Сварка цветных металлов и их сплавов
Сварка цветных металлов и их сплавов
Сварка цветных металлов и их сплавов достаточно сложная процедура, поэтому при выполнении всех операций нужно строго соблюдать все условия конструкторской документации и технологического процесса.
Техническая медь маркируется в зависимости от содержания в ней примесей. Сплавы на основе меди в зависимости от состава легирующих элементов относят к латуням, бронзам и медно-никелевым сплавам.
При сварке технической меди и ее сплавов необходимо учитывать их специфические физико-химические свойства: высокую теплопроводность, высокий коэффициент термического расширения, высокую чувствительность к водороду, низкую стойкость швов и около шовной зоны к возникновению горячих трещин, повышению текучести и др.
Перед сваркой меди или ее сплавов разделку кромок и основной металл около них на ширине не менее 20 мм очищают от масла, грязи и оксидной пленки, обезжиривают растворителем или бензином. Сварочную проволоку и присадочный металл очищают травлением в жидком растворе азотной, серной и соляной кислот с последующей промывкой в воде и щелочи и просушкой горячим воздухом. Для предупреждения пористости кромки деталей покрывают специальными флюс-пастами.
Медь хорошо сваривается в аргоне, гелии и азоте, а также в их смеси. Чаще применяют смесь в составе (70-80%) Аг +(30 – 20%) N2. Азот способствует увеличению проплавления меди. Из-за высокой теплопроводности меди трудно получить надежный провар. Поэтому перед сваркой кромки деталей подогревают до температуры 200-500°С. При сварке в аргоне подогрев необходим для деталей толщиной более 4 мм, а при сварке в азоте – более 8 мм.
Величину сварочного тока выбирают исходя из диаметра вольфрамового электрода, состава защитного газа (или смеси) и рода тока. Сварку можно производить как на переменном, так и на постоянном токе обратной полярности.
При сварке латуней, бронз и медно-никелевых сплавов предпочтительнее использовать вольфрамовые электроды. В этом случае испарение цинка и олова из сплавов будет значительно меньше, чем при сварке плавящимися электродами. Следует учесть, что сварка цветных металлов и их сплавов вольфрамовыми электродами током обратной полярности затруднена из-за сильного нагрева электрода и очень малых допустимых токов.
При сварке алюминиевых и магниевых сплавов имеются специфические трудности. Они заключаются в том, что поверхность этих сплавов покрыта тугоплавкой оксидной пленкой, которая препятствует сплавлению металла сварочной ванны с основным металлом. В процессе сварки не всегда удается полностью удалить ее из сварного шва, где она остается в виде неметаллических включений.
При сварке на токе обратной полярности происходит катодная очистка свариваемых поверхностей в зоне горения дуги. Однако действием сварочного тока разрушается лишь сравнительно тонкая оксидная пленка. Толстую пленку оксида алюминия (А1203) перед сваркой необходимо удалить механическим или химическим путем. Очень важно удалить оксидную пленку с поверхности электродной проволоки малого диаметра из алюминиевых и магниевых сплавов.
Подготовка под сварку должна осуществляться особенно тщательно, так как на поверхности оксидной пленки хорошо задерживается атмосферная влага. В процессе сварки влага разлагается и приводит к насыщению металла шва водородом и увеличению пористости металла.
Термически упрочняемые сплавы марок АВ, АК6, АКВ обладают повышенной склонностью к образованию горячих трещин. Для уменьшения склонности к горячим трещинам этих сплавов применяют в качестве присадочного металла сварочную проволоку с содержанием 4-6% Si.
Влияние на качество сварных соединений оказывает и выбор оборудования для сварки. Фирма ELECTREX предлагает новейшую разработку в области сварочного производства — сварочный полуавтомат MIG 506 M – WM « Synergic+», который прекрасно подходит для сварки алюминия, меди и алюминиевых сплавов. Это оборудование позволит Вам решить самые сложные задачи, связанные со сварочным производством.
Также большое значение имеет выбор конструктивных элементов разделки кромок, которые определяются требованиями ГОСТ 23949-80. Свариваемые детали собирают так, чтобы были обеспечены минимально возможные зазоры. Если сварку приходится производить без сборочно-сварочных приспособлений, то детали фиксируют с помощью прихваток. Прихватки выполняют той же проволокой, что и сварку.
Наилучшие механические свойства сварных швов обеспечивают при сварке неплавящимся электродом в среде Аг. Основным достоинством этого способа является высокая устойчивость горения дуги. Питание дуги осуществляется переменным током от источников с падающими внешними характеристиками.
При сварке плавящимся электродом питание дуги осуществляется от источника постоянного тока с жесткой вольтамперной характеристикой. С целью надежного разрушения оксидной пленки сварку ведут на токе обратной полярности. Сварку выполняют либо в аргоне, либо в смеси аргона с гелием (30% Аг + 70% Не).
Читайте также:
Электрическая дуга
Дефекты сварных швов
Методы контроля качества сварных соединений и наплавок
Центробежные пылеуловители. Циклоны
Станки с ЧПУ
Сварка деталей из цветных металлов и их сплавов — Студопедия
Цветные металлы и их сплавы при сварке интенсивно окисляются и поглощают газы (шов оказывается пористым), что затрудняет их сварку. Трудность сварки алюминия и его сплавов, кроме того, объясняется еще и в тугоплавкости окислов этого металла. Температура плавления алюминия 657°С, а его окисла- 2050°С.
Детали из алюминиевых сплавов можно сваривать пламенем газовой горелки или с помощью электрической дуги.
Хороший эффект дает электродуговая сварка в защитной среде инертного газа— аргона (аргонодуговая сварка) неплавящимся вольфрамовым электродом. При сварке этим способом не требуется применения флюсов и электродных покрытий, а сварной шов получается с высокими механическими и антикоррозионными свойствами(сварку производят постоянным током обратной полярности или переменным током). Для ручной аргонодуговой сварки служат специальные установки и газоэлектрические горелки. Несмотря на отмеченные преимущества применение аргонодуговой сварки в условиях ремонтных предприятий ограничивается высокой стоимостью и дефицитностью аргона.
При сварке деталей из алюминиевых сплавов в качестве присадочного материала применяют стержни того же состава, что и основной металл, или специальные — следующих составов: 1) 95% алюминия и 5% кремния;2)92% алюминия и 8% кремния.
Для растворения окислов, препятствующих сварке, применяют специальные флюсы марок АФ-4А, АЗ, ВАМИ, КМ-1, в состав которых входят в разных пропорциях хлористые соединения натрия, калия, лития, бария, а также фтористый натрий, плавиковый цитат и криолит. При газовой сварке используется флюс в виде порошка при электродуговой сварке плавящимися электродами — электродных покрытий.
Подготовка деталей к сварке состоит в разделке кромок и последующей очистке их до металлического блеска механическим (проволочной щеткой, шабером) или химическим способом (погружением в 10-процентный раствор едкого натра, а затем в 3-процентный раствор азотной кислоты с последующей промывкой водой). При подготовке к сварке трещин засверливание их по концам не требуется, детали сложной конфигурации (алюминиевые головки блоков цилиндров перед сваркой рекомендуется подогревать до температуры 150—250°С.
Газовая сварка ведется нормальным пламенем или с небольшим избытком ацетилена. Сварку деталей из алюминиевых сплавов плавящимся металлическим электродом ведут постоянным током обратной полярности. Рекомендуемые величины сварочного тока в зависимости от диаметра электрода следующие:
диаметр электрода, мм 4 5 6
Сила тока, А 100…125 до 160 до 200
длина дуги должна быть минимальной, не более диаметра электрода. Электрод необходимо держать перпендикулярно к шву и перемещать без поперечных колебаний. Сварку рекомендуется вести непрерывно.
Детали из алюминиевых сплавов свариваются также угольным электродом. Однако этот способ сварки не может быть рекомендован, так как он связан с загрязнением алюминиевого сплава и значительным снижением его коррозионной стойкости.
На некоторых ремонтных предприятиях детали из алюминиевых сплавов сваривают без флюсов. При этом способе предусматривается сохранение окисной пленки алюминия на поверхности сварочной ванны. Особой подготовки деталь не требует. Сварку ведут газовой горелкой с предварительным местным подогревом. В результате расплавления металла детали образуется сварочная ванна. При трении стального прутка о стенки сварочной ванны расплавление металла ускоряется и различные инородные включения, имеющиеся в металле, всплывают в виде шлака. В сварочную ванну вводят присадочный материал — кусочки сплава того же состава, что свариваемая деталь. Обычно для этой цели используют выбракованные детали из алюминиевых сплавов. Затем с поверхности сварочной ванны стальным прутком снимают имеющиеся шлаки. После этого деталь охлаждается, причем место сварки и прилегающие к нему зоны детали предварительно закрывают листовым асбестом.
Хорошие результаты дает применение ультразвука, позволяющего вести сварку деталей из алюминия и его сплавов без флюсов. Под действием импульсов ультразвука окисная пленка разрушается, обеспечивая высококачественную сварку.
Детали из алюминиевого сплава сложной конфигурации после сварки подвергают отжигу при температуре 300—350°С для снятия внутренних напряжений и получения мелкозернистой структуры шва. После отжига они медленно охлаждаются.
После окончания сварки остатки флюса следует удалить с поверхности охлажденной детали, так как он разъедает алюминиевые сплавы. Эти остатки удаляют травлением в 2-процентном растворе хромовой кислоты, подогретой до температуры 80°С, в течение 5 мин с последующей промывкой в горячей воде.
Места сварки или наплавки подвергают слесарно-механической обработке для получения требуемых размеров и шероховатости. Герметичность сварного шва контролируют с помощью керосина; последний не должен просачиваться через сварной шов.
Сваркой и наплавкой восстанавливать такие детали из алюминиевых сплавов: головки, и блоки цилиндров двигателей, картеры сцеплений при наличии трещин, пробои обломов, износе или повреждении резьбовых отверстий и др.
Детали из цинковых сплавов (корпуса бензонасосов и карбюраторов) сваривают пламенем газовой гор. без применения флюсов. Места деталей, подлежащие сварке, подготавливают непосредственно перед сваркой, чтобы избежать окисления поверхностей. Трещины расфасовывают по всей длине на глубину до 4 мм. Затем места сварки тщательно зачищают стальной щеткой. С целью уменьшения отвода тепла под свариваемую деталь подкладывают листовой асбест. Пламенем газовой горелки расплавляют присадочный материал, заполняя им подготовленную трещину. В процессе сварки его следует вводить под окисную пленку расплавленного металла. Присадочным материалом служат стержни того же металла, что и свариваемые детали (их получают путем сплавления выбракованных деталей). После сварки детали подвергают слесарно-механической обработке до получения требуемых размеров и шероховатости поверхности.
Детали из свинца (решетки пластин баретки, выводные штыри аккумуляторных батарей) сваривают водородно-воздушным пламенем газовой горелки или угольным электродом током прямой полярности. В последнем случае используют источник тока, имеющий напряжение 12В. Для сварки может быть использован любой горючий газ (ацетилен, водород, природный газ и др.), для поддержания горения при сварке применяют как кислород, так и воздух. Сварку ведут нейтральным или слабо восстановительным пламенем, используя газовые горелки малой мощности (наконечники №0 или №1)
Свинец плавится при температуре 327°С. При его нагревании образуется тугоплавкая окись РЬО, температура плавления которой 850°С. Учитывая легкоплавкость свинца, сварку следует вести с большой скоростью, а пламя горелки держать под углом 45° к поверхности детали. При свариваемой детали более 1,5 мм сварочный шов накладывают в несколько слоев, перекрывающих друг друга. При этом первый слой создают без присадки. Окись свинца удаляют с поверхности сварочной ванны механическим путем. Флюсы при сварке деталей из свинца не применяют. Присадочным материалом служит свинец.
Сварка цветных металлов покрытыми электродами
Медь толщиной до 4 мм сваривают без разделки кромок, до 10 мм — с односторонней V-образной разделкой с углом 60…70° и притуплением 1,5…3 мм, при больших толщинах рекомендуется двух сторонняя Х-образная разделка. Для сварки применяют электроды согласно табл. 17 на параметрах режима, приведенных в табл. 87, на постоянном токе обратной полярности.
Таблица 87. Ориентировочные параметры режима сварки стыковых соединений меди и ее сплавов
s, мм | dэ, мм | Ісв, А | Uд, В | Тподогрева, оС |
2…4 | 3 | 120…140 | 25…27 | — |
4…6 | 5 | 160…220 | 25…27 | 220…250 |
8…10 | 6…7 | 380…420 | 28…30 | 280…320 |
Сварку ведут короткой дугой с возвратно-поступательным движением электрода в нижнем положении или «на подъем» При использовании электродов «Комсомолец-100» достигается равнопрочностъ сварного шва основному металлу. Электроды марки АНЦ-1, разработанные в ИЭС им. Е.О. Патона, благодаря наличию экзотермических компонентов в покрытии позволяют сваривать без подогрева медь толщиной до 15 мм.
Сварку никеля толщиной до 15 мм ведут на постоянном токе обратной полярности без подогрева, большие толщины сваривают с подогревом до 200…250 °C. Металл толщиной 4…12 мм подготавливают с V-образной разделкой, а 12…20 мм — с Х-образной. Сварку ведут электродами согласно табл. 17. Параметры режима приведены в табл. 88.
Таблица 88. Ориентировочные параметры режима сварки никеля
s, мм | dэ, мм | Ісв, А |
2…3 | 2…3 | 40…80 |
4…5 | 3…4 | 80…140 |
6…8 | 4 | 120…180 |
9…12 | 4…5 | 140…220 |
Для лучшего газоудаления на медных подкладках сварку ведут с незначительными продольными колебаниями электродов.
Сварка технического алюминия и его сплавов типа AMг и АМц покрытыми электродами применяется при изготовлении малонагруженных конструкций и для заварки дефектов силуминового литья.
Металл толщиной до 20 мм сваривают без разделки кромок с зазором 0,5…1 мм, большие толщины подготавливают с V-образной разделкой с углом 70…90о, притуплением 3…5 мм и с зазором 1,5…2 мм. Сварку выполняют на стальных подкладках с использованием электродов, согласно табл. 17, на постоянном токе обратной полярности и остальных параметрах режима, приведенных в табл. 89.
Прихватку кромок выполняют с предварительным подогревом до 200… 250 оС, а сварку ведут при большей температуре подогрева — 300…400 оС. Нужно тщательно зачищать от шлака прихватки и нижележащие слои, а после сварки смывать остатки шлака теплой водой, после чего протравить шов 5…10% раствором азотной кислоты и промыть водой.
Таблица 89. Ориентировочные параметры режима сварки алюминия и его сплавов
s, мм | dэ, мм | Ісв, А | Uд, В |
6…8 | 5…6 | 280…320 | 30…34 |
10…12 | 7…8 | 320…400 | 32…56 |
14…16 | 8 | 400…550 | 32…36 |
18…20 | 8…10 | 450…550 | 32…36 |
Просмотров: 787
ГАЗОВАЯ СВАРКА ЦВЕТНЫХ МЕТАЛЛОВ И СПЛАВОВ
СВАРКА, РЕЗКА МЕТАЛЛОВ
Наиболее часто в домашнем хозяйстве возникает необходимость в сварке деталей (изделий) из цветных металлов, поэтому начнем с описания технологии именно этих работ. На первом месте по статистике стоят работы с металлами и сплавами медной группы (медь, латунь, бронза). За ними следуют алюминий и его сплавы.
Работы с медью. Первое, что надо помнить, — медь сильно окисляется. Образующийся оксид снижает пластичность и механическую прочность сварного шва. Помимо всего, появляются мелкие трещины в расплавленном металле (упомянутая «водородная болезнь»). Это и объясняет необходимость обязательного использования флюсов при работах с медью. Роль флюсов заключается в растворении образующихся оксидов. Оксиды трансформируются в легкоплавкие шлаки. А чтобы закиси меди (Си20) не образовывались в металле шва, необходимы присадки (марганец, кремний). Для указанных целей рекомендуется и использование меди с пониженным содержанием кислорода (до 0,01%).
Флюсы и присадочные металлы даны в таблицах.
Флюсы для газовой сварки меди
|
Назначение | Марка меди | Состав |
Для ответственных конструкций небольшой толщины | М-1 | Медь чистая электролитическая |
Для ответственных конструкций | МСр-1 | Медь с 0,8—1,2% серебра |
То же | МНЖ-5-1 | Медь с раскислителем — 0,2% фосфора |
То же | МНЖКТ-5- 1-0,2-0,2 | Медь с раскислителем — 0,2% фосфора и 0,3% кремния, 0,2% марганца |
Для слабонагружен — ных конструкций | М-0 | Медь для раскислигелей |
Дополнительные трудности возникают при газовой сварке меди из-за ее уникальных теплофизических свойств. Медь обладает высокой теплоемкостью и теплопроводностью (в 6—7 раз выше, чем у стали), повышенным коэффициентом линейного расширения при нагревании (в 1,5 раза выше, чем у стали).
Эти свойства обусловливают большую, чем при сварке стали, зону термического влияния и приводят к появлению значительных тепловых деформаций, которые могут вызывать при охлаждении сварного шва значительные напряжения.
Некоторыми технологическими приемами можно устранить нежелательные последствия при сварке меди. К примеру, сварку можно вести на увеличенных скоростях. Это уменьшит время соприкосновения пламени с жидким металлом. Для этого надо предварительно подогреть свариваемые кромки. Наконечник для сварки меди всегда будет на 1—2 номера больше, чем наконечник для сварки стали. Это общее правило и его надо знать без обращения к специальным источникам. Разрушить оксидные прослойки после сварки можно путем проковки шва в горячем состоянии. Обычно медь сваривается в виде стыковых и угловых соединений. Сварка впритык (тавровое соединение) и сварка в кромку применяется только при ремонте. Внахлестку медь не сваривается. И последнее — медь сваривается только в один слой. При накладывании второго слоя большая вероятность появления трещин. При сварке меди надо соблюдать технологическую последовательность операций. В противном случае полученный сварной шов не будет соответствовать предъявляемым требованиям. Опишем все стадии процесса сварки.
Первое — подготовка свариваемых деталей. Для этого надо зачистить как кромки свариваемых изделий (деталей), так и прилегающую к ним поверхность металла. Очищать можно как механическим, так и химическим путем. Затем надо собрать свариваемые детали, закрепить их (лучше всего в кондукторе) и сделать прихватки.
Прихватки — это короткие швы (не более 5 мм) с интервалом между ними в 70—100 мм. Если свариваются детали, имеющие значительную толщину, то длина прихваток составит не менее 20 мм при интервале между ними в 400—500 мм.
Второе — установка свариваемой детали (свариваемых деталей). Свариваемые детали надо располагать под углом 7—10° к горизонтальной плоскости, чтобы лучше заполнялись зазоры кромок (разделка кромок).
Третье—установка. режима сварки. Мощность горелки регулируется, исходя из следующего расчета, — 155— 175 л/ч ацетилена на 1мм свариваемой толщины (при толщине 3—4 мм). Если толщина больше, порядка 8— 10 мм, — 175—225 л/ч на 1 мм толщины. Пламя должно быть нормальным, мягким.
Четвертое — сам процесс сварки. Свариваемые кромки нагреваются, на них в виде пасты наносится флюс. Флюсом покрывается и присадочный пруток.
Расплавить присадочный пруток, расположив его над местом сварки близко от сварочной ванны, для уменьшения ее оксидирования.
Установить горелку под углом наклона к свариваемому изделию 30—40°, присадочной проволоки — 30— 40% расположить гядро пламени на расстоянии 6—10 мм от расплавленного металла и выполнить сварку восстановительной зоной пламени в один прр — ход снизу вверх: левым способом при толщине листов до 5 мм, а
при большей толщине — правым способом.
Во время сварки периодически добавлять флюс непосредственно в зону сварки на кончике присадочной проволоки, непрерывно перемешивая жидкий металл присадкой, извлекая ее возможно реже из ванночки.
Пятое — завершение процесса сварки.
После сварки шов проковать: при толщине листов до 4 мм — в холодном состоянии, при больших толщинах — при температуре до 500°С, принять меры предосторожности против резкого охлаждения сварного соединения под воздействием сквозняков или притока холодного воздуха.
Очистить шов 2% раствором серной или азотной кислоты и промыть водой для удаления остатков флюса.
Работы с латунью. Латунь, как уже упоминалось, это сплав меди с цинком (цинка может быть до 55%). Если речь идет о специальных латунях, то это означает, что в сплав включаются дополнительно различные легирующие добавки (свинец, никель, олово). Как и медь, латунь является труцносвариваемым сплавом. Основные трудности процесса—это выгорание цинка и поглощение газов расплавленным металлом. Последствия — образование пор и снижение механической прочности соединения. К тому же, сплав с содержанием цинка более 20% очень часто растрескивается после деформации в холодном состоянии. Чтобы добиться устранения этого, применяются особые технологические приемы. Попытаемся объяснить это в доходчивой форме. Обратимся к таблице.
Обработка сварных соединений из латуни после сварки производится так же, как при сварке меди. Однако, в отличие от меди, температура проковки латуни зависит не от толщины свариваемой детали, а от содержания цинка в основном металле.
Холодную проковку латуней алюминиевым молотком или пневмомолотком применяют для латуней, содержащих менее 40% цинка.
Латуни, содержащие более 40% цинка, подвергают проковкел npji температуре 650°С, что соответствует нагреву металла до темно-красного цвета.
Дефект | Методы устранения | Результат |
1 | 2 | 3 |
Образование трещин | Производить многослойную сварку методом ступенчатой и обратноступенчатой сварки Легировать шов кремнием и бором применением соответствующих марок присадочного металла (ЛК62-0,5иЛКБО) Подвергать сварное соединение после сварки низкотемпературному отжигу при температуре 270— 300°С | Уменьшение горяче ломкое ти лат}ии Уменьшение горячелом — кости латуни в интервале температур 200— 600°С Снятие остаточных напряжений, возникающих при изготовлении сварных конструкций Предохранение латуни от Коррозионного растекания |
Выгорание цинка | Использовать присадочные проволоки типов ЛК и ЛКБО, содержащие добавки кремния и бора Выполнять сварку левым способом Вести сварку окислительным пламенем с соотношением кислорода к aife — тилечу 1,3—1,4 Применять специальные флюсы на основе бористых соединений с добавками кремния, алюминия, олова и т. д. Нагревать металл не ядром пламени, а с расположением его на расстоянии 7 — 10 Мм от сварочной ванны | На поверхности сварочной ванны образуется пленка шлакового покрова, которая затрудняет испарение цинка, но не является препятствием для выделения газов га расплава Уменьшается перегрев металла шва, а следовательно, и испарение цинка, так как пламя не направлено на свареннутЬ часть шва На поверхности расплавленного металла образуется пленка оксидов, которая уменьшает угар цинка На поверхности жидкой ванны образуется защитная пленка, предохраняющая металл от испарения цинка Уменьшается перегрев жидкого металла и испарение га него цинка |
1 | 2 | 3 |
Образование пор | Применять присадочные металлы и флюсы на основе бористых соединений Производить сварку окислительным пламенем | На поверхности расплавленного металла образуется шлаковый покров, который не является препятствием для выделения водорода и других газов из расплава при кристаллизации шва Избыточный кислород связывает свободный водород пламени и способствует уплотнению металла шва |
Не следует забывать, что пары цинка, содержащиеся в латуни, ядовиты и это требует принятия мер для защиты органов дыхания. Лучше всего применять респиратор или постараться обеспечить бездымный технологический процесс. В заключение данной темы — о порошкообразных флюсах, применяемых при сварке латуни: флюс № 1 состоит исключительно из прокаленной буры; флюс № 3 состоит из 80% борной кислоты и 20% прокаленной буры;
флюс № 200 состоит из 70% борной кислоты, 21% прокаленной буры и 9% фтористого кальция.
Работы с бронзой. Бронза — это сплав меди с оловом (оловянные бронзы) алюминием (алюминиевые бронзы), кремнием (кремнистые бронзы) и т. д. В состав бронзы могут входить и другие элементы.
Процесс газовой сварки применим преимущественно для оловянной бронзы, алюминиевые и кремнистые бронзы свариваются в основном дуговой или аргонодуговой сваркой.
Есть необходимость подробнее остановиться на существующих марках различных бронз и изложить в виде таблицы способы их сварки.
Группа | Марка | Применение | Способы сварки |
Оловянные бронзы с содержанием олова до 20% | БрОЦ8-4 БрОЦЮ-2 БрОЦС6-6-3 | Фасонное литье и арматура | Газовая сварка |
Алюминиевые бронзы. Состав алюминий до 10%, легированный марганцем, железом, никелем | БрАМ10-3-7-5 БрАЖ9-4 БрАЖН — 10-4-4 БрАЖН-11-6-6 | Фасонное литье и арматура | Из-за пониженной свариваемости сварку лучше вести угольным электродом. Газовая сварка применяется редко |
Кремнистые бронзы кремнемарган — цевистые, бронзы легированные кремнием и марганцем, с добавкой железа, никеля и ДР- | БрКМцЗ-1 | Применяются в химической и пищевой промышленности (возможно применение и в других отраслях) | Хорошая свариваемость. Хорошо соединяются дуговой сварной Газовая сварка применяется крайне редко |
Практика показывает, что хорошее знание технологических подробностей всегда дает хороший результат при выполнении сварочных работ. В быту и в объеме работ небольших сварочных мастерских большое место занимают оловянные бронзы. Поэтому есть необходимость глубже вникнуть в вопрос газовой сварки оловянных бронз.
Первое, что мы делаем, готовясь к сварке — готовим соединяемые детали. Это очистка поверхности от окалины, от остатков формовочной смеси (если таковые имеются), других отложений. Зачистку надо проводить металлической щеткой до появления блеска металла. Затем следует этап разделки кромок V-образного профиля под 70—90°. После этого, учитывая вредность испарений оловянных бронз, закрепить соединяемые детали в зоне действия вытяжной вентиляции в нижнем положении, т. к. бронза обладает большой текучестью в расплавленном состоянии. Под будущий шов необходимо подвести подкладки из графита или асбеста. Сварку производить лучше всего ацетиленом, но можно применить и га
зы-заменители (бутан, пропан). На горелке отрегулировать мягкое нормальное пламя из расчета 70—120 литров в час на 1 мм свариваемой толщины. На кромки деталей и на присадочный металл нанести флюс. Флюсы используются те же, что и при сварке меди. Если металл холодный, подогреть его до температуры 250—300°С. Затем располагаем мундштук горелки под прямым углом к поверхности металла и расплавляем соединяемые кромки и присадочный материал. Ядро пламени горелки должно находиться на расстоянии 7—10 мм от уровня расплавленного металла (сварочной ванны). Это необходимо для того, чтобы сварочная ванна не перегрелась и не началось выгорание олова. Хорошо перемешивать сварочную ванну присадочным прутком и периодически добавлять в жидкий металл флюс, который будет удалять образующиеся окислы. В качестве присадочного материала при сварке оловянных бронз надо использовать проволоку БрОФб,5-0,4 или БрОЦ4-3 с добавкой фосфора. Если таковых нет под рукой, можно использовать бронзовые полоски, но только обязательно той же марки, что и свариваемый металл.
По окончании сварочных работ произвести термообрабопу детали (изделия) и удалить остатки флюса путем промывки шва 2% раствором серной или азотной кислоты.
Работы с алюминием и его сплавами. Уже упоминалось, что сварка алюминия затруднена из-за того, что на расплавленном участке сразу образуется тугоплавкая пленка оксида алюминия. Для устранения этого явления используется присадочная проволока со специальными флюсами, которые растворяют пленку, преобразуя ее в шлак.
Алюминиевые сплавы делятся на две группы: деформируемые и литейные.
Наиболее распространенные деформируемые сплавы — это сплавы алюминия с марганцем (АМц) и магнием (АМг), а также термоупрочняемые сплавы с медью типов Д1 и Д6 (дюралюминий). Из литейных сплавов чаще всего применяются различный виды силумина (сплава алюминия с кремнием) типов Ал2. Ал4 й Ал9.
В последние годы сварка деформируемых алюминиевых сплавов производится преимущественно дуговыми методами и, в част —
ности, аргонодуговой сваркой. Газовая сварка используется при отсутствии такой возможности.
Литейные алюминиевые сплавы хорошо поддаются газовой сварке и этот метод, наравне с аргонодуговой сваркой, широко применяется при заварке дефектов литья и при ремонте.
Еще одна особенность, которую проявляют алюминиевые сплавы при сварке, — это наличие высокого коэффициента линейного расширения (почти в два раза больше, чем у низкоуглеродистой стали). Следствием является то, что возникающие при сварке напряжения и деформации при сочетании с чрезмерно быстрым охлаждением ведут к появлению трещин. Поэтому всякое отклонение от правильного режима сварки и охлаждения может привести к браку всего изделия. Итак, еще раз о правильном режиме охлаждения.
Укрыть отливку асбестом или засыпать песком и обеспечить после сварки медленное ее охлаждение, не оставляя ее на сквозняке или в холодном помещении. Произвести проковку отливки, совмещая ее с отжигом при температуре 300—350°С и с выдержкой в печи в течение 2—5 ч для снятия остаточных напряжений и улучшения механических свойств сварного соединения
Наконец, при сварке алюминиевых сплавов необходимо учитывать их склонность к порообразованию из-за растворения водорода, содержащегося в пламени. Для уменьш
Газовая сварка цветных металлов
Медь и ее сплавы обладают большой теплопроводностью, что создает дополнительные трудности при их газопламенной обработке. Для преодоления теплопроводности меди требуется концентрация большего количества тепла, что влечет за собой перегрев металла и укрупнение его структуры. Кроме того, медь обладает низкой стойкостью к образованию трещин в массиве сварочного шва и склонностью к образованию газовых включений. Свариваемость меди во многом зависит от наличия примесей и, в первую очередь, оксидов. Чем меньше в меди содержится оксидов, тем выше ее свариваемость. Кроме того, образовавшийся при повышенных температурах оксид меди размещается по границам кристаллической решетки, что приводит к повышению хрупкости сварочного шва.
Подготовка к сварке медных деталей заключается в тщательной зачистке до металлического блеска кромок и протравке их в азотной кислоте. Детали плотно сжимают между собой без скоса кромок. Медь варят нормальным пламенем с применением защитных флюсов, что препятствует образованию оксидов меди. Сварку ведут быстро, без перерывов в работе. В качестве присадочного материала можно использовать обычную медную проволоку, диаметр которой зависит от толщины свариваемого металла. Кроме того, для сварки меди часто используют специальную проволоку марки МСр-1. Зависимость толщины присадочной поволоки от толщины свариваемых деталей отражена в таблице 1.
Таблица 1. Соотношение толщин присадочной проволоки и свариваемой детали
Диаметр присадочной проволоки, мм | 1,5 | 2 | 3 | 4-5 | 6 | 8 |
Сварку медных деталей ведут в один слой, а при необходимости сварки листов толщиной более 10 мм работают одновременно двумя горелками с двух сторон. Для защиты сварочной ванны используют флюсы, примерный состав которых приведен в таблице 2.
Таблица 2. Состав флюсов для защиты сварочной ванны
№1 | №2 | №3 | №4 | №5 | №6 | №7 | №8 | |
Бура прокаленная | 100 | — | 50 | 75 | 50 | 50 | 70 | 56 |
Борная кислота | — | 100 | 50 | 25 | 35 | — | 10 | |
Поваренная соль | — | — | — | — | 20 | 22 | ||
Фосфорнокислый натрий | — | — | — | — | 15 | 15 | — | — |
Кварцевый песок | — | — | — | — | — | — | — | |
Древесный уголь | — | — | — | — | — | — | — | |
Углекислый калий (поташ) | — | — | — | — | — | — | — | 22 |
Флюсы вводят в виде порошков, пасты или подают зону сварочной ванны в парообразном состоянии.
Для придания сварочному шву необходимых механических свойств после сварки осуществляют проковку, которую для листов толщиной до 4 мм выполняют в холодном состоянии. Листы толщиной более 4 мм перед проковкой подогревают до температуры 500 — 600°С. Необходимую вязкость сварочных швов получают при термической обработке. Для этого деталь нагревают до температуры 550 — 600°С и быстро охлаждают в воде.
Латунь представляет собой сплав меди с цинком. В специальную латунь могут вводить дополнительные добавки алюминия, свинца, никеля, кремния и других легирующих элементов. Сварочная ванна, получающаяся при газопламенной обработке, активно впитывает в себя газы, что способствует образованию пор и трещин. Кроме того, цинк, имеющийся в составе латуни, под действием высоких температур кипит и испаряется, что сказывается на свойствах сварочного шва. Зависимость температуры кипения цинка от состава латуни отражена на рис.1.
Рис.1. Зависимость температуры кипения цинка от состава латуни: 1 — температура кипения цинка; 2 — температура сварки; 3 — температура полного расплавления |
Для того чтобы уменьшить это отрицательное явление, при сварке создают избыток кислорода, который способствует созданию окислов. Оксиды покрывают сварочную ванну пленкой, которая снижает испарения цинка. С этой же целью вводят в виде присадки кремний, который активно окисляется под действием кислорода, создавая над сварочной ванной тугоплавкую пленку. Диаметр присадочного материала подбирают в зависимости от толщины свариваемой латуни по таблице 3.
Таблица 3. Соотношение толщины латуни и диаметра присадочного материала
Диаметр присадочной проволоки, мм | 2 | 3 | 5 | 7 | 9 |
Марку присадочного материала подбирают, исходя из марки свариваемой латуни. Ацетилено-кислородную сварку ведут окислительным пламенем с применением флюсов, состав которых приведен в таблице 4.
Таблица 4. Флюсы для ацетилено-кислородной сварки
№1 | №2 | №3 | Марки БМ-1 | |
Бура прокаленная | 100 | 50 | 20 | — |
Борная кислота | — | 35 | 80 | — |
Фтористый натрий | — | 15 | — | — |
Метилборат | — | — | — | 75 |
Метиловый сирт | — | — | — | 25 |
При толщине свариваемой латуни более 6 мм используют многослойную сварку, накладывая каждый последующий шов после тщательной зачистки предыдущего. Сварку латуни можно выполнять пропан-бутановыми смесями и керосино-кислородным пламенем.
Кромки металла перед сваркой зачищают до металлического блеска и протравливают 10%-ным раствором азотной кислоты с последующей промывкой и просушкой. Швы после сварки проковывают или проколачивают, придавая им нужные механические свойства.
Бронза представляет собой сплав меди с любым металлом кроме цинка, поэтому при ее сварке нет необходимости выполнять защиту кремнием. В зависимости от состава бронза может быть оловянистой (когда в сплаве присутствует олово) и безоловянистой, содержащей в составе алюминий, кремний, никель, хром и другие металлы, кроме олова.
Олово является легкоплавким металлом, поэтому во избежание его выгорания не допускается избыток в пламени кислорода. Избыток в пламени ацетилена может привести к пористости шва, поэтому оловянистые бронзы варят строго нормальным пламенем. Жидкотекучесть оловянистой бронзы не позволяет выполнять сварку в других положениях шва, кроме нижнего. Присадочный материал следует подбирать того же состава, что и основной. Допускается применение в качестве присадочного материала фосфористой бронзы, потому что фосфор является хорошим раскислителем. Сварочный шов после сварки подвергают отжигу при температуре 750°С и закалке при температуре 600 — 650°С. Это позволит придать шву необходимые физико-механические свойства, что особенно важно в ответственных конструкциях.
Бронза, имеющая в своем составе алюминий, требует нормального пламени, так как тугоплавкие окислы алюминия А120„ получающиеся при избытке кислорода, оседают на дно сварочной ванны. Флюсы используют те же, что и при сварке меди, а присадочный материал лучше использовать того же состава, что и свариваемая бронза. При наличии в бронзе кремния ответственные детали перед сваркой подвергают предварительному нагреву до температуры 300 — 350°С.
Газовая сварка алюминия и его сплавов
Алюминий плавится при относительно низких температурах (660°С), а его оксиды являются тугоплавкими, поэтому сварка алюминия и его сплавов при помощи газопламенной обработки требует высокой квалификации сварщика. В противном случае швы получаются с микротрещинами и с повышенной пористостью. Основной причиной образования пор является водород, который при кристаллизации алюминия остается в массиве шва. С трещинами, причиной которых является кремний, борются добавлением в алюминий железа. Для снижения вероятности образования оксидов сварку следует выполнять нормальным или слегка науглераживающим пламенем с пониженным содержанием кислорода. Не допускается применение окислительного пламени.
Трудности, связанные со сваркой алюминия и его сплавов, требуют тщательной предсварочной подготовки свариваемых кромок, которые зачищают от окисных пленок и загрязнений. Для этого пользуются напильниками, шаберами металлическими щетками и абразивными кругами. В ответственных деталях свариваемые кромки дополнительно обезжиривают ацетоновой смывкой, бензином, дихлорэтаном или подвергают травлению 10%-ным раствором едкого натра. После обезжиривания или травления кромки промывают горячей водой и высушивают при температуре 100 — 120°С. После травления кромки подвергают дополнительной нейтрализации 10%-ным раствором азотной кислоты. Подготовку кромок для сварки выполняют не позже, чем за 3 — 6 часов до сварки. Если за это время сварку не производили, то кромки готовят вторично, так как на поверхности успевают образоваться новые окислы.
Сборку деталей перед сваркой выполняют, исходя из толщины свариваемых деталей. При необходимости перед сваркой накладывают прихваточные швы, расстояние между которыми устанавливают по таблице 5.
Таблица 5. Интервалы между прихваточными швами
Высота | Длинна | ||
До 1,5 | 20-30 | 1-1,5 | 2-4 |
1, 5-3 | 30-50 | 1,5-2,5 | 4-6 |
3-5 | 50-80 | 2,5-4 | 6-8 |
5-10 | 80-120 | 4-6 | 8-12 |
10-25 | 120-200 | 6-12 | 12-26 |
25-50 | 200-360 | 12-20 | 26-60 |
Присадочную проволоку выбирают того же состава, что и основной металл. Термически упрочняемые сплавы «АМц» варят проволокой Св АК5, содержащей кремний, который повышает жидкотекучесть сварочной ванны и снижает величину усадки шва. Сплавы типа «АМг» варят присадочным материалом с несколько большим содержанием магния, чем в основном металле. После сварки шов проковывают в холодном состоянии. Составы флюсов, применяемых при газопламенной обработке алюминия и его сплавов, приведены в таблице 6. Все флюсы, применяемые для сварки алюминия и его сплавов, гигроскопичны, поэтому они активно поглощают влагу. Во избежание повышенного влагосодержания флюсы следует хранить в герметической таре. Оставшиеся после сварки флюсы удаляют промывкой в горячей воде, так как они способствуют возникновению коррозии шва.
Таблица 6. Флюсы для газопламенной обработки алюминия
АФ-4А | АН-А201 | АН-4А | ВАМИ | КМ-1 | |
Хлористый калий | 55 | — | — | 50 | 45 |
Хлористый натрий | 28 | — | 30 | 20 | |
Хлористый литий | 14 | 15 | — | — | — |
Хлористый барий | — | 70 | — | — | 70 |
Фтористый натрий | 3 | — | 70 | — | 15 |
Фтористый литий | — | 15 | 30 | — | — |
Криолит | — | — | — | 20 | — |
Газовая сварка свинца
Трудности, возникающие при сварке свинца, вызваны большой разницей температуры плавления основного металла и его оксидов. Так, свинец плавится при температуре 327°С, а его оксиды — при температуре около 888°С. Поэтому сварку свинца следует вести нормальным пламенем после тщательной предсварочной подготовки. Предсварочная подготовка свинцовых кромок подобна той, которую применяют при сварке алюминия и его сплавов. Защиту сварочной ванны выполняют флюсом, в качестве которого при небольших толщинах свариваемого металла применяют стеарин, которым натирают кромки свариваемых деталей перед сваркой. При больших толщинах свариваемых кромок в качестве флюса используют смесь стеарина с канифолью.
Жидкотекучесть свинца вызывает трудности при сварке вертикальных швов. Такие швы в большинстве случаев накладывают при помощи кристаллизатора, представляющего собой полукольцо (рис. 2). Кристаллизатор прикладывают к свариваемым кромкам и после кристаллизации сварочной ванны, заполняющей его полость, перемещают вверх. В качестве присадочного материала применяют свинцовую проволоку или полоски свинца.
Рис. 2. Сварка вертикального шва с кристаллизатором: 1 — кристаллизатор; 2 — присадочный пруток; 3 — горелка
|
подготовка кромок, цветных, как отличить от шлака, толстого, как нагреть электросваркой, детали и изделия из сплавов, индукционная – Определенных металлов на Svarka.guru

Ее используют на производстве, в быту, при изготовлении строительных конструкций и автомобилей, деталей механизмов, украшений. Выполняют под водой и в космическом пространстве.
Современные технологии позволяют достигать такой прочности полученного изделия, как если бы оно изначально было цельным.
Свариваемость металлов изучают профильные институты разных стран мира, а сварщик одна из самых востребованных сегодня рабочих профессий.
Основные понятия процесса
Задача сварки — создание неразъемного соединения деталей. Чтобы его получить, необходимо сдвинуть атомы, образующие металл настолько близко, чтобы начали действовать межатомные силы сцепления. Почему это происходит, какие при этом протекаю физические процессы, изучено достаточно слабо, но самим свойством пользуются давно.
Добиваются соединения тремя методами:
- Термическим, расплавляя металл самих соединяемых деталей, либо дополнительной присадки. Пример — распространенная дуговая и газовая, лазером, струей плазмы. Сюда относится и пайка.
- Термомеханическим, при котором изделия раскаляют, после чего сжимают либо выполняют проковку. Это самый древний способ, которым владели кузнецы уже пятого тысячелетия до Н.Э. Кроме ковки это диффузионная сварка, контактная, индукционно-прессовая.
- Механическим методом изделия сваривают, подвергая различным воздействиям без специального нагрева. Пример — ультразвуковые методики, соединения взрывом, трением, давлением.

Второй и третий методы применяют на промышленных линиях, при серийных выпусках, а также для изготовления уникальных изделий.
Не зависимо от используемой методики, существует всего две разновидности процесса:
- Бесшовный, когда соединяется металл непосредственно самих деталей.
- С образованием шва. При этом применяют вспомогательные присадки. Они могут как точно соответствовать основному металлу, так и отличаться. Пример — соединение стали медным электродом, пайка оловом, все виды сварки с использованием плавкого электрода.
История
До второй половины XIX единственным методом сварных соединений была ковка, а также пайка. Кузнецы раскаляли и накладывали друг на друга заготовки, после чего били молотами. Разумеется, о надежности и точности говорить не приходилось.


Пайка отличается тем, что при ней не происходит расплав кромок соединяемых деталей. Это своего рода «склеивание», где роль клеящего состава играет расплавленный металл.

Настоящая революция сварочных процессов началась с открытием процесса электрической дуги. Для соединения деталей ее сумели применить русские инженеры. Методику дуговой сварки угольными электродами изобрел Н.Н. Бенардос, а спустя буквально несколько месяцев, Н. Г. Славянов сумел выполнить первое соединение металлов плавящимся электродом.
Настоящим сварочным бумом отмечен век XX. Французские инженеры изобрели газовую сварку, в 1956 г. токарь А. И. Чудиков сумел соединить вращающиеся на токарном станке детали трением. К концу 60-х люди узнали, как сварить металл лазером. Примерно тогда же появились промышленные аппараты плазменного напыления, сварка индукционная, диффузионная и пр.
Основные способы
На сегодня насчитывается более 150 различных способов сварных работ. Отличаясь деталями, все они входят в несколько основных категорий, которые мы вкратце рассмотрим.
Электродуговая
Наиболее распространенная на сегодня технология. Ее разделяют на два основных типа: неплавящимся и плавким электродом.
Оба они основаны на температурном воздействии вольтовой дуги. В первом случае задача как нагреть металл электросваркой решается с помощью тугоплавкого электрода из вольфрама. Сам он не плавится, а только образует дугу, формируя сварочную ванну из материала самих деталей либо с добавлением присадки.
Последнюю вносят рукой, как сварочный пруток, либо автоматической подачей, как тонкую проволоку.
Во втором варианте дуга образуется между свариваемым металлом и плавящимся электродом. Последний одновременно служит для формирования шва, который образуется струйным переносом его металла.
Для концентрации дуги, а также образования защитного слоя, металлический стержень покрывают слоем специальной обмазки. К обмазке так же добавляют ряд компонентов, перенос которых улучшает качество шва.


Впервые синтетический рутил, основу обмазки большинства видов электродов, был получен при разработке технологии изготовления белой краски: титановых белил, в 50-х годах прошлого века. Сегодня этот метод является основным источником для электродной промышленности.

- Сварку в углекислом газе. Как правило ведут полуавтоматическими инверторами. Скорость сварки полуавтоматом в зависимости от толщины металла, диктует и необходимый объем подачи углекислоты. Таким способом сваривают тонколистовой металл, скажем, при ремонтах кузова автомобиля.
- Соединение в среде инертных газов аргона, либо гелия. К примеру, так варят трубопроводы из нержавейки, алюминия, специальных сплавов.
- Сварку в активном газе.
Оборудование, которыми ведут работы отличаются устройством, но как правило это различного типа трансформаторы и генераторы.
Методика дуговой сварки универсальна, позволяет как варить тонкий металл полуавтоматом, так и соединять толстостенные стальные трубы ручным способом.
Автоматическая под флюсом
Сварочный флюс представляет собой порошок из различных веществ. Его задача двойная:
- Защитить расплав металла от окисления.
- Внести в соединение вещества для усиления прочности стыка.
Процесс происходит следующим образом.
Предварительно подготовленные детали фиксируют на специальном стенде. После этого, на место стыка специальной трубкой подают слой флюса, образующего длинный холмик. За ней идет сварочная головка, образующая дугу. Далее может следовать еще одна трубка, засасывающая не использованный порошок флюса.
Работа ведется неплавящимся или плавящимся электродом. Флюс при этом частично расплавляется. Как отличить металл от шлака при сварке задача не ставится: после завершения работы, достаточно простучать шов, чтобы шлаковая корка, образованная расплавом флюса, отскочила.
Электрошлаковая

Расплав поддерживается проходящим через него электрическим током. При этом, прогрев ведется сразу по всей длине соединения.
Металл образующий соединительный шов одновременно является плавким электродом, подающим ток в расплав. Это может быть проволока, пластина, либо трубчатый мундштук.
Постепенный нагрев и такое же плавное охлаждение исключает перекаливание изделия, не создает дополнительных напряжений.
Метод требует специфического оборудования и выполняется в заводских условиях. Зато, ему доступна сварка толстого металла, сразу на весь массив деталей.
Электронно-лучевая и плазменная, диффузионная и контактная
При различии методов и принципов соединений изделий все эти виды объединяет отсутствие вольтовой дуги (либо ее особая разновидность, как при сварке плазменной). Более того, при контактной технологии дуга нежелательна.
Электронно-лучевое соединение деталей впервые получили еще в 50-е годы. Процесс схож с соединением лазером, но вместо луча фотонов выступает направленный пучок электронов. Таким способом возможно, как соединять крохотные детали, размеры которых измеряются долями миллиметра, так производить сварку листового металла размером в десятки квадратных метров.


Обязательное требование процесса, специфическая особенность электронно-лучевой технологии — помещение соединяемых деталей в вакуум. Поэтому, этому типу сварки ученые пророчат будущее как основной технологии при сборке конструкций космических станций и кораблей.

Диффузная сварка основана на взаимопроникновении атомов металлов плотно сжатых, предварительно нагретых деталей. Этот процесс, называемый диффузией, дал название методу. Эффективен метод в сложных случаях, к примеру с его помощью выполняется сварка цветных металлов.
Сварка контактная также относится к соединению давлением. При сжатии деталей в месте контакта проходит импульс эл. тока, который обеспечивает связь.
Холодное сваривание деталей и индукционный способ
Основа холодной сварки: деформация соединяемых деталей. Иначе — холодная ковка. При всей привлекательности метода (отсутствие эл. тока) с его помощью удается соединять только неокисляющиеся детали.
Индукционный способ является полной противоположностью холодному. Детали греют, причем не пламенем или дугой, а высокочастотным электромагнитным полем. При этом сварные изделия из металла прогреваются на значительную глубину.
Способ технологичен, поэтому применяется, к примеру, на автоматизированных. трубопрокатных линиях.
Как свариваются разные металлы и сплавы?
Особым качеством металлов является такое понятие как свариваемость, то есть способность соединятся сваркой с помощью того, или иного метода. Зависеть она может от многих причин: химический состав, специфические свойства металла либо сплава, методика подготовки деталей под сварку и многое другое.
ГОСТ разделяет это свойство на следующие группы, свариваемые:
- хорошо;
- удовлетворительно;
- ограниченно;
- плохо.

- окисная пленка, препятствующая контакту;
- наличие легирующих добавок, в частности углерода делающих шов хрупким и непрочным.
Свариваемость улучшают предварительной специфической подготовкой металла к сварке.
Особенно сложны в отношении свариваемости цветные металлы, каждый со своей спецификой.
Процедура
Хотя технология создания сварных соединений отличается, во всех случаях процесс начинается с подготовительных операций. Для дуговых методов это подготовка кромок под сварку, или как говорят, их разделка. Для холодной ковки — тщательная зачистка (вплоть до полировки) соединяемых деталей и т.п. Подготовка может включать очистку от грязи, обезжиривание.
Еще одно негативное явление, объединяющее все виды сварочных контактов — температурные деформации и напряжения.
Борются с этим по-разному. В некоторых случаях изделия заранее фиксируют струбцинами. Еще один распространенный способ — термическая обработка готового изделия: нагрев с последующим медленным охлаждением (отпуск).
В заключение
Мы рассмотрели далеко не все виды и способы сварки. Кроме того, постоянно развиваются существующие технологии, изобретаются новые.
При этом технологические решения диктуются задачами. В одном случае вопрос стоит как правильно сварить байпас из металла отопительной системы квартиры используя простейший ручной способ, в другом — создать сверхточное изделие для авиапромышленности. Соответственно подход требуется разный.
На смену существующим, неизбежно придут новые методы, более быстрые и надежные.
Черные и цветные металлы | Примеры и списки металлов
В чем разница между черными и цветными металлами? В случае черных металлов (железо = железо) основным металлом является железо. Они составляют значительную часть всех металлов, используемых сегодня. Это стало возможным благодаря их свойствам, которые подходят для многих различных отраслей и сценариев использования.
Цветные металлы, с другой стороны, не включают железо. Это различие сделано потому, что оно приводит к определенному характерному изменению, которого не могут обеспечить цветные металлы.
Свойства черных металлов
Черные металлы могут содержать множество различных легирующих элементов. Некоторые примеры — хром, никель, молибден, ванадий, марганец. Они придают черным сталям свойства материала, благодаря которым они широко используются в машиностроении.
Список свойств черных металлов:
- Долговечность
- Высокая прочность на разрыв
- Обычно магнитная
- Низкая устойчивость к коррозии
- Серебристый цвет
- Пригоден для вторичной переработки
- Хорошие проводники электричества
Эти качества делают их можно использовать в строительстве долговечных небоскребов.Кроме того, они используются в производстве инструментов, автомобильных двигателей, трубопроводов, контейнеров, автомобилей, столовых приборов и т. Д.
Примеры черных металлов
Все они имеют разные спецификации, что позволяет находить множество применений. Для лучшего обзора мы составили список черных металлов:
Нелегированные стали
Нелегированные стали также известны как углеродистые стали, потому что углерод является там легирующим элементом. Да, это немного сбивает с толку, поскольку название предполагает одно, но именно так часто бывает в мире металлов.Хотя присутствуют и другие элементы, их содержание достаточно низкое, чтобы не влиять на свойства материала. Эти элементы — сера, фосфор, кремний и марганец. Сера и фосфор на самом деле могут отрицательно сказаться на качестве стали, но опять же, не с таким низким содержанием.
Хотя термин «нелегированные стали» не часто упоминается в типичной машиностроительной компании как таковой, наши любимые конструкционные стали, такие как S235, S355 и т. Д., Относятся к этой группе.
Нелегированные стали классифицируются по содержанию углерода на стали с низким, средним и высоким содержанием углерода. Каждый из них имеет собственное применение и характеристики различаются. Также доступны разные методы лечения.
Низкоуглеродистая сталь
Низкоуглеродистая или мягкая сталь содержит 0,05… 0,25% углерода. Они довольно дешевы и очень хорошо подходят для операций гибки. Поверхностную твердость можно повысить за счет науглероживания.
Широко используются недорогие и ковкие низкоуглеродистые стали.Некоторые примеры включают болты и гайки, поковки, детали со средней нагрузкой и т. Д.
Примеры низкоуглеродистых сталей: C10E / 1.1121, C15E / 1.1141
Среднеуглеродистая сталь
Среднеуглеродистые стали содержат 0,25… 0,6% углерода. Более высокое содержание углерода увеличивает их прочность и твердость по сравнению с низкоуглеродистыми сталями. При этом снижается пластичность. Повышение содержания углерода и марганца позволяет производить отпуск и закалку.
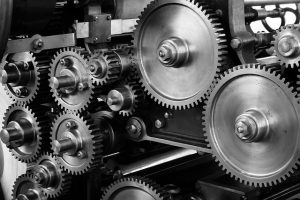
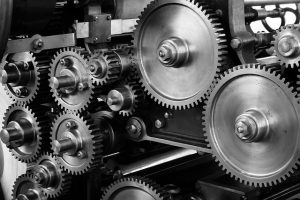
Среднеуглеродистые стали в основном используются для изготовления различных компонентов автомобильной промышленности, таких как шестерни, оси, валы, а также болты, гайки, винты и т. Д.Стали от 0,4… 0,6% также подходят для всего, что связано с локомотивами и рельсами.
Примеры среднеуглеродистых сталей: C40E / 1.1186, C60E / 1.1221
Высокоуглеродистая сталь
Цифры содержания углерода для высокоуглеродистых сталей варьируются в зависимости от различных источников. Некоторые из них имеют больше подгрупп, в то время как другие останавливаются на высокоуглеродистых сталях, которые начинаются с содержания углерода 0,6% и заканчиваются примерно 1%. Мы будем придерживаться второй интерпретации.
Это самые прочные из этой группы, что делает их пригодными для применений, где требуется устойчивость к механическому износу материала.Еще одно качество высокоуглеродистых сталей — их способность сохранять форму. Вот почему инструментальная сталь находит множество различных применений в области машиностроения.
С другой стороны, свариваемость, пластичность и ударная вязкость хуже, чем у сталей с меньшим содержанием углерода.
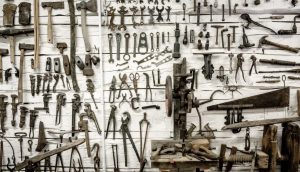
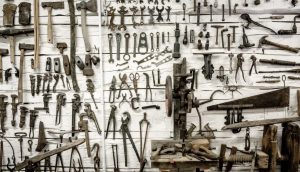
Сохранение формы делает их полезными в качестве пружин. Другие варианты использования включают лезвия, рельсовые стали, трос, износостойкие пластины, все виды инструментов и т. Д.
Примеры высокоуглеродистых сталей: C70U / 1.1520, C105U / 1.1545
Легированные стали
Легированные стали составляют еще одну подгруппу черных металлов. Легирующими элементами стали являются хром, никель, кремний, медь, титан и т. Д. Каждый из них по-своему влияет на свойства материала. Конечно, их обычно совмещают, поэтому в конечных продуктах есть всего понемногу. Мы обсуждаем, как наиболее распространенные элементы влияют на результат.
Хром
Хром — это элемент, ответственный за создание нержавеющей стали.Содержание хрома в количестве более 11% делает металл устойчивым к коррозии. Как обсуждалось в статье «Материал износостойкого материала», защита осуществляется путем создания слоя окисленного хрома на поверхности металла. Это означает, что основной металл не контактирует с кислородом, и опасность коррозии значительно снижается.
Таким образом, он готов к использованию без какого-либо защитного покрытия. Вы можете добиться отличного эстетического результата, выбрав подходящую для вашего применения поверхность из нержавеющей стали.
Кроме того, хром также увеличивает прочность на разрыв, твердость, ударную вязкость, износостойкость и т. Д.
Марганец
Марганец улучшает пластичность, износостойкость и способность к упрочнению. Последнее осуществляется путем закалки, при которой марганец оказывает значительное влияние. Это снижает опасность образования дефектов в процессе, делая его более стабильным.
Также исключает образование вредных сульфидов железа, повышая прочность при высоких температурах.
Никель
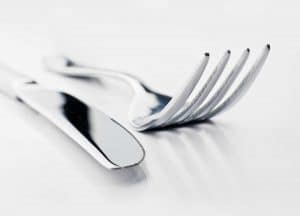
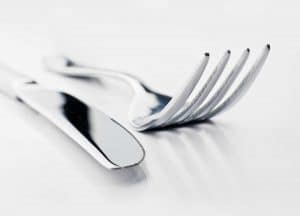
Его основная цель — повысить пластичность и коррозионную стойкость в сочетании с другими элементами, а именно с хромом.Когда содержание хрома составляет около 18%, а никеля — 8%, мы получаем чрезвычайно прочные нержавеющие стали.
Кремний
Повышает прочность и эластичность пружин. Еще один значительный эффект — повышение магнитных свойств металла.
Титан
Повышает прочность и коррозионную стойкость, ограничивает размер зерна аустенита.
Ванадий
Образование карбидов ванадия ограничивает размер зерна. Это влияет на повышение пластичности материала.
Он также увеличивает прочность, твердость, износостойкость и ударопрочность. Из-за его эффективности суммы должны быть низкими. В противном случае это может негативно сказаться на свойствах материала.
Молибден
Молибден оказывает большое влияние на стальные сплавы при высоких температурах. Он улучшает механические свойства, а также устойчивость к коррозии и действует как усилитель для эффектов других легирующих элементов.
Чугун
Чугун — это сплав железа и углерода с содержанием углерода где-то между 1.5 и 4 процента. Также присутствуют другие элементы, а именно кремний, марганец, сера и фосфор.
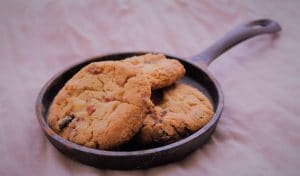
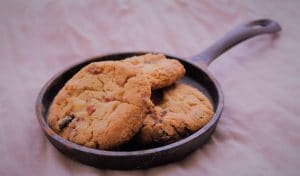
Хотя они хрупкие, их твердость делает их износостойкими. Окончательная форма изделия из чугуна достигается путем литья. Этот процесс требует лишь незначительной обработки после обработки, чтобы можно было сформировать необходимую форму.
Свойства чугуна:
- Отличная литье
- Относительно дешевый
- Высокая прочность на сжатие
- Хорошая износостойкость
- Низкая температура плавления
Что такое цветной металл?
Цветные металлы не содержат железа.Они более мягкие и, следовательно, более податливые. Они используются как в промышленности, так и в эстетических целях — драгоценные металлы, такие как золото и серебро, являются цветными. На самом деле все чистые формы металлов, кроме чистого железа, являются цветными.
Свойства цветных металлов
Преимущества цветных металлов позволяют использовать их во многих областях вместо железа и стали.
Свойства цветных металлов:
- Высокая коррозионная стойкость
- Простота изготовления — обрабатываемость, литье, сварка и т. Д.
- Отличная теплопроводность
- Отличная электропроводность
- Низкая плотность (меньшая масса)
- Цветной
- Немагнитный
Список цветных металлов
Опять же, мы собираемся предоставить некоторую информацию о каждом металле и его свойствах.Примеры цветных металлов:
Медь
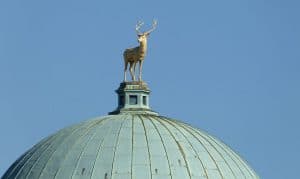
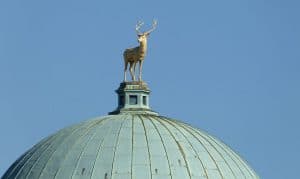
Медь довольно широко распространена в промышленной сфере. Добавьте сплавы латуни (медь и цинк) и бронзу (медь и олово), и вы, возможно, уже увидите множество применений меди. Если нет, мы можем вам помочь. Для инженеров-механиков наиболее известны подшипники скольжения и втулки.
Тем не менее, свойства меди и медных сплавов позволяют использовать больше:
- Высокая теплопроводность — теплообменники, нагревательные сосуды, приборы и т. Д.
- Высокая электропроводность — используется в качестве электрического проводника в проводке и двигателях
- Хорошая коррозионная стойкость — красиво но дорогая кровля
- Высокая пластичность — делает материал очень легко формуемым и подходящим для изготовления статуй.
Алюминий
С инженерной точки зрения, очень особенный и важный металл.Может быть не так полезен в повседневном применении из-за цены, но его сочетание небольшого веса и отличной обрабатываемости делает его основным металлом на яхтах, самолетах и многих автомобильных деталях.
Алюминий также является основным металлом во многих сплавах. Наиболее известными марками алюминия, вероятно, являются дюралюминий, Y-сплав и магналий.
Свойства алюминия включают:
- Устойчивость к коррозии
- Хорошая проводимость тепла и электричества (но меньше, чем у меди) — в сочетании с пластичностью и пластичностью в некоторых случаях заменяет медь
- Высокая пластичность и легкий вес
- Становится твердым после холодной обработки , поэтому требуется отжиг
Лазерная резка алюминия — это то, что требует опыта и правильного оборудования.Так что внимательно выбирайте субподрядчика для производства.
Свинец
Свойства свинца
Свойства свинца (металла)Для обычного человека свинец может вызвать тревогу, связанную с пулями (которые теперь не содержат свинца) и газом (имеющим знак «неэтилированный»). Хотя сначала его добавляли в топливо, чтобы уменьшить детонацию двигателя, оказалось, что он очень вреден для здоровья при испарении в атмосферу.
То же самое с патронами и работниками стрельбища, у которых возникли проблемы со здоровьем.Но зачем вообще это добавлять? Потому что свинец — самый тяжелый из обычных металлов. Поскольку он не вступает в реакцию с другими веществами, они все еще используются в батареях и силовых кабелях, резервуарах для кислоты и водопроводах.
Свойства свинца:
- Очень тяжелый
- Устойчивый к коррозии — не вступает в реакцию со многими химическими веществами
- Мягкий и податливый
Цинк
Сам по себе цинк не имеет большого значения для обычного человека. С другой стороны, как легирующий элемент он имеет широкий спектр применения.Он в основном используется для цинкования стали во всех областях. Цинкование делает материал более устойчивым к коррозии.
Черные и цветные металлы, Fractory позаботится о ваших работах по изготовлению листового металла.
.Цветные металлы и сплавы
Цветные металлы и сплавы — Мы уже обсуждали, что цветные металлы — это те металлы, которые содержат в качестве своей основной составляющей металл, отличный от железа. В инженерной практике используются различные цветные металлы: алюминий, медь, свинец, олово, цинк, никель и т. Д. И их сплавы. Эти цветные металлы и их сплавы рассматриваются вкратце следующим образом:1. Алюминий и его сплавы: Основным источником алюминия является глинистый минерал, называемый бокситом, который представляет собой гидратированный оксид алюминия.Он широко используется в компонентах самолетов и автомобилей, где экономия веса является преимуществом. Основными алюминиевыми сплавами являются:
(а) Дуралюминий. Состав этого сплава следующий:
Медь = 3,5 — 4,5%; Марганец = 0,40 — 0,70%; Магний = 0,40 — 0,70%; а остальное — алюминий.
Этот сплав обладает максимальной прочностью (около 400 МПа) после термической обработки и старения. Если после работы дать металлу состариться в течение 3-4 дней, он затвердеет.Это явление известно как старение.
(б) Y-сплав. Его еще называют медно-алюминиевым сплавом. Состав этого сплава следующий:
Медь = 3,5 4,5%; Марганец = 1,2—1,7%; Никель = 1,8 — 2,3%; кремний, магний, железо = 0,6% каждый; а остальное — алюминий.
Этот сплав подвергается термообработке и старению, как дюралюминий. Он имеет лучшую прочность, чем дюралюминий, при высоких температурах.
(в) Магналиум. Его получают путем плавления алюминия с 2-10% магния в вакууме с последующим охлаждением в вакууме или под давлением от 100 до 200 атмосфер.Он также содержит около 1,75% меди.
(d) Хиндалий. Это сплав алюминия и магния с небольшим количеством хрома. Выпускается в виде проката калибра 16, в основном для изготовления анодированной посуды.
2. Медь и ее сплавы: Медь — один из наиболее широко используемых цветных металлов в промышленности. В чистом виде под землей не встречается. Он встречается в некоторых минералах, таких как медь, медный колчедан, малахит и азурит.
Медные сплавы в целом подразделяются на следующие две группы:
(a) Медно-цинковые сплавы (латуни) , в которых цинк является основным легирующим металлом, и
(b) Медь-олово сплавы (бронзы) , в которых олово является основным легирующим металлом.
Самым распространенным сплавом меди с цинком является латунь. По сути, это бинарный сплав меди с цинком по 50%. В зависимости от пропорции меди и цинка существуют различные типы латуни.Латунь очень устойчива к атмосферной коррозии и легко поддается пайке.
Сплавы меди и олова обычно называют бронзой. Полезный диапазон состава составляет от 75 до 95% меди и от 5 до 25% олова. По коррозионным свойствам бронза превосходит латунь. Вот некоторые из распространенных типов бронзы:
(i) Фосфорная бронза. Бронза, содержащая фосфор, называется фосфористой бронзой. Фосфор увеличивает прочность, пластичность и прочность отливок.Он содержит 87-90% меди, 9-10% олова и 0,1-0,3% фосфора. Сплав обладает хорошими износостойкими качествами и высокой эластичностью. Применяется для подшипников, червячных колес, шестерен, гаек, накладок. Он также подходит для изготовления пружин.
(ii) Кремниевая бронза. Содержит 96% меди, 3% кремния и 1% марганца или цинка. Он обладает хорошей общей коррозионной стойкостью меди в сочетании с более высокой прочностью. Он широко используется для котлов, резервуаров, печей или там, где требуется высокая прочность и хорошая коррозионная стойкость.
(iii) Бериллиевая бронза. Это сплав на основе меди, содержащий около 97,75% меди и 2,25% бериллия. Он имеет высокий предел текучести, высокий предел выносливости и отличную стойкость к холодной и горячей коррозии. Это особенно подходящий материал для пружин, электрических переключателей, кулачков и втулок. Обладает пленкообразованием и обладает мягкими смазывающими свойствами, что делает его более подходящим в качестве металла подшипников.
(iv) Марганцевая бронза. Содержит 60% меди, 35% цинка и 5% марганца.Этот металл отличается высокой устойчивостью к коррозии. Из этой бронзы часто изготавливают червячные передачи.
(в) Алюминиевая бронза. Это сплав меди и алюминия. Алюминиевая бронза с содержанием алюминия 6-8% обладает ценными свойствами холодной обработки. Алюминиевый сплав с содержанием 6% алюминия имеет цвет чистого золота, который используется для изготовления бижутерии и в декоративных целях.
3. Оружейный металл: Это сплав меди, олова и цинка. Обычно он содержит 88% меди, 10% олова и 2% цинка.Этот металл также известен как оружейный металл Адмиралтейства. Цинк добавляется для очистки металла и повышения его текучести. Он широко используется для литья арматуры котлов, втулок, подшипников, сальников и т. Д.
4. Баббитовый металл: Сплав на основе олова, содержащий 88% олова, 8% сурьмы и 4% меди, называется металлическим баббитом. Это мягкий материал с низким коэффициентом трения и небольшой прочностью.
5. Сплавы на основе никеля: Наиболее важными сплавами на основе никеля являются:
(a) Металлический монель. Это важный сплав никеля и меди. Он содержит 68% никеля, 29% меди и 3% других компонентов. По внешнему виду он напоминает никель, он прочный, пластичный и вязкий. По коррозионным свойствам он превосходит латунь и бронзу.
(б) К-сплав. Состоит из алюминия на 3% и титана на 0,5% в дополнение к составу монель. Он имеет лучшие механические свойства, чем монель.
(c) Инконель. Он состоит из 80% никеля, 14% хрома и 6% железа.Этот сплав обладает прекрасными механическими свойствами при обычных и повышенных температурах. Он используется для изготовления пружин, которые должны выдерживать высокие температуры и подвергаться коррозионному воздействию.
(г) Нихром. Состоит из 65% никеля, 15% хрома и 20% железа. Применяется для изготовления проволоки электрического сопротивления для электропечей и нагревательных элементов.
e) Нимоник. Состоит из 80% никеля и 20% хрома. Он широко используется в газотурбинных двигателях.
.СВАРКА ЦВЕТНЫХ МЕТАЛЛОВ — Скачать PDF бесплатно
1 СВАРКА ЦВЕТНЫХ МЕТАЛЛОВ Р. ГХОШ Резюме В статье рассматриваются различные методы сварки, как газовой, так и электросварной, хотя в основном речь идет о кислородно-ацетиленовом процессе.Введение Цветные металлы, такие как алюминий, медь, магний, свинец, олово, цинк, никель и т. Д., А также их различные сплавы сегодня составляют одну из наиболее важных групп материалов, доступных для взыскательных инженеров. Хотя производство чугуна и стали намного превышает общий тоннаж цветных металлов, их истинную стоимость можно оценить, исходя из особого широкого диапазона представленных свойств. Чаще всего их стоимость больше, чем у низкоуглеродистой стали или чугуна, но их особые характеристики делают их выбор очевидным и экономичным.Поэтому вполне естественно, что в настоящее время сварка этих цветных металлов привлекает внимание инженеров. Вначале можно сказать, что почти все цветные металлы и сплавы поддаются сварке тем или иным способом. Слово «свариваемость», которое очень часто используется на практике, можно определить как «способность металла свариваться в условиях изготовления, налагаемых на конкретную, соответствующим образом спроектированную конструкцию, и удовлетворительно работать в предполагаемой эксплуатации».Хотя это определение довольно выразительно, его нельзя оценить количественно и можно выразить только как личное мнение. Процессы, обычно используемые для сварки цветных металлов, можно условно разделить на две группы: процессы плавления и процессы давления. Процессы сварки: газовая сварка, дуговая сварка в среде защитного газа (аргонодуговая сварка и сварка аргонавтом), металлическая дуговая сварка, 223 углеродная дуговая сварка и прополка атомарным водородом. К процессам давления относятся: точечная, шовная, стыковая и оплавление (все процессы контактной сварки), ручная кузнечная сварка и сварка давлением.Существенное различие между сваркой плавлением и сваркой под давлением состоит в том, что в первом случае сварка выполняется путем плавления основного металла с добавлением или без добавления дополнительного металла и позволяя металлу затвердеть, а во втором случае соединение осуществляется давлением без плавления. металла, но эта желательная цель не всегда реализуется на практике, и может иметь место некоторое плавление. Здесь будет уместно сослаться на процессы пайки, которые широко используются при производстве алюминия и некоторых ее сплавов, меди и ее сплавов, никеля и его сплавов, а также некоторых драгоценных металлов с использованием соответствующих присадочных прутков.Процесс сварки Теперь кратко описаны процессы, используемые для сварки цветных металлов. Процесс газовой сварки. Кислородно-ацетиленовая сварка является наиболее важной и широко используемой. Кислородно-ацетиленовое пламя имеет очень высокую температуру, превышающую 3000 ° С, и многогранность получаемого пламени добавляет его преимуществу. Оборудование, используемое для кислородно-ацетиленовой сварки, слишком хорошо известно и не нуждается в представлении. Подача кислорода обычно осуществляется из баллонов, заполненных до 2000 фунтов./ кв. дюйм., или от трубопровода. где такая установка существует. Ацетилен поступает либо из генераторов, либо из цилиндров, последний обычно известен как растворенный ацетилен. Для сварки
2 224 СИМПОЗИУМ ПО ПРОМЫШЛЕННОСТИ ЦВЕТНЫХ МЕТАЛЛОВ В ИНДИИ для некоторых металлов предпочтительнее использовать растворенный ацетилен из-за его более высокой чистоты. Сварочные выдувные трубы в основном бывают двух типов: инжекторного типа для использования с образовавшимся ацетиленом и неинжекторного типа для использования с системой высокого давления, т.е.е. с растворенным ацетиленом. Также необходимы регуляторы для регулирования расхода газов из баллонов. Для сварки цветных металлов используются три типа пламени; это нейтральное пламя, науглероживающее пламя (избыток ацетилена) и окислительное пламя (избыток кислорода). Манипуляции с выдувной трубкой для сварки важны и зависят от различных факторов. Есть три хорошо известных техники манипуляции: «Влево», «Вправо» и «Вертикально вверх».Что касается других топливных газов, таких как водород, угольный газ и т. Д., Их использование очень ограничено и часто ограничивается сваркой цинка, свинца и в некоторых случаях пайкой. Дуговые процессы в среде защитного инертного газа. Внедрение технологии защиты инертным газом в области сварки произошло совсем недавно, но, несомненно, очень важно. Наиболее важными в этой области являются: аргонодуговая сварка и сварка аргонавтом — в первой используется неплавящийся вольфрамовый электрод, а во второй — плавящийся электрод, который также является присадочным стержнем.Основное преимущество этого процесса заключается в том, что его можно использовать для сварки большинства цветных металлов без использования флюса. Are Welding — Влияние дуговой сварки на производство цветных металлов ощущается каждый день. Оборудование, используемое для дуговой сварки цветных металлов этим процессом, аналогично тому, что используется для стали, и знакомо каждому инженеру. Широко используются сварочные агрегаты как электродвигателя-генератора, так и сварочные агрегаты трансформаторного типа. Однако важно отметить, что для сварки некоторых цветных металлов с помощью сварочного агрегата трансформаторного типа необходимо использовать стабилизатор напряжения, который накладывает высокочастотный переменный ток порядка 5–3 Мегациклов в секунду. .Этот высокочастотный ток не только стабилизирует дугу в рабочих условиях, но также увеличивает легкость зажигания дуги. Ввиду очень ограниченного использования угольной дуги и сварки атомарным водородом не предлагается распространяться на эти два процесса. Процесс под давлением — большинство сварочных процессов, используемых в этой группе, представляют собой ту или иную форму контактной сварки. В то короткое время, которое имеется в нашем распоряжении, невозможно подробно описать типы установок, используемых для этих сварочных процессов.Используются как переменный, так и постоянный ток, последний в основном используется в машинах для контактной сварки конденсаторного типа, которые выдают большой импульс тока в течение чрезвычайно короткого периода. На таких машинах сваривают некоторые цветные металлы. Выбор процесса и техники сварки цветных металлов во многом определяется их физическими, механическими, химическими и металлургическими свойствами. Это: i) Физические — точка плавления, удельная и скрытая теплота, температура кипения, проводимость, коэффициент расширения, изменение объема при замерзании (влияние легирующих компонентов на физические свойства).ii) Механические свойства и. изменения, вызванные изменением температуры. iii) химические, включая физико-химические свойства — окисление и растворимость в газах. iv) Металлургические свойства — Литой металл, деформируемые изделия, термообработанные сплавы и воздействие тепла на основной металл. В этом кратком резюме невозможно подробно описать процедуры сварки всех цветных металлов и сплавов. Поэтому будет подробно описана процедура сварки двух основных цветных металлов — алюминия и меди.
3 GHOSH — СВАРКА ЦВЕТНЫХ МЕТАЛЛОВ 225 Сварка алюминия и его сплавов Алюминий и его сплавы из-за их низкого удельного веса, высокой проводимости, хорошей устойчивости к коррозии и других характеристик, необходимых для конкретного применения, используются все чаще для производственных целей. Таким образом, чистый алюминий широко используется для химических заводов и оборудования для пищевой промышленности, некоторые алюминиево-магниевые сплавы для морских работ, высокопрочные термообработанные сплавы для самолетов и т. Д.В общих чертах, для целей сварки алюминий и его сплавы можно разделить на две основные группы, а именно нетермообрабатываемые и термически обрабатываемые. Основными характеристиками, влияющими на свариваемость алюминия и его сплавов, являются их (1) низкая температура плавления (нет видимого изменения цвета при нагревании), (ii) высокая удельная теплоемкость, (iii) высокая электрическая и теплопроводность, (iv) высокая температура. -короткость, (v) высокое тепловое расширение и сжатие, (vi) быстрое окисление поверхности при всех температурах, (vii) способность поглощать водород в расплавленном и твердом состоянии, и, наконец, (viii) влияние сварки на их свойства, особенно в случай термообработанных сплавов.Газовая сварка. До появления аргонно-дуговой сварки или сварки аргонавтом, кислородно-ацетиленовая сварка была самым распространенным методом сварки алюминия и его сплавов, не поддающихся термической обработке. (i) Конструкция. Конструкция сварных конструкций из этих металлов требует тщательного рассмотрения в основном из-за необходимости использования коррозионного флюса. Это требует доступа к обеим сторонам соединений, чтобы обеспечить надлежащее удаление остатков флюса после сварки, и запрещает использование соединений внахлестку, угловых, краевых и угловых соединений во избежание захвата флюса.Таким образом, необходимость использования стыковых соединений и обеспечения доступности с обеих сторон соединения; это часто вызывает проблемы в дизайне. (ii) Подготовка кромок — очень важно, чтобы кромки были хорошо очищены непосредственно перед сваркой. Масло или жир необходимо удалить путем обезжиривания, а края металла можно очистить щеткой от царапин, чтобы удалить оксидную пленку, но. не рекомендуется пользоваться наждачной бумагой. Сразу после очистки следует произвести флюсование. Листы толщиной до J дюймов не нужно скашивать, их нужно делать поверх I дюйма.кромки должны быть скошены до 30 или 45 _ Совмещение кромок должно быть сохранено прихватками или с помощью зажимов и зажимов. Также можно использовать конусность, позволяющую примерно до U дюймов на фут соединения. В случае длинных швов предпочтительнее прихватка или использование зажимных приспособлений, сварку следует начинать в дюймах от конца, а затем заканчивать короткую несваренную часть. (iii) Флюс — важно использовать флюс хорошего качества, и многие проверенные патентованные марки легко доступны. Флюс, который в основном представляет собой смесь, содержащую галогениды щелочных металлов, легко растворяет тугоплавкий оксид и обеспечивает адекватную защиту металла во время сварки.Обычный метод нанесения флюса — это приготовление пасты с водой или спиртом и последующее окрашивание сварочного стержня и сварных кромок. Сварочный пруток также можно флюсовать, окунув нагретый конец сварочной проволоки в порошкообразный флюс и расплавив «пучок» пламенем. Использование флюса необходимо держать под контролем, иначе использование чрезмерного флюса может привести к некоторому захвату флюса. (iv) Сварочное пламя и мартипуляция горелки — для сварки алюминия и его сплавов необходимо строго мягкое нейтральное пламя; любая тенденция к использованию окислительного пламени будет пагубной, поэтому следует избегать использования резкого пламени.Некоторые часто используют пламя с дымкой излишка ацетилена, но в этом нет необходимости. В случае сварки тяжелых секций может потребоваться использование сопла на один размер больше, чем у стали той же толщины, а также для предварительного нагрева участка с помощью наддувной трубы перед началом сварочных работ.
4 226 СИМПОЗИУМ ПО ПРОМЫШЛЕННОСТИ ЦВЕТНЫХ МЕТАЛЛОВ В ИНДИИ Для легких секций используется техника налево или вперёд; но очень часто, особенно для более тяжелых секций, вертикальный метод, предпочтительно вертикальный метод двойного оператора, используется с преимуществом.(v) Присадочный стержень. Как правило, желательно использовать присадочный стержень, который при осаждении дает такой же состав, как и основной металл. Это очень важно, если условия эксплуатации не допускают каких-либо отклонений между составом основного металла и наплавленного металла. Однако можно отметить, что стержни из алюминиево-кремниевого (5%) сплава часто используются для сварки различных алюминиевых сплавов, включая некоторые термически обработанные сплавы. Доступно большое количество присадочных стержней запатентованных марок, подходящих для сварки алюминия и его сплавов.(vi) Обработка сварных швов — изделие после сварки следует тщательно протереть горячей водой и щеткой, чтобы удалить все следы флюса, после чего следует окончательная промывка 5-процентной азотной кислотой и водой. Холодная обработка и отжиг наддува улучшают механические свойства сварного шва. Аргонодуговая сварка и сварка аргонавтом — эти процессы быстро заменяют другие традиционные методы сварки алюминия и его сплавов. Поскольку эти процессы не требуют использования флюса, никаких ограничений на конструкцию не накладывается, с вытекающими отсюда преимуществами; а также скорость сварки значительно выше.Are Welding — Этот процесс сварки алюминия и его сплавов появился сравнительно недавно. Обычно используется постоянный ток, но переменный ток может использоваться со стабилизатором дуги ВЧ. Обычно используемые электроды имеют сердечник из алюминиево-кремниевого сплава, хотя также доступны несколько других типов с магнием, магнием и кремнием в качестве легирующих компонентов. Покрытие из флюса, используемое для этих электродов, очень гигроскопично и вызывает коррозию. Процесс контактной сварки. Применение контактной сварки для алюминия и его сплавов за последние несколько лет очень быстро развивалось, в основном из-за требований авиационной промышленности.Точечная, шовная и оплавливая сварка широко используются для сварки алюминия и его сплавов, в том числе многих термообработанных сплавов. Ввиду высокой теплопроводности и электропроводности этого металла и его сплавов для их удовлетворительной сварки необходимы машины специального типа. Ввиду очень ограниченного использования других процессов их ссылка здесь вряд ли заслуживает внимания. Сварка меди кислородно-ацетиленовая сварка — для сварки плавлением предпочтительна раскисленная медь, но для сварки бронзы подходит медь с твердым шагом.Наиболее выдающимися характеристиками, определяющими свариваемость меди, являются: (i) высокая теплопроводность, (ii) высокое тепловое расширение, (iii) жаростойкость, (iv) высокая текучесть в расплавленном состоянии, (v) реакция с кислородом при высокой температуре, и (vi) способность растворять водород при высокой температуре. (i) Подготовка кромок — для сварки плавлением следует использовать только стыковые соединения, соединения внахлестку или угловые соединения не рекомендуются из-за чрезвычайной жаропрочности металла. Края следует очистить и освободить от поверхностной окалины.Края тонких листов могут быть отбортованы, но если толщина превышает дюйм, края должны быть квадратными, более дюйма, они должны быть скошены с небольшим выступом. Длинные швы должны быть сужены, оставляя зазор около дюйма на фут. Из-за жаростойкости металла прихватки не рекомендуется. Можно использовать выравнивающие зажимы и приспособления, но не следует ограничивать расширение и сжатие. При сварке вниз используется подкладочная лента, покрытая сухим асбестом в качестве опоры. (ii) Флюс — использование флюса не обязательно, но его рекомендуется использовать для предотвращения образования оксида во время сварки.Сварочные кромки, верхняя и нижняя стороны листа
5 GHOSH — СВАРКА ЦВЕТНЫХ МЕТАЛЛОВ 227 должны быть окрашены флюсом, нанесенным в пасту. (iii) Сварочное пламя и манипуляции с паяльной трубкой — Пламя должно быть нейтральным, и для обеспечения этого часто пламя регулируется с небольшим избытком ацетиленового перышка. Также из-за высокой проводимости меди желательно использовать сопло размером на один или два размера больше, чем то, которое используется для стали той же толщины.Часто для сварки толстых секций желательно использовать две выдувные трубы, одну для предварительного нагрева, а другую для сварки. В зависимости от свариваемой толщины используются методы направления влево или вправо. Вертикальная сварка и часто вертикальная сварка с двумя операторами используются с преимуществом. (iv) Заполняющие стержни. Наиболее распространенными типами являются полностью раскисленные присадочные стержни, содержащие фосфор или серебро или и то, и другое в качестве раскислителя. Использование кремния в качестве раскислителя также не является редкостью, но лучшие результаты были получены с первыми типами.Хорошие удочки запатентованной марки легко доступны. (v) Окончательная обработка сварного шва — прочность сварного шва повышается, а усадке металла шва противодействуют удары молотком. Делать это нужно от красного до черного тепла; если металл забить слишком горячим молотком, могут появиться трещины, а холодная штамповка затвердеет и сделает металл хрупким. Сварка в среде защитного инертного газа — Медь также может быть успешно сваривается с помощью процесса аргонодуговой сварки. Другие процессы сварки меди обычно не используются. Краткое описание процессов, обычно используемых для сварки алюминия, меди и их сплавов А.Алюминий и его сплавы i) Алюминий — кислородно-ацетиленовая сварка, сварка аргоном и аргонавтом, пайка, металлическая дуговая сварка. ii) Алюминиевые сплавы (без термической обработки) — кислородно-ацетиленовая сварка, аргонодуговая сварка и сварка аргонавтом, металлическая дуговая сварка, точечная и шовная сварка. iii) Алюминиевые сплавы (термообработанные) — аргонная, точечная, шовная и оплавленная сварка. Б. Медь и ее сплавы i) Медно-кислородно-ацетиленовая сварка, аргонодуговая сварка и сварка аргонавтом и пайка. ii) Медно-цинковые сплавы, включая никель-серебро и высокопрочную латунь — кислородно-ацетиленовая сварка, аргонодуговая сварка (только для сплавов, содержащих менее 30 процентов цинка), металлическая дуговая сварка и пайка.iii) Медно-оловянные сплавы Кислородно-ацетиленовая сварка, металлическая дуговая сварка, пайка, сварка угольной дугой и аргонодуговая сварка. iv) Медно-алюминиевые сплавы Кислородно-ацетиленовая сварка, аргонодуговая сварка, углеродно-дуговая сварка и точечная сварка. v) Медно-кремниевые сплавы — кислородно-ацетиленовая сварка, аргонодуговая сварка, металлическая дуговая сварка, точечная и шовная сварка. vi) Медно-никелевые (медно-никелевые) сплавы — кислородно-ацетиленовая сварка, аргонная сварка, металлическая дуговая сварка и пайка. C. Свинец Свинец — кислородно-ацетиленовый, кислородно-водородный, кислородно-угольный газ, воздух-ацетилен, воздух-угольный газ.D. Магниевые сплавы Кислородно-ацетиленовая сварка, кислородно-водородная и угольно-газовая сварка, аргонодуговая сварка, точечная сварка. Д. Никель и его сплавы i) Никель — кислородно-ацетиленовая сварка, аргонодуговая сварка, металлическая дуговая сварка, углеродно-дуговая сварка, точечная, шовная, стыковая и оплавление, ii) Никель-медные сплавы (кусочки) — кислородно-ацетиленовая сварка, аргон это сварка, сварка металлической дугой, сварка угольной дугой, пайка и точечная, шовная, стыковая и оплавленная сварка. iii) Никель-хром-нелегированный инконель — кислородно-ацетиленовая сварка, аргонная сварка, металлическая дуговая сварка.F. Цинк и литье под давлением на основе цинка Кислородно-ацетиленовая и кислородно-водородная сварка.
.Цветные металлы — медь, никель, алюминий, титан и их сплавы
Перейти к содержанию- На главную
- Развернуть / свернуть трубопровод
- Развернуть / свернуть трубопровод
- Направляющая
- Размеры и график труб
- Графики трубопроводов
- Цветовые коды трубопроводов
- Производство бесшовных и сварных труб
- Осмотр труб
- ФитингиРазвернуть / свернуть
- Руководство по трубным фитингам
- Производство трубных фитингов
- Размеры и материалы трубных фитингов
- Осмотр и испытания фитингов
Осмотр и испытания фитингов
Размеры — 90 и 45 градусов - Развернуть / свернуть трубопровод
- Размеры отводов и возвратных труб
- Размеры тройника
- Размеры трубного редуктора
- Размеры заглушки
- Размеры трубной муфты
- Направляющая для фланцев
- Фланец шейки
- Номинальные характеристики фланца
- Размеры фланца приварной шейки
- Размеры фланца RTJ
- Размеры фланца для соединения внахлест
- Размеры фланца с длинной приварной шейкой
- Размеры фланца приварной внахлест
- Размеры фланца с муфтой
- Размеры фланца
- Размеры заглушки
- Направляющая
- Клапаны
- Детали клапана и трим клапана
- Задвижка
- Шаровой клапан
- Шаровой клапан
- Обратный клапан
- Дроссельный клапан
- Пробковый клапан
- Клапан сброса давления
- Направляющая материала трубы
- Углеродистая сталь
- Легированная сталь
- Нержавеющая сталь
- Цветные материалы
- Неметаллические
- ASTM A53 04
- Оле tsExpand / Collapse
- Направляющая Olets
- Weldolet и размеры
- Sockolet и размеры
- Threadolet и размеры
- Latrolet и размеры
- Elbolet и размеры
- Шпильки Процедура затяжки шпильки 9000 9000 Болт
- Направляющая
- Таблица фланцевых болтов
- Размеры тяжелой шестигранной гайки
- Направляющая прокладок
- Спирально-навитая прокладка
- Размеры спирально-навитой прокладки
- Прокладка
- и размер
- Spectac4 Размеры слепых очков