Сварка — это… Что такое Сварка?
технологический процесс соединения твёрдых материалов в результате действия межатомных сил, которое происходит при местном сплавлении или совместном пластическом деформировании свариваемых частей. С. получают изделия из металла и неметаллических материалов (стекла, керамики, пластмасс и др.). Изменяя режимы С., можно наплавлять слои металла различной толщины и различного состава. На специальном оборудовании в определенных условиях можно осуществлять процессы, противоположные по своей сущности процессу соединения, например огневую, или термическую, резку металлов.
Историческая справка. Простейшие приёмы С. были известны в 8—7-м тыс. до н. э. В основном сваривались изделия из меди, которые предварительно подогревались, а затем сдавливались. При изготовлении изделий из меди, бронзы, свинца, благородных металлов применялась т. н. литейная С. Соединяемые детали заформовывали, подогревали и место соединения заливали заранее приготовленным расплавленным металлом. Изделия из железа и его сплавов получали их нагревом до «сварочного жара» в кузнечных горнах с последующей проковкой. Этот способ известен под названием горновая, или кузнечная, С. Только эти два способа С. были распространены вплоть до конца 19 в. Толчком к появлению принципиально новых способов соединения металлов явилось открытие в 1802 дугового разряда (См. Дуговой разряд)К электрическим способам С. плавлением относится электрошлаковая С., при которой процесс начинается, как при дуговой С. плавящимся электродом — зажиганием дуги, а продолжается без дугового разряда. При этом значительное количество шлака закрывает сварочную ванну. Источником нагрева металла служит тепло, выделяющееся при прохождении электрического тока через шлак. Способ разработан в институте электросварки им. Е. О. Патона и получил промышленное применение (в конце 50-х гг.). Возможна электрошлаковая С. металлов толщиной до 200 мм (одним электродом), до 2000 мм (одновременно работающими несколькими электродами). Она целесообразна и экономически выгодна при толщине основного металла более 30 мм. Электрошлаковым способом можно выполнять ремонтные работы, производить наплавку, когда требуется значительная толщина наплавляемого слоя. Способ нашёл применение в производстве паровых котлов, станин прессов, прокатных станов, строительных металлоконструкций и т. п.
Осуществление дуговой электросварки возможно также в воде (пресной и морской). Первый практически пригодный способ С. под водой был создан в СССР в Московском электромеханическом институте инженеров ж.-д. транспорта в 1932 под руководством К. К. Хренова. Дуга в воде горит устойчиво, охлаждающее действие воды компенсируется небольшим повышением напряжения дуги, которая плавит металл в воде так же легко, как и на воздухе. С. производится вручную штучным плавящимся стальным электродом с толстым (до 30% толщины электрода) водонепроницаемым покрытием. Качество С. несколько ниже, чем на воздухе, металл шва недостаточно пластичен. В 70-е гг. в СССР в институте электросварки им. Е. О. Патона осуществлена С. под водой полуавтоматом, в котором в качестве электрода использована т. н. порошковая проволока (тонкая стальная трубка, набитая смесью порошков), непрерывно подаваемая в дугу. Порошок является флюсом. Подводная С. ведётся на глубине до 100Один из перспективных способов С. — плазменная С. — производится плазменной горелкой. Сущность этого способа С. состоит в том, что дуга горит между вольфрамовым электродом и изделием и продувается потоком газа, в результате чего образуется плазма, используемая для высокотемпературного нагрева металла. Перспективная разновидность плазменной С. — С. сжатой дугой (газы столба дуги, проходя через калиброванный канал сопла горелки, вытягиваются в тонкую струю). При сжатии дуги меняются её свойства: значительно повышается напряжение дуги, резко возрастает температура (до 20000—30000 °С). Плазменная С. получила промышленное применение для соединения тугоплавких металлов, причём автоматы и полуавтоматы для дуговой С. легко могут быть приспособлены для плазменной при соответствующей замене горелки. Плазменную С. используют как для соединения металлов больших толщин (многослойная С. с защитой аргоном), так и для соединения пластин и проволоки толщиной от десятков мкм до 1 мм (микросварка, С. игольчатой дугой). Плазменной струей можно осуществлять также др. виды плазменной обработки, в том числе плазменную резку металлов.
Газовая С. относится к способам С. плавлением с использованием энергии газового пламени, применяется для соединения различных металлов обычно небольшой толщины — до 10 мм. Газовое пламя с такой температурой получается при сжигании различных горючих в кислороде (водородно-кислородная, бензино-кислородная, ацетилено-кислородная С. и др.). Промышленное применение получила ацетилено-кислородная газовая С. Существенное отличие газовой С. от дуговой С. — более плавный и медленный нагрев металла, Это обстоятельство определяет применение газовой С. для соединения металлов малых толщин, требующих подогрева в процессе С. (например, чугун и некоторые специальные стали), замедленного охлаждения (например, инструментальные стали) и т. д. Благодаря универсальности, сравнительной простоте и портативности оборудования газовая С. целесообразна при выполнении ремонтных работ. Промышленное применение имеет также Газопрессовая сварка стальных труб и рельсов, заключающаяся в равномерном нагреве ацетилено-кислородным пламенем металла в месте стыка до пластического состояния и последующей осадке с прессованием или проковкой.Сварка давлением. Способы С. в твёрдой фазе дают сварное соединение, прочность которого иногда превышает прочность основного металла. Кроме того, в большинстве случаев при С. давлением не происходит значительных изменений в химическом составе металла, т. к. металл либо не нагревается, либо нагревается незначительно. Это делает способы С. давлением незаменимыми в ряде отраслей промышленности (электротехнической, электронной, космической и др.).
Холодная С. выполняется без применения нагрева, одним только приложением давления, создающим значительную пластическую деформацию (до состояния текучести), которая должна быть не ниже определённого значения, характерного для данного металла. Перед С. требуется тщательная обработка и очистка соединяемых поверхностей (осуществляется обычно механическим путём, например вращающимися проволочными щётками). Этот способ С. достаточно универсален, пригоден для соединения многих металлических изделий (проводов, стержней, полос, тонкостенных труб и оболочек) и неметаллических материалов, обладающих достаточной пластичностью (смолы, пластмассы, стекло и т. п.). Перспективно применение холодной С. в космосе.
Для С. можно использовать механическую энергию трения. С. трением осуществляется на машине, внешне напоминающей токарный станок Детали зажимаются в патронах и сдвигаются до соприкосновения торцами. Одна из деталей приводится во вращение от электродвигателя. В результате трения разогреваются и оплавляются поверхностные слои на торцах, вращение прекращается и производится осадка деталей, С. высокопроизводительна, экономична, применяется, например, для присоединения режущей части металлорежущего инструмента к державке.
Ультразвуковая С. основана на использовании механических колебаний частотой 20 кгц. Колебания создаются магнитострикционным преобразователем, превращающим электромагнитные колебания в механические. На сердечник, изготовленный из магнитострикционного материала (См. Магнитострикционные материалы), намотана обмотка. При питании обмотки токами ВЧ из электрической сети в сердечнике возникают продольные механические колебания. Металлический наконечник, соединённый с сердечником, служит сварочным инструментом. Если наконечник с некоторым усилием прижать к свариваемым деталям, то через несколько секунд они оказываются сваренными в месте давления инструмента. В результате колебаний сердечника поверхности очищаются и немного разогреваются, что способствует образованию прочного сварного соединения. Этот способ С. металлов малых толщин (от нескольких мкм до1,5 мм) и некоторых пластмасс нашёл применение в электротехнической, электронной, радиотехнической промышленности. В начале 70-х гг. этот вид С. использован в медицине (работы коллектива сотрудников Московского высшего технического училища им. Н. Э. Баумана под руководством Г. А. Николаева в содружестве с медиками) для соединения, наплавки, резки живых тканей. При С. и наплавке костных тканей, например отломков берцовых костей, рёбер и пр., конгломерат из жидкого мономера циакрина и твёрдых добавок (костной стружки и разных наполнителей и упрочнителей) наносится на поврежденное место и уплотняется ультразвуковым инструментом, в результате чего ускоряется полимеризация. Эффективно применение ультразвуковой резки в хирургии. Сварочный инструмент ультразвукового аппарата заменяется пилой, скальпелем или ножом. Значительно сокращаются время операции, потеря крови и болевые ощущения. Одним из способов электрической С. является контактная С., или С. сопротивлением (в этом случае электрический ток пропускают через место С., оказывающее омическое сопротивление прохождению тока). Разогретые и обычно оплавленные детали сдавливаются или осаживаются, т. о. контактная С. по методу осадки относится к способам С. давлением (см. Контактная электросварка). Этот способ отличается высокой степенью механизации и автоматизации и получает всё большее распространение в массовом и серийном производстве (например, соединение деталей автомобилей, самолётов, электронной и радиотехнической аппаратуры), а также применяется для стыковки труб больших диаметров, рельсов и т. п.Наплавка. От наиболее распространённой соединительной С. отличается наплавка, применяемая для наращения на поверхность детали слоя материала, несколько увеличивающего массу и размеры детали. Наплавкой можно осуществлять восстановление размеров детали, уменьшенных износом, и облицовку поверхностного слоя. Восстановительная наплавка имеет высокую экономическую эффективность, т. к. таким способом восстанавливают сложные дорогие детали; распространена при ремонте на транспорте, в сельском хозяйстве, строительстве, горной промышленности и т. д. Облицовочная наплавка применяется для создания на поверхности детали слоя материала с особыми свойствами — высокой твёрдостью, износостойкостью и т. д. не только при ремонте, но и при производстве новых изделий. Для этого вида наплавки изготовляют наплавочные материалы с особыми свойствами (например, износостойкий сплав сормайт). Наплавочные работы ведут различными способами С.: дуговой, газовой, плазменной, электронной и т. п. Процесс наплавки может быть механизирован и автоматизирован. Выпускаются специальные наплавочные установки с автоматизацией основных операций.
Термическая резка. Резка технологически отлична от С. и противоположна ей по смыслу, но оборудование, материалы, приёмы выполнения операций близки к применяемым в сварочной технике. Под термической, или огневой, резкой подразумевают процессы, при которых металл в зоне резки нагревается до высокой температуры и самопроизвольно вытекает или удаляется в виде размягченных шлаков и окислов, а также может выталкиваться механическим действием (струей газа, электродом и т. п.). Резка выполняется несколькими способами. Наиболее важный и практически распространённый способ — кислородная резка, основанная на способности железа сгорать в кислороде, применяется обычно для резки сталей толщиной от 5 до 100 мм, возможно разделение материала толщиной до 2000 мм. Кислородной резкой выполняют также операции, аналогичные обработке режущим инструментом, — строжку, обточку, зачистку и т. п. Резку некоторых легированных сталей, чугуна, цветных металлов, для которых обычный способ малопригоден, осуществляют кислородно-флюсовым способом. Кислородная обработка нашла применение на металлургических и машиностроительных заводах, ремонтных предприятиях и т. п.
Дуговая резка, выполняемая как угольным, так и металлическим электродами, применяется при монтажных и ремонтных работах (например, в судостроении). Для поверхностной обработки и строжки металлов используют воздушно-дуговую резку, при которой металл из реза выдувается струей воздуха, что позволяет существенно улучшить качество резки.
Резку можно выполнять высокотемпературной плазменной струей. Для резки и прожигания отверстий перспективно применение светового луча, струи фтора, лазерного излучения (см. Лазерная технология). Дальнейшее развитие и совершенствование методов сварки и резки связано с внедрением и расширением сферы применения новых видов обработки — плазменной, электронной, лазерной, с разработкой совершенных технологических приёмов и улучшением конструкции оборудования. Возможно значительное расширение использования С. и резки для подводных работ и в космосе. Направление прогресса в области сварочной техники характеризуется дальнейшей механизацией и автоматизацией основных сварочных работ и всех вспомогательных работ, предшествующих С. и следующих за ней (применение манипуляторов, кантователей, Роботов). Актуальной является проблема улучшения контроля качества С., в том числе применение аппаратов с обратной связью, способных регулировать в автоматическом режиме работу сварочных автоматов. См. также Вибрационная (вибродуговая) наплавка (См. Вибрационная наплавка), Высокочастотная сварка, Взрывная сварка, Диффузионная сварка, Конденсаторная сварка, Термитная сварка, Электролитическая сварка, Сварка пластмасс, Сварка в космосе.
Лит.: Справочник по сварке, т. 1—4, М., 1960—71; Глизманенко Д. Л., Евсеев Г. Б., Газовая сварка и резка металлов, 2 изд., М., 1961; Технология электрической сварки плавлением, под ред. Б. Е., Патона, М. — К., 1962; Багрянский К. В., Добротина 3. А., Хренов К. К., Теория сварочных процессов, Хар., 1968; Хренов К. К., Сварка, резка и пайка металлов, 4 изд., М., 1973; Словарь-справочник по сварке, сост. Т. А. Кулик, К., 1974.
К. К. Хренов.
СВАРКА — это… Что такое СВАРКА?
Сварка — – получение неразъемных соединений посредством установления межатомных связей между соединяемыми частями при их нагревании и (или) пластическом деформировании. [ГОСТ 2601 84] Сварка – получение неразъемных соединений посредством… … Энциклопедия терминов, определений и пояснений строительных материалов
Сварка — стального каркаса будущего небоскреба. СВАРКА, процесс получения неразъемного соединения деталей из металлов, керамики, пластмасс, стекла и других материалов или их сочетаний (например, стекла с металлом) чаще всего путем местного или общего… … Иллюстрированный энциклопедический словарь
СВАРКА — СВАРКА, сварки, жен. (тех.). Соединение металлических частей путем заливки промежутков между ними расплавленным металлом. Автогенная сварка. || Соединение металлических частей, нагретых до высокой температуры, путем ковки или сжимания их.… … Толковый словарь Ушакова
СВАРКА — технологический процесс получения неразъёмных соединений твёрдых материалов из металла и неметалла (стекла, керамики, пластмасс и др.) путём образования межатомных связей между соединяемыми частями при их нагревании (плавлении) или пластическом… … Большая политехническая энциклопедия
СВАРКА — процесс соединения металл. частей путем нагрева места соединения до пластического состояния или расплавления. В первом случае (С. давлением) после нагрева производится проковка или сильное сжатие свариваемых концов, во втором (С. плавлением)… … Технический железнодорожный словарь
сварка — Получение неразъемных соединений посредством установления межатомных связей между соединяемыми частями при их нагревании и (или) пластическом деформировании [ГОСТ 2601 84] сварка Процесс получения неразъёмных соединений посредством установления… … Справочник технического переводчика
сварка — автоген, сваривание, соединение, состыковывание Словарь русских синонимов. сварка сущ., кол во синонимов: 20 • автоген (2) • … Словарь синонимов
СВАРКА — процесс получения неразъемного соединения деталей машин, конструкций и сооружений при их местном или общем нагреве, пластическом деформировании или при совместном действии того и другого в результате установления межатомных связей в месте их… … Большой Энциклопедический словарь
СВАРКА — СВАРКА, процесс соединения металлических деталей, как правило, с помощью регулируемого плавления. Автомашины, домашняя техника, мосты, электронные приборы это только часть объектов, в которых содержатся детали, соединенные сваркой. Сварочные… … Научно-технический энциклопедический словарь
сварка — СВАРИТЬ, сварю, сваришь; сваренный; сов. Толковый словарь Ожегова. С.И. Ожегов, Н.Ю. Шведова. 1949 1992 … Толковый словарь Ожегова
СВАРКА — (Welding) способ соединения металлических частей путем соприкасания при расплавлении этих частей (С. плавлением) или при приведении их в тестообразное состояние с последующей ковкой (С. давлением). Последняя применяется к металлам (железо, сталь) … Морской словарь
Что такое сварка — Виды сварки в википедии строительного инструмента
На вопрос, что такое сварка, ответит даже школьник.

Сварщик с помощью оборудования и электрода «сваривает» 2 материала, на этом месте получается шов.
Но это сложный технологический процесс и со времен, когда была открыта (1802 г.) и применена на практике электрическая дуга (1881 г.), произошло много инновационных изменений. Разработаны различные методы, чтобы получать ровные неразъемные соединения, совмещая металлы местным или общим нагревом. От структуры сырья зависит, какие виды для крепкой фиксации приемлемы в конкретном случае.
Что такое сварка?
Сварка – это ремесло, которое придумал и использует человек для своих хозяйственных нужд. Часто в жизнедеятельности встречаются вещи, изготовленные сварочной технологией, но разными способами. Ушло в прошлое, когда сваривали только металлические части. Созданы вещества, в состав которых входит разный молекулярный уровень, их тоже стали межатомно связывать между собой.
Поэтому и разработаны разные технологические процессы для соединения поверхностей:
- металлических;
- пластмассовых;
- керамических.
Для получения красивого и незаметного шва необходим был энергетический источник.
В ход пошло использование:
- электрической дуги и тока;
- газового пламени;
- лазерного излучения;
- электронного луча;
- различных трений;
- ультразвука.
Технологии развиваются стремительно, но последовательно и постепенно появились основные виды сварки.
Соединять конструкции в единое целое начали в самых неожиданных местах
Со временем стало возможным выполнять работу в условиях:
- бытовых;
- промышленных организаций;
- полевых;
- открытого моря;
- космоса.
Сваривают части деталей во время ремонта оборудования под водой, в безвоздушном пространстве и дома, выполняя монтажные работы. Только после обучения можно проводить ряд действий, так как они опасны.
Нарушения техники безопасности угрожают жизни и здоровью самому работнику, его окружению:
- пожарами;
- электрическими поражениями;
- отравлениями от вредных газов;
- ослеплением ярким светом, вплоть до полной потери зрения;
- воздействием на организм теплового, ультрафиолетового, инфракрасного излучения, металлических брызг.
Склеивание деталей происходит с помощью:
- большого удельного давления, сжатием элементов, без использования температурных режимов;
- нагревания соединяющей черты, когда на объекты оказывают умеренное силовое воздействие;
- увеличения температуры в местах соединений до пластического деформирования, когда металл начинает плавиться, его не нужно сжимать, давить, после остывания и затвердения он крепко соединяется, остается только шов.
Мастера стараются выполнить линию как можно ровней и тоньше, а полосу, объединяющую 2 материала — прочной. Этим все виды сварщиков подчеркивают свой профессионализм, навыки, опыт.
Сварочный аппарат и экипировка
Соединять металлы начали давно, а когда стали работать с разными материалами, создали удобное оборудование для выполнения рабочих операций.
сварочный аппарат
Вначале появился сварочный аппарат довольно непростой и громоздкий, который считается до сих пор традиционным.
Этот тип устройств основан на понижающих свойствах трансформатора в преобразовании силы тока до нужного уровня. При выполнении работ сварочными трансформаторами металл разбрызгивается во все стороны, отчего получаются некрасивые, толстые швы.
Со временем с развитием технологий, разработали новые способы и создали аппараты для сварки:
- электродуговой;
- полуавтоматической;
- ручной;
- с применением флюсов;
- газопламенной;
- электрошлаковой;
- термитной;
- аргонодуговой;
- плазменной;
- электронно-лучевой;
- лазерной;
- контактной;
- точечной;
- стыковой;
- диффузионной;
- с использованием высокочастотных токов.
Кроме основного оборудования для выполнения качественных сварных соединений важна дополнительная оснастка:
- электродами;
- щетками;
- держателями и клеммами;
- электрическими кабелями, протяжными роликами и горелками.
сварочное оборудование
В сварочном оборудовании мелочей не бывает, каждая деталь может как защитить сварщика, так и исключить брак в работе.
Для безопасных действий важна экипировка работника, включающая надлежащее состояние:
- специального костюма;
- обуви;
- перчаток.
Комплекты спецодежды шьют легкие и мягкие, предохраняющие тело от ожогов искрами, расплавленным металлом.
Предусмотрена специальная пропитка брюк и курток:
- парусиновых;
- брезентовых;
- кожаных.
Такая обработка создает устойчивость от горячих капель, раскаленных брызг. Руки тоже подвергаются опасным воздействиям, их защищают толстыми рукавицами, рабочими перчатками.
Сварщик
Сварщик должен быть одет в одежду, сшитую по ГОСТу из огнестойкой ткани, обработанной химическим составом.
Широкое применение получено изготовление курток от спилок со шкур животных. Изделия покрывают полимерной основой с акриловыми смолами, что дает надежную защиту от ожогов.
Существуют нормативы и для обуви. Работник не должен выполнять сварку в ботинках, подбитых металлическими гвоздями или со шнурками. В сапогах должны быть короткие голенища.
Особое внимание уделяют маске. Там окошко вставлено из светового фильтра, который предохраняет зрение от попадания горячих окалин. Существуют разные модели. В «хамелеонах» вставлено стекло, автоматически реагирующее на световые импульсы, а жидкокристаллические слои блокируют свет в начале сварки.
Технология сварочных работ
Если рассматривать технологию на примере электросварки, там создают электрическую дугу 2 проводника тока с разными зарядами. Для этого берут свариваемые детали и электроды. В ручном электродуговом соединении используют металлический сердечник, покрытый веществом – это электрод. Для отдельных видов работ, этот же элемент может быть графитовым или угольным. Когда разнополярные проводники прикасаются друг с другом происходит электрический разряд, процесс в виде дуги. Мастер направляет её в нужное место, там начинается деформация или плавление, уложенных рядом материалов и электрода.
Тот момент, когда расплавляется металл, происходит формирование шва, называют сварочной ванной. Где высокая температура размягчает детали, а плазменная сила или давление от горячего газа перемешивает молекулярные частицы. Окружающие испарения создают защиту металлическим частям от кислорода, чтобы не произошла химическая реакция. Расплавленным шлаком поддерживается температура.
Сварщик следит, чтобы образование полностью распространилось по сварной ванне, она в свою очередь двигается вслед за электродом, в это время происходит формирование шва.
электрод
Мастерство специалиста заключено в передвижении электрода при нужной скорости, под правильным углом наклона, в соответствии с параметрами напряжения.
Газы после горения оставляют сформированную застывшую корку, пока она мягкая излишки убирают, сбивая молотком.
Виды сварки
Классификация
Классификация производственных процессов основана на физическом происхождении сварных соединений.
С помощью:
- плавления – в этом случае отсутствует давление, являться в качестве источника будет пламя газа, лучевая энергия;
- давления — происходят мероприятия благодаря механической энергии;
- термомеханики – с использованием физической нагрузки совместно с подогревом элементов.
Ручная дуговая сварка с применением неплавящихся электродов
Дуговую сварку применяют для соединения частей:
- алюминиевых;
- магниевых;
- из нержавейки;
- никелевых;
- медных;
- бронзовых;
- циркониевых.
Техника производства с использованием неплавящихся электродов идентична с автогенной сваркой, так работники добиваются качественных швов.
В этом методе отстает производительность по сравнению с плавящимся стержнем.
Преимущество технологического метода в соединении стали:
- низкоуглеродистой;
- высоколегированной;
- мартенситной.
Способ успешно используют, соединяя разнородные материалы — углеродистую с нержавеющей сталью, медную с латунной. Хотя в швах могут быть поры, что снижает их качество. В технологии сварки применяют неплавящиеся вольфрамовые электроды из чистого материала или с добавлением сплава.
Существует и другой метод с применением инертного газа:
- аргона;
- гелия;
- водорода;
- азота.
Выбранный газ служит защитной атмосферой для сварочной ванны и электрода.
Ручная дуговая сварка с применением плавящихся электродов
Эту сварку относят к универсальному подходу, когда работы нужно проводить при сложных производственных условиях.
К достоинствам такого метода относятся:
- соединение труднодоступных участков;
- выполнение работ из разных положений;
- совмещение возможно разных видов металлов — стальных, чугунных, цветных с широким выбором электродов;
- дешевое оборудование.
Из недостатков можно подчеркнуть:
- не каждый сварщик сможет выполнить хороший шов, это зависит от его навыков и способностей;
- низкая производительность по сравнению с остальными сварочными процессами;
- вредное производство как для сварщика, так и для окружающих.
Отличие в сварках состоит в электродах, изготовление стержня происходит из легкоплавкого металла.
Дуговая сварка с использованием защитного газа
В этом случае применяют электроды 2 видов – плавящиеся и неплавящиеся. Сваривают разные по составу металлы по технологии одинаковой с традиционной. Дополнительной защитой для сварочных ванн служит подача газа, поставляемого в баллонах. На эту область негативно влияет кислород отчего шов окисляется. Поэтому он нуждается в дополнительной защите, что и выполняет образование в виде газового облака, которое не дает проникать кислороду.
Автоматическая и полуавтоматическая сварка с использованием флюса или газа
Считается, что этот способ в скреплении металлических частей наиболее совершенный. Электроды подают в зону сварки не ручным, а механизированным способом, также происходит и дальнейшее их движение.
Полуавтоматическая сварка
В полуавтоматическом методе только стержни вставляют автоматически, остальную процедуру сварщик выполняет своими руками.
Защитить сварочную ванну при использовании такой сварки необходимо в обязательном порядке. Для этого берут жидкий, пастообразный или кристаллический флюс, который улучшает шов.
Прочие методы соединения металлов
В природе существуют разные по своей уникальности материалы, которые человек старается соединить. При этом у них могут быть отличные химические и тугоплавкие свойства, которые не подходят для традиционной сварки. Применение разных способов важно для промышленности, где создают ответственные детали.
Если необходимо приварить детали на небольших по площади участках поможет лазерный или плазменный метод.
В первом случае нагревают деталь, затем плавят лазерным лучом.
В первом случае нагревают деталь затем плавят лазерным лучом
Плазмой называют ионизированный газ, который подают в зону сварки, он же служит проводником тока.
Такую работу применяют для соединения 9 мм. металлов.
Технологический процесс сварки
На производственных участках, в строительстве к сварке не допускается человек без специальной подготовки. Для проведения работ тоже нужен документальный комплект. Такие строгости не относятся к обустройству забора возле дома или металлических ограждений, понадобятся только умения в обращении с аппаратом. Для серьезных объектов:
- разрабатывают чертеж;
- составляют технологическую карту;
- подготавливают рабочее место и металл;
- выполняют сварку;
- очищают обработанное место;
- контролируют проведенный процесс.
Проведение технологического процесса означает поэтапную разработку всех мероприятий на конкретном объекте. Заполняют документ на бланке, который является технологической картой, где описаны все подробности сварки. После завершения работ оценивают швы, вносят все огрехи, если они имеются.
В домашних условиях для сварщика теория важна, но начинать нужно под наблюдением сварщика, который сможет поправить неправильные действия, подскажет все секреты. Только на практике можно правильно поставить руку, это избавит от приобретения «зайчиков» в глазах и прочих неприятностей
Summary

Article Name
Что такое сварка
Description
Виды сварки — полуавтомат, ручная, холодная сварка, дуговая, сварка металла, сварка аргоном, точечная, контактная, ручная дуговая сварка, сварка своими руками.
Author
Сарычев Александр Викторович — судебный строительно-технический эксперт, кандидат технических наук
Publisher Name
Википедия строительного инструмента
Publisher Logo

Поделиться новостью в соцсетях


Виды сварки металла, обозначения ГОСТ и общая классификация

Если вы занимаетесь сварочными работами и считаете, что хорошо знаете все и ориентируетесь в новых технологиях, то вы, наверное, ошибаетесь. Сварочных способов очень много. В каждом плюсы, минусы, нюансы, которые нужно знать и понимать.
Для чего? – спросите вы. Для грамотного выбора самого оптимального способа «здесь и сейчас» – ответим мы. Читаем, разбираемся, принимаем решения. Поехали.
Физика, химия, немного лирики
Сварка – процесс неразрывного соединения разных конструкций нагреванием, деформированием или использованием того и другого.
Если коротко с точки зрения физики, в сварке используется либо тепло, либо давление, либо тепло с давлением вместе. Если коротко с химической точки зрения, в сварочном деле используется огромное количество разного рода порошковых лент, флюсов, газов и других комплектующих. Это зависит от материалов и условий. Благодаря химии мы имеем огромное число технических вариантов.
Важно! Мы не будет грузить вас полными списками видов сварки или всеми классификациями, какие существуют. Нам не хватит бумаги писать, вам не хватит терпения читать. Разобраться в логике группировки сварочных способов, чтобы потом легко находить информацию по каждому конкретному виду. В сети много сайтов, посвященных сварке: есть где найти все, что нужно.
Принципы классификаций, обзор

Классификация способов дуговой сварки.
Классификация видов сварки проводится по самым разным критериям, они аккуратно укладываются в смысловые рамки. Какие критерии самые важные? Пройдемся по некоторым, для начала лучше увидеть общую картинку.
Сколько видов сварки существует на сегодняшний день? Можно назвать цифру 150 со словом «около». Можно 250. Но цифры называть не советуем. Пока вы читаете эту статью, число видов может измениться – технологии на месте не стоят. А вот какая бывает сварка по материалам, физическим процессам, популярности, способам управления – говорить нужно, это как раз те самые принципы классификации, которые нам нужно понимать.
Пример простой понятной классификации по источнику энергии в сварке:
- электрический ток;
- электрическая дуга;
- трение;
- газовое пламя;
- лазерное излучение;
- электронный луч;
- ультразвук.
Еще один пример списка по типу сварочных швов. Их много, целые гроздья разных видов:
- стыковые, угловые швы – по соединению краев;
- по форме, длине – швы горизонтальные, вертикальные, кольцевые, прямолинейные, прерывистые, сплошные, длинные, короткие, средние;
- по виду используемого материала – швы для стали, цветных металлов, биметаллов, полиэтилена и др.;
- по объему наплавливаемого металла – усиленные, ослабленные, нормальные швы;
- по форме – продольные, поперечные швы;
- по количеству наложения слоев – сплошные, прерывистые, прихваточные, многослойные.
«Швейный» список можно продолжить, но нам важно понять общие принципы, поэтому заканчиваем с лирикой, двигаемся к главным способам.
Приварим намертво, недорого, звоните

Прихватка конструкций перед сваркой.
Основные способы сварки – частое, но неверное определение классификации в данном контексте. Правильнее будет «самые популярные».
Перед вами тройка заслуженных призеров:
- Ручная дуговая – золото.
- Газовая – серебро.
- – бронза.
Каждый призер относится к разным сварочным семействам, по идее их лучше описывать на своих законных местах вместе с близкими «родственниками». Но мы поступим неправильно – представим сварочных чемпионов в начале обзора.
Ручная дуговая сварка РД
Народная любимица №1, самый распространенный вид в быту и в промышленности. Три главных слова в РД – простота, дешевизна, транспортабельность. Физика процесса заключается в плавке специального покрытого электрода, который оставляет за собой след в виде варочного шва. Электроды применяются разные, в зависимости от металла. Дуга – это расстояние между электродом и поверхностью металла, который играет роль второго электрода.
По сути дуга представляет собой сильнейший разряд в газовом пространстве (воздухе). При РД плавятся три предмета: края двух соединяемых поверхностей с электродом. Чем лучше смешиваются продукты тройной плавки (для этого электрод двигают влево и вправо), тем качественнее шов.
Сварка РД имеет серьезные преимущества перед другими видами:
- способу РД легко научиться;
- варить можно в любых положениях в пространстве;
- варить можно самые разные металлы, в продаже есть электроды на любой вкус;
- доступное транспортабельное оборудование
Газовая сварка
Народная чемпионка №2, заслуженная серебряная медаль. Вот когда сварщики возят с собой газовые баллоны: им нужна смесь кислорода с каким-нибудь горючим газом – ацетиленом, пропаном или бутаном. Физика процесса – тоже плавление, но тепло подается не электродом, а газовой горелкой. Металл поверхностей плавится факелом горелки, процесс происходит плавно и довольно медленно. Чем толще слой металла, тем медленнее он плавится.
В чем газовая сварка лучше других способов:
- отлично варятся цветные металлы;
- оборудование проще, чем электрических методов;
- возможность контролировать смесь и пламя;
- не нужен мощный источник энергии, метод автономен.
Без минусов не обойтись, «газовые» недостатки следующие:
- очень медленный нагрев поверхностей;
- низкая концентрация тепла из-за рассеивания;
- высокая стоимость электричества.
По стоимости электричества дуговые способы могут поспорить с газовыми: при РД электричество тоже тратится нещадно. Но в итоге газовый метод из-за своей «тихоходности» обходится значительно дороже.
Важно! Там, где есть пара слов «горючий газ», обязательно присутствует вторая пара «техника безопасности». Правила по безопасности хорошо регламентированы, но выполнение требований несет дополнительные затраты денег и времени. Кстати, газовой сварке больше 100 лет – вот она, нержавеющая классика, аплодисменты.
Полуавтоматическая сварка

Классификация сварочной дуги.
Бронзовый чемпион, замыкает популярную тройку, но по своим перспективам легко обойдет первых призеров. По сути это вид знакомого нам дугового вида, прогрессивная эволюция РД. Отличается большим количеством технологических нюансов, вариантов, инструкций. Нам достаточно знать то, что «автоматическая часть» метода – это подача сварочной проволоки.
Ручная часть – сам процесс сварки с контролем подачи проволоки. Варить можно с газом (углекислым газом для новичков, аргоном для профессионалов), можно без газа, с подачей прямого тока. Вариант без газа любят в гаражах и на дачных участках, в этом случае нужна специальная порошковая или флюсовая проволока. Когда она горит, образуется газ с парами, которые защищают область горения.
Полуавтомат – безальтернативный метод на СТО: кузовные работы проводятся только с его помощью. В полуавтомате используются газ и специальная проволока вместо привычного электрода. Газ из горелки с проволокой подаются в сварочный рукав. В итоге процесс защищен от воздействия внешней среды. Режимы процесса определяет сварщик в зависимости от толщины металла.
У полуавтоматического метода серьезные преимущества перед другими видами:
- отличное качество шва;
- высокая скорость работы;
- удобство в работе;
- варятся как цветные и черные металлы;
- можно варить заржавевшие или оцинкованные металлы;
- широкий выбор материалов, скромные финансовые затраты.
Варим металлы
С народными любимцами разобрались, приступаем к «правильным» классификациям.
Начнем с настоящих тяжеловесов – типов сварки металлов, которые подразделяются на три группы по:
- Физическим признакам.
- Техническим признакам (механизация, непрерывность процесса, защита металла).
- Технологическим признакам (отдельные классификации для каждого способа – например, виды электродов).
По физическим признакам мы имеем три главных класса для всех видов сварки металлов:
Термический класс – сварочный процесс заключается в плавлении тепловой энергией:
- газовой;
- дуговой;
- лазерной;
- лучевой, термитной и т.д.
Важно! Основные виды сварки плавлением – самые распространенные в быту и в промышленности. Это самый густонаселенный класс, подавляющее большинство сварочных методов относится к нему.
Механический класс с использованием механической энергии:
- ;
- холодной;
- трением;
- взрывом и т.д.

Таблица сварки металлов.
Термомеханический класс, способы совместного действия тепловой энергии и давления:
- кузнечные;
- диффузионные;
- контактные и т.д.
В качестве примера варки металлов представляем МАДП – механизированную аргонодуговую сварку плавящимся электродом. Настоящий гибрид для электро-газового соединения металлов. Без него невозможная сварка цветных металлов или сложных сплавов.
Преимущества МАДП:
- соединение любых сплавов;
- устойчивость формы изделия из-за слабого нагрева;
- электроды нужно менять редко;
- широчайшая сфера использования;
Недостатки:
- сложно для новичков;
- невысокая скорость выполнения.
Варим полиэтилен

Области применения сварки пластмасс.
Что можно варить кроме металлов? Керамику. Стекло. Но на втором почетном месте стоят пластмассы или полимеры, прежде всего это полиэтиленовые трубы. С полиэтиленом можно работать терморезисторным, электромуфтовым методами, можно электросопротивлением: эти термины перечисляются в технической литературе. Не пугайтесь, все варианты можно называть коротко – сварка НЗ. НЗ – закладные нагреватели.
Суть процесса – расплавление полиэтилена в местах соединения с помощью металлических спиралей электрического нагревателя, который заложен в деталь. Способ чрезвычайно популярен, у него большие перспективы в промышленности: применяется в различных трубопроводах, замене старых металлических труб новыми полиэтиленовыми, установке и ремонте, развитии новых полимерных технологий.
В работе с пластмассами применяется еще один способ НИ или сварка нагретым инструментом. Самый простой вариант подвода тепла для нагрева полимерных поверхностей. Для работ с НИ существует множество вариантов сварочных инструментов – от простого электропаяльника для маленьких деталей до специальных сварочных аппаратов различной величины. Уважающие себя сантехники держат в своих рабочих чемоданах такого рода аппараты в обязательном порядке.
Кстати, способы сварки НЗ и НИ входят в том числе в список владения обязательными методами профессионального сварщика с подтвержденной квалификацией, например, аттестацией от НАКС – Национального Агентства Контроля Сварки.
Теперь классификация по типу механизации процесса:
- Автоматизированная
- Механизированная
- Ручная, начнем с нее.
Ручная сварка

Примеры сварных соединений.
Несмотря на быстрый рост новых автоматизированных способов, ручные методы незаменимы во многих случаях, этот вид сварки давно занимает законное важное место в современных технологиях.
Преимущества ручных способов:
- можно варить в труднодоступных местах;
- в разных положениях в пространстве;
- можно быстро переходить от одного материала, которые плавим, к другому;
- выбор электродов на любой вкус для любых видов стали;
- оборудование легко перевозить, просто обслуживать.
Кроме знакомого нам электрического дугового способа к этой группе относится ручной вариант аргонодуговой сварки с теми же принципами действия, как и механизированный вариант, о котором писалось выше.
К ручным видам относится точечная сварка своими руками, контактная метод, который возможен в домашних условиях в отличие от других контактных способов, применяемых только в промышленности.
Классическая газовая сварка также относится к ручным способам.
Автоматические способы
Классификация способов сварки с помощью автоматизации:
- Электродуговая технология.
- Газоэлектрическая, электрическая дуга защищена газом, чаще всего – инертным типа аргона или гелия.
- Электрошлаковая технология.

Сварка вольфрамом – схемы применения.
Электродуговой способ: близкая родственница ручной дуговой – автоматическая сварка под флюсом или АФ – разновидность дугового способа с великолепными показателями производительности. Здесь тоже используется плавящийся электрод, вся работа проводится под специальным защитным слоем флюса. В ручном дуговом способе серьезный риск горения в воздухе самой дуги, поэтому сила подаваемого тока ограничена.
При АФ защищена слоем флюса, риска горения нет. Сила сварочного тока никак не ограничена. Это делает возможным глубокое проплавление металла, в результате чего получается шов отличного качества. Слой флюса предотвращает разбрызгивание металла, его потери в процессе. Полная механизация метода позволяет допускать к АФ менее квалифицированных сварщиков. В итоге производительность способа АФ выше ручного дугового в 5 – 10 раз. Будем честными и представим недостатки АФ, их немного:
- флюсы стоят недешево;
- имеется вредное воздействие на оператора;
- работать можно только в ограниченном пространстве.
Электрошлаковая технология, «тяжелая артиллерия» на современном промышленном фронте. Это принципиально новый бездуговой способ плавления. Источником тепловой энергии выступает не дуга, а переменный ток, который проходит сквозь расплавленный шлак. Поверхности металла покрываются шлаком, который нагревается. Таким образом можно варить металлы практически любой толщины.
Преимущества бездуговой технологии:
- качественные плотные швы;
- швы сложной формы;
- отсутствие деформаций, особенно угловых;
- не нужно обрабатывать кромки;
- простота выполнения
- автоматизация труда, минимальное участие человека
Метод применяется в основном для крупногабаритных конструкций.
Дуговые способы
Выше мы разбирались с основными понятиями и физикой дуги (знаменитая РДС – ручная дуговая, абсолютный чемпион по популярности).
Но классификация способов сварки – дело строгое, поэтому представляем виды дуговой сварки отдельно взятым семейством:

Строение и свойства электрической дуги.
Ручные дуговые:
- РАД – ручная аргонодуговая неплавящимся электродом;
- РАДН – ручная аргонодуговая наплавка.
Автоматические способы дуговых:
- ААД, ААДН, АЛСН, АППГН и т.д. – обширная семья способов с применением либо электродов (плавящихся и неплавящихся), либо проволок, либо порошковых проволок. Варить можно с газом и без.
Дуговые под флюсом:
- знакомая нам АФ, автоматическая дуговая под флюсом;
- различные приварки, наплавки с ленточными или проволочными электродами;
- механизированная дуговая.
Дуговые с покрытыми электродами:
- вот где правильное место для народной чемпионки РДС;
- ручная дуговая наплавка;
Механизированные дуговые:
- МАДП, МПГН, МСОД и т.д. – многочисленная «механическая» семья.
Механический класс
Все виды, о которых говорилось выше, относятся к первому термическому классу. Главным героем в нем выступает тепловая энергия с плавлением. Следующий класс – механический. Главные «механические» слова в данном контексте – давление и пластическая деформация.
В нем также есть стройная классификация сварки:
- Холодная сварка (ковка)
- Сварка трением
- Ультразвуковая
Иногда механические методы объединяют под названием «сварка давлением», здесь есть логика, но речь идет об одном и том же.
Одна из перспективных механических технологий – сварка трением. Тепло в ней тоже присутствует, но образуется оно от силы трения. Поверхности, которые нужно сварить, вращаются, с силой сжимаются. Технология сварки трением особенно эффективна при работе с деталями круглого сечения – сверл, резцов, разверток.

Таблица видов сварки.
Виды сварки трением:
- Сварка трением с перемешиванием.
- Радиальная сварка трением.
- Штифтовая сварка трением.
- Линейная.
- Инерционная.
Рассмотрим эти типы сварки подробнее:
- Сварка трением с перемешиванием – довольно новый способ, в нем необходимо специальное оборудование для сварки трением – инструмент для вращения с двумя элементами – основанием (буртом) и наконечником (пином). Шов формируется с помощью двух процессов выдавливания и перемешивания.
- Радиальная сварка трением применяется в работах с трубами: в ней вращается кольцо между стыками, которое создает трение.
- Штифтовая сварка трением: просверливается отверстие, вводится штифт из того же металла, что детали. Штифт вращается, выделяет тепло, формирует соединение в виде металлических нитей. Великолепная технология сварки трением, когда «нужно заделать дырку».
- Линейный способ. Здесь вращения нет. Детали просто трут друг об друга до выделения тепла, повышения пластичности, затем увеличивают давление, вплоть до необратимого соединения. При этом способе образуется идеальная ровная поверхность, ни в каких других методах такой нет.
- Инерционная сварка. Движение поверхностей происходит за счет массивного вращающегося маховика, который разгоняется специальным двигателем.
Термомеханический класс
Третий класс с точки зрения физики: здесь используются оба вида воздействия на поверхности: тепло и давление. Представляем виды и способы сварки термомеханическим способом:
- Диффузионная. Поверхности сдавливают, затем нагревают в высоком вакууме, добиваясь взаимной диффузии атомов. Эффективен, когда металлы для сварки плохо совмещаются друг с другом или материалы разные по своей природе, например, металл с керамикой. Способ недешевый, применяется в основном в аэрокосмической сфере, других высокотехнологических отраслях.

Разновидности сварки давлением.
Все следующие пункты – виды контактной сварки
- электрическая. Здесь все просто: перед тем, как надавить, нужно хорошенько разогреть. Поверхности разогревают током в местах соединения, затем сдавливают или осаживают. Отличный высокопроизводительный способ, хорошо поддается автоматизации. Широко применяется в строительстве, машиностроении.
- Шовная контактная – разновидность контактной сварки: шов формируется электродами внахлестку.
- Точечная контактная. Между двумя электродами размещают поверхности. Ток включается после плотного сжимания, в результате чего образуется сварная точка с диаметром, равным диаметру поверхности электрода. Чрезвычайно интересна разновидность – рельефная сварка. Контакт электродов проводят по определенным заранее выступам – рельефам, которые в итоге деформируются, поверхность выравнивается.
- Точечная конденсаторная – «сварка с запасенной энергией в конденсаторах». Отличается малым потреблением мощности, применяется в работе с мелкими деталями и при использовании оптических приборов – часовых механизмов, авиационных приборов и т.д.
И на десерт
Особые виды сварки – понятие размытое, учитывая огромное число технических вариантов, групп, видов, подвидов. Каждый видит этот список по-своему.
В нашем списке классификация сварки определена по технологичности. Это уникальные способы, которые по праву относятся к технологиям высшего пилотажа.
Электронно-лучевая и плазменная сварка:
- Электронно-лучевая сварка. Здесь применяется электронная пушка и пучок ускоренных электронов из этой пушки. Работы проводятся в больших вакуумных камерах. Концентрация энергии и тепловая мощность – фантастические. получаются узкими, глубокими. Применяется для производства высокоточных деталей из специальных сплавов – удовольствие недешевое.
- Плазменная сварка. Один из самых высокотехнологичных видов – название говорит само за себя. Плазма – струя ионизированного газа (аргона, гелия, водорода) высочайшей температуры. Такая струя варит все – от самых тугоплавких металлов до неметаллических поверхностей. Великолепная производительность с фантастическим качеством швов и поверхностей.
Обобщаем и закольцовываем
Сваркой называется процесс формирования неразъединимых соединений поверхностей разных конструкций.
Сначала все виды и способы сварки делятся на три мощных класса с точки зрения физики:
- Термический (греем и плавим)
- Механический (трем, давим, толкаем и пр.)
- Термомеханический (греем и давим одновременно)

Аргонодуговая сварка алюминия.
Внутри этих классов методы можно группировать как угодно:
- с дугой или без дуги;
- с газом или без него, можно с дугой и газом вместе;
- ручные или автоматические. Или полуавтоматические;
- какие виды сварочных электродов используешь;
- все виды контактной сварки;
- виды сварок металла или наоборот, полимеров;
- и так далее, список вариантов длиннейший.
Главное – узнавать, пробовать, учиться и двигаться вперед к профессиональным вершинам. Не забывать читать обзоры, нужно быть в курсе. Нам на месте стоять нельзя. Желаем чистого металла, хороших заказов и рабочего настроения.
Свариваемость — Википедия
Материал из Википедии — свободной энциклопедии
Свариваемость — свойство металлов или сочетания металлов образовывать при установленной технологии сварки неразъемное соединение, отвечающее требованиям, обусловленным конструкцией и эксплуатацией изделия. В сварочной практике существуют такие понятия, как физическая и технологическая свариваемость.
Свариваемость оценивается степенью соответствия свойств сварного соединения тем же свойствам основного материала и его склонностью к образованию дефектов. Материалы делятся на хорошо, удовлетворительно, плохо и ограниченно свариваемые.
Физическая свариваемость — подразумевает возможность получения монолитных сварных соединений с химической связью. Такой свариваемостью обладают практически все технические сплавы и чистые металлы, а также ряд сочетаний металлов с неметаллами.
Технологическая свариваемость — это характеристика металла, определяющая его реакцию на воздействие сварки и способность образовывать сварное соединение с заданными эксплуатационными свойствами. В этом случае свариваемость рассматривается как степень соответствия свойств сварных соединений одноименным свойствам основного металла или их нормативным значениям.
Определение свариваемости по ГОСТ 29273-92: металлический материал считается поддающимся сварке до установленной степени при данных процессах и для данной цели, когда сваркой достигается металлическая целостность при соответствующем технологическом процессе, чтобы свариваемые детали отвечали техническим требованиям, как в отношении их собственных качеств, так и в отношении их влияния на конструкцию, которую они образуют.
Свариваемость металлов зависит от их химических и физических свойств, наличия примесей и др. От свариваемости металла зависит выбор технологии его сварки.
Свариваемость сталей определяется по склонности к образованию трещин и механическим свойствам шва, по ней стали разделяются на четыре группы:
- — хорошая свариваемость; сварка выполняется без подогрева до, в процессе сварки и после.
- — удовлетворительная свариваемость; сварка для предотвращения трещин предварительно нагревается, после сварки нужна термообработка.
- — ограниченная свариваемость; сталь склонна к образованию трещин, её предварительно подвергают термообработке, термически обрабатывается после сварки.
- — плохая свариваемость, склонность к образованию трещин. Сварка производится с предварительной термообработкой, подогрев проводится и после сварки.
Нормативная литература[править | править код]
Техническая литература[править | править код]
- Николаев Г. А. Сварка в машиностроении: Справочник в 4-х т. М.: Машиностроение, 1978.
- Сварка, резка и пайка металлов / К. К. Хренов. М.: Машиностроение, 1970, 408 с.
- Справочник конструктора–машиностроителя. Т. 3. / В. И. Анурьев. М.: Машиностроение. 2000. 859 с.
- Марочник сталей и сплавов / В. Г. Сорокин, А. В. Волосникова. – М.: Машиностроение, 1989. – 640 с.
- Инструментальные стали. Справочник / Л. А. Позняк. М.: Металлургия, 1977, 168 с.
Сварка. Процесс сварки и его виды
Сваркой называют технологический процесс получения неразъемных соединений посредством установления межатомных связей между свариваемыми заготовками при их нагревании и (или) пластическом деформировании. Это позволяет в результате сварки получить непрерывность структуры соединяемых металлических изделий. Сварочные процессы применяют для изготовления разнообразных конструкций, исправления брака литья, восстановления поломанных и изношенных деталей (ГОСТ Р ИСО 857-1–2009).
Существенным преимуществом сварки является плотность швов, обеспечивающая герметичность резервуаров, котлов, вагонов-цистерн, трубопроводов, корпусов судов. Сварка позволяет соединять элементы, имеющие различную толщину, и упрощать технологию изготовления сложных узлов и конструкций. Возможность механизации и автоматизации производственных процессов, высокое качество сварных соединений и рациональное использование металла сделали сварку прогрессивным высокопроизводительным и экономически выгодным технологическим процессом.
Сущность процесса сварки заключается в возникновении атомномолекулярных связей между контактирующими поверхностями. Для этого необходимо поверхности сблизить на расстояние, соизмеримое с атомным радиусом. В реальных условиях сближению поверхностей препятствуют микронеровности, окисные и органические пленки, адсорбированные газы. Для получения качественного соединения необходимо устранить причины, препятствующие сближению контактирующих поверхностей, и сообщить атомам твердого тела некоторую энергию для повышения энергии поверхностных атомов, которая называется энергией активации. Эта энергия может сообщаться в виде теплоты (термическая активация) и в виде упругопластической деформации (механическая активация).
В зависимости от типа активации образование связей между атомами соединяемых поверхностей происходит в твердой или жидкой фазах. В соответствии с этим все способы сварки можно разделить на две основные группы: сварка пластическим деформированием (давлением) и сварка плавлением.
Сварка давлением осуществляется приложением внешней силы и сопровождается пластическим деформированием сопрягаемых поверхностей, обычно без присадочного металла. При этой сварке сближение атомов и активация соединяемых поверхностей достигаются в результате совместной упругопластической деформации. В контактирующих слоях заготовок выравниваются микронеровности, разрушается адсорбированный слой и увеличивается число активных центров взаимодействия, атомы активизированных поверхностей вступают во взаимодействие, и между ними образуется металлическая связь.
Методы сварки давлением разделяются на две подгруппы – термомеханические и механические.
Сварку давлением можно проводить:
- без предварительного нагрева места соединения (холодная, взрывом, ультразвуковая, трением), когда применяется только механическая энергия;
- с предварительным нагревом (контактная, диффузионная, газопрессовая), когда наряду с механической, применяется и тепловая энергия от внешних или внутренних источников теплоты.
Предварительный нагрев до пластического состояния или до оплавления применяют для металлов и сплавов, обладающих повышенным сопротивлением пластическим деформациям в холодном состоянии, что затрудняет их совместное деформирование, так как требует больших давлений на единицу поверхности.
Нагрев металла при сварке давлением осуществляется либо за счет дополнительных энергетических затрат (пропускание тока, сжигание газов, индуктирование в деталях токов высокой частоты), либо за счет частичного преобразования сообщаемой энергии в тепловую.
Сварка плавлением осуществляется оплавлением свариваемых поверхностей без приложения внешней силы. Расплавляется либо только основной металл (заготовки) по кромкам, либо основной металл с дополнительным – электродным или присадочным.
Расплавленный металл заготовок с дополнительным образуют общую сварочную ванну. При этом достигается разрушение окисных пленок, покрывающих поверхность соединяемых элементов, и сближение атомов до расстояния, при котором возникают металлические связи. После кристаллизации металла образуется сварной шов, имеющий литую структуру.
Для расплавления основного и электродного (или присадочного) металлов применяют источники теплоты с температурой не ниже 3 000 °С.
В зависимости от характера источника теплоты различают электрическую и химическую сварку плавлением.
При электрической сварке плавлением источником теплоты служит электрический ток. Существуют следующие виды электрической сварки плавлением:
- дуговая, при которой нагрев осуществляется электрической дугой;
- плазменная, при которой нагрев осуществляется сжатой дугой;
- электрошлаковая, при которой нагрев и плавление металла осуществляются за счет термической энергии, выделяемой шлаком при прохождении через него электрического тока;
- лучевые способы сварки, к которым относятся лазерная и электронно-лучевая сварки. При лазерной сварке для нагрева используется монохроматический когерентный луч, а при электронно-лучевой сварке – сфокусированный электронный луч;
- газовая сварка, где в качестве источника теплоты используют экзотермическую реакцию горения горючего газа или смеси горючих газов и кислорода.
Свариваемость – свойство металла или сочетания металлов образовывать при установленной технологии сварки соединение, отвечающее требованиям, обусловленным конструкцией и эксплуатацией изделия. Понятие свариваемости часто применяют при сравнительной оценке существующих и разработке новых материалов.
Свариваемость материалов оценивают степенью соответствия заданных свойств сварного соединения одноименным свойствам основного металла и их склонностью к образованию таких сварочных дефектов, как трещины, поры, шлаковые включения и др. По этим признакам материалы разделяют на хорошо, удовлетворительно и плохо сваривающиеся. Многие разнородные материалы, особенно металлы с неметаллами, не вступают во взаимодействие друг с другом. Такие материалы относятся к числу практически несваривающихся.
Свариваемость материалов в основном определяется типом и свойствами структуры, возникающей в сварном соединении при сварке. При сварке однородных металлов и сплавов в месте соединения, как правило, образуется структура, идентичная или близкая структуре соединяемых заготовок. Этому случаю соответствует хорошая свариваемость материалов.
При сварке разнородных материалов, в зависимости от различия их физико-химических свойств, в месте соединения образуется твердый раствор с решеткой одного из материалов либо химическое или интерметаллидное соединение с решеткой, отличающейся от решеток исходных материалов. Механические и физические свойства твердых растворов, особенно химических или интерметаллидных соединений, могут значительно отличаться от свойств соединяемых материалов. Такие материалы относятся к удовлетворительно сваривающимся.
Если образуются хрупкие и твердые структурные составляющие в сварном соединении, то в условиях действия сварочных напряжений возможно возникновение трещин в шве или околошовной зоне. В последнем случае материалы относятся к категории плохо сваривающихся.
Свариваемость, с одной стороны, зависит от материала, технологии сварки, конструктивного оформления соединения, а с другой – от эксплуатационных свойств сварной конструкции, которые определяются предъявляемыми к ним техническими требованиями. Это может быть одно свойство или комплекс свойств, в зависимости от назначения конструкции. Если эксплуатационные требования удовлетворяются, то свариваемость материалов считается достаточной. Если не обеспечивается хотя бы одно из этих свойств, то свариваемость материала считается недостаточной.
Для исследования свариваемости, как правило, применяют сварные образцы специальной конструкции или образцы с имитацией сварочных циклов. В результате испытания сварных образцов определяются условия появления дефектов, механические и специальные свойства соединений. Наряду с экспериментальными используют расчетные методы определения показателей свариваемости, учитывающие химический состав, тип соединения, вид, режим сварки и другие факторы.
В каждом конкретном случае основные показатели выбирают с учетом того, какие свойства и характеристики связаны с наиболее частыми отказами сварных соединений при эксплуатации.
При сварке однородных металлов в месте соединения, как правило, образуется структура, близкая к структуре соединяемых заготовок. В этом случае свариваемость оценивается как хорошая или удовлетворительная. В процессе сварки разнородных материалов в зависимости от степени их взаимной растворимости в соединении могут образовываться твердые растворы, химические и интерметаллические соединения. Механические и физические свойства соединений могут существенно отличаться от свойств свариваемых материалов. При этом высока вероятность образования несплошностей в виде трещин и несплавлений. Свариваемость в этом случае оценивается как ограниченная или плохая.
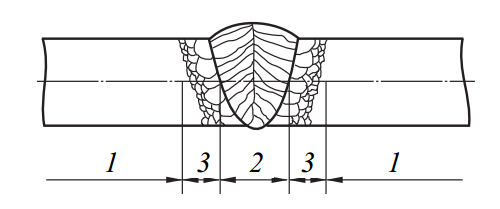
Рис. 1. Неоднородность механических свойств различных зон сварного соединения легированной стали: 1 – основной металл; 2 – шов с литой структурой; 3 – зона термического влияния
Прочность и твердость шва при сварке сплавов, как правило, ниже, чем у основного материала. Это объясняется тем, что для предотвращения образования трещин при сварке плавлением применяют менее легированный присадочный материал, чем металл заготовок. Пониженная пластичность шва также может быть обусловлена крупнокристаллической литой макроструктурой (рис. 1) и повышенным содержанием газов.
Просмотров: 489
Развитие сварки и ее значение
Сварка металлов является одним из выдающихся русских изобретений и впервые была освоена в России.
В 1802 г. русский академик Василий Владимирович Петров обратил внимание на то, что при пропускании электрического тока через два стержня из угля или металла между их концами возникает ослепительно горящая дуга (электрический разряд), имеющая очень высокую температуру. Он изучил и описал это явление, а также указал на возможность использования тепла электрической Дуги для расплавления металлов и тем заложил основы дуговой сварки металлов.
Результаты опытов В. В. Петрова тогда не были известны за границей, а в России не использовались. Только спустя 80 лет русские инженеры — Николай Николаевич Бенардос и Николай Гаврилович Славянов применили открытие В. В. Петрова на практике и разработали различные промышленные способы сварки металлов электрической «дугой Петрова».
Н.Н.Бенардос | Н.Г.Славянов |
Н.Н. Бенардос в 1882 г. изобрел способ дуговой сварки с применением угольного электрода. В последующие годы им были разработаны способы сварки дугой, горящей между двумя или несколькими электродами; сварки в атмосфере защитного газа; контактной точечной электросварки с помощью клещей; создан ряд конструкций сварочных автоматов. Н.Н. Бенардосом запатентовано в России и за границей большое количество различных изобретений в области сварочного оборудования и процессов сварки.
Автором метода дуговой сварки плавящимся металлическим электродом, наиболее распространенного в настоящее время, является Н.Г. Славянов, разработавший его в 1888 г.
Н.Г. Славянов не только изобрел дуговую сварку металлическим электродом, описал ее в своих статьях, книгах и запатентовал в различных странах мира, но и сам широко внедрял ее в практику. С помощью обученного им коллектива рабочих-сварщиков Н.Г. Славянов дуговой сваркой исправлял брак литья и восстанавливал детали паровых машин и различного крупного оборудования. Н.Г. Славянов создал первый сварочный генератор и автоматический регулятор длины сварочной дуги, разработал флюсы для повышения качества наплавленного металла при сварке. Созданные Н.Н. Бенардосом и Н.Г. Славяновым способы сварки явились основой современных методов электрической сварки металлов.
В настоящее время создано большое количество типов сварочного оборудования, марок электродов, разработаны новые прогрессивные сварочные процессы, в том числе высокомеханизированные и автоматизированные, освоена техника сварки многих металлов и сплавов, глубоко и всесторонне разработана теория сварочных процессов.
Сейчас сварка является основным способом соединения деталей при изготовлении металлоконструкций. Широко применяется сварка в комплексе с литьем, штамповкой и специальным прокатом отдельных элементов заготовок изделий, почти полностью вытеснив сложные и дорогие цельнолитые и цельноштампованные заготовки.
Сварка обеспечивает ряд преимуществ, основные из которых приводятся ниже:
1. Экономия металла вследствие наиболее полного использования рабочих сечений элементов сварных конструкций, придания им наиболее целесообразной формы в соответствии с действующими нагрузками и уменьшения веса соединительных элементов. В сварных конструкциях вес металла сварных швов обычно составляет от 1 до 2%, в то время как в клепаных вес заклепок и косынокне менее 4% от веса изделия. Сварка дает до 25% экономии металла по сравнению с клепкой, а по сравнению с литьем в отдельных случаях — до 50%
Использование сварки на строительстве зданий позволяет уменьшить вес стальных конструкций на 15%, облегчает изготовление и увеличивает жесткость всей конструкции.
Сокращение сроков работ и уменьшение стоимости изготовления конструкций за счет снижения расхода металла и уменьшения трудоемкости работ.
2. Возможность изготовления сварных изделий сложной формы из штампованных элементов взамен ковки или литья. Такие конструкции называются штампосварными и широко применяются в автомобилестроении, самолетостроении, вагоностроении. С помощью сварки можно изготовлять детали из металла, прошедшего различную предварительную обработку, например сваривать прокатанные профили со штампованными, литыми или коваными заготовками. Можно сваривать и разнородные металлы: нержавеющие стали с углеродистыми, медь со сталью и др.
3. Возможность широкого использования сварки и резки при ремонте, где эти способы обработки металла позволяют быстро и с наименьшими затратами восстанавливать изношенное или вышедшее из строя оборудование и разрушенные сооружения.
4. Удешевление технологического оборудования, так как отпадает необходимость в использовании дорогих сверлильных, дыропробивных станков и клепальных машин.
5. Герметичность получаемых сварных соединений.
6. Уменьшение производственного шума и улучшение условий труда рабочих.
Сваркой можно получить сварное соединение прочностью выше основного металла. Поэтому сварку широко применяют при изготовлении весьма ответственных конструкций, работающих при высоких давлениях и температурах, а также при динамических (ударных) нагрузках — паровых котлов высокого давления, мостов, самолетов, гидросооружений, арматуры железобетонных конструкций и др.