Ультразвуковой контроль (УЗК) швов и сварных соединений, труб и трубопроводов
Прочность и герметичность швов — важные условия нормального функционирования сварных конструкций. Низкое качество соединений при помощи сварки может привести к катастрофическим последствиям вплоть до обрушений, поэтому после сварочных работ обязательно проводится контроль качества сварных соединений. Особенно тщательно проверка выполняется для систем и резервуаров, находящихся под давлением, обязателен и контроль сварных соединений трубопроводов. Порядок и ход процедур по контролю регламентируются соответствующим отраслевым ГОСТом, здесь же перечислены допустимые погрешности и дефекты, не влияющие на качество шва. По окончании работ составляется протокол контроля.
Все методы контроля качества делятся на две большие группы: разрушающие и неразрушающие. Разрушающие подразумевают изъятие из партии нескольких изделий и их всесторонняя проверка. Неразрушающие методы проверки проводятся с помощью специальных инструментов, которые позволяют оценить качество шва, не разрушая всю конструкцию. Наиболее часто применимыми способами контроля качества сварки металла являются визуальный, радиационный, магнитный, капиллярный, визуальный, ультразвуковой, проверка на проницаемость. Ультразвуковой контроль сварных соединений в последнее время получил широкое распространение — с его помощью можно провести измерение толщины металла на труднодоступных участках трубопроводов.
Принцип действия ультразвукового аппарата для контроля качества сварки труб основан на разнице акустических сред на месте соединения металлов. Ультразвук проходит через металл, отражается от задней стенки и принимается сенсором, который выводит полученный результат на экран. Дефекты сварки показываются на экране как искажения волны, причем они типичны для определенных видов дефектов. Опытный специалист по ультразвуковому методу контроля быстро распознает вид брака в сварном шве. Ультразвуковой неразрушающий контроль безопасен в отличие от радиационного контроля, оборудование стоит недорого, а проводить его просто и удобно.
Ультразвуковый контроль швов позволяет выявить следующие дефекты соединения:
- Трещины,
- Свищи,
- Несплавления шва,
- Коррозия,
- Участки с другим химическим составом,
- Искажения геометрической формы.
УЗК швов используется при сварке определенных металлов:
- Медь,
- Легированная сталь,
- Чугун,
- Аустенитные стали.
Строительная лаборатория “Прометей” работает по всей территории России — наши специалисты проводят ультразвуковой контроль сварных соединений и трубопроводов. Проведение ультразвукового контроля непосредственно на объекте экономит время заказчика. Контроль проводится в строгом соответствии с отраслевыми ГОСТами. Мы гарантируем заказчикам качественную проверку, короткие сроки и выгодные цены на УЗК сварных швов и соединений.
Ультразвуковой контроль сварных соединений в Москве и Санкт-Петербурге
Неразрушающий метод проверки швов – ультразвуковая дефектоскопия – предназначен для оперативного и максимально эффективного отслеживания надежности работы соединений металлоконструкций, газопроводов, труб, арматуры по невысокой цене. Ультразвуковой контроль сварных соединений трубопроводов (УЗК) является безопасным для человека способом отслеживания качества и надежности, характерной для стыковых соединений металлоконструкций.
Сделать заказ
рассчитать стоимость работ
Из-за несвоевременного выявления дефектов могут возникнуть крупные неприятности, связанные с ростом риска прорывов на трубопроводах, созданием условий для проявления разнообразных аварийных ситуаций, включая автомобильные катастрофы. Потому недопустима экономия, связанная с проведением ультразвукового контроля стыковых соединений, особенно в строительной сфере либо при проведении ремонтных работ.
Ключевые особенности
Неразрушающий метод является достаточно популярным способом проверки прочности швов металла. Впервые ультразвуковой контроль сварных соединений использовали еще в 1930-ом году. В основе принципа действия лежат проникающие свойства, присущие высокочастотному ультразвуку, в металл. Данные свойства способствуют отталкиванию диагностической волны от возникших пустот, сколов или царапин. Оператору при ультразвуковом контроле стыковых соединений остается лишь обнаружить дефект в соответствии с отклонениями графика волны. Данный метод хорошо отработан и имеет невысокую цену.
Ультразвуковой контроль сварных соединений не приводит к нарушениям в целостности швов и способствует выявлению дефектов, невидимых человеческому глазу. Отметим преимущество данной технологии для обнаружения как наружных, так и внутренних дефектов в тавровых, угловых или любых других видах швов. Можно также эффективно определиться с отклонениями от стандартного химического состава, с наличием пустотных образований, присутствием неметаллических элементов.
Наши предложения
Наша компания специализируется на проведении ультразвукового контроля стыковых соединений с использованием современного высокоточного оборудования, позволяющего справляться с выявлением любых дефектов сварных швов металла указанным методом. Определение стоимости неразрушающего ультразвукового контроля сварных соединений трубопроводов осуществляется индивидуально, в соответствии с видом и маркой материала, его толщиной, конструктивными особенностями сооружений и некоторыми другими параметрами.
Мы проводим процедуры контроля для тавровых, угловых, стыковых и других соединений:
- труб;
- газопроводов;
- металлоконструкций;
- арматуры.
Почему именно мы?
- Срочный выезд — можем произвести испытания в день обращения.
- Наши протоколы принимают проверяющие органы (ГАСН…)
- Мы делаем скидки в зависимости от объема испытаний
- Решаем уникальные задачи по невысокой цене
- Несколько испытательных центров позволяет обрабатывать большой объем испытаний в максимально короткие сроки не жертвуя качеством
- Реализованная система менеджмента качества позволяет оперативно реагировать на любой запрос клиента- максимальное время ответа на запрос 1 час
Ультразвуковой контроль сварных соединений и швов трубопроводов в Екатеринбурге
Для проверки качества изделия без нарушения структуры материала, из которого оно изготовлено, применяют неразрушающий ультразвуковой контроль. В основе метода УЗК лежит применение ультразвуковых волн, которые проникают в материал проверяемого изделия и отражаются от границ нарушения его целостности при наличии дефектов. Ультразвуковой неразрушающий контроль безопасен для проверяемых материалов. Ультразвуковые дефектоскопы позволяют контролировать качество изделий, выполненных из металла, пластмассы, керамики и композитных материалов.
Контроль качества изделий посредством ультразвуковых дефектоскопов применяется в металлургии, судостроении, машиностроении, энергетике и многих других отраслях. УЗК необходим при строительстве железных дорог, газопроводов, объектов химической промышленности.
Для повышения качества строительства и обеспечения необходимого уровня надежности металлических конструкций применяют ультразвуковой контроль сварных соединений. Используя данный метод, проверяют стыковые, нахлесточные, угловые и тавровые соединения, металлических частей конструкций, выполненные различными способами сварки.
В большинстве случаев УЗК сварных швов практически невозможно заменить другими видами контроля качества. Ультразвуковая дефектоскопия позволяет заранее спрогнозировать и предотвратить аварийные ситуации, связанные с непредвиденными неисправностями механизмов, нефтепроводов, газопроводов, сосудов и агрегатов, постоянно находящихся под давлением. УЗК подвергаются участки железнодорожные пути, стальные сооружения и конструкции, детали летательных аппаратов, паровые котлы, газовые баллоны, листовой прокат и многие другие виды продукции.
Работы, связанные с ультразвуковой диагностикой материалов выполняют операторы дефектоскописты. Они проверяют конструкции технологического оборудования на наличие дефектов, выполняют ультразвуковой контроль трубопроводов, проводят работы связанные с толщинометрией резервуаров, трубопроводов, элементов и узлов различных конструкций. Метод отличается оперативностью при испытаниях и подходит для контроля качества большинства типов соединений выполненных сваркой.
С помощью ультразвукового метода контроля качества можно выявить следующие дефектные области:
- Область неоднородной плотности материала
- Область, в которой материал имеет неоднородную структуру
- Область, пораженную коррозией
- Область с несоответствием химического состава
- Область с несоответствием размеров
При помощи ультразвуковой дефектоскопии можно проверить характеристики твердых образцов, а также контролировать состояние:
- Сварных, паянных и клееных соединений
- Заготовок и готовых деталей
- Деталей установок во время их эксплуатации
- Технологических трубопроводов и аппаратов в нефтегазовой и химической отраслях
- Конструкций в строительной отрасли
- Энергетических установок
Работы, связанные с УЗК могут проводиться как в лабораторных, так и в полевых условиях. Объективность полученных результатов существенно зависит от квалификации, теоретической подготовки и практического опыта оператора дефектоскописта. Чтобы повысить объективность информации о качестве изделия и обеспечить оперативность получения новых данных на многих предприятиях внедряют автоматизацию ультразвукового контроля. Что, в свою очередь, положительно влияет на рост производительности труда.
Метод УЗК способствует выявлению в структуре материала трещин, пор, царапин и других дефектов. Ультразвуковые исследования позволяют определить параметры объекта, от которых зависит уровень надежности его эксплуатации. Чаще всего ультразвуковому контролю подвергают сварные швы и участки конструкции, при наличии дефектов в которых может выйти из строя весь объект.
Износ материалов деталей, а также скрытые дефекты производства со временем могут набрать критическое напряжение. В результате может выйти из строя ответственная конструкция, что приведет к созданию аварийной ситуации с разрушительными последствиями. Ультразвуковые исследования позволяют заблаговременно выявить слабые места конструкций, не подвергая их механическим воздействиям и не разрушая материал из которого они изготовлены.
Ультразвуковая дефектоскопия применяется для исследования состояния конструкций, чтобы определить качество швов, соединяющих элементы. Метод отличается оперативностью выполнения замеров. Современные приборы для ультразвуковых исследований производят измерения, используя сочетание различных измерительных способов:
- Измерения дельта-методом
- Измерения с использованием зеркального метода
- Зеркально теневой метод
- Теневой метод
- Эхо-метод
Критическая усталость металла способствует постепенному образованию трещин. Однако явное проявление дефекта приводит к поломке. При помощи ультразвукового контроля процессы разрушения можно выявить еще в самом начале их формирования. Во многих случаях ультразвуковые исследования позволяют определить предрасположенность элемента к появлению критического дефекта еще до начала его образования.
Образовавшийся в сварном шве, при сварке стыка воздушный пузырек, с течением времени может вырасти в большую проблему. Ультразвуковая дефектоскопия позволяет обнаружить скрытую разность в плотности материала, которая означает наличие дефекта. Ультразвуковая дефектоскопия обязательна для проверки качества колесных пар, а также трамвайных и железнодорожных путей при эксплуатации трамваев и железнодорожного транспорта.
В настоящее время ультразвуковой контроль в Екатеринбурге чаще всего применяют производители элементов и конструкций, необходимых для обеспечения нормальной жизнедеятельности населения, а также для безопасной эксплуатации объектов на предприятиях. Ультразвуковая дефектоскопия основана на свойстве полнотелых материалов отзываться вибрациями на воздействие ультразвука, при наличии в них полостей, коррозии, растрескиваний и других дефектов. В нашей компании вы можете заказать весь спектр услуг, связанный с ультразвуковым контролем в Екатеринбурге. Квалификация наших сотрудников и новейшее высококачественное оборудование, позволяют получать объективные и точные результаты.
Лаборатория компании оснащена современными ультразвуковыми дефектоскопами и толщинометрами, позволяющими проводить ультразвуковой контроль швов и толщинометрию деталей конструкций из различных материалов. Элементная база приборов обеспечивает высокую помехоустойчивость. Все приборы оснащены функцией записи полученных результатов, которые потом можно распечатать на бумажные носители. Параллельно с дефектоскопией проводится и визуально измерительный контроль.
Ультразвуковое тестирование и дефектоскопия сварных швов
Нижний Новгород.
ООО «ЛКС» — это полностью оборудованная и аккредитованная лаборатория неразрушающего контроля и механических испытаний, проводящая исследования на всей территории России. ЛКС специализируется на испытании заготовок и готовых деталей из металлов, сплавов, керамики, композитов и полимеров.
Приоритетная сфера деятельности – оценка качества сварных соединений. Опыт и квалификация сотрудников лаборатории позволяют им выбрать правильные методы и процедуры для обнаружения дефектов оборудования, производственных мощностей, строительных и жилищно-коммунальных объектов и предоставить все необходимые данные для принятия обоснованных решений. Испытания проводятся во время или после производства деталей или на оборудовании которое уже находится в эксплуатации.
Ультразвуковой аудит — это один из самых универсальных и точных методов неразрушающего контроля, проводимых в полевых условиях. Благодаря использованию портативного оборудования, специалисты ЛКС оперативно выполняют выездные проверки промышленных объектов и предоставляют экспертные заключения по результатам их проведения. Ультразвуковой контроль выполняемый непосредственно в лаборатории идеально применим для исследования деталей сложной геометрии.
Применение ультразвукового тестирования варьируется от контроля сварных швов до измерения толщины стенок и обнаружения скрытых дефектов, таких как трещины, включения, пустоты и другие неоднородности в металлах, пластмассах, керамике и композитах. Также данный метод исследований позволяет проводить картирование коррозии.
Типичная область применения методов НРК включает в себя:
- объекты нефтегазовой промышленности, в том числе предназначенные для бурения, эксплуатации и ремонта скважин;
- системы газоснабжения, включая газопроводы и газовое оборудование;
- строительные объекты, в том числе здания, сооружения, мосты и другие металлоконструкции различных отраслей промышленности;
- объекты котельного надзора, в том числе паровые и водогрейные котлы, сосуды и трубопроводы;
- подъемные устройства, включая управление кранами, подъемниками и манипуляторами.
Комплекс услуг по неразрушающему контролю лаборатории ЛКС
ЛКС работает с широким спектром отраслей промышленности, включая нефтегазовую, аэрокосмическую, энергетическую, нефтехимическую, автомобильную, железнодорожную, общее машиностроение, производство и строительство. Вне зависимости от величины компании, от самой крупной до небольшого производства, и сложности проверяемого объекта, инженеры ЛКС подберут подходящий под конкретный случай комплекс испытаний. Наиболее часто применяемые способы исследований включают в себя:
- магнитопорошковый контроль;
- ультразвуковое исследование;
- пенетратный контроль;
- акустико-эмиссионные испытания;
- визуально-измерительный контроль;
- рентгенография.
Стоимость и время выполнения работ по неразрушающему контролю зависит от множества факторов: способа и объема испытаний, накладных расходов и др. Если вы заинтересованы в том, чтобы узнать больше о услугах по комплексному обеспечению качества производственных объектов, пожалуйста, свяжитесь с нами по телефону 8 (800) 333-67-99 или по электронной почте: [email protected].
*На правах рекламы.Все новости раздела «Новости ПФО»
Провести ультразвуковой УЗК контроль качества сварных соединений в Салавате
УЗК контроль в Салавате
Ультразвуковой метод контроля является одним из основных методов неразрушающего контроля.
Ультразвуковой контроль основан на способности высокочастотных колебаний проникать в металл и отражаться от поверхности трещин, пустот и других несплошностей.
Контролируемые объекты:Методы ультразвуковой дефектоскопии позволяют производить контроль сварных соединений, сосудов и аппаратов высокого давления, трубопроводов, поковок, листового проката и другой продукции.
Полезно знать, что ультразвуковой метод контроля, помимо своего прямого назначения, а именно, обнаружения дефектов, также применяется для измерения толщины. Ультразвуковая толщинометрия, в свою очередь, является не менее важной процедурой для контроля качества и безопасности изделий.Преимущества:
- высокая чувствительность к наиболее опасным дефектам типа трещин и непроваров;
- высокая точность и скорость исследования;
- возможность вести контроль непосредственно на рабочих местах без прерывания технологического процесса;
- не требуется выведения контролируемой детали или всего объекта из эксплуатации;
- исследуемый объект не повреждается;
- возможность проводить контроль изделий из разнообразных материалов, как металлов, так и неметаллов.
Трудности при контроле металлов с крупнозернистой структурой из-за большого рассеяния и сильного затухания ультразвука, а также повышенные требования к состоянию поверхности контроля (шероховатости и волнистости)
Применяемое оборудование:- А1214 «Expert»
- Peleng 307
- Уралец А9812
Перед тем, как приступить к УЗК, необходимо подготовить поверхность контролируемого объекта. Подготовка заключается в том, чтобы придать поверхности шероховатость. Если диагностируется сварные соединения, то шероховатостям требуется задать направление, которое расположится перпендикулярно шву. Для устранения воздушного зазора, исследуемый участок обрабатывается контактными жидкостями (водой, маслом, глицерином).Нормативные документы в Салавате:
РД СТО 02495307-002-2008 Ультразвуковой контроль сварных соединений арматуры в железобетонных конструкциях.
РД ПНАЭ Г-7-030-91 «Ультразвуковой контроль. Часть II. Контроль сварных соединений и наплавки».
РД 34. 17.450-98 МЕТОДИЧЕСКИЕ УКАЗАНИЯ ПО УЛЬТРАЗВУКОВОМУ КОНТРОЛЮ БЕЗ РАЗЛОПАЧИВАНИЯ ОБОДА ДИСКА В РАЙОНЕ ВЕРХНИХ КОНЦЕНТРАТОРОВ Т-ОБРАЗНОГО ПАЗА.
РД 34.17.302-97 (ОП-501, ЦД-97) «Котлы паровые и водогрейные. Трубопроводы пара и горячей воды, сосуды. Сварные соединения. Контроль качества. Ультразвуковой контроль. Основные положения».
РД РОСЭК-001-96 «Машины грузоподъемные. Конструкции металлические. Контроль ультразвуковой. Основные положения».
РД СТО 00220256-005-2005 «Швы стыковых, угловых и тавровых сварных соединений сосудов и аппаратов, работающих под давлением. Методика ультразвукового контроля».
РД СНиП 3.05.03-85 (2000) «Тепловые сети».
РД ВСН 012-88 «Строительство магистральных и промысловых трубопроводов. Контроль качества и приемка работ. Часть1».
РД ПБ 03-585-03 «Правила устройства и безопасной эксплуатации технологических трубопроводов».
РД СТО Газпром-2006 «Инструкция по неразрушающим методам контроля качества сварных соединений при строительстве и ремонте промысловых и магистральных газопроводов».
РДИ 38.18.016-94 «Инструкция по УЗК сварных соединений технологического оборудования».
РД ОСТ-32-100-87″Ультразвуковой контроль швов сварных соединений мостов, локомотивов и вагонов».
РДСНиП 3.03.01-87 «Несущие и ограждающие конструкции».
РДПБ 03-576-03 «Правила устройства и безопасной эксплуатации сосудов, работающих под давлением».
РД 153-34.1-003-01 (РТМ-1С) «Сварка, термообработка и контроль трубных систем котлов и трубопроводов при монтаже и ремонте энергетического оборудования».
ГОСТ 17624-87 «Бетоны. Ультразвуковой метод определения прочности бетона».
Методические рекомендации по статистической оценке прочности бетона при испытании неразрушающими методами (МДС 62-1.2000)
УЗК контроль — универсальный метод выявления дефектов
Ультразвуковое исследование объекта возглавляет перечень методов контроля. Ведь его проведение основывается на свойствах высокочастотных колебаний, а значит может применяться как для металлов, так и не металлических материалов. В Салавате ультразвуковой контроль качества на самых выгодных условиях сотрудничества, выполняет наша лаборатория. Опытные специалисты готовы выполнить исследование любого объекта, не зависимо от размеров и характеристик, ориентируясь на сроки заказчика. Результатом такой работы станет детальное заключение экспертной комиссии установленного законодательством образца.
Проводятся исследования контролируемого объекта с помощью мощное современного оборудования, что позволяет гарантировать заказчику:
- Выявление дефектов любого размера;
- Определение дополнительных параметров;
- Оперативность получения информации.
Высокая чувствительность применяемого оборудования позволяет не только провести дефектовку, но и классифицировать выявленные изъяны. Такая максимальная точность и конкретика значительно облегчает пути поиска решений и планирования ремонтных работ. В конце исследования, наши эксперты предоставят письменное заключение, а также окажут консультативную поддержку относительно самого эффективного и практичного метода устранения выявленных дефектов.
Ультразвуковой контроль сварных соединений — швов. Ультразвуковой неразрушающий контроль
Ультразвуковой неразрушающий контроль – это эффективный способ исследования металлических изделий, сварных швов, пайки, склейки на предмет наличия в них инородных вкраплений, пустот, пор, трещин, а также для определения толщины стенок обследуемых объектов из различных материалов. У этого метода есть ряд преимуществ, среди которых:
- Высокая точность результатов – до 0,01 мм, чувствительность, что делает метод высокоэффективным при проверке качества сварных швов, в которых дефекты даже минимального размера наиболее опасны
- Безопасность для человека и окружающей среды – ультразвуковой прибор не генерирует опасных излучений
- Компактность, малая масса – до 1,5-2 кг
- Возможность проведения обследования с сохранением целостности образца – ультразвуковой контроль материалов является неразрушающим
- Быстрота получения данных – они моментально выводятся на дисплей устройства в цифровом или графическом виде
- Минимальные материальные затраты при осуществлении контроля
Ультразвуковые преобразователи для неразрушающего контроля могут работать в различных режимах – эхо, зеркальном, зеркально-теневом, а также применяться для проведения вихревой диагностики – в фазовом, амплитудном динамическом, статическом.
Принцип методики
Ультразвуковой контроль металла и других материалов основывается на физических свойствах звуковых волн – их способности равномерно распространяться в толще веществ в заданном направлении. Если на их пути возникает препятствие, которым может быть инородное вкрапление, участок с другой плотностью, пустота, то волна отражается от них определенным образом, возвращаясь к приемнику. В результате на дисплее формируется график или выдается числовое значение, по которому специалист делает выводы о качестве образца.
Важно, чтобы поверхность, в области которой будет прикладываться датчик, соответствовала пятому классу шершавости. При проведении обследования необходимо использовать контактные жидкости или смазки, чтобы исключить возможность попадания воздуха в пространство между поверхностью образца и наконечником.
Области применения
Наиболее распространенным является ультразвуковой контроль сварных швов, так как он позволяет выявлять мельчайшие дефекты без каких-либо последствий для изделия. Поэтому метод применяется во всех сферах промышленности, связанных с производством, контролем ответственных изделий, конструкций. При помощи представленных в каталоге компании «ПОВЕРКОН» устройств можно осуществлять:
- Ультразвуковой контроль сварных соединений трубопроводов – в производственных условиях, на эксплуатируемых магистралях
- Измерение толщины материалов в диапазоне 0,7-300 мм
- Ультразвуковой контроль осей колесных пар – для эффективного контроля подвижных ЖД составов, прицепов и других видов транспорта
- Приемку, плановые обследования ответственных конструкций
Также можно осуществлять ультразвуковой контроль отливок из стали, сплавов, других материалов на предмет несплошности в массе.
Оборудование от компании «ПОВЕРКОН»
В компании «ПОВЕРКОН» представлены следующие виды ультразвукового оборудования:
- Толщиномеры – ручные устройства с автономными источниками питания.
Отличаются компактностью, простотой использования
- Дефектоскопы – мультифункциональные, высокой точности, поставляются с гарантиями качества, поверкой
- Комплекты с калибровочными образцами
С любыми дополнительными вопросами обращайтесь к нашим компетентным специалистам по номерам телефонов, указанным в верхней части страницы и в разделе «Контакты».
Качественный ультразвуковой контроль, неразрушающий сварных соединений, заклепок, описание устройства контроля
Неразрушающий ультразвуковой контроль широко используется в таких отраслях промышленности, как строительство, металлургия, энергетика, машиностроение и пр. Он позволяет повысить качество и безопасность выпускаемой продукции.
Особенности метода
Подобный способ контроля заключается в учете и анализе характеристик звуковых волн, проходящих через объект от внешнего источника. Суть метода довольно проста.
Распространяющийся в любой среде ультразвук отражается от малейших внутренних препятствий (дефектов), границ обследуемого объекта (металлические трубы, балки). При данном способе контроля дает обратная волна принимается специальным прибором и анализируется.
Используя различные импульсные методы работы, можно быстро получить подробную информацию о внутреннем состоянии материала. Использование ультразвукового обследования объектов является обязательным условием при проведении любых строительных экспертиз.
Способ позволяет точно определить уровень качества сварного шва или клепочного крепления. При этом контролироваться могут стройматериалы, здания, сооружения и готовая продукция.
Из-за значительных отличий в распространении звука в воздухе и твердых предметах с помощью данного неразрушающего метода можно выявить даже очень мелкие дефекты. Кроме того, легко определяется качество шлифовки материала.
Ультразвуковое исследование может применяться для обнаружения недостатков, как на внутренней, так и на внешней поверхности объектов, изготовленных из металла, сплава или неметаллов. Выявляется полость, трещина или поры даже небольшого размера.
Определение мест расположения и глубины залегания повреждений позволяет заблаговременно изменить схему раскроя металлического листа или, например, поменять расположение заготовок на нем.
Регулярный УЗ-контроль дает возможность безопасно эксплуатировать оборудование и компании денежные средства, благодаря упреждающему устранению аварий.
Дефекты, которые выявляются:
- некачественные сварные или спаечные швы;
- недостатки склеенных мест;
- межкристальная коррозия.
Также применение данного способа контроля позволяет точно определить геометрические параметры даже у предметов со сложной формой.
Ультразвуковую дефектоскопию в компании «Экспертсистема» осуществляют аттестованные специалисты с использованием современных измерительных приборов.
Технология
Контроль материалов с использованием фазированной решетки в настоящее время считается наиболее достоверным способом обнаружения дефектов, которые образовались при проведении сварочных работ. Легко определяется и целостность любых конструкций из металла, которые ранее подверглись, каким-либо воздействиям. Применение УЗ-приборов существенно снижает затраты на различные строительные экспертизы, т.к. полноценное обследование оборудования или продукции проводится без использования дорогого и громоздкого оборудования.
Ультразвуковой контроль наиболее востребован при:
- исследовании любых металлов, трубопроводов и сырьевого металла;
- проверке стыков балок;
- исследовании мест заготовок, соединенных методом литья.
Используемый при этом принцип крайне прост. Например, ультразвуковой контроль сварных соединений труб заключается в выявлении микроскопических полостей с газом, который не успел выйти наружу после сварки стыков, особенно, когда длина шва значительна.
Эффективность дефектоскопа при обнаружении в толщине металла скоплений воздуха зависит от длины волны. На нее, в свою очередь, влияет частота создаваемых прибором, колебаний.
Устройства с низкими частотами потребуются в следующих ситуациях:
- проверка объектов или материалов с большой толщиной;
- обследование отливок, сварного шва;
- проверка металла, с крупнозернистой структурой.
В промышленной сфере ультразвуковое исследование металлов проводится, как правило, в волновом диапазоне 0,5-10 МГц. При решении определенных задач, когда необходимо обнаружить совсем небольшие дефекты, используют приборы с излучением до 20 МГц.
Контроль сварного шва
Дефектоскопию сварных швов используют во многих сферах промышленности, но наибольшие сложности связаны с применением ее в строительстве из-за полевых условий проверки. Нередко объекты находятся в областях с затрудненной транспортной доступностью, когда возводятся линии электропередач, дорожные магистрали, промышленные здания.
Использование фазированных решеток и S-скана позволяет проводить дефектоскопию даже в сложных условиях, благодаря своей простоте по сравнению с обычными методиками обследования.
Например, проверяя сварной шов, не потребуется водить прибором по всей плоскости объекта. Простой наклонное устройство ультразвуковое блок питания и контроля генерирует узконаправленный луч в направлении шва и осуществляет прием отраженных импульсов. При этом, для выявления возможных огрехов специалисту приходится перемещать свой прибор так, чтобы он, как можно тщательнее «просветил» всю поверхность шва.
Обычное устройство работает как с прямым лучом, так и с отраженным от донной плоскости. Оператору потребуется точно определить траекторию расхождения звуковых волн в обследуемом материале с учетом всех положений аппарата.
Устройство с фазированной решеткой, благодаря широкому УЗ-пучку позволяет покрыть всю поверхность шва не меняя угол наклона. Сдвиг дефектоскопа по отношению к исследуемому месту приведет только к смещению картинки на мониторе аппарата.
Для полноценного контроля нужно лишь установить устройство по возможности в непосредственной близости от валика усиления (чтобы воздействие звуковых волн на проверяемый шов было максимальным) и проанализировать зафиксированные данные с помощью S-скана. Перемещать прибор понадобится только для обследования следующего шва.
Определяется брак сварного шва сразу по нескольким параметрам, среди них время, за которое звуковые волны перемещаются в конкретном материале. Так можно с высокой точностью определить глубину залегания дефекта. Площадь повреждения определяется в зависимости от амплитуды отраженных звуковых колебаний.
Контроль клепочных соединений
Заклепочные соединения повсеместно распространены в судостроении, производстве авиационной и космической техники. Без проверки качества работу в данных отраслях представить невозможно.
Чаще других используется ультразвуковой контроль заклепок (метод инфракрасной термографии), позволяющий выявлять дефекты в таких сложных соединениях. При этом, обязательной проверке должна подвергаться четвертая часть всех болтов или заклепок от их общего количества. Если, в процессе обследования обнаруживается хотя бы один бракованный элемент, число контролируемых соединений должно быть удвоено.
Контроль композитных материалов
Ультразвуковой неразрушающий контроль с помощью фазированной решетки изделия из однородного изотропного мелкоструктурного неметалла, (капрон, поливинилхлорид, полистирол и пр.) очень похож на обследование металлических объектов. Просто используется меньшая скорость ультразвука с большим затуханием при распространении.
Существенное распространение объема полимеров и других композиционных материалов в строительстве и производственной сфере потребовало принципиально новых способов при проведении контроля и определения качества. Для решения подобных проблем при проверке неметаллов дефектоскопами с фазированными решетками разрабатываются специальные методы реконструкции получаемых изображений.
Преимущества методики
Ультразвуковой неразрушающий контроль качества продукции, материалов или сварных швов отличается целым рядом преимуществ. Во-первых, метод полностью безопасен для человека. Во-вторых, весь процесс проверки займет минимум времени, гарантировав высокую точность обследования.
По сравнению с другими способами обнаружения дефектов ультразвуковой контроль обойдется заказчику намного дешевле, не потребуется использование какого-либо громоздкого оборудования, проверку можно проводить непосредственно на действующем объекте. При этом не нужно будет останавливать строительные работы или повреждать элементы конструкций, чтобы обследовать внутреннюю структуру материала.
Применение ультразвуковой дефектоскопии стало востребованным и необходимым мероприятием, осуществляемым при проведении обязательных экспертиз жилых или промышленных объектов. заказывают ее при изменении планировок, возведении дополнительных этажей, определении изношенности конструкций здания.
Ультразвуковую дефектоскопию специалисты компании «Экспертсистема» проводят в сжатые сроки. По требованию заказчика возможно провести контроль сварных соединений, проверяя любой участок на присутствие каких-либо скрытых дефектов.
Ультразвуковой онлайн-метод оценки сварных швов тонких стальных листов на линии непрерывного цинкования
Marder AR (2000) Металлургия оцинкованной стали. Prog Mater Sci 45 (3): 191–271. DOI: 10.1016 / S0079-6425 (98) 00006-1
Артикул Google Scholar
Питтнер Дж., Симан М.А. (2010) Управление тандемным станом холодной прокатки: использование передовых практических методов. Springer Science & Business Media, Нью-Йорк
Google Scholar
Лю Г.М., Ди Х.С., Чжоу К.Л., Ли Х.С., Цзян Ли (2012) Анализ стратегии контроля натяжения и толщины двухклетевого реверсивного стана холодной прокатки. J Iron Steel Res Int 19 (10): 20–25
Артикул Google Scholar
Ziyou HY, Shouqun C (1997) Анализ разрыва полосы в сварном шве при непрерывном отжиге холоднокатаной полосы. Bao Steel Technology, том 1
Чой И.С., Росситер Дж.А., Флеминг П.Дж. (2007) Петлеобразователь и контроль натяжения на станах горячей прокатки: обзор.J Process Control 17 (6): 509–521
Статья Google Scholar
Tominaga N, Ishii H, Tadokoro H, Satoh K, Tagata H, Watanabe Y (2012) Разработка нового сварочного аппарата для сварных швов (сварка поперечных швов, CSW), совместимого с непрерывной прокаткой стальных листов толщиной до 6 мм. Технический обзор Mitsubishi Heavy Industries, том 49. Mitsubishi Heavy Industries
Kaga S, Tominaga N, Saito T, Onose M, Yoshimura Y, Tagata H, Watanabe Y, Zenitani S, Wakamoto I (2008) Соединение металлических пластин способ и аппарат.Mitsubishi-Hitachi Metals Machinery Inc., заявка на патент США US 13/002663
Fricke W (2003) Анализ усталости сварных соединений: состояние разработки. Mar Struct 16 (3): 185–200
Статья Google Scholar
Поуранвари М., Абеди А., Мараши П., Гударзи М. (2008) Влияние вытеснения на пиковую нагрузку и поглощение энергии точечной сваркой сопротивлением низкоуглеродистой стали. Sci Technol Weld Join 13 (1): 39–43
Статья Google Scholar
Wan X, Wang Y, Zhao D (2016) Мониторинг качества на основе анализа динамического сопротивления и главных компонентов в мелкомасштабном процессе точечной сварки сопротивлением. Int J Adv Manuf Technol 86 (9): 3443–3451. DOI: 10.1007 / s00170-016-8374-1
Артикул Google Scholar
Дикинсон Д. , Франклин Дж., Станя А. (1980) Определение характеристик точечной сварки с помощью динамического мониторинга электрических параметров. Сварка J 59 (6): 170–176
Google Scholar
Cho Y, Rhee S (2002) Мониторинг динамического сопротивления первичной цепи и его применение для оценки качества во время точечной контактной сварки. Сварка J 81 (6): 104–111
Google Scholar
Эль-Банна М., Филев Д., Ценг Ф. (2011) Алгоритм контроля качества сварки на основе силы. Int J Intell Syst Technol Appl 10 (1): 1–14
Google Scholar
Подржай П., Симончич С. (2013) Контроль контактной точечной сварки на основе измерения температуры.Sci Technol Weld Join 18 (7): 551–557. DOI: 10.1179 / 1362171813Y.0000000131
Артикул Google Scholar
Salzburger HJ, Dobmann G, Mohrbacher H (2001) Контроль качества лазерной сварки специальных заготовок с использованием волноводных волн и ЭМАП. IEE Proc Sci Meas Technol 148 (4): 143–148. DOI: 10.1049 / IP-SMT: 20010534
Артикул Google Scholar
Бернига Г., Холь СП, Зальцбургер Х. Дж., Арнольд В. (2007) Неразрушающий контроль лазерных сварных швов в специально изготовленных заготовках с использованием электромагнитных преобразователей. Оценка на неразрушающий контроль 22 (1): 1–18. DOI: 10.1080 / 10589750701327874
Артикул Google Scholar
Контроль сварного шва заторного шва для соединения рулонов. Innerspec Technologies Inc. http://innerspec.com/wp-content/uploads/2016/03/temate%C2%AE-Si-MWC.pdf. По состоянию на 23 ноября 2016 г.
Lopez B, Green P (2004) Ультразвуковые ЭМАП для контроля сварных швов. Innerspec Technologies Inc. https://app.aws.org/itrends/2004/07/it0704-23.pdf. По состоянию на 23 ноября 2016 г.
Babcock M (2004) RR301-замена рентгенографии. Колегейт, Норвич
Google Scholar
Ван Г., Ляо Т.В. (2002) Автоматическое определение различных типов сварочных дефектов на радиографических изображениях. NDT & E Int 35 (8): 519–528.DOI: 10.1016 / S0963-8695 (02) 00025-7
Артикул Google Scholar
Hayes C (1997) Азбука неразрушающего контроля сварных швов. Сварка J 76 (5): 46–51
Google Scholar
Лю Дж, Сюй Дж., Рен Л., Цюань З., Рен Л. (2016) Интеллектуальная идентификация дефектов при ультразвуковом обнаружении контактной точечной сварки на основе вейвлет-пакета и нейронной сети.Int J Adv Manuf Technol. DOI: 10.1007 / s00170-016-9588-y
Google Scholar
Кумар А., Раджкумар К.В., Паланичами П., Джаякумар Т., Челлапандиан Р., Касивисванатан К.В., Радж Б., Патанкар В.Х., Джоши В.М., Ланде Б.К. (2007) Разработка и применение ультразвукового оборудования для С-сканирования. Бюллетень BARC 285: 49–57
Google Scholar
Zhou G, Xu G, Gu X, Liu J (2016) Исследование по оценке качества лазерной сварки на основе двумерного матричного ультразвукового датчика.Int J Adv Manuf Technol 84 (5): 1717–1723. DOI: 10.1007 / s00170-015-8243-3
Google Scholar
Хасиотис Т., Бадогианнис Э., Цувалис Н.Г. (2011) Применение ультразвуковых методов C-сканирования для отслеживания дефектов в слоистых композитных материалах. Стройнишки вестник-Машиностроительный журнал 57 (3): 192–203
Статья Google Scholar
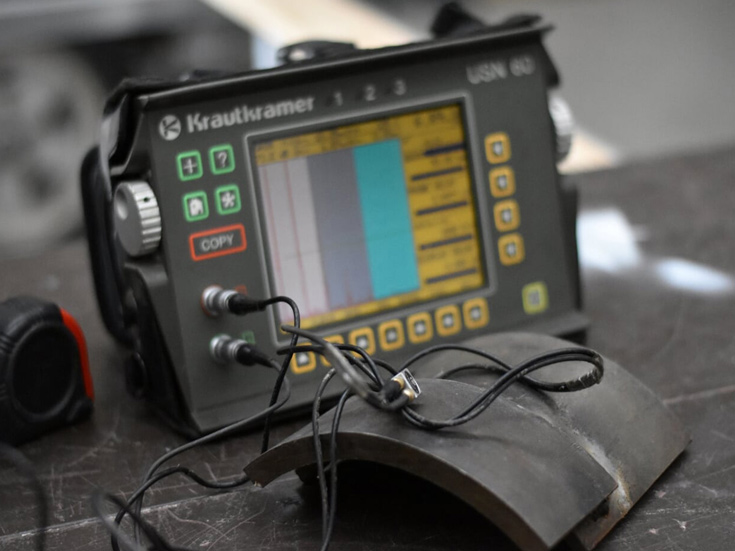
Jasiūnienė E, Raišutis R, Šliteris R, Voleišis A, Jakas M (2008) Ультразвуковой неразрушающий контроль лопастей ветряных турбин с использованием контактного импульсно-эхо-иммерсионного тестирования с движущимся резервуаром для воды. УЗИ 63 (3): 28–32
Google Scholar
Джонсон П., Галбалли Д., Митчелл III В.А., Дэвис Т.Дж. (2008) Методы и аппаратура для обнаружения трещин в сварных швах. Патент США US7412890 B1
Krautkrämer J, Krautkrämer H (1983) Ультразвуковой контроль материалов, 3-е изд.Springer, Берлин
Google Scholar
Хуанг Дж. Х., Динг Д. (2009) Простая приближенная формула для физического фокусного расстояния сферически сфокусированных преобразователей. IEEE Trans Ultrason Ferroelectr Freq Control 56 (12): 2764–2768. DOI: 10.1109 / TUFFC.2009.1368
Артикул Google Scholar
Hickling R (2012) Бесконтактные сфокусированные ультразвуковые датчики для виброметрии, измерения, мониторинга состояния и управления роботами с обратной связью.Патент США US8296084 B1
Ультразвуковой онлайн-метод оценки сварных швов между тонкими стальными листами на линии непрерывного цинкования
ОРИГИНАЛЬНАЯ СТАТЬЯ
S. S. Indimath
1
& R. Шунмугасундарам
1
& S. Баламуруган
1
и М. Дутта
1
и
С. К. Гудиметла
1
и К. Кант
1
Получено: 12 сентября 2016 г. / Принято: 2 января 2017 г. / Опубликовано онлайн: 24 января 2017 г.
Аннотация Рулоны стали свариваются встык для обработки на линии непрерывного цинкования
стана холодной прокатки.Отказ
сварных швов на линии во время обработки приводит к остановке стана —
страниц, что приводит к огромным простоям производства. Описывается автоматизированная ультразвуковая система неразрушающего контроля
для
оценки целостности сварных швов стальных листов
толщиной 0,6–2 мм сразу после сварки. Система была де-
подписана для обнаружения любых физических дефектов сварных швов, а именно отсутствия плавления, выталкивания
, трещин и т. Д., Что ставит под угрозу целостность сварного шва
, что приводит к его выходу из строя на технологической линии.Ультразвуковой датчик высокой частоты
со встроенной водяной камерой
был разработан для обеспечения возможности высокоскоростной бесконтактной автоматической проверки сварного шва
на линии с учетом ограниченного времени проверки, доступного на стане (40 с) . Прототип сканирующей системы
был изготовлен с использованием разработанного ультразвукового датчика, который
смог успешно обнаружить дефекты сварного шва, образовавшиеся в
реальных образцах завода.
Ключевые слова Бесконтактный ультразвуковой контроль.Машинный шов сварной.
Дефекты сварного шва .Тонкий шов .НДТ .Скоростной контроль.
Линия непрерывного цинкования. Стан холодной прокатки
1 Введение
Линия непрерывного цинкования — одна из нескольких технологических линий
в прокатном комплексе сталеплавильного завода. Изначально сталь
производится в листовой форме на стане холодной прокатки. Эти листы могут иметь длину
в несколько километров и, таким образом, свертываться в бухты для хранения и транспортировки
.Линия непрерывного цинкования — это технологическая линия
, на которой стальные листы покрываются цинком для придания устойчивости к коррозии
[1]. Линия называется «непрерывной», потому что
нет остановок в линии между обработкой
последовательных бухт листов [2]. Это достигается путем сварки катушек
встык в начале линии. Таким образом, на линию цинкования подается непрерывный стальной лист
. Линия цинкования в вопросе
обрабатывает листы в диапазоне толщины 0.От 6 до
2 мм при скорости до 200 м / мин. Чтобы сохранить стабильность
стального листа во время нанесения покрытия и других процессов на линии
, на листе
всегда поддерживается определенное натяжение [2,3]. Сварка должна быть достаточно сильной, чтобы выдерживать
это натяжение в течение всего времени обработки. . Кроме того, лист
подвергают сгибанию на различных рулонах, которые используются для направления листа
по линии обработки.Любые дефекты в сварном шве листа могут привести к обрыву сварного шва на линии
. Такие поломки требуют длительных остановок на техническое обслуживание —
простоев, что приводит к огромным простоям производства [2,4]. Таким образом,
любая система для оценки целостности сварного шва в оперативном режиме с помощью методов разрушающего контроля (NDT), отличных от
, может помочь в предотвращении такого простоя
.
Скорость обработки и натяжение могут варьироваться между
различных секций / клетей в пределах линии цинкования.Ролики петлителей
,[2,5] используются для хранения определенных избыточных длин листов, так что
натяжение / скорость между двумя последовательными клетями остается основным —
поддерживаются при непрерывной работе линии. Поскольку сварка
требует, чтобы лист оставался неподвижным во время сварки,
набор роликов петлителя сразу после того, как сварщик продолжает подавать
на стан во время сварки. Ролики петлителя
, однако, могут хранить только конечную длину листа, которая
позволяет листу оставаться неподвижным в течение примерно 2 минут для сварки
и проверки на рассматриваемом стане.При этом необходимо иметь в виду, что осмотр сварного шва должен производиться
на очень высокой скорости. Малая толщина листов и характер ожидаемых дефектов сварного шва
также создают значительные
* S. С. Индимат
1
Tata Steel Ltd., Джамшедпур 831001, Индия
Int J Adv Manuf Technol (2017) 91: 3481–3491
DOI 10.1007 / s00170-017 9995-8
Ультразвуковой онлайн-метод оценки сварных швов затор
тонких стальных листов на линии непрерывного цинкования
# Springer-Verlag London 2017
Содержание предоставлено Springer Nature, применяются условия использования.Права защищены.
(PDF) Ультразвуковой контроль стыковых сварных соединений методом TOFD
Ссылки
[1] ЛАНГЕНБЕРГ, К., Дж., МАРКЛЕЙН, Р., МЕЙЕР, К. (2012). Ультразвуковой неразрушающий контроль материалов
— Теоретические основы. п. 772. CRC Press, Нью-Йорк. ISBN 978-14-398-5588-1
[2] МОРАВЕК, Дж., НОВАКОВА, И., БРАДАК, Дж., (2014) Влияние условий старения на механические свойства
сварных швов из сплава AW 6082. В кн .: Технология производства: научно-исследовательский и производственный журнал —
, 2016, Т.16, № 1, стр. 192–198. Университет J.E. Purkyne, Усти-над-Лабем. ISSN 1213-2489.
[3] КРЕЙЧИ, Л., ХЛАВАТЫЙ, И., ШЕВЧИКОВА, X. (2013) Исследование переходных зон неоднородных сварных швов
. Металл 2013. Брно: 2013, стр. 785-789, ISBN 978-80-87294-41-3.
[4] HLAVAT, I., KOZAK, J., KREJČI, L. (2016) Исследование свойств отложений, содержащих карбиды вольфрама
в железной матрице. Металл 2016. Брно: 2016, стр. 1056-1060, ISBN 978-80-87294-67-3.
[5] КОНАР, Р., МИЦИАН, М. (2014). Неразрушающий контроль сварных швов при ремонте газопроводов ультразвуковым методом Phased Array
. В кн .: Технология производства: научно-исследовательский и производственный журнал, Вып. 14, No.
1, pp. 42-47. Университет J.E. Purkyne, Усти-над-Лабем. ISSN 1213-2489.
[6] ОЛИМП (2013). Компания Olympus NDT. В Интернете:
[7] KOPEC, B. et al. (2008) Неразрушающий контроль материалов и конструкций, стр. 573, CERM, s.r.o .: Брно,
2008, ISBN 978-80-7204-591-4.
[8] БОХАЦИК, М. (2016). Сравнение достоверности выявления внутренних дефектов стыковых сварных стыков
с помощью ультразвукового и рентгенологического контроля: Дипломная работа. Жилина: Жилинский университет в Жилине, 2016. 67с.
[9] ФАТУРИК, М. — МИЧЯН, М. — КОНАР, Р. (2016) Ультразвуковая идентификация дефектов сварных швов, выполненных электролитической сваркой плавлением
на пластиковых трубопроводах. В кн .: Технология производства: научно-исследовательский и производственный журнал —
.- ISSN 1213-2489. — Т. 16, нет. 1 (2016), с. 76-81.
[10] ВРЗГУЛА, П. — ФАТУРИК, М. — МИЧЯН. (2014) Новые технологии контроля для выявления отказов в
материалах и сварных соединениях для области газа. В кн .: Технология производства: научно-исследовательский журнал
и производственный. — ISSN 1213-2489. — Т. 14, вып. 3 (2014), с. 487-492.
[11] KOŇÁR, R. — MIČIAN, M. — HLAVATÝ, I. (2014) Обнаружение дефектов в трубопроводах во время эксплуатации с использованием ультразвукового метода утечки магнитного потока Mag-
и фазированной решетки В: Технология производства: журнал для науки,
НИОКР.- ISSN 1213-2489. — Т. 14, вып. 3 (2014), с. 337-341.
[12] ZRAK, A. — MEŠKO, J. — MORAVEC, J. — NIGROVIČ, R. — KADÁŠ, D. (2016) Бесконтактная термическая гибка
стальных листов. В кн .: Технология производства: научно-исследовательский и производственный журнал. — ISSN 1213-2489.
— Том. 16, нет. 1 (2016), с. 309-313.
[13] НИГРОВИЧ, Р. — МЕШКО, Дж. (2016) Лазерная резка неметаллических материалов. В: Технология производства:
научно-исследовательский и производственный журнал.- ISSN 1213-2489. — Т. 16, нет. 2 (2016), с. 402-406
[14] СЕЙЧ, П. — БИЕЛАК, Р. — ШВЕЦ, П. — РОШКО, М. (2006) Компьютерное моделирование зоны термического влияния при пайке
MIG оцинкованных стальных листов. В Kovové materiály. Металлические материалы. Roč. 44, корп. 4 (2006), s.225-
234. ISSN 0023-432X.
Ультразвуковой контроль сварных швов с использованием технологии фазированных решеток
Щелкните изображение, чтобы увеличить
https: //www.vogt-ultrasonics.de / en / homepage / объявила о внедрении полностью автоматизированного решения для ультразвукового контроля с фазированной решеткой для электронно-лучевой сварки роторов асинхронных двигателей для поставщика автомобильной промышленности.
Система разработана как неотъемлемая часть производственной линии. Система ультразвукового контроля с фазированной решеткой Vogt работает без погружения с использованием барботера. Компонент локально смачивается водой для воздействия ультразвука, а это означает, что не требуется сложная и дорогостоящая стадия сушки.
Использование ультразвуковой технологии с фазированной решеткой приводит к значительному сокращению времени тестирования. Ультразвуковые системы с фазированной решеткой основаны на принципе многоэлементного тестирования. Зонд может иметь до 128 элементов, которые можно активировать электронным способом по отдельности или в группе. Это создает сфокусированный ультразвук.
Программа проверки создает двух- и трехмерные виды компонента с областями проверки, показывающими размеры и расположение обнаруженных дефектов. Преимущества этого метода включают фокусировку луча и управление, а также возможность линейного или секторального тестирования.Это позволяет быстро и надежно обнаруживать дефекты одним датчиком независимо от направления.
Система ультразвукового контроля, разработанная для этого заказчика, позволяет сократить время цикла в 30 раз по сравнению с обычным контролем.
После того, как роторы были сварены системой, они подвергаются автоматическому контролю качества на следующем этапе процесса. Робот круглосуточно подает роторы в систему ультразвукового контроля Vogt. Осмотр включает проверку сварных швов медных компонентов с обеих торцевых поверхностей на наличие дефектов. По желанию, маркировка 0 ° цилиндрической детали может быть сделана с помощью оправки, вбиваемой в деталь с помощью пневматического штампа. Это позволяет проводить локальный металлургический контроль компонента на месте дефекта. Программное обеспечение
Inspection автоматически оценивает данные испытаний на основе ранее определенных критериев оценки и передает результат испытаний («ОК» / «НЕПРАВИЛЬНО») в центральную систему управления заказчика. Программное обеспечение растрового сканирования с модулем синхронизации трафарета используется из-за сложной, несмежной тестовой области.Впоследствии компоненты передаются роботом в дальнейшее производство или сортируются как «НЕ в порядке».
УЛЬТРАЗВУКОВАЯ ИСПЫТАТЕЛЬНАЯ СИСТЕМА ON-LINE — PRD
СОДЕРЖАНИЕ
А- СИСТЕМА:
1. Электроника для ультразвуковой оценки (включая шкаф, кондиционер)
1.1. Оценочная электроника на базе ПК (включая монитор, клавиатуру и мышь)
1.2. Датчики и кабели датчиков
2. Механика тестирования
2.1. Механика для испытания сварных швов
2.1.1. Консоль — регулируемая по высоте подъемная рама
2.1.2. Поворотный стол
2.1.3. Механизм держателя зонда (включая устройство отслеживания сварного шва)
2.1.4. Держатели зондов (включая баллон с воздухом и клапан)
2.2. Механика теста ламинации тела
2.2.1. Консоль — регулируемая по высоте подъемная рама
2.2.2. Качающийся механизм
2.2.3. Держатели зондов
3. Блок водоснабжения
3.1. Резервуар для воды
3.2. Муфта распределителя воды
3.3. Сопло для охлаждения труб (включая фиксирующие стержни и соединители)
3.4. Шланги, электромагнитные клапаны, клапаны
4.Блок подачи воздуха
4.1. Клапаны давления
4.2. Водоотделитель
4.3. Масленка
4.4. Шланги
5. Узел маркировки краской
5.1. Пистолет-распылитель и резервуар для краски
5.2. Электромагнитные клапаны
5.3. Штанги и соединители для пистолета-распылителя
6. Запись данных
6.1. Программное обеспечение
6.2. Принтер
7. Отслеживание сварного шва
7.2. Автоматический (лазерное отслеживание шва)
7.3. Стержни и соединители для лазерной указки и камеры
8.Панель электрического управления (реле, контакторы, переключатели)
9. Панель управления оператора (кнопки, переключатели, освещение)
B-ТЕХНИЧЕСКИЕ ХАРАКТЕРИСТИКИ ТРУБ:
Диаметр трубы: 200 мм — 3000 мм
Толщина стенки: 3 мм — 25 мм
Длина трубы: Линия — бесконечная
Скорость сварки: макс. 2,5 м / мин.
ТИПЫ ТЕСТОВ C:
Испытание на сварку под флюсом (S.A.W.)
1.1. Продольный дефект сварного шва
1.2. Поперечный дефект сварного шва
2.1. Ламинирование
2.2. Включение
Тест на ламинацию тела (основной материал)
3.1. Ламинирование
3.2. Включение
D-ДЕТАЛИ ВИДОВ ИСПЫТАНИЙ:
- 1. Дуговая сварка под флюсом (S.A.W.) Испытание:
Датчики опускаются до верха трубы до достижения установочного расстояния между поверхностью трубы и механизмом.
Держатели зонда опускаются с помощью пневмоцилиндра, чтобы коснуться поверхности трубы, и позиционируются с помощью устройства смещения на заданное расстояние между центром сварного шва и индексной точкой зонда.Калибровка выполняется согласно соответствующей спецификации после получения надлежащей водяной связи между поверхностью трубы и датчиками.
Испытание проводится методом эхо-импульса для продольных дефектов сварного шва и методом сквозного прохождения для поперечных дефектов шва. Угловые зонды используются для обнаружения продольных и поперечных дефектов сварных швов.- 1.1. Дефект продольного сварного шва:
Два датчика с угловым лучом обращены друг к другу и работают в режиме эхо-импульса для выявления дефектов и в режиме сквозной передачи для соединения и проверки рабочих характеристик датчиков. - 1.2. Поперечный дефект сварного шва:
Два датчика с угловым лучом работают в режиме сквозного прохода. Передающий зонд передает звуковой луч под углом 45 градусов к сварному шву. При наличии поперечного дефекта звуковой луч отражается оттуда и принимается вторым зондом, обращенным к первому.
- 1.1. Дефект продольного сварного шва:
- 2. Испытание на зону теплового воздействия (H.A.Z.):
Ламинарный дефект в зоне теплового воздействия обнаруживается с помощью иммерсионных зондов с прямым лучом.Погружные зонды
подключены через столб воды. Датчики работают в эхо-импульсном режиме. Тест выполняется посредством оценки между эхосигналом от границы раздела и первым эхо-сигналом от задней стенки. Возможное изменение толщины воды во времени компенсируется системой запуска эхо. - 3. Тест на расслоение корпуса:
Основной материал испытывается после формирования трубы и завершения внутренней / внешней дуговой сварки под флюсом на расслоение и включение.
Колебательный механизм опускается консольной подъемной рамой.Держатели зондов опускаются с помощью пневмоцилиндра до тех пор, пока они не окажутся на поверхности трубы. Колебательный привод регулируется по диапазону в соответствии с шириной полосы основного материала трубы. Зонды перемещаются вперед и назад с помощью колебательного устройства по поверхности трубы. Зонды соединяются через водяной зазор. Любое расслоение или включение можно обнаружить с помощью электронной оценки, отобразить на мониторе и отметить на поверхности трубы с помощью краскопульта. Испытание проводится по методу эхо-импульса с использованием прямолинейных двухкристаллических зондов.Каждый зонд сканирует часть расстояния между двумя соседними сварными швами. Датчики также могут быть расположены слева и справа от сварного шва.
Сравнение технологий ультразвукового неразрушающего контроля для измерения аномалий длинных сварных швов в трубах, сваренных методом низкочастотного электросопротивления | IPC
В трубопроводной промышленности широко распространенная методология управления трещинами целостности включает использование технологий ультразвукового контроля на линии (ILI). После того, как прогон инструмента ILI завершен, эффективность инструмента обычно подтверждается путем рытья трубопровода и проведения исследований в канаве.Методы ультразвуковой неразрушающей оценки (NDE) используются в полевых условиях для определения характеристик и измерения трещиноподобных элементов. Эти измерения в канаве сравниваются с результатами ILI, чтобы проверить производительность инструмента и стимулировать постоянное совершенствование технологии. Поскольку валидация инструмента ILI основана на измерениях неразрушающего контроля, получение точных и репрезентативных данных в полевых условиях является критическим шагом в этом подходе к управлению трещинами целостности. Достижение точной инспекции в полевых условиях сопряжено со своими проблемами, некоторые из которых связаны со сложными условиями сварки длинных швов, присутствующими в старых старых трубопроводах, включая смещение сварного шва, проблемы с обрезкой сварного шва и большое количество производственных аномалий.Чтобы лучше понять проблемы, связанные со сложными условиями сварки длинных швов, была проведена оценка и сравнение характеристик доступных в настоящее время технологий неразрушающего контроля.
В этом исследовании часть канадского трубопровода со сложными условиями сварки длинных швов была вырезана и выведена из эксплуатации. Для оценки состояния длинного сварного шва использовались различные технологии и методы контроля неразрушающего контроля трещин от трех разных поставщиков. Обычный ультразвуковой контроль (UT), ультразвуковой контроль с фазированной решеткой (PAUT), времяпролетная дифракция (TOFD) и вариации полного матричного ультразвукового контроля (FMCUT) использовались для оценки длинного сварного шва и сравнивались их результаты.Эффективность всех технологий неразрушающего контроля оценивается путем сравнения их с разрушающим исследованием участков длинного сварного шва. Было показано, что новые методики оценки неразрушающего контроля неизменно более точны при определении характеристик длинных пластов.