Π‘Π²Π°ΡΠΊΠ°, Π²ΠΈΠ΄Ρ ΡΠ²Π°ΡΠΊΠΈ, ΠΈΡΡΠΎΡΠΈΡ ΡΠ²Π°ΡΠΊΠΈ
Π‘Π²Π°ΡΠΊΠ° —Β ΡΠ΅Ρ Π½ΠΎΠ»ΠΎΠ³ΠΈΡΠ΅ΡΠΊΠΈΠΉ ΠΏΡΠΎΡΠ΅ΡΡ ΡΠΎΠ΅Π΄ΠΈΠ½Π΅Π½ΠΈΡ ΡΠ²ΡΡΠ΄ΡΡ ΠΌΠ°ΡΠ΅ΡΠΈΠ°Π»ΠΎΠ² Π² ΡΠ΅Π·ΡΠ»ΡΡΠ°ΡΠ΅ Π΄Π΅ΠΉΡΡΠ²ΠΈΡ ΠΌΠ΅ΠΆΠ°ΡΠΎΠΌΠ½ΡΡ ΡΠΈΠ», ΠΊΠΎΡΠΎΡΠΎΠ΅ ΠΏΡΠΎΠΈΡΡ ΠΎΠ΄ΠΈΡ ΠΏΡΠΈ ΠΌΠ΅ΡΡΠ½ΠΎΠΌ ΡΠΏΠ»Π°Π²Π»Π΅Π½ΠΈΠΈ ΠΈΠ»ΠΈ ΡΠΎΠ²ΠΌΠ΅ΡΡΠ½ΠΎΠΌ ΠΏΠ»Π°ΡΡΠΈΡΠ΅ΡΠΊΠΎΠΌ Π΄Π΅ΡΠΎΡΠΌΠΈΡΠΎΠ²Π°Π½ΠΈΠΈ ΡΠ²Π°ΡΠΈΠ²Π°Π΅ΠΌΡΡ ΡΠ°ΡΡΠ΅ΠΉ. Π‘Π²Π°ΡΠΊΠΎΠΉ ΠΏΠΎΠ»ΡΡΠ°ΡΡ ΠΈΠ·Π΄Π΅Π»ΠΈΡ ΠΈΠ· ΠΌΠ΅ΡΠ°Π»Π»Π° ΠΈ Π½Π΅ΠΌΠ΅ΡΠ°Π»Π»ΠΈΡΠ΅ΡΠΊΠΈΡ ΠΌΠ°ΡΠ΅ΡΠΈΠ°Π»ΠΎΠ² (ΡΡΠ΅ΠΊΠ»Π°, ΠΊΠ΅ΡΠ°ΠΌΠΈΠΊΠΈ, ΠΏΠ»Π°ΡΡΠΌΠ°ΡΡ ΠΈ Π΄Ρ.). ΠΠ·ΠΌΠ΅Π½ΡΡ ΡΠ΅ΠΆΠΈΠΌΡ ΡΠ²Π°ΡΠΊΠΈ, ΠΌΠΎΠΆΠ½ΠΎ Π½Π°ΠΏΠ»Π°Π²Π»ΡΡΡ ΡΠ»ΠΎΠΈ ΠΌΠ΅ΡΠ°Π»Π»Π° ΡΠ°Π·Π»ΠΈΡΠ½ΠΎΠΉ ΡΠΎΠ»ΡΠΈΠ½Ρ ΠΈ ΡΠ°Π·Π»ΠΈΡΠ½ΠΎΠ³ΠΎ ΡΠΎΡΡΠ°Π²Π°.
ΠΠ° ΡΠΏΠ΅ΡΠΈΠ°Π»ΡΠ½ΠΎΠΌ ΠΎΠ±ΠΎΡΡΠ΄ΠΎΠ²Π°Π½ΠΈΠΈ Π² ΠΎΠΏΡΠ΅Π΄Π΅Π»Π΅Π½Π½ΡΡ ΡΡΠ»ΠΎΠ²ΠΈΡΡ ΠΌΠΎΠΆΠ½ΠΎ ΠΎΡΡΡΠ΅ΡΡΠ²Π»ΡΡΡ ΠΏΡΠΎΡΠ΅ΡΡΡ, ΠΏΡΠΎΡΠΈΠ²ΠΎΠΏΠΎΠ»ΠΎΠΆΠ½ΡΠ΅ ΠΏΠΎ ΡΠ²ΠΎΠ΅ΠΉ ΡΡΡΠ½ΠΎΡΡΠΈ ΠΏΡΠΎΡΠ΅ΡΡΡ ΡΠΎΠ΅Π΄ΠΈΠ½Π΅Π½ΠΈΡ, Π½Π°ΠΏΡΠΈΠΌΠ΅Ρ ΠΎΠ³Π½Π΅Π²ΡΡ, ΠΈΠ»ΠΈ ΡΠ΅ΡΠΌΠΈΡΠ΅ΡΠΊΡΡ, ΡΠ΅Π·ΠΊΡ ΠΌΠ΅ΡΠ°Π»Π»ΠΎΠ².
ΠΡΡΠΎΡΠΈΡΠ΅ΡΠΊΠ°Ρ ΡΠΏΡΠ°Π²ΠΊΠ°
ΠΡΠΎΡΡΠ΅ΠΉΡΠΈΠ΅ ΠΏΡΠΈΡΠΌΡ ΡΠ²Π°ΡΠΊΠΈ Π±ΡΠ»ΠΈ ΠΈΠ·Π²Π΅ΡΡΠ½Ρ Π² 8-7-ΠΌ ΡΡΡ. Π΄ΠΎ Π½. Ρ. Π ΠΎΡΠ½ΠΎΠ²Π½ΠΎΠΌ ΡΠ²Π°ΡΠΈΠ²Π°Π»ΠΈΡΡ ΠΈΠ·Π΄Π΅Π»ΠΈΡ ΠΈΠ· ΠΌΠ΅Π΄ΠΈ, ΠΊΠΎΡΠΎΡΡΠ΅ ΠΏΡΠ΅Π΄Π²Π°ΡΠΈΡΠ΅Π»ΡΠ½ΠΎ ΠΏΠΎΠ΄ΠΎΠ³ΡΠ΅Π²Π°Π»ΠΈΡΡ, Π° Π·Π°ΡΠ΅ΠΌ ΡΠ΄Π°Π²Π»ΠΈΠ²Π°Π»ΠΈΡΡ. ΠΡΠΈ ΠΈΠ·Π³ΠΎΡΠΎΠ²Π»Π΅Π½ΠΈΠΈ ΠΈΠ·Π΄Π΅Π»ΠΈΠΉ ΠΈΠ· ΠΌΠ΅Π΄ΠΈ, Π±ΡΠΎΠ½Π·Ρ, ΡΠ²ΠΈΠ½ΡΠ°, Π±Π»Π°Π³ΠΎΡΠΎΠ΄Π½ΡΡ
ΠΌΠ΅ΡΠ°Π»Π»ΠΎΠ² ΠΏΡΠΈΠΌΠ΅Π½ΡΠ»Π°ΡΡ Ρ. Π½. Π»ΠΈΡΠ΅ΠΉΠ½Π°Ρ ΡΠ²Π°ΡΠΊΠ°. Π‘ΠΎΠ΅Π΄ΠΈΠ½ΡΠ΅ΠΌΡΠ΅ Π΄Π΅ΡΠ°Π»ΠΈ Π·Π°ΡΠΎΡΠΌΠΎΠ²ΡΠ²Π°Π»ΠΈ, ΠΏΠΎΠ΄ΠΎΠ³ΡΠ΅Π²Π°Π»ΠΈ ΠΈ ΠΌΠ΅ΡΡΠΎ ΡΠΎΠ΅Π΄ΠΈΠ½Π΅Π½ΠΈΡ Π·Π°Π»ΠΈΠ²Π°Π»ΠΈ Π·Π°ΡΠ°Π½Π΅Π΅ ΠΏΡΠΈΠ³ΠΎΡΠΎΠ²Π»Π΅Π½Π½ΡΠΌ ΡΠ°ΡΠΏΠ»Π°Π²Π»Π΅Π½Π½ΡΠΌ ΠΌΠ΅ΡΠ°Π»Π»ΠΎΠΌ.
ΠΠ·Π΄Π΅Π»ΠΈΡ ΠΈΠ· ΠΆΠ΅Π»Π΅Π·Π° ΠΈ Π΅Π³ΠΎ ΡΠΏΠ»Π°Π²ΠΎΠ² ΠΏΠΎΠ»ΡΡΠ°Π»ΠΈ ΠΈΡ
Π½Π°Π³ΡΠ΅Π²ΠΎΠΌ Π΄ΠΎ «ΡΠ²Π°ΡΠΎΡΠ½ΠΎΠ³ΠΎ ΠΆΠ°ΡΠ°» Π² ΠΊΡΠ·Π½Π΅ΡΠ½ΡΡ
Π³ΠΎΡΠ½Π°Ρ
Ρ ΠΏΠΎΡΠ»Π΅Π΄ΡΡΡΠ΅ΠΉ ΠΏΡΠΎΠΊΠΎΠ²ΠΊΠΎΠΉ. ΠΡΠΎΡ ΡΠΏΠΎΡΠΎΠ± ΠΈΠ·Π²Π΅ΡΡΠ΅Π½ ΠΏΠΎΠ΄ Π½Π°Π·Π²Π°Π½ΠΈΠ΅ΠΌ Π³ΠΎΡΠ½ΠΎΠ²Π°Ρ, ΠΈΠ»ΠΈ ΠΊΡΠ·Π½Π΅ΡΠ½Π°Ρ, ΡΠ²Π°ΡΠΊΠ°. Π’ΠΎΠ»ΡΠΊΠΎ ΡΡΠΈ Π΄Π²Π° ΡΠΏΠΎΡΠΎΠ±Π° ΡΠ²Π°ΡΠΊΠΈ Π±ΡΠ»ΠΈ ΡΠ°ΡΠΏΡΠΎΡΡΡΠ°Π½Π΅Π½Ρ Π²ΠΏΠ»ΠΎΡΡ Π΄ΠΎ ΠΊΠΎΠ½ΡΠ° 19 Π². Π’ΠΎΠ»ΡΠΊΠΎΠΌ ΠΊ ΠΏΠΎΡΠ²Π»Π΅Π½ΠΈΡ ΠΏΡΠΈΠ½ΡΠΈΠΏΠΈΠ°Π»ΡΠ½ΠΎ Π½ΠΎΠ²ΡΡ
ΡΠΏΠΎΡΠΎΠ±ΠΎΠ² ΡΠΎΠ΅Π΄ΠΈΠ½Π΅Π½ΠΈΡ ΠΌΠ΅ΡΠ°Π»Π»ΠΎΠ² ΡΠ²ΠΈΠ»ΠΎΡΡ ΠΎΡΠΊΡΡΡΠΈΠ΅ Π² 1802 Π΄ΡΠ³ΠΎΠ²ΠΎΠ³ΠΎ ΡΠ°Π·ΡΡΠ΄Π° Π. Π. ΠΠ΅ΡΡΠΎΠ²ΡΠΌ. Π 1882 Π. Π. ΠΠ΅Π½Π°ΡΠ΄ΠΎΡ ΠΈ Π² 1890 Π. Π. Π‘Π»Π°Π²ΡΠ½ΠΎΠ² ΠΏΡΠ΅Π΄Π»ΠΎΠΆΠΈΠ»ΠΈ ΠΏΠ΅ΡΠ²ΡΠ΅ ΠΏΡΠ°ΠΊΡΠΈΡΠ΅ΡΠΊΠΈ ΠΏΡΠΈΠ³ΠΎΠ΄Π½ΡΠ΅ ΡΠΏΠΎΡΠΎΠ±Ρ ΡΠ²Π°ΡΠΊΠΈ Ρ ΠΈΡΠΏΠΎΠ»ΡΠ·ΠΎΠ²Π°Π½ΠΈΠ΅ΠΌ ΡΠ»Π΅ΠΊΡΡΠΈΡΠ΅ΡΠΊΠΎΠΉ Π΄ΡΠ³ΠΈ. Π Π½Π°ΡΠ°Π»Π΅ 20 Π². Π΄ΡΠ³ΠΎΠ²Π°Ρ ΡΠ»Π΅ΠΊΡΡΠΎΡΠ²Π°ΡΠΊΠ° ΠΏΠΎΡΡΠ΅ΠΏΠ΅Π½Π½ΠΎ ΡΡΠ°Π»Π° Π²Π΅Π΄ΡΡΠΈΠΌ ΠΏΡΠΎΠΌΡΡΠ»Π΅Π½Π½ΡΠΌ ΡΠΏΠΎΡΠΎΠ±ΠΎΠΌ ΡΠΎΠ΅Π΄ΠΈΠ½Π΅Π½ΠΈΡ ΠΌΠ΅ΡΠ°Π»Π»ΠΎΠ². Π Π½Π°ΡΠ°Π»Ρ 20 Π². ΠΎΡΠ½ΠΎΡΡΡΡΡ ΠΈ ΠΏΠ΅ΡΠ²ΡΠ΅ ΠΏΠΎΠΏΡΡΠΊΠΈ ΠΏΡΠΈΠΌΠ΅Π½Π΅Π½ΠΈΡ Π΄Π»Ρ ΡΠ²Π°ΡΠΊΠΈ ΠΈ ΡΠ΅Π·ΠΊΠΈ Π³ΠΎΡΡΡΠΈΡ
Π³Π°Π·ΠΎΠ² Π² ΡΠΌΠ΅ΡΠΈ Ρ ΠΊΠΈΡΠ»ΠΎΡΠΎΠ΄ΠΎΠΌ. ΠΠ΅ΡΠ²ΡΡ Π°ΡΠ΅ΡΠΈΠ»Π΅Π½ΠΎ-ΠΊΠΈΡΠ»ΠΎΡΠΎΠ΄Π½ΡΡ ΡΠ²Π°ΡΠΎΡΠ½ΡΡ Π³ΠΎΡΠ΅Π»ΠΊΡ ΡΠΊΠΎΠ½ΡΡΡΡΠΈΡΠΎΠ²Π°Π» ΡΡΠ°Π½ΡΡΠ·ΡΠΊΠΈΠΉ ΠΈΠ½ΠΆΠ΅Π½Π΅Ρ Π. Π€ΡΡΠ΅, ΠΊΠΎΡΠΎΡΡΠΉ ΠΏΠΎΠ»ΡΡΠΈΠ» Π½Π° Π½Π΅Ρ ΠΏΠ°ΡΠ΅Π½Ρ Π² ΠΠ΅ΡΠΌΠ°Π½ΠΈΠΈ Π² 1903. Π Π ΠΎΡΡΠΈΠΈ ΡΡΠΎΡ ΡΠΏΠΎΡΠΎΠ± ΡΡΠ°Π» ΠΈΠ·Π²Π΅ΡΡΠ΅Π½ ΠΏΡΠ΅Π΄ΠΏΠΎΠ»ΠΎΠΆΠΈΡΠ΅Π»ΡΠ½ΠΎ ΠΊ 1905, ΠΏΠΎΠ»ΡΡΠΈΠ» ΡΠ°ΡΠΏΡΠΎΡΡΡΠ°Π½Π΅Π½ΠΈΠ΅ ΠΊ 1911. ΠΡΠΎΡΠ΅ΡΡ Π΄ΡΠ³ΠΎΠ²ΠΎΠΉ ΡΠ²Π°ΡΠΊΠΈ ΡΠΎΠ²Π΅ΡΡΠ΅Π½ΡΡΠ²ΠΎΠ²Π°Π»ΡΡ, ΠΏΠΎΡΠ²ΠΈΠ»ΠΈΡΡ Π΅Ρ ΡΠ°Π·Π½ΠΎΠ²ΠΈΠ΄Π½ΠΎΡΡΠΈ: ΠΏΠΎΠ΄ ΡΠ»ΡΡΠΎΠΌ, Π² ΡΡΠ΅Π΄Π΅ Π·Π°ΡΠΈΡΠ½ΡΡ
Π³Π°Π·ΠΎΠ² ΠΈ Π΄Ρ.
ΠΠ»Π°ΡΡΠΈΡΠΈΠΊΠ°ΡΠΈΡ
Π‘ΠΎΠ²ΡΠ΅ΠΌΠ΅Π½Π½ΡΠ΅ ΡΠΏΠΎΡΠΎΠ±Ρ ΡΠ²Π°ΡΠΊΠΈ. ΠΌΠ΅ΡΠ°Π»Π»ΠΎΠ² ΠΌΠΎΠΆΠ½ΠΎ ΡΠ°Π·Π΄Π΅Π»ΠΈΡΡ Π½Π° Π΄Π²Π΅ Π±ΠΎΠ»ΡΡΠΈΠ΅ Π³ΡΡΠΏΠΏΡ: ΡΠ²Π°ΡΠΊΠ° ΠΏΠ»Π°Π²Π»Π΅Π½ΠΈΠ΅ΠΌ, ΠΈΠ»ΠΈ ΡΠ²Π°ΡΠΊΠ° Π² ΠΆΠΈΠ΄ΠΊΠΎΠΉ ΡΠ°Π·Π΅, ΠΈ ΡΠ²Π°ΡΠΊΠ° Π΄Π°Π²Π»Π΅Π½ΠΈΠ΅ΠΌ, ΠΈΠ»ΠΈ ΡΠ²Π°ΡΠΊΠ° Π² ΡΠ²ΡΡΠ΄ΠΎΠΉ ΡΠ°Π·Π΅. ΠΡΠΈ ΡΠ²Π°ΡΠΊΠ΅ ΠΏΠ»Π°Π²Π»Π΅Π½ΠΈΠ΅ΠΌ ΡΠ°ΡΠΏΠ»Π°Π²Π»Π΅Π½Π½ΡΠΉ ΠΌΠ΅ΡΠ°Π»Π» ΡΠΎΠ΅Π΄ΠΈΠ½ΡΠ΅ΠΌΡΡ
ΡΠ°ΡΡΠ΅ΠΉ ΡΠ°ΠΌΠΎΠΏΡΠΎΠΈΠ·Π²ΠΎΠ»ΡΠ½ΠΎ, Π±Π΅Π· ΠΏΡΠΈΠ»ΠΎΠΆΠ΅Π½ΠΈΡ Π²Π½Π΅ΡΠ½ΠΈΡ
ΡΠΈΠ» ΡΠΎΠ΅Π΄ΠΈΠ½ΡΠ΅ΡΡΡ Π² ΠΎΠ΄Π½ΠΎ ΡΠ΅Π»ΠΎΠ΅ Π² ΡΠ΅Π·ΡΠ»ΡΡΠ°ΡΠ΅ ΡΠ°ΡΠΏΠ»Π°Π²Π»Π΅Π½ΠΈΡ ΠΈ ΡΠΌΠ°ΡΠΈΠ²Π°Π½ΠΈΡ Π² Π·ΠΎΠ½Π΅ ΡΠ²Π°ΡΠΊΠΈ ΠΈ Π²Π·Π°ΠΈΠΌΠ½ΠΎΠ³ΠΎ ΡΠ°ΡΡΠ²ΠΎΡΠ΅Π½ΠΈΡ ΠΌΠ°ΡΠ΅ΡΠΈΠ°Π»Π°. ΠΡΠΈ ΡΠ²Π°ΡΠΊΠ΅ Π΄Π°Π²Π»Π΅Π½ΠΈΠ΅ΠΌ Π΄Π»Ρ ΡΠΎΠ΅Π΄ΠΈΠ½Π΅Π½ΠΈΡ ΡΠ°ΡΡΠ΅ΠΉ Π±Π΅Π· ΡΠ°ΡΠΏΠ»Π°Π²Π»Π΅Π½ΠΈΡ Π½Π΅ΠΎΠ±Ρ
ΠΎΠ΄ΠΈΠΌΠΎ Π·Π½Π°ΡΠΈΡΠ΅Π»ΡΠ½ΠΎΠ΅ Π΄Π°Π²Π»Π΅Π½ΠΈΠ΅. ΠΡΠ°Π½ΠΈΡΠ° ΠΌΠ΅ΠΆΠ΄Ρ ΡΡΠΈΠΌΠΈ Π³ΡΡΠΏΠΏΠ°ΠΌΠΈ Π½Π΅ Π²ΡΠ΅Π³Π΄Π° Π΄ΠΎΡΡΠ°ΡΠΎΡΠ½ΠΎ ΡΡΡΠΊΠ°Ρ, Π½Π°ΠΏΡΠΈΠΌΠ΅Ρ Π²ΠΎΠ·ΠΌΠΎΠΆΠ½Π° ΡΠ²Π°ΡΠΊΠ° Ρ ΡΠ°ΡΡΠΈΡΠ½ΡΠΌ ΠΎΠΏΠ»Π°Π²Π»Π΅Π½ΠΈΠ΅ΠΌ Π΄Π΅ΡΠ°Π»Π΅ΠΉ ΠΈ ΠΏΠΎΡΠ»Π΅Π΄ΡΡΡΠΈΠΌ ΡΠ΄Π°Π²Π»ΠΈΠ²Π°Π½ΠΈΠ΅ΠΌ ΠΈΡ
(ΠΊΠΎΠ½ΡΠ°ΠΊΡΠ½Π°Ρ ΡΠ»Π΅ΠΊΡΡΠΎΡΠ²Π°ΡΠΊΠ°). Π ΠΏΡΠ΅Π΄Π»Π°Π³Π°Π΅ΠΌΠΎΠΉ ΠΊΠ»Π°ΡΡΠΈΡΠΈΠΊΠ°ΡΠΈΠΈ Π² ΠΊΠ°ΠΆΠ΄ΡΡ Π³ΡΡΠΏΠΏΡ Π²Ρ
ΠΎΠ΄ΠΈΡ Π½Π΅ΡΠΊΠΎΠ»ΡΠΊΠΎ ΡΠΏΠΎΡΠΎΠ±ΠΎΠ². Π ΡΠ²Π°ΡΠΊΠ΅ ΠΏΠ»Π°Π²Π»Π΅Π½ΠΈΠ΅ΠΌ ΠΎΡΠ½ΠΎΡΡΡΡΡ: Π΄ΡΠ³ΠΎΠ²Π°Ρ, ΠΏΠ»Π°Π·ΠΌΠ΅Π½Π½Π°Ρ, ΡΠ»Π΅ΠΊΡΡΠΎΡΠ»Π°ΠΊΠΎΠ²Π°Ρ, Π³Π°Π·ΠΎΠ²Π°Ρ, Π»ΡΡΠ΅Π²Π°Ρ ΠΈ Π΄Ρ.
Π‘Π²Π°ΡΠΊΠ° ΠΏΠ»Π°Π²Π»Π΅Π½ΠΈΠ΅ΠΌ
ΠΡΠΎΡΡΠ΅ΠΉΡΠΈΠΉ ΡΠΏΠΎΡΠΎΠ± ΡΠ²Π°ΡΠΊΠΈ — ΡΡΡΠ½Π°Ρ Π΄ΡΠ³ΠΎΠ²Π°Ρ ΡΠ²Π°ΡΠΊΠΈ — ΠΎΡΠ½ΠΎΠ²Π°Π½ Π½Π° ΠΈΡΠΏΠΎΠ»ΡΠ·ΠΎΠ²Π°Π½ΠΈΠΈ ΡΠ»Π΅ΠΊΡΡΠΈΡΠ΅ΡΠΊΠΎΠΉ Π΄ΡΠ³ΠΈ. Π ΠΎΠ΄Π½ΠΎΠΌΡ ΠΏΠΎΠ»ΡΡΡ ΠΈΡΡΠΎΡΠ½ΠΈΠΊΠ° ΡΠΎΠΊΠ° Π³ΠΈΠ±ΠΊΠΈΠΌ ΠΏΡΠΎΠ²ΠΎΠ΄ΠΎΠΌ ΠΏΡΠΈΡΠΎΠ΅Π΄ΠΈΠ½ΡΠ΅ΡΡΡ Π΄Π΅ΡΠΆΠ°ΡΠ΅Π»Ρ, ΠΊ Π΄ΡΡΠ³ΠΎΠΌΡ — ΡΠ²Π°ΡΠΈΠ²Π°Π΅ΠΌΠΎΠ΅ ΠΈΠ·Π΄Π΅Π»ΠΈΠ΅. Π Π΄Π΅ΡΠΆΠ°ΡΠ΅Π»Ρ Π²ΡΡΠ°Π²Π»ΡΠ΅ΡΡΡ ΡΠ³ΠΎΠ»ΡΠ½ΡΠΉ ΠΈΠ»ΠΈ ΠΌΠ΅ΡΠ°Π»Π»ΠΈΡΠ΅ΡΠΊΠΈΠΉ ΡΠ»Π΅ΠΊΡΡΠΎΠ΄. ΠΡΠΈ ΠΊΠΎΡΠΎΡΠΊΠΎΠΌ ΠΏΡΠΈΠΊΠΎΡΠ½ΠΎΠ²Π΅Π½ΠΈΠΈ ΡΠ»Π΅ΠΊΡΡΠΎΠ΄Π° ΠΊ ΠΈΠ·Π΄Π΅Π»ΠΈΡ Π·Π°ΠΆΠΈΠ³Π°Π΅ΡΡΡ Π΄ΡΠ³Π°, ΠΊΠΎΡΠΎΡΠ°Ρ ΠΏΠ»Π°Π²ΠΈΡ ΠΎΡΠ½ΠΎΠ²Π½ΠΎΠΉ ΠΌΠ΅ΡΠ°Π»Π» ΠΈ ΡΡΠ΅ΡΠΆΠ΅Π½Ρ ΡΠ»Π΅ΠΊΡΡΠΎΠ΄Π° (ΠΏΡΠΈ ΠΌΠ΅ΡΠ°Π»Π»ΠΈΡΠ΅ΡΠΊΠΎΠΌ ΡΠ»Π΅ΠΊΡΡΠΎΠ΄Π΅), ΠΎΠ±ΡΠ°Π·ΡΡ ΡΠ²Π°ΡΠΎΡΠ½ΡΡ Π²Π°Π½Π½Ρ, Π΄Π°ΡΡΡΡ ΠΏΡΠΈ Π·Π°ΡΠ²Π΅ΡΠ΄Π΅Π²Π°Π½ΠΈΠΈ ΡΠ²Π°ΡΠ½ΠΎΠΉ ΡΠΎΠ². Π’Π΅ΠΌΠΏΠ΅ΡΠ°ΡΡΡΠ° ΡΠ²Π°ΡΠΎΡΠ½ΠΎΠΉ Π΄ΡΠ³ΠΈ 6000-10000 Π‘ (ΠΏΡΠΈ ΡΡΠ°Π»ΡΠ½ΠΎΠΌ ΡΠ»Π΅ΠΊΡΡΠΎΠ΄Π΅).
ΠΡΠΈ Π΄ΡΠ³ΠΎΠ²ΠΎΠΉ ΡΠ²Π°ΡΠΊΠ΅ ΠΊΠΈΡΠ»ΠΎΡΠΎΠ΄ ΠΈ Π°Π·ΠΎΡ Π°ΡΠΌΠΎΡΡΠ΅ΡΠ½ΠΎΠ³ΠΎ Π²ΠΎΠ·Π΄ΡΡ
Π° Π°ΠΊΡΠΈΠ²Π½ΠΎ Π²Π·Π°ΠΈΠΌΠΎΠ΄Π΅ΠΉΡΡΠ²ΡΡΡ Ρ ΡΠ°ΡΠΏΠ»Π°Π²Π»Π΅Π½Π½ΡΠΌ ΠΌΠ΅ΡΠ°Π»Π»ΠΎΠΌ, ΠΎΠ±ΡΠ°Π·ΡΡΡ ΠΎΠΊΠΈΡΠ»Ρ ΠΈ Π½ΠΈΡΡΠΈΠ΄Ρ, ΡΠ½ΠΈΠΆΠ°ΡΡΠΈΠ΅ ΠΏΡΠΎΡΠ½ΠΎΡΡΡ ΠΈ ΠΏΠ»Π°ΡΡΠΈΡΠ½ΠΎΡΡΡ ΡΠ²Π°ΡΠ½ΠΎΠ³ΠΎ ΡΠΎΠ΅Π΄ΠΈΠ½Π΅Π½ΠΈΡ. Π‘ΡΡΠ΅ΡΡΠ²ΡΡΡ Π²Π½ΡΡΡΠ΅Π½Π½ΠΈΠ΅ ΠΈ Π²Π½Π΅ΡΠ½ΠΈΠ΅ ΡΠΏΠΎΡΠΎΠ±Ρ Π·Π°ΡΠΈΡΡ ΠΌΠ΅ΡΡΠ° ΡΠ²Π°ΡΠΊΠΈ Π²Π²Π΅Π΄Π΅Π½ΠΈΠ΅ ΡΠ°Π·Π»ΠΈΡΠ½ΡΡ
Π²Π΅ΡΠ΅ΡΡΠ² Π² ΠΌΠ°ΡΠ΅ΡΠΈΠ°Π» ΡΠ»Π΅ΠΊΡΡΠΎΠ΄Π° ΠΈ ΡΠ»Π΅ΠΊΡΡΠΎΠ΄Π½ΠΎΠ³ΠΎ ΠΏΠΎΠΊΡΡΡΠΈΡ (Π²Π½ΡΡΡΠ΅Π½Π½ΡΡ Π·Π°ΡΠΈΡΠ°), Π²Π²Π΅Π΄Π΅Π½ΠΈΠ΅ Π² Π·ΠΎΠ½Ρ ΡΠ²Π°ΡΠΊΠΈ ΠΈΠ½Π΅ΡΡΠ½ΡΡ
Π³Π°Π·ΠΎΠ² ΠΈ ΠΎΠΊΠΈΡΠΈ ΡΠ³Π»Π΅ΡΠΎΠ΄Π°, ΠΏΠΎΠΊΡΡΡΠΈΠ΅ ΠΌΠ΅ΡΡΠ° ΡΠ²Π°ΡΠΊΠΈ ΡΠ²Π°ΡΠΎΡΠ½ΡΠΌΠΈ ΡΠ»ΡΡΠ°ΠΌΠΈ (Π²Π½Π΅ΡΠ½ΡΡ Π·Π°ΡΠΈΡΠ°). ΠΡΠΈ ΠΎΡΡΡΡΡΡΠ²ΠΈΠΈ Π²Π½Π΅ΡΠ½ΠΈΡ
ΡΡΠ΅Π΄ΡΡΠ² Π·Π°ΡΠΈΡΡ ΡΠ²Π°ΡΠΎΡΠ½Π°Ρ Π΄ΡΠ³Π° Π½Π°Π·ΡΠ²Π°Π΅ΡΡΡ ΠΎΡΠΊΡΡΡΠΎΠΉ, ΠΏΡΠΈ Π½Π°Π»ΠΈΡΠΈΠΈ ΠΈΡ
— Π·Π°ΡΠΈΡΠ΅Π½Π½ΠΎΠΉ ΠΈΠ»ΠΈ ΠΏΠΎΠ³ΡΡΠΆΠ΅Π½Π½ΠΎΠΉ. ΠΠ°ΠΈΠ±ΠΎΠ»ΡΡΠ΅Π΅ ΠΏΡΠ°ΠΊΡΠΈΡΠ΅ΡΠΊΠΎΠ΅ Π·Π½Π°ΡΠ΅Π½ΠΈΠ΅ ΠΈΠΌΠ΅Π΅Ρ ΡΠ»Π΅ΠΊΡΡΠΎΡΠ²Π°ΡΠΊΠ° ΠΎΡΠΊΡΡΡΠΎΠΉ Π΄ΡΠ³ΠΎΠΉ ΠΏΠΎΠΊΡΡΡΡΠΌ ΠΏΠ»Π°Π²ΡΡΠΈΠΌΡΡ ΡΠ»Π΅ΠΊΡΡΠΎΠ΄ΠΎΠΌ. ΠΡΡΠΎΠΊΠΎΠ΅ ΠΊΠ°ΡΠ΅ΡΡΠ²ΠΎ ΡΠ²Π°ΡΠ½ΠΎΠ³ΠΎ ΡΠΎΠ΅Π΄ΠΈΠ½Π΅Π½ΠΈΡ ΠΏΠΎΠ·Π²ΠΎΠ»ΡΠ΅Ρ ΠΈΡΠΏΠΎΠ»ΡΠ·ΠΎΠ²Π°ΡΡ ΡΡΠΎΡ ΡΠΏΠΎΡΠΎΠ± ΠΏΡΠΈ ΠΈΠ·Π³ΠΎΡΠΎΠ²Π»Π΅Π½ΠΈΠΈ ΠΎΡΠ²Π΅ΡΡΡΠ²Π΅Π½Π½ΡΡ
ΠΈΠ·Π΄Π΅Π»ΠΈΠΉ. ΠΠ΄Π½ΠΎΠΉ ΠΈΠ· Π²Π°ΠΆΠ½Π΅ΠΉΡΠΈΡ
ΠΏΡΠΎΠ±Π»Π΅ΠΌ ΡΠ²Π°ΡΠΎΡΠ½ΠΎΠΉ ΡΠ΅Ρ
Π½ΠΈΠΊΠΈ ΡΠ²Π»ΡΠ΅ΡΡΡ ΠΌΠ΅Ρ
Π°Π½ΠΈΠ·Π°ΡΠΈΡ ΠΈ Π°Π²ΡΠΎΠΌΠ°ΡΠΈΠ·Π°ΡΠΈΡ Π΄ΡΠ³ΠΎΠ²ΠΎΠΉ ΡΠ²Π°ΡΠΊΠΈ . ΠΡΠΈ ΠΈΠ·Π³ΠΎΡΠΎΠ²Π»Π΅Π½ΠΈΠΈ ΠΈΠ·Π΄Π΅Π»ΠΈΠΉ ΡΠ»ΠΎΠΆΠ½ΠΎΠΉ ΡΠΎΡΠΌΡ ΡΠ°ΡΡΠΎ Π±ΠΎΠ»Π΅Π΅ ΡΠ°ΡΠΈΠΎΠ½Π°Π»ΡΠ½ΠΎΠΉ ΠΎΠΊΠ°Π·ΡΠ²Π°Π΅ΡΡΡ ΠΏΠΎΠ»ΡΠ°Π²ΡΠΎΠΌΠ°ΡΠΈΡΠ΅ΡΠΊΠ°Ρ Π΄ΡΠ³ΠΎΠ²Π°Ρ ΡΠ²Π°ΡΠΊΠΈ , ΠΏΡΠΈ ΠΊΠΎΡΠΎΡΠΎΠΉ ΠΌΠ΅Ρ
Π°Π½ΠΈΠ·ΠΈΡΠΎΠ²Π°Π½Π° ΠΏΠΎΠ΄Π°ΡΠ° ΡΠ»Π΅ΠΊΡΡΠΎΠ΄Π½ΠΎΠΉ ΠΏΡΠΎΠ²ΠΎΠ»ΠΎΠΊΠΈ Π² Π΄Π΅ΡΠΆΠ°ΡΠ΅Π»Ρ ΡΠ²Π°ΡΠΎΡΠ½ΠΎΠ³ΠΎ ΠΏΠΎΠ»ΡΠ°Π²ΡΠΎΠΌΠ°ΡΠ°.
ΠΡΠΈ ΠΌΠ΅Ρ
Π°Π½ΠΈΠ·ΠΈΡΠΎΠ²Π°Π½Π½ΡΡ
ΡΠΏΠΎΡΠΎΠ±Π°Ρ
ΡΠ²Π°ΡΠΊΠΈ ΠΏΡΠΈΠΌΠ΅Π½ΡΡΡ Π³Π°Π·ΠΎΠ²ΡΡ Π·Π°ΡΠΈΡΡ — ΡΠ²Π°ΡΠΊΠ° Π² Π·Π°ΡΠΈΡΠ½ΡΡ
Π³Π°Π·Π°Ρ
, ΠΈΠ»ΠΈ Π³Π°Π·ΠΎΡΠ»Π΅ΠΊΡΡΠΈΡΠ΅ΡΠΊΠ°Ρ ΡΠ²Π°ΡΠΊΠ°. ΠΠ΄Π΅Ρ ΡΡΠΎΠ³ΠΎ ΡΠΏΠΎΡΠΎΠ±Π° ΠΏΡΠΈΠ½Π°Π΄Π»Π΅ΠΆΠΈΡ Π. Π. ΠΠ΅Π½Π°ΡΠ΄ΠΎΡΡ (ΠΊΠΎΠ½Π΅Ρ 19 Π².). Π‘Π²Π°ΡΠΊΠ° ΠΎΡΡΡΠ΅ΡΡΠ²Π»ΡΠ΅ΡΡΡ ΡΠ²Π°ΡΠΎΡΠ½ΠΎΠΉ Π³ΠΎΡΠ΅Π»ΠΊΠΎΠΉ ΠΈΠ»ΠΈ Π² ΠΊΠ°ΠΌΠ΅ΡΠ°Ρ
, Π·Π°ΠΏΠΎΠ»Π½Π΅Π½Π½ΡΡ
Π³Π°Π·ΠΎΠΌ. ΠΠ°Π·Ρ Π½Π΅ΠΏΡΠ΅ΡΡΠ²Π½ΠΎ ΠΏΠΎΠ΄Π°ΡΡΡΡ Π² Π΄ΡΠ³Ρ ΠΈ ΠΎΠ±Π΅ΡΠΏΠ΅ΡΠΈΠ²Π°ΡΡ Π²ΡΡΠΎΠΊΠΎΠ΅ ΠΊΠ°ΡΠ΅ΡΡΠ²ΠΎ ΡΠΎΠ΅Π΄ΠΈΠ½Π΅Π½ΠΈΡ.
Π ΡΠ»Π΅ΠΊΡΡΠΈΡΠ΅ΡΠΊΠΈΠΌ ΡΠΏΠΎΡΠΎΠ±Π°ΠΌ ΡΠ²Π°ΡΠΊΠΈ ΠΏΠ»Π°Π²Π»Π΅Π½ΠΈΠ΅ΠΌ ΠΎΡΠ½ΠΎΡΠΈΡΡΡ ΡΠ»Π΅ΠΊΡΡΠΎΡΠ»Π°ΠΊΠΎΠ²Π°Ρ ΡΠ²Π°ΡΠΊΠ°, ΠΏΡΠΈ ΠΊΠΎΡΠΎΡΠΎΠΉ ΠΏΡΠΎΡΠ΅ΡΡ Π½Π°ΡΠΈΠ½Π°Π΅ΡΡΡ, ΠΊΠ°ΠΊ ΠΏΡΠΈ Π΄ΡΠ³ΠΎΠ²ΠΎΠΉ ΡΠ²Π°ΡΠΊΠ΅ ΠΏΠ»Π°Π²ΡΡΠΈΠΌΡΡ ΡΠ»Π΅ΠΊΡΡΠΎΠ΄ΠΎΠΌ — Π·Π°ΠΆΠΈΠ³Π°Π½ΠΈΠ΅ΠΌ Π΄ΡΠ³ΠΈ, Π° ΠΏΡΠΎΠ΄ΠΎΠ»ΠΆΠ°Π΅ΡΡΡ Π±Π΅Π· Π΄ΡΠ³ΠΎΠ²ΠΎΠ³ΠΎ ΡΠ°Π·ΡΡΠ΄Π°. ΠΡΠΈ ΡΡΠΎΠΌ Π·Π½Π°ΡΠΈΡΠ΅Π»ΡΠ½ΠΎΠ΅ ΠΊΠΎΠ»ΠΈΡΠ΅ΡΡΠ²ΠΎ ΡΠ»Π°ΠΊΠ° Π·Π°ΠΊΡΡΠ²Π°Π΅Ρ ΡΠ²Π°ΡΠΎΡΠ½ΡΡ Π²Π°Π½Π½Ρ. ΠΡΡΠΎΡΠ½ΠΈΠΊΠΎΠΌ Π½Π°Π³ΡΠ΅Π²Π° ΠΌΠ΅ΡΠ°Π»Π»Π° ΡΠ»ΡΠΆΠΈΡ ΡΠ΅ΠΏΠ»ΠΎ, Π²ΡΠ΄Π΅Π»ΡΡΡΠ΅Π΅ΡΡ ΠΏΡΠΈ ΠΏΡΠΎΡ
ΠΎΠΆΠ΄Π΅Π½ΠΈΠΈ ΡΠ»Π΅ΠΊΡΡΠΈΡΠ΅ΡΠΊΠΎΠ³ΠΎ ΡΠΎΠΊΠ° ΡΠ΅ΡΠ΅Π· ΡΠ»Π°ΠΊ. Π‘ΠΏΠΎΡΠΎΠ± ΡΠ°Π·ΡΠ°Π±ΠΎΡΠ°Π½ Π² ΠΈΠ½ΡΡΠΈΡΡΡΠ΅ ΡΠ»Π΅ΠΊΡΡΠΎΡΠ²Π°ΡΠΊΠΈ ΠΈΠΌ. Π. Π. ΠΠ°ΡΠΎΠ½Π° ΠΈ ΠΏΠΎΠ»ΡΡΠΈΠ» ΠΏΡΠΎΠΌΡΡΠ»Π΅Π½Π½ΠΎΠ΅ ΠΏΡΠΈΠΌΠ΅Π½Π΅Π½ΠΈΠ΅ (Π² ΠΊΠΎΠ½ΡΠ΅ 50-Ρ
Π³Π³.). ΠΠΎΠ·ΠΌΠΎΠΆΠ½Π° ΡΠ»Π΅ΠΊΡΡΠΎΡΠ»Π°ΠΊΠΎΠ²Π°Ρ ΡΠ²Π°ΡΠΊΠ° ΠΌΠ΅ΡΠ°Π»Π»ΠΎΠ² ΡΠΎΠ»ΡΠΈΠ½ΠΎΠΉ Π΄ΠΎ 200 ΠΌΠΌ (ΠΎΠ΄Π½ΠΈΠΌ ΡΠ»Π΅ΠΊΡΡΠΎΠ΄ΠΎΠΌ), Π΄ΠΎ 2000 ΠΌΠΌ (ΠΎΠ΄Π½ΠΎΠ²ΡΠ΅ΠΌΠ΅Π½Π½ΠΎ ΡΠ°Π±ΠΎΡΠ°ΡΡΠΈΠΌΠΈ Π½Π΅ΡΠΊΠΎΠ»ΡΠΊΠΈΠΌΠΈ ΡΠ»Π΅ΠΊΡΡΠΎΠ΄Π°ΠΌΠΈ). ΠΠ½Π° ΡΠ΅Π»Π΅ΡΠΎΠΎΠ±ΡΠ°Π·Π½Π° ΠΈ ΡΠΊΠΎΠ½ΠΎΠΌΠΈΡΠ΅ΡΠΊΠΈ Π²ΡΠ³ΠΎΠ΄Π½Π° ΠΏΡΠΈ ΡΠΎΠ»ΡΠΈΠ½Π΅ ΠΎΡΠ½ΠΎΠ²Π½ΠΎΠ³ΠΎ ΠΌΠ΅ΡΠ°Π»Π»Π° Π±ΠΎΠ»Π΅Π΅ 30 ΠΌΠΌ. ΠΠ»Π΅ΠΊΡΡΠΎΡΠ»Π°ΠΊΠΎΠ²ΡΠΌ ΡΠΏΠΎΡΠΎΠ±ΠΎΠΌ ΠΌΠΎΠΆΠ½ΠΎ Π²ΡΠΏΠΎΠ»Π½ΡΡΡ ΡΠ΅ΠΌΠΎΠ½ΡΠ½ΡΠ΅ ΡΠ°Π±ΠΎΡΡ, ΠΏΡΠΎΠΈΠ·Π²ΠΎΠ΄ΠΈΡΡ Π½Π°ΠΏΠ»Π°Π²ΠΊΡ, ΠΊΠΎΠ³Π΄Π° ΡΡΠ΅Π±ΡΠ΅ΡΡΡ Π·Π½Π°ΡΠΈΡΠ΅Π»ΡΠ½Π°Ρ ΡΠΎΠ»ΡΠΈΠ½Π° Π½Π°ΠΏΠ»Π°Π²Π»ΡΠ΅ΠΌΠΎΠ³ΠΎ ΡΠ»ΠΎΡ. Π‘ΠΏΠΎΡΠΎΠ± Π½Π°ΡΡΠ» ΠΏΡΠΈΠΌΠ΅Π½Π΅Π½ΠΈΠ΅ Π² ΠΏΡΠΎΠΈΠ·Π²ΠΎΠ΄ΡΡΠ²Π΅ ΠΏΠ°ΡΠΎΠ²ΡΡ
ΠΊΠΎΡΠ»ΠΎΠ², ΡΡΠ°Π½ΠΈΠ½ ΠΏΡΠ΅ΡΡΠΎΠ², ΠΏΡΠΎΠΊΠ°ΡΠ½ΡΡ
ΡΡΠ°Π½ΠΎΠ², ΡΡΡΠΎΠΈΡΠ΅Π»ΡΠ½ΡΡ
ΠΌΠ΅ΡΠ°Π»Π»ΠΎΠΊΠΎΠ½ΡΡΡΡΠΊΡΠΈΠΉ ΠΈ Ρ. ΠΏ.
ΠΡΡΡΠ΅ΡΡΠ²Π»Π΅Π½ΠΈΠ΅ Π΄ΡΠ³ΠΎΠ²ΠΎΠΉ ΡΠ»Π΅ΠΊΡΡΠΎΡΠ²Π°ΡΠΊΠΈ Π²ΠΎΠ·ΠΌΠΎΠΆΠ½ΠΎ ΡΠ°ΠΊΠΆΠ΅ Π² Π²ΠΎΠ΄Π΅ (ΠΏΡΠ΅ΡΠ½ΠΎΠΉ ΠΈ ΠΌΠΎΡΡΠΊΠΎΠΉ). ΠΠ΅ΡΠ²ΡΠΉ ΠΏΡΠ°ΠΊΡΠΈΡΠ΅ΡΠΊΠΈ ΠΏΡΠΈΠ³ΠΎΠ΄Π½ΡΠΉ ΡΠΏΠΎΡΠΎΠ± ΡΠ²Π°ΡΠΊΠΈ ΠΏΠΎΠ΄ Π²ΠΎΠ΄ΠΎΠΉ Π±ΡΠ» ΡΠΎΠ·Π΄Π°Π½ Π² Π‘Π‘Π‘Π Π² ΠΠΎΡΠΊΠΎΠ²ΡΠΊΠΎΠΌ ΡΠ»Π΅ΠΊΡΡΠΎΠΌΠ΅Ρ
Π°Π½ΠΈΡΠ΅ΡΠΊΠΎΠΌ ΠΈΠ½ΡΡΠΈΡΡΡΠ΅ ΠΈΠ½ΠΆΠ΅Π½Π΅ΡΠΎΠ² ΠΆ.-Π΄. ΡΡΠ°Π½ΡΠΏΠΎΡΡΠ° Π² 1932 ΠΏΠΎΠ΄ ΡΡΠΊΠΎΠ²ΠΎΠ΄ΡΡΠ²ΠΎΠΌ Π. Π. Π₯ΡΠ΅Π½ΠΎΠ²Π°. ΠΡΠ³Π° Π² Π²ΠΎΠ΄Π΅ Π³ΠΎΡΠΈΡ ΡΡΡΠΎΠΉΡΠΈΠ²ΠΎ, ΠΎΡ
Π»Π°ΠΆΠ΄Π°ΡΡΠ΅Π΅ Π΄Π΅ΠΉΡΡΠ²ΠΈΠ΅ Π²ΠΎΠ΄Ρ ΠΊΠΎΠΌΠΏΠ΅Π½ΡΠΈΡΡΠ΅ΡΡΡ Π½Π΅Π±ΠΎΠ»ΡΡΠΈΠΌ ΠΏΠΎΠ²ΡΡΠ΅Π½ΠΈΠ΅ΠΌ Π½Π°ΠΏΡΡΠΆΠ΅Π½ΠΈΡ Π΄ΡΠ³ΠΈ, ΠΊΠΎΡΠΎΡΠ°Ρ ΠΏΠ»Π°Π²ΠΈΡ ΠΌΠ΅ΡΠ°Π»Π» Π² Π²ΠΎΠ΄Π΅ ΡΠ°ΠΊ ΠΆΠ΅ Π»Π΅Π³ΠΊΠΎ, ΠΊΠ°ΠΊ ΠΈ Π½Π° Π²ΠΎΠ·Π΄ΡΡ
Π΅. Π‘Π²Π°ΡΠΊΠ° ΠΏΡΠΎΠΈΠ·Π²ΠΎΠ΄ΠΈΡΡΡ Π²ΡΡΡΠ½ΡΡ ΡΡΡΡΠ½ΡΠΌ ΠΏΠ»Π°Π²ΡΡΠΈΠΌΡΡ ΡΡΠ°Π»ΡΠ½ΡΠΌ ΡΠ»Π΅ΠΊΡΡΠΎΠ΄ΠΎΠΌ Ρ ΡΠΎΠ»ΡΡΡΠΌ (Π΄ΠΎ 30% ΡΠΎΠ»ΡΠΈΠ½Ρ ΡΠ»Π΅ΠΊΡΡΠΎΠ΄Π°) Π²ΠΎΠ΄ΠΎΠ½Π΅ΠΏΡΠΎΠ½ΠΈΡΠ°Π΅ΠΌΡΠΌ ΠΏΠΎΠΊΡΡΡΠΈΠ΅ΠΌ. ΠΠ°ΡΠ΅ΡΡΠ²ΠΎ ΡΠ²Π°ΡΠΊΠΈ Π½Π΅ΡΠΊΠΎΠ»ΡΠΊΠΎ Π½ΠΈΠΆΠ΅, ΡΠ΅ΠΌ Π½Π° Π²ΠΎΠ·Π΄ΡΡ
Π΅, ΠΌΠ΅ΡΠ°Π»Π» ΡΠ²Π° Π½Π΅Π΄ΠΎΡΡΠ°ΡΠΎΡΠ½ΠΎ ΠΏΠ»Π°ΡΡΠΈΡΠ΅Π½. Π 70-Π΅ Π³Π³. Π² Π‘Π‘Π‘Π Π² ΠΈΠ½ΡΡΠΈΡΡΡΠ΅ ΡΠ»Π΅ΠΊΡΡΠΎΡΠ²Π°ΡΠΊΠΈ ΠΈΠΌ. Π. Π. ΠΠ°ΡΠΎΠ½Π° ΠΎΡΡΡΠ΅ΡΡΠ²Π»Π΅Π½Π° ΡΠ²Π°ΡΠΊΠ° ΠΏΠΎΠ΄ Π²ΠΎΠ΄ΠΎΠΉ ΠΏΠΎΠ»ΡΠ°Π²ΡΠΎΠΌΠ°ΡΠΎΠΌ, Π² ΠΊΠΎΡΠΎΡΠΎΠΌ Π² ΠΊΠ°ΡΠ΅ΡΡΠ²Π΅ ΡΠ»Π΅ΠΊΡΡΠΎΠ΄Π° ΠΈΡΠΏΠΎΠ»ΡΠ·ΠΎΠ²Π°Π½Π° Ρ. Π½. ΠΏΠΎΡΠΎΡΠΊΠΎΠ²Π°Ρ ΠΏΡΠΎΠ²ΠΎΠ»ΠΎΠΊΠ° (ΡΠΎΠ½ΠΊΠ°Ρ ΡΡΠ°Π»ΡΠ½Π°Ρ ΡΡΡΠ±ΠΊΠ°, Π½Π°Π±ΠΈΡΠ°Ρ ΡΠΌΠ΅ΡΡΡ ΠΏΠΎΡΠΎΡΠΊΠΎΠ²), Π½Π΅ΠΏΡΠ΅ΡΡΠ²Π½ΠΎ ΠΏΠΎΠ΄Π°Π²Π°Π΅ΠΌΠ°Ρ Π² Π΄ΡΠ³Ρ. ΠΠΎΡΠΎΡΠΎΠΊ ΡΠ²Π»ΡΠ΅ΡΡΡ ΡΠ»ΡΡΠΎΠΌ. ΠΠΎΠ΄Π²ΠΎΠ΄Π½Π°Ρ ΡΠ²Π°ΡΠΊΠ° Π²Π΅Π΄ΡΡΡΡ Π½Π° Π³Π»ΡΠ±ΠΈΠ½Π΅ Π΄ΠΎ 100 ΠΌ, ΠΏΠΎΠ»ΡΡΠΈΠ»Π° ΡΠ°ΡΠΏΡΠΎΡΡΡΠ°Π½Π΅Π½ΠΈΠ΅ Π² ΡΡΠ΄ΠΎΡΠ΅ΠΌΠΎΠ½ΡΠ½ΡΡ
ΠΈ Π°Π²Π°ΡΠΈΠΉΠ½ΠΎ-ΡΠΏΠ°ΡΠ°ΡΠ΅Π»ΡΠ½ΡΡ
ΡΠ°Π±ΠΎΡΠ°Ρ
.
ΠΠ΄ΠΈΠ½ ΠΈΠ· ΠΏΠ΅ΡΡΠΏΠ΅ΠΊΡΠΈΠ²Π½ΡΡ
ΡΠΏΠΎΡΠΎΠ±ΠΎΠ² ΡΠ²Π°ΡΠΊΠΈ — ΠΏΠ»Π°Π·ΠΌΠ΅Π½Π½Π°Ρ ΡΠ²Π°ΡΠΊΠ° — ΠΏΡΠΎΠΈΠ·Π²ΠΎΠ΄ΠΈΡΡΡ ΠΏΠ»Π°Π·ΠΌΠ΅Π½Π½ΠΎΠΉ Π³ΠΎΡΠ΅Π»ΠΊΠΎΠΉ. Π‘ΡΡΠ½ΠΎΡΡΡ ΡΡΠΎΠ³ΠΎ ΡΠΏΠΎΡΠΎΠ±Π° ΡΠ²Π°ΡΠΊΠΈ ΡΠΎΡΡΠΎΠΈΡ Π² ΡΠΎΠΌ, ΡΡΠΎ Π΄ΡΠ³Π° Π³ΠΎΡΠΈΡ ΠΌΠ΅ΠΆΠ΄Ρ Π²ΠΎΠ»ΡΡΡΠ°ΠΌΠΎΠ²ΡΠΌ ΡΠ»Π΅ΠΊΡΡΠΎΠ΄ΠΎΠΌ ΠΈ ΠΈΠ·Π΄Π΅Π»ΠΈΠ΅ΠΌ ΠΈ ΠΏΡΠΎΠ΄ΡΠ²Π°Π΅ΡΡΡ ΠΏΠΎΡΠΎΠΊΠΎΠΌ Π³Π°Π·Π°, Π² ΡΠ΅Π·ΡΠ»ΡΡΠ°ΡΠ΅ ΡΠ΅Π³ΠΎ ΠΎΠ±ΡΠ°Π·ΡΠ΅ΡΡΡ ΠΏΠ»Π°Π·ΠΌΠ°, ΠΈΡΠΏΠΎΠ»ΡΠ·ΡΠ΅ΠΌΠ°Ρ Π΄Π»Ρ Π²ΡΡΠΎΠΊΠΎΡΠ΅ΠΌΠΏΠ΅ΡΠ°ΡΡΡΠ½ΠΎΠ³ΠΎ Π½Π°Π³ΡΠ΅Π²Π° ΠΌΠ΅ΡΠ°Π»Π»Π°. ΠΠ΅ΡΡΠΏΠ΅ΠΊΡΠΈΠ²Π½Π°Ρ ΡΠ°Π·Π½ΠΎΠ²ΠΈΠ΄Π½ΠΎΡΡΡ ΠΏΠ»Π°Π·ΠΌΠ΅Π½Π½ΠΎΠΉ ΡΠ²Π°ΡΠΊΠΈ — ΡΠ²Π°ΡΠΊΠ° ΡΠΆΠ°ΡΠΎΠΉ Π΄ΡΠ³ΠΎΠΉ (Π³Π°Π·Ρ ΡΡΠΎΠ»Π±Π° Π΄ΡΠ³ΠΈ, ΠΏΡΠΎΡ
ΠΎΠ΄Ρ ΡΠ΅ΡΠ΅Π· ΠΊΠ°Π»ΠΈΠ±ΡΠΎΠ²Π°Π½Π½ΡΠΉ ΠΊΠ°Π½Π°Π» ΡΠΎΠΏΠ»Π° Π³ΠΎΡΠ΅Π»ΠΊΠΈ, Π²ΡΡΡΠ³ΠΈΠ²Π°ΡΡΡΡ Π² ΡΠΎΠ½ΠΊΡΡ ΡΡΡΡΡ). ΠΡΠΈ ΡΠΆΠ°ΡΠΈΠΈ Π΄ΡΠ³ΠΈ ΠΌΠ΅Π½ΡΡΡΡΡ Π΅Ρ ΡΠ²ΠΎΠΉΡΡΠ²Π°: Π·Π½Π°ΡΠΈΡΠ΅Π»ΡΠ½ΠΎ ΠΏΠΎΠ²ΡΡΠ°Π΅ΡΡΡ Π½Π°ΠΏΡΡΠΆΠ΅Π½ΠΈΠ΅ Π΄ΡΠ³ΠΈ, ΡΠ΅Π·ΠΊΠΎ Π²ΠΎΠ·ΡΠ°ΡΡΠ°Π΅Ρ ΡΠ΅ΠΌΠΏΠ΅ΡΠ°ΡΡΡΠ° (Π΄ΠΎ 20000-30000 Π‘). ΠΠ»Π°Π·ΠΌΠ΅Π½Π½Π°Ρ ΡΠ²Π°ΡΠΊΠ° ΠΏΠΎΠ»ΡΡΠΈΠ»Π° ΠΏΡΠΎΠΌΡΡΠ»Π΅Π½Π½ΠΎΠ΅ ΠΏΡΠΈΠΌΠ΅Π½Π΅Π½ΠΈΠ΅ Π΄Π»Ρ ΡΠΎΠ΅Π΄ΠΈΠ½Π΅Π½ΠΈΡ ΡΡΠ³ΠΎΠΏΠ»Π°Π²ΠΊΠΈΡ
ΠΌΠ΅ΡΠ°Π»Π»ΠΎΠ², ΠΏΡΠΈΡΡΠΌ Π°Π²ΡΠΎΠΌΠ°ΡΡ ΠΈ ΠΏΠΎΠ»ΡΠ°Π²ΡΠΎΠΌΠ°ΡΡ Π΄Π»Ρ Π΄ΡΠ³ΠΎΠ²ΠΎΠΉ ΡΠ²Π°ΡΠΊΠΈ Π»Π΅Π³ΠΊΠΎ ΠΌΠΎΠ³ΡΡ Π±ΡΡΡ ΠΏΡΠΈΡΠΏΠΎΡΠΎΠ±Π»Π΅Π½Ρ Π΄Π»Ρ ΠΏΠ»Π°Π·ΠΌΠ΅Π½Π½ΠΎΠΉ ΠΏΡΠΈ ΡΠΎΠΎΡΠ²Π΅ΡΡΡΠ²ΡΡΡΠ΅ΠΉ Π·Π°ΠΌΠ΅Π½Π΅ Π³ΠΎΡΠ΅Π»ΠΊΠΈ. ΠΠ»Π°Π·ΠΌΠ΅Π½Π½ΡΡ ΡΠ²Π°ΡΠΊΡ ΠΈΡΠΏΠΎΠ»ΡΠ·ΡΡΡ ΠΊΠ°ΠΊ Π΄Π»Ρ ΡΠΎΠ΅Π΄ΠΈΠ½Π΅Π½ΠΈΡ ΠΌΠ΅ΡΠ°Π»Π»ΠΎΠ² Π±ΠΎΠ»ΡΡΠΈΡ
ΡΠΎΠ»ΡΠΈΠ½ (ΠΌΠ½ΠΎΠ³ΠΎΡΠ»ΠΎΠΉΠ½Π°Ρ ΡΠ²Π°ΡΠΊΠ° Ρ Π·Π°ΡΠΈΡΠΎΠΉ Π°ΡΠ³ΠΎΠ½ΠΎΠΌ), ΡΠ°ΠΊ ΠΈ Π΄Π»Ρ ΡΠΎΠ΅Π΄ΠΈΠ½Π΅Π½ΠΈΡ ΠΏΠ»Π°ΡΡΠΈΠ½ ΠΈ ΠΏΡΠΎΠ²ΠΎΠ»ΠΎΠΊΠΈ ΡΠΎΠ»ΡΠΈΠ½ΠΎΠΉ ΠΎΡ Π΄Π΅ΡΡΡΠΊΠΎΠ² ΠΌΠΊΠΌ Π΄ΠΎ 1 ΠΌΠΌ (ΠΌΠΈΠΊΡΠΎΡΠ²Π°ΡΠΊΠ°, ΡΠ²Π°ΡΠΊΠ°. ΠΈΠ³ΠΎΠ»ΡΡΠ°ΡΠΎΠΉ Π΄ΡΠ³ΠΎΠΉ). ΠΠ»Π°Π·ΠΌΠ΅Π½Π½ΠΎΠΉ ΡΡΡΡΠ΅ΠΉ ΠΌΠΎΠΆΠ½ΠΎ ΠΎΡΡΡΠ΅ΡΡΠ²Π»ΡΡΡ ΡΠ°ΠΊΠΆΠ΅ Π΄Ρ. Π²ΠΈΠ΄Ρ ΠΏΠ»Π°Π·ΠΌΠ΅Π½Π½ΠΎΠΉ ΠΎΠ±ΡΠ°Π±ΠΎΡΠΊΠΈ, Π² ΡΠΎΠΌ ΡΠΈΡΠ»Π΅ ΠΏΠ»Π°Π·ΠΌΠ΅Π½Π½ΡΡ ΡΠ΅Π·ΠΊΡ ΠΌΠ΅ΡΠ°Π»Π»ΠΎΠ².
ΠΠ°Π·ΠΎΠ²Π°Ρ ΡΠ²Π°ΡΠΊΠ°
ΠΠ°Π·ΠΎΠ²Π°Ρ ΡΠ²Π°ΡΠΊΠ° ΠΎΡΠ½ΠΎΡΠΈΡΡΡ ΠΊ ΡΠΏΠΎΡΠΎΠ±Π°ΠΌ ΡΠ²Π°ΡΠΊΠ° ΠΏΠ»Π°Π²Π»Π΅Π½ΠΈΠ΅ΠΌ Ρ ΠΈΡΠΏΠΎΠ»ΡΠ·ΠΎΠ²Π°Π½ΠΈΠ΅ΠΌ ΡΠ½Π΅ΡΠ³ΠΈΠΈ Π³Π°Π·ΠΎΠ²ΠΎΠ³ΠΎ ΠΏΠ»Π°ΠΌΠ΅Π½ΠΈ, ΠΏΡΠΈΠΌΠ΅Π½ΡΠ΅ΡΡΡ Π΄Π»Ρ ΡΠΎΠ΅Π΄ΠΈΠ½Π΅Π½ΠΈΡ ΡΠ°Π·Π»ΠΈΡΠ½ΡΡ
ΠΌΠ΅ΡΠ°Π»Π»ΠΎΠ² ΠΎΠ±ΡΡΠ½ΠΎ Π½Π΅Π±ΠΎΠ»ΡΡΠΎΠΉ ΡΠΎΠ»ΡΠΈΠ½Ρ — Π΄ΠΎ 10 ΠΌΠΌ. ΠΠ°Π·ΠΎΠ²ΠΎΠ΅ ΠΏΠ»Π°ΠΌΡ Ρ ΡΠ°ΠΊΠΎΠΉ ΡΠ΅ΠΌΠΏΠ΅ΡΠ°ΡΡΡΠΎΠΉ ΠΏΠΎΠ»ΡΡΠ°Π΅ΡΡΡ ΠΏΡΠΈ ΡΠΆΠΈΠ³Π°Π½ΠΈΠΈ ΡΠ°Π·Π»ΠΈΡΠ½ΡΡ
Π³ΠΎΡΡΡΠΈΡ
Π² ΠΊΠΈΡΠ»ΠΎΡΠΎΠ΄Π΅ (Π²ΠΎΠ΄ΠΎΡΠΎΠ΄Π½ΠΎ-ΠΊΠΈΡΠ»ΠΎΡΠΎΠ΄Π½Π°Ρ, Π±Π΅Π½Π·ΠΈΠ½ΠΎ-ΠΊΠΈΡΠ»ΠΎΡΠΎΠ΄Π½Π°Ρ, Π°ΡΠ΅ΡΠΈΠ»Π΅Π½ΠΎ-ΠΊΠΈΡΠ»ΠΎΡΠΎΠ΄Π½Π°Ρ ΡΠ²Π°ΡΠΊΠ° ΠΈ Π΄Ρ.).
ΠΡΠΎΠΌΡΡΠ»Π΅Π½Π½ΠΎΠ΅ ΠΏΡΠΈΠΌΠ΅Π½Π΅Π½ΠΈΠ΅ ΠΏΠΎΠ»ΡΡΠΈΠ»Π° Π°ΡΠ΅ΡΠΈΠ»Π΅Π½ΠΎ-ΠΊΠΈΡΠ»ΠΎΡΠΎΠ΄Π½Π°Ρ Π³Π°Π·ΠΎΠ²Π°Ρ ΡΠ²Π°ΡΠΊΠ°. Π‘ΡΡΠ΅ΡΡΠ²Π΅Π½Π½ΠΎΠ΅ ΠΎΡΠ»ΠΈΡΠΈΠ΅ Π³Π°Π·ΠΎΠ²ΠΎΠΉ ΡΠ²Π°ΡΠΊΠΈ ΠΎΡ Π΄ΡΠ³ΠΎΠ²ΠΎΠΉ ΡΠ²Π°ΡΠΊΠΈ — Π±ΠΎΠ»Π΅Π΅ ΠΏΠ»Π°Π²Π½ΡΠΉ ΠΈ ΠΌΠ΅Π΄Π»Π΅Π½Π½ΡΠΉ Π½Π°Π³ΡΠ΅Π² ΠΌΠ΅ΡΠ°Π»Π»Π°, ΠΡΠΎ ΠΎΠ±ΡΡΠΎΡΡΠ΅Π»ΡΡΡΠ²ΠΎ ΠΎΠΏΡΠ΅Π΄Π΅Π»ΡΠ΅Ρ ΠΏΡΠΈΠΌΠ΅Π½Π΅Π½ΠΈΠ΅ Π³Π°Π·ΠΎΠ²ΠΎΠΉ ΡΠ²Π°ΡΠΊΠΈ Π΄Π»Ρ ΡΠΎΠ΅Π΄ΠΈΠ½Π΅Π½ΠΈΡ ΠΌΠ΅ΡΠ°Π»Π»ΠΎΠ² ΠΌΠ°Π»ΡΡ ΡΠΎΠ»ΡΠΈΠ½, ΡΡΠ΅Π±ΡΡΡΠΈΡ ΠΏΠΎΠ΄ΠΎΠ³ΡΠ΅Π²Π° Π² ΠΏΡΠΎΡΠ΅ΡΡΠ΅ ΡΠ²Π°ΡΠΊΠΈ (Π½Π°ΠΏΡΠΈΠΌΠ΅Ρ, ΡΡΠ³ΡΠ½ ΠΈ Π½Π΅ΠΊΠΎΡΠΎΡΡΠ΅ ΡΠΏΠ΅ΡΠΈΠ°Π»ΡΠ½ΡΠ΅ ΡΡΠ°Π»ΠΈ), Π·Π°ΠΌΠ΅Π΄Π»Π΅Π½Π½ΠΎΠ³ΠΎ ΠΎΡ Π»Π°ΠΆΠ΄Π΅Π½ΠΈΡ (Π½Π°ΠΏΡΠΈΠΌΠ΅Ρ, ΠΈΠ½ΡΡΡΡΠΌΠ΅Π½ΡΠ°Π»ΡΠ½ΡΠ΅ ΡΡΠ°Π»ΠΈ) ΠΈ Ρ. Π΄. ΠΠ»Π°Π³ΠΎΠ΄Π°ΡΡ ΡΠ½ΠΈΠ²Π΅ΡΡΠ°Π»ΡΠ½ΠΎΡΡΠΈ, ΡΡΠ°Π²Π½ΠΈΡΠ΅Π»ΡΠ½ΠΎΠΉ ΠΏΡΠΎΡΡΠΎΡΠ΅ ΠΈ ΠΏΠΎΡΡΠ°ΡΠΈΠ²Π½ΠΎΡΡΠΈ ΠΎΠ±ΠΎΡΡΠ΄ΠΎΠ²Π°Π½ΠΈΡ Π³Π°Π·ΠΎΠ²Π°Ρ ΡΠ²Π°ΡΠΊΠ° ΡΠ΅Π»Π΅ΡΠΎΠΎΠ±ΡΠ°Π·Π½Π° ΠΏΡΠΈ Π²ΡΠΏΠΎΠ»Π½Π΅Π½ΠΈΠΈ ΡΠ΅ΠΌΠΎΠ½ΡΠ½ΡΡ ΡΠ°Π±ΠΎΡ. ΠΡΠΎΠΌΡΡΠ»Π΅Π½Π½ΠΎΠ΅ ΠΏΡΠΈΠΌΠ΅Π½Π΅Π½ΠΈΠ΅ ΠΈΠΌΠ΅Π΅Ρ ΡΠ°ΠΊΠΆΠ΅ Π³Π°Π·ΠΎΠΏΡΠ΅ΡΡΠΎΠ²Π°Ρ ΡΠ²Π°ΡΠΊΠ° ΡΡΠ°Π»ΡΠ½ΡΡ ΡΡΡΠ± ΠΈ ΡΠ΅Π»ΡΡΠΎΠ², Π·Π°ΠΊΠ»ΡΡΠ°ΡΡΠ°ΡΡΡ Π² ΡΠ°Π²Π½ΠΎΠΌΠ΅ΡΠ½ΠΎΠΌ Π½Π°Π³ΡΠ΅Π²Π΅ Π°ΡΠ΅ΡΠΈΠ»Π΅Π½ΠΎ-ΠΊΠΈΡΠ»ΠΎΡΠΎΠ΄Π½ΡΠΌ ΠΏΠ»Π°ΠΌΠ΅Π½Π΅ΠΌ ΠΌΠ΅ΡΠ°Π»Π»Π° Π² ΠΌΠ΅ΡΡΠ΅ ΡΡΡΠΊΠ° Π΄ΠΎ ΠΏΠ»Π°ΡΡΠΈΡΠ΅ΡΠΊΠΎΠ³ΠΎ ΡΠΎΡΡΠΎΡΠ½ΠΈΡ ΠΈ ΠΏΠΎΡΠ»Π΅Π΄ΡΡΡΠ΅ΠΉ ΠΎΡΠ°Π΄ΠΊΠ΅ Ρ ΠΏΡΠ΅ΡΡΠΎΠ²Π°Π½ΠΈΠ΅ΠΌ ΠΈΠ»ΠΈ ΠΏΡΠΎΠΊΠΎΠ²ΠΊΠΎΠΉ.
ΠΠ΅ΡΡΠΏΠ΅ΠΊΡΠΈΠ²Π½ΡΠΌΠΈ ΡΠ²Π»ΡΡΡΡΡ ΠΏΠΎΡΠ²ΠΈΠ²ΡΠΈΠ΅ΡΡ Π² 60-Π΅ Π³Π³. ΡΠΏΠΎΡΠΎΠ±Ρ Π»ΡΡΠ΅Π²ΠΎΠΉ ΡΠ²Π°ΡΠΊΠΈ , ΡΠ°ΠΊΠΆΠ΅ ΠΎΡΡΡΠ΅ΡΡΠ²Π»ΡΠ΅ΠΌΡΠ΅ Π±Π΅Π· ΠΏΡΠΈΠΌΠ΅Π½Π΅Π½ΠΈΡ Π΄Π°Π²Π»Π΅Π½ΠΈΡ. ΠΠ»Π΅ΠΊΡΡΠΎΠ½Π½ΠΎΠ»ΡΡΠ΅Π²Π°Ρ (ΡΠ»Π΅ΠΊΡΡΠΎΠ½Π½Π°Ρ) ΡΠ²Π°ΡΠΊΠ° ΠΏΡΠΎΠΈΠ·Π²ΠΎΠ΄ΠΈΡΡΡ ΡΡΠΎΠΊΡΡΠΈΡΠΎΠ²Π°Π½Π½ΡΠΌ ΠΏΠΎΡΠΎΠΊΠΎΠΌ ΡΠ»Π΅ΠΊΡΡΠΎΠ½ΠΎΠ². ΠΠ·Π΄Π΅Π»ΠΈΠ΅ ΠΏΠΎΠΌΠ΅ΡΠ°Π΅ΡΡΡ Π² ΠΊΠ°ΠΌΠ΅ΡΡ, Π² ΠΊΠΎΡΠΎΡΠΎΠΉ ΠΏΠΎΠ΄Π΄Π΅ΡΠΆΠΈΠ²Π°Π΅ΡΡΡ Π²Π°ΠΊΡΡΠΌ (10-2-10-4 Π½/ΠΌ2), Π½Π΅ΠΎΠ±Ρ
ΠΎΠ΄ΠΈΠΌΡΠΉ Π΄Π»Ρ ΡΠ²ΠΎΠ±ΠΎΠ΄Π½ΠΎΠ³ΠΎ Π΄Π²ΠΈΠΆΠ΅Π½ΠΈΡ ΡΠ»Π΅ΠΊΡΡΠΎΠ½ΠΎΠ² ΠΈ ΡΠΎΡ
ΡΠ°Π½Π΅Π½ΠΈΡ ΠΊΠΎΠ½ΡΠ΅Π½ΡΡΠΈΡΠΎΠ²Π°Π½Π½ΠΎΠ³ΠΎ ΠΏΡΡΠΊΠ° ΡΠ»Π΅ΠΊΡΡΠΎΠ½ΠΎΠ². ΠΡ ΠΌΠΎΡΠ½ΠΎΠ³ΠΎ ΠΈΡΡΠΎΡΠ½ΠΈΠΊΠ° ΡΠ»Π΅ΠΊΡΡΠΎΠ½ΠΎΠ² (ΡΠ»Π΅ΠΊΡΡΠΎΠ½Π½ΠΎΠΉ ΠΏΡΡΠΊΠΈ) Π½Π° ΠΈΠ·Π΄Π΅Π»ΠΈΠ΅ Π½Π°ΠΏΡΠ°Π²Π»ΡΠ΅ΡΡΡ ΡΠΏΡΠ°Π²Π»ΡΠ΅ΠΌΡΠΉ ΡΠ»Π΅ΠΊΡΡΠΎΠ½Π½ΡΠΉ Π»ΡΡ, ΡΠΎΠΊΡΡΠΈΡΡΠ΅ΠΌΡΠΉ ΠΌΠ°Π³Π½ΠΈΡΠ½ΡΠΌ ΠΈ ΡΠ»Π΅ΠΊΡΡΠΎΡΡΠ°ΡΠΈΡΠ΅ΡΠΊΠΈΠΌΠΈ ΠΏΠΎΠ»ΡΠΌΠΈ. ΠΠΎΠ½ΡΠ΅Π½ΡΡΠ°ΡΠΈΡ ΡΠ½Π΅ΡΠ³ΠΈΠΈ Π² ΡΡΠΎΠΊΡΡΠΈΡΠΎΠ²Π°Π½Π½ΠΎΠΌ ΠΏΡΡΠ½Π΅ Π΄ΠΎ 109 Π²Ρ/ΡΠΌ2. ΠΠ΅ΡΠ΅ΠΌΠ΅ΡΠ°Ρ Π»ΡΡ ΠΏΠΎ Π»ΠΈΠ½ΠΈΠΈ ΡΠ²Π°ΡΠΊΠΈ , ΠΌΠΎΠΆΠ½ΠΎ ΡΠ²Π°ΡΠΈΠ²Π°ΡΡ ΡΠ²Ρ Π»ΡΠ±ΠΎΠΉ ΠΊΠΎΠ½ΡΠΈΠ³ΡΡΠ°ΡΠΈΠΈ ΠΏΡΠΈ Π²ΡΡΠΎΠΊΠΎΠΉ ΡΠΊΠΎΡΠΎΡΡΠΈ. ΠΠ°ΠΊΡΡΠΌ ΡΠΏΠΎΡΠΎΠ±ΡΡΠ²ΡΠ΅Ρ ΠΌΠ΅Π½ΡΡΠ΅ΠΌΡ ΠΎΠΊΠΈΡΠ»Π΅Π½ΠΈΡ ΠΌΠ΅ΡΠ°Π»Π»Π° ΡΠ²Π°. ΠΠ»Π΅ΠΊΡΡΠΎΠ½Π½ΡΠΉ Π»ΡΡ ΠΏΠ»Π°Π²ΠΈΡ ΠΈ Π΄ΠΎΠ²ΠΎΠ΄ΠΈΡ Π΄ΠΎ ΠΊΠΈΠΏΠ΅Π½ΠΈΡ ΠΏΡΠ°ΠΊΡΠΈΡΠ΅ΡΠΊΠΈ Π²ΡΠ΅ ΠΌΠ΅ΡΠ°Π»Π»Ρ ΠΈ ΠΈΡΠΏΠΎΠ»ΡΠ·ΡΠ΅ΡΡΡ Π½Π΅ ΡΠΎΠ»ΡΠΊΠΎ Π΄Π»Ρ ΡΠ²Π°ΡΠΊΠΈ , Π½ΠΎ ΠΈ Π΄Π»Ρ ΡΠ΅Π·ΠΊΠΈ, ΡΠ²Π΅ΡΠ»Π΅Π½ΠΈΡ ΠΎΡΠ²Π΅ΡΡΡΠΈΠΉ ΠΈ Ρ. ΠΏ. Π‘ΠΊΠΎΡΠΎΡΡΡ ΡΠ²Π°ΡΠΊΠΈ ΡΡΠΈΠΌ ΡΠΏΠΎΡΠΎΠ±ΠΎΠΌ Π² 1,5- 2 ΡΠ°Π·Π° ΠΏΡΠ΅Π²ΡΡΠ°Π΅Ρ ΡΠΊΠΎΡΠΎΡΡΡ Π΄ΡΠ³ΠΎΠ²ΠΎΠΉ ΠΏΡΠΈ Π°Π½Π°Π»ΠΎΠ³ΠΈΡΠ½ΡΡ
ΠΎΠΏΠ΅ΡΠ°ΡΠΈΡΡ
. ΠΠ΅Π΄ΠΎΡΡΠ°ΡΠΎΠΊ ΡΡΠΎΠ³ΠΎ ΡΠΏΠΎΡΠΎΠ±Π° — Π±ΠΎΠ»ΡΡΠΈΠ΅ Π·Π°ΡΡΠ°ΡΡ Π½Π° ΡΠΎΠ·Π΄Π°Π½ΠΈΠ΅ Π²Π°ΠΊΡΡΠΌΠ° ΠΈ Π½Π΅ΠΎΠ±Ρ
ΠΎΠ΄ΠΈΠΌΠΎΡΡΡ Π²ΡΡΠΎΠΊΠΎΠ³ΠΎ Π½Π°ΠΏΡΡΠΆΠ΅Π½ΠΈΡ Π΄Π»Ρ ΠΎΠ±Π΅ΡΠΏΠ΅ΡΠ΅Π½ΠΈΡ Π΄ΠΎΡΡΠ°ΡΠΎΡΠ½ΠΎ ΠΌΠΎΡΠ½ΠΎΠ³ΠΎ ΠΈΠ·Π»ΡΡΠ΅Π½ΠΈΡ.
ΠΡΠΈΡ
Π½Π΅Π΄ΠΎΡΡΠ°ΡΠΊΠΎΠ² Π»ΠΈΡΡΠ½ Π΄Ρ. ΡΠΏΠΎΡΠΎΠ± Π»ΡΡΠ΅Π²ΠΎΠΉ ΡΠ²Π°ΡΠΊΠΈ — ΡΠΎΡΠΎΠ½Π½Π°Ρ (ΡΠ²Π΅ΡΠΎΠ²Π°Ρ) ΡΠ²Π°ΡΠΊΠ°. Π ΠΎΡΠ»ΠΈΡΠΈΠ΅ ΠΎΡ ΡΠ»Π΅ΠΊΡΡΠΎΠ½Π½ΠΎΠ³ΠΎ Π»ΡΡΠ°, ΡΠ²Π΅ΡΠΎΠ²ΠΎΠΉ Π»ΡΡ ΠΌΠΎΠΆΠ΅Ρ ΠΏΡΠΎΡ
ΠΎΠ΄ΠΈΡΡ Π·Π½Π°ΡΠΈΡΠ΅Π»ΡΠ½ΡΠ΅ ΡΠ°ΡΡΡΠΎΡΠ½ΠΈΡ Π² Π²ΠΎΠ·Π΄ΡΡ
Π΅, Π½Π΅ ΡΠ΅ΡΡΡ Π·Π°ΠΌΠ΅ΡΠ½ΠΎ ΡΠ½Π΅ΡΠ³ΠΈΠΈ (Ρ. Π΅. ΠΎΡΠΏΠ°Π΄Π°Π΅Ρ Π½Π΅ΠΎΠ±Ρ
ΠΎΠ΄ΠΈΠΌΠΎΡΡΡ Π² Π²Π°ΠΊΡΡΠΌΠ΅), ΠΌΠΎΠΆΠ΅Ρ ΠΏΠΎΡΡΠΈ Π±Π΅Π· ΠΎΡΠ»Π°Π±Π»Π΅Π½ΠΈΡ ΠΏΡΠΎΡΠ²Π΅ΡΠΈΠ²Π°ΡΡ ΠΏΡΠΎΠ·ΡΠ°ΡΠ½ΡΠ΅ ΠΌΠ°ΡΠ΅ΡΠΈΠ°Π»Ρ (ΡΡΠ΅ΠΊΠ»ΠΎ, ΠΊΠ²Π°ΡΡ ΠΈ Ρ. ΠΏ.), Ρ. Π΅. ΠΎΠ±Π΅ΡΠΏΠ΅ΡΠΈΠ²Π°Π΅ΡΡΡ ΡΡΠ΅ΡΠΈΠ»ΡΠ½ΠΎΡΡΡ Π·ΠΎΠ½Ρ ΡΠ²Π°ΡΠΊΠΈ ΠΏΡΠΈ ΠΏΡΠΎΠΏΡΡΠΊΠ°Π½ΠΈΠΈ Π»ΡΡΠ° ΡΠ΅ΡΠ΅Π· ΠΏΡΠΎΠ·ΡΠ°ΡΠ½ΡΡ ΠΎΠ±ΠΎΠ»ΠΎΡΠΊΡ. ΠΡΡ ΡΠΎΠΊΡΡΠΈΡΡΠ΅ΡΡΡ Π·Π΅ΡΠΊΠ°Π»ΠΎΠΌ ΠΈ ΠΊΠΎΠ½ΡΠ΅Π½ΡΡΠΈΡΡΠ΅ΡΡΡ ΠΎΠΏΡΠΈΡΠ΅ΡΠΊΠΎΠΉ ΡΠΈΡΡΠ΅ΠΌΠΎΠΉ (Π½Π°ΠΏΡΠΈΠΌΠ΅Ρ, ΠΊΠ²Π°ΡΡΠ΅Π²ΠΎΠΉ Π»ΠΈΠ½Π·ΠΎΠΉ). ΠΡΠΈ ΠΏΠΎΡΡΠ΅Π±Π»ΡΠ΅ΠΌΠΎΠΉ ΠΌΠΎΡΠ½ΠΎΡΡΠΈ 50 ΠΊΠ²Ρ Π² Π»ΡΡΠ΅ ΡΠ΄Π°ΡΡΡΡ ΡΠΊΠΎΠ½ΡΠ΅Π½ΡΡΠΈΡΠΎΠ²Π°ΡΡ ΠΎΠΊΠΎΠ»ΠΎ 15 ΠΊΠ²Ρ.
ΠΠ»Ρ ΡΠΎΠ·Π΄Π°Π½ΠΈΡ ΡΠ²Π΅ΡΠΎΠ²ΠΎΠ³ΠΎ Π»ΡΡΠ° ΠΌΠΎΠΆΠ΅Ρ ΡΠ»ΡΠΆΠΈΡΡ Π½Π΅ ΡΠΎΠ»ΡΠΊΠΎ ΠΈΡΠΊΡΡΡΡΠ²Π΅Π½Π½ΡΠΉ ΠΈΡΡΠΎΡΠ½ΠΈΠΊ ΡΠ²Π΅ΡΠ°, Π½ΠΎ ΠΈ Π΅ΡΡΠ΅ΡΡΠ²Π΅Π½Π½ΡΠΉ — Π‘ΠΎΠ»Π½ΡΠ΅. ΠΡΠΎΡ ΡΠΏΠΎΡΠΎΠ± ΡΠ²Π°ΡΠΊΠΈ , Π½Π°Π·ΡΠ²Π°Π΅ΡΡΡ Π³Π΅Π»ΠΈΠΎΡΠ²Π°ΡΠΊΠΎΠΉ, ΠΏΡΠΈΠΌΠ΅Π½ΡΠ΅ΡΡΡ Π² ΡΡΠ»ΠΎΠ²ΠΈΡΡ Π·Π½Π°ΡΠΈΡΠ΅Π»ΡΠ½ΠΎΠΉ ΡΠΎΠ»Π½Π΅ΡΠ½ΠΎΠΉ ΡΠ°Π΄ΠΈΠ°ΡΠΈΠΈ, ΠΠ»Ρ ΡΠ²Π°ΡΠΊΠΈ ΠΈΡΠΏΠΎΠ»ΡΠ·ΡΠ΅ΡΡΡ ΡΠ°ΠΊΠΆΠ΅ ΠΈΠ·Π»ΡΡΠ΅Π½ΠΈΠ΅ ΠΎΠΏΡΠΈΡΠ΅ΡΠΊΠΈΡ ΠΊΠ²Π°Π½ΡΠΎΠ²ΡΡ Π³Π΅Π½Π΅ΡΠ°ΡΠΎΡΠΎΠ² — Π»Π°Π·Π΅ΡΠΎΠ², ΠΠ°Π·Π΅ΡΠ½Π°Ρ ΡΠ²Π°ΡΠΊΠ° Π·Π°Π½ΠΈΠΌΠ°Π΅Ρ Π²ΠΈΠ΄Π½ΠΎΠ΅ ΠΌΠ΅ΡΡΠΎ Π² Π»Π°Π·Π΅ΡΠ½ΠΎΠΉ ΡΠ΅Ρ Π½ΠΎΠ»ΠΎΠ³ΠΈΠΈ.
Π‘Π²Π°ΡΠΊΠ° Π΄Π°Π²Π»Π΅Π½ΠΈΠ΅ΠΌ
Π‘ΠΏΠΎΡΠΎΠ±Ρ ΡΠ²Π°ΡΠΊΠΈ Π² ΡΠ²ΡΡΠ΄ΠΎΠΉ ΡΠ°Π·Π΅ Π΄Π°ΡΡ ΡΠ²Π°ΡΠ½ΠΎΠ΅ ΡΠΎΠ΅Π΄ΠΈΠ½Π΅Π½ΠΈΠ΅, ΠΏΡΠΎΡΠ½ΠΎΡΡΡ ΠΊΠΎΡΠΎΡΠΎΠ³ΠΎ ΠΈΠ½ΠΎΠ³Π΄Π° ΠΏΡΠ΅Π²ΡΡΠ°Π΅Ρ ΠΏΡΠΎΡΠ½ΠΎΡΡΡ ΠΎΡΠ½ΠΎΠ²Π½ΠΎΠ³ΠΎ ΠΌΠ΅ΡΠ°Π»Π»Π°. ΠΡΠΎΠΌΠ΅ ΡΠΎΠ³ΠΎ, Π² Π±ΠΎΠ»ΡΡΠΈΠ½ΡΡΠ²Π΅ ΡΠ»ΡΡΠ°Π΅Π² ΠΏΡΠΈ ΡΠ²Π°ΡΠΊΠ΅ Π΄Π°Π²Π»Π΅Π½ΠΈΠ΅ΠΌ Π½Π΅ ΠΏΡΠΎΠΈΡΡ
ΠΎΠ΄ΠΈΡ Π·Π½Π°ΡΠΈΡΠ΅Π»ΡΠ½ΡΡ
ΠΈΠ·ΠΌΠ΅Π½Π΅Π½ΠΈΠΉ Π² Ρ
ΠΈΠΌΠΈΡΠ΅ΡΠΊΠΎΠΌ ΡΠΎΡΡΠ°Π²Π΅ ΠΌΠ΅ΡΠ°Π»Π»Π°, Ρ. ΠΊ. ΠΌΠ΅ΡΠ°Π»Π» Π»ΠΈΠ±ΠΎ Π½Π΅ Π½Π°Π³ΡΠ΅Π²Π°Π΅ΡΡΡ, Π»ΠΈΠ±ΠΎ Π½Π°Π³ΡΠ΅Π²Π°Π΅ΡΡΡ Π½Π΅Π·Π½Π°ΡΠΈΡΠ΅Π»ΡΠ½ΠΎ. ΠΡΠΎ Π΄Π΅Π»Π°Π΅Ρ ΡΠΏΠΎΡΠΎΠ±Ρ ΡΠ²Π°ΡΠΊΠΈ Π΄Π°Π²Π»Π΅Π½ΠΈΠ΅ΠΌ Π½Π΅Π·Π°ΠΌΠ΅Π½ΠΈΠΌΡΠΌΠΈ Π² ΡΡΠ΄Π΅ ΠΎΡΡΠ°ΡΠ»Π΅ΠΉ ΠΏΡΠΎΠΌΡΡΠ»Π΅Π½Π½ΠΎΡΡΠΈ (ΡΠ»Π΅ΠΊΡΡΠΎΡΠ΅Ρ
Π½ΠΈΡΠ΅ΡΠΊΠΎΠΉ, ΡΠ»Π΅ΠΊΡΡΠΎΠ½Π½ΠΎΠΉ, ΠΊΠΎΡΠΌΠΈΡΠ΅ΡΠΊΠΎΠΉ ΠΈ Π΄Ρ.).
Π₯ΠΎΠ»ΠΎΠ΄Π½Π°Ρ ΡΠ²Π°ΡΠΊΠ° Π²ΡΠΏΠΎΠ»Π½ΡΠ΅ΡΡΡ Π±Π΅Π· ΠΏΡΠΈΠΌΠ΅Π½Π΅Π½ΠΈΡ Π½Π°Π³ΡΠ΅Π²Π°, ΠΎΠ΄Π½ΠΈΠΌ ΡΠΎΠ»ΡΠΊΠΎ ΠΏΡΠΈΠ»ΠΎΠΆΠ΅Π½ΠΈΠ΅ΠΌ Π΄Π°Π²Π»Π΅Π½ΠΈΡ, ΡΠΎΠ·Π΄Π°ΡΡΠΈΠΌ Π·Π½Π°ΡΠΈΡΠ΅Π»ΡΠ½ΡΡ ΠΏΠ»Π°ΡΡΠΈΡΠ΅ΡΠΊΡΡ Π΄Π΅ΡΠΎΡΠΌΠ°ΡΠΈΡ (Π΄ΠΎ ΡΠΎΡΡΠΎΡΠ½ΠΈΡ ΡΠ΅ΠΊΡΡΠ΅ΡΡΠΈ), ΠΊΠΎΡΠΎΡΠ°Ρ Π΄ΠΎΠ»ΠΆΠ½Π° Π±ΡΡΡ Π½Π΅ Π½ΠΈΠΆΠ΅ ΠΎΠΏΡΠ΅Π΄Π΅Π»ΡΠ½Π½ΠΎΠ³ΠΎ Π·Π½Π°ΡΠ΅Π½ΠΈΡ, Ρ
Π°ΡΠ°ΠΊΡΠ΅ΡΠ½ΠΎΠ³ΠΎ Π΄Π»Ρ Π΄Π°Π½Π½ΠΎΠ³ΠΎ ΠΌΠ΅ΡΠ°Π»Π»Π°. ΠΠ΅ΡΠ΅Π΄ ΡΠ²Π°ΡΠΊΠΎΠΉ ΡΡΠ΅Π±ΡΠ΅ΡΡΡ ΡΡΠ°ΡΠ΅Π»ΡΠ½Π°Ρ ΠΎΠ±ΡΠ°Π±ΠΎΡΠΊΠ° ΠΈ ΠΎΡΠΈΡΡΠΊΠ° ΡΠΎΠ΅Π΄ΠΈΠ½ΡΠ΅ΠΌΡΡ
ΠΏΠΎΠ²Π΅ΡΡ
Π½ΠΎΡΡΠ΅ΠΉ (ΠΎΡΡΡΠ΅ΡΡΠ²Π»ΡΠ΅ΡΡΡ ΠΎΠ±ΡΡΠ½ΠΎ ΠΌΠ΅Ρ
Π°Π½ΠΈΡΠ΅ΡΠΊΠΈΠΌ ΠΏΡΡΡΠΌ, Π½Π°ΠΏΡΠΈΠΌΠ΅Ρ Π²ΡΠ°ΡΠ°ΡΡΠΈΠΌΠΈΡΡ ΠΏΡΠΎΠ²ΠΎΠ»ΠΎΡΠ½ΡΠΌΠΈ ΡΡΡΠΊΠ°ΠΌΠΈ). ΠΡΠΎΡ ΡΠΏΠΎΡΠΎΠ± ΡΠ²Π°ΡΠΊΠΈ Π΄ΠΎΡΡΠ°ΡΠΎΡΠ½ΠΎ ΡΠ½ΠΈΠ²Π΅ΡΡΠ°Π»Π΅Π½, ΠΏΡΠΈΠ³ΠΎΠ΄Π΅Π½ Π΄Π»Ρ ΡΠΎΠ΅Π΄ΠΈΠ½Π΅Π½ΠΈΡ ΠΌΠ½ΠΎΠ³ΠΈΡ
ΠΌΠ΅ΡΠ°Π»Π»ΠΈΡΠ΅ΡΠΊΠΈΡ
ΠΈΠ·Π΄Π΅Π»ΠΈΠΉ (ΠΏΡΠΎΠ²ΠΎΠ΄ΠΎΠ², ΡΡΠ΅ΡΠΆΠ½Π΅ΠΉ, ΠΏΠΎΠ»ΠΎΡ, ΡΠΎΠ½ΠΊΠΎΡΡΠ΅Π½Π½ΡΡ
ΡΡΡΠ± ΠΈ ΠΎΠ±ΠΎΠ»ΠΎΡΠ΅ΠΊ) ΠΈ Π½Π΅ΠΌΠ΅ΡΠ°Π»Π»ΠΈΡΠ΅ΡΠΊΠΈΡ
ΠΌΠ°ΡΠ΅ΡΠΈΠ°Π»ΠΎΠ², ΠΎΠ±Π»Π°Π΄Π°ΡΡΠΈΡ
Π΄ΠΎΡΡΠ°ΡΠΎΡΠ½ΠΎΠΉ ΠΏΠ»Π°ΡΡΠΈΡΠ½ΠΎΡΡΡΡ (ΡΠΌΠΎΠ»Ρ, ΠΏΠ»Π°ΡΡΠΌΠ°ΡΡΡ, ΡΡΠ΅ΠΊΠ»ΠΎ ΠΈ Ρ. ΠΏ.). ΠΠ΅ΡΡΠΏΠ΅ΠΊΡΠΈΠ²Π½ΠΎ ΠΏΡΠΈΠΌΠ΅Π½Π΅Π½ΠΈΠ΅ Ρ
ΠΎΠ»ΠΎΠ΄Π½ΠΎΠΉ ΡΠ²Π°ΡΠΊΠΈ Π² ΠΊΠΎΡΠΌΠΎΡΠ΅.
ΠΠ»Ρ ΡΠ²Π°ΡΠΊΠΈ ΠΌΠΎΠΆΠ½ΠΎ ΠΈΡΠΏΠΎΠ»ΡΠ·ΠΎΠ²Π°ΡΡ ΠΌΠ΅Ρ Π°Π½ΠΈΡΠ΅ΡΠΊΡΡ ΡΠ½Π΅ΡΠ³ΠΈΡ ΡΡΠ΅Π½ΠΈΡ. Π‘Π²Π°ΡΠΊΠ° ΡΡΠ΅Π½ΠΈΠ΅ΠΌ ΠΎΡΡΡΠ΅ΡΡΠ²Π»ΡΠ΅ΡΡΡ Π½Π° ΠΌΠ°ΡΠΈΠ½Π΅, Π²Π½Π΅ΡΠ½Π΅ Π½Π°ΠΏΠΎΠΌΠΈΠ½Π°ΡΡΠ΅ΠΉ ΡΠΎΠΊΠ°ΡΠ½ΡΠΉ ΡΡΠ°Π½ΠΎΠΊ. ΠΠ΅ΡΠ°Π»ΠΈ Π·Π°ΠΆΠΈΠΌΠ°ΡΡΡΡ Π² ΠΏΠ°ΡΡΠΎΠ½Π°Ρ ΠΈ ΡΠ΄Π²ΠΈΠ³Π°ΡΡΡΡ Π΄ΠΎ ΡΠΎΠΏΡΠΈΠΊΠΎΡΠ½ΠΎΠ²Π΅Π½ΠΈΡ ΡΠΎΡΡΠ°ΠΌΠΈ. ΠΠ΄Π½Π° ΠΈΠ· Π΄Π΅ΡΠ°Π»Π΅ΠΉ ΠΏΡΠΈΠ²ΠΎΠ΄ΠΈΡΡΡ Π²ΠΎ Π²ΡΠ°ΡΠ΅Π½ΠΈΠ΅ ΠΎΡ ΡΠ»Π΅ΠΊΡΡΠΎΠ΄Π²ΠΈΠ³Π°ΡΠ΅Π»Ρ. Π ΡΠ΅Π·ΡΠ»ΡΡΠ°ΡΠ΅ ΡΡΠ΅Π½ΠΈΡ ΡΠ°Π·ΠΎΠ³ΡΠ΅Π²Π°ΡΡΡΡ ΠΈ ΠΎΠΏΠ»Π°Π²Π»ΡΡΡΡΡ ΠΏΠΎΠ²Π΅ΡΡ Π½ΠΎΡΡΠ½ΡΠ΅ ΡΠ»ΠΎΠΈ Π½Π° ΡΠΎΡΡΠ°Ρ , Π²ΡΠ°ΡΠ΅Π½ΠΈΠ΅ ΠΏΡΠ΅ΠΊΡΠ°ΡΠ°Π΅ΡΡΡ ΠΈ ΠΏΡΠΎΠΈΠ·Π²ΠΎΠ΄ΠΈΡΡΡ ΠΎΡΠ°Π΄ΠΊΠ° Π΄Π΅ΡΠ°Π»Π΅ΠΉ, ΡΠ²Π°ΡΠΊΠ° Π²ΡΡΠΎΠΊΠΎΠΏΡΠΎΠΈΠ·Π²ΠΎΠ΄ΠΈΡΠ΅Π»ΡΠ½Π°, ΡΠΊΠΎΠ½ΠΎΠΌΠΈΡΠ½Π°, ΠΏΡΠΈΠΌΠ΅Π½ΡΠ΅ΡΡΡ, Π½Π°ΠΏΡΠΈΠΌΠ΅Ρ, Π΄Π»Ρ ΠΏΡΠΈΡΠΎΠ΅Π΄ΠΈΠ½Π΅Π½ΠΈΡ ΡΠ΅ΠΆΡΡΠ΅ΠΉ ΡΠ°ΡΡΠΈ ΠΌΠ΅ΡΠ°Π»Π»ΠΎΡΠ΅ΠΆΡΡΠ΅Π³ΠΎ ΠΈΠ½ΡΡΡΡΠΌΠ΅Π½ΡΠ° ΠΊ Π΄Π΅ΡΠΆΠ°Π²ΠΊΠ΅.
Π£Π»ΡΡΡΠ°Π·Π²ΡΠΊΠΎΠ²Π°Ρ ΡΠ²Π°ΡΠΊΠ° ΠΎΡΠ½ΠΎΠ²Π°Π½Π° Π½Π° ΠΈΡΠΏΠΎΠ»ΡΠ·ΠΎΠ²Π°Π½ΠΈΠΈ ΠΌΠ΅Ρ
Π°Π½ΠΈΡΠ΅ΡΠΊΠΈΡ
ΠΊΠΎΠ»Π΅Π±Π°Π½ΠΈΠΉ ΡΠ°ΡΡΠΎΡΠΎΠΉ 20 ΠΊΠ³Ρ. ΠΠΎΠ»Π΅Π±Π°Π½ΠΈΡ ΡΠΎΠ·Π΄Π°ΡΡΡΡ ΠΌΠ°Π³Π½ΠΈΡΠΎΡΡΡΠΈΠΊΡΠΈΠΎΠ½Π½ΡΠΌ ΠΏΡΠ΅ΠΎΠ±ΡΠ°Π·ΠΎΠ²Π°ΡΠ΅Π»Π΅ΠΌ, ΠΏΡΠ΅Π²ΡΠ°ΡΠ°ΡΡΠΈΠΌ ΡΠ»Π΅ΠΊΡΡΠΎΠΌΠ°Π³Π½ΠΈΡΠ½ΡΠ΅ ΠΊΠΎΠ»Π΅Π±Π°Π½ΠΈΡ Π² ΠΌΠ΅Ρ
Π°Π½ΠΈΡΠ΅ΡΠΊΠΈΠ΅. ΠΠ° ΡΠ΅ΡΠ΄Π΅ΡΠ½ΠΈΠΊ, ΠΈΠ·Π³ΠΎΡΠΎΠ²Π»Π΅Π½Π½ΡΠΉ ΠΈΠ· ΠΌΠ°Π³Π½ΠΈΡΠΎΡΡΡΠΈΠΊΡΠΈΠΎΠ½Π½ΠΎΠ³ΠΎ ΠΌΠ°ΡΠ΅ΡΠΈΠ°Π»Π°, Π½Π°ΠΌΠΎΡΠ°Π½Π° ΠΎΠ±ΠΌΠΎΡΠΊΠ°. ΠΡΠΈ ΠΏΠΈΡΠ°Π½ΠΈΠΈ ΠΎΠ±ΠΌΠΎΡΠΊΠΈ ΡΠΎΠΊΠ°ΠΌΠΈ ΠΠ§ ΠΈΠ· ΡΠ»Π΅ΠΊΡΡΠΈΡΠ΅ΡΠΊΠΎΠΉ ΡΠ΅ΡΠΈ Π² ΡΠ΅ΡΠ΄Π΅ΡΠ½ΠΈΠΊΠ΅ Π²ΠΎΠ·Π½ΠΈΠΊΠ°ΡΡ ΠΏΡΠΎΠ΄ΠΎΠ»ΡΠ½ΡΠ΅ ΠΌΠ΅Ρ
Π°Π½ΠΈΡΠ΅ΡΠΊΠΈΠ΅ ΠΊΠΎΠ»Π΅Π±Π°Π½ΠΈΡ. ΠΠ΅ΡΠ°Π»Π»ΠΈΡΠ΅ΡΠΊΠΈΠΉ Π½Π°ΠΊΠΎΠ½Π΅ΡΠ½ΠΈΠΊ, ΡΠΎΠ΅Π΄ΠΈΠ½ΡΠ½Π½ΡΠΉ Ρ ΡΠ΅ΡΠ΄Π΅ΡΠ½ΠΈΠΊΠΎΠΌ, ΡΠ»ΡΠΆΠΈΡ ΡΠ²Π°ΡΠΎΡΠ½ΡΠΌ ΠΈΠ½ΡΡΡΡΠΌΠ΅Π½ΡΠΎΠΌ. ΠΡΠ»ΠΈ Π½Π°ΠΊΠΎΠ½Π΅ΡΠ½ΠΈΠΊ Ρ Π½Π΅ΠΊΠΎΡΠΎΡΡΠΌ ΡΡΠΈΠ»ΠΈΠ΅ΠΌ ΠΏΡΠΈΠΆΠ°ΡΡ ΠΊ ΡΠ²Π°ΡΠΈΠ²Π°Π΅ΠΌΡΠΌ Π΄Π΅ΡΠ°Π»ΡΠΌ, ΡΠΎ ΡΠ΅ΡΠ΅Π· Π½Π΅ΡΠΊΠΎΠ»ΡΠΊΠΎ ΡΠ΅ΠΊΡΠ½Π΄ ΠΎΠ½ΠΈ ΠΎΠΊΠ°Π·ΡΠ²Π°ΡΡΡΡ ΡΠ²Π°ΡΠ΅Π½Π½ΡΠΌΠΈ Π² ΠΌΠ΅ΡΡΠ΅ Π΄Π°Π²Π»Π΅Π½ΠΈΡ ΠΈΠ½ΡΡΡΡΠΌΠ΅Π½ΡΠ°. Π ΡΠ΅Π·ΡΠ»ΡΡΠ°ΡΠ΅ ΠΊΠΎΠ»Π΅Π±Π°Π½ΠΈΠΉ ΡΠ΅ΡΠ΄Π΅ΡΠ½ΠΈΠΊΠ° ΠΏΠΎΠ²Π΅ΡΡ
Π½ΠΎΡΡΠΈ ΠΎΡΠΈΡΠ°ΡΡΡΡ ΠΈ Π½Π΅ΠΌΠ½ΠΎΠ³ΠΎ ΡΠ°Π·ΠΎΠ³ΡΠ΅Π²Π°ΡΡΡΡ, ΡΡΠΎ ΡΠΏΠΎΡΠΎΠ±ΡΡΠ²ΡΠ΅Ρ ΠΎΠ±ΡΠ°Π·ΠΎΠ²Π°Π½ΠΈΡ ΠΏΡΠΎΡΠ½ΠΎΠ³ΠΎ ΡΠ²Π°ΡΠ½ΠΎΠ³ΠΎ ΡΠΎΠ΅Π΄ΠΈΠ½Π΅Π½ΠΈΡ. ΠΡΠΎΡ ΡΠΏΠΎΡΠΎΠ± ΡΠ²Π°ΡΠΊΠΈ ΠΌΠ΅ΡΠ°Π»Π»ΠΎΠ² ΠΌΠ°Π»ΡΡ
ΡΠΎΠ»ΡΠΈΠ½ (ΠΎΡ Π½Π΅ΡΠΊΠΎΠ»ΡΠΊΠΈΡ
ΠΌΠΊΠΌ Π΄ΠΎ1,5 ΠΌΠΌ) ΠΈ Π½Π΅ΠΊΠΎΡΠΎΡΡΡ
ΠΏΠ»Π°ΡΡΠΌΠ°ΡΡ Π½Π°ΡΡΠ» ΠΏΡΠΈΠΌΠ΅Π½Π΅Π½ΠΈΠ΅ Π² ΡΠ»Π΅ΠΊΡΡΠΎΡΠ΅Ρ
Π½ΠΈΡΠ΅ΡΠΊΠΎΠΉ, ΡΠ»Π΅ΠΊΡΡΠΎΠ½Π½ΠΎΠΉ, ΡΠ°Π΄ΠΈΠΎΡΠ΅Ρ
Π½ΠΈΡΠ΅ΡΠΊΠΎΠΉ ΠΏΡΠΎΠΌΡΡΠ»Π΅Π½Π½ΠΎΡΡΠΈ. Π Π½Π°ΡΠ°Π»Π΅ 70-Ρ
Π³Π³. ΡΡΠΎΡ Π²ΠΈΠ΄ ΡΠ²Π°ΡΠΊΠΈ ΠΈΡΠΏΠΎΠ»ΡΠ·ΠΎΠ²Π°Π½ Π² ΠΌΠ΅Π΄ΠΈΡΠΈΠ½Π΅ (ΡΠ°Π±ΠΎΡΡ ΠΊΠΎΠ»Π»Π΅ΠΊΡΠΈΠ²Π° ΡΠΎΡΡΡΠ΄Π½ΠΈΠΊΠΎΠ² ΠΠΎΡΠΊΠΎΠ²ΡΠΊΠΎΠ³ΠΎ Π²ΡΡΡΠ΅Π³ΠΎ ΡΠ΅Ρ
Π½ΠΈΡΠ΅ΡΠΊΠΎΠ³ΠΎ ΡΡΠΈΠ»ΠΈΡΠ° ΠΈΠΌ. Π. Π. ΠΠ°ΡΠΌΠ°Π½Π° ΠΏΠΎΠ΄ ΡΡΠΊΠΎΠ²ΠΎΠ΄ΡΡΠ²ΠΎΠΌ Π. Π. ΠΠΈΠΊΠΎΠ»Π°Π΅Π²Π° Π² ΡΠΎΠ΄ΡΡΠΆΠ΅ΡΡΠ²Π΅ Ρ ΠΌΠ΅Π΄ΠΈΠΊΠ°ΠΌΠΈ) Π΄Π»Ρ ΡΠΎΠ΅Π΄ΠΈΠ½Π΅Π½ΠΈΡ, Π½Π°ΠΏΠ»Π°Π²ΠΊΠΈ, ΡΠ΅Π·ΠΊΠΈ ΠΆΠΈΠ²ΡΡ
ΡΠΊΠ°Π½Π΅ΠΉ. ΠΡΠΈ ΡΠ²Π°ΡΠΊΠ΅ ΠΈ Π½Π°ΠΏΠ»Π°Π²ΠΊΠ΅ ΠΊΠΎΡΡΠ½ΡΡ
ΡΠΊΠ°Π½Π΅ΠΉ, Π½Π°ΠΏΡΠΈΠΌΠ΅Ρ ΠΎΡΠ»ΠΎΠΌΠΊΠΎΠ² Π±Π΅ΡΡΠΎΠ²ΡΡ
ΠΊΠΎΡΡΠ΅ΠΉ, ΡΡΠ±Π΅Ρ ΠΈ ΠΏΡ., ΠΊΠΎΠ½Π³Π»ΠΎΠΌΠ΅ΡΠ°Ρ ΠΈΠ· ΠΆΠΈΠ΄ΠΊΠΎΠ³ΠΎ ΠΌΠΎΠ½ΠΎΠΌΠ΅ΡΠ° ΡΠΈΠ°ΠΊΡΠΈΠ½Π° ΠΈ ΡΠ²ΡΡΠ΄ΡΡ
Π΄ΠΎΠ±Π°Π²ΠΎΠΊ (ΠΊΠΎΡΡΠ½ΠΎΠΉ ΡΡΡΡΠΆΠΊΠΈ ΠΈ ΡΠ°Π·Π½ΡΡ
Π½Π°ΠΏΠΎΠ»Π½ΠΈΡΠ΅Π»Π΅ΠΉ ΠΈ ΡΠΏΡΠΎΡΠ½ΠΈΡΠ΅Π»Π΅ΠΉ) Π½Π°Π½ΠΎΡΠΈΡΡΡ Π½Π° ΠΏΠΎΠ²ΡΠ΅ΠΆΠ΄Π΅Π½Π½ΠΎΠ΅ ΠΌΠ΅ΡΡΠΎ ΠΈ ΡΠΏΠ»ΠΎΡΠ½ΡΠ΅ΡΡΡ ΡΠ»ΡΡΡΠ°Π·Π²ΡΠΊΠΎΠ²ΡΠΌ ΠΈΠ½ΡΡΡΡΠΌΠ΅Π½ΡΠΎΠΌ, Π² ΡΠ΅Π·ΡΠ»ΡΡΠ°ΡΠ΅ ΡΠ΅Π³ΠΎ ΡΡΠΊΠΎΡΡΠ΅ΡΡΡ ΠΏΠΎΠ»ΠΈΠΌΠ΅ΡΠΈΠ·Π°ΡΠΈΡ.
ΠΡΡΠ΅ΠΊΡΠΈΠ²Π½ΠΎ ΠΏΡΠΈΠΌΠ΅Π½Π΅Π½ΠΈΠ΅ ΡΠ»ΡΡΡΠ°Π·Π²ΡΠΊΠΎΠ²ΠΎΠΉ ΡΠ΅Π·ΠΊΠΈ Π² Ρ
ΠΈΡΡΡΠ³ΠΈΠΈ. Π‘Π²Π°ΡΠΎΡΠ½ΡΠΉ ΠΈΠ½ΡΡΡΡΠΌΠ΅Π½Ρ ΡΠ»ΡΡΡΠ°Π·Π²ΡΠΊΠΎΠ²ΠΎΠ³ΠΎ Π°ΠΏΠΏΠ°ΡΠ°ΡΠ° Π·Π°ΠΌΠ΅Π½ΡΠ΅ΡΡΡ ΠΏΠΈΠ»ΠΎΠΉ, ΡΠΊΠ°Π»ΡΠΏΠ΅Π»Π΅ΠΌ ΠΈΠ»ΠΈ Π½ΠΎΠΆΠΎΠΌ. ΠΠ½Π°ΡΠΈΡΠ΅Π»ΡΠ½ΠΎ ΡΠΎΠΊΡΠ°ΡΠ°ΡΡΡΡ Π²ΡΠ΅ΠΌΡ ΠΎΠΏΠ΅ΡΠ°ΡΠΈΠΈ, ΠΏΠΎΡΠ΅ΡΡ ΠΊΡΠΎΠ²ΠΈ ΠΈ Π±ΠΎΠ»Π΅Π²ΡΠ΅ ΠΎΡΡΡΠ΅Π½ΠΈΡ.
ΠΠ΄Π½ΠΈΠΌ ΠΈΠ· ΡΠΏΠΎΡΠΎΠ±ΠΎΠ² ΡΠ»Π΅ΠΊΡΡΠΈΡΠ΅ΡΠΊΠΎΠΉ ΡΠ²Π°ΡΠΊΠΈ ΡΠ²Π»ΡΠ΅ΡΡΡ ΠΊΠΎΠ½ΡΠ°ΠΊΡΠ½Π°Ρ ΡΠ²Π°ΡΠΊΠ°, ΠΈΠ»ΠΈ ΡΠ²Π°ΡΠΊΠ° ΡΠΎΠΏΡΠΎΡΠΈΠ²Π»Π΅Π½ΠΈΠ΅ΠΌ (Π² ΡΡΠΎΠΌ ΡΠ»ΡΡΠ°Π΅ ΡΠ»Π΅ΠΊΡΡΠΈΡΠ΅ΡΠΊΠΈΠΉ ΡΠΎΠΊ ΠΏΡΠΎΠΏΡΡΠΊΠ°ΡΡ ΡΠ΅ΡΠ΅Π· ΠΌΠ΅ΡΡΠΎ ΡΠ²Π°ΡΠΊΠΈ , ΠΎΠΊΠ°Π·ΡΠ²Π°ΡΡΠ΅Π΅ ΠΎΠΌΠΈΡΠ΅ΡΠΊΠΎΠ΅ ΡΠΎΠΏΡΠΎΡΠΈΠ²Π»Π΅Π½ΠΈΠ΅ ΠΏΡΠΎΡ ΠΎΠΆΠ΄Π΅Π½ΠΈΡ ΡΠΎΠΊΠ°). Π Π°Π·ΠΎΠ³ΡΠ΅ΡΡΠ΅ ΠΈ ΠΎΠ±ΡΡΠ½ΠΎ ΠΎΠΏΠ»Π°Π²Π»Π΅Π½Π½ΡΠ΅ Π΄Π΅ΡΠ°Π»ΠΈ ΡΠ΄Π°Π²Π»ΠΈΠ²Π°ΡΡΡΡ ΠΈΠ»ΠΈ ΠΎΡΠ°ΠΆΠΈΠ²Π°ΡΡΡΡ, Ρ. ΠΎ. ΠΊΠΎΠ½ΡΠ°ΠΊΡΠ½Π°Ρ ΡΠ²Π°ΡΠΊΠ° ΠΏΠΎ ΠΌΠ΅ΡΠΎΠ΄Ρ ΠΎΡΠ°Π΄ΠΊΠΈ ΠΎΡΠ½ΠΎΡΠΈΡΡΡ ΠΊ ΡΠΏΠΎΡΠΎΠ±Π°ΠΌ ΡΠ²Π°ΡΠΊΠΈ Π΄Π°Π²Π»Π΅Π½ΠΈΠ΅ΠΌ (ΡΠΌ. ΠΠΎΠ½ΡΠ°ΠΊΡΠ½Π°Ρ ΡΠ»Π΅ΠΊΡΡΠΎΡΠ²Π°ΡΠΊΠ°). ΠΡΠΎΡ ΡΠΏΠΎΡΠΎΠ± ΠΎΡΠ»ΠΈΡΠ°Π΅ΡΡΡ Π²ΡΡΠΎΠΊΠΎΠΉ ΡΡΠ΅ΠΏΠ΅Π½ΡΡ ΠΌΠ΅Ρ Π°Π½ΠΈΠ·Π°ΡΠΈΠΈ ΠΈ Π°Π²ΡΠΎΠΌΠ°ΡΠΈΠ·Π°ΡΠΈΠΈ ΠΈ ΠΏΠΎΠ»ΡΡΠ°Π΅Ρ Π²ΡΡ Π±ΠΎΠ»ΡΡΠ΅Π΅ ΡΠ°ΡΠΏΡΠΎΡΡΡΠ°Π½Π΅Π½ΠΈΠ΅ Π² ΠΌΠ°ΡΡΠΎΠ²ΠΎΠΌ ΠΈ ΡΠ΅ΡΠΈΠΉΠ½ΠΎΠΌ ΠΏΡΠΎΠΈΠ·Π²ΠΎΠ΄ΡΡΠ²Π΅ (Π½Π°ΠΏΡΠΈΠΌΠ΅Ρ, ΡΠΎΠ΅Π΄ΠΈΠ½Π΅Π½ΠΈΠ΅ Π΄Π΅ΡΠ°Π»Π΅ΠΉ Π°Π²ΡΠΎΠΌΠΎΠ±ΠΈΠ»Π΅ΠΉ, ΡΠ°ΠΌΠΎΠ»ΡΡΠΎΠ², ΡΠ»Π΅ΠΊΡΡΠΎΠ½Π½ΠΎΠΉ ΠΈ ΡΠ°Π΄ΠΈΠΎΡΠ΅Ρ Π½ΠΈΡΠ΅ΡΠΊΠΎΠΉ Π°ΠΏΠΏΠ°ΡΠ°ΡΡΡΡ), Π° ΡΠ°ΠΊΠΆΠ΅ ΠΏΡΠΈΠΌΠ΅Π½ΡΠ΅ΡΡΡ Π΄Π»Ρ ΡΡΡΠΊΠΎΠ²ΠΊΠΈ ΡΡΡΠ± Π±ΠΎΠ»ΡΡΠΈΡ Π΄ΠΈΠ°ΠΌΠ΅ΡΡΠΎΠ², ΡΠ΅Π»ΡΡΠΎΠ² ΠΈ Ρ. ΠΏ.
ΠΠ°ΠΏΠ»Π°Π²ΠΊΠ°
ΠΡ Π½Π°ΠΈΠ±ΠΎΠ»Π΅Π΅ ΡΠ°ΡΠΏΡΠΎΡΡΡΠ°Π½ΡΠ½Π½ΠΎΠΉ ΡΠΎΠ΅Π΄ΠΈΠ½ΠΈΡΠ΅Π»ΡΠ½ΠΎΠΉ ΡΠ²Π°ΡΠΊΠΈ ΠΎΡΠ»ΠΈΡΠ°Π΅ΡΡΡ Π½Π°ΠΏΠ»Π°Π²ΠΊΠ°, ΠΏΡΠΈΠΌΠ΅Π½ΡΠ΅ΠΌΠ°Ρ Π΄Π»Ρ Π½Π°ΡΠ°ΡΠ΅Π½ΠΈΡ Π½Π° ΠΏΠΎΠ²Π΅ΡΡ
Π½ΠΎΡΡΡ Π΄Π΅ΡΠ°Π»ΠΈ ΡΠ»ΠΎΡ ΠΌΠ°ΡΠ΅ΡΠΈΠ°Π»Π°, Π½Π΅ΡΠΊΠΎΠ»ΡΠΊΠΎ ΡΠ²Π΅Π»ΠΈΡΠΈΠ²Π°ΡΡΠ΅Π³ΠΎ ΠΌΠ°ΡΡΡ ΠΈ ΡΠ°Π·ΠΌΠ΅ΡΡ Π΄Π΅ΡΠ°Π»ΠΈ. ΠΠ°ΠΏΠ»Π°Π²ΠΊΠΎΠΉ ΠΌΠΎΠΆΠ½ΠΎ ΠΎΡΡΡΠ΅ΡΡΠ²Π»ΡΡΡ Π²ΠΎΡΡΡΠ°Π½ΠΎΠ²Π»Π΅Π½ΠΈΠ΅ ΡΠ°Π·ΠΌΠ΅ΡΠΎΠ² Π΄Π΅ΡΠ°Π»ΠΈ, ΡΠΌΠ΅Π½ΡΡΠ΅Π½Π½ΡΡ
ΠΈΠ·Π½ΠΎΡΠΎΠΌ, ΠΈ ΠΎΠ±Π»ΠΈΡΠΎΠ²ΠΊΡ ΠΏΠΎΠ²Π΅ΡΡ
Π½ΠΎΡΡΠ½ΠΎΠ³ΠΎ ΡΠ»ΠΎΡ. ΠΠΎΡΡΡΠ°Π½ΠΎΠ²ΠΈΡΠ΅Π»ΡΠ½Π°Ρ Π½Π°ΠΏΠ»Π°Π²ΠΊΠ° ΠΈΠΌΠ΅Π΅Ρ Π²ΡΡΠΎΠΊΡΡ ΡΠΊΠΎΠ½ΠΎΠΌΠΈΡΠ΅ΡΠΊΡΡ ΡΡΡΠ΅ΠΊΡΠΈΠ²Π½ΠΎΡΡΡ, Ρ. ΠΊ. ΡΠ°ΠΊΠΈΠΌ ΡΠΏΠΎΡΠΎΠ±ΠΎΠΌ Π²ΠΎΡΡΡΠ°Π½Π°Π²Π»ΠΈΠ²Π°ΡΡ ΡΠ»ΠΎΠΆΠ½ΡΠ΅ Π΄ΠΎΡΠΎΠ³ΠΈΠ΅ Π΄Π΅ΡΠ°Π»ΠΈ; ΡΠ°ΡΠΏΡΠΎΡΡΡΠ°Π½Π΅Π½Π° ΠΏΡΠΈ ΡΠ΅ΠΌΠΎΠ½ΡΠ΅ Π½Π° ΡΡΠ°Π½ΡΠΏΠΎΡΡΠ΅, Π² ΡΠ΅Π»ΡΡΠΊΠΎΠΌ Ρ
ΠΎΠ·ΡΠΉΡΡΠ²Π΅, ΡΡΡΠΎΠΈΡΠ΅Π»ΡΡΡΠ²Π΅, Π³ΠΎΡΠ½ΠΎΠΉ ΠΏΡΠΎΠΌΡΡΠ»Π΅Π½Π½ΠΎΡΡΠΈ ΠΈ Ρ. Π΄. ΠΠ±Π»ΠΈΡΠΎΠ²ΠΎΡΠ½Π°Ρ Π½Π°ΠΏΠ»Π°Π²ΠΊΠ° ΠΏΡΠΈΠΌΠ΅Π½ΡΠ΅ΡΡΡ Π΄Π»Ρ ΡΠΎΠ·Π΄Π°Π½ΠΈΡ Π½Π° ΠΏΠΎΠ²Π΅ΡΡ
Π½ΠΎΡΡΠΈ Π΄Π΅ΡΠ°Π»ΠΈ ΡΠ»ΠΎΡ ΠΌΠ°ΡΠ΅ΡΠΈΠ°Π»Π° Ρ ΠΎΡΠΎΠ±ΡΠΌΠΈ ΡΠ²ΠΎΠΉΡΡΠ²Π°ΠΌΠΈ — Π²ΡΡΠΎΠΊΠΎΠΉ ΡΠ²ΡΡΠ΄ΠΎΡΡΡΡ, ΠΈΠ·Π½ΠΎΡΠΎΡΡΠΎΠΉΠΊΠΎΡΡΡΡ ΠΈ Ρ. Π΄. Π½Π΅ ΡΠΎΠ»ΡΠΊΠΎ ΠΏΡΠΈ ΡΠ΅ΠΌΠΎΠ½ΡΠ΅, Π½ΠΎ ΠΈ ΠΏΡΠΈ ΠΏΡΠΎΠΈΠ·Π²ΠΎΠ΄ΡΡΠ²Π΅ Π½ΠΎΠ²ΡΡ
ΠΈΠ·Π΄Π΅Π»ΠΈΠΉ. ΠΠ»Ρ ΡΡΠΎΠ³ΠΎ Π²ΠΈΠ΄Π° Π½Π°ΠΏΠ»Π°Π²ΠΊΠΈ ΠΈΠ·Π³ΠΎΡΠΎΠ²Π»ΡΡΡ Π½Π°ΠΏΠ»Π°Π²ΠΎΡΠ½ΡΠ΅ ΠΌΠ°ΡΠ΅ΡΠΈΠ°Π»Ρ Ρ ΠΎΡΠΎΠ±ΡΠΌΠΈ ΡΠ²ΠΎΠΉΡΡΠ²Π°ΠΌΠΈ (Π½Π°ΠΏΡΠΈΠΌΠ΅Ρ, ΠΈΠ·Π½ΠΎΡΠΎΡΡΠΎΠΉΠΊΠΈΠΉ ΡΠΏΠ»Π°Π² ΡΠΎΡΠΌΠ°ΠΉΡ). ΠΠ°ΠΏΠ»Π°Π²ΠΎΡΠ½ΡΠ΅ ΡΠ°Π±ΠΎΡΡ Π²Π΅Π΄ΡΡ ΡΠ°Π·Π»ΠΈΡΠ½ΡΠΌΠΈ ΡΠΏΠΎΡΠΎΠ±Π°ΠΌΠΈ ΡΠ²Π°ΡΠΊΠΈ Π΄ΡΠ³ΠΎΠ²ΠΎΠΉ, Π³Π°Π·ΠΎΠ²ΠΎΠΉ, ΠΏΠ»Π°Π·ΠΌΠ΅Π½Π½ΠΎΠΉ, ΡΠ»Π΅ΠΊΡΡΠΎΠ½Π½ΠΎΠΉ ΠΈ Ρ. ΠΏ. ΠΡΠΎΡΠ΅ΡΡ Π½Π°ΠΏΠ»Π°Π²ΠΊΠΈ ΠΌΠΎΠΆΠ΅Ρ Π±ΡΡΡ ΠΌΠ΅Ρ
Π°Π½ΠΈΠ·ΠΈΡΠΎΠ²Π°Π½ ΠΈ Π°Π²ΡΠΎΠΌΠ°ΡΠΈΠ·ΠΈΡΠΎΠ²Π°Π½. ΠΡΠΏΡΡΠΊΠ°ΡΡΡΡ ΡΠΏΠ΅ΡΠΈΠ°Π»ΡΠ½ΡΠ΅ Π½Π°ΠΏΠ»Π°Π²ΠΎΡΠ½ΡΠ΅ ΡΡΡΠ°Π½ΠΎΠ²ΠΊΠΈ Ρ Π°Π²ΡΠΎΠΌΠ°ΡΠΈΠ·Π°ΡΠΈΠ΅ΠΉ ΠΎΡΠ½ΠΎΠ²Π½ΡΡ
ΠΎΠΏΠ΅ΡΠ°ΡΠΈΠΉ.
Π’Π΅ΡΠΌΠΈΡΠ΅ΡΠΊΠ°Ρ ΡΠ΅Π·ΠΊΠ°
Π Π΅Π·ΠΊΠ° ΡΠ΅Ρ
Π½ΠΎΠ»ΠΎΠ³ΠΈΡΠ΅ΡΠΊΠΈ ΠΎΡΠ»ΠΈΡΠ½Π° ΠΎΡ ΡΠ²Π°ΡΠΊΠΈ ΠΈ ΠΏΡΠΎΡΠΈΠ²ΠΎΠΏΠΎΠ»ΠΎΠΆΠ½Π° Π΅ΠΉ ΠΏΠΎ ΡΠΌΡΡΠ»Ρ, Π½ΠΎ ΠΎΠ±ΠΎΡΡΠ΄ΠΎΠ²Π°Π½ΠΈΠ΅, ΠΌΠ°ΡΠ΅ΡΠΈΠ°Π»Ρ, ΠΏΡΠΈΡΠΌΡ Π²ΡΠΏΠΎΠ»Π½Π΅Π½ΠΈΡ ΠΎΠΏΠ΅ΡΠ°ΡΠΈΠΉ Π±Π»ΠΈΠ·ΠΊΠΈ ΠΊ ΠΏΡΠΈΠΌΠ΅Π½ΡΠ΅ΠΌΡΠΌ Π² ΡΠ²Π°ΡΠΎΡΠ½ΠΎΠΉ ΡΠ΅Ρ
Π½ΠΈΠΊΠ΅. ΠΠΎΠ΄ ΡΠ΅ΡΠΌΠΈΡΠ΅ΡΠΊΠΎΠΉ, ΠΈΠ»ΠΈ ΠΎΠ³Π½Π΅Π²ΠΎΠΉ, ΡΠ΅Π·ΠΊΠΎΠΉ ΠΏΠΎΠ΄ΡΠ°Π·ΡΠΌΠ΅Π²Π°ΡΡ ΠΏΡΠΎΡΠ΅ΡΡΡ, ΠΏΡΠΈ ΠΊΠΎΡΠΎΡΡΡ
ΠΌΠ΅ΡΠ°Π»Π» Π² Π·ΠΎΠ½Π΅ ΡΠ΅Π·ΠΊΠΈ Π½Π°Π³ΡΠ΅Π²Π°Π΅ΡΡΡ Π΄ΠΎ Π²ΡΡΠΎΠΊΠΎΠΉ ΡΠ΅ΠΌΠΏΠ΅ΡΠ°ΡΡΡΡ ΠΈ ΡΠ°ΠΌΠΎΠΏΡΠΎΠΈΠ·Π²ΠΎΠ»ΡΠ½ΠΎ Π²ΡΡΠ΅ΠΊΠ°Π΅Ρ ΠΈΠ»ΠΈ ΡΠ΄Π°Π»ΡΠ΅ΡΡΡ Π² Π²ΠΈΠ΄Π΅ ΡΠ°Π·ΠΌΡΠ³ΡΠ΅Π½Π½ΡΡ
ΡΠ»Π°ΠΊΠΎΠ² ΠΈ ΠΎΠΊΠΈΡΠ»ΠΎΠ², Π° ΡΠ°ΠΊΠΆΠ΅ ΠΌΠΎΠΆΠ΅Ρ Π²ΡΡΠ°Π»ΠΊΠΈΠ²Π°ΡΡΡΡ ΠΌΠ΅Ρ
Π°Π½ΠΈΡΠ΅ΡΠΊΠΈΠΌ Π΄Π΅ΠΉΡΡΠ²ΠΈΠ΅ΠΌ (ΡΡΡΡΠ΅ΠΉ Π³Π°Π·Π°, ΡΠ»Π΅ΠΊΡΡΠΎΠ΄ΠΎΠΌ ΠΈ Ρ. ΠΏ.). Π Π΅Π·ΠΊΠ° Π²ΡΠΏΠΎΠ»Π½ΡΠ΅ΡΡΡ Π½Π΅ΡΠΊΠΎΠ»ΡΠΊΠΈΠΌΠΈ ΡΠΏΠΎΡΠΎΠ±Π°ΠΌΠΈ. ΠΠ°ΠΈΠ±ΠΎΠ»Π΅Π΅ Π²Π°ΠΆΠ½ΡΠΉ ΠΈ ΠΏΡΠ°ΠΊΡΠΈΡΠ΅ΡΠΊΠΈ ΡΠ°ΡΠΏΡΠΎΡΡΡΠ°Π½ΡΠ½Π½ΡΠΉ ΡΠΏΠΎΡΠΎΠ± — ΠΊΠΈΡΠ»ΠΎΡΠΎΠ΄Π½Π°Ρ ΡΠ΅Π·ΠΊΠ°, ΠΎΡΠ½ΠΎΠ²Π°Π½Π½Π°Ρ Π½Π° ΡΠΏΠΎΡΠΎΠ±Π½ΠΎΡΡΠΈ ΠΆΠ΅Π»Π΅Π·Π° ΡΠ³ΠΎΡΠ°ΡΡ Π² ΠΊΠΈΡΠ»ΠΎΡΠΎΠ΄Π΅, ΠΏΡΠΈΠΌΠ΅Π½ΡΠ΅ΡΡΡ ΠΎΠ±ΡΡΠ½ΠΎ Π΄Π»Ρ ΡΠ΅Π·ΠΊΠΈ ΡΡΠ°Π»Π΅ΠΉ ΡΠΎΠ»ΡΠΈΠ½ΠΎΠΉ ΠΎΡ 5 Π΄ΠΎ 100 ΠΌΠΌ, Π²ΠΎΠ·ΠΌΠΎΠΆΠ½ΠΎ ΡΠ°Π·Π΄Π΅Π»Π΅Π½ΠΈΠ΅ ΠΌΠ°ΡΠ΅ΡΠΈΠ°Π»Π° ΡΠΎΠ»ΡΠΈΠ½ΠΎΠΉ Π΄ΠΎ 2000 ΠΌΠΌ. ΠΠΈΡΠ»ΠΎΡΠΎΠ΄Π½ΠΎΠΉ ΡΠ΅Π·ΠΊΠΎΠΉ Π²ΡΠΏΠΎΠ»Π½ΡΡΡ ΡΠ°ΠΊΠΆΠ΅ ΠΎΠΏΠ΅ΡΠ°ΡΠΈΠΈ, Π°Π½Π°Π»ΠΎΠ³ΠΈΡΠ½ΡΠ΅ ΠΎΠ±ΡΠ°Π±ΠΎΡΠΊΠ΅ ΡΠ΅ΠΆΡΡΠΈΠΌ ΠΈΠ½ΡΡΡΡΠΌΠ΅Π½ΡΠΎΠΌ, — ΡΡΡΠΎΠΆΠΊΡ, ΠΎΠ±ΡΠΎΡΠΊΡ, Π·Π°ΡΠΈΡΡΠΊΡ ΠΈ Ρ. ΠΏ. Π Π΅Π·ΠΊΡ Π½Π΅ΠΊΠΎΡΠΎΡΡΡ
Π»Π΅Π³ΠΈΡΠΎΠ²Π°Π½Π½ΡΡ
ΡΡΠ°Π»Π΅ΠΉ, ΡΡΠ³ΡΠ½Π°, ΡΠ²Π΅ΡΠ½ΡΡ
ΠΌΠ΅ΡΠ°Π»Π»ΠΎΠ², Π΄Π»Ρ ΠΊΠΎΡΠΎΡΡΡ
ΠΎΠ±ΡΡΠ½ΡΠΉ ΡΠΏΠΎΡΠΎΠ± ΠΌΠ°Π»ΠΎΠΏΡΠΈΠ³ΠΎΠ΄Π΅Π½, ΠΎΡΡΡΠ΅ΡΡΠ²Π»ΡΡΡ ΠΊΠΈΡΠ»ΠΎΡΠΎΠ΄Π½ΠΎ-ΡΠ»ΡΡΠΎΠ²ΡΠΌ ΡΠΏΠΎΡΠΎΠ±ΠΎΠΌ. ΠΠΈΡΠ»ΠΎΡΠΎΠ΄Π½Π°Ρ ΠΎΠ±ΡΠ°Π±ΠΎΡΠΊΠ° Π½Π°ΡΠ»Π° ΠΏΡΠΈΠΌΠ΅Π½Π΅Π½ΠΈΠ΅ Π½Π° ΠΌΠ΅ΡΠ°Π»Π»ΡΡΠ³ΠΈΡΠ΅ΡΠΊΠΈΡ
ΠΈ ΠΌΠ°ΡΠΈΠ½ΠΎΡΡΡΠΎΠΈΡΠ΅Π»ΡΠ½ΡΡ
Π·Π°Π²ΠΎΠ΄Π°Ρ
, ΡΠ΅ΠΌΠΎΠ½ΡΠ½ΡΡ
ΠΏΡΠ΅Π΄ΠΏΡΠΈΡΡΠΈΡΡ
ΠΈ Ρ. ΠΏ.Β
ΠΡΠ³ΠΎΠ²Π°Ρ ΡΠ΅Π·ΠΊΠ°, Π²ΡΠΏΠΎΠ»Π½ΡΠ΅ΠΌΠ°Ρ ΠΊΠ°ΠΊ ΡΠ³ΠΎΠ»ΡΠ½ΡΠΌ, ΡΠ°ΠΊ ΠΈ ΠΌΠ΅ΡΠ°Π»Π»ΠΈΡΠ΅ΡΠΊΠΈΠΌ ΡΠ»Π΅ΠΊΡΡΠΎΠ΄Π°ΠΌΠΈ, ΠΏΡΠΈΠΌΠ΅Π½ΡΠ΅ΡΡΡ ΠΏΡΠΈ ΠΌΠΎΠ½ΡΠ°ΠΆΠ½ΡΡ
ΠΈ ΡΠ΅ΠΌΠΎΠ½ΡΠ½ΡΡ
ΡΠ°Π±ΠΎΡΠ°Ρ
(Π½Π°ΠΏΡΠΈΠΌΠ΅Ρ, Π² ΡΡΠ΄ΠΎΡΡΡΠΎΠ΅Π½ΠΈΠΈ). ΠΠ»Ρ ΠΏΠΎΠ²Π΅ΡΡ
Π½ΠΎΡΡΠ½ΠΎΠΉ ΠΎΠ±ΡΠ°Π±ΠΎΡΠΊΠΈ ΠΈ ΡΡΡΠΎΠΆΠΊΠΈ ΠΌΠ΅ΡΠ°Π»Π»ΠΎΠ² ΠΈΡΠΏΠΎΠ»ΡΠ·ΡΡΡ Π²ΠΎΠ·Π΄ΡΡΠ½ΠΎ-Π΄ΡΠ³ΠΎΠ²ΡΡ ΡΠ΅Π·ΠΊΡ, ΠΏΡΠΈ ΠΊΠΎΡΠΎΡΠΎΠΉ ΠΌΠ΅ΡΠ°Π»Π» ΠΈΠ· ΡΠ΅Π·Π° Π²ΡΠ΄ΡΠ²Π°Π΅ΡΡΡ ΡΡΡΡΠ΅ΠΉ Π²ΠΎΠ·Π΄ΡΡ
Π°, ΡΡΠΎ ΠΏΠΎΠ·Π²ΠΎΠ»ΡΠ΅Ρ ΡΡΡΠ΅ΡΡΠ²Π΅Π½Π½ΠΎ ΡΠ»ΡΡΡΠΈΡΡ ΠΊΠ°ΡΠ΅ΡΡΠ²ΠΎ ΡΠ΅Π·ΠΊΠΈ.
Π Π΅Π·ΠΊΡ ΠΌΠΎΠΆΠ½ΠΎ Π²ΡΠΏΠΎΠ»Π½ΡΡΡ Π²ΡΡΠΎΠΊΠΎΡΠ΅ΠΌΠΏΠ΅ΡΠ°ΡΡΡΠ½ΠΎΠΉ ΠΏΠ»Π°Π·ΠΌΠ΅Π½Π½ΠΎΠΉ ΡΡΡΡΠ΅ΠΉ. ΠΠ»Ρ ΡΠ΅Π·ΠΊΠΈ ΠΈ ΠΏΡΠΎΠΆΠΈΠ³Π°Π½ΠΈΡ ΠΎΡΠ²Π΅ΡΡΡΠΈΠΉ ΠΏΠ΅ΡΡΠΏΠ΅ΠΊΡΠΈΠ²Π½ΠΎ ΠΏΡΠΈΠΌΠ΅Π½Π΅Π½ΠΈΠ΅ ΡΠ²Π΅ΡΠΎΠ²ΠΎΠ³ΠΎ Π»ΡΡΠ°, ΡΡΡΡΠΈ ΡΡΠΎΡΠ°, Π»Π°Π·Π΅ΡΠ½ΠΎΠ³ΠΎ ΠΈΠ·Π»ΡΡΠ΅Π½ΠΈΡ. ΠΠ°Π»ΡΠ½Π΅ΠΉΡΠ΅Π΅ ΡΠ°Π·Π²ΠΈΡΠΈΠ΅ ΠΈ ΡΠΎΠ²Π΅ΡΡΠ΅Π½ΡΡΠ²ΠΎΠ²Π°Π½ΠΈΠ΅ ΠΌΠ΅ΡΠΎΠ΄ΠΎΠ² ΡΠ²Π°ΡΠΊΠΈ ΠΈ ΡΠ΅Π·ΠΊΠΈ ΡΠ²ΡΠ·Π°Π½ΠΎ Ρ Π²Π½Π΅Π΄ΡΠ΅Π½ΠΈΠ΅ΠΌ ΠΈ ΡΠ°ΡΡΠΈΡΠ΅Π½ΠΈΠ΅ΠΌ ΡΡΠ΅ΡΡ ΠΏΡΠΈΠΌΠ΅Π½Π΅Π½ΠΈΡ Π½ΠΎΠ²ΡΡ
Π²ΠΈΠ΄ΠΎΠ² ΠΎΠ±ΡΠ°Π±ΠΎΡΠΊΠΈ — ΠΏΠ»Π°Π·ΠΌΠ΅Π½Π½ΠΎΠΉ, ΡΠ»Π΅ΠΊΡΡΠΎΠ½Π½ΠΎΠΉ, Π»Π°Π·Π΅ΡΠ½ΠΎΠΉ, Ρ ΡΠ°Π·ΡΠ°Π±ΠΎΡΠΊΠΎΠΉ ΡΠΎΠ²Π΅ΡΡΠ΅Π½Π½ΡΡ
ΡΠ΅Ρ
Π½ΠΎΠ»ΠΎΠ³ΠΈΡΠ΅ΡΠΊΠΈΡ
ΠΏΡΠΈΡΠΌΠΎΠ² ΠΈ ΡΠ»ΡΡΡΠ΅Π½ΠΈΠ΅ΠΌ ΠΊΠΎΠ½ΡΡΡΡΠΊΡΠΈΠΈ ΠΎΠ±ΠΎΡΡΠ΄ΠΎΠ²Π°Π½ΠΈΡ. ΠΠΎΠ·ΠΌΠΎΠΆΠ½ΠΎ Π·Π½Π°ΡΠΈΡΠ΅Π»ΡΠ½ΠΎΠ΅ ΡΠ°ΡΡΠΈΡΠ΅Π½ΠΈΠ΅ ΠΈΡΠΏΠΎΠ»ΡΠ·ΠΎΠ²Π°Π½ΠΈΡ ΡΠ²Π°ΡΠΊΠΈ ΠΈ ΡΠ΅Π·ΠΊΠΈ Π΄Π»Ρ ΠΏΠΎΠ΄Π²ΠΎΠ΄Π½ΡΡ
ΡΠ°Π±ΠΎΡ ΠΈ Π² ΠΊΠΎΡΠΌΠΎΡΠ΅. ΠΠ°ΠΏΡΠ°Π²Π»Π΅Π½ΠΈΠ΅ ΠΏΡΠΎΠ³ΡΠ΅ΡΡΠ° Π² ΠΎΠ±Π»Π°ΡΡΠΈ ΡΠ²Π°ΡΠΎΡΠ½ΠΎΠΉ ΡΠ΅Ρ
Π½ΠΈΠΊΠΈ Ρ
Π°ΡΠ°ΠΊΡΠ΅ΡΠΈΠ·ΡΠ΅ΡΡΡ Π΄Π°Π»ΡΠ½Π΅ΠΉΡΠ΅ΠΉ ΠΌΠ΅Ρ
Π°Π½ΠΈΠ·Π°ΡΠΈΠ΅ΠΉ ΠΈ Π°Π²ΡΠΎΠΌΠ°ΡΠΈΠ·Π°ΡΠΈΠ΅ΠΉ ΠΎΡΠ½ΠΎΠ²Π½ΡΡ
ΡΠ²Π°ΡΠΎΡΠ½ΡΡ
ΡΠ°Π±ΠΎΡ ΠΈ Π²ΡΠ΅Ρ
Π²ΡΠΏΠΎΠΌΠΎΠ³Π°ΡΠ΅Π»ΡΠ½ΡΡ
ΡΠ°Π±ΠΎΡ, ΠΏΡΠ΅Π΄ΡΠ΅ΡΡΠ²ΡΡΡΠΈΡ
ΡΠ²Π°ΡΠΊΠ΅ ΠΈ ΡΠ»Π΅Π΄ΡΡΡΠΈΡ
Π·Π° Π½Π΅ΠΉ (ΠΏΡΠΈΠΌΠ΅Π½Π΅Π½ΠΈΠ΅ ΠΌΠ°Π½ΠΈΠΏΡΠ»ΡΡΠΎΡΠΎΠ², ΠΊΠ°Π½ΡΠΎΠ²Π°ΡΠ΅Π»Π΅ΠΉ, ΡΠΎΠ±ΠΎΡΠΎΠ²). ΠΠΊΡΡΠ°Π»ΡΠ½ΠΎΠΉ ΡΠ²Π»ΡΠ΅ΡΡΡ ΠΏΡΠΎΠ±Π»Π΅ΠΌΠ° ΡΠ»ΡΡΡΠ΅Π½ΠΈΡ ΠΊΠΎΠ½ΡΡΠΎΠ»Ρ ΠΊΠ°ΡΠ΅ΡΡΠ²Π° Π‘. , Π² ΡΠΎΠΌ ΡΠΈΡΠ»Π΅ ΠΏΡΠΈΠΌΠ΅Π½Π΅Π½ΠΈΠ΅ Π°ΠΏΠΏΠ°ΡΠ°ΡΠΎΠ² Ρ ΠΎΠ±ΡΠ°ΡΠ½ΠΎΠΉ ΡΠ²ΡΠ·ΡΡ, ΡΠΏΠΎΡΠΎΠ±Π½ΡΡ
ΡΠ΅Π³ΡΠ»ΠΈΡΠΎΠ²Π°ΡΡ Π² Π°Π²ΡΠΎΠΌΠ°ΡΠΈΡΠ΅ΡΠΊΠΎΠΌ ΡΠ΅ΠΆΠΈΠΌΠ΅ ΡΠ°Π±ΠΎΡΡ ΡΠ²Π°ΡΠΎΡΠ½ΡΡ
Π°Π²ΡΠΎΠΌΠ°ΡΠΎΠ².
Π‘ΡΡΠ½ΠΎΡΡΡ ΠΈ ΠΊΠ»Π°ΡΡΠΈΡΠΈΠΊΠ°ΡΠΈΡ ΠΏΡΠΎΡΠ΅ΡΡΠ° ΡΠ²Π°ΡΠΊΠΈ. ΠΠΎΠ½ΡΠΏΠ΅ΠΊΡ
ΠΠΎΠ½ΡΠΏΠ΅ΠΊΡ. Π ΡΡΠ½Π°Ρ ΡΠ»Π΅ΠΊΡΡΠΎ-Π΄ΡΠ³ΠΎΠ²Π°Ρ ΡΠ²Π°ΡΠΊΠ°.
… … …
ΠΠ²Π΅Π΄Π΅Π½ΠΈΠ΅:
Π‘Π²Π°ΡΠΊΠ° ΡΠ²Π»ΡΠ΅ΡΡΡ ΠΎΠ΄Π½ΠΈΠΌ ΠΈΠ· ΡΠ΅Ρ Π½ΠΎΠ»ΠΎΠ³ΠΈΡΠ΅ΡΠΊΠΈΡ ΠΏΡΠΎΡΠ΅ΡΡΠΎΠ², ΠΊΠ°ΠΊ Π² ΠΎΠ±Π»Π°ΡΡΠΈ ΠΌΠ°ΡΠΈΒΠ½ΠΎΡΡΡΠΎΠ΅Π½ΠΈΡ, ΡΠ°ΠΊ ΠΈ Π² ΡΡΡΠΎΠΈΡΠ΅Π»ΡΠ½ΠΎΠΉ ΠΈΠ½Π΄ΡΡΡΡΠΈΠΈ.
ΠΠ΅ΡΠΌΠΎΡΡΡ Π½Π° Π±ΠΎΠ»ΡΡΠΈΠ΅ ΠΌΠ°ΡΡΡΠ°Π±Ρ ΠΈΡΠΏΠΎΠ»ΡΠ·ΠΎΠ²Π°Π½ΠΈΡ Π² ΠΏΡΠΎΠΌΡΡΠ»Π΅Π½Π½ΠΎΡΡΠΈ ΡΠ°Π·Π»ΠΈΡΒΠ½ΡΡ Π²ΠΈΠ΄ΠΎΠ² ΠΌΠ΅Ρ Π°Π½ΠΈΠ·ΠΈΡΠΎΠ²Π°Π½Π½ΠΎΠΉ ΡΠ²Π°ΡΠΊΠΈ, ΠΎΠ±ΡΠ΅ΠΌ ΠΏΡΠΈΠΌΠ΅Π½Π΅Π½ΠΈΡ ΡΡΡΠ½ΠΎΠΉ Π΄ΡΠ³ΠΎΠ²ΠΎΠΉ ΡΠ²Π°ΡΠΊΠΈ ΡΠ΅ΒΠ³ΠΎΠ΄Π½Ρ Π½Π΅ ΡΠΎΠ»ΡΠΊΠΎ Π½Π΅ ΡΠ½ΠΈΠΆΠ°Π΅ΡΡΡ, Π½ΠΎ ΠΈ Π²ΠΎΠ·ΡΠ°ΡΡΠ°Π΅Ρ, ΡΡΠΎ ΡΠ²ΡΠ·Π°Π½ΠΎ Ρ ΡΠΎΠ·Π΄Π°Π½ΠΈΠ΅ΠΌ Π½ΠΎΠ²ΡΡ ΠΌΠ°ΡΠ΅ΒΡΠΈΠ°Π»ΠΎΠ² ΠΈ Π½ΠΎΠ²ΠΎΠ³ΠΎ ΠΎΠ±ΠΎΡΡΠ΄ΠΎΠ²Π°Π½ΠΈΡ Π΄Π»Ρ ΡΡΡΠ½ΠΎΠΉ Π΄ΡΠ³ΠΎΠ²ΠΎΠΉ ΡΠ²Π°ΡΠΊΠΈ.
ΠΠ»Π΅ΠΊΡΡΠΈΡΠ΅ΡΠΊΠ°Ρ Π΄ΡΠ³Π° Π²ΠΏΠ΅ΡΠ²ΡΠ΅ Π±ΡΠ»Π° ΠΎΡΠΊΡΡΡΠ° Π² 1802 Π³. ΠΏΡΠΎΡΠ΅ΡΡΠΎΡΠΎΠΌ ΡΠΈΠ·ΠΈΠΊΠΈ Π‘Π°Π½ΠΊΡ-ΠΠ΅ΡΠ΅ΡΠ±ΡΡΠ³ΡΠΊΠΎΠΉ ΠΌΠ΅Π΄ΠΈΠΊΠΎ-Ρ ΠΈΡΡΡΠ³ΠΈΡΠ΅ΡΠΊΠΎΠΉ Π°ΠΊΠ°Π΄Π΅ΠΌΠΈΠΈ Π.Π. ΠΠ΅ΡΡΠΎΠ²ΡΠΌ.
Π Π² 1882 Π³ΠΎΠ΄Ρ ΡΡΡΡΠΊΠΈΠΉ ΠΈΠ·ΠΎΠ±ΡΠ΅ΡΠ°ΡΠ΅Π»Ρ Π.Π. ΠΠ΅Π½Π°ΡΠ΄ΠΎΡ ΠΏΡΠΈΠΌΠ΅Π½ΠΈΠ» ΡΠ»Π΅ΠΊΡΡΠΈΡΠ΅ΡΠΊΡΡ Π΄ΡΠ³Ρ Π΄Π»Ρ ΡΠΎΠ΅Π΄ΠΈΠ½Π΅Π½ΠΈΡ ΠΌΠ΅ΡΠ°Π»Π»ΠΎΠ². Π 1885 Π³ΠΎΠ΄Ρ ΠΎΠ½ ΠΏΠΎΠ»ΡΡΠΈΠ» ΠΏΠ°ΡΠ΅Π½Ρ ΠΏΠΎΠ΄ Π½Π°Π·Π²Π°Π½ΠΈΠ΅ΠΌ Β«ΡΠΏΠΎΒΡΠΎΠ± ΡΠΎΠ΅Π΄ΠΈΠ½Π΅Π½ΠΈΡ ΠΈ ΡΠ°Π·ΡΠ΅Π΄ΠΈΠ½Π΅Π½ΠΈΡ ΠΌΠ΅ΡΠ°Π»Π»ΠΎΠ² Π½Π΅ΠΏΠΎΡΡΠ΅Π΄ΡΡΠ²Π΅Π½Π½ΡΠΌ Π΄Π΅ΠΉΡΡΠ²ΠΈΠ΅ΠΌ ΡΠ»Π΅ΠΊΡΡΠΈΡΠ΅ΒΡΠΊΠΎΠ³ΠΎ ΡΠΎΠΊΠ°Β», ΠΈΡΠΏΠΎΠ»ΡΠ·ΡΡ Π΄Π»Ρ ΡΡΠΎΠ³ΠΎ Π΄ΡΠ³Ρ, Π³ΠΎΡΡΡΡΡ ΠΌΠ΅ΠΆΠ΄Ρ ΡΠ³ΠΎΠ»ΡΠ½ΡΠΌ ΡΠ»Π΅ΠΊΡΡΠΎΠ΄ΠΎΠΌ ΠΈ ΠΌΠ΅ΒΡΠ°Π»Π»ΠΎΠΌ ΠΈ ΠΏΠΈΡΠ°ΡΡΡΡ ΡΠ»Π΅ΠΊΡΡΠΈΡΠ΅ΡΠΊΠΎΠΉ ΡΠ½Π΅ΡΠ³ΠΈΠ΅ΠΉ ΠΎΡ Π°ΠΊΠΊΡΠΌΡΠ»ΡΡΠΎΡΠ°.
Π ΡΡΡΠΊΠΈΠΉ ΠΈΠ½ΠΆΠ΅Π½Π΅Ρ-ΠΌΠ΅ΡΠ°Π»Π»ΡΡΠ³ ΠΈ ΠΈΠ·ΠΎΠ±ΡΠ΅ΡΠ°ΡΠ΅Π»Ρ Π.Π. Π‘Π»Π°Π²ΡΠ½ΠΎΠ² Π² 1888 Π³ΠΎΠ΄Ρ ΡΠ°Π·ΡΠ°ΒΠ±ΠΎΡΠ°Π» ΡΠΏΠΎΡΠΎΠ± ΡΠ²Π°ΡΠΊΠΈ ΠΌΠ΅ΡΠ°Π»Π»ΠΈΡΠ΅ΡΠΊΠΈΠΌ ΡΠ»Π΅ΠΊΡΡΠΎΠ΄ΠΎΠΌ, Π² 1891 Π³ΠΎΠ΄Ρ ΠΎΠ½ ΠΏΠΎΠ»ΡΡΠΈΠ» Π΄Π²Π° ΠΏΠ°ΡΠ΅Π½ΡΠ° ΠΏΠΎΠ΄ Π½Π°Π·Π²Π°Π½ΠΈΠ΅ΠΌ Β«ΡΠΏΠΎΡΠΎΠ± ΠΈ Π°ΠΏΠΏΠ°ΡΠ°ΡΡ Π΄Π»Ρ ΡΠ»Π΅ΠΊΡΡΠΈΡΠ΅ΡΠΊΠΎΠΉ ΠΎΡΠ»ΠΈΠ²ΠΊΠΈ ΠΌΠ΅ΡΠ°Π»Π»ΠΎΠ²Β» ΠΈ Β«ΡΠΏΠΎΡΠΎΠ± ΡΠ»Π΅ΠΊΡΡΠΈΡΠ΅ΡΠΊΠΎΠ³ΠΎ ΡΠΏΠ»ΠΎΡΠ½Π΅Π½ΠΈΡ ΠΌΠ΅ΡΠ°Π»Π»ΠΈΡΠ΅ΡΠΊΠΈΡ ΠΎΡΠ»ΠΈΠ²ΠΎΠΊΒ». ΠΠ΅Π½Π°ΡΠ΄ΠΎΡ ΠΏΡΠ΅Π΄Π»ΠΎΠΆΠΈΠ» ΡΠ°Π·Π»ΠΈΡΒΠ½ΡΠ΅ ΡΠΏΠΎΡΠΎΠ±Ρ ΡΠ²Π°ΡΠΊΠΈ Π½Π°ΠΊΠ»ΠΎΠ½Π½ΡΠΌΠΈ ΠΌΠ΅ΡΠ°Π»Π»ΠΈΡΠ΅ΡΠΊΠΈΠΌΠΈ ΡΠ»Π΅ΠΊΡΡΠΎΠ΄Π°ΠΌΠΈ ΠΈ ΡΡΡΡΠΎΠΉΡΡΠ²Π°, Π² ΠΊΠΎΡΠΎΒΡΡΡ ΠΏΠΎΠ΄Π°ΡΠ° ΡΠ»Π΅ΠΊΡΡΠΎΠ΄Π° Π² Π·ΠΎΠ½Ρ Π΄ΡΠ³ΠΈ Π²ΡΠΏΠΎΠ»Π½ΡΠ»Π°ΡΡ Π·Π° ΡΡΠ΅Ρ Π΄Π°Π²Π»Π΅Π½ΠΈΡ ΠΏΡΡΠΆΠΈΠ½Ρ.
ΠΠ΄Π½Π°ΠΊΠΎ Π½ΠΈΠ·ΠΊΠΈΠΉ ΡΡΠΎΠ²Π΅Π½Ρ ΡΠ°Π·Π²ΠΈΡΠΈΡ ΡΠ΅Ρ Π½ΠΈΠΊΠΈ Π² Π ΠΎΡΡΠΈΠΈ Ρ ΡΠ΅Ρ Π»Π΅Ρ Π½Π΅ ΠΏΠΎΠ·Π²ΠΎΠ»ΡΡΡ ΠΈΡΠΏΠΎΠ»ΡΠ·ΠΎΠ²Π°ΡΡ ΠΈ ΡΠΈΡΠΎΠΊΠΎ ΡΠ°Π·Π²ΠΈΠ²Π°ΡΡ ΠΈΠ΄Π΅ΠΈ ΠΠ΅ΡΡΠΎΠ²Π°, ΠΠ΅Π½Π°ΡΠ΄ΠΎΡΠ°, Π‘Π»Π°Π²ΡΠ½ΠΎΠ²Π°.
ΠΡΠ΄Π°ΡΡΡΡΡΡ ΡΠΎΠ»Ρ Π² ΡΠ΅ΠΎΡΠ΅ΡΠΈΡΠ΅ΡΠΊΠΎΠΉ ΡΠ°Π·ΡΠ°Π±ΠΎΡΠΊΠ΅ ΡΠ²Π°ΡΠ½ΡΡ ΠΏΡΠΎΡΠ΅ΡΡΠΎΠ² ΡΡΠ³ΡΠ°Π»ΠΈ Π²ΠΈΠ΄Π½ΡΠ΅ ΡΡΠ΅Π½ΡΠ΅ Π.Π. ΠΡΠ±Π°Π²ΡΠΊΠΈΠΉ, Π.Π. Π₯ΡΠ΅Π½ΠΎΠ², Π.Π. ΠΠΈΠΊΠΎΠ»Π°Π΅Π², Π.Π. ΠΠΊΠ΅ΡΠ±Π»Π°ΠΌ, Π.Π. Π ΡΠΊΠ°Π»ΠΈΠ½, Π.Π. ΠΠ°ΡΠΎΠ½, Π.Π. ΠΠΈΠΊΠΈΡΠΈΠ½ ΠΈ Π΄Ρ.
Π‘Π²Π°ΡΠΊΠ° — ΠΏΡΠΎΡΠ΅ΡΡ ΠΏΠΎΠ»ΡΡΠ΅Π½ΠΈΡ Π½Π΅ΡΠ°Π·ΡΠ΅ΠΌΠ½ΠΎΠ³ΠΎ ΡΠΎΠ΅Π΄ΠΈΠ½Π΅Π½ΠΈΡ Π΄Π²ΡΡ
ΠΈΠ»ΠΈ Π±ΠΎΠ»Π΅Π΅ Π΄Π΅ΡΠ°Π»Π΅ΠΉ ΠΈΠ· ΡΠ²Π΅ΡΠ΄ΡΡ
ΠΌΠ΅ΡΠ°Π»Π»ΠΎΠ² (ΠΌΠ°ΡΠ΅ΡΠΈΠ°Π»ΠΎΠ²) ΠΏΡΡΠ΅ΠΌ ΠΈΡ
ΠΌΠ΅ΡΡΠ½ΠΎΠ³ΠΎ ΡΠΏΠ»Π°Π²Π»Π΅Π½ΠΈΡ ΠΈΠ»ΠΈ ΡΠΎΠ²ΠΌΠ΅ΡΡΠ½ΠΎΠ³ΠΎ Π΄Π΅ΡΠΎΡΠΌΠΈΡΠΎΠ²Π°Π½ΠΈΡ Ρ Π½Π°Π³ΡΠ΅Π²ΠΎΠΌ ΠΈ Π±Π΅Π· Π½Π°Π³ΡΠ΅Π²Π° Ρ ΠΏΠΎΠ»ΡΡΠ΅Π½ΠΈΠ΅ΠΌ Π½Π° Π³ΡΠ°Π½ΠΈΡΠ΅ ΠΈΡ
ΡΠ°Π·Π΄Π΅Π»Π° ΠΏΡΠΎΡΠ½ΡΡ
ΠΌΠ΅ΠΆΠ°ΡΠΎΠΌΠ½ΡΡ
ΡΠ²ΡΠ·Π΅ΠΉ, Π·Π° ΡΡΠ΅Ρ ΡΠΏΠ»Π°Π²Π»Π΅Π½ΠΈΡ ΠΎΡΠ½ΠΎΠ²Π½ΠΎΠ³ΠΎ ΠΈ ΠΏΡΠΈΡΠ°Π΄ΠΎΡΠ½ΠΎΠ³ΠΎ ΠΌΠ°ΡΠ΅ΡΠΈΠ°Π»Π°.
ΠΡΠ΅ Π²ΠΈΠ΄Ρ ΡΠ²Π°ΡΠΊΠΈ ΠΌΠΎΠΆΠ½ΠΎ ΡΠ°Π·Π΄Π΅Π»ΠΈΡΡ Π½Π° Π΄Π²Π΅ ΠΎΡΠ½ΠΎΠ²Π½ΡΠ΅ Π³ΡΡΠΏΠΏΡ: ΡΠ²Π°ΡΠΊΠ° ΠΏΠ»Π°Π²Π»Π΅Π½ΠΈΠ΅ΠΌ ΠΈ ΡΠ²Π°ΡΠΊΠ° Π΄Π°Π²Π»Π΅Π½ΠΈΠ΅ΠΌ.
ΠΡΠΈ ΡΠ²Π°ΡΠΊΠ΅ ΠΏΠ»Π°Π²Π»Π΅Π½ΠΈΠ΅ΠΌ, ΠΊΡΠΎΠΌΠΊΠΈ ΡΠ²Π°ΡΠΈΠ²Π°Π΅ΠΌΡΡ Π΄Π΅ΡΠ°Π»Π΅ΠΉ ΠΈ ΠΏΡΠΈΡΠ°Π΄ΠΎΡΠ½ΡΠΉ ΠΌΠ°ΡΠ΅ΡΠΈΠ°Π» ΡΠ°ΡΠΏΠ»Π°Π²Π»ΡΡΡΡΡ ΡΠ΅ΠΏΠ»ΠΎΡΠΎΠΉ ΡΠ²Π°ΡΠΎΡΠ½ΠΎΠΉ Π΄ΡΠ³ΠΈ ΠΈΠ»ΠΈ Π³Π°Π·ΠΎΠ²ΡΠΌ ΠΏΠ»Π°ΠΌΠ΅Π½Π΅ΠΌ, ΠΎΠ±ΡΠ°Π·ΡΡ ΡΠ²Π°ΡΠΎΡΠ½ΡΡ Π²Π°Π½Π½Ρ. ΠΡΠΈ ΠΊΡΠΈΡΡΠ°Π»Π»ΠΈΠ·Π°ΡΠΈΠΈ ΠΌΠ΅ΡΠ°Π»Π»Π° ΡΠ²Π°ΡΠΎΡΠ½ΠΎΠΉ Π²Π°Π½Π½Ρ ΡΠΎΡΡ ΠΊΡΠΈΡΡΠ°Π»Π»ΠΎΠ² Π½Π°ΡΠΈΠ½Π°Π΅ΡΡΡ Ρ ΡΠΏΠ»Π°Π²Π»Π΅Π½Π½ΡΡ ΠΊΡΠΈΡΡΠ°Π»Π»ΠΎΠ² ΠΎΡΠ½ΠΎΠ²Π½ΠΎΠ³ΠΎ ΠΌΠ΅ΡΠ°Π»Π»Π°.
ΠΡΠΈ ΡΠ²Π°ΡΠΊΠ΅ Π΄Π°Π²Π»Π΅Π½ΠΈΠ΅ΠΌ ΡΠΎΠ²ΠΌΠ΅ΡΡΠ½Π°Ρ Π½Π°ΠΏΡΠ°Π²Π»Π΅Π½Π½Π°Ρ ΠΏΠ»Π°ΡΡΠΈΡΠ΅ΡΠΊΠ°Ρ Π΄Π΅ΡΠΎΡΠΌΠ°ΡΠΈΡ ΡΠ²Π°ΡΠΈΠ²Π°Π΅ΠΌΡΡ ΠΌΠ΅ΡΠ°Π»Π»ΠΎΠ² ΡΠΏΠΎΡΠΎΠ±ΡΡΠ²ΡΠ΅Ρ ΡΠΎΠΏΡΠΈΠΊΠΎΡΠ½ΠΎΠ²Π΅Π½ΠΈΡ ΠΈ ΠΏΠ΅ΡΠ΅ΠΌΠ΅ΡΠΈΠ²Π°Π½ΠΈΡ ΠΈΡ Π°ΡΠΎΠΌΠΎΠ² ΠΈ ΠΎΠ±ΡΠ°Π·ΠΎΠ²Π°Π½ΠΈΡ ΠΌΠ΅ΠΆΠ°ΡΠΎΠΌΠ½ΠΎΠΉ ΡΠ²ΡΠ·ΠΈ.
ΠΠ»Π°ΡΡΠΈΡΠΈΠΊΠ°ΡΠΈΡ Π²ΠΈΠ΄ΠΎΠ² ΡΠ²Π°ΡΠΊΠΈ ΠΌΠ΅ΡΠ°Π»Π»ΠΎΠ² ΠΏΠΎ ΡΠΈΠ·ΠΈΡΠ΅ΡΠΊΠΈΠΌ ΠΏΡΠΈΠ·Π½Π°ΠΊΠ°ΠΌ. Π Π·Π°Π²ΠΈΡΠΈΠΌΠΎΡΡΠΈ ΠΎΡ ΡΠΎΡΠΌΡ ΡΠ½Π΅ΡΠ³ΠΈΠΈ, ΠΈΡΠΏΠΎΠ»ΡΠ·ΡΠ΅ΠΌΠΎΠΉ Π΄Π»Ρ ΠΎΠ±ΡΠ°Π·ΠΎΠ²Π°Π½ΠΈΡ ΡΠ²Π°ΡΠ½ΠΎΠ³ΠΎ ΡΠΎΠ΅Π΄ΠΈΠ½Π΅Π½ΠΈΡ, ΡΠ°Π·Π»ΠΈΡΠ°ΡΡ ΡΡΠΈ ΠΊΠ»Π°ΡΡΠ° ΡΠ²Π°ΡΠΎΡΠ½ΡΡ ΠΏΡΠΎΡΠ΅ΡΡΠΎΠ²: ΡΠ΅ΡΠΌΠΈΡΠ΅ΡΠΊΠΈΠΉ, ΡΠ΅ΡΠΌΠΎΠΌΠ΅Ρ Π°Π½ΠΈΡΠ΅ΡΠΊΠΈΠΉ, ΠΌΠ΅Ρ Π°Π½ΠΈΡΠ΅ΡΠΊΠΈΠΉ.
ΠΠΈΠ΄ ΡΠ²Π°ΡΠΊΠΈ β ΠΎΠ±ΡΠ΅Π΄ΠΈΠ½ΡΠ΅Ρ ΡΠ²Π°ΡΠΎΡΠ½ΡΠ΅ ΠΏΡΠΎΡΠ΅ΡΡΡ ΠΏΠΎ Π²ΠΈΠ΄Ρ ΠΈΡΡΠΎΡΠ½ΠΈΠΊΠ° ΡΠ½Π΅ΡΠ³ΠΈΠΈ Π½Π΅ΠΏΠΎΡΡΠ΅Π΄ΡΡΠ²Π΅Π½Π½ΠΎ ΠΈΡΠΏΠΎΠ»ΡΠ·ΡΠ΅ΠΌΠΎΠ³ΠΎ Π΄Π»Ρ ΠΎΠ±ΡΠ°Π·ΠΎΠ²Π°Π½ΠΈΡ ΡΠ²Π°ΡΠ½ΠΎΠ³ΠΎ ΡΠΎΠ΅Π΄ΠΈΠ½Π΅Π½ΠΈΡ.
Π ΡΠ΅ΡΠΌΠΈΡΠ΅ΡΠΊΠΎΠΌΡ ΠΊΠ»Π°ΡΡΡ ΠΎΡΠ½ΠΎΡΡΡΡΡ Π²ΠΈΠ΄Ρ ΡΠ²Π°ΡΠΊΠΈ ΠΎΡΡΡΠ΅ΡΡΠ²Π»ΡΠ΅ΠΌΡΠ΅ ΠΏΠ»Π°Π²Π»Π΅Π½ΠΈΠ΅ΠΌ Ρ ΠΈΡΠΏΠΎΠ»ΡΠ·ΠΎΠ²Π°Π½ΠΈΠ΅ΠΌ ΡΠ΅ΠΏΠ»ΠΎΠ²ΠΎΠΉ ΡΠ½Π΅ΡΠ³ΠΈΠΈ, Π° ΠΈΠΌΠ΅Π½Π½ΠΎ: Π΄ΡΠ³ΠΎΠ²Π°Ρ, ΡΠ»Π΅ΠΊΡΡΠΎΡΠ»Π°ΠΊΠΎΠ²Π°Ρ ΡΠ²Π°ΡΠΊΠ°, ΡΠ»Π΅ΠΊΡΡΠΎΠ½Π½ΠΎ-Π»ΡΡΠ΅Π²Π°Ρ, ΠΏΠ»Π°Π·ΠΌΠ΅Π½Π½ΠΎ-Π»ΡΡΠ΅Π²Π°Ρ, ΡΠ»Π΅ΡΡΠΈΠΌ ΡΠ°Π·ΡΡΠ΄ΠΎΠΌ, ΡΠ²Π΅ΡΠΎΠ²Π°Ρ, ΠΈΠ½Π΄ΡΠΊΡΠΈΠΎΠ½Π½Π°Ρ, Π³Π°Π·ΠΎΠ²Π°Ρ ΡΠ²Π°ΡΠΊΠ°, ΡΠ΅ΡΠΌΠΈΡΠ½Π°Ρ ΡΠ²Π°ΡΠΊΠ° ΠΈ Π»ΠΈΡΠ΅ΠΉΠ½Π°Ρ.
Π ΡΠ΅ΡΠΌΠΎΠΌΠ΅Ρ Π°Π½ΠΈΡΠ΅ΡΠΊΠΎΠΌΡ ΠΊΠ»Π°ΡΡΡ ΠΎΡΠ½ΠΎΡΡΡΡΡ Π²ΠΈΠ΄Ρ ΡΠ²Π°ΡΠΊΠΈ, ΠΎΡΡΡΠ΅ΡΡΠ²Π»ΡΠ΅ΠΌΡΠ΅ ΠΏΠ»Π°Π²Π»Π΅Π½ΠΈΠ΅ΠΌ Ρ ΠΈΡΠΏΠΎΠ»ΡΠ·ΠΎΠ²Π°Π½ΠΈΠ΅ΠΌ ΡΠ΅ΠΏΠ»ΠΎΠ²ΠΎΠΉ ΡΠ½Π΅ΡΠ³ΠΈΠΈ ΠΈ Π΄Π°Π²Π»Π΅Π½ΠΈΡ, Π° ΠΈΠΌΠ΅Π½Π½ΠΎ: ΠΊΠΎΠ½ΡΠ°ΠΊΡΠ½Π°Ρ ΡΠ²Π°ΡΠΊΠ°, Π΄ΠΈΡΡΡΠ·ΠΈΠΎΠ½Π½Π°Ρ, ΠΈΠ½Π΄ΡΠΊΡΠΈΠΎΠ½Π½ΠΎ-ΠΏΡΠ΅ΡΡΠΎΠ²Π°Ρ, Π³Π°Π·ΠΎΠΏΡΠ΅ΡΡΠΎΠ²Π°Ρ, Π΄ΡΠ³ΠΎΠ²ΠΎ-ΠΏΡΠ΅ΡΡΠΎΠ²Π°Ρ, ΡΠ»Π°ΠΊΠΎΠΏΡΠ΅ΡΡΠΎΠ²Π°Ρ, ΡΠ΅ΡΠΌΠΈΡΠ½ΠΎ-ΠΏΡΠ΅ΡΡΠΎΠ²Π°Ρ, ΠΏΠ΅ΡΠ½Π°Ρ ΠΈ Π΄Ρ.
Π ΠΌΠ΅Ρ Π°Π½ΠΈΡΠ΅ΡΠΊΠΎΠΌΡ ΠΊΠ»Π°ΡΡΡ ΠΎΡΠ½ΠΎΡΡΡΡΡ Π²ΠΈΠ΄Ρ ΡΠ²Π°ΡΠΊΠΈ, ΠΎΡΡΡΠ΅ΡΡΠ²Π»ΡΠ΅ΠΌΡΠ΅ Ρ ΠΈΡΠΏΠΎΠ»ΡΠ·ΠΎΠ²Π°Π½ΠΈΠ΅ΠΌ ΠΌΠ΅Ρ Π°Π½ΠΈΡΠ΅ΡΠΊΠΎΠΉ ΡΠ½Π΅ΡΠ³ΠΈΠΈ ΠΈ Π΄Π°Π²Π»Π΅Π½ΠΈΡ, Π° ΠΈΠΌΠ΅Π½Π½ΠΎ Ρ ΠΎΠ»ΠΎΠ΄Π½Π°Ρ ΡΠ²Π°ΡΠΊΠ°, Π²Π·ΡΡΠ²ΠΎΠΌ, ΡΠ»ΡΡΡΠ°Π·Π²ΡΠΊΠΎΠ²Π°Ρ ΡΠ²Π°ΡΠΊΠ°, ΡΠ²Π°ΡΠΊΠ° ΡΡΠ΅Π½ΠΈΠ΅ΠΌ ΠΈ ΠΌΠ°Π³Π½ΠΈΡΠΎΠΈΠΌΠΏΡΠ»ΡΡΠ½Π°Ρ.
ΠΠ»Π°ΡΡΠΈΡΠΈΠΊΠ°ΡΠΈΡ Π²ΠΈΠ΄ΠΎΠ² ΡΠ²Π°ΡΠΊΠΈ ΠΌΠ΅ΡΠ°Π»Π»ΠΎΠ² ΠΏΠΎ ΡΠ΅Ρ Π½ΠΈΡΠ΅ΡΠΊΠΈΠΌ ΠΏΡΠΈΠ·Π½Π°ΠΊΠ°ΠΌ:
Π ΡΠ΅Ρ Π½ΠΈΡΠ΅ΡΠΊΠΈΠΌ ΠΏΡΠΈΠ·Π½Π°ΠΊΠ°ΠΌ ΠΎΡΠ½ΠΎΡΡΡΡΡ: ΡΠΏΠΎΡΠΎΠ± Π·Π°ΡΠΈΡΡ ΠΌΠ΅ΡΠ°Π»Π»Π° Π² Π·ΠΎΠ½Π΅ ΡΠ²Π°ΡΠΊΠΈ, Π½Π΅ΠΏΡΠ΅ΡΡΠ²Π½ΠΎΡΡΡ ΠΏΡΠΎΡΠ΅ΡΡΠ° ΠΈ ΡΡΠ΅ΠΏΠ΅Π½Ρ ΠΌΠ΅Ρ Π°Π½ΠΈΠ·Π°ΡΠΈΠΈ ΡΠ²Π°ΡΠΊΠΈ.
ΠΠΎ ΡΠΏΠΎΡΠΎΠ±Ρ Π·Π°ΡΠΈΡΡ ΠΌΠ΅ΡΠ°Π»Π»Π° ΡΠ°Π·Π»ΠΈΡΠ°ΡΡ ΡΠ²Π°ΡΠΊΡ Π² Π²ΠΎΠ·Π΄ΡΡ Π΅, Π² Π²Π°ΠΊΡΡΠΌΠ΅, Π² Π·Π°ΡΠΈΡΠ½ΡΡ Π³Π°Π·Π°Ρ , ΠΏΠΎΠ΄ ΡΠ»ΡΡΠΎΠΌ, Π² ΠΏΠ΅Π½Π΅ ΠΈ Ρ ΠΊΠΎΠΌΠ±ΠΈΠ½ΠΈΡΠΎΠ²Π°Π½Π½ΠΎΠΉ Π·Π°ΡΠΈΡΠΎΠΉ.
ΠΠΎ Π½Π΅ΠΏΡΠ΅ΡΡΠ²Π½ΠΎΡΡΠΈ ΠΏΡΠΎΡΠ΅ΡΡΠ°: ΠΏΡΠ΅ΡΡΠ²ΠΈΡΡΡΠ΅ ΠΈ Π½Π΅ΠΏΡΠ΅ΡΡΠ²Π½ΡΠ΅.
ΠΠΎ ΡΡΠ΅ΠΏΠ΅Π½ΠΈ ΠΌΠ΅Ρ Π°Π½ΠΈΠ·Π°ΡΠΈΠΈ: ΡΡΡΠ½ΡΠ΅, ΠΌΠ΅Ρ Π°Π½ΠΈΠ·ΠΈΡΠΎΠ²Π°Π½Π½ΡΠ΅, Π°Π²ΡΠΎΠΌΠ°ΡΠΈΠ·ΠΈΡΠΎΠ²Π°Π½Π½ΡΠ΅ ΠΈ Π°Π²ΡΠΎΠΌΠ°ΡΠΈΡΠ΅ΡΠΊΠΈΠ΅.
- < Π ΡΡΠ½Π°Ρ Π΄ΡΠ³ΠΎΠ²Π°Ρ ΡΠ²Π°ΡΠΊΠ°
- Π₯Π°ΡΠ°ΠΊΡΠ΅ΡΠΈΡΡΠΈΠΊΠΈ ΠΎΡΠ½ΠΎΠ²Π½ΡΡ
Π²ΠΈΠ΄ΠΎΠ² ΡΠ²Π°ΡΠΊΠΈ.
ΠΠΎΠ½ΡΠΏΠ΅ΠΊΡ >
Π‘Π²Π°ΡΠΊΠ° ΠΊΠ°ΠΊ ΠΏΡΠΎΡΠ΅ΡΡ. ΠΠΈΠ΄Ρ ΡΠ²Π°ΡΠΊΠΈ
ΠΠ°ΠΊ ΠΏΡΠΎΠΈΡΡ ΠΎΠ΄ΠΈΡ ΡΠ²Π°ΡΠΊΠ°.
Π ΡΠ»Π΅ΠΊΡΡΠΎΠ΄Ρ ΠΈ ΡΠ²Π°ΡΠΈΠ²Π°Π΅ΠΌΠΎΠΌΡ ΠΈΠ·Π΄Π΅Π»ΠΈΡ Π΄Π»Ρ ΠΎΠ±ΡΠ°Π·ΠΎΠ²Π°Π½ΠΈΡ ΠΈ ΠΏΠΎΠ΄Π΄Π΅ΡΠΆΠ°Π½ΠΈΡ ΡΠ»Π΅ΠΊΡΡΠΈΡΠ΅ΡΠΊΠΎΠΉ Π΄ΡΠ³ΠΈ ΠΎΡ ΠΈΡΡΠΎΡΠ½ΠΈΠΊΠΎΠ² ΡΠ²Π°ΡΠΎΡΠ½ΠΎΠ³ΠΎ ΡΠΎΠΊΠ° ΠΏΠΎΠ΄Π²ΠΎΠ΄ΠΈΡΡΡ ΡΠ»Π΅ΠΊΡΡΠΎΡΠ½Π΅ΡΠ³ΠΈΡ. ΠΠΎΠ΄ Π΄Π΅ΠΉΡΡΠ²ΠΈΠ΅ΠΌ ΡΠ΅ΠΏΠ»ΠΎΡΡ ΡΠ»Π΅ΠΊΡΡΠΈΡΠ΅ΡΠΊΠΎΠΉ Π΄ΡΠ³ΠΈ ΠΊΡΠΎΠΌΠΊΠΈ ΡΠ²Π°ΡΠΈΠ²Π°Π΅ΠΌΡΡ
Π΄Π΅ΡΠ°Π»Π΅ΠΉ ΠΈ ΡΠ»Π΅ΠΊΡΡΠΎΠ΄Π½ΡΠΉ ΠΌΠ΅ΡΠ°Π»Π» ΡΠ°ΡΠΏΠ»Π°Π²Π»ΡΡΡΡΡ, ΠΎΠ±ΡΠ°Π·ΡΡ ΡΠ²Π°ΡΠΎΡΠ½ΡΡ Π²Π°Π½Π½Ρ, ΠΊΠΎΡΠΎΡΠ°Ρ Π½Π΅ΠΊΠΎΡΠΎΡΠΎΠ΅ Π²ΡΠ΅ΠΌΡ Π½Π°Ρ
ΠΎΠ΄ΠΈΡΡΡ Π² ΡΠ°ΡΠΏΠ»Π°Π²Π»Π΅Π½Π½ΠΎΠΌ ΡΠΎΡΡΠΎΡΠ½ΠΈΠΈ. Π ΡΠ²Π°ΡΠΎΡΠ½ΠΎΠΉ Π²Π°Π½Π½Π΅ ΡΠ»Π΅ΠΊΡΡΠΎΠ΄Π½ΡΠΉ ΠΌΠ΅ΡΠ°Π»Π» ΡΠΌΠ΅ΡΠΈΠ²Π°Π΅ΡΡΡ Ρ ΡΠ°ΡΠΏΠ»Π°Π²Π»Π΅Π½Π½ΡΠΌ ΠΌΠ΅ΡΠ°Π»Π»ΠΎΠΌ ΠΈΠ·Π΄Π΅Π»ΠΈΡ (ΠΎΡΠ½ΠΎΠ²Π½ΡΠΌ ΠΌΠ΅ΡΠ°Π»Π»ΠΎΠΌ), Π° ΡΠ°ΡΠΏΠ»Π°Π²Π»Π΅Π½Π½ΡΠΉ ΡΠ»Π°ΠΊ Π²ΡΠΏΠ»ΡΠ²Π°Π΅Ρ Π½Π° ΠΏΠΎΠ²Π΅ΡΡ
Π½ΠΎΡΡΡ, ΠΎΠ±ΡΠ°Π·ΡΡ Π·Π°ΡΠΈΡΠ½ΡΡ ΠΏΠ»ΡΠ½ΠΊΡ. ΠΡΠΈ Π·Π°ΡΠ²Π΅ΡΠ΄Π΅Π²Π°Π½ΠΈΠΈ ΠΌΠ΅ΡΠ°Π»Π»Π° ΠΎΠ±ΡΠ°Π·ΡΠ΅ΡΡΡ ΡΠ²Π°ΡΠ½ΠΎΠ΅ ΡΠΎΠ΅Π΄ΠΈΠ½Π΅Π½ΠΈΠ΅. ΠΠ½Π΅ΡΠ³ΠΈΡ, Π½Π΅ΠΎΠ±Ρ
ΠΎΠ΄ΠΈΠΌΠ°Ρ Π΄Π»Ρ ΠΎΠ±ΡΠ°Π·ΠΎΠ²Π°Π½ΠΈΡ ΠΈ ΠΏΠΎΠ΄Π΄Π΅ΡΠΆΠ°Π½ΠΈΡ ΡΠ»Π΅ΠΊΡΡΠΈΡΠ΅ΡΠΊΠΎΠΉ Π΄ΡΠ³ΠΈ, ΠΏΠΎΠ»ΡΡΠ°Π΅ΡΡΡ ΠΎΡ ΡΠΏΠ΅ΡΠΈΠ°Π»ΡΠ½ΡΡ
ΠΈΡΡΠΎΡΠ½ΠΈΠΊΠΎΠ² ΠΏΠΈΡΠ°Π½ΠΈΡ ΠΏΠΎΡΡΠΎΡΠ½Π½ΠΎΠ³ΠΎ ΠΈΠ»ΠΈ ΠΏΠ΅ΡΠ΅ΠΌΠ΅Π½Π½ΠΎΠ³ΠΎ ΡΠΎΠΊΠ°.
Π ΠΏΡΠΎΡΠ΅ΡΡΠ΅ ΡΠ»Π΅ΠΊΡΡΠΎΡΠ²Π°ΡΠΊΠΈ ΠΌΠΎΠ³ΡΡ Π±ΡΡΡ ΠΈΡΠΏΠΎΠ»ΡΠ·ΠΎΠ²Π°Π½Ρ ΠΏΠ»Π°Π²ΡΡΠΈΠ΅ΡΡ ΠΈ Π½Π΅ΠΏΠ»Π°Π²ΡΡΠΈΠ΅ΡΡ ΡΠ»Π΅ΠΊΡΡΠΎΠ΄Ρ. Π ΠΏΠ΅ΡΠ²ΠΎΠΌ ΡΠ»ΡΡΠ°Π΅ ΡΠΎΡΠΌΠΈΡΠΎΠ²Π°Π½ΠΈΠ΅ ΡΠ²Π°ΡΠ½ΠΎΠ³ΠΎ ΡΠ²Π° ΠΏΡΠΎΠΈΡΡ
ΠΎΠ΄ΠΈΡ ΠΏΡΠΈ ΡΠ°ΡΠΏΠ»Π°Π²Π»Π΅Π½ΠΈΠΈ ΡΠ°ΠΌΠΎΠ³ΠΎ ΡΠ»Π΅ΠΊΡΡΠΎΠ΄Π°, Π²ΠΎ Π²ΡΠΎΡΠΎΠΌ ΡΠ»ΡΡΠ°Π΅ β ΠΏΡΠΈ ΡΠ°ΡΠΏΠ»Π°Π²Π»Π΅Π½ΠΈΠΈ ΠΏΡΠΈΡΠ°Π΄ΠΎΡΠ½ΠΎΠΉ ΠΏΡΠΎΠ²ΠΎΠ»ΠΎΠΊΠΈ (ΠΏΡΡΡΠΊΠΎΠ² ΠΈ Ρ. ΠΏ.), ΠΊΠΎΡΠΎΡΡΡ Π²Π²ΠΎΠ΄ΡΡ Π½Π΅ΠΏΠΎΡΡΠ΅Π΄ΡΡΠ²Π΅Π½Π½ΠΎ Π² ΡΠ²Π°ΡΠΎΡΠ½ΡΡ Π²Π°Π½Π½Ρ.
ΠΠ»Ρ Π·Π°ΡΠΈΡΡ ΠΎΡ ΠΎΠΊΠΈΡΠ»Π΅Π½ΠΈΡ ΠΌΠ΅ΡΠ°Π»Π»Π° ΡΠ²Π°ΡΠ½ΠΎΠ³ΠΎ ΡΠ²Π° ΠΏΡΠΈΠΌΠ΅Π½ΡΡΡΡΡ Π·Π°ΡΠΈΡΠ½ΡΠ΅ Π³Π°Π·Ρ (Π°ΡΠ³ΠΎΠ½, Π³Π΅Π»ΠΈΠΉ, ΡΠ³Π»Π΅ΠΊΠΈΡΠ»ΡΠΉ Π³Π°Π· ΠΈ ΠΈΡ ΡΠΌΠ΅ΡΠΈ), ΠΏΠΎΠ΄Π°ΡΡΠΈΠ΅ΡΡ ΠΈΠ· ΡΠ²Π°ΡΠΎΡΠ½ΠΎΠΉ Π³ΠΎΠ»ΠΎΠ²ΠΊΠΈ Π² ΠΏΡΠΎΡΠ΅ΡΡΠ΅ ΡΠ»Π΅ΠΊΡΡΠΎΡΠ²Π°ΡΠΊΠΈ.
Π Π°Π·Π»ΠΈΡΠ°ΡΡ ΡΠ»Π΅ΠΊΡΡΠΎΡΠ²Π°ΡΠΊΡ ΠΏΠ΅ΡΠ΅ΠΌΠ΅Π½Π½ΡΠΌ ΡΠΎΠΊΠΎΠΌ ΠΈ ΡΠ»Π΅ΠΊΡΡΠΎΡΠ²Π°ΡΠΊΡ ΠΏΠΎΡΡΠΎΡΠ½Π½ΡΠΌ ΡΠΎΠΊΠΎΠΌ. ΠΡΠΈ ΡΠ²Π°ΡΠΊΠ΅ ΠΏΠΎΡΡΠΎΡΠ½Π½ΡΠΌ ΡΠΎΠΊΠΎΠΌ ΡΠΎΠ² ΠΏΠΎΠ»ΡΡΠ°Π΅ΡΡΡ Ρ ΠΌΠ΅Π½ΡΡΠΈΠΌ ΠΊΠΎΠ»ΠΈΡΠ΅ΡΡΠ²ΠΎΠΌ Π±ΡΡΠ·Π³ ΠΌΠ΅ΡΠ°Π»Π»Π°, ΠΏΠΎΡΠΊΠΎΠ»ΡΠΊΡ Π½Π΅Ρ ΠΏΠ΅ΡΠ΅Ρ ΠΎΠ΄Π° ΡΠ΅ΡΠ΅Π· Π½ΡΠ»Ρ ΠΈ ΡΠΌΠ΅Π½Ρ ΠΏΠΎΠ»ΡΡΠ½ΠΎΡΡΠΈ ΡΠΎΠΊΠ°.
Π Π°ΠΏΠΏΠ°ΡΠ°ΡΠ°Ρ Π΄Π»Ρ ΡΠ»Π΅ΠΊΡΡΠΎΡΠ²Π°ΡΠΊΠΈ ΠΏΠΎΡΡΠΎΡΠ½Π½ΡΠΌ ΡΠΎΠΊΠΎΠΌ ΠΏΡΠΈΠΌΠ΅Π½ΡΡΡΡΡ Π²ΡΠΏΡΡΠΌΠΈΡΠ΅Π»ΠΈ.
ΠΠ»Π°ΡΡΠΈΡΠΈΠΊΠ°ΡΠΈΡ
ΠΠ»Π°ΡΡΠΈΡΠΈΠΊΠ°ΡΠΈΡ Π΄ΡΠ³ΠΎΠ²ΠΎΠΉ ΡΠ²Π°ΡΠΊΠΈ ΠΏΡΠΎΠΈΠ·Π²ΠΎΠ΄ΠΈΡΡΡ Π² Π·Π°Π²ΠΈΡΠΈΠΌΠΎΡΡΠΈ ΠΎΡ ΡΡΠ΅ΠΏΠ΅Π½ΠΈ ΠΌΠ΅Ρ
Π°Π½ΠΈΠ·Π°ΡΠΈΠΈ ΠΏΡΠΎΡΠ΅ΡΡΠ°, ΡΠΎΠ΄Π° ΡΠΎΠΊΠ° ΠΈ ΠΏΠΎΠ»ΡΡΠ½ΠΎΡΡΠΈ, ΡΠΈΠΏΠ° ΡΠ²Π°ΡΠΎΡΠ½ΠΎΠΉ Π΄ΡΠ³ΠΈ, ΡΠ²ΠΎΠΉΡΡΠ² ΡΠ²Π°ΡΠΎΡΠ½ΠΎΠ³ΠΎ ΡΠ»Π΅ΠΊΡΡΠΎΠ΄Π°, Π²ΠΈΠ΄Π° Π·Π°ΡΠΈΡΡ Π·ΠΎΠ½Ρ ΡΠ²Π°ΡΠΊΠΈ ΠΎΡ Π°ΡΠΌΠΎΡΡΠ΅ΡΠ½ΠΎΠ³ΠΎ Π²ΠΎΠ·Π΄ΡΡ
Π° ΠΈ Π΄Ρ.
ΠΠΎ ΡΡΠ΅ΠΏΠ΅Π½ΠΈ ΠΌΠ΅Ρ Π°Π½ΠΈΠ·Π°ΡΠΈΠΈ ΡΠ°Π·Π»ΠΈΡΠ°ΡΡ:
* ΡΡΡΠ½ΡΡ Π΄ΡΠ³ΠΎΠ²ΡΡ ΡΠ²Π°ΡΠΊΡ
* ΠΏΠΎΠ»ΡΠ°Π²ΡΠΎΠΌΠ°ΡΠΈΡΠ΅ΡΠΊΡΡ Π΄ΡΠ³ΠΎΠ²ΡΡ ΡΠ²Π°ΡΠΊΡ
* Π°Π²ΡΠΎΠΌΠ°ΡΠΈΡΠ΅ΡΠΊΡΡ Π΄ΡΠ³ΠΎΠ²ΡΡ ΡΠ²Π°ΡΠΊΡ
ΠΡΠ½Π΅ΡΠ΅Π½ΠΈΠ΅ ΠΏΡΠΎΡΠ΅ΡΡΠΎΠ² ΠΊ ΡΠΎΠΌΡ ΠΈΠ»ΠΈ ΠΈΠ½ΠΎΠΌΡ ΡΠΏΠΎΡΠΎΠ±Ρ Π·Π°Π²ΠΈΡΠΈΡ ΠΎΡ ΡΠΎΠ³ΠΎ, ΠΊΠ°ΠΊ Π²ΡΠΏΠΎΠ»Π½ΡΡΡΡΡ Π·Π°ΠΆΠΈΠ³Π°Π½ΠΈΠ΅ ΠΈ ΠΏΠΎΠ΄Π΄Π΅ΡΠΆΠ°Π½ΠΈΠ΅ ΠΎΠΏΡΠ΅Π΄Π΅Π»ΡΠ½Π½ΠΎΠΉ Π΄Π»ΠΈΠ½Ρ Π΄ΡΠ³ΠΈ, ΠΌΠ°Π½ΠΈΠΏΡΠ»ΡΡΠΈΡ ΡΠ»Π΅ΠΊΡΡΠΎΠ΄ΠΎΠΌ Π΄Π»Ρ ΠΏΡΠΈΠ΄Π°Π½ΠΈΡ ΡΠ²Ρ Π½ΡΠΆΠ½ΠΎΠΉ ΡΠΎΡΠΌΡ, ΠΏΠ΅ΡΠ΅ΠΌΠ΅ΡΠ΅Π½ΠΈΠ΅ ΡΠ»Π΅ΠΊΡΡΠΎΠ΄Π° ΠΏΠΎ Π»ΠΈΠ½ΠΈΠΈ Π½Π°Π»ΠΎΠΆΠ΅Π½ΠΈΡ ΡΠ²Π° ΠΈ ΠΏΡΠ΅ΠΊΡΠ°ΡΠ΅Π½ΠΈΡ ΠΏΡΠΎΡΠ΅ΡΡΠ° ΡΠ²Π°ΡΠΊΠΈ.
ΠΡΠΈ ΡΡΡΠ½ΠΎΠΉ Π΄ΡΠ³ΠΎΠ²ΠΎΠΉ ΡΠ²Π°ΡΠΊΠ΅ ΡΠΊΠ°Π·Π°Π½Π½ΡΠ΅ ΠΎΠΏΠ΅ΡΠ°ΡΠΈΠΈ, Π½Π΅ΠΎΠ±Ρ ΠΎΠ΄ΠΈΠΌΡΠ΅ Π΄Π»Ρ ΠΎΠ±ΡΠ°Π·ΠΎΠ²Π°Π½ΠΈΡ ΡΠ²Π°, Π²ΡΠΏΠΎΠ»Π½ΡΡΡΡΡ ΡΠ΅Π»ΠΎΠ²Π΅ΠΊΠΎΠΌ Π²ΡΡΡΠ½ΡΡ Π±Π΅Π· ΠΏΡΠΈΠΌΠ΅Π½Π΅Π½ΠΈΡ ΠΌΠ΅Ρ Π°Π½ΠΈΠ·ΠΌΠΎΠ².
ΠΡΠΈ ΠΏΠΎΠ»ΡΠ°Π²ΡΠΎΠΌΠ°ΡΠΈΡΠ΅ΡΠΊΠΎΠΉ Π΄ΡΠ³ΠΎΠ²ΠΎΠΉ ΡΠ²Π°ΡΠΊΠ΅ ΠΏΠ»Π°Π²ΡΡΠΈΠΌΡΡ ΡΠ»Π΅ΠΊΡΡΠΎΠ΄ΠΎΠΌ ΠΌΠ΅Ρ Π°Π½ΠΈΠ·ΠΈΡΡΡΡΡΡ ΠΎΠΏΠ΅ΡΠ°ΡΠΈΠΈ ΠΏΠΎ ΠΏΠΎΠ΄Π°ΡΠ΅ ΡΠ»Π΅ΠΊΡΡΠΎΠ΄Π½ΠΎΠΉ ΠΏΡΠΎΠ²ΠΎΠ»ΠΎΠΊΠΈ Π² ΡΠ²Π°ΡΠΎΡΠ½ΡΡ Π·ΠΎΠ½Ρ, Π° ΠΎΡΡΠ°Π»ΡΠ½ΡΠ΅ ΠΎΠΏΠ΅ΡΠ°ΡΠΈΠΈ ΠΏΡΠΎΡΠ΅ΡΡΠ° ΡΠ²Π°ΡΠΊΠΈ ΠΎΡΡΡΠ΅ΡΡΠ²Π»ΡΡΡΡΡ Π²ΡΡΡΠ½ΡΡ.
ΠΡΠΈ Π°Π²ΡΠΎΠΌΠ°ΡΠΈΡΠ΅ΡΠΊΠΎΠΉ Π΄ΡΠ³ΠΎΠ²ΠΎΠΉ ΡΠ²Π°ΡΠΊΠ΅ ΠΏΠΎΠ΄ ΡΠ»ΡΡΠΎΠΌ ΠΌΠ΅Ρ Π°Π½ΠΈΠ·ΠΈΡΡΡΡΡΡ ΠΎΠΏΠ΅ΡΠ°ΡΠΈΠΈ ΠΏΠΎ Π²ΠΎΠ·Π±ΡΠΆΠ΄Π΅Π½ΠΈΡ Π΄ΡΠ³ΠΈ, ΠΏΠΎΠ΄Π΄Π΅ΡΠΆΠ°Π½ΠΈΡ ΠΎΠΏΡΠ΅Π΄Π΅Π»ΡΠ½Π½ΠΎΠΉ Π΄Π»ΠΈΠ½Ρ Π΄ΡΠ³ΠΈ, ΠΏΠ΅ΡΠ΅ΠΌΠ΅ΡΠ΅Π½ΠΈΡ Π΄ΡΠ³ΠΈ ΠΏΠΎ Π»ΠΈΠ½ΠΈΠΈ Π½Π°Π»ΠΎΠΆΠ΅Π½ΠΈΡ ΡΠ²Π°. ΠΠ²ΡΠΎΠΌΠ°ΡΠΈΡΠ΅ΡΠΊΠ°Ρ ΡΠ²Π°ΡΠΊΠ° ΠΏΠ»Π°Π²ΡΡΠΈΠΌΡΡ ΡΠ»Π΅ΠΊΡΡΠΎΠ΄ΠΎΠΌ Π²Π΅Π΄ΡΡΡΡ ΡΠ²Π°ΡΠΎΡΠ½ΠΎΠΉ ΠΏΡΠΎΠ²ΠΎΠ»ΠΎΠΊΠΎΠΉ Π΄ΠΈΠ°ΠΌΠ΅ΡΡΠΎΠΌ 1-6 ΠΌΠΌ; ΠΏΡΠΈ ΡΡΠΎΠΌ ΡΠ΅ΠΆΠΈΠΌ ΡΠ²Π°ΡΠΊΠΈ (ΡΠΎΠΊ, Π½Π°ΠΏΡΡΠΆΠ΅Π½ΠΈΠ΅, ΡΠΊΠΎΡΠΎΡΡΡ ΠΏΠ΅ΡΠ΅ΠΌΠ΅ΡΠ΅Π½ΠΈΡ Π΄ΡΠ³ΠΈ ΠΈ Π΄Ρ.) Π±ΠΎΠ»Π΅Π΅ ΡΡΠ°Π±ΠΈΠ»Π΅Π½, ΡΡΠΎ ΠΎΠ±Π΅ΡΠΏΠ΅ΡΠΈΠ²Π°Π΅Ρ ΠΎΠ΄Π½ΠΎΡΠΎΠ΄Π½ΠΎΡΡΡ ΠΊΠ°ΡΠ΅ΡΡΠ²Π° ΡΠ²Π° ΠΏΠΎ Π΅Π³ΠΎ Π΄Π»ΠΈΠ½Π΅, Π² ΡΠΎ ΠΆΠ΅ Π²ΡΠ΅ΠΌΡ ΡΡΠ΅Π±ΡΠ΅ΡΡΡ Π±ΠΎΠ»ΡΡΠ°Ρ ΡΠΎΡΠ½ΠΎΡΡΡ Π² ΠΏΠΎΠ΄Π³ΠΎΡΠΎΠ²ΠΊΠ΅ ΠΈ ΡΠ±ΠΎΡΠΊΠ΅ Π΄Π΅ΡΠ°Π»Π΅ΠΉ ΠΏΠΎΠ΄ ΡΠ²Π°ΡΠΊΡ.
ΠΠΎ ΡΠΎΠ΄Ρ ΡΠΎΠΊΠ° ΡΠ°Π·Π»ΠΈΡΠ°ΡΡ:
* ΡΠ»Π΅ΠΊΡΡΠΈΡΠ΅ΡΠΊΠ°Ρ Π΄ΡΠ³Π°, ΠΏΠΈΡΠ°Π΅ΠΌΠ°Ρ ΠΏΠΎΡΡΠΎΡΠ½Π½ΡΠΌ ΡΠΎΠΊΠΎΠΌ ΠΏΡΡΠΌΠΎΠΉ ΠΏΠΎΠ»ΡΡΠ½ΠΎΡΡΠΈ (ΠΌΠΈΠ½ΡΡ Π½Π° ΡΠ»Π΅ΠΊΡΡΠΎΠ΄Π΅)
* ΡΠ»Π΅ΠΊΡΡΠΈΡΠ΅ΡΠΊΠ°Ρ Π΄ΡΠ³Π°, ΠΏΠΈΡΠ°Π΅ΠΌΠ°Ρ ΠΏΠΎΡΡΠΎΡΠ½Π½ΡΠΌ ΡΠΎΠΊΠΎΠΌ ΠΎΠ±ΡΠ°ΡΠ½ΠΎΠΉ (ΠΏΠ»ΡΡ Π½Π° ΡΠ»Π΅ΠΊΡΡΠΎΠ΄Π΅) ΠΏΠΎΠ»ΡΡΠ½ΠΎΡΡΠΈ
* ΡΠ»Π΅ΠΊΡΡΠΈΡΠ΅ΡΠΊΠ°Ρ Π΄ΡΠ³Π°, ΠΏΠΈΡΠ°Π΅ΠΌΠ°Ρ ΠΏΠ΅ΡΠ΅ΠΌΠ΅Π½Π½ΡΠΌ ΡΠΎΠΊΠΎΠΌ
ΠΠΎ ΡΠΈΠΏΡ Π΄ΡΠ³ΠΈ ΡΠ°Π·Π»ΠΈΡΠ°ΡΡ
* Π΄ΡΠ³Ρ ΠΏΡΡΠΌΠΎΠ³ΠΎ Π΄Π΅ΠΉΡΡΠ²ΠΈΡ (Π·Π°Π²ΠΈΡΠΈΠΌΡΡ Π΄ΡΠ³Ρ)
* Π΄ΡΠ³Ρ ΠΊΠΎΡΠ²Π΅Π½Π½ΠΎΠ³ΠΎ Π΄Π΅ΠΉΡΡΠ²ΠΈΡ (Π½Π΅Π·Π°Π²ΠΈΡΠΈΠΌΡΡ Π΄ΡΠ³Ρ)
Π ΠΏΠ΅ΡΠ²ΠΎΠΌ ΡΠ»ΡΡΠ°Π΅ Π΄ΡΠ³Π° Π³ΠΎΡΠΈΡ ΠΌΠ΅ΠΆΠ΄Ρ ΡΠ»Π΅ΠΊΡΡΠΎΠ΄ΠΎΠΌ ΠΈ ΠΎΡΠ½ΠΎΠ²Π½ΡΠΌ ΠΌΠ΅ΡΠ°Π»Π»ΠΎΠΌ, ΠΊΠΎΡΠΎΡΡΠΉ ΡΠ°ΠΊΠΆΠ΅ ΡΠ²Π»ΡΠ΅ΡΡΡ ΡΠ°ΡΡΡΡ ΡΠ²Π°ΡΠΎΡΠ½ΠΎΠΉ ΡΠ΅ΠΏΠΈ, ΠΈ Π΄Π»Ρ ΡΠ²Π°ΡΠΊΠΈ ΠΈΡΠΏΠΎΠ»ΡΠ·ΡΠ΅ΡΡΡ ΡΠ΅ΠΏΠ»ΠΎΡΠ°, Π²ΡΠ΄Π΅Π»ΡΠ΅ΠΌΠ°Ρ Π² ΡΡΠΎΠ»Π±Π΅ Π΄ΡΠ³ΠΈ ΠΈ Π½Π° ΡΠ»Π΅ΠΊΡΡΠΎΠ΄Π°Ρ
; Π²ΠΎ Π²ΡΠΎΡΠΎΠΌ β Π΄ΡΠ³Π° Π³ΠΎΡΠΈΡ ΠΌΠ΅ΠΆΠ΄Ρ Π΄Π²ΡΠΌΡ ΡΠ»Π΅ΠΊΡΡΠΎΠ΄Π°ΠΌΠΈ.
ΠΠΎ ΡΠ²ΠΎΠΉΡΡΠ²Π°ΠΌ ΡΠ²Π°ΡΠΎΡΠ½ΠΎΠ³ΠΎ ΡΠ»Π΅ΠΊΡΡΠΎΠ΄Π° ΡΠ°Π·Π»ΠΈΡΠ°ΡΡ:
* ΡΠΏΠΎΡΠΎΠ±Ρ ΡΠ²Π°ΡΠΊΠΈ ΠΏΠ»Π°Π²ΡΡΠΈΠΌΡΡ ΡΠ»Π΅ΠΊΡΡΠΎΠ΄ΠΎΠΌ
* ΡΠΏΠΎΡΠΎΠ±Ρ ΡΠ²Π°ΡΠΊΠΈ Π½Π΅ΠΏΠ»Π°Π²ΡΡΠΈΠΌΡΡ ΡΠ»Π΅ΠΊΡΡΠΎΠ΄ΠΎΠΌ (ΡΠ³ΠΎΠ»ΡΠ½ΡΠΌ, Π³ΡΠ°ΡΠΈΡΠΎΠ²ΡΠΌ ΠΈ Π²ΠΎΠ»ΡΡΡΠ°ΠΌΠΎΠ²ΡΠΌ)
Π‘Π²Π°ΡΠΊΠ° ΠΏΠ»Π°Π²ΡΡΠΈΠΌΡΡ ΡΠ»Π΅ΠΊΡΡΠΎΠ΄ΠΎΠΌ ΡΠ²Π»ΡΠ΅ΡΡΡ ΡΠ°ΠΌΡΠΌ ΡΠ°ΡΠΏΡΠΎΡΡΡΠ°Π½ΡΠ½Π½ΡΠΌ ΡΠΏΠΎΡΠΎΠ±ΠΎΠΌ ΡΠ²Π°ΡΠΊΠΈ; ΠΏΡΠΈ ΡΡΠΎΠΌ Π΄ΡΠ³Π° Π³ΠΎΡΠΈΡ ΠΌΠ΅ΠΆΠ΄Ρ ΠΎΡΠ½ΠΎΠ²Π½ΡΠΌ ΠΌΠ΅ΡΠ°Π»Π»ΠΎΠΌ ΠΈ ΠΌΠ΅ΡΠ°Π»Π»ΠΈΡΠ΅ΡΠΊΠΈΠΌ ΡΡΠ΅ΡΠΆΠ½Π΅ΠΌ, ΠΏΠΎΠ΄Π°Π²Π°Π΅ΠΌΡΠΌ Π² Π·ΠΎΠ½Ρ ΡΠ²Π°ΡΠΊΠΈ ΠΏΠΎ ΠΌΠ΅ΡΠ΅ ΠΏΠ»Π°Π²Π»Π΅Π½ΠΈΡ. ΠΡΠΎΡ Π²ΠΈΠ΄ ΡΠ²Π°ΡΠΊΠΈ ΠΌΠΎΠΆΠ½ΠΎ ΠΏΡΠΎΠΈΠ·Π²ΠΎΠ΄ΠΈΡΡ ΠΎΠ΄Π½ΠΈΠΌ ΠΈΠ»ΠΈ Π½Π΅ΡΠΊΠΎΠ»ΡΠΊΠΈΠΌΠΈ ΡΠ»Π΅ΠΊΡΡΠΎΠ΄Π°ΠΌΠΈ. ΠΡΠ»ΠΈ Π΄Π²Π° ΡΠ»Π΅ΠΊΡΡΠΎΠ΄Π° ΠΏΠΎΠ΄ΡΠΎΠ΅Π΄ΠΈΠ½Π΅Π½Ρ ΠΊ ΠΎΠ΄Π½ΠΎΠΌΡ ΠΏΠΎΠ»ΡΡΡ ΠΈΡΡΠΎΡΠ½ΠΈΠΊΠ° ΠΏΠΈΡΠ°Π½ΠΈΡ Π΄ΡΠ³ΠΈ, ΡΠΎ ΡΠ°ΠΊΠΎΠΉ ΠΌΠ΅ΡΠΎΠ΄ Π½Π°Π·ΡΠ²Π°ΡΡ Π΄Π²ΡΡ
ΡΠ»Π΅ΠΊΡΡΠΎΠ΄Π½ΠΎΠΉ ΡΠ²Π°ΡΠΊΠΎΠΉ, Π° Π΅ΡΠ»ΠΈ Π±ΠΎΠ»ΡΡΠ΅ β ΠΌΠ½ΠΎΠ³ΠΎΡΠ»Π΅ΠΊΡΡΠΎΠ΄Π½ΠΎΠΉ ΡΠ²Π°ΡΠΊΠΎΠΉ ΠΏΡΡΠΊΠΎΠΌ ΡΠ»Π΅ΠΊΡΡΠΎΠ΄ΠΎΠ².
ΠΡΠ»ΠΈ ΠΊΠ°ΠΆΠ΄ΡΠΉ ΠΈΠ· ΡΠ»Π΅ΠΊΡΡΠΎΠ΄ΠΎΠ² ΠΏΠΎΠ»ΡΡΠ°Π΅Ρ Π½Π΅Π·Π°Π²ΠΈΡΠΈΠΌΠΎΠ΅ ΠΏΠΈΡΠ°Π½ΠΈΠ΅ β ΡΠ²Π°ΡΠΊΡ Π½Π°Π·ΡΠ²Π°ΡΡ Π΄Π²ΡΡ
Π΄ΡΠ³ΠΎΠ²ΠΎΠΉ (ΠΌΠ½ΠΎΠ³ΠΎΠ΄ΡΠ³ΠΎΠ²ΠΎΠΉ) ΡΠ²Π°ΡΠΊΠΎΠΉ. ΠΡΠΈ Π΄ΡΠ³ΠΎΠ²ΠΎΠΉ ΡΠ²Π°ΡΠΊΠ΅ ΠΏΠ»Π°Π²Π»Π΅Π½ΠΈΠ΅ΠΌ ΠΠΠ Π΄ΡΠ³ΠΈ Π΄ΠΎΡΡΠΈΠ³Π°Π΅Ρ 0,7-0,9.
ΠΠΎ ΡΡΠ»ΠΎΠ²ΠΈΡΠΌ Π½Π°Π±Π»ΡΠ΄Π΅Π½ΠΈΡ Π·Π° ΠΏΡΠΎΡΠ΅ΡΡΠΎΠΌ Π³ΠΎΡΠ΅Π½ΠΈΡ Π΄ΡΠ³ΠΈ ΡΠ°Π·Π»ΠΈΡΠ°ΡΡ:
* ΠΎΡΠΊΡΡΡΡΡ
* Π·Π°ΠΊΡΡΡΡΡ
* ΠΏΠΎΠ»ΡΠΎΡΠΊΡΡΡΡΡ Π΄ΡΠ³Ρ
ΠΡΠΈ ΠΎΡΠΊΡΡΡΠΎΠΉ Π΄ΡΠ³Π΅ Π²ΠΈΠ·ΡΠ°Π»ΡΠ½ΠΎΠ΅ Π½Π°Π±Π»ΡΠ΄Π΅Π½ΠΈΠ΅ Π·Π° ΠΏΡΠΎΡΠ΅ΡΡΠΎΠΌ Π³ΠΎΡΠ΅Π½ΠΈΡ Π΄ΡΠ³ΠΈ ΠΏΡΠΎΠΈΠ·Π²ΠΎΠ΄ΠΈΡΡΡ ΡΠ΅ΡΠ΅Π· ΡΠΏΠ΅ΡΠΈΠ°Π»ΡΠ½ΡΠ΅ Π·Π°ΡΠΈΡΠ½ΡΠ΅ ΡΡΡΠΊΠ»Π° β ΡΠ²Π΅ΡΠΎΡΠΈΠ»ΡΡΡΡ. ΠΡΠΊΡΡΡΠ°Ρ Π΄ΡΠ³Π° ΠΏΡΠΈΠΌΠ΅Π½ΡΠ΅ΡΡΡ ΠΏΡΠΈ ΠΌΠ½ΠΎΠ³ΠΈΡ
ΡΠΏΠΎΡΠΎΠ±Π°Ρ
ΡΠ²Π°ΡΠΊΠΈ: ΠΏΡΠΈ ΡΡΡΠ½ΠΎΠΉ ΡΠ²Π°ΡΠΊΠ΅ ΠΌΠ΅ΡΠ°Π»Π»ΠΈΡΠ΅ΡΠΊΠΈΠΌ ΠΈ ΡΠ³ΠΎΠ»ΡΠ½ΡΠΌ ΡΠ»Π΅ΠΊΡΡΠΎΠ΄ΠΎΠΌ ΠΈ ΡΠ²Π°ΡΠΊΠ΅ Π² Π·Π°ΡΠΈΡΠ½ΡΡ
Π³Π°Π·Π°Ρ
.
ΠΠ°ΠΊΡΡΡΠ°Ρ Π΄ΡΠ³Π° ΡΠ°ΡΠΏΠΎΠ»Π°Π³Π°Π΅ΡΡΡ ΠΏΠΎΠ»Π½ΠΎΡΡΡΡ Π² ΡΠ°ΡΠΏΠ»Π°Π²Π»Π΅Π½Π½ΠΎΠΌ ΡΠ»ΡΡΠ΅ β ΡΠ»Π°ΠΊΠ΅, ΠΎΡΠ½ΠΎΠ²Π½ΠΎΠΌ ΠΌΠ΅ΡΠ°Π»Π»Π΅ ΠΈ ΠΏΠΎΠ΄ Π³ΡΠ°Π½ΡΠ»ΠΈΡΠΎΠ²Π°Π½Π½ΡΠΌ ΡΠ»ΡΡΠΎΠΌ, ΠΈ ΠΎΠ½Π° Π½Π΅Π²ΠΈΠ΄ΠΈΠΌΠ°.
ΠΠΎΠ»ΡΠΎΡΠΊΡΡΡΠ°Ρ Π΄ΡΠ³Π° Ρ
Π°ΡΠ°ΠΊΡΠ΅ΡΠ½Π° ΡΠ΅ΠΌ, ΡΡΠΎ ΠΎΠ΄Π½Π° Π΅Ρ ΡΠ°ΡΡΡ Π½Π°Ρ
ΠΎΠ΄ΠΈΡΡΡ Π² ΠΎΡΠ½ΠΎΠ²Π½ΠΎΠΌ ΠΌΠ΅ΡΠ°Π»Π»Π΅ ΠΈ ΡΠ°ΡΠΏΠ»Π°Π²Π»Π΅Π½Π½ΠΎΠΌ ΡΠ»ΡΡΠ΅, Π° Π΄ΡΡΠ³Π°Ρ Π½Π°Π΄ Π½ΠΈΠΌ. ΠΠ°Π±Π»ΡΠ΄Π΅Π½ΠΈΠ΅ Π·Π° ΠΏΡΠΎΡΠ΅ΡΡΠΎΠΌ ΠΏΡΠΎΠΈΠ·Π²ΠΎΠ΄ΠΈΡΡΡ ΡΠ΅ΡΠ΅Π· ΡΠ²Π΅ΡΠΎΡΠΈΠ»ΡΡΡΡ. ΠΡΠΏΠΎΠ»ΡΠ·ΡΠ΅ΡΡΡ ΠΏΡΠΈ Π°Π²ΡΠΎΠΌΠ°ΡΠΈΡΠ΅ΡΠΊΠΎΠΉ ΡΠ²Π°ΡΠΊΠ΅ Π°Π»ΡΠΌΠΈΠ½ΠΈΡ ΠΏΠΎ ΡΠ»ΡΡΡ.
ΠΠΎ ΡΠΎΠ΄Ρ Π·Π°ΡΠΈΡΡ Π·ΠΎΠ½Ρ ΡΠ²Π°ΡΠΊΠΈ ΠΎΡ ΠΎΠΊΡΡΠΆΠ°ΡΡΠ΅Π³ΠΎ Π²ΠΎΠ·Π΄ΡΡ Π° ΡΠ°Π·Π»ΠΈΡΠ°ΡΡ:
* Π΄ΡΠ³ΠΎΠ²Π°Ρ ΡΠ²Π°ΡΠΊΠ° Π±Π΅Π· Π·Π°ΡΠΈΡΡ (Π³ΠΎΠ»ΡΠΌ ΡΠ»Π΅ΠΊΡΡΠΎΠ΄ΠΎΠΌ, ΡΠ»Π΅ΠΊΡΡΠΎΠ΄ΠΎΠΌ ΡΠΎ ΡΡΠ°Π±ΠΈΠ»ΠΈΠ·ΠΈΡΡΡΡΠΈΠΌ ΠΏΠΎΠΊΡΡΡΠΈΠ΅ΠΌ)
* Π΄ΡΠ³ΠΎΠ²Π°Ρ ΡΠ²Π°ΡΠΊΠ° ΡΠΎ ΡΠ»Π°ΠΊΠΎΠ²ΠΎΠΉ Π·Π°ΡΠΈΡΠΎΠΉ (ΡΠΎΠ»ΡΡΠΎΠΏΠΎΠΊΡΡΡΡΠΌΠΈ ΡΠ»Π΅ΠΊΡΡΠΎΠ΄Π°ΠΌΠΈ, ΠΏΠΎΠ΄ ΡΠ»ΡΡΠΎΠΌ)
* Π΄ΡΠ³ΠΎΠ²Π°Ρ ΡΠ²Π°ΡΠΊΠ° ΡΠΎ ΡΠ»Π°ΠΊΠΎΠ³Π°Π·ΠΎΠ²ΠΎΠΉ Π·Π°ΡΠΈΡΠΎΠΉ (ΡΠΎΠ»ΡΡΠΎΠΏΠΎΠΊΡΡΡΡΠΌΠΈ ΡΠ»Π΅ΠΊΡΡΠΎΠ΄Π°ΠΌΠΈ)
* Π΄ΡΠ³ΠΎΠ²Π°Ρ ΡΠ²Π°ΡΠΊΠ° Ρ Π³Π°Π·ΠΎΠ²ΠΎΠΉ Π·Π°ΡΠΈΡΠΎΠΉ (Π² ΡΡΠ΅Π΄Π΅ Π·Π°ΡΠΈΡΠ½ΡΡ
Π³Π°Π·ΠΎΠ²)
* Π΄ΡΠ³ΠΎΠ²Π°Ρ ΡΠ²Π°ΡΠΊΠ° Ρ ΠΊΠΎΠΌΠ±ΠΈΠ½ΠΈΡΠΎΠ²Π°Π½Π½ΠΎΠΉ Π·Π°ΡΠΈΡΠΎΠΉ (Π³Π°Π·ΠΎΠ²Π°Ρ ΡΡΠ΅Π΄Π° ΠΈ ΠΏΠΎΠΊΡΡΡΠΈΠ΅ ΠΈΠ»ΠΈ ΡΠ»ΡΡ)
Π‘ΡΠ°Π±ΠΈΠ»ΠΈΠ·ΠΈΡΡΡΡΠΈΠ΅ ΠΏΠΎΠΊΡΡΡΠΈΡ ΠΏΡΠ΅Π΄ΡΡΠ°Π²Π»ΡΡΡ ΡΠΎΠ±ΠΎΠΉ ΠΌΠ°ΡΠ΅ΡΠΈΠ°Π»Ρ, ΡΠΎΠ΄Π΅ΡΠΆΠ°ΡΠΈΠ΅ ΡΠ»Π΅ΠΌΠ΅Π½ΡΡ, Π»Π΅Π³ΠΊΠΎ ΠΈΠΎΠ½ΠΈΠ·ΠΈΡΡΡΡΠΈΠ΅ ΡΠ²Π°ΡΠΎΡΠ½ΡΡ Π΄ΡΠ³Ρ. ΠΠ°Π½ΠΎΡΡΡΡΡ ΡΠΎΠ½ΠΊΠΈΠΌ ΡΠ»ΠΎΠ΅ΠΌ Π½Π° ΡΡΠ΅ΡΠΆΠ½ΠΈ ΡΠ»Π΅ΠΊΡΡΠΎΠ΄ΠΎΠ² (ΡΠΎΠ½ΠΊΠΎΠΏΠΎΠΊΡΡΡΡΠ΅ ΡΠ»Π΅ΠΊΡΡΠΎΠ΄Ρ), ΠΏΡΠ΅Π΄Π½Π°Π·Π½Π°ΡΠ΅Π½Π½ΡΡ
Π΄Π»Ρ ΡΡΡΠ½ΠΎΠΉ Π΄ΡΠ³ΠΎΠ²ΠΎΠΉ ΡΠ²Π°ΡΠΊΠΈ.
ΠΠ°ΡΠΈΡΠ½ΡΠ΅ ΠΏΠΎΠΊΡΡΡΠΈΡ ΠΏΡΠ΅Π΄ΡΡΠ°Π²Π»ΡΡΡ ΡΠΎΠ±ΠΎΠΉ ΠΌΠ΅Ρ Π°Π½ΠΈΡΠ΅ΡΠΊΡΡ ΡΠΌΠ΅ΡΡ ΡΠ°Π·Π»ΠΈΡΠ½ΡΡ ΠΌΠ°ΡΠ΅ΡΠΈΠ°Π»ΠΎΠ², ΠΏΡΠ΅Π΄Π½Π°Π·Π½Π°ΡΠ΅Π½Π½ΡΡ ΠΎΠ³ΡΠ°ΠΆΠ΄Π°ΡΡ ΡΠ°ΡΠΏΠ»Π°Π²Π»Π΅Π½Π½ΡΠΉ ΠΌΠ΅ΡΠ°Π»Π» ΠΎΡ Π²ΠΎΠ·Π΄Π΅ΠΉΡΡΠ²ΠΈΡ Π²ΠΎΠ·Π΄ΡΡ Π°, ΡΡΠ°Π±ΠΈΠ»ΠΈΠ·ΠΈΡΠΎΠ²Π°ΡΡ Π³ΠΎΡΠ΅Π½ΠΈΠ΅ Π΄ΡΠ³ΠΈ, Π»Π΅Π³ΠΈΡΠΎΠ²Π°ΡΡ ΠΈ ΡΠ°ΡΠΈΠ½ΠΈΡΠΎΠ²Π°ΡΡ ΠΌΠ΅ΡΠ°Π»Π» ΡΠ²Π°.
ΠΠ°ΠΈΠ±ΠΎΠ»ΡΡΠ΅Π΅ ΠΏΡΠΈΠΌΠ΅Π½Π΅Π½ΠΈΠ΅ ΠΈΠΌΠ΅ΡΡ ΡΡΠ΅Π΄Π½Π΅ β ΠΈ ΡΠΎΠ»ΡΡΠΎΠΏΠΎΠΊΡΡΡΡΠ΅ ΡΠ²Π°ΡΠΎΡΠ½ΡΠ΅ ΡΠ»Π΅ΠΊΡΡΠΎΠ΄Ρ, ΠΏΡΠ΅Π΄Π½Π°Π·Π½Π°ΡΠ΅Π½Π½ΡΠ΅ Π΄Π»Ρ ΡΡΡΠ½ΠΎΠΉ Π΄ΡΠ³ΠΎΠ²ΠΎΠΉ ΡΠ²Π°ΡΠΊΠΈ ΠΈ Π½Π°ΠΏΠ»Π°Π²ΠΊΠΈ, ΠΈΠ·Π³ΠΎΡΠΎΠ²Π»ΡΠ΅ΠΌΡΠ΅ Π² ΡΠΏΠ΅ΡΠΈΠ°Π»ΡΠ½ΡΡ ΡΠ΅Ρ Π°Ρ ΠΈΠ»ΠΈ Π½Π° Π·Π°Π²ΠΎΠ΄Π°Ρ .
Π ΠΏΠΎΡΠ»Π΅Π΄Π½Π΅Π΅ Π²ΡΠ΅ΠΌΡ ΠΏΠΎΠ»ΡΡΠ°Π΅Ρ ΡΠ°ΡΠΏΡΠΎΡΡΡΠ°Π½Π΅Π½ΠΈΠ΅ ΠΏΠ»Π°Π·ΠΌΠ΅Π½Π½Π°Ρ ΡΠ²Π°ΡΠΊΠ°, Π³Π΄Π΅ Π΄ΡΠ³Π° ΠΌΠ΅ΠΆΠ΄Ρ ΠΈΠ½Π΅ΡΡΠ½ΡΠΌΠΈ Π½Π΅ΠΏΠ»Π°Π²ΡΡΠΈΠΌΠΈΡΡ ΡΠ»Π΅ΠΊΡΡΠΎΠ΄Π°ΠΌΠΈ ΠΈΡΠΏΠΎΠ»ΡΠ·ΡΠ΅ΡΡΡ Π΄Π»Ρ Π²ΡΡΠΎΠΊΠΎΡΠ΅ΠΌΠΏΠ΅ΡΠ°ΡΡΡΠ½ΠΎΠ³ΠΎ Π½Π°Π³ΡΠ΅Π²Π° ΠΏΡΠΎΠΌΠ΅ΠΆΡΡΠΎΡΠ½ΠΎΠ³ΠΎ Π½ΠΎΡΠΈΡΠ΅Π»Ρ, Π½Π°ΠΏΡΠΈΠΌΠ΅Ρ β Π²ΠΎΠ΄ΡΠ½ΠΎΠ³ΠΎ ΠΏΠ°ΡΠ°. ΠΠ·Π²Π΅ΡΡΠ½Π° ΡΠ°ΠΊΠΆΠ΅ ΡΠ²Π°ΡΠΊΠ° Π°ΡΠΎΠΌΠ°ΡΠ½ΡΠΌ Π²ΠΎΠ΄ΠΎΡΠΎΠ΄ΠΎΠΌ, ΠΏΠΎΠ»ΡΡΠ°Π΅ΠΌΡΠΌ Π² Π΄ΡΠ³Π΅ ΠΌΠ΅ΠΆΠ΄Ρ Π²ΠΎΠ»ΡΡΡΠ°ΠΌΠΎΠ²ΡΠΌΠΈ ΡΠ»Π΅ΠΊΡΡΠΎΠ΄Π°ΠΌΠΈ, ΠΈ Π²ΡΠ΄Π΅Π»ΡΡΡΠ΅ΠΌ ΡΠ΅ΠΏΠ»ΠΎ ΠΏΡΠΈ ΡΠ΅ΠΊΠΎΠΌΠ±ΠΈΠ½Π°ΡΠΈΠΈ Π² ΠΌΠΎΠ»Π΅ΠΊΡΠ»Ρ Π½Π° ΡΠ²Π°ΡΠΈΠ²Π°Π΅ΠΌΡΡ Π΄Π΅ΡΠ°Π»ΡΡ .
ΠΠ°Π·ΠΎΠΏΠ»Π°ΠΌΠ΅Π½Π½Π°Ρ ΡΠ²Π°ΡΠΊΠ°
ΠΡΡΠΎΡΠ½ΠΈΠΊΠΎΠΌ ΡΠ΅ΠΏΠ»ΠΎΡΡ ΡΠ²Π»ΡΠ΅ΡΡΡ Π³Π°Π·ΠΎΠ²ΡΠΉ ΡΠ°ΠΊΠ΅Π», ΠΎΠ±ΡΠ°Π·ΡΡΡΠΈΠΉΡΡ ΠΏΡΠΈ ΡΠ³ΠΎΡΠ°Π½ΠΈΠΈ ΡΠΌΠ΅ΡΠΈ ΠΊΠΈΡΠ»ΠΎΡΠΎΠ΄Π° ΠΈ Π³ΠΎΡΡΡΠ΅Π³ΠΎ Π³Π°Π·Π°. Π ΠΊΠ°ΡΠ΅ΡΡΠ²Π΅ Π³ΠΎΡΡΡΠ΅Π³ΠΎ Π³Π°Π·Π° ΠΌΠΎΠ³ΡΡ Π±ΡΡΡ ΠΈΡΠΏΠΎΠ»ΡΠ·ΠΎΠ²Π°Π½Ρ Π°ΡΠ΅ΡΠΈΠ»Π΅Π½, Π²ΠΎΠ΄ΠΎΡΠΎΠ΄, ΠΏΡΠΎΠΏΠ°Π½, Π±ΡΡΠ°Π½, Π±Π»Π°ΡΠ³Π°Π·, ΠΠΠ€, Π±Π΅Π½Π·ΠΈΠ½, Π±Π΅Π½Π·ΠΎΠ», ΠΊΠ΅ΡΠΎΡΠΈΠ½ ΠΈ ΠΈΡ
ΡΠΌΠ΅ΡΠΈ. Π’Π΅ΠΏΠ»ΠΎ, Π²ΡΠ΄Π΅Π»ΡΡΡΠ΅Π΅ΡΡ ΠΏΡΠΈ Π³ΠΎΡΠ΅Π½ΠΈΠΈ ΡΠΌΠ΅ΡΠΈ ΠΊΠΈΡΠ»ΠΎΡΠΎΠ΄Π° ΠΈ Π³ΠΎΡΡΡΠ΅Π³ΠΎ Π³Π°Π·Π°, ΡΠ°ΡΠΏΠ»Π°Π²Π»ΡΠ΅Ρ ΡΠ²Π°ΡΠΈΠ²Π°Π΅ΠΌΡΠ΅ ΠΏΠΎΠ²Π΅ΡΡ
Π½ΠΎΡΡΠΈ ΠΈ ΠΏΡΠΈΡΠ°Π΄ΠΎΡΠ½ΡΠΉ ΠΌΠ°ΡΠ΅ΡΠΈΠ°Π» Ρ ΠΎΠ±ΡΠ°Π·ΠΎΠ²Π°Π½ΠΈΠ΅ΠΌ ΡΠ²Π°ΡΠΎΡΠ½ΠΎΠΉ Π²Π°Π½Π½Ρ. ΠΠ»Π°ΠΌΡ ΠΌΠΎΠΆΠ΅Ρ Π±ΡΡΡ ΠΎΠΊΠΈΡΠ»ΠΈΡΠ΅Π»ΡΠ½ΡΠΌ, Β«Π½Π΅ΠΉΡΡΠ°Π»ΡΠ½ΡΠΌΒ» ΠΈΠ»ΠΈ Π²ΠΎΡΡΡΠ°Π½ΠΎΠ²ΠΈΡΠ΅Π»ΡΠ½ΡΠΌ, ΡΡΠΎ ΡΠ΅Π³ΡΠ»ΠΈΡΡΠ΅ΡΡΡ ΠΊΠΎΠ»ΠΈΡΠ΅ΡΡΠ²ΠΎΠΌ ΠΊΠΈΡΠ»ΠΎΡΠΎΠ΄Π°.
* Π ΠΏΠΎΡΠ»Π΅Π΄Π½ΠΈΠ΅ Π³ΠΎΠ΄Ρ Π² ΠΊΠ°ΡΠ΅ΡΡΠ²Π΅ Π·Π°ΠΌΠ΅Π½ΠΈΡΠ΅Π»Ρ Π°ΡΠ΅ΡΠΈΠ»Π΅Π½Π° ΠΏΡΠΈΠΌΠ΅Π½ΡΠ΅ΡΡΡ Π½ΠΎΠ²ΡΠΉ Π²ΠΈΠ΄ ΡΠΎΠΏΠ»ΠΈΠ²Π° β ΡΠΆΠΈΠΆΠ΅Π½Π½ΡΠΉ Π³Π°Π· ΠΠΠ€ (ΠΌΠ΅ΡΠΈΠ»Π°ΡΠ΅ΡΠΈΠ»Π΅Π½-Π°Π»Π»Π΅Π½ΠΎΠ²Π°Ρ ΡΡΠ°ΠΊΡΠΈΡ). ΠΠΠ€ ΠΎΠ±Π΅ΡΠΏΠ΅ΡΠΈΠ²Π°Π΅Ρ Π²ΡΡΠΎΠΊΡΡ ΡΠΊΠΎΡΠΎΡΡΡ ΡΠ²Π°ΡΠΊΠΈ ΠΈ Π²ΡΡΠΎΠΊΠΎΠ΅ ΠΊΠ°ΡΠ΅ΡΡΠ²ΠΎ ΡΠ²Π°ΡΠΎΡΠ½ΠΎΠ³ΠΎ ΡΠ²Π°, Π½ΠΎ ΡΡΠ΅Π±ΡΠ΅Ρ ΠΏΡΠΈΠΌΠ΅Π½Π΅Π½ΠΈΡ ΠΏΡΠΈΡΠ°Π΄ΠΎΡΠ½ΠΎΠΉ ΠΏΡΠΎΠ²ΠΎΠ»ΠΎΠΊΠΈ Ρ ΠΏΠΎΠ²ΡΡΠ΅Π½Π½ΡΠΌ ΡΠΎΠ΄Π΅ΡΠΆΠ°Π½ΠΈΠ΅ΠΌ ΠΌΠ°ΡΠ³Π°Π½ΡΠ° ΠΈ ΠΊΡΠ΅ΠΌΠ½ΠΈΡ (Π‘Π08ΠΠ‘, Π‘Π08Π2Π‘). ΠΠΠ€ Π³ΠΎΡΠ°Π·Π΄ΠΎ Π±Π΅Π·ΠΎΠΏΠ°ΡΠ½Π΅Π΅ Π°ΡΠ΅ΡΠΈΠ»Π΅Π½Π°, Π² 2-3 ΡΠ°Π·Π° Π΄Π΅ΡΠ΅Π²Π»Π΅, ΠΈ ΡΠ΄ΠΎΠ±Π½Π΅Π΅ ΠΏΡΠΈ ΡΡΠ°Π½ΡΠΏΠΎΡΡΠΈΡΠΎΠ²ΠΊΠ΅. ΠΠ»Π°Π³ΠΎΠ΄Π°ΡΡ Π²ΡΡΠΎΠΊΠΎΠΉ ΡΠ΅ΠΌΠΏΠ΅ΡΠ°ΡΡΡΠ΅ ΡΠ³ΠΎΡΠ°Π½ΠΈΡ Π³Π°Π·Π° Π² ΠΊΠΈΡΠ»ΠΎΡΠΎΠ΄Π΅ (2927 Β°C) ΠΈ Π²ΡΡΠΎΠΊΠΎΠΌΡ ΡΠ΅ΠΏΠ»ΠΎΠ²ΡΠ΄Π΅Π»Π΅Π½ΠΈΡ (20800 ΠΠΊΠ°Π»/ΠΌ³) Π³Π°Π·ΠΎΠ²Π°Ρ ΡΠ΅Π·ΠΊΠ° Ρ ΠΈΡΠΏΠΎΠ»ΡΠ·ΠΎΠ²Π°Π½ΠΈΠ΅ΠΌ ΠΠΠ€ Π³ΠΎΡΠ°Π·Π΄ΠΎ ΡΡΡΠ΅ΠΊΡΠΈΠ²Π½Π΅Π΅ Π΄ΡΡΠ³ΠΈΡ
Π³Π°Π·ΠΎΠ² Π² ΡΠΎΠΌ ΡΠΈΡΠ»Π΅ ΠΈ Π°ΡΠ΅ΡΠΈΠ»Π΅Π½Π°.
* ΠΠ³ΡΠΎΠΌΠ½ΡΠΉ ΠΈΠ½ΡΠ΅ΡΠ΅Ρ ΠΏΡΠ΅Π΄ΡΡΠ°Π²Π»ΡΠ΅Ρ ΠΏΡΠΈΠΌΠ΅Π½Π΅Π½ΠΈΠ΅ Π΄Π»Ρ Π³Π°Π·ΠΎΠ²ΠΎΠΉ ΡΠ²Π°ΡΠΊΠΈ ΠΈΡΠΏΠΎΠ»ΡΠ·ΠΎΠ²Π°Π½ΠΈΠ΅ Π΄ΠΈΡΠΈΠ°Π½Π° Π²Π²ΠΈΠ΄Ρ Π²Π΅ΡΡΠΌΠ° Π²ΡΡΠΎΠΊΠΎΠΉ ΡΠ΅ΠΌΠΏΠ΅ΡΠ°ΡΡΡΡ ΡΠ³ΠΎΡΠ°Π½ΠΈΡ (4500 Β°C). ΠΡΠ΅ΠΏΡΡΡΡΠ²ΠΈΠ΅ΠΌ ΠΊ ΡΠ°ΡΡΠΈΡΠ΅Π½Π½ΠΎΠΌΡ ΠΏΡΠΈΠΌΠ΅Π½Π΅Π½ΠΈΡ ΠΈΡΠΏΠΎΠ»ΡΠ·ΠΎΠ²Π°Π½ΠΈΡ Π΄ΠΈΡΠΈΠ°Π½Π° Π΄Π»Ρ ΡΠ²Π°ΡΠΊΠΈ ΠΈ ΡΠ΅Π·ΠΊΠΈ ΡΠ²Π»ΡΠ΅ΡΡΡ Π΅Π³ΠΎ ΠΏΠΎΠ²ΡΡΠ΅Π½Π½Π°Ρ ΡΠΎΠΊΡΠΈΡΠ½ΠΎΡΡΡ. Π‘ Π΄ΡΡΠ³ΠΎΠΉ ΡΡΠΎΡΠΎΠ½Ρ ΡΡΡΠ΅ΠΊΡΠΈΠ²Π½ΠΎΡΡΡ Π΄ΠΈΡΠΈΠ°Π½Π° Π²Π΅ΡΡΠΌΠ° Π²ΡΡΠΎΠΊΠ° ΠΈ ΡΡΠ°Π²Π½ΠΈΠΌΠ° Ρ ΡΠ»Π΅ΠΊΡΡΠΈΡΠ΅ΡΠΊΠΎΠΉ Π΄ΡΠ³ΠΎΠΉ, ΠΈ ΠΏΠΎΡΠΎΠΌΡ Π΄ΠΈΡΠΈΠ°Π½ ΠΈΠΌΠ΅Π΅Ρ Π·Π½Π°ΡΠΈΡΠ΅Π»ΡΠ½ΡΡ ΠΏΠ΅ΡΡΠΏΠ΅ΠΊΡΠΈΠ²Ρ Π΄Π»Ρ Π΄Π°Π»ΡΠ½Π΅ΠΉΡΠ΅Π³ΠΎ ΠΏΡΠΎΠ³ΡΠ΅ΡΡΠ° Π² ΡΠ°Π·Π²ΠΈΡΠΈΠΈ Π³Π°Π·ΠΎΠΏΠ»Π°ΠΌΠ΅Π½Π½ΠΎΠΉ ΠΎΠ±ΡΠ°Π±ΠΎΡΠΊΠΈ. ΠΠ»Π°ΠΌΡ Π΄ΠΈΡΠΈΠ°Π½Π° Ρ ΠΊΠΈΡΠ»ΠΎΡΠΎΠ΄ΠΎΠΌ ΠΈΡΡΠ΅ΠΊΠ°ΡΡΠ΅Π΅ ΠΈΠ· ΡΠ²Π°ΡΠΎΡΠ½ΠΎΠΉ Π³ΠΎΡΠ΅Π»ΠΊΠΈ ΠΈΠΌΠ΅Π΅Ρ ΡΠ΅Π·ΠΊΠΈΠ΅ ΠΎΡΠ΅ΡΡΠ°Π½ΠΈΡ, ΠΎΡΠ΅Π½Ρ ΠΈΠ½Π΅ΡΡΠ½ΠΎ ΠΊ ΠΎΠ±ΡΠ°Π±Π°ΡΡΠ²Π°Π΅ΠΌΠΎΠΌΡ ΠΌΠ΅ΡΠ°Π»Π»Ρ, ΠΊΠΎΡΠΎΡΠΊΠΎΠ΅ ΠΈ ΠΈΠΌΠ΅ΡΡΠ΅Π΅ ΠΏΡΡΠΏΡΡΠ½ΠΎ-ΡΠΈΠΎΠ»Π΅ΡΠΎΠ²ΡΠΉ ΠΎΡΡΠ΅Π½ΠΎΠΊ. ΠΠ±ΡΠ°Π±Π°ΡΡΠ²Π°Π΅ΠΌΡΠΉ ΠΌΠ΅ΡΠ°Π»Π» (ΡΡΠ°Π»Ρ) Π±ΡΠΊΠ²Π°Π»ΡΠ½ΠΎ Β«ΡΠ΅ΡΠ΅ΡΒ», ΠΈ ΠΏΡΠΈ ΠΈΡΠΏΠΎΠ»ΡΠ·ΠΎΠ²Π°Π½ΠΈΠΈ Π΄ΠΈΡΠΈΠ°Π½Π° Π΄ΠΎΠΏΡΡΡΠΈΠΌΡ ΠΎΡΠ΅Π½Ρ Π±ΠΎΠ»ΡΡΠΈΠ΅ ΡΠΊΠΎΡΠΎΡΡΠΈ ΡΠ²Π°ΡΠΊΠΈ ΠΈ ΡΠ΅Π·ΠΊΠΈ ΠΌΠ΅ΡΠ°Π»Π»Π°.
* ΠΠ½Π°ΡΠΈΡΠ΅Π»ΡΠ½ΡΠΌ ΠΏΡΠΎΠ³ΡΠ΅ΡΡΠΎΠΌ Π² ΡΠ°Π·Π²ΠΈΡΠΈΠΈ Π³Π°Π·ΠΎΠΏΠ»Π°ΠΌΠ΅Π½Π½ΠΎΠΉ ΠΎΠ±ΡΠ°Π±ΠΎΡΠΊΠΈ Ρ ΠΈΡΠΏΠΎΠ»ΡΠ·ΠΎΠ²Π°Π½ΠΈΠ΅ΠΌ ΠΆΠΈΠ΄ΠΊΠΈΡ
Π³ΠΎΡΡΡΠΈΡ
ΠΌΠΎΠΆΠ΅Ρ Π΄Π°ΡΡ ΠΏΡΠΈΠΌΠ΅Π½Π΅Π½ΠΈΠ΅ Π°ΡΠ΅ΡΠΈΠ»Π΅Π½Π΄ΠΈΠ½ΠΈΡΡΠΈΠ»Π° ΠΈ Π΅Π³ΠΎ ΡΠΌΠ΅ΡΠ΅ΠΉ Ρ ΡΠ³Π»Π΅Π²ΠΎΠ΄ΠΎΡΠΎΠ΄Π°ΠΌΠΈ Π²Π²ΠΈΠ΄Ρ ΡΠ°ΠΌΠΎΠΉ Π²ΡΡΠΎΠΊΠΎΠΉ ΡΠ΅ΠΌΠΏΠ΅ΡΠ°ΡΡΡΡ ΡΠ³ΠΎΡΠ°Π½ΠΈΡ (5000 Β°C). ΠΡΠ΅ΡΠΈΠ»Π΅Π½Π΄ΠΈΠ½ΠΈΡΡΠΈΠ» ΡΠΊΠ»ΠΎΠ½Π΅Π½ ΠΏΡΠΈ ΡΠΈΠ»ΡΠ½ΠΎΠΌ Π½Π°Π³ΡΠ΅Π²Π΅ ΠΊ Π²Π·ΡΡΠ²Π½ΠΎΠΌΡ ΡΠ°Π·Π»ΠΎΠΆΠ΅Π½ΠΈΡ, Π½ΠΎ Π² ΡΠΎΡΡΠ°Π²Π΅ ΡΠΌΠ΅ΡΠ΅ΠΉ Ρ ΡΠ³Π»Π΅Π²ΠΎΠ΄ΠΎΡΠΎΠ΄Π°ΠΌΠΈ Π³ΠΎΡΠ°Π·Π΄ΠΎ Π±ΠΎΠ»Π΅Π΅ ΡΡΠ°Π±ΠΈΠ»Π΅Π½. Π Π½Π°ΡΡΠΎΡΡΠ΅Π΅ Π²ΡΠ΅ΠΌΡ ΠΏΡΠΎΠΈΠ·Π²ΠΎΠ΄ΡΡΠ²ΠΎ Π°ΡΠ΅ΡΠΈΠ»Π΅Π½Π΄ΠΈΠ½ΠΈΡΡΠΈΠ»Π° ΠΎΡΠ΅Π½Ρ ΠΎΠ³ΡΠ°Π½ΠΈΡΠ΅Π½Π½ΠΎΠ΅ ΠΈ ΠΏΡΠΎΠ΄ΡΠΊΡ Π΄ΠΎΡΠΎΠ³ΠΎΠΉ, Π½ΠΎ ΠΏΡΠΈ ΡΠ°Π·Π²ΠΈΡΠΈΠΈ ΠΏΡΠΎΠΈΠ·Π²ΠΎΠ΄ΡΡΠ²Π° Π°ΡΠ΅ΡΠΈΠ»Π΅Π½Π΄ΠΈΠ½ΠΈΡΡΠΈΠ» ΠΌΠΎΠΆΠ΅Ρ Π²Π΅ΡΡΠΌΠ° ΠΎΡΡΡΠΈΠΌΠΎ ΡΠ°Π·Π²ΠΈΡΡ ΠΎΠ±Π»Π°ΡΡΠΈ ΠΏΡΠΈΠΌΠ΅Π½Π΅Π½ΠΈΡ Π³Π°Π·ΠΎΠΏΠ»Π°ΠΌΠ΅Π½Π½ΠΎΠΉ ΠΎΠ±ΡΠ°Π±ΠΎΡΠΊΠΈ Π²ΠΎ Π²ΡΠ΅Ρ
Π΅Π΅ ΠΎΠ±Π»Π°ΡΡΡΡ
ΠΏΡΠΈΠΌΠ΅Π½Π΅Π½ΠΈΡ.
ΠΠ»Π΅ΠΊΡΡΠΎΡΠ»Π°ΠΊΠΎΠ²Π°Ρ ΡΠ²Π°ΡΠΊΠ°
ΠΡΡΠΎΡΠ½ΠΈΠΊΠΎΠΌ ΡΠ΅ΠΏΠ»ΠΎΡΡ ΡΠ»ΡΠΆΠΈΡ ΡΠ»ΡΡ, Π½Π°Ρ ΠΎΠ΄ΡΡΠΈΠΉΡΡ ΠΌΠ΅ΠΆΠ΄Ρ ΡΠ²Π°ΡΠΈΠ²Π°Π΅ΠΌΡΠΌΠΈ ΠΈΠ·Π΄Π΅Π»ΠΈΡΠΌΠΈ, ΡΠ°Π·ΠΎΠ³ΡΠ΅Π²Π°ΡΡΠΈΠΉΡΡ ΠΏΡΠΎΡ ΠΎΠ΄ΡΡΠΈΠΌ ΡΠ΅ΡΠ΅Π· Π½Π΅Π³ΠΎ ΡΠ»Π΅ΠΊΡΡΠΈΡΠ΅ΡΠΊΠΈΠΌ ΡΠΎΠΊΠΎΠΌ. ΠΡΠΈ ΡΡΠΎΠΌ ΡΠ΅ΠΏΠ»ΠΎΡΠ°, Π²ΡΠ΄Π΅Π»ΡΠ΅ΠΌΠ°Ρ ΡΠ»ΡΡΠΎΠΌ, ΡΠ°ΡΠΏΠ»Π°Π²Π»ΡΠ΅Ρ ΠΊΡΠΎΠΌΠΊΠΈ ΡΠ²Π°ΡΠΈΠ²Π°Π΅ΠΌΡΡ Π΄Π΅ΡΠ°Π»Π΅ΠΉ ΠΈ ΠΏΡΠΈΡΠ°Π΄ΠΎΡΠ½ΡΡ ΠΏΡΠΎΠ²ΠΎΠ»ΠΎΠΊΡ. Π‘ΠΏΠΎΡΠΎΠ± Π½Π°Ρ ΠΎΠ΄ΠΈΡ ΡΠ²ΠΎΡ ΠΏΡΠΈΠΌΠ΅Π½Π΅Π½ΠΈΠ΅ ΠΏΡΠΈ ΡΠ²Π°ΡΠΊΠ΅ Π²Π΅ΡΡΠΈΠΊΠ°Π»ΡΠ½ΡΡ ΡΠ²ΠΎΠ² ΡΠΎΠ»ΡΡΠΎΡΡΠ΅Π½Π½ΡΡ ΠΈΠ·Π΄Π΅Π»ΠΈΠΉ.
Π‘Π²Π°ΡΠΎΡΠ½ΡΠ΅ ΡΠ°Π±ΠΎΡΡ: Π²ΠΈΠ΄Ρ ΠΈ ΠΎΠ±Π»Π°ΡΡΠΈ ΠΏΡΠΈΠΌΠ΅Π½Π΅Π½ΠΈΡ
Π‘Π²Π°ΡΠΊΠ° ΡΠ²Π»ΡΠ΅ΡΡΡ ΠΎΠ΄Π½ΠΈΠΌ ΠΈΠ· ΡΠ°ΠΌΡΡ
ΡΠ°ΡΠΏΡΠΎΡΡΡΠ°Π½Π΅Π½Π½ΡΡ
ΡΠΏΠΎΡΠΎΠ±ΠΎΠ² ΡΠΎΠ΅Π΄ΠΈΠ½Π΅Π½ΠΈΡ ΡΠ°Π·Π»ΠΈΡΠ½ΡΡ
ΠΌΠ΅ΡΠ°Π»Π»ΠΈΡΠ΅ΡΠΊΠΈΡ
Π΄Π΅ΡΠ°Π»Π΅ΠΉ ΠΈ ΠΊΠΎΠ½ΡΡΡΡΠΊΡΠΈΠΉ, ΠΏΠΎΡΠΊΠΎΠ»ΡΠΊΡ ΠΎΠ±Π΅ΡΠΏΠ΅ΡΠΈΠ²Π°Π΅Ρ ΠΎΡΠ΅Π½Ρ Π²ΡΡΠΎΠΊΡΡ ΠΏΡΠΎΡΠ½ΠΎΡΡΡ Π³ΠΎΡΠΎΠ²ΡΡ
ΠΈΠ·Π΄Π΅Π»ΠΈΠΉ. ΠΠ°ΠΊ ΠΏΡΠ°Π²ΠΈΠ»ΠΎ, ΡΠΈΠ·ΠΈΠΊΠΎ-ΠΌΠ΅Ρ
Π°Π½ΠΈΡΠ΅ΡΠΊΠΈΠ΅ Ρ
Π°ΡΠ°ΠΊΡΠ΅ΡΠΈΡΡΠΈΠΊΠΈ ΡΠ²Π°ΡΠ½ΠΎΠ³ΠΎ ΡΠ²Π° Π½Π΅ ΡΡΡΡΠΏΠ°ΡΡ Π°Π½Π°Π»ΠΎΠ³ΠΈΡΠ½ΡΠΌ ΠΏΠ°ΡΠ°ΠΌΠ΅ΡΡΠ°ΠΌ ΠΎΡΠ½ΠΎΠ²Π½ΠΎΠ³ΠΎ ΠΌΠ°ΡΠ΅ΡΠΈΠ°Π»Π° Π΄Π΅ΡΠ°Π»Π΅ΠΉ, Π° Π²ΠΎ ΠΌΠ½ΠΎΠ³ΠΈΡ
ΡΠ»ΡΡΠ°ΡΡ
ΠΈ ΠΏΡΠ΅Π²ΠΎΡΡ
ΠΎΠ΄ΡΡ ΠΈΡ
.
ΠΠΈΠ΄Ρ ΡΠ²Π°ΡΠΊΠΈ:
- ΡΠ»Π΅ΠΊΡΡΠΎΠ΄ΡΠ³ΠΎΠ²Π°Ρ. ΠΠ±Π΅ΡΠΏΠ΅ΡΠΈΠ²Π°Π΅Ρ ΡΠΎΠ΅Π΄ΠΈΠ½Π΅Π½ΠΈΠ΅ Π΄Π΅ΡΠ°Π»Π΅ΠΉ Ρ ΠΏΠΎΠΌΠΎΡΡΡ Π½Π°Π³ΡΠ΅Π²Π°, ΠΈΡΡΠΎΡΠ½ΠΈΠΊΠΎΠΌ ΠΊΠΎΡΠΎΡΠΎΠ³ΠΎ ΡΠ²Π»ΡΠ΅ΡΡΡ ΡΠ»Π΅ΠΊΡΡΠΈΡΠ΅ΡΠΊΠ°Ρ Π΄ΡΠ³Π°, Π²ΠΎΠ·Π½ΠΈΠΊΠ°ΡΡΠ°Ρ ΠΌΠ΅ΠΆΠ΄Ρ ΡΠ²Π°ΡΠΈΠ²Π°Π΅ΠΌΡΠΌ ΠΌΠ°ΡΠ΅ΡΠΈΠ°Π»ΠΎΠΌ ΠΈ ΡΠ²Π°ΡΠΎΡΠ½ΡΠΌ ΡΠ»Π΅ΠΊΡΡΠΎΠ΄ΠΎΠΌ. ΠΠΌΠ΅Π½Π½ΠΎ ΡΠ»Π΅ΠΊΡΡΠΎΠ΄ΡΠ³ΠΎΠ²Π°Ρ ΡΠ΅Ρ Π½ΠΎΠ»ΠΎΠ³ΠΈΡ ΡΠ°ΡΠ΅ Π²ΡΠ΅Π³ΠΎ ΠΈΡΠΏΠΎΠ»ΡΠ·ΡΠ΅ΡΡΡ ΠΏΡΠΈ Π²ΡΠΏΠΎΠ»Π½Π΅Π½ΠΈΠΈ ΡΠ²Π°ΡΠΎΡΠ½ΡΡ ΡΠ°Π±ΠΎΡ Ρ ΠΎΠ±ΡΡΠ½ΡΠΌΠΈ ΡΠ³Π»Π΅ΡΠΎΠ΄ΠΈΡΡΡΠΌΠΈ ΡΡΠ°Π»ΡΠΌΠΈ;
- Π°ΡΠ³ΠΎΠ½Π½ΠΎ-Π΄ΡΠ³ΠΎΠ²Π°Ρ. Π’Π°ΠΊΠΆΠ΅ Π²ΡΠΏΠΎΠ»Π½ΡΠ΅ΡΡΡ ΡΠ»Π΅ΠΊΡΡΠΈΡΠ΅ΡΠΊΠΎΠΉ Π΄ΡΠ³ΠΎΠΉ, Π½ΠΎ ΠΏΡΠΈ ΡΡΠΎΠΌ ΠΈΡΠΏΠΎΠ»ΡΠ·ΡΠ΅Ρ Π·Π°ΡΠΈΡΠ½ΡΡ Π·Π°Π²Π΅ΡΡ ΠΈΠ· ΠΈΠ½Π΅ΡΡΠ½ΠΎΠ³ΠΎ Π³Π°Π·Π°. Π‘ Π΅Π΅ ΠΏΠΎΠΌΠΎΡΡΡ ΠΏΡΠ΅Π΄ΠΎΡΠ²ΡΠ°ΡΠ°Π΅ΡΡΡ ΠΏΠΎΠΏΠ°Π΄Π°Π½ΠΈΠ΅ Π²ΠΎΠ·Π΄ΡΡ Π° Π² Π·ΠΎΠ½Ρ ΡΠ²Π°ΡΠΊΠΈ ΠΈ ΠΎΠΊΠΈΡΠ»Π΅Π½ΠΈΠ΅ ΡΠ²Π°ΡΠΎΡΠ½ΠΎΠΉ Π²Π°Π½Π½Ρ. ΠΡΠ³ΠΎΠ½Π½ΠΎ-Π΄ΡΠ³ΠΎΠ²Π°Ρ ΡΠ²Π°ΡΠΊΠ° ΠΏΠΎΠ΄Ρ ΠΎΠ΄ΠΈΡ Π΄Π»Ρ ΡΠΎΠ΅Π΄ΠΈΠ½Π΅Π½ΠΈΡ Π·Π°Π³ΠΎΡΠΎΠ²ΠΎΠΊ ΠΈΠ· Π½Π΅ΡΠΆΠ°Π²Π΅ΡΡΠ΅ΠΉ, ΠΆΠ°ΡΠΎΠΏΡΠΎΡΠ½ΠΎΠΉ, ΠΊΠΈΡΠ»ΠΎΡΠΎΡΡΠΎΠΉΠΊΠΎΠΉ ΡΡΠ°Π»ΠΈ, Π°Π»ΡΠΌΠΈΠ½ΠΈΡ, ΠΌΠ°Π³Π½ΠΈΡ ΠΈ ΡΠ°Π·Π»ΠΈΡΠ½ΡΡ ΡΠ²Π΅ΡΠ½ΡΡ ΡΠΏΠ»Π°Π²ΠΎΠ²;
- ΠΊΠΎΠ½ΡΠ°ΠΊΡΠ½Π°Ρ. ΠΡΠ° ΡΠ΅Ρ Π½ΠΎΠ»ΠΎΠ³ΠΈΡ ΠΏΡΠ΅Π΄ΡΡΠΌΠ°ΡΡΠΈΠ²Π°Π΅Ρ ΡΠΎΠ΅Π΄ΠΈΠ½Π΅Π½ΠΈΠ΅ ΠΈΠ·Π΄Π΅Π»ΠΈΠΉ ΠΏΠΎΡΡΠ΅Π΄ΡΡΠ²ΠΎΠΌ Π΄Π²ΡΡ ΠΏΠΎΡΠ»Π΅Π΄ΠΎΠ²Π°ΡΠ΅Π»ΡΠ½ΡΡ ΠΏΡΠΎΡΠ΅ΡΡΠΎΠ² β Π½Π°Π³ΡΠ΅Π²Π° ΠΌΠ΅ΡΠ°Π»Π»Π° Π΄ΠΎ ΠΏΠ»Π°ΡΡΠΈΡΠ΅ΡΠΊΠΎΠ³ΠΎ ΡΠΎΡΡΠΎΡΠ½ΠΈΡ Ρ Π΄Π°Π»ΡΠ½Π΅ΠΉΡΠΈΠΌ ΠΌΠ΅Ρ Π°Π½ΠΈΡΠ΅ΡΠΊΠΈΠΌ Π΄Π΅ΡΠΎΡΠΌΠΈΡΠΎΠ²Π°Π½ΠΈΠ΅ΠΌ Π΄Π΅ΡΠ°Π»Π΅ΠΉ. ΠΠΎΠ½ΡΠ°ΠΊΡΠ½Π°Ρ ΡΠ²Π°ΡΠΊΠ° Π±ΡΠ²Π°Π΅Ρ ΡΠΎΡΠ΅ΡΠ½ΠΎΠΉ, ΡΡΡΠΊΠΎΠ²ΠΎΠΉ, ΡΠΎΠ²Π½ΠΎΠΉ, ΡΠ΅Π»ΡΠ΅ΡΠ½ΠΎΠΉ;
- Π³Π°Π·ΠΎΠ²Π°Ρ.
Π ΡΡΠΎΠΌ ΡΠ»ΡΡΠ°Π΅ ΡΠ²Π°ΡΠΎΡΠ½ΡΠ΅ ΡΠ°Π±ΠΎΡΡ Π·Π°ΠΊΠ»ΡΡΠ°ΡΡΡΡ Π² ΡΠ°ΡΠΏΠ»Π°Π²Π»Π΅Π½ΠΈΠΈ ΠΊΡΠΎΠΌΠΎΠΊ ΡΠ²Π°ΡΠΈΠ²Π°Π΅ΠΌΡΡ Π΄Π΅ΡΠ°Π»Π΅ΠΉ ΠΈ Π²Π²Π΅Π΄Π΅Π½ΠΈΠΈ Π² ΠΆΠΈΠ΄ΠΊΡΡ Π²Π°Π½Π½Ρ ΠΏΡΠΈΡΠ°Π΄ΠΎΡΠ½ΠΎΠ³ΠΎ ΠΌΠ°ΡΠ΅ΡΠΈΠ°Π»Π°. Π§Π°ΡΠ΅ Π²ΡΠ΅Π³ΠΎ Π΄Π°Π½Π½ΡΡ ΡΠ΅Ρ Π½ΠΎΠ»ΠΎΠ³ΠΈΡ ΠΈΡΠΏΠΎΠ»ΡΠ·ΡΡΡ ΠΏΡΠΈ ΠΏΡΠΎΠΈΠ·Π²ΠΎΠ΄ΡΡΠ²Π΅ Π»ΠΈΡΡΠΎΠ²ΡΡ ΠΈ ΡΡΡΠ±ΡΠ°ΡΡΡ ΡΡΠ°Π»ΡΠ½ΡΡ ΠΊΠΎΠ½ΡΡΡΡΠΊΡΠΈΠΉ Π½Π΅Π±ΠΎΠ»ΡΡΠΎΠΉ ΡΠΎΠ»ΡΠΈΠ½Ρ. Π Π°ΡΠΏΠ»Π°Π²Π»Π΅Π½ΠΈΠ΅ ΠΌΠ΅ΡΠ°Π»Π»Π° ΠΎΡΡΡΠ΅ΡΡΠ²Π»ΡΠ΅ΡΡΡ Π·Π° ΡΡΠ΅Ρ Π³ΠΎΡΠ΅Π½ΠΈΡ Π°ΡΠ΅ΡΠΈΠ»Π΅Π½Π° ΠΏΡΠΈ Π²Π·Π°ΠΈΠΌΠΎΠ΄Π΅ΠΉΡΡΠ²ΠΈΠΈ Ρ ΡΠΈΡΡΡΠΌ ΠΊΠΈΡΠ»ΠΎΡΠΎΠ΄ΠΎΠΌ. ΠΠ»Π°Π²Π½ΡΠΌ Π΄ΠΎΡΡΠΎΠΈΠ½ΡΡΠ²ΠΎΠΌ Π³Π°Π·ΠΎΠ²ΠΎΠΉ ΡΠ²Π°ΡΠΊΠΈ ΡΠ²Π»ΡΠ΅ΡΡΡ ΠΌΠΎΠ±ΠΈΠ»ΡΠ½ΠΎΡΡΡ ΠΈ ΠΎΡΡΡΡΡΡΠ²ΠΈΠ΅ Π·Π°Π²ΠΈΡΠΈΠΌΠΎΡΡΠΈ ΠΎΡ Π²Π½Π΅ΡΠ½ΠΈΡ ΠΈΡΡΠΎΡΠ½ΠΈΠΊΠΎΠ² ΡΠ»Π΅ΠΊΡΡΠΎΠΏΠΈΡΠ°Π½ΠΈΡ;
- ΠΏΠ»Π°Π·ΠΌΠ΅Π½Π½Π°Ρ. ΠΠ΅ ΠΏΡΠΈΠΌΠ΅Π½ΡΡΡ Π΄Π»Ρ ΡΠ²Π°ΡΠΈΠ²Π°Π½ΠΈΡ Π½Π°ΠΈΠ±ΠΎΠ»Π΅Π΅ ΡΡΠ³ΠΎΠΏΠ»Π°Π²ΠΊΠΈΡ ΠΌΠ΅ΡΠ°Π»Π»ΠΎΠ² β ΠΌΠΎΠ»ΠΈΠ±Π΄Π΅Π½Π°, Π²ΠΎΠ»ΡΡΡΠ°ΠΌΠ°, Π½ΠΈΠΊΠ΅Π»Π΅Π²ΡΡ ΡΠΏΠ»Π°Π²ΠΎΠ², ΡΠΏΠ΅ΡΠΈΠ°Π»ΡΠ½ΡΡ ΡΡΠ°Π»Π΅ΠΉ. ΠΠ±ΡΠ°Π±ΠΎΡΠΊΠ° ΠΎΡΡΡΠ΅ΡΡΠ²Π»ΡΠ΅ΡΡΡ ΡΡΡΡΠ΅ΠΉ ΠΏΠ»Π°Π·ΠΌΡ, ΡΠ΅ΠΌΠΏΠ΅ΡΠ°ΡΡΡΠ° ΠΊΠΎΡΠΎΡΠΎΠΉ Π΄ΠΎΡΡΠΈΠ³Π°Π΅Ρ 30000ΠΎΠ‘;
- Π»Π°Π·Π΅ΡΠ½Π°Ρ. Π‘Π²Π°ΡΠΊΠ° Π»Π°Π·Π΅ΡΠΎΠΌ ΡΠ²Π»ΡΠ΅ΡΡΡ ΠΎΠ΄Π½ΠΈΠΌ ΠΈΠ· ΡΠ°ΠΌΡΡ
ΡΡΡΠ΅ΠΊΡΠΈΠ²Π½ΡΡ
ΡΠΏΠΎΡΠΎΠ±ΠΎΠ² ΡΠΎΠ΅Π΄ΠΈΠ½Π΅Π½ΠΈΡ ΠΌΠ΅ΡΠ°Π»Π»ΠΈΡΠ΅ΡΠΊΠΈΡ
Π΄Π΅ΡΠ°Π»Π΅ΠΉ. ΠΠ½Π° ΠΎΡΠ»ΠΈΡΠ°Π΅ΡΡΡ ΠΎΡΠ΅Π½Ρ Π²ΡΡΠΎΠΊΠΎΠΉ ΠΏΡΠΎΠΈΠ·Π²ΠΎΠ΄ΠΈΡΠ΅Π»ΡΠ½ΠΎΡΡΡΡ, ΡΡΠ°Π±ΠΈΠ»ΡΠ½ΠΎΡΡΡΡ ΡΠΎΡΠΌΠΈΡΠΎΠ²Π°Π½ΠΈΡ ΡΠ²Π°, ΠΎΠ³ΡΠ°Π½ΠΈΡΠ΅Π½Π½ΠΎΡΡΡΡ Π·ΠΎΠ½Ρ ΡΠ΅ΡΠΌΠΈΡΠ΅ΡΠΊΠΎΠ³ΠΎ Π²ΠΎΠ·Π΄Π΅ΠΉΡΡΠ²ΠΈΡ Π½Π° ΠΈΠ·Π΄Π΅Π»ΠΈΡ, Π²ΠΎΠ·ΠΌΠΎΠΆΠ½ΠΎΡΡΡΡ ΡΠ²Π°ΡΠΈΠ²Π°ΡΡ ΠΊΡΡΠΏΠ½ΠΎΠ³Π°Π±Π°ΡΠΈΡΠ½ΡΠ΅ ΠΊΠΎΠ½ΡΡΡΡΠΊΡΠΈΠΈ.
ΠΠ΄Π΅ΡΡ ΠΏΠ΅ΡΠ΅ΡΠΈΡΠ»Π΅Π½Ρ ΡΠΎΠ»ΡΠΊΠΎ Π½Π°ΠΈΠ±ΠΎΠ»Π΅Π΅ Π²ΠΎΡΡΡΠ΅Π±ΠΎΠ²Π°Π½Π½ΡΠ΅ Π²ΠΈΠ΄Ρ ΡΠ²Π°ΡΠΎΡΠ½ΡΡ ΡΠ°Π±ΠΎΡ. Π‘ΡΡΠ΅ΡΡΠ²ΡΡΡ ΡΠ°ΠΊΠΆΠ΅ ΠΈ Π΄ΡΡΠ³ΠΈΠ΅, ΠΌΠ΅Π½Π΅Π΅ ΠΏΠΎΠΏΡΠ»ΡΡΠ½ΡΠ΅ ΠΌΠ΅ΡΠΎΠ΄Ρ ΡΠ²Π°ΡΠΊΠΈ, ΠΊΠΎΡΠΎΡΡΠ΅ ΠΎΠ±ΡΡΠ½ΠΎ ΠΈΡΠΏΠΎΠ»ΡΠ·ΡΡΡΡΡ Π΄Π»Ρ Π²ΡΠΏΠΎΠ»Π½Π΅Π½ΠΈΡ ΡΠΏΠ΅ΡΠΈΡΠΈΡΠ΅ΡΠΊΠΈΡ ΠΎΠΏΠ΅ΡΠ°ΡΠΈΠΉ. ΠΠ°ΠΏΡΠΈΠΌΠ΅Ρ, Π² Π½Π΅ΠΊΠΎΡΠΎΡΡΡ ΠΎΡΡΠ°ΡΠ»ΡΡ Π΄Π»Ρ ΠΎΠ±ΡΠ°Π·ΠΎΠ²Π°Π½ΠΈΡ ΡΠ΅Π»ΡΠ½ΡΡ ΠΊΠΎΠ½ΡΡΡΡΠΊΡΠΈΠΉ ΠΈΠ· ΡΠ°Π·Π½ΠΎΡΠΎΠ΄Π½ΡΡ ΠΌΠ΅ΡΠ°Π»Π»ΠΎΠ² ΠΏΡΠΈΠΌΠ΅Π½ΡΠ΅ΡΡΡ ΡΠ΅ΡΠΌΠΎΠΌΠ΅Ρ Π°Π½ΠΈΡΠ΅ΡΠΊΠΎΠ΅ ΡΠΎΠ΅Π΄ΠΈΠ½Π΅Π½ΠΈΠ΅ Π΄Π΅ΡΠ°Π»Π΅ΠΉ Ρ ΠΏΠΎΠΌΠΎΡΡΡ ΡΡΠ΅Π½ΠΈΡ, Π° Π΄Π»Ρ ΠΏΠΎΠ»ΡΡΠ΅Π½ΠΈΡ Π±ΠΈΠΌΠ΅ΡΠ°Π»Π»ΠΎΠ² Ρ ΠΎΡΠΎΡΠΎ ΠΏΠΎΠ΄Ρ ΠΎΠ΄ΠΈΡ ΡΠ²Π°ΡΠΊΠ° Π²Π·ΡΡΠ²ΠΎΠΌ.
ΠΠ±Π»Π°ΡΡΠΈ ΠΏΡΠΈΠΌΠ΅Π½Π΅Π½ΠΈΡ ΡΠ²Π°ΡΠΎΡΠ½ΡΡ ΡΠ°Π±ΠΎΡ
Π‘Π²Π°ΡΠΊΠ° ΠΈΡΠΏΠΎΠ»ΡΠ·ΡΠ΅ΡΡΡ Π΄Π»Ρ ΡΠ΅ΡΠ΅Π½ΠΈΡ ΠΎΡΠ΅Π½Ρ ΡΠΈΡΠΎΠΊΠΎΠ³ΠΎ ΠΊΡΡΠ³Π° ΡΠ΅Ρ Π½ΠΎΠ»ΠΎΠ³ΠΈΡΠ΅ΡΠΊΠΈΡ ΠΈ ΠΊΠΎΠ½ΡΡΡΡΠΊΡΠΈΠΎΠ½Π½ΡΡ Π·Π°Π΄Π°Ρ. Π Π°ΡΡΠΌΠΎΡΡΠΈΠΌ Π½Π΅ΡΠΊΠΎΠ»ΡΠΊΠΎ ΡΠΈΠΏΠΎΠ²ΡΡ ΠΏΡΠΈΠΌΠ΅Π½Π΅Π½ΠΈΠΉ ΡΡΠΎΠ³ΠΎ ΡΠΏΠΎΡΠΎΠ±Π° ΠΎΠ±ΡΠ°Π±ΠΎΡΠΊΠΈ ΠΌΠ΅ΡΠ°Π»Π»ΠΎΠ²:
- ΠΈΠ·Π³ΠΎΡΠΎΠ²Π»Π΅Π½ΠΈΠ΅ ΠΌΠ΅ΡΠ°Π»Π»ΠΎΠΊΠΎΠ½ΡΡΡΡΠΊΡΠΈΠΉ. Π‘ ΠΏΠΎΠΌΠΎΡΡΡ ΡΠ²Π°ΡΠΊΠΈ ΠΌΠΎΠΆΠ½ΠΎ ΡΠΎΠ·Π΄Π°Π²Π°ΡΡ ΡΠ΅Π»ΡΠ½ΡΠ΅ ΠΌΠ΅ΡΠ°Π»Π»ΠΈΡΠ΅ΡΠΊΠΈΠ΅ ΠΊΠΎΠ½ΡΡΡΡΠΊΡΠΈΠΈ ΠΏΡΠ°ΠΊΡΠΈΡΠ΅ΡΠΊΠΈ Π»ΡΠ±ΠΎΠΉ ΡΠ»ΠΎΠΆΠ½ΠΎΡΡΠΈ ΠΈ ΡΠ°Π·ΠΌΠ΅ΡΠΎΠ², Π½Π°ΠΏΡΠΈΠΌΠ΅Ρ, ΠΏΠ°Π½Π΄ΡΡΡ, ΠΎΠ³ΡΠ°ΠΆΠ΄Π΅Π½ΠΈΡ, Π½Π΅ΡΡΡΠΈΠ΅ ΡΠ»Π΅ΠΌΠ΅Π½ΡΡ Π·Π΄Π°Π½ΠΈΠΉ, ΠΊΠΎΡΠΏΡΡΠ° ΡΡΠ°Π½ΡΠΏΠΎΡΡΠ½ΡΡ ΡΡΠ΅Π΄ΡΡΠ², ΡΠΏΠΎΡΡΠΈΠ²Π½ΡΠ΅ ΡΠ½Π°ΡΡΠ΄Ρ, Π°Π½Π³Π°ΡΡ ΠΈ Π±ΠΎΠΊΡΡ, ΡΠ°Π·Π»ΠΈΡΠ½ΡΠ΅ ΡΠ°ΠΌΡ ΠΈ ΠΊΠ°ΡΠΊΠ°ΡΡ;
- ΠΏΡΠΎΠΈΠ·Π²ΠΎΠ΄ΡΡΠ²ΠΎ Π²ΠΎΡΠΎΡ. ΠΡΠΏΠΎΠ»ΡΠ·ΡΡ ΡΠ²Π°ΡΠΊΡ, ΠΌΠΎΠΆΠ½ΠΎ ΠΈΠ·Π³ΠΎΡΠ°Π²Π»ΠΈΠ²Π°ΡΡ Π½Π΅ ΡΠΎΠ»ΡΠΊΠΎ ΠΏΡΠΎΡΠ½ΡΠ΅, Π½ΠΎ ΠΈ ΡΡΡΠ΅ΡΠΈΡΠ½ΡΠ΅ ΠΊΠΎΠ½ΡΡΡΡΠΊΡΠΈΠΈ.
Π’Π΅Ρ Π½ΠΎΠ»ΠΎΠ³ΠΈΡ ΠΏΠΎΠ·Π²ΠΎΠ»ΡΠ΅Ρ ΠΈΠ·Π³ΠΎΡΠ°Π²Π»ΠΈΠ²Π°ΡΡ ΠΎΡΠΊΠ°ΡΠ½ΡΠ΅ ΠΈ ΡΠ°ΡΠΏΠ°ΡΠ½ΡΠ΅ Π²ΠΎΡΠΎΡΠ° ΠΈΠ· ΠΏΡΠΎΡΠ½Π°ΡΡΠΈΠ»Π°, ΠΊΠΎΡΠΎΡΡΠΉ ΡΠ²Π»ΡΠ΅ΡΡΡ ΠΎΠ΄Π½ΠΈΠΌ ΠΈΠ· ΡΠ°ΠΌΡΡ ΠΏΠΎΠΏΡΠ»ΡΡΠ½ΡΡ ΠΌΠ°ΡΠ΅ΡΠΈΠ°Π»ΠΎΠ² Π΄Π»Ρ ΠΎΠ³ΡΠ°ΠΆΠ΄Π΅Π½ΠΈΡ Π·Π°Π³ΠΎΡΠΎΠ΄Π½ΡΡ ΡΡΠ°ΡΡΠΊΠΎΠ², ΡΠ΅ΡΡΠΈΡΠΎΡΠΈΠΉ ΠΏΡΠΎΠΌΡΡΠ»Π΅Π½Π½ΡΡ ΠΏΡΠ΅Π΄ΠΏΡΠΈΡΡΠΈΠΉ. ΠΡΠΈ ΡΡΠΎΠΌ ΡΠ²Π°ΡΠΊΠ° ΠΌΠΎΠΆΠ΅Ρ ΠΎΡΡΡΠ΅ΡΡΠ²Π»ΡΡΡΡΡ Π½Π΅ ΡΠΎΠ»ΡΠΊΠΎ Π² Π·Π°Π²ΠΎΠ΄ΡΠΊΠΈΡ ΡΡΠ»ΠΎΠ²ΠΈΡΡ , Π½ΠΎ ΠΈ Π½Π΅ΠΏΠΎΡΡΠ΅Π΄ΡΡΠ²Π΅Π½Π½ΠΎ Π½Π° ΠΎΠ±ΡΠ΅ΠΊΡΠ΅ ΠΌΠΎΠ½ΡΠ°ΠΆΠ°;
- ΠΈΠ·Π³ΠΎΡΠΎΠ²Π»Π΅Π½ΠΈΠ΅ Π»Π΅ΡΡΠ½ΠΈΡ. ΠΡΡΠΈ ΡΠ²Π°ΠΊΡΠ°ΡΠΈΠΈ ΠΏΡΠΈ ΠΏΠΎΠΆΠ°ΡΠ΅ ΠΈΠ»ΠΈ Π΄ΡΡΠ³ΠΈΡ ΡΡΠ΅Π·Π²ΡΡΠ°ΠΉΠ½ΡΡ ΡΠΈΡΡΠ°ΡΠΈΡΡ Π΄ΠΎΠ»ΠΆΠ½Ρ ΠΎΡΠ²Π΅ΡΠ°ΡΡ ΠΎΡΠ΅Π½Ρ ΠΆΠ΅ΡΡΠΊΠΈΠΌ ΡΡΠ°Π½Π΄Π°ΡΡΠ°ΠΌ. ΠΠ±Π΅ΡΠΏΠ΅ΡΠΈΡΡ Π½Π΅ΠΎΠ±Ρ ΠΎΠ΄ΠΈΠΌΡΡ ΠΏΡΠΎΡΠ½ΠΎΡΡΡ ΠΈ Π½Π°Π΄Π΅ΠΆΠ½ΠΎΡΡΡ ΠΌΠΎΠ³ΡΡ ΡΠΎΠ»ΡΠΊΠΎ ΡΠ²Π°ΡΠ½ΡΠ΅ ΠΏΠΎΠΆΠ°ΡΠ½ΡΠ΅ Π»Π΅ΡΡΠ½ΠΈΡΡ. ΠΠ½ΠΈ ΡΡΡΠ°Π½Π°Π²Π»ΠΈΠ²Π°ΡΡΡΡ Π²Π½ΡΡΡΠΈ ΠΈΠ»ΠΈ ΡΠ½Π°ΡΡΠΆΠΈ ΠΆΠΈΠ»ΡΡ Π²ΡΡΠΎΡΠ½ΡΡ Π΄ΠΎΠΌΠΎΠ², Π΄Π΅Π»ΠΎΠ²ΡΡ ΠΈ ΡΠΎΡΠ³ΠΎΠ²ΡΡ ΡΠ΅Π½ΡΡΠΎΠ², ΠΏΡΠΎΠΌΡΡΠ»Π΅Π½Π½ΡΡ ΠΈ ΠΎΠ±ΡΠ΅ΡΡΠ²Π΅Π½Π½ΡΡ Π·Π΄Π°Π½ΠΈΠΉ.
ΠΠ»Ρ Π²ΡΠΏΠΎΠ»Π½Π΅Π½ΠΈΡ ΡΠ²Π°ΡΠΎΡΠ½ΡΡ ΡΠ°Π±ΠΎΡ ΠΈΡΠΏΠΎΠ»ΡΠ·ΡΠ΅ΡΡΡ ΡΠ°Π·Π½ΠΎΠΎΠ±ΡΠ°Π·Π½ΠΎΠ΅ ΠΎΠ±ΠΎΡΡΠ΄ΠΎΠ²Π°Π½ΠΈΠ΅ β ΠΎΡ ΠΏΡΠΎΡΡΡΡ ΠΈ ΠΊΠΎΠΌΠΏΠ°ΠΊΡΠ½ΡΡ Π±ΡΡΠΎΠ²ΡΡ ΡΡΠ°Π½ΡΡΠΎΡΠΌΠ°ΡΠΎΡΠΎΠ² ΡΠΎΠΊΠ° Π΄ΠΎ ΠΌΠΎΡΠ½ΡΡ ΠΏΡΠΎΠΌΡΡΠ»Π΅Π½Π½ΡΡ Π°Π²ΡΠΎΠΌΠ°ΡΠΈΠ·ΠΈΡΠΎΠ²Π°Π½Π½ΡΡ Π»ΠΈΠ½ΠΈΠΉ.
ΠΠΠΠ‘Π‘ΠΠ€ΠΠΠΠ¦ΠΠ― ΠΠΠΠΠ Π‘ΠΠΠ ΠΠ | ΠΠ½ΡΡΡΡΠΌΠ΅Π½Ρ, ΠΏΡΠΎΠ²Π΅ΡΠ΅Π½Π½ΡΠΉ Π²ΡΠ΅ΠΌΠ΅Π½Π΅ΠΌ
Π Π½Π°ΡΡΠΎΡΡΠ΅Π΅ Π²ΡΠ΅ΠΌΡ ΡΠ°Π·Π»ΠΈΡΠ°ΡΡ Π±ΠΎΠ»Π΅Π΅ 150 Π²ΠΈΠ΄ΠΎΠ² ΡΠ²Π°ΡΠΎΡΠ½ΡΡ
ΠΏΡΠΎΡΠ΅ΡΒΡΠΎΠ². ΠΠΠ‘Π’ 19521-74 ΡΡΡΠ°Π½Π°Π²Π»ΠΈΠ²Π°Π΅Ρ ΠΊΠ»Π°ΡΡΠΈΡΠΈΠΊΠ°ΡΠΈΡ ΡΠ²Π°ΡΠΎΡΠ½ΡΡ
ΠΏΡΠΎΡΠ΅ΡΒΡΠΎΠ² ΠΏΠΎ ΠΎΡΠ½ΠΎΠ²Π½ΡΠΌ ΡΠΈΠ·ΠΈΡΠ΅ΡΠΊΠΈΠΌ, ΡΠ΅Ρ
Π½ΠΈΡΠ΅ΡΠΊΠΈΠΌ ΠΈ ΡΠ΅Ρ
Π½ΠΎΠ»ΠΎΠ³ΠΈΡΠ΅ΡΠΊΠΈΠΌ ΠΏΡΠΈΠ·Π½Π°ΒΠΊΠ°ΠΌ.
ΠΡΠ½ΠΎΠ²ΠΎΠΉ ΡΠΈΠ·ΠΈΡΠ΅ΡΠΊΠΈΡ ΠΏΡΠΈΠ·Π½Π°ΠΊΠΎΠ² ΠΊΠ»Π°ΡΡΠΈΡΠΈΠΊΠ°ΡΠΈΠΈ ΡΠ²Π»ΡΠ΅ΡΡΡ ΡΠΎΡΠΌΠ° ΡΠ½Π΅ΡΠ³ΠΈΠΈ, ΠΈΡΠΏΠΎΠ»ΡΠ·ΡΠ΅ΠΌΠ°Ρ Π΄Π»Ρ ΠΏΠΎΠ»ΡΡΠ΅Π½ΠΈΡ ΡΠ²Π°ΡΠ½ΠΎΠ³ΠΎ ΡΠΎΠ΅Π΄ΠΈΠ½Π΅Π½ΠΈΡ. ΠΠΎ ΡΠΈΠ·ΠΈΡΠ΅ΒΡΠΊΠΈΠΌ ΠΏΡΠΈΠ·Π½Π°ΠΊΠ°ΠΌ Π²ΡΠ΅ Π²ΠΈΠ΄Ρ ΡΠ²Π°ΡΠΊΠΈ ΠΎΡΠ½ΠΎΡΡΡ ΠΊ ΠΎΠ΄Π½ΠΎΠΌΡ ΠΈΠ· ΡΡΠ΅Ρ ΠΊΠ»Π°ΡΡΠΎΠ²: ΡΠ΅ΡΒΠΌΠΈΡΠ΅ΡΠΊΠΎΠΌΡ, ΡΠ΅ΡΠΌΠΎΠΌΠ΅Ρ Π°Π½ΠΈΡΠ΅ΡΠΊΠΎΠΌΡ ΠΈ ΠΌΠ΅Ρ Π°Π½ΠΈΡΠ΅ΡΠΊΠΎΠΌΡ (ΡΠ°Π±Π». 1.2).
ΠΠ»Π°ΡΡ ΡΠ²Π°ΡΠΊΠΈ | ΠΠΏΡΠ΅Π΄Π΅Π»Π΅Π½ΠΈΠ΅ | ΠΠΈΠ΄ ΡΠ²Π°ΡΠΊΠΈ |
1 | 2 | 3 |
Π’Π΅ΡΠΌΠΈΡΠ΅ΡΠΊΠΈΠΉ | ΠΠΈΠ΄Ρ ΡΠ²Π°ΡΠΊΠΈ, ΠΎΡΡΡΠ΅ΡΡΠ²ΒΠ»ΡΠ΅ΠΌΡΠ΅ ΠΏΠ»Π°Π²Π»Π΅Π½ΠΈΠ΅ΠΌ Ρ ΠΈΡΠΏΠΎΠ»ΡΠ·ΠΎΠ²Π°Π½ΠΈΠ΅ΠΌ ΡΠ΅ΠΏΠ»ΠΎΒΠ²ΠΎΠΉ ΡΠ½Π΅ΡΠ³ΠΈΠΈ | ΠΡΠ³ΠΎΠ²Π°Ρ ΠΠ»Π΅ΠΊΡΡΠΎΡΠ»Π°ΠΊΠΎΠ²Π°Ρ ΠΠ»Π΅ΠΊΡΡΠΎΠ½Π½ΠΎ-Π»ΡΡΠ΅Π²Π°Ρ ΠΠ»Π°Π·ΠΌΠ΅Π½Π½ΠΎ-Π»ΡΡΠ΅Π²Π°Ρ ΠΠΎΠ½Π½ΠΎ-Π»ΡΡΠ΅Π²Π°Ρ Π’Π»Π΅ΡΡΠΈΠΌ ΡΠ°Π·ΡΡΠ΄ΠΎΠΌ Π‘Π²Π΅ΡΠΎΠ²Π°Ρ ΠΠ½Π΄ΡΠΊΡΠΈΠΎΠ½Π½Π°Ρ ΠΠ°Π·ΠΎΠ²Π°Ρ Π’Π΅ΡΠΌΠΈΡΠ½Π°Ρ ΠΠΈΡΠ΅ΠΉΠ½Π°Ρ |
Π’Π΅ΡΠΌΠΎΠΌΠ΅Ρ Π°Π½ΠΈΡΠ΅ΡΠΊΠΈΠΉ | ΠΠΈΠ΄Ρ ΡΠ²Π°ΡΠΊΠΈ, ΠΎΡΡΡΠ΅ΡΡΠ²ΒΠ»ΡΠ΅ΠΌΡΠ΅ Ρ ΠΈΡΠΏΠΎΠ»ΡΠ·ΠΎΠ²Π°Π½ΠΈΒΠ΅ΠΌ ΡΠ΅ΠΏΠ»ΠΎΠ²ΠΎΠΉ ΡΠ½Π΅ΡΠ³ΠΈΠΈ Π΄Π°Π²Π»Π΅Π½ΠΈΡ | ΠΠΎΠ½ΡΠ°ΠΊΡΠ½Π°Ρ ΠΠΈΡΡΡΠ·ΠΈΠΎΠ½Π½Π°Ρ ΠΠ½Π΄ΡΠΊΡΠΈΠΎΠ½Π½ΠΎ-ΠΏΡΠ΅ΡΡΠΎΠ²Π°Ρ ΠΠ°Π·ΠΎΠΏΡΠ΅ΡΡΠΎΠ²Π°Ρ Π’Π΅ΡΠΌΠΎΠΊΠΎΠΌΠΏΡΠ΅ΡΡΠΈΠΎΠ½Π½Π°Ρ ΠΡΠ³ΠΎΠΏΡΠ΅ΡΡΠΎΠ²Π°Ρ Π¨Π»Π°ΠΊΠΎΠΏΡΠ΅ΡΡΠΎΠ²Π°Ρ Π’Π΅ΡΠΌΡΠ½ΠΎ-ΠΏΡΠ΅ΡΡΠΎΠ²Π°Ρ ΠΠ΅ΡΠ½Π°Ρ |
ΠΠ΅Ρ Π°Π½ΠΈΡΠ΅ΡΠΊΠΈΠΉ | ΠΠΈΠ΄Ρ ΡΠ²Π°ΡΠΊΠΈ, ΠΎΡΡΡΠ΅ΡΡΠ²ΒΠ»ΡΠ΅ΠΌΡΠ΅ Ρ ΠΈΡΠΏΠΎΠ»ΡΠ·ΠΎΠ²Π°Π½ΠΈΒΠ΅ΠΌ ΠΌΠ΅Ρ Π°Π½ΠΈΡΠ΅ΡΠΊΠΎΠΉ ΡΠ½Π΅ΡΒΠ³ΠΈΠΈ ΠΈ Π΄Π°Π²Π»Π΅Π½ΠΈΡ | Π₯ΠΎΠ»ΠΎΠ΄Π½Π°Ρ ΠΠ·ΡΡΠ²ΠΎΠΌ Π£Π»ΡΡΡΠ°Π·Π²ΡΠΊΠΎΠ²Π°Ρ Π’ΡΠ΅Π½ΠΈΠ΅ΠΌ ΠΠ°Π³Π½ΠΈΡΠ½ΠΎ-ΠΈΠΌΠΏΡΠ»ΡΡΠ½Π°Ρ |
ΠΡΠΈΠΌΠ΅ΡΠ°Π½ΠΈΠ΅: Π ΠΊΠΎΠΌΠ±ΠΈΠ½ΠΈΡΠΎΠ²Π°Π½Π½ΡΡ ΡΠ΅Ρ Π½ΠΎΠ»ΠΎΠ³ΠΈΡΠ΅ΡΠΊΠΈΡ ΠΏΡΠΎΡΠ΅ΡΡΠ°Ρ Π²ΠΎΠ·ΠΌΠΎΠΆΠ½ΠΎ ΠΎΠ΄Π½ΠΎΠ²ΡΠ΅ΒΠΌΠ΅Π½Π½ΠΎΠ΅ ΠΈΡΠΏΠΎΠ»ΡΠ·ΠΎΠ²Π°Π½ΠΈΠ΅ ΡΠ°Π·Π½ΡΡ Π²ΠΈΠ΄ΠΎΠ² ΡΠ²Π°ΡΠΊΠΈ |
ΠΠ»Π°ΡΡΠΈΡΠΈΠΊΠ°ΡΠΈΡ ΡΠ²Π°ΡΠΊΠΈ ΠΌΠ΅ΡΠ°Π»Π»ΠΎΠ² ΠΏΠΎ ΠΠΠ‘Π’ 19521-74 |
Π ΡΠ΅Ρ
Π½ΠΈΡΠ΅ΡΠΊΠΈΠΌ ΠΏΡΠΈΠ·Π½Π°ΠΊΠ°ΠΌ ΠΊΠ»Π°ΡΡΠΈΡΠΈΠΊΠ°ΡΠΈΠΈ ΡΠ²Π°ΡΠΎΡΠ½ΡΡ
ΠΏΡΠΎΡΠ΅ΡΡΠΎΠ² ΠΎΡΠ½ΠΎΡΡΡ ΡΠΏΠΎΡΠΎΠ±Ρ Π·Π°ΡΠΈΡΡ ΠΌΠ΅ΡΠ°Π»Π»Π° Π² Π·ΠΎΠ½Π΅ ΡΠ²Π°ΡΠΊΠΈ, Π½Π΅ΠΏΡΠ΅ΡΡΠ²Π½ΠΎΡΡΡ ΠΏΡΠΎΡΠ΅ΡΒΡΠ° ΠΈ ΡΡΠ΅ΠΏΠ΅Π½Ρ Π΅Π³ΠΎ ΠΌΠ΅Ρ
Π°Π½ΠΈΠ·Π°ΡΠΈΠΈ (ΡΠΈΡ. 1.1).
Π’Π΅Ρ Π½ΠΎΠ»ΠΎΠ³ΠΈΡΠ΅ΡΠΊΠΈΠ΅ ΠΏΡΠΈΠ·Π½Π°ΠΊΠΈ ΠΊΠ»Π°ΡΡΠΈΡΠΈΠΊΠ°ΡΠΈΠΈ ΡΡΡΠ°Π½Π°Π²Π»ΠΈΠ²Π°ΡΡΡΡ Π΄Π»Ρ ΠΊΠ°ΠΆΠ΄ΠΎΠ³ΠΎ Π²ΠΈΠ΄Π° ΡΠ²Π°ΡΠΊΠΈ ΠΎΡΠ΄Π΅Π»ΡΠ½ΠΎ. ΠΠ°ΠΏΡΠΈΠΌΠ΅Ρ, Π²ΠΈΠ΄ Π΄ΡΠ³ΠΎΠ²ΠΎΠΉ ΡΠ²Π°ΡΠΊΠΈ ΠΌΠΎΠΆΠ΅Ρ Π±ΡΡΡ ΠΊΠ»Π°ΡΡΠΈΡΠΈΡΠΈΡΠΎΠ²Π°Π½ ΠΏΠΎ ΡΠ»Π΅Π΄ΡΡΡΠΈΠΌ ΠΏΡΠΈΠ·Π½Π°ΠΊΠ°ΠΌ: Π²ΠΈΠ΄Ρ ΡΠ»Π΅ΠΊΡΡΠΎΠ΄Π°, Ρ Π°ΒΡΠ°ΠΊΡΠ΅ΡΡ Π·Π°ΡΠΈΡΡ, ΡΡΠΎΠ²Π½Ρ Π°Π²ΡΠΎΠΌΠ°ΡΠΈΠ·Π°ΡΠΈΠΈ.
Π ΠΈΡ. 1.1. ΠΠ»Π°ΡΡΠΈΡΠΈΠΊΠ°ΡΠΈΡ ΡΠΏΠΎΡΠΎΠ±ΠΎΠ² Π΄ΡΠ³ΠΎΠ²ΠΎΠΉ ΡΠ²Π°ΡΠΊΠΈ |
ΠΡΠ½ΠΎΠ²Π½ΡΠ΅ Π²ΠΈΠ΄Ρ ΡΠ²Π°ΡΠΊΠΈ ΠΌΠ΅ΡΠ°Π»Π»ΠΎΠ² | ΠΠΎΠ»Π΅Π·Π½ΡΠ΅ ΡΡΠ°ΡΡΠΈ ΠΎ ΠΌΠ΅ΡΠ°Π»Π»ΠΎΠΏΡΠΎΠΊΠ°ΡΠ΅
Π‘Π²Π°ΡΠΊΠ° β ΠΏΡΠΎΡΠ΅ΡΡ ΠΎΠ±ΡΠ°Π±ΠΎΡΠΊΠΈ ΠΌΠ΅ΡΠ°Π»Π»ΠΎΠ², ΠΎΠ±Π΅ΡΠΏΠ΅ΡΠΈΠ²Π°ΡΡΠΈΠΉ ΠΈΡ ΠΏΠ»ΠΎΡΠ½ΠΎΠ΅ ΡΠΈΠ·ΠΈΡΠ΅ΡΠΊΠΎΠ΅ ΡΠΎΠ΅Π΄ΠΈΠ½Π΅Π½ΠΈΠ΅ ΠΏΡΡΠ΅ΠΌ Π½Π°Π³ΡΠ΅Π²Π° ΠΈ ΠΏΠ»Π°Π²Π»Π΅Π½ΠΈΡ Π² ΠΌΠ΅ΡΡΠ΅ ΡΡΡΠΊΠΎΠ²ΠΊΠΈ, Ρ Π΄ΠΎΠ±Π°Π²Π»Π΅Π½ΠΈΠ΅ΠΌ ΡΠ²ΡΠ·ΡΡΡΠ΅Π³ΠΎ ΠΈΠ»ΠΈ Π±Π΅Π· Π½Π΅Π³ΠΎ. ΠΠ° ΠΏΡΠΎΡΡΠΆΠ΅Π½ΠΈΠΈ ΠΌΠ½ΠΎΠ³ΠΈΡ Π»Π΅Ρ Π±ΡΠ»ΠΈ ΡΠ°Π·ΡΠ°Π±ΠΎΡΠ°Π½Ρ ΡΠ°Π·Π»ΠΈΡΠ½ΡΠ΅ ΠΌΠ΅ΡΠΎΠ΄Ρ ΡΠ²Π°ΡΠΊΠΈ ΠΎΠ±ΡΠ΅ΠΊΡΠΎΠ², ΠΊΠ°ΠΆΠ΄ΡΠΉ ΠΈΠ· ΠΊΠΎΡΠΎΡΡΡ ΠΏΡΠ΅Π΄Π½Π°Π·Π½Π°ΡΠ΅Π½ Π΄Π»Ρ ΡΠ°Π·Π½ΡΡ ΡΠΈΠΏΠΎΠ² ΠΌΠ°ΡΠ΅ΡΠΈΠ°Π»ΠΎΠ² ΠΈ ΠΈΡΠΏΠΎΠ»ΡΠ·ΡΠ΅ΡΡΡ Π² ΠΎΠΏΡΠ΅Π΄Π΅Π»Π΅Π½Π½ΠΎΠΉ ΠΎΠ±Π»Π°ΡΡΠΈ. ΠΠ»Π°ΡΡΠΈΡΠΈΠΊΠ°ΡΠΈΡ ΠΌΠ΅ΡΠΎΠ΄ΠΎΠ² Π·Π°Π²ΠΈΡΠΈΡ ΠΎΡ ΡΠΈΠΏΠ° ΡΠ½Π΅ΡΠ³ΠΈΠΈ, ΠΈΡΠΏΠΎΠ»ΡΠ·ΡΠ΅ΠΌΠΎΠΉ Π΄Π»Ρ ΡΠΎΠ·Π΄Π°Π½ΠΈΡ ΡΠ²Π°, Π±Π»Π°Π³ΠΎΠ΄Π°ΡΡ Π΅ΠΉ ΡΠ°Π·Π»ΠΈΡΠ°ΡΡ ΡΠ»Π΅Π΄ΡΡΡΠΈΠ΅ Π²ΠΈΠ΄Ρ ΡΠ²Π°ΡΠΊΠΈ ΠΌΠ΅ΡΠ°Π»Π»ΠΎΠ²:
- Π’Π΅ΡΠΌΠΈΡΠ΅ΡΠΊΠΈΠΉ
- Π’Π΅ΡΠΌΠΎΠΌΠ΅Ρ Π°Π½ΠΈΡΠ΅ΡΠΊΠΈΠΉ
- ΠΠ΅Ρ Π°Π½ΠΈΡΠ΅ΡΠΊΠΈΠΉ
ΠΠ° Π½Π°ΡΠ΅ΠΌ ΡΠ°ΠΉΡΠ΅ ΠΌΠΎΠΆΠ½ΠΎ Π·Π°ΠΊΠ°Π·Π°ΡΡ ΡΠ»Π΅Π΄ΡΡΡΠΈΠ΅ ΡΡΠ»ΡΠ³ΠΈ:
Π’Π΅ΡΠΌΠΈΡΠ΅ΡΠΊΠ°Ρ ΡΠ²Π°ΡΠΊΠ°
Π ΠΎΡΠ½ΠΎΠ²Π΅ ΡΠ΅ΡΠΌΠΈΡΠ΅ΡΠΊΠΈΡ ΡΠΏΠΎΡΠΎΠ±ΠΎΠ² ΡΠ²Π°ΡΠΊΠΈ ΠΈΡΠΏΠΎΠ»ΡΠ·ΡΠ΅ΡΡΡ Π½Π°Π³ΡΠ΅Π²:
- ΠΠ»Π΅ΠΊΡΡΠΎΠ΄ΡΠ³ΠΎΠ²Π°Ρ β ΠΎΠ΄ΠΈΠ½ ΠΈΠ· ΠΎΡΠ½ΠΎΠ²Π½ΡΡ
Π²ΠΈΠ΄ΠΎΠ² ΡΠ²Π°ΡΠΊΠΈ ΠΌΠ΅ΡΠ°Π»Π»ΠΎΠ².
ΠΠ»Π°Π³ΠΎΠ΄Π°ΡΡ ΠΏΡΠΎΠΈΠ·Π²ΠΎΠ΄ΡΡΠ²Ρ Π²ΡΡΠΎΠΊΠΎΠΉ ΡΠ΅ΠΌΠΏΠ΅ΡΠ°ΡΡΡΡ (Π½Π΅ ΠΌΠ΅Π½Π΅Π΅ 3000 Π³ΡΠ°Π΄ΡΡΠΎΠ²) ΠΌΠ΅ΠΆΠ΄Ρ ΡΠ»Π΅ΠΊΡΡΠΎΠ΄ΠΎΠΌ ΠΈ ΡΠ²Π°ΡΠΈΠ²Π°Π΅ΠΌΠΎΠΉ ΠΏΠΎΠ²Π΅ΡΡ Π½ΠΎΡΡΡΡ, ΠΏΠΎΠ»ΡΡΠ°Π΅ΡΡΡ ΡΠ²Π°ΡΠΈΠ²Π°ΡΡ Π±ΠΎΠ»ΡΡΠΈΠ΅ ΠΌΠ΅ΡΠ°Π»Π»ΠΈΡΠ΅ΡΠΊΠΈΠ΅ Π΄Π΅ΡΠ°Π»ΠΈ. ΠΠ»Π΅ΠΊΡΡΠΈΡΠ΅ΡΠΊΠ°Ρ Π΄ΡΠ³Π° ΠΏΠΎΠ·Π²ΠΎΠ»ΡΠ΅Ρ Π»Π΅Π³ΠΊΠΎ ΡΠΎΠ΅Π΄ΠΈΠ½ΡΡΡ ΡΡΠ°Π»Ρ, ΠΆΠ΅Π»Π΅Π·ΠΎ, Π°Π»ΡΠΌΠΈΠ½ΠΈΠΉ, ΠΌΠ΅Π΄Π½ΡΠ΅ ΡΠΏΠ»Π°Π²Ρ ΠΈ Π½ΠΈΠΊΠ΅Π»Ρ, ΡΠΎΠ·Π΄Π°Π²Π°Ρ Π΄ΠΎΠ»Π³ΠΎΠ²Π΅ΡΠ½ΡΠ΅ ΠΈ ΠΏΡΠΎΡΠ½ΡΠ΅ ΡΠ²Π°ΡΠ½ΡΠ΅ ΡΠ²Ρ.
- ΠΠ»Π΅ΠΊΡΡΠΎΡΠ»Π°ΠΊΠΎΠ²Π°Ρ β ΡΠ²Π°ΡΠΊΠ°, ΠΏΡΠΎΡ ΠΎΠ΄ΡΡΠ°Ρ Π² Π²Π΅ΡΡΠΈΠΊΠ°Π»ΡΠ½ΠΎΠΌ ΠΈΠ»ΠΈ Π±Π»ΠΈΠ·ΠΊΠΎΠΌ ΠΊ Π½Π΅ΠΌΡ ΠΏΠΎΠ»ΠΎΠΆΠ΅Π½ΠΈΠΈ, ΠΏΡΠΈ ΠΊΠΎΡΠΎΡΠΎΠΌ Π²ΡΠ΄Π΅Π»ΡΠ΅ΠΌΠΎΠ΅ ΡΠ»Π΅ΠΊΡΡΠΈΡΠ΅ΡΠΊΠΈΠΌ ΡΠΎΠΊΠΎΠΌ ΡΠ΅ΠΏΠ»ΠΎ ΠΏΡΠΎΡ ΠΎΠ΄ΠΈΡ ΡΠ΅ΡΠ΅Π· ΡΠ»ΠΎΠΉ ΠΆΠΈΠ΄ΠΊΠΎΠ³ΠΎ ΡΠ»Π°ΠΊΠ°. Π§Π°ΡΠ΅ Π²ΡΠ΅Π³ΠΎ ΠΏΡΠΈΠΌΠ΅Π½ΡΠ΅ΡΡΡ Π΄Π»Ρ ΡΠΎΠ΅Π΄ΠΈΠ½Π΅Π½ΠΈΡ ΠΌΠ°ΡΠ΅ΡΠΈΠ°Π»ΠΎΠ² Π±ΠΎΠ»ΡΡΠΎΠΉ ΡΠΎΠ»ΡΠΈΠ½Ρ, ΠΎΡΠ»ΠΈΡΠ°Π΅ΡΡΡ Π²ΡΡΠΎΠΊΠΎΠΉ ΡΡΡΠ΅ΠΊΡΠΈΠ²Π½ΠΎΡΡΡΡ ΠΈ ΠΌΠΈΠ½ΠΈΠΌΠ°Π»ΡΠ½ΡΠΌ ΡΠΈΡΠΊΠΎΠΌ ΡΡΠ΅ΡΠΈΠ½ΠΎΠΎΠ±ΡΠ°Π·ΠΎΠ²Π°Π½ΠΈΡ, ΠΎΡΡΡΡΡΡΠ²ΠΈΠ΅ΠΌ Π΄Π΅ΡΠΎΡΠΌΠ°ΡΠΈΠΈ ΡΡΡΠΊΠΎΠ²ΡΡ ΡΠΎΠ΅Π΄ΠΈΠ½Π΅Π½ΠΈΠΉ.
- ΠΠ»Π΅ΠΊΡΡΠΎΠ½Π½ΠΎ-Π»ΡΡΠ΅Π²Π°Ρ β ΡΠ΅Ρ
Π½ΠΈΠΊΠ° ΡΠΎΠ΅Π΄ΠΈΠ½Π΅Π½ΠΈΡ ΠΌΠ΅ΡΠ°Π»Π»ΠΎΠ², ΠΏΡΠΈ ΠΊΠΎΡΠΎΡΠΎΠΉ Π½Π°Π³ΡΠ΅Π² ΠΎΡΡΡΠ΅ΡΡΠ²Π»ΡΠ΅ΡΡΡ Π±Π»Π°Π³ΠΎΠ΄Π°ΡΡ ΡΠ½Π΅ΡΠ³ΠΈΠΈ ΡΡΠΊΠΎΡΠ΅Π½Π½ΡΡ
ΡΠ»Π΅ΠΊΡΡΠΎΠ½ΠΎΠ². ΠΠ°Π³ΡΠ΅Π² ΡΡΠΎΠΊΡΡΠΈΡΠΎΠ²Π°Π½Π½ΡΠΌ ΠΏΡΡΠΊΠΎΠΌ Π²ΡΡΠΎΠΊΠΎΡΠ½Π΅ΡΠ³Π΅ΡΠΈΡΠ΅ΡΠΊΠΈΡ
ΡΠ»Π΅ΠΊΡΡΠΎΠ½ΠΎΠ² ΠΎΡΡΡΠ΅ΡΡΠ²Π»ΡΠ΅ΡΡΡ Π»ΠΎΠΊΠ°Π»ΡΠ½ΠΎ, ΠΏΠΎΡΡΠΎΠΌΡ Π±ΠΎΠ»ΡΡΠ°Ρ ΡΠ°ΡΡΡ ΡΠ±ΠΎΡΠΊΠΈ ΠΎΡΡΠ°Π΅ΡΡΡ Ρ
ΠΎΠ»ΠΎΠ΄Π½ΠΎΠΉ ΠΈ ΡΡΠ°Π±ΠΈΠ»ΡΠ½ΠΎΠΉ. Π ΡΠ΅Π·ΡΠ»ΡΡΠ°ΡΠ΅ ΠΏΠΎΠ»ΡΡΠ°Π΅ΡΡΡ ΠΎΡΠ΅Π½Ρ ΡΠ·ΠΊΠΈΠΉ ΡΡΡΠΊ Ρ ΠΌΠΈΠ½ΠΈΠΌΠ°Π»ΡΠ½ΠΎΠΉ Π·ΠΎΠ½ΠΎΠΉ ΡΠ΅ΡΠΌΠΈΡΠ΅ΡΠΊΠΎΠ³ΠΎ Π²Π»ΠΈΡΠ½ΠΈΡ.
- ΠΠ»Π°Π·ΠΌΠ΅Π½Π½Π°Ρ β ΡΠΈΠΏ ΡΠ²Π°ΡΠΊΠΈ ΠΌΠ΅ΡΠ°Π»Π»Π°, Π² ΠΊΠΎΡΠΎΡΠΎΠΌ Π΄Π»Ρ Π½Π°Π³ΡΠ΅Π²Π° ΠΈΡΠΏΠΎΠ»ΡΠ·ΡΠ΅ΡΡΡ ΡΠΆΠ°ΡΠ°Ρ Π΄ΡΠ³Π°, Π° Π² ΠΊΠ°ΡΠ΅ΡΡΠ²Π΅ ΠΈΡΡΠΎΡΠ½ΠΈΠΊΠ° ΡΠ½Π΅ΡΠ³ΠΈΠΈ Π²ΡΡΡΡΠΏΠ°Π΅Ρ ΠΏΠ»Π°Π·ΠΌΠ΅Π½Π½ΡΠΉ ΡΠΎΠΊ.
- Π’Π΅ΡΠΌΠΈΡΠ½Π°Ρ β Π²ΠΈΠ΄ ΡΠ²Π°ΡΠΊΠΈ ΠΏΠΎ ΠΌΠ΅ΡΠ°Π»Π»Ρ, Π½Π°Π·Π²Π°Π½ΠΈΠ΅ ΠΊΠΎΡΠΎΡΠΎΠ³ΠΎ ΠΏΠΎΡΠ»ΠΎ ΠΎΡ ΠΏΡΠΈΠΌΠ΅Π½ΡΠ΅ΠΌΡΡ Π² ΠΏΡΠΎΡΠ΅ΡΡΠ΅ ΡΠΎΠ΅Π΄ΠΈΠ½Π΅Π½ΠΈΡ ΡΠ΅ΡΠΌΠΈΡΠΎΠ². Π’Π΅ΡΠΌΠΈΡ β ΡΠΌΠ΅ΡΡ ΠΎΠΊΡΠΈΠ΄Π° ΠΆΠ΅Π»Π΅Π·Π° ΠΈ ΠΏΠΎΡΠΎΡΠΊΠΎΠ²ΠΎΠ³ΠΎ Π°Π»ΡΠΌΠΈΠ½ΠΈΡ. ΠΡΠΈ Π΅Π³ΠΎ Π½Π°Π³ΡΠ΅Π²Π°Π½ΠΈΠΈ Π΄ΠΎ 1000 Π³ΡΠ°Π΄ΡΡΠΎΠ² ΠΏΡΠΎΠΈΡΡ ΠΎΠ΄ΠΈΡ Π±ΡΡΠ½Π°Ρ ΡΠΊΠ·ΠΎΡΠ΅ΡΠΌΠΈΡΠ΅ΡΠΊΠ°Ρ ΡΠ΅Π°ΠΊΡΠΈΡ Π²ΠΎΡΡΡΠ°Π½ΠΎΠ²Π»Π΅Π½ΠΈΡ ΠΎΠΊΡΠΈΠ΄Π° ΠΆΠ΅Π»Π΅Π·Π°. Π’Π΅ΡΠΌΠΈΠ½ Π²ΡΠ³ΠΎΡΠ°Π΅Ρ Ρ ΠΎΠ³ΡΠΎΠΌΠ½ΡΠΌ ΡΠ΅ΠΏΠ»ΠΎΠ²ΡΠ΄Π΅Π»Π΅Π½ΠΈΠ΅ΠΌ (ΠΏΠΎΡΡΠ΄ΠΊΠ° 3000 Π³ΡΠ°Π΄ΡΡΠΎΠ² ΠΏΠΎ Π¦Π΅Π»ΡΡΠΈΡ) ΠΈ ΡΠΏΠΎΡΠΎΠ±ΡΡΠ²ΡΠ΅Ρ ΠΎΠ±ΡΠ°Π·ΠΎΠ²Π°Π½ΠΈΡ ΠΆΠΈΠ΄ΠΊΠΎΠ³ΠΎ ΠΆΠ΅Π»Π΅Π·Π°, ΠΊΠΎΡΠΎΡΠΎΠ΅ Π·Π°ΠΏΠΎΠ»Π½ΡΠ΅Ρ ΠΏΡΠ°Π²ΠΈΠ»ΡΠ½ΠΎ ΠΏΠΎΠ΄Π³ΠΎΡΠΎΠ²Π»Π΅Π½Π½ΡΠ΅ ΡΠΎΡΠΌΡ, ΡΠΎΠ·Π΄Π°Π²Π°Ρ ΠΏΡΠΎΡΠ½ΡΠΉ ΡΠΎΠ². ΠΡΠΈΠΌΠ΅Π½ΡΠ΅ΡΡΡ Π΄Π»Ρ:
- ΡΠΎΠ΅Π΄ΠΈΠ½Π΅Π½ΠΈΡ ΡΡΠ°Π»ΡΠ½ΡΡ ΠΈ ΡΡΠ³ΡΠ½Π½ΡΡ ΠΈΠ·Π΄Π΅Π»ΠΈΠΉ Π±ΠΎΠ»ΡΡΠΎΠ³ΠΎ ΡΠ΅ΡΠ΅Π½ΠΈΡ;
- ΡΠ΅ΠΌΠΎΠ½ΡΠ° ΠΆΠ΅Π»Π΅Π·Π½ΠΎΠ΄ΠΎΡΠΎΠΆΠ½ΡΡ ΡΠ΅Π»ΡΡΠΎΠ² ΠΈ Π΄Π΅ΡΠ΅ΠΊΡΠΎΠ² ΠΎΡΠ»ΠΈΠ²ΠΊΠΈ;
- ΡΠ΅ΠΌΠΎΠ½Ρ Π²Π°Π»ΠΎΠ² Ρ ΡΡΠ΅ΡΠΈΠ½Π°ΠΌΠΈ.
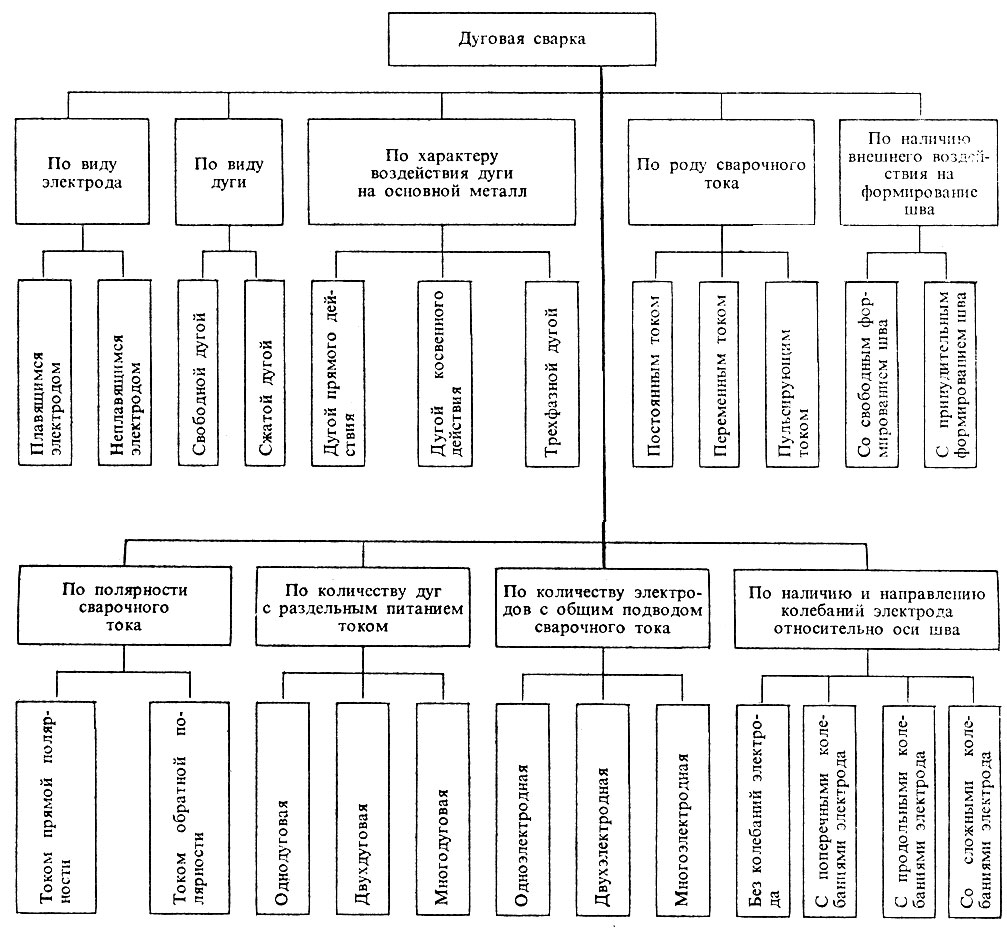
Π’Π΅ΡΠΌΠΎΠΌΠ΅Ρ Π°Π½ΠΈΡΠ΅ΡΠΊΠΈΠ΅ ΠΌΠ΅ΡΠΎΠ΄Ρ
Π ΡΠ΅ΡΠΌΠΎΠΌΠ΅Ρ Π°Π½ΠΈΡΠ΅ΡΠΊΠΎΠΌΡ ΠΈΠ»ΠΈ ΠΊΠΎΠΌΠ±ΠΈΠ½ΠΈΡΠΎΠ²Π°Π½Π½ΠΎΠΌΡ Π²ΠΈΠ΄Ρ ΡΠ²Π°ΡΠΊΠΈ ΠΎΡΠ½ΠΎΡΡΡ ΡΠΏΠΎΡΠΎΠ±Ρ ΡΠΎΠ΅Π΄ΠΈΠ½Π΅Π½ΠΈΡ ΠΌΠ΅ΡΠ°Π»Π»ΠΎΠ² ΠΏΡΡΠ΅ΠΌ ΠΈΡ Π½Π°Π³ΡΠ΅Π²Π° ΠΈ Π΄Π°Π²Π»Π΅Π½ΠΈΡ:
- ΠΡΠ΅ΡΡΠΎΠ²Π°Ρ β ΡΠ»Π΅ΠΌΠ΅Π½ΡΡ ΡΠΎΠ΅Π΄ΠΈΠ½ΡΡΡΡΡ Π±Π»Π°Π³ΠΎΠ΄Π°ΡΡ ΡΠ°Π²Π½ΠΎΠΌΠ΅ΡΠ½ΠΎΠΌΡ Π½Π°Π³ΡΠ΅Π²Ρ ΠΈ ΠΏΠΎΡΠ»Π΅Π΄ΡΡΡΠ΅ΠΌΡ ΡΡΠ°ΠΌΠΏΠΎΠ²ΠΎΠΌΡ ΡΠΆΠ°ΡΠΈΡ.
- ΠΠΎΠ½ΡΠ°ΠΊΡΠ½Π°Ρ β Π½Π°Π³ΡΠ΅Π² ΠΏΡΠΎΠΈΠ·Π²ΠΎΠ΄ΠΈΡΡΡ ΡΠ»Π΅ΠΊΡΡΠΈΡΠ΅ΡΠΊΠΈΠΌ ΡΠΎΠΊΠΎΠΌ, ΠΏΠΎΡΠ»Π΅ ΡΠ΅Π³ΠΎ ΠΌΠ΅ΡΡΠ° ΡΠΎΠ΅Π΄ΠΈΠ½Π΅Π½ΠΈΡ ΠΏΠΎΠ΄Π²Π΅ΡΠ³Π°ΡΡΡΡ ΠΏΠ»Π°ΡΡΠΈΡΠ΅ΡΠΊΠΎΠΉ Π΄Π΅ΡΠΎΡΠΌΠ°ΡΠΈΠΈ.
- ΠΠΈΡΡΡΠ·ΠΈΠΎΠ½Π½Π°Ρ β ΡΠΎΠ΅Π΄ΠΈΠ½Π΅Π½ΠΈΠ΅ ΠΏΠΎΠ»ΡΡΠ°ΡΡ Π±Π»Π°Π³ΠΎΠ΄Π°ΡΡ Π²Π·Π°ΠΈΠΌΠ½ΠΎΠΉ Π΄ΠΈΡΡΡΠ·ΠΈΠΈ Π°ΡΠΎΠΌΠΎΠ².
ΠΠΈΡΡΡΠ·ΠΈΡ ΠΏΡΠΎΠΈΡΡ ΠΎΠ΄ΠΈΡ Π² Π²Π΅ΡΡ Π½ΠΈΡ ΡΠ»ΠΎΡΡ ΠΌΠ΅ΡΠ°Π»Π»Π° Π·Π° ΡΡΠ΅Ρ Π½Π°Π³ΡΠ΅Π²Π° ΠΈ ΡΠΆΠ°ΡΠΈΡ Ρ Π΄Π»ΠΈΡΠ΅Π»ΡΠ½ΠΎΠΉ Π²ΡΠ΄Π΅ΡΠΆΠΊΠΎΠΉ.
- Π‘Π²Π°ΡΠΊΠ° Π’ΠΠ§ β ΡΠ²Π°ΡΠ½ΡΠ΅ ΡΠ²Ρ Π½Π°Π³ΡΠ΅Π²Π°ΡΡΡΡ ΡΠΎΠΊΠ°ΠΌΠΈ Π²ΡΡΠΎΠΊΠΎΠΉ ΡΠ°ΡΡΠΎΡΡ.
- ΠΠ΅ΡΠ½Π°Ρ β ΠΌΠ΅ΡΠ°Π»Π» Π½Π°Π³ΡΠ΅Π²Π°ΡΡ Π² Π³ΠΎΡΠ½Π΅ Π»ΠΈΠ±ΠΎ ΠΏΠ΅ΡΠΈ, ΡΠΎΠ΅Π΄ΠΈΠ½ΡΡ Π΅Π³ΠΎ ΡΠ΄Π°ΡΠ°ΠΌΠΈ ΠΌΠΎΠ»ΠΎΡΠ°.
- Π’Π΅ΡΠΌΠΈΡΠ½Π°Ρ Ρ Π΄Π°Π²Π»Π΅Π½ΠΈΠ΅ΠΌ β Π½Π°Π³ΡΠ΅Π² ΠΏΡΠΎΠΈΠ·Π²ΠΎΠ΄ΠΈΡΡΡ Π·Π° ΡΡΠ΅Ρ ΠΈΡΠΏΠΎΠ»ΡΠ·ΠΎΠ²Π°Π½ΠΈΡ ΡΠ΅ΡΠΌΠΈΡΠ° (ΡΠΌΠ΅ΡΠΈ ΠΎΠΊΡΠΈΠ΄Π° ΠΆΠ΅Π»Π΅Π·Π° ΠΈ ΠΏΠΎΡΠΎΡΠΊΠΎΠ²ΠΎΠ³ΠΎ Π°Π»ΡΠΌΠΈΠ½ΠΈΡ Π»ΠΈΠ±ΠΎ ΠΌΠ°Π³Π½ΠΈΡ), ΠΏΠΎΡΠ»Π΅ ΡΠ΅Π³ΠΎ ΡΠ»Π΅ΠΌΠ΅Π½ΡΡ ΡΠΎΠ΅Π΄ΠΈΠ½ΡΡΡΡΡ ΠΏΠΎΠ΄ Π΄Π°Π²Π»Π΅Π½ΠΈΠ΅ΠΌ.
ΠΠ΅Ρ Π°Π½ΠΈΡΠ΅ΡΠΊΠΈΠ΅ ΠΌΠ΅ΡΠΎΠ΄Ρ
ΠΠ°ΠΊΠΈΠ΅ Π΅ΡΠ΅ Π΅ΡΡΡ Π²ΠΈΠ΄Ρ ΡΠ²Π°ΡΠΊΠΈ ΠΌΠ΅ΡΠ°Π»Π»ΠΎΠ²? Π‘ΡΡΠ΅ΡΡΠ²ΡΠ΅Ρ Π½Π΅ΡΠΊΠΎΠ»ΡΠΊΠΎ ΡΠΈΠΏΠΎΠ² ΡΠ²Π°ΡΠΊΠΈ Ρ ΠΈΡΠΏΠΎΠ»ΡΠ·ΠΎΠ²Π°Π½ΠΈΠ΅ΠΌ ΠΌΠ΅Ρ Π°Π½ΠΈΡΠ΅ΡΠΊΠΎΠΉ ΡΠ½Π΅ΡΠ³ΠΈΠΈ ΠΈ Π΄Π°Π²Π»Π΅Π½ΠΈΡ. Π Π½ΠΈΠΌ ΠΎΡΠ½ΠΎΡΡΡ:
- Π£Π»ΡΡΡΠ°Π·Π²ΡΠΊΠΎΠ²Π°Ρ ΡΠ²Π°ΡΠΊΠ° β ΡΠ°Π·Π½ΠΎΠ²ΠΈΠ΄Π½ΠΎΡΡΡ ΡΠ²Π°ΡΠΊΠΈ, Π² ΠΊΠΎΡΠΎΡΠΎΠΉ ΠΌΠ΅ΡΠ°Π»Π»Ρ ΡΠΎΠ΅Π΄ΠΈΠ½ΡΡΡΡΡ ΠΏΠΎΠ΄ Π΄Π΅ΠΉΡΡΠ²ΠΈΠ΅ΠΌ ΡΠ»ΡΡΡΠ°Π·Π²ΡΠΊΠΎΠ²ΡΡ ΠΊΠΎΠ»Π΅Π±Π°Π½ΠΈΠΉ.
- Π₯ΠΎΠ»ΠΎΠ΄Π½Π°Ρ β ΡΠ²Π°ΡΠΊΠ° ΡΠ»Π΅ΠΌΠ΅Π½ΡΠΎΠ² Π±Π»Π°Π³ΠΎΠ΄Π°ΡΡ ΠΏΠ»Π°ΡΡΠΈΡΠ΅ΡΠΊΠΎΠΉ Π΄Π΅ΡΠΎΡΠΌΠ°ΡΠΈΠΈ Π·ΠΎΠ½Ρ ΡΠΊΡΠ΅ΠΏΠ»Π΅Π½ΠΈΡ, Π±Π΅Π· Π½Π°Π³ΡΠ΅Π²Π° ΠΎΡ Π²Π½Π΅ΡΠ½Π΅Π³ΠΎ ΠΈΡΡΠΎΡΠ½ΠΈΠΊΠ° ΡΠ΅ΠΏΠ»Π°. Π Π°Π·Π»ΠΈΡΠ°ΡΡ ΡΡΠ΅ΡΠ½Π΅Π½Π½ΡΠΉ ΠΈ ΡΠ²ΠΎΠ±ΠΎΠ΄Π½ΡΠΉ ΡΠΏΠΎΡΠΎΠ±Ρ.
- Π‘Π²Π°ΡΠΊΠ° Π²Π·ΡΡΠ²ΠΎΠΌ β ΠΌΠ΅ΡΠΎΠ΄ ΡΠΎΠ΅Π΄ΠΈΠ½Π΅Π½ΠΈΡ ΠΌΠ΅ΡΠ°Π»Π»ΠΎΠ², ΠΏΡΠΈ ΠΊΠΎΡΠΎΡΠΎΠΌ ΠΏΡΠΎΠΈΡΡ
ΠΎΠ΄ΠΈΡ ΠΏΡΠΎΡΠ΅ΡΡ Π΄ΠΈΠ½Π°ΠΌΠΈΡΠ΅ΡΠΊΠΎΠ³ΠΎ Π΄Π°Π²Π»Π΅Π½ΠΈΡ ΡΠΎΠ΅Π΄ΠΈΠ½ΡΠ΅ΠΌΡΡ
ΠΏΠΎΠ²Π΅ΡΡ
Π½ΠΎΡΡΠ΅ΠΉ Π·Π° ΡΡΠ΅Ρ ΡΠ½Π΅ΡΠ³ΠΈΠΈ, Π²ΡΠ΄Π΅Π»ΡΡΡΠ΅ΠΉΡΡ Π² ΡΠ΅Π·ΡΠ»ΡΡΠ°ΡΠ΅ Π΄Π΅ΡΠΎΠ½Π°ΡΠΈΠΈ Π²Π·ΡΡΠ²ΡΠ°ΡΠΎΠ³ΠΎ Π²Π΅ΡΠ΅ΡΡΠ²Π°.
- ΠΠ°Π³Π½ΠΈΡΠ½ΠΎ-ΠΈΠΌΠΏΡΠ»ΡΡΠ½ΠΎΠ΅ ΡΠΎΠ΅Π΄ΠΈΠ½Π΅Π½ΠΈΠ΅ β ΡΡΠΎ ΠΏΡΠΎΡΠ΅ΡΡ ΡΠ²Π°ΡΠΊΠΈ Π΄Π²ΡΡ ΡΠ»Π΅ΠΌΠ΅Π½ΡΠΎΠ² Ρ ΠΈΡΠΏΠΎΠ»ΡΠ·ΠΎΠ²Π°Π½ΠΈΠ΅ΠΌ ΠΌΠ°Π³Π½ΠΈΡΠ½ΡΡ ΡΠΈΠ». Π‘Π°ΠΌΡΠΌ Π±ΠΎΠ»ΡΡΠΈΠΌ ΠΏΡΠ΅ΠΈΠΌΡΡΠ΅ΡΡΠ²ΠΎΠΌ ΠΈΡΠΏΠΎΠ»ΡΠ·ΠΎΠ²Π°Π½ΠΈΡ ΠΌΠ°Π³Π½ΠΈΡΠ½ΠΎ-ΠΈΠΌΠΏΡΠ»ΡΡΠ½ΠΎΠΉ ΡΠ²Π°ΡΠΊΠΈ ΡΠ²Π»ΡΠ΅ΡΡΡ ΠΏΡΠ΅Π΄ΠΎΡΠ²ΡΠ°ΡΠ΅Π½ΠΈΠ΅ ΠΎΠ±ΡΠ°Π·ΠΎΠ²Π°Π½ΠΈΡ Ρ ΡΡΠΏΠΊΠΈΡ ΠΈΠ½ΡΠ΅ΡΠΌΠ΅ΡΠ°Π»Π»ΠΈΡΠ΅ΡΠΊΠΈΡ ΡΠ°Π·, ΡΠ»Π΅Π΄ΠΎΠ²Π°ΡΠ΅Π»ΡΠ½ΠΎ, ΠΌΠΎΠΆΠ½ΠΎ ΡΠ²Π°ΡΠΈΠ²Π°ΡΡ ΡΠ°Π·Π½ΡΠ΅ ΠΌΠ΅ΡΠ°Π»Π»Ρ, ΠΊΠΎΡΠΎΡΡΠ΅ Π½Π΅Π»ΡΠ·Ρ ΡΠΎΠ΅Π΄ΠΈΠ½ΠΈΡΡ ΡΠ΅ΡΠΌΠΈΡΠ΅ΡΠΊΠΎΠΉ ΡΠ²Π°ΡΠΊΠΎΠΉ.
ΠΡΠ½ΠΎΠ²Π½ΡΠ΅ ΠΌΠ΅ΡΠΎΠ΄Ρ ΡΠ²Π°ΡΠΊΠΈ
Π ΠΎΡΠ½ΠΎΠ²Π½ΡΠΌ (Π½Π°ΠΈΠ±ΠΎΠ»Π΅Π΅ ΡΠ°ΡΠΏΡΠΎΡΡΡΠ°Π½Π΅Π½Π½ΡΠΌ) ΠΌΠ΅ΡΠΎΠ΄Π°ΠΌ ΡΠ²Π°ΡΠΊΠΈ ΠΎΡΠ½ΠΎΡΡΡ ΡΠ»Π΅ΠΊΡΡΠΎ- ΠΈ Π³Π°Π·ΠΎΠ²ΡΡ ΡΠ²Π°ΡΠΊΡ.
ΠΠ»Π΅ΠΊΡΡΠΎΡΠ²Π°ΡΠΊΠ° β ΠΏΠΎΠ»ΡΡΠ΅Π½ΠΈΠ΅ Π½Π°Π΄Π΅ΠΆΠ½ΡΡ
ΠΈ Π΄ΠΎΠ»Π³ΠΎΠ²Π΅ΡΠ½ΡΡ
ΡΠΎΠ΅Π΄ΠΈΠ½Π΅Π½ΠΈΠΉ Ρ ΠΈΡΠΏΠΎΠ»ΡΠ·ΠΎΠ²Π°Π½ΠΈΠ΅ΠΌ ΡΠ»Π΅ΠΊΡΡΠΈΡΠ΅ΡΠΊΠΎΠΉ Π΄ΡΠ³ΠΈ. Π‘Π²Π°ΡΠΎΡΠ½ΡΠ΅ ΡΠ°Π±ΠΎΡΡ ΠΌΠΎΠ³ΡΡ ΠΏΡΠΎΠΈΠ·Π²ΠΎΠ΄ΠΈΡΡΡΡ ΠΊΠ°ΠΊ Π½Π° Π²ΠΎΠ·Π΄ΡΡ
Π΅, ΡΠ°ΠΊ ΠΈ Π² ΠΏΠΎΠΌΠ΅ΡΠ΅Π½ΠΈΠΈ. Π Π°Π·Π»ΠΈΡΠ°ΡΡ Π°Π²ΡΠΎΠΌΠ°ΡΠΈΡΠ΅ΡΠΊΡΡ, ΠΏΠΎΠ»ΡΠ°Π²ΡΠΎΠΌΠ°ΡΠΈΡΠ΅ΡΠΊΡΡ ΠΈ ΡΡΡΠ½ΡΡ ΡΠΈΠΏΡ ΡΠ²Π°ΡΠΊΠΈ. ΠΠΎΡΠ»Π΅Π΄Π½ΡΡ ΠΌΠΎΠΆΠ½ΠΎ Π½Π°Π·Π²Π°ΡΡ ΡΠ°ΠΌΠΎΠΉ ΡΠ°ΡΠΏΡΠΎΡΡΡΠ°Π½Π΅Π½Π½ΠΎΠΉ. ΠΡΠΈ ΠΏΡΠΎΠ²Π΅Π΄Π΅Π½ΠΈΠΈ ΡΡΡΠ½ΠΎΠΉ ΡΠ²Π°ΡΠΊΠΈ, ΡΠ²Π°ΡΡΠΈΠΊ ΠΈΠΌΠ΅Π΅Ρ Π²ΠΎΠ·ΠΌΠΎΠΆΠ½ΠΎΡΡΡ ΡΠ°ΠΌ ΠΎΠΏΡΠ΅Π΄Π΅Π»ΡΡΡ Π½ΡΠΆΠ½ΡΠΉ Π΄Π»Ρ Π½Π΅Π³ΠΎ Π² Π΄Π°Π½Π½ΠΎΠΉ ΡΠΈΡΡΠ°ΡΠΈΠΈ ΡΠ΅ΠΆΠΈΠΌ ΠΏΠΎΠ΄Π°ΡΠΈ ΡΠ»Π΅ΠΊΡΡΠΎΠ΄Π°. ΠΠΎΠ»ΡΠ°Π²ΡΠΎΠΌΠ°ΡΠΈΡΠ΅ΡΠΊΠΈΠΉ ΡΠΏΠΎΡΠΎΠ± ΠΏΡΠ΅Π΄ΠΏΠΎΠ»Π°Π³Π°Π΅Ρ ΠΏΠΎΠ΄Π°ΡΡ ΡΠ»Π΅ΠΊΡΡΠΎΠ΄Π½ΠΎΠΉ ΠΏΡΠΎΠ²ΠΎΠ»ΠΎΠΊΠΈ Π² Π·ΠΎΠ½Ρ ΡΠΎΠ·Π΄Π°Π½ΠΈΡ ΡΠ²Π° ΡΠΏΠ΅ΡΠΈΠ°Π»ΡΠ½ΡΠΌ ΡΡΡΡΠΎΠΉΡΡΠ²ΠΎΠΌ.
Π ΠΏΡΠΎΡΠ΅ΡΡΠ΅ ΡΠ²Π°ΡΠΊΠΈ ΠΌΠ΅ΡΠ°Π»Π»ΠΎΠ² ΠΏΡΠΈΠΌΠ΅Π½ΡΠ΅ΡΡΡ ΡΠΏΠ΅ΡΠΈΠ°Π»ΡΠ½ΠΎΠ΅ ΡΠ²Π°ΡΠΎΡΠ½ΠΎΠ΅ ΠΎΠ±ΠΎΡΡΠ΄ΠΎΠ²Π°Π½ΠΈΠ΅: ΠΊΠΎΠΌΠΏΠ°ΠΊΡΠ½ΡΠ΅ ΠΈΠ½Π²Π΅ΡΡΠΎΡΡ, ΡΡΠ°Π½ΡΡΠΎΡΠΌΠ°ΡΠΎΡΡ, Π²ΡΠΏΡΡΠΌΠΈΡΠ΅Π»ΠΈ ΡΠ»Π΅ΠΊΡΡΠΈΡΠ΅ΡΠΊΠΎΠ³ΠΎ ΡΠΎΠΊΠ°.
ΠΠ°Π·ΠΎΡΠ²Π°ΡΠΊΠ° β ΠΌΠ΅ΡΠΎΠ΄, ΠΏΠΎΠ·Π²ΠΎΠ»ΡΡΡΠΈΠΉ ΠΏΠΎΠ»ΡΡΠ°ΡΡ Π²ΡΡΠΎΠΊΠΎΠΏΡΠΎΡΠ½ΡΠ΅ ΡΠΎΠ΅Π΄ΠΈΠ½Π΅Π½ΠΈΡ Π΄Π΅ΡΠ°Π»Π΅ΠΉ ΠΈΠ· ΡΡΠ°Π»ΠΈ, Π»Π°ΡΡΠ½ΠΈ, Π±ΡΠΎΠ½Π·Ρ ΠΈ ΡΡΠ³ΡΠ½Π°.
Π‘Π²Π°ΡΠΎΡΠ½ΡΠ΅ ΡΠ°Π±ΠΎΡΡ. ΠΡΠ΅ Π²ΠΈΠ΄Ρ ΡΠ²Π°ΡΠΎΡΠ½ΡΡ ΡΠ°Π±ΠΎΡ. ΠΡΠ±ΡΠ΅ ΠΌΠ΅ΡΠ°Π»Π»Ρ
ΠΠΎΠΌΠΈΠΌΠΎ Π²ΡΡΠΎΠΊΠΎΠΊΠ°ΡΠ΅ΡΡΠ²Π΅Π½Π½ΠΎΠΉ Π»Π°Π·Π΅ΡΠ½ΠΎΠΉ ΡΠ΅Π·ΠΊΠΈ, Π½Π°ΡΠ° ΠΊΠΎΠΌΠΏΠ°Π½ΠΈΡ ΠΏΡΠ΅Π΄Π»Π°Π³Π°Π΅Ρ ΡΠ²ΠΎΠΈΠΌ ΠΊΠ»ΠΈΠ΅Π½ΡΠ°ΠΌ ΡΠΈΡΠΎΠΊΠΈΠΉ ΡΠΏΠ΅ΠΊΡΡ Π΄ΠΎΠΏΠΎΠ»Π½ΠΈΡΠ΅Π»ΡΠ½ΡΡ ΡΡΠ»ΡΠ³. ΠΠΎ ΠΠ°ΡΠ΅ΠΌΡ ΠΆΠ΅Π»Π°Π½ΠΈΡΒ ΡΠΏΠ΅ΡΠΈΠ°Π»ΠΈΡΡΡ Π½Π°ΡΠ΅ΠΉ ΠΊΠΎΠΌΠΏΠ°Π½ΠΈΠΈ ΠΎΡΡΡΠ΅ΡΡΠ²ΡΡ Π³ΠΈΠ±ΠΊΡ, ΡΠ²Π°ΡΠΊΡ, Π²Π°Π»ΡΡΠΎΠ²ΠΊΡ, Π·ΠΈΠ³ΠΎΠ²ΠΊΡ ΠΈ Π΄ΡΡΠ³ΠΈΠ΅ Π²ΠΈΠ΄Ρ ΡΠ°Π±ΠΎΡ, ΡΠ²ΡΠ·Π°Π½Π½ΡΠ΅ Ρ ΠΎΠ±ΡΠ°Π±ΠΎΡΠΊΠΎΠΉ ΠΌΠ΅ΡΠ°Π»Π»Π°.
Π‘ΠΠΠ ΠΠ β ΠΎΠ΄Π½Π° ΠΈΠ· ΡΠ°ΠΌΡΡ Π½Π΅ΠΎΠ±Ρ ΠΎΠ΄ΠΈΠΌΡΡ ΡΠ΅Ρ Π½ΠΎΠ»ΠΎΠ³ΠΈΠΉ Π² ΠΏΡΠΎΡΠ΅ΡΡΠ΅ ΠΌΠ΅ΡΠ°Π»Π»ΠΎΠΎΠ±ΡΠ°Π±ΠΎΡΠΊΠΈ. ΠΠ°ΡΠΈ ΠΏΡΠΎΠΈΠ·Π²ΠΎΠ΄ΡΡΠ²Π΅Π½Π½ΡΠ΅ ΠΌΠΎΡΠ½ΠΎΡΡΠΈ ΠΏΠΎΠ·Π²ΠΎΠ»ΡΡΡ Π½Π°ΠΌ Π²ΡΠΏΠΎΠ»Π½ΡΡΡ ΡΠ»Π΅Π΄ΡΡΡΠΈΠ΅ Π²ΠΈΠ΄Ρ ΡΠ²Π°ΡΠΎΡΠ½ΡΡ ΡΠ°Π±ΠΎΡ:
- ΠΠ»Π΅ΠΊΡΡΠΎΠ΄ΡΠ³ΠΎΠ²Π°Ρ ΡΠ²Π°ΡΠΊΠ°. ΠΡΡΠΎΡΠ½ΠΈΠΊΠΎΠΌ ΡΠ΅ΠΏΠ»ΠΎΡΡ ΡΠ²Π»ΡΠ΅ΡΡΡ ΡΠ»Π΅ΠΊΡΡΠΈΡΠ΅ΡΠΊΠ°Ρ Π΄ΡΠ³Π°, Π²ΠΎΠ·Π½ΠΈΠΊΠ°ΡΡΠ°Ρ ΠΌΠ΅ΠΆΠ΄Ρ ΡΠΎΡΡΠΎΠΌ ΡΠ»Π΅ΠΊΡΡΠΎΠ΄Π° ΠΈ ΡΠ²Π°ΡΠΈΠ²Π°Π΅ΠΌΡΠΌ ΠΈΠ·Π΄Π΅Π»ΠΈΠ΅ΠΌ ΠΏΡΠΈ ΠΏΡΠΎΡΠ΅ΠΊΠ°Π½ΠΈΠΈ ΡΠ²Π°ΡΠΎΡΠ½ΠΎΠ³ΠΎ ΡΠΎΠΊΠ° Π² ΡΠ΅Π·ΡΠ»ΡΡΠ°ΡΠ΅ Π·Π°ΠΌΡΠΊΠ°Π½ΠΈΡ Π²Π½Π΅ΡΠ½Π΅ΠΉ ΡΠ΅ΠΏΠΈ ΡΠ»Π΅ΠΊΡΡΠΎΡΠ²Π°ΡΠΎΡΠ½ΠΎΠ³ΠΎ Π°ΠΏΠΏΠ°ΡΠ°ΡΠ°.
ΠΡΠ½ΠΎΠ²Π½ΡΠΌΠΈ ΡΠ°Π·Π½ΠΎΠ²ΠΈΠ΄Π½ΠΎΡΡΡΠΌΠΈ ΡΠ»Π΅ΠΊΡΡΠΎΠ΄ΡΠ³ΠΎΠ²ΠΎΠΉ ΡΠ²Π°ΡΠΊΠΈ ΡΠ²Π»ΡΡΡΡΡ: ΡΡΡΠ½Π°Ρ Π΄ΡΠ³ΠΎΠ²Π°Ρ ΡΠ²Π°ΡΠΊΠ°, ΡΠ²Π°ΡΠΊΠ° Π½Π΅ΠΏΠ»Π°Π²ΡΡΠΈΠΌΡΡ ΡΠ»Π΅ΠΊΡΡΠΎΠ΄ΠΎΠΌ, ΡΠ²Π°ΡΠΊΠ° ΠΏΠ»Π°Π²ΡΡΠΈΠΌΡΡ ΡΠ»Π΅ΠΊΡΡΠΎΠ΄ΠΎΠΌ, ΡΠ²Π°ΡΠΊΠ° ΠΏΠΎΠ΄ ΡΠ»ΡΡΠΎΠΌ, ΡΠ»Π΅ΠΊΡΡΠΎΡΠ»Π°ΠΊΠΎΠ²Π°Ρ ΡΠ²Π°ΡΠΊΠ°.
- ΠΠΎΠ½ΡΠ°ΠΊΡΠ½Π°Ρ ΡΠ²Π°ΡΠΊΠ°. ΠΡΠΈ ΡΠ²Π°ΡΠΊΠ΅ ΠΏΡΠΎΠΈΡΡ ΠΎΠ΄ΡΡ Π΄Π²Π° ΠΏΠΎΡΠ»Π΅Π΄ΠΎΠ²Π°ΡΠ΅Π»ΡΠ½ΡΡ ΠΏΡΠΎΡΠ΅ΡΡΠ°: Π½Π°Π³ΡΠ΅Π² ΡΠ²Π°ΡΠΈΠ²Π°Π΅ΠΌΡΡ ΠΈΠ·Π΄Π΅Π»ΠΈΠΉ Π΄ΠΎ ΠΏΠ»Π°ΡΡΠΈΡΠ΅ΡΠΊΠΎΠ³ΠΎ ΡΠΎΡΡΠΎΡΠ½ΠΈΡ ΠΈ ΠΈΡ ΡΠΎΠ²ΠΌΠ΅ΡΡΠ½ΠΎΠ΅ ΠΏΠ»Π°ΡΡΠΈΡΠ΅ΡΠΊΠΎΠ΅ Π΄Π΅ΡΠΎΡΠΌΠΈΡΠΎΠ²Π°Π½ΠΈΠ΅. ΠΡΠ½ΠΎΠ²Π½ΡΠΌΠΈ ΡΠ°Π·Π½ΠΎΠ²ΠΈΠ΄Π½ΠΎΡΡΡΠΌΠΈ ΠΊΠΎΠ½ΡΠ°ΠΊΡΠ½ΠΎΠΉ ΡΠ²Π°ΡΠΊΠΈ ΡΠ²Π»ΡΡΡΡΡ: ΡΠΎΡΠ΅ΡΠ½Π°Ρ ΡΠ»Π΅ΠΊΡΡΠΎΡΠ²Π°ΡΠΊΠ°, ΡΡΡΠΊΠΎΠ²Π°Ρ ΡΠ²Π°ΡΠΊΠ°, ΡΠ΅Π»ΡΠ΅ΡΠ½Π°Ρ ΡΠ²Π°ΡΠΊΠ°, ΡΠΎΠ²Π½Π°Ρ ΡΠ²Π°ΡΠΊΠ°.
- ΠΡΠ³ΠΎΠ½Π½ΠΎ-Π΄ΡΠ³ΠΎΠ²Π°Ρ ΡΠ²Π°ΡΠΊΠ°. ΠΡΠΏΠΎΠ»Π½ΡΠ΅ΡΡΡ Π³ΠΎΡΠ΅Π»ΠΊΠ°ΠΌΠΈ, ΠΏΠΎΠ·Π²ΠΎΠ»ΡΡΡΠΈΠΌΠΈ ΠΎΠΊΡΡΠΆΠ°ΡΡ ΡΠ»Π΅ΠΊΡΡΠΈΡΠ΅ΡΠΊΡΡ Π΄ΡΠ³Ρ Π·Π°Π²Π΅ΡΠΎΠΉ ΠΈΠ· ΠΈΠ½Π΅ΡΡΠ½ΠΎΠ³ΠΎ Π³Π°Π·Π° Π°ΡΠ³ΠΎΠ½Π°, ΠΏΠΎΠ΄Π²ΠΎΠ΄ΠΈΠΌΠΎΠ³ΠΎ ΠΊ Π³ΠΎΡΠ΅Π»ΠΊΠ΅ ΠΈΠ· Π±Π°Π»Π»ΠΎΠ½Π°. ΠΠ°Π·ΠΎΠ²Π°Ρ Π·Π°Π²Π΅ΡΠ° ΠΏΡΠ΅ΠΏΡΡΡΡΠ²ΡΠ΅Ρ ΠΎΠΊΠΈΡΠ»Π΅Π½ΠΈΡ ΡΠ²Π°ΡΠΎΡΠ½ΠΎΠΉ Π²Π°Π½Π½Ρ, ΠΏΠΎΡΡΠΎΠΌΡ Π°ΡΠ³ΠΎΠ½Π½ΠΎ-Π΄ΡΠ³ΠΎΠ²ΡΡ ΡΠ²Π°ΡΠΊΡ ΡΠ΅Π»Π΅ΡΠΎΠΎΠ±ΡΠ°Π·Π½ΠΎ ΠΏΡΠΈΠΌΠ΅Π½ΡΡΡ ΠΏΡΠΈ ΡΠ²Π°ΡΠΊΠ΅ Π»Π΅Π³ΠΊΠΎ ΠΎΠΊΠΈΡΠ»ΡΠ΅ΠΌΡΡ
ΠΌΠ΅ΡΠ°Π»Π»ΠΎΠ² ΠΈ ΡΠΏΠ»Π°Π²ΠΎΠ². ΠΡΠΎΡ ΡΠΏΠΎΡΠΎΠ± ΡΠ²Π°ΡΠΊΠΈ ΠΏΠΎΠ·Π²ΠΎΠ»ΡΠ΅Ρ ΡΠ²Π°ΡΠΈΠ²Π°ΡΡ Π΄Π΅ΡΠ°Π»ΠΈ ΠΌΠ°Π»ΠΎΠΉ ΡΠΎΠ»ΡΠΈΠ½Ρ, Π΄Π°Π΅Ρ ΠΌΠΈΠ½ΠΈΠΌΠ°Π»ΡΠ½ΠΎΠ΅ ΠΊΠΎΡΠΎΠ±Π»Π΅Π½ΠΈΠ΅ ΠΈ ΠΏΠΎΠ·Π²ΠΎΠ»ΡΠ΅Ρ ΠΏΠΎΠ»ΡΡΠΈΡΡ ΡΠΎΠ΅Π΄ΠΈΠ½Π΅Π½ΠΈΠ΅ Ρ Π²ΡΡΠΎΠΊΠΈΠΌΠΈ ΠΌΠ΅Ρ
Π°Π½ΠΈΡΠ΅ΡΠΊΠΈΠΌΠΈ ΠΈ ΠΏΡΠΎΡΠΈΠ²ΠΎΠΊΠΎΡΡΠΎΠ·ΠΈΠΎΠ½Π½ΡΠΌΠΈ ΡΠ²ΠΎΠΉΡΡΠ²Π°ΠΌΠΈ.
ΠΡΠ³ΠΎΠ½Π½ΠΎ-Π΄ΡΠ³ΠΎΠ²ΠΎΠΉ ΡΠ²Π°ΡΠΊΠΎΠΉ ΠΌΠΎΠΆΠ½ΠΎ ΡΠ²Π°ΡΠΈΠ²Π°ΡΡ Π½Π΅ΡΠΆΠ°Π²Π΅ΡΡΡΡ, ΠΆΠ°ΡΠΎΠΏΡΠΎΡΠ½ΡΡ ΠΈ ΠΊΠΈΡΠ»ΠΎΡΠΎΡΠΏΠΎΡΠ½ΡΡ ΡΡΠ°Π»ΠΈ, Π°Π»ΡΠΌΠΈΠ½ΠΈΠΉ, ΠΌΠ°Π³Π½ΠΈΠΉ ΠΈ ΠΈΡ ΡΠΏΠ»Π°Π²Ρ.
- ΠΠ°Π·ΠΎΠ²Π°Ρ ΡΠ²Π°ΡΠΊΠ°. ΠΡΠΎΡΠ΅ΡΡ Π·Π°ΠΊΠ»ΡΡΠ°Π΅ΡΡΡ Π² ΡΠ°ΡΠΏΠ»Π°Π²Π»Π΅Π½ΠΈΠΈ ΠΊΡΠΎΠΌΠΎΠΊ ΡΠ²Π°ΡΠΈΠ²Π°Π΅ΠΌΡΡ Π΄Π΅ΡΠ°Π»Π΅ΠΉ ΠΈ Π²Π²ΠΎΠ΄ΠΈΠΌΠΎΠ³ΠΎ Π² ΠΆΠΈΠ΄ΠΊΡΡ Π²Π°Π½Π½Ρ ΠΏΡΠΈΡΠ°Π΄ΠΎΡΠ½ΠΎΠ³ΠΎ ΠΌΠ°ΡΠ΅ΡΠΈΠ°Π»Π° ΡΠ΅ΠΏΠ»ΠΎΠΌ ΡΠ²Π°ΡΠΎΡΠ½ΠΎΠ³ΠΎ ΠΏΠ»Π°ΠΌΠ΅Π½ΠΈ. ΠΠ°Π·ΠΎΠ²Π°Ρ ΡΠ²Π°ΡΠΊΠ° ΠΏΡΠΈΠΌΠ΅Π½ΡΠ΅ΡΡΡ ΠΏΡΠΈ ΠΈΠ·Π³ΠΎΡΠΎΠ²Π»Π΅Π½ΠΈΠΈ Β Π»ΠΈΡΡΠΎΠ²ΡΡ ΠΈ ΡΡΡΠ±ΡΠ°ΡΡΡ ΠΊΠΎΠ½ΡΡΡΡΠΊΡΠΈΠΉ ΠΈΠ· ΠΏΡΠΎΡΡΡΡ , ΡΠ³Π»Π΅ΡΠΎΠ΄ΠΈΡΡΡΡ ΠΈ ΡΠΏΠ΅ΡΠΈΠ°Π»ΡΠ½ΡΡ ΡΡΠ°Π»Π΅ΠΉ Π½Π΅Π±ΠΎΠ»ΡΡΠΈΡ ΡΠΎΠ»ΡΠΈΠ½.
Π‘ΠΏΠ΅ΡΠΈΠ°Π»ΠΈΡΡΡ Π½Π°ΡΠ΅ΠΉ ΠΊΠΎΠΌΠΏΠ°Π½ΠΈΠΈ ΠΈΠΌΠ΅ΡΡ Π±ΠΎΠ»ΡΡΠΎΠΉ ΠΎΠΏΡΡ Π² ΠΎΠ±Π»Π°ΡΡΠΈ ΠΏΡΠΎΠ²Π΅Π΄Π΅Π½ΠΈΡ ΡΠ²Π°ΡΠΎΡΠ½ΡΡ ΡΠ°Π±ΠΎΡ, ΠΈΡΠΏΠΎΠ»ΡΠ·ΡΡΡ ΡΠΎΠ»ΡΠΊΠΎ Π»ΡΡΡΠΈΠ΅ ΠΌΠ°ΡΠ΅ΡΠΈΠ°Π»Ρ ΠΈ ΡΠΎΠ²ΡΠ΅ΠΌΠ΅Π½Π½ΠΎΠ΅ ΠΎΠ±ΠΎΡΡΠ΄ΠΎΠ²Π°Π½ΠΈΠ΅.Β Π‘ΡΠΎΠΈΠΌΠΎΡΡΡ ΡΠ²Π°ΡΠΎΡΠ½ΡΡ ΡΠ°Π±ΠΎΡ ΠΎΠ³ΠΎΠ²Π°ΡΠΈΠ²Π°Π΅ΡΡΡ ΠΈΠ½Π΄ΠΈΠ²ΠΈΠ΄ΡΠ°Π»ΡΠ½ΠΎ.
ΠΡ Π³Π°ΡΠ°Π½ΡΠΈΡΡΠ΅ΠΌ ΠΊΠ°ΡΠ΅ΡΡΠ²ΠΎ ΠΈ ΡΠ²ΠΎΠ΅Π²ΡΠ΅ΠΌΠ΅Π½Π½ΠΎΡΡΡ Π²ΡΠΏΠΎΠ»Π½Π΅Π½ΠΈΡ Π·Π°ΠΊΠ°Π·Π°Π½Π½ΡΡ Ρ Π½Π°Ρ ΡΠ²Π°ΡΠΎΡΠ½ΡΡ ΡΠ°Π±ΠΎΡ!
Β Β Β Β Β Β Β Β Β Β Β Β Β Β
ΠΠΎΠ»ΡΡΠ΅ ΡΠΎΡΠΎ Π·Π΄Π΅ΡΡ.
.
Π‘Π²Π°ΡΠΊΠ°, Π²ΠΈΠ΄Ρ ΡΠ²Π°ΡΠΊΠΈ, ΠΈΡΡΠΎΡΠΈΡ ΡΠ²Π°ΡΠΊΠΈ
Π‘Π²Π°ΡΠΊΠ° — ΡΠ΅Ρ
Π½ΠΎΠ»ΠΎΠ³ΠΈΡΠ΅ΡΠΊΠΈΠΉ ΠΏΡΠΎΡΠ΅ΡΡ ΡΠΎΠ΅Π΄ΠΈΠ½Π΅Π½ΠΈΡ ΡΠ²ΡΡΠ΄ΡΡ
ΠΌΠ°ΡΠ΅ΡΠΈΠ°Π»ΠΎΠ² Π² ΡΠ΅Π·ΡΠ»ΡΡΠ°ΡΠ΅ Π΄Π΅ΠΉΡΡΠ²ΠΈΡ ΠΌΠ΅ΠΆΠ°ΡΠΎΠΌΠ½ΡΡ
ΡΠΈΠ», ΠΊΠΎΡΠΎΡΠΎΠ΅ ΠΏΡΠΎΠΈΡΡ
ΠΎΠ΄ΠΈΡ ΠΏΡΠΈ ΠΌΠ΅ΡΡΠ½ΠΎΠΌ ΡΠΏΠ»Π°Π²Π»Π΅Π½ΠΈΠΈ ΠΈΠ»ΠΈ ΡΠΎΠ²ΠΌΠ΅ΡΡΠ½ΠΎΠΌ ΠΏΠ»Π°ΡΡΠΈΡΠ΅ΡΠΊΠΎΠΌ Π΄Π΅ΡΠΎΡΠΌΠΈΡΠΎΠ²Π°Π½ΠΈΠΈ ΡΠ²Π°ΡΠΈΠ²Π°Π΅ΠΌΡΡ
ΡΠ°ΡΡΠ΅ΠΉ. Π‘Π²Π°ΡΠΊΠΎΠΉ ΠΏΠΎΠ»ΡΡΠ°ΡΡ ΠΈΠ·Π΄Π΅Π»ΠΈΡ ΠΈΠ· ΠΌΠ΅ΡΠ°Π»Π»Π° ΠΈ Π½Π΅ΠΌΠ΅ΡΠ°Π»Π»ΠΈΡΠ΅ΡΠΊΠΈΡ
ΠΌΠ°ΡΠ΅ΡΠΈΠ°Π»ΠΎΠ² (ΡΡΠ΅ΠΊΠ»Π°, ΠΊΠ΅ΡΠ°ΠΌΠΈΠΊΠΈ, ΠΏΠ»Π°ΡΡΠΌΠ°ΡΡ ΠΈ Π΄Ρ.). ΠΠ·ΠΌΠ΅Π½ΡΡ ΡΠ΅ΠΆΠΈΠΌΡ ΡΠ²Π°ΡΠΊΠΈ, ΠΌΠΎΠΆΠ½ΠΎ Π½Π°ΠΏΠ»Π°Π²Π»ΡΡΡ ΡΠ»ΠΎΠΈ ΠΌΠ΅ΡΠ°Π»Π»Π° ΡΠ°Π·Π»ΠΈΡΠ½ΡΡ
ΡΠΎΠ»ΡΠΈΠ½Ρ ΠΈ ΡΠ°Π·Π»ΠΈΡΠ½ΠΎΠ³ΠΎ ΡΠΎΡΡΠ°Π²Π°.
ΠΠ° ΡΠΏΠ΅ΡΠΈΠ°Π»ΡΠ½ΠΎΠΌ ΠΎΠ±ΠΎΡΡΠ΄ΠΎΠ²Π°Π½ΠΈΠΈ Π² ΠΎΠΏΡΠ΅Π΄Π΅Π»Π΅Π½Π½ΡΡ ΡΡΠ»ΠΎΠ²ΠΈΡΡ ΠΌΠΎΠ³ΡΡ ΠΎΡΡΡΠ΅ΡΡΠ²Π»ΡΡΡΡΡ ΠΏΡΠΎΡΠ΅ΡΡΡ, ΠΏΡΠΎΡΠΈΠ²ΠΎΠΏΠΎΠ»ΠΎΠΆΠ½ΡΠ΅ ΠΏΠΎ ΡΠ²ΠΎΠ΅ΠΉ ΡΡΡΠ½ΠΎΡΡΠΈ ΠΏΡΠΎΡΠ΅ΡΡΡΠ°Π»ΡΠ½ΡΠ΅ ΡΠΎΠ΅Π΄ΠΈΠ½Π΅Π½ΠΈΡ, Π½Π°ΠΏΡΠΈΠΌΠ΅Ρ ΠΎΠ³Π½Π΅Π²ΡΡ, ΠΈΠ»ΠΈ ΡΠ΅ΡΠΌΠΈΡΠ΅ΡΠΊΡΡ, ΡΠ΅Π·ΠΊΡ ΠΌΠ΅ΡΠ°Π»Π»ΠΎΠ².
ΠΡΡΠΎΡΠΈΡΠ΅ΡΠΊΠ°Ρ ΡΠΏΡΠ°Π²ΠΊΠ°
ΠΡΠΎΡΡΠ΅ΠΉΡΠΈΠ΅ ΠΏΡΠΈΡΠΌΡ ΡΠΎΠ΅Π΄ΠΈΠ½Π΅Π½ΠΈΡ Π±ΡΠ»ΠΈ ΠΈΠ·Π²Π΅ΡΡΠ½Ρ Π² 8-7-ΠΌ ΡΡΡ. Π ΡΠ±. Π΄ΠΎ Π½. Ρ. Π ΠΎΡΠ½ΠΎΠ²Π½ΠΎΠΌ ΡΠ²Π°ΡΠΈΠ²Π°Π»ΠΈΡΡ ΠΈΠ·Π΄Π΅Π»ΠΈΡ ΠΈΠ· ΠΌΠ΅Π΄ΠΈ, ΠΊΠΎΡΠΎΡΡΠ΅ ΠΏΠΎΠ΄ΠΎΠ³ΡΠ΅Π²Π°Π»ΠΈΡΡ, Π° Π·Π°ΡΠ΅ΠΌ ΡΠ΄Π°Π²Π»ΠΈΠ²Π°Π»ΠΈΡΡ. ΠΡΠΈ ΠΈΠ·Π³ΠΎΡΠΎΠ²Π»Π΅Π½ΠΈΠΈ ΠΈΠ·Π΄Π΅Π»ΠΈΠΉ ΠΈΠ· ΠΌΠ΅Π΄ΠΈ, Π±ΡΠΎΠ½Π·Ρ, ΡΠ²ΠΈΠ½ΡΠ°, Π±Π»Π°Π³ΠΎΡΠΎΠ΄Π½ΡΡ ΠΌΠ΅ΡΠ°Π»Π»ΠΎΠ² ΠΏΡΠΈΠΌΠ΅Π½ΡΠ»Π°ΡΡ Ρ. Π½. Π»ΠΈΡΠ΅ΠΉΠ½Π°Ρ ΡΠ²Π°ΡΠΊΠ°. Π‘ΠΎΠ΅Π΄ΠΈΠ½ΡΠ΅ΠΌΡΠ΅ Π΄Π΅ΡΠ°Π»ΠΈ Π·Π°ΡΠΎΡΠΌΠΎΠ²ΡΠ²Π°Π»ΠΈ, ΠΏΠΎΠ΄ΠΎΠ³ΡΠ΅Π²Π°Π»ΠΈ ΠΈ Π·Π°Π»ΠΈΠ²Π°Π»ΠΈ Π·Π°ΡΠ°Π½Π΅Π΅ ΠΏΡΠΈΠ³ΠΎΡΠΎΠ²Π»Π΅Π½Π½ΡΠΌ ΡΠ°ΡΠΏΠ»Π°Π²Π»Π΅Π½Π½ΡΠΌ ΠΌΠ΅ΡΠ°Π»Π»ΠΎΠΌ.
ΠΠ·Π΄Π΅Π»ΠΈΡ ΠΈΠ· ΠΆΠ΅Π»Π΅Π·Π° ΠΈ Π΅Π³ΠΎ ΡΠΏΠ»Π°Π²ΠΎΠ² ΠΈΡ
Π½Π°Π³ΡΠ΅Π²ΠΎΠΌ Π΄ΠΎ «ΡΠ²Π°ΡΠΎΡΠ½ΠΎΠ³ΠΎ ΠΆΠ°ΡΠ°» Π² ΠΊΡΠ·Π½Π΅ΡΠ½ΡΡ
Π³ΠΎΡΠ½Π°Ρ
Ρ ΠΏΠ΅ΡΠ²ΠΎΠΉ ΠΏΡΠΎΠΊΠΎΠ²ΠΊΠΎΠΉ.ΠΡΠΎΡ ΡΠΏΠΎΡΠΎΠ± ΠΈΠ·Π²Π΅ΡΡΠ΅Π½ ΠΏΠΎΠ΄ Π½Π°Π·Π²Π°Π½ΠΈΠ΅ΠΌ Π³ΠΎΡΠ½ΠΎΠ²Π°Ρ, ΠΈΠ»ΠΈ ΠΊΡΠ·Π½Π΅ΡΠ½Π°Ρ, ΡΠ²Π°ΡΠΊΠ°. Π’ΠΎΠ»ΡΠΊΠΎ ΡΡΠΈ Π΄Π²Π° ΠΌΠ΅ΡΠΎΠ΄Π° ΡΠ²Π°ΡΠΊΠΈ Π±ΡΠ»ΠΈ ΡΠ°ΡΠΏΡΠΎΡΡΡΠ°Π½Π΅Π½Ρ Π΄ΠΎ ΠΊΠΎΠ½ΡΠ° 19 Π². Π’ΠΎΠ»ΡΠΊΠΎΠΌ ΠΊ ΠΏΠΎΡΠ²Π»Π΅Π½ΠΈΡ ΠΏΡΠΈΠ½ΡΠΈΠΏΠΈΠ°Π»ΡΠ½ΠΎ Π½ΠΎΠ²ΡΡ
ΡΠΏΠΎΡΠΎΠ±ΠΎΠ² ΡΠΎΠ΅Π΄ΠΈΠ½Π΅Π½ΠΈΡ ΠΌΠ΅ΡΠ°Π»Π»ΠΎΠ² ΡΠ²ΠΈΠ»ΠΎΡΡ ΠΎΡΠΊΡΡΡΠΈΠ΅ Π² 1802 Π³ΠΎΠ΄Ρ Π΄ΡΠ³ΠΎΠ²ΠΎΠ³ΠΎ ΡΠ°Π·ΡΡΠ΄Π° Π. Π. ΠΠ΅ΡΡΠΎΠ²ΡΠΌ. Π 1882 Π. Π. ΠΠ΅Π½Π°ΡΠ΄ΠΎΡ ΠΈ Π² 1890 Π. Π. Π‘Π»Π°Π²ΡΠ½ΠΎΠ² ΠΏΡΠ΅Π΄Π»ΠΎΠΆΠΈΠ»ΠΈ ΠΏΠ΅ΡΠ²ΡΠ΅ ΠΏΡΠ°ΠΊΡΠΈΡΠ΅ΡΠΊΠΈ ΠΏΡΠΈΠ³ΠΎΠ΄Π½ΡΠ΅ ΡΠΏΠΎΡΠΎΠ±Ρ ΡΠ²Π°ΡΠΊΠΈ Ρ ΠΈΡΠΏΠΎΠ»ΡΠ·ΠΎΠ²Π°Π½ΠΈΠ΅ΠΌ ΡΠ»Π΅ΠΊΡΡΠΈΡΠ΅ΡΠΊΠΎΠΉ Π΄ΡΠ³ΠΈ. Π Π½Π°ΡΠ°Π»Π΅ 20 Π². Π΄ΡΠ³ΠΎΠ²Π°Ρ ΡΠ»Π΅ΠΊΡΡΠΎΡΠ²Π°ΡΠΊΠ° ΠΏΠΎΡΡΠ΅ΠΏΠ΅Π½Π½ΠΎ ΡΡΠ°Π»Π° Π²Π΅Π΄ΡΡΠΈΠΌ ΠΏΡΠΎΠΌΡΡΠ»Π΅Π½Π½ΡΠΌ ΡΠΏΠΎΡΠΎΠ±ΠΎΠΌ ΡΠΎΠ΅Π΄ΠΈΠ½Π΅Π½ΠΈΡ ΠΌΠ΅ΡΠ°Π»Π»ΠΎΠ².Π Π½Π°ΡΠ°Π»Ρ 20 Π². ΠΏΡΠΈΡΡΡΠΏ ΠΈ ΠΏΠ΅ΡΠ²ΡΠ΅ ΠΏΠΎΠΏΡΡΠΊΠΈ ΠΏΡΠΈΠΌΠ΅Π½Π΅Π½ΠΈΡ ΡΠ²Π°ΡΠΊΠΈ ΠΈ ΡΠ΅Π·ΠΊΠΈ Π³ΠΎΡΡΡΠΈΡ
Π³Π°Π·ΠΎΠ² Π² ΡΠΌΠ΅ΡΡΡ
Ρ ΠΊΠΈΡΠ»ΠΎΡΠΎΠ΄ΠΎΠΌ. ΠΠ΅ΡΠ²ΡΡ Π°ΡΠ΅ΡΠΈΠ»Π΅Π½ΠΎ-ΠΊΠΈΡΠ»ΠΎΡΠΎΠ΄Π½ΡΡ ΡΠ²Π°ΡΠΎΡΠ½ΡΡ Π³ΠΎΡΠ΅Π»ΠΊΡ ΡΠΊΠΎΠ½ΡΡΡΡΠΈΡΠΎΠ²Π°Π» ΡΡΠ°Π½ΡΡΠ·ΡΠΊΠΈΠΉ ΠΈΠ½ΠΆΠ΅Π½Π΅Ρ Π. Π€ΡΡΠ΅, ΠΊΠΎΡΠΎΡΡΠΉ ΠΏΠΎΠ»ΡΡΠΈΠ» Π½Π° Π½Π΅Π΅ ΠΏΠ°ΡΠ΅Π½Ρ Π² ΠΠ΅ΡΠΌΠ°Π½ΠΈΠΈ Π² 1903. Π Π ΠΎΡΡΠΈΠΈ ΡΡΠΎΡ ΡΠΏΠΎΡΠΎΠ± ΡΡΠ°Π» ΠΈΠ·Π²Π΅ΡΡΠ΅Π½ ΠΏΡΠ΅Π΄ΠΏΠΎΠ»ΠΎΠΆΠΈΡΠ΅Π»ΡΠ½ΠΎ ΠΊ 1905 Π³ΠΎΠ΄Ρ, ΠΏΠΎΠ»ΡΡΠΈΠ» ΡΠ°ΡΠΏΡΠΎΡΡΡΠ°Π½Π΅Π½ΠΈΠ΅ ΠΊ 1911 Π³ΠΎΠ΄Ρ. ΠΠΎ 2-ΠΉ ΠΏΠΎΠ»ΠΎΠ²ΠΈΠ½Π΅ 20 Π². Π΄Π»Ρ ΡΠ²Π°ΡΠΊΠΈ ΡΡΠ°Π»ΠΈ ΠΈΡΠΏΠΎΠ»ΡΠ·ΠΎΠ²Π°ΡΡ Π΄Ρ.Π²ΠΈΠ΄Ρ ΡΠ½Π΅ΡΠ³ΠΈΠΈ: ΠΏΠ»Π°Π·ΠΌΡ, ΡΠ»Π΅ΠΊΡΡΠΎΠ½Π½ΡΠΉ, ΡΠΎΡΠΎΠ½Π½ΡΠΉ ΠΈ Π»Π°Π·Π΅ΡΠ½ΡΠΉ Π»ΡΡΠΈ, Π²Π·ΡΡΠ², ΡΠ»ΡΡΡΠ°Π·Π²ΡΠΊ ΠΈ Π΄Ρ.
ΠΠ»Π°ΡΡΠΈΡΠΈΠΊΠ°ΡΠΈΡ
Π‘ΠΎΠ²ΡΠ΅ΠΌΠ΅Π½Π½ΡΠ΅ ΡΠΏΠΎΡΠΎΠ±Ρ ΡΠ²Π°ΡΠΊΠΈ. ΠΌΠ΅ΡΠ°Π»Π»ΠΎΠ² ΠΌΠΎΠΆΠ½ΠΎ ΡΠ°Π·Π΄Π΅Π»ΠΈΡΡ Π½Π° Π΄Π²Π΅ Π±ΠΎΠ»ΡΡΠΈΠ΅ Π³ΡΡΠΏΠΏΡ: ΡΠ²Π°ΡΠΊΠ° ΠΏΠ»Π°Π²Π»Π΅Π½ΠΈΠ΅ΠΌ, ΠΈΠ»ΠΈ ΡΠ²Π°ΡΠΊΠ° Π² ΠΆΠΈΠ΄ΠΊΠΎΠΉ ΡΠ°Π·Π΅, ΠΈ ΡΠ²Π°ΡΠΊΠ° ΠΏΠΎΠ΄ Π΄Π°Π²Π»Π΅Π½ΠΈΠ΅ΠΌ, ΠΈΠ»ΠΈ ΡΠ²Π°ΡΠΊΠ° Π² ΡΠ²ΡΡΠ΄ΠΎΠΉ ΡΠ°Π·Π΅. ΠΡΠΈ ΡΠ²Π°ΡΠΊΠ΅ ΠΏΠ»Π°Π²Π»Π΅Π½ΠΈΠ΅ΠΌ ΡΠ°ΡΠΏΠ»Π°Π²Π»Π΅Π½Π½ΡΠΉ ΠΌΠ΅ΡΠ°Π»Π» ΡΠΎΠ΅Π΄ΠΈΠ½ΡΠ΅ΠΌΡΡ
ΡΠ°ΡΡΠ΅ΠΉ ΡΠ°ΠΌΠΎΠΏΡΠΎΠΈΠ·Π²ΠΎΠ»ΡΠ½ΠΎ, Π±Π΅Π· ΠΏΡΠΈΠ»ΠΎΠΆΠ΅Π½ΠΈΡ Π²Π½Π΅ΡΠ½ΠΈΡ
ΡΠΈΠ» ΡΠΎΠ΅Π΄ΠΈΠ½ΡΠ΅ΡΡΡ Π² ΠΎΠ΄Π½ΠΎ ΡΠ΅Π»ΠΎΠ΅ Π² ΡΠ΅Π·ΡΠ»ΡΡΠ°ΡΠ΅ ΡΠ°ΡΠΏΠ»Π°Π²Π»Π΅Π½ΠΈΡ ΠΈ ΡΠΌΠ°ΡΠΈΠ²Π°Π½ΠΈΡ Π² Π·ΠΎΠ½Π΅ ΡΠ²Π°ΡΠΊΠΈ ΠΈ Π²Π·Π°ΠΈΠΌΠ½ΠΎΠ³ΠΎ ΡΠ°ΡΡΠ²ΠΎΡΠ΅Π½ΠΈΡ ΠΌΠ°ΡΠ΅ΡΠΈΠ°Π»Π°.ΠΡΠΈ ΡΠ²Π°ΡΠΊΠ΅ Π΄Π°Π²Π»Π΅Π½ΠΈΡ Π΄Π»Ρ ΡΠΎΠ΅Π΄ΠΈΠ½Π΅Π½ΠΈΡ ΡΠ°ΡΡΠ΅ΠΉ Π±Π΅Π· ΡΠ°ΡΠΏΠ»Π°Π²Π»Π΅Π½ΠΈΡ Π·Π½Π°ΡΠΈΡΠ΅Π»ΡΠ½ΠΎΠ΅ Π΄Π°Π²Π»Π΅Π½ΠΈΠ΅. ΠΡΠ°Π½ΠΈΡΠ° ΠΌΠ΅ΠΆΠ΄Ρ ΡΡΠΈΠΌΠΈ Π½Π΅ Π²ΡΠ΅Π³Π΄Π° Π΄ΠΎΡΡΠ°ΡΠΎΡΠ½ΠΎ ΡΡΡΠΊΠ°Ρ, Π½Π°ΠΏΡΠΈΠΌΠ΅Ρ Π²ΠΎΠ·ΠΌΠΎΠΆΠ½Π° ΡΠ²Π°ΡΠΊΠ° Ρ ΡΠ°ΡΡΠΈΡΠ½ΡΠΌ ΠΎΠΏΠ»Π°Π²Π»Π΅Π½ΠΈΠ΅ΠΌ Π΄Π΅ΡΠ°Π»Π΅ΠΉ ΠΈ ΠΏΠΎΡΠ»Π΅Π΄ΡΡΡΠΈΠΌ ΡΠ΄Π°Π²Π»ΠΈΠ²Π°Π½ΠΈΠ΅ΠΌ ΠΈΡ
(ΠΊΠΎΠ½ΡΠ°ΠΊΡΠ½Π°Ρ ΡΠ»Π΅ΠΊΡΡΠΎΡΠ²Π°ΡΠΊΠ°). ΠΡΠ΅Π΄Π»Π°Π³Π°Π΅ΠΌΠΎΠΉ ΠΊΠ»Π°ΡΡΠΈΡΠΈΠΊΠ°ΡΠΈΠΈ Π² ΠΊΠ°ΠΆΠ΄ΡΡ Π³ΡΡΠΏΠΏΡ Π²Ρ
ΠΎΠ΄ΠΈΡ Π½Π΅ΡΠΊΠΎΠ»ΡΠΊΠΎ ΡΠΏΠΎΡΠΎΠ±ΠΎΠ². Π ΡΠ²Π°ΡΠΊΠ΅ ΠΏΠ»Π°Π²Π»Π΅Π½ΠΈΠ΅ΠΌ: Π΄ΡΠ³ΠΎΠ²Π°Ρ, ΠΏΠ»Π°Π·ΠΌΠ΅Π½Π½Π°Ρ, ΡΠ»Π΅ΠΊΡΡΠΎΡΠ»Π°ΠΊΠΎΠ²Π°Ρ, Π³Π°Π·ΠΎΠ²Π°Ρ, Π»ΡΡΠ΅Π²Π°Ρ ΠΈ Π΄Ρ .; ΠΊ ΡΠ²Π°ΡΠΊΠ΅ Π΄Π°Π²Π»Π΅Π½ΠΈΠ΅ΠΌ — Π³ΠΎΡΠ½ΠΎΠ²Π°Ρ, Ρ
ΠΎΠ»ΠΎΠ΄Π½Π°Ρ, ΡΠ»ΡΡΡΠ°Π·Π²ΡΠΊΠΎΠ²Π°Ρ, ΡΡΠ΅Π½ΠΈΠ΅ΠΌ, Π²Π·ΡΡΠ²ΠΎΠΌ ΠΈ Π΄Ρ.Π ΠΎΡΠ½ΠΎΠ²Ρ ΠΊΠ»Π°ΡΡΠΈΡΠΈΠΊΠ°ΡΠΈΠΈ ΠΌΠΎΠΆΠ΅Ρ Π±ΡΡΡ ΠΏΠΎΠ»ΠΎΠΆΠ΅Π½ ΠΈ ΠΊΠ°ΠΊΠΎΠΉ-Π»ΠΈΠ±ΠΎ Π΄Ρ. ΠΏΡΠΈΠ·Π½Π°ΠΊ. ΠΠ°ΠΏΡΠΈΠΌΠ΅Ρ, ΠΏΠΎ ΡΠΎΠ΄Ρ ΡΠ½Π΅ΡΠ³ΠΈΠΈ ΠΌΠΎΠ³ΡΡ Π±ΡΡΡ Π²ΡΠ΄Π΅Π»Π΅Π½Ρ ΡΠ»Π΅Π΄ΡΡΡΠΈΠ΅ Π²ΠΈΠ΄Ρ ΡΠ²Π°ΡΠΊΠΈ ΡΠ»Π΅ΠΊΡΡΠΈΡΠ΅ΡΠΊΠ°Ρ (Π΄ΡΠ³ΠΎΠ²Π°Ρ, ΠΊΠΎΠ½ΡΠ°ΠΊΡΠ½Π°Ρ, ΡΠ»Π΅ΠΊΡΡΠΎΡΠ»Π°ΠΊΠΎΠ²Π°Ρ, ΠΏΠ»Π°Π·ΠΌΠ΅Π½Π½Π°Ρ, ΠΈΠ½Π΄ΡΠΊΡΠΈΠΎΠ½Π½Π°Ρ ΠΈ Ρ.
Π.), ΠΠ΅Ρ
Π°Π½ΠΈΡΠ΅ΡΠΊΠ°Ρ (ΡΡΠ΅Π½ΠΈΠ΅ΠΌ, Ρ
ΠΎΠ»ΠΎΠ΄Π½Π°Ρ, ΡΠ»ΡΡΡΠ°Π·Π²ΡΠΊΠΎΠ²Π°Ρ ΠΈ Ρ. Π.), Π₯ΠΈΠΌΠΈΡΠ΅ΡΠΊΠ°Ρ (Π³Π°Π·ΠΎΠ²Π°Ρ, ΡΠ΅ΡΠΌΠΈΡΠ½Π°Ρ), Π»ΡΡΠ΅Π²Π°Ρ (ΡΠΎΡΠΎΠ½Π½Π°Ρ, ΡΠ»Π΅ΠΊΡΡΠΎΠ½Π½Π°Ρ, Π»Π°Π·Π΅ΡΠ½Π°Ρ).
Π‘Π²Π°ΡΠΊΠ° ΠΏΠ»Π°Π²Π»Π΅Π½ΠΈΠ΅ΠΌ
ΠΡΠΎΡΡΠ΅ΠΉΡΠΈΠΉ ΡΠΏΠΎΡΠΎΠ± ΡΠ²Π°ΡΠΊΠΈ — ΡΡΡΠ½Π°Ρ Π΄ΡΠ³ΠΎΠ²Π°Ρ ΡΠ²Π°ΡΠΊΠ° — ΠΎΡΠ½ΠΎΠ²Π°Π½Π° Π½Π° ΠΈΡΠΏΠΎΠ»ΡΠ·ΠΎΠ²Π°Π½ΠΈΠΈ ΡΠ»Π΅ΠΊΡΡΠΈΡΠ΅ΡΠΊΠΎΠΉ Π΄ΡΠ³ΠΈ.Π ΠΎΠ΄Π½ΠΎΠΌΡ ΠΏΠΎΠ»ΡΡΡ ΠΈΡΡΠΎΡΠ½ΠΈΠΊΠ° ΡΠΎΠΊΠ° Π³ΠΈΠ±ΠΊΠΈΠΌ ΠΏΡΠΎΠ²ΠΎΠ΄ΠΎΠΌ ΠΏΡΠΈΡΠΎΠ΅Π΄ΠΈΠ½ΡΠ΅ΡΡΡ Π΄Π΅ΡΠΆΠ°ΡΠ΅Π»Ρ, ΠΊ Π΄ΡΡΠ³ΠΎΠΌΡ — ΡΠ²Π°ΡΠΈΠ²Π°Π΅ΠΌΠΎΠ΅ ΠΈΠ·Π΄Π΅Π»ΠΈΠ΅. Π Π΄Π΅ΡΠΆΠ°ΡΠ΅Π»Ρ Π²ΡΡΠ°Π²Π»ΡΠ΅ΡΡΡ ΡΠ³ΠΎΠ»ΡΠ½ΡΠΉ ΠΈΠ»ΠΈ ΠΌΠ΅ΡΠ°Π»Π»ΠΈΡΠ΅ΡΠΊΠΈΠΉ ΡΠ»Π΅ΠΊΡΡΠΎΠ΄. ΠΡΠΈ ΠΊΠΎΡΠΎΡΠΊΠΎΠΌ ΠΏΡΠΈΠΊΠΎΡΠ½ΠΎΠ²Π΅Π½ΠΈΠΈ ΡΠ»Π΅ΠΊΡΡΠΎΠ΄Π° ΠΊ ΠΈΠ·Π΄Π΅Π»ΠΈΡ Π·Π°ΠΆΠΈΠ³Π°Π΅ΡΡΡ Π΄ΡΠ³Π°, ΠΊΠΎΡΠΎΡΠ°Ρ ΠΏΠ»Π°Π²ΠΈΡ ΠΎΡΠ½ΠΎΠ²Π½ΠΎΠΉ ΠΌΠ΅ΡΠ°Π»Π» ΠΈ ΡΡΠ΅ΡΠΆΠ΅Π½Ρ ΡΠ»Π΅ΠΊΡΡΠΎΠ΄Π° (ΠΏΡΠΈ ΠΌΠ΅ΡΠ°Π»Π»ΠΈΡΠ΅ΡΠΊΠΎΠΌ ΡΠ»Π΅ΠΊΡΡΠΎΠ΄Π΅), ΠΎΠ±ΡΠ°Π·ΡΡ ΡΠ²Π°ΡΠΎΡΠ½ΡΡ Π²Π°Π½Π½Ρ, Π΄Π°ΡΡΡΡ ΠΏΡΠΈ Π·Π°ΡΠ²Π΅ΡΠ΄Π΅Π²Π°Π½ΠΈΠΈ ΡΠ²Π°ΡΠ½ΠΎΠΉ ΡΠΎΠ². Π’Π΅ΠΌΠΏΠ΅ΡΠ°ΡΡΡΠ° ΡΠ²Π°ΡΠΎΡΠ½ΠΎΠΉ Π΄ΡΠ³ΠΈ 6000-10000 Π‘ (ΠΏΡΠΈ ΡΡΠ°Π»ΡΠ½ΠΎΠΌ ΡΠ»Π΅ΠΊΡΡΠΎΠ΄Π΅). ΠΠ»Ρ ΠΏΠΈΡΠ°Π½ΠΈΡ Π΄ΡΠ³ΠΈ ΠΈΡΠΏΠΎΠ»ΡΠ·ΡΠΉΡΠ΅ ΡΠΈΠ»Ρ 100-350 Π°, Π½Π°ΠΏΡΡΠΆΠ΅Π½ΠΈΠ΅ΠΌ 25-40 Π² ΠΎΡ ΡΠΏΠ΅ΡΠΈΠ°Π»ΡΠ½ΡΡ ΠΈΡΡΠΎΡΠ½ΠΈΠΊΠΎΠ².
ΠΡΠΈ Π΄ΡΠ³ΠΎΠ²ΠΎΠΉ ΡΠ²Π°ΡΠΊΠ΅ ΠΊΠΈΡΠ»ΠΎΡΠΎΠ΄ ΠΈ Π°Π·ΠΎΡ Π°ΡΠΌΠΎΡΡΠ΅ΡΠ½ΠΎΠ³ΠΎ Π²ΠΎΠ·Π΄ΡΡ
Π° Π°ΠΊΡΠΈΠ²Π½ΠΎ Π²Π·Π°ΠΈΠΌΠΎΠ΄Π΅ΠΉΡΡΠ²ΡΡΡ Ρ ΡΠ°ΡΠΏΠ»Π°Π²Π»Π΅Π½Π½ΡΠΌ ΠΌΠ΅ΡΠ°Π»Π»ΠΎΠΌ, ΠΎΠ±ΡΠ°Π·ΡΡΡ ΠΎΠΊΠΈΡΠ»Ρ ΠΈ Π½ΠΈΡΡΠΈΠ΄Ρ, ΡΠ½ΠΈΠΆΠ°ΡΡΠΈΠ΅ ΠΏΡΠΎΡΠ½ΠΎΡΡΡ ΠΈ ΠΏΠ»Π°ΡΡΠΈΡΠ½ΠΎΡΡΡ ΡΠ²Π°ΡΠ½ΠΎΠ³ΠΎ ΡΠΎΠ΅Π΄ΠΈΠ½Π΅Π½ΠΈΡ. Π‘ΡΡΠ΅ΡΡΠ²ΡΡΡ Π²Π½ΡΡΡΠ΅Π½Π½ΠΈΠ΅ ΠΈ Π²Π½Π΅ΡΠ½ΠΈΠ΅ ΡΠΏΠΎΡΠΎΠ±Ρ Π·Π°ΡΠΈΡΡ ΠΌΠ΅ΡΡΠ° ΡΠ²Π°ΡΠΊΠΈ, Π²Π²Π΅Π΄Π΅Π½ΠΈΠ΅ ΡΠ°Π·Π»ΠΈΡΠ½ΡΡ
Π²Π΅ΡΠ΅ΡΡΠ² Π² Π·ΠΎΠ½Ρ ΡΠ²Π°ΡΠΊΠΈ ΠΈΠ½Π΅ΡΡΠ½ΡΡ
Π³Π°Π·ΠΎΠ² ΠΈ ΠΎΠΊΠΈΡΠΈ ΡΠ³Π»Π΅ΡΠΎΠ΄Π°, ΠΏΠΎΠΊΡΡΡΠΈΠ΅ ΠΌΠ΅ΡΡΠ° ΡΠ²Π°ΡΠΊΠΈ ΡΠ²Π°ΡΠΎΡΠ½ΡΠΌΠΈ ΡΠ»ΡΡΠ°ΠΌΠΈ (Π²Π½Π΅ΡΠ½ΡΡ Π·Π°ΡΠΈΡΠ°). ΠΡΠΈ ΠΎΡΡΡΡΡΡΠ²ΠΈΠΈ Π²Π½Π΅ΡΠ½ΠΈΡ
ΡΡΠ΅Π΄ΡΡΠ² Π·Π°ΡΠΈΡΡ ΡΠ²Π°ΡΠΎΡΠ½Π°Ρ Π΄ΡΠ³Π° Π½Π°Π·ΡΠ²Π°Π΅ΡΡΡ ΠΎΡΠΊΡΡΡΠΎΠΉ, ΠΏΡΠΈ Π½Π°Π»ΠΈΡΠΈΠΈ ΠΈΡ
Π·Π°ΡΠΈΡΠ΅Π½Π½ΠΎΠΉ ΠΈΠ»ΠΈ ΠΏΠΎΠ³ΡΡΠΆΠ΅Π½Π½ΠΎΠΉ.ΠΠ° Π½Π°ΠΈΠ±ΠΎΠ»ΡΡΠ΅Π΅ Π·Π½Π°ΡΠ΅Π½ΠΈΠ΅ ΠΈΠΌΠ΅Π΅Ρ ΡΠ»Π΅ΠΊΡΡΠΎΡΠ²Π°ΡΠΊΠ° ΠΎΡΠΊΡΡΡΠΎΠΉ Π΄ΡΠ³ΠΎΠΉ ΠΏΠΎΠΊΡΡΡΡΠΌ ΠΏΠ»Π°Π²ΡΡΠΈΠΌΡΡ ΡΠ»Π΅ΠΊΡΡΠΎΠ΄ΠΎΠΌ. ΠΡΡΠΎΠΊΠΎΠ΅ ΠΊΠ°ΡΠ΅ΡΡΠ²ΠΎ ΡΠ²Π°ΡΠ½ΠΎΠ³ΠΎ ΡΠΎΠ΅Π΄ΠΈΠ½Π΅Π½ΠΈΡ ΠΏΠΎΠ·Π²ΠΎΠ»ΡΠ΅Ρ ΠΈΡΠΏΠΎΠ»ΡΠ·ΠΎΠ²Π°ΡΡ ΡΡΠΎΡ ΡΠΏΠΎΡΠΎΠ± ΠΈΠ·Π³ΠΎΡΠΎΠ²Π»Π΅Π½ΠΈΡ ΠΎΡΠ²Π΅ΡΡΡΠ²Π΅Π½Π½ΡΡ
ΠΈΠ·Π΄Π΅Π»ΠΈΠΉ. ΠΠ΄Π½ΠΎΠΉ ΠΈΠ· Π²Π°ΠΆΠ½Π΅ΠΉΡΠΈΡ
ΠΏΡΠΎΠ±Π»Π΅ΠΌ ΡΠ²Π°ΡΠΎΡΠ½ΠΎΠΉ ΡΠ΅Ρ
Π½ΠΈΠΊΠΈ ΡΠ²Π»ΡΠ΅ΡΡΡ ΠΌΠ΅Ρ
Π°Π½ΠΈΠ·Π°ΡΠΈΡ ΠΈ Π°Π²ΡΠΎΠΌΠ°ΡΠΈΠ·Π°ΡΠΈΡ Π΄ΡΠ³ΠΎΠ²ΠΎΠΉ ΡΠ²Π°ΡΠΊΠΈ. ΠΡΠΈ ΠΈΠ·Π³ΠΎΡΠΎΠ²Π»Π΅Π½ΠΈΠΈ ΠΈΠ·Π΄Π΅Π»ΠΈΠΉ ΡΠ»ΠΎΠΆΠ½ΠΎΠΉ ΡΠΎΡΠΌΡ ΡΠ°ΡΡΠΎ ΠΈΡΠΏΠΎΠ»ΡΠ·ΡΠ΅ΡΡΡ ΠΏΠΎΠ»ΡΠ°Π²ΡΠΎΠΌΠ°ΡΠΈΡΠ΅ΡΠΊΠ°Ρ Π΄ΡΠ³ΠΎΠ²Π°Ρ ΡΠ²Π°ΡΠΊΠ°, ΠΊΠΎΡΠΎΡΠ°Ρ ΠΌΠ΅Ρ
Π°Π½ΠΈΠ·ΠΈΡΠΎΠ²Π°Π½Π° ΠΏΠΎΠ΄Π°ΡΠ° ΡΠ»Π΅ΠΊΡΡΠΎΠ΄Π½ΠΎΠΉ ΠΏΡΠΎΠ²ΠΎΠ»ΠΎΠΊΠΈ Π² Π΄Π΅ΡΠΆΠ°ΡΠ΅Π»Π΅ ΡΠ²Π°ΡΠΎΡΠ½ΠΎΠ³ΠΎ ΠΏΠΎΠ»ΡΠ°Π²ΡΠΎΠΌΠ°ΡΠ°.Π’Ρ Π΄ΡΠ³ΠΈ ΠΎΡΡΡΠ΅ΡΡΠ²Π»ΡΡΡ ΡΠ°ΠΊΠΆΠ΅ ΡΠ²Π°ΡΠΎΡΠ½ΡΠΌ ΡΠ»ΡΡΠΎΠΌ. ΠΠ΄Π΅Ρ ΡΡΠΎΠ³ΠΎ ΠΌΠ΅ΡΠΎΠ΄Π°, ΠΏΠΎΠ»ΡΡΠΈΠ²ΡΠ΅Π³ΠΎ Π½Π°Π·Π²Π°Π½ΠΈΠ΅ ΡΠ²Π°ΡΠΊΠΈ ΠΏΠΎΠ΄ ΡΠ»ΡΡΠΎΠΌ, ΠΏΡΠΈΠ½Π°Π΄Π»Π΅ΠΆΠΈΡ Π. Π. Π‘Π»Π°Π²ΡΠ½ΠΎΠ²Ρ (ΠΊΠΎΠ½Π΅Ρ 19 Π².), ΠΡΠΈΠΌΠ΅Π½ΠΈΠ²ΡΠ΅ΠΌΡ Π² ΠΊΠ°ΡΠ΅ΡΡΠ²Π΅ ΡΠ»ΡΡΠ° Π΄ΡΠΎΠ±Π»ΡΠ½ΠΎΠ΅ ΡΡΠ΅ΠΊΠ»ΠΎ. ΠΡΠΎΠΌΡΡΠ»Π΅Π½Π½ΡΠΉ ΡΠΏΠΎΡΠΎΠ± Π²Π½Π΅Π΄ΡΠ΅Π½ΠΈΡ ΠΈ Π²Π½Π΅Π΄ΡΠ΅Π½ΠΈΡ Π² ΠΏΡΠΎΠΈΠ·Π²ΠΎΠ΄ΡΡΠ²ΠΎ ΠΏΠΎΠ΄ ΡΡΠΊΠΎΠ²ΠΎΠ΄ΡΡΠ²ΠΎΠΌ Π°ΠΊΠ°Π΄Π΅ΠΌΠΈΠΊΠ° Π.
Π. ΠΠ°ΡΠΎΠ½Π° (40-Π΅ Π³Π³. 20 Π².). ΡΠ²Π°ΡΠΊΠ° ΠΏΠΎΠ΄ ΡΠ»ΡΡΠΎΠΌ ΠΏΠΎΠ»ΡΡΠΈΠ»Π° Π·Π½Π°ΡΠΈΡΠ΅Π»ΡΠ½ΠΎΠ΅ ΠΏΡΠΎΠΌΡΡΠ»Π΅Π½Π½ΠΎΠ΅ ΠΏΡΠΈΠΌΠ΅Π½Π΅Π½ΠΈΠ΅, Ρ. ΠΊ. ΠΏΠΎΠ·Π²ΠΎΠ»ΡΠ΅Ρ Π°Π²ΡΠΎΠΌΠ°ΡΠΈΠ·ΠΈΡΠΎΠ²Π°ΡΡ ΠΏΡΠΎΡΠ΅ΡΡ, ΡΠ²Π»ΡΠ΅ΡΡΡ Π΄ΠΎΡΡΠ°ΡΠΎΡΠ½ΠΎ ΠΏΡΠΎΠΈΠ·Π²ΠΎΠ΄ΠΈΡΠ΅Π»ΡΠ½ΠΎΠΉ, ΠΏΡΠΈΠ³ΠΎΠ΄Π½ΠΎΠΉ Π΄Π»Ρ ΠΎΡΡΡΠ΅ΡΡΠ²Π»Π΅Π½ΠΈΡ ΡΠ°Π·Π»ΠΈΡΠ½ΠΎΠ³ΠΎ ΡΠΎΠ΄Π° ΡΠ²Π°ΡΠ½ΡΡ
ΡΠΎΠ΅Π΄ΠΈΠ½Π΅Π½ΠΈΠΉ, ΠΎΠ±Π΅ΡΠΏΠ΅ΡΠΈΠ²Π°Π΅Ρ Ρ
ΠΎΡΠΎΡΠ΅Π΅ ΠΊΠ°ΡΠ΅ΡΡΠ²ΠΎ ΡΠ²Π°.Π ΠΏΡΠΎΡΠ΅ΡΡΠ΅ Π‘. ΡΠ°Π±ΠΎΡΠ°Π΅Ρ ΠΏΠΎΠ΄ ΡΠ»ΠΎΠ΅ΠΌ ΡΠ»ΡΡΠ°, ΠΊΠΎΡΠΎΡΡΠΉ Π·Π°ΡΠΈΡΠ°Π΅Ρ Π³Π»Π°Π·Π° ΠΎΡ ΡΠ°Π±ΠΎΡΠ°ΡΡΠΈΡ
ΠΎΡ ΠΈΠ·Π»ΡΡΠ΅Π½ΠΈΡ.
ΠΡΠΈ ΠΌΠ΅Ρ
Π°Π½ΠΈΠ·ΠΈΡΠΎΠ²Π°Π½Π½ΡΡ
ΡΠΏΠΎΡΠΎΠ±Π°Ρ
ΡΠ²Π°ΡΠΊΠΈ ΠΏΡΠΈΠΌΠ΅Π½ΡΡΡ Π³Π°Π·ΠΎΠ²ΡΡ Π·Π°ΡΠΈΡΡ — ΡΠ²Π°ΡΠΊΠ° Π² Π·Π°ΡΠΈΡΠ½ΡΡ
Π³Π°Π·Π°Ρ
, ΠΈΠ»ΠΈ Π³Π°Π·ΠΎΡΠ»Π΅ΠΊΡΡΠΈΡΠ΅ΡΠΊΠ°Ρ ΡΠ²Π°ΡΠΊΠ°. ΠΠ΄Π΅Ρ ΡΡΠΎΠ³ΠΎ ΠΌΠ΅ΡΠΎΠ΄Π° ΠΏΡΠΈΠ½Π°Π΄Π»Π΅ΠΆΠΈΡ Π. Π. ΠΠ΅Π½Π°ΡΠ΄ΠΎΡΡ (ΠΊΠΎΠ½Π΅Ρ 19 Π².). Π‘Π²Π°ΡΠΊΠ° ΠΎΡΡΡΠ΅ΡΡΠ²Π»ΡΠ΅ΡΡΡ ΡΠ²Π°ΡΠΎΡΠ½ΠΎΠΉ Π³ΠΎΡΠ΅Π»ΠΊΠΎΠΉ ΠΈΠ»ΠΈ Π² ΠΊΠ°ΠΌΠ΅ΡΠ°Ρ
, Π·Π°ΠΏΠΎΠ»Π½Π΅Π½Π½ΡΡ
Π³Π°Π·ΠΎΠΌ. ΠΠ°Π·Ρ Π½Π΅ΠΏΡΠ΅ΡΡΠ²Π½ΠΎ ΠΏΠΎΠ΄Π°ΡΡΡΡ Π² Π΄ΡΠ³Ρ ΠΈ ΠΎΠ±Π΅ΡΠΏΠ΅ΡΠΈΠ²Π°Π΅Ρ Π²ΡΡΠΎΠΊΠΎΠ΅ ΠΊΠ°ΡΠ΅ΡΡΠ²ΠΎ ΡΠΎΠ΅Π΄ΠΈΠ½Π΅Π½ΠΈΡ. ΠΡΠΏΠΎΠ»ΡΠ·ΡΡΡ ΠΈΠ½Π΅ΡΡΠ½ΡΠ΅ ΠΈ Π°ΠΊΡΠΈΠ²Π½ΡΠ΅ Π³Π°Π·Ρ.ΠΠ°ΠΈΠ»ΡΡΡΠΈΠ΅ ΡΠ΅Π·ΡΠ»ΡΡΠ°ΡΡ Π΄Π°ΡΡ ΠΏΡΠΈΠΌΠ΅Π½Π΅Π½ΠΈΠ΅ Π³Π΅Π»ΠΈΡ ΠΈ Π°ΡΠ³ΠΎΠ½Π°. ΠΠ΅Π»ΠΈΠΉ ΠΈΠ·-Π·Π° Π²ΡΡΠΎΠΊΠΎΠΉ ΡΡΠΎΠΈΠΌΠΎΡΡΠΈ Π΅Π³ΠΎ ΠΈΡΠΏΠΎΠ»ΡΠ·ΠΎΠ²Π°Π½ΠΈΡ ΠΈΡΠΏΠΎΠ»ΡΠ·ΡΠΉΡΠ΅ ΡΠΎΠ»ΡΠΊΠΎ ΠΏΡΠΈ Π²ΡΠΏΠΎΠ»Π½Π΅Π½ΠΈΠΈ ΡΠΏΠ΅ΡΠΈΠ°Π»ΡΠ½ΡΡ
ΠΎΡΠ²Π΅ΡΡΡΠ²Π΅Π½Π½ΡΡ
ΡΠ°Π±ΠΎΡ. ΠΠΎΠ»Π΅Π΅ ΡΠΈΡΠΎΠΊΠΎ ΡΠ°ΡΠΏΡΠΎΡΡΡΠ°Π½Π΅Π½Π° Π°Π²ΡΠΎΠΌΠ°ΡΠΈΡΠ΅ΡΠΊΠ°Ρ ΠΈ ΠΏΠΎΠ»ΡΠ°Π²ΡΠΎΠΌΠ°ΡΠΈΡΠ΅ΡΠΊΠ°Ρ ΡΠ²Π°ΡΠΊΠ° Π² Π°ΡΠ³ΠΎΠ½Π΅ ΠΈΠ»ΠΈ Π² ΡΠΌΠ΅ΡΠΈ Π΅Π³ΠΎ Ρ Π΄ΡΡΠ³ΠΈΠΌΠΈ Π³Π°Π·Π°ΠΌΠΈ Π½Π΅ΠΏΠ»Π°Π²ΡΡΠΈΠΌΡΡ Π²ΠΎΠ»ΡΡΡΠ°ΠΌΠΎΠ²ΡΠΌ ΠΈ ΠΏΠ»Π°Π²ΡΡΠΈΠΌΡΡ ΡΡΠ°Π»ΡΠ½ΡΠΌ ΡΠ»Π΅ΠΊΡΡΠΎΠ΄Π°ΠΌΠΈ. ΠΡΠΎ ΡΠΏΠΎΡΠΎΠ± ΡΠΎΠ΅Π΄ΠΈΠ½Π΅Π½ΠΈΡ Π΄Π΅ΡΠ°Π»Π΅ΠΉ ΠΎΠ±ΡΡΠ½ΠΎ Π½Π΅Π±ΠΎΠ»ΡΡΠΈΡ
ΡΠΎΠ»ΡΠΈΠ½ ΠΈΠ· Π°Π»ΡΠΌΠΈΠ½ΠΈΡ, ΠΌΠ°Π³Π½ΠΈΡ ΠΈ ΠΈΡ
ΡΡΠ°Π»Π΅ΠΉ, Π²ΡΠ΅Π²ΠΎΠ·ΠΌΠΎΠΆΠ½ΡΡ
ΡΠΏΠ»Π°Π²ΠΎΠ², ΠΆΠ°ΡΠΎΠΏΡΠΎΡΠ½ΡΡ
ΡΠΏΠ»Π°Π²ΠΎΠ², ΡΠΈΡΠ°Π½Π° ΠΈ Π΅Π³ΠΎ ΡΠΏΠ»Π°Π²ΠΎΠ², Π½ΠΈΠΊΠ΅Π»Π΅Π²ΡΡ
ΠΈ ΠΌΠ΅Π΄Π½ΡΡ
ΡΠΏΠ»Π°Π²ΠΎΠ², Π½ΠΈΠΎΠ±ΠΈΡ, ΡΠΈΡΠΊΠΎΠ½ΠΈΡ, ΡΠ°Π½ΡΠ°Π»Π° ΠΈ Π΄Ρ.Π‘Π°ΠΌΡΠΉ Π΄Π΅ΡΡΠ²ΡΠΉ ΡΠΏΠΎΡΠΎΠ±, ΠΎΠ±Π΅ΡΠΏΠ΅ΡΠΈΠ²Π°ΡΡΠΈΠΉ Π²ΡΡΠΎΠΊΠΎΠ΅ ΠΊΠ°ΡΠ΅ΡΡΠ²ΠΎ, — ΡΠ²Π°ΡΠΊΠ° Π² ΡΠ³Π»Π΅ΠΊΠΈΡΠ»ΠΎΠΌ Π³Π°Π·Π΅, ΠΏΡΠΎΠΌΡΡΠ»Π΅Π½Π½ΠΎΠ΅ ΠΏΡΠΈΠΌΠ΅Π½Π΅Π½ΠΈΠ΅ ΠΊΠΎΡΠΎΡΠΎΠΉ ΡΠ°Π·ΡΠ°Π±ΠΎΡΠ°Π½ΠΎ Π² 50-Π΅ Π³Π³. 20 Π². Π² Π¦Π΅Π½ΡΡΠ°Π»ΡΠ½ΠΎΠΌ Π½Π°ΡΡΠ½ΠΎ-ΠΈΡΡΠ»Π΅Π΄ΠΎΠ²Π°ΡΠ΅Π»ΡΡΠΊΠΎΠΌ ΠΈΠ½ΡΡΠΈΡΡΡΠ΅ ΡΠ΅Ρ
Π½ΠΎΠ»ΠΎΠ³ΠΈΠΉ ΠΈ ΠΌΠ°ΡΠΈΠ½ΠΎΡΡΡΠΎΠ΅Π½ΠΈΡ (Π¦ΠΠΠΠ’ΠΠΠ¨) ΠΏΠΎΠ΄ ΡΡΠΊΠΎΠ²ΠΎΠ΄ΡΡΠ²ΠΎΠΌ Π. Π. ΠΡΠ±Π°Π²ΡΠΊΠΎΠ³ΠΎ. ΠΠ»Ρ ΡΠ²Π°ΡΠΊΠΈ Π² ΡΠ³Π»Π΅ΠΊΠΈΡΠ»ΠΎΠΌ Π³Π°Π·Π΅ ΠΈΡΠΏΠΎΠ»ΡΠ·ΡΡΡ ΡΠ»Π΅ΠΊΡΡΠΎΠ΄Π½ΡΡ ΠΏΡΠΎΠ²ΠΎΠ»ΠΎΠΊΡ. Π‘ΠΏΠΎΡΠΎΠ± ΠΏΡΠΈΠ³ΠΎΠ΄Π΅Π½ Π΄Π»Ρ ΡΠΎΠ΅Π΄ΠΈΠ½Π΅Π½ΠΈΡ ΠΈΠ·Π΄Π΅Π»ΠΈΠΉ ΠΈΠ· ΡΡΠ°Π»ΠΈ ΡΠΎΠ»ΡΠΈΠ½ΠΎΠΉ 1-30 ΠΌΠΌ.
Π ΡΠ»Π΅ΠΊΡΡΠΈΡΠ΅ΡΠΊΠΎΠΌΡ ΡΠΏΠΎΡΠΎΠ±Ρ ΡΠ²Π°ΡΠΊΠΈ ΠΏΠ»Π°Π²Π»Π΅Π½ΠΈΠ΅ΠΌ ΠΎΡΠ½ΠΎΡΠΈΡΡΡ ΡΠ»Π΅ΠΊΡΡΠΎΡΠ»Π°ΠΊΠΎΠ²Π°Ρ ΡΠ²Π°ΡΠΊΠ°, ΠΏΡΠΈ ΠΊΠΎΡΠΎΡΠΎΠΉ ΠΏΡΠΎΡΠ΅ΡΡ Π½Π°ΡΠΈΠ½Π°Π΅ΡΡΡ, ΠΊΠ°ΠΊ ΠΏΡΠΈ Π΄ΡΠ³ΠΎΠ²ΠΎΠΉ ΡΠ²Π°ΡΠΊΠ΅ ΠΏΠ»Π°Π²ΠΈΡΡΡ ΡΠ»Π΅ΠΊΡΡΠΎΠ΄ΠΎΠΌ — Π·Π°ΠΆΠΈΠ³Π°Π½ΠΈΠ΅ΠΌ Π΄ΡΠ³ΠΈ, Π° ΠΏΡΠΎΠ΄ΠΎΠ»ΠΆΠ°Π΅ΡΡΡ Π±Π΅Π· Π΄ΡΠ³ΠΎΠ²ΠΎΠ³ΠΎ ΡΠ°Π·ΡΡΠ΄Π°.ΠΡΠΈ ΡΡΠΎΠΌ Π·Π½Π°ΡΠΈΡΠ΅Π»ΡΠ½ΠΎΠ΅ ΠΊΠΎΠ»ΠΈΡΠ΅ΡΡΠ²ΠΎ ΡΠ»Π°ΠΊΠ° Π·Π°ΠΊΡΡΠ²Π°Π΅Ρ ΡΠ²Π°ΡΠΎΡΠ½ΡΡ Π²Π°Π½Π½Ρ. ΠΡΡΠΎΡΠ½ΠΈΠΊΠΎΠ²ΡΠΌ ΠΌΠ΅ΡΠΎΠ΄ΠΎΠΌ ΠΈΡΠΏΠΎΠ»ΡΠ·ΠΎΠ²Π°Π½ΠΈΡ ΡΠ΅ΠΏΠ»ΠΎ, Π²ΡΠ΄Π΅Π»ΡΡΡΠ΅Π³ΠΎΡΡ ΠΏΡΠΈ ΠΏΡΠΎΡ
ΠΎΠΆΠ΄Π΅Π½ΠΈΠΈ ΡΠ»Π΅ΠΊΡΡΠΈΡΠ΅ΡΠΊΠΎΠ³ΠΎ ΡΠΎΠΊΠ° ΡΠ΅ΡΠ΅Π· ΡΠ»Π°ΠΊ. Π‘ΠΏΠΎΡΠΎΠ± ΡΠ°Π·ΡΠ°Π±ΠΎΡΠ°Π½ Π² ΠΈΠ½ΡΡΠΈΡΡΡΠ΅ ΡΠ»Π΅ΠΊΡΡΠΎΡΠ²Π°ΡΠΊΠΈ ΠΈΠΌ. Π. Π. ΠΠ°ΡΠΎΠ½Π° ΠΈ ΠΏΠΎΠ»ΡΡΠΈΠ» ΠΏΡΠΎΠΌΡΡΠ»Π΅Π½Π½ΠΎΠ΅ ΠΏΡΠΈΠΌΠ΅Π½Π΅Π½ΠΈΠ΅ (Π² ΠΊΠΎΠ½ΡΠ΅ 50-Ρ
Π³Π³.). ΠΠΎΠ·ΠΌΠΎΠΆΠ½Π° ΡΠ»Π΅ΠΊΡΡΠΎΡΠ»Π°ΠΊΠΎΠ²Π°Ρ ΡΠ²Π°ΡΠΊΠ° ΠΌΠ΅ΡΠ°Π»Π»ΠΎΠ² ΡΠΎΠ»ΡΠΈΠ½ΠΎΠΉ Π΄ΠΎ 200 ΠΌΠΌ (ΠΎΠ΄Π½ΠΈΠΌ ΡΠ»Π΅ΠΊΡΡΠΎΠ΄ΠΎΠΌ), Π΄ΠΎ 2000 ΠΌΠΌ (ΠΎΠ΄Π½ΠΎΠ²ΡΠ΅ΠΌΠ΅Π½Π½ΠΎ ΡΠ°Π±ΠΎΡΠ°ΡΡΠΈΠΌΠΈ ΡΠ»Π΅ΠΊΡΡΠΎΠ΄Π°ΠΌΠΈ). ΠΠ½Π° ΡΠ΅Π»Π΅ΡΠΎΠΎΠ±ΡΠ°Π·Π½Π° ΠΈ ΡΠΊΠΎΠ½ΠΎΠΌΠΈΡΠ΅ΡΠΊΠΈ Π²ΡΠ³ΠΎΠ΄Π½Π° ΠΏΡΠΈ ΡΠΎΠ»ΡΠΈΠ½Π΅ ΠΎΡΠ½ΠΎΠ²Π½ΠΎΠ³ΠΎ ΠΌΠ΅ΡΠ°Π»Π»Π° Π±ΠΎΠ»Π΅Π΅ 30 ΠΌΠΌ.ΠΠ»Π΅ΠΊΡΡΠΎΡΠ»Π°ΠΊΠΎΠ²ΡΠΌ ΡΠΏΠΎΡΠΎΠ±ΠΎΠΌ ΠΌΠΎΠΆΠ½ΠΎ Π²ΡΠΏΠΎΠ»Π½ΡΡΡ ΡΠ΅ΠΌΠΎΠ½ΡΠ½ΡΠ΅ ΡΠ°Π±ΠΎΡΡ, Π½Π°ΠΏΠ»Π°Π²ΠΊΡ, ΠΊΠΎΠ³Π΄Π° ΡΡΠ΅Π±ΡΠ΅ΡΡΡ Π·Π½Π°ΡΠΈΡΠ΅Π»ΡΠ½Π°Ρ ΡΠΎΠ»ΡΠΈΠ½Π° Π½Π°ΠΏΠ»Π°Π²Π»ΡΠ΅ΠΌΠΎΠ³ΠΎ ΡΠ»ΠΎΡ. Π‘ΠΏΠΎΡΠΎΠ± Π½Π°ΡΡΠ» ΠΏΡΠΈΠΌΠ΅Π½Π΅Π½ΠΈΠ΅ Π² ΠΏΡΠΎΠΈΠ·Π²ΠΎΠ΄ΡΡΠ²Π΅ ΠΏΠ°ΡΠΎΠ²ΡΡ
ΠΊΠΎΡΠ»ΠΎΠ², ΡΡΠ°Π½ΠΈΠ½ ΠΏΡΠ΅ΡΡΠΎΠ², ΠΏΡΠΎΠΊΠ°ΡΠ½ΡΡ
ΡΡΠ°Π½ΠΎΠ², ΡΡΡΠΎΠΈΡΠ΅Π»ΡΠ½ΡΡ
ΠΌΠ΅ΡΠ°Π»Π»ΠΎΠΊΠΎΠ½ΡΡΡΡΠΊΡΠΈΠΉ ΠΈ Ρ. ΠΏ.
ΠΡΡΡΠ΅ΡΡΠ²Π»Π΅Π½ΠΈΠ΅ Π΄ΡΠ³ΠΎΠ²ΠΎΠΉ ΡΠ»Π΅ΠΊΡΡΠΎΡΠ²Π°ΡΠΊΠΈ Π²ΠΎΠ·ΠΌΠΎΠΆΠ½ΠΎ ΡΠ°ΠΊΠΆΠ΅ Π² Π²ΠΎΠ΄Π΅ (ΠΏΡΠ΅ΡΠ½ΠΎΠΉ ΠΈ ΠΌΠΎΡΡΠΊΠΎΠΉ). ΠΠ΅ΡΠ²ΡΠΉ ΠΏΡΠ°ΠΊΡΠΈΡΠ΅ΡΠΊΠΈ ΠΏΡΠΈΠ³ΠΎΠ΄Π½ΡΠΉ ΡΠΏΠΎΡΠΎΠ± ΡΠ²Π°ΡΠΊΠΈ Π±ΡΠ» ΡΠΎΠ·Π΄Π°Π½ Π² ΠΠΎΡΠΊΠΎΠ²ΡΠΊΠΎΠΌ ΡΠ»Π΅ΠΊΡΡΠΎΠΌΠ΅Ρ
Π°Π½ΠΈΡΠ΅ΡΠΊΠΎΠΌ ΠΈΠ½ΡΡΠΈΡΡΡΠ΅ ΠΈΠ½ΠΆΠ΅Π½Π΅ΡΠΎΠ² ΠΆ.-Π΄. ΡΡΠ°Π½ΡΠΏΠΎΡΡΠ° Π² 1932 ΠΏΠΎΠ΄ Π.Π. Π₯ΡΠ΅Π½ΠΎΠ²Π°. ΠΡΠ³Π° Π² Π²ΠΎΠ΄Π΅ Π³ΠΎΡΠΈΡΠΎ, ΠΎΡ
Π»Π°ΠΆΠ΄Π°ΡΡΠ΅Π΅ Π΄Π΅ΠΉΡΡΠ²ΠΈΠ΅ Π²ΠΎΠ΄Ρ ΠΊΠΎΠΌΠΏΠ΅Π½ΡΠΈΡΡΠ΅ΡΡΡ Π½Π΅Π±ΠΎΠ»ΡΡΠΈΠΌ ΠΏΠΎΠ²ΡΡΠ΅Π½ΠΈΠ΅ΠΌ Π½Π°ΠΏΡΡΠΆΠ΅Π½ΠΈΡ Π΄ΡΠ³ΠΈ, ΠΊΠΎΡΠΎΡΠ°Ρ ΠΏΠ»Π°Π²ΠΈΡ ΠΌΠ΅ΡΠ°Π»Π» Π² Π²ΠΎΠ΄Π΅ ΡΠ°ΠΊ ΠΆΠ΅ Π»Π΅Π³ΠΊΠΎ, ΠΊΠ°ΠΊ ΠΈ Π½Π° Π²ΠΎΠ·Π΄ΡΡ
Π΅. Π‘Π²Π°ΡΠΊΠ° ΠΏΡΠΎΠΈΠ·Π²ΠΎΠ΄ΠΈΡΡΡ Π²ΡΡΡΠ½ΡΡ ΡΡΡΡΠ½ΡΠΌ ΠΏΠ»Π°Π²ΠΈΠΌΡΡ ΡΡΠ°Π»ΡΠ½ΡΠΌ ΡΠ»Π΅ΠΊΡΡΠΎΠ΄ΠΎΠΌ Ρ ΡΠΎΠ»ΡΡΡΠΌ (Π΄ΠΎ 30% ΡΠΎΠ»ΡΠΈΠ½Ρ ΡΠ»Π΅ΠΊΡΡΠΎΠ΄Π°) Π²ΠΎΠ΄ΠΎΠ½Π΅ΠΏΡΠΎΠ½ΠΈΡΠ°Π΅ΠΌΡΠΌ ΠΏΠΎΠΊΡΡΡΠΈΠ΅ΠΌ. ΠΠ°ΡΠ΅ΡΡΠ²ΠΎ ΡΠ²Π°ΡΠΊΠΈ Π½Π΅ΡΠΊΠΎΠ»ΡΠΊΠΎ Π½ΠΈΠΆΠ΅, ΡΠ΅ΠΌ Π½Π° Π²ΠΎΠ·Π΄ΡΡ
Π΅, ΠΌΠ΅ΡΠ°Π»Π» ΡΠ²Π° Π½Π΅Π΄ΠΎΡΡΠ°ΡΠΎΡΠ½ΠΎ ΠΏΠ»Π°ΡΡΠΈΡΠ΅Π½. Π 70-Π΅ Π³Π³. Π² Π‘Π‘Π‘Π Π² ΠΈΠ½ΡΡΠΈΡΡΡΠ΅ ΡΠ»Π΅ΠΊΡΡΠΎΡΠ²Π°ΡΠΊΠΈ ΠΈΠΌ. Π. Π. ΠΠ°ΡΠΎΠ½Π° ΠΎΡΡΡΠ΅ΡΡΠ²Π»Π΅Π½Π° ββΡΠ²Π°ΡΠΊΠ° ΠΏΠΎΠ΄ ΠΏΠΎΠ»ΡΠ°Π²ΡΠΎΠΌΠ°ΡΠΎΠΌ, Π² ΠΊΠΎΡΠΎΡΠΎΠΌ Π² ΠΊΠ°ΡΠ΅ΡΡΠ²Π΅ ΡΠ»Π΅ΠΊΡΡΠΎΠ΄Π° ΠΏΡΠ΅Π΄Π»ΠΎΠΆ Ρ.Π½. ΠΏΠΎΡΠΎΡΠΊΠΎΠ²Π°Ρ ΠΏΡΠΎΠ²ΠΎΠ»ΠΎΠΊΠ° (ΡΠΎΠ½ΠΊΠ°Ρ ΡΡΠ°Π»ΡΠ½Π°Ρ ΡΡΡΠ±ΠΊΠ°, Π½Π°Π±ΠΈΡΠ°Ρ ΡΠΌΠ΅ΡΡΡ ΠΏΠΎΡΠΎΡΠΊΠΎΠ²), Π½Π΅ΠΏΡΠ΅ΡΡΠ²Π½ΠΎ ΠΏΠΎΠ΄Π°Π²Π°Π΅ΠΌΠ°Ρ Π² Π΄ΡΠ³Ρ. ΠΠΎΡΠΎΡΠΎΠΊ ΡΠ²Π»ΡΠ΅ΡΡΡ ΡΠ»ΡΡΠΎΠΌ. ΠΠΎΠ΄Π²ΠΎΠ΄Π½Π°Ρ ΡΠ²Π°ΡΠΊΠ° Π²Π΅Π΄ΡΡΡΡ Π½Π° Π³Π»ΡΠ±ΠΈΠ½Π΅ Π΄ΠΎ 100 ΠΌ, ΠΏΠΎΠ»ΡΡΠΈΠ»Π° ΡΠ°ΡΠΏΡΠΎΡΡΡΠ°Π½Π΅Π½ΠΈΠ΅ Π² ΡΡΠ΄ΠΎΡΠ΅ΠΌΠΎΠ½ΡΠ½ΡΡ
ΠΈ Π°Π²Π°ΡΠΈΠΉΠ½ΠΎ-ΡΠΏΠ°ΡΠ°ΡΠ΅Π»ΡΠ½ΡΡ
ΡΠ°Π±ΠΎΡΠ°Ρ
.
ΠΠ΄ΠΈΠ½ ΠΈΠ· ΠΏΠ΅ΡΡΠΏΠ΅ΠΊΡΠΈΠ²Π½ΡΡ
ΡΠΏΠΎΡΠΎΠ±ΠΎΠ² ΡΠ²Π°ΡΠΊΠΈ — ΠΏΠ»Π°Π·ΠΌΠ΅Π½Π½Π°Ρ ΡΠ²Π°ΡΠΊΠ° — ΡΠΎΠ·Π΄Π°Π΅ΡΡΡ ΠΏΠ»Π°Π·ΠΌΠ΅Π½Π½ΠΎΠΉ Π³ΠΎΡΠ΅Π»ΠΊΠΎΠΉ. Π‘ΡΡΠ½ΠΎΡΡΡ ΡΡΠΎΠ³ΠΎ ΠΌΠ΅ΡΠΎΠ΄Π° ΡΠ²Π°ΡΠΊΠΈ ΡΠΎΡΡΠΎΠΈΡ Π² ΡΠΎΠΌ, ΡΡΠΎ Π΄ΡΠ³Π° Π³ΠΎΡΠΈΡ ΠΌΠ΅ΠΆΠ΄Ρ Π²ΠΎΠ»ΡΡΡΠ°ΠΌΠΎΠ²ΡΠΌ ΡΠ»Π΅ΠΊΡΡΠΎΠ΄ΠΎΠΌ ΠΈ ΠΈΠ·Π΄Π΅Π»ΠΈΠ΅ΠΌ ΠΈ ΠΏΡΠΎΠ΄ΡΠ²Π°Π΅ΡΡΡ ΠΏΠΎΡΠΎΠΊΠΎΠΌ Π³Π°Π·Π°, Π² ΡΠ΅Π·ΡΠ»ΡΡΠ°ΡΠ΅ ΡΠ΅Π³ΠΎ ΠΎΠ±ΡΠ°Π·ΡΠ΅ΡΡΡ ΠΏΠ»Π°Π·ΠΌΠ°, ΠΈΡΠΏΠΎΠ»ΡΠ·ΡΠ΅ΠΌΠ°Ρ Π΄Π»Ρ Π²ΡΡΠΎΠΊΠΎΡΠ΅ΠΌΠΏΠ΅ΡΠ°ΡΡΡΠ½ΠΎΠ³ΠΎ ΠΌΠ΅Ρ
Π°Π½ΠΈΠ·ΠΌΠ° ΠΌΠ΅ΡΠ°Π»Π»Π°.ΠΠ΅ΡΡΠΏΠ΅ΠΊΡΠΈΠ²Π½Π°Ρ ΡΠ°Π·Π½ΠΎΠ²ΠΈΠ΄Π½ΠΎΡΡΡ ΠΏΠ»Π°Π·ΠΌΠ΅Π½Π½ΠΎΠΉ ΡΠ²Π°ΡΠΊΠΈ — ΡΠ²Π°ΡΠΊΠ° ΡΠΆΠ°ΡΠΎΠΉ Π΄ΡΠ³ΠΎΠΉ (Π³Π°Π·Ρ ΡΡΠΎΠ»Π±Π° Π΄ΡΠ³ΠΈ, ΠΏΡΠΎΡ
ΠΎΠ΄Ρ ΡΠ΅ΡΠ΅Π· ΠΊΠ°Π»ΠΈΠ±ΡΠΎΠ²Π°Π½Π½ΡΠΉ ΠΊΠ°Π½Π°Π» ΡΠΎΠΏΠ»Π° Π³ΠΎΡΠ΅Π»ΠΊΠΈ, Π²ΡΡΡΠ³ΠΈΠ²Π°ΡΡΡΡ Π² ΡΠΎΠ½ΠΊΡΡ ΡΡΡΡΡ). ΠΡΠΈ ΡΠΆΠ°ΡΠΈΠΈ Π΄ΡΠ³ΠΈ ΠΌΠ΅Π½ΡΡΡΡΡ Π΅Π΅ ΡΠ²ΠΎΠΉΡΡΠ²Π°: Π·Π½Π°ΡΠΈΡΠ΅Π»ΡΠ½ΠΎ ΠΏΠΎΠ²ΡΡΠ°Π΅ΡΡΡ Π½Π°ΠΏΡΡΠΆΠ΅Π½ΠΈΠ΅, ΡΠ΅Π·ΠΊΠΎ Π²ΠΎΠ·ΡΠ°ΡΡΠ°Π΅Ρ ΡΠ΅ΠΌΠΏΠ΅ΡΠ°ΡΡΡΠ° (Π΄ΠΎ 20000-30000 Π‘). ΠΠ»Π°Π·ΠΌΠ΅Π½Π½Π°Ρ ΡΠ²Π°ΡΠΊΠ° ΠΏΠΎΠ»ΡΡΠΈΠ»Π° ΠΏΡΠΎΠΌΡΡΠ»Π΅Π½Π½ΠΎΠ΅ ΠΏΡΠΈΠΌΠ΅Π½Π΅Π½ΠΈΠ΅ Π΄Π»Ρ ΡΠΎΠ΅Π΄ΠΈΠ½Π΅Π½ΠΈΡ ΡΡΠ³ΠΎΠΏΠ»Π°Π²ΠΊΠΈΡ
ΠΌΠ΅ΡΠ°Π»Π»ΠΎΠ², ΠΏΡΠΈΡΡΠΌ Π°Π²ΡΠΎΠΌΠ°ΡΡ ΠΈ ΠΏΠΎΠ»ΡΠ°Π²ΡΠΎΠΌΠ°ΡΡ Π΄Π»Ρ Π΄ΡΠ³ΠΎΠ²ΠΎΠΉ ΡΠ²Π°ΡΠΊΠΈ Π»Π΅Π³ΠΊΠΎ Π±ΡΡΡ ΠΏΡΠΈΡΠΏΠΎΡΠΎΠ±Π»Π΅Π½Ρ Π΄Π»Ρ ΠΏΠ»Π°Π·ΠΌΠ΅Π½Π½ΠΎΠΉ ΠΏΡΠΈ ΠΈΡΠΏΠΎΠ»ΡΠ·ΠΎΠ²Π°Π½ΠΈΠΈ Π·Π°ΠΌΠ΅Π½Π΅ Π³ΠΎΡΠ΅Π»ΠΊΠΈ.ΠΠ»Π°Π·ΠΌΠ΅Π½Π½ΡΡ ΡΠ²Π°ΡΠΊΡ ΠΈΡΠΏΠΎΠ»ΡΠ·ΡΡΡ ΠΊΠ°ΠΊ Π΄Π»Ρ ΡΠΎΠ΅Π΄ΠΈΠ½Π΅Π½ΠΈΡ ΠΌΠ΅ΡΠ°Π»Π»ΠΎΠ² Π±ΠΎΠ»ΡΡΠΈΡ
ΡΠΎΠ»ΡΠΈΠ½ (ΠΌΠ½ΠΎΠ³ΠΎΡΠ»ΠΎΠΉΠ½Π°Ρ ΡΠ²Π°ΡΠΊΠ° Ρ Π·Π°ΡΠΈΡΠΎΠΉ Π°ΡΠ³ΠΎΠ½ΠΎΠΌ), ΡΠ°ΠΊ ΠΈ Π΄Π»Ρ ΡΠΎΠ΅Π΄ΠΈΠ½Π΅Π½ΠΈΡ ΠΏΠ»Π°ΡΡΠΈΠ½ ΠΈ ΠΏΡΠΎΠ²ΠΎΠ»ΠΎΠΊΠΈ ΡΠΎΠ»ΡΠΈΠ½ΠΎΠΉ ΠΎΡ Π΄Π΅ΡΡΡΠΊΠΎΠ² ΠΌΠΊΠΌ Π΄ΠΎ 1 ΠΌΠΌ (ΠΌΠΈΠΊΡΠΎΡΠ²Π°ΡΠΊΠ°, ΡΠ²Π°ΡΠΊΠ°. ΠΠ³ΠΎΠ»ΡΡΠ°ΡΠΎΠΉ ββΠ΄ΡΠ³ΠΎΠΉ). ΠΠ»Π°Π·ΠΌΠ΅Π½Π½ΠΎΠΉ ΡΡΡΡΠ΅ΠΉ ΠΌΠΎΠΆΠ½ΠΎ ΠΎΡΡΡΠ΅ΡΡΠ²Π»ΡΡΡ ΡΠ°ΠΊΠΆΠ΅ Π΄Ρ. Π²ΠΈΠ΄Ρ ΠΏΠ»Π°Π·ΠΌΠ΅Π½Π½ΠΎΠΉ ΠΎΠ±ΡΠ°Π±ΠΎΡΠΊΠΈ, Π² ΡΠΎΠΌ ΡΠΈΡΠ»Π΅ ΠΏΠ»Π°Π·ΠΌΠ΅Π½Π½ΡΡ ΡΠ΅Π·ΠΊΡ ΠΌΠ΅ΡΠ°Π»Π»ΠΎΠ².
ΠΠ°Π·ΠΎΠ²Π°Ρ ΡΠ²Π°ΡΠΊΠ°
ΠΠ°Π·ΠΎΠ²Π°Ρ ΡΠ²Π°ΡΠΊΠ° ΠΎΡΠ½ΠΎΡΠΈΡΡΡ ΠΊ ΡΠΏΠΎΡΠΎΠ±Π°ΠΌ ΡΠ²Π°ΡΠΊΠΈ Ρ ΠΈΡΠΏΠΎΠ»ΡΠ·ΠΎΠ²Π°Π½ΠΈΠ΅ΠΌ ΡΠ½Π΅ΡΠ³ΠΈΠΈ Π³Π°Π·ΠΎΠ²ΠΎΠ³ΠΎ ΠΏΠ»Π°ΠΌΠ΅Π½ΠΈ, ΠΏΡΠΈΠΌΠ΅Π½ΡΠ΅ΠΌΡΠΌΠΈ Π΄Π»Ρ ΡΠΎΠ΅Π΄ΠΈΠ½Π΅Π½ΠΈΡ ΡΠ°Π·Π»ΠΈΡΠ½ΡΡ ΠΌΠ΅ΡΠ°Π»Π»ΠΎΠ² ΠΎΠ±ΡΡΠ½ΠΎ Π½Π΅Π±ΠΎΠ»ΡΡΠΈΠΌΠΈ ΡΠΎΠ»ΡΠΈΠ½Π°ΠΌΠΈ — Π΄ΠΎ 10 ΠΌΠΌ.ΠΠ°Π·ΠΎΠ²ΠΎΠ΅ ΠΏΠ»Π°ΠΌΡ Ρ ΡΠ°ΠΊΠΎΠΉ ΡΠ΅ΠΌΠΏΠ΅ΡΠ°ΡΡΡΠΎΠΉ ΠΏΠΎΠ»ΡΡΠ°Π΅ΡΡΡ ΠΏΡΠΈ ΡΠΆΠΈΠ³Π°Π½ΠΈΠΈ ΡΠ°Π·Π»ΠΈΡΠ½ΡΡ Π³ΠΎΡΡΡΠΈΡ Π² ΠΊΠΈΡΠ»ΠΎΡΠΎΠ΄Π΅ (Π²ΠΎΠ΄ΠΎΡΠΎΠ΄Π½ΠΎ-ΠΊΠΈΡΠ»ΠΎΡΠΎΠ΄Π½Π°Ρ, Π±Π΅Π½Π·ΠΈΠ½ΠΎ-ΠΊΠΈΡΠ»ΠΎΡΠΎΠ΄Π½Π°Ρ, Π°ΡΠ΅ΡΠΈΠ»Π΅Π½ΠΎ-ΠΊΠΈΡΠ»ΠΎΡΠΎΠ΄Π½Π°Ρ ΡΠ²Π°ΡΠΊΠ° ΠΈ Π΄Ρ.).
ΠΡΠΎΠΌΡΡΠ»Π΅Π½Π½ΠΎΠ΅ ΠΏΡΠΈΠΌΠ΅Π½Π΅Π½ΠΈΠ΅ ΠΏΠΎΠ»ΡΡΠΈΠ»Π° Π°ΡΠ΅ΡΠΈΠ»Π΅Π½ΠΎ-ΠΊΠΈΡΠ»ΠΎΡΠΎΠ΄Π½Π°Ρ Π³Π°Π·ΠΎΠ²Π°Ρ ΡΠ²Π°ΡΠΊΠ°. Π‘ΡΡΠ΅ΡΡΠ²Π΅Π½Π½ΠΎΠ΅ ΠΎΡΠ»ΠΈΡΠΈΠ΅ Π³Π°Π·ΠΎΠ²ΠΎΠΉ ΡΠ²Π°ΡΠΊΠΈ ΠΎΡ Π΄ΡΠ³ΠΎΠ²ΠΎΠΉ ΡΠ²Π°ΡΠΊΠΈ — Π±ΠΎΠ»Π΅Π΅ ΠΏΠ»Π°Π²Π½ΡΠΉ ΠΈ ΠΌΠ΅Π΄Π»Π΅Π½Π½ΡΠΉ Π½Π°Π³ΡΠ΅Π² ΠΌΠ΅ΡΠ°Π»Π»Π°, ΠΡΠΎ ΠΎΠ±ΡΡΠΎΡΡΠ΅Π»ΡΡΡΠ²ΠΎ ΠΎΠΏΡΠ΅Π΄Π΅Π»ΡΠ΅Ρ ΠΏΡΠΈΠΌΠ΅Π½Π΅Π½ΠΈΠ΅ Π³Π°Π·ΠΎΠ²ΠΎΠΉ ΡΠ²Π°ΡΠΊΠΈ Π΄Π»Ρ ΡΠΎΠ΅Π΄ΠΈΠ½Π΅Π½ΠΈΡ ΠΌΠ΅ΡΠ°Π»Π»ΠΎΠ² ΠΌΠ°Π»ΡΡ
ΡΠΎΠ»ΡΠΈΠ½, ΡΡΠ΅Π±ΡΡΡΠΈΡ
ΠΏΠΎΠ΄ΠΎΠ³ΡΠ΅Π²Π° Π² ΠΏΡΠΎΡΠ΅ΡΡΠ΅ ΡΠ²Π°ΡΠΊΠΈ (Π½Π°ΠΏΡΠΈΠΌΠ΅Ρ, ΡΡΠ³ΡΠ½ ΠΈ Π½Π΅ΠΊΠΎΡΠΎΡΡΠ΅ ΡΠΏΠ΅ΡΠΈΠ°Π»ΡΠ½ΡΠ΅ ΡΡΠ°Π»ΠΈ), Π·Π°ΠΌΠ΅Π΄Π»Π΅Π½Π½ΠΎΠ³ΠΎ ΠΎΡ
Π»Π°ΠΆΠ΄Π΅Π½ΠΈΡ (Π½Π°ΠΏΡΠΈΠΌΠ΅Ρ, ΠΈΠ½ΡΡΡΡΠΌΠ΅Π½ΡΠ°Π»ΡΠ½ΡΠ΅ ΡΡΠ°Π»ΠΈ) ΠΈ Ρ.Π΄. ΠΠ»Π°Π³ΠΎΠ΄Π°ΡΡ ΡΡΠ°Π²Π½ΠΈΡΠ΅Π»ΡΠ½ΠΎΠΉ ΠΏΡΠΎΡΡΠΎΡΠ΅ ΠΈ ΡΠ½ΠΈΠ²Π΅ΡΡΠ°Π»ΡΠ½ΠΎΡΡΠΈ ΠΎΠ±ΠΎΡΡΠ΄ΠΎΠ²Π°Π½ΠΈΡ Π³Π°Π·ΠΎΠ²Π°Ρ ΡΠ²Π°ΡΠΊΠ° ΡΠ΅Π»Π΅ΡΠΎΠΎΠ±ΡΠ°Π·Π½Π° ΠΏΡΠΈ Π²ΡΠΏΠΎΠ»Π½Π΅Π½ΠΈΠΈ ΡΠ΅ΠΌΠΎΠ½ΡΠ½ΡΡ
ΡΠ°Π±ΠΎΡ. ΠΡΠΎΠΌΡΡΠ»Π΅Π½Π½ΠΎΠ΅ ΠΏΡΠΈΠΌΠ΅Π½Π΅Π½ΠΈΠ΅ ΠΈΠΌΠ΅Π΅Ρ ΡΠ°ΠΊΠΆΠ΅ Π³Π°Π·ΠΎΠΏΡΠ΅ΡΡΠΎΠ²Π°Ρ ΡΠ²Π°ΡΠΊΠ° ΡΡΠ°Π»ΡΠ½ΡΡ
ΡΡΡΠ± ΠΈ ΡΠ΅Π»ΡΡΠΎΠ², Π·Π°ΠΊΠ»ΡΡΠ°ΡΡΠ°ΡΡΡ Π² ΡΠ»ΡΡΡΠ΅Π½Π½ΠΎΠΌ Π½Π°Π³ΡΠ΅Π²Π΅ ΡΠΎΡΡΠΎΡΠ½ΠΈΡ Π°ΡΠ΅ΡΠΈΠ»Π΅Π½ΠΎ-ΠΊΠΈΡΠ»ΠΎΡΠΎΠ΄Π½ΡΠΌ ΠΏΠ»Π°ΠΌΠ΅Π½Π΅ΠΌ ΠΌΠ΅ΡΠ°Π»Π»Π° Π² ΠΌΠ΅ΡΡΠ΅ ΡΡΡΠΊΠ° Π΄ΠΎ ΠΏΠ»Π°ΡΡΠΈΡΠ΅ΡΠΊΠΎΠ³ΠΎ ΠΌΠ°ΡΠ΅ΡΠΈΠ°Π»Π° ΠΈ ΠΎΡΠ°Π΄ΠΊΠ΅ Ρ ΠΏΡΠ΅ΡΡΠΎΠ²Π°Π½ΠΈΠ΅ΠΌ ΠΈΠ»ΠΈ ΠΏΡΠΎΠΊΠΎΠ²ΠΊΠΎΠΉ.
ΠΠ΅ΡΡΠΏΠ΅ΠΊΡΠΈΠ²Π½ΡΠΌΠΈ ΠΏΠΎΡΠ²ΠΈΠ²ΡΠΈΠΌΠΈΡΡ Π² 60-Π΅ Π³Π³. ΡΠΏΠΎΡΠΎΠ±Ρ Π»ΡΡΠ΅Π²ΠΎΠΉ ΡΠ²Π°ΡΠΊΠΈ, ΡΠ°ΠΊΠΆΠ΅ ΠΎΡΡΡΠ΅ΡΡΠ²Π»ΡΠ΅ΠΌΡΠ΅ Π±Π΅Π· ΠΏΡΠΈΠΌΠ΅Π½Π΅Π½ΠΈΡ Π΄Π°Π²Π»Π΅Π½ΠΈΡ.ΠΠ»Π΅ΠΊΡΡΠΎΠ½Π½ΠΎΠ»ΡΡΠ΅Π²Π°Ρ (ΡΠ»Π΅ΠΊΡΡΠΎΠ½Π½Π°Ρ) ΡΠ²Π°ΡΠΊΠ° ΠΏΡΠΎΠΈΠ·Π²ΠΎΠ΄ΠΈΡΡΡ ΡΡΠΎΠΊΡΡΠΈΡΠΎΠ²Π°Π½Π½ΡΠΌ ΠΏΠΎΡΠΎΠΊΠΎΠΌ ΡΠ»Π΅ΠΊΡΡΠΎΠ½ΠΎΠ². ΠΠ·Π΄Π΅Π»ΠΈΠ΅ ΠΏΠΎΠΌΠ΅ΡΠ°Π΅ΡΡΡ Π² ΠΊΠ°ΠΌΠ΅ΡΡ, Π² ΠΊΠΎΡΠΎΡΠΎΠΉ ΠΈΠΌΠ΅Π΅ΡΡΡ Π²Π°ΠΊΡΡΠΌ (10-2-10-4 Π½ / ΠΌ2), Π½Π΅ΠΎΠ±Ρ
ΠΎΠ΄ΠΈΠΌΠΎΠ΅ Π΄Π»Ρ ΡΠ²ΠΎΠ±ΠΎΠ΄Π½ΠΎΠ³ΠΎ Π΄Π²ΠΈΠΆΠ΅Π½ΠΈΡ ΡΠ»Π΅ΠΊΡΡΠΎΠ½ΠΎΠ² ΠΈ ΠΊΠΎΠ½ΡΠ΅Π½ΡΡΠΈΡΠΎΠ²Π°Π½Π½ΠΎΠ³ΠΎ ΠΏΡΡΠΊΠ° ΡΠ»Π΅ΠΊΡΡΠΎΠ½ΠΎΠ². ΠΡ ΠΌΠΎΡΠ½ΠΎΠ³ΠΎ ΠΈΡΡΠΎΡΠ½ΠΈΠΊΠ° ΡΠ»Π΅ΠΊΡΡΠΎΠ½ΠΎΠ² (ΡΠ»Π΅ΠΊΡΡΠΎΠ½Π½ΠΎΠΉ ΠΏΡΡΠΊΠΈ) Π½Π° ΡΡΡΡΠΎΠΉΡΡΠ²ΠΎ Π½Π°ΠΏΡΠ°Π²Π»ΡΠ΅ΡΡΡ ΡΠΏΡΠ°Π²Π»ΡΠ΅ΠΌΡΠΉ ΡΠ»Π΅ΠΊΡΡΠΎΠ½Π½ΡΠΉ Π»ΡΡ, ΡΠΎΠΊΡΡΠΈΡΡΠ΅ΠΌΡΠΉ ΠΌΠ°Π³Π½ΠΈΡΠ½ΡΠΌ ΠΈ ΡΠ»Π΅ΠΊΡΡΠΎΡΡΠ°ΡΠΈΡΠ΅ΡΠΊΠΈΠΌΠΈ ΠΏΠΎΠ»ΡΠΌΠΈ. ΠΠΎΠ½ΡΠ΅Π½ΡΡΠ°ΡΠΈΡ ΡΠ½Π΅ΡΠ³ΠΈΠΈ Π² ΡΡΠΎΠΊΡΡΠΈΡΠΎΠ²Π°Π½Π½ΠΎΠΌ ΠΏΡΡΠ½Π΅ Π΄ΠΎ 109 Π²Ρ / ΡΠΌ2. ΠΠ΅ΡΠ΅ΠΌΠ΅ΡΠ°Ρ Π»ΡΡ ΠΏΠΎ Π»ΠΈΠ½ΠΈΠΈ ΡΠ²Π°ΡΠΊΠΈ, ΠΌΠΎΠΆΠ½ΠΎ ΡΠ²Π°ΡΠΈΠ²Π°ΡΡ ΡΠ²Ρ Π»ΡΠ±ΠΎΠΉ ΠΊΠΎΠ½ΡΠΈΠ³ΡΡΠ°ΡΠΈΠΈ ΠΏΡΠΈ Π²ΡΡΠΎΠΊΠΎΠΉ ΡΠΊΠΎΡΠΎΡΡΠΈ.ΠΠ°ΠΊΡΡΠΌ ΡΠΏΠΎΡΠΎΠ±ΡΡΠ²ΡΠ΅Ρ ΠΌΠ΅Π½ΡΡΠ΅ΠΌΡ ΠΎΠΊΠΈΡΠ»Π΅Π½ΠΈΡ ΠΌΠ΅ΡΠ°Π»Π»Π° ΡΠ²Π°. ΠΠ»Π΅ΠΊΡΡΠΎΠ½Π½ΡΠΉ Π»ΡΡ ΠΏΠ»Π°Π²ΠΈΡ ΠΈ Π΄ΠΎΠ²ΠΎΠ΄ΠΈΡ Π΄ΠΎ ΠΊΠΈΠΏΠ΅Π½ΠΈΡ ΠΏΡΠ°ΠΊΡΠΈΡΠ΅ΡΠΊΠΈ Π²ΡΠ΅ ΠΌΠ΅ΡΠ°Π»Π»Ρ ΠΈ ΠΈΡΠΏΠΎΠ»ΡΠ·ΡΠ΅ΡΡΡ Π½Π΅ ΡΠΎΠ»ΡΠΊΠΎ Π΄Π»Ρ ΡΠ²Π°ΡΠΊΠΈ, Π½ΠΎ ΠΈ Π΄Π»Ρ ΡΠ΅Π·ΠΊΠΈ, ΡΠ²Π΅ΡΠ»Π΅Π½ΠΈΡ ΠΎΡΠ²Π΅ΡΡΡΠΈΠΉ ΠΈ Ρ. ΠΏ. Π‘ΠΊΠΎΡΠΎΡΡΡ ΡΠ²Π°ΡΠΊΠΈ ΡΡΠΈΠΌ ΡΠΏΠΎΡΠΎΠ±ΠΎΠΌ Π² 1,5β2 ΡΠ°Π·Π° Π±ΠΎΠ»ΡΡΠ΅ ΠΏΡΠΈ ΠΏΠΎΠ΄ΠΎΠ±Π½ΡΡ
ΠΎΠΏΠ΅ΡΠ°ΡΠΈΡΡ
. ΠΠ΅Π΄ΠΎΡΡΠ°ΡΠΎΠΊ ΡΡΠΎΠ³ΠΎ ΠΌΠ΅ΡΠΎΠ΄Π° — Π±ΠΎΠ»ΡΡΠΈΠ΅ Π·Π°ΡΡΠ°ΡΡ Π½Π° ΡΠΎΠ·Π΄Π°Π½ΠΈΠ΅ Π²Π°ΠΊΡΡΠΌΠ° ΠΈ Π½Π΅ΠΎΠ±Ρ
ΠΎΠ΄ΠΈΠΌΠΎΡΡΡ Π½Π°ΠΏΡΡΠΆΠ΅Π½ΠΈΡ Π΄Π»Ρ ΠΎΠ±Π΅ΡΠΏΠ΅ΡΠ΅Π½ΠΈΡ ΠΌΠΎΡΠ½ΠΎΠ³ΠΎ ΠΈΠ·Π»ΡΡΠ΅Π½ΠΈΡ. ΠΡΠΈΡ
Π½Π΅Π΄ΠΎΡΡΠ°ΡΠΊΠΎΠ² Π»ΠΈΡΡΠ½ Π΄Ρ. ΡΠΏΠΎΡΠΎΠ± Π»ΡΡΠ΅Π²ΠΎΠΉ ΡΠ²Π°ΡΠΊΠΈ — ΡΠΎΡΠΎΠ½Π½Π°Ρ (ΡΠ²Π΅ΡΠΎΠ²Π°Ρ) ΡΠ²Π°ΡΠΊΠ°.Π ΠΎΡΠ»ΠΈΡΠΈΠ΅ ΠΎΡ ΡΠ»Π΅ΠΊΡΡΠΎΠ½Π½ΠΎΠ³ΠΎ Π»ΡΡΠ°, ΡΠ²Π΅ΡΠΎΠ²ΠΎΠΉ Π»ΡΡ ΠΌΠΎΠΆΠ΅Ρ ΠΏΡΠΎΠΉΡΠΈ ΡΠ΅ΡΠ΅Π· Π±ΠΎΠ»ΡΡΠΈΠ΅ ΡΠ°ΡΡΡΠΎΡΠ½ΠΈΡ Π² Π²ΠΎΠ·Π΄ΡΡ
Π΅, Π½Π΅ ΡΠ΅ΡΡΡ ΡΠ½Π΅ΡΠ³ΠΈΠΈ Π·Π°ΠΌΠ΅ΡΠ½ΠΎ (Ρ. Π. ΠΡΠΏΠ°Π΄Π°Π΅Ρ Π² Π²Π°ΠΊΡΡΠΌΠ΅), ΠΌΠΎΠΆΠ΅Ρ Π±Π΅Π· ΠΎΡΠ»Π°Π±Π»Π΅Π½ΠΈΡ ΠΏΡΠΎΡΠ²Π΅ΡΠΈΠ²Π°ΡΡ ΠΏΡΠΎΠ·ΡΠ°ΡΠ½ΡΠ΅ ΠΌΠ°ΡΠ΅ΡΠΈΠ°Π»Ρ (ΡΡΠ΅ΠΊΠ»ΠΎ, ΠΊΠ²Π°ΡΡ ΠΈ Ρ.
Π.), Π’. Π΅. ΠΎΠ±Π΅ΡΠΏΠ΅ΡΠΈΠ²Π°Π΅ΡΡΡ ΡΡΠ΅ΡΠΈΠ»ΡΠ½ΠΎΡΡΡ Π·ΠΎΠ½Ρ ΡΠ²Π°ΡΠΊΠΈ ΠΏΡΠΈ ΠΏΡΠΎΠΏΡΡΠΊΠ°Π½ΠΈΠΈ Π»ΡΡΠ° ΡΠ΅ΡΠ΅Π· ΠΏΡΠΎΠ·ΡΠ°ΡΠ½ΡΡ ΠΎΠ±ΠΎΠ»ΠΎΡΠΊΡ. ΠΡΡ ΡΠΎΠΊΡΡΠΈΡΡΠ΅ΡΡΡ Π·Π΅ΡΠΊΠ°Π»ΠΎΠΌ ΠΈ ΠΊΠΎΠ½ΡΠ΅Π½ΡΡΠΈΡΡΠ΅ΡΡΡ ΠΎΠΏΡΠΈΡΠ΅ΡΠΊΠΎΠΉ ΡΠΈΡΡΠ΅ΠΌΠΎΠΉ (Π½Π°ΠΏΡΠΈΠΌΠ΅Ρ, ΠΊΠ²Π°ΡΡΠ΅Π²ΠΎΠΉ Π»ΠΈΠ½Π·ΠΎΠΉ). ΠΡΠΈ ΠΏΠΎΡΡΠ΅Π±Π»ΡΠ΅ΠΌΠΎΠΉ ΠΌΠΎΡΠ½ΠΎΡΡΠΈ 50 ΠΊΠ²Ρ Π² Π»ΡΡΠ΅ ΡΠ΄Π°ΡΡΡΡ ΡΠΊΠΎΠ½ΡΠ΅Π½ΡΡΠΈΡΠΎΠ²Π°ΡΡ ΠΎΠΊΠΎΠ»ΠΎ 15 ΠΊΠ²Ρ.
ΠΠ»Ρ ΡΠΎΠ·Π΄Π°Π½ΠΈΡ ΡΠ²Π΅ΡΠΎΠ²ΠΎΠ³ΠΎ Π»ΡΡΠ° ΠΌΠΎΠΆΠ΅Ρ ΡΠ»ΡΠΆΠΈΡΡ Π½Π΅ ΡΠΎΠ»ΡΠΊΠΎ ΠΈΡΠΊΡΡΡΡΠ²Π΅Π½Π½ΡΠΉ ΠΈΡΡΠΎΡΠ½ΠΈΠΊ ΡΠ²Π΅ΡΠ°, Π½ΠΎ ΠΈ Π΅ΡΡΠ΅ΡΡΠ²Π΅Π½Π½ΡΠΉ — Π‘ΠΎΠ»Π½ΡΠ΅. ΠΡΠΎΡ ΡΠΏΠΎΡΠΎΠ± ΡΠ²Π°ΡΠΊΠΈ, Π½Π°Π·ΡΠ²Π°Π΅ΡΡΡ Π³Π΅Π»ΠΈΠΎΡΠ²Π°ΡΠΊΠΎΠΉ, ΠΈΡΠΏΠΎΠ»ΡΠ·ΡΠ΅ΡΡΡ Π² ΡΡΠ»ΠΎΠ²ΠΈΡΡ ΡΠΎΠ»Π½Π΅ΡΠ½ΠΎΠΉ ΡΠ°Π΄ΠΈΠ°ΡΠΈΠΈ. ΠΡΠΏΠΎΠ»ΡΠ·ΡΠ΅ΡΡΡ ΡΠ°ΠΊΠΆΠ΅ ΠΈΠ·Π»ΡΡΠ΅Π½ΠΈΠ΅ ΠΎΠΏΡΠΈΡΠ΅ΡΠΊΠΈΡ ΠΊΠ²Π°Π½ΡΠΎΠ²ΡΡ Π³Π΅Π½Π΅ΡΠ°ΡΠΎΡΠΎΠ² — Π»Π°Π·Π΅ΡΠΎΠ². ΠΠ°Π·Π΅ΡΠ½Π°Ρ ΡΠ²Π°ΡΠΊΠ° Π·Π°Π½ΠΈΠΌΠ°Π΅Ρ Π²ΠΈΠ΄Π½ΠΎΠ΅ ΠΌΠ΅ΡΡΠΎ Π² Π»Π°Π·Π΅ΡΠ½ΠΎΠΉ ΡΠ΅Ρ Π½ΠΎΠ»ΠΎΠ³ΠΈΠΈ.
Π‘Π²Π°ΡΠΊΠ° Π΄Π°Π²Π»Π΅Π½ΠΈΠ΅ΠΌ
Π‘ΠΏΠΎΡΠΎΠ±Ρ ΡΠ²Π°ΡΠΊΠΈ Π² ΡΠ²ΡΡΠ΄ΠΎΠΉ ΡΠ°Π·Π΅ Π΄Π°ΡΡ ΡΠ²Π°ΡΠ½ΠΎΠ΅ ΡΠΎΠ΅Π΄ΠΈΠ½Π΅Π½ΠΈΠ΅, ΠΏΡΠΎΡΠ½ΠΎΡΡΡ ΠΊΠΎΡΠΎΡΠΎΠ³ΠΎ ΠΈΠ½ΠΎΠ³Π΄Π° ΠΏΡΠ΅Π²ΡΡΠ°Π΅Ρ ΠΏΡΠΎΡΠ½ΠΎΡΡΡ ΠΎΡΠ½ΠΎΠ²Π½ΠΎΠ³ΠΎ ΠΌΠ΅ΡΠ°Π»Π»Π°.ΠΡΠΎΠΌΠ΅ ΡΠΎΠ³ΠΎ, Π² Π±ΠΎΠ»ΡΡΠΈΠ½ΡΡΠ²Π΅ ΡΠ»ΡΡΠ°Π΅Π² ΠΏΡΠΈ ΡΠ²Π°ΡΠΊΠ΅ Π΄Π°Π²Π»Π΅Π½ΠΈΡ Π½Π΅ ΠΏΡΠΎΠΈΡΡ
ΠΎΠ΄ΠΈΡ Π·Π½Π°ΡΠΈΡΠ΅Π»ΡΠ½ΡΡ
ΠΈΠ·ΠΌΠ΅Π½Π΅Π½ΠΈΠΉ Π² Ρ
ΠΈΠΌΠΈΡΠ΅ΡΠΊΠΎΠΌ ΡΠΎΡΡΠ°Π²Π΅ ΠΌΠ΅ΡΠ°Π»Π»Π°, Ρ. ΠΊ. ΠΌΠ΅ΡΠ°Π»Π» Π»ΠΈΠ±ΠΎ Π½Π΅ Π½Π°Π³ΡΠ΅Π²Π°Π΅ΡΡΡ, Π»ΠΈΠ±ΠΎ Π½Π°Π³ΡΠ΅Π²Π°Π΅ΡΡΡ Π½Π΅Π·Π½Π°ΡΠΈΡΠ΅Π»ΡΠ½ΠΎ. ΠΡΠΎ Π΄Π΅Π»Π°Π΅Ρ ΡΠΏΠΎΡΠΎΠ±Ρ ΡΠ²Π°ΡΠΊΠΈ Π΄Π°Π²Π»Π΅Π½ΠΈΡ Π½Π΅Π·Π°ΠΌΠ΅Π½ΠΈΠΌΡΠΌΠΈ Π² ΡΠ°Π·Π»ΠΈΡΠ½ΡΡ
ΠΎΡΡΠ°ΡΠ»ΡΡ
ΠΏΡΠΎΠΌΡΡΠ»Π΅Π½Π½ΠΎΡΡΠΈ (ΡΠ»Π΅ΠΊΡΡΠΎΡΠ΅Ρ
Π½ΠΈΡΠ΅ΡΠΊΠΎΠΉ, ΡΠ»Π΅ΠΊΡΡΠΎΠ½Π½ΠΎΠΉ, ΠΊΠΎΡΠΌΠΈΡΠ΅ΡΠΊΠΎΠΉ ΠΈ Π΄Ρ. ).
Π₯ΠΎΠ»ΠΎΠ΄Π½Π°Ρ ΡΠ²Π°ΡΠΊΠ° Π²ΡΠΏΠΎΠ»Π½ΡΠ΅ΡΡΡ Π±Π΅Π· ΠΏΡΠΈΠΌΠ΅Π½Π΅Π½ΠΈΡ ΡΠΈΡΡΠ΅ΠΌΡ ΠΎΠ΄Π½ΠΈΠΌ ΡΠΎΠ»ΡΠΊΠΎ ΠΏΡΠΈΠ»ΠΎΠΆΠ΅Π½ΠΈΠ΅ΠΌ Π΄Π°Π²Π»Π΅Π½ΠΈΡ, ΡΠΎΠ·Π΄Π°ΡΡΠ΅ΠΉ Π·Π½Π°ΡΠΈΡΠ΅Π»ΡΠ½ΡΡ ΠΏΠ»Π°ΡΡΠΈΡΠ΅ΡΠΊΡΡ Π΄Π΅ΡΠΎΡΠΌΠ°ΡΠΈΡ (Π΄ΠΎ ΡΠΎΡΡΠΎΡΠ½ΠΈΡ ΡΠ΅ΠΊΡΡΠ΅ΡΡΠΈ), ΠΊΠΎΡΠΎΡΠ°Ρ Π΄ΠΎΠ»ΠΆΠ½Π° Π±ΡΡΡ Π½Π΅ Π½ΠΈΠΆΠ΅ ΡΡΡΠ°Π½ΠΎΠ²Π»Π΅Π½Π½ΠΎΠ³ΠΎ Π·Π½Π°ΡΠ΅Π½ΠΈΡ, Ρ Π°ΡΠ°ΠΊΡΠ΅ΡΠ½ΠΎΠ³ΠΎ Π΄Π»Ρ Π΄Π°Π½Π½ΠΎΠ³ΠΎ ΠΌΠ΅ΡΠ°Π»Π»Π°.ΠΠ΅ΡΠ΅Π΄ ΡΠ²Π°ΡΠΊΠΎΠΉ ΡΡΠ΅Π±ΡΠ΅ΡΡΡ ΡΡΠ°ΡΠ΅Π»ΡΠ½Π°Ρ ΠΎΠ±ΡΠ°Π±ΠΎΡΠΊΠ° ΠΈ ΠΎΡΠΈΡΡΠΊΠ° ΡΠΎΠ΅Π΄ΠΈΠ½ΡΠ΅ΠΌΡΡ ΠΏΠΎΠ²Π΅ΡΡ Π½ΠΎΡΡΠ΅ΠΉ (ΠΎΡΡΡΠ΅ΡΡΠ²Π»ΡΠ΅ΡΡΡ ΠΎΠ±ΡΡΠ½ΠΎ ΠΌΠ΅Ρ Π°Π½ΠΈΡΠ΅ΡΠΊΠΈΠΌ ΠΏΡΡΡΠΌ, Π½Π°ΠΏΡΠΈΠΌΠ΅Ρ Π²ΡΠ°ΡΠ°ΡΡΠΈΠΌΠΈΡΡ ΠΏΡΠΎΠ²ΠΎΠ»ΠΎΡΠ½ΡΠΌΠΈ ΡΡΡΠΊΠ°ΠΌΠΈ). ΠΡΠΎΡ ΡΠΏΠΎΡΠΎΠ± ΡΠ²Π°ΡΠΊΠΈ Π΄ΠΎΡΡΠ°ΡΠΎΡΠ½ΠΎ ΡΠ½ΠΈΠ²Π΅ΡΡΠ°Π»Π΅Π½, ΠΏΡΠΈΠ³ΠΎΠ΄Π΅Π½ Π΄Π»Ρ ΡΠΎΠ΅Π΄ΠΈΠ½Π΅Π½ΠΈΠΉ ΠΌΠ½ΠΎΠ³ΠΈΡ ΠΌΠ΅ΡΠ°Π»Π»ΠΈΡΠ΅ΡΠΊΠΈΡ ΠΈΠ·Π΄Π΅Π»ΠΈΠΉ (ΠΏΡΠΎΠ²ΠΎΠ΄ΠΎΠ², ΡΡΠ΅ΡΠΆΠ½Π΅ΠΉ, ΠΏΠΎΠ»ΠΎΡ, ΡΠΎΠ½ΠΊΠΎΡΡΠ΅Π½Π½ΡΡ ΡΡΡΠ± ΠΈ ΠΎΠ±ΠΎΠ»ΠΎΡΠ΅ΠΊ) ΠΈ Π½Π΅ΠΌΠ΅ΡΠ°Π»Π»ΠΈΡΠ΅ΡΠΊΠΈΡ ΠΌΠ°ΡΠ΅ΡΠΈΠ°Π»ΠΎΠ², ΠΎΠ±Π»Π°Π΄Π°ΡΡΠΈΡ Π΄ΠΎΡΡΠ°ΡΠΎΡΠ½ΠΎΠΉ ΠΏΠ»Π°ΡΡΠΈΡΠ½ΠΎΡΡΡΡ (ΡΠΌΠΎΠ»Ρ, ΠΏΠ»Π°ΡΡΠΌΠ°ΡΡΡ, ΡΡΠ΅ΠΊΠ»ΠΎ ΠΈ Ρ. Π.). ΠΠ΅ΡΡΠΏΠ΅ΠΊΡΠΈΠ²Π½ΠΎ ΠΏΡΠΈΠΌΠ΅Π½Π΅Π½ΠΈΠ΅ Ρ ΠΎΠ»ΠΎΠ΄Π½ΠΎΠΉ ΡΠ²Π°ΡΠΊΠΈ Π² ΠΊΠΎΡΠΌΠΎΡΠ΅.
ΠΠ»Ρ ΡΠ²Π°ΡΠΊΠΈ ΠΌΠΎΠΆΠ½ΠΎ ΠΈΡΠΏΠΎΠ»ΡΠ·ΠΎΠ²Π°ΡΡ ΠΌΠ΅Ρ
Π°Π½ΠΈΡΠ΅ΡΠΊΡΡ ΡΠ½Π΅ΡΠ³ΠΈΡ ΡΡΠ΅Π½ΠΈΡ.Π‘Π²Π°ΡΠΊΠ° ΡΡΠ΅Π½ΠΈΠ΅ΠΌ ΠΎΡΡΡΠ΅ΡΡΠ²Π»ΡΠ΅ΡΡΡ Π½Π° ΠΌΠ°ΡΠΈΠ½Π΅, Π²Π½Π΅ΡΠ½Π΅ Π½Π°ΠΏΠΎΠΌΠΈΠ½Π°ΡΡΠ΅ΠΉ ΡΠΎΠΊΠ°ΡΠ½ΡΠΉ ΡΡΠ°Π½ΠΎΠΊ. ΠΠ΅ΡΠ°Π»ΠΈ Π·Π°ΠΆΠΈΠΌΠ°ΡΡΡΡ Π² ΠΏΠ°ΡΡΠΎΠ½Π°Ρ
ΠΈ ΡΠ΄Π²ΠΈΠ³Π°ΡΡΡΡ Π΄ΠΎ ΡΠΎΠΏΡΠΈΠΊΠΎΡΠ½ΠΎΠ²Π΅Π½ΠΈΡ ΡΠΎΡΡΠ°ΠΌΠΈ. ΠΠ΄Π½Π° ΠΈΠ· Π΄Π΅ΡΠ°Π»Π΅ΠΉ Π²ΠΎ Π²ΡΠ°ΡΠ΅Π½ΠΈΠ΅ ΠΎΡ ΡΠ»Π΅ΠΊΡΡΠΎΠ΄Π²ΠΈΠ³Π°ΡΠ΅Π»Ρ. Π ΡΠ΅Π·ΡΠ»ΡΡΠ°ΡΠ΅ ΡΡΠ΅Π½ΠΈΡ ΡΠ°Π·ΠΎΠ³ΡΠ΅Π²Π°ΡΡΡΡ ΠΈ ΠΎΠΏΠ»Π°Π²Π»ΡΡΡΡΡ ΠΏΠΎΠ²Π΅ΡΡ
Π½ΠΎΡΡΠ½ΡΠ΅ ΡΠ»ΠΎΠΈ Π½Π° ΡΠΎΡΡΠ°Ρ
, Π²ΡΠ°ΡΠ°ΡΡΠ΅Π΅ΡΡ Π²ΡΠ°ΡΠ΅Π½ΠΈΠ΅ ΠΈ ΠΏΡΠΎΠΈΡΡ
ΠΎΠ΄ΠΈΡ ΠΎΡΠ°Π΄ΠΊΠ° Π΄Π΅ΡΠ°Π»Π΅ΠΉ, ΡΠ²Π°ΡΠΊΠ° Π²ΡΡΠΎΠΊΠΎΡΠΊΠΎΡΠΎΡΡΠ½ΠΎΠΉ, ΡΠΊΠΎΠ½ΠΎΠΌΠΈΡΠ½ΠΎΠΉ, ΠΏΡΠΈΠΌΠ΅Π½ΡΠ΅ΠΌΠΎΠΉ, Π½Π°ΠΏΡΠΈΠΌΠ΅Ρ, Π΄Π»Ρ ΠΏΡΠΈΡΠΎΠ΅Π΄ΠΈΠ½Π΅Π½ΠΈΡ ΡΠ΅ΠΆΡΡΠ΅ΠΉ ΡΠ°ΡΡΠΈ ΠΌΠ΅ΡΠ°Π»Π»ΠΎΡΠ΅ΠΆΡΡΠ΅Π³ΠΎ ΠΈΠ½ΡΡΡΡΠΌΠ΅Π½ΡΠ° ΠΊ Π΄Π΅ΡΠΆΠ°Π²ΠΊΠ΅.
Π£Π»ΡΡΡΠ°Π·Π²ΡΠΊΠΎΠ²Π°Ρ ΡΠ²Π°ΡΠΊΠ° Π½Π° ΠΎΡΠ½ΠΎΠ²Π΅ ΠΈΡΠΏΠΎΠ»ΡΠ·ΠΎΠ²Π°Π½ΠΈΡ ΠΌΠ΅Ρ
Π°Π½ΠΈΡΠ΅ΡΠΊΠΈΡ
ΠΊΠΎΠ»Π΅Π±Π°Π½ΠΈΠΉ ΡΠΈΠΏΠ° 20 ΠΊΠ³Ρ.ΠΠΎΠ»Π΅Π±Π°Π½ΠΈΡ ΠΌΠ°Π³Π½ΠΈΡΠΎΡΡΡΠΈΠΊΡΠΈΠΎΠ½Π½ΡΠΌ ΠΏΡΠ΅ΠΎΠ±ΡΠ°Π·ΠΎΠ²Π°ΡΠ΅Π»Π΅ΠΌ, ΠΏΡΠ΅Π²ΡΠ°ΡΠ°ΡΡΠΈΠΌ ΡΠ»Π΅ΠΊΡΡΠΎΠΌΠ°Π³Π½ΠΈΡΠ½ΡΠ΅ ΠΊΠΎΠ»Π΅Π±Π°Π½ΠΈΡ Π² ΠΌΠ΅Ρ
Π°Π½ΠΈΡΠ΅ΡΠΊΠΈΠ΅. ΠΠ° ΡΠ΅ΡΠ΄Π΅ΡΠ½ΠΈΠΊ, ΠΈΠ·Π³ΠΎΡΠΎΠ²Π»Π΅Π½Π½ΡΠΉ ΠΈΠ· ΠΌΠ°Π³Π½ΠΈΡΠΎΡΡΡΠΈΠΊΡΠΈΠΎΠ½Π½ΠΎΠ³ΠΎ ΠΌΠ°ΡΠ΅ΡΠΈΠ°Π»Π°, Π½Π°ΠΌΠΎΡΠ°Π½Π° ΠΎΠ±ΠΌΠΎΡΠΊΠ°. ΠΡΠΈ ΠΏΠΈΡΠ°Π½ΠΈΠΈ ΠΎΠ±ΠΌΠΎΡΠΊΠΈ ΡΠΎΠΊΠ°ΠΌΠΈ ΠΠ§ ΠΈΠ· ΡΠ»Π΅ΠΊΡΡΠΈΡΠ΅ΡΠΊΠΎΠΉ ΡΠ΅ΡΠΈ Π² ΡΠ΅ΡΠ΄Π΅ΡΠ½ΠΈΠΊΠ΅ Π²ΠΎΠ·Π½ΠΈΠΊΠ°ΡΡ ΠΏΡΠΎΠ΄ΠΎΠ»ΡΠ½ΡΠ΅ ΠΌΠ΅Ρ
Π°Π½ΠΈΡΠ΅ΡΠΊΠΈΠ΅ ΠΊΠΎΠ»Π΅Π±Π°Π½ΠΈΡ. ΠΠ΅ΡΠ°Π»Π»ΠΈΡΠ΅ΡΠΊΠΈΠΉ Π½Π°ΠΊΠΎΠ½Π΅ΡΠ½ΠΈΠΊ, ΡΠΎΠ΅Π΄ΠΈΠ½Π΅Π½Π½ΡΠΉ Ρ ΡΠ΅ΡΠ΄Π΅ΡΠ½ΠΈΠΊΠΎΠΌ, ΡΠ»ΡΠΆΠΈΡ ΡΠ²Π°ΡΠΎΡΠ½ΡΠΌ ΠΈΠ½ΡΡΡΡΠΌΠ΅Π½ΡΠΎΠΌ. ΠΡΠ»ΠΈ Π½Π°ΠΊΠΎΠ½Π΅ΡΠ½ΠΈΠΊ Π½Π΅ΠΊΠΎΡΠΎΡΡΠΌ ΡΡΠΈΠ»ΠΈΠ΅ΠΌ ΠΏΡΠΈΠΆΠ°ΡΡ ΠΊ ΡΠ²Π°ΡΠΈΠ²Π°Π΅ΠΌΡΠΌ Π΄Π΅ΡΠ°Π»ΡΠΌ, ΡΠΎ ΡΠ΅ΡΠ΅Π· Π½Π΅ΡΠΊΠΎΠ»ΡΠΊΠΎ ΡΠ΅ΠΊΡΠ½Π΄ ΠΎΠ½ΠΈ ΠΎΠΊΠ°Π·ΡΠ²Π°ΡΡΡΡ ΡΠ²Π°ΡΠ΅Π½Π½ΡΠΌΠΈ Π² ΠΌΠ΅ΡΡΠ΅ ΠΈΠ½ΡΡΡΡΠΌΠ΅Π½ΡΠ° Π΄Π°Π²Π»Π΅Π½ΠΈΡ.Π ΡΠ΅Π·ΡΠ»ΡΡΠ°ΡΠ΅ ΡΠΎΠ·Π΄Π°Π½ΠΈΡ ΡΠ΅ΡΠ΄Π΅ΡΠ½ΠΈΠΊΠ° ΠΏΠΎΠ²Π΅ΡΡ
Π½ΠΎΡΡΠΈ ΠΎΡΠΈΡΠ°ΡΡΡΡ ΠΈ Π½Π΅ΠΌΠ½ΠΎΠ³ΠΎ ΡΠ°Π·ΠΎΠ³ΡΠ΅Π²Π°ΡΡΡΡ, ΡΡΠΎ ΠΎΠ±ΡΠ°Π·ΠΎΠ²Π°Π½ΠΈΠ΅ ΠΏΡΠΎΡΠ½ΠΎΠ³ΠΎ ΡΠ²Π°ΡΠ½ΠΎΠ³ΠΎ ΡΠΎΠ΅Π΄ΠΈΠ½Π΅Π½ΠΈΡ. ΠΡΠΎΡ ΡΠΏΠΎΡΠΎΠ± ΡΠ²Π°ΡΠΊΠΈ ΠΌΠ΅ΡΠ°Π»Π»ΠΎΠ² ΠΌΠ°Π»ΡΡ
ΡΠΎΠ»ΡΠΈΠ½ (ΠΎΡ Π½Π΅ΡΠΊΠΎΠ»ΡΠΊΠΈΡ
ΠΌΠΊΠΌ Π΄ΠΎ1,5 ΠΌΠΌ) ΠΈ Π½Π΅ΠΊΠΎΡΠΎΡΡΡ
ΠΏΠ»Π°ΡΡΠΌΠ°ΡΡ Π½Π°ΡΡΠ» ΠΏΡΠΈΠΌΠ΅Π½Π΅Π½ΠΈΠ΅ Π² ΡΠ»Π΅ΠΊΡΡΠΎΡΠ΅Ρ
Π½ΠΈΡΠ΅ΡΠΊΠΎΠΉ, ΡΠ»Π΅ΠΊΡΡΠΎΠ½Π½ΠΎΠΉ, ΡΠ°Π΄ΠΈΠΎΡΠ΅Ρ
Π½ΠΈΡΠ΅ΡΠΊΠΎΠΉ ΠΏΡΠΎΠΌΡΡΠ»Π΅Π½Π½ΠΎΡΡΠΈ. Π Π½Π°ΡΠ°Π»Π΅ 70-Ρ
Π³Π³. ΡΡΠΎΡ Π²ΠΈΠ΄ ΡΠ²Π°ΡΠΊΠΈ ΠΈΡΠΏΠΎΠ»ΡΠ·ΡΠ΅ΡΡΡ Π² ΠΌΠ΅Π΄ΠΈΡΠΈΠ½Π΅ (ΡΠ°Π±ΠΎΡΡ ΠΊΠΎΠ»Π»Π΅ΠΊΡΠΈΠ²Π° ΡΠΎΡΡΡΠ΄Π½ΠΈΠΊΠΎΠ² ΠΠΎΡΠΊΠΎΠ²ΡΠΊΠΎΠ³ΠΎ Π²ΡΡΡΠ΅Π³ΠΎ ΡΠ΅Ρ
Π½ΠΈΡΠ΅ΡΠΊΠΎΠ³ΠΎ ΡΡΠΈΠ»ΠΈΡΠ° ΠΈΠΌ. Π. Π. ΠΠ°ΡΠΌΠ°Π½Π° ΠΏΠΎΠ΄ ΡΡΠΊΠΎΠ²ΠΎΠ΄ΡΡΠ²ΠΎΠΌ Π. Π. ΠΠΈΠΊΠΎΠ»Π°Π΅Π²Π° Π² ΡΠΎΠ΄ΡΡΠΆΠ΅ΡΡΠ²Π΅ Ρ ΠΌΠ΅Π΄ΠΈΠΊΠ°ΠΌΠΈ) Π΄Π»Ρ ΡΠΎΠ΅Π΄ΠΈΠ½Π΅Π½ΠΈΡ, Π½Π°ΠΏΠ»Π°Π²ΠΊΠΈ, ΡΠ΅Π·ΠΊΠΈ ΠΆΠΈΠ²ΡΡ
ΡΠΊΠ°Π½Π΅ΠΉ.ΠΡΠΈ ΡΠ²Π°ΡΠΊΠ΅ ΠΈ Π½Π°ΠΏΠ»Π°Π²ΠΊΠ΅ ΠΊΠΎΡΡΠ½ΡΡ
ΡΠΊΠ°Π½Π΅ΠΉ, Π½Π°ΠΏΡΠΈΠΌΠ΅Ρ ΠΎΡΠ»ΠΎΠΌΠΊΠΎΠ² Π±Π΅ΡΡΠΎΠ²ΡΡ
ΠΊΠΎΡΡΠ΅ΠΉ, ΡΡΠ±Π΅Ρ ΠΈ ΠΏΡ., ΠΠΎΠ½Π³Π»ΠΎΠΌΠ΅ΡΠ°Ρ ΠΈΠ· ΠΆΠΈΠ΄ΠΊΠΎΠ³ΠΎ ΠΌΠΎΠ½ΠΎΠΌΠ΅ΡΠ° ΡΠΈΠ°ΠΊΡΠΈΠ½Π° ΠΈ ΡΠ²ΡΡΠ΄ΡΡ
Π΄ΠΎΠ±Π°Π²ΠΎΠΊ (ΠΊΠΎΡΡΠ½ΠΎΠΉ ΡΡΡΡΠΆΠΊΠΈ ΠΈ ΡΠ°Π·Π½ΡΡ
Π½Π°ΠΏΠΎΠ»Π½ΠΈΡΠ΅Π»Π΅ΠΉ ΠΈ ΡΠΏΡΠΎΡΠ½ΠΈΡΠ΅Π»Π΅ΠΉ) Π½Π°Π½ΠΎΡΠΈΡΡΡ Π½Π° ΠΏΠΎΠ²ΡΠ΅ΠΆΠ΄Π΅Π½Π½ΠΎΠ΅ ΠΌΠ΅ΡΡΠΎ ΠΈ ΡΠΏΠ»ΠΎΡΠ½ΡΠ΅ΡΡΡ ΡΠ»ΡΡΡΠ°Π·Π²ΡΠΊΠΎΠ²ΡΠΌ ΠΈΠ½ΡΡΡΡΠΌΠ΅Π½ΡΠΎΠΌ, Π² ΡΠ΅Π·ΡΠ»ΡΡΠ°ΡΠ΅ ΡΠ΅Π³ΠΎ ΡΡΠΊΠΎΡΡΠ΅ΡΡΡ ΠΏΠΎΠ»ΠΈΠΌΠ΅ΡΠΈΠ·Π°ΡΠΈΡ. ΠΡΡΠ΅ΠΊΡΠΈΠ²Π½ΠΎ ΠΏΡΠΈΠΌΠ΅Π½Π΅Π½ΠΈΠ΅ ΡΠ»ΡΡΡΠ°Π·Π²ΡΠΊΠΎΠ²ΠΎΠΉ ΡΠ΅Π·ΠΊΠΈ Π² Ρ
ΠΈΡΡΡΠ³ΠΈΠΈ. Π‘Π²Π°ΡΠΎΡΠ½ΡΠΉ ΠΈΠ½ΡΡΡΡΠΌΠ΅Π½Ρ ΡΠ»ΡΡΡΠ°Π·Π²ΡΠΊΠΎΠ²ΠΎΠ³ΠΎ Π°ΠΏΠΏΠ°ΡΠ°ΡΠ° Π·Π°ΠΌΠ΅Π½ΡΠ΅ΡΡΡ ΠΏΠΈΠ»ΠΎΠΉ, ΡΠΊΠ°Π»ΡΠΏΠ΅Π»Π΅ΠΌ ΠΈΠ»ΠΈ Π½ΠΎΠΆΠΎΠΌ. ΠΠ½Π°ΡΠΈΡΠ΅Π»ΡΠ½ΠΎ ΡΠΎΠΊΡΠ°ΡΠ°ΡΡΡΡ Π²ΡΠ΅ΠΌΡ ΠΎΠΏΠ΅ΡΠ°ΡΠΈΠΈ, ΠΏΠΎΡΠ΅ΡΡ ΠΊΡΠΎΠ²ΠΈ ΠΈ Π±ΠΎΠ»Π΅Π²ΡΠ΅ ΠΎΡΡΡΠ΅Π½ΠΈΡ.
ΠΠ΄Π½ΠΈΠΌ ΠΈΠ· ΡΠΏΠΎΡΠΎΠ±ΠΎΠ² ΡΠ»Π΅ΠΊΡΡΠΈΡΠ΅ΡΠΊΠΎΠΉ ΡΠ²Π°ΡΠΊΠΈ ΡΠ²Π»ΡΠ΅ΡΡΡ ΠΊΠΎΠ½ΡΠ°ΠΊΡΠ½Π°Ρ ΡΠ²Π°ΡΠΊΠ°, ΠΈΠ»ΠΈ ΡΠ²Π°ΡΠΊΠ° ΡΠΎΠΏΡΠΎΡΠΈΠ²Π»Π΅Π½ΠΈΠ΅ΠΌ (Π² ΡΡΠΎΠΌ ΡΠ»ΡΡΠ°Π΅ ΡΠ»Π΅ΠΊΡΡΠΈΡΠ΅ΡΠΊΠΈΠΉ ΡΠΎΠΊ ΠΏΡΠΎΠΏΡΡΠΊΠ°ΡΡ ΡΠ΅ΡΠ΅Π· ΠΌΠ΅ΡΡΠΎ ΡΠ²Π°ΡΠΊΠΈ, ΠΎΠΊΠ°Π·ΡΠ²Π°ΡΡΠ΅Π΅ ΠΎΠΌΠΈΡΠ΅ΡΠΊΠΎΠ΅ ΡΠΎΠΏΡΠΎΡΠΈΠ²Π»Π΅Π½ΠΈΠ΅ ΠΏΡΠΎΡ
ΠΎΠΆΠ΄Π΅Π½ΠΈΠ΅ ΡΠΎΠΊΠ°). Π Π°Π·ΠΎΠ³ΡΠ΅ΡΡΠ΅ ΠΈ ΠΎΠ±ΡΡΠ½ΠΎ ΠΎΠΏΠ»Π°Π²Π»Π΅Π½Π½ΡΠ΅ Π΄Π΅ΡΠ°Π»ΠΈ ΡΠ΄Π°Π²Π»ΠΈΠ²Π°ΡΡΡΡ ΠΈΠ»ΠΈ ΠΎΡΠ°ΠΆΠΈΠ²Π°ΡΡΡΡ, Ρ. ΠΎ. ΠΊΠΎΠ½ΡΠ°ΠΊΡΠ½Π°Ρ ΡΠ²Π°ΡΠΊΠ° ΠΏΠΎ ΠΌΠ΅ΡΠΎΠ΄Ρ ΠΎΡΠ°Π΄ΠΊΠΈ ΠΎΡΠ½ΠΎΡΠΈΡΡΡ ΠΊ ΡΠΏΠΎΡΠΎΠ±Π°ΠΌ ΡΠ²Π°ΡΠΊΠΈ Π΄Π°Π²Π»Π΅Π½ΠΈΠ΅ΠΌ (ΡΠΌ. ΡΠΌ. ΡΠ»Π΅ΠΊΡΡΠΎΡΠ²Π°ΡΠΊΠ°). ΠΡΠΎΡ ΡΠΏΠΎΡΠΎΠ± ΠΎΡΠ»ΠΈΡΠ°Π΅ΡΡΡ Π²ΡΡΠΎΠΊΠΎΠΉ ΡΡΠ΅ΠΏΠ΅Π½ΡΡ ΠΌΠ΅Ρ
Π°Π½ΠΈΠΊΠΈ ΠΈ ΠΏΠΎΠ»ΡΡΠ°Π΅Ρ Π²ΡΡ Π±ΠΎΠ»ΡΡΠ΅Π΅ ΡΠ°ΡΠΏΡΠΎΡΡΡΠ°Π½Π΅Π½ΠΈΠ΅ Π² ΠΌΠ°ΡΡΠΎΠ²ΠΎΠΌ ΠΈ ΡΠ΅ΡΠΈΠΉΠ½ΠΎΠΌ ΠΏΡΠΎΠΈΠ·Π²ΠΎΠ΄ΡΡΠ²Π΅ (Π½Π°ΠΏΡΠΈΠΌΠ΅Ρ, ΡΠΎΠ΅Π΄ΠΈΠ½Π΅Π½ΠΈΠ΅ Π΄Π΅ΡΠ°Π»Π΅ΠΉ Π°Π²ΡΠΎΠΌΠΎΠ±ΠΈΠ»Π΅ΠΉ, ΡΠ°ΠΌΠΎΠ»ΡΡΠΎΠ², ΠΈ ΡΠ°Π΄ΠΈΠΎΡΠ΅Ρ
Π½ΠΈΡΠ΅ΡΠΊΠΎΠΉ Π°ΠΏΠΏΠ°ΡΠ°ΡΡΡΡ), Π° ΡΠ°ΠΊΠΆΠ΅ ΠΈΡΠΏΠΎΠ»ΡΠ·ΡΠ΅ΡΡΡ Π΄Π»Ρ ΡΡΡΠΊΠΎΠ²ΠΊΠΈ ΡΡΡΠ± Π±ΠΎΠ»ΡΡΠΈΡ
Π΄ΠΈΠ°ΠΌΠ΅ΡΡΠΎΠ², ΡΠ΅Π»ΡΡΠΎΠ² ΠΈ Ρ.ΠΏ.
ΠΠ°ΠΏΠ»Π°Π²ΠΊΠ°
ΠΡ Π½Π°ΠΈΠ±ΠΎΠ»Π΅Π΅ ΡΠ°ΡΠΏΡΠΎΡΡΡΠ°Π½Π΅Π½Π½ΠΎΠΉ ΡΠΎΠ΅Π΄ΠΈΠ½ΠΈΡΠ΅Π»ΡΠ½ΠΎΠΉ ΡΠ²Π°ΡΠΊΠΈ Π½Π°ΠΏΠ»Π°Π²ΠΊΠ°, ΠΏΡΠΈΠΌΠ΅Π½ΡΠ΅ΠΌΠ°Ρ Π΄Π»Ρ Π½Π°ΡΠ°ΡΠ΅Π½ΠΈΡ Π½Π° ΠΏΠΎΠ²Π΅ΡΡ
Π½ΠΎΡΡΠΈ Π΄Π΅ΡΠ°Π»ΠΈ ΡΠ»ΠΎΡ ΠΌΠ°ΡΠ΅ΡΠΈΠ°Π»Π°, Π½Π΅ΡΠΊΠΎΠ»ΡΠΊΠΎ ΡΠ²Π΅Π»ΠΈΡΠΈΠ²Π°ΡΡΠ°Ρ ΠΌΠ°ΡΡΠ° ΠΈ ΡΠ°Π·ΠΌΠ΅ΡΡ Π΄Π΅ΡΠ°Π»Π΅ΠΉ. ΠΠ°ΠΏΠ»Π°Π²ΠΊΠΎΠΉ ΠΌΠΎΠΆΠ½ΠΎ ΠΎΡΡΡΠ΅ΡΡΠ²ΠΈΡΡ Π²ΠΎΡΡΡΠ°Π½ΠΎΠ²Π»Π΅Π½ΠΈΠ΅ ΡΠ°Π·ΠΌΠ΅ΡΠΎΠ², ΡΠΌΠ΅Π½ΡΡΠ΅Π½Π½ΡΡ
ΠΈΠ·Π½ΠΎΡΠΎΠΌ, ΠΈ ΠΎΠ±Π»ΠΈΡΠΎΠ²ΠΊΡ ΠΏΠΎΠ²Π΅ΡΡ
Π½ΠΎΡΡΠ½ΠΎΠ³ΠΎ ΡΠ»ΠΎΡ. ΠΠΎΡΡΡΠ°Π½ΠΎΠ²ΠΈΡΠ΅Π»ΡΠ½Π°Ρ Π½Π°ΠΏΠ»Π°Π²ΠΊΠ° ΠΈΠΌΠ΅Π΅Ρ ΡΠΊΠΎΠ½ΠΎΠΌΠΈΡΠ΅ΡΠΊΡΡ ΡΡΡΠ΅ΠΊΡΠΈΠ²Π½ΠΎΡΡΡ, Ρ. ΠΊ. ΡΠ°ΠΊΠΈΠΌ ΡΠΏΠΎΡΠΎΠ±ΠΎΠΌ Π²ΠΎΡΡΡΠ°Π½Π°Π²Π»ΠΈΠ²Π°ΡΡ ΡΠ»ΠΎΠΆΠ½ΡΠ΅ Π΄ΠΎΡΠΎΠ³ΠΈΠ΅ Π΄Π΅ΡΠ°Π»ΠΈ; ΡΠ°ΡΠΏΡΠΎΡΡΡΠ°Π½Π΅Π½Π° ΠΏΡΠΈ ΡΠ΅ΠΌΠΎΠ½ΡΠ΅ Π½Π° ΡΡΠ°Π½ΡΠΏΠΎΡΡΠ΅, Π² ΡΠ΅Π»ΡΡΠΊΠΎΠΌ Ρ
ΠΎΠ·ΡΠΉΡΡΠ²Π΅, ΡΡΡΠΎΠΈΡΠ΅Π»ΡΡΡΠ²Π΅, Π³ΠΎΡΠ½ΠΎΠΉ ΠΏΡΠΎΠΌΡΡΠ»Π΅Π½Π½ΠΎΡΡΠΈ ΠΈ Ρ.Π΄. ΠΠ±Π»ΠΈΡΠΎΠ²ΠΎΡΠ½Π°Ρ Π½Π°ΠΏΠ»Π°Π²ΠΊΠ° Π΄Π»Ρ ΡΠΎΠ·Π΄Π°Π½ΠΈΡ Π½Π° ΠΏΠΎΠ²Π΅ΡΡ
Π½ΠΎΡΡΠΈ Π΄Π΅ΡΠ°Π»Π΅ΠΉ ΡΠ»ΠΎΡ ΠΌΠ°ΡΠ΅ΡΠΈΠ°Π»Π° Ρ ΠΎΡΠΎΠ±ΡΠΌΠΈ ΡΠ²ΠΎΠΉΡΡΠ²Π°ΠΌΠΈ — Π²ΡΡΠΎΠΊΠΎΠΉ ΡΠ²ΡΡΠ΄ΠΎΡΡΡΡ, ΠΈΠ·Π½ΠΎΡΠΎΡΡΠΎΠΉΠΊΠΎΡΡΡΡ ΠΈ Ρ. Π΄. Π½Π΅ ΡΠΎΠ»ΡΠΊΠΎ ΠΏΡΠΈ ΡΠ΅ΠΌΠΎΠ½ΡΠ΅, Π½ΠΎ ΠΈ ΠΏΡΠΈ ΠΏΡΠΎΠΈΠ·Π²ΠΎΠ΄ΡΡΠ²Π΅ Π½ΠΎΠ²ΡΡ
ΠΈΠ·Π΄Π΅Π»ΠΈΠΉ. ΠΠ»Ρ ΡΡΠΎΠ³ΠΎ Π²ΠΈΠ΄Π° Π½Π°ΠΏΠ»Π°Π²ΠΊΠΈ ΠΈΠ·Π³ΠΎΡΠΎΠ²Π»ΡΡΡ Π½Π°ΠΏΠ»Π°Π²ΠΎΡΠ½ΡΠ΅ ΠΌΠ°ΡΠ΅ΡΠΈΠ°Π»Ρ Ρ ΠΎΡΠΎΠ±ΡΠΌΠΈ ΡΠ²ΠΎΠΉΡΡΠ²Π°ΠΌΠΈ (Π½Π°ΠΏΡΠΈΠΌΠ΅Ρ, ΠΈΠ·Π½ΠΎΡΠΎΡΡΠΎΠΉΠΊΠΈΠΉ ΡΠΏΠ»Π°Π² ΡΠΎΡΠΌΠ°ΠΉΡ). ΠΠ°ΠΏΠ»Π°Π²ΠΎΡΠ½ΡΠ΅ ΡΠ°Π±ΠΎΡΡ Π²ΡΠΏΠΎΠ»Π½ΡΡΡ ΠΌΠ΅ΡΠΎΠ΄Ρ ΡΠ²Π°ΡΠΊΠΈ Π΄ΡΠ³ΠΎΠ²ΠΎΠΉ, Π³Π°Π·ΠΎΠ²ΠΎΠΉ, ΠΏΠ»Π°Π·ΠΌΠ΅Π½Π½ΠΎΠΉ, ΡΠ»Π΅ΠΊΡΡΠΎΠ½Π½ΠΎΠΉ ΠΈ Ρ. ΠΏ. ΠΡΠΎΡΠ΅ΡΡ Π½Π°ΠΏΠ»Π°Π²ΠΊΠΈ ΠΌΠΎΠΆΠ΅Ρ Π±ΡΡΡ ΠΌΠ΅Ρ
Π°Π½ΠΈΠ·ΠΈΡΠΎΠ²Π°Π½ ΠΈ Π°Π²ΡΠΎΠΌΠ°ΡΠΈΠ·ΠΈΡΠΎΠ²Π°Π½. ΠΡΠΏΡΡΠΊΠ°ΡΡΡΡ ΡΠΏΠ΅ΡΠΈΠ°Π»ΡΠ½ΡΠ΅ Π½Π°ΠΏΠ»Π°Π²ΠΎΡΠ½ΡΠ΅ ΡΡΡΠ°Π½ΠΎΠ²ΠΊΠΈ Ρ Π°Π²ΡΠΎΠΌΠ°ΡΠΈΠ·Π°ΡΠΈΠ΅ΠΉ ΠΎΡΠ½ΠΎΠ²Π½ΡΡ
ΠΎΠΏΠ΅ΡΠ°ΡΠΈΠΉ.
Π’Π΅ΡΠΌΠΈΡΠ΅ΡΠΊΠ°Ρ ΡΠ΅Π·ΠΊΠ°
Π Π΅Π·ΠΊΠ° ΡΠ΅Ρ
Π½ΠΎΠ»ΠΎΠ³ΠΈΡΠ΅ΡΠΊΠΈ ΠΎΡΠ»ΠΈΡΠ½Π°Ρ ΠΎΡ ΡΠ²Π°ΡΠΊΠΈ ΠΈ ΠΏΡΠΎΡΠΈΠ²ΠΎΠΏΠΎΠ»ΠΎΠΆΠ½Π° Π΅ΠΉ ΠΏΠΎ ΡΠΌΡΡΠ»Ρ, Π½ΠΎ ΠΎΠ±ΠΎΡΡΠ΄ΠΎΠ²Π°Π½ΠΈΠ΅, ΠΌΠ°ΡΠ΅ΡΠΈΠ°Π»Ρ, ΠΏΡΠΈΡΠΌΡ Π²ΡΠΏΠΎΠ»Π½Π΅Π½ΠΈΡ Π±Π»ΠΈΠ·ΠΊΠΈ ΠΊ ΠΏΡΠΈΠΌΠ΅Π½ΡΠ΅ΠΌΡΠΌ Π² ΡΠ²Π°ΡΠΎΡΠ½ΠΎΠΉ ΡΠ΅Ρ
Π½ΠΈΠΊΠ΅. ΠΠΎΠ΄ ΡΠ΅ΡΠΌΠΈΡΠ΅ΡΠΊΠΎΠΉ ΠΈΠ»ΠΈ ΠΎΠ³Π½Π΅Π²ΠΎΠΉ, ΡΠ΅Π·ΠΊΠΎΠΉ ΠΏΠΎΠ΄ΡΠ°Π·ΡΠΌΠ΅Π²Π°ΡΡ ΠΏΡΠΎΡΠ΅ΡΡΡ, ΠΏΡΠΈ ΠΊΠΎΡΠΎΡΡΡ
ΠΌΠ΅ΡΠ°Π»Π» Π² Π³Π°Π·ΠΎΠ²ΠΎΠΉ ΡΠ΅Π·ΠΊΠ΅ Π½Π°Π³ΡΠ΅Π²Π°Π΅ΡΡΡ Π΄ΠΎ Π²ΡΡΠΎΠΊΠΎΠΉ ΡΠ΅ΠΌΠΏΠ΅ΡΠ°ΡΡΡΡ ΠΈ ΡΠ°ΠΌΠΎΠΏΡΠΎΠΈΠ·Π²ΠΎΠ»ΡΠ½ΠΎ Π²ΡΡΠ΅ΠΊΠ°Π΅Ρ ΠΈΠ»ΠΈ ΡΠ΄Π°Π»ΡΠ΅ΡΡΡ Π² Π²ΠΈΠ΄Π΅ΡΠ³ΡΠ΅Π½Π½ΡΡ
ΡΠ»Π°ΠΊΠΎΠ² ΠΈ ΠΎΠΊΠΈΡΠ»ΠΎΠ², Π° ΡΠ°ΠΊΠΆΠ΅ ΠΌΠΎΠΆΠ΅Ρ Π²ΡΡΠ°Π»ΠΊΠΈΠ²Π°ΡΡΡΡ ΠΌΠ΅Ρ
Π°Π½ΠΈΡΠ΅ΡΠΊΠΈΠΌ Π΄Π΅ΠΉΡΡΠ²ΠΈΠ΅ΠΌ (ΡΡΡΡΠ΅ΠΉ Π³Π°Π·Π°, ΡΠ»Π΅ΠΊΡΡΠΎΠ΄ΠΎΠΌ ΠΈ Ρ.ΠΏ.). Π Π΅Π·ΠΊΠ° Π²ΡΠΏΠΎΠ»Π½ΡΠ΅ΡΡΡ Π±Π΅Π·ΠΎΠΏΠ°ΡΠ½ΡΠΌΠΈ ΡΡΠ΅Π΄ΡΡΠ²Π°ΠΌΠΈ. ΠΠ°ΠΈΠ±ΠΎΠ»Π΅Π΅ Π²Π°ΠΆΠ½ΡΠΉ ΠΈ ΠΏΡΠ°ΠΊΡΠΈΡΠ΅ΡΠΊΠΈ ΡΠ°ΡΠΏΡΠΎΡΡΡΠ°Π½ΡΠ½Π½ΡΠΉ ΡΠΏΠΎΡΠΎΠ± — ΠΊΠΈΡΠ»ΠΎΡΠΎΠ΄Π½Π°Ρ, ΠΎΡΠ½ΠΎΠ²Π°Π½Π½Π°Ρ Π½Π° ΡΠΏΠΎΡΠΎΠ±Π½ΠΎΡΡΠΈ ΠΌΠ΅ΡΠ°Π»Π»Π°, ΠΎΠ±ΡΡΠ½ΠΎ Π΄Π»Ρ ΡΠ΅Π·ΠΊΠΈ ΡΠΎΠ»ΡΠΈΠ½ΠΎΠΉ ΠΎΡ 5 Π΄ΠΎ 100 ΠΌΠΌ, Π²ΠΎΠ·ΠΌΠΎΠΆΠ½ΠΎ ΡΠ°Π·Π΄Π΅Π»Π΅Π½ΠΈΠ΅ ΠΌΠ°ΡΠ΅ΡΠΈΠ°Π»Π° ΡΠΎΠ»ΡΠΈΠ½ΠΎΠΉ Π΄ΠΎ 2000 ΠΌΠΌ. ΠΠΈΡΠ»ΠΎΡΠΎΠ΄Π½ΠΎΠΉ ΡΠ΅Π·ΠΊΠΎΠΉ Π²ΡΠΏΠΎΠ»Π½ΡΡΡΡΡ ΡΠ°ΠΊΠΆΠ΅ ΠΎΠΏΠ΅ΡΠ°ΡΠΈΠΈ, Π°Π½Π°Π»ΠΎΠ³ΠΈΡΠ½ΡΠ΅ ΠΎΠ±ΡΠ°Π±ΠΎΡΠΊΠΈ ΡΠ΅ΠΆΡΡΠΈΠΌ ΠΈΠ½ΡΡΡΡΠΌΠ΅Π½ΡΠΎΠΌ, — ΡΡΡΠΎΠΆΠΊΡ, ΠΎΠ±ΡΠΎΡΠΊΡ, Π·Π°ΡΠΈΡΡΠΊΡ ΠΈ Ρ. ΠΏ. Π Π΅Π·ΠΊΡ Π½Π΅ΠΊΠΎΡΠΎΡΡΡ
Π»Π΅Π³ΠΈΡΠΎΠ²Π°Π½Π½ΡΡ
, ΡΡΠ³ΡΠ½Π°, ΡΠ²Π΅ΡΠ½ΡΡ
ΠΌΠ΅ΡΠ°Π»Π»ΠΎΠ², Π΄Π»Ρ ΠΊΠΎΡΠΎΡΡΡ
ΠΎΠ±ΡΡΠ½ΡΠΉ ΡΠΏΠΎΡΠΎΠ± ΠΌΠ°Π»ΠΎΠΏΡΠΈΠ³ΠΎΠ΄Π΅Π½, ΠΎΡΡΡΠ΅ΡΡΠ²Π»ΡΡΡ ΠΊΠΈΡΠ»ΠΎΡΠΎΠ΄Π½ΠΎ-ΡΠ»ΡΡΠΎΠ²ΡΠΌ ΡΠΏΠΎΡΠΎΠ±ΠΎΠΌ.ΠΠΈΡΠ»ΠΎΡΠΎΠ΄Π½Π°Ρ ΠΎΠ±ΡΠ°Π±ΠΎΡΠΊΠ° Π½Π°ΡΠ»Π° ΠΏΡΠΈΠΌΠ΅Π½Π΅Π½ΠΈΠ΅ Π½Π° ΠΌΠ΅ΡΠ°Π»Π»ΡΡΠ³ΠΈΡΠ΅ΡΠΊΠΈΡ
ΠΈ ΠΌΠ°ΡΠΈΠ½ΠΎΡΡΡΠΎΠΈΡΠ΅Π»ΡΠ½ΡΡ
Π·Π°Π²ΠΎΠ΄Π°Ρ
, ΡΠ΅ΠΌΠΎΠ½ΡΠ½ΡΡ
ΠΏΡΠ΅Π΄ΠΏΡΠΈΡΡΠΈΡΡ
ΠΈ Ρ. ΠΏ.
ΠΡΠ³ΠΎΠ²Π°Ρ ΡΠ΅Π·ΠΊΠ°, Π²ΡΠΏΠΎΠ»Π½ΡΠ΅ΠΌΠ°Ρ ΠΊΠ°ΠΊ ΡΠ³ΠΎΠ»ΡΠ½ΡΠΌ, ΡΠ°ΠΊ ΠΈ ΠΌΠ΅ΡΠ°Π»Π»ΠΈΡΠ΅ΡΠΊΠΈΠΌ ΡΠ»Π΅ΠΊΡΡΠΎΠ΄Π°ΠΌΠΈ, ΠΏΡΠΈΠΌΠ΅Π½ΡΠ΅ΠΌΡΠΌ ΠΏΡΠΈ ΠΌΠΎΠ½ΡΠ°ΠΆΠ½ΡΡ ΠΈ ΡΠ΅ΠΌΠΎΠ½ΡΠ½ΡΡ ΡΠ°Π±ΠΎΡΠ°Ρ (Π½Π°ΠΏΡΠΈΠΌΠ΅Ρ, Π² ΡΡΠ΄ΠΎΡΡΡΠΎΠ΅Π½ΠΈΠΈ). ΠΠ»Ρ ΠΏΠΎΠ²Π΅ΡΡ Π½ΠΎΡΡΠ½ΠΎΠΉ ΠΎΠ±ΡΠ°Π±ΠΎΡΠΊΠΈ ΠΈ ΡΡΡΠΎΠΆΠΊΠΈ ΠΌΠ΅ΡΠ°Π»Π»Π° ΠΈΡΠΏΠΎΠ»ΡΠ·ΡΡΡ Π²ΠΎΠ·Π΄ΡΡΠ½ΠΎ-Π΄ΡΠ³ΠΎΠ²ΡΡ ΡΠ΅Π·ΠΊΡ, ΠΏΡΠΈ ΠΊΠΎΡΠΎΡΠΎΠΉ ΠΌΠ΅ΡΠ°Π»Π» ΠΈΠ· ΡΠ΅Π·Π° Π²ΡΠ΄ΡΠ²Π°Π΅ΡΡΡ ΡΡΡΡΠ΅ΠΉ Π²ΠΎΠ·Π΄ΡΡ Π°, ΡΡΠΎ ΠΏΠΎΠ·Π²ΠΎΠ»ΡΠ΅Ρ ΠΌΠ°ΠΊΡΠΈΠΌΠ°Π»ΡΠ½ΠΎ ΡΠ»ΡΡΡΠΈΡΡ ΠΊΠ°ΡΠ΅ΡΡΠ²ΠΎ ΡΠ΅Π·ΠΊΠΈ.
Π Π΅Π·ΠΊΡ ΠΌΠΎΠΆΠ½ΠΎ Π²ΡΠΏΠΎΠ»Π½ΡΡΡ Π²ΡΡΠΎΠΊΠΎΡΠ΅ΠΌΠΏΠ΅ΡΠ°ΡΡΡΠ½ΠΎΠΉ ΠΏΠ»Π°Π·ΠΌΠ΅Π½Π½ΠΎΠΉ ΡΡΡΡΠ΅ΠΉ.ΠΠ»Ρ ΡΠ΅Π·ΠΊΠΈ ΠΈ ΠΏΡΠΎΠΆΠΈΠ³Π°Π½ΠΈΡ ΠΎΡΠ²Π΅ΡΡΡΠΈΠΉ ΠΏΠ΅ΡΡΠΏΠ΅ΠΊΡΠΈΠ²Π½ΠΎ ΠΏΡΠΈΠΌΠ΅Π½Π΅Π½ΠΈΠ΅ ΡΠ²Π΅ΡΠΎΠ²ΠΎΠ³ΠΎ Π»ΡΡΠ°, ΡΡΡΡΠΈ ΡΡΠΎΡΠ°, Π»Π°Π·Π΅ΡΠ½ΠΎΠ³ΠΎ ΠΈΠ·Π»ΡΡΠ΅Π½ΠΈΡ. ΠΠ°Π»ΡΠ½Π΅ΠΉΡΠ΅Π΅ ΡΠ°Π·Π²ΠΈΡΠΈΠ΅ ΠΈ ΡΠΎΠ²Π΅ΡΡΠ΅Π½ΡΡΠ²ΠΎΠ²Π°Π½ΠΈΠ΅ ΠΌΠ΅ΡΠΎΠ΄ΠΎΠ² ΡΠ²Π°ΡΠΊΠΈ ΠΈ ΡΠ²ΡΠ·Π°Π½ΠΎ Π²Π½Π΅Π΄ΡΠ΅Π½ΠΈΠ΅ ΠΈ ΡΠ°ΡΡΠΈΡΠ΅Π½ΠΈΠ΅ ΡΡΠ΅ΡΡ ΠΏΡΠΈΠΌΠ΅Π½Π΅Π½ΠΈΡ Π½ΠΎΠ²ΡΡ
Π²ΠΈΠ΄ΠΎΠ² ΠΎΠ±ΡΠ°Π±ΠΎΡΠΊΠΈ — ΠΏΠ»Π°Π·ΠΌΠ΅Π½Π½ΠΎΠΉ, ΡΠ»Π΅ΠΊΡΡΠΎΠ½Π½ΠΎΠΉ, Π»Π°Π·Π΅ΡΠ½ΠΎΠΉ, Ρ ΠΈΡΠΏΠΎΠ»ΡΠ·ΠΎΠ²Π°Π½ΠΈΠ΅ΠΌ ΡΠΎΠ²Π΅ΡΡΠ΅Π½Π½ΡΡ
ΡΠ΅Ρ
Π½ΠΎΠ»ΠΎΠ³ΠΈΡΠ΅ΡΠΊΠΈΡ
ΠΏΡΠΈΡΠΌΠΎΠ² ΠΈ ΡΠ»ΡΡΡΠ΅Π½ΠΈΠ΅ΠΌ ΠΊΠΎΠ½ΡΡΡΡΠΊΡΠΈΠΈ ΠΎΠ±ΠΎΡΡΠ΄ΠΎΠ²Π°Π½ΠΈΡ. ΠΠΎΠ·ΠΌΠΎΠΆΠ½ΠΎ Π·Π½Π°ΡΠΈΡΠ΅Π»ΡΠ½ΠΎΠ΅ ΡΠ°ΡΡΠΈΡΠ΅Π½ΠΈΠ΅ ΠΈΡΠΏΠΎΠ»ΡΠ·ΠΎΠ²Π°Π½ΠΈΡ ΡΠ²Π°ΡΠΊΠΈ ΠΈ ΡΠ΅Π·ΠΊΠΈ Π΄Π»Ρ ΠΏΠΎΠ΄Π²ΠΎΠ΄Π½ΡΡ
ΡΠ°Π±ΠΎΡ ΠΈ Π² ΠΊΠΎΡΠΌΠΎΡΠ΅. ΠΠ°ΠΏΡΠ°Π²Π»Π΅Π½ΠΈΠ΅ ΠΏΡΠΎΠ³ΡΠ΅ΡΡΠ° Π² ΠΎΠ±Π»Π°ΡΡΠΈ ΡΠ²Π°ΡΠΎΡΠ½ΠΎΠΉ ΡΠ΅Ρ
Π½ΠΈΠΊΠΈ Π΄Π°Π»ΡΠ½Π΅ΠΉΡΠ°Ρ ΠΌΠ΅Ρ
Π°Π½ΠΈΠ·Π°ΡΠΈΡ ΠΈ Π°Π²ΡΠΎΠΌΠ°ΡΠΈΠ·Π°ΡΠΈΡ ΠΎΡΠ½ΠΎΠ²Π½ΡΡ
ΡΠ²Π°ΡΠΎΡΠ½ΡΡ
ΡΠ°Π±ΠΎΡ ΠΈ Π²ΡΠ΅Ρ
Π²ΡΠΏΠΎΠΌΠΎΠ³Π°ΡΠ΅Π»ΡΠ½ΡΡ
ΡΠ°Π±ΠΎΡ, ΠΏΡΠ΅Π΄ΡΠ΅ΡΡΠ²ΡΡΡΠΈΡ
ΡΠ²Π°ΡΠΊΠ΅ ΠΈ ΡΠ»Π΅Π΄ΡΡΡΠΈΡ
Π·Π° Π½Π΅ΠΉ (ΠΏΡΠΈΠΌΠ΅Π½Π΅Π½ΠΈΠ΅ ΠΌΠ°Π½ΠΈΠΏΡΠ»ΡΡΠΎΡΠΎΠ², ΠΊΠ°Π½ΡΠΎΠ²Π°ΡΠ΅Π»Π΅ΠΉ, ΡΠΎΠ±ΠΎΡΠΎΠ²).ΠΠΊΡΡΠ°Π»ΡΠ½ΠΎΠΉ ΡΠ²Π»ΡΠ΅ΡΡΡ ΠΏΡΠΎΠ±Π»Π΅ΠΌΠ° ΡΠ»ΡΡΡΠ΅Π½ΠΈΡ ΠΊΠΎΠ½ΡΡΠΎΠ»Ρ ΠΊΠ°ΡΠ΅ΡΡΠ²Π° Π‘., Π² ΡΠΎΠΌ ΡΠΈΡΠ»Π΅ ΠΏΡΠΈΠΌΠ΅Π½Π΅Π½ΠΈΠ΅ Π°ΠΏΠΏΠ°ΡΠ°ΡΠΎΠ² ΠΎΠ±ΡΠ°ΡΠ½ΠΎΠΉ ΡΠ²ΡΠ·ΡΡ, ΡΠΏΠΎΡΠΎΠ±Π½ΡΡ
ΡΠ΅Π³ΡΠ»ΠΈΡΠΎΠ²Π°ΡΡ Π² Π°Π²ΡΠΎΠΌΠ°ΡΠΈΡΠ΅ΡΠΊΠΎΠΌ ΡΠ΅ΠΆΠΈΠΌΠ΅ ΡΠ°Π±ΠΎΡΡ ΡΠ²Π°ΡΠΎΡΠ½ΡΡ
Π°Π²ΡΠΎΠΌΠ°ΡΠΎΠ².
Π€ΠΈΠ·ΠΈΡΠ΅ΡΠΊΠ°Ρ ΡΡΡΠ½ΠΎΡΡΡ ΠΈ ΠΊΠ»Π°ΡΡΠΈΡΠΈΠΊΠ°ΡΠΈΡ Π²ΠΈΠ΄ΠΎΠ² ΡΠ²Π°ΡΠΊΠΈ
Π‘Π²Π°ΡΠΊΠ° — ΡΠ΅Ρ Π½ΠΎΠ»ΠΎΠ³ΠΈΡΠ΅ΡΠΊΠΈΠΉ ΠΏΡΠΎΡΠ΅ΡΡ Π²Π½Π΅Π΄ΡΠ΅Π½ΠΈΡ Π½Π΅ΡΠ°Π·ΡΡΠΌΠ½ΡΡ ΡΠΎΠ΅Π΄ΠΈΠ½Π΅Π½ΠΈΠΉ ΠΌΠ΅ΠΆΠ΄Ρ ΡΠΎΠ΅Π΄ΠΈΠ½ΡΠ΅ΠΌΡΠΌΠΈ ΡΠ»Π΅ΠΌΠ΅Π½ΡΠ°ΠΌΠΈ ΡΠΎΡΠΌΡ Π»ΡΠ±ΠΎΠΉ ΠΊΠΎΠ½ΡΡΡΡΠΊΡΠΈΠΈ ΠΏΡΠΈ Π²Π½Π΅ΡΠ΅Π½ΠΈΠΈ ΡΠ½Π΅ΡΠ³ΠΈΠΈ ΠΈΠ·Π²Π½Π΅ Π² ΡΠ΅ΠΏΠ»ΠΎΡΡ ΠΈΠ»ΠΈ ΡΠ°Π±ΠΎΡΡ ΠΌΠ΅Ρ Π°Π½ΠΈΡΠ΅ΡΠΊΠΎΠ³ΠΎ ΡΠΆΠ°ΡΠΈΡ.
Π‘Π²Π°ΡΠ½ΠΎΠ΅ ΡΠΎΠ΅Π΄ΠΈΠ½Π΅Π½ΠΈΠ΅ — ΡΡΠΎ ΡΠ°ΡΡΡ ΠΊΠΎΠ½ΡΡΡΡΠΊΡΠΈΠΈ Π² ΠΌΠ΅ΡΡΠ΅, Π³Π΄Π΅ Π²ΡΠΏΠΎΠ»Π½Π΅Π½Π° ΡΠ²Π°ΡΠΊΠ° Π΄Π΅ΡΠ°Π»Π΅ΠΉ.
Π‘Π²Π°ΡΠ½ΠΎΠΉ ΡΠΎΠ² — ΡΠ°ΡΡΡ ΡΠ²Π°ΡΠΎΡΠ½ΠΎΠ³ΠΎ ΡΠΎΠ΅Π΄ΠΈΠ½Π΅Π½ΠΈΡ, Π³Π΄Π΅ Π΄ΠΎΡΡΠΈΠ³Π½ΡΡΠΎ Π²Π·Π°ΠΈΠΌΠΎΠ΄Π΅ΠΉΡΡΠ²ΠΈΠ΅ ΠΌΠ΅ΠΆΠ°ΡΠΎΠΌΠ½ΡΡ
ΡΠΈΠ» ΡΡΠ΅ΠΏΠ»Π΅Π½ΠΈΡ Π² ΡΠ΅Π·ΡΠ»ΡΡΠ°ΡΠ΅ ΠΊΡΠΈΡΡΠ°Π»Π»ΠΈΠ·Π°ΡΠΈΠΈ ΡΠ°ΡΠΏΠ»Π°Π²Π»Π΅Π½Π½ΠΎΠ³ΠΎ ΠΌΠ΅ΡΠ°Π»Π»Π°, ΠΏΠ»Π°ΡΡΠΈΡΠ΅ΡΠΊΠΎΠ³ΠΎ Π΄Π΅ΡΠΎΡΠΌΠΈΡΠΎΠ²Π°Π½ΠΈΡ ΠΏΡΠΈ ΡΠΆΠ°ΡΠΈΠΈ Π΄Π΅ΡΠ°Π»Π΅ΠΉ, ΠΈΠ»ΠΈ ΡΠΎΡΠ΅ΡΠ°Π½ΠΈΡ ΠΊΡΠΈΡΡΠ°Π»Π»ΠΈΠ·Π°Β¬ΡΠΈΠΈ ΠΈ Π΄Π΅ΡΠΎΡΠΌΠΈΡΠΎΠ²Π°Π½ΠΈΡ. ΠΠΎ ΡΡΠ°Π²Π½Π΅Π½ΠΈΡ Ρ ΡΠΎΠ΅Π΄ΠΈΠ½Π΅Π½ΠΈΡΠΌΠΈ, ΠΏΠΎΠ»ΡΡΠ΅Π½Π½ΡΠΌΠΈ Π΄ΡΡΠ³ΠΈΠΌΠΈ ΡΠΏΠΎΡΠΎΠ±Π°ΠΌΠΈ, ΡΠ²Π°ΡΠ½ΡΠ΅ ΡΠΎΠ΅Π΄ΠΈΠ½Π΅Π½ΠΈΡ ΠΎΠ±Π»Π°Π΄Π°ΡΡ ΠΌΠΎΠ½ΠΎΠ»ΠΈΡΠ½ΠΎΡΡΡΡ, Π½Π΅ΠΏΡΠΎΠ½ΠΈΡΠ°Π΅ΠΌΠΎΡΡΡΡ, Π³Π΅ΡΠΌΠ΅ΡΠΈΡΠ½ΠΎΡΡΡΡ, ΠΌΠ΅Π½ΡΡΠ΅ΠΉ ΠΌΠ°ΡΡΠΎΠΉ, Π±ΠΎΠ»Π΅Π΅ ΡΠ°ΡΠΈΠΎΠ½Π°Π»ΡΠ½ΡΠΌ ΠΈΡΠΏΠΎΠ»ΡΠ·ΠΎΠ²Π°Π½ΠΈΠ΅ΠΌ, ΠΌΠ΅Π½ΡΡΠΈΠΌΠΈ ΡΠ΅Ρ
Π½ΠΎΠ»ΠΎΠ³ΠΈΡΠΌΠΈ ΡΡΡΠ΄Π°, ΠΈΡΠΏΠΎΠ»ΡΠ·ΡΡ ΠΌΠ΅Ρ
Π°Π½ΠΈΡΠ΅ΡΠΊΡΡ ΠΈ Π°Π²ΡΠΎΠΌΠ°ΡΠΈΠ·ΠΈΡΠΎΠ²Π°Π½Π½ΡΡ ΠΎΠ±ΡΠ°Π±ΠΎΡΠΊΡ ΠΈΡ
ΠΏΡΠΎΡΠ΅ΡΡΠ°.
ΠΡΠΈ ΡΠΈΠ»Π΅ ΠΏΡΠΈΡΡΠΆΠ΅Π½ΠΈΡ Π°ΡΠΎΠΌΠΎΠ² (ΠΊΠ°ΠΊ ΡΠ°ΡΡΠΈΡ Π²Π΅ΡΠ΅ΡΡΠ²Π°) ΠΏΡΠΎΠΈΡΡ ΠΎΠ΄ΠΈΡ ΠΏΡΠ΅ΠΎΠ±Π»Π°Π΄Π°ΡΡ Π½Π°Π΄ ΡΠΈΠ»Π°ΠΌΠΈ ΠΎΡΡΠ°Π»ΠΊΠΈΠ²Π°Π½ΠΈΡ. ΠΡΠΈ ΡΡΠΎΠΌ ΠΏΡΠΎΠΈΡΡ ΠΎΠ΄ΠΈΡ ΡΠ±Π»ΠΈΠΆΠ΅Π½ΠΈΠ΅ Π°ΡΠΎΠΌΠΎΠ² Ρ Π°ΡΠΎΠΌΠ½ΡΠΌ ΡΠ°Π΄ΠΈΡΡΠΎΠΌ ΠΈ (ΡΠΌ. Π ΠΈΡ. 1.2). ΠΈΡ (ΠΊΠ°ΠΊ ΠΎΠ΄Π½ΠΎΠΈΠΌΡΠ½Π½ΠΎ Π·Π°ΡΡΠΆΠ΅Π½Π½ΡΡ ΡΠ°ΡΡΠΈΡ). Π‘ΡΠΌΠΌΠΈΡΠΎΠ²Π°Π½ΠΈΠ΅ ΡΡΠΈΡ ΡΠΈΠ» ΠΈΠ·ΠΎΠ±ΡΠ°ΠΆΠ΅Π½ΠΎ ΠΏΡΠ½ΠΊΡΠΈΡΠ½ΠΎΠΉ ΠΊΡΠΈΠ²ΠΎΠΉ.
Π£ΡΡΠ°Π½ΠΎΠ²Π»Π΅Π½ΠΈΠ΅ ΠΌΠ΅ΠΆΠ°ΡΠΎΠΌΠ½ΡΡ
ΡΠ²ΡΠ·Π΅ΠΉ Π½Π° Π³ΡΠ°Π½ΠΈΡΠ°Ρ
ΡΠ°Π·Π΄Π΅Π»Π° ΡΠΎΠ΅Π΄ΠΈΠ½ΡΠ΅ΠΌΡΡ
Π΄Π΅ΡΠ°Π»Π΅ΠΉ ΠΌΠΎΠΆΠ΅Ρ Π±ΡΡΡ Π΄ΠΎΡΡΠΈΠ³Π½ΡΡΠΎ ΡΠ°Π·Π»ΠΈΡΠ½ΡΠΌΠΈ ΡΠ΅Ρ
Π½ΠΎΠ»ΠΎΠ³ΠΈΡΠ΅ΡΠΊΠΈΠΌΠΈ ΠΏΡΠΈΡΠΌΠ°ΠΌΠΈ, ΠΎΠΏΡΠ΅Π΄Π΅Π»ΡΡΡΠΈΠΌΠΈ Π²ΡΠ΅ ΡΠ»Π΅ΠΊΡΡΠΈΡΠ΅ΡΠΊΠΈΠ΅ Π²ΠΈΠ΄Ρ ΠΈ ΡΠ°Π·Π½ΠΎΠ²ΠΈΠ΄Π½ΠΎΡΡΠΈ ΡΠ²Π°ΡΠΊΠΈ.ΠΡΠΈ ΠΏΡΠΈΡΠΌΡ ΠΏΡΠ΅Π΄ΡΡΠ°Π²Π»ΡΡΡ ΡΠΎΠ±ΠΎΠΉ ΡΠ»Π΅ΠΌΠ΅Π½ΡΡ Π·Π°ΡΠΈΡΡ ΡΠ²Π°ΡΠΎΡΠ½ΠΎΠΉ Π²Π°Π½Π½Ρ ΠΈ ΠΌΠ΅ΡΠ°Π»Π»Π°, ΠΈΡΠΏΠΎΠ»ΡΠ·ΡΡ ΡΡΠ΅Π΄ΡΡΠ²Π° ΠΌΠ΅Ρ
Π°Π½ΠΈΠ·Π°ΡΠΈΠΈ ΠΈ Π΄ΡΡΠ³ΠΈΠΌΠΈ ΠΏΡΠΈΠ·Π½Π°ΠΊΠ°ΠΌΠΈ. ΠΠΎΠ»ΡΡΠ΅Π½Π½Π°Ρ Π² ΡΠ΅Π·ΡΠ»ΡΡΠ°ΡΠ΅ ΡΠ²Π°ΡΠΊΠΈ ΡΠΈΡΡΠ΅ΠΌΠ° Π² ΡΠ΅ΡΠΌΠΎΠ΄ΠΈΠ½Π°ΠΌΠΈΡΠ΅ΡΠΊΠΎΠΌ ΡΠΌΡΡΠ»Π΅ ΠΏΡΠ΅Π΄ΡΡΠ°Π²Π»ΡΠ΅Ρ ΡΠΎΠ±ΠΎΠΉ ΡΡΡΠΎΠΉΡΠΈΠ²ΡΡ ΡΠΈΡΡΠ΅ΠΌΡ, Π² ΠΊΠΎΡΠΎΡΠΎΠΉ Π² ΠΏΡΠΎΡΠ΅ΡΡΠ΅ ΡΠ²Π°ΡΠΊΠΈ ΠΏΡΠΎΠΈΠ·ΠΎΡΠ»ΠΎ ΡΠΌΠ΅Π½ΡΡΠ΅Π½ΠΈΠ΅ ΡΠ½Π΅ΡΠ³ΠΈΠΈ. ΠΠ΄Π½Π°ΠΊΠΎ ΡΠ°ΠΌΠΎΠΏΡΠΎΠΈΠ·Π²ΠΎΠ»ΡΠ½ΡΠΉ ΠΏΡΠΎΡΠ΅ΡΡ ΠΎΠ±ΡΠ°Π·ΠΎΠ²Π°Π½ΠΈΡ ΡΠ²Π°ΡΠ½ΠΎΠ³ΠΎ ΡΠΎΠ΅Π΄ΠΈΠ½Π΅Π½ΠΈΡ Π½Π΅Π²ΠΎΠ·ΠΌΠΎΠΆΠ½ΠΎ, ΡΠ°ΠΊ ΠΊΠ°ΠΊ ΡΠ΅Π°Π»ΡΠ½ΡΠ΅ ΡΠ²Π°ΡΠΈΠ²Π°Π΅ΠΌΡΠ΅ Π΄Π΅ΡΠ°Π»ΠΈ Π½Π΅ ΠΈΠΌΠ΅ΡΡ ΠΈΠ΄Π΅Π°Π»ΡΠ½ΠΎ ΡΠΈΡΡΡΡ
ΠΈ Π³Π»Π°Π΄ΠΊΠΈΡ
ΠΏΠΎΠ²Π΅ΡΡ
Π½ΠΎΡΡΠ΅ΠΉ.
ΠΠΎΡΡΠΎΠΌΡ Π² ΡΠ»ΡΡΠ°Π΅ ΡΠ±Π»ΠΈΠΆΠ΅Π½ΠΈΡ ΠΎΠ±ΡΠ΅ΠΊΡΠΎΠ² Π΄ΠΎ ΡΠ°ΡΡΡΠΎΡΠ½ΠΈΡ, ΡΠΎΠΈΠ·ΠΌΠ΅ΡΠΈΠΌΠΎΠ³ΠΎ ΠΏΠ°ΡΠ°ΠΌΠ΅ΡΡΠ° Ρ ΠΏΠ°ΡΠ°ΠΌΠ΅ΡΡΠΎΠΌ ΠΊΡΠΈΡΡΠ°Π»Π»ΠΈΡΠ΅ΡΠΊΠΎΠΉ ΡΠ΅ΡΡΡΠΊΠΈ, Π·Π° ΡΡΡΡ ΡΠΆΠ°ΡΠΈΡ (ΡΠΈΡ.1.3, Π°) (ΡΠ²Π°ΡΠΊΠ° Π΄Π°Π²Π»Π΅Π½ΠΈΠ΅ΠΌ — ΠΌΠ΅Ρ Π°Π½ΠΈΡΠ΅ΡΠΊΠΈΠΉ ΠΊΠ»Π°ΡΡ ΡΠ²Π°ΡΠΊΠΈ) Π½Π΅ΠΎΠ±Ρ ΠΎΠ΄ΠΈΠΌΠΎ ΠΎΠ±ΡΠ·Π°ΡΠ΅Π»ΡΠ½ΠΎ Π²Π·Π°ΠΈΠΌΠ½ΠΎ Π΄Π΅ΡΠΎΡΠΌΠΈΡΠΎΠ²Π°ΡΡ ΠΏΠΎΠ²Π΅ΡΡ Π½ΠΎΡΡΡ ΡΠΎΠ΅Π΄ΠΈΠ½ΡΠ΅ΠΌΡΡ Π΄Π΅ΡΠ°Π»Π΅ΠΉ Π΄Π»Ρ ΡΠΌΡΡΠΈΡ Π½Π΅ΡΠΎΠ²Π½ΠΎΡΡΠ΅ΠΉ ΠΈ Π½Π°Π΄ΡΠΆΠ½ΠΎΠ³ΠΎ ΡΠΈΠ·ΠΈΡΠ΅ΡΠΊΠΎΠ³ΠΎ Π²ΠΎΠ·Π΄Π΅ΠΉΡΡΠ²ΠΈΡ, Π° ΡΠ°ΠΊΠΆΠ΅ Π°ΠΊΡΠΈΠ²ΠΈΠ·ΠΈΡΠΎΠ²Π°ΡΡ ΠΈΡ , ΡΠΎΠΎΠ±ΡΠΈΡΡ ΠΏΠΎΠ²Π΅ΡΡ Π½ΠΎΡΡΠ½ΡΠΌ Π°ΡΠΎΠΌΠ°ΠΌ Π½Π΅ΠΊΠΎΡΠΎΡΡΡ Π°ΠΊΡΠΈΠ²Π°ΡΠΈΡ Π°ΠΊΡΠΈΠ²Π°ΡΠΈΠΈ.
ΠΡΠΈ ΡΡΠΎΠΌ Π²Π½Π΅ΡΠ½ΠΈΠ΅ ΠΎΡΠ±ΠΈΡΡ ΡΠ»Π΅ΠΌΠ΅Π½ΡΠΎΠ² Π΄ΠΎΠ»ΠΆΠ½Ρ ΠΏΠ΅ΡΠ΅ΠΊΡΡΡΡ Π΄ΡΡΠ³ Π΄ΡΡΠ³Π° ΡΠ°ΠΊΠΈΠΌ ΠΎΠ±ΡΠ°Π·ΠΎΠΌ, ΡΡΠΎΠ±Ρ ΡΠ»Π΅ΠΊΡΡΠΎΠ½Ρ ΠΌΠΎΠ³Π»ΠΈ ΡΠ²ΠΎΠ±ΠΎΠ΄Π½ΠΎ ΠΏΠ΅ΡΠ΅ΠΌΠ΅ΡΠ°ΡΡΡΡ Ρ ΠΎΠ΄Π½ΠΎΠΉ ΠΎΡΠ±ΠΈΡΡ Π½Π° Π΄ΡΡΠ³ΡΡ. ΠΡΠΎ ΡΠ²Π»ΡΠ΅ΡΡΡ ΡΡΠ»ΠΎΠ²ΠΈΠ΅ΠΌ ΠΎΠ±ΡΠ°Π·ΠΎΠ²Π°Π½ΠΈΡ Π² ΡΠΎΠ΅Π΄ΠΈΠ½Π΅Π½ΠΈΠΈ ΡΠΊΠ²ΠΎΠ·Π½ΠΎΠΉ ΠΌΠ΅ΡΠ°Π»Π»ΠΈΡΠ΅ΡΠΊΠΎΠΉ ΡΠ²ΡΠ·ΠΈ.Π£ΡΠΈΠ»ΠΈΡ ΡΠΆΠ°ΡΠΈΡ ΠΌΠΎΠΆΠ½ΠΎ ΡΠΌΠ΅Π½ΡΡΠΈΡΡ, Π΅ΡΠ»ΠΈ Π½Π°Π³ΡΠ΅Π²Π°ΡΡ ΡΠ²Π°ΡΠΈΠ²Π°Π΅ΠΌΡΠ΅ ΠΏΠΎΠ²Π΅ΡΡ Π½ΠΎΡΡΠΈ (ΡΠ΅ΡΠΌΠΎΠΌΠ΅Ρ Π°Π½ΠΈΡΠ΅ΡΠΊΠΈΠΉ ΠΊΠ»Π°ΡΡ ΡΠ²Π°ΡΠΊΠΈ).
ΠΠ±ΡΠ°Π·ΠΎΠ²Π°Π½ΠΈΠ΅ ΡΠΎΠ΅Π΄ΠΈΠ½Π΅Π½ΠΈΠΉ ΠΌΠ΅ΡΠ°Π»Π»ΠΈΡΠ΅ΡΠΊΠΈΡ
Π΄Π΅ΡΠ°Π»Π΅ΠΉ Π²ΠΎΠ·ΠΌΠΎΠΆΠ½ΠΎ ΠΈ Π±Π΅Π· ΠΏΡΠΈΠΌΠ΅Π½Π΅Π½ΠΈΡ ΡΠΆΠ°ΡΠΈΡ (Π°Π²ΡΠΎΠ³Π΅Π½Π½ΠΎ) Π·Π° ΡΡΡΡ Π²ΡΠ΅ΠΌΠ΅Π½Π½ΠΎΠ³ΠΎ ΠΌΠ΅ΡΡΠ½ΠΎΠ³ΠΎ ΡΠ°ΡΠΏΠ»Π°Π²Π»Π΅Π½ΠΈΡ ΠΊΡΠΎΠΌΠΎΠΊ Π΄Π»Ρ ΠΎΠ±ΡΠ°Π·ΠΎΠ²Π°Π½ΠΈΡ ΠΎΠ±ΡΠ΅ΠΉ ΡΠ²Π°ΡΠΎΡΠ½ΠΎΠΉ Π²Π°Π½Π½Ρ (ΡΠ²Π°ΡΠΊΠ° ΠΏΠ»Π°Π²Π»Π΅Π½ΠΈΠ΅ΠΌ ΡΠ΅ΡΠΌΠΈΡΠ΅ΡΠΊΠΈΠΉ ΠΊΠ»Π°ΡΡ ΡΠ²Π°ΡΠΊΠΈ). Π ΠΆΠΈΠ΄ΠΊΠΎΠΌ ΠΌΠ΅ΡΠ°Π»Π»Π΅ ΠΈ Π½Π° ΠΎΠ±ΡΠ°Π·ΠΎΠ²Π°Π²ΡΠΈΡ
ΡΡ ΠΌΠ΅ΠΆΡΠ°Π·ΠΎΠ²ΡΡ
Π³ΡΠ°Π½ΠΈΡΠ°Ρ
(ΡΠΈΡ. 1.3, 6) ΡΠ²ΡΠ·ΠΈ ΠΌΠ΅ΠΆΠ΄Ρ Π°ΡΠΎΠΌΠ°ΠΌΠΈ ΡΠΎΡ
ΡΠ°Π½ΡΡΡΡΡ. Π‘ΠΊΠ²ΠΎΠ·Π½Π°Ρ ΠΌΠ΅ΠΆΠ°ΡΠΎΠΌΠ½Π°Ρ ΡΠ²ΡΠ·Ρ Π² ΡΠΎΠ΅Π΄ΠΈΠ½Π΅Π½ΠΈΠΈ ΠΎΠ±ΡΠ°Π·ΡΠ΅ΡΡΡ Π² ΡΠ΅Π·ΡΠ»ΡΡΠ°ΡΠ΅ ΠΊΡΠΈΡΡΠ°Π»Π»ΠΈΠ·Π°ΡΠΈΠΈ ΠΆΠΈΠ΄ΠΊΠΎΠΉ ΡΠ²Π°ΡΠΎΡΠ½ΠΎΠΉ Π²Π°Π½Π½Ρ, Π° ΡΠ°ΠΊΠΆΠ΅ ΡΠ°Π·Π²ΠΈΡΠΈΡ Π΄ΠΈΡΡΡΠ·ΠΈΠΎΠ½Π½ΡΡ
ΠΏΡΠΎΡΠ΅ΡΡΠΎΠ² Ρ ΠΌΠ°ΡΡΠΎΠΏΠ΅ΡΠ΅Π½ΠΎΡΠΎΠΌ ΡΠ΅ΡΠ΅Π· Π³ΡΠ°Π½ΠΈΡΡ ΡΠ²Π°.
Π’Π°ΠΊΠΈΠΌ ΠΎΠ±ΡΠ°Π·ΠΎΠΌ, ΠΏΡΠΎΡΠ΅ΡΡ ΠΎΡΠ½ΠΎΠ²Π½ΠΎΠΉ ΡΠ²Π°ΡΠΊΠΈ (ΡΠ²Π°ΡΠ½ΠΎΠ³ΠΎ ΡΠ²Π°) Π²ΠΊΠ»ΡΡΠ°Π΅Ρ ΡΡΡΠ°Π½ΠΎΠ²Π»Π΅Π½ΠΈΠ΅ ΡΠΈΠ·ΠΈΡΠ΅ΡΠΊΠΎΠ³ΠΎ ΠΊΠΎΠ½ΡΠ°ΠΊΡΠ° ΠΌΠ΅ΠΆΠ΄Ρ ΠΏΠΎΠ²Π΅ΡΡ Π½ΠΎΡΡΡΠΌΠΈ Π΄Π΅ΡΠ°Π»Π΅ΠΉ ΠΈΠ»ΠΈ ΡΠ΅ΡΠ΅Π· ΠΆΠΈΠ΄ΠΊΠΈΠΉ ΠΌΠ΅ΡΠ°Π»Π», ΡΠ²Π°ΡΠΎΡΠ½ΠΎΠΉ Π²Π°Π½Π½Ρ, ΠΎΠ±ΡΠ°Π·ΠΎΠ²Π°Π½ΠΈΠ΅ ΠΏΡΠΎΡΠ½ΡΡ ΠΌΠ΅ΠΆΠ°ΡΠΎΠΌΠ½ΡΡ ΡΠ²ΡΠ·Π΅ΠΉ ΠΈ ΡΠ°Π·Π²ΠΈΡΠΈΠ΅ Π΄ΠΈΡΡΡΠ·ΠΈΠΈ.
ΠΠ°ΡΠ΅ΡΡΠ²ΠΎ ΡΠ²Π°ΡΠ½ΡΡ ΡΠΎΠ΅Π΄ΠΈΠ½Π΅Π½ΠΈΠΉ, ΠΎΠΏΠΈΡΡΠ²Π°Π΅ΠΌΠΎΠ΅ ΠΏΡΠΎΡΠ½ΠΎΡΡΡΡ ΡΡΠΎΠΉΠΊΠΎΡΡΠΈ, ΠΎΡΡΡΡΡΡΠ²ΠΈΠ΅ΠΌ Π²Π½ΡΡΡΠ΅Π½Π½ΠΈΡ ΠΊΠΎΠΌΠΏΠΎΠ½Π΅Π½ΡΠΎΠ², Π·Π°Π²ΠΈΡΠΈΡ Π½Π΅ ΡΠΎΠ»ΡΠΊΠΎ ΠΎΡ ΠΎΡΠ½ΠΎΠ²Π½ΠΎΠ³ΠΎ, Π½ΠΎ ΠΈ ΠΎΡ ΡΠΎΠΏΡΡΡΡΠ²ΡΡΡΠΈΡ Π΄Π΅ΡΠ΅ΠΊΡΠΎΠ² ΠΏΡΠΎΡΠ΅ΡΡΠΎΠ². Π’Π°ΠΊ ΠΊΠ°ΠΊ ΠΏΡΠΈ ΡΠ²Π°ΡΠΊΠ΅ ΠΏΠ»Π°Π²Π»Π΅Π½ΠΈΠ΅ΠΌ Π² ΡΠ²Π°ΡΠ½ΠΎΠΌ ΡΠΎΠ΅Π΄ΠΈΠ½Π΅Π½ΠΈΠΈ ΠΏΠΎΡΠ²Π»ΡΠ΅ΡΡΡ Π·ΠΎΠ½Π° ΡΠ΅ΡΠΌΠΈΡΠ΅ΡΠΊΠΎΠ³ΠΎ Π²Π»ΠΈΡΠ½ΠΈΡ (ΠΠ’Π), ΡΠΎ ΡΠΎΠΏΡΡΡΡΠ²ΡΡΡΠΈΠΌΠΈ Π·Π΄Π΅ΡΡ ΡΠ²Π»ΡΡΡΡΡ:
- ΠΈΠ·ΠΌΠ΅Π½Π΅Π½ΠΈΠ΅ ΡΡΡΡΠΊΡΡΡΡ ΠΈ ΡΠ²ΠΎΠΉΡΡΠ² ΠΌΠ΅ΡΠ°Π»Π»Π° Π² ΠΠ’Π;
- ΠΌΠ΅ΡΠ°Π»Π»ΡΡΠ³ΠΈΡΠ΅ΡΠΊΠΈΠ΅ ΠΏΡΠΎΡΠ΅ΡΡΡ Π² ΡΠ²Π°ΡΠΎΡΠ½ΠΎΠΉ Π²Π°Π½Π½Π΅;
- ΠΏΡΠΎΡΠ΅ΡΡΡ ΠΊΡΠΈΡΡΠ°Π»Π»ΠΈΠ·Π°ΡΠΈΠΈ ΡΠ²Π°ΡΠ½ΠΎΠ³ΠΎ ΡΠ²Π°;
- Π²ΠΎΠ·Π½ΠΈΠΊΠ½ΠΎΠ²Π΅Π½ΠΈΠ΅ ΡΠ²Π°ΡΠΎΡΠ½ΡΡ
Π½Π°ΠΏΡΡΠΆΠ΅Π½ΠΈΠΉ ΠΈ Π΄Π΅ΡΠΎΡΠΌΠ°ΡΠΈΠΉ.
ΠΠ»ΠΈΡΠ½ΠΈΠ΅ ΠΎΡΠ½ΠΎΠ²Π½ΡΡ ΡΠ°ΠΊΡΠΎΡΠΎΠ² ΠΈ ΡΠΎΠΏΡΡΡΡΠ²ΡΡΡΠΈΡ ΠΏΡΠΎΡΠ΅ΡΡΠΎΠ² ΡΠ²Π°ΡΠ½ΡΡ ΡΠΎΠ΅Π΄ΠΈΠ½Π΅Π½ΠΈΠΉ Π·Π°Π²ΠΈΡΠΈΡ ΠΎΡ ΡΠΎΡΡΠ°Π²Π° ΠΈ ΡΠ²ΠΎΠΉΡΡΠ² ΡΠ²Π°ΡΠΈΠ²Π°Π΅ΠΌΡΡ ΠΈ ΠΏΡΠΈΡΠ°Π΄ΠΎΡΠ½ΡΡ ΠΌΠ΅ΡΠ°Π»Π»ΠΎΠ², Π° ΡΠ°ΠΊΠΆΠ΅ ΠΎΡ ΡΠ΅Ρ Π½ΠΎΠ»ΠΎΠ³ΠΈΡΠ΅ΡΠΊΠΈΡ ΡΠ°ΠΊΡΠΎΡΠΎΠ²: ΡΠ΅ΠΆΠΈΠΌΠ° ΡΠ²Π°ΡΠΊΠΈ, Π·Π°ΡΠΈΡΡ ΡΠ²Π°ΡΠΎΡΠ½ΠΎΠΉ Π²Π°Π½Π½Ρ ΠΈ Π΄Ρ.
Π ΠΏΡΠΎΡΠ΅ΡΡΠ΅ ΡΠ²Π°ΡΠΊΠΈ ΡΠ΅Ρ Π½ΠΎΠ»ΠΎΠ³ΠΈΡΠ΅ΡΠΊΠΈΠΌΠΈ ΡΠ°ΠΊΡΠΎΡΠ°ΠΌΠΈ ΠΌΠΎΠΆΠ½ΠΎ Π°ΠΊΡΠΈΠ²Π½ΠΎ ΡΠΏΡΠ°Π²Π»ΡΡΡ. Π‘ΠΎΡΡΠ°Π² ΠΈ ΡΠ²ΠΎΠΉΡΡΠ²Π° ΡΠ²Π°ΡΠΈΠ²Π°Π΅ΠΌΠΎΠ³ΠΎ ΠΌΠ΅ΡΠ°Π»Π»Π° ΠΎΡΡΠ°ΡΡΡΡ Π½Π΅ΠΈΠ·ΠΌΠ΅Π½Π½ΡΠΌΠΈ. ΠΠ»Ρ ΠΎΡΠ΅Π½ΠΊΠΈ ΡΡΠ΅ΠΏΠ΅Π½ΠΈ Π²Π»ΠΈΡΠ½ΠΈΡ ΠΈ ΡΠ²ΠΎΠΉΡΡΠ² ΡΠ²Π°ΡΠΈΠ²Π°Π΅ΠΌΠΎΠ³ΠΎ ΠΌΠ΅ΡΠ°Π»Π»Π° Π½Π° ΠΏΡΠΎΡΠ΅ΠΊΠ°Π½ΠΈΠ΅ ΠΎΡΠ½ΠΎΠ²Π½ΠΎΠ³ΠΎ ΠΈ ΡΠΎΠΏΡΡΡΡΠ²ΡΡΡΠ΅Π³ΠΎ ΠΏΡΠΎΡΠ΅ΡΡΠΎΠ² Π²Π²Π΅Π΄Π΅Π½ΠΎ ΠΏΠΎΠ½ΡΡΠΈΠ΅ ΠΎ ΡΠ²Π°ΡΠΈΠ²Π°Π΅ΠΌΠΎΡΡΠΈ ΠΌΠ΅ΡΠ°Π»Π»ΠΎΠ² ΠΊΠ°ΠΊ ΡΠΏΠΎΡΠΎΠ±Π½ΠΎΡΡΠΈ ΠΎΠ±ΡΠ°Π·ΠΎΠ²ΡΠ²Π°ΡΡ Π½Π΅ΡΠ°Π·ΡΡΠΌΠ½ΠΎΠ΅ ΡΠΎΠ΅Π΄ΠΈΠ½Π΅Π½ΠΈΠ΅ Ρ Π·Π°Π΄Π°Π½Π½ΡΠΌΠΈ ΡΠ²ΠΎΠΉΡΡΠ²Π°ΠΌΠΈ Π² ΡΡΠ»ΠΎΠ²ΠΈΡΡ ΠΏΡΠΈΠ½ΡΡΠΎΠ³ΠΎ ΡΠ΅Ρ Π½ΠΎΠ»ΠΎΠ³ΠΈΡΠ΅ΡΠΊΠΎΠ³ΠΎ ΠΏΡΠΎΡΠ΅ΡΡΠ°.ΠΡΠΈ ΡΡΠ»ΠΎΠ²ΠΈΡ Π² ΠΏΡΠΎΠΈΠ·Π²ΠΎΠ΄ΡΡΠ²Π΅ ΠΌΠΎΠ³ΡΡ Π±ΡΡΡ Π½Π΅ΠΎΠ΄Π½ΠΎΠ·Π½Π°ΡΠ½ΠΎΠΉ.
Π ΡΠΎΠΎΡΠ²Π΅ΡΡΡΠ²ΠΈΠΈ Ρ Π΄Π΅ΠΉΡΡΠ²ΡΡΡΠΈΠΌΠΈ ΡΡΠ°Π½Π΄Π°ΡΡΠ°ΠΌΠΈ ΡΠ²Π°ΡΠΊΡ ΠΊΠ»Π°ΡΡΠΈΡΠΈΡΠΈΡΡΡΡ ΠΏΠΎ ΡΡΡΠΌ ΠΏΡΠΈΠ·Π½Π°ΠΊΠ°ΠΌ: ΡΠΈΠ·ΠΈΡΠ΅ΡΠΊΠΈΠΌ, ΡΠ΅Ρ Π½ΠΈΡΠ΅ΡΠΊΠΈΠΌ ΠΈ ΡΠ΅Ρ Π½ΠΎΠ»ΠΎΠ³ΠΈΡΠ΅ΡΠΊΠΈΠΌ (ΡΠΈΡ. 1.4).
ΠΠΎ ΡΠΈΠ·ΠΈΡΠ΅ΡΠΊΠΈΠΌ ΠΏΡΠΈΠ·Π½Π°ΠΊΠ°ΠΌ, Π² Π·Π°Π²ΠΈΡΠΈΠΌΠΎΡΡΠΈ ΠΎΡ ΡΠΎΡΠΌΡ ΡΠ½Π΅ΡΠ³ΠΈΠΈ, ΠΈΡΠΏΠΎΠ»ΡΠ·ΡΠ΅ΠΌΠΎΠΉ Π΄Π»Ρ ΠΎΠ±ΡΠ°Π·ΠΎΠ²Π°Π½ΠΈΡ ΡΠ²Π°ΡΠ½ΠΎΠ³ΠΎ ΡΠΎΠ΅Π΄ΠΈΠ½Π΅Π½ΠΈΡ, ΡΠ°Π·Π»ΠΈΡΠ°ΡΡ ΡΡΠΈ ΠΊΠ»Π°ΡΡΠ° ΡΠ²Π°ΡΠΊΠΈ: ΡΠ΅ΡΠΌΠΈΡΠ΅ΡΠΊΠΈΠΉ, ΡΠ΅ΡΠΌΠΎΠΌΠ΅Ρ
Π°Π½ΠΈΡΠ΅ΡΠΊΠΈΠΉ ΠΈ ΠΌΠ΅Ρ
Π°Π½ΠΈΡΠ΅ΡΠΊΠΈΠΉ. Π Π·Π°Π²ΠΈΡΠΈΠΌΠΎΡΡΠΈ ΠΎΡ ΠΈΡΡΠΎΡΠ½ΠΈΠΊΠΎΠ² ΡΠ½Π΅ΡΠ³ΠΈΠΈ, ΠΈΡΠΏΠΎΠ»ΡΠ·ΡΠ΅ΡΡΡ Π΄Π»Ρ ΠΎΠ±ΡΠ°Π·ΠΎΠ²Π°Π½ΠΈΡ ΡΠ²Π°ΡΠ½ΠΎΠ³ΠΎ ΡΠΎΠ΅Π΄ΠΈΠ½Π΅Π½ΠΈΡ, ΠΏΠΎ ΠΊΠ°ΠΆΠ΄ΠΎΠΌΡ ΠΊΠ»Π°ΡΡΡ Π²ΡΠ΄Π΅Π»Π΅Π½ΠΎ Π½Π΅ΡΠΊΠΎΠ»ΡΠΊΠΎ Π²ΠΈΠ΄ΠΎΠ² ΡΠ²Π°ΡΠΊΠΈ.
ΠΠΎ ΡΠ΅Ρ Π½ΠΈΡΠ΅ΡΠΊΠΈΠΌ ΠΏΡΠΈΠ·Π½Π°ΠΊΠ°ΠΌ ΡΠ²Π°ΡΠΊΡ ΠΊΠ»Π°ΡΡΠΈΡΠΈΡΠΈΡΡΡΡ Π² Π·Π°Π²ΠΈΡΠΈΠΌΠΎΡΡΠΈ ΠΎΡ ΡΠΏΠΎΡΠΎΠ±Π° Π·Π°ΡΠΈΡΡ ΡΠ°ΡΠΏΠ»Π°Π²Π»Π΅Π½Π½ΠΎΠ³ΠΎ ΠΌΠ΅ΡΠ°Π»Π»Π° ΠΎΡ Π²ΠΎΠ·Π΄ΡΡ Π°, ΡΠΈΠΏΠ° Π·Π°ΡΠΈΡΡ Π³Π°Π·Π° ΠΈ ΡΡΠ΅ΠΏΠ΅Π½ΠΈ ΠΌΠ΅Ρ Π°Π½ΠΈΠ·Π°ΡΠΈΠΈ.
ΠΠΎ ΡΠ΅Ρ Π½ΠΎΠ»ΠΎΠ³ΠΈΡΠ΅ΡΠΊΠΈΠΌ ΠΏΡΠΈΠ·Π½Π°ΠΊΠ°ΠΌ ΡΠ²Π°ΡΠΊΡ ΠΊΠ»Π°ΡΡΠΈΡΠΈΡΠΈΡΡΡΡ ΠΏΠΎ Π²ΠΈΠ΄Ρ ΡΠ»Π΅ΠΊΡΡΠΎΠ΄Π°, ΠΏΠΎ ΡΠΎΠ΄Ρ ΡΠΎΠΊΠ°, ΠΏΠΎ Π²ΠΈΠ΄Ρ ΠΈ Ρ Π°ΡΠ°ΠΊΡΠ΅ΡΡ Π΄ΡΠ³ΠΈ, ΠΏΠΎ Π²ΠΎΠ·Π΄Π΅ΠΉΡΡΠ²ΠΈΡ Π½Π° ΠΆΠΈΠ΄ΠΊΠΈΠΉ ΠΌΠ΅ΡΠ°Π»Π».
ΠΠΈΡΠ΅ΡΠ°ΡΡΡΠ°
ΠΡΠ½ΠΎΠ²Ρ ΡΠ²Π°ΡΠΊΠΈ ΠΈ Π³Π°Π·ΠΎΡΠ΅ΡΠΌΠΈΡΠ΅ΡΠΊΠΈΡ ΠΏΡΠΎΡΠ΅ΡΡΠΎΠ² Π² ΡΡΠ΄ΠΎΡΡΡΠΎΠ΅Π½ΠΈΠΈ ΠΈ ΡΡΠ΄ΠΎΡΠ΅ΠΌΠΎΠ½ΡΠ΅ — ΠΡΡΠΌΠΈΡΡΡΠΎΠ² Π.Π. [2017]
ΠΠΎΡ ΠΎΠΆΠΈΠ΅ ΡΡΠ°ΡΡΠΈ
Π‘ΡΡΠ½ΠΎΡΡΡ ΠΈ ΠΊΠ»Π°ΡΡΠΈΡΠΈΠΊΠ°ΡΠΈΡ ΠΏΡΠΎΡΠ΅ΡΡΠ° ΡΠ²Π°ΡΠΊΠΈ. ΠΠΎΠ½ΡΠΏΠ΅ΠΊΡ
ΠΠΎΠ½ΡΠΏΠ΅ΠΊΡ. Π ΡΡΠ½Π°Ρ ΡΠ»Π΅ΠΊΡΡΠΎ-Π΄ΡΠ³ΠΎΠ²Π°Ρ ΡΠ²Π°ΡΠΊΠ°.
… … …
ΠΠ²Π΅Π΄Π΅Π½ΠΈΠ΅:
Π‘Π²Π°ΡΠΊΠ° ΡΠ²Π»ΡΠ΅ΡΡΡ ΠΎΠ΄Π½ΠΈΠΌ ΠΈΠ· ΡΠ΅Ρ Π½ΠΎΠ»ΠΎΠ³ΠΈΡΠ΅ΡΠΊΠΈΡ ΠΏΡΠΎΡΠ΅ΡΡΠΎΠ², ΠΊΠ°ΠΊ Π² ΠΎΠ±Π»Π°ΡΡΠΈ ΠΌΠ°ΡΠΈΠ½ΠΎΡΡΡΠΎΠ΅Π½ΠΈΡ, ΡΠ°ΠΊ ΠΈ Π² ΠΈΠ½Π΄ΡΡΡΡΠΈΠΈ ΠΈΠ½Π΄ΡΡΡΡΠΈΠΈ.
ΠΠ΅ΡΠΌΠΎΡΡΡ Π½Π° Π±ΠΎΠ»ΡΡΠΈΠ΅ ΠΌΠ°ΡΡΡΠ°Π±Ρ ΠΈΡΠΏΠΎΠ»ΡΠ·ΠΎΠ²Π°Π½ΠΈΡ Π² ΡΠ°Π·Π»ΠΈΡΠ½ΡΡ
Π²ΠΈΠ΄Π°Ρ
ΠΌΠ΅Ρ
Π°Π½ΠΈΠ·ΠΈΡΠΎΠ²Π°Π½Π½ΠΎΠΉ ΡΠ²Π°ΡΠΊΠΈ, ΠΎΠ±ΡΠ΅ΠΌ ΠΏΡΠΈΠΌΠ΅Π½Π΅Π½ΠΈΡ ΡΡΡΠ½ΠΎΠΉ Π΄ΡΠ³ΠΎΠ²ΠΎΠΉ ΡΠ²Π°ΡΠΊΠΈ ΡΠ΅Π³ΠΎΠ΄Π½Ρ Π½Π΅ ΡΠΎΠ»ΡΠΊΠΎ Π½Π΅ ΡΠ½ΠΈΠΆΠ°Π΅ΡΡΡ, Π½ΠΎ ΠΈ Π²ΠΎΠ·ΡΠ°ΡΡΠ°Π΅Ρ, ΡΡΠΎ ΡΠ²ΡΠ·Π°Π½ΠΎ Ρ ΡΠΎΠ·Π΄Π°Π½ΠΈΠ΅ΠΌ Π½ΠΎΠ²ΡΡ
ΠΌΠ°ΡΠ΅ΡΠΈΠ°Π»ΠΎΠ² ΠΈ ΠΎΠ±ΠΎΡΡΠ΄ΠΎΠ²Π°Π½ΠΈΡ Π΄Π»Ρ ΡΡΡΠ½ΠΎΠΉ Π΄ΡΠ³ΠΎΠ²ΠΎΠΉ ΡΠ²Π°ΡΠΊΠΈ.
ΠΠ»Π΅ΠΊΡΡΠΈΡΠ΅ΡΠΊΠ°Ρ Π΄ΡΠ³Π° Π²ΠΏΠ΅ΡΠ²ΡΠ΅ Π±ΡΠ»Π° ΠΎΡΠΊΡΡΡΠ° Π² 1802 Π³. ΠΏΡΠΎΡΠ΅ΡΡΠΎΡΠΎΠΌ ΡΠΈΠ·ΠΈΠΊΠΈ Π‘Π°Π½ΠΊΡ-ΠΠ΅ΡΠ΅ΡΠ±ΡΡΠ³ΡΠΊΠΎΠΉ ΠΌΠ΅Π΄ΠΈΠΊΠΎ-Ρ ΠΈΡΡΡΠ³ΠΈΡΠ΅ΡΠΊΠΎΠΉ Π°ΠΊΠ°Π΄Π΅ΠΌΠΈΠΈ Π.Π. ΠΠ΅ΡΡΠΎΠ²ΡΠΌ.
Π Π² 1882 Π³ΠΎΠ΄Ρ ΡΡΡΡΠΊΠΈΠΉ ΠΈΠ·ΠΎΠ±ΡΠ΅ΡΠ°ΡΠ΅Π»Ρ Π.Π. ΠΠ΅Π½Π°ΡΠ΄ΠΎΡ ΠΏΡΠΈΠΌΠ΅Π½ΠΈΠ» ΡΠ»Π΅ΠΊΡΡΠΈΡΠ΅ΡΠΊΡΡ Π΄ΡΠ³Ρ Π΄Π»Ρ ΡΠΎΠ΅Π΄ΠΈΠ½Π΅Π½ΠΈΠΉ ΠΌΠ΅ΡΠ°Π»Π»ΠΎΠ². Π 1885 Π³ΠΎΠ΄Ρ ΠΎΠ½ ΠΏΠΎΠ»ΡΡΠΈΠ» ΠΏΠ°ΡΠ΅Π½Ρ ΠΏΠΎΠ΄ Π½Π°Π·Π²Π°Π½ΠΈΠ΅ΠΌ Β«ΡΠΏΠΎΡΠΎΠ± ΡΠΎΠ΅Π΄ΠΈΠ½Π΅Π½ΠΈΡ ΠΈ ΡΠ°Π·ΡΠ΅Π΄ΠΈΠ½Π΅Π½ΠΈΡ ΠΌΠ΅ΡΠ°Π»Π»ΠΎΠ² Π½Π΅ΠΏΠΎΡΡΠ΅Π΄ΡΡΠ²Π΅Π½Π½ΡΠΌ ΡΠ»Π΅ΠΊΡΡΠΈΡΠ΅ΡΠΊΠΈΠΌ ΡΠΎΠΊΠΎΠΌΒ», ΠΈΡΠΏΠΎΠ»ΡΠ·ΡΡ Π΄Π»Ρ ΡΡΠΎΠ³ΠΎ Π΄ΡΠ³Ρ, Π³ΠΎΡΡΡΡΡ ΠΌΠ΅ΠΆΠ΄Ρ ΡΠ³ΠΎΠ»ΡΠ½ΡΠΌ ΡΠ»Π΅ΠΊΡΡΠΎΠ΄ΠΎΠΌ ΠΈ ΠΌΠ΅ΡΠ°Π»Π»ΠΎΠΌ ΠΈ ΠΏΠΈΡΠ°ΡΡΡΡ ΡΠ»Π΅ΠΊΡΡΠΈΡΠ΅ΡΠΊΡΡ ΡΠ½Π΅ΡΠ³ΠΈΡ ΠΎΡ Π°ΠΊΠΊΡΠΌΡΠ»ΡΡΠΎΡΠ°.
Π ΡΡΡΠΊΠΈΠΉ ΠΈΠ½ΠΆΠ΅Π½Π΅Ρ-ΠΌΠ΅ΡΠ°Π»Π»ΡΡΠ³ ΠΈ ΠΈΠ·ΠΎΠ±ΡΠ΅ΡΠ°ΡΠ΅Π»Ρ Π.Π. Π‘Π»Π°Π²ΡΠ½ΠΎΠ² Π² 1888 Π³ΠΎΠ΄Ρ ΡΠ°Π·ΡΠ°Π±ΠΎΡΠ°Π» ΡΠΏΠΎΡΠΎΠ± ΡΠ²Π°ΡΠΊΠΈ ΠΌΠ΅ΡΠ°Π»Π»ΠΈΡΠ΅ΡΠΊΠΈΠΌ ΡΠ»Π΅ΠΊΡΡΠΎΠ΄ΠΎΠΌ, Π² 1891 Π³ΠΎΠ΄Ρ ΠΎΠ½ ΠΏΠΎΠ»ΡΡΠΈΠ» Π΄Π²Π° ΠΏΠ°ΡΠ΅Π½ΡΠ° ΠΏΠΎΠ΄ Π½Π°Π·Π²Π°Π½ΠΈΠ΅ΠΌ Β«ΡΠΏΠΎΡΠΎΠ± ΠΈ Π°ΠΏΠΏΠ°ΡΠ°ΡΡ Π΄Π»Ρ ΡΠ»Π΅ΠΊΡΡΠΈΡΠ΅ΡΠΊΠΎΠΉ ΠΎΡΠ»ΠΈΠ²ΠΊΠΈ ΠΌΠ΅ΡΠ°Π»Π»ΠΎΠ²Β» ΠΈ Β«ΡΠΏΠΎΡΠΎΠ± ΡΠ»Π΅ΠΊΡΡΠΈΡΠ΅ΡΠΊΠΎΠ³ΠΎ ΡΠΏΠ»ΠΎΡΠ½Π΅Π½ΠΈΡ ΠΌΠ΅ΡΠ°Π»Π»ΠΈΡΠ΅ΡΠΊΠΈΡ ΠΎΡΠ»ΠΈΠ²ΠΎΠΊΒ». ΠΠ΅Π½Π°ΡΠ΄ΠΎΡ ΠΈΡΠΏΠΎΠ»ΡΠ·ΡΠ΅Ρ ΡΠ°Π·Π»ΠΈΡΠ½ΡΠ΅ ΡΠΏΠΎΡΠΎΠ±Ρ ΡΠ²Π°ΡΠΊΠΈ Π½Π°ΠΊΠ»ΠΎΠ½Π½ΡΠΌΠΈ ΠΌΠ΅ΡΠ°Π»Π»ΠΈΡΠ΅ΡΠΊΠΈΠΌΠΈ ΡΠ»Π΅ΠΊΡΡΠΎΠ΄Π°ΠΌΠΈ ΠΈ ΡΡΡΡΠΎΠΉΡΡΠ²Π°, Π² ΠΊΠΎΡΠΎΡΡΡ ΠΏΠΎΠ΄Π°ΡΠ° ΡΠ»Π΅ΠΊΡΡΠΎΠ΄Π° Π² Π·ΠΎΠ½Ρ Π΄ΡΠ³ΠΈ Π²ΡΠΏΠΎΠ»Π½ΡΠ»Π°ΡΡ Π·Π° ΡΡΠ΅Ρ Π΄Π°Π²Π»Π΅Π½ΠΈΡ ΠΏΡΡΠΆΠΈΠ½Ρ.
ΠΠΈΠ·ΠΊΠΈΠΉ ΡΡΠΎΠ²Π΅Π½Ρ ΡΠ°Π·Π²ΠΈΡΠΈΡ ΡΠ΅Ρ
Π½ΠΈΠΊΠΈ Π² Π ΠΎΡΡΠΈΠΈ Ρ ΡΠ΅Ρ
Π»Π΅Ρ Π½Π΅ ΠΏΠΎΠ·Π²ΠΎΠ»ΡΠ΅Ρ ΠΈΡΠΏΠΎΠ»ΡΠ·ΠΎΠ²Π°ΡΡ ΠΈ ΡΠΈΡΠΎΠΊΠΎ ΠΈΡΠΏΠΎΠ»ΡΠ·ΠΎΠ²Π°ΡΡ ΠΈΠ΄Π΅ΠΈ ΠΠ΅ΡΡΠΎΠ²Π°, ΠΠ΅Π½Π°ΡΠ΄ΠΎΡΠ°, Π‘Π»Π°Π²ΡΠ½ΠΎΠ²Π°.
ΠΡΠ΄Π°ΡΡΠ°ΡΡΡ ΡΠΎΠ»Ρ Π² ΡΠ΅ΠΎΡΠ΅ΡΠΈΡΠ΅ΡΠΊΠΎΠΉ ΡΠ°Π·ΡΠ°Π±ΠΎΡΠΊΠ΅ ΡΠ²Π°ΡΠ½ΡΡ ΠΏΡΠΎΡΠ΅ΡΡΠΎΠ² ΡΡΠ³ΡΠ°Π»ΠΈ Π²ΠΈΠ΄Π½ΡΠ΅ ΡΡΠ΅Π½ΡΠ΅ Π.Π. ΠΡΠ±Π°Π²ΡΠΊΠΈΠΉ, Π.Π. Π₯ΡΠ΅Π½ΠΎΠ², Π.Π. ΠΠΈΠΊΠΎΠ»Π°Π΅Π², Π.Π. ΠΠΊΠ΅ΡΠ±Π»Π°ΠΌ, Π.Π. Π ΡΠΊΠ°Π»ΠΈΠ½, Π.Π. ΠΠ°ΡΠΎΠ½, Π.Π. ΠΠΈΠΊΠΈΡΠΈΠ½ ΠΈ Π΄Ρ.
Π‘Π²Π°ΡΠΊΠ° — ΠΏΡΠΎΡΠ΅ΡΡ ΠΏΠΎΠ»ΡΡΠ΅Π½ΠΈΡ Π½Π΅ΡΠ°Π·ΡΠ΅ΠΌΠ½ΠΎΠ³ΠΎ ΡΠΎΠ΅Π΄ΠΈΠ½Π΅Π½ΠΈΡ Π΄Π²ΡΡ ΠΈΠ»ΠΈ Π±ΠΎΠ»Π΅Π΅ Π΄Π΅ΡΠ°Π»Π΅ΠΉ ΠΈΠ· ΡΠ²Π΅ΡΠ΄ΡΡ ΠΌΠ΅ΡΠ°Π»Π»ΠΎΠ² (ΠΌΠ°ΡΠ΅ΡΠΈΠ°Π»ΠΎΠ²) ΠΏΡΡΠ΅ΠΌ ΠΈΡ ΠΏΠΎΠ»ΡΡΠ΅Π½ΠΈΡ ΠΏΡΡΠ΅ΠΌ ΠΌΠ΅ΡΡΠ½ΠΎΠ³ΠΎ ΡΠΏΠ»Π°Π²Π»Π΅Π½ΠΈΡ ΠΈΠ»ΠΈ ΡΠΎΠ²ΠΌΠ΅ΡΡΠ½ΠΎΠ³ΠΎ Π΄Π΅ΡΠΎΡΠΌΠΈΡΠΎΠ²Π°Π½ΠΈΡ Ρ ΠΈΡΠΏΠΎΠ»ΡΠ·ΠΎΠ²Π°Π½ΠΈΠ΅ΠΌ Π½Π°Π³ΡΠ΅Π²Π°ΡΠ΅Π»Ρ ΠΈ Π±Π΅Π· ΠΎΠ±ΡΠ°Π·ΠΎΠ²Π°Π½ΠΈΡ Π³ΡΠ°Π½ΠΈΡΡ ΡΠ°Π·Π΄Π΅Π»Π° ΠΏΡΠΎΡΠ½ΡΡ ΠΌΠ΅ΠΆΠ°ΡΠΎΠΌΠ½ΡΡ ΡΠ²ΡΠ·Π΅ΠΉ, Π·Π° ΡΡΠ΅Ρ ΡΠΏΠ»Π°Π²Π»Π΅Π½ΠΈΡ ΠΎΡΠ½ΠΎΠ²Π½ΠΎΠ³ΠΎ ΠΈ ΠΏΡΠΈΡΠ°Π΄ΠΎΡΠ½ΠΎΠ³ΠΎ ΠΌΠ°ΡΠ΅ΡΠΈΠ°Π»Π°.
ΠΡΠ΅ Π²ΠΈΠ΄Ρ ΡΠ²Π°ΡΠΊΠΈ ΠΌΠΎΠΆΠ½ΠΎ ΡΠ°Π·Π΄Π΅Π»ΠΈΡΡ Π½Π° Π΄Π²Π΅ Π³ΡΡΠΏΠΏΡ: ΡΠ²Π°ΡΠΊΠ° ΠΏΠ»Π°Π²Π»Π΅Π½ΠΈΠ΅ΠΌ ΠΈ ΡΠ²Π°ΡΠΊΠ° Π΄Π°Π²Π»Π΅Π½ΠΈΠ΅ΠΌ.
ΠΡΠΈ ΡΠ²Π°ΡΠΊΠ΅ ΠΏΠ»Π°Π²Π»Π΅Π½ΠΈΠ΅ΠΌ, ΠΊΡΠΎΠΌΠΊΠΈ ΡΠ²Π°ΡΠΈΠ²Π°Π΅ΠΌΡΡ Π΄Π΅ΡΠ°Π»Π΅ΠΉ ΠΈ ΠΏΡΠΈΡΠ°Π΄ΠΎΡΠ½ΡΠΉ ΠΌΠ°ΡΠ΅ΡΠΈΠ°Π» ΡΠ°ΡΠΏΠ»Π°Π²Π»ΡΡΡΡΡ ΡΠ΅ΠΏΠ»ΠΎΡΠΎΠΉ ΡΠ²Π°ΡΠΎΡΠ½ΠΎΠΉ Π΄ΡΠ³ΠΈ ΠΈΠ»ΠΈ Π³Π°Π·ΠΎΠ²ΡΠΌ ΠΏΠ»Π°ΠΌΠ΅Π½Π΅ΠΌ, ΠΎΠ±ΡΠ°Π·ΡΡ ΡΠ²Π°ΡΠΎΡΠ½ΡΡ Π²Π°Π½Π½Ρ. ΠΡΠΈ ΠΊΡΠΈΡΡΠ°Π»Π»ΠΈΠ·Π°ΡΠΈΠΈ ΠΌΠ΅ΡΠ°Π»Π»Π° ΡΠ²Π°ΡΠΎΡΠ½ΠΎΠΉ Π²Π°Π½Π½Ρ ΡΠΎΡΡ ΠΊΡΠΈΡΡΠ°Π»Π»ΠΎΠ² Π½Π°ΡΠΈΠ½Π°Π΅ΡΡΡ Ρ ΡΠΏΠ»Π°Π²Π»Π΅Π½Π½ΡΡ ΠΊΡΠΈΡΡΠ°Π»Π»ΠΎΠ² ΠΎΡΠ½ΠΎΠ²Π½ΠΎΠ³ΠΎ ΠΌΠ΅ΡΠ°Π»Π»Π°.
ΠΡΠΈ ΡΠ²Π°ΡΠΊΠ΅ Π΄Π°Π²Π»Π΅Π½ΠΈΠ΅ΠΌ ΡΠΎΠ²ΠΌΠ΅ΡΡΠ½Π°Ρ Π½Π°ΠΏΡΠ°Π²Π»Π΅Π½Π½Π°Ρ ΠΏΠ»Π°ΡΡΠΈΡΠ΅ΡΠΊΠ°Ρ Π΄Π΅ΡΠΎΡΠΌΠ°ΡΠΈΡ ΡΠ²Π°ΡΠΈΠ²Π°Π΅ΠΌΡΡ
ΠΌΠ΅ΡΠ°Π»Π»ΠΎΠ² ΡΠΏΠΎΡΠΎΠ±ΡΡΠ²ΡΠ΅Ρ ΡΠΎΠΏΡΠΈΠΊΠΎΡΠ½ΠΎΠ²Π΅Π½ΠΈΡ ΠΈ ΠΏΠ΅ΡΠ΅ΠΌΠ΅ΡΠΈΠ²Π°Π½ΠΈΡ ΠΈΡ
ΡΠ»Π΅ΠΌΠ΅Π½ΡΠΎΠ² ΠΈ ΠΎΠ±ΡΠ°Π·ΠΎΠ²Π°Π½ΠΈΡ ΠΌΠ΅ΠΆΠ°ΡΠΎΠΌΠ½ΠΎΠΉ ΡΠ²ΡΠ·ΠΈ.
ΠΠ»Π°ΡΡΠΈΡΠΈΠΊΠ°ΡΠΈΡ Π²ΠΈΠ΄ΠΎΠ² ΡΠ²Π°ΡΠΊΠΈ ΠΌΠ΅ΡΠ°Π»Π»ΠΎΠ² ΠΏΠΎ ΡΠΈΠ·ΠΈΡΠ΅ΡΠΊΠΈΠΌ ΠΏΡΠΈΠ·Π½Π°ΠΊΠ°ΠΌ. Π Π·Π°Π²ΠΈΡΠΈΠΌΠΎΡΡΠΈ ΠΎΡ ΡΠΎΡΠΌΡ ΡΠ½Π΅ΡΠ³ΠΈΠΈ, ΠΈΡΠΏΠΎΠ»ΡΠ·ΡΠ΅ΠΌΠΎΠΉ Π΄Π»Ρ ΠΎΠ±ΡΠ°Π·ΠΎΠ²Π°Π½ΠΈΡ ΡΠ²Π°ΡΠ½ΠΎΠ³ΠΎ ΡΠΎΠ΅Π΄ΠΈΠ½Π΅Π½ΠΈΡ, ΡΠ°Π·Π»ΠΈΡΠ°ΡΡ ΡΡΠΈ ΠΊΠ»Π°ΡΡΠ° ΡΠ²Π°ΡΠΎΡΠ½ΡΡ ΠΏΡΠΎΡΠ΅ΡΡΠΎΠ²: ΡΠ΅ΡΠΌΠΈΡΠ΅ΡΠΊΠΈΠΉ, ΡΠ΅ΡΠΌΠΎΠΌΠ΅Ρ Π°Π½ΠΈΡΠ΅ΡΠΊΠΈΠΉ, ΠΌΠ΅Ρ Π°Π½ΠΈΡΠ΅ΡΠΊΠΈΠΉ.
ΠΠΈΠ΄ ΡΠ²Π°ΡΠΊΠΈ — ΠΎΠ±ΡΠ΅Π΄ΠΈΠ½ΡΠ΅Ρ ΡΠ²Π°ΡΠΎΡΠ½ΡΠ΅ ΠΏΡΠΎΡΠ΅ΡΡΡ ΠΏΠΎ Π²ΠΈΠ΄Ρ ΠΈΡΡΠΎΡΠ½ΠΈΠΊΠ° ΡΠ°ΠΌΠΎΠ³ΠΎ ΠΈΡΡΠΎΡΠ½ΠΈΠΊΠ° ΡΠΎΠ±ΡΡΠ²Π΅Π½Π½ΠΎΠ³ΠΎ ΠΎΠ±ΡΠ°Π·ΠΎΠ²Π°Π½ΠΈΡ ΡΠ²Π°ΡΠ½ΠΎΠ³ΠΎ ΡΠΎΠ΅Π΄ΠΈΠ½Π΅Π½ΠΈΡ.
Π ΡΠ΅ΡΠΌΠΈΡΠ΅ΡΠΊΠΎΠΌΡ ΠΊΠ»Π°ΡΡΡ ΡΠ²Π°ΡΠΊΠΈ ΠΏΡΠΈΠΌΠ΅Π½ΡΠ΅ΠΌΡΠΌ ΠΏΠ»Π°Π²Π»Π΅Π½ΠΈΠ΅ΠΌ Ρ ΠΈΡΠΏΠΎΠ»ΡΠ·ΠΎΠ²Π°Π½ΠΈΠ΅ΠΌ ΡΠ΅ΠΏΠ»ΠΎΠ²ΠΎΠΉ ΡΠ½Π΅ΡΠ³ΠΈΠΈ, Π° ΠΈΠΌΠ΅Π½Π½ΠΎ: Π΄ΡΠ³ΠΎΠ²Π°Ρ, ΡΠ»Π΅ΠΊΡΡΠΎΡΠ»Π°ΠΊΠΎΠ²Π°Ρ ΡΠ²Π°ΡΠΊΠ°, ΡΠ»Π΅ΠΊΡΡΠΎΠ½Π½ΠΎ-Π»ΡΡΠ΅Π²Π°Ρ, ΠΏΠ»Π°Π·ΠΌΠ΅Π½Π½ΠΎ-Π»ΡΡΠ΅Π²Π°Ρ, ΡΠ»Π΅ΡΡΠΈΠΌ ΡΠ°Π·ΡΡΠ΄ΠΎΠΌ, ΡΠ²Π΅ΡΠΎΠ²Π°Ρ, ΠΈΠ½Π΄ΡΠΊΡΠΈΠΎΠ½Π½Π°Ρ, Π³Π°Π·ΠΎΠ²Π°Ρ ΡΠ²Π°ΡΠΊΠ°, ΡΠ΅ΡΠΌΠΈΡΠ½Π°Ρ ΡΠ²Π°ΡΠΊΠ° ΠΈ Π»ΠΈΡΠ΅ΠΉΠ½Π°Ρ.
Π ΡΠ΅ΡΠΌΠΎΠΌΠ΅Ρ Π°Π½ΠΈΡΠ΅ΡΠΊΠΎΠΌΡ ΠΊΠ»Π°ΡΡΡ ΡΠΈΠΏΠ° ΡΠ²Π°ΡΠΊΠΈ, ΠΎΡΡΡΠ΅ΡΡΠ²Π»ΡΠ΅ΠΌΡΠΌ ΠΏΠ»Π°Π²Π»Π΅Π½ΠΈΠ΅ΠΌ Ρ ΠΈΡΠΏΠΎΠ»ΡΠ·ΠΎΠ²Π°Π½ΠΈΠ΅ΠΌ ΡΠ½Π΅ΡΠ³ΠΈΠΈ ΠΈ Π΄Π°Π²Π»Π΅Π½ΠΈΡ, Π° ΠΈΠΌΠ΅Π½Π½ΠΎ: ΠΊΠΎΠ½ΡΠ°ΠΊΡΠ½Π°Ρ ΡΠ²Π°ΡΠΊΠ°, Π΄ΠΈΡΡΡΠ·ΠΈΠΎΠ½Π½Π°Ρ, ΠΈΠ½Π΄ΡΠΊΡΠΈΠΎΠ½Π½ΠΎ-ΠΏΡΠ΅ΡΡΠΎΠ²Π°Ρ, Π³Π°Π·ΠΎΠΏΡΠ΅ΡΡΠΎΠ²Π°Ρ, Π΄ΡΠ³ΠΎΠ²ΠΎ-ΠΏΡΠ΅ΡΡΠΎΠ²Π°Ρ, ΡΠ»Π°ΠΊΠΎΠΏΡΠ΅ΡΡΠΎΠ²Π°Ρ, ΡΠ΅ΡΠΌΠΈΡΠ½ΠΎ-ΠΏΡΠ΅ΡΡΠΎΠ²Π°Ρ, ΠΏΠ΅ΡΠ½Π°Ρ ΠΈ Π΄Ρ.
Π ΠΌΠ΅Ρ
Π°Π½ΠΈΡΠ΅ΡΠΊΠΎΠΉ ΠΊΠ»Π°ΡΡΡ Π²ΠΈΠ΄Ρ ΡΠ²Π°ΡΠΊΠΈ, ΠΏΡΠΈΠΌΠ΅Π½ΡΠ΅ΠΌΡΠ΅ Ρ ΠΈΡΠΏΠΎΠ»ΡΠ·ΠΎΠ²Π°Π½ΠΈΠ΅ΠΌ ΠΌΠ΅Ρ
Π°Π½ΠΈΡΠ΅ΡΠΊΠΎΠΉ ΡΠ½Π΅ΡΠ³ΠΈΠΈ ΠΈ Π΄Π°Π²Π»Π΅Π½ΠΈΡ, ΡΠ»ΡΡΡΠ°Π·Π²ΡΠΊΠΎΠ²Π°Ρ ΡΠ²Π°ΡΠΊΠ°, ΡΠ²Π°ΡΠΊΠ° ΡΡΠ΅Π½ΠΈΠ΅ΠΌ ΠΈ ΠΌΠ°Π³Π½ΠΈΡΠΎΠΈΠΌΠΏΡΠ»ΡΡΠ½Π°Ρ.
ΠΠ»Π°ΡΡΠΈΡΠΈΠΊΠ°ΡΠΈΡ Π²ΠΈΠ΄ΠΎΠ² ΡΠ²Π°ΡΠΊΠΈ ΠΌΠ΅ΡΠ°Π»Π»ΠΎΠ² ΠΏΠΎ ΡΠ΅Ρ Π½ΠΈΡΠ΅ΡΠΊΠΈΠΌ ΠΏΡΠΈΠ·Π½Π°ΠΊΠ°ΠΌ:
Π’Π΅Ρ Π½ΠΈΡΠ΅ΡΠΊΠΈΠΉ ΠΏΡΠΈΠ·Π½Π°ΠΊ: ΡΠΏΠΎΡΠΎΠ± Π·Π°ΡΠΈΡΡ ΠΌΠ΅ΡΠ°Π»Π»Π° Π² Π·ΠΎΠ½Π΅ ΡΠ²Π°ΡΠΊΠΈ, Π½Π΅ΠΏΡΠ΅ΡΡΠ²Π½ΠΎΡΡΡ ΠΏΡΠΎΡΠ΅ΡΡΠ° ΠΈ ΡΡΠ΅ΠΏΠ΅Π½Ρ ΠΌΠ΅Ρ Π°Π½ΠΈΠ·Π°ΡΠΈΠΈ ΡΠ²Π°ΡΠΊΠΈ.
ΠΠΎ ΡΠΏΠΎΡΠΎΠ±Ρ Π·Π°ΡΠΈΡΡ ΠΌΠ΅ΡΠ°Π»Π»Π° ΡΠ°Π·Π»ΠΈΡΠ°ΡΡ ΡΠ²Π°ΡΠΊΡ Π² Π²ΠΎΠ·Π΄ΡΡ Π΅, Π² Π²Π°ΠΊΡΡΠΌΠ΅, Π² Π·Π°ΡΠΈΡΠ½ΡΡ Π³Π°Π·Π°Ρ , ΠΏΠΎΠ΄ ΡΠ»ΡΡΠΎΠΌ, Π² ΠΏΠ΅Π½Π΅ ΠΈ Ρ ΠΊΠΎΠΌΠ±ΠΈΠ½ΠΈΡΠΎΠ²Π°Π½Π½ΠΎΠΉ Π·Π°ΡΠΈΡΠΎΠΉ.
ΠΠΎ Π½Π΅ΠΏΡΠ΅ΡΡΠ²Π½ΠΎΡΡΠΈ ΠΏΡΠΎΡΠ΅ΡΡΠ°: ΠΏΡΠ΅ΡΡΠ²ΠΈΡΡΡΠ΅ ΠΈ Π½Π΅ΠΏΡΠ΅ΡΡΠ²Π½ΡΠ΅.
ΠΠΎ ΡΡΠ΅ΠΏΠ΅Π½ΠΈ ΠΌΠ΅Ρ Π°Π½ΠΈΠ·Π°ΡΠΈΠΈ: ΡΡΡΠ½ΡΠ΅, ΠΌΠ΅Ρ Π°Π½ΠΈΠ·ΠΈΡΠΎΠ²Π°Π½Π½ΡΠ΅, Π°Π²ΡΠΎΠΌΠ°ΡΠΈΠ·ΠΈΡΠΎΠ²Π°Π½Π½ΡΠ΅ ΠΈ Π°Π²ΡΠΎΠΌΠ°ΡΠΈΡΠ΅ΡΠΊΠΈΠ΅.
- <Π ΡΡΠ½Π°Ρ Π΄ΡΠ³ΠΎΠ²Π°Ρ ΡΠ²Π°ΡΠΊΠ°
- Π₯Π°ΡΠ°ΠΊΡΠ΅ΡΠΈΡΡΠΈΠΊΠΈ ΠΎΡΠ½ΠΎΠ²Π½ΡΡ Π²ΠΈΠ΄ΠΎΠ² ΡΠ²Π°ΡΠΊΠΈ. ΠΠΎΠ½ΡΠΏΠ΅ΠΊΡ>
ΠΠΈΠ΄Ρ ΡΠ²Π°ΡΠΊΠΈ. ΠΠ»Π°ΡΡΠΈΡΠΈΠΊΠ°ΡΠΈΡ ΠΎΡΠ½ΠΎΠ²Π½ΡΡ ΡΠΏΠΎΡΠΎΠ±ΠΎΠ² ΡΠ²Π°ΡΠΊΠΈ
Π ΠΈΡ. 1 ΠΠ»Π°ΡΡΠΈΡΠΈΠΊΠ°ΡΠΈΡ ΡΠΏΠΎΡΠΎΠ±Ρ ΡΠ²Π°ΡΠΊΠΈ
Π‘Π²Π°ΡΠΊΠΎΠΉ Π½Π°Π·ΡΠ²Π°Π΅ΡΡΡ ΠΏΡΠΎΡΠ΅ΡΡ ΠΏΠΎΠ»ΡΡΠ΅Π½ΠΈΡ
Π½Π΅ΡΠ°Π·ΡΠ΅ΠΌΠ½ΠΎΠ³ΠΎ ΡΠΎΠ΅Π΄ΠΈΠ½Π΅Π½ΠΈΡ ΡΠ²Π΅ΡΠ΄ΠΎΠ³ΠΎ ΡΠ΅Π»Π°
ΠΌΠ°ΡΠ΅ΡΠΈΠ°Π»ΠΎΠ² ΠΏΡΡΠ΅ΠΌ ΠΈΡ
ΠΌΠ΅ΡΡΠ½ΠΎΠ³ΠΎ
ΡΠΏΠ»Π°Π²Π»Π΅Π½ΠΈΡ ΠΈΠ»ΠΈ ΡΠΎΠ²ΠΌΠ΅ΡΡΠ½ΠΎΠ³ΠΎ
Π΄Π΅ΡΠΎΡΠΌΠΈΡΠΎΠ²Π°Π½ΠΈΡ, Π² ΡΠ΅Π·ΡΠ»ΡΡΠ°ΡΠ΅ ΡΠ΅Π³ΠΎ
Π½Π°ΠΉΠ΄ΠΈΡΠ΅ ΠΏΡΠΎΡΠ½ΡΠ΅ ΡΠ²ΡΠ·ΠΈ ΠΌΠ΅ΠΆΠ΄Ρ
Π°ΡΠΎΠΌΠ°ΠΌΠΈ ΡΠ²Π°ΡΠΈΠ²Π°Π΅ΠΌΡΡ
ΠΌΠ°ΡΠ΅ΡΠΈΠ°Π»ΠΎΠ².
Π‘Π²Π°ΡΠΊΠ° ΠΏΠ»Π°Π²Π»Π΅Π½ΠΈΠ΅ΠΌ
ΠΡΠ³ΠΎΠ²Π°Ρ ΡΠ²Π°ΡΠΊΠ°. ΠΠ΅ΠΎΠ±Ρ ΠΎΠ΄ΠΈΠΌΠΎΠ΅ Π΄Π»Ρ ΠΌΠ΅ΡΡΠ½ΠΎΠ³ΠΎ ΡΠ°ΡΠΏΠ»Π°Π²Π»Π΅Π½ΠΈΡ Π΄Π΅ΡΠ°Π»Π΅ΠΉ ΠΈ ΠΏΡΠΈΡΠ°Π΄ΠΎΡΠ½ΠΎΠ³ΠΎ ΠΌΠ°ΡΠ΅ΡΠΈΠ°Π»Π° ΡΠ΅ΠΏΠ»ΠΎ ΠΎΠ±ΡΠ°Π·ΡΠ΅ΡΡΡ ΠΏΡΠΈ Π³ΠΎΡΠ΅Π½ΠΈΠΈ ΡΠ»Π΅ΠΊΡΡΠΈΡΠ΅ΡΠΊΠΎΠΉ Π΄ΡΠ³ΠΈ ΠΌΠ΅ΠΆΠ΄Ρ ΡΠ²Π°ΡΠΈΠ²Π°Π΅ΠΌΡΠΌ ΠΌΠ΅ΡΠ°Π»Π»ΠΎΠΌ ΠΈ ΡΠ»Π΅ΠΊΡΡΠΎΠ΄ΠΎΠΌ. ΠΠΎ ΡΠΏΠΎΡΠΎΠ±Ρ ΠΌΠ΅Ρ Π°Π½ΠΈΠ·Π°ΡΠΈΠΈ ΡΠ²Π°ΡΠΊΠ° ΠΌΠΎΠΆΠ΅Ρ Π±ΡΡΡ ΡΡΡΠ½Π°Ρ, ΠΏΠΎΠ»ΡΠ°Π²ΡΠΎΠΌΠ°ΡΠΈΡΠ΅ΡΠΊΠ°Ρ ΠΈ Π°Π²ΡΠΎΠΌΠ°ΡΠΈΡΠ΅ΡΠΊΠ°Ρ. ΠΠ΅Ρ Π°Π½ΠΈΠ·ΠΈΡΠΎΠ²Π°Π½Π½Π°Ρ (ΠΏΠΎΠ»ΡΠ°Π²ΡΠΎΠΌΠ°ΡΠΈΡΠ΅ΡΠΊΠ°Ρ ΠΈ Π°Π²ΡΠΎΠΌΠ°ΡΠΈΡΠ΅ΡΠΊΠ°Ρ) ΡΠ²Π°ΡΠΊΠ° ΠΌΠΎΠΆΠ΅Ρ Π±ΡΡΡ ΠΏΠΎΠ΄ ΡΠ»ΡΡΠΎΠΌ ΠΈ Π² Π·Π°ΡΠΈΡΠ½ΡΡ Π³Π°Π·Π°Ρ .
ΠΠ»Π΅ΠΊΡΡΠΎΡΠ»Π°ΠΊΠΎΠ²Π°Ρ ΡΠ²Π°ΡΠΊΠ°. ΠΠ»Π°Π²Π»Π΅Π½ΠΈΠ΅ ΠΎΡΠ½ΠΎΠ²Π½ΠΎΠ³ΠΎ ΠΌΠ΅ΡΠ°Π»Π»Π° ΠΈ ΠΏΡΠΈΡΠ°Π΄ΠΎΡΠ½ΠΎΠ³ΠΎ ΠΌΠ°ΡΠ΅ΡΠΈΠ°Π»Π° ΠΏΡΠΎΠΈΡΡ ΠΎΠ΄ΠΈΡ Π·Π° ΡΡΠ΅Ρ ΡΠ΅ΠΏΠ»Π°, Π²ΡΠ΄Π΅Π»ΡΡΡΠ΅Π³ΠΎΡΡ ΠΏΡΠΈ ΠΏΡΠΎΡ ΠΎΠΆΠ΄Π΅Π½ΠΈΠΈ ΡΠ»Π΅ΠΊΡΡΠΈΡΠ΅ΡΠΊΠΈΠΉ ΡΠΎΠΊ ΡΠ΅ΡΠ΅Π· ΡΠ°ΡΠΏΠ»Π°Π²Π»Π΅Π½Π½ΡΠΉ ΡΠ»Π°ΠΊ (Π² ΠΏΠ΅ΡΠΈΠΎΠ΄ ΡΡΡΠ°Π½ΠΎΠ²ΠΈΠ²ΡΠ΅Π³ΠΎΡΡ ΠΏΡΠΎΡΠ΅ΡΡΠ°).
ΠΠ»Π΅ΠΊΡΡΠΎΠ½Π½ΠΎΠ»ΡΡΠ΅Π²Π°Ρ
ΡΠ²Π°ΡΠΊΠ°. Π‘Π²Π°ΡΠΊΠ° Π²ΡΠΏΠΎΠ»Π½ΡΠ΅ΡΡΡ Π²
ΠΊΠ°ΠΌΠ΅ΡΠ°Ρ
Ρ ΡΠ°Π·ΡΠ΅ΠΆΠ΅Π½ΠΈΠ΅ΠΌ Π΄ΠΎ 10 -4 -10 -6 ΠΌΠΌ ΡΡ. ΡΡ. Π’Π΅ΠΏΠ»ΠΎ Π²ΡΠ΄Π΅Π»ΡΠ΅ΡΡΡ Π·Π° ΡΡΠ΅Ρ
Π±ΠΎΠΌΠ±Π°ΡΠ΄ΠΈΡΠΎΠ²ΠΊΠΈ Π·ΠΎΠ½Ρ ΡΠ²Π°ΡΠΊΠΈ
ΡΠ»Π΅ΠΊΡΡΠΎΠ½Π½ΡΠΌ ΠΏΠΎΡΠΎΠΊΠΎΠΌ, ΠΏΡΠΈΠΎΠ±ΡΠ΅ΡΠ°ΡΡΠΈΠΌ
Π²ΡΡΠΎΠΊΠ°Ρ ΡΠΊΠΎΡΠΎΡΡΡ Π² Π²ΡΡΠΎΠΊΠΎΠ²ΠΎΠ»ΡΡΠ½ΠΎΠΉ
ΡΡΡΠ°Π½ΠΎΠ²ΠΊΠ΅, ΠΈΠΌΠ΅ΡΡΠ΅ΠΉ ΠΌΠΎΡΠ½ΠΎΡΡΡ Π΄ΠΎ 50 ΠΊΠΡ. ΠΠ½ΠΎΠ΄ΠΎΠΌ ΡΠ²Π»ΡΠ΅ΡΡΡ ΡΠ²Π°ΡΠΈΠ²Π°Π΅ΠΌΠ°Ρ Π΄Π΅ΡΠ°Π»Ρ,
Π° ΠΊΠ°ΡΠΎΠ΄ΠΎΠΌ — Π²ΠΎΠ»ΡΡΡΠ°ΠΌΠΎΠ²Π°Ρ Π½ΠΈΡΡ ΠΈΠ»ΠΈ
ΡΠΏΠΈΡΠ°Π»Ρ, Π½Π°Π³ΡΠ΅ΡΠ°Ρ Π΄ΠΎ ΡΠ΅ΠΌΠΏΠ΅ΡΠ°ΡΡΡΡ 2300
Π³ΡΠ°Π΄ Π‘.
ΠΠ°Π·ΠΎΠ²Π°Ρ ΡΠ²Π°ΡΠΊΠ°. ΠΡΠ½ΠΎΠ²Π½ΠΎΠΉ ΠΈ ΠΏΡΠΈΡΠ°Π΄ΠΎΡΠ½ΡΠΉ ΠΌΠ΅ΡΠ°Π»Π»Ρ ΡΠ°ΡΠΏΠ»Π°Π²Π»ΡΡΡΡΡ Π²ΡΡΠΎΠΊΠΎΡΠ΅ΠΌΠΏΠ΅ΡΠ°ΡΡΡΠ½ΡΠΌ Π³Π°Π·ΠΎΠΊΠΈΡΠ»ΠΎΡΠΎΠ΄Π½ΡΠΌ ΠΏΠ»Π°ΠΌΠ΅Π½Π΅ΠΌ (ΡΠ΅ΠΌΠΏΠ΅ΡΠ°ΡΡΡΠ° 3200 Π³ΡΠ°Π΄ Π‘)
ΠΠΌΠΏΡΠ»ΡΡΠ½ΠΎ-Π΄ΡΠ³ΠΎΠ²Π°Ρ ΡΠ²Π°ΡΠΊΠ°. Π‘ΡΡΠ½ΠΎΡΡΡ ΡΠΏΠΎΡΠΎΠ±Π° Π² ΠΏΠΎΡΡΠ΄ΠΊΠ΅ Π² ΡΠΎΠΌ, ΡΡΠΎ ΡΠ²Π°ΡΠΎΡΠ½ΡΠΉ ΡΠΎΠΊ Π½Π΅ ΡΠΎΡ ΡΠ°Π½ΡΠ΅Ρ ΠΏΠΎΡΡΠΎΡΠ½Π½ΡΡ ΡΡΡΠ°Π½ΠΎΠ²ΠΊΡ, Π° ΠΏΠΎΡΡΡΠΏΠ°Π΅Ρ Π² Π΄Π΅ΠΆΡΡΠ½ΡΡ ΡΠ²Π°ΡΠΎΡΠ½ΡΡ Π΄ΡΠ³Ρ ΠΎΠΏΡΠ΅Π΄Π΅Π»Π΅Π½Π½ΡΠΌΠΈ ΠΊΡΠ°ΡΠΊΠΎΠ²ΡΠ΅ΠΌΠ΅Π½Π½ΡΠΌΠΈ ΠΈΠΌΠΏΡΠ»ΡΡΠ°ΠΌΠΈ.
ΠΠ»Π°Π·ΠΌΠ΅Π½Π½Π°Ρ ΡΠ²Π°ΡΠΊΠ°. ΠΠ»Π°Π²Π»Π΅Π½ΠΈΠ΅ ΠΌΠ΅ΡΠ°Π»Π»ΠΎΠ² ΠΎΡΡΡΠ΅ΡΡΠ²Π»ΡΠ΅ΡΡΡ ΠΏΠ»Π°Π·ΠΌΠ΅Π½Π½ΠΎ-Π΄ΡΠ³ΠΎΠ²ΠΎΠΉ ΡΡΡΡΠ΅ΠΉ, ΠΈΠΌΠ΅ΡΡΠ΅ΠΉ ΡΠ΅ΠΌΠΏΠ΅ΡΠ°ΡΡΡΡ Π²ΡΡΠ΅ 10 000 Π³ΡΠ°Π΄ Π‘.
ΠΠ°Π·Π΅ΡΠ½Π°Ρ ΡΠ²Π°ΡΠΊΠ°. Π‘Π²Π°ΡΠΊΠ° Π½Π° ΠΎΡΠ½ΠΎΠ²Π΅ ΠΈΡΠΏΠΎΠ»ΡΠ·ΠΎΠ²Π°Π½ΠΈΠ΅ ΡΠΎΡΠΎΡΠ»Π΅ΠΊΡΡΠΎΠ½Π½ΠΎΠΉ ΡΠ½Π΅ΡΠ³ΠΈΠΈ. ΠΡΠΈ Π±ΠΎΠ»ΡΡΠΎΠΌ ΡΡΠΈΠ»Π΅Π½ΠΈΠΈ ΡΠ²Π΅ΡΠΎΠ²ΠΎΠΉ Π»ΡΡ ΡΠΏΠΎΡΠΎΠ±Π΅Π½ ΠΏΠ»Π°Π²ΠΈΡΡ ΠΌΠ΅ΡΠ°Π»Π». ΠΠ»Ρ ΠΏΠΎΠ»ΡΡΠ΅Π½ΠΈΡ ΡΠ°ΠΊΠΎΠ³ΠΎ Π»ΡΡΠ° ΠΏΡΠΈΠΌΠ΅Π½ΡΡΡ ΡΠΏΠ΅ΡΠΈΠ°Π»ΡΠ½ΡΠ΅ ΡΡΡΡΠΎΠΉΡΡΠ²Π° — Π»Π°Π·Π΅ΡΡ.
Π‘Π²Π°ΡΠΊΠ° Π΄Π°Π²Π»Π΅Π½ΠΈΠ΅
ΠΠΎΠ½ΡΠ°ΠΊΡΠ½Π°Ρ
ΡΠ²Π°ΡΠΊΠ°. ΠΠ΅ΡΡΠΎ ΡΠ²Π°ΡΠΊΠΈ
ΡΠ°Π·ΠΎΠ³ΡΠ΅Π²Π°Π΅ΡΡΡ ΠΈΠ»ΠΈ ΡΠ°ΡΠΏΠ»Π°Π²Π»ΡΠ΅ΡΡΡ
ΡΠ΅ΠΏΠ»ΠΎΠΌ, ΠΎΠ±ΡΠ°Π·ΠΎΠ²Π°Π½Π½ΡΠΌ ΠΏΡΠΈ
ΠΏΡΠΎΡ
ΠΎΠΆΠ΄Π΅Π½ΠΈΠ΅ ΡΠ»Π΅ΠΊΡΡΠΈΡΠ΅ΡΠΊΠΎΠ³ΠΎ ΡΠΎΠΊΠ°
ΡΠ΅ΡΠ΅Π· ΠΊΠΎΠ½ΡΠ°ΠΊΡΠΈΡΡΠ΅ΠΌΡΠ΅ ΠΌΠ΅ΡΡΠ° ΠΈΠ·Π΄Π΅Π»ΠΈΠΉ.
Π£Π»ΡΡΡΠ°Π·Π²ΡΠΊΠΎΠ²Π°Ρ ΡΠ²Π°ΡΠΊΠ°. Π‘Π²Π°ΡΠΊΠ° ΠΎΡΡΡΠ΅ΡΡΠ²Π»ΡΠ΅ΡΡΡ Π·Π° ΡΡΠ΅Ρ ΠΏΡΠ΅Π²ΡΠ°ΡΠ΅Π½ΠΈΡ ΠΏΡΠΈ ΠΏΠΎΠΌΠΎΡΠΈ ΡΠΏΠ΅ΡΠΈΠ°Π»ΡΠ½ΠΎΠ³ΠΎ ΠΏΡΠ΅ΠΎΠ±ΡΠ°Π·ΠΎΠ²Π°ΡΠ΅Π»Ρ ΡΠ»ΡΡΡΠ°Π·Π²ΡΠΊΠΎΠ²ΡΡ ΠΊΠΎΠ»Π΅Π±Π°Π½ΠΈΠΉ Π² ΠΌΠ΅Ρ Π°Π½ΠΈΡΠ΅ΡΠΊΠΈΠ΅ Π²ΡΡΠΎΠΊΠΈΠ΅ ΡΠ°ΡΡΠΎΡΡ ΠΈ ΠΏΡΠΈΠΌΠ΅Π½Π΅Π½ΠΈΡ Π½Π΅Π±ΠΎΠ»ΡΡΠΎΠ³ΠΎ ΡΠ΄Π°Π²Π»ΠΈΠ²Π°ΡΡΠ΅Π³ΠΎ ΡΡΠΈΠ»ΠΈΡ.
Π‘Π²Π°ΡΠΊΠ° ΡΡΠ΅Π½ΠΈΠ΅ΠΌ. Π‘Π²Π°ΡΠΊΠ° Π·Π°ΠΊΠ»ΡΡΠ°Π΅ΡΡΡ Π² ΡΠΎΠΌ, ΡΡΠΎ ΠΏΠΎΡΡΡΠΈΡΡ ΡΡΠ΅Π½ΠΈΡ ΠΎΠ΄Π½ΠΎΠ³ΠΎ ΠΈΠ· ΡΠ²Π°ΡΠΈΠ²Π°Π΅ΠΌΡΡ ΡΡΠ΅ΡΠΆΠ½Π΅ΠΉ ΠΎ Π΄ΡΡΠ³ΠΎΠ΅ ΠΌΠ΅ΡΡΠΎ ΡΠΎΠ΅Π΄ΠΈΠ½Π΅Π½ΠΈΡ ΡΠ°Π·ΠΎΠ³ΡΠ΅Π²Π°Π΅ΡΡΡ; ΠΏΡΠΈ ΠΏΡΠΈΠ»ΠΎΠΆΠ΅Π½ΠΈΠ΅ ΠΎΡΠ΅Π²ΠΎΠ³ΠΎ ΡΡΠΈΠ»ΠΈΡ ΡΠΎΠ΅Π΄ΠΈΠ½ΡΠ΅ΠΌΡΠ΅ ΠΌΠ΅ΡΠ°Π»Π»Ρ ΡΠ²Π°ΡΠΈΠ²Π°ΡΡΡΡ.
Π₯ΠΎΠ»ΠΎΠ΄Π½Π°Ρ ΡΠ²Π°ΡΠΊΠ°. Π‘Π²Π°ΡΠΊΠ° Π½Π° ΠΎΡΠ½ΠΎΠ²Π΅ ΡΠΏΠΎΡΠΎΠ±Π½ΠΎΡΡΠΈ ΠΌΠ΅ΡΠ°Π»Π»Π° ΠΎΠ±ΡΠ°Π·ΠΎΠ²ΡΠ²Π°ΡΡ ΠΎΠ±ΡΠΈΠ΅ ΠΊΡΠΈΡΡΠ°Π»Π»Ρ ΠΏΡΠΈ Π·Π½Π°ΡΠΈΡΠ΅Π»ΡΠ½ΠΎΠΌ Π΄Π°Π²Π»Π΅Π½ΠΈΠ΅.
ΠΠ°Π·ΠΎΠΏΡΠ΅ΡΡΠΎΠ²Π°Ρ
ΡΠ²Π°ΡΠΊΠ°. Π‘Π²Π°ΡΠΊΠ° ΠΎΡΡΡΠ΅ΡΡΠ²Π»ΡΠ΅ΡΡΡ
Π½Π°Π³ΡΠ΅Π²Π°Π½ΠΈΠ΅ΠΌ ΠΊΠΎΠ½ΡΠΎΠ² ΡΡΠ΅ΡΠΆΠ½Π΅ΠΉ ΠΈΠ»ΠΈ
ΡΡΡΠ± Π²ΡΠ΅ΠΌΡ ΠΏΠ΅ΡΠΈΠΌΠ΅ΡΡΡ ΠΎΠΊΡΡΠΆΠ½ΠΎΡΡΠΈ
ΠΌΠ½ΠΎΠ³ΠΎΠΏΠ»Π°ΠΌΠ΅Π½Π½ΡΠΌΠΈ Π³ΠΎΡΠ΅Π»ΠΊΠ°ΠΌΠΈ Π΄ΠΎ
ΠΏΠ»Π°ΡΡΠΈΡΠ΅ΡΠΊΠΎΠ³ΠΎ ΡΠΎΡΡΠΎΡΠ½ΠΈΡ ΠΈΠ»ΠΈ
Π‘ΠΆΠΈΠΌΠ°ΡΡΠΈΠΌ ΠΏΠ»Π°Π²Π»Π΅Π½ΠΈΠ΅ΠΌ Ρ ΠΈΡ
ΠΏΠΎΡΠ»Π΅Π΄ΡΡΡΠΈΠΌ ΡΠΆΠ°ΡΠΈΠ΅ΠΌ.
Π’Π΅ΡΠΌΠΈΡΠ½Π°Ρ ΡΠ²Π°ΡΠΊΠ°. ΠΡΠΎΡΠ΅ΡΡ ΡΠ²Π°ΡΠΊΠΈ Π·Π°ΠΊΠ»ΡΡΠ°Π΅ΡΡΡ Π² ΡΠΎΠΌ, ΡΡΠΎ ΡΠ²Π°ΡΠΈΠ²Π°Π΅ΠΌΡΠ΅ Π·Π°ΠΊΠ»Π°Π΄ΡΠ²Π°ΡΡΡΡ Π² ΠΎΠ³Π½Π΅ΡΠΏΠΎΡΠ½ΡΡ Π΄Π΅ΡΠ°Π»ΠΈ ΡΠΎΡΠΌΡ, Π° Π² ΡΡΡΠ°Π½ΠΎΠ²Π»Π΅Π½Π½ΡΠΉ ΡΠ²Π΅ΡΡ Ρ ΡΠΈΠ³Π΅Π»Ρ Π·Π°ΡΡΠΏΠ°Π΅ΡΡΡ ΡΠ΅ΡΠΌΠΈΡ — ΠΏΠΎΡΠΎΡΠΎΠΊ ΠΈΠ· Π°Π»ΡΠΌΠΈΠ½ΠΈΡ ΠΈ ΠΎΠΊΡΠΈΠ΄Π° ΠΆΠ΅Π»Π΅Π·Π°.ΠΡΠΈ Π³ΠΎΡΠ΅Π½ΠΈΠΈ ΡΠ΅ΡΠΌΠΈΡΠ° ΠΎΠΊΠΈΡΡ ΠΆΠ΅Π»Π΅Π·Π° Π²ΠΎΡΡΡΠ°Π½Π°Π²Π»ΠΈΠ²Π°Π΅ΡΡΡ, Π° ΠΎΠ±ΡΠ°Π·ΡΡΡΠΈΠΉΡΡ ΠΏΡΠΈ ΡΡΠΎΠΌ ΠΆΠΈΠ΄ΠΊΠΈΠΉ ΠΌΠ΅ΡΠ°Π»Π» ΠΏΡΠΈ Π·Π°ΠΏΠΎΠ»Π½Π΅Π½ΠΈΠΈ ΡΠΎΡΠΌΡ ΠΎΠΏΠ»Π°Π²Π»ΡΠ΅Ρ ΠΈ ΡΠΎΠ΅Π΄ΠΈΠ½ΡΠ΅Ρ ΠΊΡΠΎΠΌΠΊΠΈ ΡΠ²Π°ΡΠΈΠ²Π°Π΅ΠΌΡΡ ΠΈΠ·Π΄Π΅Π»ΠΈΠΉ.
ΠΠ½Π΄ΡΠΊΡΠΈΠΎΠ½Π½Π°Ρ ΡΠ²Π°ΡΠΊΠ°. ΠΡΠΎΡ ΡΠΏΠΎΡΠΎΠ± ΡΠ²Π°ΡΠΊΠΈ ΠΎΡΠ½ΠΎΠ²Π°Π½ Π½Π° ΡΠΎΠ·ΠΎΠ³ΡΠ΅Π²Π΅ ΡΠΎΠΊΠ°ΠΌΠΈ Π²ΡΡΠΎΠΊΠΎΠΉ ΡΠΊΠΎΡΠΎΡΡΠΈ ΠΊΠΎΠ½ΡΠΎΠ² ΡΡΡΠΊΡΠ΅ΠΌΡΡ ΡΡΠ΅ΡΠΆΠ½Π΅ΠΉ ΠΈΠ»ΠΈ ΡΡΡΠ± Π΄ΠΎ ΠΏΠ»Π°ΡΡΠΈΡΠ΅ΡΠΊΠΎΠ³ΠΎ ΡΠΎΡΡΠΎΡΠ½ΠΈΡ Ρ ΠΏΠΎΡΠ»Π΅Π΄ΡΡΡΠΈΠΌ ΠΏΡΠΈΠ»ΠΎΠΆΠ΅Π½ΠΈΠ΅ΠΌ ΠΎΡΠ΅Π²ΡΡ ΡΡΠΈΠ»ΠΈΡ Π΄Π»Ρ Π΄ΠΎΡΡΠΈΠΆΠ΅Π½ΠΈΡ Π½Π΅ΡΠ°Π·ΡΠ΅ΠΌΠ½ΠΎΠ³ΠΎ ΡΠΎΠ΅Π΄ΠΈΠ½Π΅Π½ΠΈΡ
Π‘Π²Π°ΡΠΊΠ° Π²ΠΈΠ΄ΠΎΠ² ΡΠ²Π°ΡΠΊΠΈ — ΠΠ½ΡΠΈΠΊΠ»ΠΎΠΏΠ΅Π΄ΠΈΡ ΠΏΠΎ ΠΌΠ°ΡΠΈΠ½ΠΎΡΡΡΠΎΠ΅Π½ΠΈΡ XXL
Π’Π΅Ρ Π½ΠΎΠ»ΠΎΠ³ΠΈΡ ΡΠ²Π°ΡΠΊΠΈ (Π²ΠΈΠ΄ ΡΠ²Π°ΡΠΊΠΈ, ΡΠ²Π°ΡΠΎΡΠ½ΡΠ΅ ΠΌΠ°ΡΠ΅ΡΠΈΠ°Π»Ρ, ΡΠ΅Ρ Π½ΠΈΠΊΠ° ΡΠ²Π°ΡΠΊΠΈ) Π²ΡΠ±ΠΈΡΠ°Π΅ΡΡΡ Π² Π·Π°Π²ΠΈΡΠΈΠΌΠΎΡΡΠΈ ΠΎΡ ΠΎΡΠ½ΠΎΠ²Π½ΠΎΠ³ΠΎ ΠΏΠΎΠΊΠ°Π·Π°ΡΠ΅Π»Ρ ΡΠ²Π°ΡΠΈΠ²Π°Π΅ΠΌΠΎΡΡΠΈ (ΠΈΠ»ΠΈ ΡΠΎΡΠ΅ΡΠ°Π½ΠΈΡ Π½Π΅ΡΠΊΠΎΠ»ΡΠΊΠΈΡ ΠΏΠΎΠΊΠ°Π·Π°ΡΠ΅Π»Π΅ΠΉ) Π΄Π»Ρ ΠΊΠ°ΠΆΠ΄ΠΎΠ³ΠΎ ΠΊΠΎΠ½ΠΊΡΠ΅ΡΠ½ΠΎΠ³ΠΎ ΠΌΠ°ΡΠ΅ΡΠΈΠ°Π»Π°. [c.40] ΠΠ½Π΄Π΅ΠΊΡΡ ΡΠ²Π°ΡΠΊΠΈ ΠΠΈΠ΄Ρ ΡΠ²Π°ΡΠΊΠΈ ΠΠ½Π΄Π΅ΠΊΡΡ ΠΌΠ΅ΡΠΎΠ΄Π° ΠΈΠ·Π³ΠΎΡΠΎΠ²Π»Π΅Π½ΠΈΡ [c. 176]
Π’Π΅ΡΠΌΠΎΠΎΠ±ΡΠ°Π±ΠΎΡΠΊΠ° Π΄ΠΎ ΡΠ²Π°ΡΠΊΠΈ ΠΠΈΠ΄ ΡΠ²Π°ΡΠΊΠΈ Π’Π΅ΡΠΌΠΎΠΎΠ±ΡΠ°Π±ΠΎΡΠΊΠ° ΠΏΠΎΡΠ»Π΅ ΡΠ²Π°ΡΠΊΠΈ ΠΈ ΠΌΠ΅Ρ Π°Π½ΠΈΡΠ΅ΡΠΊΠΈΠ΅ ΡΠ²ΠΎΠΉΡΡΠ²Π° ΠΠΎΠΊΡΡΡΠΈΠ΅ Π‘ΡΠ΅Π΄Π½Π΅Π΅ Π²ΡΠ΅ΠΌΡ Π΄ΠΎ ΡΠ°Π·ΡΡΡΠ΅Π½ΠΈΡ, ΡΡΡΠΊΠΈ [c.134]
ΠΠ»Π°ΡΡ ΡΠ²Π°ΡΠΊΠΈ ΠΠΈΠ΄ ΡΠ²Π°ΡΠΊΠΈ [c.334]
Π£Π»ΡΡΡΠ°Π·Π²ΡΠΊΠΎΠ²Π°Ρ (Π£Π) ΡΠ²Π°ΡΠΊΠ° — Π²ΠΈΠ΄ ΡΠ²Π°ΡΠΊΠΈ ΠΌΠ΅Ρ Π°Π½ΠΈΡΠ΅ΡΠΊΠΎΠ³ΠΎ ΠΊΠ»Π°ΡΡΠ°, ΠΎΠ±ΡΠ΅Π΄ΠΈΠ½ΡΡΡΠΈΠΉ ΡΠΏΠΎΡΠΎΠ±Ρ (ΡΠΈΡ.6.32), ΠΏΡΠΈ ΠΏΠΎΠΌΠΎΡΠΈ ΠΈΠ½ΡΡΡΡΠΌΠ΅Π½ΡΠ° ΡΠΎΠ΅Π΄ΠΈΠ½ΡΠ΅ΠΌΡΠΌ ΠΏΠΎΠ²Π΅ΡΡ Π½ΠΎΡΡΠ½ΡΠΌ ΠΏΠΎΠ΄Π²ΠΎΠ΄ΡΡΡΡ ΠΌΠ΅Ρ Π°Π½ΠΈΡΠ΅ΡΠΊΠΈΠ΅ ΠΊΠΎΠ»Π΅Π±Π°Π½ΠΈΡ Π£ 3-Ρ ΡΠ°ΡΡΠΎΡΠ½ΠΎΠΉ ΡΠΎΡΠΌΡ, ΠΏΡΠ΅ΠΎΠ±ΡΠ°Π·ΠΎΠ²ΡΠ²Π°Π΅ΠΌΡΠ΅ Π² ΡΠ²Π°ΡΠΈΠ²Π°Π΅ΠΌΠΎΠΌ ΠΌΠ°ΡΠ΅ΡΠΈΠ°Π»Π΅ Π² ΡΠ΅ΠΏΠ»ΠΎΡΡ. [c.390]
ΠΡΡΠ΅Π²Π°Ρ ΠΏΡΠ΅ΡΡΠΎΠ²Π°Ρ ΡΠ²Π°ΡΠΊΠ° — Π²ΠΈΠ΄ ΡΠ²Π°ΡΠΊΠΈ ΡΠ΅ΡΠΌΠΎΠΌΠ΅Ρ Π°Π½ΠΈΡΠ΅ΡΠΊΠΎΠ³ΠΎ ΠΊΠ»Π°ΡΡΠ°, ΠΎΠ±ΡΠ΅Π΄ΠΈΠ½ΡΡΡΠΈΠΉ ΡΠΏΠΎΡΠΎΠ±Ρ ΡΠ²Π°ΡΠΊΠΈ, ΠΏΡΠΈ ΠΊΠΎΡΠΎΡΡΡ Π΄Π»Ρ ΠΏΠ΅ΡΠ΅Π΄Π°ΡΠΈ ΡΠ½Π΅ΡΠ³ΠΈΠΈ Π² ΡΠΎΡΠΌΠ΅ ΡΠ΅ΠΏΠ»ΠΎΡΡ ΠΊ ΡΠΎΠ΅Π΄ΠΈΠ½ΡΠ΅ΠΌΡΠΌ ΠΏΠΎΠ²Π΅ΡΡ Π½ΠΎΡΡΡΠΌ ΠΈΡΠΏΠΎΠ»ΡΠ·ΡΡΡ ΡΠ»Π΅ΠΊΡΡΠΎΠΌΠ°Π³Π½ΠΈΡΠ½ΠΎΠ΅ ΠΈΠ·Π»ΡΡΠ΅Π½ΠΈΠ΅ Π²ΠΈΠ΄ΠΈΠΌΠΎΠΉ ΠΈΠ»ΠΈ ΠΈΠ½ΡΡΠ°ΠΊΡΠ°ΡΠ½ΠΎΠΉ ΠΎΠ±Π»Π°ΡΡΠΈ (Π΄ΠΈΠ°ΠΏΠ°Π·ΠΎΠ½ Π΄Π»ΠΈΠ½ Π²ΠΎΠ»Π½ 0,4-15) ΠΌΠΊΠΌ), Π° ΠΎΠ±ΡΠ°Π·ΠΎΠ²Π°Π½ΠΈΠ΅ ΡΠ²Π°ΡΠ½ΠΎΠ³ΠΎ ΡΠΎΠ΅Π΄ΠΈΠ½Π΅Π½ΠΈΡ ΠΎΡΡΡΠ΅ΡΡΠ²Π»ΡΡΡ Ρ ΠΏΡΠΈΠ»ΠΎΠΆΠ΅Π½ΠΈΠ΅ΠΌ Π΄Π°Π²Π»Π΅Π½ΠΈΡ.Π Π»ΠΈΡΠ΅ΡΠ°ΡΡΡΠ΅ ΡΡΠΎΡ Π²ΠΈΠ΄ ΡΠ²Π°ΡΠΊΠΈ ΡΠ°ΡΠ΅ Π½Π°Π·ΡΠ²Π°Π΅ΡΡΡ ΡΠ²Π°ΡΠΊΠΎΠΉ ΠΈΠ·Π»ΡΡΠ΅Π½ΠΈΠ΅ΠΌ. [c.415]
Π ΡΡΠ½Π°Ρ Π°ΡΠ³ΠΎΠ½ΠΎΠ΄ΡΠ³ΠΎΠ²Π°Ρ ΡΠ²Π°ΡΠΊΠ° — Π²ΠΈΠ΄ ΡΠ²Π°ΡΠΊΠΈ, ΠΏΡΠΈ ΠΊΠΎΡΠΎΡΠΎΠΉ ΡΠ»Π΅ΠΊΡΡΠΈΡΠ΅ΡΠΊΠ°Ρ Π΄ΡΠ³Π° Π³ΠΎΡΠΈΡ ΠΌΠ΅ΠΆΠ΄Ρ Π½Π΅ΠΏΠ»Π°Π²ΡΡΠΈΠΌΡΡ Π²ΠΎΠ»ΡΡΡΠ°ΠΌΠΎΠ²ΡΠΌ ΡΠ»Π΅ΠΊΡΡΠΎΠ΄ΠΎΠΌ ΠΈ ΡΠ²Π°ΡΠΈΠ²Π°Π΅ΠΌΡΠΌ ΠΈΠ·Π΄Π΅Π»ΠΈΠ΅ΠΌ Π² ΡΡΠ΅Π΄Π΅ ΠΈΠ½Π΅ΡΡΠ½ΠΎΠ³ΠΎ Π³Π°Π·Π°, Π·Π°ΡΠΈΡΠ°ΡΡΠ΅Π³ΠΎ ΡΠ°ΠΊΠΆΠ΅ Π·ΠΎΠ½Ρ ΠΏΠ»Π°Π²Π»Π΅. Π½ΠΈΡ ΠΎΡΠ½ΠΎΠ²Π½ΠΎΠ³ΠΎ ΠΈ ΠΏΡΠΈΡΠ°Π΄ΠΎΡΠ½ΠΎΠ³ΠΎ ΠΌΠ΅ΡΠ°Π»Π»Π° (ΡΠΈΡ. 2). [c.5]
Π ΡΠ΄ΠΎΡΡΠΎΠ²Π΅ΡΠ΅Π½ΠΈΠΈ ΠΎ ΠΌΠΎΠ½ΡΠ°ΠΆΠ΅ ΡΠΊΠ°Π·ΡΠ²Π°ΡΡ ΠΌΠ°ΡΠ΅ΡΠΈΠ°Π»Ρ, ΠΏΡΠΈΠΌΠ΅Π½Π΅Π½Π½ΡΠ΅ ΠΏΡΠΈ ΡΠ²Π°ΡΠΊΠ΅, ΠΏΡΠΈΠ²ΠΎΠ΄ΡΡ ΡΠ²Π΅Π΄Π΅Π½ΠΈΡ ΠΎ ΠΏΡΠΎΠ²ΠΎΠ΄ΠΊΠ΅ (Π²ΠΈΠ΄ ΡΠ²Π°ΡΠΊΠΈ, ΡΠΈΠΏ ΠΈ ΠΌΠ°ΡΠΊΠ° ΡΠ»Π΅ΠΊΡΡΠΎΠ΄ΠΎΠ², ΡΠ°ΠΌΠΈΠ»ΠΈΠΈ ΡΠ²Π°ΡΡΠΈΠΊΠΎΠ² ΠΈ Π½ΠΎΠΌΠ΅ΡΠ° ΡΠ΄ΠΎΡΡΠΎΠ²Π΅ΡΠ΅Π½ΠΈΠΉ, ΡΠ΅Π·ΡΠ»ΡΡΠ°ΡΡ ΠΈΡΠΏΡΡΠ°Π½ΠΈΠΉ ΠΊΠΎΠ½ΡΡΠΎΠ»ΡΠ½ΡΡ ΡΡΡΠΊΠΎΠ²), Π΄Π°Π½Π½ΡΠ΅ ΠΎ ΠΏΡΠΎΠ²Π΅ΡΠΊΠ΅ ΡΠΈΡΡΠ΅ΠΌΡ ΡΡΡΠ± ΠΏΡΠΎΠΏΡΡΠΊΠΎΠΌ ΠΏΠ°ΡΠ° ΠΈ ΠΏΡΠΎΠΌΡΠ²ΠΊΠ΅ ΠΊΠΎΡΠ»Π°, ΠΎΠ±ΡΠ΅Π΅ Π·Π°ΠΊΠ»ΡΡΠ΅Π½ΠΈΠ΅ ΠΏΠΎ ΠΌΠΎΠ½ΡΠ°ΠΆΡ ΠΏΡΠΎΠ΅ΠΊΡΡ, ΠΏΡΠ°Π²ΠΈΠ»Π°ΠΌ ΠΠΎΡΠ³ΠΎΡΡΠ΅Ρ Π½Π°Π΄Π·ΠΎΡΠ° Π‘Π‘Π‘Π ΠΈ ΠΏΡΠΈΠ³ΠΎΠ΄Π½ΠΎΡΡΠΈ ΠΊΠΎΡΠ»Π° ΠΊ ΡΠΊΡΠΏΠ»ΡΠ°ΡΠ°ΡΠΈΠΈ. [c.115]
ΠΠ»Ρ ΡΠ΅Π³ΠΈΡΡΡΠ°ΡΠΈΠΈ ΠΊΠΎΡΠ»Π° Π°Π΄ΠΌΠΈΠ½ΠΈΡΡΡΠ°ΡΠΈΡ ΠΏΡΠ΅Π΄ΠΏΡΠΈΡΡΠΈΡ (Π²Π»Π°Π΄Π΅Π»Π΅Ρ ΠΊΠΎΡΠ»Π°) Π²ΠΌΠ΅ΡΡΠ΅ Ρ ΠΏΠΈΡΡΠΌΠ΅Π½Π½ΡΠΌ Π·Π°ΡΠ²Π»Π΅Π½ΠΈΠ΅ΠΌ ΠΏΡΠ΅Π΄ΡΡΠ°Π²Π»ΡΠ΅Ρ Π² ΠΎΡΠ³Π°Π½Π°Ρ
ΠΠΎΡΠ³ΠΎΡΡΠ΅Ρ
Π½Π°Π΄Π·ΠΎΡΠ° ΠΏΠ°ΡΠΏΠΎΡΡ ΠΏΠ°ΡΠΎΠ²ΠΎΠ³ΠΎ (Π²ΠΎΠ΄ΠΎΠ³ΡΠ΅ΠΉΠ½ΠΎΠ³ΠΎ) ΠΊΠΎΡΠ»Π° Ρ ΠΏΠΎΠ΄ΡΠΈΡΡΠΌΠΈ ΡΠ΅ΡΡΠ΅ΠΆΠ°ΠΌΠΈ ΠΊΠΎΡΠ»Π°, ΡΠΎΠΏΠΎΡΠ½ΠΎΠ³ΠΎ ΡΡΡΡΠΎΠΉΡΡΠ²Π°, ΠΊΠΎΡΠ΅Π»ΡΠ½ΠΎΠ³ΠΎ (ΠΏΠ»Π°Π½, ΠΏΡΠΎΠ΄ΠΎΠ»ΡΠ½ΡΠΉ ΠΈ ΠΏΠΎΠΏΠ΅ΡΠ΅ΡΠ½ΡΠΉ ΡΠ°Π·ΡΠ΅Π·Ρ) Π°ΠΊΡ ΠΎΠ± ΠΈΡΠΏΡΠ°Π²Π½ΠΎΡΡΠΈ ΠΊΠΎΡΠ»Π° Π»Π°Π±ΠΎΡΠ°ΡΠΎΡΠ½ΡΠΉ Π°Π½Π°Π»ΠΈΠ· ΠΏΠΈΡΠ°ΡΠ΅Π»ΡΠ½ΠΎΠΉ Π²ΠΎΠ΄Ρ ΡΠΏΡΠ°Π²ΠΊΡ (Ρ Ρ
Π°ΡΠ°ΠΊΡΠ΅ΡΠΈΡΡΠΈΠΊΠΎΠΉ) ΠΏΠΈΡΠ°ΡΠ΅Π»ΡΠ½ΡΡ
ΡΡΡΡΠΎΠΉΡΡΠ² ΡΠ΄ΠΎΡΡΠΎΠ²Π΅ΡΠ΅Π½ΠΈΠ΅ ΠΎ ΠΊΠ°ΡΠ΅ΡΡΠ²Π΅ ΠΌΠΎΠ½ΡΠ°ΠΆΠ½ΠΎΠΉ ΠΎΡΠ³Π°Π½ΠΈΠ·Π°ΡΠΈΠΈ, ΠΏΡΠΎΠΈΠ·Π²ΠΎΠ΄ΠΈΠ²ΡΠ΅ΠΉ ΠΌΠΎΠ½ΡΠ°ΠΆ Π΄Π°Π½Π½ΠΎΠ³ΠΎ ΠΊΠΎΡΠ»Π°.Π ΡΠ΄ΠΎΡΡΠΎΠ²Π΅ΡΠ΅Π½ΠΈΠΈ ΡΠΊΠ°Π·ΡΠ²Π°Π΅ΡΡΡ Π½Π° ΠΎΠ±ΠΎΠ·Π½Π°ΡΠ΅Π½ΠΈΠ΅ ΠΌΠΎΠ½ΡΠ°ΠΆΠ½ΠΎΠΉ ΠΎΡΠ³Π°Π½ΠΈΠ·Π°ΡΠΈΠΈ, ΡΡΡΠ΅ΠΆΠ΄Π΅Π½ΠΈΡ, ΠΏΡΠ΅Π΄ΠΏΡΠΈΡΡΠΈΡ (Π²Π»Π°Π΄Π΅Π»Π΅Ρ ΠΊΠΎΡΠ»Π°), Π·Π°Π²ΠΎΠ΄Π°-ΠΈΠ·Π³ΠΎΡΠΎΠ²ΠΈΡΠ΅Π»Ρ ΠΈ Π·Π°Π²ΠΎΠ΄ΡΠΊΠΎΠΉ Π½ΠΎΠΌΠ΅Ρ ΠΊΠΎΡΠ»Π° ΡΠ²Π΅Π΄Π΅Π½ΠΈΡ ΠΎ ΠΌΠ°ΡΠ΅ΡΠΈΠ°Π»Π°Ρ
ΡΡΡΠ±, ΡΡΡΡΠ΅ΡΠΎΠ², ΡΠ»Π°Π½ΡΠ΅Π², ΡΠΊΠ°Π·Π°Π½Π½ΡΠΌ Π΄Π°Π½Π½ΡΠΌ Π² ΠΏΠ°ΡΠΏΠΎΡΡΠ΅ ΠΊΠΎΡΠ»Π° ΡΠ²Π΅Π΄Π΅Π½ΠΈΡ ΠΎ ΡΠ²Π°ΡΠΊΠ΅, Π²ΠΈΠ΄ ΡΠ²Π°ΡΠΊΠΈ , ΠΌΠ°ΡΠΊΠΈ ΡΠ»Π΅ΠΊΡΡΠΎΠ΄ΠΎΠ², ΠΏΡΠΈΠΌΠ΅Π½ΡΠ²ΡΠΈΡ
ΡΡ ΠΏΡΠΈ ΡΠ²Π°ΡΠΎΡΠ½ΡΡ
ΡΠ°Π±ΠΎΡΠ°Ρ
Π½Π° ΠΊΠΎΡΠ»Π΅ Π·Π°ΠΊΠ»ΡΡΠ΅Π½ΠΈΡ ΠΎ ΡΠ΅Π·ΡΠ»ΡΡΠ°ΡΠ°Ρ
ΠΈΡΠΏΡΡΠ°Π½ΠΈΠΉ ΠΊΠΎΠ½ΡΡΠΎΠ»ΡΠ½ΡΡ
ΡΡΡΠΊΠΎΠ² ΡΠΏΡΠ°Π²ΠΊΠ° ΠΎ Π½Π°Π»ΠΈΡΠΈΠΈ ΠΏΡΠΈΠ±ΠΎΡΠΎΠ² Π±Π΅Π·ΠΎΠΏΠ°ΡΠ½ΠΎΡΡΠΈ. [c.168]
Π ΠΆΡΡΠ½Π°Π»Π΅ ΡΠ²Π°ΡΠΎΡΠ½ΡΡ ΡΠ°Π±ΠΎΡ ΡΠΊΠ°Π·ΡΠ²Π°ΡΡΡΡ Π½ΠΎΠΌΠ΅Ρ ΡΡΡΠΊΠ°, ΡΠ°Π·ΠΌΠ΅Ρ ΡΡΡΠ±Ρ, Π½ΠΎΠΌΠ΅Ρ ΡΠ΅ΡΡΠΈΡΠΈΠΊΠ°ΡΠ° Π½Π° ΡΡΡΠ±Ρ, ΠΏΠΎΠ»ΠΎΠΆΠ΅Π½ΠΈΠ΅ Π²ΠΎ Π²ΡΠ΅ΠΌΡ ΡΠ²Π°ΡΠΊΠΈ, Π΄Π°ΡΠ° ΡΠ²Π°ΡΠΊΠΈ, Π°ΡΠΌΠΎΡΡΠ΅ΡΠ½ΡΠ΅ ΡΡΠ»ΠΎΠ²ΠΈΡ Π²ΠΎ Π²ΡΠ΅ΠΌΡ ΡΠ²Π°ΡΠΊΠΈ, Π²ΠΈΠ΄ ΡΠ²Π°ΡΠΊΠΈ (Π°Π²ΡΠΎΠΌΠ°ΡΠΈΡΠ΅ΡΠΊΠ°Ρ, ΠΏΠΎΠ»ΡΠ°Π²ΡΠΎΠΌΠ°ΡΠΈΡΠ΅ΡΠΊΠ°Ρ, Π³Π°Π·ΠΎΠ²Π°Ρ, ΡΠ»Π΅ΠΊΡΡΠΎΠ΄ΡΠ³ΠΎΠ²Π°Ρ) , Π½ΠΎΠΌΠ΅ΡΠ° ΡΠ΅ΡΡΠΈΡΠΈΠΊΠ°ΡΠΎΠ² Π½Π° ΡΠ»Π΅ΠΊΡΡΠΎΠ΄Ρ, ΡΠ²Π°ΡΠΎΡΠ½ΡΡ ΠΏΡΠΎΠ²ΠΎΠ»ΠΎΠΊΡ ΠΈ ΡΠ»ΡΡ ΡΠ°ΠΌΠΈΠ»ΠΈΡ, ΠΈΠΌΡ ΠΈ ΠΎΡΡΠ΅ΡΡΠ²ΠΎ ΡΠ²Π°ΡΡΠΈΠΊΠ°, ΠΊΠ»Π΅ΠΉΠΌΠΎ ΡΠ²Π°ΡΡΠΈΠΊΠ°.ΠΡΡΠ½Π°Π» ΠΏΠΎΠ΄ΠΏΠΈΡΡΠ²Π°Π΅ΡΡΡ ΠΌΠ°ΡΡΠ΅ΡΠΎΠΌ ΠΈ ΡΡΡΡΠΎΠΉΡΡΠ²ΠΎΠΌ ΡΠ°Π±ΠΎΡ (ΠΈΠ»ΠΈ ΠΏΡΠ΅Π΄ΡΡΠ°Π²ΠΈΡΠ΅Π»Π΅ΠΌ ΠΠ’Π ΠΌΠ°ΡΡΠ΅ΡΡΠΊΠΎΠΉ ΠΌΠΎΠ½ΡΠ°ΠΆΠ½ΡΡ Π·Π°Π³ΠΎΡΠΎΠ²ΠΎΠΊ). [c.728]
ΠΠ»Π΅ΠΊΡΡΠΎΠ½Π½ΠΎ-Π»ΡΡΠ΅Π²Π°Ρ ΡΠ²Π°ΡΠΊΠ° — Π²ΠΈΠ΄ ΡΠ²Π°ΡΠΊΠΈ ΠΏΠ»Π°Π²Π»Π΅Π½ΠΈΠ΅ΠΌ ΠΏΠΎΡΠ²ΠΈΠ»Π°ΡΡ Π² ΡΡΠΈΠ΄ΡΠ°ΡΡΡ Π³ΠΎΠ΄Π°Ρ Π½Π°ΡΠ΅Π³ΠΎ ΡΡΠΎΠ»Π΅ΡΠΈΡ Π²ΠΎ Π€ΡΠ°Π½ΡΠΈΠΈ Π² Π‘Π‘Π‘Π Π²ΠΏΠ΅ΡΠ²ΡΠ΅ Π² 1958 Π³. ΡΠΎΠ·Π΄Π°Π½Π° Π΄Π»Ρ ΡΠ²Π°ΡΠΊΠΈ ΡΠ»Π΅ΠΊΡΡΠΎΠ½Π½ΡΠΌ Π»ΡΡΠΎΠΌ ΡΡΡΠ°Π½ΠΎΠ²ΠΊΠ° ΠΌΠΎΠ΄Π΅Π»ΠΈ ΠΠΠ’Π£-ΠΠΠ. ΠΡΠΎΠΌΡΡΠ»Π΅Π½Π½ΠΎΡΡΡ Π²ΡΠΏΡΡΠΊΠ°Π΅Ρ ΡΡΡΠ°Π½ΠΎΠ²ΠΊΡ ΡΠ»Π΅ΠΊΡΡΠΎΠ½Π½ΠΎΠ»ΡΡΠ΅Π²ΠΎΠΉ ΡΠ²Π°ΡΠΊΠΈ ΠΌΠΎΡΠ½ΠΎΡΡΡΡ, ΠΏΠΎΠ·Π²ΠΎΠ»ΡΡΡΠ΅ΠΉ ΡΠ²Π°ΡΠΈΠ²Π°ΡΡ Π»ΠΈΡΡΡ ΡΠΎΠ»ΡΠΈΠ½ΠΎΠΉ Π΄ΠΎ 50 ΠΌΠΌ, Π³ΠΎΡΠΎΠ²ΠΈΡΡΡ ΠΎΠ±ΠΎΡΡΠ΄ΠΎΠ²Π°Π½ΠΈΠ΅ Π΄Π»Ρ ΡΠ²Π°ΡΠΊΠΈ ΡΡΠ°Π»ΠΈ ΡΠΎΠ»ΡΠΈΠ½ΠΎΠΉ 100 ΠΌΠΌ ΠΈ Π±ΠΎΠ»Π΅Π΅. [c.10]
ΠΠΈΡΡΡΠ·ΠΈΠΎΠ½Π½Π°Ρ ΡΠ²Π°ΡΠΊΠ°-Π²ΠΈΠ΄ ΡΠ²Π°ΡΠΊΠΈ Π΄Π°Π²Π»Π΅Π½ΠΈΠ΅ΠΌ. ΠΠΏΠ΅ΡΠ²ΡΠ΅ Π² ΠΌΠΈΡΠ΅ ΠΏΡΠ΅Π΄Π»ΠΎΠΆΠ΅Π½Π° ΠΈ Π±ΡΠ΄ΠΆΠ΅ΡΠ½ΠΎ Π² Π‘Π‘Π‘Π ΠΏΡΠΎΡ. Π. Π€. ΠΠ°Π·Π°ΠΊΠΎΠ²ΡΠΌ. ΠΡΠΎΡΠ΅ΡΡ ΡΠ²Π°ΡΠΊΠΈ Ρ 1953 Π³. Π‘ΡΡΠ½ΠΎΡΡΡ ΠΏΡΠΎΡΠ΅ΡΡΠ° Π΄ΠΈΡΡΡΠ·ΠΈΠΎΠ½Π½ΠΎΠΉ ΡΠ²Π°ΡΠΊΠΈ ΡΠΎΡΡΠΎΠΈΡ Π² ΡΠΎΠΌ, ΡΡΠΎ Π΄Π΅ΡΠ°Π»ΠΈ Ρ ΠΏΠΎΠ»ΠΈΡΠΎΠ²Π°Π½Π½ΡΠΌΠΈ ΠΏΠΎΠ²Π΅ΡΡ
Π½ΠΎΡΡΡΠΌΠΈ ΠΏΠ»ΠΎΡΠ½ΠΎ ΠΏΡΠΈΠΆΠΈΠΌΠ°ΡΡΡΡ Π΄ΡΡΠ³ ΠΊ Π΄ΡΡΠ³Ρ ΠΈ Π½Π°Π³ΡΠ΅Π²Π°ΡΡΡΡ Π² ΡΡΠ»ΠΎΠ²ΠΈΡΡ
Π²Π°ΠΊΡΡΠΌΠ°. ΠΡΠΈ ΡΡΠ»ΠΎΠ²ΠΈΡ ΠΏΡΠΈΠ²ΠΎΠ΄ΡΡ ΠΊ Π²Π·Π°ΠΈΠΌΠ½ΠΎΠΉ Π΄ΠΈΡΡΡΠ·ΠΈΠΈ ΡΠ»Π΅ΠΌΠ΅Π½ΡΠΎΠ² ΠΏΠΎ ΠΊΠΎΠ½ΡΠ°ΠΊΡΠΈΡΡΡΡΠΈΠΌ ΠΏΠΎΠ²Π΅ΡΡ
Π½ΠΎΡΡΡΠΌ. [c.12]
Π₯ΠΎΠ»ΠΎΠ΄Π½Π°Ρ ΡΠ²Π°ΡΠΊΠ°-Π²ΠΈΠ΄ ΡΠ²Π°ΡΠΊΠΈ Π΄Π°Π²Π»Π΅Π½ΠΈΠ΅ΠΌ.ΠΠ½Π° ΠΎΡΡΡΠ΅ΡΡΠ²Π»ΡΠ΅ΡΡΡ Π±Π΅Π· ΡΠΎΠ·Π΄Π°Π½ΠΈΡ ΠΏΠ»Π°ΡΡΠΈΡΠ΅ΡΠΊΠΎΠΉ Π΄Π΅ΡΠΎΡΠΌΠ°ΡΠΈΠΈ ΡΠ΅ΠΏΠ»Π°. Π‘Π²Π°ΡΠΊΠ΅ ΠΏΠΎΠ΄Π²Π΅ΡΠ³Π°ΡΡΡΡ Π² ΠΎΡΠ½ΠΎΠ²Π½ΠΎΠΌ ΠΏΠ»Π°ΡΡΠΈΡΠ½ΡΠ΅ ΠΌΠ°ΡΠ΅ΡΠΈΠ°Π»Ρ (Π°Π»ΡΠΌΠΈΠ½ΠΈΠΉ, ΠΌΠ΅Π΄Ρ, ΡΠ²ΠΈΠ½Π΅Ρ ΠΈ Π΄Ρ.). ΠΠ»Π°ΡΡΠΈΡΠ΅ΡΠΊΠ°Ρ Π΄Π΅ΡΠΎΡΠΌΠ°ΡΠΈΡ ΠΏΡΠΈ ΡΠ²Π°ΡΠΊΠ΅ ΠΎΠ±ΡΠ°Π·ΡΠ΅Ρ ΠΎΡ Π±ΠΎΠ»ΡΡΠΎΠΉ ΡΡΠ°ΡΠΈΡΠ΅ΡΠΊΠΎΠΉ ΠΈΠ»ΠΈ Π±ΠΎΠ»ΡΡΠΎΠΉ ΡΠ΄Π°ΡΠ½ΠΎΠΉ ΡΠΆΠΈΠΌΠ°ΡΡΠ΅ΠΉ ΡΠΈΠ»Ρ. [c.14]
Π‘Π²Π°ΡΠΊΠ° — ΠΠΈΠ΄Ρ ΡΠ²Π°ΡΠΊΠΈ 213 [c.333]
Π’Π΅Ρ Π½ΠΎΠ»ΠΎΠ³ΠΈΡ ΡΠ²Π°ΡΠΊΠΈ (Π²ΠΈΠ΄ ΡΠ²Π°ΡΠΊΠΈ, ΡΠ²Π°ΡΠΎΡΠ½ΡΠ΅ ΠΌΠ°ΡΠ΅ΡΠΈΠ°Π»Ρ, ΡΠ΅Ρ Π½ΠΈΠΊΠ° ΡΠ²Π°ΡΠΊΠΈ) Π²ΡΠ±ΠΈΡΠ°Π΅ΡΡΡ Π² Π·Π°Π²ΠΈΡΠΈΠΌΠΎΡΡΠΈ ΠΎΡ ΠΎΡΠ½ΠΎΠ²Π½ΠΎΠ³ΠΎ ΠΏΠΎΠΊΠ°Π·Π°ΡΠ΅Π»Ρ ΡΠ²Π°ΡΠΈΠ²Π°Π΅ΠΌΠΎΡΡΠΈ Π΄Π»Ρ ΠΊΠ°ΠΆΠ΄ΠΎΠ³ΠΎ ΠΌΠ°ΡΠ΅ΡΠΈΠ°Π»Π°. [c.25]
ΠΠ«ΠΠΠ ΠΠΠΠΠ Π‘ΠΠΠ ΠΠ Π Π‘ΠΠΠ ΠΠ§ΠΠ«Π₯ ΠΠΠ’ΠΠ ΠΠΠΠΠ [c.264]
ΠΡΠΈ Π²ΡΠ±ΠΎΡΠ΅ Π²ΠΈΠ΄Π° ΡΠ²Π°ΡΠΊΠΈ, ΡΠ²Π°ΡΠΎΡΠ½ΡΡ
ΠΌΠ°ΡΠ΅ΡΠΈΠ°Π»ΠΎΠ² ΠΈ ΡΠ΅ΠΆΠΈΠΌΠ° ΡΠ²Π°ΡΠΊΠΈ Π²ΡΡΠΎΠΊΠΎΡ
ΡΠΎΠΌΠΈΡΡΡΡ
ΡΡΠ°Π»Π΅ΠΉ, ΠΎΡΠΎΠ±Π΅Π½Π½ΠΎ ΠΆΠ°ΡΠΎΠΏΡΠΎΡΠ½ΡΡ
, Π½Π΅ΠΎΠ±Ρ
ΠΎΠ΄ΠΈΠΌΠΎ ΡΡΠΈΡΡΠ²Π°ΡΡ, ΡΡΠΎ Π½Π΅Π±ΠΎΠ»ΡΡΠΈΠ΅ Π΄Π°ΠΆΠ΅ ΠΎΡΠΊΠ»ΠΎΠ½Π΅Π½ΠΈΡ Π² Ρ
ΠΈΠΌΠΈΡΠ΅ΡΠΊΠΎΠΌ ΡΠΎΡΡΠ°Π²Π΅ ΠΌΠ΅ΡΠ°Π»Π»Π° ΡΠ²ΠΎΠ² (Π½ΠΎ ΡΡΠ΄Ρ ΡΠ»Π΅ΠΌΠ΅Π½ΡΠΎΠ² Π² ΠΏΡΠ΅Π΄Π΅Π»Π°Ρ
Π΄Π΅ΡΡΡΡΡ
Π΄ΠΎΠ»Π΅ΠΉ ΠΏΡΠΎΡΠ΅Π½ΡΠ°) ΠΌΠΎΠΆΠ΅Ρ ΠΏΡΠΈΠ²ΠΎΠ΄ΠΈΡΡ ΠΊ Π·Π½Π°ΡΠΈΡΠ΅Π»ΡΠ½ΠΎΠΌΡ ΠΈΠ·ΠΌΠ΅Π½Π΅Π½ΠΈΡ ΠΈΡ
ΡΠ»ΡΠΆΠ΅Π±Π½ΡΡ
ΡΠ²ΠΎΠΉΡΡΠ². ΠΡΠΈΡΠΈΠ½ΠΎΠΉ ΡΡΠΎΠ³ΠΎ, ΠΊΠ°ΠΊ ΠΏΡΠ°Π²ΠΈΠ»ΠΎ, ΡΠ²Π»ΡΠ΅ΡΡΡ Π³Π΅ΡΠ΅ΡΠΎΠ³Π΅Π½Π½ΠΎΡΡΡ ΡΡΡΡΠΊΡΡΡΡ (Π½Π°ΠΏΡΠΈΠΌΠ΅Ρ, Π½Π°Π»ΠΈΡΠΈΠ΅ Π·Π΅ΡΠ΅Π½ ΡΡΡΡΠΊΡΡΡΠ½ΠΎ-ΡΠ²ΠΎΠ±ΠΎΠ΄Π½ΠΎΠ³ΠΎ ΡΠ΅ΡΡΠΈΡΠ° Π² ΡΠΎΡΠ±ΠΈΡΠ½ΠΎΠΉ ΠΎΡΠ½ΠΎΠ²Π΅ ΠΎΡΠΏΡΡΠ΅Π½Π½ΠΎΠ³ΠΎ ΠΌΠ°ΡΡΠ΅Π½ΡΠΈΡΠ°). [c.266]
ΠΠΎΠ»Π΅Π΅ ΠΏΠΎΠ΄ΡΠΎΠ±Π½ΡΠ΅ ΡΠ²Π΅Π΄Π΅Π½ΠΈΡ ΠΎ ΠΏΠΎΠ»Π½ΠΎΠΌ ΡΠ²Π°ΡΠΊΠ΅, ΠΏΡΠΈΠΌΠ΅Π½ΡΠ΅ΠΌΠΎΠΉ Π°ΠΏΠΏΠ°ΡΠ°ΡΡΡΠ΅ ΠΈ ΡΠ΅Ρ Π½ΠΎΠ»ΠΎΠ³ΠΈΠΈ ΡΠ²Π°ΡΠΊΠΈ ΠΌΠΎΠΆΠ½ΠΎ ΠΏΠΎΠ»ΡΡΠΈΡΡ Π² ΡΠΏΠ΅ΡΠΈΠ°Π»ΡΠ½ΡΡ ΠΊΡΡΡΠ°Ρ . [c.289]
ΠΡΠΈ ΠΏΡΠΈΠ·Π½Π°ΠΊΠΈ ΠΎΡΡΠ°ΠΆΠ΅Π½Ρ Π² ΡΡΠ°Π½Π΄Π°ΡΡΠ°Ρ Π½Π° ΡΠ²Ρ ΡΠ²Π°ΡΠ½ΡΡ ΡΠΎΠ΅Π΄ΠΈΠ½Π΅Π½ΠΈΠΉ Π΄Π»Ρ ΡΠ°Π·Π»ΠΈΡΠ½ΡΡ Π²ΠΈΠ΄ΠΎΠ² ΡΠ²Π°ΡΠΊΠΈ, ΡΡΡΠ°Π½ΠΎΠ²Π»Π΅Π½Ρ ΡΠΈΡΡΡ ΡΠ²ΠΎΠ², ΠΎΠ±ΠΎΠ·ΡΠ΅Π½ΠΈΡ Π½Π°ΡΠ΅Π½ΠΈΡ ΡΠΏΠΎΡΠΎΠ±ΠΎΠ² ΡΠ²Π°ΡΠΊΠΈ. [c.289]
ΠΡΠΈΠ²Π΅Π΄Π΅Π½Ρ ΡΠΈΡΡΡ Π½Π°ΠΈΠ±ΠΎΠ»Π΅Π΅ ΡΠ°ΡΠΏΡΠΎΡΡΡΠ°Π½Π΅Π½Π½ΡΡ ΡΠ²ΠΎΠ² ΡΠΎΠ»ΡΠΊΠΎ Π΄Π»Ρ ΡΠ΅ΡΡΠΈ Π²ΠΈΠ΄ΠΎΠ² ΡΠ²Π°ΡΠΊΠΈ (ΡΠΌ. Π‘ΠΎΠΎΡΠ²Π΅ΡΡΡΠ²ΡΡΡΠΈΠ΅ ΠΏΠΎΡΡΠ΄ΠΊΠΎΠ²ΡΠ΅ Π½ΠΎΠΌΠ΅ΡΠ° ΠΏΠΎ ΠΏΠ΅ΡΠ΅ΡΠ½Ρ ΡΡΠ°Π½Π΄Π°ΡΡΠΎΠ² Π½Π° ΡΠ²Ρ, ΠΏΡΠΈΠ²Π΅Π΄Π΅Π½Π½ΠΎΠΌΡ Π² ΠΏΡΠΈΠ»ΠΎΠΆΠ΅Π½ΠΈΠΈ 4).ΠΠΎΠΌΠ΅ΡΠ° ΡΡΠ°Π½Π΄Π°ΡΡΠΎΠ², ΡΠΎΠΎΡΠ²Π΅ΡΡΡΠ²ΡΡΡΠΈΠ΅ ΠΏΠΎΡΡΠ΄ΠΊΠΎΠ²ΡΠΌ Π½ΠΎΠΌΠ΅ΡΠ°ΠΌ 1, 3, 5. 6, 9, 10 ΡΠ»Π΅Π΄ΡΡΡΠΈΠ΅ ΠΠΠ‘Π’ 5264-69, ΠΠΠ‘Π’ 8713-70. ΠΠΠ‘Π’ 14771-69. ΠΠΠ‘Π’ 15164-69, ΠΠΠ‘Π’ 14806-69, ΠΠΠ‘Π’ 16037-70, [c.293]
ΠΠ° ΡΠΈΡ. 227 ΠΏΠΎΠΊΠ°Π·Π°Π½ ΡΠ΅ΡΡΠ΅ΠΆΡΡΠ΅ΠΉΠ½Π° ΠΊΠ°ΠΊ ΠΏΡΠΈΠΌΠ΅Ρ Π±ΠΎΠ»Π΅Π΅ ΡΠ»ΠΎΠΆΠ½ΠΎΠ³ΠΎ ΡΠ΅ΡΡΠ΅ΠΆΠ° ΡΠ²Π°ΡΠ½ΠΎΠΉ ΡΠ±ΠΎΡΠΎΡΠ½ΠΎΠΉ Π΅Π΄ΠΈΠ½ΠΈΡΡ. ΠΡΠΎΠ½ΡΡΠ΅ΠΉΠ½ ΠΎΠ±ΡΠ°Π·ΠΎΠ²Π°Π½ ΠΈΠ· Π³Π½ΡΡΡΡ
, ΠΏΠ»ΠΎΡΠΊΠΈΡ
ΠΈ ΡΡΠ°ΠΌΠΏΠΎΠ²Π°Π½Π½ΡΡ
Π΄Π΅ΡΠ°Π»Π΅ΠΉ, Π²ΡΠΏΠΎΠ»Π½Π΅Π½ ΠΏΡΠΈ ΠΏΠΎΠΌΠΎΡΠΈ ΡΠ°Π·Π»ΠΈΡΠ½ΡΡ
Π²ΠΈΠ΄ΠΎΠ² ΡΠ²Π°ΡΠΊΠΈ, ΡΠΎΠ΄Π΅ΡΠΆΠΈΡ ΡΠ°Π·Π»ΠΈΡΠ½ΡΠ΅ ΡΠΈΠΏΡ ΡΠ²ΠΎΠ², Π° ΠΏΠΎΡΡΠΎΠΌΡ ΠΈ ΠΈΠ·ΠΎΠ±ΡΠ°ΠΆΠ΅Π½ΠΈΡ, ΠΈ ΠΎΠ±ΠΎΠ·Π½Π°ΡΠ΅Π½ΠΈΡ ΠΈΡ
ΡΠ°Π·Π»ΠΈΡΠ°ΡΡΡΡ. [c.295]
ΠΡΠΈ ΠΏΡΠΈΠ·Π½Π°ΠΊΠΈ ΠΎΡΡΠ°ΠΆΠ΅Π½Ρ Π² ΡΡΠ°Π½Π΄Π°ΡΡΠ΅ Π½Π° ΡΠ²Ρ ΡΠ²Π°ΡΠ½ΡΡ ΡΠΎΠ΅Π΄ΠΈΠ½Π΅Π½ΠΈΠΉ Π΄Π»Ρ ΡΠ°Π·Π»ΠΈΡΠ½ΡΡ Π²ΠΈΠ΄ΠΎΠ² ΡΠ²Π°ΡΠΊΠΈ, ΡΡΡΠ°Π½ΠΎΠ²Π»Π΅Π½Ρ ΡΠΈΡΡΡ ΡΠ²ΠΎΠ², ΠΎΠ±ΠΎΠ·Π½Π°ΡΠ΅Π½ΠΈΡ ΡΠΏΠΎΡΠΎΠ±ΠΎΠ² ΡΠ²Π°ΡΠΊΠΈ. ΠΠΠ‘Π’ΠΎΠΌ 2.312β72 ΡΡΡΠ°Π½ΠΎΠ²Π»Π΅Π½Ρ ΠΈ ΠΈΠ·ΠΎΠ±ΡΠ°ΠΆΠ΅Π½ΠΈΡ Π½Π° ΡΠ΅ΡΡΠ΅ΠΆΠ°Ρ ΡΠ°Π·Π»ΠΈΡΠ½ΡΡ ΡΠ²Π°ΡΠ½ΡΡ ΡΠ²ΠΎΠ². [c.248]
Π’Π΅ΡΠΌΠΈΠ½Ρ ΠΈ ΠΎΠΏΡΠ΅Π΄Π΅Π»Π΅Π½ΠΈΡ, ΠΎΡΠ½ΠΎΡΡΡΠΈΠ΅ΡΡ ΠΊ ΡΠ²Π°ΡΠΊΠ΅ (ΠΏΡΠΎΡΠ΅ΡΡ ΡΠ²Π°ΡΠΊΠΈ, Π²ΠΈΠ΄Ρ ΡΠ²Π°ΡΠ½ΡΡ ΡΠΎΠ΅Π΄ΠΈΠ½Π΅Π½ΠΈΠΉ, ΡΠ²Π°ΡΠ½ΡΠ΅ ΡΠ²Ρ ΠΈ Ρ. Π.), Π£ΡΡΠ°Π½ΠΎΠ²Π»Π΅Π½Ρ Π (Π₯Π’ 2601β74.Π‘Π²Π°ΡΠΈΠ²Π°ΡΡ ΠΌΠΎΠΆΠ½ΠΎ ΠΌΠ΅ΡΠ°Π»Π»Ρ, ΡΡΠ΅ΠΊΠ»ΠΎ, Π½Π΅ΠΊΠΎΡΠΎΡΡΠ΅ Π²ΠΈΠ΄Ρ ΠΏΠ»Π°ΡΡΠΌΠ°ΡΡ ΠΈ Ρ. Π΄. ΠΡΠΈΠΌΠ΅Π½Π΅Π½ΠΈΠ΅ ΡΠ²Π°ΡΠΊΠΈ Π²ΠΌΠ΅ΡΡΠΎ ΠΊΠ»Π΅ΠΏΠΊΠΈ ΠΏΠΎΠ·Π²ΠΎΠ»ΡΠ΅Ρ ΡΠΊΠΎΠ½ΠΎΠΌΠΈΡΡ ΠΌΠ°ΡΠ΅ΡΠΈΠ°Π», ΠΎΠ±Π»Π΅Π³ΡΠ°ΡΡ ΠΊΠΎΠ½ΡΡΡΡΠΊΡΠΈΡ, ΡΠΌΠ΅Π½ΡΡΠ°ΡΡ ΡΡΡΠ΄ΠΎΠ΅ΠΌΠΊΠΎΡΡΡ ΠΏΡΠΎΠΈΠ·Π²ΠΎΠ΄ΡΡΠ²Π΅Π½Π½ΡΡ ΠΏΡΠΎΡΠ΅ΡΡΠΎΠ², ΠΎΠ±Π»Π΅Π³ΡΠ°ΡΡ ΡΡΠ»ΠΎΠ²ΠΈΡ ΡΠ°Π±ΠΎΡΡ ΠΈ Ρ. Π΄. [c.194]
Π ΡΠΎΠ²ΡΠ΅ΠΌΠ΅Π½Π½ΠΎΠΌ ΠΏΡΠΎΠΈΠ·Π²ΠΎΠ΄ΡΡΠ²Π΅ ΠΏΡΠΈΠΌΠ΅Π½ΡΡΡΡΡ Π΄Π²Π° ΠΎΡΠ½ΠΎΠ²Π½ΡΡ
Π²ΠΈΠ΄Π° ΡΠ²Π°ΡΠΊΠΈ Π΄Π°Π²Π»Π΅Π½ΠΈΠ΅ΠΌ (Π³ΠΎΡΠ½Π°Ρ ΡΠ²Π°ΡΠΊΠ°, Ρ
ΠΎΠ»ΠΎΠ΄Π½Π°Ρ ΡΠ²Π°ΡΠΊΠ° ΠΈ Π΄Ρ. ) Π ΠΏΠ»Π°Π²Π»Π΅Π½ΠΈΠ΅ΠΌ (Π³Π°Π·ΠΎΠ²Π°Ρ ΡΠ²Π°ΡΠΊΠ°, Π΄ΡΠ³ΠΎΠ²Π°Ρ ΡΠ²Π°ΡΠΊΠ° ΠΈ Π΄Ρ.). [c.194]
ΠΠΎΠ΄ΡΠΎΠ±Π½Π΅Π΅ ΠΎΠ± ΡΡΠ»ΠΎΠ²Π½ΡΡ ΠΈΠ·ΠΎΠ±ΡΠ°ΠΆΠ΅Π½ΠΈΡΡ ΠΈ ΠΎΠ±ΠΎΠ·Π½Π°ΡΠ΅Π½ΠΈΡΡ ΡΠ²Π°ΡΠ½ΡΡ ΡΠ²ΠΎΠ² ΠΈ Π²ΠΈΠ΄ΠΎΠ² ΡΠ²Π°ΡΠΊΠΈ ΡΠΌ.Π² ΠΠΠ‘Π’ 5264-80, 8713-79, 11533-75, 11534-75, 14771-76, 14776-79, 14806-80, 15164-78, 16037-80, 16038-80, 16098-80. [c.305]
ΠΠ°ΠΊΠΈΠ΅ Π±ΡΠΊΠ²Π΅Π½Π½ΡΠ΅ ΠΎΠ±ΠΎΠ·Π½Π°ΡΠ΅Π½ΠΈΡ ΠΏΡΠΈΠΌΠ΅Π½ΡΡΡΡΡ Π΄Π»Ρ ΠΎΠ±ΠΎΠ·Π½Π°ΡΠ΅Π½ΠΈΡ ΡΠ°Π·Π»ΠΈΡΠ½ΡΡ Π²ΠΈΠ΄ΠΎΠ² ΡΠ²Π°ΡΠΊΠΈ [c.227]
ΠΡΠΈ ΡΠ²Π°ΡΠΊΠ΅ Π΄ΠΎΠ»ΠΆΠ½ΠΎ ΠΏΠΎΠ»ΡΡΠ°ΡΡΡΡ ΠΏΠ»ΠΎΡΠ½ΠΎΠ΅ ΠΈ ΡΠ°Π²Π½ΠΎΠΏΡΠΎΡΠ½ΠΎΠ΅ Ρ ΠΎΡΡΠ°Π»ΡΠ½ΡΠΌ ΠΈΠ·Π΄Π΅Π»ΠΈΠ΅ΠΌ ΡΠΎΠ΅Π΄ΠΈΠ½Π΅Π½ΠΈΠ΅. ΠΡΠ½ΠΎΠ²Π½ΠΎΠΉ Π²ΠΈΠ΄ ΡΠ²Π°ΡΠΊΠΈ — ΡΠ²Π°ΡΠΊΠ° ΠΏΠ»Π°Π²Π»Π΅Π½ΠΈΠ΅ΠΌ, ΠΏΡΠΈ ΠΊΠΎΡΠΎΡΠΎΠΉ Π½Π°ΠΏΠ»Π°Π²Π»ΡΠ΅ΡΡΡ ΡΠΎΠ² ΠΆΠΈΠ΄ΠΊΠΎΠ³ΠΎ ΠΌΠ΅ΡΠ°Π»Π»Π° ΠΈ ΠΏΠΎΠ΄ Π΅Π³ΠΎ ΡΠ΅ΠΌΠΏΠ΅ΡΠ°ΡΡΡΡ Π½Π°Π³ΡΠ΅Π²Π°Π΅ΡΡΡ ΠΎΠΊΠΎΠ»ΠΎΡΠΎΠ²-ΠΏΠ°Ρ Π·ΠΎΠ½Π°.Π ΡΠ²Π°ΡΠ½ΠΎΠΌ ΡΠ²Π΅ ΡΠ»Π΅Π΄ΡΠ΅Ρ ΡΠ°Π·Π»ΠΈΡΠ°ΡΡ ΡΡΠΈ Π·ΠΎΠ½Ρ (ΡΠΈΡ. 305) I — ΡΠΎΠ² (Π»ΠΈΡΠ°Ρ ΡΡΡΡΠΊΡΡΡΠ°) II — ΠΎΠΊΠΎΠ»ΠΎΡΠΎΠ²Π½Π°Ρ Π·ΠΎΠ½Π°, Π½Π°Π³ΡΠ΅ΡΠ°Ρ Π² ΠΏΡΠΎΡΠ΅ΡΡΠ΅ ΡΠ²Π°ΡΠΊΠΈ Π²ΡΡΠ΅ ΠΊΡΠΈΡΠΈΡΠ΅ΡΠΊΠΈΡ ΡΠΎΡΠ΅ΠΊ III — ΠΎΠΊΠΎΠ»ΠΎΡΠΎΠ²Π½Π°Ρ Π·ΠΎΠ½Π°, Π½Π°Π³ΡΠ΅ΡΠ°Ρ Π² ΠΏΡΠΎΡΠ΅ΡΡΠ΅ ΡΠ²Π°ΡΠΊΠΈ Π½ΠΈΠΆΠ΅ ΠΊΡΠΈΡΠΈΡΠ΅ΡΠΊΠΈΡ ΡΠΎΡΠ΅ΠΊ. [c.397]
Π Π·Π°Π²ΠΈΡΠΈΠΌΠΎΡΡΠΈ ΠΎΡ ΡΠΎΡΠΌΡ ΡΠ½Π΅ΡΠ³ΠΈΠΈ, ΠΈΡΠΏΠΎΠ»ΡΠ·ΡΠ΅ΠΌΠΎΠΉ Π΄Π»Ρ ΠΎΠ±ΡΠ°Π·ΠΎΠ²Π°Π½ΠΈΡ ΡΠ²Π°ΡΠ½ΠΎΠ³ΠΎ ΡΠΎΠ΅Π΄ΠΈΠ½Π΅Π½ΠΈΡ, Π²ΡΠ΅ Π²ΠΈΠ΄Ρ ΡΠ²Π°ΡΠΊΠΈ ΡΠ°Π·Π΄Π΅Π»ΡΡΡ Π½Π° ΡΡΠΈ ΠΊΠ»Π°ΡΡΠ° ΡΠ΅ΡΠΌΠΈΡΠ΅ΡΠΊΠΈΠΉ, ΡΠ΅ΡΠΌΠΎΠΌΠ΅Ρ
Π°Π½ΠΈΡΠ΅ΡΠΊΠΈΠΉ ΠΈ ΠΌΠ΅Ρ
Π°Π½ΠΈΡΠ΅ΡΠΊΠΈΠΉ. [c.182]
Π ΠΌΠ΅Ρ Π°Π½ΠΈΡΠ΅ΡΠΊΠΎΠΌΡ ΠΊΠ»Π°ΡΡΡ Π·Π°ΡΠΈΡΡ, ΠΈΡΠΏΠΎΠ»ΡΠ·ΡΠ΅ΠΌΡΠΌ Ρ ΠΈΡΠΏΠΎΠ»ΡΠ·ΠΎΠ²Π°Π½ΠΈΠ΅ΠΌ ΠΌΠ΅Ρ Π°Π½ΠΈΡΠ΅ΡΠΊΠΎΠΉ ΡΠ½Π΅ΡΠ³ΠΈΠΈ ΠΈ Π΄Π°Π²Π»Π΅Π½ΠΈΡ (ΡΠ»ΡΡΡΠ°Π·Π²ΡΠΊΠΎΠ²Π°Ρ, Π²Π·ΡΡΠ²ΠΎΠΌ, ΡΡΠ΅Π½ΠΈΠ΅ΠΌ, Ρ ΠΎΠ»ΠΎΠ΄Π½Π°Ρ ΠΈ Π΄Ρ.)). [c.183]
ΠΡΡΠΎΠΊΠΎΡΠ°ΡΡΠΎΡΠ½Π°Ρ (ΠΠ§) ΡΠ²Π°ΡΠΊΠ° — Π²ΠΈΠ΄ ΡΠ²Π°ΡΠΊΠΈ ΡΠ»Π΅ΠΊΡΠΎΡΠΌΠ΅Ρ Π°Π½ΠΈΡΠ΅ΡΠΊΠΎΠ³ΠΎ ΠΊΠ»Π°ΡΡΠ°, ΠΎΡΠ½ΠΎΠ²Π°Π½Π½Π°Ρ Π½Π° Π΄ΠΈΡΠ»Π΅ΠΊΡΡΠΈΡΠ΅ΡΠΊΠΎΠΌ Π½Π°Π³ΡΠ΅Π²Π΅ Ρ ΠΈΡΠΏΠΎΠ»ΡΠ·ΠΎΠ²Π°Π½ΠΈΠ΅ΠΌ ΡΠ»Π΅ΠΊΡΡΠΎΠΌΠ°Π³Π½ΠΈΡΠ½ΠΎΠΉ ΡΠ½Π΅ΡΠ³ΠΈΠΈ ΠΠ§-Π΄ΠΈΠ°ΠΏΠ°Π·ΠΎΠ½Π° [39, Ρ. 130]. [c.412] ΠΠ»Π΅ΠΊΡΡΠΎΡΠ»Π°ΠΊΠΎΠ²Π°Ρ ΡΠ²Π°ΡΠΊΠ° — Π²ΠΈΠ΄ ΡΠ²Π°ΡΠΊΠΈ, ΠΏΡΠΈ ΠΊΠΎΡΠΎΡΠΎΠΌ ΡΠ°ΡΠΏΠ»Π°Π²Π»Π΅Π½ΠΈΠ΅ ΡΠ²Π°ΡΠΈΠ²Π°Π΅ΠΌΡΡ
ΠΊΡΠΎΠΌΠΎΠΊ ΠΈ ΡΠ»Π΅ΠΊΡΡΠΎΠ΄Π½ΠΎΠΉ ΠΏΡΠΎΠ²ΠΎΠ»ΠΎΠΊΠΈ ΠΏΡΠΎΠΈΡΡ
ΠΎΠ΄ΠΈΡ Π·Π° ΡΡΠ΅Ρ ΡΠ΅ΠΏΠ»Π°, Π²ΡΠ΄Π΅Π»ΡΠ΅ΠΌΠΎΠ³ΠΎ Π² ΡΠ»Π΅ΠΊΡΡΠΎΠ΄Π΅ (ΠΏΠΎ Π·Π°ΠΊΠΎΠ½Ρ ΠΠΆΠΎΡΠ»Ρ ΠΠ΅Π½ΡΠ°), ΠΊΠΎΡΠΎΡΡΠΉ ΠΏΠΎΠ΄Π°Π΅ΡΡΡ Π· ΡΠ»Π°ΠΊΠΎΠ²ΡΡ Π²Π°Π½Π½Ρ (ΡΠΈΡ.8). Π‘Π²Π°ΡΠΊΠ° ΠΏΡΠ΅ΠΈΠΌΡΡΠ΅ΡΡΠ²Π΅Π½Π½ΠΎ Π² Π²Π΅ΡΡΠΈΠΊΠ°Π»ΡΠ½ΠΎΠΌ ΠΏΠΎΠ»ΠΎΠΆΠ΅Π½ΠΈΠΈ ΠΈ ΠΈΡΠΏΠΎΠ»ΡΠ·ΡΠ΅ΡΡΡ Π΄Π»Ρ ΡΠΎΠ΅Π΄ΠΈΠ½Π΅Π½ΠΈΡ ΡΠ»Π΅ΠΌΠ΅Π½ΡΠΎΠ² ΡΠΎΠ»ΡΠΈΠ½ΠΎΠΉ 50 … 100 ΠΌΠΌ ΡΠΎΠ² ΡΠΎΡΠΌΠΈΡΡΠ΅ΡΡΡ Ρ ΠΏΠΎΠΌΠΎΡΡΡ ΠΎΡ
Π»Π°ΠΆΠ΄Π°Π΅ΠΌΡΡ
ΠΌΠ΅Π΄Π½ΡΡ
ΠΏΠΎΠ»Π·ΡΠ½ΠΎΠ². ΠΠΎΠ·ΠΌΠΎΠΆΠ½ΠΎ ΠΏΠΎΡΠ²Π»Π΅Π½ΠΈΠ΅ Π½Π°ΡΡΠΆΠ½ΡΡ
ΠΈ Π²Π½ΡΡΡΠ΅Π½Π½ΠΈΡ
Π΄Π΅ΡΠ΅ΠΊΡΠΎΠ², ΡΠ²ΡΠ·Π°Π½Π½ΠΎΠ΅ Ρ Π½Π°ΡΡΡΠ΅Π½ΠΈΠ΅ΠΌ ΡΠ΅ΠΆΠΈΠΌΠ° ΡΠ²Π°ΡΠΊΠΈ, ΠΏΠ»ΠΎΡ
ΠΎΠΉ ΠΎΡΠΈΡΡΠΊΠΎΠΉ ΡΠ²Π°ΡΠΎΡΠ½ΠΎΠΉ ΠΏΡΠΎΠ²ΠΎΠ»ΠΎΠΊΠΈ, Π½Π΅Π΄ΠΎΡΡΠ°ΡΠΎΡΠ½ΠΎ ΡΡΡ
ΠΈΠΌ ΡΠ»ΡΡΠΎΠΌ. ΠΡΡΠ³ΠΈΠ΅ Π²ΠΈΠ΄Ρ ΡΠ²Π°ΡΠΊΠΈ ΠΏΡΠΈΠΌΠ΅Π½ΡΡΡΡΡ ΠΏΡΠΈ ΠΌΠΎΠ½ΡΠ°ΠΆΠ½ΡΡ
ΡΠ°Π±ΠΎΡΠ°Ρ
ΡΡΠ°Π²Π½ΠΈΡΠ΅Π»ΡΠ½ΠΎ ΡΠ΅Π΄ΠΊΠΎ ΠΈ ΠΈΡΡΠ»Π΅Π΄ΡΡΡΡΡ Π² ΡΠΏΠ΅ΡΠΈΠ°Π»ΡΠ½ΡΡ
ΠΊΡΡΡΠ°Ρ
. [c.9]
Π‘ΠΠΠ’ΠΠΠΠ― Π‘ΠΠΠ ΠΠ, ΡΠΎΡΠΎΠ½Π½Π°Ρ ΡΠ²Π°ΡΠΊΠ° βΠ²ΠΈΠ΄ ΡΠ²Π°ΡΠΊΠΈ ΠΏΠ»Π°Π²Π»Π΅Π½ΠΈΠ΅ΠΌ, ΠΏΡΠΎΠΈΠ·Π²Π΅Π΄Π΅Π½Π½Π°Ρ ΡΠ²Π΅ΡΠΎΠ²ΡΠΌ Π»ΡΡΠΎΠΌ Π΄ΡΠ³ΠΎΠ²ΠΎΠΉ Π»Π°ΠΌΠΏΡ, Π·Π°ΠΏΠΎΠ»Π½Π΅Π½Π½ΠΎΠΉ ΠΊΡΠ΅Π½ΠΎΠ½ΠΎΠΌ.ΠΠΎΠ·ΠΌΠΎΠΆΠ½Π° Π‘. Ρ. ΠΈΠ·Π»ΡΡΠ΅Π½ΠΈΠ΅ΠΌ Π‘ΠΎΠ»Π½ΡΠ° (Π³Π΅Π»ΠΈΠΎΡΠ²Π°ΡΠΊΠ°). [c.148]
Π’Π΅ΡΠΌΠΈΡΠ½Π°Ρ ΡΠ²Π°ΡΠΊΠ° — Π²ΠΈΠ΄ ΡΠ²Π°ΡΠΊΠΈ ΠΏΠ»Π°Π²Π»Π΅Π½ΠΈΠ΅ΠΌ. ΠΠ΅ΡΡΠ½ΡΠΉ Π½Π°Π³ΡΠ΅Π² ΠΏΡΠΎΠΈΠ·Π²ΠΎΠ΄ΠΈΡΡΡ ΡΠ³ΠΎΡΠ°Π½ΠΈΠ΅ΠΌ ΡΠ΅ΡΠΌΠΈΡΠ° — ΠΆΠ΅Π»Π΅Π·Π½ΠΎΠΉ ΠΎΠΊΠ°Π»ΠΈΠ½Ρ Π² ΡΠΌΠ΅ΡΠΈ Ρ ΠΏΠΎΡΠΎΡΠΊΠΎΠΎΠ±ΡΠ°Π·Π½ΡΠΌ Π°Π»ΡΠΌΠΈΠ½ΠΈΠ΅ΠΌ. ΠΡΠΈ ΡΠ΅ΡΠΌΠΈΡΠ½ΠΎΠΉ ΡΠ²Π°ΡΠΊΠ΅ ΠΏΡΠΈΠΌΠ΅Π½ΡΡΡΡΡ ΡΠΏΠ΅ΡΠΈΠ°Π»ΡΠ½ΡΠ΅ ΡΠΈΠ³Π»ΠΈ Π΄Π»Ρ ΡΠΆΠΈΠ³Π°Π½ΠΈΡ ΡΠ΅ΡΠΌΠΈΡΠ°. Π’Π΅Ρ.ΠΌΠΈΡΠ½Π°Ρ ΡΠΌΠ΅ΡΡ ΠΏΠΎΠ΄ΠΆΠΈΠ³Π°Π΅ΡΡΡ ΡΠΏΠ΅ΡΠΈΠ°Π»ΡΠ½ΡΠΌΠΈ ΡΠ΅ΡΠΌΠΈΡΠ½ΡΠΌΠΈ ΡΠΏΠΈΡΠΊΠ°ΠΌΠΈ (ΠΌΠ°Π³Π½ΠΈΠ΅Π²ΡΠΉ ΡΠ΅ΡΠΌΠΈΡ). Π‘ΠΌΠ΅ΡΡ Π³ΠΎΡΠΈ Π·Π° ΡΡΠ΅Ρ ΠΊΠΈΡΠ»ΠΎΡΠΎΠ΄Π° ΠΎΠΊΠ°Π»ΠΈΠ½Ρ ΠΈ Π½Π΅ Π½ΡΠΆΠ΄Π°Π΅ΡΡΡ Π² ΠΊΠΈΡΠ»ΠΎΡΠΎΠ΄Π΅ Π²ΠΎΠ·Π΄ΡΡ
Π°. ΠΠΎΡΠ΅Π½ΠΈΠ΅ ΠΏΡΠΎΡΠ΅ΠΊΠ°Π΅Ρ ΡΠ°Π²Π½ΠΎΠΌΠ΅ΡΠ½ΠΎ, Π±Π΅Π· Π²Π·ΡΡΠ²ΠΎΠ².Π ΡΠΈΠ³Π»Π΅ ΠΎΡ ΡΠ³ΠΎΡΠ°Π½ΠΈΡ ΡΠ΅ΡΠΌΠΈΡΠ° ΠΎΠ±ΡΠ°Π·ΡΡΡΡΡ ΡΠ°ΡΠΏΠ»Π°Π²Π»Π΅Π½Π½ΡΠΉ ΠΌΠ΅ΡΠ°Π»Π» ΠΈ ΡΠ»Π°ΠΊ. ΠΠ· ΠΎΡΠ²Π΅ΡΡΡΠΈΡ Π½Π° Π΄Π½Π΅ ΡΠΈΠ³Π»Ρ ΡΠ°ΡΠΏΠ»Π°Π²Π»Π΅Π½Π½ΡΠΉ ΠΌΠ΅ΡΠ°Π»Π» Π²ΡΠ»ΠΈΠ²Π°Π΅ΡΡΡ Π² Π·Π°ΡΠΎΡΠΌΠΎΠ²Π°Π½Π½ΠΎΠ΅ ΠΈ ΠΏΠ΅ΡΠ²ΠΎΠ΅ Π½Π°Π³ΡΠ΅ΡΠΎΠ΅ ΠΌΠ΅ΡΡΠΎ ΡΠ²Π°ΡΠΊΠΈ. Π Π°ΡΠΏΠ»Π°Π²Π»Π΅Π½Π½ΡΠΉ ΠΌΠ΅ΡΠ°Π»Π» ΠΏΠΎΠ΄ΠΎΠ³ΡΠ΅Π²Π°Π΅Ρ ΠΊΡΠΎΠΌΠΊΠΈ ΠΌΠ΅ΡΠ°Π»Π»Π° Π΄Π΅ΡΠ°Π»Π΅ΠΉ Π΄ΠΎ ΡΠ°ΡΠΏΠ»Π°Π²Π»Π΅Π½ΠΈΡ ΠΈ ΠΏΠΎΡΠ»Π΅ ΠΎΡ
Π»Π°ΠΆΠ΄Π΅Π½ΠΈΡ ΠΎΠ±ΡΠ°Π·ΡΠ΅Ρ ΡΠΎΠ². Π Π°Π·ΡΠ΅ΠΌΠ½Π°Ρ ΡΠΎΡΠΌΠ° ΡΠ½ΠΈΠΌΠ°Π΅ΡΡΡ, Π° ΡΠ»Π°ΠΊ Ρ ΠΏΠΎΠ²Π΅ΡΡ
Π½ΠΎΡΡΠΈ ΡΡΡΠΊΠ° ΡΡΡΠ±Π°Π΅ΡΡΡ ΠΈ Π·Π°ΡΠΈΡΠ°Π΅ΡΡΡ. ΠΠ»Ρ ΡΠ²Π΅Π»ΠΈΡΠ΅Π½ΠΈΡ ΠΊΠΎΠ»ΠΈΡΠ΅ΡΡΠ²Π° ΡΠ°ΡΠΏΠ»Π°Π²Π»Π΅Π½Π½ΠΎΠ³ΠΎ ΠΌΠ΅ΡΠ°Π»Π»Π° Π² ΡΠ΅ΡΠΌΠΈΡ Π΄ΠΎΠ±Π°Π²ΠΈΡΡ Π΄ΠΎ 50% ΠΎΠ±ΡΠ΅ΡΠΊΠΈ, Π³Π²ΠΎΠ·Π΄Π΅ΠΉ ΠΈΠ»ΠΈ ΡΡΡΡΠΆΠΊΠΈ, Π° Π΄Π»Ρ Π»Π΅Π³ΠΈΡΠΎΠ²Π°Π½ΠΈΡ — ΡΠ΅ΡΡΠΎΡΠΏΠ»Π°Π²Ρ ΠΈ Π³ΡΠ°ΡΠΈΡ. [c.198]
ΠΡΠΈ ΡΠ²Π°ΡΠΊΠ΅ Π°Π»ΡΠΌΠΈΠ½ΠΈΠ΅Π²ΡΡ ΡΠΏΠ»Π°Π²ΠΎΠ² Π±ΠΎΠ»ΡΡΠΈΡ ΡΠΎΠ»ΡΠΈΠ½ ΠΈ Π²ΡΡΠΎΠΊΠΎΠΉ ΠΏΡΠΎΠΈΠ·Π²ΠΎΠ΄ΠΈΡΠ΅Π»ΡΠ½ΠΎΡΡΡΡ ΠΏΡΠΈΠΌΠ΅Π½ΡΡΡ ΡΡΠ΅Ρ ΡΠ°Π·Π½ΡΡ Π΄ΡΠ³Ρ ΠΈ Π½Π΅ΠΏΠ»Π°Π²Π½ΡΠΈΠ΅ΡΡ Π²ΠΎΠ»ΡΡΡΠ°ΠΌΠΎΠ²ΡΠ΅ ΡΠ»Π΅ΠΊΡΡΠΎΠ΄Ρ. ΠΡΡΠΎΡΠ½ΠΈΠΊΠΈ ΠΏΠΈΡΠ°Π½ΠΈΡ Π΄Π»Ρ ΡΠ°ΠΊΠΎΠ³ΠΎ Π²ΠΈΠ΄Π° ΡΠ²Π°ΡΠΊΠΈ ΡΠ°ΠΊΠΆΠ΅ ΠΈΠΌΠ΅ΡΡ ΠΏΠ°Π΄Π°ΡΡΠΈΠ΅ Π²Π½Π΅Π½1ΠΏΠΈΠ΅ Ρ Π°ΡΠ°ΠΊΡΠ΅ΡΠΈΡΡΠΈΠΊΠΈ ΠΈ ΠΏΠΎΠ·Π²ΠΎΠ»ΡΡΡ ΡΠ΅Π³ΡΠ»ΠΈΡΠΎΠ²Π°ΡΡ ΡΠ΅ΠΆΠΈΠΌ Ρ ΠΏΠΎΠΌΠΎΡΡΡ ΠΏΠ΅ΡΠ΅ΠΊΠ»ΡΡΠ°ΡΠ΅Π»Ρ ΡΡΡΠΏΠ΅Π½Π΅ΠΉ ΠΈΠ»ΠΈ ΠΏΠΎΠ΄ΠΌΠ°Π³Π½ΠΈΡΠΈΠ²Π°Π΅ΠΌΡΡ ΡΡΠ½ΡΠΎΠ². ΠΠ΄Π΅ΡΡ ΡΠ°ΠΊΠΆΠ΅ Π½Π΅ΠΎΠ±Ρ ΠΎΠ΄ΠΈΠΌΠ° ΠΊΠΎΠΌΠΏΠ΅Π½ΡΠ°ΡΠΈΡ ΠΏΠΎΡΡΠΎΡΠ½Π½ΡΡ ΠΊΠΎΠΌΠΏΠΎΠ½Π΅Π½ΡΠΎΠ² ΠΏΡΡΠ΅ΠΌ Π²ΠΊΠ»ΡΡΠ΅Π½ΠΈΡ ΠΊΠΎΠ½Π΄Π΅Π½ΡΠ°ΡΠΎΡΠΎΠ² Π² ΡΠ²Π°ΡΠΎΡΠ½ΡΡ ΡΠ΅ΠΏΡ. ΠΠ°ΠΊ ΠΏΡΠ°Π²ΠΈΠ»ΠΎ, ΡΡ Π΅ΠΌΡ ΠΈΡΡΠΎΡΠ½ΠΈΠΊΠ° ΠΏΠΈΡΠ°Π½ΠΈΡ ΠΊΠΎΠΌΠΏΠ»Π΅ΠΊΡΡΡΡ ΠΎΡΡΠΈΠ»Π»ΡΡΠΎΡΠΎΠΌ ΠΈ ΡΠΈΡΡΠ΅ΠΌΠΎΠΉ Π·Π°Π²Π°ΡΠΊΠΈ ΠΊΡΠ°ΡΠ΅ΡΠ°. [c.150]
ΠΠ΅ΡΡΠΌΠ° Π±Π»Π°Π³ΠΎΠΏΡΠΈΡΡΠ½ΡΠ΅ ΠΌΠ΅ΡΠ°Π»Π»ΡΡΠ³ΠΈΡΠ΅ΡΠΊΠΈΠ΅ ΡΡΠ»ΠΎΠ²ΠΈΡ ΠΏΡΠΈ ΡΠ²Π°ΡΠΊΠ΅ Π²ΡΡΠΎΠΊΠΎΡ
ΡΠΎΠΌΠΈΡΡΡΡ
ΡΡΠ°Π»Π΅ΠΉ ΡΠΎΠ·Π΄Π°Π΅Ρ ΡΠ²Π°ΡΠΊΡ Π² ΠΈΠ½Π΅ΡΡΠ½ΡΡ
Π·Π°ΡΠΈΡΠ½ΡΡ
Π³Π°Π·Π°Ρ
, ΠΊΠ°ΠΊ ΠΏΡΠ°Π²ΠΈΠ»ΠΎ, Π² Π°ΡΠ³ΠΎΠ½Π΅ ΠΈ Π² ΡΠΌΠ΅ΡΡΡ
Π½Π° Π΅Π³ΠΎ ΠΎΡΠ½ΠΎΠ²Π΅. ΠΡΠΈΡΠ΅ΠΌ Π² ΠΎΡΠ½ΠΎΠ²Π½ΠΎΠΌ ΠΈΡΠΏΠΎΠ»ΡΠ·ΡΡΡ ΡΠ²Π°ΡΠΊΡ Π½Π΅ΠΏΠ»Π°Π²Π»Π΅Π½Π½ΠΎΠ³ΠΎ Π²ΠΎΠ»ΡΡΡΠ°ΠΌΠΎΠ²ΡΠΌ ΡΠ»Π΅ΠΊΡΡΠΎΠ΄ΠΎΠΌ, Π° ΠΏΡΠΈΡΠ°Π΄ΠΎΡΠ½ΡΠΉ ΠΌΠ°ΡΠ΅ΡΠΈΠ°Π» ΠΏΠΎΠ΄Π±ΠΈΡΠ°ΡΡ Π΄ΡΡΠ³ΠΈΠΌ ΠΆΠ΅Π»Π°Π΅ΠΌΠΎΠΌΡ ΡΠΎΡΡΠ°Π²Ρ Π½Π°ΠΏΠ»Π°Π²Π»Π΅Π½Π½ΠΎΠ³ΠΎ ΠΌΠ΅ΡΠ°Π»Π»Π°. ΠΡΠΈ ΡΡΠΎΠΌ Π²ΠΈΠ΄Π΅ ΡΠ²Π°ΡΠΊΠΈ Π² ΡΠΎΠΏ ΡΠ΄Π°Π΅ΡΡΡ Π²Π²Π΅ΡΡΠΈ ΠΏΠΎΡΡΠΈ Π±Π΅Π· ΠΏΠΎΡΠ΅ΡΡ ΡΠ°ΠΊΠΈΠ΅ Π°ΠΊΡΠΈΠ²Π½ΡΠ΅ ΡΠ»Π΅ΠΌΠ΅Π½ΡΡ (ΡΠ»ΡΡΡΠ°ΡΡΠΈΠ΅ ΡΠ²ΠΎΠΉΡΡΠ²Π° ΠΌΠ΅ΡΠ°Π»Π»Π° ΡΠ²Π°), ΠΊΠ°ΠΊ ΡΠΈΡΠ°Π½ ΠΈ Π°Π»ΡΠΌΠΈΠ½ΠΈΠΉ.ΠΠ΄Π½Π°ΠΊΠΎ ΠΏΠΎ ΠΏΡΠΈΡΠΈΠ½Π°ΠΌ ΠΏΠΎΠ½ΠΈΠΆΠ΅Π½ΠΈΡ ΠΏΡΠΎΠΈΠ·Π²ΠΎΠ΄ΠΈΡΠ΅Π»ΡΠ½ΠΎΡΡΠΈ ΠΌΠ΅ΡΠΎΠ΄Π° ΡΠ²Π°ΡΠΊΠΈ ΠΎΠ³ΡΠ°Π½ΠΈΡΠΈΠ²Π°Π΅ΡΡΡ ΠΈΠ·Π³ΠΎΡΠΎΠ²Π»Π΅Π½ΠΈΠ΅ΠΌ ΠΈΠ·Π΄Π΅Π»ΠΈΠΉ ΠΌΠ°Π»ΡΡ
ΡΠΎΠ»ΡΠΈΠ½ ΠΈ Π²ΡΠΏΠΎΠ»Π½Π΅Π½ΠΈΠ΅ΠΌ ΠΊΠΎΡΠ½Π΅Π²ΠΎΠ³ΠΎ Π²Π°Π»ΠΈΠΊΠ° Π² ΠΌΠ½ΠΎΠ³ΠΎΡΠ»ΠΎΠΉΠ½ΡΡ
ΡΠ²Π°Ρ
ΠΌΠ΅ΡΠ°Π»Π»Π° Π±ΠΎΠ»ΡΡΠΈΡ
ΡΠΎΠ»ΡΠΈΠ½, Π½Π°ΠΏΡΠΈΠΌΠ΅Ρ, Π² ΠΈΠ·Π΄Π΅Π»ΠΈΡΡ
ΡΡΡΠ±ΠΎΡΡΡΠΎΠ΅Π½ΠΈΡ. [c.265]
ΠΡΠΈΠΌΠ΅Π½Π΅Π½ΠΈΠ΅ Π²ΠΈΠ΄ΠΎΠ² ΡΠ²Π°ΡΠΊΠΈ, Π² ΠΎΡΠ½ΠΎΠ²Π½ΠΎΠΌ ΡΡΡΠ½ΠΎΠΉ Π΄ΡΠ³ΠΎΠ²ΠΎΠΉ, ΠΏΠΎΠ»ΡΡΠ΅Π½ΠΈΠ΅ ΠΏΠΎΠ»ΡΡΠ΅Π½ΠΈΡ ΠΈΠ°ΠΏΠ»Π°Π²Π»Π΅Π½ΠΈΠΎ-Π³ΠΎ ΠΌΠ΅ΡΠ°Π»Π»Π° Ρ Π°ΡΡΡΠ΅Π½ΠΈΡΠ½ΠΎ-ΡΠ΅ΡΡΠΈΡΠ½ΠΎΠΉ [c.270]
Π ΡΠ΅ΡΠΌΠΈΡΠ΅ΡΠΊΠΎΠΌΡ ΠΊΠ»Π°ΡΡΡ Π·Π°ΡΠΈΡΡ, ΠΎΡΡΡΠ΅ΡΡΠ²Π»ΡΠ΅ΠΌΠΎΠΌΡ Ρ ΠΈΡΠΏΠΎΠ»ΡΠ·ΠΎΠ²Π°Π½ΠΈΠ΅ΠΌ ΡΠ΅ΠΏΠ»ΠΎΠ²ΠΎΠΉ ΡΠ½Π΅ΡΠ³ΠΈΠΈ (Π΄ΡΠ³ΠΎΠ²Π°Ρ, ΠΏΠ»Π°Π·ΠΌΠ΅Π½Π½Π°Ρ, ΡΠ»Π΅ΠΊΡΡΠΎΡΠ»Π°ΠΊΠΎΠ²Π°Ρ, ΡΠ»Π΅ΠΊΡΡΠΎΠ½Π½ΠΎ-Π»ΡΡΠ΅Π²Π°Ρ, Π»Π°Π·Π΅ΡΠ½Π°Ρ, Π³Π°Π·ΠΎΠ²Π°Ρ ΠΈ Π΄Ρ.)). [c.182]
ΠΠΎΠ½ΡΠ°ΠΊΡΠ½Π°Ρ ΡΠ²Π°ΡΠΊΠ° ΠΎΡΠ½ΠΎΡΠΈΡΡΡ ΠΊ Π²ΠΈΠ΄Ρ ΡΠ²Π°ΡΠΊΠΈ Ρ ΠΊΡΠ°ΡΠΊΠΎ-BpeMeiiHijiM Π½Π°Π³ΡΠ΅Π²ΠΎΠΌ ΠΌΠ΅ΡΡΠ° ΡΠΎΠ΅Π΄ΠΈΠ½Π΅Π½ΠΈΡ Π±Π΅Π· ΠΎΠΈΠ»Π°Π²Π»Π΅Π½Π½Ρ ΠΈΠ»ΠΈ Ρ ΠΎΠΏΠ»Π°Π²Π»Π΅Π½ΠΈΠ΅ΠΌ ΠΈ ΠΎΡΠ°Π΄ΠΊΠΎ11 ΡΠ°Π·ΠΎΠ³ΡΠ΅ΡΡΡ
Π·Π°Π³ΠΎΡΠΎΠ²ΠΎΠΊ. Π₯Π°ΡΠ°ΠΊΡΠ΅ΡΠ½Π°Ρ ΠΎΡΠΎΠ±Π΅Π½Π½ΠΎΡΡΡ ΡΡΠΈΡ
ΠΏΡΠΎΡΠ΅ΡΡΠΎΠ² — ΠΏΠ»Π°ΡΡΠΈΡΠ΅ΡΠΊΠ°Ρ Π΄Π΅ΡΠΎΡΠΌΠ°ΡΠΈΡ, Π² Ρ
ΠΎΠ΄Π΅ ΠΊΠΎΡΠΎΡΠΎΠΉ ΡΠΎΡΠΌΠΈΡΡΠ΅ΡΡΡ ΡΠ²Π°ΡΠ½ΠΎΠ΅ ΡΠΎΠ΅Π΄ΠΈΠ½Π΅Π½ΠΈΠ΅. [c.211]
Π‘Π²Π°ΡΠΊΡ Π²Π·ΡΡΠ²ΠΎΠΌ ΠΌΠΎΠΆΠ½ΠΎ ΠΎΡΠ½Π΅ΡΡΠΈ ΠΊ Π²ΠΈΠ΄Ρ ΡΠ²Π°ΡΠΊΠΈ Ρ ΠΎΠΏΠ»Π°Π²Π»Π΅Π½ΠΈΠ΅ΠΌ ΠΏΡΠΈ ΠΊΡΠ°ΡΠΊΠΎΠ²ΡΠ΅ΠΌΠ΅Π½Π½ΠΎΠΌ Π½Π°Π³ΡΠ΅Π²Π΅ Π² Π²ΠΎΠ·Π΄ΡΡ Π΅, ΡΠ°ΠΊ ΠΊΠ°ΠΊ Π½Π° ΠΎΡΠ΄Π΅Π»ΡΠ½ΡΡ ΡΡΠ°ΡΡΠΊΠ°Ρ Π½Π°Π±Π»ΡΠ΄Π°ΡΡΡΡ Π·ΠΎΠ½Ρ ΠΌΠ΅ΡΠ°Π»Π»Π°, Π½Π°Π³ΡΠ΅ΡΡΠ΅ Π΄ΠΎ ΠΎΠΏΠ»Π°Π²Π»Π΅Π½ΠΈΡ.ΠΠ΄Π½Π°ΠΊΠΎ Π½Π° Π΄ΡΡΠ³ΠΈΡ ΡΡΠ°ΡΡΠΊΠ°Ρ ΠΌΠΎΠΆΠ΅Ρ Π±ΡΡΡ ΠΏΠ΅Π²ΡΡΠΎΠΊΠ°, ΠΈ Π·Π΄Π΅ΡΡ ΠΏΡΠΎΡΠ΅ΡΡ ΠΏΡΠΈΠ±Π»ΠΈΠΆΠ°Π΅ΡΡΡ ΠΊ Ρ ΠΎΠ»ΠΎΠ΄Π½ΠΎΠΉ ΡΠ²Π°ΡΠΊΠ΅. [c.225]
ΠΡΠΈ ΠΏΡΠΎΠ΅ΠΊΡΠΈΡΠΎΠ²Π°Π½ΠΈΠΈ ΡΠ²Π°ΡΠ½ΡΡ Π·Π°Π³ΠΎΡΠΎΠ²ΠΎΠΊ ΡΠ»Π΅Π΄ΡΠ΅Ρ ΡΡΠΈΡΡΠ²Π°ΡΡ ΡΡΠ΅Π±ΠΎΠ²Π°Π½ΠΈΡ ΠΊ ΡΠ΅Ρ Π½ΠΎΠ»ΠΎΠ³ΠΈΡΠ½ΠΎΡΡΠΈ ΠΈΡ ΠΈΠ·Π³ΠΎΡΠΎΠ²Π»Π΅Π½ΠΈΡ. ΠΠ±Π΅ΡΠΏΠ΅ΡΠΈΠ²Π°Π΅Ρ ΡΠ΄ΠΎΠ±ΡΡΠ²ΠΎ ΠΈ ΠΏΡΠΎΡΡΠΎΡΡ ΠΈΠ·Π³ΠΎΡΠΎΠ²Π»Π΅Π½ΠΈΡ Π»ΡΠ±ΡΠΌΠΈ Π²ΠΈΠ΄Π°ΠΌΠΈ ΡΠ²Π°ΡΠΊΠΈ ΠΈ ΠΏΡΠΈ ΡΠ°Π·Π»ΠΈΡΠ½ΡΡ ΡΠ΅ΠΆΠΈΠΌΠ°Ρ ΠΏΡΠΈΠΌΠ΅Π½Π΅Π½ΠΈΡ Π²ΡΡΠΎΠΊΠΎ-ΠΏΡΠΎΠΈΠ·Π²ΠΎΠ΄ΡΡΠ²Π΅Π½Π½ΠΎΠΉ ΡΠ²Π°ΡΠΊΠΈ Π°Π²ΡΠΎΠΌΠ°ΡΠΈΠ·Π°ΡΠΈΡ ΠΈ ΠΌΠ΅Ρ Π°Π½ΠΈΠ·Π°ΡΠΈΡ ΠΎΠΏΠ΅ΡΠ°ΡΠΈΠΉ ΡΠ΅Ρ Π½ΠΎΠ»ΠΎΠ³ΠΈΡΠ΅ΡΠΊΠΎΠ³ΠΎ ΠΏΡΠΎΡΠ΅ΡΡΠ° Π½ΠΈΠ·ΠΊΡΡ ΡΠ΅Π±Π΅ΡΡΠΎΠΈΠΌΠΎΡΡΡ ΠΏΡΠΎΡΠ΅ΡΡΠ° ΡΠ²Π°ΡΠΊΠΈ Π·Π° ΡΡΠ΅Ρ ΡΠΊΠΎΠ½ΠΎΠΌΠΈΠΈ ΡΠ²Π°ΡΠΎΡΠ½ΡΡ ΠΌΠ°ΡΠ΅ΡΠΈΠ°Π»ΠΎΠ², ΠΏΠΎΠ²ΡΡΠ΅Π½ΠΈΡ ΠΏΡΠΎΠΈΠ·Π²ΠΎΠ΄ΠΈΡΠ΅Π»ΡΠ½ΠΎΡΡΠΈ ΠΈ Π²ΡΡΠΎΠΊΠΎΠ³ΠΎ ΡΡΠΎΠ²Π½Ρ ΠΌΠ΅Ρ Π°Π½ΠΈΠ·Π°ΡΠΈΠΈ ΡΠ²Π΅Π΄Π΅Π½ΠΈΡ ΠΊ ΠΌΠΈΠ½ΠΈΠΌΡΠΌΡ ΠΈΡΠΊΠ°ΠΆΠ΅Π½ΠΈΠΉ ΡΠΎΡΠΌΡ, Π²ΡΠ·ΡΠ²Π°Π΅ΠΌΡΡ ΡΠ΅ΠΏΠ»ΠΎΠ²ΡΠΌ ΠΈ ΠΌΠ΅Ρ Π°Π½ΠΈΡΠ΅ΡΠΊΠΈΠΌ Π²ΠΎΠ·Π΄Π΅ΠΉΡΡΠ²ΠΈΡΠΌΠΈ ΠΏΡΠΈ ΡΠ²Π°ΡΠΊΠ΅. [c.245]
Π‘ΠΏΠΎΡΠΎΠ±Ρ ΡΠ²Π°ΡΠΊΠΈ ΠΈ Π²ΠΈΠ΄Ρ ΡΠ²Π°ΡΠ½ΡΡ
ΡΠΎΠ΅Π΄ΠΈΠ½Π΅Π½ΠΈΠΉ ΠΏΡΠΈ ΠΏΠΎΠΌΠΎΡΠΈ ΡΡΡΠΎΠΈΡΠ΅Π»ΡΠ½ΡΡ
ΠΊΠΎΠ½ΡΡΡΡΠΊΡΠΈΠΉ: ΡΠ»Π΅ΠΊΡΡΠΎΠ΄ΡΠ³ΠΎΠ²Π°Ρ ΠΈ Π³Π°Π·ΠΎΠ²Π°Ρ ΡΠ²Π°ΡΠΊΠ°.
ΠΡΠΆΠ½Π° ΠΏΠΎΠΌΠΎΡΡ Π² Π½Π°ΠΏΠΈΡΠ°Π½ΠΈΠΈ ΡΠ°Π±ΠΎΡΡ?
ΠΠΈΠ΄Ρ ΡΠ²Π°ΡΠ½ΡΡ
ΡΠ²ΠΎΠ² ΠΈ ΡΠ²Π°ΡΠ½ΡΡ
ΡΠΎΠ΅Π΄ΠΈΠ½Π΅Π½ΠΈΠΉ.
Π‘Π²Π°ΡΠ½ΡΠΌΠΈ ΡΠΎΠ΅Π΄ΠΈΠ½Π΅Π½ΠΈΡΠΌΠΈ Π½Π°Π·ΡΠ²Π°ΡΡ Π΄Π²Π΅, ΠΈ Π±ΠΎΠ»Π΅Π΅ Π΄Π΅ΡΠ°Π»Π΅ΠΉ ΡΠΎΠ΅Π΄ΠΈΠ½Π΅Π½Π½ΡΡ
ΠΌΠ΅ΠΆΠ΄Ρ ΡΠΎΠ±ΠΎΠΉ ΡΠ²Π°ΡΠ½ΡΠΌΠΈ ΡΠ²Π°ΠΌΠΈ. ΠΡΠΈ ΡΠ²Π°ΡΠΊΠ΅ ΠΈΠ·Π΄Π΅Π»ΠΈΠΉ ΠΈ ΠΊΠΎΠ½ΡΡΡΡΠΊΡΠΈΠΉ ΠΏΡΠΈΠΌΠ΅Π½ΡΡΡΡΡ ΡΠ»Π΅Π΄ΡΡΡΠΈΠ΅ Π²ΠΈΠ΄Ρ ΡΠ²Π°ΡΠ½ΡΡ
ΡΠΎΠ΅Π΄ΠΈΠ½Π΅Π½ΠΈΠΉ: Π½Π°Ρ
Π»Π΅ΡΡΠΊΡ, ΡΡΡΠΊΠΎΠ²ΡΠ΅, ΡΠ°Π²ΡΠΎΠ²ΡΠ΅, ΡΠ³Π»ΠΎΠ²ΡΠ΅, ΠΏΡΠΎΡΠ΅Π·Π½ΡΠ΅, Ρ ΡΠ»Π΅ΠΊΡΡΠΎΠ·Π°ΠΊΠ»Π΅ΠΏΠΊΠ°ΠΌΠΈ, ΡΠΎΡΡΠ΅Π²ΡΠ΅.
Π°) Π‘ΡΡΠΊΠΎΠ²ΠΎΠ΅ ΡΠΎΠ΅Π΄ΠΈΠ½Π΅Π½ΠΈΠ΅ . ΠΠ΄ΠΈΠ½ ΠΈΠ· ΡΠ°ΠΌΡΡ
ΡΠ°ΡΠΏΡΠΎΡΡΡΠ°Π½Π΅Π½Π½ΡΡ
Π²ΠΈΠ΄ΠΎΠ² ΡΠ²Π°ΡΠ½ΡΡ
ΡΠΎΠ΅Π΄ΠΈΠ½Π΅Π½ΠΈΠΉ. Π’Π°ΠΊΠΈΠ΅ ΡΠΎΠ΅Π΄ΠΈΠ½Π΅Π½ΠΈΡ ΠΈΠΌΠ΅ΡΡ ΠΌΠ΅Π½ΡΡΠΈΠ΅ Π²Π½ΡΡΡΠ΅Π½Π½ΠΈΠ΅ ΠΈ Π½Π°ΠΏΡΡΠΆΠ΅Π½ΠΈΡ ΠΌΠ΅Π½ΡΡΠ΅ Π΄Π΅ΡΠΎΡΠΌΠ°ΡΠΈΠΈ ΠΏΡΠΈ ΡΠ²Π°ΡΠΊΠ΅. Π ΡΠΎΠΌΡ ΠΆΠ΅ ΠΈΠΌΠ΅ΡΡ Π±ΠΎΠ»Π΅Π΅ Π²ΡΡΠΎΠΊΡΡ ΠΏΡΠΎΡΠ½ΠΎΡΡΡ ΠΏΡΠΈ ΡΡΠ°ΡΠΈΡΠ΅ΡΠΊΠΈΡ
ΠΈ Π΄ΠΈΠ½Π°ΠΌΠΈΡΠ΅ΡΠΊΠΈΡ
Π½Π°Π³ΡΡΠ·ΠΊΠ°Ρ
.
Π±) ΠΠ½Π°Ρ
Π»Π΅ΡΡΠΊΡ . Π§Π°ΡΡΠΎ ΠΏΡΠΈΠΌΠ΅Π½ΡΡΡ ΠΏΡΠΈ Π΄ΡΠ³ΠΎΠ²ΠΎΠΉ ΡΠ²Π°ΡΠΊΠ΅ ΡΡΡΠΎΠΈΡΠ΅Π»ΡΠ½ΡΡ
ΠΊΠΎΠ½ΡΡΡΡΠΊΡΠΈΠΉ ΠΏΡΠΈ ΡΠΎΠ»ΡΠΈΠ½Π΅ ΠΌΠ΅ΡΠ°Π»Π»Π° Π½Π΅ Π±ΠΎΠ»Π΅Π΅ 10 — 12 ΠΌΠΌ. ΠΠΎ ΡΡΠ°Π²Π½Π΅Π½ΠΈΡ Ρ ΡΠΎΠ΅Π΄ΠΈΠ½Π΅Π½ΠΈΡΠΌΠΈ Π²ΡΡΡΠΊ Π½Π΅ ΡΡΠ΅Π±ΡΠ΅Ρ ΡΠ°ΠΊΠΎΠΉ ΡΡΠ°ΡΠ΅Π»ΡΠ½ΠΎΠΉ ΠΏΠΎΠ΄Π³ΠΎΠ½ΠΊΠΈ ΡΡΡΠΊΠΎΠ².ΠΡΠΈ ΡΠ²Π°ΡΠΊΠ΅ Π²Π½Π°Ρ
Π»Π΅ΡΡΠΊΡ ΡΠ΅ΠΊΠΎΠΌΠ΅Π½Π΄ΡΠ΅ΡΡΡ ΠΏΠΎ Π²ΠΎΠ·ΠΌΠΎΠΆΠ½ΠΎΡΡΠΈ ΡΠ²Π°ΡΠΈΠ²Π°ΡΡ Π»ΠΈΡΡΡ Ρ ΡΡΠ΅Ρ
ΡΡΠΎΡΠΎΠ½.
Π²) Π£Π³Π»ΠΎΠ²ΡΠ΅ ΡΠΎΠ΅Π΄ΠΈΠ½Π΅Π½ΠΈΡ . ΠΡΠΈΠΌΠ΅Π½ΡΡΡ ΠΏΡΠΈ ΡΠ²Π°ΡΠΊΠ΅ Π΄Π΅ΡΠ°Π»Π΅ΠΉ ΠΏΠΎ ΠΊΡΠΎΠΌΠΊΠ°ΠΌ ΠΏΠΎΠ΄ ΠΎΠΏΡΠ΅Π΄Π΅Π»Π΅Π½Π½ΡΠΌ ΡΠ³Π»ΠΎΠΌ Π΄ΡΡΠ³ ΠΊ Π΄ΡΡΠ³Ρ.
Π³) Π’Π°Π²ΡΠΎΠ²ΡΠ΅ ΡΠΎΠ΅Π΄ΠΈΠ½Π΅Π½ΠΈΡ . ΠΠ°ΠΈΠ±ΠΎΠ»Π΅Π΅ ΡΠ°ΡΡΠΎ ΠΏΡΠΈΠΌΠ΅Π½ΡΡΡ Π΄Π»Ρ ΡΠ²Π°ΡΠΊΠΈ ΠΊΠΎΠ»ΠΎΠ½Π½, Π±Π°Π»ΠΎΠΊ, ΡΠ°Π·Π»ΠΈΡΠ½ΡΡ
ΡΡΠΎΠ΅ΠΊ, ΡΠ΅ΡΠΌ ΠΈ ΠΏΡΠΎΡΠΈΡ
ΡΡΡΠΎΠΈΡΠ΅Π»ΡΠ½ΡΡ
ΠΊΠΎΠ½ΡΡΡΡΠΊΡΠΈΠΉ.
Π΄) ΠΡΠΎΡΠ΅Π·Π½ΡΠ΅ . Π’Π°ΠΊΠΈΠ΅ ΡΠΎΠ΅Π΄ΠΈΠ½Π΅Π½ΠΈΡ ΠΏΡΠΈΠΌΠ΅Π½ΡΡΡ, ΠΊΠΎΠ³Π΄Π° ΠΎΠ±ΡΡΠ½Π°Ρ ΡΠΎΠ»ΡΠΈΠ½Π°, ΡΠ²Π° Π²Π½Π°Ρ
Π»Π΅ΡΡ Π½Π΅ ΠΌΠΎΠ³ΡΡ ΠΎΠ±Π΅ΡΠΏΠ΅ΡΠΈΡΡ Π½Π΅ΠΎΠ±Ρ
ΠΎΠ΄ΠΈΠΌΠΎΠΉ ΠΏΡΠΎΡΠ½ΠΎΡΡΠΈ.
Π΅) Π‘ΠΎΠ΅Π΄ΠΈΠ½Π΅Π½ΠΈΡ ΡΠ»Π΅ΠΊΡΡΠΎΠ·Π°ΠΊΠ»Π΅ΠΏΠΊΠ°ΠΌΠΈ . ΠΡΠΈΠΌΠ΅Π½ΡΡ ΡΠ°ΠΊΠΎΠΉ ΠΌΠ΅ΡΠΎΠ΄, ΡΠΎΠ΅Π΄ΠΈΠ½Π΅Π½ΠΈΠ΅ ΠΏΠΎΠ»ΡΡΠ°Π΅ΡΡΡ Π΄ΠΎΡΡΠ°ΡΠΎΡΠ½ΠΎ ΠΏΡΠΎΡΠ½ΠΎΠ΅, Π½ΠΎ Π½Π΅ ΠΏΠ»ΠΎΡΠ½ΠΎΠ΅. Π Π²Π΅ΡΡ
Π½Π΅ΠΌ Π»ΠΈΡΡΠ΅ ΠΏΡΠΎΡΠ²Π΅ΡΠ»ΠΈΠ²Π°ΡΡΡΡ ΠΈΠ»ΠΈ ΠΏΡΠΎΡΠ΅Π·Π°ΡΡΡΡ ΠΎΡΠ²Π΅ΡΡΡΠΈΡ ΠΈ Π·Π°Π²Π°ΡΠΈΠ²Π°ΡΡΡΡ ΡΠ°ΠΊΠΈΠΌ ΠΎΠ±ΡΠ°Π·ΠΎΠΌ, ΡΡΠΎΠ±Ρ ΠΌΠ΅ΡΠ°Π»Π» Π½ΠΈΠΆΠ½Π΅Π³ΠΎ Π»ΠΈΡΡΠ° ΡΠ²Π°ΡΠΈΠ»ΡΡ Ρ Π²Π΅ΡΡ
Π½ΠΈΠΌ.
ΠΆ) Π’ΠΎΡΡΠ΅Π²ΡΠ΅ ΡΠΎΠ΅Π΄ΠΈΠ½Π΅Π½ΠΈΡ . ΠΠΎΠ³Π΄Π° Π»ΠΈΡΡΡ ΡΠ²Π°ΡΠΈΠ²Π°ΡΡΡΡ ΠΏΠΎ ΡΠΎΠ²ΠΌΠ΅ΡΠ΅Π½Π½ΡΠΌ ΡΠΎΡΡΠ°ΠΌ.
ΠΠΈΠ΄Ρ ΡΠ²Π°ΡΠ½ΡΡ
ΡΠ²ΠΎΠ².
1) ΠΠΎ ΠΏΠΎΠ»ΠΎΠΆΠ΅Π½ΠΈΡ Π² ΠΎΡΠ²Π΅ΡΠ΅Π½ΠΈΠΈ: Π² Π½ΠΈΠΆΠ½Π΅ΠΌ (1), Π³ΠΎΡΠΈΠ·ΠΎΠ½ΡΠ°Π»ΡΠ½ΠΎΠΌ (3), Π²Π΅ΡΡΠΈΠΊΠ°Π»ΡΠ½ΠΎΠΌ (2) ΠΈ ΠΏΠΎΡΠΎΠ»ΠΎΡΠ½ΠΎΠΌ (4) ΠΈΡΠΏΠΎΠ»Π½Π΅Π½ΠΈΠΈ.
2) ΠΠΎ ΠΎΡΠ½ΠΎΡΠ΅Π½ΠΈΡ ΠΊ Π΄Π΅ΠΉΡΡΠ²ΡΡΡΠΈΠΌ Π½Π°Π³ΡΡΠ·ΠΊΠ°ΠΌ: ΡΠ»Π°Π½ΠΊΠΎΠ²ΡΠ΅ (1), Π»ΠΎΠ±ΠΎΠ²ΡΠ΅ (2), ΠΊΠΎΡΡΠ΅ (4), ΠΊΠΎΠΌΠ±ΠΈΠ½ΠΈΡΠΎΠ²Π°Π½Π½ΡΠ΅ 3) ΠΠΎ ΠΊΠΎΠ»ΠΈΡΠ΅ΡΡΠ²Ρ Π½Π°ΠΏΠ»Π°Π²Π»Π΅Π½Π½ΠΎΠ³ΠΎ ΠΌΠ΅ΡΠ°Π»Π»Π° ΡΠ²Ρ Π±ΡΠ²Π°ΡΡ: ΡΡΠΈΠ»Π΅Π½Π½ΡΠ΅, Π½ΠΎΡΠΌΠ°Π»ΡΠ½ΡΠ΅, Π²ΠΎΠ³Π½ΡΡΡΠΉ (ΠΎΡΠ»Π°Π±Π»Π΅Π½Π½ΡΠΉ).
ΠΠ°Π·ΠΎΠ²Π°Ρ ΡΠ²Π°ΡΠΊΠ°. Π‘ΡΡΠ½ΠΎΡΡΡ Π³Π°Π·ΠΎΠ²ΠΎΠΉ ΡΠ²Π°ΡΠΊΠΈ ΡΠΎΡΡΠΎΠΈΡ Π² ΡΠΎΠΌ, ΡΡΠΎ ΡΠΎΠ΅Π΄ΠΈΠ½Π΅Π½ΠΈΠ΅ ΡΠ°ΡΡΠ΅ΠΉ ΠΎΡΡΡΠ΅ΡΡΠ²Π»ΡΠ΅ΡΡΡ ΠΏΡΡΠ΅ΠΌ ΡΠ°ΡΠΏΠ»Π°Π²Π»Π΅Π½ΠΈΡ ΠΊΡΠΎΠΌΠΎΠΊ ΡΠ²Π°ΡΠΈΠ²Π°Π΅ΠΌΡΡ
Π΄Π΅ΡΠ°Π»Π΅ΠΉ ΠΏΠ»Π°ΠΌΠ΅Π½Π΅ΠΌ ΡΠ²Π°ΡΠΎΡΠ½ΠΎΠΉ Π³ΠΎΡΠ΅Π»ΠΊΠΈ ΠΈ Π·Π°ΠΏΠΎΠ»Π½Π΅Π½ΠΈΡ ΠΏΡΠΎΠΌΠ΅ΠΆΡΡΠΊΠ° ΠΌΠ΅ΠΆΠ΄Ρ Π½ΠΈΠΌΠΈ ΡΠ°ΡΠΏΠ»Π°Π²ΠΎΠΌ ΠΏΡΠΈΡΠ°Π΄ΠΎΡΠ½ΠΎΠΉ ΠΏΡΠΎΠ²ΠΎΠ»ΠΎΠΊΠΈ. ΠΠΎΡΠ»Π΅ Π·Π°ΡΡΡΠ²Π°Π½ΠΈΡ ΠΎΠ±ΡΠ°Π·ΡΠ΅ΡΡΡ ΡΠ²Π°ΡΠ½ΠΎΠΉ ΡΠΎΠ², ΡΠΎΠ΅Π΄ΠΈΠ½ΡΡΡΠΈΠΉ Π΄Π΅ΡΠ°Π»ΠΈ Π² ΠΎΠ΄Π½ΠΎ ΡΠ΅Π»ΠΎΠ΅.ΠΠ»Ρ ΠΏΠΎΠ»ΡΡΠ΅Π½ΠΈΡ Π³Π°Π·ΠΎΠ²ΠΎΠ³ΠΎ ΠΏΠ»Π°ΠΌΠ΅Π½ΠΈ Π² Π³ΠΎΡΠ΅Π»ΠΊΡ ΠΈΠ· Π΄Π²ΡΡ
Π±Π°Π»Π»ΠΎΠ½ΠΎΠ² ΠΏΠΎ Π³ΠΈΠ±ΠΊΠΈΠΌ ΡΠ΅Π·ΠΈΠ½ΠΎΠ²ΡΠΌ ΡΠ»Π°Π½Π³Π°ΠΌ ΠΏΠΎΠ΄Π°Π΅ΡΡΡ Π°ΡΠ΅ΡΠΈΠ»Π΅Π½ ΠΈ ΠΊΠΈΡΠ»ΠΎΡΠΎΠ΄. ΠΠ°Π·ΠΎΠ²ΠΎΠΉ ΡΠ²Π°ΡΠΊΠΎΠΉ ΡΠ²Π°ΡΠΈΠ²Π°ΡΡ ΡΡΠ°Π»ΠΈ, ΡΡΠ³ΡΠ½ ΠΈ ΡΠ²Π΅ΡΠ½ΡΠ΅ ΠΌΠ΅ΡΠ°Π»Π»Ρ.
ΠΡΠ³ΠΎΠ²Π°Ρ ΡΠ²Π°ΡΠΊΠ°. . ΠΡΠΈ Π΄ΡΠ³ΠΎΠ²ΠΎΠΉ ΡΠ²Π°ΡΠΊΠ΅ ΠΌΠ΅ΡΠ°Π»Π» ΠΏΠ»Π°Π²ΠΈΡΡΡ ΠΏΠΎΠ΄ Π΄Π΅ΠΉΡΡΠ²ΠΈΠ΅ΠΌ ΡΠ΅ΠΏΠ»Π° ΡΠ»Π΅ΠΊΡΡΠΈΡΠ΅ΡΠΊΠΎΠΉ Π΄ΡΠ³ΠΈ, ΠΎΠ±ΡΠ°Π·ΡΡΡΠ΅ΠΉΡΡ ΠΏΡΠΈ ΠΏΡΠΎΡ
ΠΎΠΆΠ΄Π΅Π½ΠΈΠΈ ΡΠ»Π΅ΠΊΡΡΠΈΡΠ΅ΡΠΊΠΎΠ³ΠΎ ΡΠΎΠΊΠ° ΡΠ΅ΡΠ΅Π· Π²ΠΎΠ·Π΄ΡΡΠ½ΡΠΉ ΠΏΡΠΎΠΌΠ΅ΠΆΡΡΠΎΠΊ ΠΌΠ΅ΠΆΠ΄Ρ ΡΠ²Π°ΡΠΈΠ²Π°Π΅ΠΌΡΠΌ ΠΌΠ΅ΡΠ°Π»Π»ΠΎΠΌ ΠΈ ΡΠ³ΠΎΠ»ΡΠ½ΡΠΌ ΠΈΠ»ΠΈ ΠΌΠ΅ΡΠ°Π»Π»ΠΈΡΠ΅ΡΠΊΠΈΠΌ ΡΠ»Π΅ΠΊΡΡΠΎΠ΄ΠΎΠΌ. ΠΠ»Ρ ΠΎΠ±ΡΠ°Π·ΠΎΠ²Π°Π½ΠΈΡ ΡΠ»Π΅ΠΊΡΡΠΈΡΠ΅ΡΠΊΠΎΠΉ Π΄ΡΠ³ΠΈ Π½Π°Π΄ΠΎ ΠΊΠΎΡΠ½ΡΡΡΡΡ ΡΠ²Π°ΡΠΈΠ²Π°Π΅ΠΌΠΎΠ³ΠΎ ΠΌΠ΅ΡΠ°Π»Π»Π° ΠΈ ΡΠΎΡΡΠ°Ρ ΠΎΡΠ²Π΅ΡΡΠΈ Π΅Π³ΠΎ Π½Π° 2β4 ΠΌΠΌ.Π’ΠΎΠ³Π΄Π° ΡΠ»Π΅ΠΊΡΡΠΈΡΠ΅ΡΠΊΠΈΠΉ ΡΠΎΠΊ, ΠΏΡΠΎΡ
ΠΎΠ΄Ρ ΡΠ΅ΡΠ΅Π· Π²ΠΎΠ·Π΄ΡΡΠ½ΡΠΉ ΠΏΡΠΎΠΌΠ΅ΠΆΡΡΠΎΠΊ, ΠΎΠ±ΡΠ°Π·ΡΠ΅Ρ Π΄ΡΠ³Ρ, ΡΠ΅ΠΌΠΏΠ΅ΡΠ°ΡΡΡΠ° ΠΊΠΎΡΠΎΡΠΎΠΉ Π΄ΠΎΡ
ΠΎΠ΄ΠΈΡ Π΄ΠΎ 3500 Β° Π‘. ΠΡΠΈ ΡΠ²Π°ΡΠΊΠ΅ ΠΌΠ΅ΡΠ°Π»Π»ΠΈΡΠ΅ΡΠΊΠΈΠΉ ΡΠ»Π΅ΠΊΡΡΠΎΠ΄ ΠΏΠ»Π°Π²ΠΈΡΡΡ, ΠΈ ΠΎΠ±ΡΠ°Π·ΡΡΡΠΈΠΉΡΡ ΠΆΠΈΠ΄ΠΊΠΈΠΉ ΠΌΠ΅ΡΠ°Π»Π» Π·Π°ΠΏΠΎΠ»Π½ΡΠ΅Ρ ΡΠΎΠ². ΠΠ°ΡΠ΅ΡΡΠ²ΠΎ ΡΠ²Π° Π·Π°Π²ΠΈΡΠΈΡ ΠΎΡ ΡΠΎΡΡΠ°Π²Π° ΡΠ»Π΅ΠΊΡΡΠΎΠ΄Π°.
ΠΠΎΠΌΠΎΠΆΠ΅ΠΌ Π½Π°ΠΏΠΈΡΠ°ΡΡ Π»ΡΠ±ΡΡ ΡΠ°Π±ΠΎΡΡ Π½Π° Π°Π½Π°Π»ΠΎΠ³ΠΈΡΠ½ΡΡ ΡΠ΅ΠΌΡ
ΠΠΎΠ»ΡΡΠΈΡΡ Π²ΡΠΏΠΎΠ»Π½Π΅Π½Π½ΡΡ ΡΠ°Π±ΠΎΡΡ ΠΈΠ»ΠΈ ΠΊΠΎΠ½ΡΡΠ»ΡΡΠ°ΡΠΈΡ ΡΠΏΠ΅ΡΠΈΠ°Π»ΠΈΡΡΠ° ΠΏΠΎ Π²Π°ΡΠ΅ΠΌΡ ΡΡΠ΅Π±Π½ΠΎΠΌΡ ΠΏΡΠΎΠ΅ΠΊΡΡ
Π£Π·Π½Π°ΡΡ ΡΡΠΎΠΈΠΌΠΎΡΡΡ ΠΠΎΠ΄Π΅Π»ΠΈΡΡ Ρ Π΄ΡΡΠ·ΡΡΠΌΠΈΠΠ»Π°ΡΡΠΈΡΠΈΠΊΠ°ΡΠΈΡ Π²ΠΈΠ΄ΠΎΠ² ΠΈ ΡΠΏΠΎΡΠΎΠ±ΠΎΠ² ΡΠ²Π°ΡΠΊΠΈ Π΄Π»Ρ ΡΠ²Π°ΡΡΠΈΠΊΠΎΠ²
ΠΡΠ»ΠΈΡΠ½ΠΎΠ³ΠΎ ΡΠ²Π°ΡΠ½ΠΎΠ³ΠΎ ΡΠΎΠ΅Π΄ΠΈΠ½Π΅Π½ΠΈΡ ΠΌΠΎΠΆΠ½ΠΎ Π΄ΠΎΠ±ΠΈΡΡΡΡ ΠΎΠ΄Π½ΠΈΠΌ ΠΈΠ· ΡΡΡΡ ΠΈΠ·Π²Π΅ΡΡΠ½ΡΡ Π²ΠΈΠ΄ΠΎΠ² ΡΠ²Π°ΡΠΊΠΈ: ΠΏΠΎΠ΄ Π΄Π°Π²Π»Π΅Π½ΠΈΠ΅ΠΌ, ΡΠΏΠ»Π°Π²Π»Π΅Π½ΠΈΠ΅ΠΌ ΠΈ ΡΠ΅ΡΠΌΠΎΠΌΠ΅Ρ Π°Π½ΠΈΡΠ΅ΡΠΊΠΈΠΌ ΠΌΠ΅ΡΠΎΠ΄ΠΎΠΌ.Π ΡΡΠΎΠΉ ΡΡΠ°ΡΡΠ΅ ΠΌΡ ΡΠ°ΡΡΠΌΠΎΡΡΠΈΠΌ Π²ΡΠ΅ ΡΡΠΈ Π²Π°ΡΠΈΠ°Π½ΡΠ°, ΡΠ²Π°ΡΠΎΡΠ½ΡΠ΅ Π°ΠΏΠΏΠ°ΡΠ°ΡΡ ΠΌΠΎΠΆΠ½ΠΎ ΠΏΠΎΡΠΌΠΎΡΡΠ΅ΡΡ Π² ΠΊΠ°ΡΠ°Π»ΠΎΠ³Π΅ ΡΠΎΠ²Π°ΡΠΎΠ² ΡΠ°Π·Π΄Π΅Π»Π° ΡΠ²Π°ΡΠΎΡΠ½ΠΎΠ΅ ΠΎΠ±ΠΎΡΡΠ΄ΠΎΠ²Π°Π½ΠΈΠ΅ — ΡΠ²Π°ΡΠΎΡΠ½ΡΠ΅ Π°ΠΏΠΏΠ°ΡΠ°ΡΡ.
ΠΠ»Ρ ΠΏΠ΅ΡΠ²ΠΎΠ³ΠΎ ΠΌΠ΅ΡΠΎΠ΄Π° Ρ
Π°ΡΠ°ΠΊΡΠ΅ΡΠ½ΠΎ ΠΌΠ΅Ρ
Π°Π½ΠΈΡΠ΅ΡΠΊΠΎΠ΅ Π²ΠΎΠ·Π΄Π΅ΠΉΡΡΠ²ΠΈΠ΅. ΠΠΎΠ΄ Π±ΠΎΠ»ΡΡΠΈΠΌ Π΄Π°Π²Π»Π΅Π½ΠΈΠ΅ΠΌ, Π΄Π΅ΡΠΎΡΠΌΠΈΡΠΎΠ²Π°Π½Π½ΡΠΉ ΠΌΠ΅ΡΠ°Π»Π» ΡΡΠ°Π½ΠΎΠ²ΠΈΡΡΡ ΡΠ΅ΠΊΡΡΠΈΠΌ ΠΈ ΠΏΠ΅ΡΠ΅ΠΌΠ΅ΡΠ°Π΅ΡΡΡ ΠΏΠΎ ΠΏΠΎΠ²Π΅ΡΡ
Π½ΠΎΡΡΠΈ, Π²ΡΡΡΠΏΠ°Π΅Ρ Π² ΡΠ΅Π°ΠΊΡΠΈΡ Ρ ΠΏΠΎΠΌΠΎΡΡΡ ΡΠ°ΡΡΡΠΌΠΈ, ΡΡΠΎ ΠΈΡ
Π½Π°Π΄ΡΠΆΠ½ΠΎΠΌΡ ΡΠΎΠ΅Π΄ΠΈΠ½Π΅Π½ΠΈΡ.
Π‘Π²Π°ΡΠΊΡ ΠΏΠ»Π°Π²Π»Π΅Π½ΠΈΠ΅ΠΌ Π±Π΅Π· Π΄Π°Π²Π»Π΅Π½ΠΈΡ Π½Π° ΡΠΎΠ΅Π΄ΠΈΠ½ΡΠ΅ΠΌΡΠ΅ ΠΈΠ·Π΄Π΅Π»ΠΈΡ. ΠΠ»Π°Π²Π½ΡΠΌ ΠΈΡΡΠΎΡΠ½ΠΈΠΊΠΎΠΌ ΡΠ΅ΠΏΠ»Π° ΡΠ²Π»ΡΠ΅ΡΡΡ ΡΠ²Π°ΡΠΎΡΠ½Π°Ρ Π΄ΡΠ³Π°.
ΠΠ½Π° Π½Π°Π³ΡΠ΅Π²Π°Π΅Ρ ΠΌΠ΅ΡΠ°Π»Π» Π΄ΠΎ Π΅Π³ΠΎ ΠΏΠ»Π°Π²Π»Π΅Π½ΠΈΡ, ΠΏΠΎΡΠ»Π΅ ΡΠ΅Π³ΠΎ ΠΏΡΠΎΠΈΡΡ ΠΎΠ΄ΠΈΡ ΡΠΎΠ΅Π΄ΠΈΠ½Π΅Π½ΠΈΠ΅. ΠΡΡΡΠ², ΡΠ°ΡΠΏΠ»Π°Π² ΠΎΠ±ΡΠ°Π·ΡΠ΅Ρ ΡΠΎΠ².
ΠΠΎΡΠ»Π΅Π΄Π½ΠΈΠΉ ΡΠΈΠΏ ΠΏΡΠ΅Π΄ΡΡΠ°Π²Π»ΡΠ΅Ρ ΡΠΎΠ±ΠΎΠΉ Π³ΠΈΠ±ΡΠΈΠ΄ Π΄Π²ΡΡ ΠΏΠ΅ΡΠ²ΡΡ — ΡΠ½Π°ΡΠ°Π»Π° Π·Π°Π³ΠΎΡΠΎΠ²ΠΊΠΈ Π½Π°Π³ΡΠ΅Π²Π°ΡΡΡΡ, Π° ΠΎΠ½ΠΈ ΡΠΎΠ΅Π΄ΠΈΠ½ΡΡΡΡΡ ΠΏΡΡΡΠΌ ΠΌΠ΅Ρ Π°Π½ΠΈΡΠ΅ΡΠΊΠΎΠ³ΠΎ Π΄Π°Π²Π»Π΅Π½ΠΈΡ.
Π‘ΠΎΠ·Π΄Π°Π½ΠΈΠ΅ ΡΠΏΠ»ΠΎΡΠ½ΠΎΠ³ΠΎ ΡΠ²Π° ΠΎΡΡΡΠ΅ΡΡΠ²Π»ΡΠ΅ΡΡΡ ΠΏΡΡΡΠΌ ΡΠ°ΡΠΏΠ»Π°Π²Π»Π΅Π½ΠΈΡ ΠΌΠ΅ΡΠ°Π»Π»Π° Π² ΡΡΡΠ°Π½ΠΎΠ²Π»Π΅Π½Π½ΡΡ ΠΌΠ΅ΡΡΠ°Ρ .
ΠΠΌΠΏΡΠ»ΡΡΠ½Π°Ρ Π΄ΡΠ³Π° Π·Π°ΠΌΠ΅ΡΠ½ΠΎ ΡΠ°ΡΡΠΈΡΡΠ΅Ρ Π²ΠΎΠ·ΠΌΠΎΠΆΠ½ΠΎΡΡΡ ΠΊΠ»Π°ΡΡΠΈΡΠ΅ΡΠΊΠΎΠΉ ΡΠ²Π°ΡΠΊΠΈ Π΄ΡΠ³ΠΎΠΉ, ΠΏΡΠΎΠ²ΠΎΠ΄ΠΈΠΌΠΎΠΉ Π² ΡΡΠ΅Π΄Π΅ Π·Π°ΡΠΈΡΠ½ΡΡ Π³Π°Π·ΠΎΠ².
ΠΠΎ Π²ΡΠ΅ΠΌΡ ΡΠ²Π°ΡΠΊΠΈ Π½Π΅ΠΏΠ»Π°Π²ΡΡΠΈΠΌΡΡ ΡΠ»Π΅ΠΊΡΡΠΎΠ΄ΠΎΠΌ ΠΏΡΠΎΠΈΡΡ ΠΎΠ΄ΠΈΡ Π²ΠΎΠ·Π΄Π΅ΠΉΡΡΠ²ΠΈΠ΅ ΠΈΠΌΠΏΡΠ»ΡΡΠ½ΠΎΠΉ Π΄ΡΠ³ΠΈ Π½Π° ΠΌΠ΅ΡΠ°Π»Π»ΠΈΡΠ΅ΡΠΊΡΡ ΠΏΠΎΠ²Π΅ΡΡ Π½ΠΎΡΡΡ, Π² ΡΠ΅Π·ΡΠ»ΡΡΠ°ΡΠ΅ ΡΠ΅Π³ΠΎ ΠΎΠ±ΡΠ°Π·ΡΠ΅ΡΡΡ ΡΠΎΠ².
Π‘Π²Π°ΡΠΊΠ° ΠΏΠ»Π°Π²ΡΡΠΈΠΌΡΡ ΡΠ»Π΅ΠΊΡΡΠΎΠ΄ΠΎΠΌ ΠΏΠΎΠ·Π²ΠΎΠ»ΡΠ΅Ρ ΡΠ΅Π³ΡΠ»ΠΈΡΠΎΠ²Π°ΡΡ ΠΎΠΏΠ΅ΡΠ°ΡΠΈΡ ΠΏΠ»Π°Π²Π»Π΅Π½ΠΈΡ ΠΈ ΠΏΠ΅ΡΠ΅ΠΌΠ΅ΡΠ΅Π½ΠΈΡ ΡΠ»Π΅ΠΊΡΡΠΎΠ΄Π½ΠΎΠ³ΠΎ ΠΌΠ΅ΡΠ°Π»Π»Π°.
ΠΠ°ΠΆΠ½Π΅ΠΉΡΠΈΠΌ ΠΏΠ°ΡΠ°ΠΌΠ΅ΡΡΠΎΠΌ ΡΠ΅Ρ
Π½ΠΎΠ»ΠΎΠ³ΠΈΠΈ ΡΠ²Π»ΡΠ΅ΡΡΡ Π΄Π»ΠΈΡΠ΅Π»ΡΠ½ΠΎΡΡΡ ΠΈΠΌΠΏΡΠ»ΡΡΠΎΠ² Ρ ΠΏΠ°ΡΠ·Π°ΠΌΠΈ ΠΎΠ±ΡΠ΅Π³ΠΎ ΠΈ ΡΠΈΠΊΠ»Π° ΡΠΎΡΠ΅ΡΠ½ΠΎΠ³ΠΎ ΡΠΎ ΡΠΊΠΎΡΠΎΡΡΡΡ ΡΠ²Π°ΡΠΊΠΈ. ΠΠΎΠ·ΠΌΠΎΠΆΠ½ΠΎΡΡΡ ΠΈΡ
ΡΠ΅Π³ΡΠ»ΠΈΡΠΎΠ²Π°Π½ΠΈΡ ΠΏΠΎΠ·Π²ΠΎΠ»ΡΠ΅Ρ ΡΠΏΡΠ°Π²Π»ΡΡΡ Π΄Π΅ΠΉΡΡΠ²ΠΈΠ΅ΠΌ Π½Π° ΡΠ°Π·ΠΌΠ΅ΡΡ, ΡΠΎΡΠΌΡ Π·ΠΎΠ½Ρ, ΠΎΠ±ΡΠ°Π·ΠΎΠ²Π°Π½ΠΈΠ΅ ΡΠ²Π° ΠΈ ΠΏΡΠΎΡΠ΅Π³ΠΎ.
ΠΠ° ΠΏΠ΅ΡΠΈΠΎΠ΄ ΠΌΠ°ΠΊΡΠΈΠΌΠ°Π»ΡΠ½ΠΎΠ³ΠΎ ΡΡΡΠ΅ΠΊΡΠ° Π΄Π°Π½Π½ΡΠΉ ΡΠ΅ΠΆΠΈΠΌ ΠΎΠ±Π΅ΡΠΏΠ΅ΡΠΈΠ²Π°Π΅Ρ ΡΠ°Π±ΠΎΡΡ Ρ Π°Π»ΡΠΌΠΈΠ½ΠΈΠ΅Π²ΡΠΌΠΈ Π΄Π΅ΡΠ°Π»ΡΠΌΠΈ ΡΠΎΠ»ΡΠΈΠ½ΠΎΠΉ ΠΌΠ΅Π½Π΅Π΅ ΡΡΡΡ ΠΌΠΈΠ»Π»ΠΈΠΌΠ΅ΡΡΠΎΠ².
ΠΠ»ΡΡΠΎΠΌ ΡΠ²Π»ΡΠ΅ΡΡΡ ΠΈ ΡΠ°ΡΠΈΠΎΠ½Π°Π»ΡΠ½ΠΎΠ΅ ΠΏΡΠΈΠΌΠ΅Π½Π΅Π½ΠΈΠ΅ ΠΏΠΎΠ²Π΅ΡΡ Π½ΠΎΡΡΠ½ΠΎΠ³ΠΎ Π½Π°ΡΡΠΆΠ΅Π½ΠΈΡ, ΡΡΠΎ ΠΏΠΎΠ·Π²ΠΎΠ»ΡΠ΅Ρ ΡΠΎΡΠΌΠΈΡΠΎΠ²Π°ΡΡ ΡΠΎΠ² Π² Π»ΡΠ±ΠΎΠΌ ΠΏΠΎΠ»ΠΎΠΆΠ΅Π½ΠΈΠΈ ΠΎΠ±ΡΠ΅ΠΊΡΠ°.
ΠΠΎΡΡΠΎΠΌΡ Π½Π΅ ΡΠ΄ΠΈΠ²ΠΈΡΠ΅Π»ΡΠ½ΠΎ Π°ΠΊΡΠΈΠ²Π½ΠΎΠ΅ ΠΈΡΠΏΠΎΠ»ΡΠ·ΠΎΠ²Π°Π½ΠΈΠ΅ ΠΈΠΌΠΏΡΠ»ΡΡΠΈΠ²Π½ΠΎΠΉ ΡΠ²Π°ΡΠΊΠΈ Π² ΡΠ°Π±ΠΎΡΠ°Ρ Π½Π° Π²Π΅ΡΡΠΈΠΊΠ°Π»ΡΠ½ΡΡ ΠΈ Π³ΠΎΡΠΈΠ·ΠΎΠ½ΡΠ°Π»ΡΠ½ΡΡ Π½Π°ΠΏΡΠ°Π²Π»Π΅Π½ΠΈΡΡ — ΠΏΡΠΈ Π²Π°ΡΠΊΠ΅ ΠΌΠ΅ΡΠ°Π»Π»ΠΈΡΠ΅ΡΠΊΠΈΡ ΠΈΠ·Π΄Π΅Π»ΠΈΠΉ ΡΠΎΠ»ΡΠΈΠ½Ρ ΠΈ ΡΠΎΠ΅Π΄ΠΈΠ½Π΅Π½ΠΈΠΈ ΡΡΠ°Π³ΠΌΠ΅Π½ΡΠΎΠ² ΡΡΡΠ±Ρ, ΠΈΠΌΠ΅ΡΡΠΈΡ Π½Π΅ΠΏΠΎΠ²ΠΎΡΠΎΡΠ½ΡΠ΅ ΡΡΡΠΊΠΈ.
ΠΡΡΠΎΡΠ½ΠΈΠΊΠΎΠΌ ΠΏΠΈΡΠ°Π½ΠΈΡ ΡΡΠΎΠ³ΠΎ Π²ΠΈΠ΄Π° Π°ΠΏΠΏΠ°ΡΠ°ΡΠΎΠ² ΠΎΠ±ΡΡΠ½ΠΎ ΠΏΡΠ΅ΠΎΠ±ΡΠ°Π·ΠΎΠ²Π°ΡΠ΅Π»ΠΈ, ΡΡΠ½ΠΊΡΠΈΠΎΠ½ΠΈΡΡΡΡΠΈΠ΅ Π½Π° ΠΏΠΎΡΡΠΎΡΠ½Π½ΠΎΠΌ ΡΠΎΠΊΠ΅.Π Π½ΠΈΡ ΠΏΠ»Π°Π²ΡΡΠΈΠ΅ΡΡ ΡΠ»Π΅ΠΊΡΡΠΎΠ΄Ρ Π»ΡΡΡΠ΅ ΠΈΡΠΏΠΎΠ»ΡΠ·ΠΎΠ²Π°ΡΡ ΠΏΡΠΈ ΠΏΠΎΡΡΠΎΡΠ½Π½ΠΎΠΌ Π³ΠΎΡΠ΅Π½ΠΈΠΈ Π΄ΡΠ³ΠΈ Ρ ΠΏΠ΅ΡΠΈΠΎΠ΄ΠΈΡΠ΅ΡΠΊΠΎΠΉ Π½Π°ΠΊΠ»Π°Π΄ΠΊΠΎΠΉ Π½Π° ΠΎΠ±ΡΡΠ½ΡΠΉ ΡΠ²Π°ΡΠΎΡΠ½ΡΠΉ ΡΠΎΠΊ ΠΈΠΌΠΏΡΠ»ΡΡΠΈΠ²Π½ΠΎΠ³ΠΎ.
ΠΡΠΌΠ΅ΡΠ°Π΅ΡΡΡ ΠΏΡΠ΅ΠΎΠ±Π»Π°Π΄Π°Π½ΠΈΠ΅ ΡΠ»Π΅ΠΊΡΡΠΎΠ΄ΠΈΠ½Π°ΠΌΠΈΡΠ΅ΡΠΊΠΎΠΉ ΡΠΈΠ»Ρ, Π²ΡΠ·ΡΠ²Π°ΡΡΠ΅ΠΉ ΠΎΡΠ΄Π΅Π»Π΅Π½ΠΈΠ΅ ΠΊΠ°ΠΏΠ»ΠΈ. ΠΡΠΎ ΠΏΡΠΈΠ²ΠΎΠ΄ΠΈΡ Π½Π°ΠΏΡΠ°Π²Π»Π΅Π½Π½ΠΎΠΌΡ ΠΏΠ΅ΡΠ΅Π½ΠΎΡΡ ΠΌΠ΅ΡΠ°Π»Π»Π° ΠΏΠΎ ΡΠ°ΡΡΠΎΡΠ΅ ΡΠΎΠΈΠ·ΠΌΠ΅ΡΠΈΠΌΠΎΠΌΡ Ρ ΠΈΠΌΠΏΡΠ»ΡΡΠ°ΠΌΠΈ ΠΏΡΠΈ Π·Π½Π°ΡΠ΅Π½ΠΈΠΈ ΡΠΎΠΊΠ°, ΠΌΠ΅Π½ΡΡΠ΅Π³ΠΎ, ΡΠ΅ΠΌ ΠΊΡΠΈΡΠΈΡΠ΅ΡΠΊΠΎΠ΅.
ΠΡΠΎΠ±Π΅Π½Π½ΠΎΡΡΠΈ ΡΠ»Π΅ΠΊΡΡΠΎΡΠ»Π°ΠΊΠΎΠ²ΠΎΠΉ ΡΠ²Π°ΡΠΊΠΈ
ΠΡΠΎ Π½ΠΎΠ²ΡΠΉ ΡΠΈΠΏΠΎΠΌ, ΠΏΡΠΈ ΠΏΠΎΠΌΠΎΡΠΈ ΠΊΠΎΡΠΎΡΠΎΠ³ΠΎ ΠΌΠΎΠΆΠ½ΠΎ ΡΠΎΠ΅Π΄ΠΈΠ½ΠΈΡΡ Π΄Π΅ΡΠ°Π»ΠΈ Π·Π° ΠΎΠ΄ΠΈΠ½ ΡΠ°Π·.
ΠΡΠΎΠ±Π΅Π½Π½ΠΎΡΡΡ ΠΌΠ΅ΡΠΎΠ΄Π° Π² ΡΠΎΠΌ, ΡΡΠΎ Π½Π° ΠΏΠΎΠ²Π΅ΡΡ Π½ΠΎΡΡΠΈ Π΄Π΅ΡΠ°Π»Π΅ΠΉ Π½Π°Π½ΠΎΡΠΈΡΡΡ ΡΠ»ΠΎΠΉ ΡΠ»Π°ΠΊΠ°, Π΄Π»Ρ ΡΠ°ΡΠΏΠ»Π°Π²Π»Π΅Π½ΠΈΡ ΠΊΠΎΡΠΎΡΠΎΠ³ΠΎ ΡΡΠ΅Π±ΡΠ΅ΡΡΡ Π±ΠΎΠ»ΡΡΠ°Ρ ΡΠ΅ΠΌΠΏΠ΅ΡΠ°ΡΡΡΠ°, ΡΠ΅ΠΌ Π΄Π»Ρ ΠΏΠ»Π°Π²Π»Π΅Π½ΠΈΡ Π·Π°Π³ΠΎΡΠΎΠ²ΠΊΠΈ.
ΠΠ°ΡΠ°Π»ΠΎ Π΄Π°Π½Π½ΠΎΠΉ ΠΌΠ΅ΡΠΎΠ΄ΠΈΠΊΠΈ ΡΡ ΠΎΠΆΠ΅ Ρ ΡΠΎΠ΅Π΄ΠΈΠ½Π΅Π½ΠΈΠ΅ΠΌ Ρ ΠΏΠΎΠΌΠΎΡΡΡ Π°Π²ΡΠΎΠΌΠ°ΡΠΈΡΠ΅ΡΠΊΠΎΠΉ ΡΠ²Π°ΡΠΊΠΈ Ρ ΠΏΡΠΈΠΌΠ΅Π½Π΅Π½ΠΈΠ΅ΠΌ ΡΠ»ΡΡΠ°.
ΠΠΎΡΠ»Π΅ ΠΏΠΎΠ»Π½ΠΎΠ³ΠΎ ΡΠ°ΡΠΏΠ»Π°Π²Π»Π΅Π½ΠΈΡ ΡΠ»Π°ΠΊΠ° ΠΏΡΠ΅ΠΊΡΠ°ΡΠ΅Π½ΠΈΡ Π³ΠΎΡΠ΅Π½ΠΈΡ Π΄ΡΠ³ΠΈ, ΠΊΡΠΎΠΌΠΊΠΈ ΡΠΎΠ΅Π΄ΠΈΠ½ΡΠ΅ΠΌΡΡ Π΄Π΅ΡΠ°Π»Π΅ΠΉ ΠΎΠΏΠ»Π°Π²Π»ΠΈΠ²Π°ΡΡΡΡ Π·Π° ΡΡΡΡ ΡΠ΅ΠΏΠ»Π°, ΠΎΠ±ΡΠ°Π·ΡΡΡΠ΅Π³ΠΎΡΡ ΠΏΡΠΈ ΠΏΡΠΎΡ ΠΎΠΆΠ΄Π΅Π½ΠΈΠΈ ΡΠΊΠ²ΠΎΠ·Ρ ΡΠ°ΡΠΏΠ»Π°Π² ΡΠΎΠΊΠ°. ΠΠ°Π½Π½ΡΠΉ Π²Π°ΡΠΈΠ°Π½Ρ ΠΈΠ΄Π΅Π°Π»ΡΠ½ΠΎ ΠΏΠΎΠ΄Ρ ΠΎΠ΄ΠΈΡ Π΄Π»Ρ ΡΠΎΠ»ΡΡΡΡ ΠΌΠ΅ΡΠ°Π»Π»ΠΈΡΠ΅ΡΠΊΠΈΡ Π΄Π΅ΡΠ°Π»Π΅ΠΉ.
ΠΡΠ°ΠΊΡΠΈΠΊΡΡΡΡΡ ΡΡΠΈ ΠΊΠ»Π°ΡΡΠΈΡΠΈΠΊΠ°ΡΠΈΠΈ:
- ΠΏΡΠΈ 1-ΠΌ ΡΠΈΠΏΠ΅ ΡΠ»Π΅ΠΊΡΡΠΎΠ΄Π½Π°Ρ ΠΏΡΠΎΠ²ΠΎΠ»ΠΎΠΊΠ° ΠΏΠΎΠ΄Π°ΡΡΡΡ Π² ΡΠ»Π°ΠΊΠΎΠ²ΡΡ Π²Π°Π½Π½Ρ ΠΏΠΎ ΠΌΠ΅ΡΠ΅ ΡΠ°ΡΠΏΠ»Π°Π²Π»Π΅Π½ΠΈΡ.ΠΡΠ΅Π΄ΠΏΠΎΠ»Π°Π³Π°Π΅ΡΡΡ, ΡΡΠΎ ΡΠ»Π΅ΠΊΡΡΠΎΠ΄ ΠΈΠΌΠ΅Π΅Ρ Π²ΠΎΠ·Π²ΡΠ°ΡΠ½ΠΎ-ΠΏΠΎΡΡΡΠΏΠ°ΡΠ΅Π»ΡΠ½ΠΎΠ΅ Π΄Π²ΠΈΠΆΠ΅Π½ΠΈΠ΅ ΠΏΠΎ Π³ΠΎΡΠΈΠ·ΠΎΠ½ΡΠ°Π»ΡΠ½ΠΎΠΉ ΠΏΠ»ΠΎΡΠΊΠΎΡΡΠΈ, ΡΡΠΎ ΠΏΠΎΠ·Π²ΠΎΠ»ΡΠ΅Ρ ΡΠ°Π²Π½ΠΎΠΌΠ΅ΡΠ½ΠΎ ΠΏΡΠΎΠ³ΡΠ΅ΡΡ ΡΠΎΠ΅Π΄ΠΈΠ½ΡΠ΅ΠΌΡΠ΅ Π΄Π΅ΡΠ°Π»ΠΈ Π½Π° Π²ΡΡ ΡΠΎΠ»ΡΠΈΠ½Ρ;
- Π΄Π»Ρ Π²ΡΠΎΡΠΎΠ³ΠΎ Π²ΠΈΠ΄Π° Ρ Π°ΡΠ°ΠΊΡΠ΅ΡΠ½ΠΎ ΠΈΡΠΏΠΎΠ»ΡΠ·ΠΎΠ²Π°Π½ΠΈΠ΅ ΠΈΠ»ΠΈ ΠΏΠ»Π°ΡΡΠΈΠ½Ρ ΡΠ»Π΅ΠΊΡΡΠΎΠ΄Π° Ρ Π±ΠΎΠ»ΡΡΠΈΠΌ Π΄ΠΈΠ°ΠΌΠ΅ΡΡΠΎΠΌ. ΠΠ°ΡΠΈΠΊΡΠΈΡΠΎΠ²Π°Π½Π½Π°Ρ Π² Π·Π°Π·ΠΎΡΠ΅ ΠΏΠ»Π°ΡΡΠΈΠ½Π°Π·ΠΎΡ ΠΎΠΊΠ°Π·ΡΠ²Π°Π΅ΡΡΡ Π² ΡΠ»Π°ΠΊΠΎΠ²ΠΎΠΉ Π²Π°Π½Π½Π΅, ΠΊΠΎΠ³Π΄Π° Π½Π΅ Ρ Π²Π°ΡΠ°Π΅Ρ ΡΠ°ΡΠΏΠ»Π°Π²Π»Π΅Π½Π½ΠΎΠ³ΠΎ ΠΌΠ΅ΡΠ°Π»Π»Π°, Π° Π³Π°Π±Π°ΡΠΈΡΠ½ΡΠΉ ΡΠ»Π΅ΠΊΡΡΠΎΠ΄ ΠΏΡΠΎΡΡΠΎ ΠΏΠ΅ΡΠ΅ΠΊΡΡΠ²Π°Π΅Ρ Π·Π°Π·ΠΎΡ;
- Π²ΠΎΠ·Π½ΠΈΠΊΠ°Π΅Ρ ΡΡΠ΅ΡΠΈΠΉ Π²ΠΈΠ΄ ΠΏΡΠΈ ΠΈΡΠΏΠΎΠ»ΡΠ·ΠΎΠ²Π°Π½ΠΈΠΈ ΠΏΠ»Π°Π²ΡΡΠ΅Π³ΠΎ ΠΌΡΠ½Π΄ΡΡΡΠΊΠ°.