Сварка металлов в вакууме — Справочник химика 21
Для того чтобы металлы не окислялись при нагревании в процессе технологических операций, надо эти операции проводить в вакууме. Современное машино- и приборостроение широко используют вакуум для изготовления деталей и узлов машин диффузионная сварка в вакууме, сварка электронным лучом в вакууме, вакуумная пайка деталей и узлов, вакуумная плавка металлов, нанесение на металл слоев других металлов и неорганических материалов в вакууме и т. д. [c.167]Электронно-лучевые установки применяются не только для переплава металлов и сварки в вакууме, но и для нагрева под термообработку тугоплавких металлов. Примером могут служить установки непрерывного действия для нагрева металлической ленты. Лента продвигается в вакуумированной камере под аксиальной пушкой, пучок которой движется непрерывно с большой скоростью перпендикулярно движению ленты.

ЭТУ, использующие электронно-луче-вой нагрев применяются для плавки и литья металлов в высоком вакууме сварки металлов размерной обработки материалов термообработки металлического проката нанесения в вакууме металлических покрытий на прокат. [c.329]
СВАРКА МЕТАЛЛОВ В ВАКУУМЕ [c.350]
Диффузионная сварка. Способом диффузионной сварки в вакууме можно сваривать как однородные, так и разнородные металлы, сплавы и неметаллические материалы, которые трудно или совершенно невозможно сваривать другими способами. Большой экономический эффект достигается при сварке стали и алюминия, титана и стали, чугуна и стали, металлокерамики и стали. [c.350]
Этот способ соединения основан на использовании взаимной диффузии атомов или молекул соединяемых веществ в условиях вакуума при нагреве их выше температуры рекристаллизации одного или нескольких компонентов свариваемых тел без расплавления поверхностей металла.
Кривошей А. В. и др. Диффузионная сварка в вакууме некоторых тугоплавких металлов. Сварочное производство , 1964, № 7.
Так, например, очищенные от слоя оксидов поверхности металлов при нагреве в вакууме до температуры, равной 0,7, — температуры плавления при сжатии образуют между собой соединение — ди у-зионная сварка в вакууме. При исследовании стыка соединения под микроскопом мы видим взаимное проникновение атомов соприкасающихся поверхностей с образованием твердых растворов или даже с образованием интерметаллидов, что, вообще говоря, нежелательно, так как они могут образовать хрупкие прослойки. Регулируя время диффузии, этого можно избежать. [c.234]
Значительные затруднения вызвали соединения труб из нержавеющей стали с кожухом из алюминиевого сплава АМц. В настоящее время известны три принципиально различных способа соединения алюминия (или его сплавов) с остальными металлами непосредственное соединение с никелем пайкой гальваническое меднение и лужение с последующей пайкой с другими металлами и диффузионная сварка под вакуумом. [c.124]
Наконец, без вакуума невозможны новые технологические процессы, весьма перспективные для прогресса промышленности. Прецизионная обработка металлов тонкими электронными пучками позволяет получить точное профилирование сложных контуров. Диффузионная сварка в вакууме соединяет материалы, обычно не поддающиеся сварке сталь с алюминием, чугуном и порошкообразными материалами, керамику с металлами и т. д. [c.10]
Сварка металлов в вакууме [c. 261]
Простейшая схема. Сварку металлов взрывом можно производить по схеме, которая изображена на рис. 150. Свариваемые пластины устанавливаются в воздухе или в вакууме на некотором расстоянии друг ог друга так, чтобы плоскости пластин составляли между собой угол а. Нижняя пластина прочно устанавливается на некоторой опоре, а на поверхности второй (иногда че-)ез какой-либо инертный подслой) размещается слой ЗВ. Пусть плотности и толщины ВВ, верхней и нижней пластин будут соответственно ро, бо, р1, 61 и рг, 62.
Б качестве примеров вакуумных систем, в которых откачиваемый объект можно присоединить к насосу трубопроводом с большой пропускной способностью, следует указать вакуумную систему для прокаливания металлических деталей токами высокой частоты под колпаком (рис. 5-86), для вакуумных печей различного назначения, например для обезгаживания материалов или деталей (рис. 5-85), для плавки или сварки металлов в вакууме и т. п. Если в указанных вакуумных системах технологический процесс и насосы позволяют полностью убрать ц вентили и Соединительные трубы, то, присоединяя их непосредственно к насосу, можно добиться полного равенства 5 = 5,,.
Основным элементом корпуса является обечайка — барабан цилиндрической или конической формы, изготовленный из листового металла. Обечайки корпусов, работающих под вакуумом и при давлении до 10 МН/м , изготовляют главным образом сваркой, при давлении выше 10 МН/м — соответствующей механической обработкой поковок. [c.42]
Были приняты меры, предохраняющие металл от попадания примесей внедрения (использовали чистые шихтовые материалы выплавку, сварку электродов, термическую обработку проводили в условиях высокого вакуума поверхность слитка и заготовок после каждой операции зачищали механически). Сплавы выплавляли в вакуумной печи с расходуемым электродом (вакуум 1 10 мм рт.ст.) и с нерасходуемым вольфрамовым электродом. [c.13]
Технические признаки различных видов сварки различаются по способу защиты металла в зоне сварки от воздействия компонентов воздуха (под флюсом, в защитном газе, в вакууме) по непрерывности процесса по степеням механизации.
Процессы сварки, которые используют неплавящиеся покрытия электродов и способствуют повышению содержания водорода в наплавленном металле, непригодны, и следует применять методы сварки в атмосфере защитного газа, такие, как сварка в атмосфере инертного газа металлическим электродом, сварка в атмосфере инертного газа вольфрамовым электродом и плазменная сварка, а также сварка электронным лучом в вакууме. [c.393]
Электронно-лучевая сварка. Электронно-лучевая сварка за счет большой концентрации энергии дает возможность сваривать стали и сплавы толщиной 40—50 мм без разделки кромок и подачи дополнительного металла. При этом расход энергии снижается в 5—10 раз по сравнению с другими методами сварки. При проведении электронно-лучевой сварки место сварки подвергают интенсивной бомбардировке быстролетящими электронами в высоком вакууме. Во время электронной бомбардировки большая часть энергии выделяется в виде тепла, которое используется для расплавления металла при сварке.
Основным элементом корпуса является обечайка — барабан цилиндрической или конической формы. Обечайки корпусов, работающих под вакуумом и под давлением до 10 МПа, изготовляют главным образом из листового металла сваркой, под давлением выше 10 МПа — соответствующей механической обработкой поковок. [c.36]
Ниобий хорошо сваривается с титаном, медью, цирконием и другими металлами. Сварку ведут в вакууме или нейтральной среде, приме няя различные виды дуговой и электронно-лучевой сварки. При пайка на ниобий предварительно наносят электролитическим путем слой меди или никеля.
Большой интерес представляет лучевая сварка, где для нагрева металла используется направленный поток элементарных частиц.
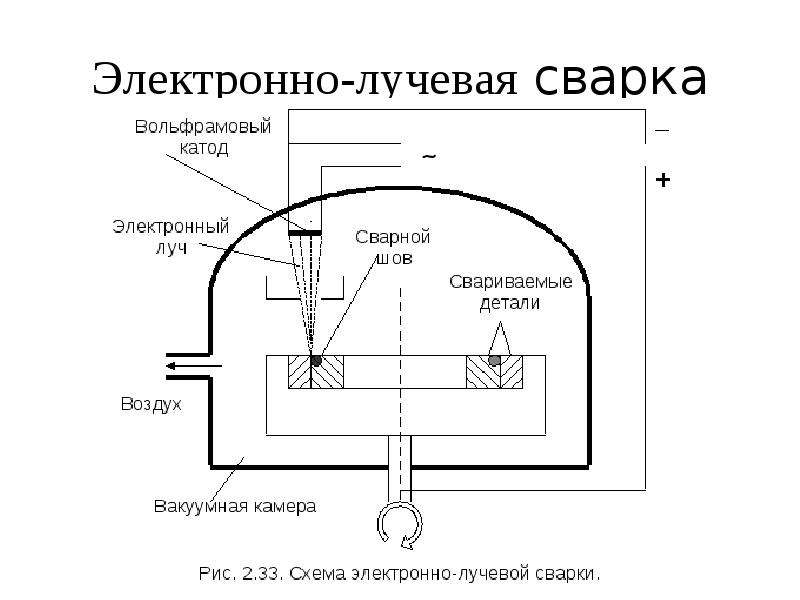
Помимо наиболее распространенных способов получения ПТА (гальванического нанесения слоя платины и наварки платиновой фольги на поверхность титанового анода), предложены другие разнообразные методы. ПТА можно подучать нанесением на титан платины диффузионной сваркой в вакууме, напылением расплавленного металла, конденсацией паров платины на титане, помещенном в вакуумной камере [1631, холодной прокаткой титана с листовой платиной с последующей термообработкой в инертной атмосфере или вакууме при 600—1000 °С [164J, покрытием титана платиной или металлами — платиновой группы методом взрыва [165[, методами порошковой металлургии, при получении металлокерамических электродов, в состав которых входят металлы платииовой группы [166), или нанесением их на поверхность в виде тонкого слоя [167]. Применяют нанесение солей платиновых металлов на титан в виде растворов их солей или пасты с последующим термическим разложением их [16Я] и образованием активного слоя, содержащего платиновые металлы, их окислы или смешанные окислы платиновых металлов с окислами неблагородных металлов. Окисные слои платиповых. металлов могут быть получены па поверхности электрода нанесениел гальваническим или каким-либо другим способом тонкого слоя платинового металла или его сплава с последующим его окислением.
При сварке металл нагревается до температуры плавления циркония и затем охлаждается с достаточно высокой скоростью. При этом происходит мартенситное превращение с образованием нестабильных а -фазы и пересыщенного твердого раствора ниобия) в а-цирконий. Коррозионная стойкость сварного соединения при этом снижается. Для ее увеличения сварные соединения отжигаются в вакууме при температурах, отвечающих существованию а-циркония. Контроль за коррозионным состоянием сварных соединений осуществляется путем автоклавирования изделий. Браковочным признаком является побеление металла сварного шва и пришовной зоны. [c.220]
Металлы и сплавы, предназначенные для сварки, не должны содержать окислов. В процессе сварки в вакууме окислы разлагаются с образованием газообразных продуктов, которые в большом количестве остаются в сварном шве, образуя газовые поры и раковины. Наличие окислов недопустимо также в припоях, так как при плавлении такие припои вскипают , и паяный шов получается пористым и невакуум-плотным. Вредное влияние на вакуум в приборе оказывает содержащийся в металлах и сплавах углерод, который в условиях глубокого вакуума является источником дополнительного газоотделения. Поэтому его содержание в металлах должно быть также строго ограничено [9, 10, 19]. [c.9]
Весьма удобным и надежным способом вакуумноплотной сварки является диффузионная сварка в вакууме. Она производится в специальных вакуумных печах при давлении -10″ Па, причем этим методом надежно соединяются и разнородные металлы, вплоть до пар алюминий-медь и алюминий-сталь 12Х18Н10Т . Сварка выполняется при температуре, равной 0,7г л (1 — температура плавления) более легкоплавкого из соединяемых металлов, и при удельном давлении порядка 0,7…0,8 предела текучести менее прочного из свариваемых металлов для температуры сварки. Соединение получается вакуумноплотным и — вследствие взаимной диффузии материалов — очень прочным разрушается, как правило, не по сварному шву, а по менее прочному металлу. [c.153]
ООО, охрупчивания не происходит. Контакт платины с танталом может быть осуществлен с помощью клепки, сварки или электролитическим осаждением. Металл, охрупченный при катодном выделении на нем водорода или вследствие наводорожи-вания при повышенных температурах, можно восстановить до обычного состояния только нагревом в вакууме. [c.383]
При этом виде сварки сплошность соединения достигается в пластическом состоянии нагретого металла с приложением сжима-юш,его усилия. Перед сваркой с соединяемых деталей удаляют поверхностные пленки, а для предупреждения их дальнейшего образо-ванкя сварка производится в вакууме при давлении 10- —10 » Па. В процессе сварки происходит взаимная диффузия атомов в поверхностных слоях свгариваемых материалов, [c.320]
Для получения герметичных швов для установок высокого и сверхвысокого вакуума чаще всего используется дуговая сварка в среде инертного газа. Это объясняется следующими преимуществами применимостью для большинства металлов и сплавов, большой концентрацией выделяющегося тепла, практическим отсутствием изиос электрода, плотностью, чистотой и прочностью шва. [c.45]
Для проверки герметичности сварных швов перед сборкой (методы см. в табл. 1-4) сваренные детали подсоединяются к вакуумному сосуду с помощью двойных уплотнений, между которыми со- здается охранный вакуум (разд. 3, 8-2). Максимально допустимая скорость натекания воздуха через сварной шов составляет около 2Х Х10 л-мкм рт. ст. .сек на 1 см длины шва. Если натекание в шве больше этой величины, то шов должен быть отшлифован до основного металла и сварка должна быть произведена снова. Это также относится к швам, в которых при работе образовались трещины. Неправильно думать, что, наложив сверху новый шов на шов с натеканием, можно последний исправить. Таким способом течи устраняются редко, так как в шве возникают напряже-66 [c.66]
Детали ТВЭЛов и технологических каналов обычно со0п[йняют электронно-лучевой сваркой, осуществляемой в вакууме. Цирконий и его сплавы являются хорошим геттером. В связи с этим при ухудшении вакуума металл шва и пришовной зоны поглощает азот и кислород. Это обстоятельство уменьшает коррозионную стойкость сварного соединения сплавов циркония. [c.220]
Для защиты от контакта с атмосферой сварку плавлением всех тугоплавких металлов выполняют в струе инертного газа или в камере, заполненной инертным газом, после предварительного вакууми-рования до давления 3 10- мм рт. ст. или ниже, а также в вакууме. В качестве защитных газов используют аргон состава А ( 0,003% Ог, гелий высокой чистоты (ВЧ МРТУ51-04-24-65). Инертные газы недостаточной чистоты предварительно очищают от влаги пропусканием через силикагель марки КСМ и ШСМ (ГОСТ 3956—54) и алюмогель (ТУ ГХП 65—53), а от кислорода — через нагретую до 900—1000° С титановую стружку или губку. [c.272]
Большая часть материалов и продуктов проходит тепловую обработку в пламенных печах. Так, подавляющее количество стали получается в мартеновских печах и в конверторах с кислородным и парокислородным дутьем. Сталь, выплавляемая в указанных агрегатах, широко используется в народном хозяйстве и в том Числе в машиностроении. Но некоторое количество вырабатываемой стали, а именно высококачественная высоколегированная сталь, получается в электрических печах, главным образом в дуговых. Эта область металлургии называется электрометаллургией. Она непрерывно развивается, так как народному хозяйству требуются высококачественные стали. История металлургии— это борьба за качество и чистоту. металлов и лх сплавов. Современное электронное машиностроение развивается с использова-ние. м особо чистых металлов и сплавов. Даже незначительное количество растворенных в металле газообразных примесей может при нагреве деталей испортить вакуум в электровакуумных приборах. Современной технике необходимы металлы и сплавы, выдерживающие большие нагрузки при высоких температурах (лопатки газовых турбин, детали ракетных двигателей и т. д.). Для этой цели применяются ниобий, молибден, тантал, вольфрам и их сплавы. Но даже ничтожно малые примеси газов (азот, кислород, водород), а также твердые примеси (углерода и др.) резко снижают механические свойства этих металлов, увеличивают их хрупкость и ухудшают качество сварки. Получение перечисленных металлов производится в электрических печах, позволяющих развить высокие температуры (3 500— 5000°С и выше). [c.87]
Дуговая сварка в атмосфере защитных газов
Технический титан обрабатывается давлением, сваривается дуговой сваркой в атмосфере защитных газов н контактной сваркой но плохо обрабатывается резанием.
Технический титан используется для изготовления химических и пищевых емкостей, а как конструкционный материал — в криогенной технике, в восстановительной хирургии и т.д. Его поставляют в виде листов, труб, проволоки и других полуфабрикатов. Технический титан хорошо обрабатывается давлением, сваривается дуговой сваркой в атмосфере защитных газов и контактной сваркой, но плохо обрабатывается резанием. Карбид титана, обладающий высокой твердостью, входит в состав твердых сплавов, применяемых для изготовления режущих инструментов. Губчатый титан широко используется в вакуумной технике. Оксид титана применяется в лакокрасочном производстве. Ограничивает повсеместное использование титана его очень высокая стоимость. [c.195]
Способ дуговой сварки в атмосфере защитных газов был впервые предложен и 1883 г. знаменитым русским инженером Н. Н. Бенардосом.

Обработка давлением. Титан удовлетворительно обрабатывается давлением (ковкой, прессованием, прокаткой) и сваривается дуговой сваркой в атмосфере защитных газов. Он имеет высокую стойкость против коррозии в пресной и морской воде и в некоторых кислотах. [c.289]
Дуговая сварка в атмосфере защитного газа [c.326]
Титан удовлетворительно обрабатывается давлением (ковкой, прессованием,» прокаткой) и сваривается дуговой сваркой в атмосфере защитных газов. Он имеет высокую стойкость против коррозии в пресной и морской воде и в некоторых кислотах. Примеси резко повышают прочность титана, одновременно снижая его пластичность. [c.192]
При сварке титана возникают трудности, обусловленные его большой химической активностью. В связи с этим в процессе сварки необходимо защищать от взаимодействия с газами не только расплавленный металл шва, но и все сильно нагретые части, в том числе и противоположную сторону шва. Несмотря на этп трудности, в настоящее время успешно применяется дуговая сварка в атмосфере защитных газов (гелия и аргона). Широко используют также контактные методы сварки точками, швом и в стык.
[c.376]
Дуговая сварка в атмосфере защитного газа. Для защиты наплавляемого металла от окисления и азотирования при сварке жароупорных, магниевых, алюминиевых сплавов и нержавеющей стали, а также для получения сварного соединения, обладающего высокой коррозионной стойкостью, сварку производят в среде нейтральных газов (аргона, гелия). Поэтому и сварка этого вида называется аргонной. При аргоно-дуговой сварке дуга возбуждается между концом вольфрамового электрода и деталью в защитной среде аргона, с помощью специальной [c.305]
Самое широкое применение имеет дуга с жесткой характеристикой (т. е. на участке, где напряжение дуги не зависит от тока) при ручной дуговой сварке, автоматической сварке под флюсом, аргонодуговой сварке неплавящимся электродом и др.

Дуговая сварка в среде защитного газа предложена в конце XIX в. Н. Н. Бенардосом. Зтот процесс основан на оттеснении окружающей атмосферы из зоны плавильного пространства защитным газо.м (см. рис. 28.5). [c.276]
Технология сварки. В настоящее время для сварки ниобия применяется электроннолучевая сварка в вакууме и дуговая сварка в среде защитных газов. Электроннолучевая сварка выполняется на высоковольтных и на низковольтных установках в вакууме не ниже 10 мм рт. ст. Дуговая сварка производится главным образом в камерах с контролируемой атмосферой неплавящимся вольфрамовым электродом с присадкой или без присадки. Для сварки применяется постоянный ток прямой полярности. В качестве защитного газа используется аргон марки А или гелий, при условии, что его чистота не ниже чистоты аргона марки А . Металл шва, полученного электроннолучевой сваркой, имеет несколько меньшую твердость по сравнению с полученным аргоно-дуговой сваркой.
[c.122]
За последние годы все более широкое применение находит сварка в атмосфере защитных газов (аргоно-дуговая сварка и сварка в среде углекислого газа). [c.184]
Н. Н. Бенардос в 1882 г. изобрел способ дуговой сварки с применением угольного электрода. В последующие годы им были разработаны способы сварки дугой, горящей между двумя или несколькими электродами сварки в атмосфере защитного газа контактной точечной электросварки с помощью клещей создан рад конструкций сварочных автоматов. Н. Н. Бенардосом запатентовано в России и за границей большое количество различных изобретений в области сварочного оборудования и процессов сварки. [c.8]Вредными примесями титана, снижающими его пластические свойства, являются кислород, азот и углерод с углеродом титан образует очень твердые карбиды. Титан удовлетворительно куется, прокатывается и прессуется. Сварка (дуговая) титана производится в атмосфере защитных газов.
[c.203]
Для повышения стойкости швов к межкристаллитной коррозии и создания в их металле аустенитно-ферритной структуры при сварке их обычно легируют титаном или ниобием. Однако титан обладает высоким сродством к кислороду и поэтому при способах сварки, создающих в зоне сварки окислительную атмосферу (ручная дуговая сварка, сварка под окислительными флюсами), выгорает в количестве 70. .. 90 %. Легирование швов титаном возможно при сварке в инертных защитных газах, при дуговой и электрошлаковой сварке с использованием фторидных флюсов. В металле швов содержание титана должно соответствовать соотношению Ti/ > 5. Ниобий при сварке окисляется значительно меньше и его чаще используют для легирования шва при ручной дуговой сварке. Его содержание в металле шва должно соответствовать Nb/ >10. Однако он может вызвать появление в швах горячих трещин.
[c.364]
При дуговой сварке в защитном газе (рис. 373, г) электрическая дуга 1 возникает в атмосфере защитных газов 2. В качестве защитных газов применяют аргон, гелий, углекислый газ и др. Газ подводится непосредственно к зоне сварочной дуги. Сварка производится плавящимся или неплавящимся электродом 3. [c.386]
Источники с падающей и пологой характеристиками применяются при ручной дуговой сварке и автоматической сварке под флюсом. Сварочные генераторы с жесткой и возрастающей внешними характеристиками применяются для сварки плавящимся электродом в атмосфере защитных газов. [c.306]
Из всех тугоплавких материалов самое щирокое применение в промышленности получил титан и его сплавы. Сварку титана и его сплавов проводят в атмосфере защитных газов с дополнительной газовой защитой корня щва и еще не остывшего участка шва до 400° С. Перед сваркой проволоку подвергают вакуумному отжигу. Для сварки титана больших толщин применяют автоматическую сварку под специальным бескислородным флюсом (АНТ-1 ПНТ-3 и т. д.). Защита обратной стороны осуществляется применением остающейся или флюсомедной подкладки или флюсовой подушки. При этом используют постоянный ток обратной полярности. Кроме того, для сварки титана и его сплавов можно применять и другие способы сварки вакуумно-дуговую, электроннолучевую, диффузионную и т, п.
[c.681]
Сварка дугой прямого действия плавящимися электродами в атмосфере защитных газов. Этот способ применяется в некоторых случаях при аргоно-дуговой сварке. Широкое распространение получает сварка малоуглеродистой и нержавеющих сталей и других сплавов в углекислом газе плавящимися электродами. [c.198]
Газоэлектрическая сварка. Газоэлектрическая сварка (рис. 1,( ) является разновидностью дуговой сварки. При этом способе сварки электрическая дуга 1 горит в атмосфере защитных газов 12, которыми могут являться аргон, гелий, углекислый газ и др. Газ подводится непосредственно к зоне сварочной дуги. Сварка производится плавящимся или неплавящимся электродом 3.
[c.8]
Дефекты, встречающиеся в сварных соединениях, выполненных дуговой (ручной и автоматической), газовой, в атмосфере защитных газов, контактной и другими видами сварки, а также причины их появления весьма разнообразны и имеют характерные особенности для каждого из видов сварки. [c.363]
При дуговой сварке в атмосфере аргона требуется высокая чистота металла и инертного газа. Обычно защитный газ (аргон или гелий) дополнительно очищают, пропуская его над раскаленным активным металлом. [c.171]
В книге описаны электрические, магнитные и тепловые свойства сварочной дуги изложены данные о конструкциях современных сварочных автоматов и полуавтоматов для сварки под флюсом и в атмосфере защитных газов приведены краткие сведения по устройству и обслуживанию источников питания дуговой сварки освещены вопросы сварки цветных металлов и сплавов описаны методы контроля и испытания сварных соединений и конструкций.
[c.223]
Сущностью и отличительной особенностью дуговой сварки в защитных га.зах является защита расплавленного и нагретого до высокой температуры основного и электродного металла от вредного влияния воздуха защитными газами, которые обеспечивают физическую изоляцию металла и зоны сварки от воздуха и заданную атмосферу в зоне сварки. [c.79]
Сварка в атмосфере атомарного водорода нлн инертного защитного газа дает самые лучшие по качеству швы и в относительно массивных изделиях и в листах толщиной более 0,8 мм. Таким образом можно сваривать н более тонкие листы. При сварке при.меняются вольфрамовые электроды с сварочной проволокой или без нее. Можно производить н ручную дуговую сварку, но она менее надежна, чем автоматическая. В качестве инертных газов, создающих защитную атмосферу, при электродуговой сварке используются гелий и аргон. [c.423]
При дуговой сварке ниобия в защитной атмосфере [38, 159] в качестве защитного газа применяется аргон или гелии электродом служит вольфрамовый наконечник сварочной горелки. Такая сварка наиболее эффективна для соединения листов, расположенных плотно в стык (краевая или стыковая сварка). Края свариваемых листов помещают в паз шириной примерно 9,6 мм и глубиной 3,2 мм. Электрод вводят через крышку камеры или экран, заполненный аргоном или гелием. За счет инертного газа должно поддерживаться избыточное давление в экране. Защита сварного шва достигается путем заполнения паза инертным газом со стороны, обратной сварке. Вольфрамовый электрод Делают отрицательным для получения ковкого шва (как при сварке циркония), а дугу зажигают с помощью высокочастотного разряда, чтобы предотвратить загрязнение шва вольфрамом. Дуга постоянного тока по сравнению с дугой переменного тока глубже пронизывает металл, что способствует образованию более узкой лужи из расплавленного металла, которую легче защитить инертным газом. Минимальная толщина листа, который можно удовлетворительно сваривать этим способом, составляет 0,33—0,38 мм.
[c.459]
Новыми металлическими материалами, занимающими видное место в машиностроении, являются титан и сплавы на его основе. Это серебристо-белый металл с температурой плавления 1665° С и плотностью 4,5. Технический титан высокой чистоты содержит не более 0,1 % примесей (Fe, Мп, А1, С, Si, Ni), имеет невысокую прочность, хорошую пластичность, по свойствам приближаясь к чистому железу с углеродом образует очень твердые карбиды титана. Титан удовлетворительно обрабатывается давлением (ковкой, прессованием, прокаткой), сваривается дуговой сваркой в атмосфере защитных газов. Титан имеет высокую стойкость против коррозии в пресной, морской воде и в некоторых кислотах. Примеси резко повышают прочность, одновременно снижая пластичность титана. Изготовляемый в СССР технический титан, содержащий до 0,5% примесей, имеет ов = 55—75 кПмм 1550—750 Мн/мЧ, 8 = 20— 25%.
[c.163]
Новым металлическим материалом, занимающим видное место в машиностроении, являются титан и сплавы на его основе. Это серебристо-белый металл с температурой плавления 1660° и удельным весом 4,5 г/сж .
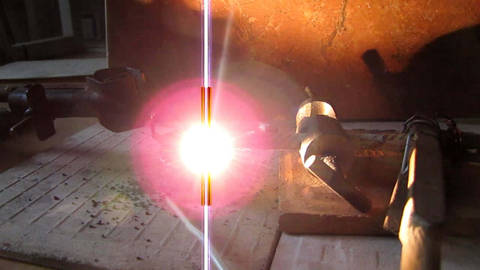
Допускаемые напряжения в сварных швах 137 Дуговая сварка в атмосфере защитных газов 145. 432 Дендритная структура 164 Дуга прямого действия 222 Дуга косвенного действия 222 Дуга комбинированного действия 222 Дроссель 234, 631 Деформации прн сварке 299. 302 Дюралюмии 94, 509 Дефекты сварки 581. 582 Динамическая нагрузка 584 Дефектометр 589
[c.637]
При выполнении сварочных работ обезуглероженный КЧ (так называемый бело-сердечный или европейский КЧ) пригоден для сварки и пайки любыми методами без прел-варительной и последующей ТО. В отливках из этого материала пря толщине стенки до 8 мм содержание С снижается до 0,3%. В сердцевине при большей толщине стенок конечное содержание С остается более или менее значительным. При открытой дуговой сварке чугуна применяются электроды средней толщины с покрытиями типа TiOa или СаО. Дуговая сварка в атмосфере защитного газа позволяет использовать обычные электроды из низколегированных сталей, которые годятся также и для газосварки плавлением. Для отдельных узлов возможно применение стыковой сварки оплавлением. [c.688]
В определенных случаях при изготовлении узлов из жаропрочных сталей применяется и дуговая сварка в атмосфере защитных газов. Так, для тонкостенных катаных хромоникелевых сталей применяется аргонодуговая сварка непласящимся вольфрамовым электродом. Этот метод используется для выполнения стыков различных трубных систем [178], а также при изготовлении регенераторов газотурбинных установок. Иногда при сварке стыков труб большой толщины аргонодуговую сварку применяют только для выполнения корневого валика, осуществляя заполнение шва плавящимся электродом.
[c.69]
Для предотвращения указанных дефектов при дуговой сварке меди рекомендуются сварка в атмосфере защитных газов (аргона, гелия, азота и их смесей) применение сварочной и присадочио проволок, содержащих сильные раскислители (титан, цирконий, бор, фосфор, кремний и др.). [c.235]
При сварке углеродистых сталей уменьшения склонности к образованию горячих трещин добиваются снижением содержания углерода в наплавленном металле вследствие применения сварочной проволоки с меньшим содержанием углерода по сравнению с основным металлом. Одновременно шов легируют марганцем и кремнием, которые обеспечивают сохранение необходимых механических свойств металла шва. Кроме того, присутствие марганца связывает серу в соединение MnS, в котором сера находится в виде твердого раствора. Температура плавления такого раствора выше 1180°С, поэтому в шве снижается количество легкоплавких примесей, способствующих образованию горячих трещин. Для сварки углеродистых сталей можно рекомендовать ручную дуговую сварку покрытыми электродами, сварку са-мозащитной порошковой проволокой, под флюсом, сварку в атмосфере защитных газов (аргона, аргона с добавлением кислорода или углекислого газа), электрошлаковую, газовую или контактную сварку.
[c.508]
Gas shielded ar welding — Газовая дуговая сварка в среде защитного газа. Общий термин, используемый для описания газовой дуговой сварки металлическим электродом, газовой дуговой сварки вольфрамовым электродом и дуговой сварки под флюсом, когда использована защитная атмосфера. Типичные используемые газы включают аргон, гелий, аргоноводородную смесь или диоксид углерода. [c.968]
Качество сварных соединений в значительной степени определяется надежностью защиты сварочной ванны и максимально разогретой зоны от воздействия окружающей среды, а также отсутствием в шве нор, шлаковых включений и других дефектов. Обеспечение указанных условий получения качественных соединений также связано с выбором способа сваркп. Наиболее эффективны в этом отношении сварка в атмосфере защитных газов и вакууме. Особенно важно правильно выбрать способ сварки при применении материалов, свойства которых ухудшаются при незначительном насыщении газами из окружающего воздуха. Например, для таких тугоплавких металлов, как титан, ниобий, а также для алюминия, магния и высоколегированных сталей предпочтительна дуговая сварка в атмосфере аргона высокой чистоты, а для молибдена и его сплавов — электронным лучом в вакууме. В то же время углеродистые и легированные конструкционные стали успешно сваривают всеми способами дуговой и электрошлаковой сварки. При соответствующем выборе режима и сварочных материалов получают сварные соединения, равнопрочные основному металлу при статических и динамических нагрузках.
[c.377]
При изготовлении сварных конструкций из разнородных сталей может быть прим енено большинство имеющихся методов сварки. Наибольшее распространение из них получила в настоящее время ручная дуговая сварка. Перспективным является использование автоматической сварки под флюсом [75], сварки в атмосфере защитных газов [45], стыковой [23], а также сварки в вакууме [60], трением [157] и других видов сварки.
[c.137]
Наиболее широко применяют сварку алюминия и его сплавов в атмосфере защитных газов неплавящимся (толщины 0,5—10 мм) и плавящимся (толщины более 10 мм) электродом. В этом случае получают более высокое качество сварных швов по сравнению с другими видами дуговой сварки. Применяют также автоматическую сварку плавящимся электродом полуоткрытой дугой по слою флюса, при которой для формирования корня шва используют медные или стальные подкладки. Возможна газовая (ацетилено-кислородная) сварка алюминия и его сплавов. Флюс наносят на свариваемые кромки в виде пасты или вводят в сварочную ванну на разогретом конце присадочного прутка. Алюминий и его сплавы также сваривают плазменной и электрошлаковой сваркой они достаточно хорошо свариваются контактной сваркой. Учитывая высокую теплопроводность и электропроводимость алюминия, для его сварки необходимо применять большие силы тока.
[c.237]
В процессе обычной сварки вследствие образования окислов, нитридов и карбидов гафний становится хрупким. Сварка гафнии с гафпием и гафния с титаном, цирконием и циркониевыми сплавами (циркалой-2) производится электродуговым способом с применением вольфрамового электрода в инертной защитной атмосфере [53, 57, 65, 1141. Однако этот метод не вполне удовлет-ворнтелен. Длительный контакт с электродом приводит к загрязнению гафния вольфрамом 1114]. Поскольку стандартное оборудование для дуговой сварки в атмосфере гелия не обеспечивает пластичных швон, приходится применять специальную сварочную камеру, заполненную инертным газом гелием или аргоном. Для сварки в вакууме необходима на 60% большая сила тока, поэтому сварочная камера заполняется инертным газом до атмосферного давления. [c.197]
При этом процессе дуга тоже образуется между одиночным электродом, в данном случае вольфрамовым, и заготовкой.

Ручную дуговую сварку довольно широко применяют в производстве металлоконструкций для самых различных металлов и сплавов малых и средних толщин (2—30 мм). Ручная сварка удобна при выполнении коротких и криволинейных швов в любых пространственных положениях (нижнем, вертикальнодт, горизонтальном, потолочном рис. У.Ю), а также прн наложении швов в труднодоступных местах. Она все еще остается незаменимой при монтажных работах и сборке конструкций сложной формы. Ручная сварка обеспечивает хорошее качество сварных швов, но обладает более низкой производительностью по сравнению с автоматической дуговой сваркой под флюсом. Производительность процесса сварки в основном определяется силой сварочного тока. Однако ток при ручной сварке покрытыми э.лектро-дами ограничен, так как повышение тока сверх рекомендованной величины приводит к разогреву стержня электрода, отслаиванию покрытия, сильному разбрызгиванию и угару расплавленного металла сварочной ванны. Ручную сварку постепенно заменяют полуавтоматической в атмосфере защитных газов,
[c.283]
При плазменной резке нужно соблюдать те же требования безопасности, что и при дуговой сварке в защитных газах, в частности при сварке сжатой дугой. Особенности плазменной резки — сильный шум и более интенсивное излучение. Поэтому при машинной резке рабочее место резчика должно быть по возможности удалено от места реза, а управление установкой должно быть дистанционным. При ручной резке надо применять защитные стекла с повышенной затемненнос-тью, а при шуме более 110 дБ наушники или противошумную каску. Кроме того, при плазменной резке выделяется в атмосферу много металлического пара и газов, поэтому должна быть усилена вентиляция.
[c.313]
Сварка вуглекислом газе отличается от аргоно-дуговой сварки окислительным характером защитной атмосферы. Считают, что по окислительной способности эта атмосфера отвечает сварке в смеси аргона с 8—10% кислорода. Углекислый газ создает более совершенную защиту дуги и жидкого металла, чем это достигается при сварке открытой дугой покрытыми электродами. Так, при сварке в углекислом газе из проволоки переходит в шов до 50% содержащегося в ней титана. При сварке открытой дугой, как известно, переход титана в 3—4 раза меньше, а при аргоно-дуговой сварке он составляет обычно 80%. [c.338]
Ele trogas welding (EGW) — Электрогазовая сварка (ЭГС). Процесс дуговой сварки в вертикальном положении, который производит соединение металлов, нагревая их дугой между непрерывно подающимся присадочным металлом (потребляемым электродом) и заготовкой. Медные ограничители (молдинговые башмаки) используются, чтобы ограничить распространение расплавленного свариваемого металла. Электроды могут быть покрыты флюсом или твердой обмазкой. Может применяться защитная атмосфера путем внешней подачи газа или газовой смеси.
[c.947]
Аргоно-дуговую сварку плавлением можно выполнять в струе защитных газов или в камере с атмосферой защитных газов. Для защиты используют чистый аргон, гелий высокой чистоты и техиич. водород с дополнит, очисткой. Имеются сведения о применении при дуговой сварке Та, Nb защиты погружением в 4-хло-ристый углерод. При сварке в струе газа, для защиты разогретого металла с наружной стороны шва, сопло сварочной горелки снабжают дополнит, колпачком (соответствующим конфигурации изделия), обычно с самостоят системой подачи защитного газа. Обратная сторона шва защищается подачей газа в канавку подкладки. При струйной защите неизбежно нек-рое насыщение газами нагреваемых участков метал-
[c. 156]
В следующем периоде сварочная техника развивалась в направлении совершенствования ранее известных способов и разработки новых эффектив-пых с точки зрения их технологических возможностей и производительности с применепием современных источников энергии, таких как электронный луч, высокотемпературная плазма, ультразвук и др. В результате появились дуговая сварка в защитной атмосфере аргона и углекислого газа, электрошлаковая, а также автоматизированные способы контактной сварки. Разработаны и внедрены в производство сварных конструкций из специальных сталей, цветных и тугоплавких металлов и сплавов следующие способы сварки электронно-лучевая, дуговая в вакууме, плазменной струей, ультразвуковая U др. В последнее время для сварки начали применять оптические [c.266]
Сварочные термины
С
Сборка (под сварку) — технологическая операция, при которой подлежащие сварке деталей занимают необходимое взаиморасположение и закрепляются специальными приспособлениями или прихватками.
Свариваемость — свойство металла или сочетаний металлов образовывать при установленной технологии сварки соединение, отвечающее требованиям, обусловленным конструкцией и эксплуатацией изделия.
Сварка — получение неразъемных соединений посредством установления межатомных связей между соединяемыми частями при их нагревании и (или) пластическом деформировании.
Сварка аргонодуговая — дуговая сварка в защитном газе, при которой в качестве защитного газа используется аргон.
Сварка блоками — сварка, при которой многослойный шов сваривают отдельными участками, а промежутки между ними заполняют до того, как будет завершена сварка корня шва.
Сварка взрывом — сварка, при которой соединение осуществляется в результате вызванного взрывом соударения быстро движущихся частиц.
Сварка в углекислом газе — дуговая сварка в защитном газе, при которой в зону дуги подается углекислый газ.
Сварка газовая — сварка плавлением, при которой нагрев кромок соединяемых частей производится пламенем газов, сжигаемых на выходе из горелки для газовой сварки.
Сварка давлением — осуществляется при температурах ниже точки плавления свариваемых металлов без использования припоя и с приложением давления, достаточного для создания необходимой пластической деформации соединяемых частей.
Сварка дуговая — сварка плавлением, при которой нагрев осуществляется электрической дугой.
Сварка дуговая автоматическая — дуговая сварка, при которой подача плавящего электрода и перемещение дуги вдоль свариваемых кромок механизированы.
Сварка дуговая в защитном газе — дуговая сварка, при которой в зону дуги подается защитный газ.
Сварка дуговая неплавящимся электродом — дуговая сварка, выполняемая нерасплавляющимся при сварке электродом.
Сварка дуговая плавящимся электродом — дуговая сварка, выполняемая электродом, который, расплавляясь при сварке, служит присадочным металлом.
Сварка дуговая полуавтоматическая — дуговая сварка, при которой механизирована только подача электродной проволоки.
Сварка дуговая ручная — сварка штучными электродами, при которой подача электрода и перемещение дуги вдоль свариваемых кромок производится вручную
Сварка каскадом — сварка, при которой каждый последующий участок многослойного шва перекрывает весь или часть предыдущего участка.
Сварка контактная — сварка с применением давления, при которой нагрев производится теплом, выделяемым при прохождении электрического тока через находящиеся в контакте соединяемые части.
Сварка контактная стыковая — контактная сварка, при которой соединение свариваемых частей происходит по поверхности стыкуемых торцов.
Сварка контактная точечная — контактная сварка, при которой соединение элементов происходит на участках, ограниченных площадью торцов электродов, подводящих ток и передающих усилие сжатия.
Сварка контактная шовная — контактная сварка, при которой соединение элементов выполняется внахлестку вращающимися дисковыми электродами в виде непрерывного или прерывистого шва.
Сварка кузнечная — сварка давлением, при которой осадка выполняется ударами молотка.
Сварка лежачим электродом — дуговая сварка, при которой неподвижный плавящийся электрод укладывается вдоль свариваемых кромок, а дуга перемещается по мере расплавления электрода.
Сварка многодуговая — дуговая сварка, осуществляемая одновременно более чем двумя электродами с раздельным питанием их током.
Сварка многоэлектродная — дуговая сварка, осуществляемая одновременно более чем двумя электродами с общим подводом сварочного тока.
Сварка на весу — односторонняя сварка плавлением без подкладок.
Сварка наклонным электродом — дуговая сварка, при которой плавящийся электрод располагается наклонно вдоль свариваемых кромок и по мере расплавления движется под действием силы тяжести или пружины.
Сварка на подъем — сварка в наклонном положении, при которой сварочная ванна перемещается снизу вверх.
Сварка на проход — сварка, при которой направление сварки неизменно.
Сварка на спуск — сварка в наклонном положении, при которой сварочная ванна перемещается сверху вниз.
Сварка неповоротных стыков — сварка стыковых швов по замкнутому контуру, при которой объект сварки неподвижен.
Сварка обратноступенчатая — сварка, при которой сварной шов выполняется следующими один за другим участками в направлении, обратном общему приращению шва.
Сварка открытой дугой — дуговая сварка плавящимся электродом, осуществляемая без подачи защитного газа или сварочного флюса, при которой зона дуги доступна наблюдению.
Сварка под флюсом — дуговая сварка, при которой дуга горит под слоем сварочного флюса.
Сварка сверху вниз — сварка в вертикальном положении, при которой сварочная ванна перемещается сверху вниз.
Сварка снизу вверх — сварка в вертикальном положении, при которой сварочная ванна перемещается снизу вверх.
Сварка трением — сварка давлением, при которой нагрев осуществляется трением, вызываемым вращением одной из свариваемых частей.
Сварочная дуга — мощный устойчивый электрический разряд в газовой среде, образованной между электродом и изделием (либо между электродами).
Сварочный выпрямитель — источник питания постоянного тока сварочной дуги, предназначенный для понижения напряжения сети (220 или 380 В) до напряжения холостого хода, необходимого для зажигания и стабильного горения дуги, а также преобразования переменного тока в постоянный.
Сварочный пост — рабочее место сварщика, оснащенное необходимым оборудованием для выполнения сварочных работ.
Сварочный трансформатор — источник питания переменного тока сварочной дуги предназначенной для понижения напряжения электрической сети (220 или 380 В) до напряжения холостого тока, необходимого для зажигания и стабильного горения сварочной дуги.
Светофильтр — темное защитное стекло в щитке или маске, предназначенное для защиты глаз, кожи лица от лучей дуги, брызг металла и шлака.
Скос кромки — прямолинейный или криволинейный срез кромки, подлежащий сварке.
Слой — часть металла сварного шва, образованная одним или несколькими валиками, располагающимися на одном уровне поперечного сечения шва.
Соединение нахлесточное — сварное соединение, в котором свариваемые элементы расположены параллельно и перекрывают друг друга.
Соединение сварное — неразъемное соединение, выполненное сваркой.
Соединение стыковое — сварное соединение двух элементов, расположенных в одной плоскости или на одной поверхности.
Соединение тавровое — сварное соединение, в котором к боковой поверхности одного элемента примыкает под углом и приварен торцом другой элемент.
Соединение угловое — сварное соединение двух элементов, расположенных под прямым углом и сваренных в месте примыкания их краев.
Спецодежда сварщика — рабочая одежда для защиты сварщика от брызг металла, шлака, вредных излучений, электрического тока.
СВАРКА И РОДСТВЕННЫЕ ТЕХНОЛОГИИ В ОСВОЕНИИ КОСМОСА И МИРОВОГО ОКЕАНА. XXI ВЕК
Ученый с мировым именем, организатор науки Борис Евгеньевич Патон вот уже 47 лет возглавляет Научно-исследовательский институт электросварки им. Е. О. Патона в Киеве. Под его руководством здесь развиваются научные основы и техника сварки, создаются и внедряются в промышленность новые, прогрессивные сварочные технологии. Много раз Б. Е. Патон, бессменный член редакционного совета «Науки и жизни», выступал на страницах журнала со статьями о путях развития науки и научно-технического прогресса (см. «Наука и жизнь» № 5, 1969 г.; № 10, 1972 г.; № 9, 1974 г.; № 7, 1976 г.; № 4, 1977 г.; № 10, 1981 г.; № 5, 1986 г.; № 1, 1988 г.).Борис Евгеньевич Патон.
Грузовая стрела-манипулятор транспортирует космонавта-оператора и оборудование к месту проведения работ на внешней поверхности станции «Мир».
Схема прокладки сварного газопровода по дну Черного моря между Джубгой (Россия) и Самсуном (Турция).
Орбитальная станция «Мир» полной конфигурации, на которой из года в год проводятся эксперименты по космическим технологиям.
Летчики-космонавты СССР В. Н. Кубасов и Г. С. Шонин.
Наука и жизнь // Иллюстрации
Подводная механизированная сварка при ремонте трубопровода на дне Волги.
Так в перспективе будут выглядеть сборка и сварка трубопроводов на дне океана.
‹
›
Сегодня ученый обращает взгляд в будущее и размышляет о том, какие проблемы придется решать сварочной науке в XXI веке и какое место займут сварочные технологии в освоении космоса и Мирового океана.
Президент Национальной академии наук Украины, академик Российской академии наук Б. ПАТОН, директор Института электросварки им. Е. О. Патона (Киев).
В преддверии нового века возникает естественное желание поразмышлять над тем, что нас ожидает впереди, куда мы идем, какими путями. Это в полной мере относится к научно-техническому прогрессу, к сварочной науке и технике, без которых просто невозможно представить себе современное производство и строительство.
БУДУЩЕЕ СВАРОЧНЫХ ТЕХНОЛОГИЙ
В соответствии с терминологией, предложенной Европейской сварочной федерацией, термин «сварка» означает соединение, резку и обработку поверхности материалов всех типов с использованием таких процессов, как сварка, пайка (твердая и мягкая), термическая резка, газотермическое напыление, адгезионное сцепление, микросоединение. Этот перечень включает и управление, обеспечение качества, неразрушающий контроль, гигиену труда и охрану здоровья персонала.
Основная задача сварочного производства — проектирование и изготовление сварных конструкций. Сварными в наше время делают конструкции из стали, цветных металлов и сплавов. Все глубже проникает сварка в производство изделий из синтетических материалов, создаются технологии сварки разнородных металлов и сплавов, освоена сварка композиционных материалов. Наиболее ответственные гражданские и военные машины и инженерные сооружения изготовляются в сварном исполнении. Год от года растут требования к качеству сварных конструкций, повышаются их надежность и долговечность.
О масштабах применения сварки можно судить по данным статистики: примерно 70% всего выпускаемого в мире стального проката используется в сварных конструкциях; годовой объем мирового производства сварочных материалов и оборудования достигнет в нынешнем году в денежном выражении 40 миллиардов долларов. В разных странах мира в сварочном производстве заняты миллионы сварщиков, резчиков, дефектоскопистов и других специалистов.
Конечно, все это относится к производству и строительству в земных условиях. Однако на всех этапах развития человечества его привлекали Вселенная (ближний и дальний космос) и гидросфера (Мировой океан). Во все века люди стремились овладеть небесным и водным пространствами.
Эпохой активного вторжения человека в космос, в глубины океанов и морей стала вторая половина XX века. И это естественно и закономерно. Вместе с тем благодаря достижениям научно-технического прогресса появилась иллюзорная надежда на то, что человек обретет безграничную власть над окружающей средой, над природой. Такая философия очень опасна. Она может привести к глобальной катастрофе. Мы должны всегда помнить об этом.
Несомненно, в наступающем XXI веке будут интенсивно развиваться космические исследования, направленные на решение земных проблем, продолжатся глубокие фундаментальные исследования происхождения жизни на планете и эволюции человека. Дальнейшее проникновение человека в космос позволит создать такие новые жизненно важные отрасли, как глобальная информационная система, добыча внеземных ресурсов, космическая биотехнология, космическая энергетика, технология производства полупроводниковых монокристаллов, и другие.
Сейчас на орбите объединенными усилиями космических держав сооружается международная космическая станция. Реально рассматривается задача освоения Луны, ее минеральных и энергетических ресурсов. Продолжается штурм Марса. Чтобы осуществить эти грандиозные планы, нужно строить совершенно новые сооружения, создавать принципиально новые материалы. При этом решающую роль будут играть микрогравитация и вакуум, наличием которых определяются характеристики различных конструкций. Принципиально изменятся условия и методы труда человека.
Новую космическую технику будут создавать как в земных, так и в орбитальных условиях. И здесь очень важная роль отводится сварке и связанным с ней совершенно новым процессам и технологиям.
Говоря о гидросфере, прежде всего стоит вспомнить, что три четверти поверхности нашей планеты составляют океаны, моря, озера, реки. Они всегда привлекали людей своими необъятными просторами и глубинами. И хотя складывались легенды об ихтиандрах, до недавнего времени человек мог проникнуть лишь в верхние, мелководные зоны Мирового океана.
Практическое освоение континентального шельфа началось во второй половине нашего столетия. Сегодня в крупных промышленных масштабах добывают нефть и газ. Согласно прогнозу, в 2004 году мировая добыча нефти составит 3150 миллионов тонн, из них 32% будет получено со дна морей и океанов. Примерно такую же долю составит объем добытого на шельфе природного газа. Развитие этой отрасли было бы невозможно без строительства мощных буровых и эксплуатационных платформ, терминалов, обустройства подводных месторождений. Кроме этого создана современная технология укладки мощных подводных трубопроводов. Так, в Северном море сооружен газопровод «Zip Pipe» диаметром до 1220 миллиметров, протяженностью более 1000 километров.
Пока все эти объекты построены на шельфе, глубина которого, как правило, не превышает 300 метров, правда, газопровод из Алжира в Европу уложен на глубине 600 метров. И это, конечно, не предел. Россия уже приступила к осуществлению грандиозного проекта — прокладке газопровода протяженностью около 400 километров на глубине свыше 2000 метров по дну Черного моря.
Сейчас разрабатывается технология строительства и эксплуатации на дне морей и океанов газоперекачивающих и нефтяных насосных станций без непосредственного участия человека. В этой связи возникают чрезвычайно сложные задачи диагностики и ремонта всех подводных сооружений топливно-энергетического комплекса. Нужно заметить, что пока самые квалифицированные водолазы могут действовать на глубине лишь до 300 метров.
Грандиозный шаг вперед сделала Япония. Здесь на сравнительно мелководном шельфе строятся целые города. При этом широко используются сварные сваи, опоры, платформы, трубопроводы.
В глубинах океанов таятся огромные запасы минеральных ресурсов. Их добыча, в частности марганцевых конкреций, пока нерентабельна. Но по мере исчерпания этих полезных ископаемых на суше и дальнейшего мощного развития научно-технического прогресса человечество неизбежно придет к добыче минеральных ресурсов со дна океанов и морей, глубины которых достигают 5000 метров.
Самостоятельную задачу представляет подъем затонувших кораблей и других конструкций. Эти огромные «запасы» металла, веками скапливавшиеся на дне морей и океанов, могут и должны быть введены в процесс рециклинга.
Совершенно очевидно, что проблемы освоения гидросферы, так же как и космического пространства, не могут быть решены без широкого применения разнообразных процессов и технологий сварки, резки, нанесения покрытий. Водная среда и громадные гидростатические давления — очень сложные условия для практического применения сварочных и сопутствующих им технологий, поэтому для их создания понадобятся дорогие и трудоемкие исследования.
Подводя итог вышесказанному, можно утверждать, что в наступающем XXI веке нас ожидают большие, чрезвычайной сложности работы в космосе и в глубинах Мирового океана. При этом громадное значение будут иметь сварочные технологии, используемые для создания сложного оборудования и аппаратуры в земных условиях. Частично они уже существуют, но для дальнейшего освоения космоса и гидросферы необходимо разрабатывать новые процессы сварки, резки, пайки и нанесения различных покрытий. В XXI веке появятся новые, экзотические материалы. Для их обработки и соединения опять-таки понадобятся совершенно новые технологии. К выполнению этих работ сварочная наука и техника достаточно подготовлены.
Иначе обстоит дело с созданием материалов и технологий их обработки непосредственно в космосе и гидросфере, где условия необычайно сложны и принципиально отличаются от земных. И те и другие технологии объединяет то, что они заведомо должны быть ориентированы на экстремальные условия. Для космоса характерны не только микрогравитация и вакуум, но и термоциклирование, неизбежное при работах на орбите. В гидросфере же приходится иметь дело с непрерывной водной средой и со все большими и большими гидростатическими давлениями. При этом, в отличие от космоса, в глубинах мирового океана всегда сохраняется постоянная положительная температура. Обитание и, главное, работа человека в таких экстремальных условиях связаны с громадными трудностями, а иногда и просто невозможны. В обоих случаях нужны скафандры и высоконадежные системы жизнеобеспечения. Скафандры для работы в открытом космосе уже многократно проверены в деле, они существуют около 40 лет. Водолазные скафандры позволяют работать на глубине только до 300 метров. Погружение на большую глубину пока неосуществимо, и связано это в том числе с физиологическими особенностями организма человека.
И в космосе, и в гидросфере возникают трудности со снабжением электроэнергией, особенно если речь идет об ее длительном потреблении. Чтобы вырабатывать электроэнергию в космических условиях, понадобятся огромные солнечные батареи и мощные аккумуляторы. Полагаю, в дальнейшем будут использоваться и другие источники, в частности ядерные. Они могут функционировать на автономной необитаемой орбитальной станции-платформе, а излучаемый поток энергии будут принимать на обитаемой станции.
Ряд технологических операций в космосе может выполняться только при дистанционном управлении рабочими процессами с применением всевозможных роботов и манипуляторов. Некоторые образцы таких устройств уже действуют на американских шаттлах и на российской орбитальной станции «Мир». В большинстве случаев в их работу может вмешиваться оператор-космонавт, в том числе и в открытом космосе.
Немалые трудности представляет снабжение электроэнергией оборудования, работающего в подводных условиях на больших глубинах. Чтобы передать значительное количество электроэнергии с надводного корабля на глубину, нужны специальные кабели достаточно большого сечения. Потери электроэнергии в них окажутся весьма существенными, и будет относительно трудно добиться жестких вольт-амперных нагрузочных характеристик. Видимо, предпочтение следует отдать аккумуляторным батареям, которые можно снабдить соответствующими преобразователями энергии. Вполне реально использовать в будущем сверхпроводниковые кабельные линии, соединяющие мощный источник питания на надводном корабле с приемной подстанцией на дне. Здесь предстоит искать оптимальные решения.
Что касается роботов и всевозможных манипуляторов, то их применение для глубоководных работ исключает возможность непосредственного вмешательства оператора. Человек будет управлять рабочими процессами дистанционно, из глубоководного обитаемого подводного судна (батискафа). Подводные суда можно оборудовать достаточно мощными подъемно-транспортными устройствами, оснастить телевизионными камерами и различными сенсорами. Батискафы будут использовать как для визуального наблюдения, так и для инструментального контроля за состоянием подводных трубопроводов и другого оборудования.
Сварка в космосе и гидросфере сможет получить серьезное распространение только в том случае, если удастся разработать весьма совершенные методы неразрушающего контроля сварных соединений, методологию технической диагностики сварных конструкций. Для этого потребуются мощные банки данных и компьютерное моделирование. Режимы сварки в широком понимании этого термина будут выбираться с помощью компьютеров. В целом без компьютеризации создать новые технологии сварки и применить их в космосе и гидросфере просто невозможно.
Как видим, строительно-монтажные и ремонтные работы в космосе и гидросфере очень сложны и кардинально отличаются от таковых в наших земных условиях. Остановимся несколько подробнее на собственно сварочных и сопутствующих технологиях.
КОСМОС
Сначала несколько слов о наиболее распространенной в земных условиях дуговой сварке. В космосе, где вакуум и микрогравитация оказывают существенное влияние на процессы сварки, резки, пайки и напыления, очень трудно обеспечить устойчивое горение дуги и стабильное протекание процесса сварки. Особенно это относится к сварке плавящимся электродом. Еще в шестидесятых годах в Институте электросварки им. Е. О. Патона Национальной академии наук Украины (сокращенно ИЭС НАНУ) были проведены опыты, включающие реальную сварку в космических условиях. Они показали, что дуговая сварка в открытом космосе не имеет больших перспектив.
Не дает положительных результатов и плазменная сварка, также опробованная в космосе. Тем не менее в дальнейшем дуговая и плазменная сварка и резка все же смогут найти применение в космосе, например при сооружении различных объектов на Луне. Совершенствовать и тот и другой вид сварки, а также электродуговую металлизацию, безусловно, необходимо. Для этого потребуются серьезные исследования физики дуги и металлургических процессов, протекающих при дуговой сварке в вакууме, в условиях микрогравитации.
Тем не менее сварка плавлением нужна в космосе уже сейчас при сооружении крупных орбитальных станций и платформ, а также при ремонтных операциях. Самый оптимальный процесс — электронно-лучевая сварка, поскольку необходимый для нее вакуум присутствует в космосе постоянно, а микрогравитация не составляет непреодолимых трудностей. В ИЭС созданы оборудование и технология, позволившие еще в 1984 году совместно с НПО «Энергия» осуществить электронно-лучевую сварку, резку, пайку и напыление различных металлов в открытом космосе. Эти работы превосходно выполнили космонавты С. Е. Савицкая и В. А. Джанибеков. В 1986 году в расширенном виде опыты повторили. Их провели в открытом космосе космонавты В. А. Соловьев и Л. Д. Кизим.
В девяностых годах специалисты ИЭС создали новое оборудование для применения электронно-лучевой технологии в космосе. Это установка «Универсал», снабженная сменным инструментом для сварки, резки, пайки и напыления. Она питается электроэнергией от бортовой сети космической станции. «Универсал» можно либо использовать как ручной инструмент, либо встраивать в механизированные дистанционно управляемые установки, применяемые в основном для восстановления деградировавших поверхностей теплозащитных экранов, антенн и других объектов на космических станциях. Установка «Универсал» прошла весь комплекс предполетных испытаний, сертифицирована и готова к проведению серии запланированных натурных экспериментов на орбитальной станции «Мир». Во время подготовки к полету установку «Универсал» осваивала группа американских астронавтов, прошли также «горячие» тренировки несколько российских экипажей, которым предстоит проводить сварочные эксперименты в космосе.
Работы, связанные с применением электронно-лучевой технологии в космосе, продолжаются: совершенствуется оборудование, увеличивается его мощность. Все это позволит сваривать и резать металл практически любой толщины.
Весьма интересна для применения в открытом космосе лазерная технология. От электронно-лучевой ее отличают по крайней мере два существенных преимущества: во-первых, нет высокого ускоряющего напряжения и, во-вторых, может быть применена волоконная оптика. Это значит, что можно установить лазер стационарно и транспортировать световой луч в любую точку орбитальной станции снаружи (в открытом космосе), а также внутри ее. Присущие лазерной технологии недостатки — низкий, по сравнению с электронным лучом, кпд процесса и сравнительно большие масса и габариты установки — устранимы, но над этим нужно работать. В недалеком будущем лазерная технология, видимо, найдет применение на космических орбитах. Особые надежды мы возлагаем на диодные лазеры.
Нет препятствий и для применения в открытом космосе контактной сварки (в частности, точечная сварка была проверена еще в шестидесятых годах). Это относится и к шовной (роликовой) сварке. Нужно создать своего рода установку «Универсал» со сменным инструментом для точечной и роликовой сварки, а также с устройствами, защищающими оператора от возможных выплесков металла. Контактную сварку можно будет использовать в космосе при сооружении различных конструкций из тонколистовых материалов и для их ремонта. Она может найти применение при сооружении объектов на Луне.
Представляют интерес различные сварные трансформируемые конструкции, изготовленные на Земле. Их можно доставлять на орбитальную станцию либо на Луну в компактном виде. Оболочечные металлоконструкции способны «раздуваться» с помощью небольшого избыточного внутреннего давления и приобретать заданную форму и габариты. Соединяя с помощью сварки отдельные преобразуемые элементы, можно собирать в космосе более сложные и крупные сооружения. Найдут применение и трансформируемые раздвигающиеся и складывающиеся конструкции, состоящие из унифицированных узлов. Их можно использовать как на орбитальных космических станциях, так и на Луне.
Словом, сварочные технологии в космосе — это не научная фантастика. Думаю, они будут востребованы уже в начале XXI века, по мере развития работ на международной орбитальной космической станции.
ГИДРОСФЕРА
Существуют «мокрая» и «сухая» технологии подводной сварки. В первом случае сварка (это же касается и резки) осуществляется непосредственно в воде, во втором — сварка и резка проводятся в локальных и крупногабаритных камерах, где можно создать либо газовую атмосферу, либо вакуум.
Конечно, весьма интересна и перспективна «мокрая» сварка, например, при сооружении в гидросфере крупных сварных конструкций и их ремонте. Такая технология применяется в наше время на глубине до 100 метров, при этом, как правило, в работе участвует оператор-водолаз. Однако в перспективе будут освоены глубины порядка сотен и тысяч метров, где работа оператора невозможна. Сварка и резка в таких экстремальных условиях должны быть полностью автоматическими.
Задача несколько облегчается благодаря тому, что за процессом сварки можно наблюдать и частично управлять им из находящегося поблизости батискафа. Решающую роль в работе сварочного оборудования должны играть подводные роботы и дистанционно управляемые манипуляторы. Но, как видим, на пути подготовки и сборки изделий под сварку и в процессе собственно сварки возникают громадные трудности.
Наибольший интерес для гидросферы представляет дуговая сварка. Однако следует иметь в виду, что на больших глубинах, где гидростатические давления достигают нескольких сотен атмосфер, свойства дуги и протекание металлургических процессов совершенно не изучены. В этом направлении нужны серьезные и длительные исследования, результаты которых сегодня трудно предсказать. Но постановка таких исследований крайне необходима.
Речь может и должна идти также о применении в гидросфере других способов сварки и резки. Определенную перспективу представляют различные варианты контактной сварки. Собственно точечная сварка, в том числе металлов больших толщин, видимо, возможна. Но для этого предстоит разработать такие конструкции и их сварные узлы, в которых точечные соединения будут иметь необходимый комплекс свойств.
Несколько сложнее обстоит дело с контактной стыковой сваркой. Получить качественные соединения, выполненные «мокрой» стыковой сваркой оплавлением, не удастся. Значит, необходимо развивать «сухую» сварку. То же самое относится к стыковой сварке сопротивлением.
В гидросфере может быть применена взрывная технология. Прежде всего это касается резки взрывом, используемой при ремонтных работах. Примером может служить вырезка дефектного участка подводного трубопровода либо резка трубчатых свай, на которых установлены исчерпавшие ресурс буровые или эксплуатационные платформы. Разработанные в ИЭС технологии резки взрывом безопасны для окружающей водной среды и ее обитателей. Опыт использования этой технологии на глубинах в несколько десятков метров позволяет предположить, что «резать» взрывом можно и на большей глубине. Но для этого необходимы серьезные исследования.
Возможно использование и лазерной технологии с применением твердотельного лазера и волоконной оптики. Лазер можно установить на надводном корабле, а световой луч транспортировать по волоконному световоду. Другой вариант — опустить лазер в герметичном корпусе на дно или поместить в батискаф, из которого «выпускается» световод с «горелкой». Словом, заставить работать под водой световой луч лазера в наших силах. Однако получить качественное сварное соединение очень трудно. Первые опыты по лазерной сварке под водой уже проводятся, но опять-таки необходимы серьезные эксперименты в гипербарических камерах. Видимо, предстоят длительные исследования, в том числе связанные с созданием новых присадочных материалов. Таким образом, при всей заманчивости «мокрой» сварки и резки, чтобы использовать их при строительстве и ремонте различных конструкций и сооружений под водой на больших глубинах, нужны очень серьезные, длительные и дорогие исследования и опытно-конструкторские работы.
Что касается «сухой» сварки, то выполнить ее в вакуумной камере под водой очень сложно. Ведь речь идет о том, чтобы поместить в крупногабаритную камеру либо всю сооружаемую конструкцию, либо ее узлы. Создать в такой камере вакуум при давлениях в окружающей водной среде в несколько десятков и даже сотен атмосфер чрезвычайно трудно. Полагаю, что разработки в этой области малоперспективны.
Реально можно осуществить сварку на больших глубинах в локальных камерах, которые устанавливаются в зоне сварки. В них подается газ под давлением, несколько превышающим гидростатическое давление окружающей среды. Вода вытесняется, и создается контролируемая газовая среда. Нужны только насосы высокого давления и достаточный запас газа. Необходимо следить за тем, чтобы плотность посадки камеры в зоне сварки была максимальной. В противном случае существенно возрастает расход газа, и это вызывает дополнительные трудности. Полагаю, что пока можно говорить лишь о необитаемых камерах.
Процесс сварки (резки) в камерах под водой должен быть автоматизирован. Управлять им и вести наблюдение можно только дистанционно — из батискафа либо из надводного корабля. Для этого в камере надо установить телевизионные мониторы и различные сенсоры. Информация от них будет выводиться на центральный пульт в батискафе или надводном корабле. Если батискаф оборудовать механической рукой и другими манипуляторами, то оператор сможет вмешиваться в работу при сооружении и сварке конструкции.
В случае необходимости в такой камере можно проводить антикоррозионное напыление различных конструкций. Это, например, газотермическое и плазменно-дуговое напыление, а также электродуговая металлизация. Однако о целесообразности использования этих процессов говорить пока рано. У нас нет опыта применения технологий, основанных на использовании электрической дуги при столь высоких давлениях. В этом направлении также предстоят серьезные длительные исследования в гипербарических камерах.
В камерах с контролируемой газовой атмосферой можно применять лазерный луч. Но и в этом случае предстоит добиться стабильного качества сварных соединений, создать новые присадочные материалы и технологии собственно сварки. Нужна также технология лазерной резки в условиях высокого давления газовой среды в камерах.
Все процессы сварки в камерах должен сопровождать неразрушающий контроль качества сварных швов — ультразвуковой, магнитный или рентгеновский. Естественно, процессы контроля тоже должны быть автоматизированы.
Электроснабжение сварочных и сопутствующих технологических процессов на больших глубинах представляет самостоятельную и достаточно сложную задачу. Видимо, оптимальными, как уже было сказано, будут источники энергии, состоящие из аккумуляторной батареи и преобразователей, прежде всего инверторов. Источники питания можно поместить в герметичные кожухи с устройствами для теплообмена, опустить на дно, а после окончания работ поднять на надводный корабль либо «захоронить» на дне. Выбор варианта будет определяться экономическими соображениями. Можно разместить источники питания и в батискафе. В обоих случаях потребители электроэнергии подключаются к ним дистанционно с помощью манипуляторов, размещенных на батискафе, либо роботов.
Чрезвычайно сложная и актуальная задача — ремонт на больших глубинах сварных конструкций. Для него нужны дистанционно управляемые сборочные стапели, кондукторы и манипуляторы. Оказалось, что ремонтные работы значительно сложнее сварочных. Сегодня ремонт одного сварного стыка подводного трубопровода на глубине 100 метров и более стоит несколько миллионов долларов. Поэтому строители всегда стремятся выполнить максимальный объем сборки и сварки на берегу. Очень сложным будет неразрушающий контроль качества сварных соединений.
Огромное значение приобретает техническая диагностика сварных подводных сооружений. Эта задача решается сегодня во многих промышленно развитых странах. Систематический контроль, в том числе ультразвуковой контроль за эксплуатационным состоянием сварных соединений, ведется на сотнях морских буровых скважин на весьма больших глубинах.
Таким образом, сварка, резка, напыление и пайка в гидросфере представляют собой очень сложную комплексную задачу. Особенно, когда речь идет о больших глубинах, которые, несомненно, будут осваиваться в XXI веке.
Ученым и специалистам в области сварочной науки и техники предстоит выполнить сложнейшие исследования и опытно-конструкторские разработки, без них просто невозможно создать и освоить технологии соединения металлов, нанесения покрытий и сооружения уникальных конструкций в открытом космосе и гидросфере. При этом возникают огромные проблемы и в области экологии. Словом, нам предстоит решать чрезвычайно увлекательную научную и инженерную задачу.
Масштабность и комплексный характер всех этих проблем заставляют говорить об интеграции мировой сварочной науки и техники, это особенно важно, когда национальные ассигнования на науку сокращаются. Необходимо общими усилиями создавать крупные международные проекты, которые будут реализовываться на основе специализации и кооперации многих сварочных и других научных центров ведущих стран мира.
(PDF) Особенности сварки шаробаллонов в вакууме полым катодом
140
луч создается специальным прибором – электронной пушкой.
Применение низкого давления (до 1·10-5 мм рт.ст.) позволяет зна-
чительно повысить качество сварных соединений за счет сниже-
ния содержания вредных примесей в вакууме (рис. 3).
Этот метод сварки требует специального оборудования для
проведения сварочного процесса и контроля параметров им-
пульсного магнитного поля. Он обеспечивает большую глубину
проплавления при очень маленькой ширине шва.
При этом способе сварки с нити накала испускаются элек-
троны, поток которых контролируется (фокусируется и концен-
трируется) магнитными линзами. Электронный луч создается тем
же путем, что и световой луч в телевизионном приемнике. Энер-
гия этой сварки контролируется током, подаваемым на нить нака-
ла. Сварка в основном проводится в вакууме, так как молекулы
воздуха мешают движению луча. Вакуумная камера имеет защиту
от радиационного излучения, появляющегося в процессе сварки.
Дуговая сварка титана под бескислородным флюсом иссле-
дована в работах /2, 4, 5/. Титан и его сплавы можно сваривать
под флюсами АНТ-1, АНТ-3 при толщине металла 2,5–8 мм и
АНТ-7 для металла большей толщины. Перед сваркой флюс про-
каливают при температуре 400 оС, чтобы содержание влаги в нем
не превышало 0,05% по массе. Сварка выполняется на стандарт-
ном оборудовании при постоянном токе обратной полярности.
Получаемые сварные соединения не уступают по прочности
и пластичности основному металлу и имеют более мелкозерни-
стую структуру, чем при сварке в инертных газах. Данный способ
экономически эффективен для металла толщиной более 6-8 мм.
При сварке по флюсу-пасте типа АН-ТА, наносимому тон-
ким слоем на поверхность кромок свариваемых деталей, на
меньших токах можно сваривать без разделки кромок металл
толщиной до 12 мм. Данная технология позволяет увеличить глу-
бину проплавления, снизить деформации сварных конструкций,
изменить форму провара, уменьшить зону термического влияния,
снизить вероятность образования пор и прожогов. Такими же
преимуществами обладает и сварка порошковой проволокой с
флюсом в качестве наполнителя.
история развития и первые достижения
Возможность проведения сварочных работ за пределами земной атмосферы впервые всерьез рассматривалась еще во времена Советского Союза. При этом до определенного момента сварка в космосе считалась попросту невозможной, о чем неоднократно заявляли ученые и инженеры того времени. Первым, кто предложил заняться поиском способов решения подобной задачи был великий советский ученый Сергей Королев.
Существовало несколько причин, которые по мнению многих специалистов делали процесс сваривания металлов в отрытом космосе невозможным. Основная причина заключалась в значительном отличии условий на Земле и за ее пределами. Это действительно так, ведь при выполнении такой работы в космическом пространстве ситуацию осложняли такие факторы, как:
- глубокий вакуум;
- неограниченная скорость диффузии газообразных веществ из зоны сваривания;
- значительные изменения температуры (от минус 150 до плюс 130 градусов по Цельсию).
Еще одной проблемой являлось полное отсутствие гравитации, в связи с чем было важно полностью пересмотреть сам подход к выполнению сварочных работ. Кроме того, процесс сварки в космосе был существенно осложнен ограниченной подвижностью космонавта, связанной с тем, что он должен был выполнять такую задачу в громоздком и сковывающем движения скафандре. Нельзя было забывать и о риске повреждения защитного костюма, ведь это несло угрозу самому астронавту.
Космическая сварка: первые эксперименты
Для начала советские ученые решили определить, возможно ли провести сваривание металлических изделий в условиях невесомости. Для этого в 1965 году была использована лаборатория, установленная на борту самолета ТУ-104.
В процессе свободного падения авиатранспортного средства удавалось создавать условия, полностью аналогичные условиям невесомости в околоземном космическом пространстве. Хотя такие условия обеспечивались лишь на очень непродолжительное время (порядка 30 секунд), этого было достаточно для того, чтобы убедится — сварка в невесомости является возможной.
Далее пришло время экспериментов непосредственно в космосе. Самый первый из них был осуществлен в октябре 1969 года внутри космического пилотируемого корабля «Союз-6». Для этого советскими учеными, возглавляемыми Борисом Патоном, был создан уникальный сварочный прибор под названием «Вулкан». Этот прибор позволял варить металлические детали с применением сразу трех различных способов – электронно-лучевого, плазменного и дугового.
В результате выяснилось, что метод сваривания с применением сжатой дуги низкого давления не подходит для работ в невесомости. В то же время электронно-лучевая технология оказалась наиболее эффективной и позволила обеспечить прочное соединение деталей высокого качества.
К слову, об особенностях и сферах применения такой технологии вы можете прочитать в нашем отдельном материале – по электронно-лучевой сварке.
Дальнейшие разработки и улучшения
Впоследствии перед советскими учеными возникла новая задача – добиться улучшения показателей эффективности устройства, используемого для сваривания металлов с применением электронно-лучевой технологии. Ведь для того, чтобы космическая сварка могла проводиться повсеместно, требовалось обеспечить:
- Снижение общего веса сварочного оборудования. Во время космического полета каждый лишний килограмм может иметь ключевое значение.
- Низкое потребление электроэнергии. В космосе использование мощных источников электрического тока является более сложным и затратным, чем на Земле.
- Высокая надежность. Оборудование должно быть безотказным и функционировать даже в самых экстремальных условиях окружающей среды.
- Универсальность в применении. Была поставлена задача, согласно которой прибор для сваривания металла должен был быть приспособлен и для решения других задач, например, резки такого материала.
- Простоту и безопасность. Космонавт должен иметь возможность выполнять сварочные работы в открытом космическом пространстве, находясь при этом в скафандре, а также с минимальным риском для себя.
Первая сварка в открытом космосе
Уже спустя пять лет после предыдущего эксперимента к работе был готов новый вид оборудования – аппарат с автономным источником питания, получивший название «УРИ». Он был разработан сотрудниками Института электросварки имени Патона в городе Киеве.
Прибор «УРИ» позволяет проводить сваривание металлических конструкций в условиях вакуума, невесомости, а также при экстремальных изменениях температуры. При этом он обладает более компактными размерами и легким весом, чем его предшественники, а также может быть использован для резки, пайки и нагрева деталей, как и для нанесения на их поверхность тонких покрытий.
С помощью прибора «УРИ» в 1984 году была проведена первая в истории сварка в открытом космическом пространстве. Она была выполнена с применением электронно-лучевого метода советскими космонавтами Светланой Савицкой и Владимиром Джанибековым.
Сваривание металлов в космосе в наше время
В настоящее время проведение космической сварки позволяет решать различные задачи, связанные с ремонтом космических аппаратов, а также монтажом и сборкой металлических конструкций, являющихся их конструкционными элементами.
Наибольшее распространение получил метод электронно-лучевой варки металла. Созданные много лет назад устройства модернизируются и улучшаются, что позволяет повысить коэффициент полезного действия и уменьшить их вес.
Заключение
Сварка в космосе впервые была проведена на борту советского космического аппарата. Перед этим долгое время это считалось практически невыполнимой задачей ввиду многих причин. Разработки ученых позволили достичь значительного прогресса в этой области, а также в усовершенствованном виде используются и сегодня.
Стоит отметить, что процесс сваривания металлических изделий часто невозможен без применения качественных газовых смесей. При желании вы можете изучить ассортимент такой продукции и приобрести ее на сайте компании «ПРОМТЕХГАЗ», проследовав по этой ссылке. Кроме того, предлагаем вам прочесть нашу статью о лазерной резке металлов.
Дуговая сварка в камерах с контролируемой атмосферой
В промышленности сварка многих металлов осуществляется дуговой сваркой с защитой места сварки инертными газами: аргоном или гелием.
При дуговой сварке в инертных газах различаются следующие способы защиты металлов от атмосферы;
rn- rn
- сварка с применением стандартных сварочных горелок для сварки в струе инертных газов; rn
- сварка с применением подвижных защитных микрокамер; rn
- сварка с использованием стационарных камер с контролируемой инертной атмосферой.
Самым распространенным и простейшим способом предохранения металла от действия атмосферы является использование аргоно-дуговых горелок с защитой инертным газом ванны расплавленного металла: в некоторых случаях используется также защита и нижней стороны соединяемых кромок. Однако такой способ не обеспечивет стабильного качества сварных соединений и по-этому он ограниченно применяется при сварке таких активных и тугоплавких металлов как титан, молибден, вольфрам и др.
rnrn
Электрическая дуговая сварка с защитой места сварки струей инертных газов широко применяется при изготовлении изделий из высоколегированных сталей, алюминиевых и магниевых сплавов, сплавов на основе никеля. Однако, как показывает практика, при сварке активных и тугоплавких металлов, а также при сварке листов большой толщины и поковок из высоколегированных сталей, алюминиевых и магниевых сплавов с использованием обычных сварочных горелок не обеспечивается необходимое качество сварного соединения вследствие недостаточной защиты металла, нагретого до высоких температур.
rn
Более совершенным методом сварки с защитой инертными газами является сварка с использованием защитных кожухов (микрокамер), представляющих собой небольшие подвижные камеры, которые позволяют защитить не только ванну расплавленного металла, но и значительную область металла в околошовной зоне, нагретого до высоких температур.
rnРазмеры микрокамер и их форма выбираются в зависимости от вида свариваемого металла и его толщины, режимов сварки, формы изделия. При этом микрокамеры должны обеспечивать надежную защиту инертным газом зоны металла, нагретого до температур, при которых еще может происходить активное взаимодействие металла с кислородом и азотом воздуха. При сварке циркония необходимо защищать зону металла с температурой выше 500° С (773° К).
rnrn
Представлена схема сварки с применением защитной подвижной микрокамеры. Инертный газ подается в подвижную камеру через сопло и специальный газоподводящий шланг. Защита корня шва, как видно из рисунка, производится инертным газом, поступающим в подкладку, имеющую канавку. При сварке сосудов или труб оба конца изделия закрываются, а инертный газ непрерывно в процессе сварки подается внутрь изделия.
Сварка в космосе | Онлайн-обучение Американского общества сварщиков
Автор: Джеймс Уилки
1 секунда.
Почти мгновенно ваша кровь начинает пузыриться, ваша кожа начинает замерзать, воздух вытягивается из ваших легких.
5 секунд.
С каждым мгновением ваши клетки бомбардируются фотонами и частицами , вызывающими опасные мутации.
10 секунд.
Ваше тело начинает расширяться при быстрой декомпрессии.
30 секунд.
В тканях не осталось кислорода. Вся ваша кровеносная система вышла из строя.
31 секунда.
Ты мертв.
Искры в космосе
Космос — это не только последний рубеж; это также самое враждебное. Потенциал смертельной опасности так же велик, как и романтические исследования, поэтому аэрокосмическая инженерия уделяет такое внимание качеству конструкции и безопасности.
Однако, при всем тщательном планировании строительства космического корабля, чрезвычайные ситуации все же случаются. В конце концов, космические путешествия зависят от людей, летящих на огненных столбах с невероятной скоростью, пока они не выскользнут из живительной хватки Земли.
Когда необходимо произвести ремонт, многие из процессов, которые мы считаем само собой разумеющимися, включая сварку, сильно осложняются отсутствием гравитации внутри космического корабля и ледяной, надвигающейся пустотой космоса по другую сторону стены.
Георгий Шонин и Валерий Кубасов, российские космонавты, участвовавшие в космическом полете советского корабля «Союз-6» в 1969 году, первыми экспериментировали со сваркой в космосе, используя универсальный инструмент, известный как «Вулкан».Шонин и Кубасов также первыми ощутили, насколько опасным может быть космический ремонт. Пара протестировала три сварочных процесса, чтобы увидеть, как они будут работать в среде с пониженным давлением: электронно-лучевая сварка, дуговая сварка сжатым воздухом под низким давлением и дуговая сварка плавящимся электродом.
Во время испытаний Кубасов чуть не прожег корпус жилого отсека корабля «Союз-6» — ошибка, из-за которой пара без скафандров отправилась бы в космос на последние 30 секунд своей жизни.К счастью, корпус остался целым, но с предупреждением о жесткости и сложности сварки в космосе. Качество сварки образцов из титана, алюминиевого сплава и нержавеющей стали было сравнимо с найденным на Земле.
Испытания и невзгоды
За более чем 40 лет, прошедших после полета «Союза-6», космические путешествия стали все более изощренными, предлагая гораздо большую защиту от потенциальных опасностей при сварке внутри и снаружи корабля. Инженеры из таких групп, как НАСА, строят космические аппараты из материалов, специально подобранных для преодоления суровых условий космических путешествий, особенно из керамики и алюминия.
Хотя «Союз-6» продемонстрировал, что в космосе могут работать несколько процессов, эксперименты также продемонстрировали проблемы, с которыми традиционные процессы сварки сталкиваются за пределами планеты. Структура, состав и качество сварного шва чрезвычайно зависят от распределения температуры в сварочной ванне и распределения расплавленных материалов по мере формирования сварного шва — условия, которые усложняются в космосе независимо от того, находитесь ли вы внутри или снаружи сварочной ванны. судно.Даже такие простые вещи, как брызги, представляют серьезную проблему, когда понятия «вниз» и «вверх» не имеют смысла.
Короче говоря, даже если процесс может функционировать в космосе, этот процесс не обязательно является идеальным решением, особенно когда сварка должна выполняться в жестком вакууме. Хотя многие стандартные процессы сварки могут работать внутри космического корабля, универсальность имеет решающее значение, когда инженеры таких групп, как НАСА и SpaceX, оснащают свои корабли.
Помните, космический корабль должен бороться с ограниченным пространством и необходимостью оставаться как можно более легким для запуска. Таким образом, идеальный процесс сварки должен хорошо работать как внутри , так и снаружи корабля, чтобы оправдать включение необходимого оборудования. Например, хотя сварка электродом может показаться простым и гибким решением для аварийного ремонта, любая сварка, которая должна выполняться в сильном вакууме, затруднит зажигание дуги. Процессами, основанными на тщательно сбалансированных защитных газах, также будет трудно управлять, поскольку газы ведут себя по-разному в невесомости и безвоздушной среде.
Источники сварочного тока также являются проблемой, поскольку традиционные бензиновые или дизельные двигатели представляют собой астрономические трудности на орбите. Портативные генераторы протягивают окружающий воздух через машину для охлаждения, что невозможно в космосе.
Принимая во внимание легкий алюминий, выступающий в качестве основного металла в космических конструкциях, TIG может показаться очевидным выбором, однако ловкость и точность, которые делают TIG таким выгодным процессом, также ограничивают его полезность в постоянном свободном падении космоса.
Электронно-лучевая сварка, при которой для защиты сварного шва требуется вакуум, а не защитные газы, может быть полезна при сварке вне космического корабля, но создание изолированного вакуума внутри космического корабля делает внутреннюю сварку проблемой.
Первоначально разработанный НАСА для более легкого доступа и ремонта компонентов двигателя космического корабля «Шаттл», ручной фонарик теперь доступен для коммерческого применения.
Лазер в день избавляет от вакуума
Сегодня инструмент, называемый ручным лазерным резаком переменной мощности, предназначенный для сварки и пайки металлов, представляет собой компактное и эффективное средство повышения точности сварки, уменьшения зон термического влияния и для легкой маневренности.Устройство также простое в использовании, предлагая простую кривую обучения для астронавтов, уже увязших в годах обучения.
Лазерная сварка не требует ни защитных газов, ни вакуума (как при электронно-лучевой сварке), и была рекомендована учеными НАСА еще в 1989 году для аварийных ремонтных комплектов на космических кораблях и станциях.
Сварка лазером позволяет точно контролировать температуру сварочной ванны, что обеспечивает формирование чистого и прочного шва без чрезмерного плавления или загрязнения расплавленного металла.
Факел был специально разработан для ремонта компонентов двигателя космического челнока, хотя версии устройства также были разработаны для коммерческих рынков.
Несмотря на развитие сварочных технологий и их роль во внеземных чрезвычайных ситуациях, лучший способ предотвратить проблемы — это в первую очередь избегать их.С этой целью НАСА, Space X и другие частные организации также разрабатывают передовые новые методы наземной сварки, особенно с использованием процесса перемешивания трением.
Есть надежда, что, построив более прочный корабль с первого раза, можно будет избежать трудностей сварки в космосе, просто сделав аварийный ремонт маловероятным и ненужным.
AWS Learning предлагает блоги, подкасты, виртуальные конференции, онлайн-курсы и другие цифровые инструменты, которые помогут вам расширить свою карьеру в области сварки.
Кстати, если вы сварщик, вы можете быть удивлены, обнаружив, что у космоса очень знакомый запах.
Нажмите на изображение слева, чтобы узнать, как пахнет космос!
Сварка
В вакуумном оборудовании используются компоненты из мягкой и нержавеющей стали.
обычно свариваются вместе для сосудов и соединений. Кроме того, это
также возможна сварка алюминиевых компонентов. Чтобы убедиться, что
полученные сварные швы герметичны, необходимо использовать
надлежащие материалы, не имеющие трещин и пустот, и поверхности которых
гладкие и обезжиренные.Кроме того, особый геометрический дизайн
также требуется, что иногда отличается от обычного сварного
соединения, которые используются для невакуумных применений. Где бы
возможно с инженерной точки зрения, внутренние сварные швы должны быть предусмотрены в
чтобы избежать зазоров и трещин со стороны вакуума, так называемых скрытых или
виртуальные утечки. Если это невозможно, сварной шов должен проходить через
в сторону вакуума. При необходимости дополнительная атмосферная сторона
Сварка может быть использована для повышения механической стабильности. В этом
соединение, важно, чтобы этот дополнительный сварной шов не
непрерывным, чтобы при необходимости можно было обнаружить утечку, и не иметь
воздушные включения.
Сварка вакуумных компонентов и камер требует специальных знания, а сварочный персонал должен иметь профессиональную квалификация. Обычно сварочная компания регулярно документирует это. испытания своих сварщиков через независимые испытательные институты. В Кроме того, испытания процедуры сварки для каждого свариваемого материала и необходимо соблюдать геометрию шва.Специально обученные сварщики персонал, например, инженеры-сварщики или техники, сопровождают и оценить сварочные работы.
Сварочное тепло и относительно быстрое охлаждение могут изменить
свойства материалов. Например, изменения в структуре во время
сварка аустенитных нержавеющих сталей может увеличить
намагничиваемость или привести к порам и горячим трещинам, возникающим во время
сварка алюминия (об этом уже упоминалось в главе 3.2.1.1
«Нержавеющая сталь» и 3. 2.1.3 «Алюминий»). В
Кроме того, высокие остаточные напряжения в зоне сварного шва приводят к
деформация компонентов, которая должна быть сведена к минимуму.
Если затрагиваются функциональные области, такие как уплотнительные поверхности, их необходимо
переработано. Если это невозможно, это может привести к потере всего
заготовка. Тем не менее, могут быть приняты различные сварочные меры для предотвращения
это, включая выбор подходящего метода сварки в сочетании
с подходящей геометрией сварного шва и последовательностью сварки, сварка
подготовка и послесварочная обработка, и не в последнюю очередь квалификация
и опыт сварщика.
В вакуумной технологии применяется сварка вольфрамовым электродом в среде инертного газа (TIG).
довольно часто. Кроме того, другие виды дуговой сварки в среде защитных газов
используемые, а также специальные методы, такие как микроплазменная сварка для
тонкостенные компоненты или орбитальная сварка для трубных компонентов.
Значительно более сложными машинными процедурами являются лазерная сварка и
электронно-лучевая сварка. Оба подходят для деликатных компонентов и
для глубоких швов. Для сварки крупных алюминиевых корпусов клапанов, фрикционных
используется сварка с перемешиванием, которая представляет собой сложную машинную процедуру с низким
сварочные перекосы.
Сварка вольфрамовым электродом в среде инертного газа (TIG) не требует расходных материалов электрод, а соединительные детали могут быть сварены напрямую без каких-либо дополнительные материалы. При необходимости выполнения дополнительных сварных швов например, из соображений стабильности можно использовать сварочные материалы. Другими преимуществами этого метода являются практически полное отсутствие брызг, отсутствие шлака. форма и универсальность: нержавеющая сталь, алюминий, а также медь можно сваривать TIG. Метод TIG предпочтительнее, если сварка высокого качества желательна по отношению к скорости сварки.
Рисунок 3.4: Изображение поперечного сечения лазерной сварки
Лазерная сварка , или сокращенно лазерная сварка, характеризуется
за счет высокой скорости сварки и низкой термической деформации. Высота
концентрированный ввод энергии лазера приводит к узкой зоне сварки и
ограничивает диапазон зоны нагрева. Тонкие пленки, а также глубокие и
узкие сварные швы для несущих конструкций могут быть созданы путем установки
ширина фокуса и мощность лазера.Таким образом, компоненты камеры могут
могут быть выполнены без дополнительных сварных швов, или могут быть приварены фланцевые кольца.
быть приварены к концам труб методом глубокого провара без необходимости сложных
доработка геометрии уплотнительной поверхности. Большая ширина зазора на
суставы могут быть соединены в определенной степени. Используемые дополнительные материалы
здесь используются частично. Недостатком являются высокие инвестиционные затраты.
Рисунок 3.5: Изображение поперечного сечения орбитального сварного шва WIG
Орбитальная сварка представляет собой полностью механизированный процесс сварки в среде инертного газа.
что обеспечивает стабильно высокое качество шва, так как дуга свинцовая
механически и в контролируемых условиях вокруг труб или
круглый компонент. Стоимость системы выше, чем при сварке TIG. Ан
орбитальный сварочный ключ охватывает только ограниченный диапазон диаметров труб.
Для каждого наружного диаметра трубы также требуется устройство, подходящее для удерживания
труба.
При электронно-лучевой сварке ускоренных, сфокусированных электронов обеспечивают необходимую энергию в зоне сварки. Чтобы предотвратить рассеяние и поглощение электронов, процесс осуществляется в высоком вакууме. Это также позволяет сваривать высокореактивные материалы.Высокая стоимость системы и подготовка под сварку с возможно, необходимая конструкция оборудования, обычно это приводит к высоким цены на процедуру и в основном ограничивает ее применение сериями компоненты.
После сварки аустенитной нержавеющей стали металлически
гладкая поверхность должна снова присутствовать, поэтому ровный оксид хрома
пассивный слой может формироваться без перерывов. Например,
защита инертным газом (в том числе для основания корня) предотвращает образование накипи
поверхности при температурах выше 600°С. Механический или химический
отделка с последующим тщательным ополаскиванием удаляет изменение цвета на
поверхность и очищает компонент.
Ebflow — Cambridge Vacuum Engineering
Ebflow в 20-30 раз быстрее, чем обычная дуговая сварка, что обеспечивает радикальное повышение производительности.
Он также потребляет меньше энергии, чем обычные процессы дуговой сварки, что снижает выбросы углекислого газа.
Среди множества других преимуществ можно отметить возможность выполнения сварных швов с низким подводом тепла, что приводит к уменьшению деформации, обеспечивая качество, а также возможность проведения неразрушающего контроля сразу после сварки, ускорение производственного процесса и снижение затрат.Другие преимущества:
1. Снижение углеродного следа
Энергия, потребляемая на один метр сварного шва, при использовании Ebflow на 75 % меньше, чем при стандартной дуговой сварке под флюсом. В дополнение к этому есть:
- Снижение затрат на транспортировку и установку
- Нет необходимости в наполнителях, камере и сопутствующем насосном оборудовании
- Без предварительного нагрева
- Нет погрузочно-разгрузочных работ
2. Повышение производительности
Термическая обработка после сварки (PWHT) может создать сварной шов, металлургически неотличимый от основного материала, что позволяет использовать сварные компоненты вместо одной поковки. Ebflow также способствует повышению производительности, предоставляя:
- Более высокая скорость изготовления
- Возможность сварки на месте
- Скос сварного шва не требуется
- Возможность сварки объектов любого размера
- Предварительный нагрев не требуется
- Без погрузочно-разгрузочных работ
- Возможность немедленной проверки после сварки
- Сварка в один проход
3.Улучшенная эконом-класса
Энергия, потребляемая на один метр сварного шва, при использовании Ebflow на 75 % меньше, чем при стандартной дуговой сварке под флюсом (SAW). Кроме этого есть:
- Меньшие потребности в оборотном капитале
- Снижение расходов на персонал
- Без камеры и сопутствующего насосного оборудования
- Снижение транспортных расходов
- Отсутствие наполнителей – снижение затрат на расходные материалы
- Возможна меньшая занимаемая площадь
4. Высшее качество
Ebflow обеспечивает непрерывно воспроизводимые и точные высококачественные сварные швы с локализованными остаточными напряжениями. Сварной шов становится металлургически неотличимым от основного материала, а также имеет минимальную деформацию.
УСТК-1 АППАРАТ ДЛЯ РУЧНОЙ АРГОНОДУГОВОЙ СВАРКИ
Установка УСТК-1 предназначена для ручной аргонно-дуговой сварки наружных деталей отсеков из титановых сплавов.
Размеры и материалы сварных узлов:
материалы отсеков | ВТ20 |
диаметр отсеков, мм | 360 |
длина отсеков, мм | 600 |
толщина отсеков в зоне сварки, мм | 2,5 |
внешние детали макс.габариты, мм | 35х15х1,5 |
В состав сварочного аппарата УСТК-1 входят:
1. Вакуумная камера представляет собой горизонтальную сварную оболочку ствола со сварной коробкой, расположенной вдоль образующего луча на верхней стороне ствола
2. В камере есть отверстия для перчаток и осветители для наблюдения за процессом сварки.
3. Текущий вывод.
4. Рабочий стол.
5. Протектор для защиты глаз сварщика.
6. Контрольно-регулировочный блок для автоматического поддержания необходимого давления аргона внутри вакуумной камеры.
7. Освещение внутри камеры.
8. Текущая пусковая педаль.
9. Пульт управления сварочным током.
10. Вакуумная система, состоящая из предварительного и высоковакуумного насосов, трубопроводов и системы арматуры.
11. Вакуумметры.
12. Электрический шкаф
13. Электропроводка
14. Клапан предохранительный для регулировки давления аргона на входе.
15. Станция контрольно-измерительных приборов для контроля состава атмосферы в рабочей зоне вакуумной камеры
(концентрация Н2О и О2).
16. Горелки сварочные.
17. Коллектор заправки аргоном.
18. Пневматические (гидравлические) зажимы крышки.
19. Механические зажимы крышки.
20. Тип источника ГЕНЕЗИС-400.
21. Ресивер для экономии защитного газа.
22. Камера закреплена неподвижно и не перемещается при сборке деталей.
23. Одна крышка камеры фиксируется наглухо (не снимая).
24. Вторая крышка сдвижная (для загрузки и выгрузки деталей).
25. Охлаждение автономным охладителем (чиллером).
покрытий | Бесплатный полнотекстовый | Термоэлектронная вакуумная дуга — универсальная технология для нанесения тонких пленок и ее применение
1. Введение
Вакуумная дуга обычно рассматривается как сильноточный низковольтный электрический разряд, который создает плазму, состоящую из испаренного и ионизированного материала электрода.В [1] дуга определяется как «разряд в газе или паре, имеющий падение напряжения на катоде порядка минимального ионизирующего или минимального возбуждающего потенциала газа или пара».
Целью этого обзора является представление универсального метода нанофабрикации на основе плазмы, называемой термоэлектронной вакуумной дугой (ТВА). Он состоит из катода с внешним нагревом, окруженного цилиндром Венельта, который концентрирует ускоренные электроны высокого напряжения на материале анода.За счет мощности электронного луча происходит непрерывное испарение материала анода и обеспечивается его плотность паров в установившемся режиме. При достижении определенной плотности паров подаваемое высокое напряжение зажигает и поддерживает яркий разряд в межэлектродном пространстве. Газ, поддерживающий разряд, представляет собой испаряющиеся атомы в вакууме, поэтому напыление тонкой пленки производится в условиях высокой чистоты.
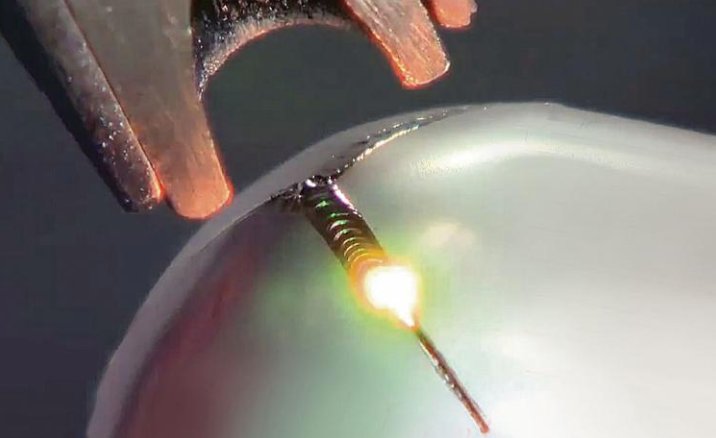




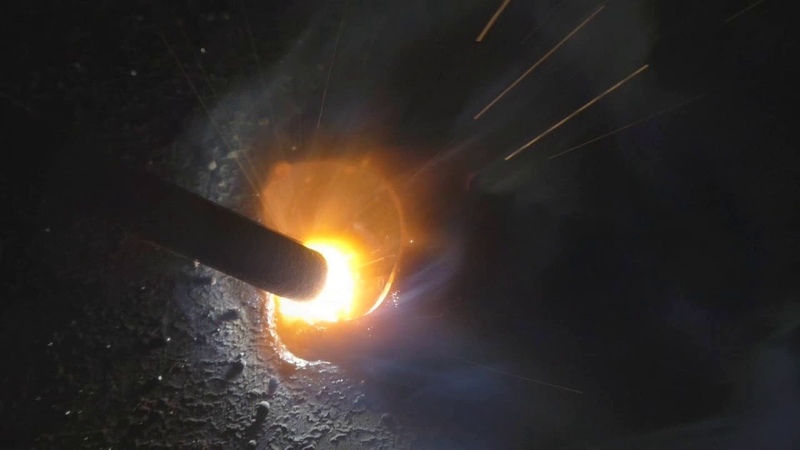


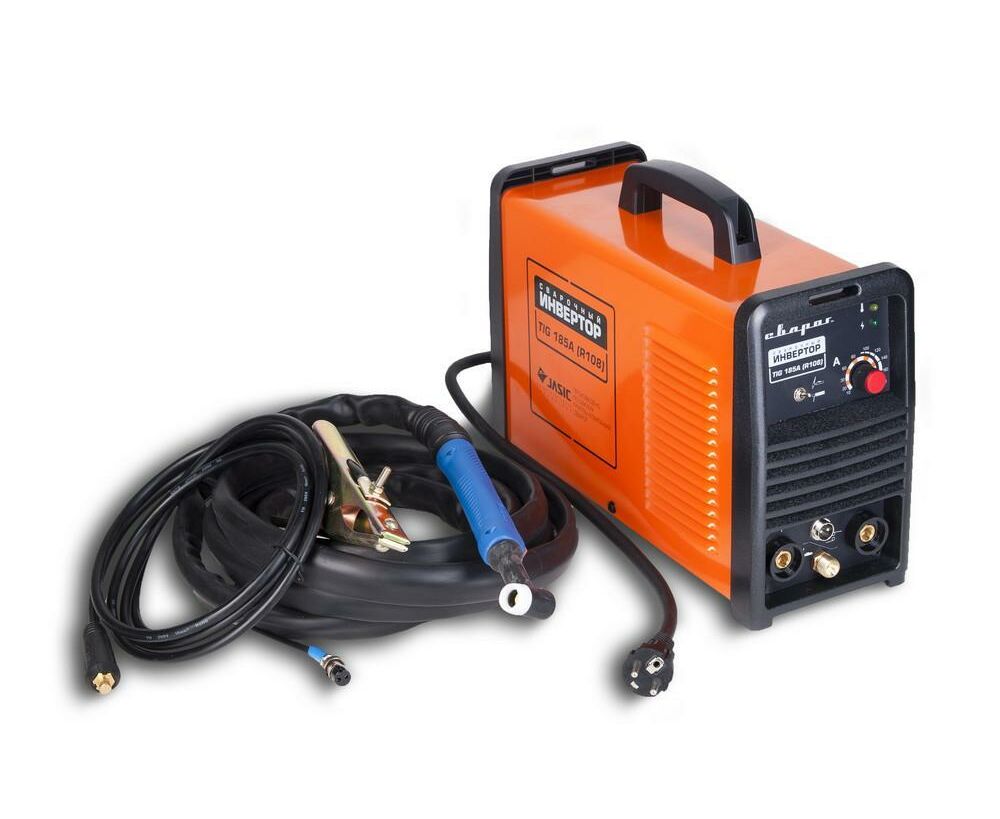
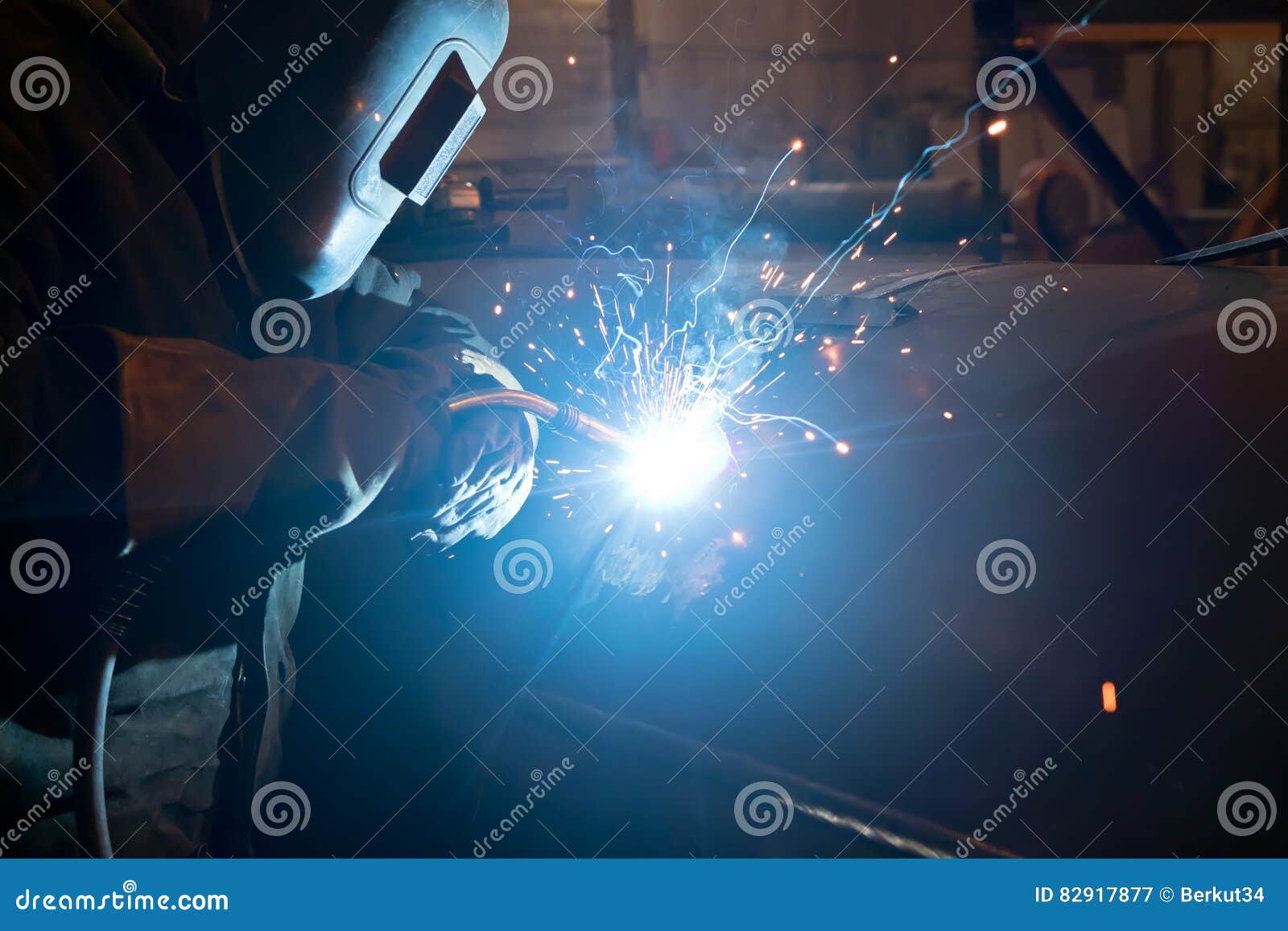
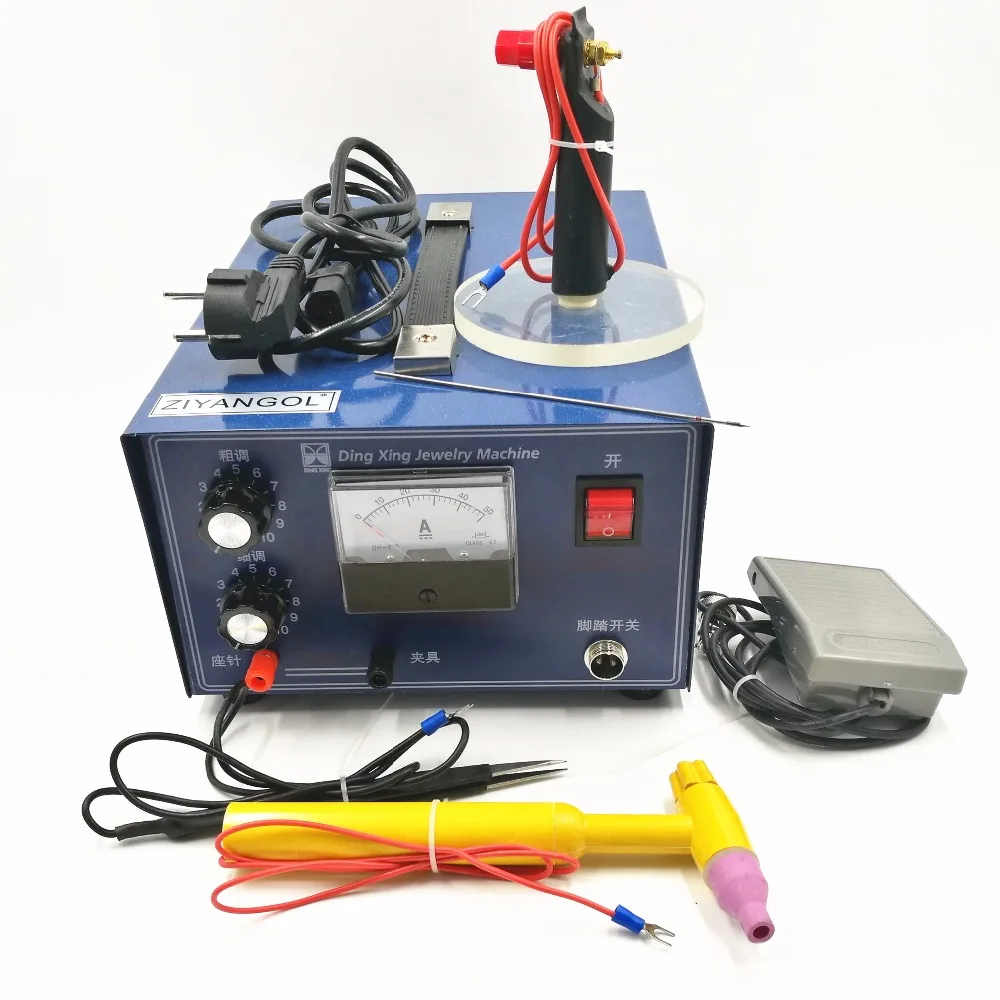
Технология TVA изучена и успешно используется для синтеза большого количества металлов, оксидов и углерода. Это подтверждается опубликованными документами, патентами и проектами, финансируемыми на международном уровне. В настоящее время метод TVA был усовершенствован до доступного, универсального и надежного метода обработки нескольких материалов, таких как тонкие пленки из сплава / композита, в нанометрическом масштабе для широкого спектра применений.
4. Применение системы осаждения TVA
За более чем 25 лет с момента изобретения системы TVA исследователи приложили усилия, чтобы использовать все ее преимущества для эффективной разработки новых материалов. Спектр приложений TVA очень широк; они охватывают новые механические свойства (твердые покрытия, покрытия с низким коэффициентом трения), области применения, связанные с термоядерным синтезом (покрытия Be и W), биомедицинские применения (покрытия DLC и т. д.), термобарьерные покрытия, материалы для оптоэлектроники (CuO, TiO 2 , ZnO , и т.д.), материалы для микроэлектроники, материалы для твердотельных аккумуляторов и материалы, обладающие гигантскими магниторезистивными (ГМС) свойствами; см. рис. 23. Мы попытались представить эту часть нашего обзора как обзор, который мы организуем в группы в соответствии с соответствующим применением новых материалов. Однако во многих случаях нельзя сказать, что тот или иной материал можно использовать только для одной практической цели. Существует много примеров материалов, полезных для оптоэлектроники, а также для микроэлектроники, для биомедицинских применений и/или материалов с низким коэффициентом трения, для термоядерных применений, а также для твердых или коррозионно-стойких покрытий.Поэтому мы хотели бы попросить читателя быть щедрым, находя тот или иной материал в одной главе, а не в другой.
Для проверки/оценки свойств тонких пленок, таких как их структура, шероховатость, состав, проводимость, твердость, коэффициент трения, биосовместимость и другие, использовалось множество различных методов анализа поверхности. К ним относятся оптический микроскоп, трансмиссионный электронный микроскоп (ПЭМ), сканирующий трансмиссионный электронный микроскоп (STEM), сканирующий электронный микроскоп (SEM), метод сфокусированного ионного пучка (FIB), сканирующий туннельный микроскоп (STM), сканирующий электронный микроскоп с полевой эмиссией (FESEM). ), рентгеновские оже-электронные спектры C KLL (XAES), атомно-силовая микроскопия (АСМ), энергодисперсионная рентгеновская спектроскопия (EDX), рентгеновская спектроскопия с дисперсией по длине волны (WDS), рентгеновская фотоэлектронная спектроскопия (XPS) , Спектрометрия обратного рассеяния Резерфорда (RBS), Резонансный анализ ядерных реакций (RNRA), Рентгеноструктурный анализ (XRD), Дифракция электронов на выбранных участках (SAED), Инфракрасная спектроскопия с преобразованием Фурье, Рамановская спектроскопия, эллипсометрия, наноиндентирование, измерение удельного сопротивления, износ измерения сопротивления и коррозионной стойкости и др. Мы предполагаем, что читатель знаком с принципами этих методов и информацией, которую эти методы дают о тестируемом слое.
4.1. Материалы с новыми механическими свойствами
Более ранние работы по осаждению тонких пленок методом ТВА, представленные, например, в [32, 50, 72], выполнялись при достаточно малой мощности в разряде ТВА (анодное напряжение несколько сотен вольт, разрядный ток десятки мА). ). Таким образом, выбор материалов для осаждения с помощью TVA был ограничен материалами с довольно низкой температурой плавления.Тем не менее были созданы слои с привлекательными свойствами: слой Cu в [32, 33], идея металлизации пластиковых поверхностей медными пленками в [72], пленка MgO в [50, 89] и т. д. Новая эра для применения ТВА начинали с нанесения слоев, содержащих углерод; первой статьей, описывающей углеродную пленку, нанесенную ТВА, является [90]. При направленной энергии энергии ионов углерода, достигающих подложки порядка 500 эВ, на подложках NaCl или KCl создавалась наноструктурированная углеродная пленка.
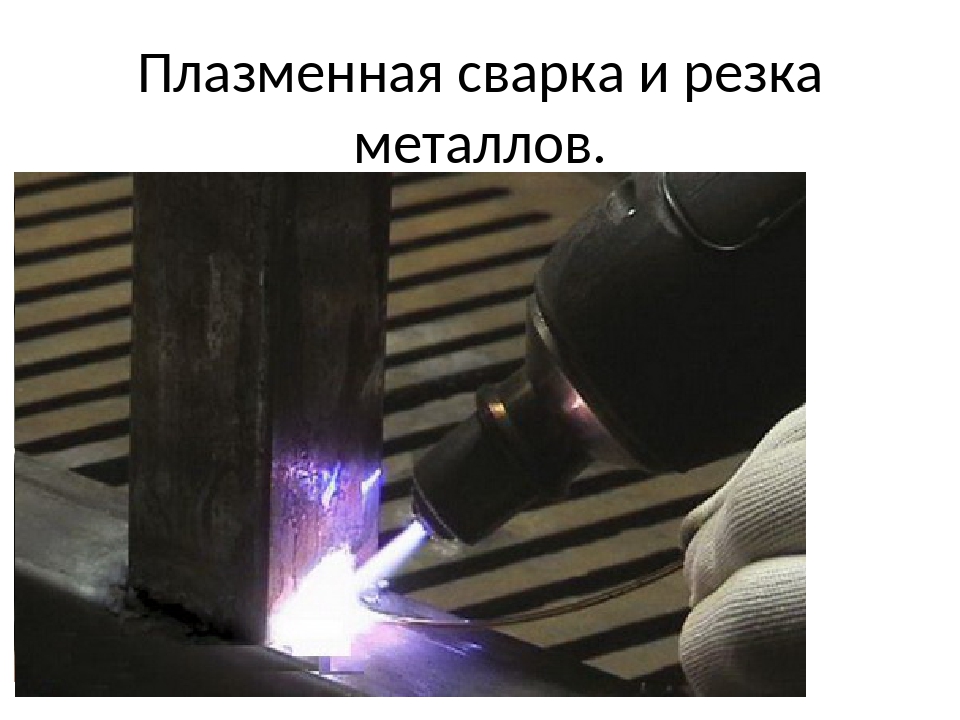
4.2. Покрытия с низким коэффициентом трения
Нанокомпозиты углерод-металл .В работе [93] сообщается о покрытии с низким коэффициентом трения, состоящем из углерода, внедренного в серебряную матрицу с помощью TVA. В результате коэффициент трения бронзовой подложки снизился с ~0,8 до ~0,35. Аналогичные трибологические свойства пленок Ag-DLC описаны в [94]. Осаждены и исследованы нанокомпозитные тонкие пленки серебро/аморфный углерод, Ag/a-C на Si, стекле и нержавеющей стали OLC45 [95]. Авторы использовали единую систему электронной пушки, и оба материала C и Ag были помещены в виде зерен в один вольфрамовый тигель.Мягкий металл, включенный в пленку, может действовать как твердая смазка, кроме того, серебросодержащие слои обладают антибактериальными свойствами. Авторы обнаружили существенные различия в структуре пленок, обусловленные природой подложки: они получили поликристаллическую пленку и кубическую CFC Ag (CFC — Cubic Face Centered) с размерами зерен 16 нм (на стали) и 23 нм (на подложке Si).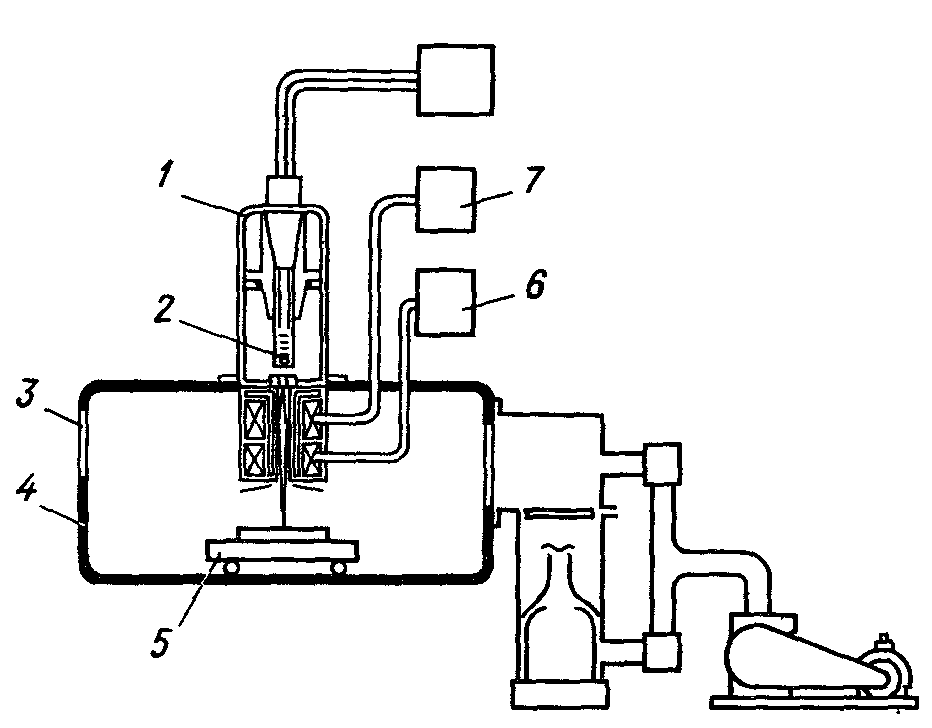
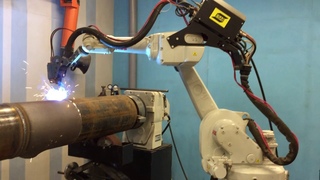
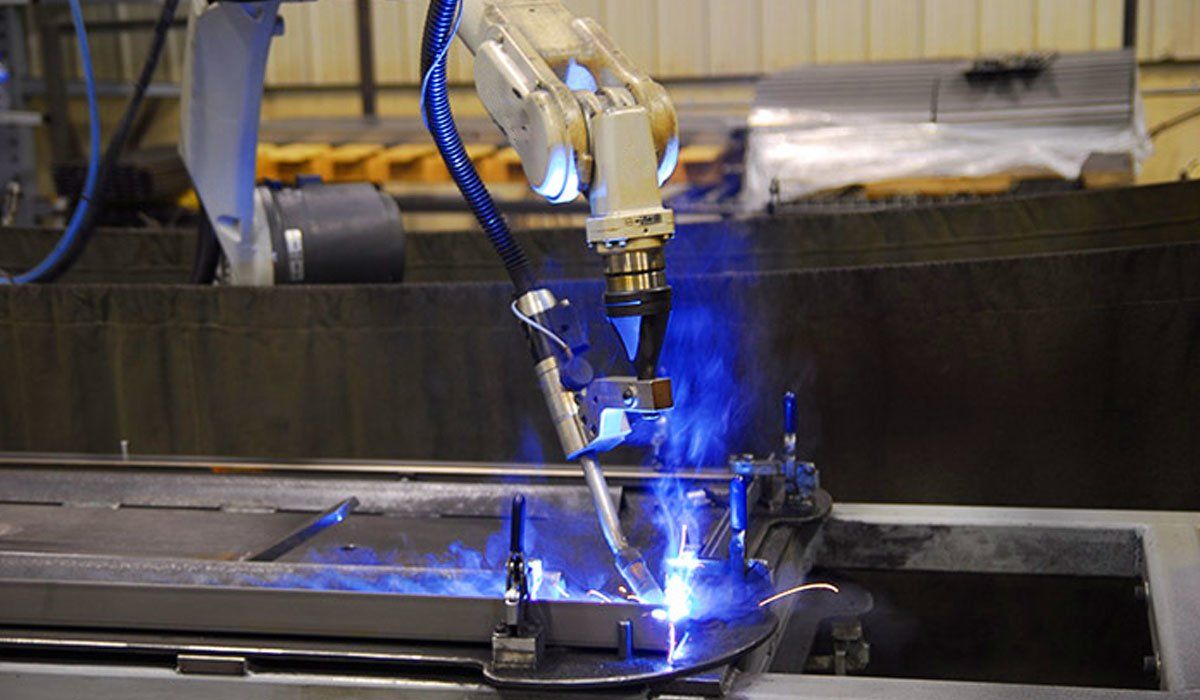

4.3. Твердые и стойкие к окислению покрытия
4.3.1. Выдающиеся свойства осажденных тонких пленок DLC
Наилучшие свойства технологии TVA проявляются при осаждении слоев материалов, которые было трудно или невозможно получить с помощью других методов осаждения. Первый вывод заключался в том, что технология TVA подходит для высококачественного гладкого, чистого и компактного DLC и осаждения углеродной пленки без водорода [90]. Благодаря своей электронной пушке TVA обеспечивает необходимое высокое значение энергии, необходимой для испарения/сублимации чистого углерода.Кроме того, можно контролировать потенциал плазмы TVA, а значит, и энергию ионов, падающих на подложку. С целью увеличения срока службы подшипников пленки DLC наносились на подложки из бронзы, железа и подшипниковой стали [107]. Достигнутая твердость пленок DLC составляла от 50 до 60 ГПа. Коэффициент трения пленки находился в диапазоне 0,05–0,1, что почти в 10 раз ниже, чем у материалов подложки.

4.3.2. Анализ поверхности и границы раздела
Оценка поверхностной энергии тонкой пленки алмазоподобного углерода, не содержащей водорода, нанесенной методом TVA на различные поверхности (цинковая и алюминиевая фольга, нержавеющая сталь, стекло), была проведена в [113].Это исследование показало, что свободная энергия поверхности и смачиваемость осажденной негидрированной пленки DLC сильно зависят от расстояния между образцами и точки зажигания разряда. ПЭМ-анализ и электрические измерения тонких углеродных пленок на стеклянных и кремниевых подложках, созданных с помощью TVA, можно найти в [114]. Для получения информации использовались следующие методы: просвечивающая электронная микроскопия в светлом поле (BF-TEM), просвечивающая электронная микроскопия в темном поле (DF-TEM), просвечивающая электронная микроскопия высокого разрешения (HRTEM), электронная дифракция в выбранной области (SAED) и функция радиального распределения.
4.3.3. Огнеупорные материалы и суперсплавы
TVA можно использовать и для нанесения вольфрама на графитовые подложки [115]. Измерения АСМ подтвердили гладкость осажденных пленок с шероховатостью от пика до впадины в диапазоне 20–30 нм. В исх. [116], попытка осаждения рения (Re) в составе так называемых жаропрочных сплавов на основе никеля, т.е.г., Re–Cr–Ni. Температура плавления Re 3450 К, температура кипения 5903 К. Авторы исследовали проблему осаждения Re, связанную с взаимодействием атомов Re с горячей нитью накала электронной пушки. Поскольку работа выхода Re (5,1 эВ) больше, чем у вольфрама (4,5 эВ), и даже больше, чем у обычно используемого торированного вольфрама (4 эВ), Re, нанесенный на горячую нить, со временем осаждения уменьшал мощность электронной пушки и, следовательно, процесс осаждения. Авторы окончательно решили проблему, увеличив ток накала до 120 А.
4.3.

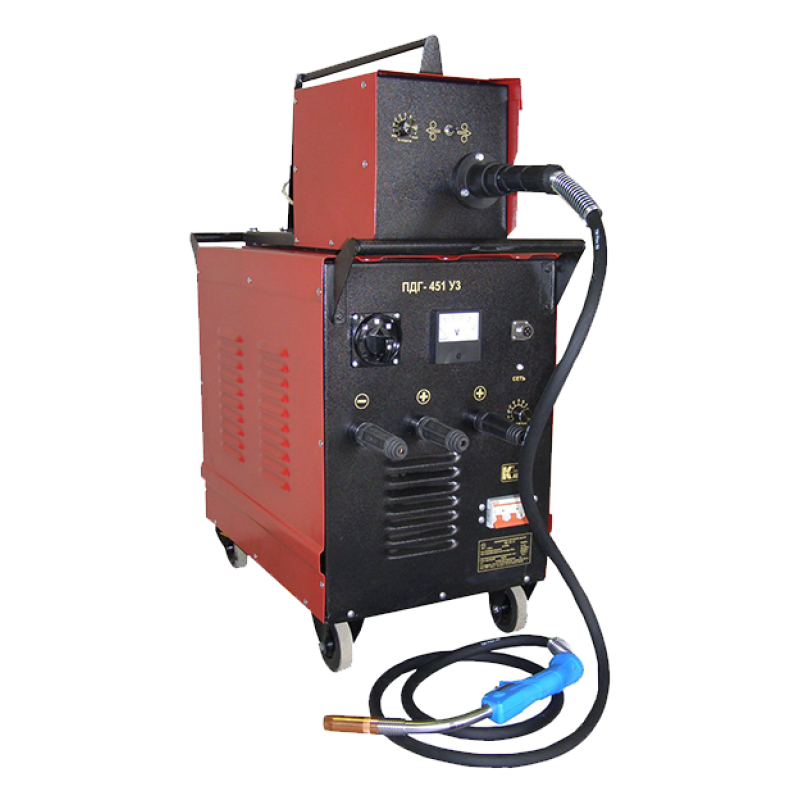
4.3.5. Адгезия к подложке
Одной из проблем при разработке новых технологий производства углеродных пленок является плохая адгезия к подложке из-за остаточных напряжений при осаждении.Адгезия углеродных пленок может быть увеличена путем одновременного осаждения углерода и нескольких металлов: Fe, Cr, Al и Ni [48].

4.3.6. Адаптация структуры алмазоподобного углерода
Попытка повлиять на содержание sp 3 в пленках алмазоподобного углерода, осажденных с помощью TVA, раскрыта в [54]. Установлено, что существенными являются следующие параметры ТВА: ток накала катода электронной пушки, ток дуги, приложенное напряжение и расстояние от анода до подложки. Авторы добились соотношения sp 3 :sp 2 от 20 до 50% в зависимости от условий разряда TVA.Применение алмазоподобных пленок в качестве наноабразивов представлено в [87]. При этом была обнаружена прямая зависимость размера зерен нанокристаллитов, внедренных в аморфную структуру, с расстоянием подложки от анода. Это показало способность метода TVA синтезировать DLC-пленки с контролируемой наноразмерной шероховатостью и содержанием sp 3 . Ссылка [131] предлагает для оценки содержания sp 3 так называемый метод D-value.
4.4. Материалы для микроэлектроники/оптоэлектроники
Универсальность технологии TVA нашла свое отражение в многочисленных приложениях для оптоэлектроники и микроэлектроники.Даже если в некоторых случаях указанные ниже материалы можно создать другими методами, TVA использует его чистоту, отсутствие капель и простоту регулировки энергии ионов, образующих тонкую пленку.
4.4.1. Материалы на основе магния
Покрытия, содержащие магний, представляют интерес как для опто-, так и для микроэлектроники. Например, MgO осаждались TVA непосредственно из гранул MgO (температура плавления MgO 2852 °C), с прозрачностью пленки >94,5% и показателем преломления 1.73; значения, значительно отличающиеся от значений, соответствующих объемному материалу [50]. Пленки чистого магния осаждали и исследовали толщиной около 200 нм на стеклянную подложку [132]. Пленки оказались поликристаллическими с преимущественной ориентацией (0 0 2). Ссылка В работе [133] исследованы мультислои MgO/Co на стеклянных и латунных подложках.
4.4.2. Тонкие пленки, нанесенные в качестве диэлектриков
TVA также подходит для создания диэлектрических пленок. В исх. [136] из композита Ag-Al 2 O 3 был создан конденсатор емкостью 2–4 пФ.
4.4.3. Deposition for Solar-Cell Technology
В нескольких работах также показана полезность метода TVA в технологии солнечных элементов. Ссылка [139] получили тройное соединение CuInSe (CIS) методом электроосаждения на пластиковых подложках, покрытых никелем, с использованием метода TVA. CIS имеет потенциальное применение в качестве поглотительного материала для тонкопленочных солнечных элементов. Исследовался пентаоксид тантала на кремниевых подложках для применения в качестве просветляющих или высокоотражающих пленочных зеркал для солнечных элементов, для двулучепреломляющих покрытий или в качестве компонента многослойных интерференционных фильтров в оптических устройствах [140].
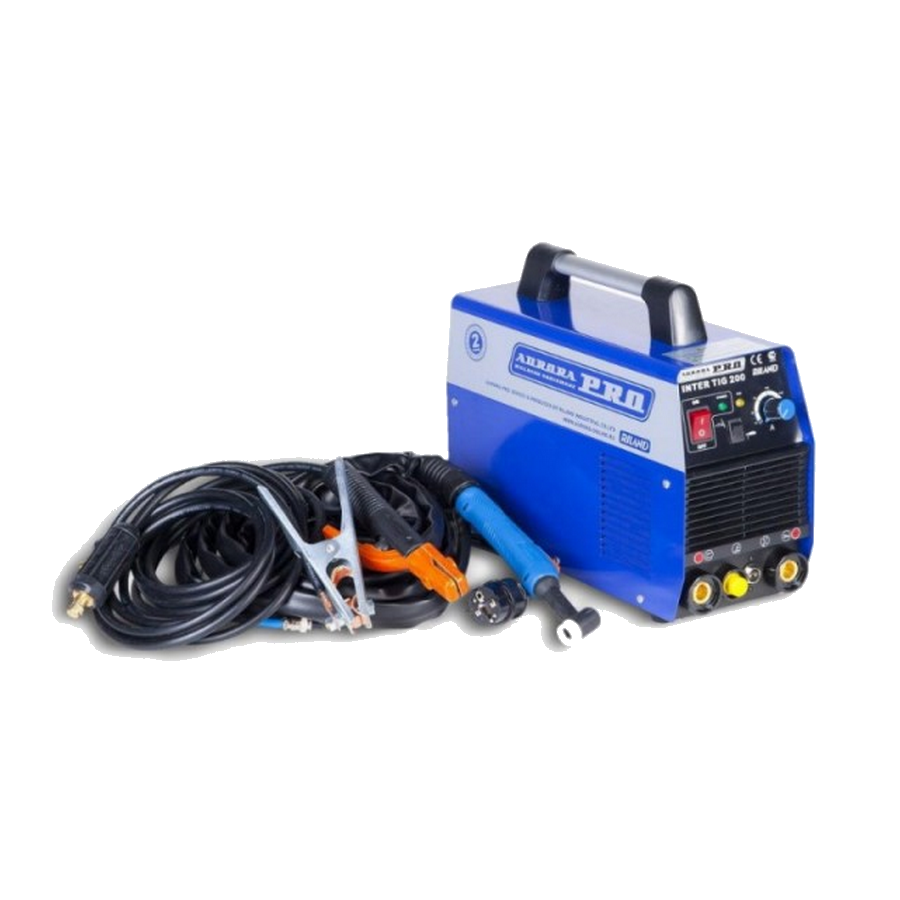
4.4.4. Осаждение тонкой пленки на специальные подложки
В системе TVA подложки могут располагаться сравнительно далеко от расплавленного материала анода. Следовательно, возможно осаждение на термопластичные подложки; обычно в сочетании с напылением на стандартную стеклянную или кремниевую подложку.покрытие прозрачных подложек из полиэтилентерефталата (ПЭТФ) SiO 2 и ZrO 2 , проведенное в [147]. Поскольку в системе TVA нет фонового газа, оба оксида могут быть нанесены «как есть». Это означает, что оксид как материал в тигле просто плавится, без опасности изменить свой химический состав, например, из-за кислорода, оставшегося в разрядном сосуде.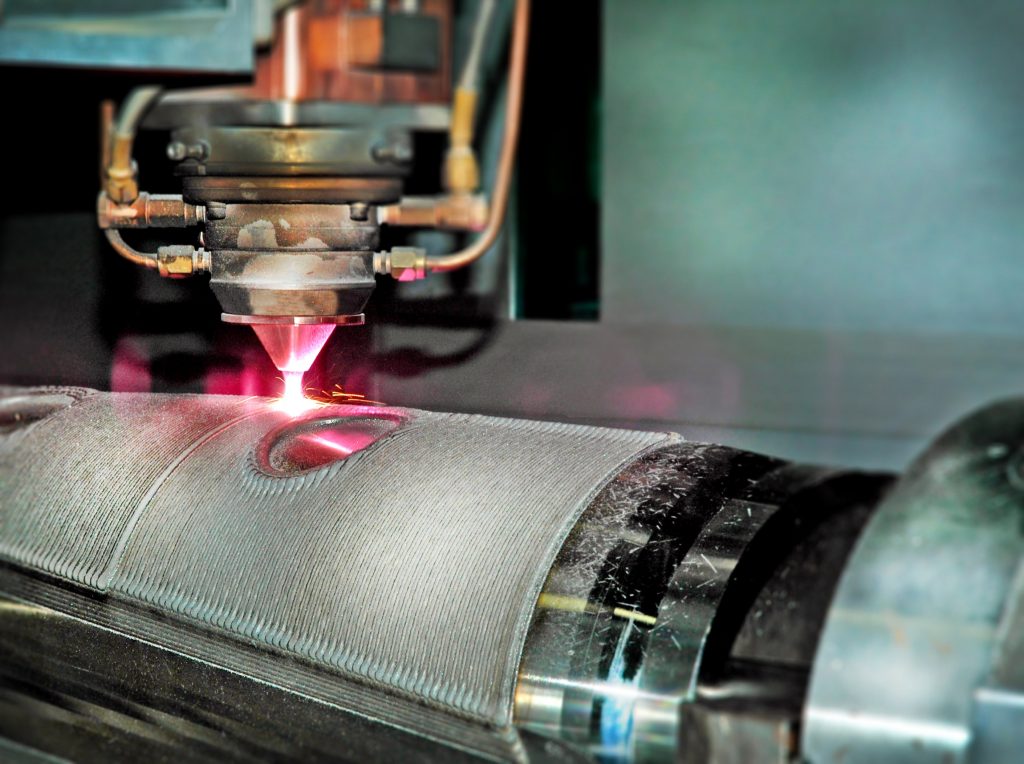
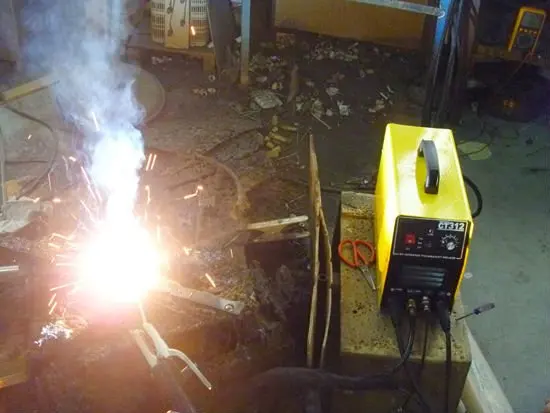
4.4.5. Материалы на основе галлия
В работе [152] монокристаллические слои арсенида галлия (GaAs) микронной толщины на стеклянные и ПЭТ-подложки наносились методом ТВА в течение двух минут. Полупроводник GaAs, возможно, наиболее известен благодаря его применению в диодах Ганна, используемых для выработки микроволновой энергии в радарах, однако также важны его дальнейшие применения в ИК-светодиодах, лазерных диодах, солнечных элементах и оптических окнах.

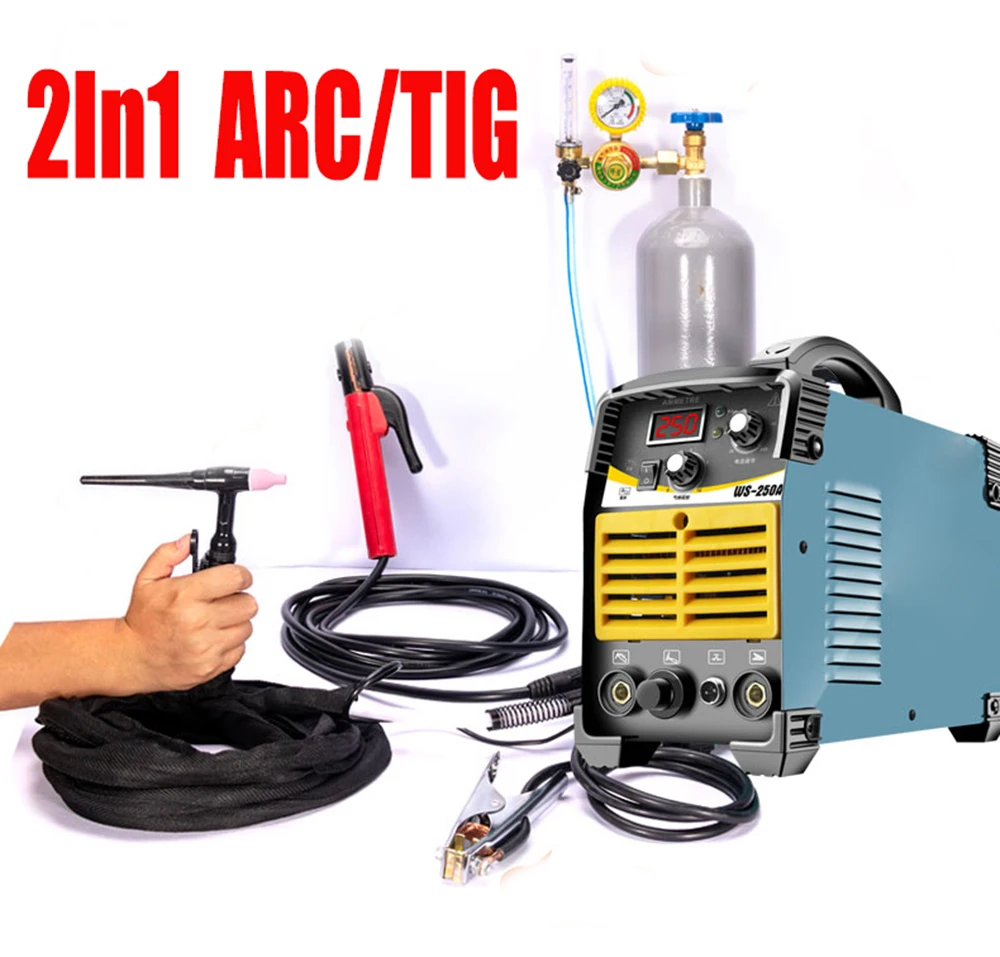

4.4.6. Deposition of the Semiconductors
Пожалуй, самая большая группа приложений TVA в опто- и микроэлектронике касается полупроводниковой техники. [181] покрыли кремниевые и стеклянные подложки сульфидом цинка (ZnS).ZnS представляет собой бинарный составной полупроводник, важный для исследований в области фотоники и оптоэлектроники. Опять же, ZnS наносился непосредственно из купленного материала, помещенного в вольфрамовый тигель. Показатель преломления слоя ZnS толщиной 167 нм был оценен как 2,05, а ширина запрещенной зоны 3,7 эВ. Аналогичный эксперимент, но с нанесением бинарного полупроводника ZnSe на подложку Si, был проведен в [182].


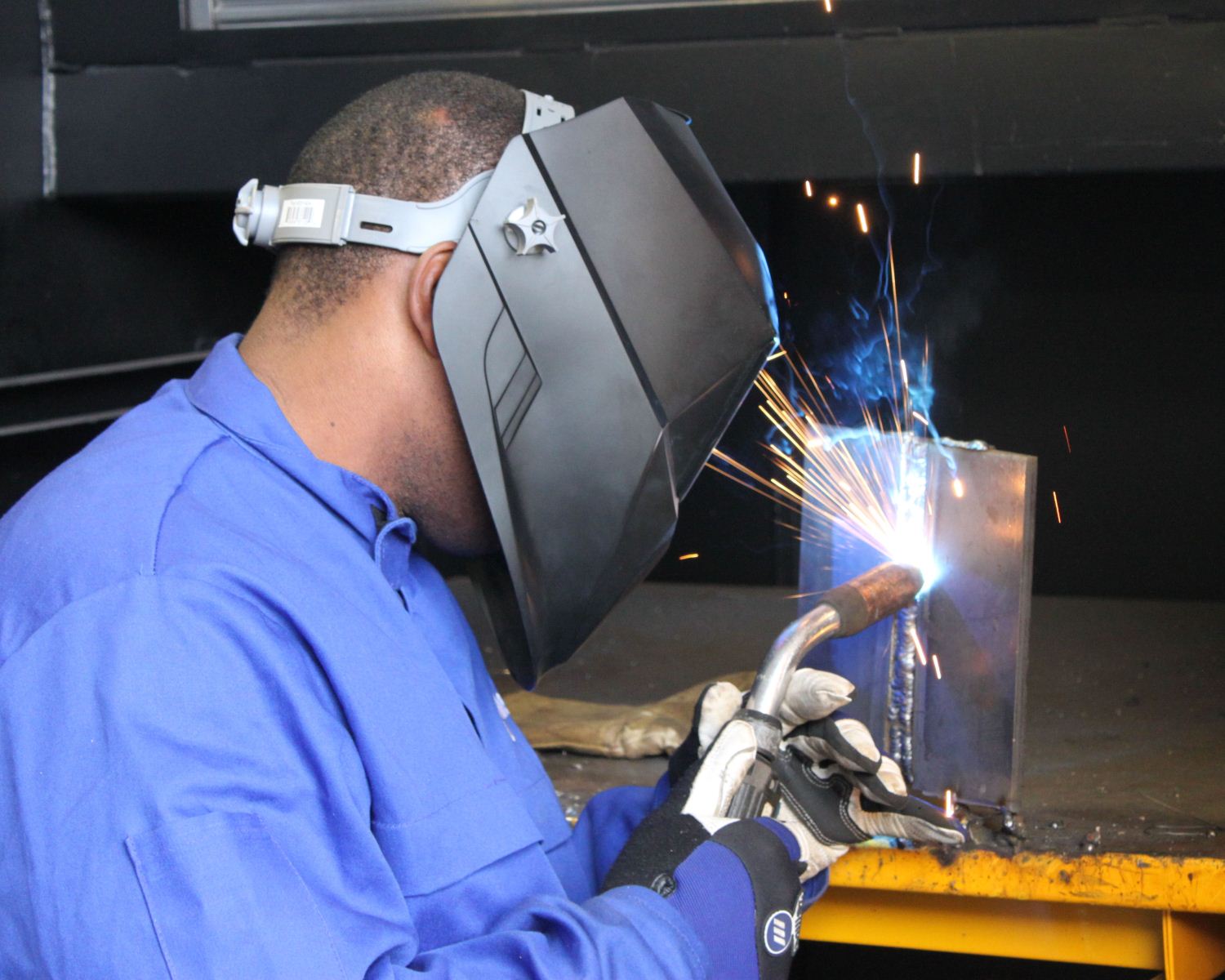

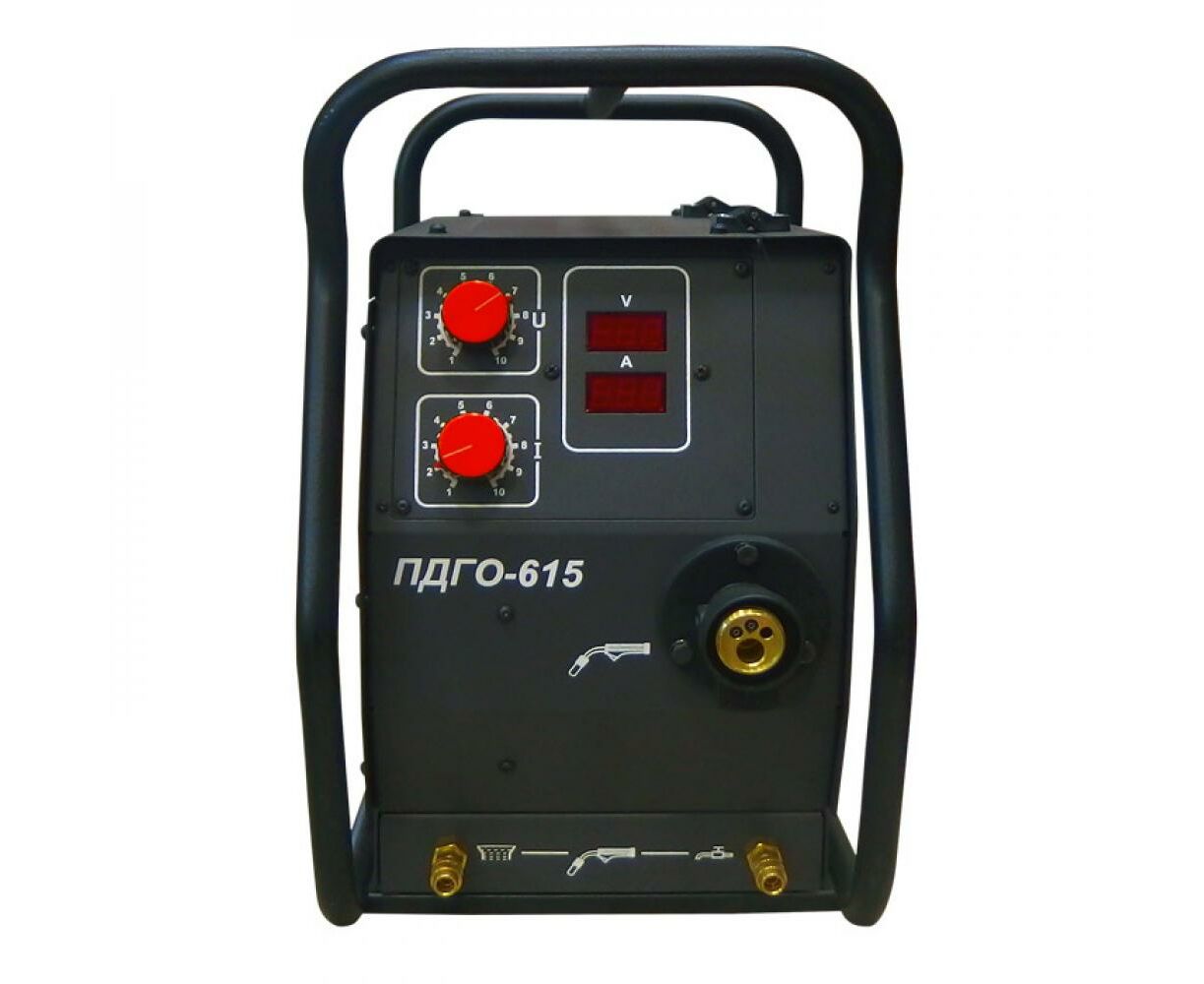

4.4.7. Осаждение диоксида титана
Еще одним материалом, представляющим интерес для микро- и оптоэлектроники, является диоксид титана, TiO 2 .Его применения в виде тонкой пленки охватывают катализ, газовые датчики, солнечные элементы, оптические фильтры и т. д. Авторы исх. [198] изготовили пленки TiO 2 методом TVA на стеклянных подложках, покрытых оксидом индия-олова (ITO) и оксидом фтор-олова (FTO). Установлено, что осажденные пленки находятся в кристаллических фазах анатаза и рутила. Исследованы электрохромные свойства пленок TiO 2 и проведено сравнение результатов с литературными данными. Были получены тонкие пленки прозрачного диоксида титана (TiO 2 ) на предметном стекле и на подложке из ПЭТФ [199].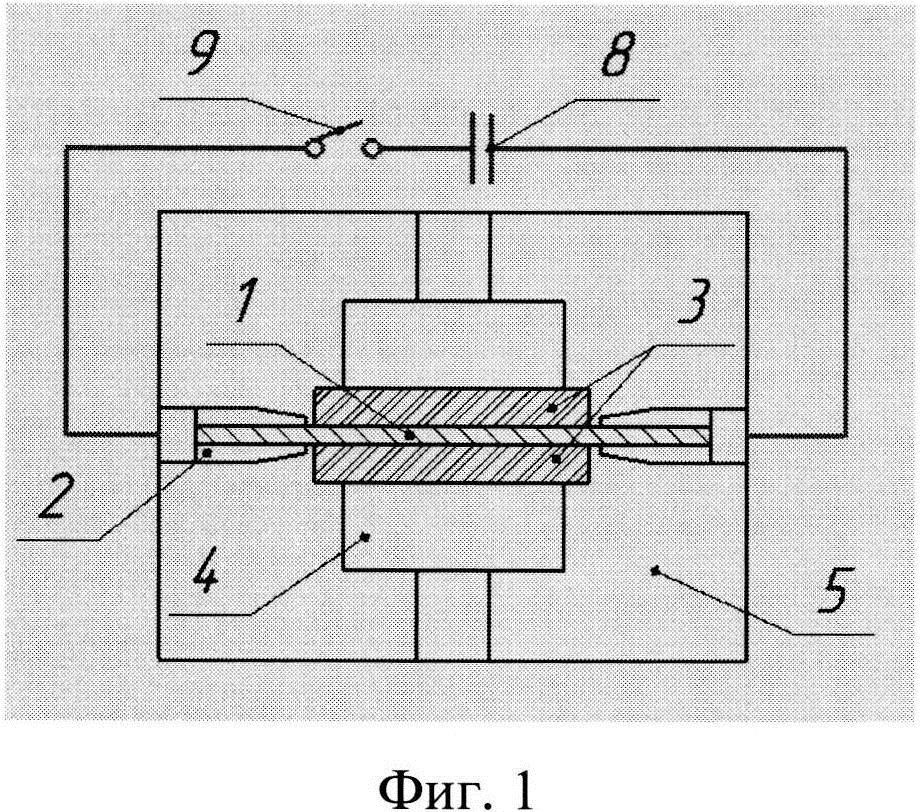
4.5. Бериллий и вольфрам — материалы, относящиеся к термоядерному синтезу
4.5.1. Роль метода TVA в покрытиях Be для термоядерного синтеза
Первым шагом в процессе исследований и разработок цельнометаллической стенки токамака JET, подобной ИТЭР, был поиск и оценка подходящего метода покрытия так называемых маркерных плиток путем бериллий.Первая попытка использовать технику TVA для этой цели описана в [200] как совместная работа Румынии, Швеции и Великобритании. Чтобы можно было контролировать эрозию Be от ограничителей токамака, свойства маркерной пленки должны были точно соответствовать свойствам объемного Be. Пленка была нанесена на так называемую металлическую промежуточную прослойку с высоким Z, которую необходимо было сначала нанести на маркерную плитку.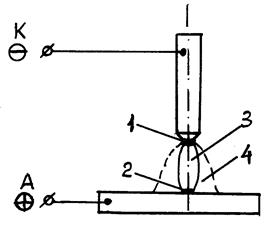



4.5.2. Смешанные слои, связанные с термоядерным синтезом
В большинстве работ, посвященных материалам, связанным с термоядерным синтезом, Be и W изучаются отдельно. В качестве альтернативы, в [210] были охарактеризованы углерод-вольфрамовые и углерод-бериллиевые наноструктурные пленки для потенциального применения в диверторных покрытиях методами SEM, TEM и AFM.Пленки были износостойкими с достаточно низким коэффициентом трения 0,15–0,35. Аналогичное исследование, включающее построение двойной системы ТВА для одновременного последовательного осаждения углеродного и вольфрамового слоев, было выполнено в работах [211, 212].

4.5.3. Углерод-металлические нанокомпозиты для термоядерных применений
Важную группу материалов, связанных с термоядерным синтезом, образуют нанокомпозиты углерод-металл.
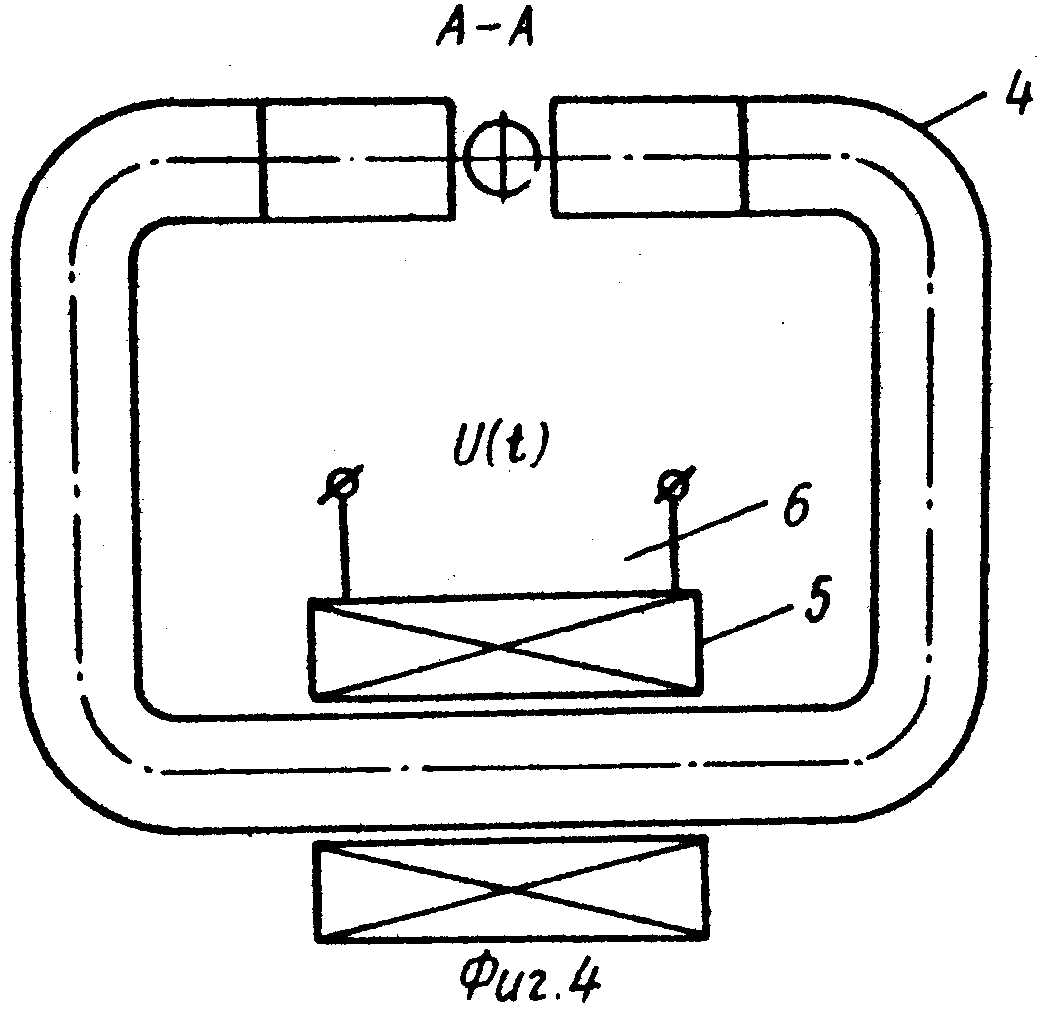
4.6. Материалы, обладающие свойствами ГМС/ТМС
Гигантское магнитосопротивление (ГМС) или туннельное магнитосопротивление (ТМС) представляет собой квантово-механический эффект, возникающий в тонкопленочных структурах, состоящих либо из чередующихся ферромагнитных и немагнитных слоев, либо в слоях зернистого типа, где трехмерный магнитный металлический кластер равномерно распределены внутри изолирующей матрицы.Эффект проявляется как изменение электрического сопротивления в присутствии магнитного поля.
Многослойные слои со свойствами GMR/TMR . Оба типа структур GMR/TMR, как в виде сэндвича, так и в виде гранул, могут быть сравнительно легко изготовлены TVA с использованием устройства с двумя электронными пушками и двумя (или более) тиглями с соответствующими материалами.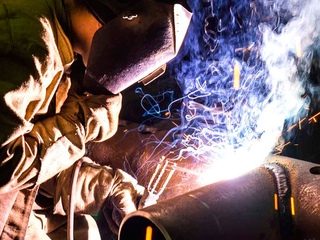

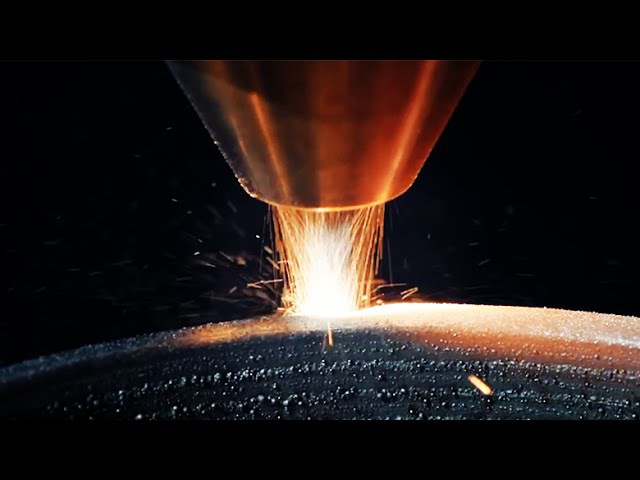
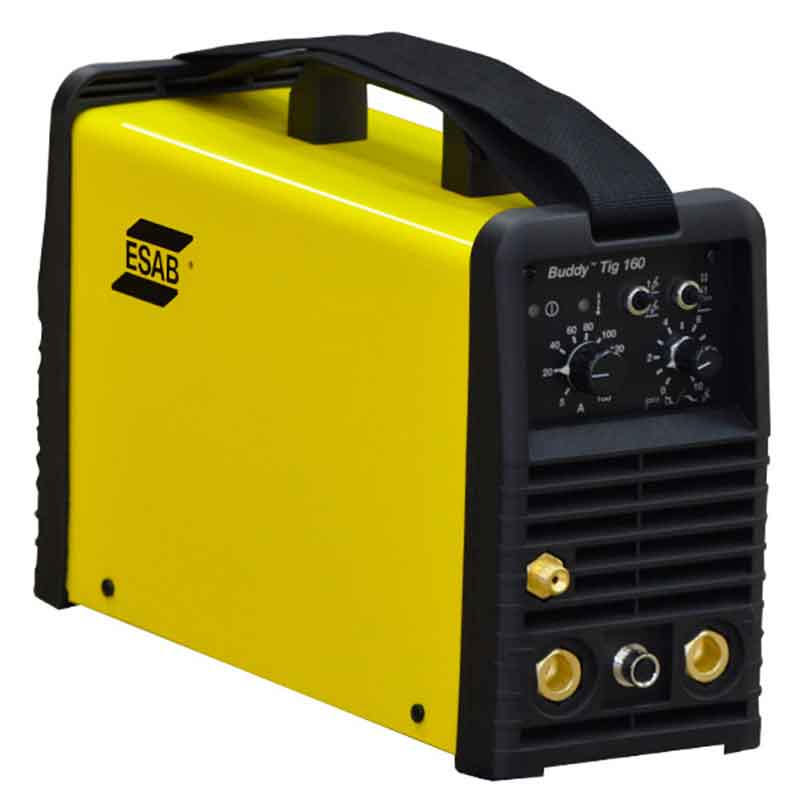

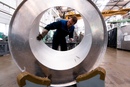
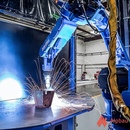


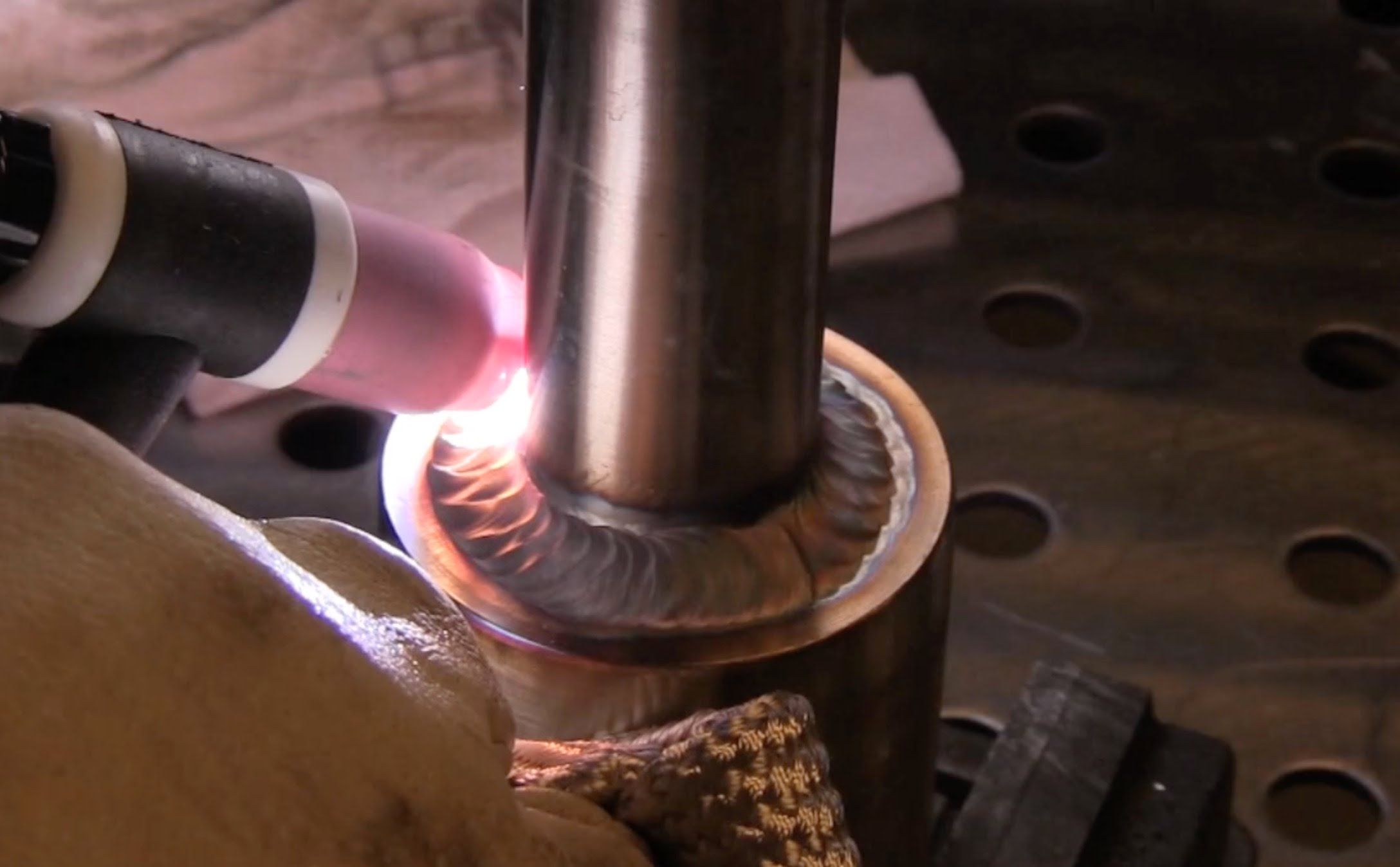
4.7. Материалы для биомедицинских применений
Многие из уже упомянутых материалов, например материалы с низким коэффициентом трения, нашли применение в биомедицине. Например, они могут служить покрытиями на тазобедренных суставах, стентами или зубными имплантатами. Однако материалы, используемые в этой области, также должны быть биосовместимыми, нетоксичными и не вызывать аллергических реакций.Они должны быть гибкими и прочными, иметь высокую прочность на растяжение, предельную прочность, низкую плотность и низкий модуль упругости.
4.7.1. Зубные имплантаты
Авторы [233] изучили материалы, подходящие для зубных имплантатов, и сравнили материалы с DLC-покрытием с материалами без покрытия.

4.7.2. Имплантируемые медицинские устройства
Хорошо известно, что устройства, содержащие нанокристаллическое серебро и платину, могут обеспечивать улучшенные противомикробные и противовоспалительные свойства имплантируемых медицинских устройств.Поэтому металлсодержащий аморфный углерод (а-С:Ме) и тетраэдрический (алмазоподобный) аморфный углерод (та-С:Ме) изучались в [235]. Использовалась двойная система TVA с двумя электронными пушками и двумя источниками материала: углеродным стержнем диаметром 10 мм и длиной 150 мм и тиглем TiB 2 , содержащим серебро. В качестве подложек стальные полированные диски и диски из оптического стекла БК7; использовались оба диаметром 25 мм. Диагностика поверхности пленок толщиной 2 мкм выявила кубическую кристаллическую фазу Ag в слое со средним размером кристаллитов 15–19 нм.
4.7.3. Биомедицинские покрытия
В то время как для твердых покрытий предпочтительны углеродные пленки, не содержащие водорода, для биомедицинских применений больше подходят пленки a-C:H. Было доказано, что гидрогенизированные углеродные пленки очень полезны для биомедицинских покрытий (тазобедренных суставов, стентов, приводов и т. д.) и биосенсоров, они антикоррозийны и химически стабильны. Однако плотность и твердость этих пленок ниже, чем у безводородных углеродных пленок; именно поэтому они включены в категорию так называемых мягких пленок.Количество водорода в пленке лучше всего контролировать с помощью G-TVA для осаждения пленки. Тонкие пленки a-C:H с точными характеристиками в нанометрическом масштабе представляют собой работу [51]. Гладкие пленки a-C:H без точечных отверстий были нанесены с помощью G-TVA и описаны в [60]. Пленки показали хорошую вязкость разрушения, износостойкость и хорошую адгезию к кремниевым и углеродным подложкам.
4.7.4. Антибактериальные материалы
Ионы металлов являются антибактериальными материалами.Антибактериальные эффекты ионов металлов связаны с их энергией ионизации и номером группы в периодической таблице. Атомы с меньшей энергией ионизации могут оказывать более сильное антибактериальное действие; чем выше номер группы, тем ниже антибактериальный эффект. Антибактериальные свойства нанослоистых пленок Au, Ag и Al, нанесенных методом ТВА на гибкие органические подложки, изучались в работе [236]. Антибактериальные свойства покрытий исследовали с использованием бактерий Escherichia coli (ATCC 25922).Время контакта составляло 3 часа, а антибактериальные свойства определяли через 24 часа. Авторы утверждают, что антибактериальные эффекты ионов металлов связаны с их энергией ионизации и номером группы в периодической таблице. Атомы с меньшей энергией ионизации обладают более сильным антибактериальным действием; атом в более высокой группе обладают более слабым антибактериальным эффектом.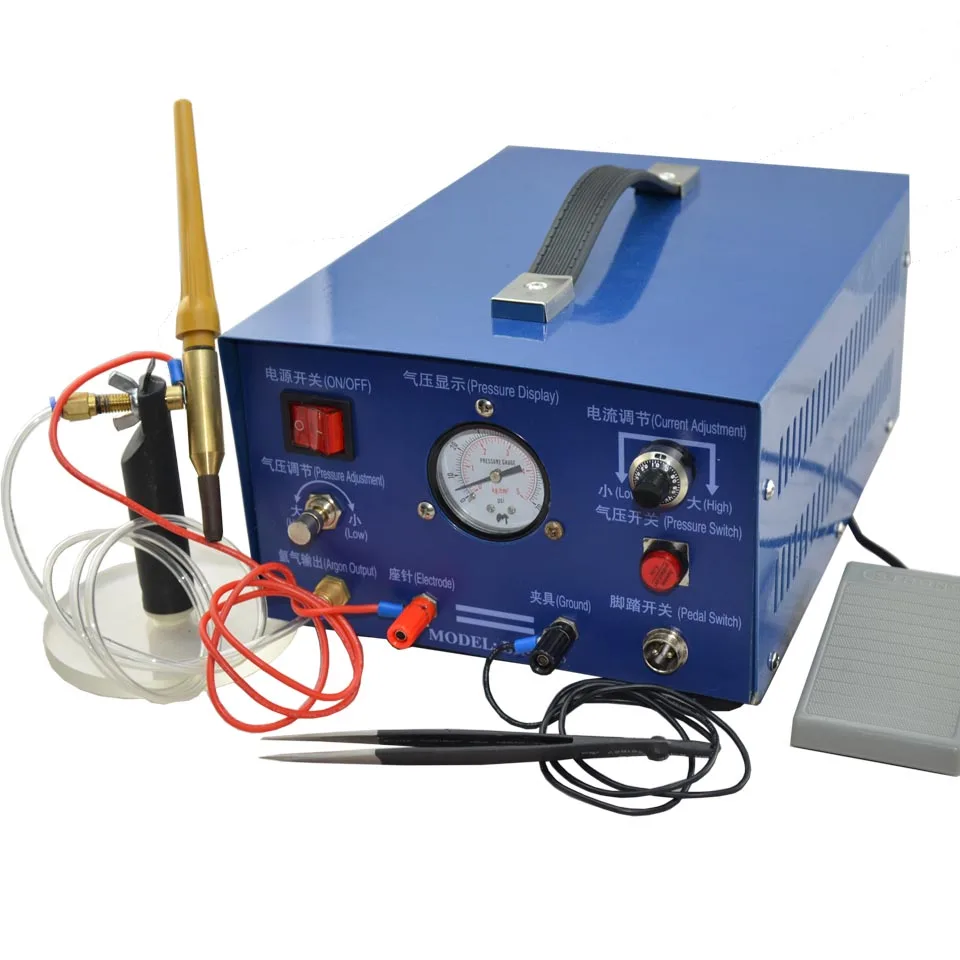
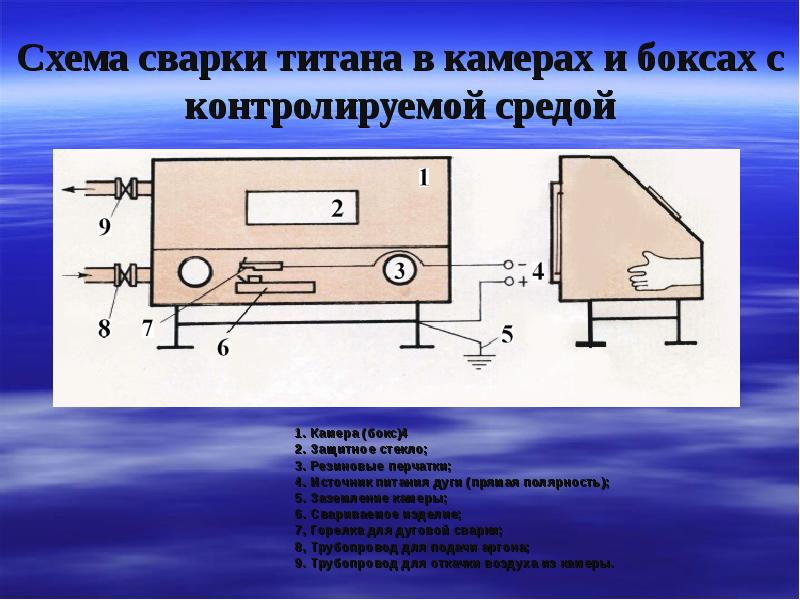
4.7.5. Сенсоры для биомедицинского анализа
Новый одноразовый стохастический сенсор для биомедицинского анализа был разработан в [239].Цель состояла в том, чтобы упростить обнаружение интерлейкина-6 (ИЛ-6), который является биомаркером сердечно-сосудистых и ряда других заболеваний.

4.8. Материалы для твердотельных аккумуляторов и топливных элементов
В нашем мире мобильных телефонов, планшетов и другой легкой портативной электроники все большее значение приобретают аккумуляторы с малой толщиной. В таких батареях используется твердотельный электролит. Как следует из литературы, см., например, [241], идеальные твердотельные электролиты должны обладать высокой ионной проводимостью. Li 3 PO 4 полностью твердотельный электролит имеет самую высокую ионную проводимость 4 × 10 −7 См/см при 25 °C, он электрохимически стабилен и поэтому представляет собой хороший сепаратор для тонкопленочных аккумуляторов.Прозрачные нанослоистые покрытия Li 3 PO 4 на чистом стекле и стекле с покрытием ITO от TVA представлены [242].4.8.1. Thin Rechargeable Batteries
В работе [243] впервые представлены попытки изготовления тонких аккумуляторных батарей методами TVA и RF (Radio Frecquency) напыления.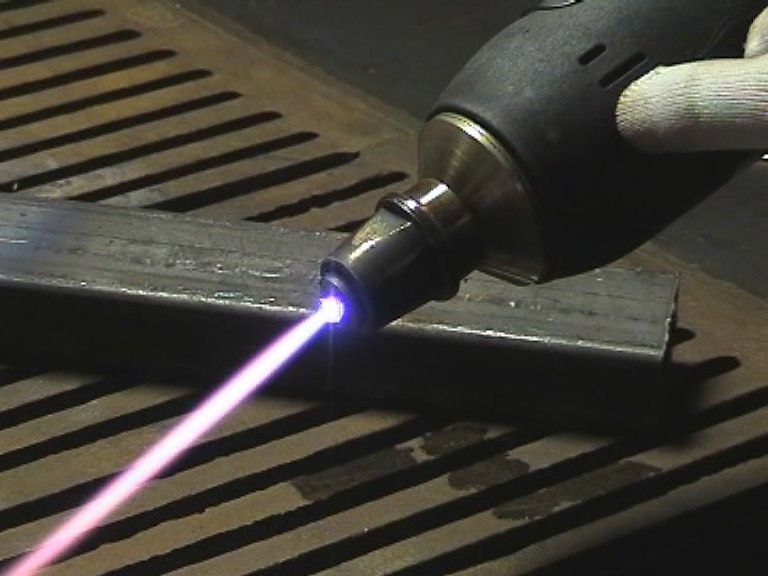
4.8.2. Материалы на основе лития
Вышеупомянутый успех стимулировал дальнейшие исследования в этой области. Применение ТВА-технологии для получения полностью твердого электролита Li 3 ПО 4 впервые подробно описано в [245].
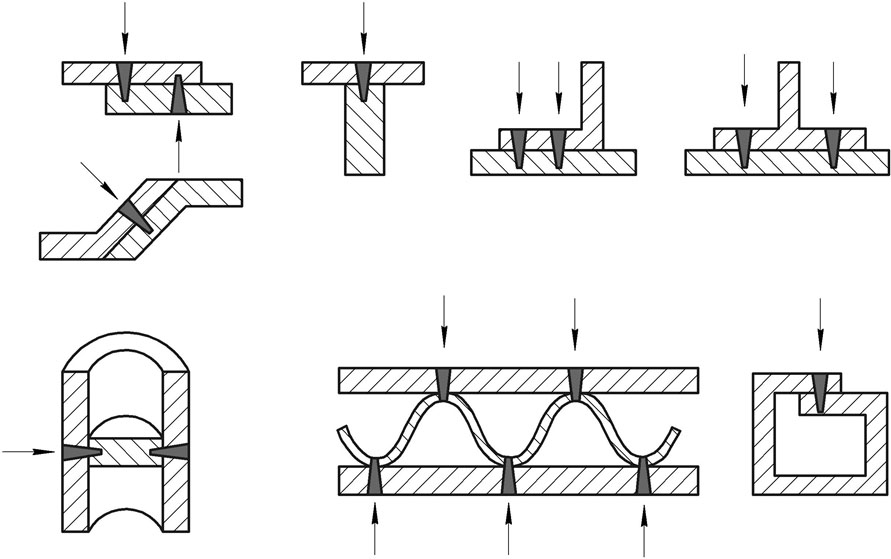
4.8.3. Материалы на основе платины
В работе [247] исследованы углеродно-платиновые катализаторы для технологии топливных элементов. Для приготовления наноструктурированных пленок на основе углерода (C-Glass + Pt) на стекле для использования в анодной и катодной частях топливных элементов метод TVA был использован в одной конфигурации электронной пушки. Сначала стеклянная подложка была покрыта углеродной пленкой толщиной около 50 нм.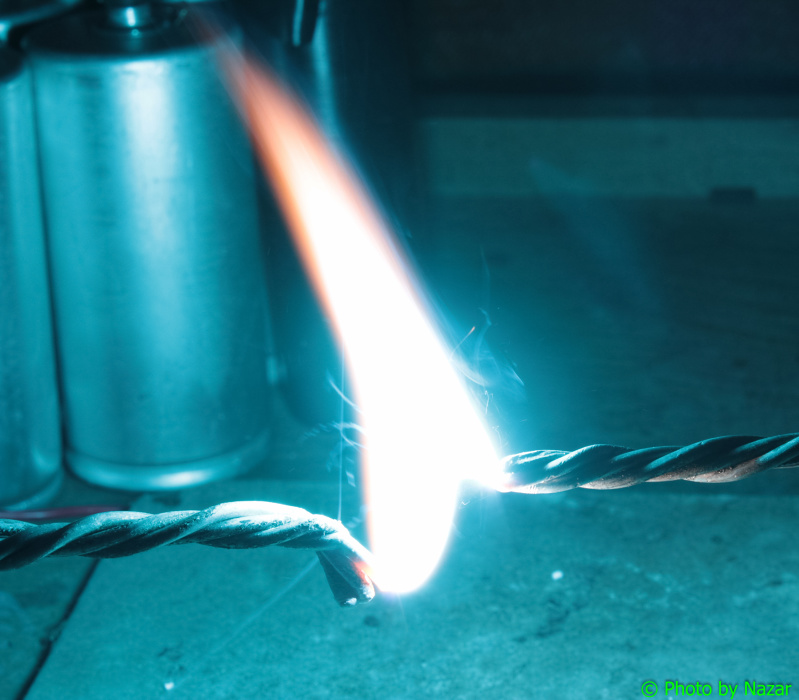
4.
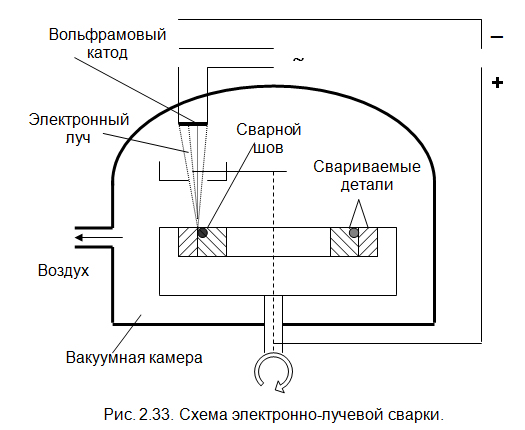
4.9.1. Сплавы на основе никеля
В работе [250] исследованы сплавы на основе никеля, которые высокоэффективны при повышенных температурах, обладают стабильностью поверхности, коррозионной стойкостью и стойкостью к окислению. Сплавы на основе никеля содержат такие материалы, как рутений (Ru), рений (Re), титан (Ti), кобальт (Co), хром (Cr) и другие. В работе [250] исследованы смешанные сплавы Re, Ni, Cr, приготовленные на подложках из кремния, графита, стекла и нержавеющей стали с использованием нескольких (трех) источников TVA с кольцевой конфигурацией катодов и трех стержневых источников соответствующего материала.
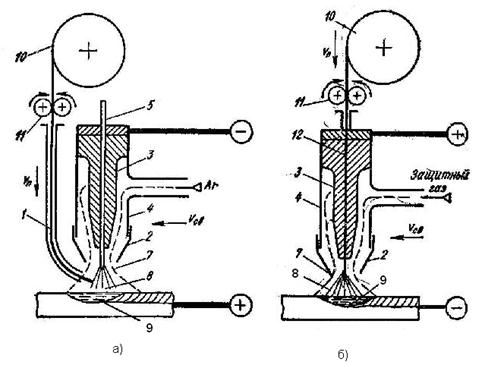
4.9.2. Углерод-титановые многослойные пленки
Углерод-титановые многослойные пленки на кремниевых подложках были приготовлены в [104]. Конечная толщина пленки составляла до 400 нм. Сначала был нанесен слой углерода толщиной 100 нм, а затем попеременно нанесены семь слоев углерода и титана. Использовался двойной ТВА с двумя кольцеобразными катодами и двумя стержнями из соответствующего материала (C, Ti) в качестве анодов.Различные образцы были изготовлены путем изменения температуры подложки от 0°С до 400°С и изменения отрицательного напряжения подложки до -700В. Для получения слоев точной толщины применялась низкая скорость осаждения. Помимо исследования характеристики ГМС, рассмотренной выше, теплопроводность мультислоев была рассчитана с использованием измеренной электропроводности. Оказалось, что такие многослойные конструкции также являются хорошими теплоизоляторами.
4.10. Борсодержащие пленки
Бор имеет температуру плавления при атмосферном давлении 2076 °C и температуру кипения 3927 °C.Он используется в качестве составного элемента в большом количестве химических веществ. Кроме того, наблюдаемая сверхпроводимость диборида магния (MgB 2 ) вызвала повышенный интерес к обработке бора. С точки зрения высокой температуры плавления бор можно рассматривать как близкий к тугоплавким металлам. Поэтому он был хорошим кандидатом для проверки способностей TVA с самого открытия техники TVA. Насколько нам известно, первой статьей, описывающей осаждение борной пленки, была [251], представленная на 4-й -й -й Международной конференции по новым направлениям исследований в материаловедении ARM-4.Анализ пленки различными методами показал, что пленки были высокого качества. Процесс испарения был достаточно стабильным, даже если ввиду высокой температуры плавления бора приходилось использовать высокие разрядные напряжения и токи TVA.
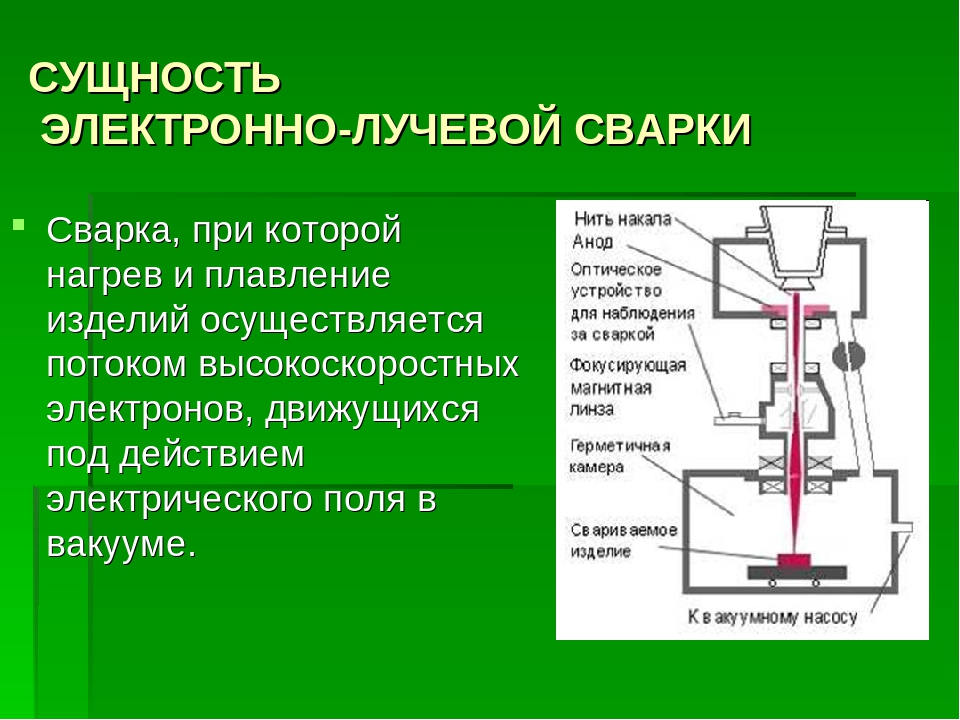
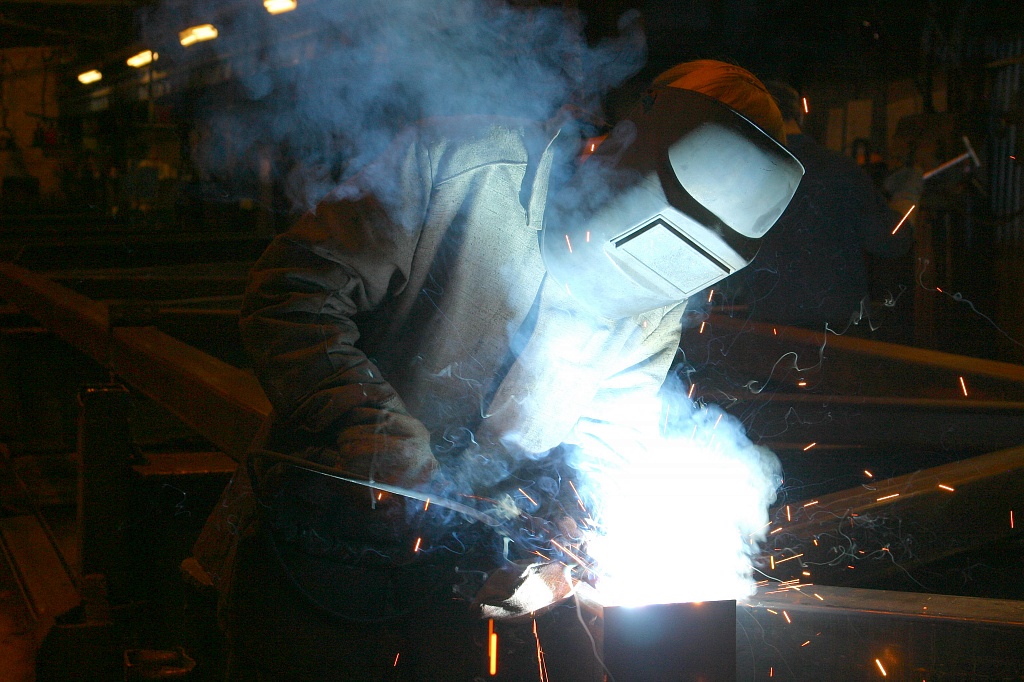

Разработка шестигорелочной автоматической сварочной установки для алюминиевых вакуумных камер
Действия
‘) var buybox = документ.
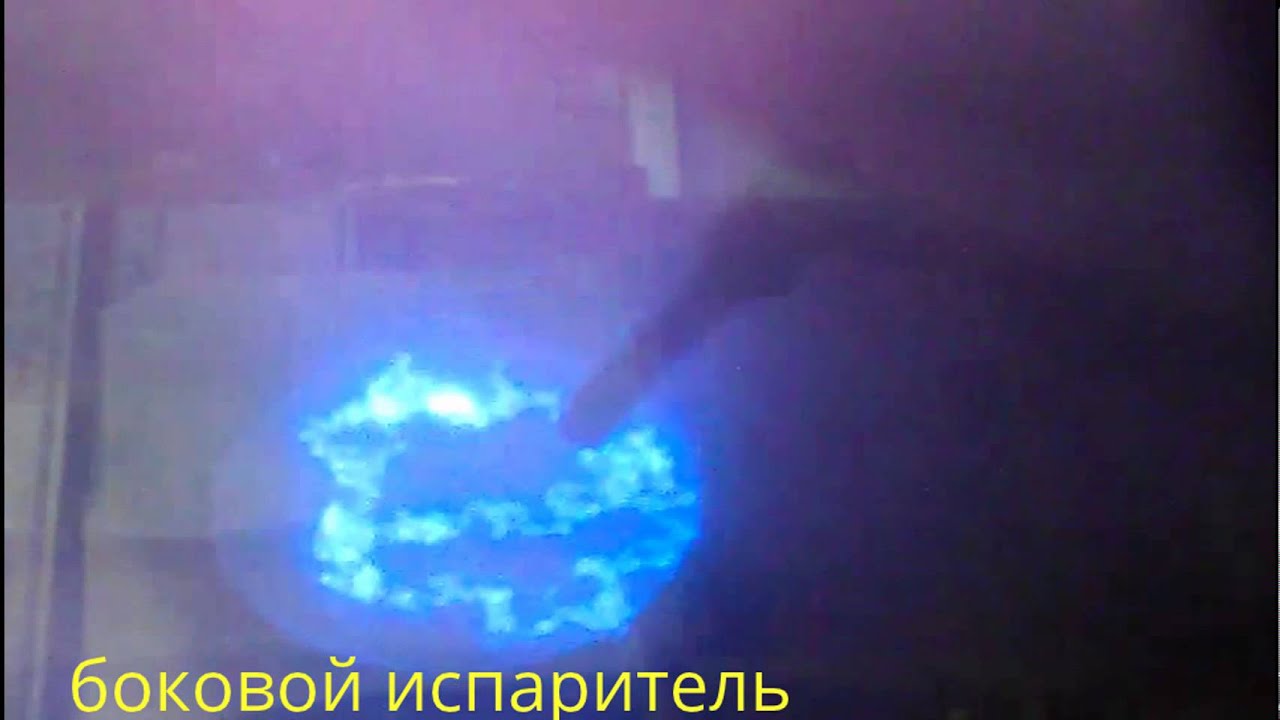
Как BEPeterson отвечает всем требованиям клиентов в области сварки — BEPeterson
С 1935 года компания BEPeterson предоставляет первоклассные услуги по производству сосудов под давлением.Среди наших разнообразных услуг нас хвалят за наши универсальные и ориентированные на решения сварочные процессы. Мы предлагаем широкий спектр сварочных услуг, которые могут удовлетворить различные требования к изготовлению металла различных клиентов.Предлагает широкий спектр методов сварки Наша команда состоит из опытных и сертифицированных сварщиков, которые обладают знаниями для выполнения различных типов сварочных процедур:
- Дуговая сварка под флюсом (SAW): Сварка под флюсом включает создание дуги между заготовкой и постоянно подаваемым электродом.Гранулированный флюс используется для создания защитного экрана вокруг зоны сварки. Дуга погружена в флюс, который покрывает зону расплава и предотвращает разбрызгивание. Многие из наших клиентов запрашивают эту процедуру сварки, поскольку она известна своей высокой производительностью. В BEPeterson мы используем автоматическое и полуавтоматическое оборудование для выполнения этого процесса сварки.
- Сварка МИГ: Сварка МИГ, также известная как дуговая сварка металлическим газом (GMAW), включает формирование электрической дуги между металлическими заготовками и расходуемой проволокой.Дуга нагревает заготовки, заставляя их сливаться. Мы предлагаем нашим клиентам полуавтоматическую сварку MIG. В зависимости от требований клиента, мы также можем предоставить услуги традиционной сварки MIG или импульсной сварки MIG.
- Сварка ВИГ: Также известная как дуговая сварка вольфрамовым электродом в среде защитного газа (GTAW), сварка ВИГ предполагает использование вольфрамового электрода для выполнения процесса сварки. В процессе в качестве защитного газа используется аргон, а присадочный материал добавляется отдельно.Это делает процесс достаточно гибким. Мы предоставляем это как автоматический процесс сварки, и он поддерживает высокий уровень качества сварки.
- Дуговая сварка с флюсовой сердцевиной (FCAW): Этот метод включает использование трубчатого электрода, заполненного флюсом, для создания дуги. Это может быть выполнено с защитными газами или без них. Что делает FCAW уникальным, так это то, что с помощью этой технологии можно разработать специальные химические составы свариваемых сплавов. Дуговая сварка с флюсовой сердцевиной — это процесс автоматической сварки, который мы предлагаем нашим клиентам в соответствии с индивидуальными требованиями .
- Дуговая сварка защищенным металлом (SMAW): Простой, но универсальный процесс сварки SMAW требует только источника питания, кабелей и электрододержателя.Электрод имеет покрытие и создает дугу, касаясь заготовки и быстро отдергивая ее. Мы в BEPeterson можем обеспечить этот процесс сварки как в автоматическом, так и в ручном режиме.
Использование новейшего сварочного оборудования
Вместе с нашей командой сертифицированных сварщиков мы используем ручное, полуавтоматическое и автоматическое сварочное оборудование для удовлетворения потребностей клиентов в сварке. Мы выполняем все сварочные процессы собственными силами с использованием передового сварочного оборудования:
- Два сварочных манипулятора 12x▓
- Тридцать сварочных постов
- Внешняя продольная закаточная машина 72″ (толщиной до 3/8″)
- Различные автоматические сварочные позиционеры весом до 5000 фунтов.
- Полуавтоматическая сварка под дугой
Работа с эклектичными производственными материалами
Наш многолетний опыт и новейшее сварочное оборудование позволяют нам работать с различными типами материалов для удовлетворения потребностей наших промышленных клиентов. В BEPeterson мы используем следующие материалы для сварки и изготовления металлов:
- Углеродистая сталь
- Нержавеющая сталь 200, серия 300
- Алюминиевые никелевые сплавы
- Нержавеющая сталь серии 1000, 5000, 6000
- Сплавы Hastelloy и Monel
- Нержавеющая сталь 2205 и 2207 дуплекс
- Твердый материал
Испытано и сертифицировано!
Сертификацияявляется одним из важнейших аспектов успеха в производстве сосудов под давлением.Наши сварочные процессы соответствуют положениям следующих стандартов:
- ASME Раздел 9
- АМС Д1.1, Д1.6
Мы также гарантируем, что все компоненты, изготовленные с использованием любого процесса сварки, проходят тщательные испытания. Наши процедуры тестирования включают:
- Рентген – неразрушающий контроль
- Ультразвуковой контроль
- Вихретоковый контроль
- Гидростатические и вакуумные испытания
- Оценка проникающей способности жидких красителей
BEPeterson всегда обеспечивает качественную сварку.Наши сварочные процессы поддерживаются высококачественным оборудованием, авторизованными сварщиками и сертификатами. Наши процессы получили высокую оценку клиентов из многих отраслей, включая нефтегазовую, судостроительную, строительство и производство трубопроводов.
.