Электронно-лучевая сварка — Википедия
Материал из Википедии — свободной энциклопедии
Электронно-лучевая сварка — сварка, источником энергии при которой является кинетическая энергия электронов в электронном пучке, сформированном электронной пушкой.
Используется для сварки тугоплавких, высокоактивных металлов в космической, авиационной промышленности, приборостроении и др. Электронно-лучевая сварка используется и при необходимости получения высококачественных швов с глубоким проплавлением металла, для крупных металлоконструкций.
История
Первая установка для электронно-лучевой сварки была создана в МЭИ в 1958 году. В настоящее время выпускаются установки ЭЛУ-27, ЭЛСТУ-60, MEBW-60 и др.
Сущность
Электронно-лучевая сварка проводится электронным лучом в вакуумных камерах. Размеры камер зависят от размеров свариваемых деталей и составляют от 0.1 до нескольких сотен кубических метров.
Плавление металла при электронно-лучевой сварке и образование зоны проплавления обусловлено давлением потока электронов в электронно-лучевой пушке, выделением теплоты в объеме твердого металла, реактивным давлением испаряющегося металла, вторичных и тепловых электронов и излучением.
Сварка производится непрерывным или импульсным электронным лучом. Импульсные лучи с большой плотностью энергии и частотой импульсов 100—500 Гц используются при сварке легкоиспаряющихся металлов, таких как алюминий, магний. При этом повышается глубина проплавления металла. Использование импульсных лучей позволяет сваривать тонкие металлические листы.
В камере, формирующей электронный луч, откачивается воздух вплоть до давлений 1—10 Па. Это приводит к высокой защите расплавленного металла от газов воздуха.
Приемы сварки электронными лучами
Электронная пушка. 1 — катод, 2 — электрод, 3 — анод, 4 — электромагнитная линза, 5 — отклоняющая катушка, 6 — свариваемое изделиеВ электронно-лучевой сварке применяют следующие технологические приемы для улучшения качества шва:
- сварку наклонным лучом (отклонение на 5—7°) для уменьшения пор и несплошностей в металле;
- сварку с присадкой для легирования металла шва;
- сварку на дисперсной подкладке для улучшения выхода паров и газов из металла;
- сварку в узкую разделку;
- сварку двумя электронными пушками, при этом одна пушка производит проплавление металла, а вторая формирует корень канала;
- предварительные проходы для очистки и обезгаживания кромок свариваемых металлов;
- двустороннюю сварку одновременно или последовательно ;
- развертку электронного луча: продольную, поперечную, Х-образную, круговую, по эллипсу, дуге и т. п.;
- расщепление луча для одновременной сварки двух и более стыков;
- модуляцию тока луча частотой 1—100 Гц. для управления теплоподачей в сварной шов.
Преимущества
Электронно-лучевая сварка имеет следующие преимущества:
- Высокая концентрация теплоты позволяет за один проход сваривать металлы толщиной от 0,1 до 200 мм;
- Для сварки требуется в 10-15 раз меньше энергии чем для дуговой сварки;
- Отсутствует насыщение расплавленного металла газами.
Недостатки
- Образование непроваров и полостей в корне шва;
- Необходимость создания вакуума в рабочей камере.
Оборудование
Электронно-лучевые установки подразделяются на универсальные и специализированные, высоковакуумные (давление менее <10-1 Па), промежуточного вакуума (давление 10—10-1 Па), сварка в защитном газе (103—105 Па), на камерные (изделие внутри рабочей камеры) и с локальным вакуумированием (герметизация изделия в зоне сварки).
В состав установок для электронно-лучевой сварки входит электронная пушка, блоки питания. Электронно-лучевая пушка формирует пучок электронов с высокой плотностью энергии.
См. также
Примечания
Литература
- Николаев Г. А. Сварка в машиностроении: Справочник в 4-х т. — М.: Машиностроение, 1978 (1-4 т).
- Электронно-лучевая сварка/О. К. Назаренко, А. А. Кайдалов, С. Н. Ковбасенко и др./Под ред. Б. Е. Патона.— Киев: Наукова думка, 1987.— 256 с.
- З. Шиллер, У. Гайзиг, З. Панцер. Электронно-лучевая технология. — М.: Энергия, 1980. — 528 с.
- Попов В. Ф., Горин Ю. Н. Процессы и установки электронно-ионной технологии. — М.: Высш. шк., 1988. — 255 с. — ISBN 5-06-001480-0.
- Виноградов М.И., Маишев Ю.П. Вакуумные процессы и оборудование ионно — и электронно-лучевой технологии. — М.: Машиностроение, 1989. — 56 с. — ISBN 5-217-00726-5.
Ссылки
оборудование и установка, технология и обозначение, требования по ГОСТу
Долгое время электродуговая сварочная практика была единственным вариантом. Но техника не стоит на месте, и неизбежно появлялись новые методики. Для любого толкового специалиста важно хотя бы в общих чертах знакомиться с электронно-лучевой сваркой, чтобы понимать, на что она способна и что может дать.
Особенности и область применения
Говоря про электронно-лучевую сварку, следует подчеркнуть прежде всего, что это бурно развивающаяся и неуклонно совершенствующаяся технология. Ее можно использовать при работе с плохо расплавляемыми при обычных условиях или очень активными химически веществами. Электронно-лучевая методика лучше традиционных вариантов справляется с соединением разнородных веществ. Специальные установки находят применение:
- в обработке алюминиевых и легированных стальных заготовок;
- в манипуляциях со сплавами титана, ниобием, цирконием, танталом;
- в производстве изделий из бериллия и сплавов на его основе.
Эта технология востребована в производстве ракет, иных летательных аппаратов и атомных систем. Именно лучевое воздействие позволяет создать очень ровный и однородный по составу шов. Процесс сварки совершается за счет применения кинетической энергии электронов. Соударение их с поверхностью является причиной прогрева металла или сплава. В ГОСТ на электронно-лучевую сварку введены обозначения уровней качества:
- D – минимальный уровень;
- C – среднее качество;
- B – максимально высокой уровень.
Достоинства и недостатки
Вакуумная среда, создающаяся в электронно-лучевой установке, помогает защищать поверхность обрабатываемого изделия. В этом смысле она куда совершеннее, чем даже самые продуманные варианты газовой сварки или сварочных работ под флюсом. Катод тоже очень хорошо защищен в химическом отношении.
Еще одним плюсом оказывается повышенная эффективность дегазации в сварочной ванне. Тот же вакуум является абсолютной гарантией против образования оксидных пленок. Однако все это не означает, что электронно-лучевая методика есть абсолютный идеал. На поверхность попадает сравнительно немного тепла.
Традиционное дуговое воздействие отличается большей мощностью.
Потому ЭЛС резко меняет кристаллическую структуру металла или сплава. Обрабатываемые участки могут подвергнуться короблению. Вернувшись к достоинствам методики, стоит подчеркнуть, что она позволяет обрабатывать керамику и тугоплавкие металлы. Фокусированный луч может обработать участки величиной меньше 1 мм. Отработана технология изготовления ответственных элементов и декоративной продукции, в том числе из стойких к коррозии сплавов.
Еще стоит отметить:
- существенную гибкость регулировки мощности;
- возможность получения узких швов на большой глубине;
- минимизацию риска повреждений при импульсной подаче энергии;
- пригодность для общей термообработки и перфорации металла, для нарезки заготовок.
Но очевидно, что вакуумная среда создается за определенное время. Потому, несмотря на относительно высокую производительность самого рабочего цикла, суммарный выход продукции будет меньше, чем при других технологиях. Корень шва может иметь полость. Предотвратить это помогает только специальная контрольная техника. В любом случае электронно-лучевая сварка невозможна в домашних условиях, она относительно дорога и требует квалифицированных операторов.
Необходимое оборудование
Специальная установка, создающая электронный поток, генерирует его при помощи одной или нескольких «пушек». Сама заготовка находится во время работы в специальной вакуумной камере. Для контроля хода работы используется либо смотровое окошко, либо удаленный монитор с датчиками и магистралями передачи информации. Непосредственное управление работой установки происходит через пульт специальной конструкции. Создание электронного потока в «пушке» происходит при помощи катода, который нагревает обычная спираль сопротивления.
Фокусировка потока выполняется с помощью вспомогательных электродов. На катоде формируют напряжение с отрицательным зарядом. Избежать отталкивания электродов помогает специальный фокусирующий блок. Точность управления обеспечивает система отклонения луча. Стоит учесть, что камеры есть не во всех приборах: многие системы электронно-лучевой сварки создают лишь локальный вакуум непосредственно в рабочей зоне.
Камерные электронно-лучевые аппараты классифицируют по напряжению. Низковольтными считают системы, сконструированные для тока от 10 до 30 кВ. К среднему классу относят сварочные комплексы, рассчитанные на 40-60 кВ. В высоковольтную категорию попадают аппараты, работающие на токе 100-200 кВ.
Также системы электронно-лучевой сварки подразделяют на универсальную и специализированную группу. Первый тип позволяет выполнять ремонтную и экспериментальную сварку. Второй рассчитан только на изготовление однородных элементов. Часть выпускаемого оборудования имеет блоки горизонтального вращения, помогающие обрабатывать трубчатые детали.
Применяемые в микроэлектронной отрасли сварочные комплексы имеют максимально возможную точность расположения лучей.
Технология
Разогрев идет по всему зазору, разделяющему детали. Зона воздействия частиц ограничивается долями микрона, но поскольку их много, особых ограничений на размер обрабатываемого участка нет. Зазоры между соединяемыми конструкциями стараются делать максимально малыми; если толщина металла 20 мм и менее, разрыв должен составлять не более 0,1 мм. Если уменьшить зазор не получается, применяют присадочные металлы. Однако на долю присадки должно приходиться максимум 50% массы шва.
Отклонение электронного луча может составлять максимум 0,3 мм от заданного значения. Катод в электронно-лучевых установках может быть плазменным (тогда говорят о косвенном накале). Катодный элемент прямого накаливания — это вольфрамовая, танталовая либо иная тугоплавкая спираль. Для изготовления анодов применяют сталь либо медь. Вакуумная среда не только обеспечивает защиту свариваемых изделий, но и помогает избежать перегрева катода.
В следующем видео показано, как происходит электронно-лучевая сварка алюминия.
Электронно-лучевая сварка, технология, оборудование, особенности и принцип работы
пер.Каштановый 8/14 51100 пгт.Магдалиновка
Nikolaenko Dmitrij
Электронно-лучевая сварка, технология, оборудование, особенности и принцип работы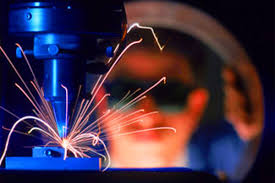
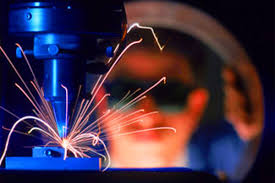
- 5
- 4
- 3
- 2
- 1
Впервые такой метод сварки появился в 1958 году. С помощью электронного луча можно производить сваривание металлов. Электронно-лучевая сварка сводится к соединению двух металлов на их стыке. Проводится она в вакууме, и сваривает детали самой разной конструкции и размеров, с высокой чистотой соединяемого шва.
Источником кинетической энергии электронов, собранных в электронный пучок, который формируется специальным приспособлением, производится соединение металла. Импульсным лучом происходит сваривание металла. Плотность энергии такого луча очень большая, частота импульсов составляет 100-500 Гц, используется при сварке легкоиспаряющихся металлов, например магний и алюминий. При таких параметрах глубина проплавления повышается. Варить можно металл разной толщины, но всегда учитывается какого рода этот металл, его толщина, структура.
Успешно соединяются и тонкие листы, но, перед процессом сварки проводят контрольную подготовку, чтобы правильно установить соотношение времени паузы и импульса. Теплоотвод во время пауз позволяет уменьшить протяженность зоны термического влияния. Когда сваривают мелкие детали, очень важно, чтобы луч точно попадал на малую ширину шва, поэтому, сначала положения луча проверяют на пробном образце. Луч должен точно попадать на соединяемый шов, ни ниже, ни выше, иначе результат соединения не будет качественным. Параметры пучка проверяют путем технологического эксперимента. После этого производят серийное сваривание всех необходимых деталей.
В электронно-лучевой сварке для перемещения луча применяют перемещение самого луча или изделия с помощью отклоняющейся системы. Эта система дает возможность осуществлять колебания луча поперек и вдоль шва, а также по более сложной траектории. Существуют низковольтные и высоковольтные установки. Первые используют при сварке толщины металла 0,5 мм и выше, высоковольтные для более толстого металла.
Созданный вакуум в электронно-лучевой сварке позволяет значительно уменьшить потери кинетической энергии электронов за счет соударения с молекулами газов воздуха и для тепловой и химической защиты катода в электронной пушке. Вакуум составляет порядка 10-4-10-6 мм рт. ст. Проплавление металла происходит в основном давлением потока электронов, выделением теплоты в объеме твердого металла, а также мощным давлением испаряющегося металла. Качество и вид обработки лучом зависит от теплофизических свойств материала, параметра пучка, длительности импульса и не зависит от механических свойств материала. Следовательно, электронным лучом можно обрабатывать: кварц, керамику, драгоценные камни. Успешно применяется для сварки тугоплавких металлов, а также металлов, применяемых в авиационной промышленности, приборостроении. В зависимости от размера вакуумной камеры, можно соединять детали большой толщины.
Преимущества электронно-лучевой сварки:
- можно сваривать детали толщиной от 0,1 до 200 мм. за один проход, а при других условиях и более толстые детали;
- экономичность процесса, требуется в 10-15 раз меньше энергии, чем при дуговой сварке;
- нет газового насыщения металла, что придает прочность шву;
- высокое качество швов, глубокое проплавление металла.
Недостатки такой сварки:
- в корне шва иногда недоваренный шов;
- привязанность к рабочей камере, для создания вакуума.
Электронно-лучевая сварка – от изобретения до наших дней Текст научной статьи по специальности «Нанотехнологии»
УДК 621.791
Е.С. Саломатова E.S. Salomatova
Пермский национальный исследовательский политехнический университет Perm National Research Polytechnic University
ЭЛЕКТРОННО-ЛУЧЕВАЯ СВАРКА -ОТ ИЗОБРЕТЕНИЯ ДО НАШИХ ДНЕЙ
ELECTRON BEAM WELDING:
FROM INVENTION TO OF OUR DAYS
Рассмотрены предпосылки, подтолкнувшие ученых на изобретение электронно-лучевой сварки. Перечислены персоналии, чьи изобретения и научные теории стали общепринятыми в теории электронно-лучевой сварки.
Ключевые слова: ученые и изобретатели в области ЭЛС, предпосылки возникновения ЭЛС, электронно-лучевая сварка, вакуумная техника, высококонцентрированные источники тепла, трудносвариваемые материалы.
The prerequisites considered that prompted scientists to the invention of electron beam welding. Are personalities whose inventions and scientific theories are generally accepted in the electron-beam welding.
Keywords: scientists and inventors in the field of EBW, predictors of EBW, electron-beam welding, vacuum equipment, highly concentrated heat source, difficult to weld materials.
Электронно-лучевая сварка (ЭЛС) явилась одним из перспективных и быстро развивающихся способов соединения различных металлов, в первую очередь тугоплавких, химически активных и разнородных качественных сталей, высокопрочных сплавов на основе алюминия и титана. Также этот способ сварки обладает широкими технологическими возможностями, позволяя соединять за один проход металлы и сплавы толщиной от 0,1 до 400 мм. При этом обеспечивается максимальная пластичность и вязкость сварных соединений.
Наиболее перспективным является соединение деталей из термически упрочненных материалов, когда затруднена или невозможна последующая термообработка. Максимальная пластичность и вязкость сварных соединений, минимальные сварочные деформации позволяют также успешно использовать ЭЛС при изготовлении изделий после завершающей механической обработки [1].
ЭЛС основана на использовании тепла, которое выделяется при торможении остросфокусированного потока электронов, ускоренных до высоких энергий. Явление термического воздействия электронных пучков на твердые материалы было известно давно. В частности, оно было отмечено в докладе В. Гроува (рис. 1), прочитанного в Лондонском Королевском обществе в апреле 1852 г.
Однако только благодаря развитию вакуумной техники и электронной оптики этот источник нагрева получил широкое применение сначала в сварочной, а затем в металлургической технике. Толчком, послужившим поиску новых способов соединения материалов, явились трудности сварки молибдена, тантала, ниобия, вольфрама, циркония, которые обнаружились в середине 60-х гг. прошлого века. Эти металлы составляют группу труд-Рис. 1 Вильям Роберт Гроув носвариваемых, так как обладают вы-
сокими температурой плавления и химической активностью. Это предполагает использование высококонцентрированных источников тепла и серьезной защиты зоны сварки [2].
В процессе ЭЛС в вакууме порядка 10-4 мм рт. ст. обеспечивается практически полное отсутствие примеси вредных газов. Высокая концентрация энергии в электронном луче до 109 Вт/см2 при минимальной площади пятна нагрева до 10-7 см2 способствует уменьшению термических деформаций при сварке, незначительным структурным превращениям в зоне нагрева и обеспечивает формирование сварного шва с ярко выраженной кинжальной формой проплавления.
Разработка техники и технологии ЭЛС связана с работами французских и американских инженеров Д.А. Стора, Д. Бриолы, В.Л. Вимена, которые были опубликованы в 1957-1958 гг. У истоков появления ЭЛС стоял также К.Г. Штайгервальд (ФРГ). В эти же годы в СССР в Московском энергетическом институте под руководством Н.А. Ольшанского и в Институте электросварки им. Е.О. Патона под руководством Б.А. Мовчана, независимо от работ иностранных ученых, также были проведены исследования по применению электронного луча для сварки [2].
В начале 60 гг. XX в. Н.А. Ольшанский (рис. 2) и О.К. Назаренко одни из первых предложили теорию кинжального проплавления: электронный луч образует конус проплавления деталей, на передней стенке которого происходит равномерное распределение энергии. Перемещение луча относительно
детали приводит к непрерывному плавлению металла и переносу его в сторону, противоположную лучу (рис. 3). По этой теории образование глубокого проплавления представляется как стационарный процесс.
В 1964 г. на основе экспериментальных данных, полученных при помощи скоростной киносъемки, американский ученый М. Шварц установил, что процесс взаимодействия луча и металла происходит за счет испарения и носит прерывистый характер. Им было также установлено, что распределение температур по глубине канала неравномерно: в корневой части канала Т ~ 5000 К, а у выходной части канала она минимальна и составляет 2500-3000 К.
И.В. Зуев в 1968-1967 гг. показал, что процесс внедрения электронного Рис. 2. Николай Александрович ЛуЧа в металл с образованием канала Ольшанский
происходит за счет периодического выброса вещества вследствие взрывообразного испарения (вскипания) металла. Было установлено, что при плотностях мощности ц = 109…1010 Вт скорость ввода тепла намного превышает скорость его отвода за счет теплопроводности, что приводит к взрывному вскипанию микрообъема вещества. Эта «взрывная гипотеза» позволила перейти к первым полуколичественным оценкам параметров процесса и получила подтверждение в ряде других работ.
4 3 12
Рис. 3. Канал проплавления: 1 — электронный луч; 2 — основной металл; 3 — расплавленный металл; 4 — сварной шов
Рис. 4. Николай Николаевич Рыкалин
Теория формирования канала проплавления за счет периодических взрывов, предложенная И.В. Зуевым и Н.Н. Рыкалиным (рис. 4), оказалась очень плодотворной [3].
В 1969 г. американские ученые Гид и Тонг провели экспериментальные исследования процесса образования канала с помощью киносъемки в рентгеновских лучах. Было установлено, что в жидком металле вокруг электронного луча существует полость. Эта полость все время находится в движении: глубина ее периодически колеблется от нулевой до максимальной с частотой 10-60 Гц. На основе этих исследований была предложена модель образования канала проплавления, основанная на гидродинамическом анализе процесса внедрения в жидкость тела, имеющего форму снаряда.
Красноярские ученые В.Д. Лаптенок, В.Я. Браверман внесли большой вклад в исследование возможности управления ЭЛС по рентгеновскому излучению из зоны сварки. В 1997 г. В.М. Язовских (рис. 5) и В.В. Уточкиным была установлена термодинамическая зависимость температуры испарения с давлением пара в канале проплавления при электроннолучевой сварке, позволяющая с точностью прогнозировать глубину проплавления при ЭЛС.
С начала 90-х гг. учеными В.Я. Беленьким, В.М. Язовских, Д.Н. Трушнико-вым ведется активное изучение механизма вторично-эмиссионных процессов при ЭЛС с глубоким проплавлением, с модуляцией электронного луча, со сквозным проплавлением, а также исследуется возможности контроля процесса формирования сварного шва при ЭЛС [4-6]. В.Я. Беленький занимается вопросом формирования передней стенки каналов проплавления в металле при ЭЛС [7-9]. На счету этих ученых разработка целого ряда способов контроля процессов формирования сварных швов при ЭЛС и управления ими.
Рис. 5. Валерий Михайлович Язовских
В.В. Мелюковым (рис. 6) разработан метод численного определения оптимальных режимов ЭЛС. Он нашел, как получать новые по форме конфигурации зон нагрева металла при сварке, и определил оптимальные комбинации источников, действующих одновременно, если этого требуют условия сварки. В.В. Ме-люков разработал алгоритм непрерывного управления мощностью теплового источника при ЭЛС и предложил новшевство — термоциклическую обработку, осуществляемую с помощью сварочного электронного луча путем многочисленных циклов нагрева-охлаждения по особой программе [10].
Стоит также отметить ученых из Санкт-Петербурга В.В. Башенко, Г.А. Туричина, которые внесли неоценимый вклад в исследования в области ЭЛС. Г.А. Туричин работает в области теоретических исследований, моделирования и разработки технологий лучевой обработки материалов, является одним из ведущих специалистов в этой области не только в России, но и за рубежом. Под его руководством и при его непосредственном участии проводятся исследования в области разработки новых и перспективных лазерных и гибридных технологий, в том числе технологического комплекса и базовой технологии для лазерно-дуговой сварки труб большого диаметра, разработаны программные комплексы для инженерного компьютерного анализа процессов лазерной, электронно-лучевой и гибридной сварки различных материалов [11-13].
Таким образом, ЭЛС является современным, прогрессивным способом соединения различных видов материалов и находит все новые и новые области применения в производстве.
Список литературы
1. Башенко В.В., Вихман В.Б. Состояние и перспективы развития электронно-лучевой сварки // Технологии и оборудование электронно-лучевой сварки-2008: материалы I Санкт-Петербур. Междунар. науч.-техн. конф. -СПб.: ВиТ-Принт, 2008. — 210 с.
2. Шалимов М.П., Панов В.П. История сварки. Электронно-лучевые технологии [Электронный ресурс]. — иЯГ: http://www.svarkainfo.ru/rus/lib/ history/h8.
3. Рыкалин Н.Н., Зуев И.В., Углов А.А. Основы электронно-лучевой обработки материалов. — М.: Машиностроение, 1978. — 239 с. — (Библиотека Технолога).
4. Язовских В.М., Трутников Д.Н., Беленький В.Я. Тепловые процессы при электронно-лучевой сварке дуговых швов // Сварка и диагностика. -2012. — № 5. — С. 26-31.
5. Математическое описание и анализ сварочных высококонцентрированных тепловых источников / В.Я. Беленький [и др.] // Вестник Ижев. гос. техн. ун-та. — 2012. — № 3. — С. 46-50.
6. Использование параметров вторично-эмиссионного сигнала для управления проплавлением при электронно-лучевой сварке / Д.Н. Трушников [и др.] // Интеллектуальные системы в производстве. — 2012. — № 1. — С. 175-181.
7. Структура вторично-эмиссионного сигнала при электронно-лучевой сварке с глубоким проплавлением / Д.Н. Трушников, В.М. Язовских, В.Я. Беленький, Л.Н. Кротов // Сварка и диагностика. — 2008. — № 4. — С. 22-24.
8. Беленький В.Я. О формировании передней стенки канала проплавления в металле при электронно-лучевой сварке // ФХОМ. — 1987. — № 1. — С. 116.
9. Структура вторично-эмиссионного сигнала при электронно-лучевой сварке с глубоким проплавлением / Д.Н. Трушников, В.М. Язовских, В.Я. Беленький, Л.Н. Кротов // Сварка и диагностика. — 2008. — № 4. — С. 22-24.
10. Шишкин В.В. Валерий Мелюков: новое слово в электронно-лучевой
сварке [Электронный ресурс]. — URL: http://www.vyatsu.ru/nash-
universitet/obrazovatel-naya-deyatel-nost/istoriya-kafedr/valeriy-melyukov-novoe-slovo-v-svarke.html.html.
11. Моделирование динамического поведения сварочной ванны при лазерной и гибридной сварке с глубоким проплавлением / Г.А. Туричин, Е.А. Валдайцева, Е.Ю. Поздеева, Е.В. Земляков, А.В. Гуменюк // Автоматическая сварка. — 2008. — № 7. — С. 15.
12. Гибридная лазерно-дуговая сварка металлов больших толщин / Г.А. Туричин, И.А. Цибульский, Е.А. Валдайцева, А.В. Лопота // Сварка и диагностика. — 2009. — № 3. — С. 16-23.
13. Kinetic description of keyhole plasma in laser welding / U. Dilthey, A. Goumeniouk, V. Lopota, G. Turichin // Journal of Physics D: Applied Physics. -2000. — Vol. 33, № 21. — C. 2747-2753.
Получено 15.02.2012
Саломатова Екатерина Сергеевна — старший преподаватель, Пермский национальный исследовательский политехнический университет (614990, г. Пермь, Комсомольский пр., 29, e-mail: [email protected]).
Salomatova Ekaterina Sergeevna — Senior Lecturer, Perm National Research Polytechnic University (614990, Perm, Komsomolsky av., 29, e-mail: [email protected]).
Электронно-лучевая сварка — Студопедия
Этот способ сварки основан на использовании для Нагрева и расплавления свариваемых деталей энергии электронного луча.
Электронный луч представляет собой сжатый поток электронов, перемещающихся с большой скоростью от катода к аноду в сильном электрическом поле. При соударении электронного потока с твердым телом более 99 % кинетической энергии электронов переходит в тепловую, которая расходуется на нагрев этого тела. Температура в месте соударения может достигать 5000…6000 °С.
В установках для электронно-лучевой сварки (рис. 19.29) происходит эмиссия электронов на катоде 1 электронной пушки. Электроны формируются в пучок прикатодным электродом 2, расположенным непосредственно за катодом, и ускоряются под действием разности потенциалов между катодом и анодом 3, составляющей 20…150 кВ и выше. Затем они фокусируются в виде луча и направляются специальной отклоняющей магнитной системой 4 на обрабатываемое изделие 5. Фокусировкой достигается высокая удельная мощность (от 5 до 105 кВт/м2 и выше). Ток электронного луча невелик (от нескольких миллиампер до единиц ампер).
б
Рис. 19.29. Схема установки (а) и «кинжальное» проплавление(б) при электронно-лучевой сварке(F.lt F2— сечения швов при дуговой и электронно-лучевой сварке) |
При перемещении заготовки под неподвижным лучом образуется сварной шов. Иногда при сварке перемещают сам луч вдоль неподвижных кромок с помощью отклоняющих систем. Отклоняющие системы используют также и для колебаний электронного луча поперек и вдоль шва, что позволяет регулировать тепловое воздействие на металл. Процесс сварки осуществляется в вакуумных камерах.
Параметрами процесса электронно-лучевой сварки являются ускоряющее напряжение Е/уск; сила тока пучка /п; расстояние от пушки до изделияdи до плоскости фокусировки пучка Ь; скорость сварки ися; глубина вакуума р. Изменяя перечисленные параметры процесса сварки, удается в широких пределах изменять форму сварочной ванны.
Сварку тонколистовых металлов (до 1…3 мм) обычно выполняют расфокусированным пучком электронов при небольших значениях удельной мощности в пятне нагрева (рис. 19.30, а). По термодеформационному циклу такая сварка почти не отличается от аргонно-дуговой сварки неплавящимся электродом.
малой (а) и большой (б) толщины: 1 — направление испарения металла;2 — пучок электронов; 3 — направление выноса металла в верхней части сварочной ванны;4 — фронт кристаллизации; 5 — направление перемещения изделия; 6 — поперечная усадка металла сварного шва |
При сварке толстолистовых металлов (рис. 19.30, б) используют острофокусные пучки электронов. Процесс сварки толстолистового металла состоит из следующих этапов. Вначале ввиду высокой концентрации энергии в пятне нагрева и высокого температурного градиента происходит преимущественное испарение металла. Далее по мере нагрева металл плавится и образуется сварочная ванна. Потоки паров, истекая в вакуум, силой реакции воздействуют на жидкий металл, вытесняя его из зоны нагрева. При этом оголяемые глубинные слои металла, воспринимая энергию электронов, плавятся, испаряются и вытесняются, пока не наступает динамическое равновесие всех сил, действующих на жидкий металл. В результате в его толще образуется канал с большим отношением глубины к диаметру. Воспринимающая энергию электронного пучка боковая поверхность канала имеет площадь, во много раз превышающую сечение пучка. Канал устойчив, так как при заполнении хотя бы части его жидким металлом резко увеличивается количество поглощаемой этим металлом энергии, он вскипает и испаряется.
Характерной особенностью электронно-лучевой сварки при высокой мощности являются большие скорости переноса жидкого металла из зоны плавления в зону кристаллизации. В верхней части сварочной ванны жидкий металл выносится на поверхность свариваемого изделия и образует усиление, площадь поперечного сечения которого достигает 10…15 % общей площади поперечного сечения сварочной ванны. Электронно-лучевой сварке толстого металла присущи колебания глубины проплав- ления, но при правильной фокусировке и стабильных параметрах пучка они не превышают 5 % общей глубины проплавления.
Применение электронно-лучевой сварки при изготовлении изделий из тугоплавких и химически активных материалов (Мо, W, Nb, Та и др.) позволяет получить сварные соединения с узкой зоной термического влияния и малыми деформациями без обогащения металла шва вредными примесями. При сварке высокотеплопроводных материалов (меди, алюминия и их сплавов) обеспечиваются высокий термический коэффициент плавления и возможность получения узких и глубоких швов при сравнительно малой мощности электронных пучков. При сварке изделий из сталей обеспечивается большая глубина проплавления и, следовательно, высокая производительность процесса при изготовлении конструкций из толстостенных заготовок.
Для электронно-лучевой сварки характерны как обычные типы соединений, так и принципиально новые. Общее требование ко всем типам соединений — точная сборка деталей перед сваркой.
Обычно отклонение оси пучка электронов от сварного стыка в процессе сварки не должно превышать 0,2…0,3 мм. При толщине свариваемых пластин до 5 мм допустимая величина зазора, как правило, не превышает 0,05…0,07 мм. При увеличении толщины пластин до 20 мм допустимая величина зазора возрастает до 0,1 мм, но не более.
Лазерная сварка
В последнее время в сварочной практике находят применение оптические квантовые генераторы (ОКГ), так называемые лазеры. При лазерной сварке нагрев и плавление металла осуществляются мощным световым лучом, получаемым от специальных твердых или газовых излучателей. Для управления сформированным излучателем лучом служат специальные оптические системы. Вакуум при сварке лазером не нужен, и сварка может осуществляться на воздухе даже на значительном расстоянии от генератора.
Лазерная сварка вследствие высоких значений плотности тепловой мощности в облучаемой зоне характеризуется высокой локальностью нагрева. Она позволяет сваривать металлы с различными теплофизическими характеристиками, в труднодоступных местах, поскольку это бесконтактный способ сварки, а также в любой прозрачной для данного излучения атмосфере или среде. В настоящее время для данной сварки применяются импульсные твердотельные лазеры и газовые лазеры непрерывного действия.
Принципиальная схема импульсной сварочной установки показана на рис. 19.31. Стержень активного материала 4 (например, рубина) и импульсная лампа накачки 3 размещены в полости осветителя 2. Электрическая энергия источника питания 1 преобразуется лампой накачки в световую энергию. Под воздействием света активный материал переходит в состояние, в котором он способен усиливать и генерировать свет определенрой длины волны. Чтобы улучшить условия генерации, стержень активного вещества помещают между двумя зеркалами, очень точно отъюстированными по отношению к стержню. Эти два зеркала и стержень активной среды образуют резонатор. Для вывода из-
Лучения из полости резонатора одно из зеркал делают частично прозрачным. Вышедший из резонатора пучок 5 собирается линзой 6, ив плоскости, где размеры пучка наименьшие, а плотность мощности наиболее высокая, располагают свариваемые детали 7.
Режим импульсной лазерной сварки определяется вводимой в свариваемые детали энергией лазерного излучения, длительностью импульса и радиусом светового пятна на облучаемой поверхности свариваемых деталей.
При сварке стыковых соединений возможны три технологические схемы нагрева:
1) фокусировка пятна нагрева на стык соединения — применяется при сходных теплофизических свойствах свариваемых металлов. В результате получается практически симметричный сварной шов;
2) смещение пятна нагрева в сторону более тугоплавкого металла — применяется в том случае, когда один из свариваемых металлов значительно более тугоплавкий. При этом происходит преимущественный нагрев и плавление более тугоплавкого металла. Плавление менее тугоплавкого металла осуществляется за счет теплоты, передаваемой его кромке от расплава;
3) сварка с преимущественным нагревом менее тугоплавкого металла. В этом случае сварное соединение образуется в результате процесса сварки-пайки.
Импульсная лазерная сварка стыковых соединений требует тщательной подгонки кромок свариваемых деталей.
Импульсные твердотельные лазеры применяют для сварки деталей в микроэлектронике и приборостроении, где важно получать малоразмерные швы с минимальным разогревом окружающего зону сварки материала. Сварка может вестись как отдельными точками, так и герметичными швами при последовательном наложении точек с их перекрытием.
Мощные газовые лазеры позволяют проплавлять за один проход, как и при электронно-лучевой сварке, значительные толщины.
Так же как и электронно-лучевая сварка, сварка лазером дает узкий шов «кинжального» типа с малыми деформациями свариваемых деталей, что позволяет применять этот способ для соединения окончательно обрабатываемых узлов и деталей-
Лазерную сварку можно с успехом применять для получения различных типов сварных соединений из многих однородных и разнородных металлов.
Электронно-лучевая сварка | Лазерная сварка
Поскольку мы продолжаем внимательно следить за развитием коронавируса (COVID-19), здоровье и благополучие наших сотрудников, клиентов и партнеров-поставщиков остается важнейшим приоритетом для Electron Beam Engineering, Inc.
Как ключевой поставщик для вашего бизнеса, мы понимаем, что крайне важно ограничить любое влияние, которое это нарушение здоровья может оказать на наши услуги для вас, и наши сотрудники прекрасно осознают важность продолжения выполнения ваших критических заказов.
Что касается Общего Калифорнийского приказа о домоседе, наша компания попадает в критически важные производственные условия и может продолжать свою деятельность. Компания Electron Beam Engineering, Inc. продолжает свою деятельность. На сегодняшний день мы открыты для бизнеса во время пандемии. Обычные сроки поставки могут быть увеличены, и мы по-прежнему привержены как удовлетворению ваших производственных потребностей, так и обеспечению безопасности наших сотрудников.
Electron Beam Engineering, Inc. предприняла упреждающие и превентивные действия на основе текущих рекомендаций США.Центры по контролю и профилактике заболеваний (CDC) и Всемирной организации здравоохранения (ВОЗ) о предотвращении распространения вируса COVID-19.
Чтобы свести к минимуму сбои в бизнес-операциях, мы внедрили следующие меры:
- Мы предоставили нашим сотрудникам информацию и передовые методы предотвращения распространения, включая напоминания о частом мытье рук и, по возможности, соблюдение дистанции 6 футов
- Выключатели света, дверные ручки, туалеты, телефоны, рабочие поверхности, стойка администратора и кухонные столешницы теперь очищаются ежедневно антибактериальным дезинфицирующим средством.
- Мы приказываем нашим сотрудникам оставаться дома, если они плохо себя чувствуют или у них есть нездоровые члены семьи.
- Мы ограничили все посещения второстепенных клиентов и внедрили процесс проверки анкеты посетителей
- Мы включили возможности работы из дома
Мы продолжим внимательно следить за этой ситуацией, чтобы обеспечить вам доступность основных услуг. Благодарим вас за то, что вы являетесь клиентом компании Electron Beam Engineering, Inc. Мы продолжим делать все возможное, чтобы заслужить ваше доверие.Если у вас есть вопросы, позвоните мне по телефону (714) 491-5990 x109 или напишите по электронной почте [email protected]. Мы будем держать вас в курсе по мере поступления новой информации.
Спасибо, Грант Триллвуд
.Принципы электронно-лучевой сварки | Электронно-лучевая сварка | Основы автоматизированной сварки
Электронно-лучевая (световая) сварка — это метод сварки, основанный на принципе испускания электронов в вакуумной трубке или трубке Брауна. Сварка в основном выполняется в вакууме (сварка в высоком вакууме) и характеризуется минимальным искажением для применений от толстых до тонких листов и даже для сварки деталей. Однако в последние годы были разработаны аппараты для электронно-лучевой сварки, способные выполнять сварку даже без идеального вакуума (аппарат для низковакуумной сварки) или путем перемещения электронной пушки (сварочный аппарат с подвижной электронной пушкой), что еще больше расширило область применения.
Обязательно к прочтению всем, кто занимается сваркой! Это руководство включает в себя базовые знания о сварке, такие как типы и механизмы сварки, а также подробные знания, касающиеся автоматизации сварки и устранения неисправностей. СкачатьКогда катод в вакууме нагревается нитью накала, он испускает электроны. Испускаемые электроны ускоряются напряжением и сходятся электромагнитной катушкой, и при столкновении с основным материалом выделяют высокую тепловую энергию.Электронно-лучевая сварка использует это тепло для сварки.
Диаметр пятна луча типичного аппарата для электронно-лучевой сварки составляет примерно 0,2 мм, а плотность энергии электронного луча примерно в 1000 раз больше, чем у дуги. Тепло, прикладываемое к области вокруг сварного шва, невелико, что позволяет производить сварку с меньшими искажениями. Управление выходом электронного луча позволяет регулировать проникновение, что делает этот метод применимым к широкому спектру основных материалов, от толстых до тонких пластин.Электронно-лучевая сварка также может использоваться для сварки металлов с высокими температурами плавления (например, вольфрама), а также активных металлов, которые могут окисляться во время сварки (например, титана).
Возможные области применения: обшивка кораблей, мосты, резервуары для хранения, детали самолетов и электронные компоненты.
В электронных компонентах используется процесс, называемый запечатыванием электронного луча, для герметизации кварцевых генераторов, которые необходимо соединять в вакууме. В этом процессе вакуумная пайка выполняется путем плавления присадочного материала между металлической крышкой и керамической упаковкой за счет теплопроводности, индуцированной электронным лучом.
Аппарат для электронно-лучевой сварки
Как электронно-лучевая сварка, так и лазерная сварка позволяют достичь глубокого проплавления при небольшом нагреве. При лазерной сварке вакуум не требуется, оборудование может быть меньше, чем оборудование для электронно-лучевой сварки, и возможны высокие скорости сварки.
Однако лазерные лучи имеют меньшую мощность, чем электронные лучи, поэтому глубина проникновения меньше, поэтому лазерная сварка не подходит для сварки толстых листов. Кроме того, если коэффициент отражения поверхности основного материала высок, эффективность использования энергии снизится.
В таблице ниже сравниваются различные аспекты каждого метода. Сравнение показывает, что у обоих методов есть преимущества и недостатки, и что преимущества каждого метода должны использоваться соответственно.
Электронно-лучевая сварка | Лазерная сварка | ||
---|---|---|---|
CO 2 (углекислый газ) лазер | YAG лазер | ||
Устройство источника тепла | Генератор высокого напряжения + электронная пушка | Оптический резонатор с CO 2 в качестве основной среды | Оптический резонатор со стержнем из YAG в качестве среды |
Диапазон выпуска серийно выпускаемого оборудования | от 3 кВт до 100 кВт | 0.От 5 кВт до 45 кВт | от 0,1 кВт до 6 кВт |
Максимальная плавильная мощность | Прибл. 150 мм (100 кВт) | Прибл. 30 мм (45 кВт) | Прибл. 10 мм (6 кВт) |
Энергоэффективность луча | Прибл. 100% | Прибл. 20% Значительные потери из-за отражений от поверхности и поглощения плазмы | Коэффициент поверхностного поглощения немного выше, чем у CO 2 с меньшим поглощением плазмы |
Практическая максимальная толщина листа | Прибл.100 мм | Несколько мм или меньше | То же, что слева |
Сварочная атмосфера | Вакуум (<10-2 мм рт. Ст.) Сварка должна выполняться в вакууме | Окружающий воздух Требуется защита инертным газом, как при дуговой сварке | То же, что слева |
Сварные материалы | Только металлы Отсутствуют металлические материалы с высоким давлением пара, такие как цинк и магний | Металлы, неметаллы | То же, что слева |
Электронно-лучевая сварка используется для плавления и соединения основных материалов.Поскольку при сварке выделяется небольшое пятно с минимальным тепловым воздействием, идеально подходят муфты без зазоров. Однако при сварке на макс. глубина проплавления от 3 до 5 мм, допускаются зазоры до 0,1 мм. Более глубокие проникновения позволяют увеличить порог зазора. При глубине проплавления 50 мм сварка возможна даже с зазором 3 мм с использованием присадочного материала (сварочной проволоки).
- Типичные сварные соединения, возможные при электронно-лучевой сварке
(EB = электронно-лучевая сварка)
Дом
.Электронно-лучевая или лазерная сварка?
Лазерный луч сваривает кольцевой шов вращающейся детали.
«Что работает лучше всего?» Кто не слышал этот вопрос, когда консультировался с заказчиком по поводу изготовления детали? В некоторых случаях на вопрос есть простой ответ, но часто нет, и решение использовать процесс A или процесс B сводится к сравнению плюсов и минусов, при этом стоимость как большой палец на шкале, подсказывающий баланс.
Для прецизионной сварки обычно выбирают между электронно-лучевой сваркой и лазерной сваркой. Иногда другие типы сварки плавлением, такие как GMAW или GTAW, могут быть вариантом, но процессы дуговой сварки не имеют проплавления, небольшой площади термического влияния, высокой точности и чистоты сварки, как при электронно-лучевой и лазерной сварке. Электронные лучи и лазеры могут быть сфокусированы и нацелены с исключительной точностью, необходимой для сварки самых маленьких имплантируемых медицинских устройств, и в то же время обеспечивать огромную мощность, необходимую для сварки больших частей космического корабля.Электронно-лучевая и лазерная сварка — это универсальные, мощные, автоматизированные процессы. Оба могут создавать красивые сварные швы с металлургической и эстетической точек зрения. Оба могут быть рентабельными.
Но, несмотря на все сходства, электронно-лучевая и лазерная сварка сильно отличаются друг от друга с точки зрения физики и функциональности в реальном мире цеха. Именно в этих различиях один конкретный процесс может иметь преимущество для конкретного приложения. Ключом к определению характеристик, которые могут сделать одну более подходящей, чем другую, является понимание того, как работают электронно-лучевая сварка и лазерная сварка.На первый взгляд они кажутся одинаковыми, но дьявол кроется в деталях.
Электронно-лучевая сварка
Электронно-лучевая сварка была разработана в конце 1950-х годов. Он был быстро воспринят высокотехнологичными отраслями, такими как аэрокосмическая промышленность, за точность и прочность получаемых сварных швов. Электронный луч может быть размещен очень точно, и сварной шов может сохранить до 97 процентов первоначальной прочности материала. Не будет преувеличением сказать, что электронно-лучевая сварка с точки зрения качества сварки не имеет себе равных: это лучшая собака сварочных процессов.
СваркуEB объяснить просто. Вольфрамовая нить накаливания нагревается, и к точке, где нить накала испускает электроны, подается мощность. Эти свободные электроны ускоряются и фокусируются с помощью электрических полей и магнитных «линз». Этот невидимый поток быстро движущихся электронов обладает огромной кинетической энергией. Когда эти электроны ударяются о металлическую деталь, кинетическая энергия передается молекулярной решетке материала, нагревая ее почти мгновенно.
Мощность электронного пучка может быть огромной — до 10 000 кВт / мм. 3 .Фактически, система электронно-лучевой сварки может выдавать достаточно энергии, чтобы просто испарить металл (процесс, называемый электронно-лучевой обработкой). Сварочные аппараты EB обычно бывают двух классов мощности: низкого напряжения (60 кВ) или высокого напряжения (150 кВ). Типичная высоковольтная машина мощностью 7500 Вт может производить сварной шов в стали глубиной 2 дюйма с шириной примерно 10 процентов глубины проплавления.
Однако логистика эксплуатации системы электронно-лучевой сварки непроста. Процесс должен происходить в вакууме; в противном случае частицы воздуха / газа рассеивают и диффундируют электроны.Для вакуума требуется вакуумная камера, поэтому размер свариваемой детали ограничен размером камеры. Вакуумные камеры могут быть маленькими или большими, но чем больше камера, тем больше времени потребуется для установления надлежащего уровня вакуума, который составляет минимум 1,0 x 10 -3 торр. Использование вакуума, а также присутствие рентгеновского излучения (побочного продукта луча) исключает вмешательство человека, поэтому весь процесс должен контролироваться извне, как правило, с использованием таблиц ЧПУ.
СваркаEB была полностью автоматизирована на протяжении десятилетий.Сочетание всей этой технологии — высокого напряжения, вакуума и высокотехнологичной автоматизации — означает, что для электронно-лучевой сварки требуются хорошо обученные операторы и очень компетентное обслуживание, а установка и эксплуатация системы электронно-лучевой сварки может быть дорогостоящей.
СваркаEB — это процесс сварки плавлением, поэтому требуется точная подгонка между свариваемыми деталями, поскольку присадочный материал обычно не используется или не требуется. Детали также должны быть надежно прикреплены к столу с регулируемым перемещением, чтобы точно перемещать свариваемые области в контакт с электронным лучом.В большинстве аппаратов для электронно-лучевой сварки используется неподвижная балка, под которой с помощью ЧПУ управляют деталью.
Надежное крепление также сводит к минимуму эффект усадки и деформации во время сварки. Электронный луч должен быть тщательно откалиброван, сфокусирован и синхронизирован с движением ЧПУ, чтобы обеспечить однородный сварной шов с равномерным проплавлением и минимальной пористостью. Каждый цикл сварки включает загрузку сварочной камеры, откачку вакуума, сварку детали и затем сброс вакуума.
Электронно-лучевая сварка позволяет получать очень качественные сварные швы, но процесс должен выполняться в вакууме.(Точки и небольшие искажения на этой фотографии вызваны взаимодействием процесса с объективом камеры.)
Узлы — это откачка вакуумной камеры и загрузка / разгрузка деталей. Следовательно, крайне важно, чтобы задействованные инженеры и техники увеличивали количество деталей, свариваемых в каждом цикле, и оптимизировали движение стола с ЧПУ. Когда все это сделано правильно, электронно-лучевая сварка может обеспечить очень высокое качество и высокую рентабельность.
Системы электронно-лучевой сварки могут сваривать все свариваемые металлы и некоторые металлы, которые обычно не свариваются. Электронно-лучевые швы невероятно прочны и чисты. Примеси в сварном шве испаряются, а сварка в вакууме означает, что нет газов или воздуха, которые могут вступить в реакцию и вызвать образование оксидов.
СваркаEB позволяет также соединять разнородные материалы, которые в противном случае были бы несвариваемыми из-за разницы в точках плавления, что приводит к образованию интерметаллических соединений, вызывающих хрупкость. Точная природа электронного луча и плотная зона термического влияния позволяют электронно-лучевой сварке в основном расплавлять низкотемпературный материал на нерасплавленный, высокотемпературный материал, в результате чего получается компактный, герметичный сварной шов.Это может быть немного обременительно, но продукты для электронно-лучевой сварки первоклассны во всех отношениях.
Лазерная сварка
Лазеры были разработаны в начале 1960-х годов, а к середине 1960-х годов для сварки использовались CO 2 лазера. Десять лет спустя автоматизированные лазеры начали сваривать на производственных линиях, и эта технология продолжала совершенствоваться и находить широкое применение во многих отраслях промышленности.
Система лазерной сварки способна очень быстро и с максимальной точностью передать огромное количество энергии.Луч можно сфокусировать и отразить к труднодоступным сварным швам, а также направить по оптоволоконному кабелю, чтобы обеспечить еще больший контроль и универсальность.
Лазеры в основном работают за счет быстрого повышения и понижения энергетического состояния материала, что вызывает испускание фотонов. Как это происходит, зависит от типа лазера, будь то CO 2 или твердотельная система, такая как Nd: YAG или волоконный лазер.
Независимо от того, как производятся фотоны, они концентрируются и становятся когерентными (выстраиваются в фазе друг с другом), а затем проецируются.Когда фотоны фокусируются на поверхности детали, излучаемое тепло плавит материал в зоне теплового воздействия и распространяется вниз через деталь за счет проводимости.
Этот способ нагрева сильно отличается от метода сварки EB. Выходная мощность лазера может варьироваться от нескольких ватт до сотен киловатт, а разные типы лазеров имеют разные сварочные характеристики.
Лазерная сварка обычно требует использования покровного газа, чтобы не допустить попадания кислорода в зону сварки и повысить эффективность и чистоту сварного шва.Тип используемого газа зависит от типа лазера, свариваемого материала и конкретного применения. Некоторые области применения лазерной сварки, такие как герметизация, требуют использования герметичного перчаточного ящика для обеспечения полностью контролируемой среды. Последние несколько лет ведутся работы по лазерной сварке в вакууме. Этот метод дал интересные результаты, но еще не получил широкого распространения в отрасли.
Одна из проблем лазерной сварки связана с отражательной способностью. Многие материалы имеют склонность отражать часть света (и энергии) лазерного луча от детали и соединения, особенно когда материал плавится и становится более зеркальным.Это может свести к минимуму проникновение и повреждение материала в области сварного шва.
Чтобы решить эту проблему, лазер может работать в импульсном режиме или изменять его энергию для «разрушения» поверхности. Импульсный режим в целом является полезным методом лазерной сварки, поскольку количество тепла, прикладываемого к детали, сводится к минимуму, что ограничивает деформацию детали. Альтернативой импульсному режиму является непрерывная волна (CW). Как следует из названия, в непрерывных лазерах используется непрерывный лазерный луч.
ЛазерыCW используются для резки или когда важна скорость сварки.Например, автоматическая машина GTAW может иметь скорость сварки 10 дюймов в минуту (IPM), тогда как CW-лазер может легко работать со скоростью 100 IPM.
При сварке лазерным лучом можно добиться хорошего проплавления, как правило, на глубину до 0,040 дюйма в стали для типичного 350-ваттного лазера. Лазерная сварка обычно может соединять материалы, склонные к образованию трещин, такие как определенные типы стали и алюминия, и, как и электронная сварка, лазеры могут соединять разные материалы.
Лазеры умеют подводить минимальное количество тепла к деталям, что делает их хорошим выбором для сварки корпусов электроники, особенно герметичных.Минимальный нагрев означает, что сварка может происходить очень близко к чувствительным электронным компонентам и паяным соединениям, не повреждая их. Лазеры также популярны в медицинских устройствах, поскольку сварные швы могут быть довольно небольшими с минимальным обесцвечиванием детали, и часто сварной шов можно наносить без необходимости какой-либо вторичной обработки.
Итак, какой процесс использовать?
Какой процесс лучше всего, обычно зависит от особенностей приложения. Лазерная сварка — это обычно процесс, на который мы в первую очередь обращаем внимание при новом применении.Без необходимости в вакууме лазерная сварка, как правило, дешевле, чем электронно-лучевая сварка, а детали легче обрабатывать и закреплять. Если требуется глубокое проплавление, лучше всего подойдет электронно-лучевая сварка. Более глубокое проникновение также может иметь значение, когда речь идет о материалах с высокой теплопроводностью, таких как медь.
Типичная система лазерной сварки может проникать в медь только на 0,020 дюйма, в то время как машина EB может проникать в 0,500 дюйма. Разные комбинации металлов обычно лучше свариваются с EB, но есть некоторые области применения, в которых лазеры работают лучше.
Хотя на самом деле нет никакой разницы между этими двумя процессами с точки зрения качества, существует огромная разница в доступных стандартах качества и спецификациях, которые определяют способ нанесения сварных швов. Следовательно, требования к качеству сварки могут повлиять на выбор процесса.
СваркаEB возникла в аэрокосмической отрасли до того, как стали доступны лазеры. В результате спецификации для EB-сварки являются полными и широко признанными. Эти спецификации контролируют все аспекты процесса, включая конструкцию стыков, очистку, требования к вакууму, квалификацию машины, обучение операторов и критерии проверки.Лазерная сварка не так жестко контролируется. Это возлагает на инженера большую ответственность за понимание всех аспектов процесса, чтобы убедиться, что он выполняется правильно.
Откровенно говоря, сложно и несколько неискренне перечислить типичные области применения электронно-лучевой сварки или типичные области применения лазерной сварки, поскольку каждый вариант использования уникален. Да, электронно-лучевая сварка, вероятно, лучший способ сваривать титан, но если деталь не помещается в вакуумную камеру, электронно-лучевую сварку использовать нельзя. Лазерная сварка может хорошо работать для небольших деталей, но динамика тепловой чувствительности деталей может сделать электронный луч лучшим вариантом.
Часто один или два критических фактора делают выбор процесса очень простым. При прочих равных, лазерная сварка, как правило, более рентабельна, тогда как электронно-лучевая сварка обеспечивает наилучшее сварное соединение. Но в некоторых случаях даже это неверно: электронно-лучевая сварка позволяет достичь высоких производственных скоростей с использованием правильной детали и правильного крепления, а лазерные лучи могут создавать красивые, чистые сварные швы с использованием правильных материалов и правильных настроек.
Электронно-лучевая и лазерная сварка — отличные средства для плавления металлов.Оба процесса являются гибкими, универсальными и при правильном применении позволяют получить прочные сварные швы. Выбор того, что использовать, зависит от требований к сварке и особенностей каждого процесса.
.Виды электронно-лучевой сварки | Электронно-лучевая сварка | Основы автоматизированной сварки
Машины для электронно-лучевой сварки подразделяются на категории в зависимости от ускоряющего напряжения, давления в камере обработки и положения установки электронной пушки. Эти различия влияют на масштабирование и управляемость оборудования, а также на выполняемые сварочные процессы.
Обязательно к прочтению всем, кто занимается сваркой! Это руководство включает в себя базовые знания о сварке, такие как типы и механизмы сварки, а также подробные знания, касающиеся автоматизации сварки и устранения неисправностей.Скачать Ускоряющее напряжение существенно влияет на выход электронного пучка. Как правило, устройства с ускоряющим напряжением от 100 до 150 кВ считаются высоковольтными, а устройства от 30 до 60 кВ — с низким напряжением.
Высоковольтные устройства могут сваривать стальные материалы толщиной от 0,1 до 200 мм и алюминиевые сплавы толщиной от 0,1 до 300 мм.
Для неспециализированных приложений проще использовать низковольтные устройства.Такие устройства используются в различных областях, включая промышленность электронных компонентов.
Одной из основных характеристик аппаратов для электронно-лучевой сварки является то, что сварка выполняется в камере вакуумной обработки. Однако в последние годы были разработаны аппараты для электронно-лучевой сварки, способные выполнять сварку даже без идеального вакуума.
Как правило, камеры для обработки с давлением примерно до 0,067 Па считаются камерами высокого вакуума, а камеры с давлением примерно до 6.67 Па считаются низковакуумными камерами. Давление в камере обработки варьируется от примерно 6,67 Па до 1,3 × 10 -6 Па в зависимости от области применения, и объемы увеличиваются с некоторым оборудованием, имеющим внутренний объем в несколько сотен кубических метров.
К универсальным вытяжным устройствам высокого вакуума относятся:
- Насосы масляные диффузионные
- Механические подкачивающие насосы
- Насосы масляные роторные
Устройства низкого вакуума, с другой стороны, включают следующее:
- Механические подкачивающие насосы
- Насосы масляные роторные
В последнее время разрабатываются устройства, оснащенные спиральными насосами и турбомолекулярными насосами, обеспечивающими меньший шум, вибрацию и тепло, благодаря улучшениям в среде установки и энергоэффективности.
Электронная пушка, используемая для испускания электронного луча, может быть установлена как внутри, так и снаружи камеры обработки
Внешние устройства с электронной пушкой, установленной вне рабочей камеры, обычно классифицируются как фиксированные и подвижные со специальным скользящим уплотнением. В устройствах с фиксированной электронной пушкой положение сварки изменяется путем перемещения основного материала.
С другой стороны, в устройствах с подвижной электронной пушкой положение сварки изменяется путем перемещения электронной пушки.Подвижные устройства с электронной пушкой могут иметь ход в несколько метров, что позволяет выполнять сварку в самых разных положениях.
Внутренние устройства с подвижной электронной пушкой, установленной внутри обрабатывающей камеры, имеют электронную пушку, прикрепленную к роботу, способную управлять одновременно по пяти осям (X, Y, Z, A и C). Эти устройства могут выполнять трехмерную сварку, а некоторые устройства предлагают зону сварки 10 м и более. Трехмерное сканирование положения сварного шва выполняется маломощным лучом, расположенным поперек линии сварки.Рентгеновские лучи, генерируемые во время сварки, регистрируются датчиком, встроенным в электронную пушку, что обеспечивает точную сварку канавок.
Дом
.