Ультразвуковой контроль (ультразвуковая дефектоскопия)
Ультразвуковой контроль (УЗК) является одним из акустических методов неразрушающего контроля
Акустические методы неразрушающего контроля включают в себя испытания материалов и изготовленных из них изделий, основанные на использовании упругих колебаний и волн. В частности, осуществляется регистрация параметров упругих волн, возбуждаемых или возникающих в интересующем вас объекте. В зависимости от полученных результатов можно сделать выводы о свойствах материала и наличии дефектов. Наиболее распространены, кроме УЗК ,акустическая эмиссия и ультразвуковая толщинометрия.
Общепризнанным первооткрывателем ультразвуковой дефектоскопии является российский ученый, профессор, член-корреспондент Академии наук Сергей Яковлевич Соколов.
Он первым в мире предложил использовать ультразвук для обнаружения внутренних дефектов в изделиях, получил первый патент на метод и устройство для дефектоскопии [ Патент № 11371.
Работы были проведены на кафедре специальной радиотехники в Ленинградском Электротехническом институте (ЛЭТИ) в 1927-28 гг.
Физические основы ультразвукового контроля (УЗК) достаточно подробно описаны в работах А.К. Гурвича, И.Н. Ермолова, В.Г. Щербинского и многих других отечественных и зарубежных ученых.
В настоящее время объем применения акустических методов контроля в энергетическом машиностроении, на железнодорожном транспорте, в судостроении , в химическом машиностроении как в нашей стране, так и за рубежом достиг 70-80% от общего объема неразрушающего контроля (НК).
При контроле сварных соединений УЗК, по сравнению с другим основным методом — радиографией обладает более высокой чувствительностью и достоверностью к обнаружению трещиноподобных дефектов, более высокой оперативностью и производительностью, меньшей стоимостью и безопасностью в работе.
При контроле таких изделий как крупногабаритные поковки, массивные литые изделия, листовой и сортовой прокат УЗК является основным, а порой и единственным методом контроля внутренних дефектов.
Лаборатория «ЛЕНТЕСТ» имеет большой опыт в проведении неразрушающего контроля разнообразных изделий с помощью акустических методов.
Преимущества акустических методов неразрушающего контроля:— волны легко проникают в объекты контроля, в том числе металлы, бетон и другие материалы;
— волны эффективны при выявлении дефектов с малым раскрытием, поскольку чувствительны к изменению структуры и физико-механических свойств материалов,
— различные типы волн (нормальные, продольные, поперечные, поверхностные и др.) позволяют получить больше информации в ходе проведения неразрушающего контроля.
— волны безопасны для персонала.
Использование акустических методов неразрушающего контроля в различных отраслях промышленности (машиностроение, металлургия, энергетика, строительства, транспортная промышленность и др.
Опытные специалисты ООО «ЛЕНТЕСТ» всегда готовы найти нестандартное методическое решение для контроля изделий не прошедших технологическую проработку по вопросам НК.
Наши специалисты оперативно осуществляют работы по непосредственному проведению УЗК, а также по инспекционному контролю на предприятиях различных отраслей от Дальнего Востока до Западных границ России.
Дополнительную информацию об акустических методах неразрушающего контроля и стоимости работ можно получить, обратившись к нашим сотрудникам
Узк сварных швов | Машиностроительный завод «МИАН»
Содержание
- Разновидности УЗК
- Особенности ультразвукового анализа
- Процедура проведения дефектоскопии
- Преимущества ультразвукового контроля
- Сфера применения
Разновидности УЗК
В различных отраслях промышленности применяют 5 методов УЗК (ГОСТ 23829 – 79). Они различаются лишь способом регистрации и оценивания полученных данных:
- Зеркально-теневой. Служит для обнаружения дефектов швов по коэффициенту затухания отраженного колебания.
- Теневой метод. Основан на контроле уменьшения амплитуды ультразвуковых колебаний прошедшего и отраженного импульсов.
- Дельта-метод. Базируется на контроле ультразвуковой энергии, которая исходит от дефекта.
- Эхо-зеркальный. Основан на использовании улавливающего приемника, ловящего отраженные волны, и датчика, который генерирует волну.
- Зеркально-теневой. Фиксирует дефекты швов по коэффициенту затухания отраженного колебания.
- Эхо-импульсная УЗД. Прибор излучает и принимает волны. Дефекты отсутствуют, если датчик не зафиксировал аудиоволну.
Как правило, чаще всего применяют теневой метод и эхо-импульсную УЗД.
Особенности ультразвукового анализа
Метод основан на возможности высокочастотных колебаний (около 20000 Гц) проникать в металл и отражаться от пустот, царапин и других дефектов. Если имеются какие-либо неровности, волна, проникая в соединение, отклоняется от своего нормального распространения. Это отклонение передается на экраны приборов. Оператор УЗД по определенным показаниям сможет охарактеризовать дефект.
Процедура проведения дефектоскопии
Специалисты при проведении ультразвукового контроля ориентируются на стандарт диагностики сварных соединений трубопроводов и других металлоконструкций. Алгоритм выполнения дефектоскопии:
- Очистка стыков от краски, ржавчины с обеих сторон не менее чем на 5-7 см.
- Обработка поверхности стыка и металла солидолом, глицерином или маслом (трансформаторным, машинным, турбинным). Такая обработка позволяет получить более точный результат.
- Настройка проверочного прибора в соответствии с необходимыми параметрами. Если толщина материала не превышает 2 мм, используются стандартные настройки. Для металлов с толщиной более 20 мм настраивают АРД-диаграммы.
Качество проверяют с помощью DGS или AVG-диаграмм.
- Перемещение излучателя прибора вдоль сварного соединения зигзагообразными движениями. При этом излучатель поворачивается на 10-15 градусов вокруг своей оси.
- Перемещение искателя по материалу до появления устойчивого и максимально четкого сигнала. Затем прибор разворачивают для поиска сигнала наивысшей амплитуды.
Когда характер повреждения не удается определить с помощью УЗК, проводятся более детальные исследования. Для этого применяют гамма-дефектоскопию или рентгенодефектоскопию.
Преимущества ультразвукового контроля
Метод имеет ряд преимуществ, за которые его особенно ценят специалисты. Так, ультразвуковой контроль позволяет получить максимально точные результаты при минимальных затратах времени и денег. Также используемые во время анализа приборы полностью безопасны для человека. Этого не сказать о других способах диагностики.
При проведении УЗК сварных швов объект не нужно выводить из эксплуатации: контроль возможен прямо во время работы.
Таким образом, ультразвуковой контроль сварочных соединений – залог безопасной работы сооружений и изделий из металла. При регулярном проведении проверок удастся вовремя устранить дефекты, продлить срок службы конструкции и повысить эффективность ее работы.
Сфера применения
УЗК-диагностику применяют при проведении следующих видов работ:
- Анализ узлов, агрегатов, деталей различного назначения.
- Диагностика объектов в нефтяной и газовой промышленностях, а также в машиностроении.
- Исследование конструкций магистральных трубопроводов на предмет износа.
- Обнаружение дефектов в соединениях металлов крупнозернистой структуры.
- Исследование прочности сварных соединений и других деталей в сфере тепловой и атомной энергетики.
- Анализ прочности сварных швов в местах соединения изделий, имеющих сложные очертания.
- Лабораторная диагностика объектов и исследование в полевых условиях.
- Анализ сварных соединений и крепежа оборудования, используемых в условиях перепада температур и давления.
Метод УЗК сварки часто применяют для обнаружения дефектов в процессе эксплуатации. По этой причине такой анализ проводят не только на входном и выходном контроле, но и во время следующих обследований и технического обслуживания.
Возможно вас заинтересует
ультразвуковой контроль сварных швов узк контроль узк сварных швов дефектоскопия ультразвуковой неразрушающий контроль ультразвуковой контроль сварных соединений оказание услуги по ультразвуковой дефектоскопии сварочных проверка сварных швов ультразвуком контроль стыковых сварных соединений ультразвуковая дефектоскопия металлов ультразвуковой контроль качества сварных соединений
Ультразвуковая дефектоскопия
металлов (ультразвуковой контроль качества сварных соединений) —
метод, предложенный С. Я. Соколовым в 1928 году и основанный на исследовании
процесса распространения ультразвуковых колебаний с частотой 0,5 — 25 МГц в
контролируемых изделиях с помощью специального оборудования — ультразвукового
дефектоскопа. Является одним из самых распространенных методов неразрушающего
контроля.
Принцип
работы
Звуковые волны не изменяют траектории движения в однородном
материале. Отражение акустических волн происходит от раздела сред с различными
удельными акустическими сопротивлениями. Чем больше различаются акустические
сопротивления, тем большая часть звуковых волн отражается от границы раздела
сред. Так как включения в металле обычно содержат газ (смесь газов) возникающих
вследствие процесса сварки, литья и т. п. И не успевают выйти наружу при
затвердевании металла, смесь газов имеет на пять порядков меньшее удельное
акустическое сопротивление, чем сам металл, то отражение будет практически
полное.
Разрешающая способность акустического исследования, то есть способность выявлять мелкие дефекты раздельно друг от друга, определяется длиной звуковой волны, которая в свою очередь зависит от частоты ввода акустических колебаний. Чем больше частота, тем меньше длина волны. Эффект возникает из-за того, что при размере препятствия меньше четверти длины волны, отражения колебаний практически не происходит, а доминирует их дифракция. Поэтому, как правило, частоту ультразвука стремятся повышать. С другой стороны, при повышении частоты колебаний быстро растет их затухание, что сокращает возможную область контроля. Практическим компромиссом стали частоты в диапазоне от 0,5 до 10 МГц.
Преимущества
Ультразвуковой
неразрушающий контроль (контроль стыковых сварных соединений) не разрушает и не
повреждает исследуемый образец, что является его главным преимуществом.
Возможно проводить контроль изделий из разнообразных материалов, как металлов,
так и неметаллов. Кроме того можно выделить высокую скорость исследования при
низкой стоимости и опасности для человека (по сравнению с рентгеновской
дефектоскопией) и высокую мобильность ультразвукового дефектоскопа.
Недостатки
Использование пьезоэлектрических преобразователей требует подготовки
поверхности для ввода ультразвука в металл, в частности создания шероховатости
поверхности не ниже класса 5, в случае со сварными соединениям ещё и
направления шероховатости (перпендикулярно шву). Ввиду большого акустического
сопротивления воздуха, малейший воздушный зазор может стать неодолимой
преградой для ультразвуковых колебаний. Для устранения воздушного зазора, на
контролируемый участок изделия предварительно наносят контактные жидкости,
такие как вода, масло, клейстер. При контроле вертикальных или сильно
наклоненных поверхностей необходимо применять густые контактные жидкости с
целью предотвращения их быстрого стекания.
Ультразвуковой контроль качества сварных соединений изделий с внешним диаметром менее 200 мм, необходимо использовать преобразователи, с радиусом кривизны подошвы R, равным 0,9−1,1R радиуса контролируемого объекта, так называемые притертые преобразователи, которые в таком виде непригодны для контроля изделий с плоскими поверхностями. Например для контроля цилиндрической поковки, необходимо производить перемещение преобразователя в двух взаимно перпендикулярных направлениях, что подразумевает под собой использование двух притёртых преобразователей — по одному для каждого из направлений.
Как правило ультразвуковая
дефектоскопия металлов не может дать ответ на вопрос о реальных размерах
дефекта, лишь о его отражательной способности в направлении приемника. Эти
величины коррелируют, но не для всех типов дефектов. Кроме того, некоторые
дефекты практически невозможно выявить ультразвуковым методом в силу их
характера, формы или расположения в объекте контроля.
Практически невозможно производить достоверный ультразвуковой контроль металлов с крупнозернистой структурой, таких как чугун или аустенитный сварной шов (толщиной свыше 60 мм) из-за большого рассеяния и сильного затухания ультразвука. Кроме того, затруднителен контроль малых деталей или деталей со сложной формой. Также затруднен ультразвуковой контроль сварных соединений из разнородных сталей (например аустенитных сталей с перлитными сталями) ввиду крайней неоднородности металла сварного шва и основного металла.
Ультразвуковой контроль сварных швов
(узк сварных швов)
Сварные швы являются самой массовой областью применения ультразвуковой
дефектоскопии. Это достигается за счёт мобильности ультразвуковой установки,
высокой производительности контроля, высокой точности, высокой чувствительности
к любым внутренним (объёмным — поры, металлические и неметаллические включения;
плоскостным — непровары, трещины), а также внешним, то есть поверхностным
дефектам сварных швов (подрезы, обнижения валика усиления и т. п.).
Многие ведомственные документы подразумевают обязательный ультразвуковой контроль сварных швов (контроль стыковых сварных соединений), либо альтернативный выбор ультразвукового или радиационного контроля, либо контроль обоими методами.
Основным документом в России по ультразвуковому контролю сварных швов является ГОСТ 14782−86, в котором рассмотрены в полном объёме методы контроля стыковых, тавровых, нахлесточных и угловых сварных швов, выполненных различными способами сварки. Также в нём подробно описаны стандартные образцы (эталоны) СО-1,СО-2(СО-2А),СО-3и СО-4 и стандартные образцы предприятия, необходимые для настройки дефектоскопа, а также их параметры для их изготовления.
Объёмы контроля и нормы оценки
качества сварного соединения (проверка сварных швов ультразвуком)
устанавливаются различными нормативными документами в соответствии с
требованиями прочности к конкретной сварной конструкции. На предприятиях,
изготавливающих особо ответственные изделия, а также различными надзорными
органами могут выпускаться собственные методические материалы для оценки
качества сварных швов. Примером может служить РД РОСЭК-001−96, разработанный
Ростехнадзором для оценки качества сварных соединений для грузоподъёмных
машин.
Контроль сварных швов | ||||
1 | Ультразвуковой контроль сварных соединений толщиной 0 — 10 мм (1 п.м.) | — Подготовка и настройка оборудования — Проведение контроля — Обработка результатов — Ведение журналов — Оформление протоколов |
ГОСТ Р 55724-2013 СП 70.13330.2012 |
1 000 |
2 | Ультразвуковой контроль сварных соединений толщиной 10 — 20 мм (1 п.м.) | — Подготовка и настройка оборудования — Проведение контроля — Обработка результатов — Ведение журналов — Оформление протоколов |
ГОСТ Р 55724-2013 СП 70. ![]() |
1 200 |
3 | Ультразвуковой контроль сварных соединений толщиной 20 — 30 мм (1 п.м.) | — Подготовка и настройка оборудования — Проведение контроля — Обработка результатов — Ведение журналов — Оформление протоколов |
ГОСТ Р 55724-2013 СП 70.13330.2012 |
1 500 |
4 | Ультразвуковой контроль сварных соединений толщиной 30 — 40 мм (1 п.м.) | — Подготовка и настройка оборудования — Проведение контроля — Обработка результатов — Ведение журналов — Оформление протоколов |
ГОСТ Р 55724-2013 СП 70.13330.2012 |
2 000 |
5 | Ультразвуковой и визуальный контроль качества (дефектоскопия) сварных соединений арматуры (1 стык) | — Подготовка и настройка оборудования — Проведение контроля — Обработка результатов — Оформление протоколов |
РД 03-606-03 ГОСТ 23858-79 ГОСТ Р 55724-2013 |
700 |
6 | Ультразвуковая дефектоскопия одним преобразователем сварных соединений перлитного класса с двух сторон, прозвучивание поперечное.![]() |
— Подготовка и настройка оборудования — Проведение контроля — Обработка результатов — Ведение журналов — Оформление протоколов |
ГОСТ Р 55724-2013 РД 153-34.1-003-01 |
590 |
7 | Ультразвуковая дефектоскопия одним преобразователем сварных соединений перлитного класса с двух сторон, прозвучивание поперечное. Трубопроводов диаметром до 57 мм, толщина стенки до 6 мм. (1 стык) | — Подготовка и настройка оборудования — Проведение контроля — Обработка результатов — Ведение журналов — Оформление протоколов |
ГОСТ Р 55724-2013 РД 153-34.1-003-01 |
630 |
8 | Ультразвуковая дефектоскопия одним преобразователем сварных соединений перлитного класса с двух сторон, прозвучивание поперечное. Трубопроводов диаметром до 76 мм, толщина стенки до 6 мм. (1 стык) | — Подготовка и настройка оборудования — Проведение контроля — Обработка результатов — Ведение журналов — Оформление протоколов |
ГОСТ Р 55724-2013 РД 153-34. ![]() |
680 |
9 | Ультразвуковая дефектоскопия одним преобразователем сварных соединений перлитного класса с двух сторон, прозвучивание поперечное. Трубопроводов диаметром до 89 мм, толщина стенки до 6 мм. (1 стык) | — Подготовка и настройка оборудования — Проведение контроля — Обработка результатов — Ведение журналов — Оформление протоколов |
ГОСТ Р 55724-2013 РД 153-34.1-003-01 |
720 |
10 | Ультразвуковая дефектоскопия одним преобразователем сварных соединений перлитного класса с двух сторон, прозвучивание поперечное. Трубопроводов диаметром до 108 мм, толщина стенки до 8 мм. (1 стык) | — Подготовка и настройка оборудования — Проведение контроля — Обработка результатов — Ведение журналов — Оформление протоколов |
ГОСТ Р 55724-2013 РД 153-34.1-003-01 |
690 |
11 | Ультразвуковая дефектоскопия одним преобразователем сварных соединений перлитного класса с двух сторон, прозвучивание поперечное.![]() |
— Подготовка и настройка оборудования — Проведение контроля — Обработка результатов — Ведение журналов — Оформление протоколов |
ГОСТ Р 55724-2013 РД 153-34.1-003-01 |
790 |
12 | Ультразвуковая дефектоскопия одним преобразователем сварных соединений перлитного класса с двух сторон, прозвучивание поперечное. Трубопроводов диаметром до 159 мм, толщина стенки до 8 мм. (1 стык) | — Подготовка и настройка оборудования — Проведение контроля — Обработка результатов — Ведение журналов — Оформление протоколов |
ГОСТ Р 55724-2013 РД 153-34.1-003-01 |
960 |
13 | Ультразвуковая дефектоскопия одним преобразователем сварных соединений перлитного класса с двух сторон, прозвучивание поперечное. Трубопроводов диаметром до 219 мм, толщина стенки до 8 мм. (1 стык) | — Подготовка и настройка оборудования — Проведение контроля — Обработка результатов — Ведение журналов — Оформление протоколов |
ГОСТ Р 55724-2013 РД 153-34. ![]() |
1 160 |
14 | Ультразвуковая дефектоскопия одним преобразователем сварных соединений перлитного класса с двух сторон, прозвучивание поперечное. Трубопроводов диаметром до 273 мм, толщина стенки до 8 мм. (1 стык) | — Подготовка и настройка оборудования — Проведение контроля — Обработка результатов — Ведение журналов — Оформление протоколов |
ГОСТ Р 55724-2013 РД 153-34.1-003-01 |
1 280 |
15 | Ультразвуковая дефектоскопия одним преобразователем сварных соединений перлитного класса с двух сторон, прозвучивание поперечное. Трубопроводов диаметром до 325 мм, толщина стенки до 8 мм. (1 стык) | — Подготовка и настройка оборудования — Проведение контроля — Обработка результатов — Ведение журналов — Оформление протоколов |
ГОСТ Р 55724-2013 РД 153-34.1-003-01 |
1 480 |
16 | Ультразвуковая дефектоскопия одним преобразователем сварных соединений перлитного класса с двух сторон, прозвучивание поперечное.![]() |
— Подготовка и настройка оборудования — Проведение контроля — Обработка результатов — Ведение журналов — Оформление протоколов |
ГОСТ Р 55724-2013 РД 153-34.1-003-01 |
1 920 |
17 | Ультразвуковая дефектоскопия одним преобразователем сварных соединений перлитного класса с двух сторон, прозвучивание поперечное. Трубопроводов диаметром до 426 мм, толщина стенки до 10 мм. (1 стык) | — Подготовка и настройка оборудования — Проведение контроля — Обработка результатов — Ведение журналов — Оформление протоколов |
ГОСТ Р 55724-2013 РД 153-34.1-003-01 |
2 240 |
18 | Ультразвуковая дефектоскопия одним преобразователем сварных соединений перлитного класса с двух сторон, прозвучивание поперечное. Трубопроводов диаметром до 530 мм, толщина стенки до 10 мм.![]() |
— Подготовка и настройка оборудования — Проведение контроля — Обработка результатов — Ведение журналов — Оформление протоколов |
ГОСТ Р 55724-2013 РД 153-34.1-003-01 |
2 560 |
19 | Ультразвуковая дефектоскопия одним преобразователем сварных соединений перлитного класса с двух сторон, прозвучивание поперечное. Трубопроводов диаметром до 720 мм, толщина стенки до 8 мм. (1 стык) | — Подготовка и настройка оборудования — Проведение контроля — Обработка результатов — Ведение журналов — Оформление протоколов |
ГОСТ Р 55724-2013 РД 153-34.1-003-01 |
2 760 |
20 | Ультразвуковая дефектоскопия одним преобразователем сварных соединений перлитного класса с двух сторон, прозвучивание поперечное. Трубопроводов диаметром до 820 мм, толщина стенки до 14 мм. (1 стык) | — Подготовка и настройка оборудования — Проведение контроля — Обработка результатов — Ведение журналов — Оформление протоколов |
ГОСТ Р 55724-2013 РД 153-34. ![]() |
2 920 |
21 | Ультразвуковая дефектоскопия одним преобразователем сварных соединений перлитного класса с двух сторон, прозвучивание поперечное. Трубопроводов диаметром до 1020 мм, толщина стенки до 14 мм. (1 стык) | — Подготовка и настройка оборудования — Проведение контроля — Обработка результатов — Ведение журналов — Оформление протоколов |
ГОСТ Р 55724-2013 РД 153-34.1-003-01 |
3 200 |
22 | Ультразвуковая дефектоскопия одним преобразователем сварных соединений перлитного класса с двух сторон, прозвучивание поперечное. Трубопроводов диаметром до 1220 мм, толщина стенки до 14 мм. (1 стык) | — Подготовка и настройка оборудования — Проведение контроля — Обработка результатов — Ведение журналов — Оформление протоколов |
ГОСТ Р 55724-2013 РД 153-34.1-003-01 |
3 760 |
60 — новейшая версия популярного ультразвукового дефектоскопа
Легендарный ультразвуковой дефектоскоп УСД-60 теперь в новом эргономичном корпусе и с возможностью последующего обновления до версии дефектоскопа на фазированных решетках УСД-60ФР.![]() После глубокой модернизации прибор представляет собой новую универсальную платформу, позволяющую пользователю наращивать возможности прибора по мере необходимости. Дефектоскоп снабжен мощным регулируемым генератором и малошумящим широкополосным приемником последнего поколения с набором узколополосных фильтров для повышения соотношения сигнал/шум. База данных преобразователей позволяет в одно нажатие загружать из памяти все их параметры, включая АРД-диаграммы. Богатый функционал, включающий функции ВРЧ и АРК, различные степени демпфирования сигнала, огибающую сигнала и функцию усреднения нескольких эхо-сигналов, а также две независимые зоны контроля с индивидуальной логикой определения дефекта, позволяет реализовывать любые современные методики контроля. Функция автоматической калибровки призмы преобразователя на стандартных образцах СО-3 и V-2, автоматическая калибровка реальной скорости в материале объекта контроля, автоматическая калибровка зоны контроля по прямому и однократному лучу, встроенный помощник расчета геометрии при контроле сварных соединений — позволяют сделать процедуру настройки легкой и понятной. Вход для двухканального оптического энкодера обеспечивает построение B-скана c координатной разверткой изделия, а также С- и D- сканов в специальных версиях. Масштабируемая программная структура новой версии дефектоскопа позволяет пользователю самостоятельно в дальнейшем наращивать возможности прибора по мере необходимости работы с TOFD сканерами, 16-и канальными фазированными решетками, многоэлементными сканерами. Прибор имеет специально разработанный ударопрочный корпус с классом защиты IP65. Уникальный морозостойкий современный экран с цветной TFT матрицей 640х480, великолепным быстродействием и широким углом обзора — это наилучший выбор для проведения работ в полевых условиях на ярком солнце, а также при отрицательных температурах. |
Инструкции, ГосРеестр, и др документы
Процесс оформления для юридических и физических лиц:
Для покупки товара в нашем интернет-магазине выберите понравившийся товар и добавьте его в корзину. Далее перейдите в Корзину и нажмите на «Оформить заказ» или «Быстрый заказ».
- Выберите тип покупателя (Юридическое лицо или Физическое лицо) и регион доставки
- Укажите способ доставки до терминала транспортной компании в вашем городе (самовывоз) или доставка курьером (DHL, СДЭК и т др.) в любом случае доставку можно будет изменить после разговора с менеджером компании или в личном кабинете в разделе заказы
- Укажите Счёт для банковского перевода с вашего расчётного счёта Юр. лица (или личного счёта для Физ. лица)
Оформление заказа в полном режиме выглядит следующим образом. Заполняете полностью форму начиная с обязательных полей: Название компании* (или ФИО),Контактное лицо*,E-Mail*
Телефон*, адрес, способ доставки, оплаты, данные о себе. Советуем в комментарии к заказу написать информацию, которая поможет сотруднику более детально ответить на ваши вопросы.
Нажмите кнопку «Оформить заказ».
Как во время оформления заказа так и после вы можете связаться с нами для уточнения любых вопросов
Оплачивайте покупки удобным способом. В интернет-магазине доступно 3 варианта оплаты:
- Банковский перевод для Юридических лиц при самовывозе или доставке курьером. Специалист свяжется с вами после оформления заказа. Вы переводите денежные средства после формирования счёта в личном кабинете или разговора с нашим сотрудником который отправит вам счёт для оплаты. Дальше стандартно подписываете товаросопроводительные документы (УПД) при получении товара.
- Безналичный расчет при самовывозе или оформлении в интернет-магазине: карты Visa и MasterCard.
Чтобы оплатить покупку, система перенаправит вас на сервер системы ASSIST. Здесь нужно ввести номер карты, срок действия и имя держателя.Доступно для карт привязанных к расчетному счёту Юридических лиц.
- Электронные системы при онлайн-заказе: PayPal, WebMoney и Яндекс.Деньги. Для совершения покупки система перенаправит вас на страницу платежного сервиса. Здесь необходимо заполнить форму по инструкции.
Экономьте время на получении заказа. В интернет-магазине федеральной компании NDT Rus доступно 3 варианта доставки:
- Курьерская доставка работает с 9.
00 до 19.00. Когда товар поступит на склад, курьерская служба свяжется для уточнения деталей. Специалист предложит выбрать удобное время доставки и уточнит адрес. Осмотрите упаковку на целостность и соответствие указанной комплектации.
- Самовывоз из пункта выдачи. Список точек для выбора появится в корзине. Когда заказ поступит на склад, вам придет уведомление. Для получения заказа обратитесь к сотруднику в кассовой зоне и назовите номер.
- Самовывоз из терминала транспортной компании
Наш интернет магазин создан в первую очередь для удобной работы с Юридическими лицами
Мы сохраняем возможность нашим клиентам «старыми» способами оформить заказ: когда вы звоните по телефону и диктуете своему менеджеру заявку или отправляете сформированное ТЗ на e-mail и дополняем возможность оформить заказ через социальные сети, мессенджеры, онлайн консультант на сайте.
Но самое главное мы внедрили удобную систему создания счёта для оплаты Юридическим лицом прямо в личном кабинете. Больше не прийдётся ждать ответа от сотрудника, если вы сами знаете какой прибор или расходные материалы вам сейчас необходимо приобрести.
Оформив заказ один раз вы сохраните данные для последующих заказов.
В любой момент можно позвонить нам для получения консультации.
Ультразвуковой контроль (УЗК) — Аттестационный центр «НАКС-Иваново»
Лаборатория НАКС-Иваново осуществляет работу по ультразвуковому контролю — одному из самых популярных методов неразрушающего контроля, использующему для выявления дефектов материалов и сварных швов ультразвуковые волны путём излучения и принятия ультразвуковых колебаний, отраженных от внутренних несплошностей (дефектов) с дальнейшим анализом их амплитуды, времени прихода, формы и других характеристик с помощью специального оборудования — ультразвукового дефектоскопа.
Ультразвуковой контроль предназначен для выявления в сварных швах и околошовной зоне трещин, непроваров, несплавлений, пор, шлаковых включений, расслоений и других видов дефектов без расшифровки их характера, но с указанием координат, условных размеров и количества обнаруженных дефектов.
Ультразвуковое исследование не разрушает и не повреждает исследуемый образец, что является его главным преимуществом. Можно проводить контроль изделий из разнообразных материалов, как металлов, так и неметаллов. Кроме того можно выделить высокую скорость исследования при сравнительно низкой стоимости и безопасности для человека (по сравнению с рентгеновской дефектоскопией), а также высокую мобильность ультразвукового дефектоскопа.
Ультразвуковой контроль сварных швов
Сварные швы являются самой массовой областью применения ультразвуковой дефектоскопии. Это достигается за счёт мобильности ультразвуковой установки, высокой производительности контроля, высокой точности, высокой чувствительности к любым внутренним (объёмным — поры, металлические и неметаллические включения; плоскостным — непровары, трещины), а также внешним, т. е. поверхностным дефектам сварных швов (подрезы, несоответствия валика усиления и т.п.).
Многие ведомственные документы подразумевают обязательный ультразвуковой контроль сварных швов, либо альтернативный выбор ультразвукового или радиационного контроля, либо контроль обоими методами.
Ультразвуковой контроль сварных соединений является эффективным способом выявления дефектов сварных швов и металлических изделий, залегающих на глубинах от 1-2 миллиметров до 6-10 метров.
Ультразвуковой контроль сварных соединений проводится по ГОСТ 14782-86 «Контроль неразрушающий. Соединения сварные. Методы ультразвуковые» и позволяет осуществлять ультразвуковую диагностику качества сварных соединений, выявлять и документировать участки повышенного содержания дефектов, классифицируя их по типам и размерам. Для разных типов сварных соединений применяются соответствующие методики ультразвукового контроля.
Ультразвуковой контроль сварных соединений позволяет провести полную диагностику сварных соединений без использования дорогостоящих методов неразрушающего контроля качества сварных швов, таких как рентгенографический, гаммаграфический, магнитопорошковый или капиллярный.
Диапазон измерения | 0,03~590,5 дюйма (1,0~15000 мм) |
Разрешение | 0,000393 дюйма (3,93 дюйма) (0,01 мм (<100 мм)) |
Скорость | 500~2000 м/с 20 фиксированная скорость звука |
Задержка отображения | -20~3400 мкс разрешение: 0,1 мкс |
Задержка датчика | 0~99 мкс Разрешение: 0,01 мкс |
Автокалибровка | Измерение и настройка скорости звука и задержки зонда с использованием двух известных эхосигналов калибровки (калибровка по двум точкам) |
Линейная ошибка | Ошибка горизонтальной линейности≤0.1% Ошибка вертикальной линейности ≤3% |
Динамический диапазон | ≥36 дБ |
Остатки чувствительности | ≥64дБ отверстие 200ммФ2 с плоским дном |
Размер | 9,44×7,08×1,96 дюйма (240×180×50 мм) |
Вес | 4,188 фунта (1,9 кг) (включая аккумулятор) |
Рабочая среда | Температура: 32F~140F (0℃~60℃) Влажность: 20%~90% |
Импульс передачи | |
Импульс привода | Отрицательный импульс/прямоугольная волна |
Длительность импульса | 50~2000нс |
Амплитуда импульса | 50-500В |
Частота повторения импульсов | Частота повторения импульсов PRF может регулироваться |
Демпфирование | 50/150/250/400 Ом |
Приемная система | |
Режим тестирования | Эхо-импульс/передача и прием/передача |
Режим измерения | Пик/Грань |
Усиление | от 0 до 110 дБ Клиенты определяют шаги 0/0.![]() |
Шаблон детектора | ВЧ/полная волна/положительная/отрицательная полуволна |
Диапазон частот | 0,3~1 / 0,5~4 /2~15 МГц широкополосный фильтр Узкополосный фильтр 1/2,5/5/10/15 МГц |
Дисплей | |
ЖК-дисплей | Цветной жидкокристаллический TET-экран с широким диапазоном температур и высокой яркостью, 5,7 дюйма, промышленный класс |
Подсветка | Можно выбрать 5 классов |
Частота обновления дисплея | Не менее 60 Гц |
Тема графического интерфейса | 5 цветовых тем графического интерфейса: простая/классическая/серая/яркий свет/темный свет Клиенты могут выбирать тему, устанавливая цвет символов Фоновый цвет координат волнового сканирования |
Ворота/Измерение/Тревога | |
Ворота | Две раздельные ворота A/B |
Значение измерения | 5 областей отображения значений, одна из них в основном область.![]() |
Тревога | Все ворота могут сигнализировать логично и независимо |
Память | |
Параметры канала | 20 групп |
Волна А-скана | 3200 группа |
Значение толщины | 320000линейный |
Волновое видео | 10 мин |
Опорная волна | 4 |
Ввод/вывод | |
Кабель зонда | ЛЕМО/БНК |
Связь | RS232/USB |
Регион | |
Время | Дата и время в реальном времени |
Язык | китайский английский |
Блок | мм/дюйм |
Мощность | |
Аккумулятор | Мощный литиевый аккумулятор с защитой от перезарядки и разрядки |
Индикатор питания | Мониторинг мощности на основе кулонметра, показывающего оставшуюся емкость батареи в процентах и срок службы батареи |
Рабочее время | Непрерывная работа более 20 часов |
Блок питания | Вход 100~240 В/50~60 Гц Выход 9 В постоянного тока/4 А |
Высококачественный | |
Динамическое эхо | Производительность моделирования цифровой природы |
Ключ памяти Сохранить | 3 вида скриншота отчета о данных значение толщины волны |
Решетка | Анализ деталей зоны широких ворот |
двумерное кодирование B сканирование | Сканирование толщины/формы Серая/цветная доска Дизайн |
Эхо-кодирование | Два выбранных значения кодирования: координата/форма волны удобно вычислять интервал |
Кривая замораживания | Все/пиковое значение/контракт/огибающая/огибающая задержки |
Индикатор функции | Измерение фронта и амплитуды звуковой волны |
Калибровка кривой CSC | Коррекция значения в зависимости от угла наклона датчика, толщины деталей и диаметра кривизны |
Замок | Одиночное меню независимо блокируется, чтобы избежать системной настройки связанных данных; Группа данных может быть заблокирована, чтобы избежать ошибочного удаления |
Экранная заставка | Режим ожидания/персонаж/отключение питания |
Эквивалентная кривая | |
Кривая DAC | Запись 30 калибровочных точек; автоматическое усиление; калибровка любого заказа; две корректировки калибровки/редактирования; учет коэффициента затухания материала и экономии поверхности; 5 оценочных кривых скорректированного усиления соответствуют стандарту JIS&API |
Кривая АРД | Кривая DGS соответствует трем каталожным номерам, включая сквозные отверстия с плоским дном; учет коэффициента затухания материала и сохранения поверхности при оценке содержания дефектов; эквивалентный размер/эквивалентный прирост/процент; |
ДЕФЕКТОСКОП – ИНСПЕКЦИОННАЯ КОМПАНИЯ ALMAWSOAA
Sitescan серии D – легкие цифровые ультразвуковые дефектоскопы
Серия Sitescan D представляет новое поколение портативных цифровых дефектоскопов. Его новаторский эргономичный дизайн был разработан, чтобы сделать его удобным для использования в течение всего дня.
Sitescan D-10 использует широкополосный усилитель, совместимый с широким спектром датчиков, в то время как модель D-20 использует несколько узкополосных для улучшения характеристик. «Аналоговое ощущение» от высококачественного широкополосного усилителя показывает все детали, необходимые для определения типов дефектов, таких как дыры или трещины, и достаточное разрешение для идентификации слабых сигналов. Типичными областями применения являются контроль сварных швов, испытания на коррозию, небольшие отливки, поковки и проверка расслоения.
Характеристики D10 и D20 | ||||||||||||||||||||
|
Обнаружение дефекта
Функция DetectFlaw используется для выявления дефектов путем сравнения обученных данных, содержащихся либо в допустимой структуре данных TrainFlawModel, возвращаемой функцией TrainFlawModel, либо в структуре данных FlexFlawModel, возвращаемой функцией FlexFlawModel, и в текущем полученном изображении.Функция DetectFlaw способна идентифицировать следующие три типа дефектов: дефекты области, дефекты отсутствующих краев и/или дополнительные дефекты краев. Дополнительные сведения о TrainFlawModel см. в разделе TrainFlawModel. Дополнительные сведения о FlexFlawModel см. в разделе FlexFlawModel.
Осмотр участка проверяет наличие дефектов, таких как царапины или пятна на поверхности предмета/детали. Проверка краев позволяет проверить, есть ли лишние или отсутствующие края, а также соответствие границ объекта/детали. Сочетание площадных и краевых дефектов обеспечивает наивысшую степень инспекционной проверки.
- Одна или несколько функций DetectFlaw могут быть связаны с одной функцией TrainFlawModel, что позволяет каждой функции DetectFlaw проверять разные части объекта/детали, используя при необходимости разные настройки.
- Дополнительная обработка изображения может выполняться для выходного изображения DetectFlaw, если для параметра Display Image установлено значение Edge Image, Model Image, Mask Image или Residual Image.Например, можно выполнить дополнительный анализ изображения блоба, задав для параметра Image функции ExtractBlobs значение Residual Image функции DetectFlaw в качестве входных данных.
- Чтобы сократить время выполнения функции, задайте для параметра Разрешение изображения функции значение Среднее или Грубое, что уменьшает разрешение изображения и снижает чувствительность функции к шуму изображения и очень небольшим изменениям.
Обнаружение дефекта Входы
Вкладка «Общие»
Синтаксис: DetectFlaw(Ссылка на модель дефекта,Область контроля.X,Область проверки.Y,Область проверки.Высокая,Область проверки.Широкая,Область проверки.Угол,Область проверки.Кривая,Внешняя область проверки или путь,Разрешение изображения,Элементы управления изображением маски.Добавить остаточное,Элементы управления изображением маски.Маска по умолчанию, Параметры дефекта. Минимальный контраст, Параметры дефекта. Нормализация, Параметры дефекта. Тип дефекта области, Параметры дефекта. Минимальный размер дефекта области, Параметры дефекта. Тип дефекта кромки, Параметры дефекта. Изображение, Показать )
Параметр | Описание | ||||||||||||||||||||||||||||||||
---|---|---|---|---|---|---|---|---|---|---|---|---|---|---|---|---|---|---|---|---|---|---|---|---|---|---|---|---|---|---|---|---|---|
Ссылка на модель дефекта | Указывает ссылку на ячейку электронной таблицы, содержащую либо допустимую структуру данных TrainFlawModel, возвращаемую функцией TrainFlawModel, либо структуру данных FlexFlawModel, возвращаемую функцией FlexFlawModel.![]() | ||||||||||||||||||||||||||||||||
Зона осмотра | Указывает область изображения, также известную как область интереса (ROI). который подвергается анализу изображения; создает прямоугольный область изображения, которую можно трансформировать и вращать.С этим параметром выбрано, нажав кнопку Развернуть кнопку «Регион» на панели инструментов листа свойств, регион автоматически быть растянутым, чтобы покрыть все изображение. Примечание :
| ||||||||||||||||||||||||||||||||
Внешняя область проверки или путь | Указывает ссылку на ячейку электронной таблицы, содержащую функцию управления. Примечание : Если этот параметр был установлен как ссылка на внешнюю область или путь, чтобы использовать внутреннюю область функции, этот параметр необходимо вручную установить на ноль, введя значение 0 вместо ссылки на ячейку. В противном случае функция продолжит ссылаться на внешний регион или путь. | ||||||||||||||||||||||||||||||||
Разрешение изображения | Указывает разрешение обработки изображения для функции, что позволяет функции понижать разрешение контрольного изображения. Совет : используйте настройки Medium или Coarse, чтобы сократить время выполнения функции или уменьшить чувствительность функции к шуму изображения и очень небольшим изменениям. Примечание : Если параметр Model Reference ссылается на структуру данных FlexFlawModel, возвращаемую функцией FlexFlawModel, этот параметр будет отключен, и вместо него будут использоваться настройки параметра Image Resolution функции FlexFlawModel.
| ||||||||||||||||||||||||||||||||
Элементы управления изображением маски | Указывает внешнюю ссылку на кнопку или функцию события для управления тем, как функция обрабатывает изображение маски.
| ||||||||||||||||||||||||||||||||
Параметры дефекта | Задает пределы для определения площадных и/или краевых дефектов.Дефекты области измеряются отклонениями значения шкалы серого пикселя и обычно включают дефекты, такие как пятна или обесцвечивание. Кромочные дефекты измеряются наличием/отсутствием краевых элементов и обычно включают такие дефекты, как царапины, надрывы или дополнительные элементы. Примечание : При применении функции DetectFlaw, если допуски для параметров дефекта узкие (например, ≤ 15 пикселей) и изображение имеет незначительные отклонения в шуме изображения, параметры «Игнорировать дефект» и «Добавить остаток» могут не учитываться.
| ||||||||||||||||||||||||||||||||
Маркировка кромок | Указывает, будет ли функция рисовать на изображении обнаруженные краевые метки зеленым цветом.
| ||||||||||||||||||||||||||||||||
Нанесение маркировки дефектов | Указывает, будет ли функция рисовать обнаруженные дефекты красным цветом на изображении.Выходные метки указывают, какие пиксели совпадают с пикселями в обученном изображении модели. Пиксели в полученном изображении, совпадающие с сегментом обученного края в обученном изображении модели, будут окрашены в зеленый цвет. Пиксели, которые выходят за пределы допусков и классифицируются как дефекты краев или областей, отображаются красным цветом, и вокруг них помещается красная ограничивающая рамка.
| ||||||||||||||||||||||||||||||||
Изображение на дисплее | Указывает тип вывода, который будет генерировать функция.
| ||||||||||||||||||||||||||||||||
Показать | Указывает режим отображения для DetectFlaw
графические наложения поверх изображения. Примечание : Когда лист свойств DetectFlaw открыт, все маркировки будут нарисованы на изображении, если включены параметры Draw Edge Markings и Draw Flaw Markings.
|
Вкладка «Редактировать маску»
Элементы управления редактированием изображения маски
Элементы управления редактированием изображения маски предоставляют средства для управления изображением маски, сохраненным в указанной структуре данных TrainFlawModel. Пока выбрана вкладка «Редактировать маску», изображение будет отображаться, и если параметр «Тип дефекта кромки» включен, маскированные края будут отмечены, а если параметр «Тип дефекта области» включен, будет отображаться изображение маски.
- Настройка изображения маски повлияет на любые другие функции DetectFlaw, которые ссылаются на ту же функцию TrainFlawModel, которая содержит изображение маски.
- При применении функции DetectFlaw, если допуски для параметров дефекта узкие (т.е. ≤ 15 пикселей, например), и на изображении наблюдаются незначительные вариации шума изображения, параметры «Игнорировать дефект» и «Добавить остаток» могут не учитывать эти вариации. В таких ситуациях попытайтесь расширить допуски для параметров дефекта, прежде чем применять параметры «Игнорировать дефект» или «Добавить остаток».
Добавить остаточное изображение | Указывает, что остаточное изображение и остаточные края будут добавлены к маске.Этот параметр приводит к изменению дефектов, обнаруженных на изображении, на недефекты. |
Расширенная маска | Указывает, что область пикселей в маске расширяется. Примечание : для использования этой опции должны быть включены типы дефектов области. |
Термоусадочная маска | Указывает, что площадь пикселей в маске уменьшается. Примечание : для использования этой опции должны быть включены типы дефектов области. |
Снять маску | Указывает, что все данные маски удаляются. |
Маска по умолчанию | Указывает, что изображение маски сбрасывается в первоначальное обученное состояние путем повторного создания данных маски из изображения модели. |
Вкладка «Список дефектов»
Таблица списка дефектов
Список дефектов представляет собой сортируемую таблицу обнаруженных дефектов.Выбор дефекта в списке выделит его на изображении, а также активирует кнопку Игнорировать дефект ; можно выбрать несколько дефектов, используя клавиши CTRL или SHIFT при выборе дефектов в списке.
Примечание : При применении функции DetectFlaw, если допуски для параметров дефекта узкие (например, ≤ 15 пикселей) и изображение имеет незначительные отклонения в шуме изображения, параметры «Игнорировать дефект» и «Добавить остаток» могут не учитываться. для вариаций.В таких ситуациях попытайтесь расширить допуски для параметров дефекта, прежде чем применять параметры «Игнорировать дефект» или «Добавить остаток».
Номер | Указывает порядковый номер обнаруженных дефектов, от 1 до N. |
Тип | Указывает тип дефекта: дополнительная кромка, недостающая кромка или область. |
Размер | Задает размер дефекта в пикселях.![]() |
Контраст | Задает контраст дефекта. |
Ряд | Указывает координату строки ограничивающей рамки, окружающей дефект. |
Столбец | Указывает координату столбца ограничивающей рамки, окружающей дефект. |
Высота | Указывает значение высоты ограничивающей рамки, окружающей дефект. |
Ширина | Указывает значение ширины ограничивающей рамки вокруг дефекта. |
Кнопка «Игнорировать дефект» | Указывает, что выбранные дефекты будут добавлены к изображению маски, больше не будут отображаться как дефекты и удалены из списка.![]() |
Выходы DetectFlaw
Возвращает | Структура данных DetectFlaw, содержащая обнаруженные дефекты или #ERR, если какой-либо из входных параметров недействительны. Примечание : Структура данных DetectFlaw может использоваться в качестве входных данных изображения для других инструментов технического зрения. Дополнительные сведения см. в разделе Инструменты машинного зрения. |
Результаты | Когда DetectFlaw изначально вставляется в
ячейка, таблица результатов
создается в электронной таблице.
|
Обнаружение дефекта Функции доступа к данным Vision
Следующие функции доступа к данным Vision автоматически вставляются в электронную таблицу для создания Таблица результатов структуры данных DetectFlaw. Дополнительные сведения о функциях доступа к данным Vision см. в разделе Обнаружение дефектов.
Имя электронной таблицы | Имя функции | Описание |
---|---|---|
Суммарное общее количество | GetTotalFlawCount(DetectFlaw, Тип) | Возвращает общее количество обнаруженных дефектов независимо от их типа.![]() |
Общий размер дефекта | GetTotalFlawSize(DetectFlaw, Тип) | Возвращает общее количество пикселей, классифицированных как дефекты. |
Кол-во | ||
Зона | GetTotalFlawCount(DetectFlaw, Тип) | Возвращает общее количество обнаруженных дефектов области. |
Отсутствующие края | GetTotalFlawCount(DetectFlaw, Тип) | Возвращает общее количество обнаруженных недостающих дефектов кромки.![]() |
Дополнительные кромки | GetTotalFlawCount(DetectFlaw, Тип) | Возвращает общее количество обнаруженных дополнительных дефектов кромок. |
Размер дефекта | ||
Зона | GetTotalFlawSize(DetectFlaw, Тип) | Возвращает общее количество пикселей, которые классифицируются как дефекты области. |
Отсутствующие края | GetTotalFlawSize(DetectFlaw, Тип) | Возвращает общее количество пикселей, которые классифицируются как недостающие края.![]() |
Дополнительные кромки | GetTotalFlawSize(DetectFlaw, Тип) | Возвращает общее количество пикселей, которые классифицируются как дополнительные краевые пиксели. |
Тип дефекта Примечание : Для каждого из типов дефектов (область, недостающая кромка и лишняя кромка) отображаются первые пять обнаруженных дефектов. | ||
Размер | GetFlawSize(DetectFlaw, Тип, Индекс) | Возвращает размер дефекта в пикселях.![]() |
Контраст | GetFlawContrast(DetectFlaw, Тип, Индекс) | Возвращает контраст дефекта. |
Ряд | GetFlawRow(DetectFlaw, Тип, Индекс) | Возвращает координату строки ограничивающей рамки, окружающей дефект. |
Col | GetFlawCol(DetectFlaw, Тип, Индекс) | Возвращает координату столбца ограничивающей рамки вокруг дефекта. |
Высокий | GetFlawHigh(DetectFlaw, Тип, Индекс) | Возвращает значение высоты ограничивающей рамки вокруг дефекта.![]() |
Широкий | GetFlawWide(DetectFlaw, Тип, Индекс) | Возвращает значение ширины ограничивающей рамки вокруг дефекта. |
Обнаружение дефектов на основе правил на КТ-изображениях бревен лиственных пород
Обнаружение дефектов на основе правил на КТ-изображениях бревен лиственных пород | Поиск по дереву Перейти к основному содержанию .gov означает, что это официально.
Веб-сайты федерального правительства часто заканчиваются на .gov или .mil. Прежде чем делиться конфиденциальной информацией, убедитесь, что вы находитесь на сайте федерального правительства.
Сайт защищен.
https:// гарантирует, что вы подключаетесь к официальному веб-сайту и что любая предоставленная вами информация шифруется и передается безопасно.
Автор(ы):
Эрол Саригул
А.Линн Эбботт
Дэниел Л. Шмольдт
Тип публикации:
Разное Публикация
Первичная(ые) станция(и):
Южная исследовательская станция
Источник:
Материалы 4-й Международной конференции по обработке изображений и сканированию древесины. 37-49.
Описание
Эта статья посвящена автоматизированному обнаружению и идентификации внутренних дефектов в бревнах лиственных пород с использованием изображений компьютерной томографии (КТ). Мы разработали систему, использующую искусственные нейронные сети для предварительной классификации бревен попиксельно. Этот подход позволяет достичь высокого уровня точности классификации нескольких лиственных пород (дуб северный красный, Quercus rubra, L., водяной дуб, Q. nigra, L., тополь желтый, Liriodendron tulipifera, L., и черешня, Prunus serotina, Ehrh.), и три распространенных типа дефектов (сучки, трещины и гниение). Хотя статистически результаты очень удовлетворительны, субъективное исследование выявляет ситуации, которые могут быть уточнены на последующем этапе постобработки. В настоящее время мы разрабатываем основанный на правилах подход к уточнению региона, чтобы усилить первоначальный акцент на местной информации. Результирующие правила зависят от области, используя информацию, которая зависит от формы области и типа дефекта.Например, расщепления имеют тенденцию быть длинными и узкими, и это знание можно использовать для слияния меньших, непересекающихся областей, которые предварительно были помечены как расщепления. Точно так же области изображения, представляющие сучки, гниение и чистую древесину, можно улучшить, удалив мелкие ложные точки и сгладив границы этих областей. Для большинства этих задач можно использовать операторы математической морфологии. В этой статье представлены подробные сведения о доменно-зависимых правилах, по которым выбираются морфологические операторы, а также о слиянии результатов различных операций.
Цитата
Саригул, Эрол; Эбботт, А. Линн; Шмольдт, Даниэль Л. 2000. Обнаружение дефектов на основе правил в изображениях КТ бревен твердой древесины. Материалы 4-й Международной конференции по обработке изображений и сканированию древесины. 37-49.
Примечания к публикации
- Мы рекомендуем вам также распечатать эту страницу и прикрепить ее к распечатке статьи, чтобы сохранить полную информацию о цитировании.
- Эта статья была написана и подготовлена служащими правительства США в официальное время и поэтому находится в открытом доступе.
https://www.fs.usda.gov/treesearch/pubs/1860
Sonatest — цифровой дефектоскоп Masterscan D-70
Описание
Masterscan Series D-70, ВЫСОКОПРОИЗВОДИТЕЛЬНЫЙ УЗКОПОЛОСНЫЙ ЦИФРОВОЙ УЛЬТРАЗВУКОВОЙ ДЕФЕКТОСКОП
Наследие Sonatest в дизайне продукции и имя Masterscan всегда гарантировали техническим специалистам надежность
Конструкция прибора в сочетании с исключительными характеристиками. Серия Masterscan несет эстафету
и обновления, выполняемые в рабочей среде, что сокращает время простоя и повышает гибкость работы.
Высокие уровни разрешения вблизи поверхности, проникающая способность (импульсный генератор 450 В — прямоугольный и пиковый) и отличные характеристики
Соотношение сигнал/шумявляется ключевой функцией в линейке Masterscan.
Типичные области применения: изготовление сварных швов, обнаружение коррозии, проверка композитных материалов, испытание сцепления,
Поковки и отливки, производство электроэнергии (включая EMATS) и общий контроль УЗК.
Особенности серии Masterscan
• Настраиваемое встроенное программное обеспечение.
• Настраиваемые и интуитивно понятные меню.
• Раздельный ЦАП/СРЕДНИЙ.
• Режим измерения угла.
• Возможность сухого сканирования.
• Возможность модернизации на месте.
• Кодированный B-скан.
• Затухание А-скана.
• 4 ГБ встроенной памяти.
• USB-интерфейс для импорта/экспорта ПК
Дисплей повышенной видимости
Для любого дефектоскопа дисплей является важным элементом. Серия Masterscan оснащена цветным трансфлективным дисплеем VGA,
, обеспечивающий высокую видимость в любых условиях освещения.Максимальная читаемость достигается за счет регулируемой яркости
и выбор из 9 цветовых палитр, включая режим эмуляции черно-белого ЖК-дисплея.
Простота царит благодаря усовершенствованному пользовательскому интерфейсу и полноэкранному дисплею A-Scan, доступному в модели
.нажатием кнопки, чтобы можно было легко увидеть каждую деталь А-скана.
3Rs – надежный, прочный и прочный
Способность работать в суровых условиях с проверенной надежностью является важным аспектом владения дефектоскопом
.Максимальному времени работы способствует выдающаяся производительность батареи. До 18 часов
от полной зарядки. Корпус Masterscan изготовлен из ударопрочных автомобильных материалов
и соответствует стандартам IP67, обеспечивая превосходную водонепроницаемость.
Испытания на взрывоопасность соответствуют стандартам MIL810-G, а испытания на воздействие окружающей среды
подтвердили полную работоспособность прибора при температурах выше 55°C.
Стандартный комплект Masterscan
• Цифровой дефектоскоп D70
• Аккумулятор, зарядное устройство, сетевой кабель зарядного устройства.
• Руководство пользователя и сертификат калибровки.
• Сертификат соответствия
• Сумка для переноски.
• Кабель UTLity и USB.
• Крышка окна дисплея.
• Ультразвуковая контактная жидкость
Что такое ультразвуковой контроль с фазированной решеткой (PAUT) и как он работает?
Как упоминалось выше, ультразвуковые контрольные преобразователи с фазированной решеткой состоят из нескольких пьезоэлектрических кристаллов, которые передают/принимают сигналы независимо друг от друга в разное время. Ультразвуковой луч фокусируется с помощью временных задержек, которые применяются к элементам для создания конструктивной интерференции волновых фронтов.Эта интерференция позволяет сфокусировать энергию на любой глубине и под любым углом в испытуемом образце.
Каждый элемент излучает сферическую волну в указанное время, создавая волны, которые сходятся и расходятся, создавая почти плоский волновой фронт в указанном месте. Изменение прогрессивной временной задержки позволяет электронным образом управлять лучом и проводить его через исследуемый материал, как прожектор. Когда несколько лучей соединяются вместе, создается визуальное изображение, показывающее срез тестового объекта.
Существуют различные методы, которые можно использовать с системами PAUT.
Метод полной фокусировки (TFM)
Этот метод включает в себя применение основного принципа фокусировки с фазированной решеткой в определенной интересующей области. Область проверки сегментируется на сетку позиций или пикселей, при этом формирование луча применяется к каждому пикселю в сетке.
Электронное сканирование
Электронное сканирование воспроизводит осмотр, выполняемый путем ручного перемещения стандартного ультразвукового датчика.Ультразвуковой луч электронно перемещается по всему зонду, что позволяет ускорить осмотр и ограничить механическое смещение. Этот метод может быть выполнен с S- или L-зубцом и может сочетаться с фокусировкой луча и управлением лучом.
Сканирование секторов
При сканировании секторов используются электронные законы задержки для электронного изменения углов ультразвукового луча в определенном секторе. Это означает, что для осмотра компонентов под разными углами требуется только один преобразователь, а также он намного быстрее, чем стандартный УЗК с наклонным лучом, отображая поперечные сечения образца в режиме реального времени и упрощая интерпретацию.Этот метод можно комбинировать с электронной фокусировкой и использовать для L- и S-волн.
Преимущества фазированных решеток по сравнению с обычными ультразвуковыми датчиками включают улучшенную портативность, удобство, скорость проверки и безопасность. Фазированная решетка более надежна и проста в использовании, чем обычные одноэлементные датчики, обеспечивая повышенную эффективность, захват сотен сигналов одновременно и снижение количества ложных срабатываний. Стратегии контроля PAUT могут быть оптимизированы для улучшения обнаружения дефектов при использовании вместе с моделированием, в то время как запись данных и отслеживаемость также значительно улучшаются.
Ультразвуковой контроль с фазированной решеткой обеспечивает постоянную запись, не создает излучения и может использоваться для нескольких приложений. Поскольку PAUT может обнаруживать дефекты на поверхности и в объеме сварного шва (без мертвой зоны), он также дает информацию о боковом положении дефекта (глубина и высота).
Основные преимущества ультразвукового контроля с фазированной решеткой:
Упрощенный осмотр и интерпретация
Датчик с фазированной решеткой может заменить несколько обычных ультразвуковых датчиков, упрощая сложные процедуры и устраняя необходимость в настройке и калибровке нескольких датчиков. Это также позволяет упростить функциональность, включая визуализацию в реальном времени.
Расширенное обнаружение дефектов
Поскольку для управления направлением и формой луча используется датчик, поверхность можно сканировать под разными углами. Это позволяет увеличить зону обнаружения дефектов, а также проверку сложной геометрии. PAUT также эффективен для определения толщины материала, что полезно для ультразвукового определения коррозии или эрозии образца.
Более высокая скорость проверки
Используя электронное сканирование для запуска последовательных групп элементов массива, PAUT снижает потребность в механическом сканировании и сокращает время проверки.Скорость проверки также повышается по сравнению с обычными датчиками, поскольку фазированные решетки позволяют пользователю изменять форму и фокус ультразвукового луча для оптимизации каждой проверки. Это означает, что нет необходимости в ручной настройке и реконфигурации для каждого уникального тестирования. Кроме того, динамическая фокусировка по глубине позволяет проводить измерения на нескольких глубинах за то же время, которое требуется для выполнения одного измерения глубины с помощью обычного датчика. Кроме того, поскольку цифровая обратная связь может быть получена мгновенно, идентификация дефектов и оценка качества сварки могут выполняться быстрее.
Более надежные результаты
Сокращение или отказ от механического сканирования не только сокращает время проверки, но и повышает надежность измерений за счет устранения изменений или потери связи, которая возникает при перемещении датчика. Это также означает, что датчики с фазированной решеткой обеспечивают превосходную воспроизводимость результатов испытаний.
Хотя PAUT имеет ряд преимуществ, необходимо учитывать и несколько недостатков.
К ним относятся:
Применимость
Несмотря на диапазон применений, в которых PAUT блистает, это не предпочтительный метод испытаний для обнаружения поверхностных трещин, усталости металла или проверки отверстий под болты и труб. В этих случаях обычно предпочтительнее вихретоковый контроль, в то время как PAUT эффективен для обнаружения коррозии и контроля композитных материалов и более толстых сварных швов. Кроме того, угол падения не всегда оптимален при использовании S-скана.
Сложность
ОборудованиеPAUT является более совершенным, чем обычное ультразвуковое испытательное оборудование, с множеством функций оптимизации данных, оборудование должно использоваться обученным специалистом, чтобы устранить риск неточных испытаний и получить все преимущества PAUT.
Стоимость
ОборудованиеPAUT также обычно стоит дороже, чем обычные системы ультразвукового контроля. Это связано с расширенными функциями, предлагаемыми системами PAUT, хотя они могут привести к более быстрым, точным и эффективным проверкам, что в конечном итоге может привести к снижению общей стоимости владения.
Фазированные решетки могут выполнять любую работу, выполняемую с помощью обычного ультразвука, и используются для широкого спектра задач контроля и измерения, в том числе для медицинской визуализации и промышленного неразрушающего контроля (НК).
Идеально подходит для неинвазивного исследования материалов, обнаружения дефектов сварных швов и оценки качества заклепок. PAUT также может обнаруживать трещины, пустоты и ямки, вызванные коррозией. Эта технология позволяет измерять толщину материала и покрытия, обнаруживать изменения в свойствах материала и проверять соединения и поверхности раздела, включая картирование адгезии.
В качестве передового метода неразрушающего контроля он используется для обнаружения несплошностей для определения качества компонентов, что делает его идеальным для:
- Проверка сварных швов
- Измерение толщины
- Контроль коррозии
- Валидационные/демонстрационные блоки PAUT
- Осмотр колес и осей подвижного состава
- Стандартные калибровочные блоки PAUT и TOFD
- Сосуды под давлением
Этот диапазон приложений означает, что фазированные решетки широко используются в нескольких отраслях промышленности, таких как строительство, трубопроводы и производство электроэнергии.
Преобразователь — это устройство, которое преобразует одну форму энергии в другую. В случае ультразвукового контроля с фазированной решеткой пьезоэлектрический кристалл преобразует электрическую энергию в энергию ультразвука.
Фазированные решетки объединяют несколько ультразвуковых преобразователей, которые активируют отдельные элементы в определенной последовательности, чтобы направить звуковую волну в нужном направлении.
Ультразвуковой контроль с фазированной решеткой обеспечивает ряд преимуществ и может использоваться в различных приложениях и отраслях.Как метод неразрушающего контроля, он более надежен, эффективен и быстрее, чем многие другие методы, такие как радиографический контроль.
Несмотря на некоторые недостатки, при правильном обучении и при использовании в подходящих приложениях пользователи могут выполнять проверки толщины материала, сварных швов, коррозии, клея и многого другого.
Связанные часто задаваемые вопросы (FAQ)
Трещина трубопровода была тонкой.

Рабочие убирают загрязненный пляж в Ньюпорт-Бич, Калифорния., после крупного разлива нефти у побережья. Ринго Х.В. Чиу/АП скрыть заголовок
переключить заголовок Ринго Х.В. Чиу/АПРабочие убирают загрязненный пляж в Ньюпорт-Бич, Калифорния, после крупного разлива нефти у побережья.
Ринго Х.В. Чиу/АП ХАНТИНГТОН-БИЧ, Калифорния. На видео прорыва трубопровода, из которого вылились десятки тысяч галлонов сырой нефти у побережья Южной Калифорнии, видна тонкая трещина вдоль верхней части трубы, которая может указывать на медленную утечку, которую изначально было трудно обнаружить, говорят эксперты. Четверг.
Узкая щель длиной 13 дюймов может объяснить, почему признаки нефтяного пятна были замечены в пятницу вечером, но разлив ускользал от оператора трубопровода до утра субботы, сказал Ричард Купревич, частный исследователь и консультант по авариям на трубопроводе.
«Мой опыт подсказывает, что это чертовски сложная утечка, которую можно быстро определить удаленно», — сказал Купревич. «Отверстие такого типа на подводной трубе длиной 17 миль очень трудно обнаружить по дистанционным признакам. Эти выбросы в виде трещин имеют более низкую скорость и могут продолжаться довольно долго».
Когда трубы терпят катастрофический отказ, разрыв обычно намного больше, что называется в отрасли разрывом «рыбьей пасти», потому что он зияет широко, как пасть рыбы, сказал он.
Amplify Energy, компания из Хьюстона, которая владеет и управляет тремя морскими нефтяными платформами и трубопроводом к югу от Лос-Анджелеса, заявила, что не знала о разливе, пока ее рабочие не обнаружили масляный блеск на воде в субботу в 8 часов. :09 утра
Рабочие проходят мимо, пока мертвые морские обитатели выброшены на берег после разлива нефти. Ринго Х.В. Чиу/AP скрыть заголовок
переключить заголовок Ринго Х.В. Чиу/АПРабочие проходят мимо мертвых морских обитателей, выброшенных на берег после разлива нефти.
Ринго Х.В. Чиу/АППричина разлива расследуется многочисленными агентствами, поскольку очистка продолжается вдоль береговой линии на побережье округа Ориндж к югу от портов Лос-Анджелеса и Лонг-Бич.
Береговая охрана расследует, мог ли корабельный якорь зацепить и погнуть трубопровод. Amplify публично заявила, что утекло не более 126 000 галлонов. Но он также сообщил федеральным следователям, что общее количество может составлять всего 29 400 галлонов.
Официальные лица заявили в среду, что они расследуют, может ли корабль, ожидающий разгрузки, иметь какое-то отношение к утечке. Следователи береговой охраны поднялись на борт огромного контейнеровоза Rotterdam Express под немецким флагом, чтобы определить, был ли он причастен к разливу.На прошлой неделе «Роттердам» был ближайшим к трубопроводу якорем.
Hapag-Lloyd, судоходная компания, которая управляет судном, подтвердила в четверг, что следователи поднялись на борт корабля, когда он стоял в порту Окленда в заливе Сан-Франциско. По словам Нильса Хаупта, представителя штаб-квартиры Hapag-Lloyd в Гамбурге, Германия, береговая охрана опросила капитана и команду и получила доступ к бортовому журналу с указанием местонахождения корабля.
После этого береговая охрана позвонила в компанию и сообщила, что судно Rotterdam больше не находится под пристальным вниманием в связи с разливом, сказал Хаупт. Корабль получил разрешение на отплытие из Окленда и направлялся в Мексику.
По словам следователей, утечка произошла примерно в 5 милях от берега на глубине около 98 футов. По словам генерального директора Amplify Мартина Уилшера, участок трубопровода длиной 4000 футов был смещен на 105 футов, согнутый назад, как тетива на луке.
Люди наслаждаются пляжем на заднем плане, пока рабочие чистят загрязненный песок. Ринго Х.В. Чиу/AP скрыть заголовок
переключить заголовок Ринго Х.В. Чиу/АПНа заднем плане люди наслаждаются пляжем, пока рабочие убирают зараженный песок.
Ринго Х.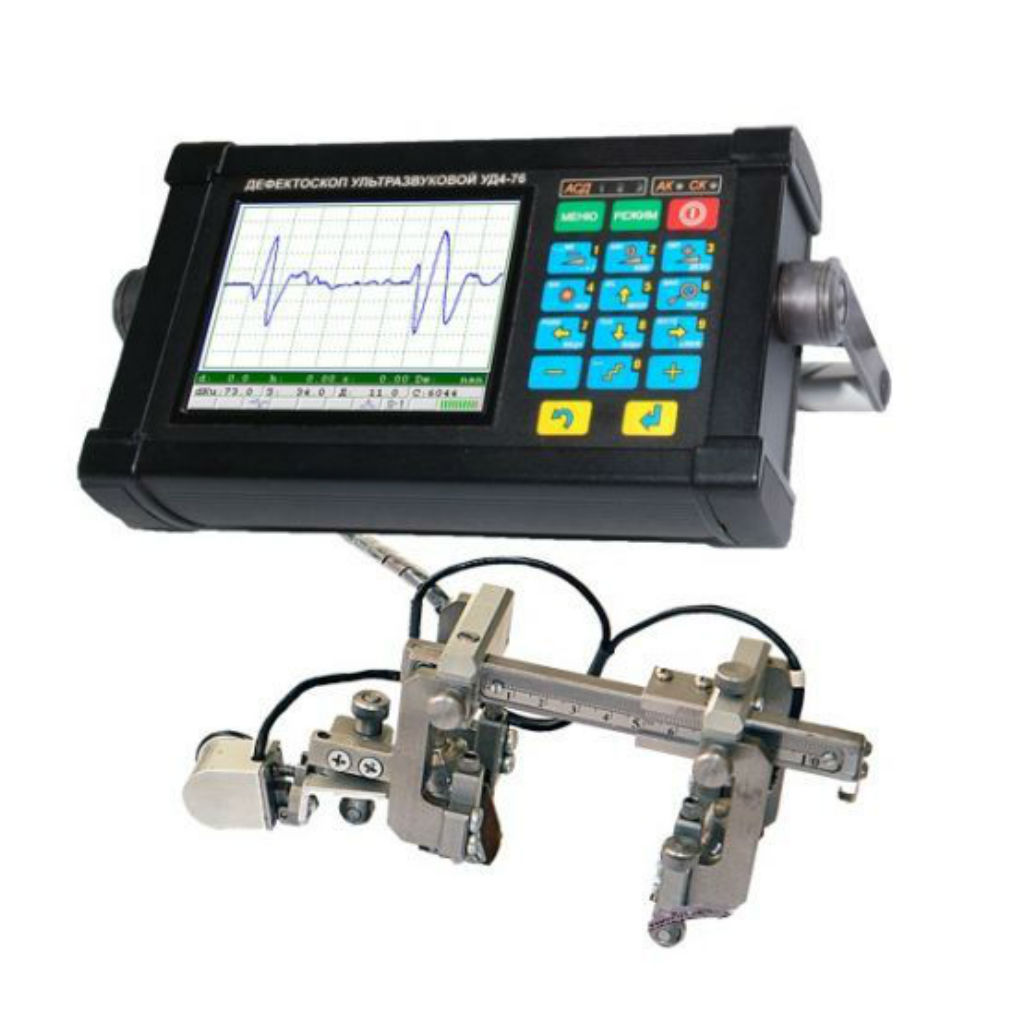
Остаются вопросы о том, когда нефтяная компания узнала, что у нее есть проблема, и о задержках с сообщением о разливе.
Иностранное судно, стоявшее на якоре в водах у Хантингтон-Бич, сообщило береговой охране, что сразу после 18:00 увидело сияние длиной более 2 миль. Спутниковый снимок, сделанный Европейским космическим агентством, показал вероятное нефтяное пятно в этом районе около 19:00. и было сообщено береговой охране после 2 часов ночи Национальным управлением океанических и атмосферных исследований.
Федеральные регуляторы безопасности трубопроводов установили время инцидента в 2:30 утра в субботу, но говорят, что компания не отключала трубопровод до 6:01.м. и не сообщал об утечке береговой охране до 9:07 утра. Федеральные правила и правила штата требуют немедленного уведомления о разливах.
Трещина, показанная на видео береговой охраны, достаточно велика, чтобы позволить утечке некоторого количества масла, что может привести к срабатыванию сигнализации низкого давления, сказал Купревич. Но, поскольку трубопровод работал при относительно низком давлении, оператор диспетчерской, возможно, просто отклонил сигнал тревоги, потому что давление было не очень высоким, чтобы начать работу, сказал он.
Раманан Кришнамурти, профессор нефтяной инженерии Хьюстонского университета, сказал, что трубопровод мог протекать в течение нескольких дней, прежде чем его обнаружили.
«Если у вас есть массивная трещина или массивная дыра, вы получаете огромный перепад давления, и поэтому вы знаете, что у вас есть массивная утечка», — сказал он. «Когда у вас есть такая трещина на волоске, возможно, это могло продолжаться в течение двух, трех, четырех дней».
Тот факт, что линия залива Сан-Педро на видео все еще была забетонирована, является еще одним признаком того, что утечка нефти, вероятно, происходила с небольшой скоростью. По словам Купревича, в случае крупного прорыва на линии с высоким давлением бетон сорвется.
Поскольку линия залита бетоном, что позволяет удерживать ее на морском дне, видео береговой охраны не показывает состояние стальной трубы толщиной в полдюйма под ней.