Электросварка — это… Что такое Электросварка?
- Электросварка
Электродуговая ручная сварка покрытым электродом
Электросварка — один из способов сварки, использующий для нагрева и расплавления металла электрической дугой.
Температура электрической дуги превосходит температуры плавления всех существующих металлов. Электросварка не изменяет химического состава материала.
История
1803 год — В. В. Петров опубликовал книгу в которой описал явление электрической дуги и возможность её применения для электросварки.
1882 год — Н. Н. Бенардос изобрёл электрическую сварку с применением угольных электродов.
1888 год — Н. Г. Славянов впервые в мире применил на практике дуговую сварку металлическим (плавящимся) электродом под слоем флюса. В присутствии государственной комиссии он сварил коленчатый вал паровой машины.
19ХХ год — Патон, электросварные башни танков, электросварной мост.
Описание процесса
К электроду и свариваемому изделию для образования и поддержания электрической дуги от источников сварочного тока подводится электроэнергия. Под действием теплоты электрической дуги кромки свариваемых деталей и электродный металл расплавляются, образуя сварочную ванну, которая некоторое время находится в расплавленном состоянии. В сварочной ванне электродный металл смешивается с расплавленным металлом изделия (основным металлом), а расплавленный шлак всплывает на поверхность, образуя защитную плёнку. При затвердевании металла образуется сварное соединение.
В процессе электросварки могут быть использованы плавящиеся и неплавящиеся электроды. В первом случае формирование сварного шва происходит при расплавлении самого электрода, во втором случае — при расплавлении присадочной проволоки (прутков и т.п.), которую вводят непосредственно в сварочную ванну.
Для защиты от окисления металла сварного шва применяются защитные газы (аргон, гелий, углекислый газ и их смеси), подающиеся из сварочной головки в процессе электросварки.
Различают электросварку переменным током и электросварку постоянным током. При сварке постоянным током шов получается с меньшим количеством брызг металла, поскольку нет перехода через нуль и смены полярности тока.
В аппаратах для электросварки постоянным током применяются выпрямители.
Источники
Ссылки
См. также
Wikimedia Foundation. 2010.
- Москвина, Марина Львовна
- Кубок Федерации футбола СССР
Смотреть что такое «Электросварка» в других словарях:
электросварка — электросварка … Орфографический словарь-справочник
ЭЛЕКТРОСВАРКА
к месту сварки ток подводится помощью тонкого … Большая медицинская энциклопедия
ЭЛЕКТРОСВАРКА — контактная электросварка, сварка … Большая политехническая энциклопедия
ЭЛЕКТРОСВАРКА — сварка, при которой свариваемые части нагреваются электрическим током. Различают электросварку дуговую и контактную … Большой Энциклопедический словарь
ЭЛЕКТРОСВАРКА — ЭЛЕКТРОСВАРКА, электросварки, мн. нет, жен. (тех.). Сварка металлов при помощи электрического тока. см. электро…. Толковый словарь Ушакова. Д.Н. Ушаков. 1935 1940 … Толковый словарь Ушакова
ЭЛЕКТРОСВАРКА
— (Electric welding) см. Сварка. Самойлов К. И. Морской словарь. М. Л.: Государственное Военно морское Издательство НКВМФ Союза ССР, 1941 … Морской словарьэлектросварка — сущ., кол во синонимов: 2 • сварка (20) • электрогазосварка (3) Словарь синонимов ASIS. В.Н. Тришин.
2013 … Словарь синонимов
Электросварка — Электросварка: способ получения сварного шва путем контактной электросварки сопротивлением, при которой свариваемые кромки механически прижимают друг к другу, а тепло для сварки выделяется вследствие сопротивления приложенному или наведенному… … Официальная терминология
электросварка — Группа способов сварки, использующая для нагрева металла электрическую энергию. Примечание Электрический нагрев позволяет получить температуры, превосходящие температуры плавления существующих металлов, не изменяет химического состава материала,… … Справочник технического переводчика
электросварка — 4.54 электросварка (electric welding): Способ получения шва сваркой электросопротивлением, при которой свариваемые кромки прижимаются друг к другу под механическим воздействием, а тепло для сварки выделяется вследствие сопротивления приложенному… … Словарь-справочник терминов нормативно-технической документации
Электросварка — это.
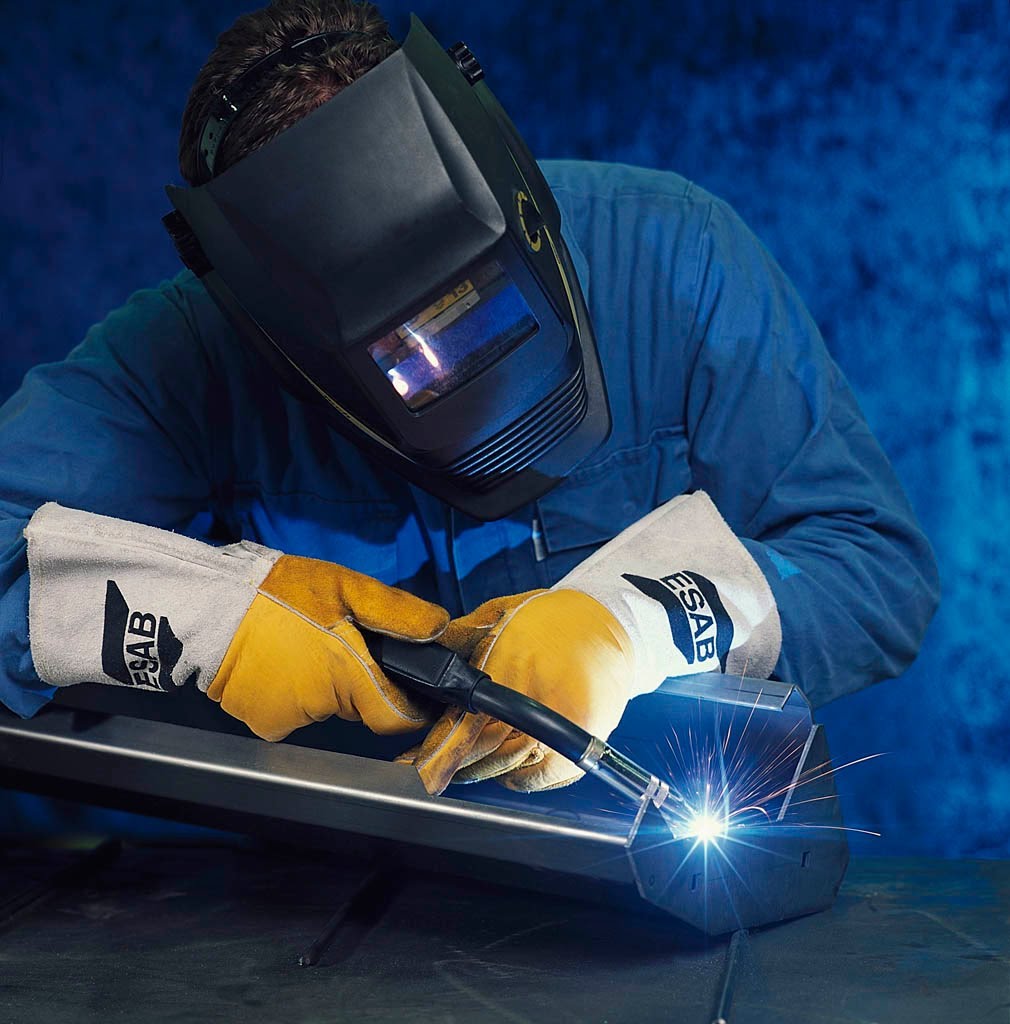
- Электросварка
Электродуговая ручная сварка покрытым электродом
Электросварка — один из способов сварки, использующий для нагрева и расплавления металла электрической дугой.
Температура электрической дуги превосходит температуры плавления всех существующих металлов. Электросварка не изменяет химического состава материала.
История
1803 год — В. В. Петров опубликовал книгу в которой описал явление электрической дуги и возможность её применения для электросварки.1882 год — Н. Н. Бенардос изобрёл электрическую сварку с применением угольных электродов.
1888 год — Н. Г. Славянов впервые в мире применил на практике дуговую сварку металлическим (плавящимся) электродом под слоем флюса. В присутствии государственной комиссии он сварил коленчатый вал паровой машины.
19ХХ год — Патон, электросварные башни танков, электросварной мост.
Описание процесса
К электроду и свариваемому изделию для образования и поддержания электрической дуги от источников сварочного тока подводится электроэнергия. Под действием теплоты электрической дуги кромки свариваемых деталей и электродный металл расплавляются, образуя сварочную ванну, которая некоторое время находится в расплавленном состоянии. В сварочной ванне электродный металл смешивается с расплавленным металлом изделия (основным металлом), а расплавленный шлак всплывает на поверхность, образуя защитную плёнку. При затвердевании металла образуется сварное соединение.
В процессе электросварки могут быть использованы плавящиеся и неплавящиеся электроды. В первом случае формирование сварного шва происходит при расплавлении самого электрода, во втором случае — при расплавлении присадочной проволоки (прутков и т.п.), которую вводят непосредственно в сварочную ванну.
Для защиты от окисления металла сварного шва применяются защитные газы (аргон, гелий, углекислый газ и их смеси), подающиеся из сварочной головки в процессе электросварки.
Различают электросварку переменным током и электросварку постоянным током. При сварке постоянным током шов получается с меньшим количеством брызг металла, поскольку нет перехода через нуль и смены полярности тока.
В аппаратах для электросварки постоянным током применяются выпрямители.
Источники
Ссылки
См. также
Wikimedia Foundation. 2010.
- Москвина, Марина Львовна
- Кубок Федерации футбола СССР
Смотреть что такое «Электросварка» в других словарях:
электросварка — электросварка … Орфографический словарь-справочник
ЭЛЕКТРОСВАРКА — ЭЛЕКТРОСВАРКА. При контактной Э. через свариваемые металлы пропускают электрический ток, к рый нагревает их до точки плавления. Она производится специальными электросварочными машинами. При дуговой Э.
к месту сварки ток подводится помощью тонкого … Большая медицинская энциклопедия
ЭЛЕКТРОСВАРКА — контактная электросварка, сварка … Большая политехническая энциклопедия
ЭЛЕКТРОСВАРКА — сварка, при которой свариваемые части нагреваются электрическим током. Различают электросварку дуговую и контактную … Большой Энциклопедический словарь
ЭЛЕКТРОСВАРКА — ЭЛЕКТРОСВАРКА, электросварки, мн. нет, жен. (тех.). Сварка металлов при помощи электрического тока. см. электро…. Толковый словарь Ушакова. Д.Н. Ушаков. 1935 1940 … Толковый словарь Ушакова
ЭЛЕКТРОСВАРКА — (Electric welding) см. Сварка. Самойлов К. И. Морской словарь. М. Л.: Государственное Военно морское Издательство НКВМФ Союза ССР, 1941 … Морской словарь
электросварка — сущ., кол во синонимов: 2 • сварка (20) • электрогазосварка (3) Словарь синонимов ASIS. В.Н. Тришин.
2013 … Словарь синонимов
Электросварка — Электросварка: способ получения сварного шва путем контактной электросварки сопротивлением, при которой свариваемые кромки механически прижимают друг к другу, а тепло для сварки выделяется вследствие сопротивления приложенному или наведенному… … Официальная терминология
электросварка — Группа способов сварки, использующая для нагрева металла электрическую энергию. Примечание Электрический нагрев позволяет получить температуры, превосходящие температуры плавления существующих металлов, не изменяет химического состава материала,… … Справочник технического переводчика
электросварка — 4.54 электросварка (electric welding): Способ получения шва сваркой электросопротивлением, при которой свариваемые кромки прижимаются друг к другу под механическим воздействием, а тепло для сварки выделяется вследствие сопротивления приложенному… … Словарь-справочник терминов нормативно-технической документации
Виды электросварки: дуговая и точечная
Что такое электросварка и её виды
Электрический ток даёт возможность нагревать любые вещества. В обычных условиях окружающей среды может быть достигнута температура, когда твёрдое вещество либо расплавится, либо начнёт гореть, то есть окисляться. Если при этом в контакте находятся два или более веществ, которые прочно соединяются друг с другом за время существования электрического тока, нагревающего их, они оказываются приваренными друг другу. Процесс соединения тех или иных объектов с использованием тока, протекающего через эти объекты, называется электросваркой.
Она может быть:
- дуговая;
- точечная.
Электрический ток обеспечивает и другие виды сварки, такие как
- индукционная;
- сверхвысокочастотная;
- лазерная.
Но при этом создаётся электромагнитное излучение определённой частоты, нагревающее только те предметы, на которые это излучение воздействует из-за их природы. Таким способом можно нагревать и сваривать даже те вещества, которые не проводят ток.
Каждому виду электросварки соответствует определённый тип оборудования.
Дуговая электросварка
Дуговая разновидность наиболее широко распространена при сварке деталей из металлов, нагреваемых с помощью вольтовой дуги. Наиболее часто этот вид используется по швам. Для возникновения и существования вольтовой дуги необходимы определённые условия, которые обеспечиваются сварщиком и оборудованием. Оборудование для такой сварки включает два контакта и источник электропитания.
Один контакт это специальный сменный электрод, а другой – надёжный зажимной контакт. Сменный электрод сделан из специального сплава и покрыт специальным флюсом. К тому же электроды имеют различную толщину, которая прямо пропорциональна мощности дуги. Зажимной контакт закрепляется так, чтобы надёжный контакт получился хотя бы на одной из деталей.
Процесс дуговой электросварки начинается с того, что сварщик делает короткое замыкание на шве, прикасаясь к нему. Затем он плавно приподнимает электрод над швом. При этом за электродом тянется вольтова дуга, которая может существовать при определённой мощности источника питания и расстоянии между ними. Дуга расплавляет электрод и края шва. Расплавленный электрод заполняет пространство шва в месте расположения дуги, а флюс создаёт наилучшие условия для сцепления оплавленного шва с материалом электрода.
Классическим сварочным аппаратом для дуговой сварки является сварочный трансформатор. Он не только понижает напряжения и обеспечивает безопасность сварщика гальванической развязкой от сети, но при этом ограничивает потребляемый от сети ток и в определённых пределах позволяет регулировать мощность дуги. Для этого с помощью подвижного сердечника и витками вторичной обмотки меняются величины индуктивности трансформатора.
Также он отличается очень большой надёжностью и долговечностью. Но уже при минимальных мощностях его вес настолько велик, что ограничивает возможности сварки. Из-за больших величин токов провода, соединяющие электрод и зажим имеют ограниченную длину. А у сварщика не всегда хватает сил для перемещения этого трансформатора. К тому же переменный ток, который питает дугу, не способствует качественной сварке.
По мере развития электроники появились мощные полупроводниковые приборы, которые позволили создать высокочастотные трансформаторные генераторы с мощностью достаточной для сварки. Это так называемые инверторные сварочные аппараты. Поскольку увеличение частоты намагничивающего тока позволяет в разы уменьшить габариты и вес трансформатора, новые аппараты стали небольшими и лёгкими. К тому же высокочастотный выпрямленный ток существенно улучшает качество сварного шва.
Для промышленных целей, например при постройке трубопроводов, судов, и прочих крупных объектов применяются специальные автоматизированные и роботизированные аппараты. Дуга уже при небольшой мощности излучает широкий спектр электромагнитного излучения. Это излучение оказывает вредное воздействие на человека, особенно на зрение и кожу. Поэтому сварщик должен работать в специальном защитном костюме и маске, которые полностью закрывают его от света дуги.
- Пренебрежительное отношение к применению средств защиты при выполнении электросварки может привести к утрате зрения и сильным ожогам не только от капель металла, но и от излучения дуги.
Детали из некоторых металлов и сплавов могут быть скреплены электросваркой только в специальной газовой среде. Это так называемая аргоновая сварка, которая применяется для деталей из нержавеющей стали и специальных сплавов. Для выполнения таких работ используются соответствующие камеры, заполненные газовой смесью определённого состава. Сварщики работают в них с системами автономного обеспечения дыхания и под наблюдением.
Точечная электросваркаНекоторые металлические детали, особенно с малой толщиной, и те, которые не требуют сварных швов, не могут быть скреплены с помощью дуговой электросварки. Вольтова дуга либо оставит грубый след на такой детали, либо повредит её из-за малой толщины. В таких случаях применяются специальные аппараты для точечной сварки, которые содержат два электрода сжимающие скрепляемые детали и мощный разрядный источник питания.
В источнике питания содержится конденсаторная батарея. Эта батарея разряжается через электроды либо напрямую, либо через специальный трансформатор и вызывает моментальный нагрев в месте контакта электродов и скрепляемых деталей. Сопротивление электрическому току, создаваемое скрепляемыми деталями, невелико. Но оно существенно больше, чем сопротивление проводов и электродов. Поэтому в месте точечной сварки происходит нагрев, который лавинообразно нарастает из-за увеличения сопротивления, обусловленного нагревом.
Процесс протекает очень быстро. Но и величина электрической мощности, потраченная за это малое время огромна. В результате детали в месте точечной сварки размягчаются и поверхностно оплавляются, сцепляясь друг с другом из-за сдавливания электродами. Прочность такого соединения намного меньше, чем у сварного шва. Поэтому точечная сварка имеет соответствующие ограничения.
Электросварка в значительной мере способствовала развитию современного машиностроения. И сейчас технологии продолжают совершенствоваться и обеспечивают новые недостижимые ранее результаты.
«Электрик» для электросварки
В 1932 году был построен завод для необходимого оборудования.
Сварка – это многогранный процесс и целая наука, без которой невозможно представить современную цивилизацию. В наши дни ни одно производство не обходится без применения сварочных работ, которые сейчас проводятся и под водой, и в открытом космосе, и в условиях Арктики.
Сварочный процесс, каким бы современным он ни казался, появился примерно в VIII–VII веках до нашей эры. В Древнем Египте, о чем свидетельствуют находки археологов, оловом спаивали украшения из золота. Разогретый на углях легкосплавный материал наносился на золотые украшения и, застывая, образовывал некоторое соединение.
Во время раскопок Помпеи найдены остатки водопроводных коммуникаций, которые имели поперечные швы на свинцовых трубах. Поскольку свинец тоже легко плавился на огне, он поддавался заливанию в формы и созданию соединений.
Но возможности человечества были ограничены температурой углей, поэтому другие металлы для соединения были недоступны.
Наши приоритеты
История развития сварки и сварочного производства имеет множество открытий и этапов развития. О возможности применения «электрических искр» для плавления металлов еще в 1753 году говорил соратник и друг Михаила Ломоносова, академик Российской академии наук Георг Рихман. Однако прорыв в технологии сварочного производства был сделан позднее, и связан он с открытиями в области электричества.
В 1802 году русский физик, академик Петербургской военно–хирургической академии Василий Владимирович Петров обратил внимание на то, что при пропускании электрического тока через два стержня из угля или металла между их концами возникает ослепительно горящая дуга – электрический разряд. Возможность использования высокой температуры электрической дуги для расплавления металлов и их дуговой сварки он описал в книге «Известия о гальвани–вольтовых опытах», опубликованной в 1803 году. Впоследствии Петров предложил возможное практическое применение электросварки и электропайки металлов. Однако на момент открытия им особо никто не заинтересовался.
В 1881 году инженер и изобретатель Николай Николаевич Бенардос продолжил дело, начатое академиком Петровым. Работая над созданием аккумуляторных батарей, он открыл способ электродуговой сварки металлов угольными и металлическими электродами. Позднее создал ряд конструкций сварочных автоматов. Свои изобретения в области сварочного оборудования и процессов сварки ученый запатентовал в России, Германии, Англии, Франции, Италии и США.
Его современник Николай Гаврилович Славянов в 1888 году впервые в мире на практике применил наиболее распространенный в настоящее время метод дуговой сварки – плавящимся металлическим электродом. В присутствии государственной комиссии он сварил коленчатый вал паровой машины.
Славянов создал первый сварочный генератор и автоматический регулятор длины сварочной дуги, разработал флюсы для повышения качества наплавленного металла при сварке, организовал первый в мире электросварочный цех в Пермских пушечных мастерских, где работал с 1883 по 1897 год. С помощью обученных им рабочих–сварщиков Славянов дуговой сваркой восстанавливал детали паровых машин и различного крупного оборудования.
Однако царская Россия не сумела реализовать возможности, открытые изобретениями Бенардоса и Славянова, и великое русское изобретение – дуговая сварка, как это случалось неоднократно, реализовано было за границей – в США, Германии, Англии. Началось стремительное развитие сварочной техники – за десятилетие она совершенствовалась больше, чем за столетие предшествующего периода. Быстро развивались и новые источники нагрева, легко расплавлявшие железо – электрический ток и газокислородное пламя.
К огромному спросу на производство вооружения, которое было невозможно без развития сварочного процесса, привела Первая мировая война. В Америке и Европе появилось множество компаний, которые производили сварочные аппараты и электроды.
В нашей стране дуговая сварка нашла широкое применение только после Октябрьской революции. Уже в начале 1920–х под руководством профессора Валентина Вологдина на Дальнем Востоке производили ремонт судов дуговой сваркой, а также изготовление сварных котлов, а несколько позже – сварку судов и ответственных конструкций.
Новый этап в истории сварки начинается в 1929 году, когда было принято постановление Совета труда и обороны о развитии сварочной техники. Для производства электросварочного оборудования в 1932 году был построен завод «Электрик», в то время – самый мощный в Европе завод по электросварочному оборудованию. Созданные специальные учебные заведения занялись подготовкой кадров – рабочих, техников и инженеров–сварщиков. Большое внимание было уделено научным исследованиям: появились многочисленные лаборатории и институты по проблемам сварки.
Применение сварки в промышленных объемах требовало создания и скорейшего внедрения в массовое производство надежных источников питания, гарантирующих стабильное горение дуги. В 1924 году на Ленинградском заводе «Электрик» запустили производство сварочных генераторов и сварочных трансформаторов.
Легендарные академики
Над технологиями сварки работали многие выдающиеся советские специалисты, а наиболее заметными были Евгений Оскарович и Борис Евгеньевич Патоны, отец и сын.
Евгений Оскарович – известный мостостроитель, профессор, декан инженерно–строительного факультета Киевского политехнического института. Десять изданий выдержали три тома учебника «Железные мосты» и два издания – «Деревянные мосты».
Предвидя огромное будущее электросварки в мостостроении и других отраслях хозяйства, он резко сменил поле своей научной деятельности и в 1929 году организовал в Киеве сначала лабораторию, а позднее первый в мире Институт электросварки, где разработал и предложил немало эффективных технологических процессов электросварки. В годы войны в короткий срок под его руководством были разработаны технология и автоматические стенды для сварки башен и корпусов танков, самоходных орудий, авиабомб.
Его сын, будущий президент Национальной академии наук Украины, дважды Герой Социалистического Труда, заслуженный изобретатель СССР, лауреат множества престижных премий, получил диплом об окончании Киевского политехнического института 21 июня 1941 года. На следующий день немецкие самолеты бомбили Киев. Очень символично – большой объем будущих работ Борис Патон выполнил именно по заказу военно–промышленного комплекса СССР, лучшие технологии создавались им для производства вооружения.
Его инженерная деятельность началась на Сормовском оборонном заводе в Горьком (теперь – Нижний Новгород). Позднее Борис стал работать в Нижнем Тагиле, куда был эвакуирован Институт электросварки. Туда же прибыли более 600 вагонов Харьковского завода №183 с людьми, оборудованием, заготовками танков Т–34, а также эшелоны с оборудованием Днепропетровского и Мариупольского металлургических заводов. Так был создан Уральский танковый завод № 183. Здесь развернулось производство танков.
Однако ручная сварка толстой брони занимала много времени, сварщиков катастрофически не хватало. Под руководством Патона–старшего впервые в мире удалось решить проблему скоростной автоматической сварки броневых сталей. Также впервые в мире был создан новый класс сварочного оборудования. Сотрудники института научили подростков 12–14 лет управлять аппаратами. Одна установка заменяла до 14 опытных сварщиков–ручников. На 52 заводах были смонтированы линии сборки и сварки танков всех типов, авиабомб и других вооружений. Патон–младший участвовал в разработке нового оборудования, работал его наладчиком и инструктором.
В 1941–1944 годах на территории страны, где проходили военные действия, было разрушено значительное количество металлоконструкций и производственного оборудования. Начиная с 1944 года, с возвращением Института электросварки в Киев, Евгений Патон организовал работу сотрудников по восстановлению промышленности страны. Для этой цели, в частности, был создан новый класс сварочных аппаратов – сварочные трактора.
В послевоенные годы его сын – старший научный сотрудник, заведующий электротехническим отделом Института электросварки, решал сложные технические и научные вопросы создания универсальной аппаратуры, пригодной для широкой номенклатуры изделий, а также специализированных сборочно–сварочных установок для конвейеров, участвовал во внедрении новейшей техники в промышленность, создал полуавтоматы для дуговой сварки под флюсом, порошковой проволокой и в среде активных газов.
В 1953 году Борис Евгеньевич возглавил Институт, носящий имя его отца, со временем превратив его в крупнейший мировой центр по сварке. Сотрудники института создали большое количество типов сварочного оборудования, марок электродов, разработали новые прогрессивные сварочные процессы, в том числе высокомеханизированные и автоматизированные, освоили технику сварки многих металлов и сплавов, глубоко и всесторонне разработали теорию сварочных процессов.
Вот что рассказывал бывший министр транспортного строительства СССР Владимир Аркадьевич Брежнев: «При конструировании мостов, разработке технологии, подборе материалов, обучении кадров, контроле качества специалисты Минтрансстроя работали в тесном сотрудничестве с учеными киевского Института электросварки имени Патона и его руководителем – академиком Борисом Патоном. Мы познакомились в начале 70–х. Сошлись потому, что Борис Патон быстро реагировал на новые и интересные идеи, прикладывал максимум усилий для их реализации.
Но достижения Института электросварки и его бессмертного руководителя транспортные строители использовали не только в мостостроении. Строительство дорог требовало применения большого объема электросварочных работ, да и на стройке сварщик – ведущая профессия. С помощью специалистов Института электросварки было внедрено немало новейших технологических процессов, был разработан и четко выполнялся план совместных работ. Удалось механизировать и даже автоматизировать сварочный процесс, что значительно повысило производительность труда и ускорило строительство…»
В 1970–1980–е годы фундаментальные научные исследования привели к созданию уникальных конструкций, оборудования, материалов и прорывных технологий. Были решены многие проблемы машиностроения, судостроения, ракетно–космического комплекса, авиастроения, энергетики, горнопромышленного комплекса, металлургии и химического производства, создания трубопроводного транспорта, строительной индустрии и других отраслей промышленности.
Для изделий из алюминия, титана, циркония и других металлов и сплавов, пластмасс, керметов и других материалов в авиации, производстве ракет и судостроении, атомной и химической промышленности, радиоэлектронике, приборостроении и других отраслях промышленности были предложены аргонодуговая, электронно–лучевая, контактная, плазменная, диффузная и др. виды сварки, пайки, напыления, наплавки.
В 1963 году Борис Евгеньевич инициировал работы по созданию оборудования и технологий сварки, пайки и напыления в условиях космоса и непосредственно участвовал в работе специального отдела. В 1969 году на пилотируемом космическом корабле «Союз–6» на созданной в Институте электросварки установке «Вулкан» космонавты Валерий Кубасов и Георгий Шонин впервые в мире провели электронно–лучевую, дуговую, плазменную сварку и резку металлов. В 1984 году Светлана Савицкая и Владимир Джанибеков провели в открытом космосе сварку, резку и пайку различных металлов, а в 1986 году в космосе впервые была проведена пайка узлов фермы для солнечных батарей орбитальной стации «Мир».
В настоящее время широкое развитие получили новые способы сварки – ультразвуком, диффузионная, электронно–лучевая, холодная, плазменная, сварка трением и другие. Применение этих сварочных процессов позволяет соединять детали толщиной от нескольких микрометров, что нашло широкое применение в медицине, до десятков метров.
Владимир Гондусов
КСТАТИ
Отрасли сварщики нужны!
Механизм непрерывной подготовки высококвалифицированных специалистов сварочного производства обсудили ведущие представители сварочного производства и системы образования России во время научно–практической конференции «Сварка. Подготовка сварщиков различного уровня», которая прошла в Российском университете транспорта.
Организаторами мероприятия выступили Российский университет транспорта (МИИТ), профессиональное сообщество «Союз наставников по повышению производительности труда».
Как сообщил директор Департамента государственной политики в сфере СПО и профессионального обучения Министерства просвещения РФ Виктор Неумывакин, сегодня более 800 учебных заведений обучают по программам среднего профессионального образования по профессии «сварщик» и специальности «сварочное производство».
Ректор Российского университета транспорта Александр Климов отметил, что развитие сварочных технологий и подготовка кадров по этому направлению являются одними из ключевых задач транспортной отрасли, так как строительство, в том числе железнодорожное, не может без этого обойтись.
Участники конференции обсудили методическую базу и вопросы подготовки профессиональных сварщиков и сформировали предложения для Министерства просвещения и Министерства науки и высшего образования РФ.
Для объединения передовых ученых и отраслевых центров необходимо создание Института сварки России. Такое решение было принято на общероссийском совещании сварщиков в октябре 2019 года. С течением времени актуальность создания института возрастает, об этом и об основных вопросах подготовки сварщиков различного уровня в своем выступлении говорил начальник Головного центра сварочных технологий на транспорте Российского университета транспорта Сергей Петров.
«Сварка должна быть включена в те стратегии и госпрограммы, которые связаны с транспортной отраслью и промышленностью в целом. Или же должна быть разработана отдельная программа по развитию технологии сварочного процесса», – заявил он.
Что такое электросварка? (с изображением)
Электросварка — это процесс нагрева и сварки двух металлических частей вместе с помощью мощного электрического тока. Его изобрел профессор Элиху Томсон. Это требует использования специального устройства, называемого динамо-машиной, которое высвобождает ток, используемый для сварки.
В отличие от более традиционных методов, электросварка требует минимальных навыков и понимания со стороны оператора динамо-машины. Он должен только изучить надлежащую температуру сварки используемого металла, но не обязан изучать более сложные процессы традиционной сварки. Использование динамо-машины при этом типе сварки является саморегулирующимся, и для нормальной работы требуется лишь периодическая смазка. Это делает этот метод идеальным для начинающего сварщика.
и любые два подобных куска металла могут быть соединены электросваркой.Таким же образом можно сваривать два разных куска металла, если точка сварки одного из них не превышает точку сварки другого. Если разница в температуре сварки является проблемой, металлы все еще можно сваривать с использованием заусенцев в точке сварки.
В процессе электросварки металлические детали соединяются между собой медными зажимами.Электричество пропускается через детали, нагревая их и соединяя в точке, где встречаются две металлические детали. Кажется, что тепло будет самым большим в точке встречи двух металлов, но область, где металлы закручены и не соприкасаются, сначала нагревается, а затем излучается наружу к стыкам.
Распределение тепла регулируется путем обеспечения равномерного движения с помощью регулирующего рычага. Это гарантирует, что оба металла станут мягкими и одновременно соединятся друг с другом. По окончании процесса электросварки образуется бесшовное соединение.
Преимущества электросварки заключаются в том, что этот метод не расходует лишнее топливо и обеспечивает заданную точность.Тепло не выходит далеко за пределы точки сварки. Это делает его идеальным для изолированных проводов. Концы каждого провода можно сваривать, оставляя изоляцию нетронутой.
Хотя электросварка может потреблять до 50 000 ампер электричества, она использует электродвижущую силу, которая содержит только половину вольта электричества. Это делает динамо-машину неспособной поражать человека электрическим током или поражать его током во время использования. Сварка с использованием электричества может занять от долей секунды до нескольких минут в зависимости от работы, и этот метод можно использовать как для больших, так и для небольших работ.
Что такое электродуговая сварка и ее преимущества
Сегодня я расскажу о процессе дуговой сварки.Ранее по сварочному процессу публиковались статьи. проверьте ниже:
Что такое электродуговая сварка?
Дуговая сварка — это процесс сварки, в котором используется электрическая дуга для создания тепла, достаточного для расплавления металла, охлаждения и соединения металлов. Эта сварка плавлением использует источник питания переменного или постоянного тока в качестве источника тепла. Этот источник питания создает дугу между расходуемым или неплавящимся электродом, пропуская переменный или постоянный ток к основному материалу.
Другими словами, это тип процесса сварки, в котором источник сварочного тока используется для создания электрической дуги между металлической палкой (электродом) и основным металлом.Он плавит металлы в точке соприкосновения. Сварщики могут выбирать и стабильно использовать постоянный или переменный ток, а также расходуемые или неплавящиеся электроды в зависимости от рассматриваемых факторов.
Дуговая сварка была впервые разработана в конце 19 -го века, применялась в судостроении во время Второй мировой войны. Сегодня этот процесс становится одним из самых быстрых и распространенных сварочных процессов на производственных предприятиях.
Приложения
Дуговая сварка сегодня широко используется во многих областях, поскольку бывает разных типов. Ниже приведены области применения дуговой сварки;
- Судостроение
- Строительная промышленность
- Автомобильная промышленность
- Машиностроение.
Вот некоторые другие области применения дуговой сварки
- В аэрокосмической промышленности используется дуговая сварка вольфрамовым электродом в газе во многих областях соединения, особенно в случае листового металла
- Большинство обрабатывающих производств используют GTAW для сварки тонких деталей, особенно цветных металлов
- Дуговая сварка широко применяется при производстве космических аппаратов
- Используется для сварки деталей небольшого диаметра и тонкостенных труб, что делает его применимым в велосипедной промышленности.
- Дуговая сварка GTAW используется для выполнения гаек или сварных швов за первый проход трубопроводов различных размеров.
- Используется для ремонта инструментов или штампов, в основном деталей из алюминия и магния.
- GTAW обладают высокой устойчивостью к коррозии и растрескиванию в течение длительного периода времени, они используются там, где эти качества необходимы.
Преимущества
Дуговая сварка имеет большие преимущества по сравнению со многими другими сварочными процессами. Некоторые преимущества дуговой сварки:
- Сварочное оборудование переносное, что упрощает транспортировку для работы вне дома
- Может сваривать пористые и грязные металлы
- Его оборудование недорогое
- Это быстрый процесс сварки по сравнению с другими
- Может работать во время ветра или дождя
- Прочный шарнир
- С помощью валиков для дуговой сварки можно создавать рисунки на тонких металлах
- Его источник питания можно использовать там, где есть электричество, и в качестве альтернативы, если нет электричества, кроме генератора.
Недостатки
- Увеличение стоимости проекта, так как отходы неизбежны в процессе
- Для выполнения задачи необходим хорошо обученный и опытный оператор
- Не все тонкие металлы можно сваривать дуговой сваркой
Также проверьте:
И что это для этой статьи, что такое электродуговая сварка? Я также рассказываю о его приложениях, преимуществах и недостатках. Надеюсь, вам понравится читать, свободно задавайте вопросы через поле для комментариев. Пожалуйста, поделитесь с другими и спасибо за чтение!
Электродуговая сварка — Сварочная цепь
Это вторая часть серии статей, состоящей из двух частей.Для начала прочтите «Электродуговая сварка — полезный метод для прочных сварных швов» (часть 1).
Сварочная цепь
Слово «цепь» должно быть вам знакомо, даже если вы не электрик, но и из других источников, например, из мотоспорта. Термин относится к полному пути или маршруту, на котором происходит любое действие, например гоночное мероприятие. Теперь, если вы знаете об электронике, ток состоит из потока электронов, которые устремляются от одной полярности к другой {Конечно, не путайте переменный и постоянный ток — просто обратитесь к некоторым учебным материалам для этого разъяснения, если я начну объясните это здесь, я сильно сбился с пути}, а трасса, по которой они следуют, известна как электрическая цепь, которая может варьироваться в зависимости от типа устройства и применения, так же как гоночная трасса будет зависеть от факторов, будь то гонка на велосипеде , автогонки, ралли и так далее.
Базовая сварочная схема состоит из трансформатора, который питается от источника электроэнергии и преобразует типичное электричество высокого напряжения — низкого тока в электричество высокого напряжения — низкого напряжения, как объяснялось ранее. Две клеммы выхода трансформатора подключены к заготовке и сварочному электроду соответственно. Это было графически изображено на изображении, сопровождающем эту страницу.
Трансформатор имеет элементы управления, с помощью которых вы можете увеличивать или уменьшать ток в зависимости от типа сварного шва и соединяемого материала, о чем на данном этапе вам не нужно беспокоиться.
Заготовка подключается к одной из клемм трансформатора, который «заземлен». Заготовка на рисунке показана в виде двух металлических частей, которые должны быть соединены по своей длине, что изображено в виде небольшого зазора между двумя частями
Электрод подсоединяется к другому концу трансформатор через электрододержатель, который изготовлен из изоляционного материала, чтобы избежать любой возможности поражения электрическим током человека, выполняющего сварку.
Как следует из названия, электродуговая сварка использует электрическую энергию для зажигания и поддержания дуги, которая является источником интенсивного тепла, достаточного для расплавления соединяемых материалов и их сплавления. Но как возникает эта дуга и каковы в ней основополагающие принципы?
Если бы мы просто прикоснулись электродом к заготовке, электрическая цепь замкнулась бы сама собой, что означало бы, что ток начал бы течь по пути, как показано проводами.Но тогда просто спросите себя, достигнет ли это какой-либо цели, и ответом на это будет большое НЕТ! Итак, как мы на самом деле выполняем этот процесс? Что мы делаем, так это то, что мы просто ударяем электродом по заготовке и быстро оттягиваем его на очень короткое расстояние порядка миллиметров. Это воссоздает то, что происходит, когда вы выключаете тяжелый электроприбор в своем доме — генерируется искра, которая прыгает через две стороны, замыкая цепь. Эта искра или дуга генерирует интенсивное тепло, которого достаточно для расплавления соответствующих металлов при осаждении дополнительного материала с электрода, который затвердевает для завершения сварки.
Как выполнить электродуговую сварку стальных конструкций? [PDF]
В процессе электродуговой сварки используется электрическая дуга для выработки тепла для плавления основного материала и присадочного материала (электрода) для образования расплавленной сварочной ванны в соединении. Метод электродуговой сварки предпочтительнее других методов из-за его доступности.
Наиболее часто используемые методы крепления для соединения стальных элементов стальной конструкции — это сварка, клепка и болтовое соединение. В то время как для заклепок и болтов используются заклепки и болты для соединения деталей, сварка основывается на плавлении деталей для их соединения.
В этой статье мы обсудим процедуру укладки, изготовления, сварки, сборки и монтажа металлоконструкций методом электродуговой сварки.
1. Разметка стальных стержней
- Фигура стальной конструкции, которая должна быть изготовлена, должна быть нарисована на ровной платформе в полном масштабе.
- Это может быть выполнено полностью или по частям, как показано на чертежах или в зависимости от состояния площадки.
- Стальная лента должна использоваться для измерения стальных элементов.
2. Изготовление стальных элементов
- На всех сталелитейных заводах рабочие чертежи должны содержать полную информацию о производстве стального компонента, включая расположение, тип, длину, размер и детали сварных швов. Кроме того, компонент должен быть подготовлен до фактического изготовления.
- Стальные элементы должны быть промаркированы или окрашены опознавательными знаками, как указано на рабочих чертежах.
- Работа по изготовлению должна выполняться с большой точностью, чтобы их можно было собрать без чрезмерной упаковки, принуждения или напряжения.
- В собранном виде элементы должны быть правильными и не иметь перекручивания, перегибов, изгибов или открытых стыков.
- Затем на стальных элементах маркируются шаблоны и на них указываются места сварки.
- Концы стальных элементов должны быть промаркированы для резки в соответствии с требуемыми размерами.
- Стальной профиль должен быть прямым или выпрямляться или сплющиваться под давлением и не иметь скручиваний.
- Никакие две части не должны быть сварены или соединены для обеспечения необходимой длины элемента.
3. Электродуговая сварка
- Сварка стальных элементов должна производиться электродуговым способом.
- В местах, где нет электричества, следует применять метод газовой сварки с использованием кислородно-ацетиленового пламени.
- Сварку должны выполнять только обученные и опытные сварщики.
- Процесс сварки должен выполняться, как показано на заводских чертежах, на которых должны быть указаны все детали сварных соединений, заводских и строительных швов, типа сварных швов и типов используемых электродов.
- Насколько это возможно, должны быть приложены усилия для ограничения сварки после монтажа, чтобы избежать неправильной или неисправной сварки, которая может произойти из-за высоты и трудного положения на строительных лесах и т. Д., Помимо аспекта экономии.
- Максимальный диаметр электродов для любых сварочных работ должен соответствовать IS: 814 и приложению «B» IS: 823.
- Соединяемые поверхности должны быть очищены от рыхлой прокатной окалины, ржавчины, краски, смазки или других посторонних веществ, которые могут отрицательно повлиять на качество сварки и качество изготовления.
- Если сварка выполняется на открытом воздухе, необходимо принять меры для защиты мест сварки от ветра или дождя.
- Сварной шов должен соответствовать проектным формам и размерам.
- Сварной шов не должен иметь дефектов, таких как трещины, непровар, подрезы сплавлением, шероховатые поверхности, ожоги, раковины, пористость и т. Д. За пределами допустимых пределов.
- Испытания и осмотр должны проводиться во время операции сварки, а готовые элементы одобрены, как показано в Таблице 1 ниже —
Таблица 1: Контроль и испытания для сварки
Sl.Нет | Инспекция теста | Покрытие | Процедура | Оценка и устранение дефектов |
1 | Контроль внешнего вида сварного шва | Все сварные швы | Невооруженный глаз или линза | Все дефектные сварные швы должны быть устранены. |
2 | Проверка размеров | Не менее одного на каждый сварной шов | Обычные средства измерений (шаблон правил) | При обнаружении дефектного сварного шва необходимо проверить все сварные швы и устранить все дефекты. |
4.
Сборка стальных стержней- Перед тем, как начать сварку, свариваемые элементы должны быть сначала собраны вместе и прочно зажаты или приварены прихваточными швами, чтобы удерживать их на месте.
- Временное соединение должно быть достаточно прочным, чтобы детали точно удерживались на месте без каких-либо нарушений.
- Прихваточные швы, расположенные в местах, где впоследствии будут выполнены окончательные сварные швы, должны соответствовать качеству окончательного шва и должны быть зачищены перед выполнением окончательного шва.
5. Монтаж стальных сварных стержней
- Во время возведения сварной конструкции должны использоваться соответствующие средства для временного скрепления элементов друг с другом и фиксации каркаса до тех пор, пока соединения не будут сварены.
- Временное крепление состоит из монтажных болтов, прихваток или других положительных устройств, придающих достаточную прочность и жесткость, чтобы выдерживать все временные нагрузки и боковые силы, включая ветер.
- Все различные элементы, которые должны свариваться угловым швом, должны находиться в тесном контакте.
- Зазоры из-за дефектов изготовления или неправильной подгонки, если таковые имеются, не должны превышать 1,5 мм. Если зазор превышает 1,5 мм или более, размер углового шва в этом месте должен быть увеличен на величину, равную ширине зазора.
Часто задаваемые вопросы по дуговой сварке
Что такое электродуговая сварка?В процессе электродуговой сварки используется электрическая дуга для генерирования тепла для плавления основного материала и присадочного материала (электрода) для образования расплавленной сварочной ванны в соединении.
Какие испытания и проверки проводятся на сварном стальном элементе?Сварной шов не должен иметь каких-либо дефектов, таких как трещины, непровар, подрезы от оплавления, шероховатости поверхностей, ожогов, раковин, пористости и т. Д. Сверх допустимых.
Подробнее: Контроль и испытание сварных швов в конструкционной стали
Системы преобразования электроэнергии — Системы отопления
Системы преобразования энергии обычно называют функцией они выступают.Преобразование энергии происходит в нагрузке электрического система питания. Общие типы нагрузок энергосистемы — это те, которые преобразуют электрическую энергию в тепло, свет или механическую энергию. Есть разные виды освещения, отопления и механических нагрузок, применяемые в промышленности, торговле здания и дома. Некоторые из этих систем преобразования энергии будут обсуждается в разделах 12, 13 и 14.
ТЕРМИНОЛОГИЯ
Этот раздел посвящен системам отопления.Изучив этот раздел, вы должны понимать следующие термины:
- Резистивный нагрев
- Индукционный нагрев
- Диэлектрический нагрев
- Электросварка
- Сварка сопротивлением
- Дуговая сварка
- Индукционная сварка
- Контакторы SCR
- Системы электрического отопления
- Британские тепловые единицы (Btus)
- Расчетная разница температур
- Градус Дней
- Термическое сопротивление (R)
- Коэффициент теплопередачи (U)
- Тепловой насос
- Система кондиционирования
ОСНОВНЫЕ ТЕПЛОВЫЕ НАГРУЗКИ
Большинство нагрузок, подключенных к системам электроснабжения, производят определенную количество тепла, в основном в результате протекания тока через резистивный устройств.Во многих случаях тепло представляет собой потерю мощности в цепи, поскольку тепловая энергия не является типом энергии, для которой предназначена система производить. Например, светильники производят тепловую энергию так же, как и свет. энергия.
Преобразование электрической энергии в тепловую при производстве света нагрузка снижает эффективность этого загрузочного устройства, поскольку не все доступная энергия источника преобразуется в световую энергию. Однако есть несколько типов систем преобразования энергии, которые в основном являются тепловыми нагрузками.Их основная функция — преобразовывать электрическую энергию в тепловую. Некоторые базовые системы включают резистивный нагрев, индукционный нагрев и диэлектрический нагрев. (емкостный) нагрев.
Нагрев сопротивления
Тепловая энергия вырабатывается при прохождении электрического тока через резистивную материал. Во многих случаях тепловая энергия, производимая электрическим ток нежелателен; однако для некоторых приложений требуется контролируемый резистивный нагрев.Полезное тепло может передаваться от резистивного элемента. до точки использования обычными методами теплопередачи-конвекции, излучение или проводимость. Корпус нагревательного элемента необходим для управления передача тепла конвекцией и излучением. Для передачи тепла проводимость, нагревательный элемент находится в прямом контакте с материалом быть нагретым. Фактическая теплопередача обычно включает комбинацию этих методы.
РИС. 1 иллюстрирует принцип резистивного нагрева.Самостоятельный В нагревательном элементе используется спиральный резистивный провод, который помещается внутри теплопроводный материал и заключен в металлическую оболочку. Этот принцип может использоваться для нагрева воды, масла, окружающей атмосферы или различных другие СМИ. Этот тип обогревателя может использоваться на открытом воздухе или под водой. в нагреваемых средах. Срок службы элементов сопротивления зависит от в основном от рабочей температуры. С повышением температуры тепловая мощность также увеличивается.2 р).
Индукционный нагрев
Принцип индукционного нагрева показан на фиг. 2. Вырабатывается тепло в магнитных материалах, когда они подвергаются воздействию переменного тока (AC) поле. В показанном примере ток индуцируется в нагретом материале. электромагнитной индукцией. Это вызвано приложением переменного тока к нагревательной катушке. Нагреваемый материал должен быть проводником. для индукции тока.Обычно это высокочастотный источник переменного тока. в диапазоне 100-500 кГц используется для получения высокой тепловой мощности. Этот высокая тепловая мощность связана с большим наведенным напряжением.
(вверху) РИС. 1. Принцип резистивного нагрева; (внизу) ФИГ. 2. Индукционный нагрев
принцип
Поскольку магнитное поле, создаваемое высокочастотным источником переменного тока, движется через нагреваемого материала, индуцированное напряжение вызывает вихревые токи (циркулирующие токи) течь в материале.Тепло из-за сопротивления материала к течению вихревых токов. Вырабатывается тепло быстро этим методом, что является преимуществом.
Основное применение процесса индукционного нагрева — обработка металлов. промышленности, для таких процессов, как закалка, пайка, плавка и отжиг металлов. По сравнению с другими методами нагрева производство тепла этого процесса чрезвычайно быстро. Площадь металла, которая на самом деле нагрев можно регулировать размером и положением нагревательных спиралей индукционного нагревателя.Такой контроль сложно осуществить. другими методами. Индукционные печи используют принцип индукционного нагрева.
Путем изменения частоты напряжения, подаваемого на индукционный нагреватель. обмоток можно варьировать глубину проникновения тепла в нагретый металл. На более высоких частотах тепло, выделяемое индуцированным током от нагревательных спиралей не проникает так глубоко из-за так называемой «кожицы» эффект ». Таким образом, тепло будет проникать глубже на более низких частотах.Когда тепло должно быть локализовано только на поверхности материала, например, для поверхностного упрочнения металла используются более высокие частоты. Цена индукционных нагревателей более высокой частоты больше, потому что более сложные схемы генератора необходимы для создания этих частот.
РИС. 3. Принцип емкостного нагрева
Диэлектрический (емкостный) нагрев
Индукционный нагрев можно использовать только с токопроводящими материалами.Следовательно, какой-то другой метод должен использоваться для нагрева непроводящих материалов.
Такой способ проиллюстрирован на фиг. 3 и называется диэлектрическим или емкостный нагрев. Непроводники можно нагреть, поместив их в электростатическое поле, создаваемое между двумя металлическими электродами, на которые подается питание. от источника высокочастотного переменного тока. Нагреваемый материал становится диэлектриком. или изоляция емкостного устройства. Металлические электроды составляют две тарелки.
Когда высокочастотный переменный ток подается на диэлектрическую нагревательную сборку, изменение характера применяемого переменного тока вызывает внутреннюю атомную структуру диэлектрического материала искажаться. Поскольку частота AC увеличивается, количество внутренних атомных искажений также увеличивается.
Это внутреннее трение вызывает большое количество тепла в непроводящей материал. Частоты в диапазоне 50 МГц могут использоваться для нагрева диэлектрика.Диэлектрический нагрев вызывает быстрый нагрев, который равномерно распределяется по всей поверхности. нагретый материал. Обычно этот метод нагрева применяется в склейка фанеры и склейка пластиковых листов.
ЭЛЕКТРИЧЕСКИЕ СВАРОЧНЫЕ НАГРУЗКИ
Электросварка — еще один распространенный вид преобразования энергии с выделением тепла. система. Типы электросварочных систем включают контактную сварку, электродуговая сварка, индукционная сварка.
Сварка сопротивлением
Несколько знакомых методов сварки, например точечная сварка, шовная сварка, и стыковая сварка — это процессы контактной сварки. Все эти процессы полагаться на принцип резистивного нагрева. Точечная сварка, изображенная на ИНЖИР. 4А, выполняется на листах металла внахлест, которые обычно толщиной менее 1/4 дюйма. Металлические листы зажимаются между двумя электродами, и электрический ток проходит через электроды и металлические листы.Ток заставляет металлы плавиться вместе. Мгновенный ток через электроды обычно превышает 5000 ампер, в то время как напряжение между электродами менее 2 вольт.
Шовная сварка, показанная на РИС. 4B, достигается пропусканием листов металла между двумя прижимными роликами, при этом непрерывно прерываемый ток проходит через электроды. Принцип работы шовной сварки такая же, как при точечной сварке.Несколько других подобных методов, которые называются стыковой сваркой, сваркой кромок и сваркой выступов, также широко используются.
Электродуговая сварка
В то время как при контактной сварке используется давление на свариваемые материалы, Электродуговая сварка позволяет получать сварные металлы путем локального нагрева без давление, как показано на фиг. 5. Электрическая дуга возникает, когда электрод сварщика приводят в контакт со свариваемым металлом.Углерод Электроды используются для дуговой сварки постоянным или переменным током цветных металлов и сплавов. Не все металлы можно сваривать дуговой сваркой. Когда металлы при сварке, часть свариваемых металлов расплавляется, создавая металлический бассейн, который при необходимости добавляется с помощью присадочного стержня. Затем лужа (ванна расплавленного металла) заполняет зазор (кратер дуги), который была создана дуга электрода. Различные типы и различное вольтамперное напряжение имеются рейтинги электродуговых сварщиков.
Для дуговой сварки требуется меньшее количество тока, чем для сварки сопротивлением. сварка. Сила тока может составлять от 50 до 200 ампер или выше для некоторых. Приложения. Напряжение обычно составляет от 10 до 50 вольт. Электрический Аппарат для дуговой сварки может питаться от переносного генератора, аккумуляторного блока, понижающий трансформатор, или блок выпрямления.
РИС. 4. Методы контактной сварки: (A) точечная сварка, (B) шовная сварка
Индукционная сварка
В процессе индукционной сварки используется принцип индукционного нагрева. сплавить металлы вместе.Высокочастотный переменный ток подается на нагревательную спираль, в которую помещаются свариваемые материалы. Трубчатый металл часто бывает сварены таким образом.
ЭНЕРГОСБЕРЕЖЕНИЕ ДЛЯ ЭЛЕКТРОСВАРОЧНЫХ МАШИН
Электросварщики — достаточно специализированный вид оборудования, так как они используйте очень большой ток при низких уровнях напряжения. У них есть своеобразное влияние на работу энергосистемы. Они тянут большие суммы тока на короткие промежутки времени.Выпрямители с кремниевым управлением (SCR) обычно используются для управления запуском и остановкой больших токов связанных с электросварщиками. Текущий рейтинг этих устройств должен быть очень высоким, иногда в диапазоне от 1000 до 100000 ампер, а оборудование для распределения энергии должно выдерживать эти высокие токи. SCR обсуждаются в Разделе 17.
РИС. 5. Электродуговая сварка
РИС. 6 иллюстрирует типичную электросварочную систему.Подача питания переменного тока от параллельной цепи энергосистемы понижается на трансформатор для подачи переменного напряжения на сварщика или выпрямленный для производства Напряжение постоянного тока для сварщиков постоянного тока. В любом типе машины контактор SCR может использоваться для контроля времени включения и выключения сварочного аппарата.
РИС. 6. Блок-схема типовой электросварочной установки
Контакторы SCR
КонтакторыSCR — это электронные устройства управления, предназначенные для работы с большими количества тока.SCR запускаются или включаются подаваемыми импульсами. синхронизацией или последовательностью цепей сварщика. SCR обычно охлаждается оборотной водой. Обсуждаются принципы работы SCR. в Разделе 17.
СИСТЕМЫ ОТОПЛЕНИЯ И КОНДИЦИОНИРОВАНИЯ ВОЗДУХА
Очень важным видом преобразования электроэнергии является тот, который требует место в системах отопления и кондиционирования домов, производств, и коммерческие здания.Эти нагрузки преобразуют высокий процент общий объем поставленной электроэнергии. Хотя природный газ и системы подогрева мазута все еще используются, электрическое отопление становится с каждым годом все больше. Системы кондиционирования также становятся все более популярными. обычно используется для охлаждения зданий. Использование электрического отопления и кондиционирования системы сделали нас еще более зависимыми от электроэнергии. Теперь мы используем электроэнергия для поддержания комфортной среды внутри зданий.
Основы электрического отопления
Есть несколько важных факторов, которые вы должны понимать, чтобы иметь знания в области электрического отопления. Тепло измеряется в британских термиках. единиц (BTUS). Одна британская тепловая единица — это количество тепла, необходимое для повышения температуры. одного фунта воды на один градус Фаренгейта. Тепловая энергия в количестве 3,4 БТЕ в час эквивалентно одному ватту электроэнергии.
Еще один важный фактор, который следует учитывать при изучении электрического отопления расчетная разница температур.В этом разница между внутри и температура наружного воздуха в градусах Фаренгейта. Внешняя температура считается самой низкой температурой, которая ожидается в течение нескольких раз в год. Внутренняя температура — это желаемая температура (термостат параметр).
Коэффициент, используемый вместе с расчетной разницей температур, называется градусные дни. Фактор градус-день используется для определения среднего числа. градусов, что средняя температура ниже 65 ° F.Эти данные усреднены в сезонные периоды для рассмотрения при теплоизоляции зданий.
Важность изоляции
Изоляция здания — очень важный фактор в электрическом системы отопления. Изоляция используется для предотвращения утечки тепла. Качество изоляции выражается коэффициентом термического сопротивления (R). Общая тепловое сопротивление здания определяется исходя из теплового сопротивления всей конструкции (дерево, бетон, изоляция и т. д.).Обратный теплового сопротивления называется коэффициентом теплопередачи (U), который это выражение количества теплового потока через площадь, выраженное в британских британских фунтах стерлингов на квадратный фут в час на градус Фаренгейта. Следующие формулы используются для преобразования U или R в электрические единицы (ватты):
1
термическое сопротивление = ————- коэффициент теплопередачи
коэффициент теплопередачи
Вт = ———— 3.4 или:
Вт = 0,29 × U
Производители изоляции могут предоставить различные таблицы, которые могут быть используется для оценки потерь тепла, которые могут возникнуть в зданиях разного типа строительства. Потери тепла происходят, в частности, через окна и двери зданий. Периодическое открывание дверей также имеет значительную влияние на теплопотери. Здание должно иметь достаточную изоляцию, чтобы уменьшить потери тепла; в противном случае электрические системы отопления и кондиционирования быть очень неэффективным.Теплопотери здания в первую очередь зависят от конструкции здания, а также от расчетного коэффициента температурного перепада в районе, где расположено здание. Здания из бетона имеют другое количество теплопотерь по сравнению с конструкцией из деревянного каркаса. Потеря тепла будет происходить через стены, пол, окна и потолок. Каждый из этих факторов необходимо учитывать при оценке теплопотерь здания.
Следующий пример задачи поможет вам понять важность добавления теплоизоляции в здание.
Пример задачи:
Дано: здание, построенное для обеспечения следующего теплового сопротивления (R) факторы:
(a) Наружная черепица R = 0,80
(б) Обшивка фанерная R = 0,75
(c) Используемая строительная бумага R = 0,04
(г) Конструкция стены R = 0,85
(д) Штукатурка стен R = 0,35
(е) Изоляция R = 11,0
Найдите: полное тепловое сопротивление (R), коэффициент теплопередачи. (U) и мощность потерь тепла (Вт) как с изоляцией, так и без нее.
Раствор (без изоляции):
Из результатов этой задачи видно, что добавление изоляции в стены здания оказывает большое влияние на теплопотери. Изоляция имеет гораздо больший эффект в контроле теплопотерь, чем конструкция материалы, использованные для постройки.
Системы электрического отопления и охлаждения
Сегодня используется несколько типов систем электрического отопления. Некоторые общие это обогреватели для плинтусов, настенные или потолочные обогреватели и обогреватели. насосы.В большинстве этих систем для циркуляции тепла используется принудительный воздух.
У одних электронагревателей есть индивидуальные термостаты, другие — подключаемые. к одному центральному термостату, который контролирует температуру во всем здании. Возможность иметь контроль температуры в каждой комнате является преимуществом. систем электрического отопления.
Тепловые насосы
В последние годы большой популярностью стали пользоваться тепловые насосы как комбинированные. отопительно-охлаждающая установка для зданий.Тепловой насос — это теплообменник. Блок. Когда наружная температура теплая, тепловой насос действует как воздушный кондиционер и передает внутреннее тепло наружу. Этот рабочий цикл реверсируется при низких температурах наружного воздуха. В зимой наружное тепло передается внутрь здания. Этот процесс может происходить при низких температурах, так как всегда есть определенное количество тепла в наружном воздухе даже при отрицательных температурах.Однако при более низких температурах снаружи меньше тепла. воздуха.
Таким образом, тепловые насосы передают тепло, а не производят его. Поскольку тепловые насосы не выделяют тепло, как блоки резистивного нагрева, они более экономичны с точки зрения энергосбережения. Нагрев и охлаждение — обратимые процессы в тепловом насосе; таким образом, устройство является автономным.
Реверсивная функция тепловых насосов снижает потребность в пространстве для раздельные нагревательные и охлаждающие агрегаты.Еще одно преимущество заключается в том, что изменение переход от нагрева к охлаждению может производиться автоматически. Эта функция может быть желанным в весеннее и осеннее время года во многих районах, где температуры очень изменчивы. В очень холодных регионах тепловой насос может быть дополнен дополнительным блоком резистивного нагрева.
Этот вспомогательный агрегат будет работать при очень высоких температурах наружного воздуха. холод, и будет полезен для поддержания температуры в помещении на комфортном уровень.Воздух циркулирует мимо этих нагревательных элементов в вентиляционные отверстия. здания.
Тепловые насосы используются как в жилых, так и в коммерческих и промышленных помещениях. приложений, и с каждым годом они используются все более широко.
РИС. 7 показана упрощенная схема теплового насоса, в котором компрессор забирает хладагент из низкотемпературного низкого давления испаритель и переводит его на высокую температуру и высокое давление.
Затем хладагент поступает в конденсатор почти таким же образом. как в холодильнике.
Системы кондиционирования воздуха
Более широкое использование систем кондиционирования воздуха обеспечивает больший комфорт в домах, на промышленных предприятиях и коммерческих объектах. Большинство кондиционеров агрегаты используются для регулирования внутренней температуры зданий, чтобы сделать условия труда и проживания более комфортными. Однако многие агрегаты используются для охлаждения внутренней части различного оборудования. Кондиционер изменяет температуру и относительную влажность воздуха. единицы измерения.При проектировании систем кондиционирования все тепловыделяющие элементы в ближайшем окружении. Тепло тела, электрическое бытовые приборы и светильники представляют собой некоторые общие источники тепла. Распространение тепла проходит через полы, стены, потолки и окна здания. Показана упрощенная схема комнатного кондиционера. на фиг. 8.
РИС. 7. Упрощенная электрическая схема теплового насоса
Соображения относительно нагревательных нагрузок
Системы отопления для жилых, коммерческих и промышленных помещений обычно называются системами HVAC.Это означает отопительную вентиляцию и система кондиционирования. Требования к электроэнергии для HVAC Системы — это основная проблема при проектировании электрических систем здания. Электрические системы отопления, вентиляции и кондиционирования воздуха обеспечивают индивидуальный термостатический контроль температуры, имеют длительный срок службы оборудования и безопасны в использовании. Хорошо изолированное здание необходимо для снижения потерь тепла для экономичного использования систем отопления, вентиляции и кондиционирования воздуха.
РИС. 8. Упрощенная схема комнатного кондиционера.
Системы комфортного отопления с электропитанием широко используются сегодня. для производства тепла для коммерческих, промышленных и жилых зданий. Электроэнергия доступна практически на любой строительной площадке, и он имеет ряд преимуществ по сравнению с методами сжигания топлива для получения тепла. С экологической точки зрения любое топливо, необходимое для производства электроэнергии, сжигается или потребляется. на электростанции, которая обычно находится на некотором расстоянии от здания где это используется.При таком способе отопления меньше загрязнений. чем было бы, если бы топливо сжигалось в каждом здании.
Электрический обогреватель также чист в использовании, прост в управлении и очень эффективен.
Электрическое отопление сегодня важно из-за его высокого уровня эффективности. Теоретически, когда в систему подается электрическая энергия, практически все это превращается в тепловую энергию. По сути, это означает, что когда применяется определенное количество электричества, он производит эквивалент Выход BTU.Одна тысяча ватт или 1 кВт электроэнергии при преобразовании в тепла, производит 3412 БТЕ тепловой энергии.
Отопление может быть достигнуто различными способами за счет использования электричества. Комфортные системы отопления содержат источник энергии, тракт передачи, управление. загрузочное устройство, а также возможность использования одного или нескольких дополнительных индикаторов. В первичная разница между тепловым насосом и электрическими системами сопротивления находится в производстве тепловой энергии. Выполнен резистивный нагрев. пропуская электрический ток через провода или проводники к нагрузке устройство.Для сравнения, тепловой насос работает за счет циркуляции газа или жидкости. через трубы, которые соединяют внутреннюю катушку с внешней катушкой. Электричество требуется в обоих случаях в качестве источника энергии для обеспечения работоспособности систем.
Сопротивление отопления в зданиях
Когда электрический ток протекает через проводящий материал, он встречает тип оппозиции, называемый сопротивлением. В большинстве схем это противостояние неизбежно, в некоторой степени, из-за материала проводника, его длина, площадь поперечного сечения и температура.Дирижер провода системы отопления намеренно имеют низкое сопротивление, чтобы свести к минимуму производство тепла между источником и нагрузочным устройством.
Для этой части системы используется изолированный медный провод большого сечения.
Нагрузочное устройство системы резистивного нагрева несет основную ответственность для производства тепловой энергии. Количество тепла, выделяемого нагрузка зависит от величины тока, который проходит через резистивный элемент.Сопротивление элемента специально спроектировано так, чтобы быть довольно высоким по сравнению к соединительным проводам системы. Сплав никеля и хрома Нихром обычно используется для нагревательных элементов.
Резистивные элементы можно размещать под окнами или в стратегических местах. по всему зданию. В этом типе установки элементы заключен в корпус, обеспечивающий электробезопасность и эффективное использование доступного тепла. Воздух, поступающий в нижнюю часть блока, циркулирует вокруг плавников, чтобы нагреться, чем выходит наверху.Различные конфигурации могут быть выбраны в соответствии с желаемым методом циркуляции, единичной длиной, и теплоплотное производство.
Резистивные элементы также используются в качестве источника тепла в приточно-вытяжных системах. системы отопления. В этом приложении элемент устанавливается непосредственно в основной воздушный поток системы. Количество элементов, выбранных для конкретная установка основана на желаемой тепловой мощности. Отдельные элементы обычно располагаются в шахматном порядке. для обеспечения равномерного теплообмена и устранения горячих точек.Элемент имеет пружинную конструкцию, поддерживаемую керамическими изоляторами.
Агрегаты этого типа обеспечивают дополнительный источник тепла, когда снаружи температура становится довольно холодной. Воздух, циркулирующий вокруг элемента, нагревается и помещается в сеть воздуховодов для распределения по всему зданию.
Тепловые насосы в зданиях
Тепловой насос определяется как реверсивная система кондиционирования воздуха, передающая нагреть либо внутрь кондиционируемой зоны, либо от нее.
Когда наружная температура теплая, тепловой насос забирает тепло из помещения. и перемещает его наружу, действуя таким образом как кондиционер. Операция в холодную погоду заставляет забирать тепло с улицы и перемещать его в помещение, функционирует как отопительный агрегат. Обогрев можно производить даже в холодное время года. температуры, потому что на выходе всегда присутствует определенное количество тепла. боковой воздух. Например, при 0 ° F (-22 ° C) в воздухе будет примерно 89 процентов тепла, которое он имеет при температуре 100 ° F (38 ° C).Даже при минусовых температурах, можно выделять тепло из наружного воздуха. Однако это труднее выделять тепло, когда температура опускается ниже 20 ° F (-6 ° C). Для установок, работающих при более низких температурах, тепловые насосы оснащены нагревательными змеевиками сопротивления для дополнения системы.
Тепловой насос, как и кондиционер, состоит из компрессора, наружного змеевик, расширительное устройство и внутренний змеевик. Компрессор отвечает для перекачивания хладагента между внутренним и наружным змеевиками.Хладагент попеременно переключается между жидким и газообразным состояниями, в зависимости от его расположение в системе. Электрические вентиляторы или воздуходувки используются для принуждения воздух через соответствующие змеевики, а также для циркуляции холодного или теплого воздуха по всей здание.
Большинство работающих в настоящее время тепловых насосов состоят из внутренних и наружные блоки, соединенные между собой изолированными трубами или трубками.
Внутренний блок содержит дополнительные электрические нагревательные элементы, вентилятор и двигатель в сборе, электронный воздухоочиститель, увлажнитель, регулятор панель и внутренняя катушка.Наружный блок покрыт толстым слоем стальной шкаф, в котором находится наружный змеевик, вентиляторный вентилятор в сборе, компрессор, расширительное устройство и реверсивный клапан.
Оба блока рассчитаны на максимальную производительность, высокую эффективность, и низкое потребление электроэнергии.
Цикл нагрева теплового насоса
Если кондиционер развернулся в окне во время его работы цикл, он будет извлекать тепло из наружного воздуха и перекачивать его в здание.Это условие, которое является оперативной основой тепловой насос, часто называют принципом кондиционера с обратным потоком. Тепловой насос по существу «переворачивается» после охлаждения. цикл с помощью специального клапана, который меняет направление потока хладагента через система.
Когда происходит цикл нагрева, внутренний змеевик, наружный змеевик и вентиляторы поменяны местами. Наружный змеевик теперь отвечает за отвод тепла от наружный воздух и прохождение его по внутреннему змеевику, где он выпускается в сеть воздуховодов для распределения.
Во время цикла нагрева любой хладагент, циркулирующий снаружи змеевик заменен на низкотемпературный газ. Это сделано специально, чтобы быть существенно холоднее наружного воздуха. Поскольку тепловая энергия всегда движется от горячего к холодному происходит передача тепла от наружного воздуха к холодный хладагент. В некотором смысле можно сказать, что жара от холода снаружи воздух поглощается гораздо более холодным хладагентом.
Компрессор системы отвечает за сжатие нагруженный теплом газ, прошедший через внешний змеевик.Это действие разработан, чтобы вызвать повышение давления перекачиваемого газа к внутренней катушке. Когда воздух обдувается внутренним змеевиком, газ отдает свое тепло воздуху. Затем теплый воздух циркулирует через сеть воздуховодов в соответствующие помещения системы.
Когда хладагент внутреннего змеевика отдает тепло, он охлаждается. и конденсируется в жидкость. Затем он перекачивается обратно во внешний змеевик. действием компрессора.Еще раз переходит в холодное газообразное состояние. и применяется к внешней катушке для повторения цикла. Если снаружи температура падает слишком низко, хладагент может не собрать достаточно тепло для удовлетворения системы. Когда это происходит, электронагреватели сопротивления находятся под напряжением, чтобы дополнить процесс нагрева. Место, где электрические тепло, поступающее в систему, называется точкой баланса.
РИС. 9 показано изображение работы теплового насоса во время его нагрева. цикл.В точке (1) тепло от холодного наружного воздуха поглощается находящийся под давлением низкотемпературный хладагент, циркулирующий снаружи катушка. Как (2), хладагент подается в компрессор и сжимается. в высокотемпературный газ под высоким давлением. В (3) нагретый газ переносится к внутреннему змеевику и выделяется в виде тепла. В точке (4) циркулирует теплый воздух. через сеть воздуховодов. Обратите внимание, что дополнительный нагревательный элемент сопротивления размещается в этой части системы.В (5) возвращается хладагент. к компрессору, а затем к расширительному устройству, где жидкий хладагент конденсируется, а затем возвращается в наружный змеевик. Цикл повторяется с этого момента.
РИС. 9. Работа цикла нагрева
Цикл охлаждения теплового насоса
Тепловой насос предназначен для работы в качестве кондиционера во время летние месяцы. Для этого необходимо установить реверсивный клапан. в положении цикла охлаждения.В некоторых системах это достигается переключателем вручную, в то время как в других это достигается автоматически, в соответствии с настройкой термостата. Рабочее положение клапана просто направляет поток хладагента.
Когда цикл охлаждения запускается, он сначала вызывает охлаждение хладагента. течь от компрессора во внутренний змеевик. Во время этой части В цикле хладагент находится в газообразном состоянии низкого давления и достаточно прохладен.По мере продолжения процесса циркуляции внутренний змеевик начинает поглощать тепло из внутреннего воздуха здания. Воздух проходит над змеевиком внутри помещения охлаждается и циркулирует в сети воздуховодов для распределения по всей здание.
После выхода из внутреннего змеевика хладагент должен пройти через реверсивный клапан и в компрессор. Компрессор отвечает за увеличение давление хладагента и его циркуляция наружу катушка.В этой точке цикла хладагент отдает свое тепло наружный воздух охлаждается и переходит в жидкое состояние. Тогда это возвращается в компрессор, где перекачивается через расширительное устройство и вернулся к внутренней катушке. Затем процесс повторяется.
РИС. 10 показано изображение теплового насоса во время кондиционирования воздуха. цикл. В точке (1) тепло поглощается из внутреннего воздуха, а холодный воздух перенесен в здание. В (2) давление нагруженного теплом хладагент увеличивается компрессором и циркулирует наружу змеевик для передачи в воздух.