Электрическая сварка. Виды сварки. Сварочные аппараты и машины.
1.1. Основные сведения об электрической дуге
Процесс возникновения электрической дуги состоит в следующем. В точке соприкосновения электрода с шихтой или свариваемой металлической деталью выделяется большое количество тепла. Конец электрода раскаляется и после отрыва электрода от детали разогревается и воздушный промежуток. Из катода начинается мощная термоэлектронная эмиссия. Электроны производят ионизацию атомов и молекул воздуха в промежутке между электродом и металлом. Воздух становится проводником электричества, что создаёт мощный разряд, называемый электрической дугой. Ток в дуге поддерживается в основном движением электронов, так как положительные ионы движутся медленно.
Напряжение на дуге очень мало по сравнению с напряжением на электродах у других видов разрядов в газах (искра, корона, тлеющий разряд). Это объясняется более сильной ионизацией газа между электродами дуги. При первом зажигании дуги с холодным промежутком необходима большая кинетическая энергия электронов для ионизации.
Рис. 1.1. Элементы дуги
Электрическая дуга состоит из следующих элементов (рис. 1.1): катодного пятна 1, катодного пространства 2 (где скапливаются вылетевшие из катодного пятна электроны), столба дуги 3 (он занимает почти всю длину дуги), анодного пространства 4 (состоящего из слоя электронов и положительных ионов).
Напряжение в электрической дуге делится на три характерные части (рис. 1.2):
1. Падение напряжения в катодном пространстве Uк, затрачиваемое на эмиссию электронов из катода.
2. Падение напряжения в столбе дуги Uс, затрачиваемое на перемещение зарядов через газовый промежуток l.
3. Падение напряжения в анодном пространстве Uа, затрачиваемое на преодоление объёмных зарядов и нагрев анода.
Рис. 1.2. Распределение напряжения в электрической дуге
Характеристики дуги
Статическая характеристика
При токах порядка 200 А и выше падение напряжения в столбе дуги не зависит от силы тока и пропорционально длине столба, но меняется в зависимости от рода газа, материала электродов и давления (рис. 1.3). Катодное и анодное падение напряжения также не зависят от силы тока:
Uа+Uk = const,
но величина их разная в зависимости от материала электродов, рода газа и давления.
С увеличением тока ионизация столба дуги (вследствие нагрева газа) усиливается, возрастает проводимость столба, а это приводит к уменьшению напряжения, необходимого для поддержания горения дуги с увеличением силы тока.
Рис. 1.3. Статические характеристики электрической дуги:
1 – короткая дуга; 2 – средняя дуга; 3 – длинная дуга
Динамическая характеристика
Рассмотренное выше изменение напряжения дуги с ростом тока справедливо при медленном нарастании тока (статическая характеристика).
Рис. 1.4. Динамическая характеристика дуги
При быстрых изменениях тока (на рис. 1.4 от I1 до I2) ионизация в промежутке отстаёт от роста тока, проводимость дуги увеличивается медленнее и напряжение на дуге изменяется меньше, чем по статической характеристике (из точки 1 приходим в точку 2’, а не в точку 2). При внезапном уменьшении тока степень ионизации промежутка снижается медленнее тока, и из точки 2 приходим в точку 1’, а не в точку 1.
Изложенные выше явления имеют место в дуге независимо от рода тока, питающего дугу. Однако поддержание дуги на переменном токе труднее, т. к. он меняет свою величину и направление 100 раз в секунду (при промышленной частоте), а изменение направления тока приводит к перемещению катодного пятна с одного электрода на другой вследствие изменения полярности электродов.
Особенность открытой дуги постоянного тока при атмосферном давлении и относительно небольших токах заключается в том, что её статическая вольтамперная характеристика имеет падающий вид, причём электрическая дуга будет гореть устойчиво, лишь в том случае если во внешней цепи последовательно включено сопротивление. Для электрической дуги переменного тока имеет смысл говорить только о её динамических характеристиках. Изменение тока и напряжения на разрядном промежутке существенно зависит от электрических параметров контура дуги и условий её охлаждения.
Дуга переменного тока при активном и индуктивном сопротивлениях цепи
На рис. 1.5 видно, что пока напряжение источника тока Uи меньше напряжения дуги Uз, дуга не загорается (до точки А пройдёт время t1). В точке А дуга загорается и горит в течение промежутка t2.
В точке В дуга гаснет и время t3+t1 (до точки А’) дуга не горит. Во время перерыва столб дуги остывает и происходит процесс деионизации, а это приводит к повышению напряжения для повторного зажигания дуги.
Повторное зажигание дуги происходит в момент А’ пересечения кривой А’ В’ с синусоидой напряжения источника тока. Повторное зажигание дуги переменного тока облегчается, если газовый промежуток искусственно сильно ионизирован (например, при обмазке электродов составом, содержащим калий, кальций и др.).
Рис. 1.5. Дуга переменного тока при активном сопротивлении цепи
При токах дуги больше 100 А диаграмма дуги переменного тока в чисто активной цепи (рис. 1.6) упрощается, так как при больших токах промежуток не успевает остывать, ионизация сохраняется достаточной величины, а поэтому напряжение зажигания дуги почти не отличается от напряжения горения дуги. Кроме того, напряжение горения дуги мало изменяется с изменением тока.
Рис. 1.6. Дуга переменного тока при активном сопротивлении цепи и больших токах
Из рис. 1.6 следует, что время перерыва тока уменьшается:
— при снижении напряжения зажигания дуги;
— при увеличении напряжения тока источника;
— при повышении частоты тока.
Дуга переменного тока при наличии в цепи индуктивности и газового промежутка, представляющего некоторое омическое сопротивление, имеет сдвиг по фазе между напряжением и током (рис. 1.7).
Рис. 1.7. Непрерывное горение дуги в цепи переменного тока при наличии индуктивности
Подбором индуктивности можно создать такой сдвиг фаз, что (при снижении напряжения тока ниже напряжения горения дуги) э. д. с. самоиндукции, складываясь с напряжением источника тока, может обеспечить дуге напряжение, необходимое для её поддержания до момента, пока ток не перейдёт через нулевое значение. В этот момент напряжение источника будет иметь другой знак и величину, достаточную для повторного зажигания дуги, и она возникнет без всякого перерыва. Для устойчивого горения дуги коэффициент мощности должен быть в пределах 0,35–0,45. Таким образом, для устойчивого горения дуги в цепи переменного тока необходимо иметь значительную индуктивность. Увеличение же омического сопротивления снижает устойчивость горения дуги, поэтому длинная дуга горит менее устойчиво.
1.2. Дуговая сварка
Дуговая сварка имеет несколько разновидностей (рис. 1.8). Соединяемые детали обычно нагреваются вместе с присадочным материалом при помощи электрической дуги, температура которой превышает 5000 oС.
В зоне сварки создаётся ванночка расплавленного металла, которая при охлаждении затвердевает и образует сварной шов, прочно соединяющий свариваемые детали.
Рис. 1.8. Классификация разновидностей дуговой сварки
— Сварка открытой дугой с плавящимся электродом (а) получила самое широкое применение для чёрных металлов. Дуга получает питание от источника переменного или постоянного тока, горит в воздухе между свариваемыми деталями и электродом. В процессе сварки электрод плавится и участвует в образовании сварного шва. Электрод из проволоки, по химическому составу близкой к металлу свариваемых деталей, покрыт обмазкой. Она содержит вещества, которые при расплавлении образуют шлаки и газы, повышающие устойчивость дуги и защищающие расплавленный металл от окисления.
— Ручная сварка открытой дугой с неплавящимся электродом (б) применяется обычно для соединения цветных металлов и сплавов. Питание дуги – от источника постоянного тока. Дуга горит между свариваемыми деталями и угольным или графитовым электродом, а в зону сварки вводится присадочный пруток.
— Сварка (полуавтоматическая или автоматическая) закрытой дугой с плавящимся электродом (в) под слоем флюса применяется для соединения любых металлов.
механизма подачи. Под действием высокой температуры флюс плавится и образует газовый пузырь, оболочка которого защищает металл от действия кислорода и азота воздуха. При полуавтоматической сварке дуга перемещается вручную, а при автоматической все операции автоматизированы. Автоматическая сварка под флюсом обеспечивается высокое качество сварного соединения и высокую производительность (в 6–12 раз выше, чем при ручной дуговой сварке).
— Сварка защищённой дугой и неплавящимся электродом (г) применяется для соединения нержавеющих и жаропрочных сталей. Защитной средой является аргон, смесь аргона с небольшим количеством активных газов или углекислый газ. Питание дуги – от источника переменного или постоянного тока. Вольфрамовый электрод помещён в газоэлектрическую горелку, к которой под давлением подводится газ из баллона.
— Сварка (полуавтоматическая или автоматическая) защищённой дугой (среда аргона или углекислого газа) и плавящимся электродом (д). Неизолированная электродная проволока подаётся в зону сварки через горелку с помощью механизма подачи. В горелку подаётся газ. Сварка в среде аргона применяется при питании дуги как от источника переменного, так и постоянного тока. Сварка в среде углекислого газа для сталей любого состава – на постоянном токе. При этом возможна «прямая полярность» сварки (деталь соединена с положительным полюсом, а электрод с отрицательным) или
«обратная» (электрод является анодом). «Обратная» полярность применяется при сварке тонких листов цветных металлов в среде углекислого газа.
1.2.1. Автоматическая дуговая сварка под слоем флюса
Электрическая дуга горит между свариваемыми деталями и концом голой электродной проволоки, имеющей значительную длину и намотанной на кассету. По мере расплавления проволока подается в зону сварки механизмом подачи.
Применение длинной проволоки в данном случае позволяет исключить перерыва в сварке для замены электрода. Для защиты дуги сварки, ванны и сварного шва от действия атмосферного кислорода и азота используется порошкообразный флюс. Дуга горит под слоем флюса в газовом пузыре, наполненном парами металла и флюса. Стабилизирующие добавки, имеющиеся во флюсе, обеспечивают устойчивость дуги. Высокое давление в газовом пузыре позволяет исключить разбрызгивание металла, даже при высоких мощностях дуги.
Расплавленный флюс покрывает сварной шов и, застывая, образует шлаковую корку. Взаимодействие расплавленного флюса с металлом позволяет обеспечить его высокие механические свойства. Флюс подается в зону сварки и отсасывается из этой зоны с помощью специальных пневматических устройств. Подвод сварочного тока к электродной проволоке осуществляется через контактный мундштук.
Обычно кассета с электродной проволокой, механизм и электропривод подачи, мундштук, а также механизмы подачи и отсоса флюса объединяются в единой конструкции, называемой сварочной головкой (сварочным автоматом). Сварочная головка может быть подвешена над изделием, и перемещаться по направляющим. Часто сварочную головку устанавливают на колеса и снабжают электроприводом перемещения. В этом случае получают самоходный сварочный аппарат (сварочный трактор). Сварочный трактор перемещается либо по поверхности изделия, либо по переносному рельсовому пути.
Практическая реализация автоматической сварки требует решения задачи автоматического поддержания длины дуги. Данная задача может решаться двумя способами:
1. использованием регулирования скорости подачи электрода в зависимости от режима дуги, т.е. ее тока или напряжения;
2. использованием явления саморегулирования электрической дуги.
При первом способе обычно используют поддержание пропорциональности между скоростью подачи проволоки и напряжением на дуге. Автоматы данного типа применяют при относительно низких сварочных токах. В наиболее производительных автоматах используется явление саморегулирования дуги, проявляющееся при больших плотностях тока. Автоматы такого типа имеют постоянную скорость подачи электродной проволоки.
Учтем, что при больших токах ВАХ имеет положительное дифференциальное сопротивление. Скорость плавления электрода пропорциональна мощности дуги, следовательно, линии разной мощности одновременно являются линиями разной скорости плавления электрода. Для нормальной работы автомата скорость плавления должна быть равна скорости подачи.
Допустим, VПОД = VПЛ2 (рис. 1.9). В этом случае рабочей точкой системы будет точка «б». Предположим, что вследствие каких-либо возмущений длина дуги увеличилась, стала равна L3, тогда рабочая точка системы перейдет в точку «а». Однако данная точка соответствует меньшей мощности и меньшей скорости плавления электрода (VПЛ3). Поэтому длина дуги начнет снижаться до тех пор, пока вновь не наступит равенство VПОД = VПЛ2.
Рис. 1.9. ВАХ дуги
Для обеспечения эффективного саморегулирования внешняя характеристика источника питания должна быть более жесткой, чем при ручной сварке. Такие характеристики – пологопадающие. Для дуговой сварки под слоем флюса в зависимости от технологических требований используют
либо переменный, либо постоянный ток. Причем при токах свыше 300–400 А используют переменный ток. Автоматическая сварка позволяет резко увеличить производительность и поднять качество сварки.
Иногда сказываются такие недостатки, как невидимость места сварки и возможность выполнения сварных швов только простой формы. Поэтому наряду с автоматической сваркой широко применяется полуавтоматическая сварка.
1.2.2 Специальные виды дуговой сварки
Дуговая сварка в углекислом газе
Сущность этого способа сварки заключается в том, что в зону сварки подаётся с постоянной скоростью электродная проволока диаметром 0,5–2 мм в струе углекислого газа, защищающего расплавляемый электродный и основной металл от вредного воздействия окружающего воздуха. С целью компенсации окислительного влияния углекислого газа на расплавленный металл, применяется электродная проволока из металла с повышенным содержанием раскисляющих элементов (марганца, кремния и др. ). Этот способ более прост по сравнению со сваркой под слоем флюса, особенно он эффективен при сварке металлов небольшой толщины. Наиболее целесообразна полуавтоматическая сварка в углекислом газе для тонкостенных изделий сложной формы со значительным количеством коротких перекрещивающихся швов. Сварка плавящимся электродом в среде углекислого газа выполняется автоматами и полуавтоматами.
Аргоно-дуговая сварка
Наиболее распространена аргоно-дуговая сварка неплавящимся электродом (вольфрамом). При аргоно-дуговой сварке дуга горит в струе аргона. Аргон не только защищает дугу и место сварки, но и исключает окисление вольфрамового электрода. Для формирования шва в зону сварки вводится проволока из присадочных материалов. Применение неплавящегося электрода и аргоновой защиты придает технологическому процессу следующие особенности:
1. при прямой полярности дуги на электроде имеет место мощная термоэлектродная эмиссия. Дуга имеет высокую проводимость и устойчивость. Поэтому в большинстве случаев аргоно-дуговая сварка ведется на переменном токе прямой полярности;
2. при обратной полярности дуги температура катода падает, соответственно падает интенсивность эмиссии. Дуга обратной полярности имеет меньшую проводимость и устойчивость. При обратной полярности дуги имеет место интенсивная бомбардировка свариваемых деталей тяжелыми положительными ионами аргона. Такая бомбардировка разрушает окисные пленки даже на таких активных металлах, как медь и алюминий;
3. питание переменным током позволяет сочетать устойчивость дуги прямой полярности с очищающей способностью дуги обратной полярности. Поэтому сварка меди и алюминия ведется на переменном токе;
4. различие калорийности дуг прямой и обратной полярности приводит к частичному выпрямлению тока в цепи дуги и возникновению постоянной составляющей тока, подмагничивающей трансформатор. Кроме этого, эффект выпрямления снижает очищающую способность дуги, поэтому постоянную составляющую убирают, включая в сварочную цепь последовательно конденсаторы. При аргоно-дуговой сварке используют источники с крутопадающей характеристикой, т. к. какое-либо саморегулирование режима горения в данном случае отсутствует.
Для облегчения зажигания дуги переменного тока применяют специальные устройства – осцилляторы. Иногда повышают напряжение холостого хода (UХХ) трансформатора до 130–200 В. Аргоно-дуговая сварка может быть автоматической и полуавтоматической.
Электрошлаковая сварка
Электрошлаковой сваркой можно соединять металлические части большой толщины. Источником теплоты служит шлаковая ванна, образуемая при расплавлении флюса. В отличие от дуговой сварки для расплавления основного и присадочного металлов используют теплоту, выделяющуюся при прохождении сварочного тока через расплавленный электропроводный шлак (флюс). В начале процесса дугой расплавляют небольшое количество флюса. Затем электрод погружают в шлаковую ванну, горение дуги прекращается, и ток начинает проходить через расплавленный шлак. Сварку выполняют снизу вверх чаще всего при вертикальном положении свариваемых деталей с зазором между ними.
Рис. 1.10. Установка электрошлаковой сварки
Электрошлаковую сварку различают:
— по виду электрода: проволочным, пластинчатым электродом и плавящимся мундштуком;
— по наличию колебаний электрода: без колебаний и с колебаниями электрода;
— по числу электродов: одно-, двух- и многоэлектродную.
Обычно электрошлаковую сварку применяют для соединения деталей толщиной от 50 мм до нескольких метров. Электрошлаковый процесс используют также для переплавки отходов стали и получения отливок.
1.3. Электрическая контактная сварка
При электроконтактной или электрической сварке сопротивлением нагрев производят пропусканием через место сварки тока достаточной величины. Разогретые детали механически сдавливают (сварка давлением).
Нагрев зоны сварки осуществляется электрическим током, проходящим через место сварки двух деталей. Осадочное давление создается электродами, проводящими ток. Контактная сварка обычно осуществляется на переменном токе. Это объясняется тем, что ток в тысячи и десятки тысяч ампер, необходимый для такой сварки, проще всего получить с помощью понижающего трансформатора. Получение постоянного тока такой величины требует создания специальных генераторов.
Сварочный трансформатор, снабженный необходимой функциональной аппаратурой, устройство токоподвода, механизм для создания осадочного давления обычно собирают в виде единой конструкции, которую называют машиной для контактной сварки. Различают машины для стыковой, роликовой, точечной сварки.
Рис. 1.10. Основные разновидности контактной сварки
1.3.1. Стыковая сварка
Существует два вида стыковой сварки: с оплавлением и без оплавления.
При сварке без оплавления детали с обработанными концами приводят в соприкосновение и сжимают значительными усилиями. После этого через детали пропускают ток. За счет контактного сопротивления в месте стыка возникает концентрированное выделение тепла. При достижении определенной температуры пластические свойства металла становятся достаточными для сварки. При окончании цикла сварки сначала снимают ток, потом осадочное давление.
При стыковой сварке оплавлением нагрев деталей производится до полного оплавления их поверхностей (стыков). Процесс имеет 3 стадии: предварительный подогрев, оплавление, окончательная осадка (либо только 2 последние стадии).
В начальный момент детали сжимают для обеспечения надежного контакта и пропускают электрический ток. Таким образом, обеспечивают быстрый разогрев до необходимой температуры (для стали 600–800°С). После этого давление некоторым образом снижают. Соответственно, увеличивается сопротивление контакта и сварной ток падает. Ухудшение контакта приводит к тому, что линии тока концентрируются в этот период времени в немногих точках соприкосновения.
Рис. 1.11. Цикл сварки
В этих точках концентрируются большие мощности, и начинается оплавление. Контактирующие выступы разрушаются. Весьма быстро оплавляется поле свариваемой поверхности. После этого увеличивают осадочное давление, и детали можно сварить. При этом избыток расплавленного металла выдавливается из контакта.
Рис. 1.12. Графики тока и сжимающего усилия при стыковой сварке оплавлением с предварительным подогревом
Грат (венчик) содержит большое количество окислов. Он механически непрочен и легко удаляется со сваренного стыка. Сварка плавлением имеет ряд преимуществ по сравнению со сваркой без оплавления. Она даёт большую прочность шва, не требует предварительной зачистки торцов детали, позволяет сваривать сечения сложной формы, детали из разнородных металлов. Недостаток – потери металла с гратом.
На рис. 1.13 показана машина для стыковой сварки.
Рис. 1.13. Машина для стыковой сварки
Стыковая сварка применяется для сварки проволоки, арматуры, всевозможных колец, ободов, цепей, труб, рельсов.
1.3.2. Точечная сварка
Наиболее распространенный способ контактной сварки. Применяется для сварки различных полос, листов небольшой величины (5–6 мм). Наиболее распространен цикл, когда в течение всей сварки давление не меняется. Однако лучшие результаты получают в том случае, если в конце сварки повышается осадочное давление.
Рис. 1.14. Графики тока и сжимающего усилия при точечной сварке
Рис. 1.15. Машина точечной сварки
Машины точечной сварки (рис. 1.15) имеют высокую производительность. Они могут давать до 600 точек в минуту. При такой производительности трудно коммутировать сварочный ток и выдерживать необходимую длительность его протекания. Лишь в самых простейших машинах используют механические переключатели или контакторы с эффективным дугогашением.
1.3.3. Роликовая (шовная) сварка
Три режима роликовой сварки:
1. с непрерывным движением роликов и непрерывной подачей тока (не применяется, так как дает сварку низкого качества). Применение способа возможно лишь при очень больших скоростях сварки, когда в каждый полупериод питающего тока сваривается одна точка;
2. с непрерывным движением роликов и импульсной подачей тока;
3. с прерывистым движением роликов. Ток подается только в моменты остановки. Машины для роликовой сварки (рис. 3.16) отличаются от точечных машин наличием подвижных электродов (роликов), снабженных механизмом электропривода и более напряженным режимом работы. Машины снабжают бесконтактными прерывателями.
Рис. 1.16. Машина шовной сварки
Шовная сварка позволяет соединить плотным швом непроницаемые для жидкостей и газов листы металла небольшой толщины (от доли мм до 5–6 мм).
3.4. Источники питания дуговой сварки
Источником питания (ИП) сварочной дуги называют устройство, которое обеспечивает необходимый род и силу тока дуги. Источник питания и сварочная дуга образуют взаимосвязанную энергитическую систему, в которой ИП выполняет следующие основные функции: обеспечивает условия начального возбуждения дуги, её устойчивое горение в процессе сварки и возможность производить настройку параметров режима. По роду тока в сварочной цепи различают:
— источники переменного тока – сварочные однофазные и трехфазные трансформаторы;
— специализированные установки для сварки алюминиевых сплавов;
— источники постоянного тока – сварочные выпрямители и генераторы с приводами различных типов.
По количеству обслуживаемых постов могут быть однопостовые и многопостовые, а по применению – общепромышленные источники питания. К общепромышленным относятся источники питания для ручной дуговой сварки покрытыми электродами, а также для механизированной сварки под флюсом.
1.4.1. Источники питания переменного тока
К этой группе относятся трансформаторы и специальные установки.
Сварочные трансформаторы
Рис. 1.9. Сварочный трансформатор ТДМ–315
Сварочный трансформатор – это электромагнитный аппарат, преобразующий напряжение 220–380 В промышленной сети переменного тока в более низкое напряжение, регламентируемое ГОСТами на сварочное оборудование, и обеспечивающий необходимую силу сварочного тока. Наибольшее распространение получила конструкция сварочного трансформатора с подвижными обмотками. Серийно выпускаются несколько типов таких трансформаторов: ТД и ТСК – основные из них. Серийно выпускаются несколько типов таких трансформаторов: ТД и ТСК – основные из них. Трансформаторы с подвижными обмотками чаще других применяются для ручной дуговой сварки. Кроме них применяют трансформаторы, в которых поток рассеяния изменяют поворотом магнитного шунта – среднего подвижного звена сердечника, а также малогабаритные трансформаторы типов ТДП, ТСП, АДЗ, в которых регулирование тока производят с помощью переключения секций вторичной обмотки или с помощью дополнительных обмоток. Для автоматической и полуавтоматической сварки плавящимся электродом под слоем флюса выпускаются и специальные трансформаторы типа ТДФ. Для дуговой сварки алюминиевых сплавов в защитных газах применяют специальные установки однофазного и трехфазного токов.
1.4.2. Источники питания постоянного тока
К ИП постоянного тока относятся сварочные выпрямители, вращающиеся электромашинные преобразователи (генераторы), сварочные агрегаты и инвертеры. ИП постоянного тока используются при ручной дуговой сварке штучными электродами, при сварке плавящимися и неплавящимися электродами в среде защитного газа.
Сварочные выпрямители
Сварка на постоянном токе обеспечивает получение сварного соединения более высокого качества по сравнению со сваркой на переменном токе. Из-за отсутствия нулевых значений тока повышается стабильность горения дуги, увеличивается глубина проплавления, снижается разбрызгивание, улучшается защита дуги, повышаются прочностные характеристики металла сварного шва, снижается количество дефектов шва, а пониженное разбрызгивание улучшает использование присадочного материала и упрощает операции зачистки сварного соединения от шлака и застывших брызг металла. Всё это привело к тому, что для сварки качественных швов ответственных соединений больше применяют сварку на постоянном токе. Кроме того, многие материалы – высоколегированные и теплоустойчивые стали, чугуны, титан, сплавы на основе меди и никеля – свариваются только на постоянном токе. В частности, для полуавтоматической сварки металлической проволокой в среде защитных газов (метод MIG/MAG) – наиболее производительного и универсального метода сварки – применяют именно ИП постоянного тока. Сварочными выпрямителями называются источники питания, в которых постоянный ток получается путём выпрямления переменного тока промышленной частоты с использованием полупроводниковых вентилей.
Рис. 1.10. Выпрямитель Aristotig DTG405 AC/DC
Общими элементами для сварочных выпрямителей являются:
— силовой трансформатор;
— выпрямительный блок;
— блоки пускорегулирующей, измерительной и защитной аппаратуры.
Наиболее рациональным в выпрямителях оказывается применение трёхфазного тока. Для питания выпрямительного блока (ВБ) обычно используют понижающие трёхфазные силовые трансформаторы, по устройству и принципу действия аналогичные описанным в предыдущем разделе. Сам ВБ собирается либо по трёхфазной мостовой схеме, либо по шестифазной мостовой схеме с уравнительным реактором – разнесёнными вторичными обмотками силового трансформатора, соединёнными в две «звезды» (схема Ларионова – Гретца). У обеих схем повторяемость напряжения равна шестикратной частоте питающего тока (для обычного переменного тока промышленной частоты – 300 Гц).Это позволяет получить выпрямленный ток, у которого пульсации напряжения меньше, чем при использовании обычной однофазной мостовой двухполупериодной схемы, собранной на четырёх вентилях (четырёхвентильные мостовые схемы обычно используются в более простых выпрямителях бытового класса). Регулирование тока сварки в сварочных выпрямителях осуществляется двумя путями – электромеханическим и электрическим. В выпрямителях с электромеханической регулировкой изменение тока происходит до ВБ, т. е. на выпрямляющие вентили в каждой фазе поступает переменный ток, имеющий силу тока и напряжение заданных сварочных параметров.
Применяемые в этом случае силовые трансформаторы с увеличенным магнитным рассеиванием (с раздвижными катушками) и трансформаторы с нормальным магнитным рассеиванием (с управляемым магнитным шунтом) описаны в предыдущем разделе.
Сварочные генераторы
Во всех рассмотренных выше источниках питания преобразование тока происходит за счёт электрических и электромагнитных процессов при отсутствии вращающихся деталей и узлов (за исключением элементов механических систем регулировки тока), поэтому такие ИП называют статическими. Однако раньше статических ИП были разработаны вращающиеся источники питания, называемые сварочными генераторами. Отличительной особенностью сварочных генераторов является наличие в них вращающегося якоря, приводимого в движение внешним приводом. Принцип действия сварочного генератора аналогичен работе любого генератора постоянного тока. Сварочные установки на основе генераторов с приводом от электродвигателя называются сварочными преобразователями, с приводом от двигателя внутреннего сгорания (бензинового или дизельного) – сварочными агрегатами.
Рис. 1.11. Генератор КНМ 190 YS
За счёт взаимодействия магнитных потоков в якоре и статоре генератора происходит формирование сварочного тока. Генераторы имеют широкий спектр вольт-амперных характеристик: крутопадающие в сочетании с пологопадающими, жёсткие в сочетании с возрастающими. Конструктивно различают генераторы с независимыми обмотками возбуждения
статора и генераторы с самовозбуждающимися обмотками. Генераторы с независимыми обмотками возбуждения требуют дополнительно отдельного источника тока. Двойные вольт-амперные характеристики генераторов формируются за счёт подключения намагничивающих последовательных обмоток возбуждения; при их включении вольт-амперная характеристика будет иметь крутопадающую форму, при отключенной намагничивающей обмотке вольт-амперная характеристика генератора будет пологопадающей. Для питания намагничивающих обмоток возбуждения требуется автономный источник постоянного тока, поэтому такой тип генератора обычно применяют в тех случаях, когда в качестве привода используется электродвигатель переменного тока. В генераторах с самовозбуждением для получения постоянного напряжения на коллекторе устанавливают промежуточную щетку, расположенную между двумя основными. За счет постоянного сдвига фаз между промежуточной и основными щетками, равному p/4, напряжение между промежуточной щеткой и опережающей ее основной щеткой будет постоянным, и может быть использовано для питания намагничивающих обмоток возбуждения. Такие генераторы обычно применяют в мобильных сварочных агрегатах с приводом от двигателя внутреннего сгорания. Вращающиеся сварочные источники питания просты и дёшевы в изготовлении и эксплуатации, однако вредные условия действующего производства (высокая влажность, масляные пары, пыль с наличием абразивных частиц) приводят к быстрому выходу из строя пары трения «щётки – коллектор», поэтому более совершенной является схема вентильного генератора, в котором роль коллектора выполняет бесконтактное полупроводниковое выпрямительное устройство. В этих генераторах обмотка возбуждения закреплена на корпусе статора, а обмотка самого статора является трехфазной и размещена на статоре с постоянным сдвигом фаз.
При вращении якоря его магнитное поле индуцирует в статоре синусоидальные трехфазные токи со сдвигом фаз 2p/3. Частота этих токов определяется частотой вращения якоря и числом пар полюсов статора. Далее трехфазный ток, снимаемый с обмотки статора, преобразуется в постоянный в выпрямительном блоке, построенном обычно по трёхфазной мостовой схеме. За счёт большого индуктивного сопротивления обмотки статора вольт-амперная характеристика такого генератора будет падающей. Бесколлекторные генераторы (например, ГД-4004) надёжнее в работе, но более требовательны к температурным перепадам, условиям охлаждения полупроводниковых вентилей и точности выдерживания частоты вращения привода.
Сварочные инверторы
Наиболее современными и технически сложными источниками сварочного тока являются сварочные инверторы (рис. 1.12). В отличие от статических ИП так называемых «классических» типов (т. е. трансформаторов и выпрямителей), у инверторов отсутствует силовой трансформатор. Вся работа сварочного инвертора построена на принципе фазового сдвига (инверсии) напряжения, осуществляемого электронной микропроцессорной схемой с покаскадным усилением тока (обычно микропроцессором типа IGBT). За счёт применения такого принципа удаётся получить широкий спектр вольт- амперных характеристик: от крутопадающей до возрастающей – с очень гладкой кривой тока, отклонения которого снижены до уровня десятых долей процента, что позволяет добиваться высокого качества сварки. Включение в схему высокочастотного генератора расширяет сферу применения инверторных источников питания и позволяет использовать их практически для любого метода дуговой сварки и для плазменной резки. За счёт небольшой массы инверторы малой мощности очень перспективны для использования при монтаже особо ответственных металлоконструкций и трубопроводов, к сварным соединениям которых предъявляются повышенные требования, а условия работы не позволяют применять громоздкое промышленное оборудование, предназначенное для работы в цеховых условиях.
Наличие сложной и дорогой электроники, требующей особых условий охлаждения, резко увеличивает стоимость инверторных источников, но высокое качество получаемых сварных соединений и широкий спектр методов сварки делает их наиболее перспективными для промышленного применения, особенно при производстве сложных и ответственных металлоконструкций из различныхматериалов.
Рис. 1.12. Сварочный инвертор Caddy LHQ 150
1.4.3. Основные требования к источникам питания
Источник питания должен обеспечивать надежное зажигание дуги, ее устойчивое горение и иметь возможность настройки требуемого режима сварки.
Чтобы удовлетворить эти требования, необходимо:
1. иметь UXX источника больше напряжения зажигания дуги (UЗАЖ). Например, при сварке постоянным током металлическим электродом UЗАЖ = 30–40 В, на переменном токе UЗАЖ = 50–60 В. По условиям безопасности UXX общепромышленных источников постоянного тока не превышает 90 В, переменного тока – 80 В;
2. обеспечение соответствия способа сварки и внешней характеристики источника. Внешняя характеристика должна быть круто падающей для ручной дуговой или аргоно-дуговой сварки, пологопадающей – для автоматической сварки под слоем флюса и жесткой для сварки в углекислом газе;
3. обеспечить достаточную выходную индуктивность источника переменного тока;
4. иметь возможность регулировать UXX или выходное сопротивление источника питания.
Источники питания работают в одном из следующих режимов:
1. перемежающемся;
2. повторно-кратковременном;
3. длительном.
В перемежающемся режиме работы под нагрузкой в течение времени tH работа продолжается с работой на холостом ходу tX. Такой режим характерен для ручной дуговой сварки. Источники питания для ручной сварки выпускают на номинальную продолжительность нагрузки 60 %.
В повторно-кратковременном режиме работа под нагрузкой в течение времени tH чередуется с периодическими отключениями источника от сети на время t0. Такой режим характерен для автоматической или полуавтоматической сварки.
В случае продолжительного включения имеем длительный режим работы (характерен для многопостовых источников питания).
Выводы: Электрическая сварка позволяет создавать сплошные неразъемные соединения за счет воздействия электрической дуги или прямого протекания тока. Источниками сварочного тока являются сварочные трансформаторы специальной конструкции, а также сварочные выпрямители, инверторы и генераторы.
Электрическая сварка | Слесарное дело
Электрическая сварка и оборудование для сварки
Назвать виды электрической сварки.
При электрической сварке нагрев металла производится с помощью электричества. В зависимости от принципа превращения электрической энергии в тепловую различают следующие виды сварки: дуговая, электрошлаковая, контактная, индукционная и электронно-лучевая.
Назвать виды дуговой сварки.
Вид дуговой сварки зависит от используемого электрода. Применяются угольные (способ Бенардеса) или металлические электроды (способ Словянова или трехфазным током).
При какой толщине материала можно использовать дуговую электрическую сварку?
Дуговую электрическую сварку можно применять для сварки металлических листов толщиной 1—80 мм. Применение электрошлаковой сварки позволяет сваривать значительно большие толщины.
Что такое электрическая дуга и когда она возникает?
Электрическая дуга представляет собой мощный продолжительный электрический разряд в газах, который сопровождается выделением значительного количества тепла и света.
Электрическая дуга при сварке называется сварочной. Она служит для расплавления свариваемых частей изделия и электрода, металлом которого заполняется сварной шов. Дуга может возникнуть вследствие проскакивания искры между электродами, расположенными на небольшом расстоянии друг от друга или вследствие соприкосновения электродов и последующего их некоторого разведения.
Какова температура электрической сварочной дуги?
Температура электрической сварочной дуги достигает 6000° С при рабочей температуре в зоне сварки порядка 3500° С. Электрическая дуга постоянного тока имеет более высокую температуру на положительном полюсе, в то время как дуга переменного тока имеет наивысшую температуру на обоих полюсах. Температура электрической сварочной дуги зависит от силы электрического тока, протекающего через дугу. Чем больше сила тока, тем больше выделяется тепла, а потому можно расплавить более толстый материал и использовать толстый электрод. По мере отдаления электрода от свариваемого материала количество выделяемого тепла уменьшается.
Какой ток может быть подведен к инструменту для дуговой сварки?
Страницы: 1 2 3 4 5
Автор admin | Категория Без рубрики |
Теги: ГОСТ 2. 312-72, ГОСТ 5264-69, дуга, дуговая сварка, искра, место, металл, молот, отжиг, ремонт, сварка, сварочный аппарат, сварщик, сила тока, сплав, стали, сталь, температура, ток, уголь, чугун, шлак, электрическая сварка, электрод
Принцип действия электродуговой сварки
Электродуговая сварка в настоящее время является одной из наиболее широко применяемых технологией в процессе сварки металлических элементов. Она при помощи электродугового разряда расплавляет кромки элементов, которые необходимо соединить. Для процесса сварки необходим источник питания с низким напряжением и сильным током, к которому подсоединяется сварочный электрод и свариваемая деталь.Принцип действия дуговой электросварки: дуговой разряд преобразует электрическую энергию в тепловую. Температура достигает 3000–5500 градусов Цельсия, тогда газ в разряде переходит в ионизированные частицы, влияющие на присадочный металл. На характер разряда влияют используемый присадочный металл, характеристики электрической цепи и защитной среды. Напряжение дуги зависит от ее длины. Электродуговая сварка может быть ручной или выполняться с помощью сварочного оборудования. Ручная сварка с защитой зоны сварки является наиболее распространенным видом электросварки. Данная технология используется для сварки стали легированной и мягкой, нержавейки, чугуна и цветных металлов. Электрод представляет собой стержень диаметром до 1 см, который закрепляется электрододержателем. Затем, электрод прикасается к свариваемой детали и замыкает электрическую цепь. При этом происходит нагревание конца электрода. После этого электрод отводится от детали на 3–5 мм, и возникает дуговой разряд, который продолжает поддерживать ток в цепи. В непосредственной близости от дугового разряда происходит интенсивный нагрев и в месте стыка основной металл детали расплавляется. Конец электрода также начинает расплавляться, и оба металла соединяются в сварочной ванне.
Важно следить за тем, чтобы размер дуги не менялся, и вести электрод таким образом, вдоль кромок стыка. В процессе прохождения электрода вдоль кромок стыка образуется сварочная ванна из расплавленного основного и электродного металлов, которая сразу же затвердевает. В результате чего образуется сварочный валик по контуру сварки. В данной технологии важным является создание плотного флюса — защитной обмазки электрода, который защищает дугу и сварочную ванну от загрязнения атмосферными газами, способствует очистке сварочного металла окислителями, повышает стабильность дугового разряда и ускоряет наплавку. При работе сварочным оборудованием можно использовать переменный или постоянный ток. Также существует сварка неплавящимся электродом из вольфрама или графита, когда расплавляется только основной или дополнительный присадочный металл, сварка косвенной дугой между двумя неплавящимися электродами и сварка трехфазной дугой, которая идет между самими электродами и между электродом и основным металлом.
Двухфазные портативные сварочные трансформаторы. Плавная регулировка тока. Защита от перегрузки. Укомплектованы аксессуарами.
Контактная электрическая сварка
Темы: Контактная сварка, Технология сварки.
Контактная сварка -это один из наиболее эффективных, экономичных, высокомеханизированных и автоматизированных способов сварки, обеспечивающих высокую прочность, качество и надежность сварного соединения и широко используемых в строительстве для сварки арматуры, трубопроводов, рельсов и т.д. Изготовление наиболее дорогих и сложных узлов легковых и грузовых автомобилей — кузовов и кабин тоже основывается на электроконтактной сварке. Многие конструктивно сложные детали в машиностроении изготовляются путем точечной сварки штампованных из листового проката заготовок.
Способы электроконтактной сварки подразделяются на три группы: стыковая сварка, точечная сварка и шовная сварка.
Электроконтактная сварка деталей выполняется следующим образом: детали сжимают усилием Р , через стык их пропускается электрический ток J в течении времени t , происходит нагрев металла в зоне контакта до температуры плавления, выключается электрический ток, деталь охлаждается и кристаллизуется сварной шов, снимается нагрузка.
Количество тепла, выделившегося при прохождении электрического тока находится по формуле:
Q= J 2 R t, Дж.
Напряжение сварки U по сравнению с электродуговой сваркой очень низкое (всего 1-6 В), а токи измеряются сотнями и тысячами А. Поэтому понижающий трансформатор конструктивно отличается от сварочных трансформаторов для электродуговой сварки: вторичная обмотка имеет от 1 до 6 витков, а сила тока J регулируется изменением количества витков первичной обмотки (рис. 1). Сопротивление R зависит от чистоты, шероховатости и загрязнения поверхности свариваемых деталей, электрического сопротивления материала, давления сжатия деталей и др. Время сварки t изменяется от сотых долей секунды до нескольких минут. Из-за малого времени сварки снижаются окисляемость материалов деталей и величина зоны термического влияния, поэтому при сварке будут минимальные деформации и хорошее качество наплавленного металла.
Стыковой сваркой (рис. 1) свариваются арматурные стержни, полосы, трубы, фланцы, швеллера, рельсы. Применяются три разновидности стыковой сварки: сопротивлением, непрерывным и периодическим оплавлением.
Рис.1. Схема электроконтактной стыковой сварки
При сварке сопротивлением торцы свариваемых деталей тщательно обрабатывают, детали сводят до соприкосновения и включают электрический ток. После нагрева металла до пластичного состояния выключают ток и снимают нагрузку. Сваркой сопротивлением можно сваривать детали сечением до 300 мм2, например, трубы — диаметром до 40 мм.При сварке непрерывным оплавлением после сжатия деталей производят нагрев стыка до его оплавления электрическим током. С торца выдавливается жидкий металл, а с ним окислы и загрязнения с поверхности контакта, поэтому особой подготовки детали перед сваркой не надо. После выключения электрического тока кристаллизуется расплавленный металл и образуется сварной шов. Этим способом можно сварить детали значительно большего сечения (до 3000 мм2 ) чем при сварке сопротивлением.
Сварка прерывистым оплавлением выполняется периодическими короткими замыканиями и размыканиями электрического тока за счет перемещения детали . При этом появляются искры и разбрызгивание металла. Этот способ сварки эффективен для легированных сталей (30ХГСА,…).
Точечная сварка используется в основном для сварки листовых конструкций, соединения пересекающих стержней (арматура железобетонных конструкций). Суммарная толщина листов обычно не превышает 10-12 мм (возможна до 20 мм для листовой сварки), а других элементов до 30 мм.
Рис.2. Способы получения точечных сварных швовСварные соединения могут реализовываться по разному ( рис. 2) : одноточечная 2-х сторонняя; 2-х точечная односторонняя и многоточечная односторонняя. Последний способ обеспечивается аналогично как и 2-х точечная односторонняя, только в этом случае для каждой пары точек сварки необходима своя вторичная обмотка, так, например, для 40 -точечной контактной сварки необходимо 20 вторичных обмоток трансформатора.
При двухсторонней одноточечной сварке нижний электрод неподвижен, а верхний перемещается с помощью механизма сжатия (механический, пневматический или электрический привод).
После установки и сжатия (рис.3) деталей включается трансформатор, металл нагревается в зоне контакта до образования ядра из расплавленного металла, увеличивается нагрузка сжатия и выключается ток, кристаллизуется расплавленный металл и детали свариваются. Место контакта электрода с деталью нагревается меньше, т.к. тепло отводится через водоохлаждаемые медные электроды. Для сварки конкретных деталей могут использоваться схемы выполнения сварки. отличающиеся от схемы, представленной на рис. 3.
Для сварки углеродистых и низколегированных сталей применяются мягкие режимы (большое время выдержки ( t=0,2-3 с и небольшая плотность тока J=80-160 А/ мм2), а для сварки низкоуглеродистых и высоколегированных сталей, не склонных к закалке, – жесткие режимы (t=0,001-0,1 с , J=150-350 А/ мм2).
Разновидность точечной сварки — рельефная (рис.4). Сначала создаются холодной пластической деформацией выступы на свариваемых поверхностях, а затем детали сжимаются и через них пропускается электрический ток, т.е. производится электроконтактная сварка.
Рис.4. Рельефная сварка
Рис. 5. Шовная сварка
Шовная контактная сварка ( рис.5) применяется для получения прочных и герметичных швов (тонкостенные сосуды, тонкостенные сварные трубы ,..) Листы толщиной 0,3-3 мм собирают внахлестку, сжимают двумя медными роликами, пропускают через них электрический ток, ролики вращаются, листы или ролики перемещаются, происходит контактная сварка.Есть два способа шовной сварки :
- При непрерывной контактной сварке изделий из малоуглеродистой стали толщиной менее 1мм выполняется непрерывная подача электрического тока.
- Для более толстых изделий используется прерывистая сварка : ролики вращаются непрерывно, а ток подается периодическими импульсами ; образуется ряд непрерывных точек, которые перекрывая друг друга в итоге образуют сплошной сварной шов.
Конденсаторная сварка. Энергия накапливается в конденсаторах, которые разряжаются или непосредственно через изделие или через дополнительный трансформатор на изделие. Чаще всего используется второй способ. Конденсаторной сваркой соединяют металлические детали толщиной 0,005 … 2 мм., но можно приварить тонкий металл (толщиной 0,2…0,3 мм ) к металлическим деталям большой толщины (до 10…15 мм). Конденсаторные установки имеют маленькую мощность и обеспечивают высокое качество сварных соединений.
Для повышения твердости и износостойкости рабочих поверхностей деталей и при ремонте посадочных мест под подшипники качения валов, отверстий редукторов, коробок перемены передачи, шеек коленчатых валов двигателей широко используется электроконтактная приварка ленты, проволоки или порошка. Технология приварки ленты включает в себя : подготовку детали (шлифование до размера : dн -0,3мм), нарезку заготовок ленты по ширине и длине (периметру) и очистку ленты, предварительную приварку ленты в середине. Далее выполняется приварка ленты (порошка, проволоки) с помощью роликов установки электроконтактной сварки.
Тепловые деформации при этом малы, материал подбирается высокой износостойкости, обеспечивается долговечность не ниже новых деталей, исключается термическая деформация деталей.
Другие материалы относящиеся к теме »
Контактная электрическая сварка
» :
Машины ( аппараты ) для контактной сварки
- < Дефекты контактной сварки
Сварка электрическая сопротивлением (контактная) — Энциклопедия по машиностроению XXL
Электрическое сопротивление контактных соединений шин, выполненных холодной сваркой в двух и более точках, практически не меняется с течением времени и по абсолютной величине вполне удовлетворяет требованиям, предъявляемым к шинным контактам.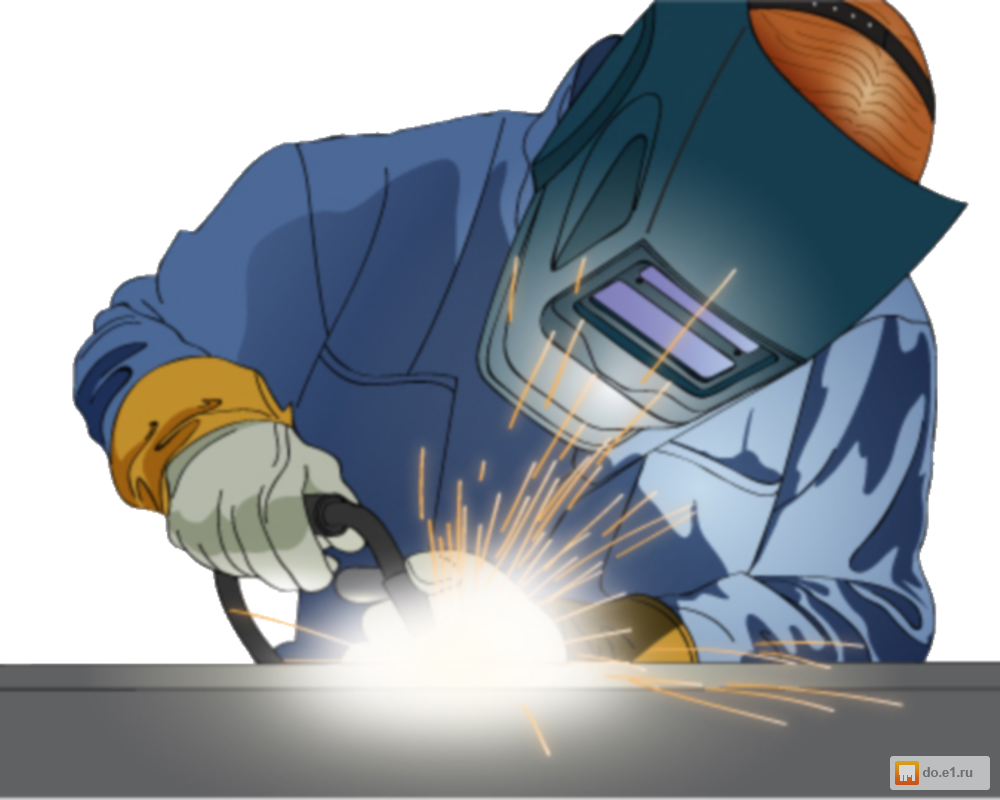
Контактная сварка. Этот процесс применяют только для сварки металлов и основным источником энергии в нем служит теплота, выделяемая электрическим током в зоне контакта соединяемых деталей, электрическое сопротивление которой выше сопротивления основного металла. Некоторое количество теплоты при контактной сварке может выделяться и в объеме свариваемых деталей вследствие работы электрического тока при прохождении через внутренний объем деталей, имеющих некоторое электрическое сопротивление. [c.132]
К устройствам регулирования процессов точечной сварки относятся стабилизаторы сварочного тока и напряжения, устройства для поддержки неизменной величины тока, действующие по принципу изменения электрического сопротивления и т. д. В СССР созданы контактные машины с управлением процессами путем регулирования температуры зон соединения (ЦНИИТМАШ), дилатометрического эффекта, основанного на из-114 [c.
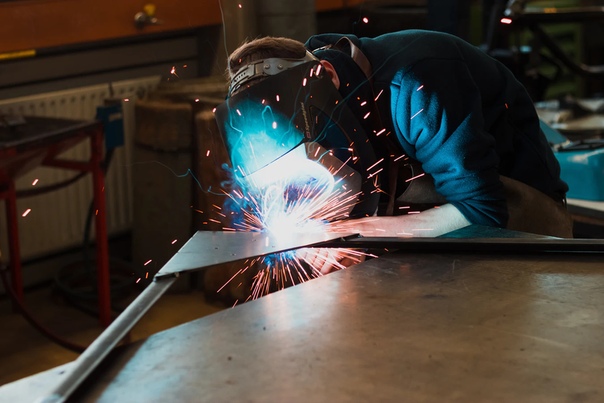
На рис. 1.2 приведены схемы трехфазных машин контактной сварки. Использование для контактной сварки выпрямленного тока повышает технические характеристики оборудования и расширяет его технологические возможности. Сварочный контур большинства машин представляет собой электрическую цепь, индуктивное сопротивление которой на переменном токе промышленной частоты в несколько раз превышает ее активное сопротивление. Отношение это тем выше, чем больше вылет электродов и раствор сварочного контура. Так, в серийно выпускаемой машине переменного тока МТ-4019, имеющей вылет электродов 500 мм, индуктивное сопротивление сварочного контура составляет 260 мкОм. [c.169]
Электроконтактная сварка. При пропускании тока через свариваемые детали в месте их соприкосновения (контакта) вследствие повышенного электрического сопротивления выделяется большое количество тепла, нагревающего металл до пластического состояния. Наибольшее применение нашли 3 основных способа электро-контактной сварки.
[c.325]
Широко применяется электрическая контактная сварка. Различают стыковую (контактную) сварку сопротивлением и стыковую сварку оплавлением. В первом случае через свариваемые детали, прижатые друг к другу торцами, пропускают электрический ток, нагревающий детали до сварочной темпера-212 [c.212]
Для сварки стержней встык применяют контактную электрическую сварку (методами сопротивления, оплавления и оплавления с подогревом) и сварку трением. Эффективность контактной электросварки обусловливается большой скоростью сварочного процесса, обеспечивающей высокую производительность электросварочного оборудования, и отсутствием необходимости в присадочном материале. [c.15]
Контактная сварка — сварка с применением давления, при которой используется тепло, выделяющееся в контакте свариваемых частей при прохождении электрического тока. Этот вид сварки, в свою очередь, подразделяется на несколько видов точечная контактная сварка, рельефная сварка, шовная контактная сварка, стыковая контактная сварка оплавлением и контактная сварка сопротивлением.
[c.17]
Последовательность операций точечной сварки следующая. Заготовки устанавливают и затем плотно сжимают между электродами контактной машины. Включают ток, и заготовки быстро нагреваются особенно быстро нагреваются участки металла, прилегающие к контакту между заготовками, так как эти участки имеют повышенное электрическое сопротивление. Кроме того, они менее подвержены охлаждающему действию электродов. В момент образования в зоне сварки расплавленного ядра заданных размеров ток выключают. После выключения тока заготовки кратковременно выдерживают между электродами под действием усилия сжатия, в результате чего происходит охлаждение зоны сварки, кристаллизация расплавленного металла и уменьшение усадочной раковины в ядре сварной точки. [c.245]
При контактной сварке участки металла нагреваются проходящим по ним электрическим током. Большое влияние на процессы нагрева и сварки оказывает сопротивление контакта между соединяемыми деталями.
[c.394]
Контактная сварка применяется только для металлов. Основной источник энергии — теплота, выделяемая электрическим током в зоне контакта соединяемых деталей, электрическое сопротивление которой выше сопротивления основного металла. Давление, сжимающее детали, формирует сварное соединение, на что затрачивается всего несколько процентов от общей вводимой энергии. [c.27]
СВАРКА МЕТОДОМ СОПРОТИВЛЕНИЯ, электромеханическая сварка — устарелый термин, применявшийся ранее для обозначения совокупности разновидностей сварки давлением, при которых для нагрева металла используется тепло, выделяемое в соединяемых деталях при прохождении по ним электрического тока (к таким разновидностям относили контактную сварку и сварку по методу Игнатьева). [c.134]
При сварке к двум (или более) сжатым между собой деталям с помощью специальных электродов подводят ток небольшого напряжения (обычно 3—8 В) и большой силы (до нескольких десятков кА). Теплота, используемая при сварке, выделяется непосредственно в деталях, контактах между ними и контактах деталей с электродами. Электрическое сопротивление имеет существенное значение в процессах контактной сварки.
[c.3]
При контактной сварке методом сопротивления (рис. 174) электрический ток подводится к сформованной трубной заготовке посредством вращающихся электродных колец, являющихся составной частью вращающегося сварочного трансформатора. [c.312]
Другие способы сварки. Медь, как металл высокой пластичности, хорошо сваривается всеми видами сварки термомеханического класса, кроме контактной, так как медь характеризуется малым переходным электрическим сопротивлением. Для приварки выводов из тонких медных проволок в изделиях электронной техники используют термокомпрессионную сварку. Для более крупных изделий сложной конфигурации широко применяют диффузионную сварку в вакууме, позволяющую получать соединения меди не только с медью, но и с другими металлами и даже неметаллическими материалами.
[c.123]
На рис. 111 дана схема участков электрического сопротивления при контактной сварке. Большое значение при контактной сварке имеют сопротивления Гх и Гг, так как переходные сопротивления между токоподводящими колодками при стыковой сварке расположены сравнительно далеко от зоны сварки, а при точечной и шовной контактной сварке тепло, выделяемое ими, в значительной степени отводится за счет охлаждения водой конических или роликовых электродов. [c.169]
Величина электрического сопротивления свариваемых деталей и контактов между ними существенно влияет на процесс выделения тепла при точечной сварке, а следовательно, должна влиять и на размеры и прочность сварной точки. Для получения сварных точек стабильной прочности необходимо, чтобы эти сопротивления по возможности колебались в узких пределах. Для обеспечения постоянства контактного сопротивления обычно применяется специальная подготовка поверхности деталей перед их точечной сваркой.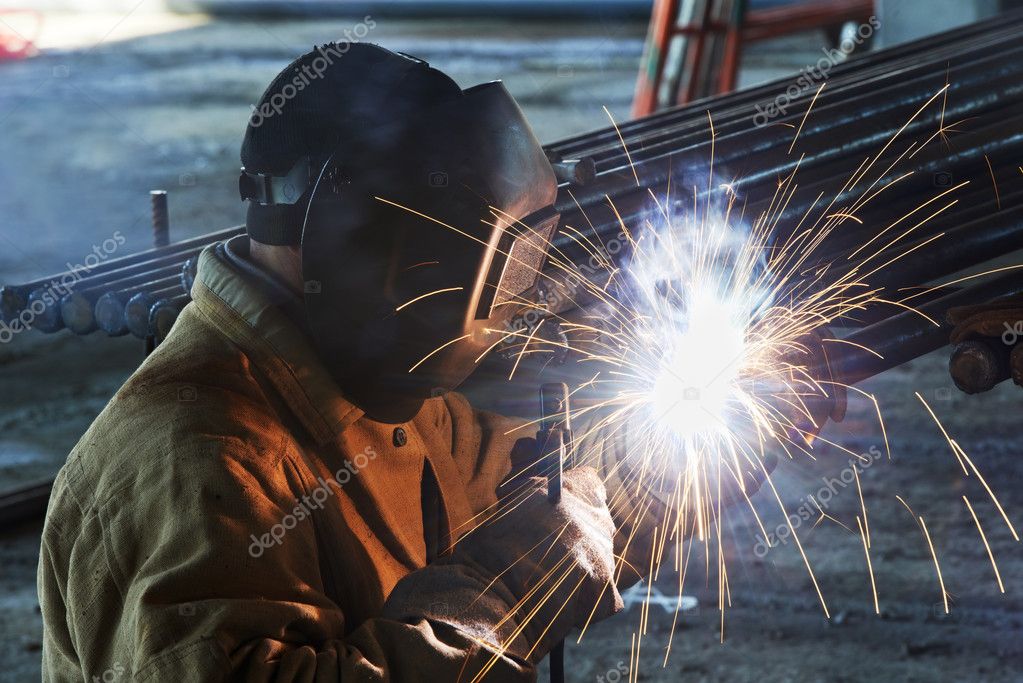
Н е д 3 в ец к и й Г. В. Исследование электрической контактной сварки встык сопротивлением. Кандидатская диссертация. 1939. 157 с. [c.130]
Для контактной сварки важен надежный и постоянный электрический контакт электродов с заготовками. При плохой очистке заготовок электрическое сопротивление и потери мощности растут, сварочный ток уменьшается, что может привести к снижению качества соединения. Так же влияет окисление переходных контактов сварочной цепи и загрязнение электродов. Из-за грязи материал заготовок пригорает к поверхности электрода, что, наряду с ухудшением контакта, нарушает центрирование заготовок и увеличивает износ электродов. [c.79]
При контактной сварке, или сварке сопротивлением, металл нагревается проходящим по нему электрическим током при этом значительное влияние на процесс сварки имеет сопротивление контакта между соединяемыми деталями. Контактная сварка почти всегда выполняется как сварка давлением с осадкой разогретых деталей. Нередко осадка сочетается с полным расплавлением основного металла, и зона сварки имеет структуру литого металла, например при точечной контактной сварке.
[c.12]
В книге изложены основные вопросы теории и элементы технологии современных процессов сварки давлением взрывом, холодной, ультразвуковой, диффузионной, трением и контактной. Для этих способов сварки рассмотрены металлофизические, деформационные и электротепловые явления и процессы в Металлических свариваемых контактах. Исследованы н показаны в применении критерии подобия для расчета электрических сопротивлений свариваемых контактов и для расчета режимов некоторых способов сварки давлением. [c.2]
Для идеально чистых поверхностей весьма рациональным является представление полного электрического сопротивления контакта как суммы внутреннего и геометрического сопротивлений. На целом ряде примеров можно убедиться, что для контактной сварки принципиально неверно рассматривать в качестве электрического сопротивления контакта только его внутреннюю составляющую, а геометрическое сопротивление контакта считать сопротивлением самой детали, самого стержня, самой пластины и т. д. (в зависимости от конструкции свариваемых изделий).
[c.67]
Электрические сопротивления между электродом и свариваемыми деталями будем называть переходными сопротивлениями, в отличие от исследованных выше контактных. Разумеется, между переходными и контактными сопротивлениями в их холодном состоянии никакой принципиальной разницы нет. Однако терминологическое различие весьма удобно. Для обозначения переходных сопротивлений вместо индекса /о> будем использовать индекс п (рис. 33). Рассматривая опытные кривые этого рисунка, убеждаемся, что при одинаковых площадях контактирования переходное сопротивление (рис. 33, а) Си + Fe значительно меньше контактного Fe + Fe. Если же медный электрод (рис. 33, б) создает явно меньшую площадь контактирования со стальной деталью (Си -f Fe), то это переходное сопротивление может быть заметно увеличенным по сравнению с контактным (Fe + Fe), если площадь этого контактного сопротивления больше площади переходного. Как видно по кривым и rI (рис. 33, б), принятое в практике расчетов контактной сварки половинное со-
[c.70]
Сварочные машины для контактной сварки. . Электропечи сопротивления и электрические ванны. ………………… [c.296]
Контактный наконечник является ответственной деталью газоэлектрической горелки. От его состояния зависит устойчивость процесса сварки, производительность работы и качество сварного шва. При сварке наконечник находится в зоне разлета-ния брызг электродного металла. Часть стальных брызг прилипает к поверхности сапожка наконечника. Брызги, попавшие на сапожок, ухудшают передачу сварочного тока с наконечника на электродную проволоку, так как увеличивается между ними переходное электрическое сопротивление. Внешне это проявляется в неустойчивом горении дуги и увеличении разбрызгивания электродного металла. [c.77]
При контактной сварке для нагрева свариваемых частей используется тепло, выделяемое при прохождении тока через место сварки. В месте контакта частей наблюдается увеличенное электрическое сопротивление по сравнению с другими участками цепи. После достижения в зоне сварки необходимой температуры свариваемые части для их соединения сдавливают.
[c.270]
Контактно-тепловая сварка (сварка нагретыми инструментами). Контактно-тепловая сварка является наиболее простым и широко распространенным методом сварки полимерных пленок. Нагрев материала до необходимых для сварки температур достигается при одностороннем либо двустороннем контакте материала с поверхностью рабочих инструментов (роликов, полозов, клина), нагреваемых электрическими спиралями, а также непосредственно пропускаемым через инструмент током. В последнем случае в качестве рабочего инструмента наиболее час(го используется металлическая лента с высоким омическим сопротивлением. Продолжитель-4 [c.4]
КОНТАКТНОЕ СОПРОТИВЛЕНИЕ (при стыковой и точечной сварке) — электрическое сопротивление сварочного контакта. К. с. существенно зависит от сжимающего усилия, прикладываемого к соединяемым деталям в процрсге спарки.
[c.66]
При контактной сварке электрическое сопротивление в месте контакта электродов и двух свариваемых деталей состо1 т из суммы сопротивлений / = 2Д д + А ь- -2аол, где / д — электрическое сопротивление металла свариваемых детален. Ом контактное электрическое сопротивление между сваривае.мыми деталями, Ом [c.283]
Контактную сварку можно выполнять под водой, получая при этом по существу непрерывный точечныГ шов между двумя плотно прижатыми плоскими поверхностями. Эти поверхности прижимаются друг к другу с помощью фасонных зажимов, между которыми при их контакте через тантал проходит ток тантал в месте касания поверхностей (т. е. в месте наибольшего электрического сопротивления) разогревается и сваривается. Кроме того, этим способом можно выполнять сварку труб внахлестку, однако присутствие напуска удвоенной толщины по длине трубы ограничивает применение таких труб в химическом машиностроении.
[c.738]
Перед контактной сваркой алюминия лучший способ удаления окисной пленки с поверхности деталей — ультразвуковая обработка. Одна из проблем контактной сварки алюминия — это низкая стойкость электродов из-за налипания алюминия на их поверхность. Сплавы алюминия имеют малое электрическое сопротивление и высокую теплопроводность, поэтому их сваривают на жестких режимах. Деформируемые сплавы типа АМц, АМг и особенно термоупрочняемые сплавы типа Д16Т обладают склонностью к трещинам. При их контактной сварке нужно в конце цикла увеличивать усилие проковки в 3…6 раз по сравнению со сварочным усилием. [c.198]
При подготовке поверхностей к контактной сварке должны выполняться три основных требования в контактах электрод — деталь должно быть обеспечено как можно меньшее электрическое сопротивление (/ э-д -> niin), в контакте деталь — деталь сопротивление должно быть одинаковым по всей площади контакта. Сопрягаемые поверхности де-
[c. 287]
Алюминий, (Как и медь, в воздухе окисляется (соединяется с кислородом воздуха), и на его поверхности по-я1вляется пленка окиси. У меди в обычных условиях пленка окиси образуется медленно, она легко удаляется и незначительно влияет на ухудшение контактного соединения. Пленка же окиси алюминия образ1уется в воздухе очень быстро, обладает большой твердостью и значительным электрическим сопротивлением, вследствие чего -состояние контактного соединения быстро ухудшается. Пленка окиси алюминия тугоплавка (температура плавления пленки около 2 000° С, алюминия 565—576° С) и препятствует пайке и сварке. [c.4]
Контактичя сварка. Благодаря высокому электрическому сопротивлению и малой теплопроводности титана контактная сварка последнего значительно облегчается п может выполняться па обычных машинах средней мощности. Происходящее в процессе точечной, роликовой и стыковой сварки сопротивлением плотное сжатие свариваемых деталей между собой препятствует доступу воздуха в зону сварки и не требует в связи с. зтим при.менения специальной защиты инертными газами. В случае сварки методом оплавления свариваемые поверхности защищены интенсивным выделением из зоны сварки паров и газов, оттесняющих окружающий воздух, однако дополнительная защита аргоном повышает нластд1чность стыковых соединений. Режпмы сварки приведены в табл.
[c.369]
Нержавеющие стали обладают весьма высокой стойкостью против окисления и даже, находясь в тяжелых условиях эксплуатации, не коррозируют. Они имеют предел прочности, превышающий в 1,5—2 раза предел прочт ности малоуглеродистой стали. Благодаря таким преимуществам нержавеющие стали все более широко применяются в современной промышленности. Поэтому их свариваемость представляет особый интерес. Большое удельное электрическое сопротивление и малая теплопроводность нержавеющих сталей — свойства, благоприятствующие контактной сварке. Однако опыт предприятий показывает, что контактная электросварка нержавеющих сталей должна выполняться на жестких режимах. Это объясняется, во-первых, ухудшением физических и химических свойств нержавеющих сталей при медленном нагреве и охлаждении и, во-вторых, большим коэффициентом линейного расширения при нагреве, в силу чего крупногабаритные детали и узлы могут покоробиться.
[c.9]
Контроль качества подготовки поверхности производится измерением контактного (переходного) электрического сопротивления сопрягаемых деталей, выполняемом на специальном стенде СККС-1 (рис. 1) на сложенных внахлестку образцах-свидетелях. Величина сопротивления измеряется микроомметром М246 или иным измерителем малых сопротивлений, подключенным к электродам измерительного устройства. При правильной подготовке поверхности контактное сопротивление не должно превышать 120 мком в течение всего цикла сварки деталей. [c.54]
Лучшие результаты дает химическая очистка (травление), осуществляемая погружением деталей в специальные ванны (после предварительного их обезжиривания). Основные требования, которым должен удовлетворять травитель а) энергичное растворение окислов при минимальном воздействии на основной, неокисленный сплав и б) образование на поверхности деталей после их травления новой пленки с умеренным электрическим сопротивлением, достаточно стойкой против воздействия кислорода сопротивление этой пленки при хранении деталей перед сваркой не должно быстро увеличиваться. Хорошие результаты дает травление при температуре 17—25 в водном растворе концентрированной ортофосфорной кислоты (Н3РО4) с добавкой 0,1 — 0,3 /о хромпика (Ka fjOj). Травление продолжается 10—15 мин,, после чего детали просушиваются лри комнатной температуре (30 мин.) или, лучше, горячим воздухом при Т = 70- -80°. Детали после такого травления могут храниться перед сваркой на машинах переменного тока до 3 суток, а при сварке запасенной энергией — до 24 час. Контроль качества травления производится измерением контактного сопротивления (специальным чувствительным прибором).
[c.149]
Величину контактного (переходного) сопротивления измеряют микроомметром типа М246, ПКС-1 или иными приборами, измеряющими малые электрические сопротивления. При правильном режиме подготовки поверхности деталей величина контактного сопротивления не должна превышать 120 мком в течение всего цикла сварки деталей. [c.102]
Хромоникелевые аустенитные стали характеризуются высоким удельным электрическим сопротивлением, примерно в пять раз ббльщим, чем у обычных малоуглеродистых сталей. Это определяет выбор режимов сварки этих сталей как при контактной сварке, так и при дуговой плавящимся электродом и электрощла-ковой сварке. Так, например, при сварке плавящимся электродом высокое удельное электрическое сопротивление q при низкой удельной теплопроводности % металла приводит к увеличению скорости плавления электрода и ограничивает при определенных диаметре и длине электрода допустимые значения силы тока. Поэтому при ручной дуговой сварке штучными электродами, имеющими стержень из аустенитной стали, приходится применять меньшую предельную силу тока для данного диаметра электрода и уменьшать длину электрода в сравнении с электродами из малоуглеродистой стали.
[c.54]
область применения, сущность, техника работы, безопасность
Электродуговая сварка – самый старый и распространенный вид сварки, который можно отнести к разряду универсальных.
Сущность электродуговой сварки
Сущность электродуговой сварки заключается в том, что соединение осуществляется электродом, который равномерно покрыт горючей силикатной обсыпкой, которая при горении оплавляет электрод, соединяющие две металлические поверхности.
В Российской и зарубежной технической номенклатуре дуговую сварку принято обозначать следующими буквенными обозначениями:
- РДС – ручная дуговая сварка, обозначение которое является единым для всех обозначений дуговой электродной сварки;
в зарубежных обозначениях выделяют следующие:
- MMA – металлическая ручная сварка электрической дугой;
- SMAW – дуговая сварка в среде-протекторе, например, в среде флюса для защиты сварных поверхностей от воздуха.
Основная цель применения газосварочного оборудования – это соединение или резка металлических элементов. Как и любое оборудование, оно может быть стационарным или переносным. Читайте подробнее о газосварочном оборудовании.
Аргонодуговая сварка получила такое название из-за специфики своего действия: в среде инертного газа-аргона возникает дуговой разряд, который ведет к образованию плавильной ванны и соединения металлических поверхностей между собой. Детальнее читайте здесь.
Технологически и функционально дуговую сварку можно применять в двух случаях:
- соединение однородных металлических поверхностей – задача, которая является первостепенной;
- выполнение наплавок и восстановление деталей электродуговой сваркой. Актуально при возникновении трещин, каверн или в случае, когда требуется усиление ребер жесткости и т.п.
Технология электродуговой сварки
Принцип работы дуговой сварки отличается простотой и элементарной электрической схемой: от баласного инвертора или трансформатора ток подается к “держаку”, состоящему из трех жестких жил – катода, анода и фазной перемычки.
Между “плюсом” и “минусом” зажимается электрод. От сварных поверхностей необходимо пустить заземляющий провод, для того, чтобы контур “сварная поверхность – баласник” был замкнутым.
Также очень важно помнить о заземлении при выполнении сварных наплавок на подшипник, так как при воздействии РДС на подшипник могут возникнуть блуждающие токи, что приведет к поломке подшипниковой обоймы при эксплуатации.
Также необходимо помнить о длине дуги, при высоких токах дуга возникает при близком расстоянии электрода от поверхности (ток для резки поверхностей).
Баласник и инвертор устроены таким образом, что при повышении тока и уменьшении напряжения сварочный аппарат работает на сварку, при пропорциональном изменении параметров на резку металла.
Виды электродов:
- электрод в силикатной обсыпке. Такие электроды служат для соединения или резки, являются самыми распространенными. Выполняются в различных диаметрах: 3 и 4 миллиметра для грубых и более тонких работ;
- вольфрамовые электроды. Такими электродами пользуются для того, чтобы варить цветные металлы или разнородные поверхности.Электроды из вольфрама не плавятся, благодаря свойствам металла, но создают достаточную температуру для использования присадочных прутков.
- электроды в стеклянной обсыпке. Такие электроды чаще всего используются для электродуговой сварки труб, так как шлаковый шлейф отстает самостоятельно, сбивать его не требуется, соответственно уменьшается риск повреждения трубы при ударе.
Сварочный карандаш по внешнему виду представляет трубку или стержень, который туго заполнен сухим спрессованным горючем веществом, вещество при сгорании образует номинальное количество тепла, которого достаточно для оплавления металлических кромок и возникновения сварочной ванны.
Полуавтоматическая сварка в защитной газовой среде, широко применяется при кузовном ремонте на специализированных СТО, при строительно-монтажных работах и многих других областях производства. Подробнее читайте здесь.
Виды дуговой сварки в зависимости от положения
Сварка электрической дугой в нижнем положении. Соединение металлических поверхностей таким способом чаще всего чревато непроварами или возникновением прожогов, для того, чтобы этого избежать поверхности
устанавливают на съемных стальных подставках, а после выкладки основного шва проводят еще один “проварочный” шов с обратной стороны.
Сварочными роботами принято называть полностью автоматизированные системы для выполнения сварочных работ с возможностью программирования.
Читайте подробнее о сварочном роботе.
Аппараты контактной сварки применяются в тех случаях, когда сваривание металлических запчастей происходит при их нагревание посредством электрического тока дуги. Подробнее о технологии и аппаратах контактной сварки.
Сварка РДС в верхнем положении. Такой вид сварки несколько опасен, так как сварочная ванна может “пролиться” на сварщика и привести к серьезным повреждениям, как правило, сварку в вернем положении выполняют коротким швами-прихватами, после чего шов проваривается полностью так же короткими промежутками по 3-4 сантиметра.
Правила безопасности при электродуговой сварке
Поскольку основными поражающими факторами являются электрический ток и температура, то к сварщикам предъявляются следующие требования:
- использование поляризационного затемняющего щитка, который убережет глаза от ожогов при дуговой вспышке. Так же щиток убережет лицо от ожогов;
- все работы желательно производить в резиновых перчатках на слое диэлектрика, чтобы ток не пошел через тело человека на замыкание контура “баласник-сварочная поверхность”;
- сварочные поверхности раскаляются и оплавляются, необходимо соблюдать осторожность, чтобы не обжечься;
- электрические кабеля не должны находится лужах или в снегу, во избежание короткого замыкания.
Соблюдение этих простых правил убережет сварщика от повреждений, которые могут привести к инвалидности или смерти.
Плюсы и минусы электродуговой сварки
К положительным критериям можно отнести следующие:
- возможность сварки в любых пространственных позициях, в зависимости от умения сварщика;
- возможность сварки практически любых видов сталей;
- возможность быстрого перехода с металла на металл для формирования стяжек и наплавок электродами;
- технологическая простота и эффективность;
Сварочная горелка – это основная часть сварочного оборудования. Она отвечает за обеспечение подвода электрического тока при электросварке к электроду. Читайте подробнее о сварочной горелке.
Читайте подробнее о ремонте сварочных аппаратов тут.
К минусам относятся:
- вредные условия труда, электромагнитное излучение;
- качественный сварщик – качественный шов;
- по сравнению с автоматической сваркой несколько низкий КПД.
Читайте также:
- Роботизированная сварка Сварочными роботами принято называть полностью автоматизированные системы для выполнения сварочных работ с возможностью […]
- Преимущества плазменной сварки Чрезвычайно похожая на аргонную, плазменная сварка, происходит при помощи потока плазменной дуги. Дуга должна быть направлена в нужное русло, […]
Контактная электрическая сварка
Контактная сварка -это один из наиболее эффективных, экономичных, высокомеханизированных и автоматизированных способов сварки, обеспечивающих высокую прочность, качество и надежность сварного соединения и широко используемых в строительстве для сварки арматуры, трубопроводов, рельсов и т.д. Изготовление наиболее дорогих и сложных узлов легковых и грузовых автомобилей — кузовов и кабин тоже основывается на электроконтактной сварке. Многие конструктивно сложные детали в машиностроении изготовляются путем точечной сварки штампованных из листового проката заготовок.
Способы электроконтактной сварки подразделяются на три группы (рис. 2.36): стыковая, точечная и шовная.
Электроконтактная сварка деталей (рис. 2. 37) выполняется следующим образом: детали сжимают усилием Р, через стык их пропускается электрический ток J в течении времени t , происходит нагрев металла в зоне контакта до температуры плавления, выключается электрический ток, деталь охлаждается и кристаллизуется сварной шов, снимается нагрузка.
Количество тепла, выделившегося при прохождении электрического тока находится по формуле:
Q= J 2 R t, Дж.
Напряжение сварки U по сравнению с электродуговой сваркой очень низкое (всего 1…6 В), а токи измеряются сотнями и тысячами А. Поэтому понижающий трансформатор конструктивно отличается от сварочных трансформаторов для электродуговой сварки: вторичная обмотка имеет от 1 до 6 витков, а сила тока J регулируется изменением количества витков первичной обмотки (рис. 2.38). Сопротивление R зависит от чистоты, шероховатости и загрязнения поверхности свариваемых деталей, электрического сопротивления материала, давления сжатия деталей и др. Время сварки t изменяется от сотых долей секунды до нескольких минут. Из-за малого времени сварки снижаются окисляемость материалов деталей и величина зоны термического влияния, поэтому при сварке будут минимальные деформации и хорошее качество наплавленного металла.
Стыковой сваркой (рис. 2.38) свариваются арматурные стержни, полосы, трубы, фланцы, швеллера, рельсы. Применяются три разновидности стыковой сварки: сопротивлением, непрерывным и периодическим оплавлением.
При сварке сопротивлением торцы свариваемых деталей тщательно обрабатывают, детали сводят до соприкосновения и включают электрический ток. После нагрева металла до пластичного состояния выключают ток и снимают нагрузку. Сваркой сопротивлением можно сваривать детали сечением до 300 мм2, например, трубы — диаметром до 40 мм.
При сварке непрерывным оплавлением после сжатия деталей производят нагрев стыка до его оплавления электрическим током. С торца выдавливается жидкий металл, а с ним окислы и загрязнения с поверхности контакта, поэтому особой подготовки детали перед сваркой не надо. После выключения электрического тока кристаллизуется расплавленный металл и образуется сварной шов. Этим способом можно сварить детали значительно большего сечения (до 3000 мм2) чем при сварке сопротивлением.
Сварка прерывистым оплавлением выполняется периодическими короткими замыканиями и размыканиями электрического тока за счет перемещения детали. При этом появляются искры и разбрызгивание металла. Этот способ сварки эффективен для легированных сталей (30ХГСА,…).
Точечная сварка используется в основном для сварки листовых конструкций, соединения пересекающих стержней (арматура железобетонных конструкций). Суммарная толщина листов обычно не превышает 10 …12 мм (возможна до 20 мм для листовой сварки), а других элементов до 30 мм.
Сварные соединения могут реализовываться по разному (рис. 2.39): одноточечная 2-х сторонняя; 2-х точечная односторонняя и многоточечная односторонняя. Последний способ обеспечивается аналогично как и 2-х точечная односторонняя, только в этом случае для каждой пары точек сварки необходима своя вторичная обмотка, так, например, для 40 -точечной контактной сварки необходимо 20 вторичных обмоток трансформатора.
При двухсторонней одноточечной сварке нижний электрод неподвижен, а верхний перемещается с помощью механизма сжатия (механический, пневматический или электрический привод).
После установки и сжатия (рис.2.40) деталей включается трансформатор, металл нагревается в зоне контакта до образования ядра из расплавленного металла, увеличивается нагрузка сжатия и выключается ток, кристаллизуется расплавленный металл и детали свариваются. Место контакта электрода с деталью нагревается меньше, т.к. тепло отводится через водоохлаждаемые медные электроды. Для сварки конкретных деталей могут использоваться схемы выполнения сварки. отличающиеся от схемы, представленной на рис. 2.40.
Для сварки углеродистых и низколегированных сталей применяются мягкие режимы (большое время выдержки (t=0,2…3 с и небольшая плотность тока J=80…160 А/ мм2), а для сварки низкоуглеродистых и высоколегированных сталей, не склонных к закалке, – жесткие режимы (t=0,001…0,1 с, J=150…350 А/ мм2).
Разновидность точечной сварки — рельефная (рис. 2.41.). Сначала создаются холодной пластической деформацией выступы на свариваемых поверхностях, а затем детали сжимаются и через них пропускается электрический ток, т.е. производится электроконтактная сварка..
Шовная контактная сварка (рис. 2.42) применяется для получения прочных и герметичных швов (тонкостенные сосуды, тонкостенные сварные трубы,..) Листы толщиной 0,3.. 3 мм собирают внахлестку, сжимают двумя медными роликами, пропускают через них электрический ток, ролики вращаются, листы или ролики перемещаются, происходит контактная сварка. Два способа шовной сварки: непрерывная и прерывистая. При непрерывной контактной сварке изделий из малоуглеродистой стали толщиной менее 1мм выполняется непрерывная подача электрического тока. Для более толстых изделий используется прерывистая сварка: ролики вращаются непрерывно, а ток подается периодическими импульсами ; образуется ряд непрерывных точек, которые перекрывая друг друга в итоге образуют сплошной сварной шов.
Конденсаторная сварка. Энергия накапливается в конденсаторах, которые разряжаются или непосредственно через изделие или через дополнительный трансформатор на изделие. Чаще всего используется второй способ. Конденсаторной сваркой соединяют металлические детали толщиной 0,005 … 2 мм., но можно приварить тонкий металл (толщиной 0,2…0,3 мм) к металлическим деталям большой толщины (до 10…15 мм). Конденсаторные установки имеют маленькую мощность и обеспечивают высокое качество сварных соединений.
Для повышения твердости и износостойкости рабочих поверхностей деталей и при ремонте посадочных мест под подшипники качения валов, отверстий редукторов, коробок перемены передачи, шеек коленчатых валов двигателей широко используется электроконтактная приварка ленты, проволоки или порошка. Технология приварки ленты включает в себя: подготовку детали (шлифование до размера: dн — 0,3 мм), нарезку заготовок ленты по ширине и длине (периметру) и очистку ленты, предварительную приварку ленты в середине. Далее выполняется приварка ленты (порошка, проволоки) с помощью роликов установки электроконтактной сварки.
Тепловые деформации при этом малы, материал подбирается высокой износостойкости, обеспечивается долговечность не ниже новых деталей, исключается термическая деформация деталей.
Сортировать по: актуальность —
Дата 30,23 доллара в час
26,88 долларов в час
30 долларов.
27,18 долларов в час
31 586 долларов в год
19,32 доллара в час
| Будьте первыми, кто увидит новыеэлектросварочные работы Создавая оповещение о вакансиях, вы соглашаетесь с нашими Условиями.![]() |
Урок 1 — Основы дуговой сварки
Урок 1 — Основы дуговой сварки © АВТОРСКИЕ ПРАВА 1999 УРОК ГРУППЫ ЭСАБ ИНК. I, ЧАСТЬ B 1.8 ЭЛЕКТРИЧЕСТВО ДЛЯ СВАРКИ 1.8.1 Принципы электричества — Дуговая сварка — это метод соединения металлов вместе с обработан путем применения достаточного электрического давление на электрод для поддержания пути тока (дуги) между электродом и заготовкой.В этом процессе электрическая энергия заменяется на тепловая энергия, переводящая металлы в расплавленное состояние; посредством чего они соединяются. Электрод (проводник) либо плавится и добавляется к основному металлу или остается в твердом состоянии государственный. Вся дуговая сварка использует передачу электрической энергии в тепло. энергия, и понять этот принцип, базовые знания об источниках электричества и сварочного тока необходимо.
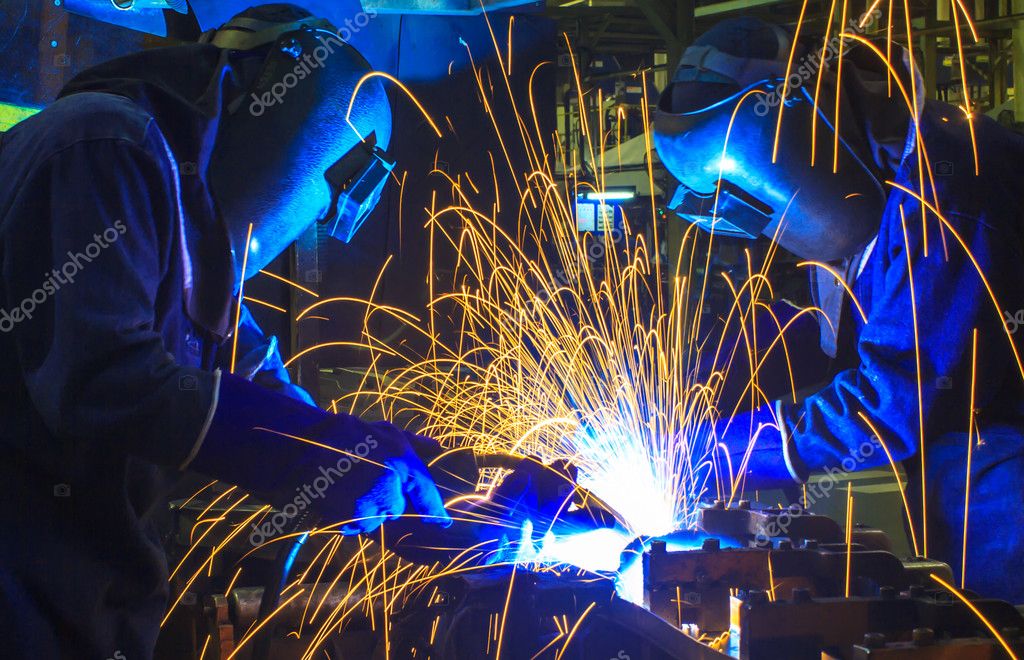
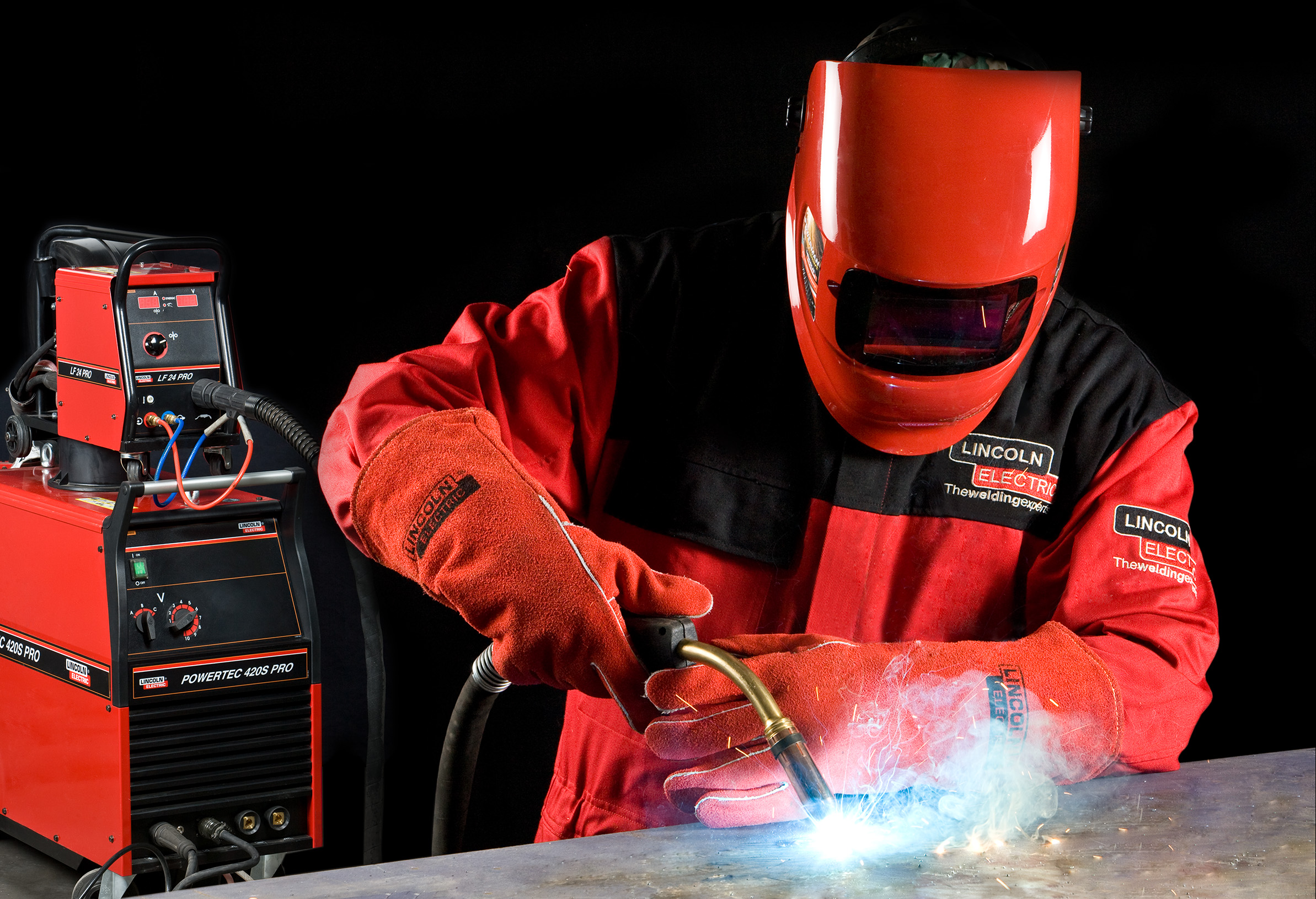
Электросварка изобретена Элиу Томсоном в 1877 году
Изобретен: Элиху Томсон
Изобретен в год: 1877
Процесс нагрева и сварки двух металлических частей вместе с помощью мощного электрического тока известен как электросварка.Процесс электросварки включает соединение двух металлических деталей с помощью медных зажимов. Электричество пропускается через детали, нагревая их и соединяя в точке, где встречаются две металлические детали. Похоже, что тепло будет самым большим в точке встречи двух металлов, но область, где металлы закручиваются и не соприкасаются, сначала нагревается, а затем излучается наружу к стыкам. Распределение тепла регулируется путем обеспечения равномерного движения с помощью регулирующего рычага.Это гарантирует, что оба металла станут мягкими и соединятся друг с другом одновременно. После завершения процесса электросварки образуется бесшовное соединение.
История и развитие электросварки
В 1802 году Василий Петров, русский физик-экспериментатор, открыл непрерывную электрическую дугу и впоследствии предложил ее возможные практические применения, включая сварку. Но какое-то время его видение не находило применения. Но в другом месте Элиу Томсон (29 марта 1853 — 13 марта 1937), британский инженер и изобретатель, страстно увлекался механическими и электрическими материалами и их применением.В 1877 году он изобрел электросварку. Он подал заявку на свое изобретение 14 июня 1890 года, и 28 апреля 1891 года ему был выдан номер патента: 451345. Преобладающий метод электросварки до изобретения Элиху Томсона предполагал одновременное применение давления, удара или другой объединяющей силы. с применением нагревающего электрического тока, предназначенного для приведения материала в надлежащее пластичное состояние. Изобретение Томаса позволяло электрическому току течь до тех пор, пока куски металла не были доведены до желаемой температуры сварки или рабочей температуры, прежде чем их можно было соединить.Другими словами — в изобретении Томсона сварка, ковка или формовка выполнялись после того, как материал был доведен до надлежащего пластичного состояния.
После этого ток был отключен, а затем материал был сварен, кован или обработан молотками, валками, штампами или другими подходящими устройствами в соответствии с требованиями клиента. Это была многоэтапная процедура, а не одна громоздкая процедура.
К концу 19 века были разработаны различные способы сварки.
Различные методы электросварки
Дуговая сварка — Дуговая сварка — это тип сварки, в котором используется источник сварочного тока для создания электрической дуги между электродом и основным материалом для плавления металлов при сварке точка.Он используется для соединения металла путем плавления основного металла и добавления металла в соединение, обычно обеспечиваемое расходуемым электродом. Этот метод был изобретен в 1881-82 годах русским изобретателем Николаем Бернардосом. Он создал первый метод электродуговой сварки, известный как углеродная дуговая сварка, с использованием углеродных электродов. К концу 19 века русский Николай Славянов и американец К. Л. Коффин изобрели металлические электроды. Около 1900 г. А. П. Штроменгер выпустил в Великобритании металлический электрод с покрытием, который давал более стабильную дугу.В 1905 году русский ученый Владимир Миткевич предложил использовать для сварки трехфазную электрическую дугу. В 1919 году сварка на переменном токе была изобретена К.Дж. Холслагом.
Дуговая сварка под флюсом — Он был изобретен в 1930 году и пользуется популярностью до сих пор.
Подводная электродуговая сварка — В 1932 году россиянин Константин Хренов успешно осуществил первую подводную электродуговую сварку.
Газовая дуговая сварка вольфрамом — усовершенствована в 1941 году.
Газовая дуговая сварка металлов — Изобретенный в 1948 году, он позволял осуществлять быструю сварку цветных металлов.
Порошковая сварка — Этот метод сварки был изобретен в 1957 году. В этом методе самозащитный проволочный электрод можно использовать с автоматическим оборудованием, что значительно увеличивает скорость сварки.
Плазменно-дуговая сварка — также была изобретена в 1958 году.
Электрошлаковая сварка — Изобретена в 1958 году.
Электрогазовая сварка — двоюродный брат электрошлаковой сварки, она была изобретена в 1961 году.
Роль электросварки в улучшении жизни человека
- Электросварка не тратит лишнее топливо и обеспечивает заданную точность. Тепло не выходит далеко за пределы точки сварки. Это делает его идеальным для изолированных проводов. Концы каждого провода можно сваривать, оставляя изоляцию нетронутой.
- Thomas’s Electric Welding привел к разработке и производству различных машин для электросварки.Эти машины упростили процесс сварки до такого уровня, что некоторые из них работают автоматически.
Они сводят к минимуму ручной труд, и им могут управлять даже механики с ограниченными техническими знаниями.
- Электросварка также привела к развитию различных методов электросварки, отличающихся друг от друга как по принципу, так и по применению.
- Электросварка сегодня используется во многих промышленных целях, превосходя ее первоначальное применение в различных отраслях промышленности.
Дуговая сварка и опасность поражения электрическим током
Для дуговой сварки требуется электрическая цепь под напряжением. Это означает, что все сварщики, использующие ручное оборудование, подвергаются риску поражения электрическим током и ожогов. Риск при сварке MIG / MAG и TIG намного меньше, поскольку сварочный ток обычно включается и выключается с помощью куркового или ножного переключателя. Опасность поражения электрическим током — одна из самых серьезных и непосредственных опасностей, с которыми вы сталкиваетесь как сварщик. Контакт с металлическими частями, которые являются «электрически горячими», может привести к травмам или смерти из-за воздействия удара на ваше тело или падения, которое может возникнуть в результате вашей реакции на удар. Во время большинства операций ручной дуговой сварки электрический ток составляет от 10 до 600 ампер. Помните, что для того, чтобы убить большинство людей, требуется всего от 70 до 100 миллиампер, а 70 миллиампер — это лишь часть одного усилителя. Лучшая защита — не стать заземленным.
Опасность поражения электрическим током, связанная с дуговой сваркой, можно разделить на две совершенно разные категории:
— Удар первичного напряжения (т. Е. 230, 460 В)
— Удар вторичного напряжения (т. Е., 20-100 вольт)
Удар первичного напряжения
Поражение первичным напряжением очень опасно, поскольку оно намного превышает вторичное напряжение. Вы можете получить удар от первичного (входного) напряжения, если прикоснетесь к проводу внутри сварочного аппарата при включенном питании к сварочному аппарату , когда вы держите тело или руку на корпусе сварочного аппарата или другом заземленном металле.
- Помните, что выключение выключателя питания сварочного аппарата не приводит к отключению питания внутри сварочного аппарата.
Входной шнур питания должен быть отключен, или выключатель питания должен быть выключен.
- Никогда не снимайте фиксированные панели со сварочного оборудования, это всегда должен устанавливать квалифицированный электрик.
- Когда к сварочному аппарату подключены линии электропитания, проверьте паспортную табличку сварочного аппарата и инструкции по подключению, чтобы убедиться, что на входе правильная фаза (однофазная или трехфазная) и напряжение.
- Многие сварочные аппараты могут быть настроены для работы в однофазном или трехфазном режиме и на несколько входных напряжений.Убедитесь, что сварочный аппарат настроен на электропитание, к которому он подключен.
- Только квалифицированный электрик должен подключать входное питание.
- Корпус необходимо заземлить, чтобы при возникновении проблемы внутри сварочного аппарата перегорел предохранитель, отключив питание и сообщив о необходимости ремонта.
Никогда не игнорируйте перегоревший предохранитель, потому что это предупреждение о том, что что-то не так.
Разряд вторичного напряжения
Вторичный электрический разряд возникает, когда вы касаетесь части цепи электрода — возможно, оголенного участка на кабеле электрода — в то же время, когда другая часть вашего тела касается металла, с которым вы свариваете (работаете).Чтобы получить удар, ваше тело должно одновременно коснуться обеих сторон сварочного контура — электрода и рабочего (или сварочного заземления). Чтобы предотвратить поражение вторичным напряжением, вы должны выработать и использовать безопасные рабочие привычки:
- Помните, что напряжение на электроде самое высокое, когда вы не ведете сварку (напряжение холостого хода).
- При сварке надевайте сухие перчатки в хорошем состоянии.
- Не прикасайтесь к электроду или металлическим частям электрододержателя кожей или влажной одеждой.
- Держите сухим. Изоляция между вашим телом (включая руки и ноги) и свариваемым или шлифуемым металлом (например, металлический пол, мокрая земля).
- Поддерживайте сварочный кабель и электрододержатель в хорошем состоянии. Отремонтировать или заменить поврежденную изоляцию
Помните, что стержневой электрод всегда «электрически горячий», когда сварщик включен — обращайтесь с ним уважительно. Если вы действительно испытали электрический ток, воспринимайте это как предупреждение — проверьте свое оборудование, рабочие привычки и рабочую зону, чтобы увидеть, что не так, прежде чем продолжить сварку.
РЕЗЮМЕ
ОПАСНОСТЬ | ФАКТОРЫ ДЛЯ РАССМОТРЕНИЯ | РЕЗЮМЕ |
---|---|---|
Поражение электрическим током может убить |
|
|
Что такое электросварка? (с изображением)
Электросварка — это процесс нагрева и сварки двух металлических частей вместе с помощью мощного электрического тока. Его изобрел профессор Элиху Томсон. Это требует использования специального устройства, называемого динамо-машиной, которое выпускает ток, используемый для сварки.
В отличие от более традиционных методов, электросварка требует минимальных навыков и понимания со стороны оператора динамо-машины.Он должен только изучить надлежащую температуру сварки используемого металла, но не обязан изучать более сложные процессы традиционной сварки. Использование динамо-машины при этом типе сварки является саморегулирующимся, и для нормальной работы требуется лишь периодическая смазка. Это делает этот метод идеальным для начинающего сварщика.
Сплав и любые два подобных куска металла можно соединить электросваркой. Таким же образом можно сваривать два разных куска металла, если точка сварки одного из них не превышает точку сварки другого. Если разница в температуре сварки является проблемой, металлы все еще можно сваривать с использованием заусенцев в точке сварки.
В процессе электросварки металлические детали соединяются между собой медными зажимами. Электричество пропускается через детали, нагревая их и соединяя в точке, где встречаются две металлические детали.Кажется, что тепло будет самым большим в точке встречи двух металлов, но область, где металлы закручены и не соприкасаются, сначала нагревается, а затем излучается наружу к стыкам.
Распределение тепла регулируется путем обеспечения равномерного движения с помощью регулирующего рычага. Это гарантирует, что оба металла станут мягкими и соединятся друг с другом одновременно. После завершения процесса электросварки образуется бесшовное соединение.
Преимущества электросварки заключаются в том, что этот метод не расходует лишнее топливо и обеспечивает заданную точность. Тепло не выходит далеко за пределы точки сварки. Это делает его идеальным для изолированных проводов.Концы каждого провода можно сваривать, оставляя изоляцию нетронутой.
Хотя электросварка может потреблять до 50 000 ампер электричества, она использует электродвижущую силу, которая содержит только половину вольта электричества. Это делает динамо-машину неспособной поражать человека электрическим током или шокировать его во время использования. Сварка с использованием электричества может занимать от долей секунды до нескольких минут в зависимости от задачи, и этот метод можно использовать как для больших, так и для небольших работ.
Школа электросварки Линкольна объявляет расписание на четвертый квартал 2010 года
КЛИВЛЕНД — Школа электросварки Линкольна, которая обучила более 120 000 студентов с момента ее основания в 1917 году, объявляет о своем расписании на четвертый квартал 2010 года.
Школа электросварки Линкольна — старейшая и одна из самых уважаемых школ дуговой сварки в Соединенных Штатах. Занятия проводят семь штатных преподавателей школы, которые имеют более чем 100-летний опыт работы в отрасли. Курсы предназначены для обучения навыкам дуговой сварки, которые необходимы работодателям. Студенты, прошедшие обучение в компании Lincoln, пользуются большим спросом у производителей сварочного оборудования с уровнем оплаты труда, который обычно превышает средний по отрасли.
Классы на четвертый квартал варьируются от шестинедельного базового курса до продвинутого 15-недельного комплексного курса, а также недельные занятия по конкретным сварочным процессам, сертификации и индивидуальным программам.Студенты проводят 80 процентов своего времени в кабине, обучаясь сварке. Кроме того, Lincoln ограничивает размер классов до 15 студентов в классе, чтобы максимизировать обучение и гарантировать индивидуальное обучение.
Курсы, запланированные на октябрь-декабрь 2010 г., включают:
Введение в сварку: знакомит сварщиков со всеми стандартными сварочными процессами. Этот недельный курс длится 18 октября.
Комплексная программа: обучите сварщиков правилам дуговой сварки и всем обычным сварочным процессам.Курс длится 15 недель и включает более 540 часов практических занятий. Этот курс предлагается 25 — 11 марта 2011.
Подготовительный курс к сертификации сварщиков: готовит их к семинару и экзамену сертифицированного инспектора по сварке (CWI) Американского общества сварщиков (AWS). Этот недельный курс предлагается в течение недели, начиная с 11 октября.
Семинар и экзамен AWS CWI: Lincoln Electric является местом проведения семинара и экзамена по AWS CWI. На семинаре под руководством инструктора AWS рассказывается, как ссылаться на код AWS, исследовать сварные швы и подготовиться к экзамену CWI в следующую субботу (под контролем AWS).Эти курсы предлагаются 1-23 октября.
Основной листовой и листовой металл: инструктирует сварщиков по процессу сварки штангой. Шестинедельные занятия предлагаются с 25 октября по декабрь. 3.
Сварка труб: инструктирует сварщиков по процессу сварки труб штангой в соответствии со стандартами сварки Американского общества инженеров-механиков (ASME) (вертикально вверх) или Американского института нефти (API) (вертикально вниз). Шестинедельный курс будет предлагаться в течение нескольких недель октября.25 дек. 3.
Плазма, кислородное топливо, сплавы и закалка: инструктирует сварщиков по плазменной резке и дуговой строжке, кислородно-топливному процессу, теории сплавов и их применениям, а также наплавке твердым сплавом. Трехнедельные занятия будут проводиться с 25 октября по ноябрь. 12.
Дуговая сварка вольфрамовым электродом в газовой среде: инструктирует сварщиков по процессу сварки TIG. Недельный курс предлагается 4 октября, 15 ноября, 6 декабря и 13 декабря.
Газовая дуговая сварка металла / полуавтоматическая сварка: инструктирует сварщиков по процессу сварки MIG.Недельный курс проводится с 11 октября, 1 ноября, 22 ноября, 6 декабря и 13 декабря.
Дуговая сварка порошковой проволокой / полуавтоматическая сварка: инструктирует сварщиков по процессу сварки порошковой проволокой для как с самозащитой, так и с газовой защитой. Недельные занятия проходят с 18 октября по 29 ноября.
Классы заполняются быстро, поэтому заинтересованным студентам рекомендуется зарегистрироваться по крайней мере за месяц. Чтобы зарегистрироваться, позвоните в школу сварки Линкольна по телефону 216 / 383-8325 или посетите сайт www.lincolnelectric.com.
Lincoln Electric подписывает окончательное соглашение о приобретении компании Air Liquide Welding Nasdaq: LECO
КЛИВЛЕНД, 27 апреля 2017 г. (GLOBE NEWSWIRE) — Lincoln Electric Holdings, Inc., («Компания») (Nasdaq: LECO) объявила сегодня, что она заключила окончательное соглашение с Air Liquide о приобретении своей дочерней компании Air Liquide Welding («Предлагаемое приобретение»). По завершении Предполагаемого приобретения дополнительный бизнес расширит глобальный портфель расходных материалов Lincoln Electric и расширит охват каналов сбыта систем оборудования и решений Harris Product Group в Европе. Комбинация также предложит европейским клиентам более комплексные решения для сварки и резки, более широкий технический опыт применения и более высокий уровень обслуживания.
Lincoln Electric ожидает, что предлагаемое приобретение после его завершения приведет к немедленному увеличению прибыли, за исключением транзакционных издержек, и обеспечит привлекательную рентабельность капитала в первые пять лет.
«Мы воодушевлены перспективой объединения двух ведущих организаций по сварке и резке, которые стремятся предоставлять лучшие в своем классе инженерные решения», — сказал Кристофер Л.Мейпс, председатель, президент и главный исполнительный директор Lincoln Electric. «Взаимодополняющий характер бизнеса усилит наше географическое присутствие и продвинет нашу« Стратегию на 2020 год », чтобы стимулировать рост в привлекательных конечных секторах и приложениях. Это также обеспечит большую эффективность в цепочке поставок, инфраструктуре обслуживания, коммерческом охвате и разработке новых продуктов, что укрепит долгую историю Lincoln Electric по созданию стоимости для наших акционеров ».
Предлагаемая информация о приобретении
Окончательное соглашение отражает покупную цену в 115 миллионов евро (приблизительно 125 миллионов долларов США) для бизнеса Air Liquide Welding, оцениваемую примерно в 7x Скорректированная EBITDA (полный 2016 год).Предполагается, что предлагаемое приобретение, за исключением транзакционных издержек, немедленно приведет к увеличению прибыли Lincoln Electric на уровне примерно 0,03 доллара США на одну разводненную обыкновенную акцию (EPS) в квартал, или 0,12 доллара США в год, в первый год после приобретения и примерно 0,06 доллара США на акцию в квартал. , или 0,24 доллара в год на второй год работы.
Предполагаемое приобретение требует обычных разрешений регулирующих органов и других условий закрытия и, как ожидается, завершится во второй половине 2017 года.До закрытия Предполагаемого приобретения Lincoln Electric и Air Liquide Welding будут продолжать работать как независимые компании и будут продолжать обслуживать своих клиентов и создавать ценность для своих акционеров.
Для получения дополнительной информации о предлагаемом приобретении посетите веб-сайт Lincoln Electric по связям с инвесторами по адресу: http://ir.lincolnelectric.com.
Информация о веб-трансляции
Lincoln Electric проведет телефонную конференцию для инвесторов в пятницу, 28 апреля 2017 г., в 9:00.м. (ET) для более подробного обсуждения Предлагаемого приобретения.
Конференц-звонок будет транслироваться в прямом эфире, а доступ к веб-трансляции, а также к сопроводительным презентационным материалам можно будет получить на домашней странице компании по связям с инвесторами http://ir.lincolnelectric.com. Слушатели должны зайти на веб-сайт до звонка, чтобы зарегистрироваться, загрузить и установить любое необходимое аудио программное обеспечение. Инвесторы, которые не могут получить доступ к веб-трансляции, могут послушать конференц-звонок в прямом эфире по телефону, набрав (877) 344-3899 (внутренний) или (315) 625-3087 (международный), и должны использовать код подтверждения 14202988. Участников по телефону просят набрать за 10–15 минут до начала конференц-связи.
Повтор звонка будет доступен через веб-трансляцию на сайте Компании.
О компании Lincoln Electric
Lincoln Electric является мировым лидером в области проектирования, разработки и производства оборудования для дуговой сварки, роботизированных систем дуговой сварки, оборудования для плазменной и газокислородной резки, а также занимает лидирующие позиции на мировом рынке припоев и припоев. .Компания Lincoln со штаб-квартирой в Кливленде, штат Огайо, имеет 47 производственных предприятий, включая производственные предприятия и совместные предприятия в 19 странах, а также всемирную сеть дистрибьюторов и офисов продаж, охватывающую более 160 стран. Для получения дополнительной информации о Lincoln Electric, ее продуктах и услугах посетите веб-сайт компании www.lincolnelectric.com.
О компании Air Liquide Welding
Air Liquide Welding, дочерняя компания Air Liquide, является ключевым игроком в производстве технологий сварки и резки. В Air Liquide Welding работает около 2000 сотрудников по всему миру, а объем продаж в 2016 году составил около 350 миллионов евро. Он предлагает через несколько всемирно известных брендов (SAF-FRO и OERLIKON в области промышленности, CEMONT для профессионалов) широкий спектр сопутствующего оборудования, расходных материалов и услуг на рынке.
Заявления о перспективах
Ожидания и убеждения Компании в отношении будущего, содержащиеся в этом пресс-релизе, являются прогнозными заявлениями по смыслу Закона о реформе судебных разбирательств по частным ценным бумагам 1995 года.Эти заявления отражают текущие ожидания руководства и включают ряд рисков и неопределенностей, которые могут привести к тому, что фактические события или результаты будут существенно отличаться от явно выраженных или подразумеваемых. Заявления о перспективах обычно можно идентифицировать с помощью таких слов, как «может», «будет», «ожидать», «намереваться», «оценивать», «ожидать», «полагать», «прогнозировать», «руководствоваться».