Ручная дуговая сварка плавящимся электродом
Ручная дуговая сварка плавящимся электродом
Категория:
Сварка металлов
Ручная дуговая сварка плавящимся электродом
Наибольший объем среди других видов сварки занимает ручная дуговая сварка плавящимся электродом. Сварку выполняют электродами, которые вручную подают в зону горения дуги и перемещают вдоль свариваемого изделия. Дуга горитмеж-ду стержнем электрода и основным металлом. Под действием тепла дуги электрод и основной металл плавятся, образуя металлическую сварочную ванну. Капли жидкого металла с расплавляемого электродного стержня переносятся в ванну через дуговой промежуток. Вместе со стержнем плавится покрытие электрода, образуя газовую защиту вокруг дуги и жидкую шлаковую ванну на поверхности расплавленного металла.
Металлическая и шлаковая ванны вместе образуют сварочную ванну. По мере движения дуги сварочная ванна затвердевает и образуется сварной шов.
Рис. 1. Ручная дуговая сварка металлическим электродом с покрытием (стрелкой указано направление сварки)
Рис. 2. Схема питания дуги при ручной дуговой сварке (на постоянном токе): а — электрическая схема, б — общая компоновка поста для сварки; 1 — изделие, 2 — сварочная дуга, 3 — электрод, 4 — электрододержатель, 5 — сварочные провода, 6 — источник питания, 7 — щит с приборами контроля и регулирования параметров режима сварки
Рабочим местом для ручной сварки служит сварочный пост, оснащенный источником питания, токоподводом, необходимыми инструментами, принадлежностями и приспособлениями. Схема питания дуги приведена на рис. 2.
Сварочные посты могут быть стационарными и передвижными.
ремонтных работах. При этом часто используют переносные источники питания.
В зависимости от свариваемых материалов и применяемых электродов для ручной дуговой сварки применяют источники переменного или постоянного тока с крутопадающей характеристикой.
Основным рабочим инструментом сварщика при ручной сварке служит электрододержатель, который предназначен для зажима электрода и подвода сварочного тока. Применяют электрододержатели пружинного и пластинчатого типов.
Согласно ГОСТ 14651—78, электрододержатели выпускают трех типов в зависимости от силы сварочного тока: I типа — для тока 125 А; II — 125—315 А, III — 315—500 А.
Для подвода тока от источника питания к электрододержателю и изделию используют сварочные провода. Сечения проводов выбирают по установленным нормативам для электротехнических установок — 5—7 А/мм2.
Для предохранения лица и глаз сварщика от лучей электрической дуги служат специальные защитные приспособления — щитки и маски из жаростойких диэлектриков (фибры, пропитанной специальным раствором фанеры и т. п.) с защитными стеклами —светофильтрами (размер 52×102 мм). Для предохранения тела применяют спецодежду из плотного брезента или сукна, иногда из асбестовой ткани.
К вспомогательным инструментам для ручной сварки относятся стальные проволочные щетки для зачистки кромок перед сваркой и для удаления с поверхности швов остатков шлака, молоток-шлако-отделитель для удаления шлаковой корки, особенно с угловых и корневых швов в глубокой разделке, зубило, набор шаблонов для проверки размеров швов, стальное клеймо для клеймения швов, выполненных сварщиком, метр, стальная линейка, отвес, угольник, чертилка, мел, а также ящик для хранения и переноски инструмента.
Реклама:
Читать далее:
Техника ручной дуговой сварки
Статьи по теме:
Механизм дуговая сварка плавящимся электродом
Автор zamolotkom. ru На чтение 23 мин. Просмотров 1.6k. Опубликовано
Сварка плавящимся электродом: технология процесса, необходимое оборудование, типы переноса электродного метала
Дуговая сварка плавящимся электродом — это метод, при котором между свариваемым изделием и концом электрода возникает электрическая дуга, под действием которой основной металл и электрод начинают плавиться, образуя сварочную ванну, а обмазочный материал электрода при этом создает газовую защитную среду, необходимую для качественного шва.
Плюсы и минусы метода
Плюсами этого способа сваривания всегда считались:
- простота эксплуатации и низкая цена оборудования для сварного процесса;
- возможность сваривания большого количества разновидностей металлов при широком спектре выбора электродного материала;
- возможность выполнять сварные работы в труднодоступных местах;
- уместно сваривание в любых пространственных положениях.
Из недостатков стоит выделить:
Оборудование для ручной дуговой сварки
Оборудование, необходимое для ручного дугового сваривания, состоит:
- из источника питания, который может быть как переносным, так и стационарным в зависимости от вида выполняемых сварщиком работ;
- из кабеля с электродержателем, в котором фиксируется покрытый специальной обмазкой электрод;
- из кабеля обратного заземления для соединения свариваемого изделия с источником питания.
Также не стоит забывать о дополнительных средствах, таких, как: защитная маска, перчатки сварщика, разнообразные приспособления для удаления шлака и другие вещи, необходимые для удобства специалиста.
Перенос электродного металла делится на три типа:
- крупнокапельный перенос. Случается, если процесс происходит с высоким напряжением на электрической дуге и невысокими параметрами тока при сваривании.
Размер капель плавящегося электрода при этом имеет диаметр больше сечения самого электрода. Процесс сварки в таком случае возможен только в вертикальном пространственном положении, так как сварочная ванна при таком переносе имеет большие размеры и её становится сложно контролировать.
- мелкокапельный перенос. При данном виде переноса металла капли расплавленного электродного материала равны или меньше по диаметру, чем сам электрод. Процесс сварки проходит с высоким напряжением на дуге и высокими параметрами тока. При мелкокапельном переносе увеличивается скорость выполнения работ, шов имеет более аккуратный вид. Такой тип переноса наиболее подходит для сваривания толстостенных металлов.
- струйный перенос. Струйный перенос металла обычно происходит при высокой силе тока и использовании электрода с прямой полярностью. При данном переносе очень мелкие капли металла идут одна за другой непрерывной цепочкой, обеспечивая ровную и гладкую на ощупь поверхность шва.
Этот же тип переноса характерен для полуавтоматической сварки в среде защитного газа.
Сварочный процесс
От источника сварочного тока к электроду поступает электроэнергия. Во время контакта электрода со свариваемым металлом образуется электрическая дуга, которая расплавляет изделие и электрод, вследствие чего возникает сварочная ванна. Электродный материал, поступая в эту ванну, сплавляет кромки металла, который нужно сварить, а обмазка обеспечивает защиту в области формирования шва и образует защитный слой по окончании процесса сваривания.
Сварка плавящимся электродом в защитных газах
Этот тип сварки подразумевает собой сварку с помощью автоматических или полуавтоматических сварочных аппаратов, в процессе сварочная проволока подается в зону формирования шва. В роли защитного газа чаще всего выступают аргон либо углекислый газ, которые подаются в зону действия электрической дуги для обеспечения хорошего соединения металлов и отсутствия дефектов сварочного шва.
Этот способ отличается высокой производительностью и большой скоростью процесса, что способствует его распространению в сфере промышленного производства металлоконструкций, машиностроении.
Из-за отсутствия шлаковых включений и возможности аккуратного выполнения сварки при очень малых толщинах материала данный метод получил широкое распространение на разнообразных СТО и других предприятиях по обслуживанию и ремонту автомобилей.
Опишите ручную дуговую сварку плавящимся электродом
Ручная дуговая сварка выполняется плавящимся или неплавящимся (угольным, графитовым, вольфрамовым, гафниевым) электродом. При сварке плавящимся электродом (рис. 5.1) дуга горит между ним и изделием. Формирование металла шва осуществляется за счет материала электрода и расплавления основного металла в зоне действия дуги.
Наибольшее применение нашла сварка плавящимся электродом, так как ее можно применять во всех пространственных положениях, сваривая черные, цветные металлы и различные сплавы. При этом используются электроды диаметром 1÷ 12 мм. Однако основной объем работ выполняется электродами диаметром 3 ÷ 6 мм.
Электроды классифицируются по материалу, из которого они изготовлены, по назначению, по виду покрытия, по свойствам металла шва, по допустимым пространственным положениям сварки или наплавки, по роду и полярности тока.
По назначению электроды подразделяются на следующие группы: для сварки углеродистых и низколегированных конструкционных сталей – У; для сварки теплоустойчивых легированных сталей – Т; для сварки высоколегированных сталей с особыми свойствами – В; для наплавки слоев с особыми свойствами – Н.
48. Свариваемость. Основные технологические приемы для трудно и ограниченно свариваемых сталей.
Ограниченно свариваемые стали имеют содержание углерода от 0,36 до 0,45% и склонны к образованию трещин. Сварка требует обязательного подогрева. Плохо свариваемые стали содержат углерод в количестве более 0,45%. При их сварке требуются специальные технологические процессы.
Легирование стали одним или несколькими легирующими элементами придает ей определенные физико-механические свойства. Как правило, повышение уровня легирования и прочности стали приводит к ухудшению ее свариваемости и первостепенная роль в этом принадлежит углероду.
Низколегированные стали хорошо свариваются всеми способами плавления. Получение же при сварке равнопрочного сварного соединения, особенно у термоупрочненных сталей, вызывает определенные трудности. В зонах, удаленных от высокотемпературной области, возникает холодная пластическая деформация. При наложении последующих швов эти зоны становятся участками деформационного старения. Это в конечном итоге приводит к снижению пластических и повышению прочностных свойств металла и соответственно к появлению холодных трещин. В среднелегированных сталях увеличивается склонность к закалке, в связи с чем такие стали имеют высокую чувствительность к термическому циклу сварки. Их околошовная зона оказывается резко закаленной, а следовательно, и непластичной при всех режимах сварки, обеспечивающих удовлетворительное формирование шва. Поэтому с целью снижения скорости охлаждения околошовной зоны при сварке этих сталей необходим предварительный подогрев свариваемого изделия.
При сварке высоколегированных хромистых 08X13, 08Х17Т и некоторых других сталей существуют отличительные особенности: высокий порог хладноломкости стали, находящийся обычно в области положительных температур; склонность к значительному охрупчиванию в околошовной зоне;
низкая пластичность и вязкость металла шва, выполненного сварочными материалами аналогичного со сталью химического состава; невозможность устранить охрупчивание термообработкой.
Сварку таких сталей необходимо выполнять с минимальным тепловложением, так как с увеличением погонной энергии возрастает склонность зон сварного соединения к росту зерен, появлению микротрещин и падению пластичности. При этом снижается сопро-тивляемость сварного соединения локальным повреждениям и межкристаллической коррозии. В процессе сварки возникает опасность коробления и появляется повышенный уровень остаточных напряжений. После сварки в ряде случаев требуется термообработка.
Сварка плавящимся электродом.
Выполняется при расплавлении электродной проволоки, подаваемой в плавильное пространство, его защита от воздуха осуществляется подачей защитного газа — инертного, активного или их смесей под давлением, большим атмосферного, вследствие чего воздух оттесняется и образуется соответствующая газовая среда (рис. 7.4). При этом способе сварки дуга горит между электродом 5, который подается в зону сварки с помощью специального механизма со скоростью Упэ, и изделием 4.
Рис. 7.4. Схема сварки плавящимся электродом в среде защитных газов
Капли расплавленного электродного металла 3 смешиваются с расплавленным основным металлом, образуя общую сварочную ванну 2, которая после кристаллизации превращается в сварной шов 1. Перемещение горелки вдоль сварного шва выполняется вручную сварщиком со скоростью сварки VCB. Защита плавильного пространства осуществляется инертным или активным газом б, который подается через сопло 7 под давлением, большим атмосферного. Образованная газовая среда определяет характер взаимодействия между газами и расплавленным металлом. Как и при сварке неплавящимся электродом, надо обеспечивать ламинарное течение газа из сопла, для чего используют такие же средства. Основными параметрами режима являются следующие:
- • род тока, полярность — сварка ведется на постоянном токе обратной полярности, что обеспечивает наиболее стабильное горение дуги;
- • диаметр электродной проволоки — зависит от толщины свариваемого металла и пространственного положения; находится в пределах 0,5—2,0 мм для полуавтоматической сварки и 2—4 мм для автоматической;
- • сила сварочного тока /св = 50—500 А — зависит от диаметра электродной проволоки, пространственного положения и скорости ее подачи;
- • напряжение на дуге Ua = 18—35 В — зависит от пространственного положения, силы сварочного тока, диаметра и состава электродной проволоки и рода защитного газа;
- • скорость сварки VCB при полуавтоматической сварке не задается по тем же соображениям, что и при ручной, при автоматической находится в пределах 10-60 м/ч;
- • вылет электрода /э = 10—30 мм — зависит от диаметра электродной проволоки и ее электрофизических свойств.
При малом вылете возможны оплавление мундштука, увеличение забрызгивания внутренней поверхности сопла, что приводит к нарушению ламинарного течения защитного газа. При большом вылете ухудшается защита плавильного пространства, проволока вследствие перегрева теряет свою жесткость, ухудшается направление ее в место сварки. Однако вследствие подогрева проволоки на участке увеличенного вылета возрастают скорость ее плавления и производительность процесса. Это явление можно реализовать, используя специальные керамические направляющие мундштуки;
- • расход защитного газа QT = 5—30 л/мин — зависит от силы сварочного тока, защитного газа (расход аргона и диоксида углерода в 3—4 раза меньше, чем гелия), состава свариваемого металла, скорости сварки и т.д.
Выбор защитного газа определяется в первую очередь свойствами свариваемого металла. Одни высоколегированные стали и сплавы, титан и его сплавы требуют лишь инертной защитной атмосферы, а другие высоколегированные стали и сплавы, алюминий и его сплавы могут быть сварены как в инертной атмосфере, так и с примесями к ней активных газов, например 2—5 % кислорода. При этом достигается струйный перенос металла, уменьшается разбрызгивание и не появляется пористость от водорода. Сварку углеродистых и низколегированных сталей можно выполнять в активных газах (С02 по ГОСТ 8050—85, С02 + 20—30 % 02), в смеси активных и инертных газов. Так, смесь Аг + 25 % 02 способствует струйному переносу электродного металла и позволяет предотвратить разбрызгивание. Состав защитных газов влияет и на другие технологические характеристики процесса. При сварке в аргоне короткая и длинная дуга обеспечивает благоприятные условия сварки металлов малых и средних толщин в нижнем положении. При сварке в гелии и азоте и в их смесях с аргоном благодаря повышенной тепловой мощности обеспечиваются большая глубина провара и благоприятная его форма, что способствует повышению скорости сварки.
При выборе рассмотренных взаимосвязанных характеристик следует руководствоваться данными, приведенными в табл. 7.1.
Рекомендованные соотношения между диаметром электрода и силой тока, напряжением на дуте и вылетом электрода
Техника полуавтоматической сварки в среде защитных газов плавящимся электродом достаточно проста и имеет много общего с техникой ручной дуговой сварки. Роль сварщика сводится к поддержанию постоянного вылета электрода и расстояния сопла до изделия, равномерного перемещения горелки вдоль свариваемых кромок и иногда к выполнению необходимых манипуляций и колебаний электродом. Форма колебаний зависит от диаметра проволоки; при сварке тонкой проволокой (до 1,6 мм), как и при ручном процессе при больших диаметрах, зависит от типа соединения. Корневые швы сваривают при возвратно-поступательном перемещении электрода, средние слои стыковых швов при перемещении электрода по вытянутой спирали, а верхние слои — с поперечными колебаниями «змейкой». Сварку ведут с наклоном электрода углом вперед и углом назад до 10—30°. В первом случае глубина провара меньше, чем во втором, вследствие подтекания жидкого металла под основание дуги.
Возвратно-поступательные движения горелки уменьшают пористость, особенно при применении активных газов вследствие улучшения защиты, перемешивания и замедления охлаждения жидкой ванны, что способствует извлечению из нее газов.
Подготовка кромок под сварку и размеры сварных швов регламентирует ГОСТ 14771—76, согласно которому можно качественно сваривать металл толщиной начиная с 0,8 мм.
Сварку стыковых швов тонкостенных изделий во всех случаях лучше вести в вертикальном положении сверху вниз или «на весу», а дугу направлять на ванну жидкого металла и выполнять такой шов за один проход. Если детали собраны с зазором, процесс ведут с периодическими остановками, уменьшением мощности или поперечными колебаниями. Кольцевые стыковые швы сваривают, как и прямолинейные. Металл толщиной до 4 мм сваривают в по- лупотолочном или вертикальном положении сверху вниз проволокой малого диаметра или импульсной дугой. Более толстые изделия сваривают в нижнем положении со смещением электрода с зенита в сторону, противоположную вращению детали; размер смещения зависит от диаметра детали, силы тока и скорости сварки. Соединение металла внахлест толщиной до 1,5 мм сваривают, направляя дугу на верхнюю кромку, при большей толщине сваривают «на весу» с наклоном электрода поперек шва, а дугу направляют в угол среза кромки верхнего листа.
Угловые соединения сваривают «лодочкой» наклонным электродом под углом 50—60° к полке. Если толщина металла менее 5 мм, дугу направляют в угол. При большей толщине электрод смещают в сторону полки на 0,8—1,5 мм, а сварку ведут углом вперед.
Сварку электрозаклепками и точками применяют для стыковых, угловых и соединений внахлест металла толщиной до 2 мм во всех пространственных положениях с пробивкой или без пробивки отверстий в верхних листах, а стык деталей обеспечивают прижатием сопла, которое имеет отверстия для выхода газа.
При сварке вертикальных швов на тонком металле используют свободное формирование шва: процесс ведут сверху вниз, углом назад, направляя дугу на переднюю часть ванны, что обеспечивает проплавление кромок и исключает прожоги. Сварка сверху вниз не требует высокой точности сборки деталей и выполняется в 2—2,5 раза быстрее, чем снизу вверх. Сварку металла толщиной более 6 мм выполняют снизу вверх, что обеспечивает надежный провар и отсутствие несплавления по краям шва, короткими частыми замыканиями, пересаживая электродный металл капля за каплей в сварочную ванну. При значительной длине прямолинейные вертикальные швы на стали толщиной от 8 до 40 мм рекомендуется сваривать с принудительным формированием шва с помощью медных водоохлаждаемых ползунов, используя порошковую проволоку или подавая небольшое количество флюса в плавильное пространство. Сварка выполняется специальным автоматом. Использование импульсно-дугового процесса значительно упрощает сварку таких швов.
Сварку горизонтальных швов ведут с наклоном электрода, снизу вверх и углом назад без поперечных колебаний, направляя дугу на сварочную ванну. При толщине металла более 4 мм производят разделку верхней кромки листа, а металл толщиной более 6 мм сваривают с наклоном электрода сверху вниз. При этом корневой шов сваривают тонкой проволокой с частыми короткими замыканиями, импульсной дугой или неплавящимся электродом. Основную разделку заплавляют плавящимся электродом на больших токах, а облицовочный шов — тем же способом, что и корневой.
Потолочные швы — сложные в исполнении, их сваривают углом назад на минимальных силах тока и напряжении, а диаметр электрода выбирают в пределах 0,5—1,4 мм. Дугу и поток защитного газа направляют на ванну жидкого металла для уменьшения ее стекания при увеличенном расходе газа, поперечных колебаниях электрода, частых коротких замыканиях.
Полуавтоматическая сварка в среде защитных газов полностью вытеснила полуавтоматическую сварку под флюсом и стала доминирующей среди механизированных способов сварки при изготовлении металлоконструкций ответственного и особо ответственного назначения благодаря таким преимуществам, как высокая производительность, легкость транспортирования защитной среды к плавильному пространству, отсутствие шлаковой корки и шлаковых включений, уменьшение ширины зоны термического влияния и сварочных деформаций, сварка во всех пространственных положениях, возможность наблюдения за дугой и управления ею.
Углеродистые, низколегированные и некоторые среднелегированные стали можно сваривать в сильно- или слабоокислительной среде, используя электродную проволоку с повышенным содержанием элементов-раскислителей. Дело в том, что углекислый газ только защищает от азота плавильное пространство, а сам образует в нем кислую среду за счет диссоциации:
Жидкий металл в головной части сварочной ванны может реагировать как с самим диоксидом углерода, так и с продуктами его реакции:
в результате чего сварочная ванна насыщается кислородом. При охлаждении расплавленного металла углерод, который присутствует в стали, может окисляться, образуя оксид углерода:
Выделяясь из сварочной ванны в виде пузырей, СО может вызвать пористость; если сварочная проволока легирована кремнием и марганцем, оксиды железа будут раскисляться главным образом в результате взаимодействия с ними, а не с углеродом, обеспечив качественный металл шва и отсутствие пор:
Эти реакции протекают в хвостовой части сварочной ванны, поэтому оксиды кремния и марганца в виде очень тонкой шлаковой корки покрывают поверхность сварного шва. Существенным недостатком использования углекислого газа для сварки является повышенное разбрызгивание: забрызгиваются внутренняя поверхность сопла горелки и околошовная зона, а отделение брызг от основного металла требует применения тяжелого непрестижного ручного труда.
Для предотвращения этого явления используют специальные источники питания, применяют газовые смеси, которые способствуют мелкокапельному переносу электродного металла (С02 + 02) или струйному (Ат + СОД, ведут сварку специальными порошковыми или активированными проволоками или наносят на около- шовную поверхность специальные лакокрасочные покрытия, которые, однако, эффективно действуют только при однопроходной сварке, после чего их нужно обновлять.
С учетом специфики защиты плавильного пространства углекислым газом сварку различных соединений из углеродистых и низколегированных сталей ведут с использованием специальных электродных проволок Св-08Г2С, Св-08ГСМТ, Св-08ХГСМФ и т.д.
При сварке высоколегированных сталей, которые имеют в своем составе элементы, высокоактивные к кислороду (алюминий, титан, ниобий и т.д.), нужно использовать только инертные газы, в других случаях возможно применение смеси аргона с кислородом в комбинации с соответствующими проволоками: Св-01Х19Н9, Св-08Х19Н10Г2Б, Св-08Н50, Св-ХН75М6ТЮит.п.
Медь и ее сплавы сваривают в аргоне, гелии и азоте. С целью экономии аргона и повышения производительности труда рекомендуется газовая смесь 70—80 % Аг + 30—20 % N2. Однако лучшее формирование шва достигается при сварке в аргоне и гелии. В качестве присадки используется проволока из кремнисто-марганцевой бронзы БрКМцЗ—1. Перед началом процесса требуется подогрев кромок до 200—500 °С.
Для механизированной сварки высокопрочной коррозионно-стойкой бронзы марки БрАНМцЖ-8,5—4—4—1,5 разработана специальная композитная проволока, которая обеспечивает получение сварного шва того же состава на параметрах режима: d3 = 2,8 мм, /св — 350-380 А, 1/Д = 24—26 В, QM = 16—17 л/мин.
Титан и его сплавы толщиной более 4 мм сваривают только в среде инертных газов высокой степени чистоты. Размеры сварных швов и их формирование зависят от рода газа. В гелии швы имеют более плавный переход усиления к основному металлу, в аргоне проплавление шва глубже и шов уже. Рекомендуется вести сварку присадочной проволокой марки ВТ 1—00.
Для сварки на монтаже рекомендуется использовать импульсно-дуговой процесс с использованием гелия.
Сварка должна выполняться в палатке, чтобы исключить сдувание защитной струи из плавильного пространства. В цеху надо пользоваться камерой с контролируемой атмосферой.
Алюминий и его ставы толщиной более 4 мм сваривают в среде аргона или в смеси 30 % Аг + 70 % Не. В качестве присадочной проволоки используются сплавы типа АМц и АМг, а также сплавы состава, близкого к основному металлу.
По сравнению со сваркой вольфрамовым электродом сварные швы имеют пониженную на 15 % прочность вследствие большего перегрева электродного металла при переходе через дуговой промежуток. Преимуществами являются надежное перемешивание сварочной ванны и ее очистка от оксидных включений, а также высокая производительность, которую можно значительно увеличить, применяя импульсно-дуговой процесс. Введение модификаторов (циркония, титана, бора) в проволоку повышает стойкость сварных швов к кристаллизационным трещинам.
При сварке высоколегированных термически упрочняемых сплавов прочность может снижаться почти наполовину, поэтому после сварки изделия надо подвергать термической обработке — закалке с последующим старением. Повышение устойчивости куста- лости соединения достигается снятием усиления сварного шва.
Сварку магниевых сплавов плавящимся электродом в аргоне целесообразно выполнять для толщин металла начиная с 6 мм. Лучшие результаты можно получить на параметрах режима сварки, соответствующих струйному переносу металла. При этом скорость плавления магниевой проволоки вдвое больше, чем алюминиевой при той же силе сварочного тока.
Надежная защита обеспечивается при расстоянии от сопла до поверхности изделия и от токоведущего мундштука до среза сопла соответственно 10—15 и 5—10 мм. Листы толщиной до 5 мм сваривают встык без разделки кромок, 10—20 мм — с V-образной разделкой с углом 50—60° и притуплением 2—6 мм, более 20 мм — с Х-образной разделкой с углом 60—80° и притуплением 2—3 мм. Ось электрода составляет угол 90° к изделию при сварке стыковых соединений без разделки или с небольшой разделкой. При большей глубине разделки сварку ведут углом вперед с углом 7—15° к вертикали.
Сварка плавящимся электродом в среде защитных газов производится с помощью полуавтоматов и автоматов, причем наиболее распространены первые.
Для полуавтоматической сварки предназначена установка, основные составные части которой даны на рис. 7.5. Сварочная проволока 7подается из катушки с помощью подающего механизма 5 по специальному шлангу 4к горелке 3. Источник 9 питает как сварочную дугу, которая горит между проволокой горелки 3 и изделием, так и блок управления 6, где размещены элементы пускорегулирующей аппаратуры, источник питания подающего механизма, рукоятка регулирования скорости подачи проволоки, электрогазовый клапан и т. д. Защитный газ подается из баллона через редуктор 10 по шлангу 8 к блоку управления 6 на электрогазовый клапан. Эта магистраль до начала сварки заполнена газом. От электрогазового клапана к подающему шлангу идет магистраль подачи газа 4 к горелке 3, которая перед сваркой заполнена воздухом. С блока управления к подающему шлангу идут провода управления 1 на кнопку, расположенную на горелке. На источнике питания находятся рукоятка регулирования напряжения на дуге, а также амперметр и вольтметр для контроля электрических параметров сварки. Сварочные кабели 2 соединяют изделие с подающими роликами механизма 5. При сварке в среде С02 на газовой магистрали после вентиля баллона устанавливаются подогреватель и осушитель газа.
Рис. 7.5. Монтажная схема установки для полуавтоматической сварки плавящимся электродом в среде защитного газа:
1 — провода управления; 2 — сварочные провода; 3 — горелка; 4 — шланг; 5 — механизм подачи; 6 — блок управления; 7 — кассета; 8 — шланг для газа; 9— источник питания; 10— аппаратура для регулирования и измерения параметров защитного газа
В работе полуавтомата очень важно обеспечить надежность подачи электродной проволоки специальным механизмом по шлангу к горелке. Подавляющее большинство подающих механизмов проталкивает проволоку к горелке по шлангу, и требуемое усилие достигается прижатием проволоки двумя роликами. Эта схема упрощает подающий механизм, уменьшает его габаритные размеры и массу. Однако подача проволоки, особенно тонкой и нежесткой, требует значительных усилий прижима, что ведет к ее деформации, затрудняет прохождение направляющего канала в шланге, приводит к его преждевременному износу, а иногда делает невозможной надежную постоянную работу. Поэтому сейчас применяют четырехроликовые подающие механизмы, значительно улучшающие надежность подачи электродной проволоки. Подающий механизм 5 соединяется с горелкой 3 шлангом 4, по которому транспортируется сварочная проволока, подаются сварочный ток, ток цепи управления, защитный газ и в случае необходимости вода, охлаждающая сопло горелки (при сварке на токах выше 350 А).
Устройство рабочей части горелки для сварки плавящимся электродом показано на рис 7.6. Горелка содержит изогнутый мундштук 7с переходной втулкой 2 и наконечником 5, рукоятку 1 с гашеткой 9, пусковую кнопку, защитный щиток 8 и сопло 4 для создания вокруг зоны сварки защитной атмосферы 6. Сопло электрически изолировано от наконечника и может легко заменяться. Переходная втулка имеет ряд отверстий 3, расположенных перпендикулярно направлению подачи проволоки и предназначенных для подвода защитного газа в зону сопла. Это обеспечивает получение ламинарного газового потока.
При сварке в углекислом газе образующиеся брызги прилипают к соплу и наконечнику, ухудшая газовую защиту зоны сварки и образуя токоведущую перемычку между соплом и наконечником горелки. Для снижения прилипания брызг применяют охлаждаемые сопла, составные с изоляционной прокладкой, металлокерамические и др., а также теплостойкие покрытия или хромирование сопла и защитные смазки, например силиконовые (раствор кремнийорганических соединений). При наличии смазки на поверхности сопла и наконечника брызги металла не привариваются, а только прилипают и потом легко удаляются.
Некоторые зарубежные производители изготовляют горелки, в которых наконечник тела между рукояткой и соплом выполнен из эластичного гибкого материала, что позволяет выгибать сопло под любым углом для достижения любого места сварки.
Для сварки в защитных газах плавящимся электродом используют выпрямители с пологопадающими или жесткими внешними характеристиками.
Р и с. 7.6. Устройство рабочей части горелки для сварки плавящимся электродом в среде защитных газов
В табл. 7.2 приведены итоговые сведения относительно возможности сварки конструкционных материалов с учетом их особенностей, специфики способов и использования оборудования.
Возможности использования сварки металлов и сплавов в среде защитных
Ручная дуговая сварка плавящимся электродом
Ручная сварка производится плавящимся металлическим электродом по способу Славянова (рис. 10.3).
Ручная электродуговая сварка универсальна и широко распространена, так как может выполняться в любом пространственном положении. Она часто применяется при монтаже в труднодоступных местах, где механизированные способы сварки не могут быть применены. Меньшая глубина проплавления основного металла и меньшая производительность ручной сварки из-за пониженной силы применяемого тока, а также меньшая стабильность ручного процесса (по сравнению с автоматической сваркой под флюсом) являются недостатками ручной сварки.
Электродуговая сварка металла представляет собой один из способов сваривания металлов, суть которого заключается в нагреве и расплавлении металла электрической дугой. Это один из самых распространенных методов сварки. Впервые этот способ был открыт ученым Славяновым Н.Г. в 1888 году. Для этого он использовал металлический плавящийся электрод. Сварка происходила под слоем флюса. Электродуговая сварка металла осуществляется постоянным током. При этом плюс находится на свариваемой детали, а минус на электроде. Процесс электросварки выполняется как плавящимся электродом, так и неплавящимся. Такой способ сварки широко применяется в ремонтных работах, монтажных, машиностроении, в строительстве и др. областях.
Электродуговая сварка плавящимся электродом
Электродуговая сварка плавящимся электродом заключается в расплавлении поверхности металла и электрода. При этом электрод служит материалом для получения сварного шва. Чтобы предотвратить окисление шва, применяют такие газы как: гелий, аргон, углекислый, а также их смеси. В процессе работы они подаются из сварочной головки. Легко ионизируемые элементы, входящие в состав электрода, делают электрическую дугу более устойчивой. Такими элементами могут быть: натрий, калий, кальций. Преимущество сварки постоянным током в том, что шов получается более чистым. Это происходит благодаря тому, что при расплавлении электрода количество брызг минимальное. Электродуговая сварка металла плавящимся электродом включает в себя:
- Подготовка свариваемой поверхности металла. Зачищается от грязи и масляных пятен;
- Для образования сварочной дуги, к электроду и заготовке подводится электрический ток;
- Происходит образование дуги. Она достигает 7000 0 С и начинает расплавлять металл;
- Образуется сварочная ванна из расплавленного электрода и поверхности металла. Шлак всплывает и образует защитную пленку. Затем сварочный шов застывает и образуется сварное соединение.
При сварке плавящимся электродом в защитном газе, сварочная проволока похожа по своему химическому составу к свариваемому металлу. Для сварки цветных металлов и их сплавов используют инертные газы: гелий, аргон, а также их смеси.
Параметры тока влияют на глубину проплава. Увеличение тока глубже проплавляет металл, а уменьшение наоборот. Величина тока не влияет на ширину шва, а род тока оказывает влияние. Шов более узкий когда применяют постоянный ток.
Сварочная дуга также влияет на качество шва. Чем меньше сварочная дуга, тем сварной шов более чистый. При этом металл проплавляется спокойно, а количество металлических капель значительно меньше. Это позволяет достичь более глубокое проплавление. Электродуговая сварка металла плавящимся электродом имеет свои преимущества:
- возможность сваривания в любом месте и любом положении;
- можно варить самые разные виды стали;
- сварка достаточно простая, легко транспортировать.
Недостатки такого способа сварки:
- вредность газов во время работы;
- низкий КПД и, в сравнении с другими видами сварки, невысокая производительность;
- качество сварного шва зависит от квалификации сварщика.
Ручная дуговая сварка плавящимся электродом.
Несмотря на большое распространение автоматов для дуговой сварки, ручная дуговая сварка сохранилась и в машиностроении, и в строительстве. Она применяется в монтажных условиях, при сварке швов сложной конфигурации или в труднодоступных местах.
Применение ручной дуговой сварки плавящимся электродом стало возможным только после создания покрытий электродов, предохраняющих зону сварки от воздействия окружающей воздушной атмосферы или уменьшающих это воздействие.
Это позволило значительно повысить качество сварных соединений и сварка стала широко применяться для производства ответственных изделий (паровых котлов, мостов, железнодорожного транспорта и т. д. ).
В самом деле, если сваривать шов обычной стальной проволокой без покрытия, то капли электродного металла, проходя через дуговой разряд, подвергнутся воздействию кислорода и азота воздуха. В результате этого произойдет выгорание углерода, марганца и других активных элементов — металл шва будет насыщаться азотом из атмосферы дугового разряда. Это вызовет резкое ухудшение механических свойств сварного соединения, так как металл шва будет резко отличаться от основного металла по составу и свойствам.
При таких условиях сварки особенно сильно понизятся пластические свойства наплавленного металла, что увеличит его склонность к образованию горячих трещин.
Для того чтобы повысить качество сварных соединений, облегчить труд сварщика и увеличить производительность сварки, разработаны специальные электродные покрытия, содержащие различные вещества, необходимые для улучшения технологии сварки.
Электроды с покрытием, обеспечивающие определенное качество сварных соединений, получили название качественных электродов.
Для вытеснения воздушной атмосферы из зоны сварки в покрытие вводят вещества (мел, мрамор или органические вещества — крахмал, декстрин), при разложении которых в дуговом разряде образуется большое количество газов.
Очень надежную защиту сварочной ванны от окружающей среды обеспечивает слой жидкого шлака. С этой целью в состав электродного покрытия вводят шлакообразующие вещества — полевой шпат, плавиковый шпат, кварцевый песок и другие компоненты. Шлак, взаимодействуя с жидким металлом, извлекает из сварочной ванны окислы, соединения с серой и фосфором, значительно улучшая свойства металла шва.
В состав покрытия вводят также раскислители — сплавы, содержащие высокоактивные элементы (ферросилиций, ферромарганец, ферротитан). Для сохранения определенного состава металла шва и улучшения его свойств можно вводить легирующие элементы в виде порошков ферросплавов (феррохром, ферромолибден и т. д.), которые при плавлении покрытия переходят в металл сварочной ванны.
Для повышения устойчивости дугового разряда в состав покрытия вводят вещества, легко переходящие в ионное состояние, — ионизаторы (соли натрия, калия, кальция).
Введение таких веществ облегчает работу сварщика, так как возрастает устойчивость дугового разряда, обрывы дугового разряда возникают реже, качество сварного шва улучшается.
Все эти перечисленные компоненты покрытий тщательно перемешивают в тонкоизмельченном состоянии и добавляют жидкое стекло (силикат натрия). Оно затвердевает при повышении температуры и связывает все порошковые материалы в общую систему покрытия.
Покрытие наносят на зачищенную до металлического блеска электродную проволоку, предварительно выпрямленную и разрезанную на мерные куски (400— 500 мм), наносят окунанием в жидкий замес (единичное производство) или напрессовкой вязкого замеса в специальных прессах (массовое производство). После сушки и прокаливания электроды испытывают, составляют паспорт, упаковывают в герметичную тару.
При ручной сварке электрод зачищенным концом вставляют в электрододержатель, подключенный к одному полюсу источника питания, другой полюс источника присоединяют к изделию.
Детальный просмотр
Автоматические способы (виды) дуговой сварки (наплавки)
ААД -Автоматическая аргонодуговая сварка неплавящимся электродом
ААДН- Автоматическая аргонодуговая наплавка неплавящимся электродом
ААДП -Автоматическая аргонодуговая сварка плавящимся электродом
АПГ -Автоматическая сварка плавящимся электродом в среде активных газов и смесях
АПС- Автоматическая сварка самозащитной порошковой проволокой
Газовая сварка (наплавка)
Г-Газовая сварка
Дуговая сварка (наплавка) покрытыми электродами
РД-Ручная дуговая сварка покрытыми электродами
РДН-Ручная дуговая наплавка покрытыми электродами
Дуговые способы (виды) сварки (наплавки) под флюсом
АФ-Автоматическая сварка под флюсом
АФЛН-Автоматическая наплавка ленточным электродом под флюсом
АФПН-Автоматическая наплавка проволочным электродом под флюсом
МФ-Механизированная сварка под флюсом
Контактная сварка
КСО-Контактная стыковая сварка оплавлением
КСС-Контактная стыковая сварка сопротивлением
КТС-Контактно-точечная сварка
КШС-Контактная шовная сварка
Механизированные способы (виды) дуговой сварки (наплавки)
МАДП-Механизированная аргонодуговая сварка плавящимся электродом
МП-Механизированная сварка плавящимся электродом в среде активных газов и смесях
МПГ-Механизированная сварка порошковой проволокой в среде активных газов и смесях
МПС-Механизированная сварка самозащитной порошковой проволокой
МСОД-Механизированная сварка открытой дугой легированной проволокой
Плазменная сварка (наплавка)
П-Плазменная сварка
Ручная дуговая сварка (наплавка) в защитных газах
РАД-Ручная аргонодуговая сварка неплавящимся электродом
РАДН-Ручная аргонодуговая наплавка
Способы (виды) сварки (наплавки) не вошедшие в группы
ВЧС-Высокочастотная сварка
ЗН-Сварка с закладными нагревателями
НГ-Сварка нагретым газом
НИ-Сварка нагретым инструментом
ПАК-Пайка
СТ-Сварка трением
Т-Термитная сварка
Э-Экструзионная сварка
ЭЛ-Электронно-лучевая сварка
ЭШ-Электрошлаковая сварка
Ручная дуговая сварка плавящимся электродом
Опыт показал, что уравнение (2.
К первой схеме нагрева относятся ручная дуговая сварка плавящимся электродом, электрошлаковая сварка пластинами, электрошлаковый переплав, электрошлаковая сварка плавящимся мундштуком (по отношению к мундштуку), ручная газовая сварка с присадкой, сварка неплавящимся электродом (по отношению к вольфрамовому или угольному электроду). [c.223]
Для алюминия и его сплавов используют все виды сварки плавлением, Наибольшее применение нашли автоматическая и полуавтоматическая дуговая сварка неплавящимся и плавящимся электродом в среде инертных защитных газов, автоматическая дуговая сварка с использованием флюса (открытой и закрытой дугой), электрошлаковая сварка, ручная дуговая сварка плавящимся электродом, электронно-лучевая сварка. Сварка, как правило, осуществляется в цехах с высокой культурой производства [c.
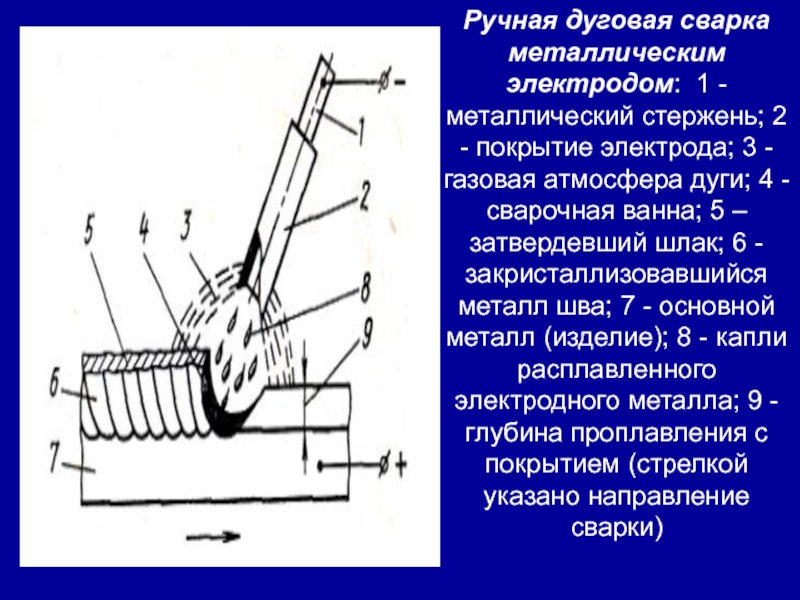
Из большого разнообразия существующих видов сварки в машиностроении применяют ручную дуговую сварку плавящимся электродом, авто.матическую дуговую сварку плавящимся электродом под флюсом, электрошлаковую сварку и контактную сварку — стыковую, шовную и точечную. Первые три способа относятся к сварке плавлением, последний — к сварке плавлением или давлением. [c.46]
Ручная дуговая сварка плавящимся электродом, при которой подача электрода и перемещение дуги вдоль свариваемых кромок осуществляются вручную. Нагрев производится электрической дугой между изделием и электродом. Электрод, расплавляясь при сварке, служит присадочным материалом для образования сварного шва. При данном способе возможна сварка стальных деталей толщиной 1…60 мм и более. Этот вид сварки применяют для конструкций с короткими и неудобно расположенными сварными швами, а также в единичном производстве.
[c.46]
Аргоно-дуговая сварка неплавящимся и плавящимся электродами Ручная дуговая сварка плавящимся электродом на постоянном токе Газовая сварка [c.616]
Ручная дуговая сварка плавящимся электродом на постоянном токе (в особенности при изготовлении секций и узлов шинопроводов сложного и круглого сечений) [c.616]
ЧТО ручная дуговая сварка плавящимся электродом выполняется сварщиком с помощью инструмента, получающего энергию от специального источника расплавляемый при сварке электрод, закрепленный в инструменте, служит присадочным металлом, вводимым в сварочную ванну в дополнение к расплавленному основному металлу. Этот вид сварки в настоящее время занимает по объему выполненных сварочных работ первое место в строительно-монтажном производстве.
[c.10]
Кроме перечисленных сварных соединений и швов при ручной дуговой сварке применяют соединения под острыми и тупыми углами по ГОСТ 11534—75, но они встречаются значительно реже. Для сварки в защитном газе, сварки алюминия, меди, других цветных металлов и их сплавов применяют сварные соединения и швы, предусмотренные отдельными стандартами. Например, форма подготовки кромок и швов конструкций трубопроводов предусмотрена ГОСТ 16037—80, в котором определены основные размеры швов для различных видов сварки. На рис. 2.6, а показана подготовка кромок шва С-1 с толщиной элементов 2—4 мм для ручной дуговой сварки плавящимся электродом и 2—3 мм для сварки неплавящимся электродом в защитном газе. На рис. 2.6, б показана форма подготовки кромок шва С-6 с толщиной 3— 20 мм для комбинированной ручной сварки плавящимся или неплавящимся электродом подварочного шва и последующей механизированной сварки основного шва, а также для сварки стали толщиной 3 мм неплавящимся электродом в защитном газе.
[c.26]
Сварочный пост для ручной дуговой сварки плавящимся электродом [c.153]
Сварные соединения из углеродистых и низколегированных сталей, выполняемые ручной дуговой сваркой плавящимся электродом во всех пространственных положениях прн толщине свариваемого металла до 60 мм включительно с расположением свариваемых деталей под острыми и тупыми углами [c.36]
В автомашине (рис. 52) смонтирован главный щит 7, обеспечивающий управление работой генераторов, а также быструю настройку на один из видов сварки ручной дуговой сварки плавящимся электродом на постоянном токе любой полярности и на переменном токе аргоно-дуговой сварки неплавящимся электродом на переменном токе (с осциллятором) и постоянным током (только при прямой полярности). Наружные сварочные кабели постоянно подключены к щиту и при переездах мастерской находятся в бухтах на кронштейне в специальном отсеке 13 под верстаком. [c.129]
Ручная дуговая сварка плавящимся электродом является наиболее распространенной она применяется для сварки и наплавки углеродистых и легированных сталей, чугуна и цветных металлов.
[c.7]
Ручная дуговая сварка плавящимся электродом является наиболее распространенной, ее применяют для сварки и [c.6]
Ручная дуговая сварка плавящимся электродом на постоянном токе [c.208]
Отсталая промышленность дореволюционной России так и не смогла в должном объеме использовать дуговую сварку. Промышленное применение этого вида сварки в нашей стране началось только после победы Великой Октябрьской социалистической революции. Уже в начале 20-х годов под руководством В. П. Вологдина были изготовлены сварные котлы, а несколько позже — суда и другие ответственные конструкции. В конце первой четверти XX в. ручная дуговая сварка плавящимся электродом стала основным способом сварки в нашей стране и во всем мире. [c.7]Сварные соединения строительных конструкций, изделий и деталей из алюминия и алюминиевых сплавов могут выполняться ручной дуговой сваркой плавящимся электродом газовой [c.
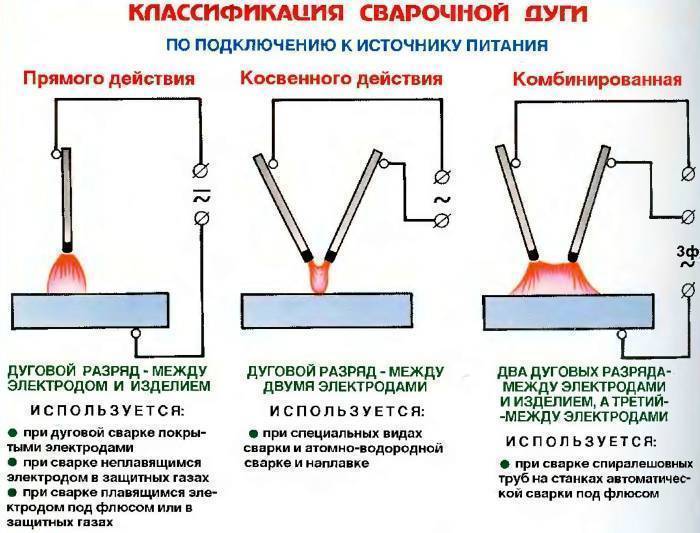
На фиг. 3, г приведен способ сварки плавящимся электродом под флюсом (порошкообразное вещество определенного состава) дуга горит в пузыре из расплавленного флюса, который надежно изолирует зону сварки от соприкосновения с воздухом. Сварка под слоем флюса производится только автоматами и полуавтоматами, причем производительность этого способа в несколько раз выше, чем при ручной дуговой сварке плавящимся электродом открытой дугой. Питание дуги осуществляется как переменным, так и постоянным током. Сварка под слоем флюса может производиться также и неплавящимся (угольным или вольфрамовым) электродом. [c.7]
Аппарат Разряд-250 предназначен для ручной дуговой сварки плавящимся электродом углеродистой стали, а также сварки неплавящимся электродом в защитных газах коррозионно-стойкой стали и алюминия. [c.13]
Основными видами сварки меди являются ручная дуговая покрытыми электродами, автоматическая под флюсом, в защитных газах плавящимся и неплавящимся электродом, газовая. В связи с высокой теплопроводностью меди сварку ведут на повышенных по сравнению со сталью величинах тока. Например, при ручной дуговой сварке покрытыми электродами величина тока выбирается из расчета /диаметр электрода сварка ведется на постоянном токе с подогревом до 200—250°С. Мощность газового пламени по расходу ацетилена выбирают из расчета для толщин бЮ мм Ос.н.=200-6 л/ч е использованием, нормального пламени и флюсов на основе буры.
[c.137]
ИП постоянного тока используются при ручной дуговой сварке штучными электродами, при сварке плавящимся и неплавящимся электродом в среде защитного газа. [c.102]
Примечания. 1. Условные обозначения по ГОСТ 16037-80 Р — ручная дуговая сварка покрытым электродом . Ф — автоматическая дуговая сварка под флюсом ЗН — дуговая сварка в защитном газе не-плавящимся электродом ЗП — то же, но плавящимся электродом. [c.205]
Сварку листовых конструкций, в том числе трубных изделий, когда не допускается применение стальных подкладок, выполняют после под-варки корня шва. Подварку корня шва высотой 5…6 мм выполняют ручной дуговой сваркой покрытым электродом или ручной аргонодуговой сваркой с присадочной проволокой. Стыковые соединения трубных изделий диаметром более 800 мм обычно сваривают автоматами с двух сторон, при этом первым выполняют поворотный шов с внутренней стороны на флюсовой подушке (рис. 4.10), а затем сваривают шов с наружной стороны. Плавящийся электрод сварочного автомата располагается со смещением относительно точки зенита с целью получения швов оптимальной формы (см. рис. 3.18).
[c.302]
Многослойные швы соединений отдельных стальных конструкций выполняют с применением одновременно нескольких видов и способов сварки, в том числе механизированной дуговой сварки плавящимся электродом порошковой проволокой, в углекислом газе, ручной дуговой покрытым электродом и автоматической дуговой под флюсом. Так, кольцевые и продольные соединения листовых трубных конструкций с толщиной стенки 8… 10 мм при таком подходе сваривают на режимах в зависимости от положения выполняемого слоя в шве, вида и способа сварки (табл. 4.31).
[c.335]
Каждый способ сварки имеет свою проплавляющую способность и оптимальные форму и параметры разделки для конкретной толщины. На рис. 1.11 представлены разделки кромок для сварки стыков труб толщиной 11. .. 18 мм магистральных трубопроводов ручной дуговой сваркой покрытыми электродами (е), дуговой сваркой плавящимся электродом в среде защитных газов ж), автоматической дуговой сваркой под флюсом (э) и электронно-лучевой сваркой и). [c.17]
ГОСТ 27580-88 «Дуговая сварка алюминия и алюминиевых сплавов в инертных газах. Соединения сварные под острыми и тупыми углами» распространяется на сварку деталей толщиной от 0,8 до 60 мм (включительно) ручной, полуавтоматической и автоматической дуговой сваркой неплавящимся электродом в инертных газах с присадочным металлом, полуавтоматической и автоматической дуговой сваркой плавящимся электродом, а также автоматической сваркой неплавящимися электродами трехфазной дугой с присадочным металлом.
[c.20]
В отличие от ручной дуговой сварки металлическом электродом при сварке под флюсом, так же как и при сварке плавящимся электродом в защитных газах, токоподвод 2 к электродной проволоке осуществляется на небольшом расстоянии (вылет электрода) от дуги (до 70 мм). Это позволяет без перегрева электрода использовать повышенные сварочные токи (до 2000 А). Плотность сварочного тока достигает 200. .. 250 А/мм в то время как при ручной дуговой сварке не превышает 15 А/мм . В результате повышается глубина проплавления основного металла и скорость расплавления электродной проволоки, т.е. достигается высокая производительность процесса. [c.110]
Наибольший объем среди других видов сварки занимает ручная дуговая сварка плавящимся электродом. Сварку выполняют электродами, которые вручную подают в зону горения дуги и перемещают вдоль свариваемого изделия. Схема процесса сварки металлическим покрытым электродом показана на рис. 35. Дуга горитмеж-ду стержнем электрода I и основным металлом 7. Под действием тепла дуги электрод и основной металл плавятся, образуя металлическую сварочную ванну 4. Капли жидкого металла 8 с расплавляемого электродного стержня переносятся в ванну через дуговой промежуток.
[c.65]
Для перехода от значений внешних нагрузок (номинальных напряжений) к локальным напряжениям и деформациям необходимо располагать в соответствии с нормами расчета энергетических конструкций на малоцикловую усталость [2] значениями кэффициен-тов концентрации напряжений (при упругих деформациях) и коэффициента концентрации деформаций К , если местные напряжения превышают предел текучести материала. Если для геометрических концентраторов напряжений типа отверстий, галтелей, выточек и т. п. такие данные в области упругих деформа ий широко представлены в работах [3, 4], то применительно к сварным соединениям строительных конструкций такая систематизация до настоящего времени отсутствует.

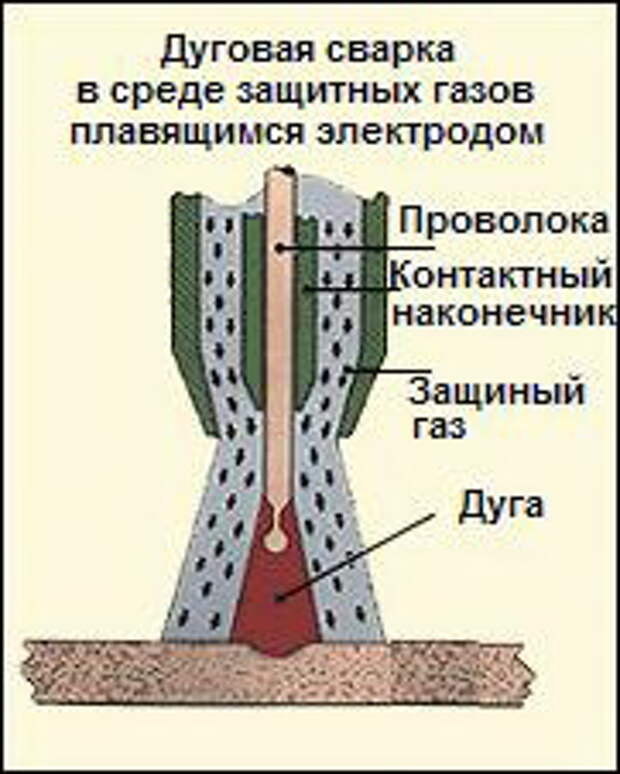
Режимы ручной аргонодуговой сварки стыков труб и положение при сварке неплавяшегося электрода и присадочной проволоки представлены в табл. 3.13 и на рис. 3.9 для ручной дуговой сварки плавящимся электродом с основным покрытием — в табл. 3.12 и на рис. 3.7 и 3.8 схема многослойных стыковых и угловых швов — на рис. 3.5 и 3.6. Режимы автоматической дуговой сварки под флюсом стыков трубопроводов представлены в табл. 3.31. [c.253]
Использование в различных отраслях новой техники в качестве конструкционных материалов редких и тугоплавких металлов (молибдена, тантала, ниобия, вольфрама, циркония и др.), которые ранее находили ограниченное применение, в основном,-лишь в качестве легирующих добавок, выдвинуло проблему разработки методов их сварки. Эти металлы составляют группу труд-носваривающихся вследствие того, что помимо высокой температуры плавления они характеризуются высокой химической активностью при повышенных температурах. Большинство из них реагирует со всеми известными флюсами, а некоторые являются гетерами. Поэтому применительно к этим металлам оказались неприемлемыми такие методы сварки, как ручная дуговая сварка плавящимся электродом, сварка под флюсом и газовая.
[c.5]
Источник питания для ручной дуговой сварки плавящимся электродом и автоматической сварки под флюсом должен иметь падающую внешнюю характеристику. Жесткая характеристика источников питания (рис. 56, кривая 3) необходима при выполнении сварки в защитных газах (аргоне, углекислом газе, гелии) и некоторыми видами. порошковых проволок, например ЭПС-15/2. Для сварки в защитных газах допустимы также источники питания с пологовозрастающи-м и в н е ш н и м и характеристиками (рис. 56, кривая 4). [c.136]
Алюминий и его сплавы, обладающие рядом физических и технологических особенностей, успешно сваривают в инертных газах. Однако при необходимости применяют ручную дуговую сварку плавящимися электродами и ручную сварку неплавлящимися электродами, например угольными. В табл. 11.1 приводится состав некоторых марок алюминиевой сварочной проволоки, которую употребляют для изготовления электродов для механизированной сварки, а также в качестве присадочного металла при ручной аргонодуговой сварке неплавящимся вольфрамовым электродом.
[c.143]
Передвижная сварочная двухпостовая установка СДУ2 [16]. Установка СДУ2 предназначена для ручной дуговой сварки плавящимся электродом в полевых условиях при монтаже трубопроводов. Установка предназначена для сварки углеродис-122 [c.122]
ГОРЕЛКИ ДЛЯ РУЧНОЙ ДУГОВОЙ СВАРКИ ПЛАВЯЩИМСЯ ЭЛЕКТРОДОМ в АКТИВНОМ и ИНЕРТНОМ ЗАЩИТНОМ ГАЗЕ (ИЗГОТОВИТЕЛЬ — PLAST) [c.135]
Доля основного металла в металле однопроходного шва (одиночного наплавленного валика) зависит от способа сварки, режима сварки (например, при дуговой сварке плавящимся электродом — от Ug, leg и Ктеплофизических свойств свариваемого металла, формы и размеров разделки кромок под сварку. Для обычных режимов ручной дуговой сварки плавящимся электродом, а также обычных типовых режимов сварки под флюсом малоуглеродистых и низколегированных сталей доля основного металла ф, в металле шва при отсутствии разделки (согласно рис. 1.3, а) изменяется в следующих пределах при ручной сварке — от 0,25 до 0,40 при сварке под флюсом — от 0,65 до 0,70.
[c.19]
При ручной дуговой Bapjie плавящимся электродом размеры сварного шва в большинстве случаев определяются размерами разделки кромок соединений, подготовленных под сварку. Поэтому необходимости определения глубины провара при ручной дуговой сварке, как правило, не возникает. Исключение может составлять только сварка стыковых соединений без разделки кромок, диапазон толщин которых согласно ГОСТ 5264—69 ограничен. Этим ГОСТом регламентированы также конструктивные элементы подготовки кромок соединений различных видов исходя из условий получения необходимой величины проплавления и формы шва при использовании режимов сварки в ншроком диапазоне.
[c.183]
Однако даже при получении швов, подобных по составу основному металлу, необходимо учитывать, что часть наиболее важных свойств сварных соединений может быть получена, когда металл шва по составу несколько отличается от свариваемой стали, например имеет меньшую концентрацию углерода, содержит некоторое количество титана и т.д. В связи с тем, что такое регулирование состава металла шва легче обеспечивается при дуговой сварке, этот способ сварки наиболее распространен при изготовлении и ремонте изделий из высокохромистых сталей. Большинство сварочных работ с этими сталями выполняют ручной дуговой сваркой стальными покрытыми электродами. Наряду с этим используют дуговую сварку плавящимся электродом в углекислом газе, в инертных газах (аргоне, аргоногелиевых смесях) и сварку под спещ1альными флюсами. [c.328]
Ручная дуговая сварка — Сварка MMA штучными электродами — Статьи о сварке
Ручная дуговая сварка MMA – сварка покрытыми штучными плавящимися электродами.
Сварка ММА (Manual Metal Arc) – это электродуговая сварка, которая была открыта русским ученым Н.Н. Бернандосом в 1882 году. Он впервые использовал электрический ток для соединения заготовок стали с помощью угольного электрода. В то время сварка осуществлялась непокрытыми электродами, то есть стальной проволокой. В 1904 году швед Оскар Челльберг (основатель концерна «ESAB») изобрел покрытый обмазкой сварочный электрод. Ручная дуговая сварка MMA – это сварка покрытыми штучными электродами, которая заключается в том, что источник сварочного тока, подключенный к сети, имеет два кабеля с разной полярностью, при помощи которых сварочный ток подается к свариваемым деталям. Один кабель, с зажимом на конце, именуется массой (клемма заземления) и крепится к стальной заготовке. Второй кабель имеет держатель для сварочного электрода, при помощи которого происходит сварка металла. При данном типе сварки тепловая энергия вызывает плавление металла и образование сварочной ванны, при остановке теплового воздействия электрического тока металл остывает и кристаллизуется – так образуется сварочный шов. Металл сварочного электрода переходит в сварочную ванну. Благодаря различным химическим составам обмазки сварочного электрода меняется химический состав и свойства металла сварного шва, а также образуются газообразные соединения, защищающие сварочную ванну от воздействия окружающей среды.
Основы ручной дуговой сварки.
Электродуговая сварка может проходить на переменном (AC) и постоянном (DC) токе. При сварке на переменном токе сварочная дуга слабоустойчива, необходимы профессиональные навыки сварки в сравнении с постоянным током. Сварка на постоянном токе является единственным способом электросварки некоторых металлов и сплавов. При ручной дуговой сварке особую роль играет выбор полярности подключения сварочного аппарата.
-
Прямая полярность – это когда «минус» подключен к электроду, а «плюс» на клемме заземления или на массе. При это способе подключения ток поступает от электрода к заготовке металла, которая нагревается, а электрод остается при этом холодным.
В основном сварка MMA при прямой полярности применяется для сварки листового металла, имеет узкую сферу применения.
- Обратная полярность – это когда «плюс» подключен к электроду, а «минус» на клемме массы или заземления. В таком случае сварочный ток подается от металла на электрод, происходит нагрев и плавление сварочного электрода. Сварка на обратной полярности наиболее распространена.
Следующий шаг – это выбор сварочного тока в зависимости от толщины свариваемого металла. За основу можно взять правило: около 40 А тока на 1 мм металлической заготовки. То есть при сварке металла толщиной 3 мм используется сварочный ток в 100 – 140 А. Немаловажным понятием является значение ПВ% сварочного аппарата, не забывайте про него при выставлении нужного Вам значения сварочного тока на сварочном аппарате.
Розжиг дуги. Сварочная дуга разжигается двумя способами: касание кончика электрода и заготовки металла и резкий отрыв электрода; несколько чиркающих прикосновений сварочного электрода к заготовке свариваемого металла. При соблюдении одинакового расстояния между электродом и свариваемым металлом при сварке обеспечивается стабильная не затухающая дуга. При слишком маленьком расстоянии между заготовкой и электродом, сварочный электрод попросту прилипнет к металлу; при слишком большом расстоянии — сварочная дуга потухнет (погаснет). Для стабильной и качественной ручной дуговой сварки необходимы практические навыки сварочного дела, качественные и правильно выбранные сварочные материалы и сварочное оборудование.
Тесты по профессиональному модулю пмо2 «Ручная дуговая сварка плавящимся покрытым электродом»
Тема: Оборудование для ручной дуговой сварки.
Какое сварочное оборудование преобразовывает переменное напряжение в постоянное?
а) трансформатор;
б) выпрямитель;
в) двигатель.
В каком устройстве напряжение понижается?
а) трансформатор;
б) выпрямитель;
в) двигатель.
При помощи чего подводится питание к электрододержателю?
а) шланга;
б) провод;
в) кабель.
При помощи чего фиксируется электрод?
а) электромуфта;
б) электрододержатель;
в) зубило.
Выпрямитель – это источник питания сварочной дуги
а) преобразующий переменный ток в переменный;
б) преобразующий переменный ток в постоянный;
в) преобразующий постоянный ток в переменный.
В каком устройстве есть якорь и коллектор?
а) трансформатор;
б) выпрямитель;
в) генератор.
Неплавящиеся электроды:
а) угольный, металлический, пластмассовый;
б) вольфрамовый, графитовый, угольный;
в) бумажный, алюминиевый, медный.
Что входит в состав обмазки электрода постоянного тока?
а) уголь, кварц, мел, песок;
б) мел, жидкое стекло, целлюлоза, крахмал, металлические опилки;
в) жидкое стекло, крахмал, мел, древесная мука, песок.
Для устойчивого горения электрической дуги обмазку электрода переменного тока добавляют:
а) магний, калий, марганец;
б) кальций, калий, натрий;
в) крахмал, мел, калий.
Что относится к оборудованию для электросварочных работ?
а) защитная маска;
б) сварочный шланг;
в) баллон;
г) сварочный кабель;
д) сварочный трансформатор;
е) электрододержатель;
ж) газовая горелка.
На какую обмотку в сварочном трансформаторе подается напряжение 380 В?
а) вторичную;
б) возбуждения;
в) первичную.
Перечислите источники питания сварочной дуги?
а) трансформатор, преобразователь, выпрямитель ;
б) трансформатор, генератор, редуктор;
в) выпрямитель, двигатель, генератор.
13. Как классифицируются сварочные трансформаторы по фазности?
а) однофазные, двухфазные;
б) однофазные, трехфазные;
в) двухфазные, трехфазные.
14. Самый простой в обслуживании и работе сварочный аппарат:
а) сварочный выпрямитель постоянного тока;
б) сварочный преобразователь постоянного тока;
в) сварочный трансформатор переменного тока.
Тема: Технология ручной дуговой сварки.
Длиной дуги называется:
а) расстояние между торцом электрода и поверхностью сварочной ванны;
б) расстояние от середины;
в) первичную.
2. Виды сварных швов в пространственном положении:
а) стыковой, угловой, вертикальный;
б) вертикальный, горизонтальный, нижний, потолочный;
в) тавровый, потолочный, нижний.
3. Виды сварных соединений:
а) стыковое, угловое, тавровое, нахлесточное, торцевое;
б) вертикальное, горизонтальное, угловое;
в) тавровое, кольцевое, нижние.
Гидравлические испытания сварных швов заключается:
а) в испытании воздухом;
б) в испытании аммиаком;
в) в испытании водой.
Зона наиболее высоких температур в сварочной дуге находится:
а) в середине столба дуги;
б) на катоде;
в) на аноде.
Какими бывают электроды по виду покрытия?
а) ионизирующие, газообразующие, легирующие, связывающие;
б) кислые, основные, целлюлозные, рутиловые;
в) вольфрамовые, графитовые.
7. Для чего применяются светофильтры марки Г -3?
а) для выполнения электрогазосварочных работ;
б) для резки средней мощности;
в) для мощной газосварке и резке.
8. Горячие трещины в сталях при электросварке возникают при:
а) температуре 30000С;
б) температуре 10000С;
в) температуре 5000С.
9. Холоде трещины в сталях при электросварке возникают при:
а) температуре 5000С;
б) температуре 1000С;
в) ниже температуры 10000С.
10. Температура сварочной дуги:
а) 50000С — 80000С;
б) 10000С — 20000С;
в) 20000С — 25000С.
11. Обработка кромки на металле:
а) Т – образная, Х – образная, М — образная;
б) V – образная, Х – образная, У — образная;
в) V – образная, C – образная, М — образная.
12. На электросварочном аппарате переменного тока подвижная обмотка:
а) вторичная;
б) первичная;
в) первичная и вторичная.
13. Дефект шва «шлаковые включения» относится к:
а) внешнему;
б) внутреннему;
в) внешнему и внутреннему.
14. Какая электрическая дуга называется неустойчивой?
а) дуга более 3мм горящая устойчиво;
б) дуга более 5мм горящая плохо;
в) дуга более 6мм горящая неустойчиво.
15. Источники образования шлака:
а) образуется при сгорании основного металла и электрода;
б) образуется при сгорании электродного покрытия;
в) образуется при сгорании электрода, окислении металла, реакции самого металла.
16. Что называется сварочной ванной?
а) соединение шва с основным металлом;
б) участок расплавленного металла;
в) участок расплавленного соединения.
17. Причины образования газовых пор в металле шва?
а) интенсивное выделение газов при кристаллизации шва;
б) охлаждение металла шва;
в) интенсивное выделение газов при кристаллизации шва, наличие окалины, ржавчины в металле, наличие влаги в электроде.
18. Какую роль играют газовые поры и пузырьки в наплавленном металле?
а) повышают прочность металла;
б) повышают закалку металла;
в) понижают механическую прочность металла.
19. Какая температура плавления шлака при дуговой сварке?
а) ниже температуры плавления металла;
б) выше температуры плавления металла;
в) средняя температура плавления металла.
20. Что называется усадкой наплавленного металла?
а) уменьшение объёма сплава шва при охлаждении;
б) увеличение объёма сплава шва при охлаждении;
в) увеличение и уменьшение объёма сплава шва при охлаждении.
Чем отличается симметричный стыковый шов от других сварных швов стыковых соединений?
а) одинаковые формы и размеры;
б) одинаковая толщина металла;
в) одинаковая длина и ширина.
22. Пневматическое испытание сварных швов заключается:
а) в испытании воздухом;
б) в испытании аммиаком;
в) в испытании водой.
23. Какой самый простой метод проверки сварочного шва?
а) внешний осмотр, рентген;
б) промыть водой, керосином;
в) пневматический контроль.
24. Каким методом можно проверить дефект шва «Внутренние трещины»?
а) водой, воздухом;
б) керосином, водой;
в) гамма – лучами, рентгеном.
25. Защищать сварной шов от шлаков следует:
а) До сварки.
б) Во время сварки.
в) Сразу после сварки.
26. Гидравлические испытания сварных швов заключается:
а) в испытании воздухом;
б) в испытании аммиаком;
в) в испытании водой.
27. Диаметр электрода при ручной дуговой сварке выбирают в зависимости от.
а) Сварочного тока;
б) Марки стали;
в) Толщины свариваемой детали.
28. Что может быть причиной дефекта?
а) режим сварки;
б) плохое оборудование;
в) плохое качество электрода;
г) плохая обработка кромок;
б) электрододержатель;
в) некачественное соединение проводов.
29. Когда применяется наплавка?
а) при восстановлении изношенных поверхностей;
б) при изготовлении новых деталей;
в) при сборке конструкций.
30. Каковы причины появления брызг электродного металла?
а) короткая дуга;
б) большая ширина сварочного шва;
в) большая длина сварочной дуги.
31. Сварной шов в ручной дуговой сварке защищается с помощью:
а) нет зашиты;
б) обмазки;
в) флюса.
32. Сварным соединением называется:
а) неразъемное соединение, выполненное сваркой;
б) неразъемное соединение, выполненное пайкой;
в) разъемное соединение, выполненное сваркой.
33. Что считают дефектом сварного соединения?
а) каждую трещину;
б) некоторые поры;
в) оба ответы верны.
34. Как можно устранить подрез?
а) зачисткой;
б) подваркой;
в) зачисткой и подваркой.
35. Что способствует непровару корня шва?
а) малая мощность дуги;
б) большая скорость сварки;
в) оба ответы верны.
36. Для чего необходим контроль качества шва?
а) для определения качества свариваемости металла;
б) для определения марки электрода;
в) для определения металла и его свойств.
Техника безопасности
Что заземляется в сварочном трансформаторе?
а) первичная обмотка, корпус;
б) вторичная обмотка, корпус;
в) первичная обмотка, вторичная обмотка, корпус.
Что заземляется в сварочном оборудовании электросварщика?
а) первичная обмотка;
б) вторичная обмотка;
в) корпус;
г) магнитопровод;
д) электрододержатель;
е) деталь;
ж) стол;
з) стул.
3. Электросварочные работы запрещены на высоте без площадки и ограждения:
а) 1 – 2 м;
б)2,5 – 3 м;
в)1,4 – 1,5.
4. Как правильно соединять сварочные кабели?
а) болтовое соединение, пайка, жимок;
б) скрутка, пайка, жимок;
в) гайка, скрутка, жимок.
5. Что служит для защиты зрения от электросварки?
а) щиток и маска;
б)очки, щиток;
в)маска, шапка.
6. При каких условиях сварочные работы на высоте запрещаются?
а) сильный ветер, дождь и обледенение;
б) жара, дождь, снег;
в)мороз, дождь, снег.
7.Что заземляется в сварочном преобразователе?
а) первичная обмотка;
б) вторичная обмотка;
в) корпус;
г) стол.
8. Какое освещение при сварке в металлических резервуарах и колодцах?
а) 4 -6 – 12В;
б) 220В;
в) 36В.
9. Что заземляется в сварочном выпрямителе постоянного тока?
а) первичная обмотка, корпус;
б) корпус, сердечник вторичной обмотки;
в) вторичная обмотка, корпус сварочного аппарата.
Что используется в качестве заземляющего проводника?
а) алюминиевый провод;
б) медный провод;
в) латунный провод.
Ручная дуговая сварка стержневыми электродами
Процесс ручной дуговой сварки металла
В процессах дуговой сварки используется источник электроэнергии для создания и поддержания электрической дуги между электродом и основным материалом для плавления металлов в точке сварки. Они могут использовать как постоянный (DC), так и переменный (AC) ток, а также расходуемые или неплавящиеся электроды. Область сварки защищена инертным или полуинертным газом определенного типа, известным как защитный газ.
Ручной процесс металлической дуги происходит, когда два провода, которые составляют часть электрической цепи, соединяются, а затем медленно растягиваются, на их концах образуется электрическая искра.Эта искра, или дуга, как ее еще называют, имеет температуру до 3600 ° C. Поскольку дуга ограничена очень небольшой площадью, она может почти мгновенно расплавить металл. Если один из этих проводов подключен к заданию, а другой — к катанке или электроду, как его обычно называют, тепло дуги расплавляет как металл задания, так и острие электрода. Расплавленный металл от электрода смешивается с расплавленным металлом, образуя сварной шов. Важно понимать, что крошечные шарики расплавленного металла от электрода проталкиваются через дугу (они не падают под действием силы тяжести).Если бы это было не так, было бы невозможно использовать этот процесс для сварки над головой.
Для создания дуги для сварки требуется напряжение от 60 до 100 Вольт для создания дуги, но как только оно установилось, для ее поддержания требуется 20–40 Вольт. При создании дуги происходят следующие этапы:
- При включенной сварочной установке и до начала сварки через провода не проходит ток, и амперметр показывает ноль. Однако на цепь было подано напряжение, и вольтметр покажет напряжение холостого хода или холостого хода (т.е. от 60 до 100 В).
- Когда электрод соприкасается с изделием, через провода проходит большой ток, называемый током короткого замыкания, и амперметр отклоняется на большую величину. Однако пока это происходит, напряжение падает почти до нуля.
Кончик электрода нагревается из-за сопротивления, возникающего между ним и работой.
- Если электрод немного выдвинут, между электродом и деталью образуется дуга.Воздух между ними проводит сварочный ток. По мере образования дуги напряжение повышается до 20–40 В, а ток падает до установленного значения (т. Е. Сварочного тока). После этого дуга переходит в нормальное состояние сварки. Тепло, генерируемое дугой, плавит и заготовку, и электрод, а металл осаждается в сварочной ванне. Во время наплавки металла шва могут возникать колебания как напряжения, так и тока дуги, и сварочная установка должна быть способна справиться с этими изменениями.
Ключевые пункты обучения
- Обозначение оборудования, используемого для ручной дуговой сварки металлическим электродом
Основное оборудование, используемое при ручной дуговой сварке, включает:
- Источник сварочного тока
- Кабели
- Электрододержатель
- Зажим заземления.
Ручной источник питания металлической дуги и сварочные провода
2.1 Источники питания для сварки MMA
Существует два типа источников сварочного тока, используемых для подачи тока при дуговой сварке металлом.
- Тип переменного тока (AC).
- Тип постоянного тока (DC).
Источник питания переменного тока
Этот источник питания получает питание непосредственно от основного источника электроэнергии. В нем используется трансформатор для подачи напряжения, соответствующего условиям сварки. Специальное устройство в трансформаторе позволяет регулировать ток во вторичной катушке.Первичная катушка подключена к источнику питания, а вторичная катушка подключена к зажиму заземления и держателю электрода.
Источник питания постоянного тока
Используются два типа установок для сварки постоянным током:
- Генератор постоянного тока
- Трансформатор-выпрямитель.
Генератор постоянного тока использует двигатель (электрический, бензиновый или дизельный) для выработки электроэнергии. Генератор обеспечивает постоянный ток для дуги.
Трансформатор-выпрямитель — это в основном трансформатор с электрическим устройством для преобразования переменного тока в выход постоянного тока.Это устройство известно как выпрямитель. Трансформатор-выпрямитель имеет то преимущество, что он может питать переменный или постоянный ток.
2.2 Типы источников питания для дуговой сварки
Для обеспечения электрической энергией, необходимой для процессов дуговой сварки, можно использовать несколько различных источников питания. Наиболее распространенная классификация — источники питания постоянного тока и источники питания постоянного напряжения. При дуговой сварке напряжение напрямую связано с длиной дуги, а сила тока связана с количеством подводимого тепла.Источники питания постоянного тока чаще всего используются для процессов ручной сварки, таких как дуговая сварка вольфрамовым электродом и дуговая сварка в среде защитного металла, поскольку они поддерживают относительно постоянный ток даже при изменении напряжения. Это важно, потому что при ручной сварке может быть трудно удерживать электрод идеально устойчивым, и в результате длина дуги и, следовательно, напряжение имеют тенденцию колебаться. Источники питания с постоянным напряжением поддерживают постоянное напряжение и изменяют ток, поэтому они чаще всего используются для автоматизированных сварочных процессов, таких как дуговая сварка металлическим газом, дуговая сварка порошковой проволокой и дуговая сварка под флюсом.В этих процессах длина дуги поддерживается постоянной, поскольку любые колебания расстояния между проволокой и основным материалом быстро устраняются за счет большого изменения тока. Например, если проволока и основной материал подойдут слишком близко, ток будет быстро увеличиваться, что, в свою очередь, приведет к увеличению тепла и расплавлению кончика проволоки, возвращая его на исходное расстояние разделения.
2.3 Настройки полярности сварочных электродов
Тип тока, используемый при дуговой сварке, также играет важную роль при сварке. В процессах с плавящимся электродом, таких как дуговая сварка в защитном металлическом корпусе и газовая дуговая сварка, обычно используется постоянный ток, но электрод может заряжаться как положительно, так и отрицательно. При сварке положительно заряженный анод будет иметь большую концентрацию тепла, и в результате изменение полярности электрода влияет на свойства сварного шва. Если электрод заряжен положительно, он будет плавиться быстрее, увеличивая проплавление и скорость сварки. В качестве альтернативы, отрицательно заряженный электрод приводит к более мелким сварным швам.В процессах с использованием неплавящихся электродов, таких как сварка газовой вольфрамовой дугой, можно использовать как постоянный, так и переменный ток любого типа. Однако при постоянном токе, поскольку электрод только создает дугу и не обеспечивает присадочный материал, положительно заряженный электрод вызывает неглубокие сварные швы, а отрицательно заряженный электрод — более глубокие сварные швы. Между ними быстро проходит переменный ток, что приводит к сварным швам со средним проплавлением.
Один из недостатков переменного тока, тот факт, что дуга должна повторно зажигаться после каждого перехода через нуль, был устранен с помощью изобретения специальных блоков питания, которые вырабатывают прямоугольную форму волны вместо нормальной синусоидальной волны, что делает возможным быстрое пересечение нуля и сводит к минимуму последствия проблемы.
2.4 Преимущества и недостатки Сварка стержневыми электродами
Преимущества сварки стержневыми электродами
- Ручная дуговая сварка металла в защитном флюсе — это самый простой из всех процессов дуговой сварки.
- Оборудование может быть портативным, и его стоимость довольно низкая.
- Этот процесс находит бесчисленное множество применений из-за наличия большого количества электродов.
- Можно сваривать широкий спектр металлов и их сплавов.
- Сварка может выполняться в любом положении с высочайшим качеством сварки.
- Процесс может быть очень хорошо использован для наплавки твердым сплавом и наплавки металла для восстановления деталей или для улучшения других характеристик, таких как износостойкость и т.
Д.
- Стыки (например, между соплами и кожухом в сосуде высокого давления), которые из-за их положения трудно сваривать с помощью автоматических сварочных аппаратов, легко выполняются дуговой сваркой металла в защитном флюсе.
Недостатки сварки MMA
- Из-за ограниченной длины каждого электрода и хрупкого флюсового покрытия трудно автоматизировать процесс.
- При сварке длинных швов (например, в сосудах высокого давления) по окончании обработки одного электрода сварка должна выполняться следующим электродом. При отсутствии должного ухода в месте возобновления сварки с новым электродом может возникнуть дефект (например, включение шлака или недостаточное проплавление).
- В этом процессе используются стержневые электроды, поэтому он более медленный по сравнению со сваркой MIG.
2.5 Преимущества и недостатки установок для сварки переменным и постоянным током
Преимущества сварочных установок A.C.

- Их дешевле покупать, чем наборы DC. Начальная стоимость ок. V от того, что требуется для набора постоянного тока эквивалентного рейтинга.
- Небольшие затраты на техническое обслуживание или их отсутствие, потому что в A.C. Трансформатор.
- Нет «дуги», как в случае с D.C.
Недостатки сварочных установок A.C.
- Электроды из цветных металлов не так хорошо осаждаются.
- Опасность поражения электрическим током более выражена с переменным током, чем с постоянным током.
Преимущества сварки на постоянном токе
- Их можно использовать для наплавки электродов как из черных, так и из цветных металлов.
- Более плавная сварка дает преимущество при сварке тонких листов.
- Безопаснее использовать во влажных условиях, где риск поражения электрическим током выше, например, при работе котла и т. Д.
- Бензиновые или дизельные агрегаты можно использовать в удаленных районах, где нет электросети.
Строительные работы на объекте и т. Д.
Недостатки сварки на постоянном токе
- Дороже, чем наборы переменного тока.
- Периодическое обслуживание установки необходимо из-за движущихся частей.
- Проблемы от «Дуги дуги».
Удар дуги
«Удар дуги» встречается на сварочном оборудовании постоянного тока. Дуга отводится от точки сварки, особенно при сварке в углах. Проводники, по которым проходит ток, а именно сварочный провод от установки и обратный провод от обрабатываемой детали, проводят ток в противоположном направлении, так что создается отталкивающая магнитная сила, которая влияет на сварочную дугу постоянного тока.
Чаще всего это происходит при использовании токов выше 200 или ниже 40 ампер.Лучший способ подключения:
- Приваривайте вдали от заземления.
- Изменить положение заземляющего провода на работе.
- Оберните сварочный кабель на несколько оборотов вокруг изделия, если возможно, на балках и т.
Д.
- Измените положение работы на столе, если работаете за верстаком.
2.6 Кабели для сварки MMA
Назначение кабелей — проводить ток, необходимый для дуги. Один кабель заканчивается зажимом заземления.Другой идет к держателю электрода. Важно, чтобы кабели не были слишком маленькими в диаметре. Кабели небольшого диаметра могут иметь слишком высокое сопротивление и перегреваться во время сварки. Большинство кабелей содержат множество жил из тонкой медной проволоки. Это позволяет им переносить электрический ток и делает их очень гибкими.
Держатель электрода
Электрододержатель представляет собой электрически изолированное зажимное устройство, которое удерживает электрод. Он подключается к одному из кабелей, идущих от сварочной установки.Ток проходит от кабеля через электрододержатель к электроду.
Зажим заземления
Он подключен к другому кабелю, идущему от электростанции. Крепится к работе с помощью винтового зажима или прочной пружинной скобы.
2.7 Создание установки для сварки стержневыми электродами
Работа подключена к источнику электропитания (сварочный комплект). Держатель электрода, удерживаемый оператором, подключен к тому же источнику.Электрическая дуга замыкает цепь.
Установка для ручной дуговой сварки металла
Дуга не загорится, пока электрод не коснется изделия. Это завершает схему. Когда электрод слегка приподнимается и зазор снова появляется, электричество проходит через зазор, используя выстроенные в ряд атомы (ионизированного) воздуха в качестве проводника. Дуга останавливается или разрывается при удалении электрода. Вырабатывается сильный жар; Температура при ручной дуговой сварке металла достигает 6000 ° C.Тепло на верхнем конце дуги плавит расходуемый электрод, в то время как тепло на нижнем конце дуги плавит основной металл (свариваемый металл).
Ключевые пункты обучения
- Определите особые опасности, относящиеся к сварке стержневыми электродами
- Определите, как эти опасности устраняются или сводятся к минимуму
- Определите, как минимизировать опасность для других
- Указать меры безопасности, которые необходимо соблюдать при сварке стержневыми электродами
3.
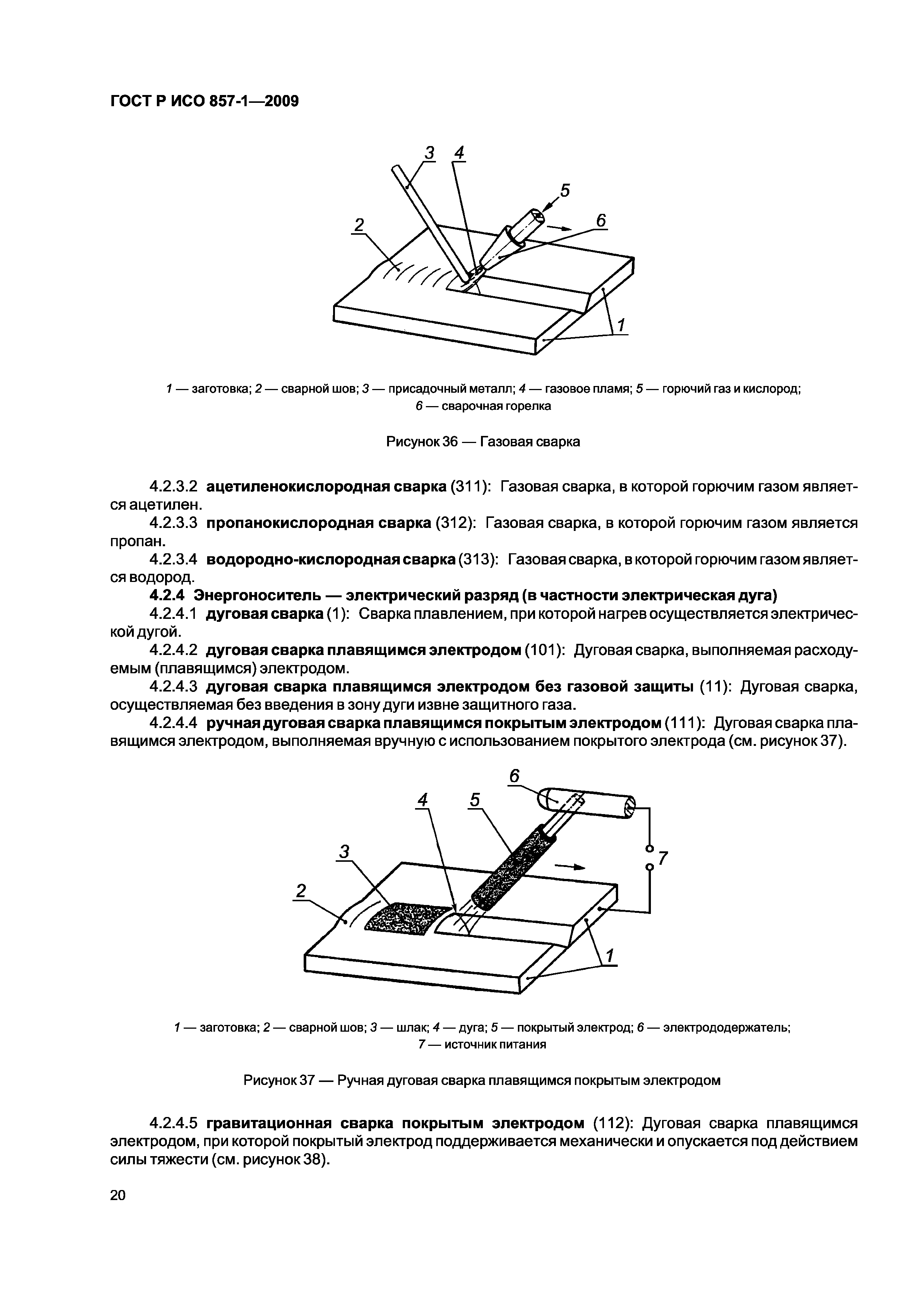
При сварке оператор должен соблюдать все общие безопасные рабочие процедуры, необходимые для термических процессов, некоторые из которых относятся к сварке стержневыми электродами:
- Убедитесь, что нет открытых участков кожи, так как ультрафиолетовые лучи от сварочной дуги могут обжечь кожу.
- Носите только легковоспламеняющуюся спецодежду, так как при дуговой сварке образуется большое количество горячих искр, которые воспламеняют легковоспламеняющуюся одежду. Для защиты от искр при сварке над головой следует надевать соответствующий кожух.
- При дуговой сварке образуются тепло, блики, искры, ультрафиолетовые и инфракрасные лучи и вредные пары. Сварочные рукавицы необходимо носить постоянно.
- Маски для лица предназначены для отвода паров, поэтому их следует держать близко к лицу.
- Убедитесь, что на лицевой маске установлены фильтры EW подходящего оттенка 11 для ручной дуговой сварки металлическим электродом.
- Очки для газовой сварки не обеспечивают защиту лица от сильного света или излучения, и их нельзя использовать.
- Всегда надевайте защитные очки при измельчении шлака.
- При сварке внутри зданий обеспечить соответствующую вентиляцию источника. Это требование закона, предназначенное для защиты оператора и других лиц. При сварке некоторых материалов (например, оцинкованной стали) выделяются высокотоксичные пары
- Проверьте свое окружение: когда вы работаете за темной маской, вы не замечаете, что происходит вокруг вас. Очистите окружающую среду от легковоспламеняющихся материалов и убедитесь в наличии огнетушителя.
- Проверьте все сварочные кабели на наличие ослабленных соединений, которые могут вызвать искривление и создать опасность. Убедитесь, что ваше окружение сухое и, по возможности, поставьте на деревянную «утиную доску».
- При сварке в ограниченном пространстве, пожалуйста, обратитесь к отдельному обучению, необходимому для входа и работы в ограниченном пространстве, поскольку для этого требуются специальные знания, обучение и оборудование.
- Не допускайте пролегания краски / масел / смазок / растворителей, так как зажигание дуги будет затруднено и будут выделяться токсичные пары
3.2 Защита для других
- Перед сваркой убедитесь, что окружающие защищены от лучей дуги, установив экраны. Ультрафиолетовые лучи вызывают состояние, известное как «дугообразный глаз», которое на самом деле является конъюнктивитом. При поражении глаза следует тщательно промыть глазной ванночкой. Если состояние не исчезнет, следует обратиться за медицинской помощью.
- Человек, получивший удар электрическим током, все еще может находиться в контакте с источником энергии, поэтому его следует удалить с помощью непроводящего материала для защиты спасателя.
- Наблюдатели за процессом сварки должны быть проинформированы о необходимости носить защитную одежду и СИЗ.
3.3 Общие меры безопасности
- Убедитесь, что подходящий огнетушитель и противопожарное одеяло всегда под рукой и легко доступны в случае небольшого пожара.
Противопожарные покрытия могут использоваться для защиты небольших окружающих территорий от искр при выполнении врезных или локальных сварных швов.
- Убедитесь, что рабочая зона чистая, и все горючие / легковоспламеняющиеся материалы удалены из рабочей зоны, чтобы гарантировать, что они не воспламеняются из-за чрезмерного тепла или случайных искр.
- Обеспечьте свободный доступ к рабочей зоне в случае аварии или травмы. На выходах не должно быть препятствий.
- Убедитесь, что соблюдаются соответствующие меры предосторожности при обращении с горячими материалами и что они не остаются без присмотра, чтобы ничего не подозревающие прохожие могли прикоснуться к ним.
3.4 Меры безопасности при сварке стержневыми электродами
- Полностью контролируйте резак / пистолет и держите его неподвижно. Сосредоточьтесь на наблюдении за процессом сварки.
- Поддержите гибкий шланг в сборе, чтобы уменьшить сопротивление резаку / пистолету.
- Удерживайте резак / пистолет только за точку равновесия, достаточную для контроля. В противном случае это вызовет утомление мышц. Расположитесь так, чтобы избежать чрезмерного баланса.
- Предупредить посторонних о зажигании дуги.
- Убедитесь, что все необходимые переносные экраны установлены.
- Обеспечьте защиту от излучения, отраженного от ярких поверхностей.Закройте или временно накройте полированные поверхности поблизости.
- Держите сварочную сетку перед глазами, пока дуга не пропадет.
- Выполните процедуру закрытия в конце рабочего периода или при длительном перерыве.
Перед выполнением каких-либо сварочных работ проконсультируйтесь с вашим инструктором по поводу требований безопасности на рабочем месте.
Меры предосторожности
Ключевые пункты обучения
- Определите основные параметры, влияющие на качество сварного шва
- Определите, как можно настроить эти параметры для достижения желаемых результатов.
4.1 Слишком низкий ток
Если текущее значение слишком мало, полученный сварной шов будет иметь плохой проплав из-за отсутствия нагрева для полного плавления. Сварочный присадочный металл имеет тенденцию скапливаться на поверхности пластины, не прилипая к ней, и дуга издает неустойчивый звук распыления.
Слишком низкий ток
4.2 Слишком высокий ток
Когда используемое значение тока слишком велико, электрод нагревается докрасна, и происходит большое количество брызг.Это может привести к образованию раковин в пластине, чрезмерному провару, что приведет к образованию валиков металла сварного шва на нижней стороне пластины, подрезанию по краю сварного шва и чрезмерному окислению и образованию шлака, который трудно удалить. Дуга издает резкий треск.
Слишком высокий ток
4.3 Правильный ток
При правильном токе дуга издает устойчивый треск. Сформированный шов имеет хорошее проплавление и легко контролируется.
Правильный ток
4.4 Длина дуги
Длина дуги — это расстояние между концом электрода и поверхностью сварочной ванны. Он должен быть примерно равен диаметру жилы используемого электрода. Когда это расстояние является правильным, электродный металл осаждается постоянным потоком металлических частиц в сварочную ванну. Если длина дуги уменьшается, становится трудно поддерживать дугу из-за увеличения сварочного тока, и это может привести к привариванию электрода к сварочной ванне.Кроме того, если длина дуги увеличивается, сварочный ток уменьшается, что приводит к плохому сварному шву, и защитный газовый экран, создаваемый электродом, окружающим сварочную ванну, не может эффективно предотвращать образование оксидов и т.д. в сварном шве.
Длина дуги
4.5 Скорость передвижения
Слишком быстро
Высокая скорость перемещения приводит к образованию тонкого слоя присадочного металла и может привести к недостаточному сплавлению присадочного металла с основным металлом. Поверхность сварного шва имеет вытянутую рябь и пористую кратер.
Скорость движения — слишком высокая
Слишком медленно
Слишком низкая скорость перемещения приводит к образованию широких толстых отложений наполнителя и может позволить шлаку затопить сварочную ванну, затрудняя осаждение присадочного металла. Поверхность сварного шва выглядит как грубая рябь и имеет плоскую кратер.
Скорость движения — слишком низкая
Ключевые пункты обучения
- Назначение сварочных электродов и их покрытий
- Определите, как электроды классифицируются в соответствии со стандартами AWS.
5.1 Сварочные электроды
Когда кусок металла нагревается в атмосфере, он соединяется с кислородом и азотом с образованием оксидов и нитридов, которые соединяются с металлом. Если бы они образовались в сварном шве, это привело бы к низкому качеству, слабому и хрупкому сварному шву. Поэтому необходимо защищать зону сварки от воздуха. Это можно сделать, окружив зону сварного шва инертным газом или используя подходящие флюсы. При ручной дуговой сварке металла обычно используются электроды с покрытием.Эти электроды состоят из металлического сердечника, окруженного слоем подходящего флюсового покрытия.
5.2 Функции электродного покрытия
Шесть основных функций электродного покрытия следующие:
- Действует как флюс и удаляет загрязнения с свариваемых поверхностей.
- Для образования защитного слоя (шлака) на сварном шве, который предотвращает контакт с воздухом, когда он начинает остывать. Это предотвращает хрупкость сварного шва и обеспечивает более гладкую поверхность, предотвращая возникновение волнистости во время процесса сварки.
- Образует нейтральную газовую атмосферу, которая помогает защитить сварочную ванну от кислорода и азота из окружающего воздуха.
- Помогает стабилизировать дугу, позволяя использовать переменный ток (AC).
- Может добавлять в сварной шов определенные компоненты, заменяя любые потери, потерянные в процессе сварки.
- Может ускорить процесс сварки за счет увеличения скорости плавления металла и электрода.
5.3 Система классификации сварочных электродов
Метод классификации электродов в соответствии с Американским обществом сварщиков (AWS) основан на использовании четырехзначного числа, которому предшествует буква «E», обозначающая «электрод». Первые две цифры обозначают минимальную прочность на разрыв металла сварного шва (в 1000 фунтов на кв. Дюйм) в состоянии после сварки. Третья цифра указывает положение, в котором электрод может выполнять удовлетворительные сварные швы. Четвертая цифра указывает используемый ток и тип покрытия из флюса.
Например, классификация электродов E6012 получена следующим образом:
E = Металлический электрод для дуговой сварки.
60 = сварной металл UTS мин. 60 000 фунтов на кв. Дюйм.
1 = Может использоваться во всех положениях.
2 = Покрытие рутилового типа: отрицательный переменный или постоянный ток.
Детали классификации показаны ниже:
Первые и вторые цифры
E 60xx Наплавка после сварки.UTS 60,000 фунтов на квадратный дюйм мин. для E 6010, E 6011,
E 6012, E 6013, E 6020, E 6027 UTS.
E 70xx Наплавка после сварки, UTS мин. 70,000 psi. для E 7014, E7015, E7016, E7018, E 7024 и E 7028.
Третья и четвертая цифры
Третья и четвертая цифры указывают на удобство позиционирования и типы покрытия флюсом, например
Exx10 = Покрытие с высоким содержанием целлюлозы, связанное силикатом натрия, глубоко проникающее, мощное, дуга распылительного типа, тонкий, рыхлый шлак, универсальное положение.(Постоянный ток, постоянный ток), только положительный электрод.
Exx11 = Очень похоже на Exx10, но связан силикатом калия, что позволяет использовать его как на положительном, так и на постоянном токе.
Exx12 = Покрытие с высоким содержанием рутила, связанное силикатом натрия. Тихая дуга, средний провар, всепозиционный, включен (переменный или постоянный ток) отрицательный.
5.4 Уход за электродами
Электроды для сварки низкоуглеродистой стали следует держать сухими, чтобы избежать образования пористости. Их следует хранить в той упаковке, в которой они были доставлены, чтобы гарантировать правильную идентификацию и избежать повреждения покрытия.
Их нельзя гнуть, чтобы избежать разрыва покрытия и последующего загрязнения сварного шва.
Ключевые пункты обучения
- Выявление дефектов сварных швов
- Определите причину дефектов сварного шва
- Определите, как можно избежать дефектов сварного шва
6.1 Дефекты сварных швов и их причины
Недостаток проникновения
Непровар — это неспособность присадочного металла проникнуть в шов.Это вызвано:
- Неправильная пропила кромки.
-
Неправильная техника сварки. - Неадекватное удаление шлака.
Непробиваемость
Отсутствие Fusion
Отсутствие плавления — это неспособность присадочного металла сплавиться с основным металлом. Это вызвано:
- Недостаточный нагрев.
- Слишком быстрое путешествие.
-
Неправильная техника сварки.
Отсутствие плавления
Пористость
Пористость — это группа небольших отверстий в металле сварного шва. Это вызвано улавливанием газа во время процесса сварки, химическими веществами в металле, влажностью или слишком быстрым охлаждением сварного шва.
Пористость
Включение шлака
Шлаковые включения — это улавливание шлака или других примесей в сварном шве. Это вызвано тем, что шлак от предыдущих прогонов не был очищен, или недостаточная очистка и подготовка основного металла перед началом сварки.
Включение шлака
Выточка
Поднутрения — это бороздки или щели по краям сварного шва, вызванные:
- Слишком быстрое путешествие.
- Слишком большое тепловыделение.
- Плохая сварочная техника.
Выточка
Накладки
Накладки состоят из металла, который растекся по основному металлу, но не сплавился с ним. Причина дефекта:
- Недостаточный нагрев.
- Загрязнение поверхности основного металла.
- Плохая сварочная техника.
Накладка
Треск
Растрескивание — это образование трещин либо в металле сварного шва, либо в основном металле. Это вызвано:
-
Плохая техника сварки. - В сварном шве использованы неподходящие основные металлы.
Треск
Пузыри
Горы — это большие дыры в сварном шве, вызванные:
- Газ из-за влажности.
- Загрязнение наполнителя или основного металла.
Унитазы
Прожигать
Прожог — это обрушение сварочной ванны из-за:
-
Плохая подготовка края. - Слишком большая концентрация тепла.
Прогорание
Чрезмерное проникновение
Чрезмерный провар — это место, где металл шва выступает из основания сварного шва.Это вызвано:
- Слишком большая концентрация тепла.
- Слишком медленное движение.
Чрезмерное проникновение
6.2 Контроль искажений
Расширение и сжатие в процессах сварки и резки
При нагревании кусок металла расширяется, а при остывании сжимается. При сварке и резке нагревание происходит в определенной области металла, а расширение может происходить только в этой части металла.Последующее сжатие, которое происходит при охлаждении, может привести к силам, вызывающим деформацию или, что еще хуже, растрескивание металла. Когда сварной шов наносится на стык между двумя пластинами, расплавленный металл, проходящий через дугу, имеет очень высокую температуру. Дуга плавит края шва, а присадочный материал и основной металл сливаются вместе. По мере того, как дуга перемещается по стыку, наплавленный валик начинает охлаждаться, и в зоне сварки возникают значительные силы сжатия.
Поскольку наплавленный металл имел более высокую температуру, чем основной металл, он будет сжиматься больше, а также, поскольку его объем больше, происходит большая усадка металла.Результат — деформация сустава. Ниже приведены несколько способов управления эффектом деформации во время сварки. предварительная настройка; обратная или ступенчатая сварка, отсадка и предварительный нагрев. Они описаны и показаны ниже:
Предварительная настройка
Это влечет за собой смещение стыка перед сваркой, чтобы после сжатия стык был выровнен.
Backstepping или Stepwelding
Это влечет за собой сварку соединения в короткие этапы, гарантируя, что зоны расширения и сжатия расположены рядом друг с другом.
Отсадка
Это влечет за собой удержание свариваемого металла в зажимном приспособлении с механическим ограничением деформации.
Предварительный нагрев
Это влечет за собой нагрев свариваемого металла перед сваркой и позволяет добиться равной усадки как в сварном шве, так и в основном металле.
Искажение / предварительная установка / обратный шаг / сварка с пропуском
Ключевые пункты обучения
- Определите, почему используются символы сварных швов на чертежах.
- Определение стандартных символов сварных швов и их значения
- Определите, как символы сварных швов наносятся на инженерные чертежи
7.1 Условные обозначения сварных швов на чертежах
Технические чертежи — это описания изготавливаемых объектов по форме. поверхность, отделка и материал. Во многих отраслях промышленности принято рисовать форму компонента, не указывая, как эта форма получена. Чертеж представляет собой описание требований, предъявляемых проектировщиком по инструкции производителя.Теоретически производитель лучше всех знает, как произвести объект с имеющимися у него ресурсами. На практике, конечно. дизайнер идет на компромисс и создает проекты, которые можно производить с помощью техник, о которых он знает. Например, круглое отверстие можно просверлить, просверлить или пробить. и может быть закончен путем рассверливания, но какой бы метод ни использовался, линии на чертеже одинаковы, и какой бы метод ни использовался, характеристики материала не меняются.
Сварное соединение предлагает ряд соображений, которые не возникают при других формах производства.Во-первых, способов выполнения сварного соединения гораздо больше, чем во многих других производственных операциях. Это означает, что у дизайнера гораздо меньше шансов предугадать методы производителя. Во-вторых, свойства и целостность соединения будут зависеть от способа выполнения сварного шва. Несмотря на это, проектировщик может указать тип требуемого соединения. при условии, что он готов признать, что он не сможет полностью определить соединение на ранних этапах проектирования.
В некоторых отраслях промышленности принято, чтобы производитель составлял рабочие чертежи, которые содержат подробные сведения о подготовке к сварке и ссылки на установленные процедуры сварки, которые подробно не показаны на чертежах проектировщика. Здесь описывается ряд символов Британского стандарта, которые могут использоваться на чертеже для обозначения сварных деталей.
7.2 Обозначения на чертежах стандартов сварки
Базовый B.S. 499 сварных швов
Базовый B.S. 499 применены особенности сварного шва
7.3 Пояснения к стандартным обозначениям сварных швов
Символы сварных швов B.S 1.
Символы сварных швов B.S 2.
Пример 1 обозначений сварных швов B.S
Пример обозначения сварных швов B.S 2.
Размер сварного шва может быть указан на символе. Угловой шов диаметром 6 мм. На чертеже должно быть указано, указан ли размер горла или ноги.
Угловой шов 6 мм
Угловой шов с неравномерной опорой.Это должно определяться длиной ноги. Здесь требуется схема формы сварного шва.
Угловой шов неравнополочной опоры
Схема здесь не требуется, поскольку размер элементов указывает ориентацию сварного шва.
Размер элементов
7.4 Прерывистые сварные швы
Справа от символа может быть указана информация, отличная от размера сварного шва. Цифра в скобках — длина пространства. 50 перед (100) означает, что сварка находится в начале.(100) 50 будет указывать сначала промежуток, а затем сварной шов, хотя такое расположение не является хорошей практикой.
Информация на стороне символа
Прерывистые швы
Источник: http://local.ecollege.ie/Content/APPRENTICE/liu/pipefitting/word/M2_U3_Manual%20Metal%20Arc%20Welding.doc
Если вы являетесь автором приведенного выше текста и не согласны с этим Чтобы поделиться своими знаниями для обучения, исследований, стипендий (для добросовестного использования, как указано в авторских правах США), отправьте нам электронное письмо, и мы быстро удалим ваш текст.Добросовестное использование — это ограничение и исключение из исключительного права, предоставленного законом об авторском праве автору творческой работы. В законодательстве США об авторском праве добросовестное использование — это доктрина, которая разрешает ограниченное использование материалов, защищенных авторским правом, без получения разрешения от правообладателей. Примеры добросовестного использования включают комментарии, поисковые системы, критику, новостные сообщения, исследования, обучение, архивирование библиотек и стипендии. Он предусматривает легальное, нелицензионное цитирование или включение материалов, защищенных авторским правом, в работы другого автора в соответствии с четырехфакторным балансирующим тестом.(источник: http://en.wikipedia.org/wiki/Fair_use)
Информация о медицине и здоровье, содержащаяся на сайте, имеет общий характер и цель, которая является чисто информативной и по этой причине не может в любом случае заменить совет врача или квалифицированного лица, имеющего законную профессию.
Тексты являются собственностью соответствующих авторов, и мы благодарим их за предоставленную нам возможность бесплатно делиться своими текстами с учащимися, преподавателями и пользователями Интернета, которые будут использоваться только в иллюстративных образовательных и научных целях.
Как сваривать медные сплавы с помощью дуговой сварки защитным слоем металла или дуговой сварки порошковой проволокой
При сварке медных сплавов необходимо выбрать правильный процесс сварки. Это может быть сложной задачей. Чтобы внести немного света в темноту и помочь вам принять правильное решение, мы даем вам представление о дуговой сварке защитным металлом и дуговой сварке порошковой проволокой.
Сварка — это ремесло с великой тысячелетней традицией. Тем не менее, в этом сообщении в блоге мы пролили свет на два довольно молодых процесса сварки.Тем не менее, они являются одними из самых распространенных сварочных процессов. Это потому, что они не требуют большого количества оборудования и, следовательно, очень портативны. Следовательно, эти два метода можно использовать и на открытом воздухе.
Что такое SMAW?Дуговая сварка в защищенном металлическом корпусе (SMAW) — это процесс ручной дуговой сварки с использованием плавящегося электрода. Она также известна как ручная дуговая сварка металлом. Качество конечного продукта во многом зависит от навыков оператора и зависит от того, как он устанавливает и перемещает электрод.Характерной особенностью этого процесса является возникновение дуги между управляемым вручную стержневым электродом и заготовкой. Используется плавящийся электрод, плавящийся при сварке.
Этот плавимый электрод имеет еще одну характеристику, типичную для дуговой сварки в среде защитного металла: он содержит флюс, который отвечает за защитную функцию, образуя инертные газы и шлак, защищающий расплав от химических реакций с окружающим воздухом. Слой шлака можно удалить после его застывания.
Какие преимущества SMAW?Большие преимущества этого процесса заключаются во флюсе, который находится внутри расходуемого электрода. Из-за этого не требуется никакого большого оборудования, вроде отдельного бензобака. Это делает дуговую сварку защищенным металлом наиболее портативным из всех сварочных процессов. Следовательно, его можно использовать в широком диапазоне сред, в том числе на открытом воздухе, в производственных цехах, на трубопроводах и нефтеперерабатывающих заводах, на судах и мостах, среди прочего.
Что такое FCAW?Дуговая сварка порошковой проволокой (FCAW) была фактически разработана в 1950-х годах как альтернатива дуговой сварке защитным металлом. В отличие от SMAW, которым управляют вручную, FCAW является полуавтоматическим или полностью автоматическим. В этом процессе сварки используется плавящийся трубчатый электрод с непрерывной подачей. Следует различать два разных процесса.
В первом процессе нет необходимости во внешнем защитном газе, поскольку электрод уже состоит из флюсового материала, который защищает расплавленный металл в сварном шве.Поскольку флюс является частью электрода, этот процесс называется процессом самоэкранирования. Второй процесс называется процессом в защитном газе. Здесь дополнительный защитный газ защищает расплавленный металл от окисления.
Каковы преимущества FCAW?
Дуговая сварка порошковой проволокой имеет различные преимущества. Прежде всего, это позволяет получить высококачественные и стабильные сварные швы с меньшим количеством дефектов. Еще одним большим плюсом является то, что с правильным присадочным металлом ее можно выполнять во всех положениях сварки.И, наконец, как и SMAW, он подходит как для сварки на открытом воздухе, так и для заводской сварки.
Когда использовать SMAW или FCAWПоскольку процесс SMAW является портативным, а необходимое оборудование общедоступным, это лучший выбор для многих сварщиков, занимающихся техническим обслуживанием и ремонтом. Тем не менее, хорошая подготовка основного металла является ключевым моментом. Для получения наилучших результатов сварки необходимо заранее очистить поверхность и выбрать идеальный присадочный металл.Для этого процесса очень хорошо подходят AMPCO-TRODE® 10, 46 и 150, а также AMPCO-CORE® 200, 250 и 300.
Поскольку FCAW также может выполняться на открытом воздухе, он широко используется в морской промышленности — например, для ремонта судов. Для FCAW мы рекомендуем следующие присадочные металлы: AMPCO-CORE® 200, 250, 250 и 300.
Если вы хотите узнать больше о различных сварочных процессах и глубже понять мир сварки, загрузите нашу бесплатную Техническую статью «Полное руководство по сварке разнородных металлов».
Что такое дуговая сварка экранированного металла (SMAW)?
Если вы интересуетесь сваркой и задаетесь вопросом: «Что такое SMAW?» мы здесь, чтобы помочь объяснить. SMAW расшифровывается как «дуговая сварка защищенным металлом». SMAW — это тип сварки, который используется в самых разных областях, включая техническое обслуживание и ремонт, строительство, промышленное производство и т. Д.
SMAW — один из старейших видов сварки, созданный в 1890 году, когда Чарльз Л. Коффин запатентовал этот процесс. SMAW — это процесс ручной дуговой сварки, который остается одним из наиболее часто используемых сварочных процессов. Его можно использовать как для ремонтной сварки, так и для производства, и его можно использовать во всех положениях сварки на всех черных металлах.
Что такое дуговая сварка металлом в экранированном металле?Экранированная дуговая сварка (SMAW), также известная как ручная дуговая сварка металлическим электродом (MMA или MMAW), дуговая сварка под защитным флюсом или, неофициально, как сварка стержнем, представляет собой процесс ручной дуговой сварки, в котором используется плавящийся электрод, покрытый флюсом. уложить сварной шов.
Дуговая сварка защищенным металлическим электродом (SMAW) — это ручной процесс с использованием плавящегося электрода с флюсовым покрытием и металлическим стержнем в сердечнике. Переменный или постоянный ток образует дугу между электродом и основным металлом, что создает необходимое тепло. В Соединенных Штатах это наиболее распространенный метод.
Покрытие флюса распадается и выделяет пары, которые служат защитным газом и образуют защитный слой шлака. Оба защищают зону сварного шва от атмосферного загрязнения.Когда металлический стержень внутри электрода плавится, он образует ванну расплава, которая становится сварным швом.
Сварщик может управлять несколькими переменными, которые влияют на ширину и высоту сварного шва, проплавление сварного шва и количество брызг. Сварка палкой стоит недорого по сравнению с другими методами, такими как TIG. Он портативный и работает с любой толщиной и в любом положении.
Основным недостатком является шлак, образующийся в процессе сварки при более низких скоростях (если вы не обладаете высокой квалификацией).
SMAW по-прежнему широко используется в строительстве тяжелых стальных конструкций и в промышленном производстве. Этот процесс используется в основном для сварки чугуна и стали (включая нержавеющую сталь), но этим методом также можно сваривать алюминиевые, никелевые и медные сплавы.
Теперь, когда вы знаете основы SMAW, продолжайте читать, чтобы узнать больше о том, как это работает.
Как работает SMAW?SMAW использует тепло дуги для плавления верхней части расходуемого покрытого электрода и основного металла.И электрод, и свариваемый предмет являются частью электрической цепи. Эта схема также включает источник питания, сварочные кабели, электрододержатель и зажим заземления.
Кабели от источника питания присоединены к изделию и электрододержателю. Сварка начинается, когда между основным металлом и концом электрода образуется дуга. Поверхность изделия и кончика электрода оплавляется.
Затем на конце электрода образуется металл, переходящий из дуги в ванну. Наполнитель откладывается при израсходовании электрода.Дуга в SMAW становится очень горячей — температура может превышать 9000 градусов по Фаренгейту!
SMAW НапряжениеНапряжение — одна из основных переменных при дуговой сварке. В некоторых сварочных процессах для поддержания этого может использоваться заданная система постоянного напряжения, но при сварке SMAW напряжение регулируется вручную. Это достигается перемещением палки ближе или дальше от работы.
SMAW Сварочный токИсточники питания постоянного тока используются для большинства SMAW и других процессов ручной сварки.Это обеспечивает постоянный предварительно установленный ток и поддерживает настройку силы тока.
Полярность SMAWПри сварке SMAW почти всегда используется обратная полярность. Это помогает обеспечить наилучший профиль валика и проплавление, а также снижает чрезмерное разбрызгивание, которое представляет собой капли расплавленного материала, которые образуются на сварочной дуге или рядом с ней. включают:
- Источник питания для дуговой сварки (сварочный аппарат)
- Кабель вывода электрода
- Держатель электрода
- Выводы
- Кабели
- Кабельные соединители
- Зажим заземления
- Отбойный молоток
Как и при любом другом процессе сварки, сварщик использует средства безопасности.Сюда входят шлем, перчатки и защитная одежда.
Для чего используется SMAWSMAW можно использовать для различных типов металлов и различной толщины. Он часто используется для тяжелых работ, связанных с промышленным чугуном и сталью, например углеродистой сталью и чугуном, а также для работ с низко- и высоколегированными сталями и никелевыми сплавами.
SMAW используется в различных отраслях промышленности, в том числе:
- Строительство
- Трубопроводы
- Судостроение
- Подводная сварка
- Производство сельскохозяйственной техники
Оборудование SMAW легко переносится и может использоваться в различных средах, от помещения до улицы и на корабле в море.И хотя SMAW является одним из старейших видов сварки, новые технологии всегда совершенствуют процессы и делают их все более эффективными.
Если сварщик SMAW знает, как правильно выбрать электрод, скорость сварки и длину дуги (и работает с чистыми материалами), сварка SMAW обеспечивает надежную сварку в различных отраслях промышленности.
Преимущества SMAWSMAW имеет много больших преимуществ, которые делают его незаменимым продуктом в большинстве промышленных предприятий.К этим преимуществам относятся:
- Относительно простое оборудование
- Наиболее портативное из всех сварочных процессов
- Отсутствие необходимости в отдельной газовой защите
- Может использоваться в широком диапазоне сред, включая наружные, в производственных цехах, на трубопроводах и нефтеперерабатывающих заводах, на корабли и мосты и многое другое.
- Не чувствителен к ветру и сквознякам
- Хорошо подходит для широкого спектра широко используемых металлов и сплавов
- Может работать на бензине или дизельном топливе в удаленных районах без электрических подключений
- Оборудование и технические знания уже широко распространены в большинстве промышленных предприятий
SMAW имеет несколько больших преимуществ, но, конечно, есть и недостатки, которые не могут сделать его лучшим выбором для определенных проектов.Некоторые из недостатков включают:
- Не автоматизирован и поэтому обычно имеет более низкую производительность, чем автоматизированные процессы
- Скорость наплавки обычно ниже, чем для других сварочных процессов
- Требуется больше навыков оператора, чем во многих других процессах
- Не подходит для металлов, которые являются химически активными, включая: титан, колумбий и цирконий
- Может разбрызгиваться и требовать дополнительной очистки.
СВЯЗАННЫЕ ЗАПИСИ
Урок 2 — Общие процессы электродуговой сварки
Урок 2 — Общие процессы электродуговой сварки © АВТОРСКИЕ ПРАВА 1998 ГРУППА ЭСАБ, ИНК.УРОК II ОБЩИЙ ЭЛЕКТРИЧЕСКАЯ ДУГА СВАРОЧНЫЕ ПРОЦЕССЫ 2.1 ВВЕДЕНИЕ После долгого эксперименты других в начале 1800-х, англичанин по имени Уайлд получена первая электросварка патент в 1865 году. Он успешно соединил две небольшие части утюг, пропуская электрический ток через обе детали, образуя сварной шов.Примерно двадцать лет спустя Бернадо, русский, получил патент на процесс электродуговой сварки в котором он поддерживал дугу между угольным электродом и деталями, которые должны быть соединились, сплавив металлы вместе поскольку дуга вручную пропускалась через свариваемый стык. 2.1.0.1 Во время в 1890-х годах дуговая сварка выполнялась неизолированными металлическими электродами, которые были сожжены в расплавленной луже и стал частью наплавленного металла. Сварные швы были из низкое качество из-за азота и кислород в атмосфере с образованием вредных оксидов и нитридов в металле шва.В начале двадцатого века важность защиты дуга из атмосфера была реализована. Покрытие электрода разложившимся материалом в пылу дуга для образования газового экрана оказалась лучшим методом это конец. В результате различные методы покрытия электродов, такие как оборачивание и окунание, были опробованы. Эти усилия завершились в электроде с экструдированным покрытием в середине 1920-х гг. улучшение качества металла шва и обеспечение того, что многие считают наиболее значительный прогресс в области электрической дуги сварка.2.1.0.2 Поскольку сварка покрытыми электродами это довольно медленная процедура, более быстрая сварка были разработаны процессы. В этом уроке будут рассмотрены наиболее часто используемые электродуговая сварка процессы, используемые сегодня. 2.2 ЗАЩИТНЫЙ ДУГОВАЯ СВАРКА МЕТАЛЛА Экранированный Дуговая сварка металла *, также известная как ручная металлическая дуговая сварка, ручная сварка или электрическая Дуговая сварка — это наиболее широко используемый из различных процессов дуговой сварки. Сварка выполняется с тепло электрической дуги, которое сохраняется между концом металла с покрытием электрод и заготовку (см. рис. 1).Тепло, производимое дугой, плавит основной металл, стержень сердечника электрода и покрытие. Поскольку капли расплавленного металла передан через дуги и в расплавленную сварочную ванну, они защищены от атмосферы производимыми газами от разложения флюсового покрытия. Расплавленный шлак всплывает в вершина сварного шва лужа, в которой он защищает металл шва от воздействия атмосферы во время затвердевания.Расходные материалы для дуговой сварки: полное руководство
Что такое дуговая сварка?
Дуговая сварка использует поток электронов, проходящих через воздух / газ, известный как «дуга», для нагрева металлических деталей в определенной области с образованием лужи расплава, известной как «сварочная ванна».После того, как дуга переместилась или исчезла, сварочная ванна затвердевает, создавая связь между ранее отдельными деталями.
Что такое сварочные материалы?
Существует два основных типа сварочных материалов : один — это материалы, составляющие часть самого сварного шва (часто называемые «присадочным металлом»), а другой — части, которые потребляются для обеспечения процесса сварки. В этой статье мы сконцентрируемся на расходных деталях, которые позволяют производить сварку, с акцентом на процессы MIG / MAG , TIG и MMA .
Расходные материалы для сварки MIG / MAG
Мы ставим сварку MIG / MAG на первое место не потому, что это лучший способ сварки с точки зрения целостности сварного шва, а потому, что это то, с чем знакомо большинство сварщиков. Его главные сильные стороны — продуктивность, гибкость и то, что этому относительно легко научиться.
Сварка МИГ / МАГ — это процесс, при котором дуга зажигается между непрерывно подаваемой расходной проволокой (присадочным металлом) и заготовкой.Эта проволока плавится в «сварочную ванну» (расплавленную «лужу»), образованную дугой на заготовке, и добавляет дополнительный материал к сварному шву. Поскольку большинство металлов будут гореть на воздухе при этих температурах, вводится защитный газ, чтобы не допустить попадания кислорода (и других химически активных газов) в расплавленный металл.
Таким образом, проблема, с которой сталкивается тот, кто хочет произвести сварочный аппарат MIG , заключается не только в том, как создать правильные электрические условия для зажигания и поддержания сварочной дуги, но не менее критична доставка присадочного металла и защитного газа в область, сваренная точно и последовательно.
Обычный метод подачи сварочной дуги, защитного газа и присадочного металла к заготовке достигается с помощью сварочной горелки (или «пистолета»), которая обычно имеет длину от 3 до 4 метров и присоединяется к положительному электрическому выводу. сварочного аппарата. Устройство подачи проволоки проталкивает присадочный металл (в форме проволоки) вдоль горелки через «лайнер», выходящий из конца через «контактный наконечник», который передает ему электрический заряд. В то же время защитный газ подается в горелку под давлением сжатого цилиндра, который выходит через сопло (или «кожух»), окружающее контактный наконечник.Провод заземления, присоединенный к отрицательной электрической клемме сварочного аппарата, зажимается на заготовке для обеспечения целостности цепи; сварочная горелка и заземляющий провод обычно называют «вторичными» расходными материалами.
Расходные детали для сварки MIG могут быть товаром, но они играют решающую роль в обеспечении качества сварки и могут напрямую влиять на общую производительность и стоимость операции. Плохо спроектированная горелка MIG может быть не только неудобной для оператора, но также может создавать такие проблемы, как плохая подача присадочной проволоки и непостоянная газовая защита.
Переходя к основным расходным деталям, они обычно включают гильзу, контактный наконечник, газовое сопло и газовый диффузор. Именно эти детали в первую очередь отвечают за равномерную подачу сварочной проволоки, поддержание газовой защиты и создание электропроводности, необходимой для хорошей сварочной дуги. Расходные детали более высокого качества обычно изготавливаются из материалов высшего сорта с более точными допусками, чтобы максимально продлить срок их службы, повысить качество сварки и снизить неудовольствие оператора.Детали низкого качества создают ненужные проблемы для оператора, который уже может быть сложной работой, например:
- Отжиг (оплавление конца проволоки на наконечник), требующий длительной повторной подачи
- Резкая подача проволоки, вызывающая чрезмерное разбрызгивание и плохой внешний вид сварного шва
- Дополнительное время простоя при частой замене перегоревших деталей
- Плохая газовая защита, вызывающая пористость сварного шва и, следовательно, возможную переделку
По оценкам, расходные материалы составляют менее 1% стоимости метра сварного шва по сравнению с 76%, приходящимися на заработную плату.Это веский аргумент в пользу покупки качественных деталей, а не только самых дешевых из тех, что рекламируются.
Расходные детали для сварки TIG
Сварка TIG — один из наиболее распространенных способов получения высокопрочных и эстетически красивых сварных швов. Это очень гибкий процесс, позволяющий сваривать практически все металлы на одном типе оборудования и в защитном газе (аргон).
Как и сварка MIG / Mag, процесс TIG соединяет металлы путем локального нагрева их до температуры плавления с помощью электрической дуги.Однако в этом случае дуга зажигается между термостойким вольфрамовым электродом и заготовкой, в то время как присадочная проволока обычно подается в сварочную ванну независимо. Опять же, вводится защитный газ, чтобы удерживать химически активные газы, присутствующие в воздухе, вдали от расплавленного металла.
Электрическая дуга и защитный газ подаются на обрабатываемую деталь сварочной горелкой, длина которой обычно составляет 4 или 8 метров, а вольфрамовый электрод, из которого излучается дуга, удерживается в цанге внутри головки горелки.В то же время защитный газ подается в горелку под давлением сжатого цилиндра и выходит через сопло, из которого выступает вольфрам. Цепь замыкается заземляющим проводом, который и горелка являются «вторичными» расходными материалами для сварки TIG.
Основные расходные детали, обычно состоящие из цанги, корпуса цанги и керамического сопла, должны иметь точные размеры, чтобы вольфрамовый электрод оставался концентричным относительно керамического сопла. Эксцентрично установленный вольфрам будет вызывать блуждание сварочной дуги и затруднять управление сварочной ванной.Как и в случае с расходными материалами для сварки MIG , расходные материалы более высокого качества обычно изготавливаются из материалов высшего качества, которые лучше справляются с интенсивным нагревом. Это особенно касается цанг для небольших горелок TIG , а также керамических сопел для высокоамперных приложений. Опять же, детали низкого качества вызывают ненужное разочарование у операторов, гордящихся своей работой, например:
- Блуждание дуги, приводящее к ухудшению внешнего вида сварного шва
- Падение вольфрама в сварочную ванну из-за деформации цанги под действием тепла
- Плохая газовая защита, вызывающая пористость в сварном шве и возможную доработку
- Дополнительное время простоя при частой замене перегоревших деталей
- Керамическое сопло трескается и отваливается
MMA (ручная дуговая сварка металла или «палка») — это широко распространенный метод дуговой сварки.Это простой и гибкий процесс, который можно использовать в первую очередь для обработки черных металлов, но, тем не менее, требует высокого уровня навыков оператора.
Сварка стержневыми электродами работает путем создания электрической дуги между металлическим плавящимся электродом, покрытым флюсом, и заготовкой. Как и в случае других процессов дуговой сварки, упомянутых выше, при этом происходит локальное плавление металлической сердцевины электрода и заготовки, образуя прочную связь при охлаждении. Однако фундаментальное отличие заключается в покрытии электрода из флюса, которое «выгорает» во время сварки, создавая газовую защиту от кислорода в воздухе.Этот процесс очень надежен и позволяет получать сварные швы с высокой степенью целостности в атмосферных условиях вне помещений, чего нельзя было добиться с помощью сварки MIG или TIG.
Сварочная дуга подводится к изделию с помощью провода с ручкой на одном конце для удержания плавящегося электрода. В некотором смысле, в процессе сварки MMA нет фактически расходуемых деталей. Однако держатели электродов, зажимы заземления и сварочные провода изнашиваются в процессе эксплуатации, вызывая такие проблемы, как:
- Изношенный электрододержатель, из-за которого электрод выпадает или меняет положение во время сварки
- Снижение мощности сварки из-за плохой проводимости земли и электрода
- Искрение из розеток машины из-за изношенных соединителей / заглушек сварочных проводов
- Оплавление изоляции сварочного провода из-за ослабления разъемов
Рекомендуется регулярно заменять сварочные провода и использовать кабель, держатели и зажимы заземления правильного размера; полезное руководство показано ниже;
Где найти поставщиков качественных сварочных материалов в Великобритании?
Если вы сварщик или работаете в отрасли, то вы знаете, насколько важны правильные расходные материалы для ваших сварщиков.В PWP мы стремимся помочь металлообрабатывающей промышленности добиться максимальных результатов. Это означает предоставление лучших инструментов для проектов, чтобы каждый готовый результат был безупречным.
Наш обширный ассортимент продукции ориентирован на предоставление решений, с которыми могут работать наши клиенты. В конце концов, наша цель — предоставить сварщикам качественное оборудование, чтобы помочь им во всех отраслях стать более эффективными, производительными и прибыльными.
Не говоря уже о том, что мы предлагаем быструю доставку, чтобы ваши задержки и простои были по возможности сведены к минимуму.Опять же, это лишь часть нашего стремления, чтобы сварщики повсюду добивались своих целей! Так что, если вам нужна консультация специалиста или новый сварочный аппарат или расходные материалы , свяжитесь с нами сегодня. Позвоните нам по телефону 01234 345111 или по электронной почте [адрес электронной почты защищен] , чтобы разместить запрос или узнать больше от нашей знающей и преданной команды.
Биография автора:
Эта статья написана Ричардом Фрайером, партнером PWP Industrial с 24-летним опытом.
Страстно поддерживая профессиональных сварщиков и демонстрируя историю поставок продукции для индустрии сварки и производства, Ричард является бесценным активом для PWP Industrial и вносит свой вклад в конечную цель предоставления инновационных решений. Связаться с Ричардом в Linkedin.
Преимущества и недостатки дуговой сварки
Компания Wasatch Steel часто покупает изделия для сварки стали. Мы предлагаем инструменты и продукты для всех видов сварочных работ, а также знания и ноу-хау, которые помогут вам приступить к реализации вашего последнего сварочного проекта.
Один из этих форматов, широко используемых в мире сварки, — это дуговая сварка. Что такое дуговая сварка, и каковы ее преимущества и недостатки? Давайте посмотрим.
Что такое дуговая сварка?Дуговая сварка — это процесс соединения металла, в данном случае стали, с помощью электричества. В отличие от большинства других форматов, в которых обычно используется газ, в этом процессе используется электричество, чтобы создать достаточно тепла, чтобы расплавить металл и сплавить его во время охлаждения.
Для дуговой сварки можно использовать как постоянный, так и переменный ток, а также использовать плавящиеся или неплавящиеся электроды, покрытые флюсом. Температура при дуговой сварке достигает 6500 градусов по Фаренгейту. Некоторые из наиболее распространенных применений дуговой сварки включают монтаж стали, ремонт тяжелого оборудования, сварку трубопроводов и многие крупные строительные проекты.
ПреимуществаИспользование дуговой сварки имеет ряд преимуществ по сравнению со многими другими форматами:
- Стоимость — оборудование для дуговой сварки стоит по хорошей цене и доступно, и для этого процесса часто требуется меньше оборудования в первую очередь из-за отсутствия газа
- Портативность — эти материалы очень легко транспортировать
- Работы по грязному металлу
- В защитном газе нет необходимости — процессы можно завершить во время ветра или дождя, и разбрызгивание не является серьезной проблемой.
Есть несколько причин, по которым некоторые люди ищут другие варианты помимо дуговой сварки для определенных типов проектов.Эти недостатки могут включать:
- Более низкая эффективность — при дуговой сварке обычно образуется больше отходов, чем при сварке многих других типов, что в некоторых случаях может увеличить стоимость проекта
- Высокий уровень квалификации — операторам проектов по дуговой сварке требуется высокий уровень навыков и подготовки, и не все профессионалы обладают им.
- Тонкие материалы — использование дуговой сварки некоторых тонких металлов может быть затруднительным
Готовы узнать больше об этой или любой другой нашей металлургической компании? Наши профессионалы в Wasatch Steel всегда рядом.
Основы дуговой сварки
Дуговая сварка — это один из нескольких способов соединения металлов плавлением. Под воздействием сильного тепла металл на стыке между двумя частями расплавляется и смешивается — непосредственно или чаще с промежуточным расплавленным присадочным металлом. После охлаждения и затвердевания создается металлургическая связь. Поскольку соединение представляет собой смесь металлов, окончательная сварка потенциально имеет те же прочностные свойства, что и металл деталей. Это резко контрастирует с процессами соединения без слияния (т.е. пайка, пайка и т. д.), в которых механические и физические свойства основных материалов не могут быть воспроизведены в месте соединения.Рис.1 Базовая схема дуговой сварки |
При дуговой сварке сильное тепло, необходимое для плавления металла, вырабатывается электрической дугой. Дуга образуется между реальной работой и электродом (стержнем или проволокой), который вручную или механически направляют вдоль стыка.Электродом может быть стержень, который просто пропускает ток между наконечником и изделием. Или это может быть специально подготовленный пруток или проволока, которая не только проводит ток, но также плавит и подает присадочный металл к стыку. В большинстве сварочных операций при производстве стальных изделий используется электрод второго типа.
Базовая сварочная цепь
Базовая схема дуговой сварки проиллюстрирована на рис. 1. Источник переменного или постоянного тока, оснащенный любыми элементами управления, которые могут потребоваться, подключается рабочим кабелем к заготовке и «горячим» «кабель к электрододержателю какого-либо типа, который обеспечивает электрический контакт со сварочным электродом.
Дуга возникает в зазоре, когда цепь под напряжением и кончик электрода касаются заготовки и извлекаются, но все еще находятся в тесном контакте.
Дуга создает температуру около 6500 ° F на конце. Это тепло плавит и основной металл, и электрод, образуя лужу расплавленного металла, которую иногда называют «кратером». Кратер затвердевает за электродом по мере его перемещения по стыку. Результат — сплавление.
Дуговое экранирование
Однако для соединения металлов требуется нечто большее, чем просто перемещение электрода по стыку.Металлы при высоких температурах склонны химически реагировать с элементами воздуха — кислородом и азотом. Когда металл в ванне расплава вступает в контакт с воздухом, образуются оксиды и нитриды, которые снижают прочность и ударную вязкость сварного соединения. Таким образом, многие процессы дуговой сварки предоставляют некоторые средства для покрытия дуги и ванны расплава защитным экраном из газа, пара или шлака. Это называется дуговой защитой. Эта защита предотвращает или сводит к минимуму контакт расплавленного металла с воздухом. Экранирование также может улучшить сварной шов.Примером может служить гранулированный флюс, который фактически добавляет в сварной шов раскислители.
Рис. 2 Это показывает, как покрытие на покрытом (стержневом) электроде обеспечивает газовый экран вокруг дуги и шлаковое покрытие на горячем сварном шве. |
На рис. 2 показано экранирование сварочной дуги и сварочной ванны стержневым электродом. Экструдированное покрытие стержня присадочного металла обеспечивает защитный газ в точке контакта, а шлак защищает свежий сварной шов от воздуха.
Сама по себе дуга — очень сложное явление. Глубокое понимание физики дуги не имеет большого значения для сварщика, но некоторые знания ее общих характеристик могут быть полезны.
Природа дуги
Дуга — это электрический ток, протекающий между двумя электродами через ионизированный столб газа. Отрицательно заряженный катод и положительно заряженный анод создают интенсивный нагрев сварочной дуги. Отрицательные и положительные ионы отскакивают друг от друга в плазменном столбе с ускоренной скоростью.
При сварке дуга не только обеспечивает тепло, необходимое для плавления электрода и основного металла, но при определенных условиях также должна обеспечивать средства для транспортировки расплавленного металла от кончика электрода к изделию. Существует несколько механизмов переноса металла. Два (из многих) примеров включают:
- Surface Tension Transfer® — капля расплавленного металла касается ванны расплавленного металла и втягивается в нее за счет поверхностного натяжения
- Spray Arc — капля выбрасывается из расплавленного металла на кончике электрода с помощью электрического пинцета, толкающего ее в ванну расплава (отлично подходит для сварки над головой)
Если электрод расходный, наконечник плавится под действием тепла дуги а капли расплава отделяются и транспортируются к работе через столб дуги.Любая система дуговой сварки, в которой электрод расплавляется, чтобы стать частью сварного шва, описывается как металлическая дуга. При сварке углеродом или вольфрамом (TIG) капли расплава не попадают в зазор и не попадают на изделие. Присадочный металл вплавляется в стык из отдельного прутка или проволоки.
Большая часть тепла, выделяемого дугой, передается сварочной ванне с плавящимися электродами. Это обеспечивает более высокую термическую эффективность и более узкие зоны термического влияния.
Так как должен быть ионизированный путь для проведения электричества через зазор, простое включение сварочного тока с электрически холодным электродом, наложенным на него, не вызовет зажигания дуги.Дуга должна быть зажжена. Это вызвано либо подачей начального напряжения, достаточно высокого, чтобы вызвать разряд, либо прикосновением электрода к изделию, а затем его извлечением по мере того, как область контакта нагревается.
Дуговая сварка может выполняться постоянным током (DC) с электродом либо положительным, либо отрицательным, либо переменным током (AC). Выбор тока и полярности зависит от процесса, типа электрода, атмосферы дуги и свариваемого металла.
.