Визуальный контроль
Визуальный и измерительный контроль.
ООО «Диаформ» имеет аттестованных специалистов по визуальному и измерительному контролю, а также все необходимое оборудование для его проведения.
ВИК — это один из методов неразрушающего контроля оптического вида. Он основан на получении первичной информации о контролируемом объекте при визуальном наблюдении или с помощью оптических приборов и средств измерений. Это органолептический контроль, т.е. воспринимаемый органами чувств (органами зрения) ГОСТ 23479-79 «Контроль неразрушающий. Методы оптического вида» устанавливает требования к методам контроля оптического вида.
Перед проведением визуального контроля поверхность в зоне контроля должна быть очищена от ржавчины, окалины, грязи, краски, масла, брызг металла, и других загрязнений, препятствующих осмотру.
Получить консультацию
При Визуально-Измерительном Контроле сварных швов зоной контроля является сварной шов и прилегающие к нему участки основного металла на ширине не менее 20 мм в каждую сторону от шва с двух поверхностей, если обе они доступны для осмотра.
Визуальный контроль выполняется до проведения других методов контроля. Дефекты, обнаруженные при визуальном контроле, должны быть устранены до проведения контроля другими методами.
Внешним осмотром (ВИК-ом) проверяют качество подготовки и сборки заготовок под сварку, качество выполнения швов в процессе сварки и качество готовых сварных соединений. Как правило, внешним осмотром контролируют все сварные изделия независимо от применения других видов контроля. Визуальный контроль во многих случаях достаточно информативен и является наиболее дешевым и оперативным методом контроля.
Визуальный контроль, как правило, производится невооруженным глазом или с использованием увеличительных луп до 7 х. В сомнительных случаях и при техническом диагностировании допускается применение луп с увеличением до 20 х. Визуальный метод контроля позволяет обнаруживать несплошности, отклонения размера и формы от заданных более 0,1 мм при использовании приборов с увеличением до 10 х.
Измерения производятся с использованием приборов и инструментов:
— лупы измерительные;
— штангенциркули;
— линейки измерительные металлические;
— угломеры;
— угольники;
— щупы;
— шаблоны и др.
Визуальный контроль в «бережливом производстве»
Системы технического зрения – как средство реализации методов Lean производства.
Непрерывное устранение потерь – одна из главных задач концепции «бережливого производства». Рассмотрим некоторые идеи реализации этого подхода с точки зрения внедрение систем технического зрения.
Перепроизводство.
Производство продукции «на склад» и связанные с обслуживанием и хранением операции являются потерями, не несущими ценности для потребителя.
Для решения этой проблемы «бережливое производство» предлагает производить продукцию точно под заказ или минимальными партиями. Эту систему называют «Just-in-time».
Контроль качества динамично меняющихся видов продукции осложнен для человека.
Возникает риск возникновения других потерь: предпосылки к выпуску продукции с отклонениями, возрастанию потерь времени на переналадку оборудования.
Системы технического зрения хранят настройки для очень большого числа задач и моментально переключаются на другой вид продукции или задачу.
В арсенале контроллера FH более 100 инструментов анализа изображений, что делает его очень универсальным средством. А количество оперативно хранимых сценариев настройки – 128.
Предотвращение ошибочных действий.
«POKA-YOKE» или «Защита от дурака» — методика исключения неправильных действий.
Идентификация продукции в процессе сборки, выполняемая тех. зрением может создавать инструкции для сборщика, подсказывающие или разрешающие соблюдение требуемой последовательности и комплектации изделия.
Контроль перед финальной операцией сборки. Операция контролирует правильность сборки и полную комплектность изделия перед финальной операцией, исключающей изготовление бракованного изделия.
Еще один момент — избыточность интерфейсов систем управления. При необходимости создания интерактивного воздействия оператором на процесс визуального контроля, с системой нашего технического зрения пользовательский интерфейс может быть индивидуально приспособлен под конкретную задачу. Делается это путём свободного выбора места размещения элементов интерфейса, а ненужные элементы могут быть скрыты. Программное обеспечение позволяет иметь различные виды интерфейса для разработчика и конечного пользователя.
Снижение допустимых отклонений.
Автоматизированный визуальный контроль способен сделать новый шаг в воздействии на причину возникновения отклонений качества продукции. Анализ с помощью технического зрения дает возможность произвести детальные и количественные измерения отклонений. И что, также важно, делать это непрерывно, накапливая статистику. Техническое зрение может сохранять результаты анализа и непосредственно изображения инспектируемых изделий. Порой, только анализ таких данных дает возможность понять причину отклонений и исследовать качество влияния корректирующих воздействий. Результатом может быть достижение качества изделий выше необходимых требований.
1. Систематический анализ процесса
2. Корректировка
3. Уменьшение рассеивания
Отслеживание перемещения продукции в цикле производства.
Для сбора и сохранения информации о процессе производства продукта в пределах всего производственного цикла, – от сырья (или исходных комплектующих) до склада готовой продукции, применяются технологии прослеживаемости продукта. А для некоторых продуктов, прослеживаемость может выходить и за рамки производственного процесса, помогая предпринять действия, направленные на улучшение качества изделий, находящихся уже в эксплуатации. Такое отслеживание проводится путем присвоения и контроля серийных номеров изделий. В большинстве случаев маркировка осуществляется штрих-кодами.
Коммуникационные возможности наших систем на основе стандартных интерфейсов позволяют встраивать их в распределенные системы. Камеры умеют считывать все наиболее используемые штрих-коды, а также распознавать текст, если маркировка нанесена в виде, предназначенном для чтения человеком.
Идея непрерывного улучшения и модернизации лежит в основе философии «бережливого производства». И перед тем, как сделать первый шаг и начать, даже, маленький проект, который сегодня что-то улучшит в технологической цепочке, нужно принять во внимание некоторые идеи, как это решение может развиваться в будущем. Каким должно быть решение, которое отвечает идее постоянного улучшения:
Масштабируемое:
- начиная с одного продукта, оно может быть применимо ко всем продуктам
- от одной линии, до других линий и производственных площадок
Интегрируемое:
- в создаваемую систему должны легко интегрироваться новые элементы
- последующее использование наработок снижает затраты на новые разработки
Обслуживаемое:
- минимальное время поиска неисправностей и переналадки
Легко применимое:
- использование должно быть простым для всех подразделений и новых пользователей
- унификация настройки оборудования.
Наши линейки технического зрения разработаны как модульная система с гибкими возможностями. Для коммуникации используются стандартные интерфейсы и протоколы, облегчающие интеграцию с различным оборудованием.
Контроллеры серии FH комбинируются с очень широкой линейкой камер: от 0.3 МП до 12 МП и большим количеством вариантов объективов.
Возможность высокоскоростной обработки изображений с высоким разрешением обеспечена благодаря оснащению контроллеров мощными многоядерными процессорами. Но, в то же время, сохранена гибкость выбора оптимальной цены за счет наличия в линейке модели FH-Lite.
Системы технического зрения разработаны, как продукт, входящий в единую «экосистему» решений Омрон. Где программирование и настройка оборудования осуществляются в единой программной среде, обеспечивая прозрачность, переносимость настроек и легкую совместимость.
Следить за подразделением промышленной автоматизации OMRON на LinkedIn
Контроль визуальный — Энциклопедия по машиностроению XXL
Дефектоскопия.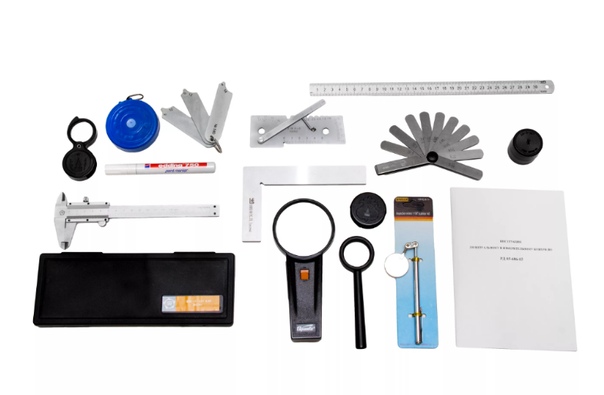
Система оптико-электронного сканирования для магнитно-люминесцентного и люминесцентного контроля (Англия). В капиллярной дефектоскопии механизированные полуавтоматические линии действуют уже более 20 лет, Основной источник низкой надежности контроля — визуальный осмотр объектов контроля. Прежние попытки автоматизировать осмотр были неудачными из-за влияния фона и невозможности учета общей визуальной информации об объекте контроля. Данная система не только фиксирует, но интерпретирует индикаторные следы дефектов по размерам, форме и положению, принимая решение о годности объекта. [c.180]
Были рассмотрены все возможные комбинации использования четырех выше указанных способов, дл5 каждой из которых определялись значения параметров, характеризующих эффективность системы контроля, г строился обобщенный показатель качества контроля функция желательности.

Методы производства контроля (визуальный, инструментальный или лабораторный) устанавливаются в каждом конкретном случае а зависимости от специфики объектов контроля. [c.186]
Различают следующие виды контроля визуальный контроль изделий после покрытия (цвет, блеск, шероховатость поверхности) определение пористости и толщины слоя покрытий испытание на коррозионную стойкость определение механических и физических свойств покрытий (пластичности, стойкости к высоким температурам и др.).
Контроль объектов или стадий процесса производства может быть летучим — срок проведения его не регламентирован периодическим — проводится через определенный промежуток времени (часы, сутки, месяцы) непрерывным — ведется непрерывно (постоянно). В зависимости от средств контроля различают контроль визуальный, когда
[c.95]
При автоматических методах сварки и допустимости контроля визуальным осмотром обратной стороны допускается применение устройств для местной защиты. [c.332]
Визуальные МНК применяются не только для армированных пластиков. Использование композитов в Сандвичевых конструкциях вызывает необходимость и в этом случае применять такие методы контроля. Визуальный осмотр непосредственно после отверждения еще не остывших сотовых сандвичевых конструкций позволяет обнаружить пузыри, непроклеенные участки или расслоенные участки. Эти пузыри могут исчезнуть после охлаждения конструкции при пониженном давлении. Когда необходимо определить визуально наличие или отсутствие открытых пор в слоистых пластиках, желательно использовать специальные световые установки, которые могут помочь увидеть дефекты в структуре. Однако таким способом в основном могут наблюдаться только большие дефекты.
[c.469]
Методика выявления дефектов уплотнительных поверхностей и деталей разъемных соединений включает методы контроля (визуальный и инструментальный) контролируемые параметры уплотнительных поверхностей и деталей узла уплотнения (отклонение формы уплотнительных поверхностей — некруглость, прямолинейность образующей уплотнительной поверхности, угол наклона уплотнительной поверхности к оси сосуда, трещины на уплотнительных поверхностях и на резьбовой и гладкой частях крепежных шпилек, дефекты уплотнительных поверхностей механического и коррозионного происхождения резьба шпилек и гаек основного крепежа — размеры, механические повреждения, коррозия, шероховатость) методы проведения и средства измерений контролируемых параметров деталей разъемных соединений. [c.81]
По виду проверяемых параметров качества применяются следующие методы контроля визуальный (внешний осмотр), геометрический (контроль размеров и форм изделий), качественный (качество металлов и материалов), химический,, физический и др.

Контроль (визуальный, пыжом) Укупорка [c.25]
Производственный контроль. У заготовок перед зубообработкой на специальных приспособлениях контролируют поверхности, которые используют в качестве установочных баз на зубообрабатывающих операциях и контроле. Визуально проверяют наличие забоин и заусенцев на установочных поверхностях. [c.417]
Отливки должны подвергаться следующим видам контроля визуально с измерениями основных размеров контролю химического состава (поплавочно) контролю механических свойств (включая твердость) гидравлическому испытанию неразрушающему контролю сплошности металла отливок (МПД радиусных переходов и рентгенопросвечивание или гаммаграфия концов присоединительных патрубков). [c.116]
Таким образом, в описанном случае измерительное устройство работает на полуавтоматическом цикле управление подачей приспособления осуществляется автоматически, процесс контроля — визуально. Однако данная конструкция измерительного приспособления легко может быть переведена на автоматический цикл рабо-218
[c.218]
Кроме того, отливки должны проходить следующие виды контроля визуальный с измерениями основных размеров химического состава (по плавкам) механических свойств (включая твердость) гидравлические испытания неразрушающий контроль сплошности металла отливок (МПД радиусных переходов и рентгенопросвечивание или гаммаграфия концов присоединительных патрубков). [c.136]
Контроль отливок прежде всего осуществляют визуально для выявления брака или отливок, подлежащих исправлению. Правильность конфигурации и размеров проверяют разметкой, плотность металла отливки — гидравлическими испытаниями под давлением воды до 200 МПа. Внутренние дефекты выявляют в специализированных лабораториях. Технический контроль возложен на отдел технического контроля завода. [c.180]
К механическим устройствам относятся главным образом трехконтактные индикаторные скобы, предназначенные для визуального контроля. — При шлифовании шеек ступенчатого вала целесообразно применять устройство (рис. 61) с поворотным барабаном 1, на котором смонтировано необходимое количество трехконтактных индикаторных скоб 2, каждая из которых отрегулирована на требуемый диаметр.
[c.192]
На линии выполняются следующие операции I — полная токарная обработка наружного кольца 2 — черновая токарная обработка внутреннего кольца 3 — чистовая токарная обработка внутреннего кольца 4 — клеймение 5 — магазины задела 5 и 7 — термическая обработка наружного и внутреннего колец 8 — визуальный контроль 9 — плоское шлифование наружного и внутреннего колец (поочередно) а — базового торца б — противоположной поверхности 10 — бесцентровое шлифование наружной поверхности наружного кольца 11 — черновое бесцентровое шлифование дорожки качения наружного кольца 12 — чистовое бесцентровое шлифование дорожки качения наружного кольца 13 — бесцентровая доводка дорожки качения наружного кольца 14 — снятие наката 15 — визуальный контроль 16 — промывка и сушка наружного кольца 17 — автома-
[c. 465]
Здесь на позиции 10 нижний пуансон приподнимает балку до упора в верхний пуансон, создавая прогиб кромок банджо примерно на 2°. Затем на позиции 11 подающее устройство захватывает балку и выносит ее из линии для визуального контроля на позиции 11а. Контролер осматривает швы и, ес 1и картер требует подварки, нажимает кнопку Дефект . По этой команде подающее устройство опускает балку на склиз, направляя ее на под-варку, а из накопителя забирает ранее подваренную балку и подает ее в линию. При качественных швах контролер нажимает [c.364]
Все сварные соединения сосудов и их элементов подлежат визуальному и измерительному контролю с целью выявления в них следующих дефектов [c.49]
Активными методами являются визуальный и измерительный контроль, ультразвуковая дефектоскопия, магнитные, радиографические капиллярные, метод вихревых токов, электрический. [c.176]
Визуальный и измерительный контроль (ВИК) [c.
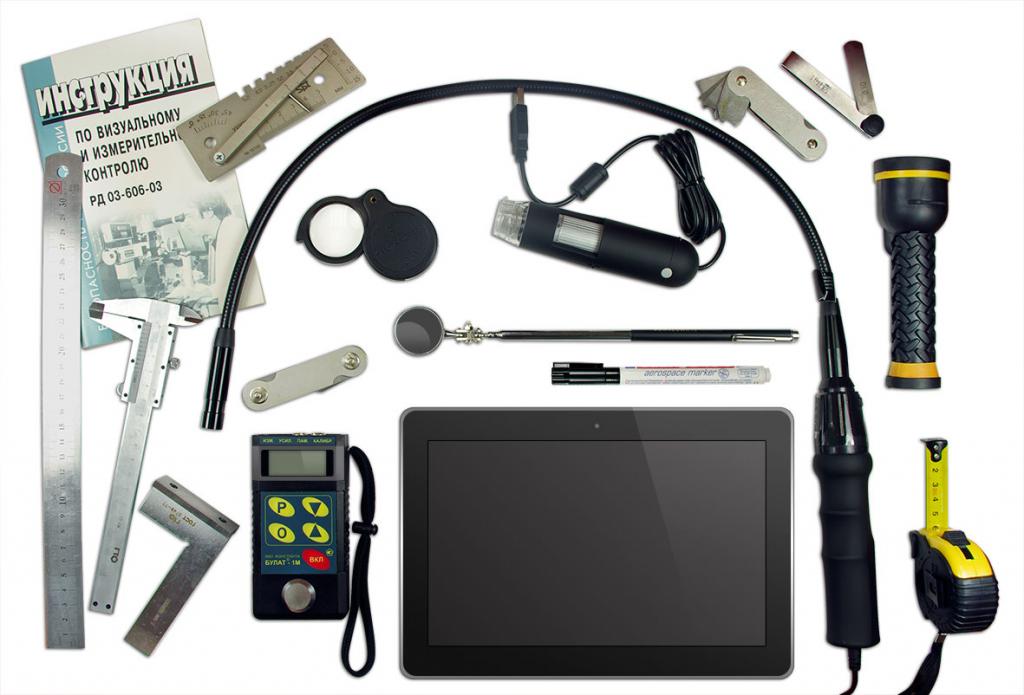
Визуальный осмотр и при необходимости выполнения текущего контроля измерениями являются необходимыми и обязательными условиями контроля качества как при изготовлении, так и при эксплуатации технологического оборудования, работающего под внутренним давлением. [c.179]
В 10—30-х годах текущего столетия были опробованы методы микроскопического анализа изучение под микроскопом поперечного шлифа электролитически покрытой поверхности, измерение под микроскопом неровностей поверхности по репликам из желатина и т. д. Предпринимали попытки косвенной оценки неровностей поверхности по потерям энергии маятника при торможении его неровностями поверхности во время качания, по разности размеров деталей до и после доводки, по предельному углу регулярного отражения света, по теневой картине поверхности на экране с увеличенными изображениями поверхностных дефектов, по расходу воздуха через участок контакта сопла с испытуемой поверхностью, по четкости изображения растра на испытуемой поверхности или на экране после отражения от нее светового пучка, по электрической емкости контактирующей пары испытуемая поверхность — диэлектрик с нанесенным слоем серебра , по нагрузке на индентер при определенном его сближении с испытуемой поверхностью, по изображению мест плотного соприкосновения призмы с неровностями поверхности и т. д. Были опробованы методы исследования рельефа поверхности с помощью стереофотограмм и стереокомпаратора. На производстве в этот период доминировали органолептические методы контроля визуальное сравнение с образцом, сравнение с помощью луп, сравнение на ощупь ногтем, краем монеты и т. п. В 30-х годах был предложен и реализован в двойном микроскопе метод светового сечения (Линник, Шмальц), а также метод микроинтерференции и основанные на нем микроинтерферометры, сочетающие схемы микроскопа и интерферометра Майкельсона. В этот же период
[c.58]
Светорассеивающее (молочное) МС13 Пластинка стекла толщиной 2 мм должна иметь коэффициент пропускания То для источника света А не менее 50+3%, определяемый на фотометрической установке при отсутствии света, проходящего прямо через стекло. Отступление от нейтральности 40%. Глушение стекла равномерное. Контроль визуальный Прессованные диаметром не больше 120 мм, по ГОСТ 3514-57 [c.729]
Размеры коррозионньЕх повреждений определяются неразрушающими методами контроля (визуальный, ультразвуковой, вихретоковый, рентгеновский и др. ). Остаточная прочность силовых элементов с коррозионными повреждениями должна быть определена, как правило, на основе экспериментальных исследований. Приближенная оценка может быть сделана по величине коэффшщента интенсивности напряжений К = К = ). При этом, зона коррозионного повреждения представляется в виде усталостной трещины соответствующего размера.
[c.423]
Гидравлические системы. Визуальным методом выявляют места возможной утечки. Преимуществом метода является то, что система заполнена рабочей жидкостью, испытания совмещаются с опрессовкой и проверкой функционирования. Недостаток метода — невозможность контроля визуально недоступных мест утечки, низкая чувствительность и субъективность. Критерии оценки образование подтеков без каплепадения, подтекания с каплеобразованием, капельные утечки. Соответствующий диапазон утечек для масел и нефтепродуктов 0,025… 10 mmV(m ). Визуальный метод контроля со сбором утечек на фильтровальную бумагу несколько точ-
[c. 52]
В системе УСП существует два вида контроля, определяющего пригодность компоновки к зксплуатации контроль визуальный и контроль с помощью мерительных средств. Под визуальным контролем подразумевается внешний осмотр приспособления, который должен определить правильность его конструкции. Оценивается, правильно ли сделан выбор типа конструкции, удачно ли расположение на базовой плоскости всех входящих в компановку узлов, посадоч1ных мест, крепежно-прижимных устройств и установочно-направляющих элементов и, наконец, пол1ож0ние самой обрабатываемой детали в приспособлении. [c.163]
Цвет можно контролировать путем визуального сравнения образца со стандартными цветными эталонами. Можно доказывать, что в конечном счете глаз является единственным справедливым арбитром, но возникает много вопросов, из которых самым трудным, вероятно, является Чей глаз Помимо генетических аномалий, которые рассматривались выще, известно, что цветовосприятие изменяется с возрастом из-за возникновения в глазах желтой пятноподобной пигментации, и что стандартный наблюдатель — это статистическая абстракция. Все это — сильные аргументы в пользу контроля цвета путем физических измерений. Эти измерения и их интерпретация должны быть тесно связаны с визуальным восприятием наблюдателя. На практике имеется два вида цветового контроля — визуальный и инструментальный.
[c.450]
Диагностика технологических коммуникаций и оборудования ГРС осуществляется при помощи комплекса измерительных средств и методов неразрушающего контроля визуально-оптический вибродиагностический акустико-эмиссионный метод измеритель твердости ультразвуковая дефектоскопия толщинометрия термографический магнитный. 49 [c.49]
Затем балка снова возвращается к сборщику для визуального контроля и подварки в случае необходимости, после чего он освобождает балку от закрепления п приспособлении, и автоопера- [c.104]
После визуального контроля технологических швов и приварки технологических планок трубы поступают на сварку йнутренних рабочих швов. Сварку осуществляют трехдуговым аппаратом А-1448, слежение за направлением электродов по стыку производится автоматически или визуально путем совмещения иертикаль-ной линии креста на экране телевизора с риской на внутренней
[c. 298]
Auto AD обладает широкими возможностями отображения различных видов рисунка. Предусмотрены команды, которые позволяют при редактировании рисунка быстро перемещаться от одного его фрагмента к другому для визуального контроля внесенных изменений. Можно производить зумирование, изменяя экранное увеличение выводимого изображения, или панорамирование, перемещая рисунок по видовому экрану сохранять выбранный вид, а затем восстанавливать его для вывода на печать или просмотра. Допускается также одновременный просмотр различных участков изображения при разделении области рисунка на несколько неперекрывающихся видовых экранов. [c.184]
Экспертное обследование предполагает получение информации о фактическом состоянии элементов длительно проработавшего оборудования, наличия в нем повреждений, выявления причин и механизмов возникновения повреждений. Оно должно проводиться в соответствии с программой, разработанной на основе анализа технической документации, а также данных функциональной диагностики и должно включать визуальный (внешний и внутр)енний) контроль измерение геометрических параметров и толщины стенок замер твердости и определения механических характеристик, металлографические исследования основного металла и сварных соединений определение химического состава дефектоскопический контроль (вид и объем которого устанавливаются с учетом требований полноты и достаточности выявления дефектов и повреждений) испытания на прочность и герметичность и др.

Визуальный управленческий контроль ключевых показателей компании
Характерной областью применения визуального контроля является мониторинг ключевых показателей исполнения соглашений об уровне сервиса ИТ-службы компании (SLA).
В последнее время на руководителей, менеджеров усиливается давление ответственности за успешность компаний на рынке, за выполнение планов. Визуальный управленческий контроль – один из наиболее понятных и эффективных инструментов современного руководителя, менеджера. Попытаемся дать краткий обзор принципов формирования показателей управления, описать возможности визуального управленческого контроля и приведем несколько примеров из практики.
Руководители, менеджеры и ключевые показатели
В названии должностей часто встречаются слова руководитель
и менеджер. В этих терминах существует некоторое различие. Руководитель
определяет цели и ставит задачи, отслеживает выполнение задач и достижение целей. Менеджер координирует работу и распределяет ресурсы для выполнения поставленных задач и достижения целей. Совсем четкой границы между менеджером и руководителем не существует, но, если кратко: руководитель отвечает за правильную постановку целей, а менеджер – за их достижение в рамках своих полномочий. Часто менеджер одновременно является руководителем для менеджеров в своем подчинении.
Руководителю и менеджеру необходимо постоянно управлять процессом достижения целей (CPM[1]), а для этого им надо иметь не только измеримые ключевые целевые показатели (KGI[2]), но и измеримые текущие ключевые показатели исполнения (KPI[3]). Показатели цели фактически являются критериями достижения цели: если этот показатель выполнен, то цель можно считать достигнутой, задачи выполненными. Показатель цели – эта та планка, финишная черта, к которой стремятся менеджеры. Показатели исполнения носят промежуточный характер, и их невыполнение свидетельствует заранее о реальных проблемах с достижением поставленных целей.
В текущей работе менеджеров и руководителей крайне важно быть в курсе действительного состояния дел в своей зоне ответственности, а поэтому постоянно владеть всеми актуальными KPI. Только зная реальное положение дел здесь и сейчас, зная причины тех или иных событий, понимая спектр возможных последствий, можно рассчитывать на принятие правильных решений. И в этом плане визуализация KPI оказывает руководителям, менеджерам неоценимую услугу: графическое представление KPI позволяет в интуитивно схватываемой форме быстро, в требуемом объеме оценить подчас огромные объемы информации, при необходимости – сделать детализацию или агрегирование, увидеть реальное положение дел.
Если все идет по плану, то такая экспресс-оценка KPI в графическом представлении практически не занимает времени и позволяет спокойно переключиться на решение других задач. Но если что-то идет не так, то именно графическое визуальное представление KPI позволяет моментально увидеть проблему, сделать экспресс-анализ причин, по трендам оценить возможные последствия. Сделать все это, имея колонки безликих цифр электронной таблицы, либо затруднительно, либо практически невозможно.
Управление компанией и ключевые показатели
В январском номере «Гарвардского бизнес-обозрения» за 2008 год Роберт Каплан и Дэвид Нортон (Robert S. Raplan, David P. Norton, Mastering the Managment System, HBR, January, 2008) блестяще описали схему выстраивания системы управления компанией. По сути, все достаточно просто. Вырабатывается стратегия компании: миссия, ценности, цели. Определяются стратегические инициативы, их цели и измерения. И все это представляется в форме стратегического плана, который структурно соответствует «системе сбалансированных показателей»[4].
Стратегический план определяет направления операционной деятельноссти компании, по которым формируются оперативные планы (планы инноваций процессов, продаж, потребности в ресурсах, бюджет), система ключевых показателей, формы отчетов.
Менеджмент компании ежедневно, еженедельно, ежемесячно и ежеквартально отвечает за исполнение планов, проводит оценку исполнения в соответствии с поставленными целями. По результатам исполнения планов выполняется анализ достижения стратегических целей и при необходимости делается корректировка стратегии компании. Таким образом, получается типичный годичный замкнутый цикл управления компанией.
Правильно разработанная система ключевых показателей работы компании дает руководству уверенность в достижении поставленных целей, а менеджменту – определенность в работе. Разработать такую систему непросто, поскольку со временем смещаются приоритеты потребителей, меняется внешняя среда, совершенствуются внутренние процессы, соответственно меняются приоритеты бизнеса компании. Поэтому вчерашние ключевые показатели сегодня могут оказаться уже неактуальными и требуются их пересмотр, корректировка, вывод неактуальных показателей, добавление новых, что является абсолютно нормальной практикой. Разработка, согласование и принятие ключевых показателей являются логическим продолжением построения планов компании, и это неотъемлемая функция высшего менеджмента.
Характерной областью применения визуального контроля является мониторинг ключевых показателей исполнения соглашений об уровне сервиса ИТ-службы компании (SLA[5]).
Классическим и наиболее востребованным показателем в управлении ИТ-сервисами (ITSM[6]) является доступность сервиса – будь то Интернет, электронная почта, корпоративная сеть, бизнес-приложения. Доступность определяется как процентное отношение времени, когда данный сервис был доступен, к длительности периода наблюдения, например за сутки. Также интересными являются показатели обращаемости пользователей, клиентов в службу поддержки, процент обращений, закрытых в оговоренный сервисным соглашением срок.
В одном динамично развивающемся банке в качестве стратегического направления развития выбрали быстрое и качественное обслуживание клиентов. Для этого было принято решение о переходе с распределенной на централизованную банковскую систему, что в условиях развитой филиальной сети потребовало кардинального обновления корпоративной сети передачи данных. Естественно, сеть оказалась на достаточно длительный период самым узким местом всех процессов обслуживания клиентов и к качеству ее работы было приковано внимание руководства, менеджмента банка и, конечно, менеджеров ИТ.
Для обеспечения качественного функционирования корпоративной сети требовалось не только постоянное владение информацией, но и быстрое принятие правильных решений. В этой ситуации контроль доступности сети в целом, а также отдельных региональных сегментов сети, функциональных решений играл решающую роль. Причем важен был контроль не только за текущим состоянием корпоративной сети, но и наличие информации за последнюю неделю, месяц, квартал, а по некоторым показателям – и за год. Неоценимую помощь оказало визуальное представление информации о параметрах сети: это позволяло не только адекватно оценивать проблематику, но и получать представление о возможных угрозах и рисках на будущее, а кроме того, лишало руководство оптимистических иллюзий, помогая реально смотреть на вещи, сформировать разумные ожидания, грамотно выстроить отношения с клиентами в переходный период, а в итоге помогло банку занять лидирующие позиции по обслуживанию клиентов в макрорегионе.
Мониторинг KPI необходим для своевременного принятия управленческих решений. Снижается удовлетворенность клиентов, падает объем продаж определенной группы товаров в данном сегменте рынка, растет спрос в конкретном регионе – во всех этих случаях надо принимать управленческие решения. Визуальный контроль с доступной историей на определенную глубину, с возможностью агрегирования и детализации помогает увидеть не только сиюминутное состояние дел, но и картину в целом, понять возможные причины происходящего. Целостное владение информацией, понимание ситуации являются основой для выбора и принятия руководителем, менеджером правильного решения.
В истории с банком визуальный управленческий контроль сыграл еще одну важную роль. Централизованная система оказалась очень требовательной к не так давно крайне дорогостоящим ресурсам хранения данных. Цифры по потребностям в ресурсах хранилища данных были противоречивы: то наблюдался значительный прирост объемов данных, то он существенно замедлялся, а после профилактических работ отмечался и вовсе переизбыток ресурсов хранения. Тем не менее инженеры, отвечавшие за функционирование центра обработки данных, приняли на вооружение методику статистического контроля процессов (SPC[7]), основой которой является мониторинг KPI по критичным системам, в том числе и системам хранения данных. Когда сухие цифры KPI были визуализированы, то быстро обнаружились закономерности, выявились тренды и удалось не только увидеть надвигающиеся проблемы, но и оперативно и наглядно проинформировать руководство. Результатом стали вовремя принятые правильные решения по модернизации, и система в дальнейшем работала без каких-либо серьезных сбоев и рисков.
Рис. 1. Практика BI – cтатистический контроль процессов
Визуальный контроль и мобильность
Пожалуй, главным технологическим трендом последнего времени стал тотальный переход на мобильные платформы. Практически все руководители, менеджеры в своей работе используют смартфоны, планшеты. В отличие от настольных компьютеров, где сеанс работы занимает от нескольких минут до нескольких часов, сеанс работы на планшете гораздо короче – длится минуты, десятки минут, а на смартфоне еще короче – считаные минуты. При этом практика показывает, что сеансов работы с мобильными устройствами оказывается тем больше в течение дня, чем эти сеансы короче. Поэтому приложения для мобильных устройств рассчитаны на короткие и простые, но частые сеансы работы, и эти приложения отличаются упрощенным по сравнению с традиционными пользовательским интерфейсом. Это то, что нужно руководителям для визуального контроля: беглый взгляд на экран, моментальный анализ ситуации, максимум пара уточнений и переключение на другие задачи. Неудивительно, что основным трендом разработчиков систем визуального контроля является акцент на мобильные приложения, и в первую очередь для планшетов.
Так или иначе, большинство из нас в повседневной жизни используют визуальный контроль: погода, курсы валют, пробки на дорогах – вся эта информация доступна и легко воспринимается в графической форме как на мобильных устройствах, так и на своем компьютере.
В любой компании существует множество информационных систем, в которых собирается, обрабатывается, хранится информация о текущей работе. Ключевые показатели исполнения собираются из корпоративных информационных систем на специальном сервере управленческого контроля, а откуда раздаются подписчикам – руководителям и менеджерам компании – в соответствии со служебной необходимостью. На сервере управленческого контроля показатели проходят предварительную обработку, в том числе проводятся агрегация данных и шифровка, если предполагается передача на мобильные или удаленные устройства по открытым каналам связи.
Таким образом, решение визуального управленческого контроля архитектурно представляет собой три основные компоненты: сервер, BI-программную[8] реализацию для мобильного устройства или рабочего места на персональном компьютере и механизмы защищенной передачи данных. Серверная часть включает в себя базу данных для хранения показателей контроля с предусмотренной историей, не требует каких-то больших ресурсов и может быть установлена на виртуальной машине в корпоративном центре обработки данных.
Рис. 2. Архитектура решений визуального управленческого контроля
Следует отметить, что важной составляющей решения визуального управленческого контроля является механизм передачи и генерации ключевых показателей из корпоративных информационных систем на сервер управленческого контроля. В ряде случаев требуются не только дизайн и уточнение самих ключевых показателей, но и нормализация, очистка исходных данных для получения искомых ключевых показателей, то есть подготовка данных для сервера визуального управленческого контроля. Эта задача оказывается сложнее, чем кажется не первый взгляд, и, как правило, лежит на стороне самой компании, которая повышает эффективность своего бизнеса. Помощь в решении этой задачи – подготовке исходных данных для управленческого контроля – могут оказать опытные консультанты, которые уже не раз выполняли подобные проекты.
Конечно, данные на сервер управленческого контроля идеально получать из корпоративного хранилища данных (КХД), но на практике оно есть далеко не у всех даже крупных компаний, и поэтому решение с прямой передачей минимально достаточной информации на сервер управленческого контроля является наиболее оптимальным с точки зрения практики использования показателем эффективности и стоимости владения.
[1] CPM или Corporate Performance Management или управление деятельностью компании
[2] KGI или Key Goal Indicators — ключевые показатели цели
[3] KPI или Key Performance Indicators — ключевые показатели исполнения
[4] BSC или Balanced Score Cards — Система Сбалансированных Показателей была предложена Р.Капланом и Д.Нортоном и в настоящее время является основой структуры стратегий подавляющего большинства крупных компаний. Все показатели компании делятся на четыре крупных блока — финансовые, отношения с клиентами, процессы, инновации и обучение. Инновации и знания позволяют совершенствовать процессы компании, компания постоянно улучшает отношения с клиентами и это отражается на финансовых результатах
[5] SLA или Service Level Agreement — соглашение об уровне сервиса
[6] ITSM или IT Service Management — управление ИТ сервисами
[7] SPC или Statistic Process Control — статистический контроль процессов
[8]
BI (Business Intelligence) – анализ деловой информации.
Средства визуального управления Lean: 5 типов визуальных элементов управления
Управляющий директор Тим Маклин объясняет различные типы визуальных элементов управления в вашем распоряжении.
Типы визуального контроляВизуальный менеджмент и визуальный контроль идут рука об руку, они являются источником жизненной силы системы бережливого производства. Визуальное управление предназначено для создания визуального рабочего места с органами управления, которые общаются без слов и прерываний процесса. Визуальный контроль может помочь выявить проблемы, сократить количество отходов, сократить производственные затраты, сократить время выполнения заказа, сократить запасы, создать безопасную рабочую среду и даже увеличить вашу прибыль.
Средства визуального контроля стандартизируют принятие решений на основе фактов. Например, если горит красный, я не могу ехать, если зеленый, то могу. Цвет светофора — это факт, который позволяет нам принять решение ехать или останавливать машину. Точно так же визуальный контроль дает нам возможность сразу отличить нормальное от ненормального. Таким образом, продолжая аналогию, машина, проезжающая на красный свет, явно ненормальна, в то время как движение транспорта на зеленый свет является нормальным явлением.
На самом деле, средства визуального контроля присутствуют в нашей повседневной жизни повсюду: от парковок супермаркетов до линий метро с цветовой кодировкой и зеленых знаков аварийного выхода. К сожалению, когда мы выходим на работу, эти полезные коды, управляющие нашим поведением, имеют тенденцию исчезать, и мы повсюду сталкиваемся с двусмысленностью.
Средства визуального контроля можно использовать в вашем бизнесе, они одинаково эффективны в офисе, на производстве или в проектировании. Визуальный контроль также может быть эффективным средством поддержания качества и безопасности.Существует множество различных визуальных элементов управления, которые можно реализовать для создания среды, в которой нестандартное можно отличить от стандартного. Ниже приводится краткое описание некоторых из наиболее распространенных средств визуального контроля, которые наши консультанты используют в полевых условиях.
Простейшая форма визуального контроля — это цветовое кодирование, когда мы используем цвета для передачи статуса. После внедрения он позволяет сотрудникам легко определить, какие действия предпринять дальше.Наличие стандартов цветового кодирования на вашем рабочем месте поможет обеспечить единый стиль для всего бизнеса.
Цветовая маркировка может применяться ко всем отделам, включая цветовую маркировку теневых досок для инструментов, цветовую маркировку пола и даже офисные документы. Другой инструмент, который можно использовать, — это визуальная доска с цветовой кодировкой. Эти доски регулярно обновляются и содержат инструкции по задачам каждого на рабочем месте. Внедрение визуальной доски с цветовой кодировкой может помочь сотрудникам отслеживать свои рабочие задачи.
Andon относится к системе, которая уведомляет руководство, техническое обслуживание и операторов о проблемах качества или процесса. Это работает, когда в процессе обнаруживается проблема, член команды имеет возможность немедленно уведомить персонал службы поддержки, чтобы проблему можно было решить. На производстве это позволяет рабочему остановить производство при обнаружении проблемы и немедленно обратиться за помощью.Это может быть распространено на офисный процесс, где поднятие флага андона означает, что процесс не переходит к следующему шагу, пока проблема не будет решена.
Андон можно активировать вручную с помощью кнопки, шнура или даже флажков. Распространенными причинами активации Andon могут быть нехватка деталей, созданный или обнаруженный дефект, неисправность инструмента/машины или наличие проблемы с безопасностью.
Часто всегда есть несколько способов выполнить задачу, но только один из этих способов является наиболее эффективным использованием ресурсов на основе текущих знаний.Со временем навыки, необходимые для выполнения задачи, могут быть утеряны, и процесс повторного обучения повторяется.
Стандартная работа обеспечивает сотрудникам всех уровней структуру и предсказуемость их рабочей недели, чтобы они могли максимально повысить свою эффективность и результативность. Процесс разработки стандартной работы гарантирует, что сотрудники понимают все свои «обязательные» задачи и выделяют наиболее подходящее время для выполнения этих задач.
В производственной системе Toyota есть четыре аспекта стандартизации:
- Содержание – это согласование с шагами, которые включены в задачу.Иногда возникают споры о том, нужны ли конкретные шаги. Для разработки стандартизированной работы команда должна согласовать необходимые шаги.
- Последовательность – шаги каждый раз должны выполняться в одной и той же последовательности. Это необходимо для обеспечения стабильного результата
- Сроки – должно быть установлено стандартное время, которое требуется обученному человеку со средней квалификацией для выполнения задачи. Знание этого стандартного времени позволяет нам сбалансировать эту задачу с другими задачами для создания уровня производства.
- Результат — Результат задачи должен быть четко определен с точки зрения качества, безопасности и производительности.
Стандартный подход к работе разработан таким образом, чтобы он был практичным, полезным для всех и не вызывал затруднений. Стандартная работа не идеальна и считается живым документом, который со временем развивается. Но помните, стандартная работа очень быстро умрет, если ее игнорировать.
Примеры стандартной работы:
- Рабочие инструкции на каждой рабочей ячейке, позволяющие легко переключаться между оператором и производством.
- Стандартные рабочие листы с инструкциями и схемами для производственных процессов.
Напольная разметка и указатели, показывающие проходы, полосы для транспортных средств, рабочие зоны и перекрестки. Они состоят из цветовой маркировки пола, вывесок с различными логотипами и маркировкой, позволяющей легко и быстро их идентифицировать.
Напольная маркировка и указатели в качестве средств визуального контроля показывают, где потоки материалов и людей должны в конечном итоге укреплять культуру безопасности без прерывания производственного процесса.
TXM Lean Case Study: Global Pneumatic Manufacturer Kamishbai Board + Tee Cards Kamashibai Boards и Tee Cards можно использовать на заводе и в офисе. Это простой и удобный способ для сотрудников определить, выполнена ли определенная задача или нет, просто взглянув на указывающую карточку. Совет Kamishibai впервые был создан для производственной системы Toyota.
Система красных/зеленых карт позволяет быстро и легко понять визуальный контроль, включая:
- Используется ли плата
- Выполняются ли задачи в правильной последовательности
- Отображение обнаруженных и зарегистрированных проблем
Наличие стандартов качества для продуктов помогает вашим операторам визуально контролировать свои решения при определении качества.Эти стандарты должны быть доступны операторам для удобства использования. Визуальный контроль применительно к качеству помогает уменьшить количество дефектов и исключить контроль качества из вашего процесса.
Существует множество визуальных элементов управления, которые вы можете внедрить в свою организацию для достижения целей визуального управления. Визуальные элементы управления используются, чтобы помочь вашей организации увидеть потери, сократить время на поиск информации и материалов и продвигать культуру непрерывного совершенствования «Планируй, делай, проверяй, действуй».
Как инструменты визуального управления запускают и поддерживают совершенствование
Инструменты визуального управления окружают нас. Хотя они настолько вездесущи, мы можем даже не думать о них. Например, когда в вашей машине скоро закончится бензин, свет предупредит вас о проблеме. Ваше фитнес-приложение может даже показать вам, насколько вы близки к своей ежедневной цели. Ваш мозг может быстро обрабатывать эти простые для понимания визуальные подсказки и использовать информацию для принятия решений.
Бережливый бизнес-подход использует этот факт и использует несколько мощных инструментов для управления и улучшения. Вам не нужно полностью использовать Lean, чтобы воспользоваться ими. Любая организация, стремящаяся к постоянному совершенствованию, может извлечь из этого пользу.
Что делают инструменты визуального управления?
Через минуту мы рассмотрим особенности некоторых из наиболее популярных инструментов визуального управления Lean, но полезно отметить, что целью визуальных инструментов является выполнение одного или нескольких из следующих действий:
- Делитесь информацией с другими
- Оптимизация управления проектами
- Сообщить стандартные рабочие инструкции
- Обеспечение соблюдения стандартов
- Обратите внимание на неровности
- Реакция на нарушения, когда они происходят
- Предотвращение возникновения нарушений
Бережливые организации сосредоточены на обеспечении максимальной ценности для клиента за счет устранения потерь и получения стабильных и предсказуемых результатов. Эти практические инструменты визуального управления используются для достижения этих целей.
Карты управления процессом
Карты контроля процесса (иногда называемые «диаграммами поведения процесса») представляют собой графики или диаграммы, отображающие данные процесса или данные управления (выходные данные) в упорядоченной по времени последовательности. Обычно они включают осевую линию, верхний контрольный предел 3 сигма и нижний контрольный предел 3 сигма. Также могут быть установлены пределы в 1 или 2 сигмы.Осевая линия представляет среднее или среднее значение процесса (а иногда и медиану).
Контрольные пределы представляют отклонения процесса и помогают пользователям распознавать отклонения «общей причины», которые ожидаются в рамках процесса, и отклонения «особых причин», которые указывают на проблему. Кроме того, можно анализировать тенденции, чтобы определить, является ли процесс стабильным.
Организации, которые практикуют постоянное улучшение качества, используют контрольные карты, чтобы обеспечить общий язык для обсуждения производительности и поведения процессов и принятия обоснованных решений о том, какие процессы оставить в покое, а какие нацелить на улучшение. Наряду со стандартной работой контрольные карты ограничивают потребность в проверке и определяют производительность процесса на основе прошлой производительности и тенденций. Они также создают основу для будущих улучшений и облегчают решение проблем.
Канбан
Kanban — это метод визуализации, разработанный как часть производственной системы Toyota для управления и улучшения рабочего процесса. Этот подход использует визуальные подсказки, чтобы сбалансировать спрос с доступной емкостью и устранить узкие места на уровне системы. Рабочие элементы представлены визуально, чтобы дать участникам представление о прогрессе и процессе от начала до конца — обычно с помощью доски Kanban Managemen.Работа протягивается через процесс по мере возможности, а не по запросу.
Если рабочий процесс визуализируется, а незавершенная работа ограничена, любой прерывающий поток может быть идентифицирован, нацелен и устранен до того, как накопится или станет слишком большим отставание. Это важно в любой отрасли, поскольку невыполненные работы связывают инвестиции, создают конфликты приоритизации и увеличивают расстояние до потребительской ценности.
Toyota впервые применила подход Канбан для ограничения незавершенного производства и минимизации запасов с помощью карточек, указывающих на необходимость пополнения запасов.Сегодня многие организации используют цифровые доски Канбан для представления рабочего процесса и уменьшения трения внутри процессов.
Доски для совещаний
Доски для совещаний служат ценной цели визуализации прогресса проектов по улучшению. Через определенные промежутки времени команды собираются для обсуждения возможностей позитивных изменений и совместной работы над устранением любых препятствий на пути к улучшению. Таким образом, доски для совещаний визуализируют работу, способствуют командному сотрудничеству и делают акцент на улучшении.
Хотя некоторые организации используют физические доски для совещаний, переход к цифровым визуальным доскам идет полным ходом.Новые программные приложения позволяют получить все преимущества визуализации и совместной работы без ограничений физической доски, висящей на стене. Кросс-функциональные команды могут работать над проектами по улучшению, даже если они находятся в разных местах. Результаты улучшения могут быть измерены в долгосрочной перспективе и переданы всей организации, а вся работа по улучшению фиксируется, пополняя хранилище племенных знаний.
Андон Лампы
Andon в производстве относится к визуализации состояния дисплея.Происхождение термина Андон — это японское слово, обозначающее традиционный бумажный фонарь. Андон — одна из наиболее распространенных форм визуального управления, используемая в бережливом производстве. Это ценный инструмент, поскольку он позволяет работать бесперебойно без каких-либо узких мест.
Огни Андона — это сигнал, очень похожий на светофор с тремя цветами на вершине каждого уровня производственной сборочной линии. Всякий раз, когда рабочий обнаруживает проблему на производственной линии или обнаруживает, что не может идти в ногу с линией, он может остановить операцию, потянув за шнур, называемый шнуром «андон», который запускает систему сигнализации и включает цветную маркировку. световая доска.
5С
5S — это метод организации рабочей области, в котором используется список из пяти японских слов, которые были переведены на английский язык как «сортировать», «установить порядок», «чистить», «стандартизировать» и «поддерживать». Пять слов, которые начинаются с буквы S, описывают, как организовать рабочее пространство для повышения эффективности и результативности, определяя и сохраняя используемые предметы, сохраняя площадь и предметы и поддерживая новый порядок. 5S также известен как «визуальный контроль, визуальное рабочее место или визуальная фабрика».
5S часто включает цветовое кодирование, при этом желтый используется в основном для управления дорожным движением.Синий, зеленый или черный используются для маркетинговых материалов и компонентов, включая сырье, незавершенное производство и готовую продукцию. Оранжевый часто используется для материалов или продуктов, которые были подвергнуты проверке, а красный используется для обозначения дефектов, брака, переделки и областей с красными метками.
Карты потока создания ценности
Картирование потока создания ценности — еще один полезный визуальный метод управления, в котором все виды деятельности и сырьевые товары, создающие ценность для клиента, изображаются в виде непрерывного потока.Этот метод удобен для выявления процессов, которые не добавляют ценности, и их устранения.
Независимо от того, используете ли вы один или все эти методы, добавление элемента визуального управления, особенно при поддержке технологий, поможет вам ускорить темпы улучшения, уменьшить неравномерность и привлечь всех.
Как внедрить визуальный контроль на вашем складе
Визуальный контроль — одна из самых популярных концепций, проникающих сегодня в складскую отрасль, но компании, считающие это необходимым, должны помнить, что эта мощная концепция не является панацеей.Подобно многоуровневой подотчетности или любому другому инструменту бережливого производства, для правильной работы он должен быть частью системы. Это означает небольшое исследование и изучение того, как ваша команда внедряет инструменты бережливого производства.
Склад, который демонстрирует «системное мышление», активно использует инструменты и методы для улучшения бизнеса и разработал эффективные системы для обеспечения непрерывности и последовательности применения инструментов во всей бизнес-структуре.
Это может быть неудобно, и вы можете даже столкнуться с противодействием со стороны некоторых отделов компании — слово «новый» может быть пугающим, в конце концов.Если вы наткнетесь на пресловутую стену, имейте в виду: даже если визуальное управление реализовано идеально, если поддержки, поддерживающей его, нет на месте, оно в конечном итоге исчезнет. Когда-нибудь менеджеры оглянутся и обнаружат, что «то, как мы всегда поступали», снова вернулось на свои места.
Внедряйте инновации в свои рабочие процессы правильно планируя и ориентируясь на конечные цели, и вы обнаружите, что эта мощная концепция изменит способ ведения бизнеса в стенах вашего склада.
В отличие от некоторых методов улучшения бизнеса, временная шкала, связанная с визуальным управлением, не обязательно привязана к общим показателям, таким как размер компании, капитал и т. д.; это связано со сложностью. Чем больше движущихся частей в ваших складских операциях, тем больше точек соприкосновения вам нужно будет охватить при внедрении. Как правило, для получения существенных результатов может потребоваться от 6 месяцев до 2 лет, если вы имеете дело с очень сложной рабочей средой.Если вы сочетаете производство с визуальным контролем, временная шкала может растянуться на 3-4 года. Независимо от того, сколько времени требуется, чтобы начать показывать результаты; визуальное управление стоит вложений.
Помните, что хорошо отработанный визуальный менеджмент — это не только прямая экономия затрат, но и сокращение дорогостоящих ошибок, неэффективных или устаревших методов и даже несчастных случаев на рабочем месте .
Склад с поддерживаемым визуальным контролем будет рабочим пространством, где все, что может понадобиться сотруднику, будет легко найти— без помощи .Их направляющие и инструменты удобно расположены в соответствующем месте и промаркированы.
Это означает меньше времени на бег вверх и вниз по цепочке команд, меньше путаницы в процедурах и меньше затрат времени и денег на «обходные пути» для неработающих или устаревших звеньев в цепочке рабочего процесса. Новый персонал быстрее акклиматизируется, и больной или отсутствующий член команды с индивидуальными знаниями не остановит все; задержки — самая большая операционная неудача, которая может случиться с компанией.
При поддержке руководства вы можете повысить эффективность каждого аспекта вашего рабочего процесса с помощью трех очень простых вопросов:
Что прошло хорошо?
Что пошло не так?
Как мы можем его улучшить?
Имея эти ответы на руках, привлеките своих сотрудников — даже и особенно неуправленческих должностей — чтобы получить дополнительную обратную связь и внедрить модель «планируй-делай-проверяй-действуй».
По мере того, как вы продвигаетесь дальше от C-suite к «сапогам на земле», вы получите ценную информацию о ваших фактических складских процедурах в их нынешнем виде, что позволит вам создать надежную, самостоятельную и самоотчетную структуру. для сохранения визуального контроля.
Это еще один ключевой способ преобразования ваших складов: ваши сотрудники станут уполномоченными экспертами . Это люди, которые могут сказать вам, что нужно пометить, почему это нужно пометить, где это нужно разместить, а что нужно полностью вырезать.Отчеты, цифры и данные могут сделать не так много: чтобы добиться реальных результатов, вам нужно сначала сосредоточиться на фундаменте, а не на представлении вашей организации сверху вниз.
Визуальное управление — это, опять же, просто инструмент, помогающий вам приспособиться к эффективности. Это не может быть единственным инструментом в поясе инструментов. Ему нужны планы, которые в настоящее время заперты в знаниях и опыте вашего складского персонала.
Обучение должно быть вашим первым шагом к успешному визуальному контролю, независимо от того, с чего вы начинаете.Прямо сейчас существует разрыв между обычными сотрудниками и их опытными менеджерами с дипломами.
Это может быть тонкое различие, такое как несоответствие диалекта в отличие от совершенно другого языка, но его все равно нужно исправить. Так же, как изучение нового языка, ваш новый общий язык должен быть построен с нуля с помощью простых соглашений: стрелки для процесса, нумерация активов, таких как вилочные погрузчики, нумерация мест для вилочных погрузчиков, публикация ваших словесных правил и так далее.
Это может показаться слишком упрощенным для опытных, штатных инженеров, но попросите своих менеджеров приостановить скептицизм, пока они не прогуляются по Гемба, как только этот язык будет установлен. Результаты будут говорить сами за себя. Помните, что даже простые линии, нарисованные на парковке, представляют собой разницу между упорядоченным использованием и кошмаром борцов с правым проездом: если простые линии так сильны в «гражданском» мире, представьте, что они могут сделать в вашем мире. склад.
Если вы готовы внедрить принципы бережливого склада, начните с нашей бесплатной электронной книги о 7 стратегиях, которые вам необходимо знать.
Что мешает реализации визуального контроля?Самые большие затраты на добавление визуального управления на ваш склад — это просто время. Признание, исследование, общение, внедрение вывесок: все эти задачи требуют усилий ваших сотрудников и руководства для демонстрации и обслуживания.
Также будет учеба и противодействие со стороны тех, кто не любит покидать свои зоны комфорта. Однако изменение чего-либо в вашем фонде будет иметь такие же затраты, а визуальный контроль предлагает преимущества, которые будут длиться намного дольше нескольких лет.Необходимо будет информировать и поощрять руководство более высокого уровня на протяжении всего процесса, поскольку потребуется некоторое время, чтобы указать на конкретные результаты. Предоставление отличных отчетов об опыте до и после и записи скорости рабочего процесса значительно ускорит процесс.
Если вы готовы освоить систему визуального контроля на собственном складе, вот несколько советов, которые помогут вам встать на правильный путь:
1. Повесьте хозяйственные «теневые доски» , на которых есть силуэт каждого инструмента, где он должен храниться.Когда вы убираете инструмент, тень показывает, что инструмент пропал и его нужно вернуть.
2. Разместите свои сжато отредактированные правила склада на видном месте, чтобы каждый мог их видеть. Больше никаких передаваемых знаний, молвы или «так, как мы всегда это делали».
3. Наклейте скотчем или, в идеале, нарисуйте линии на полу, чтобы все было видно на своем месте. Линии не обязательно должны быть точными, но они должны указывать членам вашей команды на каждое действие.
4.Пометьте все шкафы с припасами, чтобы сократить время, необходимое для погони за дикими гусями в моменты оперативной необходимости.
5. Нарисуйте, выгравируйте или наклейте номера на оборудование, чтобы ускорить обсуждение и отчеты о неисправностях.
6. Упростите и централизуйте процесс работы с документами: больше не нужно рыться в разбросанных картотеках в поисках разных папок.
Еще одним препятствием, которое может помешать вашему визуальному контролю добиться окончательного успеха, является недопонимание. Иногда мы путаем «улучшение процесса» с дополнительным надзором и контролем, чтобы указывать сотрудникам, что делать .Мы пытаемся усложнить простые принципы визуального контроля.
Высокопоставленные инженеры говорят: «Зачем клеить пол скотчем? Мы просто запланируем больше офисных совещаний и дискуссионных групп». Эти усилия всегда терпят неудачу по нескольким причинам: Очевидная нехватка участия со стороны сотрудников (которые являются вашими повседневными экспертами). Кроме того, руководство очень разочаровывается, потому что не может понять, почему улучшения не поддерживаются. Они говорят: «Мы приняли меры на основании сообщений… почему это не сработало?»
Если вы столкнулись с таким мышлением, пытаясь улучшить свои процессы, вы не начали с сотрудников, которые понимают все тонкости того, насколько важными могут быть маленькие визуальные подсказки.
Визуальный контроль работает. При должной самоотверженности и поддержке руководства это сработает и для вас . В период с 2011 по 2015 год Kenco сэкономила более 25 миллионов долларов на проектах LSS; конкретное доказательство того, что благодаря таким усилиям можно добиться существенной экономии средств.
Уделяя особое внимание визуальному управлению, стандартизации и средствам наблюдения, таким как прогулки по гемба, Kenco эффективно устранила ненужные процессы и принесла максимально возможную пользу нашим клиентам.
Хотите узнать больше, прежде чем сделать решительный шаг в собственной компании? Узнайте историю операционного успеха Kenco благодаря использованию визуального управления.
Вы также можете узнать больше об эффективности склада в нашей электронной книге ниже:
Визуальный менеджмент – хороший, плохой и безобразный
Визуализация – это хорошо. Мы все это знаем. И многие из нас в бережливом сообществе практикуют его с большей или меньшей степенью эффективности. Помимо других преимуществ, наглядность таких вещей (см. примеры ниже), как темп или качество работы, облегчает решение проблем и сохранение результатов.Цитируя доктора Торальфа Сундта из клиники Майо: «Если я это увижу, я смогу это исправить». Обратное тоже должно быть верным — трудно исправить то, чего не видишь. В прошлом месяце я наткнулся на три примера визуализации — хороший, плохой и безобразный — и хочу поделиться с вами.
Хороший
В первом случае молодая женщина проводила проверку качества в конце сборочной линии электромеханических компонентов. В течение двух лет она собирала одну и ту же качественную информацию. Выполнив серию проверок, она подтвердит, что все разъемы надежно закреплены, все компоненты собраны и находятся в рабочем состоянии.Находя проблемы, она записывала их в компьютерную базу данных, которая затем объединялась в большую базу данных. База данных была просмотрена, проанализирована, и результаты были переданы производственной группе и другим лицам.
Вот так:
Не было прямой связи между рабочими, допустившими ошибки, и инспектором, обнаружившим ошибки, и информация, которая в конечном итоге была передана, следовала за длинной и неравномерной временной шкалой. Руководство начало анализировать ситуацию из-за предполагаемого «отсутствия мотивации» у рабочих и инспекторов.Когда руководство завода исследовало различные способы повышения вовлеченности и мотивации работников, инженер по качеству заметил несоответствие между рабочими и отзывами об их работе . Проблемы, которые можно было решить сразу, выявлялись спустя дни и недели, а время, необходимое для исправления ошибок, могло занять гораздо больше времени. Инженер хотел решить свою техническую проблему.
Предложение внесла женщина, производившая осмотр. «Как насчет того, — предложила она, — вместо того, чтобы просто вводить информацию об ошибках в базу данных, я буду отмечать каждый пример по мере его появления на этой неиспользуемой доске?» Ей было легко просто быстро записать каждую задачу на доске, а затем внести ее в базу данных.
Вот так:
То, что произошло дальше, было незапланированным. Начальник производственной линии начал замечать, что она делает. Он немного нервничал, видя выступление — ошибки — членов его команды, выставленные на всеобщее обозрение. Следующее предложение было его. «Как насчет того, — предложил он, — если я приведу свою команду посмотреть на доску в конце каждого дня, чтобы мы могли посмотреть, как у нас дела?»
Дальше было интересно. Когда инспектор и рабочие вместе посмотрели на ее доску, они начали говорить об этом.Выяснилось, что один из рабочих, допустивший множество ошибок, упомянул, что у него всегда была проблема с одним из разъемов. Два конца разъема были очень маленькими, его руки — нет, а пространство, в котором ему приходилось работать, было очень тесным. Была обнаружена повторяющаяся проблема, установлена ее причина, и инженер был в восторге, так как знал, что может исправить ситуацию с помощью относительно простой инженерной корректировки. Другие возникшие проблемы часто было еще проще решить, часто прямо на месте.
Что мотивирует?
Дальнейшее было еще интереснее. По мере того, как инспектор и рабочие лучше узнавали друг друга, вместо того, чтобы ждать до конца смены, они стали заходить во время обеденного перерыва. Они могли видеть, как они продвинулись до сих пор в смене. Вскоре инспектор и команда целый день обсуждали, как продвигается производство. Важно отметить, что рабочие меньше боролись, производя больше, и сама роль инспектора в этом процессе резко изменилась.Руководство стремилось улучшить мотивацию, и они это сделали. Но совсем не так, как они ожидали. Выяснилось, что для повышения мотивации сотрудников необходима более эффективная поддержка, помогающая им быть успешными и вовлеченными в свою работу.
Плохой
Второй случай касался платы производственного анализа (PAB), которая, на первый взгляд, работала хорошо. Производственный план был составлен на почасовой основе, а не на фактической основе. На доске было выделено достаточно места для того, чтобы сотрудники могли фиксировать свои проблемы, идеи, замечания.Но пара вещей выглядела не так, и разговор с руководителем группы показал, что доска работает не очень хорошо. Более глубокий разговор и небольшое наблюдение показали, почему.
Все переделки плохи, хуже всего переделки вовлеченности рабочих.
Первая проблема в этом случае была слишком распространенной. Руководство попросило рабочих записать проблемы, с которыми они столкнулись в ходе выполнения своей повседневной работы. Благородное усилие благонамеренных менеджеров.Проблема заключалась в том, что произошло дальше, а это было… ничего. Немногим больше деморализует рабочую силу, чем настроить ее на то, чтобы заниматься своим умом только для того, чтобы пропустить смену и обнаружить, что вы идете в обратном направлении. Рабочим не составило труда найти проблемы для захвата на бумаге для сухого стирания. Трудность возникла, когда руководство не смогло эффективно на них отреагировать. Список стал длиннее. Это было плохо. Потом список сократился. Но это было нехорошо — он стал короче не потому, что руководство отреагировало на удаление предметов; список сократился, потому что рабочие перестали отчитываться.Пустая трата времени, говорили они.
В следующий раз, когда руководство попытается нанять этих рабочих, они обнаружат, что рабочие, которые были убеждены, что их снова обманули, настроены более скептически, чем когда-либо.
Что сказать, если вы хотите создать отходы и скрыть проблемы: «Производите столько, сколько можете».
Следующую проблему в этом примере можно различить при внимательном рассмотрении плана в сравнении с фактическими — P/A — числами на доске. Цифры плана не менялись изо дня в день, просто стабильный план по производству 240 единиц в смену, далее разбитый на 30 единиц в час.Ладно, может быть, все в порядке. Затем реальные цифры — записи фактического производства — были по всей карте. Это было интересно и могло указать на множество проблем — их выявление и является целью платы P/A. Но, исследуя чуть дальше, оказалось, что цифры плана вовсе не были реальными. Из-за различных проблем с продуктом, правда заключалась в том, что никто не ожидал производства 240 единиц продукции в смену. Реальная производительность в час варьировалась от 10 до 40, в день от 120 до 240, в одном экземпляре 260.Объяснение? «Ну, у нас есть много технических изменений, поэтому мы не можем удовлетворить наш спрос, но цель по-прежнему составляет 240». Итак, я спросил: «Сколько вы на самом деле рассчитываете произвести сегодня — сколько вы хотите, чтобы произвел ?» Ответ: «Ну, мы не знаем, сколько мы можем сделать, но мы хотим сделать как можно больше…»
Очень важно обеспечить однозначные ожидания – цели. «Сегодня нам нужно производить 240 единиц, по 30 штук в час. Не 239. Не 241. 240. Однозначная цель облегчает решение проблемы — «Мы произвели только 230 из запланированных 240 единиц — куда именно делись недостающие десять единиц?» Мы можем проследить причинно-следственную связь между недостающими 10 единицами и различными факторами, их вызывающими. По мере того, как мы совершенствуем свои навыки, мы можем сократить время реагирования руководства (прививая важнейшее чувство срочности) до часа и даже меньше. Дело в том, что без четкой цели трудно проводить PDCA. Без P не может быть PDCA — это как раз то, что касается «план против факта». Число, которое я, как лидер, записываю в пространстве P, представляет собой число, которое я — без шуток — прошу команду произвести. Решение проблем — это вызов, который я прошу принять, чтобы достичь цели.(Существует роль «расширенных целей», но это другой разговор.) Такие инструкции, как «Производить как можно больше», создают динамику двусмысленности, поощряют оправдания и ведут непосредственно к тем непрекращающимся циклам пожаротушения, которые мы желаю избежать.
См. объяснение PAB на стр. 110-111 в Kaizen Express
Уродливый
Интересный пример уродливой визуализации можно найти в этой записи блога.
Этот пример напоминает мне о «бережливых офисах», в которых теневой дозор каждого предмета на каждом рабочем столе, даже если ход работы остается туманным, проблемы вне поля зрения и путь вперед совершенно невидим.
Лучше
Сделать видимым нормальное из ненормального, упорядочить физическую среду так, чтобы она представляла то, как мы хотим работать, и убедиться, что наше мышление о работе воплощается в том, как мы настраиваем нашу физическую среду, — это методы, помогающие нам использовать естественные человеческие мотивы.Случайная визуализация приведет к случайным результатам и непредвиденным последствиям. Контрмера состоит в том, чтобы убедиться, что каждый визуальный артефакт имеет четкую и конкретную цель, определенных владельцев и пользователей, а также правила и ритм использования. Дэйв Логоццо из LEI рекомендует ответить на эти три простых вопроса, чтобы убедиться, что ваши визуальные доски полезны и могут принести ожидаемые результаты:
- Какова цель?
- Для кого это?
- Как часто вы используете и/или реагируете на признаки отклонения от нормы – каков ваш пульс PDCA ?
Гораздо лучше, чем теневые доски (ничего не имею против теневых досок — я люблю их!), которые гарантируют, что никто не уйдет с нашими степлерами, давайте сосредоточимся на этом: организуйте поток работы так, чтобы проблемы выявлялись по мере их возникновения, позволяя и поощрение отдельных лиц и групп к их немедленному решению. Визуализация, которая поддерживает ту визуализацию, которую я могу поддерживать.
Джон
Джон Шук
Председатель и главный исполнительный директор
Lean Enterprise Institute, Inc.
[email protected]
PS: Другой пример визуального управления можно найти прямо здесь, в LEI. С момента переезда в новый офис в марте мы удвоили усилия, чтобы сделать нашу работу как можно более заметной. Мы вложили средства в белые доски различных видов, панели для белых досок (металлические, поэтому они также магнитные), умную доску и покрасили многие стены белой краской для досок.Когда вы посетите нас, вы сможете увидеть наш годовой план работы — цели, мероприятия, сроки — на стене 3х4 метра.
Здесь мы делаем офисную работу, и ни требования к объему работы, ни показатели качества не являются такими четкими, как в приведенных выше примерах операций, но мы стараемся сделать их настолько четкими, насколько это необходимо. Поскольку мы планируем проводить больше семинаров в нашей новой тренировочной комнате (пока я пишу это, Дэвид Вербл проводит семинар по навыкам агента изменений, а в июле Майк Ротер и его команда проведут трехдневный семинар по ката совершенствования), я надеюсь, что вы найдите возможность посетить нас в ближайшее время и поделиться своими отзывами и идеями по улучшению нашего визуального офиса. Вы можете сказать нам, хорошие мы, плохие или уродливые.
Visual Controls: применение визуального управления на заводе
Содержание
Важность Visual Factory
Общий грунт производственных сред
Люди
Процессы
Инженерные изменения, ускоренные и неконформные продукты
Инвентаризация
Информация о снижении доступа к снижению доступов Доступна
Роль управления
Основы визуального завода: 5S
Визуальная планировка завода
Визуальные инструменты
Визуальные детали и расходные материалы
Визуальное техническое обслуживание и общая производительность
Платы технического обслуживания
Визуальная коммуникация
Основы визуального фабрики: 5s
Сортировка
SORT
Набор в порядке
Shine или Scrub
Стандартизируется
Sustain
Пусть 5S событие начнется
5s День 1: Сортировка
5s День 2 и 3-й день: установлен в Order and Shine
5S День 4.
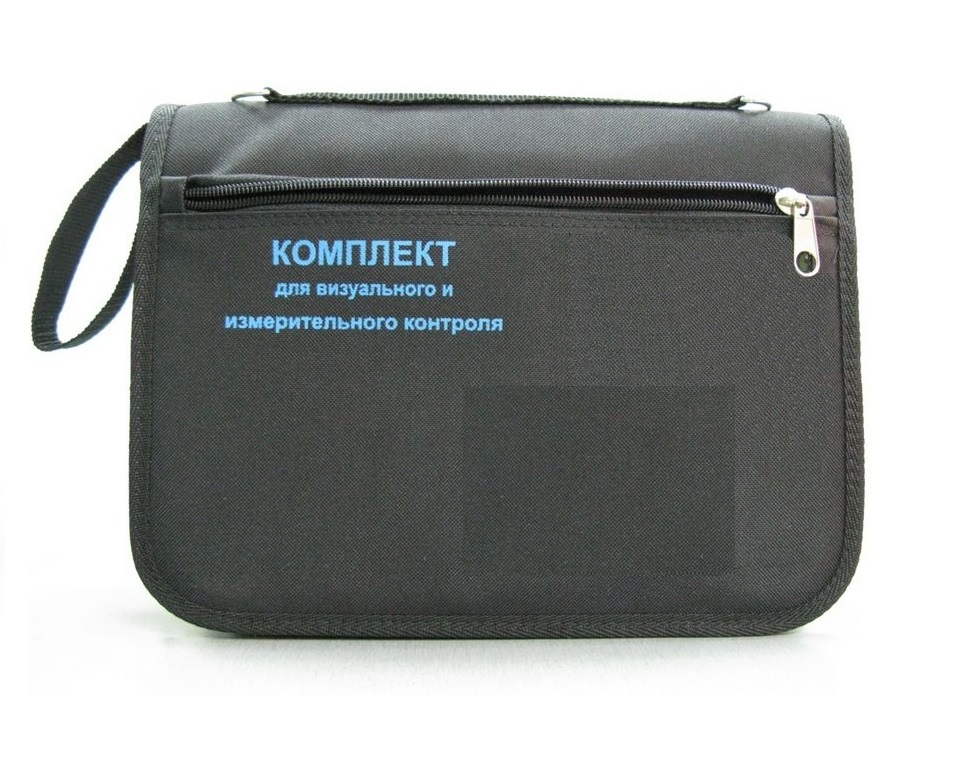
5S День 5. Начало поддержки
5S в отделах технического обслуживания
Советы по поддержанию 5S
Создание процедуры очистки в конце дня Лист аудита
Создание и ведение листа отслеживания 5S
Разработка программы стимулирования 5S
Visual Factory Layout
Визуализация вашего Visual Factory
Актуализация вашего Visual Factory
Общие рекомендации
Устранение потерь при планировании Visual
Factory
Четыре основных условия для создания 14 макетов Factory 901 Добавление 50104 Процессы
Процессы
Добавляется
Процесс реконфигурирован (настройка или замена)
Запланированная остановка
Незапланированная остановка
Визуальный инвентарь
Материалы питания и расходные материалы
Купленный инвентарь
WIP
Готовая продукция
Укладка функций поддержки
Функции прямой поддержки
Функции косвенной поддержки
Назад к планировке завода-изготовителя будущего
Визуальные инструменты
Визуальные инструментальные доски или теневые доски
Материалы для инструментальной доски
Проектирование и создание инструментальной доски
Персональные инструменты: дилемма или решение?
Контрольные карточки для инструментов
Инструменты для позиционирования над головой
Подбор правильного размера
Визуальные детали и расходные материалы
Основы инвентаризации
Когда мы используем термин инвентаризация, о чем конкретно мы говорим?
Почему иметь больше запасов, чем необходимо для удовлетворения потребительского спроса, плохо?
Почему ваша компания поддерживает существующие уровни запасов?
Можно ли снизить уровень запасов, не ставя под угрозу обязательства по производству и отгрузке?
Какую роль играет система визуального управления в снижении уровня запасов?
Несколько общих точек по управлению цепочками поставок
Роль производственных программных систем
Текущие глобальные тенденции
Прием проверка
Тур по идеальному акционому
Материалы Общая площадь
Расположенный вход площадью
Разгрузка док
Приемный осмотр площадь
Главный объект площадью
Соображения
Стратегия сокращения запасов
5S и Канбан
5S на складе
Пополнение: Канбан и системы с двумя контейнерами
Визуальный техническое обслуживание и общий производительный производственный
Технические доски
Роль обслуживания
Общие заблуждения
Первый ответчик
Влияние неконформ продукта
Общее производственное обслуживание — обзор
Три подхода к TPM
Три уровня TPM
, реализующие TPM и TPM Visuals
Cross-Training
Визуальный макет для зоны обслуживания
Создание общей площади
Общая площадь Расположение
Обслуживание Макет на производстве
Техническое обслуживание 5S
Визуальные инструменты Доски для инструментов
Наименование Теги
Технические материалы и Канбан
Общее оборудование Эффективность
Менеджер по техническому обслуживанию
Visual Communications
Производительность объекта
Продажа
Средняя доставка
Продажа
Качество
Производительность
Качество
Безопасность
Экологические
Метрики Доски коммуникаций на производстве
Уровень
Доплатные доски
Светы
Острые процедуры
Блог по бережливому строительству
Иллюзия контроля
Многие специалисты в области машиностроения и строительства работают в иллюзии, что они контролируют свои капитальные проекты, пока не стало слишком поздно. Для многих рецепт контроля состоит из нескольких ключевых ингредиентов, включая, помимо прочего, базовый график, чтобы можно было измерить прогресс.
Почему бережливое строительство применимо к строительству ветряных турбин?
В качестве вступления к этому посту вы кратко расскажете о модульной конструкции ветряных турбин, тенденциях планирования и о том, почему здесь применимо бережливое строительство.Во-первых, строительство ветряных турбин относится к категории модульных конструкций с последовательной стратегией сборки модулей [1].
Действительно ли мне нужен инструктаж по бережливому строительству?
«Мне нужен тренер по бережливому производству!» Это здорово слышать! Но если вы нанимаете одного, вам действительно нужен коучинг или вам действительно нужно что-то еще? Как тренеры, мы тратим много времени на коучинг, но многие из нас тратят еще больший процент времени на обучение и фасилитацию.
Применение бережливого производства для сокращения переделок в цепочке поставок жилья
Цепочка поставок жилья в Великобритании часто подвергается критике за низкое качество продукции, низкий уровень производительности и высокий уровень отходов. Проблема плохого предложения и качества успешно решается автомобильной промышленностью.
Внедрение системы последнего планировщика — как вы это делаете?
Жизнь может подкидывать неожиданные мячи.Один из них появился на семинаре под руководством Кристин Паскуайр много лет назад в Университете Лафборо в Великобритании. Говоря о системе последнего планировщика (LPS), она раскрыла подход, который казался логичным и интуитивным.
Визуальный контроль…{Стратег}
Visual Control предоставляет информацию для управления повседневными действиями.
Сигналы светофора и знаки являются наиболее распространенными примерами. Это мощный инструмент для обеспечения хорошего
принятие решений на микроуровне. В таблице ниже приведены различные типы визуального контроля.
и приводит примеры. Визуальный контроль является естественным партнером 5S и используется в границах и во многих других целях. гарантировать, что инструменты заменяются, что люди следуют безопасным методам и что проверки качества
Выполнено.
Индикатор
Мощность | Описание | Примеры |
Низкий | Индикатор предоставляет информацию только о ближайшем окружении или ситуация. Индикаторы пассивны, и люди могут не замечать их или реагировать на них. | — Уличные знаки -Индикаторы уровня -Автоматический указатель уровня топлива — Разметка проходов |
Сигнал
Мощность | Описание | Примеры |
Средний | Сигналы привлекают внимание визуальными (или звуковыми) сигналами тревоги.Люди могут по-прежнему предпочитают игнорировать сигналы, но обычно они их воспринимают. | — Светофор |
Управление
Мощность | Описание | Примеры |
Высокий | Контролирует ограничение поведения с помощью четких визуальных сообщений или физических ограничений во время действия. |