Информация о методе дуговая сварка под флюсом
Сварка под флюсом является разновидностью дуговой сварки. Особенностью такого вида дуговой сварки является ведение сварочного процесса с использованием специального порошкового сварочного флюса. Сварочная дуга в процессе сварки горит под слоем флюса.
Флюс – это специальное вещество в виде порошка или гранул с положительными характеристиками. Флюс подается прямо в зону сварки толстым слоем и используется для защиты сварочной ванны от попадания воздуха в процессе сварки. В этом смысле порошковый флюс аналогичен использованию для сварки инертного газа, защищающего ванну от кислорода.
Дуговая сварка под флюсом имеет ряд особенностей, выгодно отличающих метод от стандартной дуговой сварки:
- максимальная защита сварочной зоны в процессе работы,
- значительное сокращение потерь электрода и присадочной проволоки,
- практически полное отсутствие брызг металла,
- повышение производительности сварочного процесса,
- снижение чувствительности к появлению оксидов на поверхности металла,
- дополнительная защита операторов от дугового свечения,
- высокое качество шва и улучшенные свойства металла шва благодаря пониженной скорости остывания материала в процессе.
Но при этом сварка с использованием защитного флюса имеет ряд недостатков, которые могут быть существенны при выборе метода:
- повышение общих расходов на сварочный процесс,
- повышение сложности корректировать положение дуги,
- необходимость дополнительной защиты органов дыхания операторов от газов,невозможность визуально контролировать непосредственное место сварки,
- невозможность сварки в любом пространственном положении,
- повышение текучести металла и флюса в процессе работы,
- высокая зависимость качества выполнения работы от сборки сварочных кромок в связи с угрозой вытекания расплавленного флюса или металла с последующим образованием дефектов.
Техника проведения дуговой сварки под флюсом
Дуговая сварка под флюсом выполняется полуавтоматическим или автоматическим способом. Это связано с необходимостью автоматизации процесса подачи сварочной проволоки и флюса. Электродная проволока, используемая в процессе, автоматически вытягивается в дугу специальными роликами автомата. Используемая проволока должна по составу соответствовать свариваемым материалам.
Сварочный ток подводится к проволоке и к изделию. В зависимости от задач может использоваться постоянны или переменный ток прямой или обратной полярности. Сварочные работы следует начинать с тщательной обработки и зачистки свариваемых материалов от краски, ржавчины, пыли и других загрязнений, в том числе с использованием металлической щетки или шлифовального круга при необходимости.
Флюс подается к месту сварки перед дугой. Толщина слоя флюса должна составлять не меньше 40-80мм, а ширина слоя – 40-100мм. Количество флюса зависит от условий сварки и толщины сварочной проволоки.
Из-за высокой температуры от дуги флюс и металл начинают плавиться и испаряться. В результате образуется газовое облако, защищающее дугу и сварочную ванну от попадания воздуха. Расплавленный флюс после гашения дуги остывает и образует шлаковую корку, которая после завершения работ легко отделяется от сварочного шва.
В зависимости от свариваемых материалов и других условий ведения процесса могут использоваться различные виды флюсов. Флюсы делятся на несколько классов и подгрупп:
- по способу производства: плавленые или неплавленые (керамические),
- по химическому составу: оксидные, солевые или смешанные (солеоксидные),
- по активности (скорости окисления): пассивные, малоактивные, активные и высокоактивные,
- по строению гранул: стекловидные, пемзовидные или цементированные.
Область применения сварки под флюсом
Сварка с использованием флюса в первую очередь была разработана для работы с различными видами стали. В настоящее время с развитием технологий дуговую сварку под флюсом используют и для сваривания алюминия, меди, различных тугоплавких металлов.
Флюс используется для соединения вертикальных швов, сваривания труб различного диаметра (в том числе очень больших размеров, а также для сваривания кольцевых швов в других ситуациях. Это позволяет применять дуговую сварку под флюсом в кораблестроении, трубопрокатной промышленности, нефтегазовой отрасли и многих других промышленных сферах.
Автоматическая сварка под слоем флюса
- Автоматическая сварка под флюсом
- это разновидность дуговой сварки, при которой электрическая дуга горит под слоем сварочного флюса, который препятствует проникновению атмосферного воздуха в зону сварки.
Сварка вертикальных швов автоматическим способом производится под флюсом с принудительным формированием.
Для сварки вертикальные стыковые соединения (без скоса кромок) собирают с зазором 8—12 мм.
Технология автоматической сварки под флюсом
С одной стороны стыка закрепляется медная полая накладка (рис. 1), охлаждаемая проточной водой
Изогнутая электродная проволока 4 занимает положение между кромками 5. Автоматическая головка имеет медный полый ползун 2, также охлаждаемый водой.
Наплавка происходит снизу вверх в «форму», образованную свариваемыми кромками и медными планками, в которой удерживается жидкая ванна металла 3.
Вследствие соприкосновения ее с неподвижной медной планкой и подвижным медным ползуном происходит охлаждение и застывание металла шва.
Сварка стыковых соединений в вертикальном положении с принудительным формированием может производиться как дуговым, так и бездуговым— электрошлаковым процессом.
Бездуговой процесс с принудительным формированием применяется при сварке металла больших толщин (более 30 мм).
Полуавтоматическая шланговая сварка осуществляется при механической подаче сварочной проволоки диаметром 1,2—2 мм из катушки через гибкий шланг в трубчатый мундштук, закрепленный в держателе.
К мундштуку подводятся также сварочный ток и флюс. Держатель перемещается вдоль свариваемого шва вручную.
С 1940 г. началось повсеместное применение автоматической сварки закрытой дугой под слоем порошкообразных флюсов.
Схема установки для автоматической дуговой сварки под флюсом
Голая электродная проволока 1, помещенная в кассете 2, с помощью подающего механизма сварочной головки перемещается к изделию.
Дуга горит в толстом слое (50—70 мм) стекловидного гранулированного флюса 3, поступающего в зону сварки из специального бункера 4.
При поступательном перемещении автомата или изделия образуется сварной шов 5, покрытый шлаковой коркой 6.
Большая часть флюса, оставшаяся нерасплавленной, инжекторным флюсоотсасывающим устройством 7 собирается с поверхности изделия и вновь поступает в бункер.
Основная особенность описанного процесса сварки заключается в повышении качества металла шва благодаря тому, что флюс обеспечивает устойчивое горние дуги и защиту сварочной зоны от влияния воздуха.
Так же флюс способствует замедлению скорости охлаждения шва.
Подбором состава флюса можно осуществить легирование металла шва.
Рис.2 Схема установки для автоматической сварки под флюсом
При автоматической сварке наиболее широко применяются флюсы, представляющие собой шлаковые системы, построенные на базе силикатов и окислов марганца, кальция или магния.
Составы флюсов-силикатов
Таблица. Плавленные флюсы, применяемые при сварке малоуглеродистых сталей
Марка флюса | Химический состав, % | |||||||
Si02 | МпО | CaF2 | MgO | СаО | Аl2O3 | FeO | Fe2О3 | |
не более | ||||||||
ОСЦ-45 | 38,0-44,0 | 38,0-47,0 | 6,0-9,0 | до 2,5 | до 6,5 | до 5,0 | — | 2,0 |
АН-348А | 41,0-44,0 | 34,0-38,0 | 4,0-5,5 | 5,5-7,5 | до 6,5 | до 4,5 | — | 2,0 |
ФЦ-7 | 46,0-48,0 | 24,0-26,0 | 5,0-6,0 | 16,0-18,0 | до 3,0 | до 3,0 | 1,5 | — |
АН-10 | 20,0-23,0 | 29,5-33,5 | 18,0-24,0 | до 1,2 | 3,0-7,0 | 19,0-21,0 | 1,5 | — |
Химическая активность этих шлаков относительно невелика, но при высоких содержаниях окислов марганца и кремния наблюдается восстановление их железом.
Высокая степень легирования различными элементами легко достигается при сварке под керамическими флюсами, которые состоят из шлакообразующих компонентов и ферросплавов, сцементированных жидким стеклом.
В последнее время начинают находить применение бескислородные флюсы, изготавливаемые из различных фтористых соединений.
При автосварке под флюсом производительность повышается в 10—40 раз в сравнении с ручной сваркой. Это обусловлено применением больших сил токов (1000-3000 а), а также лучшим использованием тепла дуги.
Благодаря лучшему использованию тепла и отсутствию потерь электродного металла при автосварке под флюсом уменьшается расход электроэнергии и проволоки.
Весьма существенны и эксплуатационные достоинства сварки под флюсом.
Они выражаются в улучшении условий труда в сварочных цехах, что обусловлено уменьшением выделения пыли и газов и отсутствием светового излучения дуги.
Для выполнения автоматической дуговой сварки под флюсом широко применяют самоходные сварочные головки и тракторы.
Оборудование для автоматической сварки под флюсом
Универсальная самоходная головка АБС
Этот аппарат состоит из трех отдельных узлов.
- Узел А представляет собой подвесную сварочную головку с пультом управления, которая предназначена для правки и подачи проволоки с постоянной скоростью к изделию.
- Узел Б состоит из бункера для флюса, устройств для подачи и отсоса флюса, кассеты со сварочной проволокой и механизма вертикального перемещения.
- Узел С — это самоходная тележка для перемещения всего аппарата вдоль свариваемого изделия.
Технические данные аппарата АБС приведены в табл. 2.
Рис.3 Универсальный сварочный аппарат АБС
1 — указатель; 2 — мундштук; 5 —механизм подачи; 4 -корректор; 5 — маховичок вертикального подъема; 6 — рукоятка фрикциона; 7 — кассета со сварочной проволокой; 8 — флюсоаппарат; 9 — направляющая воронка
Особенно широко распространены одноэлектродные сварочные тракторы — легкие самоходные тележки, перемещающиеся непосредственно по свариваемому изделию.
Универсальный сварочный трактор ТС-17-Р
Этот аппарат предназначен для сварки под флюсом прямолинейных и круговых швов стыковых, угловых и нахлесточных соединений.
Рис.4 Сварочный трактор ТС-17-Р
Трактор опирается на изделие обрезиненными ведущими бегунками 9 и передними съемными бегунками 2.
Электродвигатель 10 с постоянным числом оборотов приводит в движение механизм вращения бегунков 9 и механизм подачи сварочной проволоки 3.
Оба Механизма с коробками сменных шестерен смонтированы вместе с электромотором в одном общем корпусе, имеющем, мундштук 1 для подвода тока к электродной проволоке, бункер 5 для флюса, пульты управления 5 и 8 и кассету 7 со сварочной проволокой.
В комплекте трактора имеется ряд сменных узлов и деталей, которые осуществляют настройку его на сварку различных типов соединений вертикальным или наклонным электродом. Направление трактора по линии шва производится копирами. Кроме того, можно выполнить направление электрода по линии шва, пользуясь указателем 11 и механизмом поперечной корректировки 4.
Технические характеристики трактора ТС-17-Р приведены, в таблице.
Технические данные самоходных головок и тракторов для сварки под флюсом.
Тип аппарата | Наибольший сварочный ток, а | Диаметр сварочной проволоки, мм | Скорость подачи проволоки, м/ч | Скорость сварки, м/ч | Масса, кг |
АБС | 1500 | 2,0-6,0 | 29—220 | 14—110 | 160 |
ТС-17-Р | 1200 | 1,6-5,0 | 56-435 | 16-126 | 42 |
АДС-1000-2 | 1200 | 3,0-6,0 | 30-120 | 15—70 | 65 |
Двухмоторный трактор АДС-1000-2
Другим широко распространенным аппаратом для автоматической сварки под флюсом является двухмоторный трактор АДС-1000-2 (рис. 5) .
В этом тракторе электромотор, расположенный на тележке 1, служит для привода механизма двигателя, а электромотор головки 13 — предназначен для подачи сварочной проёолоки со скоростью, зависящей от напряжения дуги.
Рис. 5 Сварочный трактор АДС-1000-2
На четырехколесной тележке укреплена на поперечном суппорте стойка 3, которая несет на себе горизонтальную штангу 9. На левом конце этой штанги укреплены пульт управления 6 и кассета с проволокой 7, а на правом— сварочная головка 13 и бункер с флюсом 10.
Штанга может поворачиваться как около своей оси, так и относительно оси стойки. Сварочная головка может также изменять свое положение, так как она укреплена на штанге при помощи шарнира, фиксируемого зубчатыми полумуфтами.
Таким образом, можно придавать электроду при сварке различные положения в пространстве, фиксируй головку рукоятками 8, II и маховичком 5.
Для вертикального перемещения головки служит рукоятка 12.
Перемещение стойки по направлению, перпендикулярному к линии движения трактора, осуществляется маховичком 2.
Рукоятка 4 служит для выключения фрикционного сцепления передачи от мотора к ведущим бегункам трактора.
Достоинства автоматической сварки под флюсом
- широкий спектр возможного применения: сварка тонких и толстых пластин, сварка слаболегированных, легированных и нержавеющих сталей, наплавка и ремонтные работы;
- высокая скорость сварки достигается благодаря использованию высоких сварочных токов;
- высокоэффективное сплавление существенно снижает или исключает необходимость в дополнительной обработке;
- меньшая стоимость работ, так как расход сварочных материалов ниже, чем при использовании других методов сварки;
- низкий уровень сварочных деформаций;
- качественное формирование и отличный внешний вид сварного шва; превосходная компактность сварных швов;
- высокие механические свойства металла сварного шва;
- горение дуги во время сварки происходит под слоем флюса, что позволяет не применять индивидуальные средства защиты и снизить затраты на вентиляцию;
- отсутствие дымовыделения обеспечивает оператору большой комфорт и позволяет сэкономить на оборудовании для отвода и утилизации выделяющегося при сварке дыма.
Недостатки автоматической сварки под флюсом
- Определенные затраты связанные с производством, подготовкой, хранением вспомогательных материалов, в данном случае флюсов.
- Достаточно сложно установить дугу в правильном положении относительно краев соединяемых изделий.
- Оператор при сварочном процессе подвергается неблагоприятному воздействию.
- Ограничение пространства во время выполнения работ. Но эта проблема решается при помощи специального оборудования.
Автоматическая сварка под флюсом — один из основных способов выполнения сварочных работ в промышленности и строительстве. Обладая рядом важных преимуществ, она существенно изменила технологию изготовления сварных конструкций, таких как металлоконструкции, трубы большого диаметра, котлы, корпуса судов.
Сущность процесса электродуговой сварки под слоем флюса
Благодаря высокой производительности электродуговая сварка под слоем флюса широко применяется во многих отраслях народного хозяйства.
Как уже отмечалось, применение флюса обеспечивает надежную защиту расплавленного металла от окисления и азотирования. Это позволяет получить металл шва с высокими механическими свойствами.
При сварке под слоем флюса разбрызгивания металла, имеющего место при сварке открытой дугой, не происходит. Расход электроэнергии при сварке под флюсом ниже, чем при ручной дуговой сварке. Последнее связано с меньшими потерями тепла в окружающую среду. Схема сварки под слоем флюса представлена на фиг. 70.
При полуавтоматической сварке подача проволоки производится механизмом, а перемещение держателя вручную. Флюс при полуавтоматической сварке подается в зону горения дуги или из бункера, закрепленного на держателе, или по шлангу от специального флюсопитателя.
При автоматической сварке перемещение сварочной проволоки относительно изделия производится механизмом. Кроме того, уборка нерасплавившейся части флюса при автоматической сварке производится специальным флюсоотсасывающим механизмом.
Процесс сварки под слоем флюса может вестись на переменном токе, а также на постоянном токе при прямой и обратной полярности.
Поскольку при сварке под слоем флюса разбрызгивание электродного металла не происходит, ее можно вести при значительно больших плотностях тока, чем ручную сварку. В связи с этим при сварке под слоем флюса значительно повышается скорость сварки и соответственно производительность труда.
Следует также отметить, что при сварке под слоем флюса качество сварных соединений получается высоким.
Фиг.70.Схема процесса сварки под слоем флюса
Обязательным условием для получения высокого качества сварных соединений является настройка оборудования, правильная подготовка кромок под сварку, а также правильная сборка сварных конструкций.
Cварка под флюсом: особенности, описание технологии
Сварка под слоем флюса – одна из наиболее производительных промышленных технологий сборки металлоконструкций. Ее используют для получения неразъемных соединений деталей из углеродистых и легированных сталей, а также цветных металлов. Современное технологическое оборудование для сварки под флюсом позволяет добиться высокой степени автоматизации процессов. Поэтому целесообразность применения метода определяется длиной шва и толщиной свариваемых деталей.
Особенности технологии сварки под флюсом
В зависимости от материала соединяемых деталей сварка может выполняться как переменным, так и постоянным током. В качестве электрода используется проволока или лента, намотанная на бобину. Для защиты сварочной ванны от воздействия атмосферного кислорода используется флюс – гранулированный или порошкообразный материал. Как правило, его основу составляют силикаты. Возбуждение, прерывание дуги и подача электрода выполняются автоматически, а флюс засыпается из бункера через воронку под собственным весом. В процессе сварки перемещение головки вдоль шва может выполняться оператором при помощи механических средств или приводом используемого оборудования.
Расплавление электрода и флюса происходит под воздействием температуры электрической дуги. Образующиеся пузыри газа являются защитной атмосферой для ванны. Сварочный шлак оказывается легче металла и всегда остается на поверхности шва, а после остывания механически удаляется. Слой флюса и газы создают избыточное давление, достаточное для того, чтобы предотвратить разбрызгивание металла. Поэтому полученный шов оказывается значительно чище, чем при аргонодуговой или ручной сварке штучными электродами. Оставшийся флюс может быть использован повторно. Технология широко применяется в промышленном производстве и восстановлении деталей.
Сферы применения сварки под флюсом
- Производство труб большого диаметра. Сварка под флюсом позволяет получать кольцевые, прямолинейные и спиральные швы. Оборудование дает возможность полностью автоматизировать процесс.
- Изготовление емкостей и резервуаров. Метод сварки под флюсом позволяет получить шов практически без пор и шлаковых вкраплений.
Резервуары подходят для хранения и транспортировки жидкостей и газообразных веществ, а также используются в аппаратах, работающих под давлением.
- Производство металлоконструкций. Сварка под флюсом позволяет значительно снизить себестоимость монтажа.
- Производство и восстановление деталей. Технология сварки дает возможность наносить слой металла на всю поверхность изделия. Метод наплавки используется для восстановления поверхностей деталей и нанесения износостойких покрытий.
Виды оборудования для сварки под флюсом
Современное оборудование для сварки под флюсом сделано так, чтобы оператор мог выбрать положение аппарата и настроить режим. Остальные операции выполняются автоматически. Производителями разработано множество серийных и уникальных конструкций для сварки под флюсом, позволяющих решать широкий спектр задач в производственных и полевых условиях. Наибольшее распространение получили следующие виды оборудования.
- Тракторы.
Эти мобильные аппараты для сварки под флюсом имеют сравнительно небольшие габариты и массу. При настройке они перемещаются вручную, а при прохождении шва – автоматически. Также существуют аппараты с механическим приводом: в режиме сварки оператор регулирует скорость перемещения тележки вручную, а подача флюса и проволоки выполняется приводом. В зависимости от конструкции тележка может перемещаться по рельсам либо по самой детали.
- Мобильные сварочные установки. Такие аппараты применяются как в производственных цехах, так и в полевых условиях (например, при прокладке трубопроводов). Чаше всего они имеют модульную конструкцию и состоят из консоли, на которой расположена сварочная головка, роликовых опор с приводом для установки и вращения детали, а также источника тока.
- Стационарные сварочные установки. Для серийного изготовления металлоконструкций чаще всего создается уникальный проект, учитывающий особенности производства.
Однако существует ряд универсальных аппаратов для сварки под флюсом, которые можно адаптировать под любые задачи. Степень автоматизации таких устройств позволяет автоматически менять направления перемещения детали и головки во всех осях, а также изменять направление и скорость вращения. Существует возможность создания технологических линий, в состав которых входит сразу несколько таких аппаратов.
Решение для промышленной сварки под флюсом: STTNF-II + ASAW 1000
Преимущества и недостатки технологии
Среди преимуществ сварки под флюсом можно выделить следующие.
- Использование высоких токов (1000–2000 А) и проволоки позволяет добиться высокой производительности аппаратов.
- Применение флюса помогает снизить потери металла на разбрызгивание, улучшить условия защиты шва и сократить затраты электроэнергии.
- Сварка на высоких токах позволяет контролируемо увеличить глубину проплавления основного металла.
- Шлаковая корка, образующаяся в результате плавления флюса, снижает скорость остывания шва и предохраняет его от растрескивания.
- Зона сварки закрыта, что позволяет оператору работать без щитка.
У технологии также есть недостатки. К ним относят следующие.
- Высокая начальная стоимость оборудования для сварки под флюсом.
- Сложность коррекции положения дуги относительно кромок деталей.
- Невидимость зоны сварки создает повышенные требования к качеству подготовительных операций.
- Флюс является источником пыли.
Как выбрать оборудование
Наиболее важными критериями служат геометрические параметры и материал деталей, которые предстоит соединять, а также массовость и условия производства. Для сварки под флюсом применяются универсальные источники. Их выбирают в зависимости от сечения электрода по максимальной силе тока.
Чтобы оборудование для сварки под флюсом соответствовало всем рабочим параметрам, лучше всего обратиться к производителям или официальным дилерам. У них всегда есть возможность адаптации устройств под конкретные задачи.
Сварка под флюсом — теория и практическая реализация
Сварка, как технология соединения металлических элементов, достаточно молода. И эту технологию делают всё совершеннее – например, сварка под флюсом позволяет не только сэкономить энергию, но и обеспечить более качественный шов. Почему же она не получила широкого распространения? Причина проста – использовать сварка под слоем флюса возможна только на относительно горизонтальной поверхности. Уклон больше 10-15 градусов делает её применение бессмысленным.
Но в ряде случаев ручная сварка под флюсом может стать достойной альтернативой классическому варианту. Так что иметь представление о данном процессе будет полезно любому сварщику.
Теория
При классической сварке энергия тратится не только на расплав металла, но и на нагрев окружающей среды. С целью минимизации подобных потерь используют флюс – дуга и точка контакта укрываются слоем материала (чаще всего порошкового типа). В результате не только повышается КПД процесса, но и снижается воздействие окружающей среды – шлак раскаленного флюса обеспечивает защиту зоны сварки. Дополнительно обеспечивается равномерный расплав металла по шву, что самым положительным образом влияет на его качество.
С точки зрения экономии расходных материалов толщина сварки под флюсом выгодна при работе с металлом толщиной 6 мм и более. Это еще одна причина, по которой данный тип сварки в быту используется редко. Хотя на рынке представлены профессиональные модели сварочных аппаратов, осуществляющие сварку проволокой с флюсом, широкого распространения они не получили.
Практическая реализация
Чаще всего флюс для сварки реализуется в виде порошка, который необходимо насыпать на место будущего шва. Основа такого флюса – силикат кремния (его доля может составлять от 35 до 80%). Материал выбран не случайно – кремний хороший раскислитель и подавляет образование оксидов в месте сварки. Результат – низкая пористость металла на сварном шве. А что еще входит в состав флюса?
— если мы рассматриваем флюс для сварки стали – то соединения марганца, магния и кальция;
— работа с легированными сортами потребует присадок в виде соединений хрома, молибдена или титана;
— ну а флюс для сварки алюминия содержит в составе плавиковый шпат или его аналоги (фториды и хлориды щелочных металлов).
Купить флюс для сварки можно на нашем сайте – широкий ассортимент удовлетворит запросы самых требовательных клиентов.
Сварка под флюсом – Осварке.Нет
Сварка под флюсом — дуговая сварка при которой электрическая дуга горит под слоем сыпучего зернистого флюса, который выполняет функции защиты дуги и сварочной ванны.
Рис. 1. Условная схема сварки под флюсом
Международные обозначения сварки под флюсом
SWA (Submerged Arc Welding) — сварка погруженной дугой.
Сущность процесса сварки под флюсом
[context] Отличительной особенностью сварки под флюсом является то, что сварочная дуга горит под слоем сыпучего зернистого флюса. Под воздействием сварочной дуги электродная проволока, основной металл и часть флюса расплавляются. Сварочную проволоку подают в направлении основного металла с помощью механизмов. По мере заполнения сварочной ванны проволока и дуга перемещается вдоль сварочного соединения. В зоне горения дуги создается среда из парами металла, расплавленным флюсом и газами, давление которых удерживает корку что образовывается над сварочной ванной. Так сварочная ванна надежно, дуга и остывающий шов надежно защищены от вредного воздействия кислорода и азота воздуха, а также предотвращает разбрызгивание металла.Давление газов толкает жидкий металл в противоположную направлению сварки сторону. По мере удаления сварочной дуги, ванна кристаллизуется и получается сварочный шов покрытый коркой шлака.
Как было сказано выше, флюс защищает зону сварки, а также влияет на металла сварочной ванны и препятствует разбрызгиванию. Низкая теплопроводность расплавленного флюса позволяет медленнее охлаждать сварочный шов. При этом шлаковые включения и газы легче подымаются на поверхность, металл шва становиться очищенным от загрязнений.
Флюс который не расплавился после сварки убирают со шва специальными приборами и их можно использовать при следующей сварке. Шлаковая корка легко удаляется с поверхности металла.
Способы сварки под флюсом
В зависимости от степени механизации сварочного процесса сварку под флюсом можно выполнять автоматическим и полуавтоматическим методом.
Автоматическая сварка под флюсом
Автоматическая сварка под флюсом подразумевает что все операции выполняются автоматически, а именно возбуждение дуги, поддержание горения дуги, подача электрода, перемещение электрода вдоль сварочного соединения, защита зоны сварки, заварка кратера по окончанию сварки. При сварке под флюсом также можно добавить операции с насыпания и уборки флюса.
Этот метод используется при серийном производстве однотипных конструкций с продольными швами.
Полуавтоматическая сварка под флюсом
При полуавтоматической сварки под флюсом механизированными способами в зону сварки подаются сварочные материалы — проволока и флюс. Перемещение дуги вдоль шва выполняется сварщиков вручную.
Такой метод используется не обязательно при серийном производстве. Его можно применять для сварки протяжных швов и удобных для удержания флюса соединений.
Преимущества сварки под флюсом
- Значительное повышение продуктивности сварки (в 6-12 раз) за счет отсутствия потери металла на разбрызгивание, использования высокой силы тока, увеличения глубины провара.
- Полная или частичная механизация процесса сварки.
- Надежная защита сварочной ванны и как следствие высокие показатели качества сварных соединений выполненных сваркой под слоем флюса.
- Более безопасные условия труда для сварщиков и операторов.
Недостатки сварки под флюсом
- Сварку можно выполнять только в нижнем положении (± 15°) так как требуется удержать флюс на поверхности сварочного соединения.
- Ограниченные возможности сварки в монтажных условиях и сварки коротких швов.
- Трудно контролировать процесс сварки, горение дуги и формирование шва закрыто флюсом.
- Пары образующиеся во время сварки под флюсом, а также флюсовая пыль вредны для здоровья человека.
- Сварка под флюсом требует применения сложного оборудования.
- Необходимость тщательной сборки деталей под сварку, использование приемов и приспособлений для предотвращения вытекания металла и флюса.
Автоматическая сварка и наплавка под слоем флюса
Рис. 137. Сварка под слоем флюса:
а — схема процесса сварки; б — продольный разрез зоны сварки; 1 и 4 — трубки; 2 — бункер; 3—кассета с электродной проволокой; 5 — подающий механизм; 6 — шлаковая корка; 7 — деталь; 8 — электродная проволока; 9 — газовый пузырь; 10 — расплавленный металл; 11 — сыпучий флюс
Дуга горит между свариваемой деталью и электродной проволокой, диаметр которой принимается 2, 6 и 8 мм. По мере расплавления сварочной проволоки она постепенно подается из катушки (бухты) в зону сварки механизмом сварочного аппарата (головкой, трактором, полуавтоматом и т. д.). Флюс поступает в зону шва из бункера, при этом некоторое количество его плавится вместе с проволокой и кромками детали. По мере удаления дуги жидкий металл затвердевает, образуя сварочный шов, а расплавленный флюс образует легкоудаляемую шлаковую корку. Часть неиспользованного флюса отсасывается в бункер и может быть использована повторно.
При увеличении сварочного тока возрастают объем жидкой ванны и глубина провара основного металла, ширина же провара остается практически неизменной.
При увеличении сечения электрода при неизменном токе увеличивается ширина и уменьшается глубина провара. Уменьшение диаметра электрода при неизменном токе увеличивает глубину провара.
Опыт показывает, что при увеличении скорости сварки более 40 м/ч глубина и ширина провара заметно уменьшаются, а высота валика увеличивается.
Высокая производительность при сварке под флюсом достигается благодаря применению больших токов (высоких плотностей тока — 70—150 а/мм2) и использованию тонкой проволоки.
Значительные успехи в области разработки технологии механизированной сварки и наплавки под слоем флюса, конструкции сварочного оборудования и составов специальных флюсов достигнуты институтом электросварки им. Е. О. Патона АН УССР.
Флюсы, применяемые для автоматической и полуавтоматической сварки и наплавки, совместно с соответствующей электродной проволокой должны обеспечивать устойчивое горение дуги, требуемый химический состав и механические свойства металла шва, отсутствие пор и трещин в шве, а также легкое удаление шлаковой корки с поверхности шва.
По способу изготовления флюсы делятся на плавленые, получаемые путем сплавления компонентов шихты в печах, и неплавленые, или керамические. Наличие различных ферросплавов в составе керамического флюса при наплавке способствует получению легированного наплавленного металла, в то время как при использовании плавленых флюсов легирующие примеси вводятся только через легированную электродную проволоку.
Наиболее широко при ремонте деталей дорожных машин применяются плавленые флюсы АН-348Ш и АН-348А, используемые совместно с электродной проволокой марок Св-08А, Св-08ГА, Св-ЗОХГСА, Св-20ХГСА и Св-13ГДХ.
Химический состав флюса АН-348А, %: Si02 — 41,0—43,5; МпО — 34,5—37,5; CaF2 — 3,5—5,5; А1203 — до 3; MgO — 5,5—7,5; S —до 0,15; Р — до 0,75.
При применении мягкой проволоки практикуется добавка к флюсу АН-348 75%-ного ферромарганца в количестве 3,5—4,0% и графита 1 % по весу, что позволяет увеличить износостойкость и твердость наплавленного металла с НВ 200-240 до НВ 420. Однако твердость наплавленного металла получается по всей поверхности неоднородной.
В последнее время испытан и применяется флюс марки ДН-ЮЛ8, состав которого следующий, %: Si02— 20—23; А1203 — 19—21; МпО — 29,5—33,5; СаО — 3—7; MgO — до 1,2; К20 и Na20 — 0,4—0,6; Fe —до 1,2; CaF2—18—24; S —до 0,15 и Р — до 0,2.
К флюсу АН-10 добавляется в количестве 6—8% по весу специальная порошкообразная лигатура из А1 (85%) и Fe (15%).
Твердость металла, наплавленного малоуглеродистой проволокой под флюсом АН-10Л8, составляет НВ 340—400 и получается равномерной. Указанный флюс используется при наплавке верхних и нижних катков, натяжных колес и звеньев гусениц, ножей бульдозеров и автогрейдеров, а также для других деталей, где требуется высокая поверхностная твердость.
Флюс ОСЦ-45 предназначен для автоматической сварки стали марок МСт.1, МСт.2, МСт.З и МСт.4, электродной проволокой марок Св-08; Св-08А, СВ-08Г и Св-08ГА.
Химический состав флюса ОСЦ-45, %: Si02 — 43—45; МпО — 38—45; CaF — 6—8; СаО — до 5; MgO — до 1; А1 — до 2,5; F203— до 1,5; S — до 0,15; Р — до 0,15.
При флюсе ОСЦ-45 качественные швы получаются на малоуглеродистых сталях; в швах, сваренных по умеренно коррозированному металлу, отсутствует пористость и механические свойства шва высокие. К недостаткам рассмотренного флюса относятся выделение сравнительно большого количества вредных фтористых газов и недостаточная устойчивость дуги при питании от источника переменного тока с напряжением холостого хода 65—70 в.
Оборудование для механизированной наплавки под слоем флюса должно обеспечить подачу электрода, регулирование и перемещение дуги вдоль свариваемого шва.
Регулирование дуги сводится к поддержанию постоянства длины дугового промежутка. Надежное возбуждение дуги получается при относительно высоких плотностях тока.
Гашение дуги для окончания сварки производится прекращением подачи электродной проволоки. Подвод сварочного тока к электроду производится мундштуком, расположенным на небольшом расстоянии от детали.
При автоматической сварке подача электрода и передвижение Дуги вдоль шва механизированы. При полуавтоматической сварке механизирована только подача электрода, а продвижение дуги вдоль шва производится сварщиком вручную.
На ремонтных предприятиях для восстановления деталей тракторов и дорожных машин (катков и натяжных колес гусениц, валов, осей и др.) применяется наплавочный аппарат типа А-409 конструкции института электросварки им. Е. О. Патона АН УССР, предназначенный для автоматической наплавки тонкой электродной проволокой под слоем флюса деталей, имеющих поверхности тел вращения диаметром от 40 до 700 мм.
Наплавка аппаратом А-409 производится на специальном или токарном станке, непригодном для эксплуатации по прямому назначению. Аппарат устанавливают и закрепляют на суппорте станка, а наплавляемую деталь — в патроне или центрах. Подкладками под переднюю и заднюю бабки повышают высоту центров станка до 300—350 мм.
Рис. 138. Установка для наплавки цилиндрических деталей аппаратом А-409:
1 — замедляющий редуктор; 2 — наплавляемая деталь; 3 — бункер; 4 — наплавочный аппарат А-409; 5 — поддон для шлаковой корки; 6 — токарный станок; 7 — аппаратный ящик; 8 — сварочный преобразователь ПС-300
Для получения малых окружных скоростей детали при наплав-, ке со скоростью 12—40 м/ч:число оборотов шпинделя станка необходимо снизить за счет дополнительного редуктора в пределах 0,5; 1,5; 2; 3 и 4 об/мин. Наплавка производится на постоянном токе от сварочных агрегатов типа СУГ-2Р, ПС-300 или ПС-500.
Установка для наплавки аппаратом А-409 на токарном станке показана на рис. 138.
Аппарат А-409 (рис. 139) состоит из следующих основных узлов: сварочной головки, мундштука, вертикального суппорта 2У бункера и пульта управления, установленных на суппорте токарного стана.
Рис. 139. Наплавочный аппарат А-409
Кроме того, можно наплавлять детали из высокоуглеродистых сталей без риска получения в наплавленном металле горячих трещин.
Наплавка цилиндрических поверхностей деталей производится непрерывно по винтовой линии с заданным шагом, что обеспечивает высокую производительность работы. Вследствие равномерного нагрева деталь во время наплавки не деформируется.
Детали, ранее наплавлявшиеся электродами с меловой обмазкой, должны быть предварительно проточены до полного удаления металла прежней наплавки.
Рис. 140. Схема наплавки цилиндрических деталей:
1 — сварочный генератор; 2— подача флюса; 3 — электрод; 4 — электрическая дуга; 5 —шлаковая корка; 6 — наплавленный металл; 7 — деталь
Вовремя наплавки сварщик сбивает шлак, следит за показанием приборов и нормальным поступлением флюса в зону горения дуги.
Процесс дуговой сварки под флюсом — TWI
Особенности процесса
Подобно сварке MIG, сварка SAW включает образование дуги между неизолированным проволочным электродом и заготовкой. В процессе используется флюс для образования защитных газов и шлака, а также для добавления легирующих элементов в сварочную ванну. Защитный газ не требуется. Перед сваркой на поверхность заготовки наносится тонкий слой порошка флюса. Дуга движется вдоль линии стыка, и при этом излишки флюса рециркулируют через бункер.Оставшиеся слои расплавленного шлака легко удаляются после сварки. Поскольку дуга полностью покрыта слоем флюса, потери тепла чрезвычайно низки. Это дает тепловой КПД до 60% (по сравнению с 25% для ручной металлической дуги). Отсутствие видимого дугового света, сварка без брызг и вытяжки дыма.
Рабочие характеристики
SAW обычно работает как полностью механизированный или автоматический процесс, но может быть и полуавтоматическим. Параметры сварки: ток, напряжение дуги и скорость перемещения — все это влияет на форму валика, глубину проплавления и химический состав наплавленного металла шва. Поскольку оператор не видит сварочную ванну, следует больше полагаться на настройки параметров.
Варианты процесса
В зависимости от толщины материала, типа соединения и размера компонента изменение следующих параметров может увеличить скорость наплавки и улучшить форму валика.
Провод
SAW обычно работает с одним проводом переменного или постоянного тока. Общие варианты:
- сдвоенный провод
- многопроволочный (тандемный или тройной)
- однопроволочный с добавлением горячей или холодной проволоки
- добавка металлического порошка
- Трос трубчатый
Все это способствует повышению производительности за счет значительного увеличения скорости наплавки металла шва и / или скорости движения.
Также разработан вариант процесса с узким зазором, который использует технику осаждения двух или трех валиков на слой. См. Что такое сварка в узкий зазор?
Флюс
Флюсы, используемые в SAW, представляют собой гранулированные легкоплавкие минералы, содержащие оксиды марганца, кремния, титана, алюминия, кальция, циркония, магния и другие соединения, такие как фторид кальция. Флюс специально разработан, чтобы быть совместимым с данным типом электродной проволоки, так что комбинация флюса и проволоки дает желаемые механические свойства.Все флюсы вступают в реакцию со сварочной ванной, определяя химический состав и механические свойства металла шва. Обычно флюсы называют «активными», если они добавляют марганец и кремний в сварной шов, количество добавленных марганца и кремния зависит от напряжения дуги и уровня сварочного тока. Основные типы флюсов для SAW:
- Связанные флюсы — получаются путем сушки ингредиентов с последующим их связыванием с помощью соединения с низкой температурой плавления, такого как силикат натрия.Большинство флюсов на связке содержат металлические раскислители, которые помогают предотвратить пористость сварных швов. Эти флюсы эффективны против ржавчины и прокатной окалины.
- Плавленые флюсы — получают путем смешивания ингредиентов, затем плавления их в электрической печи с образованием химически однородного продукта, охлаждения и измельчения до необходимого размера частиц.
Гладкие стабильные дуги со сварочным током до 2000 А и неизменными свойствами металла сварного шва являются основным преимуществом этих флюсов.
Приложения
SAW идеально подходит для выполнения продольных и кольцевых стыковых и угловых швов.Однако из-за высокой текучести сварочной ванны, расплавленного шлака и рыхлого слоя флюса сварка обычно выполняется на стыковых соединениях в плоском положении и угловых соединениях как в плоском, так и в горизонтально-вертикальном положениях. Для кольцевых соединений заготовка вращается под неподвижной сварочной головкой, при этом сварка происходит в горизонтальном положении. В зависимости от толщины материала могут выполняться однопроходные, двухпроходные или многопроходные сварочные процедуры. Фактически нет ограничений по толщине материала при условии соответствующей подготовки шва.Чаще всего свариваются углеродисто-марганцевые стали, низколегированные стали и нержавеющие стали, хотя с помощью этого процесса можно сваривать некоторые цветные металлы с разумным выбором присадочной проволоки и комбинаций флюсов.
Сварка под флюсом (SAW): рабочий процесс, оборудование, детали и области применения
Сварка под флюсом (SAW) — это процесс сварки, при котором трубчатый электрод непрерывно подается для соединения двух металлов путем выделения тепла между электродом и металлом.
Область дуги и зона расплава получают защиту от атмосферного загрязнения путем погружения под слой гранулированного флюса. Слой флюса покрывает поверхность, полностью предотвращая разбрызгивание, искры, пары и УФ-излучение.
Более высокая производительность наплавки по сравнению с другими сварочными процессами.
Удобство для оператора — без видимой дуги и брызг.
Принципы дуговой сварки под флюсомИщете:
- Увеличение производства
- Повышение скорости сварки
- Повышение производительности наплавки
👇 Это решение.
Оборудование для резки металла Образование дуги между проволочным электродом и деталью происходит так же, как при сварке MIG. Но этот процесс имеет дополнительное преимущество, заключающееся в защите гранулированным флюсом, что делает сварку SAW свободной от брызг, дыма и УФ-излучения. В инвентаре имеется следующее оборудование.
Сварку под флюсом можно использовать как на постоянном, так и на переменном токе.
- Источник питания
- Сварочная горелка / горелка и кабель в сборе
- Бункер флюса и его подача
- Механизм хода для автоматической сварки
Нам нужен источник питания для этой дуговой сварки под флюсом со 100% -ным рабочим циклом. Процесс сварки SAW является непрерывным, и длина одного шва может достигать 10 минут. Обычные источники питания с рабочим циклом 60% могут иметь снижение номинальных характеристик в соответствии с кривой рабочего цикла 100%. Механизм подачи проволоки с датчиком напряжения должен использоваться, когда применяется постоянный ток переменного / постоянного тока. Механизм подачи проволоки с фиксированной скоростью использует постоянное напряжение, в то время как система CV работает с постоянным током.
Можно использовать как технологический генератор постоянного тока, так и трансформатор переменного тока, но выпрямительные машины более популярны. Аппарат для дуговой сварки под флюсом доступен в диапазоне от 300 до 1500 ампер.
Оборудование постоянного тока подходит для полуавтоматических приложений, в то время как источник переменного тока подходит только для автоматизации. Дополнительная мощность может быть достигнута путем параллельного соединения обоих. С оборудованием переменного тока возможно использование нескольких электродов в специализированных областях применения.
2. Узел сварочной горелки и устройства подачи кабеля Эта часть оборудования должна подавать электрод и даже флюс к месту возникновения дуги. К концу кабельной сборки прикреплен небольшой бункер для флюса. В нижней части бункера имеется выход для электродной проволоки через токоприемник дуги.
На подачу флюса действует сила тяжести. Количество подаваемого флюса зависит от высоты пушки, удерживаемой над рабочей станцией.
3. Бункер для флюсаПистолет с бункером имеет мягкий переключатель для начала сварки. Он может использовать горячие электроды, так как когда он касается заготовки, подача начинается автоматически. В автоматическом режиме он присоединяет горелку к двигателям подачи проволоки и наконечнику датчика тока для процесса сварки. Этот бункер обычно прикреплен к горелке, которая имеет клапан с магнитным приводом, который открывается и закрывается системой управления.
4. Механизм перемещения Процесс сварки настраивается в очень быстром темпе с помощью ходовой тележки.Это может быть доступно в конструкциях, подобных трактору. Блок регенерации флюса обычно собирает неиспользованный флюс и возвращает его в бункер для подачи. Обычно трактор движется в горизонтальном направлении.
Основные достоинства процесса дуговой сварки под флюсом:
- Отличная скорость, лучшая производительность наплавки в более быстром темпе.
- Превосходное качество сварки.
- Без дыма
- Гладкая, качественная и равномерная сварка без брызг
- Безопасно для сварщика, без брызг и вспышки дуги
- Автоматизация здесь проста.
- Отличное использование электродов.
- Отсутствие навыков манипуляций
- Минимальная деформация металла
- Может работать на станке в ветреную местность
- Отсутствие подготовки кромок материала толщиной менее 12 мм
Изготовление — Процесс, необходимый для изготовления труб, затворов, котлов, профилей, сосудов высокого давления, железных дорог, вращающихся печей, землеройных машин, кранов, балок, мостов, локомотивов и нижних конструкций железнодорожных вагонов.
Автомобилестроение — Авиация, судостроение и атомная энергетика.
Восстановление изношенных деталей и износостойких сплавов, тракторных катков, холостых колес, крановых шкивов.
Подходит для металлов , таких как низкоуглеродистая сталь, средне- и высокопрочные сплавы.
Ограничения SAW- Оператор не видит процесса сварки. Он не может судить о качестве или каких-либо дефектах.Чтобы преодолеть эти недостатки, могут быть добавлены различные приспособления, приспособления, указатель, световой луч и роликовые направляющие для оценки и улучшения результата.
- Предварительная установка флюса на свариваемый стык не всегда возможна.
- Может сваривать только в горизонтальном направлении.
- Толщина металла должна составлять 4,8 мм, меньшая толщина обожжет металл.
- Кромки свариваемого металла должны быть чистыми и точно подогнанными.
Нанесение флюса на неровные кромки невозможно, и это может привести к подгоранию кромок.
- Качество флюса может вызывать беспокойство. Низкое качество может привести к пористости.
- Чугун, алюминиевый сплав, магниевый сплав и цинковый сплав не подходят для сварки под SAW.
- Химический состав металла сварного шва сложно контролировать, поскольку флюсовые сплавы полностью изменят характер низколегированной стали.
В процессе дуговой сварки под флюсом покрытый флюсом электрод заменяется гранулированным флюсом и неизолированным электродом.Дуга между электродом и работой является источником тепла и остается скрытой под слоем флюса. Этот флюс защищает от атмосферного загрязнения. Процесс может быть автоматическим или полуавтоматическим.
При нажатии на спусковой крючок флюс начинает оседать на свариваемом соединении. Холодный флюс не является проводником электричества, поэтому дуга может возникнуть при прикосновении электрода к основному металлу. Дугу можно зажечь, поместив стальную вату между электродом и рабочим металлом и используя ток высокой частоты.
Зажигает дугу под прикрытием флюса. как только флюс нагревается и расплавляется, чтобы получить высокую проводимость. Верхний слой остается неизменным и действует как защита, в то время как нижний слой остается электропроводящим для поддержания дуги. Верхний слой остается неизменным и зернистым, и его можно использовать повторно.
Электрод непрерывно движется с заданной скоростью для подачи на свариваемое соединение. Расплавленный металл от электрода переносится на заготовку и осаждается.Флюс вблизи дуги плавится и смешивается с расплавленными металлами. Этот флюс в качестве защитного слоя образует шлак, более легкий, чем наплавленный металл. Сварочный шов остается под слоем флюса и шлака, поэтому так называется сварка под флюсом.
Подача электродов непрерывная катушкой. Дуга автоматически сохраняется флюсом. Путешествие может управляться вручную или с помощью машины.
Популярными методами нанесения SAW являются машинный метод и автоматический метод.Машинный метод — наиболее распространенный метод, при котором оператор следит за процессом сварки. Автоматический метод — это кнопочная техника, и процесс применяется полуавтоматически, но не очень популярный метод сварки под флюсом.
Процесс нельзя искать вручную, так как невозможно управлять невидимой дугой. Процесс дуговой сварки под флюсом — это процесс сварки в ограниченном положении. Ограничение связано с тем, что большие лужи расплава и шлак представляют собой жидкость, которую трудно удерживать на месте.Для них лучше всего подходит плоское положение с горизонтальным положением скругления. Мы умеем сваривать в 3 часа в контролируемых условиях.
Процесс невозможно использовать в вертикальном положении или над головой, потому что он не может удерживать расплавленный металл и флюс на месте.
Этот процесс лучше всего подходит для сварки низко-среднеуглеродистых сталей, низколегированных и высокопрочных сталей, закаленных сталей, закаленной стали и нержавеющей стали.Сварка под флюсом экспериментально опробована на таких металлах, как никелевый сплав, медный сплав и уран.
Толщина 1,6–12,7 мм сваривается без подготовки кромок. Металл толщиной 6,4-25,4 мм требует подготовки кромок и сваривается за один проход. При использовании многопроходной техники толщина практически не ограничивается этой процедурой. Горизонтальный угловой шов позволяет выполнять сварной шов толщиной до 9,5 мм за один проход.
Детали совместной конструкции Мы можем использовать те же детали конструкции соединения, что и при сварке штучной сваркой.На нем показаны различные детали соединений, обеспечивающие первостепенное использование и производительность дуговой сварки под флюсом. Мы можем использовать квадратную канавку толщиной до 16 мм. Для большей толщины могут потребоваться конструкции со скосом. Открытые корни сварной конструкции с опорными стержнями обязательно должны удерживать расплавленный металл.
В случае более толстого металла на одной стороне сварного шва с большой корневой поверхностью, мы можем удалить опорный стержень. Для получения лучших результатов при полном проникновении требуется подкладная планка. Можно сделать проект, в котором обе поверхности доступны через сварной шов, который будет плавиться с оригиналом, обеспечивая полное проплавление.
Сварочные цепи и токВ процессе дуговой сварки под флюсом используется постоянный или переменный ток, но постоянный ток используется в большинстве приложений. Используются как положительный электрод постоянного тока (DCEP), так и отрицательный электрод постоянного тока (DCEN).
Постоянное напряжение с мощностью постоянного тока популярно для сварки под флюсом с проволокой малого диаметра 3,2 мм. Система постоянного тока обычно используется для сварки электродов диаметром 4 мм и более.Схема управления постоянным током более сложна, поскольку она пытается скопировать действия сварочного аппарата для поддержания определенной длины дуги.
Механизм подачи проволоки должен определять напряжение на дуге и поддерживать электродную проволоку в дуге для поддержания напряжения. Подача проволоки может замедляться или увеличиваться для поддержания заданного напряжения на дуге. Это добавит сложности системе управления. Система не реагирует быстро. Зажигание дуги затруднено, поскольку для запуска, отвода и поддержания заданной дуги необходимо использовать реверсивную систему.
При сварке SAW неизменно используется постоянный ток. Многоэлектродная проволока используется с дугами переменного и постоянного тока. Мы используем здесь систему постоянного питания. Он прикладывает постоянное напряжение, когда двухэлектродная проволока подается в дугу, питаемую от одного источника сварочного тока. Сварочный ток при дуговой сварке под флюсом может варьироваться от 50 до 2000 ампер. Самая распространенная сварка SAW выполняется в диапазоне 200-1200 ампер.
Дуговая сварка под флюсом имеет самую высокую скорость наплавки по сравнению с другими процессами дуговой сварки.Есть четыре причины для увеличения количества осаждений при сварке SAW.
- Полярность
- Длинный вылет
- Добавки флюса
- Дополнительный электрод
Скорость осаждения является самой высокой для отрицательного электрода постоянного тока (DCEN). Осаждение в переменном токе находится между DCEP и DCEN. Полярность с максимальным нагревом способствует отрицательному полюсу. Скорость наплавки при любой сварке увеличивается с увеличением «вылета». Точка, в которой ток должен вводиться в электрод и дуга, является вылетом.Чем длиннее вылет, тем хуже проникновение.
Мы можем увеличить скорость наплавки, добавляя металлические добавки во флюс и используя дополнительные электроды.
Металл шва, наплавленный дуговой сваркой под флюсом, высочайшего качества. По прочности и пластичности наплавленный металл превосходит низкоуглеродистую сталь и низколегированный материал. Это может произойти, если мы используем правильную комбинацию электрода, флюса и источника питания. Дуговая сварка под флюсом, используемая на машине или автомате, исключает врожденную человеческую ошибку, и сварка будет более однородной и без дефектов.
Ширина сварного шва при сварке под флюсом намного больше, чем при любой другой дуговой сварке. Подвод тепла намного выше, поэтому его охлаждение занимает больше времени. Газы успевают выйти. Шлак здесь имеет более низкую плотность и всплывает к верхней части валика. Автоматический процесс обеспечивает единообразие и последовательность.
Неполадки при сварке под флюсом- Проблем много, но одна из них заключается в том, что электродная проволока может искривляться при выходе из сопла и пистолета.
Кривизна проволоки не приведет к осаждению того места, где она предназначена. Если вы выполняете сварку в глубокую канавку, налет будет в стене, а не в корне, что приведет к неполному сращиванию корня. Это может захватить флюс в корне сварного шва.
- Поддержание точного размера сварного шва и заполнение сварной канавки вслепую может оказаться нелегкой задачей. Мы можем переусердствовать, наложив дополнительный сварной шов, или можем перестараться, сделав меньше депозита. Подготовленный сварщик справится с этой проблемой.
- Другой проблемой является растрескивание по средней линии. Чрезвычайно большой однопроходный сварной шов может захватывать примеси, а при затвердевании они собираются, что приводит к растрескиванию по средней линии. Это возможность с однопроходным плоским галтелем с углом 45 градусов. Многократные проходы позволяют избежать этого или изменить угол на 10 градусов.
- Чрезмерная твердость сварного шва, превышающая 225 единиц по Бринеллю, является результатом твердого углеродного шва, быстрого охлаждения и недостаточной обработки после сварки.
Этому может способствовать чрезмерное количество сплава в электроде.
- Дефект может возникать в начале и в конце, что можно контролировать, используя вкладку биения для начала и остановки, а не на продукте.
Параметры сварки аналогичны другим процессам дуговой сварки, за некоторыми исключениями. Тип электрода и флюс выбираем в зависимости от свариваемого металла. Размер электрода прямо пропорционален размеру сварного шва и рекомендуемому току.Количество проходов / размер валика, которые необходимо учитывать и определять соединение. Сварочный шов одного и того же размера может быть выполнен за несколько проходов или за несколько проходов, как предлагает металлургия. За несколько проходов получается лучший и более качественный сварной шов. Первоначально необходимо принять решение о полярности, нужно ли нам максимальное проникновение или максимальная ставка по депозитам.
Сварочный ток Важные переменные, влияющие на тепло при сварке, включают сварочный ток, напряжение, скорость перемещения. Сварочный ток имеет первостепенное значение, так как для однопроходного шва тока должно быть достаточно для достаточного проплавления без прожигания основного металла.
Чем выше сила тока, тем глубже проникновение. Требуется многопроходная сварка, сила тока должна соответствовать размеру сварного шва в каждом проходе. Размер электрода может быть параметром для выбора силы тока для сварного шва.
Напряжение дугиИзменение напряжения дуги находится в узких пределах. Это влияет на ширину и форму валика, поскольку при более высоком напряжении дуги валик будет плоским и широким.
Чрезвычайно высокое напряжение дуги может вызвать растрескивание, поскольку чрезмерное плавление флюса с избытком раскислителей, переносимых в зону сварки, снижает пластичность.При высоком напряжении дуги расходуется больше флюса. Низкое напряжение создает более жесткую дугу для улучшения проплавления глубокой канавки. Низкое напряжение приводит к получению узкого валика с высоким гребнем и затруднению удаления шлака.
Скорость перемещения влияет на сварной шов и проплавление. Чем выше скорость, тем тоньше валик с меньшим проникновением. Это идеальная ситуация для листового металла, когда требуется небольшой валик с минимальным проникновением.Слишком высокая скорость может привести к образованию поднутрений и пористости из-за более быстрого замораживания. Слишком низкая скорость приводит к образованию плохих шариков, чрезмерного разбрызгивания и вспышек.
Вторичные переменныеУгол электрода, рабочий угол, толщина флюсового слоя и расстояние между текущим наконечником и дугой (вылет). Нормальное расстояние между наконечником и дугой 25-38 мм.
Увеличение вылета увеличивает скорость наплавки. Мы должны рассмотреть этот фактор подробно для получения лучших результатов.
Вылет проволоки должен быть примерно в 8 раз больше диаметра проволоки.
Глубина потока Тонкий слой флюса вызывает большее количество дугового разряда и вспышки дуги, вызывая пористость. Тяжелый флюс приведет к образованию узкого и выпуклого сварочного валика. Небольшие примеси во флюсе оставляют следы на валике.
Ситуация с кольцевым сварным швом, когда детали вращаются под неподвижной головкой. Необходимость сварки может быть внутреннего или внешнего диаметра.Большая ванна расплавленного металла со шлаком движется для работы в процессе сварки SAW. Наплавленный слой по внешнему диаметру, электрод должен располагаться вверху в положении «12 часов». Металл шва опускается вниз по мере затвердевания. Меньший диаметр может быть проблемой при сварке. Неправильная установка электрода может привести к включению шлака и плохой сварке. В процессе сварки для внутренней окружности могут потребоваться электроды, расположенные под углом 6o по часовой стрелке.
Сварка под уклон и под уклон дает разные контуры сварного шва.На спуске борт будет иметь меньшее проникновение и шире. Подъем обеспечивает глубокое проникновение узким бортом.
Возможна односторонняя сварка при полном проплавлении корня под флюсом. При соединении с плотным корнем и большой гранью используется сильный ток с положительным электродом. Минимальная поверхность с широким основанием требует подкладки, так как нет ничего, что могло бы поддерживать расплавленный металл.
Медные опорные стержни являются полезным оборудованием при сварке тонкой стали. Бруски удерживают расплавленный материал, пока он не затвердеет.Опорные стержни могут иметь устройство водяного охлаждения для более быстрого охлаждения металла.
Уголок для проволоки Варианты процесса сварки под флюсом- Существует множество вариантов процесса, которые добавляют дополнительные возможности процессу дуговой сварки под флюсом. Некоторые из распространенных вариантов:
- Одинаковый источник питания с двухпроводной системой
- Отдельный источник питания с двухпроводной системой
- Отдельный источник питания с трехпроводной системой
- Наплавочный ленточный электрод
- Добавки железа в флюс
- Длинный вылет
- Электрическая проволока для холодной присадки
Многопроволочная система — Многопроволочная система повышает скорость наплавки за счет использования большего количества электродов. При одном источнике питания для обоих электродов используется один и тот же приводной валок. При использовании двух источников питания отдельные механизмы подачи проволоки используются для изоляции между двумя электродами в сварном шве. С двумя источниками питания и двумя электродами. Можно использовать разную полярность и разместить оба электрода рядом. Мы называем это поперечным положением электрода. В положении тандемного электрода мы можем разместить один электрод перед другим.
Двухпроводная тандемная система — Это положение электрода требуется, если требуемая глубина проникновения очень велика.Здесь ведущий электрод положительный, а задний электрод отрицательный. Первый электрод выполняет копание, а второй электрод заполняет шов. Если две дуги постоянного тока расположены близко друг к другу, возникает тенденция к интерференции дуги.
Система сварки полос — Используется для низкоуглеродистой и легированной стали с широким валиком с минимальным и равномерным проплавлением. Мы используем его для покрытия внутренней части сосудов, чтобы обеспечить коррозионную стойкость нержавеющей стали.В нем используется ленточный механизм подачи проволоки со специальным флюсом.
Железная основа под флюсом — Мы можем увеличить осаждение, добавив железосодержащий основной материал в стык под слоем флюса. Здесь утюг расплавится и станет частью металлического шва. Осаждение металла увеличивается без ухудшения свойств основного материала.
Проволока для холодной присадки — Пруток для холодной присадки может быть добавлен в виде специального сплава для увеличения наплавки металла. Улучшает свойства наплавленного материала.Здесь можно использовать порошковый электрод.
Материал, используемый при сварке под флюсом Сварочный флюс и плавящаяся электродная проволока — это материалы, которые используются при сварке под флюсом. Слой флюса защищает дугу и расплавленный металл от атмосферных примесей кислорода и азота. Он обладает свойствами поглотителя и раскислителя, который удаляет эти загрязнения из сварочной ванны. Флюс придает свойства сплава, но после охлаждения он образует стеклообразный шлак. Шлак защищает сварочную поверхность.Нерасплавленный флюс остается неизменным и собирается для повторного использования для дальнейшей эксплуатации.
Флюс при плавлении образует шлак, который легко отслаивается без особых усилий. Для удаления шлака в сварном шве с разделкой кромок может потребоваться отбойный молоток. Они разрабатывают флюсы для определенных целей. Эти флюсы бывают разных размеров, а частицы предназначены для конкретного применения.
Заключение Он использует процесс дуговой сварки под флюсом для сварки тяжелых металлов и тяжелых конструкций.Самый быстрый и мощный процесс дуговой сварки с наилучшей производительностью наплавки. Сварка SAW — это процесс сварки, выбранный в соответствии с потребностями проекта. Если вам нужно сварить тяжелую сварку на заводе, трубопроводах, котлах или рельсах, ваш выбор — это аппарат для дуговой сварки под флюсом.
Теперь ваша очередь задать мне вопрос. Мы готовы помочь в выборе.
Часто задаваемые вопросыДля чего используется процесс сварки пилой?
Промышленности, где требуется длительная свадьба в толстых сталях.Процесс включает в себя соединение между стальными компонентами с помощью электрической дуги, погруженной под слой флюса.
Почему сварка под флюсом считается под флюсом?
Процесс показывает, как дуга и зона сварки покрываются слоем флюса. Он погружен под флюс, при нагревании становится электропроводным и помогает в создании дуги.
Какой тип электрода используется при сварке пилой?
При сварке под флюсом и используются два материала.Сварочный флюс и плавящаяся электродная проволока. Флюс защищает дугу и расплавленный металл от примесей, таких как кислород и азот.
Каковы ограничения при сварке пилой?
Есть несколько основных ограничений, это может быть выполнено в одном положении для плоской сварки. Расплавленный металл подходит только для позиций 1F, 1G и 2F. Он также не подходит для тонких металлов.
Какой тип электрода используется при сварке под флюсом?
Используются как положительный (DCEP), так и отрицательный (DCEN) ток.Постоянный тип прямой мощности более популярен при сварке под флюсом проволокой 3,2 мм и проволокой малого диаметра.
Справочные материалы по дуговой сварке под флюсом
Дуговая сварка под флюсом — Википедия
Дуговая сварка под флюсом pdf
Дуговая сварка под флюсом — обзор
3.5 Дефекты сварного шва под флюсом
Дуговая сварка под флюсом была впервые проведена на линейных трубах в 1930 году [11]. Это процесс, при котором края пластины сводятся и свариваются дуговой сваркой с использованием расходуемого электрода и флюса.В отличие от ВПВ и оплавления, нагрев происходит с помощью электрической дуги между электродом и металлической трубой [12]. Кроме того, в отличие от сварных швов внахлест, ВПВ или оплавления (которые являются самопроизвольными), при сварке на ПАВ используется добавленный присадочный металл. Дуга и сварочная ванна погружены во флюс, чтобы защитить расплавленный металл сварного шва от атмосферы, где в противном случае он может собирать посторонние газы и приводить к появлению неметаллических включений или пористости. Процесс SAW — это не процесс ковки, как ERW, и в процессе сварки не применяется механическое давление.Первые трубы, сваренные дугой под флюсом, были сварены только по наружному диаметру и известны как одиночные сварные швы под флюсом. Примерно в 1948 году компания Consolidated Western впервые разработала процесс двойной дуговой сварки под флюсом (DSAW), при котором труба сваривалась как по внешнему, так и по внутреннему диаметру [11]. Процесс SAW универсален, так как можно соединять трубы различного диаметра и толщины [12]. Процесс SAW и DSAW, в частности, остаются одними из наиболее распространенных методов производства труб сегодня [11].
Хотя SAW, как правило, считается надежным процессом, он может иметь многие из тех же проблем сварки, что и другие процессы, такие как (не ограничиваясь) отсутствие плавления, недостаточное проплавление, пористость и поднутрение. В дополнение к этим довольно распространенным проблемам, трубы, сваренные дугой под флюсом, также могут иметь трещины в металле сварного шва, которые вызваны перемещением пластин до затвердевания металла шва [11], а также трещины на подошвах, которые могут образовываться при сварке. корень или носок сварного шва на внутреннем или внешнем диаметре. Трещины на носке могут быть вызваны холодным расширением после процесса сварки, когда труба имеет некруглую форму, или если сварной шов слишком большой, вызывая локально высокие напряжения на носке сварного шва, поскольку труба вынуждена принимать круглую форму [11,13 ].Трещины на носке, наряду с недостаточным проваром и трещинами сварных швов (трещины затвердевания), являются наиболее частыми механизмами разрушения при сварке под флюсом [5].
Другие дефекты могут включать несоосность между внутренним и наружным сварными швами в трубе DSAW — это может вызвать изгибающие напряжения при воздействии внутреннего давления [11]. Также известно, что транзитная усталость вызывает растрескивание труб, сваренных дугой под флюсом [4,11,13]. При усталости при транспортировке трубы отскакивают во время транспортировки по железной дороге или автомобильным транспортом, что может вызвать локальные высокие напряжения, вызвать образование трещин и рост трещин.Это усугубляется плохой загрузкой труб (недостаточное рассеивание энергии между трубами и т. Д.) И ранее существовавшими условиями в трубе (то есть смещением кромок пластин) [11,13].
Сварка под флюсом (SAW): области применения, работа, детали
Сегодня я буду обсуждать определение, применение, схему, оборудование, работу, преимущества и недостатки дуговой сварки под флюсом (SAW). Ранее была опубликована статья о дуговой сварке порошковой проволокой (FCAW). Проверить!
Подробнее: Принцип работы дуговой сварки порошковой проволокой
Что такое сварка под флюсом (SAW)?
Сварка под флюсом — это еще один тип процесса дуговой сварки, в котором используется плавящийся трубчатый электрод с непрерывной подачей.Может эксплуатироваться в автоматическом или механизированном режиме. Он также может работать с полуавтоматическими (ручными) пушками для резки SAW с подачей флюса под давлением или под действием силы тяжести. Этот процесс не подходит для плоских или горизонтальных положений присадочной сварки, поскольку горизонтальное положение было выполнено с помощью специального приспособления для поддержки флюса.
В этом процессе сварки зона дуги и сварочная ванна защищены от атмосферного загрязнения за счет слоя гранулированного флюса, состоящего из извести, кремния, оксида марганца, фторида кальция и некоторых других соединений.Расплавленный флюс становится проводящим и создает ток между электродами и основным металлом. Толстый слой флюса полностью покрывает металл, предотвращая образование искр и брызг, а также поддерживая интенсивное ультрафиолетовое излучение и пары, которые являются частью процесса сварки.
SAW был первым патентом в 1935 году и покрыл электрическую дугу под слоем гранулированного флюса. Первоначально он был разработан Джонсом, Кеннеди и Ротермундом.
Схема дуговой сварки под флюсом:
Подробнее: Что такое сварка в среде защитной дуги (SMAW)
Приложения
Ниже приведены приложения SAW:
ПроцессSAW подходит для сварки углеродистых сталей (конструкционных и судостроительных).Он также используется для обработки низколегированных сталей, нержавеющих сталей, сплавов на основе никеля и для наплавки.
Дуговая сварка под флюсом может использоваться для сварки сосудов под давлением, таких как котлы.
Множество контуров конструкций, труб, землеройных инструментов, судостроения, строительства железных дорог и локомотивов.
Наконец, сварка под флюсом может использоваться для ремонта деталей машин.
Этот процесс имеет некоторые отличительные особенности, которые отличают его от других процессов дуговой сварки, в том числе:
- Сварочная головка: подает флюс и присадочный металл к сварному шву.
- Бункер для флюса: он помогает накапливать флюс и контролирует скорость осаждения флюса на сварное соединение.
- Флюс: гранулированный флюс защищает сварной шов от атмосферного загрязнения. Он также очищает металл шва и снижает его химическое загрязнение. Хотя некоторые другие процессы дуговой сварки, такие как MIG, SMAW, предлагают это.
- Электрод: присадочный материал представляет собой стандартную проволоку, а также другие специальные формы. Толщина этих проводов обычно составляет от 1,6 до 6 мм.
Подробнее: Сварка вольфрамовым электродом в среде инертного газа (TIG)
Детали машин SAW
Дуговая сварка под флюсом состоит из основных частей или оборудования, таких как сварочная головка, бункер для флюса, флюс, блок подачи электродной проволоки, электрод и блок регенерации флюса.Сварочную головку можно использовать для подачи присадочного металла, а также флюса к стыку для сварки. Другие общие части машины включают:
- Расходный электрод
- Источники энергии
- Гранулированный флюс
- Основной металл
- Держатель электрода
Аппарат для дуговой сварки под флюсом:
Подробнее: Электрошлаковая сварка
Принцип работы SAW
Как и другие процессы дуговой сварки, SAW передает ток на электрод от сварочного аппарата переменного или постоянного тока. Он отдельно наносил флюс в зону сварного шва до того, как произойдет соединение. Этот флюс не проводит электричество в холодном состоянии, но становится хорошим проводником при расплавлении с помощью тепла дуги. Это также позволяет току течь между электродом и заготовкой. Поток, видимый для атмосферы, остается зернистым (неизменным), что позволяет использовать его повторно. Низкоплавкий флюс становится шлаком, превращается в отходы и должен быть удален после сварки,
Электрод непрерывно подается в соединение с заданной скоростью.В полуавтоматических сварочных установках сварка выполняется вручную вдоль стыка. В автоматическом режиме отдельный привод перемещает либо сварочную головку над стационарной работой, либо работа вращается под неподвижной сварочной головкой.
Подробнее: Общие сведения о плазменно-дуговой сварке (PAW)
Посмотрите видео ниже, чтобы узнать, как работает SAW:
youtube.com/embed/_jdk0q9dccc?feature=oembed» frameborder=»0″ allow=»accelerometer; autoplay; clipboard-write; encrypted-media; gyroscope; picture-in-picture» allowfullscreen=»»/>
Подробнее: Знакомство с дуговой сваркой шпилек и ее методами
Преимущества и недостатки сварки под флюсом
Преимущества:
Ниже приведены преимущества SAW:
- Высокая производительность наплавки.
- Процесс автоматизирован.
- Получается меньше дыма.
- Обучение кромке не требуется.
- Это можно делать в помещении и / или на открытом воздухе.
- Нет шансов для оксидных искр, потому что он погружен в слой флюса.
Недостатки
Несмотря на хорошие преимущества SAW, некоторые ограничения все же имеют место. Ниже приведены недостатки SAW:
- Для некоторых металлов процесс не завершен.
- Может быть несовершенным для прямых швов сосудов и труб. Использование
- Flux может быть утомительным.
- Проблема со здоровьем может возникнуть из-за флюса.
- Удаление шлака желательно после сварки.
Подробнее: Приварка шпилек
Вот и все для этой статьи, где обсуждаются определение, применение, схема, оборудование, работа, преимущества и недостатки. Я надеюсь, что вы многое узнали из чтения, если да, пожалуйста, поделитесь с другими студентами. Спасибо за чтение, увидимся в следующий раз!
Сварка под флюсом: технология, которая совершенствуется с возрастом
Технологии производства сегодня очень сильно отличаются от методов и процессов, использовавшихся в начале 20 века.Однако в случае дуговой сварки под флюсом (SAW), уникального безопасного и последовательного метода сварки, который используется с 1930-х годов, новые технологии не снизили его значимость для производства деталей, подвергнутых механической обработке. Фактически, технология автоматизированной сварки гарантирует, что ПАВ остается важной частью наших производственных процессов здесь, в Allis Roller.
Сварка под флюсом (SAW) была впервые запатентована в 1935 году и наиболее широко использовалась при производстве танков во время Второй мировой войны.Те же элементы, которые сделали SAW идеальным процессом для сварки деталей резервуаров, также делают его идеальным для продольных и кольцевых стыковых швов, необходимых сегодня для трубопроводных трубопроводов и сосудов под давлением. SAW использует порошковый флюс, который действует как проводник между сварочным электродом и заготовкой и предотвращает утечку искр, дыма и брызг во время процесса. В результате отпадает необходимость в защитном экране во время процесса сварки, а большое количество металла может быть наплавлено за короткое время, что делает SAW отличным выбором для сварки тяжелых элементов оборудования.
Преимущества использования SAW для безопасной и эффективной сварки тяжелых деталей — вот почему Allis Roller продолжает использовать ее на нашем собственном предприятии при производстве тяжелых деталей со сложной механической обработкой для сельскохозяйственной, строительной и горнодобывающей промышленности.
В Allis Roller большая часть наших процессов обработки и производства включает использование компьютеризированного оборудования, которым управляет один из наших квалифицированных специалистов, и наше применение SAW ничем не отличается.Во время механизированного или автоматизированного процесса SAW программа ЧПУ вращает деталь с заданной скоростью, контролируя при этом нагрев и скорость сварки, чтобы гарантировать оптимальное качество и стабильность детали. В отличие от ранней технологии SAW, использовавшейся во время Второй мировой войны, автоматическая SAW стала более быстрой, экономичной и точной.
В дополнение к включению как традиционных, так и автоматизированных процессов SAW по требованию заказчика, наши инженеры продолжают совершенствовать наши собственные системы для производства более крупных деталей.Чаще всего мы используем SAW для изготовления структурных поперечных труб длиной три фута в тракторных погрузчиках CNH, но прямо сейчас Allis Roller работает над созданием гораздо большего приводного вала — 7 дюймов в диаметре на 5 футов в длину — для размещения SAW даже более тяжелое оборудование. Allis Roller также обновила наш сварочный аппарат до MillerDC650 и добавила новую горелку / устройство подачи, чтобы увеличить нашу производительность и приспособить сварочную проволоку большего диаметра. Каждое из этих обновлений помогает нам максимально использовать потенциал исторически актуальных сварочных технологий в производстве более крупных и качественно обработанных деталей.
Allis Roller являются экспертами в области инноваций и совершенствования методов сварки под флюсом в интересах наших клиентов. Каждый проект, который проходит через наши двери, тщательно проверяется, и выбираются лучшие машины для работы, чтобы обеспечить точное и экономичное изготовление деталей для наших клиентов. Для получения дополнительной информации об использовании SAW в Allis Roller свяжитесь с одним из членов нашей команды через страницу «Контакты».
Вам понравился этот пост? Поделись:
Назад к основам — дуговая сварка и сварка электродом
GTAW, GMAW, поддуговая и электродная сварка — в чем разница? Часть 2
Я надеялся, что к тому времени, когда я сел писать эту статью, у меня будет для вас история о сварке, но этому помешала чудесная зима MN. В тот день, когда я должен был пойти вниз и взять урок, у нас была ужасная снежная буря, и я работал из дома. Кто еще думает, что мать-природа и старик Зима должны просто поцеловаться и помириться? Пришло время весны! В любом случае, ни у Джо (нашего тренера по сварке), ни у меня с тех пор на это не было времени, но это произойдет! Я ничто иное, как настойчивый!
На этот раз я расскажу о разнице между дуговой сваркой и сваркой электродом. Начнем с дуговой сварки или дуговой сварки под флюсом.Этот вид сварки используется, когда необходимо соединить толстые листы металла. Он создает длинные швы, экономит время и создает более плотные сварные швы. Сам сварной шов нельзя увидеть, пока он не будет завершен, потому что флюс, который используется вместо защитного газа, необходимо удалить, чтобы увидеть сварной шов. Мне удалось провести небольшой промежуток времени в магазине, наблюдая за этим процессом, и, хотя я был очарован, сварщик, обслуживающий органы управления, сообщил мне, что это не так весело, как кажется, и через некоторое время становится довольно скучно наблюдать. Хотя я не сомневаюсь, что она, вероятно, права, для меня это было весело! На мой взгляд, самое интересное в Sub-Arc заключается в том, что сварка выполняется под слоем флюса.
Что такое флюс, спросите вы? (Да, я тоже!) Флюс — это материал, похожий на серый песок. Надеюсь, вы все помните Шона из моей последней статьи, он снова согласился мне помочь. Он говорит, что флюс — это гранулированный легкоплавкий материал, содержащий оксиды марганца, кремния, титана, алюминия, кальция, циркония, магния и другие соединения.Поддуговая сварка в основном используется на наших продольных (прямых) и кольцевых (круглых) швах на наших судах. Его также можно использовать для угловых швов.
Ручная сварка — SMAW (дуговая сварка защищенного металла) — это еще один процесс дуговой сварки, в котором всегда используется присадочный металл. Обычно это металлический стержень, покрытый флюсом, который защищает сварной шов и стабилизирует дугу, благодаря чему отпадает необходимость в защитном газе, как в GTAW и GMAW . Этот процесс используется при тяжелом ремонте или строительстве, а также при работе с более толстыми материалами, такими как чугун, потому что он создает такой прочный сварной шов.Этот сварной шов сложнее создать, и он предназначен для более опытных сварщиков, но как для новичка, так и для новичка этот процесс оставляет сварной шов, который наименее привлекателен для взгляда из всех типов. Следовательно, почему это последний, о котором я говорю…
Итак, подведем итог: GTAW, — самый красивый, GMAW — наиболее часто используемый, Sub-Arc — самый сильный, а Stick — самый уродливый. Но всем им есть свое место в нашем магазине, и все они используются, чтобы мы могли создавать все, что встречается на нашем пути.Вам интересно, что будет дальше? Решил немного переключить передачи. Моя следующая статья будет посвящена нашему механическому отделу. Вернитесь через пару недель, чтобы узнать разницу между фрезерными, торцевыми и токарными операциями.
Принципы и способы применения дуговой сварки под флюсом (SAW)
перейти к основному | перейти на боковую панельПринципы и способы применения дуговой сварки под флюсом (SAW)
Дуговая сварка под флюсом или SAW — один из наиболее распространенных процессов дуговой сварки.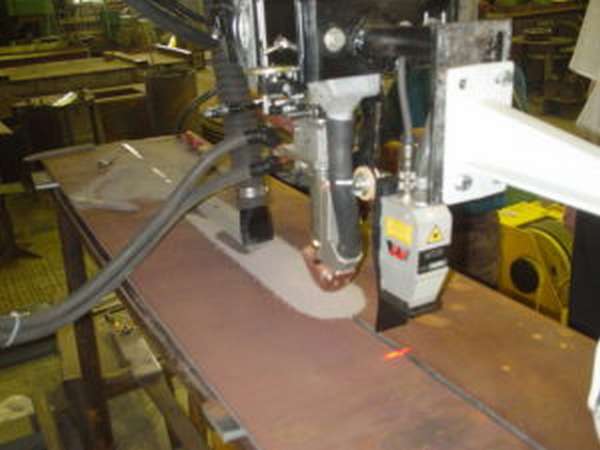

Преимущества
- Этот процесс сварки отличается высокой скоростью наплавки.Можно отложить почти 45 кг / ч.
- Для механизированного применения.
- Видно очень мало сварочного дыма. .
- Подготовка кромок не требуется.
- Этот процесс применим как внутри помещений, так и снаружи.
- Отсутствие брызг при сварке, так как он погружен в слой флюса.
Недостатки
- Эксплуатация ограничена некоторыми конкретными металлами.
- Область применения ограничена прямыми швами, трубами и сосудами.
- Обработка флюса может быть сложной.
- Проблема со здоровьем может быть вызвана потоком.
- Удаление шлака необходимо после сварки.
Приложения
- Присоединение сосудов под давлением, таких как котлы.
- Многие строительные профили, землеройное оборудование, трубы.