Технологические трубопроводы
Трубопроводами называются устройства, которые служат для транспортирования жидких, газообразных и сыпучих веществ. Трубопроводы состоят из соединенных между собой прямых участков труб, деталей трубопроводов, запорнорегулирующей арматуры, контрольноизмерительных приборов, средств автоматики, опор и подвесок, крепежных материалов (болтов, шпилек, гаек), прокладок и уплотнений.
Технологическими трубопроводами называются такие трубопроводы промышленных предприятий, по которым транспортируются сырье, полуфабрикаты и готовые продукты, пар, вода, топливо, реагенты и другие материалы, обеспечивающие ведение технологического процесса и эксплуатацию оборудования; отработанные реагенты и газы, различные промежуточные продукты, полученные и использованные в технологическом процессе.
В проектной документации и технической литературе приняты следующие названия отдельных составляющих трубопровода:
- Линия — участок трубопровода, соединяющий между собой аппараты, установки, цехи и другие линии с аппаратами, установками, цехами.
- Узел — часть линии трубопровода, состоящая из нескольких элементов, собранных между собой иа разъемных и неразъемных соединеинях.
Узлы подразделяются на:
- Плоские, состоящие из нескольких элементов, расположенных в одной плоскости.
- Пространственные, состоящие из нескольких элементов, расположенных в двух и более плоскостях.
Элемент — часть узла трубопровода, подлежащая самостоятельному изготовлению; она состоит из гнутых участков или прямых отрезков труб и деталей, все стыки которых выполнены с помощью автоматической сварки.
Деталь — элементарная часть трубопровода, ие имеющая соединений, например отвод, фланец, отрезок трубы, тройиик, заглушка, переход, а также отдельные изделия, входящие в конструкцию трубопровода — метизы, комлеисаторы, арматура, опоры, подвески и др.
Блок — линия или часть линии трубопровода, состоящая из узлов, собранных на разъемных и неразъемных соединениях. Укрупнение узлов в блоки производят перед монтажом.
Секция — одноосный узел, состоящий из нескольких сваренных между собой труб одного диаметра, ось которых составляет одну прямую линию.
Плеть — несколько сваренных между собой секций (сварка секций в плеть производится на месте прокладки трубопровода).
Сварочные работы. Сварка трубопроводов, металлоконструкций, емкостей
Компания «100 ТОНН МОНТАЖ» обладает широкими компетенциями в области сварочно-монтажного производства. В нашем референс-листе крупные проекты, включающие:
Узнать стоимость или получить бесплатную консультацию
Оставьте заявку сегодня и получите бесплатный выезд специалиста на объект для изучения задачи, проведения замеров и осмотра площадки.
Нажимая на кнопку, вы даёте согласие на обработку своих персональных данных. Пользовательское соглашение
География и сроки сварочных работ«100 ТОНН МОНТАЖ» реализует сварочные проекты на территории всей России и стран СНГ, в том числе в особых климатических зонах. Наша опытная служба материально-технического обеспечения быстро организует доставку необходимого оборудования и материалов на любой удаленный объект.
Мы уделяем много времени работе с персоналом и готовы укомплектовать бригады сварщиков и ИТР для работы в несколько смен. Имеем опыт реализации сварочно-монтажных проектов в период останова производства. Еще до начала проекта наши специалисты точно рассчитают сроки завершения работ.
На объекте заказчика мы оперативно разворачиваем инфраструктуру, необходимую для эффективной работы сварочного производства. Обычно она включает площадку укрупнения, склады для хранения сварочного оборудования и материалов.
Узнать стоимость или получить бесплатную консультацию
Оставьте заявку сегодня и получите бесплатный выезд специалиста на объект для изучения задачи, проведения замеров и осмотра площадки.
Нажимая на кнопку, вы даёте согласие на обработку своих персональных данных. Пользовательское соглашение
Контроль качества сваркиВ «100 ТОНН МОНТАЖ» тщательно отработаны:
- Входной контроль основных и сварочных материалов
- Пооперационный контроль сборки и сварки на объекте
- Контроль качества сварных соединений с выдачей всей необходимой документации, в соответствии с действующими нормативными требованиями
Это значит, что наши заказчики могут быть уверены в качестве, надёжной безопасной эксплуатации и долговечности сварных изделий любого назначения.
Квалифицированный персонал и современное сварочное оборудование ручной дуговой, аргонодуговой и механизированной сварки, позволяет реализовывать крупные проекты (включая работы на опасных производственных объектах) и производить сварку различных групп материалов (углеродистые стали, стали аустенитного класса, теплоустойчивые хромомолибденовые стали) в широком диапазоне толщин и диаметров.
Применяемое на предприятии сварочное оборудование и технологии сварки имеют свидетельства об аттестации в соответствии с требованиями руководящих документов системы аттестации сварочного производства. Свидетельства НАКС, выданные «100 ТОНН МОНТАЖ», могут быть представлены по вашему запросу. Свяжитесь с нами и получите необходимую информацию.
Сварка технологических трубопроводовРучная дуговая и аргонодуговая сварка трубопроводов требует высокой квалификации персонала. Чтобы обеспечить качество сварного шва стыков трубопроводов, надо уметь одинаково хорошо варить во всех пространственных положениях и в совершенстве владеть теорией. Мы гордимся, что в нашем штате есть такие редкие специалисты, за которых обычно идёт конкурентная борьба у работодателей.
«100 ТОНН МОНТАЖ» успешно реализует проекты по сварке трубопроводов в целлюлозно-бумажной промышленности, на горно-обогатительных комбинатах, нефтеперерабатывающих заводах и других отраслях.
Узнать стоимость или получить бесплатную консультацию
Оставьте заявку сегодня и получите бесплатный выезд специалиста на объект для изучения задачи, проведения замеров и осмотра площадки.
Нажимая на кнопку, вы даёте согласие на обработку своих персональных данных. Пользовательское соглашение
Ремонт трубопроводов. Восстановление сварных и разъемных соединений трубопроводов
Мар 25, 2020
Восстановление сварных соединений трубопроводов.
Наземные сварные соединения наиболее многочисленны. При их ремонте проводят сварочно-ремонтные операции при выявлении в сварных соединениях недопустимых дефектов и эксплуатационных повреждений [1, 2].
Выбор сварочной технологии зависит от типа трубопровода (параметров эксплуатации — давления и температуры, длительности наработки), типоразмера сварного соединения и технологии его изготовления или предыдущего ремонта (способа сварки, сварочного материала, марки стали, вида термообработки), характера и размера повреждения, места и ориентации трещин (поперечные или продольные, по металлу шва или в зоне термического влияния).
Основные положения сварочно—ремонтной технологии включают требования и рекомендации по анализу особенностей и причин повреждения, измерению твердости и химическому анализу металла, организации места ремонта, выбору и прокалке покрытых электродов, удалению поврежденного металла механическим способом с получением углубления — выборки оптимальной чашеобразной формы и размера, многослойному заполнению выборки с подогревом, выполнению при необходимости усиливающих наплавок, проведению послесварочной термообработки, механической обработки и контроля качества отремонтированного сварного соединения [1].
Для сварных соединений технологических трубопроводов химических, газо— и нефтеперерабатывающих и добывающих предприятий ремонт заключается в выполнении подварочных швов в местную выборку. Поверхностный дефект удаляется механическим способом (вырубкой ударным инструментом, фрезерованием, абразивным инструментом) с засверловкой концов трещин. Разделка под сварку подготавливается чашеобразной формы с отлогими стенками без резких переходов по краям разделки. Процесс сварки ведется на спокойном воздухе (без сквозняков) при положительной температуре. При ручной дуговой сварке низко— и легированных сталей, включая высоколегированные аустенитного класса, используются электроды с основным покрытием, при сварке углеродистых сталей — электроды с рутиловым покрытием [1].
Причинами повреждений сварных соединений паропроводов из хромомолибденованадиевых сталей являются технологические, конструкционные и эксплуатационные факторы [1, 2]. К типичным относятся повреждения в виде продольных и поперечных трещин в металле шва и в зоне термического влияния.
Для сварных соединений тепловых сетей горячей воды с температурой эксплуатации до 250° технология ремонта соединений трубопроводов 100 ≤ Дн ≥ 920 мм и с S ≤20 мм проводится путем выполнения подварочных швов в зоне появления свищей или трещин, а также путем переварки поврежденных сварных швов, либо замены разрушившихся сварных деталей на новые [1].
Ремонт сварных соединений магистральных газо- и нефтепроводов проводится несколькими способами, в том числе [1]:
— с применением ручной дуговой сварки. Одним из вариантов технологии является нанесение наплавки при ремонте поверхностных дефектов без прекращения перекачки продукта (нефти, газа) .в трубопроводе. Другим вариантом является замена дефектного участка трубопровода (сварного стыка, трубы) с вваркой нового трубного элемента, что связано с остановкой транспортировки продукта. При любом варианте технологии ремонта принимаются специальные меры по пожаро— и взрывобезопасности;
— с использованием холодной сварки без прекращения транспортировки продукта в трубопроводе. По технологии, разработанной АО «ВНИИСТ», полость поверхностного дефекта заполняется композиционным материалом в виде полимерной основы с дисперсным металлическим наполнителем. В течение короткого времени нанесенный материал твердеет однако по прочности он заметно уступает показателям металла труб, что сдерживает широкое применение этого способа ремонта;
— с применением кольцевых пластиковых муфт (возможно в сочетании с холодной сваркой) без прекращения транспортировки продукта в трубопроводе. Такой способ является эффективным как обеспечивающий несущую способность сварных соединений (или участков труб) с поверхностными дефектами, Кольцевая муфта изготавливается путем многослойной намотки высокопрочной пластиковой ленты на дефектный кольцевой сварной стык трубы без применения электрической дуги или открытого пламени. Целостное сцепление муфты между слоями и с металлом трубы обеспечивается связующим материалом-адгезивом.
Рекомендации по ремонту сварных соединений трубопроводов, включая режимы сварки, даны в [1‚ 2, 3].
Восстановление разъемных соединений трубопроводов.
При ремонте и замене фланцы и крепежные детали технологических трубопроводов независимо от наличия сертификата и заводской маркировки (Pу‚ Dу, марка стали), допускается применять только после проверки марки стали (химический анализ, стилоскопирование и т. п.) [4].
Все детали перед ремонтными работами должны проверяться. Поверхности фланцев, прокладок не должны иметь трещин, раковин, плен, заусенцев и других дефектов, снижающих их прочность и работоспособность.
Маркировка должна соответствовать документации.
Фланцы отбраковываются при:
— неудовлетворительном состоянии привалочных поверхностей;
— наличии трещин, раковин и других дефектов;
— деформации;
— уменьшении толщины стенки воротника фланца до отбраковочных размеров трубы;
— срыве, смятии и износе резьбы в резьбовых фланцах высокого давления, а также при наличии люфта в резьбе, превышающего допустимые пределы.
Крепежные детали отбраковываются:
— при появлении трещин, срыва или коррозионного износа резьбы;
— в случаях изгиба болтов и шпилек;
— при остаточной деформации, приводящеи к изменению профиля резьбы;
— в случае износа боковых граней головок болтов и гаек;
— в случае снижения механических свойств металла ниже допустимого уровня.
Прокладочпый материал для уплотнения соединений фланцев должен соответствовать действующим стандартам.
Прокладки отбраковываются при наличии трещин, забоин, сколов, смятии уплотнительных поверхностей, деформации.
Замена прокладок фланцевых соединении газопровода допустима при условии установки кабельной перемычки между их разъединяемыми частями.
Станции электрохимической защиты при производстве работ выключаются.
При ремонте перед сборкой фланцевых соединений уплотнительные поверхности, а также металлические прокладки и линзы должны промываться и насухо протираться. Торцы труб, соединяемых на фланцах (муфтах), должны быть паралельными в пределах установленных допусков.
На поверхности резьбы крепежных деталей не должно быть следов коррозии, вмятин, надрывов и других дефектов, снижающих прочность.
При сборке фланцев под сварку с различными деталями (патрубками, фасонными частями, бесфланцевой арматурой, компенсаторами и т.п.) следует обеспечивать перпендикулярность и соосность уплотнительной поверхности фланцев к оси смежной детали в соответствии с правилами [4, 5].
При сборке фланцевых соединений деталей трубопроводов и арматуры следует обеспечивать соосность уплотнительных поверхностей фланцев. При сборке фланцев с деталями следует симметрично располагать отверстия под болты и шпильки относительно оси фланцевого соединения. Смещение отверстий двух смежных фланцев не должно превышать половины разности номинальных диаметров отверстия и устанавливаемого болта (или шпильки). При сборке деталей с плоскими приварными фланцами расстояние между уплотнительной поверхностью фланца и торцом трубы (недовод трубы) должно приниматься равным толщине трубы +1 мм или выбираться в зависимости от условного диаметра прохода трубы (табл.
Таблица 1
Dy трубы, мм | 20 | 20-50 | 70-150 | 200 | 225 | 250-300 | 350-450 |
Недовод, мм | 4 | 5 | 8 | 8 | 9 | 10 | 11 |
Для разъемных соединений трубопроводов при ремонте целесообразна замена их деталей: фланцев, прокладок, крепежа.
ЛИТЕРАТУРА
1. Хромченко Ф.А. Сварочная технология ремонта трубопроводов. М.: ИПК гослужбы, 2004. 92 с.
2. Хромченко Ф.А. Ресурс сварных соединений паропроводов. М.: Машиностроение, 2002. 352 с.
3. Юхин Н.А. Ручная сварка при сооружении и ремонте трубопроводов пара и горячей воды. М.: СОУЭЛО, 2003. 56 с.
4. Правила устройства и безопасной эксплуатации технологических трубопроводов (ПБ 03-585-03). Серия 03. Выпуск 25, 2004. 152 с.
5. Правила устройства и безопасной эксплуатации трубопроводов пара и горячей воды (ПБ 10-573-03). Серия 10. Выпуск 28, 2005. 128 с.
Контроль качества сварных соединений технологических трубопроводов
Рекомендуем приобрести:
Установки для автоматической сварки продольных швов обечаек — в наличии на складе!
Высокая производительность, удобство, простота в управлении и надежность в эксплуатации.
Сварочные экраны и защитные шторки — в наличии на складе!
Защита от излучения при сварке и резке. Большой выбор.
Доставка по всей России!
Сварные соединения трубопроводов подвергают следующим видам контроля: внешнему осмотру и измерению, ультразвуковому и магнитографическому контролю, просвечиванию гамма- или рентгеновскими лучами, металлографическим исследованиям, механическим, гидравлическим и пневматическим испытаниям. Все указанные виды контроля выполняют после термической обработки сварных соединений (если она предусмотрена).
Для контроля отбирают наихудшие (по результатам внешнего осмотра) стыки в количестве: для трубопроводов I и II категорий — 3% общего количества стыков, сваренных каждым сварщиком; III категории — 2%; IV категории — 1%.
Шов бракуют, если выявляются следующие дефекты: трещины любых размеров; непровар глубиной более 15% толщины стенки трубы, если она не превышает 20 мм, и не более 3 мм при толщине стенки свыше 20 мм шлаковые включения и поры глубиной более 10% толщины стенки трубы, если она не превышает 20 мм, и 3 мм при толщине свыше 20 мм; скопление включений и пор в виде сплошной сетки.
Механические свойства сварных соединений проверяют на образцах, вырезанных из контрольных или производственных стыков.
Предел прочности образцов должен быть не ниже нормативного; угол загиба для всех видов сварки (кроме газовой) — не менее 100° для углеродистой, низколегированной и высоколегированной, не менее 50° — для среднелегированной стали при толщине стенки до 20 мм и 40° — при толщине выше 20 мм. Для газовой сварки угол загиба углеродистой и низколегированной стали должен составлять не менее 70°, среднелегированной — не менее 30°. Ударная вязкость металла шва при дуговой сварке трубопроводов I и II категорий с толщиной стенки более 12 мм должна быть не менее 5 кгс • м/см2 для среднелегированных сталей и 7 кгс•м/см2 для прочих сталей.
Показатели механических свойств определяют как среднее арифметическое по трем образцам, при этом для отдельных образцов допускается снижение величин предела прочности и угла загиба на 10%, а ударной вязкости — на 2 кгс•м/см2.
По материалам: Л.П. Шебеко, А.П. Яковлев. «Контроль качества сварных соединений»
Безопасность труда при сварке технологических трубопроводовУчастки монтажной площадки, на которых ведется сварка трубопроводов, должны быть ограждены ширмами, щитами из листовой стали или фанеры, обработанной огнестойким материалом, занавесями из асбестового полотна или брезента на высоту не менее навесами из асбестового полотна или брезента на высоту не менее 1,8 м, ограждения должны быть окрашены в серый, желтый или голубой цвет матового тона. Сварочные работы внутри трубопроводов допускаются при условном их диаметре 1020 мм и более. Женщины не допускаются к сварке внутри трубопроводов. Все люки, штуцера и другие отверстия должны быть открыты. У каждого торца трубопровода должен постоянно дежурить наблюдающий, который располагается так, чтобы в течение сварочных работ видеть и слышать сварщика. Читать далее: |
Сварка, сборка узлов технологических трубопроводов
Одна из возможных причин возникновения аварий трубопровода – это брак при проведении строительно-монтажных работ. При проведении СМР возникает сложность правильного выполнения сборочных и сварочных работ в полевых условиях, при котором могут возникать дефекты сварных швов: поры, внутренние трещины, непровар корня шва, отслоений в результате неправильно подобранных материалов, низкой квалификации персонала, отсутствия контроля качества и т.д. Эти дефекты образуют внутренние остаточные напряжения, которые приводят к разрушениям трубопроводов на ранних стадиях эксплуатации.
Компания ООО «ЛивингСнаб» предлагает вам качественную заводскую сборку и сварку узлов технологических трубопроводов с возможностью дальнейшего нанесения антикоррозионного покрытия. На предприятии имеется собственное сварочное производство, аттестованное в НАКС. Высококвалифицированные специалисты выполняют входной контроль материалов, межоперационный и приемо-сдаточный контроль готовых изделий. Для подтверждения качества сварных швов проводятся испытания разрушающими и неразрушающими методами контроля аттестованной лабораторией.
Применение готовых узлов при строительстве трубопроводов нефтегазовой отрасли дает Заказчику ряд существенных преимуществ:
- Качественное заводское изготовление с полным антикоррозионным покрытием и паспортом на изделие.
- Удешевление продукции, поскольку проведение сварочных работ и испытаний изделия в заводских условиях обходятся гораздо дешевле.
- Сокращение сроков выполнения строительно-монтажных работ за счет более быстрой и легкой сборки уже готового узла.
Наше предприятие постоянно проводит изыскания и улучшает способы и средства нанесения антикоррозионных покрытий на особо сложные конфигурации изделий. При отсутствии такой технологической возможности нанесения покрытия, ООО «ЛивингСнаб» совместно с Заказчиком оптимизирует конструкцию узла посредством минимальных изменений.
Продукция предприятия сертифицирована в системе ГОСТ Р. Качество нашей продукции соответствует ГОСТ и ТУ и подтверждается сертификатами качества.
Технология сварки трубопровода природного газа
Трубопровод природного газа относится к трубопроводу, который транспортирует природный газ (включая попутный газ, добываемый на нефтяном месторождении) от производственной площадки или очистных сооружений к городскому газораспределительному центру или промышленному предприятию, также известному как газопровод. Использование газопровода для транспортировки природного газа — это способ транспортировки природного газа по суше. Трубопроводы природного газа составляют около половины всех трубопроводов в мире.Современная газопроводная промышленность Китая в основном сосредоточена в провинции Сычуань, которая является основным районом добычи природного газа. В 1963 году был построен первый газопровод Баю диаметром 426 мм и общей протяженностью 54,7 км. К 1983 г. построена сеть магистральных газопроводов от востока Сычуани до Чэнду, Дэян и других мест через Чунцин, Лучжоу, Вэйюань и др., диаметром 426-720 мм, общей протяженностью более 2200 км, 178 газосборных пунктов. и распределительных станций и годовой мощностью 5-6 миллиардов кубометров.Кроме того, в Дацине, Шэнли, Северном Китае и других нефтяных месторождениях есть трубопроводы для транспортировки попутного газа на нефтехимические заводы.
Технология сварки газопровода
я . Универсальный метод сварки
Как правило, полуавтоматическая сварка является основным методом инженерной сварки, а ручная дуговая сварка вниз может использоваться для локально сложных участков и соединений. Правила выполнения сварки вниз должны соответствовать положениям «Правил проведения сварки трубопроводов вниз».
- 1. Электрод из целлюлозы AWS_E6010 используется для ручной дуговой сварки, электрод AWS_E8010 используется для заполнения, а электрод с низким содержанием водорода AWS_E8018G используется для покрытия.
- 2. Для полуавтоматической корневой сварки используется электрод AWS_E6010, для заполнения и укупорки используется порошковая проволока E71T8-Ni1 или 71T8-K6.
II . Сварщики
- 1. Внедрить систему управления качеством сварки в соответствии со сварочным процессом до строительства.Обучайте и тестируйте сварщиков в соответствии с требованиями процесса сварки, утвержденными владельцем, чтобы техническое качество и технический уровень сварщиков могли соответствовать соответствующим правилам критериев приемки строительства этого проекта.
- 2. Все сварщики, участвующие в строительстве данного объекта, должны иметь «Квалификационный аттестат сварщика», выданный Главным государственным управлением технического надзора или провинциальными и муниципальными бюро технического надзора, и «Рабочий сертификат», выданный руководителем работ. , чтобы сертификат работал.
III. Основное сварочное оборудование
Источник питания: Источником питания сварочного полуавтомата является передвижная электростанция ДЗ-80 производства компании «Трубопроводное оборудование». Электростанция оснащена многосистемной сварочной машиной DC-400 Lincoln, которая одновременно может выполнять ручную сварку.
IV. ОБЩИЕ ТРЕБОВАНИЯ
- 1. Сварка трубопроводов материалом X70 требует предварительного нагрева перед сваркой. Кольцевой нагреватель и ручка для выпечки используются для предварительного нагрева.Ширина предварительного нагрева: канавка с обеих сторон (> 50 мм), температура предварительного нагрева, температура межслойного нагрева: в соответствии с температурой, указанной в процедуре сварки для термообработки. Температура предварительного нагрева измеряется инфракрасным термометром на расстоянии 50 мм от отверстия трубы.
- Для других материалов предварительный нагрев не требуется.
- 2. Начало дуги или закрытие валиков сварного шва смещены более чем на 30 мм. Зажигание сварочной дуги осуществляется в разделке, а зажигание дуги на разделке вне сварочного слоя не допускается, тем более на стенке трубы вне разделки.
Каждая точка начала дуги и стык должны быть отремонтированы перед сваркой. После завершения первого слоя сварки начинается следующий слой сварки.
- 3. После завершения корневой сварки угловая полировальная машина используется для шлифовки и очистки шлака, брызг, дефектов и выступов шва на внешней поверхности корневой сварки. Форма разделки на наружной поверхности трубы не должна быть нарушена шлифовкой, а интервал времени между корневой сваркой и заливкой не должен превышать 10 минут.
- 4. Все валики должны быть сварены непрерывно, а межслойная температура валиков должна соответствовать требуемым требованиям. После окончания сварки брызги и шлак на поверхности шва необходимо очистить. До завершения сварки валика в этот день должно быть выполнено более 50 % всего валика сварного шва в каждом сварном соединении и не менее трех слоев. В сварочном строительстве «протокол сварочного процесса» должен быть заполнен тщательно в соответствии с правилами.
- 5. Для покрытия несварных швов в этот день следует использовать сухие водонепроницаемые и теплоизоляционные материалы.
Перед сваркой на следующий день необходимо предварительно нагреть до температуры, требуемой процедурой сварки. Для неиспользованной сварочной проволоки в тот же день механизм подачи проволоки следует снять с механизма подачи проволоки или положить вместе с механизмом подачи проволоки на склад, оборудованный осушителем, на строительной площадке для осушения. На следующий день после прибытия на строительную площадку немедленно снимите ленту, намотанную на горловину трубы, зашлифуйте корень, а затем кольцевым нагревателем прогрейте левое устье.Требования к температуре нагрева такие же, как и к температуре горловины трубы. Качество нагрева должно быть одобрено инженером по надзору на месте.
- 6. В процессе сварки резиновый защитный слой шириной 800 мм наматывается на два конца антикоррозионного слоя для предотвращения брызг и ожогов при сварке.
- 7. Требования к сварочным материалам
- (1) Каждая партия сварочных материалов должна иметь сертификат качества, сертификат соответствия и акт повторной экспертизы.
Ввозимые материалы также должны иметь сертификат товарной инспекции.
- (2) Внешний вид сварочных материалов должен быть гладким, чистым, без трещин, ржавчины, масла и других загрязнений.
- (3) Категорически запрещается разрушать сварочные материалы сыростью, дождевой водой и маслом. Хранить их следует в сухих и проветриваемых помещениях с влажностью не более 60%.
- (4) Полка сварочного материала находится на высоте более 300 мм над землей, на расстоянии более 300 мм от стены, а высота укладки не превышает установленного количества слоев.
- (5) Следует избегать повреждения сварочных материалов и упаковки во время хранения и обращения. После вскрытия упаковки ее следует беречь от порчи. Сварочные материалы с признаками повреждения или износа не должны применяться в технике.
- (6) Назначить специального человека для хранения и распределения сварочных материалов, а также вести надлежащие записи о распределении и восстановлении, метеорологические записи и записи об отжиге.
- (7) При использовании электрода его следует помещать в корпус электрода.При относительной влажности окружающей среды более 80% использование электрода должно быть ограничено в течение двух часов, а при относительной влажности окружающей среды менее 80% использование электрода должно быть ограничено в течение четырех часов. .
- (8) Неиспользованные электроды в этот день должны быть изъяты и сохранены. Электрод с низким содержанием водорода следует использовать первым после повторной сушки, и количество повторных сушек не должно превышать двух раз.
- (9) Каждый электрод должен быть приварен непрерывно, и сварщик должен по возможности избегать разрыва дуги.
- (10) Сварочную проволоку нельзя сушить. Его следует хранить в сухом и проветриваемом помещении и держать в сухости.
- (11) При большом эксцентриситете электрода, трещинах покрытия, каплеобразовании и других явлениях, влияющих на качество сварки, их нельзя использовать для сварки.
- (12) После завершения сварки оставшиеся электроды не выбрасываются по собственному желанию, а за восстановление и централизованную обработку несут ответственность специальные лица.
V. Среда сварки
Сварка строго запрещена в следующих случаях, например, без эффективных защитных мер (таких как укрытие, обогреватель и т. д.).
- Когда скорость ветра превышает требования процедуры сварки, необходимо предусмотреть специальное ветровое стекло для обеспечения требований к герметизации места сварки.
- Если скорость окружающего ветра влияет на сварочные работы, необходимо принять эффективные ветрозащитные меры для защиты зоны сварки.Согласно прошлому опыту строительства, мы обычно используем метод ветрозащиты.
Ⅵ. Проверка сварки
1. Визуальный осмотр
После сварки, ремонта или ремонта должен быть своевременно проведен визуальный осмотр. Перед осмотром необходимо удалить шлак, брызги и другие загрязнения с поверхности. Внешний вид сварного шва должен соответствовать стандарту приемки, установленному для сварки и приемки стального трубопровода. Неразрушающий контроль не должен проводиться для сварных швов, не прошедших визуальный контроль.Проверка внешнего вида сварного шва должна соответствовать следующим требованиям.
- (1) Внешний вид сварного шва однородный, а поверхность сварного шва и его зона термического влияния не должны иметь дефектов, таких как трещины, непровары, воздушные отверстия, шлаковые включения, брызги, сварные швы и т. д.
- (2) Поверхность сварного шва не должна быть ниже поверхности основного металла, а усиление сварного шва не должно превышать 1,6 мм.
- (3) Ширина каждой стороны поверхности сварного шва должна быть равна 0.на 5-2 мм шире поверхности канавки.
- (4) Непригодность после сварки должна быть менее 2 мм
- (5) Максимальный размер поднутрения должен соответствовать требованиям.
- (6) След дуги должен быть заполирован, а оставшаяся толщина стенки трубы после шлифовки не должна быть уменьшена меньше минимальной толщины, разрешенной стандартом на материал.
В противном случае весь участок трубы со следом от дуги должен быть отрезан.
2.Неразрушающий контроль сварных швов
Все стыковые сварные швы должны быть подвергнуты 100% радиографическому контролю, а повторный ультразвуковой контроль (обычно известный как контроль двойной сотни) должен проводиться в соответствии со следующими требованиями. Требования к конструкции должны быть проверены в соответствии с фактическими требованиями:
(1) Выполните 100% ut на следующих сварных швах:
- а. Все стыки труб в зонах класса III и класса IV;
- б. Сварные соединения трубопроводов, пересекающих крупные и средние реки, горные тоннели, болота, водохранилища, автомобильные и железные дороги выше III класса;
- в.Сварное соединение трубопровода, пересекающее подземный трубопровод, кабель и оптический кабель;
- д. Сварное соединение прямой трубы и колена;
- эл. Сварка встык после испытания давлением в разрезе;
- ф.
Первые 100 сварных швов, изначально сваренных каждым агрегатом;
(2) После 100 % радиографического контроля 10 % всех сварных соединений, выполненных в один и тот же день каждой единицы, подлежат ультразвуковой дефектоскопии: неквалифицированные сварные соединения должны быть отремонтированы в соответствии с требованиями, а сроки устранения дефектов тех же часть не должна превышать 1, а отремонтированные части подлежат 100%-ному ультразвуковому контролю.
Ⅶ. Ремонт
- 1. Дефекты, не связанные с трещинами, в сварном шве могут быть отремонтированы напрямую. Если процесс ремонта отличается от первоначального процесса сварки, необходимо использовать квалифицированный процесс ремонтной сварки.
- 2. Когда длина трещины составляет менее 8% длины сварного шва, для ремонта должна использоваться аттестованная процедура ремонтной сварки. При длине трещины более 8 % все сварные швы с трещинами должны быть отрезаны от трубопровода.
- 3.
Сроки устранения дефектов в одной и той же детали не должны превышать 1 раза, в противном случае сварной шов срезается. После ремонта проверьте в соответствии с первоначальным стандартом.
Источник: Китай Производитель газопроводов — Yaang Pipe Industry Co., Limited (www.yaang.com)
Технология сварки трубопроводов обеспечивает более реактивную дугу и больший контроль
Сварка магистральных трубопроводов требует высококачественных сварных швов и быстрого выполнения работы.Технология Dynamic DIG может помочь.
Экономьте время благодаря технологии динамической сварки DIG
Как сварщик трубопроводов повышенной проходимости, вы ежедневно сталкиваетесь с необходимостью выполнять высококачественную работу как можно быстрее. Для этого требуется надежный сварочный аппарат/генератор, который поможет вам добиться максимальной производительности, эффективности и качества работы.
Поскольку каждый сварной шов подвергается самым высоким стандартам неразрушающего контроля, нет места для дефектов — они требуют времени и денег — и могут задержать всю операцию. Слишком большое количество дефектов может в конечном итоге стоить сварщику трубопроводов работы.
Для решения конкретных задач, связанных со сваркой магистральных трубопроводов, компания Miller Electric Mfg. LLC собрала отзывы представителей отрасли и внедрила новые технологии в свои сварочные дуги. Новая технология Dynamic DIG обеспечивает более плавную и стабильную дугу электродуговой сварки, которую можно настроить в соответствии с областью применения, материалом, вариантами монтажа труб и техникой сварки.
Результаты? Улучшенный контроль сварочной ванны, большая гибкость дуги и возможность выполнения высококачественных сварных швов на более высоких скоростях.
Соответствие требованиям качества и производительности
Для сварщика трубопроводов наиболее важными задачами являются высококачественная сварка электродами и быстрое завершение работы. Чем больше металла сварного шва вы можете наложить за каждый проход, тем быстрее вы сможете перейти к следующему сварному соединению и, в конечном итоге, к следующей работе.
Одной из распространенных проблем при сварке трубопроводов является неравномерная подгонка, что может привести к чрезвычайно узким или несоответствующим зазорам при укладке в корневом шве. Поскольку труба сваривается сверху вниз, зазор в стыке может меняться от надлежащего до очень малого зазора или вообще без зазора, что требует от оператора внесения изменений в свою технику, чтобы учесть это отклонение.Для этого требуется машина с достаточным приводом, чтобы позволить сварщикам вставлять стержень, прикладывая большее усилие к электроду, при этом поддерживая горящую дугу и обеспечивая необходимое проплавление с посадкой с узким зазором.
Источники питания в прошлом не обладали достаточным приводом, чтобы обеспечить эту способность, что приводило к гашению дуги при попытках проникнуть в тесные зазоры. С развитием технологий сварочные аппараты/генераторы Miller ® теперь имеют привод и адаптируемость дуги, которые обеспечивают значительные преимущества для производительности и качества сварки.
Тонкая настройка дуги рукояти
Dynamic DIG — это программная технология формирования сигнала для приводов двигателей Miller Big Blue ® , включая сварочный аппарат/генератор Big Blue 400 PipePro ® . Разработанный специально для конвейеров, Dynamic DIG автоматически регулирует величину тока, необходимого для устранения короткого замыкания. В результате дуга более чувствительна к тому, как сварщик использует свой электрод, обеспечивая лучший контроль дуги и контроль сварочной ванны. Это изменяет характеристики корневого прохода и верхнего прохода, которые вы обычно видите.Если для корневого прохода требуется большой привод, вы можете настроить дугу для обеспечения достаточного проникновения. Когда вам нужно смягчить дугу и высушить ванну, чтобы сделать более широкий горячий или верхний проход, технология также может предоставить эти возможности.
Характеристики дуги могут быть оптимизированы для заполняющего и закрывающего проходов, чтобы укладывать больше металла шва, что позволяет выполнять сварку быстрее. Конечным результатом является более точная настройка дуги, поэтому сварщики могут легко изменять дугу в зависимости от того, что они видят при каждом проходе.
Еще одним преимуществом новой технологии является возможность предварительно задавать ток и поддерживать равномерный нагрев в течение всего дня сварки по сравнению с конкурентными технологиями, где сила тока падает в течение дня. Аппарат с технологией Dynamic DIG обеспечивает стабильную производительность в течение всего дня, при этом сварщику не нужно регулировать силу тока на передней панели, чтобы компенсировать изменение производительности аппарата. Эта способность выводит традиционные характеристики генератора на новый уровень с возможностями современной сварочной дуги.
Взять под контроль
Как подрядчик трубопровода, вы должны уложиться в жесткие сроки проекта. Для этой работы требуется сварочный аппарат/генератор с технологией, которая поможет вам справиться с требованиями долгих рабочих дней и выполнить работу.
Требуется машина, которая обеспечивает большую адаптацию к конкретным условиям применения и предпочтениям сварщика. Измените свой подход к работе с помощью новой технологии, которая обеспечивает больший контроль над дугой и сварочной ванной, чем это было возможно ранее.
Благодаря Dynamic DIG от Miller результаты помогают сэкономить время и повысить производительность и эффективность конвейеров без ущерба для качества сварки, чтобы вы могли выполнять свою работу наилучшим образом.
Обеспечение более безопасных условий сварки при строительстве трубопроводов
Рэйчел Далтон, Xiris Automation
Действуя как жилы региона, трубопроводы транспортируют воду, газ, нефть и многое другое.Через сеть трубопроводов эти материалы распределяются по электростанциям, предприятиям и домам потребителей. Везде, где есть эти трубопроводы, требуется сварка.
Фото: Daniel Acker
Сварщикам трубопроводов требуются опыт и знания для выполнения требований работы. Им приходится иметь дело с потенциально опасными материалами, часто в суровых погодных условиях. Они также должны знать, как и когда использовать различные методы автоматизированной сварки.
Существуют серьезные потенциальные экономические и экологические последствия, если в процессе сварки будут допущены какие-либо ошибки, которые могут поставить под угрозу трубопроводную сеть. Это означает, что при строительстве трубопроводов особое внимание уделяется качеству и последовательности, и поэтому, как правило, трубопроводные компании используют автоматизированные процессы орбитальной сварки.
В процессе орбитальной сварки горелка перемещается по внешней стороне трубы с зажимами, приводимыми в действие гидравлическим давлением, удерживая два куска трубы на месте для соединения в полевых условиях.
Опасные условия
Строительство трубопровода часто может представлять опасные сценарии, как это было на примере одного из наших клиентов. Заказчик является подрядчиком по сварке, который развертывает автоматизированное сварочное оборудование и операторов на месте для выполнения соединения сегментов трубы.
Хотя используемое оборудование представляет собой автоматизированную систему орбитальной сварки, все же требуется присутствие оператора для наблюдения за процессом сварки и обеспечения оптимизации всех параметров процесса во время процесса сварки.
Перед внедрением нового комплекта сварочного оборудования наш клиент провел оценку рисков, связанных с использованием нового оборудования в полевых условиях. Они определили, что существует повышенный риск для их операторов, поскольку некоторые гидравлические шланги для используемых зажимов могут протечь в рабочей зоне, что приведет к распылению гидравлического масла в воздухе. Это было сочтено потенциальной пожарной опасностью для оператора.
Существует вероятность возгорания тумана гидравлической жидкости в процессе сварки открытой дугой, используемой при сварке труб.Оператор, которому необходимо было наблюдать и контролировать процесс сварки, находился в опасной близости от потенциальной опасности возгорания.
Сварочные камеры
Чтобы удалить оператора из опасной зоны, заказчик решил внедрить сварочную камеру Xiris, чтобы сварщик трубопровода мог удаленно наблюдать за процессом сварки.
Установка включала в себя две сварочные камеры на орбитальном сварочном оборудовании, одну перед сварочной горелкой и одну ведомую. Видеосигналы передавались в кабину оператора на расстоянии 66 футов (20 метров) от сварочного процесса, что позволяло операторам выполнять и удаленно контролировать сварку из более безопасной среды.
Связанные статьи
Надежная сварочная технология ремонта нефтегазопроводов
Надежная технология ремонта сваркой для нефтегазопроводов
Номер проекта
FWP-FEAA139
Последний отзыв датирован
Цель
Целью этого проекта является усовершенствование и оптимизация инновационной низкотемпературной сварочной проволоки/расходных материалов Окриджской национальной лаборатории (ORNL) для низкотемпературного фазового превращения для устранения водородной коррозии и улучшения свойств разрушения и усталости отремонтированной области сварного шва нефти/газа. стальные трубопроводы.
Исполнитель(и)
Окриджская национальная лаборатория (ORNL)
Фон
Сварочный ремонт является одной из широко применяемых технологий обеспечения целостности конструкции и продления срока службы нефтегазопроводов. По сравнению со сваркой при строительстве оригинального трубопровода ремонтная сварка на месте или в полевых условиях, как правило, намного сложнее во многих аспектах. Например, доступность и установка оборудования могут быть затруднены или затруднены из-за ограничений по пространству и местоположению.Предварительный нагрев и/или термообработка после сварки (PWHT), которые являются обычными и обязательными при сварке исходных конструкций, могут быть невозможны или скомпрометированы. Кроме того, возможно, придется использовать сварочные материалы с более низкой прочностью для преодоления водородного растрескивания (HIC) из-за невозможности предварительного нагрева или PWHT. HIC будет вызывать особую озабоченность в отношении старых трубопроводов, изготовленных из сталей с высоким углеродным эквивалентом, из-за технологий производства стали до 1970 года. HIC также представляет собой серьезную проблему для трубопроводов из высокопрочной стали (например, стали X80 или более высокой прочности), которые были установлены. за последние 20 лет или около того.По этим причинам сварка, в том числе ремонтная сварка трубопровода, может быть дорогостоящей, и, если она не будет выполнена должным образом, может поставить под угрозу запас прочности вариантов трубопровода, что приведет к катастрофическому отказу трубопровода, такому как инцидент 2010 года в Сан-Бруно, Калифорния, в результате которого было разрушено 38 домов, повредил 120 домов и убил 8 человек.
Группа по обработке и соединению материалов в ORNL имеет долгую историю разработки практических решений для соединения конструкционных материалов для широкого спектра отраслей промышленности, включая автомобилестроение, электростанции на ископаемом топливе, нефтегазовую, нефтехимическую и атомную энергетику. Темы исследований варьируются от фундаментальных научных проектов в области сварки до разработки сварочных технологий, предназначенных для решения конкретных отраслевых проблем.
Воздействие
Аналитика, которую предстоит разработать, позволит заблаговременно обнаруживать деградацию в действующих трубопроводах, чтобы поддерживать решения о том, на чем сосредоточить проверки, повышать ситуационную осведомленность об объеме проверок, которые необходимо выполнить, позволит отслеживать тенденции между проверками и информировать о сроках профилактического обслуживания.Исследования позволят снизить стоимость ремонта и повысить структурную целостность и надежность ремонтируемых конструкций.
Достижения (последние в списке первыми)
- Решена проблема низкой ударной вязкости сварочной проволоки первого витка. Две сварочные проволоки во втором раунде дали сварные швы с ударной вязкостью по Шарпи 259 Дж и 178 Дж соответственно, что намного выше, чем значение ударной вязкости по Шарпи с V-образным надрезом (показатель ударной вязкости материала в условиях ударной нагрузки) для стали высшего сорта ( X120) 108 Дж по спецификации API 5L.
- Продемонстрированы три различных низкотемпературных сварочных проволоки с фазовым превращением для успешной сварки трубопроводной стали X60 со сталью 100 без HIC. Все сварные швы не подвергались предварительной и послесварочной термообработке и соответствовали или превышали требования по прочности и другим требованиям отраслевых партнеров для этих сталей для трубопроводов.
- Завершены конкретные целевые показатели для исследований, основанные как на технологиях, так и на бизнес-соображениях.
Текущее состояние
Следующие шаги включают доработку химического состава сварочной проволоки для снижения прочности для лучшего соответствия трубопроводам X80-X100, выполнение дополнительной сварки и испытаний сталей X65 и других трубных сталей с бедным и обогащенным химическим составом, а также проведение углубленного исследования микроструктура области частичного плавления и микротвердость.
Начало проекта
Конец проекта
Современные технологии сварки ускорят строительство газопроводов
Сохранить в список для чтения
Опубликовано
Лидия Веллварт,
редактор
мировые трубопроводы,
Автоматизация, более быстрая сварка и меньший расход дополнительного материала – основные преимущества новой методики сварки, одобренной ГАЗ-СИСТЕМ.Компания впервые применила его при строительстве газопровода Страхочина-Подгурска-Воля.
Сварка по технологии CRC Evans осуществляется автоматически шестью сварочными головками, размещенными внутри свариваемой трубы, плюс четырьмя внешними головками. Автоматизм этого метода обеспечивает высокую повторяемость качества сварных швов. Дополнительным преимуществом является скорость работы. Один сварной шов на трубе DN 1000 выполняется примерно в три раза быстрее, чем при использовании старых методов, — сказал Анджей Федор, руководитель технического отдела филиала ГАЗ-СИСТЕМ в Тарнове.Кроме того, в технологии CRC Evans используется специальная фаска, которая в четыре раза снижает расход дополнительного материала, необходимого для сварки, по сравнению со стандартной фаской.
Апробация метода, т.е. его приемка в ГАЗ-СИСТЕМ, проходит в несколько этапов. Наиболее важным из них является выполнение сварных швов в точно заданных условиях и контроль их качества в лаборатории. Первый этап был завершен в мае 2018 года с участием представителей технического отдела ГАЗ-СИСТЕМ, Управления технического надзора, команды CRC Evans, группы надзора инвестора и подрядчиков строительных работ на Страхочина-Погурска-Воля. газопровод.Утверждение 135 метода технологии соединения труб с наружным диаметром 1016 мм и толщиной стенки 22,2 мм состоялось на голландском предприятии CRC Evans. Разрушающие и неразрушающие испытания сварных швов были проведены в июне в лаборатории Palab, аккредитованной Польским центром аккредитации и Управлением технического надзора. Испытания подтвердили правильность сварных швов, и подрядчик строительных работ рекомендовал использовать метод, разработанный CRC Evans, при строительстве газопровода Страхочина-Погурска-Воля.
Газопровод Страхочина-Погурска Воля диаметром DN 1000 и рабочим давлением 8,4 МПа будет расположен в Подкарпатском и Малопольском воеводствах. Его завершение улучшит техническое состояние и безопасность транспортировки газа в юго-западной части Польши, заявил вице-президент «ГАЗ-СИСТЕМ» Артур Завартко. Это также позволит транспортировать газ в Подкарпатье и Словакию по планируемому межсистемному соединению Польша-Словакия, а также в сторону Украины, т.е.е. в направлении, противоположном текущему. Газ также будет транспортироваться на запад напрямую из подземного хранилища газа в Страхоцине.
Прочтите статью онлайн по адресу: https://www.worldpipelines.com/project-news/16072018/state-of-the-art-welding-techniques-will-speed-up-the-construction-of-gas- трубопроводы/
Вам также может понравиться
Пакистан укрепит сеть газопроводов для удовлетворения растущего спроса на газ, говорится в отчете GlobalData.
Технологии сварки | ГКТС
Что такое технология сварки?
Программа «Технология сварки» посвящена сварочному обучению, технологиям и обучению студентов.
успех. Сварочные работы в основном связаны с соединением, наплавкой или ремонтом
конструкции или детали из металла или других свариваемых материалов.Навыки и знания
необходимо определить соответствующую технику сварки, требуемую для конкретного проекта
и успешно выполнять эту технику, полученные в ходе курсовой работы и практических занятий. опыт.
Для получения дополнительной информации посетите наш информационный лист программы.
Каков мой выбор карьеры?
Сварочные работы встречаются на производстве и в строительстве.Рабочие места сосредоточены в производство готовых металлических изделий, производство транспортного оборудования, машиностроение производство, производство архитектурных и конструкционных металлов. Сварщики-технологи можно найти соединительные балки при строительстве зданий, мостов и других сооружений и соединение труб в трубопроводах, электростанциях и нефтеперерабатывающих заводах.
Какие у меня есть степени, дипломы или сертификаты?
Диплом
Сертификаты
- Дугообразный резак
- Аппарат дуговой сварки
- Национальные стандарты навыков AWS, уровень 1
- Газовый сварочный аппарат для дуговой сварки металла
- Аппарат дуговой сварки вольфрамовым электродом
- Газосварочный аппарат
- Сварочный аппарат для трубопроводов
- Сварочный аппарат производственной линии
- Аппарат для дуговой сварки экранированного металла
- Прихваточный сварочный аппарат
- Помощник сварщика
Длина программы
Вы можете получить степень младшего специалиста по прикладным наукам за два года, если будете работать полный рабочий день. статус.
Эта информация не должна рассматриваться как замена каталогу KCTCS. Вы всегда должны выбирать классы в сотрудничестве с вашим преподавателем, чтобы обеспечить что вы соответствуете всем требованиям степени.
Подводные трубопроводы и технология сварки, супердуплексная нержавеющая сталь, Sunny Steel Enterprise Ltd.
Морской нефтепровод (газопровод)
Подводный нефтепровод (газопровод) является основным компонентом морской системы разработки и добычи нефти (газа).Он непрерывно поставляет большое количество нефти (газа) самым быстрым, безопасным, экономичным и надежным видом транспорта. Связанные подводным трубопроводом морские месторождения нефти (газа) могут быть системами сбора и хранения промысловой продукции, также связанными с морскими месторождениями нефти (газа) и наземными нефтепромысловыми системами. В последние десятилетия, с непрерывным освоением морских нефтяных (газовых) месторождений, подводный нефтепровод (газопровод) фактически стал эффективным транспортным средством, широко используемым в морской нефтяной промышленности.
Нефтяной (газовый) трубопровод морского дна океана в Китае в основном распространен в Бохайском заливе, заливе Ляодун, Желтом море, северной части Восточно-Китайского моря, устье Жемчужной реки в Южно-Китайском море и море Ингэ и других местах. Согласно статистическим данным на сегодняшний день, подводные трубопроводы были построены более чем на 2000 км, 11 из которых Бохайское море нефти (газа) подводного трубопровода Тянь Цзяньчэн накопили более 200 км в Южно-Китайском море 15 нефтяных (газовых) месторождений, прокладывающих подводный трубопровод накоплено более 1000 км определенного морского газового месторождения от острова Хайнань до Гонконга 711 пленки (28 дюймов) в диаметре подводного газопровода длиной около 800 км, является самым длинным подводным трубопроводом. Кроме того, газовое месторождение в Восточно-Китайском море недалеко от Шанхая, прокладка нефтегазового подводного трубопровода общей протяженностью 800 км.
Характеристики и классификация подводного трубопровода
Преимуществом подводного трубопровода является непрерывная передача, практически свободная от влияния условий окружающей среды, не форсирующая добычу на месторождении или прекращенная из-за нехватки мощностей морских нефтехранилищ, или несвоевременный подбор челночных танкеров.Высокая эффективность, поэтому емкость нефтяного танкера. Продолжительность прокладки другого подводного трубопровода невелика, а ввод в эксплуатацию осуществляется быстро, легко в управлении и с низкими эксплуатационными расходами. Недостатком является то, что в трубопроводе на морском дне большинство из них необходимо закапывать на определенную глубину в грунт морского дна, трудности с осмотром и техническим обслуживанием, более высокая стоимость. Некоторые в приливно-отливном диапазоне или при срыве волны с трубы (стояка), подверженные влиянию ветра и волнения, прилива, льда и т. д., иногда могут быть повреждены поплавки в море и кораблекрушение или поломка.В наших водах было много инцидентов рыболовных судов для борьбы с разрушением сетей подводного трубопровода аварии.
Среда передачи подводного трубопровода может быть разделена на подводные трубопроводы, подводный газопровод, подводные нефтегазовые смешанные транспортные трубопроводы и подводный акведук со структурной точки зрения можно разделить на трубу и одинарную трубу с двойной изоляцией.
Китайский подводный трубопровод с разработкой трубы
Выбор материала подводного трубопровода должен соответствовать требованиям проектирования, а также требованиям к прокладке и строительству морского трубопровода.С промышленным развитием подводных трубопроводов надежность труб становится все более требовательной, но методы производства подводных трубопроводов не предъявляют особых требований, таких как бесшовные стальные трубы, различные прямошовные стальные трубы с дуговой сваркой и т. д. можно использовать. Чтобы соответствовать требованиям конструкции и монтажа под помещение, выбрать наиболее экономичную трубу.
С расширением морской разработки нефти в Китае, строительство подводных трубопроводов после многих лет непрерывной разведки и улучшения с точки зрения ключевых процессов строительной группы, сварки, испытаний и других более научно обоснованных.Тенденции строительства подводных трубопроводов, высокая эффективность и высокое качество строительства, технологические процессы становятся все более требовательными, особенно от имени уровня технологии сварки строительства подводных трубопроводов, повышения класса прочности стали подводных трубопроводов, производительности технологии сварки трубопроводов и высоких эффективность производства, высокая рентабельность процесса автоматической сварки является приоритетом, чтобы адаптироваться к темпам развития строительства подводных трубопроводов.
.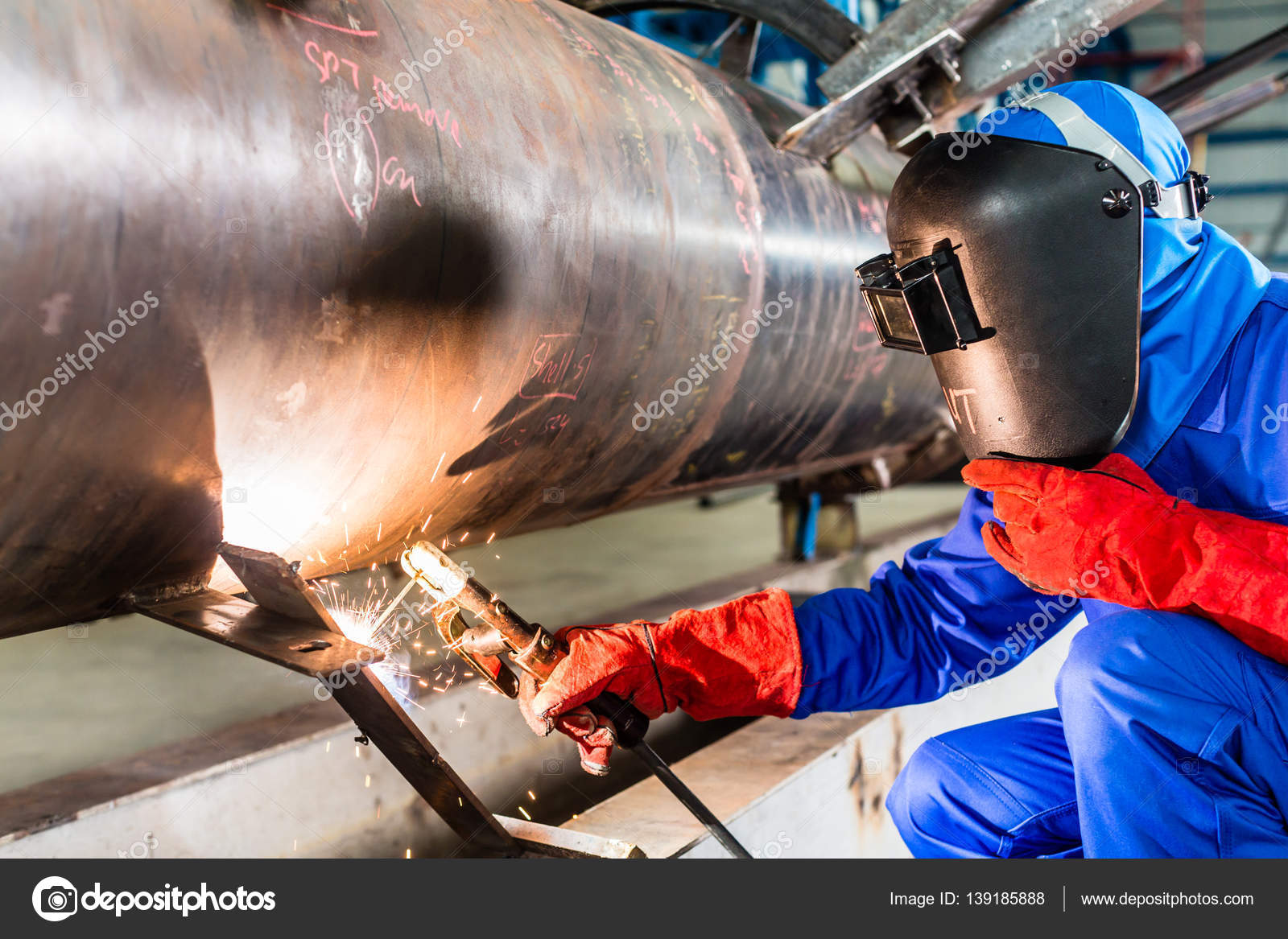