Технология MIG/MAG сварки. Характерные дефекты и способы борьбы с ними.
Технология сварки. Характерные дефекты MIG/MAG сварки и способы борьбы с ними.
Технология
Как и любой тип дуговой сварки, процесс GMA сварки начинается с зажигания дуги. Для легкого зажигания дуги электрод (электродная проволока) должен получить хороший контакт со свариваемой поверхностью. Для этого на свариваемой поверхности не должно быть масла, грязи, окалины и прочих веществ, затрудняющих контакт. Вылет провода следует установить согласно рис. 1, поскольку при увеличении вылета электрода трудно инициализировать дугу. Угол наклона горелки должен быть 5-20°.
Рис. 1. Вылет электродной проволоки из мундштука сварочной горелки (а), расположение контактной трубки в сопле сварочной горелки при циклическом режиме сварки короткой дугой (б) и при струйном переносе металла (в)
Для компенсации веса подающего рукава и сварочного кабеля (при раздельном подводе) для облегчения манипулирования горелкой необходимо перебросить их через плечо.
Переместите горелку по отношению к изделию, касаясь проволочным электродом поверхности, как бы царапая ее. Чтобы предотвратить прилипание проволоки, необходимо быстро протянуть горелку на 10-15 мм в направлении, противоположном направлению сварки, и приподнять ее. Как только появился контакт проволоки с изделием, начинает работать электродвигатель механизма подачи проволоки и работает до тех пор, пока нажата кнопка триггера.
Правильно установленная дуга имеет мягкий, шипящий звук. Регулирование скорости подачи электродной проволоки необходимо только тогда, когда дуга издает неправильный звук, например, громкий треск указывает на то, что высока скорость подачи проволоки. Проволока касается сварочной ванны и кратковременно гаснет.
Чтобы погасить дугу, необходимо отпустить кнопку триггера. Это отключит сварочную цепь, при этом остановится двигатель подачи электродной проволоки. Если при сварке произошло прилипание электрода, необходимо отпустить кнопку триггера и бокорезами откусить проволоку.
При сварке в защитном газе плавящимся электродом большое значение имеет положение горелки по отношению к свариваемой детали. Если свариваемые части равны по толщине, то поперечный угол между деталями должен быть строго одинаков. Если детали не равны по толщине, то горелка наклоняется в сторону тонкого металла (поперечный угол уменьшается). Продольный угол, в зависимости от характера переноса электродного металла, должен быть в пределах 5-25°.
Сварка может производиться как углом вперед, так и углом назад. Сварка углом назад означает — горелка позиционируется так, что направление подачи электродной проволоки противоположно направлению перемещения горелки. Сварка углом вперед означает, что направление подачи электродной проволоки совпадает с направлением движения горелки. Следует отметить, что для изменения способа сварки не нужно изменять направление перемещения горелки, достаточно изменить ее наклон в продольном направлении.
Скорость перемещения сварочной горелки определяет скорость сварки, которая выражается в м/мин. На скорость сварки влияет:
- толщина свариваемого изделия: с увеличением толщины металла уменьшается скорость сварки и наоборот;
- скорость подачи электродной проволоки: с увеличением скорости подачи — увеличивается скорость сварки;
- направление сварки: при сварке углом вперед скорость сварки выше.
При сварке углом назад достигается большая стабильность дуги и меньшее брызгообразование. Сварка углом назад применяется для соединения толстого металла, при этом достигается большая глубина проплавления. Кроме того, сварщик видит сварочную ванну, что позволяет повысить качество сварки. Сварка углом вперед применяется для соединения тонкого металла, при этом достигается меньшая глубина провара, но сварка производится с большей скоростью.
Легче всего производить сварку в нижнем положении, причем качество сварного соединения получается наилучшее. В нижнем положении лучше растекание расплавленного металла и лучше газовая защита. Освоив сварку в нижнем положении, можно производить ее и в других пространственных положениях. Сварка в горизонтальном, вертикальном снизу вверх и вертикальном сверху вниз положениях производится при уменьшенном на 10% сварочном токе. На рис. 2 показан угол наклона сварочной горелки при сварке в различных пространственных положениях.
Рис. 2. Угол наклона сварочной горелки при выполнении различных швов в нижнем и вертикальном положениях при циклическом режиме сварки короткой дугой (а-г) и при струйном переносе металла (д)
Поперечный угол наклона сварочной горелки при сварке угловых швов должен быть 45°. Для стыковых швов поперечный наклон горелки должен быть всего несколько градусов, иначе ухудшается расплавление металла на боковой поверхности стыка и, соответственно, ухудшается слияние металла шва и основного металла.
Сварка в вертикальном положении может осуществляться как снизу вверх, так и сверху вниз, при этом огромное значение имеет положение горелки. Сварка должна производиться только в положении, показанном на рис. 10в,г, при этом, чтобы обеспечить полное проплавление металла, дуга должна располагаться на переднем краю сварочной ванны.
Проплавление. Проплавление — это глубина сплавления основного металла. Величина сварочного тока является основным параметром, влияющим на глубину проплавления. Увеличение или уменьшение тока вызывает увеличение или уменьшение соответственно глубины проплавления. Глубину проплавления можно также увеличить, увеличивая скорость подачи электродной проволоки, при той же скорости перемещения горелки. При этом уменьшается длина дуги и, соответственно, увеличивается сварочный ток, т. е., изменяя скорость подачи проволоки, можно изменять глубину проплавления.
Изменение остальных параметров сварки оказывает сравнительно небольшое влияние на глубину проплавления. 24 В — оптимальное напряжение для выбранного тока. С уменьшением напряжения уменьшается глубина проплавления и наоборот. Кроме того, при данном напряжении наиболее стабильная дуга. Нестабильность дуги уменьшает глубину проплавления.
Изменение скорости перемещения сварочной горелки, т. е. изменение скорости сварки, похоже на изменение напряжения дуги — глубина проплавления максимальна при определенной скорости сварки и уменьшается как при ее снижении, так и при ее повышении. При скорости 30,5 см/мин для выбранного диаметра проволоки глубина проплавления максимальна. При скоростях 17,8 см/мин и 43,2 см/мин проплавление уменьшилось.
При низких скоростях большое количество расплавленного металла сварного шва создает <подушку> между дугой и основным металлом, что препятствует дальнейшему проплавлению. При больших скоростях сварки тепло, создаваемое дугой, не успевает достаточно глубоко проплавить основной металл.
Изменение наклона сварочной горелки в меньшей степени, чем изменение напряжения и скорости сварки, влияет на глубину проплавления.
Размер валика сварного шва. Валик сварного шва характеризуется высотой (выпуклостью) и шириной. Правильность этих характеристик гарантирует, что валик сварного шва выполняется с минимумом дефектов, особенно при многопроходной сварке. В случае большой выпуклости шва при многопроходной сварке трудно наложить последующий шов, обеспечивая качественное слияние. Очень зауженный шов не обеспечивает хорошего слияния металла шва и основного металла.
Характеристика валика сварного шва зависит как от его размера, так и от формы. Для изменения размера сварного шва (количество наплавленного металла на погонный метр шва) необходимо изменить режим сварки. Основное влияние на размер сварного шва оказывает величина сварочного тока и скорость перемещения сварочной горелки. Размер сварного шва прямо пропорционален сварочному току и обратно пропорционален скорости перемещения горелки.
Изменение сварочного тока и скорости перемещения горелки изменяет размер сварного шва, но мало влияет на его форму.
Изменяя напряжение на дуге (изменяя длину дуги), можно изменять форму сварного шва. Увеличение длины дуги вызывает увеличение ширины шва и уменьшение его высоты, причем объем шва (количество наплавленного металла на единицу длины) остается неизменным. Возрастает ширина валика сварного шва, выпуклость уменьшается, и более жидкий металл сварного шва более эффективно соединяется с основным металлом, т. е. слияние улучшено.
Увеличение длины дуги для увеличения производительности сварки (скорости наплавки) вызывает увеличение выпуклости в большей степени, чем увеличение ширины шва. Валик сварного шва становится чрезмерно выпуклым. Сварка углом назад также дает узкий и высокий валик сварного шва. Уменьшая угол продольного наклона горелки, можно уменьшить высоту валика сварного шва и увеличить его ширину. Сварка углом вперед дает более плоский и более широкий валик сварного шва.
Манипулирование сварочной горелкой. Описание технологии сварки без описания приемов манипулирования сварочной горелкой будет далеко не полным. Приведенные ниже рекомендации являются справочными. Каждый сварщик по мере повышения квалификации вырабатывает свои приемы перемещения горелки.
Сварка в нижнем положении. Рекомендуемое перемещение сварочной горелки при выполнении однопроходного и многопроходного стыкового сварного шва в нижнем положении показано на рис. 3. Как видно из рисунка, при выполнении однопроходного шва совершаются пилообразные, с легким сдвигом назад перемещения горелки. В многопроходном сварном шве с разделкой кромок при выполнении корневого шва совершают зигзагообразные колебания горелки, при этом нужно следить, чтобы не было прожогов. Заполняющие и облицовочный швы выполняют с такими же, но более широкими колебаниями. Отличие в том, что при выполнении этих швов производят поперечный наклон горелки и при достижении крайнего положения делают задержку горелки.
Угловой шов в нижнем положении выполняют, совершая сварочной горелкой круговые движения.
Рис. 3. Манипулирование горелкой при выполнении стыкового шва в нижнем положении
Сварка в горизонтальном положении. Стыковой шов в горизонтальном положении выполняется с использованием той же технологии перемещения сварочной горелки, что и при выполнении стыкового шва в нижнем положении. Отличие только в том, что заполняющие валики при сварке в горизонтальном положении более узкие. При выполнении сварки не следует забывать, что наклон горелки составляет 90° по отношению к поверхности, на которую накладывается валик сварного шва.
Сварка в вертикальном положении. Сварка однопроходного стыкового шва без разделки кромок в положении снизу вверх производится путем пилообразных колебаний горелки. Выполнение корневого шва при многопроходной сварке производится путем зигзагообразных перемещений сварочной горелки. Заполняющие валики и облицовочный шов выполняют при ступенчатом перемещении горелки, причем при достижении крайней точки при горизонтальном перемещении необходимо сделать задержку и спуститься вниз на величину, равную диаметру электродной проволоки, а затем подняться вверх и переместиться по горизонтали на противоположную сторону. Там снова сделать задержку и опуститься вниз и т. д.
Сварка углового шва в вертикальном положении снизу вверх производится движением горелки, как бы рисуя <елочку>, с задержкой на боковых поверхностях изделия.
Стыковой сварной шов с разделкой кромок при сварке сверху вниз — корневой, заполняющий и облицовочный швы выполняются путем зигзагообразных перемещений сварочной горелки с задержкой в крайних точках. Поперечный наклон горелки составляет 90° к поверхности сварки. Производя манипулирование горелкой, нужно следить, чтобы дуга располагалась на переднем крае сварочной ванны. Нельзя допускать прогона расплавленного металла впереди дуги. Это ухудшает качество сварки.
Сварка в потолочном положении. При выполнении стыкового шва с разделкой кромок в потолочном положении необходимо совершать зигзагообразное перемещение сварочной горелки. Поперечный наклон горелки составляет 90° к поверхности сварки.
В крайних точках перемещения необходимо делать небольшую задержку. Все вышесказанное применимо при выполнении как корневого, так и заполняющего и облицовочного прохода.
Характерные дефекты MIG/MAG сварки и способы борьбы с ними
Техника выполнения GMA сварки более простая, чем других видов сварки, но, тем не менее, как и любая другая сварка, имеет свои характерные дефекты.
Поверхностная пористость. Поверхностная пористость возникает из-за атмосферного загрязнения. Это может быть вызвано засорением сопла горелки, недостаточной подачи защитного газа или сваркой на ветру. Для предупреждения образования пористости необходимо систематически очищать сопло от налипших брызг, правильно отрегулировать расход защитного газа, при сварке на ветру использовать защитные противоветровые экраны.
Воронкообразная пористость. Воронкообразная пористость возникает, когда в конце сварного шва горелка убирается раньше, чем произошла кристаллизация расплавленного металла, или когда после прекращения горения дуги слишком рано прекращается подача защитного газа. Чтобы устранить образование этого дефекта, необходимо замедлить перемещение горелки в конце сварного шва или приподнять горелку.
Наплыв. Наплыв возникает, когда металл сварочной ванны затекает на нерасплавленный дугой основной металл. Наплыв часто возникает, когда сварочная ванна становится слишком большой. Чтобы устранить образование этого дефекта, необходимо держать дугу на переднем крае сварочной ванны. Для уменьшения объема сварочной ванны необходимо повысить скорость перемещения горелки или уменьшить скорость подачи электродной проволоки.
Малая глубина проплавления. Малая глубина проплавления возникает при слишком малом тепловложении в зоне сварки. При недостаточном тепловложении необходимо увеличить скорость подачи электродной проволоки, что, в свою очередь, увеличит сварочный ток. Можно также попробовать уменьшить диаметр проволоки.
Прожог сварного шва. Прожог сварного шва возникает при слишком большой глубине проплавления, т. е. при слишком большом тепловложении в зоне горения дуги. Чтобы устранить образование этого дефекта, необходимо уменьшить скорость подачи электродной проволоки, что, в свою очередь, уменьшит сварочный ток. Можно также увеличить скорость сварки (скорость перемещения горелки). Прожог сварного шва может также произойти при большом зазоре в корне шва. В этом случае необходимо увеличить диаметр сварочной проволоки и совершать небольшие поперечные колебания сварочной горелкой.
Независимо от свариваемого материала, существуют мероприятия, способствующие предупреждению пористости и образованию наплывов.
- Свариваемое изделие должно быть максимально чистым. Жир, нефтепродукты и замазученность должны быть удалены. Для получения качественного шва окалина, ржавчина и различные оксидные покрытия необходимо удалить либо механически, либо химически.
Огромное значение это имеет при сварке алюминия.
- При сварке углеродистых спокойных, полуспокойных и кипящих сталей использовать только рекомендуемую газовую смесь.
- Устанавливать расход защитного газа согласно рекомендациям на выбранный режим сварки. Защищать свариваемое изделие от ветра и сквозняков.
- Электродная проволока должна выходить из сопла горелки строго по центру. При смещении проволоки к какому-либо краю следует, произвести регулировку сварочной горелки.
- При двухсторонней сварке, когда проплавление не достигло противоположной стороны, нужно убедиться, что второй проход глубоко проходит в первый шов. Если проплавление от первого прохода достигло противоположной стороны или когда имеется зазор в корне шва, необходимо зашлифовать противоположную строну шва до устранения дефектов. Это требование обязательно при сварке алюминия и при высококачественной сварке углеродистой и нержавеющей сталей.
- Избегать условий, когда расплавленный металл затекает вперед дуги.
Это основная причина образования наплывов, особенно при сварке под уклон.
- При многопроходной сварке зашлифовать до получения плоской поверхности все сварные валики, которые имеют большую выпуклость и в которых обнаружится плохое сплавление металла шва и основного металла.
- При многопроходной сварке произвести зачистку поверхности предыдущего валика, если на его поверхности обнаружены включения окислов или шлака.
Основные неисправности инверторов и методы их устранения
Сварочный аппарат часто встречается в домашних мастерских — для личного использования его приобретают даже новички: этот вид техники удобнее, чем трансформатор или выпрямитель.
Пользователи сварочного оборудования отмечают следующие преимущества:
- доступность — приобрести инвертор можно в каждом магазине строительной техники;
- мобильность — самый тяжелый агрегат весит не более 10 килограммов, что упрощает транспортировку инвертора;
- универсальность — подходит для обработки любых металлов;
- малотребовательность — для сварки электродом 3 мм достаточно напряжения 170 В;
- простота эксплуатации — новички предпочитают работать с инвертором благодаря устойчивой рабочей дуге: сварочный шов получается ровным и аккуратным.
Причины поломок
Инверторы, как и любое оборудование, могут выйти из строя. Большинство поломок происходят из-за неправильно выбранного сварочного режима, выхода из строя некоторых электронных элементов или попадания пыли и посторонних частиц в корпус блока питания.
Зная типовые поломки, вы легко определите и устраните неисправность — чаще всего диагностика и домашний ремонт сварочного оборудования не вызывают трудностей.
Основные неисправности и пути их решения:
- Дуга горит нестабильно, материал электрода неконтролируемо разбрызгивается. Скорее всего вы выбрали неподходящую силу тока: на каждый миллиметр электрода должно приходиться от 20 до 40 ампер.
- Сварка прилипает к металлу — недостаточно напряжения. Замерьте напряжение в сети и не забудьте очистить клеммы инвертора.
- Нет дуги при включенной аппаратуре — силовые кабели повреждены или перегреты.
- Аварийное отключение — скорее всего сработала защита от короткого замыкания.
Проверьте элементы силовой цепи сварочного оборудования — скорее всего, какой-то из них вышел из строя и требует замены.
- Большое энергопотребление при холостом ходе — возникает из-за замыкания витков на токопроводящих катушках. Проблема устраняется полной перемоткой катушек и наложением дополнительных слоев изоляции.
- Отключение аппарата через одинаковые промежутки времени характерно для чрезмерно перегревающихся моделей. Если инвертор внезапно выключился, дайте ему остыть в течение 30–40 минут, прежде чем продолжать работу.
- Блок питания при работе издает посторонние звуки. Необходимо проверить и затянуть в случае ослабления болты, которые стягивают элементы магнитопровода. Если проблема заключается не в этом — проверьте крепеж сердечника или замыкание между кабелями.
Важно! Если из корпуса инвертора идет густой белый дым — не пытайтесь выполнить самостоятельный ремонт, сразу несите оборудование в сервисный центр.
Ремонт в домашних условиях
Чтобы установить причину поломки, проведите визуальный осмотр всех узлов сварочного аппарата, тщательно зачистите окислившиеся контакты с помощью щетки и растворителя. Внимательно изучите инструкцию: возможно, там уже указана типовая неисправность этой модели.
В первую очередь, выходят из строя:
- транзисторы;
- диодный мост;
- система охлаждения.
Их неисправность устанавливается по существенному изменению геометрии.
В таком случае весь ремонт сводится к замене элементов с помощью паяльника. В работе вам также пригодится дополнительное оборудование — мультиметр, вольтметр и осциллограф.
Если по окончании первичных ремонтных работ сварочный инвертор не включается, переходите к более глубокой диагностике — проверьте блоки питания, управления а также силовой блок.
- При возникновении неисправности необходимо немедленно отключить прибор от электросети, дать ему остыть и только после этого снимать кожух.
- Диагностику начинайте с малого — нередки случаи, когда ремонт инвертора заключается в простейшей замене деталей или пропайке контактов.
- Для проверки транзисторов используйте мультиметры, вольтметры и осциллографы.
- Заменив электротехнические элементы, проверьте печатные проводники.
- Не забудьте об обслуживании разъемов после работы с дорожками.
- Проверяйте диодные мосты: они нечасто выходят из строя, но это лишним не будет.
- Если в процессе поиска неисправностей вы дошли до проверки плат и пультов управления, обязательно используйте высокоразрешающий осциллограф.
Если вы провели все диагностики и проверки, но обнаружить поломку так и не удалось — рекомендуем прекратить поиски проблемы и обратиться специализированные мастерские по ремонту сварочного оборудования.
основы сварки металла полуавтоматом в среде углекислого газа для новичков, все азы.
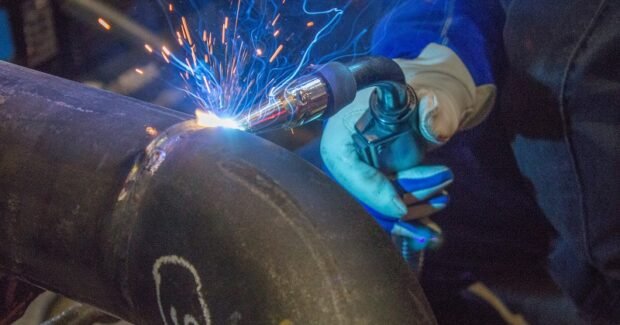
Ремонтные и обслуживающие работы в частном доме нужны довольно часто. Да и в квартире такой запрос – не редкость. Владельцы автомобилей тоже знают, что ремонт своими руками обходится гораздо дешевле, чем регулярное привлечение помощи специалистов. И сварка является тем ремонтным процессом, овладение которым выручает в самых разных ситуациях. И учиться сварке, конечно, никогда не поздно. В данной статье рассмотрим основы сварки для начинающих.
Основные правила
Лучший способ освоить сварку для начинающих – записаться на профессиональные курсы либо просто пойти в подмастерья: попросить мастера взять себя в помощники. Активное наблюдение за процессом с комментариями специалиста быстрее поможет научиться основам сварки. Но если обе вышеописанные возможности не являются доступными, есть другой вариант – даже теоретические азы полезны для новичков. Сначала теория, общее понимание процесса, а потом можно и практиковаться.
Электросварка – метод, при котором для нагрева и дальнейшего расплавления металлов применяют электродугу.
Термические показатели электродуги способны достичь 7000 градусов, что превысит температуру плавления большей части металлов. Процесс сварки происходит следующим образом:
- чтобы электродуга поддерживалась и работала, ток подают от агрегата к электроду;
- электродный стержень, касающийся основания варки, вызывает прохождение сварочного тока;
- под действием такого тока и формируемой дуги электрод и в дополнении к нему металлокромки элементов действия будут плавиться;
- из данного расплава выходит сварочная ванна, в ней расплавленный электрод смешивается с базовым металлом;
- на ванне появляется плавленый шлак, образующий пленку защиты;
- когда дуга отключается, металл постепенно остывает, так получается шов с окалиной, когда материал остынет полностью, окалину счищают.
Для этого процесса используют плавящиеся и неплавящиеся электроды. Если это плавящийся электрод, то сварочный шов образуется за счет введения в расплав присадочной проволоки. Если электрод неплавящийся, ничего такого не потребуется. Чтобы образовать и поддержать в рабочем состоянии электродугу, пользуются спецоборудованием. Это сварочный агрегат.
Выбираем сварочный аппарат
На сегодняшний день выбор такого оборудования велик, есть несколько его основных разновидностей.
- Сварочный генератор. Он может продуцировать электрическую энергию, которая будет использоваться на создание дуги. Он полезен в тех местах, где еще не удалось провести электричество. Но он слишком большой по весу, такие габариты не дают право сказать, что аппарат действительно удобен в использовании.
- Сварочный трансформатор. Данный агрегат может преобразовывать переменное напряжение, которое подается от сети, в переменное напряжение той частоты, что и требуется для сварки. Такое оборудование легче в использовании, но также не самое компактное. Еще один потенциальный «минус» – скачки напряжения в сети.
- Сварочный выпрямитель. Данная техника трансформирует напряжение, подаваемое от сети, в постоянный ток, без которого не образуется дуга. И уже выпрямители считаются компактной техникой с высоким КПД.
Для домашних нужд эксперты советуют приобретать выпрямители инверторного типа. Их чаще зовут просто инверторами. Это компактное оборудование, которое в ходе манипуляций вешается на плечо.
А принцип его устройств прост и понятен даже новичку. Инверторы хороши и тем, что экономичны. Работать могут от бытовой сети. Главное, что они обеспечивают стабильную дугу.
Правда, у такого оборудования есть и недостаток – стоимость. На него придется раскошелиться. А еще удобный и маловесный инвертор чувствителен к увлажнению, запылению, к перепадам напряжения. Когда приходится выбирать такое оборудование, непременно нужно смотреть на возможные значения сварочного тока. Минимум – 160–200 А.
Если в таком сложном виде деятельности человек еще совсем неопытен, а консультант в магазине техники начинает сыпать словами «автомат и полуавтомат», «электрод двойка», «переноска», следует попросить его вначале просто показать инверторы. И именно те, которые будут полезны для опыта в сварке и безопасны, а уже потом – все остальное.
Подбор экипировки
К остальному относится и экипировка. Это защитный костюм сварщика. Он защитит человека от металлических брызг, вспышек ультрафиолета и его потоков. Обычный комплект, как правило, включает маску, подшлемник, рабочий костюм/робу и плотные спецперчатки. Эксперты советуют приобретать маску «хамелеон», оснащенную автоматическим затемнением. Если такого костюма нет, теоретически можно использовать и другую одежду, скроенную из очень плотной ткани.
В домашних условиях этого может быть достаточно.
Но маска и перчатки все равно обязательны.
В этом пункте стоит сказать о правилах безопасности.
- Категорически запрещено проводить сварочные работы в помещении, где нет огнетушителя. Его наличие обязательно.
- Всю экипировку надевать нужно строго до начала работ. Если дугу зажечь без защитной маски, получится ожог сетчатки глаз. И, что особенно тревожно, симптомы этого недуга проявляются не сразу, то есть человек продолжает работать со сваркой, ухудшая положение.
- Капли для глаз – такая же необходимая вещь, как и огнетушитель. Они могут не пригодиться, но быть рядом должны. Даже опытные сварщики страдают от ожогов сетчатки (они это называют – «нахвататься зайчиков»), вот только в их случаи зрение страдает из-за высокого объема работ. Новички же рискуют в силу своей неопытности.
- При сварке металла человек находится в окружении деталей, которые нагреты до высоких термических показателей.
И к ним нельзя прикасаться до полного остывания, иначе ожоги неизбежны.
Если с правилами знакомы, экипировка в полном порядке, работать будет безопасно. Осталось только теоретически разобраться, что же представляет собой технология сварки.
Технология
Сначала следует найти верстак либо иное подходящее основание. Оно должно быть сделано из негорючего материала. То есть деревянный стол как основание под сварку никак не подойдет. Рядом со сварочным оборудованием не должно находиться ничего, что может легко воспламениться.
Подготовка
Рядом с собой сварщик должен поставить ведро с водой – на случай спасения от угрозы возгорания. Надо найти безопасную зону, где будут складироваться остатки уже использованных электродов. Все же даже маленький электрод способен стать причиной пожара.
Необходимо настроить сварочный ток и взять электрод. Электроды берутся 2–5 мм. Ток выставляется зависимо от того, какой толщины будут детали, и как именно будет свариваться материал. На корпусе агрегата обычно указана сила тока.
Если электроды только приобретены в магазине, их качество обычно не вызывает сомнений. Но если электроды не новые, и хранились они в помещении без отопления, достаточно влажном, их обязательно нужно высушить.
И не просто высушить, а сделать это при температурном показателе +200 градусов.
Старый духовой шкаф (электрический) подойдет для этого.
При выборе электродов необходимо придерживаться следующих советов:
- тройкой обычно варят металл толщиной до 5 мм;
- для металла толщиной 1,5–3 мм берут электрод диаметром 2–2,5 мм;
- электроды в 4 мм в домашних условиях практически не используют, домовая сеть с ними не справится.
Об ориентировании деталей: для новичка проще работать на горизонтали. Контроль сварочной ванны выполнять в таком виде проще. Сила тяжести будет давить на расплав в направлении сверху вниз, не сдвигая его. Присадочный металл электрода перенесется в образуемый шов. Поэтому начинающие сваркой занимаются на столе, а сбор укрупненных деталей ведут «по месту». Но и вертикальной сварке несложно научиться, вопрос времени.
А вот потолочной методикой занимаются исключительно профессионалы, новичкам лучше на нее не замахиваться.
И еще о выставлении тока: сварочный ток коррелирует с толщиной электрода. Техника ограничивает лишь нижние границы тока. Для электрода-двойки переключатель ставится на 70–80 А, для тройки – 100–140 А. Сначала нужно выставлять ток немного выше минимума, а потом поднимать его показатель.
Важно! Силовой режим выбран грамотно, если звук сварки похож на растрескивание, неправильно – если та гудит либо булькает.
Сварочные работы
Следует рассказать о вариантах сварки, прежде чем перейти к пошаговой инструкции. Сварка бывает стыковой, внахлест, угловой и тавровой. В первом виде работает практически прямой электрод, в других случаях электрод придется наклонять. Провариваться будут две детали, которые расположены в перпендикулярных областях.
Чтобы научиться правильно варить, нужно придерживаться нескольких шагов.
- Поджиг. Чтобы зажечь дугу, нужно осуществить чирканье электродом по детали, как сделали бы это спичкой. Чиркать надо по траектории шва, иначе есть риск испортить базу. Электрод немного наклоняется к вертикали, выдерживая угол примерно в 30 градусов.
- Контроль электродуги и образование сварочной ванны. Когда дуга разогрелась, ее надо подвести к началу шва и ждать, пока металл расплавится. Так, под электродом через пару секунд образуется красный фрагмент, так горит флюс. Потом пятно появится оранжевое, с рябью – это плавится металл.
- Как держать электрод.
Практически вертикально, с уходом в сторону шва не далее чем на 40 градусов. Между элементом и электродом выдерживается дистанция в 3 мм.
- Образование шва. Появляется сварочная ванна, когда возникает оранжевое пятно, и поверхность этого пятна рябит, подрагивает. С начала поджига электродуги металлический расплав (то есть ванна) появится через 2 или 3 секунды, и электрод надо перенаправить на 1–2 мм к шву. Потом снова нужно дождаться оранжевого пятна, только уйдет на это меньше секунды. И вот так, поступательно, по миллиметру выполняется сварка.
- О положении и типе движения. Обязательно следует выдерживать корректный наклон, не играть с отрывом от рекомендованного угла. Если электрод наклонить сильнее, дуга потолком просто оттолкнет назад сварочную ванну. И шов выйдет высоким, отчего прогрев металла усложнится.
Получается, что электродный наклон руководит высотой будущего шва. Правильным можно назвать шов, по параметрам высоты выходящий «заподлицо» к свариваемым основаниям. Важно держать дуговой интервал. Если слишком откровенно касаться электродом элемента, возникнет замыкание. На агрегате система защиты даст об этом знать. Поэтому ориентироваться надо на высоту, при которой при наклоне электрода деталей выйдет касаться лишь его обмазкой.
- Контролировать качество сварочной ванны надо зрительно. Оценивать важно и ее саму, и задний шов. На саму дугу смотреть не надо. Шов должен быть равномерным. Поначалу не все будет идеально, и не нужно стремиться сварить шов только одной электродугой. Надо замедлиться, разглядеть шовное сечение. Если на шве кратеры и прожиг до получения тонкого металла и явных «дырок», значит, сила чрезмерна. Если на ножке шва шарик – значит, силы тока недостаточно.
А вот если на шве чешуйка/бугорок – это правильно.
- Завершение сварки. В завершении работы не нужно убирать электрод одномоментно. Имеет смысл в зоне действия сделать маленький круг, с внесением металла. В противном случае в месте отрыва дуги появится совсем нежелательный кратер. Отрывать электрод стоит легким чирканьем. Остывший и почерневший в результате шлак удается со шва молотком и жесткой щеткой. Если процесс выполнен корректно, он отскочит большими хлопьями, в металлическом шве включений шлака не будет.
Такие уроки – только теоретическая подготовка, без претензии на детальное руководство. Но сварка и не требует быстрого научения, придется вспомнить и курс школьной физики с его переменным и постоянным током, процессами в среде углекислого газа. А главное – требуется вспомнить все правила безопасности. Не стоит жалеть время на подготовку: информирован – значит, вооружен и риски неудачной работы низки.
Об основах сварки для начинающих смотрите далее.
ArcTest, PAS и HDCM в процессе сварки волокон Fibertool
Данный материал рекомендован для ознакомления специалистам всех уровней. У вас есть желание углубиться в сварочные аппараты оптических волокон? Тогда смиритесь с некоторыми сложностями. Нужна терминология, привычка к ней, проверенные факты и специалисты, которым можно верить.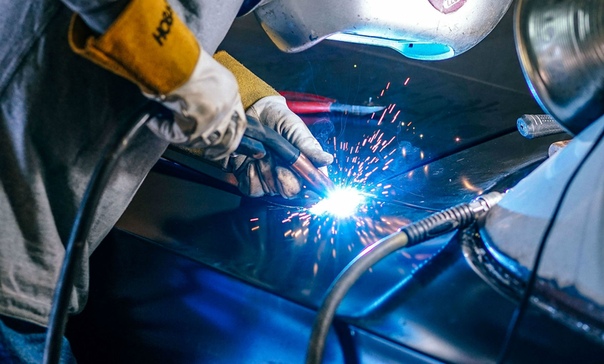
Сварок серий Type-36 и Type-37 практически не осталось, а существующие модели Type-39 и Type-71c вытесняются конкурентами, поэтому делясь с вами секретной информацией о них, мы ничем не рискуем.
Итак, в 2005 году лондонский офис прислал в Россию письмо, в котором попытался объяснить разницу между PAS и HDCM. Объяснили неудачно. В российской рекламе HDCM (англ. High Definition Core Monitoring) до сих пор называют системой юстировки, путая ее с DCM (англ. Direct Core Monitoring), так в Sumitomo называют юстировку по сердцевине. Очень часто ее выдают за передовое достижение, видимо не зная, что понятие HDCM появилось в 1995 году. Спустя 7 лет, в сентябре 2012 года специалисты Fibertool выяснили, что разницы между PAS и HDCM не существует, по сути дела, это обработка профиля яркости волокна, а разные названия ей даны только потому, что она происходит на разных стадиях сварного процесса. Рассмотрим же этот процесс.
Тест дуги
Тест дуги и калибровка дуги применительно к сваркам оптики выражают одно и то же понятие. Разница состоит только в физическом воплощении у разных сварочных аппаратов. Мы будем пользоваться термином «арктест» (калька с английского слова Arctest).
Существует три основных вида арктеста:
1. Простой арктест. Встречается у аппаратов производства Sumitomo и Fitel, а также у Jilong KL-280 и DVP-730. Два волокна выводятся на экран и устанавливаются на расстоянии зазора друг от друга. После дугового разряда неподвижные волокна оплавляются. Анализируя величину оплавлений, аппарат устанавливает позицию выхода волокон на экран и мощность дуги.
2. Продвинутый арктест. Используется на сварочных аппаратах Jilong KL-300T, Jilong KL-300 и в INNO IFS-10. Два волокна выводятся на экран и устанавливаются на расстоянии зазора друг от друга, только оплавляются они последовательно двумя разрядами разной мощности, а затем аппарат устанавливает позицию выхода волокон на экран и мощность дуг.
3. Арктест Fujikura. Позиция выхода волокон на экран устанавливается в том месте, где на экране регистрируются вспышки разрядов. Установка мощности происходит на сваренных волокнах, исходя из осевых сдвигов после серии последовательных дуговых разрядов. Такой способ калибровки используется на магистральных аппаратах Fujikura. Исключение составляет FSM-60S, у которого последняя функция находится в секретном меню, а в открытом меню мощность и позиция дуги калибруется простым арктестом как в случае 1.
Арктест в китайских аппаратах реализован весьма удачно. Несмотря на затянутость самого теста, его результаты гораздо стабильнее по сравнению с японскими сварками. Дуге не требуется дополнительная подстройка, которая была нужна, к примеру, на Sumitomo Type-39. Как результат, китайские Jilong более стойки к изменению внешних условий, нежели японские аппараты. Физика сварки, реализованная китайскими инженерами в Jilong, заключается в том, что волокна при включенной дуге подаются к месту сварного стыка одновременно с двух сторон сразу (в японских аппаратах одно волокно во время дуги стоит на месте). За счет этой отлично реализованной физики «Джилонгам» значительное время удавалось нивелировать недостатки родных скалывателей. Эти сварки «прощали» своим хозяевам плохие сколы, несовпадающие виды свариваемых волокон и старые электроды, выдавая отличный результат там, где начинались проблемы с японскими аппаратами.
Назначение арктеста двояко. Во-первых, на основании его результатов аппарат устанавливает мощность дуги. Во-вторых, и это более важно, при арктесте устанавливается позиция дуги. Это координата, на которую будет выведено волокно перед сваркой. Она не является постоянной и со временем из-за нагара на электродах дуга может переместиться. Как правило, это сопровождается снижением качества сварки, но вновь сделанный арктест скорректирует позицию дуги в памяти аппарата.
Когда-то считалось, что у Fujikura тест дуги необязателен, так как аппарат в программе AUTO сам производил подстройку мощности дуги перед каждой сваркой. Однако при этом упускался факт, что позиция дуги в процессе работы не подстраивается. Калибровать дугу необходимо именно из-за позиции, и первой рекомендацией при неполадках у «Фуджикур» является именно калибровка дуги.
В INNO IFS-10 тоже производится калибровка мощности перед каждой сваркой, но тем не менее, в кратком руководстве подчеркивается, что калибровка дуги является обязательным условием начала работы. Во многих источниках, особенно там, где дело касается Sumitomo, арктест подается как компенсация внешних воздействий: температуры, влажности, высоты над уровнем моря, изношенности электродов. Такая формулировка второстепенная. Что бы арктест ни компенсировал, он всё равно подстраивает мощность (которая может быть избыточной или недостаточной при данной температуре, влажности и атмосферном давлении) и устанавливает позицию дуги, на которую подадутся волокна (смещение дуги вызвано изменением формы электродов вследствие нагара). Эти два параметра являются главными в любой программе сварки любого сварочного аппарата.
Можно привести несколько интересных постулатов на эту тему:
• Электроды стоят на месте, но дуга, которую они создают, может двигаться.
• Позиция дуги — это координата, на которую выводятся волокна перед сваркой.
• Координата, на которую выводятся волокна перед сваркой, не всегда совпадает с реальным местонахождением дуги.
• С помощью арктеста аппарат пытается поставить волокна именно в то место, где находится дуга.
• Позицию дуги можно выставить вручную или доверить ее аппарату. Во втором случае нужно активировать в меню аппарата калибровку или тест дуги, после теста сварка выставит позицию дуги сама, используя информацию о оплавлении волокон.
• Аппарат двигает позицию дуги в сторону того волокна, которое при арктесте оплавилось больше.
Позиция дуги — это координата на экране сварочного аппарата. Место, где стоят электроды, не обязательно совпадает с позицией дуги. Более того, электроды вообще могут быть не соосны, хотя человек их представляет идеально ровными и стоящими четко друг против друга.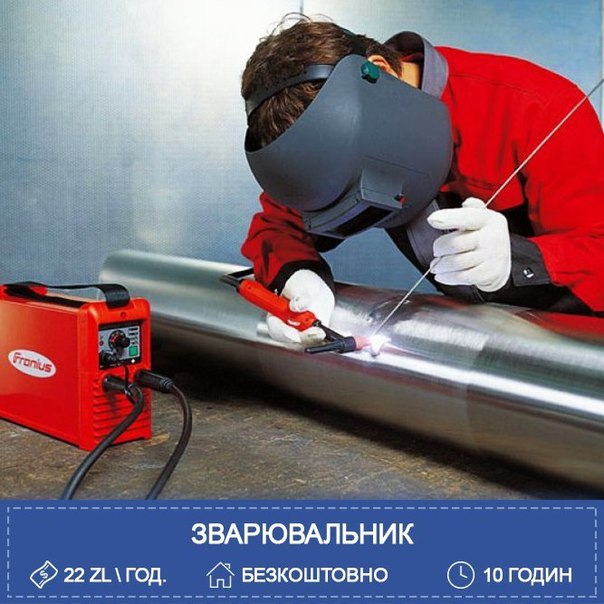
Интересный факт: В Sumitomo Type-39, в меню «Функции» на странице номер 6, видимой в режиме администратора (пароль 0000), начиная с версии Firmware 1.69 существует пункт «Комп. влияния на дугу окруж. среды» (англ. Arc Environment Compensation). Если этот пункт активировать, то параметры программ сварки блокируются, и пользователь не сможет их изменить. Монтажник, работающий на Type-39, всегда реагировал на плохое качество сварки тем, что вручную повышал мощность дуги. При включенной «Arc Environment Compensation» такая возможность пропала. Всем пользователям Type-39 рекомендуется перед работой войти в режим администратора и убедиться, что эта функция выключена.
Профиль яркости волокна как основа процессов HDCM, PAS и APDS
Международная аббревиатура PAS (англ. Profile Aligning System) означает выравнивание волокон с использованием профиля яркости волокна. Аббревиатуры HDCM (англ. High Definition Core Monitoring) и APDS (англ. Automatic Profile Detection System) сумитомовские, мы используем их потому, что другие производители не давали аналогичным процессам отдельных имен. HDCM означает оценку потерь сварного шва с повышенной точностью, а APDS — автоматическое определение типа волокна по его профилю яркости.
Сразу надо оговориться, что часть параметров юстировки и оценки качества применима только к сваркам с юстировкой по сердцевине. Бесполезно искать их в Swift F1, Fujikura FSM-18S и т.п. Там упрощенная оптика и обработка изображения, а юстировки нет вообще как и определения типа волокон. В общем, программное обеспечение аппаратов с «выравниванием по канавке» (fixed V-groove) не содержит тонкостей, перечисленных ниже. Синоним юстировки — слово выравнивание. Когда говорят, что волокна разъюстированы, это значит, что они не соосны, то есть вышли на экран со смещением. Когда говорят, что аппарат имеет юстировку по сердцевине, это значит, что он может выравнивать волокна по сердцевине, устраняя осевые смещения, возникшие из-за грязи или неровно уложенного волокна. Точную последовательность операций, которую проводит аппарат перед включением дуги, мы рассмотрим в отдельной статье, на примере Sumitomo Type-36.
А сейчас дадим описание двух — трех важных моментов, без которых невозможно обойтись. Обработку изображения волокна аппарат начинает немедленно, сразу после закрытия ветрозащитной крышки. Но он вынужден придерживаться определенного порядка действий, например, сварка не может сначала выровнять волокна по сердцевине, а потом по оболочке. Это невозможно в силу алгоритма работы аппарата. Волокно необходимо сначала подготовить и один из важнейших этапов — фокусировка. При команде «сфокусировать волокно» сварочный аппарат подсчитывает два параметра, их еще называют отношениями Black and White (сокращенно B/W) и Black and Black (сокращенно B/B).
Следующий важный момент состоит в том, что PAS (англ. Profile Aligning System), HDCM (англ. High Definition Core Monitoring) и APDS (англ. Automatic Profile Detection System) имеют общую основу, а именно профиль яркости волокна. По сути дела, PAS, HDCM и APDS — одна и та же обработка изображения, только на разных стадиях сварного процесса: PAS — использует профиль яркости при юстировке волокон. APDS — использует профиль яркости при определении типа волокон. HDCM — использует профиль яркости при оценке качества сварного шва. Профиль яркости волокна на экране сварочного аппарата (отражающий изменение показателя преломления волокна в поперечном сечении) напоминает трезубец или корону, он используется во всех сварках оптики, обладающих юстировкой. Способ юстировки PAS обязан своим названием именно профилю яркости. Упрощенное изображение профиля яркости волокна можно встретить в презентациях: Реально, на экране сварочного аппарата, он выглядит так:
Слева показана диаграмма яркости всего волокна, а справа обработка изображения его сердцевины. Черной линией показан график яркости в зависимости от координаты, а красной линией график его производной по яркости. Форма трезубца должна быть приблизительно одинакова, хотя его зубцы и впадины могут сдвигаться в зависимости от типа волокна или состояния оптики аппарата. За форму трезубца отвечают коэффициенты «k», о них сказано чуть ниже. Обратите внимание, что в точках перегиба черного графика, производная (красный график) проходит через свои максимумы и минимумы, в этих точках изменение яркости наиболее интенсивно. Центр сердцевины волокна обозначен зеленой вертикальной линией, проходящей через весь экран. Для аппарата центр сердцевины лежит в точке, находящейся между двумя экстремумами производной, эти экстремумы обозначены желтыми вертикальными линиями. Самая яркая координата не является центром, она всего лишь максимум яркости, располагается немного левее центра сердцевины и отмечена короткой зеленой линией. Координаты зубцов и впадин (в точках, где красный график пересекает горизонтальную ось) используются при расчете коэффициентов «k», их всего пять: k1, k2, k3, k4, k5.
Коэффициенты «k» являются количественным выражением качества изображения волокна. Каждый из них может меняться строго в определенном диапазоне. Пока все коэффициенты находятся в допуске, аппарат обрабатывает изображение корректно. Стоит хотя бы одному коэффициенту выйти за допустимые рамки, и Sumitomo начинает давать сбои. Это происходит при повреждении зеркал, загрязнении матрицы или объектива микроскопа. В лучшем случае аппарат начнет врать при оценке потерь, в худшем — потеряет способность юстировать волокна.
До появления волокон с пониженной чувствительностью к изгибам (стандарт G.657), сварочные аппараты умели обрабатывать только диаграмму яркости в форме простого трезубца. Когда же волокна с пониженной чувствительностью к изгибам стали появляться, выяснилось, что их диаграмма яркости содержит не три зубца, как у обычных волокон SMF, а целых пять (обусловлено дополнительным изменением показателя преломления в профиле волокна для обеспечения отражения излучения, прошедшего первый барьер из изменения показателя преломления, обратно в сердцевину волокна, что обеспечивает сохранение излучения в волокне при изгибах). Центральный пик диаграммы волокон G.657 в свою очередь представляет собой трезубец. Это выбивалось из стандартной схемы обработки изображения Sumitomo Type-37 и ранних Type-39. Аппараты Type-37, Type-37SE и Type-39 ранних версий оказались не в состоянии юстировать такие волокна по сердцевине, их требовалось переключать в режим юстировки по оболочке. Модернизировать программное обеспечение Sumitomo Type-37 не стали, а Type-39 потребовалось на это почти 2 года.
Ниже представлена диаграмма яркости волокна Draka BendBrightXS, отчетливо видны 5 зубцов его сердцевины.
PAS — юстировка волокон с использованием профиля яркости
Свет проходит сквозь волокна и попадает в камеры, на тыльной части которых расположен детектор-матрица, на ней и формируется картинка. Свет, проходя сквозь волокно, преломляется как в линзе. Яркость света, измеренная аппаратом, меняется в поперечном сечении волокна, так как показатель преломления сердцевины и отражающей оболочки волокна разные. Светодиоды монохромные, красного цвета, их свечение можно увидеть только при закрытой крышке. Линза это объектив камеры. Сама камера снимает увеличенное изображение, поэтому ее часто называют микроскопом. CMOS это тип матрицы, раньше на аппаратах стояли матрицы CCD. Зеркала отражают красный свет и направляют его на волокно в микроскоп. Такая схема позволяет получить изображение волокон с двух взаимно перпендикулярных точек зрения, и выравнивать волокна в двух плоскостях: X и Y. Изображение волокон выводится с детектора на монитор, где его наблюдает оператор.
Чтобы вы поняли степень абстракции, мы выложили реальный вид сварочного аппарата с того же ракурса.
Как видите, он совершенно не похож на свою функциональную схему. Данная схема с зеркалами на крышке является классической. Большинство сварочных аппаратов построено по ней. Исключение составляют только аппараты последних поколений типа Fitel S178, Sumitomo Type-71c, где на ветрозащитной крышке установлены светодиоды, а зеркал вообще нет. Самым первым аппаратом без зеркал был Sumitomo Type-36 (выпускался до 2002 года), ниже показана схема его оптического тракта.
С небольшой натяжкой ее можно считать оптической схемой для Fitel S178 и Sumitomo Type-71, с тем отличием, что у Type-36 был всего один детектор на два микроскопа, поэтому одновременно изображение в двух полях X и Y он не показывал. Как появляется картинка на экране сварочного аппарата, мы разобрались. Теперь переходим к обработке изображения. Программное обеспечение аппарата обрабатывает картинку вдоль секущих линий, проходящих перпендикулярно оси волокна на экране. В результате получается диаграмма яркости.
Абстрактный вид диаграммы показан на схеме слева, а реальный вид справа, так выглядит диаграмма яркости на экране аппарата Sumitomo Type-37. Каждая секущая представляет собой такую диаграмму, для простоты ее называют профилем яркости волокна.
Аппарат оперирует производной графика яркости, это дает ему возможность определять координаты, где происходит изменение яркости, а они происходят на границах раздела оптических сред с разным показателем преломления. Таким образом, он определяет границы сердцевины волокна и границы его оболочки.
Эксцентриситет (ошибка концентричности волокна) является важным параметром, входящим в формулу оценки потерь. Чтобы свести влияние эксцентриситета к минимуму, его значение должно быть около 0.5 мкм. Это стало возможным после 2000 года, когда технология производства волокна стала более развитой. Значение эксцентриситета измеряется до включения дуги, каждое из двух волокон (правое и левое) имеет свой эксцентриситет. Используя информацию о профилях яркости, аппарат в каждый момент времени обсчитывает геометрическую модель волокон и юстирует их в двух взаимно перпендикулярных плоскостях.
Волокна SM, DS, NZDS, PSC, CS, ED и BIF выравниваются по осям сердцевин в обоих полях. У волокон MM 50 и 62.5 сердцевина настолько велика, что нет необходимости выравнивать оси сердцевин. Система выравнивает волокна по осям их оболочек (диаметров).
Сварка волокон
Программа сварки для волокон SMF в аппаратах «Сумитомо» одна из самых простых с точки зрения параметров. Они уже много лет не менялись. Скриншот снят с Sumitomo Type-39. Первым идет не параметр, а тест. А точнее, тест дуги, который мы разбирали вначале. Он регулирует Позицию дуги (англ. Arc Center) и мощность дуги (англ. Arc Power). Мы будем считать, что тест уже проведен, и оптимальные позиция и мощность установлены.
Далее идут уже параметры программы сварки:
• Позиция дуги (англ. Arc Center) измеряется в точках, по-английски «dot».
• Время дуги (англ. Fusion Time) секунды
• Предварительная дуга (англ. Prefusion Time) сотые доли секунды
• Зазор (англ. Gap) микрометры
• Перекрытие (англ. Overlap) микрометры
• Мощность дуги (англ. Arc power) безразмерные «стэпы», калька с английского «step», то есть шаг. Мы так и говорим: «мощность двадцать пять стэп». Русское слово «шаг» не прижилось. Сначала аппарат очищает волокна коротким разрядом дуги, а после предварительной фокусировки проверяет углы скола, наличие выступов и пыли. Критическое значение угла скола, при котором аппарат останавливает работу, программируется пользователем.
Установка зазора между волокнами: Левое волокно становится на позицию дуги, а правое волокно подходит к левому на расстояние, определяемое параметром Зазор (англ. Gap).
Юстировка волокон: после того как волокна вышли на экран, идет их юстировка по оболочке, а после установки зазора происходит уже точное выравнивание волокон по сердцевине. Используя данные профиля волокна, аппарат выравнивает волокна в плоскостях X и Y, идет та стадия обработки изображения, которую обычно называют PAS (англ. Profile Aligning System).
Помимо абстрактной картинки показан реальный вид линий PAS на экране Sumitomo Type-37.
Включение дуги: Зажигается дуга. В течение 0.05 секунды волокна стоят на месте и «греются». Это и есть предварительная дуга (англ. prefusion time). На самом деле дуга не делится на предварительную и основную, её время едино и прописано в параметре Время дуги (англ. fusion time), оно равно 1.65 секунды. Просто из этого времени 0.05 секунды волокна будут стоять на месте, а оставшиеся 1.6 секунды они будут двигаться и сплавляться. Момент предварительной дуги в одномодовой программе поймать трудно, потому что он очень короткий. Выглядит он примерно так:
Подача волокна: Сварка подает правое волокно, находящееся на позиции зазора, влево на расстояние перекрытия. При этом правое волокно вдавливается в левое. Видно как стык между волокнами, который еще не успел расплавиться, сдвигается влево.
Вдавливание происходит у каждого аппарат по своему. У Fujikura, независимо от модели, всегда левое волокно вдавливается в правое, у Fitel S178 левое волокно подаётся в правое, а на ранних моделях S175, S176 было наоборот. У Sumitomo всегда правое волокно подается в неподвижное левое. А у Jilong оба волокна подаются к месту сварного стыка одновременно, этим объясняется малое значение их параметра «Перекрытие» (англ. overlap), оно в 2 раза меньше, чем у других сварок, ведь не одно, а оба волокна сдвигаются к центру дуги на эту величину.
Сплавление волокон: скорость вдавливания достаточно велика и расстояние в 25 мкм правое волокно проходит почти мгновенно, всё оставшееся время дуги волокна вновь стоят на месте. Дальше работает уже физика, а конкретнее, силы поверхностного натяжения расплава.
Оценка потерь: Аппарат снова начинает обрабатывать профиль яркости волокна. При этом он использует два вида секущих. Одни представляют собой ряд отдельно взятых линий, проходящих под углом 90° к оси волокна ближе к краю экрана. Для определенности мы их называем секущими PAS. Вторые линии расположены гораздо ближе друг к другу и начинаются сразу возле центральной линии сварного соединения. Мы называем их секущими HDCM.
На экране сварочного аппарата эти линии по умолчанию не видны, и не все современные аппараты позволяют их увидеть, поэтому мы вновь обращаемся к Sumitomo Type-37.
Впервые название HDCM для дополнительного ряда измерительных линий прозвучало в 1995 году. При помощи этих линий повышается точность оценки вносимого сваркой затухания. Все эти секущие, и PAS, и HDCM, на стадии оценки используют профиль яркости для получения параметров, входящих в формулу расчета потерь. С помощью секущих PAS измеряется параметр «смещение» (англ. offset)
С помощью секущих HDCM измеряется два параметра: смещение сердцевин (англ. core offset) и угловая деформация (англ. deformation). Смещение выражается в микрометрах, а угловая деформация в градусах.
Смещение сердцевин и простое смещение по сути дела одно и то же, просто смещение сердцевин (англ. Core offset) считается более точным. Вот как выглядят параметры сварного стыка в журнале сварок Sumitomo Type-39.
Параметры, измеренные с помощью линий PAS, выделены красным шрифтом. Параметры, выделенные зеленым шрифтом, измерены с помощью линий HDCM. Значения Est(L) и Est(R) означают смещение между осями сердцевины и оболочки (эксцентриситет) – левого и правого волокна соответственно.
Неженская профессия. Рязанка более 30 лет преподаёт технологию сварочных работ — Общество
О женской хрупкости на время приходится забыть, у сварщика должна быть твердая рука, ни каких рывков и остановок, одно неловкое движение и образуется дефект сварного шва. Елена Васяткина в профессии уже более 30 лет. Говорит, идти в сварщицы не планировала, училась на радиомонтажника, но всегда верила в судьбу.
Знаки Земли, знаки Огня по гороскопу. Вот так случилось, что мой знак Огня, и, наверное, поэтому мне все это достаточно приятно, не пугает, нравится. Это горячая профессия, горячо там бывает, 7000 градусов на дуге и надо управлять, она горит моментально и быстро. Видеть и управлять, сварщики должны быть ловкими.
Елена Васяткина, преподаватель Рязанского колледжа электроники.
У неё свой женский подход к мужской специальности, даже звук сварки ласкает слух. Ученики — сплошь юноши, а значит, завоевывать авторитет в мужском коллективе приходится с первого занятия.
Мальчишки, они, конечно, когда идут: о! Женщина! И идут к мужчинам, вроде как мужчина, им повезло. А потом, когда чувствуют нашу заботу, чувствуют наше к ним отношение, и понимают, что они точно так же учатся, и они нисколько не жалеют.
Елена Васяткина, преподаватель Рязанского колледжа электроники.
В учебной мастерской всё как в настоящем цехе, пренебрегать положенными перерывами на отдых нельзя. Свои «побочные эффекты» есть у любой профессии. Работа сварщика не проста физически, напряжены спина и шея, от светового излучения страдают глаза. Но те, кто выбрал эту специальность, остаются ей верны.
Трудоемкая работа, все время выполнение сложных элементов, конструкций. Вот это все нравится, нравится работать со сваркой, как держать дугу, всё это интересно.
Дмитрий Федин, учащийся Рязанского колледжа электроники.
Сегодня профессия сварщика входит в рейтинг 50 самых востребованных в стране. В последние годы произошли изменения профстандартов, вместо 6 разрядов ввели 4 квалификационных уровня. И мастера замечают, в работе сварщика множество аспектов изменилось, а, значит, это та профессия, учиться которой придётся всю жизнь.
Как выполнять дуговую сварку
Сварка защищенной дугой – процесс соединения двух металлических частей с использованием электродов, покрытых флюсом, которые плавятся в электрической дуге и становятся неотъемлемой частью свариваемых частей. В данной статье описывается процесс использования при дуговой сварке электродов, а также сварочного аппарата обычного, трансформаторного, исполнения.
Понимание процесса сварки защищенной дугой.
Электрическая дуга формируется на кончике сварочного электрода при протекании тока через воздушный промежуток и через заземленный свариваемый металл. Здесь приведены некоторые термины, используемые в данной статье, и их описания.
- Сварочный аппарат. Данное понятие применимо к аппарату, который преобразует переменное напряжение 120-240 В в напряжение для сварки. Обычно это переменное напряжение 40-70 В или постоянное напряжение различных диапазонов. В состав данного аппарата обычно входит большой, тяжелый трансформатор, схема регулятора напряжения, внутренний вентилятор охлаждения и переключатель диапазонов силы тока. Понятие «сварщик» применимо к человеку, который выполняет сварку. Сварщик также осуществляет управление сварочным аппаратом.
- Провода, или сварочные кабеля. Это – изолированные медные проводники, по которым подводится к свариваемой рабочей поверхности ток большой величины и низкого напряжения.
- Электрододержатель, или стингер – это устройство на конце проволоки, которое держит электрод, с помощью которого сварщик выполняет сварочные работы.
- Заземление и заземляющий зажим. Заземление – это проводник, который заземляет или замыкает электрическую цепь. Заземляющий зажим присоединяется к рабочей поверхности и обеспечивает протекание электрического тока через свариваемый металл.
- Ампераж, или амперы. Это – электрический термин, который используется для описания величины электрического тока, подводимого к электроду.
- Постоянный ток и обратная полярность. Это – альтернативная конфигурация, которая используется в дуговой/электродной системе сварки. Данная конфигурация обеспечивает большую гибкость, особенно при сварке потолочным швом и при сваривании определенных видов сплавов, которые невозможно сварить с помощью переменного тока.
В состав сварочного аппарата, который генерирует данный род тока, входит выпрямительная схема, или же ток вырабатывается генератором. Он намного дороже по сравнению с традиционным сварочным аппаратом переменного тока.
- Электроды. Существует множество специализированных сварочных электродов для сваривания конкретных сплавов и типов металлов, таких как твердый и ковкий чугун, нержавеющая или легированная сталь, алюминий, а также различных видов закаленных и высокоуглеродистых сталей. Традиционно электрод состоит из тонкого стержня в центре, который покрыт специальным слоем (флюсом). Флюс, сгорая в процессе горения дуги, потребляет кислород и насыщает область шва двуокисью углерода, предохраняя свариваемый металл от окисления и от его горения в пламени дуги в процессе сварки.
Традиционные типы электродов и их назначение:
Электроды E6011 – это электроды из мягкой стали, покрытые древесно-целлюлозным слоем. Первые две цифры в обозначении электрода – это предел его прочности, измеряемый в фунтах на квадратный дюйм, умноженный на 1000. В приведенном примере предел прочности электрода составляет 60000 фунтов на кв. дюйм.
Электроды E6010 – это электроды обратной полярности, обычно используемые для сваривания паровых и водяных трубопроводов. Их целесообразно использовать для потолочной сварки, так как при плавлении металл, обладающий определенной формой, переходя из твердого состояния в расплавленное, втягивается потоком постоянного тока от электрода к обрабатываемой поверхности.
Существуют и другие виды специальных электродов E60XX. Однако они не будут изучаться подробно в данной статье в связи с тем, что электроды E6011s являются стандартными электродами общего применения, а электроды E6010s являются стандартными электродами для сварки постоянного тока обратной полярности.
Электроды E7018 – это электроды с низким содержанием водорода, из стали, покрытые флюсом, с высоким пределом прочности – 70000 фунтов на кв. дюйм. Часто применяются при сваривании сборок металлической конструкции в строительной отрасли, а также и в других случаях, когда применяется твердый присадочный материал и требуется прочный сварной шов. Хотя эти стержни и обеспечивают большую прочность, обратите внимание на то, что они не обеспечивают чистый, качественный шов при отклонении величины силы тока от требуемой величины, а также при наличии загрязнения (ржавчины, краски или оцинковки) конструкций. Их называют электродами с низким содержанием водорода, так как принимаются постоянные меры по снижению содержания водорода. Эти электроды должны храниться в печи при температуре от 120ºС до 150ºС. Данный уровень температуры выше температуры кипения воды на уровне моря – 100ºС. Данный уровень температуры препятствует образованию влаги (росы)(h3O) в воздухе и не дает ей накапливаться во флюсе.
Никелевые электроды, электроды из литейного сплава, электроды с никелевым стержнем. Это – специальные электроды, предназначенные для сваривания твердого, высокопрочного и ковкого чугуна, которые обладают большей податливостью при расширении и сжатии свариваемого материала.
Стержни из разнородного металла. Эти стержни изготовлены из специального сплава и обеспечивают лучший результат при сварке закаленных, твердых или легированных сталей.
Алюминиевые стержни. Существуют более современные технологии, обеспечивающие дуговую сварку алюминиевым стержнем в конвекционной среде, вместо сварки электродом в среде защитных газов. Это – сварочные аппараты MIG (газ, инертный к металлу) или TIG (газ, инертный к вольфраму), называемые часто гелиевыми, так как гелий – это газ, ранее используемый для защиты пламени дуги в процессе сварки. Официальное название было дано Американским обществом сварки (AWS), так как в этих случаях дуговая сварка производится плавящимся покрытым электродом (стержнем) в среде газа, инертного к вольфраму (tig) и газа, инертного к металлу (mig).
Размеры электродов. Выпускаются электроды различных размеров, в зависимости от диаметра металлического сердечника стержня. В зависимости от силы тока сварки, а также плотности свариваемого материала, стержни из мягкой стали могут быть диаметром от 16 мм до 1 см. Стержень, выпускаемый под определенную силу тока, обладает наибольшей производительностью при данной силе тока. Диапазон тока, протекающий через электрод выбранного диаметра, обусловлен материалом подложки и желаемой глубиной проникновения. Далее в этой статье будет приведен выбор конкретного диапазона тока сварки.
Средства защиты:
Важнейшим условием для безопасной сварки является выбор подходящих средств защиты для конкретной работы, а также их правильное использование. Здесь приводится перечень предметов, необходимых для безопасной сварки.
Защитный щиток (шлем). Это – маска, которая надевается сварщиком для того, чтобы защититься от яркой вспышки дуги, а также от искр, выбрасываемых в процессе сварки. Стандартные стекла для дуговой сварки очень затемнены, так как вспышки дуги негативно воздействуют на сетчатку глаза. Для дуговой сварки уровень затемнения 10 является минимальным. Защитные шлемы с линзами-раскладушками являются более эффективными, так как затемненные линзы могут быть подняты, а дополнительные прозрачные линзы защитят сварщика от частичек шлака, отлетающих в процессе сварки. Самозатемняемые защитные щитки являются наиболее эффективными на сегодняшний день защитными щитками, которые сегодня можно купить. Линзы данного сварочного щитка слабо затемнены и пригодны для шлифовки и газовой резки. При обнаружении дуги эти линзы затемняются автоматически на 10 единиц. Современный рынок предлагает различные модификации автоматических самозатемняемых линз.
Сварочные перчатки. Это – специальные изолированные кожаные перчатки, до 15 сантиметров выше запястий, которые защищают руки и предплечья сварщика (человека, выполняющего сварку). Они также обеспечивают частичную защиту от ожога при случайном контакте человека с электродом.
Сварочная кожаная одежда. Это – передник в виде кожаной куртки, защищающий плечи и грудь сварщика. Применяется при выполнении работ выше уровня головы, когда искры могут воспламенить одежду сварщика или причинить ожоги.
Рабочие ботинки. Для предотвращения ожога ног от раскаленного шлака и горячих искр, человек, выполняющий сварку, должен носить ботинки с областью зашнуровки как минимум 15 сантиметров. Ботинки должны быть с изолирующими подошвами из материала, который не плавится и не является легковоспламеняемым.
Меры, гарантирующие качественную сварку.
Сварка – это не просто процесс манипулирования сварочным стержнем с листом стали для его соединения с другим листом стали. Процесс сварки начинается с правильной установки и закрепления свариваемых деталей, или соединения вместе двух свариваемых поверхностей. Для поверхностей большой толщины скос можно заточить, чтобы наплывы твердого материала полностью заполнили паз. Далее приводится последовательность основных действий, необходимых для сваривания простого шва.
Зажигание дуги. Это – процесс создания электрической дуги между электродом и рабочей поверхностью. Тепло, необходимое для плавления и сваривания частей металла вместе, невозможно высвободить. если просто передавать ток от электрода к заземленной заготовке.
Перемещение дуги для создания валика. Валик – это смесь расплавленных металлов сварочного электрода и свариваемой поверхности. Служит в качестве наполнителя пространства между свариваемыми частями металла.
Формирование сварного шва. Это достигается за счет переплетения дуги взад и вперед через путь шва, или за счет движений в виде зигзага, или за счет движений в виде восьмерки. Благодаря этому металл распространяется по всей ширине, и, тем самым, достигается цель – формируется сварной шов.
Стружка и чистка шва между проходами. Каждый раз, по окончании прохода, или пути, от одного конца шва до другого, необходимо удалить шлак, или материал расплавленного флюса электрода, с поверхности сварного шва. Это необходимо повторять до тех пор, пока при последующем проходе не обнаружится, что шов заполнен лишь чистым расплавленным металлом.
Набор инструментов и материалов, необходимых для начала сварки.
Сюда входит сварочный аппарат, электроды, кабели и заземляющие зажимы, а также свариваемый металл.
Подготовка безопасной рабочей зоны.
Предпочтительно, чтобы был стол, изготовленный из стали или другого негорючего материала. В действительности подойдет несколько листов мягкой стали. Минимальная толщина – 0,5см.
Подготовка свариваемого металла.
В случае, если свариваемый металл состоит из двух частей, которые необходимо соединить в процессе сварки, может потребоваться подготовка, или сварочная подготовка этих частей, которая заключается в срезе фасок по сторонам, которые должны быть соединены. Благодаря этому обеспечивается в достаточной степени проникновение сварочной дуги, необходимой для перевода металла с обоих сторон в расплавленное состояние. В результате присадочный металл проникает в по всему сечению в глубину свариваемого металла. Как минимум, необходимо удалить краску, жир, ржавчину или другие загрязнения и убедиться в том, что шов с расплавленным металлом в процессе сварки будет чистым.
Присоединение зажимов для фиксации свариваемых поверхностей вместе.
Обычно используются плоскогубцы с зажимом, С-образные струбцины, тиски или пружинные зажимы с захватом. При выполнении определенных видов сварочных работ необходимо комбинировать различные методы для обеспечения надежного соединения поверхностей.
Подключение заземляющего зажима к большей по размеру части, которая подлежит свариванию.
Убедитесь в чистоте поверхности и в том, что выбрано правильное местоположение заземляющего зажима – электрическая цепь должна замыкаться на заземление по пути наименьшего сопротивления. Опять же, ржавчина или краска мешают надежному заземлению свариваемой части. А это препятствует образованию дуги вначале процесса сварки.
Выбор подходящего стержня и диапазона тока для выполнения требуемой работы.
Например, для эффективного сваривания 0,6-мм. листовой стали применяется 0,32-см. электрод E6011 и подается ток 80-100 А. Установите электрод в электрододержатель (далее по тексту – стингер). Убедитесь в чистоте проводящего материала зажима стингера, который держит конец электрода.
Включение сварочного аппарата.
Вы услышите жужжащий звук, исходящий от трансформатора. Звук вращения вентилятора охлаждения может быть или слышен, или не слышен. Вентиляторы некоторых сварочных аппаратов начинают вращаться только тогда, когда требуется охлаждение аппарата. В случае необходимости проверьте схему подключения питания и выключатель, расположенный на щите управления. Так как сварочные аппараты, во время их работы, потребляют значительную мощность, они требуют специальную схему подключения, рассчитанную на ток 60 А или выше, на напряжение 240 В.
Правильное удержание электрода.
Удержание стингера с электродом за изолированную ручку в правой (для левши – в левой) руке в положении, которое обеспечит естественность движений при сваривании сразу после того, как Вы ударите кончиком электрода по свариваемой поверхности. Удерживайте сварочный щиток на достаточной высоте таким образом, чтобы Вам был виден процесс движения электрода у рабочей поверхности в пределах нескольких дюймов. Вы должны быть готовы опустить затемняющие линзы для защиты глаз. До подачи напряжения питания можно выполнить пробное соприкосновение электрода с рабочей поверхностью для того, чтобы почувствовать электрод. Однако, никогда не зажигайте электрическую дугу без защиты глаз.
Выбор точки начала сварки.
Поднесите кончик стержня к точке начала сварки и опустите защитный шлем. Прислоните кончик электрода к рабочей поверхностью и, тем самым, замкните электрическую цепь. После этого немедленно возвратите электрод назад на некоторое расстояние для зажигания электрической дуги между электродом и свариваемым металлом. Альтернативный способ зажигания дуги, подобный зажиганию спички. Дуговой промежуток, или воздушное пространство, создает большое сопротивление в электрической цепи. За счет этого вспыхивает пламя дуги, или плазмы, с температурой, достаточной для плавления электрода и металла зоны сварки.
Ударение электрода о рабочую поверхность, взятие электрода назад при появлении электрической дуги.
Так как расстояние от кончика электрода до свариваемой поверхности зависит от диаметра электрода и силы тока, данное действие требует большой практики. Но если Вы научились правильно выдерживать это расстояние, между электродом и рабочей поверхностью будет наблюдаться устойчивое горение дуги. Обычно длина дугового промежутка не более, чем диаметр электрода. Поддерживайте устойчивое горение дуги, соблюдая расстояние от электрода до рабочей поверхности от 0,32 до 0,5 см. Перемещайте электрод по направлению сварки. При перемещении электрода металл будет расплавляться и заполнять шов. Тем самым будет осуществляться процесс сварки.
Опыт перемещения электрода от одного до другого края шва с поддержанием стабильной дуги и постоянной скорости и с выдерживанием правильного направления движения. Научившись управлять дугой, Вы перейдете к процессу прокладки, или наращивания, сварного шва. Это – слой металла, который соединяет две свариваемых поверхности. Процесс формирования валика зависит от ширины (если шов однородный) наполнения и от глубины проникновения наплавленного металла. Чем меньше скорость движения электрода, тем глубже проникает наплавленный металл. А широкий шов обеспечивается при зигзагообразных или узорообразных движениях электрода.
Поддержка дуги стабильной по всей траектории сварки.
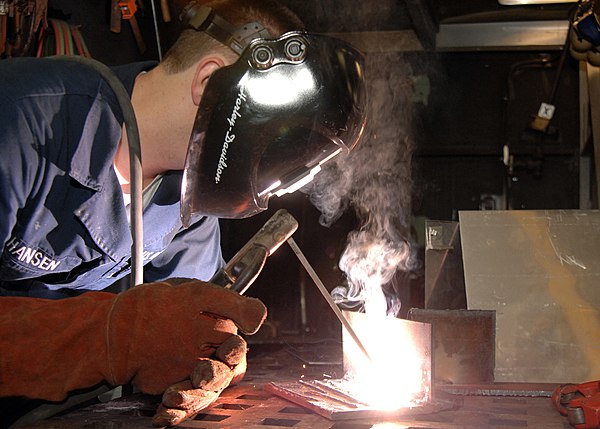
При замыкании электрода на металл и его заклинивании, резкий рывок электрода на себя может легко привести к переламыванию стержня, повреждению стингера или сварного шва. При потере дуги из-за удаления электрода слишком далеко, необходимо остановить процесс сварки и очистить сварной шов от шлака. После этого следует выбить дугу и продолжить сваривание шва, очищенного от шлака, с места потери или нарушения дуги. Никогда не кладите слой наплавленного металла поверх шлака, так как он растворится в плазме дуги и создаст пузырьки в глубине наплавленного металла. Сварка получится непрочной и грязной.
Перемещение электрода по радиальной траектории для формирования более широкого валика.
Данный прием позволяет сформировать более объемный шов в один проход. Сварка получается чистой и без дефектов. Используется поперечное движение электрода относительно продольной оси сварного шва, либо зигзагообразное, криволинейное, а также движение в виде восьмерки.
Регулирование выходной силы тока сварочного аппарата в зависимости от свариваемого материала и желаемой глубины проникновения дуги.
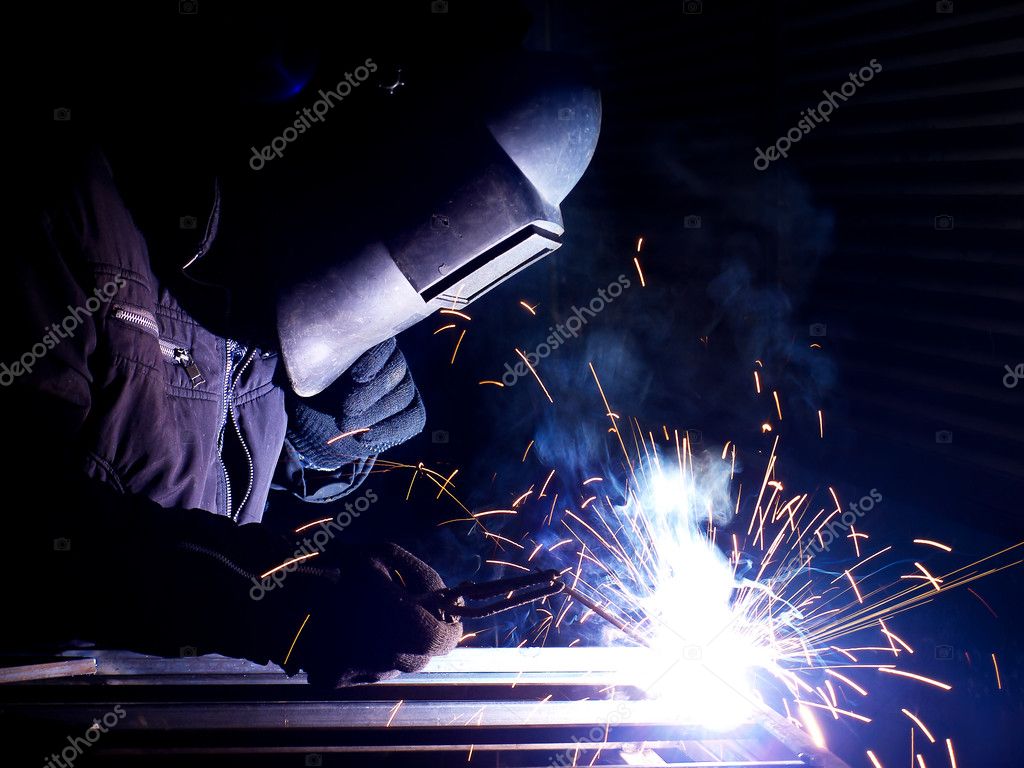
Если в процессе сварки шов получается пористым, с глубокими кратерами по краям, или металл интенсивно плавится и прогорает, необходимо постепенно уменьшать силу тока до тех пор, пока ситуация не придет в норму. Если существуют трудности в зажигании или поддержке дуги, необходимо увеличить силу тока.
Очистка выполненного сварного шва.
По завершении сварки может потребоваться очистка шва от шлака с целью его последующей покраски либо из косметических соображений. Обломайте шлак. Обработайте шов проволочной щеткой для его очистки от инородного материала и остатков шлака. Если необходимо обеспечить ровную поверхность, чтобы в дальнейшем ее приварить к другой поверхности, воспользуйтесь угловой шлифмашиной для удаления верхней кромки или верхней части валика. Чистый сварной шов, особенно после обработки, легче проверить на слоистость или на наличие раковин и других дефектов сварки.
Окраска шва.
Используйте антикоррозионную грунтовку для предотвращения коррозии. Если свежий сварной шов подвергается атмосферным воздействиям, таким как влага, его быстро разъест коррозия
Советы:
- При сваривании больших по размеру заготовок, которые невозможно эффективным образом зажать, для предотвращения сдвига, соедините части воедино с помощью маленьких сварных швов, находящихся на небольшом расстоянии друг от друга.
- Некоторые люди вслушиваются в звуки, издаваемые электрической дугой, чтобы судить о качестве сварки. Хлопки и щелкающие звуки могут свидетельствовать о несогласованном дуговом промежутке или о неправильно выбранной силе тока.
Предостережения:
- Металл остается горячим в течение длительного периода времени после завершения сварки. Поэтому, до полного остывания материалов, держите животных и детей отдельно.
- Во избежание поражения электрическим током, выполняйте периодический осмотр кабелей и соединений.
- Ток большой силы, генерируемый дуговым сварочным аппаратом, крайне опасен.
Поэтому пользуйтесь кабелями и стингером с осторожностью. Никогда не выполняйте сварочные работы во влажных условиях. Не сваривайте влажный материал без предварительной подготовки.
- Защитите себя от ожогов, покрыв кожу перчатками, лицо – маской, в зависимости от того, какие части тела необходимо покрыть. Никогда не выполняйте сварку без защитного шлема.
- Избегайте вдыхания паров сварки. Это особенно актуально при сваривании металлов с оцинкованными поверхностями и с электролитическим покрытием, а также при сваривании металлов, окрашенных оксидными грунтовками.
- Яркий свет электрической дуги может вызвать ожог, подобный солнечному ожогу. Поэтому, для уменьшения воздействия света дуги, необходимо носить рубашки с длинными рукавами и длинные брюки.
- В подборке ниже дается ссылка, где можно ознакомиться со специальными предостережениями и мерами предосторожности.
Что Вам понадобится:
- Сварочный аппарат с проводами, зажимами и электродами;
- Инструменты для подготовки и очистки сварных швов, в том числе обрубочный молоток, проволочная щетка и угловая шлифовальная машина;
- Средства защиты.
Ремонт сварочных аппаратов в СПб
Предлагаем все виды ремонта сварочных аппаратов трансформаторного типа. Беремся за любые поломки, возвращаем технику в рабочее состояние, устраняем последствия короткого замыкания и перегрева, меняем поврежденные части, зачищаем контакты, восстанавливаем изоляцию, обмотку.
Сварочный трансформатор — это простой, надежный аппарат, который часто продолжает работать даже после критических повреждений. Главное требование при ремонте сварочного аппарата — установить и устранить причину неполадки, тогда ситуация не повторится.
Причины поломок трансформаторного сварочного аппарата
- Ослабление контактов
Неплотный контакт образуется в результате неправильного закрепления сварочных проводов, вибраций, размыкания внутри корпуса, заводских дефектов. Иногда достаточно один раз неправильно закрепить провод — и начнется постепенный процесс разрушения. Контакты нагреваются, искрят, повреждается изоляция. Если вовремя не принять меры неизбежна поломка или травма.
- Пыль и посторонние предметы в корпусе
Сварочный трансформатор хорошо переносит работу в условиях строительной площадки (пыль, влажность), но и за ним необходимо следить.Грязь внутри корпуса ухудшает теплообмен, катушки перегреваются, трескается изоляция. Посторонние предметы могут повредить вентилятор, вызвать короткое замыкание.
- Физическое повреждение кабеля
Дефект изоляции или жилы устраняется путем замены поврежденного участка, кабеля целиком, местного восстановления изоляции.
- Проблемы с напряжением сети
Эффективность трансформаторного сварочного аппарата зависит от параметров сети, изменение параметров влияет на сварочный ток. Если настройка не помогает, значит мощности сети недостаточно и необходимо подключить генератор.
- Нарушение режимов работ
Каждый сварочный аппарат предусматривает определенную продолжительность включения (ПВ) в максимальных режимах работы.
Параметр зависит от мощности, стандартное значение 70%: 7 минут работы, 3 минуты перерыв. При использовании электродов меньшего диаметра с понижением сварочного тока допускается увеличение продолжительности включения. Несоблюдение режима приводит к перегреву оборудования.
Когда нужен ремонт сварочных аппаратов в СПб: признаки неисправности
- Аппарат не включается. Нужно искать повреждения питающего кабеля, контактов внутри корпуса. Если визуально причину определить невозможно — требуется провести диагностику.
- Оборудование самопроизвольно отключается. Скорее всего, причина — перегрев. Проверьте вентилятор, затяжку пластин трансформатора, послушайте звук работы.
- Прерывание дуги, залипание электрода. Проблемы с настройкой оборудования, напряжением сети. Нужно настроить, заменить электрод, проверить параметры сети.
- Гудение трансформатора. Короткое замыкание между обмотками, ослабление болтов, которые стягивают пластины.
- Шум при работе прибора. Вентилятор задевает за посторонние предметы, скопления грязи, начинает скрипеть, шуршать. Необходимо почистить лопасти, решетку, пространство вокруг.
Особенности ремонта сварочных аппаратов
В трансформаторных сварочных аппаратах нет слишком сложных систем управления, поэтому ремонт часто сводится к механическому обслуживанию и устранению дефектов:
- Зачистка, замена контактов. Неплотный контакт приводит к нагару, зазор увеличивается, соединение перегревается, полностью выходит из строя.
- Удаление поврежденных частей силового кабеля, установка новых элементов, замена вентилятора, регулятора, блока питания.
- Перемотка трансформатора и подтяжка болтов помогают избежать межвиткового короткого замыкания, перегрева, снижают громкость гудения.
- Восстановление изоляции. Поврежденная, оплавленная изоляция приводит к дальнейшему разрушению проводки и поломке устройства.
Преимущества ремонта сварочных аппаратов в ООО «АНДИ»
- Бесплатная диагностика. Не придется платить даже при отказе от ремонта;
- Гарантия на работы 1 месяц;
- Собственный склад деталей, материалов для восстановления. Быстро находим любой элемент, без задержек приступаем к работе;
- Токарный станок для производства мелких деталей поштучно. Возможно изготовление металлических запчастей для ремонта;
- Низкая стоимость;
- Наличный и безналичный расчет.
Как заказать ремонт сварочных аппаратов в Санкт-Петербурге
Ремонтируем сложную силовую технику: трансформаторы, инверторные аппараты, плазменные резаки, электронные блоки управления, переключатели, вентиляторы, контакты, механическую часть.
Позвоните, проконсультируйтесь с мастером или приезжайте и привозите аппарат. Ремонт занимает от 2 до 6 дней.
Если нужно срочно — предупредите механиков, сделаем без очереди.
Как звучит сварка? GMAW
Каждый вид сварки имеет уникальный звук. Иногда этот звук может указывать на проблемы. В других случаях он сообщает оператору, что все идет правильно. Компания Xiris добавила аудиомониторинг в наши ведущие в отрасли сварочные камеры. Эта инновационная система дает сварщикам новый инструмент для контроля и улучшения своей работы.
Однако часто требуются годы опыта, чтобы отличить небольшие различия в звуке, которые отделяют хороший сварной шов от плохого.А если вы новичок в сварке или раньше не пользовались звуком, как узнать, к чему прислушиваться?
Сегодня мы рассмотрим сварку GMAW или MIG и поделимся различными звуками, которые вы можете слышать, и их значением.
- — Frying Bacon: Это наиболее распространенное описание того, как звучит GMAW. Факел будет шипеть, время от времени будет хлопать. Обычно это означает, что ваш сварочный аппарат правильно настроен и вы укладываете качественный валик.
- – Попкорн : Если ваша сварка больше похожа на попкорн, чем на бекон, с большим количеством щелчков и хлопков, это может означать, что ваша скорость подачи проволоки слишком высокая.«Проволока ударяется о поверхность и не плавится в металле полностью, создавая слабый и опасный сварной шов». 1
- — Шипение, , как будто идет утечка газа : Часто означает слишком низкую скорость подачи проволоки. Это также слабый и небезопасный сварной шов. 1
- — Щелчки и шипение: Обычно это означает проблему с защитным газом. Вы также увидите чрезмерное количество искр, шлака и пор в готовом сварном шве. Убедитесь, что газ включен, в баллоне есть газ и давление в баллоне правильное. 1
- – Необычно: Еще одна проблема, которую можно определить по звуку, — это вылет провода. Если вылет слишком большой, дуга может звучать нерегулярно — постоянно меняясь по высоте и / или громкости.
2
Настройки напряжения и тока сварочного аппарата, а также металл, который вы свариваете, влияют на звук дуги в GMAW. 3 Например, при сварке нержавеющей стали используются три различных подхода: перенос погружением, шаровидный перенос или дуговая струя.Каждый из этих методов звучит по-разному, поскольку дуга переходит от низкой мощности к высокой в течение цикла переноса металла. 4
При переносе погружением (сварка с низким током, которая идеально подходит для более тонких материалов) вы слышите быстрое потрескивание — желанный звук бекона. Шаровая передача, которая используется не часто, издает неравномерный, разбрызгивающийся звук с периодическим шипением. Перенос распылением имеет постоянный шипящий звук, поскольку горячий металл равномерным потоком переходит на основной материал.
Важно изучить свое оборудование, понять используемые материалы и поэкспериментировать с различными настройками.Следите за звуком и внешним видом дуги и критически оценивайте качество сварных швов. Скоро вы будете знать, к чему прислушиваться.
Посмотрите видео, в котором показано, как изменение скорости подачи проволоки и напряжения влияет на звук сварки MIG: https://www.youtube.com/watch?v=kmcO0lFfn1k.
Лучшие изображения. Лучшие решения. Лучшее управление процессом.
Подпишитесь на Xiris в социальных сетях, чтобы получать регулярные обновления и видеоролики о сварке!
Источники:
1 https: // гараж.eastwood.com/eastwood-chatter/listen-to-your-mig/
2 https://www.millerwelds.com/resources/article-library/mig-welding-the-basics-for-mild-steel
3 https://forum.millerwelds.com/forum/welding-discussions/4179-mig-welding-sound
4 https://www.theshedmag.co.nz/home/2018/7/8/tackling-stronic-a-guide-to-stronic-steel-welding
Длинная сварка 1 (бесплатный звуковой эффект) • BigSoundBank.com
Длинная сварка, выполняемая сварочным аппаратом «Mig Mag» от Stanley.
❮❯
Продолжительность : 00:20
Категория UCS : ЭЛЕКТРИЧЕСТВО / ДУГА (ELECArc) ⊕ UCS, для «Универсальной системы категорий», является общественным достоянием Тима Нильсена, Джастина Друри и Кая Пакуина, среди других. Это список фиксированных и последовательных категорий для классификации звуковых эффектов. Он обеспечивает согласованность в структуре имени файла, чтобы упростить именование и категоризацию для всех, кто поддерживает свою личную или профессиональную библиотеку. Щелкните, чтобы отобразить полный список ПСК.
Тип : Один звук
Каналы : Моно ⊕ — Моно: Одноканальный. Обычно есть только один микрофон, один динамик.
— Стерео: Это метод воспроизведения звука, который создает иллюзию направленности и слышимой перспективы.
Условия : На открытом воздухе ⊕Звук « studio » был записан в месте без реверберации.
Звук « на открытом воздухе » содержит мешающие элементы. Звук не совсем чистый.Иногда дует ветер, ходят слухи и т. Д.
Звук « в помещении » обычно содержит сильную реверберацию. Например, его нельзя использовать для озвучивания изображения, сделанного на открытом воздухе.
Частота дискретизации : 48 000 Гц ⊕ Поиск : Определяет количество отсчетов в секунду, взятых из непрерывного сигнала для создания дискретного сигнала. Единица измерения частоты дискретизации — герцы.
— 44,100 Гц: CD Качество звука.
— 48000 Гц: Стандарт, используемый профессиональным цифровым видеооборудованием, таким как магнитофоны, видеосерверы, видеомикшеры и т. Д.
— 96 000 Гц: DVD-Audio, некоторые дорожки DVD LPCM, звуковые дорожки BD-ROM (Blu-ray Disc), звуковые дорожки HD DVD (DVD высокой четкости).
Битовая глубина : 16 бит ⊕ Подробнее : В цифровом аудио битовая глубина описывает количество битов информации, записанной для каждой выборки.
— 16 бит: Качество звука CD. Стандарт, используемый профессионалами в области СМИ.
— 24 бита: DVD-Audio, который может поддерживать до 24-битного звука.
Оборудование : Регистратор Tascam DR-40 и микрофон Sennheiser ME66 ⊕
Автор : Джозеф САРДИН
Звук № : 950
Обозначения
Оценить, Комментарий!
Они также загрузили
Ключевые слова
О BigSoundBank.com
BigSoundBank.com — это библиотека звуков, не требующая лицензионных отчислений, а также звуки, являющиеся общественным достоянием. Лучший звуковой банк для коммерческих и личных проектов. Звуковые эффекты, окружение, звуковые ландшафты и атмосферы в форматах MP3, WAV, BWF, AIFF, OGG, FLAC, AAC и M4A. Слушай и качай! Для аудиовизуальных материалов, кино, театра, видеоигр, аудиосаг, радио, разработки, PowerPoint и других медиа-проектов.
— «Да здравствует свободная культура !!!» — Mournful Skank — Musician — другие отзывы>
Джозеф САРДИН — основатель BigSoundBank. com и LaSonotheque.org — Контакты
Вьетнам Звуковые эффекты — Звуковые эффекты сварки
Вьетнам звуковые эффекты! Звуковые эффекты сварки!
Если меня спросят, скучаю ли я по Вьетнаму, я отвечу, конечно! Я люблю страну, людей и миллион разных звуков, подобных этим звукам сварки!
Мы уже две недели на Бали, и звуки здесь другие, что неудивительно, но также труднее найти, если речь идет о звуках строительства или машин.
Во Вьетнаме я мог просто гулять по Хойану или Данангу со своим диктофоном и слышать всевозможные звуки от старых машин!
Эти звуки определенно труднее найти на Бали, но мы вернемся в июле, и я буду больше записывать вокруг Денпасара!
В любом случае, этот звук сварки, который я записал, из Дананга! Мы побывали у наших друзей, и район, где они живут, — это просто огромная строительная зона.
Я видел, как этот мужчина сваривает трубы на улице, подошел и спросил его, могу ли я записать звук! Он и еще один мужчина посмотрели на меня с удивительным лицом. «Конечно»
Я поместил рекордер H6 как можно ближе, чтобы получить этот звуковой эффект.
Из всех сварочных технологий эта одна из самых сложных и очень сложных. Сварка алюминия, безусловно, является наиболее продвинутой, но сварка электродами — это удобное занятие, и вы должны знать, что делаете.
Его сварочная техника была очень хорошей.
Да, конечно, без перчаток и только в шлепанцах, но это нормально во Вьетнаме! 🙂
Я записал звук в течение пяти минут и получил самые важные звуки сварки плюс приятную ночную атмосферу.Вы можете слушать звук сварочного аппарата, постукивание клинкера, запуск электрода и, как я уже упоминал, приятную ночную атмосферу.
Надеюсь, вам понравится и вы сможете использовать звук! 🙂
Работаете ли вы сварщиком или инспектором, законы физики — неумолимые детекторы лжи. Вы можете обмануть мужчин. Металл не обманешь.
Лоис Макмастер Буджолд
Скачать Звуковые эффекты сварки!
Загрузить файл
(PDF) Оценка звукового сигнала на основе сварочного тока в процессе газовой дуговой сварки
Страница: 13/13
Образец цитирования: J. Презель, М. Кудина, Шум как сигнал для онлайн-оценки и мониторинга процесса сварки
, Acta acustica, объединенная с Acustica, Vol. 89 (2), 2003, pp.280-286
12. Beckmann, HJ, Timm K .: Die akustische Emission der Lichtbögen im Elektrostahl-
ofen, Elektrowärme International Vol.42, Nr.10, (1984), pp. 220-227,
13. Beckmann, HJ: Die akustische Emission der Lichtbögen im Elektroofen. Диссертация
an der Hochschule der Bundeswehr, 1983.
14. Манц, А. Ф .: Звук сварочной дуги, Welding Journal, (1981), стр. 23-27 ,.
15. Yaowe, W., Pensheng, Z .: Бесконтактный акустический анализ, мониторинг плазменной дуги
Welding, Int. J. Сосуды под давлением и трубопроводы, том 78, (2001), стр. 43-47 ,.
16. Polajnar, I. Prezelj, J., Grad, L. Čudina, M .: Исследование звуковых волн в газе
Дуговая сварка металла. Труды 7-й Международной научной конференции по
Технологии производства, Лумбарда, Корчула, Хорватия 2001, стр. В-059 — В-068.
17. Град, Л., Презель, Дж., Лангус, Д .: Исследование форм акустических волн, генерируемых
во время GMAW в режиме короткого замыкания, IIW D. XII-1680-01, Любляна 2001.
18. Град, Л. Презель, Дж., Полайнар, И. Грум, Дж .: Оценка сварочного процесса путем анализа на линии
— измеренные акустические сигналы. Труды 6-й Международной конференции
Словенского общества неразрушающего контроля, Порторож, Словения (2001), стр.185-189.
19. Ким, Дж. С., Игар, Т. В.: Перенос металла при импульсной газовой сварке металлической дугой,
Welding Journal, Том 72, № 7, (1993), стр. 279-284,
20. Чой , JH, Lee, JY, Yoo, CD: Моделирование динамического поведения в системе GMAW,
Welding journal, (2001), стр. 239-245.
21. Морита Т., Огава Ю., Сумитомо Т .: Анализ акустических сигналов при сварке и резке
, Материаловедение, ASME, Vol. III, (1995), стр.547-552.
22. Хамерник, Р. П., Хсеуэ, К. Д . : Импульсный шум: некоторые определения, физическая акустика и
другие соображения; J. Acoust. Soc. Являюсь. Том 90 (1), (1991,) стр. 189–196.
23. Беранек, Л.Л .: Контроль шума и вибрации, Институт техники контроля шума,
1988, Глава 17, стр. 549-553.
24. Фью, А. А. Младший: Справочник по атмосфере, глава: Акустическое излучение от молнии,
CRC Press, 1982.
25.Друэ, М., Надо, Ф .: Акустическое измерение напряжения дуги, применимое к дуговой сварке
и дуговым печам. J. Phys. E: Sci. Instrum. Том 15, (1982), стр. 268-269.
26. Мансур, А. М., Хьюиссон, Дж. П .: Акустическая идентификация процесса GMAW, специальный
Публикация 9-й Международной конференции по компьютерным технологиям в сварке,
(1999), стр. 312-323.
27. Сайни, Д., Флойд, С .: Исследование звуковой сигнатуры газовой дуговой сварки для контроля качества линии On-
, Welding Journal, апрель 1998 г., стр.172-179.
Сварочное оборудование | Общественный колледж Саут-Пьюджет-Саунд
CCS101 Пути к успеху 3 График поиска кредитов Развивает мышление и навыки, необходимые учащимся, чтобы они стали уверенными в себе, размышляющими, самостоятельными и успешными учениками. Предварительное условие: соответствует требованиям ENGL 090 или выше.
Для WELD 102, 103, 104 и 106 требуется одновременная запись.
Требуется предварительное условие: соответствует требованиям MATH 101 и ENGL 090.
WELD102 Теория сварки I 5 График поиска кредитов
Знакомит с инструментами и оборудованием, используемыми при сварке, в том числе с технической ориентацией на отдельные процессы сварки и резки. Предварительное условие: соответствует требованиям MATH 101 и ENGL 090. Одновременное участие в курсах WELD 103, WELD 104, WELD 106.
WELD103 Термическая резка и строжка 1 График поиска кредитаРазвивает навыки газокислородной резки, плазменно-дуговой резки, а также резки и строжки угольной дугой.Предварительное условие: соответствует требованиям MATH 101 и ENGL 090. Одновременное участие в курсах WELD 102, WELD 104, WELD 106.
WELD104 Кислородно-ацетиленовая сварка 3 График поиска кредитов Развивает навыки работы с сталью для кислородно-ацетиленовой сварки (OAW) в различных конструкциях и положениях соединений. Предварительное условие: соответствует требованиям MATH 101 и ENGL 090. Одновременное участие в курсах WELD 102, WELD 103, WELD 106.
Представляет дуговую сварку защищенного металла (SMAW) с упором на электроды с глубоким проникновением.Предварительное условие: соответствует требованиям MATH 101 и ENGL 090. Одновременное участие в курсах WELD 102, WELD 103, WELD 104.
WELD125 Теория сварки II 5 График поиска кредитов
Вводит методы контроля и испытаний сварных швов, основы металлургии и продолжение технической ориентации по выбору сварочных процессов. Предпосылка: WELD 102.
WELD127 Дуговая сварка защищенного металла II 9 График поиска кредитовПродолжает повышать квалификацию в области дуговой сварки экранированных металлов (SMAW), уделяя особое внимание применению и технологиям электродов с низким содержанием водорода.Предпосылка: WELD 102.
WELD134 Печатные материалы для сварщиков 5 График поиска кредитов Развивает способность интерпретировать отпечатки, используемые при сварке и производстве, включая использование символов сварки. Предпосылка: WELD 102.
Развивает знания и навыки в области газовой дуговой сварки (GMAW) углеродистой стали и алюминия на всех должностях.Предпосылка: WELD 102 и WELD 127.
WELD210 Дуговая сварка порошковой проволокой График поиска 12 кредитовРазвивает знания и навыки использования дуговой сварки газом и самозащитой порошковой проволокой (FCAW) для соединения углеродистой стали во всех позициях. Предпосылка: WELD 125 и WELD 127.
WELD220 Газовая вольфрамовая дуговая сварка График поиска 12 кредитовРазвивает знания и навыки в области газо-вольфрамо-дуговой сварки (GTAW) углеродистой стали и алюминия на всех должностях.Предпосылка: WELD 125 и WELD 127.
WELD230 Сварочное производство и сертификация График поиска 12 кредитов Предоставляет заключительный опыт для развития знаний в области изготовления металлов с применением методов сварки, полученных в ходе предыдущей курсовой работы. Этот курс даст студентам возможность стать сварщиком, сертифицированным Вашингтонской ассоциацией строительных служащих (WABO). Предварительное условие: WELD 134, WELD 135, WELD 210 и WELD 220.
Звуковые волны определяют прочность сварного шва
Рисунок 1
Хотя пьезоэлектрические преобразователи и электромагнитно-акустические преобразователи выполняют
то же самое, распространить ультразвуковую раневую волну через исследуемый материал,
они делают это по-разному.
Неразрушающий контроль (NDT) играет две важные роли в производстве сварных труб и труб.Во-первых, испытания, проводимые на ранних этапах производственного процесса, могут сэкономить время и деньги компании, обнаружив проблемы, которые могут привести к низкому качеству сварки. Во-вторых, при возникновении проблем немедленное обнаружение может предотвратить образование большого количества брака или некачественной продукции.
Процесс контактной сварки сопротивлением (ERW) несовершенен. Типичные дефекты включают защемление (черные пенетраторы), преддуги (белые пенетраторы), отсутствие плавления (LOF), LOF на краях (складки) или промежуточной стенке, литой сварной шов, пористость, сшивание, трещины с крючками и пастообразные сварные швы (холодные сварные швы).После сварки обрезка по внутреннему и внешнему диаметру (подрез или перерез) может привести к ухудшению качества продукта или браку. Перед сваркой скелп, входящий в линию, может содержать поверхностные или внутренние дефекты или не соответствовать спецификации по толщине.
В традиционных методах проверки ВПВ используются пьезоэлектрические преобразователи. Несмотря на то, что пьезоэлектрические преобразователи являются высокоэффективными и универсальными, их необходимо подсоединять к проверяемой детали, находящейся под высоким давлением или в жидкой среде. Это может ограничивать возможности сканирования или создавать помехи, соответственно.
Альтернативный процесс, электромагнитно-акустический преобразователь (ЭМАП), является более поздней разработкой, в которой используются два взаимодействующих магнитных поля для генерации ультразвуковых звуковых волн в детали. Относительно высокочастотное (RF) поле, создаваемое электрическими катушками, взаимодействует с низкочастотным или статическим полем, создаваемым магнитами, для создания силы Лоренца аналогично тому, как это происходит в электродвигателе. Это возмущение передается решетке материала, создавая упругую волну.При обратном процессе взаимодействие упругих волн в присутствии магнитного поля индуцирует токи в цепи приемной катушки ЭМАП. Для ферромагнитных проводников магнитострикция создает дополнительные напряжения, которые усиливают сигналы до гораздо более высоких уровней, чем можно было бы получить только с помощью силы Лоренца. Различные типы волн могут генерироваться с помощью различных комбинаций радиочастотных катушек и магнитов. См. Рисунок 1 .
Поскольку звук генерируется в проверяемой детали, а не в преобразователе, EMAT имеет несколько характеристик, которые нравятся производителям трубок и трубок:
- Сухой осмотр. Поскольку в EMAT не используется связующее вещество, он хорошо подходит для проверки очень горячих и очень холодных деталей. Это свойство также облегчает интеграцию EMAT в автоматизированные системы контроля.
- Состояние поверхности. EMAT невосприимчив к обычным условиям поверхности скелпа, таким как загрязнения, прокатная окалина и шероховатость поверхности.
- Развертывание датчика. Поскольку EMAT генерирует звуковые волны в испытуемом материале, закон преломления Снеллиуса не применяется, и угол датчика не влияет на направление распространения.Один датчик EMAT может применяться к трубам нескольких диаметров без необходимости замены клиньев. Кроме того, небольшие изменения угла наклона датчика не изменяют направление звука и качество контроля.
- Волноводные. ЭМАП эффективен для генерации направленных волн, которые можно использовать для проверки труб малого диаметра без изменения положения датчиков на детали.
- Широкая вертикальная балка. Катушки EMAT генерируют широкий вертикальный луч, который заполняет объем материала.В то время как для некоторых процессов неразрушающего контроля требуется несколько датчиков или фазированная решетка, один датчик EMAT позволяет обнаруживать дефекты ID, OD и межслойные дефекты.
Контроль сварных швов
На небольших трубах направленные волны идеально подходят для проверки ВПВ. Передатчик EMAT может быть расположен под углом 90 градусов, посылая звуковые волны по часовой стрелке, а приемник — под углом 270 градусов, чтобы обнаруживать отражения от сварного шва. Второй набор датчиков с передатчиком под углом 270 градусов и приемником под углом 90 градусов отправляет звук против часовой стрелки, чтобы дополнить первый набор.Направленные волны заполняют объем материала, тем самым позволяя обследовать весь сварной шов за один прием для обнаружения трещин от крюка, сварных швов, отсутствия плавления и несоответствия с большей надежностью, чем наклонные балки на небольших трубках. EMAT также может быть дополнен вихретоковой технологией для обнаружения точечных дефектов и допускает смещение сварного шва до 55 градусов во время контроля (см. , рис. 2, ).
На трубах большого диаметра сварные швы можно проверять с помощью EMAT сразу после процесса сварки, что сводит к минимуму отходы.Осмотр без связующего вещества позволяет производить установку сразу после сварочной головки для обнаружения всех дефектов сварного шва, дефектов стандарта API (пенетраторы, LOF, литой сварной шов, пористость, трещины от крючка и сшивание) и дефекты обрезки (внутренний и внешний диаметр). Одни только проблемы обрезки могут составлять большую часть списанных труб, поскольку они обнаруживаются спустя долгое время после возникновения проблемы.
Проверка и измерение толщины скелпа
Скелп-осмотр на предмет плоских дефектов выполняется с использованием массивов датчиков, генерирующих нормальный пучок 0-градусных волн.Датчики могут быть размещены по всей ширине скелпа или сосредоточены только в зонах сварного шва. EMAT гораздо менее чувствителен к вибрациям или перемещению датчика и может использоваться на очень высоких скоростях для просеивания скелпа. Тот же метод нормального луча можно использовать для измерения толщины скелпа с разрешением ± 0,0001 дюйма (2,5 мкм).
Рисунок 2
Возможности EMAT с направленными волнами означают, что
расположение сварного шва не обязательно
будь непоколебимым.Он может измерять сварку
прочность, несмотря на смещение сварного шва
аж 55 градусов.
Можно ли выполнить качественную сварку с помощью подводной мокрой сварки?
Мокрая подводная сварка требует значительных навыков и, в зависимости от материалов и расходных материалов, сопряжена с высоким риском водородного растрескивания. В критических случаях это должно выполняться только опытными сварщиками-водолазами с соблюдением установленных процедур. Кроме того, поскольку существуют большие различия в работоспособности и результирующем качестве сварного шва, получаемого с использованием различных имеющихся в продаже электродов, к выбору сварочных материалов следует подходить с осторожностью.
Хотя удовлетворительные сварные швы, как правило, можно выполнять в плоском положении, а с лучшими электродами в вертикальном положении, сварка над головой представляет значительную проблему, и качество сварки в этом положении, вероятно, будет хуже, чем в других положениях сварки. Несмотря на эту трудность, в течение многих лет было признано, что с помощью этого процесса можно наплавить сварные швы приемлемой целостности.
Сообщалось о удовлетворительном ремонте кораблей [1-3] ВМС США и морских сооружений. [1,2] Успешный ремонт был также проведен на морских сооружениях в Мексиканском заливе после повреждений, нанесенных ураганом [4,5] и в Северном море. [6] Целостность и механические свойства мокрых подводных сварных швов были оценены рядом авторов, например, [3,7] , а сварные швы, соответствующие требованиям AWS D3.6 [8] класса A (которые такие же, как для сварных швов, наплавленных на воздухе), были зарегистрированы как [9-11] . Ферритные наплавленные швы обычно демонстрируют лишь умеренную пластичность и ударную вязкость, а отложения на основе никеля дают лучшие механические свойства.
В ядерных установках удовлетворительный ремонт нержавеющей стали был проведен под водой с использованием ручных металлических электродуговых электродов из нержавеющей стали. [12,13] Однако следует отметить, что сварка ферритной стали электродами из нержавеющей стали, как правило, не приносит успеха, так как происходит растрескивание на границе сплавления, а иногда и трещинообразование при затвердевании. [1,14]
Полуавтоматические процессы мокрой подводной сварки «сварка водяной завесой» (с действием конической водяной струи, содержащей газовую защиту) и сварка порошковой проволокой (без газовой защиты) были использованы с некоторым успехом.Первый позволяет производить сварные швы высокой прочности. [15,16] В то время как последний был заявлен об успехе при ремонте судов [17] и трубопроводов, [18,19] качество сварных швов, как правило, не достигало того, что было достигнуто с другими сварочные процессы.
Список литературы
- Горелка W K: «Обобщенное изложение современного состояния подводной сварки» Журнал морских инженеров, апрель 1978 г. 90 68-74.
- Grubbs C.E. и Seth OW: «Подводная мокрая сварка ручными электродуговыми электродами» Proc.Int. Конф. по подводной сварке для морских установок, 1977 г., Институт сварки, 1977 г., стр. 17-33.
- West T. C., Mitchell G и Lindberg E: «Оценка мокрого сварочного электрода для ремонта судов» Weld J. 1988 69 (8) 46-56.
- Cayll D. R и Marino J A: «Инспекционная оценка и ремонт поврежденных морских платформ» Proc. Int. семинар по подводной сварке морских конструкций, 7-9 декабря 1994 г., Новый Орлеан, США, С. Лю, Д. Л. Олсон, С. Смит и Дж. С. Спенсер, редакторы, Американское бюро судоходства, 1995 247-277.
- Мэгес А. Дж., Рейнольдс Т. Дж. И Смит Р. Л.: «Ураган Эндрю повредил платформу для ремонта мокрой сварки», Там же 279–293.
- Ибарра С., Рид Р. Л., Смит Дж. К., Пачнюк И. и Граббс К. Э .: «Ремонт подводной мокрой сваркой шва на морской платформе в Северном море» Proc. Первый Int. Конференция по морской и полярной инженерии, Эдинбург, Великобритания, 11–16 августа 1991 г., С. П. Эллинас, Р. С. Путли, И. Уэда и С. Берга, ред. Международное общество морских и полярных инженеров, 191, Vol. 4 339-346, и «Ремонт конструкции платформы в Северном море с использованием методов мокрой сварки» Proc.23 rd Ежегодная конференция оффшорных технологий. 1991 Т. 3 Paper OTC 6652, p 57-66.
- Кокрейн Д. Дж. И Светнам Д.: «Мокрая сварка — жизнеспособная технология?» Встретились. Против. 1986 18 (11) 680-685.
- AWS D3.6M: 2010: «Спецификация для подводной сварки», Американское сварочное общество, Майами, США, 2010 г.
- Граббс К. Э. и Рейнольдс Т. Дж .: «Подводная сварка: высокое качество на больших глубинах», Welding J. 1998, 77 (9) 35-39.
- Петт, М. «Мокрая сварка — значительный прогресс в качестве»: сварка и изготовление металлов, 2000 68 (4) 22-24.
- Йонсен М. Р.: «Сохранение формы с помощью подводной сварки», Welding J, 2001, 79 (11) 54-57.
- O’Sullivan JE: «Ремонт мокрого подводного сварного шва паровой сушилки Susquehana №1» Weld J. 1988 67 (6) 19-23.
- O’Sullivan JE: «Подводная сварка в ядерных приложениях» в Proc. Конф. по техническому обслуживанию и ремонту сварки на электростанциях, Орландо, США, 9-11 декабря 1992 г., AWS и EPRI 75-83.
- Gooch T G: «Свойства подводных сварных швов» Met. Против. 1983, «Часть 1 Процессуальные процессы» 15 (3) 164-167; «Часть 2 Механические свойства» 15 (4) 206-215.
- Hoffmeister H, Küster K и Schafstall H-G: «Свойства сварных швов сталей средней прочности после подводной мокрой MIG-сварки методом водяной завесы» Proc. Второй Int. Конф. по морским сварным конструкциям, 16-18 ноября 1982 г., Лондон, Институт сварки, 1983 г., стр. 17-1 — стр. 17-8.
- Ирие, Т; Оно, Й; Сато, М; Китамура, N; Огава, Ю. «Подводная стыковая сварка на глубине до 10 м», Proc. 17-й Int. Морская механика и арктическая инженерная конф. (OMAE 1998), 5-9 июля 1998 г., Лиссабон, Португалия, Ред: К.Guedes-Soares, ASME International, Нью-Йорк, США, 1998.
- Кононенко В.Я., Грицай П.М., Семенкин В.И.: «Использование мокрой механизированной сварки при ремонте корпусов судов в море». Журнал сварочного процесса Патона, 1994 г., 6 (12) 498-501.
- Кононенко В. Я., Рыбченков: «Опыт мокрой механизированной сварки самозащитной порошковой проволокой при подводном ремонте газонефтепроводов», Там же. 1994 6 (9-10) 401-404.
- Кононенко В.