания материала. Длина печи составляет 60 м.
Прокаленный материал после печи попадает в холодильник, который представляет собой тоже металлический барабан, установленный на роликоопорах под углом 1,5 градуса к горизонту, при этом его горячая головка расположена выше холодной. Барабан вращается также при помощи электродвигателя. Корпус холодильника орошается водой для более эффективного охлаждения.
7.
Электрокальцинатор. Температура обработки в электрокальцинаторе достигает 1800 °С. Он также задействован в операции прокаливания. Из себя он представляет печь сопротивления, где тепловыделяющим элементом служит прокаливаемый материал, через который пропускается электрический ток. Работает он в постоянном режиме. Электрокальцинатор состоит из металлической шахты, внутри выложенной огнеупорным кирпичом, также имеются два токоподвода. Верхним токоподводом служит электрод, расположенный по оси шахты, а в качестве нижнего токоподвода используется угольный электрод, навинченный на водоохлаждаемый фальшниппель, расположенный также вдоль оси шахты. Расстояние между токоподводами составляет 2-2,5 м.
8.
9.
10. Управление всеми процессами прокаливания осуществляется отсюда.
11.
12. Каменноугольный пек поступает на завод в жидком виде в вагон-цистернах, собственно, одна такая прямо перед нами.
13.
14.
3 июля 1974 года Министерство цветной металлургии СССР издало приказ «О создании Новосибирского электродного завода». Этот день и стал официальной датой рождения нашего сегодняшнего предприятия.
15.
16.
В целях мотивации и ускорения процесса, в 1976 году завод был объявлен всесоюзной ударной комсомольской стройкой. И как это обычно было тогда, сюда со всех концов нашей страны стали массово приезжать строители, монтажники, водители, крановщики и т.д. Как результат, уже 26 сентября 1977 года была разожжена первая печь цеха обжига, а 1 ноября 1977 года была выпущена первая электродная масса. В связи с этим был подписан акт Государственной комиссии «О приеме промышленных мощностей НовЭЗа». Дальше больше – в 1978 году запустили цех механической обработки углеграфитовых изделий (в настоящее время ЦМОЭП), 19 апреля 1979 года был отпрессован первый подовый блок, а 10 октября 1982 года — получена первая графитовая заготовка.
17.
В 2006 году завод попадает под крыло Группы Энергопром, что позволило предприятию дальше расти и успешно развиваться. Кстати, в состав Группы компаний «Энергопром» входят ещё два электродных завода — Челябинский и Новочеркасский, а также ООО «Донкарб Графит» (площадки в Новочеркасске и Челябинске). Сегодня, как и раньше, Новосибирский электродный завод является градообразующим для посёлка, а также вносит существенный вклад в целом в экономику Новосибирской области. Выпускаемый ассортимент довольно широк: это крупногабаритные угольные электроды, электроды графитированные и ниппели, катодная продукция, блоки угловые и боковые, антрацит прокаленный, доменные блоки, масса электродная, масса холоднонабивная низкоусадочная, фасонные и мелкофасонные изделия, нефтяные прокаленные коксы. Между прочим, свыше 60 % стран мира охотно покупают их продукцию.
18.
19. Рядом по соседству находится ещё одно крупное предприятие — Сибирский Антрацит. Я к ним тоже напрашиваюсь, может и у них когда-нибудь побываю. А так эта компания- ведущий в России и в мире производитель высококачественного антрацита Ultra High Grade (UHG). Именно они как раз и ведут добычу угля на месторождениях Горловского угольного бассейна в Искитимском районе Новосибирской области. Предприятие объединяет 2 угольных разреза и 2 обогатительные фабрики.
Далее мы попадаем смесильно-прессовый цех, где производится размол, рассев прокаленных материалов по заданной рецептуре и составу, а также смешивание определенных фракций и прессование заготовок.
20.
Этот цех занимает целое здание в несколько этажей (44 метра вверх и ещё 4 метра вниз), где сырье, как на американских горках, то поднимается вверх, то также стремительно падает вниз, потом снова вверх и так до тех пор, пока не придёт к нужной кондиции. Итак, первоначально мы поднимаемся вверх.
Вкратце техпроцесс выглядит следующим образом. Прокаленный материал, поступивший сюда, поступает вначале в бункера запаса и потом по транспортёрам подаётся наверх по элеваторам в рассеиватели. Учитывая, что сырьё сюда поступает разных размеров его, ещё подвергают дроблению. После сортирования по бункерам уже по нужным фракциям, шихта и пек подогреваются, после чего они уже поступают на смешивание. Всего тут семь технологических линий.
21.
22. Один из транспортёров, по которому путешествует сырьё.
23. Бункера, в которых находятся уже разбитые по нужным фракциям и составу материалы.
24. Напорный бак, в них осуществляется подогрев пека
25.
26. Дозировочные телеги
27. Эта телега работает в автоматическом режиме. Стоит только оператору захотеть, как нужное количество материала уже там.
28.
29. Это тоже дозировочные телеги, но уже другого типа.
30. Участок смешения
31.
32. Смесильная машина
33.
34.
35. Смесильная машина в разрезе
36.
37.
38.
39. Склад набивной подовой массы, в данном случае мы наблюдаем Массу холоднонабивную низкоусадочную.
40.
41. Прессовый участок.
42.
Прессование заготовок производится двумя способами: виброформованием и экструзии (прошивное прессование). Прошивное прессование — это выдавливание массы через мундштук пресса, затем её охлаждение и усреднение массы в охладительном барабане прошивного пресса. Здесь установлены пресса: 3 550У (3 т.н.), 6 300 У (4 т.н.), 3 550Н (5 т.н.) и 6 300Н (5 т.н.). Виброформование (в прессформе) проходит на 2 технологической нитке (немецкий вибропресс КХД) и на 7 технологической нитке вибропресс RUEF. Процессы всех технологических ниток автоматизированы, что позволяет производить их контроль в режиме реального времени.
43.
44.
45. Завод работает круглые сутки, без праздников и выходных.
46.
47. Охлаждение прессованной продукции.
48.
49.
50.
51.
52.
53.
54. Участок обжига. Главная цель обжига — это обеспечить максимальный выход коксового остатка из связующего. Это как раз и обеспечивает прочность спекания частиц наполнителя, придаёт ему конечную механическую прочность, а также получение однородной структуры по всему объёму заготовки.
Процесс обжига ведется по заданному температурному режиму и его длительность варьируется в зависимости от марок и габаритов загруженных полуфабрикатов. Продолжительность обжига составляет не менее 396 часов. Обжиг проходит в специальных 32-х камерных кольцевых печах закрытого типа с газовым обогревом при температуре в газовой среде не ниже 1265 °С.
55.
На участке обжига находятся десять печей, восемь печей по 32 камеры каждая, работают на двух системах «огня», печь 10 по 12 камер, печь 10А по 14 камер. Размеры кассет камер обжиговых печей позволяют производить обжиг заготовок шириной (диаметром) до 1440 мм и высотой до 4100 мм. Печи имеют, в зависимости от сечения загружаемой продукции, по 4 или 6 кассет.
56. Управление процессами обжига полностью автоматизировано.
57.
58.
59. Участок графитации. Цель процесса графитации — это переход углерода используемого сырья в графит под действием высоких температур, т.е. превращение двумерной структуры углеродных сеток в трехмерную (кристаллическую), в следствии чего происходит снижение удельного электросопротивления заготовок, повышается теплопроводность и термостойкость.
Обожженные заготовки марки МГВ проходят процесс графитации. Графитация производится вот в таких электрических печах сопротивления по методу Ачесона (печь косвенного нагрева) или Кастнера (прямого нагрева). В качестве пересыпки для печи Ачесона используют коксовый орешек (керновая пересыпка) и антрацит марки АСШ (теплоизоляционная шихта), а для печи Кастнера коксовая мелочь. Температура в них достигает 3000 °C. Продолжительность процесса графитации в печах Ачесона составляет 3-4 суток и далее постепенное охлаждение в печи в течении 12-15 суток в зависимости от диаметра заготовки. А в печах Кастнера («прямая» графитация) — 18-20 часов. Выгрузка заготовок производится при температуре около 700 градусов. Кстати, в печь Ачесона заготовки укладываются горизонтально, перпендикулярно продольной оси печи и параллельно друг другу на расстоянии 02 диаметра (ширины) заготовки, а в печах Кастнера заготовки укладываются параллельно продольной оси печи.
60.
61. Участок механической обработки заготовок угольных электродов.
62. На этом участке могут обрабатываться заготовки длиной до 3 600 мм.
63. Ниппели к электродам графитированным
64.
65.
66. Визуальный контроль качества изделий.
Кроме визуального осмотра, обожженные электроды проходят проверку и ультразвуковым методом неразрушающего контроля. Между прочим, его разработали в собственном НТЦ Группы ЭНЕРГОПРОМ. Данный метод позволяет визуализировать внутреннюю структуру тела электрода и определить наличие любых внутренних дефектов.
67.
68.
69. После проверки, вся продукция упаковывается и направляется на склад.
В качестве закрепления материала, ещё раз предлагаю остановиться на том, для кого день изо дня трудится новосибирский завод. Итак, угольные электроды предназначены для электротермических процессов производства кристаллического кремния, карбида кальция и фосфора. Подовые и боковые электроды отправляются к производителям алюминия. Доменные блоки нужны для выкладки металлургических печей, которые выплавляют чугун. Графитированные электроды, ниппели используются для в электродуговых печах при выплавке сталей. А электродная масса нужна для получения непрерывных самообжигающихся электродов электротермических печей черной, цветной и химической промышленности.
70.
71.
72. Большое спасибо Группе «ЭНЕРГОПРОМ» за организацию такой интересной поездки, а заводу «ЭНЕРГОПРОМ-Новосибирский электродный завод» за тёплый приём! Отличный завод, нужная продукция, да ещё и открыты, жадничать не буду, ЗаводычЛайк от меня одназначно, получите-распишитесь.
Ещё по теме:
Р. S. Уважаемые собственники и акционеры, представители пресс-служб компаний, отделы маркетинга и другие заинтересованные лица, если на Вашем предприятие есть, что показать — «Как это делается и почему именно так!», мы всегда рады принять участие. Не стесняйтесь, пишите нам сами [email protected] и расскажите о себе, пригласив нас к ВАМ в гости. Берите пример с лидеров!
Уже более 250 организаций открыли перед нами свои двери, а вот и наши репортажи оттуда:
Почему наша промышленность самая лучшая в мире: http://zavodfoto.livejournal.com/4701859.html
ZAVODFOTO — Шагает по стране! — ЭНЕРГЕТИКА РОССИИ: http://zavodfoto. livejournal.com/2133307.html
«Пермский край — Нам есть, чем гордиться!»: http://zavodfoto.livejournal.com/1823939.html
Лучшие Корпоративные музеи России и другие промрепортажи: http://zavodfoto.livejournal.com/5338699.html
Мы всегда рады новым друзьям, добавляйтесь и читайте нас в:
А ещё прошу всех в гости: http://ok.ru/zavodfoto и https://www.facebook.com/groups/ZAVODFOTO/
Электроды для резки металла: виды, достоинства и недостатки
Чем варить медь: способы
Для успешной и качественной сварки меди чаще всего применяют инверторы, полуавтоматы, газовые аппараты, аргоновые. Ручную, полуавтоматическую и автоматическую сварку купрума и его соединений можно выполнить плавящимися и неплавящимися электродами. Для работы с медью и сталью используется автоматическая дуговая технология, флюс.
Электрошлаковый метод рекомендуется для соединения изделий толщиной 30-55 миллиметров. Используя инвертор можно применить угольный электрод, например, ESAB OK Carbon, Weldline CARBONAIR PLUS. В магазине представлен широкий выбор производителей. Отлично зарекомендовала себя сварка меди графитовым типом электрода. Ниже приведены несколько подзаголовков, в которых дано более подробное описание лучших способов сварки меди и ее сплавов.
Сварочный аппарат для меди
Качественные сварочные аппараты для меди:
- – полуавтоматы и автоматы;
- – TIG – аппараты;
- – инверторы.
Популярные модели производит TESLA, СПЕЦЭЛЕКТРОМАШ, ЭСАБ.
BUDDY TIG 160 от ESAB (на фото справа) имеет двух и четырехтактные режимы включения горелки. С его помощью можно соединять нержавейку и большинство других видов металлов. Он совместим практически с любыми генераторами.
Инвертор RENEGADE ES 300i ESAB сохраняет в памяти несколько параметров сварки. Автоматически устанавливает лучшие параметры пуска по настроенному току. Он легкий, но у него высокая мощность.
Инверторные аппараты позволяют сваривать медные прутки, они вырабатывают ток 60-110 ампер. Для них нужно покупать медь/угольные электроды. Компания HUNTER выпускает полупрофессиональные модели, например, ММА 257D, рассчитанные на непрерывную работу продолжительностью два часа.
TESLA известна надежными аппаратами типа ММА 265, 275, 255. У них есть функция возбуждения бесконтактной дуги. Они без проблем подключаются к обычной бытовой сети. Ими удобно сваривать медь и ее сплавы, цветные металлы.
Какие марки электродов применяются для сварки меди
Для сварки, наплавки меди и цветных металлов, сварки медных труб и проч. применяются специальные медные электроды для сварки. К данному типу относятся электроды
- Комсомолец-100,
- ОЗБ-2М,
- ОЗБ-3,
- АНЦ/ОЗМ-2,
- АНЦ/ОЗМ-3,
- ESAB ОК 94.25,
- ESAB OK 94.35,
- ESAB OK 94.55,
- ESAB OK NiCu-7 (OK 92.
86),
- ESAB OK Ni-1 (OK 92.05),
- ZELLER 390.
Работать ими нужно начинать, зная некоторые их особенности и характеристики.
Комсомолец-100 предназначен для наплавки, сварки меди марки М1-М3. Работа должна производится на постоянном токе (о сварочных токах здесь), в нижнем или наклонном положениях. Выпускаются электроды Комсомолец-100 толщиной 3-5 миллиметров. Рекомендуемая сила тока для диаметра 3 мм 90-180 ампер, 4 мм 120-140, 5 мм 150-190. Эти показатели зависят от положения шва. Перед началом работы рекомендуется нагреть свариваемое изделие до 300-700 градусов, в зависимости от его толщины.
ОЗБ-2М предназначен и для работы с бронзой, используемой в художественном литье. Ими можно наплавлять ее на сталь, исправлять дефекты чугуна. При этом необходимо включать ток обратной полярности, производить работу в вертикальном или горизонтальном положении. ОЗБ-2М состоят из меди, железа, фосфора, марганца, никеля и олова. Их длина 350 мм. Для успешной работы необходимо устанавливать сварочный ток следующих значений: для диаметра 3 мм/ 90 – 120 ампер, 4 мм/120 – 160.
ОЗБ-3 используются в работе с цветными металлами, медью и бронзой. Они делаются со специальным покрытием (узнайте тут больше о покрытиях электродов). Сварку нужно производить только в нижнем положении. Используется постоянный ток. Коэффициент и производительность наплавки ОЗБ-3 12,5 г/А.ч – 3,5 кг.ч при диаметре изделия 4 мм.
АНЦ/ОЗМ-2 применяется для работы с чистой медью, при этом ее нет необходимости нагревать, если она не очень толстая. Сварка должна производиться в наклонном или нижнем положениях. Используется постоянный ток обратной полярности. Расходуется АНЦ/ОЗМ-2 1,6 кг на то, чтобы наплавить килограмм металла.
АНЦ/ОЗМ-3 нужны для работы с изделиями из меди технических марок по ГОСТ 859-78. Они выпускаются толщиной 4-6 мм. Чтобы успешно выполнить сварку нужно настроить ток на 220-300 ампер для диаметра 4 мм, 350-400 для 5 мм, 420-600 для 6 мм. Положение шва должно быть нижнее. Работать нужно короткой дугой, с медью толщиной до 10 мм, без подогрева, без разделки кромок одно или двусторонним швом с небольшими поперечными колебаниями электрода.
ESAB ОК 94.25 хорошо подходит для работы с многими цветными металлами, сплавами. Особенно с медью, оловянной бронзой, пережженным чугуном, латунью. Они могут использоваться для наплавки на сталь, для ее защиты от коррозийного воздействия. Толстые медные изделия рекомендуется нагреть до 300 градусов. Лучше всего работать маркой ESAB ОК 94.25 в пространственных положениях 1-4.
Металлические электроды.
Достаточно распространены и часто используются для резки металла металлические электроды со специальным электродным покрытием, улучшающим качество разреза и сам процесс резки. Как правило, покрытие состоит из смеси различных материалов — марганцевая руда, поташ, мрамор и др. Материалы покрытия обладают определённым набором свойств:
- изолирующих, предотвращающих переход дуги на боковые поверхности разреза;
- стабилизирующих, обеспечивающих постоянство горения дуги и предотвращающих её гашение;
- газообразующих, способствующих окислению металла в месте разреза и создающих давление газа в месте плавления.
Соотношение компонентов тщательно сбалансировано, что позволяет сварщику лучше управлять ходом работ. С точки зрения физики процесса принцип применения специальных покрытий состоит в том, что используемые материалы плавятся с меньшей скоростью, чем металл электрода, в нём образуется углубление 3-5 мм (рис. 1), при этом выгорающие изнутри вещества покрытия создают струю газа, которая выдувает расплавленный металл и шлак.
Состав защитных покрытий электродов
Покрытые электроды часто требуются для электросварки. В табличке указаны основные марки и варианты их покрытий:
Компоненты покрытия | № состава и марка электродов | |||||||||
1 | 2 | 3 | 4 | 5 | 6 | 7 | 8 | 9 | ||
К-100 | ЗТ | Комсо- молец | ММ3-2 | – | – | ОЗЧ-1 | ОЗМ-1 | ММ3-1 | ||
1-ый слой | 2-ой слой | |||||||||
Плавиковый шпат | 10 | 32 | 10 | 30 | 82 | 12,5 | 7,5 | 12,5 | 30 | 32 |
Полевой шпат | 12 | – | 12 | 14 | – | – | – | 15 | 20 | – |
Железный порошок | – | – | – | – | – | – | 50 | – | – | – |
Гранит | – | – | – | – | – | 15 | – | – | – | – |
Кремнистая медь | 20 | – | – | – | – | – | – | 25 | – | – |
Ферротитан | – | – | – | – | – | – | 6 | – | – | – |
Диоксид титана | – | – | – | – | 8 | – | – | – | – | – |
Ферромарганец | 38 | – | 50 | – | – | 47,5 | 2,5 | 47,5 | – | – |
Марганцевая руда | – | 17,5 | – | – | – | – | – | – | 5 | 17,5 |
Серебристый графит | – | 16 | – | 8 | – | – | – | – | – | 16 |
Ферросилиций (Si=45%) | – | 32 | 8 | – | – | 25 | 2,4 | – | – | 32 |
Алюминий (порошок) | – | 2,5 | – | – | – | – | – | – | – | 2,5 |
Кварц | – | – | – | – | – | – | 4,5 | – | – | – |
Мрамор | – | – | – | – | 10 | – | 27 | – | – | – |
Поташ | – | – | – | 5 | – | – | – | – | – | – |
Симанал* | – | – | – | 43 | – | – | – | – | 20 | – |
Криолит | – | – | – | – | – | – | – | – | – | – |
Сумма, % | 80 | 100 | 80 | 100 | 100 | 100 | 100 | 100 | 75 | 100 |
Жидкое стекло, % | 20 | замес | 20 | замес | замес | замес | замес | замес | 25 | замес |
Примечания.![]() |
Ручная дуговая сварка меди металлическими электродами
Целесообразность применения дуговой сварки плавящимся электродом взамен газовой сварки меди продиктована технико-экономическими преимуществами, также как и при сварке сталей. Прежде всего, этот способ отличается высокой производительностью. Скорость дуговой сварки металлическим плавящимся электродом намного превосходит скорость при другом способе сварки. Дуговая сварка меди может производиться вручную, автоматически под флюсом или в защитных газах. О сварке меди на полуавтоматах и автоматах изложено ниже по тексту. Сейчас рассмотрим ручную дуговую сварку меди.
Подготовка места сварки
Если толщина свариваемой меди составляет 6-12мм, то рекомендуется выполнять V-образную разделку с суммарным углом раскрытия кромок 60-70°. Если предусматривается подварочный шов с оборотной стороны, то угол можно уменьшить до 50°.
Перед сваркой необходимо раздвигать медные листы или полосы под углом друг к другу, с зазором 2-2,5% от длины шва, см. рисунок справа. Если сварка выполняется без предварительного раздвигания листов, то рекомендуется предварительно прихватить их короткими швами длиной около 30мм на расстоянии, примерно, 300мм друг от друга. Прихватки выполняют электродом меньшего диаметра и обеспечивают зазор между кромками 2-4мм. При отсутствии зазора возрастает вероятность перегрева металла и появления горячих трещин при сварке. При выполнении прихваток следует учитывать, что повторный нагрев меди приводит к появлению пор в металле, поэтому, по мере приближения к прихваткам их необходимо вырубать и зачищать. Это не потребует много времени, т.к. прихватки выполняются на малую глубину.
При толщине металла более 12мм рекомендуется Х-образная разделка кромок, что потребует двухсторонней сварки. Если нет возможности выполнить Х-образную разделку, то выполняют V-образную. При этом возрастает почти в полтора раза расход электродов и время сварки. При Х-образной подготовке кромок прихватку выполняют с оборотной стороны первого шва и удаляют её перед началом выполнения второго шва.
Сварка стыкового соединения без разделки кромок или с V-образной разделкой выполняется на подкладках, которые прижимаются вплотную к стыку, либо на флюсовой подкладке-подушке. Применяются стальные, медные, либо графитовые подкладки шириной 40-50мм с выполнением формирующей канавки.
Перед сваркой рекомендуется предварительный подогрев кромок. Подогрев может быть местным, общим или сопутствующим, в зависимости от габаритов изделия и толщины свариваемой меди. Обычно температура подогрева составляет 300-400°C.
Электроды для дуговой сварки меди и покрытия для них
Для дуговой сварки меди применяют покрытые электроды. Применение электродом без защитного покрытия приводит к окислению шва, нестабильному горению дуги и появлению дефектов в сварном шве (пористости). Электродные стержни используют в виде медной проволоки (которая может быть легирована кремнием и марганцем), бронзы марки Бр.КМц 3-1 или бронзы марок Бр.ОФ 4-03 и БР.ФО 9-03.
Электродные стержни такого состава легируют металл шва кремнием, марганцем, фосфором (иногда оловом) и оказывают раскисляющее действие. Защитные покрытия подбираются с таким составом, который обеспечивает стабильность дуги, раскисление металла и образование шлаков. Всё это способствует хорошему формированию шва и повышению качества сварки.
Подробнее о марках электродов для сваривания медных изделий и о том, какие защитные покрытия применяются для них в том или ином случае подробно рассказано в статье: «Электроды для сварки меди».
Режимы ручной дуговой сварки меди
Сварка выполняется постоянным током обратной полярности. Применение переменного тока часто не позволяет обеспечить нужной стабильности дуги. Переменным током возможно производить сварку лишь в том случае, если в составе защитного покрытия присутствует железо. При этом необходимо повысить силу тока, примерно, на 40-50%. Но следует иметь в виду, что применение переменного тока может привести к разбрызгиванию электродного металла. Ориентировочные режимы сварки указаны в таблице ниже.
Режимы ручной дуговой сварки в стык листовой меди медными электродами на постоянном токе:
Толщина меди, мм
2 | 3 | 4 | 5 | 6 | 7-8 | 9-10 | |
Диаметр электрода, мм | 2-3 | 3-4 | 4-5 | 5-6 | 5-7 | 6-7 | 6-8 |
Сила тока, А | 100-120 | 120-160 | 160-200 | 240-300 | 260-340 | 380-400 | 300-420 |
Рабочее напряжение, В | 25-27 | 25-27 | 25-27 | 25-27 | 26-28 | 26-28 | 28-30 |
Скорость сварки составляет 15-18 м/час. Если применяются электроды из бронзы, то скорость сварки увеличивается, т. к. бронзовый электрод плавится быстрее медного.
При сварке меди толщиной более 10-12мм при диаметре электрода 6-8мм, силу сварочного тока увеличивают до 500А.
При сварке тавровых соединений режимы сварки примерно такие же, как и для сварки стыковых соединений. При этом необходимо установить сварное соединение «в лодочку».
Техника ручной дуговой сварки меди
Сварку меди большой толщины сваривают в несколько слоёв. Каждый предыдущий слой тщательно зачищают перед наплавкой последующего. Но малые и средние толщины меди лучше сваривать за один проход.
Сварка выполняется обратноступенчатыми швами, с длиной участка 200-300мм. Всю длину свариваемого участка делят на два участка: в 2/3 длины шва и с другой стороны 1/3 от длины. Вначале заваривается длинный участок по направлению к малому, а затем короткий. Схема этой сварки показана на рисунке слева. Подобная техника сварки значительно снижает риск возникновения трещин в металле.
Сварка производится в нижнем положении, или слегка наклонённом и выполняется она «углом вперёд», т. е. электрод должен быть наклонен в противоположную от сварки сторону на угол 15-20°. При сварке может происходить «вспучивание» сварных кромок, при уменьшении зазора между ними. В этом случае шов необходимо периодически править молотком или кувалдой. При этом следует иметь в виду, если сварка выполняется на графитовой подкладке, то она может расколоться. Поэтому, предпочтительнее стальные подкладки, или медные.
Качество ручной сварки меди
Ручная дуговая сварка меди способна обеспечить хорошее качество сварки. При этом проковка увеличивает прочность сварного шва, примерно, на 10-15%, но может уменьшать пластичность. К примеру, прочность сварного соединения, выполненного медными покрытыми электродами «Комсомолец 100», составляет 200-215МПа без проковки и 230-240МПа. Угол загиба 180° без проковки и 140-180° без проковки.
Ручная сварка медных трубопроводов
Одними из первых ручную сварку медных трубопроводов с толщиной стенки от 3мм начали выполнять ещё в Советском Союзе на Николаевском судостроительном заводе. Для сварки выбираются электроды с покрытием Комсомолец-100. Сварка выполняется на постоянном токе обратной полярности при плотности сварочного тока 50а/мм.
Сварка производится с предварительным подогревом до температуры 250-300°C. Для трубопроводов, диаметром до 50мм выполняют полный подогрев, а при большем диаметре — местный, периодический подогрев по участкам. Перед сваркой выполняют прихватки. Прихватки необходимо вырубать, т.к. их заварка приведёт к повышенной пористости в этих участках из-за повторного нагрева. Рекомендуемая максимальная скорость сварки составляет 15м/час. При сварке не следует допускать перегрева основного металла свыше температуры 350°C.
Материал для стержней
Стержни, которые устанавливаются в электродах и предназначены для сплавов меди, производятся из прутков и проволоки. Их состав соответствует ГОСТу. Главным образом это бронза и медь. Часто находят применение в производстве сплавы металлов. Медные стержни выполняют в диаметре от 2 до 6 мм. Они могут быть обернуты жестью толщиной 0,3 мм. На них наносится различное покрытие. Оно может быть рутиловым и основным.
Для электродов Комсомолец-100 стержень изготавливается из меди М1. Бронзовые изделия выполняются из специального металла и покрываются смесью различных веществ. Иногда их производят из оловянно-фосфористой бронзы. Бронзовый стержень придает отличное качество швам. Они меньше окисляют металлы, нежели медные. Бронзовые стержни снижают механическую прочность при определённых условиях.
Ключевые принципы сварки
Проводя сварочные работы по сварке меди и ее сплавов, сварщик сталкивается с определенными трудностями. На шве может формироваться трещина. При работе легкоплавкие соединения скапливаются на границах кристаллов. Соответственно, образуются поры. Надо это учитывать и предотвращать. Медь толщиной до 4 мм соединяют без разделки кромок, до 10 мм — с односторонней разделкой. Скос кромок должен иметь угол не более 70 градусов.
Допускается притупление от 1,5 до 3 мм. Текучесть заметно осложняет работу в потолочном, горизонтальном и вертикальном положениях. Дуговая сварка производится при повышенном сварочном токе из-за высокой теплопроводности металла. Кромки соединяются с минимальным зазором из-за высокой текучести меди. Нередко рекомендуют использовать стальную подкладку.
Изделия толщиной больше 6 мм необходимо нагревать до 250 градусов. Делать это заранее, учитывая при этом характеристики плавления металла и особенности сплавов. Тонкий металл не следует нагревать. Лучше производить дугой от 10 до 15 мм такую сварку. Это позволяет манипулировать электродом намного легче.
При постоянном токе обратной полярности сваривается медь. Это также нужно учитывать. Дуговая сварка латуни и бронзы выполняется мощной дугой. Это происходит при увеличенном напряжении за счёт соответствующей силы тока. Работа выполняется быстро и на большой скорости. Сварку по возможности рекомендуется делать в нижнем положении, а также при угле наклона 20 градусов по отношению к вертикали.
Дуга направляется на поверхность сварочной ванны. Лучше применять специальные подкладки. Их делают из графита и асбеста. Характеристики металла при этом надо обязательно учитывать. Медь плавится при плюс 1080 градусах. Прочность ее составляет 20 кг на квадратный миллиметр. Если изделие толстое, надо обрабатывать его постепенно. Наполняется один слой за другим.
Сварка выполняется обратноступенчатым швом. Длина каждого участка составляет от 20 до 30 см. Его делят на две части: в соотношении 75% и 25%. Обрабатывается длинный участок по направлению к меньшему. За счет этого понижается риск возникновения трещин. Работа выполняется снизу. Шов правится кувалдой или молотком по причине вспенивания. В процессе сварки необходимо уменьшить ток, так как разогрев тонкой меди может привести к ожогам. Перед началом работы электроды прокаливаются при рекомендуемой производителем температуре.
Сварка графитовым электродом.
Угольным электродом медь сваривается легко. Но процесс весьма нестабильный: легко возникает пористый шов. Что там получается с металлургией непонятно, но твердость шва несколько выше, чем твердость отпущенной меди рядом. Иногда удается получить шов и без пор, но подобрать условия, при которых процесс стабилен, трудно. Хорошо заточенный электрод более-менее позволяет управлять дугой, но обгорает, и тогда дуга начинает гулять как по электроду, так и на металле. Так что электрод приходится подтачивать периодически напильником. Электроды от батарейки служат недолго, так как выгорают не только в дуге, но и сбоку по образующей цилиндра,- разогрев ведь идет еще и на 1-2 см от, собственно, дуги. Однако для небольшой работы их хватает. Гораздо лучше использовать омедненные угольные электроды, Таковые использовались раньше в кинопроекторах (дуговая лампа), но и теперь их нетрудно купить, поискав в интернете. За счет медной рубашки электрод выгорает значительно медленнее. Так на сотню метров стыкового шва по меди М1 толщиной 1 мм потребно около 10-12 штук их. Теперь о флюсах. По меди они не нужны и даже вредны.
В дуге углерод электрода испаряется и окисляется сначала до СО и затем до СО2 , то есть вы имеете четкую восстановительную зону, как в газосварке. Через маску отчетливо видно, как при приближении дуги очищается до медного блеска область шва. Использование флюсов может привести только к сложностям с управлением дугой (начинает гулять) из-за их изолирующих свойств и изменения состава газа и его течения в дуге. Это точно также, как применение флюсов усложняет пайку, если греть стык в аргоне. Работа с угольным электродом интересна еще и тем, что если вы хотите приостановить разогрев ванны, то вместо того, чтобы отвести электрод, вам достаточно окунуть в ванну конец электрода. Дуга погаснет, а чисто джоулево тепло в месте контакта имеет значительно меньшую мощность. Сей замечательный эффект позволяет «подпирать» концом электрода ванну, готовую провалиться вам на маску при выполнении потолочного шва (а потолочный шов по меди в аргоне почти немыслим, но угольком его выполнить легко. Таким же манером вы можете буквально «запихивать» конец присадки в ванну.
Уголь не прилипает к меди и вы восстанавливаете процесс сварки просто снова вынув конец электрода из ванны. Кроме того, работа с угольным электродом гораздо производительнее сварки меди в аргоне. И если вас не очень волнует качество шва (например, при сварке скульптур из листа), то этот метод много удобнее работы в аргоне. Антикоррозийные свойства меди сохраняются, т.к. задаются окислением поверхности меди, защищающим металл впоследствии.
Все сказанное не болтовня, а личный опыт автора, по сварке сотен метров листовой меди в условиях стройплощадки.
Да, и не вздумайте варить сталь углем — науглероживание; паять — можно, но результат не так уж и хорош.
Особенности применения
Мало просто выбрать электроды по меди, необходимо также знать, как их правильно использовать. Также важно учитывать физико-химические свойства самого металла, чтобы полученный шов соответствовал нормам качества.
Медь, медные сплавы, бронза и латунь — текучие металлы. При плавлении они быстро теряют твердую форму. К тому же, обладают повышенной теплопроводностью. Это означает, что сквозь них тепло проходит гораздо быстрее, чем при сварке других металлов. Медь и ее сплавы плавятся быстро, поэтому важно подобрать оптимальный температурный режим, чтобы не образовались прожоги. Учитывайте, что медь может быть химически активна по отношению к некоторым газам. Например, при взаимодействии с водородом или кислородом она видоизменяется и теряет стойкость к образованию пор. В некоторых случаях возможно даже образование горячих трещин.
Правильное использование
Недостаточно грамотно выбрать электроды для меди, следует разобраться в правилах их использования. Чтобы шов соответствовал всем требованиям, необходимо учитывать свойства меди.
Медь обладает такой характеристикой, как текучесть. Сразу после начала процесса плавления исчезает ее твердая форма. Кроме этого меди свойственна повышенная теплопроводность. Тепло через медь проходит гораздо быстрее, чем через другие металлы, что может привести к образованию прожогов.
Также следует учитывать, что вследствие существенно повышенной активности при взаимодействии с газами возможно образование пор и даже горячих трещин.
Поэтому так важен установленный правильно режим сваривания и проведение подготовительных работ. Перед началом сварочного процесса необходима закалка электродов не менее одного часа. Также следует подготовить свариваемые детали: очистить их от загрязнений, следов краски и масел, и разделать их кромки.
При работе электроды для пайки меди следует водить со средней скоростью. Формирование шва должно происходить равномерно, чтобы исключить прожоги, наплывы и непровары. Силу тока устанавливают на 10% меньше, чем обычно.
Правильное использование включает в себя регулярную заточку медных электродов. Инструмент для заточки медных электродов предназначается для того, чтобы зачищать контактную поверхность электродов от нагара.
Различия угольных и графитовых электродов
Сварка угольным электродом с подачей присадочного металла в дугу: а — «левый» способ; б — «правый» способ.
Несмотря на схожесть угольных и графитовых стержней в области применения, характеристики их несколько различаются:
- Первое различие – цена. Графитовые изделия более доступны.
- Если стержни из угля абсолютно черные, то электроды из графита обладают темно-серым цветом с металлическим отливом.
- Сварка угольным электродом требует от сварщика определенного опыта, так как этот стержень создает дугу очень высокой температуры, которая может стать причиной разрушения скрутки. В то же время высокие температурные значения достигаются при минимальном токе, поэтому электроды из угля пригодятся обладателям слабых трансформаторных устройств.
- Владельцам инверторных аппаратов, оснащенных регуляторами силы тока, лучше использовать графитовые стержни. Они менее требовательны к квалификации мастера. Кроме того, сварное соединение после их использования отличается лучшим качеством, большей прочностью, повышенной сопротивляемостью к окислению, нежели после сварки углем.
Нюансы эксплуатации
Вы можете подобрать идеальные электроды для работы с медью, но просто на просто, не знать с какой стороны к ним подойти. Не мало важен и сам металл, его химико-физические характеристики, не зная этого вы никогда не получите шов высокой пробы.
Также нужно помнить что такие металлы как медь, латук, бронза, их сплавы имеют свойство течь. Когда вы начинаете их расправлять они очень быстро деформируются. Ещё имеют очень высокую теплопроводность.
То есть при сварке тепло действует на них сильнее нежели на другие металлы. Помните про теплопроводность, если при работе с медью или её сплавами вы подбираете не подходящую мощность то будете готовы до прожогов в металле.
Если вы используете газовую сварку, то так же, будет осторожны поскольку медь химически активный элемент которые взаимодействует с газами.
Если медь начинает взаимодействие с водородом или же кислородом, то оно изменяет свои свойства становиться при сварке не цельной, это очень сильно снижает качество сварки. Также в редких ситуациях появляются трещины ещё по-горячему.
Желательно перед началом сварки очень нагреть электроды, в печи. Показатели времени, температуры при которой нужно прогревать зависеть он марки электрода.
Также важно подготовить к работе сам металл с которым будет проводиться работа, разделите кромки, идеально их отчистить, работа с загрязнённым материалам, в пыли или же с коррозиями полностью исключена.
Скорость нанесения должна быть не очень высокой, но и не низкой. Делайте шов аккуратным без наплывов, не проверенных мест, прожжённого металла равномерно.
Что бы вас не тронулось большинство проблем нужно подобрать правильный режим на сварочном аппарате. Уменьшите силу тока процентом на десять.
Если вы ещё совсем новичок, то лучше сразу сделать не высокую силу тока и по немного её увеличивать, одновременно наблюдал как на это реагирует металл.
Сфера использования стержней и особенности работы с ними
Графитовые электроды используются не только в случаях, когда необходимо соединить медные или алюминиевые провода. Сфера их применения намного обширней. К примеру, стержни из графита востребованы для предварительной обработки поверхности перед выполнением сварочных работ, зачисткой кромок, сварка заготовок и целого ряда других видов обработки. Расходные материала данного типа активно используются как в металлообработке, так и в производстве судов.
Графитированные электроды дают возможность эффективно срезать заклепки, прошивать детали из углеродистой и легированной марок стали. Они актуальны при термической обработке (сплавлении) чугуна и стали. Специальные ниппели позволяют соединять электроды между собой, что позволяет организовать непрерывную подачу электродов в рабочую зону. Таким образом, несложно наладить процесс потоковой подачи расходного материала в печь.
Как показывает практический опыт, графитовые стержни при дуговой резке металла или сварке медной проводки уменьшают количество дефектов. Главное требование при использовании расходников данного типа – соблюдение требований техники безопасности и технологического процесса.
Кроме того, применение стержней из графита актуально для выполнения таких операций:
- сваривание тонкого листового проката или заготовок из цветного металла;
- устранение дефектов, образованных во время литья;
- наплавка твердосплавных покрытий к деталям разного назначения.
Нередко работа с графитовыми электродами подразумевает использование присадки. Она может быть ранее уложенной в определенные места сварки или же подаваться в рабочую зону во время формирования шва.
Следует помнить, что для получения высококачественных сварных соединений с использование графитовых электродов, нужно учитывать особенности работы с таким расходным материалом:
- Добиться экономичного расхода стержня и при этом удерживать стабильную дугу длительный период времени легче при прямой полярности. Другими словами, минус подается на электрод.
- При выполнении сварочных работ важно учитывать воздействие внешних факторов на стабильность горения дуги. Это способствует получению лучшего результата.
- При использовании графитовых электродов КПД специалиста будет меньшим, чем во время сварочных работ плавящимися расходниками.
- Сварка графитом дает возможность получать сварные соединения со средними показателями пластичности.
- Не исключается образование пустот внутри швов, что отрицательно сказывается на их прочности и долговечности.
Учитывая сложность технологического процесса, сварочный работы с использование графитовых электродов поручают опытным специалистам. Новичкам для такой работы желательно хорошо попрактиковаться.
Для работы с электродами из графита применяются два технологических приема:
- Подача материала непосредственно в пламя дуги. Присадка располагается между стыком и электродом под углом в тридцать градусов. При этом в рабочую зону первой подается проволока и только после нее – сам электрод. Для ускорения рабочего процесса расходник удерживается под углом 70 градусов.
- Сначала наплавляется валик, состоящий из основного металла.
После этого в зону плавления подается присадочный материал. В отличие от первого технологического приема здесь подается прежде стержень и только после него – проволока.
Наибольший недостаток второго способа заключается в том, что существует высокая вероятность образования прожога. Поэтому он не подходит при работе с тонкими заготовками и нежелателен для использования новичками в таком деле. А вот для соединения заготовок с толстыми стенками такая технология подходит.
Работая с графитовыми электродами, специалист должен помнить, что определяющим параметром для их применения является плотность тока. Если в силу каких-либо объективных причин данный показатель выше допустимых норм, то работу следует прекратить. В противном случае с высокой степенью вероятности графит придет в негодность.
Продлить срок службы графитовых электродов несложно. Для этого достаточно с обеих сторон вкрутить специальные удлиняющие ниппели. Благодаря такому решению не только сокращаются издержки на приобретения расходных материалов, но и повышается их надежность.
Часто задаваемые вопросы по продукции Керхер
«Из чего сделаны помпы в мойках высокого давления KÄRCHER?» Покупатели часто задают нам этот вопрос, однако, чтобы корректно ответить на него, необходимо небольшое пояснение.
Помпа АВД представляет собой соединение узлов и элементов, функцией которых является перекачивание воды и создание высокого давления, поэтому можно с уверенностью сказать, что именно от нее зависят рабочие характеристики аппарата. Два основных конструктивных узла помпы – это электродвигатель и блок насоса, которые, в свою очередь, также состоят из нескольких узлов и деталей. Поэтому, задаваясь вопросом, из чего сделана помпа – из пластика или металла, нужно понимать, о каком конкретно элементе идет речь. Например, плунжера во всех насосах выполнены из нержавеющей стали, что повышает их долговечность.
Неотъемлемой и очень важной частью насоса является также крышка насосного блока – именно в ней сосредоточены каналы, соединяющие области низкого и высокого давления, а также впускные и выпускные клапаны насоса. От вида материала, из которого изготовлена крышка, во многом зависит надежность аппарата. В ходе многолетней работы инженеры лаборатории KÄRCHER точно установили закономерности поведения различных металлов и композитов при разных нагрузках и выяснили диапазон значений давления, при котором оптимально применение того или иного материала.
N-COR
Высококачественный композитный материал
Долговечен, устойчив к механической усталости
Обладает малым весом
Устойчив к коррозии
Оптимален для АВД с максимальным давлением до 130 бар
Применяется в бытовых АВД
БИ-КОМПОНЕНТ
Устойчив к коррозии на всех участках, контактирующих с водой, благодаря покрытию внутренней поверхности материалом N-Cor
Отличается высокой устойчивостью к напорным нагрузкам благодаря прочному внешнему алюминиевому корпусу
Оптимален для АВД с максимальным давлением от 130 до 145 бар
Применяется в бытовых АВД
АЛЮМИНИЙ
Отличается очень долгим сроком службы, стойкостью к высоким нагрузкам
Сверхпрочный и надежный
Оптимален для АВД с максимальным давлением от 145 до 160 бар.
Применяется в бытовых АВД
ЛАТУНЬ
Применяется в профессиональных АВД
Оптимален во всех диапазонах давлений
Углеродные электроды в электрохимическом анализе биомолекул и биоактивных веществ: роли поверхностных структур и химических групп
Abstract
наноструктуры, химия поверхностного обрыва, влияние этих характеристик на перенос электронов и адсорбционные характеристики электродов.Их свойства обсуждаются в связи с электрохимическими откликами, измеренными для типичных групп аналитов, таких как нуклеиновые кислоты и белковые компоненты или другие электроактивные соединения. Как правило, базисные плоскости графитовых материалов являются местами преимущественной адсорбции органических соединений, тогда как краевые плоскости и дефекты являются местами быстрого переноса электронов для ряда аналитов. При BDD кинетика быстрого переноса электронов наблюдается, в частности, на гидрогенизированных и полированных поверхностях. Терминация поверхности кислородсодержащими группами вызывает снижение скорости переноса электронов и придает углеродной поверхности гидрофильные свойства, проявляющиеся в уменьшении адсорбции гидрофобных молекул и вовлечении кулоновских сил и водородных связей во взаимодействие соответствующих аналитов с поверхностью электрода. Кратко рассмотрены примеры приложений в области электроанализа биомолекул и их компонентов.
Ключевые слова
Электроды3
графит
графит
графин
графен
гетерогенный электрон
Гетерогенный электрон Передача
Электрод-электрод
Adsorption
BiomoLecules
Рекомендуемые статьи со статей (0)
Авторское право © 2018 Elsevier Inc.Все права защищены.
Рекомендуемые статьи
Ссылки на статьи
Произошла ошибка при настройке пользовательского файла cookie
Этот сайт использует файлы cookie для повышения производительности. Если ваш браузер не принимает файлы cookie, вы не можете просматривать этот сайт.
Настройка браузера на прием файлов cookie
Существует множество причин, по которым файл cookie не может быть установлен правильно. Ниже приведены наиболее распространенные причины:
- В вашем браузере отключены файлы cookie.Вам необходимо сбросить настройки браузера, чтобы принять файлы cookie, или спросить вас, хотите ли вы принимать файлы cookie.
- Ваш браузер спрашивает, хотите ли вы принимать файлы cookie, и вы отказались. Чтобы принять файлы cookie с этого сайта, нажмите кнопку «Назад» и примите файл cookie.
- Ваш браузер не поддерживает файлы cookie. Попробуйте другой браузер, если вы подозреваете это.
- Дата на вашем компьютере в прошлом. Если часы вашего компьютера показывают дату до 1 января 1970 г.,
браузер автоматически забудет файл cookie.Чтобы это исправить, установите правильное время и дату на своем компьютере.
- Вы установили приложение, которое отслеживает или блокирует установку файлов cookie. Вы должны отключить приложение при входе в систему или проконсультироваться с системным администратором.
Почему этому сайту требуются файлы cookie?
Этот сайт использует файлы cookie для повышения производительности, запоминая, что вы вошли в систему, когда переходите со страницы на страницу. Предоставить доступ без файлов cookie потребует от сайта создания нового сеанса для каждой посещаемой вами страницы, что замедляет работу системы до неприемлемого уровня.
Что сохраняется в файле cookie?
Этот сайт не хранит ничего, кроме автоматически сгенерированного идентификатора сеанса в файле cookie; никакая другая информация не фиксируется.
Как правило, в файле cookie может храниться только та информация, которую вы предоставляете, или выбор, который вы делаете при посещении веб-сайта. Например, сайт
не может определить ваше имя электронной почты, если вы не решите ввести его. Разрешение веб-сайту создавать файлы cookie не дает этому или любому другому сайту доступ к
остальной части вашего компьютера, и только сайт, создавший файл cookie, может его прочитать.
Угольные электроды что означает? угольные электроды для электролиза воды
Автор: Ивонн 02 сентября 2020 г.
Углеродный электрод представляет собой электрод, состоящий из углеродных элементов, включая электроды из природного графита, электроды из искусственного графита, угольные электроды и специальные углеродные электроды.
Угольные электроды что значит?
Углеродные электроды обладают отличной электро- и теплопроводностью, термостойкостью, химической стойкостью, высокой механической прочностью, простотой обработки и формовки.Широко применяется в металлургии, химической промышленности, электрохимии и других отраслях промышленности, например, электроды для электродуговых печей, электроды для электролиза, электроды для аккумуляторов и т.
Углеродные электроды изготавливаются путем смешивания пекового кокса, нефтяного кокса и клея, а затем обугливания. Степень графитации невысокая, а проводимость не такая хорошая, как у графитовых электродов. Его можно использовать для электролизных электродов, таких как алюминий и магний, а также аккумуляторных электродов.
Технические параметры угольного электрода:
Углеродные электроды используются для
Углеродный электрод представляет собой проводящий материал, изготавливаемый из антрацита и металлургического кокса в качестве основного сырья (иногда с небольшим количеством природного графита или графитизированной крошки).Удельное сопротивление угольного электрода в 2-3 раза больше, чем у графитированного электрода, а прочность на сжатие при комнатной температуре выше, чем у графитированного электрода, но теплопроводность и стойкость к окислению не так хороши, как у графитированного электрода. электрод. Поскольку основным сырьем являются антрацит и металлургический кокс с высокой зольностью, зольность угольных электродов обычно составляет 6-10%.
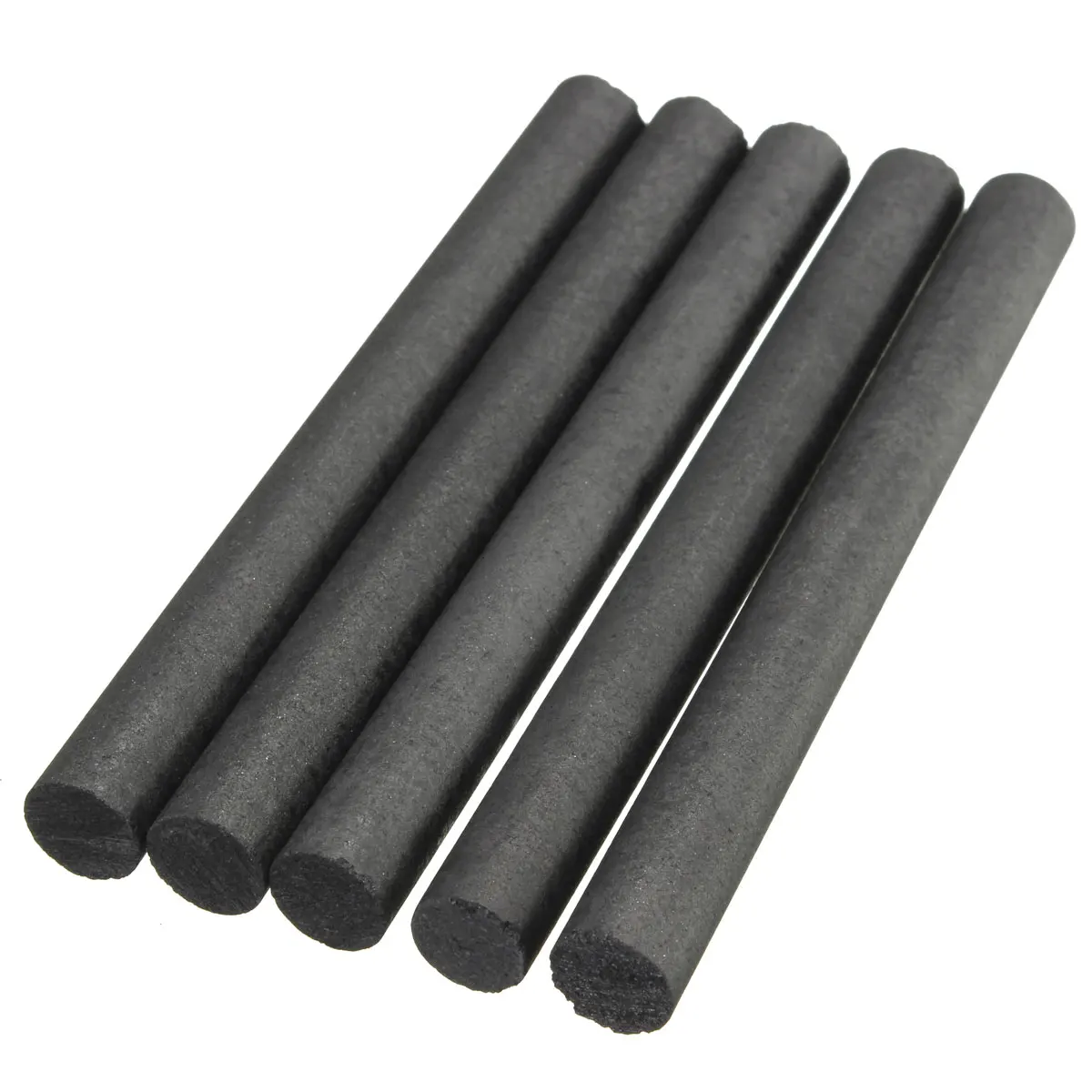
Углеродные электроды подходят для плавки некоторых распространенных электропечных сталей и ферросплавов в средних и малых электропечах и ферросплавных печах.Поскольку угольный электрод имеет относительно высокую зольность, он не подходит для плавки высокосортной легированной стали.
Сырье угольных электродов относительно легко растворяется, при производстве нет необходимости графитировать, а стоимость продукта намного ниже, чем у графитированных электродов.
После обжаривания сырья его подвергают механической обработке. Механическая обработка включает в себя гладкую поверхность и резьбовые отверстия для соединения на обоих концах, а также соединение для соединения двух продуктов.
Для лучшего соединения двух электродов на тонну готового изделия следует подать одновременно несколько килограммов угольной пасты, приготовленной из графитового порошка, сиропа и воды, которую следует нанести в отверстие стыка при соединении изделия.
Электроды угольные для электролиза воды
Обычно для электролиза воды используют инертные электроды, такие как графит, платина.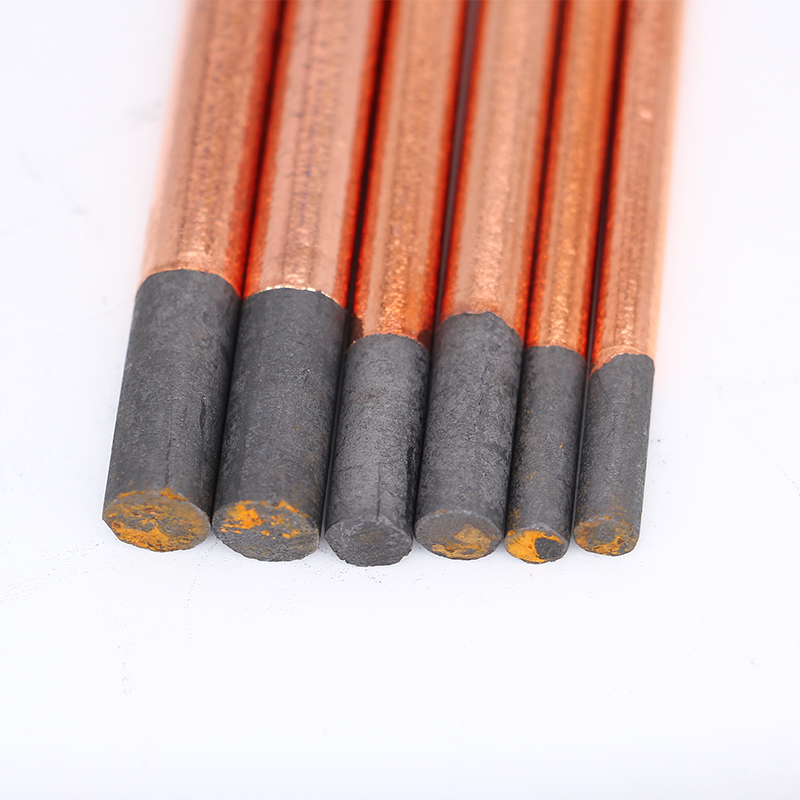
Углерод и графит обладают хорошей электропроводностью и более высокой температурой плавления (около 3800-4200°С). Сопротивление угольных электродов в 2-3 раза больше, чем у графитовых, а зольность значительно больше. Поэтому допустимая плотность тока графитовых электродов составляет 200-600 А/см2, а угольных — 100-200 А/см2. Форма поперечного сечения электрода обычно круглая, квадратная или плоская. Угол кончика электрода обычно составляет 45° ~ 70°. . Электрод расходуется быстрее, когда угол мал, но это может повысить стабильность дуги.При зажиме электрода проводящая часть электрода должна быть как можно короче для удобства работы. Если удлинение слишком длинное, потеря окисления электрода будет ускорена.
Электроды угольные для контактной пайки
Он использует дугу, образующуюся между угольным электродом или графитовым стержнем и заготовкой, в качестве источника тепла для сварки.
Углеродная дуговая сварка, как правило, представляет собой плоскую сварку, вертикальную сварку и более сложную потолочную сварку.Он может сваривать сталь, чугун, цветные металлы и т. д., а также может использоваться для поверхностной наплавки. Однако из-за плохого защитного эффекта он подходит только для случаев с низкими требованиями.
Электроды угольные цена
Рынок цен на угольные электроды сильно изменился и приведен только для справки. Пожалуйста, обратитесь к производителю угольного электрода для получения предложения или в магазин Amazon, чтобы найти его.
Электрохимия угольных электродов | Уайли
Список участников XIII
Редакторы серии Предисловие XIX
Предисловие XXI
1 Свойства углерода: обзор 1
Шэнси Хуан, Йохан ЭкВейс, Сара Коста, Мартин Калбак и Милдред С.Dresselhaus
1.1 Обзор свойств 1
1.2 Различные формы углерода 2
1. 2.1 графена 2
1.2.1. Оптические свойства 2
1.2.1.2 Электрические свойства и настраивание 4
1.2.1.3 Спектроскопические свойства 5
1.2.2 ВОПГ 11
1.2.3 Углеродные нанотрубки 12
1.2.3.1 Структура и электронные свойства 12
1.2.3.2 Спектроскопия и спектроэлектрохимия углеродных нанотрубок 14
1.2.3.22.4 Графен Нанориббон 18
1.2.5 Diamond 20
1.2.6 Пористый углерод 20
1.3 Outlook 21
Список литературы 21
Список литературы 21
2 Электрохимия на высокоориединном пиролитическом графите (HOPG): к новой перспективе 31
Aleix G. Güell, Sze-yin Tan, Patrick R. Unwin и Guohui Zhang
2.1 Введение 31
2.2 Структура и электронные свойства HOPG 33
2.2.1 Структура и формирование 33
2.2.2 Электронные свойства 39
2.2.3 Значение для электрохимических исследований 44
2.3 Формирующие исследования электрохимии ВОПГ 45
2. 3.1 Ранние макроскопические вольтамперометрические измерения и корреляции 45
2.3.2 Макроскопическая вольтамперометрия и моделирование 45
2.3.2 Макроскопическая вольтамперометрия и моделирование 45 Вольтамперометрические методы переменного тока (AC) 50
2.3.4 Критическое сравнение макроскопических данных 50
2.4 Микроскопические взгляды на электрохимию в ВОПГ 53
2.4.1 Окислительно-восстановительные системы Outer-Sphere 53
2.4.1.1 Контактный метод сканирующей микропипетки 53
2.4.1.2 ВОПГ с пленочным покрытием Nafion 55
2.4.1.3 Сканирующая электрохимическая клеточная микроскопия (SECCM) (сканирующая микроскопия) SECM) 60
2.4.1.5 Исследования SECM-AFM 61
2.4.1.6 Недавние макроскопические исследования 62
2.4.2 Сложные многоступенчатые реакции: окисление нейротрансмиттера 64
2.2 90 Адсорбированные системы 684.4 Функционализация диазония HOPG 71
2.5 Выводы 75
Благодарности 75
ссылки 75
ссылки 75
3 Электрохимия в одном измерении: применение углеродных нанотрубок 83
Emiliano N. Primo, Fabiana Gutiérrez, Mar’ © ¥ A Рубианес, Нэнси Ф. Феррейра, Марсела С. Родресгес, Марья. Л. Педано, Орельен Гаснье, Алехандро Гутьеррес, Маркос Эгулас, Пабло Дальмассо, Гильермина Луке, Соледад Болло, Консепсьон Паррадо и Густаво А.RIVAS
3.1 Нанотрубки углерода: Общие соображения 83
3.2 Структура и синтез СНТС 84
3.3 Структура СНК по сравнению с электрохимическими свойствами 86
3.4 Стратегии для приготовления углеродных нанотрубок электродов 89
3.4.1 Функционализация 89
3.4.1.1 Ковалентная функционализация 90
3.4.1.2 Нековалентная функционализация 90
3.4.2 Приготовление электродов из пасты углеродных нанотрубок с использованием различных связующих 106
3.4.2.1 Электроды для трафаретной печати (SPE) 108
3.5 ProspectiveWork 108
Ссылки 109
4 Электрохимия графена 121
Холли В. Паттен, Матень Велицкий, Dryfe
4.1 Обзор свойств графена 121
4. 2 Подготовка графена 123
4.2.1 Изготовление сверху вниз графена 123
4.2.2 «Поднимок» Маршруты до производства графена 128
4.3 емкости графена Электроды 130
4.4 электронные трансферные кинетики на графеновых электродах 137
4.4.1 модификация и допинг графена для применения в электрокатализе 149
4.5 Заключение и будущие направления 151
Собеты 152
Символы 152
Символы 153
5 Использование Проводящий алмаз в электрохимии 163
Джули В. Макферсон
1.2 Выращивание синтетического легированного бором алмаза для электрохимических применений 166
5.1.2.1 Выращивание при высоких давлениях и высоких температурах (HPHT) 166
5.1.2.2 Выращивание методом химического осаждения из газовой фазы 167
5.2 Геометрия и расположение электродов 1800 9009
1 Характеристика электрохимических и материальных свойств BDD 174
5.2.1.1 Оценка морфологии поверхности 174
5. 2.1.2 Расширенное окно растворителя и низкая емкость 175
5.2.1.3 Рамановский анализ отношения sp2/sp3 в BDD 177
5.2.1.4 Характеристика окислительно-восстановительных компонентов внешней сферы 180
5.3 Влияние поверхностного обрыва на электрохимический отклик BDD 182
Сферические механизмы переноса электронов 182
5.3.2 Алмаз с концевыми водородными и кислородными концевыми группами 183
5.3.2.1 Кинетика гетерогенного переноса электронов на электродах с концевыми водородными и кислородными концевыми группами 186
5.4 Электрохимия поликристаллов и монокристаллов 190
5.4.1 Электрохимическая визуализация поликристаллических BDD 191
5.4.2 Электрохимия монокристаллов BDD 193
5.5 Придание каталитической активности BDD 195
5.5. 195
5.5.2 Ионная имплантация 197
5.6 Химическая функционализация электродов BDD 197
5.7 Электроаналитическое применение BDD 199
5.8 Выводы 201
Благодарности 202
Ссылки 202
6 Модификация поверхностей углеродных электродов 211
Мухаммед Танзирул Алам и Дж. Джастин хорошее
6.1 Введение 211
6.2 Ковалентная модификация 212
6.2.1 катиона диазония 212
6.2.2 Окисление амина 220
6.2.3 Окисление карбоксилата 223
6.2.4 Окисление спирта 225
6.2.5 Гидрирование и галогенирование углерода 226
6.3 некоммерческая модификация 228
6.3.1 π-π укладка 228
6.3.2 48
6.3.2 6.4
6.4 Направления на будущее 234
Благодарности 235
ссылки 235
7 углеродных материалов в низкотемпературных полимерно-электролитных мембранных топливных элементах 241
Майкл Брон и Кристина Рот
1.2 Характеристика углерода 246
7.1.2.1 Рамановская спектроскопия 247
7.1.2.2 Методы малоуглового рассеяния 249
7.1.2.3 Химия поверхности с помощью рентгеновской фотоэлектронной спектроскопии (XPS) и ближнекраевой рентгеновской абсорбционной спектроскопии. (NEXAFS) 249
7.1.2.4 Другие методы и исследования на месте 251
7. 2 Углерод как вспомогательный материал в электрокатализаторах топливных элементов 251
7.2.1 Сажи 254
7.2.2 УНТ и графен 251
7.2.22.3 (Заказ) Мезопористый углерод 257
7.2.4 Графитизация как средство борьбы с углеродной коррозией 258
7.3 Углерод как каталитически активный компонент в топливных элементах 259
7.3.1 ORR активность углерода 259
8 Допированные углеки и функционализированные CNT 260
7.3.3 Модификация углеродных и других углеродных материалов 261
7.3.3.1 Материалы на основе CNT 262
7.3.3.2 Графен 262
7.3.3.3 Наноструктурированный углерод, выращенный над металлическими катализаторами 262
7.4 Углерод как структурообразующий элемент в электродах пористых топливных элементов 263
7.4.1 Влияние материала подложки на структуру электрода 264
7.4.2 Влияние выбранного этапа изготовления на структуру электрода 266
7.4.3 Влияние на структуру электрода Обещано улучшить характеристики электродов 267
7. 4.4 Классические конструкции электродов 268
7.4.5 Усовершенствованные конструкции 268
7.4.5.1 Горизонтальное структурирование с помощью LbL 269
7.4.5.2 Наноструктурированные электроды 270
7.4.4.6 Новые концепции 270
7.4.6.1 Электроспинация в технологии топливных элементов 271
7.4.6.2 «Самостоятельно узел» путем парилирования эмульсий 272
7.5 Сводка и Outlook 274
Благодарности 275
Ссылки 275
8 Электрохимические конденсаторы на основе угольных электродов в водных электролитах 285
1 Введение 285
8.2 Основы двухслойных электрических конденсаторов 286
8.3 Углерод и электролиты для электрических двухслойных конденсаторов 290
8.3.1 Электрические двухслойные конденсаторы на основе углеродных электродов 290
8.3.1 Электрические двухслойные конденсаторы на основе углеродных электродов 290
8.3. Электролиты для электрических двухслойных конденсаторов 295
8. 4 Привлекательные электрохимические конденсаторы в водных растворах 296
8.4.1 Расширение окна стабильности в нейтральных водных электролитах 296
8.4.2 Определение пределов стабильности клеточного потенциала путем плавания 300
8.4.3 Повышение емкости посредством фарадиевских реакций на границе раздела углерод-электролит в водной среде 305
8.5 Выводы и перспективы 308
Ссылки 309
9008 313Дерек Плетчер
9.1 Введение 313
9.2 Комментарии по углероду, встречающемуся в электрохимической технологии 314
9.3 Производство химикатов 315
9.3.1 Хлор-щелочная промышленность 316
9.3.2 Извлечение алюминия 317
9.3.3 Извлечение металлов группы 1 и 2 318
9.3.4 Поколение фтора 318
9.3.4 Поколение фтора 317
9.3.4 5 Генерация озона 319
9.3.6 Перекись водорода 322
9.3.7 Другие сильные окислительные агенты 323
9.3.8 Органические продукты 323
9. 4 Водные и сточные процедуры 327
9.4.1 Удаление органика 328
9.4.1.1 Doped Boron Doped Diamond 328
9.4.1.2 Химия пероксида водорода 329
9.4.1.3 Другие технологии 329
9.4.2 Удаление неорганических батарей 330
9.5 Расходные батареи 331
Ссылки 332
10 углерода Электроды в молекулярной электронике 339
Адам Йохан Бергрен и Алексей Ивашенко
3.1 Графен 350
10.3.1.1 Электрохимия графена (см. Также глава 4) 350
10.3.1.2 Графен в молекулярной электронике 351
10.3.2 Углеродные нанотрубки 355
10.3.2.1 Электрохимия электродов CNT 357
10.3. 2.2 Электронные свойства УНТ 357
10.3.2.3 Электронные устройства на основе УНТ 357
10.4 Транспортировка заряда 360
10.4.1 Транспортировка заряда зависит от системы 365
10.4.2 Механизмы переходов 367
10.5 Выводы и перспективы 367
Благодарности 368
ссылки 368
ссылки 368
11 Электроды углерода 379
Иван Švancara и Kurt Kalcher
11. 1 Введение: Электроды углерода — состояние искусства 379
11.2 Угольная паста как электродный материал 380
11.2.1 Основные положения и классификация 380
11.2.2 Характеристика двух основных компонентов угольной пасты 384
11.2.2.1 Углеродистая часть 384
11.2.2.2 Связующая/пастообразная жидкая часть 386
11.2.3 Физико-химические и электрохимические характеристики угольных паст и соответствующих электродов из угольной пасты 387
11.2.3.1 Несколько замечаний по получению обычного углерода Смеси паст 387
11.2.3.2 Типичные свойства и поведение традиционной угольной пасты (электрод) 388
11.2.3.3 Особенности новых типов двухкомпонентных углеродных паст 391
11.2.4 Обзор применения двухкомпонентных и немодифицированных угольных паст 394
11.2.5 Современные тенденции использования угольных паст и некоторые перспективы на будущее 398
11.3 Электроды из модифицированной угольной пасты 399
11. 3.1 Модификация – как изменить свойства электрода in an IntentionalWay 399
11.3.2 Процессы модификации 400
11.3.3 Типы модификаторов 401
11.3.4 Биосенсоры с углеродной пастой 406
11.3.5 Применение CMCPE и CP
11.4 последних достижения в электроанализ с CMCPES и CP-биосенсорами и перспективами для будущего 412
ссылки 413
12
12 напечатанные на экране углеродные электроды 425
Стивен Флетчер
12.1 Введение 425
12.2 Проводимость композитов 426
12.3 Полиморфы углерода 427
12.4 Кислородные функциональные группы 427
12.5 Активированные угли 428
12.6 Комбинации связующее-растворитель 429
12.7 PVDF Properties 430
12.8 PVDF Solubility 432
12.9 Гибкие подложки 433
12.10 Процесс экрана 434
12.11 Экран печати Материалы 435
12.12 The Ink Flow 436
12.13 Подложка 436
12.14 Коммерческие чернил-добавки 437
12. 15 Процентное содержание связующего 438
12.16 Многослойные электроды 438
12.17 ИК-капля 439
12.18 Поверхностная емкость 439
12.19 Эквивалентная схема 440
Ссылки 441
Алфавитный указатель 445
Оценка покрытия поверхности аминофенильных связей на электродах из диазотированного стеклоуглерода для оптимизации работы электрохимического биосенсора
Электрохимические биосенсоры с использованием углеродных электродов широко разрабатываются для обнаружения ряда различных заболеваний. Поскольку их чувствительность зависит от покрытия поверхности частями биорецепторов, она обязательно зависит от покрытия поверхности предшественниками аминов.Электрохимические методы с использованием ферроценкарбоновой кислоты в качестве быстрого и дешевого анализа использовались для оценки покрытия поверхности аминофенильными группами, присоединенными к угольному электроду. В то время как количество электронов, перенесенных на первой стадии диазотирования, указывало на покрытие поверхности 8,02 ± 0,2 × 10 -10 (моль/см 2 ), а электронов, перенесенных на второй стадии, на восстановление нитрофенила до амино- фенила, указывало на покрытие поверхности амином 4-5 × l0 -10 (моль/см 2 ), количество электронов, перенесенных во время присоединения соединения для анализа аминового сочетания, ферроценкарбоновой кислоты, указывало на гораздо более низкое количество доступного амина покрытие всего 2. 2 × l0 -11 (моль/см 2 ). Кроме того, доступное покрытие амином критически зависело от количества циклов циклической вольтамперометрии, используемых при восстановлении, и, таким образом, процедуры, используемые на этом этапе, влияли на чувствительность любого последующего датчика. Связывание амина антитела против бета-амилоида с концевыми карбоксильными группами, специфичного к пептиду Aβ(1-42), потенциальному маркеру болезни Альцгеймера, происходило по той же схеме покрытия, что и с ферроценкарбоновой кислотой, и при оптимальном покрытии амином чувствительность датчика дифференциальной импульсной вольтамперометрии находилась в диапазоне 0-200 нг/мл с крутизной 5.07 мкА/нг.мл -1 и R 2 = 0,98.
Ключевые слова: 4-нитробензол диазония; амилоид-β-пептид; электрохимический; функционализация; покрытие поверхности.
Углеродный электрод с трафаретной печатью
pH/ионы, растворенный кислород и проводимость Ищете титратор?Вы ищете правильный титратор для ваших требований?
ОМНИС Новая система титрования для современной лаборатории: более быстрый анализ, более безопасное обращение с химическими веществами, новое программное обеспечение, больше автоматизации.
Высококлассный потенциометрический титратор, отвечающий любым требованиям: гибкий, совместимый, настраиваемый и автоматизированный.
Ти-ТачКомпактный и простой в использовании потенциометрический титратор для широкого спектра рутинных титрований.
Эко титраторНовый базовый титратор для всех стандартных приложений потенциометрического титрования
Титрино плюсУниверсальный потенциометрический титратор начального уровня для основных задач
ТитротермТермометрический титратор для быстрых определений, если невозможно применить потенциометрическое титрование.
Ищете титратор KF?Вы ищете подходящий титратор KF для ваших требований?
ОМНИС КФНовый волюметрический титратор Карла Фишера для безопасного, простого и быстрого определения содержания воды
КФ ТитрандоВысококачественные титраторы для определения любого содержания воды от 0.от 001 до 100%
КФ Ти-ТачКомпактный автономный волюмометрический (> 0,1 % воды) или кулонометрический (до 0,001 % воды) титратор со встроенным блоком управления с сенсорным экраном
Eco KF ТитраторБазовый волюметрический титратор Карла Фишера для простого, безопасного и надежного рутинного определения содержания воды
КФ Титрино плюсТитратор начального уровня для кулонометрического (содержание воды: от 0,001 до 1%) или волюмометрического (до 100%) определения воды
Кулонометры Наш ассортимент кулонометров для определения низкого содержания воды (0. 001 на 1%).
Базовый кулонометр для определения низкого содержания воды (до 0,001%)
ГазоанализаторКомплексная система для определения содержания воды в сжиженных и постоянных газах
Ищете систему IC?Здесь вы найдете подходящую ИС-систему, соответствующую вашим требованиям.
Быстрый контроль качества с ICУвеличьте производительность при одновременном снижении затрат на контроль качества продуктов питания и напитков с помощью ионной хроматографии.
940 Professional IC VarioВысококачественная система ионной хроматографии для исследовательских приложений и разработки методов
930 Компактный IC FlexСистема компактной ионной хроматографии для рутинного анализа
Эко СКИонный хроматограф начального уровня для анализа воды и использования в качестве учебного пособия.
Методы через дефис Расширьте область применения ионной хроматографии, соединив свою ИС Metrohm с различными системами отбора проб и методами детектирования.
Столбцы
Аксессуары и расходные материалы
Ищете счетчик?Найдите подходящий прибор для измерения pH, проводимости, кислорода или ионов
912/913/914 pH/DO/кондуктометрПростые в использовании измерители для использования в лаборатории и в полевых условиях
780/781 pH/иономерУсовершенствованные рН-метры и ионометры для использования в лаборатории
Модули 867/856Модули высокого класса для индивидуального измерения pH, ионов и проводимости
Обзор нашего ассортимента продукции для спектроскопииНайдите спектрометр, соответствующий вашим требованиям.
Быстрый контроль качества с NIRSУзнайте, как NIRS может повысить вашу производительность и снизить затраты в вашей лаборатории контроля качества.
Анализаторы спектроскопии ближнего инфракрасного диапазонаСпектроскопические анализаторы ближнего инфракрасного диапазона для рутинного анализа химических и физических свойств
Мгновенные рамановские анализаторы MetrohmРучной спектрометр для быстрой и простой идентификации неизвестных веществ
Решения для мобильной спектроскопии B&W Tek Лабораторные, портативные и портативные рамановские спектрометры для простой и быстрой идентификации и проверки материалов.
Здесь вы найдете подходящую систему VA или CVS, соответствующую вашим требованиям.
Профессиональные инструменты VA/CVSУсовершенствованные системы VA с высокопроизводительным программным обеспечением viva для определения следов тяжелых металлов с помощью полярографии и вольтамперометрии с высокой чувствительностью
Портативный анализатор ВАПортативный вольтамперометрический анализатор для определения следовых количеств мышьяка, ртути и меди в воде
Базовые приготовления
Процесс ВА
Волтик ПрофессионалСистема, сочетающая ионную хроматографию и вольтамперометрию для анализа следовых ионов.
Пионеры в области анализа процессовНам нравится решать аналитические задачи в Metrohm Process Analytics.
Обзор анализатора процессовУзнайте больше о наших семействах анализаторов процессов
Анализаторы процессов 2060 Платформа модульного анализатора для максимальной гибкости в индивидуальном мониторинге процессов.
Полностью автономная система мониторинга ионов в аэрозолях и газов в окружающем воздухе
Анализаторы процессов NIRS XDSМногоканальный анализатор для неразрушающего спектроскопического анализа в реальном времени
Анализаторы процессов NIRS PROАнализатор для непрерывного неразрушающего контроля с помощью контактных датчиков или бесконтактных измерений над конвейерной лентой или через стеклянное окно
2035 Анализаторы процессовТехнологические анализаторы доступны в потенциометрической, фотометрической и термометрической версиях, а также дополнительные измерения pH и электропроводности.
Серия 202X – анализаторы процессов с одним методомУниверсальные технологические анализаторы для мониторинга воды и сточных вод с использованием методов титрования, pH, ISE или фотометрии.
ADI 204Y – многофункциональные анализаторы технологических процессовМногофункциональные анализаторы процессов, адаптированные к вашим требованиям для многопараметрических измерений и потоков
Служба качества МПА Наши качественные услуги варьируются от консультаций и поддержки приложений до установки, обучения, профилактического обслуживания и ремонта.
Найдите правильное электрохимическое решение для ваших требований.
VIONIC на базе INTELLOОдин прибор, чистое открытие для всех ваших электрохимических исследований.
Компактная линияВысококачественные потенциостатические/гальваностатические приборы небольшого размера.
Модульная линияМодульные потенциостаты/гальваностаты для любых требований электрохимических исследований
Многоканальная линияМногоканальные потенциостатические/гальваностатические приборы для одновременных измерений
Портативная линияКомпактный портативный потенциостат, управляемый ПК, для обучения и базовых приложений
СпектроэлектрохимияИнтегрированное решение для комбинированного электрохимического и спектроскопического анализа.
Электрохимические электродыИндивидуальные решения
Обзор измерения стабильности Узнайте больше о наших решениях для измерения стабильности.
Прибор для определения устойчивости к окислению натуральных масел и жиров
Биодизель РанциматПрибор для определения устойчивости к окислению биодизеля и биодизельных смесей
Термомат ПВХПрибор для определения термостойкости ПВХ
Обзор работы с жидкостямиУзнайте больше о наших решениях для обработки жидкостей.
Эко ДосиматСовременная система для работы с жидкостями, обеспечивающая точность и аккуратность швейцарского производства по доступной цене.
846 Интерфейс дозированияПрибор для работы с жидкостями для автономного использования или интеграции в существующие системы Metrohm
Дозимат плюсВысокоточный прибор с ручным управлением для всех задач по работе с жидкостями
Поиск аксессуаровНайдите дозаторы, пробирки, стеклянную посуду, стаканы и другие аксессуары и запасные части.
Поиск столбцов Найдите аналитические, ловушки и защитные колонки для определения анионов и катионов.
Найдите подходящий электрод для вашего приложения: титрование, IC, измерение pH, VA, CVS, электрохимия и многое другое.
Поиск программного обеспеченияНайдите программное обеспечение Metrohm для титрования, IC, VA/CVS, измерения стабильности, электрохимии, спектроскопии и многого другого.
Бутылочные диспенсеры BrinkmannБутылочные дозаторы Brinkmann и дозаторы ChemSaver обладают уникальными и полезными функциями для надежного и удобного дозирования реагентов.
С.Рабочие электроды — Химия LibreTexts
1. Типы электродов
Рабочий электрод (РЭ) представляет собой важнейший компонент электрохимической ячейки. Именно на границе между WE и раствором происходят наиболее интересные переносы электронов. Выбор материала рабочего электрода имеет решающее значение для успеха эксперимента. Следует учитывать несколько важных факторов. Во-первых, материал должен демонстрировать благоприятное окислительно-восстановительное поведение с аналитом, в идеале быстрый, воспроизводимый перенос электронов без загрязнения электрода. Во-вторых, окно потенциала , в котором электрод работает в данном растворе электролита, должно быть как можно шире, чтобы обеспечить наибольшую степень характеризации аналита. Дополнительные соображения включают стоимость материала, его способность подвергаться механической обработке или придавать ему полезную геометрию, легкость обновления поверхности после измерения и токсичность.
Наиболее часто используемые материалы для рабочих электродов: платина , золото , углерод и ртуть .Среди них платина, вероятно, является фаворитом, демонстрируя хорошую электрохимическую инертность и простоту изготовления во многих формах. Самым большим недостатком использования платины, помимо ее высокой стоимости, является то, что присутствие даже небольшого количества воды или кислоты в электролите приводит к восстановлению иона водорода с образованием газообразного водорода (выделение водорода) при довольно скромных отрицательных потенциалах. (Е = -0,059 х рН). Это уменьшение скрывает любой полезный аналитический сигнал.
Золотые электроды ведут себя аналогично платиновым, но имеют ограниченную полезность в положительном диапазоне потенциалов из-за окисления их поверхности.Однако это оказалось очень полезным для изготовления модифицированных электродов , содержащих поверхностные структуры, известные как самособирающиеся монослои (SAM) .
Углеродные электроды позволяют сканировать более отрицательные потенциалы, чем платиновые или золотые, а также хорошие окна анодного потенциала. Наиболее распространенной формой угольного электрода является стеклоуглерод , который относительно дорог и сложен в обработке. Электроды из угольной пасты также используются во многих областях.Эти электроды изготовлены из пасты мелко гранулированного углерода, смешанного с масляной подложкой, такой как Nujol. Затем паста помещается в полость инертного корпуса электрода. Электроды из угольной пасты имеют тот недостаток, что они подвержены механическим повреждениям во время использования.
Ртуть исторически была широко используемым электродным материалом, главным образом в виде сферической капли, образованной на конце стеклянного капилляра, по которому течет жидкий металл. Он демонстрирует превосходное потенциальное окно в катодном направлении, но сильно ограничен в анодном направлении из-за легкости окисления.Капля ртутного электрода (DME) , в котором капли образуются и падают многократно во время сканирования потенциала, заменяясь «свежим» электродом каждую секунду или около того, обычно в прошлые годы был первым электродом, с которым многие студенты сталкивались в своих исследованиях. исследования. Токсичность ртути привела к ограниченному использованию в наши дни, хотя она по-прежнему является очень полезной поверхностью в методах, включающих предварительное концентрирование металлического аналита перед потенциальным сканированием, как это делается в анодной инверсионной вольтамперометрии (ASV) .В настоящее время многие практикующие врачи используют ртутные пленки , сформированные на поверхности твердых электродов, а не на чистом металле. В этих условиях небольшой объем пленки позволяет анализируемому веществу концентрироваться при больших значениях с быстрым временем диффузии.
2. Преимущества и ограничения
В таблице 1 перечислены часто используемые электродные материалы, а также приведены преимущества и ограничения каждого из них.
Материал | Преимущества | Ограничения |
---|---|---|
Пт | доступный провод, плоская пластина и трубка большой выбор размеров Сплав Pt-Rh для жесткости | низкое водородное перенапряжение, поэтому диапазон катодного потенциала ограничен дорогой |
Золото | Конфигурации аналогичны Pt больший диапазон катодного потенциала | больший диапазон катодного потенциала анодное окно, ограниченное поверхностным окислением дорогой |
Углерод | много типов и конфигураций хороший диапазон катодного потенциала | качество сильно различается трудно поддается формовке |
С-паста | широкий потенциальный диапазон низкий фоновый ток недорогой | нестабилен в проточных кюветах нельзя использовать в органических растворителях |
рт.![]() | отличное катодное окно легко «обновить» формы амальгамы | ограниченное анодное окно из-за окисления ртути токсичный |
Приблизительные диапазоны полезных потенциалов для платиновых, ртутных и угольных электродов в водных растворах электролитов, а также для платины в ряде неводных систем можно найти в приложении к ссылке 2.
Твердые электроды для вольтамперометрических измерений чаще всего изготавливаются путем заключения материала электрода в непроводящую оболочку из стекла или инертного полимерного материала, такого как тефлон, Kel-F (полихлортрифторэтилен) или PEEK (полиэфирэфиркетон). Чаще всего открытый электродный материал имеет форму диска. Обычные имеющиеся в продаже диаметры дисков составляют 1,0, 3,0 и 10,0 мм. Электроды такого размера обычно производят измеренные токи в диапазоне от мкА до малого мА для аналитов при концентрациях около 1 мМ.Два распространенных коммерческих источника рабочих электродов: ESA, Inc. (www.esainc.com) 23 и Bioanalytical Systems, Inc. (www.bioanalytical.com) 24 .
На рис. 35 показаны примеры рабочих электродов этих двух производителей. Слева показаны дисковые электроды макроразмеров, заключенные в непроводящий полимер, а справа показаны микроэлектродов (см. ниже), которые были изготовлены путем запаивания проволок из инертных металлов в стеклянные изолирующие тела.
Рисунок 35
Электроды диаметром менее примерно 25 мкм, называемые микроэлектродами или ультрамикроэлектродами , разработанные Р. М. Вайтманом и его сотрудниками, обладают уникальными электрохимическими характеристиками. К ним относятся, в дополнение к их чрезвычайно малому размеру, минимизация эффектов сопротивления раствора и быстрое время отклика. Важными областями применения этих электродов являются высокоскоростная вольтамперометрия (> 10 000 В/с), электрохимия растворителей с высоким сопротивлением и вольтамперометрия in vivo .Электроды могут быть изготовлены в диапазоне малых диаметров путем герметизации платиновых или золотых микропроводов или углеродных волокон в стекле. Электроды таких размеров также могут быть изготовлены методом осаждения металла или фотолитографии.
Электрохимическое поведение микроэлектродов может заметно отличаться от поведения электродов обычного размера. Чтобы проиллюстрировать различие, сначала рассмотрим случай плоского электрода миллиметровых размеров в кювете объемом несколько мл.Если изменить приложенный потенциал либо на ступеньку, либо на развертку, от значения, при котором не происходит переноса электронов к окислительно-восстановительным активным частицам в растворе, до значения, при котором происходит перенос электронов, концентрация окислительно-восстановительных активных частиц будет снижена. на поверхности электрода, что приводит к образованию градиента концентрации (см. для обзора хроноамперометрия , раздел II А, часть 1-а). Чем дольше электрод находится под потенциалом, достаточным для переноса электронов, тем дальше от электрода в раствор распространяется градиент концентрации.
Наличие градиента вызывает диффузию электроактивного материала из областей с высокой концентрацией (основной объем раствора) в области с низкой концентрацией (вблизи поверхности электрода). Эту диффузию можно описать законами Фика, которые принимают несколько иную форму для изменения геометрии электродов. Для большого плоского электрода, описанного здесь, диффузионный слой очень быстро перемещается вглубь раствора, превышая расстояние, на которое молекула может диффундировать в масштабе времени типичного эксперимента.В этих условиях диффузия из объема раствора, где концентрация постоянна, к поверхности электрода почти полностью носит линейный характер в направлении, перпендикулярном поверхности электрода.
В циклической вольтамперометрии (см. Раздел II A, часть 2-b) эти условия обычно дают традиционную пиковую вольтамперограмму. CV, записанная для ферроцена на дисковом электроде из стеклоуглерода диаметром 3 мм, показана слева на рис. 36 .Ферроцен присутствовал в концентрации 0,6 мМ в ацетонитриле с 0,1 М гексафторфосфатом тетрабутиламмония в качестве фонового электролита. Скорость сканирования составляла 0,10 В/с.
Рисунок 36
Далее рассмотрим планарный микроэлектрод микрометрового или меньшего размера. Справа от Рисунок 36 показана вольтамперограмма для 0,6 мМ ферроцена, снятая на стеклоуглеродном электроде диаметром всего 10 мкм. При прочих равных условиях эксперимента наблюдалась сигмоидальная, а не пиковая вольтамперограмма.Это было результатом стационарного состояния между диффузией и переносом электронов, когда скорость диффузии соответствует скорости переноса электронов. Почему разница? Из-за небольшого размера электрода вклад в ток за счет диффузии от краев электрода становится важным в общем массопереносе электроактивных частиц. Этот краевой эффект, или радиальная диффузия , обычно очень мал при больших электродах по сравнению с упомянутой выше линейной диффузией.Для микроэлектродов поток в единицу времени и площади больше, чем для больших электродов, потому что область, из которой электроактивные частицы диффундируют к поверхности, имеет форму полусферы .
Важно понимать, что вольтамперограммы Рисунок 36 относятся к одному набору условий. Существуют условия, при которых ЦВА, зарегистрированная на большом плоском электроде, будет демонстрировать стационарное поведение, и условия, при которых на микроэлектродах наблюдаются пиковые вольтамперограммы.{1/2}}\]
, где D 0 — коэффициент диффузии (см 2 /с). Когда d мало по сравнению с радиусом электрода, будет преобладать линейная диффузия, и наблюдаемая вольтамперограмма будет иметь форму пика. Для малых размеров электрода d часто будет большим по сравнению с радиусом электрода, и в результате будет получена стационарная вольтамперограмма.