Ванная сварка арматуры
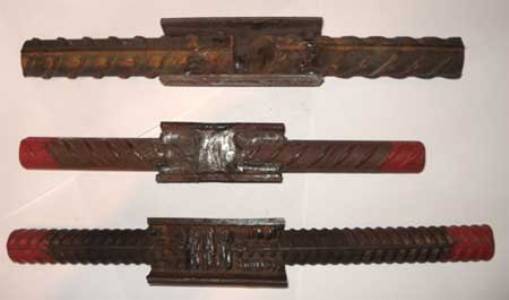
Арматурные пруты из-за небольшой контактной поверхности и упроченных марок стали считаются сложно свариваемыми изделиями. Качество соединения формируется за счет нескольких факторов. Одним из определяющих факторов является точность стыка, который нередко смещается во время сварки. Во избежание этого возникает необходимость применения специальных технологий. Наибольшее распространение в строительстве на сегодняшний день приобрела так называемая ванная сварка арматуры, которая позволяет получить надежное соединение прутьев.
Сварка арматуры ванным способом
Арматурные прутья широко используются для сооружения железобетонных конструкций. При построении каркаса металлические прутья могут соединяться как продольно, так и перпендикулярно. Как правило, при этом площадь сварного шва получается небольшой, в то время как соединение подвержено значительным нагрузкам. Использование специальных ванночек позволяет не только упростить работу сварщика, но и повысить качество соединения.
Данная технология обладает рядом преимуществ, хотя она не лишена и недостатков.
Преимущества
- Ванная сварка арматуры позволяет рационально распределять наплавочный материал при его минимальных потерях.
- Оптимальный уровень качества соединения.
- Технология, проверенная временем и доведенная до совершенства.
- Наличие широкого выбора ванночек для арматуры различного сечения.
Недостатки
- Стальные ванночки являются расходным материалом, используемым единожды.
- Стоимость медных ванночек достаточно высока.
- Необходимость более тщательной и длительной подготовки свариваемых элементов.
Принцип сварки арматуры ванным способом
Наиболее часто данная технология применяется при соединении стержней большого сечения. Накладки для ванной сварки арматуры устанавливаются в вертикальном или горизонтальном положении на стык прутьев, между которыми остается небольшой зазор, заполняемый при сваривании наплавом. Наличие этого подковообразного элемента практически полностью исключает возможность смещения арматуры. Помимо того, бортики ванночек не позволяют растекаться расплавляемому при сварке металлу, который надежно обволакивает соединяемые поверхности. Аналогичным образом проводится и ванная сварка арматуры колонн.
Расходные материалы и инструмент
Сварка арматуры ванным способом достаточно простой технологический процесс, не требующий наличия специальных инструментов и материалов. Единственным требованием является достаточно точная установка свариваемых металлических прутьев и закрепление на стыках ванночек.
В качестве основного расходного материала выступают электроды марки УОНИ 13/55, предназначенные для сваривания упроченных металлов. Другим расходным материалом являются подковообразные металлические накладки подходящей размерности.
Источником энергии служит стандартный сварочный трансформатор, способный обеспечивать повышенные токи.
Из прочих инструментов сварщику понадобятся измерительный шаблон, щетка по металлу и резак.
Процесс сварки арматуры ванным способом
Сваривание металлической арматуры посредством указанной технологии проводится в несколько этапов.
- Подготовка поверхности заготовок. Свариваемые концы прутьев тщательно очищаются от коррозии щеткой по металлу. Необходимо чтобы концы арматуры были прямыми. При наличии скосов, изгибов и прочих неровностей дефектную часть следует обрезать.
- Установка арматуры. На этом этапе соединяемые стержни устанавливаются соответственно друг другу с минимальными отклонениями и зазором, составляющим около 1,5 см. Зазор между прутьями в процессе сваривания заполняется слоем наплава, способным выдерживать расчетные нагрузки.
- Фиксирование ванночек. На стыке арматурных стержней устанавливаются и фиксируются штампованные накладки для ванной сварки арматуры соответствующего диаметра, формирующие сварной шов.
- Сваривание. После появления дуги сварщик проводит электродом колебательные движения поперек оси стержней, равномерно покрывая все сечение наплавом. При прерывании процесса следует удалить с поверхности шлак, после чего продолжить операцию до полного заполнения штампованной заготовки наплавом.
Накладки для ванной сварки арматуры
Литые или штампованные формочки доступны в разных размерах как по длине, так и по диаметру. Подбирать их следует в соответствии с размерами арматурных стержней. Указанные заготовки изготавливаются и стали и меди. При этом если стальные ванночки используются в качестве разового расходного материала, медные заготовки могут применяться неоднократно.
Соблюдение техники безопасности
Как и при ведении любого другого вида сварки, здесь необходимо строго придерживаться правил электробезопасности. Следует помнить, что сварочные операции ведутся с использованием повышенных токов, что требует уделить особое внимание качеству заземления, контролю оборудования и расходных материалов.
Сварщики должны быть оснащены полным комплектом индивидуальных средств защиты – маской, щитком, диэлектрической обувью и рукавицами, одеждой из огнеупорных тканей. Территория, где проводятся сварочные работы, должна быть оборудована средствами пожарной безопасности.
что это такое, как выполняется, особенности техники и где используется
На данный момент существует больше ста разновидностей сварки. Между ними много отличительных особенностей.
Однако общим для всех является то, что соединение получается в результате плавки металлических частей.
Чтобы правильно выбрать необходимый вид неразъемного соединения, необходимо принять во внимание характеристику изделий, которые планируются к стыковке.
В этой публикации мы поговорим о технике ванной сварки.
Содержание статьиПоказать
Общие сведения
В частности, для варки арматурных частей часто используется метод ванной сварки (еще он называется «сварка встык»).
Здесь мы осветим технологические процессы ванной сварки с применением полукруглых скоб и особенности работы с арматурой. Этом метод также может применяться для сварки стальных конструкций.
Необходимо отметить, что при сварочном соединении арматурных деталей колонн самой используемой является ванная сварка встык.
Ванная сварка осуществляется путем соединения металлов при помощи специальных подковообразных полос, которые так и называются «ванночки для сварки» или «скобы накладки для сварки».
Свое название данная технология получила от приспособлений, которые в ней используются. Суть данного метода заключается в том, что в скобу-ванночку помещаются концы арматуры и заливаются до краев расплавленным металлом.
После того как металл застывает, образуется прочное соединение.
Обычно устанавливают дополнительные ограничивающие приспособления, препятствующие вытеканию металла с торцов ванночки. Для изготовления скоб -ванночек обычно используют сталь низкоуглеродную.
После использования подобных изогнутых полос для сварочных соединений они сплавляются воедино с арматурным стержнем и расплавленным железом.
Но есть скобы для многократного использования ванным методом, которые изготавливают из сплавов меди, из керамики или графита. Они более удобны и практичны.
Особенности техники

Для процесса получения неразъемных соединений применяются один или несколько электродов. Соединять арматурные стержни, используя метод ванной сварки можно в любом положении за исключением потолочного.
Но для этого нужно придерживаться определенных параметров.
Например, диаметр арматурного стержня должен быть меньше, чем скоба. Отступ до стрежня от краев скобы допускается от 1,5 сантиметра.
Есть также определенные особенности сварочных соединений ванным методом при вертикальном расположении.
Для этого берут изогнутую железную полосу из стали (одноразовую) и приваривают ее к ниже расположенной детали. Расплавляется нижний конец арматурного стержня и после этого верхнюю часть арматурного стержня состыковывают с нижним обработанным концом и расплавляют стык.
Скобу, неспешно, наполняют расплавленным железом. Иногда, чтобы избежать образования большого количества шлака, в ванной делают небольшое отверстие. По окончанию процесса его тоже заваривают.
Метод «в стык»

У метода ванной варки в стык, как у любой полноценной технологии, есть ряд своих нюансов и определенных особенностей, которые надо учитывать в работе.
Во-первых, этот метод требует беспрерывности процесса. Именно это дает гарантию равномерной расплавки, поскольку температура плавки многих групп металлов очень высока и требует длительного временного промежутка.
А при непрерывности процесса металлические детали расплавляются существенно быстрее.
Во-вторых, как указывалось ранее, при ванной сварке могут появляться пузырики из шлака. Именно для того, чтобы они не накапливались и выходили, делают маленькое отверстие в скобе-ванночке.
Важно, что на поверхности металла они осуществляют функцию защиты соединения от окисления. По верху шва на арматуре после сварки ванным методом образуется защитная корка.
Она является свидетельством того, что работы выполнены правильно, с соблюдением необходимой технологии. Когда температура металла опустится, эту корку можно счистить.
Пока деталь еще горячая, для выведения излишнего напряжения, ее можно немного обстучать.
При использовании электрода в процессе ванной сварки, профессионалы все делают поступательными движениями, при этом захватываю нерасплавленные кромки.
Будет ошибкой держать электрод без движения на месте стыка, поскольку тепловая энергия не может самостоятельно распределяться, и в результате металлические элементы расплавляются неравномерно.
Все действия необходимо выполнять без спешки, но и без промедления.
При слишком быстрой ванной сварке металл может не успеть расплавиться и приобрести необходимую температуру, и в результате даже внешне хорошее соединение может оказаться некачественным.
При слишком медленной работе металл будет расплавляться и растекаться по ванночке неравномерно, и соединение в итоге может получится хрупким и пористым. Существуют ГОСТы, в которых указана подходящая скорость создания неразъемных соединений.
Сварка встык со скобой
Для ванной сварки встык со скобой не нужно никакого особого специального оборудования. Вполне хватит аппарата для сварки, который способен выдавать мощные показатели сварочного тока, и работать от обычной бытовой розетки.
С этим заданием даже справится небольшой бытовой сварочник или любой другой инвертор в среднем ценовом диапазоне.
Отдельно необходимо приобрести скобы-ванночки, учитывая тип необходимого соединения и характеристики самой детали, которую необходимо варить.
Для соединения в горизонтальной плоскости самыми распространенными являются ванные скобы С-14 -Мn, с15-Рс и С16-Мо.
При этом следует принимать во внимание и длину скобы-ванночки, поскольку объем сваренного металла влияет на качество соединения самым непосредственным образом. Выбирая подходящую ванночку, необходимо обращать внимание на температуру ee плавления.
Она должны быть выше температуры плавления самой арматурной детали.
Применяемые методы соединения металлических конструкций сварочным способом можно совмещать. Сваривание в стык по ванной технологии можно использовать параллельно с методами, где используется газ.
Для этого будет нужен баллон с аргоном или другим инертным газом Кроме того, для сварочного шва могут использоваться плавящиеся электроды с покрытием, например, МР- 3 или АНО.
Это особенно важно для новичков. Учитывая толщину металла, подбирается соответствующий диаметр электрода. Хорошим вариантом для более опытных сварщиков будут расходные материалы торговой марки УОНИ.
Заключение

При выполнении сварочных работ для индивидуальной защиты рекомендуется использовать специальные средства: маски (неплохим вариантом будет маска- хамелеон), робы, перчатки и обувь с подошвой, непроводящей электрический ток.
Это все необходимо в первую очередь для безопасности самого рабочего-сварщика.
В заключении, хотелось бы сказать, что метод ванной сварки в стык с использованием скоб-ванночек надежен, и по своей технологии довольно прост. Он вполне может использоваться сварщиками-новичками без опыта и особой квалификации.
Если понять саму суть данного способа, ознакомится с видео в интернете, то вполне хватит базовых навыков. Надеемся, что данная статья оказалась для Вас полезной!
контактная, внахлест, встык ванным методом
Арматура может применяться как по отдельности, так в составе сложных конструкций. Для создания сложных конструкций арматурные запчасти часто соединяются друг с другом. Основной способ соединения — это проведение сварочных работ. Сварка осуществляется с помощью оборудования, которое выполняет локальный нагрев краев деталей с последующим расплавлением и затвердеванием. Сварка арматуры может выполняться различными способами — внахлест, встык, ванным способом, контактным методом. Но какие электроды следует применять для сваривания арматурных изделий? Как правильно определить силу тока? И как проконтролировать качество проведенных работ? В нашей статье мы узнаем ответы на эти вопросы.
Краткие сведения
Сварка арматуры является основным методом соединения арматурных прутков. С помощью сваривания можно соединить прутки любой длины и формы. Сварка может вестись встык, нахлестом и крестообразным способом. В фабричном производстве также применяется точечная контактная сварка. Для проведения работ применяется стандартное сварочное оборудование с автоматической или полуавтоматической подачей электрода в активную зону. Сварение прутков рекомендуется проводить при подаче в активную зону инертных газов — это улучшает качество сварного шва, препятствует появлению коррозии в активной зоне.
Сварка помогает создать конструкцию любой формы — сетку, квадраты, треугольники, многоугольники. Сварка арматуры ГОСТ проводится в защитной одежде (костюм, маска, рукавицы), которая будет защищать человека от воздействия высоких температур. Сварочные работы рекомендуется проводить в сухом проветриваемом помещении, хотя при необходимости сварку можно проводить в любое время при отсутствии сильного ветра и/или осадков (дождь, туман, снег). Сварочные работы регулируются отечественными и международными нормами. Основной регулирующий закон — ГОСТ 14098-2014 (обратите внимание, что старый ГОСТ 14098-91 действовал до 2014 года).
Сварочные методики
Для сварки арматуры применяется несколько технологий. Основные методики — сварка арматуры ванным способом, сварное соединение внахлест, создание крестообразных соединений, контактная технология. Ниже мы рассмотрим каждую методику более подробно.
Встык ванным методом
Ванная сварка арматуры — оптимальный метод сварения арматурных прутков. Ванночкой называют U-образную скобу, к которой будет привариваться стальные прутки. Ванная технология позволяет получить качественный надежный шов, который не растрескается под действием механических ударов или химически активных веществ. К тому же ванная технология уменьшает контакт прутков с окружающей средой, поэтому риск коррозии в данном случае будет минимальным.
Сварочные работы проводятся так:
- С помощью металлической щетки нужно зачистить края стержней на 3-4 сантиметра (у концов должен появиться характерный металлический блеск). Для более качественной, быстрой обработки щетка должна иметь оцинкованное покрытие. После зачистки нужно промыть и обезжирить края, чтобы они стали чистыми.
- Теперь нужно поместить края внутрь ванночки. Некоторые мастера для более надежной фиксации обвязывают ванночку проволокой, а во время сварки проволока быстро удаляется из активной зоны. Новичкам манипуляции с проволокой делать не рекомендуется, поскольку есть большой риск приваривания проволоки к поверхности ванночки.
- Сварку следует проводить на высоких токах (оптимальная сила тока — 400 ампер при диаметре электрода 5 миллиметров) с помощью автоматического или полуавтоматического оборудования. Сперва выполняется плавление края одного прутка — потом второго. После этого операция повторяется до тех пор, пока ванночка полностью не покроется расплавленным металлом.
Главным преимуществом ванной технологии является небольшой расход расходного материала. Еще один крупный плюс — возможность проведения сварочных работ при отрицательных температурах (силу тока нужно увеличить на 15-20%). В качестве ванночки могут использовать как стальные скобы, так и скобы из других металлических сплавов (медь, латунь, дюралюминий, чугун). Также допускается применение графитовых ванночек.
Сварка арматуры внахлест
Если сварная конструкция не будет подвергается серьезной механической нагрузке, то в таком случае можно применять сварение арматуры внахлест. Главные плюсы технологии — простота, высокая скорость работ, минимум расходных материалов, неплохая надежность. Нахлест арматуры при сварке должен быть полным, чтобы получился прочный большой шов. Сварочные работы рекомендуется проводить с нижнего, а не с верхнего положения (это обеспечит более активное расплавление металла в активной зоне). Также можно выполнять боковую сварку внахлест под углом наклона до 15-20 градусов.
Оптимальный алгоритм действий:
- Зачистите поверхность арматуры с помощью металлической щетки или грубой наждачной бумаги. Также рекомендуется сделать обезжиривание поверхности, чтобы получить высококачественный сварной шов в активной зоне.
- Наложите сварные прутки друг на друга. Оптимальный уровень нахлеста — от 15 до 30 сантиметров. Скреплять детали проволокой не рекомендуется, поскольку при нагреве проволока быстро расплавится.
- Выполните обварку сверху минимум в двух местах (по краям). Потом выполните обварку снизу (по центру).
Крестообразное сварение
Если делать большую объемную решетку, то можно выполнить крестообразную сварку арматурных прутков. Все работы нужно проводить в строго горизонтальном или вертикальном положении, чтобы прутки надежно давили друг на друга. Делать сварку под углом не рекомендуется, поскольку будет проблематично получить надежный качественный шов (расплавленный металл будет активно стекать или испаряться). Крестообразную технологию также не рекомендуется выполнять при отрицательной температуре окружающей среды.
Особенности крестообразной технологии:
- Оптимальным методом соединения прутков является дуговая сварка в среде защитных газов. Соединение арматуры следует выполнять короткими прихватами с короткой подачей дуги в активную зону.
- Во время подачи электрод должен находиться под углом 30-45 градусов относительно плоскости стержней. В противном случае расплавление будет идти менее активно, что увеличит время проведения работ и снизит качество шва.
- Для улучшения фиксации прутков можно приварить на арматуру прихватки. Накладывать их рекомендуется с двух сторон, чтобы зафиксировать детали как в нижнем, так и верхнем положении.
Контактная сварка
Точечная контактная сварка арматуры является надежным методом соединения прутков друг с другом. Для сварения требуется применения станкового сварочного оборудования, которое обладает большой массой. Поэтому на практике эта технология получила мало распространения, хотя ее часто применяют в фабричном производстве. Контактное точечное сварение выглядит так:
- Прутки помещаются в станок, который имеет вид промышленных клещей. Станочные клещи надежно фиксируют детали, а во время сварения их положение не меняется.
- Потом рабочий выполняет настройку станка с помощью электронной панели. Рабочий может выбрать все технологические особенности операции (сила тока, глубина обработки, температура нагрева).
- Потом рабочий запускает станок, который выполняет сварку контактным методом. При работе сдавливающие поверхности нагреваются до высоких температур, что приводит к расплавлению арматуры.
- Во время работы возможно перемещение прутков с помощью подвижной консоли. Новые станки могут также выполнять перемещение сдавливающих нагревателей, что делает такие станки более универсальными, простыми в использовании.
Правила подбора электродов
Для сварения арматурных прутков рекомендуется использоваться электроды марок Э42, СМ-11, АНО-5, АНО-6, ВСЦ-4, УОНИ-13. Преимущества — высокое качество сварного шва, минимальный расход во время сварочных работ, хорошая температурная устойчивость, отсутствие коррозийного риска. Электроды этих марок могут работать при низких температурах окружающей среды, что будет весьма кстати в зимнее время. Для сварения стандартной арматуры диаметром 5-10 миллиметров применяются электроды диаметром 2-4 миллиметра. Для более крупных запчастей применяются электродные детали диаметром 4-6 миллиметров.
Также не забудьте проконтролировать силу сварочного тока:
- Для работы с популярными электродами диаметром 3 мм марки Э42 или СМ-11 лучше применять ток силой от 100 до 150 ампер. Для более толстых электродов силу тока нужно увеличить до 150-220 ампер (4 мм) или до 180-290 ампер (5 мм).
- Электроды АНО-5 и АНО-6 диаметром 4 мм варятся с помощью тока, сила которого составляет 170-220 ампер. Если диаметр составляет 5 мм, то силу тока нужно увеличить на 40-60 ампер.
- Маломощные электроды ВСЦ-4 варятся с помощью небольшого тока — 90-100 ампер (диаметр 3 миллиметра) или 120-150 ампер (диаметр 4 миллиметра).
- Также на рынке Вы можете встретить новые электроды марки УОНИ-13. Их следует варить слабым током — для устройств диаметром 2 миллиметра нужно применять ток силой 30-50 ампер. За каждый дополнительный миллиметр диаметра нужно увеличить силу тока на 50-70 ампер.
Качество работы
После проведения сварочных работ рекомендуется проконтролировать качество полученного шва. Правила ГОСТ не дают точных указаний относительно проведения проверочных работ. Обратите внимание, что следует выполнять после полного остывания соединения (в идеале проверку нужно проводить на следующий день). Большинство мастеров на практике применяют следующие методы проверки:
- Небольшие удары молотком по месту шва. С помощью металлического молотка выполняется простукивание конструкции на местах швов. Удары должны быть несильными, но точными. Перед простукиванием ударную часть молотка желательно помыть и вытереть насухо (мусор или частички воды могут негативно сказываться на качестве удара). Во время проверки сварной шов не должен растрескиваться и облущиваться — в противном случае сварочную процедуру нужно повторить.
- Сброс получившейся конструкции с высоты 1-2 метров. Если сварочные работы были проведены качественно, то падение с небольшой высоты не должно нанести конструкции какие-либо повреждения. Сбрасывать конструкцию желательно на плоскую ровную поверхность, на которой отсутствует мусор. Сбрасывать конструкцию рекомендуется 2 раза — это повысит качество проверки.
- Рентгенологическое исследование. Если сварка была проведена некачественно, то на рентгенограмме будут видны все микротрещины и неровности. Рентгенографическое исследование является очень точным, надежным, а с его помощью можно получить точные сведения о качестве шва. Метод имеет множество недостатков — дополнительные траты на покупку оборудования, нельзя часто проводить исследования, сложность при работе с большими конструкциями.
Заключение
Подведем итоги. Для соединения арматурных прутков можно применять сварку. Основные сварочные методики — стыковое соединение ванным методом, сварка внахлест, крестообразное соединение, контактная сварка. Каждая из технологий обладает своими преимуществами и недостатками. Оптимальным методом соединения арматуры является сварка встык ванным методом, при котором прутки соединяются друг с другом с помощью U-образной металлической дуги.
Еще один хороший метод соединения арматуры — это точечная технология сварки. Она позволяет получить очень прочный качественный шов, однако для ее применения требуются тяжелые станки. Для проведения сварочных работ могут применяться различные электроды — Э42, СМ-11, АНО-5, АНО-6, ВСЦ-4, УОНИ-13. После сварочных работ посмотрите качество шва.
Используемая литература и источники:
- Яковлев, С. К. Расчет железобетонных конструкций по Еврокоду EN 1992. В 2 частях. Часть 1. Изгибаемые и сжатые железобетонные элементы без предварительного напряжения. Определение снеговых, ветровых и крановых нагрузок. Сочетание воздействий / С.К. Яковлев, Я.И. Мысляева. — М.: МГСУ, 2015.
- Ферстер, М. Справочная книга для инженеров-строителей. Часть I. Математика, механика, сопротивление материалов, статика сооружений, железобетон, геодезия / М. Ферстер. — М.: Государственное научно-техническое издательство, 1976.
- Салов, Александр Монолитное строительство: от теории к практике: моногр. / Александр Салов. — М.: LAP Lambert Academic Publishing, 2013.
- Статья на Википедии
Ванная сварка арматуры колонн
Ванная сварка арматуры
Арматурные пруты из-за небольшой контактной поверхности и упроченных марок стали считаются сложно свариваемыми изделиями. Качество соединения формируется за счет нескольких факторов. Одним из определяющих факторов является точность стыка, который нередко смещается во время сварки. Во избежание этого возникает необходимость применения специальных технологий. Наибольшее распространение в строительстве на сегодняшний день приобрела так называемая ванная сварка арматуры, которая позволяет получить надежное соединение прутьев.
Сварка арматуры ванным способом
Арматурные прутья широко используются для сооружения железобетонных конструкций. При построении каркаса металлические прутья могут соединяться как продольно, так и перпендикулярно. Как правило, при этом площадь сварного шва получается небольшой, в то время как соединение подвержено значительным нагрузкам. Использование специальных ванночек позволяет не только упростить работу сварщика, но и повысить качество соединения.
Данная технология обладает рядом преимуществ, хотя она не лишена и недостатков.
Преимущества
- Ванная сварка арматуры позволяет рационально распределять наплавочный материал при его минимальных потерях.
- Оптимальный уровень качества соединения.
- Технология, проверенная временем и доведенная до совершенства.
- Наличие широкого выбора ванночек для арматуры различного сечения.
Недостатки
- Стальные ванночки являются расходным материалом, используемым единожды.
- Стоимость медных ванночек достаточно высока.
- Необходимость более тщательной и длительной подготовки свариваемых элементов.
Принцип сварки арматуры ванным способом
Наиболее часто данная технология применяется при соединении стержней большого сечения. Накладки для ванной сварки арматуры устанавливаются в вертикальном или горизонтальном положении на стык прутьев, между которыми остается небольшой зазор, заполняемый при сваривании наплавом. Наличие этого подковообразного элемента практически полностью исключает возможность смещения арматуры. Помимо того, бортики ванночек не позволяют растекаться расплавляемому при сварке металлу, который надежно обволакивает соединяемые поверхности. Аналогичным образом проводится и ванная сварка арматуры колонн.
Расходные материалы и инструмент
Сварка арматуры ванным способом достаточно простой технологический процесс, не требующий наличия специальных инструментов и материалов. Единственным требованием является достаточно точная установка свариваемых металлических прутьев и закрепление на стыках ванночек.
В качестве основного расходного материала выступают электроды марки УОНИ 13/55, предназначенные для сваривания упроченных металлов. Другим расходным материалом являются подковообразные металлические накладки подходящей размерности.
Источником энергии служит стандартный сварочный трансформатор, способный обеспечивать повышенные токи.
Из прочих инструментов сварщику понадобятся измерительный шаблон, щетка по металлу и резак.
Процесс сварки арматуры ванным способом
Сваривание металлической арматуры посредством указанной технологии проводится в несколько этапов.
- Подготовка поверхности заготовок. Свариваемые концы прутьев тщательно очищаются от коррозии щеткой по металлу. Необходимо чтобы концы арматуры были прямыми. При наличии скосов, изгибов и прочих неровностей дефектную часть следует обрезать.
- Установка арматуры. На этом этапе соединяемые стержни устанавливаются соответственно друг другу с минимальными отклонениями и зазором, составляющим около 1,5 см. Зазор между прутьями в процессе сваривания заполняется слоем наплава, способным выдерживать расчетные нагрузки.
- Фиксирование ванночек. На стыке арматурных стержней устанавливаются и фиксируются штампованные накладки для ванной сварки арматуры соответствующего диаметра, формирующие сварной шов.
- Сваривание. После появления дуги сварщик проводит электродом колебательные движения поперек оси стержней, равномерно покрывая все сечение наплавом. При прерывании процесса следует удалить с поверхности шлак, после чего продолжить операцию до полного заполнения штампованной заготовки наплавом.
Накладки для ванной сварки арматуры
Литые или штампованные формочки доступны в разных размерах как по длине, так и по диаметру. Подбирать их следует в соответствии с размерами арматурных стержней. Указанные заготовки изготавливаются и стали и меди. При этом если стальные ванночки используются в качестве разового расходного материала, медные заготовки могут применяться неоднократно.
Соблюдение техники безопасности
Как и при ведении любого другого вида сварки, здесь необходимо строго придерживаться правил электробезопасности. Следует помнить, что сварочные операции ведутся с использованием повышенных токов, что требует уделить особое внимание качеству заземления, контролю оборудования и расходных материалов.
Сварщики должны быть оснащены полным комплектом индивидуальных средств защиты – маской, щитком, диэлектрической обувью и рукавицами, одеждой из огнеупорных тканей. Территория, где проводятся сварочные работы, должна быть оборудована средствами пожарной безопасности.
svarkagid.com
Ванная сварка арматуры
Арматура относится к сложно свариваемым изделиям, так как у нее достаточно низкая контактная поверхность и делается она из упрочненных материалов. На итоговый результат влияет большое количество факторов. Одним из них является точность построения стыка. Нередко бывает так, что при выставлении правильного пространственного положения оно смещается во время сваривания. Чтобы этого не случилось, следует использовать специальные технологии. Сварка ванным способом является одним из них, так как стала самым распространенным методом в строительстве.
Сварка арматуры ванным способом
Арматура находит широкое применение при изготовлении металлоконструкций, где она выступает в качестве каркаса или основы для производства железомедных изделий. Она относительно недорогая и обладает высокой прочностью, благодаря чему удовлетворяет всем основным требованиям. Изделия соединяются продольно, когда один конец сваривается с другим, а также перпендикулярно. В любом случае, площадь шва получается небольшой, а нагрузки на нее воздействуют существенные. Благодаря использованию специальных ванночек, сварка арматуры А500С и других марок становится значительно проще. Эти изделия не позволяют растекаться расплавленному металлу и все остается в области шва, образуя полезное усиление.
Арматура А500С
Преимущества
- Ванный способ сварки арматуры обеспечивает рациональный расход наплавочных материалов с минимальными лишними растратами;
- Здесь получается высокий уровень качества, чего трудно достичь другими методами в таких условиях;
- Устоявшийся метод, технология которого проверена множеством мастеров, обладающий отточенной технологией;
- Широкое разнообразие самих ванночек, которые можно без труда подобрать для каждого диаметра арматуры.
Недостатки
- Стальные ванночки, как правило, используются всего один раз, так как они привариваются к конструкции;
- Медные ванночки обладают достаточно высокой стоимостью;
- Процесс сварки требует более тщательного подхода и занимает больше времени на подготовку.
Принцип ванной сварки
Сварка арматуры ванным способом подходит лучше всего для стержней с большим диаметром. В большинстве случаев это арматура диаметром от 20 до 100 мм. Ванная помогает охватить весь стык арматуры с небольшим зазором для заполнения расплавленным металлом. Данный способ обеспечивает сохранение жесткости и прочности на всей длине
Ванная сварка арматуры — описание технологии
При строительстве зданий и сооружений монолитно-каркасного типа для армирования железобетона используются стальные прутья различного типа и диаметра. Такой железобетон идет на изготовление плит перекрытия, балок, возведение свай и колонн. Армированный железобетон в гражданском и промышленном строительстве нашел широкое применение. Фундаменты, цокольные помещения, балконные плиты, лестничные марши – все это изделия из железобетона. Надежное соединение каркасных деталей между собой обеспечивается сваркой арматуры.
При возведении монолитных конструкций также требуется соединение стержней каркаса для придания жесткости сооружению. Тонкие металлические прутья используются для укрепления цементной стяжки пола. Во всех этих случаях используется соединения, самым надежным из которых на сегодня является ванная сварка арматуры.
Виды соединений арматуры
Армирующие стыки можно соединить в единую надежную конструкцию несколькими способами. Применение каждого из них требует точного соблюдения технологии, что обеспечивает надежность всей конструкции. Прочность соединений стальных прутьев, в зависимости от предполагаемой нагрузки, обеспечивается разными способами.
Различают три основных вида соединения:
- Методом нахлеста;
- Перекрестное;
- Встык.
Нахлесточное
Соединение арматуры внахлест чаще всего применяется при необходимости распределения сжимающих и растягивающих нагрузок по всей поверхности. Существует несколько правил, которым необходимо неукоснительно следовать при использовании этого метода:
- Соединение внахлест можно применять лишь на участках с наименьшим напряжением;
- Соединяемые прутья должны быть одного диаметра. Допускается лишь небольшое отклонение в исключительных случаях;
- Этот способ разрешается использовать лишь для соединения прутьев, диаметр которых не превышает 20 мм.
При соединении арматуры сваркой внахлест образуются швы в месте соприкосновения обеих частей, что обеспечивает равностороннюю опору для готового изделия. Чаще всего такое соединение применяется для создания металлических каркасов под будущий монолит.
Иногда применяют соединение арматуры внахлест без сварки. В этом случае стальные прутья в местах пересечения связываются с помощью проволоки. Это возможно при создании металлоконструкций, которые не будут подвергаться большим нагрузкам. В промышленном производстве такой метод не используется, а для частного строительства иногда возможен. Выбор, вязать или варить арматуру, зависит от того, для каких нагрузок монтируется армированная конструкция.
Перекрестное
Крестообразное соединение прутьев металлического каркаса рекомендуется сваривать методом контактной точечной сварки. Этим способом изготавливаются сварные сетки, а также плоские каркасы из арматуры, с последующей их сборкой в пространственные конструкции.
Контактная сварка арматуры крестообразным способом осуществляется с использованием:
- В единичных случаях или мелком производстве – одноточечных машин стационарного или подвесного типа;
- Для массового промышленного производства – специализированных контактных многоточечных машин.
Для крестообразных соединений также может быть использован метод вязки. Он позволяет соединять между собой прутья арматуры любого диаметра, преимущественно до 20 мм. Стержни диаметром свыше 20 мм рекомендуется соединять сварным способом, при этом они создают большую площадь соприкосновения во время варки.
Стыковое
Сварка арматуры встык характерна соединением концов прутов по всей площади касания путем нагрева. Соединение стыков можно осуществлять двумя способами:
- Оплавление соприкасающихся плоскостей – стыки нагреваются до состояния оплавления;
- Нагрев соединяемых деталей методом сопротивления – при нагревании стык доводится до пластического состояния.
Выбор того или иного способа зависит от марки используемого металла, диаметра арматуры, а также от требований к прочности соединения. С особенностями сварки стыков и применения видов соединений можно ознакомиться, посмотрев данное видео:
Основные способы сварки арматуры
Соединения сварные арматуры осуществляются несколькими способами:
- Стыковое сваривание контактное;
- Сварка продольными швами;
- Точечное контактное сваривание;
- Электродуговая сварка;
- Сварка ванным способом.
Какой из этих видов сварного соединения выбрать, зависит от каждого конкретного случая с учетом используемого материала и расчётной нагрузки на них. Нередко применяются одновременно несколько способов сразу. Очень часто доминантным при выборе является простота или надежность конкретного метода.
Сварку встык контактную применяют для соединения стальных прутьев, имеющих одинаковые или немного различные сечения.

Контактная сварка арматуры оплавлением
Контактная стыковая сварка арматуры осуществляется значительно быстрее, чем при плавлении. Это позволяет повысить производительность строительных работ. При этом свариваемый стык не подвергается значительному короблению.
Данные преимущества позволяют использовать контактную стыковую сварку в промышленных масштабах, поскольку этот метод можно легко автоматизировать и использовать в конвейерном производстве. Однако у него есть один существенный недостаток: происходит большой расход стальных прутов и электродов для сварки.
Для того, чтоб соединить тяжелые элементы крупногабаритных железобетонных конструкций, предпочтительнее использовать сварочный метод продольными швами. Он наиболее надежен, однако из-за затратности применяется достаточно редко.
Точечную сварку применяют для соединения стыков сечением до 50 мм. Чаще всего ею соединяют малогабаритные элементы, имеющие небольшой вес. Преимущества метода – более низкий расход материалов, чем при контактном способе, однако точечная сварка уступает контактной в надежности.
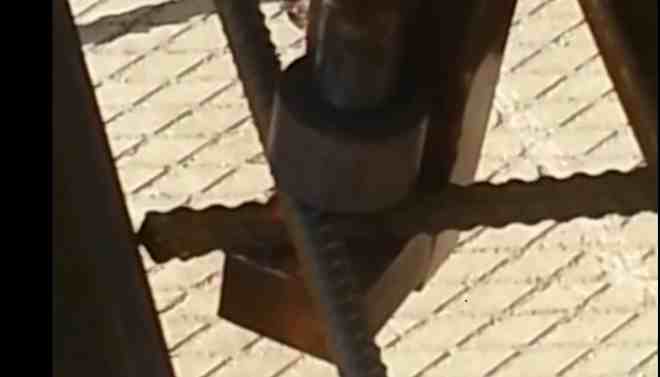
Точечная контактная сварка арматуры
Для надежного скрепления арматуры из стали разных марок используется электродуговая сварка. Однако ее можно применять лишь на отдельных участках, поскольку она стыки, полученные методом электродуговой сварки, не выдерживают повышенных нагрузок.
Ванный способ соединения стыков позволяет сваривать стержни с большим диаметром – от 20 до 100 мм. Этот метод широко используется в промышленном и гражданском строительстве, где требуется большое количество соединения стыков.
Он является самым надежным методом создания цельного жесткого силового каркаса будущего сооружения. Многих интересует вопрос – можно ли этим способом сваривать арматуру в разных плоскостях.
Сваривание арматуры ванным методом возможно в любой плоскости – горизонтальной и вертикальной.
Особенности технологии ванного способа
Сваривание ванным способом обеспечивает возведение прочных армированных конструкций при значительной экономии металла и трудозатрат.
Наибольшее распространение в отечественной промышленности получили разновидности ванной сварки:
- Ручная сварка в стальной скобе методом с трехфазной и однофазной дугой;
- Полуавтоматическое сваривание ванным способом в керамической форме;
- Автоматическая сварка стыков в медной форме с использованием шлака.

Формы для ванной сварки
Ванная сварка горизонтальных и вертикальных стыков имеет свои особенности. Стоит отметить, что наибольшее распространение получил первый метод, как менее затратный.
При сварке горизонтально расположенной арматуры применяются стальные формы – ванны, имеющие форму скобы. Для вертикальных – усеченный конус. Форма приваривается к концам арматуры в месте соединения, в ней посредством высокой температуры дуги создается ванна жидкого металла. От высокой температуры расплавленного металла начинают плавиться концы арматуры, образуя в месте шва после остывания единое сварное соединение.
Качественная сварка этим способом может быть обеспечена лишь при правильной предварительной подготовке торцов металлических стержней:
- Зачищаются жесткой металлической щеткой концы прутков от окалины, грязи или коррозии;
- Торцы прутьев размещаются соосно, зазор между ними не должен превышать полтора диаметра сварочных стержней.
Главное требование при ванном способе – торцы металлических прутков должны быть четко совмещены друг с другом, их оси не должны быть смещены по отношению друг к другу больше чем на половину диаметра.
Такой точности можно добиться, если для стыковки концов применять специальные кондукторы, фиксирующие расположение арматуры в течение всей сварки.
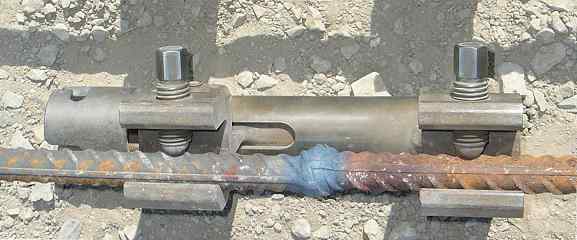
Кондуктор для сварки арматуры
Ванное сваривание требует токов с большими величинами – до 450 А, при использовании электродов, имеющих диаметр 5-6 мм. Пониженная температура воздуха увеличивает эту норму еще на 10%.

Сварка горизонтальных стыков
При сварке швов вертикально расположенных прутков в качестве ванны используется штампованная металлическая форма. Ее приваривают к нижнему пруту арматуры и используют без присадок.
Затем верхний прут с помощью кондуктора стыкуется с нижним и фиксируется. После этого в форму направляется наплавленный горячий металл. Для выпуска шлака в форме с помощью электрода прожигается отверстие, которое затем снова заваривают.
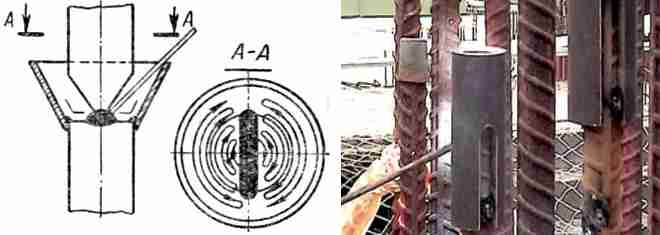
Сварка вертикальных стыков
Преимущества и недостатки сваривания стыков ванным способом
К несомненным плюсам ванного сваривания относятся:
- Возможность использования обычного сварочного оборудования, как и для электродуговой сварки;
- Не требуется поворачивание конструкции для полноценного сваривания;
- Сваренный шов на качество можно проверить, используя гамма-лучи;
- Стыки, соединенные ванным способом без накладок, позволяют экономить электроды – на каждом от 0,5 до 2,5 кг, и по 10-60 кг металла;
- Значительная экономия трудозатрат по отношению к другим способам сваривания.
Недостатком ванного сваривания являются случаи зашлаковывания торцов стальных прутов из-за раннего отвода от места сварки тепла. Из-за этого соединение может быть лишено необходимой прочности и надежности. Чтобы уменьшить риск зашлаковки соединения, необходимо перед началом сваривания прогреть торцы прутьев, а также предпочтительно использовать формы из теплопроводных материалов.
Ванный способ сварки
Для сварки стержней арматуры большого диаметра в настоящее время широко применяется ванный способ сварки. Этот способ сварки имеет следующие преимущества:
1. По сравнению со сваркой с накладками на каждом стыке экономится от 10 до 60 кг арматурной стали и от 0,5 до 2,5 кг электродов в зависимости от сечения свариваемых стержней.
2. Может быть использовано стандартное сварочное оборудование для дуговой сварки.
3. Отпадает необходимость в поворачивании (кантовке) конструкций.
4. Имеется возможность проверки качества сварки с помощью гамма-лучей.
В нашей стране технологически разработаны следующие три варианта ванного способа сварки: 1) ручная сварка ванным способом в стальной скобе однофазной и трехфазной дугой;
2) полуавтоматическая ванная сварка в керамической форме;
3) автоматическая ванно-шлаковая сварка в медной форме.
Фиг.64.Схема сварки ванным способом в скобе.
Ручная сварка ванным способом в стальной скобе. Подготовка под сварку горизонтальных стыков осуществляется следующим образом. Торцы и поверхности стержней перед сваркой должны быть зачищены от грязи, ржавчины и окалины стальной щеткой или другим способом на длину не менее 30 мм. Свариваемые стержни устанавливаются соосно, с зазором между торцами, не превышающим полтора диаметра электрода.
В случае сварки трехфазной дугой зазор следует устанавливать на 1,5—2,0 мм больше максимального размера электрода в поперечнике. Несовпадение осей свариваемых стержней не должно превышать более 5% от диаметра стержней. Для предохранения от последующей деформации и в случае значительной длины стержней рекомендуется придать им «обратный прогиб» перед сваркой. Место стыка охватывается снизу стальной скобой из листового металла или стержней, которая предохраняет от вытекания жидкий металл ванны (фиг. 64).
При сварке трехфазной дугой дополнительно по краям скобы ставятся еще боковые ограничители, чтобы предотвратить растекание шлака по стержню. Изготовляются скобы и ограничители из малоуглеродистой стали.
Размеры заготовок скоб даны в табл. 55.
Табл. 55.Размеры пластин для изготовления скоб
Дуговая ванная сварка стыков арматурных стержней
За последние несколько лет в практику арматурных работ начинает внедряться так называемый ванный способ ручной дуговой электросварки арматуры, являющийся разновидностью обычной дуговой сварки. Ванным способом может осуществляться стыковая сварка как горизонтальных, так и вертикальных или наклонных стержней.
Стыкуемые горизонтальные стержни укладывают в медную форму (рис. 94) с зазором между их торцами.
Рис. 94. Стык горизонтальных стержней, приготовленных для ванной дуговой сварки в медной форме: 1 — стыкуемые стержни; 2 — медная форма
Рис. 95. Схема дуговой ванной сварки стыка стержней гребенкой электродов:
1 — свариваемые стержни; 2 — медная форма; 5 — электрододержатель; 4 — электроды
Рис. 96. Вид сверху готового стыка, сваренного ванным способом: (форма не отнята)
Рис. 97. Стыкование вертикальных стержней ванным способом:
а — схема стыка, подготовленного для сварки: 1 — верхний стержень; 2 — форма; 3 — нижний стержень; б — готовый стык
Электроды, собранные в виде так называемой гребенки и закрепленные в специальном двуручном электрододержателе, опускают в зазор между торцами стержней (рис. 95). Величина зазора, а также количество и диаметр электродов берутся в соответствии с диаметром свариваемых стержней и по данным табл. 18.
Диаметры стыкуемых стержней в мм | Зазор между торцами свариваемых стержней в мм | Диаметр электрода в мм | Число электродов в гребенке при рекомендуемом зазоре и диаметре электрода в мм | Сварочный ток в A | |||
минимальный и рекомендуемый | наибольший | 4 | 5 | 6 | |||
25—32 | 9 | 12 | 4 | 4 |
— | — | 250 |
36 | 10 | 15 | 4—5 | 5* | 6 |
— | 300—500 |
40; 45 | 11 | 18 | 5 | — | 8 | — | 650 |
50; 55 | 12 | 21 | 5—6 | — | 7* | 5* | 550—600 |
60 | 13 | 25 | 5—6 | — | 10* |
7* | 700 |
70 |
14 | 28 | 6 | — | — | 9* | 700 |
Между гребенкой электродов и дном медной формы возбуждают электрическую дугу. После накопления на дне формы жидкого металла от расплавляющихся электродов электрическая дуга образуется между гребенкой электродов и поверхностью расплавленного металла.
Перегретый жидкий металл передает тепло торцам стержней, которые при этом частично оплавляются и соединяются с расплавленным металлом, заполняющим зазор. Вид готового сварного стыка с неотнятой еще формой показан на рис. 96.
При сварке ванным способом вертикальных или наклонных стержней конец верхнего стержня обрабатывается в виде усеченного конуса (рис. 97, а) с диаметром притуплённого конца, равного 4—6 мм. На конце нижнего из стыкуемых стержней устанавливается форма в виде конусообразной чашки. При сварке электрод или гребенку электродов перемещают по окружности стыка, производя оплавление, как было описано выше. Вид готового стыка показан на рис. 97, б.
Электрододержатель при ванном способе сварки может быть двуручный: на нем удобно крепить защитный щиток с цветным стеклом.
Рекомендуются электроды Э-42 с покрытиями марок ОММ-5, МЭЗ-04 или ЦМ7 при сварке стержней диаметрами до 40 мм из сталей Ст. 0—Ст. 3 и электроды Э50А с покрытием марки УОНИИ-13/55 или УП2/55 при сварке стержней больших диаметров из стали тех же марок или стержней из стали Ст. 5 диаметрами 25—70 мм включительно.
Преимуществами сварки ванным способом по сравнению с обычной дуговой сваркой являются:
а) большая производительность в результате применения электродных гребенок вместо одиночных электродов;
б) меньший расход стали благодаря применению медных форм по нескольку сотен раз.
Определение содержания воды методом песчаной бани
Метод песчаной бани — это полевой метод определения влажности почвы. Этот метод быстр, но результат не так точен, как метод сушки в духовке.
Также читайте: Определение содержания воды методом сушки в печи и пикнометром
Процедура и расчет, используемые в методе песочной бани для определения содержания воды в почве, объясняются ниже.
Требуемый материал для метода песчаной ванны
Материалы требуются:
- Песочная баня: Это поднос или посуда из прочного металла.Поднос представляет собой жаропрочную посуду с чистым песком на глубину 25 мм.
- Контейнеры или лоток: Контейнеры для содержания влаги необходимы для мелкозернистых почв. Если почва более крупная, используются жаростойкие лотки глубиной от 50 до 70 мм и квадратные от 200 до 250 мм. Диапазон фиксирован в зависимости от размера и количества выбранного грубого материала.
- Отопительное оборудование: Любое отопительное оборудование, такое как парафиновая плита под давлением, электрическая плита или газовая горелка в баллонах.
- Шпатель, совок и мелкие инструменты.
Порядок Метод песчаной ванны
Песочный метод выполняет следующую процедуру:
- Образец почвы крошится и свободно кладется на поддон. Вес образца плюс лоток определяется и записывается как м2. Вес только лотка записывается как m1.
- Песочная баня размещается над каким-либо нагревательным оборудованием. Образец почвы с лотком помещается поверх песка, содержащегося в песочной бане. Следует проявлять особую осторожность, чтобы не нагревать лоток.
- Образец непрерывно перемешивают, чтобы избежать пригорания почвы. Чтобы определить перегрев, к образцу почвы можно добавить крошки бумаги.
- Образец можно проверить, полностью ли он высох, сняв его с огня и взвесив массу. После этого образец снова нагревают в течение 15 минут и взвешивают. Если обе массы остаются одинаковыми (допустима вариация 0,1 г для мелкозернистой почвы, 0,5 г для среднезернистой почвы и 5 г для крупнозернистой почвы), это означает, что почва полностью высохла.
- После высыхания образцу дают остыть и принимают массу сухой почвы в м3.
- Процедура повторяется для 3 испытаний и берется среднее значение.
Наблюдение и Расчет
Sl. Нет | Наблюдение | Испытание 1 | Испытание 2 | Испытание 3 |
1 | Номер контейнера / номер лотка | |||
2 | Масса влажного грунта + контейнер (м2) (граммы) | |||
3 | Масса контейнера (м1) | |||
4 | Масса сухого грунта + емкость (м3) | |||
5 | Масса сухой почвы (Ms) = м3-м1 | |||
6 | Масса влаги (Mw) = м2-м3 | |||
7 | Содержание воды(%) w = (Mw / Ms) x 100 (%) | w1 | w2 | w3 |
Среднее содержание воды (%) ш ср = (w1 + w2 + w3) / 3 |
Вода содержание получается по формуле:
w = [(Масса влаги) / (Масса сухой почвы)] x 100 = Mw / Ms
Результат
Средняя влажность образца почвы = -%
В методе песчаной бани используется высокая температура, которая может повлиять на кристаллическую структуру почвы.Следовательно, он не рекомендуется для органических почв и почв с высоким содержанием гипса.
Также читайте: Определение содержания воды методом торсионных весов
.Автоматический сварочный аппарат коммутатора якоря
Компания Nide, основанная в 2007 году, занимается производством электродвигателей и предоставляет своим клиентам комплексные услуги.
Nide имеет три основных бизнес-подразделения.
Первое подразделение должно предоставить различных видов оборудования для производства двигателей, — это наша основная сфера деятельности, включая стенд вдоль станка, полностью автоматическую комплектную линию для производства якоря и статора, а также линию сборки двигателей.
Второе подразделение должно поставить полный спектр компонентов двигателя , таких как коллектор, шарикоподшипник, угольная щетка, изоляционная бумага, вал, магнит, вентилятор, крышка двигателя и т. Д.
Третье подразделение обеспечивает техническую поддержку и консультации, сопровождение проектов и услуги «под ключ» для некоторых производителей двигателей.
Наши машины в основном применяются к асинхронным двигателям , двигателям BLDC, универсальным двигателям, трехфазным двигателям, однофазным двигателям, двигателям переменного тока, двигателям постоянного тока, таким как двигатель стиральной машины, двигатель кондиционера, двигатель насоса, двигатель охладителя, двигатель генератора переменного тока , мотор вентилятора, мотор потолочного вентилятора, мотор компрессора, мотор электроинструмента, мотор пылесоса, мотор смесителя, мотор серии, мотор электромобиля, мотор ступицы колеса, мотор электрической зубной щетки, мотор фена, мотор электробритвы и т. д.
Благодаря хорошему сервису, уникальной философии, профессиональной команде и надежному качеству мы постепенно завоевываем доверие клиентов во всем мире. Мы прямо и косвенно поставляем нашу продукцию в более чем 50 стран, таких как Германия, Великобритания, Испания, Италия, Турция, Бразилия, Аргентина, Мексика и т. Д. Среди наших клиентов многие из них являются всемирно известными компаниями.
Индивидуальное обслуживание | 1. Разработка и производство продукции по индивидуальному заказу |
2.Индивидуальный перевод | |
3.Технические предложения | |
Сервисное обслуживание | 1. Гарантийный срок: обычно 12 месяцев |
2. Доступен зарубежный сервисный центр | |
3. Инженеры, работающие за рубежом |
Решение проблем сварки сталей с покрытием
Увеличение использования сталей с покрытием (особенно оцинкованных) привело к усиленному поиску решений проблем, возникающих при соединении этих материалов. Часто встречаются высокие уровни брызг и сварочного дыма, пористость сварного шва и плохая форма валика. Эти проблемы приводят к увеличению затрат на очистку после сварки, снижению качества, увеличению количества доработок и общему снижению производительности.Наиболее часто используемые материалы с покрытием включают горячеоцинкованную и гальванизированную углеродистую сталь, стальной лист с цинковым покрытием (Galvanneal®) и сталь с алюминиевым покрытием.
Электролитически осажденные покрытия являются тонкими, однородными и обеспечивают прочное покрытие, необходимое при формовании. Лист горячего окунания, покрытый в ванне расплавленного цинка или алюминия, имеет менее однородное покрытие, но все же обеспечивает отличную коррозионную стойкость. Отожженный оцинкованный материал, покрытый любым способом, подвергается термообработке для увеличения адгезии покрытия и улучшения его свариваемости. и характеристики окраски.
Почему возникают проблемы со сваркой?
При сварке оцинкованного материала сварщики часто сталкиваются с проблемами разбрызгивания, пористости, образования дыма и потенциального растрескивания сварного шва в результате улетучивания цинка в покрытии.
Когда для соединения этого материала используется короткое замыкание или перенос металла распылением, улетучивающийся цинк, поднимающийся с поверхности пластины, вызывает нестабильность дуги и образование значительных брызг. Пары цинка иногда могут задерживаться в затвердевающей сварочной ванне, вызывая пористость.
Количество сварочного дыма, образующегося при сварке, зависит от состава и толщины покрытия, а также от используемых параметров сварки. Более толстое покрытие увеличивает количество выделяемого дыма.Трещины также могут возникать в результате захвата цинка сварным швом.
В отличие от оцинкованного покрытия, алюминиевое покрытие не является летучим, но при этом образует оксид с высокой температурой плавления, который может повлиять на стабильность дуги и вызвать разбрызгивание. Этот оксид также препятствует хорошему смачиванию поверхности, что может привести к ухудшению формы валика.
Современные методы сварки терпят неудачу
Большая часть оцинкованной стали сваривается, как и ее аналоги без покрытия, с небольшими изменениями в процессах и параметрах.Сплошная проволока, используемая с короткозамкнутым переносом, и защитный газ аргон / 25% CO2 (C-25) является обычным явлением.
Иногда цинк удаляют с поверхностей соединения перед сваркой, чтобы улучшить качество сварки, или в стыке делают зазоры, чтобы пары цинка выходили из области соединения во время сварки, что снижает разбрызгивание и пористость. Напряжение и ток могут быть немного увеличены, чтобы улучшить стабильность дуги и увеличить удаление цинкового покрытия до того, как лужа достигнет области соединения. Качество может немного улучшиться, но постоянные проблемы — снижение производительности, плохой внешний вид и прочность сварных швов.
Комбинации проволока-газ для улучшения сварки стали с покрытием
Правильный размер и тип проволоки в сочетании с наиболее подходящим защитным газом могут существенно улучшить характеристики газовой дуговой сварки (GMAW) оцинкованной стали и стали с покрытием.
Оценка различных комбинаций проволоки и газа в технологическом центре Praxair в Тонаванде, штат Нью-Йорк, показала, что сплошная проволока с низким содержанием кремния (ER 70S-3, в среднем 0,55 процента кремния) снижает вероятность горячих трещин в металле сварного шва, в котором присутствует цинк. покрытие.Использование проволоки диаметром 0,045 дюйма, а не обычно выбираемой 0,035 дюйма. диаметр для этого калибра материала — сгенерированный более высокая скорость перемещения и удаление меньшего количества покрытия вблизи фактической области сварного шва.
Оценка газовой смеси показала, что защита аргоном / кислородом приводит к образованию неприлипающего оксида, который снижает коррозионную стойкость в области, окружающей сварное соединение. Сочетание аргона и CO2 улучшает форму валика и качество сварки по мере увеличения содержания CO2, но обычно это увеличивает образование брызг и дыма при сварке.
Продолжение оценки показало, что экспериментальная смесь аргона, CO2 и небольшого количества гелия снижает разбрызгивание и образование дыма при сварке, а также улучшает внешний вид валика. Эта газовая смесь со сплошной проволокой с низким содержанием кремния обеспечивает оптимальные характеристики при коротком замыкании (см. «Производитель оборудования для игровых площадок обеспечивает лучшую сварку» боковая панель).
Производитель оборудования для игровых площадок улучшает сварные швы
BCI Burke, разработчику и производителю игрового оборудования в Фон-дю-Лак, штат Висконсин, потребовалось сократить время, затрачиваемое на шлифовку, чтобы удалить брызги и улучшить внешний вид сварных швов. Окрашенные оцинкованные трубы используются для многих компонентов игрового набора компании, и, поскольку хорошее качество сварки и внешний вид имеют решающее значение для приемлемости и безопасности использования этого оборудования, чрезмерное разбрызгивание является причиной
большая проблема. Его удаление приводит к непроизводительным затратам труда, а также к значительным расходам, связанным с шлифовальными кругами и другими необходимыми принадлежностями. |
Импульсный металлический переходник с твердым телом
Импульсный перенос металла GMAW может помочь еще больше улучшить качество сварки оцинкованной стали. За счет уменьшения разбрызгивания увеличивается эффективность процесса и сводится к минимуму очистка. Управляемый перенос мелкокапельной струи, создаваемый импульсным GMAW, приводит к более стабильной дуге, чем при коротком замыкании, поэтому можно соединять больше типов соединений и более широкий диапазон толщин материала. Его более низкие средние текущие уровни а большая стабильность приводит к более низкому уровню дыма, поскольку меньше цинка испаряется.Хорошие результаты достигаются при использовании проволоки с низким содержанием кремния и смеси газов аргон / CO2.
В примере 1 листовой материал толщиной от 16 до 12 (от 0,060 до 0,10 дюйма) соединялся с использованием короткозамкнутого переноса. Замена импульсной GMAW смесью аргон / газ с низким содержанием CO2 уменьшила разбрызгивание и повысила эффективность осаждения с 85 до 98,5%. Было выполнено небольшое повторное покрытие основного материала и сварного шва после сварки. обязательный.
Изменения в конструкции с использованием новой технологии сварки
Из-за обширной шлифовки и очистки, которые ранее были связаны со сваркой сталей с покрытием, некоторые производители вынуждены производить компоненты из стали без покрытия, а затем очищать и цинковать погружением перед порошковой окраской эти детали для обеспечения необходимой коррозионной стойкости.Эти дополнительные операции значительно увеличивают производственные затраты и время для завершения изготовления. Теперь дизайн которые включают предварительно покрытый или предварительно оцинкованный материал и детали, такие как трубы, могут обеспечить коррозионную стойкость без последующего цинкования и порошковой окраски. Это значительно увеличивает производительность и снижает затраты.
Соединение алюминированного стального листа
Алюминированная сталь представляет другие проблемы при сварке, которые легче решить. Здесь также ключевыми проблемами являются контроль формы валика и уровня разбрызгивания.Алюминиевое покрытие образует трудно удаляемый оксид, который препятствует смачиванию валика и вызывает нестабильность дуги из-за разбрызгивания. Поскольку это покрытие не является летучим, как покрытия, содержащие цинк, прочность сварного шва не является такой большой проблемой. подобно оцинкованный материал, короткозамкнутый переход с C-25 является наиболее часто используемым методом сварки.
В технологическом центре Praxair была проведена оценка переноса короткого замыкания с использованием нескольких комбинаций проволока-газ для улучшения свариваемости алюминированной стали.Форма сварного шва и глубина проплавления были ключевыми факторами при выборе наилучшего сочетания проволоки и газа. Аргон с низким содержанием CO2 (от 5 до 10 процентов) работает лучше всего за счет минимизации разбрызгивания и улучшение контроля формы борта.
Импульсный перенос металла значительно снижает разбрызгивание при соединении алюминированных листов. Лучшая общая форма бусинок — более плоская, с меньшим «выступом» — была получена при использовании смесей аргон / CO2. Аргон / 8% CO2 — лучшая двухкомпонентная газовая смесь. Из трех оцениваемых смесей смесь аргон-гелий / CO2 дает лучшую форму шариков и дополнительно снижает разбрызгивание по сравнению с обычными двухкомпонентными смесями аргон / CO2.
MIG-пайка сталей с покрытием
Альтернативой сварке стали с покрытием (особенно оцинкованной) является пайка с использованием сплавов меди с низкой температурой плавления (1500–1600 градусов по Фаренгейту) (бронза) или алюминия, меди и кремния (алюминиевая бронза) (1000–1100 градусов по Фаренгейту). Более низкие рабочие температуры процесса исключают коррозию сварных швов и уменьшают разбрызгивание и потери покрытия. Низкое тепловложение уменьшает искажения и снижает образование дыма уровни поколения. Прочность связи эквивалентна силе любого процесса пайки.
Исторически пайка выполнялась с использованием пламени в качестве источника тепла. Последние разработки оборудования привели к появлению разновидности импульсной сварки GMAW, известной как пайка MIG.
При пайке оцинкованного листа методом MIG рекомендуется использовать 3-процентный кремний-бронзовый сплав для повышения текучести лужи. В качестве материала с алюминиевым покрытием можно выбрать один из нескольких сплавов алюминия и бронзы. В качестве защитных газов для этих сплавов предпочтительны аргон или аргон с небольшой добавкой CO2.
Решающее значение для успеха этого процесса имеет импульсное оборудование, которое может регулировать перенос одной капли материала за импульс.Короткая длина дуги со стабильным переносом металла необходима для минимизации тепловложения. Оптимальные результаты могут быть достигнуты с помощью смеси аргон / CO2 / водород, так как улучшенное управление дугой и слегка восстановительная атмосфера могут способствовать даже лучший внешний вид поверхности борта.
Если механические свойства соединения позволяют использовать пайку, а стоимость расходных материалов может быть оправдана, этот процесс может предложить некоторые значительные преимущества по сравнению с традиционной дуговой сваркой. 2
Несмотря на то, что при соединении сталей с покрытием возникает множество проблем, новые расходные материалы и технологические процессы могут улучшить качество сварки и повысить производительность.Новые смеси газов и правильные сварочные процессы могут сэкономить производителям как время, так и деньги, поскольку они сталкиваются с проблемой конкурентоспособности в глобальной экономике.
Кевин А. Литтл — менеджер отдела исследований и разработок в области сварки, Praxair Inc., 175 E. Park Drive, Tonawanda, NY 14150, 716-879-7290, факс 716-879-7275, www.praxair.com.
Примечания:
1. «Импульсная мощность GMAW, идеально подходящая для гальванического отжига стального листа, проектирования и изготовления сварки, май 1998 г., стр. 28-29.
2.М. Эббингаус, Генрих Хакль и Р. Ланштайнер, «MIG-пайка оцинкованных листовых металлов и профилей», в материалах Комиссии XII Международного института сварки (IIW), документ № 1501-97, Сан-Франциско, 1997, стр. 121–137.
Модификатор арматуры — Руководство Blender
Модификатор Armature используется для построения скелетных систем (ригов) для анимации позы персонажей и все, что нужно позировать.
Путем добавления арматурной системы к объекту, этот объект можно точно деформировать, так что геометрию не нужно анимировать вручную.
Опции
Модификатор арматуры.
- Объект
Имя объекта арматуры, используемого этим модификатором.
- Vertex Group
Группа вершин объекта, веса которой будут использоваться для определения влияния этого результаты модификатора при смешивании с результатами других Арматура .
Имеет значение только при наличии хотя бы двух из этих модификаторов на одном и том же объекте, с активированным мульти-модификатором .
- Инвертировать
<->
Инвертирует влияние, заданное группой вершин, определенной в предыдущей настройке (я.е. меняет значения веса этой группы на противоположные).
- Инвертировать
- Сохранить объем
Используйте кватернионы для сохранения объема объекта во время деформации. Во многих ситуациях может быть лучше.
Без этого вращения в соединениях имеют тенденцию уменьшать соседнюю геометрию, почти до нуля при 180 градусах от исходного положения. С его помощью геометрия больше не уменьшается в масштабе, но есть «пробел», нарушение непрерывности при достижении 180 градусов из положения покоя.
Исходное состояние. | Вращение на 100 °, Сохранение объема отключено. | Поворот на 180 °, Сохранение объема отключено. |
Вращение на 100 °, Сохранение объема включено. | Вращение на 179,9 °, Сохранение объема включено. | Поворот на 180,1 °, Сохранение объема включено. |
- Мульти модификатор
Используйте те же данные, что и предыдущий модификатор (обычно также Арматура ) в качестве входных данных. Это позволяет вам использовать несколько арматур для деформации одного и того же объекта, все на основе «недеформированных» данных. (т.е. это позволяет избежать того, чтобы второй модификатор Armature искажал результат первого…).
Затем результаты модификаторов Якоря смешиваются вместе с использованием весов Vertex Group как «направляющие для смешивания».
Подсказка
Арматура модификаторов могут быть быстро добавлены к объектам посредством родительского контроля их к арматуре.
- Bind to
Методы привязки арматуры к сетке.
- Группы вершин
Только сетки и решетки. Когда этот параметр включен, кости с заданным именем будут деформировать вершины, принадлежащие одноименные группы вершин. Например. кость с именем «предплечье» будет влиять только на вершины в группе вершин «предплечье».
Влияние одной кости на данную вершину контролируется весом этой вершины в соответствующей группе. Гораздо более точный метод, чем Bone Envelopes , но, как правило, дольше настраивается.
- Bone Envelopes
При включении кости будут деформировать вершины или контрольные точки рядом с ними, определяется радиусом оболочки каждой кости и расстоянием. Это позволяет костным оболочкам контролировать деформацию (т.е. кости деформируют вершины по соседству).
Пример методов снятия шкуры. Веса вершинной группы «рука».
Веса вершинной группы «предплечье».
Результат при постановке арматуры.
Та же поза, но с использованием метода конвертов, а не групп вершин.
Подсказка
Когда конверты отключены, Blender использует набор существующих имен групп вершин для определить, какие кости действительно необходимы для оценки модификатора.Удаление пустых групп вершин помогает уменьшить зависимости и может иметь важное значение. если сетка используется во время оценки других костей в той же арматуре, например как цель ограничения Shrinkwrap.