Вибродуговая наплавка
Этот способ обычно используется для наплавки деталей типа тел вращения диаметром 8…10 мм и более. Сущность метода заключается в том, что основной и электродный металл нагревается до расплавления теплотой, которая выделяется в результате возникновения периодически повторяющихся электрических разрядов, т. е. прерывисто горящей электрической дуги. Наплавленный слой образуется в процессе кристаллизации расплавленных основного и электродного металлов. Малая длительность и прерывистость горения электрической дуги обусловлены вибрациями электродной проволоки, которые создаются с помощью электромагнитных или механических вибраторов.
Вибродуговая наплавка – разновидность механизированной дуговой наплавки плавящимся металлическим электродом. Процесс наплавки осуществляется при вибрации электрода с подачей охлаждающей жидкости на наплавленную поверхность (рис. 1).
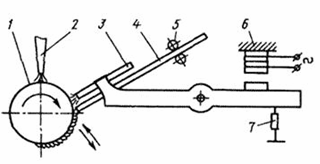
Рис. 1. Схема вибродуговой наплавки: 1 – наплавляемое изделие; 2 – сопло для подачи охлаждающей изделие жидкости; 3 – сопло для подачи жидкости в зону сварки; 4 – электродная проволока; 5 – подающие ролики; 6 – электромагнитный вибратор; 7 – пружина
Вибродуговая наплавка отличается тремя особенностями:
- в цепь нагрузки источника питания включена индуктивность L;
- напряжение источника питания недостаточно для поддержания непрерывного дугового разряда;
- электродная проволока совершает колебания относительно детали с частотой 50…100 Гц и амплитудой 1…3 мм с периодическим касанием наплавляемой поверхности.
Весь процесс наплавки состоит из весьма коротких и непрерывно повторяющихся циклов, каждый из которых можно разбить на три части: короткое замыкание цепи, разрыв этой цепи и холостой ход. При коротком замыкании напряжение в сварочной цепи падает до нуля, а ток быстро возрастает. Далее наступает разрыв цепи, при котором возможно кратковременное возникновение микродуги. При частоте тока вибратора 50 Гц продолжительность одного цикла составляет 0,01 секунды. Из этого времени 65 % приходится на холостой ход. Следовательно, КПД – весьма низкий.
Во время короткого замыкания цепи через место контакта проходит ток плотностью до 400 А/мм2. Вследствие этого металл в месте контакта нагревается до высокой температуры. Далее торец электродной проволоки отрывается вибратором от наплавляемой детали, оставляя на ней часть металла электрода. Возникающая затем электрическая дуга расплавляет этот металл. В это время расстояние между торцом электродной проволоки и наплавляемой деталью увеличивается, электрическая дуга гаснет и наступает период холодного хода. Частым повторением таких циклов наращивается металл наплавляемого валика.
Введение индуктивности в цепь дуги обеспечивает накопление электрической энергии в индуктивности во время разомкнутого состояния цепи, сдвиг фаз тока и напряжения, поэтому переход тока через нуль происходит при наличии напряжения источника питания и возникновении электродвижущей силы самоиндукции, которая совпадает по направлению с напряжением источника питания. Это обеспечивает повторное возникновение дугового разряда после разрыва сварочной цепи и устойчивое горение дуги.
Вибродуговую наплавку выполняют вибрирующим электродом диаметром 1,5…2 мм. При каждом коротком замыкании часть наплавляемого электрода остается на поверхности. Толщина слоя получается небольшой. Так как в зону наплавки все время подаются охлаждающая жидкость (обычно водный раствор кальцинированной соды) или потоки воздуха, изделие прогревается и деформируется очень мало. Ускоренное охлаждение способствует повышению твердости наплавленного металла. Наиболее часто этот способ применяют при наплавке цилиндрических изделий небольшого диаметра (рис. 2). Выполняют вибродуговую наплавку и под слоем флюса.
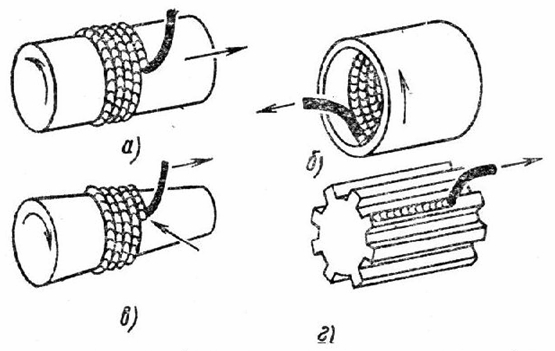
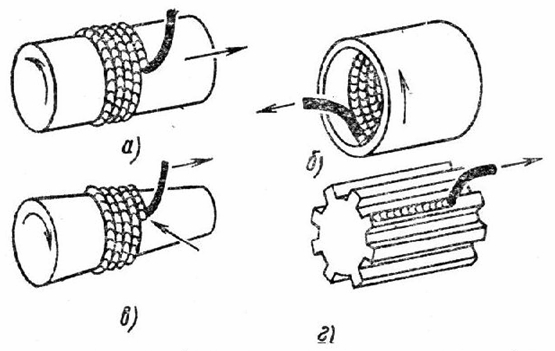
Рис. 2. Схемы вибродуговой наплавки изделий различной формы: а – цилиндрической; б – внутренней поверхности трубы; в – конической; г – шестерни
Вибродуговая наплавка под слоем флюса имеет ряд преимуществ: дает возможность наплавлять металл только на изношенную часть, что уменьшает трудоемкость последующей механической обработки; позволяет получать наплавленный слой без пор и трещин; деформация детали минимальная и не превышает полей допусков посадочных мест; минимальная зона термического влияния.
Для комбинированной наплавки под слоем флюса вибрирующим электродом можно применять головки ОКС-1252 и ОКС-6569. При использовании электродной проволоки марки Нп-80 и флюса АН-348А твердость наплавленного слоя составляет 36…38 HRС. Для увеличения твердости наплавленного слоя до 52…54 HRC к флюсу АН-348А добавляют по 2 % феррохрома и серебристого графита.
Аппараты для автоматической вибродуговой наплавки (автоматические вибродуговые аппараты) являются основной частью наплавочных вибродуговых установок и служат для подачи к месту наплавки электродной проволоки и вибрации конца проволоки с заданной частотой и амплитудой.
Степень совершенства аппаратов для вибродуговой наплавки в значительной мере определяется конструкцией их колебательной системы, особенно видом привода системы, который может быть электромагнитным, электромоторным или пневматическим. Наиболее распространены вибродуговые аппараты с электромагнитными вибраторами. Они достаточно просты в устройстве, позволяют легко настраивать систему на заданный размах вибрации конца электродной проволоки и обеспечивают синусоидальную форму вибрации с частотой 100 Гц (при включении вибратора в стандартную сеть переменного тока с частотой 50 Гц) (рис. 2).

Рис. 2. Схема вибродугового аппарата ВДГ-3: 1 – электромагнитный вибратор; 2 – гидравлический амортизатор; 3 – наплавляемая деталь; 4 – хоботок; 5 – вибрирующий кронштейн; 6 – пружины
При необходимости наплавки деталей с различной частотой вибрации используют вибродуговые аппараты, снабженные колебательными системами с электромоторным приводом. В этом случае
вибрация рычага, на котором закреплен хоботок, осуществляется с помощью вращающегося кулачка, поджатого пружиной к вибрирующему рычагу. Эксцентриситет кулачка определяет размах вибрации конца электродной проволоки, а частота вращения кулачка – частоту вибрации. В аппаратах с такими колебательными системами предусмотрены наборы сменных кулачков и сравнительно простые способы изменения частоты их вращения.
Вибродуговые аппараты могут иметь верхний или боковой подвод электродной проволоки. Боковой подвод электрода применяют преимущественно для наплавки цилиндрических деталей. При этом вращение наплавляемой детали устанавливается таким, чтобы сварочная ванна располагалась над электродом. Жидкий металл ванны будет стремиться стечь вниз, растекаясь по ширине ванны, что приведет к образованию маловыпуклых, слегка уширенных валиков. При затекании жидкого металла под дугу уменьшается глубина проплавления основного металла, меньше разбавляется наплавленный слой металлом детали, что имеет важное значение при наплавке тонких слоев, особенно проволокой с повышенным содержанием углерода и легирующих элементов.
Просмотров: 519
Вибродуговая наплавка: описание процесса, оборудование, материал
Лучшим способом восстановления изношенных частей деталей в виде обода колеса, диска и вообще любых тел вращения является вибродуговая наплавка. Которая, в отличие от газокислородного и обычного сварочного дугового метода обеспечивает равномерность нанесения навариваемого/наплавляемого металла на объект ремонта.
Принцип устройства для нанесения равномерного нанесения металла несложен. Это совмещение детали вращения, закреплённой на валу токарного станка с необходимой для этой детали свободной зоной и вибро-электродуговой насадки, или наплавочной головки, которая размещается на месте штатного суппорта станка или крепится на нём.
Вибро-электродуговая насадка
Это несложное устройство представляет собой механический вибратор или специальную электромагнитную установку, работающую по принципу соленоида в реле, когда подаваемый переменный ток колеблет взад-вперёд внутри обмотки металлический стержень-электрод.
Вибраторы механического типа только называются так, на самом деле они тоже связаны с частотой переменного тока, и являются по сути электромеханическими. И у электромагнитных, и у механических вибраторов частота колебаний наплавной проволоки, или стержня-электрода, может быть в пределах 50-100 гц.
Перемещения стержня в обмотке вызывают кратковременные касания его к наплавляемой детали, а затем отрывы от неё. Во время касания стержня-электрода детали, зажатой и вращающейся в станке, происходит короткое замыкание, напряжение становится нулевым, а ток, наоборот, скачкообразно нарастает. Во время отрыва происходит скачок напряжения, ток прерывается, а между деталью и электродом возникает дуга. Так как в цепь включена катушка индуктивности, постоянного напряжения в цепи не хватает для постоянной дуги разряда, но импульсная подача тока и напряжения способна вызвать такую дугу, которая выглядит как серия сливающихся для глаза коротких вспышек, которые выглядят как непрерывная дуга, но на деле таковой не являющейся.
Конструктивно электродуговая насадка является частью комплекса, в который входят источник сварочного тока и наплавочная головка ВДГ-5 (или её аналоги). Главное – нет нужды применять какие-то кустарные устройства, промышленностью давно освоены разные типы таких насадок на токарные станки – с разными узлами крепления и с разными способами подачи проволоки, из которой формируется наплавочный слой.
В вибродуговую головку в качестве неотъемлемых составных частей входят также
- Ролики подачи со стандартных мотков проволоки разных типов.
- Опорные узлы.
- Вибратор с двигателем, обеспечивающим колебания электрода.
- Наконечник обеспечения подвода электрода к заготовке.
Как происходит вибродуговая наплавка
Нужно иметь в виду, что КПД этого процесса весьма низок. Это происходит оттого, что при условной частоте тока вибратора в 50 гц касание электрода к детали составляет 0,01 сек. То есть 65% времени процесса падает на холостой ход. Но без фазы холостого хода полноценной наплавки тоже не получится. Чтобы понять, почему так происходит, нужно рассматривать процесс с дискретностью в доли секунд.
- За период касания обрабатываемой детали и электрода в месте контакта ток возрастает до 400 А на кв. миллиметр, и проволочный электрод в месте касания от огромного скачка температуры нагревается до критических состояний..
- Вибратор отрывает электрод от заготовки, и на ней остаётся часть электрода.
- Возникающая дуга расплавляет эту каплю.
- Электрод под воздействием остаточного импульса в обмотке продолжает удаление от наплавляемой детали, расстояние увеличивается, ток падает до нуля и дуга гаснет. Наступает фаза холостого хода.
Всё это происходит от 50 до 100 раз в секунду, и именно в чередовании холостого хода и касаний с дугой между ними происходит наплавка металла на изношенную заготовку.
Введённая в цепь дуги индуктивность служит источником накопления энергии во время разомкнутого состояния электрической цепи. Она вызывает фазовый сдвиг напряжения и тока, поэтому переход тока через фазу нуля способствует возникновению ЭДС самоиндукции, совпадающей по направлению с напряжением выпрямленной сети. Что способствует повторному возникновению дуги после разрыва цепи и её устойчивому горению в короткий промежуток времени между касанием и холостым ходом.
Электроды для вибродуговой наплавки имеют толщину 1,5-2 мм, и являются, по сути, проволокой из стали определённой марки, в той или иной степени совпадающей с маркой стали ремонтируемой детали. После короткого замыкания и отрыва в результате импульса в обмотке часть этой проволоки остаётся на детали в расплавленном состоянии.
Дополнительные технические условия
Чтобы не возникало перегрева ремонтируемой заготовки и, как следствие, её деформации, наплавляемую поверхность охлаждают следующими составами:
- 10-20% раствор технического глицерина,
- 3-4% водный раствор кальцинированной соды.
Может быть также охлаждение потоками холодного воздуха.
Восстановление изношенных в результате долгой эксплуатации деталей имеет под собой вполне оправданную экономическую подоплёку. Дело в том, что восстанавливают обычно старые, незаменимые части изделий (чаще всего уникальные по характеристикам валы вращения), которые давно сняты с производства и не выпускаются в виде запасных частей.
Охлаждения деталей растворами или воздушной струёй направленного действия выглядит в этих условиях не только оправданной, но и остро необходимой мерой, предохраняющей поверхность изделий и от деформаций и оберегая их габариты.
Точка подачи охлаждающих растворов не должна совпадать с местом горения дуги, иначе может пострадать качество наплавки. Для этого одновременно с вибраторами устанавливают магистраль, по которой подаётся охлаждение, с регулировочными механизмами подачи глицериновой или водной смеси, или воздушный вентиль. Но у охлаждающего раствора есть ещё одна функция — предохранение навариваемого металла от процессов азотирования, от которого он сделается чрезмерно хрупким, и кислородного окисления.
Стабильность процесса
О стабильности и отсутствии технологических сбоев процесса наплавки будет свидетельствовать равномерность характерного трескучего звука в момент наваривания и показания амперметра. Так как частота колебаний тока и напряжения в секунду бывает равной 50-100 гц, стрелка аналогового прибора будет не успевать колебаться туда-сюда и будет просто стоять на месте – но это как раз и будет свидетельствовать о стабильности процесса.
Если же плавление проволочного электрода сопровождается неприятным и неравномерным треском с разной частотой и периодичностью, а стрелка амперметра совершает беспорядочные колебания, это свидетельствует о неравномерности нанесения металла на заготовку, при которой могут образовываться каверны, а слой будет нервным и рыхлым.
От чего зависит толщина слоя
На толщину наплавляемого на деталь слоя металла влияют два параметра:
- Скорость вращения заготовки (окружная скорость, зависящая от диаметра вала, колеса, обода той ремонтируемой детали, что закреплена на валу станка)
- Скорость подачи сварочного проволочного электрода.
При увеличении скорости вращения будет получаться узкий и тонкий валик с медленной скоростью наращивания металла. Наоборот, снижение темпа вращения с одновременным увеличением числа и силы колебаний проволоки наплавляемая поверхность будет быстрее увеличиваться в диаметре. Но для увеличения толщины наращиваемого слоя металла нужна ещё и более толстая проволока.
Увеличения скорости вращения заготовки стараются всячески избегать и выставляют обычно минимально-возможную скорость – иначе в наращиваемом слое неизбежно появление каверн. И чем быстрее вращается деталь – тем большее количество каверн будет образовываться.
Пористый некачественный металл наплавки получается также в случае загрязнения детали маслами и смазками.
Расходные материалы для наращивания металла
Это в первую очередь проволока для наплавки. Используют два её основных типа:
- СВ-15 для наплавки металла на изделия из чугуна (придаёт поверхности особую твёрдость при определённой хрупкости)
- Св-08А Св-18ХГСА, Нп-50 (65Г), Нп-30ХГСА – для наплавки стальных слоёв.
- Проволока пружинного типа по ГОСТу 9389–75.
Уход за оборудованием электродуговой наплавки
Для обеспечения стабильной и бесперебойной работы дуговых насадок для наплавки металлических слоёв на ремонтируемые детали нужен постоянный мониторинг работоспособности оборудования, с выставлением точных параметров с применением аппаратуры КИП. Продолжительная работа головки без замены и регулировки подающего мундштука приводит к поломке роликов, что вызывает изъяны в образуемом слое в виде пропусков, раковин, каверн и резко снижает качество ремонта.
Заключение
Оборудовать вибродуговой головкой можно токарный станок практически любого года выпуска – даже такого, когда о методе наращивания металла способом дуговой сварки не имели ни малейшего понятия. Если не подходит стандартный адаптер, всегда при наличии некоторой технической смекалки можно изготовить переходник для крепления и подачи проволоки-электрода к поверхности, которая нуждается в реставрации. Продляя таким образом жизнь многим устройствам, на которые запасных частей можно просто не найти.
А размер в данном случае не имеет значения – вибродуговая наплавка позволяет ремонтировать и огромные гребные валы океанских судов, и оси микродвигателей размером в 5-6 см.
Вибродуговая наплавка | Сварка металлов и материалов
Основным преимуществом дуговой наплавки является низкая температура нагрева детали, которая не превышает 90-100° С. Подобный нагрев не вызывает деформаций и понижения твердости соседних закаленных участков наплавляемой детали. Вибродуговой наплавкой можно наращивать слой толщиной до 4 мм. При значительном износе можно производить многослойную наплавку без предварительной обработки наплавленного металла.
Сущность метода
Сущность метода вибродуговой наплавки состоит в том, что в процессе наплавки электроду сообщаются колебания с частотой 50-100 в секунду. Во время наплавки в зону дуги подается охлаждающая жидкость — 5%-ный раствор кальцинированной соды. Охлаждающая жидкость уменьшает тепловое воздействие дуги на деталь и повышает скорость охлаждения наплавленного и основного металла, благодаря чему уменьшаются деформация и самоотпуск соседних участков детали. Кроме того, жидкость служит защитой расплавленного металла от вредного действия кислорода и азота.
Область применения
Вибродуговая наплавка используется преимущественно для восстановления деталей, имеющих форму тел вращения диаметром 15-40 мм из среднеуглеродистых и низколегированных цементируемых сталей. Вибродуговая наплавка также применима для термически обработанных деталей сложной конфигурации, где недопустимы глубокий прогрев, отпуск закаленной поверхности и коробление деталей.
Восстановление валов, осей, фланцев и других подобных деталей типа тел вращения вибродуговон наплавкой возможно на токарном станке, на суппорт которого устанавливается внброголовка, получающая продольную или поперечную подачи, а в центрах или патроне закрепляется деталь (рис. 17).
Рис. 17. Схема вибродуговон наплавки: 1 — барабан с электродной проволокой’. 2 — подающие ролики; 3 -пружина; 4 — насос; 5 — направляющий наконечник; 5 -деталь; 7 — электромагнит; 8-генератор; 9 — двигатель; 10 — редуктор.
Электрический ток подведен к детали и к электроду, который подается роликами 2 с барабана 1. В результате вибрации электрода с помощью пружинно-электромагнитного устройства происходят замыкание и разрыв электрической цепи в зоне контакта электрода с поверхностью детали. Вследствие большой плотности тока (до 400 А/мм2) при касании электрода детали зона контакта оплавляется, и электрод оставляет на поверхности детали часть расплавленного металла. Процесс повторяется с заданной частотой вибрации.
При вибродуговой наплавке вибрация электрода уменьшает глубину плавления основного металла и повышает коэффициент расплавления электрода, вследствие чего снижаются потери металла и расход электроэнергии.
Благодаря интенсивному охлаждению зоны дуги струей жидкости вибродуговая наплавка позволяет наращивать слой металла на тонкостенные втулки и детали, армированные резиной и пластмассой, восстановление которых другими методами затруднительно. В процессе вибродуговой наплавки детали намагничиваются, поэтому после восстановления их размагничивают.
Выполнение вибродуговой наплавки
Технологическая последовательность вибродуговой наплавки может быть следующей:
- Подготовка деталей к наплавке: очистка, промывка, обезжиривание.
- Вибродуговая наплавка; при необходимости — в несколько проходов.
- Размагничивание.
- Контроль детали с целью определения припусков для механической обработки.
Следует отметить, что биение свыше 0,3 мм поверхностей детали, глубокие риски и задиры, вызванные износом, устраняются механической обработкой до наплавки. Шпоночные пазы и отверстия, не подлежащие восстановлению, заделываются медными или графитовыми вставками. Поверхности, ие подлежащие наплавке, закрываются мокрым асбестом.
Похожие материалы
Восстановление деталей вибродуговой наплавкой (сущность процесса, применяемые материалы и оборудование, область применения).
Этот способ наплавки является разновидностью наплавки под слоем флюса и защитных газов процесс осуществляется при вибрации электрода с подачей охлаждающей жидкостью на наплавленную поверхность выше дана схема вибродуговой установки с электромеханическим вибратором деталь «3» подлежащий наплавки устанавливаются в патроне или в центрах токарного станка, на суппорте станка монтируются наплавочная головка. Состоящая из механизма подачи проволоки «5» с кассетой для электродной проволоки «6» электромагнитного вибратора «7» с мундштуком «4» вибратор создает колебание конца электрода с частотой 110 Гц и амплитудой колебания от 1 до 4 мм обеспечивая размыкание и замыкание сварочной цепи
Вибрация электрода существенно влияет на качество наплавки.
В связи с разрывом происходит мелкокапельный переход металла с электрода на основную деталь, образуя минимально воздушную сварочную ванну, способствующую достаточно хорошему наплавлению электродного металла с основным, небольшому нагреву и созданию малой по глубине зоны термического влияния. Кроме того уменьшается выгорание легирующих элементов электродной проволоки.
Вибродуговой наплавкой можно получить сравнительно тонкие и весьма прочные покрытия толщиной от 0,8 до 2,5 мм на круглых деталях диаметром от15 мм и больше.
Электроснабжение установок осуществляется от источника тока величиной 24 V последовательно с ним включен дроссель «9» низкой частоты который стабилизирует силу сварочного тока. Реостат служит для легировки силы тока в цепи
в зону наплавки при помощи насоса «1» из фильтрующего отстойника. В бак
«2» подается охлаждающая жидкость 4-6 % водный раствор кальцинированной соды которая защищает месталл от окисления.
Преимущество небольшой нагрев поверхности детали небольшая зона техническая слияния :
Возможность получать
Качество наплавки зависит от полярности тока зависит от полярности тока шага наплавки угла подвода электрода к детали качество очистки и подготовка поверхности детали и толщины слоя наплавки.
Высокое качество наплавки получают при токе обратной полярности (+) на электроде (-) на детали , шаг наплавки 2,3-2,8 мм и углу подвода проволоки к детали 15-30градусов скорость подачи электродной проволоки не должна превышать 1,05 м/мин при однослойном наплавки 0,5 -0,65 м/мин при однослойной наплавке толщина слоя колеблется от 0,5 до 3 мм а при многослойной наплавки можно получать слой любой толщины.
14. Электроконтактная сварка и наплавка (приварка ленты, проволоки, порошка). Сущность процесса, область применения, достоинства и недостатки.
По форме выполняемых соединений различают три основных вида контактной сварки : стыковую, точечную и шовную или роликовую.
При стыковой сварке через стык соединяемых деталей пропускают электрический ток. После разогрева зоны сварки производится осадка.
При точечной сварке соединяемые детали, чаще всего листы, собирают внахлёстку и зажимают между двумя медными, охлаждаемыми изнутри проточной водой электродами, подводящими ток к месту сварки и имеющими вид усечённого конуса. Ток проходит от одного электрода к другому через толщу соединяемых металлов и контакт между ними и производит местный нагрев их(вплоть до температуры расплавления). Давлением Р, приложеныым к электрода, производят осадку. Полученное сваренное соединение в плане имеет форму пятна диаметром в несколько миллиметров. Это пятно называют точкой.
При шовной сварке электроды, подводящие ток к изделию и осуществляющие сварку, имеют форму роликов, катящихся по изделию, в связи с чем эту разновидность контактной сварки называют также роликовой. При шовной сварке листы соединяются непрерывным плотным швом.
Энергия, выделяемая на контактах между электродами и основным металлом, расходуется на подогрев поверхности свариваемых деталей и ускоряет износ электродов, в связи с чем является вредной. Для уменьшения износа электродов обычно предусматривается водяное охлаждение их.
Все разновидности электрической контактной сварки широко используют в промышленности, а в ряде отраслей (например в автомобилестроении и др.) находят наибольшее по сравнению с другими способами сварки применение.
Сущность способа ЭКН заключается в нагреве присадочного материала и приконтактного объема металла восстанавливаемой детали импульсами электрического тока и их совместной пластической деформации, обеспечивающей образование физического контакта, активацию контактных поверхностей и объемное взаимодействие покрытия и материала основы.
В качестве присадки при ЭКН применяются как порошковые материалы, так и компактные материалы (сплошные металлические ленты и проволоки, порошковые ленты и проволоки). В случае использования в качестве присадки порошковых материалов процесс называется электроконтактное припекание (ЭКП). Припекание – технологический процесс, заключающийся в нанесении на поверхность восстанавливаемой детали порошковой формовки или слоя порошка с целью получения двухслойного материала путем нагрева до температуры, обеспечивающей спекание порошкового материала и образования прочной диффузионной связи с деталью.
Наварка стальной ленты. Металлическая лента используется для восстановления деталей типа тел вращения (валы, оси, ролики). Для этого используют отожженные СЛ. В этом случае теплота выделяется в основном на переходном сопротивлении лента – деталь. Наплавленный слой (определение «наплавленный слой» в принципе некорректно.) формируется в результате соединения СЛ с поверхностью детали. Его толщина практически равна толщине СЛ. Ленты почти всех марок стали при наварке значительно упрочняются (наблюдали даже упрочнение слоя, наплавленного лентой стали 08). Получаемая твердость пропорциональна содержанию углерода в стали.
Упрочнение происходит неравномерно. Наиболее интенсивно упрочнение происходит в зонах наплавленного слоя, не подвергающихся термическому воздействию последующих импульсов тока . Площадь этих зон составляет 50–90% от общей площади наплавленной поверхности. Остальная часть наплавленного слоя разупрочняется при наварке смежных участков в результате повторного термического воздействия. Степень разупрочнения повышается при увеличении содержания углерода в стали и снижении содержания легирующих элементов.
При правильном выборе режима наплавленные слои являются практически беспористыми. Однако с повышением содержания углерода возрастает вероятность образования в наплавленном слое сетки трещин. Поэтому электроконтактную наварку СЛ наиболее целесообразно применять для восстановления и упрочнения деталей, имеющих большой запас усталостной прочности.
Недостатками наплавки металлической лентой являются сравнительно низкая прочность сцепления покрытия с основой, тонкий слой наплавленного металла. Увеличить толщину наплавки в данном случае не представляется возможным. Более толстое покрытие позволяет получить ЭКН сварочной проволокой.
Наплавка сварочной проволокой .Электроконтактную наплавку осуществляют на специальной установке совместным деформированием наплавляемого металла и поверхностного слоя металла основы, нагретых в очаге деформации до пластического состояния короткими (0,02–0,04 с) импульсами тока 10–20 кА. В результате каждого из последовательных электромеханических циклов процесса на поверхности металла основы образуется единичная площадка наплавленного металла, перекрывающая соседние. Деформация наплавляемого металла за цикл составляет 40 – 60%. Наличие пластической деформации присадочного материала дает возможность повысить прочность сцепления покрытия с основой.
Наварка порошковых материалов. Использование свободных порошков позволяет готовить широкую гамму композиций различных технологических и эксплуатационных свойств, имея в наличии небольшую номенклатуру порошков матричных, технологических и упрочняющих материалов. Наварку производят сухими порошками со свободной их подачей под сварочные ролики.
Для уменьшения износа электрода, а также для устранения налипания порошковых материалов на контактную поверхность роликового электрода между последними и порошковым слоем целесообразно вводить технологическую медную или латунную ленту толщиной 0,1–0,2 мм (рис. 10, в). При нанесении твердосплавных металлических порошков, когда требуется приложение к слою значительных давлений (DР>О,7 МН/м), возможен токоподвод непосредственно через технологическую прокладку. Верхний ролик выполняется из жаропрочной стали.
В настоящее время широко применяется ЭКПП предварительно сформированных покрытий. Порошок с помощью плазмы или газопламенного устройства напыляют на поверхность заготовки , после чего она подвергается воздействию давления с одновременным пропусканием электрического тока. Указанный способ позволяет эффективно упрочнять крупногабаритные детали, оплавление которых после напыления практически невозможно. Электроконтактное припекание предварительно напыленных покрытий дает возможность получать слои с высокими физико-механическими свойствами, которые существенно превосходят характеристики оплавленных покрытий.
Применяющиеся в настоящее время дозирующие устройства для электроконтактной наплавки металлических порошков не позволяют решить поставленную задачу. Это связано с тем, что требуемый расход порошкового материала определяется сечением крана бункера и давлением порошка, масса которого изменяется в процессе упрочнения. Вследствие значительного удельного веса металлических порошков давление на слои, прилегающие к отверстию крана, в процессе наплавки существенно изменяется. Кроме того, требуемая величина толщины слоя порошка регулируется вручную, что приводит к ошибкам, снижающим качество металлопокрытия.
НАПЕКАНИЕ И НАПЛАВКА
Электроконтактное напекание металлических порошков применяют для восстановления деталей типа валов и осей. Технология этого процесса разработана в Челябинском институте механизации и электрификации сельского хозяйства. Сущность его заключается в следующем:
Между вращающейся деталью 4 (рис. 4), установленной в шпиндель токарного станка, и медным роликом-электродом 2, подают присадочный порошок 3. Ролик 2, при помощи
пневмо- или гидро — цилиндра 1 прижимается к детали с усилием 0,75…1,2 кН. При прокатывании детали и ролика и в результате большлого электрического сопротивления в месте их контакта порошок нагревается до температуры 1000…1300’С. Раскаленные частицы порошка спекаются межд собой и с поверхностью детали. Для напеканияпорошка применяют большуюсилу тока 2500…3500 А напряжение 0,7…1,2 В от трансформатора 6.
Рис. 40. Схема электроконтактного напекания металлических порошков:
1 – силовой цилиндр; 2 – ролик; 3 – металлический порошок; 4 – деталь;
5 – напекаемый слой; 6 – трансформатор; Р – прижимное усилие.
Основные виды сварки. Подготовка поверхностей перед сваркой.
Сваркой называют технологический процесс получения механически неразъемных соединений, характеризующихся непрерывностью структур – непрерывной структурной связью.
Механическая сварка.
Она же сварка взрывом. Выделение тепла происходит за счет трения между соединяемыми материалами. Трение происходит за счет взрыва, который сжимает соприкасающиеся поверхности деталей. Данный метод применяется для плакирования металлов инородным материалом. Например, сталь плакируется алюминием.
Термическая сварка.
Данный тип сварки включает в себя несколько разновидностей, которые мы сейчас и рассмотрим.
Электродуговая сварка.
Данный вид сварки наиболее часто используемый. Расплавление свариваемых материалов и/или деталей происходит за счет выделяемой электрической дугой теплоты. После застывания свариваемые поверхности образуют единое сварное соединение. Для данного типа сварки необходим сильноточный источник питания низкого напряжения. К его зажиму присоединяется сварочный электрод, к которому, в свою очередь, прикасается свариваемая деталь.
Основными «подвидами» электродуговой сварки являются: ручная дуговая сварка, сварка неплавящимся электродом, сварка плавящимся электродом, сварка под флюсом, электрошлаковая сварка.
Ручная дуговая сварка.
Является универсальным технологическим процессом. С её помощью можно производить сварочные работы в любом пространственном положении, из различных марок сталей, даже при отсутствии необходимого оборудования. Используется специальный покрытый флюсом электрод. Покрытие используется для защиты шва металла от внешних воздействий. Сварка проводится на постоянном токе прямой или обратной полярности и на переменном токе. Данный вид сварки применяется для выполнения коротких и криволинейных швов в труднодоступных местах, а также при монтажных работах.
Сварка неплавящимся электродом.
В качестве электрода используется стержень из графита или вольфрама. Температура плавления данных материалов выше температуры, при которой протекает сварочный процесс. Сварка чаще всего проводится в среде защитного газа (аргон, гелий, азот и их смесях) для защиты шва и электрода от влияния атмосферы. Сварку может проводить как без присадочного материала, так и с ним. В качестве присадочного материала используются металлические прутки, проволока, полосы.
Сварка плавящимся электродом.
В качестве электрода используется проволока (стальная, медная или алюминиевая), к которой через токопроводящий наконечник подводится ток. Электрическая дуга расплавляет проволоку, и для обеспечения её постоянной длины проволока подаётся автоматически механизмом подачи. Для защиты от атмосферы применяются защитные газы (аргон, гелий, углекислый газ и их смеси), подающиеся из сварочной головки вместе с электродной проволокой.
Сварка под флюсом.
В этом виде сварки конец электрода также представлен в виде металлической проволоки или стержня, на конец которой (-го) подается слой флюса. В качестве флюсов применяют прокаленную буру, борную кислоту, кремниевую кислоту и др. Флюсы используются в виде порошков, паст, водных растворов. Горение дуги происходит в газовом пузыре, находящемся между металлом и слоем флюса. Сама дуга при этом не видна. Благодаря этой технологии усиливается защита металла от вредного воздействия атмосферы и улучшается глубина проплавления металла.
Электрошлаковая сварка.
При электрошлаковой сварке в качестве электродов служат: электродная проволока, стержни, пластины. Источником теплоты является расплавленный шлак, через который протекает электрический ток. При этом теплота, выделяемая флюсом, расплавляет кромки свариваемых деталей и присадочную проволоку. Способ находит своё применение при сварке вертикальных швов толстостенных изделий. Электрошлаковую сварку используют в машиностроении для изготовления ковано-сварных и лито-сварных конструкций.
Плазменная сварка.
Источником теплоты является плазменная струя, получаемая при нагреве электрическим током электрода. Струя плазмы сжимается и ускоряется под действием электромагнитных сил, оказывая на свариваемое изделие как тепловое, так и газодинамическое воздействие. Теплом струи расплавляется основной металл около дуги, а также присадочный металл. Помимо сварки этот способ часто используется для наплавки, напыления и резки.
Электронно-лучевая сварка.
Источником теплоты является электронный луч. Луч получается за счёт термоэлектронной эмиссии с катода электронно-лучевой пушки. Данный вид сварки применяется в промышленных условиях в вакуумных камерах. Известна также технология сварки электронным лучом в атмосфере нормального давления, когда электронный луч покидает область вакуума непосредственно перед свариваемыми деталями.
Лазерная сварка.
Источником теплоты служит сфокусированный лазерный луч. Применяют твердотельные, газовые, жидкостные и полупроводниковые лазерные установки. Лазерный луч также используется для резки различных материалов. Основными достоинствами лазерной сварки являются: возможность вести процесс на больших скоростях, практически отсутствие деформаций изделия и узкий шов.
Газопламенная сварка.
Источником теплоты является газовый факел, образующийся при сгорании смеси кислорода и горючего газа. В качестве горючего газа могут быть использованы ацетилен, водород, пропан, бутан и их смеси. Тепло, выделяющееся при горении смеси кислорода и горючего газа, оплавляет свариваемые поверхности и присадочный материал с образованием сварочной ванны. Пламя может быть «окислительным» или «восстановительным», это регулируется количеством кислорода.
Термомеханическая сварка
Сварка происходит за счет нагревания свариваемых поверхностей. У этого вида сварки тоже имеются свои разновидности.
Контактная сварка.
При данном типе сварки изделия нагреваются, и происходит их деформация, что обеспечивает их взаимное проникновение. Свариваемые детали зажимаются в сварочных клещах, и по электродам пускают ток высокого напряжения, который плавит детали. Затем ток отключают и сильно сжимают клещи, из-за чего металл кристаллизируется, образуя, сварной шов.
Диффузионная сварка.
При диффузионной сварке соединяемые поверхности сдавливают и нагревают. Обычно этот процесс происходит в вакууме. В результате этого действия образуется сварочный шов. Данная технология весьма дорогостоящая и поэтому находит свое применение в основном в авиакосмической, электронной и инструментальной промышленности.
Кузнечная сварка.
Сваривание поверхностей происходит за счет ударов кованым молотом по раскаленным деталям. Данный тип сварки не надежен, малопроизводителен и пригоден для ограниченного числа сплавов. Кузнечная сварка на сегодняшний день практически нигде не используется.
Сварка высокочастотными токами.
Свариваемые изделия располагают вплотную друг к другу и разогревают за счет пропускания тока высокой частоты, затем детали сжимают. После этого полученному изделию необходимо остыть, и оно готово. Метод применяется в основном для изготовления труб и фасонных изделий из сортовой стали.
Разнообразие способов сварки, отраслей промышленности, в которых её используют, свариваемых материалов, видов конструкций и огромные объёмы применения позволяют охарактеризовать технологический процесс сварки, как один из важнейших в металлообработке
Подготовка к сварке предусматривает разметку, правку, резку, гибку, обработку кромок.
Правка. Цель этой операции — устранение деформаций. Сортовой и листовой металл небольшой толщины правится в холодном состоянии, а толстый (как и значительно деформированный) предварительно надо подогреть до 250—300°С.
Разметка выполняется с целью нанесения размеров Детали на металл. Разметка может быть выполнена индивидуально, по шаблонам, а также оптическим и машинным методами. Индивидуальная разметка — очень трудоемкий процесс. Шаблоны обычно изготовляют из алюминиевого листа. Для разметки используют инструменты: линейку, угольник, рулетку и чертилку.
Резка как этап подготовки к сварке может быть термической или механической. По производительности термическая резка уступает механической, но она более универсальна и позволяет точно выкроить заготовки разной геометрической формы (в том числе криволинейной). Механическая резка не может дать такой результат, так как возможности ножниц и прессов ограничены.
Кромки подготавливаются также двумя способами — термическим и механическим. Но чаще используется механический способ.
Кромки с односторонним или двусторонним скосом можно получить, используя одновременно два или три резака, расположенных под соответствующими углами. Механическая обработка кромок на станках выполняется для обеспечения требуемой точности сборки, для образования фасок, имеющих заданное очертание, в случаях, если технические условия требуют удаления металла с поверхности кромок после резки.
Гибка может осуществляться разным инструментом и разными способами, но классическим является гибка на листогибочных вальцах. Кроме этого используется и штамповка (в промышленных условиях).
Кроме этих операций обязательно надо хорошо очистить поверхности свариваемых деталей от грязи, ржавчины, окалины, масел.
Вибродуговая наплавка
В последние годы все большее применение в ремонтном деле получает восстановление изношенных деталей вибродуговой наплавкой, представляющей собой разновидность автоматической электродуговой наплавки металлическим электродом.
Сущность этого способа состоит в том, что деталь, вращающаяся в центрах токарного станка, наплавляется с помощью специальной головки. Головка обеспечивает подачу на деталь и вибрацию электродной проволоки диаметром 1,0—3,0 мм. К детали и проволоке подводится напряжение от источника питания. Для уменьшения зоны термического влияния и коробления наплавляемых деталей, а также увеличения твердости наплавленного слоя в зону дуги и на деталь подается охлаждающая жидкость — водный раствор кальцинированной соды. Охлаждающая жидкость защищает также расплавленный металл от окисления и азотирования.
Вибрация электрода осуществляется с помощью электромагнитного вибратора, включенного в цепь переменного тока с частотой 50 пер/сек., или с помощью механического вибратора. Частота вибрации электрода при использовании электромагнитного вибратора составляет 100 гц. Механические вибраторы в зависимости от их конструкций могут обеспечивать различную частоту вибрации.
В результате вибрации электрода в процессе наплавки происходит чередование периодов горения дуги и короткого замыкания.
Основная часть тепла (98—99,5%), идущая на расплавление электродной проволоки и детали, выделяется при горении дуги. Во время горения дуги на конце электрода образуются капли расплавленного металла, которые переходят на деталь преимущественно при коротких замыканиях. Таким образом, вибрация электрода способствует переносу электродного металла на деталь в виде мелких порций, облегчающих формирование тонких наплавленных слоев. Кроме того, вибрация способствует стабилизации процесса путем частых возбуждений дуговых разрядов, происходящих в каждый момент размыкания цепи (отрыва электрода от детали).
Вибродуговая наплавка обладает существенными преимуществами по сравнению с другими способами восстановления изношеиных деталей. К числу таких преимуществ относятся: незначительные деформации наплавляемых деталей, малая глубина зоны термического влияния, получение наплавленных слоев повышенной твердости без дополнительной термической обработки, возможность наплавки тонких слоев (от 0,5—0,7 мм до 2—3 мм). Эти преимущества обусловили широкое применение описываемого способа для восстановления изношенных деталей, в частности для восстановления автомобильных и тракторных деталей, деталей сельхозмашин, электродвигателей, различного промышленного и горнорудного оборудования, деталей судовых механизмов и машин.
На фиг. 85 показана принципиальная схема процесса вибродуговой наплавки, а на фиг. 86 — общий вид вибродуговой головки ВДГ-5, разработанной Челябинским политехническим институтом и Челябинским автомеханическим заводом.
Для питания дуги используются различные сварочные преобразователи, низковольтные генераторы типа НД 500/250, сварочные выпрямители типа ВС-200, выпрямители ВСГ-ЗМ и другие источники постоянного тока.
Для наплавки в зависимости от требуемой твердости применяются сварочная проволока Св-08, Св-08А, Св-18ХГСА и других марок, а также проволока из конструкционных и инструментальных углеродистых сталей с содержанием углерода до 0,8%. В большинстве случаев проволока берется диаметром 1,8—2,5 мм.
Фиг.85.Принципиальная схема вибродуговой наплавки
Фиг.86.Общий вид вибродуговой головки ВДГ-5
Основные параметры процесса вибродуговой наплавки: скорость подачи электродной проволоки 60—75 м/час, размах вибраций конца электрода 1,5—2 мм, среднее напряжение на дуге 15—23 в, расход охлаждающей жидкости 0,5—2,5 л/мин.
Вибродуговой процесс иногда применяется для сварки металла небольшой толщины.
Вибродуговая наплавка и сварка может осуществляться не только в среде жидкости, но также в среде защитных газов и под слоем флюса.
ВИБРОДУГОВАЯ НАПЛАВКА ДЕТАЛЕЙ
⇐ ПредыдущаяСтр 24 из 42Следующая ⇒
Вибродуговая наплавка отличается от ранее рассмотренных способов наплавки, тем что в процессе восстановления детали конец электродной проволоки совершает колебательные движения в плоскости, перпендикулярной наплавляемой поверхности, а также тем, что наплавленный слой металла принудительно охлаждается.
Процесс осуществляется нестабильной дугой (дуга на стадии тлеющего разряда) в сочетании с периодически повторяющимся коротким замыканием электрической сварочной цепи. Это способствует смягчению теплового режима наплавки. Перенос металла в режиме коротких замыканий облегчает формирование наплавляемых валиков. Вибродуговую наплавку осуществляют на установке стальной проволокой (рис. 7.14), которая подается через мундштук 9 до соприкосновения с поверхностью детали 1. К детали и проволоке подводится сварочный ток низкого напряжения. В момент соприкосновения электрода 10 с деталью 1 по проволоке протекает ток короткого замыкания. Это способствует расплавлению поверхности детали в месте контакта, и торец электрода быстро нагревается до температуры плавления. В результате такого взаимодействия достигается структурная связь между деталью и наплавленным металлом. Благодаря колебательному движению мундштука 9 торец электрода 10на короткое время отходит от поверхности детали 1, и в разрыве сварочной электрической цепи возникает искровой разряд с переходом в стадию тлеющего разряда, который длится до момента очередного соприкосновения торца электрода с поверхностью детали.
Рис. 7.14. Схема установки для вибродуговой наплавки:
1— источник сварочного тока; 2 — штуцер для подачи охлаждающей жидкости; 3 — механизм подачи электродной проволоки; 4 — электровибратор; 5 — кассета с электродной проволокой; 6 — уравновешивающие пружины; 7 — насос для подачи охлаждающей жидкости; 8 — мундштук; 9 — электрод; 10 — наплавляемая деталь; 11 — дроссель
Полезность выполнения электродом данного колебательного цикла состоит в том, что при коротком замыкании сварочной цепи основное количество тепла практически аккумулируется в вылете электрода и небольшом микрообъеме поверхностного слоя детали. При этом температура жидкой ванны достигает 1450 — 1500 °С, т. е. не превышает температуры плавления металла. Это не только смягчает тепловой режим наплавки, но и предотвращает возможность выгорания и испарения химических компонентов металла. Стадия тлеющего разряда при удалении торца электрода от поверхности детали используется для предварительного подогрева поверхности детали перед наплавлением очередной порции металла. В отличие от стабильной дуги, температура которой составляет в средней части около 6000 °С, дуга на стадии тлеющего разряда имеет температуру меньше 4000 °С, что также является фактором, смягчающим тепловой режим наплавки. Кроме того, молекула содержащегося в воздухе азота при этой температуре не диссоциирует и поэтому азот остается химически нейтральным по отношению к железу. Это способствует тому, что процесс вибродуговой автоматической наплавки деталей может обеспечить достаточно хорошее качество наплавки без применения защитных средств (флюса, газа и др.).
В ряде случаев в зону наплавки подают охлаждающую жидкость (2,5 — 6 %-ный водный раствор кальцинированной соды или 20 %-ный водный раствор глицерина). Образующийся водяной пар дополнительно защищает расплавленный металл от воздействия азота воздуха, чем способствует получению валика с более высокими механическими свойствами.
Учеными Института электросварки им. Е. О. Патона АН Украины разработан метод вибродуговой наплавки под слоем флюса, который с успехом применяют для наплавки, тонкостенных изделий большого диаметра. Применение флюса обеспечивает замедленное остывание металла и предотвращает образование трещин. Весьма эффективной защитной средой в процессе вибродуговой автоматической наплавки является углекислый газ.
Аккумуляция тепла с последующим быстрым охлаждением малых порций поверхностного слоя металла обеспечивает возможность наплавки вибродуговым способом малогабаритных деталей цилиндрической формы. При этом нет опасности стекания жидкого металла с поверхности детали. Практически диапазон размеров деталей, пригодных для наплавки этим способом, колеблется в пределах 3 — 200 мм.
Вибродуговая наплавка дает возможность получать равномерные слои толщиной от нескольких сотых миллиметра до 3 мм за один проход. Уникальным свойством этой наплавки является то, что в определенном интервале режимов возможно ведение процесса на воздухе без применения защитных средств. Вибродуговой наплавкой восстанавливают стальные и чугунные детали. При наплавке низкоуглеродистой проволокой, например марки Св-08, поверхность легко обрабатывают резцом. Для получения износостойких поверхностей применяют проволоку марки Нп-50Г, Нп-65Г, Нп-ЗОХГСА, Нп-40X13 и др.
Наплавку ведут на переменном и постоянном токе обратной полярности. Режимы вибродуговой наплавки приведены в табл. 7.18.
Вибродуговая наплавка обладает рядом серьезных недостатков. Так, ограниченные объемы сварочной ванны не обеспечивают хорошего перемешивания основного и наплавленного металлов, что приводит к образованию в последнем пор и микротрещин. В процессе восстановления деталей охлаждающая жидкость, подаваемая в зону сварки, обеспечивает закалку наплавленного валика, а накладываемый последующий валик частично расплавляет предыдущий и создает зону отжига, что приводит к возникновению напряженного состояния и увеличению трещин в наплавленном металле. Наращенный слой сплава имеет неоднородную структуру и соответственно физико-механические свойства. Поэтому у деталей, восстановленных вибродуговой наплавкой, усталостная прочность снижается более чем в 2 раза. Кроме того, производительность вибродуговой наплавки по сравнению с наплавкой подслоем флюса значительно ниже, а безвозвратные потери электродной проволоки на угар и разбрызгивание увеличиваются в 3 — 4 раза.
Вследствие указанных причин, вибродуговая наплавка для восстановления автомобильных деталей применяется в настоящее время редко. Детали, восстанавливающиеся ранее данным способом, в настоящее время успешно наплавляются более прогрессивными методами, например, электроконтактной приваркой металлического слоя.
Т а б л и ц а 7.18. Ориентировочные режимы вибродуговой автоматической наплавки в струе жидкости (4 %-ный водный раствор кальцинированной соды)
СВАРКА ЧУГУННЫХ ДЕТАЛЕЙ
Общие сведения о чугуне. В автомобильном производстве чугун имеет довольно широкое распространение. Он используется для изготовления базовых, корпусных и других деталей, например, блоков цилиндров, картеров, маховиков, тормозных барабанов, шкивов, ступиц колес и пр. Наибольшее распространение при восстановлении чугунных деталей получила электродуговая сварка.
Чугун относится к трудносвариваемым материалам. Эти трудности обусловлены наличием большого количества свободного углерода и структурой. В процессе восстановления сваркой свободный углерод частично выгорает с образованием углекислого газа, который растворяется в расплавленном сплаве. Некоторая часть газа не успевает выделиться из сварного шва, что приводит к образованию пористости. Кроме того, детали из чугуна после эксплуатации содержат в порах(своеобразных капиллярах) остатки масел, которые при нагреве выгорают и также способствуют образованию пористости в металле шва. Это снижает физико-механические характеристики сварного соединения.
Чугун обладает высокой жидкотекучестью и очень быстро переходит из жидкой фазы в твердую, минуя пластическое состояние. При быстром охлаждении сварочной ванны в шве или околошовной зоне может образовываться цементит (Ре3С), обладающий высокой твердостью и практически нулевой пластичностью. Такое явление получило название отбела чугуна в процессе сварки. Отбел приводит, как правило, к возникновению больших внутренних напряжений и трещинам в сварочном шве или околошовной зоне.
Поэтому для получения качественного сварного соединения при восстановлении чугунных деталей необходимо выполнение особых мер и приемов, направленных в первую очередь на предварительный нагрев деталей до начала сварки, охлаждение наплавленного металла с заданной скоростью, использование специальных электродов с более низкой температурой плавления, чем основной материал, и пр.
Выбор способа и приемов сварки чугунной детали зависит от ее размеров, формы, структуры, характера и места расположения дефекта, наличия тех или других сварочных материалов и других факторов. В ремонтном производстве в зависимости от состояния восстанавливаемой детали используют, в основном, два способа сварки чугуна: холодный и горячий.
Холодная сварка чугуна. Эта сварка наиболее широко используется при восстановлении автомобильных деталей. При данном способе используют специальные сварочные материалы или определенные приемы, например, способ отжигающих валиков, постановкой шпилек и пр.
Одной из основных задач при восстановлении чугунных деталей холодной сваркой является получение швов с минимально возможным количеством малопластинных цементита и ледебурита. Электродные материалы для сварки (на плавки) без предварительного подогрева детали разрабатывались, в направлении получения металла шва с достаточной степенью пластичности, который не образовывал бы закалочных структур при больших скоростях охлаждения. Требуемая пластичность материала шва достигается подбором электродного металла с большим значением предела текучести по сравнению с основным материалом, а также благодаря уменьшению количества углерода в наплавленном слое {с повышением количества углерода повышается вероятность образования ледебурита и мартенсита). Однако в процессе сварки избежать разбавления присадочного металла с основным не удается, поэтому в качестве электродных материалов используют металлы и сплавы, не образующие карбидов с углеродом (медь, никель). Так, при сварке высоконикелевыми электродными материалами возникают благоприятные условия для диффузии никеля в зону неполного расплавления из-за большого градиента концентрации этого элемента и большого коэффициента диффузии в жидком расплаве по сравнению с другими элементами. Для предупреждения образования карбидов на границах сплавления, когда сварка ведется на режим ах с малой погонной энергией (без сквозного проплавления), применяют электродные материалы с содержанием никеля более 90 %.
В ремонтном производстве для восстановления чугунных деталей наиболее широкое распространение получила механизированная сварка самозащитной электродной проволокой на основе никеля ПАНЧ-11, разработанной в Институте электросварки им. Е. О. Патона. Данный вид сварки чугуна обеспечивает высокое качество и производительность, позволяет восстанавливать самые разнообразные по форме и размерам автомобильные чугунные детали.
Рассмотрим устранение основных выбраковочных дефектов чугунных корпусных деталей. После дефектации при обнаружении трещин или пробоев деталь поступает в слесарно-механическое отделение, где ее подготавливают к восстановлению сваркой (рис. 7,15) электродной проволокой ПАНЧ-11. Поверхность с трещиной зачищают при помощи шлифовального круга электро- или пневмошлифовальной машиной до металлического блеска по обе стороны трещины на8— 10мм. Концы трещин обваривают или сверлят сквозные отверстия диаметром 3 — 4 мм, отступив 6 — 10 мм от видимого конца трещин в направлении ее развития. После зачистки поверхностей выполняют разделку трещин (рис. 7.16), причем, сквозные трещины в тонких стенках — с одной стороны (рис. 7.16, а), в толстых (более 12мм) — с двух сторон (рис. 7.16, в). Стенки средней толщины разделывают, как показано на рис. 7.16, 6. Несквозные трещины разделывают до сплошного металла. Операцию разделки трещин выполняют фрезерованием с использованием ручной сверлильной пневматической машины ИП-1011. При разделке прорезным шлифовальным камнем применяют пневмошлифовальную машину ИП-2009А. Сварка проволокой ПАНЧ-11 выполняется на постоянном токе прямой полярности без дополнительной защиты газом или флюсом. При сварке чугуна проволокой ПАНЧ-11 рекомендуются следующие режимы: диаметр проволоки— 1,2 мм, сварочный ток — 80 — 180 А, напряжение дуги—14—18 В, скорость подачи проволоки — ПО — 120 м/ч, скорость сварки — 4 — 5 м/ч.
Небольшой диаметр проволоки ПАНЧ-11 дает возможность использовать разделку кромок до 5 мм, что позволяет уменьшить тепловложение в деталь и сужает зону структурных превращений в основном металле. При данном виде сварки металл шва имеет достаточно высокие механические характеристики: предел прочности — до 500 МН/м2, предел текучести — до 300 МН/н2, удлинение — до 25 %, твердость — НВ 160 — 180. На небольшом участке околошовной зоны наблюдается повышение твердости до НВ 280 — 310. При испытании на растяжении образцы разрушаются, как правило, по чугуну.
Для сварки можно использовать один из серийных шланговых полуавтоматов типа А-547, А-825, «Варио-Стар» 240.
Техника сварки следующая. Трещины заваривают участками длиной 30 — 50 мм с проковкой и охлаждением каждого участка до температуры 50 — 60 °С. Заплаты на пробоины в деталях приваривают вразброс участками длиной 50 — 60 мм по контуру заплаты. Следующий участок на заплате начинают варить после проковки и охлаждения предыдущего до температуры 50 — 60 °С.
Для холодной сварки чугуна нашли применение медно-железные электроды ОЗЧ-2, которые изготавливают из медного стержня с фтористо-кальциевым покрытием с добавкой в него 50 % железного порошка. Эти электроды применяют для заварки трещин в водяных рубашках блоков цилиндров двигателей, головках блоков. Сварку ведут короткой дугой
на постоянном токе обратной полярности с перерывами на проковку (для снижения внутренних напряжений и повышения плотности шва) и охлаждение детали до температуры 50 — 60 °С. Силу сварочного тока для электродов диаметром 3 — 5 мм выбирают в пределах 110 — 190 А.
Медь, как и никель, не образует соединений с углеродом и практически не растворяется в железе. Поэтому наплавленный слой неоднороден, в медной основе расположены включения высокоуглеродистой стали с высокой твердостью. В околошовной зоне наблюдаются участки отбела. Шов обладает высокой твердостью.
Рис. 7.16. Разделка сквозных трещин
Таким образом, наплавка электродами с медными стержнями не обеспечивает получения сварного соединения свободного от отбела и закаленных переходных зон. Прочность сплава сварного шва составляет примерно 50 — 60 % прочности основного материала. Поэтому при заварке трещин электродами ОЗЧ-2, учитывая пониженную прочность чугуна в околошовной зоне, необходимо применять усиление шва, захватывая часть детали, прилегающую к кромке.
Более высокое качество восстановления достигается при холодной сварке чугуна электродами МНЧ-2, изготовленными из монельметалла (28 % меди, 2,5 % железа, 1,5 % марганца, остальное никель). Сварной шов при этом пластичен, имеет малую твердость, не имеет пор и раковин, зона отбела практически отсутствует, зона закаленного чугуна имеет невысокую твердость, которая может быть снижена небольшим отпуском. Однако твердость и прочность металла сварного шва невысока. Электродами МНЧ-2 устраняют практически все дефекты, которые встречаются в автомобильных деталях из чугуна: трещины, пробои, сколы, обломы и пр.
С целью экономии дорогостоящих электродов из монельметалла и получения материала шва более высокого качества иногда применяют комбинированную сварку в сочетании с электродами ОЗЧ-2. При таком варианте первый и последний слои наплавляют .электродами МНЧ-2, а промежуточные варят электродами ОЗЧ-2.
При отсутствии специальных сварочных материалов, рассмотренных выше, допускается проводить холодную сварку чугуна стальными электродами с содержанием в них углерода не более 0,1 %, например, марок УОНИ-13/45 или ОММ-5. В данном случае применяют специальный способ, получивший название сварки наложением отжигающих валиков (рис. 7.17). При таком способе первый валик, накладываемый на чугун, из-за перемешивания электродного материала с основным представляет собой сталь с содержанием углерода 0,6 — 0,8 %. При охлаждении -шов с таким высоким содержанием углерода закаливается. Последующие сварочные валики накладывают на первые таким образом, что происходит отжиг нижележащих слоев. Это позволяет получить относительно невысокую твердость сварочного шва. Перед сваркой трещину разделывают так, чтобы ширина разделки в верхней части в 2 — 3 раза превышала толщину свариваемой детали. Первоначально выполняют обварку кромок, а затем заполняют разделку. После сварки наложением отжигающих валиков материал шва по химическому составу представляет собой высокоуглеродистую сталь с неоднородной структурой. Данный способ отличается низкой производительностью, невысоким качеством и требует повышенного расхода электродов.
Для восстановления размеров поверхностей трения в ИЭС им. Е. О. Патона разработана самозащитная порошковая проволока марки ПП-АН160 диаметром 1,6мм. Проволока используется для наплавки изношенных шеек коленчатых валов, изготовленных из высокопрочного чугуна ВЧ-50-2. Наплавка производится с поперечными на всю ширину шейки колебаниями электрода. Наплавленный слой представляет собой белый износостойкий чугун доэвтектического состава с твердостью ИКС 48—54. Применение самозащитной порошковой проволоки позволило исключить флюс или защитный газ, что значительно снизило трудоемкость и себестоимость процесса.
От применяющихся в ремонтном производстве способов дуговой наплавки разработанную технологию отличает хорошо сформированный наплавленный слой высокой макрохимической однородности с низкой склонностью к образованию трещин. Это объясняется тем, что скорость распространения температурного поля в тело шейки выше скорости наплавки, а это способствует явлению автоподогрева.
Существенные различия во взаимном расположении коренных и шатунных шеек вала определили целесообразность проведения наплавки на двух специализированных станках УД-289 и УД-290. Основные параметры процесса (скорость подачи проволоки, частота колебаний, скорость наплавки) находятся во взаимной функциональной зависимости и устанавливаются один раз при настройке станка. В качестве источника питания применяют сварочные выпрямители с жесткой внешней характеристикой ВДУ-В04, ВДУ-505,- ВС-300 и др. Род тока постоянный, полярность обратная.
Описанная технология используется для восстановления чугунных коленчатых валов автомобилей ГАЗ-24, УАЗ-469. К недостаткам данного процесса следует отнести укорочение коленчатого вала после наплавки на 2 —З мм.
Горячая сварка чугуна. Эта сварка заключается в том, что деталь предварительно нагревают до температуры 650 — 680 °С в печи и в таком состоянии устраняют дефекты сваркой и наплавкой. Используют электродуговую и газовую сварку. В качестве присадочного материала применяют чугунные прутки марки А , химический состав которых характеризуется повышенным содержанием углерода и особенно кремния. Это необходимо для компенсации их угара при сварке и обеспечения полной графитизации металла шва.
При сварке используют специальный флюс ФСЧ-1, допускается применение технической буры и 50 % смеси углекислого калия к натрия. В процессе сварки нельзя — допускать снижение температуры восстанавливаемой детали ниже 500 °С. После окончания сварки деталь охлаждают в специальных термосах или вместе с печью со скоростью 50 — 100 °С в час для нормализации и снятия внутренних напряжений.
При горячей сварке наблюдается наилучшее качество восстановления детали — сварной шов прочный, плотный, однородный по химическому составу и структуре, отсутствуют хрупкие структуры отбеленного чугуна. Однако высокая трудоемкость и стоимость восстановления, а также тяжелые условия труда сварщика ограничивают использование данного способа. По данной причине на авторемонтных заводах в настоящее время горячая сварка и наплавка деталей из чугуна практически не используется.
Рекомендуемые страницы:
Вибродуговая наплавка | Обслуживание и ремонт автомобиля
Вибродуговая наплавка отличается от других сварочных процессов наличием колебаний электродной проволоки с частотой 50-100 Гц и низким напряжением источника сварочного тока. Перенос металла электродной проволоки на деталь происходит за счет чередования электрических разрядов и коротких замыканий цепи.
Вибродуговую наплавку применяют для восстановления изношенных поверхностей стальных и чугунных деталей довольно широкой номенклатуры.
Оборудование
В состав оборудования для вибродуговой наплавки входит переоборудованный токарный станок, обеспечивающий медленное вращение детали, наплавочная головка и источник сварочного тока.
В качестве наплавочных головок используют те же механизмы, что и при автоматической наплавке под слоем флюса. В них изменена только конструкция мундштука и отсутствует устройство для подачи флюса.
Одной из новых разработок для вибродуговой наплавки является головка ОКС-6569М ГОСНИТИ. Она предназначена для наплавки деталей диаметром более 15 мм, имеющих износ от 0,5 до 3 мм. Наплавка производится в среде жидкости или углекислого газа проволокой сплошного сечения диаметром от 1,2 до 3 мм. Головка пригодна также для наплавки порошковой проволокой. При использовании специальной проволоки Св-15 наплавку ведут при отключенном вибраторе.
В качестве источников сварочного тока при вибродуговой наплавке используют то же оборудование, что и при автоматической наплавке под слоем флюса.
Электродная проволока
Для восстановления деталей вибродуговой наплавкой применяют следующие марки проволоки: Св-08А, Св-18ХГСА, Св-15; Нп-50, Нп-65Г, Нп-30ХГСА; пружинную проволоку 2-го класса. Марка проволоки выбирается в зависимости от требуемых свойств наплавленного металла (в основном твердости). Стальные детали, требующие высокой твердости, наплавляют пружинной проволокой 2-го класса, другой высоко-углеродистой проволокой. Этими же проволоками наплавляют чугунные детали. Кроме того, чугунные детали, требующие высокую твердость поверхностного слоя, наплавляют проволокой Св-15. Для наплавки деталей двигателя применяют в основном проволоку диаметром 1,4-1,8 мм.
Подготовка деталей
Поверхность, подлежащая наплавке, должна быть зачищена до металлического блеска.
Зачистку делают непосредственно перед наплавкой при помощи шлифовальной шкурки при тех же частотах вращения детали, что и при ее наплавке. Биение наплавляемой поверхности не должно превышать 0,5 мм. При большем изгибе детали ее перед наплавкой необходимо выправить либо обработать на станке. Поврежденные резьбовые отверстия перед наплавкой необходимо обработать до полного удаления старой резьбы.
Технология вибродуговой наплавки
Процесс осуществляют на постоянном токе обратной полярности. Оптимальное напряжение при наплавке 17-20 В.
Для охлаждения детали применяют 3-4 %-ный раствор кальцинированной соды или 10-20 %-ный раствор технического глицерина. Количество жидкости, подаваемой в зону наплавки, регулируют краном, установленным на наплавочной головке. Струя жидкости не должна попадать в столб дуги, так как от этого нарушается процесс наплавки.
Толщина наплавляемого слоя зависит от соотношения скоростей подачи электродной проволоки и окружной скорости вращения детали. Чем больше скорость подачи проволоки и меньше окружная скорость вращения детали, тем толще будет наплавленный слой. С увеличением окружной скорости вращения детали наплавляемый валик металла при прочих равных условиях наплавки становится тоньше и уже.
Если толщина наплавленного слоя должна быть минимальной, то применяют тонкую проволоку, а если требуется получить более толстый слой, то применяют проволоку большего диаметра.
Стабильность процесса наплавки контролируют по показаниям амперметра и по равномерности издаваемого звука. При нормальном ходе процесса стрелка амперметра почти не колеблется и слышен равномерный характерный звук плавящейся проволоки. При неправильно выбранных режимах наплавки процесс идет при непрерывном резком потрескивании, стрелка амперметра резко колеблется, шов получается прерывистым.
Большая пористость наплавленного металла указывает на загрязненность охлаждающей жидкости либо недостаточно хорошую очистку поверхностей основного металла и проволоки. При слишком большой окружной скорости детали в наплавленном металле образуется большое количество раковин.
После длительной работы наплавочной головки изнашиваются направляющая трубка мундштука, рифления подающего ролика в механизме подачи проволоки, ослабевает затяжка конусного болта шатуна наплавочной головки и пр. Все эти неисправности приводят к нарушению стабильности процесса и образованию дефектов наплавки. Поэтому необходимо своевременно производить обслуживание установки.
Другие статьи по теме:
с вашего сайта.