Ручная дуговая сварка стыковых швов – Осварке.Нет
Ручную дуговую сварку стыковых швов без скоса кромок выполняют односторонним швом. Электрод выбирают равным толщине металла, если его толщина не превышает 4 мм. Тонколистовой металл толщиной до 1-2 мм сваривают на медной или стальной подкладке, чтобы избежать прожогов.
Листы без скоса кромок толщиной 4-8 мм сваривают двусторонним швом.
Однослойные и однопроходные швы с V-образным скосом кромок для деталей толщиной 4-8 мм выполняют с колебательными движениями. Дугу зажигают с края кромки и постепенно перемещают в низ к корню шва. На кромках движение замедляют, чтобы лучше проварить их. Во время перехода с одной кромки на другую движение ускоряют чтобы не прожечь металл (для толщины 4 мм). Сварку деталей толщиной 8 мм можно выполнять без ускорения в корне шва.
Сварка толстостенных конструкций
Для сварки толстостенных конструкций более 8 мм используют однослойную, многослойную и многопроходную сварку с V-образным, X-образным, U-образным скосом кромок (рис.
Большой угол скоса кромок (80-90°) более удобный для сварщика, уменьшает вероятность непровара, но увеличивается объем наплавленного металла, деформации и падает производительность. Нормальным считается угол 60°. Его можно увеличить до 65° для сварки тонких листов и уменьшают до 55° для листов более 15 мм.
Зазор между кромками должен быть 1,5-4,0 мм в зависимости от толщины листов, режимов сварки и конструкции изделия
Выбор многопроходного или многослойного шва зависит от типа соединения, толщины металла и его химического состава. Многослойный шов выполняется быстрее многопроходного. После наложения каждого следующего необходимо очистить от шлака предыдущий. Многопроходный шов следует выполнять тонкими валиками без колебательных движений.
Каждый слой многослойного шва в разрезе больше за предыдущий, поэтому многослойная сварка более производительная. Многослойный шов чаще используют для сварки стыковых соединений. Преимущества многослойного выполнения шва над многопроходным:
- объем сварной ванны уменьшается, а значит скорость охлаждения увеличивается и формируются более мелкие зерна металла;
- каждый слой выполняет функцию термической обработки для предыдущего и околошовная зона имеет большую пластичность с мелкозернистой структурой.
Каждый слой должен быть толщиной не более 4-5 мм и не меньше 2 мм чтобы металл прогрелся и отжогся. Сварка металла толщиной 12 мм с X-образным скосом кромок требует наложения 4-6 слоев, а металл толщиной 40 мм — 10-16 слоев. Соединения с X-образной формой имеет следующие преимущества над V-образным:
- повышения продуктивности за счет уменьшения количества наплавленного металла;
- меньше деформаций;
- непровар корня шва находится по середине соединения двух деталей, поэтому менее опасен.
Стыковые швы толщиной более 20 мм следует сваривать с U-образным скосом кромок. Это дает возможность использовать электроды большого диаметра, обеспечивает надежный провар и равномерную усадку металла шва.
Швы рекомендуется выполнять по очереди с разных сторон чтобы избежать коробления деталей.
Сварка декоративного и подварного шва
Сварка ответственных конструкций должна выполняться с заваркой корня шва с обратной стороны. Для этого изделие переворачивают и зубылом, резцом или фрезой делают канавку шириной 8-10 мм и глубиной 3-4 мм. Канавку заваривают электродом диаметром 3 мм в один проход с незначительным усилением на силе тока 100 A.
Последними проходами делается усиление на 2-3 мм от поверхности металла. Последний (декоративный) шов выполняется электродом 5-6 мм. Толщина слоя должна быть 1-2 мм, сила тока 200-300 A.
Сварка стыковых соединений на подкладках
Прочность сварного соединения обеспечивает хороший провар кромок, корня шва, отсутствие дефектов несплошности, плавный переход шва к основному металлу.
Наибольшее внимание следует уделять корню шва. Даже маленькая несплошность в этой части шва может привести к разрушению. Для избежания разрушения шва используют двусторонние швы с промежуточным струганием для удаления корневой части первого шва или сварку на подкладках.
Сегодня существует большое количество подкладок изготовленных из разных материалов:
- стальные;
- медные;
- графитовые;
- флюсо-керамические;
- на латексной основе;
- стеклянные.
Подкладки размещают со стороны корня шва симметрично кромкам.
Регулирование и устранение перемещений при сварке толстостенных конструкций
Рекомендуем приобрести:
Установки для автоматической сварки продольных швов обечаек — в наличии на складе!
Высокая производительность, удобство, простота в управлении и надежность в эксплуатации.
Сварочные экраны и защитные шторки — в наличии на складе!
Защита от излучения при сварке и резке. Большой выбор.
Доставка по всей России!
При электрошлаковой сварке могут возникать сварочные деформации нескольких видов. Электрошлаковой сваркой соединяют элементы большого сечения, борьба с деформациями в этом случае представляет непростую задачу.
Перемещение кромок 2vmax от нагрева их сварочным источником тепла предотвратить невозможно. Увеличивая скорость сварки и уменьшая мощность q, можно лишь несколько уменьшить поперечное сближение кромок в зоне сварки. Не удается также сколько-нибудь значительно повлиять на величину поступательного перемещения (сближения) деталей вследствие поперечного сокращения заваренной части соединения.
Угловые перемещения от температурных и структурных деформаций удается регулировать в широких пределах. Существует несколько приемов их уменьшения, но во всех случаях положительный результат достигается созданием изгибающего момента в плоскости свариваемых деталей. Наиболее естественный способ создания момента — использование веса деталей, расположенных на опорах (рис. 136, а) М = G1l1.
В производстве широкое применение нашел способ, основанный на использовании жесткости свариваемой конструкции. Это достигается скреплением деталей скобами, установкой «сухарей» или использованием притупления кромок (см. рис. 136). Скобы препятствуют закрыванию и открыванию зазора. Недостаток скоб в их малой прочности по сварному соединению, а также в том, что их можно располагать только снаружи зазора f.
«Сухари» могут препятствовать только закрыванию зазора. Усилия, развиваемые ими, достигают десятков и сотен тонн. Скобы и «сухари» особенно эффективны, когда сваривают протяженные в направлении шва детали. Например, два «сухаря» размером 100×100 мм могут развивать усилие до 6000 кн., что, очевидно, намного превосходит возможности весовой нагрузки. При сварке плавящимися мундштуками роль «сухарей» могут с успехом выполнять изоляционные шайбы, расположенные между мундштуками и изделием.
Сборку деталей по притуплению нередко применяют при сварке двумя магнитошагающими автоматами в общую ванну (рис. 136, б). Роль притупления может выполнять закладная деталь в виде полоски, расположенной по всей длине стыка (рис. 136, в). Особенно эффективным может оказаться притупление при сварке кольцевых швов (рис. 136, г).
Распространенным в производстве приемом компенсации деформаций является сборка деталей с переменным зазором. Такойспособ удобен для компенсации закрывания зазора, так как обычно нет никаких препятствий для сборки с расширяющимся кверху зазором.
При электрошлаковой сварке стыковых соединений могут возникать значительные временные деформации в плоскости свариваемых деталей, которые следует принимать во внимание.
а) При сварке деталей, протяженных в направлении, перпендикулярном шву (рис. 137, а), угловые деформации в плоскости могут привести к заметному искажению формы и появлению прогиба.
б) При сварке деталей, поперечный размер которых должен быть выдержан с определенным допуском (рис. 137, б), необходимо учитывать величину поперечной усадки после сварки.
в) При выполнении соединения встык в жестком контуре в процессе ремонтной сварки (рис. 137, в) необходимо иметь в виду, что после остывания вследствие возникшей поперечной усадки появятся значительные остаточные напряжения. Эти напряжения могут вызвать разрушение конструкции. В таких случаях рекомендуется перед сваркой подогревать противоположный участок (зона А на рис. 137, в), а сам шов сваривать на режимах, обеспечивающих минимальную поперечную усадку.
При расчленении конструкции, например литой, на две части (рис. 137, г) во избежание значительных напряжений рекомендуется одновременно сваривать оба шва.
г) При электрошлаковой сварке протяженных швов сварочные деформации могут привести к такому изменению зазора, что это вызовет нарушение выбранного режима сварки, короткое замыкание вследствие уменьшения зазора или вытекание металла ванны из-за чрезмерного открывания зазора.
д) При определении фактической скорости электрошлаковой сварки и расхода электродной проволоки необходимо учитывать, что в момент сварки зазор уменьшается на величину 2vmax, даже если никаких перемещений деталей в процессе сварки и не происходит.
Угловые деформации особенно интенсивно происходят в начальный период сварки. Но именно в этот период, когда сечение заваренного шва невелико, их наиболее легко устранить.
Нередко возникает необходимость определить длину шва, начиная с которой преодолевается сопротивление разного рода закреплений и появляются заметные деформации. Эта задача весьма сложная, так как заваренная часть соединения представляет собой пластину с переменными модулями упругости и пределом текучести.
Если ожидаемые угловые деформации весьма значительны, то в заваренном соединении будут протекать пластические деформации. Это, разумеется, будет справедливо при условии, что противодействие превосходит внутренний момент, возникающий во время пластической деформации. Деформации будут отсутствовать по крайней мере до тех пор, пока внутренний момент, вычисленный с учетом пластического сопротивления сечения, не превзойдет момент от внешнего противодействия. Максимальный внутренний момент, который может возникнуть в сечении при образовании в нем пластического шарнира, равен
где h — высота заваренного шва;
ho — расстояние от ванны до изотермы 1300° С;
σh — предел текучести металла при температуре, которая имеется на расстоянии h от ванны, т. е. предел текучести металла в нижней части шва.
Коэффициент 2/3 при σh в формуле (243) означает, что принимается некоторый средний предел текучести всего сечения с учетом того, что в верхней части шва температура больше, а предел текучести меньше, чем в нижней части шва. Формулой (243) можно пользоваться, если температура в начале шва не ниже 250° С.
Распределение усадочных поперечных напряжений в металле шва при сварке
Распределение усадочных поперечных напряжений в металле шва по его сечению неравномерно (рис. 21). В верхней части шва, где объем наплавляемого металла наибольший, образуются наибольшие растягивающие поперечные напряжения, которые уменьшаются и переходят в сжимающие в середине сечения шва.
Усадочные поперечные напряжения так же, как и продольные, суммируются с тепловыми напряжениями. Наряду с плоскостными (продольными и поперечными) напряжениями при сварке толстостенных элементов образуются дополнительные остаточные напряжения, направленные по толщине свариваемых элементов.
Совокупность этих напряжений с плоскостными создает в металле шва и в околошовной зоне объемно-напряженное состояние, что иногда приводит к образованию трещин и уменьшению срока эксплуатации изделия.
Опыт эксплуатации сварных конструкций из низкоуглеродистых и низколегированных сталей, а также специальные исследования показали, что остаточные сварочные напряжения оказывают сильное влияние на работоспособность сварных соединений лишь в том случае, когда сварные швы имеют дефекты — трещины, непровары, подрезы, поры и др.
В этом случае напряжения от внешних нагрузок суммируются в сварных соединениях с собственными сварочными напряжениями и, концентрируясь в местах дефектов, могут вызвать разрушение конструкции.
Сварочные напряжения могут быть также опасными, если сварные изделия изготовлены из закаливающихся сталей и эксплуатируются в нетермообработанном состоянии (без отпуска).
Собственные напряжения и хрупкие структуры металла в околошовной зоне и шве могут явиться причиной разрушения конструкции, тем более если она при эксплуатации испытывает ударные внешние нагрузки.
Рис. 21. Распределение по высоте шва поперечных остаточных напряжений, вызванных его усадкой при затвердевании
Если конструкция изготовлена из пластичных металлов и сварные швы не имеют дефектов, то сварочные напряжения не оказывают заметного влияния на ее работоспособность.
Поэтому при сварке изделий из низкоуглеродистых и низколегированных (незакаливающихся) сталей стремятся прежде всего предотвратить их коробление, так как последующая правка конструкций увеличивает их стоимость и нередко ухудшает свойства сварных соединений.
На рис. 22 показаны деформации некоторых листовых конструкций, сваренных в незакрепленном состоянии. Стыковые и угловые соединения под действием поперечных напряжений деформируются в сторону большего сечения шва, т. е. в направлении максимальных напряжений.
Наряду с этим сварные элементы деформируются в направлении действия продольных тепловых и усадочных напряжений, образующихся в шве.
Рис. 22. Деформация (коробление) различных соединений, свариваемых в свободном состоянии: а — стыкового с односторонним швом, б — углового с наружным швом, в — таврового с одной полкой, г — таврового с двумя полками (двутавра).
Величина короблений свариваемых элементов в значительной степени зависит от концентрации нагрева при сварке и скорости теплоотвода.
Чем больше концентрация нагрева и лучше теплоотвод, тем меньше объемы металла нагреваются до пластичного состояния и претерпевают остаточную пластичную деформацию сжатия и, следовательно, тем меньше будет коробиться свариваемое изделие.
Так, например, при газовой сварке тонколистовой металл коробится значительно больше, чем при ручной дуговой сварке. При сварке в углекислом газе с применением тонкой электродной проволоки величина короблений изделий наименьшая.
Сварочный флюс OP 76
Флюорид-основной типСтандарт:
OP 76 – агломерированный основной специальный сварочный флюс флюорид-основного типа для сварки нержавеющих аустенитных, жаростойких и жаропрочных сталей в комбинации со сварочной проволокой по DIN EN 12072. OP 76 применяется для сварки дуплекс-сталей, полностью аустенитных сталей и никелевых сплавов. При сварке флюсом ОР 76 в наплавленный металл отсутствует перенос углерода, по этому настоящий флюс можно применять для сварки низко углеродистых сталей. Металлургическое поведение флюса ОР 76 относительно кремния и марганца является нейтральным, что означает, что в процессе сварки эти элементы не привносятся в наплавленный металл, но и не выгорают. Выгорание марганца наблюдалось только в случае использования для сварки высоко марганцовистых проволок. Высокая устойчивость к трещинообразованию при сварке аустенитных сталей и никелевых сплавов позволяет применять этот флюс для сварки толстостенных конструкций. При сварке ОР 76 в металл сварного шва привносится минимальное количество диффузионного водорода. Возможно использовать настоящий флюс так же для сварки тандемом или несколькими проволоками. Поверхность наплавленного металла гладкая без подрезов при переходе к основному металлу. OP 76 сваривается на постоянном токе (обратная полярность) до 800 А. Влажный флюс прокаливать при 300-350 0С.
Фракция по DIN 760: 2-20.
Химический состав наплавленного металла, % (типичное содержание):
Наименование проволоки |
C |
Cr |
Ni |
Mo |
Nb |
N |
Cu |
OE-19 9 nC |
< 0,04 |
> 18 |
> 9 |
— |
— |
— |
— |
OE-19 9 Nb |
< 0,07 |
> 18 |
> 9 |
— |
> 8 x C |
— |
— |
OE-19 12 3 nC |
< 0,04 |
> 18 |
> 10 |
> 2,5 |
— |
— |
— |
OE 19 12 3 Nb |
< 0,07 |
>18 |
>10 |
>2,5 |
>8xC |
— | |
OE 20 16 nC |
<0,04 |
20 |
16 |
3,0 |
— |
0,15 |
— |
OE 20 25 Cu |
< 0,03 |
20 |
25 |
4.![]() |
— |
— |
1.5 |
OE 23 3 nC |
< 0.04 |
23 |
9 |
3.0 |
— |
0.15 |
— |
OE 22 12 |
<0.15 |
22 |
12 |
— |
— |
— |
— |
Nifil 600 |
<0,03 |
20 |
Rest |
— |
2,5 |
— |
— |
Nifil 650 |
<0.![]() |
21 |
>60 |
9.0 |
3.5 |
— |
— |
Основность по Бонишевскому: ~ 2,7
Одобрения: TÜV, UDT, DB
Упаковка: полиэтиленовые мешки 25 кг
Механические свойства сварного шва (типичные значения):
Наименование проволоки |
Предел прочности, Н/мм2 |
Предел текучести 0,2 %, Н/мм2 |
Удлинение, % |
Ударная вязкость (KCV), Дж |
+ 200С | ||||
OE-19 9 nC |
> 510 |
> 320 |
> 30 |
> 75 |
OE-19 9 Nb |
> 550 |
> 350 |
> 25 |
> 65 |
OE-19 12 3 nC |
> 510 |
> 320 |
> 25 |
> 75 |
OE 19 12 3 Nb |
>550 |
>350 |
>25 |
>65 |
OE 20 16 nC |
>510 |
>320 |
>25 |
>120 |
OE 20 25 Cu |
>510 |
>320 |
>25 |
>100 |
OE-23 3 nC |
> 550 |
> 450 |
> 20 |
> 100 |
OE-22 12 |
> 550 |
> 350 |
> 25 |
> 75 |
Nifil 600 |
>600 |
>380 |
>30 |
>100 |
Nifil 650 |
>680 |
>420 |
>30 |
>75 |
Материал:
№ материала |
EN-обозначение |
сварочная проволока |
Сварка с двух сторон в один проход |
1.![]() |
X2CrNi19-11 |
ОЕ 19 9 nC |
1.4316 |
1.4301 |
(X5CrNi18 10) |
ОЕ 19 9 nC |
1.4316 |
1.4541 |
X6CrNiTi18-10 |
OE 19 9 Nb |
1.4551 |
1.4543 |
(X5 CrNiNb 18 9) |
OE 19 9 Nb |
1.4551 |
1.4550 |
X6CrNiNb18-10 |
OE 19 9 Nb |
1.![]() |
1.4878 |
(X 12 CrNiTi 18 9) |
OE 19 9 Nb |
1.4551 |
1.4404 |
X2CrNiMo17-12-2 |
OE 19 12 3 nC |
1.4430 |
1.4435 |
X2CrNiMo18-14-3 |
OE 19 12 3 nC |
1.4430 |
1.4401 |
X4CrNiMo17-12-2 |
OE 19 12 3 nC |
1.4430 |
1.![]() |
X6CrNiMoTi17-12-2 |
OE 19 12 3 Nb |
1.4576 |
1.4573 |
(X 10 CrNiMoTi 18 12) |
OE 19 12 3 Nb |
1.4576 |
1.4580 |
(X 6 CrNiMoNb 17 12 2) |
OE 19 12 3 Nb |
1.4576 |
1.4583 |
(X 10 CrNiMoNb 18 12) |
OE 19 12 3 Nb |
1.4576 |
1.4462 |
X2CrNiMoN22-5-3 |
OE 23 3 nC |
1.![]() |
1.4828 |
X15CrNiSi20-12 |
OE 22 12 |
1.4829 |
1.4878 |
X10CrNiTi18-10, X12CrNiTi18-9 |
OE 22 12 |
1.4829 |
1.4306 |
X2CrNi19-11 |
OE 20 16 nC |
1.4455 |
1.4301 |
(X 5 CrNi18 10) |
OE 20 16 nC |
1.4455 |
1.![]() |
X6CrNiTi18-10 |
OE 20 16 nC |
1.4455 |
1.4543 |
(X 5 CrNiNb 18 9) |
OE 20 16 nC |
1.4455 |
1.4550 |
X6CrNiNb18-10 |
OE 20 16 nC |
1.4455 |
1.4878 |
(X 12 CrNiTi 18 9) |
OE 20 16 nC |
1.4455 |
1.4404 |
X2CrNiMo 17-12-2 |
OE 20 16 nC |
1.![]() |
1.4435 |
X2CrNiMo18-14-3 |
OE 20 16 nC |
1.4455 |
1.4401 |
X4CrNiMo17-12-2 |
OE 20 16 nC |
1.4455 |
1.4571 |
X6CrNiMoTi17-12-2 |
OE 20 16 nC |
1.4455 |
1.4571 |
(X 10 CrNiMoTi 18 12) |
OE 20 16 nC |
1.4455 |
Тип тока/ Полярность/Позиции для сварки
Вертикальный шов | «снизу-вверх» или «сверху-вниз»? | Euro Welder
Один из вопросов, который так часто можно услышать, в особенности от молодых сварщиков. Так как же все таки правильно? Развеем все сомнения и поставим точку в этом вопросе.
Вертикальный шов, на ряду с потолочным, один из самых сложных и незаменимых в сварке. Им, как правило, сваривают стыки, которые невозможно или тяжело развернуть в более удобное горизонтальное или нижнее положение. Итак, как же всё таки сваривать?
Вертикальный шов «снизу-вверх» требует определённых навыков и может быть выполнен всеми видами сварки (РДС, РАДС, полуавтомат) на всех видах соединений (тавровом, нахлёсточном, стыковом). Такой вертикал всегда сваривается на максимально уместном малом токе, для того, чтобы расплавленный металл не вытекал из сварочной ванны — поэтому является низкопроизводительным (медленным). Метод «снизу-вверх» применяется на толщине свариваемого металла (или притуплении кромок) свыше 2-3 мм. Все ответственные конструкции с толщиной выше указанной свариваются только «снизу-вверх», потому что такой способ даёт более высокое и плотное проникновение.
На фото сварщик сваривает вертикальный шов полуавтоматом «снизу-вверх». Соединение «в стык» с зазором и разделкой с притуплением кромок. Металл 6 мм. Чётко прорисовывается необходимый обратный валик шва.
Вертикальный шов «сверху-вниз» не требует высокого мастерства и так же может быть выполнен всеми видами сварки на разных стыковых соединениях, однако сварочный ток может быть в значительной степени увеличен, за счёт чего увеличивается скорость сварки — это и является самым значимым преимуществом. Все виды металла с толщиной менее 2-3 мм(а в некоторых случаях неответственные стыки свыше 3-4-мм) рекомендуется сваривать сверху вниз. При таком способе можно быстро и качественно сформировать обратный валик на стыковом соединении с зазором на тонком металле без прожогов, а так же повысить производительность работы на неответственных конструкциях. Как уже стало понятно из вышеописанного, вертикальный шов «снизу-верх» нельзя применять на ответственных конструкциях с толстым металлом. Однако есть исключение: специальные электроды для сварки труб «сверху-вниз», которые специально разработаны для сварки толстостенных ответственных конструкций/труб этим методом для увеличения производительности сварки.
На фото парная работа сварщиков трубопровода. Сварка ведётся специальными электродами «сверху-вниз».
Спасибо, что дочитали до конца! Не забываем оставлять комментарии и лайки, а так же подписываться на канал в Дзен и наш канал EURO WELDER Вконтакте.
Численный расчет и экспериментальное измерение температур и остаточных напряжений при сварке в толстостенной конструкции таврового соединения
Takazawa H, Yanagida N. Влияние определяющего уравнения ползучести на смоделированное поведение снижения напряжения в трубе из легированной стали во время после сварки термическая обработка. Int J Press Vessels Pip. 2014; 117–118:42–8. https://doi.org/10.1016/j.ijpvp.2013.10.008.
КАС Статья Google Scholar
Перич М., Гарашич И., Нижетич С., Дедич-Яндрек Х. Численный анализ продольных остаточных напряжений и прогибов в сварной конструкции таврового соединения с использованием метода локального предварительного нагрева. Энергии. 2018;11(12):3487. https://doi.org/10.3390/en11123487.
Артикул Google Scholar
Coules HE, Colegrove P, Cozzolino LD, Wen SW. Прокатка под высоким давлением сварных швов низкоуглеродистой стали: часть 1 – влияние на механические свойства и микроструктуру.Sci Technol Weld Join. 2013;18(1):63–78. https://doi.org/10.1179/1362171812Y.0000000079.
КАС Статья Google Scholar
Coules HE, Colegrove P, Cozzolino LD, Wen SW, Kelleher JF. Прокатка сварных швов низкоуглеродистой стали под высоким давлением: часть 2 — геометрия ролика и остаточное напряжение. Sci Technol Weld Join. 2013;18(1):84–90. https://doi.org/10.1179/1362171812Y.0000000080.
КАС Статья Google Scholar
Дэн Д., Лян В., Муракава Х. Определение сварочной деформации в угловом сварном соединении с помощью численного моделирования и сравнения с экспериментальными измерениями. J Mater Process Technol. 2007; 183: 219–25. https://doi.org/10.1016/j.jmatprotec.2006.10.013.
КАС Статья Google Scholar
Гэннон Л., Лю Ю., Пегг М., Смит М. Влияние последовательности сварки на остаточное напряжение и деформацию в пластинах с ребрами жесткости из плоских стержней.Влияние остаточных напряжений и деформаций, вызванных сваркой, на предел прочности корабельной балки. Мар Структура. 2010;23(3):375–404. https://doi.org/10.1016/j.marstruc.2010.05.002.
Артикул Google Scholar
Кейвани Р. , Джахази М., Фам Т., Ходабанде А.Р., Афшар М.Р. Прогнозирование остаточных напряжений и деформации при многопоследовательной сварке крупногабаритных конструкций с использованием МКЭ. Int J Adv Manuf Technol. 2014;73(1–4):409–19. https://дои.орг/10.1007/s00170-014-5833-4.
Артикул Google Scholar
Li Y, Wang K, Jin Y, Xu M, Lu H. Прогноз деформации сварки в усиленной конструкции путем введения термомеханического элемента интерфейса. J Mater Process Technol. 2015; 216:440–6. https://doi.org/10.1016/j.jmatprotec.2014.10.012.
Артикул Google Scholar
Ронг И, Чжан Г, Хуан Ю.Исследование сварочной деформации и остаточного напряжения с учетом нелинейных кривых предела текучести и уравнений с несколькими ограничениями. J Mater Eng Perform. 2016;25(10):4484–94. https://doi.org/10.1007/s11665-016-2259-1.
КАС Статья Google Scholar

Перич М., Тонкович З., Родич А., Сурьяк М., Гарашич И., Борас И., Швайч С. Численный анализ и экспериментальное исследование сварочных остаточных напряжений и деформаций в тавровом угловом шве.Матер Дес. 2014;53:1052–63. https://doi.org/10.1016/j.matdes.2013.08.011.
КАС Статья Google Scholar
Ван С., Ким Ю.Р., Ким Дж.В. Сравнение моделей КЭ для прогнозирования сварочной деформации в процессе дуговой сварки Т-образного соединения в среде защитного газа. Int J Adv Manuf Technol. 2014;18(8):1637–931. https://doi.org/10.1007/s12541-014-0513-8.
Артикул Google Scholar
Tian L, Luo Y. Сравнительное исследование моделей прогнозирования BPN и SVM для собственных деформаций тавровых сварных соединений. Mech Adv Mater Struct. 2019. https://doi.org/10.1080/15376494.2019.1567881 (в печати) .
Артикул Google Scholar
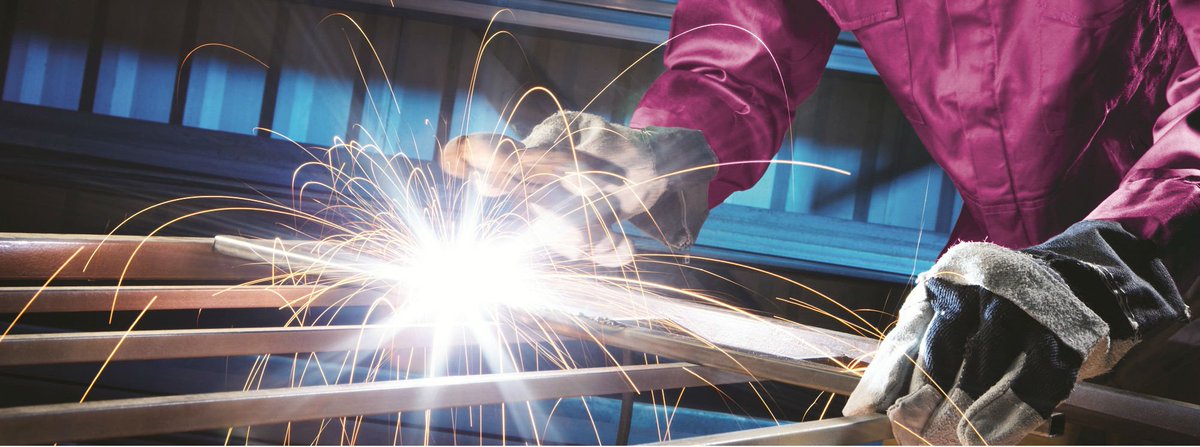
Тянь Л., Луо Ю. Исследование прогнозирования внутренней деформации в угловом сварном соединении с использованием метода опорных векторов и алгоритма генетической оптимизации. Дж Интелл Мануф. 2019.https://doi.org/10.1007/s10845-019-01469-w (в печати) .
Артикул Google Scholar
Лостадо Р., Фернандес Мартинес Р., Мак Дональд Б.Дж., Вильянуэва П.М. Сочетание методов мягких вычислений и метода конечных элементов для проектирования и оптимизации сложных сварных изделий. Integr Comput-Aid E. 2015;22(2):153–70. https://doi.org/10.3233/ICA-150484.
Артикул Google Scholar
Бхатти А.А., Барсум З., Муракава Х., Барсум И. Влияние термомеханических свойств материалов различных марок стали на сварочные остаточные напряжения и угловую деформацию. Матер Дес. 2015;65:878–89. https://doi.org/10.1016/j.matdes.2014.10.019.
КАС Статья Google Scholar
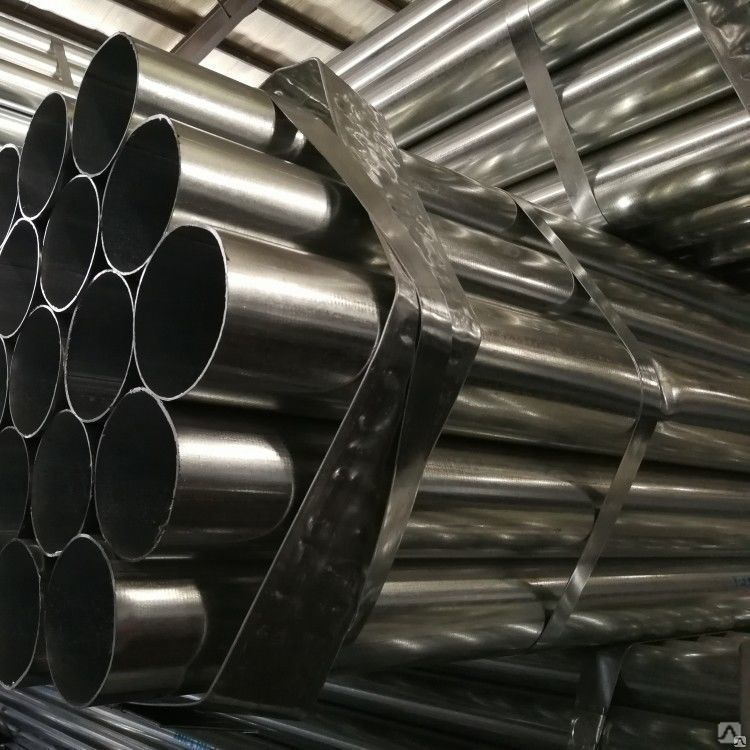
Перич М., Тонкович З., Гарашич И., Вухерер Т. Инженерный подход к моделированию угловой сварки таврового соединения с использованием упрощенных свойств материала.океан инж. 2016; 128:13–21. https://doi.org/10.1016/j.oceaneng.2016.10.006.
Артикул Google Scholar
Баба Х., Эра Т., Уэяма Т., Танака М. Однопроходное соединение с полным проплавлением толстолистовой стали с использованием сильноточного процесса GMA. Мир сварки. 2017;61(5):963–9. https://doi.org/10.1007/s40194-017-0464-7.
КАС Статья Google Scholar
Перич М., Гарашич И., Тонкович З., Вухерер Т., Нижетич С., Дедич-Яндрек Х.Численное прогнозирование и экспериментальная проверка распределения температуры и остаточных напряжений в толстых листах, сваренных подземной дугой. Int J Energy Res. 2019;43(8):3590–600. https://doi.org/10.1002/er.4506.
Артикул Google Scholar

Пилипенко А.В. Компьютерное моделирование остаточных напряжений и деформации толстых листов при многоэлектродной сварке под флюсом. Их приемы смягчения. Докторская диссертация, Тронхейм, 2001 г.
Хуан Х., Цуцуми С., Ван Дж., Ли Л., Муракава Х. Высокопроизводительный расчет остаточного напряжения и деформации в сваренных лазером листах из нержавеющей стали 301L. конечный элем анальный дез. 2017; 135:1–10. https://doi.org/10.1016/j.finel.2017.07.004.
Артикул Google Scholar
Lin J, Ma N, Lei Y, Murakawa H. Измерение остаточного напряжения в соединениях внахлест дуговой сваркой методом cosα рентгеновской дифракции. J Mater Process Technol.2017; 243:387–94. https://doi.org/10.1016/j.jmatprotec.2016.12.021.
КАС Статья Google Scholar
Перич М., Тонкович З., Каршай И., Стаменкович Д. Упрощенный инженерный метод моделирования сварки таврового соединения. Терм. наук. 2018;22(3):S867–73. https://doi.org/10.2298/TSCI171108020P.
Артикул Google Scholar
Селеш К., Перич М., Тонкович З.Численное моделирование процесса сварки с использованием заданного температурного подхода. J Строительная сталь Res. 2018;145:49–57. https://doi.org/10.1016/j.jcsr.2018.02.012.
Артикул Google Scholar
Венкаткумар Д., Равиндран Д. Влияние граничных условий на остаточные напряжения и деформации в пластине из нержавеющей стали 316, сваренной встык. Высокотемпературный материал Proc. 2019; 38: 827–36. https://doi.org/10.1515/htmp-2019-0048.
КАС Статья Google Scholar
Насури Р., Нгуен К., Монтойя А., Матаморос А., Беннетт С., Ли Дж. Термические требования из-за горячего цинкования высоких опор освещения мачты. Часть I: разработка конечно-элементной модели. J Строительная сталь Res. 2019;162:105705. https://doi.org/10.1016/j.jcsr.2019.105705.
Артикул Google Scholar
Zhang J, Yu L, Liu Y, Ma Z, Li H, Liu C, Wu J, Ma J, Li Z. Анализ влияния последовательностей сварки вольфрамовым электродом в среде инертного газа на остаточное напряжение и деформацию CFETR вакуумный сосуд с использованием моделирования методом конечных элементов.Металлы-Базель. 2018;8(11):912. https://doi.org/10.3390/met8110912.
КАС Статья Google Scholar
Дэн Д. Прогноз остаточного напряжения и деформации при сварке углеродистой стали методом конечных элементов с учетом эффектов фазового превращения. Матер Дес. 2009;30(2):359–66. https://doi.org/10.1016/j.matdes.2008.04.052.
КАС Статья Google Scholar
Перич М., Селеш К., Тонкович З., Ловренич-Югович М. Численное моделирование сварочных деформаций в крупных конструкциях с упрощенным инженерным подходом. Открыть физ. 2019;17:719–30. https://doi.org/10.1515/phys-2019-0076.
Артикул Google Scholar
Перич М., Тонкович З., Максимович С.К., Стаменкович Д. Численный анализ остаточных напряжений в угловом шве таврового соединения с использованием метода субмоделирования. ФМЭ транс. 2019;47(1):183–9. https://doi.org/10.5937/fmet1
Артикул Google Scholar
Маренич Э., Скозрит И., Тонкович З. О расчете коэффициентов интенсивности напряжений и J-интегралов с использованием метода субмоделирования. J Press Vessel-Technol ASME. 2010;132(4):041203. https://doi.org/10.1115/1.4001267.
Артикул Google Scholar
Расчет теплопроводности при сварке толстостенных корпусов реакторов
Сентябрь 2017 г.
Сварка реакторов на нефтеперерабатывающих заводах сложна из-за различного фазообразования во время и после сварки.Каждая фаза уникальна, успех сварки заключается в контроле фазового состава при затвердевании шва.
С Чидамбарам
Numaligarh Refinery Limited
Резюме статьи
Разработано математическое моделирование с определяющими уравнениями движущегося источника тепла для получения прогноза температуры в зоне теплового влияния. Максимальная температура 737°С получена на расстоянии 0,5 см от зоны сплавления шва при благоприятной микроструктуре сварных швов реактора из аустенитной нержавеющей стали.
Введение
Теплообмен при сварке анализируется для стенки реактора как в окружном, так и в радиальном направлении. Теплопередача в окружном направлении анализируется с использованием трехмерной определяющей теплопроводности, а теплопередача в радиальном направлении анализируется с использованием уравнения Розенталя.
Математическое моделирование сварного соединения реактора
Математическое моделирование теплопередачи в окружном направлении или направлении сварки:
Тепловыделение сварного соединения анализируется для измерения пиковой температуры, скорости нагрева, скорости охлаждения и температурных профилей различных термических циклов, возникающих во время сварки.Переходное определяющее уравнение теплопроводности записывается как:
(1)
α — коэффициент температуропроводности в квадратных метрах в секунду, а T — температура
x, y, z – осевые координаты
Наплавка юбки на стык стенки реактора, сваренный дуговой сваркой в защитных газах электродом Э347, электрод движется в направлении X. Граничные условия, определяемые как скорость изменения перемещения во времени, определяются как скорость электрода Vx.Также предполагая, что электрод отдает все тепло от электрода к заготовке, скорость изменения температуры во времени равна нулю в любой пространственной точке во время сварки, ∂T/∂t=0. Используя постоянные стационарные условия и применяя граничные условия, уравнение теплопроводности первого порядка решается как:
(2)
Q – мощность тепла, подаваемого при сварке, в ваттах
r, продольное расстояние от зоны сварки, м
k, теплопроводность в ваттах на метр по Кельвину
x — расстояние, пройденное за n секунд 90 192
Теплопроводность SS347 k = 22.8 ватт на метр Кельвин
Температуропроводность SS347 составляет α = 4,2 кв.м в секунду
Скорость подачи тепла определяется как произведение максимальной подводимой теплоты на скорость движения. Максимальная погонная энергия дана 1,6 кДж/мм, скорость перемещения 165 мм/мин, мощность подвода тепла рассчитана как 4400 Вт. Скорость электрода Vx составляет 0,00233 м/с, а расстояние, пройденное от зоны сварки r = 0,5 см при скорости перемещения электрода в течение 10 секунд, x = «V»x X 10. При подстановке вышеприведенных данных в уравнение 2 получаем результат температуры как 34 °С при 0. Расстояние 5 см от зоны сплавления шва по окружности. В направлении X (по окружности) при движении электрода со скоростью 140 мм/мин пиковая температура не достигалась, и термоциклы не происходили. На расстоянии 1 см от зоны сплавления шва температура рассчитывается как 30°С и остается постоянной на различных расстояниях от зоны сплавления шва за пределами 1 см. Из вышеприведенных температурных расчетов было подтверждено, что металлургическая структура остается стабилизированной аустенитной без существенных изменений по окружности в любой точке расстояния вблизи сварки.
Математическое моделирование теплопередачи в радиальном направлении или перпендикулярно направлению сварки:
Тепловой поток в направлении, перпендикулярном или перпендикулярном сварке, анализируется для измерения пиковой температуры, скорости нагрева, скорости охлаждения и температурных профилей различных тепловых циклов во время сварки.
Распределение температуры полубесконечной пластины, полученное по уравнению Розенталя, которое выглядит следующим образом:
n, эффективность процесса сварки SMAW = 0.
E напряжение в вольтах, I ток в амперах, r — радиальное расстояние по нормали к направлению сварки,
T0 — комнатная температура в Кельвинах.
Набор расчетов температуры был выполнен относительно интересующего расстояния от зоны сплавления сварного шва, которая представлена на рисунке 2, где температура является функцией времени в соответствии с уравнением 3. Пиковая температура отмечена точкой на графике и на расстоянии 0,5 см от Пиковая температура зоны сплавления шва достигала 737°С, тогда как на расстоянии 1 см от зоны сплавления шва пиковая температура достигала 203°С.Пиковая температура уменьшается с увеличением расстояния от зоны сплавления шва, а также скорость нагрева и охлаждения уменьшается с увеличением расстояния от зоны сплавления шва. Время, необходимое для достижения пиковой температуры, увеличивается с увеличением расстояния от зоны сплавления. На расстоянии более 1 см пиковая температура ниже, и не происходит вредного воздействия на микроструктуру из-за сварки.
Результаты и обсуждения
Максимальная достигнутая пиковая температура составляет около 737°C от 0.5 см от зоны сплавления шва. Картина затвердевания во время сварки из зоны сплавления шва четко указывает на зародыши аустенитных зерен и выросшие с очень небольшим количеством зародышей ферритных фаз около 800°C. Содержание ферритных фаз снижается после температуры выше 400°C, а также присутствуют основные аустенитные фазы наряду с небольшим количеством ферритной фазы или ее отсутствием. Микроструктура зависит от состава основного материала, как показано на рис. 3. Максимально достигаемая пиковая температура составляет около 203°C на расстоянии 0,5 см от зоны сплавления. . Картина затвердевания во время сварки из зоны сплавления шва четко указывает на то, что аустенитное зерно нагревается примерно до 203°C и снова охлаждается, не влияя на микроструктуру, как показано на рисунке 3.Приведенные выше результаты были предсказаны не на основе ни микроструктуры, восприимчивой к остаточному водороду, ни явления высокотемпературного воздействия водорода.
Заключение
Из математических расчетов и из приведенного выше обсуждения ясно видно, что сварка приводит к зарождению дельта-феррита, из которого зерна аустенита растут по металлу шва, а дельта-феррит на границах зерен предотвращает растрескивание при затвердевании во время сварки реакторов. Зона термического влияния на расстоянии 0,5 см от границы сплавления подвергалась воздействию температуры 737 °C, тогда как 1 см подвергалась воздействию температуры 203 °C. Математически это показывает, что металл сварного шва, зона термического влияния и основной металл не были затронуты сваркой в условиях выше идеальных.
, толстостенная стальная труба большого диаметра
Соотношение диаметра трубы и толщины стенки менее 20 называется толстостенной стальной трубой , которая в основном используется в буровых трубах для нефтяной геологии, нефтехимических крекинговых трубах, котельных трубах, трубах и автомобильных подшипниках, тракторах, авиационных конструкциях с высокой прецизионные трубки.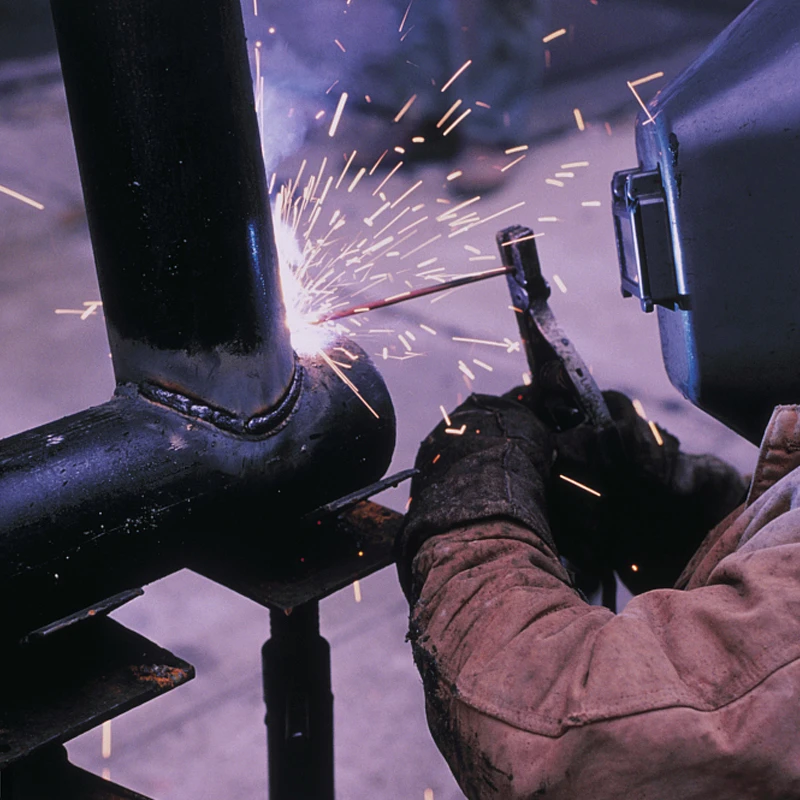
Толстостенная сталь в основном используется в гидротехнике, нефтехимической промышленности, химической промышленности, энергетике, сельскохозяйственном орошении, городском строительстве.Для перевозки жидкостей: водопровод, канализация. Для транспортировки газа: газ, пар, СУГ. Для конструкционных целей: в качестве трубы для свай для мостов; опоры, дороги, трубы и другие строительные конструкции.
При сварке толстостенной трубы сначала очистите сварочное масло, краску, воду, ржавчину и т. д., а затем, в зависимости от толщины стенки скашивания, откройте большое количество толстых, тонкие, чтобы открыть небольшое количество ( УШМ), то что есть на изделии Зазор обычно 1 или диаметр катанки — 1.5 раз, если не осторожно срезать открытые большие слова, они могут оставаться маленькими. Прихватка минимум в трех точках, в четырех точках лучше общая работа. Сварка при сварке должна быть пополам, лучшая начальная точка находится примерно на одном сантиметре ниже нижнего, поэтому через разъем. Если толщина стенки трубы, она должна быть многослойной, не менее двух слоев, первый слой сварки по кругу может сваривать готовый второй слой.
Ключом к качеству толстостенной стальной трубы является однородность толщины стенки, которая не находится под контролем, что напрямую повлияет на качество и полезность, толстостенная стальная труба большого диаметра обычно используется при различных обработках, толстостенных деталях обработки, даже стенка толстостенной стальной трубы напрямую влияет на качество постобработки деталей, толстостенная труба не контролируется, общее качество стали не является строгим. Выберите подходящее место и хранение толстостенного стального склада или склада, следует выбирать в чистой, гладкой дренажной зоне, вдали от вредных газов или пыли в шахтах. Наличие на земле необходимо очистить от всего мусора и сорняков, толстостенную стальную трубу содержать в чистоте. На складе нельзя складывать вместе кислоту, щелочь, соль, цемент и другую толстостенную сталь для коррозионно-активных материалов. Различные сорта толстостенных труб следует укладывать отдельно, чтобы не допустить путаницы и предотвратить контактную коррозию.Крупногабаритная сталь, рельсы, позорная сталь, бесшовные стальные трубы большого диаметра, поковки и т. д. могут открывать свалки.
Усовершенствованный конструктивно-технологический способ уменьшения деформации тонкостенных сварных конструкций
Разработанная численная модель позволяет рассчитать напряженное состояние и деформацию конструкции после сварки. В анализируемом случае было подтверждено, что напряжения, вызванные процессом сварки в основной конструкции, превышают величину пластифицирующих напряжений и приводят к неконтролируемым деформациям конструкции (σ Y < σ R ). Для анализируемого случая максимальное отклонение от плоскостности составляет Δh = −8,5 · 10 −3 (м), что является величиной, аналогичной наблюдаемой в эксперименте.
С целью повышения жесткости конструкции образца для анализируемого случая было внесено конструктивное и технологическое изменение, состоящее в замене существующего отверстия в оболочке фланцем соответствующей высоты. Такое решение повысит жесткость перпендикулярно базовой поверхности. Пластическое выдавливание фланца увеличивает жесткость и дополнительно создает благоприятные сжимающие напряжения, вызванные растяжением отверстия по окружности.Предполагается, что привносимые во фланец напряжения уменьшат сварочные напряжения и, следовательно, снизят деформацию сварного соединения до приемлемой величины.
Моделирование строительного процесса Повышение жесткости экструдированной системы фланцев
Чтобы определить требуемую высоту экструдированного фланца для создания желаемого напряженного состояния, сначала было определено отношение напряженного состояния к высоте фланца. Затем в результате решения обратной задачи определялась необходимая высота полки.Поперечный разрез спроектированного образцового инструмента для выдавливания фланцев высотой h 1 = 6 × 10 −3 (м) (название модели h6) и высотой h 2 = 10 −2 (м) (названная модель h20), показана на .
Поперечные сечения инструментов, используемых для кольцевого растяжения отверстий: инструмент для формирования фланцев, высота 1 = 6 × 10 −3 (м), высокий ( a ), инструмент для формирования фланцев, высота 2 = 10 −2 (м) высоты ( b ) и теоретических геометрических параметров фасонного фланца ( c ).
Зная ранее принятые допущения, можно вычислить ориентировочное значение начального диаметра отверстия d o . Для теоретической высоты полки h 1 = 6 × 10 −3 (м), диаметр отверстия выполняется d 0 = 19,225 × 10 −3 (м), а для теоретической высоты полки h 1 = 10 −2 (м) – значение d 0 = 11,225 × 10 −3 (м). Из расчетного значения на основании [44, 45, 46, 47] была рассчитана теоретическая толщина стенки t вытянутой полки.Для h 1 = 6 × 10 −3 (м) и r = 1 результат составил t = 1,278 × 10 −3 (м), а для h 2 = 10 −2 ( м) и r = 1, t = 0,976 × 10 −3 (м). Для оценки напряженного состояния в изделии после процесса формообразования полки арматуры и оценки возможности формообразования полки арматуры было выполнено компьютерное моделирование процесса. Численный анализ был выполнен с использованием FEM. Процесс рисования рассматривался как геометрически и физически нелинейная краево-начальная задача, в которой присутствуют нелинейные, подвижные и переменные во времени и пространстве граничные условия.Граничные условия в местах контакта инструмента с заготовкой неизвестны. Нелинейность процесса и высокая сложность физических явлений при незнании граничных условий в зоне контакта инструмента с заготовкой требуют применения современных методов моделирования и анализа.
Математическое описание нелинейных явлений требует применения иных, чем в линейных задачах, принципов постановки гранично-начальных задач и более сложных методов их решения.В этой статье обновленное описание Лагранжа было принято для описания процесса механической обработки на типичном шаге приращения. Согласно этому описанию, в текущий момент времени t известны начальная конфигурация тела C0 и текущая конфигурация Ct. Это означает, что в эти моменты времени и во все остальные моменты времени t<τ значения всех функций, входящих в задачу, известны. Вместо этого находится следующая равновесная конфигурация C t+Δt, в следующий момент времени τ=t+Δt. Записав частные уравнения движения для всех конечных элементов, отделенных от инструмента и заготовки, после их суммирования получают уравнение движения технологического процесса.Общее уравнение движения дискретного объекта в уточненном лагранжевом описании при типичном шаге приращения t→τ имеет вид [37,38,39,40,41,46,47,48]:
М⋅ Δr¨+C⋅Δr˙+(K+ΔK)⋅Δr=ΔR+ΔF+F+R,
(12)
где: M – мгновенная матрица масс системы, C – мгновенная матрица демпфирования, K и ∆K – мгновенная матрица жесткости и ее приращение соответственно, F, ∆F – мгновенная a внутренних нагрузок узлов и ее приращение, R, ∆R – вектор поверхностных нагрузок и ее приращения соответственно, Δr – вектор приращений перемещений узлов, Δr˙ – вектор приращений узловых скоростей, Δr¨ – вектор приращений узловых ускорений.
Матричное уравнение (12) представляет собой систему N дифференциальных уравнений второго порядка с постоянными (с шагом приращения) коэффициентами с соответствующими начальными условиями {r(t=0)}={r0}, {r˙(t=0) )}={r˙0} и граница являются инкрементальной формулировкой динамического равновесия деформируемых твердых тел в контакте для анализируемого случая. Система уравнения (12) содержит N уравнений с N известными элементами вектора внутренних сил F и 3N2 элементами матриц M, C , и K, при 4N неизвестных, т.е.е., компоненты вектора: прирост перемещения Δr, прирост скорости узлов Δr˙, прирост ускорений узлов Δr¨, прирост внутренних нагрузок объекта ΔF и N2 неизвестных элементов матрицы прироста жесткости объекта ΔK. В этом уравнении также неизвестна часть компонент вектора возрастания внешних нагрузок ΔR (в зонах контакта). В данной работе для решения уравнения движения использовались его частичная линеаризация, явные и неявные методы аппроксимации.В процедуре частичной линеаризации нелинейного инкрементного уравнения (12) предполагается, что приращение времени ∆t очень мало. Тогда можно считать, что увеличение матрицы жесткости объекта ΔK и увеличение вектора внутренних нагрузок объекта ΔF пренебрежимо мало. Таким образом, N + N 2 неизвестных исключаются, и уравнение (12) принимает вид:
M⋅Δr¨+C⋅Δr˙+K⋅Δr=F+ΔR+R.
(13)
В системе уравнений (13) имеется 3N неизвестных, т.е.е., компоненты вектора: приращение перемещения узлов Δr, приращение узловой скорости Δr˙, приращение узлового ускорения Δr¨. Кроме того, неизвестны некоторые компоненты вектора прироста внешних нагрузок ΔR (т. е. касающиеся площадей контакта тел). Полученное уравнение далее является нелинейным относительно вектора приращения перемещений узловых точек Δr и его производных по времени Δr¨, Δr˙. Далее использовались известные методы явной и неявной аппроксимации [42,43], выражающие возрастания скорости перемещений и ускорений Δr¨, Δr˙ через приращение смещения Δr, получая вид уравнения, из которого определялся искомый вектор приращения смещения узловых точек.
Упругая/вязкопластическая модель Купера-Саймондса использована для моделирования предела текучести σ Y материала в процессе формообразования фланца при радиальном растяжении отверстия. В этой модели использовались критерий текучести Хубера-Мизеса-Хенки и связанный с ним закон движения материала. Модель Каупера-Саймондса допускает линейно-изотропное (β=1) или кинематическое (β=0) пластическое упрочнение и влияние интенсивности скорости пластической деформации в соответствии со следующим степенным соотношением:
σY=[1 +(φ˙z(p)/C)]m(Re+β⋅Ep⋅φz(p)),
(14)
где:
β — параметр пластического упрочнения,
R e — начальный, статический предел текучести (Па),
φ˙z(p) — интенсивность скорости пластической деформации (с −1),
C – параметр материала, определяющий влияние интенсивности скорости пластической деформации (с−1),
м=1/P – постоянная материала, определяющая чувствительность материала к скорости пластической деформации,
φz(p)(−) – интенсивность пластической деформации,
Ep=ET⋅EE−ET – параметр материала, зависящий от модуля пластического упрочнения ET=∂σp/∂φz(p) и модуль Юнга Е.
Соответствующая дискретизация является важным шагом в моделировании процесса формирования полки во время радиального растяжения отверстия для трехмерного напряженного состояния и трехмерного состояния деформации. Это особенно важно в контактных зонах. Неадекватная сетка вызывает проникновение элементов инструмента и листа и недостаточное представление явления выдавливания материала. Слишком высокая плотность сетки приводит к значительному увеличению времени вычислений. представлена геометрическая модель и адекватная дискретная модель (эффективность модели проверена на основе анализа чувствительности) процесса формообразования фланца при радиальной вытяжке отверстия.
Геометрическая модель ( a ) и дискретная модель ( b ) в процессе формирования полки — радиальное растяжение отверстия.
После проведения численных расчетов [46,47,48,49] была разработана зависимость σR= f(h) напряжений от высоты полки, показанная на , и разработанное уравнение имеет следующий вид:
Зависимость между действующими напряжение и высота полки определяются численно.
Примеры результатов численных расчетов для модели h6 показаны на , а для модели h20 на .
Действующее напряжение в рельефном фланце с пуансоном для модели h6: вид всей модели ( a ), вид внутренней стороны ( b ), вид внешней стороны ( c ).
Действующее напряжение в рельефном фланце с пуансоном для модели h20: вид с внутренней стороны ( a ), вид с внешней стороны ( b ).
Эффективное напряжение для модели h6 () достигает максимального значения 380×10 6 (Па) в верхней части полки, где произошло наибольшее изменение толщины листа, до значения около 1.24 × 10 −3 (м). Эффективные напряжения для модели h20 () достигают максимального значения 556×10 6 (Па) в верхней части полки, где произошло наибольшее изменение толщины листа, до величины около 1,04 × 10 −3 (м). На основании проведенных анализов можно сделать вывод, что модель h20 получает высокие значения эффективных напряжений и для анализируемого материала — аустенитной стали 1. 4301 существует риск разрыва фасонного фланца уже в процессе изготовления.
Разработанная зависимость напряжений от высоты полки σ R = f(h) () позволяет определить необходимую высоту прессованной полки, при которой напряженное состояние соответствует напряжению сварки. В результате наложения этих напряжений результирующие напряжения значительно снижаются до необходимого уровня (обратная задача). Например, в анализируемом случае высота фланца должна быть h = 6×10 −3 (м), что обеспечивает правильность технологического процесса изготовления фланца и обеспечивает снижение деформации после сварки.
Что такое остаточное напряжение? — ТВИ
Остаточные напряжения – это такие напряжения, которые сохраняются в объекте (в частности, в сварной детали) даже при отсутствии внешней нагрузки или температурных градиентов. В ряде случаев остаточные напряжения приводят к значительным пластическим деформациям, приводящим к короблению и деформации объекта. В других они влияют на склонность к разрушению и усталость.
Щелкните здесь , чтобы посмотреть наши последние технические подкасты на YouTube .
Содержимое
Остаточные напряжения возникают, когда объект (особенно сварной компонент) подвергается напряжению, превышающему его предел упругости, что приводит к пластической деформации. Существуют три основные причины возникновения этих напряжений:
Термические вариации
Когда объект охлаждается от высокой температуры (например, после сварки), часто наблюдается большая разница в скорости охлаждения по всему телу. Разница в скорости охлаждения поверхности и внутренней части объекта приводит к локальным изменениям теплового сжатия.Различные термические сжатия вызывают неравномерные напряжения. Во время охлаждения поверхность остывает быстрее, сжимая нагретый материал в центре. Поскольку материал в центре пытается охладиться, он ограничивается более холодным внешним материалом. Следовательно, внутренняя часть будет иметь остаточное напряжение растяжения, а внешняя часть компонента будет иметь остаточное напряжение сжатия.
Фазовые превращения
Когда материал подвергается фазовому превращению, возникает разница в объеме между новообразованной фазой и окружающим материалом, который еще не претерпел фазового превращения.Разница в объеме вызывает расширение или сжатие материала, что приводит к остаточным напряжениям.
Механическая обработка
Остаточное напряжение также возникает, когда пластическая деформация неравномерна по поперечному сечению объекта, подвергающегося производственному процессу, такому как гибка, волочение, выдавливание и прокатка. Когда материал подвергается деформации, одна его часть эластична, а другая пластична. После снятия нагрузки материал пытается восстановить упругую часть деформации, но полностью восстанавливается из-за соседнего пластически деформированного материала.
В зависимости от применения остаточные напряжения могут быть положительными или отрицательными. Например, остаточные напряжения реализуются в конструкциях некоторых приложений для получения положительного эффекта. Этого можно достичь с помощью лазерной наклепа, которая придает сжимающие остаточные напряжения поверхности объекта, что позволяет упрочнить тонкие срезы или упрочнить хрупкие поверхности.
Однако обычно остаточные напряжения имеют негативные последствия. Остаточные напряжения часто незаметны для производителя, если только они не приводят к значительным деформациям, но могут отрицательно сказаться на целостности конструкции.Например, толстостенные конструкции в состоянии после сварки более склонны к хрупкому разрушению, чем конструкции со снятыми напряжениями.
Нежелательные напряжения также влияют на усталостные характеристики.
Давно признано, что для несварных материалов в условиях усталостного нагружения только растягивающие части цикла приложенного напряжения способствуют росту усталостной трещины (см. нижнюю часть рисунка 1). В сварном состоянии к эффекту приложенного циклического напряжения необходимо добавить эффекты остаточных сварочных напряжений, в результате чего весь усталостный цикл (растяжение и сжатие) вызывает усталостное повреждение (см. верхнюю часть рисунка 1).
Рис. 1 Влияние остаточного напряжения при сварке на усталостное повреждение.
К счастью, влияние остаточных сварочных напряжений как на разрушение, так и на усталость прописано в нормах и стандартах таким образом, что большинство пользователей не знают о них, и им не нужно учитывать их в явном виде. Тем не менее, есть частные случаи, когда необходима количественная оценка остаточных напряжений.
Существует множество методов измерения остаточных напряжений.Они в целом подразделяются на три области: разрушающие, полуразрушающие и неразрушающие. Используемый подход часто зависит от требуемой информации. Из-за сложности некоторых методов измерения измерение должно выполняться в специализированном помещении. Это особенно верно для многих неразрушающих методов.
Ниже перечислены три основные категории:
Разрушительный
Эти методы включают разрушение измеряемого объекта и обычно используются с точки зрения исследований и разработок. Разрушающий контроль часто намного дешевле в реализации, чем неразрушающий контроль.
Примеры методов включают:
- Контурный метод. Контурный метод определяет остаточное напряжение путем разрезания объекта на две части и измерения карт высот поверхности вдоль свободной плоскости, созданной разрезом. Средний контур определяет деформации, вызванные перераспределением остаточных напряжений, и используется для расчета остаточных напряжений с помощью упругой конечно-элементной модели образца.Результатом является двумерная карта остаточного напряжения, перпендикулярная плоскости измерения.
- Резка. Метод продольной резки — это метод измерения остаточного напряжения по толщине, нормального к плоскости, проходящей через объект. Он включает в себя нарезание тонкой щели с шагом глубины по толщине заготовки и измерение результирующих деформаций в зависимости от глубины щели. Остаточное напряжение затем рассчитывается как функция положения по толщине, определяемого путем решения обратной задачи с использованием измеренных деформаций.
Полуразрушающий
Методы полуразрушения сравнимы с методами разрушения тем, что они используют принцип снятия напряжения для определения остаточного напряжения. Однако удаляется лишь небольшое количество материала, что позволяет конструкции лучше сохранять свою целостность.
Примеры:
- Глубокое сверление. Сверление глубоких отверстий включает в себя просверливание отверстия через толщину объекта, измерение диаметра отверстия, прорезание круглой прорези вокруг отверстия для удаления сердцевины материала вокруг отверстия, а затем повторное измерение диаметра отверстия.Остаточное напряжение определяется по геометрическому изменению.
- Сверление центрального отверстия. Сверление центрального отверстия работает по принципу сверления небольшого отверстия в объекте. Когда материал, содержащий остаточное напряжение, удаляется, оставшийся материал достигает нового состояния равновесия, которое имеет связанные с ним деформации вокруг отверстия.
Деформации вокруг отверстия измеряются во время анализа с помощью тензодатчиков или оптических методов. Исходное остаточное напряжение в материале рассчитывается по измеренным деформациям.
Неразрушающий
Существует множество методов, используемых для неразрушающего контроля, которые включают измерение влияния отношений между остаточными напряжениями и их материальными изменениями в интервале кристаллической решетки.
Примеры неразрушающих методов включают:
- Нейтронная дифракция. Использует нейтроны для измерения шага кристаллической решетки в объекте. Нейтроны, выходящие из объекта, имеют энергию, сравнимую с энергией падающих нейтронов, что позволяет определить остаточное напряжение по расстоянию решетки.
- Синхротронная рентгеновская дифракция. Требуется синхротрон для ускорения электромагнитного излучения, чтобы обеспечить понимание расстояния между решетками объектов по толщине. В этом процессе используется подход, аналогичный дифракции нейтронов, для расчета остаточного напряжения.
- Рентгеновская дифракция. Этот процесс позволяет измерять остаточное поверхностное напряжение, поскольку рентгеновское излучение проникает в поверхность объекта только на несколько сотен микрон.
Существует ряд методов, которые можно использовать для перераспределения или снятия остаточных напряжений.Соответствующая производственная схема и выбор параметров сварки могут уменьшить образование остаточных напряжений. Например, методы обработки сварки, которые уменьшают температурный градиент внутри объекта, уменьшают величину создаваемых напряжений.
После производственного процесса могут быть предприняты дополнительные шаги для радикального снижения остаточных напряжений внутри объекта. Этого можно добиться с помощью термической или механической обработки. Термическая обработка после сварки часто используется для снятия или перераспределения остаточных напряжений в свариваемом объекте.С механической точки зрения для достижения желаемого эффекта можно применять такие методы, как дробеструйная обработка, холодная прокатка и растяжение.
Чем может помочь TWI?
TWI в настоящее время предоставляет ряд услуг своим членам в отношении остаточных напряжений, вызванных процессом, в том числе:
- Измерение
- Численное моделирование
- Рекомендации по:
Влияние остаточных напряжений на целостность конструкции (в первую очередь разрушение и усталость)
Методы снижения остаточных напряжений (например,г. послесварочная термообработка, упрочнение и т.д.)
Контроль деформации
Кроме того, несколько прошлых и настоящих проектов NSIRC касаются измерения, моделирования или интерпретации различных аспектов остаточных напряжений при сварке.
Таким образом,Экспертиза остаточного напряжения в TWI охватывает весь спектр уровней технологической готовности (TRL), от исследований и разработок, связанных с университетом, до применения мер по снижению остаточного напряжения на месте.
TWI имеет долгую историю работы со своими членами над преодолением проблем, связанных с остаточными напряжениями. Пожалуйста, свяжитесь с нами, чтобы узнать больше.
Микроструктурная характеристика толстостенной сверхвысокопрочной стали S1100, сваренной в различных положениях сварки — Технологический университет Граца
TY — CONF
T1 — Микроструктурная характеристика толстостенной сверхвысокопрочной стали S1100, сваренной в различных положениях сварки
AU — Тюмер , Mustafa
AU — Enzinger, N
PY — 2020/9/22
Y1 — 2020/9/22
N2 — Использование сверхвысокопрочных конструкционных сталей позволяет создавать не только легкие конструкции, за счет уменьшения толщины листа и тем самым веса и наполнителя, но также способствует решению текущих задач в различных областях техники.Благодаря их точно подобранному химическому составу и точно контролируемым термомеханическим процессам во время производства поддерживается очень эффективная микроструктура в отношении прочности и пластичности. Для достижения желаемой прочности, пластичности, ударной вязкости и усталостных свойств применяются различные механизмы упрочнения. Процессы соединения этих сталей имеют особое значение во многих областях применения. Сварка в горизонтальном (PA) и вертикальном (PF) положениях играет важную роль в производстве или крупных конструктивных элементах, таких как краны, крановые стрелы, бетононасосы, сосуды под давлением, трубы для транспортировки нефти/газа, судостроение и морская промышленность.Однако для разных положений сварки требуются разные параметры с подведением тепла, обобщающими наиболее важные из них. Это исследование фокусируется на микроструктурных изменениях в зависимости от тепловложения сварных соединений MAG из S1100 с использованием соответствующего присадочного материала с металлическим сердечником. Процесс сварки выполнялся полностью автоматически для получения однородных сварных швов в положениях PA и PF с различными значениями тепловложения в соответствии с их собственными характеристиками. Детально исследовано влияние погонной энергии на металл шва и зоны термического влияния (ЗТВ).Полученная микроструктура зоны сплавления состоит из ферритных форм, а зона термического влияния представлена преимущественно мартенситом и мартенситом отпуска.
Структура прежних границ аустенитных зерен (ПАГ) различается в зависимости от применяемых положений сварки.
AB — Использование сверхвысокопрочных конструкционных сталей позволяет не только создавать легкие конструкции за счет уменьшения толщины листа и, следовательно, веса и присадочного материала, но также способствует решению текущих задач в различных областях техники.Благодаря их точно подобранному химическому составу и точно контролируемым термомеханическим процессам во время производства поддерживается очень эффективная микроструктура в отношении прочности и пластичности. Для достижения желаемой прочности, пластичности, ударной вязкости и усталостных свойств применяются различные механизмы упрочнения. Процессы соединения этих сталей имеют особое значение во многих областях применения. Сварка в горизонтальном (PA) и вертикальном (PF) положениях играет важную роль в производстве или крупных конструктивных элементах, таких как краны, крановые стрелы, бетононасосы, сосуды под давлением, трубы для транспортировки нефти/газа, судостроение и морская промышленность. Однако для разных положений сварки требуются разные параметры с подведением тепла, обобщающими наиболее важные из них. Это исследование фокусируется на микроструктурных изменениях в зависимости от тепловложения сварных соединений MAG из S1100 с использованием соответствующего присадочного материала с металлическим сердечником. Процесс сварки выполнялся полностью автоматически для получения однородных сварных швов в положениях PA и PF с различными значениями тепловложения в соответствии с их собственными характеристиками. Детально исследовано влияние погонной энергии на металл шва и зоны термического влияния (ЗТВ).Полученная микроструктура зоны сплавления состоит из ферритных форм, а зона термического влияния представлена преимущественно мартенситом и мартенситом отпуска. Структура прежних границ аустенитных зерен (ПАГ) различается в зависимости от применяемых положений сварки.
M3 — плакат
T2 — Advanced Materials Day 2020
Y2 — с 28 по 28 сентября 2020 г.
ER —
%PDF-1. 4
%
1 0 объект
>
эндообъект
2 0 объект
>
эндообъект
3 0 объект
>
эндообъект
4 0 объект
>
/ExtGState >
/Шрифт >
/ProcSet [/PDF /текст]
/XОбъект >
>>
/Повернуть 0
/StructParents 0
/Тип /Страница
>>
эндообъект
5 0 объект
>
/ExtGState >
/Шрифт >
/ProcSet [/PDF /текст]
/XОбъект >
>>
/Повернуть 0
/StructParents 1
/Тип /Страница
>>
эндообъект
6 0 объект
>
/ExtGState >
/Шрифт >
/ProcSet [/PDF /текст /ImageC]
/XОбъект >
>>
/Повернуть 0
/StructParents 2
/Тип /Страница
>>
эндообъект
7 0 объект
>
/ExtGState >
/Шрифт >
/ProcSet [/PDF /текст /ImageC /ImageI]
/XОбъект >
>>
/Повернуть 0
/StructParents 3
/Тип /Страница
>>
эндообъект
8 0 объект
>
/ExtGState >
/Шрифт >
/ProcSet [/PDF /текст /ImageC]
/XОбъект >
>>
/Повернуть 0
/StructParents 4
/Тип /Страница
>>
эндообъект
9 0 объект
>
/ExtGState >
/Шрифт >
/ProcSet [/PDF /текст /ImageC]
/XОбъект >
>>
/Повернуть 0
/StructParents 5
/Тип /Страница
>>
эндообъект
10 0 объект
>
/ExtGState >
/Шрифт >
/ProcSet [/PDF /текст]
/XОбъект >
>>
/Повернуть 0
/StructParents 6
/Тип /Страница
>>
эндообъект
11 0 объект
>
/ExtGState >
/Шрифт >
/ProcSet [/PDF /текст /ImageC]
/XОбъект >
>>
/Повернуть 0
/StructParents 7
/Тип /Страница
>>
эндообъект
12 0 объект
>
/ExtGState >
/Шрифт >
/ProcSet [/PDF /текст /ImageC]
/XОбъект >
>>
/Повернуть 0
/StructParents 8
/Тип /Страница
>>
эндообъект
13 0 объект
>
/ExtGState >
/Шрифт >
/ProcSet [/PDF /текст]
/XОбъект >
>>
/Повернуть 0
/StructParents 9
/Тип /Страница
>>
эндообъект
14 0 объект
>
/ExtGState >
/Шрифт >
/ProcSet [/PDF /текст]
/XОбъект >
>>
/Повернуть 0
/StructParents 10
/Тип /Страница
>>
эндообъект
15 0 объект
>
/ExtGState >
/Шрифт >
/ProcSet [/PDF /текст]
/XОбъект >
>>
/Повернуть 0
/StructParents 11
/Тип /Страница
>>
эндообъект
16 0 объект
>
/ExtGState >
/Шрифт >
/ProcSet [/PDF /текст /ImageC]
/XОбъект >
>>
/Повернуть 0
/StructParents 12
/Тип /Страница
>>
эндообъект
17 0 объект
>
/ExtGState >
/Шрифт >
/ProcSet [/PDF /текст]
/XОбъект >
>>
/Повернуть 0
/StructParents 13
/Тип /Страница
>>
эндообъект
18 0 объект
>
/ExtGState >
/Шрифт >
/ProcSet [/PDF /текст]
/XОбъект >
>>
/Повернуть 0
/StructParents 14
/Тип /Страница
>>
эндообъект
19 0 объект
>
/ExtGState >
/Шрифт >
/ProcSet [/PDF /текст]
/XОбъект >
>>
/Повернуть 0
/StructParents 15
/Тип /Страница
>>
эндообъект
20 0 объект
>
/ExtGState >
/Шрифт >
/ProcSet [/PDF /текст]
/XОбъект >
>>
/Повернуть 0
/StructParents 16
/Тип /Страница
>>
эндообъект
21 0 объект
>
ручей
xVKO0v9ty%G8q»% Z+!@*Ry
*؞??nH6گUx ‘6qxrJ
.