Сварка AISI 304 в промышленных условиях
Сделать заказ можно по телефону
Наши специалисты с радостью вам помогут
+7 495 775-50-79
Сварка AISI 304, как и любой другой нержавеющей стали, требует определенного подхода и соответствующего оборудования. Основной задачей процесса является получение соединения, которое по своим свойствам будет превосходить основной металл и иметь определенные геометрические параметры.
Характеристики материала
AISI 304 соответствует ГОСТовской марке 08Х18Н10. По своему классу это коррозионно-стойкая сталь жаропрочная. Высокое содержание легирующих веществ определяет устойчивость к химическому и температурному воздействию.
Это позволяет использовать AISI 304 при производстве теплообменников и коллекторов различных типов, оборудования для химического производства, труб и пр.
Содержание химических элементов:
- Углерод: 0,08%.
- Кремний: 0,8%.
- Марганец: 0,2%. Он хорошо влияет на свариваемость, выступая в качестве раскислителя.
- Никель: от 9,0 до 11,0%.
- Хром: от 17,0 до 19,0%. Именно никель и хром определяют принадлежность к нержавеющему классу.
- Титан: до 0,5%.
- Сера и фосфор – в незначительных количествах. Их переизбыток ведет к, так называемой, горячей или холодной ломкости. Это значит, при сварке могут появиться трещины в процессе нагревания или остывания. Содержание этих элементов тщательно контролируется, и их переизбыток является основанием для признания материала некачественным.
Неограниченная свариваемость и подверженность другим видам обработки, делает востребованным AISI 304 в промышленности.
Процесс сварки
Наиболее применяемый стальной прокат: лист, труба, пруток, уголок. Подход к ним в сварочном производстве примерно одинаков. Качество готовой продукции зависит от следующих аспектов:
- Использование оборудования, способное поддерживать стабильный процесс.
Для любой нержавейки важно соблюдение замыкания, напряжения, подачи присадки и т.д. Оптимальны последние поколения сварочных полуавтоматов, использующие инвертеры.
- Назначение правильных сварочных режимов.
- Подготовка поверхности материала: обезжиривание и зачистка непосредственно перед сваркой.
- Материалы. Учитывая хорошую теплопроводность и подверженность термической деформации, оптимальны защитные газовые смеси на основе аргона. Этот инертный газ обеспечивает локальный нагрев и глубокое проплавление при сравнительно небольшой площади. Выбор сварочной проволоки выбирается по ГОСТУ. Содержание легирующих элементов в месте соединения не должно быть ниже, так же, как и его физические свойства. Имеет значение, с чем соединяют AISI 304 – одно дело. Если это углеродистая сталь, а другое – если высоколегированная.
- Заключительные операции. Желательно готовому изделию дать остыть в зафиксированном состоянии – это уменьшит масштаб деформаций.
Преимущества образования неразъемных соединений
Сварка дает высокую прочность и не теряет своих параметров даже после многих лет службы. дополнительными преимуществами являются:
- Универсальность. AISI 304 можно варить с любыми другими сталями с неограниченной свариваемостью.
- Высокая производительность.
- Получение сложной конфигурации швов. Ограничением является лишь доступ горелки к месту сварки. От формы стыка ничего не зависит – важно лишь найти сварщика с соответствующей квалификацией.
- Возможность автоматизации.
- Аккуратный стык, который, к тому же, можно зачистить и сделать полностью незаметным.
Сварка AISI 304 широко применяется в машиностроении. Данный процесс можно наладить не только на большом заводе, но и в маленькой мастерской. Необходимые навыки достаточно легко получить, имея опыт в сварочных процессах.
#TITLE# || KOBELCO — KOBE STEEL, LTD.

Сварка нержавеющей стали
Предыдущая страница Следующая страница4. Рекомендуемые сваркаприсадочные материалы для одинаковых сварных швов
(1) Рекомендуемые сваркаприсадочные материалы для нержавеющей мартенситной и ферритной стали
Сваркаприсадочные материалы с химическим составом в основном идентичны материалам из основных металлов (См. Таблицу 5)
Сваркаприсадочные материалы типа 309 также можно использовать для хромовой нержавеющей стали. Однако в этом случае требуется осторожность в связи с риском возникновения термической усталости в термоциклах, т.к. коэффициенты теплового расширения основного металла и металла шва различны
(2) Рекомендуемые сваркаприсадочные материалы для нержавеющей аустенитной стали
- ①
- Сваркаприсадочные материалы с химическим составом в основном идентичны материалам из основных металлов (См. Таблицу 6)
- Когда порошковая проволока применяется для сварки конструкции, состоящей из аустенитной нержавеющей стали марки SUS304 (AISI 304) или SUS316 (AISI 316) для температуры 500℃ и выше, рекомендуется использовать специальную проволоку для для высоких температур
- ③
- Малоуглеродистые сваркаприсадочные материалы можно использовать для таких типов нержавеющей обычной углеродистой стали, как SUS304 (AISI 304) и SUS316 (AISI 316). Не рекомендуется использовать в среде, где требуется жаропрочность (ползучестойкость)
- ④
- Такие типы малоуглеродистой нержавеющей стали, как SUS304L (AISI 304L) и SUS316L (AISI 316L) содержат не более 0.03% углерода, в то время как соответствующие сваркаприсадочные материалы содержат не более 0.04% углерода в соответствии с принятыми стандартами. В этой связи, когда одинаковое содержание углерода требуется как для металла швов, так и для основного металла, рекомендуется использоватьсваркаприсадочные материалы с пониженным содержанием углерода
Сварочные материалы для нержавеющей стали (только на английском)
Краткий справочник по сварочным материалам для нержавеющих сталей и никелевых сплавов
Сварочные материалы для дуплексной нержавеющей стали
5.
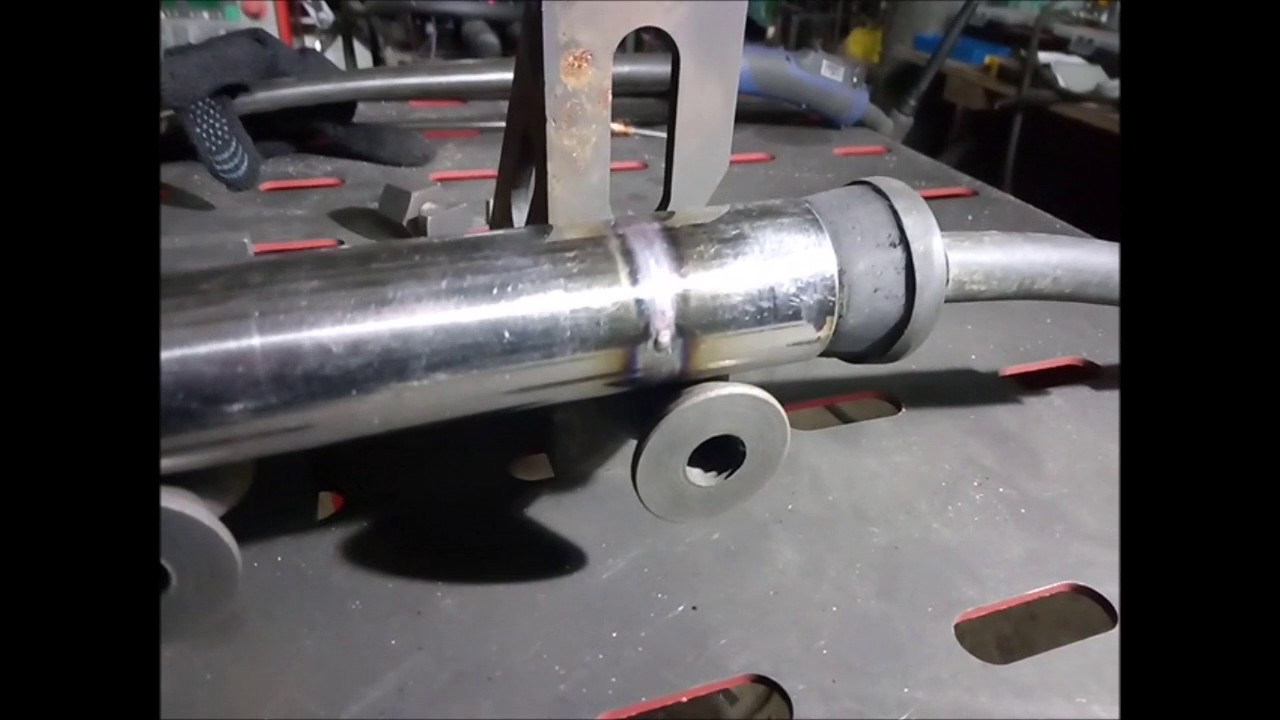
Сварка двух типов стали с различным химическим содержанием называется сваркой разнородных металлов. Данный тип сварки предусматривает выбор сваркаприсадочных материалов с учётом трещиноустойчивости, коррозиоустойчивости и прочностных свойств в зависимости от комбинации основных металлов
В Таблице 7 представлены распространённые сваркаприсадочные материалы, используемые для сварки разнородных металлов. Такие сваркаприсадочные материалы рекомендуется использовать для поддержания прочностных свойств хотя бы одного металла в соединении.
Ниже представлены дополнительные комментарии к Таблице 7.
- ①
- В сварке углеродистой стали с аустенитной нержавеющей сталью обычно используются сваркаприсадочные материалы типа 309 с повышенными хромом и никелем. Это вызвано тем, что при использовании сваркаприсадочных материалов типа 308 хром и никельмогут быть разжижены основным металлом углеродистой стали, что приведёт к формированию мартенситной структуры на базе металла шва (хрупкая структура)
- ②
- В сварке углеродистой стали с аустенитной нержавеющей сталью, в связи с различными коэффициентами теплового расширения обоих металлов, рекомендуется использовать сваркаприсадочные материалы инконельного типа с высоким содержанием никеля со средним коэффициентом теплового расширения. В этом случае сварная деталь подвергается интенсивному термоциклу.
- ③
- В сварке углеродистой стали с нержавеющей Cr-сталью могут использоваться сваркаприсадочные материалылюбого типа нержавеющей Cr-стали, аустенитной нержавеющей стали и высокопрочной Ni-стали, причём каждая категория материалов имеет собственные преимущества и недостатки. Материалы нержавеющей Cr-стали пригодны в случае интенсивных термоциклов или Ni−чувствительной коррозионной среды. При этом во избежание замедленного трещинообразования рекомендуются предварительный нагрев и термическая обработка после сварки.
Материалы аустенитной нержавеющей стали характеризуются высокой свариваемостью, но при этом вызывают термостресс в среде, где сварная деталь подвергается интенсивному термоциклу. Материалы высокопрочной Ni-стали дорогостоящие и подвержены трещинам. Вместе с тем, в связи с длительной выдержкой при интенсивных термоциклах, они пригодны для сварных деталей в ситуации, когда затруднительна термическая обработка после сварки и имеются интенсивные термоциклы. - ④
- Во время сварки разнородных металлов не рекомендуется использовать дуговую сварку под флюсом с повышенным коэффициентом разбавления
- ⑤
- Когда во время сварки разнородных металлов применяются MIG and TIG-сварки, рекомендуется минимизировать поступление в углеродистую сталь
Здесь можно найти СПРАВОЧНИК СВАРКИ KOBELCO
6. Подогрев и послесварочный отжиг
(1) Сварка идентичных металлов
В Таблице 4 — 8 представлены надлежащие условия подогрева и послесварочного отжига для сварки основных металлов с идентичным химическим составом. При контроле за сварочным процессом ключевым моментом является контроль за температурой, особенно при использовании ферритной и мартенситной нержавеющей стали (также известна как нержавеющая Cr-сталь). Контроль за температурой в ходе подогрева и послесварочного отжига во многом определяет результаты сварки
Ниже объяснены положения ①~⑤ Таблицы 8.
① Защита от замедленного трещинообразования
Замедленное трещинообразование случается после того, как сварная деталь охлаждена до температуры окружающей среды. Выделяются 3 основные причины: диффундирующий водород в металле шва, затвердение металла шва и зоны термического влияния , а также совместное сдерживание.
Подогрев и отжиг для снятия напряжений эффективны при защите от замедленного трещинообразования. В связи с тем, что
в ходе подогрева снижается скорость охлаждения сварной детали, замедляется затвердение металла шва и зоны термического влияния, и ускоряется процесс выхода диффундирующего водорода. Замедленное трещинообразование свойственно сварной детали скорее из нержавеющей Cr-стали, чем из нержавеющей аустенитной стали, т.к. деталь из аустенитной стали затвердевает в прямой зависимости от скорости охлаждения, а растворённый водород не становится диффундирующим.
Следовательно, подогрев не рекомендуется при сварке нержавеющей аустенитной стали, иначе возникнет риск снижения коррозионной стойкости.
② Гомогенизация
Гомогенизация, осуществляемая в основном на сварных деталях из нержавеющей аустенитной стали, применяется во время сварки при температуре 1000~1150℃ в течение 2 мин. и более на 1 мм толщины плиты, после чего наступает быстрое охлаждение. Охлаждение должно пройти как можно скорее при температуре 500~800℃ во избежание образования карбида хрома. Во время сварки при температуре 1000~1150℃ карбид хрома, сигма-фаза и ферриты в металле шва разъединяются в матрице. С помощью гомогенизации возможно усиление коррозионной стойкости, вязкости и прочности, а также удаление внутренних напряжений, вызванных процессом сварки
③ Отжиг для снятия напряжений (SR)
SR предусматривает защиту от замедленного трещинообразования в сварных деталях из нержавеющей Cr-стали и повышение прочностных свойств. В то же время для сварных деталей из нержавеющей аустенитной стали основной задачей становится защита от трещинообразования от коррозии под напряжением. Однако применение SR во многом наносит вред, когда важна коррозионная стойкость или ускоряется образование сигмы-фазы, как в случае с металлом-швом типа 347 или 316. Следовательно, использование SR в случае со сварными деталями из нержавеющей аустенитной стали должно проводиться только после определения марки стали, анализа условий сварки и на основании предыдущего опыта.
④ Горячие трещины
Трещины в сварной детали из нержавеющей Cr-стали могут возникнуть при температуре окружающей среды и называются замедленными разрушенями. Трещины металла шва из нержавеющей аустенитной стали и высокого никелевого сплава в большинстве случаев могут возникнуть сразу же после затвердевания и называются горячими трещинами. Во избежание их возникновения, сваркаприсадочные материалы для нержавеющей аустенитной стали общего типа изготавливают с пониженным (до нескольких процентов) содержанием ферритических структур аустенитной матрицы в составе металла шва. Для измерения процентного содержания ферритических структур в металле шва используются несколько методов: диаграммы металлографической структуры, измерительные приборы и микроскоп. В отличие от трещин на сварных деталях из нержавеющей Cr-стали, трещин на сварных деталях из нержавеющей аустенитной стали нельзя избежать с помощью подогрева и послесварочной термообработки. Для этого необходимо выбрать подходящий сваркапосадочный материал с пониженным содержанием примесей и правильный тип сварки
⑤ Коррозионная стойкость зоны термического влияния
Нержавеющая аустенитная сталь производится с целью демонстрации уникальной коррозионной стойкости посредством гомогенизации. Однако в ходе сварки коррозионная стойкость зоны термического влияния снижается до уровня зоны с неизменённой структурой основного металла, т.к. карбиды ускоряются в зоне термического влияния. Эта зона ускорения карбидов называется зоной коррозии сварного шва, образующейся в ходе подогрева при сварке 500~800℃. В результате карбиды хрома ускоряются и понижают количество хрома в матрице, эффективного в усилении коррозионной стойкости. Следовательно, коррозионная стойкость зоны термического влияния разрушается. Хотя имеются случаи, когда коррозия сварного шва не наносила никакого вреда в повседневном использовании, некоторые меры защиты всё же рекомендуются, когда сварочная деталь используется в среде с межзеренной коррозией или возникает трещинообразование от коррозии под напряжением.
Существуют следующие превентивные меры против коррозии сварного шва :
- (a)
- Гомогенизация при температуре 1000~1150℃ после окончания сварки — чтобы расщепить карбиды хрома.
- (b)
- Превентивное ускорение карбидов хрома с помощью малоуглеродистой нержавеющей стали марки SUS304L (AISI 304L) или SUS316L (AISI 316L), или стабильной нержавеющей стали марки SUS321 (AISI 321) или SUS347 (AISI 347).
- (c)
- Переплавить поверхность HAZ с помощью TIG-сварки с минимальной погонной энергией
(2) Сварка разнородных металлов
Температура подогрева сварки разнородных металлов — высокая температура подогрева между двумя основными металлами определяется стандартно. Примеры таких температур подогрева представлены в Таблице 9. Требуется соблюдение мер предосторожности, т.к. слишком высокая температура во время сварки разнородных металлов может привести к превышению проплава и нарушению химического состава металла шва. Использование сваркапосадочных материалов для нержавеющей аустенитной стали приводит к снижению температуры подогрева во избежание коррозии сварного шва. Однако низкие температуры подогрева могут ослабить защиту от затвердевания зоны термического влияния
Примеры температур термической обработки после сварки (PWHT) разнородных металлов представлены в Таблице 10. Поскольку PWHT сварного шва разнородных металлов по-разному затрагивает оба основных металла и металл шва, рекомендуется тщательно изучить условия проведения PWHT и даже необходимость в ней.
Если для проведения термической обработки после сварки (PWHT) разнородных металлов выбирается средняя или высокая температура в сравнении с подходящей PWHT-температурой для каждого основного металла, она может превысить температуру превращения основного металла, чья PWHT-температура ниже (обычно это металл с менее легирующими элементами). Это может привести к полному изменению свойств металла. Следовательно, необходимо заранее определить PWHT-температуру.
Комбинация ферритных и аустенитных типов стали, наблюдаемая в месте сварного шва мягкой и нержавеющей аустенитной стали даёт возможность определить низкую PWHT-температуру из списка рекомендуемых температур для ферритной стали. Низкая температура необходима для минимизации перемещения углерода на поверхности контакта между свариваемыми деталями. Надо также знать, что эти PWHT-температуры наблюдаются там, где нержавеющая аустенитная сталь ускоряет карбиды и сигма-фазы.
1.Свойства нержавеющей стали2.Разные типы нержавеющей стали3.Физические свойства нержавеющей стали 7.Сварка плакированной нержавеющей стали8.Ключевые моменты сварочного процесса для нержавеющей стали
Верх страницы
Сталь AISI 304
Главная >> Продукция >> Металлопродукция >>Нержавеющая сталь AISI >>304Химический состав стали AISI 304
Углерод (С) ≤0,08Хром (Cr) 18,0-20,0
Марганец (Mn) ≤2,0
Кремний (Si) ≤0,75
Фосфор (Р) ≤0,045
Сера (S) ≤0,03
Селен (Se) 0,15
Железо (Fe) остальное
Физические свойства AISI 304
Плотность 8,00 г /см³Температура плавления 1450°C
Тепловое расширение 17,2 x10-6/K
Модуль упругости 193 ГПа
Теплопроводность 16,2 Вт/мK
Удельное электрическое сопротивление 0,072 x10-6 ΩМ
Механические свойства AISI 304
Прочность на сжатие 210 МПаПредел текучести 210 МПа Мин
Прочность на разрыв 520 до 720 МПа
Деформация растяжения 45% мин
Применение
Помимо высокой коррозионной стойкости аустенитная сталь AISI 304 обладает высокой пластичностью, что позволяет широко использовать AISI 304 в штампованных изделиях с высоким уровнем вытяжки и сложным рельефом, например при изготовлении моек, раковин и тому подобных предметов обихода. Благодаря низкому содержанию углерода сталь AISI 304 обладает улучшенными сварочными характеристиками.
Основная сфера применения стали AISI 304 — пищевая промышленность: изготовление различных емкостей, передающих устройств. Практически во всех молочных и пивоваренных производствах используется сталь AISI 304 в качестве основного материала для изготовления оборудования, инструмента и приборов.
Пожалуй, второй по значимости отраслью промышленности, которая не может обойтись без стали AISI 304, без преувеличения можно назвать фармацевтическую и медицинскую промышленности. В этих отраслях AISI 304 применяют при производстве медицинского и фармакологического оборудования и инструмента, имплантатов и медицинской мебели.
Самый большой объем потребления стали AISI 304 в нефтехимических и химических производствах. Благодаря высокой сопротивляемости агрессивным средам трубы AISI 304 в этих производствах повсеместно применяются повсеместно. Кроме того, имеется специфическое оборудование, например щелевые фильтры, которые производятся только из проволоки марок AISI 304 и AISI 321.
Еще одна область применения стали марки AISI 304 – ресторанный бизнес и производство домашней утвари, в том числе посуды.
Аналоги AISI 304
Сталь марки AISI 304 является наиболее часто применяемой из всех коррозионностойких сталей. По физическим механическим свойствам химическому составу наиболее близко она подходит российской марке 08Х18Н10. По стандартам Евросоюза сталь AISI 304 имеет обозначение 1.4301. Отличительной особенностью аустенитной стали AISI 304 является оптимальное содержание никеля и хрома. До сих пор ее иногда называют 18/8, что подчеркивает содержание этих металлов в составе AISI 304 – 18% хрома и 8% никеля. В зависимости от содержания углерода в стали AISI 304 выделяют два дополнительных подкласса – с пониженным содержанием углерода AISI 304L (аналог российской 03Х18Н11) и с повышенным содержанием углерода AISI 304H использующаяся в основном при высокотемпературных производствах.
Коррозионная стойкость
Сталь марки AISI 304 обладает отличной коррозионной стойкостью во многих средах и при контакте с различными агрессивными средами. Кроме того изделия из стали AISI 304 имеют низкую подверженность точечной (питтинговой) и щелевой коррозии, даже в средах, содержащих хлориды. Трещинообразование от коррозии под напряжением может произойти при температурах выше 60 °C.
Жаростойкость
AISI 304 имеет хорошую стойкость к окислению при температурах до 870 °C, а при длительной эксплуатации и до 925 °C.
Тем не менее, длительное пребывание при температуре 425-860 °C не рекомендуется если требуется коррозионная стойкость в водной среде. В этом случае больше подходит сталь марки AISI 304L из-за ее устойчивости к выделению карбидов.
В случаях, когда требуется высокая прочность при температурах от 500 °C до 800 °C, лучше применять сталь AISI 304H. Этот материал будет дольше сохранять коррозионную стойкость в воде.
Обработка стали AISI 304
Изготовление всех изделий из нержавеющей стали марки AISI 304 должно выполняться только предназначенными для обработки нержавеющей стали инструментами. Рабочая поверхность заготовки и применяемый в процессе обработки стали AISI 304 рабочий инструмент должен быть тщательно очищен перед использованием. Эти меры предосторожности необходимы во избежание вторичного загрязнения (контаминирования) из-за соприкосновения нержавеющей стали AISI 304 с подверженными коррозии металлами, которые могут загрязнить поверхность изготавливаемого изделия.
Холодная обработка стали AISI 304 достаточно эффективна, так как она очень быстро затвердевает. При обработке стали AISI 304 холодным способом могут потребоваться промежуточные стадии отжига, необходимые для облегчения упрочнения и предупреждения разрывов или трещин. Изделие из стали AISI 304 после завершения его изготовления должно быть подвержено процедуре полного отжига. Данная операция необходима для уменьшения внутреннего напряжения металла.
Горячая обработка стали AISI 304 такая, как и ковка должна сопровождаться равномерным нагревом до температуры 1149-1260°C. Непосредственно после обработки деталь должна быть быстро охлаждена для обеспечения максимальной защиты от коррозии.
Механическая обработка
Благодаря высокой текучести нержавеющая сталь AISI 304 обладает высокой обрабатываемостью. Для повышения способности стали AISI 304 подвергаться обработке необходимо соблюдать следующие правила.
Края металлорежущего инструмента должна быть острыми во избежание избыточного уплотнения в местах обработки. Для этой же цели желательно, чтоб резка была быстрой, но глубокой.
При обработке желательно использовать стружколомные устройства для своевременного отделения обрезков и во избежание деформации заготовки.
В связи с низкой теплопроводностью аустенитных сплавов, таких как AISI 304, высока вероятность перегрева режущей кромки инструмента. Поэтому при обработке изделий из стали AISI 304 необходимо использование охлаждающих и смазочных материалов
Термообработка
Нержавеющая сталь AISI 304 не может улучшать свои физические характеристики при термической обработке, поэтому термообработка применяется только для снижения напряжения поверхностного слоя посредством быстрого охлаждения после нагревания до 1010-1120 °С.
Сварка стали AISI 304
Показатели плавкости нержавеющей стали AISI 304 довольно высокие, поэтому она неплохо подвергается автогенной сварке (сварке плавлением) даже без использования присадочных материалов.
При электрической сварке в качестве наполнителя для электрода и присадочного материала для стали AISI 304 рекомендуется использовать сталь AISI 308 или ее российский аналог Св-04Х19Н9, для стали AISI 304L лучше подойдут электроды из стали AISI 308L с рутилово-кислотным покрытием (AC/DC).
После проведения сварочных операций места сварных соединений стали AISI 304 желательно подвергать отжигу. Эта операция необязательна для стали 304L. В случае, если после сварки термическая обработка металла невозможна, желательно применять сталь марки AISI 321.
Другие обозначения AISI 304
1.4301, SUS304, S30400, 304S15, 304S16, 304S31, EN58E
Формат поставки
Первичные формы поставки стали: лист AISI 304, полоса (штрипс) AISI 304, плита AISI 304, пруток AISI 304, труба AISI 304, фитинги и фланцы AISI 304.
Текст страницы в формате *.pdf ~ 225 кБ Скачать текст в формате *.doc ~ 226 кБ
AISI 430. Goodner (ГудНер) — хорошая нержавейка!
Обозначение по международным стандартам
Международный стандарт |
Американский ASTM A240 |
Европейский ЕN 10088-2 |
Российский ГОСТ 5632-72 |
---|---|---|---|
Обозначение марки | AISI 430 | 1.4016 | 08Х17 |
Применяемые стандарты и одобрения
AMS 5503
ASTM A 240
EN 10088-2
Классификация
коррозионная сталь общего применения
Применение
- камеры сгорания и печи
- мойки
- посудомоечные и стиральные машины
- вытяжки
- газовые плиты
- желоба и сливные трубы
- дымоходы
- утюги с отпаривателем
- столовые приборы
- декоративные компоненты
- оборудование, находящееся в контакте с азотной кислотой
- заводское оборудование по очистке нефти
- кровля (в экологически чистых районах)
- ресторанное оборудование
- автомобильная отделка и тюнинг
Основные характеристики
- одна из наиболее широко используемых «не упрочняемых» ферритных марок
- имеет хорошее сопротивление коррозии в мягко коррозийных окружающих средах
- имеет хорошее сопротивление окислению в высоких температурах
- в отожженном состоянии податлива, не укрепляется чрезмерно в течение холодной обработки и может быть легко формуема
- обладает хорошей способностью к вытяжке и полируемости
- имеет ограниченную свариваемость и не должна использоваться в сваренных конструкциях, подвергающихся нагрузкам
- имея ферритную структуру, проявляет хрупкость при низких температурах, и не может использоваться в криогенных конструкциях
Химический состав (% к массе)
стандарт | марка | C | Si | Mn | P | S | Cr | Ni |
---|---|---|---|---|---|---|---|---|
ASTM A240 | AISI 430 |
≤0.![]() |
≤1.0 | ≤1.0 | ≤0.04 | ≤0.030 | 16.00 — 18.00 | ≤0.5 |
Механические свойства
AISI 430 |
Сопротивление на разрыв (σв), Н/мм² |
Предел текучести (σ0,2), Н/мм² |
Предел текучести (σ1,0), Н/мм² |
Относительное удлинение (σ), % | Твердость по Бринеллю (HB) | Твердость по Роквеллу (HRB) |
---|---|---|---|---|---|---|
В соответствии с EN 10088-2 | ≥430 | ≥260 | - | ≥20 | - | - |
В соответствии с ASTM A 240 | ≥450 | ≥205 | - | ≥22 | - | 88 |
Механические свойства при высоких температурах
Физические свойства
Физические свойства | Условные обозначения | Единица измерения | Температура | Значение |
---|---|---|---|---|
Плотность | d | - | 4°C |
7.![]() |
Температура плавления | °C | 1500 | ||
Удельная теплоемкость | c | J/kg.K |
20°C 400°C 800°C |
460 600 800 |
Тепловое расширение | k | W/m.K | 20°C | 26 |
Средний коэффициент теплового расширения | α | 10-6.K-1 |
20-200°C 20-400°C 20-600°C 20-800°C |
10.5 11.5 11.7 12.5 |
Электрическое удельное сопротивление | ρ | Ωmm2/m | 20°C | 0.60 |
Магнитная проницаемость | μ |
в 0.80 kA/m DC или в/ч AC |
20°C μ μ разряж.возд. |
1.0 |
Модуль упругости | E | MPa x 103 | 20°C | 205 |
Сопротивление коррозии
AISI 430 не чувствительна к коррозии под напряжением и растрескиванию при солидификации.
Имеет хорошую коррозийную устойчивость при эксплуатации:
- в домашних условиях, при регулярной очистке поверхности
- кухонной утвари
- при контакте с мылом и моющими средствами
- в щелочных растворах при температуре окружающей среды
- с некоторыми разбавленными органическими кислотами при температуре окружающей среды
- с другими нейтральными, щелочными и соляными растворами, кроме тех, которые содержат галиды (хлориды, фториды, бромиды, йодиды)
- с многочисленными органическими веществами
Температурный предел постоянной эксплуатации из-за окисления ограничен 800°C.
Степень защиты металла в кислотных средах
Температура, °C | 20 | 80 | ||||||||||
---|---|---|---|---|---|---|---|---|---|---|---|---|
Концентрация, % к массе | 10 | 20 | 40 | 60 | 80 | 100 | 10 | 20 | 40 | 60 | 80 | 100 |
Серная кислота | 2 | 2 | 2 | 2 | 2 | 1 | 2 | 2 | 2 | 2 | 2 | 2 |
Азотная кислота | 0 | 0 | 0 | 0 | 1 | 2 | 0 | 0 | 0 | 1 | 1 | 2 |
Фосфорная кислота | 0 | 0 | 2 | 2 | 1 | 0 | 0 | 0 | 2 | 2 | 1 | 1 |
Муравьиная кислота | 0 | 0 | 1 | 1 | 1 | 0 | 0 | 2 | 2 | 2 | 2 | 0 |
0 — высокая степень защиты — Скорость коррозии менее чем 100 мкм/год
1 — частичная защита — Скорость коррозии от 100 до 1000 мкм/год
2 — нет защиты — Скорость коррозии более чем 1000 мкм/год
Атмосферные воздействия
Сравнение AISI 430 с другими металлами в различных окружающих средах
(Скорость коррозии рассчитана при 10-летнем воздействии).
Окружающая среда | Скорость коррозии (мкм/год) | ||
---|---|---|---|
AISI 430 | Алюминий-3S | Углеродистая сталь | |
Сельская | 0.0025 | 0.028 | 4.3 |
Морская | 0.0381 | 0.424 | 25.7 |
Индустриальная Морская | 0.0406 | 0.546 | 37.1 |
Максимальные рекомендуемые температуры эксплуатации
(Температура образования окалины)
Непрерывное воздействие 750 °C
Прерывистые воздействия 850 °C
Примечание: эксплуатация в температурном диапазоне 350 — 525°C свыше 100 часов сделает сталь хрупкой при комнатной температуре.
Сварка
- Сталь трудно свариваемая
- Плохо подходит для сварки, так как при нагревании происходит рост зерен в микроструктуре металла, что ведет к хрупкому и не способному деформироваться соединению
- Однако удовлетворительные результаты могут быть получены после последующей обработки шва травильной пастой
- Не рекомендуется для тяжелых сварных конструкций из-за хрупкости соединений
- Сварные швы должны быть механически или химически очищены от окалины, затем пассивированы
- Нет необходимости в термической обработке после сварки
- Если существует риск возникновения межкристаллитной коррозии, предпочтительнее использовать марку 430Ti (439)
Формовка
AISI 430 может холодно формоваться всеми стандартными процессами (изгиб, штамповка, волочение, ротационная вытяжка и т. д.). Глубокая вытяжка, требующая значительного растягивания, может быть облегчена начальной формовкой — для создания больших радиусов искривления.
О формовке с растяжением
В процессе формовки с растяжением заготовку подвергают «торможению» во время вытяжки. Стенки становятся более тонкими и во избежание разрывов для AISI 430 желательно предусмотреть свойства повышенного упрочнения при формовке.
Степень растяжения определяется эриксоновским испытанием на вытяжку (деформация производится до начала утончения стенок).
Число Эриксена (Характеристика обрабатываемости листового металла давлением) |
|
---|---|
AISI 430 | 8.7 мм |
AISI 304 | 11.8 мм |
Тесты на Глубокую вытяжку
При чистой глубокой вытяжке на прессе заготовку не подвергают «торможению», а материалу дают свободно течь в штампе. На практике это происходит редко. Например, при вытяжке хозяйственной посуды всегда присутствует также элемент формовки с растяжением.
Характеристики листового материала при глубокой вытяжке описываются предельным коэффициентом вытяжки — LDR (отношение наибольшего возможного диаметра образца до момента разрыва к диаметру пресса) и пределом фестонообразования (при формовочном тесте – относительный размер образующихся язычков).
Испытание на выдавливание по Эриксену
LDR* (При толщине образца 0.8 мм и диаметре пресса равном 20 мм) |
|
---|---|
AISI 430 | 2.05 |
AISI 304 |
2.![]() |
*Limiting drawing ratio — предельный коэффициент вытяжки
Оценка фестонообразования
Фестонообразование (Относительный размер образующихся язычков) |
|
---|---|
AISI 430 | 5-7% |
AISI 304 | 3-5% |
Гибка
Хорошая 180° гибкость, с очень маленьким радиусом изгиба для толщин менее 0.8 мм (продольные и поперечные направления), для листов толщиной более 0.8 мм рекомендуется радиус не меньше половины толщины.
Приближенные пределы изгиба:
s < 3мм → мин r = 0
3мм < s < 6мм → мин r = ½ s, угол 180°
6мм < s < 12мм → мин r = ½ s, угол 90°
Рекомендуют следующие минимумы:
s < 0,8 мм → мин r = ½ s, 180°
0,8 < s < 6 мм → мин r = s, 180°
6 < s < 12мм → мин r = s, 90°
где s — толщина листа, r — радиус изгиба
Обработка
Отжиг
Отожженная AISI 430 является самой мягкой и податливой и может использоваться для холодной формовки. Диапазон температуры отжига 780-800°C сопровождается последующим охлаждением на воздухе.
Отпуск
Отпуск после сварки обычно не требуется, хотя 200-300°C — рекомендованный диапазон.
Обработка, отделка, полировка, шлифовка поверхности
Легко поддается полировке, щеточной обработке, шлифовке.
Травление (очистка поверхности)
- Смесь азотной кислоты и фтористоводородной/плавиковой кислоты (10 % HNO3 + 2% HF)
- Паста для очистки от окалины в зоне сварки
Пассивация
- 20-25 % раствор HNO3 при 20°C
- Пассивирующие пасты для зоны сварки
Ковка
Начальная температура: 1100 — 1150°C
Конечная температура: ниже 750°C
Избегайте длительного воздействия температурой выше 1000°C, поскольку возможен чрезмерный рост зерна, который уменьшает податливость.
Следует обращать особое внимание на следующий факт: для нержавеющей стали требуется для однородного прогрева время, в 2 раза превышающее время для той же самой толщины углеродистой стали.
Чем отличаются нержавеющие стали AISI 304 и 430?
Информационная статьяВ этой статье мы разбираемся, чем же друг от друга отличаются нержавеющие стали AISI 304 и 430, почему одна дешевле, а другая дороже. Давайте разберемся в этом вместе на примере банных печей из нержавейки. Вы узнаете как отличить эти стали при покупке банной печи, чтобы вас не обманули и под видом настоящей нержавейки не продали обычную печь для бани из AISI 430 стали.
На рынке банных печей много различных моделей, при изготовлении которых используется нержавеющая сталь, но не всякая нержавеющая сталь одинаково хороша. Давайте попробуем разобраться, чем же друг от друга отличаются нержавеющие стали. Возьмем за пример самые распространенные стали AISI 430 (17Х18 по ГОСТ) и AISI 304 (12X18h20 по ГОСТ).
Многие производители банных печей используют в производстве именно сталь AISI 430, так как по таблице жаростойкости она выше. Использование этой стали также оправдано и её относительно невысокой ценой, по сравнению со сталью AISI 304. Сталь AISI 304 же обладает чуть меньшей жаростойкостью, по сравнению с AISI 430, но это её единственное незначительное отличие. Так как есть более важные показатели, которые напрямую влияют на работу и долговечность изделия.
Для начала давайте узнаем поподробнее, что же это за стали.
Нержавеющая жаропрочная (аустенитная) сталь AISI 304 (INOX)
Жаропрочность – это способность металла сопротивляться пластической деформации и разрушению при высоких температурах.
Основными жаропрочными аустенитными сталями являются хромоникелевые стали. Стали содержат 15…20 % хрома и 10…20 % никеля. Обладают жаропрочностью и жаростойкостью, пластичны, хорошо свариваются.
Марка стали AISI 304 (INOX) — относится к хромоникелевому классу низкоуглеродистых высоколегированных сталей. Высокое содержание хрома и никеля определяет превосходные прочностные и антикоррозионные свойства, востребованные повсеместно – их определяют, как универсальные. Именно поэтому данный сплав относится к числу наиболее применяемых.
В системе ГОСТ данной марке соответствует 12X18h20 сталь.
Основные качества, дающие преимущества именно AISI 304: устойчивость к окислению и к повышенной температуре, повышенная надежность сварных швов из-за хорошей свариваемости.
AISI 304 обладает такими эксплуатационными свойствами как:
- Кислотоустойчивость. Устойчивость к агрессивным воздействиям техногенного или природного характера.
- Жаропрочность. Способность металла сопротивляться пластической деформации и разрушению при высоких температурах.
- Жаростойкость. Способность металлов и сплавов сопротивляться газовой коррозии при высоких температурах в течение длительного времени (до 850oC).
- Слабые магнитные свойства. Они достигаются за счет структуры материала и способа его обработки. Сталь AISI 304 не магнитится.
- Экологичность. Производители AISI 304 позиционируют данный материал, также называемый Inox, как пищевую нержавеющую сталь. В ней не содержится токсических веществ.
Нержавеющая жаростойкая (ферритная) сталь AISI 430
Жаростойкость (окалиностойкость) – это способность металлов и сплавов сопротивляться газовой коррозии при высоких температурах в течение длительного времени.
Если изделие работает в окислительной газовой среде при температуре 500..550 oC без больших нагрузок, то достаточно, чтобы они были только жаростойкими (например, отдельные детали нагревательных печей). Являясь экономлегированной и коррозионностойкой сталь AISI 430 обладает хорошей стойкостью к образованию окалины до температуры 850-900 oC, сохраняя свои полезные эксплуатационные свойства.
Для повышения жаростойкости в состав стали вводят элементы, которые образуют с кислородом оксиды с плотным строением кристаллической решетки (хром, кремний, алюминий).
В системе ГОСТ данной марке соответствует сталь 17Х18.
AISI 430 обладает такими эксплуатационными свойствами как:
- Жаростойкость. Способность металлов и сплавов сопротивляться газовой коррозии при высоких температурах в течение длительного времени (до 900oC).
- Экологичность. В ней не содержится токсических веществ.
Сравнение нержавеющих сталей AISI 304 и 430
Сталь AISI 430 при большей жаростойкости является более хрупкой и плохо поддается сварке. Чтобы её качественно сварить требуется специальная сложная технология и точное её соблюдение на всех этапах работы. Эта сталь в основном используется в декоративных целях. Сварные конструкции из нее очень хрупкие и самым слабым местом всегда будет сварочный шов.
Эта сталь AISI 430 обладает более низкой кислотостойкостью, по сравнению с 304 нержавейкой, и при работе в жестких условиях воды, сажи и конденсата постепенно приходит в негодность, поэтому, например, дымоходные трубы из такой стали все равно прогорают. Их просто разъедает получаемая в результате работы печи кислота. Также, сталь AISI 430 магнитится, что легко ее выдает при любой проверке магнитом. Так вы легко сможете определить какая нержавеющая сталь перед вами – AISI 430 или настоящая немагнитная нержавейка AISI 304.
Сталь AISI 304 (INOX) – это жаропрочная сталь и не боится высоких температур при работе банной печи. Она прекрасно сваривается благодаря более качественному составу стали и высокому содержанию никеля. Никель – очень дорогой металл, но при его высоком содержании в нержавеющей стали она приобретает повышенную прочность и стойкость к перепадам температур, а также приобретает отличную свариваемость. Именно благодаря никелю данная сталь теряет свои магнитные свойства.
Также нержавеющая сталь AISI 304 устойчива к химическим и кислотным воздействиям, не выделяет вредных или токсичных веществ. Поэтому данная сталь в основном используется в пищевой и медицинской промышленности и входит в разряд пищевой нержавейки.
Сталь AISI 304 является более дорогой по сравнению со сталью AISI 430 из-за применения более качественных и дорогих сплавов никеля и хрома в большом количестве.
Печи из такой нержавейки могут использоваться постоянно и при этом смогут прослужить практически вечно. Поэтому, такие печи рекомендованы производителем ERMAK для использования даже в коммерческих банях с гарантией до 5 лет.
Резюме
Не все печи из нержавейки одинаковы, как вы уже поняли. И прежде, чем сделать выбор в сторону той или иной печи проверяйте, из какой нержавейки будет сделана ваша печь для бани. От этого будет сильно зависеть ее качество и срок службы.
Завод Ермак производит банные печи и из стали AISI 430, соблюдая всю технологию сварки. Это классическая серия банных печей Ермак-Элит из нержавейки.
Но в новой линейке банных печей из нержавейки ERMAK в сериях «Премиум» и «Люкс» уже используется при изготовлении топки и всех дымовых каналов нержавеющая сталь AISI 304 (INOX), из-за этого и цена печей сильно отличается.
Поставив себе такую печь из настоящей нержавейки, можно будет забыть о проблемах навсегда и просто наслаждаться качеством банных процедур и расслабляться.
Как выбрать банную печь из настоящей нержавейки? Как отличить её от обычной жаростойкой стали? Достаточно воспользоваться магнитом. Топка печи из настоящей жаропрочной нержавейки не будет магнититься! До 90% печей на рынке под видом нержавейки продаются из обычной жаростойкой стали. Не дайте себя обмануть!
Почему ржавеет нержавейка?
Иногда приходится слышать от заказчиков пожелание, чтобы при изготовлении изделия из нержавейки под заказ была использована сталь, которая не будет ржаветь. Иногда просят, чтобы была «не китайская». От чего зависит будет ли ржаветь нержавейка? Почему вообще это происходит?
По сути могут быть две причины. Первая — условия эксплуатации в агрессивной среде. И вторая — дефекты материала.
Рассмотрим эти явления подробнее.
Не все виды нержавеющей стали предназначены для эксплуатации в агрессивных средах. Например на пищевых производствах при технологических процессах используются хлорсодержащие моющие средства и там могут должна применяться нержавеющая сталь с повышенной коррозионной устойчивостью. То же самое относится к условиям эксплуатации в морской воде. По этой причине оборудование, например, из AISI 304 может попросту придти в негодность. Для агрессивных сред имеет смысл использовать AISI 316 или дуплексные виды нержавеющей стали, такие как Ferralium SD40, SAF 2205 или Zeron 100.
Вторая причина более распространена — ржавчина может возникнуть на поверхности металла в следствии механических повреждений или термической обработки(вызванные сваркой). Это так называемая точечная коррозия. Этот вид коррозии может начаться в металле где присутствуют посторонние примеси, например такие как сера.
Гладкая поверхность нержавеющего металла менее подвержена точечной коррозии чем шероховатая. На графике приведенном ниже показана зависимость коррозионной устойчивости от шероховатости поверхности. Эксперимент проводился с коррозионноустойчивой маркой нержавеющей стали AISI 316 в хлорсодержащей среде. На графике видно, что после того как шероховатость поверхности превышает Ra > 0,5 мкм, устойчивость к коррозии резко снижается. Таким образом, шероховатая поверхность AISI 316 делает ее коррозионную устойчивость даже хуже, чем полированная поверхность AISI 304.
Следы ржавчины могут появиться даже в местах куда попала раскаленная окалина. Это происходит потому, что при температуре сварки выгорают легирующие элементы, в первую очередь хром. На металле в местах сварки образуются «следы побежалости»(иногда называют следы термического воздействия). В этих местах нержавейка неизбежно начнет ржаветь. Слой ржавчины, однако, может остаться только на поверхности металла, там где нет оксидной пленки, которая образуется благодаря хрому. То есть в глубь ржавчина развиваться не будет. Но выглядят следы побежалости и тем более ржавчина очень не эстетично. Чтобы этого не произошло сварочный шов обрабатывают специальными эмульсиями, травильными пастами или при помощи абразивных материалов. При очистке шва от железных окислов(окалины окисей) травильными пастами, следует работать в защитных очках и наносить только на остывший металл, поскольку в них может содержатся плавиковая кислота. После очистки зону сварного шва необходимо подвергнуть операции пассивации. Пассивация металла — это процесс обработки поверхности с целю образования на ней слоев соединений препятствующих коррозии. То есть недостаточно только очистить сварной шов от продуктов сварки, необходимо так же восстановить защитный слой. Для этого так же существует разнообразная химия: гели, пасты. Иногда используют для пассивации нержавейки азотную или лимонную кислоту.
Существуют инновационные методы очистки и пассивации. Например метод электро-химической пассивации нержавеющего металла. Причем этот процесс осуществляется без применения продуктов травления, которые очень вредны для здоровья и окружающей среды. Компания «Строй Металл» использует оборудование компании Surfox. Благодаря этому производительность и качество работ позволяют нам выполнять заказы по изготовлению изделий из зеркальной нержавейки для элитных магазинов одежды, ресторанов, элементов интерьера.
Рекомендуем ознакомиться со статьями:
Виды нержавеющей стали
Виды коррозии нержавеющей стали
Шлифованная или полированная нержавейка.
УралСибМет холдинг | Типы рекомендуемых электродов для сварки следующих сталей
Типы рекомендуемых электродов для сварки следующих сталей
AISI марка стали | 430 | 410, 420 | 321, 348, 347 | 317 | 316L | 316 | 316Ti | 310, 310S | 309, 309S | 304L | 201, 202, 301, 302, 302B 304, 305, 308 |
304 | 310, 312, 309 | 309, 310, 312 | 308 | 308 | 308 | 309, 316 | 308, 318 | 308 | 308 | 308 | 308 |
304L | 310, 309, 312 | 309, 310, 312 | 308 | 308 | 308-L | 308 | 308, 318 | 308 | 308 | 308-L | 308 |
309, 309S | 310, 309, 312 | 309, 310, 312 | 308 | 317, 316, 309 | 316 | 316 | 316, 309 | 309 | 308 | 308 | 308 |
310, 310S | 310, 309, 312 | 310, 309, 312 | 309 | 317, 316, 309 | 316 | 316 | 310, 309, 318 | 310 | 309, 310 | 309 | 309 |
316 | 310, 309, 312 | 309, 310, 312 | 308 | 316 | 316 | 316 | 318 | 310, 309, 316 | 309, 310, 316 | 309, 316 | 309, 316 |
316L | 310, 309, 312 | 309, 310, 312 | 308 | 316, 317, 308 | 316L | 316 | 318 | 310, 309, 316 | 316, 309 | 308, 316 | 308, 316 |
316Ti | 310, 309, 312 | 309, 310, 312 | 308 | 318 | 318 | 318 | 318 | 310, 309, 318 | 316, 309 | 308, 318 | 308, 318 |
317 | 310, 309, 312 | 309, 310, 312 | 308 | 317 | 316, 308 | 316, 308 | 318 | 317, 316, 309 | 317, 316, 309 | 308, 316, 317 | 308, 316, 317 |
321, 348, 347 | 310, 309, 312 | 309, 310, 312 | 347, 308 | 308, 347 | 347, 308 | 347, 308 | 308 | 347, 308 | 347, 308 | 347, 308L | 347, 308 |
420, 410 | 310, 309, 312 | 410* 309** | 309, 310 | 309, 310 | 309, 310 | 309, 310 | 309, 310, 312 | 310, 309 | 309, 310 | 309, 310 | 309, 310 |
430 | 430, 310, 309 | 310, 309 | 310, 309 | 310, 309 | 310, 309 | 310, 309 | 310, 309, 312 | 310, 309 | 310,309 | 310, 309 | 310, 309 |
* Предварительный нагрев
** Нет необходимости в предварительном нагреве
— Проволочные электроды
]]> Железо Вступление Материалы Не Железо Материалы Вариации- Металл Перевод Оборудование Мощность Поставлять Экранирование Газы Проволока Электроды Безопасность Сварка Методы Сварка Условия Экономика Сварка Дефекты Миг Место Сварка Таблицы 6 ЭЛЕКТРОДЫ ИЗ НЕРЖАВЕЮЩЕЙ СТАЛИ При выборе подходящего провода для сварка нержавеющей стали, как правило, нужно учитывать меньше факторов как: 1) Экранирование газы обычно ограничиваются Ar-1% 0 2 для струйной дуги и A-1025 для короткой дуги.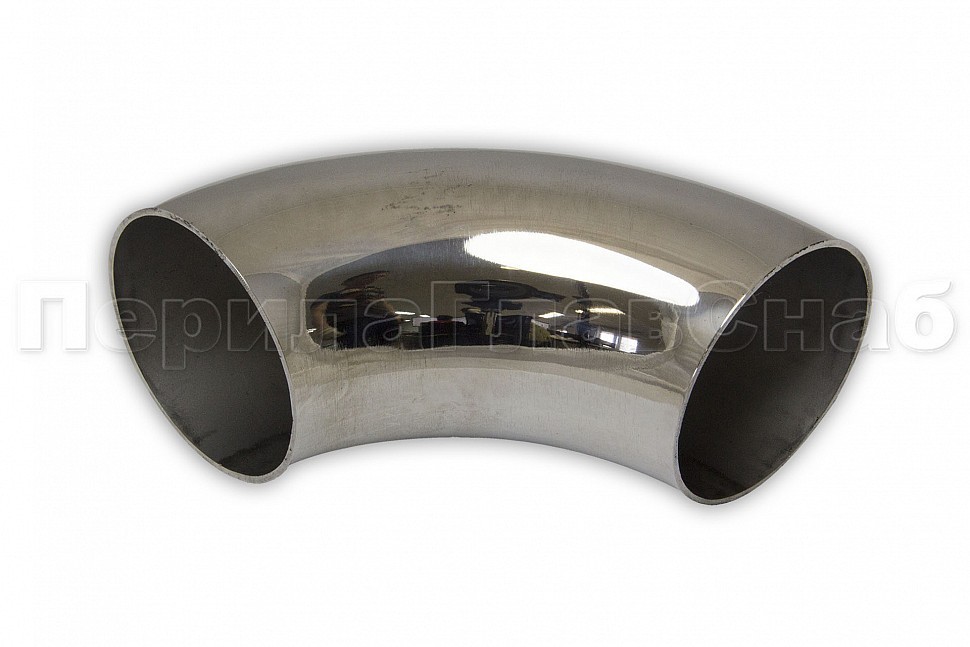

Поддержание коррозионной стойкости и повышение производительности
(Примечание читателя: из журнала The Welding Journal (Американское сварочное общество)).
Когда дело доходит до сварки труб и труб из нержавеющей стали, здесь нет вуду — правильный выбор присадочных металлов, подготовка стыков, чистота и процессы сварки помогают гарантировать, что конечный продукт соответствует установленным стандартам качества и сохраняет свои заданные свойства устойчивости к коррозии.Тем не менее, есть эволюция хорошо зарекомендовавших себя процессов и технологий, которые позволяют производителям труб повышать производительность без ущерба для коррозионной стойкости нержавеющей стали.
В этой статье будут рассмотрены основы сварки труб из нержавеющей стали для различных применений, от продуктов питания и напитков высокой чистоты, фармацевтических и нефтехимических труб до нефтегазовых приложений. В рамках этих основ мы представим передовой опыт и новые особенности установленных методов, которые могут помочь повысить производительность вашего цеха при одновременном улучшении или поддержании желаемой стойкости к коррозии.
В качестве примечания: критические приложения, в которых процессы сертифицированы, не должны изменяться без прохождения соответствующих процессов сертификации. Каждый процесс, описанный в этой статье, был сертифицирован для критически важных приложений и призван стимулировать идеи о том, как продвигать вперед ваши собственные методы сварки.
Выбор присадочного металла имеет решающее значение для контроля уровня углерода
Выбор присадочного металла для труб из нержавеющей стали связан с улучшением свойств сварного шва и соответствием требованиям применения.Присадочные материалы с обозначением «L», такие как ER308L, обеспечивают более низкое максимальное содержание углерода, что может помочь сохранить коррозионную стойкость в низкоуглеродистых нержавеющих сплавах. В качестве примера: если вы сварите основной металл 304L со стандартным присадочным металлом 308, вы фактически увеличите содержание углерода в этом соединении и увеличите вероятность коррозии. В областях применения с высокой степенью чистоты — продуктов питания, напитков, фармацевтики — это низкое содержание углерода имеет решающее значение для поддержания коррозионной стойкости. Напротив, присадочный металл с обозначением «H» обеспечивает более высокое содержание углерода для применений, требующих большей прочности, особенно при высоких температурах.Присадочные металлы с более высоким содержанием кремния, такие как ER309LSi, увеличивают текучесть сварочной ванны, улучшают врезку и увеличивают скорость перемещения для повышения производительности. Присадочные металлы серии 309 также особенно хорошо подходят для соединения разнородных нержавеющих сталей и для наплавки.
При сварке нержавеющих сталей также важно выбирать присадочный металл с низким содержанием следов (или «попутных») элементов. Это остаточные элементы в сырье, используемом для изготовления присадочных металлов. Они включают олово, сурьму, мышьяк, фосфор и серу и могут оказывать сильное влияние на коррозионную стойкость.
Контроль сенсибилизации с помощью присадочных металлов, контроль температуры между проходами
Сенсибилизация является основной причиной потери коррозионной стойкости и зависит от химического состава основного материала и присадочного металла, а также от температуры, при которой сварной шов остывает. Оксид хрома — это «нержавеющий» слой нержавеющей стали. Если вы повысите уровень углерода в сварном шве и в соседней зоне термического влияния, он образует карбиды хрома, которые связывают хром, предотвращая образование оксида хрома.Это, в свою очередь, приводит к коррозии стали, иначе она не будет иметь заданной коррозионной стойкости.
Существует три основных способа борьбы с сенсибилизацией: первый — использовать низкоуглеродистую основу и присадочный металл для уменьшения или устранения углерода при сварке. Однако этот метод не всегда практичен, поскольку углерод является жизненно важным легирующим ингредиентом в некоторых областях применения.
Второй — минимизировать время, в течение которого сварной шов и зона термического влияния проводят при температурах, способствующих сенсибилизации.Этот диапазон будет варьироваться в зависимости от того, кого вы спрашиваете, но по общему мнению, этот диапазон составляет от 500 до 800 градусов Цельсия. Чем короче время пребывания в этой температурной зоне, тем меньше повреждений от тепла сварки. Таким образом, важно соблюдать максимальные температуры между проходами, указанные в процедурах сварки. Целью многопроходных приложений должно быть использование как можно меньшего количества проходов и сварка с минимально возможным тепловложением для достижения более быстрого охлаждения.
Третий — использование присадочных металлов со специальными легирующими ингредиентами для предотвращения образования карбидов хрома.Например, титан и ниобий могут быть добавлены в присадочный металл и помогают предотвратить реакции между хромом и углеродом. Эти элементы также сильно влияют на прочность и ударную вязкость, ограничивая области применения, в которых они могут быть полезны. Они также не приносят никакой пользы в зонах термического влияния, наиболее удаленных от сварного шва.
Защитный газ, имеющий критическое значение для сохранения коррозионной стойкости
Для сварки труб из нержавеющей стали традиционно требуется продувка обратным потоком аргона.В некритических областях применения, где стоимость является определяющим фактором, азот также можно использовать в качестве обратной продувки, но это может привести к образованию некоторых нитридных соединений в корне шва, что в некоторой степени снижает коррозионную стойкость. Это может быть приемлемым компромиссом в таких областях применения, как трубопроводы из нержавеющей стали для больших систем сжатого воздуха и гидравлических жидкостных систем, где вода обычно не присутствует внутри труб и риск коррозии изнутри невелик.
Прямой аргон рекомендуется для дуговой сварки газом вольфрамовым электродом (TIG) труб из нержавеющей стали. Выбор защитного газа для проволочных процессов более сложен.
Традиционно для сварки MIG используются смеси аргона и диоксида углерода, аргона и кислорода, а также 3 газовые смеси на основе гелия, аргона и диоксида углерода. Эти смеси обычно содержат в основном аргон или гелий, причем диоксид углерода составляет менее 5 процентов от общей газовой смеси. Это связано с тем, что углекислый газ может разлагаться в дуге и вносить углерод в сварочную ванну, создавая чувствительный сварной шов, уязвимый для коррозии.Чистый аргон не используется в процессах MIG, поскольку он не обеспечивает стабильную сварочную дугу. Другие следовые составляющие, такие как углекислый газ и кислород, могут выполнять эту роль. Смеси газов аргона и кислорода можно использовать только для сварки в плоском положении, потому что кислород создает очень жидкую сварочную ванну. Аргон / диоксид углерода в сочетании с импульсной сваркой MIG можно использовать для сварки во всех положениях, как и смеси защитных газов Tri-Mix.
Порошковая проволокадля сварки нержавеющей стали предназначена для работы на традиционных смесях аргона и диоксида углерода на 75/25 процентов.Ингредиенты флюса предотвращают загрязнение сварного шва углеродом, вносимым защитным газом, а флюсирующее действие шлакового покрытия улавливает избыточный углерод и не дает ему попасть в сварочный шов. Нержавеющую сталь 304 можно успешно сваривать с использованием процесса регулируемого осаждения металла (RMD ™) без обратной продувки. Это не относится к дуплексным нержавеющим сталям. Их необходимо продуть инертным газом, например аргоном.
Подготовка к сварке и важность подгонки
Обсуждение сварки труб из нержавеющей стали не будет полным без обсуждения подготовки стыков.Применяются обычные атрибуты сварки нержавеющей стали: используйте специальные щетки, напильники и шлифовальные машины, которые никогда не касаются углеродистой стали или алюминия. Чистота имеет решающее значение. Даже микроэлементы посторонних материалов, попавшие в сварное соединение, могут вызвать дефекты и снизить коррозионную стойкость и прочность. Поскольку нержавеющая сталь настолько чувствительна к тепловыделению, чтобы сохранять свои свойства — как по форме, так и по стойкости к коррозии, — способ резки и фаски трубы также может отрицательно сказаться на сварном шве.Любой зазор или отсутствие подгонки требует, чтобы сварщик добавил больше присадочного металла, что может замедлить процесс сварки, что приведет к накоплению тепла в пораженной области. Вы хотите максимально приблизиться к идеальной подгонке, особенно на санитарных и высокочистых трубках.
Управление подводом тепла и скоростью определяет эволюцию процесса
Сам процесс сварки также играет решающую роль в управлении подводом тепла и охлаждением, и, следовательно, стойкостью к коррозии и деформации. Сварка TIG традиционно используется для сварки труб из нержавеющей стали и остается оптимальным решением для труб или труб с очень высокой степенью чистоты диаметром 6 дюймов или меньше и толщиной стенки 10.Предпочтительным методом обработки пищевой нержавеющей стали высокой чистоты является сварка встык квадратным сварным швом методом TIG методом автогенной сварки. Возможность плавления трубы без добавления присадочного металла помогает снизить нагрев и устраняет любые химические изменения, которые могут быть вызваны добавлением присадочного металла. Эта практика обычно работает с любой трубкой или трубой тоньше 1/8 дюйма. толстый. По мере того, как труба становится толще — в диапазоне от 10 до 40 — возникает необходимость в фаске трубы и добавлении присадочного металла. Существуют трубы меньшего диаметра с более толстыми стенками, например, диаметр 2 дюйма, сортамент 80, для которых TIG остается идеальным вариантом, поскольку переход на проволочный процесс на трубах такого малого диаметра нецелесообразен.
Современные инверторы для сварки TIG отлично справляются с этой задачей, поскольку импульсные возможности значительно улучшились со времен более крупных трансформаторных машин и помогают снизить подвод тепла. Старая технология сварки TIG ограничивалась импульсной частотой около 20 импульсов в секунду. Более новая инверторная технология TIG, такая как Maxstar® 200, позволяет использовать высокоскоростную сварку TIG на постоянном токе со скоростью до 500 импульсов в секунду. Возможность управления импульсами в этом диапазоне позволяет сварщикам значительно снизить среднюю силу тока и тепловложение, что помогает контролировать проплавление и уменьшать искажения.Импульсы на этих более высоких частотах увеличивают фокус дуги за счет быстрых пульсаций между высоким пиковым и низким фоновым током, что позволяет получить большее проникновение, двигаться быстрее и уменьшить зону термического влияния. Испытания показали, что частота импульсов от 250 до 400 импульсов в секунду увеличивает скорость перемещения до 35 процентов без ущерба для проплавления сварного шва.
MIG-процессы развивают и упрощают производство труб из нержавеющей стали
В то время как остаются более толстые трубы высокой чистоты, для которых по-прежнему требуется корень TIG или горячий проход TIG, корневые проходы MIG на нержавеющей стали регулярно сертифицируются для менее критических применений, а в некоторых случаях более ответственных применений, традиционно выполняемых с использованием TIG.Некоторые приложения даже завершаются без помощи обратной продувки, относительно недавняя разработка, ставшая возможной благодаря модифицированному процессу сварки MIG с коротким замыканием, например RMD, доступному с системой сварки труб PipeWorx — хотя это никогда не должно выполняться в приложениях с высокой степенью чистоты. с дуплексными нержавеющими сталями, такими как фармацевтическая, полупроводниковая или пищевая промышленность. Обычной последовательностью сварки на трубе большего диаметра, такой как 12-дюймовая труба сортамента 40, используемая в нефтегазопереработке, является укладка корня RMD с последующим переключением на импульсную сварку MIG (с использованием того же защитного газа и проволоки, что и для корневого прохода) или дуговой сварки порошковой проволокой (FCAW) для заполняющих и закрывающих проходов, что устраняет необходимость в горячем проходе TIG.
RMD представляет собой усовершенствование по сравнению с традиционной сваркой MIG с коротким замыканием в том, что сварочная система предугадывает и контролирует короткое замыкание, а затем снижает сварочный ток для обеспечения стабильного переноса металла. Точно контролируемый перенос металла обеспечивает равномерное осаждение капель и облегчает сварщику управление лужей и, следовательно, подводом тепла и скоростью сварки. Плавный перенос металла компенсирует несоосность между секциями трубы, устраняя несовершенную подгонку трубы в некоторых случаях и создавая более равномерное армирование корня на внутренней стороне трубы.Точно так же защитный газ выходит из пистолета, относительно не нарушенный управляемой передачей, и проталкивается через корневое отверстие, чтобы предотвратить окисление на тыльной стороне. Эта особенность позволила производителям труб сертифицировать процессы без вспомогательного газа в некоторых областях применения аустенитной нержавеющей стали, полностью исключив значительное время и затраты, связанные с обратной продувкой больших труб.
RMD также значительно упрощает обучение новых сварщиков использованию, поскольку контролируемый перенос металла упрощает управление сварочной ванной.Этот процесс также поддерживает постоянную длину дуги независимо от вылета электрода и обеспечивает отличный обзор сварочной ванны. В поисках опытных сварщиков эти функции требуют обучения работе с исторически сложным приложением с нескольких недель до нескольких дней.
Этот процесс позволяет производителям труб увеличить скорость и производительность, не нагревая детали, помогая сохранить коррозионную стойкость и механические свойства, обеспечиваемые нержавеющей сталью.Скорость сварки с этим модифицированным процессом короткого замыкания составляет от 6 до 12 дюймов в минуту (дюйм / мин) по сравнению с 3–5 дюймами в минуту при сварке TIG. Такое увеличение скорости, а также возможность исключить горячий проход TIG и, возможно, исключить резервный газ в некоторых приложениях, обеспечивают значительную экономию времени и средств.
Пониженное тепловложение с помощью RMD также помогает избежать деформации нержавеющей стали по сравнению с другими процессами MIG. Некоторые компании сообщают, что могут использовать процессы изготовления труб, которые ранее были модульными — сборка по частям, а затем объединение для полной сборки для управления подводом тепла — и теперь изготавливать всю конструкцию за один присест из-за более низкого тепловложения и уменьшения деформации.Это упрощает процесс и позволяет собирать его быстрее, что значительно сокращает рабочее время.
Подходящие присадочные металлы к нержавеющей стали
Появление в 1913 году нержавеющей стали обещало лучшую коррозионную стойкость по сравнению с углеродистой сталью. И это удалось, но с некоторыми издержками и проблемами. Оригинальная нержавеющая сталь соответствовала своим требованиям к коррозии, но имела гораздо более низкую пластичность, чем ее стандартный аналог. На протяжении многих лет металлурги экспериментировали с разным количеством легирующих материалов для повышения производительности, но даже сегодня, с развитием технологии производства стали, сварка нержавеющей стали остается сложной задачей.
Хотя техника сварки нержавеющей стали практически не отличается от той, которая используется при сварке стандартной углеродистой стали, есть два исключения. Сварщикам необходимо уделять пристальное внимание нагреву и охлаждению нержавеющей стали. Кроме того, они должны правильно подбирать присадочные металлы с типом свариваемого нержавеющего материала.
ПОНИМАНИЕ ОБЫЧНОЙ НЕРЖАВЕЮЩЕЙ СТАЛИ
Пять видов стали, каждый с многочисленными вариациями, подпадают под действие зонта из нержавеющей стали. Все они классифицируются на основе их микроструктуры — результата как химического состава, так и способа нагрева и обработки стали.Микроструктура оказывает большое влияние на прочность, пластичность и другие физические и химические свойства стали.
В стандартных производственных цехах вы обычно встретите три типа нержавеющей стали: аустенитную, мартенситную и ферритную. Аустенитная нержавеющая сталь является наиболее распространенным типом, используемым в производственных цехах. Обычно ее обозначают как «серия 300». Эта серия не требует предварительного нагрева, но имеет максимальную температуру промежуточного прохода 350 градусов F. И некоторые из нержавеющих сталей серии 300 — 310, 320 и 330 — классифицируются как «полностью аустенитные» и могут быть подвержены растрескиванию, если вы не используйте процесс с низким тепловложением и делайте сварные швы плоскими или вогнутыми вместо выпуклых.
Твердая мартенситная нержавеющая сталь часто используется в областях, связанных с повышенным износом, таких как наплавки и для создания износостойких материалов, и в меньшей степени для соединения. При высокой температуре между проходами крайне важно, чтобы вы достигли точной температуры предварительного нагрева и поддерживали минимальную температуру между проходами в течение всего времени сварки. Если вы этого не сделаете, вы рискуете взломать.
Менее дорогая, чем другие нержавеющие стали, ферритная нержавеющая сталь является фаворитом для расходных материалов, таких как компоненты, используемые в автомобильных выхлопах.Двумя наиболее распространенными марками в этой заявке являются 409 и 439. Поскольку ферритная нержавеющая сталь бывает толщиной ¼ дюйма или меньше, большая часть сварки выполняется за один проход. Сварка ферритной нержавеющей стали наиболее успешна при низком тепловложении и максимальной температуре промежуточного прохода 300 ° F.
Четвертый тип, дуплексная нержавеющая сталь, представляет собой комбинацию микроструктур аустенита и феррита, что делает ее более прочной, чем любой из ее компонентов, но с которой труднее работать. Наконец, дисперсионно-твердеющие нержавеющие стали включают другие легирующие элементы, например ниобий, которые увеличивают как прочность, так и стоимость. Как дуплексная, так и дисперсионно-твердеющая нержавеющая сталь — это специальные типы, используемые в основном в высокопроизводительных приложениях, таких как аэрокосмическая и перерабатывающая промышленность, и мы не будем вдаваться в подробности о них.
СОБИРАЕМ СООТВЕТСТВИЕ
Каждый из трех распространенных типов нержавеющей стали, используемых в промышленных цехах, имеет определенные факторы, которые необходимо учитывать при выборе правильного присадочного металла. Во многом это связано с тепловыми условиями, которые могут определять тип используемого присадочного металла.И во многих случаях сопоставление так же просто, как выбор присадочного металла с тем же номером, что и у основного металла. Так часто бывает, например, с ферритной нержавеющей сталью.
Другие параметры, такие как состав основного материала и присадочного металла, могут немного усложнить этот, казалось бы, простой метод согласования. Например, у вас есть марка нержавеющей стали серии 300 с обозначением «L», например 316L. Этот L показывает, что материал обычно имеет низкое содержание углерода.03 процента углерода. В этом случае вам нужно будет сопоставить номер присадочного металла, 316, но также и L. Таким образом, для нержавеющей стали 316L вам нужно будет использовать присадочный металл с тем же обозначением — 316L.
Но это еще не все. У вас может быть под рукой основной металл 316H, но проволока 316L. Цифры такие же, правда? Это не совпадение. Буква «H» указывает на то, что основной материал имеет высокое содержание углерода. Несмотря на то, что вы можете сварить его с использованием присадочного металла 316L, сварной шов не выдержит, когда свариваемая деталь будет возвращена в эксплуатацию.Или рассмотрим проблему поиска подходящего присадочного металла для аустенитной нержавеющей стали марки 304. Сделать это непросто, потому что присадочного металла 304 не существует. Вместо этого вы должны сопоставить этот материал с присадочным металлом 308L. Его химический состав позволяет присадочному металлу проходить быстрое затвердевание и охлаждение, связанное со сваркой, без образования трещин.
Другой пример, 321 основной металл, включает небольшое количество титана. Однако любой титан в присадочном металле может выгореть в процессе сварки.Таким образом, точное совпадение числа невозможно. Вместо этого, если вы используете присадочный металл 347, вы получите расходный материал, который по химическому составу аналогичен 321, но вместо титана содержит ниобий.
Все становится еще сложнее, когда вы выполняете наплавку или соединяете разнородные металлы. Приложения с использованием мартенситной нержавеющей стали часто попадают в эту категорию. Как и в случае со многими другими разновидностями нержавеющей стали, если вы соединяете мартенситные неблагородные металлы, вы, вероятно, будете использовать присадочный металл с тем же номером.Но иногда для соединения можно использовать присадочный металл из аустенитной нержавеющей стали. Или, для наплавочных работ, которые часто выполняются на углеродистой стали, 410 является стандартным выбором присадочного металла.
ОБРАЩЕНИЕ С СМЕШАННЫМИ ИЛИ НЕИЗВЕСТНЫМИ МАТЕРИАЛАМИ
Иногда вы оказываетесь в ситуации, когда вам нужно сваривать разнородные металлы или неизвестные основные металлы, например, во время ремонта в полевых условиях. Подобрать присадочный металл проще, чем вы думаете. Фактически, присадочные металлы с химическим составом, специально разработанным для таких ситуаций, действительно существуют.Например, нередко соединяют нержавеющую сталь 304L с углеродистой сталью. Для успешной сварки используйте присадочный материал 309L. Обычно это хороший выбор для разнородных металлов при температурах до 750 градусов F.
Если вы совершенно не уверены в составе основного металла, используйте электроды специальной конструкции для ремонта. Универсальный электрод из нержавеющей стали 312, который продается под различными торговыми марками, рекламирующими всестороннюю совместимость расходных материалов, предлагает возможность сварки на все случаи жизни. Его химический состав обеспечивает высокую прочность, коррозионную стойкость и хорошую пластичность. Он также совместим с большинством типов недрагоценных металлов. Эти электроды, как правило, стоят дороже, чем стандартный провод, но их универсальность и производительность окупаются.
В конечном счете, соответствие присадочного металла и основного металла сводится к использованию металла одной марки. А если у вас есть вопросы о составе основного металла, но вам все еще нужно обеспечить качественную сварку, вы можете выбрать один из универсальных специальных электродов, которые помогут вам справиться со своей работой, и сделать это хорошо.Если вы столкнетесь с трудностями при поиске точного соответствия вашим требованиям, ваша компания-поставщик сварочных материалов может помочь вам найти подходящий присадочный металл, соответствующий свариваемому материалу.
[PDF] ЭКСПЕРИМЕНТАЛЬНОЕ ИССЛЕДОВАНИЕ АСПЕКТОВ СВАРКИ АУСТЕНИТНОЙ НЕРЖАВЕЮЩЕЙ СТАЛИ (AISI 304) НА ПРОЧНОСТЬ НА РАЗРЫВ ПО ТЕХНИКЕ TAGUCHI
1 Инт. J. Mech. Англ. И Роб. Рес Мохит Сингмар и Нишант Верма, Исследовательская статья 2015 г. ISSN Vol. 4, No. 1, январь IJ …
Int.J. Mech. Англ. И Роб. Res. 2015Мохит Сингмар и Нишант Верма, 2015 ISSN 2278-0149 www.ijmerr.com Vol. 4, No. 1, январь 2015 © 2015 IJMERR. Все права защищены.
Research Paper
ЭКСПЕРИМЕНТАЛЬНОЕ ИССЛЕДОВАНИЕ АСПЕКТОВ СВАРКИ АУСТЕНИТНОЙ НЕРЖАВЕЮЩЕЙ СТАЛИ (AISI 304) НА ПРОЧНОСТЬ НА РАСТЯЖЕНИЕ ПО ТЕХНИКЕ TAGUCHI Mohit Singhmar1 * и Nishant Verma1
, автор: Целью данного исследования было изучение параметров влияния, влияющих на механические свойства аустенитной нержавеющей стали марки 304 (AISI 304) при газовой дуговой сварке (GMAW).В исследовании применялся метод Тагучи на образце из анаустенитной нержавеющей стали размерами 110 × 40 × 3 мм, который имел следующие интересующие параметры: ток дуги при 150, 200 и 250 А, расход газа при 10, 20 и 30 кг / час. и напряжение дуги 15, 20 и 25 В. Исследование проводилось по следующим аспектам: Предел прочности на разрыв. Настоящая работа направлена на изучение факторов, влияющих на механические свойства аустенитной нержавеющей стали при газовой дуговой сварке (GMAW) при различных параметрах сварки.Ключевые слова: аустенитная нержавеющая сталь (AISI 304), метод Тагучи, предел прочности на разрыв
Фактически, идеальная дуга может быть получена, когда все параметры соответствуют. Такие параметры, как сварочный ток, напряжение дуги и расход газа, в значительной степени влияют на характеристики сварного шва. Поскольку эти факторы могут изменяться в широком диапазоне, они считаются основными при любых сварочных операциях. Их значения следует записывать для каждого типа сварного шва, чтобы обеспечить воспроизводимость.
ВВЕДЕНИЕ Газовая дуговая сварка металла — один из наиболее широко используемых процессов в промышленности. Входные параметры играют очень важную роль в определении качества сварного соединения. Фактически, геометрия сварного шва напрямую влияет на сложность графиков сварки и, следовательно, на стоимость строительства и производства стальных конструкций и механических устройств. Следовательно, эти параметры, влияющие на дугу и сварку, должны быть оценены, а их изменяющиеся условия во время процесса должны быть известны заранее, чтобы получить оптимальные результаты; in 1
GMAW может выполняться тремя различными способами Полуавтоматическая сварка: оборудование контролирует только подачу электродной проволоки.
Кафедра машиностроения, Омский институт технологий и менеджмента, Хисар, Харьяна, Индия.
493
Внутр. J. Mech. Англ. И Роб. Res. 2015
Mohit Singhmar и Nishant Verma, 2015
Таким образом, произведено. Электрод плавится от тепла, и расплавленный присадочный металл попадает на нагретое соединение.
Движение сварочной горелки контролируется вручную. Это можно назвать ручной сваркой. Машинная сварка: используется пистолет, подключенный к какому-либо манипулятору (не ручной). Оператор должен постоянно настраивать и настраивать элементы управления, которые перемещают манипулятор.
Дуга может образовываться между непрерывно подаваемой проволокой и изделием. Непрерывная сварка спиральной проволокой обеспечивает высокую скорость наплавки металла и высокую скорость сварки. Присадочную проволоку обычно подключают к источнику постоянного тока положительной полярности, образующему один из электродов. Заготовка подключена с отрицательной полярностью. Источником питания может быть источник постоянного напряжения постоянного напряжения с положительным электродом, который обеспечивает стабильную дугу и плавный перенос металла с наименьшим разбрызгиванием во всем диапазоне тока.Газовая защита вокруг него не ионизируется, что предотвращает атмосферное загрязнение и окисление поверхности сварного шва. Некоторые горелки имеют системы водяного охлаждения. Сварка МИГ также называется дуговой сваркой металла в газовой среде. Присадочный металл передается от электрода к стыку разными способами. Это зависит от тока, проходящего через электрод, и напряжения.
Автоматическая сварка: Использует оборудование, которое выполняет сварку без постоянной регулировки органов управления сварщиком или оператором. На некотором оборудовании автоматические датчики контролируют правильное выравнивание пистолета в сварном шве.Принцип работы сварки MIG. Как показано на рисунке 1, электрод в этом процессе имеет форму проволоки и непрерывно подается на работу во время процесса. В то же время инертный газ (например, аргон, гелий или др.) Проходит вокруг электрода от той же горелки. Для предотвращения контакта атмосферы с расплавленным металлом и зоной термического воздействия (HAZ) используется инертный газ, обычно аргон, гелий или подходящая их смесь. Когда подается газ, он ионизируется, и между электродом и заготовкой возникает дуга.Heat is
Сварка GMAW / MIG
Рис. 1: Принципы работы GMAW
MIG может работать в полуавтоматическом, машинном или автоматическом режимах. Все коммерчески важные применимые металлы, такие как углеродистая сталь, высокопрочная, низколегированная сталь и нержавеющая сталь, алюминий, медь, титан и никелевые сплавы, могут быть сварены во всех положениях с помощью этого процесса путем выбора подходящего защитного газа, электрода и др. и параметры сварки. Влияние параметров сварки MIG На качество сварки и скорость наплавки очень сильно влияют различные параметры сварки и геометрия соединения.По сути, сварное соединение может быть выполнено различными 494
Int. J. Mech. Англ. И Роб. Res. 2015
Mohit Singhmar and Nishant Verma, 2015
сочетания параметров сварки, а также геометрии стыков. Эти параметры являются переменными процесса, которые контролируют скорость наплавки и качество сварки. Геометрия сварного шва, глубина проплавления и общее качество сварного шва зависят от следующих рабочих параметров.
параметров, идентифицированных с помощью анализа S / N.Подтверждающий тест был проведен в оптимальных условиях, чтобы гарантировать правильность анализа. Омар Батаине и Омар Баркави определили и оптимизировали основные факторы, которые оказывают значительное влияние на прочность сварного соединения, с помощью экспериментов по факторному проектированию. Сварочные эксперименты проводились с использованием процесса MIG Welding, в качестве плавящегося электрода использовалась присадочная проволока ER1100 диаметром 1,2 мм. В качестве защитного газа использовался аргон 100% -ной чистоты. Образцы для испытаний состояли из двух частей каждая, каждая из которых имела размер 100 мм × 50 мм × 8 мм и была сделана из алюминиевого сплава 1070.
• Размер электрода, сварочный ток, напряжение дуги • Скорость движения дуги, положение сварки • Скорость потока газа, состав защитного газа • Удлинение электрода (длина вылета) • Скорость подачи проволоки
ОБЗОР ЛИТЕРАТУРЫ
Факторы, которые были изучены — напряжение дуги, скорость подачи присадки, расход газа, угол кромки образца и температура предварительного нагрева. Результаты экспериментов по факторному дизайну и дисперсионного анализа (ANOVA) показали, что напряжение дуги и скорость подачи наполнителя являются единственными значимыми факторами из пяти.Оптимальные настройки напряжения дуги и скорости подачи присадки были достигнуты с помощью регрессионного анализа при 24 В и 7 дюймов / с, соответственно, при которых средняя прочность сварного шва является максимальной (Aagakhani et al., 2011).
Haragopal et al. (2011) представили метод разработки параметров процесса, оптимизирующих механические свойства сварного образца из алюминиевого сплава (Al-65032), используемого для строительства аэрокосмических крыльев. Параметры процесса, рассматриваемые для исследования, включали давление газа, ток, угол канавки и температуру предварительного нагрева.Параметры процесса задавались для каждого эксперимента. Эксперименты проводились на ортогональной решетке L9. Получено оптимальное сочетание параметров процесса. Наряду с этим, также была проведена идентификация параметров, оказавших наибольшее влияние. Это было выполнено с использованием анализа S / N, анализа среднего отклика и ANOVA. Были получены механические свойства, полученные для трех образцов каждого цикла. Отношение сигнал / шум для каждого отношения качества (S / N) для каждой характеристики качества было вычислено, значимые параметры были определены, и оптимальный входной параметр для каждой характеристики качества был спрогнозирован на основе значений S / N и среднего отклика.Дисперсионный анализ (ANOVA) подтвердил значимость
Иззатулайни Ибрагим, Сярулашрафмохамат, Амалина Амир провели эксперименты по влиянию различных параметров на сварку. Рисунок 2: Геометрия соединения для сварочных образцов
495
Int. J. Mech. Англ. И Роб. Res. 2015
Mohit Singhmar and Nishant Verma, 2015
Измерения проплавления, микроструктуры и твердости были измерены в низкоуглеродистой стали с толщиной основного металла 6 мм с помощью роботизированной газовой дуговой сварки металла. Переменными параметрами являются напряжение дуги, сварочный ток и скорость сварки. Плавность, микроструктура и твердость были измерены для каждого образца после процесса сварки, и было изучено влияние на него. В результате очевидно, что увеличение значения параметра сварочного тока увеличивает значение глубины проплавления. Помимо этого, еще одним фактором, влияющим на значение глубины проплавления, является напряжение дуги и скорость сварки. В этих экспериментах используется 100% защитный газ и проволочный электрод ER70S 6 с 1.Расстояние от сопла 2 диаметра до рабочей поверхности составляет 12 мм и выполняется только один проход на сварной пластине. На рисунке влияние сварочного тока на проплавление присутствовало при постоянной скорости сварки 20 см / мин, а значение проплавления было увеличено за счет увеличения значения сварочного тока 90, 150 и 210 А. Наибольшее провар составляет 2,98 мм при сварке. 22 В и 210 А. Скорость сварки была постоянной, равной 40 см / мин, а значение проплавления было увеличено за счет увеличения значения сварочного тока на 90, 150 и 210 А. Наибольшее провар — 3.26 мм при 22 В и 210 А. Изменение значения глубины проплавления аналогично при напряжении 26 В и 30 В. Скорость сварки оставалась постоянной, равной 60 см / мин, а значение проплавления было увеличено за счет увеличения значения сварочный ток 90, 150 и 210 А. Наибольшее провар составляет 2,79 мм при 26 В и 210 А (Ashok Mishra et al., 2012).
обсуждались. Влияние конструкции инструмента, скорости вращения инструмента и скорости перемещения инструмента на механические свойства было проанализировано с использованием методики моделирования экспериментов с ортогональным массивом Тагучи.Исследование показывает, что конструкция инструмента является основным параметром процесса, который имеет наибольшее статистическое влияние на механические свойства. Однако другие параметры, такие как скорость вращения инструмента и скорость перемещения инструмента, также оказывают значительное влияние на механические свойства (Sandip Bhattacharya et al. , 2011). Хуанг и Тарнг используют метод Тагучи для анализа геометрии сварочной ванны при сварке нержавеющей стали вольфрамовым электродом в среде инертного газа (TIG). Были выбраны входные параметры: высота лицевой стороны, высота спинки, ширина лицевой стороны и ширина спинки.Модифицированный метод Тагучи применяется для определения оптимальной геометрии сварочной ванны с четырьмя характеристиками качества «меньше — лучше». Результаты экспериментов показали, что качественные характеристики, т. Е. Высота фасада; При использовании этого подхода значительно улучшаются передняя ширина, задняя высота и задняя ширина сварочной ванны при сварке TIG нержавеющей стали (Abbasi et al., 2011).
ВЫБОР МАТЕРИАЛА Аустенитная сталь — наиболее широко используемый тип нержавеющей стали. Он имеет содержание никеля не менее 7%, что делает структуру стали полностью аустенитной и придает ей пластичность, широкий диапазон рабочих температур, немагнитные свойства и хорошую свариваемость.Область применения аустенитной нержавеющей стали включает изделия для дома, контейнеры, промышленные трубопроводы и сосуды, архитектурные фасады и строительные конструкции.
Ваг и Пандья изучали влияние параметров процесса сварки трением с перемешиванием на механические свойства соединений из сплава AA 2014-T6, полученных сваркой трением с перемешиванием 496
Int. J. Mech. Англ. И Роб. Res. 2015
Mohit Singhmar and Nishant Verma, 2015
При сварке нержавеющих сталей рекомендуется следовать общим правилам сварки, действующим для данного типа стали, например.g., аустенитные нержавеющие стали из-за своего химического состава имеют более высокое термическое удлинение по сравнению с мягкими сталями. Это может увеличить деформацию сварного шва. В зависимости от микроструктуры металла сварного шва они также могут быть более чувствительными к образованию горячих трещин и интерметаллическим выделениям по сравнению с мягкими сталями.
Таблица 1: Химический состав для 304 C Состав
Аустенитные сорта — это сплавы, которые обычно используются для нержавеющих сталей. Аустенитные марки немагнитны.Наиболее распространенными аустенитными сплавами являются железо-хромоникелевые стали, широко известные как серия 300. Аустенитные нержавеющие стали из-за высокого содержания хрома и никеля являются наиболее устойчивыми к коррозии из группы нержавеющих сталей, обеспечивая необычайно прекрасные механические свойства. Их нельзя упрочнить термической обработкой, но можно значительно упрочнить путем холодной обработки.
Тип 304%
Углерод
0,08 макс.
Марганец
2,00 макс.
Фосфор
0.045 макс.
Сера
0,030 макс.
Кремний
0,75 макс.
Хром
18.00-20.00
Никель
8.00-10.05
Азот
0,10 макс.
• Нержавеющая сталь имеет плохие характеристики стружкодробления. Поскольку нержавеющая сталь классифицируется по различным категориям, таким как аустенитная, ферритная, мартенситная и т. Д., Мы выбрали аустенитную нержавеющую сталь (304) из-за ее низкой стоимости и доступности в рынок и широкое применение.
МЕТОД ТАГУЧИ Планирование эксперимента Тагучи является одним из широко используемых методов. Метод Тагучи предполагает уменьшение вариативности процесса за счет надежного планирования экспериментов. Общая цель метода — производить продукт высокого качества по низкой цене для производителя. Метод Тагучи был разработан Геничи Тагучи из Японии, который поддержал этот вариант. Тагучи разработал метод планирования экспериментов, чтобы исследовать, как различные параметры влияют на среднее значение и дисперсию характеристики производительности процесса, которая определяет, насколько хорошо этот процесс функционирует.План эксперимента, предложенный Тагучи, включает использование ортогональных массивов для организации параметров, влияющих на процесс, и уровней, на которых они должны варьироваться.
Особые свойства материала нержавеющей стали влияют на все четыре фактора обрабатываемости: в целом можно сказать, что чем выше содержание сплава в нержавеющей стали, тем сложнее ее обрабатывать. Особые свойства, затрудняющие обработку нержавеющей стали, в большей или меньшей степени проявляются у всех марок нержавеющих сталей, но наиболее заметны у аустенитных марок.Их можно резюмировать по пяти пунктам: • Нержавеющие стали значительно затвердевают • Нержавеющие стали имеют низкую теплопроводность Нержавеющие стали обладают высокой вязкостью • Нержавеющие стали имеют тенденцию к липкости 497
Int. J. Mech. Англ. И Роб. Res. 2015
Mohit Singhmar and Nishant Verma, 2015
Ортогональный массив — это метод планирования эксперимента, который обычно требует лишь части полных факторных комбинаций. Ортогональный массив означает, что план сбалансирован, так что уровни факторов взвешиваются одинаково.Благодаря этому каждый фактор можно оценивать независимо от всех других факторов, поэтому влияние одного фактора не влияет на оценку другого фактора.
• Выбор качественных характеристик • Выбор ортогонального массива • Выбор основного металла и присадочного материала • Подготовка образца стальной пластины • После выполнения операции GMAW образцы были вырезаны из сварной пластины для проведения различных испытаний. Тесты, проведенные для достижения цели:
Таблица 2: Ортогональная матрица L-9 S.№
A
B
C
1.
1
1
1
2.
1
2
2
3.
3
4.
2
1
2
5.
2
2
3
6.
2
3
1
7.
3
8.
3
2
1
9.
3
3
2
• Испытание на растяжение на UTM
ЭКСПЕРИМЕНТ Эксперименты проводились с использованием источника питания Auto K 400 и ручной сварочной установки. В сварочном аппарате предусмотрены автоматические устройства подачи проволоки. Для экспериментов настраиваются разные параметры. Экспериментальные параметры
Отношение сигнал / шум
Входные параметры
Отношение сигнал / шум (S / N) было получено с использованием методологии Тагучи. «Сигнал» — это желаемое значение (среднее значение), а «шум» — это нежелательное значение (стандартное отклонение). Таким образом, отношение сигнал / шум представляет собой величину отклонения, присутствующего в характеристике производительности. В зависимости от цели характеристики производительности могут быть различные типы отношений сигнал / шум. Есть 3 отношения сигнал / шум, представляющих общий интерес для оптимизации.
1. Сварочный ток 2. Сварочное напряжение 3. Расход газа Выходные параметры 1. Предел прочности на разрыв Подготовлен сварочный образец для изготовления сварных соединений MIG Образец AS 304 размером 110 мм x 40 мм x 3 мм Таблица 3: Параметры сварки и их уровни
МЕТОДОЛОГИЯ Ниже приведены шаги, которые были выполнены для достижения цели:
Параметры
• Выбор параметров процесса и их уровней
Блок
Уровень 1
Уровень 2
Уровень 3
Текущий
Ампер
150
200
250
Напряжение
Вольт
15
20
25
кг / ч
10
20
20
30
Внутр.J. Mech. Англ. И Роб. Res. 2015
Mohit Singhmar and Nishant Verma, 2015
экспериментальные значения преобразуются в отношение сигнал / шум. Влияние управляющих параметров, таких как ток дуги, напряжение дуги и расход газа, на прочность на разрыв было проанализировано с использованием таблицы отклика для отношения сигнал / шум.
Таблица 4: Ортогональный массив L-9 после назначения параметров Exp. №
Ток (А)
Напряжение (В)
Расход газа (кг / ч)
1.
150
15
10
2.
150
20
20
3.
150
25
30
4.
200
5.200
20
30
6.
200
25
10
7.
250
15
30
8.
250
9.
250
25
20
В таблицах ответов показано среднее значение каждой характеристики ответа (отношения сигнал / шум) для каждого уровня каждого фактора. Таблицы включают ранги, основанные на статистике Дельта, которые сравнивают относительную величину эффектов. Дельта-статистика — это наивысший минус наименьшее среднее значение для каждого фактора. Minitab присваивает ранги на основе значений Delta; ранг 1 соответствует наивысшему значению дельты, ранг 2 — второму по величине и так далее. Используйте средние значения уровней в таблицах ответов, чтобы определить, какой уровень каждого фактора обеспечивает лучший результат.
рассматривался для сварки с разными параметрами. Сварка производилась на сварочном аппарате МИГ. Эксперименты проводились по методу Тагучи.
РЕЗУЛЬТАТЫ И ИХ ОБСУЖДЕНИЕ
Таблица 5: Результаты ортогональной матрицы L9 для прочности на растяжение
Целью экспериментального плана является определение влияния параметров сварной конструкции, влияющих на предел прочности при растяжении. Эксперименты были разработаны на основе ортогонального массива с целью соотнести влияние сварочного тока, напряжения дуги и расхода газа.Эти проектные параметры являются отличительными и неотъемлемыми характеристиками процесса, которые влияют и определяют характеристики композита.
Предел прочности при растяжении газа (кг / ч) (МПа)
Exp. №
Ток (А)
Напряжение (В)
1.
150
15
10
385,69
51.7248
2.
150
20
53.0174
3.
150
25
30
571.95
55.1472
4.
200
15
20
536.97
54.5990
5.
200
20
30
561.9000
561.9000
25
10
636,92
56,0817
Результаты статистического анализа экспериментов
7.
250
15
30
546,66
54.7543
8.
250
20
10
538,42
54,6224
Результаты для различных комбинаций параметров были получены путем проведения эксперимента по ортогональному массиву. Результаты измерений были проанализированы с использованием коммерческого программного обеспечения MINITAB 15, специально используемого для разработки экспериментальных приложений. Для измерения качественных характеристик используется
9.
250
25
20
486.22
53,7367
Отношение сигнал / шум
Анализ Иитагучи для прочности на разрыв В таблице 6 показан экспериментальный анализ прочности на разрыв. В нашем экспериментальном анализе ранги показывают, что ток имеет наибольшее влияние как на отношение сигнал / шум, так и на среднее значение. 499
Внутр. J. Mech. Англ. И Роб. Res. 2015
Mohit Singhmar and Nishant Verma, 2015
Цель состоит в том, чтобы увеличить предел прочности на разрыв, нам нужны уровни факторов, которые дают наивысшее среднее значение.В экспериментах Тагучи мы всегда хотим максимизировать отношение сигнал / шум. Средние значения уровней в таблицах отклика показывают, что отношения сигнал / шум и средние значения были максимальными, когда расход газа составлял 30, напряжение дуги составляло 20, а ток дуги составлял 200.
Таблица 6: Таблица отклика для отношения сигнал / шум Коэффициент (прочность на разрыв, чем больше, тем лучше) Напряжение дуги
Расход газа
Уровень
Ток дуги
1
53,30
53,69
54,14
2
55.22
54,21
53,78
3
54,37
54,99
54,96
Дельта
1,93
1,30
1,18
000 3
000 3
000 Анализ
000 3 Отношение / N (предел прочности на разрыв)
Для отношения сигнал / шум, напряжение дуги имеет следующее наибольшее влияние, за ним следует скорость потока газа. Значит, напряжение дуги имеет следующее наибольшее влияние, за ним следует скорость потока газа. Здесь, потому что наш
Таблица 7 показывает результат дисперсионного анализа (ANOVA) для прочности на разрыв.Дисперсионный анализ проводился с доверительной вероятностью 95%. Основная цель дисперсионного анализа — исследовать влияние проектных параметров на предел прочности при растяжении путем указания того, какие параметры существенно влияют на качественные характеристики.
Рисунок 3: График основных эффектов для отношения сигнал / шум — прочность на разрыв
Целью дисперсионного анализа является исследование того, какие параметры процесса сварки существенно влияют на характеристики качества. Это достигается путем разделения общей изменчивости отношения сигнал / шум, которая измеряется суммой квадратов отклонений от общего среднего значения отношения сигнал / шум, на вклад каждого параметра процесса сварки и ошибки.Процентный вклад каждого из параметров процесса сварки в общую сумму квадратов Таблица 7: Анализ дисперсии для отношения сигнал / шум Источник
DF
Seq SS
Adj SS
Adj MS
F
P
% Вклад
Ток дуги
2
5.602
5.602
2.801
1,86
0,350
41
Напряжение дуги
2
2.552
2,552
1,276
0,85
0,542
20
Расход газа
2
2,198
2,198
1,099
0,73
000
0,73
3,015
3,015
1,507
Всего
8
13,367
500
23
Внутр. J. Mech. Англ. И Роб. Res. 2015
Mohit Singhmar and Nishant Verma, 2015
Прочность аустенитной нержавеющей стали (AISI 304).
Рисунок 4: Круговая диаграмма для% возрастного вклада различных параметров в предел прочности на растяжение
ОБЪЕМ БУДУЩИХ РАБОТ В этом исследовании представлен эффективный метод определения оптимальных параметров дуговой сварки металлическим газом для повышения свариваемости аустенитной нержавеющей стали (AISI 304) при меняющиеся условия за счет использования процесса расчета параметров Тагучи. Этот процесс применялся с использованием определенного набора элементов управления и переменной отклика прочности на разрыв. Использование ортогонального массива L9 (3 3) с тремя управляющими параметрами (ток дуги, напряжение дуги и расход газа), используемое для этого исследования, должно проводиться с образцом из 9 деталей.
отклонений можно использовать для оценки важности изменения параметра процесса для характеристики качества.
Он также проводится для других материалов из нержавеющей стали с большим количеством управляющих факторов и по сравнению с нержавеющими сталями AISI, чтобы рекомендовать, какой материал является подходящим процессом, рекомендовать процесс с минимальными затратами и максимальной прибылью для организации и минимизировать дефекты сварных швов, поскольку а также проблемы со сваркой для дальнейшей работы.
Из рисунка 4 можно сделать вывод, что ток дуги значительно влияет на предел прочности на разрыв с вкладом 41%, за которым следует напряжение дуги с вкладом 20% и расход газа с вкладом 16%.
ЗАКЛЮЧЕНИЕ Настоящее исследование может быть заключено в следующие этапы:
СПИСОК ЛИТЕРАТУРЫ
1. Методика экспериментов Тагучи может быть очень эффективно использована при оптимизации параметров сварки в производственных операциях.
1. Аагахани М., Мехардад Э. и Хаяти Э. (2011), «Параметрическая оптимизация процесса GMAW с помощью метода Тагаучи на глобальном уровне», Журнал моделирования и оптимизации, Vol. 1, № 3.
2.Ток дуги имеет наибольшее влияние на предел прочности при растяжении с вкладом 41%, за ним следует напряжение дуги с вкладом 20% и расход газа с вкладом 16%.
2. Аббаси К., Алам С. и Хан М. И. (2011), «Экспериментальное исследование влияния повышенного давления на сварочную дугу MIG», Международный журнал прикладных инженерных исследований, Vol. 2, № 1, Диндигул.
3. Таким образом, план экспериментов методом Тагучи был успешно использован для определения оптимальных параметров сварки для Tensile 501
Int. J. Mech. Англ. И Роб. Res. 2015
Мохит Сингмар и Нишант Верма, 2015
3. Ашок Кр. Мишра, Ракеш Шеок и Шривастава Р.К. (2012), «Трибологическое поведение металлического матричного композита Al-6061 / SiC по методам Тагучи», Международный журнал научных и исследовательских публикаций, Vol. 2, № 10, ISSN: 2250-3153.
9. Ганджигатти Дж. П., Пратихар Д. К. и Рой Чоудхури А. (2008 г.), «Моделирование процесса сварки MIG с использованием статистических подходов», Международный журнал передовых производственных технологий, Vol.35, ноябрь, стр. 1166-1190. 10. Гарг М. П., Сарбджит Сингх и Джодх Сингх (2011), «Экспериментальное исследование механических свойств сварных швов MIG пластин из легированного сплава», Journal of Engineering and Technology, Vol. 1, No. 2, июль-декабрь.
4. Баппа Ачерджи, Сурен Митра, Арунаншу С. Куар и Диптен Мишра (2009 г.), «Использование функции потери качества Тагаучи для оптимизации характеристик качества с использованием процесса лазерной передачи и сварки термопластов», Технический журнал ASME Early Career, ASME.
11. Харагопал Г., Равиндра Редди П. В. Р., Чандра Мохан Редди Г. и Субраманьям Дж. В. (2001), «Параметрический расчет для MIG-сварки сплава Al-65032 с использованием метода Тагаучи», Журнал научных и промышленных исследований, Vol. 70, October, pp. 844-850.
5. Беньюнис К. И. и Олаби А. Г. (2008), «Оптимизация различных процессов сварки с использованием статистических и численных подходов — справочное руководство», «Достижения в инженерном программном обеспечении», Vol. 39, March, pp. 483-496, Elsevier.
12.Хер-Юэ Хуанг (2010), «Влияние активирующего флюса на сварочные характеристики в GMAW», Vol. 31, ноябрь, стр. 2488-2495, Elsevier.
6. Эмили Ле Гуен, Мюриэль Карин и Реми Фаббро (2011 г.), «Трехмерная модель теплопередачи гибридной лазерной сварки стали S355 и экспериментальная проверка», Международный журнал тепломассопереноса, Vol. 54, декабрь, стр. 1313-1322.
13. Ханна О.П. (2000), Технология сварки, Публикации Дханпат Рай.
7. Фархад Кохалан и Мехди Хейдари (2010 г.), «Новый подход к прогнозированию и оптимизации геометрии сварного шва в GMAW», Международный журнал науки и инженерии механических систем, том.2.
14. Кишор К., Гопал Кришна П. В., Веладри К. и Сайед Касим Али (2010), «Анализ дефектов дуговой сварки в среде защитного газа стали AISI 1040 с использованием метода Тагаучи», Журнал инженерных и прикладных наук ARPN, Vol. 5, No. 1.
8. Ганджигатти Дж. П., Дилип Кумар Пратихар и Рой Чоудхури А. (2006 г.), «Кластерный регрессионный анализ Global Verses для прогнозирования геометрии шва в процессе сварки MIG», декабрь, Elsevier.
15. Ленин Н., Шива Кумар М. и Винешкумар Д. (2010), «Оптимизация параметров процесса при дуговой сварке разнородных металлов», ThammasatInt.J. Sc. Tech., Vol. 15, No. 3. 502
Внутр. J. Mech. Англ. И Роб. Res. 2015
Мохит Сингхмар и Нишант Верма, 2015
21. Сатоши Ямане, Такуя Ямадзаки, Томоаки Канета и Тору Наказима (2011), «Экспериментальное и численное моделирование температурного распределения и деформации сварного шва при сварке GMA», Журнал Японского сварочного общества , Vol. 29.
16. Современные технологии дуговой сварки, Публикация Ador Welding. 17. Росс П. Дж. (1996), «Методы Тагучи для инженерии качества», Макгроу Хилл, Нью-Йорк.18. Рой Р. К. (1990), «Учебник по методу Тагучи», Ван Ностранд Рейнхольд, Нью-Йорк.
22. Сухомай Пал, Сантош К. Мальвия и Сурджа К. Пал (2009), «Оптимизация параметров характеристик качества в импульсном процессе GMAW с использованием метода Тагаучи на основе серого», Международный журнал передовых производственных технологий, Vo l. 4 4, Январь, стр. 1250–1260.
19. Сандип Бхаттачарья, Камал Пал и Сурджья К. Пал (2012), «Прогнозирование осаждения металлов в импульсном GMAW с использованием различных моделей мягких вычислений на основе нескольких датчиков», Applied Soft Computing, Vol. 12, август, стр. 498-505, Elsevier.
23. Суреш Кумар Л., Верма С.М., Киран Кумар П. и Шива Шанкер Т. (2011), «Экспериментальное исследование сварочных аспектов AISI 304 и 316 с помощью техники Tagauchi для процесса сварки TIG и MIG», Международный инженерный журнал Тенденции и технологии, Vol. 2, No. 2.
20. Санджай Кумар, Шриниваса Рао П. и Рамакришна А. (2011), «Влияние эксцентриситета и скорости вращения дуги на геометрию сварного шва в импульсной GMAW сплава 5083», Журнал исследований в области машиностроения, Vol.3, No. 6, pp. 186-196.
503
Сварка нержавеющей стали Orange County — 17-4, 304 и 316L
Pendarvis Manufacturing располагает собственным оборудованием и квалифицированным персоналом для сварки широкого спектра материалов, включая нержавеющую сталь. Мы способны сваривать различные формы, такие как каналы, стержни, листы, уголки, пластины и трубки. Как опытный сварщик из Калифорнии, мы можем выполнять сварку нержавеющей стали на компонентах, деталях и узлах от 10 тонн до 10 тонн, которые поместятся на ладони вашей руки.
Марки нержавеющей стали, такие как 304L и 316L, легко поддаются сварке и обладают очень хорошей прочностью, что делает их отличными кандидатами для многих применений при сварке нержавеющей стали. Нержавеющая сталь 17-4 использовалась в проектах, требующих специальной термической обработки после завершения сварки. В Pendarvis Manufacturing нержавеющая сталь сваривается дуговой / стержневой сваркой или сваркой TIG.
ЗАПРОСИТЬ ИНФОРМАЦИЮ ПО сварке нержавеющей стали
Применение сварки нержавеющей стали
За последние 10–20 лет в мире наблюдался взрывной рост применения нержавеющей стали.По мере того, как во всем мире росли рынки для использования нержавеющей стали, растет и доступность материалов из нержавеющей стали. В настоящее время Индия и Россия являются крупнейшими производителями сырья для производства нержавеющей стали.
Некоторые примеры продукции, производимой Pendarvis Manufacturing с использованием сварки нержавеющей стали:
- Транспортная промышленность — различные узлы, используемые внутри железнодорожных вагонов для сбора жидких отходов, изготавливаются из тонколистовой нержавеющей стали.
- Очистка сточных вод — из-за свойств коррозионной стойкости узлы из нержавеющей стали используются во всех отраслях очистки сточных вод.
- Промышленность чистой воды — компоненты технологических трубопроводов и конструкции, используемые для удержания компонентов, собранных на заводах, создающих чистую воду.
- Строительные компоненты — опорные плиты, используемые в основе строительного проекта.
В дополнение к нашим услугам по сварке MIG и TIG, у нас есть и другие внутренние услуги, в том числе услуги по отливке стекла, электрике, окраске и сантехнике.
Выбор лучших марок стали
Что делает нержавеющую сталь пригодной для сварки? Секрет в соотношении сплавов.
Для качественной сварки необходим материал высокого качества. Свариваемость . Свариваемость зависит от химического состава металла. Например, стали с более высоким содержанием углерода не так хорошо свариваются из-за их низкой пластичности.
Итак, какие типы нержавеющей стали следует использовать при сварке? Давайте взглянем.
Виды нержавеющей стали для сварки
При выборе подходящей нержавеющей стали для вашего проекта необходимо учитывать, будет ли она свариваться. Различные типы нержавеющей стали по-разному реагируют на сварку. Некоторые из них лучше других подходят для этого типа изготовления.
Вот основные виды нержавеющей стали и их свойства.
Аустенитный
Аустенитная нержавеющая сталь — лучший вариант для сварки. Они содержат низкое содержание углерода, что означает, что они более пластичны.Более высокая пластичность означает лучшую свариваемость.
Они также имеют самый высокий уровень хрома, что делает их самыми блестящими и долговечными. Аустенитные стали являются наиболее распространенными нержавеющими сталями во всех отраслях промышленности и лучше всего подходят для высококоррозионных сред. В эту категорию входят обычные и прочные марки 304 (L), 316 (L) и 347. Вот полный список:
-201
-202
-301
-302
-303
-304 / л
-305
-309S
-310S
-316 / L
-317 / LMN
-321
-347
Мартенситный
Мартенситные стали являются вторым лучшим вариантом, хотя их состав может потребовать предварительной и послесварочной обработки.По химическому составу они находятся между аустенитными и ферритными сталями по содержанию углерода и хрома. Martensitics включает популярную и блестящую серию 400.
-403
-410
-416
-420 / F
-440 / A / C / F
Ферритный
Ферритные стали не подходят для сварки. Они имеют более высокий уровень углерода, что вызывает низкую пластичность, высокий рост зерна и сенсибилизацию. Ферритные стали не такие блестящие из-за большего количества углерода и более низкого содержания хрома.
-405
-430 / F
-439
-442
-446
Дуплекс
Дуплексные нержавеющие сталиотлично подходят для сварки, и их популярность в последние годы растет. Дуплексы представляют собой сочетание ферритных и аустенитных сталей. По химическому составу они ближе к аустенитам, но обладают более высоким пределом текучести и большей устойчивостью к нагрузкам.
-LDX 2101
-LDX 2404
-DX 2202
-RDN 903
-2304
-2205
-2507
-Zeron 100
-Ferrinox 205 / Uranus 2507Cu
Выбирайте нержавеющую сталь с умом!
Это самый тонкий вопрос о том, как выбрать материал для сварки нержавеющей стали. Если ваша область применения связана с большим количеством сварочных работ, выберите нержавеющую сталь с высоким соотношением хрома и углерода . Аустенитная серия — ваш лучший выбор.
Почему нержавеющая сталь ржавеет после сварки?
Нержавеющая сталь | Понедельник, 10 апреля 2017
Агрессивные условия вызывают ржавчину на нержавеющей стали
Хотя нержавеющая сталь действительно подвержена коррозии, важно отметить, что сплав не ржавеет в нормальных атмосферных условиях или на водной основе.
Другими словами, коррозия нержавеющей стали происходит в особых агрессивных условиях , которые способствуют коррозии.
Основные типы нержавеющей стали, такие как 304 и 316, могут легче подвергаться коррозии в определенных средах, и тогда можно использовать более высоколегированную нержавеющую сталь.
Следовательно, использование основных форм из нержавеющей стали не рекомендуется в более агрессивных условиях.
Чтобы гарантировать, что изделие или конструкция из нержавеющей стали остаются неповрежденными, неповрежденными и неповрежденными в более неблагоприятных условиях, в требуется использование высоколегированной нержавеющей стали.
Коррозионная стойкость количественная
Другими словами, нержавеющая сталь более или менее устойчива к коррозии и очень хорошо работает практически в любой среде.
Характеристика коррозионной стойкости как качественная, так и количественная .
Каждый тип нержавеющей стали имеет определенную степень коррозионной стойкости . Как только предел прочности будет превышен, обязательно произойдет образование ржавчины.
Предел коррозионной стойкости нержавеющей стали определяется в первую очередь тем, что в первую очередь используется при производстве нержавеющей стали. Это означает, что предел сопротивления зависит от составляющих элементов.
В результате этого нержавеющая сталь разных сортов по-разному реагирует, когда их оставляют в среде, способствующей коррозии.
Марка нержавеющей стали — не единственный способ судить о ее коррозионной стойкости.
Детализация и качество изготовления каждой нержавеющей стали имеет большое значение в , решая, насколько уязвимой будет сталь к появлению пятен и коррозии.
6 Общие типы и формы коррозии нержавеющей стали
Понимание механизмов коррозии нержавеющей стали помогает нам понять, почему нержавеющая сталь ржавеет. Механизмы коррозии нержавеющей стали можно условно разделить на 6 категорий. Их:
a) Питтинговая коррозия
Это локализованная версия коррозии, которая возникает в нержавеющей стали, когда она подвергается воздействию окружающей среды, содержащей хлориды.
б) Щелевая коррозия
Это еще одна форма локальной коррозии, которая возникает, когда уровень кислорода в щели чрезвычайно низок. Этот конкретный тип коррозии не представляет большой проблемы, если нержавеющая сталь не находится в застойном растворе, где могут накапливаться хлориды.
c) Биметаллическая коррозия
Когда разнородные металлы в общем электролите контактируют с другим, может иметь место биметаллическая коррозия, также известная как гальваническая коррозия.Самый распространенный сценарий — коррозия нержавеющей стали под дождем.
d) Коррозионное растрескивание под напряжением
Растягивающие напряжения в сочетании с конкретными условиями окружающей среды приводят к коррозионному растрескиванию под напряжением.
д) Общая коррозия
Когда нержавеющая сталь имеет значение pH менее 1, имеет место общая коррозия.
е) Межгранулярная атака
Когда аустенитная нержавеющая сталь нагревается до температуры от 450 до 850 градусов Цельсия, углерод в стали превращается в границы зерен, что приводит к коррозии.
Удаление и предотвращение ржавчины на сварных швах из нержавеющей стали
Сварка — один из самых распространенных видов металлообработки.
Несмотря на то, что этот процесс полезен, он может серьезно повредить антикоррозионные свойства поверхностей из нержавеющей стали.
Плавление в результате высоких температур во время сварки лишает сталь защитного слоя и, следовательно, присущей способности противостоять коррозии.
По этой причине важно уделять одинаковое внимание двум связанным, но немного различным процессам:
- Удаление ржавчины, перекрестного загрязнения и тепловых оттенков — Если ржавчина уже появилась на сварном шве, необходимо полностью удалить ее, но также важно избавиться от всех загрязняющих частиц, которые образуются в результате промышленной обработки металлов.Кроме того, необходимо удалить тепловые оттенки, которые появляются вокруг сварного шва и в зоне термического влияния.
- Репассивация поверхности — В нормальных условиях защитный пассивный слой самовосстанавливается при незначительном повреждении. Однако обычно этого не происходит при обсуждении побочных эффектов сварки и других форм металлообработки. Следовательно, ваше вмешательство в имеет важное значение для предотвращения будущей коррозии .
Но что именно вы можете сделать для эффективной очистки сварных швов и достижения поверхностной (ре) пассивации?
К счастью, теперь может выполнять обе задачи одновременно, , используя метод электрохимической очистки сварных швов .
Чем отличается (и лучше) электрохимическая очистка сварных швов от аналогичных методов?
Традиционные методы очистки сварных швов, такие как химическое травление и абразивное шлифование, связаны с рядом проблем безопасности и производительности .
Из-за использования токсичных кислот химическая очистка сварных швов считается опасностью как для окружающей среды, так и для человеческого организма. Строгие правовые нормы, регулирующие использование и утилизацию опасных травильных кислот, существенно усложняют весь процесс.
Кроме того, этот метод не подходит для очистки поверхностей из нержавеющей стали, которые предназначены для контакта с пищевыми продуктами, водой и другими «чувствительными» материалами, где загрязнение любого рода просто недопустимо.
Ручное шлифование часто бывает слишком трудоемким и может вызвать значительный шум и загрязнение воздуха. Однако наибольшее беспокойство вызывает отсутствие репассивации поверхности.
Конечно, вы можете использовать абразивные диски для успешного удаления ржавчины и других загрязнений с поверхности.Однако, когда речь идет о нержавеющей стали, восстановление ее защитного пассивного слоя имеет не меньшее или даже большее значение. При шлифовании и других механических методах репассивация не гарантируется , поскольку поверхность может быть разорвана, и другие материалы могут попасть в поверхность в результате шлифования, что делает поверхность уязвимой и подверженной коррозии в будущем.
Итак, чем помогает электрохимическая очистка сварных швов?
Во-первых, этот метод несравнимо безопаснее, чем химическое травление и шлифование.
Используя слабый электрический ток и мягкие электролитические жидкости, вы сможете эффективно удалить все загрязнения, возникающие в результате сварки . Сюда входят ржавчина, тепловые оттенки, обесцвечивание, следы ожогов и другие формы загрязнения.
Электрохимическая очистка не только удалит загрязнения с ваших сварных швов, но также повторно пассивирует поверхность , что означает, что останется очень устойчивым к коррозии.
Все это без тяжелых ручных инструментов и опасных химикатов.
Очистители сварных швов Cougartron — правильный выбор для быстрой и безопасной очистки сварных швов TIG и MIG
Очистители сварных швов Cougartron являются эффективным оружием против ржавчины и всех других форм загрязнения, появляющихся на сварных швах и поверхностях нержавеющей стали после изготовления.
В ассортимент нашей продукции входят машины для ежедневных тяжелых работ и периодической легкой очистки сварных швов , поэтому вы обязательно найдете правильное решение для своей области применения.Для работы с нашим оборудованием не требуется специального обучения, оно обеспечит исключительные результаты в руках , как любителей, так и промышленных профессионалов .
В дополнение к очистке, машины Cougartron будут одновременно выполнять полную репассивацию поверхности , так что вам не придется беспокоиться о коррозии в будущем.
Как отмечалось выше, это достигается очень быстрым и безопасным способом .
Если вам нужна помощь в выборе подходящего оборудования для вашего производства, оставьте свои данные ниже, и один из наших специалистов свяжется с вами в ближайшее время.
НУЖНА ПОМОЩЬ ПРИ ВЫБОРЕ ОБОРУДОВАНИЯ COUGARTRON?Если вы хотите узнать больше об очистке сварных швов и преимуществах электролитического процесса, вы можете продолжить свое исследование, используя некоторые из наших полезных статей:
.