Как проверить сварочный шов на герметичность
При строительстве протяженных трубопроводов образуется большое количество сварных соединений, от качества которых во многом зависит работоспособность системы. Дефекты сварного шва возникают из-за низкого качества труб, нарушения технологии сварки, недостаточной квалификации работника. Они приводят к ухудшению внешнего вида, снижению прочностных характеристик трубопровода, его долговечности. Могут быть поверхностными и внутренними, для выявления которых требуются специальные методы и оборудование. Чтобы проверить трубу на трещины и другие дефекты без нарушения целостности шва, применяют методы неразрушающего контроля.
Разновидности дефектов сварных швов
Появляются в результате затекания расплавленного металла на холодные участки трубы, находящиеся в околошовной области. Могут иметь вид отдельных капель или протяженных образований.
- слишком большой сварочный ток;
- неправильное движение электрода;
- неправильный угол наклона труб при их соединении.
Сопровождающие явления: неравномерный провар шва, наружные и внутренние трещины.
Представляют собой канавки, появляющиеся на околошовных участках. Негативные последствия – снижение сечения шва, избыточные напряжения, провоцирующие образование трещин с возможным полным разрушением сварного соединения.
Отверстия, через которые протекает расплав из сварочной ванны.
- недостаточная скорость сварочного процесса;
- слишком большой зазор между торцами соединяемых труб;
- превышение силы тока.
Внимание! Трещины – наиболее опасный вид брака. Могут образоваться в любой точке шва или околошовной области. Располагаются продольно или поперечно.
Подразделяются на микротрещины и трещины. Причины появления: неправильная технология сварки или повышенное содержание вредных примесей.
Особенно опасными являются остатки шлака на поверхности швов, ускоряющие коррозию стали.
Внутренние дефекты. Могут располагаться по отдельности, цепочками, группами. Этот вид брака снижает прочность. Цепочки пор провоцируют разгерметизацию системы.
Ультразвуковая дефектоскопия
Принцип действия ультразвуковых дефектоскопов основан на том, что в среде одинаковой структуры звуковая волна движется в постоянном направлении. При возникновении препятствия волна меняет направление – отражается.
Основные способы ультразвуковой дефектоскопии: эхолокация, теневой, зеркальный, зеркально-теневой, дельта.
Магнитный способ
Заключается в намагничивании исследуемой зоны и изучении магнитного рассеивания при возникновении структурных неоднородностей. Различают следующие подвиды способа:
- Порошковый. Для его реализации применяют опилки железа, которые рассыпают на поверхности сварного шва. При создании магнитного поля частицы железа формируют картину магнитного спектра и сигнализируют о наличии глубинных трещин и пор.
- Индукционный. В этом случае используются искатели, подающие звуковой или визуальный сигнал при рассеивании магнитного потока.
- Магнитографический. Рассеивание потока регистрируется на магнитной ленте, находящейся на шовной поверхности. Поиск дефектов осуществляется сравнением полученных результатов с эталоном.
Как проверить сварной шов на герметичность?
Существует несколько способов проверки герметичности собранного трубопровода.
Герметичность сварного шва проверяется с помощью керосина, имеющего свойство проникать через внутренние поры и трещины. На сварной шов наносят водный меловой раствор с дальнейшим просушиванием. На сторону, противоположную поверхности, обработанной мелом, наносят керосин (в большом количестве). Если сварной шов поврежден, керосин проступит на меловом покрытии.
Проверка воздухом, подаваемым под давлением. Швы смазывают мыльной водой. При подаче сжатого воздуха на негерметичном шве появляются мыльные пузыри.
С помощью газоэлектрического искателя
Этот способ используется для проверки ответственных трубопроводных систем. Для его реализации применяют высокопроницаемый газообразный гелий. Появление газа фиксируется специальным щупом, а его количество определяется с помощью электронного блока.
Как проверить трубы системы «теплого пола»?
Перед укладкой чистового пола обязательно проводят проверку тепловых труб на герметичность. Способ определяется материалом трубопровода.
Проверку металлопластиковых труб проводят в течение суток холодной водой, подаваемой под давлением в 6 бар. Если давление не изменилось, то считается, что система успешно прошла испытание.
Трубопровод из сшитого полиэтилена проверяют холодной водой при давлении, превышающем рабочее в 2 раза, но не менее 6 бар. Давление будет падать. Через полчаса необходимо восстановить проверочное давление. Эта процедура повторяется 3 раза. После третьего раза доводят давление до проверочного и оставляют на сутки. Если после этого протечки не появились, а давление упало не более чем на 1,5 бара, то система считается работоспособной.
После опрессовки трубопровода с холодной водой под давлением проводится дополнительная проверка системы «теплого пола» при максимальной рабочей температуре. Систему разогревают на 30 минут. После этого проверяют на герметичность все цанговые соединения. При необходимости их подтягивают.
Внимание! Стяжку можно заливать после остывания системы. Трубы обязательно должны быть под давлением.
Объекты, предназначенные для транспортировки или хранения жидких и газообразных веществ, должны подвергаться контролю герметичности сварных соединений. Проверка непроницаемости проводится работниками ОТК предприятия. Периодический контроль во время эксплуатации выполняет владелец в сроки, определяемые нормативными документами.
Суть контроля герметичности сварных соединений
Проверка герметичности ― это метод неразрушающего контроля, основанный на способности газов или жидкостей просачиваться сквозь мельчайшие отверстия. После его проведения визуально оценивают или измеряют массу просочившейся через изъяны сварного соединения рабочей среды. Полученный результат сравнивают с допустимыми значениями, указанными в нормативных документах. При назначении периодичности проверки непроницаемости и способа выполнения учитывают:
- физико-химические свойства рабочей среды;
- величину давления;
- температуру окружающей среды;
- условия эксплуатации.
Способы проверки сварных швов на герметичность
Перед контролем на непроницаемость сварочный шов должен быть подготовлен. Поверхность очищают от шлака и окалины при необходимости протравливают. Если при осмотре не выявлены крупные дефекты, выбирают приемлемый способ проверки герметичности.
Гидравлическое испытание
В зависимости от назначения и размеров объекта для проверки сварных швов на герметичность выбирают один из 3 вариантов:
- Трубопроводы и сосуды, работающие под давлением, герметизируют, через штуцер закачивают воду, создавая давление выше рабочего на 25 — 50%. Испытание проводят в течение 10 — 15 минут при плюсовой температуре. О результате судят по протеканиям, запотеванию, величине падения давления.
- Резервуары и цистерны для хранения жидкостей на сутки заполняют водой с температурой не меньше 5⁰ Степень герметичности определяют по понижению уровня. После устранения дефектов проверку повторяют.
- У объектов большой протяженности стыки на герметичность проверяют струей воды, направляемой по швам под давлением от 1 атм. Брандспойт держат на расстоянии не больше 2 метров от поверхности. Дефекты проявляются с обратной стороны в виде протечек, водяных капелек, запотевания швов.
Пневматическое испытание
Небольшие, герметично закрытые емкости, заполняют сжатым воздухом под давлением на 10 — 20% больше рабочего. После погружения в воду места неплотностей выявляют по пузырькам. У объектов большого размера сварные швы обмазывают мыльным раствором. После подачи внутрь сжатого воздуха дефекты обнаруживают по вздувшимся пузырям. При проверке на герметичность сварных швов газопроводов и резервуаров большой емкости, у которых много соединений, мыльную пену не наносят. О степени непроницаемости судят по величине падения давления сжатого воздуха в течение суток.Проверка керосином
Этим способом выявляют дефекты размером от 0,1 мм в металле толщиной до 16 мм у объектов без давления. Чтобы начать проверять сварочный шов на герметичность, поверхность окрашивают разведенным в воде мелом или каолином. После просушки с обратной стороны 2 — 3 раза наносят керосин. Величину изъянов определяют по размерам жирных пятен желтого цвета, выступивших на окрашенной поверхности. Длительность проведения испытания 12 часов, если температура воздуха плюсовая, ниже 0⁰C ― 26 часов.
Проверка аммиаком
В основу метода заложено свойство химических индикаторов (нитрата ртути или фенолфталеина) изменять цвет при контакте с аммиаком. Метод применяют для проверки непроницаемости сварных швов на замкнутых сосудах.
Перед началом испытания подготавливают бумажные полоски или отрезки медицинского бинта пропитанные 5% раствором нитрата ртути. Их накладывают поверх сварных соединений, сосуд заполняют сжатым воздухом, в который добавлен аммиак до концентрации 1%. При прохождении его паров через изъяны окраска индикатора в этих местах становится серебристо-черной. Когда для пропитки берут фенолфталеин бумага над дефектами меняет цвет на ярко-красный. Вид и величину неплотностей определяют по размеру, форме, скорости проявления окрашенных пятен.
В зависимости от толщины металла испытание проводят в течение 10 — 30 минут.
Испытание вакуумом
Проверку сварных швов с односторонним доступом проводят вакуумным прибором. Швы предварительно покрывают мыльным раствором. Затем закрепляют камеру, после включения насоса внутри образуется вакуум. Наружный воздух за счет атмосферного давления проходит через изъяны, создавая вздутия. За образованием мыльных пузырей следят через прозрачное окно прибора. В раствор добавляют поваренную соль, если испытания проводят при минусовой температуре.
При проверке герметичности под давлением нельзя обстукивать швы. Для проведения испытаний должно быть выделено изолированное помещение с хорошей вентиляцией. Контроль крупных объектов выполняют, соблюдая осторожность.
После завершения сварочных работ, изделия должны подвергаться контролю сварных соединений с целью обнаружения и исправления дефектов. Невооруженным глазом можно рассмотреть лишь часть из них — крупные наружные трещины и поры, непровары, подрезы и т.п. Большая часть дефектов скрыта в глубине металла или имеет такие малые размеры, что обнаружить их можно только с использованием специальных приборов и материалов.
Существует много способов контроля сварных швов, различающихся по принципу действия, способности к обнаружению тех или иных видов дефектов, техническому оснащению. Методы контроля сварных соединений подразделяются на разрушающие и неразрушающие. Последние, в силу понятных причин, являются наиболее широко используемыми. Применяются следующие основные методы неразрушающего контроля сварных соединений:
- внешний осмотр;
- радиационная дефектоскопия;
- магнитный контроль;
- ультразвуковая дефектоскопия;
- капиллярная дефектоскопия;
- контроль сварных швов на проницаемость;
- прочие методы (проверка с использованием вихревых токов и т.п.).
Внешний осмотр
Перед осмотром, швы тщательного очищаются от шлака, окалины и брызг металла. Более тщательная очистка в виде обработки шва промывкой спиртом и травлением 10%-ным раствором азотной кислоты придает шву матовую поверхность, на которой легче заметить мелкие трещины и поры. После использования кислоты нужно не забыть удалить ее спиртом во избежание разъедания металла.
Визуальный контроль сварных соединений выявляет, прежде всего, наружные дефекты — геометрические отклонения шва (высоты, ширины, катета), наружные поры и трещины, подрезы, непровары, наплывы.
Для эффективности контроля используют дополнительное местное освещение и лупу с 5-10 кратным увеличением. Лупа — очень полезный инструмент в данном случае, она помогает выявить многие дефекты, которые нельзя рассмотреть невооруженным глазом — тонкие волосяные трещины, выходящие на поверхность, пережег металла, малозаметные подрезы. Она позволяет также проследить, как ведет себя конкретная трещина в процессе эксплуатации — разрастается или нет.
При внешнем осмотре применяется также измерительный инструмент для замера геометрических параметров сварного соединения и дефектов — штангенциркуль, линейка, различные шаблоны.
Капиллярный контроль
С помощью капиллярного контроля можно контролировать материалы любого вида и формы — ферромагнитные и неферромагнитные, цветные и черные металлы и их сплавы, керамику, пластмассы, стекло. В основном, капиллярный метод применяют для обнаружения невидимых или слабовидимых невооруженным глазом поверхностных дефектов с открытой полостью. Однако с помощью некоторых материалов (керосина, например) можно с успехом обнаруживать и сквозные дефекты.
Для капиллярного контроля разработан ГОСТ 18442-80 «Контроль неразрушающий. Капиллярные методы. Общие требования».
Контроль сварных швов с помощью пенетрантов. К наиболее распространенным способам контроля качества сварных швов с использованием явления капиллярности относится контроль пенетрантами (англ. penetrant — проникающий) — веществами, обладающими малым поверхностным натяжением и высокой световой и цветовой контрастностью, позволяющей легко их увидеть. Сущность метода состоит в окраске дефектов, заполненных пенетрантами.
Существуют десятки рецептур пенетрантов, обладающих различными свойствами. Есть пенетранты на водной основе и на основе различных органических жидкостей (керосина, скипидара, бензола, уайт-спирита, трансформаторного масла и пр.). Последние (на основе различных органических жидкостей) особенно эффективны и обеспечивают высокую чувствительность выявления дефектов.
Если в рецептуру пенетрантов входят люминесцирующие вещества, то их называют люминесцентными, а способ контроля — люминесцентной дефектоскопией. Наличие таких пенетрантов в трещинах определяется при облучении поверхности ультрафиолетовыми лучами. Если в состав смеси входят красители, видимые при дневном свете, пенетранты называются цветными, а метод контроля — цветной дефектоскопией. Обычно в качестве красителей используются вещества ярко-красного цвета.
У разных пенетрантов разная чувствительность. Самые чувствительные (1-й класс чувствительносьи) способны выявлять капилляры с поперечным размером 0,1-1 мкм. Верхний предел капиллярного метода — 0,5 мм. Глубина капилляра должна быть минимум в 10 раз больше ширины.
Пенетрант может храниться в любой емкости и наноситься на контролируемый шов любым способом, но наиболее удобная форма выпуска — аэрозольные баллончики, с помощью которых смесь распыляется на поверхность металла. Обычно в комплект средства контроля швов входят три баллончика:
- сам пенетрант;
- очиститель, предназначенный для очистки поверхности от загрязнений перед проведением контроля и удаления излишков пенетранта с поверхности перед проявлением;
- проявитель — материал, предназначенный для извлечения пенетранта из дефекта и создания фона, для образования четкого индикаторного рисунка.
Баллончики могут быть разборными, позволяющими заряжать их на специальном зарядном стенде, входящем в комплект.
Методы контроля сварных соединений с использованием разных пенетрантов могут незначительно отличатся друг от друга, но в основном они сводятся к трем операциям — очистке поверхности, нанесению на неё пенетранта и проявлению дефектов с помощью проявителя. В деталях это выглядит следующим образом.
Поверхность шва и околошовной зоны очищается от загрязнения, обезжиривается и сушится. При очистке важно не внести в дефекты новых загрязнений, поэтому механический способ очистки, при котором повреждения могут забиться посторонними включениями, использовать нежелательно. Обычно рекомендуется заканчивать операцию очистки очистителем, идущим в комплекте, — протерев им поверхность материалом не оставляющим волокон. Если сварной шов перед контролем подвергался травлению, травящий состав нужно нейтрализовать 10-15% раствором соды (Na2CO3).
При контроле в условиях минусовых температур (если свойства используемого пенетранта допускают это), поверхность изделия рекомендуется протереть чистой тканью, смоченной в этиловом спирте.
Затем на поверхность распыляют пенетрант и дают выдержку в течение 5-20 минут (в соответствии с инструкций для конкретного состава). Это время необходимо на проникновение жидкости в имеющиеся дефекты.
После выдержки излишки пенетранта удаляются с поверхности. Способ удаления может различаться в зависимости от используемого состава. Водорастворимые смеси удаляют тканью без волокон, смоченной в воде, но обычно излишки пенетранта удаляются очистителем, входящим в состав комплекта. Независимо от способа удаления, нужно добиться того, чтобы поверхность была полностью очищена от препарата.
В заключительной стадии операции, из третьего баллончика наносится индикаторная жидкость, которая вытягивает пенетрант из полостей дефектов по принципу промокашки, отображая их расположение и форму в виде цветового рисунка. В случае необходимости, при осмотре применяют лупу с двукратным увеличением.
Проверка качества сварных швов с использованием пенетрантов имеет как достоинства, так и недостатки. В числе первых — простота использования, высокая чувствительность и достоверность обнаружения дефектов, многообразие контролируемых по виду и форме материалов, высокая производительность, относительная дешевизна. К основным недостаткам относится возможность обнаружения только поверхностных дефектов, необходимость тщательной очистки шва, невозможность применения после механической обработки поверхностного слоя. Применяя пенетранты, следует также иметь в виду, что широко раскрытые дефекты (более 0,5 мм) могут не проявиться — из-за особенности капиллярного явления.
Контроль швов на непроницаемость с помощью керосина. Несмотря на свою простоту, контроль качества сварных соединений с помощью керосина достаточно эффективен и к тому же не требует сколько-нибудь значительных материальных затрат. Недаром им продолжают широко пользоваться и в наше время, богатое на различные высокофункциональные устройства и приборы.
Керосин способен проникать сквозь мельчайшие трещины в сварных швах, благодаря чему позволяет обнаруживать мельчайшие дефекты. По своей эффективности способ контроля керосином эквивалентен гидравлическому испытанию с давлением 3-4 кгс/мм 2 . Он основан на том же явлении капиллярности, что и контроль пенетрантами. К слову сказать, в некоторые пенетранты фирменного изготовления керосин входит в качестве составляющего компонента.
Проверка керосином сводится к ряду последовательных операций:
- Очистка шва с двух сторон от шлака, грязи и ржавчины.
- Покрытие одной из сторон (той, за которой удобнее наблюдать) водной суспензией каолина или мела (350-450 г на 1 л воды). После нанесения суспензии необходимо подождать, пока она высохнет. Для ускорения процесса покрытие можно просушить горячим воздухом.
- Обильное смачивание обратной стороны керосином — 2-3 раза в течение 15-30 минут, в зависимости от толщины металла. Это можно делать струей из краскопульта или паяльной лампы, а также с помощью кисти или кусочка ветоши.
- Наблюдение за стороной, на которую нанесена меловая или каолиновая суспензия, и маркирование проявляющихся дефектов.
Негерметичность швов обнаруживает себя появлением темных полос или точек на меловом или каолиновом покрытии, которые с течением времени расплываются в более обширные пятна. Именно поэтому наблюдать за обратной стороной нужно сразу после нанесения керосина — чтобы зафиксировать первые проявления керосина, точно указывающие на место и форму дефекта. Проявляющиеся точки свидетельствуют о порах и свищах, полоски — о сквозных трещинах.
Продолжительность испытания при комнатной температуре должна составлять несколько часов. Скорость проникновения керосина в дефекты зависит от его вязкости, которая уменьшается с повышением температуры.
Контроль сварных швов с помощью керосина предназначен в основном для стыковых соединений, в отношении нахлесточных он менее эффективен. Повысить его действенность в этом случае можно, просверлив отверстие и закачав или залив керосин между швами. Применяя этот прием нужно иметь в виду, что керосин, попавший в стык деталей, может впоследствии вызвать коррозию, поэтому его необходимо удалить после испытания подогревом детали горелкой или паяльной лампой.
Контроль сварных швов на проницаемость
Существует довольно много методов контроля сварных швов на проницаемость с использованием различных материалов — газов (в основном воздуха или азота), жидкостей (воды или масла). Сутью испытаний является создание избыточного давления или разрежения и обнаружение мест, через которые под их воздействием рабочий компонент (газ или жидкость) проникает через сварной шов.
По виду используемого рабочего компонента и способа создания разности давлений различают пневматический, гидравлический, пневмогидравлический, вакуумный контроль.
Пневматический способ контроля. При пневматическом способе проверяемая емкость надувается воздухом, азотом или инертным газом до давления, составляющего 100-150% от рабочего (в зависимости от технических условий на изделие). Наружные швы смачиваются пенообразующим составом, который представляет собой раствор туалетного или хозяйственного мыла в воде (50-100 г мыла на 1 литр воды).
Если испытания проводятся при минусовой температуре, часть воды (до 60%) заменяется спиртом. Появившиеся на поверхности швов пузырьки свидетельствуют о наличии сквозных дефектов.
Рекомендуется подключать к емкости манометр и предохранительный клапан. По показаниям манометра контролируется давление и его падение — в случае наличия сквозных дефектов. Предохранительный клапан обеспечивает безопасность испытаний, сбросом давления при превышении его значения выше допустимого уровня.
Небольшие сосуды можно не промазывать мыльным раствором, а помещать в ванну с водой. Дефекты обнаружат себя появлением воздушных пузырьков. Этот способ проверки даже более прост и надежен, чем промазка швов пенообразующим раствором.
Проверка аммиаком. К разновидностям пневматического испытания относится контроль качества сварки с помощью аммиака, который подают под давлением в проверяемую емкость в количестве сотой части всего объема воздуха. Перед подачей аммиачно-воздушной смеси, швы, подлежащие контролю, покрывают бумажной летной или медицинским бинтом, пропитанными фенолфталеином. Проходя через сквозные дефекты, аммиак оставляет на ленте или бинте красные пятна. Метод проверки с помощью аммиака очень достоверен.
Обдув сварных соединений воздухом. В тех случаях, когда изделие нельзя накачать воздухом, можно применить упрощенный вариант пневматического испытания, обдувая шов с одной стороны струей воздуха под давлением, а с другой — обмазав его мыльным раствором. В этом случае в зоне обдува создается подпор воздуха, который проявляет себя появлением пузырьков с обратной стороны (при наличии сквозных дефектов).
Чтобы получить необходимый эффект, необходимо соблюдать определенные условия: давление воздуха должно быть до 2,5 кгс/см 2 , струя должна направляться перпендикулярно шву, конец шланга должен быть увенчан ниппелем с отверстием 10-15 мм. Ниппель удерживают на расстоянии 50-100 мм от шва. Как и в случае пневматического испытания, наличие сквозных дефектов определяется по появлению пузырьков воздуха на обратной стороне шва. Способ наиболее эффективен при проверке угловых швов, поскольку в этом случае создается больший подпор.
Гидравлический контроль. Гидравлическое испытание предполагает использование в качестве компонента, создающего давление, воды или масла. После создания необходимого давления (100-150% от рабочего), емкость выдерживают в таком состоянии около 5-10 минут, обстукивая легкими ударами молотка с круглым бойком околошовную зону. Если шов имеет сквозной дефект, он проявится течью жидкости.
Емкости, работающие без значительного избыточного давления, необходимо выдерживать наполненными более длительное время — не менее двух часов.
Магнитная дефектоскопия
Более совершенный магнитографический способ предполагает наложение на шов ферромагнитной ленты, на которой после пропускания ее через прибор проявляются имеющиеся дефекты.
Магнитным способам контроля могут подвергаться только ферромагнитные металлы. Хромоникелевые стали, алюминий, медь, не являющиеся ферромагнетиками, магнитному контролю не подлежат.
Ультразвуковая дефектоскопия
Контроль качества сварных соединений с помощью ультразвуковых дефектоскопов в силу удобства его проведения получил очень широкое распространение — гораздо большее, чем магнитная и радиационная дефектоскопия. К его недостаткам относится сложность расшифровки сигнала (качественно сделать контроль сварного соединения способен только специалист, прошедший обучение), ограниченность использования для металлов с крупным зерном (аустенитные стали, чугун и пр.).
Как проверить качество и герметичность сварного шва трубы?
При строительстве протяженных трубопроводов образуется большое количество сварных соединений, от качества которых во многом зависит работоспособность системы. Дефекты сварного шва возникают из-за низкого качества труб, нарушения технологии сварки, недостаточной квалификации работника. Они приводят к ухудшению внешнего вида, снижению прочностных характеристик трубопровода, его долговечности. Могут быть поверхностными и внутренними, для выявления которых требуются специальные методы и оборудование. Чтобы проверить трубу на трещины и другие дефекты без нарушения целостности шва, применяют методы неразрушающего контроля.
Разновидности дефектов сварных швов
Наплывы
Появляются в результате затекания расплавленного металла на холодные участки трубы, находящиеся в околошовной области. Могут иметь вид отдельных капель или протяженных образований.
Причины появления:
- слишком большой сварочный ток;
- неправильное движение электрода;
- неправильный угол наклона труб при их соединении.
Сопровождающие явления: неравномерный провар шва, наружные и внутренние трещины.
Подрезы
Представляют собой канавки, появляющиеся на околошовных участках. Негативные последствия – снижение сечения шва, избыточные напряжения, провоцирующие образование трещин с возможным полным разрушением сварного соединения.
Прожоги
Отверстия, через которые протекает расплав из сварочной ванны.
Причины образования:
- недостаточная скорость сварочного процесса;
- слишком большой зазор между торцами соединяемых труб;
- превышение силы тока.
Трещины
Внимание! Трещины – наиболее опасный вид брака. Могут образоваться в любой точке шва или околошовной области. Располагаются продольно или поперечно.
Подразделяются на микротрещины и трещины. Причины появления: неправильная технология сварки или повышенное содержание вредных примесей.
Инородные включения
Особенно опасными являются остатки шлака на поверхности швов, ускоряющие коррозию стали.
Газовые поры
Внутренние дефекты. Могут располагаться по отдельности, цепочками, группами. Этот вид брака снижает прочность. Цепочки пор провоцируют разгерметизацию системы.
Ультразвуковая дефектоскопия
Принцип действия ультразвуковых дефектоскопов основан на том, что в среде одинаковой структуры звуковая волна движется в постоянном направлении. При возникновении препятствия волна меняет направление – отражается.
Основные способы ультразвуковой дефектоскопии: эхолокация, теневой, зеркальный, зеркально-теневой, дельта.
Магнитный способ
Заключается в намагничивании исследуемой зоны и изучении магнитного рассеивания при возникновении структурных неоднородностей. Различают следующие подвиды способа:
- Порошковый. Для его реализации применяют опилки железа, которые рассыпают на поверхности сварного шва. При создании магнитного поля частицы железа формируют картину магнитного спектра и сигнализируют о наличии глубинных трещин и пор.
- Индукционный. В этом случае используются искатели, подающие звуковой или визуальный сигнал при рассеивании магнитного потока.
- Магнитографический. Рассеивание потока регистрируется на магнитной ленте, находящейся на шовной поверхности. Поиск дефектов осуществляется сравнением полученных результатов с эталоном.
Как проверить сварной шов на герметичность?
Существует несколько способов проверки герметичности собранного трубопровода.
Капиллярный
Герметичность сварного шва проверяется с помощью керосина, имеющего свойство проникать через внутренние поры и трещины. На сварной шов наносят водный меловой раствор с дальнейшим просушиванием. На сторону, противоположную поверхности, обработанной мелом, наносят керосин (в большом количестве). Если сварной шов поврежден, керосин проступит на меловом покрытии.
Пузырьковый
Проверка воздухом, подаваемым под давлением. Швы смазывают мыльной водой. При подаче сжатого воздуха на негерметичном шве появляются мыльные пузыри.
С помощью газоэлектрического искателя
Этот способ используется для проверки ответственных трубопроводных систем. Для его реализации применяют высокопроницаемый газообразный гелий. Появление газа фиксируется специальным щупом, а его количество определяется с помощью электронного блока.
Как проверить трубы системы «теплого пола»?
Перед укладкой чистового пола обязательно проводят проверку тепловых труб на герметичность. Способ определяется материалом трубопровода.
Проверку металлопластиковых труб проводят в течение суток холодной водой, подаваемой под давлением в 6 бар. Если давление не изменилось, то считается, что система успешно прошла испытание.
Трубопровод из сшитого полиэтилена проверяют холодной водой при давлении, превышающем рабочее в 2 раза, но не менее 6 бар. Давление будет падать. Через полчаса необходимо восстановить проверочное давление. Эта процедура повторяется 3 раза. После третьего раза доводят давление до проверочного и оставляют на сутки. Если после этого протечки не появились, а давление упало не более чем на 1,5 бара, то система считается работоспособной.
После опрессовки трубопровода с холодной водой под давлением проводится дополнительная проверка системы «теплого пола» при максимальной рабочей температуре. Систему разогревают на 30 минут. После этого проверяют на герметичность все цанговые соединения. При необходимости их подтягивают.
Внимание! Стяжку можно заливать после остывания системы. Трубы обязательно должны быть под давлением.
12 способов проверить качество одежды :: Инфониак
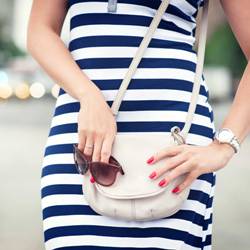
Как часто бывает, вы нашли платье нужного цвета и формы, и цена при этом не «кусается». Но прежде чем вы поспешите расплатиться за покупку, попробуйте ее изучить, чтобы оценить ее качество.
Качественная одежда дольше носится, более удобна и приятна в носке.
Читайте также: Как выбрать правильный цвет в одежде
Вот несколько способов, как можно проверить насколько качественной является одежда.
Одежда хорошего качества
1. Чтобы быстро оценить качество одежды, посмотрите на ткань при ярком свете.
Вот пример двух разных шелковых блузок, рассматриваемых при ярком свете. Чем толще материал, тем выше качество.
2. Проделайте тест, скомкав ткань.
Скомкайте ткань в кулаке, подержите несколько секунд и отпустите. Ткань осталась смятой или быстро разгладилась? Если она осталась смятой после того, как вы подержали ее в руках, она вряд ли выдержит испытание временем.
3. Слегка потяните ткань.
Немного потяните ткань и отпустите ее. Это особенно хорошо видно на юбке или нижней части платья. Посмотрите, сохранила ли ткань форму или материал видоизменился.
4. Избегайте открытых молний.
Молния на одежде должна быть плоской и закрыта планкой, за исключением случаев, когда она является элементом дизайна. Кроме того, строчка, которая держит молнию, должна подходить к ткани.
5. Проверьте, чтобы у юбок и брюк был достаточный подгиб.
Если у вас высокий рост, то вероятно вы знаете, что дополнительный припуск на ткани может существенно помочь удлинить изделие. Обычно на прямых юбках, сделанных из плотного материала, должен быть подгиб 4 — 5 см, а у конических юбок — около 3-4 см.
6. У хорошо пошитых брюк должен быть французский шов.
Французский шов — самый распространенный способ обработки швов у дизайнеров, так как необработанный край ткани спрятан в обработанном шве.
Качество материалов одежды
7. Проверяйте этикетку по уходу за изделием.
Натуральные ткани, такие как шелк, хлопок и шерсть лучше противостоят износу, чем синтетические материалы.
8. Проверьте, чтобы рисунок совпадал по швам.
Проверьте боковые швы на блузке и вокруг карманов, чтобы сразу понять, является ли изделие качественным или нет. Чтобы совместить рисунок в клетку или горизонтальную полосу, может потребоваться дополнительная ткань, что повышает цену изделия.
Читайте также: 10 табу в офисной одежде
9. Проверьте швы, чтобы убедиться, что нитки совпадают.
Качественные расстрочные швы должны быть прямыми, сделанными нитками такого же цвета, с большим количеством стежков на один сантиметр.
Оценка качества одежды
10. Проверьте пуговицы и петли для пуговиц
Петли для пуговиц должны быть плотно обметаны и аккуратно прорезаны. Посмотрите на пуговицу и убедитесь в том, что она плотно пришита, а нитки не торчат.
11. Слегка потяните швы, чтобы увидеть пробелы между строчек.
Изделия хорошего качества имеют большое количество стежков на сантиметр, и у них более плотные швы, что предотвращает расхождение.
12. Подкладка — всегда хороший признак.
У хорошо пошитого пиджака подкладка сделана из качественного материала, и она достаточно просторная, что позволит вам комфортно сидеть, двигать руками и наклоняться.
Предложения со словосочетанием ПРОВЕРИТЬ ШВЫ
Мне нужно проверить швы, чтобы сделать окончательный вывод о твоих дальнейших перспективах. Он заказал новую резину к нашему «Тайменю» по интернету и принял покупку, расписался, а потом разложил этого выдохнувшего полосатого кита пяти метров длиной у нас в коридоре, тщательно проверил швы, посыпал какой-то присыпкой, свернул и запаковывал в «снасть». Вскоре она была уже здорово навеселе, вышла в ванную, накрасила губы, поправила глаза, проверила швы на чулках. Затем проверил шов, в который был заделан проводок, и микрофон-пуговицу. Возвратив плиту на место, он тщательно проверил шов.
Привет! Меня зовут Лампобот, я компьютерная программа, которая помогает делать
Карту слов. Я отлично
умею считать, но пока плохо понимаю, как устроен ваш мир. Помоги мне разобраться!
Спасибо! Я обязательно научусь отличать широко распространённые слова от узкоспециальных.
Насколько понятно значение слова околпачивать (глагол), околпачивает:
Кристально
понятно
Понятно
в общих чертах
Могу только
догадываться
Понятия не имею,
что это
Другое
Пропустить
Неточные совпадения
Кроме того, проверьте нижнюю часть шагового шва, там, где штанины прилегают друг к другу, а также места на коленях. Проверить рану, обработать шов, оставайся, если желаешь, заодно поможешь мне. Проверив правильность вмётанного рукава, его втачивают со стороны проймы швом шириной 1 см, Оба среза обмётывают вместе. Чтобы удостовериться, готов ли раствор к использованию, нужно проверить, не растекается ли он по мастерку и выдавливается ли из шва при нажатии на кирпич. Проницательный молодой человек даже ощупал швы в её сумках и проверил наличие второго дна. Также проверьте качество швов: в них не должно быть пропущенных стежков, торчащих ниток и т.Как проверить прочность сварного шва? — Полуавтоматическая сварка — MIG/MAG
Реставрирую свое авто,дело дошло до ремонта кузова,замена гнилых деталий, первое что начал варить, это один злосчастный лонжерон гнивший изнутри.Вопрос вот в чем, как проверить прочность шва,чтоб быть точно уверенным что заварил как надо,варю недавно,и не могу понять шов надежный или нет,пробовал приваривать два кусочка стык в стык шов 40мм с одной стороны метал 3ка, потом зажимал в тиски и бил молотком с противоположной стороны шва, и примерно с одного двух ударов молотком весом грамм 300 свариваемые детали разрываются,пробовал так же варить с одной стороны и с другой просто делать прихватки в нескольких местах то в этом варианте при проверке детали не разрываются, а просто гнется металл. Ну тогда я подумал что провар достаточный и решился начать варить сделал заготовки для замены ржавых сегментов и начал варить,вертикальные швы вроде получились не плохо, а вот с потолочным пришлось помучатся но в итоге вроде гуд.Теперь меня стали мучать сомнения а в друг все что я наварил одним словом «Г».Подскажите пожалуйста как возможно проверить швы?очень мучает этот вопрос, спать не смогу,пока не найду истину)))
вот такие две детали в ставленые друг в друга,как бы продолжение основного лонжерона
На втором фото как раз видно ту самую железяку которую испытывал на прочность последним способом,изогнулась но не треснула,в последующем использовалась для массы(ну эт чтоб вопросов не было для чего это она там весит))
на третьем тот самый шов который меня волнует