Ультразвуковой неразрушающий контроль
|
Наша лаборатория оказывает услуги по ультразвуковому контролю (УЗК) различных объектов. Лаборатория укомплектована оборудованием для ультразвуковой дефектоскопии, измерения толщины и твердости. Все допущенные к работам специалисты аттестованы на II уровень согласно ПБ 03-440-02. По результатам измерений выдается заключение установленного образца. Мы работаем с юридическими и физическими лицами. Проведение ультразвукового контроля возможно как лабораторно, так и с выездом.
Ультразвуковой метод контроля был предложен советским физиком С.Я. Соколовым в 1928 году и в настоящее время является одним из основных методов неразрушающего контроля. Методы ультразвуковой дефектоскопии позволяют производить контроль сварных соединений, сосудов и аппаратов высокого давления, трубопроводов, поковок, листового проката и другой продукции. Ультразвуковой контроль является обязательной процедурой при изготовлении и эксплуатации многих ответственных изделий, таких как части авиационных двигателей, трубопроводы атомных реакторов или железнодорожные рельсы.
По сравнению с другими методами неразрушающего контроля ультразвуковой метод обладает важными преимуществами:
- высокая чувствительность к наиболее опасным дефектам типа трещин и непроваров
- низкая стоимость
- безопасность для человека (в отличие от рентгеновской дефектоскопии)
- возможностью вести контроль непосредственно на рабочих местах без нарушения технологического процесса
- при проведении УЗК исследуемый объект не повреждается
- возможность проводить контроль изделий из разнообразных материалов, как металлов, так и неметаллов.
К недостаткам ультразвукового метода контроля можно отнести невозможность оценки реального размера и характера дефекта, трудности при контроле металлов с крупнозернистой структурой из-за большого рассеяния и сильного затухания ультразвука, а также повышенные требования к состоянию поверхности контроля по шероховатости и волнистости. Согласно РД 03-606-03 максимально допустимая шероховатость при ультразвуковом контроле составляет Ra 6,3 / Rz 40
Сущность ультразвукового метода неразрушающего контроля (видео ИКБ Градиент)
Многообразие задач, возникающих при необходимости проведения неразрушающего контроля различных изделий, привело к разработке и использованию ряда различных акустических методов контроля. Согласно ГОСТ 23829-85 акустические методы контроля делятся на 2 большие группы: использующие излучение и приём акустических колебаний и волн (активные методы) и основанные только на приёме колебаний и волн (пассивные методы).
Методы | Описание |
Методы прохождения | выявляют глубинные дефекты типа нарушения сплошности, расслоения. |
выявляют дефекты типа нарушения сплошности, определяет их координаты, размеры, ориентацию путём прозвучивания изделия и приёма отраженного от дефекта эхо-сигнала. | |
Импедансный метод | предназначен для контроля клеевых, сварных и паяных соединений, имеющих тонкую обшивку, приклеенную или припаянную к элементам жёсткости. |
Методы свободных колебаний | применяются для обнаружения глубинных дефектов. |
Методы вынужденных колебаний (резонансные) | применяются в основном для измерения толщины изделия и для обнаружения зоны коррозионного поражения, расслоений в тонких местах из металлов.![]() |
Акустико-эмиссионный метод | обнаруживает и регистрирует только развивающиеся трещины или способные к развитию под действием механической нагрузки (квалифицирует дефекты по степени их опасности во время эксплуатации). |
Наиболее широкое распространение в практике ультразвуковой дефектоскопии нашли методы прохождения и отражения (импульсные методы), реже применяют другие методы: резонансный, импедансный и метод акустической эмиссии.
Импульсные методы (прохождения и отражения)
Среди многочисленных методов прохождения и отражения на сегодняшний день наибольшее применение в дефектоскопии нашли: теневой, зеркально-теневой, и эхо-метод. Эхо-метод, в отличии от других, применим при одностороннем доступе к исследуемому объекту, и при этом позволяет определить размеры дефекта, его координаты и характер. В общем случае, суть перечисленных методов заключается в излучении в изделие и последующем принятии отраженных ультразвуковых колебаний с помощью специального оборудования — ультразвукового дефектоскопа и пьезоэлектрического преобразователя (ПЭП) и дальнейшем анализе полученных данных с целью определения наличия дефектов, а также их эквивалентного размера, формы, вида, глубины залегания и пр.
Самой массовой областью применения ультразвуковой дефектоскопии являются сварные соединения. Основным документом в России по ультразвуковому контролю сварных швов является ГОСТ Р 55724-2013
«Контроль неразрушающий. Соединения сварные. Методы ультразвуковые» (pdf), в котором рассмотрены в полном объёме методы контроля стыковых, тавровых, нахлесточных и угловых сварных швов, выполненных различными способами сварки. Также в нём подробно описаны меры (калибровочные образцы) СО-2, СО-3 и СО-3Р, V-1, V-2 и настроечные образцы, а также параметры для их изготовления. Проведение ультразвукового контроля сварных соединений и наплавок оборудования и трубопроводов атомных энергетических установок регламентируется документом ПНАЭ Г-7-030-91 «Унифицированные методики контроля основных материалов (полуфабрикатов), сварных соединений и наплавки оборудования и трубопроводов атомных энергетических установок.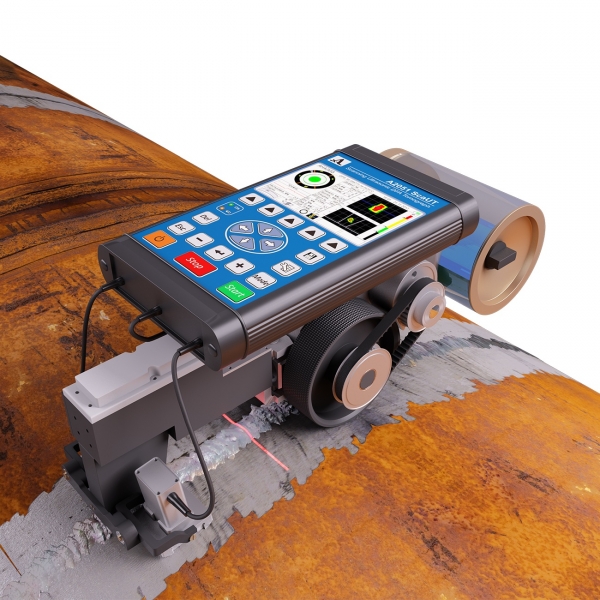
В зависимости от области использования, различают ультразвуковые дефектоскопы общего и специального назначения. Дефектоскопы общего назначения могут использоваться для контроля самой разнообразной продукции, а специализированные дефектоскопы созданы для решения узкоцелевых задач. К наиболее популярным моделям ультразвуковых дефектоскопов общего назначения относятся:
Ультразвуковая толщинометрия (резонансный и импульсный метод)
Как правило, ультразвуковой метод толщинометрии применяют в случаях недоступности или труднодоступности объекта для измерения его толщины механическим измерительным инструментом. Ультразвуковая толщинометрия — неотъемлемая процедура при определении толщины стенок труб, котлов, сосудов, то есть объектов замкнутого типа или с односторонним доступом, а также объектов судостроительного и судоремонтного производства. Современные ультразвуковые толщиномеры позволяют измерять толщины от 1 до 50 мм с точностью ±0,001 мм. По физическим принципам, используемым для измерения толщины, акустические толщиномеры делят на резонансные и эхо-импульсные.
Резонансный метод контроля основан на возбуждении и анализе резонансных колебаний в исследуемом объеме изделия, при этом исследование проводится при доступности одной стороны изделия, а погрешность метода составляет менее 1%. Резонансным методом измеряют толщину стенок металлических и некоторых неметаллических изделий (керамика, стекло, фарфор). Кроме того, при помощи резонансной дефектоскопии можно выявлять зоны коррозионного поражения, зоны непроклея и непропоя листовых соединений, зоны расслоения в биметаллах, тонких листах. Резонансные методы вынужденных колебаний в настоящее время не имеют широкого применения, так как задачи дефектоскопии и толщинометрии более точно решают импульсные ультразвуковые методы.
Принцип ультразвуковой импульсной толщинометрии основан на измерении времени прохождения ультразвукового импульса в изделии или в слое и умножении измеренного времени на коэффициент, учитывающий скорость звука в материале изделия.
- ГОСТ Р 55614-2013 «Контроль неразрушающий. Толщиномеры ультразвуковые. Общие технические требования».
- ГОСТ Р ИСО 16809-2015 «Контроль неразрушающий. Контроль ультразвуковой. Измерение толщины».
К наиболее популярным моделям ультразвуковых толщиномеров можно отнести:
Импедансные дефектоскопы и твердомеры (импедансный метод)
Импедансный метод разработан советским ученым Ю.В. Ланге в 1958 году. Он основан на использовании зависимости полного механического сопротивления (импеданса) контролируемого изделия от качества соединения отдельных его элементов между собой. Этим методом можно выявлять дефекты в клеевых, паяных и других соединениях, между тонкой обшивкой и элементами жёсткости или заполнителями в многослойных конструкциях. Импедансные дефектоскопы широко используются в авиастроении, автомобильной и космической промышленности. Они способны обнаружить непроклеенные участки, расслоения, нарушения целостности и пустоты в различном оборудовании, приборах, конструкциях. Кроме того, метод ультразвукового контактного импеданса широко применяется для измерения твёрдости изделий из металлов и сплавов, таких как сосуды давления различного назначения (реакторы, парогенераторы, коллекторы, котельные барабаны) роторы турбин и генераторов, трубопроводы, детали различных транспортных средств, промышленные полуфабрикаты (отливки, поковки, листы) и т.д. Метод контактного импеданса основан на измерении режима колебаний преобразователя, соприкасающегося с объектом. По амплитудам и резонансным частотам такого преобразователя (часто имеющего вид стержня) судят о твердости материала изделия, податливости (упругому импедансу) его поверхности.
К наиболее популярным моделям ультразвуковых твердомеров можно отнести:
Средства для проведения ультразвукового контроля
Следующим важнейшим инструментом для проведения ультразвукового контроля являются пьезоэлектрические преобразователи (ПЭП), которые выступают в качестве излучателя и приемника ультразвукового импульса, обрабатываемого дефектоскопом или толщиномером. Принцип действия пьезоэлектрических преобразователей основан на использовании прямого или обратного пьезоэлектрических эффектов. Прямой пьезоэффект представляет собой способность некоторых материалов образовывать электрические заряды на поверхности при приложении механической нагрузки, обратный пьезоэффект заключается в изменении механического напряжения или геометрических размеров образца материала под воздействием электрического поля. В качестве пьезоэлектрических материалов обычно используют естественный материал кварц, турмалин, а также искусственно поляризованную керамику на основе титаната бария (ВаТiO3), титаната свинца (PbTiO3) и цирконата свинца (PbZrO3)
Основные требования к ультразвуковым преобразователям указаны в:
- ГОСТ Р 55725-2013 «Преобразователи ультразвуковые пьезоэлектрические. Общие технические требования» (pdf)
- ГОСТ Р 55808-2013 «Преобразователи ультразвуковые. Методы испытаний» (pdf)
Подробнее о ультразвуковых преобразователях, их классификации, маркировке и применении можно посмотреть здесь.
Для обеспечения хорошего контакта между ультразвуковым преобразователем и контролируемой поверхностью, а также для предотвращения образования воздушного зазора, создающего помехи звуковому импульсу, необходимо использовать различные контактные жидкости или гели. Контактная жидкость должна иметь специальный химический состав, соответствующий диапазону температур той или иной контролируемой поверхности и ее структуре. Так, для контроля арматурных стержней и неровных поверхностей необходимо использовать контактный гель высокой степени вязкости, при контроле нагревающихся поверхностей рекомендуется применять контактные гели на водной основе, а при очень низких температурах (до -60ºC) в качестве контактной жидкости можно использовать пропиленгликоль. Также стоит отметить, что в некоторых случаях (в частности, при контроле оборудования, используемого в ядерной промышленности) требуются контактные среды с ограниченным галогенным и серным составом. Подробнее о контактных жидкостях для ультразвукового контроля можно посмотреть здесь.
Одним из важных факторов качественного ультразвукового контроля изделий является обеспечение достоверности и единообразия при проведении контроля, особенно при диагностике объектов повышенной опасности. Метрологическое обеспечение оборудования подразумевает обязательную проверку работоспособности аппаратуры перед проведением ультразвукового контроля с использованием специальных образцов. Существует два вида образцов: меры (калибровочные образцы) и настроечные образцы (ранее стандартные образцы предприятия СОП).
Комплект калибровочных образцов необходим для проверки основных параметров аппаратуры (разрешающей способности, мертвой зоны, угла ввода, стрелы ПЭП), а по контрольным образцам предприятия СОП осуществляют настройку глубиномера дефектоскопа и определение уровней чувствительности для проведения контроля конкретного изделия по определенному НД. К используемым калибровочным образцам (мерам) относятся:
Калибровочный образец | Материал | Основное назначение | |
Основные калибровочные образцы (входят в обязательный перечень оборудования необходимого для аттестации лабораторий) |
|||
СО-1 | органическое стекло марки ТОСП |
|
|
СО-2 | Сталь марки 20 или сталь марки 3 |
|
|
СО-3 | Сталь марки 20 или сталь марки 3 |
|
|
Специальные калибровочные образцы | |||
ISO/DIS 19675 | сталь марки S355J0 | Образец выполнен в соответствии с ISO/DIS 19675 и предназначен для для настройки дефектоскопов на фазированной решетке.![]() |
|
СО-3Р | Сталь марки 20 | Специальный образец для калибровки ультразвуковых дефектоскопов при контроле качества рельсов, а также деталей и узлов железнодорожного подвижного состава при совмещенной и раздельной схеме работы ПЭП с частотой более 1,5 МГц. | |
V-1 | Образец из углеродистой стали с цилиндром из органического стекла | Образец применяют в соответствии с рекомендациями Международного института сварки (МИС) и требованиями EN 12223-2000, ISO 2400-2013 для настройки и проверки параметров дефектоскопа и ПЭП. | |
V-2 | Образец из углеродистой мелкозернистой стали | Образец применяют в соответствии с рекомендациями Международного института сварки (МИС) и требованиями EN 12223-2000 , ISO2400-2013 для настройки и проверки параметров дефектоскопа с использованием малогабаритных и миниатюрных преобразователей.![]() |
|
Подробнее о калибровочных образцах, их классификации и схемах применения можно посмотреть здесь |
Контрольные образцы предприятия (СОП) предназначены для настройки глубиномера и чувствительности при проведении ультразвукового контроля конкретного изделия. Наиболее распространенными типами применяемых отражателей при контроле сварных соединений являются: плоскодонные отражатели, «зарубки» и сегменты. Подробнее о назначении, типах и области применения контрольных образцов можно посмотреть здесь.
Помимо технических требований, предъявляемых к процессу ультразвукового контроля, существует и установленный порядок организации работ. Так лаборатории, выполняющие ультразвуковой контроль должны быть аттестованы в соответствии с
- СДАНК-01-2020 «Правила аттестации и основные требования к лабораториям неразрушающего контроля»
Необходимость аттестации лабораторий НК регламентирована Письмом Госгортехнадзора России № 02-35/213 от 27 июня 2001 г. (pdf) в соответствии с которым, для проведения контроля оборудования, материалов и сварных соединений неразрушающими методами (в том числе и для сторонних организаций) организациям необходимо иметь лаборатории неразрушающего контроля, аттестованные в соответствии с вышеуказанным документом. По результатам аттестации лаборатории выдаётся свидетельство об аттестации в соответствующей области. Подробнее о порядке проведения аттестации, перечне необходимых документов и оборудования можно посмотреть здесь.
В зависимости от сферы деятельности, специалисты, проводящие ультразвуковой контроль должны быть аттестованы в соответствии с:
- ПБ 03-440-02 «Правила аттестации персонала в области неразрушающего контроля»
- ПНАЭ Г-7-010-89 «Федеральные нормы и правила в области использования атомной энергии»
Аттестацию специалистов в целях подтверждения их уровня теоретической и практической подготовки, необходимого для выполнения работ по конкретному методу контроля проводят независимые органы по аттестации персонала в сфере неразрушающего контроля (НОАП). НТЦ «Эксперт» является экзаменационным центром Независимого органа по аттестации персонала АЦ «НИКИМТ» АО «НИКИМТ-Атомстрой». При подготовке к аттестации специалистами могут быть использованы следующие учебные материалы:
- Комплект образцов для обучения и аттестации специалистов
- Учебные плакаты по ультразвуковому методу контроля
- Нормативные документы по ультразвуковому методу контроля
- Учебная литература по неразрушающим методам контроля
Подробнее о порядке проведения аттестации персонала, перечне необходимых документов и стоимости аттестации можно посмотреть здесь.
Кроме того, в соответствии с требованиями ПНАЭ Г-7-010-89 и СДАНК-01-2020 для проведения ультразвукового контроля конкретного объекта должны быть разработаны технологические карты, содержащие перечень используемого оборудования, последовательность, параметры и схемы проведения контроля, оценку качества объекта с указанием информативных признаков выявляемых дефектов. Для объектов атомной энергетики технологические карты должны быть согласованы в Головных материаловедческих организациях (ГМО)
Подробнее о разработке и согласовании технологических карт, а также примеры технологических карт на различные методы неразрушающего контроля можно посмотреть здесь.
УЗК для Чайников
Купить оборудование для ультразвукового контроля можно по цене, указанной в прайс-листе. Цена оборудования указана с учетом НДС. Смотрите также разделы: Визуальный и измерительный контроль, Радиографических контроль, Капиллярный контроль.
Купить оборудование и заказать услуги по ультразвуковому контролю можно в следующих городах: Москва, Санкт-Петербург, Екатеринбург, Саратов, Амурск, Ангарск, Архангельск, Астрахань, Барнаул, Белгород, Бийск, Брянск, Воронеж, Великий Новгород, Владивосток, Владикавказ, Владимир, Волгоград, Волгодонск, Вологда, Иваново, Ижевск, Йошкар-Ола, Казань, Калининград, Калуга, Кемерово, Киров, Кострома, Краснодар, Красноярск, Курск, Липецк, Магадан, Магнитогорск, Мурманск, Муром, Набережные Челны, Нальчик, Новокузнецк, Нарьян-Мар, Новороссийск, Новосибирск, Нефтекамск, Нефтеюганск, Новочеркасск, Нижнекамск, Норильск, Нижний Новгород, Обнинск, Омск, Орёл, Оренбург, Оха, Пенза, Пермь, Петрозаводск, Петропавловск-Камчатский, Псков, Ржев, Ростов, Рязань, Самара, Саранск, Смоленск, Сочи, Сыктывкар, Таганрог, Тамбов, Тверь, Тобольск, Тольятти, Томск, Тула, Тюмень, Ульяновск, Уфа, Ханты-Мансийск, Чебоксары, Челябинск, Череповец, Элиста, Ярославль и других городах, кроме того, в Республике Крым. А так же Республики Казахстан, Белоруссия и другие страны СНГ.
Настроечные образцы (СОПы) | НТЦ Эксперт
Настроечные образцы (ранее СОПы) используются для настройки ультразвуковых приборов на решение конкретных задач НК. Образцы изготавливаются из материала, аналогичного материалу ОК и содержат определенные отражатели, используемые для настройки амплитудной и временной шкалы путем сравнения показаний от несплошностей ОК с показаниями от известных отражателей. Наиболее распространенными типами отражателей при контроле сварных соединений являются плоскодонные отражатели, «зарубки» и сегменты.
Настроечные образцы изготавливаются в соответствии с требованиями ГОСТ Р 55724-2013 (взамен ГОСТ 14782-86). Данный норматив, вместо используемого ранее термина «стандартный образец предприятия» или «СОП» вводит понятие «настроечный образец». Помимо ГОСТ Р 55724-2013 среди документов, регламентирующих изготовление отраслевых настроечных образцов можно выделить следующие:
Развернуть
- РД 153-34.
1-003-01 (РТМ-1С) Сварка, термообработка и контроль трубных систем котлов и трубопроводов при монтаже и ремонте энергетического оборудования.
- РД 34.17.302-97(ОП-501 ЦД-97) Котлы паровые и водогрейные. Трубопроводы пара и горячей воды, сосуды. Сварные соединения. Контроль качества. Ультразвуковой контроль. Основные положения.
- РД РОСЭК-001-96 Машины грузоподъемные, конструкции металлические, контроль ультразвуковой, основные положения.
- СТО 00220256-005-2005 Швы стыковых, угловых и тавровых сварных соединений сосудов и аппаратов, работающих под давлением. Методика ультразвукового контроля.
- СНиП 3.05.03-85 (2000) Строительные нормы и правила. Тепловые сети.
- СНиП 3.03.01-87 Строительные нормы и правила. Несущие и ограждающие конструкции.
- ВСН 012-88 Строительство магистральных и промысловых трубопроводов. Контроль качества и приемка работ. Часть II. Формы документации и правила ее оформления в процессе сдачи-приемки.
- ПБ 03-585-03 Правила устройства и безопасной эксплуатации технологических трубопроводов
- СТО Газпром-2006 Инструкция по неразрушающим методам контроля качества сварных соединений при строительстве и ремонте промысловых и магистральных газопроводов
Калибровка настроечных образцов осуществляется в добровольном порядке. Поверка и внесение в Госреестр в отношении данных образцов не производится, т.к. они не имеют статуса «стандартного образца» или «меры» для которых поверка в большинстве случаев является обязательной. Методика калибровки настроечных образцов регламентирована в том числе документом Р 08-01-2000. Периодичность калибровки в зависимости от конкретного норматива может отличаться:
- ПНАЭ Г-7-014, ПНАЭ Г-7-030, ПНАЭ Г-7-031, ПНАЭ Г-7-032 – 1 раз в год;
- ОСТ 26-2044, РД 34.17.302, ВСН 012 – 1 раз в 3 года;
- РД РОСЭК-001 – 1 раз в 5 лет.
Плоские настроечные образцы (СОПы) с отражателями различного типа применяются для настройки длительности развертки и чувствительности дефектоскопов при контроле листовых изделий. СОПы изготавливаются в соответствии с требованиями нормативной документации регулирующей порядок проведения УЗК в соответствующих областях промышленности. Каждый образец имеет паспорт и сертификат калибровки сроком действия 3 года. Возможно изготовление настроечных образцов из материалов, аналогичных материалам ОК.
Подробнее…
Трубные настроечные образцы (СОПы) с отражателями различного типа применяются для настройки длительности развертки и чувствительности дефектоскопов при контроле трубных изделий. СОПы изготавливаются в соответствии с требованиями нормативной документации регулирующей порядок проведения УЗК в соответствующих областях промышленности. Каждый образец имеет паспорт и сертификат калибровки сроком действия 3 года. Возможно изготовление настроечных образцов из материалов, аналогичных материалам ОК.
Подробнее…
Стандартный образец типа «ступенька» предназначен для настройки толщиномера перед проведением ультразвукового контроля. Образец изготавливается из стали марки СТ20 и алюминия. По заявке возможно изготовления образца из других материалов по размерам заказчика.
Подробнее…
В соответствии с ПНАЭ Г-7-014-89 УЗК данные образцы необходимы для определения параметров УЗ дефектоскопа и преобразователя при работе на объектах атомной энергетики. Более подробное описание контрольных образцов содержится в разделе 4 ПНАЭ Г-7-014-89. В комплект контрольных образцов по ПНАЭ Г-7-014-89 УЗК входят:
Подробнее…
Настроечный образец (СОП) с общепринятым названием «Утюг» предназначен для настройки чувствительности дефектоскопа и определения эквивалентных размеров дефектов при работе с прямыми и наклонными ПЭП.
Подробнее…
Настроечные образцы (меры) для контроля на расслоение предназначены для настройки предельной чувствительности, блока ВРЧ и глубиномера ультразвуковых дефектоскопов при контроле прямыми преобразователями.
Подробнее. ..
Настроечные образцы (меры) для контроля шпилек и анкерных болтов в соответствии с требованиями РД-19.100.00-КТН-036-13 предназначены для настройки чувствительности при проведении УЗК прямыми совмещенными ультразвуковыми преобразователями.
Подробнее…
Настроечные образцы (меры) для ультразвукового контроля валов в соответствии с требованиями РД-19.100.00-КТН-036-13 предназначены для настройки чувствительности при проведении УЗК прямыми раздельно-совмещенными ультразвуковыми преобразователями.
Подробнее…
Стандартные образцы предприятия (меры) с отражателем типа «плоскодонное отверстие» в соответствии с требованиями РД-19.100.00-КТН-036-13 предназначены для настройки предельной чувствительности, блока ВРЧ и глубиномера ультразвуковых дефектоскопов при проведении УЗК наклонными совмещенными ультразвуковыми преобразователями.
Подробнее…
Плоские настроечные образцы (меры) с угловым сварным швом с плоскими угловыми отражателями типа «зарубка» и отражателем типа «боковое цилиндрическое отверстие» применяют для настройки чувствительности и длительности развертки дефектоскопов при проведении УЗК сварных соединений и основного металла наклонными совмещенными и наклонными раздельно-совмещенными ультразвуковыми преобразователями в соответствии с требованиями РД-25. 160.10-КТН-016-15.
Подробнее…
Плоские настроечные образцы (меры) с нахлесточным сварным швом и с отражателями типа «зарубка» применяют для настройки чувствительности и длительности развертки дефектоскопов при контроле сварных соединений и основного металла наклонными совмещенными и наклонными раздельно-совмещенными преобразователями в соответствии с требованиями РД-25.160.10-КТН-016-15.
Подробнее…
Стандартные образцы предприятия (меры) с отражателями типа «сегмент» в соответствии с требованиями СТО 00220256-005-2005 применяют для настройки предельной чувствительности, блока ВРЧ и глубиномера ультразвуковых дефектоскопов при проведении УЗК прямыми и наклонными совмещенными и раздельно-совмещенными ультразвуковыми преобразователями.
Подробнее…
Стандартные образцы предприятия (меры) с отражателями типа «плоскодонное отверстие» и «зарубка» в соответствии с требованиями РД РОСЭК-001-96 применяют для настройки предельной чувствительности, блока ВРЧ и глубиномера ультразвуковых дефектоскопов при проведении УЗК прямыми и наклонными совмещенными и раздельно-совмещенными ультразвуковыми преобразователями.
Подробнее…
Стандартные образцы предприятия (меры) с отражателями типа «плоскодонное отверстие» в соответствии с требованиями ОСТ 108.961.07-83 применяют для настройки предельной чувствительности, блока ВРЧ и глубиномера ультразвуковых дефектоскопов при проведении УЗК прямыми и наклонными совмещенными и раздельно-совмещенными ультразвуковыми преобразователями.
Подробнее…
Комплект образцов для аттестации по УЗК, используется для обучения специалистов ультразвуковому контролю. Комплект для аттестации состоит из четырех образцов, каждый из которых имеет характерные дефекты, возникающие в процессе производства и эксплуатации сварных швов и основного металла (трещины, поры, непровары, шлаковые и вольфрамовые включения и т.д.).
Подробнее…
Стандартные (настроечные) образцы предприятия (СОП) можно купить с доставкой до двери или до терминалов транспортной компании в следующих городах: Москва, Санкт-Петербург, Екатеринбург, Саратов. Амурск, Ангарск, Архангельск, Астрахань, Барнаул, Белгород, Бийск, Брянск, Воронеж, Великий Новгород, Владивосток, Владикавказ, Владимир, Волгоград, Волгодонск, Вологда, Иваново, Ижевск, Йошкар-Ола, Казань, Калининград, Калуга, Кемерово, Киров, Кострома, Краснодар, Красноярск, Курск, Липецк, Магадан, Магнитогорск, Мурманск, Муром, Набережные Челны, Нальчик, Новокузнецк, Нарьян-Мар, Новороссийск, Новосибирск, Нефтекамск, Нефтеюганск, Новочеркасск, Нижнекамск, Норильск, Нижний Новгород, Обнинск, Омск, Орёл, Оренбург, Оха, Пенза, Пермь, Петрозаводск, Петропавловск-Камчатский, Псков, Ржев, Ростов, Рязань, Самара, Саранск, Смоленск, Сочи, Сыктывкар, Таганрог, Тамбов, Тверь, Тобольск, Тольятти, Томск, Тула, Тюмень, Ульяновск, Уфа, Ханты-Мансийск, Чебоксары, Челябинск, Череповец, Элиста, Ярославль и другие города. А так же Республики Казахстан, Белоруссия и другие страны СНГ.
| Лидеры продаж УКАльбом радиографических снимков Документы
|
Ультразвуковой контроль — обучение, аттестация и сертификация специалистов в «АРЦНК»
Ультразвуковой контроль (УЗК) — акустический метод неразрушающего контроля, который основан на анализе процесса распределения ультразвуковых колебаний в проверяемых элементах. В качестве оборудования используются УЗ-преобразователи, дефектоскопы и толщиномеры.
ООО «АРЦ НК» предоставляет услуги по технической диагностике, ультразвуковой толщинометрии и ультразвуковому контролю. Компания имеет аттестованную лабораторию неразрушающего контроля, которая оснащена полным набором необходимого оборудования.
Уточнить стоимость ультразвукового контроля и толщинометрии, а также заказать услугу вы можете одним из этих способов:
- Позвоните по указанным на сайте номерам телефонов в Томске.
- Отправьте запрос по электронной почте.
- Оставьте заявку на сайте.
Мы свяжемся с вами, обсудим детали и ответим на все интересующие вопросы.
Содержание:
- Для чего нужен УЗК?
- Ключевые особенности метода
- Классификация ультразвуковых методов
- Ультразвуковой контроль от «АРЦ НК»
- Стоимость УЗК в «АРЦ НК»
Для чего нужен УЗК?
Цель ультразвукового контроля — обнаружение внутренних дефектов материалов, проверка качества исполнения работ и состояния следующих объектов:
- сварочных швов;
- сосудов под давлением;
- аппаратов высокого давления;
- трубопроводов;
- пайки, склейки и поковки;
- листового проката из металла и других материалов.
Ультразвуковой контроль — необходимое исследование при изготовлении и проверке функционирования множества узлов и деталей: оснащения атомных станций, авиадвигателей, трубопроводов или рельс на железной дороге и др.
Ультразвуковая толщинометрия используется при проверке объектов, недоступных или труднодоступных для исследования их толщины при помощи механических измерительных приборов. Данный метод обязателен для установления толщины стенок замкнутых и имеющих доступ только к одной из сторон объектов: котлов, труб, сосудов, объектов судостроения и др.
Ключевые особенности метода
Относительно остальных способов неразрушающего контроля УЗ-диагностика имеет ощутимые достоинства:
- аппаратура высокочувствительна к особо серьезным дефектам: трещинам и непроварам;
- доступная цена услуги;
- скорость процедуры УЗК;
- безопасность для людей;
- возможность проводить проверку на рабочих объектах без влияния на течение производственного дела;
- процедура контроля не приводит к повреждению проверяемых объектов;
- возможность проверки разных материалов: металлических и неметаллических;
- повышенная маневренность УЗ приборов.
Ультразвуковой метод предъявляет повышенные нормы относительно таких характеристик поверхности проверки, как шероховатость и волнистость.
Классификация ультразвуковых методов
Ультразвуковые методы контроля относятся к активным акустическим методам, которые основаны на формировании волн и последующем приеме отраженных, прошедших или дифрагированных сигналов.
Активные методы подразделяют на методы:
- прохождения, использующие излучающий и приемный преобразователи, расположенные по разные стороны объекта контроля или контролируемого участка;
- отражения, регистрирующие и анализирующие сигналы, отраженные от границы раздела двух сред с разными акустическими свойствами;
- комбинированные, использующие элементы методов прохождения и отражения.
Ультразвуковой контроль от ООО «АРЦ НК»
Опытные сотрудники нашего испытательного центра имеют надлежащую квалификацию и практические навыки проведения неразрушающего контроля ультразвуковыми методами в разных промышленных отраслях.
Наши специалисты проводят проверку таких объектов:
Сварные соединения | Все виды |
---|---|
Инфраструктура |
|
Эксплуатационный контроль |
|
Нефтехимическая отрасль |
|
Производство |
|
Композитные материалы |
|
Первичные металлы |
|
Испытательный центр ООО «АРЦ НК» оснащен современным оборудованием в области УЗК, что позволяет специалистам центра проводить ручной или механизированный ультразвуковой контроль.
В работе мы используем УЗ-дефектоскопы и толщиномеры, работающие как с традиционными пьезоэлектрическими преобразователями (ПЭП) с отображением А и В-сканов, так и использующие технологию фазированных решеток с отображением S-скана.
Перед каждым использованием приборы обязательно проверяют на работоспособность и точность. С этой целью используют стандартные образцы.
Испытательный центр ООО «АРЦ НК» оснащен образцами для калибровки двух разновидностей:
- Калибровочные образцы (меры).
Они служат для корректировки главных показателей приборов:
- угла ввода,
- мертвой зоны,
- разрешающей способности,
- стрелы ПЭП
- Настроечные.
Стандартные образцы предприятия (СОП) с распространенными видами отражателей: плоскодонные отверстия, «зарубки» и сегменты. Служат для наладки глубиномера, измерения уровней чувствительности при выполнении проверки отдельного элемента по установленной нормативной документации.
Стоимость УЗК в «АРЦ НК»
Ультразвуковой контроль представляет собой высокотехнологичный и трудоемкий процесс, зависящий от многих факторов:
- удаленности, расположения и размеров объекта контроля;
- состояния поверхности;
- доступности объекта контроля,
- условий окружающей среды и т.д.
В связи с таким количеством условий мы применяем индивидуальный подход к расчету стоимости работ в зависимости от поставленных задач. Используя этот метод расчета, мы неоднократно подбирали оптимальные предложения для наших заказчиков.
Помимо осуществления УЗК, мы проводим обучение, аттестацию, аккредитацию и оценку квалификации специалистов по данному направлению.
Чтобы задать вопросы или получить консультацию по поводу услуги ультразвукового контроля, свяжитесь с нами любым удобным вам способом.
Ультразвуковой контроль сварных соединений и швов трубопроводов в Екатеринбурге
Для проверки качества изделия без нарушения структуры материала, из которого оно изготовлено, применяют неразрушающий ультразвуковой контроль. В основе метода УЗК лежит применение ультразвуковых волн, которые проникают в материал проверяемого изделия и отражаются от границ нарушения его целостности при наличии дефектов. Ультразвуковой неразрушающий контроль безопасен для проверяемых материалов. Ультразвуковые дефектоскопы позволяют контролировать качество изделий, выполненных из металла, пластмассы, керамики и композитных материалов.
Контроль качества изделий посредством ультразвуковых дефектоскопов применяется в металлургии, судостроении, машиностроении, энергетике и многих других отраслях. УЗК необходим при строительстве железных дорог, газопроводов, объектов химической промышленности.
Для повышения качества строительства и обеспечения необходимого уровня надежности металлических конструкций применяют ультразвуковой контроль сварных соединений. Используя данный метод, проверяют стыковые, нахлесточные, угловые и тавровые соединения, металлических частей конструкций, выполненные различными способами сварки.
В большинстве случаев УЗК сварных швов практически невозможно заменить другими видами контроля качества. Ультразвуковая дефектоскопия позволяет заранее спрогнозировать и предотвратить аварийные ситуации, связанные с непредвиденными неисправностями механизмов, нефтепроводов, газопроводов, сосудов и агрегатов, постоянно находящихся под давлением. УЗК подвергаются участки железнодорожные пути, стальные сооружения и конструкции, детали летательных аппаратов, паровые котлы, газовые баллоны, листовой прокат и многие другие виды продукции.
Работы, связанные с ультразвуковой диагностикой материалов выполняют операторы дефектоскописты. Они проверяют конструкции технологического оборудования на наличие дефектов, выполняют ультразвуковой контроль трубопроводов, проводят работы связанные с толщинометрией резервуаров, трубопроводов, элементов и узлов различных конструкций. Метод отличается оперативностью при испытаниях и подходит для контроля качества большинства типов соединений выполненных сваркой.
С помощью ультразвукового метода контроля качества можно выявить следующие дефектные области:
- Область неоднородной плотности материала
- Область, в которой материал имеет неоднородную структуру
- Область, пораженную коррозией
- Область с несоответствием химического состава
- Область с несоответствием размеров
При помощи ультразвуковой дефектоскопии можно проверить характеристики твердых образцов, а также контролировать состояние:
- Сварных, паянных и клееных соединений
- Заготовок и готовых деталей
- Деталей установок во время их эксплуатации
- Технологических трубопроводов и аппаратов в нефтегазовой и химической отраслях
- Конструкций в строительной отрасли
- Энергетических установок
Работы, связанные с УЗК могут проводиться как в лабораторных, так и в полевых условиях. Объективность полученных результатов существенно зависит от квалификации, теоретической подготовки и практического опыта оператора дефектоскописта. Чтобы повысить объективность информации о качестве изделия и обеспечить оперативность получения новых данных на многих предприятиях внедряют автоматизацию ультразвукового контроля. Что, в свою очередь, положительно влияет на рост производительности труда.
Метод УЗК способствует выявлению в структуре материала трещин, пор, царапин и других дефектов. Ультразвуковые исследования позволяют определить параметры объекта, от которых зависит уровень надежности его эксплуатации. Чаще всего ультразвуковому контролю подвергают сварные швы и участки конструкции, при наличии дефектов в которых может выйти из строя весь объект.
Износ материалов деталей, а также скрытые дефекты производства со временем могут набрать критическое напряжение. В результате может выйти из строя ответственная конструкция, что приведет к созданию аварийной ситуации с разрушительными последствиями. Ультразвуковые исследования позволяют заблаговременно выявить слабые места конструкций, не подвергая их механическим воздействиям и не разрушая материал из которого они изготовлены.
Ультразвуковая дефектоскопия применяется для исследования состояния конструкций, чтобы определить качество швов, соединяющих элементы. Метод отличается оперативностью выполнения замеров. Современные приборы для ультразвуковых исследований производят измерения, используя сочетание различных измерительных способов:
- Измерения дельта-методом
- Измерения с использованием зеркального метода
- Зеркально теневой метод
- Теневой метод
- Эхо-метод
Критическая усталость металла способствует постепенному образованию трещин. Однако явное проявление дефекта приводит к поломке. При помощи ультразвукового контроля процессы разрушения можно выявить еще в самом начале их формирования. Во многих случаях ультразвуковые исследования позволяют определить предрасположенность элемента к появлению критического дефекта еще до начала его образования.
Образовавшийся в сварном шве, при сварке стыка воздушный пузырек, с течением времени может вырасти в большую проблему. Ультразвуковая дефектоскопия позволяет обнаружить скрытую разность в плотности материала, которая означает наличие дефекта. Ультразвуковая дефектоскопия обязательна для проверки качества колесных пар, а также трамвайных и железнодорожных путей при эксплуатации трамваев и железнодорожного транспорта.
В настоящее время ультразвуковой контроль в Екатеринбурге чаще всего применяют производители элементов и конструкций, необходимых для обеспечения нормальной жизнедеятельности населения, а также для безопасной эксплуатации объектов на предприятиях. Ультразвуковая дефектоскопия основана на свойстве полнотелых материалов отзываться вибрациями на воздействие ультразвука, при наличии в них полостей, коррозии, растрескиваний и других дефектов. В нашей компании вы можете заказать весь спектр услуг, связанный с ультразвуковым контролем в Екатеринбурге. Квалификация наших сотрудников и новейшее высококачественное оборудование, позволяют получать объективные и точные результаты.
Лаборатория компании оснащена современными ультразвуковыми дефектоскопами и толщинометрами, позволяющими проводить ультразвуковой контроль швов и толщинометрию деталей конструкций из различных материалов. Элементная база приборов обеспечивает высокую помехоустойчивость. Все приборы оснащены функцией записи полученных результатов, которые потом можно распечатать на бумажные носители. Параллельно с дефектоскопией проводится и визуально измерительный контроль.
Ультразвуковой контроль – где заказать услугу, стоимость
Ультразвуковой метод контроля является одним из основных (дополнительный) методов неразрушающего контроля, выполняется в соответствии ГОСТ 55724-2013 Контроль неразрушающий. Соединения сварные. Методы ультразвуковые.
Ультразвуковой контроль основан на способности высокочастотных колебаний проникать в металл и отражаться от поверхности трещин, пустот и других несплошностей.
КОНТРОЛИРУЕМЫЕ ОБЪЕКТЫ:
Методы ультразвуковой дефектоскопии позволяют производить контроль сварных соединений, сосудов и аппаратов высокого давления, трубопроводов, поковок, листового проката и другой продукции.
Определяет неразрушающие методы УЗК контроля стыковых, нахлестных, тавровых деталей с полным проваром шва, выполненные электрошлаковой, газовой, лучевой, лазерной и стыковой сваркой оплавлением в сварных деталях из металлов и их сплавов.
Определяются:
— размеры, типы, и формы несплошностей (дефекты).
— эквивалентная площадь несплошности
— координаты несплошности в сварном соединении
— условные размеры несплошности
— условное расстояние между несплошностями
— количество несплошностей
ПРЕИМУЩЕСТВА:
— высокая чувствительность к наиболее опасным дефектам типа трещин и непроваров;
— высокая точность и скорость исследования;
— возможность вести контроль непосредственно на рабочих местах без прерывания технологического процесса;
— не требуется выведения контролируемой детали или всего объекта из эксплуатации;
— исследуемый объект не повреждается;
— возможность проводить контроль изделий из разнообразных материалов, как металлов, так и неметаллов.
НЕДОСТАТКИ:
— подготовка к контролю
ПРИМЕНЯЕМОЕ ОБОРУДОВАНИЕ:
Ультразвуковые дефектоскопы А1212«MASTER», УД «PELENG», УИУ «СКАРУЧ» и другое оборудование в соответствии с поставленными задачами по контролю.
В какой документации указывается необходимость проведения и объем ультразвукового и радиографического контроля, типы и размеры несплошностей (дефектов), подлежащих обнаружению, для конкретного вида (типа) конструкции оборудования под давлением и сварного соединения?
НОРМАТИВНАЯ ДОКУМЕНТАЦИЯ ДЛЯ КОНТРОЛЯ УЗК:
• ГОСТ Р 55724-2013 Контроль неразрушающий. Соединения сварные. Методы ультразвуковые
• СТО 02495307-002-2008 Ультразвуковой контроль сварных соединений арматуры в железобетонных конструкциях.
• РД 34.17.302-97 (ОП-501, ЦД-97) «Котлы паровые и водогрейные. Трубопроводы пара и горячей воды, сосуды. Сварные соединения. Контроль качества. Ультразвуковой контроль. Основные положения».
• РД РОСЭК-001-96 «Машины грузоподъемные. Конструкции металлические. Контроль ультразвуковой. Основные положения».
• СТО 00220256-005-2005 «Швы стыковых, угловых и тавровых сварных соединений сосудов и аппаратов, работающих под давлением. Методика ультразвукового контроля».
• СНиП 3.05.03-85 (2000) «Тепловые сети».
• СТО Газпром 2-2.4-083-2006 «Инструкция по неразрушающим методам контроля качества сварных соединений при строительстве и ремонте промысловых и магистральных газопроводов».
• РДИ 38.18.016-94 «Инструкция по УЗК сварных соединений технологического оборудования».
• СНиП 3.03.01-87 «Несущие и ограждающие конструкции».
• ПБ 03-576-03 «Правила устройства и безопасной эксплуатации сосудов, работающих под давлением».
• РД 153-34.1-003-01 (РТМ-1С) «Сварка, термообработка и контроль трубных систем котлов и трубопроводов при монтаже и ремонте энергетического оборудования».
• СП 70.13330.2012 Несущие и ограждающие конструкции
• ГОСТ 22727-88 Прокат листовой. Методы ультразвукового контроля.
• ГОСТ 12.1.001-89 Межгосударственный стандарт. Система стандартов безопасности труда. Ультразвук. Общие требования безопасности.
• ТУ 2248-001-50049230-2007 Проектирование и монтаж трубопроводов из полиэтилена.
• СП 40-102-2000 Проектирование и монтаж трубопроводов систем водоснабжения и канализации из полимерных материалов. Общие требования.
В основе ультразвукового неразрушающего контроля сварных соединений лежит свойство звуковых волн отклоняться от прямолинейного распространения в пространстве при столкновении с препятствиями, в данном случае дефектами объекта. Для этого высокочастотные колебания направляют внутрь исследуемой конструкции. Если в ней есть трещины, царапины и прочие дефекты, то волна будет отражаться от их поверхности.
Компания «Веско» занимается проверкой строительных объектов с помощью различных методов неразрушающего контроля, включая ультразвуковой. Если вам необходимо провести исследование сварного соединения с помощью звуковых волн, тогда обратитесь к специалистам из этой фирмы.
Какие объекты можно проверить ультразвуком?
Метод позволяет проводить контроль сварных швов, сосудов, аппаратов высокого давления, трубопроводов. Главное, что в ходе проверки целостность объекта не нарушается.
В ходе такой проверки можно выявить:
- размер и вид дефекта;
- расположение несплошности;
- количество дефектов;
- расстояние между несплошностями и другое.
Компания «Веско» для проведения ультразвукового неразрушающего контроля сварных соединений использует высокоточное и эффективное оборудование, например, ультразвуковые дефектоскопы А1212«MASTER», УД «PELENG», УИУ «СКАРУЧ» и другие устройства, необходимые для выполнения задачи.
Ультразвуковой метод контроля имеет ряд преимуществ:
- высокий уровень чувствительности, этот метод позволяет обнаружить наиболее опасные дефекты сварных швов;
- высокая точность и скорость проведения контроля;
- исследование объекта можно вести, не прерывая технологический процесс;
- исследуемый объект не требуется изымать из эксплуатации;
- целостность объекта сохраняется;
- этот метод применим для изделий из широкого спектра материалов, включая как металлы, так и не металлы.
Ультразвуковой метод контроля можно проводить в температурном диапазоне от +5°С до +40°С.
Ультразвуковой неразрушающий контроль сварных соединений — это высокочувствительный метод, позволяющий обнаружить различные дефекты. Вы можете легко заказать проверку объекта этим способом, оставив заявку на сайте компании «Веско» или позвонив по контактному номеру.
Выбор способа прозвучивания, типа искателя, контактной жидкости, схемы контроля. В зависимости от толщины свариваемых элементов (ГОСТ 16037-80) выбирают такой способ прозвучивания, который позволяет обеспечить контроль сечения всего наплавленного металла (табл. 1).
Расстояние В, на которое по обе стороны от валика усиления шва должна быть подготовлена поверхность зоны перемещения искателя типа ИЦ, выбирается по табл. 1 или в случаях применения других типов искателей вычисляется по формулам:
B1=δ⋅tgα-l/2+d+m (1)
— при прозвучивании прямым лучом
B2=2δ⋅tgα+d+m (2)
— при прозвучивании прямым и однократно отраженным лучом
B3=3δ⋅tgα-l/2+d+m (3)
— при прозвучивании однократно и двукратно отраженным лучом
Таблица 1
Параметры ультразвукового контроля
Толщина свариваемых элементов по ГОСТ 16037-80, мм | Способ прозвучивания*) |
Угол призмы искателя, град.![]() |
Рабочая частота искателя, МГц | Зона перемещения искателя, мм | Зона зачистки В**, мм | Предельная чувствительность Sп (первый браковочный уровень), мм2 | Площадь и линейные размеры вертикальной грани углового отражателя | ||
площадь S мм2 | ширина b мм | высота h мм | |||||||
от 6 до 7,5 вкл. | Прямым и однократно отраженным лучем | 53(50) | 5,0 | 0-65 (0-55) | 85 (75) | 1,7 | 2,4(3,4) | 1,5(2,0) | 1,6(1,7) |
свыше 7,5 до 10 вкл.![]() |
53(50) | 5,0 | 0-80 (0-60) | 100 (80) | 2,0 | 3,0(4,0) | 2,0(2,0) | 1,5(2,0) | |
» 10 » 14 « | 53(50) | 5,0 | 0-105 (0-70) | 125 (90) | 2,0 | 3,0(4,0) | 2,0(2,0) | 1,5(2,0) | |
» 14 » 18 « | 50 | 2,5 | 0-100 | 120 | 2,5 | 5,0 | 2,0 | 2,5 | |
» 18 » 22 « | 50 | 2,5 | 0-115 | 135 | 3,0 | 6,0 | 2,0 | 3,0 | |
» 22 » 26 « | 50 | 2,5 | 0-130 | 150 | 3,0 | 6,0 | 2,0 | 3,0 | |
» 26 » 30 « | 50(40) | 2,5 | 0-150 (0-90) | 170(110) | 4,0 | 8,0(3,0) | 2,5(2,0) | 3,2(1,5) | |
» 30 » 34 « | 50(40) | 2,5 | 0-165 (0-95) | 185(115) | 5,0 | 10,0(3,8) | 3,0(2,0) | 3,3(1,9) | |
«34 » 38 « | 40 | 2,5 | 0-105 | 125 | 6,0 |
4.![]() |
2,0 | 2,2 | |
» 38 » 42 « | 40 | 2,5 | 0-115 | 135 | 7,0 | 5,2 | 2,5 | 2,1 | |
» 42 » 46 « | 40 | 2,5 | 0-125 | 145 | 7,0 | 5,2 | 2,5 | 2,1 | |
» 46 » 50 « | 40 | 2,5 | 0-140 | 160 | 7,0 |
Схема определения зон зачистки поверхности около шва сварного соединения
δ — толщина свариваемых элементов, мм; α — угол ввода, град; d — расстояние от точки ввода до задней грани искателя, мм; — половина ширины валика усиления шва, мм; B1, B2, B3, — зоны зачистки поверхности при прозвучивании прямым, однократно и двукратно отраженным лучом, мм; m=20 мм
Разметка кольцевого сварного соединения трубопровода на участки и их нумерация
Сварное соединение должно быть разделено на 12 равных участков по окружности свариваемых элементов. 2. Границы участков нумеруются цифрами от 1 до 12 по ходу часовой стрелки с указанным направлением движения продукта в трубопроводе. 3. Участки нумеруются двумя цифрами: 1-2, 2-3 и т.д. 4. Граница между участками 11-12 и 12-1 должна проходить через клеймо сварщика, перпендикулярно шву.
Частоту и угол призмы искателя выбирают, исходя из толщины свариваемых элементов и способа прозвучивания по таблице №1.
Перед настройкой дефектоскопа на контроль конкретного изделия должны быть проверены следующие основные параметры контроля в соответствии с требованиями ГОСТ Р 55724-2013 в замен ГОСТ 14782-86 (Применяется в ЕАЭС):
- стрела искателя;
- угол ввода ультразвукового луча в металл;
- мертвая зона;
- предельная чувствительность;
- разрешающая способность.
ПАРАМЕТРЫ ИСКАТЕЛЯ
Угол призмы (β) искателя, град.![]() |
Рабочая частота (f), МГц | Диаметр преобразователя, мм | Стрела искателя, мм | Угол ввода (α) ультразвукового луча (оргстекло-сталь), град. |
30 | 1,8 | 18 | 24 | 39 |
40 | « | « | 22 | 50 |
30 | 2,5 | 12 | 14 | 39 |
40 | « | « | « | 50 |
50 | « | « | 10 | 65 |
53 | « | « | « | 70 |
54 | « | « | 12 | 72 |
55 | « | « | 14 | 74 |
40 | 5,0 | 8 | 12 | 50 |
50 | « | « | 10 | 65 |
53 | « | « | 8 | 70 |
54 | « | « | « | 72 |
55 | « | « | 8 | 74 |
Материал испытательных образцов по акустическим свойствам и чистоте поверхности должен быть аналогичен контролируемому изделию. В испытательных образцах не должно быть дефектов (кроме искусственных отражателей), выявляемых эхо-импульсным методом.
Проведение контроля включает операции прозвучивания металла шва и околошовной зоны и определения измеряемых характеристик дефектов.
Прозвучивание швов выполняют способом поперечно-продольного перемещения искателя.
Скорость перемещения искателя должна быть не более 30 мм/с.
Акустический контакт искателя с поверхностью, по которой он перемещается, обеспечивают через контактную жидкость легким нажатием на искатель. О стабильности акустического контакта свидетельствует уменьшение уровней амплитуд сигналов на заднем фронте зондирующего импульса, создаваемых акустическими шумами искателя, по сравнению с их уровнем при ухудшении или отсутствии акустического контакта искателя с поверхностью изделия.
Прозвучивание сварных соединений производят на поисковой чувствительности, а определение характеристик выявленных дефектов — на первом и втором браковочных уровнях. Анализируют только те эхо-сигналы, которые наблюдаются в строб-импульсе и имеют высоту не менее 30 мм на поисковой чувствительности.
В процессе контроля необходимо не реже двух раз в смену проверять настройку дефектоскопа на первый браковочный уровень.
На первом браковочном уровне дефекты оценивают по амплитуде, а на втором браковочном уровне оценивают условную протяженность, условное расстояние между дефектами и количество дефектов.
Швы сварных соединений прозвучивают прямым и однократно отраженным лучами с двух сторон.
Схема прозвучивания шва при одностороннем доступе
Оценка качества швов сварных соединений.
Измеренные характеристики дефектов швов сварных соединений оценивают в соответствии с требованиями действующей нормативно-технической документации. Предельно допустимые значения измеряемых характеристик дефектов, установленные с учетом требований нормативно технической документации на контролируемый объект. Качество швов сварных соединений оценивают по результатам контроля по принципу: «годен» — «негоден».
Каким образом оформляются результаты проводимого контроля качества сварных соединений?
По окончанию работ выдается заключение установленной формы:
Рекомендуемое
(наименование объекта) |
(наименование организации, проводившей контроль- |
|
Линия № |
монтажное управление треста, лаборатория) |
|
ЗАКЛЮЧЕНИЕ №___ Чертеж (формуляр, монтажная схема) №___________________________________________________________________________ Фамилия, имя, отчество и номер клейма сварщика____________________________________________________________________ Тип дефектоскопа и его заводской номер________________________________________________________________________ №№ пп Номер стыка Наружный диаметр и толщина стенки трубопровода, (Дн×δ), мм Рабочая частота искателя,
МГц Угол призмы искателя, град. Начальник лаборатории_______________________________________________________ подпись (фамилия, имя, отчество) Дефектоскопист по ультразвуковому контролю___________________________________ подпись (фамилия, имя, отчество) |
||
Примечание: 1. Номер заключения должен являться порядковым номером соответствующей записи в журнале ультразвукового контроля.
2. Схема контроля приведена на обороте.
Рекомендуемое
ДЕФЕКТОГРАММА №8 СВАРНОГО СОЕДИНЕНИЯ №8 ЗАПИСЬ №8 В ЖУРНАЛЕ УЛЬТРАЗВУКОВОГО КОНТРОЛЯ
Примечание: стрелка «+» указывает направление движения продукта от нас перпендикулярно плоскости чертежа
Рекомендуемое
ЖУРНАЛ УЛЬТРАЗВУКОВОГО КОНТРОЛЯ
Номер заключения и дата его выдачи |
Дата проведения контроля |
Наименование объекта контроля и его адрес |
Объем контроля |
Характеристика сварного соединения |
Параметры контроля |
Результаты контроля |
Оценка качества шва сварного соединения |
Сведения о повторном контроле |
Фамилия дефектоскописта |
Подпись дефектоскописта |
Примечание |
||||||||||
Тип соединения | Индекс (номер) шва по чертежу | Диаметр и толщина свариваемых элементов, мм | Марка стали | Способ сварки | Тип дефектоскопа и его номер | Рабочая частота, МГц | Тип и гол призмы искателя, град | Площадь предельно допустимого эквивалентного дефекта | Номер участка сварного соединения | Сокращенное описание обнаруженных дефектов | Кол-во обнаруженных дефектов на 100 мм длины шва | Условная протяженность дефектов на 100 мм длины шва, мм |
Что такое ультразвуковой контроль и для чего он нужен?
Одним из основных способов проверки сварных соединений является ультразвуковой контроль. Специальные приборы образуют высокочастотные колебания, которые обладают способностью проникать вглубь металла и отражаться от неровностей, пустот и иных дефектов. Специалист, проводящий ультразвуковой контроль, на экране прибора видит несоответствия и по определенным показаниям может точно охарактеризовать дефект.
Какими преимуществами обладает ультразвуковой контроль?
Ультразвуковой контроль имеет обширную область применения, так как обладает огромным количеством преимуществ:
- Высокая точность и безопасность проведения исследований.
- Мобильность. Благодаря переносным дефектоскопам контроль может проводиться по вызову на объект заказчика.
- В процессе проведения ультразвуковой диагностики не требуется вывод объекта из эксплуатации.
- При ультразвуковом контроле полностью отсутствуют повреждения исследуемого объекта.
Ультразвуковой контроль позволяет исследовать изделия, состоящие из разнообразных материалов – металлы, неметаллы, а также их сплавы. Стоит отметить, что подобный вид диагностики применяется не только в промышленных отраслях, но и в строительстве и реконструкции жилых объектов.
Где заказать ультразвуковой контроль?
Научно-исследовательская лаборатория технического центра «ВЕСКО» предлагает услуги по проведению всех видов диагностики, включая и ультразвуковой контроль. Наши специалисты обладают огромным опытом и знаниями, которые постоянно совершенствуют. Они ответственно подходят к своей работе и выполняют ее на самом высоком уровне. Заказав у нас ультразвуковое исследование, вы получите точные результаты, оформленные надлежащим образом в самые кратчайшие сроки. Связаться с нами вы можете по номеру телефона, указанному на сайте компании или оставив электронную заявку. Наш специалист профессионально ответит на все интересующие вас вопросы и подробно расскажет о процедуре ультразвукового контроля, стоимости проводимых работ, а также о способах оплаты.
Научно-исследовательская лаборатория технического центра «ВЕСКО» – это точность и надежность. Мы индивидуально подходим к каждому клиенту и качество нашего сервиса на высоте. Наша компания дорожит своей репутацией, и мы гарантированно выполняем свои обязательства.
Что такое ультразвуковой контроль и как он работает?
Ультразвуковой контроль (УЗК) включает ряд методов неразрушающего контроля (НК), при которых ультразвуковые волны проходят через объект или материал. Эти высокочастотные звуковые волны передаются в материалы для определения характеристик материала или обнаружения дефектов. В большинстве приложений ультразвукового контроля используются короткие импульсные волны с частотами в диапазоне от 0,1 до 15 МГц, хотя могут использоваться частоты до 50 МГц. Одним из распространенных применений этого метода испытаний является ультразвуковое измерение толщины, которое используется для определения толщины объекта, например, при оценке коррозии трубопровода.
Как это работает?
Ультразвуковой контроль использует пьезоэлектрический преобразователь, соединенный с дефектоскопом, который в своей основной форме представляет собой импульсный приемник и дисплей осциллографа. Преобразователь проходит над проверяемым объектом, который обычно связан с объектом контроля гелем, маслом или водой. Эта контактная жидкость необходима для эффективной передачи звуковой энергии от преобразователя в деталь, однако она не требуется при проведении испытаний с помощью бесконтактных методов, таких как электромагнитный акустический преобразователь (ЭМАП) или лазерное возбуждение.
Эхо-импульс и сквозное пропускание
Ультразвуковой контроль можно проводить двумя основными методами – эхо-импульсным и сквозным.
При импульсном эхо-контроле один и тот же преобразователь излучает и принимает энергию звуковой волны. В этом методе используются эхо-сигналы на границе раздела, например, на задней стороне объекта или дефекта, для отражения волн обратно к датчику. Результаты представлены в виде линейного графика, где амплитуда по оси ординат представляет интенсивность отражения, а расстояние или время по оси абсцисс показывает глубину прохождения сигнала через материал.
При тестировании сквозного пропускания используется излучатель для отправки ультразвуковых волн с одной поверхности и отдельный приемник для приема звуковой энергии, достигшей противоположной стороны объекта. Несовершенства материала уменьшают количество принимаемого звука, позволяя обнаружить дефекты.
Контактный и иммерсионный контроль
Ультразвуковой контроль также можно разделить на два основных типа: контактный или иммерсионный контроль .
Контактный ультразвуковой контроль обычно используется для проверки доступности или портативности на месте. Контактный ультразвуковой контроль можно проводить, когда доступна только одна сторона испытуемого образца, или когда испытуемые детали имеют большие размеры, неправильную форму или их трудно транспортировать.
Иммерсионный ультразвуковой контроль – это лабораторный или заводской неразрушающий контроль, который лучше всего подходит для изогнутых компонентов, сложной геометрии и для разработки ультразвуковой техники. В этом методе компонент или материал погружают в воду, которая действует как контактная жидкость вместо гелей, используемых для контактного ультразвука. Иммерсионный УЗ обычно использует метод эхо-импульса, а траектории роботизированного датчика можно использовать для проверки сложных поверхностей, которые было бы трудно покрыть контактными датчиками. Иммерсионный УЗК можно использовать для широкого диапазона толщин стенок и типов материалов, что делает его подходящим методом испытаний для различных областей применения и отраслей.
Для чего используется?
В качестве метода неразрушающего контроля ультразвуковой контроль идеально подходит для обнаружения недостатков и дефектов, не повреждая проверяемый объект или материал. Периодические ультразвуковые проверки также могут использоваться для проверки коррозии или роста известных дефектов и, таким образом, потенциально предотвращать выход из строя детали, компонента или всего актива. Он используется в различных отраслях промышленности, включая аэрокосмическую, автомобильную, строительную, медицинскую, металлургическую и обрабатывающую.
Какие материалы можно тестировать?
Ультразвуковой контроль используется в самых разных отраслях промышленности благодаря его пригодности для многих различных материалов. УЗ идеально подходит для контроля плотных кристаллических структур, таких как металлы. Керамика, пластмассы, композиты и бетон также могут успешно контролироваться, но с меньшим разрешением, поскольку затухание в этих материалах выше.
Ультразвуковая технология успешно используется в медицинском секторе на протяжении многих десятилетий и становится все более предпочтительным вариантом как для рутинной диагностической визуализации, так и для медицинских исследований из-за отсутствия ионизирующего излучения.
Преимущества
К преимуществам ультразвукового контроля относятся:
- Высокая проникающая способность, позволяющая обнаруживать дефекты глубоко внутри детали
- Высокая чувствительность, позволяющая обнаруживать очень маленькие дефекты
- Может использоваться для проверки, когда доступна только одна сторона объекта
- Более высокая по сравнению с другими методами неразрушающего контроля точность определения глубины внутренних дефектов и толщины деталей с параллельными поверхностями
- Способен оценить размер, форму, ориентацию и природу дефектов
- Способность оценивать структуру сплава компонентов с различными акустическими свойствами
- Неопасный для находящихся рядом людей, оборудования или материалов
- Возможны высокоавтоматизированные и портативные операции
- Можно получить немедленные результаты, позволяющие принимать незамедлительные решения
Ограничения
Однако есть несколько ограничений для ультразвукового контроля, а именно:
- Требуются опытные техники для проверки и интерпретации данных
- Ложноположительные результаты, также известные как ложные сигналы, могут быть результатом допустимых аномалий, а также самой геометрии компонента
- Объекты шероховатые, неправильной формы, очень маленькие, тонкие или неоднородные, трудно поддающиеся контролю
- Перед началом испытаний необходимо удалить отслоившуюся окалину или краску, хотя можно оставить чистую, надлежащим образом закрепленную краску
- Соединения, необходимые для испытаний с использованием обычного UT
- UT может иметь меньшую чувствительность к объемным дефектам, особенно металлическим включениям, чем рентгенографический контроль
Области применения
Ультразвуковой контроль имеет множество применений в различных отраслях промышленности, включая проверку целостности материала или компонента. Это может включать в себя проверку сварных швов для определения наличия каких-либо дефектов. Это испытание может быть выполнено как для черных, так и для цветных металлов, а также для более толстых участков и тех, которые доступны только с одной стороны. УЗК также способен обнаруживать более мелкие дефекты и плоские дефекты, которые не так просто оценить с помощью радиографического контроля.
Применение УЗ включает в себя аэрокосмическую, автомобильную, строительную, железнодорожную, медицинскую и нефтегазовую отрасли.
Услуги и курсы TWI
TWI предоставляет ряд услуг по ультразвуковому контролю нашим промышленным членам, а также ряд учебных курсов по неразрушающему контролю для тех, кто хочет узнать о применяемых методах.
Мы можем предоставить полный спектр услуг по тестированию и экспертизу, включая такие методы, как ультразвуковой контроль с фазированной решеткой (PAUT), лазерный ультразвуковой контроль и ручной ультразвуковой контроль.
Ультразвуковой контроль: руководство
Ультразвуковой контроль проводится в материалах для определения наличия дефектов или изъянов в материале, а также для определения толщины материала.
Методы ультразвукового контроля используют звуковые волны для обнаружения дефектов и измерения толщины.
Ультразвуковой контроль (UT) также часто называют ультразвуковым измерением толщины (UTM), ультразвуковым контролем толщины (UTT) или ультразвуковым контролем (ST). Чаще всего он используется на металле, потому что металл проводит звуковые волны таким образом, что поддерживает этот тип измерения.
Этот метод обычно используется инспекторами как один из многих методов неразрушающего контроля (НК), позволяющий им собирать информацию о состоянии актива без необходимости его повреждения.
[Ультразвуковой контроль — это лишь один из методов неразрушающего контроля (НК), используемых инспекторами. Узнайте больше о неразрушающем контроле в этом подробном руководстве .]
Первый ультразвуковой контроль толщины был разработан после того, как Титаник затонул в 1912.
Исследователи хотели определить, как корабли могут находить айсберги до того, как они их увидят, и для этой цели они начали тестировать звуковые волны.
После этих испытаний акустические испытания получили дальнейшее развитие во время Первой мировой войны как способ обнаружения подводных лодок.
Только в 1928 году ученые приступили к испытаниям УЗ в промышленных целях, когда советский исследователь Сергей Соколов обнаружил, что звуковые волны можно использовать для выявления дефектов в металлических материалах. В течение следующих нескольких десятилетий этот метод получил широкое распространение и с тех пор стал одним из наиболее распространенных методов неразрушающего контроля.
Вот меню для этого руководства по UTM, на случай, если вы захотите пробежаться по нему:
- Что такое ультразвуковой контроль?
- Методы ультразвукового контроля
- Где используется ультразвуковой контроль?
- Ультразвуковое испытательное оборудование
- Ультразвуковой контроль и дроны
Чтобы уточнить, ультразвуковой контроль материалов проводится для определения наличия дефектов путем измерения их толщины с помощью высокочастотных звуковых волн (обычно 500 кГц–20 МГц).
При ультразвуковом контроле инспектор будет использовать датчик или другой тип преобразователя, чтобы послать звуковые волны через материал, который он хочет проверить. Если в материале нет дефектов, звуковые волны будут проходить через него, но если звуковые волны попадут в дефект, они отразятся от него, указывая на его наличие.
Инспекторы могут использовать сигнал звуковых волн для создания трехмерной визуализации материала и определения расстояний между различными обнаруженными в нем дефектами.
Вот основные преимущества использования ультразвуковых измерений толщины при контроле:
- Немедленные результаты
- Не требует особой подготовки
- Может обнаруживать дефекты как на поверхности, так и под поверхностью материала
- Это можно сделать на одной стороне материала (т. е. это можно сделать, даже если вы не можете получить доступ к другой стороне материала)
- Можно автоматизировать
- Результаты тестирования могут быть легко переданы
Методы ультразвукового контроля
Существует три основных типа методов ультразвукового контроля:
1. Сквозное пропускание
Сквозное пропускание использует два преобразователя, каждый из которых размещается на противоположных сторонах тестируемого материала. Один из преобразователей создает импульс, а другой его принимает. Если есть сбой в импульсе, инспекторы поймут, что на пути между двумя датчиками присутствует дефект.
2. Эхо-импульс
Эхо-импульс более чувствителен, чем сквозная передача. Он используется для выявления дефектов путем измерения времени, которое требуется амплитудным сигналам для прохождения между различными точками или поверхностями материала.
3. Резонанс
Резонанс аналогичен эхо-импульсу, за исключением того, что при проверке резонанса можно изменить регулярность передачи. Резонансное тестирование в основном используется, когда возможен доступ только к одной стороне материала.
Где используется ультразвуковой контроль? Основной принцип ультразвукового контроля заключается в использовании звука для проверки толщины материала в различных точках.
Ультразвуковые измерения толщины могут помочь инспекторам найти дефекты, такие как крошечные трещины, зазоры, коррозия или другие дефекты в материалах, которые слишком малы, чтобы их можно было увидеть другими методами неразрушающего контроля. Его также можно использовать для обнаружения коррозии — если одна область тоньше другой, это может быть признаком того, что область подверглась коррозии и может потребовать обслуживания.
Ультразвуковой толщиномер можно использовать не только для металлов, но и для контроля пластиков, композитов и керамики. Его также можно использовать для проверки бетона, но результаты могут быть не такими надежными.
Вот некоторые активы, обычно тестируемые с помощью ультразвукового измерения толщины:
- Факельные трубы
- Ветряные турбины
- Большие резервуары для хранения
Вот отрасли, которые обычно используют ультразвуковой контроль как часть своих процедур контроля:
- Аэрокосмическая отрасль
- Автомобилестроение
- Электроника и батарея
- Металлы и литье
- Нефть и газ
- Производство электроэнергии
- Железная дорога
Инспекторы используют несколько различных типов оборудования для ультразвукового контроля.
Некоторое из этого оборудования является узкоспециализированным и может потребовать использования специалиста, обученного его использованию. Некоторые компании нанимают третьих лиц, которые являются экспертами в использовании определенных типов оборудования УЗК и методов ультразвукового контроля, либо для обучения членов внутренней группы по его использованию, либо для самостоятельного использования инструментов и анализа полученных результатов.
При этом даже самое сложное УЗ-оборудование, как правило, несложно в уходе и использовании, а также отличается высокой надежностью.
Вот наиболее распространенные типы ультразвукового оборудования, которое используют инспекторы:
- Ультразвуковые преобразователи и зонды . Преобразователи используются в нескольких типах ультразвукового измерения толщины, включая контроль сварных швов и измерение толщины. Типы включают фазированные решетки, иммерсионные и контактные преобразователи.
- Дефектоскопы . Испытанные в полевых условиях портативные решения для ультразвукового контроля для быстрой и точной проверки внутренней целостности продукта, поиска дефектов, трещин и других дефектов. Дефектоскопы портативны, мощны и чувствительны, что позволяет инспекторам проникать в материалы на значительной глубине.
- Толщиномер . Ультразвуковые толщиномеры обычно используются для контроля толщины различных металлов, в том числе латуни, стали, никеля и свинца. Толщиномер может быть особенно полезен для выявления коррозии.
- Автоматизированные системы УЗК . Автоматизированные ультразвуковые системы измерения толщины — это системы, которые можно установить и собирать ультразвуковые показания без физического присутствия инспектора, что позволяет собирать данные, которые могут быть полезны для долговечности актива, даже когда кого-то нет. Эти системы обычно используются для мониторинга труб в нефтяной и газовой промышленности.
UT Drone Inspection
Дроны обычно используются для визуального осмотра, т. е. для сбора визуальных данных, отражающих состояние актива, но их также начинают использовать для акустических испытаний.
Двумя самыми большими преимуществами проведения проверки толщины с помощью дрона вместо проведения УЗ-контроля лично являются безопасность и экономия:
- В целях безопасности УЗ-проверку с помощью дрона можно использовать в сценариях, требующих работы человека на высоте. с помощью подъемника, подиума или строительных лесов. Использование дрона для сбора данных UT избавляет человека от необходимости подвергать себя опасности при выполнении такой работы.
- В целях экономии УЗ-инспекция может потенциально собирать данные УЗК быстрее, чем человек, а также помогает избежать необходимости в строительных лесах, которые могут быть дорогостоящими и трудоемкими для возведения и демонтажа, что приводит к увеличению затрат из-за продолжительных простоев.
.
Ультразвуковой контроль с помощью дрона все еще находится в зачаточном состоянии. На данный момент одна из немногих компаний, предлагающих дроны, — это Appelix.
Фото предоставлено: Appelix
Чтобы выполнить проверку толщины дрона, дрон должен сначала нанести контактную жидкость на поверхность, которая будет тестироваться, чтобы оптимизировать ее для распространения звуковых волн.
По мере развития технологии дронов мы обязательно увидим больше инспекционных дронов, предлагающих ультразвуковой контроль.
Мы проводим демонстрации по всему миру, чтобы продемонстрировать наш новый беспилотник для инспекции помещений.
Зарегистрируйтесь, чтобы увидеть Elios 3 в прямом эфире рядом с вами.
Неразрушающий контроль – ультразвуковой контроль
Ультразвуковой неразрушающий контроль, также известный как ультразвуковой неразрушающий контроль или просто УЗК, представляет собой метод определения толщины или внутренней структуры испытуемого образца с помощью высокочастотных звуковых волн. Частоты или высота тона, используемые для ультразвукового контроля, во много раз превышают пределы человеческого слуха, чаще всего в диапазоне от 500 кГц до 20 МГц.
В промышленности ультразвуковой контроль широко используется для металлов, пластмасс, композитов и керамики. Единственными распространенными конструкционными материалами, которые не подходят для ультразвукового контроля на обычном оборудовании, являются изделия из дерева и бумаги. Ультразвуковая технология также широко используется в биомедицинской области для диагностической визуализации и медицинских исследований.
Принцип ультразвукового контроля.
СЛЕВА.. Зонд посылает звуковую волну в исследуемый материал. Есть две индикации, одна из начального импульса зонда, а вторая из-за эхосигнала задней стенки.
ПРАВИЛЬНО.. Дефект создает третью индикацию и одновременно уменьшает амплитуду индикации задней стенки.
Как это работает..
Высокочастотные звуковые волны очень направленны, и они будут проходить через среду (например, кусок стали или пластика), пока не встретят границу с другой средой (например, воздухом), после чего они отражаются обратно к своему источнику. Анализируя эти отражения, можно измерить толщину образца или найти признаки трещин или других скрытых внутренних дефектов.
При ультразвуковом контроле ультразвуковой преобразователь, подключенный к диагностическому аппарату, проводится над проверяемым объектом. Преобразователь обычно отделяется от испытуемого объекта контактной жидкостью (например, маслом) или водой, как при иммерсионном испытании.
Существует два метода получения ультразвукового сигнала: отражение и затухание.
В режиме отражения (или эхо-импульса) преобразователь выполняет как отправку, так и прием импульсных волн, поскольку «звук» отражается обратно в устройство. Отраженный ультразвук исходит от поверхности раздела, такой как задняя стенка объекта, или от несовершенства внутри объекта. Диагностическая машина отображает эти результаты в виде сигнала с амплитудой, представляющей интенсивность отражения, и расстоянием, представляющим время прихода отражения.
В режиме затухания (или сквозного пропускания) передатчик посылает ультразвук через одну поверхность, а отдельный приемник определяет количество, достигшее его на другой поверхности после прохождения через среду. Несовершенства или другие условия в пространстве между передатчиком и приемником уменьшают количество передаваемого звука, тем самым выявляя их присутствие. Использование контактной жидкости повышает эффективность процесса за счет снижения потерь энергии ультразвуковой волны из-за разделения поверхностей.
Контроль труб ультразвуковым дефектоскопом
В чем преимущества ультразвукового контроля..
Ультразвуковой контроль полностью неразрушающий. Испытываемый образец не нужно резать, делить на секции или подвергать воздействию повреждающих химических веществ. Требуется доступ только с одной стороны, в отличие от измерения с помощью механических инструментов для измерения толщины, таких как штангенциркули и микрометры. Ультразвуковое исследование не представляет потенциальной опасности для здоровья, в отличие от рентгенографии. Когда тест настроен правильно, результаты очень воспроизводимы и надежны.
Каковы потенциальные ограничения ультразвукового контроля.

Для ультразвуковой дефектоскопии требуется обученный оператор, который может настроить испытание с помощью соответствующих эталонных стандартов и правильно интерпретировать результаты. Проверка некоторых сложных геометрий может быть сложной задачей. Ультразвуковые толщиномеры должны быть откалиброваны по отношению к измеряемому материалу, а приложения, требующие измерения толщины в широком диапазоне или измерения акустически различных материалов, могут потребовать нескольких настроек. Ультразвуковые толщиномеры дороже механических измерительных приборов.
На строительной площадке техник проверяет сварной шов трубопровода на наличие дефектов с помощью ультразвукового прибора с фазированной решеткой. Сканер, состоящий из рамы с магнитными колесами, удерживает датчик в контакте с трубой с помощью пружины. Влажная зона представляет собой ультразвуковую контактную группу, которая позволяет звуку проникать в стенку трубы.
Ультразвуковой контроль сварных швов
Одной из наиболее полезных характеристик ультразвукового контроля является его способность определять точное положение разрыва в сварном шве. Этот метод испытаний требует высокого уровня подготовки и компетентности оператора и зависит от разработки и применения подходящих процедур испытаний. Этот метод контроля можно использовать для черных и цветных металлов, он часто подходит для контроля более толстых участков, доступных только с одной стороны, и часто может обнаруживать более тонкие линии или более простые дефекты, которые могут быть не так легко обнаружены при радиографическом контроле.
Стандарты
Международная организация по стандартизации (ISO)
- ISO 7963, Неразрушающий контроль. Ультразвуковой контроль. Спецификация калибровочного образца № 2
- ISO/DIS 11666, Неразрушающий контроль сварных швов. Ультразвуковой контроль сварных соединений. Уровни приемлемости
- ISO/DIS 17640, Неразрушающий контроль сварных швов. Ультразвуковой контроль сварных соединений
- ISO 22825, Неразрушающий контроль сварных швов. Ультразвуковой контроль. Контроль сварных швов аустенитных сталей и сплавов на основе никеля
Европейский комитет по стандартизации (CEN)
- EN 583, Неразрушающий контроль – Ультразвуковой контроль
- EN 1330-4, Неразрушающий контроль.
Терминология. Часть 4. Термины, используемые в ультразвуковом контроле
- EN 1712, Неразрушающий контроль сварных швов. Ультразвуковой контроль сварных соединений. Уровни приемлемости
- EN 1713, Неразрушающий контроль сварных швов. Ультразвуковой контроль. Характеристика признаков в сварных швах
- EN 1714, Неразрушающий контроль сварных швов. Ультразвуковой контроль сварных соединений
- EN 12223, Неразрушающий контроль. Ультразвуковой контроль. Спецификация калибровочного образца № 1
- EN 12668-1, Неразрушающий контроль. Характеристика и проверка оборудования для ультразвукового контроля. Часть 1. Приборы
- EN 12668-2, Неразрушающий контроль. Характеристика и проверка оборудования для ультразвукового исследования. Часть 2. Датчики
- EN 12668-3, Неразрушающий контроль. Характеристика и проверка оборудования для ультразвукового контроля. Часть 3. Комбинированное оборудование
- EN 12680, Основание. Ультразвуковое исследование
- EN 14127, Неразрушающий контроль.
Ультразвуковое измерение толщины
Вопросы и ответы по ультразвуковому контролю
- Что такое ультразвуковой преобразователь..
Преобразователь — это любое устройство, которое преобразует одну форму энергии в другую. Ультразвуковой преобразователь преобразует электрическую энергию в механические колебания (звуковые волны), а звуковые волны — в электрическую энергию. Как правило, это небольшие ручные сборки, которые выпускаются с широким спектром частот и стилей для удовлетворения конкретных потребностей тестирования. - Что такое ультразвуковой толщиномер..
Ультразвуковой толщиномер — это прибор, который генерирует звуковые импульсы в испытуемом образце и очень точно измеряет интервал времени до получения эхосигналов. Запрограммированный на скорость звука в испытуемом материале, прибор использует эту информацию о скорости звука и измеренный временной интервал для расчета толщины с помощью простой зависимости [расстояние] равно [скорости], умноженной на [время]. - Насколько точен ультразвуковой толщиномер..
При оптимальных условиях коммерческие ультразвуковые толщиномеры могут достигать точности до +/- 0,001 мм, с точностью +/- 0,025 мм или лучше для большинства распространенных технических материалов. Факторы, влияющие на точность, включают однородность скорости звука в испытуемом материале, степень рассеяния или поглощения звука, состояние поверхности, а также точность и тщательность, с которой прибор был откалиброван для конкретного применения. - Кто использует ультразвуковые приборы.
Ультразвуковые датчики в основном используются для измерения остаточной толщины стенок проржавевших труб и резервуаров. Измерение может быть выполнено быстро и легко без необходимости доступа внутрь или опорожнения трубы или резервуара. Другие важные области применения включают измерение толщины формованных пластиковых бутылок и аналогичных контейнеров, лопастей турбин и других прецизионно обработанных или литых деталей, медицинских трубок малого диаметра, резиновых шин и конвейерных лент, корпусов лодок из стекловолокна и даже контактных линз. - Что такое ультразвуковой дефектоскоп.
Звуковые волны, проходящие через материал, будут предсказуемым образом отражаться от таких дефектов, как трещины и пустоты. Ультразвуковой дефектоскоп — это прибор, который генерирует и обрабатывает ультразвуковые сигналы для создания отображения формы сигнала, которое может использовать обученный оператор для выявления скрытых дефектов в контрольном образце. Оператор идентифицирует характерный образец отражения от хорошей детали, а затем ищет изменения в этом образце отражения, которые могут указывать на дефекты. - Какие дефекты можно обнаружить с помощью одного из них?
С помощью ультразвуковых дефектоскопов можно локализовать и измерить широкий спектр трещин, пустот, отслоений, включений и подобных проблем, влияющих на структурную целостность. Минимальный обнаруживаемый размер дефекта в данном приложении будет зависеть от типа испытуемого материала и типа рассматриваемого дефекта. - Кто использует ультразвуковые дефектоскопы..
Ультразвуковые дефектоскопы широко используются в критических областях, связанных с безопасностью и качеством, включая структурные сварные швы, стальные балки, поковки, трубопроводы и резервуары, авиационные двигатели и рамы, автомобильные рамы, железнодорожные рельсы , силовые турбины и другое тяжелое оборудование, корпуса кораблей, отливки и многие другие важные области применения. - Какие другие типы инструментов доступны.
Ультразвуковые системы визуализации используются для получения высокодетализированных изображений, подобных рентгеновским, отображающих внутреннюю структуру детали с помощью звуковых волн. Технология фазированных решеток, первоначально разработанная для медицинской диагностической визуализации, используется в промышленных условиях для создания изображений поперечного сечения. Крупные системы сканирования используются поставщиками аэрокосмической промышленности и металлообработки для проверки наличия скрытых дефектов как в сырье, так и в готовых деталях.Ультразвуковые генераторы/приемники и анализаторы сигналов используются в различных приложениях для исследования материалов.
Ссылки..www.olympus-ims.com и Welding and Cutting United States
Неразрушающий контроль материалов с помощью ультразвука
Неразрушающий контроль материалов с помощью ультразвука — Введение в основные принципыNDT.net — сентябрь 2000 г., Vol. 5 № 09 |
— Введение в основные принципы — Майкл Берке | СОДЕРЖАНИЕ |
Введение 1. Зачем использовать ультразвук для неразрушающего контроля материалов? 2. ![]() 3. Обнаружение несплошностей 4. Методика испытаний и приборостроение 4.1 Ультразвуковой дефектоскоп 4.2 Почти разрешение 4.3 Зонд 4.4 Преломление и преобразование мод 4.5 Характеристики наклонных преобразователей 4.6 Зонд TR 5. Обнаружение разрывов 5.1 Калибровка прибора 5.1.1 Калибровка с прямолучевым преобразователем 5.1.2 Калибровка с датчиком TR 5.1.3 Калибровка с помощью датчика ангельского луча 5.1.4 Обнаружение отражателей с помощью наклонного преобразователя 6. Оценка несплошностей 6.1 Метод сканирования 6.2 Оценка небольших несплошностей: метод АРД 6.3 Шумоизоляция 6.4 Метод эталонного блока 6.4.1 Сравнение амплитуд эха 6.4.2 Кривая амплитуды расстояния 7. Документация 8. Диагностика показаний (прогноз) Справочный список Автор, ответственный за переписку: Электронная почта: mberke@krautkramer. ![]() Веб-сайт: http://www.krautkramer.com |
- Неразрушающий контроль материалов с помощью ультразвука существует более 40 лет. С первых же исследований использование ультразвуковых колебаний для обнаружения дефектов в различных материалах стало классическим методом контроля, основанным на измерениях с учетом всех важных влияющих факторов. Сегодня ожидается, что ультразвуковой контроль, поддерживаемый большими достижениями в приборостроении, даст воспроизводимые результаты теста в пределах узких допусков. Это предполагает точное знание влияющих факторов и умение применять их в технологии тестирования. Не все воздействия должны серьезно учитываться оператором. Во многих случаях некоторыми влияниями можно пренебречь без превышения допустимых допусков измерений. За счет этого упрощается последовательность испытаний и сокращается время тестирования. Несмотря на это, будущее принадлежит квалифицированному оператору, ответственно выполняющему свою задачу и постоянно стремящемуся поддерживать свои знания на самом современном уровне.

- В начале 50-х годов техник знал только радиографию (рентгеновское излучение или радиоактивные изотопы) как метод обнаружения внутренних дефектов в дополнение к методам неразрушающего контроля поверхностей материалов, т.е. метод проникающей жидкости и магнитных частиц . После Второй мировой войны ультразвуковой метод, описанный Соколовиным в 1935 г. и примененный Файрстоуном в 1940 г., получил дальнейшее развитие, так что очень скоро появились приборы для ультразвукового контроля материалов. Ультразвуковой принцип основан на том факте, что твердые материалы являются хорошими проводниками звуковых волн. При этом волны отражаются не только на границах раздела, но и от внутренних дефектов (отслоений материала, включений и т. д.). Эффект взаимодействия звуковых волн с материалом тем сильнее, чем меньше длина волны, а значит, чем выше частота волны.
c = скорость звука [км/с] f = частота [МГц] l = длина волны [мм] |
Это означает, что ультразвуковые волны должны использоваться в диапазоне частот примерно от 0,5 МГц до 25 МГц, а результирующая длина волны должна быть в миллиметрах. При более низких частотах эффект взаимодействия волн с внутренними дефектами был бы настолько мал, что обнаружение становится сомнительным. Оба метода испытаний, рентгенография и ультразвуковой контроль, являются наиболее часто используемыми методами проверки различных образцов для испытаний на наличие внутренних дефектов, частично охватывая область применения и частично расширяя ее. Это означает, что сегодня многие объемные испытания возможны с помощью более экономичного и безопасного метода ультразвукового контроля, с другой стороны, специальные контрольные задачи решаются, как и раньше, с помощью рентгенографии. В случаях, когда требуются самые высокие требования безопасности (например, атомные электростанции, аэрокосмическая промышленность), используются оба метода.
- Существует ли первичная классификация задач, возложенных на оператора УЗИ? Если ограничиться проверкой объектов на наличие возможных дефектов материала, то классификация выглядит следующим образом:
- Обнаружение отражателей
- Расположение отражателей
- Оценка отражателей
- Диагностика отражателей (тип отражателя, ориентация и т.
д.)
Вместо использования слова «отражатель» , оператор УЗИ очень часто использует термин «несплошность» . Это определяется как «неполадка в объекте испытаний, которая подозревается в дефекте». На самом деле, только после определения местоположения, оценки и диагностики можно определить, есть ли дефект, влияющий на назначение объекта испытаний. Таким образом, термин «несплошность» используется всегда, пока неясно, относится ли он к дефекту, который означает недопустимую аномалию.
3. Обнаружение несплошностей- Важным «инструментом» оператора ультразвуковой диагностики является зонд, рис. 1а + 1б. Пьезоэлектрический элемент, возбуждаемый чрезвычайно коротким электрическим разрядом, излучает ультразвуковой импульс. Тот же элемент, с другой стороны, генерирует электрический сигнал, когда он получает ультразвуковой сигнал, что приводит к его колебаниям. Зонд соединяется с поверхностью испытуемого объекта с помощью жидкости или связующей пасты, так что звуковые волны от зонда могут передаваться на испытуемый объект.

Рис. 1а Прямолучевой зонд (разрез) | Рис. 1b Наклонный зонд (разрез) |
Затем оператор сканирует объект контроля, т. е. равномерно перемещает зонд взад и вперед по поверхности. При этом он наблюдает за приборным дисплеем любых сигналов, вызванных отражениями от внутренних несплошностей, рис. 2.
Рис. 2а Плоский дефект – прямолучевой зонд | Рис. 2b Плоский дефект — наклонно-лучевой преобразователь |
Рис. 3 Звуковое поле |
Каждый зонд имеет определенную направленность, т. е. ультразвуковые волны охватывают только определенный участок объекта контроля. Площадь, эффективная для ультразвукового контроля, называется «звуковым лучом», что характерно для применяемого зонда и материала, в котором распространяются звуковые волны. Звуковой пучок можно грубо разделить на сходящуюся (фокусирующую) область, ближнего поля , а расходящейся (расширяющейся) части дальнего поля , рис. 3. Длина N ближнего поля (длина ближнего поля) и угол расхождения зависит диаметр элемента, его частота и скорость звука в испытуемом материале. Центральный луч называется акустической осью .
Форма звукового луча играет важную роль при выборе преобразователя для решения тестовой задачи. Часто достаточно провести акустическую ось, чтобы показать, как выглядит решение тестовой задачи. Объемная неоднородность (полое пространство, инородный материал) отражает звуковые волны в разные стороны, рис. 4а + 4б.
Рис. ![]() | Рис. 4b Объемная несплошность — наклонный преобразователь |
Часть звуковой волны, которая возвращается к зонду после отражения от несплошности, в основном зависит от направления звуковой волны; т. е. не имеет значения, производится ли сканирование прямолучевым преобразователем или наклонно-лучевым преобразователем или осуществляется с разных поверхностей на объекте контроля, рис. 5. Если полученная часть отраженной звуковой волны от зонда достаточно, то обнаружение существующей объемной несплошности не критично, это означает, что оператор может обнаружить ее, сканируя с разных направлений. Плоская (двумерная) несплошность (например, отрыв материала, трещина) отражает ультразвуковые волны преимущественно в определенном направлении, рис. 6.
Рис. ![]() | Рис. 6 Отражение на угловом плоском разрыве |
Если отраженная часть звуковой волны не принимается зондом, маловероятно, что дефект будет обнаружен. Возможности обнаружения только увеличиваются при вертикальном попадании звукового луча в плоскую несплошность. Это относится к неоднородностям, изолированным внутри объекта испытаний.
Рис. 7 Кажущаяся деформация звукового луча на боковой стенке |

Рис. 8a Обнаружение трещин с помощью сканирования 45 | Рис. 8b Эффект углового отражения |
Рис. 9 Плоскость, вертикальный отражатель у поверхности |
Рис. ![]() | Рис. 10b Тандемное испытание: центральная зона | Рис. 10c Испытание по Тамдену: нижняя зона F |
- Часто в толстостенных объектах контроля, в которых имеются вертикальные несплошности, это условие не может быть выполнено, чтобы звуковые волны, отраженные от несплошности и поверхности объекта контроля, не возвращались к преобразователю. В этом случае второй датчик используется для приема отраженных частей звука, что позволяет обнаружить разрыв.
При этом типе испытаний, Тандемный метод , один зонд используется в качестве передатчика, а другой — в качестве приемника. Оба зонда перемещают по поверхности объекта контроля и разносят на фиксированное расстояние. Сканирование производится по вертикально расположенным несплошностям на разной глубине объекта контроля в зависимости от шага зонда, рис. 10а, 10б и 10с.
Хотя при угловом сканировании в тонких контрольных объектах существует вероятность того, что плоские несплошности не могут быть затронуты вертикально, рис. пользователь предпочитает тест с одним датчиком в отличие от более сложного тандемного метода. Обычно это имеет место при контроле сварных швов толщиной до 30 мм.
Конечно, снижается возможность обнаружения несплошностей, которые не затрагиваются вертикально. Однако часто этот недостаток компенсируется дополнительным испытанием с другим углом падения, рис. 11 б, или применением преобразователя с более низкой частотой, рис. 11 в. Типовую процедуру можно найти в соответствующих спецификациях (инструкциях по испытаниям) для испытаний сварных швов.
Рис. 11a 70 сканирование: неблагоприятный угол | Рис. 11c 70 сканирование с частотой 2 МГц; обнаружение по большому счету расходимость звукового луча |
Рис. 11b 45 сканирование: благоприятный угол |
СЛЕДУЮЩИЙ
Обзор применения ультразвукового контроля в аддитивном производстве: оценка дефектов, характеристика материалов и управление технологическим процессом
ScienceDirectRegistersign в
View PDF
- Доступ через Ваше учреждение
Том 108, декабрь 2020, 106227
HTTPS://do. orgggggg.10.10.10.10.10.10.10.10.10.10.10.10.10.10.10.10.10.10.10.10.10.10.10.10.10.10.10.10.10.10.10.10.10.10.10.10.10.10.10.10.10.10.10.10.11 и содержание
Методы ультразвукового контроля (УЗК) обладают высокой способностью обнаруживать дефекты в технических компонентах. Настоящая рукопись предназначена для обзора методов ультразвукового контроля, применяемых к продуктам аддитивного производства; либо на месте, либо в автономном режиме. Хотя применение ультразвукового контроля на месте для аддитивного производства более благоприятно, в литературе есть несколько исследовательских работ по этой теме. С другой стороны, большинство работ, посвященных ультразвуковому контролю продуктов аддитивного производства, касаются автономных приложений. Во многих из этих работ образцы с искусственными дефектами готовятся и испытываются с помощью методов ультразвукового контроля, включая лазерный ультразвук, фазированные решетки, направленные волны и иммерсионный ультразвуковой контроль. Подробно обсуждаются эти методы УЗ и их применение для обнаружения повреждений продуктов аддитивного производства. Кроме того, вводятся коды и стандарты, которые в настоящее время разрабатываются для ультразвукового контроля продуктов аддитивного производства. Выяснилось, что выбор методов ультразвукового контроля для обнаружения дефектов и определения характеристик материала в аддитивном производстве сильно зависит от производственного процесса и возможностей методов ультразвукового контроля.
Аддитивное производство (AM), также известное как 3D-печать, изготовление твердых материалов произвольной формы или быстрое прототипирование, представляет собой революционную технологию производства, которая, как ожидается, изменит будущее обрабатывающей промышленности [1]. В 2018 году индустрия AM превысила 7,3 миллиарда долларов США, что отражает рост почти на 21% по сравнению с 2017 годом, и ожидается, что к 2022 году она вырастет до 26,2 миллиарда долларов США [2], [3]. В отличие от обычного производства, при котором продукт формируется путем приложения давления или вырезания из твердого блока, в аддитивном производстве материал наносится точно в нужных местах с использованием систем автоматизированного проектирования (САПР) и 3D-сканеров [4]. 5], [6]. Материал добавляется слой за слоем для простого и недорогого изготовления компонентов сложной геометрической формы, близких к форме сетки. В процессах аддитивного производства используются различные строительные материалы, в том числе пластмассы, металлы и керамика. Основным препятствием для широкого внедрения AM в промышленности является сложность, связанная с обнаружением и оценкой дефектов в продуктах AM [7], [8]. Передовые методы неразрушающего контроля (NDT) используются для эффективного обнаружения различных дефектов на разных слоях продуктов AM. Среди этих дефектов пористость имеет жизненно важное значение. Поры могут быть как газовыми, так и несплавленными (LOF) [9].]. Многочисленные процессы аддитивного производства и различные параметры, связанные с каждым процессом, усложняют неразрушающий контроль продуктов аддитивного производства [10], [11]. Сложная геометрия многих компонентов АП требует соответствующего выбора метода неразрушающего контроля, который наилучшим образом подходит для обнаружения дефектов.
В некоторых случаях для более эффективного обнаружения дефектов жизненно важных компонентов использовалась комбинация методов неразрушающего контроля [12], [13], [14].
Недавно был опубликован ряд обзоров исследований по неразрушающему контролю [15], контролю качества [16], мониторингу и контролю процессов [11], [17], [18] процессов и компонентов аддитивного производства. НАСА также опубликовало отчет о современных методах неразрушающей оценки (NDE), используемых в AM [10]. Различные методы неразрушающего контроля (НК) были рассмотрены для обнаружения и оценки дефектов в изделиях АМ [3], [10], [11]. Эти методы использовались как во время (в процессе), так и после производственного процесса (постпроцесс). Некоторые методы НК, рассматриваемые в AM, включают рентгеновскую компьютерную томографию (КТ) [19].], вихретоковый контроль (ВТ) [20], инфракрасный термографический контроль (ТТ) [21], [22], акустико-эмиссионный контроль (АТ) [21], визуальный контроль (ВТ) [23], ультразвуковой контроль (UT) [24]. Среди этих методов НК наиболее перспективными являются КТ и УЗК [8]. Ультразвуковой контроль (УЗК) является одним из наиболее эффективных методов неразрушающего контроля, используемых для контроля промышленных компонентов [25], [26], [27], [28], [29], [30], [31], [32], [33], [34], [35]. В последние годы было разработано много новых передовых ультразвуковых методов, которые используются в различных промышленных приложениях [36], [37], [38].
В то время как в литературе имеется несколько обзорных статей о применении рентгеновской компьютерной томографии (КТ) к продуктам АП [19], [39], обзорных статей о применении методов ультразвукового контроля (УЗК) для проверка продукции AM на месте или в автономном режиме. Текущая рукопись направлена на рассмотрение различных методов УЗ, используемых для обнаружения дефектов в компонентах AM.
Фрагменты разделов
В широком смысле производственные технологии можно разделить на формирующие, субтрактивные и аддитивные. В процессах формовки, например прокатки и ковки, желаемый продукт изготавливается путем приложения контролируемых напряжений к массе сырья [40]. В субтрактивных производственных процессах, таких как сверление, точение и фрезерование, конечный продукт получается путем контролируемого удаления материала [41]. В аддитивном производстве материал наносится точно в нужные места с помощью
Ультразвуковой контроль (УЗК) является одним из наиболее мощных методов неразрушающего контроля (НОК), используемых для обнаружения и оценки поверхностных, подповерхностных и внутренних дефектов. В большинстве металлов дефекты глубиной до нескольких метров обнаруживаются с помощью УЗК, в то время как толщина материала является ограничивающим фактором для большинства методов НК [52]. Чувствительность УЗК при обнаружении дефектов сильно возрастает с увеличением частоты контроля. В широком смысле методы УЗ можно разделить на традиционные и усовершенствованные.
Ультразвуковой контроль является одним из наиболее эффективных методов неразрушающего контроля для мониторинга процессов аддитивного производства на месте, а также для контроля качества как металлических, так и пластиковых изделий аддитивного производства. В этом разделе обсуждаются исследования, проведенные в области ультразвукового контроля на месте продуктов аддитивного производства.
Установка ультразвуковых датчиков под поверхностью сборки рассматривалась как онлайн-метод мониторинга процессов АМ. Надимпалли и др. [70] установили ультразвуковой датчик 5 МГц под рабочую пластину ультразвукового
В настоящее время нет кодексов или стандартов для ультразвукового контроля или даже неразрушающего контроля продуктов AM. Тем не менее, технические группы как в ASTM, так и в ISO работают над регулированием и установлением политик в отношении методов УЗ-тестирования. Рабочая группа ASTM WK47031 [117] в настоящее время разрабатывает рекомендации по неразрушающему контролю металлических изделий AM. Руководство специально подготовлено для деталей AM, которые используются в аэрокосмической технике. Требования и политика, разработанные в этом руководстве, являются более строгими, поскольку
Серьезной проблемой в аддитивном производстве является появление дефектов в процессе производства и загрузки готовой продукции, что требует разработки соответствующих методов неразрушающего контроля (НК) для обнаружения этих дефектов [7], [8], [9], [ 119]. Методы неразрушающего контроля благоприятны для испытаний изделий АД, так как они не несут никаких повреждений изделия во время испытаний. Различные методы неразрушающего контроля классифицируются в зависимости от их возможностей, областей применения, преимуществ и
Авторы заявляют, что у них нет известных конкурирующих финансовых интересов или личных отношений, которые могли бы повлиять на работу, представленную в этой статье.
Мы выражаем благодарность компании FUJIFILM Visualsonics Inc. и доктору Казему Фаязбахшу из Университета Райерсона за сотрудничество в проведении ультразвуковых испытаний с фазированной решеткой на образце FDM, показанном на рис. 2. Финансовая поддержка осуществляется через Совет по естественным наукам и исследованиям (NSERC) Канады. также оценил.
Ссылки (126)
- A. Ladewig et al.
Влияние потока защитного газа на удаление побочных продуктов процесса селективной лазерной плавки
Доп. Произв.
(2016)
- Ю.
Сонг и др.
Неразрушающий контроль аддитивного материала на основе измерения ультразвукового рассеяния
Измерение
(2018)
- T. Sol et al.
Неразрушающий ультразвуковой контроль образцов AlSi10Mg, изготовленных аддитивным способом
Доп. Произв.
(2018)
- Д. Фостер и др.
Упругие константы ультразвукового аддитивного производства Al 3003–h28
Ультразвук
(2013)
- D. Pieris
Лазерно-индуцированные фазированные решетки (LIPA) для обнаружения вложенных элементов в компонентах, изготовленных аддитивным способом
Mater Дес.(2020)
- К. Холмс и др.
Усовершенствованная постобработка для сканированных ультразвуковых массивов: применение для обнаружения и классификации дефектов при неразрушающем анализе
Ультразвук
(2008)
- C.
Holmes et al.
Постобработка полной матрицы данных ультразвукового приемо-передающего массива для неразрушающей оценки
NDT и E Int.
(2005)
- В.К. Надимпалли и др.
Межфазная оценка качества компонентов ультразвукового аддитивного производства на месте с использованием ультразвукового NDE
NDT E Int.
(2018)
- С. Диксон и др.
Обнаружение трещин в металлических листах с использованием импульсного лазерного ультразвука и обнаружения ЭМАП
Ультразвук
(2011)
- C.-M. Вонг и др.
Разработка широкополосного 20-мегагерцового монокристаллического фазированного ультразвукового преобразователя ПМН-ПТ
Ультразвук
(2017)
Контроль стыковых швов деталей со сложной поверхностью с использованием ультразвуковой ФАР
Ультразвук
(2019)

Характеристики ультразвукового передатчика с фазированной решеткой среднего диапазона
Ультразвук
(2018)
Некоторые применения лазерного ультразвука
Ультразвук
(1989)
Обзор магнитострикционных накладных преобразователей и их применение в ультразвуковом неразрушающем контроле волноводов
Ультразвук
(2015)
Минимизация акустической отражательной способности в емкостных микромашинных ультразвуковых преобразователях (CMUT)
Ультразвук
(2017)
Конструкция ЭМАП для измерения минимальной толщины остатка с использованием горизонтальных режимов сдвига высокого порядка Declercq
Экспериментальное исследование секторов ультразвукового луча для преобразования энергии в волны Лэмба и волны Рэлея
Ультразвук
(2014)

Проверка многослойных компонентов, изготовленных аддитивным способом
Ультразвук
(2015)
Ультразвуковой контроль с фазированной решеткой образца Wire+ Arc Additive Manufactured (WAAM) с преднамеренно встроенными дефектами
Доп. Произв.
(2019)
Обзор проволочно-дуговой аддитивной обработки металлов: свойства, дефекты и улучшение качества
J. Manuf. Процессы
(2018)
Исследование эволюции микроструктуры при селективном лазерном плавлении Ti–6Al–4V
Acta Mater.
(2010)
Неразрушающий контроль сваренных взрывом плакированных стержней методом резонансно-акустической спектроскопии
Ультразвук
(2003)
Ультразвуковые матрицы для неразрушающего контроля: обзор
NDT и E Int.

(2006)
Мониторинг и контроль процесса аддитивного производства с помощью методов неразрушающего контроля: задачи и мониторинг в процессе
Virtual Phys. Прототипирование
(2018)
Обзор мониторинга процессов на месте и метрологии на месте для аддитивного производства металлов
Материал. Дес.
(2016)
Аддитивное производство: развитие технологии и потребность в методах контроля качества и контроля
Mater. оценка
(2018)

Аддитивное производство на основе порошка – обзор типов дефектов, механизмов их возникновения, обнаружения, оценки свойств и метрологии
Междунар. J. Аддитивная субтрактивная материя. Производство
(2017)
Обзор литературы по дефектам производства металлических добавок
(2018)
Кестер
и др.Неразрушающий контроль металлических деталей, изготовленных с использованием аддитивного производства на основе порошка
Матер.

(2018)
Использование лазерного ультразвука для обнаружения подповерхностных дефектов в металлических компонентах для лазерной сварки слоя порошка
JOM
(2018)
Экспериментальная неразрушающая характеристика алюминиевого сплава, полученного аддитивным производством в порошковом слое
Матер. оценка
(2018)
Обзор методов неразрушающего контроля и мониторинга процессов, используемых для производства высококачественных деталей с помощью сварки или аддитивного производства
Welding in the World, Статья2 00003
Обзор контроля качества в аддитивном производстве
Журнал быстрого прототипирования
(2018)

Обзор процессов мониторинга и контроля в аддитивном производстве на основе металлов
J. Manuf. науч. англ.
(2014)
Рентгеновская компьютерная томография для аддитивного производства: обзор
Изм. науч. Технол.
(2016)
Измерение и анализ пористости для управления технологическим процессом аддитивного производства металлов
J. Res. Нац. Инст. Стоять. Технол.
(2014)
Неразрушающая оценка плакированных стержней путем инверсии данных акустического рассеяния
J.

(2019)
Неразрушающая оценка: теория, методы и приложения
(2002)
Визуализация дефектов на основе лазерной ультразвуковой технологии фокусировки с синтезированной апертурой в частотной области с раздельной генерацией-обнаружением и двухмерным картированием эквивалентной скорости
2022, Оптика и лазерные технологии
Для лазерного ультразвукового контроля (LUT) для обнаружения и отображения внутренних дефектов в образцах предлагается точная технология фокусировки с синтезированной апертурой в частотной области (F-SAFT), основанная на двумерном отображении эквивалентной скорости. Отображение эквивалентной скорости изменяется в зависимости от глубины и пространственной частоты, чтобы соответствовать характеристикам раздельного возбуждения и обнаружения, обычно используемым в LUT. Объемные акустические волны неразрушающим образом возбуждаются линейным лазерным источником и обнаруживаются лазерным доплеровским виброметром.
Путем компенсации смещения расстояния, возникающего из-за разделения лазерных пятен, корректируется местоположение дефекта изображения. Проведен ряд оптимизаций алгоритма: сокращено время расчета эквивалентной скорости за счет упрощения ее выражения, а также улучшено качество изображения, особенно для дефектов с малой глубиной, за счет двумерного картирования эквивалентной скорости. Результаты показывают, что по сравнению с традиционным F-SAFT оптимизированный алгоритм F-SAFT может не только улучшить качество изображения, но и более точно локализовать дефект за счет разделения возбуждения и обнаружения.
Ультразвуковая характеристика дефектов с использованием матриц рассеяния во временной области и сверточного разреженного кодирования
2022, NDT and E International
В этой статье исследуется использование матрицы рассеяния во временной области для ультразвуковой характеристики дефектов. Предлагается подход, основанный на сверточном разреженном кодировании, для извлечения инвариантных к сдвигу признаков матрицы рассеяния во временной области.
Результаты моделирования показывают, что предложенный подход можно надежно использовать для классификации грубых трещин. Кроме того, средняя ошибка размера и ее стандартное отклонение также уменьшаются по сравнению с использованием матрицы рассеяния в частотной области. В экспериментах щель 1,5 мм и эллиптический дефект 1,5 мм были рассчитаны с точностью до 0,25 мм с использованием 64-элементной линейной матрицы 2,5 МГц с шагом элементов 0,5 мм. Отличные результаты определения размеров были получены для наклонных пазов с большим углом ориентации ( т.е. 60°).
Количественный алгоритм отделения оболочки от сердцевины, основанный на реконструкции шестиугольных единиц для ультразвукового C-сканирования с воздушной связью изображений сотовой сэндвич-структуры
2022, Applied Acoustics
Сотовая сэндвич-структура (HSS) широко используется в аэрокосмической промышленности . Отслоение оболочки от сердцевины в HSS может достигать критических размеров, что приводит к внезапному разрушению структур.
Из-за размытых краев на изображении C-скана, вызванных сотовыми элементами с периодическими сотовыми стенками, точная количественная оценка отслоения все еще остается проблемой. В этой статье предлагается точная количественная оценка HSS на основе ультразвукового C-сканирования с воздушной связью и реконструкции гексагональных единиц. Идентификация границы разъединения выполняется с точностью до внутренней части сотовых элементов за счет частичного разделения элементов разъединения на основе вычисления общей амплитуды всех точек сканирования внутри элемента. Подробный процесс был представлен с ключевыми этапами, такими как ультразвуковое С-сканирование с воздушной связью для HSS, реконструкция гексагональных единиц на основе пиковых точек на изображениях С-скана, классификация единиц с помощью алгоритма кластеризации K-средних и разделение единиц в соответствии с общей амплитудой. Для оценки эффективности метода используются четыре типа снятия брекетов, в том числе приклеивание пленки, удаление клея, легкое оседание и сильное оседание.
Результаты показывают, что предложенный метод может надежно описывать и количественно определять четыре вида дефектов отслоения и идеально подходит для обработки изображений периодических структур с помощью ультразвукового С-сканирования с воздушной связью.
Ультразвуковой контроль толстых и тонких сплавов Inconel 625, изготовленных методом лазерной плавки в порошковом слое
2022, Ультразвук
Аддитивное производство сплавов позволяет производить в небольших объемах функциональные металлические компоненты со сложной геометрией. Ультразвуковой контроль может гарантировать качество этих компонентов и выявить типичные дефекты, возникающие при лазерной плавке в порошковом слое (LPBF). Однако трудно найти единый метод ультразвукового контроля, который мог бы обнаруживать дефекты в большом разнообразии геометрий, созданных с использованием LPBF. В данной работе предлагается ультразвуковой контроль с фазированной решеткой (УЗКФ) для контроля толстых компонентов LPBF, в то время как направленные волны исследуются для тонких изогнутых.
PAUT используется для обнаружения цилиндрических дефектов непровара в толстых прямоугольных деталях LPBF. Практические дефекты генерируются за счет снижения мощности лазера в заранее определенных местах образцов. Форма и плотность дефектов проверяются с помощью оптической микроскопии и рентгеновской компьютерной томографии. Частично проплавленные дефекты диаметром до 0,25 мм выявляются экспериментально с помощью датчика PAUT 10 МГц с постобработкой методом полной фокусировки. Экспериментальные результаты сравниваются с изображениями дефектов, предсказанными методом конечных элементов. Для тонких компонентов с криволинейной геометрией для обнаружения заполненных порошком цилиндрических дефектов используются направленные волны. Волны генерируются с помощью пьезоэлектрических преобразователей, а пространственно-временное волновое поле измеряется с помощью сканирующего лазерного доплеровского виброметра. Используя среднеквадратичное изображение волнового поля, четко обнаруживаются дефекты размером до 1 мм, несмотря на сложные внутренние особенности образцов.
Обзор производственных дефектов и их выявление в композитах с матрицей из армированной волокном смолы
2022, Композиты, часть C: открытый доступ
Композиты с матрицей из армированной волокном смолы все шире используются в аэрокосмической и автомобильной промышленности. Однако вероятность производственных дефектов в композитах очень высока из-за сложных физико-химических свойств материалов компонентов и процессов формования. Поэтому исследование производственных дефектов и их выявление в композитах становится важным при оценке качества композитов. Во-первых, обобщается механизм образования остаточных напряжений, пустотных дефектов и дефектов с высоким содержанием смолы в матрице композитов. В частности, в этой статье описываются отверждение термореактивной смолы и термопластичной смолы, процесс инфильтрации смолы при горячем прессовании, литье смолы и трехмерная печать, а также дефекты, связанные с высоким содержанием смолы, в процессе формования. Во-вторых, представлен механизм формирования дефектов армирования волокнами, таких как морщины волокна и волнистость в композитах, и проанализировано влияние таких дефектов на свойства композитов при изгибе и сжатии, что показывает, что дефекты смещения волокон серьезно снижают модуль, прочность и устойчивость несущих конструкций.
В-третьих, разрабатываются механизм образования, причины повреждения и методы оптимизации межфазных дефектов, таких как отслоение и отслоение на границе раздела между арматурой и матрицей. В-четвертых, выявляются дефекты механической обработки, такие как дефекты сверления и резания. Основными проявлениями являются расслоения, надрывы и заусенцы, которые серьезно повлияют на прочность и надежность соединения компонентов. Наконец, в статье показано бесконтактное обнаружение дефектов в композитах. Различные методы обнаружения могут использоваться для измерения дефектов разного масштаба, чтобы заранее прогнозировать повреждение и срок службы композита. В этом обзоре анализируются производственные дефекты в ламинированных, тканых, плетеных и аддитивных композитах, обобщаются распространенные методы обнаружения дефектов, а также представлены перспективы производства композитов.
Характеристика межфазных свойств двухслойной пластины с использованием метода нелинейных низкочастотных волн Лэмба
2022, Ультразвук
В этой работе исследуется возможность использования нелинейного низкочастотного метода волн Лэмба для характеристики межфазных свойств из двухслойной пластины.
По сравнению со случаем точного согласования фазовых скоростей приближенное согласование фазовых скоростей в области низких частот все еще может гарантировать кумулятивную генерацию второй гармоники (ГВГ) распространения первичной волны Лэмба, которая преодолевает недостатки, связанные с присущим дисперсионные и многомодовые особенности распространения волн Лэмба. Для данной двухслойной пластины выбирается соответствующая пара мод на низкой частоте, состоящая из первичной волны Лэмба и двухчастотной волны Лэмба (ДФЛВ), которая удовлетворяет приблизительному согласованию фазовых скоростей и ненулевому потоку энергии, чтобы гарантировать, что амплитуда генерируемой второй гармоники растет в пределах максимального кумулятивного расстояния (МКД). Между тем, численный анализ показывает, что изменение эффективности ГВГ максимально на МКД во время межфазной деградации. Используя экспериментальную установку, основанную на нелинейных ультразвуковых измерениях, сигнал второй гармоники во временной области, генерируемый на разных расстояниях распространения, удобно извлекается, а затем получается кривая относительных нелинейных акустических параметров, согласующаяся с теоретическим предсказанием.
Для исследования влияния межфазных свойств на эффект ГВГ распространения низкочастотной волны Лэмба различные циклы отжига тонкого клеевого слоя (акрил) используются для имитации незначительных изменений межфазных свойств данной двухслойной пластины. Установлено, что относительный нелинейный акустический параметр на МКД монотонно и чувствительно уменьшается с увеличением номера цикла отжига, что подтверждает количественную корреляцию между эффективностью ГВГ распространения низкочастотной волны Лэмба и степенью межфазной деградации. Соответствие между численным анализом и экспериментальными измерениями показывает потенциал использования эффекта ГВГ распространения низкочастотной волны Лэмба для характеристики незначительного изменения межфазных свойств слоистой композитной пластины.
Научная статья
Восстановление дефектов методом неразрушающего контроля с лазерно-индуцированной ультразвуковой дефектоскопией
объемная локализация и реконструкция дефектов с использованием ультразвука, генерируемого лазером, и его применение в качестве дистанционно управляемого метода неразрушающего контроля.В качестве альтернативы полному ультразвуку или полному оптическому подходу мы предлагаем гибридную конфигурацию, в которой ультразвук генерируется воздействием лазерных импульсов, а обнаружение осуществляется с помощью обычных преобразователей. Мы реализуем этот подход для восстановления дефектов в металлических элементах и показываем, что он сочетает в себе преимущества как фотонных, так и ультразвуковых устройств, уменьшая недостатки обоих методов. Мы объединяем наши экспериментальные результаты с процедурой обработки сигналов высокого разрешения, основанной на методе фокусировки синтетической апертуры, для окончательной двумерной визуализации дефектов.
Исследовательская статья
Неразрушающий контроль аддитивно изготовленных материалов на основе измерения ультразвукового рассеяния
Измерение, том 118, 2018 г., стр. 105-112 для расчета экспериментальных доверительных границ структурного шума, которые можно рассматривать как зависящие от времени пороги для сегментации ультразвукового изображения C-скана.
Образец из нержавеющей стали 316L, изготовленный методом селективного лазерного плавления, используется для измерения рассеяния ультразвука с помощью сфокусированного преобразователя. По сравнению с фиксированным порогом, используемым в традиционной сегментации изображения C-скана, порог, зависящий от времени, может эффективно отличать эхо-сигналы от дефектов на фоне структурного шума. Результаты измерений с помощью оптической микроскопии показывают, что настоящий способ позволяет избежать как пропущенных обнаружений, так и ложных срабатываний.
Исследовательская статья
Неоднородные механические свойства в аддитивно изготовленных деталях, характеризуемые неразрушающим лазерным ультразвуковым методом
NDT & E International, Volume 116, 2020, Article 102340 стать перспективной технологией производства в архитектуре, аэрокосмической, биомедицинской и автомобильной промышленности. Однако детали, изготовленные методом аддитивного производства, должны демонстрировать свои стабильные механические свойства, такие как модуль упругости и прочность.
В этом исследовании были подготовлены четыре образца 3D-печати различной толщины для измерения модуля упругости с помощью испытаний на растяжение и метода лазерного ультразвука (LUT). Кроме того, используется метод инверсии для извлечения модуля упругости из 3D-печатных деталей с помощью кривой дисперсии, измеренной с помощью LUT. Результаты показывают, что между образцами для растяжения различной толщины наблюдались значительные различия в модуле Юнга. Все инвертированные значения модуля упругости хорошо согласовывались с экспериментальными измерениями с контролируемым процентом ошибки 0,02–1,35%. Далее модуль отдельного слоя рассчитывали по обратному среднему модулю и аппроксимировали параболическим уравнением. Формируя полученные результаты, для печати образца с 40 слоями модуль первого (верхнего) слоя составлял 3254 МПа, а нижний слой показывает 4706 МПа, что указывает на разницу в 45% с неоднородностью по печатным слоям. При печати нового слоя ультрафиолетовый (УФ) свет может подвергаться воздействию ранее напечатанных слоев, и это дополнительное облучение УФ-светом может стимулировать дополнительную полимеризацию оставшихся непрореагировавших мономеров и увеличивать модуль в нижнем слое.
Исследовательская статья
Проверка многослойных компонентов, изготовленных аддитивным способом
Ультразвук, том 62, 2015 г., стр. 292-298 3D-геометрии или для ремонта дорогостоящих компонентов. В настоящее время не существует неразрушающего метода, гарантирующего отсутствие дефектов изделий ЛПД при их изготовлении.
В данной статье предлагается лазерно-ультразвуковой метод для внутритрубного контроля компонентов LPD. Эталонные образцы были изготовлены из инконеля, и были созданы механические дефекты, чтобы установить чувствительность метода. Численные модели ультразвуковых волн, генерируемых лазером, были созданы для более глубокого понимания физики, оптимизации установки и проверки экспериментальных измерений. Показаны результаты, полученные на двух наборах эталонных образцов. Прототип для проверки концепции был продемонстрирован на некоторых конкретных образцах осаждения с индуцированными дефектами, которые были подтверждены с помощью рентгеновского метода сверхвысокой чувствительности.
Экспериментальные результаты доказывают, что могут быть обнаружены типичные микродефекты, связанные с процессом послойного напыления, такие как приповерхностные и поверхностные дефекты в однослойном наплавлении.
Исследовательская статья
Последние достижения ультразвукового контроля материалов на цементной основе в раннем возрасте
Ultrasonics, Volume 54, Issue 1, 2014, pp. ультразвукового (УЗ) контроля ранней гидратации и формирования структуры различных материалов на основе цемента (ЦВМ), в этой статье представлен обзор литературы, посвященный методам прохождения продольных и отраженных поперечных волн УЗ. Обзор показывает большую способность обоих методов УЗИ наблюдать явления залегания и определять различные вехи во время раннего возрастного формирования микроструктуры МУП. Четкая физическая основа, высокая точность и неразрушающий характер метода указывают на то, что в ближайшем будущем методы УЗИ могут стать стандартизированными.
Исследовательская статья
Метод неразрушающей оценки для стандартизации аддитивного производства на основе изготовления плавленых нитей
Аддитивное производство, том 24, 2018 г.
, стр. 154–165
микроструктур в листовых металлах с возможностью создания плоских двумерных изображений с пространственным разрешением от 1 до 200 мкм, использовался для количественной оценки трехмерной тестовой детали, обработанной методом изготовления плавленых нитей (FFF). Для ультразвуковой системы было написано специальное программное обеспечение для управления всеми компонентами схем контроля в режиме непрерывного сканирования, включая перемещение трех ортогональных поступательных столиков, а также отображение живого ультразвукового изображения во время сканирования и предоставление инструментов для расширенного поста -обработка зарегистрированных ультразвуковых сигналов. Перед сбором ультразвуковых данных для выбранного образца для испытаний использовался оптический плоский эталон для характеристики ультразвуковых датчиков и количественной оценки механической стабильности, воспроизводимости и точности системы при измерении физических размеров элементов. Ультразвуковые данные, собранные с различным пространственным разрешением, использовались для характеристики плоскостности поверхности детали, внутренних дефектов и условий сплавления; и для измерения физических размеров предполагаемых функций.
Чтобы подтвердить точность ультразвуковой внутренней характеристики, одна боковая панель испытуемого образца была удалена для визуального подтверждения, и были собраны дополнительные ультразвуковые данные и сопоставлены с исходными данными. Наконец, предлагается принять процесс для квалификации или сертификации машин для аддитивного производства на основе FFF на рынке путем применения надежного метода проверки неразрушающего контроля к стандартизированной детали с различными характеристиками, различными формами и физическими размерами.
© 2020 Elsevier B.V. Все права защищены.
Ультразвуковой контроль, ультразвуковой контроль | Laboratories Testing Inc.
Ультразвуковой контроль (UT), также известный как УЗ-контроль, ультразвуковой неразрушающий контроль и ультразвуковой неразрушающий контроль, может обнаруживать поверхностные и внутренние дефекты сырья и деталей, не вызывая повреждений во время проверки. Кроме того, службы ультразвукового контроля могут измерять толщину стенок труб и труб.
Laboratory Testing Inc., недалеко от Филадельфии, штат Пенсильвания (США), выполняет оба Услуги контактного и высокоскоростного иммерсионного ультразвукового контроля металлических материалов .
Быстрый ультразвуковой контроль с дополнительными услугами
Ультразвуковой контроль в LTI создан для получения быстрых результатов испытаний, удобного обслуживания и простого выполнения заказа. Лаборатория ультразвукового контроля работает в две смены с полным штатом сотрудников, а иммерсионный ультразвуковой контроль выполняется на девяти системах TACTIC.
Услуги по тестированию УЗ выполняются в большом помещении цеха с помощью мощных кранов и вилочных погрузчиков, позволяющих легко перемещать большие ящики и крупногабаритные образцы. У нас также есть оборудование и опыт в предоставлении дополнительных внутренних услуг, таких как приемка и окончательная проверка, резка, обрезка и снятие заусенцев, идентификация материала, а также специальная упаковка и отгрузка. Узнайте больше о нашем современном оборудовании UT/Hydro.
Наша собственная коллекция из более чем 2000 эталонных стандартов UT для испытаний труб, труб, круглых стержней и пластин значительно экономит время и упрощает быстрое выполнение работ. Любые стандарты, отсутствующие на складе, могут быть быстро изготовлены в нашем собственном механическом цехе или нашим квалифицированным местным поставщиком.
Проверка изделий различных форм и размеров
Наши иммерсионные УЗ-системы предназначены для высокоскоростной проверки труб, труб и круглых прутков диаметром от 0,125 до 6,625 дюймов с максимальным весом 1000 фунтов и длины до 70 футов.
Метод контактного ультразвукового контроля используется в LTI для проверки труб большого диаметра, труб и круглых прутков от 6 до 30 дюймов. Контактное УЗК также выполняется на других материалах, включая пластины, поковки, плоские сварные швы и сварные пластины, чтобы получить информацию о дефектах и несоответствиях.
Удовлетворение ваших требований
LTI имеет аккредитацию NADCAP для ультразвукового контроля погружением. Иммерсионное ультразвуковое испытательное оборудование компьютеризировано для безбумажной записи диаграмм и хранения файлов.
Специалисты по УЗ-тестированию сертифицированы по ASNT SNT-TC-1A, NAS410 и Pratt & Whitney PWA-NDTQ. Инспекторы НК уровня 2 и 3 рассматривают результаты испытаний. Кроме того, в штате LTI есть другие квалифицированные инспекторы для быстрого и удобного обслуживания, в том числе:
- NDT MIL-STD-2132 инспекторы и экзаменатор
- SIM-карта Pratt & Whitney уровня 3
- Представитель DCMA по обеспечению качества на месте
Методы испытаний/спецификации
LTI выполняет ультразвуковые испытания в соответствии с широким спектром военных, коммерческих и потребительских спецификаций, включая:
АМС 2631 | АСТМ А577 | МИЛ-СТД-271 |
АМС-СТД-2154 / АСТМ Э2375 | АСТМ А578 | P&W SIM-4 |
ASME B&PV Раздел III и V | АСТМ Е213 | P&W SIM-314 |
ASME B16.![]() | МИЛ-С-15726Ф | QQ-N-281D |
АСТМ А388 | МИЛ-СТД-16420К | QQ-N-286F/G |
АСТМ А435 | МИЛ-СТД-2132 | Т9074-АС-ГИБ-010/271 |
LTI — это ваш ответ для быстрой комплексной проверки. Попросите нас предоставить информацию о ценах и сроках выполнения вашего следующего заказа на ультразвуковое тестирование.
Процесс ультразвукового контроля неразрушающего контроля
Во время УЗ-контроля ультразвуковой датчик, подключенный к испытательному оборудованию, передает короткие импульсы высокочастотных звуковых волн в проверяемый объект, проходя по его поверхности. Дефект или несоответствие вызовут отражение части энергии. Звуковые импульсы отображаются на экране при отражении от элементов тестового материала. Технический специалист интерпретирует эти отраженные сигналы, чтобы определить, является ли продукт или материал дефектным или приемлемым в соответствии со спецификацией или требованиями испытаний.
Погружной ультразвуковой контроль проводится в воде, которая проводит звуковые волны между зондом и испытуемым материалом. Процесс частично автоматизирован и исключает необходимость прямого контакта с тестируемым материалом во время контроля. При контактном ультразвуковом контроле ультразвуковой зонд, излучающий звуковые волны, вручную проводится по поверхности образца. Метод погружения предпочтительнее, поскольку он может быть более быстрым и точным.
Посмотрите видео процесса УЗК с погружением.
Возможности LTI
- Системы УЗ-тестирования – иммерсионные и контактные Эталонные стандарты
- – более 1500 иммерсионных и 500 контактных стандартов на складе
- Собственные производственные мощности и местный квалифицированный поставщик для других
- Дополнительные услуги, доступные по запросу
- Приемка и окончательная проверка
- Резка, обрезка и снятие заусенцев
- Упаковка/транспортировка в соответствии с ANSI N45.