Холодная сварка: характеристики, состав, способы применения
Главная » Обработка металла » Сварка » Преимущества и недостатки холодной сварки
На чтение 6 мин
Содержание
- Состав и свойства
- Виды
- Область применения
- Критерии выбора
- Преимущества холодного сваривания
- Производители
- Как правильно использовать
- Советы и рекомендации
На производстве и в быту, часто возникают ситуации, когда необходимо соединить металлические детали или части конструкции, но оборудования нет и разогреть металл нельзя. Для соединения в этом случае подойдёт холодная сварка. Это специальный двухкомпонентный или готовый состав для склеивания деталей. Сварку можно применять для черных и цветных металлов.
Холодная сварка (Фото: Instagram / belozerautoservise)Состав и свойства
Чтобы понимать с чем придётся работать, нужно знать характеристики и состав холодной сварки. Состав:
- Эпоксидная смола — главный элемент клеящей массы.
Только благодаря ей, можно соединить различные материалы.
- Металлическая крошка (пудра). Благодаря этому наполнителю, после застывания масса становится прочной. Дополнительно к этому, повышаются защитные свойства в плане перепадов температуры.
- Дополнительные элементы. Существуют различные виды холодной сварки, которые обладают разными характеристиками. На эти показатели влияют, добавленные в состав, химические элементы и вещества.
Средство выпускается в готовом виде или вместе с отвердителем. Готовая холодная сварка представляет собой пластилинообразный брусок или цилиндр, который перед нанесением требуется размять в руках. Эпоксидная смола с отвердителем продаётся в жидком виде. Что касается отвердевшего шва, прочность склейки напрямую зависит от входящих в состав эпоксидной смолы компонентов.
Касательно прочности шва, можно сказать, что этот показатель будет зависеть не только от компонентов, входящих в состав эпоксидной смолы, но и от проведенных работ по нанесению клеящего состава.
Отвердевший шов прочнее металла, но слабее, чем при обычной сварке.
При проведении быстрого ремонта, важно знать, сколько высыхает клей и, когда можно начинать дальнейшие работы. Большинству видов холодной сварки для отвердения достаточно 2–3 часов. Однако, полное застывание происходит за 24 часа.
Касательно температуры, которую выдерживает готовый шов, все зависит от дополнительных компонентов. Классические эпоксидные смолы после затвердения сохраняют связывающие свойства при температуре до 260 градусов. Специализированные составы способны выдерживать нагревание до 1316 градусов.
Виды
Выше уже были перечислены разновидности холодной сварки в зависимости от консистенции. Любой производитель выпускает несколько разновидностей эпоксидной смолы, в зависимости от её применения:
- Клеящие составы для работы в экстремальных ситуациях. Они способны склеить металл даже под водой.
- Эпоксидные смолы для работы с автомобильными деталями.
- Универсальная холодная сварка.
С помощью таких составов, можно соединять пластик, резину, металл, дерево, керамику.
Если говорить про склейку металлических деталей или листов, необходимо использовать эпоксидную смолу для работы с металлом. Она содержит в своём составе больше металлического наполнителя и делает шов прочнее.
При использовании составов по металлу для склейки пластиковых или деревянных изделий, шов получится хрупким.
Область применения
Эпоксидная смола может применяться в различных сферах и областях:
- Применение холодной сварки для металла. Благодаря своим связывающим свойствам, её часто применяют на производстве, при починке оборудования. Важно соединять те детали, которые не будут подвергаться усиленному механическому воздействию.
- При сантехнических поломках. С её помощью, можно сваривать металлические и пластиковые трубы, восстанавливать резьбу, заделывать сколы и трещины.
- Применяется при проведении ремонта в квартире или коттедже.
С помощью холодной сварки, можно скреплять между собой листы линолеума, резины. Также с её помощью можно закреплять элементы декоративной отделки на стенах.
Часто эпоксидную смолу используют в автосервисах, ремонтных ателье и собственных мастерских.
Применение холодной сварки (Фото: Instagram / kod_remonta)Критерии выбора
Не существует единого ответа на тему, какая холодная сварка самая хорошая для металла, потому что идеальных составов не бывает. При выборе, необходимо обращать внимание на следующие факторы:
- В первую очередь необходимо изучить состав. Чтобы шов между металлическими деталями был наиболее прочным, структура эпоксидной смолы должна быть более однородной.
- При использовании склейки на высокотемпературных приборах, требуется посмотреть, какие температуры выдерживает средство после затвердевания. Шов потеряет свою прочность при разогревании выше допустимой температуры.
- Время застывания. При необходимости провести быстрые ремонтные работы, важно покупать быстрозастывающий клей.
Преимущества холодного сваривания
У любого способа соединения деталей есть как сильные, так и слабые стороны. Преимущества холодной сварки:
- Надежность соединений.
- Нет затрат электроэнергии или газа.
- Чтобы использовать холодную сварку, не нужно дополнительно учиться.
- Процесс нанесения происходит с помощью подручных средств.
- При правильном применении и качественном составе, готовый шов получается прочнее, чем склеиваемый материал.
- Быстрое застывание. Начинать использовать склеенную деталь, можно уже спустя 2–3 часа.
- Отсутствие отходов после применения.
В отличие от горячей сварки, холодный состав не подвергает предмет нагреванию и последующему разрушению.
Производители
Ниже будут обозначены известнейшие производители холодной сварки:
- Poxipol;
- Penosil;
- Zollex;
- Алмаз;
- Alteco;
- Nowax.
Существуют и другие компании, изготавливающие смеси для склейки металла, однако, здесь были представлены самые популярные.
Как правильно использовать
Чтобы не допустить ошибок, важно ознакомиться с информацией о том, как пользоваться холодной сваркой. Инструкция по применению холодной сварки для металла:
- В первую очередь, необходимо подготовить обрабатываемые поверхности. Для этого, место будущего шва зачищается с помощью наждачной бумаги и обезжиривается ацетоном.
- Смешать отвердитель со смолой, если состав двухкомпонентный. Готовые бруски размять руками.
- В течение 3 минут, необходимо нанести клеящий состав на обработанные поверхности.
- По возможности, нужно зажать место склейки в струбцинах или положить сверху груз.
Это классический способ применения холодной сварки. Шов полностью застывает в течение суток. Его долговечность будет зависеть от условий эксплуатации.
Нанесение холодной сварки на поверхностьСоветы и рекомендации
После того как стало известно для склеивания каких материалов используется сварка и сколько сохнет холодная сварка металлу, необходимо принять во внимание некоторые рекомендации:
- Перед использованием эпоксидной смолы, требуется смочить руки, чтобы клеящий состав не прилипал к ним.
- Можно применять для стали, чугуна и алюминия.
- Важно использовать при работе защитные очки.
- Не использовать смолу для склейки посуды и емкостей, контактирующих с пищей.
Если смола попала внутрь организма, необходимо выпить большое количество молока и обратиться к врачу.
Холодная сварка считается лучшим вариантом для скрепления металлических предметов и починки различных поломок. Швы получаются слабее, чем от горячей сварки, однако, гораздо крепче, чем при использовании других клеящих смесей.
window.yaContextCb.push(()=>{ Ya.Context.AdvManager.render({ renderTo: ‘yandex_rtb_R-A-1226522-57’, blockId: ‘R-A-1226522-57’ })})»; cachedBlocksArray[266488] = «window.yaContextCb.push(()=>{ Ya.Context.AdvManager.render({ renderTo: ‘yandex_rtb_R-A-1226522-52’, blockId: ‘R-A-1226522-52’ })})»; cachedBlocksArray[266497] = «window.

Поделиться
Холодная сварка для линолеума: виды, типы, технология выполнения
Одним из самых популярных напольных материалов сегодня, несомненно, является линолеум. Помимо многих его отличных качеств застройщиков привлекает также возможность сэкономить за счет укладки покрытия своими руками. Извечный вопрос, ответы на который ищут владельцы помещений с большой площадью или нестандартной геометрией, – как постелить линолеум, чтобы стыки полотен не и расклеивались, не деформировались.
Не всегда возможно уложить линолеум во всему помещению одним куском, и тогда уложенные полосы приходится соединять. С одной стороны, места стыков после этого не будут деформироваться, а с другой – под покрытие не будет попадать мусор или влага.
Как правило, для склейки полос используют два варианта: горячая и холодная сварка для линолеума.
- В первом случае на место стыка воздействуют теплом от газовой горелки. Для самостоятельного использования этот способ затруднителен.
- Что же касается второго, то для склейки не нужно никакого дополнительного оборудования, и он достаточно легкий. Более того, холодная сварка позволяет склеивать сложные участки, к примеру, с поворотом.
К достоинствам этого способа относят также:
- универсальность – он применим к любому типу материала: бытовой или коммерческий, размеру и форме стыка;
- сварку наносят на уже уложенный линолеум;
- эксплуатировать пол можно сразу после обработки швов.
Виды клея
Холодной сваркой называют особый клей, в составе которого присутствует тетрагидрофуран – порядка 80%, ПВХ и пластификаторы –до 20%. Устройство стыка технологично, выполняется быстро практически чисто химическим путем. При четком соблюдении технологии монтажа стык получается визуально практически невидимым.
Важно!
Летучие компоненты клея представляют опасность для здоровья человека, поэтому в процессе работ прибегают к защитным мерам: открывают окно, используют маску на лицо, резиновые перчатки. После испарения хлора, примерно через полчаса, клей больше не несет опасности.
Клей из тюбика подается через наконечник-иглу. Это дает возможность полностью заполнить шов составом. К тому же присутствие в составе хлора, который растворяет кромки, обеспечивает его ровность и гладкость.
Различают следующие типы клеящих составов:
- тип А: предназначен для твердого или нового покрытия из поливинилхлорида. Благодаря жидкой консистенции, дает возможность справиться даже с тонкими щелями. Следует отметить, что именно из-за этой особенности при работе следует проявлять особую осторожность. Принцип действия состава в следующем: он расплавляет линолеум по краям и сваривает их, обеспечивая точность подгонки кромок. Щель после этого практически невозможно заметить.
- тип С. Преимущественно им заделывают швы старого полотна, начавшие расходиться. По своей консистенции этот состав более густой, нежели клей типа «А». Заполнив возникшую между полосами щель, она намертво скрепляет разошедшиеся кромки, в том числе и отошедшие на расстояние до 0,5 см. При такой ширине шва нельзя исключать образования выступа, который впоследствии срезают, скажем, при помощи ножа.
- тип Т. Это прозрачный вид для линолеума на войлочной основе. При ее наложении образуется эластичное соединение. Клей укомплектован Т-образной насадкой, которую навинчивают на тюбик. Именно она и определяет название этого состава.
Популярные марки
Современный рынок отличается большим разнообразием предложений этого типа, представляем вашему вниманию полезную информацию о составах, завоевавших самые лестные отзывы как домовладельцев, самостоятельно занимающихся обустройством своего жилища, так и профессионалов.
название | расход | Стоимость |
Homakoll s401 | 100 мл/24-30 пог. м | 145–188 руб |
Синтекс | 100 мл/45–50 пог. м | 140–260 руб |
Форбо | 42г / 25 пог. м | 336–449 руб |
Технология склеивания
Каждая упаковка клея снабжена подробной инструкцией, однако, есть общие положения, которые касаются сваривания полос покрытия.
Подготовка линолеума
Чтобы образованный при сваривании шов получился незаметным, края линолеума должны плотно прилегать один к другому. Этого обычно достигают, разрезав одновременно обе полосы.
Следует отметить, что одним из важных условий незаметности шва при этом способе сварки является однородность линолеума и отсутствие утеплителей.
Полотна укладывают с нахлестом в несколько сантиметров и очищают их кромки от пыли. Для этого может подойти обычная тряпка. Сам напольный материал необходимо защитить от клея. С этой целью на нижний край реза приклеивается скотч, а после укладки полос такой же клеется на верхний.
Выровняв полотна, их одновременно разрезают по планке, скажем по металлической линейке из металла. Под стык рекомендуется укладывать фанеру. Во-первых, при этом не притупится нож, а, во-вторых, не повредится основание.
Затем обрезки полотен убирают, укладывают полосы, проследив чтобы их высота была одинакова. При необходимости края можно примять.
Можно также после выполнения двойного реза наклеить скотч таким образом, чтобы стык проходил примерно по его середине. Затем скотч разрезают по линии стыка.
Если кромки покрытия ровные, то можно не прибегать к двойному резу, просто совместить края полотен, уложить скотч и разрезать его, как и в предыдущем случае, вдоль стыка.
Нанесение клея
- Наконечник тюбика вводят в щель между полосами и нажимают на него, дозируя поступление сварки. Как только на скотче появится маленькая капелька клея, начинают плавно вести иглу по стыку.
- Полоска клея, образовавшаяся на скотче должна иметь ширину порядка 3–5 мм. Только в этом случае клей гарантированно заполнит стык и этого в достаточном количества будет достаточно, чтобы расплавить края линолеума и соединить их.
- Скотч можно удалить примерно через четверть часа, после чего острым ножом необходимо срезать образовавшиеся бугорки.
- Если точно следовать технологии, то получится аккуратный и очень прочный шов, который визуально практически не будет выделяться на поверхности.
Если же при выполнении холодной сварки клей попал на незащищенный участок напольного материала, то не рекомендуется вытирать его сразу же. Такие действия могут привести к стиранию рисунка с поверхности покрытия и ухудшению качества шва. Необходимо дать клею высохнуть, затем счистить ножом.
Обратите внимание:
свежеуложенная холодная сварка немножко пружинит, поэтому нельзя исключать, что натяжение, возникающее в процессе срезания, может способствовать образованию канавок. Вот почему лучше удалять излишки двумя заходами.
Наглядно представить, как получить ровный шов можно, просмотрев склеивание на видео.
© 2022 prestigpol.ru
Холодная сварка для металла, для линолеума, для пластика
Холодная сварка – что это? Все, кто впервые планирует испробовать метод,задаются подобным вопросом. Приподнимем завесу. Под холодной сваркой в нашем случае мы рассматриваем особый вид клеевого состава. Клей с таким наименованием свободно продается в хозяйственных магазинах и предназначается в основном, для объединения деталей из металла. Впрочем, существуют составы для линолеума и для пластика.
Вообще, с точки зрения технологического процесса, холодная сварка это “склейка” двух металлов под давлением. В результате чего, происходит пластическое деформирование. Таким образом соединяемые поверхности заготовок наподобие пластилина, перемешиваются и скрепляются. При этом нет необходимости в нагреве заготовок от внешнего источника тепла.
Люди, так или иначе знакомые с промышленными работами, не раз слышали о холодном варианте сварки. А большинство из них даже смогли использовать его на практике, и оценить по достоинству эту технологию. Достаточно просто получить крепкое соединение, если сложить два мягких металла вместе и ударить по ним молотком.
Однако, мы вернемся к холодной сварке, которая базируется на клеящем составе. Как мы понимаем, подобное соединение “сваркой” называется достаточно условно. Руководствуясь инструкцией по применению, каждый домашний мастер сможет воспользоваться холодной сваркой для ремонта. В экстренных случаях, когда отсутствует сварочный аппарат, холодная сварка определенно заслуживает внимания.
Самая большая загвоздка в том, что мы просто не читаем инструкцию. Полагаясь на авось, упускаем важные детали выполнения технологической цепочки. Давайте постараемся раскрыть основные нюансы эксплуатации и использования состава холодной сварки.
В клеевой состав холодной сварки включены:
- Металлическая пыль – наполнитель.
- Эпоксидная смола – обеспечивает пластичность массы.
- Добавки – для каждого материала используются разные варианты.
- Отвердитель
Надежность холодной сварки определяется не только ее составом, но и чистотой соединяемых поверхностей, с которыми предстоит работать. Если выполнены требования инструкции по разведению клея и условия обезжиривания, можно не волноваться о прочности клеевого шва.
Однако, необходимо понимать, что клей “холодная сварка” целесообразно применять для небольшого домашнего ремонта. Для серьезных сварочных конструкций, подобное соединение не подходит.
Холодная сварка – вариации и разновидности
Говоря простыми словами, холодная сварка – пластичное клейкое вещество, основу которого составляет преимущественно эпоксидная смола. О замечательных свойствах которой, все слышали не один раз.
Подобно эпоксидной смоле, холодная сварка состоит из пары составляющих. Впрочем, есть готовый состав в “одном флаконе”. В этом случае его требуется использовать максимально быстро, иначе можно упустить момент и клей утратит свои качества. Обращайте на условия хранения и время использования однокомпонентных составов.
С вариантом клея из двух составляющих немного проще. Двухкомпонентную “Холодную сварку” допускается хранить долгий период времени. Плюс расход материала по мере необходимости. Однако перед использованием требуется сделать качественный замес в строгих пропорциях.
Обычно, изготовители предлагают холодную сварку в формате цилиндра. Внешняя его оболочка – служит отвердителем. Внутри цилиндра располагается эпоксидная смола, перемешанная с металлизированной пылью. Добавленная в отвердитель металлическая пыль, твердея, армирует состав. Таким образом формируется повышая устойчивость к температурам и механическому повреждению.
Металлическая добавка требуется, для придания готовому сцеплению высочайшего уровня прочности. Холодная сварка содержит и прочие добавки, придающие веществу, и готовым соединениям уникальные параметры прочности. Основная номенклатура добавок содержится изготовителями в строжайшей тайне. Однако известно – сера неотъемлемый компонент холодной сварки у любого производителя.
В большей степени, холодная сварка классифицируется по маркам в зависимости от сфер применения. Иначе говоря, в зависимости от тех материалов, которые предстоит склеивать холодная сварка включает в себя специализированные добавки. С большим успехом используется три основных типа данного вещества.
Холодная сварка для металла
Она активно применяется не только домашними мастерами, но также автомобилистами, поскольку предоставляет быстрое и действенное решение множества проблем, которые связаны с использованием автомобильного транспорта.
С помощью холодной сварки для металла устраняют течь радиатора, “заваривают” поддон картера и доже сваривают головку блока цилиндров. Безусловно, подобные поломки нуждаются в надлежащем ремонте. Но что делать, если вы находитесь за городом на даче?
Вдали от автосервиса, временное решение проблемы возможно будет лучшим выходом из ситуации. Подобный клей никогда не будет лишним в ящике с инструментами. Бытовая холодная сварка способно продержаться пока вы доберетесь до ближайшего сервисного центра.
Сцепление, которое получают благодаря холодной сварке, предоставляет шанс хотя бы ненадолго позабыть о появившейся трудности. Использовать восстановленные запчасти можно достаточно долгий период времени. Если двигаться тихо и осторожно, времени должно хватить, чтобы добраться до квалифицированного мастера.
Бытовое применение холодной сварки по металлу
Холодная сварка прекрасно проявляет себя и тогда, когда необходимо объединение деталей, которые не испытывают существенную нагрузку в процессе эксплуатации. Например этот вариант сварки используют и для починки сантехники, когда требуется быстро и накрепко заделать образовавшуюся течь. Сфера где успешно применяется холодная сварка для металла:
- Водопроводные трубы.
- Радиаторы отопления.
- Дырявые кастрюли, если их дальнейшее использование не подразумевает приготовление пищи..
- Заделка сколов на чугунных или металлических ванных.
По мере отвердения, холодная сварка перестает реагировать на высокую температуру использования приборов. Если все сделать согласно инструкции по применению, то склеенные предметы можно использовать по назначению не продолжительное время.
Заметим, клей холодная сварка не предназначен для восстановления посуды пищевого назначения. Холодная сварка содержит эпоксидную смолу, которая выделяет вещества, вредные для здоровья человека.
Существует специализированная холодная сантехническая сварка. Адаптированный состав не подвержен негативному воздействию влажной среды. В противовес обычному клеевому составу, холодная сварка для сантехники применяется в соединениях для герметизации мокрых стыков. Характеристики состава сантехнической сварки позволяют схватываться ему даже под водой, надежно удерживаясь на поверхности.
Однако, каким бы крепким ни был этот вариант сцепления, холодная сварка на клеевой основе способна лишь временно разрешить образовавшуюся проблему. Как только появится подходящий случай, обязательно требуется произвести замеру трубы.
Холодная сварка для пластика
Такая вариация холодной сварки гораздо менее распространена, чего не скажешь о металлической. Обусловливается это просто. Все сферы применения холодной сварки для пластиков вытеснены более эффективным клеевым пистолетом. Клеевой пистолет обеспечивает надежную склейку горячим методом, прочно закрепляя пластиковые изделия.
Однако холодная сварка для пластмасс пригодится для починки деталей из пластика когда нет клеевого пистолета или отсутствует электросеть для его функционирования. Обычно холодная сварка используется для стыковки пластиковых труб, или прочих полимерных поверхностей.
Холодная сварка для пластика широко используется на промышленных предприятиях. Не заменима в быту для проведения домашних ремонтов. Попробуйте использовать клеящий состав холодной сварки для починки трубы из пластика и вы на долго забудете о поломке.
Холодная сварка для линолеума
Особого внимания заслуживает холодная сварка, применяемая для стыков линолеума и резины. Просто не заменимая вещь во время ремонта и отделочных работ. Качество стыков обработанных холодной сваркой для линолеума в разы превосходит двухсторонний скотч или жидкий клей. Как правило, холодная сварка для линолеума используется только на стыках. Высокая стоимость клея не позволяет ее использование по всей поверхности.
При стыковке листов линолеума всегда остаются щели, которые со временем рассыхаются и становятся более заметными. Исправить ситуацию способен цельный шов, для получения которого используют метод холодной сварки. В результате, соединенные листы линолеума выглядят как однородное полотно. А бесшовное соединение выглядит более эстетичным.
Результатом взаимодействия линолеума с клеем является химическая реакция. Материал в местах стыков становится мягким и почти жидким. После того, как места стыков затвердеют, соединение становится прочным и незаметным. Холодная сварка – достаточно легкий способ соединить линолеум. Работы способен выполнить даже начинающий мастер без навыков и профессиональных инструментов для пайки линолеума (паяльник и т. д. ).
Холодную сварку допускается применять и когда есть необходимость провести объединение деталей, выполненных их жесткой резины. Такими деталями могут стать, например, куски линолеума. Разумеется, данный вариант сварки весьма широко используется для проведения строительных работ и просто для починки.
Важно заметить, что сцепление линолеума, образованное холодной сваркой, существенно превосходит по параметрам те, что образуются зачастую посредством обыкновенного клеевого состава либо двустороннего скотча.
Отметим, что в данной статье были обозначены лишь самые востребованные разновидности холодной сварки. Но в промышленности существует еще несколько других менее популярных видов. К примеру, это сварка для сантехники или для бетона. Существует, в том числе, и универсальный вариант.
Как бы там ни было, все варианты могут похвастаться достойной скоростью и крепостью склейки. Разумеется, лишь тогда, когда в ходе работы были строго соблюдены все обозначенные правила в инструкции по применению. Иначе сцепление скоро развалится.
Применение холодной сварки для металлоизделий
Руководство по эксплуатации сварки для металлоизделий стандартно имеется в каждом цилиндре с веществом. Его использование почти не отличается от прочих видов данного состава. Однако перед работой, пренебрегать им не стоит.
Для лучшего понимания того, как использовать данный клей, вполне достаточно подробно рассмотреть пример по ремонту пробоины в трубе либо емкости, выполненной из металла. Большой плюс холодной сварки в том, что ее допускается применять вне зависимости от того, пуста емкость или наполнена. И даже тогда, когда предмет починки под давлением.
Проще говоря, если вам, например, требуется заделать дыру в автомобильном радиаторе, совершенно нет нужды сливать из него жидкость.
Как работать с холодным клеем
В ходе работы важно четко соблюдать все инструкции. Только так сцепление получится максимально качественным и крепким. Последовательность проведения ремонтных работ посредством холодной сварки такова:
Первоначально нужно подготовить рабочую основу, куда будет нанесен клеевой состав. Зачистить от загрязнений и прочего. Для этой цели отлично подойдет наждачная бумага мелкой зернистости. Выполнить подготовку требуется со всей тщательностью. Основа обязана быть идеально чистой.
Определить степень чистоты легче по царапинкам на поверхности, которые были нанесены наждачной бумагой. Стоит отметить еще одну особенность – чем больше будет таких царапин, тем надежнее в итоге выйдет соединение.
Далее важно со всей тщательностью высушить наружность, которую планируется обрабатывать. Для этой цели вполне допускается применить обыкновенный фен для волос. Никаких особенных технологических устройств для этого не потребуется. Разумеется, холодная сварка сможет склеить и влажную поверхность. Но в данном случае не стоит рассчитывать на достойный уровень надежности подобного сцепления.
Очистка поверхностей
Последующий этап – это обезжиривание рабочей поверхности. Благодаря этому простому нюансу готовое сцепление выйдет гораздо крепче. Для процедуры обезжиривания вполне можно использовать ацетон. Эта жидкость с легкостью удалит любые жировые пятна с металла. Однако будьте осторожны. Если ацетон попал на руки или глаза, срочно промойте водой.
Потом необходимо приступить к созданию самой холодной сварки. Если учесть, что она имеет не жидковатую, а намного более плотную структуру, стоит применить нож, чтобы отделить от цилиндра состава фрагмент требуемого размера.
Совет: разрез должен быть сделан точно перпендикулярно цилиндру — это позволит получить в отрезанном фрагменте нужное соотношение затвердителя со смолой. Если резать по диагонали, то баланс соотношений будет нарушен. Полученный фрагмент надо размять пальцами пока он не превратится в податливую однообразную массу. Чтобы эта масса не прилипала к ладоням, разрешается сбрызгивать ее водой.
Как только клеевая масса будет готова, ее важно быстро использовать на подготовленной к ремонту поверхности. Инженерные показатели большинства разновидностей клеевого состава таковы, что он очень быстро затвердевает сразу после подготовки, а, значит, моментально должен быть использован.
Если вы хотите использовать холодную сварку для склейки образовавшейся дырочки, стоит делать это так, чтобы часть состава попало внутрь. Малое отверстие отлично запломбируется. Если, течь слишком большая, целесообразнее применить металлическую латку, и закрепить ее клеевым составом.
После применения, важно дать сварке время высохнуть, и полностью затвердеть. На это могут уйти приблизительно сутки. И только когда она полностью возьмется, затвердеет, можно приступать к отделочным работам.
Перед работой с клеевым составом лучше всего не пренебрегать имеющимся руководством, и следовать строго ему, либо найти соответствующие видео ролики в сети, которые помогут без проблем освоить данную технологию.
Отнестись внимательно к применению обезжиривателей, большая их часть опасна для глаз. Если делать все в соответствии с инструкцией по применению, работа с холодной сваркой покажется абсолютно простым занятием.
что это такое, особенности и виды, применение жидкой термостойкой для нержавеющей стали, латуни, чугуна – Холодная сварка на Svarka.guru
Холодная сварка для металла высокотемпературная водостойкая – это наиболее качественный представитель семейства эпоксидных клеящих составов. Отличается сохранением эксплуатационных свойств даже при воздействии высоко температур.
Содержание
- 1 Область применения
- 2 Преимущества
- 3 Недостатки
- 4 Разновидности
- 5 Состав
- 6 Технические характеристики различных производителей
- 7 Форма компонентов
- 8 Какая лучше? Критерии выбора
- 8.
1 Температурный режим
- 8.2 Герметики
- 8.3 Составы для автомобилей
- 8.4 Значение наполнения
- 8.
- 9 Инструкция по применению
- 10 Производители и популярные марки
- 11 Заключение
Область применения
Термостойкость клея определяет сферы применения:
- Бытовая. Ремонт радиаторов отопления, газовых котлов, колонок, печей, кастрюль, чайников.
- Автомобильная. Ремонт всех узлов автомобиля, которые подвергаются воздействию высокой температуры: системы охлаждения, выпуска отработанных газов и двигатель.
[stextbox id=’alert’]Важно! Современный двигатель – высокотехнологичный агрегат. Не обладая профессиональными навыками, не стоит производить ремонт. Перед применением холодной сварки для ремонта двигателя рекомендуем проконсультироваться со специалистами[/stextbox]
Преимущества
Высокотемпературную холодную сварку ценят за следующие свойства:
- Широкий перечень соединяемых материалов.
- Легкость применения. Использование не требует специальной подготовки или особых навыков. Простота состава предполагает проведение срочных работ в полевых условиях.
- Качество соединения. Шов не поддается химическому воздействию, коррозии и не подвержен окислению.
- Возможность обработки. После полной полимеризации соединение поддаются любой механической обработке, включая использование пескоструйных аппаратов.
- Экологичность. Абсолютно безопасно для окружающей среды.
Недостатки
Как и любое вещество, жаростойкий клей имеет свои недостатки:
- Температурный режим. Производители рекомендуют склеивать поверхности при комнатной температуре. В противном случае не стоит ожидать высокого качества шва.
- Промышленное применение невозможно. Применение дуговой сварки, на крупных предприятиях, обходится дешевле, чем соединение холодной сваркой.
Даже с учетом высокой оплаты труда квалифицированных сварщиков.
Разновидности
Помимо формы и содержания упаковки, рассматриваемый материал различают по следующим параметрам:
- Показания к применению (универсальная, металлическая, сантехническая).
- Характеристики (влагостойкая, жаростойкая, маслостойкая).
- Время схватывания и полимеризации.
- Наличие дополнительных компонентов.
Состав
Содержит следующие компоненты:
- Эпоксидная смола. То, на чем основана так называемая холодная сварка: базовый элемент клея, который отвечает за однородность и пластичность рабочей массы.
- Металлический или минеральный наполнитель. Важная составляющая, которая придает крепость при полимеризации. Благодаря металлической составляющей состав получил название — внешний вид соединения напоминает сварочный шов от ручной дуговой сварки.
- Наполнители.
Наиболее распространенным элементом является сера. В состав входят и другие компоненты, отвечающие за качество продукции. Изготовители держат их в секрете.
Технические характеристики различных производителей
Рассмотрим перечень продуктов, которые пользуются популярностью в крупнейших городах России – Москве и Санкт-Петербурге:
- ABRO Термометалл TM-185. Страна-производитель – США. Однокомпонентный материал для заделки трещин и отверстий в стальных и железных деталях. Пригоден к использованию при ремонте автомобильных узлов, бытовых отопительных приборов, промышленного оборудования. Содержит антикоррозийные добавки. Отличается стойкостью к нефтепродуктам. Выдерживает температуру до 1316 Сº.Время полной полимеризации – 24 часа. Рекомендованная толщина слоя – 6 мм.
- Клей «холодная сварка» АЛМАЗ «ТЕРМОСТОЙКИЙ». Продукт российского производства. Используется для соединения различных поверхностей: черный металл, нержавейка, пластмасса, стекло, керамика, дерево.
Наиболее эффективен при ремонте батарей, радиаторов отопления и различных трубопроводов. Возможно применение на мокрых или замасленных поверхностях. Термостойкость до 300 Сº.Время полной полимеризации – 24 часа. Прочность при отрыве – 120 кг/см².
[stextbox id=’info’]Вышеуказанные товары, в числе прочих, можно приобрести сети строительных гипермаркетов «Леруа Мерлен».[/stextbox]
Форма компонентов
Холодная сварка отличается степенью густоты: производят пастообразный и жидкий составы.
- Пастообразный представляет собой однокомпонентное вещество, готовое к использованию. По внешнему виду напоминает детский пластилин.
- Жидкую сварку для металла выпускают в специальных контейнерах. Является двухкомпонентным клеем, который необходимо смешать перед применением.
Двухкомпонентные растворы имеют преимущество – длительный срок хранения, тогда как однокомпонентный клей необходимо использовать после вскрытия упаковки.
Какая лучше? Критерии выбора
Популярность холодной сварки породила огромное количество товаров на любой вкус, поэтому выбор должен зависть от области применения.
Температурный режим
Универсальные продукты отличаются хорошим показателем прочности на растяжение и разнообразием соединяемых материалов. Показатель химической устойчивости – средний. Можно ли таким составом заклеить кастрюлю? Да, но максимальная температура соединения не превышает 200 Сº.
Специализированный клей сохраняет свойства при температуре свыше 1000 Сº.
Герметики
Краеугольным камнем универсальных продуктов является низкая избирательность. Для устранения утечек труб отопления рекомендуем использовать специальные водостойкие продукты. В первую очередь они являются герметиками, поэтому не ждите от них высокой адгезии при заклеивании металла. Производятся в жидком виде.
Составы для автомобилей
Автомобильная холодная сварка отличается устойчивостью к негативным факторам, которые сопровождают эксплуатацию автомобиля – вибрация, удары, перепады температур. Не подходит для применения под водой. Высокий показатель прочности на разрыв.
Значение наполнения
Обращайте внимание на соединяемый материал. Для холодной сварки металла лучше всего подойдет сварка с металлическим наполнителем. Он должен соответствовать параметрам металла. Например, для соединения чугуна необходим чугунный наполнитель, для меди – медный и т. п. Это позволит добиться наилучших результатов.
Инструкция по применению
Перед работой внимательно изучите инструкцию по применению. В ней указаны технические характеристики. Также можно почерпнуть нужную информацию, касательно безопасного использования клея и рекомендуемых областей применения.
Ниже приведены общие правила при использовании холодной сварки.
Правила безопасности при работе с холодной сваркой
Холодная сварка – нетоксичный материал. Ее применения не требует использования защитных очков или средств защиты органов дыхания. Основным требованием безопасности некоторых продуктов является защита кожного покрова и слизистой оболочки от непосредственного контакта с клеем.
[stextbox id=’warning’]В случае попадания в глаза следует хорошо промыть контактный участок большим количеством воды и обратиться к врачу. Это относится к готовой смеси – контакт с высохшим продуктом не принесет вреда здоровью.[/stextbox]
Посуда для подготовки смеси должна быть чистой, без содержания посторонних элементов. Дальнейшее использование посуды для приема пищи нежелательно.
Производители и популярные марки
Рейтинг наиболее популярных производителей холодной сварки возглавляют:
- HI-GEAR;
- Liqui Moly;
- ALTECO;
- MANNOL;
- LAVR;
- АЛМАЗ;
- Done Deal.
[stextbox id=’warning’]Если вы хотите узнать больше об использовании холодной сварки, то на нашем сайте есть статьи по темам:
- Какую холодную сварку сварку лучше выбрать для металла?
- Как пользоваться холодной сваркой для пластика?
- Как заварить глушитель холодной сваркой?[/stextbox]
Заключение
Таким образом, холодная сварка является наиболее востребованным средством экстренного ремонта в бытовой и автомобильной сфере. Однако, ее применение не всегда освобождает от необходимости в проведении полноценного ремонта или замены детали.
[stextbox id=’info’]Автомеханик ООО «Алеко-Сервис» Бондаренко Сергей Анатольевич, опыт работы – 20 лет: «Я занимаюсь ремонтом автомобильного подвижного состава с 20 лет. Появление на рынке термостойкой холодной сварки существенно облегчила мне жизнь – особенно при ремонте выхлопной системы. С задачей заделки незначительных трещин она справляется «на отлично». К тому же отсутствует необходимость снятия узлов для полноценной сварки – это экономит силы и время».[/stextbox]
Холодная сварка для металла, дерева, пластика.
Содержание:
- Холодная сварка для металла, дерева, пластика: универсальная инструкция к применению.
- Холодная сварка для металла, дерева, пластика: достоинства и недостатки.
Современный рынок строительных материалов постоянно расширяется и растет. Благодаря техническому прогрессу изобретаются и внедряются новые строительные материалы, один из которых называют «холодная сварка».
Холодная сварка — это своего рода клей, похожий на пластилин, очень сильный и крепкий в затвердевшем состоянии. Этот клей, с легкостью может склеить такие материалы как: пластмассу, пластик, резину, стекло, кафель, кирпич, бетон, асбест, дерево, ДСП, а также металл! К тому же из этого материала можно сделать или восстановить недостающие, либо отколовшиеся части картинных рам, ручек, лопнувших металлических изделий, заклеить пробоину и течь в трубах и радиаторах, повесить крючки в ванной.
В состав холодной сварки входит два основных компонента и различные добавки. Основные компоненты — это эпоксидная смола и отвердитель, которые давно (еще с конца шестидесятых годов) зарекомендовали себя, как качественные и надежные, клеящие вещества. Добавки бывают такие, как оксид железа, различные металлические порошки, кварц и другие, в зависимости от типа склеиваемых поверхностей.
Холодная сварка различается по виду склеиваемых поверхностей. Причем для каждого вида характерно свое время затвердевания и свой состав.
- холодная сварка для металла и кованых изделий
Включает в свой состав стальной порошок и обладает некоторыми магнитными свойствами. Прекрасно сцепляется с металлом, не ржавеет, что позволяет использовать ее вне дома. Такой вид клея идеально склеит или отреставрирует металлические предметы и кованные изделия. Полное высыхание через 2 — 3 часа.
- холодная сварка для пластика
Основное преимущество данного вида заключается в том, что после высыхания материал остается эластичным и это позволяет применять его при работе с ПВХ и АВS (полу эластичные материалы). Такой вид клея идеально подходит для ремонта и восстановления пластиковых водопроводных и канализационных труб, садовой пластиковой мебели. Полное высыхание происходит через 3 — 4 часа.
- холодная сварка для дерева
Используется для склеивания и реставрации деревянных предметов декора, картинных рам, для устранения царапин и трещин. Полное высыхание 1 — 2 часа.
- холодная сварка для влажных поверхностей и под водой
Мокрая сварка может устранить течь в трубах, производить работы под водой, при ремонте аквариумов, даже ремонтировать мелкие течи в корпусах кораблей. Полное высыхание 1,5 -2,5 часа.
Узнайте больше про обработку металла, прочитав статью «как заточить сверло по металлу».
к содержанию ↑
Холодная сварка для металла, дерева, пластика: универсальная инструкция к применению.
Перед применением холодной сварки, как и другого клея первое что нужно сделать — это подготовить склеиваемые поверхности. Зачистить щеткой от пыли и грязи, удалить старую краску и ржавчину, обезжирить ацетоном и хорошенько просушить. Затем смочить руки водой, взять необходимое количество клея и размять его в руках. При этом два основных компонента клея смешиваются.
Размякшая холодная сварка для металла, дерева, пластика наносится на склеиваемый участок. Если это отверстие или трещина, нужно наложить клей так, чтобы от отверстия он выступал минимум по одному сантиметру со всех сторон (для надежного сцепления). После чего обрезать и удалить ненужные остатки клея, дать ему просохнуть и затвердеть. Для полного и качественного сцепления необходимое время высыхания 24 часа.
Cвайно-ростверковый фундамент – плюсы и минусы.
к содержанию ↑
Холодная сварка для металла, дерева, пластика: достоинства и недостатки.
Основное преимущество холодной сварки по металлу, дереву, пластику в том, что в отличии от традиционной сварки и пайки, она намного экономичнее и не требует специальных профессиональных навыков и оборудования. Холодная сварка для металла позволяет избежать ослабления полотна металла в местах соединения.
Также клей добавляют при винтовых соединениях, для усиления прочности. Дает возможность соединять разнородные металлы и материалы. Применяется для обеспечения герметичности соединения, не подвержена коррозии, может использоваться в агрессивных средах. Холодную сварку по металлу, дереву, пластику после высыхания можно шлифовать, сверлить, красить.
К недостаткам можно отнести: меньшую прочность соединения, в отличие от обычной сварки.
Читайте также: Фрезы для фрезера ручного — выгодное приобретение для домашнего мастера.
Краска по металлу для наружных работ: правила выбора.
Холодная сварка учимся правильно пользоваться – Мои инструменты
О таком явлении, как холодная сварка, так или иначе слышал практически каждый. Тем не менее средство для быстрого соединения металлов и пластмасс пока не достигло пика популярности. Зачастую оно имеется в домашнем арсенале у мастеров, но по причине незнания тонкостей его использования откладывается в долгий ящик.
- Виды холодной сварки для металла
- Сухая сварка
- Жидкая сварка для металла
- Холодная сварка: клей для пластика
- Клей холодная сварка для жестких типов резины
- Инструкция по применению холодной сварки для металла
- В заключение
Если также слышали о данном методе, но совершенно не знаете, как пользоваться холодной сваркой металла, то статья станет для вас полезной. В публикации разобрана основная информация о такой методике и инструкция по применению сварочных средств под конкретную цель. Для начала давайте рассмотрим виды составов для сваривания пластика и металла.
Что такое холодная сварка и какой она бывает
Холодная сварка — это специальный тип высокопрочного клея, который применяется соединения разных материалов, в том числе и стали. В основу состава входит эпоксидный клей или смола с разными наполнителями, за счет чего и обеспечивается высокая прочность соединения деталей. Только достичь высокого качества соединения удается не всегда, поэтому многие жалуются и отказываются от дальнейшего использования материала. Причиной является вовсе не плохое качество клея или его низкая эффективность, а несоблюдение инструкции по применению состава.
Чтобы холодная сварка обеспечила желаемую надежность соединения, к ее применению нужен соответствующий подход. Перед тем, как пользоваться холодной сваркой, необходимо разобраться с особенностями ее правильного применения. После появления клеящего состава высокой прочности, его начали выпускать разные производители. С целью экономии на производстве, некоторые производители нарушают стандарты изготовления холодной сварки, что отражается в итоге на качестве соединений. Чтобы этого не случилось, надо покупать сварку только с сертификатами качества, которые гарантируют эффективность материала.
Холодная сварка классифицируется на два вида:
- Однокомпонентная
- Двухкомпонентная
И обоих видах клея присутствует эпоксидное вещество, а также наполнители — сера, металлический порошок и другие составы. По типу состава холодная сварка бывает сухой и жидкой.
Сухая сварка из двух компонентов находится в цилиндрической упаковке. Когда необходимо воспользоваться средством, компоненты необходимо перемешать, получив смесь, похожую на пластилин. Работать пластилином очень удобно, поэтому обеспечить соединение холодной сваркой сухого типа можно даже в самых труднодоступных местах. Эффективность материала зависит от качества замешивания состава. Оба компонента необходимо использовать в одинаковом количестве, и тщательно произвести их перемешивание.
Жидкая сварка состоит также из двух компонентов, которыми являются эпоксидное вещество и отвердитель. Эти компоненты также следует соединить вместе перед непосредственным применением. Качество и надежность склеивания зависит от такого фактора, как тщательность смешивание. Чем тщательнее будут смешаны вещества, тем надежней место соединения.
Классифицируют холодную сварку также и по способам применения, что зависит от поставленных технологических задач:
- Шовная — применяется для создания прочного и непроницаемого шва, когда необходимо не только соединить детали, но и обеспечить их герметичность. Шовный состав подходит для случаев, когда надо предотвратить протекание металлических труб и т.п.
- Точечная — такой клей наносится точками, что позволяет достичь высокой надежности, однако герметичность при этом отсутствует. Используется преимущественно в исключительных случаях, когда надо обеспечить соединение двух деталей
- Стыковая — особый вид клея, который используется для соединения металлических деталей путем их стыкования. При использовании стыковой сварки необходимо понимать, что соединить таким клеем можно только тонкий металл
- Тавровая — такой тип клеевого состава используется исключительно в электромонтаже
- Сдвижная или нахлестная сварка — клей, применяющийся для объединения труб разного диаметра.
При помощи сдвижного клея можно соединять трубы разных диаметров, но исключительно методом объединения внахлест
Это интересно!
В зависимости от материала, который планируется соединить, различают холодную сварку для металла, пластика, линолеума и т.п. Применение такого клея значительно снижает затраты на использовании других методов соединения.
Где применяется
Чтобы соединить две металлические заготовки, можно использовать сварочный аппарат. Однако этот инструмент достаточно дорого стоит, но даже если его купить, то перед применением, понадобится научиться пользоваться. Холодной сваркой также необходимо научиться пользоваться, только обучение намного легче и проще, чем со сварочным аппаратом.
Кроме того, что холодная сварка применяется для соединения металлических деталей, ее также применяют для восстановления целостности других материалов. Сфера использования рассматриваемого соединителя достаточно широкая, и применяется сварка в следующих случаях:
- При ремонте транспортных средств — это специальные вещества, которые применяют непосредственно для заделывания трещин, старых швов, а также с целью присоединения деталей к основанию кузова
- При соединении деталей, подверженных воздействию высоких температур.
Для этого применяются специальные термостойкие клеящие составы. Кроме стойкости к высоким температурам, такие материалы должны обладать устойчивостью к перепадам, при которых происходит расширение и сужение металлов
- При выполнении соединительных работ в сантехнической сфере — применяется для заделывания и герметизации мест повреждения труб, а также для их нахлестного стыкования. Главное требование, предъявляемое к холодной сварке для сантехники, заключается в устойчивости к влаге
- Для бетона — если появилась трещина в бетоне, то попадание влаги и мусора будет приводить к увеличению размеров дефекта. Предотвратить дальнейшее разрушение материала поможет специальный состав для бетона
- Универсальные — позволяют соединять разного рода материалы, такие как пластик, линолеум, металл, пластмасса и другие
Перед тем, как научиться пользоваться холодной сваркой, нужно правильно выбрать средство для соединения тех или иных материалов. В быту и хозяйстве необходимость применения холодной сварки возникает для выполнения таких задач:
- Соединить трубы отопления
- Устранить течь, возникшую по причине прохудившейся трубы
- Заделать возникшие отверстия в посуде
- Герметизировать соединение дымоходной трубы с выводом из котла
- Склеить разные детали, предметы интерьера и т.
п.
Рано или поздно необходимость в использовании холодной сварки возникает у каждого, поэтому рекомендуется не только купить высокопрочный клей, но еще и научиться его использовать. Разобравшись с видами и особенностями высокопрочного клея, можно выяснить принцип работы с холодной сваркой.
Температурные характеристики
Процесс склеивания происходит без нагрева с пластическим деформированием. Это хорошо и плохо одновременно. Иначе – без установления глубоких межатомных связей в соединяемых частях, но достаточно прочных в обычной практике для быстрого и качественного соединения деталей, заделки трещин, устранения течи, шпатлевания поверхности.
Инструктивные рекомендации производителей почти не расходятся, когда дело касается приготовления и использования рабочего состава. Однозначно при комнатной температуре 18-20°С, с отклонением 10 градусов в ту или иную сторону, без изменения первоначальных и тем более конечных свойств.
Рабочая зона эксплуатации от -60 до +260°С. Высокотемпературная холодная сварка достигает максимального показателя в 1316 градусов по Цельсию.
Как склеить стекло
Для склеивания треснувшего стекла понадобится воспользоваться прозрачным клеем. Если сделать все правильно, то после окончания работ на стекле не будет видно никаких следов. Инструкция по применению прозрачной холодной сварки по склеиванию стекла имеет следующий вид:
- Для начала нужно подготовить поверхность. От качества выполнения подготовки зависит эффективность приклеивания стекла. Поверхность стекла следует очистить от загрязнений, а также обезжирить
- Когда поверхность готова к приклеиванию, надо приступать к подготовке клеящего состава. Если используется жидкая консистенция, то вещество соединяется с отвердителем. При использовании сухой сварки нужно соединить вещества и размешать их до получения однородной консистенции. При работе с жидким клеем понадобится использовать подручные средства, исключив контакт с кожными покровами.
Сухую сварку также нельзя брать в руки, поэтому работать необходимо в медицинских перчатках
- После того, как смесь будет готова к применению, ее следует сразу же наносить. Оставлять состав на время более 3-5 минут нельзя, так как снижаются клеящие свойства, а также происходит отвердение средства
- Соединить детали и прочно прижать их. Оставить на время, пока состав не высохнет. Обычно время высыхания указывается производителем на упаковке. Когда состав полностью застынет, можно приступать к зачистке клеящего шва
Таким простым и быстрым способом можно склеить стекло, используя для этого холодную сварку. Соединительный шов получается достаточно прочным, поэтому даже при разбивании стекла можно наблюдать такую картину, что оно не трескается в месте склеивания.
Правила работы с клеем
Для правильного применения желательно прочитать инструкцию к конкретному изделию. Однако есть несколько общих советов:
Нужно удалить грязь на склеиваемых поверхностях.- Следует позаботиться о грубых неровностях. Легкие шероховатости даже желательны: сцепление будет лучше. Поверхности обрабатываются, например, наждаком и очищаются.
- Перед склейкой их нужно обезжирить. Сделать это можно, например, при помощи ацетона.
- Лучше, чтобы склеиваемые детали были сухими. Хотя есть и водостойкие клеи.
- Двухкомпонентные составы смешиваются, однокомпонентные просто разминаются пальцами. В руках состав немного нагреется.
- Использовать пресс или сильно давить не нужно.
Особенности могут касаться, например, времени готовности: сколько сохнет, зависит от марки. Как правило, первичное застывание происходит уже через 10−20 минут. У некоторых марок — до 5 минут, у других — до часа.
Первичное застывание не означает, что можно начинать пользоваться вещью. Происходит только затвердение, и масса уже не годится для работы. Необходимо учитывать это время, чтобы весь размятый материал оставался в нужном состоянии.
Полное затвердение происходит обычно через несколько часов.
Здесь все зависит от марки холодной сварки.
Как соединить линолеум холодной сваркой
Одним из самых популярных запросов в Яндексе и Google является правило склеивания линолеума при помощи холодной сварки. Напольный линолеум пользуется популярностью, и поэтому при его укладке в больших помещениях возникает необходимость склеивания швов. Для этого применяется специальная холодная сварка для линолеума, а сам процесс приклеивания двух листов выполняется по следующей схеме:
- Сначала необходимо обеспечить идеальное стыкование двух листов линолеума. Достигается это путем наложения двух частей внахлест, с выступом не менее 5 см. Этот выступ нужен, чтобы место стыка не имело свободного пространства. Место нахлёста необходимо проклеить малярным скотчем, а затем при помощи острого строительного ножа произвести удаление верхней и нижней части выступов линолеума. Проклеивать малярным скотчем не обязательно, но рекомендуется, так как при этом место соединения не будет смещаться.
Этим простым способом достигается высокая точность соединения
- На следующем шаге нужно также воспользоваться малярным скотчем, и проклеить место стыка с двух сторон снизу и сверху. Проклеивать нижнюю часть также не обязательно, но это позволит исключить приклеивание линолеума к влагозащитной пленке. Сверху проклейка малярной лентой выполняется для того, чтобы исключить попадание холодной сварки на декоративную часть материала
- На месте стыкования нужно прорезать линию в скотче, через которую будет вноситься холодная сварка
- Взять в руки тюбик специального клея для линолеума, и наносить его в место стыка при помощи тонкой иголочки, закрученной на тюбик. Если клей будет выходить за пределы соединения, то его следует оперативно удалять при помощи тампона
- Кроме этого способа, есть и другой, который заключается в том, что на одну торцевую часть линолеума наносится равномерный слой клея, а затем выполняется его укладка и соединение со вторым листом. Этот способ подходит, если место стыка имеет практически незаметный шов, который не позволяет провести по нему тонкой иглой
Время застывания клея составляет не менее 2 часов, поэтому рекомендуется выдержать это время, и только после этого к удалению малярной ленты. Если на месте шва имеется выступ клея, то его можно удалить при помощи канцелярского ножа или шпателя.
Это интересно!
Зачистку шва рекомендуется выполнять не раньше, чем через 5 часов, пока клей полностью не застынет.
Склеиваем сваркой трубы отопления
При использовании холодной сварки для труб отопления, необходимо учитывать, что применять следует специальный термостойкий состав. Если пренебречь этим требованием, то уже при первом повышении температуры сварочный шов возьмется трещиной, и продолжит сочиться вода из системы.
Для ремонта системы отопления в случае возникновения течи необходимо использовать сухой тип холодной сварки. Принцип его применения для ремонта металлических труб отопления имеет следующий вид:
- Из системы нужно слить воду. Если место нанесения вещества будет влажным, то говорить о качестве в таком случае не приходится
- Обязательно произвести зачистку места ремонта от удаления краски и ржавчины, а также выполнить обезжиривание
- Просушить поверхность
- Замешать холодную сварку, и тщательно приклеить необходимое количество вещества для герметизации прохудившейся части трубы
- Дождаться высыхания, и только после этого можно наполнять систему водой
Использование клеящего состава для заделывания мест повреждения стальных труб отопления предусматривает соблюдение таких рекомендаций:
- Толщина сухого состава должна быть незначительная, так как от нее зависит качество приклеивания вещества
- Диаметр места повреждения должен быть не более 5-6 мм.
Чем больше диаметр отверстия, который заклеивается холодной сваркой, тем ниже надежность такого соединения. Если необходимо заделать большое отверстие холодной сваркой, то рационально воспользоваться металлической латкой
- После высыхания материала можно произвести окрашивание поверхности трубы
Надо также понимать, что заделывать таким способом можно отопительные и водопроводные трубы с незначительным давлением до 1 атмосферы. Чем больше давление, тем ниже эффективность применения рассматриваемого вещества. Аналогичным способом можно заделать не только трубы отопления, но еще и батареи. Ниже показано видео, по которому видно, что перед тем, как производить ремонт системы отопления или водопровода, находящихся под давлением, нужно хорошо подумать.
Итоги правильного применения холодной сварки
Независимо от того, какие материалы склеиваются холодной сваркой, при использовании этого состава необходимо учитывать главные требования, чтобы получить надежное соединение:
- Тщательно очистить, зачистить и обезжирить поверхности, на которые наносится состав
- Правильно приготовить клеящее вещество.
Чтобы научиться, рекомендуется для начала потренироваться
- Нанести и тщательно разгладить состав по поверхности в течение 1-2 минут после приготовления
- Дождаться полного застывания средства
Руководствуясь этими рекомендациями, можно склеивать холодной сваркой металл, пластмассу, линолеум, пластик, сантехнику и прочие материалы. При высыхании, мягкий пластилин или клей (в зависимости от типа) становятся дубовыми, и по прочности напоминают ударопрочный пластик.
Это интересно!
Достоинство холодной сварки перед горячей в том, что ее можно использовать для соединения различных материалов. Горячая сварка позволяет работать только со стальными материалами.
Даже если вы понимаете и знаете, как пользоваться холодной сваркой, то почитать инструкцию и посмотреть видео никогда не будет лишним. При ознакомлении можно узнать некоторые нюансы, которые помогут избежать ошибок. В итоге следует отметить, что применение рассматриваемого средства позволяет оперативно, недорого и эффективно устранить незначительные дефекты самостоятельно. Конечно, заменить полноценное сварочное соединение холодная сварка не сможет, однако всегда выручит при незначительных дефектах. И правильно нужно не только уметь приготовить и нанести смесь, но еще и принять решение о применении этого состава для устранения дефектов.
Особенности материала
Клей для металла наиболее эффективен там, где обычную сварку использовать невозможно. Сварочная смесь обладает необходимой пластичностью, чтобы проникать в металл, и за счет этого объединять поверхности.
Данный метод сварки относится к технологиям глубокого пластического деформирования, когда оксидный слой на поверхности разрушается, а интервал между свариваемыми элементами измеряется параметрами кристаллической решетки. Благодаря возрастанию энергетического уровня материалов формируется прочная химическая связь.
При заполнении отверстий часть холодной сварки должна попасть внутрь. Для больших дырок используют латки, которые накладывают сверху и фиксируют клеящим материалом. Готовое соединение может подвергаться зачистке под последующую отделку и покраску, а также механической обработке, включая сверление отверстий и нарезание резьбы.
Холодная сварка прекрасно работает на конструкциях из черных и цветных материалов, позволяет стыковать их между собой и оперативно устранять течь. А также является идеальным решением для изделий, чувствительных к температурному нагреву.
Соединения, полученные холодной сваркой, имеют значительный ресурс эксплуатации, но при условии отсутствия рабочих нагрузок.
Клей можно применять при низких температурах
Клей для холодной сварки — как выбрать?
Состав:
- Разновидности составов и область их применения
- Особенности состава по видам
- Область применения: какие материалы можно «сваривать»
- Технические характеристики – на что обратить внимание при выборе
- Условия использования
- Популярные производители
Среди универсальных клеев особой популярностью пользуется клей «холодная сварка». Ключевым преимуществом этого вида продукции является простота использования и доступность разных видов. Представленный ассортимент позволяет выбрать состав, который предназначен для конкретной задачи.
Разновидности составов и область их применения
Удобно, производители заботятся о своих покупателях и создают клеи универсального и узкого применения. Для покупки достаточно определиться с кругом предстоящих задач и выбрать то, что подходит лучше всего.
Основные отличия касаются материалов, с которыми справится клей, и особенностей внешних условий.
Общий перечень видов клея:
- универсальный;
- для склеивания стыков линолеума и деталей из ПВХ;
- для металла.
Есть как жидкая двухкомпонентная смесь, где вторым ингредиентом является отвердитель, так и однокомпонентная «сварка» в брикетах, внешне похожая на пластилин. Различия в составах практически не влияют на результат, а вот объем действительно важен.
Отдельным видом является высокотемпературная «сварка», по своим техническим характеристикам она имеет максимальную температуру плавления и распада клеевой композиции.
Особенности состава по видам
В зависимости от назначения в состав клея входят различные наполнители и дополнительные ингредиенты.
- В «холодную сварку» для соединения деталей из ПВХ добавляют растворители, под воздействием которых образуется прочный шов. В большинстве случаев это готовая к применению эмульсия, упакованная в металлическую тубу.
- Составы для склеивания металлов содержат оксид железа, микрогранулы металлов, кварц и другие компоненты, обладающие высокой адгезией к большинству видов материалов — стеклу, керамике, металлическим и деревянным поверхностям, пластику. Таким образом, можно эффективно комбинировать совершенно разные по химическому составу детали.
- Универсальный клей «холодная сварка» чаще всего изготавливается на основе эпоксидной смолы, дополненной разнообразными компонентами, но определенного стандарта по составу нет.
Универсальный клей самый прочный среди всех видов, устойчив к воде, растворителям, бензину и другим агрессивным жидкостям. Часто универсальный клей имеет пометку «экспресс», что говорит о сверхбыстром схватывании.
К универсальным клеям также относят контактный эпоксидный клей, изготавливаемый на основе эпоксидной смолы.
Область применения: какие материалы можно «сваривать»
Производитель всегда указывает на упаковке для склеивания, для каких материалов подходит тот или иной состав. Общая классификация по видам имеет ряд подгрупп по назначению, чаще всего это относится к «холодной сварке» для металлов: для алюминия, для чугуна, для свинца и др.
Составы узкого применения следует применять по назначению. Если на упаковке нет конкретных указаний, можно придерживаться стандартных правил использования.
- Клей по металлу Предназначен для соединения деталей из черных и цветных металлов: меди, серебра, свинца, чугуна, алюминия и др.
- ПВХ-компаунды прекрасно соединяют трубы из жесткого пластика, эффективно «сваривают» стыки линолеума, виниловой плитки и других изделий из ПВХ.
- Клей универсальный Предназначен для соединения металла, резины, керамики, в том числе пригоден для работы под водой.
- Высокотемпературный или термостойкий клей, применяемый для склеивания изделий из черных и цветных металлов, керамики, термостойких пластмасс.
- Клей эпоксидный «Контакт» применяется для склеивания фаянса, фарфора, дерева, металла и различных металлических сплавов, стекла.
Технические характеристики — на что обратить внимание при выборе
Как правило, основные характеристики клеев схожи, но учитывая разнообразие предложений от производителей, при покупке следует ознакомиться с особенностями.
- Время схватывания и время склеивания. Это разные понятия. Время схватывания определяет, когда состав начинает твердеть. Пока клей не «схватился», соединяемые детали можно более точно подгонять и перемещать.
Время схватывания указывает, когда состав полностью затвердеет.
- Рекомендуемая температура использования. У разных видов этот показатель может колебаться в среднем от –20°С до +15°С. Серьезное отклонение может повлиять на химический состав клея, и его эффективность снизится.
- Термическое сопротивление. Среднее значение для всех видов «холодной сварки» составляет до +260°С, этого более чем достаточно для внутренних и наружных работ. Если область использования связана с большими колебаниями температуры, стоит обратить внимание на высокотемпературные виды, их максимальный предел может достигать +1300°С.
- Расход клея. Этот показатель неоднозначный, все зависит от плотности соединяемых деталей и квалификации пользователя. Если используется пастообразный клей, то стандартного тюбика 60 мл хватит на шов 25-30 м. Расход пластиковых компаундов можно регулировать самостоятельно: наносить тонким или толстым слоем.
- Цветовая композиция. Это важный критерий, если клей используется для декоративных работ.
Гамма на рынке включает несколько основных цветов: прозрачный, белый, черный, серый.
Условия использования
Использовать клей «холодная сварка» достаточно просто, процесс соединения элементов не предполагает сложных манипуляций.
Склеиваемые поверхности рекомендуется подготовить:
- очистить мелкой наждачной бумагой;
- очистить от крупной и мелкой пыли;
- обезжирить ацетоном.
При использовании пластиковых составов влажные детали можно склеивать, при этом клей равномерно распределяется по поверхности до появления первого сцепления.
Если объем работы небольшой, то можно разделить нужную часть клея и отвердителя. Активированный состав следует наносить в течение 10 минут для обычных видов или сразу после смешивания – для клея с пометкой «экспресс» или «секундный».
После нанесения клея детали соединяют и выдерживают до полного схватывания, в среднем 20 минут. Если фиксация изделий невозможна, следует использовать составы с минимальным временем первого схватывания – «экспресс», «второй».
Наконечник
Для сокращения времени высыхания в 2-3 раза допускается подогрев клея. Можно использовать промышленный фен, в крайнем случае подойдет обычный бытовой с максимальным температурным режимом.
После полной полимеризации поверхность клея можно шлифовать, красить, покрывать отделочными материалами.
Популярные производители
«Холодная сварка» выполняется как иностранными, так и отечественными компаниями. Российские товары отличаются доступной стоимостью, но иногда уступают по качеству европейским фирмам.
Среди компаний-лидеров выделяется «тройка лидеров»:
- Hi-Gear;
- Абу;
- «Полимет».
Среди узкоспециализированных марок стоит отметить «Тангит» — компания производит различные средства герметизации инженерных коммуникаций и выпускает качественный клей для «сварки» труб.
Клей «Холодная сварка» сочетает в себе широкий спектр применения, простоту применения и доступную стоимость. Для достижения стойкого результата от пользователя не требуются специфические навыки или знания, достаточно соблюдать простые правила использования и следовать рекомендациям производителя.
сварка — определение холодной сварки по The Free Dictionary
холодная сварка
n.
Сварка двух материалов под высоким давлением или в вакууме без использования тепла.
холодная сварка v.
Словарь английского языка American Heritage®, пятое издание. Авторские права © 2016, издательство Houghton Mifflin Harcourt Publishing Company. Опубликовано издательством Houghton Mifflin Harcourt Publishing Company. Все права защищены.
холодная сварка
vb
(Металлургия) ( tr ) для соединения (двух металлических поверхностей) без нагрева путем прижатия их друг к другу так, чтобы оксидные пленки разрушались и происходило сцепление
холодная сварка 9 n
Коллинз английский словарь английского языка-Полный и неопроверенный, 12-е издание 2014 © Harpercollins Publishers 1991, 1994, 1998, 2000, 2003, 2006, 2007, 2009, 2011, 2014
Cold-Weld
.

Gerund: cold-welding
ImperativePresentPreteritePresent ContinuousPresent PerfectPast ContinuousPast PerfectFutureFuture PerfectFuture ContinuousPresent Perfect ContinuousFuture Perfect ContinuousPast Perfect ContinuousConditionalPast Conditional
Imperative |
---|
cold-weld |
cold-weld |
Присутствует |
---|
I холодная сварка |
you cold-weld |
he/she/it cold-welds |
we cold-weld |
you cold-weld |
they cold-weld |
Preterite |
---|
I Холодный загрязненный |
У вас холодный пакет |
HE/она/IT Cold Welled |
We/It Holdded |
We/It Holdded |
We/It Holdded |
We/It |
.![]() |
Присутствие непрерывного |
---|
I AM AM AME COLD-WELDING |
HERSE-WELDIND |
HE/SHERELDIND |
HE/SHELDIND |
HE/SHELDIND |
HE/SHELDIND |
. |
вы холодносварные |
они холодносварные |
настоящее совершенное | |
---|---|
у меня холодносварные | 0200 |
he/she/it has cold-welded | |
we have cold-welded | |
you have cold-welded | |
they have cold-welded |
Past Continuous |
---|
Я был холодным белком |
Вы были холодными.0197 |
they were cold-welding |
Past Perfect |
---|
I had cold-welded |
you had cold-welded |
he/she/it had cold-welded |
У нас были холодные варианты |
У вас были холодные |
У них были холодные |
Он/она/это будет холодно-бешеной |
We Cold-Weld |
. |
у меня будет холодносварной |
у вас будет холодносварной |
у него/неё будет холодносварной |
у нас будет холодносварной |
У них будет холодная сетка |
Future Continuous |
---|
Я буду холодным. -сварка |
у нас будет холодная сварка |
у вас будет холодная сварка |
у нас будет холодная сварка |
я занимался холодной сваркой |
ты занимался холодной сваркой |
он/она/оно занимался холодной сваркой |
ты занимался холодной сваркой |
они были холодной сваркой |
Future Perfect Continuous |
---|
я буду холодной сваркой |
он/она/оно будет холодной сварки |
мы будем холодной сварки |
вы будете холодной сварки | они будут холодной сварки |
Прошлое идеальное непрерывное |
---|
Я был холодным белдом |
Вы были холодными |
.![]() |
you had been cold-welding |
they had been cold-welding |
Conditional |
---|
I would cold-weld |
you would cold-weld |
he / она / это будет холодная сварка |
мы будем холодная сварка |
вы будете холодная сварка |
они будут холодная сварка |
Collins English Verb Tables © HarperCollins Publishers 2011
Сварка холодным переносом металла от AA6061 до AA7075: механические свойства и коррозия | Дж. Инж. Матер. Технол.
Пропустить пункт назначения навигации
Научная статья
Нилай Чомез,
Хюлья Дурмуш
Информация об авторе и статье
1Ответственный автор.
Предоставлено Отделом материалов ASME для публикации в Journal of Engineering Materials and Technology. Рукопись получена 8 декабря 2017 г.; окончательный вариант рукописи получен 6 февраля 2019 г.; опубликовано онлайн 11 марта 2019 г. Доц. Монтажер: Халед Мурси.
Дж. Инж. Матер. Технол . июль 2019 г., 141(3): 031002 (6 страниц)
Номер статьи: МАТС-17-1367 https://doi.org/10.1115/1.4042863
Опубликовано в Интернете: 11 марта 2019 г.
История статьи
Получено:
8 декабря 2017 г.
Пересмотр получено:
6 февраля 2019 г.
Принято:
6 февраля 2019 г.
- Просмотры
- Содержание артикула
- Рисунки и таблицы
- Видео
- Аудио
- Дополнительные данные
- Экспертная оценка
- Делиться
906:40
- MailTo
- Твиттер
Иконка Цитировать Цитировать
Разрешения
- 906:40 Поиск по сайту
Ссылка
Чомез Н. и Дурмуш Х. (11 марта 2019 г.). «Сварка холодным переносом металла от AA6061 до AA7075: механические свойства и коррозия». КАК Я. Дж. Инж. Матер. Технол . июль 2019 г.; 141(3): 031002. https://doi.org/10.1115/1.4042863
Скачать файл цитаты:
- Рис (Зотеро)
- Менеджер ссылок
- EasyBib
- Подставки для книг
- Менделей
- Бумаги
- КонецПримечание
- РефВоркс
- Бибтекс
- Процит
- Медларс
Расширенный поиск
Сварка холодным переносом металла (CMT) обеспечивает множество преимуществ при сварке разнородных материалов и тонких листов благодаря превосходному механизму контроля тепловложения. В этом исследовании алюминиевые сплавы AA6061 и AA7075 были соединены сваркой CMT. Исследовано влияние параметров сварки на твердость, предел прочности при растяжении и скорость коррозии. Метод экстраполяции Тафеля применялся для определения скоростей коррозии основных металлов AA6061 и AA7075 и соединений AA6061–AA7075. Было обнаружено, что увеличение тепловложения отрицательно сказывается как на механических свойствах, так и на коррозионной стойкости. Результаты показали, что при сварке СМТ получаются соединения AA6061–AA7075, соответствующие механическим свойствам и коррозионной стойкости, а также параметры сварки, обеспечивающие низкое тепловложение.
Раздел выпуска:
Научные статьи
Ключевые слова:
сварка, АА6061, АА7075, прочность, коррозия
Темы:
Основные металлы, коррозия, Нагревать, Механические свойства, Металлы, Сварка, Алюминиевые сплавы, Прочность на растяжение
1.
Matusiak
,
J.
и
Wyciślik
,
J.
,
2013
, «
Анализ Влияния Материала. Полярность MIG -сварка алюминиевых сплавов на эмиссии сварочных паров
, ”
Biuletyn Instytutu Spawalnictwa
,
4
, с.
5
—
21 99
5
—
9000 21 99 99 9 5—
21 99 999 9
—
21 99
.0003
.
2.
Ishak
,
M.
,
Noordin
,
N. F. M.
,
Hakim
,
L.
, and
Shah
,
A.
,
2015
, «
Технико-экономическое обоснование соединения разнородных алюминиевых сплавов AA6061 и AA7075 с помощью вольфрамового инертного газа (TIG)
J. Teknol J.
». (тех. наук),
75
(
7
), стр.
79
–
84
.
3.
Guo
,
J. F.
,
Chen
,
H. C.
,
Sun
,
C. N.
,
Bi
,
G.
,
Вс
,
Z.
и
WEI
,
J.
,
2014
, «
Сварка трений с разнообразными материалами между AA6061 и AA7075 AL -сплавы Эффекты параметров процесса
»,
. Mater. Дес.
,
56
, стр.
185
–
192
.
4.
Борхерс
,
Т. Е.
,
Сейд
,
A.
,
Babu
,
S. S.
,
Shafer
,
P.
, and
Zhang
,
W.
,
2015
, «
Влияние присадочного металла и послесварочной обработки трением с перемешиванием на склонность к коррозионному растрескиванию дуговых сварных швов Al–Zn–Mg
»,
Sci. Технол. Сварка. Джой.
,
20
(
6
), стр.
460
–
467
.
5.
Bahemmat
,
P.
,
Haghpanahi
,
M.
,
Besharati
,
M. K.
,
Ahsanizadeh
,
S.
и
Rezaei
,
H.
,
2010
, «
Исследование механических, микро- и макроструктурных характеристик разнородной сварки трением с перемешиванием AA6061-T6 и AA7075-T6
»,
Proc. Инст. мех. англ. Б-Дж. англ.
,
224
(
12
), стр.
1854
–
1864
6.
Мезраг
,
Б.
,
Дешо-Бом
,
F.
и
Benachour
,
M.
,
2015
, «
Контроль массы и теплопередачи для соединения стали/алюминия с использованием холодного металла
», »
Науч. Технол. Сварка. Джой.
,
20
(
3
), с.
7.
Ахсан
,
M. R.
,
Kim
,
Y. R.
,
Ashiri
,
R.
,
Cho
,
Y. J.
,
Jeong
,
C.
и
Park
,
Y. D.
,
2016
, «
Перенос холодного металла (CMT) Gmaw из стали с цинком
»,
Сварка.
,
95
(
4
), стр.
120
–
132
3 .
8.
Elrefaey
,
A.
,
2015
, «
Эффективность процесса передачи холодного металла для сварки 7075 алюминиевых сплав
»,
SCA. Технол. Сварка. Джой.
,
20
(
4
), стр.
280
–
285
.
9.
Efzan
,
E.
,
Kovalan
,
K. V.
, and
Suriati
,
G.
,
2012
, “
Обзор параметров сварки на коррозионное поведение алюминия
”,
Int. Дж. Инж.
,
1
(
1
), стр.
2305
–
8269
.
10.
Jariyaboon
,
M.
,
Davenport
,
A. J.
,
Ambat
,
R.
,
Connolly
,
B. J.
,
Williams
,
S. W.
и
Цена
,
D. A.
,
2006
, «
Коррозия разнородных алюминиевых сплавов трением с перемешиванием, соединяемых AA2024 и AA7010
0», 23 Corros

,
41
(
2
), с.
11.
Рагураман
,
Д.
,
Муруганандам
,
D.
, and
Dhas
,
L. K.
,
2014
, “
Corrosion Study in Friction Stir Welded Plates of AA6061 and AA7075
,”
Int. Дж. ХимТех Рез.
,
6
(
4
), стр.
2577
–
2582
3 9
12.
Шринивасан
,
П. Б.
,
Dietzel
,
W.
,
Zettler
,
R.
,
Dos Santos
,
J. F.
, and
Sivan
,
V.
,
2005
, «
Склонность к коррозионному растрескиванию под напряжением при сварке трением с перемешиванием AA7075–AA6056 Разнородное соединение
»,
Mater. науч. англ. А
,
392
(
1–2
), стр.
292
–
300
.
13.
Sathish
,
R.
, and
Rao
,
V. S.
,
2014
, “
Corrosion Studies on Friction Welded Dissimilar Aluminum Alloys of AA7075- T6 и AA6061-T6
»,
Междунар. Дж. Электрохим. науч.
,
9
, стр.
4104
–
4113
.
14.
Zhang
,
Y. M.
,
Pan
,
C.
, and
Male
,
A. T.
,
2000
, “
Улучшенная микроструктура и свойства сварных швов из алюминиевого сплава 6061 с использованием процесса двусторонней дуговой сварки
»,
Металл. Матер. Транс. А
,
31
(
10
), стр.
2537
–
2543
15.
Ambriz
,
R. R.
,
Froustey
,
C.
, and
Mesmacque
,
G.
,
2013
, “
Определение поведения при растяжении при средней скорости деформации сварных швов из алюминиевого сплава AA6061-T6
»,
Междунар. Дж. Воздействие. англ.
,
60
, стр.
107
–
119
.
16.
Stathers
,
P. A.
,
Hellier
,
A. K.
,
Harrison
,
R. P.
,
Ripley
,
M. I.
и
Норриш
,
J.
,
2014
, «
Взаимосвязь свойств твердости и прочности на растяжение для ЗТВ в 6061T651 Алюминий
», We
ld.
,
93
, стр.
301
–
311
.
17.
HU
,
B.
и
Richardson
,
I. M.
,
2007
, «
,
2007
,«
0003Микроструктура и механические свойства гибридных сварных швов AA7075(T6) лазером/GMA
”,
Материал. науч. англ. А
,
459
(
1–2
), стр.
94
–
100
3 .
18.
Bauccio
,
M.
,
1993
,
ASM Metals Справочник
,
ASM International
,
Округ Джога, Огайо, США
, с.
614
.
19.
Mutombo
,
K.
, and
Du Toit
,
M.
,
2011
, “
Corrosion Fatigue Behaviour of Aluminum Alloy 6061-T651 Сварка с использованием полностью автоматической дуговой сварки металлическим электродом в среде защитного газа и присадочного сплава ER5183
”,
Int. J. Усталость
,
33
(
12
), стр.
1539
–
1547
.
20.
Xie
,
W. F.
,
Fan
,
C. L.
, and
Yang
,
C. L.
,
2016
, “
Импульсная ультразвуковая волновая сварка GMAW из алюминиевого сплава 7A52
»,
Weld. Дж.
,
95
(
7
), с.
21.
Ravikumar
,
S.
,
Rao
,
V. S.
, and
Pranesh
,
R. V.
,
2014
, “
Влияние параметров процесса на механические свойства сваренных трением с перемешиванием разнородных материалов из сплавов AA6061-T651 и AA7075-T651
»,
Междунар. Дж. Адв. мех. англ.
,
4
(
1
), стр.
101
–
114
3
22.
Rajakumar
,
S.
,
Muralidharan
,
C.
, and
Balasubramanian
,
V.
,
2011
, “
Прогнозирование прочности на растяжение, твердости и скорости коррозии соединений из алюминиевого сплава AA6061-T6, сваренных трением с перемешиванием
»,
Матер. Дес.
,
32
(
5
), стр.
2878
–
2890
3 .
23.
El-Menshawy
,
K.
,
El-Sayed
,
A. W. A.
,
El-Bedawy
,
M. E.
,
Ahmed
,
Х. А.
и
El-Raghy
,
S. M.
,
2012
, «
Влияние времени старения при низких температурах старения на коррозию алюминиевого сплава 6061
»,
Corrros. науч.
,
54
, стр.
167
–
173
.
24.
Венугопал
,
А.
,
Панда
,
Р.
,
Manwatkar
,
S.
,
Sreekumar
,
K.
,
Krishna
,
L. R.
, and
Sundararajan
,
G.
,
2012
, «
Влияние обработки микродуговым оксидированием на поведение локальной коррозии алюминиевого сплава AA7075 в 3,5% растворе NaCl
»,
Trans. Цветные металлы. соц. Китай
,
22
(
3
), стр.
700
–
710
3
25.
Andreatta
,
F.
,
Terryn
,
H.
, and
De Wit
,
J. H.
,
2004
, «
Коррозионное поведение алюминиевого сплава AA7075 при различных температурах
»,
Электрохим. Acta
,
49
(
17–18
), стр.
2851
–
50002 10032 9.26.
FAHIMPOUR
,
В.
,
Sadrnezhaad
,
S. K.
и
Karimzadeh
3
.Коррозионное поведение алюминиевого сплава 6061, соединенного методами сварки трением с перемешиванием и дуговой сварки вольфрамовым электродом в среде защитного газа
»,
Матер. Дес.
,
39
, стр.
329
–
333
.
27.
Davis
,
J. R.
,
1999
,
Corrosion of Aluminum and Aluminum Alloys
,
ASM International
,
Geauga County, OH
, p .
313
.
28.
Heinz
,
B.
и
Skrotzki
,
B.
,
2002
, «
».
Металл. Матер. Транс. Б
,
33
(
3
), с.
29.
Флеминг
,
K. M.
,
ZHU
,
A.
и
Scully
,
J. R.
,
2012
, ‘
,
2012
,‘
,
2012
, ‘
. Alloy: Effects of Si on Metallurgical and Corrosion Behavior
,”
Corrosion
,
68
(
12
), pp.
1126
–
1145
.
30.
Katsas
,
S.
,
Nikolaou
,
J.
, and
Papadimitriou
,
G.
,
2007
, «
Коррозионная стойкость ремонтных сварных алюминиевых сплавов
»,
Mater. Дес.
,
28
(
3
), стр.
831
–
836
.
31.
Ghali
,
E.
,
2010
,
Коррозионная стойкость алюминия и сплавов с магниями: понимание, производительность и испытания
,
John Wiley & SN. ,
Нью-Джерси
, с.
640
.
32.
Martienssen
,
W.
и
Warlimont
,
H.
,
2006
,
Справочник Springer Справочник конденсированного вещества и материалов
,
Springer
,
New York
, стр.
,
, стр.
,
.
33.
Halambek
,
J.
,
Bubalo
,
M. C.
,
Redovniković
,
I.0150, и
Berković
,
K.
,
2014
, «
Коррозионное поведение алюминия и AA5754. . Дж. Электрохим. науч.
,
9
(
10
), стр.
5496
–
5506
3 .
34.
Варгель
,
С.
,
2004
,
Коррозия алюминия
,
Elsevier
,
Оксфорд
- 3 90
- Димидук Д.М.; Перепецко, Ю.Х. Сплавы Mo-Si-B: разработка революционного материала для газотурбинных двигателей. Миссис Бык. 2003 , 28, 639–645. [Google Scholar] [CrossRef]
- Лемберг, Дж. А.; Ричи, Р.О. Сплавы Mo-Si-B для сверхвысокотемпературных конструкционных применений. Доп. Матер. 2012 , 24, 3445–3480. [Академия Google] [CrossRef] [PubMed]
- Ochiai, S. Улучшение стойкости к окислению и структуры окалины интерметаллического сплава Mo 3 Si за счет добавления элементов хрома и алюминия.
Интерметаллиды 2006 , 14, 1351–1357. [Google Scholar] [CrossRef]
- Rioult, FA; Имхофф, С.Д.; Сакиджа, Р .; Перепецко, Ю.Х. Переходное окисление сплавов Mo-Si-B: влияние масштаба микроструктуры. Acta Mater. 2009 , 57, 4600–4613. [Google Scholar] [CrossRef]
- Росалес, И.; Мартинес, Х .; Бахена, Д.; Руис, Дж. А.; Гардиан, Р .; Колин, Дж. Характеристики окисления Mo 3 Si с добавками Al. Коррос. науч. 2009 , 51, 534–538. [Google Scholar] [CrossRef]
- Ян, Ю.; Бей, Х .; Чен, С .; Джордж, EP; Тайли, JY; Чанг А. Влияние Ti, Zr и Hf на фазовую стабильность сплавов Moss+Mo 3 Si+Mo 5 SiB 2 при 1600 °C. Acta Mater. 2010 , 58, 541–548. [Google Scholar] [CrossRef]
- Акинц, М.; Мейер, М.К.; Крамер, MJ; Том, Эй Джей; Хюбш, Дж. Дж.; Кук, Б. Силициды молибдена, легированные бором, для конструкционных применений.
Матер. науч. англ. А 1999 , 261, 16–23. [Google Scholar] [CrossRef]
- Nieh, T.G.; Ван, Дж. Г.; Лю, К.Т. Деформация многофазного сплава Mo-9,4Si-13,8B при повышенных температурах. Интерметаллиды 2001 , 9, 73–79. [Google Scholar] [CrossRef]
- Рэй, П.К.; Е, Ю.Ю.; Акинц, М .; Крамер, М. Дж. Влияние замещения Nb и W на стабильность фазы A15 Mo 3 Si. Дж. Эллой. комп. 2012 , 537, 65–70. [Google Scholar] [CrossRef]
- Сакиджа Р.; Перепецко, Дж. Х.; Ким, С .; Секидо, Н. Фазовая стабильность и структурные дефекты в жаропрочных сплавах Mo-Si-B. Acta Mater. 2008 , 56, 5223–5244. [Google Scholar] [CrossRef]
- Генг Т.; Ли, К .; Чжао, X .; Сюй, Х .; Ду, З .; Guo, C. Термодинамическая оценка системы Nb-Si-Mo. Дж. Эллой. комп. 2010 , 34, 363–376. [Google Scholar] [CrossRef]
- Таката, Н.; Секидо, Н.; Такэяма, М .
; Перепецко, Дж. Х.; Фоллетт-Фигероа, М.; Чжан, К. Затвердевание трехфазной микроструктуры Bcc/T1/T2 в сплавах Mo-Nb-Si-B. Интерметаллиды 2016 , 72, 1–8. [Академия Google] [CrossRef]
- Нуньес, Калифорния; Сакиджа, Р .; Донг, З .; Перепецко, Ю.Х. Проекция ликвидуса для богатой молибденом части тройной системы Mo-Si-B. Интерметаллиды 2000 , 8, 327–337. [Google Scholar] [CrossRef]
- Катрич С.; Грицив, А.; Бондарь, А .; Рогл, П.; Великанова Т.; Бон, М. Конструкционные материалы: металл-кремний-бор: о поведении сплавов Mo-Si-B при плавлении. Дж. Эллой. комп. 2002 , 347, 94–100. [Google Scholar] [CrossRef]
- Крюгер, М.; Франц, С .; Сейдж, Х .; Хайльмайер, М.; Шнайбель, Дж. Х.; Джеханно, П .; Бонинг, М .; Кестлер, Х. Механически легированные сплавы Mo-Si-B со сплошной матрицей α-Mo и улучшенными механическими свойствами. Интерметаллиды 2008 , 16, 933–941. [Google Scholar] [CrossRef] «> Хассомерис, О.; Шумахер, Г.; Крюгер, М .; Хайльмайер, М.; Банхарт, Дж. Непрерывность фаз в высокотемпературных сплавах Mo-Si-B: исследование FIB-томографии. Интерметаллиды 2011 , 19, 470–475. [Google Scholar] [CrossRef]
- Ли Б.; Чжан, Г.Дж.; Цзян, Ф .; Рен, С .; Лю, Г.; Сан, Дж. Получение мелкозернистых сплавов Mo-12Si-8.5B с улучшенными механическими свойствами с помощью процесса механического легирования. Дж. Эллой. комп. 2014 , 609, 80–85. [Google Scholar] [CrossRef]
- Byun, JM; Банг, С.-Р.; Ким, С.Х.; Чой, WJ; Ким, Ю.Д. Механические свойства четверного сплава Mo-Nb-Si-B, полученного методом порошковой металлургии. Междунар. Дж. Преломление. Встретились. Жесткий Матер. 2017 , 65, 14–18. [Google Scholar] [CrossRef]
- Lei, R.S.; Ван, член парламента; Ли, З .; Вэй, HG; Ян, WC; Цзя, Ю.Л.; Гонг, С. Эволюция структуры и увеличение растворимости медно-ниобиевых порошков в твердом состоянии во время механического сплавления.
Матер. науч. англ. А 2011 , 528, 4475–4481. [Google Scholar] [CrossRef]
- Ян Т.; Го, XP; Луо, Ю.К. Эволюция микроструктуры механически легированных порошков Mo-Si-B-Zr-Y. Междунар. Дж. Преломление. Встретились. Жесткий Матер. 2016 , 56, 35–43. [Google Scholar] [CrossRef]
- Zhong, Y.; Пинг, Д.; Песня, X .; Инь, Ф. Определение размера зерна с помощью анализа профиля XRD и подсчета ПЭМ в наноструктурированной меди. Дж. Эллой. комп. 2009 , 476, 113–117. [Академия Google] [CrossRef]
- Унгар, Т.; Тичи, Г .; Губича, Дж.; Хельмиг, Р.Дж. Корреляция между субзернами и доменами когерентного рассеяния. Порошок Дифф. 2005 , 20, 366–375. [Google Scholar] [CrossRef][Зеленая версия]
- Агилар, К.; Ордоньес, С.; Гусман, Д.; Рохас, П.А. Механическое легирование сплавов Cu–xCr (x = 3, 5 и 8 мас.%). Дж. Эллой. комп. 2010 , 504, 102–109. [Google Scholar] [CrossRef] «> Сурьянараяна, К. Механическое легирование и фрезерование. прог. Матер. науч. 2001 , 46, 1–184. [Google Scholar] [CrossRef]
- Чжан С.; Го, Х.П. Влияние добавки бора на микроструктуру и свойства сверхвысокотемпературных сплавов на основе силицида ниобия. Интерметаллиды 2015 , 57, 83–92. [Google Scholar] [CrossRef]
- Сакиджа Р.; Ким, С .; Парк, Дж.; Перепецко, Ю.Х. Легирование переходных металлов и фазовая стабильность в системе Mo-Si-B. Симпозиум по свойствам дефектов и связанным с ними явлениям в интерметаллических сплавах. В Proceedings of the MRS Fall Meeting 2002, Бостон, Массачусетс, США, 3–5 декабря 2002 г. [Google Scholar]
700
.
35.
Trueba
,
M.
и
Trasatti
,
S. P.
,
2010
, «
Исследование Al Alloy Corrosion в NACL NACL NACL NACL NACL. Техника сканирования
»,
Матер. хим. физ.
,
121
(
3
), с.
В настоящее время у вас нет доступа к этому содержимому.
$25,00
Покупка
Товар добавлен в корзину.

Металлы | Бесплатный полнотекстовый | Влияние содержания Nb на механическое поведение сплавов и спеченную микроструктуру сплавов Mo-Nb-Si-B
1. Введение
Сплавы Mo-Si-B, как многообещающие сверхвысокотемпературные конструкционные материалы, привлекли большое внимание в последние несколько лет. десятилетия. Типичный сплав Mo-Si-B состоит из твердого раствора Mo (Moss) и фаз Mo 3 Si (A15) и Mo 5 SiB 2 (T2) [1,2]. Как самый богатый Mo силицид молибдена, Mo 3 Si-фаза показывает плохую стойкость к окислению из-за низкого содержания Si и предельной растворимости B [3,4,5,6]. Кроме того, гораздо более высокая плотность дислокаций в Mo 3 Si, чем в Mo 5 Si 3 (T1) и Mo 5 SiB 2 в испытаниях на ползучесть при повышенных температурах [7, 8], свидетельствует о том, что сверхвысокотемпературная прочность Mo 3 Si неудовлетворительна. В результате подавление продукта Mo 3 Si в упрочняющем мох сплаве на основе Mo-Si-B может привести к повышению стойкости к окислению и прочности при повышенных температурах. Как показано в ссылках [9,10], достаточное растворение Nb, W и Ta в Mo 3 Si может привести к его дестабилизации. Как более легкий элемент по сравнению с Mo, легирование Nb может снизить плотность сплава Mo-Si-B, что демонстрирует большую привлекательность, чем легирование W и Ta. К сожалению, образование пористого и нелетучего Nb 2 O 5 во время окисления задерживает образование защитного боросиликата, который, таким образом, отрицательно влияет на стойкость к окислению сплава Mo-Si-B. В результате определение критического содержания Nb для подавления Mo 3 Si в сплаве Mo-Nb-Si-B, а не чрезмерное добавление Nb, имеет большое значение. Однако, насколько известно авторам, в предыдущих работах основное внимание уделялось стабильности Mo 3 Si в системе Mo-Nb-Si теоретически [11] или экспериментально [9].
Таката и др. В работе [12] изучено развитие микроструктуры нескольких сплавов Mo-Nb-Si-B состава Mo-32,6Nb-xSi-yB (ат. %, далее все составы даны в ат. %, если не указано иное), изготовленных с использованием дуговое литье и направленное затвердевание. Была успешно получена микроструктура Moss+T1+T2. Однако, определяемый путями их кристаллизации, первичная фаза T2 большого размера неизбежна в этих сплавах, полученных в процессе плавки [13,14]. Образование этой первичной фазы Т2 большого размера, безусловно, отрицательно сказывается на вязкости разрушения сплавов. Механическое сплавление (МА) с последующим процессом спекания облегчает изготовление сплава на основе Mo-Si-B с непрерывной матрицей Мосса [15,16,17]. Бьюн и др. [18] изготовлен Мо-16.9Сплавы Nb-3Si-1B (мас.%) методом порошковой металлургии. В их исследовании сплав, содержащий ниобий, показал более низкую твердость (425 против 590 Hv) и более высокую вязкость разрушения (14,5 против 12,6 МПа·м 1/2 ), чем у сплава, не содержащего ниобия.
Стоит отметить, что этого содержания Nb недостаточно для дестабилизации Mo 3 Si, и сплав по-прежнему состоит из Moss, Mo 3 Si и Mo 5 SiB 2 . Чтобы подавить фазу Mo 3 Si, необходимо большое количество добавленного Nb, что, безусловно, повлияет на поведение порошковых смесей Mo-Nb-Si-B при МА. В отличие от процесса затвердевания, составляющие элементы в процессе спекания проявляют более низкую диффузионную способность. В результате распределение элементарного Nb в различных фазах в спеченных сплавах может отличаться от такового в затвердевших сплавах, что повлияет на фазовые составляющие сплава и критическое содержание добавки Nb для подавления Мо 3 Si фаза. Кроме того, предварительная степень МА порошковых смесей также может влиять на микроструктуру спеченного сплава. Поэтому в настоящей статье основное внимание будет уделено влиянию содержания Nb на поведение МС и спеченную микроструктуру четверных сплавов Mo-Nb-Si-B, чтобы заложить основу для изготовления сплавов, не содержащих Si, Mo 3 с использованием порошковой металлургии.
2. Материалы и методы
Порошковые смеси элементов Mo и Nb (Zhuzhou Cemented Carbide Group Co. Ltd., Чжучжоу, Китай), Si и аморфного B (Sinopharm Chemical Reagent Co. Ltd., Шанхай, Китай), с чистотой 99% или лучше взвешивали в соответствии с Mo-12Si-10B-xNb (сокращенно xNb, x = 10, 20, 22, 24, 26, 28, 30 и 40). Размер ячеек частиц порошка Mo, Nb, Si и B составлял –300/+600 (23–48 мкм), –300/+600 (23–48 мкм), –200/+400 (38–75 мкм). и -800/+1000 (13–18 мкм) соответственно. Процессы МА проводили в планетарной шаровой мельнице (QM-1SP4-CL, Nanjing Nanda Instrument Plant, Нанкин, Китай) в атмосфере аргона с использованием ампул и шариков из закаленной нержавеющей стали. Для всех случаев скорость измельчения и соотношение шариков к порошку были зафиксированы на уровне 400 об/мин и 15:1 соответственно. Время измельчения было установлено равным 10, 30, 50 и 80 ч соответственно. Измельченные порошки массой около 2 г подвергали холодному прессованию в тонкие диски (диаметром 12 мм) при давлении около 500 МПа и времени выдержки около 60 с на машине холодного прессования (YLJ-24T-SJ, Hefei Kejing Materials). Technology Co. Ltd., Хэфэй, Китай). Спекание этих тонких дисков проводили в печи с атмосферой аргона (HVHS-II, Shenyang Jinyan New Material prepare Technology Co.Ltd., Шэньян, Китай) при 1773 К в течение 2 часов. Подробности условий переработки и сокращенные наименования продуктов приведены в табл. 1.
Рентгеноструктурный анализ (XRD, Panalytical X’Pert PRO, Malvern Panalytical, Алмело, Нидерланды) использовали для характеристики фазовых составляющих с медной мишенью (λ Kα1 = 0,154 нм). Для точного рентгеноструктурного анализа спеченные образцы после шлифовки их поверхности измельчали в порошок. Формула Вильямсона–Холла использовалась для расчета размера домена когерентного рассеяния (размера домена) и микродеформации. Для расчета параметра решетки использовались методы Коэна. Микроструктурный и композиционный анализы проводили с помощью сканирующего электронного микроскопа (SEM, Tescan Mira3, Tescan Company, Брно, Чехия), оснащенного энергодисперсионным анализатором рентгеновского спектра (EDS, Inca X-sight, Oxford Instruments, Oxford, Англия). Для наблюдения микроструктуры их поперечного сечения измельченные частицы порошка и спеченные образцы были залиты эпоксидной смолой, механически отшлифованы, а затем отполированы. Для статистического анализа применяли программное обеспечение Image-Pro Plus 6.0 (IPP, Media Cybernetics Inc., Rockville, MD, USA).
3. Результаты и обсуждение
3.1. Поведение при механическом легировании
На рис. 1 показаны морфологические изображения во вторичных электронах (SE) порошков с различным содержанием Nb после 50 ч измельчения и соответствующее распределение частиц по размерам, рассчитанное с помощью IPP. Из-за изменения содержания Nb морфология частиц показала значительные различия после тех же 50 часов измельчения. Для образца МА-10Нб/50ч можно было обнаружить как одиночные частицы, так и более крупные агломераты. Размер его частиц показал бимодальное распределение по размерам с двумя пиками при 2,1 и 10,5 мкм. Очевидно, первое представляет собой размер большинства одиночных частиц, а второе представляет собой агломераты. Образец MA-20Nb/50h также показал бимодальное распределение по размерам; однако со смещенным вправо положением пика для одиночных частиц (3,3 мкм) и влево для агломератов (8,5 мкм) по сравнению с пиками распределения по размерам образца МА-10Нб/50ч. Для образца МА-30Нб/50ч порошки в основном состоят из одиночных частиц почти сфероидальной формы. В отличие от первых двух, его размер частиц показал унимодальное распределение с одним пиком при 4,1 мкм. Подобно образцу МА-30Нб/50ч, образец МА-40Нб/50ч также показал одномодальное распределение. Однако он показал более широкое распределение и большее положение пика (4,9мкм), чем у образца МА-30Нб/50ч. Для эволюции морфологии и размера частиц во время измельчения добавление Nb показало два противоположных эффекта. С одной стороны, растворение Nb в решетке Мо увеличивало склонность частиц Мо к фрагментации и уменьшало размер частиц [19,20]. С другой стороны, замена Mo на более пластичный Nb увеличивала степень холодной сварки и, следовательно, частицы укрупнялись.
Ключевой механизм зависел от содержания добавки Nb. В образце МА-10Nb/50h низкое содержание Nb сделало преобладающим разрушение частиц и привело к образованию мелких одиночных частиц. В некоторых случаях эти частицы спонтанно собирались вместе, образуя более крупные агломераты, чтобы уменьшить энергию системы. С увеличением содержания Nb увеличивалась степень холодной сварки частиц, что приводило к укрупнению одиночных частиц и постепенному снижению образования агломератов.
На рис. 2 показаны изображения поперечного сечения в обратно рассеянных электронах (BSE) и результаты картирования EDS образцов MA-10Nb/50h и MA-20Nb/50h. В образце МА-10Нб/50ч можно было наблюдать однородную сливовую микроструктуру, аналогичную нашему предыдущему наблюдению [20]. Между тем, в образце МА-20Нб/50ч еще можно обнаружить выраженную пластинчатую структуру. Из-за их соседних атомных номеров можно было наблюдать незначительный контраст между Nb и Mo в режиме BSE. Поэтому был проведен картографический анализ EDS, чтобы выявить распределение элементов. Как показано на рисунке 2а, картографический анализ образца MA-10Nb/50h показал равномерное распределение Mo, Nb и Si. Дальнейшие анализы EDS показывают, что составы точек A и B были Mo-10,7Nb-12,7Si и Mo-11,1Nb-12,9.Si соответственно, которые приблизились к нормированному номинальному составу (76Mo-11Nb-13Si) после удаления элементного B за счет его маргинального растворения в решетке Mo [20], что означает полное растворение Nb и Si. Как показано на рис. 2b, картографический анализ образца MA-20Nb/50h методом ЭДС показал равномерное распределение Si, но неравномерное распределение Nb. Дальнейшие анализы ЭДС показали, что составы точек C и D были Mo-28,1Nb-12,5Si и Mo-16,8Nb-13,1Si соответственно, что подтверждает неравномерное распределение Nb, но полное растворение Si в этих условиях измельчения.
На рис. 3 представлены спектры РФА порошковых смесей с различным содержанием Nb после разного времени помола с результатами расчета деконволюции в диапазоне 2θ от 30° до 50° на вставке и увеличенные изображения пиков Мо(110). Во всех случаях с увеличением времени измельчения дифракционный пик уширялся, а его интенсивность уменьшалась. Увеличенные изображения пиков Mo(110) показали смещение положения пика вместе с увеличением времени измельчения, вызванное растворением Si и Nb. Расчет деконволюции для асимметричного профиля РФА образца МА-10Nb/30ч в диапазоне 2θ от 30° до 50° выявил сохранение пика Nb(110). Между тем, с увеличением времени измельчения до 50 часов хорошо симметричный профиль только для пика Mo(110) в этом диапазоне 2θ указывает на полное растворение элемента Nb. Аналогичные расчеты деконволюции показали, что для полного растворения элемента Nb в порошках 20Nb и 30Nb было необходимо 80 ч измельчения, но этого недостаточно для растворения всех атомов Nb в порошках 40Nb.
На рис. 4 показано изменение размера домена и микродеформации Мосса в четырех видах порошка (10Nb, 20Nb, 30Nb и 40Nb) с увеличением времени измельчения. Стоит отметить, что зерна в материалах, изготовленных с использованием методов интенсивной пластической деформации (ИПД), таких как МА, имеют сложную микроструктуру, включающую субзерна, блоки ячеек, ячейки дислокаций и так далее. Рентгеновская дифракция чувствительна к субструктуре зерна и концентрируется на области когерентного рассеяния [21,22,23]. В результате более разумно принять размер домена, а не размер зерна, для описания результатов расчета XRD. Во всех случаях размер домена Мосса уменьшался с увеличением времени измельчения. Однако для развития микродеформации, за исключением ее непрерывного увеличения для порошков 40Nb, микродеформация Мосса для трех других порошков показала непрерывный рост до 50 ч измельчения, за которым последовало резкое снижение. Это резкое снижение может быть связано с повышенным сопротивлением генерации новых дислокаций в решетке Мосса из-за чрезвычайно малого размера доменов [20]. Как правило, при увеличении содержания Nb от 10 до 30 ат. % размер домена Мосса уменьшался после того же времени измельчения. Усиленное растворение Nb в решетке Мо, обусловленное увеличением содержания его добавок, увеличило плотность дефектов решетки Мосса и ускорило измельчение зерна [19].]. Между тем, в порошках 40Nb избыточное добавление пластичного Nb значительно увеличивало степень холодной сварки порошков, а затем откладывало процесс измельчения зерна.
На рис. 5 показано изменение постоянной решетки Мосса для порошков 10 Nb, 20 Nb, 30 Nb и 40 Nb при увеличении времени измельчения. Как показано в нашей предыдущей работе [20], элемент B демонстрирует предельную растворимость в твердом состоянии в решетке Mo. В результате изменения постоянной решетки Мосса следует отнести к растворению атомов Si и Nb. Оба элемента образуют твердый раствор замещения с Mo. Растворение атомов Nb увеличивало постоянную решетки Мосса из-за его большего атомного радиуса по сравнению с Mo, в то время как эффект растворения Si был прямо противоположным. Для порошков 10Nb постоянная решетки Мосса непрерывно уменьшалась до 50 ч измельчения, что указывает на преобладание усадочного эффекта растворения Si в течение этого периода измельчения. После этого наблюдалось незначительное изменение постоянной решетки Мосса для последующего измельчения до 80 ч, что можно отнести к уже полному растворению Si и Nb после 50 ч измельчения, подтвержденному анализами ЭДС, как упоминалось выше. В отличие от порошков 10Nb, константа решетки Мосса для порошков 20Nb показала медленное, но монотонное увеличение до 50 часов помола, а затем явное увеличение при дальнейшем помоле до 80 часов. Это медленное увеличение постоянной решетки Мосса в течение первых 50 часов измельчения означает небольшое преобладание эффекта расширения при растворении Nb после компенсации эффекта сжатия при растворении Si. Это было вызвано повышенным растворением Nb, обусловленным более высоким содержанием его добавок в порошках 20Nb, чем в порошках 10Nb. Для порошков 20Nb, как подтверждают анализы EDS, 50 часов измельчения было достаточно, чтобы растворить все атомы Si. В результате дальнейшее измельчение до 80 ч приводило к растворению остаточных атомов Nb, что приводило к значительному увеличению постоянной решетки Мосса. В порошках 30 Nb параметр решетки Мосса показал большее значение, чем у порошков 20 Nb, после того же времени измельчения в результате дальнейшего усиленного растворения Nb при увеличении содержания Nb от 20 до 30 ат.
%. В то же время снижение постоянной решетки Мосса после того же времени измельчения, а именно ослабление растворения Nb, наблюдалось при увеличении содержания добавки Nb с 30 до 40 ат.%.
На основании приведенных выше анализов можно сделать вывод, что увеличение содержания Nb с 10 до 30 ат. % ускоряет процессы МА, такие как измельчение зерна и растворение атомов, а дальнейшее увеличение содержания Nb до 40 ат. % снижает МА процессы. МА представляет собой чередующийся процесс деформации, холодной сварки и разрушения порошков. Баланс между этими тремя подпроцессами является требованием для быстрого процесса МА [24]. Между тем добавление Nb по-разному влияет на эти три подпроцесса. Во-первых, замена Mo на более легкий Nb с тем же размером ячейки увеличила общий объем порошковых смесей при заданной общей массе. При неизменной частоте столкновений мелющих тел и объемов захваченных порошков на одно столкновение увеличение общего объема порошковых смесей замедляло подпроцесс деформации. Во-вторых, добавление Nb как более пластичного компонента, чем Mo, увеличивает степень холодной сварки порошковых смесей. Холодная сварка необходима для соединения свежей поверхности излома с целью гомогенизации состава. Между тем чрезмерная холодная сварка сдерживала разрушение частиц порошка и образование новой свежей поверхности разрушения. Это предотвратило последующую холодную сварку этих новых свежих поверхностей для дальнейшей гомогенизации состава. Наоборот, растворение Nb при помоле упрочняет частицы порошка и повышает их склонность к дроблению [19].]. Было очевидно, что от содержания Nb зависело, какой из эффектов преобладал. По-видимому, для порошков с добавкой Nb менее 30 ат. % процесс МА ускорялся с увеличением содержания добавки Nb за счет повышенной склонности к фрагментации и умеренной степени хладносваривания частиц измельченного порошка. Однако в порошках 40Nb чрезмерная холодная сварка и большой объем порошков задержали процесс МА.
3.2. Спеченная микроструктура
3.
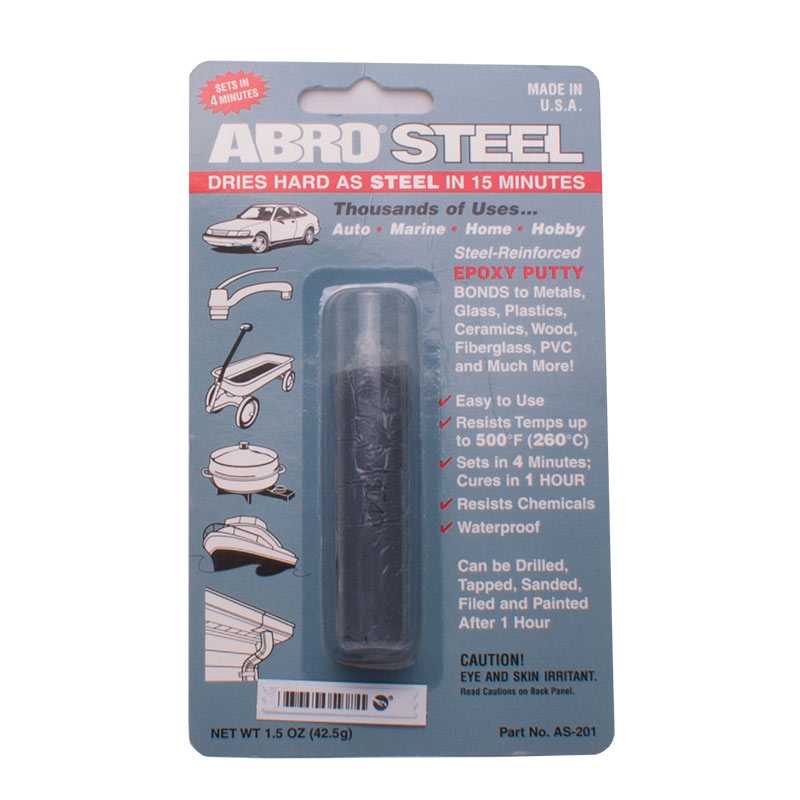
На рис. 6 представлены рентгеновские спектры спеченных образцов составов Mo-12Si-10B-xNb (x = 10, 20, 22, 24, 26, 28, 30 и 40), полученных помолом порошковых смесей для 30 ч, холодное прессование, затем спекание при 1773 К в течение 2 ч. Видно, что для этих спеченных образцов с разным содержанием Nb наблюдались два набора фазовых составляющих, а именно: Moss+Mo 3 Si+Mo 5 SiB 2 для образцов S-10Nb/30h, S-20Nb/ 30ч, С-22Нб/30ч и С-24Нб/30ч; и мох+γNb 5 Si 3 (структура D8 8 ) +Mo 5 SiB 2 для образцов S-26Nb/30h, S-28Nb/30h, S-30Nb/30h и S-40Nb/30h. Критическое содержание Nb для подавления образования фазы Mo 3 Si было найдено между 24 и 26 ат.%. На основании четырехкомпонентной фазовой диаграммы Mo-Nb-Si-B [12] для настоящих составов следует исключить фазу Nb 5 Si 3 . Образование этого неожиданного Nb 5 Si 3 следует отнести к остатку богатой Nb области после 30 ч измельчения, что подтверждается вышеупомянутыми анализами XRD и SEM, а также низкими скоростями диффузии составляющих элементы в процессе твердофазного спекания. Элементаль B стабилизировал D8 8 структура Nb 5 Si 3 в соответствии с исследованиями Zhang et al. [25].
Как показано на рис. 6, особенно на увеличенных изображениях, очевидные положения пиков, сдвинутые в сторону меньших углов, что указывает на увеличение постоянной решетки, наблюдались на дифракционных картинах Moss, Mo 3 Si и Mo 5 SiB 2 с увеличение содержания Nb. На рис. 7 показано увеличение постоянных решетки Мосса, Мо 3 Si и Мо 5 SiB 2 с увеличением содержания Nb. Независимо от образца S-40Nb/30h постоянные решетки этих трех фаз существенно линейно возрастали с увеличением содержания Nb. В то же время отклонения от результатов линейной аппроксимации в сторону меньших значений наблюдались для Moss и Mo 5 SiB 2 в образце S-40Nb/30h. Обширное образование γNb 5 Si 3 и, следовательно, подавленное растворение Nb во мхе и Mo 5 SiB 2 было ответственно за эти отклонения.
На рис. 8 представлены BSE-изображения микроструктуры спеченных образцов с различным содержанием Nb. В таблице 2 показаны соответствующие EDS-анализированные составы различных фаз, обозначенных стрелками на рисунке 8. Наблюдение BSE в сочетании с EDS-анализом подтвердило наличие яркого Moss, серого Mo 3 Si и темно-серого Mo 5 SiB 2 для образцов S-10Nb/30h и S-24Nb/30h, а также исчезновение Mo 3 Si и образование темного γNb 5 Si 3 для образцов S-26Nb/30h, S-30Nb/30h и S-40Nb/30h. Следует отметить, что из-за чрезвычайно малого размера фаз анализ ЭДС не позволяет определить состав исключительно каждой фазы. В результате результаты ЭДС использовались только для различения фазовых форм. Кроме того, хотя EDS не может точно измерить содержание B, различие между Mo 3 Si и Mo 5 SiB 2 может быть достигнуто по их очевидной разнице в содержании Si. На рис. 8g показано изменение доли площади составляющих фаз в зависимости от содержания Nb. Содержание Мо 3 Si монотонно уменьшался с увеличением содержания Nb от 10 до 24 ат.%, с последующим полным исчезновением при 26 ат.% и выше содержания Nb. При увеличении содержания Nb от 10 до 40 ат. % количество Mos непрерывно увеличивалось, а содержание Mo 5 SiB 2 сначала увеличивалось, а затем уменьшалось. В образце S-26Nb/30ч начала появляться фаза γNb 5 Si 3 , содержание которой монотонно увеличивалось с увеличением содержания Nb. Для сохранения структурной стабильности фазы Т2 геометрическое правило утверждает, что замещение Мо на Nb с большим радиусом атома в Мо 5 SiB 2 будет способствовать сопутствующей замене B на Si для относительно постоянного соотношения размеров атомов между металлом и металлоидом [26]. В результате дополнительная замена B на Si, вызванная заменой Mo на Nb в Mo 5 SiB 2 , потребляла Si, который в противном случае образовывал бы Mo 3 Si, что приводило к уменьшению Mo 3 Си содержание.
Наоборот, высвободившийся B гарантировал повышенное образование Mo 5 SiB 2 . Из-за более высокого содержания Mo в Mo 3 Si, чем в Mo 5 SiB 2 , частичная замена Mo 3 Si на Mo 5 SiB 2 способствовала образованию мха. Монотонное увеличение содержания γNb 5 Si 3 можно объяснить тем, что с увеличением содержания Nb образуется все больше и больше остатков Nb. Как показано на рисунке 8e, типичная сетка γNb 5 Si 3 наблюдалась для образца S-40Nb/30h из-за высокого остатка Nb после процесса МА. Растущее образование этого богатого кремнием и содержащего бор γNb 5 Si 3 потреблял Si и B, а затем способствовал снижению содержания Mo 5 SiB 2 , но увеличению содержания мха.
3.2.2. Влияние предшествующего процесса МА
На рис. 9 показаны рентгеновские спектры спеченных образцов с составами Mo-12Si-10B-xNb (x = 10, 20, 22, 24, 26, 28, 30 и 40), изготовленных фрезерованием. порошковых смесей в течение (а) 10 или (б) 50 ч, холодного прессования, а затем спекания при 1773 К в течение 2 ч. Взяв образцы S-xNb/30h в качестве эталона, можно увидеть, что предшествующий процесс МА оказал некоторое влияние на фазовые составляющие последующих спеченных образцов. Для образцов S-xNb/10ч уже достаточно 24 ат.% Nb для образования γNb 5 Si 3 , но для полного подавления Mo 3 Si было необходимо 28 ат.% Nb, а обогащенный Nb Nb 3 Si можно было наблюдать для образца S-40Nb/10ч. В соответствии с образцами S-xNb/30h, критическое содержание Nb для подавления образования Mo 3 Si также было обнаружено между 24 и 26 ат.% для образцов S-xNb/50h. Отличие заключалось в том, что для образца S-26Nb/50h можно было избежать γNb 5 Si 3 . Таким образом, продление предшествующего процесса измельчения способствовало подавлению Mo 3 Si и задерживает образование богатых Nb силицидов ниобия, таких как Nb 5 Si 3 и Nb 3 Si, в спеченных сплавах с увеличением содержания Nb.
Для 10-часовых измельченных порошков очевидные дифракционные пики Nb, как показано на рисунке 3, вызвали серьезное обогащение в некоторых областях частиц порошка. Низкая диффузионная способность Nb в твердом состоянии во время последующего процесса спекания способствовала предпочтительному образованию силицидов ниобия в этих богатых Nb областях. В результате растворение Nb в образующемся Mo 3 Si уменьшилось, что привело к отсроченному подавлению Mo 3 Si с увеличением содержания Nb. Для 50-часовых измельченных порошков увеличение времени измельчения способствовало однородности состава измельченных порошков, что способствовало подавлению Mo 3 Si и препятствовало образованию силицидов ниобия в спеченных сплавах.
4. Выводы
1. Повышение содержания Nb с 10 до 30 ат. % ускорило процессы МА, такие как измельчение зерна и растворение атомов, за счет повышенной склонности измельченных частиц порошка к дроблению в результате усиленного растворения Nb обусловлен повышенным содержанием добавки. Однако дальнейшее увеличение содержания Nb до 40 ат.% замедляло этот процесс из-за избыточной холодной сварки и большого объема порошков.
2. Для сплавов Mo-12Si-10B-xNb, полученных размалыванием порошков в течение 30 ч и последующим спеканием при 1773 К в течение 2 ч, критическое содержание Nb для подавления образования Mo 3 Si было найдено между 24 и 26 ат.%. Для сплавов с содержанием Nb более 26 ат. % γNb 5 Si 3 образуется за счет остатка Nb после 30 ч размола и низкой диффузионной способности Nb в твердом состоянии в процессе спекания.
3. Предыдущий процесс МА оказал некоторое влияние на фазовые составляющие последующих спеченных сплавов. Продление предшествующего процесса измельчения способствовало подавлению Мо 3 Si и задерживает образование силицидов ниобия, способствуя однородности состава размолотых порошков.
Вклад авторов
X.G. задумал и спроектировал эксперименты и руководил анализом данных; Т. Ю. проведены эксперименты и анализ экспериментальных данных. Т.Ю. написал эту рукопись. Х.Г. пересмотрел эту рукопись.
Финансирование
Работа выполнена при финансовой поддержке Национального фонда естественных наук Китая (№№ 51431003 и U1435201) и Исследовательского фонда Государственной ключевой лаборатории процессов затвердевания (NWPU), Китай (грант № 143-TZ- 2016).
Конфликт интересов
Авторы заявляют об отсутствии конфликта интересов.
Ссылки
Рисунок 1. Электронно-морфологические изображения 50-часовых помолов порошков с ( а ) 10, ( б ) 20, ( в ) 30 и ( д ) 40 ат.% Nb, и ( д ) соответствующее распределение частиц по размерам.
Рисунок 1. Электронно-морфологические изображения 50-часовых помолов порошков с ( a ) 10, ( b ) 20, ( c ) 30 и ( d ) 40 ат. % Nb и ( e )) соответствующее распределение частиц по размерам.
Рисунок 2. Изображения BSE в поперечном сечении образцов ( a ) MA-10Nb/50h и ( b ) MA-20Nb/50h и их соответствующие результаты картирования EDS.
Рисунок 2. Изображения BSE в поперечном сечении образцов ( a ) MA-10Nb/50h и ( b ) MA-20Nb/50h и их соответствующие результаты картирования EDS.
Рисунок 3. РСА порошков с ( a ) 10, ( b ) 20 , ( c ) 30 и ( d ) 40 ат.% содержания Nb после разного времени измельчения. Врезки: результаты расчета деконволюции в диапазоне 2θ от 30 до 50 градусов. ( e 1), ( e 2), ( e 3) и ( e 4 ) — увеличенные изображения для (a), (b), (c) и (d) соответственно. , в диапазоне 2θ от 39,5° до 41,5°, содержащем пики Мо(110).
Рис. 3. РФА спектры порошков с ( a ) 10, ( b ) 20, ( c ) 30 и ( d ) 40 ат.% содержания Nb после разного времени измельчения. Врезки: результаты расчета деконволюции в диапазоне 2θ от 30 до 50 градусов. ( e 1), ( e 2), ( e 3) и ( e 4 ) — увеличенные изображения для (a), (b), (c) и (d) соответственно. , в диапазоне 2θ от 39,5° до 41,5°, содержащем пики Мо(110).
Рисунок 4. Эволюция размера домена ( a ) и микродеформации ( b ) Мосса в зависимости от времени измельчения порошков 10Nb, 20Nb, 30Nb и 40Nb. Вертикальные линии — планки погрешностей.
Рисунок 4. Эволюция размера домена ( a ) и микродеформации ( b ) Мосса в зависимости от времени измельчения порошков 10Nb, 20Nb, 30Nb и 40Nb. Вертикальные линии — планки погрешностей.
Рисунок 5. Эволюция постоянной решетки Мосса в зависимости от времени измельчения для порошков 10 Nb, 20 Nb, 30 Nb и 40 Nb. Вертикальные линии — планки погрешностей.
Рисунок 5. Эволюция постоянной решетки Мосса в зависимости от времени измельчения для порошков 10 Nb, 20 Nb, 30 Nb и 40 Nb. Вертикальные линии — планки погрешностей.
Рисунок 6. Спектры XRD (логарифмические оси Y) образцов S-xNb/30h (x = 10, 20, 22, 24, 26, 28, 30 и 40). Вставка: увеличенный вид в диапазоне 2θ от 39,5° до 41,5°, содержащий Mo(110), Mo 5 SiB 2 (213) и Mo 3 Si(210) или γNb 5 Si 3 (211) пик.
Рисунок 6. Спектры XRD (логарифмические оси Y) образцов S-xNb/30h (x = 10, 20, 22, 24, 26, 28, 30 и 40). Врезка: увеличенный вид в диапазоне 2θ от 39от 0,5° до 41,5°, содержащие пики Mo(110), Mo 5 SiB 2 (213) и Mo 3 Si(210) или γNb 5 Si 3 (211).
Рисунок 7. Постоянные решетки ( a ) Moss, ( b ) Mo 3 Si и ( c ) Mo 5 SiB 2 в зависимости от содержания Nb.
Рис. 7. Постоянные решетки ( a ) Moss, ( b ) Mo 3 Si и ( c ) Mo 5 SiB 2 по сравнению с содержанием Nb.
Рисунок 8. BSE изображения микроструктуры образцов ( а ) С-10Нб/30ч, ( б ) С-24Нб/30ч, ( в ) С-26Нб/30н, ( д ) С-30Нб/ 30h, и ( e , f ) S-40Nb/30h, и ( g ) изменения доли площади составляющих фаз в зависимости от содержания Nb.
Рис. 8. BSE изображения микроструктуры образцов ( a ) S-10Nb/30h, ( b ) С-24Нб/30х, ( с ) С-26Нб/30х, ( д ) С-30Нб/30х, и ( д , ф ) С-40Нб/30х, и ( г ) изменение доли площади составляющих фаз в зависимости от содержания Nb.
Рисунок 9. Спектры РФА (логарифмические оси Y) образцов ( a ) S-xNb/10h и (b ) S-xNb/50h (x = 10, 20, 22, 24, 26, 28, 30 и 40 ).
Рис. 9. Спектры XRD (логарифмические оси Y) образцов ( a ) S-xNb/10h и ( б ) S-xNb/50h (х = 10, 20, 22, 24, 26, 28, 30 и 40).
Таблица 1. Условия и соответствующие сокращения.
Таблица 1. Условия и соответствующие сокращения.
Abbreviation of Products | Process Type | x | y |
---|---|---|---|
MA-xNb/yh | Mechanical alloying | Nb content (at.%) | Milling time (h) |
S-xNb/yh | Спекание при 1773 К в течение 2 ч измельченных порошков |
Таблица 2. ЭДС составы различных фаз в образцах С-24Нб/30ч и С-26Нб/30ч указаны стрелками на рис. 8.
Таблица 2. ЭДС составы различных фаз в образцах S-24Nb/30h и S-26Nb/30h, указанные стрелками на рис. 8.0196
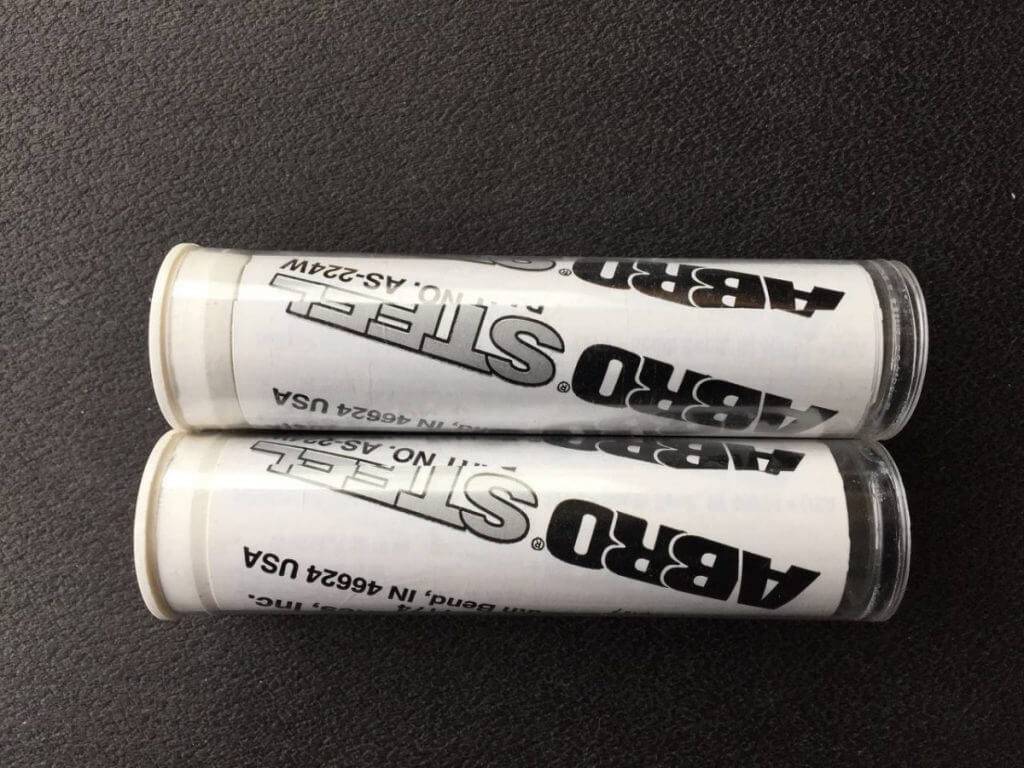

☆ Нормализованные результаты после удаления B из-за невозможности анализа EDS для измерения содержания B.
© 2019 авторами. Лицензиат MDPI, Базель, Швейцария. Эта статья находится в открытом доступе и распространяется на условиях лицензии Creative Commons Attribution (CC BY) (http://creativecommons.org/licenses/by/4.0/).
ГЕРМЕТИЧНАЯ УПАКОВКА МЭМС ДЛЯ ХОЛОДНОЙ СВАРКИ И СПОСОБ ИЗГОТОВЛЕНИЯ
Настоящая заявка частично является продолжением заявки на патент США Сер. № 11/139,960, озаглавленный «ГЕРМЕТИЧНЫЙ МЭМС-ПАКЕТ ДЛЯ ХОЛОДНОЙ СВАРКИ И СПОСОБ ИЗГОТОВЛЕНИЯ» Кертиса Н. Поттера, поданный 27 мая 2005 г., в котором испрашивается преимущество приоритета предварительной заявки на патент США № 60/574,835, поданной 28 мая 2004 г. , и раскрытие информации. Документ № 542148, поданный 17 ноября 2003 г., все из которых настоящим включены посредством ссылки, как если бы они были изложены в нем полностью.
Память Изобретение в целом относится к герметичной упаковке микроустройств, включая полупроводниковые устройства, гибридные устройства, вакуумные микроэлектронные устройства и устройства микроэлектромеханической системы (МЭМС). Сущность изобретения заключается в использовании компрессионного соединения с достаточной силой для создания герметичного холодного сварного шва для герметизации крышки и основания микроустройства в вакууме или разреженной атмосфере и при комнатной температуре. Соединение холодным сварным швом обеспечивает достаточную герметичность в течение всего срока службы устройства. Этот метод может быть использован как для одного кристалла, так и в масштабе пластины.
Герметичные корпуса микроустройств широко используются в полупроводниковой промышленности, где требуется истинная герметичность. Такая герметичность требуется, когда условия окружающей среды за пределами упаковки или изменения условий окружающей среды могут повлиять на работу устройства. В полупроводниковой промышленности были разработаны герметичные пассивирующие слои, которые наносятся на поверхности чувствительных устройств, чтобы обеспечить первичный уровень защиты от условий окружающей среды. Некоторые из этих слоев достаточно герметичны. В других случаях требуется герметичная упаковка.
Несмотря на то, что существует множество примеров осуществимости и герметичности холодной сварки в макроскопическом масштабе, как указано в этом раскрытии, количественная физическая модель более неуловима из-за сложности процесса соединения. Деформация материала является ключевым элементом успешной холодной сварки. Обычно он характеризуется поверхностным расширением на границе каждого материала, подлежащего холодной сварке. Н. Бэй, Weld Journal, том 62, 1983, с. 137, разработали модель прочности связи, основанную на расширении площади поверхности на границе раздела и силе сцепления, перпендикулярной границе раздела. Модель основана на разрушении поверхностного слоя интерфейса сдвиговым потоком материала, за которым следует достаточное усилие, перпендикулярное границе раздела сварки, чтобы вызвать тесный атомный контакт между двумя соединяемыми элементами. Утверждается, что отношение прочности связи более прочного элемента к пределу текучести более слабого элемента пропорционально выдавливанию металла через трещины в поверхностном слое плюс степень расширения площади поверхности, которая обеспечит растрескивание поверхностного слоя.
Модель прочности связи, предложенная Бэем, принимает форму отношения прочности связи/ = отношения предела текучести, приравненного к поверхностному расширению, давлению, функции предела текучести следующим образом: ·O косая черта· o =(1−) Yp−pE·O косая черта· o+Y−Y′ 1 −Y′p·O косая черта· o
. b Прочность сцепления
.O косая.o Предел текучести
β Площадь поверхности
Y Поверхностное расширение
Y′ Поверхностное расширение при изломе
P Нормальное давление
P E Давление выдавливания
Тестирование этой взаимосвязи показало удовлетворительную корреляцию (N. Bay, Trans. ASME Jour. Engn. Ind. , Vol. 101, 1979), для соединения алюминия с алюминием в диапазоне расширения поверхности долей миллиметра.
Можно провести важное различие между явлениями макроскопического и микроскопического сдвига. Такое различие может поставить под сомнение справедливость соотношения Бейса для шероховатых поверхностей. В случаях, когда на свариваемых поверхностях имеются микроскопические неровности, расширение поверхности, необходимое для того, чтобы вызвать сварку неровностей, может быть значительно уменьшено. Таким образом, возникает вопрос, насколько линейной остается связь между p-PE и Y-Y’ в зависимости от размера и плотности неровностей.
Соотношение, заявленное Бэем, определяет некоторые ключевые свойства материала, которые оптимизируют прочность соединения и, как следствие, вакуумную герметичность. Очевидно, что выгодно максимизировать поверхностное расширение и свести к минимуму поверхностные интерфейсные слои, которые могут мешать тесному контакту между двумя соединяемыми элементами. Давление соединения по нормали к свариваемым поверхностям должно быть максимальным в пределах ограничения предела текучести соединяемых материалов.
Обычный герметичный корпус состоит из основания корпуса с изолированным от него электрическим вводом для извлечения электрических сигналов от устройства, находящегося внутри корпуса. Чувствительное активное устройство монтируется на основании корпуса и выполняется микропроводное соединение для соединения выходных площадок устройства с электрическим вводом основания корпуса. Наконец, крышка или колпачок прикрепляются к основанию с помощью техники герметичного соединения, которая варьируется в зависимости от материала упаковки и ее подготовки. Технологии соединения предшествующего уровня техники требуют приложения некоторой степени тепла для обеспечения герметичного соединения колпачка с основанием.
Двумя наиболее распространенными методами герметичного соединения колпачка с основанием являются сварка колпачка и пайка. Сварка колпачка осуществляется путем пропускания высокого сварочного тока через наконечник (часто небольшой ролик), который прецессирует вокруг края узла колпачок/корпус, поскольку он локально сплавляет два металлических элемента вместе. В методе герметизации припоем используется заготовка припоя (обычно эвтектический припой золото/олово), помещаемая между позолоченной крышкой и основанием, с последующим применением нагретого кольца при номинальной температуре 320°C. расплавить припой и произвести герметизацию. Оба эти метода приводят к передаче значительного количества тепла через основание корпуса к активному устройству. Хотя существуют способы уменьшения количества теплопередачи к активному устройству, полностью исключить нагрев устройства невозможно.
МЭМС-устройства, имеющие отдельно стоящие микромеханические структуры, были герметично упакованы с использованием как сварки колпачков, так и пайки. Однако из-за остаточного напряжения в отдельно стоящих элементах и чрезвычайной чувствительности поверхностей конструкции тепло может либо полностью разрушить, либо резко снизить производительность таких МЭМС-устройств, особенно более сложных типов. Для таких устройств процесс запечатывания упаковки при комнатной температуре был бы очень полезен.
Герметизация при комнатной температуре уже несколько лет используется в оборудовании сверхвысокого вакуума (СВВ) и широко распространена в искусстве этой технологии. патент США. В US 3208758, Carlson and Wheeler, описана технология вакуумного запечатывания, пригодная для высокотемпературной выпечки после применения запечатывания при комнатной температуре. Патент ориентирован на большие фланцы, используемые в сборке вакуумной системы сверхвысокого вакуума. Описано уплотнение с медной прокладкой, в котором две сопряженные вакуумные части, имеющие вертикальную и наклонную режущие кромки, запрессовываются в медную прокладку для создания вакуумного уплотнения. Высокая сила, необходимая для деформации меди, достигается путем затягивания ряда болтов и гаек по периферии фланца. Раскрывается предпочтительная форма режущей кромки, хотя не раскрывается усилие, необходимое для создания герметичного уплотнения. Узел, включая медную прокладку и форму режущей кромки, стал известен как вакуумный фитинг типа «конфлат» и широко используется в промышленности вакуумного оборудования. Он не применялся к упаковке микроустройств. Дополнительные варианты осуществления основного метода запечатывания «совмещения» можно найти в патенте США No. №3,217,992, Глазго, и патент США No. № 3368818, Asamaki, et. al., оба описывают альтернативные геометрии крепления болтами для создания металлического уплотнения. Ни в одном из патентов не рассматривается возможность применения этой технологии для герметизации корпусов МЭМС или микроустройств.
В течение многих лет также используется макромасштабная холодная сварка. Герметизация холодной сваркой использовалась для криогенных применений, таких как герметизация матричных устройств фокальной плоскости и соединений входных/выходных сигналов, как описано в A.M. Fowler et. и др., «Орион: самая большая в производстве инфракрасная решетка в фокальной плоскости», Национальная оптическая астрономическая обсерватория, серия препринтов NOAO, № 903. Холодные сварные швы могут выполняться с материалами, имеющими различную прочность на растяжение. В то время как материалы с низкой прочностью на растяжение требуют меньшего давления для формирования сварного шва, они более подвержены деформации, вызванной, например, более поздними скачками повышенной температуры. Материалы с высокой прочностью на растяжение требуют более высокого давления для холодной сварки, но менее подвержены последующим деформациям. После сварки материала с умеренной прочностью на растяжение, такого как медь, соединение обеспечивает предел текучести, близкий к пределу текучести используемых материалов. Холодная сварка до сих пор не использовалась в герметичных микроупаковках.
Индий (точка плавления, т.пл.=156°С) широко использовался в качестве материала для холодной сварки в низкотемпературной электронике, как описано в «Техническом обзоре НАСА, Исследовательский центр Льюиса, Кливленд, Огайо, июнь 1998». Штыри из индия для холодной сварки используются для холодных соединений ввода-вывода микросхемы электроники. Давление, необходимое для образования герметичных соединений, значительно ниже предела текучести монокристаллического кремния. Однако из-за низкой температуры плавления индия ограничена допустимая степень температурного циклирования после соединения. В то время как вакуумные герметичные уплотнения были продемонстрированы с использованием индия, результирующий предел текучести запечатанных деталей низок из-за низкого предела текучести индия (порядка 1000 фунтов на квадратный дюйм).
Холодная сварка материалов со средней прочностью на растяжение, таких как медь, алюминий и золото, применялась в течение длительного времени. Так называемая «стыковая» холодная сварка используется для соединения толстой проволоки и стержня (см. «Dave Nichols, The Welding Institute, веб-сайт TWI, «Холодная сварка давлением»). В этом методе применяется гораздо более высокое давление, чем в системах пайки, и он основан на существенном течении материала на торцах, т. е. поперечном потоке, в 2-3 раза превышающем диаметр стержня, при сохранении окружности стержня. Ручные инструменты для холодной сварки (см., например, «Huestis Industrial Corporation, Инструменты для холодной сварки давлением. 2002») предназначены и используются для холодной сварки цветных металлов в диапазоне от 0,08 до 1,20 мм. Хотя холодная сварка таких материалов, как медь и алюминий, является признанным искусством в таких макроприложениях, она не использовалась в MEMS или полупроводниковых микрокорпусах. Кроме того, требуемые давления намного выше, чем предел текучести кремния, хотя они могут быть ближе к пределу текучести некоторых керамических материалов, используемых в качестве подложек МЭМС.
В связи с недавними достижениями в технологии МЭМС, которые привели к созданию более сложных устройств, предпринимаются усилия по разработке подходящей технологии упаковки, как для одиночного кристалла МЭМС, так и для упаковки на уровне пластины. Для устройств MEMS упаковка на уровне пластин особенно привлекательна из-за способа их изготовления. Практически все устройства МЭМС состоят из микромеханических элементов, подвешенных в пространстве. В процессе изготовления эти элементы должны поддерживаться жертвенным материалом, обычно через несколько уровней обработки до конца последовательности изготовления. В конце последовательности жертвенный материал удаляется, обычно путем травления, оставляя микромеханические элементы в их проектном пространстве. Этот шаг известен как процесс «выпуска». Очевидно, что с точки зрения затрат желательно выполнять этот процесс высвобождения всей пластины, а не отдельного кристалла. Однако после того, как высвобождение выполнено, устройства MEMS не могут быть отделены без повреждения отдельных механических частей из-за остатков разделения или их слипания (так называемое заедание). Пресс-формы также чрезвычайно чувствительны к загрязнению во время хранения и любой обработки после выпуска, но до упаковки. Поэтому возрос интерес к выпуску и герметичной упаковке вафельных пластин до их разделения.
Недавние разработки в области упаковки МЭМС в масштабе пластин были сосредоточены на соединении непосредственно с кремнием или другой подложкой, используемой для изготовления МЭМС. Это включает анодное соединение или соединение плавлением с использованием тепла и сильных электрических полей, эвтектическое соединение с использованием тепла для образования связи между золотом или алюминием и кремнием и термокомпрессионное соединение. Было исследовано новое применение тепла с использованием резистивного нагревательного элемента из поликремния, встроенного непосредственно в устройства MEMS. Ни в одной из этих недавних работ не использовалась описанная здесь технология холодной сварки при комнатной температуре.
В патенте США. В US 6379988 B1 Петерсен и Конли описывают предварительную пластиковую упаковку МЭМС-устройств, в которой устройство помещается в пластиковую упаковку перед выпуском. Пластиковая упаковка может быть перфорирована, чтобы позволить выпуск в упаковке с использованием процессов влажного или сухого травления. На заключительном этапе к пластиковой упаковке прикрепляют крышку с помощью различных средств, известных из уровня техники.
Патент США. № 6,400,009 B1, Bishop, et. al., раскрывает корпус МЭМС и средства соединения, в которых используется брандмауэр для образования защитной полости для устройства МЭМС во время термосваривания верхних и нижних элементов корпуса. Электрические вводы, проходящие через брандмауэр, могут быть изготовлены из проводящего материала поликремния, инкапсулированного диоксидом кремния. Все раскрытые структуры изготавливаются одновременно с устройством MEMS. В качестве средства укрепления деталей, соединенных припоем, заявлено неотъемлемое множество припоя. Описанное средство герметизации представляет собой пайку горячим припоем.
Патент США. В US 6627814B1, Дэвид Х. Старк, описана упаковка со сплошной боковой стенкой с верхней поверхностью, подготовленной для герметизации припоем. Прозрачное окно образует верхнюю крышку. Окно подготовлено с внешней металлической рамой, подходящей для припайки к основанию. Метод пайки требует применения тепла выше температуры плавления припоя. патент США. В US 6639313 B1, Martin and Harney, описан керамический корпус с углублением для размещения оптического зеркального МЭМС-устройства. Предложена стеклянная оконная крышка, которая припаивается к керамической подложке с помощью гибкой складчатой металлической прокладки, расположенной по периферии вокруг края стеклянного окна и керамического основания. Уникально то, что складчатая металлическая вставка позволяет уменьшить разницу в расширении и сжатии между окном и керамикой во время теплового цикла. Герметичность достигается термической пайкой.
Целью настоящего изобретения является создание средства герметичного закрытия микроустройства при комнатной температуре, чтобы обеспечить вакуум или разреженную атмосферу для микроустройства в течение всего срока его службы. Дополнительная цель состоит в том, чтобы использовать тот же метод герметичного запечатывания для МЭМС и других микроустройств после того, как выпуск был выполнен в масштабе пластины. Связанная с этим цель состоит в том, чтобы обеспечить гибкость, позволяющую накладывать колпачки по отдельности в пошаговой и повторяющейся операции, в группах для групповой герметизации или в колпачках в форме пластин, в которых были сформированы отдельные колпачки, которые должны быть разрезаны во время процесса. процесс выделения устройства.
Еще одной целью изобретения является использование холодной сварки металлов, прикрепленных к крышке и основанию или являющихся составными частями крышки и основания, для сохранения удерживающей силы, удерживающей крышку и основание вместе.
Еще одной целью изобретения является формирование уплотнительного кольца из подходящего материала, такого как медь, индий, сплавы индия или золото, на одном элементе крышки корпуса или узла основания посредством гальванического покрытия или плакирования. Такое уплотнительное кольцо образует прокладочный материал для холодной сварки, пригодный для герметичного уплотнения.
Другой целью изобретения является формирование осевых соединительных структур, например электрических или оптических входных и выходных соединений, как части такого уплотнительного кольца, чтобы обеспечить осевые проходы после операции сжатия холодной сваркой.
Еще одной задачей изобретения является формирование на крышке и основании ножевых или режущих кромок, которые будут усиливать силы сдвига, действующие при создании холодного сварного шва между материалами, срезаемыми вдоль этих поверхностей за счет давления, приложенного для соединения крышки и основания.
Другой целью изобретения является формирование холодного сварного шва, который будет иметь достаточную прочность, чтобы выдерживать усилие, необходимое для сохранения герметичности упаковки и основания после устранения сжимающей силы.
Еще одной целью изобретения является создание вспомогательного механического соединения между основанием упаковки и колпачком после герметизации холодной сваркой для использования в случаях, когда механический предел текучести материала холодного сварного шва недостаточен для поддержания механической целостности между колпачком и крышкой. база. Такое вспомогательное механическое соединение может иметь форму механического зажима или отверждаемого текучего материала, такого как различные эпоксидные смолы.
Другой целью изобретения является создание средства для приложения сильного электрического поля к герметизирующей поверхности между колпачком и основанием, чтобы вызвать миграцию металла уплотняющих материалов, тем самым улучшая холодную сварку и обеспечивая холодную сварку при более низких физических давлениях.
Другой целью и преимуществом изобретения является создание герметичного уплотнения при комнатной температуре с таким уплотнением, демонстрирующим скорость утечки менее 10{circumflex over( )}-9 торр л/сек.
Особым преимуществом изобретения является способ герметичной герметизации при комнатной температуре устройств МЭМС, которые проявляют чувствительность к тепловому циклу во время операции герметизации.
Другим преимуществом изобретения является очень высокая пропускная способность уплотнения, поскольку для создания герметичного уплотнения требуется только один этап сжатия. Не требуется циклов нагрева с сопутствующим расплавом припоя или временем выдержки при сварке.
Другим преимуществом изобретения является его применение к микроустройствам или наноустройствам, отличным от МЭМС, таким как НЭМС, гибридные сборки, вакуумные микроэлектронные устройства и полупроводниковые устройства, которые могут требовать высокой степени герметичности.
Изобретение, раскрытое в данном документе, обеспечивает структуру и способ соединения холодным сварным швом с компрессией с использованием прокладки или другой герметизирующей конструкции при комнатной температуре для герметичного уплотнения МЭМС и других микроустройств.
Изобретение распространяется на упаковку МЭМС и других микроустройств в виде пластин в виде пластин путем изготовления подходящих структур для прикрепления крышек во время последовательности изготовления МЭМС или микроустройств. Упаковочные конструкции могут быть изготовлены путем нанесения покрытия или травления на подложку на различных этапах изготовления устройства.
РИС. 1 a показана технология герметизации предшествующего уровня техники для прикрепления крышки упаковки к основанию с помощью средств герметизации припоем.
РИС. 1 b показывает известную технологию герметизации для прикрепления крышки упаковки к основанию с помощью сварки.
РИС. 2 показана известная технология упаковки в виде вафли, в которой используется встроенный локализованный нагреватель для последовательного прикрепления отдельных крышек к каждому месту штампа на вафле.
РИС. 3 показана известная технология упаковки в виде вафель, при которой вся вафля закрывается и герметизируется одновременно с использованием анодного, сплавляющего, ковалентного или эвтектического соединения.
РИС. 4 а и b показывает способ соединения колпачка с компрессией холодной сваркой с основанием упаковки, как раскрыто в данном изобретении.
РИС. 5 показан способ соединения колпачка с компрессионным швом холодной сваркой, раскрытый в данном изобретении, с дополнительным механическим удерживающим средством для увеличения предела текучести между колпачком и основанием.
РИС. 6 показана примерная механическая конструкция для процесса соединения сжатием при холодной сварке, выполняемого в масштабе пластины.
РИС. 7 показана деталь предпочтительного механизма удержания силы при повторном входе, показанного на фиг. 6.
Хотя нижеследующее подробное описание описывает многие конкретные признаки изобретения и описывает конкретные процедуры изготовления, специалисты в области микропроизводства поймут, что возможны многие вариации и изменения в деталях изготовления и основных структурах, не отступая от общности процессов и структур. Наиболее общие признаки изобретения относятся к конструкции и способу изготовления герметичного соединения между основанием упаковки микроустройства и колпачком при комнатной температуре. Путем изменения конструкции механизма пресса для холодной сварки и конструкций поддержания усилия герметичные швы могут выполняться на уровне одной упаковки или на уровне пластин.
Обширный предшествующий уровень техники в области упаковки микроустройств показан на ФИГ. 1, 2 и 3 . ИНЖИР. 1 показано гипотетическое МЭМС-устройство 130 , установленное на основании корпуса 120 с электрическим вводом 170 , проходящим через основание и изолированным от основания изолятором 180 . Устройство MEMS 130 прикрепляется к основанию 120 с помощью материала 140 , который обычно представляет собой припой или органический клей. Проволочные соединения 150 электрически подключите устройство MEMS к фидеру 170 . МЭМС-матрица 130 может быть снята с временной опоры как отдельная матрица перед установкой на основание корпуса или после установки на основание. Устройство MEMS также может быть испытано после установки на основание в соответствующей среде разреженного газа или в вакууме. Крышка упаковки 110 обычно прикрепляется с помощью термопайки с заготовкой для пайки 160 или может быть приварена непосредственно к основанию без припоя, как показано на РИС. 1 б . Основание упаковки и крышка обычно изготавливаются из металла (часто из ковара) и покрываются припоемным металлом в случае пайки. После герметизации пространство 190 становится герметичным, и атмосфера во время герметизации задерживается в нем и, таким образом, составляет рабочую среду в течение всего срока службы устройства. Существует ряд вариаций этой сборки в одном корпусе, связанных с методом крепления кристалла МЭМС, конфигурацией электрического ввода в основании и изменением профиля корпуса в зависимости от того, как корпус крепится на уровне печатной платы. Все варианты хорошо задокументированы в предшествующем уровне техники.
РИС. 2 представляют собой другой подход предшествующего уровня техники к упаковке МЭМС, заключающийся в том, что колпачки надеваются на устройства МЭМС до разделения матрицы. Существенным преимуществом является то, что выпуск МЭМС может выполняться сразу на всей подложке, а не на одном кристалле за раз. Кроме того, матрица MEMS защищена колпачком во время разделки, которая часто включает этап мокрого пиления. Таким образом, ссылаясь на фиг. 2, подложка 215 представляет собой часть большой подложки, содержащей множество кристаллов. Подложка может включать в себя электрический ввод 205 , изолированным от подложки изолятором 210 или может быть просто (чаще) керамической подложкой с заполненными электропроводящими сквозными переходными отверстиями с проволочными соединениями 245 , непосредственно соединенными с переходными отверстиями. Устройство МЭМС 250 устанавливается на основание 215 с использованием материала 240 . В этой концепции поликремниевый нагреватель (или другой проводящий материал) 225 осаждается в кольцевом кольце по периферии места кристалла (но внутри разметочных линий). Если подложка проводящая, кольцо нагревателя изолировано от основания изолятором 9.
0158 220 и изолирован от цоколя 255 (при необходимости) изолятором 230 . Верхнее припойное кольцо 235 предусмотрено совмещено с кольцом нагревателя и образует уплотнение между металлом на крышке и металлическим слоем (не показан) на основании под припоем. Ток подается на элемент резистивного нагревателя 225 с подложки через периферийные выводы. Таким образом, паяное соединение может быть выполнено за счет локального нагрева вблизи места припоя, что сводит к минимуму тепловой поток вблизи кристалла.
Другой известный способ упаковки в виде вафельных пластин показан на фиг. 3. Массив кристаллов MEMS 320 можно снять с временной опоры в масштабе пластины. На подложке 330 показана часть большего массива кристаллов МЭМС. Матрица разделена широкими разметочными линиями 360 . Вся согласующая подложка, часть которой показана на фиг. 3, 310 , можно соединить с подложкой 330 с помощью приложения давления и электрического поля (так называемое анодное соединение или соединение плавлением). Также можно использовать ковалентную или эвтектическую пайку. Полости 340 , сформированный в удлиненной подложке крышки, обеспечивает пространство для устройств MEMS после приклеивания. Однако для того, чтобы процесс функционировал с высокой производительностью, соответствующие подложки должны быть очень плоскими для плотного контакта повсюду, а система колпачка и основного материала должна поддаваться такому процессу. Кремниевые подложки обычно используются с кремниевыми колпачками. После склеивания чешуи пластины можно отделить матрицу путем распиливания без повреждения активных устройств МЭМС.
В описанном здесь изобретении используется совершенно иной подход к герметизации упаковки, чем в предшествующем уровне техники. ИНЖИР. 4 a и b показывают в поперечном сечении крышку корпуса, которая может быть круглой или квадратной при виде сверху и похожа на обычную крышку корпуса полупроводника. Соответствующее основание показано под колпачком на фиг. 4 a и примерно совмещены с крышкой. Крышка и основание изготавливаются отдельно, но из одного и того же металлического материала или, если они из разных материалов, коэффициент теплового расширения (ТКЭ) должен точно соответствовать друг другу. Примерным материалом для крышки и основания является стальной сплав Ковар. Также можно использовать нержавеющие стали или другие формуемые, но тугоплавкие металлы. Колпачок формируется штамповкой или механической обработкой. Необязательный нож или режущая кромка (не показаны) могут непрерывно проходить по краю колпачка и предназначены для повышения деформируемости материала холодного сварного шва.
Основание, показанное на РИС. 4, может представлять собой, например, металлическую основу обычного полупроводникового типа, стекло, керамическую подложку или саму пластину МЭМС, имеющую электрическую изоляцию через фидер, при этом кристалл МЭМС соединен с фидером посредством проволочного соединения. Если матрица прикреплена к отдельному основанию, что дает больше свободы для внешних соединений, то материалом для крепления может быть эпоксидная смола между матрицей и основанием корпуса. МЭМС можно высвободить до или после прикрепления кристалла к основанию корпуса.
Периферийная область основания может быть покрыта или плакирована уплотняющим слоем металлизации подложки, например, из сплава меди, золота или индия, который герметично прилегает к основанию или выполнен в виде прокладки. Адгезионный слой металлизации может быть использован для усиления сцепления этого слоя с основой. Структура стыкового уплотнения, более узкая, чем слой металлизации, может быть сформирована на слое металлизации уплотнения подложки. Если желательны осевые входные/выходные соединения для электрических, оптических и других взаимодействий, то они могут быть сформированы во время или до металлизации подложки, которую впоследствии можно сглаживать для обеспечения равномерного уплотнения.
Крышка, показанная на РИС. 4 также снабжен слоем металлизации, который будет соответствовать положению и форме слоя металлизации подложки. Слой металлизации крышки изготавливается из любого материала, с помощью которого можно сформировать холодный сварной шов со слоем металлизации подложки и дополнительной конструкцией контактного уплотнения подложки. Колпачок может быть, например, металлическим, стеклянным или керамическим, совпадающим по расширению с основанием. В случае оптической МЭМС оптическое окно может быть подготовлено в рамке колпачка. При необходимости геттер может быть встроен в крышку или наплавлен на крышку в отдельной камере.
Ссылаясь на деталь на РИС. 4 a показано основание упаковки 405 с МЭМС-матрицей 445 , прикрепленной к основанию с помощью связующего слоя 450 . Электрические провода 440 соединены между матрицей 445 и электрическим вводом 425 . Электрические вводы 425 изолированы от основания корпуса 405 изоляторами 420 в обычном предшествующем уровне техники. Колпачок и основание изготовлены с металлизацией 415 и состоят из адгезионного слоя хрома, за которым следует слой припойного металла, такого как медь. Слои , 415, могут быть нанесены обычным методом физического осаждения из паровой фазы (PVD). Окончательный верхний слой 415 состоит из наплавленного слоя выбранного материала для холодной сварки, который может быть идентичен заготовке или другой прокладке из материала 435 для холодной сварки. Использовались индий и сплавы индия, но другие материалы, такие как медь и золото, также могут использоваться при более высоких давлениях. Заготовка или другая прокладка 9Показано, что 0158 435 имеет круглое поперечное сечение, обеспечивающее очень высокую степень деформации и, следовательно, текучесть материала во время этапа компрессионного соединения. Возможны другие профили поперечного сечения, где возможна еще большая степень потока материала. Кроме того, возможны конструкции, изготовленные из крышки и основания упаковки, если конструкция предназначена для значительного улучшения потока металлической заготовки.
На фиг. 4 b крышка упаковки показана в тесном и герметичном контакте с основанием упаковки с заготовкой холодной сварки, деформированной в плоскую шайбовую конструкцию в результате высокого давления со стороны клеящей головки. Космос 455 теперь содержит МЭМС-устройство, герметично изолированное от внешней атмосферы, с атмосферой предварительного связывания, заключенной внутри полости 455 .
РИС. 5 показано поперечное сечение МЭМС-устройства 540 внутри крышки 510 , соединенной холодной сваркой, и основания 520 , герметизированных сжатой преформой или другой прокладкой 530 . В случаях, когда предел текучести материала холодного сварного шва 530 нежелательно низок, используйте вспомогательный материал для поддержания силы, такой как эпоксидная смола 9.0158 550 можно наносить после герметизации холодным швом. Герметичность соединения холодной сварки предотвращает нежелательный приток паров отверждения из материала 550 от загрязнения устройства МЭМС внутри упаковки.
Припои с более высокой температурой плавления (ТП) В подшипниках припои (например, Pb, Sn или Ag) также могут использоваться для металлизации уплотнения корпуса и преформы, что позволяет уплотнению выдерживать более высокие температуры. Эти материалы также могут быть покрыты и, таким образом, нанесены на устройства MEMS в масштабе пластины с использованием тех же процессов, которые используются в технологии матрицы в фокальной плоскости.
Несмотря на то, что для холодной сварки меди предлагается давление холодной сварки до 1,5 миллиона фунтов на квадратный дюйм, фактически используемое давление может быть намного ниже за счет использования энергии, генерируемой на границе раздела соединений из-за трения и разрыва металлической связи при высоких уровнях сдвигающих усилий. генерируются. Следовательно, в основании и крышке могут использоваться ножевые или скользящие кромки для увеличения таких сил сдвига.
Алюминий, медь, золото и другие материалы обладают высокой деформируемостью значительно ниже их давления холодной сварки. Таким образом, металлизация основания и крышки может использовать тонкие слои материалов с низким напряжением растяжения, наносимых на поверхности сварки в качестве вспомогательного соединения при холодной сварке. Такие интерфейсные материалы могут позволить использовать алюминий/медь/золото на кремнии в масштабе пластины.
Нанесение колпачков на массивы МЭМС-устройств, которые были выпущены в масштабе пластины, желательно, поскольку отдельный кристалл можно выделить, разрезав запечатанные устройства. Это предотвращает нарушение механической целостности микроскопических механических частей активных МЭМС-устройств любыми режущими частицами. В качестве примера герметизации пластин на фиг. 6 a показывает в поперечном сечении крышку корпуса 610 и основание 605 с МЭМС-матрицей 645 .крепится к основанию обычными средствами. Подложка 605 является частью расширенной подложки, содержащей множество устройств MEMS, выпущенных в масштабе пластины. В рамках последовательности изготовления МЭМС-устройств 645 слой 630 был нанесен на подложку 605 с использованием, например, физического осаждения из паровой фазы (PVD). Этот слой состоит из двух отдельных слоев, нанесенных последовательно. Нижний слой представляет собой адгезионный слой, например, из хрома толщиной 500 ангстрем, за которым следует слой меди номинальной толщиной 1 микрон. Очень толстая преформоподобная структура 635 наносится поверх слоя 630 и состоит из материала, поддающегося холодной сварке, такого как медь, золото или индийсодержащий припой.
Структура 635 может иметь толщину от 10 до 50 мкм. Крышка упаковки 610 может состоять из двух частей. В этом случае первичная часть 680 штампуется до нужной формы, затем изготавливается кольцевая деталь 675 и припаивается к детали 680 , чтобы образовалась значительная входящая полость 9.0158 665 в той части крышки, которая принимает материал для холодной сварки. Кроме того, к заглушке 680 может быть добавлена текучая структура для холодной сварки 660 для улучшения поверхностного течения материала для холодной сварки. Слой 615 может быть нанесен на нижнюю поверхность крышки в сборе путем металлизации и может состоять из никелевого слоя толщиной около 50 миллионных долей, за которым следует покрытие материала холодной сварки, используемого на основании упаковки. Например, толщина материала холодной сварки будет составлять от 2 до 4 микрон и состоит из медного, золотого или индийсодержащего припоя. После приклеивания колпачка к основанию, как показано на ФИГ.
6 b материал холодного сварного шва вдавливается в полость повторного входа 660 , при этом излишки выдавливаются в боковом направлении, таким образом фиксируя крышку на основании. Если предел текучести материала холодного сварного шва достаточно высок, крышка будет надлежащим образом прикреплена к основанию. Для материалов с низким пределом текучести метод, показанный на фиг. 5 используется.
При запечатывании с одинарной головкой колпачок и основание помещаются в камеру при комнатной температуре, где поддерживается вакуум, разреженный газ или другая среда, необходимая для конечной микроупаковки. Камера, которая может быть частью сложной системы герметизации, оснащена склеивающим устройством с высокой силой сжатия с головкой для литья под давлением. Выравнивание колпачка по отношению к основанию может быть достигнуто с помощью столика индексации X-Y для перемещения основания под колпачок. Затем между колпачком и основанием прикладывают достаточное усилие для образования холодного сварного шва между металлизацией колпачка и основания и, таким образом, герметизации устройства при комнатной температуре. Автоматизированная система может последовательно объединять массивы выпущенных устройств MEMS. Этот метод позволяет изготовить набор крышек, которые будут регистрироваться в массиве устройств MEMS, что устраняет необходимость обработки отдельных крышек упаковки.
При запечатывании в форме пластин МЭМС-устройства могут быть освобождены и подвергнуты электрическому зондированию на предмет функциональности перед введением в камеру запечатывания или внутри отсека камеры запечатывания. Колпачки, такие как описанные в параграфе 0057, изготавливают либо в виде отдельных колпачков для устройств, либо в виде массива колпачков на уровне пластины, в котором отдельные колпачки сформированы, например, путем штамповки. Пластина и колпачки вводятся в камеру запечатывания. Пластина поддерживается твердой пластиной на нижней стороне. Затем прикрепляют колпачки к основаниям, как описано в параграфе 0058. Колпачки могут последовательно прикрепляться к отдельным штампам на подложке. Они могут удерживаться в приспособлении для фиксации головки и скрепляться группами по частям или все сразу.
При соединении компрессионным соединением холодным сварным швом с одной головкой или в виде пластины, описанном в настоящем документе, процесс соединения может быть облегчен и, следовательно, необходимое давление снижено за счет приложения электрических полей между конструкцией основания и крышки. Поля достаточной напряженности вызывают миграцию металла между базовым и верхним слоями металлизации.
В случае клеев холодной сварки одинарной или пластинчатой формы, как описано здесь, механически прочный материал, такой как эпоксидная смола, может быть нанесен на внешнюю сторону упаковки после ее герметизации и последующего отверждения, чтобы обеспечить дополнительная прочность к соединению сжатия холодной сварки. Аналогичным образом механические опоры могут быть добавлены после запечатывания упаковок.
Настоящее изобретение хорошо адаптировано для выполнения целей и достижения целей и преимуществ, упомянутых, а также других присущих ему. Хотя настоящий вариант осуществления изобретения был дан с целью раскрытия, специалистам в данной области техники будут очевидны многочисленные изменения или изменения в деталях конструкции и этапах способа, которые охватываются духом и объемом настоящего документа. изобретение.
КРАТКОЕ РУКОВОДСТВО ПО СВАРКЕ НЕРЖАВЕЮЩЕЙ СТАЛИ — Fushun Special Steel Co., Ltd.
28 февраля 2022 г. / Часто задаваемые вопросы, Новости
КРАТКОЕ РУКОВОДСТВО ПО СВАРКЕ НЕРЖАВЕЮЩЕЙ СТАЛИ
Сварка нержавеющей стали существенно отличается от сварки других материалов. Отличие начинается с уникального химического состава нержавеющей стали.
Что такое нержавеющая сталь?
Как и другие стали, нержавеющая сталь представляет собой сплав железа и углерода. Что отличает нержавеющую сталь, так это то, что она содержит не менее 10,5% хрома, элемента, который делает полученный сплав устойчивым к коррозии. Kloeckner Metals поставляет нержавеющую сталь различных форматов, включая листовую нержавеющую сталь, листовую нержавеющую сталь, трубы из нержавеющей стали и пруток из нержавеющей стали.
Нержавеющая сталь бывает пяти типов, но в производственных цехах обычно встречаются только три из них: аустенитная нержавеющая сталь, мартенситная нержавеющая сталь и ферритная нержавеющая сталь. Наиболее распространен аустенитный. Мартенситная нержавеющая сталь используется для наплавки. А ферритная сталь, самый дешевый вариант, чаще всего используется в потребительских товарах.
Каждый из этих типов стали классифицируется на основе ее микроструктуры, которая влияет на ее пластичность и прочность. Микроструктура стали зависит от ее химического состава. Например, аустенитная сталь содержит 16-26% хрома (Cr) и 8-22% никеля (Ni). Мартенситная сталь имеет содержание Cr в пределах 11-28%. Ферритная сталь содержит 12-18% Cr. В результате материал, привариваемый к каждому типу стали, должен соответствовать составу этой стали.
В чем сложность сварки нержавеющей стали?
Сварка нержавеющей стали сложнее, чем сварка углеродистой стали.
Во-первых, нержавеющая сталь эффективно удерживает тепло, вызывая ее деформацию под воздействием высоких температур, создаваемых сваркой. Нержавеющая сталь также может деформироваться или растрескиваться в процессе охлаждения после того, как она была нагрета сварщиком. Даже если кусок нержавеющей стали не трескается и не деформируется после неудачной сварки, на нем почти всегда остаются царапины и пятна.
Каждый вид нержавеющей стали представляет собой особую проблему для сварщиков. Аустенитная сталь может растрескиваться при высокой подводимой температуре или при выполнении вогнутого или плоского сварного шва. Мартенситная сталь может треснуть, если ее не подогреть должным образом. А с низкой максимальной межпроходной температурой 300°С ферритная сталь будет терять прочность, если ее не нагреть с низким погонным теплом.
Ключом к успешной сварке нержавеющей стали является выбор правильного присадочного материала. Марка присадочного материала должна соответствовать марке основного материала, чтобы получить хороший сварной шов.
Материалы и оборудование, необходимые для сварки нержавеющей стали
Почему для сварки нержавеющей стали требуется специальное оборудование и какие инструменты и материалы необходимы для сварки нержавеющей стали?
Нержавеющая сталь может подвергаться сварке электродуговой сваркой, сваркой в среде защитного металла (MIG) или дуговой сваркой вольфрамовым электродом в среде защитного газа (TIG). Лучший выбор зависит от того, чего вы пытаетесь достичь, поскольку каждый процесс приводит к разным результатам.
Нержавеющую сталь можно сваривать палкой, но не стоит. Есть другие, лучшие варианты.
Сварочный аппарат MIG обеспечивает самые прочные и надежные сварные швы с нержавеющей сталью. Это особенно хороший выбор, если вы свариваете что-то толстое. Сварочные аппараты TIG могут быть правильным выбором для более тонких материалов и для сварки, требующей красоты и точности. Тем не менее, TIG — это сложная сварка, если у вас нет опыта и времени, чтобы сделать это правильно. Неопытный сварщик TIG может оставить неприятные следы или пятна на нержавеющей стали.
Несмотря на менее тонкий сварной шов, MIG-аппарат, как правило, является лучшим вариантом для сварки нержавеющей стали. Выберите аппарат, который поставляется со сварочным пистолетом и образцом сварочной проволоки. У большинства машин есть пистолет, но вы можете модернизировать свой, если вам нужно что-то, что обеспечит более точный сварной шов. Вы также захотите приобрести несколько насадок для сварочных пистолетов, чтобы заменить их, когда они изнашиваются.
Для защиты сварочной горелки вы можете приобрести защитный чехол. Это отличное дополнение, поскольку оно позволяет быстро и эффективно переключаться между различными типами металлической проволоки. Вам не нужен механизм подачи сварочной проволоки, если вы не профессиональный сварщик или не планируете много сваривать. Что касается самой проволоки, вы должны использовать подходящую сварочную проволоку из нержавеющей стали, которая обычно имеет диаметр 0,030 дюйма, но для более толстых деталей может подойти проволока от 0,035 до 0,045 дюйма.
Поскольку при сварке нержавеющей стали необходимо контролировать температуру, чтобы избежать проблем с производительностью, вам понадобится устройство для отслеживания температуры. Вы можете использовать традиционную палку, но помните, что ее диапазон ограничен. Другие опции включают электронный инфракрасный термометр и электронный датчик температуры поверхности.
Вам также понадобится защитный газ. Инертные газы не рекомендуются, поэтому вам, вероятно, понадобится смесь 7,5% аргона, 90% гелия и 2,5% углекислого газа. Наконец, вам нужно будет добавить щетку для соскабливания и очистки металла. Этот инструмент может помочь вам подготовить рабочее место и, в конечном итоге, добиться более прочного сварного шва.
Подготовка к сварке
На что следует обратить внимание при подготовке к сварке? Чем он отличается для разных марок стали?
Металлической щеткой удалите пыль, грязь, масло, жир или воду с рабочей станции. Вы также можете помочь предотвратить деформацию и растрескивание, зажав кусок латуни или меди за сварочным швом. Этот трюк может помочь поглотить тепло и сохранить вашу нержавеющую сталь достаточно прохладной.
Храните отдельный набор инструментов для сварки нержавеющей стали. Как только ваши инструменты коснутся углеродистой стали, на них останется нагар. Этот остаток перейдет на нержавеющую сталь во время сварки, что в конечном итоге может привести к ржавчине изделия.
Другие советы, которые следует учитывать при сварке нержавеющей стали
Как обеспечить наилучшие результаты сварки?
При сварке TIG используйте отрицательную настройку электрода DCEN или постоянного тока и силу тока 1 ампер на каждые 1/1000 дюйма толщины металла.
При сварке MIG используйте метод проталкивания. Этот подход позволяет вам более четко видеть, что вы делаете, и создает меньше бусинок. Используйте технику натяжения только тогда, когда вам нужно более глубокое проникновение.
Держите сварочный пистолет под углом 90 градусов с углом перемещения 5–15 градусов. Для Т-образных соединений и соединений внахлестку попробуйте увеличить угол примерно на 45-70 градусов.
Следите за чистотой, безопасностью и хорошей вентиляцией рабочего места.
Хотя сварка нержавеющей стали немного сложнее, чем другие сварные швы, ее можно сделать. Вы даже можете сваривать нержавеющую сталь с мягкой сталью. Используя правильное оборудование, регулируя температуру и используя правильный присадочный материал, можно получить прочный и долговечный сварной шов.