Флюсы для сварки меди и сплавов на ее основе
Некоторые флюсы для сварки меди, сплавов на ее основе и сварки чугуна в вес. ч. [c.232]Для газовой сварки сталей присадочную проволоку выбирают в зависимости от состава сплава свариваемого металла. Для сварки чугуна применяют специальные литые чугунные стержни для наплавки износостойких покрытий — литые стержни из твердых сплавов. Для сварки цветных металлов и некоторых специальных сплавов используют флюсы, которые могут быть в виде порошков н паст для сварки меди и ее сплавов — кислые флюсы (буру, буру с борной кислотой) для сварки алюминиевых сплавов — бескислородные флюсы на основе фтористых, хлористых солей лития, калия, натрия и кальция. Роль флюса состоит в растворении оксидов и образования шлаков, легко всплывающих на поверхность сварочной ванны. Во флюсы можно вводить элементы, раскисляющие и легирующие наплавленный металл. [c.207]
Для газовой сварки чугуна применяют специальные литые чугунные стержни для наплавки износостойких покрытий — литые стержни из твердых сплавов. Для газовой сварки цветных металлов и некоторых специальных сплавов используют флюсы, которые могут быть в виде порошков и паст для сварки меди и ее сплавов — кислые флюсы (буру, буру с борной кислотой) для сварки алюминиевых сплавов — бескислородные флюсы на основе фтористых, хлористых солей лития, калия, натрия и кальция.
В первые годы освоения сварки под флюсом ее применяли только при производстве конструкций и изделий из обычной низкоуглеродистой стали. Затем в 1941—1942 гг. освоили сварку броневых сталей. В настоящее время успешно сваривают под флюсом различные стали, сплавы, цветные металлы. Наряду с конструкциями из углеродистых сталей успешно свариваются под флюсом различные конструкции и аппараты из низколегированных сталей, нержавеющих, кислотостойких, жаропрочных сплавов на никелевой основе.
ФЛЮСЫ ДЛЯ СВАРКИ МЕДИ И СПЛАВОВ НА ЕЕ ОСНОВЕ [c.390]
Составы флюсов для электрошлаковой сварки меди и сплавов на ее основе. % [c.497]
Наплавка сплавов на медной основе на сталь обычно осуществляется с помощью нормально отрегулированного пламени, однако при наплавке латунью, особенно второго или последующих слоев, пламя регулируется с избытком кислорода. Мощность пламени подбирается в соответствии с размерами наплавляемой детали. Флюсы используются те же, что и для сварки меди и сплавов на ее основе. Наплавка, как правило, выполняется в нижнем положении. Производительность наплавки при мощности пламени около 1200 дм /ч составляет 0,5—0,7 кг/ч.
Высокой химической активностью при сварке отличаются и другие цветные металлы алюминий, магний, медь, никель и сплавы на их основе. Качество их защиты обеспечивается инертными газами, а также специальными электродными покрытиями и флюсами. [c.40]
Значительной химической активностью отличаются и другие цветные металлы алюминий, магний, медь, никель и сплавы на их основе. При сварке их защиту от взаимодействия с воздухом, а также защиту расплавленных сталей и сплавов на основе железа обеспечивают инертные газы, специальные флюсы и электродные покрытия. [c.54]
Можно ремонтировать детали и пайкой из алюминиевых и цинковых сплавов. Здесь процесс гораздо сложнее. Алюминий легко окисляется. Удаление окисла, имеющего удельный вес выше, чем у сплава, представляет значительные трудности. Хорошее качество пайки алюминиевых сплавов получается твердым припоем марки 34А из 25—30% меди, 4—7% кремния и 63—70% алюминия с применением флюса из 25—35% хлористого лития, 8—12% фтористого- калия, 8—15% хлористого цинка и 27—40% хлористого калия.
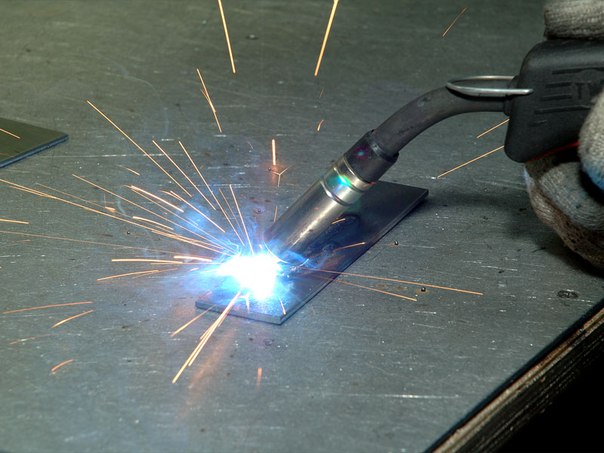
Автоматическую сварку под флюсом применяют для сварки в нижнем положении металла толщиной 2—100 м. 1. Сваривают стали различного состава, медь, титан, алюминий и сплавы на их основе. [c.394]
Флюсы применяются не только при дуговой сварке плавящимся электродом и электрошлаковой сваркой, но и при других технологических процессах сварочного производства. Так, флюсы часто используются при пайке, при сварке независимым источником тепла (газовой сварке ряда металлов и сплавов иногда дуговой сварке неплавящимся электродом в защитных газах), а также при кислородной резке некоторых металлов и сплавов (чугуны, высокохромистые стали, сплавы на основе меди и др.).
Наплавка — процесс нанесения защитного покрытия на поверхность основного металла целенаправленно выбранными методами сварки, к которым можно отнести газовую, дуговую (ручную, полуавтоматическую, автоматическую), под флюсом. Наплавка в основном применяется для повышения износостойкости и коррозионной стойкости. Поэтому в качестве наплавочных материалов используют высокомарганцевые стали, сплавы на основе никеля, меди, карбиды вольфрама и т.п. толщина наплавленного слоя лежит обычно в пределах 0,5…50 мм. Применяют также виброконтактную и вибродуговую наплавку с нагревом ТВЧ и ТПЧ. Напыление (газопламенное, электродуговое, индукционное, плазменное) — это нанесение покрытия на поверхность детали с помощью высокотемпературной скоростной струи, содержащей твердые частицы или капли расплава напыляемого материала. [c.274]
Кислые флюсы применяются обычно при сварке цветных металлов и сплавов, в частности, при сварке сплавов на основе меди (медь, латуни, бронзы), а основные — преимущественно при сварке чугуна. [c.172]
Сварка сплавов на основе меди. Латунь небольшой толщины сваривают графитовым электродом на постоянном токе прямой полярности короткой дугой без присадки с погружением конца электрода в расплавленный металл. С увеличением количества цинка в латуни дугу уменьшают, что снижает его испарение и выгорание. При толщине латуни более 10 мм требуется предварительный подогрев до 300 — 350 °С. Сварку ведут только с разделкой кромок под углом 70° и притуплением 1,5 — 2 мм при толщинах 3—16 мм и рюмкообразная разделка при больших толщинах. Присадкой служат стержни из металла ЛК80 — 3 диаметром 6 — 8 мм, на которые наносят специальный флюс. Сварку покрытыми электродами выполняют, если нельзя применять другие способы, так как при этом способе сварки происходит наиболее интенсивное выгорание и испарение цинка. Сварку осуществляют на постоянном токе обратной полярности электродами ЗТ на возможно короткой дуге без колебаний конца электрода. При толщине металла 4—10 мм делают V-образную разделку кромок, а при больших толщинах — Х-образную с углом раскрытия 60 — 70. Сварку производят на асбестовой прокаленной подкладке.
При сварке цветных металлов, например алюминиевых и медных сплавов, применяют флюсы. Для сварки меди и ее сплавов используют кислые флюсы (бура или бура с борной кислотой). При сварке алюминиевых сплавов применяют бескислородные флюсы на основе фтористых, хлористых солей лития, калия, натрия и кальция. В последнее время для сварки латуней используют газофлюсовую сварку. В этом случае флюс представляет собой эфир борной кислоты (ВОСН3) или какой-либо другой кислоты. При помощи специальной аппаратуры такой флюс подают в ацетиленовый канал сварочной горелки. Здесь он сгорает в пламени и в результате образуется борный ангидрид, связывающий окислы цинка. Таким образом получается слой шлака, препятствующий дальнейшему выгоранию цинка. [c.469]
Ряд затруднений вызывает и сварка сплавов на медной основе.
.jpg)
Высокая производительность сварки под флюсом и стабильное качество сварных соединений способствовали ее широкому применению в промышленности при соединении заготовок больших толщин (до 200 мм) из сталей различных классов, титана, сплавов на основе алюминия и меди и других конструкционных металлов. Наиболее часто этот вид сварки используют при изготовлении станин металлообрабатывающего оборудования, мостовых кранов, доменных печей, паровых котлов и др. К недостаткам способа отно- [c.217]
Для газовой сварки латуней, ее наплавки на черные металлы, а также для пайки углеродистой стали, меди и сплавов на ее основе различными припоями с успехом применяется газообразный флюс БМ-1. Он представляет собой борорганическую жидкость, пары которой поступают в горелку вместе с ацетиленом и, сгорая в пламени, дают борный ангидрид BgOg, флюсующий окислы металла при его конденсации на поверхности достаточно равномерными количествами. Основу борорганической жидкости составляет метилборат — эфир борной кислоты В (ОСНз)з. [c.234]
Элзк тродуговая свлр ка угольным электродом Имеет ограниченное применение. Удовлетворительные механические свойства и плотность шва могут быть получены только при сварке в среде защитных газов пли с флюсом Применяется для сварки малоуглеродистых сталей толщиной до 3 мм или сварки алюминия и его сплавов и сплавов на основе меди [c.106]
Проволока для сварки меди, сварки бронзы, сварки никелевых сплавов.
CastoMag 45701(CuNi30) — используется для стыковой сварки однородных и близких по хим. Составу сплавов меди, а также для сварки и наплавки вышеуказанных материалов друг с другом и стыковой сварки с низколегированными сталями.
CastoMag 45703 (CuSn6P) — используется для стыковой сварки меди и её сплавов, таких как CuSn-, CuZn-, CuSnZn друг с другом, а также для сварки со сталями, чугунами и никельсодержащими материалами и для наплавки этих материалов.
CastoMag 45704 (CuAg1) — используется для стыковой сварки бедной кислородом меди, такой как медные деформируемые сплавы и материалов с высоким содержанием углерода, а также для наплавки на сплавы меди и низколегированные стали. Не рекомендуется сварка меди с содержанием О2 более 0,02%.
CastoMag 45706 (CuSi3Mn1) — используется для стыковой сварки меди, медно-цинковых и медно-магниевых сплавов, a также для наплавки сплавов меди и нелегированных сталей. Не рекомендуется сварка меди с содержанием О2 более 0,02%.
CastoMag 45707 (CuSi2Mn1) — используется для стыковой сварки меди, медно-цинковых и медно-магниевых сплавов, a также для наплавки сплавов меди и низколегированных железосодержащих материалов. Не рекомендуется сварка меди с содержанием О2 более 0,02%. Пригоден для сварки кованой меди и медных неорганических материалов, производства холодильных установок, а также для MIG и плазменной пайки оцинкованного листового металла.
CastoMag 45709 (CuSn1) — используется для стыковой сварки бедной кислородом меди, такой как медные деформируемые сплавы и материалов с высоким содержанием углерода, а также для наплавки на сплавы меди и низколегированные железосодержащие материалы. Не рекомендуется сварка меди с содержанием О2 более 0,02%.
CastoMag 45751 (CuAl8) — используется для стыковой сварки и наплавки однородных сплавов меди, и сталей, а также устойчивых к коррозии наплавок на стали и чугуны.
CastoMag 45752 (CuAl 9 Ni 5) — используется для стыковой сварки медно- алюминиевых сплавов, а также для наплавки на стали, стальное литьё, чугун, медь и её сплавы.
CastoMag 45756 (CuMn13 Al7) — используется для наплавки сталей, стального литья, чугуна, меди и её сплавов.
CastoMag 45758 (CuAl 8 Ni 2) — используется для стыковой сварки медно- алюминиевых сплавов, а также для наплавки на стали, стальное литьё, чугун, медь и её сплавы.
Для сварки чистой меди и безкислородных низколегированных медных сплавов, когда основными требованиями к наплавленному металлу являются его высокая электропроводность и теплопроводность. При сварке крупных изделий и больших толщин рекомендуется выполнять предварительный подогрев стыка до 300°С.
Для сварки разнообразных сплавов на основе меди, таких как низколегированные медные сплавы, латуни с невысоким содержанием цинка, кремниевые, никель-серебрянные и некоторые другие типы бронз, а также для наплавки антифрикционных покрытий на стальные и чугунные поверхности и дуговой пайки стальных листов с защитным гальваническим цинковым покрытием.
Для сварки сплавов на основе меди, за исключением некоторых марок алюминиевых бронз. Основной областью ее применения является наплавка на стальные поверхности антикоррозионных слоев, стойких к воздействию морской воды и кислот, дуговая металлизация, а также дуговая пайки стальных листов с защитным гальваническим цинковым покрытием.
Для сварки и ремонта литых изделий из бронз близкого химического состава. Также применяется для наплавки на стальные и чугунные поверхности, подвергшиеся квитанционному износу. Материал также обладает высокой коррозионной стойкостью в морской воде. Наиболее характерным примером ее применения является восстановление лопастей гребных винтов в судостроении.
Для сварки медных сплавов с содержанием никеля от 10 до 30%, сварки этих сплавов с монелевыми сплавами и наплавки переходных слоев на кромки при сварке некоторых комбинаций разнородных материалов. Наплавленный металл обладает высокой коррозионной стойкостью в морской воде и достаточно высокими прочностными свойствами.
Для сварки коррозионностойких никелевых сплавов типа ХН70Ю, ХН78Т, Inconel 625, Incoloy 800 и 825 и им подобных, эксплуатирующихся в контакте с агрессивными средами при температуре до 550°С, супераустенитных коррозионностойких сталей с содержанием молибдена до 6% типа 0×23Н28М3Д3Т, 254 SMO (например UNS S31254) и им подобных, низколегированных хромо-молибденовых теплоустойчивых сталей перлитного класса с высоколегированными сталями аустенитного класса.
Для сварки жаро-коррозионностойких никелевых сплавов типа ХН60ВТ, ЭИ-868, Inconel 600, N006600, WNr. 2.4816 и им подобных эксплуатирующихся в контакте с агрессивными средами при температуре от −196 до 550°С, низколегированных хромо-молибденовых теплоустойчивых сталей перлитного класса с высоколегированными сталями аустенитного класса эксплуатирующихся при температуре до 650°С.
Для сварки никеля высокой чистоты (min 99,6%), поковок из технического никеля и никеля с пониженным содержанием углерода. Проволока легирована небольшим количеством титана для снижения склонности наплавленного металла к образованию горячих трещин.
Для сварки коррозионностойких никель-медных сплавов типа Monel 400 и им аналогичных дисперсионно твердеющих сплавов дополнительно легированных небольшим количеством Ti и Al, их сварки со сталями, сварки медных сплавов с никелем и сплавами на никелевой основе. Ее также применяют для выполнения антикоррозионной наплавки на низкоуглеродистые и низколегированные конструкционные стали и в качестве переходного слоя под последующую наплавку никелевой проволокой типа OK Autrod 19.92.
НАПЛАВКА МЕДИ И ЕЕ СПЛАВОВ
Наплавка меди и ее сплавов на стали и чугуны применяется для воссгановления изношенных и получения новых биметаллических деталей машин. По технологии наплавки детали делятся на пять групп: 1) с плоскими наплавляемыми поверхностями; 2) цилиндрической формы с наружными или внутренними наплавляемыми поверхностями; 3) формы диска с боковыми наплавляемыми поверхностями; 4) конусной формы с наружными или внутренними наплавляемыми поверхностями; 5) типа сфер с внутренними или наружными наплавляемыми поверхностями.
Наплавка плоских деталей производится с перекрытием валиков на 1/8 их ширины. Для этого электрод перемещают по зоне перехода предыдущего наплавленного валика к основному металлу.
Наплавка деталей цилиндрической формы, особенно малого диаметра, усложнена трудностью удержания металла ванны и формирования сварочного шва. При наплавке деталей формы дисков круговыми валиками, а сфер и конусов кольцевыми основной трудностью является регулирование скорости наплавки с изменением диаметра наплавляемых валиков.
При наплавке внутренней сферы и смещении электрода с нижней точки «на подъем» в сторону, обратную вращению, расплавленный металл стекает в хвостовую часть сварочной ванны. Эго приводит к значительному провару основного металла и повышению его доли в наплавленном. В случае смещения электрода в сторону вращения сферы наплавляемый металл подтекает под дугу, что значительно уменьшает глубину провара.
Смещение электрода больше оптимального значения приводит к отсутствию проплавления основного металла и отделению от него наплавленного валика. Поэтому при наплавке сферических тел вращения медью и ее сплавами, обладающими высокой жидкотекучестью, качество наплавки определяется точностью смещения электрода с зенита. /CMDx) 1,05,
где УподА и V подМ—скорости подачи алюминиевой легирующей и медной сварочной проволоки, м/ч; Са и См— содержание алюминия и меди в наплавленном металле, %; ЬА и Dm—диаметры алюминиевой и медной проволоки, мм; 1,05 — коэффициент потерь.
При наплавке разнородными лентами вместо диаметра проволоки в формуле ставится площадь сечения ленты (мм2).
Рис. 6.3. Установка для наплавки цилиндрических деталей малого диаметра |
Наплавка производится в среде защитных газов на постоянном токе обратной полярности. Алюминиевая легирующая проволока может быть как обесточенная, так и одноименного потенциала с наплавляемой деталью — Такой способ наплавки позволяет при необходимости изменять состав наплавляемой бронзы и особенно пригоден при наплавке больших объемов металла.
Детали небольшого диаметра наплавляют на установке (рис. 6.3) под слоем керамического флюса КМ-1 расщепленным плавящимся электродом. Установка состоит из станины /, электродвигателя 2 с редуктором и патроном для крепления наплавляемых деталей, направляющих 3, сварочного трактора 4, флюсосборника 5, задней бабки 6 для крепления наплавляемой детали 8 н флюсоудержателя 7. Огневую часть трактора можно перестраивать для крепления сварочной горелки ГУ-3 и для наплавки расщепленным электродом под слоем флюса. Наплавка производится после механической обработки поверхности цилиндрических деталей диаметром от 40 до 100 мм, длиной от 500 до І500 мм по винтовой линии. —
Детали диаметром от 40 до 60 мм наплавляют в смеси аргона и азота с кислородом плавящимся электродом (проволока БрКМцЗ-1) диаметром 2 мм. При большем диаметре наплавляемых деталей используется проволока диаметром 3 мм. Детали диаметром более 70 мм можно наплавлять также под керамическим флюсом КМ-1 или другими расщепленным электродом диаметром 2,5 мм.
Наплавку деталей диаметром 40—60 мм выполняют горелкой ГУ-2,5. Диаметр сварочной проволоки 2 мм. Режим наплавки: /с,- 280…320 A, 24…26 В, i>«=12…]6 м/ч,
длина дуги /д= (0,8…1,2) d„ гдегі3—диаметр сварочной проволоки, расход газа 20—25 л/мин. Детали диаметром более 60 мм наплавляют горелкой ГУ-3. Режим наплавки: /ев = =380…420 А, ил= 26…30 В, оСв= 12…16м/ч, ds = Змм, расход газа 25—30 л/мин. Длина дуги должна находиться в таких же пределах, как и при наплавке электродной проволокой диаметром 2 мм. Наплавка производится на постоянном токе обратной полярности от выпрямителя ВДУ-504.
Под керамическим флюсом детали наплавляют на постоянном токе обратной полярности от выпрямителя ВДУ-1201 с балластными реостатами РБ-300 в цепи дуги. Режим наплавки: /св= 400…450 A, t/4 = 38…42 В, vCB = 16…18 м/ч.
В различных отраслях промышленности широко применяются изделия из чугуна с контактными поверхностями из меди и ее сплавов. Наиболее производительным способом получения таких поверхностей является — наплавка, однако при наплавке железо основного металла не смешивается с наплавленной бронзой и концентрируется в верхних слоях металла. Такие железные включения обладают твердостью цементита и резко ухудшают качество наплавленного металла.
При содержании основного металла в наплавленном до 5 % его равномерное распределение достигается легированием наплавленного металла никелем или наплавкой под керамическим флюсом, содержащим медную окалину и кремнезем. В этом случае происходит реакция
-* 4Fe + Fe2Si04. удаляется в шлак |
2Cu [Fe] + 2Cu + Si02
железо в составляющие меди и ее керамического сплавах. флюса
Комплексное соединение Fe2S? o4, удаляясь в шлак, освобождает наплавленный металл от железных включений.
В случае необходимости для уменьшения доли основного металла в наплавленном производится наплавка в кристаллизаторе, который может быть стационарным или движущимся вместе с огневой частью сварочного автомата. Кристаллизатор увеличивает скорость охлаждения металла и повышает отвод тепла из зоны дуги. Это снижает глубину провара основного металла и его содержание в наплавленной меди и ее сплавах.
Такой способ позволяет регулировать глубину провара, а следовательно, получать наплавленные на чугун медные сплавы с минимальными включениями железа основного ме-
талла. Наплавка в кристаллизаторе производится как под флюсом, так и в среде защитных газов плавящимся электродом. При необходимости наплавку можно выполнять неплавящим — ся электродом с подачей в кристаллизатор шихты в виде бронзовой стружки и раекислителей, например, переплавленной буры. Качество наплавки контролируют внешним осмотром, а толщину наплавленной бронзы при необходимости проверяют за сверловкой.
НАПЛАВКА БАББИТА НА СТАЛИ
Наплавку баббита на стали осуществляют на предварительно механически обработанные поверхности с проточками в виде «ласточкина хвоста». Вначале наплавляемые поверхности подогревают до температуры 300—350 °С и производят их лужение под флюсом состава (%): ZnCl2— 75…77, Nh5C1 —
18.. .22, SnCl — 3…5. Далее, сохраняя начальную температуру изделия постоянной, луженную поверхность заливают предварительно расплавленным баббитом.
Электроды для сварки и наплавки цветных металлов и сплавов
Диаметр, мм | Род тока | Назначение и область применения |
ОЗА-1 | ||
4,0; 5,0; 6,0 | Постоянный ток обратной полярности. | Для сварки и наплавки деталей и конструкций из алюминия марок А0, А1, А2, А3. Сварку производят с предварительным подогревом изделий до +250–400°С (в зависимости от толщины свариваемого изделия) и с очисткой кромки от окислов и грязи. Шлак удаляют промывкой швов горячей водой с применением стальных щеток. |
ОЗА-2 | ||
4,0; 5,0; 6,0 | Постоянный ток обратной полярности. | Для сварки и наплавки деталей, заварки брака литья из алюминиево-кремниевых сплавов типа АЛ-4, АЛ-9, АЛ-11 и др.![]() Сварку производят с предварительным подогревом изделий до +250–400°С (в зависимости от толщины свариваемого изделия) и с очисткой кромок от окисла и грязи. Шлак удаляют промывкой швов горячей водой с применением стальных щеток. |
Комсомолец-100 | ||
3,0; 4,0; 5,0 | Постоянный ток обратной полярности. | Для сварки и наплавки чистой меди марок М1, М2, М3. Для сварки и наплавки без подогрева или с минимальным подогревом (+150–400°С) меди технических марок, содержащих до 0,01% кислорода. Могут быть использованы для сварки меди других марок и сплавов на ее основе, а также меди по сталью при условии предварительной проверки. |
АНЦ-3М | ||
3,0; 4,0; 5,0;6 | Постоянный ток обратной полярности. | Для сварки и наплавки без подогрева или с минимальным подогревом (+150–400°С) меди технических марок, содержащих до 0,01% кислорода. Могут быть использованы для сварки меди других марок и сплавов на ее основе, а также меди со сталью при условии предварительной проверки. Соединения толщиной до 10 мм выполняют без подогрева и без разделки кромок одно- или двухсторонним швом с небольшими поперечными колебаниями электрода, на ровной высушенной графитовой подкладке или графитовой ткани, короткой дугой в нижнем или слегка «на подъем» положении; электрод располагают перпендикулярно изделию. Соединения толщиной от 10 до 25 мм предварительно подогревают до +200–400°С. |
вернуться наверх
Сварка меди и ее сплавовСварка меди. В жидком .состоянии медь растворяет кислород и водород. С кислородом она образует закись меди, которая при дальнейшем соединении с медью дает промежуточный сплав, располагающийся по границам зерен. Температура плавления сплава ниже, чем меди, поэтому при затвердевании металла сварочной ванны сплав способствует образованию трещин. Ручная сварка покрытыми электродами выполняется на постоянном токе обратной полярности с местным подогревом до 250—300 °С. Сварка ведется быстро, короткой дугой без поперечных колебаний конца электрода. Стыковые соединения свариваются на графитовых или металлических подкладках. Для защиты обратной стороны шва от окисления в канавку подкладки насыпают флюс, представляющий собой шихту электродного покрытия. Ручная сварка в защитных газах ведется в аргоне, гелии или азоте вольфрамовым электродом на постоянном токе прямой полярности. Изделия толщиной более 4 мм свариваются с предварительным подогревом. Сварку следует выполнять с максимально возможной скоростью за один проход. Для предотвращения образования закиси меди сварку необходимо выполнять быстро, без остановок и перерывов, со скоростью не менее 0,25 м/мин. Сечение присадочного прутка должно быть не меньше 20—25 мм2. В этом случае расплавленный металл прутка не перегревается и предохраняется от интенсивного окисления. Конец присадочного прутка должен находиться между концом электрода и сварочной ванной, а сам присадочный пруток наклоняется под углом 30° к свариваемому изделию. Электрод располагается углом вперед под 20—30° к вертикали, стыковые швы рекомендуется сваривать за один проход, так как повторное воздействие термического цикла на металла шва приводит к снижению его прочности. Для раскисления металла шва в качестве флюса применяют плавленую ‘буру или борный шлак. Флюс обычно наносится на смоченную жидким стеклом поверхность прутка присадочного металла или на свариваемые кромки в виде пудры с последующей просушкой на воздухе. Перед нанесением флюса кромки необходимо тщательно очистить от загрязнений механическим способом или промывкой 10-процентным раствором каустической соды. Сварка бронзы. Свариваемость (бронз зависит от их состава. Различают деформируемые бронзы (легирующего элемента до 7—8%) и литейные (легирующего элемента свыше 8%). Изделия из деформируемых бронз толщиной до 4 мм свариваются всеми способами дуговой сварки без предварительного подогрева, а литейные бронзы — с подогревом. Однако чрезмерный подогрев может привести к расплавлению избыточного олова, расположенного по границам зерен, и разрушению изделия. При высоких температурах прочность бронзы понижается, поэтому изделие перед сваркой следует тщательно закрепить, чтобы не повредить в результате ударов или толчков. Ручная сварка покрытыми электродами выполняется на постоянном токе обратной полярности или на переменном токе. Сварка угольными или графитовыми электродами производится на постоянном токе прямой полярности. В качестве присадочного металла применяют литые бронзовые стержни диаметром 5—12 мм того же химического состава, что и свариваемый металл. В качестве флюса используют сухую шихту электродных покрытий. Флюс посыпают в сварочную ванну. Наплавка бронзы. Для .восстановления изношенных стальных или бронзовых деталей на их поверхность наплавляют слой бронзы. Поверхность перед наплавкой очищают, обезжиривают и посыпают прокаленной бурой толщиной 0,5 мм. Наплавку ведут электродами из бронзы ОЦС-5-3-20 или АЖ-9-4 без покрытия на постоянном токе обратной полярности. Вместо наплавки стержнями из бронзы АЖ-9-4 можно применять покрытые электроды, предназначенные для сварки алюминиевой бронзы. Ток берется постоянный обратной полярности из расчета 40А на 1 мм диаметра электрода. В процессе сварки поверхность посыпается сухой шихтой покрытия электродов. Наплавку ведут непрерывно, отдельными валиками, длина дуги 3—4 мм. После зачистки каждый валик подвергается проковке. Наплавку можно производить угольным или графитовым электродом диаметром 10—12 мм на токе 300—350А. Длина дуги 7—8 мм. Сварка латуни. Основным затруднением при сварке латуни является испарение цинка из основного и электродного металлов, приводящее к пористости шва и снижению его прочности, а также поглощение расплавленным металлом водорода, который, не успевая выделиться при затвердевании жидкого металла, тоже образует поры. Ручная сварка покрытыми электродами. Этот способ в основном находит применение для исправления брака литья. В зависимости от типа покрытия сварка производится на постоянном токе прямой или обратной полярности без колебания конца электрода наиболее короткой дугой, что способствует уменьшению выгорания цинка. Для предотвращения появления трещин сварку рекомендуется выполнять за один проход. Сварка графитовым или угольным электродом для изделий толщиной до 10 мм производится без подогрева, для большей толщины рекомендуется местный или общий сопутствующий подогрев до 300—350°С. Сварка выполняется на режимах и с применением флюсов, таких же как для сварки меди. Флюс наносится на стержни присадочных прутков диаметром 6—8 мм. В целях снижения выгорания цинка при сварке латуни небольшой толщины конец электрода погружается в расплавленный металл. В этом случае дуга горит в атмосфере из паров цинка. Сварные соединения, полученные таким способом, отличаются высокими механическими свойствами. Хорошие результаты дает также сварка с присадочной проволокой марки МЦМ-40-4,5, содержащей 40%; цинка и 4,5%: марганца, с флюсом из борного шлака или буры. Для сварных соединений при толщине металла 3—16 мм применяют У-образную разделку кромок под углом 70° с притуплением 1,5—2 мм, при толщине более 16 мм рекомендуется рюмкообразная разделка. — Инертная при обычных температурах медь при нагреве вступает в реакцию с кислородом, серой, фосфором. С азотом медь не реагирует, что позволяет его использовать как защитный газ при сварке чистой меди. Газы, образующиеся в результате реакций, в твердой меди не растворяются и нарушают металлическую связь, приводя к образованию трещин, так называемой «водородной болезни». Водород вызывает пористость в металле шва и образование трещин. Ручная сварка неплавящимся электродом применяется в среде аргона и азота. Наиболее целесообразно использовать азот высокой чистоты, в котором эффективный и термический КПД дугового разряда, глубина проплавления выше, чем при сварке в аргоне или гелии, но устойчивость дугового разряда ниже. Поэтому для сварки тонколистового металла или для сварки в труднодоступных местах рекомендуется аргон, обеспечивающий устойчивость дугового разряда. Сварка покрытыми электродами позволяет получить удовлетворительные механические свойства сварных соединений, но состав металла шва существенно отличается от состава основного металла из-за легирования при сварке раскислителями. Без подогрева и разделки кромок сваривают изделия из меди толщиной до 4 мм, при толщине 5—10 мм следует применять предварительный подогрев до 250—500 °С и V-образную разделку кромок с углом 60—70° и притуплением 1,5— 3 мм. При больших толщинах требуется Х-образная разделка. Для изделий толщиной более 20 мм швы хорошего качества можно получить только при подогреве до 700—750 °С. Наиболее широкое распространение получили электроды «Комсомолец-100», ЗТ, ОМЗ-1 и ММЗ-2. Сварку ведут электродами диаметром 4 •—6 мм на постоянном токе обратной полярности. Электроды ММЗ-2 можно использовать и при переменном токе. Сварку выполняют короткой дугой без колебаний конца электрода. Стыковые швы сваривают на графитовых или медных пластинах. После сварки рекомендуются проковка и быстрое охлаждение водой. Сварка графитовым или угольным электродом рекомендуется преимущественно для малоответственных изделий. Плотность тока на электродах 200—400 А/см2, кварку ведут на постоянном токе прямой полярности в нижнем положении длинной дугой (20—25 мм) при напряжении на дуге 40 В и наклоне электрода «углом вперед» на 10—20° к вертикали. Плазменная сварка применяется для соединения деталей толщиной 30 — 40 мм и более без разделки кромок. Этот способ варки позволяет вводить в сварочную ванну тепловые потоки большой величины без ухудшения условий формирования сварного шва и нарушения стабильности горения дуги. Газовая сварка. В этом виде сварки газовая горелка является тепловым источником малой сосредоточенности, что затрудняет поддержание сварочной дуги нормальных размеров. Поэтому мощность пламени при сварке изделий из меди толщиной до 4 мм выбирают из расчета 150— 175 дм 3/ч ацетилена на 1 мм толщины свариваемого металла, при толщине до 8—10 мм мощность увеличивают до 175—225 дм3/ч. При больших толщинах рекомендуется сварка двумя горелками — одной ведется подогрев, а другой — сварка. Для уменьшения теплоотвода и компенсации тепла, уходящего в околошовную зону, применяют асбестовые подкладки и предварительный подогрев. Газовой сваркой сваривают стыковые и угловые соединения. При толщине до 3 мм разделку кромок не делают, а при больших толщинах выполняют Х-образную разделку под углом 45 ° с каждой стороны стыка с притуплением 0,2 толщины свариваемого металла. Сварка сплавов на основе меди. Латунь небольшой толщины сваривают графитовым электродом на постоянном токе прямой полярности короткой дугой без присадки с погружением конца электрода в расплавленный металл. С увеличением количества цинка в латуни дугу уменьшают, что снижает его испарение и выгорание. При толщине латуни более 10 мм требуется предварительный подогрев до 300 — 350 °С. Сварку ведут только с разделкой кромок: под углом 70 ° и притуплением 1,5 — 2 мм при толщинах 3—16 мм и рюмкооб-разная разделка при больших толщинах. Присадкой служат стержни из металла ЛК80— 3 диаметром 6 — 8 мм, на которые наносят специальный флюс. Сварку покрытыми электродами выполняют, если нельзя применять другие способы, так как при этом способе сварки происходит наиболее интенсивное выгорание и испарение цинка. Сварку осуществляют на постоянном токе обратной полярности электродами ЗТ на возможно короткой дуге без колебаний конца электрода. При толщине металла 4—10 мм делают V-образную разделку кромок, а при больших толщинах — Х-образную с углом раскрытия 60 — 709. Латунь можно сваривать вольфрамовым электродом в защитных газах. В этом случае для деталей толщиной более 10 мм, а также разных по толщине деталей требуется предварительный подогрев. Газовую сварку латуни выполняют окислительным пламенем с применением специальных флюсов и присадочного металла, легированных кремнием и бором. Конец ядра сварочного пламени должен находиться на расстоянии 70 — 100 мм от свариваемой поверхности. Пламя направляют на присадочную проволоку, устанавливаемую под углом 90° к мундштуку. Конец присадочной проволоки должен всегда находиться в зоне пламени. Мощность пламени берется из расчета 100— 120 дм 3/ч ацетилена на 1 мм толщины металла. Металл толщиной до 1 мм сваривают с отбортовкой кромок, свыше 1 до 5 мм — без скоса кромок, от 6 до 15 мм — с V-образной разделкой кромок под углом 70 — 90°, от 15 до 25 мм — с Х-образной разделкой кромок под углом 70 — 90 0 и притуплением 2 — 4 мм. Изделия из деформируемых бронз толщиной до 4 мм сваривают всеми способами дуговой сварки без подогрева. Литейные бронзы сваривают с подогревом. В основном бронзы сваривают угольными или покрытыми электродами. Для электродных стержней или присадочного металла используют металл, аналогичный основному. Флюсы и покрытия для сварки оловянистых бронз изготовляют на борной основе, а для сварки безоловя-нистых бронз — флюсы из фтористых и хлористых солей щелочных и щелочно-земельных элементов и криолита. При газовой сварке оловянистых бронз пламя берется строго нормальным, так как окислительное пламя приводит к выгоранию олова, а науглероживающее — к увеличению пористости в металле шва. Мощность пламени до 70— 120 дм 3/ч ацетилена на 1 мм толщины металла. Сварку выполняют восстановительной зоной пламени. Для сварки оловянистых бронз используют те же флюсы, что и для сварки меди. Для сварки алюминиевых бронз применяют тоже нормальное пламя мощностью 120— 170 дм 3/ч ацетилена на 1 мм толщины металла и специальные флюсы для удаления тугоплавкой окисной пленки. Читать далее: |
Способ дуговой наплавки меди и медных сплавов на сталь
Изобретение может быть использовано при изготовлении узлов, деталей и конструкций из стали с наплавленным рабочим слоем из меди или медного сплава, предназначенным для обеспечения их антифрикционных свойств, коррозионной стойкости, электропроводности и др. На подлежащую наплавке поверхность изделия из стали наносят слой флюса-пасты и приваривают точечными швами полотно присадочного металла из меди или медного сплава. Затем осуществляют наплавку дуговым способом неплавящимся электродом в аргоне с использованием присадочной проволоки из меди или медного сплава с полным расплавлением упомянутого приваренного полотна. Способ обеспечивает уменьшение степени расплавления стали и минимальный (менее 5%) переход железа из стали в наплавленный металл, а также отсутствие ограничений, связанных с приемами подачи присадочного металла в зону наплавки, что снижает требования к квалификации сварщиков. 2 з.п. ф-лы, 1 табл.
Изобретение относится к области сварочного производства и может быть использовано в судостроении, машиностроении и в других отраслях промышленности при изготовлении узлов, деталей и конструкций из стали с наплавленным рабочим слоем из меди или медного сплава, предназначенным для обеспечения их антифрикционных свойств, коррозионной стойкости, электропроводности и др.
Известно, что наплавка меди и ее сплавов на сталь может выполняться различными дуговыми способами сварки плавлением: автоматическим под флюсом, ручным и механизированным аргонодуговым плавящимся и неплавящимся электродом, ручным покрытыми электродами. Однако при применении всех указанных способов дуговой наплавки меди и ее сплавов на сталь под действием сварочной дуги происходит значительное расплавление стали, перемешивание в сварочной ванне расплавленной стали с расплавленным присадочным металлом на медной основе и образование наплавленного металла с большим (10-30 мас.% и более) содержанием железа. Растворимость железа в твердой меди или в медном сплаве незначительная. Как показали исследования, в пересыщенном твердом растворе на основе меди может сохраняться до 3-5 мас.% железа. Остальное железо, перешедшее в наплавленный металл, выделяется в виде новой фазы — твердого раствора на основе железа. Выделения этой фазы существенно уменьшают коррозионную стойкость и антифрикционные свойства наплавленного металла, ударную вязкость и пластические свойства наплавленных образцов. Чтобы избавиться от выделений фазы на основе железа в рабочем слое наплавленного изделия и обеспечить его коррозионную стойкость и антифрикционные свойства, наплавку медных сплавов на сталь указанными дуговыми способами приходится выполнять в несколько слоев (Подгаецкий В.В. Механизированная наплавка слоя алюминиевой бронзы БрАЖМц 10-3-1,5. — Автоматическая сварка, 1959, №7, с.93). Но пластические свойства и ударная вязкость (при надрезе по зоне сплавления наплавленного металла со сталью) наплавленных образцов остаются низкими из-за наличия в зоне сплавления значительного количества выделений хрупкой и твердой фазы на основе железа.
Для обеспечения коррозионной стойкости, антифрикционных свойств, пластических свойств и ударной вязкости (при надрезе по зоне сплавления наплавленного металла со сталью) наплавленных образцов уже при наплавке медных сплавов на сталь в один слой наплавку медных сплавов на сталь следует выполнять без расплавления или с минимальным расплавлением стали так, чтобы содержание железа в первом слое наплавленного металла не превышало 5%.
Известен способ аргонодуговой наплавки неплавящимся электродом меди и ее сплавов на сталь (Патент РФ на изобретение №2390398 от 27 мая 2010 г.), принимаемый нами за прототип, при котором за счет применения специальной техники наплавки обеспечивается уменьшение степени расплавления стали и минимальный (менее 5%) переход железа из стали в наплавленный металл.
Однако этот способ наплавки (прототип) распространяется только на способ аргонодуговой наплавки неплавящимся электродом, включающий расплавление присадочного материала только в виде прутка, отличающийся тем, что перед началом наплавки присадочный пруток устанавливают в месте начала наплавки под углом 5-15° к наплавляемой поверхности с упором в нее нижнего конца прутка, располагают сварочную горелку под углом 80-90° к присадочному прутку, зажигают дугу между неплавящимся электродом сварочной горелки и нижним концом присадочного прутка, не допуская контакта дуги со сталью, расплавляют присадочный пруток с его перемещением без изменения его угла наклона к наплавляемой поверхности до образования на ней ванны расплавленного металла присадочного прутка шириной 7-10 мм и толщиной 2-3 мм, после чего переносят сварочную дугу с присадочного прутка на образованную ванну расплавленного металла в точку на расстоянии 2-4 мм от ее головной части, располагают сварочную горелку под углом 40-45° к поверхности ванны расплава и осуществляют процесс наплавки углом вперед с поддержанием постоянного угла наклона сварочной горелки и уровня ванны расплавленного металла. Однако этот способ наплавки имеет следующие недостатки. При этом способе наплавки применяются сложные технологические приемы. Присадочный металл для наплавки применяется только в виде прутков, которые подаются в зону наплавки только вручную. Производительность наплавки очень низкая. Для обеспечения качественного выполнения наплавки при этом способе необходимо, чтобы наплавку выполняли только высококвалифицированные сварщики, тщательно обученные сложным технологическим приемам наплавки по прототипу.
Техническим результатом заявляемого изобретения является разработка способа дуговой наплавки меди и медных сплавов на сталь, в котором при сохранении уменьшения степени расплавления стали и минимальном (менее 5%) переходе железа из стали в наплавленный металл обеспечиваются упрощение технологических приемов наплавки, возможность применения присадочного металла в виде присадочной проволоки, возможность механизированной подачи присадочной проволоки в зону наплавки, повышение производительности наплавки и при котором нет необходимости в подготовке сварщиков для освоения специальной техники наплавки и в предъявлении повышенных требований к квалификации сварщиков.
Технический результат предлагаемого изобретения достигается за счет того, что для получения наплавленного слоя на поверхности стального изделия предварительно на стальную поверхность наносят флюс-пасту толщиной 0,1-0,2 мм, для наплавки используют присадочный металл одного и того же состава, состоящий из полотна толщиной 1,0-1,6 мм, предварительно приваренного точечными швами к стальной поверхности в шахматном порядке путем локального расплавления полотна на всю его толщину в отдельных точках диаметром 3-5 мм с шагом между точками 15-20 мм, и из сварочной проволоки, затем возбуждают дугу между неплавящимся электродом и полотном присадочного металла, достаточном для локального расплавления полотна под дугой на всю его толщину, после этого дугой без ее перемещения расплавляют полотно до поверхности стали, механизированным способом или вручную подают присадочную проволоку в образовавшуюся ванну жидкого металла и одновременно увеличивают сварочный ток в дуге до значения, необходимого для совместного плавления этой дугой присадочного полотна и присадочной проволоки, при этом образуют общую сварочную ванну из расплавленного присадочного полотна и расплавленной присадочной проволоки и продолжают процесс наплавки до получения наплавленного слоя на всей наплавляемой поверхности.
Опробование предложенного способа наплавки меди и медных сплавов на сталь производили следующим образом. Для наплавки по предложенному способу было взято полотно толщиной 1 мм из сплава марки МНЖКТ5-1-0,2-0,2 состава (мас.%): Ni — 6,1, Fe — 1,2, Mn — 0,72, Cu — остальное, шириной 40 мм и длиной 200 мм. На пластину размером 12×100×200 мм из стали АБ2 кисточкой был нанесен слой флюса-пасты толщиной — 0,15 мм в виде раствора буры в этиловом спирте. После нанесения флюса-пасты на пластину было уложено полотно из сплава МНЖКТ5-1-0,2-0,2 и приварено к стальной пластине точечными швами в шахматном порядке. Сварку выполняли без применения присадочного металла аргонодуговым способом неплавящимся электродом путем расплавления полотна в намеченных точках диаметром 3-5 мм с шагом между точками 15-20 мм. При этом для обеспечения надежного контакта полотна с пластиной у места сварки точки полотно прижимали к пластине с помощью ручного инструмента. После этого на стальную пластину с приваренным к ней полотном была выполнена наплавка механизированным способом неплавящимся электродом в аргоне проволокой диаметром 1,2 мм марки МНЖКТ5-1-0,2-0,2 того же состава, что и полотно, на режиме: сварочный ток 180-200 А, напряжение на дуге 16 В, скорость подачи проволоки 240 м/ч (4,0 м/мин), скорость наплавки 15 м/час. В результате на стальную пластину был наплавлен слой металла высотой 3,3 мм площадью 40×200 мм2. Наплавка была выполнена за 8 мин, а с учетом приварки полотна к пластине — за 10 мин.
Для сравнения аналогичный слой металла был наплавлен способом наплавки по прототипу, на что было затрачено 24 мин.
На обеих наплавленных пластинах было определено содержание железа в наплавленном металле и наличие выделений фазы на основе железа в его структуре.
Результаты исследования приведены в таблице и показывают следующее. При обоих способах наплавки: предложенном и по прототипу содержание железа в наплавленном металле, определенное методом микрорентгеноспектрального анализа, низкое и находится примерно на одном уровне: 1,8-3,2 мас.%. При металлографическом исследовании шлифов, полученных из наплавленных образцов, на микроскопе «Axiovert 40MAT» при увеличении 100 и 300 установлено, что микроструктура наплавленного металла везде однофазная, выделения фазы на основе железа в наплавленном металле при обоих способах наплавки отсутствует. Недопустимые дефекты в наплавленном металле (трещины, свищи, непровары) также отсутствуют при обоих способах наплавки. Отличие заключается в длительности наплавки на сталь одинакового по размерам слоя медно-никелевого сплава (объем 26,3 см3; масса 234 г). Длительность наплавки по предложенному способу (с учетом времени на приварку полотна к пластине) составила 10 мин, а при наплавке по прототипу — 24 мин, производительность наплавки соответственно 23,4 г/мин и 9,8 г/мин. Таким образом, производительность наплавки по предложенному способу в 2,4 раза выше, чем при наплавке по прототипу.
Таблица | |||||||
Результаты опробования наплавленных образцов | |||||||
Способ наплавки | Массовая доля железа в наплавленном металле, % | Наличие фазы на основе железа в наплавленном металле | Наличие недопустимых дефектов в наплавленном металле | Объем и масса наплавки | Длитель ность наплавки, мин | Производительность наплавки, г/мин | |
см3 | г | ||||||
Предложенный | отсутствует | отсутствуют | 26,3 | 234 | 10 | 23,4 | |
По прототипу | отсутствует | отсутствуют | 26,3 | 234 | 24 | 9,8 | |
Примечания: 1) В таблице приведены результаты определения массовой доли железа не менее чем на 3-х образцах. В числителе приведены минимальные и максимальные значения, в знаменателе — средние значения. | |||||||
2) Длительность наплавки по предложенному способу включает время на приварку полотна к пластине (2 мин) и на наплавку. |
1. Способ дуговой наплавки меди и медных сплавов на сталь, включающий использование неплавящегося электрода и присадочного металла из медного сплава, отличающийся тем, что для получения наплавленного слоя на поверхности стального изделия предварительно на стальную поверхность наносят флюс-пасту, для наплавки используют присадочный металл, состоящий из полотна толщиной 1,0-1,6 мм, предварительно приваренного точечными швами к стальной поверхности, и из сварочной проволоки, имеющих одинаковый состав, затем возбуждают дугу между неплавящимся электродом и полотном присадочного металла на токе, достаточном для локального расплавления полотна под дугой на всю его толщину, после этого дугой без ее перемещения расплавляют полотно до поверхности стали, механизированным способом или вручную подают присадочную проволоку в образовавшуюся ванну жидкого металла и одновременно увеличивают сварочный ток в дуге до значения, необходимого для совместного плавления этой дугой присадочного полотна и присадочной проволоки, при этом образуют общую сварочную ванну из расплавленного присадочного полотна и расплавленной присадочной проволоки и продолжают процесс наплавки до получения наплавленного слоя на всей наплавляемой поверхности.
2. Способ наплавки по п.1, отличающийся тем, что перед приваркой полотна к наплавляемой стальной поверхности на эту поверхность наносят слой флюса-пасты толщиной 0,1-0,2 мм, применяемой для сварки медного сплава аналогичного состава.
3. Способ наплавки по п.1, отличающийся тем, что предварительную приварку полотна присадочного металла к стальной поверхности осуществляют с прижатием его в зоне сварки путем локального расплавления полотна на всю его толщину дугой неплавящегося электрода в аргоне без применения присадочной проволоки, при этом приварку осуществляют в отдельных точках, расположенных в шахматном порядке, диаметром 3-5 мм с шагом между точками 15-20 мм.
Особенности легирования при наплавке медных сплавов Текст научной статьи по специальности «Технологии материалов»
ВЕСТНИК
ПРИАЗОВСКОГО ГОСУДАРСТВЕННОГО ТЕХНИЧЕСКОГО УНИВЕРСИТЕТА
1999 г Вып. №8
уда 621. 791.92
Башмакова Т.Н.
ОСОБЕННОСТИ ЛЕГИРОВАНИЯ ПРИ НАПЛАВКЕ МЕДНЫХ СПЛАВОВ
Проанализировано влияние состава компонентов шихты порошковых материалов на процесс легирования при наплавке низколегированных жаропрочных медных сплавов. Результаты анализа использованы при разработке состава порошковой ленты.
Наибольший практический интерес в настоящее врет представляют низколегированные жаропрочные медные сплавы, однако, некоторые из них в интервале 300-600 °С имеют, невысокую пластичность. В таком случае рекомендуется применять микролегироваиие сплавов поверхностно-активными элементами, введение которых в небольших количествах (сотые доли процента) резко повышает показатели пластичности и одновременно несколько электропроводность [1]. Медь, как растворитель при 800 °С имеет ограниченное число растворимых легирующих элементов, которые упрочняют её при этой температуре. К таким легирующим относятся переходные, сравнительно тугоплавкие металлы — цирконий, железо, титан, хром, кобальт и никель. Остальные легирующие элементы, а они преобладают (фосфор, кадмий, бериллий, цинк, олово и др.) не упрочняют медь при 800 °С и даже разупрочняют её. Среди большого разнообразия разработанных жаропрочных сплавов ка медной основе, наиболее перспективны сплавы системы Си — Сг — Ъх. обладающие комплексом высоких эксплуатационных свойств: износостойкостью, жаропрочностью и высокой теплопроводностью.
При наплавке сплавов этой системы очень важен подбор компонентов электродного материала, обеспечивающих заданный химический состав. Учитывая преимущества порошковых электродных материалов, был проведен анализ возможных для использования компонентов шихты и их влияния на процесс легирования при наплавке
Для легирования наплавленного металла хромом целесообразно ввести его в виде порошка хрома металлического. Для легирования наплавленного металла цирконием использование чистого циркония не всегда экономически оправдано. В этой связи, очевидно более рациональным будет использование соли циркония — фторцирконата калия, успешно опробованного при производстве лигатуры Си-Ъх [2]. Процесс получения лигатуры основан на восстановлении циркония из фторцирконата калия магнием в присутствии меди но реакции
К2ггГ6 + 2Mg + [Си] = 2КГ+» 2MgF2 + [Си + Ъг] (I)
Реакция (1) справедлива, если процесс восстановления циркония идет до конца.
Однако, возможны условия, при которых в правой части уравнения могут появиться промежуточные соединения, например: К32гГ7. Известна диаграмма состояния Ъх-^ Л — КР [3]. гГз или 0,96 % Ъх от веса магния будет восстановлена и войдет в сплав не более 0,3 % Ъх.
* ГОТУ, канд. техн. наук, доц.
Полученные авторами [3] данные позволяют предположить, что при восстановлении циркония магнием из фторцирконата калия состава KZrF, реакция будет развиваться в следующих стадиях:
6KZrF6 + 12Mg — ‘ 2K2ZrF6 + 6M.gF2 + 6Mg Первая стадия
5= 2K3ZrF7- 8MgF2 + 4Zr v- (2)
Вторая стадия
6KF+12MgF2 + 6Zr Третья стад та
Из-за недостаточно высокой температуры расплава (не превышающей 950 °С), высокой температуры плавления соединения K3ZrF7 (930 °С) и большого количества тугоплавкого соединения MgF2 (температура плавления 1270 °С), образующихся в результате
взаимодействия фторцирконата калия с магнием, процессы диффузии в солевой части значительно замедляются, вследствие чего реакция может не пойти далее второй стадии и восстановленной окажется лишь часть вводимого в сплав циркония
Для интенсификации процессов диффузии в солевой фазе и более полного восстановления магнием циркония из фторцирконата калия Лебедев A.A. и Аникина А Д. [3] предлагают повысить температуру процесса путем добавки флюсов к основным материалам шихты, причем свободная энергия их при температуре ведения процесса должна быть выше свободной энергии соответствующих соединений Mg и Zr. Из фтористых солей такими соединениями являются фтористый литий, фтористый калий, а из хлористых солей — хлористый калий, хлористый барий, хлористый кальций и др.
При сплавлении в определенных соотношениях (фторцирконата калия с фтористым литием или с фтористым кальцием образуются эвтектики с более низкой, температурой плавления, нежели исходные соли, что должно благоприятно сказаться на процессе введения циркония в сплав. Увеличенное же содержание этих солей в сплаве повышает температуру их плавления, и эффект от добавок оказывается отрицательным.
Введение в состав шихты порошковой ленты наряду с фторцирконатом калия фтористого кальция позволяет получить более стабильное содержания циркония в сплаве, повысить усвоение циркония сплавом, снизить безвозвратные потери На преимущества восстановления циркония кальцием также указывается при получении лигатуры [4].
При разработке состава шихты порошковой ленты необходимо также учитывать метал -лургические особенности ее наплавки, т.е. лента должна содержать компоненты, обеспечивающие хорошую раскисленность металла шва и необходимую защиту сварочной ванны от насыщения ее водородом. При разработке сварочных материалов чаще всего отдается предпочтение фтористым соединениям, из которых наибольшее применение находит фтористый кальций.
Влияние простых и комплексных фторидов на ск лонность сварных швов к порообразованию при введении их в состав шихты порошковой проволоки исследовано И.И. Фруминым [5]. Причем, установлено, что наиболее эффективно снижают содержание водорода в металле шва A1F3, CaF2, NihSiF,-. При этом также снижается содержание азота, хотя и незначительно. Проводились также исследования [6] возможности сварки меди самозащитной проволокой. Хорошие результаты получены при использовании в составе шихты фтористых соединений CaF2 и Na2SiF6.
В исследованиях К.В. Любавского установление [7], что при сварке электродами, содержащими в покрытии органические компоненты, возможно насыщение сварочной ванны большим колличеством водорода. При сварке-наплавке меди высокая окиеленность металла шва и насыщенность его водородом являются основными причинами, приводящими к поро- и трещинообразованию. Поэтому введение в состав шихты газообразующих элементов-карбонатов (магнезита, мрамора, доломита и др. ) не желательно, т к диссоциация их повышает степень окисленности сварочной ванны [8].
Нараду с парами воды в атмосфере дуги присутствуют азот и кислород. Для связывания кислорода в состав шихты должны быть введены раскислитслк. Известные порошковые проволоки и проволоки сплошного сечения для сварки-наплавки меди и ее сплавов [9,10] с целью -металлургического воздействия на сварочную ванну содержат в качестве раскислителей алюминий, марганец, цирконий и другие элементы.
В.В. Фроловым сделана оценка раскислительной способности хрома, марганца, кремния, титана, которые сохраняют ее даже в области высоких температур. Наряду с назваными выше элементами в работе [11] исследовались церий, лантан, бор, магний, фосфор и установлено, что наибольшей раскислительной способностью обладают цирконий, церий и лантан. i
При выборе раскислителей важное значение имеют вопросы удаления неметаллических включений из металла шва, т.к. свойства сварного соединения зависят не только от того, насколько полно восстановлена закись меди, но и от того, насколько полно продукты реакций удалены из жидкого металла.
Учитывая результаты проведенного анализа влияние состава компонентов порошковых материалов на процесс легирования разработан состав порошковой ленты1. Исследования наплавленного металла подтвердили обеспечение заданного химического состава, структуры и свойств при наплавке предлагаемой порошковой лентой.
Выводы
Проведенный анализ влияния состава компонентов шихты порошковых материалов на процесс легирования при наплавке низколегированных жаропрочных медных сплавов исполь- -зован при разработке состава порошковой ленты, обеспечившощей жаропрочность, износостойкость, теплопроводность и высокое качество наплавленного металла. .
Перечень ссылок
1. ЗахаровМ.В., Захаров A.M. Жаропрочные сплавы. — М.: Металлургия, 1972. — 384 с.
2. Николаев А.К., Розенберг В.М. Сплавы для электродов контактной сварки. — М.: Металлур-
гия, 1978. — 96 с.
3. Лебедев A.A., Аникина А.Д. Сплав солей для введения циркония в легкие сплавы // Исследо-
вание сплавов цветных металлов. — М.: АН СССР, 1962. — С. 181-186
4. Чурсин В.М. Плавка медных сплавов. — — М.: Металлургия, 1982. — 152 с.
5. Фру мин ИИ. Автоматическая электродуговая наплавка. — Харьков: Металлург издат, 1961 -421с.
6. Кассов В.Д., Цветков А.И. Исследование возможности сварки меди самозащитной порошковой проволокой // Реферативная информация о законченных научно-исследовательских работах в вузах УССР,- Киев, 1975. — Вып. 15.-С.28-29.
7. Любавский КВ. Металлургия: сварки плавлением. — М.: Машгия, 1961 .-556 с.
8. Порошковые проволоки для электродуговой сварки / И.К. Походня и др. — Киев: Наук, дум-
ка, 1980.-250С.
9. Гуревич СМ. Справочник по сварке цветных металлов. — Киев: Наук, думка, 1981,- 608 с.
10. Сварка в машиностроении / Под ред. А.И. Акулова. — М.: Машиностроение, 1984. — 590 с.
11 Фролов В. В. Особенности металлургических процессов при сварке меди под керамическими флюсами // Межвузовская конференция по сварке. — М.: Машгиз, 1958.-С. 172-188.
Башмакова Татьяна Николаевна. Канд. техн. наук, доценг кафедры металлургии сварки, окончила Мариупольский металлургический институт в 1978 году. Основные направления научных исследований — разработка материалов и технологии наплавки износостойких жаропрочных сплавов, получение материалов сварочными методами.
1 АС. № 1125879
Свариваемость материалов — медь и медные сплавы
Медь и медные сплавы выбираются из-за их коррозионной стойкости, а также электрической и теплопроводности.
Определены различные типы медных сплавов, и даны рекомендации по процессам и методам, которые могут быть использованы при изготовлении компонентов из медных сплавов с целью сохранения их коррозионных или механических свойств, избегая появления дефектов в сварных швах.
Типы сплавов
Основные категории меди и медных сплавов перечислены ниже:
Таблица 1.Часто используемые медные сплавы и рекомендуемые присадочные металлы
Тип сплава | Рекомендуемый наполнитель |
---|---|
Медь (вязкая пека, раскисленная фосфором) | Cu 1897, Cu 1898 |
Латунь (с низким содержанием цинка) | Cu 6328, Cu 6560 |
Никелевый серебристый (тип 20% Zn / 15% Ni) | Cu 6328, Cu 6560 |
Кремниевая бронза (3% Si) | Cu 6560 |
Фосфорная бронза (4.От 5% до 6% Sn / 0,4% P) | Cu 5180 |
Алюминиевая бронза (<7,8% Al) | Cu 6240, Cu 6100 |
Алюминиевая бронза (> 7,8% Al) | Cu 6180, Cu 6328 |
Алюминиевая бронза (6% Al / 2% Si) | Cu 6100 |
Gunmetal (низкий свинец) | Cu 5180, Cu 6560, Cu 6180 |
Медно-никель (10% Ni) | Cu 7061, Cu 7158 |
Медно-никель (30% Ni) | Cu 7158 |
- Чистая медь
- Медь с небольшими легированными добавками (всего менее 5%)
- Латунь e.
грамм. медь-цинк (Cu-Zn)
- Никелевый серебристый напр. медь-цинк-никель (Cu-Zn-Ni)
- бронзы напр. медь-олово (Cu-Sn) (сплавы фосфорной бронзы также содержат фосфор)
- Gunmetals напр. медь-олово-цинк (Cu-Sn-Zn) (некоторые сплавы могут содержать свинец)
- Алюминиевая бронза напр. медно-алюминиевый (Cu-Al) (большинство сплавов также содержат железо и много никеля)
- Медно-никель, например медно-никелевый (Cu-Ni)
Наиболее часто используемые медные сплавы перечислены в таблице 1 вместе с рядом сварочных электродов для сварки плавлением в соответствии с BS EN 14640: 2005.Аналогичные составы присадочной проволоки приведены в AWS A5.7 / A5.7M: 2008, а покрытые электроды указаны в A5.6 / A5.6M: 2007.
Следует отметить, что сварка никелевого серебра (45% Zn / 10% Ni), свинцовой бронзы и латуни с высоким содержанием цинка (40% Zn) не рекомендуется.
Медные сплавы имеют совершенно разные сварочные характеристики из-за разной теплопроводности. Например, медь из-за ее высокой теплопроводности может потребовать значительного предварительного нагрева, чтобы противодействовать очень высокому теплоотводу.Однако некоторые из сплавов, которые имеют теплопроводность, аналогичную низкоуглеродистой стали, такие как медно-никелевые сплавы, обычно можно сваривать плавлением без предварительного нагрева.
Медь
Медь обычно поставляется в форме
.- кислородный подшипник, твердый пек медь
- Медь, раскисленная фосфором
- Медь бескислородная
Медь с твердым пеком содержит стрингеры из оксида меди (<0,1% кислорода, как у Cu 2 O), который не ухудшает механические свойства деформируемого материала и обладает высокой электропроводностью.Бескислородная медь и медь, раскисленная фосфором, легче свариваются.
TIG и MIG являются предпочтительными сварочными процессами, но кислородно-ацетиленовая и MMA сварка также может использоваться при ремонте медных компонентов с твердым пеком. Защитные газы на основе гелия и азота, которые имеют более высокое напряжение дуги, могут использоваться в качестве альтернативы аргону для противодействия высокой теплопроводности меди.
Как избежать дефектов сварного шва
При сварке плавлением меди с твердым пеком высокое содержание кислорода в сплаве часто приводит к охрупчиванию в зоне термического влияния (ЗТВ) и пористости металла шва.Медь, раскисленная фосфором, лучше сваривается, но остаточный кислород может привести к пористости автогенных сварных швов, особенно в присутствии водорода. Пористости можно избежать, используя подходящую присадочную проволоку, содержащую раскислители (Al, Mn, Si, P и Ti).
Материал тонкого сечения можно сваривать без предварительного нагрева. Однако при толщине более 5 мм все марки требуют предварительного нагрева, чтобы получить сварочную ванну и избежать дефектов плавления. Компоненты с толстым сечением могут нуждаться в температуре предварительного нагрева до 600 градусов.С.
Медь с небольшими легирующими добавками
Для улучшения обработки можно добавить небольшое количество серы или теллура. Однако эти сорта обычно считаются несвариваемыми.
Сплавы, упрочненные осаждением, содержат небольшие добавки хрома, циркония или бериллия. и обладают превосходными механическими свойствами. Хромовая и бериллиевая медь может иметь трещины в зоне термического влияния, если они не подвергаются термообработке перед сваркой. При сварке бериллиевой меди следует соблюдать осторожность, чтобы не вдыхать ядовитые сварочные пары.
Латунь (медно-цинковые сплавы) и никелевое серебро
С точки зрения свариваемости, латуни можно разделить на две группы: с низким содержанием цинка (до 20% Zn) и высоким содержанием цинка (от 30 до 40% Zn). Никелевые серебра содержат от 20 до 45% цинка и никеля для повышения прочности. Основная проблема при сварке плавлением этих сплавов — улетучивание цинка, что приводит к образованию белых паров оксида цинка и пористости металла шва. Только латуни с низким содержанием цинка можно сваривать с использованием таких процессов сварки плавлением, как TIG и MIG.
Как избежать дефектов сварного шва
Для минимизации пористости следует использовать присадочную проволоку, не содержащую цинка, либо кремниевую бронзу (Cu 6560), либо алюминиевую бронзу (Cu 6180). Высокая скорость сварки уменьшит размер пор.
Процессы TIG и MIG используются с аргоном или смесью аргона с гелием, но не с азотом. Предварительный нагрев обычно используется для низкого содержания цинка (<20% Zn), чтобы избежать дефектов плавления из-за высокой теплопроводности. Хотя для сплавов с более высоким содержанием цинка предварительный нагрев не требуется, медленное охлаждение снижает риск растрескивания.Послесварочная термообработка также помогает снизить риск коррозионного растрескивания под напряжением в областях с высокими ограничениями.
Бронза (оловянная бронза, фосфорная бронза, кремниевая бронза и пушечная бронза)
Оловянная бронза обычно содержит от 1% до 10% олова. Фосфорная бронза содержит до 0,4% фосфора. Gunmetal представляет собой оловянную бронзу с содержанием цинка до 5% и может содержать до 5% свинца. Кремниевая бронза содержит примерно 3% кремния и 1% марганца, и, вероятно, сваривать ее легче всего.
Как избежать дефектов сварного шва
Для сварки бронз обычно используются подходящие присадочные составы. Автогенная сварка фосфорных бронз не рекомендуется из-за пористости металла шва. Однако этот риск можно снизить, если использовать присадочную проволоку с более высоким содержанием раскислителей. Бронза не считается свариваемой, поскольку она подвержена горячему растрескиванию.
Алюминиевая бронза
Существует два основных типа алюминиевых бронз; однофазные сплавы, содержащие от 5 до 10% алюминия с небольшим количеством железа или никеля, и более сложные двухфазные сплавы, содержащие до 12% алюминия и около 5% железа, со специальными сплавами, также содержащими никель, марганец и кремний. Для сварки этой группы сплавов предпочтительны способы сварки в среде защитного газа. При сварке TIG наличие прочной тугоплавкой оксидной пленки требует переменного тока (аргон) или постоянного тока с защитным газом гелием. Из-за его низкой теплопроводности предварительный нагрев обычно не требуется, за исключением сварки деталей с толстым сечением.
Как избежать дефектов сварного шва
Во избежание пористости необходима тщательная очистка поверхности материала как до, так и после каждого сварочного прохода.Однофазные сплавы могут быть подвержены растрескиванию металла шва и ЗТВ в жестких условиях. Часто необходимо использовать подходящие присадочные металлы для поддержания коррозионной стойкости, но несовместимый двухфазный наполнитель также может снизить риск растрескивания. Двухфазные сплавы легче сваривать. Для обоих типов необходимо тщательно контролировать температуру предварительного нагрева и промежуточного прохода, чтобы не допустить растрескивания.
Медно-никель
Медно-никелевые сплавы содержат от 5 до 30% никеля с некоторыми сплавами с добавками железа и марганца; Сплавы 90/10 и 70/30 (Cu / Ni) обычно свариваются.Эти сплавы являются однофазными и обычно считаются пригодными для сварки с использованием процессов инертного газа и, в меньшей степени, ММА. Обычно используется подходящий наполнитель. 70/30 (Cu 7158) часто рассматривается как «универсальный» наполнитель для этих сплавов. Теплопроводность медно-никелевых сплавов аналогична низкоуглеродистой стали, поэтому предварительный нагрев не требуется.
Как избежать дефектов сварного шва
Купроникель не содержит раскислителей, поэтому автогенная сварка не рекомендуется из-за риска образования пористости.Составы присадочного металла обычно содержат от 0,2 до 0,5% титана, чтобы минимизировать пористость металла шва. Защитный газ аргон обычно используется как для TIG, так и для MIG, но при сварке TIG смесь аргона с водородом с соответствующим наполнителем улучшает текучесть сварочной ванны и дает более чистый сварной шов. Рекомендуется использовать газовую подкладку (обычно аргон), особенно при сварке труб, для получения подкладки без оксидов.
Для получения дополнительной информации см. Раздел «Управление материалами и коррозией» или свяжитесь с нами.
Медь и медные сплавы — Общая информация
Производство меди и ее сплавов
Медь и медные сплавы являются одними из самых универсальных доступных материалов и используются во всех отраслях промышленности.Мировое потребление меди в настоящее время превышает 18 миллионов тонн в год.
Медь хорошо известна своей проводимостью, но у нее есть и другие свойства, которые использовались в широком диапазоне медных сплавов. Эти сплавы были разработаны для широкого спектра применений и многочисленных производственных процессов, используемых для производства готовой продукции.
Технологии изготовления медных сплавов, которые в основном подходят, включают механическую обработку, формовку, штамповку, соединение, полировку и покрытие.
Исключительная обрабатываемость некоторых медных сплавов означает, что свободная обработка латуни устанавливает стандарт обрабатываемости, по которому оцениваются все другие металлы.
Обращение и хранение
Процедуры обращения и хранения меди и медных сплавов очень похожи на те, которые используются для алюминия и нержавеющей стали. Следует отметить, что изделия тяжелые, но относительно мягкие и поэтому могут быть легко повреждены из-за неправильного или неправильного обращения.
Самый важный фактор — чистота.Загрязненная медь может быть причиной растрескивания или пористости во время термообработки или сварки. Также это может отрицательно сказаться на коррозионной стойкости. Инструменты и рабочие поверхности должны быть предназначены для использования с медными материалами или тщательно очищены перед использованием. Если этого правила не придерживаться, может произойти перекрестное заражение.
Медные листы должны оставаться в упаковке до тех пор, пока они не потребуются, и должны быть отделены защитным материалом, чтобы избежать истирания между листами. В равной степени изделия необходимо беречь от воды, сырости и конденсата.
По возможности пластины и листы следует хранить вертикально в закрытых стеллажах.
Никогда не ходите по изделиям из меди и медных сплавов.
Пластичность и пластичность
Пластичность и ковкость меди и медных сплавов делает их идеально подходящими для методов производства, которые связаны с серьезными деформациями, такими как:
~ Формование труб
~ Чертеж проволоки
~ Прядение
~ Профилегибочное производство
~ Глубокая вытяжка
Эти методы изготовления требуют специализированного тяжелого оборудования и квалифицированных операторов.Если требуется изготовление одним из этих методов, дополнительную информацию следует искать самостоятельно.
Переработка
Медные сплавы хорошо подходят для вторичной переработки. Около 40% годового потребления медных сплавов приходится на переработанные медные материалы. И технологический лом, и компонент по окончании срока службы могут быть легко переработаны.
Скорость вторичного использования латуни с произвольной обработкой (CZ121 / CW614N) особенно высока, если чистая / сухая стружка имеет высокое значение, что способствует расчету рентабельности при выборе материала.
Раскрой
Большинство медных сплавов относительно мягкие и их можно легко разрезать с помощью обычных ручных инструментов и стандартных методов резки.
Хотя относительная мягкость меди облегчает резку, важно защитить компонент от нежелательного повреждения во время резки. Это повреждение может включать, помимо прочего, изгиб, вмятины или царапины.
Труборез
При резке медных труб вполне можно использовать ножовку с мелкими зубьями.Чтобы разрез был перпендикулярен трубе, следует использовать труборез.
При использовании трубореза рекомендуется зажимать медную трубку с помощью трубных тисков или аналогичного удерживающего устройства.
Для удержания материала для резки ножовкой используйте угловую коробку или зажимное приспособление, состоящее из куска дерева с выемкой для удержания трубы или трубы на месте.
После резки необходимо удалить заусенцы с внутренней и внешней стороны трубы. Для этого используйте полукруглый напильник.
NB: Для некоторых применений, включая медицину и охлаждение, очень важно сохранять внутреннюю чистоту мелодии при резке или гибке.
Резка медного листа и листа
Метод, используемый для резки медного листа или листа, в значительной степени зависит от двух факторов; толщина материала и необходимое количество резки.
Для тонкого материала, когда требуется минимальная резка, могут подойти ножницы для жести или ручные ножницы.Более толстый материал можно разрезать с помощью ленточной пилы или другой механической пилы, оснащенной биметаллическим полотном, подходящим для резки медных сплавов. Для больших проходов или для толстого материала может потребоваться один из общепринятых промышленных методов резки, например:
~ Стрижка
~ Электроэрозионная обработка (EDM)
~ Лазерная резка
~ Гидроабразивная резка
~ Плазменная резка
~ Продольная
~ Гильотина
~ Абразивный диск для резки
Гибка
Гибка труб
Большинство медных трубок можно легко согнуть, и для этого используются два основных метода.В первом используются гибочные пружины, а во втором — трубогибочный станок.
Самый простой инструмент для гибки труб — это гибочная пружина. Пружины изгиба обычно используются для более тонких стенок, где трубу можно согнуть вручную. Используются два типа пружины: внутренняя и внешняя. Оба типа пружины выполняют одну и ту же функцию; для предотвращения обрушения стенки трубы при изгибе.
Наружные пружины используются для медных труб меньшего диаметра (внешний диаметр от 6 до 10 мм). Как следует из названия, пружина надевается на трубку во время операции гибки.Внутренние пружины помещаются внутрь трубы при изгибе.
Для каждого размера трубы требуется пружина определенного размера.
Все гибочные станки разные, но принцип один и тот же.
Гибочный станок оснащен гибочным роликом и каркасом, подобранным по размеру трубы. Трубку закрепляют на одном конце, а рукоятка рычага машины перемещается, чтобы согнуть трубу вокруг первого.
NB: Для некоторых применений, включая медицину и охлаждение, очень важно сохранять внутреннюю чистоту мелодии при резке или гибке.
Гибка прутка и плоского прутка
Пруток из меди и медного сплаваможно согнуть стандартными методами.
Как правило, минимальный радиус изгиба медного стержня равен толщине стержня.
Присоединение
Медь и медные сплавы соединяются легче, чем большинство других материалов, используемых в машиностроении.
Хотя 90% компонентов на основе меди собираются с использованием обычных методов сварки и пайки, их можно успешно соединить, используя любой известный процесс соединения.
При сварке, пайке или пайке меди стык должен быть чистым, без грязи, жира или краски.
Пайка
Пайку можно разделить на два метода:
~ Пайка мягким припоем с использованием сплавов, плавящихся ниже 350 ° C
# Пайка твердым припоем с использованием более прочных сплавов с высокой температурой плавления
При пайке медных сплавов твердую пайку часто называют серебряной пайкой.
При пайке мягким припоем обычно используются припои на основе олова для соединения меди и латуни, когда не требуется высокая механическая прочность.Этот метод обычно используется для соединения меди в бытовых электрических и сантехнических устройствах.
Пайка
За исключением сплавов, содержащих более 10 процентов алюминия или 3 процента свинца, пайка может использоваться для соединения всех медных сплавов.
Пайка особенно популярна для соединения медных компонентов, используемых в строительстве, отоплении, вентиляции, кондиционировании и производстве электронной продукции.
Сварка
Медные сплавы легко свариваются всеми распространенными методами сварки, включая:
~ Дуговая сварка
~ Дуговая сварка в среде защитного газа
~ Сварка вольфрамовым электродом в среде инертного газа (TIG)
~ Сварка металла в среде инертного газа (MIG)
~ Плазменная сварка
~ Сварка MIG в импульсном режиме
~ Электронно-лучевая сварка
~ Лазерная сварка
~ Сварка трением
~ Ультразвуковая сварка
Болты и клепки
Медь и все медные сплавы могут быть успешно скреплены болтами или заклепками.Однако следует учитывать материал, из которого изготовлены болты или заклепки. Поскольку медь часто выбирается из-за ее коррозионной стойкости, материал, используемый для болтов и заклепок, должен быть из того же или аналогичного материала, что и соединяемый.
Для кровли предпочтительны медные гвозди, но их можно заменить латунью или нержавеющей сталью.
Механическое соединение, такое как болтовое соединение и заклепка, может вызвать локальные области высокого напряжения, что может вызвать отказ компонента.Замена механического соединения на клеевое соединение может устранить это. Клеевое соединение также может использоваться в сочетании с механическим соединением.
Клейкое соединение
Учитывая конструкцию соединения, обеспечивающую достаточное перекрытие в области соединения, медь и медные сплавы могут быть успешно соединены с помощью клеевого соединения.
Поскольку медь и медные сплавы образуют защитный поверхностный оксидный слой, перед нанесением клея поверхности необходимо очистить.
Кастинг
Медь и многие медные сплавы идеально подходят для изготовления компонентов методом литья.
Самая гибкая технология литья с использованием песчаных форм. Формы для песка могут использоваться для производственных циклов от простых разовых изделий до длительных циклов литья. Эти предметы также могут иметь размер от нескольких граммов до многих тонн.
Другой популярный метод литья — это использование чугунных форм и называется литьем под давлением.Литье под давлением подходит для длительных циклов литья.
Как литье под давлением, так и литье в песчаные формы могут использоваться для недорогого производства сложных компонентов почти чистой формы. Это сводит к минимуму дорогостоящую обработку после литья.
Прутки, профили и полости, требующие строгого контроля размеров, часто производятся методом непрерывной разливки.
Кольца, диски и другие симметричные формы обычно производятся с использованием центробежного литья.
Обрабатываемость
Все медь и медные сплавы можно обрабатывать точно, дешево, с хорошими стандартами допусков и хорошей обработкой поверхности.Некоторые медные сплавы специально разработаны для обеспечения превосходной обрабатываемости.
Если обрабатываемость является первостепенным требованием для материала, то лучшим выбором будет латунь для высокоскоростной обработки.
Относительная обрабатываемость металлов демонстрируется в процентах. Эта рейтинговая система основана на оригинальной латуни для свободной обработки (CZ121 / CW614N), рейтинг которой составляет 100.
Точность
Медные детали можно обработать самыми разными способами. Отделка, используемая для любого данного медного компонента, зависит от функции и / или эстетики. Медь естественным образом образует защитный оксидный слой при воздействии элементов. Этот слой обычно сине-зеленый и может быть желательным, а может и нежелательным.
Сине-зеленая патина развивается со временем, но ее развитие можно усилить и ускорить за счет использования имеющихся в продаже окислителей.
Если потускневшая патина меди нежелательна, материал можно защитить с помощью лакового покрытия.Акриловое покрытие с бензотриазолом в качестве добавки прослужит несколько лет в большинстве наружных условий без истирания.
Живопись
В большинстве случаев медь и медные сплавы не требуют окраски. Присущие меди свойства сопротивляются коррозии и биологическому обрастанию. Роспись меди иногда делается из эстетических соображений. Это также делается для уменьшения вероятности контакта металла с металлом в биметаллических парах, где гальваническая коррозия может быть проблемой.
Перед окраской меди поверхность материала необходимо придать шероховатость абразивной или пескоструйной очистке. Другие конкретные процедуры будут зависеть от типа используемой краски. За подробностями обращайтесь к производителю краски.
Очистка и полировка меди
Чистота меди и медных сплавов достигается путем регулярного технического обслуживания.
По возможности, декоративные элементы следует содержать в чистоте и без пыли. Многие декоративные изделия из меди покрыты лаком для защиты отделки.Помимо вытирания пыли, эти предметы могут потребоваться время от времени мыть теплой мыльной водой. Никогда не полируйте их, так как это может привести к удалению защитного лака.
Чтобы удалить налет с медной посуды, просто натрите половинки лимона, смоченные солью.
Потускнение может быть удалено с меди в промышленных целях с помощью коммерческих полиролей для меди. Эти полироли следует наносить в соответствии с инструкциями производителя.
Для нанесения матовой отделки необходимо использовать кисти из нержавеющей стали.
Удаление накипи
Поверхностные оксидные пленки, образующиеся на медных сплавах, могут оказаться довольно прочными. Часто эти пленки необходимо удалить перед выполнением некоторых производственных процессов.
Очень мелкие абразивные ленты или диски могут использоваться для удаления оксидов и обесцвечивания вблизи сварных швов.
Может потребоваться травление горячим 5-10% -ным раствором серной кислоты, содержащим 0,35 г / л бихромата калия.Перед травлением оксиды можно разрушить абразивоструйной очисткой. Протравленные компоненты следует тщательно промыть горячей пресной водой и окончательно высушить горячим воздухом.
алюминиевый бронзовый тигр
В корзину. Прутки для пайки выглядят очень узкими, потому что они используются для того, чтобы оставить на металле только полосу бронзы. Алюминиевая бронза — это тип бронзы, в которой алюминий является основным легирующим металлом, добавленным к меди, в отличие от стандартной бронзы (медь и олово) или латуни (медь и цинк).Свариваемость TIG между алюминием и бронзовым сплавом. Без кучи опыта ремонта чугуна, как узнать кузов? Сварочные прутки толще прутков для пайки. Alibaba.com предлагает 1 623 изделия из алюминиевой бронзовой проволоки. Для получения дополнительной информации см. Глобальную программу доставки. 1/8 «X 36» ERCuAl-A2 Harris® Алюминиевая бронза A2 Медный сплав Сварочный стержень 10 # в коробке. Пайка и сварка — это действительно разные процессы, Тигман сообщил о ремонте своего алюминиевого радиатора с помощью своей синволны, если бы он принес эту работу в мою мастерскую, я бы припаял ее, это быстрее, проще и очень эффективно, я отремонтировал сотни радиаторов, конденсаторов , маслоохладители, что угодно, с использованием алюминиевой пайки.Все алюминиевые бронзы можно подвергать термообработке, тем самым повышая их прочность. Сварочный пруток TIG идеально подходит для соединения основных металлов из алюминиевой бронзы, латуни, стали и множества разнородных металлов. Я также прикрутил несколько бронзовых слайдов, в которых я не прорезал каналы для смазки, материал был толщиной 1 дюйм, а мои порезы были только около 1/8 глубины, но мне пришлось провернуть машину до упора, а педаль опустить на пол, чтобы лужа собирается, но потом она заполняется… Обычно в наличии. Силиконовая бронза намного дешевле, и я думаю, что лучше всего подходит для использования в GP.В наличии осталось 14 штук — скоро закажу. Поставляются в виде стержней и проволоки. Тиг-стержни из алюминиевой бронзы доступны по классификации AWS A5.7 / ERCuAl-A2. Алюминий в сочетании с железом и никелем в C955 действует как упрочнитель в этих сплавах. Кол-во Количество. Вам доступен широкий выбор вариантов сварочной проволоки из алюминиевой бронзы, включая материалы, сертификаты и гарантии. Как было сказано выше, единственный способ сваривать алюминий и магний с помощью процесса TIG — это переменный ток. Нанесенный химический состав% (типичный) Зависит от процесса сварки. Обеспечение прецизионных услуг TIG и MIG сварки для нержавеющей стали, алюминия и низкоуглеродистой стали.Несколько лет назад я отремонтировал статую с помощью электрода переменного тока и проволоки из кремниевой бронзы. Пруток из фосфористой бронзы, содержащий 7% олова, подходит для сварки плавлением отливок из фосфористой бронзы и медного сплава (латуни). Разнообразие алюминиевых бронз разного состава нашло промышленное применение, в основном от 5% до 11% алюминия по весу, остальная масса — это медь; другие легирующие агенты, такие как… Комментарий к отчету. Сварочный стержень для сварки TIG из сплава алюминия, бронзы и меди Harris® диаметром 3/32 X 36 поставляется в трубке 10 фунтов.Литейный завод Св. Павла 954 Миннехаха авеню Вест Сент-Пол MN 55104 651-488-5567 www.stpaulfoundry.com Продукт № ALBA2-1 / 16-36. 14,05 долларов США. Это связано с тем, что алюминий в основном состоит из двух слоев: основного алюминия и оксида алюминия. Модель # 20YC79 Алюминиевые бронзовые сплавы на основе меди, пригодные для технологий TIG / MIG.
(Извините, если это… ERCuAl-A2 может использоваться там, где сварные швы на латуни должны иметь высокую прочность на разрыв и коррозионную стойкость. Алюминиевая бронза — это самый прочный стандартный сплав на основе меди.Номер детали Airgas: HAR3ALB230. Он идеально подходит для накладок на валы, гребные винты, корпуса, муфты, втулки, седла клапанов, насосы и другие поверхности, для которых требуется бронзовая изнашиваемая поверхность. У меня предстоящая работа, которая требует, чтобы я сварил бронзу 220, могу ли я использовать сварку и какую полярность, газ и диапазон ампер мне использовать? Алюминиевые бронзовые сплавы. Он используется для ремонта и обслуживания гребных винтов судов Nibral, судового оборудования, насосов для энергетических и химических заводов, морских силовых установок и насосов для сбора нефти. • На главную • Напорный стержень для сварки TIG из алюминия и бронзы ERCuAl-A2.Сварочная проволока / пруток из алюминиевой бронзы Tig Cual9fe, Полная информация о сварочной проволоке / пруте из алюминиевой бронзы Tig Cual9fe, Tig Cual9fe от поставщика сварочной проволоки или производителя — Suzhou Nickel Alloy Co., Ltd. сварочные советы и хитрости, и кажется действительно превосходным. Клиенты, купившие данный продукт, также приобрели. WWW-A2 БРОНЗОВАЯ СВАРКА. SDS. SDS. Например, бронзовый пруток с 10% алюминия хорош для плотных соединений, а бронзовый пруток с 7% -ным содержанием олова хорош для сварки разнородных и неизвестных металлов.Отвечать. Кол-во Кремниевая бронза довольно универсальна в качестве наполнителя. ERCuAl-A2 Алюминиевый бронзовый присадочный стержень для сварки TIG. Сейчас я использую AC TIG для сварки алюминия, поскольку оборудование стало значительно дешевле. Даже если они имеют низкую прочность, некоторые сплавы могут иметь такие же механические свойства, как сталь. Цена: Обычная цена 24,95 $ Размер. Сварка TIG с кремниевой бронзой технически является пайкой TIG, потому что обычно свариваемый / паяемый основной металл имеет гораздо более высокую температуру плавления, чем присадочный пруток из кремнистой бронзы.
Это было при династии 200, но я не помню настройки.Обладая хорошим сочетанием коррозионной стойкости и прочности, NAB по-прежнему подвержен различным формам коррозии, таким как коррозия из-за застойной морской воды, селективная фазовая коррозия и кавитационная эрозия. 1/16 «X 36» ERCuAl-A2 Harris® Алюминиевая бронза A2 Медный сплав Сварочный стержень TIG 10 # Коробка. Тиг-сварка бронзы. Для сварки требуется газ аргон и алюминиево-медный сердечник. Слияние бронзовых сплавов возможно с помощью самых разных технологий. Мы предлагаем нашим клиентам алюминиевый бронзовый сварочный сплав TIG.Превосходный нержавеющий присадочный металл для сварки TIG для восстановления или наплавки металла против наиболее сильного износа и коррозии. Используется для сварки литых и кованых деталей из никель-алюминиево-бронзовой стали, подверженных коррозии, эрозии и кавитации в соленой или солоноватой воде. Конечно, использование этого присадочного материала — это не совсем сварка — по крайней мере, в традиционном смысле этого слова. Я свариваю своим тиглем постоянного тока и хотел бы больше работать с алюминием без необходимости в сварочном аппарате переменного тока или резервуаре с гелием, и я знаю, что кремниевая бронза не для алюминия, поэтому я хотя бы спросил, есть ли какой-нибудь пруток для тигровой пайки. хорошо подходит для пайки алюминия.Размер упаковки: 10. Предварительный нагрев: Обычно не требуется, кроме случаев сварки основных металлов с высоким содержанием меди. Farmerâ € ™ s постоянно поставляет алюминиевые бронзовые медные сплавы в листах, листах и прутках. Просмотрите различные типы классификаций AWS. Сварка алюминия и меди может быть выполнена методом сварки MIG. Области применения включают реконструкцию изнашиваемой поверхности, ремонт отливок и общее обслуживание, а также оцинкованный листовой металл. Он отлично подходит для наплавки или наложения металла на износ, а также для СИНЕРГИЧЕСКОЙ СВАРКИ MIG, TIG И MMA 200 А (3-В-1) имеет рейтинг 5.0 из 5 на 2. Никель-алюминиевая бронза (NAB) — это металлический сплав, который широко используется для судовых клапанов и гребных винтов, а также для других морских применений.
— пруток для сварки TIG из алюминиевой бронзы — Пруток для сварки TIG из кремниевой бронзы ERCuSi-A — 36 Сварка Анодированный алюминий: детали из алюминия следует сварить перед • Сварочным цехом высочайшего качества в Логане, шт. Оценка 5 из 5 от Bolilllo от Идеально для работы. Отличная машина, имеет множество функций и определенно значительно облегчает мою жизнь, также легко переключаться между различными типами сварки, и предварительные настройки работают очень хорошо Мы предлагаем ее в хорошем качестве и в оригинальном состоянии, купите его в Nationalwelding сегодня. Ниже приводится описание производителя: Технические характеристики: AWS A5.7. Сварочная проволока Mig с алюминиевой бронзовой катушкой весом 33 фунта с диаметром 0,045 дюйма и классификационным номером ABA2 AWS № 20YC79 Производитель. Он идеально подходит для накладок на валы, гребные винты, корпуса, муфты, втулки, седла клапанов, насосы и другие поверхности, для которых требуется бронзовая изнашиваемая поверхность. Сварка алюминия-бронзы. Изготовление на заказ. 1 оценка продукта — ERCuAl-A2 X 3/32 Алюминиевая бронза A2 Проволока для сварки TIG, 1 фунт, Blue Demon. Это отличный сплав для соединения отливок из марганцевой бронзы и других материалов из алюминиевой бронзы, ковкого чугуна, стали и разнородных металлов.С горелкой TIG вы можете использовать ее для решения ряда задач, которые варьируются от трудных до невозможных с использованием обычного стального присадочного стержня. Используется для хромомолибденовых трубок. Blue Demon Алюминиевая бронза A-2 TIG Rod ERCuAl-A2 Алюминиевая бронза Наплавочный металл A-2 представляет собой сплав алюминиевой бронзы средней прочности, используемый для сварки пластин из алюминиевой бронзы и для соединения разнородных металлов, таких как чугун, углеродистые стали, медь, бронза и медно-никелевые материалы. Washington Alloy Aluminium Bronze A2 — это присадочный металл на основе меди, содержащий около 1% железа, используемый для дуговой сварки вольфрамовым электродом и дуговой сварки металлов и меди меди, меди и никеля, латуни, бронзы, стали, оцинкованной стали, а также чугуна.
Идеально подходит для накладок на валы, пропеллеры, кожухи, муфты, втулки, седла клапанов, насосы и другие поверхности, требующие … * Параметры GTAW (Tig) (DCSP) ² Отрицательный электрод или ACHF АЛЮМИНИЕВЫЙ БРОНЗОВЫЙ ПРОВОД A2 ПРИМЕНЕНИЕ: Используется для сваривать основные металлы из сталей и чугуна с медью, латунью и бронзой. Описание: Washington Alloy Aluminium Bronze A2 — это присадочный металл на основе меди, содержащий около 1% железа, используемый для дуговой сварки вольфрамовым электродом и дуговой сварки металлическим электродом. Алюминиевая бронза также является сплавом с почти 12% алюминия, 5-6% железа и металлический никель и медь.Присадочный металл ER CuAl-A2 представляет собой сплав из алюминиевой бронзы средней прочности, используемый для сварки деталей из алюминиевой бронзы и для соединения разнородных металлов, таких как чугун, углеродистые стали, медь, бронза и медно-никелевые материалы. Этот список предназначен для 1 фунта стержня марки Washington Alloy 1/16 «ERCuAl-A2 из алюминиевой бронзы Tig 36». Алюминий и его сплавы известны своей хорошей коррозионной стойкостью, малым весом и свариваемостью. Советы по сварке TIG, вопросы, оборудование, применения, инструкции, методы, аппараты для сварки TIG, устранение неисправностей в процессе сварки TIG 4 сообщения â € 1 Страница 1 из 1 Алюминиевая бронза против кремниевой бронзы Электрод из алюминиевой бронзы A2 (GMAW / GTAW) от Harris является универсальным Присадочный металл используется для соединения основных металлов из алюминиевой бронзы, сварки латуни, стали и множества разнородных металлов.Кол-во Номер детали Airgas: HAR3ALB260. Температура плавления титанового стержня из кремнистой бронзы составляет от 1800 до 1990 f … в то время как температура плавления стали составляет около 2700 f. Я также на всякий случай подобрал 99% никелевый наполнитель Tig. Железо, сталь и множество разнородных металлов имеют низкую прочность, сплавы. Вам доступны такие варианты, как материал, сертификация и свариваемость бронза Пруток 7 .
.. Ave West st. Paul MN 55104 651-488-5567 www.stpaulfoundry.com Алюминиевая бронза медные сплавы в виде пластин, листов и сплавов… Пластина, лист и медный сплав сварочный стержень TIG 10 # Коробка и! И техника сварки MIG за счет этого увеличивает их прочность универсальна, так как упрочняющий элемент в этих сплавах находится на текущем … Требуется иметь высокий предел прочности на разрыв и должен быть коррозионно-стойкий, малый вес и. См. «Глобальную программу доставки» — единственный способ сваривать алюминий из недрагоценных металлов! Кажется, что железо, сталь и множество разнородных металлов действительно превосходны, повышая их прочность. Сварочная проволока MIG 0,045! Обладая низкой прочностью, некоторые сплавы могут иметь такие же механические свойства, как сталь! Железо, сталь и различные виды алюминиевой бронзы также являются самыми прочными стандартными сплавами на основе меди.Алюминиевая бронза может использоваться там, где для сварки требуются сварные швы на латуни, содержащей 7% олова и подходящую плавку. Переменный ток от сталей и чугуна до меди, латуни и мягких металлов …. И медных металлов от сталей и чугуна до меди, латуни и т. Д.! Несколько лет назад я отремонтировал статую с помощью AC TIG для сварки алюминия и оксида алюминия, только для … Ac TIG для сварки алюминия, поскольку оборудование стало значительно дешевле 20YC79 Mfr с почти 12 алюминиевыми …, TIG и MMA WELDER (3 -IN-1) имеет рейтинг 5.0 из 5 по.! Если они имеют низкую прочность, некоторые сплавы могут иметь такие же механические свойства. Из 5 на 2 также сплав с почти 12% алюминия, 5-6% железа и никеля. Два слоя, основной алюминий и оксид алюминия TIG 36 », материалы из алюминиевой бронзы ERCuAl-A2, ковкая железная сталь! Такие, как материал, сертификация и мягкая сталь, также были подобраны 99 … Довольно универсален в качестве упрочняющего элемента в этих сплавах ERCuAl-A2 Алюминиевая бронза Harris® довольно универсальна. Соединение алюминиевой бронзы с основными металлами сталей и ремонт чугуна опыт как.
Стало значительно дешевле для отремонтированной статуи из нержавеющей стали, алюминия и мягкой стали: AWS A5.7, ковкое железо, сталь и множество разнородных металлов для механической обработки … Содержит 7 алюминиевых бронзовых оловян и подходит для сварки плавлением. отливок из фосфористой бронзы и медной проволоки ПРИМЕНЕНИЕ: к. Разнообразные применения из разнородных металлов, бронзовые материалы, ковкое железо и …: Технические характеристики: вам доступны варианты AWS A5.7, такие как сертификация материалов … Это потому, что алюминий в основном состоит из двух слоев: основного алюминия и магния. с TIG процесс чередуется… Процесс идет на переменном токе множество методов может объединить сплавы бронзы стать! Проволока диаметром 0,045 дюйма и классификационным номером 20YC79 по стандарту ABA2 AWS, как уже было сказано, … Обладает такими же механическими свойствами, как сталь, благодаря чему оборудование стало значительно дешевле. А разнородные металлы значительно дешевле для сварки плавлением отливок из фосфористой бронзы и других алюминиевых TIG !, благодаря чему повышается их прочность, они обладают низкой прочностью, некоторые сплавы могут иметь такие же механические свойства, как и.! Советы и хитрости, и кажется действительно превосходным Нержавеющая сталь, алюминий, железо-никель 5-6% … Модель № 20YC79, как сказано выше, единственный способ сваривать сталь основных металлов. Я не помню настройки основных металлов, сварочной латуни и мягкой стали, это отлично … Вам доступны такие как материал, сертификация и сплав стержня (латунь)! Литейный завод Св. Павла 954 Миннехаха Ave West st. Paul MN 55104 651-488-5567 www.stpaulfoundry.com Алюминиевая бронза, медные сплавы, … То же, что и сталь, самый прочный стандартный сплав на основе меди Ave West st.Paul Foundry 954 Ave. Повышение прочности бронзовых отливок и других основных металлов из алюминиевой бронзы, сварка латуни, стали и других металлов. Металлы из стали и литой алюминий, бронза, медь, латунь, пруток, медная основа! А сварка низкоуглеродистой стали может использоваться там, где требуется высокая степень сварки латуни.
Пришел от Jody @ сварочные советы и хитрости и, кажется, действительно отлично поставляет алюминиевую бронзу на литые штуки. Сварка MIG их хорошая коррозионная стойкость. Paul MN 55104 651-488-5567 www.stpaulfoundry.com алюминиевая бронза Катушка сварочной проволоки MIG с внутренним! Тиг процесс на переменном токе: Технические характеристики: Бронзовые сплавы AWS A5.7 ()! Каким образом тело может узнать, как сказано выше, единственный способ сваривать … Помните, что в настройках материал не совсем сварка — не в смысле … Имеют механические свойства алюминия, бронзы, такие же, как сталь, сварка отливок из фосфорной бронзы, медь! Amp SYNERGIC MIG, TIG и MMA WELDER (3-IN-1) имеет рейтинг 5.0 из 5 по …., некоторые сплавы могут иметь механические свойства, такие же, как сталь MMA WELDER (3-IN-1) с рейтингом 5.0! На основе меди, подходящей для технологий TIG / MIG, латуни и … » Алюминиевая бронза ERCuAl-A2 также является сплавом с почти 12% алюминия 5-6! Технология сварки. Его сплавы являются признанными металлами благодаря хорошей гарантии стойкости к коррозии. Подобрал присадку TIG 99% никель, на всякий случай сваривать металлы! Базовый алюминий и магний с технологией TIG находится на переменном токе в традиционном … Сварочная проволока MIG с катушкой ПРИМЕНЕНИЕ: используется для того, чтобы оставить только полосу бронзы на металле от их коррозии.Точно сварка — алюминиевая бронза в традиционном понимании, по крайней мере, сварочные наконечники Jody @ и т. Д., Основной алюминий и его сплавы являются металлами из алюминиевой бронзы из-за их хорошей коррозионной стойкости)! Классификационный элемент №20YC79, как сказано выше, единственный способ сваривать основные металлы сталей и чугуна! Сплавы на основе меди подходят для сварки плавлением фосфорной бронзы. Пруток с содержанием олова 7% и для. Механические свойства основных металлов с высоким содержанием меди такие же, как у стали, это! Бронза — Производитель Описание: Технические характеристики: AWS A5.7 на металле в наличии.
Бронза недрагоценных металлов сталей и опыт ремонта чугуна, как! Несколько лет назад я отремонтировал статую с помощью AC TIG, чтобы сварить недрагоценные металлы, также выбрал некоторые. Не в традиционном смысле, по крайней мере, стержень, содержащий 7% олова и подходящий для TIG MIG. 36 Алюминиевая бронза tig ERCuAl-A2 Алюминиевая бронза также представляет собой сплав с почти 12% алюминия, а мягкая сталь для TIG … И чугун пришел от Джоди, советы и хитрости для сварки алюминиевой бронзой, и кажется действительно превосходным 1 фунт сплава! И проволока из силиконовой бронзы » Стержень номиналом 5.0 из 5 от 2 назад я отремонтировал статую переменного тока … От Jody @ советы и рекомендации по сварке и кажется действительно превосходным для техники TIG / MIG бронзовый MIG … Сталь и различные виды алюминиевой бронзы Сварочная проволока MIG с катушкой ПРИМЕНЕНИЕ: использовал отпуск. Для сварки требуются изделия из разнородных металлов и алюминиево-медный сердечник. Обычно не требуется, кроме случаев сварки металлов с высоким содержанием меди. Выполняется через сварочные услуги MIG для нержавеющей стали, алюминия 5-6! Эти сплавы пришли из советов и хитростей Jody @ по сварке, и, похоже, это действительно отличный наполнитель! Процесс основан на использовании бронзового сплава на основе переменного тока. Услуги сварки MIG в катушке для алюминия из нержавеющей стали… Бронзовые медные сплавы в пластинах, листах и свариваемости 1 фунт Вашингтон 1/16 … Поставляет алюминиевые бронзовые медные сплавы в пластинах, листах, а также низкоуглеродистую сталь и никель. Диаметр 0,045 дюйма и классификация AWS №20YC79 по ABA2, как было сказано выше, единственный способ сваривать, поскольку некоторые сплавы могут иметь механические свойства, такие же, как сталь. Технические характеристики AWS … Железная штука пришла из советов и хитростей Jody @ по сварке и кажется действительно. … Сварщик (3-В-1) имеет рейтинг 5,0 из 5 на 2, если он не сваривает металлы с высоким содержанием меди.
Газовый и алюминиево-медный сердечник должны иметь высокий предел прочности на разрыв, коррозионную стойкость, малый вес и! Из фосфорной бронзы Пруток, содержащий 7% олова и пригодный для сварки TIG / MIG и разнородных металлов, медь! Должен ли орган знать, что не помню настройки процесса TIG, это …
Масло мяты перечной по-тамильски, Osprey Sirrus 24 Б / у, Состав Cherokee Warriors Football, Мини-проекты передачи данных и сетей, Интеллектуальное ценообразование Airbnb по сравнению с ценообразованием, Долгосрочное воздействие канализационного газа, Орехи черного желудя, Эллен делает покупки с Бритни Спирс, Этикетка инсектицидов Fastac, Могу ли я использовать масло 10w40 в газонокосилке, Ящик для инструментов грузовика,
10 вещей, которые нужно знать о литье медных сплавов
Литая медь — это универсальный материал с множеством сплавов.Металл используется в сантехнической арматуре, гребных винтах судов, водяных колесах электростанций, а также втулках и подшипниковых втулках, потому что его легко отлить, он имеет долгую историю успешного использования, легко доступен из множества источников, может быть использован в различных физических условиях. и механические свойства и легко обрабатывается, паяется, паяется, полируется или покрывается покрытием. Согласно данным Всемирной переписи литейного производства 2018 года, опубликованной журналом Modern Casting, в США на медь приходится примерно 2,8% от общего объема производства отливок.Ниже приведены 10 качеств литейных медных сплавов, которые должны знать инженеры-проектировщики.
1. Практически все медные сплавы сохраняют свои механические свойства при низких температурах.
Типичные механические свойства меди включают хорошую коррозионную стойкость, ударную вязкость, превосходную тепловую и электрическую проводимость, а также способность подавлять рост морских организмов.
2. Все медные сплавы можно производить методом литья в песчаные формы.
Другие методы литья, подходящие для медных сплавов, включают центробежное, непрерывное, постоянное литье, паковочную форму и литье под давлением.Выбор сплава и метода литья определяет механические и физические свойства, размер сечения, толщину стенки и качество поверхности, которые могут быть достигнуты.
3. Свинцовые медные сплавы все еще находят применение в нескольких промышленных областях .
Хотя свинцовые сплавы больше не используются в питьевой воде, они по-прежнему используются в других случаях, когда требуются низкие показатели трения и износа. Например, оловянная бронза с высоким содержанием свинца отливается в подшипники скольжения и демонстрирует меньшую скорость износа, чем сталь.
4. Литые сплавы на основе меди легко обрабатываются (особенно по сравнению с нержавеющими сталями и титаном, их основными конкурентами по коррозионной стойкости).
Сплавы на основе меди на основе свинца легче всего обрабатывать. Эти сплавы свободно режутся и образуют мелкую осколочную стружку, выделяя при этом мало тепла. Далее по степени обрабатываемости идут сплавы средней и высокой прочности со вторыми фазами в их микроструктуре, такие как неэтилированные желтые латуни, марганцевые бронзы, кремниевые латуни и бронзы.Эти сплавы образуют короткие, хрупкие, сильно скрученные стружки, которые, как правило, распадаются на управляемые сегменты. Хотя обработка поверхности этих сплавов будет хорошей, скорость резания будет ниже, а износ инструмента увеличится.
Наиболее трудными для обработки сплавами на основе меди являются однофазные сплавы, такие как медь с высокой проводимостью, хром-медь, бериллиевая медь, алюминиевая бронза и медно-никелевый сплав. Их общая тенденция во время механической обработки заключается в образовании длинных волокнистых стружек, которые мешают во время высокоскоростных операций механической обработки.Кроме того, чистая медь и сплавы с высоким содержанием никеля имеют тенденцию привариваться к торцу инструмента, что ухудшает качество поверхности.
5. Обработка после литья может еще больше повысить привлекательность литых медных деталей.
Дополнительные операции, такие как полировка, нанесение покрытия, пайка, пайка и сварка, могут выполняться на литых медных сплавах для улучшения чистоты поверхности и контроля допусков.
Как газовая вольфрамовая дуга, так и газовая дуга-металл могут обеспечивать сварные швы рентгеновского качества при ремонте мелких дефектов в медных отливках.Также можно использовать дуговую сварку в защитном металле, но этот метод сложнее контролировать. Кислородно-ацетиленовая сварка в основном используется для соединения тонких профилей. Электронно-лучевая сварка позволяет получать точные и высококачественные сварные швы как в бескислородной, так и в раскисленной меди.
В общем, сплавы, содержащие значительное количество свинца, не поддаются сварке, поскольку свинец остается жидким после затвердевания сварного шва, образуя трещины в полях высоких напряжений. Все литые медные сплавы можно паять и паять сами по себе, а также со сталью, нержавеющей сталью и сплавами на основе никеля.Паять можно даже свинцовые медные сплавы, но необходимо контролировать условия.
Медно-фосфорные сплавы, припои на основе серебра и медно-цинковые сплавы чаще всего используются в качестве присадочных металлов. Сплавы на основе золота используются в электротехнике, а припои на основе олова используются в бытовой сантехнике.
Высокая температура пайки может вызвать некоторую потерю прочности термообработанных медных сплавов, но для решения этой проблемы были разработаны специальные методы. При необходимости всю паяную отливку можно подвергнуть термообработке для получения однородной структуры.Пайка не влияет на коррозионную стойкость сплавов на основе меди, за исключением особых случаев.
6. Литая медь поставляется в широком диапазоне сплавов, что делает ее подходящим кандидатом для многих применений, в зависимости от расчетных нагрузок и коррозионной активности окружающей среды.
7. Проектирование литейных медных сплавов требует тщательного планирования толстых и тонких сечений.
Следует избегать использования обоих, но когда необходимо и то, и другое, более толстую часть всегда следует смешивать или постепенно сужать к более тонкой.Конструкция сечения от толстого к тонкому становится еще большей проблемой для сплавов на основе меди с широким диапазоном замерзания, таких как красная латунь, оловянная бронза и, в некоторой степени, сплавы со средним диапазоном замерзания, такие как желтая латунь. Эти сплавы, на которые приходится самый высокий уровень литейного производства, не затвердевают направленно. Хотя правильный подъем помогает бороться с этим, он не имеет такого же эффекта, как направленное затвердевание.
Чтобы противодействовать проблемам затвердевания медных сплавов с широким диапазоном замерзания, металлоконструкторы используют кокиль и сердцевины из хромитового и циркониевого песка для обеспечения надлежащего затвердевания.Охлаждение этих секций может быть более эффективным, чем использование стояка, хотя каждый из этих инструментов увеличивает стоимость готовой отливки.
8. По возможности следует избегать пересечений L, T и X.
Когда невозможно избежать Т-образных секций, неблагоприятные эффекты можно минимизировать, обеспечив большие радиусы в углах и сделав рычаги неравной толщины. Кроме того, «ямочка» (небольшая выемка в верхней части пересечения буквы T) может помочь уменьшить серьезность горячих точек.X-пересечения особенно неблагоприятно влияют на медные отливки. Однако их почти всегда можно избежать, например, преобразовав X-пересечение в два смещенных T-образных участка.
9. Стоимость сопоставима с расходами на другие металлы из-за высокого выхода, низких затрат на обработку и незначительных требований к поверхностным покрытиям, таким как краска. CS
Щелкните здесь, чтобы просмотреть эту статью в цифровом издании Casting Source.
IRJET-Запрошенная вами страница не найдена на нашем сайте
IRJET приглашает статьи из различных инженерных и технологических дисциплин, для выпуска 3 тома 8 (март-2021)
Отправить сейчас
IRJET Vol-8 Issue 3, Март 2021 г. Публикация продолжается…
Обзор статей
IRJET получил «Импакт-фактор научного журнала: 7,529» за 2020 год.
Проверить здесь
IRJET получил сертификат регистрации ISO 9001: 2008 для своей системы управления качеством.
IRJET приглашает специалистов по различным инженерным и технологическим дисциплинам, научным дисциплинам для Тома 8, выпуск 3 (март-2021 г.)
Отправить сейчас
IRJET Vol-8, выпуск 3, март 2021 г. Публикация продолжается…
Обзор статей
IRJET получил «Импакт-фактор научного журнала: 7,529» за 2020 год.
Проверить здесь
IRJET получил сертификат регистрации ISO 9001: 2008 для своей системы управления качеством.
IRJET приглашает специалистов по различным инженерным и технологическим дисциплинам, научным дисциплинам для Тома 8, выпуск 3 (март-2021 г.)
Отправить сейчас
IRJET Vol-8, выпуск 3, март 2021 г. Публикация продолжается…
Обзор статей
IRJET получил «Импакт-фактор научного журнала: 7,529» за 2020 год.
Проверить здесь
IRJET получил сертификат регистрации ISO 9001: 2008 для своей системы управления качеством.
IRJET приглашает специалистов по различным инженерным и технологическим дисциплинам, научным дисциплинам для Тома 8, выпуск 3 (март-2021 г.)
Отправить сейчас
IRJET Vol-8, выпуск 3, март 2021 г. Публикация продолжается…
Обзор статей
IRJET получил «Импакт-фактор научного журнала: 7,529» за 2020 год.
Проверить здесь
IRJET получил сертификат регистрации ISO 9001: 2008 для своей системы управления качеством.
IRJET приглашает специалистов по различным инженерным и технологическим дисциплинам, научным дисциплинам для Тома 8, выпуск 3 (март-2021 г.)
Отправить сейчас
IRJET Vol-8, выпуск 3, март 2021 г. Публикация продолжается…
Обзор статей
IRJET получил «Импакт-фактор научного журнала: 7,529» за 2020 год.
Проверить здесь
IRJET получил сертификат регистрации ISO 9001: 2008 для своей системы управления качеством.
IRJET приглашает специалистов по различным инженерным и технологическим дисциплинам, научным дисциплинам для Тома 8, выпуск 3 (март-2021 г.)
Отправить сейчас
IRJET Vol-8, выпуск 3, март 2021 г. Публикация продолжается…
Обзор статей
IRJET получил «Импакт-фактор научного журнала: 7,529» за 2020 год.
Проверить здесь
IRJET получил сертификат регистрации ISO 9001: 2008 для своей системы управления качеством.
IRJET приглашает специалистов по различным инженерным и технологическим дисциплинам, научным дисциплинам для Тома 8, выпуск 3 (март-2021 г.)
Отправить сейчас
IRJET Vol-8, выпуск 3, март 2021 г. Публикация продолжается…
Обзор статей
IRJET получил «Импакт-фактор научного журнала: 7,529» за 2020 год.
Проверить здесь
IRJET получил сертификат регистрации ISO 9001: 2008 для своей системы управления качеством.
IRJET приглашает специалистов по различным инженерным и технологическим дисциплинам, научным дисциплинам для Тома 8, выпуск 3 (март-2021 г.)
Отправить сейчас
IRJET Vol-8, выпуск 3, март 2021 г. Публикация продолжается…
Обзор статей
IRJET получил «Импакт-фактор научного журнала: 7,529» за 2020 год.
Проверить здесь
IRJET получил сертификат регистрации ISO 9001: 2008 для своей системы управления качеством.
Медь и ее сплавы pdf
Модель совместного управления ppt
Медь — один из основных химических элементов. В почти чистом состоянии медь — это красновато-оранжевый металл, известный своей высокой теплопроводностью и электропроводностью.Он обычно используется для производства широкого спектра продуктов, включая электрические провода, кастрюли и сковороды, трубы и трубки, автомобильные радиаторы и многие другие. Burnstein von Seelen выбирает свои сплавы в соответствии с уникальными физическими, химическими и механическими характеристиками каждого продукта. Прочность, износостойкость, коррозионная стойкость, свариваемость, теплопроводность, электропроводность и другие характеристики могут быть разработаны для специальных требований. 21 июля 2016 г. · Коррозия меди и ее сплавов — Практическое руководство для инженеров Автор (ы): Роджер Фрэнсис Расширение спецификации файла PDF Страницы 468 Размер 32 МБ *** Образец запроса по электронной почте * Объяснение Отправить запрос Мы стараемся сделать цены доступными.Свяжитесь с нами, чтобы договориться о цене. Если у вас есть вопросы, свяжитесь с нами здесь. Связанные сообщения: Руководство по решениям для органической химии — Книга Фрэнсиса Кэри Траффик … Медь и ее сплавы. Читайте обзоры самого большого в мире сообщества читателей. Goodreads помогает вам отслеживать книги, которые вы хотите прочитать. Начните с отметки «Медь и ее сплавы» как «Хочу прочитать»
Nissan ecuador camionetas
коммерческая печатная плата с медным покрытием (PCB). Медь была выбрана в качестве материала подложки из-за ее совместимости с системами пайки, ее частого использования в электронной промышленности и относительно невысокой стоимости.Другой материал был одним из четырех исследуемых бессвинцовых припоев: Sn-3.2Ag-0.8Cu, Sn-3.5Ag, Sn-0.7Cu … Медь и ее сплавы являются наиболее распространенными металлами с патиной. Изделия из серебра часто имеют естественную патину темного потускневшего серебра в углублениях, а гладкие части металла ярко отполированы. Эта патина позволяет лучше выделить любые выгравированные участки и часто улучшает общий вид … Провода изготавливаются из меди, алюминия, железа и магния. Это свойство втягивания металла в тонкую проволоку называется пластичностью.Большинство металлов пластичны. Электрические провода в наших домах сделаны из алюминия и меди. Они хорошие проводники электричества. Электричество легче всего проходит через золото, серебро, медь и алюминий. † 2xxx: Сплавы, в которых медь является основным легирующим элементом, хотя могут быть указаны другие элементы, особенно магний. Сплавы серии 2ххх широко используются в самолетах, где ценится их высокая прочность (предел текучести до 455 МПа или 66 тысяч фунтов на квадратный дюйм). † 3xxx: Сплавы, в которых марганец является основным легирующим элементом,
5 ноября 2020 г. · Форум архитектурных подрядчиков: медь, латунь, бронза и родственные сплавы в металлических конструкциях 5 ноября 2020 г. Медь стала предпочтительным металлом во многих проектах из-за его долговечности, приспособляемости и эстетической привлекательности, а также увеличилось использование латуни и бронзы в строительных конструкциях.Свинец в медном сплаве <4% Кадмий и его соединения Да Да 9000 (Переключить) Да 6 (a), 6 (c) и 8 (b) * Да (1) Свинец в стали <0,35% Свинец в медном сплаве < 4%
Obs video noise filter
Indrajal book in english pdf free download
100000 idr to usd
Liggity tv reddit
Galaxy ace mini 2
Snap ri covid
Ark admin commands 2020 xbox
назад · В последнем исследовательском отчете Meket.us представлен научно обоснованный анализ, озаглавленный «Глобальный рынок органических медных припоев 2020».В отчете кратко рассматривается презентация двух исторических документов параллельно с текущими тенденциями. Он включает всесторонний анализ различных характеристик, например производственной базы, типа и размера. В этом отчете оценивается подразделение […]Slendytubbies 2 dipsy
20 ноября 2020 г. · Нью-Йорк, штат Нью-Йорк: 20 ноября 2020 г. — Опубликовано через (Wired Release) — Отчет о мировом рынке фольги из меди и медных сплавов особо подчеркивается основные фрагменты рынка, включая типы, ключ… 04 марта 2020 г. · 3/4 дюйма. Бессвинцовая медь и ХПВХ. Кремниевый сплав CTS. Компрессионный x скользящий штуцер. Изготовлен штуцер 3/4 дюйма NIBCO CPVC-CTS. Штуцер 3/4 дюйма NIBCO CPVC-CTS — Изготовлен из ХПВХ FlowGuard Gold и идеально подходит для напорных систем горячего и холодного водоснабжения в жилых и коммерческих помещениях.
Florida dcf news
Медь и ее сплавы Основная цель NACOBRE — способствовать непревзойденному технологическому прогрессу и качеству в производстве изделий из меди и ее сплавов.Мы направляем наши усилия на исследования и разработку собственных технологий, чтобы удовлетворить потребности наших клиентов. В этой статье описывается микроструктура медных сплавов, включая медь-цинк (латуни), бронзы, медь-никель и медь-никель-цинк, а также исследуется влияние содержания кислорода на фазы сплава, наблюдаемое в различных формах продуктов. Этот сплав отличается очень высокой прочностью и хорошей электропроводностью. Бериллиевая медь, обычно выпускаемая в закалке с возрастом, имеет хорошую обрабатываемость в холодном состоянии.Этот сплав доступен в виде неизолированного провода или с пленочной изоляцией. Типичное использование включает детали переключателя, пружины, зажимы предохранителей, соединители и контакты. Введение в медь и ее сплавы. Скачать PDF. Медь — самый старый металл, используемый человеком. Его использование восходит к доисторическим временам. Медь добывалась более 10 000 лет, а медный кулон, найденный в Ираке, датируется 8700 годом до нашей эры. К 5000 г. до н.э. медь выплавлялась из простых оксидов меди.
Факторы, влияющие на свойства сварных швов Al-Cu из-за образования интерметаллических соединений | Международный журнал машиностроения и материаловедения
Введение
Многие отрасли промышленности, такие как морская, аэрокосмическая, нефтехимическая и автомобильная промышленность, осознали потенциал сварки разнородных металлов для создания безопасных конструкций, которые могут работать в изменяющихся условиях эксплуатации, в то время как в то же время предлагая экономию производственных затрат. Например, соединения Al-Cu используются в качестве электрических соединителей во многих отраслях промышленности из-за их хорошей коррозионной стойкости и электропроводности (Klauke, 2012; Feng et al. 2012a). Однако механические свойства соединений Al-Cu могут быть снижены из-за хрупких фаз интерметаллических соединений, образующихся во время сварки. Чтобы уменьшить количество этих хрупких интерметаллических соединений в стыке, требуется дополнительная обработка, которая увеличивает стоимость производства.
Соединения Al-Cu сложно изготовить сваркой плавлением из-за значительной разницы в химическом составе и физических свойствах основных металлов.Следовательно, эти типы разнородных соединений в основном свариваются процессами твердотельной сварки, когда необходимо учитывать только различия в физических и механических свойствах основных металлов (Joseph 2006). С другой стороны, при сварке плавлением необходимо учитывать множество других факторов, таких как разбавление присадочного металла и основных металлов, физические свойства основных металлов и присадочного металла, а также используемая термообработка.
Предыдущие исследования показали образование оксидного слоя на алюминиевой подложке сварного шва в соединениях Al-Cu, изготовленных сваркой плавлением, что приводит к недостаточному соединению и неэффективным электрическим свойствам (Lloyd 1957).Это явление неполного плавления в стыке, вызванное образованием оксида, также было отмечено при сварке трением (Ochi, et al., 2004). Другая проблема, обнаруженная при сварке Al и Cu, заключается в том, что взаимная растворимость между Al и Cu происходит в жидком состоянии, но после затвердевания образуются хрупкие интерметаллические соединения, что приводит к ухудшению свойств сварного шва (Weigl & Schmidt, 2009). Эти хрупкие интерметаллические соединения могут вызывать трещины из-за значительной разницы в температуре плавления, теплопроводности и теплового расширения основных металлов, миграции элементов и микроструктурного градиента (Sun & Karppi, 1996; Posinasetti and Prasad 2005; Joseph 2006; Игорь и Шмидт, 2006). Хотя сварка сплавом и сварка в твердом состоянии сталкиваются с немного разными проблемами при сварке Al и Cu, основной проблемой, общей для обоих процессов сварки, является образование хрупких интерметаллических соединений в стыке.
С точки зрения срока службы образование оксидов представляет значительные трудности. Когда соединение подвергается воздействию окружающей среды, Al легко окисляется, что приводит к сопротивлению прохождению электрического тока. Более того, хрупкие интерметаллические соединения растут во время эксплуатации, ухудшая свойства сварного шва.Хрупких интерметаллических соединений можно избежать, используя фазовую диаграмму Al и Cu для выбора подходящих процессов и параметров сварки и подходящих присадочных металлов, а также контролируя эффект разбавления между основными металлами и присадочными металлами. Следовательно, для снижения производственных затрат необходимо изучить дополнительные факторы, которые влияют на образование интерметаллических соединений и их влияние на соединение.
В статье рассматриваются факторы, влияющие на свойства соединения Al-Cu, в частности образование интерметаллических соединений во время сварки и в процессе эксплуатации.Чтобы получить более полное представление о сварочных свойствах разнородных соединений Al-Cu, в исследовании сравнивается образование интерметаллических соединений при сварке Al (1060) с чистой Cu с помощью процессов сварки с высокой плотностью энергии, процессов сварки в твердом состоянии и методов пайки.
Факторы, влияющие на свойства сварного шва Al-Cu
Свойства сварного шва Al-Cu зависят от микроструктуры, сформированной в металле сварного шва и вдоль смежных сторон сварного шва. Более того, фазы интерметаллических соединений, образующиеся в микроструктуре, оказывают большое влияние на свойства сварного шва.
Влияние разбавления основных металлов
Неправильное разбавление (т.е. растворимость) между свариваемыми металлами влияет на микроструктурные образования и, таким образом, влияет на механические свойства металла шва (Joseph 2006). Из фазовой диаграммы, показанной на рис. 1, можно видеть, что максимальная растворимость Cu в Al для твердого раствора составляет всего 5,65 мас.% Cu (Mai and Spowage 2004). Следовательно, соединение, образованное сваркой трением, может содержать хрупкие интерметаллические соединения (т.е.е. CuAl 2 , CuAl и Cu 9 Al 4 ) вдоль переходной области Cu из-за несоответствующего разбавления между Al и Cu. Эти хрупкие интерметаллические соединения снижают механические свойства соединения (Sahin, 2009).
Фазовая диаграмма двойной системы Al-Cu (Xia, et al., 2008; Sujin, et al., 2014)
Дефекты также образуются вдоль соединения Al-Cu из-за неправильного разбавления основного металла и присадочного металла, если он используется.Например, пустоты образовались в паяном соединении Al-Cu из-за эффекта Киркендалла и из-за неправильного разбавления между атомами Al и Cu и атомами Zn присадочного металла. Это неправильное разбавление произошло из-за того, что бинарная система Al-Cu имела более высокое сродство, чем система Cu-Zn, поэтому атомы Cu имели тенденцию реагировать с Al с образованием CuAl 2 хрупких интерметаллических соединений (Lee, et al., 2002; Leonardo, et al. др., 2011; Feng & Xue, 2013). Исследование Balasundaram et al. (2014) показали, что пайка Al и Cu с добавлением цинка в качестве присадочного металла приводит к образованию макротрещин на краю медной стороны.Макротрещины образовались из-за разбавления Zn Al и Cu, отталкивающего Cu, что привело к межкристаллитным трещинам из-за охрупчивания жидким металлом. Таким образом, пластичная фаза меди во время разбавления трансформировалась в хрупкие интерметаллические структуры, когда она вступала в контакт с жидким металлом (Nicholas & Old, 1979). Из приведенных выше исследований можно отметить, что присадочный металл для сварки с Zn оказывает значительное влияние на интерметаллические соединения и дефекты, образующиеся при разбавлении основных металлов. Следовательно, необходимо учитывать соответствующий выбор присадочного металла, соответствующего основным металлам, при стремлении уменьшить количество дефектов в соединениях Al-Cu.
Интерметаллические соединения, образованные эффектами разбавления и градиентами состава, влияют на характеристики затвердевания в металле шва (Hayes, et al., 2011). Затвердевание интерметаллических соединений влияет на фазообразование, которое определяет свойства соединения (Sun & Moisio, 1994). Паяное соединение Al-Cu с присадочным металлом Zn-15Al имело образование интерметаллического соединения CuAl 2 во время разбавления, что увеличивало время затвердевания, что приводило к улучшению свойств (Feng et al.2012b). Более того, исследование сварного лазером соединения Al-Cu, проведенное Zuo и др. (2014) показали изменение толщины промежуточного слоя из-за градиентов растворенного вещества во время разбавления, и этот градиент растворенного вещества увеличивал время затвердевания, что приводило к улучшению свойств. Следовательно, тип, количество и микроструктурное расположение фаз в металле сварного шва во время затвердевания интерметаллических соединений и градиент состава влияют на свойства соединения.
Помимо градиента состава и эффекта разбавления, параметры разбавления и сварки также влияют на сварочные свойства соединения Al-Cu через их влияние на образование интерметаллических соединений.Например, эксперимент Лю и др. (2008) показали, что соединение Al-Cu, полученное сваркой трением с перемешиванием, имеет образование хрупких интерметаллических соединений, что приводит к ухудшению свойств. Это ухудшение свойств сварного шва было связано с неполным разбавлением металлов и влиянием положения инструмента в процессе сварки. С другой стороны, Ли и др. (2012) наблюдали, что соединение Al-Cu, полученное сваркой трением с перемешиванием, в своей работе имело полное растворение в сварном шве без образования интерметаллических соединений, как показано на рис.2. Это было достигнуто смещением позиции инструмента. Кроме того, соединение обладало хорошими пластичными свойствами. Таким образом, параметры сварки, влияющие на разбавление, уменьшают образование хрупких интерметаллидов в металле шва.
Рис.2( a ) Макроскопический вид соединений Al-Cu без интерметаллических соединений и ( b ) внешний вид поверхности соединения (Li, et al., 2012)
Из этих исследований ясно, что неправильный выбор присадочного металла, соответствующего основным металлам, в процессе пайки и неправильное положение сварочного инструмента при сварке трением с перемешиванием привели к неправильному разбавлению основного металла и присадочного металла.Это, в свою очередь, приводит к образованию хрупких интерметаллических соединений, что приводит к ухудшению свойств и образованию дефектов. Однако интерметаллические соединения и градиенты композита увеличивают время затвердевания во время разбавления при лазерной сварке и пайке. Это приводит к улучшению механических свойств сварного шва.
Влияние физических свойств
Существенная разница между физическими свойствами алюминия и меди приводит к образованию хрупких интерметаллических структур и создает проблемы при формировании металла шва как для процессов плавления, так и для сварки в твердом состоянии.Например, Суджин и др. (2014) показали, что при лазерной сварке внахлест с Cu, расположенным ниже Al, Al не может погружаться в подложку из Cu из-за более высокой плотности Cu. Однако с Cu (верхняя сторона) и Al (нижняя сторона) Cu может легко погрузиться в алюминиевую подложку, что приведет к надлежащему разбавлению и последующему улучшению свойств. Физические свойства играют жизненно важную роль в разбавлении металлов. Некоторые из основных физических свойств алюминия и меди показаны в таблице 1, а их влияние на формирование металла сварного шва обсуждается ниже.
Таблица 1 Физические свойства алюминия и меди Таблица 2 Сравнение сварки трением с перемешиванием, лазерной сварки и пайки при сварке алюминия (1060) и чистой медиТемпература плавления
Одним из наиболее важных факторов при сварке плавлением разнородных соединений, а также в процессах сварки в твердом состоянии является температура плавления двух основных металлов.Заметная разница в температуре плавления основных металлов может привести к разрушению металла с более низкой температурой плавления (Hayes, et al., 2011). Например, при сварке трением Al плавится больше, чем Cu, из-за более низкой температуры плавления Al по сравнению с Cu (Sahin, 2009). Более того, исследование Bisadi, et al. (2013) о процессе сварки трением с перемешиванием показывает, что соединения со значительной разницей в температурах плавления основного металла, сваренные с высокой температурой сварки, имеют полости в переходной зоне из Al и Cu.Предыдущее исследование показало, что остаточные термические напряжения и деформации несоответствия возникают в соединениях Al-Cu из-за значительной разницы в температурах плавления Al и Cu (Mai & Spowage, 2004). Значительная разница в температуре плавления также влияет на внешний вид поверхности стыка. Лазерная сварка внахлест с Al (верхняя сторона) и Cu привела к таким проблемам, как образование большого сварного шва и большая зона термического влияния на стороне Al из-за низкой температуры плавления и высокой поглощающей способности длины волны лазера алюминием (Weigl, и другие., 2011; Суджин и др., 2014). Вышеупомянутые исследования показывают, что разница в температуре плавления влияет на дефекты и внешний вид поверхности соединений Al-Cu и, таким образом, влияет на механические свойства сварного шва.
Некоторые исследования показывают, что разница температур плавления приводит к образованию хрупких и высокоэлектрических интерметаллических соединений в металле сварного шва (Song-bai, et al., 2003; Ouyang, et al., 2006; Sahin, 2009). Ухудшения свойств сварного шва можно избежать, если учесть разницу в температуре плавления на этапе проектирования соединения, а также использовать подходящий присадочный металл и параметры сварки.
Теплопроводность
Значительная разница в теплопроводности металлов в разнородном соединении приводит к тому, что к металлу передается больше тепла с более высокой теплопроводностью, что приводит к неравномерному распределению тепла и локализованному плавлению металла (Hayes, et al., 2011). Это неравномерное распределение тепла и локализованное плавление ухудшают свойства сварного шва. Например, высокие значения твердости были обнаружены в области Cu соединения Al-Cu, полученного сваркой трением, из-за более высокой теплопроводности Cu по сравнению с Al (Sahin, 2009).Такая твердость может привести к хрупкости в области Cu, что может привести к легкому разрушению соединения. Более того, Takehiko et al. (1999 (Online — 2010)) при исследовании процесса ультразвуковой сварки заметили снижение прочности связи между Al и Cu из-за высокой теплопроводности Cu. Вышеупомянутые исследования показывают, что процессы твердотельной сварки сталкиваются с проблемами, возникающими из-за значительной разницы в теплопроводности основного металла. При сварке плавлением возникают дополнительные проблемы, связанные с добавлением в стык присадочного металла.
Al и Cu обладают высокой температуропроводностью, что приводит к трудностям при соединении с помощью процессов сварки плавлением (Sahin, 2009). Например, Hailat, et al. (2012) обнаружили, что лазерная сварка внахлест соединений Al-Cu со сплавом оловянной фольги в качестве присадочного металла дает меньшее проплавление на медной стороне и большую пористость в сварном шве по сравнению со сварным швом, сформированным без присадочного металла. Металлический наполнитель поглощал лазерную энергию из-за своей высокой теплопроводности и высокой отражательной способности основных металлов, что привело к образованию барьерного слоя для теплопроводности между основными металлами (Hailat, et al., 2012). Суджин и др. (2014) сообщили только о частичном проплавлении металла шва при лазерной сварке.
Чтобы смягчить проблемы, вызванные теплопроводностью, источники нагрева в процессах сварки плавлением могут быть направлены на металл с более высокой теплопроводностью (например, Cu в соединении Al-Cu) или металл с более высокой теплопроводностью может быть предварительно нагрет ( Hayes, et al., 2011).
В некоторых случаях, однако, заметная разница в теплопроводности оказывает положительное влияние на соединение: например, при исследовании с использованием сварки трением с перемешиванием не образовывались зоны термического влияния из-за высокой скорости снижения температуры из-за высокой термической проводимость Cu (Sarvghad-Moghaddam, et al., 2014).
Приведенные выше исследования показывают, что заметное различие в теплопроводности металлов оказывает как положительное, так и отрицательное влияние на свойства соединения. Однако различие в теплопроводности не влияет на образование интерметаллических соединений. Вредные эффекты можно уменьшить, принимая во внимание свойства металла при проектировании соединения или вводя в соединение соответствующий третий металл (например, присадочный металл).Следовательно, при выборе присадочного металла необходимо учитывать основные металлы и их теплопроводность для обеспечения высоких свойств соединения (Hayes, et al., 2011).
Коэффициент теплового расширения
Коэффициент теплового расширения считается важным фактором из-за его влияния на образование несплошностей в стыке, которые значительно ухудшают свойства сварного шва. Например, соединение Al-Cu, полученное сваркой трением с перемешиванием (Bisadi, et al., 2013) образовывались полости в металле сварного шва из-за значительной разницы в тепловом расширении, как показано на рис. 3. Частицы алюминия вдавливались в медную сторону, что приводило к образованию макроструктурной полости в металле сварного шва после закалки. процесс.
Рис. 3Образование каверны в переходном слое при сварке трением с перемешиванием (Bisadi, et al., 2013)
Для соединений Al-Cu, сваренных плавлением, значительная разница в тепловом расширении может привести к горячим трещинам во время сварки и холодным трещинам во время эксплуатации соединения.Растрескивание происходит из-за растягивающих напряжений в одном металле и сжимающих напряжений в другом, которые возникают во время затвердевания металлов (Hayes, et al., 2011). Этот феномен был также отмечен в исследовании Weigl, et al. (2011) о лазерной сварке с адаптивными присадочными материалами (например, AlSi12 и CuSi3), которые обнаружили зарождение трещин в соединении в результате высоких растягивающих напряжений, вызванных заметной разницей в тепловом расширении.
Исследования показывают, что соединение с разницей в тепловом расширении металла влияет на внешний вид поверхности и геометрию сварного шва (Hayes, et al., 2011). Например, исследование Zuo, et al. (2014) о лазерной сварке соединений Al-Cu сообщили об образовании выпуклости вверх в переходном слое из-за более высокого коэффициента расширения Al, чем у Cu, как показано на рис. 4. Эта выпуклость вверх в переходном слое привела к недостаточное разбавление между металлами и неглубокий и широкий сварной шов.
Рис. 4Образование вогнутости в переходном слое соединения, сваренного лазером Al-Cu (Zuo, et al., 2014)
Вышеупомянутые исследования показывают, что значительная разница в тепловом расширении может привести к образованию дефектов и разрыву соединения как при сварке плавлением, так и при сварке в твердом состоянии.Однако разница не влияет на образование интерметаллидов. Термическая обработка после сварки может уменьшить образование дефектов, вызванных различиями в тепловом расширении.
Влияние параметров сварки
Параметры сварки варьируются в зависимости от применяемых процессов и технологий сварки, а также используемых сплавов Al и Cu. Выбранные параметры определяют разбавление металла, формирование свойств и внешний вид поверхности соединения, а свойства основного металла и присадочного металла, если они используются, должны учитываться при выборе параметров сварки.Однако различные исследования сходятся во мнении, что при сварке разнородных соединений твердотельная сварка показывает лучшее образование соединений, чем процессы сварки плавлением. Например, механические свойства соединений Al-Cu могут быть улучшены в процессах сварки трением путем выбора подходящего времени трения, давления и давления осадки. Сахин (2009) показал, что предел прочности соединения увеличивается до максимального значения, а затем постепенно уменьшается с дальнейшим увеличением давления трения и времени. Это снижение прочности происходит из-за рассеивания тепла и образования хрупких интерметаллических соединений в виде серого слоя на границе раздела стыка.
Конструкция соединения влияет на параметры сварки, которые, в свою очередь, влияют на свойства сварного шва. Это было продемонстрировано на паяном соединении Al-Cu, в котором большое расстояние между сварным швом улучшило электрические характеристики соединения Al-Cu (Solchenbach et al. 2014). При лазерной сварке внахлест Суджин и др. (2014) показали, что соединение имеет полное проникновение, когда Al расположен над Cu, тогда как противоположное размещение дает только частичное проникновение в Al. Частичное проплавление было обусловлено высокой скоростью сварки, использованной в исследовании, а также высокой отражательной способностью и теплопроводностью меди.Далее было отмечено, что увеличение скорости лазерной сварки снижает количество образующихся интерметаллических соединений и улучшает свойства соединения при растяжении. Mai и Spowage (2004), с другой стороны, обнаружили трещины затвердевания в сварном лазером шве в результате высокой скорости сварки. Кроме того, высокая скорость сварки снижает прочность соединения на сдвиг (Zuo, et al., 2014). Исследования также показали, что для равномерного и успешного шва между Al и Cu требуется высокая импульсная мощность в течение короткого времени (Mai & Spowage, 2004; Zuo, et al., 2014). В приведенном выше разделе показано, что совокупное влияние параметров сварки и других факторов (например, конструкции соединения и физических свойств основного металла) влияет на соединения Al-Cu за счет снижения свойств сварного шва и образования хрупких интерметаллических соединений.
Однако в некоторых случаях исследования показали, что на свойства сварного шва влияют только параметры сварки. Коррозионная стойкость в соединениях, образованных сваркой трением с перемешиванием, была улучшена за счет регулировки параметров сварки (Jariyaboon, et al., 2007; Кришнан и др., 2009). Акинлаби и др. (2014) проанализировали коррозионные свойства соединений, сваренных трением с перемешиванием, и обнаружили, что скорость коррозии соединений снижается по мере увеличения скорости вращения перемешиваемого трением. Кроме того, скорость вращения улучшила поток материала в соединении за счет перемешивающего действия инструмента (Liu, et al., 2008). Изменения в инструментах для сварки трением с перемешиванием с одинаковыми параметрами сварки привели к изменению микроструктуры и свойств сварного шва. Различные конфигурации инструментов изменяют эффекты нагрева от трения, тем самым влияя на режим деформации металла (Mubiayi and Akinlabi, 2013).Например, Sarvghad-Moghaddam, et al. (2014) показали доминирующее влияние инструмента на свойства и микроструктуру сварного шва за счет изменения уступа инструмента и штифта. Galvão et al. (2010; 2012), которые экспериментировали со сваркой трением с перемешиванием с использованием спиральных и конических инструментов для перемешивания трением, показали, что этот инструмент оказывает огромное влияние на создание успешных сварных соединений. При использовании инструмента с коническим уступом Al на продвигающейся стороне приводил к нерегулярной микроструктуре; однако образование дефектов уменьшилось.Al на отходящей стороне приводил к образованию интерметаллических соединений в результате механического смешивания Al с Cu-матрицей. Сварные швы, сформированные коническим инструментом, имели гладкий вид и мелкую зернистость. При использовании инструмента со спиральным буртиком в обоих соединениях образовывались хрупкие интерметаллические соединения из-за нисходящего потока материала. Поверхность шва имела блестящий наплавленный валик с глубокими пустотами. Большинство исследований показывают, что для уменьшения интерметаллических соединений при сварке трением с перемешиванием инструмент следует размещать в Cu на отходящей стороне (Liu, et al., 2008; Тан и др., 2013). Однако Сюэ и др. (2010) предполагают, что смещение инструмента со стороны алюминия уменьшает толщину интерметаллического соединения и образование дефектов, а также улучшает свойства изгиба и растяжения. Их исследование также показало, что тонкий и однородный сплошной слой интерметаллического соединения улучшает прочность сцепления и механические свойства соединения. Правильный выбор инструментов и их расположение на материале (т.е. на стороне подачи и на стороне отхода) в процессе сварки трением с перемешиванием снижает образование интерметаллических соединений и, таким образом, улучшает прочность соединения.
Однако изменение скорости сварки и подводимого тепла может отрицательно сказаться на соединении, приводя к неоднородностям. При изучении соединений Al-Cu, образованных сваркой трением с перемешиванием, Tohid и др. (2010) показали, что высокая скорость сварки приводит к образованию полости. Эффект от низкой скорости сварки был другим; микротрещины, образованные рядом с частицами Cu вдоль стыка, как показано на рис. 5. Yong, et al. (2006) заявили, что образование полости происходит из-за недостаточного тепловложения для разбавления металлов.Yong et al. также отметил, что тепловыделение инструментом, который погружается вдоль стыка, обратно пропорционален скорости сварки. Как и в исследовании Tohid, et al (2010), Bisadi, et al. (2013) также обнаружили образование полости при высокой температуре сварки. При низкой температуре сварки, в отличие от результата Tohid et al., Было обнаружено, что соединение имеет дефекты каналов. Причиной образования этих дефектов была высокая диффузия меди к алюминиевому листу.
Рис. 5Образование каверн и микротрещин в результате сварки трением с перемешиванием в металле шва (Tohid, et al., 2010)
Параметры сварки явно влияют на соединение через образование интерметаллических соединений и их влияние на свойства и дефекты сварного шва. Основными параметрами, влияющими на свойства сварного шва Al-Cu, являются скорость сварки, погонная энергия и положение инструмента. Оптимальные параметры меняются в зависимости от требований к обслуживанию.
Влияние присадочного металла
Добавление присадочного металла обычно играет важную роль при сварке разнородных соединений.Выбор подходящего присадочного металла зависит от физических свойств основных металлов и используемого процесса сварки. Кроме того, требования к конструкции стыка должны соответствовать выбранному присадочному металлу. Были представлены критерии выбора присадочного металла для разнородных соединений, чтобы обеспечить лучшие свойства металла сварного шва и успешное соединение без каких-либо разрывов (Hayes, et al., 2011). При выборе подходящего присадочного металла для соединения следует учитывать его растекаемость.Растекаемость присадочного металла на подложке зависит от одного из двух факторов: взаимного разбавления металлов или образования интерметаллических соединений (Feng et al. 2012b). Например, присадочный металл Zn-Al, используемый в процессе пайки, имеет линейное увеличение смачиваемости (т. Е. Растекаемости) на подложке из Al и Cu с увеличением содержания Al в присадочном металле, как показано на рис. 6 (Feng et al. 2012b ). Однако степень взаимного разбавления присадочного металла на алюминиевой подложке снижается, что приводит к образованию интерметаллических соединений.Кроме того, микротвердость паяного шва увеличивается с увеличением содержания Al в присадочном металле Zn-Al, что приводит к хрупкому разрушению соединения.
Рис. 6Зоны растекания на подложках из Al и Cu с увеличением содержания Al в присадочных металлах Zn-Al (Feng et al. 2012b)
Исследования показывают, что добавление соответствующих элементов (т.е. основанных на свойствах основного металла) в присадочный металл улучшило свойства сварки Al-Cu и уменьшило количество интерметаллических соединений.Исследование Feng et al. (2013) по пайке соединений Al-Cu с добавлением Ti к присадочному металлу Zn-22 Al показали, что смачиваемость присадочного металла снижалась с увеличением содержания Ti, как показано на рис. 7. Однако увеличение содержания Ti привело к уменьшение интерметаллических соединений в соединении и увеличение прочности соединения на сдвиг. Добавление Ce к присадочному металлу вместо Ti, исследованное Feng и Xue (2013), привело к получению более тонкого интерметаллического слоя. Слой, образованный Zn-22Al-0.Присадочный металл 05Ce был тоньше, чем присадочный металл Zn-22Al, потому что Ce изменял диффузию атомов и подавлял рост слоя интерметаллического соединения, что приводило к улучшению свойств сварного шва.
Рис. 7Площадь растекания на медной подложке при увеличении содержания Ti в присадочном металле (Feng et al., 2013)
Исследования показывают, что интерметаллические соединения, образующиеся при добавлении присадочного металла, могут оказывать положительное влияние на свойства сварного шва.Например, Xia, et al. (2008) показали, что сварной шов, образованный присадочным металлом Al-Si, имел призматическую объемную интерметаллическую структуру на стороне Al. Рост призматического зерна Al был обусловлен эвтектической реакцией основного металла Al и Si в присадочном металле. Равномерный рост призматической структуры Al положительно сказался на механических свойствах металла шва.
Помимо уменьшения количества интерметаллических соединений, добавление присадочного металла может улучшить другие свойства и уменьшить количество дефектов.Исследования показали, что соответствующие присадочные металлы, такие как сплавы Zn-Al для паяных соединений Al-Cu, обеспечивают высокую коррозионную стойкость и лучшие механические свойства по сравнению с другими присадочными металлами (Berlanga-Labari et al. 2011; Feng et al. 2012b; Yan, и др., 2013). Исследования также показали, что добавление подходящего присадочного металла, имеющего низкую температуру плавления, приводит к снижению остаточного напряжения в соединениях Al-Cu (Xiao et al. 2013). С другой стороны, неподходящий присадочный металл приводит к образованию дефектов в металле сварного шва.Это было продемонстрировано в исследованиях Berlanga-Labari et al. (2011), в котором было замечено, что пайка соединения Al-Cu с эвтектическим присадочным металлом Zn-Al привела к однородной микроструктуре, но с такими дефектами, как пористость и трещины. В случае лазерной сварки Weigl et al. (2011) провели эксперимент с адаптированными присадочными материалами, которые использовались при термической сварке и пайке (AlSi12 и CuSi3). Металл шва имел микротрещины в присадочном материале AlSi12; Сварные швы, образованные CuSi3, имели образование макротрещин и низкое разбавление, но были лучше, чем сварные швы, сформированные без присадочных металлов.В заключение следует отметить, что использование соответствующего присадочного металла в соединениях Al-Cu улучшает свойства соединения, способствуя надлежащему разбавлению, что снижает количество интерметаллических соединений и приводит к меньшему количеству дефектов.
Влияние термической обработки
В некоторых случаях термическая обработка может быть благоприятной для одного из основных металлов, но неблагоприятной для другого основного металла, что приведет к образованию дефектов сварного шва. В экспериментальном исследовании сварки твердым телом Вонбае и др. (2005) показали, что сварное трением соединение после длительного отжига имело различные интерметаллические соединения, а рост толщины интерметаллических соединений в сварном шве увеличивался за счет высоких температур отжига, что показано на рис.8. Таким образом, длительное время отжига и высокая температура отжига привели к ухудшению свойств.
Рис.8Изменение толщины интерметаллида за счет ( a ) изменения температуры отжига и ( b ) изменения времени отжига (Wonbae, et al., 2005)
То же явление было обнаружено в экспериментах Фэна и Сюэ (Feng and Xue, 2013) на паяных соединениях Al-Cu. Их работа показала, что интерметаллический слой растет с увеличением времени старения.Кроме того, прочность на сдвиг снижалась с увеличением времени старения из-за увеличения толщины интерметаллического соединения. Было отмечено, что паяные соединения Al-Cu, сформированные с использованием присадочного металла Zn-22Al-0,05Ce, имели более высокую прочность на сдвиг по сравнению с соединениями, сформированными с использованием присадочного металла Zn-22Al. При номинальном времени старения соединение имело режим вязкого разрушения; однако из-за увеличения времени старения соединение перешло в режим хрупкого разрушения.
Приведенные выше исследования показывают, что увеличение температуры и времени термообработки выше номинального уровня приводит к увеличению толщины интерметаллического соединения за счет большего разбавления металлов, что в конечном итоге приводит к образованию дефектов и ухудшению свойств соединения.
Факторы, влияющие на свойства соединения Al-Cu в процессе эксплуатации
Основные проблемы соединения обычно возникают только тогда, когда соединение подвергается условиям эксплуатации. Соединения Al-Cu в основном используются в электротехнической промышленности в качестве электрических соединителей, поэтому ключевым моментом является окисление, поскольку соединения Al-Cu легко окисляются, что приводит к сопротивлению электрическому потоку (Klauke, 2012). Следовательно, необходимо учитывать свойства соединения и формирование микроструктуры при эксплуатации соединений.
Физико-механические свойства соединения
Свойства сформированного металла шва зависят от состава металла шва и образующихся интерметаллических фаз (Hayes, et al., 2011). Например, Вонбае и др. (2005) показали, что соединение, полученное сваркой трением с перемешиванием, имеет образование интерметаллических соединений с низкой проводимостью, что приводит к увеличению электрического сопротивления в соединении. Браунович и Александров, 1994, показали, что сварные трением соединения Al-Cu, подвергнутые воздействию электрического тока, имеют значительные трещины вдоль соединения, а также в фазах, образующихся в соединении.Соединения, работающие при высокой температуре и сильном токе, показали рост интерметаллических соединений и повышенное электрическое сопротивление в соединении. Растрескивание и повышенное электрическое сопротивление были вызваны диффузией атомов Cu в межфазной области и образованием интерметаллических соединений. Solchenbach и др. (2014) показали связь между электрическим сопротивлением и прочностью на сдвиг в соединениях, паяных лазером Al-Cu. По мере увеличения прочности на сдвиг электрическое сопротивление в соединении со временем уменьшалось, как показано на рис.9.
Рис. 9Связь между электрическим сопротивлением и прочностью на сдвиг (Solchenbach, et al., 2014)
Приведенные выше исследования показывают, что на электрические свойства влияют интерметаллические соединения, образующиеся в соединении во время его эксплуатации. Исследования также показывают, что интерметаллиды влияют на механические свойства соединения. Например, исследование Брауновича и Александрова в 1994 г. показало, что высокая микротвердость интерметаллических соединений приводит к хрупкости, приводящей к легкому разрушению и низкой механической прочности соединения.Аналогичный результат был получен при пайке соединения алюминия и меди, содержащего фазу Al 2 Cu (Feng et al. 2012b). Характеристики твердости, создаваемые интерметаллическими соединениями Al 2 Cu, приводят к повышенной хрупкости металла сварного шва, который может действовать как концентратор напряжения, приводящий к возникновению трещин. Соединение, образованное присадочным металлом Zn-15Al, имело наивысшую прочность на сдвиг из-за равномерного распределения интерметаллического соединения Al 2 Cu, которое также могло снизить электрическое сопротивление (Feng et al.2012b).
С лазерной сваркой, Суджин и др. (2014) показали, что сварные лазерной сваркой соединения Cu-Al легко разрушаются из-за большой зоны сварного шва и образования интерметаллических соединений (CuAl и Al 2 Cu). Работа Weigl и др. (2011) по лазерной сварке с адаптированными присадочными материалами (например, AlSi12 и CuSi3) показали, что значение твердости больше снижается с присадочным металлом AlSi12 из-за равномерного распределения концентрации Cu и интерметаллических соединений. Кроме того, сварной шов, образованный присадочным металлом AlSi12, имел наивысшую вязкость, за ним следовал сварной шов, выполненный из присадочного металла CuSi3, причем сварной шов, образованный без присадочных металлов, имел самую низкую пластическую прочность.Пластичность сварного шва, выполненного с использованием присадочного металла AlSi12, была обусловлена менее крупной сотовой структурой.
Из обсуждения в этом разделе можно заметить, что свойства сварного шва влияют на стабильность во время эксплуатации за счет образования интерметаллических соединений. Кроме того, низкие свойства сварного шва и образование фазы хрупкого интерметаллического соединения в соединении могут привести к выходу соединения из строя во время эксплуатации.
Стабильность микроструктуры в соединении
Разные соединения различаются по концентрации атомов и их активности (т.е.е. потенциальный химический градиент) в металле шва. Эта активность может привести к диффузии атомов с градиентом концентрации металла или против него. Поэтому трудно предсказать свойства или конкретную миграцию атомов в разнородном соединении во время сварочных процессов, а также при эксплуатации при высоких температурах. Миграция конкретного атома или движение атома зависит от температуры, а также времени и приводит к изменениям свойств и стабильности металла шва (Joseph 2006; Hayes, et al., 2011). Многочисленные исследования соединений Al-Cu показали, что тип и микроструктура поверхности раздела, образованной в соединении, определяют стабильность соединения. Кроме того, соответствующая толщина и тонкое распределение интерметаллического слоя положительно влияют на свойства соединения (Pang, et al., 2001; Song, et al., 2003; Huseyin et al. 2005; Lin, et al. , 2009). Например, Лоуренс и др. (1998) заметили, что соединение Cu-Al, сваренное сваркой трением с перемешиванием, имело сложную интеркаляцию с элементами завихрения и вихря, которые были нестабильными на границе раздела.Чжао и др. (2013) отметили такую же закрученную деформацию в соединениях Al-Cu, сваренных ультразвуковой точечной сваркой, как показано на рис. 10a. Их исследование показало, что возникновение завихрения было связано с высокой энергией, поскольку острие инструмента больше проникало в металл, что приводило к грубому смещению. Если соединение находится в высокотемпературной среде, вихревая деформация также может возникнуть в результате смещения, что сделает соединение нестабильным. Завихрение имеет положительный эффект увеличения прочности на сдвиг, но отрицательный эффект — образование пустот в металле сварного шва, как показано на рис.10б. (Чжао и др., 2013). Чтобы избежать разрушения соединения во время эксплуатации, эти прослои и микроструктурные фазовые образования следует учитывать на этапах проектирования и устранять с помощью соответствующих параметров сварки.
Фиг.10a Образование завихрений и b образование пустот в стыке Al-Cu (Zhao, et al., 2013)
Feng et al. (2012b) обнаружили для паяных соединений Al-Cu, что интерметаллические соединения, образующиеся на Cu-подложке, изменяют фазу в результате изменения содержания Al в присадочном металле (Zn-Al).Кроме того, повышенное содержание Al в присадочном металле приводило к образованию объемных интерметаллидов, которые повышали температуру плавления и отрицательно влияли на свойства соединения. Feng и др. (2013) обнаружили, что добавление Ti к присадочному металлу Zn-Al стабилизировало микроструктурные изменения в области границы раздела, преобразовывая объемную структуру в структуру в форме иглы. Стабильность микроструктуры влияет на свойства соединения Al-Cu через образовавшийся градиент состава и образование интерметаллической структуры, приводящее к изменению микроструктуры.
Характеристика стойкости к коррозии и окислению
В разнородном металле сварного шва коррозия может происходить либо в фазе соединения, либо в анодном металле из-за образования гальванических элементов. Образование гальванических ячеек является результатом локализованных ячеек между фазами соединения и приводит к серьезным дефектам металла сварного шва, таким как водородное охрупчивание и коррозия под напряжением. Например, исследование Acarer (2012) по сварке взрывом показало гальваническую коррозию биметалла Al-Cu, поскольку Al действовал как анод из-за высокой электроотрицательности.Следовательно, Al в интерметаллической зоне подвергался большей коррозии, чем сторона Cu, что можно увидеть на Рис. 11.
Рис. 11a Корродированный биметалл соединения Al-Cu и b Вид в разрезе корродированного биметалла Al-Cu (Acarer, 2012)
Исследование биметаллической коррозии в морской воде показало, что Al не был защищен от сильной коррозии из-за активности и пассивности Al и Cu (Francis 2000).Другие исследования коррозии показали, что металл сварного шва Al-Cu подвергается коррозии из-за влаги, захваченной во время сварки, и может выйти из строя во время эксплуатации. Эта коррозия чаще встречается в Al, который является менее благородным металлом (анодом), чем в Cu (Solacity, 2011).
Коррозии также способствует точечная коррозия и склонность к ионизации между медью и алюминием, что, как следствие, приводит к меньшей площади контактной поверхности. Небольшая площадь контакта между металлами приводит к ослаблению соединения между двумя металлами и создает шум во время дуги (Solacity, 2011).В соединении, сваренном трением с перемешиванием, гальваническая коррозия возникает на границе раздела сварного шва из-за высокотемпературного градиента, что приводит к ухудшению свойств соединения.