Автоматическая сварка под флюсом: технология и применение
Екатерина
Любому практикующему сварщику известно, что кислород оказывает негативное влияние на качество и долговечность шва. Попадая в сварочную ванну кислород способствует повышенному окислению и становится причиной трещин. Чтобы избавиться от этой проблемы существует множество способов: начиная от специальной обработки металла, заканчивая применением особых комплектующих, например, флюсов.
Один из наиболее популярных методов качественного соединения металлов — автоматическая сварка под слоем флюса. С ее помощью можно сварить такие непростые металлы, как медь, алюминий и нержавеющую сталь. Автоматическая сварка ускоряет и упрощает работу, а флюс выполняет защитную функцию. В этой статье мы кратко расскажем, что такое автоматическая дуговая сварка под флюсом и какова техника автоматической сварки под флюсом.
Содержание статьи
- Общая информация
- Область применения
- Роль флюса
- Виды применяемых флюсов
- Достоинства и недостатки
- Технология сварки
- Вместо заключения
Общая информация
Автоматическая дуговая сварка под слоем флюса — это технология, суть которой ничем не отличается от классической дуговой сварки. Металл плавится из-за высокой температуры, которая формируется благодаря электрической дуге. Ниже изображена схема автоматической дуговой сварки под флюсом.
Отличие автоматической сварки от любой другой заключается лишь в том, что большинство процессов выполняется не вручную, а с помощью специальных станков. Например, подача проволоки и движение дуги. Ну а в нашем конкретном случае все эти операции производятся под слоем флюса, нанесенного на поверхность металла.
Область применения
Автоматическая наплавка под флюсом применяется во многих сферах. С ее помощью можно организовать быстрое крупносерийное производство, в том числе конвейерное. По этой причине данная технология незаменима при сборке кораблей, производстве крупногабаритных труб и емкостей для нефтеперерабатывающей отрасли. Автоматическая сварка обеспечивает высокое качество швов, поэтому завоевала свое уважение в таких ответственных отраслях.
Роль флюса
С автоматической сваркой все ясно. А вот что насчет флюса? Что это такое?
Флюс — это специальное вещество (может выпускаться в виде порошка, гранул, паст и жидкостей), обладающее положительными свойствами. Флюсы толстым слоем подаются прямо в сварочную зону, защищая ее от негативного влияния кислорода. Также флюс защищает сам металл, способствует устойчивому горению дуги, уменьшает вероятность разбрызгивания металла и даже изменяет химический состав шва при необходимости.
Виды применяемых флюсов
Перед тем, как провести сварку под флюсом, неплохо было бы узнать, какие вообще бывать разновидности. Прежде всего, всю флюсы делятся по назначению. Они могут быть для сварки углеродистых и легированных сталей, для высоколегированных сталей и для цветных металлов. Это первое, на что стоит обратить внимание перед покупкой флюса.
Также флюсы могут быть плавлеными или керамическими. Их отличие в составе. В большинстве случаев используется именно плавленый флюс, поскольку он относительно универсальный и стоит недорого. С его помощью можно эффективно защитить сварочную ванну от кислорода. Но не ждите от плавленого флюса каких-то особых качеств. Если вам необходимы действительно отличные свойства шва, то выберите керамический флюс. Он обеспечивает отличное качество.
Также флюсы могут быть химически активными и химически пассивными. Активный флюс содержит в составе кислоты, способные не только защитить металл при сварке, но и привести к коррозии. Так что тщательно удаляйте флюс после работы. Пассивные флюсы в автоматической сварке не применяются, поскольку не обладают достаточными для этого свойствами. Зачастую вы встретите пассивный вещества при пайке в виде воска или канифоли.
Кстати, о производителях. Это давний спор всех начинающих и опытных сварщиков. Кто-то считает, что отечественные компании производят недорогой и эффективный флюс, а кто-то всеми руками за импортные комплектующие. Мы не будем однозначно говорить, что лучше, скажем лишь то, что на практике и отечественные, и импортные флюсы показывают себя хорошо, если соблюдена технология сварки.
Достоинства и недостатки
У автоматической сварки с применением флюса есть много плюсов. Ее главное достоинство — возможность полной автоматизации процесса сварки. От сварщика не нужно даже уметь варить, достаточно знать, как настроить оборудование. Также такой метод сварки гарантирует отличное качество сварочных соединений, поскольку отсутствует человеческий фактор.
У технологии сварки деталей автоматической наплавкой под слоем флюса есть и недостатки. Во-первых, вы сможете варить только нижний швы. Также детали должны быть очень точно подогнаны, ведь машина формирует шов в четко заданном месте, и любая ошибка при стыковке приведет к браку. Кроме того, нужна очень тщательная подготовка металла перед сваркой.
Учтите, что у вас не получится сварить металл на весу. Деталь нужно будет зафиксировать на горизонтальной поверхности и предварительно проварить корень сварного соединения. Еще один существенный недостаток — большая стоимость как оборудования для автоматической сварки, так и комплектующих.
Теперь, когда вам все известно, пора узнать, какова технология автоматической сварки под флюсом.
Технология сварки
Прежде всего, перед сваркой необходимо подготовить металл. Для каждого металла подготовка своя, но мы дадим общие рекомендации. Нужно очистить деталь от грязи, краски и коррозии. Затем нужна тщательная зачистка поверхности с помощью металлической щетки или шлифовального круга. Только после подготовительных операций можно приступать к сварке.
Технология сварки под флюсом проста за счет того, что многие процессы выполняет не человек, а машина. Мастеру не нужна зажигать дугу, следить за ее стабильностью, выбирать скорость подачи проволоки и так далее. Все, что от вас требуется — правильно настроить режимы сварки под флюсом. По сути, задать машине программу действий. Ниже таблица с перечислением режимов автоматической сварки под флюсом.
Это режимы автоматической сварки под флюсом для стыковых соединений. Естественно, существуют и другие типы соединений, поэтому для них нужно произвести расчет режимов сварки. Здесь мы не будем касаться этой темы, поскольку она очень обширна (сколько типов соединений, столько и формул), поэтому изучите эту информацию самостоятельно. В интернете много способов расчета.
При работе также используется специальная присадочная проволока для сварки под флюсом. Ее подача тоже автоматизирована, нужно лишь загрузить бобину в подающий механизм. Рекомендуем приобретать проволоку, изготовленную из того же металла, что и деталь.
Теперь немного о флюсе. Он тоже подается автоматически, только предварительно его нужно насыпать в специальный резервуар. Толщина слоя флюса зависит от толщины свариваемого металла. Чем металл толще, тем больше нужно флюса.
У вас может возникнуть закономерный вопрос: а плавится ли флюс? И влияет ли он на структуру шва? Да, конечно флюс плавится под действием температуры. Но при этом он никак не нарушает структура шва, а лишь улучшает ее. Но при этом застывший флюс превращается в шлак, который после сварки нужно удалить. Остатки неиспользованного флюса можно использовать повторно.
Подобная технология применения флюса при автоматической сварке позволяет существенно увеличить скорость работ, при этом не потеряв в качестве.
Вместо заключения
Похожие публикации
Автоматическая сварка под флюсом — презентация онлайн
Похожие презентации:
Автоматическая и полуавтоматическая сварка под флюсом
Полуавтоматическая сварка в среде защитных газов
Оборудование, применяемое для автоматической и полуавтоматической сварки. Его характеристика
Понятие о сварке и ее сущность
Основы технологии электродуговой сварки
Дуговая сварка
Лекция 5. Сварка металлов. Общие сведения. Физическая сущность сварочной дуги. Тепловое действие сварочной дуги
Автоматическая сварка стыков труб
Сварочные материалы
Сварка. Основные сведения о сварке. Сварочная дуга. (Лекция 8)
1.
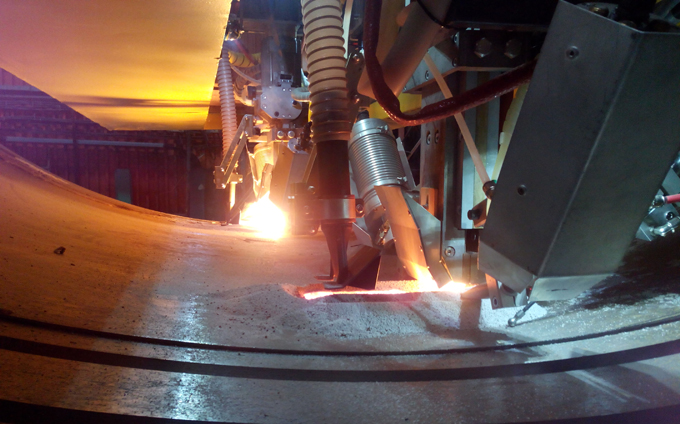
сварка под флюсом
Студент группы 13-03 СП
Громов А.Н.
2. Из истории сварки под флюсом
Идея этого способа сварки появилась не напустом месте.
Еще Н.Г. Славянов применял для защиты
расплавленного металла от воздействия
воздуха битое стекло.
В 1927 г. известный изобретатель Д.С.
Дульчевский, работавший в Одесских
железнодорожных мастерских,
разработал свой первый автомат для
сварки под флюсом.
3. Из истории сварки под флюсом
В 1939–1940 гг. коллективом Институтаэлектросварки под руководством и при
непосредственном участии Е.О. Патона на
основе идей, выдвинутых еще Н.Г. Славяновым,
был разработан отечественный способ
механизированной сварки, получивший тогда
название «скоростная автоматическая
сварка голым электродом под слоем
флюса».
Впервые этот способ соединения металлов был
продемонстрирован в лаборатории Института
электросварки в июле 1940 г.

стыковой шов металла толщиной 13 мм за
один проход с неслыханной для того времени
скоростью 32 м/ч, что во много раз
превышало скорость ручной сварки.
4. Сущность процесса
Сварочная дуга горит между изделием и торцом сварочнойпроволоки. По мере расплавления проволока
автоматически подается в зону сварки. Дуга закрыта
слоем флюса.
Сварочная проволока перемещается в направлении сварки с
помощью специального механизма (автоматическая
сварка) или вручную (полуавтоматическая сварка) .
Под влиянием тепла дуги основной металл и флюс плавятся,
причем флюс образует вокруг зоны сварки эластичную
пленку, изолирующую эту зону от доступа воздуха.
Капли расплавляемого дугой металла сварочной проволоки
переносятся через дуговой промежуток в сварочную ванну,
где смешиваются с расплавленным основным металлом.
По мере перемещения дуги вперед металл сварочной
ванны начинает охлаждаться, так как поступление тепла к
нему уменьшается.
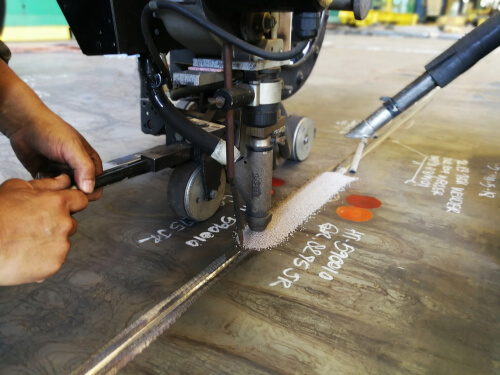
Расплавляясь, флюс превращается в жидкий шлак, который
покрывает поверхность металла и остается жидким еще
некоторое время после того, как металл уже затвердел.
Затем шлак затвердевает, образуя на поверхности шва
шлаковую корку.
Схема сварки под
флюсом
6. 1. Высокая производительность 2. Высокое качество сварки 3. Надежная защита сварочной ванны 4. Улучшаются условия работы
Достоинства сварки подфлюсом
1. ВЫСОКАЯ ПРОИЗВОДИТЕЛЬНОСТЬ
2. ВЫСОКОЕ КАЧЕСТВО СВАРКИ
3. НАДЕЖНАЯ ЗАЩИТА СВАРОЧНОЙ
ВАННЫ
4. УЛУЧШАЮТСЯ УСЛОВИЯ РАБОТЫ
ОПЕРАТОРА
7. Недостаток сварки под флюсом
Возможность сварки только внижнем положении ввиду
возможного стекания
расплавленных флюса и
металла при отклонении
плоскости шва от
горизонтали более чем
на 10-15 градусов.
8. Классификация автоматов для сварки под флюсом по способу перемещения вдоль шва
9. Классификация автоматов для сварки под флюсом по типу плавящегося электрода
10.
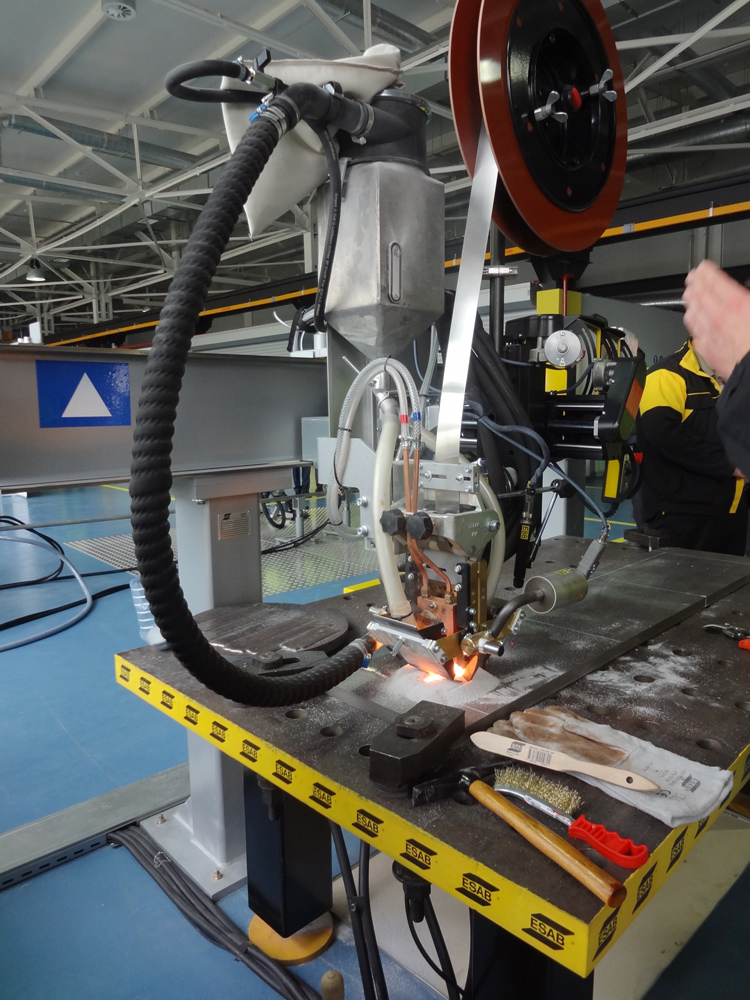
11. Классификация автоматов для сварки под флюсом по роду тока
12. Автоматическая сварка
При автоматической сваркемеханизированы и
автоматизированы следующие
операции:
— подача проволоки,
— подача и уборка флюса,
— поддержание непрерывного
горении дуги,
— перемещение по стыку
свариваемых деталей.
13. Автомат для сварки под флюсом включает следующие основные узлы:
——
—
Источник питания;
Сварочную головку;
Механизмы настроечных или
регулировочных перемещений;
Пульт управления;
Аппаратный шкаф;
Кассету с электродной
проволокой
14. Основные технические характеристики несамоходных автоматов
Модельавтомата
Назначение
Номинальная
сила
сварочного
тока, А
Диаметр
электродной
проволоки,
мм
Скорость
подачи
электродной
проволоки,
м/ч
Источники
питания
А-1416
Сварка под
слоем флюса
при
постоянном
токе
1,0
2,0-5,0
49-509
ВДУ-1202
АДФ1202У2
Сварка под
слоем флюса
1,0
3,0-5,0
60-360
ТДФЖ1002
15.

марка
Номинальный Диаметр
сварочный
электродной
ток, кА
проволоки,
мм
Скорость
подачи
проволоки
мм
Источник
питания
Масса
кг
АДФ1002
1
3,0-5,0
60-360
ТДФЖ1002
45
АДФ1202
1,25
2,0-6,0
60-360
ВДУ1201
78
16. Основные параметры режима дуговой сварки под флюсом
1. Сила сварочного тока, егород и полярность
2. Напряжение дуги
3. Скорость сварки
4. Диаметр и скорость подачи
электродной проволоки
17. Дополнительные параметры
1. Вылет электрода (расстояниеот его торца до мундштука)
2. Наклон электрода или изделия
3. Марка флюса
4. Подготовка кромок
5. Вид сварного соединения
English Русский Правила
Особенности автоматической сварки под флюсом
Содержание
- Что такое сварка под флюсом
- Сварочный флюс – что это
- Режимы сварки под флюсом
- Где применяется сварка флюсом
- Преимущества и недостатки сварки
Для улучшения качества шва, во время проведения сварочных работ используется флюс. Дуга в этом случае горит под слоем порошка, что ограничивает доступ воздуха во время плавления проволоки. Автоматическая сварка под флюсом предназначена для обработки низколегированных, низкоуглеродистых, активных, средне и высоколегированных сталей.
Что такое сварка под флюсом
Сущность сварки под флюсом сводится к тому, что дуга между сварной проволокой и обрабатываемым материалом горит под слоем гранулированного порошка. Под воздействием температуры электрод и гранулы расплавляются. В результате, вокруг сварной ванны создается эластичная пленка, полностью перекрывающая доступ воздуха и защищающая от негативного воздействия дугу и расплавленный металл.
Компоненты флюса по мере остывания превращаются в шлак покрывающий шов. После окончания работ, наплавленная корка легко отстает от металла и удаляется механическим методом. Оставшийся флюс собирается и используется в дальнейшем.
Оборудование для сварки под флюсом можно разделить на две категории:
- Роботизированная автоматическая сварка под слоем флюса угловых швов и ровных поверхностей.
Направление, скорость движения электрода задает машина. Роботизированный способ отличается максимальным качеством наложения сварного шва, прочностью соединения и скоростью работы.
В последнее время широко используется так называемая тандемная сварка – когда два электрода располагаются в одной плоскости параллельно друг другу. Технология автоматической сварки под флюсом в тандеме, существенно увеличивает качество сварного шва и скорость выполняемых работ.
Еще одним преимуществом тандемного метода является быстрое возбуждение дуги, а также минимальный размер сварочной ванны. - Полуавтоматическая сварка. Сварную проволоку направляет сварщик, он же контролирует вылет электрода. Подача проволоки осуществляется автоматически. От мастера требуется выбрать скорость и угол наклона электрода, а также подобрать наиболее подходящую мощность напряжения дуги.
Техника автоматической сварки под слоем флюса подробно описана в ГОСТ 8713 79. В нормах прописаны виды сварных соединений, обеспечивающие максимальную прочность конструкции.
Сварочный флюс – что это
По сути, флюс, это гранулированный порошок с диаметром от 0,2 до 4 мм, используемый для защиты дуги, сварной ванны и наплавляемого металла, от вредного внешнего воздействия.
Во время проведения работ создается флюсовая подушка, основным предназначением которой является:
- Создать надежную защиту сварочной ванны, в виде газового облака и шлака, от воздействия негативных факторов: сырости, пыли, низкой температуры воздуха и т.д.
- Обеспечить стабильную дугу, во время которой будет осуществляться непрерывный процесс формирования шва в сварочной ванне.
- Улучшить качество соединения и обеспечить сварной шов необходимыми свойствами.
- Вывести примеси из металла в зону шлакообразования.
Флюсовые сварочные материалы принято классифицировать на несколько категорий, в зависимости от технологии производства, составу и прямому назначению.
- Способ производства. Существуют плавленые и неплавленые разновидности флюса. Первые, рудоминеральные, предварительно плавятся в печи, после подвергаются дополнительному прокаливанию и формированию в гранулы. Неплавленые или керамические флюсы производят путем смешивания минералов и ферросплавов с добавлением жидкого стекла.
- Химический состав сварочного флюса. Существуют оксидные, солеоксидные и солевые материалы. Каждый из видов порошка используется для определенной цели.
- Область применения сварки под флюсом. Для сварки низколегированных сталей применяют оксидные материалы. Во время работ по переплавке шлака, обработки высоколегированных или углеродистых сталей, а также цветных металлов применяют солевые флюсы. Так как в составе электрода отсутствуют оксиды, обеспечивается чистота шва и сохраняется пластичность соединения. Солевые материалы используют для работ с титаном.
Расход флюса зависит от химического состава и способа производства материала. Также на количество затрат влияет мощность сварочного тока, напряжение дуги и скорость проведения работ.
Наиболее экономичным считается сварочное оборудование для автоматической сварки под флюсом. Блок управления станка рассчитывает оптимальную скорость движения электрода, а также мощность и силу тока. Дефекты сварки под флюсом, в частности, по причине человеческого фактора, сведены к нулю.
При ручной работе с полуавтоматом вносят дополнительные коэффициенты нормирования сварки, связанные с пространственным положением шва и его длиной. Если длина соединения не более 20 см, учитывают коэффициент изменений равный 1,2; от 20-50 см 1,1; свыше полуметра поправка равна 1. Полученный результат помогает точно рассчитать время, необходимое для проведения работ, а также высчитать расход флюсового материала.
Основными причинами образования пор при сварке является водород и азот. При использовании флюса создается защитное облако, не дающее этим веществам вступить в реакцию с расплавленным металлом.
Режимы сварки под флюсом
Особенностью процесса сварки под флюсом является необходимость точного расчета нескольких важных параметров, оказывающих влияние на затраты флюса:
- Род и полярность тока. Источники питания для сварки под флюсом могут быть трансформаторного и инверторного типа. Инвертор использует принцип двойного преобразования электрического тока, в результате давая на выходе стабильные высокочастотные показатели, что приводит к уменьшению расхода порошка.
- Напряжение сварной дуги.
- Диаметр используемой проволоки. Во время сварки флюсовый порошок расходуется на создание шлакового слоя вокруг шва. Соответственно, чем толще используемая проволока и стыки соединения, тем больше нужно будет гранул для защиты. Плавленые сварочные флюсы, как правило, расходуются быстрее, чем керамические. Работы с разделкой кромок также требуют больших затрат флюсового порошка.
- Скорость ведения электрода. Механизированная сварка экономнее, так как обеспечивается стабильная скорость движения электрода, отсутствуют рывки.
- Толщина обрабатываемого материала.
- Отходы сварочного флюса. В результате проведения работ, на шве образуется определенное количество защитного шлакового слоя. Расход гранулированного флюсового порошка в определенной мере зависит от того, какое количество отходов получается на выходе.
При расчете режима сварки также учитывается вылет электрода, состав и строение флюсового порошка, положение изделия при выполнении работ.
Режимы автоматической сварки под флюсом, а также параметры необходимые для выполнения работ полуавтоматом, можно рассчитать по существующим таблицам, находящимся в инструкции по эксплуатации сварного оборудования.
Где применяется сварка флюсом
В свое время характеристики процесса сварки с использованием флюса произвели настоящую революцию в промышленности. Первоначально, способ сварочных работ предназначался только для обработки низкоуглеродистой стали. Сегодня производители флюсов заявляют о возможности применения порошка практически для любых, в том числе тугоплавких сталей и металлов, тяжело поддающихся обработке.
Металлургические процессы при сварке позволили использовать полностью механизированные установки и полуавтоматы для следующих целей:
- Сварка кольцевых швов. Основной сложностью процесса является необходимость удержать сварную ванну и избежать растекания металла. Для выполнения работ используют станки ЧПУ. Может потребоваться ручная подварка.
- Сварка вертикальных швов. Выполняется с принудительным или свободным формированием шва. Лучшие характеристики прочности соединения были достигнуты при работе с металлами 20-30 мм.
- Сварка труб малого и большого диаметра. Первоначально с помощью полностью автоматических станков научились варить трубы небольшого диаметра, но впоследствии с развитием технологии обработки, получилось освоить метод позволяющий проводить работы с материалом большого диаметра.
Характеристики используемого оборудования обеспечили необходимую прочность соединения и позволили ускорить процесс сборки труб для нефте- и газопроводов.
Проведение всех производственных работ строго регламентируется в соответствии с существующей технологической картой сварки. Любые нарушения приводят к серьезным штрафным санкциям.
Преимущества и недостатки сварки
Можно выделить некоторые преимущества сварки под флюсом:
Можно выделить несколько недостатков флюсовой сварки:
- Ограниченная маневренность автоматов.
- Возможность проведения работ с максимальным отклонением от плоскости не более 10-15°.
- Влияние характеристик флюса на качество проводимых работ. Остатки порошка механизированным образом убираются в хранилище и используются повторно. Сухой порошок быстро впитывает влагу. Чтобы обеспечить высокие характеристики шва, потребуется контроль влажности флюса.
Проверку делают с помощью забора порошка, высушивания при температуре 105°С.После контрольный образец взвешивают. Если разница составляет более 0.1% от массы невысушенного состава, весь порошок отправляют на сушку.
Некоторые виды сварочных работ рекомендовано проводить только с использованием флюса. Применение гранулированного порошка позволяет сократить расходы электроэнергии и улучшить качество и прочность сварочного шва в несколько раз.
Автоматическая и полуавтоматическая сварка под флюсом
Автоматическая и полуавтоматическая сварка под флюсом является высокопроизводительным сварочным процессом при изготовлении технологических трубопроводов. При сварке под флюсом сварочная дуга горит между голой электродной проволокой и свариваемым изделием под слоем сыпучего материала, называемого флюсом. Флюс в основном играет такую же роль, как и покрытие электрода при ручной дуговой сварке и, кроме того, закрывает дугу, вследствие чего при этой сварке не требуется защищать глаза специальными стеклами.
Сварку под флюсом осуществляют с помощью сварочной головки.
Полуавтоматическая сварка отличается от автоматической тем, что сварочную головку перемещают вдоль шва вручную.
Подготовляют кромки свариваемых труб и деталей и собирают их для автоматической и полуавтоматической сварки более тщательно, чем для ручной. Глубокий провар и жидкотекучесть расплавленного металла требуют выдерживать при сборке одинаковые размеры зазоров и разделок фасок, что обеспечивает получение высокого качества сварных швов и высокую производительность процесса.
Производительность автоматической и полуавтоматической сварки под слоем флюса в 2—5 раз выше по сравнению с ручной и достигается за счет увеличения плотности тока, увеличения скорости сварки и повышения коэффициента наплавки.
Эксплуатационные преимущества заключаются в полной или частичной автоматизации процесса сварки и, как следствие, улучшении условий труда сварщика.
При автоматической и полуавтоматической сварке труб из малоуглеродистой и низколегированной стали применяют плавленые флюсы АН-348А, ОСЦ-45, ФЦ-9, а из высоколегированной стали аустенитного класса флюс ФЦЛ-2. Неплавленые керамические флюсы К-2 и КВС-19 применяют для сварки легированных и углеродистых сталей.
Для сварки под флюсом стальных труб в основном используют калиброванную холоднотянутую сварочную проволоку круглого сечения. Сварочную проволоку изготовляют диаметром от 0,3 до 12 мм из стали различного химического состава. Наиболее часто применяют проволоку диаметром от 0,8 до 5 мм.
Для сварки труб из малоуглеродистой и низколегированной стали применяют сварочную проволоку Св-08, Св-08ГА, Св-20Г2 и др. Для сварки труб из легированной и высоколегированной стали используют сварочную проволоку из сталей тех же классов (аустенитную, перлитную).
Рис. 80. Трактор ТС-17М:
1 — механизм подачи проволоки, 2 — механизм поперечной корректировки, 3 — бункер для флюса,
4 — кассета, 5 — пульт управления, 6 — коробка скоростей сварки, 7 — механизм включения передвижения трактора, 8 — электродвигатель, 9 — коробка скоростей подачи проволоки
Сварочный дуговой автомат состоит из трех основных частей: сварочной головки, источника питания сварочной дуги и аппаратного ящика с пультом управления. Для автоматической и полуавтоматической сварки под флюсом труб, узлов и деталей трубопроводов наибольшее применение нашли сварочные тракторы ТС-17М, АДС-500, АДС-1000-2, сварочные головки типа ПТ-56, ПТ-1000 и полуавтоматы ПШ-5, ПШ-54, ПДШМ-500. Сварочными тракторами называют аппараты, перемещающиеся непосредственно по свариваемому изделию.
Сварочный трактор представляет собой самоходную тележку, на которой установлены механизм подачи электродной проволоки с токоподводящим мундштуком, бункер для флюса, кассета с электродной проволокой и пульт управления. Наиболее простым, малогабаритным и легким из всех существующих в настоящее время сварочных тракторов является сварочный трактор ТС-17М (рис. 80). Поскольку этот трактор небольших габаритных размеров, его можно применять при сварке внутренних швов цилиндрических изделий диаметром от 1 м и выше. Трактор рассчитан на сварку электродной проволокой диаметром от 1,6 до 5 мм при сварочном токе 200—1000 а. Им можно сваривать любые швы в нижнем и близком к нижнему положениях.
Рис. 81. Универсальный держатель ДШ-5:
1 — бункер для флюса, 2 — щиток для регулирования подачи флюса, 3— шланг, 4 — кнопка управления, 5 — упор, 6 — электродная проволока, 7 —трубчатый наконечник
Рис. 82. схема установки для шланговой полуавтоматической сварки труб под флюсом с помощью полуавтомата ПШ-54:
1 — дроссель, 2— сварочный трансформатор, 3 — щиток, 4 — аппаратный шкаф, 5 — подающий механизм полуавтомата, 6 — крюк для подвешивания подающего механизма. 7 — кассеты для электродной проволоки, 8 — гибкий шланг, 9 —держатель
Шланговые полуавтоматы ПШ-5, ПШ-54 и ПДШМ-500 благодаря своей простоте и надежности в работе получили широкое применение в трубозаготовительных цехах и заводах. Полуавтоматы предназначены для дуговой сварки под флюсом переменным или постоянным током сплошных и прерывистых прямолинейных, круговых и криволинейных швов, угловых, стыковых и нахлесточных соединений. Полуавтоматами сваривают изделия из малоуглеродистой стали толщиной 3—20 мм и швы, расположенные на горизонтальных и наклонных (до 15°) плоскостях и в труднодоступных местах. Полуавтомат ПШ-5 работает по принципу постоянной подачи проволоки. Скорость подачи проволоки изменяется сменными шестернями. Полуавтомат рассчитан на сварку электродной проволокой диаметром 1,2— 2,5 мм при силе тока до 600 а. Область применения полуавтомата значительно расширяется с применением сменных специализированных держателей (ДШ-5, ДШ-7, ДШ-16, ДШ-17). Наибольшее применение нашел универсальный держатель ДШ-5 (рис. 81).
Полуавтомат ПШ-54 (рис. 82) комплектуется из тех же узлов, что и полуавтомат ПШ-5, но в отличие от него имеет ряд усовершенствований. В частности, вместо сменных шестерен подающий механизм 5 снабжен легкой коробкой скоростей. Держатель 9 полуавтомата ДШ-54 имеет то же устройство, что и держатель ДШ-5.
1. В чем преимущества автоматической и полуавтоматической сварки перед ручной?
2. Объясните назначение флюса при сварке?
3. Назовите основные марки сварочной проволоки.
4. Какое основное оборудование применяют для автоматической и полуавтоматической сварки под флюсом?
5. В чем отличие шланговых полуавтоматов от сварочного трактора?
Все материалы раздела «Сварка труб» :
● Способы сварки трубопроводов и виды сварных соединений
● Подготовка труб под сварку
● Технология газовой сварки и резки
● Кислородно-флюсовая и дуговая резка
● Технология ручной электродуговой сварки, электроды
● Источники питания сварочной дуги
● Автоматическая и полуавтоматическая сварка под флюсом
● Автоматическая и полуавтоматическая сварка в защитных газах
● Сварка трубопроводов из легированной стали
● Сварка трубопроводов высокого давления, термообработка сварных соединений
● Сварка трубопроводов из алюминия и его сплавов, из меди и ее сплавов
● Пайка трубопроводов, дефекты сварных швов
● Контроль качества сварных швов
● Виды сварки и применяемое оборудование
● Сварка и склеивание винипластовых труб
● Сварка полиэтиленовых трубопроводов
● Правила техники безопасности при резке и сварке трубопроводов
Сварка под флюсом: режимы, ГОСТ, схема, способы
Какой метод сварки выбрать – автоматический или полуавтоматический?
Выбрать, что именно требуется сейчас – автоматическая и полуавтоматическая дуговая сварка, поможет конкретная ситуация. Автомат необходим для изготовления швов повышенной сложности и для производства крупных партий изделий. Полуавтомат прекрасно подойдет для небольших партий продукции с качественным равномерным швом.
Настройка полуавтоматов не требует длительной подготовки, а их обслуживание экономично. Нет необходимости в создании специальных условий для соединения. Рабочие трудятся как в помещениях, так и на улице. Для размещения аппаратуры не нужна ровная поверхность с покрытием определенной плотности
И, пожалуй, самое важное свойство полуавтоматов – их мобильность
Другие ГОСТы
ГОСТ 28915-91 Сварка лазерная импульсная. Соединения сварные точечные. Основные типы, конструктивные элементы и размеры ГОСТ 25997-83 Сварка металлов плавлением. Статистическая оценка качества по результатам неразрушающего контроля ГОСТ 19521-74 Сварка металлов. Классификация ГОСТ 23338-91 Сварка металлов. Методы определения содержания диффузионного водорода в наплавленном металле и металле шва ГОСТ 2601-74 Сварка металлов. Основные понятия. Термины и определения ГОСТ 2601-84 Сварка металлов. Термины и определения основных понятий ГОСТ 11969-79 Сварка плавлением. Основные положения и их обозначения ГОСТ ISO 12932-2017 Сварка. Гибридная лазерно-дуговая сварка сталей, никеля и никелевых сплавов. Уровни качества для дефектов ГОСТ 29297-92 Сварка, высокотемпературная и низкотемператупная пайка, пайкосварка металлов. Перечень и условные обозначения процессов ГОСТ Р 56155-2014 Сварка термопластов. Экструзионная сварка труб деталей трубопроводов и листов ГОСТ Р 54793-2011 Сварка термопластов. Сварка труб, узлов трубопроводов и листов из PVDF (ПВДФ) нагретым инструментом ГОСТ EN 13705-2015 Сварка термопластов. Оборудование для сварки нагретым газом и экструзионной сварки ГОСТ 30482-97 Сварка сталей электрошлаковая. Требования к технологическому процессу ГОСТ Р 57179-2016 Сварка рельсов термитная. Методика испытаний и контроля качества
Влияние выбранных режимов автоматической сварки на глубину проплавления и ширину шва
Влияние силы тока и напряжения сварочной дуги
При увеличении силы тока, тепловая мощность и давление сварочной дуги возрастают. Это способствует увеличению глубины проплавления, но на ширину сварного шва оказывает незначительное влияние.
Если увеличить напряжение электрической дуги, то увеличивается степень её подвижности и увеличивается степень доля тепловой энергии, которая расходуется на расплавление сварочного флюса. При этом ширина сварного шва становится больше, а на глубину проплавления влияние оказывается незначительное.
Влияние диаметра электродной проволоки и скорости сварки
Если увеличить диаметр электродной проволоки, но не менять величину сварочного тока, то глубина проплавления металла уменьшится, а ширина сварного шва увеличится, вследствие увеличения подвижности сварочной дуги.
Увеличение скорости сварки уменьшит и глубину проплавления, и ширину сварного шва, т.к. металл при большей скорости сварки не будет успевать плавиться в том же количестве, в котором он плавился при меньшей скорости.
Влияние рода сварочного тока и его полярности
Род сварочного тока и его полярность существенно влияют на размеры и форму сварного шва из-за того, что количество теплоты, образующееся на катоде и аноде сварочной дуги, также сильно меняется. Если выбрать постоянный ток прямой полярности, то глубина проплавления свариваемого металла уменьшается на 40-50%, а у переменного тока на 15-20%, по сравнению с постоянным током обратной полярности.
Исходя из этого, если требуется выполнить сварной шов небольшой ширины с глубоким проплавлением металла (например, при сварке стыковых швов, или при сварке угловых швов без разделки), то рекомендуется выбирать для этого постоянный сварочный ток обратной полярности.
Влияние вылета электродной проволоки
Когда увеличивается вылет электродной проволоки, то увеличиваются также скорость его подогрева и скорость плавления. Из-за этого, объём сварочной ванны под электрической дугой увеличивается за счёт электродного металла и это препятствует расплавлению основного металла. Как следствие, глубина проплавления уменьшается. Подобную особенность иногда используют при автоматических наплавках для того, чтобы увеличить производительность наплавки.
В отдельных случаях (чаще всего при автоматической наплавке), электроду задают движение поперёк сварных кромок с разной амплитудой и частотой. Такой технологический приём позволяет существенно изменять форму и размеры сварного шва. При автоматической сварке под флюсом с поперечными движениями электродной проволоки, глубина проплавления основного металла уменьшается, а ширина сварного шва увеличивается.
Такой способ сварки применяется для того, чтобы уменьшить вероятность прожога при сварке стыковых швов с большим зазором между сварными кромками. Такой же цели можно достигнуть, если производить сварку сдвоенным электродом, при этом электроды необходимо расположить поперёк направления сварки. Если их расположить вдоль направления сварки, то это, наоборот, увеличит глубину проплавления.
Особенности сварки под флюсом
Не стоит думать, что сварка под флюсом это какой-то совершенно новый способ сварки. Придуман он очень давно, в конце в XIX века, а сущность заключается все в том же использовании присадочной проволоки и неплавящихся электродов. Однако, оборудование постоянно улучшалось, а вместо газа, покрывающего всю зону шва, используется только флюс. Он имеет порошковую консистенцию, засыпаясь поверх шва.
Такой состав под влиянием высоких температур тоже начинает выделять газ, который будет защищать свариваемые детали от окислов. Когда порошок выгорит, от него останется только легкоудаляемый шлак, а если средство не будет использовано полностью, его легко можно сохранить до следующего раза.
Перед тем, как делать варку под флюсом, потребуется выбрать:
- режим;
- электроды;
- присадочную проволоку.
Также, как при любой другой сварной работе, нужно будет правильно оформить кромки, обезжирить детали
Но здесь еще будет важно подобрать флюс, так как он существует в разных видах
Флюс защищает сварной шов от окислов
Характер сварного шва
Односторонняя сварка стыков используется для менее ответственных соединений. Применяют ее и в тех случаях, когда не удается получить доступ к изнанке. Большой размер сварочной ванны, ее относительный перегрев, большой объем расплава зачастую приводят к расплескиванию расплава и его вытеканию через зазор. Для предотвращения нежелательного эффекта используют подкладочные пластины из стали или меди, а также подсыпку флюса. Наиболее распространены следующие методы выполнения односторонних швов:
- Флюсовая подушка. Под соединяемые кромки засыпают флюсовый порошок слоем 3-7 см. Прижим осуществляется за счет собственного веса или с помощью резинового баллона, наполненного сжатым воздухом. При небольших размерах соединения используется резиновый шланг. Слой флюсового порошка препятствует вытеканию расплавленной среды и предотвращает доступ воздуха к сварочной ванне.
- Медная подкладочная пластина. Медь имеет высокий коэффициент теплопроводности. Это свойство используется для отвода избыточного тепла из рабочей зоны. Таким образом не происходит пережог материала заготовок.
Кроме того, пластина предохраняет расплав от вытекания через зазор. Напротив шва в пластине делается продольная выемка, ее засыпают флюсовым порошком. Благодаря такой выемке на изнаночной стороне соединения формируется сварочный валик. Медная пластина имеет ширину от 4 до 6 см, и толщину от 0,5 до 3 см.
- Медный ползун. Параллельно электроду с изнаночной стороны на шпильках движется массивный башмак с водяным охлаждением. Для снижения трения могут применяться ролики.
- Стальная подкладная пластина. Если позволяет конструкция, с тыльной стороны подкладывают контактную полосу шириной 2-5 см и толщиной полсантиметра из того же сплава, что и заготовки. Ее устанавливают с минимальным зазором и прихватывают через каждые 40 см конденсаторной сваркой. Пластина проваривается вместе с заготовками, входя в состав шовного материала. Таким образом не только предотвращается вытекание расплава, но и повышается прочность шва.
- Подварочный шов. Ручная подварка формирует корень шва, надежно фиксирует заготовки и предотвращает вытекание расплава.
Способы защиты от вытекания, виды подкладок.
Двустороння сварка стыков формирует более прочный и долговечный шов. Этот метод применяется в ходе сборки промышленных установок, станков, транспортных средств, строительных конструкций, ответственных и нагруженных изделий с высокой удельной прочностью. Проварка с двух сторон позволяет шву выдерживать как статические, так и динамические нагрузки наравне с основным материалом изделия.
При выполнении стыка в два прохода сначала заваривают шов с лицевой стороны, достигая глубины провара 60-70% от высоты. Перед этим заготовки тщательно подгоняют друг к другу, зазор не должен превышать 1 мм. Различные подкладочные средства при этом не применяют, сил поверхностного натяжения расплава достаточно, чтобы избежать вытекания. На следующем этапе проходят шов с изнаночной стороны, формируя его полный профиль.
Если по конструктивным или технологическим причинам обеспечить малый зазор не удается, используют те же методы для предотвращения протекания, что и при одностороннем способе:
- подкладочная пластина из меди;
- пластина из стали;
- слой флюсового порошка;
- подварка вручную.
Угловые, тавровые и нахлесточные швы заваривают, располагая заготовки в лодочку. При проварке с обратной стороны кантователь с закрепленными в нем заготовками поворачивают на необходимый угол.
Достоинства и недостатки
К преимуществам сварки под флюсом относятся:
- высокая степень автоматизации процесса;
- возможность проведения сварки под большой силой тока;
- высокая скорость сварки;
- качественный шов без окислов и раковин;
- возможность увеличения сварной ванны для более качественного провара.
Однородность шва достигается за счет изоляции сварной ванны от кислорода воздуха, а также из-за легирования шва компонентами флюса, которые можно подобрать специально для материала свариваемых деталей. Также сварка под флюсом дает возможность использования одновременно двух электродов, расположенных на расстоянии 10-20 мм друг от друга и питаемых от одного источника тока – это позволяет сделать больше сварную ванну под флюсом, увеличив таким образом скорость сварки и степень однородности готового изделия.
К недостаткам сварки под флюсом относят трудности контроля процесса и технологическую сложность. Агрегаты для сварки под флюсом занимают большие площади и требуют обслуживания квалифицированными кадрами. Сварной шов формируется под слоем флюса и у сварщика нет возможности контролировать качество шва в режиме реального времени. Избежать брака можно путем дополнения агрегата ультразвуковыми или лазерными системами контроля наличия дефектов.
Подбираем все, что нужно
Сварка под флюсом покажет себя с лучшей стороны только в том случае, если максимально правильно подобрать для нее все необходимое. Это утверждение касается как оборудования, так и флюсовых составов.
Оборудование
В промышленности чаще всего используется специальный автоматический стенд сборочного типа, позволяющий не только варить любые конструкции, но и надежно фиксировать их в том положении, в каком они должны будут пребывать постоянно после завершения работы. Подобное оборудование отличается повышенными показателями надежности крепления элементов – это позволяет гарантировать отсутствие отклонений по швам или форме будущего изделия, тем более что мастер в процессе работы сам шов не видит.
Такой агрегат удобен для выполнения стыковых и угловых швов, работает быстро, обеспечивает высокое качество и надежность соединений. Конструкция управляет собой сама, потому стоит дорого – в качестве альтернативы на стенд иногда устанавливают мобильные головки.
Полуавтомат стоит ощутимо дешевле, но требует от оператора куда большей вовлеченности в процесс. Направление проволоки и контроль вылета электрода целиком и полностью перекладываются на плечи сварщика, хотя подача проволоки все же производится автоматически. Мощность напряжения, скорость перемещения по шву и угол наклона электрода – это те параметры режима сварки, которые мастер должен выбрать самостоятельно в зависимости от специфики обрабатываемой детали.
Ручное оборудование чаще применяется в небольших мастерских или любителями, хотя есть и специфические сферы применения, где это наиболее удобный вариант для выполнения поставленной задачи. Так, ручная сварка возможна даже в труднодоступных местах и в любых положениях.
Флюсы
Сварочные флюсы бывают различных видов, их маркировка строго привязана к действующему ГОСТу. Классификация таких составов возможна по разным признакам, мы рассмотрим лишь некоторые из них. В первую очередь все флюсы делятся на классы в зависимости от материала, для сварки которого они годятся. Для высоколегированной стали нужен один класс составов, для углеродистой или легированной – другой. Третий, отдельный класс флюсов, выпускается производителями специально для цветных металлов и сплавов – меди, бронзы и так далее.
По способу производства флюсы делятся на керамические и плавленые. Керамические хороши тем, что обеспечивают повышенные качества шва и обладают легирующими свойствами. Производится масса путем экструзии сыпучих керамических компонентов с последующим добавлением жидкого стекла. Плавленые флюсы отличаются структурой, напоминающей пемзу или стекло, производятся они плавлением и спеканием ингредиентов с дальнейшим образованием гранул.
Существует также классификация флюсов по их химическому составу. Выделяют следующие классы.
- Солевые составы состоят из хлоридов и фторидов. Типичная сфера их применения – варение активных металлов и шлакового переплава.
- Оксидные смеси представляют собой металлические окислы с некоторой примесью соединений фтора. Это оптимальный выбор для сварки фтористых и низколегированных сталей.
- Смешанные флюсы, как следует из названия, представляют собой комбинацию солевых и оксидных. Лучше всего такое вещество подходит для варки легированных сталей.
Классифицируют флюсовые смеси также и по тому, в каком виде они продаются. Гранулы и порошок являются наиболее характерными формами флюса, но только в том случае, если сварка будет электрической. Состав может приобретать форму пасты или даже газа, но тогда он предназначен для более редкой газовой сварки. Некоторые начинающие сварщики по привычке стремятся определить еще и лучшего производителя флюсов, по традиции отдавая предпочтение составам импортных марок.
Технология выполнения работ
Чтобы понять, что такое сварка под флюсом стоит рассмотреть технологию ее проведения. Первым делом стоит подготовить сварочное оборудование, для этого вида сварки подходят разные автоматические аппараты – трактор и подвесной сварочный прибор.
Главным элементом конструкции автоматического аппарата является сварочная головка, которая состоит из следующих компонентов:
- устройства подачи и перемещения;
- токопроводные элементы;
- самодвижущаяся тележка;
- блок управления.
Для работы потребуется специальный флюс и проволока для сварки под флюсом или прочие электродные материалы. Ее подает сварочная головка, а уже после она осуществляет подачу электрического тока.
Обязательно для этого вида сварки требуется токопроводящий механизм, который называется горелкой или мундштуком. Встречаются разные варианты исполнения, но все они имеют общее принципиальное устройство – направляющую трубку с вкрученным токопроводящим элементом.
Трубка при помощи сапожковой вилки на шарнире соединяется с прижимным механизмом. Для увеличения срока службы вилка имеет вставку из высокопрочной основы. Прижимной механизм состоит из винта и пружины.
Для автоматической импульсной сварки под слоем флюса рекомендуется применять источники энергии с пологопадающими качествами. Если выполняются работы в газовой среде, то предпочтение стоит отдавать источникам с жесткими характеристиками.
Стоит отметить! При проведении орбитальных сварочных работ рекомендуется применять оборудование с асинхронными двигателями с постоянной частотой. За счет того, что реализуется принцип саморегуляции, скорость подачи электродов будет оставаться неизменной.
Особенности технологии
Чтобы понять, как производится автоматический сварочный процесс, стоит рассмотреть его важные особенности:
- Флюс автоматически подается на область соединяемых элементов из предварительно заполненного бункера. При этом высота слоя зависит от толщины металлической основы.
- Электродная проволока, которая используется для автоматической сварочной технологии, сматывается в бухты или на кассеты. Она подается в рабочую зону при помощи специального механизма.
- Электрод, который создает дугу, перемещается вдоль шва со скоростью, зависящей от видов используемых режимов.
- При сварочном процессе на поверхности образуется флюсовый свод, он защищает сварочную ванну и предотвращает разбрызгивание металла.
- Расплавленный флюс не оказывает негативного воздействие на качество сварочного шва, поскольку он имеет низкую плотность, поэтому он всплывает на поверхность. При остывании на поверхности образуется шлак, который обязательно требуется полностью счистить с поверхности изделия.
- Флюс, который не был израсходован, необходимо собрать в емкость. Его можно будет использовать повторно.
Автоматическая технология сваривания считается одной из лучших техник, которые активно применяются в разных областях промышленности. Но чтобы она было проведена правильно, требуется учитывать множество важных нюансов – виды флюсов, типы автоматического оборудования, расчет режимов наплавки под слоем флюса, принцип работы и многое другое. Поэтому перед тем как приступать к данному процессу стоит заранее рассмотреть его важные особенности.
Преимущества и недостатки сварки под флюсом
Сущность процесса сварки под флюсом определяет его особенности по сравнению с ручной дуговой сваркой.
Производительность по сравнению с ручной сваркой увеличивается в 5—12 раз. При сварке под флюсом ток по электродной проволоке проходит только в ее вылете (место от токоподвода до дуги). Поэтому можно использовать повышенные (25—100 А/мм2) по сравнению с ручной дуговой сваркой (10—20 А/мм2) плотности сварочного тока без опасения значительного перегрева электрода в вылете в отслаивания обмазки, как в покрытом электроде. Использование больших сварочных токов резко повышает глубину проплавления основного металла И появляется возможность сварки металла повышенной толщины без разделки кромок. При сварке с разделкой кромок уменьшается угол разделки и увеличивается величина их притупления, т. е. уменьшается количество электродного металла, необходимого для заполнения разделки. Металл шва обычно состоит приблизительно на 2/3 из переплавленного основного металла (при ручной дуговой сварке соотношение обратное). В результате вышесказанного растут скорость и производительность сварки (рис. Х.4). Под флюсом сваривают металл толщиной 2— 60 мм при скорости однодуговой сварки до 0,07 км/ч. Применение многодуговой сварки позволяет повысить ее скорость до 0,3 км/ч.
Высокое качество металлов шва и сварного соединения достигается за счет надежной защиты расплавленного металла от взаимодействия с воздухом, его металлургической обработки и легирования расплавленным шлаком. Наличие шлака на поверхности шва уменьшает скорость кристаллизации металла сварочной ванны и скорость охлаждения металла шва В результате металл шва не имеет пор, содержит пониженное количество неметаллических включений. Улучшение формы шва и стабильности его размеров, особенно глубины проплавления, обеспечивает постоянные химический состав и другие свойства па всей длине шва. Сварку под флюсом применяют для изготовления крупногабаритных резервуаров, строительных конструкций, труб и т. д. из сталей, никелевых сплавов, меди, алюминия, титана и их сплавов.
Экономичность процесса определяется снижением расхода сварочных материалов за счет сокращения потерь металла на угар и разбрызгивание (не более 3 %, а при ручной сварке достигают 15%), отсутствием потерь на огарки. Лучшее использование тепла дуги при сварке под флюсом по сравнению с ручной сваркой уменьшает расход электроэнергии на 30—40 %, Повышению экономичности способствует и снижение трудоемкости работ по разделке кромок под сварку, зачистке шва от брызг и шлака. Сварка выполняется с применением специальных автоматов или полуавтоматов. Условия работы позволяют сварщику обходиться без щитков для защиты глаз и лица. Повышаются общий уровень и культура производства.
Недостатками способа является повышенная жидкотекучесть расплавленного металла и флюса. Поэтому сварка возможна только в нижнем положении при отклонении плоскости шва от горизонтали не более чем на 10—15o. В противном случае нарушится формирование шва, могут образоваться подрезы и другие дефекты. Это одна из причин, почему сварку под флюсом не применяют для соединения поворотных кольцевых стыков труб диаметром менее 150 мм. Кроме того, этот способ сварки требует и более тщательной сборки кромок под сварку и использования специальных приемов сварки. При увеличенном зазоре между кромками возможно вытекание в него расплавленного металла и флюса и образование в шве дефектов.
Оборудование для автоматической сварки под флюсом
Универсальная самоходная головка АБС
Этот аппарат состоит из трех отдельных узлов.
- Узел А представляет собой подвесную сварочную головку с пультом управления, которая предназначена для правки и подачи проволоки с постоянной скоростью к изделию.
- Узел Б состоит из бункера для флюса, устройств для подачи и отсоса флюса, кассеты со сварочной проволокой и механизма вертикального перемещения.
- Узел С – это самоходная тележка для перемещения всего аппарата вдоль свариваемого изделия.
Технические данные аппарата АБС приведены в табл. 2.
Рис.3 Универсальный сварочный аппарат АБС
1 — указатель; 2 — мундштук; 5 —механизм подачи; 4 -корректор; 5 — маховичок вертикального подъема; 6 — рукоятка фрикциона; 7 — кассета со сварочной проволокой; 8 — флюсоаппарат; 9 — направляющая воронка
Особенно широко распространены одноэлектродные сварочные тракторы — легкие самоходные тележки, перемещающиеся непосредственно по свариваемому изделию.
Универсальный сварочный трактор ТС-17-Р
Этот аппарат предназначен для сварки под флюсом прямолинейных и круговых швов стыковых, угловых и нахлесточных соединений.
Рис.4 Сварочный трактор ТС-17-Р
Трактор опирается на изделие обрезиненными ведущими бегунками 9 и передними съемными бегунками 2.
Электродвигатель 10 с постоянным числом оборотов приводит в движение механизм вращения бегунков 9 и механизм подачи сварочной проволоки 3.
Оба Механизма с коробками сменных шестерен смонтированы вместе с электромотором в одном общем корпусе, имеющем, мундштук 1 для подвода тока к электродной проволоке, бункер 5 для флюса, пульты управления 5 и 8 и кассету 7 со сварочной проволокой.
В комплекте трактора имеется ряд сменных узлов и деталей, которые осуществляют настройку его на сварку различных типов соединений вертикальным или наклонным электродом. Направление трактора по линии шва производится копирами. Кроме того, можно выполнить направление электрода по линии шва, пользуясь указателем 11 и механизмом поперечной корректировки 4.
Технические характеристики трактора ТС-17-Р приведены, в таблице.
Технические данные самоходных головок и тракторов для сварки под флюсом.
Тип аппарата | Наибольший сварочный ток, а | Диаметр сварочной проволоки, мм | Скорость подачи проволоки, м/ч | Скорость сварки, м/ч | Масса, кг |
АБС | 1500 | 2,0-6,0 | 29—220 | 14—110 | 160 |
ТС-17-Р | 1200 | 1,6-5,0 | 56-435 | 16-126 | 42 |
АДС-1000-2 | 1200 | 3,0-6,0 | 30-120 | 15—70 | 65 |
Двухмоторный трактор АДС-1000-2
Другим широко распространенным аппаратом для автоматической сварки под флюсом является двухмоторный трактор АДС-1000-2 (рис. 5) .
В этом тракторе электромотор, расположенный на тележке 1, служит для привода механизма двигателя, а электромотор головки 13 – предназначен для подачи сварочной проёолоки со скоростью, зависящей от напряжения дуги.
Рис. 5 Сварочный трактор АДС-1000-2
На четырехколесной тележке укреплена на поперечном суппорте стойка 3, которая несет на себе горизонтальную штангу 9. На левом конце этой штанги укреплены пульт управления 6 и кассета с проволокой 7, а на правом— сварочная головка 13 и бункер с флюсом 10.
Штанга может поворачиваться как около своей оси, так и относительно оси стойки. Сварочная головка может также изменять свое положение, так как она укреплена на штанге при помощи шарнира, фиксируемого зубчатыми полумуфтами.
Таким образом, можно придавать электроду при сварке различные положения в пространстве, фиксируй головку рукоятками 8, II и маховичком 5.
Для вертикального перемещения головки служит рукоятка 12.
Перемещение стойки по направлению, перпендикулярному к линии движения трактора, осуществляется маховичком 2.
Рукоятка 4 служит для выключения фрикционного сцепления передачи от мотора к ведущим бегункам трактора.
Причины появления пор
Процесс кристаллизации сварного шва может сопровождаться образованием пор. Это заполненные газом полости различной формы. Внешние признаки отсутствуют. Обнаружение возможно посредством применения методов неразрушающего контроля. Для конструкций, которые работают в условиях повышенной нагрузки, поры считают недопустимым дефектом.
Основной причиной появления пор является перенасыщение расплава сварочной ванны газами. Кроме того, высокая скорость кристаллизации шва не позволяет сварочным газом покинуть зону соединения. Опытным путем установлено, что высокомолекулярные газы практически не влияют на процесс порообразования. Главными виновниками являются простые соединения – водород, азот и угарный газ.
Многое зависит от соединяемых материалов. При сварке под флюсом нержавющей стали причиной порообразования является водород. Углерод не способен воздействие на аустенитные сорта стали, а азот практически не вызывает пор.
Состав флюса также оказывает влияние на процесс. Учеными института Электросварки было установлено, что понижение уровня кислотности флюса способствует образованию пор. А применение ферритизаторов снижает риск появления пор при сваривании обычных сортов стали.
Формула изобретения
1. Способ автоматической электродуговой наплавки под флюсом наружных или внутренних поверхностей тел вращения, при котором электроды одной или нескольких групп электродов устанавливают со смещением в горизонтальной плоскости против направления вращения тела с линейным и угловым отклонением от «зенита» и с расстоянием между электродами каждой группы, выбранным из условия формирования общей ванны жидкого металла по всей ширине наплавляемого валика, запитывают их от одного или нескольких источников электрического тока и формируют наплавкой на обрабатываемой поверхности кольцевой валик с площадью, равновеликой площади обрабатываемой поверхности, при вращении тела и одновременном перемещении одной или нескольких групп электродов в прямом и обратном направлениях вдоль его образующей, которую совмещают с подачей флюса, отличающийся тем, что электроды устанавливают с линейным отклонением от «зенита» на 5-20 мм и угловым отклонением от «зенита» более 30°, а наплавку осуществляют на обратной полярности и одинаковом для электродов каждой группы технологическом режиме, при этом устанавливают погонную энергию, позволяющую формировать вытянутую вдоль тела вращения ванну жидкого металла и шлака с соотношением ее геометрических размеров не менее чем 3:1, а наплавку ведут со скоростью продольного перемещения электродов, в 28-32 раза превышающей линейную скорость вращения тела.
2. Способ по п.1, отличающийся тем, что при наплавке используют флюс с предельной температурой жидкотекучести шлака, близкой к температуре солидуса металла наплавляемого тела.
Виды гранулированного порошка
Гост 1139-80. основные нормы взаимозаменяемости. соединения шлицевые прямобочные. размеры и допуски (с изменениями n 1, 2)
Для осуществления сварочного процесса, флюс подразделяется на несколько типов. Все зависит от металла, который будет обрабатываться:
- Высоколегированная сталь.
- Цветные сплавы.
- Углеродистая и легированная сталь.
Методика производства также подразделяет этот гранулированный материал на несколько подвидов:
- Керамический.
- Плавленный.
Использование первого вида позволяет получить улучшенный шов. Плавленый флюс отличается своей пемзовидной структурой.
Чтобы получить керамический материал, сначала специальные элементы подвергают мелкому измельчению. Затем смешивают с экструзией, которая помогает получить однородную массу. В нее добавляют жидкое стекло. Такая смесь используется только в том случае, когда требуется провести ещё одно легирование материала сварочного шва.
После спекания исходных веществ, проведения их грануляции, получается плавленый флюс. Гранулы для проведения газовой сварки делятся на несколько подгрупп. Разделение зависит от их химического состава:
- Солевые. В их состав входит большое количество хлоридов, а также небольшое количество фторидов. Гранулы применяются для сваривания активных металлов. Их используют для переплава оставшегося шлака.
- Смешанные. Материал представляет собой смесь солевых гранул с оксидами. Используется для работы с легированными сталями.
- Оксидные. Смесь предназначена для обработки фтористой стали или низколегированного металла. В состав входят окислы металла вкупе с минимальным количеством фтористых соединений.
Технология сварки под слоем флюса
Автоматизированный процесс сварки подразумевает наличие сыпучего флюса, подаваемого непосредственно к изделию. При розжиге дуги происходит плавление проволоки электрода, воздействующего на металлическое основание. Результатом реакции металла с веществом, которые интегрируются на участке сварки, образуется газовая ванна, состоящая из сварочных паров. Сварка под флюсом применяется автоматическим либо механизированным производством.
Также конструкция электродной проволоки реагирует на флюс, подвергая обработке материал, допускает получить качественный шов.
Схема дуговой сварки под флюсом
В процессе удаления дуги, изделие переходит из расплавленного состояния в твердое, образовывая твердый слой, легко удаляемый с поверхности изделия. Технология автоматической сварки под флюсом подразумевает цикл изъятия лишнего вещества с помощью специального механизма. Технология имеет множество достоинств, позволяющих применять метод на любом предприятии.
- Возможно объединить детали, используя повышенную силу тока. На большинстве производств употребляется сила тока от 1000 до 2000 А, для сравнения показатель дуговой сварки не превышает 650 Ампер.
Обычным режимом увеличение силы тока пагубно влияет на качество, разбрызгивая металл. При использовании вещества, возможно повышение мощности до 4000 А, что позволяет получить готовый материал в сочетании со скоростью процесса.
- Процесс подразумевает образование дуги под слоем флюса, работающей при большой глубине. Данное условие дает возможность не беспокоится о предварительной обработке сварных соединений.
- Повышенная скорость сцепления позволяет производить больший объем сварочных работ. Для сравнения, изготовление шва с идентичными параметрами дуговой сваркой может отнять больше времени в 10 раз.
- Формируемый газовый пузырь в процессе позволяет избежать разбрызгивания раскаленного металла в процессе. Данное условие позволяет не только получить крепкий шов, но и соблюдать технику безопасности при работе с большими температурами. За счет этого, происходит экономия электроэнергии и инструментов.
https://youtube.com/watch?v=rMF3I_u3zjw
Режим сварки определяется при зависимости от некоторых требуемых характеристик шва. Основные критерии:
- диаметр электрода;
- электроток, его полярность;
- скоростные показатели работы и напряжение тока;
- характеристики состава.
Также существует ряд дополнительных параметров, зависящих от применяемых инструментов.
Что дает применение флюса
Химическое вещество, основанное на множестве компонентов, именуется флюсом. Применяется при необходимом следовании стандартам, защите металлических изделий от коррозионных условий при последующей эксплуатации.
Флюс сварочный
Основные задачи, которые под силу решить веществу:
- устойчивое горение сварочной дуги;
- улучшенные свойства и формы шва;
- обеспечение сварочной ванны, ей производится защита металла;
- применение различных креплений позволяет изменять состав химической смеси для получения необходимых характеристик.
Кроме вышеперечисленных достоинств, основным преимуществом является возможность построения механического процесса стыковки. Различные химические соединения применяются в автоматических линиях.
Химический состав различных марок флюса
У каждого способа существуют недостатки, использование флюса не исключение:
- работа производится только при нижнем положении стыка;
- сборка деталей должна соответствовать параметрам подгонки и обработки кромок;
- производство выполняется только на жесткой опоре, воздействие в подвешенном состоянии на материал недоступно;
- стоимость вспомогательных материалов высока, поэтому способ употребляется в ответственных конструкциях.
Сварка алюминия или других цветных металлом невозможна без применения флюса, вне зависимости от способа стыковки. Однако существует вероятность образования твердой окиси, вытесняемой на поверхность в процессе.
Автоматическая сварка под флюсом
Сварка под флюсом — это самый распространенный способ механизированной дуговой сварки плавящимся электродом. Способ нашел широкое применение и стал одним из ведущих во многих отраслях промышленности при производстве конструкций из сталей, цветных металлов (алюминия, титана, меди) и их сплавов.
Автоматическую сварку под флюсом целесообразно применять в серийном и массовом производстве для выполнения кольцевых, прямолинейных, стыковых и угловых швов протяженностью не менее 0,8 м на металле толщиной 3-100 мм со свободным входом и выходом сварочной головки.
Преимущества автоматической сварки под флюсом:
— высокая производительность;
— стабильно высокое качество и хороший внешний вид сварочных соединений;
— высокий уровень локальной механизации сварочного процесса и возможность его комплексной автоматизации;
— снижение удельного расхода электродного металла и электроэнергии.
Недостатки автоматической сварки под флюсом:
— возможность сварки только в нижнем положении шва;
— необходимость более тщательной (по сравнению с ручной сваркой) подготовки кромок и более точной сборки деталей под сварку;
— невозможность сварки стыковых швов на весу, т. е. без подкладки или предварительной подварки корня шва.
Сущностъ процесса дуговой сварки под флюсом заключается в применении непокрытой сварочной проволоки и гранулированного флюса, насыпаемого впереди дуги слоем толщиной 30-50 мм.
Автомат для сварки и схема процесса автоматической дуговой сварки под флюсом приведены на рис. 3.12.
Возбуждение и поддержание дугового разряда выполняется авто-матически сварочной головкой, которая с помощью механизма пода-чи / непрерывно подает в зону дуги сварочную проволоку 2 по мере
Рис. 3.12. Автомат АДФ-1202 (а) и схемапроцесса автоматической дуговой сварки под флюсом (б)
ее плавления. Дуга 10 горит между концом электрода и изделием. Перемещение дуги по шву осуществляется самоходной сварочной тележкой (или изделие перемещается относительно неподвижной сварочной головки).
Под действием теплоты, выделяемой сварочной дугой, плавятся электродная проволока и металл свариваемого изделия, а также часть флюса 5, примыкающего к дуге. В области горения дуги образуется полость 9 (газовый пузырь), ограниченная в верхней части оболоч-кой расплавленного флюса, а в нижней — сварочной ванной 8. Газо-вый пузырь заполнен парами металла, флюса и газами. Давление газов поддерживает флюсовый свод, образующийся над сварочной ванной. Дуга несколько отклоняется от вертикального положения в сторону, противоположную направлению сварки. Под влиянием давления дуги жидкий металл 8 оттесняется также в сторону, противоположную направлению сварки. Под электродом образуется кратер с тонким слоем расплавленного металла, а основная масса расплавленного металла занимает пространство от кратера до поверхности шва, располагаясь наклонным слоем.
Расплавленный флюс вследствие значительно меньшей плотности, чем плотность расплавленного металла шва, всплывает на его поверхность и покрывает его плотным слоем. По мере поступательного движения электрода проходит затвердевание металлической и шлаковой ванн с образованием сварного шва 7, покрытого твердой шлаковой коркой 6.
Сварку под флюсом можно осуществлять переменным и постоянным током, одной дугой, двумя дугами, расщепленным электродом и трехфазной дугой.
Расплавленньй флюс (шлак), покрывающий металлическую ванну при сварке, выполняет следующие функции:
— защищает жидкий металл сварочной ванны от непосредствен-ного контакта с воздухом;
— раскисляет, легирует и рафинирует металл шва;
— изменяет тепловой режим сварки путем уменьшения скорости охлаждения металла;
— обеспечивает устойчивое горение дуги;
— улучшает условие формирования шва.
Хороший контакт шлака и металла, наличие изолированного от внешней среды пространства обеспечивают благоприятные условия для защиты, металлургической и тепловой обработки сварочной ванны, тем самым способствуя получению швов с высокими механи-ческими свойствами.
По способу изготовления флюсы подразделяются на: п л а в л е -н ы е, получаемые сплавлением входящих в них компонентов в элек-трических или пламенных печах с последующей грануляцией при выливании расплава в воду; керамические, получаемые путем грануляции замеса из тонко измельченных компонентов, соединен-ных между собой жидким стеклом. В отличие от плавленых в кера-мических флюсах могут содержаться металлические порошки — рас-кислители и легирующие компоненты, так как в процессе изготовле-ния керамические флюсы не подвергаются нагреву до высокихтем-ператур. Наибольшее распространение в производстве получили плавленые флюсы, которые представляют собой сплав оксидов и солей метаплов.
По химическому составу различают флюсы окислительные, безо-кислительные и бескислородные.
Окислительные флюсы содержат в основном оксиды кремния и марганца. Для придания флюсу необходимых свойств в него вводят и другие компоненты, например плавиковый шпат, сни-жающий температуру плавления и вязкость шлака, а таюке весьма прочные оксиды магния, кальция, алюминия, которые при сварке практически не реагируют с металлом. Эти флюсы обычно исполь-зуют при сварке низколегированных сталей. Наиболее распростра-ненный флюс этого типа АН-348А содержит, %: 41-44 8Ю2; 34—38 МпО; до 6,5 СаО; до 7 М§О; до 4,5 А12О3; 4-6 СаР2.
Основу безокислительных флюсов составляют прочные оксиды металлов и фториды. Оксиды кремния и марганца содержатся в незначительных количествах или вообще отсутствуют. Такие флюсы преимущественно используются для сварки и наплав-ки высоколегированных сталей. Например, флюс АН-30 имеет со-став, %: 3 5Ю2; до 0,5 МпО; 41,5 А12О3; 18 СаО; 14,5 М§О; 21 СаР2; до 1 РеО.
Бескислородные флюсы состоят в основном из фторидных и хлоридных солей металлов. Их применяют при сварке химически активных металлов. Например, флюс АН-А1 для сварки алюминия и его сплавов состоит из 50 % КС1; 20 % КаС1; 30
Основные параметры режима автомапшческой сварки под флю-сом — сварочный ток, род и полярность тока, диаметр электродной проволоки, напряжение дуги, скорость сварки. Влияние сварочного тока, напряжения дуги и скорости сварки на форму и размеры шва показано на рис. 3.13.
С увеличением сварочного тока глубина провара увеличивается, ширина шва почти не изменяется.
С повышением напряжения ширина шва резко увеличивается, а глубина провара уменьшается. Это важно учитывать при сварке тон-кого металла. Несколько уменьшается и выпуклость (усиление) шва.
При одном и том же напряжении ширина шва при сварке на постоянном токе (особенно обратной полярности) значительно больше, чем ширина шва при сварке на переменном токе.
С увеличением скорости сварки сначала глубина провара возрастает (до 40—50 м/ч), а затем уменьшается. При этом ширина шва уменьшается постоянно. При скорости более 70-80 м/ч основной металл не успевает прогреваться и по обеим сторонам шва возможны подрезы.
Увеличение сварочного тока является наиболее эффективным средством повышения производительности процесса сварки. Вследствие хорошей защиты расплавленного металла от воздуха и возможности подвода тока к электроду на близком расстоянии от его торца (~70 мм) оказывается возможным повысить плотность тока до 200-250 А/мм2 (при РДС покрытым электродом плотность тока не превышает 15 А/мм2), не опасаясь перегрева и окисления электродной проволоки. При этом объем сварочной ванны достигает 10-20 см3, в то время как при РДС он составляет 1—2 см2. Сварочный ток является тем параметром режима, вследствие изменения которого в большинстве случаев сварочной практики изменяют в желаемом направлении глубину провара основного металла.
Перед сваркой детали закрепляют на стендах или иньгх устройствах с помощью различных приспособлений или прихватывают руч-ной сваркой. Режим автоматической сварки выбирают в зависимости от толщины свариваемых кромок, формы разделки и свариваемого металла. Автоматической сваркой под флюсом выполняют стыковые, тавровые и нахлесточные соединения в нижнем положении шва.
Для повышения производительности труда сварку стремятся выполнять однопроходными швами. За один проход без разделки кромок, как правило, выполняют стыковые соединения из стали толщиной 12—15 мм. Для обеспечения полного провара и необходимого усиления шва между кромками стыкуемого соединения должен быть предусмотрен зазор, размер которого зависит от толщины металла. Значительный объем расплавленного металла, большая глубина проплавления и некоторый перегрев ванны могут привести к вытеканию металла в зазор и нарушению процесса формирования шва. Чтобы избежать этого, следует использовать стальную или медную под-кладку, флюсовую подушку или проваривать шов с обратной стороны.
Двусторонняя стыковая сварка дает более высококачественный шов, обеспечивая хороший провар даже при некотором смещении свариваемых кромок. Этим способом можно сваривать стальные листы толщиной до 22 мм без разделки кромок. Сварку производятс каждой стороны на режиме, обеспечивающем расплавление основ-ного металла на глубину не менее 0,6 его толщины. При невозмож-ности выдержать зазор между кромками менее 1мм принимают меры по предупреждению подтекания жидкого металла, как и при одно-сторонней сварке.
Дата добавления: 2016-08-06; просмотров: 4744; ЗАКАЗАТЬ НАПИСАНИЕ РАБОТЫ
Описание процесса дуговой сварки под флюсом
Дуговая сварка под флюсом, чаще сокращенно SAW, или сварка под флюсом — это полностью или частично автоматизированный процесс сварки с подачей проволоки. Он в основном используется для сварки более толстых сталей, включая углеродистые стали, нержавеющие стали и некоторые никелевые сплавы. SAW идеально подходит для сварки материалов толщиной от полудюйма до 5 дюймов, однако, регулируя скорость перемещения и тепловложение, SAW можно использовать для металлов толщиной всего 3/16 9.0003-й дюйма без прожогов.
Сам термин (погруженная дуга) относится к дуге, погруженной в гранулированный флюс. Нет видимой/открытой дуги, поэтому нет дыма и сварочных брызг.
Как работает SAW
Гранулированный флюс защищает дугу от атмосферного загрязнения. Все погружено в поток. Проволока подается через сварочную горелку, которая движется вдоль стыка. Тепло от дуги расплавляет часть проволоки, при этом флюс и основной материал используются для образования расплавленной сварочной ванны. Именно здесь флюс выполняет все необходимые функции, включая раскисление и дегазацию. Расплавленный флюс застывает за дугой, образуя покрытый шлаком сварочный валик, который легко удаляется.
Оборудование для субдуговой сварки
Оборудование для сварки под флюсом различается и может быть настроено в соответствии с применением, включая все расходные материалы, такие как сплошная проволока и проволока с металлическим сердечником, а также состав флюса.
Необходимое оборудование включает в себя:
- Источник питания – регулирует потребляемый ток (переменный, постоянный или оба, чтобы обеспечить простое переключение)
- Контроллер/интерфейс – управляет параметрами сварки
- Двигатель привода проволоки – регулирует скорость подачи проволоки
- Сварочная горелка – подает присадочный металл к заготовке и может наклоняться в зависимости от области применения
- Бункер для флюса – контролирует скорость осаждения флюса. Воронки для флюса также могут иметь системы восстановления флюса для повторного использования неиспользованного флюса, подачи его обратно в воронку до тех пор, пока он не будет использован.
Источником питания может быть постоянный ток (DC) или переменный ток (AC), и их можно комбинировать, чтобы один станок на пиле обеспечивал оба типа питания, позволяя операторам легко переключаться между ними для обработки заготовок различной толщины. Для более тонкой заготовки может потребоваться слабый ток 350 ампер, тогда как для более толстой заготовки может потребоваться более 1000 ампер. Поскольку оборудование SAW в основном используется для повышения производительности, большая часть или весь процесс механизирован для обеспечения высокой продолжительности рабочего цикла. Как правило, машина должна останавливаться только тогда, когда операторы удаляют шлак, заменяют электроды и манипулируют заготовкой, хотя в автоматизированных процессах сварки сварочный манипулятор комбинируется с оборудованием SAW для автоматизации механической обработки, что еще больше увеличивает рабочий цикл, обеспечивая еще более высокая производительность. Следует отметить, что данное оборудование на ПАВ может иметь сварочную головку, перемещающуюся вдоль заготовки, либо может быть стационарной со сварочным вращателем, поворачивающим заготовку под сварочной головкой.
Контроллер/интерфейс используется для управления всеми параметрами сварки, включая…
- Угол горелки,
- Скорость движения,
- Напряжение дуги,
- Сварочный ток,
- Вылет электрода,
- Диаметр проволоки,
- Скорость подачи проволоки.
Более высокая скорость может использоваться при корневых проходах более тонкого материала, чтобы избежать прожога, и легко замедляется для более толстых материалов, при этом некоторые из них способны к глубокому проплавлению более толстых металлов за один проход.
В процессе подачи проволоки чаще всего используется подача одной проволоки, однако там, где требуется высокий уровень производительности при постоянном сохранении высочайшего качества сварных швов, можно использовать несколько проволок для тандемной поддуговой сварки, когда несколько проволок подаются в такая же лужа. Одиночная подача проволоки обеспечивает скорость наплавки 40 фунтов в час, тогда как при тандемной сварке под дугой можно достичь скорости до 100 фунтов в час.
Расходные материалы для SAW
Флюс и проволока (электроды) для процессов SAW различаются в зависимости от области применения. Стандартная проволока обычно имеет диаметр от 1,6 до 6 мм. Скрученную проволоку можно использовать для колебательного движения, чтобы облегчить сплавление сварного шва с основным металлом. Доступны различные электроды для различных металлов. Большинство из них покрыты медью для увеличения электропроводности. Различные электроды подходят для разных токов, некоторые из них подходят для токов от 150 до 350 ампер, а другие подходят для более высоких ампер 1000 и выше для более толстых сталей.
Флюс может иметь различный химический состав. Его можно склеивать, сплавлять или механически смешивать. Стандартный флюс может содержать кальций, кремний, алюминий, магний и другие химические вещества, а легирующие элементы могут быть добавлены в соответствии с требованиями.
Флюс сам по себе не является проводником, пока не вступит в контакт с дугой. Поскольку он погружен, только использованный флюс в нижней части становится шлаком (отходами), и весь видимый флюс может быть возвращен в бункер для флюса, что снижает потери. Количество извлекаемого флюса варьируется от 50% до 9%.0%, в зависимости от используемого оборудования для дуговой сварки.
Преимущества сварки под дугой
- Более высокая скорость наплавки является основным преимуществом, так как повышает производительность
- Благодаря полуавтоматическому или полностью автоматизированному процессу обеспечивается улучшенная эргономика для операторов с минимальными манипуляциями с заготовками.
- Полный контроль параметров сварки обеспечивает неизменно высокое качество сварки
- Восстановление флюса снижает потери
- Глубокий провар на толстых сталях может быть выполнен, иногда за один проход
- Сварка более тонких металлов может выполняться на высокой скорости и без прожога
- Отсутствие брызг и испарений обеспечивает более безопасную рабочую среду.
Отрасли, в которых используется дуговая сварка под флюсом
Процессы дуговой сварки под флюсом обычно используются в отраслях с тяжелыми условиями эксплуатации, включая производство железнодорожных вагонов, судостроение, ветряные башни, сосуды под давлением и морские нефтяные вышки из-за его способности проникать в толстые стали в за один проход, обеспечивая более безопасную рабочую среду для операторов и постоянно поддерживая качество сварных швов.
В то время как процессы под флюсом в основном используются для тяжелой промышленности с более толстыми сталями, более тонкие металлические профили подходят для одиночной подачи проволоки за счет увеличения скорости.
Являясь специалистом в области оборудования для автоматизации сварки, Redrock может предоставить оборудование, необходимое для высочайшего качества сварки при максимальной производительности. Чтобы узнать больше, свяжитесь с нами по телефону +44 (0)141 812 0824.
Думаете о сварке под флюсом?
Лазерное отслеживание шва генерирует, анализирует и передает трехмерные профили зоны сварки.
Ваша компания все больше занимается сваркой профилей или сосудов высокого давления для тяжелой промышленности. Скорее всего, вы хотите осаждать металл со скоростью, которую невозможно сделать вручную — в диапазоне 20, 30 или даже 40 фунтов. в час.
Дуговая сварка под флюсом (SAW) справится со сваркой, но контроль места и способа сварки может быть не менее важным, чем то, что плавит проволоку.
Покупка системы SAW без вспомогательного оборудования, такого как манипулятор или портал, аналогична покупке двигателя без остальной части автомобиля. Вы можете включить его, и он сделает немного дыма, но он не доставит вас туда, куда вам нужно.
Знание областей применения поможет вам определить, какое вспомогательное оборудование необходимо для управления сварочной головкой и достижения желаемой производительности.
Опишите соединение
При выборе вспомогательного оборудования SAW в первую очередь необходимо определиться с типом и разнообразием свариваемых соединений. Будет ли:
- Большие V-образные пазы с достаточным пространством для большой сварочной горелки?
- L Узкие, глубокие канавки для минимизации количества наплавляемого материала?
- LМногопроходные сварные швы, и если да, то сколько проходов?
- LУгловые сварные швы?
- L Облицовка, где необходимо последовательно укладывать несколько проходов?
- L Прямые и ровные или волнистые и неровные сварные швы?
Определение типового проекта
Свариваемая деталь также поможет определить требования к вспомогательному оборудованию. Следующие вопросы являются хорошими вопросами, чтобы задать:
- Соединения из длинных и прямых или круглых материалов?
- Они вертикальные?
- Насколько велика заготовка, и нужно ли ее позиционировать или поворачивать, чтобы получить доступ ко всем местам сварки?
При сварке больших заготовок время, необходимое для их позиционирования, может существенно повлиять на производительность. Переворачивание большой заготовки для достижения сварного шва требует времени и может быть опасным для операторов.
Манипулятор со стрелой и колонной, вероятно, является наиболее экономичным и универсальным методом удержания сварочной головки над заготовкой. Если соединение длинное и прямое, эффективным может быть манипулятор стрелы и колонны на рельсах с моторизованным вагоном. Важно убедиться в том, что скорость автомобиля может соответствовать ускоренному перемещению, а также обычным скоростям сварки.
Если заготовка круглая, например, ветряная башня или сосуд высокого давления, ее нужно будет вращать под факелом. Для этого обычно используются поворотные ролики и сварочные позиционеры. Валки вращают длинные и часто очень тяжелые цилиндрические заготовки, центр масс которых находится примерно на осевой линии заготовки. Позиционеры вращают заготовки с центром масс, который не лежит на оси вращения или вблизи нее.
Количество наплавляемой сварочной проволоки и толщина основного металла определяют другие требования к оборудованию. Например, для предварительного нагрева толстого материала может потребоваться обычное пламенное или индукционное нагревательное оборудование.
Размещение камеры на месте сварки позволяет оператору наблюдать за ходом и качеством сварки из удобного и безопасного места.
Ответы на два вопроса о процессе могут определить, какое вспомогательное оборудование необходимо:
- Какой ток необходим?
- Как долго мне нужно сваривать?
Если вы будете выполнять сварку с большим током в течение длительного периода времени, необходимо правильно подобрать сварочную цепь. Если ваши кабели недостаточно велики по обе стороны от дуги, вы рискуете расплавить что-то, кроме электрода.
Другим важным фактором является теплопередача. Когда ток проходит через сварочные кабели, они нагреваются и могут расплавиться. Вокруг кабелей должно быть достаточно воздуха, чтобы они оставались прохладными.
Найдите рентабельность инвестиций в автоматизацию
В некоторых случаях затраты на автоматизацию SAW окупаются в течение длительного времени. В других стоимость быстро оправдывается.
С одной стороны, многопроходные сварные швы часто трудно автоматизировать, потому что размещение последовательных валиков может быть очень важным. Трудно победить хорошо обученного оператора SAW.
С другой стороны, плакирование, конструкционные секции, толстостенные сосуды под давлением и другие процессы, требующие высокой скорости наплавки, являются первыми кандидатами на автоматизацию. Полагаться на человека-оператора для точного нанесения сотен фунтов наплавленного металла последовательными валиками в течение нескольких часов, как правило, неэкономично, непрактично или даже невозможно.
Для таких применений типичный однопроволочный процесс с дугой под флюсом может легко наплавить 15 или 20 фунтов. в час, а двойная или тандемная двухпроводная дуговая сварка под флюсом может откладывать до 40 фунтов. в час, что обеспечивает скорость наплавки в 10 раз или на 1000% выше, чем при обычной ручной дуговой сварке в среде защитного газа или дуговой сварке в среде защитного газа.
Выбрать отслеживание швов
Отслеживание швов может упростить сварку волнистых соединений по неправильной траектории. Датчик или обратная связь от сварки используются для регулировки положения сварочной головки таким образом, чтобы она оставалась в заданном месте на стыке. Это может повысить производительность во многих областях применения и помочь менее опытным операторам выполнять качественные сварные швы.
Наиболее распространенными методами отслеживания являются тактильный, лазерный и дуговой.
Тактильное отслеживание шва экономично. Механический зонд перемещается вдоль сустава и посылает сигналы поперечным суппортам с приводом, чтобы они следовали за линией движения. Для этого требуется четко определенный шов, и поэтому он не подходит для стыковых сварных швов или профилей с очень мелкими швами.
Процессы, требующие высокой скорости наплавки, хорошо подходят для автоматизированной дуговой сварки под флюсом.
Лазерное отслеживание шва проецирует лазерный луч на заготовку и использует алгоритмы обработки изображения для распознавания профиля сварного шва. Профиль используется для точного позиционирования сварочной головки. Поскольку между датчиком и заготовкой нет физического контакта, датчики слежения за лазерным швом
не подвержены заклиниванию или поломке. Их можно использовать для автоматизации многопроходных сварных швов; однако расширенная функциональность обходится дороже.
Отслеживание шва сквозной дугой требует колебания сварочной головки и использует показания напряжения и силы тока в режиме реального времени для обнаружения краев шва. Обычно это используется с системами GMAW, но также может использоваться с системами SAW.
Сочетание ваших технических требований, бюджета и поставщика или системного интегратора поможет выбрать правильную систему для отслеживания ваших сварных швов.
Восстановление неиспользованного флюса
Для больших V-образных канавок и многопроходных швов обычно требуются большие катушки или барабаны со сварочной проволокой и подходящие системы подачи и возврата флюса. Как правило, 2 фунта. флюса требуется на каждый фунт израсходованной проволоки. Вместимость флюса можно увеличить, используя систему восстановления флюса — вакуум, который всасывает флюс, который не превратился в шлак, чтобы его можно было использовать повторно. Использование системы рекуперации флюса может уменьшить отношение флюса к проволоке. Одна только экономия восстановленного флюса может компенсировать стоимость системы надлежащего размера.
Производительность потока может иметь свои собственные скрытые расходы. Бункер с гравитационной подачей должен располагаться над сварочной головкой, а это означает, что необходимо поддерживать вес бункера, сварочной головки и катушки с проволокой. Вообще говоря, чем тяжелее сварочная головка, тем дороже оборудование, необходимое для ее поддержки над заготовкой.
Мониторинг качества сварки
Мониторинг и наблюдение за ходом сварки также важны. Есть несколько подходов к размещению оператора для наблюдения за сваркой на больших заготовках: поставьте сиденье оператора рядом со сварочной головкой; добавить подмости или лестницу, чтобы оператор мог стоять рядом со сварочной головкой; или поместите камеру на сварочную головку.
Добавление сиденья оператора эффективно превращает манипулятор или портал в лифт, а дополнительные требования могут значительно увеличить стоимость системы. Лестницы и подмости могут быть громоздкими и способствовать повторяющимся травмам от перенапряжения, если оператор в течение длительного времени находится в неудобном положении. Сварочная камера может держать оператора в безопасном положении, обеспечивая четкое представление о ходе сварки.
Посмотрите на картинку целиком
Дуговая сварка под флюсом в значительной степени зависит от вспомогательного оборудования, такого как манипуляторы или порталы, системы отслеживания шва, камеры и системы управления флюсом для создания качественных сварных швов. Важно понимать ваши приложения и сообщать о своих требованиях вашему интегратору или поставщику.
Правильные вопросы помогут выбрать систему, обеспечивающую необходимую вам функциональность и безопасность, и максимизировать окупаемость инвестиций.
Проволока для дуговой сварки под флюсом جوشکاری زیر پودری 9Проволока для дуговой сварки под флюсом
Введение
Дуговая сварка под флюсом — это метод, при котором соединение металлов производится путем нагрева дугой или дугами между оголенным металлическим электродом или электродами и заготовкой.
Дуга защищена покрытием из гранулированного легкоплавкого материала на рабочем месте.
Давление не используется. Нет видимой дуги, искры, брызг или дыма. Электрод может быть сплошным или порошковым проводом или полосой.
SAW обычно представляет собой механизированный процесс.
Процесс SAW
Оборудование состоит из сварочного аппарата или источника питания, механизма подачи проволоки и системы управления, сварочной горелки для автоматической сварки или сварочной горелки и кабеля в сборе для полуавтоматической сварки, бункера для флюса и механизма подачи , обычно система рекуперации флюса, и механизм перемещения для автоматической сварки.
Источник питания для дуговой сварки под флюсом должен быть рассчитан на 100-процентный рабочий цикл, поскольку операции дуговой сварки под флюсом являются непрерывными, а продолжительность сварки может превышать 10 минут.
Используются как генераторные, так и трансформаторно-выпрямительные источники питания, но более популярны выпрямительные машины.
Сварочные аппараты для дуговой сварки под флюсом в диапазоне от 300 до 1500 ампер.
Тепло дуги расплавляет поверхность основного металла и конец электрода. Металл, расплавленный с электрода, переносится через дугу на заготовку, где он становится наплавленным металлом шва.
Защиту получают из слоя гранулированного флюса, который укладывают непосредственно на зону сварки. Флюс вблизи дуги плавится и смешивается с расплавленным металлом сварного шва, способствуя его очистке и укреплению.
Флюс образует стекловидный шлак, который легче по весу, чем наплавленный металл, и плавает на поверхности в качестве защитного покрытия.
Сварной шов погружается под этот слой флюса и шлака, отсюда и название дуговой сварки под флюсом. Флюс и шлак обычно покрывают дугу так, что ее не видно.
Нерасплавленную часть флюса можно использовать повторно. Электрод подается в дугу автоматически из катушки. Дуга поддерживается автоматически.
Перемещение может быть ручным или механическим. Дуга инициируется пуском плавкого предохранителя или реверсивной или реверсивной системой.
Нормальный метод применения и возможности положения
Наиболее популярным методом применения SAW является машинный метод, при котором оператор контролирует операцию сварки.
Вторым по популярности является автоматический метод, при котором сварка выполняется нажатием кнопки. Процесс может применяться полуавтоматически; однако этот способ применения не слишком популярен.
Этот процесс нельзя применить вручную, поскольку сварщик не может управлять невидимой дугой. Процесс сварки под флюсом представляет собой процесс сварки в ограниченном положении.
Количество позиций для сварки ограничено, так как большая масса расплавленного металла и шлака очень жидкие и имеют тенденцию вытекать из соединения. Сварку можно легко выполнять в плоском положении и в горизонтальном угловом положении.
В соответствии со специальными контролируемыми процедурами возможна сварка в горизонтальном положении, иногда называемая сваркой на 3 часа.
Для этого требуются специальные устройства для удерживания флюса, чтобы расплавленный шлак и металл сварного шва не могли утечь. Процесс нельзя использовать в вертикальном или надземном положении.
Типы SAW
Многопроволочные системы: Многопроволочные системы обладают преимуществами, поскольку скорость наплавки и скорость перемещения могут быть улучшены за счет использования большего количества электродов.
Двухпроводной тандем: положение двухпроводного тандемного электрода с отдельными источниками питания используется там, где требуется глубокое проникновение.
Трехпроводная тандемная система: Трехпроводная тандемная система обычно использует питание переменного тока на всех трех электродах, подключенных к трехфазным системам питания. Эти системы используются для изготовления скоростных продольных швов труб большого диаметра и сборных балок.
Система сварки полос: Система сварки полос используется для наплавки мягких и легированных сталей, обычно на нержавеющую сталь.
Основными преимуществами дуговой сварки под флюсом или дуговой сварки под флюсом являются:
- высокое качество металлического шва.
- чрезвычайно высокая скорость и скорость наплавки
- гладкий, равномерный сварной шов без брызг.
- мало или нет дыма.
- отсутствие вспышки дуги, поэтому минимальная потребность в защитной одежде.
- высокий коэффициент использования электродной проволоки.
- простая автоматизация для высокой производительности.
- нормально, без задействования манипулятивных навыков.
Области применения:
Процесс под флюсом широко используется при изготовлении толстолистовой стали. Сюда входит сварка профилей, продольный шов труб большего диаметра, изготовление деталей машин для всех видов тяжелой промышленности, а также изготовление сосудов и резервуаров для работы под давлением и для хранения. Процесс SAW также используется для изготовления паровых барабанов, водяных барабанов и различных коллекторов котлов на тепловых электростанциях. Он широко используется в судостроении для сращивания и изготовления узлов, а также во многих других отраслях, где используются стали средней и большой толщины. Он также используется для наплавки и наплавки, технического обслуживания и ремонта.
Поддуговые горелки — выносная установка
Стандартные цилиндры
(внутренний диаметр газового колпачка 7/16–3/4 дюйма)
Обзор
Заказ
Руководства и чертежи
Аксессуары
Больше информации
Обзор
Поддуговые горелки D/F с водяным охлаждением на наконечнике® (SAW) с выносным креплением аналогичны выносным горелкам с водяным охлаждением на наконечнике®. Эти резаки оснащены соплом с водяным охлаждением с наружным диаметром меньше 1,125 дюйма для работы в труднодоступных местах с ограниченным доступом. Узлы положительных контактов D/F Machine Automatic Sub-arc сконструированы для обеспечения длительной бесперебойной работы и идеально подходят для навесные, переносные тракторные или полуавтоматические системы для тяжелых производственных условий.Сварочные горелки для дуговой сварки под флюсом для поддуговой сварки от D/F обеспечивают максимальный контроль наплавления и провара.Эти горелки D/F для автоматизации сварки с водяным охлаждением для тяжелых режимов работы идеально подходят и были используется для наплавки металла, твердосплавной наплавки, напыления металла и строительства трубопроводов, или даже для модернизации с помощью системы подачи флюса для поддуговых применений и применений, где добавляются флюс и карбид.0005
До сих пор дуговая сварка под флюсом (SAW) в основном выполнялась с использованием субдуговой горелки с воздушным охлаждением. Большинство проблем, связанных с горелками переменного тока, вызваны нагревом и отсутствием охлаждения. Горелки с воздушным охлаждением имеют большие силовые кабели с воздушным охлаждением, которые сильно нагреваются при подаче энергии, горелки сильно нагреваются от кабелей и в процессе сварки. Из-за тепла при сварке с воздушным охлаждением у вас теперь есть горячий пистолет, удерживающий горячий наконечник. Все настолько горячо, что расходники ломаются гораздо быстрее. В сочетании с большими наконечниками для сварки под дугой, которые очень дороги, теперь вам нужно искать лучшее решение. Вот почему компания D/F предлагает сверхмощную субдуговую горелку с водяным охлаждением, которая является превосходной заменой контактного сопла для погружной дуги Lincoln K231-1 или узла сопла Profax Sub Arc PX-K231. Пистолеты с подводной дугой D/F прочны и долговечны. Простая и компактная конструкция делает их долговечными и простыми в обслуживании. Автоматические резаки D/F с водяным охлаждением до кончика, требующие минимального взаимодействия и простоя, идеально подходят для жаркой среды.
Факел прослужит годы по сравнению с месяцами у конкурентов. Благодаря превосходному водяному охлаждению горелки наконечник прослужит несколько дней, а не всего пару деталей, и переживет конкурентов как минимум в соотношении 7 к 1, а иногда и 14 к 1. Не забывайте, что поддуговые наконечники D/F стоят 1/5 стоимости больших поддуговых наконечников с воздушным охлаждением.
Процесс под флюсом широко используется в производстве тяжелых стальных листов. Сюда входит сварка профилей, продольный шов труб большего диаметра, изготовление деталей машин для всех видов тяжелой промышленности, а также изготовление сосудов и резервуаров для работы под давлением и для хранения. Он широко используется в судостроении для сращивания и изготовления узлов, а также во многих других отраслях, где используются стали средней и большой толщины. Он также используется для наплавки и наплавки, технического обслуживания и ремонта.
Основными преимуществами дуговой сварки под флюсом или дуговой сварки под флюсом являются:
- Высококачественный сварной шов
- Чрезвычайно высокая скорость и скорость наплавки
- Гладкий однородный сварной шов без брызг
- Мало дыма или совсем нет
- Отсутствие дугового разряда, поэтому потребность в защитной одежде минимальна
- Высокая степень использования электродной проволоки
- Простая автоматизация для высокой производительности.
- В норме манипулятивные навыки не задействованы
Характеристики
- Внутреннее водяное охлаждение — наконечник утоплен в водяное охлаждение
- Внешнее водяное охлаждение — газовый стакан, встроенный в водяное охлаждение
- Непрерывный рабочий цикл до 650 А
- Непрерывный ток до 850 А с двумя силовыми кабелями
- Адаптируется к любому механизму подачи проволоки или источнику питания
- Выдерживает предварительный нагрев до 900 градусов
Модель Объяснение
- NCM-W/C-T — N ORMAL DUTY, C OLLET ACTION (Slip-In Tip), M ACHINE-Barred- W Ater-Ater- COL-TO COL-TO COL-TO COL-TO COL-TO COL-TO COL-TO COL-TO COL-TO COLED-TO COL-TO COLED-TO . -the- T ip
- HTM-W/C-T Series-A — H Тяжелый режим, T Наконечник с резьбой, M Ствол станка — W ater- C 2 904 Охлаждение до 3 T 902
Технические характеристики модели — горелки 5 дюймов
МОДЕЛЬ | ТОК МОЩНОСТЬ | ВЕС с 5″ NOZ. ![]() | ВЕС с 8″ NOZ. (ПРИБЛ.) | ОХЛАЖДЕНИЕ ТРЕБУЕТСЯ | РЕКОМЕНДУЕМАЯ ПРОВОДА ДИАМ. АССОРТИМЕНТ | ИНСТРУКЦИЯ РУКОВОДСТВО |
---|---|---|---|---|---|---|
NCM-W/C-T | 450 ампер | 2,8 фунта | 3,5 фунта | 3 литра/мин | .030″-5/32″ твердый/порошковый, 3/64″-1/8″ алюминий | 534 (все 5-дюймовые патрубки) 600 |
HTM-W/C-T | 850 ампер | 2,8 фунта | 3,5 фунта | 3 литра/мин | 0,030″-5/32″ твердый/порошковый, 3/64″-1/8″ алюминий |
Размеры ствола
МОДЕЛЬ | Длина с соплом 5 дюймов | Длина с соплом 8 дюймов | Диаметр корпуса стыковочной катушки | Диаметр патрубка В/Х |
---|---|---|---|---|
NCM-W/C-T, HTM-W/C-T | 9,25 дюйма | 12,25 дюйма | 1,875 дюйма | 1,125 дюйма |
Выносное крепление с полностью водяным охлаждением стыковочной шпули® вмещает два (2) узла сопла с водяным охлаждением. Это расположение легко адаптируется к специализированным или автоматическим сварочным приложениям, таким как Lincoln Electric NA3, NA4, NA5, NA5R, Power Feed 10, LF72, LF74 Автоматические механизмы подачи проволоки, силовые штифты серии Miller, ESAB, Euro и Tweco #4. Оборудование состоит из четырех (4) основных компонентов: вспомогательной станции, промежуточного комбинированного узла коммунальных услуг, стыковочной катушки с высоким уровнем отложения® и сопла с водяным охлаждением. Docking Spool® является основным компонентом этого сварочного оборудования. Он принимает инженерные коммуникации на верхнем конце Docking Spool® и обеспечивает возможность установки сопла с водяным охлаждением на нижнем конце с превосходным водяным охлаждением. Предусмотрено несколько функций, важных для сварочной системы. В водяные каналы стыковочного золотника® встроены обратные клапаны, которые служат средством удержания остаточной воды в линиях, когда узел форсунки снимается с стыковочного золотника®. Кроме того, на верхнем конце стыковочной катушки® имеется кольцо POSIT®, которое позволяет правильно разместить его в монтажном кронштейне для сохранения стабильности размеров.
Информация для заказа (полные сборки)
ОПИСАНИЕ | КОД №. (НКМ) | КОД №. (ХТМ) |
---|---|---|
Сопло 5 дюймов | 40748 | 40749 |
Сопло 8 дюймов | 40138 | 40155 |
Добавьте цифру видеоряда к кодовому номеру товара для указания требуемой длины. Пример: требуется 40138 с 4 футами. Шланг подачи воды в сборе: 40138-4 |
Руководства и загружаемые материалы
Инструкции по эксплуатации
МОДЕЛИ ГОРЕЛОК | СКАЧАТЬ |
---|---|
NCM-W/C-T, HTM-W/C-T (все 5-дюймовые сопла) | 534 |
NCM-W/C-T, HTM-W/C-T (все 8-дюймовые сопла) | 600 |
Файлы САПР и чертежи
МОДЕЛИ ГОРЕЛОК | КОД №.![]() | САПР-ФАЙЛ | ЧЕРТЕЖ PDF |
---|---|---|---|
NCM-W/C-T 5 дюймов | 40748 | 40748 | 40748 |
HTM-W/C-T 5 дюймов | 40749 | 40749 | 40749 |
NCM-W/C-T 8″ | 40138 | 40138 | 40138 |
HTM-W/C-T 8″ | 40155 | 40155 | 40155 |
Прочие документы
ОПИСАНИЕ | СКАЧАТЬ |
---|---|
Варианты подключения горелки | |
W/C Выносной монтаж с водяным охлаждением до наконечника® Однолистовой |
Вспомогательная станция #45196
Вспомогательная станция D/F требуется для всех установок резака D/F. В типичных современных установках резака используется унифицированный кабельный узел с разъемом питания. Горелки D/F используют альтернативный подход к настройке. В горелках используется отдельный газовый шланг, шланг подачи воды, кабель подачи воды и питания, а также кожух/кабелепровод. Когда один кабель выходит из строя, его просто заменяют вместо того, чтобы прикреплять полностью новый унифицированный кабельный узел; огромная экономия средств! Здесь также вступает в игру D/F Utility Station. Газовый шланг, шланг подачи воды и кабель подачи воды и питания подключаются к существующим линиям заказчика через коммуникационную станцию. Провода резака D/F вставляются в переднюю часть (см. справа) Utility Station. В заднюю часть (см. ниже) Коммунальной станции идут коммунальные услуги клиента. Подробнее читайте на странице продукта D/F Utility Station.
Для получения дополнительной информации о правильном использовании D/F Utility Station, а также для ознакомления с различными вариантами подключения резака загрузите один лист «Варианты подключения резака».
Стойка для резака № 30418 и крепление для стойки
Дополнительный штатив для резака D/F № 30418 можно использовать с любым резаком с водоохлаждаемым соплом длиной 8 дюймов и диаметром 1,125 дюйма. Стойка надевается прямо на сопло с водяным охлаждением и крепится 4 установочными винтами. Затем подставку можно вставить в держатель стойки BUG-O BUG-5188. Стойка имеет 32-шаговое зубчатое колесо, а держатель стойки позволяет очень легко позиционировать головку резака. См. изображения ниже справа. Дополнительную информацию см. на странице продукта Torch and Rack Mount
Для получения дополнительной информации о правильном использовании D/F Utility Station, а также для ознакомления с различными вариантами подключения резака загрузите один лист «Варианты подключения резака».
D/F #30421 Поддуговая насадка
Машинные цилиндры D/F с водяным охлаждением до наконечника®, используемые с насадкой для погружной дуги D/F, являются самыми передовыми в отрасли субдуговыми горелками. для мобильного, жесткого автоматизированного и роботизированного оборудования подачи и поможет достичь новых уровней производительности сварки и операционной эффективности. Будь то настил моста, сосуды под давлением, панельные линии, закаточные машины, решения для интеграции трубных заводов или роботизированная дуговая сварка под флюсом, выбор поддуговой сварки D/F предназначен для улучшения качества сварки, снижения сварочных и эксплуатационных затрат и увеличения количества сварщиков. производительность.
D/F Water-Cooled-to-the-Tip® Sub-Arc — дополнительная информация сварка под флюсом (SAW). Они ремонтопригодны и просты в обслуживании. Наши расходные материалы всегда в наличии и стоят 1/3 стоимости конкурентов. Клиенты всегда были рады узнать, что мы отправляем каждый заказ в течение 3 дней с момента получения заказа на поставку и что мы всегда готовы сделать все возможное, чтобы отправить наше оборудование для доставки на следующий день.
Дуговая сварка под флюсом (SAW) заключается в образовании дуги между постоянно подаваемым электродом и заготовкой. Слой порошкообразного флюса, образующий защитный газовый экран и шлак (а также может использоваться для добавления легирующих элементов в сварочную ванну), защищает зону сварки. Защитный газ не требуется. Дуга находится под слоем флюса и обычно не видна во время сварки.
Способность SAW приводит к чрезвычайно высокой скорости наплавки, что обеспечивает более быстрое проникновение тепла и стабильность дуги. В традиционных источниках питания, когда волна переходит от положительной (EP) к отрицательной (EN) в своем полупериоде, может произойти запаздывание или прерывание дуги, что впоследствии вызовет проблемы со сваркой. Хотя этот фактор и связанные с ним проблемы ввода и вывода ранее ограничивали скорость и производительность, теперь он устранен в передовом энергетическом оборудовании.
Во-первых, теперь можно сваривать полярность переменного и постоянного тока в одной сварочной ванне, используя один и тот же источник питания. В прошлом требовались разные машины, и иногда сварку постоянным и переменным током приходилось выполнять за разные проходы. Сегодняшняя SAW дает возможность создавать сварные швы быстрее и с уникальными, особыми свойствами. Преимущества переменного тока для высокого наплавления, стабильности и устранения дугового разряда могут быть реализованы, в то время как DCEP/DCEN обеспечивают стабильное проплавление на гораздо более высоких скоростях. Из-за того, что происходит в задней части этих новых машин, сварщики теперь имеют гораздо больше возможностей для дуговой сварки.
Старое оборудование работало в соответствии с ограниченным набором параметров; сегодняшние источники энергии работают и реагируют.
Стыковочная катушка прямого монтажа с полным водяным охлаждением до наконечника® вмещает два (2) узла форсунок с водяным охлаждением. Это устройство легко адаптируется к специальным или автоматическим сварочным установкам, таким как Lincoln Electric NA-3, NA-4, NA-5, NA-5R, Power Feed 10, LF-72, LF-74 автоматические механизмы подачи проволоки, серия Miller Power. штифты, ESAB, Euro и Tweco #4. Оборудование состоит из четырех (4) основных компонентов: вспомогательной станции, промежуточного комбинированного узла коммунальных услуг, стыковочной катушки с высоким уровнем отложения® и сопла с водяным охлаждением. Docking Spool® является основным компонентом этого сварочного оборудования. Он принимает инженерные коммуникации на верхнем конце Docking Spool® и обеспечивает возможность установки сопла с водяным охлаждением на нижнем конце с превосходным водяным охлаждением. Предусмотрено несколько функций, важных для сварочной системы. В водяные каналы стыковочного золотника® встроены обратные клапаны, которые служат средством удержания остаточной воды в линиях, когда узел форсунки снимается с стыковочного золотника®. Кроме того, на верхнем конце стыковочной катушки® имеется кольцо POSIT®, которое позволяет правильно разместить его в монтажном кронштейне для сохранения стабильности размеров.
Горелки модели W/C Tip также могут быть оснащены двумя кабелями подачи воды/выхода и силовым кабелем, что увеличивает номинальный ток непрерывного рабочего цикла до 850 ампер. Эти силы тока требуют использования токовых наконечников HTM или серии хром-циркониевых (CrZr) резьбовых наконечников.
Горелка D/F известна тем, что при правильном охлаждении сварщик может голой рукой взяться за хромированный передний водоохлаждаемый ствол (а не за медное газовое сопло/стакан) горелки, и она быть холодным на ощупь через несколько секунд после сварки. С надлежащим чиллером это можно сделать даже после 4-часового времени дуги. Убедитесь, что подача охлаждающей воды имеет минимальный расход 1 галлон в минуту (для каждого внутреннего корпуса), давление 40 фунтов на кв. дюйм (максимум 80 фунтов на кв. дюйм) с резервуаром на 6 галлонов и рекомендуемой охлаждающей способностью 30 000 БТЕ/ч. Характеристики горелки зависят от используемого защитного газа, времени дуги, времени охлаждения и температуры воды на входе. Температура воды на выходе не должна превышать 27°C (80°F). Выход воды и силовой кабель горелки не охлаждается до тех пор, пока охлаждающая жидкость не пройдет через резак и не выйдет из воды и кабеля питания. Если вода не течет через горелку D/F в течение по крайней мере 1 минуты до зажигания дуги, когда вы включаете питание и вода попадает на «горячий» водяной/выходной и силовой кабель, вы будете генерировать пар. Пар может повредить внутренние детали горелки за считанные секунды, что приведет к утечке. Он также может выдуть факелы вода / выход и силовой кабель. Реле протока может быть установлено после обратной линии, гарантируя наличие охлаждающей жидкости в обратной линии до зажигания дуги.
При использовании GMAW с высоким напылением, высокой плотности тока, высокой силы тока, предварительного нагрева или длительных периодов времени дуги требуется охладитель охлаждающей жидкости с резервуаром большего размера. Точный контроль температуры поддерживает постоянную температуру охлаждения 13°C (55°F), что продлевает срок службы сварочного оборудования и, в частности, продлевает срок службы газового сопла и токоподвода. D/F Machine Specialties не производит и не продает чиллеры, мы только рекомендуем их. Нажмите здесь, чтобы увидеть наши рекомендуемые чиллеры.
Стационарная автоматизация — это процесс, в котором используется механизированное оборудование для выполнения повторяющихся операций с целью производства большого количества одинаковых деталей. При стационарной автоматизации последовательность технологических операций фиксируется компоновкой оборудования.
Программируемая автоматика представляет собой прикладную форму стационарной автоматизации, которая способна повторять движения в виде последовательности шагов для производства продукции партиями. Прикладные изделия в системе программируемой автоматизации изготавливаются партиями от нескольких десятков до нескольких тысяч единиц за один раз. Для каждой новой партии программируемое оборудование автоматизации должно быть перепрограммировано и изменено, чтобы соответствовать новому стилю продукта. Программируемая автоматизация обычно может включать от одной до трех осей движения горелки и/или несколько сварочных дуг.
D/F Machine Specialties является мировым лидером в производстве горелок с водяным охлаждением для систем жесткой автоматизации, включающих фиксированную и программируемую автоматику.
Каждый сварочный пистолет D/F Machine Specialties полностью собран и готов к установке. Чтобы завершить установку, укажите кодовый номер, размер проволоки, марку/модель механизма подачи проволоки (механизмы подачи проволоки Lincoln, механизмы подачи проволоки Miller, механизмы подачи проволоки Tweco, механизмы подачи проволоки ESAB и механизмы подачи проволоки EURO Quick Disconnect) и вход (при необходимости). ) необходимо указать при заказе. Если требуются специальные сварочные инструменты или принадлежности, отличные от перечисленных выше, проконсультируйтесь с заводом-изготовителем. Получите правильное соединение адаптера механизма подачи, подходящее для механизма подачи проволоки MIG.
Дуговая сварка под флюсом (SAW) Обзор
Дуговая сварка под флюсом (SAW) — это один из сварочных процессов, используемых в сварочной промышленности. В отраслях , где используются длинные сварные швы и толстые стальные листы, используется дуговая сварка под флюсом . Это высокопроизводительный автоматизированный процесс сварки. Процесс SAW обычно работает в полуавтоматическом или автоматическом режиме. Кроме того, он ограничен плоской или горизонтально-угловой сваркой. В этой статье начинающие люди могут найти различные аспекты SAW, такие как значение, расходные материалы, принципы, машины, приложения, диаграммы, ограничения, советы по безопасности и т. д.
Основные моменты сообщения:
- Дуговая сварка под флюсом Значение
- Принцип дуговой сварки под флюсом
- Схема дуговой сварки под флюсом
- Оборудование для дуговой сварки под флюсом
- Расходные материалы для дуговой сварки под флюсом
- Сварка под флюсом
- Преимущества дуговой сварки под флюсом
- Недостатки дуговой сварки под флюсом
- Распространенные ошибки SAW
- Безопасность дуговой сварки под флюсом
- Сварка под флюсом Области применения
- Работы по дуговой сварке под флюсом
- Динамика заработной платы сварщика SAW
Дуговая сварка под флюсом Значение
Дуговая сварка под флюсом — это распространенный процесс дуговой сварки. Во время процесса он образует дугу между постоянно подаваемым электродом и заготовкой. Слой порошкообразного флюса создает защитный газовый экран. Шлак защищает зону сварки. Процесс не требует защитного газа. Обычно дуга невидима во время сварки, поскольку она погружена под слой флюса.
Принцип дуговой сварки под флюсом
Как следует из названия, «под флюсом» дуга не видна. Принцип SAW включает в себя образование электрической дуги между постоянно подаваемым электродом и заготовкой . Во время сварки слой порошкообразного флюса окружает и покрывает дугу . Он обеспечивает электрическую проводимость между металлом и электродом в расплавленном состоянии. Образование защитного газа и шлак защищают зону сварки. Он также защищает глаза, так как выделяет очень мало дыма.
Схема дуговой сварки под флюсом
Схема для SAW состоит из таких названий, как гранулированный флюс, проволочный электрод, плавленый флюс, источник питания и т. д. На изображении ниже показаны различные компоненты формирования процесса SAW.
В SAW используется следующее оборудование:
1. Электрод
В процессе используется стандартная проволока и специальные формы в качестве наполнителя. Обычно толщина проволоки колеблется от 1,6 мм до 6 мм (от 1/16 до 1/4 дюйма). В некоторых случаях для придания дуге колебательного движения можно использовать витую проволоку. В результате помогает сплавление носка сварного шва с металлической основой.
Выбор электродов зависит от типа свариваемых материалов. Электроды могут состоять из электродов с легирующими элементами. Имеющиеся электроды подходят для сварки высокоуглеродистой стали, низкоуглеродистой и специальной легированной стали, мягкой стали, нержавеющей стали, а также некоторых видов цветной меди и никеля.
Как правило, электроды покрыты медью. Это увеличивает их электропроводность и предотвращает ржавление. Они доступны в прямых длинах и формах катушки. Диаметры могут быть 1,6, 2,0, 2,4, 3, 4,0, 4,8 и 6,4 мм.
2. Флюс
В процессе SAW используется гранулированный флюс для защиты и защиты расплавленного сварного шва от атмосферного загрязнения. Флюс действует как очиститель металла. Он также может изменить свой химический состав. Он гранулируется до определенного размера и может быть связанного, плавленого и механически смешанного типа. Флюс может состоять из оксидов кальция, кремния, алюминия, марганца и магния, а также фторидов кальция.
Легирующие элементы могут быть добавлены по мере необходимости. Рекомендуется использовать флюс с мелкими и крупными частицами для сварки более тяжелых и меньших толщин соответственно.
3. Сварочная головка
Основной функцией оборудования является подача флюса и присадочного металла к сварному шву. Здесь на электрод (присадочный металл) подается напряжение.
4. Бункер для флюса
Бункер для флюса хранит флюс и контролирует скорость осаждения флюса на сварном соединении во время процесса.
Переменные процесса под флюсом
Ниже приведены некоторые ключевые переменные дуговой сварки под флюсом.0005
- Напряжение дуги
- Вылет электрода (ESO) или контактный наконечник для работы (CTTW)
- Полярность и тип тока (переменный или постоянный) и регулируемый баланс переменного тока
- Скорость перемещения
- Скорость подачи проволоки (основной фактор контроля сварочного тока)
Расходные материалы для дуговой сварки под флюсом
Система AWS определяет расходные материалы под флюсом в более простой форме. Эти две спецификации относятся как к составу проволоки, так и к флюсу. Еще две спецификации касаются неизолированных проводов для нержавеющей стали и сплавов на основе никеля. Для дуговой сварки под флюсом есть два, а именно-
- 17 – Электроды и флюсы из углеродистой стали
- 23 Электроды и флюсы из низколегированной стали
Спецификации неизолированной проволоки следующие:
- 9 Проволочные электроды, ленточные электроды, проволока и стержни для дуговой сварки нержавеющих и жаропрочных сталей – Классификация
- 11/A5.
11M Сварочные электроды и стержни из никеля и никелевых сплавов без покрытия для дуговой сварки в защитных газах.
Дуговая сварка под флюсом
Сварка под флюсом используется во многих областях. Они следующие:
- Углеродистая сталь (строительство конструкций/сосудов)
- Низколегированные стали
- Сплавы на основе никеля
- Сосуды под давлением, такие как котлы и цилиндрические
- Ремонт деталей машин
- Нержавеющая сталь
- Конструктивные элементы, землеройные инструменты, трубы, строительство железных дорог, судостроение и локомотивы
- Наплавка (износостойкая, наплавочная и коррозионно-стойкая наплавка на стали)
Преимущества дуговой сварки под флюсом
- Флюс рекуперируется , перерабатывается и используется повторно (от 50% до 90%)
- Возможность глубокого провара
- Выделяет минимальное количество сварочного дыма или свет дуги или отсутствие сварочных брызг
- Высокая скорость осаждения (более 45 кг/ч (100 фунтов/ч)
- Высокие эксплуатационные факторы в механизированных применениях
- Придает высокоскоростная сварка тонколистовой стали до 5 м/мин (16 фут/мин)
- Не требуется высший уровень или продвинутая подготовка
- Отсутствие брызг при сварке из-за погружения во флюсовую подушку
- Однопроходные сварные швы могут быть выполнены на относительно толстых листах, если металлургически приемлемо
- Качественные сварные швы легко выполняются с хорошей конструкцией и контролем
- Подходит как для внутренних, так и для наружных сварочных работ
- При полной автоматизации высокая скорость наплавки и большое время работы дуги
Недостатки дуговой сварки под флюсом
Все процессы сварки имеют те или иные недостатки. Несмотря на множество преимуществ, дуговая сварка под флюсом имеет следующие ограничения:
- Не применяется для прямого шва сосудов и труб
- Системы обращения с флюсом относительно сложны
- Использование Flux затруднено
- Для правильного проникновения в корень требуются подкладочные полосы
- Нецелесообразно использовать в вертикальном или потолочном положении для сварки. В основном используется для стыковых швов (плоское положение-1G) и угловых швов (плоское/горизонтальное положение-1F/2F)
- Только для материалов большой толщины, не применяется для тонких материалов
- Ограничено некоторыми конкретными металлами, например, черными или некоторыми сплавами на основе никеля
- Потенциально опасен для здоровья из-за флюса
- Требуется удаление межпроходного и послесварочного шлака
- Желательно удаление шлака после сварки
Распространенные ошибки SAW
- Неправильное хранение флюса
- Несоответствующая плотность тока
- Несоответствие контакта наконечника и заготовки
- Выбор неверного флюса
- Плохое восстановление незакрепленного флюса
- Неправильная настройка выпрямителя проволоки
Безопасность при дуговой сварке под флюсом
Все производители сварочного оборудования прилагают к продукции инструкции по применению. Пользователи должны прочитать эти правила, прежде чем продолжить. Это меры безопасности, чтобы избежать любых возможных несчастных случаев.
1. Для защиты от поражения электрическим током
- Всегда надевайте сухие перчатки без дырок и расщепленных швов
- Если участок влажный, используйте полуавтоматический аппарат для сварки постоянным напряжением или аппарат для сварки стержнями с устройством понижения напряжения.
- Изолировать от заготовки/грунта с помощью сухой фанеры, резиновых матов, сухой изоляции
- Держите электрододержатель и изоляцию кабеля в хорошем состоянии
- Не прикасаться к горячим частям или сварочному электроду
2. Для паров/газов
- Выйдите на свежий воздух, если почувствуете дискомфорт, головокружение или тошноту
- Если невозможно контролировать сварочный дым, используйте респиратор
- Держите голову подальше от шлейфа сварочного дыма, чтобы предотвратить его
- Обеспечьте достаточную вентиляцию или вытяжку, чтобы воздух был чистым и комфортным
- Удалите краску, гальванопокрытие или покрытие со свариваемого металла, если это возможно
3. Для сварочных искр
- Всегда сваривайте контейнеры с горючими материалами в соответствии с предписанными безопасными процедурами
- Во время и после сварки нести пожарную вахту на участке
- Не допускайте попадания легковоспламеняющихся материалов в зону сварки
- В зоне сварки должен быть огнетушитель
- Носить огнеупорную одежду/головной убор без потрепанных краев
4. Для глаз/кожи
- Всегда надевайте каску во время сварки
- Выберите подходящую и удобную линзу с фильтром
- Для защиты окружающих используйте негорючие сварочные экраны
- Используйте беруши, чтобы избежать повреждения искрами/брызгами
- Носите огнеупорную одежду для защиты кожи
Сварка под флюсом Области применения
Сварка под флюсом используется во многих отраслях промышленности, таких как-
- Строительные компании
- Оборонные/космические производственные компании
- Инжиниринговые/производственные компании
- Компании-производители промышленного оборудования
- Горнодобывающие компании
- Нефтегазовые компании
- Компании-производители автомобилей
Вакансии в области дуговой сварки под флюсом
Начинающие кандидаты могут найти различные рабочие места в различных компаниях. Вот некоторые из вакансий:
- Сварщик труб
- Сварочный аппарат (сталь)
- Сварщик-изготовитель
- Сварщик/слесарь-монтажник
- Производственный сварщик
- Наладочный сварочный аппарат
- Аппарат для сварки труб
- Сварочный аппарат для сосудов под давлением
- Аппарат для дуговой сварки под флюсом
Дополнительные типы вакансий см. в разделе Сварочные работы
Тенденции заработной платы сварщика под флюсом
Почасовая или месячная заработная плата сварщика под флюсом варьируется от места к месту или от компании к компании. Разница в заработной плате вызвана такими факторами, как наличие рабочей силы, уровень образования, опыт работы, личные качества, требования к изготовлению, типы проектов, безудержные тенденции заработной платы.
По некоторым анонимным данным, средняя зарплата сварщика под дугой составляет 21,69 долларов США в час и 42 296 долларов США в год. В то время как новички могут получать 38 025 долларов США в год. Также человек с достаточным опытом может заработать 97 500 долларов США в год.
Заключение
Дуговая сварка под флюсом (SAW) является одним из важных видов сварки в промышленности. Приведенная выше информация о различных аспектах сварки под флюсом полезна начинающим рабочим и профессионалам в их повседневной жизни при взаимодействии со сваркой под флюсом.
Связанный: Другие типы сварки
Что насчет дуговой сварки под флюсом?
Лазерное отслеживание шва создает, анализирует и передает трехмерные профили зоны сварки.
Ваша компания все больше занимается сваркой профилей или сосудов высокого давления для тяжелой промышленности. Скорее всего, вы хотите осаждать металл со скоростью, которую невозможно сделать вручную — в диапазоне 20, 30 или даже 40 фунтов. в час.
Дуговая сварка под флюсом (SAW) справится со сваркой, но контроль места и способа сварки может быть не менее важным, чем то, что плавит проволоку.
Покупка системы SAW без вспомогательного оборудования, такого как манипулятор или портал, аналогична покупке двигателя без остальной части автомобиля. Вы можете включить его, и он сделает немного дыма, но он не доставит вас туда, куда вам нужно.
Знание областей применения поможет вам определить, какое вспомогательное оборудование необходимо для управления сварочной головкой и достижения желаемой производительности.
Опишите соединение
Первое, что необходимо определить при выборе вспомогательного оборудования SAW, — это тип и разнообразие соединений, которые вы будете сваривать. Будут ли:
- Большие V-образные пазы с достаточным пространством для большой сварочной горелки?
- Узкие и глубокие канавки для минимизации количества наплавляемого материала?
- Многопроходные сварные швы, и если да, то сколько проходов?
- Угловые сварные швы?
- Облицовка, где необходимо последовательно выполнять несколько проходов?
- Прямые и ровные или волнистые и неровные сварные швы?
Определение типового проекта
Свариваемая деталь также поможет определить требования к вспомогательному оборудованию. Хорошие вопросы, которые следует задать:
- Соединения выполнены из длинных и прямых или круглых материалов?
- Вертикальные?
- Насколько велика заготовка, и нужно ли ее позиционировать или поворачивать, чтобы получить доступ ко всем точкам сварки?
При сварке больших заготовок время, необходимое для их позиционирования, может существенно повлиять на производительность. Переворачивание большой заготовки для достижения сварного шва требует времени и может быть опасным для операторов.
Манипулятор со стрелой и колонной, вероятно, является наиболее экономичным и универсальным методом удержания сварочной головки над заготовкой. Если соединение длинное и прямое, эффективным может быть манипулятор стрелы и колонны на рельсах с моторизованным вагоном. Важно убедиться в том, что скорость автомобиля может соответствовать ускоренному перемещению, а также обычным скоростям сварки.
Если заготовка круглая, например, ветряная башня или сосуд высокого давления, ее нужно будет вращать под факелом. Для этого обычно используются поворотные ролики и сварочные позиционеры. Валки вращают длинные и часто очень тяжелые цилиндрические заготовки, центр масс которых находится примерно на осевой линии заготовки. Позиционеры вращают заготовки с центром масс, который не лежит на оси вращения или вблизи нее.
Количество наплавляемой сварочной проволоки и толщина основного металла определяют другие требования к оборудованию. Например, для предварительного нагрева толстого материала может потребоваться обычное пламенное или индукционное нагревательное оборудование.
Размещение камеры на месте сварки позволяет оператору наблюдать за ходом и качеством сварки из удобного и безопасного места.
Ответы на два вопроса о процессе могут определить, какое вспомогательное оборудование необходимо:
- Какой ток необходим?
- Как долго мне нужно сваривать?
Если вы будете выполнять сварку с большим током в течение длительного периода времени, необходимо правильно подобрать размер сварочной цепи. Если ваши кабели недостаточно велики по обе стороны от дуги, вы рискуете расплавить что-то, кроме электрода.
Другим важным фактором является теплопередача. Когда ток проходит через сварочные кабели, они нагреваются и могут расплавиться. Вокруг кабелей должно быть достаточно воздуха, чтобы они оставались прохладными.
Найдите рентабельность инвестиций в автоматизацию
В некоторых случаях затраты на автоматизацию SAW окупаются в течение длительного времени. В других стоимость быстро оправдывается.
С одной стороны, многопроходные сварные швы часто трудно автоматизировать, потому что размещение последовательных валиков может быть очень важным. Трудно победить хорошо обученного оператора SAW.
С другой стороны, плакирование, конструкционные секции, толстостенные сосуды под давлением и другие процессы, требующие высокой скорости наплавки, являются первыми кандидатами на автоматизацию. Полагаться на человека-оператора для точного нанесения сотен фунтов наплавленного металла последовательными валиками в течение нескольких часов, как правило, неэкономично, непрактично или даже невозможно.
Для таких применений типичный однопроволочный процесс с дугой под флюсом может легко наплавить 15 или 20 фунтов. в час, а двойная или тандемная двухпроводная дуговая сварка под флюсом может откладывать до 40 фунтов. в час, что обеспечивает скорость наплавки в 10 раз или на 1000% выше, чем при обычной ручной дуговой сварке в среде защитного газа или дуговой сварке в среде защитного газа.
Выбрать отслеживание швов
Отслеживание швов может упростить сварку волнистых соединений по неправильной траектории. Датчик или обратная связь от сварки используются для регулировки положения сварочной головки таким образом, чтобы она оставалась в заданном месте на стыке. Это может повысить производительность во многих областях применения и помочь менее опытным операторам выполнять качественные сварные швы.
Наиболее распространенными методами отслеживания являются тактильный, лазерный и дуговой.
Тактильное отслеживание шва экономично. Механический зонд перемещается вдоль сустава и посылает сигналы поперечным суппортам с приводом, чтобы они следовали за линией движения. Для этого требуется четко определенный шов, и поэтому он не подходит для стыковых сварных швов или профилей с очень мелкими швами.
Процессы, требующие высокой скорости наплавки, хорошо подходят для автоматизированной дуговой сварки под флюсом.
Лазерное отслеживание шва проецирует лазерный луч на заготовку и использует алгоритмы обработки изображения для распознавания профиля сварного шва. Профиль используется для точного позиционирования сварочной головки. Поскольку между датчиком и заготовкой нет физического контакта, датчики лазерного отслеживания шва не подвержены заклиниванию или поломке. Их можно использовать для автоматизации многопроходных сварных швов; однако расширенная функциональность обходится дороже.
Отслеживание шва сквозной дугой требует колебания сварочной головки и использует показания напряжения и силы тока в режиме реального времени для обнаружения краев шва. Обычно это используется с системами GMAW, но также может использоваться с системами SAW. Сочетание ваших технических требований, бюджетных ассигнований и поставщика или системного интегратора поможет выбрать правильную систему для отслеживания ваших сварных швов.
Восстановление неиспользованного флюса
Для больших V-образных канавок и многопроходных швов обычно требуются большие катушки или барабаны со сварочной проволокой и подходящие системы подачи и возврата флюса. Как правило, 2 фунта. флюса требуется на каждый фунт израсходованной проволоки. Вместимость флюса можно увеличить, используя систему восстановления флюса: в основном вакуум, который всасывает флюс, который не превратился в шлак, чтобы его можно было использовать повторно. Использование системы рекуперации флюса может уменьшить отношение флюса к проволоке. Одна только экономия восстановленного флюса может компенсировать стоимость системы надлежащего размера.
Производительность потока может иметь свои собственные скрытые расходы. Бункер с гравитационной подачей должен располагаться над сварочной головкой, а это означает, что необходимо поддерживать вес бункера, сварочной головки и катушки с проволокой.