Точечная электрическая контактная сварка — Энциклопедия по машиностроению XXL
Точечная электрическая контактная сварка. При точечной сварке свариваемые листы / собирают и сжимают между двумя медными электродами 2 контактной точечной машины (фиг, 20). [c.147]Теплота плавления (скрытая) 26 Теплота (скрытая) парообразования 26 Теплопроводность 30 Теплотворная способность газов 30 Трехфазный ток 30 Твердость металлов 43 Трубы стальные 115 Технологический процесс сборки 193 Точечная электрическая контактная сварка 147 Трещины в сварных швах 166 Технологические факторы, влияющие иа свариваемость металлов 181 [c.639]
Электрическая контактная сварка после дуговой и газовой является в настоящее время третьим по своему значению способом сварки, быстро прогрессирующим и претендующим на второе место. Развитие контактной сварки, требующей значительного расхода электроэнергии, тесно связано с усилением электрификации промышленности и перехода на массовое производство, так как этот метод сварки по существу является наиболее приспособленным к массовому производству однотипных изделий.

Электроконтактная сварка. Существуют три разновидности электрической контактной сварки стыковая, точечная и шовная (роликовая). . [c.159]
Приложение давления хотя бы и при наличии расплавления в зоне сварки позволяет отнести способ к группе сварки давлением, как например, при электрической контактной сварке (точечной и роликовой шовной). [c.334]
Существуют также промежуточные методы сварки, при которых металлы свариваются одновременно пластической деформацией и плавлением. К ним относят два метода электрической контактной сварки точечную и роликовую (шовную).
[c.454]
Существуют также промежуточные методы сварки с применением одновременно пластической деформации и плавления. К ним относят три метода электрической контактной сварки точечную, роликовую (шовную) и стыковую. [c.299]
Способы сварки, при которых свариваемые части деталей доводят только до состояния размягчения металла, одновременно сдавливая их друг с другом, называются электрической контактной сваркой. К ним относятся точечная, шовная, контактная стыковая и газопрессовая сварка. [c.168]
Шовная электрическая контактная сварка. Шовная контактная сварка заключается в образовании ряда перекрывающих друг друга сварных точек. Образование одной сварной точки при шовной сварке принципиально не отличается от точечной сварки. Машина для шовной сварки снабжена электродами в виде роликов, из которых один или оба имеют привод. Для сварки листы собирают внахлестку, зажимают между роликами, включают привод вращения роликов и сварочный ток. При перемещении листов относительно роликов образуется сварной шов (фиг. 21),
[c.147]
К сварке давлением относится электрическая контактная сварка, газопрессовая сварка, сварка с нагревом трением, холодная сварка. Контактная сварка производится на специальных машинах. Основными разновидностями контактной сварки являются стыковая, точечная, роликовая, рельефная, стыковая оплавлением и стыковая сопротивлением. [c.304]
Из большого разнообразия существующих в настоящее время способов с варки в машиностроении преимущественное применение имеют ручная электродуговая сварка металлическим электродом, авто.матическая электродуговая сварка металлическим электродом под слоем флюса, электрошлаковая сварка металлическим электродом и электрическая контактная сварка — стыковая, роликовая и точечная. Первые три способа относятся к сварке плавлением, а последний — к сварке плавлением или давлением.
[c.64]
Электрическая контактная сварка. По форме выполняемых соединений различают три основных вида контактной сварки стыковую, точечную и шовную или роликовую (рис. 190). [c.370]
При дуговой сварке такими характеристиками являются сварочный ток, напряжение на дуге, диаметр электрода, скорость перемещения электрода вдоль свариваемых кромок (скорость сварки), род тока, полярность и др. При электрошлаковой сварке — сварочный ток, напряжение на шлаковой ванне, скорость подъема металлической ванны (скорость сварки), глубина шлаковой ванны и др. При электрической контактной сварке — сварочный ток (мощность машины на данной ступени), время сварки, усилие на электродах (при точечной и шовной сварке), усилие осадки и установочная длинаХ(при стыковой сварке) и др.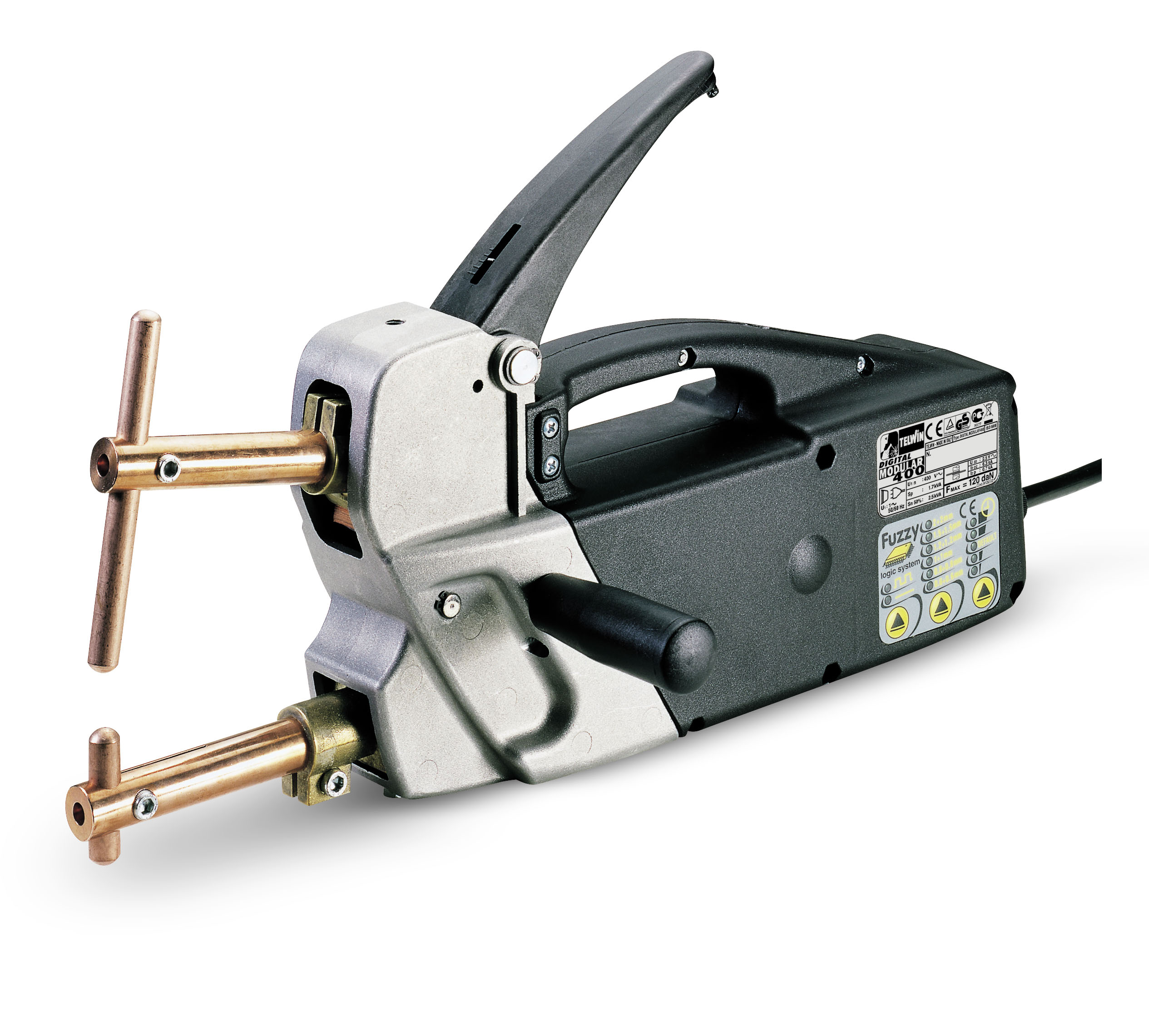
Электрическая контактная сварка. Этот вид сварки осуществляют путем местного сжатия свариваемых деталей в точке и нагрева места контакта. Местный нагрев достигается за счет повышенного сопротивления электрическому току на участках контакта между свариваемыми деталями. На рис. 13.20 показаны схемы основных видов электрической контактной сварки (а — стыковая, б — точечная, в — линейная). Во всех случаях свариваемые детали 1 зажимают электродами 2 усилием Р. [c.282]
При электрической контактной сварке разогрев концов свариваемых частей происходит вследствие прохождения через приведённые в соприкосновение детали (место контакта) тока большой силы. Основными видами контактной сварки являются стыковая, точечная и шовная. [c.378]
Однако наиболее экономичным способом сварки изделий из тонкого листового металла является электрическая контактная сварка (точечная, роликовая), которая дает шов высокого качества и вызывает наименьшие,деформации.
[c.99]
Контактная сварка (точечная, шовная и др.) —сварка давлением, пластическая с применением внешних сил, сжимающих детали в свариваемых местах где нагревания применяют электрическую энергию, превращенную в тепловую. [c.248]
Контактную сварку выполняют на специальных машинах, электрическая часть которых состоит из сварочного трансформатора, прерывателя сварочного тока, регулятора (или переключателя) тока первичной цепи трансформатора и токоподводящих устройств, а механическая часть — из механизмов и узлов, создающих необходимое давление для сжатия свариваемых деталей. В зависимости от типа выполняемого соединения контактные машины подразделяют на стыковые, точечные и шовные. [c.112]
Контактная сварка (точечная, роликовая и др.) производится за счет разогрева стыка деталей (тонких листов) теплотой, выделяемой при прохождении электрического тока через два электрода (в форме стержней или роликов), сжимающих детали.

Соединение деталей с помощью контактной электросварки происходит за счет разогрева стыка теплом, выделяющимся при прохождении электрического тока через зазор при одновременном действии силы, сжимающей соединяемые детали. Из нескольких разновидностей контактной сварки чаще всего применяются точечная, стыковая, роликовая и короткоимпульсная. [c.400]
Основным способом сварки давлением является контактная сварка, при которой неразъемное соединение образуется в результате нагрева металла проходящим электрическим током и пластической деформации зоны соединения. В зависимости от конструкции соединений и технологии их получения контактная сварка подразделяется на стыковую, точечную и шовную. Разновидностью точечной сварки является рельефная сварка. [c.362]
Наиболее полно сварочные процессы описываются детерминированными моделями, устанавливающими связь между входными и выходными параметрами на основании существующих физических закономерностей.
Большое распространение при ремонте цельнометаллических сварных конструкций корпусов получила контактно-точечная сварка, позволяющая значительно увеличить производительность труда. Для сварки в условиях авторемонтного производства применяют машину М.ТПП-75, которая предназначена для электрической контактной точечной сварки деталей из тонколистовой малоуглеродистой стали. [c.335]
По форме свариваемого соединения, определяющего тип сварочной машины, контактную сварку разделяют на стыковую, точечную и роликовую. При всех видах контактной сварки металл нагревается за счет выделения тепла при прохождении электрического тока по свариваемым деталям количество этого тепла определяется известным законом Джоуля—Ленца
[c. 322]
Контактная сварка основана на свойстве электрического тока нагревать проводник в местах значительного сопротивления, т. е. в местах соединения плотно прижатых одна к другой деталей. Различают точечную (рис. 13,1, б) и шовную (рис. 13.1, в, г) контактные сварки, которые позволяют получать хорошие соединения тонкостенных (менее 1,5—2,0 мм) деталей из низкоуглеродистых сталей. Несколько хуже свариваются алюминиевые сплавы, латунь, кремнистая бронза, никель и его сплавы. Плохо свариваются алюминий, медь и ее сплавы с высокой электрической проводимостью. [c.136]
В 1887 г. Н. Н. Бенардос запатентовал устройство для точечной контактной сварки, в котором нагрев и последующее соединение металлических листов, сложенных внахлестку, обеспечивались благодаря прохождению через них в месте контакта электрического тока, поступающего через два угольных электрода, между которыми зажимались листы.
Электросварочная точечная машина АТП-50 (рис. 138) предназначена для электрической контактной точечной сварки листового металла. Сварка производится двумя медными электродами /, расстояние между которыми меняется при помощи педали 2.
[c.217]
В 1882 г. русский инженер и изобретатель Н. Н. Бенардос разработал способ электродуговой сварки металлов неплавящимся угольным электродом. В последующие годы им были разработаны такие способы сварки, как сварка дугой, горящей между двумя или несколькими электродами в защитном газе, контактная точечная электрическая сварка, выполняемая с помощью специальных клещей, а также конструкции сварочных автоматов. В первые же годы открытия способ электродуговой сварки угольным электродом благодаря усилиям самого изобретателя, был широко использован для практических целей. [c.4]
Контактная сварка является основным видом сварки давлением термомеханического класса. Она осуществляется с применением давления и нагрева места сварки проходящим через заготовки электрическим током. Основными видами контактной сварки являются стыковая, точечная и шовная.
[c.413]
Контактная сварка основана на использовании тепла, выделяющегося при прохождении электрического тока через свариваемый участок. Свариваемые детали в месте контакта нагревают до пластического состояния и сдавливают под определенным усилием, получая таким образом неразъемное соединение. Контактная сварка делится на стыковую, точечную и шовную. [c.80]
Контактная сварка — сварка с применением давления, при которой используется тепло, выделяющееся в контакте свариваемых частей при прохождении электрического тока. Этот вид сварки, в свою очередь, подразделяется на несколько видов точечная контактная сварка, рельефная сварка, шовная контактная сварка, стыковая контактная сварка оплавлением и контактная сварка сопротивлением. [c.17]
К недостаткам контактной сварки, затрудняющим применение ее в строительстве, следует отнести большие установочные электрические мощности машин (до 1000 кВ-А и более), требующие подключения к отдельному фидеру узкую специализацию машин по видам сварных соединении (стыковые, точечные и др. ) необходимость в большинстве случаев доставки деталей к машинам сложность контроля качества сварных соединений.
[c.333]
Spot welding — Точечная сварка. Сварка перекрытых частей, в которых сплавление происходит в относительно маленькой круглой области. Обычно, это электрическая контактная сварка. [c.1049]
В зависимости от питания контактных сварочных машин электрическим током различают сварку переменным током и сварку ак-кумулированной (запасенной) энергией. По характеру соединения свариваемых заготовок электрическая контактная сварка разделяет ся на способы стыковая, точечная, рельефная, шовная (ролнко—вая), шовно-стыковая. [c.392]
Электрическая контактная сварка находит применение при ремонте кузова и оперения в одной ее разновидности— точечной сварке. Для точечной сварки чаще всего пользуются стационарными точечными аппаратами типа АТП-10 и подвесными точечными клещами типа ЗИЛ или подвесным однополюсным сварочным пистолетом типа МТПО-75 для выполнения работ непосредственно на кузове. Оснастка к однополюсному пистолету изготовлена Горьковским автозаводом.
[c.147]
Машины электросварочные контактные. Технические требования. Стандарт распространяется на точечные, шовные (роликовые) и стыковые элект1Шсварочные машины, предназначенные для электрической, контактной сварки металлов. Указываются техиические требования, предъявляемые при [c.495]
Силами MBTJy им. Баумана разработаны установки для точечной и роликовой сварки ультразвуком. Схемы этих установок, по внешнему виду сходных с обычными машинами для электрической контактной сварки, представлены на рис. 101. [c.188]
Методы соединения металлических деталей в производстве электронных ламп выбирают, учитывая специфику производства, которая О пределяется использованием небольших количеств металла, необходимостью легкого обезгаживания деталей и применения материалов с низким давлением насыщенных паров. Кроме того, следует учитывать, что в электровакуумных приборах применяются также сравнительно легкоплавкие и чувствительные к температуре стеклянные детали. Это привело к распространению и преимущественному использованию точечных и шовных соединений (электрическая контактная сварка). В последнее время в ироизводстве цельно- металлических электронных ламп СВЧ большое значение приобрело также соединение деталей пайкой твердыми припоями. Механические методы соединения, особенно так часто при.меняе.мое в обычной те.хнике резьбовое соединение, используется, за исключением некоторых специальных случаев, в вакуумной технике очень редко и только при изготовлении очень мощных электронных приборов. Обзор обычных методов сварки приведен на схеме табл. 9-3-1 (см. также (Л, 9 и 148]),
[c.508]
В 1940 г. заводом Электрик было освоено производство сложных уникальных машин для контактной сварки — стыковых машин мош ностыо 600 ква, точечных — до 450 ква, агрегатов для сварки продольных швов труб и другого оборудования. Эти машины в подавляющем большинстве имели электрические и пневматические приводы, а также тиратропные и релейно-контакторные аппараты для автоматического регулирования процесса сварки.
[c.120]
В СССР за последнее десятилетие значительно вырос объем применения всех видов контактной сварки в машиностроении, строительстве, приборостроении. Созданы десятки типов стыковых, точечных, роликовых и рельефных машин. Они оснащены игнитронными прерывателями, пневматическими, гидравлическими, электрическими и другими приводами. Машины снабжаются стабилизаторами тока, поддерживающими его среднеэффективное значение. Автоматизация и механизация управления сварочными процессами контактных машин обеспечивает получение сварных соединений надежного качества со стабильными свойствами. [c.120]
Точечная сварка — способ контактной сварки, при котором детали свариваются по отдельным офаниченным участкам касания. При точечной сварке (рис. 19.1, а) детали 1 собирают внахлестку, сжимают усилием электродами 2, к которым подключен источник J электрической энергии. Детали нафеваются при кратковременном прохождении тока до образования зоны взаимного расплавления деталей 4, называемой ядром. Нафев зоны сварки сопровождается пластической деформацией металла в зоне контакта деталей вокруг ядра.
[c.407]
Контактную сварку по форме свариваемого соединения, определяющего тип сварочной машины, разделяют (рис. 201) на стыковую а, точечную б и роликовую в. Нагрев металла при всех видах контактной сварки происходит за счет выделения тепла при прохождении электрического тока по свариваемьш деталям, количество которого определяется известным законом Джоуля—Ленца [c.480]
Контактичя сварка. Благодаря высокому электрическому сопротивлению и малой теплопроводности титана контактная сварка последнего значительно облегчается п может выполняться па обычных машинах средней мощности. Происходящее в процессе точечной, роликовой и стыковой сварки сопротивлением плотное сжатие свариваемых деталей между собой препятствует доступу воздуха в зону сварки и не требует в связи с. зтим при.менения специальной защиты инертными газами. В случае сварки методом оплавления свариваемые поверхности защищены интенсивным выделением из зоны сварки паров и газов, оттесняющих окружающий воздух, однако дополнительная защита аргоном повышает нластд1чность стыковых соединений. Режпмы сварки приведены в табл.
[c.369]
Явление нагрева контакта проводников при прохождении электрического тока также было использовано для целей сварки металлов. Так, в 1877 г. проф. Э. Томсон (США) взял патент на способ стыковой сварки сопротивлением. Поздчее, в 1887 г. И. Н. Бенардос запатентовал устройство для точечной контактной сварки, в котором нагрев и последуюш,ее соединение металлических листов, сложенных внахлестку, обеспечивались за счет прохождения электрического тока через два угольных электрода, между которыми зажимались листы. Третьей разновидностью контактной сварки является шовная или роликовая сварка, когда изделия соединяются непрерывным швом по линии качения ролика. Этот способ сварки также изобретен [c.454]
Стыковая контактная сварка основана на нагреве стыкуемых торцов дета тей теплотой, выделяющейся при прохожденщ электрического тока. Нагрев торцов деталей производится либо до оплавления их (сварка плавлением), либо до пластического состояния с последующим сдавливанием деталей (сварка давлением). Этот способ сварки самый производительный и рентабельный при массовом и крупносерийном производстве. Шовная контактная сварка, при которой соединение элементов выполняется внахлестку вращающимися дисковыми электродами в виде непрерывного или прерывного шва, применяется для получения герметичных швов в тонколистовых конструкциях (различные сосуды). Точечная контактная сварка, при которой соединение элементов происходит на участках, ограниченных площадью торцов электродов, применяется для тонколистовых конструкций, в которых не требуется герметичность швов.
[c.47]
В 1877 г. проф. Э. Томсон (США) запатентовал способ стыковой сварки сопротпвленпем, оснопанпый на нагреве поверхностей контакта между заготовками при прохождении электрического тока. В 1887 г. Н. Н. Бепардоо запатентовал устройство для точечной контактной сварки, в котором в качестве электродов были использованы угольные стержни. [c.266]
Точечная контактная сварка рис. 1.11,а), — это сварка, при которой сварное соединение получается меил ду торцами электродов 4 п 5, подводящих ток и передающих усилие сжатия. Место контакта 1 соеди-г няемых деталей расплавляется теплом, выделяемым при прохождении электрического тока, электроды сжимаются усилием, в результате чего образуется сварная точка 6. Точечную сварку щироко применяют при изготовлении арматурных сеток, в местах пересечения стержней. Для соединения пересекающихся стерм[c.17]
Контактная сварка
В связи с тем, что соединение при контактной сварке формируется за время, гораздо меньшее сварки плавлением, то это обеспечивает более высокую производительность и меньшее коробление детали, т.к. ЗТВ мала.
Т.к. процесс легко автоматизируется и более легко встраиваются поточные конвейеры, этот способ лучше применять при массовом и серийном производстве.
Этот способ нашел применение в автомобильной и авиакосмической промышленности.
Благодаря тому, что соединения, полученные контактной сваркой, обладают очень высокой прочностью и качество мало зависит от квалификации сварщика, то этот способ находит применение и в других отраслях. 2свRtu
2. Теплоотвод тепла из зоны сварки λ-теплопроводность
Т.е. в зоне между электродами действует тепло, выделяемое при прохождении тока и отводимое тепло в массу детали и электрода.
Т.к. Э. Томсон решил применить медные электроды, а λсu >> λстали, то форма литого ядра имеет благоприятную для сварного соединения чичевицеобразную форму.
Если увеличить Jсв и tсв, то начинает развиваться литое ядро.
Т.е. применение литых электродов и повышенный теплоотвод в них по сравнению с массой детали определяют развитие процесса плавления в литом ядре именно в массу детали, а не в сторону электрода.
В связи с этим снижается вероятность брака по причине плавления в ядре, т.е. прожег затруднителен, что определяет производительность точечной контактной сварки.
Рельефная сварка – ее можно отнести к одной из разновидностей точечной сварки.
Соединение при точечной сварке формируется при местном нагреве детали электрическим током и пластической деформацией в зоне соединения в счет усилия сжатия. 2R
— Qλ
Шовная контактная сварка (роликовая)
Кш – обозначение швов, детали сваривают перекрывающимися точками по линии качения роликов (электродов), сжатия детали р, подвода тока Jсв и перемещения детали со скоростью сварки Vсв – тоже с помощью этих роликов.
Применяется в тех случаях, когда нужно получить герметичное сварное соединение с помощью контактной сварки.
Герметичный шов – для сварки резервуаров, бензобаков, емкостей, полостей и др.
J = I / S – плотность тока
Jш – ток шунтирования
Процесс производится засчет выделения тепла и теплоотвода.
Шовная сварка разделяется на 3 процесса:
— непрерывная
При этом способе, когда ток протекает непрерывно, получаем сплошной шов без явно выраженных литых ядер, перекрывающих друг друга. Недостатком является повышенный нагрев электрода и необходимость их частой перезаточки.
— отдельными импульсами (прерывистая)
+ Q = J2св R tсв
— Q = f (λ) (tсв + tn)
Изменением тока Jсв по амплитуде, длительности его протекания — Jс, длительности его паузы — tn и скорости сварки — Uсв можно регулировать величину перекрытия литых ядер ln, обычно достаточно 25%, но не следует делать ln>50%.
Благодаря лучшему отводу от электродов стойкость их значительно повышается. При сварке жаропрочных сталей, обладающих низкой теплопроводностью и высокой стойкостью к деформациям при высокой t (жаростойкость) необходимо применять повышенные сварочные усилия, т.е. шаговую сварку.
Шаговая сварка – сварочный ток включают прерывисто, электроды останавливаются в момент пропускания сварочного тока.
Позволяет в момент остановки электродов и пропускания сварочного импульса осуществить более надежный контакт в зону протекания тока.
После выключения тока сварочные усилия в зоне контакта позволяют избежать горячих трещин.
Контактно – стыковая сварка
Существует несколько разновидностей контактно-стыковой сварки (Кс).
Рассмотрим способ контактной сварки сопротивлением, при этом детали сначала прижимают к электродам губками (призматические электроды) для обеспечения электрического контакта и невозможности проскальзывания детали между электродами.
Затем сжимают с усилием сварки Р нагрева, включают сварочный ток и детали в стыке нагреваются этим током Iсв. Затем прикладывают Росадки, в 1,5 – 2 раза меньше Рнагрева, потом включают ток и детали находятся под действием Р осадки.
В момент, когда деформируемое сопротивление наименьшее, прикладывают усилие осадки и выключают ток, при этом слои металла, нагретые до высокой пластичности, выдавливаются от центра стыка до периферии.
При этом из стыка выносятся остатки окисных пленок и град (металл на периферии зоны соединения).
Таким способом сваривают детали небольшого сечения, диаметром до 20-40 мм, соединение формируется в твердой фазе без расплавления металла в стыке. Нагретый пластичный металл выдавливается в град и в контакт вступают твердые нагретые частицы материала детали.
Недостатком является необходимость тщательной подготовки торцев под сварку и необходимость огромных мощностей установки для соединения больших сечений.
Второй способ – стыковая сварка оплавлением.
Технологически отличается от сварки сопротивлением тем, что напряжение на первичной обмотке трансформатора (и на вторичной) подается до момента контактирования свариваемых торцев.
Поэтому при сближении деталей в контактирование вступают отдельные микронеровности на торце, количество которых значительно меньше, чем в том случае, когда предварительно детали сдавили. Выступы сминаются и площадь контактирования возрастает. При первом контактировании возникает сварочный ток и он приходится на несколько микровыступов, отсюда плотность тока в контакте отдельных микровыступов настолько высока, что металл нагревается за тысячные доли секунды, а затем закипает. При этом происходит взрывное разрушение жидких перемычек контакта.
В контактирование вступают новые микровыступы и в зоне выступа появляются повышенные пары металлов, т.е. повышенное давление паров металлов в стыке защищает зону сварки, нагретую до tпл от взаимодействия с атмосферой.
При расплавлении торцев детали до такого состояния, когда на поверхности появляется тонкий слой жидкого металла, что гарантирует равномерный прогрев по всей площади стыка, к детали прикладывается усилие осадки. Жидкий слой с торцев выдавливается на периферию стыка – в град и под высоким давлением твердые части детали вступают в контакт, а т.к. tтв. ме вблизи жидкого слоя не намного ниже tпл и он был очень пластичный, то частично и твердый металл выдавливается в град и под давлением формируется прочное сварное соединение с минимальным количеством дефектов, т.к. продукты разложения и окисные пленки были выдавлены в град.
Стыковая сварка оплавлением обеспечивает более качественное соединение, т.к. металл на поверхности торцев, на которых могли быть загрязнения, удаляются при взрыве жидких перемычек в процессе оплавления.
Жидкий слой и часть пластичного металла также выдавливаются в град и в контакт вступает абсолютно чистые (молодые) поверхности.
Не требуется тщательной обработки свариваемых торцев как при сварке сопротивлением.
Более того, при сварке деталей с разным сечением делают специальный скос кромок, тогда площадь начального контактирования уменьшается и процесс оплавления эффективнее, а по мере процесса детали прогреваются и имеют нормальную форму.
Стыковая сварка прерывистым оплавлением или оплавлением с предварительным подогревом
При стыковой сварке крупногабаритных деталей: железнодорожных рельсов, труб, магистральных трубопроводов – для облегчения процесса начальной стадии оплавления применяют прием, заключающийся в том, что вначале детали медленно сводят до возникновения контакта и образования жидкости и паров металла. Затем разводят детали и тепло, выделившееся в зоне сплавления, распространяется в массу детали и они нагреваются.
Затем вновь создают контакт между торцами до тех пор, пока торцы не нагреются, что последующий процесс будет идти стабильно, без перерыва.
Контактная рельефная сварка (Кр)
Ее можно отнести к разновидностям точечной сварки. Применяется при сварке деталей, занимающих большое пространственное положение.
Обычно процесс по схеме 1 не получается, т.к. контактирование по всем участкам нашей детали не может быть одинаковым в связи с разницей в качестве подготовки, условиями деформирования, месторасположением контакта от токоподвода.
Данный процесс контактной рельефной сварки перекрещивающихся прутков происходит с формированием соединения в твердой фазе с выдавливанием жидкой фазы на периферию.
Для обеспечения равных условий контактирования и деформирования большого количества деталей нужно приложить сначала ковочное сварочное усилие (или усилие предварительного сжатия), которое отрихтует все прутки, обеспечит надежный контакт каждой детали с электродом и друг другом. Это должно обеспечить незначительную деформацию деталей в контакте.
Затем усилия снимаются до значения усилия сварки. Т.к. одинаковые условия контактирования всех деталей не гарантированы, но лучше сначала обеспечить импульс тока подогрева, при котором детали в контакте и под действием сварочного усилия разогреются.
Затем можно еще Jпод, после этого включают ток сварки.
Для снижения коробления прикладывается ковочное усилие и получаем многоточечное соединение с высоким качеством.
В начальный момент ток течет по вершинам, площадь мала и ток высокий, они начнут плавиться, а потом деформироваться от сварочных усилий. Получим литые ядра и незначительные следы без подгаров и пригаров.
За одну операцию контактной рельефной сварки получаем несколько сварных соединений. Но когда детали имеют защитное покрытие, которое должно остаться на поверхности после сварки, то следует применять только рельефную сварку, т.к. благодаря большой площади между электродом и деталью плотность тока будет мала и покрытие сохранится.
Физико-химические условия образования соединения Формирование сварного шва при контактной сварке. Нагрев металла сварочным током Нагревание и расплавление металлов в точке контакта энергией, выделяющейся при прохождении через него электрического тока. Шунтирование тока при точечной сварке Компенсация токов шунтирования при контактной сварке в нескольких точках. Свариваемость при контактной точечной и шовной сварке Факторы, влияющие на образование качественного сварного шва. Точечная сварка Точечные соединения при контактной сварке. Шовная сварка Соединения в виде шва из последовательных точек.
Также по теме:
Услуги по сварке деталей
Корпорация предлагает услуги по сварке деталей (сборок) со следующими характеристиками:
№ п/п | Виды сварки | Характеристики свариваемых узлов | |||
материал | толщина, мм | габариты (ДхШхВ), мм | масса, кг | ||
1 | Контактная сварка | ||||
1.![]() | Точечная контактная сварка | титан и его сплавы, алюминий и его сплавы, сталь и сплавы | 0.5 до 4.0 | 800 х350 х 350 | 20 |
1.2 | Роликовая контактная сварка | титан и его сплавы, алюминий и его сплавы, сталь и сплавы | 0.5 до 3.0 | 800 х350 х 350 | 20 |
2 | Аргонодуговая сварка неплавящимся электродом | ||||
2.1 | Ручная аргонодуговая сварка | титан и его сплавы, алюминий и его сплавы, сталь и сплавы | 0.5 до 10.0 | 3000 х450 х 350 | 300 |
2.![]() | Автоматическая аргонодуговая сварка для продольных швов | титан и его сплавы, алюминий и его сплавы, сталь и сплавы | 1.2 до 5.0 | 800 х500 х 500 | 50 |
2.3 | Автоматическая аргонодуговая сварка для кольцевых швов | титан и его сплавы, алюминий и его сплавы, сталь и сплавы | 0,5 до 20.0 | 2000 х400 х 400 | 300 |
2.4 | Ручная сварка неплавящимся электродом в контролируемой среде | титан и его сплавы, высоколегированные стали и сплавы | 0,5 до 20.0 | 800 х400 х 400 | 25 |
3 | Автоматическая плазменная сварка для кольцевых швов | титан и его сплавы, алюминий и его сплавы, сталь и сплавы | 1. | 2000 х400 х 400 | 100 |
Точечная сварка. Роликовая сварка. Рельефная сварка. История развития
Рекомендуем приобрести:
Установки для автоматической сварки продольных швов обечаек — в наличии на складе!
Высокая производительность, удобство, простота в управлении и надежность в эксплуатации.
Сварочные экраны и защитные шторки — в наличии на складе!
Защита от излучения при сварке и резке. Большой выбор.
Доставка по всей России!
Нагрев места стыка двух деталей проходящим через них электрическим током характерен для всех способов контактной сварки. Вторым существенным признаком этого вида сварки является обязательное приложение усилия сжатия контактируемых деталей. По характеру приложения такого усилия и типа соединения различают стыковую, точечную, шовную (роликовую) сварку и другие способы. Э. Томсон и его коллеги в США разрабатывали технологию стыковой контактной сварки и не пытались изменить характер приложения силы и форму соединения, несмотря на то, что прототипом нового способа контактной сварки мог послужить самый распространенный в XIX в. вид неразъемного соединения — клепка.
Неизвестно, когда и при каких обстоятельствах пришел Н. Н. Бенардос к принципу точечной контактной сварки. Первый в мире патент на этот способ (и «прибор» для его реализации) был выдан на его имя в Германии: № 46776—49 от 21.01.1888 г. В качестве электродов служили графитовые бруски, вставляемые в клещи, которые сжимали вручную (рис. 33).
В заявке на изобретение, поданной в России, Бенардос подробно описывает технологию и предлагает несколько устройств для точечной сварки. Так, один из «приборов» выполняли в виде стойки, на которой укрепляли изолированно друг от друга кронштейны: нижний жестко, а верхний — на шарнире (рис. 34).
На концах кронштейнов, к которым подавали напряжение, крепили электроды из угля или другого электропроводного «огнеупорного тела, соответственно для этого подготовленного» [20]. Свариваемые заготовки собирали встык или со скосом кромок и заводили между электродами. При этом верхний кронштейн поднимался. Перед началом сварки этот кронштейн с электродом прижимали грузом. По мере разогревания кромок до пластического состояния или до подплавления изделие передвигали, и вслед за нагревом производилось обжатие роликами.
Точечная сварка продолжала развиваться. Спустя 10 лет О. Кляйншмидт заменил угольные электроды в «приборах» Бенардоса медными электродами и усовершенствовал устройство для сварки, встроив трансформатор в клещи (рис. 35).
На разработку был выдан патент США № 616463 от 20.12.1898 г. С этого времени точечная сварка вышла из стадии лабораторных экспериментов, и началась работа над повышением производительности процесса. Бушайе разработал конструкции «дуплекс-электродов» для выполнения сразу двух сварных точек (пат. Франции № 330200 от 13.03.1903 г.). Верхний и нижний электродные узлы имели собственные трансформаторы. При параллельном подключении обмоток трансформаторов получается только одна точка, при последовательном включении — сразу две.
Оптимальную конструкцию электродов разработал Харматта (патент США № 1046066 от 3. 12.1912 г.). Тейлор предложил перекрестный процесс нагрева места сварки таким образом (рис. 36), чтобы ток проходил по диагонали между двумя разделенными на части электродами (пат. США № 1243004 от 16.10.1917 г.).
Одновременно отрабатывали оптимальную конструкцию узлов, механические и электрические схемы машин для точечной сварки (рис. 37). Были разработаны машины с качающимся плечом-хоботом, мощные стационарные и легкие переносные машины, клещи разных конструкций.
В конце XIX в. точечную сварку использовали для приварки ручек к кастрюлям и сковородкам, для изготовления других неответственных изделий, заменяя клепку, а иногда — пайку. Однако это малозаметное применение убедительно доказало, что точечная сварка намного производительнее клепки и что пригодна она для соединения многих металлов. Точечную сварку начали широко использовать в США в 1914 г., когда в автомобильной промышленности клепка была заменена приваркой листовых элементов автомобилей (крыльев, обшивки кузова, деталей шасси). Мощность установок колебалась в пределах 5—35 кВ А. Установки имели ручное или ножное управление. К 1923 г. стационарные точечные машины позволяли сваривать до 200 точек в минуту. Использование новой технологии в массовом производстве создало возможность дальнейшего развития процесса сварки, совершенствования сварочного оборудования и даже создания новых способов сварки, таких как рельефная и роликовая. Идея рельефной сварки возникла благодаря многократному появлению «ошибочных» соединений, которые выполняли в спешке неквалифицированные рабочие. В 1918 г. Гамильтон и Оберег обратили внимание на преимущества приварки деталей сразу в нескольких местах на заранее отштампованных выступах и разработали промышленную технологию рельефной сварки.
В процессе изготовления изделий цилиндрической формы часто нижний опорный электрод выполняли в виде ролика, вращающегося вместе с изделием при установке в требуемое положение, а верхний — в виде короткого цилиндрического стержня. На таких машинах осуществляли точечные соединения, они же послужили прототипом машин для шовной сварки, когда свариваемые детали проходят между двумя роликами, нагреваются мощными импульсами тока, в результате чего образуется шов из отдельных перекрывающихся точек.
В 1905 г. Снурек и Гислер предложили схему многоэлектродной точечной сварки [110]. Однако только в 1924 г. была разработана конструкция соответствующих машин, которые были применены при сборке корпусов автомобилей на заводе Форда.
В 1910 г. Джевонсом был изобретен способ контактной сварки, заключающийся в том, что между свариваемыми кромками помещали небольшие пластинки (закладки), в которых и концентрировалась теплота. Эта технология была достаточно сложной. С целью ее упрощения как при точечной, так и при шовной сварке вместо закладок были предложены тонкие полоски (ленты), которые сматывали с катушек и подавали сверху и снизу изделия (рис. 38).
В 1930 г. на верфях Германии были внедрены машины с двумя электродами и двумя трансформаторами фирмы «Оттенземер Айзенверке». Затем в короткое время различными фирмами в США и Европе были разработаны схемы многоточечной сварки — с несколькими постепенно включаемыми электродами; с одновременным включением в симметричном и несимметричном исполнении; с трансформаторами, имеющими двойную вторичную обмотку; с трансформаторами, расположенными с противоположных сторон и др. Многоэлектродными машинами можно было одновременно или почти одновременно выполнять несколько сварных точек, полностью сваривать изделие (например, узел автомобиля), не перемещая элементы и электроды до окончания процесса [111, 112].
Для многоточечной сварки были разработаны два типа машин — многоцелевые машины и сварочные прессы [113, 114]. Первые были снабжены перемещающимся столом, их использовали для сварки различных изделий; вторые применяли для сварки строго определенных изделий, когда положение электродов и опорных поверхностей было фиксированным. В 30-е годы были решены многие технические проблемы; обоснованы расстояние между электродами и расположение трансформаторов, разработаны системы подвода тока, выбрано оптимальное количество одновременно свариваемых точек, установлена последовательность постановки точек и т. д. Особое внимание было уделено конструкции электродов и системам регулирования процесса сварки.
Кляйншмидт, заменив угольные электроды Бенардоса медными, обеспечил точечной сварке практическое применение. Электролитическая медь обладает большой тепло- и электропроводностью, а при механической обработке (протяжке) — удовлетворительной твердостью. Однако в результате нагрева в процессе эксплуатации прочность меди падает. Начиная с 1915 г., поиск материала для электродов велся в двух направлениях: электролитическую медь легировали с целью придания ей твердости, добиваясь при этом незначительного снижения электропроводности; повышали электро- и теплопроводность сплавов на другой основе, добавляя медь. В 1925 г. были разработаны «псевдосплавы», названные «элколит», «элмет», «моллори» и т. п., получаемые путем спекания при высоких давлениях и температурах порошков вольфрама, покрытых медью [115]. Поскольку проводимость этого материала была ниже, чем чистой меди, из него выполняли только наконечники, которые припаивали к охлаждаемому полому стержню. В машинах для шовной сварки вольфрам медную ленту припаивали в виде обода к торцу роликов, Однако паяная конструкция стоила дорого, и, кроме того, всегда существовала опасность плохого контакта в месте соединения из-за неточной сборки и дефектов пайки.
В результате поиска достаточно прочных материалов с хорошей электро- и теплопроводностью были подобраны элементы, способные образовывать твердый раствор с медью (кобальт, хром, кадмий, бериллий и молибден) при их содержании не более 1%. Из этих сплавов начали изготавливать цельнометаллические электроды и ролики.
Серьезным недостатком первых машин для контактной сварки, особенно шовных, являлся большой расход энергии — «лишний» нагрев зоны сварки происходил из-за длительного воздействия сравнительно небольшой силы тока. В 1920 г. было предложено осуществлять подачу токов большой силы, и в машинах установили реле времени. Роликам придавалось прерывистое вращательное движение через фрикционную муфту и стопорный механизм. Для уменьшения силы тока в период перемещения изделия во вторичный контур сварочного трансформатора включался элемент индуктивности. Сердечник индуктивной катушки был связан с роликами и перемещался при их движении, возвращаясь в исходное положение с помощью пружины. Однако вскоре обнаружили, что чем больше сила сварочного тока, тем меньше точность регулирования длительности импульса. Поэтому пришлось заниматься совершенствованием системы управления.
Регулирование параметров тока и длительности сварки являются важными составляющими технологии, а аппаратура управления — существенной частью сварочных машин. В аппаратах Томсона в первичной обмотке трансформаторов находились отводы, переключением которых регулировалось напряжение во вторичной обмотке, как правило, состоявшей из одного витка. Продолжительность прохождения сварочного тока контролировалась электромагнитной системой, содержащей конденсатор, питаемый от резистора и включенный параллельно обмотке соленоида. В 1924 г. в схему была включена неоновая лампа, благодаря чему ток мог проходить через систему только при напряжении строго определенного уровня.
В 1932 г. в США в контактных машинах появилась система управления, основанная на тиратронах. Эта система нашла применение на машинах средней мощности (до нескольких кВ А), однако при их эксплуатации обнаружились серьезные недостатки, в частности, плохо работали прерыватели.
В 1934 г., практически с момента появления в США игнитронно-ртутных вентилей со вспомогательным (поджигающим) электродом, управляющим зажиганием основного дугового разряда, их стали использовать в сварочных машинах. В последующие годы система управления контактными машинами, основанная на игнитронах, совершенствовалась. Были разработаны схемы управления игнитронами, в которых использовали достижения электронной техники и применяли вспомогательные элементы (стабилизаторы, усилители и т. д.), а также элементы защиты.
В 1930-х гг. продолжали работать над проблемой перегрузки сетей однофазными машинами, что вызывало колебания напряжения. Одно из решений этой проблемы было найдено в 1941 г. братьями Марио и Давидом Сиаки: оно основывалось на применении трехфазных источников с выпрямителями [116].
К концу 1930-х гг. конструкция (узлы, компоновка, архитектоника) контактных машин претерпела серьезные изменения по сравнению с исходными образцами. Первые машины часто выполняли, кроме прочих действий, проковку или обкатку, и в некоторых из них были предусмотрены механические командоаппараты в виде валов с кулачками. Производительность машин во многом зависела от быстродействия систем захвата и сжатия свариваемых деталей. В поисках оптимальных конструкций были опробованы гидравлические, пневматические и электромагнитные системы.
В конце XIX в. машины для стыковой сварки представляли собой сравнительно простое устройство с электрическим и механическим узлами, управление работой которых осуществляли педалью (рис. 39, а, б).
Первые устройства для точечной сварки имели вид клещей. Через два-три десятилетия были созданы несколько десятков различных по назначению универсальных и специализированных машин, а по размерам — от огромных формовочных станов для производства труб и изготовления автомобилей до подвесных и переносных клещей.
Серьезной проблемой в развитии контактной точечной сварки явилось создание клещей, отличающихся высокой маневренностью, легкостью и быстродействием. В первое десятилетие XX в. в таких подвижных сварочных постах генераторы тока конструктивно отделялись от механических, пневматических или гидравлических устройств для позиционирования и сжатия. Длина кабеляи шланга водяного охлаждения составляла 2—3 м, и, учитывая потери, приходилось повышать напряжение вторичной обмотки сварочного трансформатора, а следовательно, его мощность и габаритные размеры.
Следующим этапом было создание клещей с трансформатором, вмонтированным в подвижную конструкцию. Возникли новые проблемы — необходимость уменьшения габаритных размеров трансформатора, увеличения удельной мощности, минимизации потерь, С этой целью были применены трансформаторы с броневой магнитной системой, в которых первичная и вторичная обмотки были навиты и защищены магнитной цепью, выполненной из листов кремнистой стали с ориентированными кристаллами. Первичную обмотку выполняли из медной проволоки, а вторичную — из литой меди с припаянными трубками-каналами для охлаждающей воды. В подвесных трансформаторах первичные обмотки чередовались с витками вторичной обмотки, что увеличило удельную мощность до 0,7—1 кВА/кг [117].
Первая технология стыковой сварки труб, разработанная в 1902 г. Э. Томсоном и получившая название «прямошовный» метод, по способу приложения давления была сходна с кузнечно-прессовой сваркой. В цельносварных трубах были заинтересованы многие отрасли промышленности и строительства. Технология их изготовления и соответствующее оборудование продолжали совершенствоваться. За два десятка лет были предприняты попытки использовать для производства труб все известные способы контактной сварки. В 30-х гг. фирма «А. О. Смит» разработала технологию сварки оплавлением и внедрила ее в производство труб с толщиной стенки 5 мм и диаметром 500 мм, которые сваривались по всей длине (12 м) на машинах мощностью 5000 кВА.
В контактной сварке использовали ток промышленной частоты до тех пор, пока в 1939 г. фирма «Бабкок энд Вилько Ко» не применила ток частотой 200—350 Гц, Трубы из полосового проката сваривали машинами с вращающимся трансформатором. Однако это еще не был процесс, основанный на индукционном нагреве токами, открытыми Фуко, и теоретически исследованный в 1884 г, Хевисотдом. Впервые на практике это явление использовал в 1891 г. Э. Томсон, осуществивший индукционный нагрев листового железа. В 1900 г. была пущена в эксплуатацию индукционная плавильная печь Челлина. Началом развития процессов высокочастотной сварки считается разработка фирмой «Лоррен-Эско» в 1928 г. процесса (пат. Франции № 922431), в котором индуцированный ток концентрировался в зоне сварки ферритным сердечником. Однако основное развитие сварка токами высокой частоты получила после 1940-х гг.
Много общих существенных признаков с контактной сваркой имеет и конденсаторная сварка, идея которой возникла благодаря случаю. В 1905 г. сотрудник фирмы «Вестингауз Электрик» Л. В, Чабб, экспериментируя с электрическими конденсаторами, обнаружил, что проволока приваривается к алюминиевой пластине при прохождении через них разряда накопленного электричества [118]. Это наблюдение позволило сделать определенные выводы: разряд разрушил прочную оксидную пленку, затрудняющую пайку, и поэтому появилась возможность получить прочное соединение алюминиевых проводов. Конденсаторную сварку сразу же стали применять в электротехнике (приварка серебряных, вольфрамовых и других контактов, соединение алюминиевых и медных проводов), в ювелирном деле (приварка золотых и платиновых булавок и проволочек).
Как уже отмечалось, стыковая сварка нашла применение почти сразу после создания Томсоном первых образцов машин, Сначала это было изготовление проводов для электротехнических целей, затем — производство труб и различных стержней и, наконец, наиболее эффективное применение — производство вооружения в США, в частности, снарядов в годы Первой мировой войны. В Европе в это время наиболее активно развивала и внедряла контактную сварку немецкая фирма «Альгемайне Электрише Гаэельшафт» (АЭГ). Кроме «чисто» контактных машин, эта фирма в 1930-х гг. разрабатывала и выпускала машины для приварки шпилек.
Контактная сварка нашла применение в самолетостроении уже в 1908 г., вскоре после того, как в ряде стран было решено использовать для основных узлов самолетов металл. При изготовлении стальных ланжеронов, стоек, раскосов, элеронов и т. д, применяли точечную и роликовую сварку. В 1928 г. фирма «Форд Мотор» внедрила контактную сварку для ответственных узлов самолетов из дюралюминия. В начале 1930 г. были проведены статические и усталостные испытания на натурных образцах и моделях, подтвердившие возможность применения контактной сварки алюминиевых конструкций. В США с 1935 г. ее начали использовать фирмы «Боинг», «Дуглас» и «Сикорски», почти одновременно в Европе — фирмы «Фиат» вместе с «КантьериАэронавтика д’Италия», выпустившие первый металлический итальянский самолет [119, 120].
Особенно широкое применение все способы контактной сварки находят в автомобилестроении.
Г. Форду принадлежит особая роль в развитии контактной сварки. Его заказы были стимулом для усовершенствования технологии и оборудования. В свою очередь сварка обеспечила высокие темпы производства автомобилей. В первые годы на заводах Форда выпускали до 3000 автомобилей в год, а в 1909 г. их количество достигло 10 тыс. в основном благодаря применению стыковой и точечной сварки вместо клепки.
К началу 1928 г. на заводах компании «Форд Мотор» было 320 машин для сварки оплавлением, 540 машин для точечной сварки и 25 машин для роликовой сварки. В 1928 г. на автомобиле модели «Форд-А» насчитывалось около 1300 сварных точек, на модели 1932 г. их количество составило 2000 шт. Соединение всех штампованных деталей корпуса, крепящихся к шасси, осуществлялось точечной и роликовой сваркой. В следующем году технология была усовершенствована — днище и две боковые стенки сваривали за одну операцию на машинах с двумя трансформаторами (мощностью по 250 кВ А) менее чем за 60 с, причем чистое сварочное время составляло менее 10 с. В конечном итоге развитие оборудования для точечной сварки пошло по двум направлениям — создание клещей (подвижных сварочных постов) и создание многоточечных машин (контактных машин-прессов). Также были усовершенствованы и машины для роликовой сварки.
Развитие контактной сварки в СССР также стимулировалось интенсивным ростом автомобилестроения. Нижегородский (Горьковский) автомобильный завод был спроектирован и оснащен в основном оборудованием фирмы «Форд» и, в меньшей степени, установками нескольких германских фирм. Разнообразные машины для контактной сварки, поставленные Советскому Союзу из США, а также обученный американскими специалистами инженерно-технический персонал определили направления развития Контактной сварки в СССР [121].
Развитию и внедрению высоких технологий придавалось большое значение. С середины 1930-х гг. оборудование контактной сварки, разработанное и выпускаемое заводом «Электрик» им. А. К. Скороходова, применялось на уже работающих и строящихся заводах страны. Так, на стыковых машинах АСН —25 на строительстве Уралвагонзавода в месяц сваривалось до 500 т арматурной стали.
В 1934 г. на заводе «Электрик» были также разработаны машины АС—75 и АС—100 для стыковой сварки непрерывным оплавлением, специальные роликовые машины АШ—25 для сварки продольных швов, АШ—16 для сварки поперечных швов и фланцев, аппараты для точечной сварки AT-50—1, прессы для рельефной сварки.
Кроме производства автомобилей, с применением точечной контактной сварки для прикрепления обшивки к каркасу начали выпускать цельнометаллические пассажирские вагоны. Опыт, полученный при пуске первых автомобильных и тракторных заводов, послужил толчком к организации выпуска мощных отечественных контактных машин улучшенной конструкции и одновременно способствовал освоению ряда относительно новых технологических процессов — рельефной сварки при изготовлении тормозных колодок и колес, шовностыковой сварки труб из непрерывно сворачиваемой стальной ленты, точечной и шовной сварки стальных деталей с гальваническим покрытием и т. д.
С применением контактной сварки из коррозионно-стойкой стали были изготовлены самолеты, дирижабли, скульптурная группа В. И. Мухиной «Рабочий и колхозница». Основные работы были выполнены в лаборатории акционерного общества «Оргаметалл» (впоследствии ЦНИИТМАШ) Я. М. Глуховым, П. Н. Львовым, В. И. Коровиным, в Институте гражданского воздушного флота С. М. Поповым и др. В конце 30-х гг. в СССР было начато освоение стыковой сварки железнодорожных рельсов (ЦНИИТМАШ совместно с научно-исследовательскими организациями Наркомата путей сообщения и др.).
Контактная сварка. Типовые схемы машин для контактной точечной, шовной и стыковой сварки
Балтийский Государственный Технический Университет «ВОЕНМЕХ» им. Д.Ф.Устинова
Реферат на тему:
КОНТАКТНАЯ СВАРКА
Выполнила
Капшина Л.Б. гр.А161
Санкт-Петербург, 2009
Контактная сварка — это процесс образования соединения в результате нагрева металла проходящим через него электрическим током и пластической деформации зоны соединения под действием сжимающего усилия.
Оборудование для контактной сварки…
Родоначальник контактной сварки — английский физик Уильям Томсон
(лорд Кельвин), который в 1856 г. впервые применил стыковую сварку. В 1877 г. в
США Элиху Томсон самостоятельно разработал стыковую сварку и внедрил ее в
промышленность. В том же 1877 г. в России Н.Н.Бенардос предложил способы
контактной точечной и шовной (роликовой) сварки. На промышленную основу в
России контактная сварка была поставлена в 1936 г. после освоения серийного
выпуска контактных сварочных машин.
Преимущества контактной сварки перед другими способами:
Высокая производительность (время сварки одной точки или стыка составляет 0,02… 1,0 с)
Малый расход вспомогательных материалов (воды, воздуха)
Высокое качество и надежность сварных соединений при небольшом числе управляемых параметров режима, что снижает требования к квалификации сварщика
Это экологически чистый процесс, легко поддающийся механизации и автоматизации
Основные способы контактной сварки — это точечная, шовная (роликовая) и стыковая сварка.
Машины для контактной сварки бывают стационарными,
передвижными и подвесными (сварочные клещи). По роду тока в сварочном контуре
могут быть машины переменного или постоянного тока от импульса тока,
выпрямленного в первичной цепи сварочного трансформатора или от разряда
конденсатора. По способу сварки различают машины для точечной, рельефной,
шовной и стыковой сварки.
Любая машина для контактной сварки состоит из электрической и механической частей, пневмо- или гидросистемы и системы водяного охлаждения (рис. 1).
Рис. 1. Типовые схемы машин для контактной точечной (а), шовной (б) и стыковой (в) сварки:
1 — трансформатор; 2 — переключатель ступеней; 3 — вторичный сварочный контур; 4 — прерыватель первичной цепи; 5 — регулятор; 6 — привод сжатия; 7- привод зажатия деталей; 8 — привод осадки деталей; 9 — привод вращения роликов; 10- аппаратура подготовки; 11 — орган включения
Электрическая часть включает в себя силовой сварочный
трансформатор 1 с переключателем ступеней 2 его первичной обмотки, с помощью
которого регулируют вторичное напряжение, вторичный сварочный контур 3 для
подвода сварочного тока к деталям, прерыватель 4 первичной цепи сварочного
трансформатора 1 и регулятор 5 цикла сварки, обеспечивающий заданную
последовательность операций цикла и регулировку параметров режима сварки.
Механическая часть состоит из привода сжатия 6 точечных и шовных машин, привода 7 зажатия деталей и привода 8 осадки деталей стыковых машин. Шовные машины снабжены приводом 9 вращения роликов.
Пневмогидравлическая система состоит из аппаратуры 10 подготовки (фильтры, лубрикаторы, которые смазывают движущиеся части), регулирования (редукторы, манометры, дросселирующие клапаны) и подвода воздуха к приводу 6 (электропневматические клапаны, запорные вентили, краны, штуцера).
Система водяного охлаждения включает в себя штуцера разводящей и приемной гребенок, охлаждаемые водой полости в трансформаторе 1 и вторичном контуре 3, разводящие шланги, запорные вентили и гидравлические реле, отключающие машину, если вода отсутствует или ее мало.
Все машины снабжены органом включения 11. У точечных и
шовных машин это ножная педаль с контактами, у стыковых — это комплект кнопок.
С органов управления поступают команды на сжатие «С» электродов или
зажатие «3» деталей, на включение «Т» и отключение
«О» сварочного тока, на вращение «В» роликов, на включение
«а» регулятора цикла сварки. Эти команды отрабатываются
соответствующими блоками машины, обеспечивая выполнение операций цикла сварки.
Кроме универсальных применяются специальные машины, приспособленные для сварки конкретных конструкций и типов размеров изделий. Примером могут служить машины для контактной точечной сварки кузовов автомобилей, встроенные в автоматические линии, машины для стыковой сварки оплавлением продольных швов труб в прокатном производстве.
Электроды в контактной сварке служат для замыкания вторичного контура через свариваемые детали. Кроме этого при шовной сварке электроды-ролики перемещают свариваемые детали и удерживают их в процессе нагрева и осадки.
Сварка.
Сварка
Контактная сварка.
Контактная сварка — это процесс образования соединения в результате нагрева металла проходящим через него электрическим током и пластической деформации зоны соединения под действием сжимающего усилия.
ПРЕИМУЩЕСТВА КОНТАКТНОЙ СВАРКИ ПЕРЕД ДРУГИМИ СПОСОБАМИ:
Высокая производительность (время сварки одной точки или стыка составляет 0,02.
.. 1,0 с)
Малый расход вспомогательных материалов (воды, воздуха)
Высокое качество и надежность сварных соединений при небольшом числе управляемых параметров режима, что снижает требования к квалификации сварщика
Это экологически чистый процесс, легко поддающийся механизации и автоматизации
Основные способы контактной сварки — это точечная, шовная (роликовая) и стыковая сварка.
Аргонодуговая сварка.
Аргонодуговая сварка – дуговая сварка в среде инертного газа аргона. Может осуществляться плавящимся или неплавящимся электродом. В качестве неплавящегося электрода обычно используется вольфрамовый электрод.
Область применения и преимущества аргонодуговой сварки.
Основная область применения аргонодуговой сварки неплавящимся электродом – соединения из легированных сталей и цветных металлов. При малых толщинах аргонная сварка может выполняться без присадки. Способ сварки обеспечивает хорошее качество и формирование сварных швов, позволяет точно поддерживать глубину проплавления металла, что очень важно при сварке тонкого металла при одностороннем доступе к поверхности изделия. Он получил широкое распространение при сварке неповоротных стыков труб, для чего разработаны различные конструкции сварочных автоматов. В этом виде сварку иногда называют орбитальной. Сварка неплавящимся электродом – один из основных способов соединения титановых и алюминиевых сплавов.
Аргоновая сварка плавящимся электродом используется при сварке нержавеющих сталей и алюминия. Однако объем ее применения относительно невелик.
Шовная (роликовая) контактная сварка применение, схема, ГОСТ
Технология шовной контактной сварки была разработана в конце Девятнадцатого века. Сварка проводится без плавящегося электрода и присадочного материала. Нагрев и расплавление маленькой области заготовок происходит благодаря электрического тока в газах высокой интенсивности, иногда пропускаемого между 2-мя роликовыми электродами, к которым прикладывается существенно усилие на сжатие. Шов складывается из большого количества перекрывающихся зон проплавления. Метод предназначается для сваривания тонкого листа горячей прокатки, также и содержащего непростые пространственные формы.
Описание технологии шовной сварки
Листовые заготовки кладутся один на один и сжимаются роликовыми электродами с большой силой. На электроды иногда подаются мощные импульсы тока, сила которого может достигать тысяч ампер. Текущий ток сильно нагревает контактное пятно между электродами, доводя метал до плавления. По завершении импульса территория расплавления кристаллизуется под сильным давлением, организуя шовный материал и соединяя заготовки в одно целое. Ролики перекатываются на смежный участок заготовки, подается следующий импульс и цикл работы повторяется. Вдоль линии шва образуется цепочка пятен точечной контактной сварки овальной формы. Эти пятна могут частично перекрываться, организуя непрерывную и непроницаемую шовную линию.
В зависимости от типа передвижения деталей и способа подачи импульсов тока шовная контатная сварка продразделяется на :
- Шаговая.
Давление роликов регулярно, детали перемещаются рывками, при остановке подается рабочий импульс. Выходит прерывчатая цепочка точек, сваренных контактным способом. Используется при сваривании цветных сплавов и легких металлов. Не дает герметичности шовного материала.
- Постоянная. Усилие прижима регулярно, ток также подается регулярно. Фактически применяется нечасто из-за быстрого расходования роликов, большего расхода электрической энергии и перегревания свариваемых деталей, приводящего к их короблению.
- Прерывчатая. Усилие прижима сберегается постоянным, скорость подачи заготовок также систематическая. Импульсы подаются с подобными перерывами, чтобы обеспечить непрерывную линию шва за счёт частичного перекрытия зон точечной контактной сварки.
Схема шовной сварки (рабочий принцип)
Прерывчатая контактная шовная роликовая сварка дает возможность получить надежное и герметичное шовное соединение при нормальном расходе роликов и электрической энергии. Степень перекрытия сварных зон изменяется путем подстройки скважности (периода движения) импульсов. Такая технология шовной сварки обрела самое большое распространение. Требования к проведению операции описаны в стандарте ГОСТ 15878-79.
Машины и станки контактной сварки
Для роликовых электродов очень часто применяют бронзу. Делают их в виде заостренных дисков диаметром 35-45 см, ширина рабочего обода 4-10 мм. Для сваривания трудных заготовок используют аппараты с 2-мя и более роликовых пар.
Мощность потребления аппаратов варьируется в границах от 25 до 300 киловатт.
Маломощными считают станки в 25-40 киловатт, средняя мощность — 4-100 , машины высокой мощности потребляют от 100 до 300.
Устройство средней мощности МШ-2203 просит трехфазного электрического питания 380 вольт, рабочий ток — до 22 тысяч ампер. Усилие прижима может достигать 5 тонн
Сваривает машина контактной шовной сварки стальные листы у которых толщина до 1 мм. Есть 2 вариации – с вылетом роликов 400 и 700 мм.
Устройство машины для шовной контактной сварки
Ключевой несущей конструкцией аппарата считается станина. На ней фиксируются все другие узлы:
- источник питания;
- спайдерный крепеж неподвижного ролика;
- спайдерный крепеж подвижного ролика;
- устройство прижима;
- механизм подачи заготовки
Устройство прижима может быть ручным, пневматическим, на гидравлике или комбинированным. Ручной (точнее, ножной) привод обладает наименьшей мощностью.
Роликовые электроды сделаны в виде сужающихся к краешкам бронзовых дисков, они закреплены на концах спайдерных крепежей при помощи подшипников скольжения.
Устройство машины для шовной контактной сварки
Источник питания обеспечивает периодическую подачу тока высокой мощности на электроды. Он также питает привод устройства прижима и механизма подачи. Источник питания у современных аппаратов делается по инверторной импульсной схеме с двойным преобразованием напряжения. Это дает возможность уменьшить размеры устройства и убрать броски напряжения в электросети.
Шовные машины-клещи
Помимо неподвижных сварочных машин, изготовители производят также переносные, или подвесные устройства. Они предназначаются для сваривания тонкостенных изделий сложной формы. Источник питания все также располагается на полу цеха, а ролики и устройство прижима смонтированы на подвижных клещах. Клещи при помощи шарнирного пневматического привода ставятся в положение, нужное для работы.
Роликовый стенд для контактной сварки
Для сваривания конструкций в форме цилиндра (или системы сопряженных цилиндров), применяют роликовые стенды. Они выделяются большим вылетом спайдерных крепежей роликов, что дает возможность сваривать достаточно большие и протяженные конструкции. Стенд оборудован огромным числом регулируемых опор, разрешающих зафиксировать цилиндрические заготовки различной длины и диаметра. Роликовые электроды приводятся в движение зубчато-винтовой передачей. Заготовки вращаются на стенде, и аналогичным образом ролики проходят всю линию шва. На стендах получают ровные и герметичные швы исключительной прочности.
Роликовый стенд для контактной сварки
Область использования
Шовная технология контактной сварки дает возможность делать крепкие, долговечные и герметичные швы, надежно объединяющие тонкостенные заготовки. Она находит использование в следующих ветвях:
- Тонкостенные шовные трубы для трубопроводного транспорта и технологических установок.
- Резервуары и сосуды малого давления для химической, пищевой, транспортной промышленности.
- Герметичные кожухи механизмов и приборов, ТС.
- Конструкции из тонколистового проката для оборудования которое применяется в промышленности и техники для дома.
Производство, оборудованное машинами шовной сварки
Технология отличается от других сварных технологий самой большой работоспособностью. Установка средней мощности выдаёт за час пару сотен метров шва сварки.
Как получить герметичный шов
Герметичность шва обеспечивается разработкой цепочки частично перекрывающихся точек контактной сварки. Сварное пятно после импульса, прошедшего через роликовые электроды, имеет форму овала.
Если правильно соединять скорость подачи заготовок и периодичность движения сварных импульсов, то овалы будут перекрываться собственными боковыми частями, организуя беспрерывный и герметичный шовный материал.
Если вы нашли погрешность, пожалуйста, выдилите фрагмент текста и нажмите Ctrl+Enter.
СОПРОТИВНАЯ СВАРКА С РОЛИКАМИ — MUNDOLATS
ОБЗОР
Основные принципы электросварки точками в металлургии и критерии хорошего формирования точки сварки.
Эта работа обобщает и дополняет работу, уже опубликованную на этой веб-странице под заголовком:
.– Электросварка
Анунсиос
ОПРЕДЕЛЕНИЕ
В металлических банках, сваренных с помощью электросварки, точка сварки получается между двумя соединяемыми металлическими частями без какого-либо внешнего воздействия, достаточно прохождения через эти металлические детали сильного тока в зоне, рассматриваемой как придерживаться .
Теплота, необходимая для сварки, производится за счет сопротивления материала прохождению этого тока в месте сварки.
Непрерывная линия сварки получается с помощью последовательности точек, которые образуются между двумя соединяемыми металлическими деталями, подвергаемыми давлению двух круглых электродов, через которые циркулирует электрический ток, приводимый в движение вращательным движением в направление обратное. См. чертеж №1:
Рисунок №º: Формирование непрерывной линии сварки
ОСНОВНЫЕ ПРИНЦИПЫ
А.- Понятие электрического тока: Закон Ома
Сила тока, измеренная в амперах, в любой электрической цепи равна напряжению, измеренному в вольтах, на зажимах цепи, деленному на сопротивление в омах указанной цепи:
И = В / Р
См. рисунок № 2:
Рисунок № 2: Схема места сварки
B.- Понятие теплоты: закон Джоуля
Количество теплоты, выделяемой в проводнике при прохождении электрического тока, зависит от:
– сила тока I
– сопротивление драйвера R
– времени циркуляции тока t
все связаны выражением:
2
Вт = 0.24 Р И Т
C. — Сопротивления в сварочном оборудовании
В сварочном контуре присутствуют следующие резисторы:
– R1 = сопротивление между верхним шкивом и медным проводом
– Re = сопротивление между проводом и металлом
– Ri = внутреннее сопротивление металла (1-я зона)
– Rc = контактное сопротивление (интерфейсы)
– R’i = внутреннее сопротивление металла (2-я зона)
– R’e = сопротивление металла/медной проволоки
– R2 = сопротивление резьбы/нижнего шкива
См. рисунок № 3:
Рисунок № 3: Сопротивление в сварочном контуре
Сопротивления Re, Rc и R’e изменяются в зависимости от:
– сварочное давление между электродами (шкивами)
– состояние поверхности металлов
– форма и размеры электродов
– материал электродов
– состояние поверхности электродов.
Резисторы R1, Re, R’ и R2 являются паразитными резисторами и вызывают следующие потери энергии:
Wp = W1 + We + W’e + W2
Резисторы Ri, Rc и R’i являются эффективными сопротивлениями для формирования точки сварки и вызывают энергию:
We = Wi + Wc + W’i
Наблюдения:
a.- Энергии W1 и W2 увеличиваются в зависимости от загрязнения и деформации канавок сварочных роликов.
b.- We и W’e нагревают поверхность металла и способствуют окислению сварного шва. Количество образовавшегося окисления зависит от времени и температуры.
D.- Энергетический баланс
Потребляемая энергия: Q = We + Wp
Количество тепла, необходимое для достижения температуры сварки, зависит от:
Anuncios
– объем металла. См. рисунок № 4. Этот объем:
V = 2e x c x против . Быть против скорости сварки.
Рисунок № 4: Свариваемый объем
– удельная теплоемкость металла
– потери тепла.
Эти потери тепла составляют:
– По проводимости в электроде в зависимости от:
o Поверхность электрода
o Контакт между металлом и электродом
o Погода
– По электропроводности в свариваемом металле в зависимости от:
o Теплопроводность
o Толщина металла
– По излучению
– Путем охлаждения роликов холодной водой.
E.-Основные функции сварочного давления:
1.- Сохраняет контакт со свариваемыми материалами
2.- Предотвращает попадание воздуха в зону сварки
3.- Заставляет электрический ток проходить между соприкасающимися поверхностями
4.- Поддерживает постоянное контактное сопротивление воздуха
5.- Вызывает деформацию кристаллов металла при ковке
6. — Предотвращает образование мешков и пористости в зоне сварки
7.- Обеспечивает рекристаллизацию свариваемого металла при охлаждении
8.- Предотвращает выброс расплавленного металла во время сварки
9.- Обеспечивает сопротивление вращающемуся шкиву
Вывод:
Идеальный сварочный контур должен быть спроектирован таким образом, чтобы:
– Потери энергии – Wp – минимальны
– Минимальная степень окисления
– Эффективная энергия – We – быть максимальной
– Полученная структура однородна
МЕТАЛЛИЧЕСКИЕ ХАРАКТЕРИСТИКИ
Материалы, используемые в электросварных банках, изготовлены из низкоуглеродистой стали.Его содержание в C < до 0,5% и < до 1% в других элементах.
Влияние различных элементов, входящих в состав железа при формировании стали, вызывает различные эффекты, такие как:
Углерод : Твердость стальной поверхности увеличивается с увеличением содержания углерода. Он не оказывает существенного влияния на сварку при C < 0,2 %.
Марганец : Повышает твердость и сопротивление разрушению. Если Mn > 0,6%, при высоком содержании углерода припой становится хрупким.Если Mn <0,3%, возникает пористость и сварной шов становится хрупким. Следовательно, Mn должен находиться в % между двумя предельными значениями.
Сера : Ее присутствие должно быть 0,035%, если это возможно, и никогда не должно превышать 0,05%, так как это может вызвать ослабление структуры сварного шва, особенно если углерод имеет тенденцию к увеличению.
Кремний : от 0,01% до 0,10% улучшает свариваемость.
Фосфор : Это примесь, которая должна присутствовать в минимально возможном количестве.Он не должен превышать 0,04%. Сварка становится хрупкой, вызывает трещины, снижает ударопрочность и усталостную прочность.
Влияние поверхностных покрытий:
Олово: Поверхностное олово белой жести снижает сопротивление на границе раздела, поэтому необходимо увеличивать сварочный ток в зависимости от содержания поверхностного олова, то есть его покрытия. Другой аспект заключается в том, что чем выше содержание олова, тем больше загрязнение поверхности электродов.
Анунсиос
Хром: Обработки на основе хрома и оксида хрома препятствуют прохождению тока и не подходят для электросварки.
ФОРМИРОВАНИЕ ТОЧКИ СВАРКИ
A.- Изменение контактных сопротивлений (Re, Rc и R’e)
1º.- Функция давления:
— Увеличение сварочного давления вызывает:
o Снижение паразитарной резистентности Re и R’e
o Снижение сопротивления интерфейса Rc
См. рисунок № 5:
Рисунок № 5: Изменение сопротивления в зависимости от сварочного давления
– Это уменьшение является функцией:
o Характер поверхности
o Твердость материалов
o Его проводимость
2º.- Функция температуры:
– Под действием температуры T происходит размягчение неровностей поверхности, уменьшение Rc (контактное сопротивление) и увеличение Ri (внутреннее сопротивление металла)
См. рисунок № 6:
Рисунок № 6: Изменение сопротивлений в зависимости от температуры
3º.- Эволюция в процессе сварки:
– 1) В начале сварки наибольшее потребление энергии приходится на сопротивление Rc .
– 2) Rc уменьшается до 0, до точки плавления
– 3) Ri повышается до точки плавления
– 4) После Ri уменьшается при увеличении объема точки
На графике 7 показано изменение общего количества R под действием Rc и Ri во время сварки точки.
Рисунок № 7: Изменение сопротивления в зависимости от времени сварки
Rc действует как катализатор в начале процесса сварки и позволяет увеличить Ri .
Re и R’e (сопротивление между металлом/медной проволокой) являются источником потерь энергии, величина которых незначительна, но не меняется в процессе сварки при условии, что электрод является хорошим проводником и достаточно охлажден.
B.- Сила сварочного тока – время сварки:
Чтобы явления, описанные в пункте А, хорошо переразвивались, необходимо:
– Высокая интенсивность I
– Время сварки А Ц , кратко.
2
Напомним, что согласно закону Джоуля (W = 0,24 RI t) потребляемая энергия W является функцией силы тока I от тока и времени сварки t, при равном сопротивлении R. Следовательно, такое же значение W может быть достигнуто при :
– I слабый x длинный
– I сильный x короткий t
Если мы выберем вариант слабого I, произойдет:
— Температура металлической сборки повышается, но плавления не происходит.
– Потери увеличиваются
— Электроды портятся
Во всех случаях тепловой баланс будет намного выше, т.к.:
— У меня было, на подъеме
– T слабый, уменьшающийся
Допускается, что время сварки обратно пропорционально квадрату силы тока.
Диаграмма энергии сварки ( Вт ) в зависимости от интенсивности ( I ) и времени ( t ) отражена на следующем графике №.8:
Анунсиос
Рисунок № 8: Энергетическая диаграмма сварки
В котором мы можем определить различные зоны как:
– Зона A = Зона склейки металла
– Зона B = Зона сварки металла
– Зона C = Зона внешних выступов на острие металла
Практический способ настройки сварочного аппарата для данного металла и давления сварки:
— Схема сварки должна быть построена, ищем:
o Лимит связи
o Ограничение проекции
Все это для конкретного отвода трансформатора.Та же операция затем выполняется для следующего более высокого и более низкого дубля.
Получаются три зоны сварки, из которых выберем самую большую, регулируя машину на 50% от нее.
C.- Влияние размеров точки сварки
Факторы, влияющие на размеры точки сварки:
– Толщина металла
– Величина нахлеста кромок, которую мы обозначаем C
– Длина точки сварки L , которая является функцией скорости сварки по сравнению с
Наиболее благоприятные условия даются при L / C = 1 . В такой точке тепло сварки правильно распределяется и получается равномерная цепочка горячих точек.
Если L / C = 2 , то условия не столь благоприятны, так как в этой точке теплота сварного шва плохо распределяется, и может быть получена альтернативная последовательность горячих и прилипших (холодных) точек. См. рисунок № 9
Рисунок № 9: Схемы точек сварки
МЕТАЛЛУРГИЯ СТЕКЛА СВАРОЧНОГО
1º.- Отопительный период:
— Прохождение тока вызывает локальный нагрев, который достигает сплавления материала, соответствующего двум кускам
– При нагреве чечевица материала расширяется, понимая под чечевицей зону расплавленного материала, имеющую такую форму.
— Для нейтрализации выталкивающей силы расплавленного металла требуется высокое усилие сжатия.
— Если усилие сжатия слишком слабое, металл выходит в виде выступов.
– Это приводит к значительным внутренним дефектам (полости, поры…) в сварке.
2º.- Тепловое состояние точки при отключении сварочного тока:
– Зона A = расплавленный металл
– Зона B = пастообразный металл
– Зона C = критическая температура
– Зона D = температура ниже критической
– Зона E = температура окружающей среды
См. чертеж № 10:
Рисунок № 10: Тепловое состояние точки сварки
– Градиент температуры составляет от 1500ºC до температуры окружающей среды с точностью до нескольких миллиметров.
– Отключение сварочного тока означает начало охлаждения.
3º.- Фаза охлаждения:
— Ядро расплавленного металла находится в большой остывающей массе, состоящей из:
o Детали сварные
o Электроды охлаждаемые
– Теплообмен быстрый
– Кристаллизация осуществляется сходящимся к центру точки:
Anuncios
o Зона D = без изменений структуры
o Зона C = Зерно измельчено
o Зона B = тонкая структура
o Зона A = тонкая структура
В случае неправильного охлаждения под сварочным давлением возможно образование пузырей. Тепловое сжатие также может вызывать внутренние напряжения в определенных точках.
ОСМОТР СВАРОЧНОГО КОНТУРА
1º.- Проблемы, связанные со сваркой
– Геометрия внутренней сварки.
Внутренняя сварка всегда неровная, с волнами, расплавленным металлом, острыми кромками, которые мешают хорошей защите лаковым покрытием.
– Однородность металла сварного шва
o Увеличение скорости сварки или
o Уменьшение величины нахлеста шва при равной скорости
приводит к возникновению дефектов сварки, которые материализуются разрывами внутренней сварки
2º.- Описание сварочной цепи
Рассмотрим обычный сварочный контур, который в основном состоит из:
— Шкив верхний (большого диаметра)
— Шкив нижний (малого диаметра)
— Сварочный трансформатор
Эта схема характеризуется тем, что два шкива имеют разный диаметр, поэтому контактные поверхности различны, что означает:
1º. — R2
Это означает, что сварной шов внутри горячее, чем снаружи.
2º.- Кроме того, уже сформированные точки поддерживают некоторую более высокую температуру в уже выполненной части соединения внахлест, которая в задней части еще не осознает, что будет холоднее.
3º.- Поскольку проволока остается в контакте с внешним электродом в течение более длительного времени, внешняя сварка охлаждается быстрее.
Таким образом, можно сказать, что распределение температуры является асимметричным, уменьшаясь от:
– Внутри наружу
— Передняя часть к задней
Проверка показывает, что точка на внутренней стороне сварного шва характеризуется следующими тремя элементами:
– а) След точки
– б) Кромка края листа
– в) Гирлянда из расплавленного металла, выталкиваемая из сварного шва.
Фигурка Вера № 11.
Рисунок № 11: Элементы внутренней поверхности сварки
3º. — Последствия:
Поперечное сечение сварного шва показывает, что точка сварки образует гребень вперед (самая горячая часть), поскольку:
1º.- Недостаточное распределение температуры приводит к тому, что металл остается в пастообразном состоянии между двумя последовательными точками сварного шва, этот металл нагружается шкивом в момент, когда следующий импульс отпечатывается на сварном шве.
2 .- Этот продавливаемый металл не подвергается давлению при ковке и не охлаждается шкивом, поэтому существует риск неоднородности сварного шва.
3º.- Если условия сварки таковы, что отношение L/C неблагоприятно:
– Липкие точки создаются между самыми горячими точками.
— Увеличить дефицитное распределение энергии.
Следовательно, металл в пастообразном состоянии нагружается шкивом, создавая застрявшую, но не сваренную точку.
Анунсиос
4º.- Расширение металла, вызванное нагревом, не может происходить по вертикали, находясь горизонтально в области образования гребня. Поэтому после охлаждения в области сварного шва создается усадка и зона растяжения, представляющая опасность хрупкости.
См. рис. 12:
Рисунок № 12: Напряжения при сварке после охлаждения
Роликовая сварочная машина Superb В привлекательных предложениях Местное послепродажное обслуживание
Повысьте производительность и эффективность своего сварочного бизнеса с помощью потрясающей роликовой сварочной машины , доступной по заманчивым предложениям на Алибаба.ком. Роликовый сварочный аппарат модели оснащен новаторскими инновациями, которые делают сварку простой и приятной. Они включают в себя передовые материалы и конструкции, которые обеспечивают высокую производительность на протяжении всего их непревзойденного длительного срока службы. Роликовый сварочный аппарат потребляет мало электроэнергии, сохраняя при этом заданную мощность, независимо от того, используется ли он в личных целях или в служебных целях.
Передовые изобретения, лежащие в основе конструкции и стилей этих роликовых сварочных аппаратов , делают их очень универсальными и применимыми в самых разных сварочных задачах.Роликовый сварочный аппарат не подвергается неблагоприятному воздействию экстремальных температур или холода, что делает его пригодным и применимым в широком диапазоне погодных условий. Они поставляются с широким выбором, который учитывает многочисленные факторы и предпочтения пользователей, поэтому покупатели могут быть уверены, что найдут наиболее подходящий сварочный аппарат для роликовой сварки для своих нужд.
Доступность этих роликовых сварочных аппаратов на Alibaba.com сбивает с толку, учитывая их неограниченную мощность и поразительную производительность.Затраты на эксплуатацию и техническое обслуживание роликовой сварочной машины также невероятно низки благодаря доступности запасных частей и простоте их ремонта. Они также просты в установке и использовании, гарантируя, что вы не потеряете свою производительность из-за технических проблем. Тем не менее, вы можете связаться с различными поставщиками и продавцами роликовой сварочной машины на сайте, если вам потребуются дополнительные рекомендации.
Поднимите свой сварочный бизнес на новый уровень с привлекательным роликовым сварочным аппаратом от Alibaba.ком. Вы также можете купить их для личного использования в вашем доме. Независимо от характера ваших целей, вы найдете наиболее подходящий роликовый сварочный аппарат для их достижения. Воспользуйтесь скидками сегодня и убедитесь, что вы можете платить доступные цены за качественную продукцию.
Роликовые направляющие NSK упрощают сварку башен ветряных турбин
Сотрудничество между NSK и испанской компанией Talleres Ganamagoga привело к значительному прогрессу в области сварки башен ветряных турбин. Инновационные решения линейного перемещения, основанные на новейшей технологии роликовых направляющих NSK, позволяют Talleres Ganamagoga обеспечивать плавное и точное движение сварочных аппаратов по мере увеличения длины мачт в процессе производства.
Группа Ganagoga, история которой восходит к 1974 году, имеет штаб-квартиру в Понтеведре, в регионе Галисия на северо-западе Испании. Первоначально созданная для обслуживания таких секторов, как морской, автомобильный и строительный, в последние годы на первый план вышел ряд новых отраслей, включая возобновляемые источники энергии и, в частности, энергию ветра.
Talleres Ganamagoga специализируется на производстве ответственных узлов для ветряных турбин, в том числе башен. Из-за своего размера башни состоят из нескольких отдельных сегментов конуса, которые компания впоследствии сваривает вместе. Предпосылками этого процесса являются точность и повторяемость, поэтому компания Talleres Ganamagoga полагается на технологию линейных роликовых направляющих от NSK.
Компания использует большие сварочные аппараты, основанные на концепции колонны и стрелы. Эти «круглые сварочные колонны» сваривают внутренние и внешние соединения длинных стальных обручей, образующих конусы башен ветряных турбин.Что касается производительности, машины могут обрабатывать конусы длиной до 7 м и диаметром до 5 м.
Чтобы ускорить процесс сварки, компании Talleres Ganamagoga потребовался способ перемещения машины по длине башни, поскольку она увеличивалась в размерах во время производства. Благодаря сотрудничеству с командой опытных инженеров NSK это видение вскоре стало реальностью.
Сегодня компания соединяет конусы вместе, перемещая круглую сварочную колонну по специально разработанной системе линейных направляющих и направляющих из точной и надежной серии RA от NSK.Сочетание линейных направляющих сверхвысокой нагрузки NSK и рельсов NSK (длиной 9,225 м и 7,8 м) помогает компании Talleres Ganamagoga добиться точного перемещения своих специальных сварочных аппаратов в соответствии с производственными требованиями.
Серия NSK RA использует объединенный опыт компании в технологиях роликовых подшипников и линейных направляющих. Оптимальный размер тела качения, а также особая форма роликовых направляющих и направляющих обеспечивают сверхвысокую грузоподъемность и не менее впечатляющую жесткость.
Долгий срок службы и бесперебойная работа являются обязательными требованиями при применении в компании Talleres Ganamagoga, которая стремится к отсутствию дефектов во время сварочных процессов. Здесь использование смазочных узлов NSK K1 означает длительную работу без технического обслуживания, а высокоэффективные уплотнения (входят в стандартную комплектацию) блокируют попадание посторонних предметов, что является очень важным фактором при таких операциях, как сварка, где потенциальные риски загрязнения высоки. высокий.
Роликовые направляющие серии RA также обеспечивают сверхвысокую точность и плавность хода — факторы, которые раз за разом обеспечивают воспроизводимое и стабильное позиционирование.
Рисунок 1): Круглые сварочные колонны опираются на роликовые направляющие серии NSK RA для производства башен ветряных турбин в Тальерес Ганомагога. Фото: Ганомагога
токарных роликов | Сварочное позиционирующее оборудование
Токарные валки по своей сути являются простыми позиционерами с множеством производительных опций. Они могут быть как с питанием, так и без него. Или мы можем установить ролики на поворотную раму, чтобы сделать наклонно-поворотные ролики.Мы укладываем рулоны на железнодорожные вагоны для перевозки судов через цех изготовления в дробеструйные или рентгеновские камеры. Мы также изобрели вал Trac-Tred®, который сочетает в себе поворотные валки с люлькой с гусеничным ходом, образуя бесконечный строп для обработки тонкостенных или слабостенных изделий.
Базовая установка поворотного ролика включает в себя привод с двумя приводными колесами и сопутствующий натяжной ролик, который вращается свободно. Привод поддерживает один конец заготовки и сообщает заготовке вращательное движение. Натяжной ролик просто поддерживает другой конец заготовки при ее вращении.
Компания Koike Aronson / Ransome предлагает самый широкий в мире выбор и диапазон мощности токарных роликов, которые всегда подходят для ваших задач. Доступно механическое вращение с переменной скоростью с постоянными или переменными настройками осевой линии колеса.
Предпочтительное использование различных материалов для токарных роликов:
Также доступны резиновые, стальные, уретановые и микартовые (фенольные) колеса. Традиционные, унифицированные, саморегулирующиеся (SA), Trac-Tred®, турбинные и наклонные валки — это лишь некоторые из моделей, которые мы предлагаем.
Резина — обычный материал, используемый в рулонах общего назначения. Обеспечивает поверхность для диаметров, которые могут быть обработаны, или поверхности сосудов, которые не должны быть маркированы. Для более высоких нагрузок требуется большая ширина колеса, чтобы выдержать вес.
Уретан — обычно используется для тех же целей, что и резина. Более твердый материал, который при определенных обстоятельствах может обеспечить большее тяговое усилие, когда это необходимо. Не требует такого увеличения ширины колеса при повышенной нагрузке, как резина.
Сталь — обеспечивает максимальное тяговое усилие. Используется, когда нагрузка должна быть сосредоточена на меньшей площади основания. Минимальный прогиб под нагрузкой.
Микарта — используется в особых случаях, когда нагрузка сильно сконцентрирована (например, в шейках роторов и якорей) и будет перемещаться по обработанным поверхностям. В отличие от стали, которая может повредить обработанные поверхности, Micarta этого не сделает. Кроме того, в отличие от стали, стружка, попадающая на поверхность колеса, в конечном итоге остается на поверхности микарты.Минимальная ширина колеса сильно зависит от поверхности слежения (на заготовке) и веса заготовки. Материал Micarta, используемый в колесах, при необходимости можно довольно легко заменить.
Передвижные тележки с ручным или механическим приводом могут быть включены для быстрой регулировки судов различной длины.
Специальные токарные ролики всегда доступны.
Характеристики токарных роликов- Для вращающихся труб или сосудов
- Грузоподъемность варьируется от 3000 фунтов до 2.4 миллиона фунтов стерлингов
- Колеса из резины, стали или специального композита
- Точные межосевые расстояния
- Конструкция шасси для тяжелых условий эксплуатации
- Диски перегрузки защищают резиновые шины на агрегатах весом 5000 фунтов и выше
Шовные сварочные машины WEBB одинарного или двойного действия производят продольные швы и предлагаются в различных размерах и мощностях. Наша линия сварочного оборудования поможет вам в позиционировании, сборке и автоматическом производстве. | СТАЦИОНАРНАЯ ОСНОВА и ПЕРЕНОСНЫЕ ПОВОРОТНЫЕ РОЛИКИ Поворотные валки Webb для средних нагрузок сконструированы таким образом, что любой из силовых агрегатов трех различных размеров можно легко заменить любым из наших натяжных роликов. Супермодели Аппараты для шовной сварки Webb ОДНОГО ДЕЙСТВИЯ или ДВОЙНОГО ДЕЙСТВИЯ производят продольные швы и предлагаются в различных размерах и мощностях. СМЕШИВАЮЩИЕ МАШИНЫ производят коническое соединение со смещением для облегчения сопряжения крышек резервуаров и корпусов. |
Роликовая шовная сварка
Роликовая шовная сварка (нахлестный шов) – принципиальная схема Сварочный аппарат для роликовой шовной сварки (схема) Роликовая шовная сварка сопротивлением (краткая форма: шовная сварка RR, порядковый номер 22 в соответствии с EN ISO 4063 [1] ) представляет собой шовную сварку сопротивлением, которая является одним из методов контактной сварки давлением, и от получена контактная точечная сварка. [2] Сила и ток, необходимые для сварки, передаются через пары роликовых электродов, или ролик и оправку, или ролик и плоский электрод. Электроды, выполненные в виде роликов, прижимают металлические листы друг к другу и направляют сварочный ток концентрированным образом на заготовки. Для этого используются соответствующим образом оборудованные стационарные сварочные аппараты.
Области применения процесса
Различные варианты роликовой шовной сварки используются в промышленности по обработке листового металла, при изготовлении небольших контейнеров, при изготовлении кузовов и вагонов, а также при производстве труб или упаковочного материала.При производстве листового металла рулоны бесконечно соединены в линиях прокатки и нанесения покрытия. В упаковочной промышленности бочки и жестяная упаковка для продуктов питания, напитков, химических продуктов и аэрозольных баллончиков соединяются с помощью роликовой шовной зажимной сварки. В автомобильной промышленности заготовки (специальные заготовки) или стаканы глушителя присоединяются к процессу. В производстве бытовой техники этот процесс используется для сварки корпусов нагревателей, баков и барабанов стиральных, сушильных и посудомоечных машин. Возможное применение варианта сварки фольгой встык — соединение металлических листов для изготовления фасонных деталей из листового металла большой площади, например, крыш и боковых стенок рельсовых транспортных средств и автобусов. Этот вариант роликовой шовной сварки также используется в производстве небольших контейнеров, контейнеров для пожаротушения и барабанов из оцинкованной листовой стали. [2]
Принцип и схема соединения
Как и при контактной точечной сварке, область контакта под электродами нагревается током Джоуля. В большинстве случаев электроды представляют собой пару роликов, которые, как и точечные электроды, касаются заготовки только на небольшой площади, так что ток течет от ролика к ролику через ограниченное поперечное сечение заготовки и создает точечный сварной шов. .Ролики вращаются, перемещают заготовку дальше за счет контактного давления и их не нужно поднимать, чтобы добраться до места новой точки сварки. Преимущество роликовой шовной сварки по сравнению со шовной сваркой точечными электродами заключается в гораздо меньшем износе электрода и более высокой скорости сварки. Также могут быть выполнены герметичные швы.
Параметры сварки
Количество тепла, необходимое для получения сварного шва, определяется законом Джоуля:
- Ws=∫t=0tsi2(t)r(t)dt{\displaystyle W_{\text{s}}=\int \ пределы _ {t = 0} ^ {t _ {\ text {s}}} i ^ {2} (t) r (t) {\ text {d}} t}
С
- Ws {\ displaystyle W_{\text{s}}} .
.. энергия сварки в единицах времени ts{\displaystyle t_{\text{s}}},
- i(t){\displaystyle i(t)} …сварочный ток как функция времени,
- r (t) {\ displaystyle r (t)} … сопротивление в точке сварки как функция времени,
- dt{\displaystyle {\text{d}}t} … дифференциал времени.
Сопротивление r(t){\displaystyle r(t)}зависит от действующей силы ролика, формы профиля ролика, свойств поверхности заготовок и свойства материала.Время сварки определяется длительностью импульса включенного тока и временем действия тепловой энергии на единицу объема материала через скорость ролика. В результате получаются следующие регулируемые параметры сварки:
- сварочный ток и тип тока,
- длительность импульса,
- скорость ролика (скорость сварки),
- профиль ролика;
- Сила электрода.
Сварочный ток может включаться постоянно как непрерывный ток или периодически в соответствии с программой текущего контакта.
Если переменный ток включен постоянно по всей длине шва, то такой ток называется непрерывным переменным током. Каждая полуволна создает точечный сварной шов. Расстояние между точками зависит от скорости сварки и частоты сварочного тока. При частоте сети 50 Гц и скорости сварки 6 м/мин создается одна точка сварки на миллиметр и, таким образом, герметичный шов.
При использовании программы текущего цикла подача сварочного тока периодически прерывается на регулируемые паузы тока t p по истечении выбираемого времени тока t с .Таким образом можно сваривать уплотняющие швы или прерывистые швы. Расстояние между точками определяется текущим временем перерыва и скоростью сварки.
Вращение роликов можно прервать. Говорят о сварке ступенчатым швом. Для сварки материалов, которые только частично пригодны для сварки, таких как цветные металлы с высокими требованиями к качеству шва, в дополнение к программе текущего цикла можно использовать программы тока и мощности. Так з. Б.за более сильным сварочным током следует более слабый ток повторного нагрева, во время которого усилие прижима увеличивается для улучшения качества сварки.
Варианты процесса
Типы соединений и формирование швов при роликовой шовной сварке по [2]Листы можно соединять внахлест или встык роликовой шовной сваркой.
Нахлестной шов чаще всего используется по причинам усилия. Остаточное утолщение поперечного сечения в зоне шва, отклонение силового потока при передаче усилия от одной части заготовки к другой и остающийся зазор в плоскости контакта двух листов оказывают неблагоприятное воздействие.Последний имеет эффект надреза и щелевую коррозию.
Второй вариант — сварка внахлестку. Соединяемые листы располагаются с небольшим нахлестом. Под действием тока и усилия электрода создается герметичное соединение между торцами листового металла с меньшей толщиной шва. Свариваемые кромки листового металла могут быть скошены, чтобы обеспечить как можно более ровные переходы швов. Промежуточный проволочный электрод может использоваться для соединения стальных листов с металлическими покрытиями в диапазоне толщин листа до 0.5 мм.
Другим вариантом роликовой шовной сварки является сварка швов фольгой. Полоска фольги того же типа автоматически подается между роликовыми электродами и верхней и нижней частью заготовки через направляющие устройства. Задача ленты из фольги — сконцентрировать ток и уменьшить теплоотвод охлаждаемыми электродами ролика.
Учетные данные
- ↑ DIN EN ISO 4063: 2011-03 Сварка и связанные с ними процессы — Список процессов и серийных номеров
- ↑ B C D DVS Сопротивление роликовых швов — Процесс и основы , Информационный бюллетень DVS 2906-1, 2006 г.
Патент США на процесс и устройство для взаимного направления заготовок и инструментов, которые перемещаются друг относительно друга, в частности, машины для сварки роликовым швом Патент (Патент № 4,785,153, выдан 15 ноября , 1988)
ОБЛАСТЬ И ПРЕДПОСЫЛКИ ИЗОБРЕТЕНИЯ Изобретение в целом относится к сварке и, в частности, к новому и полезному способу и устройству для взаимного направления заготовок и инструментов, которые перемещаются друг относительно друга, в частности, для осуществления сварки швом качающимся швом.
№ 29 28 620 раскрыты способ и устройство для направления заготовки на машине для сварки швом с качающимся швом, при этом заготовка направляется и перемещается относительно машины для сварки с валковым швом по заданной траектории с помощью совместное расположение и щелевое звено. Перемещение с помощью этого устройства полностью осуществляется с помощью двух приводных контактных роликов, фрикционно соединенных с заготовкой, которые тянут заготовку вместе с соединительным устройством. Он придерживается траектории подвижного шва благодаря контролю оптическим датчиком на звене, которое перемещается вместе с расположением шва.Для исправления отклонений от траектории на шарнирном устройстве предусмотрен специальный поворотный привод, который вращает поворотный удерживающий желоб, в котором находится заготовка, против направления отклонения.
Устройство предшествующего уровня техники имеет недостаток, заключающийся в том, что оно плохо подходит для компонентов больших размеров и большого веса. Кроме того, требуется дорогостоящее вспомогательное устройство для контроля и исправления отклонений от траектории, устройство, которое необходимо менять, кроме того, при смене типа или заготовки.
Настоящее изобретение предлагает устройство и способ для направления даже громоздких и тяжелых заготовок и упрощает переустановку.
Способ и устройство изобретения допускают множество вариантов. Во-первых, не имеет значения, направляется и перемещается ли заготовка относительно инструмента или инструмент относительно заготовки. Кроме того, это относительное движение может быть достигнуто в дополнение к абсолютному движению обеих частей.
Любые отклонения от заданной траектории прокатного шва могут быть обнаружены с помощью разности скоростей, которую можно легко определить прямо или косвенно. Процесс включает мониторинг в качестве первичных данных относительного отношения двух скоростей друг к другу, а не возможного отклонения от абсолютной нормы. Контроль абсолютного значения может, конечно, применяться во вторую очередь. Коррекция любых отклонений от траектории осуществляется просто без вспомогательных поворотных приводов путем уравнивания двух скоростей с кратковременной компенсацией возникшего дифференциала.В этом процессе в принципе неважно, из какого диска исходит различие. Для корректировки можно отрегулировать либо привод контактных роликов, либо привод направляющих.
Согласно изобретению способ и соответствующие устройства подходят не только для прокатных шовных сварочных машин, но также и для других инструментов или станков, в которых приводной инструмент осуществляет транспортировку заготовки.
Синхронизацию скоростей конвейера можно контролировать другим способом.Во-первых, можно считывать скорость направляющей и скорость роликового конвейера непосредственно с помощью датчиков скорости и сравнивать их. Особенно простой и точный метод контроля, который, кроме того, не зависит от размера и формы подвижной части, может быть достигнут с использованием датчика перемещения. Он определяет отклонение траектории как движение или крутящий момент одной из двух частей вокруг ее крепления. Это предпочтительно делается на подвижной части, но может применяться и к части, находящейся в покое относительно нее.
Способ согласно изобретению и соответствующее устройство позволяют отслеживать сварные швы прокатки, которые являются настолько сложными и трехмерными, насколько это необходимо. Это также верно для фланцев или прокатных сварных швов, скрученных в направлении удлинения фланца. Преимуществом также является то, что он может быстро исправить все отклонения пути, независимо от того, вызваны ли они неправильным захватом, разницей скоростей или другими факторами.
Решение согласно изобретению также обеспечивает надежное отслеживание шва на кривых, не позволяя проскальзыванию между контактными роликами и заготовкой влиять на ход шва.Это также улучшает качество сварного шва, поскольку внешние воздействия, такие как частичная замена материала, повышение температуры и т. п., компенсируются.
Для управления движущейся частью, предпочтительно заготовкой, рекомендуется использовать манипулятор с непрерывным управлением траекторией, предпочтительно многоосный промышленный робот.
Таким образом, управление траекторией осуществляется просто с помощью программы, которую можно легко изменить при смене заготовки.Промышленный робот непрерывного действия также может направлять заготовку вперед и назад.
Рекомендуется расположить датчик перемещения на монтажном кронштейне манипулятора и подать измерительные сигналы на органы управления манипулятора для регулировки скорости направляющих. Это особенно удобно при сварке деталей с криволинейными траекториями прокатки. В этой ситуации особенно рекомендуется, чтобы монтажный кронштейн и датчик смещения были расположены по отношению к заготовке таким образом, чтобы они находились примерно на одинаковом расстоянии от всех радиальных центров траектории бордюрного прокатного шва.Таким образом, можно избежать различных и слишком высоких скоростей направляющих на монтажном кронштейне.
Для работы с деталями, форма которых не позволяет такое расположение, рекомендуется, чтобы монтажный кронштейн и датчик смещения были регулируемо соединены по одной или нескольким дополнительным осям с заготовкой или ее зажимным устройством. Однако датчик перемещения также может быть прочно соединен с зажимным устройством и перемещаться вместе с зажимным устройством при регулировке относительно монтажного кронштейна.Благодаря возможности регулировки можно изменять расстояния до радиальных центров, предпочтительно сокращать, и ограничивать скорости направляющих, передаваемых через монтажный кронштейн манипулятора.
Различия между скоростью конвейера контактных роликов и направляющей скоростью заготовки в точке зажима между контактными роликами или вызванное другими факторами отклонение контактных роликов от траектории прокатного шва приводят к неправильному захвату или повороту заготовки вокруг монтажного кронштейна манипулятора.
Вследствие этого датчик перемещения имеет другую конструкцию. В предпочтительном варианте осуществления предусмотрен датчик крутящего момента, который имеет высокую чувствительность и может измерять возникающий крутящий момент с точки зрения величины и направления. Его чувствительность может быть дополнительно увеличена за счет увеличения базы измерения с помощью удлинителей. В показанном простом варианте осуществления путь прокатного шва проходит в одной плоскости, так что необходимо определять только крутящий момент вокруг нормальной оси плоскости. Для сложных траекторий раскатывания шва, соответственно более дорогих, необходимы многомерные датчики крутящего момента, способные измерять силу и крутящий момент по шести осям.
Соответственно, целью изобретения является создание устройства для регулирования движения заготовки для осуществления ее сварки, которое содержит подвижный инструмент, взаимодействующий с заготовкой для перемещения заготовки и осуществления сварки вдоль непрерывной сварки. шов и который включает в себя манипулятор, который взаимодействует с заготовкой для использования движения в направлении, аналогичном тому, которое передается подвижным инструментом, и который включает в себя датчик, подключенный между манипулятором и подвижным инструментом для обнаружения любого изменения движения между ними и который воздействует на один из подвижных инструментов или манипулятор для соответствующей регулировки скорости.
Еще одной целью изобретения является создание процесса регулирования движения заготовки для выполнения ее сварки и использования манипулятора для перемещения заготовки и использования инструмента, который зацепляет заготовку для ее сварки и перемещения, который включает определение относительное перемещение привода заготовки инструментом и привода заготовки манипулятором и воздействующее по меньшей мере на один из приводов для регулировки скорости в зависимости от измерения.
Еще одной целью изобретения является создание устройства для манипулирования инструментом с целью его сварки, которое является простым по конструкции, прочным по конструкции и экономичным в производстве.
Различные признаки новизны, которые характеризуют изобретение, подробно указаны в пунктах формулы изобретения, прилагаемых к настоящему раскрытию и являющихся его частью. Для лучшего понимания изобретения, его эксплуатационных преимуществ и конкретных целей, достигаемых при его использовании, делается ссылка на прилагаемые чертежи и описательные материалы, на которых проиллюстрированы предпочтительные варианты осуществления изобретения.
На чертежах:
РИС.1 — вид сбоку машины для сварки раскатным швом и заготовки, направляемой с помощью манипулятора;
РИС. 2 представляет собой вид снизу заготовки с зажимными средствами, если смотреть в направлении, указанном стрелкой II на фиг. 1;
ФИГ. 3 и 4 представляют собой увеличенные частичные виды сбоку, показывающие датчик смещения, показанный на фиг. 1 и возможный вариант датчика крутящего момента;
РИС. 5 — принципиальная электрическая схема цепи управления для наведения;
РИС.6 представляет собой вид, аналогичный фиг. 3, но включая монтажный кронштейн с дополнительным регулировочным устройством; и
РИС. 7 — вид заготовки, как на фиг. 2, но с регулировочным устройством по фиг. 6.
ОПИСАНИЕ ПРЕДПОЧТИТЕЛЬНЫХ ВАРИАНТОВ ВОПЛОЩЕНИЯ Со ссылкой на чертежи, в частности, воплощенное в них изобретение содержит устройство для устройства для регулирования движения заготовки 2 для осуществления ее сварки вокруг сплошного шва 11 для соединения сопрягаемых фланцев деталей заготовки, имеющих сплошной опоясывающий фланец 10. Подвижный инструмент содержит пару вращающихся роликов 3. Ролики 3 расположены друг напротив друга и входят в зацепление с заготовкой с других сторон и осуществляют сварку частей заготовки, а также непрерывное движение вдоль сварочного шва. В дополнение к движению, сообщаемому действием подвижного инструмента 3, имеется манипулятор 4, который задействует заготовку, придавая ей движение в направлении, аналогичном сообщению движения заготовке двумя рабочими роликовыми элементами 3 инструмента. .В соответствии с изобретением между инструментом 3 и манипулятором 4, воздействующим на заготовку 2, подсоединены датчики 6, чтобы воспринимать любые изменения движения, передаваемые либо инструментом 3, либо манипулятором 4.
Сенсорные средства 6 соединены в цепь, как показано на фиг. 5 через элемент управления 9 и соединительную цепь для воздействия на манипулятор 4 и/или привод инструмента, чтобы отрегулировать движение, сообщаемое заготовке, чтобы обеспечить соответствующие входы движения для заготовки 2.
РИС. На фиг.1 показана стационарная машина 1 для сварки валковым швом с двумя контактными роликами 3, устанавливаемыми друг напротив друга. Ролики 3 приводятся в движение двигателем по отдельности или совместно (не показаны). Заготовка 2 в показанном примере представляет собой бак или нечто подобное, две половины которого ранее были прихвачены к окружному фланцу 10 и теперь должны быть сварены в машине 1 для сварки подвижным швом, см. фиг. 2. Заготовка 2 крепится к зажимному устройству 13, которое через датчик перемещения 6 связано с монтажной скобой 5 манипулятора 4, в данном случае многоосного промышленного робота.Промышленный робот 4 управляется по непрерывному пути, представленному программой в блоке управления 9. Таким образом, можно обойтись без звена связи, концевых упоров и т.п.
Во время процесса сварки окружной фланец 10 удерживается от трения между двумя контактными роликами 3, которые, таким образом, продвигают заготовку 2 в направлении стрелки 30, см. ФИГ. 2. Затем процесс сварки валковым швом протекает концентрически вдоль траектории валкового шва, проходящей по всей длине фланца 10.Заготовка 2 в этом процессе направляется и приводится в движение промышленным роботом 4. Направление движения и скорость направляющей определяются блоком управления траекторией, который как ход траектории раскатного шва 11 запрограммирован в нем. Таким образом, промышленный робот 4 направляет заготовку 2 по прямой линии через контактные ролики 3 на длинных сторонах фланца 10 и поворачивает ее на углах или криволинейных участках фланца, так что оба направления перемещения всегда совпадают. Управление непрерывной траекторией так согласовано с машиной 1 для сварки швов, что скорость конвейера, с которой фланец 10 перемещается через контактные ролики 3, точно равна скорости конвейера контактных роликов 3.
Из-за износа контактных роликов 3, проскальзывания, неровностей фланца 10 или других обстоятельств может возникнуть разница между скоростью направляющей манипулятора 4 и скоростью конвейера контактных роликов 3. При фрикционном зацеплении между контактными роликами 3 и фланец 10 сохраняется, это приводит к крутящему моменту вокруг удерживающей скобы 5, удаленной от точки зажима, что проявляется в неправильном захвате или неравномерном движении заготовки 2. В обоих случаях результатом является отклонение контактных роликов 3 от заданной траектории раскатки 11.Это особенно важно в изогнутых областях полки 10. Крутящий момент также возникает, даже когда скорости конвейера одинаковы, если из-за неточности в управлении траекторией или других факторов контактные ролики 3 отклоняются от траектории 11 прокатного шва.
Подобное несоответствие усилий конвейера, приводящее к крутящему моменту, указанному выше, возникает также при проскальзывании в точке зажима между контактными роликами 3 и фланцем 10. Это также может отрицательно сказаться на качестве сварки и прилегании к шву качения. путь -1.
Как на фиг. 2, заготовка 2 удерживается зажимным устройством 13. Зажимное устройство соединено через датчик перемещения 6 с монтажной скобой 5 промышленного робота 4. Монтажной скобой 5 в данном случае является поворотный съемный конец промышленный робот 4, известный как рука робота. Как показано на фиг. 1 и 2, продольные оси монтажного кронштейна 5 и датчика перемещения 6 совпадают, и они соединены на таком расстоянии от охватывающего фланца 10 с зажимным устройством 13, что находятся на равном расстоянии от всех радиальных центров 12 изогнутых частей фланца 10.Любой крутящий момент вокруг оси монтажного кронштейна 5, введенный через зажимное устройство 13, будет определяться по степени и направлению датчиком смещения 6.
Датчик смещения 6 посылает этот измерительный сигнал по схеме, которая будет описана ниже и показана на фиг. 5, к блоку управления 9 промышленного робота 4. Величина и направление крутящего момента представляют собой аналоговые значения степени и направления отклонения траектории или разности скоростей конвейера и усилий конвейера.Блок 9 управления компенсирует эту разницу в скоростях или усилиях конвейера, накладывая управление непрерывной траекторией и увеличивая или уменьшая скорость направляющих. Направление направляющей, запрограммированное в непрерывном управлении траекторией, сохраняется в процессе. Во время перенастройки скорости направляющей происходит определенная сверхкомпенсация, которая временно устанавливает противодействующую пару сил или крутящий момент. Это приводит к тому, что отклонение траектории не только компенсируется, но даже отслеживается.Таким образом, контактные ролики 3 перемещаются по дуге назад к заданной траектории 11 прокатки шва. Когда они достигают этого положения, крутящий момент исчезает, и заготовка 2 продолжает движение, а система непрерывного управления траекторией выполняет свою обычную функцию.
В примере, показанном на фиг. 3, датчик представляет собой цилиндрическую трубку, в оболочке которой расположены углубления 16, оставляющие между собой вертикальные гибкие стержни 15. На стержнях 15 обычным образом расположены тензодатчики 14. Крутящий момент, передаваемый через зажимное устройство 13, скручивает трубку 7 датчика 8 крутящего момента, после чего стержни 15 изгибаются в соответствии с силой и направлением этого кручения.
РИС. 4 показана альтернативная конструкция датчика 6 крутящего момента. Зажимное устройство 13 и монтажный кронштейн 5 установлены аксиально друг на друге, но могут поворачиваться против друг друга вокруг продольной оси монтажного кронштейна. В этой конструкции на зажимном устройстве 13 и монтажном кронштейне 5 расположены два радиально выступающих удлинителя 8, поддерживаемых на расстоянии друг от друга, но охватывающих одну и ту же площадь и соединенных на своих концах гибкими стержнями 15 с тензодатчиками 14.За счет увеличения расстояния стержней 15 от оси кручения повышается чувствительность измерения.
ФИГ. 6 и 7 показано регулировочное устройство, с помощью которого можно изменять расстояние монтажного кронштейна 5 от радиальных центров 12 для получения различных эффектов. Возможность регулировки такого рода особенно рекомендуется для заготовок очень длинных или сложных по форме. Чем больше расстояние между центрами, тем выше скорость вращения, которую необходимо передать монтажному кронштейну 5, чтобы повернуть заготовку в точке зажима фланца 10 с необходимой скоростью конвейера. Это обстоятельство также вызывает проблемы с разгоном и торможением. С помощью регулировочного устройства, позволяющего изменить положение относительно одной или нескольких осей, эти расстояния могут быть сокращены.
В показанном варианте зажимное устройство 13 может перемещаться относительно одной оси в направляющей раме 20 и менять свое положение относительно монтажного кронштейна 5 и датчика перемещения 6 с помощью регулировочного привода 21. Направляющая рама 20 жестко соединен сбоку с датчиком перемещения 6 и передает на датчик крутящий момент, передаваемый от зажимного устройства 13.Регулировочный привод 21 имеет управление, совмещенное с управлением непрерывной траекторией, и предпочтительно состоит из электрического серводвигателя с индикатором смещения и приводного шпинделя.
Согласно фиг. 7, для работы на прямых участках фланца 10 монтажная скоба 5 и указатель перемещений 6 располагаются в центральном положении регулировочного устройства, где пересекаются прямые, соединяющие радиальные центры 12. До достижения закруглений на фланце регулировочный привод 21 перемещает зажимное устройство 13 с заготовкой 2, после чего монтажная скоба 5 с датчиком перемещения 6 оказывается в положении, указанном штрихпунктирными линиями относительно заготовки 2. , в этом положении расстояние до ближайших радиальных центров 12 заметно сокращается.Регулировочное движение контролируется непрерывным управлением траекторией и компенсируется направляющим движением промышленного робота 4, так что скорость направляющей, возникающая в точке зажима, не изменяется при регулировке. Для работы на длинных прямых участках фланца зажимное устройство 13 перемещают назад в центральное положение, а затем в другое внешнее положение.
Могут быть внесены изменения в показанный вариант осуществления, заключающиеся в том, что для целей многоосевой регулировки может быть установлена направляющая рама 20, выполненная в виде составного суппорта скольжения, или тому подобное с соответствующим регулировочным приводом 21. В качестве другого примера датчик 6 смещения может быть закреплен на зажимном устройстве 13 и сам установлен с возможностью перемещения в направляющей раме 20. Тогда он также будет перемещаться во время регулировки.
РИС. 5 показана принципиальная схема подключения для перенастройки тракта. Датчик крутящего момента с тензодатчиками 14 определяет крутящий момент, возникающий вокруг продольной оси монтажного кронштейна 5, и измеряет его по величине и направлению. Используемая измерительная схема работает с высокой частотой циклов, что позволяет ей определять крутящий момент еще до того, как контактные ролики 3 фактически отклонятся от траектории 11 прокатного шва.Сигналы измерений от тензометрических планок 14, установленных в разных направлениях, подаются на мостовой вход 17, там оцениваются и преобразуются в сигнал, представляющий крутящий момент по величине и направлению. Этот сигнал передается на блок управления 9 манипулятора 4 через схему адаптации 18 и обрабатывается в программе с наложением управления траекторией. Направляющая скорость увеличивается или уменьшается до тех пор, пока датчик 7 крутящего момента сообщает о наличии крутящего момента. С помощью балансировочной линии 19 и схемы адаптации 18 на датчике крутящего момента 7 может выполняться процедура нулевой балансировки перед подачей новой заготовки 2 в сварочный аппарат 1 с подвижным швом.
Хотя конкретные варианты осуществления изобретения были показаны и подробно описаны для иллюстрации применения принципов изобретения, следует понимать, что изобретение может быть реализовано иначе, не отступая от этих принципов.
Список деталей
(1) Инструмент, машина для сварки валковым швом, часть
(2) Заготовка, деталь
(3) Контактный ролик
(4) Манипулятор, промышленный робот
(5) Монтажный кронштейн
(6) Датчик перемещения
(7) Датчик крутящего момента
(8) Расширение
(9) Блок управления
(10) Фланец
(11) Накатной шов, накатной шов
(12) Радиальный центр
(13) Зажимное устройство
(14) Лента тензометрическая
(15) Бар
(16) Ниша
(17) Вход моста
(18) Схема адаптации
(19) Линия баланса
(20) Направляющая рама
(21) Привод регулировочный
.