Сварка трением с перемешиванием алюминиевых сплавов
Среди огромного количества различных технологий сварки следует отметить сварку трением с перемешиванием. Подобный процесс не предусматривает использование защитных газов и расходных сварочных материалов. При этом можно получить соединение высокого качества. Технология в большинстве случаев применяется при обработке алюминия и некоторых других сплавов. Рассмотрим принцип процесса и некоторые другие моменты подробнее.


Принцип процесса
Сварка трением с перемешиванием проводится при применении специального инструмента, который напоминает форму стержня. Среди особенностей сварки трением с перемешиванием можно отметить нижеприведенные моменты:
- Применяемое оборудование для сварки трением с перемешиванием состоит из двух основных частей: заплечика и бурта, а также наконечника.
- Инструмент выбирается в зависимости от толщины материала и его типа. Некоторые сплавы характеризуются низкой степенью обрабатываемостью.
- Длина наконечника устанавливается в зависимости от толщины детали.
- Этот метод сварки может выполняться с присадочным материалом. На момент сварки инструмент вращается с высокой скоростью в месте плавления. Оказываемое давление приводит к тому, что наконечника внедряется в заготовку на требуемую толщину. При этом заплечник должен коснуться обрабатываемой поверхности.
- Следующий шаг заключается в перемещении инструмента по линии шва с определенной скоростью. При сильном трении поверхность материалов начинает сильно нагреваться, за счет чего он начинает становится пластичным. Деформация проходит равномерно.


Процесс сварки
При помощи специальной установки можно создать прочное соединение, которое характеризуется довольно высоким качеством.
Основные параметры которые влияют на свойства шва
Стоит учитывать, что некоторые параметры оказывают влияние на основные качества образующегося шва. К основным можно отнести:
- Скорость перемещения инструмента определяет силу трения, возникающую между режущей поверхностью и заготовкой. От этого зависит также температура.
- Частот вращения инструмента также оказывает влияние на температуру в зоне обработке.
- Угол наклона инструмента также оказывает влияние на особенности проведения сварки трение с перемешиванием.
- Геометрические размеры применяемого прибора выбираются в зависимости от того, какой нужно получить соединение.
- Усилие прижатия и перемещения также можно считать наиболее важными параметрами.


Сварочный шов
При рассмотрении способа сварки трением отметим, что подобная технология сегодня активно развивается. Это связано с тем, что естественный процесс нагрева не приводит к появлению внутренних деформаций и иных дефектов.
Основные области применения
На сегодняшний день рассматриваемая технология применяется в большинстве случаев при выпуске транспортных средств. Это связано с нижеприведенными моментами:
- При применении технологии, которая предусматривает плавление металла, может появится перфорация тонких листов стали. Примером можно назвать обработку алюминия.
- Рассматриваемая технология СТП определяет выделение меньшего количества тепла. Именно поэтому вероятность появления подобных дефектов незначительна.
- Сварки трением с перемешиванием характеризуется высокой эффективностью, так как ее использование приводит к уменьшению степени энергопотребления в два раза.
- Применение технологии позволяет снизить вес получаемой конструкции.
Все приведенные выше моменты определяют то, что рассматриваемая технология получила следующее распространение:
- Судостроение.
- Аэрокосмическая промышленность.
- Электротехническая промышленность.
- Строительство.
- Пищевая промышленность.
- Железнодорожный транспорт.


Оборудование для сварки трением с перемешиванием
Чаще всего сварки трением с перемешиванием применяется при соединении медных сплавов. Примером можно назвать получение контейнеров, которые можно использовать для хранения ядерных отходов и ответственных деталей.
Преимущества
Рассматриваемый метод характеризуется довольно большим количеством достоинств. Перемешивая заготовки трением можно получить качественный шов. Качество сварки трением перемешиванием повышается при использовании различных инструментов. Преимуществами можно назвать следующие моменты:
- Заготовки не нужно тщательно подготавливать. Если рассматривать контактную и другую технологию, то перед непосредственной обработкой поверхность должна быть тщательно очищена от различных загрязнений и быть ровной. В противном случае качество шва будет низким, достигнуть требуемой герметичности не получится. В рассматриваемом случае достаточно очистить поверхность от крупных и сильно проявляющихся загрязнений.
- Не возникает необходимости в особой подготовке кромок. Некоторые технологии предусматривают снятие поверхностного слоя металла и проведение некоторых технологических операций, которые позволят существенно повысить прочность соединения.
- Есть возможность провести соединение металла, который нельзя обработать обычным способом. Примером можно назвать материалы, не подающиеся обычным методам сварки. При этом необходимость в предварительном подогреве зоны обработки практически не возникает.
- Прочность получаемого соединения достаточно высока. Именно поэтому технология может применяться для получения ответственных изделий с различной областью применения.
- Нет необходимости в использовании присадочной проволоки. Этот момент существенно снижает себестоимость проводимой работы.
- В месте соединения зернистость мелкая. За счет этого повышается плотность сварочного шва и его устойчивость к различного рода воздействия.
- Отсутствие пор также благоприятно сказывается на качестве полученного соединения. Это свойство можно связать с тем, что при сильном нагреве проводится выделение различных газов и веществ, которые и становятся причиной образования пористости.
- Практически полное отсутствие признаков коробления и термической деформации определяет то, что финишная обработка требуется крайне редко.
- После проведения сварочных работ при сварке трением с перемешивание изделие практически сразу готово к применению. При этом нет необходимости в проведении каких-либо подготовительных действий.
- Не повышается степень реакции поверхности на воздействие окружающей среды. Другими словами, материал не покрывается коррозией.
- При проведении процедуры на момент сварки трением с перемешиванием не образуется токсичных газов или других выделений. Кроме этого, более распространенные методы, основанные на воздействии тока, приводят к образованию электрической дуги, которая оказывает негативное воздействие на оператора и окружающих при условии отсутствия специальных средств индивидуальной защиты.
- Уменьшается продолжительность производственного цикла примерно на 50% в сравнении с другими распространенными способами.
- Экономия на количестве потребляемой энергии составляет 20%.
Как ранее было отмечено, получение бездефектных швов на сплавах определило широкое распространение сварки трением с перемешиванием. Примером можно назвать получение кузовных деталей.
Недостатки
У проводимой процедуры также есть несколько недостатков, которые нужно учитывать. Примером можно назвать возможность нарушения сплошности шва. Кроме этого, некоторые сплавы в меньшей степени подвержены воздействию силы трения.
Совершенствование рассматриваемого способа определило то, что на поверхности шва образуются дефекты в самых крайних случаях. Чаще всего это случается при нарушении технологии и использовании низкокачественного инструмента.
Технологические возможности у рассматриваемой процедуры довольно обширны. Примером назовем следующие моменты:
- Автоматизация процесса.
- Получение качественных изделий при несущественных финансовых затратах.
- Получение шва без сильного наплыва металла.


Сварка меди и стали
Как ранее было отмечено, сварка трением с перемешиванием сегодня активно развивается. Именно поэтому в будущем может появится оборудование с более высоким показателем производительности.
Особенности формирования соединений при применении СТП
Как ранее уже было отмечено, сварка трением с перемешиванием характеризуется достаточно большим количеством особенностей. Среди ключевых моментов, касающихся формирования соединения, можно отметить нижеприведенную информацию:
- Нагрев металла проводится постепенно до температуры, которая не приводит к изменению основных свойств.
- Температура повышается только в одном локальном месте. За счет этого обеспечивается высокое качество получаемого соединения.
- При соблюдении рекомендаций по проведению рассматриваемой процедуры дефекты возникают крайне редко. Именно поэтому в большинстве случаев достаточно провести визуальный осмотр места соединения для контроля качества.
Современное оборудование позволяет получать минимальный шов, которые после финишной обработки практически незаметен. Обширное распространение рассматриваемого метода также можно связать с тем, что она подходит для работы с труднообрабатываемыми металлами.
Сварка трением с перемешиванием – активно развивающаяся технология, которая сегодня все чаще внедряется в различное производство.
Сварка трением с перемешиванием конструкционных материалов и свойства соединений
Новый метод получения сварных соединений, получивший название «сварка трением с перемешиванием» (СТП) был разработан Британским институтом сварки (TWI) в 1991 г. [1]. Интенсивное изучение данного процесса, направленное на совершенствование технологии и оборудования, позволило внедрить данный способ за рубежом в производство высокотехнологичных изделий в таких отраслях как вагоно-, судо-, авиастроение и многих других. Сварка трением с перемешиванием относится к процессам соединения материалов в твердой фазе и поэтому лишена недостатков, связанных с расплавлением и испарением металла. Исследователи данного процесса считают, что если 10% общего объема сварных соединений в США заменить СТП, то будет достигнуто на 500 млн. фунтов/год меньше выделений парникового газа. Расчетная экономическая выгода промышленности США от внедрения СТП в промышленное производство составляет $4,9 млрд./год [2].
Сущность процесса заключается в следующем (рис. 1). Для сварки используют инструмент в форме стержня, состоящий из двух основных частей, а именно: заплечика или бурта (утолщенная часть) и наконечника (выступающая часть). Размеры этих конструктивных элементов выбирают в зависимости от толщины и материала свариваемых деталей.
Длину наконечника устанавливают приблизительно равной толщине детали, подлежащей сварке. Диаметр заплечика может изменяться от 1,2 до 25 мм. Вращающийся с высокой скоростью инструмент в месте стыка вводится в соприкосновение с поверхностью заготовок так, чтобы наконечник внедрился в заготовки на глубину, примерно равную их толщине, а заплечик коснулся их поверхности. После этого инструмент перемещается по линии соединения со скоростью сварки. В результате работы сил трения происходит нагрев металла до пластического состояния, перемешивание его вращающимся инструментом и вытеснение в освобождающееся пространство позади движущегося по линии стыка инструмента. Объем, в котором формируется шов, ограничивается сверху заплечиком инструмента. По окончании сварки вращающийся инструмент выводят из стыка за пределы заготовки. В связи с асимметрией структуры швов в поперечном сечении сварных соединений, полученных сваркой трением с перемешиванием, принято различать сторону набегания, где направление вращения инструмента совпадает с направлением сварки, и противоположную сторону – отхода.
Рис. 1. Схема процесса сварки трением с перемешиванием.
СТП применяют в основном для соединения материалов со сравнительно низкой температурой плавления, прежде всего алюминиевых [3] и магниевых сплавов [4]. Выполнена успешная сварка данным способом медных [5], никелевых и титановых сплавов [2], а также сталей [6]. С помощью СТП сваривают алюминиевые сплавы толщиной до 75 мм за один проход [7]. Сварка трением с перемешиванием позволяет получать нахлесточные соединения алюминиевых листов толщиной от 0,2 мм [8]. Скорость сварки сплава 6082 толщиной 5мм может достигать 6 м/мин [9]. Основными параметрами процесса СТП являются: скорость сварки, частота вращения инструмента, усилия прижатия и перемещения инструмента, угол наклона инструмента, его размеры. Усилия прижатия и перемещения зависят от типа свариваемого материала, его толщины и скорости сварки. Сварка образцов из сплава 7010 – Т7651 толщиной 6,35 мм при изменении скорости сварки в диапазоне от 59 до 159 мм/мин и скорости вращения инструмента от 180 до 660 об/мин показала, что при увеличении скорости вращения увеличивается тепловложение в металл и в сварном соединении формируется микроструктура с более однородными зернами [10]. При этом также повышаются прочностные и пластические свойства до определенного предела. При увеличении скорости сварки необходимо увеличивать скорость вращения инструмента для достижения оптимальных условий. Однако для полного отсутствия дефектов, а также для обеспечения всех необходимых свойств, надежности и технологичности необходимо строго выбирать режимы, оптимально подходящие для определенной продукции.
Большинство исследователей указывают на следующие преимущества сварки трением с перемешиванием по сравнению с другими способами получения неразъемных соединений [11, 12]:
– в зоне сварки лучше сохраняются свойства основного металла по сравнению со способами сварки плавлением;
– отсутствие вредных испарений и ультрафиолетового излучения в процессе сварки;
– возможность получения бездефектных швов на сплавах, которые при сварке плавлением склонны к образованию горячих трещин и пористости в швах;
– не требуется использование присадочного материала и защитного газа, удаление поверхностных оксидов на кромках перед сваркой, а также шлака и брызг после сварки;
– отсутствуют потери легирующих элементов металла при его сварке.
Уровни выделений Cr, Cu, Mn, Cr+6 при СТП сталей по сообщению RockwellScientific (США) значительно ниже (<0,03, <0,03, <0,02 и <0,01 мг/мм3 соответственно), чем при аргонодуговой сварке (0,25, 0,11, 1,88 и 0,02 мг/мм
Рис. 2. Распределение температур в продольном сечении образца.
Судя по экспериментальным результатам TWI, максимальная температура при сварке трением с перемешиванием составляет около 70% значения температуры плавления и для алюминия не превышает 550°С. Тепловложение при СТП меньше, чем при аргонодуговой сварке примерно в 2 раза и для сплава 6N01 – Т5 толщиной 4 мм равно соответственно 190 и 390 Дж/мм (скорость сварки 500 мм/мин) [13]. С помощью математического моделирования тепловых процессов при СТП в работе [14] построено распределение температур в свариваемой пластине (рис. 2). Более низкая температура зоны соединения при сварке трением с перемешиванием по сравнению со сваркой плавящимся электродом объясняет меньший уровень угловых деформаций в сварном соединении. При СТП угловая деформация равна 1/5÷1/7 значений при СПЭ [12] (рис. 3).
Рис. 3. Сравнение угловой деформации при сварке трением с перемешиванием и сварке плавящимся электродом (алюминиевый сплав серии 6000, толщина 2 мм).
Предполагается, что из-за невысокого уровня температур процесса, остаточные напряжения низкие. Но жесткое закрепление налагает большие ограничения на деформацию пластин. Это препятствует сокращению металла при охлаждении зоны динамической рекристаллизации и зоны термического влияния (ЗТВ) в продольном и в поперечном направлении, приводя к поперечным и продольным остаточным напряжениям. При СТП сплавов 2024 – Т3 і 6013 – Т6 обнаружено, что продольные остаточные напряжения выше поперечных (скорость сварки составляла 300 ÷ 1000 мм/мин, скорость вращения инструмента – 1000 ÷ 2500 об/мин). Высокие растягивающие напряжения преобладают в ЗТВ. Величина остаточных напряжений уменьшается при снижении скорости сварки и скорости вращения инструмента. Максимальные значения продольных растягивающих напряжений достигают значений 30 ÷ 60% предела текучести сварного соединения и 20 ÷ 50% предела текучести основного металла [15].
Рис. 4. Схема зон стыкового соединения, выполненного СТП: А – основной металл, В – зона термического влияния (ЗТВ), С – зона термомеханического влияния, D – зона динамической рекристаллизации (сторона набегания слева).
Макроструктура сварных соединений при сварке трением с перемешиванием характеризуется особенностями, не свойственными швам, полученным способами сварки плавлением. Типичным для СТП является образование в центре соединения ядра, которое содержит овальные концентричные кольца, различающиеся структурой [16]. К ядру примыкает сложный профиль, который образует верхнюю часть шва. Образование овальных колец связывается с особенностями перемешивания металла наконечником инструмента. В сварном соединении при СТП выделяют четыре зоны, которые схематически представлены на рисунке 4. Непосредственно к зоне А (основной металл) примыкает зона В, где металл заготовок остается недеформированным и изменяет свою структуру только под воздействием нагрева (зона термического влияния). Зона С, где металл подвергается значительным пластическим деформациям и нагреву, названа зоной термомеханического влияния (ЗТМВ). Зона D – это ядро соединения, где происходит динамическая рекристаллизация. Твердость металла уменьшается в направлении от основного металла к центру шва, и минимальное значение достигается в ЗТВ (рис. 5). Снижение твердости в ЗТВ происходит за счет перестаривания, уменьшения плотности дислокаций либо за счет обоих этих механизмов.
Рис. 5. Распределение твердости в зоне сварного соединения сплава 7075 – Т7351 [17].
О высоком уровне механических свойств сварных соединений сообщают многие исследователи. При СТП сварное соединение сплава 6082 –Т6 имеет предел прочности σ
Авторы [19] проводили исследования механических свойств соединений, полученных сваркой трением с перемешиванием сплава 5083 при криогенных температурах, что имело целью подготовить производство емкостей для сжиженного водорода. Образцы толщиной 30 мм были сварены со скоростью 40 мм/мин. Исследования при 77К в жидком азоте, 20К в жидком водороде и 4К в жидком гелии показали, что уровень свойств соединений при СТП выше, чем при аргонодуговой сварке.
Рис. 6. Механические свойства сварного соединения, выполненного различными способами сварки.
Проблемами СТП литейных алюминиевых сплавов занимались авторы работы [20]. В промышленном производстве литейные сплавы часто приходится сваривать с получаемыми экструдированием. Использовали сплавы ADC1 и А6061 – Т6 толщиной 4мм. Результаты, полученные при СТП, сравнивались с аналогичными при аргонодуговой и лазерной сварке. Как видно из рисунка 6, СТП обеспечивает лучшие свойства соединений. Предел прочности составляет 80% прочности А6061 – Т6. При испытании на изгиб разрушение при сварке трением с перемешиванием происходит по основному металлу. О положительных результатах сварки трением с перемешиванием разнородных сплавов, а также алюминиевых сплавов со сталями сообщается в публикации [21]. При СТП стали SS400 и сплава А5083 толщиной 2 мм предел прочности был равен 240 МПа, что составляет 86% прочности алюминиевого сплава.
Рис. 7. Установка для точечной сварки трением с перемешиванием (слева), поперечное сечение (вверху справа) и внешний вид образцов (внизу справа).
В качестве недостатка способа СТП авторы [2, 12] отмечают образование в конце шва отверстия, равного диаметру наконечника, что требует выведения шва за пределы рабочего сечения заготовки или заполнения отверстия после сварки с помощью других методов, таких как вварка трением специальных пробок.
Происходящее совершенствование технологии и оборудования позволяет преодолеть существующие недостатки, а также расширить области применения способа. Хотя сварка трением с перемешиванием применяется в основном для стыковых и нахлесточных швов, возможно также получение угловых, тавровых, точечных швов. Точечную сварку трением с перемешиванием можно реализовать двумя способами. Первый способ – это точечная сварка погружением (PFSW), который был запатентован фирмой Mazda (Япония) в 2003 году. При этом вращающийся инструмент погружается в деталь, доводя до пластического состояния и перемешивая металл под заплечиком. После этого инструмент поднимается, оставляя характерное углубление в детали. Второй способ – точечная сварка трением с заполнением шва (RFSW), который запатентован GKSS– GmbH в 2002 году [2]. Для этого способа используют инструмент, у которого наконечник и заплечик имеют раздельные системы привода. Вращающийся инструмент опускается в деталь, при этом наконечник выдавливает и перемешивает находящийся под ним металл, а после он убирается, и металл под заплечиком заполняет углубление, и, таким образом, получается шов без отверстия (рис. 7).
Рис. 8. Внешний вид инструмента из поликристаллического кубического нитрида бора [2].
Сварочный инструмент обычно изготавливается из инструментальных сталей Н13 (AISI), SKD61, SKD 11, SKH 57 (JIS), нержавеющей мартенситной стали SUS440C(JIS). При этом возможно использование составных инструментов, у которых наконечник изготовлен из кобальтового сплава МР159, а заплечик – из Н13 [22]. Для сварки методом СТП сталей толщиной до 0,5″ MegaStir разработала инструмент из поликристаллического кубического нитрида бора. Его стойкость против разрушения выше и позволяет придать наконечнику форму необходимую для благоприятного течения металла в зоне сварки (рис. 8). Инструмент по отношению к поверхности детали располагают под небольшим углом 2 ÷ 3° [16, 23]. При таком расположении инструмента под небольшим углом к поверхности детали достигаются наиболее высокие показатели качества.
Рис. 9. Конструкция инструмента Bobbin Tool.
Инструмент, одновременно выполняющий также роль подкладки соединяемых заготовок, приведен на рисунке 9 [24]. В NASA разрабатывается саморегулирующийся инструмент, длина наконечника которого определяется силами, действующими на него. При отклонении нагрузки на наконечник от заданного значения, происходит автоматическая корректировка его длины. Это позволяет сваривать заготовки переменного сечения и избегать образования отверстия при выполнении кольцевых швов.
Рис. 10. Варианты конструкции рабочего инструмента WhorlTM.
Для сварки алюминиевых сплавов значительной толщины разработаны семейства инструментов WhorlTM(рис. 10) и TrifluteTM[25], которые позволяют выполнять сварку за один проход алюминиевых сплавов толщиной 50 мм. Новыми вариантами СТП являются технологии Re– StirTM, Skew– StirTM, Com– StirTM[26]. Технология Re– StirTM с переменным вращением инструмента по часовой и против часовой стрелки позволяет исключить асимметрию шва, присущую традиционной СТП. По технологии Skew– StirTM инструмент немного наклонен по отношению к шпинделю машины так, что точка пересечения осей шпинделя и инструмента, получившая название фокусной точки, может располагаться над, под или в свариваемой заготовке в зависимости от свойств материала и параметров режима. Это позволяет получить при вращении инструмента в процессе сварки более широкий шов. Инструменты A – SkewTMи Flare – TrifluteTMобеспечивают формирование более прочных нахлесточных соединений. Технология Com– StirTM состоит в совмещении в процессе сварки вращательного и орбитального движений инструмента. В результате получают более широкие швы и в основном применяют для соединения разнородных материалов. Разработана система с двумя параллельными инструментами Twin – StirTM [27].
Рис. 11. Соединения, выполненные на автомобиле Mazda RX – 8 с помощью точечной сварки трением с перемешиванием [2].
Развитие новых технологий сварки трением с перемешиванием продолжается. В Университете Миссури – Колумбия (США) занимаются разработкой СТП с сопутствующим дополнительным нагревом при пропускании тока через наконечник инструмента. Центр обработки и соединения передовых материалов (США) разрабатывает СТП с индукционным предварительным подогревом материала, что позволит увеличить скорость сварки, уменьшить силы, действующие на инструмент, и уменьшить его износ [2]. В работе [28] изучается возможность использования лазера для предварительного подогрева металла при СТП магниевых сплавов.
Рис. 12. Оборудование для сварки трением с перемешиванием в вертикальном положении.
Благодаря небольшому количеству факторов, влияющих на процесс СТП, и достаточно простой конструкции оборудования, способ идеально подходит для автоматизации и роботизации [29]. Установка Tricept805 позволяет выполнять сварку алюминия толщиной до 10 мм.
Сварка трением с перемешиванием уже используется многими производителями различных высокотехнологичных изделий. Фирмы GDLS (GeneralDynamicsLandSystems) и EWI (EdisonWeldingInstitute) провели совместные работы, целью которых было обеспечить требуемые баллистические характеристики соединений броневых плит из алюминиевого сплава 2195 – Т87 для морских бронированных транспортеров. Сварка методом СТП вместо аргонодуговой плит толщиной 31,8 мм позволила получить приемлемые прочностные свойства соединений и более пластичные (в 2 – 3 раза) швы. В итоге сварные соединения (в том числе угловые) успешно прошли баллистические испытания [22].
Рис. 13. Установка для сварки трением с перемешиванием топливного бака ракеты «Delta» на предприятии «Boeing».
Для предотвращения ухудшения свойств сверхпроводящей Nb – Ti проволоки её необходимо соединять с жестким элементом из чистого Al при температуре ниже 400°С. Раньше для этого использовали низкотемпературную пайку, но паяные швы имели низкую прочность. СТП обеспечила требуемые свойства сварного соединения в жидком гелии [12].
В течение трех лет с 2003 года компания FordMotorCo. (США) изготовила несколько тысяч автомобилей FordGT, применяя СТП для сварки центрального отсека, который вмещает и изолирует топливный бак от внутреннего отделения и обеспечивает пространственную жесткость каркаса [2]. СТП повышает точность размеров и на 30% увеличивает прочность по сравнению со сходными узлами при дуговой сварке в защитном газе. В другой работе [30] описывается процесс изготовления точечной сваркой трением кузова автомобиля MazdaRX – 8 (рис. 11). С 2003 года было произведено свыше 100 тыс. автомобилей, двери которых изготовлены точечной сваркой трением [7]. На основании успешного применения данного способа сварки сообщается о планах фирмы выполнить подобные соединения на новом поколении автомобилей модели MX – 5.
Рис. 14. Самолет Eclipse 500 с узлами, изготовленными сваркой трением с перемешиванием.
Активно занимаются изучением процесса СТП в аэрокосмической сфере (рис. 12) [24]. В 2001 году процесс внедрен в производство внешнего бака ракеты носителя для возвращаемых космических кораблей. Технология предусматривает сварку 8 продольных швов на резервуаре из сплава 2195 для жидкого водорода и 4 продольных шва на резервуаре для жидкого кислорода. Это приблизительно ½ мили швов на каждом баке. Разрабатывается оборудование для ремонтной сварки трением с перемешиванием в условиях космического вакуума. Концепция основана на том, что высокая скорость вращения инструмента (30000 об/мин) при СТП позволит уменьшить усилия, необходимые для выполнения сварки.
Компания «Boeing» начала использовать сварку трением с перемешиванием при производстве ракеты «Delta» II и III (рис. 13) [31]. Сварка выполняется на топливном баке длиной 8,4 м, на баке для жидкого кислорода длиной 12 м и на других конструкциях. Сварка трением с перемешиванием обеспечивает повышение качества (один дефект на 76,2 м шва) по сравнению с аргонодуговой сваркой (один дефект на 8,4 м шва). При СТП уменьшается время изготовления сварной конструкции. Производство ракет «Delta» II выросло с 8 до 17 единиц в год.
О работах по СТП оребренных панелей для крыла самолета из сплавов 2024, 7475, 7050 толщиной 4 мм сообщается в статье [32]. Высокое качество соединений обеспечено при использовании СТП на самолете Airbus А350 и двух новых версиях А340 (А340 – 500 и А340 – 600) [2]. Компания EclipseAviation завершает сертификацию реактивного самолета бизнес класса Eclipse 500 с узлами, изготовленными методом СТП (рис. 14).
Рис. 15. Внешний вид экспериментальной установки для СТП тонколистовых (1,8 ÷ 2,5 мм) алюминиевых сплавов.
Приведенный анализ опубликованной информации свидетельствует о том, что сварка трением с перемешиванием успешно развивается и находит применение в различных отраслях промышленного производства. Большинство публикаций касаются сварки алюминиевых сплавов средней и сравнительно большой толщины. Следует иметь в виду, что затруднения обычно возникают при соединении заготовок толщиной 0,5 – 3 мм, а также более 40 мм. В связи с этим, а также с возникающими осложнениями при обеспечении точности сборки тонкостенных заготовок под сварку в ИЭС им. Е. О. Патона проведены исследования процесса СТП на специальной экспериментальной установке (рис. 15). Работы выполнены на алюминиевых сплавах АМг6, 1201, 1460 толщиной 1,8 … 2,5 мм. На рис. 16 приведен внешний вид сварного соединения сплава АМг6, полученного методом СТП. Одновременно проверена эффективность сварочных инструментов с различными профилями рабочей части.
Рис. 16. Внешний вид шва, полученного сваркой трением с перемешиванием (алюминиевый сплав АМг6 толщиной 2 мм).
Установлено, что соединения при данном способе сварки обладают высоким уровнем механических свойств (коэффициент прочности сварных соединений составляет 0,7 ÷ 0,9 от уровня прочности основного металла (табл.)) и подтверждена актуальность работ по усовершенствованию способа сварки трением с перемешиванием конструкций с применением тонколистовых материалов.
Таблица
Механические свойства соединений алюминиевых сплавов, полученных сваркой трением с перемешиванием
Алюминиевыйсплав | Прочность сварного соединения σвсв, МПа | Угол загиба сварного соединения α, град |
АМг6 | 343 | 180 |
1420 | 362 | 96 |
1201 | 294 | 180 |
1460 | 325 | 180 |
Литература
- US Pat. No 5460317. Friction stir butt welding/ W.M. Thomas, E.D. Nicholas, J.C. Needham et al.; Опубл. 1995.
- Arbegast W.J. Friction stir welding. After a decade of development// Welding J. – 2006. – 85, №3. – P. 28 – 35.
- Ito T., Motohashi Y., Goloborodko A. et al. Microstructures and room temperature mechanical properties in friction-stir-welded joints of 7075 aluminum alloys// Journal of the Japan Welding Society. – 2005. – 74, №3. – P. 9 – 13.
- Aritoshi M. Friction stir welding of magnesium alloys sheets// Journal of the Japan Welding Society. – 2005. – 74, №3. – P. 18 – 23.
- Nakata K. Friction stir welding of copper and copper alloys// Journal of the Japan Welding Society. – 2005. – 74, №3. – P. 14 – 17.
- Klingensmith S., Dupont J.N., Marder A.R. Microstructural characterization of a double-sided friction stir weld on a superaustenitic stainless steel// Welding J. – 2005. – May. – P. 77 – 85.
- Martin J. Pushing the boundaries – friction stir goes deeper than before// TWI Connect. – 2006. – January/February. – P. 1.
- Teh N.J. Small joints make a big difference// TWI Connect. – 2006. – 143, №4. – Р. 1.
- Эрикссон Л.Г., Ларссон Р. Ротационная сварка трением – научные исследования и новые области применения// Технология машиностроения. – 2003. – №6. – Р. 81 – 84.
- Hassan A.A., Prangnell P.B., Norman A.F. et al. Effect of welding parameters on nugget zone microstructure and properties in high strength aluminium alloy friction stir welds// Sci. Technol. Weld. Joining. – 2003. – 8, №4. – Р. 257 – 268.
- Defalco J. Friction stir welding vs. fusion welding// Welding J. – 2006. – 85, №3. – P. 42 – 44.
- Okamura H., Aota K., Ezumi M. Friction stir welding of aluminum alloy and application to structure// J. of Jap. Institute of Light Metals. – 2000. – 50, №4. – P. 166 – 172.
- Aota K., Okamura H., Masakuni E. et al. Heat inputs and mechanical properties friction stir welding// Proc. of the 3rd International Friction Stir Welding Symposium, Kobe, Japan, 27 – 28 September, 2001.
- Lambrakos S.G., Fonda R.W., Milewski J.O. et al. Analysis of friction stir welds using thermocouple measurements// Sci. Technol. Weld. Joining. – 2003. – 8, №5. – Р. 385 – 390.
- Dalle Donne C., Lima E., Wegener J. et al. Investigation on residual stresses in friction stir welds// Proc. of the 3rd International Friction Stir Welding Symposium, Kobe, Japan, 27 – 28 September, 2001.
- Volpone M., Mueller S.M. Friction stir welding (FSW): le ragioni di un successo// Rivista Italiana della Saldatura. – 2005. – №1. – Р. 23 – 30.
- Chao Y.P., Wang Y., Miller K.W. Effect of friction stir welding on dynamical properties of AA 2024-T3 and AA 7075-T7351// Welding J. – 2001. – №8. – Р. 196 – 200.
- Ericsson M., Sandstorm R. Influence of welding speed on the fatigue of friction stir welds, and comparison with MIG and TIG// International Journal of Fatigue. – 2003. – №25. – P. 1379 – 1387.
- Hayashi M., Oyama K., Eguchi H. et al. Mechanical properties of friction stir welded 5083 aluminum alloy at cryogenic temperatures// Proc. of the 3rd International Friction Stir Welding Symposium, Kobe, Japan, 27 – 28 September, 2001.
- Nagano Y., Jogan S., Hashimoto T. Mechanical properties of aluminum die casting joined by FSW// Proc. of the 3rd International Friction Stir Welding Symposium, Kobe, Japan, 27 – 28 September, 2001.
- Kimapong K., Watanabe T. Friction stir welding of aluminum alloy to steel// Welding J. – 2004. – October. – P. 277 – 282.
- Colligan K.J., Konkol P.J., Fisher J.J. et al. Friction stir welding demonstrated for combat vehicle construction// Welding J. – 2003. – March. – P. 34 – 40.
- Shibayanagi T., Maeda M. Characteristics of microstructure and hardness in friction stir welded 7075 aluminum alloy joints// Trans. JWRI. – 2004. – 33, №1. – P. 17 – 23.
- Ding J., Carter R., Lawless K. et al. Friction stir welding flies high at NASA// Welding J. – 2006. – March. – P. 54 – 59.
- Dolby R.E., Johnson K.J., Thomas W.M. The joining of aluminium extrusions// La metallurgia italiana. – 2004. – №3. – P. 25 – 30.
- Pekkari B. The future of welding and joining// Svetsaren. – 2004. – №1. – Р. 53 – 59.
- Thomas W., Staines D. Better joints using two contra – rotating FSW tools// TWI Connect. – 2006. – May/June. – P. 7.
- Kohn G., Greenberg Y., Makover I. et al. Laser – assisted friction stir welding// Welding J. – 2002. – February. – P. 46 – 48.
- Cook G.E., Smartt H.B., Mitchell J.E. et al .Controlling robotic friction stir welding//Welding J. – 2003. – June. – P. 28 – 34.
- Kato K., Sakano R. Development of spot friction welding and application for automobile body// J. of Light Metal Welding & Construction. – 2004. – 42, №11. – P. 8 – 13.
- Imuta M., Kamimuki K. Development and Application of Friction Stir Welding for Aerospace Industry// Proc. of the IIW International Conference on Technical Trends and Future Prospectives of Welding Technology for Transportation, Land, Sea, Air and Space, Osaka, Japan, 15 – 16 July, 2004. – P. 53 – 64.
- Kumagai M. Application of FSW for aircraft// Welding Technology. – 2003. – 51, №5. – P. 74 – 78.
Сварка трением с перемешиванием: виды, технология, оборудование
Существует большое многообразие сварочных методов. Среди них есть такой экзотический процесс, как сварка трением с перемешиванием. Его отличительной чертой является отсутствие расходных материалов, таких как электроды, сварочная проволока, защитные газы. Недавно разработанный метод обретает широкое распространение.
История появления
История сварки трением с перемешиванием (СТП) началась в 1991 году. Это была инновационная разработка Британского Института Сварки (TWI). Спустя несколько лет технология была использована в строительстве самолетов и морских судов.
Первыми компаниями, запустившими новую технологию в производство, были норвежская Marine Aluminium и американская Boeing. На своих предприятиях они использовали сварочное оборудование концерна ESAB, специализирующегося на разработках в области ротационной сварки трением (РСТ).
С 2003 года компания непрерывно ведет исследования возможностей сварки трением с перемешиванием. Например, были разработаны способы сваривания алюминиевых сплавов и их модификаций, применяющихся в областях строительства самолетов, морских судов и железнодорожных контейнеров.
В авиастроении была найдена возможность заменить заклепочные соединения сварными. Причем скорость сварки методом СТП значительно превышает скорость электродуговой. Сварной шов длинной 6 метров может быть сформирован за одну минуту, тогда как скорость сварки обычным способом достигает всего 0,8-2 м/мин при толщине детали 0,5 см.
Суть процесса
Соединение металлов происходит за счет разогрева в зоне сварки методом трения. Основным сварочным инструментом сварки трением с перемешиванием является металлический стержень, состоящий из двух половинок: бурта и заплечика.
Своей выступающей частью вращающийся стержень погружается в материал, вызывая сильный нагрев. Его подачу ограничивает заплечик, не позволяя пройти насквозь свариваемую деталь. В зоне нагрева материал значительно увеличивает свою пластичность и, придавливаемый заплечиком, формирует единую массу.
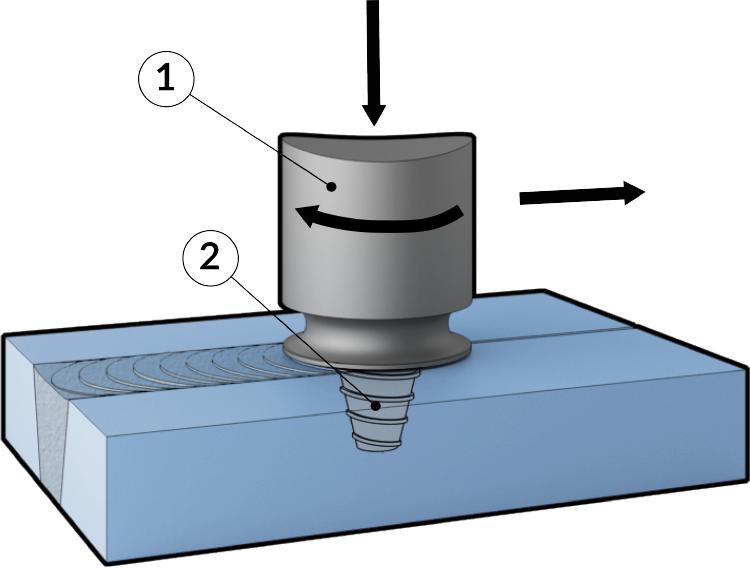
Следующим этапом происходит перемещение стержня вдоль свариваемой зоны. Двигаясь вперед, бурт перемешивает разогретую металлическую массу, которая после остывания образует прочное соединение.
Что влияет на качество СТП
Сварка трением с перемешиванием — это процесс постоянно развивающийся. Но уже сейчас можно выделить несколько параметров, влияющих на качество соединения:
- Усилие, создаваемое инструментом.
- Скорость подачи сварочной головки.
- Величина бурта.
- Окружная скорость вращения стержня.
- Угол наклона.
- Усилие подачи стержня.
Манипулирование характеристиками сварки позволяет достигать соединения разнородных металлов. Например, алюминия и лития. Литий благодаря своей малой плотности и высокой прочности может выступать как легирующий компонент деталей из алюминиевых сплавов, что позволяет применять эту технологию в аэрокосмической отрасли.
Сварка трением с перемешиванием может с легкостью заменить ковку, штамповку, литье, когда они применяются для производства деталей из трудно сочетающихся металлов. Например, сталей со структурой аустенита и перлита, стали из алюминия или бронзы.
В каких сферах применяется
Такие сферы производства, как автомобилестроение, постоянно работают над тем, как увеличить прочностные качества изделия при уменьшении его массы. В связи с этим непрерывно идет внедрение новых материалов, которые были ранее не свойственны ввиду сложности обработки. Все чаще силовые элементы, такие как подрамники, а иногда и кузова целиком, делают из алюминия или его сочетания с другими материалами.
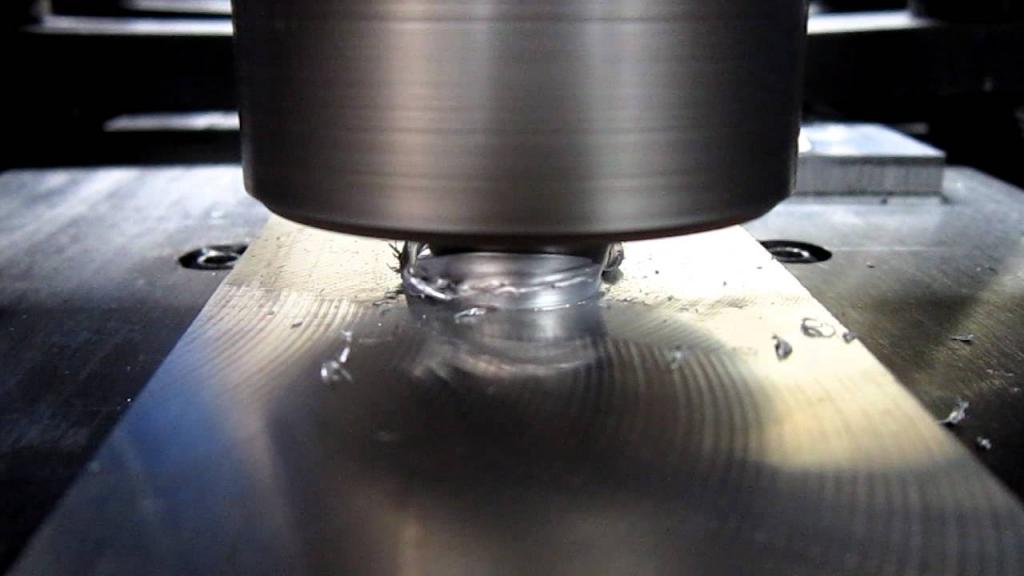
Так, в 2012 году компания “Хонда” применила аддитивные технологии и сварку трением с перемешиванием для производства подрамников для своих автомобилей. Они внедрили сочетание стали и алюминия.
При производстве сварных элементов кузова из алюминия может возникать прожиг листов металла. Этого недостатка лишена СТП. Кроме того, что потребление электричества снижается в 1,5-2 раза, снижаются затраты на расходные материалы, такие как сварочная проволока, защитные газы.
Кроме производства автомобилей СТП применяется в следующих областях:
- Строительное производство: алюминиевые опорные фермы, пролеты мостов.
- Железнодорожный транспорт: рамы, колесные тележки, вагоны.
- Судостроение: переборки, элементы конструкции.
- Авиастроение: топливные баки, части фюзеляжа.
- Пищепром: различные емкости для жидких продуктов (молоко, пиво).
- Производство электротехники: корпуса электродвигателей, параболические антенны.
Кроме алюминиевых сплавов сварка трением с перемешиванием применяется для получения соединений меди, например, при производстве медных контейнеров для захоронения отработанного радиоактивного топлива.
Достоинства СТП
Исследование СТП позволило подобрать режимы сварки при соединении различных групп сплавов. Несмотря на то, что изначально СТП разрабатывалась для работы с металлами с низкой температурой плавления, такими как алюминий (660 °C), впоследствии стала применяться для соединения никеля (1455 °С), титана (1670 °C), железа (1538 °C).
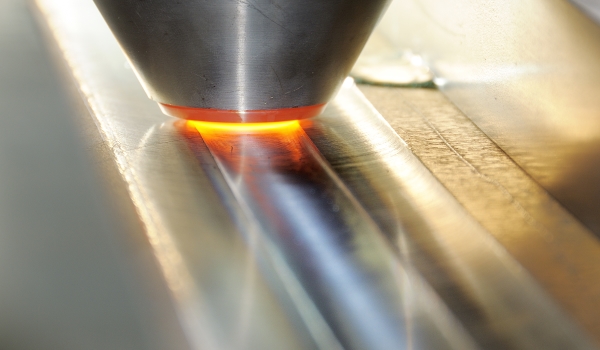
Исследования показывают, что шов, полученный таким способом, полностью соответствует по своей структуре металлу свариваемых деталей и имеет более высокие показатели прочности, меньшие затраты трудоемкости и низкую остаточную деформацию.
Правильно подобранный режим сварки гарантирует соответствие материала шва и свариваемого металла по следующим показателям:
- усталостная прочность:
- прочность на изгиб и растяжение;
- ударная вязкость.
Преимущества перед другими видами сварки
СТП имеет множество достоинств. Среди них:
- Нетоксична. В отличие от других разновидностей, здесь нет горения электрической дуги, благодаря которой расплавленный металл испаряется в зоне сварки.
- Увеличение скорости формирования шва, благодаря чему снижается время производственного цикла.
- Снижение затрат на электроэнергию в два раза.
- Отсутствие необходимости в дальнейшей обработке сварного шва. Инструмент для сварки трением с перемешиванием в процессе работы формирует идеальный шов, не требующий зачистки.
- Нет необходимости в дополнительных расходных материалах (сварочной проволоки, технических газов, флюсов).
- Возможность получения соединений металлов, недоступных для остальных видов сварки.
- Нет необходимости в особой подготовке сварочных кромок, за исключением очистки и обезжиривания.
- Получение однородной структуры шва без пор, в результате чего становится проще контроль качества, который регламентирован для сварки трением с перемешиванием ГОСТ Р ИСО 857-1-2009.
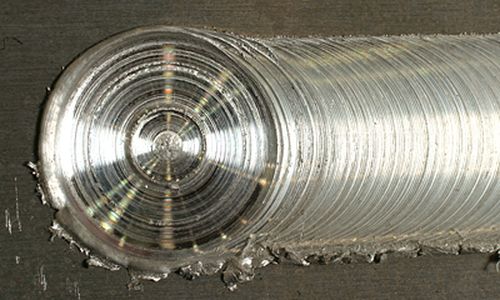
Как проверяется качество сварного шва
Качество сварки проверяется двумя разновидностями контроля. Первый подразумевает разрушение опытного образца, полученного в результате соединения двух деталей. Второй допускает проверку без разрушения. Применяются такие методы, как оптический контроль, аудиометрическое исследование. Оно помогает определить наличие пор и неоднородных включений, ухудшающих характеристики шва. Результаты звукового контроля представляют собой диаграмму, наглядно показывающую места отклонения акустического эха от нормы.
Недостатки метода
При многочисленных достоинствах метод сварки трением имеет сопутствующие минусы:
- Отсутствие мобильности. СТП предполагает соединение неподвижных деталей, жестко закрепленных в пространстве. Это накладывает на оборудование для сварки трением с перемешиванием определенные свойства, такие как неподвижность.
- Низкая универсальность. Громоздкое оборудование настраивается на выполнение однотипных операций. В связи с этим приспособления для сварки проектируются под конкретные задачи. Например, для сваривания автомобильных боковин на конвейере, и ни для чего другого.
- Сварочный шов имеет радиальную структуру. В связи с этим при определенных видах деформации или при работе детали в агрессивной среде может накапливаться усталость сварного шва.
Разновидности СТП по принципу действия
Сварочные процессы, использующие в основе трение, можно разделить на несколько типов:
- Линейное трение. Суть метода сводится к получению неразъемного соединения не в результате действия вращающегося наконечника, а по причине движения деталей друг относительно друга. Воздействуя на поверхность в точке соприкосновения, они создают трение и, как следствие, высокую температуру. Под давлением происходит расплавление примыкающих частей, и возникает сварное соединение.
- Радиальная сварка. Этот метод применяется для производства емкостей большого диаметра, железнодорожных цистерн. Он сводится к тому, что стыки деталей разогреваются вращающимся кольцом, одетым снаружи. Силой трения оно вызывает температуру, близкую к температуре плавления. Примером предприятия, использующего данную технологию, может служить чебоксарская фирма по производству цистерн “Сеспель”. Сварка трением с перемешиванием занимает основную долю сварочных работ.
- Штифтовая сварка. Данная разновидность заменяет собой заклепочное соединение. Этот вид применяется при соединениях внахлест. Вращающийся штифт в месте соприкосновения разогревает свариваемые детали. От высокой температуры происходит расплавление, и штифт проникает внутрь. Остыв, он создает прочное неразъемное соединение.
Разновидности СТП по уровню сложности
Сварочные операции, выполняемые при помощи трения, можно условно разделить на плоскостные и объемные. Главное отличие этих разновидностей в том, что в первом случае сварочный шов формируется в двухмерном пространстве, а во втором в трехмерном.
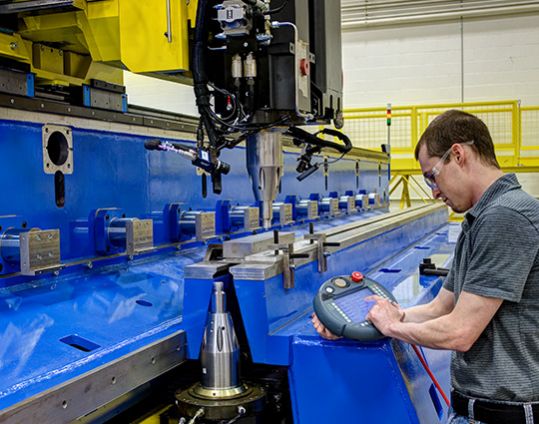
Так, для плоскостных соединений предприятие по выпуску сварочного оборудования ESAB разработало 2D-установку LEGIO. Она представляет собой настраиваемую систему для сварки трением с перемешиванием различных цветных металлов. Разные размерные группы оборудования позволяют сваривать детали малых и больших размеров. Согласно маркировке оборудование LEGIO имеет несколько компоновок, которые отличаются количеством сварочных головок, возможностью сварки по нескольким осевым направлениям.
Для сварочных работ со сложным положением в пространстве существуют 3D-роботы. Такие аппараты устанавливаются на автомобильных конвейерах, где требуются сварные швы непростой конфигурации. Одним из примеров таких роботов может служить установка Rosio производства ESAB.
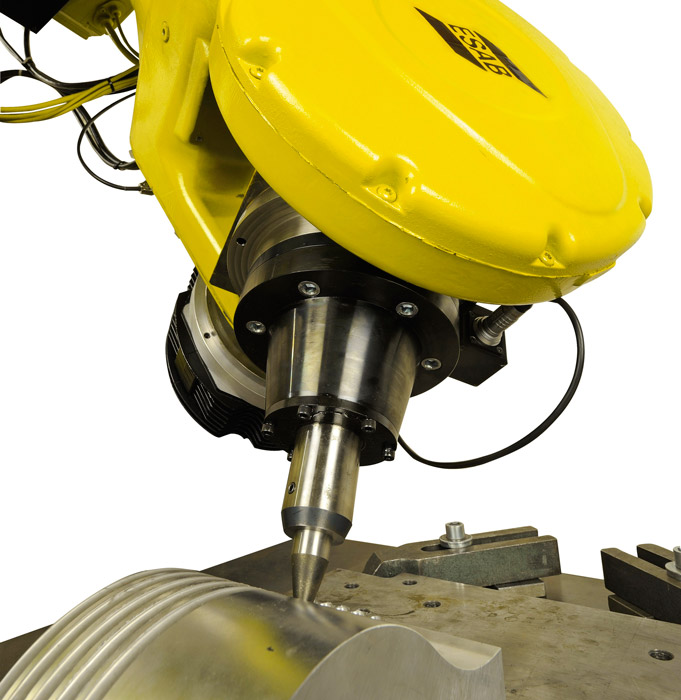
Заключение
СТП выгодно отличается от традиционных видов сварки. Ее повсеместное применение не только сулит экономическую выгоду, но и сохранение здоровья людей, занятых в производстве.
с перемешиванием, подготовка поверхности деталей, алюминиевых сплавов – Механическая сварка на Svarka.guru
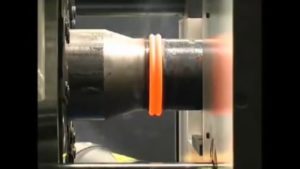
Для достижения контакта используют температуры, размягчающие металл: вольтову дугу, кислородно-ацетиленовую горелку, луч лазера и т.д.
Но есть способ, при котором дополнительный источник тепла не используется. Это сварка металла трением.
Понятие и определение
Процесс перехода кинетической (двигательной) энергии в тепловую известен с незапамятных времен. Заключается он в том, что при трении предметов друг о друга их температура повышается и может достичь точки плавления.
На этом принципе и основан способ соединения двух металлических или пластиковых изделий с помощью трения. Способ этот считается одной из разновидности сварки давлением.


Попытки соединить металл таким способом предпринимались еще в начале века. Но впервые получить по-настоящему качественный стык получилось лишь в 1956 г у А. И. Чудикова. Используя токарный станок, он, вращением нагрел, а затем сжал заготовки, тем самым став родоначальником нового вида сварных соединений.
Область применения
Сварка трением быстро приобрела популярность. С ее помощью оказалось возможным быстро и точно соединять детали. Причем из металлов, которые другим способом соединить сложно. К примеру, сталь с титаном, медь с алюминием и т.п.
Нагрев только поверхностных слоев дал возможность сваривать изделия, не допуская температурных деформаций. Соединять изделия, прошедшие чистовую обработку без порчи поверхности.
Такой способ соединения используют для редких, дорогостоящих металлов, уменьшая их расход за счет отсутствия шва, выгорания и разбрызгивания.
Преимущества и недостатки
Из минусов, точнее — ограничений метода можно назвать следующие:
- необходимость громоздкого оборудования;
- низкая универсальность процесса: невозможно либо невыгодно сваривать тяжелые, крупные изделия, ограничена конфигурация свариваемых элементов;
- требование точного соблюдения технологических регламентов;
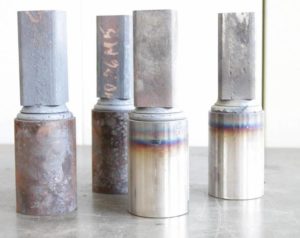
- позволяет выполнять сварное соединение металлов, плохо или совсем не поддающихся другим способам, скажем, соединить алюминиевый брусок с титановой пластиной;
- дает экономию энергозатрат, особенно при поточном изготовлении типовых деталей;
- точно выдерживает характеристики соединений;
- чтобы подготовить поверхность заготовок не требуется особых мероприятий, от большинства загрязнений она очиститься в процессе соединения;
- не требует специфических расходных и вспомогательных материалов;
- качество соединения не уступает основному металлу не только по прочности, но по пластичности и упругости;
- обладает высокими экологическими качествами: отсутствует УФ излучение, нет разбрызгивания горячего металла, пыли, вредных газов.
Высокую экономичность метода подтверждает скорость окупаемости оборудования. Она редко превышает год. При активном использовании составляет несколько месяцев.
Виды и схемы
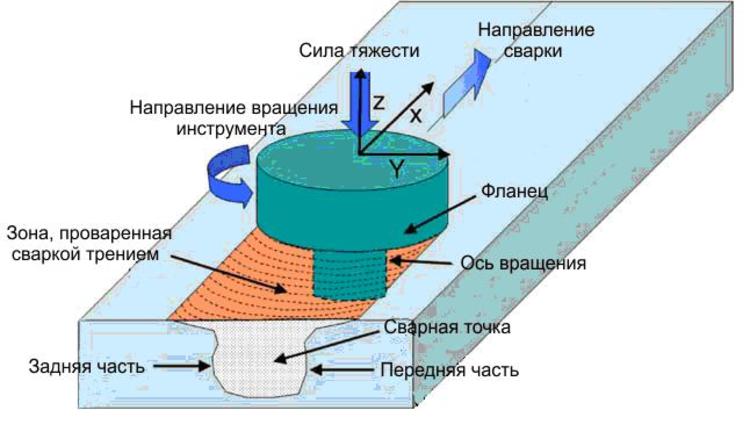
- Сварка трением с непрерывным приводом. Самый первый способ, с которого методика началась. Две детали, одна из которых неподвижна, вторая прижимается к ней одновременно вращаясь. Как только металл размягчится, вращение останавливают, детали сжимают.
- Инерционная сварка. Развитие предыдущего метода. Вращающаяся заготовка раскручивается до определенной скорости, а затем продолжает вращаться по инерции.
- Комбинированный вид сварки сочетает два предыдущих. До определенного момента вращение обеспечивает привод. Затем его отключают, а заготовку по достижению точно определенной скорости и усилия резко останавливают.
- Колебательная сварка трением. Или как ее еще называют вибрационная. Отличием является не вращательное, а возвратно поступательное движение с высокой частотой.
- Сварка трением с перемешиванием. Специфический вид позволяющий получить уникальные результаты. Сварка перемешиванием производится вращением особого валика, при неподвижных соединяемых деталях. Размягчая металл, такой наконечник погружается на определенную глубину, а затем перемещается по стыку свариваемых деталей, продолжая вращение. При этом метал перемешивается, образуя цельный стык.
- Орбитальная сварка трением. Отличается перемещением изделия по определенной орбите (обычно по окружности). При этом сама деталь не вращается.
- Радиальная сварка трением. Способ используют для соединения трубчатых заготовок. Сами детали при этом обычно неподвижны, а относительно них (внутри или снаружи) вращается еще одна — кольцеобразная.
- Роликовая сварка. С успехом используется для соединения тонких плоских элементов. Нагрев создает вращающийся ролик. Он перемещается по наложенным внахлест листам, оставляя за собой шов.
- Штифтовая сварка. Служит для создания точечных соединений, ремонта каверн и раковин. Температура создается вращающимся штифтом.
- Линейная сварка. Принцип схож с колебательной, при большей траектории перемещения. Иногда для соединения достаточно переместить деталь лишь в одном направлении.
- Ротационная сварка. Нередко встречающееся понятие — обобщенное название всех типов, при которых заготовки вращаются относительно своей оси. Сюда входит радиальная, инерционная, сварка трением с перемешиванием и пр.
- Наплавка с помощью сварки трением. Служит для образования слоя покрытия одного металла другим. Деталь вращается, одновременно перемещаясь, при этом ее металл словно намазывается на основу. Таким образом возможно получить толстый нержавеющий защитный слой, либо поверхностный сплав двух металлов.
Кроме перечисленных основных типов существуют и другие разновидности, отличающиеся незначительными нюансами.
Технология
При движении свариваемых трением деталей происходит ряд последовательных процессов:
- под воздействием механических нагрузок разрушаются пленки окислов и загрязнения;
- заготовки разогреваются, металл выдавливается из стыка, одновременно вынося все загрязнения;
- вращение резко прекращается, при этом давление на детали не убирается, а часто увеличивается.
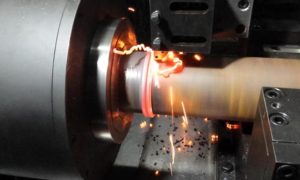
Наилучший эффект получается при использовании деталей с одинаковыми свариваемыми поверхностями. Исходя из этой особенности, в процессе подготовки, заготовки специально подрезают, выравнивая их торцы.
Сварочный процесс, выполняемый за счет трения, включает две переменных:
Скорость вращения и давление. Подбор этих параметров зависит от сочетания металлов, составляя наиболее сложную составляющую процесса. На 80% расчеты основаны на экспериментальных данных.
Динамические нагрузки возникающие при этом способе в ряде случаев требует дополнительной термической обработки. При этом она не требуется для низколегированных и некоторых классов высоколегированных сталей.
Оборудование
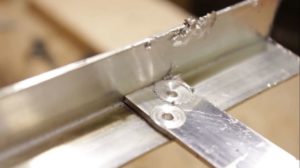
Отличает их мощность, осевое усилие вращения, проковки, размер и форма деталей которые с их помощью удается сварить и пр.
Некоторые модели оборудованы дополнительными фрезерными устройствами для снятия, выдавливаемого из зоны стыка металла.
Контроль качества соединений
В качестве руководства по контролю соединений, выполненных методом трения, используют ГОСТ 3242-79 «Соединения сварные. Методы контроля качества».
Основная методика проверки — обследование ультразвуковыми приборами. Кроме того, применяются выборочные разрушающие испытания образцов на изгиб, разрыв, поперечную деформацию.
В завершение разговора
Подводя итоги, можно сделать вывод: методика сваривания трением является инструментом инженерного арсенала промышленности. Дает эффективна при правильном использовании.
Учитывая, что с момента изобретения сварки с помощью трения не прошло еще и ста лет, велика вероятность что потенциал ее далеко не исчерпан.
СВАРКА ТРЕНИЕМ С ПЕРЕМЕШИВАНИЕМ (СТП) НА ПРИМЕРЕ НАРАЗЪЕМНОГО БИМЕТАЛЛИЧЕСКОГО СОЕДИНЕНИЯ АЛЮМИНИЙ – МЕДЬ
Основным требованием, предъявляемым к любой конструкции, применяемой в различных отраслях промышленности, является обеспечение высокого уровня работоспособности в течение определенного срока при заданных условиях эксплуатации. В настоящее время одним из эффективных способов выполнения указанных требований получения высококачественных соединений является сварка трением с перемешиванием (СТП).
Метод сварки трением с перемешиванием был разработан в Британском институте сварки в 1991 году. Он относится к твердофазным способам образования соединений материалов с использованием трения. Этот способ соединения разрабатывался для алюминиевых сплавов с целью решения многих проблем, связанных со сваркой плавлением. Дальнейшее развитие метода показал возможность его применения для широкого круга материалов [1].
Выполненные в последние годы исследования показали, что СТП является эффективным способом получения высококачественных соединений конструкций различной геометрии, включая листовые материалы, пространственные профильные конструкции, трубы, восстановления изношенных деталей, модифицирования и улучшения структуры материалов, залечивания трещин и литейных дефектов.
СТП может быть признан универсальной технологией, имеющей большие перспективы в различных отраслях производства. По мнению ведущих мировых экспертов, технология СТП является революционной в области сварки листовых материалов из легких сплавов (алюминиевых и магниевых), она оценивается как ключевая для создания авиационной техники пятого поколения. Толщины свариваемых СТП листовых материалов достигли для алюминиевых сплавов 110 мм, а для сталей и никелевых сплавов 45 мм [2].
Процесс сварки трением с перемешиванием заключается в том, что для сварки используют инструмент в форме стержня, состоящий из двух основных частей: заплечика или бурта (утолщенная часть) и наконечника (выступающая часть). Размеры этих конструктивных элементов выбирают в зависимости от толщины и материала свариваемых деталей. Так, длину наконечника устанавливают приблизительно равной толщине детали, подлежащей сварке, диаметр заплечика может изменяться от 1,2 до 25 мм. Вращающийся с высокой скоростью инструмент в месте стыка вводится в соприкосновение с поверхностью заготовок так, чтобы наконечник внедрился в заготовки на глубину, примерно равную их толщине, а заплечик коснулся их поверхности. После этого инструмент перемещается по линии соединения со скоростью сварки. В результате работы сил трения происходит нагрев металла до пластического состояния, перемешивание его вращающимся инструментом и вытеснение в освобождающееся пространство позади движущегося по линии стыка инструмента. Объем, в котором формируется шов, ограничивается сверху заплечиком инструмента. По окончании сварки вращающийся инструмент выводят из стыка за пределы заготовки. В связи с асимметрией структуры швов в поперечном сечении сварных соединений, полученных сваркой трением с перемешиванием, принято различать сторону набегания, где направление вращения инструмента совпадает с направлением сварки, и противоположную сторону – отхода [3].
Применение СТП связано с высоким качеством получаемых сварных соединений. Перемешивание металла в твердой фазе в условиях «теплой» деформации делает эффект более прочной микроструктуры чем основной материал. Прочность на растяжение и усталостная прочность сварного шва составляет 90% от характеристик основного материала на уровне, обеспечиваемом применением дорогостоящих сварок. СТП может выполняться в различных позициях вертикальной, горизонтальной, под наклоном, и т.д. Обеспечивается возможность сваривания разнородных материалов, термопластичных пластиков и композиционных материалов [4].
Целью работы является исследование микроструктуры и механических свойств неразъемного биметаллического соединения алюминиевого сплава АД0 и меди марки М1, полученного сваркой трением с перемешиванием.
В качестве материала исследования выбрано неразъемное биметаллическое СТП соединение из алюминиевого сплава АД0 и меди марки М1.Физико-химические свойства алюминия и меди представлены в таблице 1.
Таблица 1.
Физико-химические свойства алюминия и меди.
Свойство вещества | Значение | |
Алюминий | Медь | |
Плотность, г/см3 | 2.7 | 8.92 |
Температура плавления, ºС | 660 | 1083 |
Тепловодность, Вт/(м·К) | 203.5 | 401 |
Электропроводность, см/м | 37·106 | 58.1·106 |
Временное сопротивление разрыву, кг/мм2 | Литой 10-12, деформируемый 18-25 | 25-29 |
Модуль Юнга, 105 кгс/см2 | 7.1 | 12.5 |
Температурный коэффициент линейного расширения 1/ºС | 16·10-6 | 24·10-6 |
Схема СТП сплава АД0 и меди М1 представлена на рисунке 1.
Рисунок 1. Схема СТП сплава АД0 и меди М1
Для подготовки образца к исследованию использовалась шлифовальная бумага различной зернистости (P400-P2000). Для полирования использовалась алмазная паста. Далее происходило травление в два этапа. Сначала сторона Al – реактивом Келлера (HCl , HF, HNO3, H2O), затем вторая сторона Cu – FeCl3, HCl, H2O.
Для исследования поверхности сварного соединения использовался оптический микроскоп АЛЬТАМИ МЕТ-1С. С помощью оптического микроскопа были получены изображения алюминиевой и медной поверхностей образца, которые затем объединены в одно изображение всей поверхности.
Замеры микротвердости проводились микротвердометром ПМТ3 по методу Виккерса по всей длине образца с нагрузкой P=50 г., шагом 1мм и временем выдержки 12 секунд.
На рисунке 2 показано составное макроскопическое изображение неразъемного биметаллического соединения алюминиевого сплава АД0 и меди марки М1, полученного сваркой трением с перемешиванием. Красными пунктирными линиями показаны характерные структурные зоны СТП соединения.
1) Зона перемешивания (ЗП) – зона, в которой происходит деформация и образуется ядро шва.
2) Зона термомеханического влияния или ЗТМВ – зона вблизи сварочного шва. Характерна небольшая деформация. В данной зоне происходит передача тепла с зоны перемешивания.
3) Зона термического влияния или ЗТВ – зона, в которой зерна почти не отличаются от зерен основного металла, но обладают большей твердостью.
4) Основной металл (ОМ) – зона, которая не подвергается никаким воздействиям.
Рисунок 2. Составное макроскопическое изображение неразъемного биметаллического соединения алюминиевого сплава АД 0 и меди марки М1 полученного сваркой трением с перемешиванием.
1 – зона перемешивания (ЗП), 2 – зона термомеханического влияния (ЗТМВ), 3 – зона термического влияния (ЗТВ), 4 – основной металл (ОМ).
Микротвердость измерялась вдоль белой пунктирной линии
Микротвердость измерялась вдоль белой пунктирной линии (см. рис.3) равноудаленно от поверхностей с шагом 1 мм. Результаты измерений представлены в таблице 2.
Таблица 2.
Результаты измерений микротвердости образца.
x, мм | HV, кгс/м2 | x, мм | HV, кгс/м2 |
-12 | 39,688 | 1 | 43,08 |
-11 | 41,352 | 2 | 43,08 |
-10 | 48 | 3 | 31,704 |
-9 | 37,22 | 4 | 96,26 |
-8 | 37,7 | 5 | 62,66 |
-7 | 41,928 | 6 | 61,824 |
-6 | 40,776 | 7 | 69,26 |
-5 | 30,936 | 8 | 49,66 |
-4 | 35,34 | 9 | 60,78 |
-3 | 29,248 | 10 | 51,2 |
-2 | 34,924 | 11 | 62,88 |
-1 | 32,472 | 12 | 57,004 |
0 | 44,28 |
На рисунке 3 показан график распределения микротвердости, из которого следует, что в пластине меди ЗТВ и ЗТМВ она существенно меньше, чем в аналогичных зонах в алюминиевой пластине. Это связано с тем, что температура плавления и теплопроводность у меди выше, чем у алюминия, а метод СТП подразумевает асимметрию при соединении пластин. Инструмент периферийно захватывает медь, вследствие чего разогрев меди происходит в меньшей степени, а скорость теплоотдачи увеличивается.
Рисунок 3. Распределение микротвердости в неразъемном биметаллическом СТП соединении сплава АД0 и меди М1
На рисунке 4а показано увеличенное изображение ОМ меди марки М1. Средний размер зерна d=34.75±25.19 мкм. На рисунке 4б виден резкий переход от ЗТМВ к ОМ, что подтверждает ранее описанные предположения о теплопроводности меди.
Рисунок 4. Увеличенное в 200 крат изображение микроструктуры меди марки М1 в биметаллическом СТП соединении: а) ОМ, б) ЗТМВ и ЗТВ
В пластине алюминия размер зерна значительно уменьшается от ОМ к ЗП. Средний размер зерна в ОМ составляет d=211.36±67.019 мкм, что в 84.5 раз превышает средний размер зерна в ЗП (1,5-2,5 мкм), это можно заметить на рисунке 5.
Рисунок 5. Увеличенное в 50 крат изображение микроструктуры алюминия АД0 в биметаллическом СТП соединении в зоне ОМ
В ходе эксперимента было выявлено, что микротвердость материала в зоне перемешивания выше, чем в зоне термического влияния и в зоне основного металла. В медной пластине пик микротвердости наблюдается в ЗТВ.
Микроструктура исследуемого образца изменяется от ОМ к ЗП как для алюминиевой пластины, так и для меди. Средний размер зерна в ЗП существенно ниже, чем в ОМ.
Список литературы:
- Всесоюзный конструкторско-технологический Институт Сварочного Производства [Электронный ресурс] – Режим доступа: http://www.visp-ltd.com, свободный. – Загл. с экрана;
- Сварка трением с перемешиванием – Мир Сварки [Электронный ресурс] – Режим доступа: http://weldworld.ru, свободный. – Загл. с экрана
- Сварка трением с перемешиванием конструкционных материалов [Электронный ресурс] – Режим доступа: http://svarka-24.info, свободный. – Загл. с экрана.
- Промышленный интернет-портал Мир Пром. [Электронный ресурс] – Режим доступа: http://mirprom.ru, свободный. – Загл. с экрана.
Способ сварки трением с перемешиванием алюминиевых сплавов
Изобретение может быть использовано для выполнения стыковых соединений деталей из алюминиевых жаропрочных сплавов толщиной 2…6 мм. Используют сварочный инструмент с пином, выполненным в форме усеченного конуса длиной 1,8…5,7 мм с тремя «левыми» резьбовыми канавками, и опорным буртом диаметром 8…18 мм со спиральной канавкой. Погружение инструмента в стык соединяемых деталей осуществляют с минимальной скоростью вертикального перемещения 7…12 мм/мин и высокой скоростью вращения 350…500 об/мин до достижения заданной глубины, равной 90…95% толщины свариваемых деталей. Угол инструмента при этом изменяют относительно вертикальной оси с 0 до -1,5…-2,5°. Затем, сохраняя угол и скорость вращения, инструмент перемещают вдоль линии стыка со скоростью 220…300 мм/мин при постоянном осевом усилии, равном 12…15 кН, управляемом датчиками обратной связи. Способ позволяет предотвратить износ инструмента, устранить внутренние дефекты и обеспечить прочность сварного соединения до 90% от предела прочности основного материала. 2 ил.
Изобретение относится к области сварки трением с перемешиванием (СТП) и может быть использовано в различных отраслях машиностроения и авиастроения для выполнения стыковых соединений алюминиевых жаропрочных сплавов толщиной 2…6 мм.
Специфический дефект соединений, выполненных СТП, называют «kissing bonds» («несплавление» в корне шва). Дефект устраняется подбором режима сварки. Разрушение образцов в процессе испытаний происходит по данному дефекту, что является причиной снижения предела прочности сварного соединения.
Известен способ сварки трением стыковых соединений из алюминиевых сплавов, включающий предварительное выполнение в стыке деталей сквозного отверстия, погружение в него вращающегося инструмента, состоящего из наконечника в виде тела вращения с заплечником, до контакта заплечника с поверхностью деталей и перемещение инструмента вдоль стыка. В процессе сварки пропускают через инструмент и соединяемые детали импульс тока плотностью 30-50 А/мм2 при длительности протекания тока (2,0-3,5)/n, где n — частота вращения инструмента (патент РФ №2350443 от 27.03.2009).
Известный способ обеспечивает полное проплавление деталей и формирование корня шва более равномерной формы при минимальном технологическом припуске. Данный технологический прием не требует увеличения толщины заготовок, что уменьшает затраты на последующую механическую обработку сварного соединения. Подобранное соотношение длительности импульса тока, его плотности и частоты вращения инструмента способствует качественному формированию соединения деталей и мелкодисперсному распределению фрагментов оксидных пленок и выделений вторичных фаз.
Недостатком известного способа сварки трением с перемешиванием стыковых соединений алюминиевых сплавов является отсутствие постоянного усилия, действующего на материал со стороны инструмента. В совокупности с отсутствием наклона инструмента это ведет к недостаточному уплотнению и измельчению зерен материала сварного шва. Сварка без постоянного усилия при большой длине сварного шва обязательно приведет к образованию дефектов из-за неровностей станины станка или деформации самих заготовок. Другим существенным недостатком данного способа является плавление металла благодаря пропускаемому току. В результате локального плавления, а также быстрого остывания и кристаллизации, ровно, как и усадки материала будут возникать большие остаточные напряжения. Третьим недостатком является меньшая экономическая эффективность из-за наличия технологического припуска на сварной шов и большие энергозатраты.
Наиболее близким способом того же назначения к заявленному изобретению по совокупности признаков является способ сварки трением с перемешиванием алюминиевых сплавов (патент Великобритании №91259788), при котором сварку осуществляют в три этапа. На первом этапе вращающийся с высокой скоростью инструмент цилиндрической или ступенчатой формы с заплечником погружают в стык соединяемых деталей на глубину, примерно равную их толщине. Когда заплечник инструмента войдет в контакт с поверхностью деталей, погружение останавливают и включают перемещение инструмента вдоль линии соединения. На третьем этапе (по окончании сварки) вращающийся инструмент поднимают и выводят из стыка. Данный способ принят за прототип.
Признаки прототипа, совпадающие с существенными признаками заявляемого способа — погружение вращающегося с высокой скоростью инструмента, состоящего из пина и опорного бурта, в стык соединяемых деталей до контакта опорного бурта инструмента с поверхностью деталей; перемещение инструмента вдоль линии соединения; подъем вращающегося инструмента и выведение его из стыка.
Недостатком известного способа, принятого за прототип, является повышенный износ инструмента при его введении в стык деталей, а также его поломка в процессе сварки листов толщиной 5-6 мм из-за недостаточного разогрева корневой части соединения.
Задача, на решение которой направлено заявляемое изобретение, — разработка способа сварки трением с перемешиванием стыковых соединений из жаропрочных алюминиевых сплавов, позволяющего предотвратить износ инструмента, устранить внутренние дефекты и обеспечить прочность сварного соединения до 90% от предела прочности основного материала.
Поставленная задача была решена за счет того, что в известном способе сварки трением с перемешиванием стыковых соединений из алюминиевых сплавов, включающем погружение вращающегося с высокой скоростью инструмента, состоящего из пина и опорного бурта, в стык соединяемых деталей до контакта опорного бурта инструмента с поверхностью деталей, перемещение инструмента вдоль линии соединения, подъем вращающегося инструмента и выведение его из стыка, согласно изобретению используют сварочный инструмент с пином, выполненным в форме усеченного конуса длиной 1,8…5,7 мм с тремя «левыми» резьбовыми канавками, и опорным буртом диаметром 8…18 мм со спиральной канавкой, до введения пина в стык деталей производят закрепление листовых деталей толщиной 2…6 мм в тисках и фрезерование свариваемых кромок по плоскости, погружение инструмента в стык соединяемых деталей осуществляют с минимальной скоростью вертикального перемещения 7…12 мм/мин и высокой скоростью вращения 350…500 об/мин до достижения заданной глубины, равной 90…95% толщины свариваемых деталей, при этом угол инструмента изменяют относительно вертикальной оси с 0 до -1,5…-2,5°, затем, сохраняя угол и скорость вращения, инструмент перемещают вдоль линии стыка со скоростью 220…300 мм/мин при постоянном осевом усилии, равном 12…15 кН, управляемом датчиками обратной связи.
Признаки заявляемого технического решения, отличительные от прототипа — используют сварочный инструмент с пином, выполненным в форме усеченного конуса длиной 1,8…5,7 мм с тремя «левыми» резьбовыми канавками, и опорным буртом диаметром 8…18 мм со спиральной канавкой; до введения пина в стык деталей производят закрепление листовых деталей толщиной 2…6 мм в тисках и фрезерование свариваемых кромок по плоскости; погружение инструмента в стык соединяемых деталей осуществляют с минимальной скоростью вертикального перемещения 7…12 мм/мин и высокой скоростью вращения 350…500 об/мин до достижения заданной глубины, равной 90…95% толщины свариваемых деталей, при этом угол инструмента изменяют относительно вертикальной оси с 0 до -1,5…-2,5°; сохраняя угол и скорость вращения, инструмент перемещают вдоль линии стыка со скоростью 220…300 мм/мин при постоянном осевом усилии, равном 12…15 кН, управляемом датчиками обратной связи.
Отличительные признаки в совокупности с известными позволят устранить пористость в корне шва, предотвратить коагуляции зерен различных зон сварного шва и благодаря этому обеспечить прочность соединения до 90% от предела прочности основного материала. Кроме того, предотвращается износ инструмента.
Предлагаемый способ иллюстрируется чертежами, представленными на фиг. 1, 2.
На фиг. 1 показана схема закрепления листовых заготовок перед сваркой трением перемешиванием. На схеме показаны:
1 — опорный бурт инструмента для СТП;
2 — пин инструмента для СТП;
3 — подложка;
4 — сварной шов;
5 — свариваемые детали;
6 — пример установки станочных прижимов;
7 — линия стыка;
8 — ось вращения инструмента;
9 — нормаль к поверхности деталей;
10 — оси установки боковых прижимов;
11 — направление сварки;
12 — направление вращения инструмента;
13 — угол наклона инструмента.
На фиг. 2 показано поперечное сечение сварного шва после испытаний на определение кратковременных свойств.
Способ осуществляется следующим образом.
Перед процессом сварки трением с перемешиванием подготавливают кромки свариваемых деталей 5. Для этого детали 5 зажимаются в тисках свариваемыми кромками вверх и фрезеруются по плоскости без скоса кромок. В процессе сварки инструменту придается вращение 350…500 об/мин, заглубление в материал деталей производится со скоростью 7…12 мм/мин, при этом меняется угол инструмента относительно вертикальной оси с 0 до -1,5…-2,5°, при достижении заданной глубины, равной 90…95% от толщины материала, сохраняя угол и скорость вращения, инструмент начинает перемещаться вдоль линии стыка со скоростью 220…300 мм/мин, сварка осуществляется при постоянном осевом усилии, равном 12…15 кН. При таком режиме заглубление инструмента непостоянно и регулируется в соответствии со значениями осевого усилия, получаемыми с датчиков обратной связи станка.
Листовые заготовки (детали) 5 обрабатываются в паре, чтобы не допустить появления зазора между ними. Прижим боковых поверхностей деталей 5 осуществляется в плоскости станины перпендикулярно стыку 7 для обеспечения максимально полного контакта сварочных кромок. Прижим деталей 5 в вертикальной плоскости станочными прижимами 6 предотвращает движение деталей 5 относительно станины во время процесса сварки и возникновение высоких циклических нагрузок и изгиба инструмента (фиг. 1), а также обеспечивает плотный контакт деталей 5 с подложкой 3. Подложка 3 используется в виде пластины из нержавеющей стали без внешних дефектов и отполированной до зеркального блеска для предотвращения проникновения расплава алюминия в материал подложки 3 и, как следствие, прилипания к ней свариваемых деталей 5. Подложка 3 должна быть таких размеров, чтобы полностью перекрывать сварной шов 4 и места установки прижимов 6.
На формирование соединения и его качество помимо подготовки кромок и закрепления существенное влияние оказывает форма пина 2 и диаметр опорного бурта 1 (фиг. 1). Экспериментально установлено, что выполнение пина 2 в форме усеченного конуса длиной 1,8…5,7 мм с тремя «левыми» резьбовыми канавками и опорного бурта диаметром 8…18 мм со спиральной канавкой позволяет при положительном вращении инструмента направлять пластифицированный металл к центру и вниз к корню сварного шва и предотвратить повышенный износ инструмента (фиг. 2).
Для качественного формирования соединения без дефектов в виде пор в корневой части шва (фиг. 2) необходимо обеспечить пребывание металла соединяемых деталей в этой зоне в пластичном состоянии некоторый промежуток времени. В этом случае обеспечивается перемешивание металла деталей в корне шва. Вращение инструмента на стадии заглубления пина в материал детали со скоростью 350…500 об/мин способствует прогреву материала деталей до пластифицированного состояния и позволяет избежать крайних состояний: фрезерования канавки либо плавления материала деталей.
Заглубление пина 2 (фиг. 1) в материал деталей со скоростью 7…12 мм/мин при скорости вращения инструмента 350…500 об/мин и достижение заданной глубины пина, обеспечивающее полный контакт поверхности деталей с опорным буртом 1 инструмента, позволяет прогреть материал деталей в месте контакта с пином и предотвратить появление стружки или излишнего облоя, прогреть корневую зону сварного соединения и сохранить некоторый промежуток времени ее материал в пластичном состоянии, а также предотвратить нагрев и вероятность разрушения инструмента.
Отклонение инструмента относительно вертикальной оси с 0 до -1,5…-2,5° необходимо для уплотнения сварного шва позади инструмента и снижения вероятности возникновения дефектов сварного шва.
Скорость вращения инструмента 350…500 об/мин в процессе сварки трением с перемешиванием остается постоянной для поддержания твердофазного процесса сварки. Сохранение угла и скорости вращения инструмента в процессе его перемещения вдоль линии стыка позволяет получать плотную мелкозернистую структура сварного шва и достигать прочности сварного соединения более 90% от прочности основного материала.
Поддержание скорости сварки или продольной подачи инструмента 220…300 мм/мин позволяет при прочих заданных параметрах осуществлять процесс сварки деталей без внешних и внутренних дефектов, а также без значительного роста зерен различных зон сварного шва.
Сварка при постоянном осевом усилии, равном 12…15 кН, позволяет обеспечить равномерную структуру сварного шва без дефектов и пористости в корне шва. При этом сварка с постоянным усилием и управлением по обратной связи, в отличие от сварки с постоянным уровнем заглубления, позволяет ликвидировать дефекты, возникающие при отклонении от плоскостности подложки, станины станка и самих деталей. При уменьшении усилия возникает риск непровара в корне шва и возникновения дефектов в виде «червоточины» (тоннельный дефект). При увеличении усилия инструмент будет сильнее заглубляться в материал деталей, тем самым приводя к утонению сварного шва, появлению концентраторов напряжений на границах перемещения опорного бурта, а также подмешиванию материала подложки в сварочной шов, деформации подложки и риску разрушения инструмента.
По предлагаемому способу выполняли опытную сварку образцов из жаропрочного алюминиевого сплава 1151 AT толщиной 3 мм и 4 мм. Для сварки применяли инструмент с пином в форме усеченного конуса длиной 2,7 мм с тремя «левыми» резьбовыми канавками и опорным буртом диаметром 12 мм со спиральной канавкой. При сварке инструменту придается вращение 500 об/мин, заглубление в материал заготовок производится со скоростью 10 мм/мин, при этом меняется угол инструмента относительно вертикальной оси с 0 до -1,5°, по достижении заданной глубины 2,7 мм, сохраняя угол и скорость вращения, инструмент начинает перемещаться вдоль линии стыка со скоростью 280 мм/мин, сварка осуществляется при постоянном осевом усилии, равном 14 кН. При таком режиме заглубление инструмента непостоянно и регулируется в соответствии со значениями осевого усилия, получаемыми с датчиков обратной связи станка.
Испытания на определение кратковременных свойств показали, что получаемый сварной шов не содержит внутренних дефектов в виде пор и скопления пор, снижающих предела прочности сварного соединения (фиг. 2).
Предлагаемый способ позволяет получать сварные соединения с прочностью 90% от прочности основного материала без усадки шва и образования внутренних дефектов. Кроме того, предотвращается износ инструмента.
Способ сварки трением с перемешиванием стыковых соединений листовых деталей из алюминиевых сплавов, включающий погружение вращающегося инструмента, состоящего из пина и опорного бурта, в стык соединяемых деталей до контакта опорного бурта инструмента с поверхностью деталей, перемещение инструмента вдоль линии соединения, подъем вращающегося инструмента и выведение его из стыка, отличающийся тем, что используют сварочный инструмент с пином, выполненным в форме усеченного конуса длиной 1,8…5,7 мм с тремя «левыми» резьбовыми канавками, и опорным буртом диаметром 8…18 мм со спиральной канавкой, при этом до введения пина в стык деталей производят закрепление листовых деталей толщиной 2…6 мм в тисках и фрезерование свариваемых кромок по плоскости, погружение инструмента в стык соединяемых деталей осуществляют со скоростью вертикального перемещения 7…12 мм/мин и скоростью вращения 350…500 об/мин до достижения заданной глубины, равной 90…95% толщины свариваемых деталей, причем угол инструмента изменяют относительно вертикальной оси с 0 до -1,5…-2,5°, затем при сохранении угла и скорости вращения инструмент перемещают вдоль линии стыка со скоростью 220…300 мм/мин при постоянном осевом усилии, равном 12…15 кН, управляемом датчиками обратной связи.
Способ сварки трением с перемешиванием стыковых соединений алюминиевых сплавов
Изобретение может быть использовано при стыковом соединении деталей из алюминиевых сплавов, имеющих низкую свариваемость. Вращающийся инструмент, состоящий из наконечника в виде тела вращения и заплечика, погружают в стык свариваемых деталей до контакта заплечика с их поверхностью и выдерживают. Включают перемещение инструмента вдоль стыка, таким образом, что скорость перемещения инструмента вдоль стыка поддерживают в пределах 0,08-0,48 мм/об. Непосредственно за инструментом осуществляют принудительное охлаждение шва и зоны термического влияния со скоростью не менее 0,5°С/с. Охлаждение осуществляют путем подачи струи охлаждающей жидкости или ее смеси с воздухом из спрейера непосредственно за инструментом или погружением свариваемых деталей и рабочего инструмента в ванну с циркулирующей охлаждающей жидкостью. При сварке инструментом типа Боббин Тул охлаждение шва и зоны термического влияния осуществляют одновременной с лицевой и обратной стороны соединения. Способ обеспечивает повышение прочности сварных соединений нагартованных и термически упрочняемых алюминиевых сплавов. 3 з.п. ф-лы, 6 ил., 4 табл.
Изобретение относится к области сварки и может быть использовано в стыковых соединениях алюминиевых сплавов, преимущественно нагартованных и термически упрочняемых.
Из уровня техники известен способ сварки трением с перемешиванием, при котором предварительно в стыке соединяемых деталей выполняют сквозное отверстие диаметром больше диаметра наконечника инструмента (W.M. Thomas, E.D. Nicholas, E.R. Watts, D.G. Staines. Friction Based Welding Technology for Aluminum. Materials Science Forum Vols. 2002. pp. 1543-1548). Затем вращающийся инструмент погружают в отверстие до соприкосновения заплечника с поверхностью деталей. Когда заплечик инструмента войдет в контакт с поверхностью деталей, погружение останавливают и включают перемещение инструмента вдоль линии соединения. Недостатком данного способа сварки трением с перемешиванием снижение прочностных свойств соединений термически упрочняемых алюминиевых сплавов за счет интенсивного теплового воздействия и протекающих за счет этого процессов перезакалки.
Известен способ сварки трением с перемешиванием (патент Великобритании №9125978.8), при котором сварку осуществляют в три этапа. На первом этапе вращающийся с высокой скоростью инструмент цилиндрической или ступенчатой формы с заплечником погружают в стык соединяемых деталей на глубину, примерно равную их толщине. Когда заплечник инструмента войдет в контакт с поверхностью деталей, погружение останавливают и включают перемещение инструмента вдоль линии соединения. На третьем этапе (по окончании сварки) вращающийся инструмент поднимают и выводят из стыка. Недостатком упомянутого способа сварки трением с перемешиванием является снижение механических свойств сварных соединений (особенно угла изгиба) вследствие недостаточного развития процесса нагрева и перемешивания металла в корневой части соединения. Происходит образование корневого непровара в корне шва с образованием скопления частиц оксидов на оси шва.
Наиболее близким по технической сущности к заявляемому является способ сварки трением стыковых соединений из алюминиевых сплавов, при котором на стыке деталей предварительно выполняют сквозное отверстие и погружают в него наконечник вращающегося инструмента до контакта его заплечика с поверхностью деталей [Патент РФ № 2247639 МПК7В 23К 20/12]. Ось отверстия располагают под углом α к нормали к поверхности деталей в плоскости их стыка, определяемым соотношением α=(0,8–1,0) δ, где δ — толщина деталей. Диаметр отверстия задают в пределах D=d+(0,10-0,15) мм. Наконечник заглубляют в стык на (0,90-0,95)δ. Скорость перемещения инструмента вдоль стыка деталей регулируют в пределах 0,20-0,35 мм/об.
Недостатком прототипа является снижение уровня прочности сварных соединений термический упрочняемых и нагартованных алюминиевых сплавов при сварке вследствие интенсивного теплового воздействия на свариваемый металл и вызванные этим нагревом структурные изменения.
Технический результат заключается в повышении прочностных свойств сварных соединений термически упрочняемых и нагартованных алюминиевых сплавов.
Технический результат, на достижение которого направлено данное изобретение, обеспечивается за счет того, что вращающийся инструмент, состоящий из наконечника в виде тела вращения и заплечика, погружают в стык свариваемых деталей до контакта заплечика с их поверхностью, выдерживают, после чего включают перемещение инструмента вдоль стыка, отличающийся тем, что скорость перемещения инструмента вдоль стыка поддерживают в пределах 0,08-0,48 мм/об, а непосредственно за инструментом осуществляют охлаждение шва и зоны термического влияния со скоростью не менее 0,5°С/с.
Охлаждение можно осуществлять разными вариантами: путем подачи охлаждающей жидкости или ее смеси с воздухом из спрейера, путем погружения свариваемых деталей и инструмента в охлаждающую жидкость и любым другими, обеспечивающими необходимую скорость охлаждения.
Подробнее сущность заявляемого способа сварки трением с перемешиванием поясняется чертежами:
— на фиг. 1 показана схема осуществления заявляемого способа;
— на фиг. 2 представлена микроструктура металла шва сплава 1460 при сварке с подачей 0,07 мм/об;
— на фиг. 3 показано несплавление в металле шва при сварке с подачей инструмента 0,49 мм/об;
— на фиг. 4 — представлена схема расположения зоны охлаждения в плане при осуществлении заявляемого способа;
— на фиг. 5 представлена схема осуществления заявляемого способа сварки трением с перемешиванием при погружении свариваемых деталей и инструмента в ванну с циркулирующей водой;
— на фиг. 6 приведена схема выполнения охлаждения сварного соединения при использовании при сварке инструмента Боббин Тул.
Предложенный способ сварки трением осуществляется следующим образом. Свариваемые заготовки из алюминиевого сплава 1 и 2 собирают встык до их соприкосновения по торцовым поверхностям в плоскости стыка 3. Затем рабочий инструмент, состоящий из заплечика 4 и наконечника 5, приводят во вращение и погружают в материал заготовок 1 и 2 в плоскости стыка 3 до соприкосновения поверхности свариваемых заготовок с заплечиком 4. После некоторой выдержки (примерно 2-40 с), которая требуется для разогрева металла заготовок в зоне введения наконечника до пластичного состояния, включается перемещение рабочего инструмента вдоль стыка 3 соединяемых заготовок. Непосредственно позади инструмента при его перемещении вдоль стыка будет формироваться шов 6 (фиг. 1).
Позади рабочего инструмента расположен спрейер 7, через который подается охлаждающая жидкость или смесь ее с воздухом 8, охлаждающая зону 9 сварного соединения, в которую включается шов и зона термического влияния.
По завершении сварки всей длины стыка линейное перемещение инструмента останавливают и его выводят из материала свариваемых заготовок.
Формирование качественного сварного шва без внутренних дефектов определяется технологическим параметром режима сварки трением с перемешиванием, который представляет собой отношение скорости линейного перемещения инструмента вдоль стыка к его частоте вращения,и по сути является величиной подачи инструмента при сварке. Величину подачи инструмента поддерживают в диапазоне 0,08-0,48 мм/об. При величине подачи менее 0,08 мм/об наблюдается чрезмерный разогрев металла свариваемых заготовок с появлением жидкой фазы по границам зерен и интенсивным образованием грата по границам шва (фиг. 2).
Увеличение подачи инструмента свыше 0,48 мм/об сопровождается резкимснижением нагрева металла заготовок в зоне формирования шва, что влечет за собой образование внутренних дефектов в виде несплавлений и микротрещин (фиг. 3). При этом для каждого алюминиевого сплава имеется свой оптимальный диапазон величин подачи инструмента, укладывающийся в интервал 0,08-0,48 мм/об.
Высказанные положения подтверждаются результатами механических испытаний соединений листовых полуфабрикатов толщиной 4 мм сплавов 1565чН и 1460Т1, выполненных на различных режимах (таблица 1). Полученные результаты испытаний подтвердили оптимальность выбранного диапазона подачи рабочего инструмента на один оборот для повышения прочности сварных соединений стыковых соединений алюминиевых сплавов, выполненных сваркой трением с перемешиванием.
Дальнейшее повышение механических свойств сварных соединений при сварке трением с перемешиванием возможно только за счет регулирования термического цикла сварки с использованием принудительного охлаждения металла шва и зоны термического влияния.
Таблица 1
Номер режима | Параметры режима СТП | Механические свойства соединений | ||||
Частота вращения инструмента ω, об/мин | Скорость сварки Vсв, мм/мин | Подача инструмента на один оборот Vсв/ω, мм/об | Прел прочности сварного соединенияσВ, МПа | Предел прочности металла шва σВш, МПа | Угол изгиба α, град. | |
Термически неупрочняемый нагартованный алюминиевый сплав 1565чН | ||||||
1 | 720 | 57,6 | 0,08 | 375 | 335 | 155 |
2 | 720 | 86,4 | 0,12 | 398 | 368 | 160 |
3 | 720 | 129,6 | 0,18 | 411 | 430 | 180 |
4 | 720 | 180 | 0,25 | 419 | 465 | 180 |
5 | 720 | 237,6 | 0,33 | 415 | 422 | 165 |
Термически упрочняемый алюминиевый сплав 1460Т1 | ||||||
6 | 900 | 63 | 0,07 | 295 | 248 | 67 |
7 | 900 | 117 | 0,13 | 300 | 305 | 102 |
8 | 900 | 261 | 0,29 | 319 | 336 | 145 |
9 | 900 | 369 | 0,41 | 315 | 320 | 133 |
10 | 900 | 450 | 0,50 | 310 | 298 | 100 |
С этой целью позади заплечика 4 рабочего инструмента с помощью спрейера 7 производится охлаждение зоны 9, ширина которой L ширину зоны воздействия заплечика (зона шва) и ширину двух зон термического влияния по обе стороны от шва (фиг. 4). Эксперименты по сварке трением с перемешиванием листов алюминиевых сплавов толщиной 3-8 мм показывают, что ширина зоны термического влияния составляет 2-5 мм на сторону. С учетом диаметра заплечика, применяемого при сварке таких заготовок в диапазоне 12-16 мм и принимая во внимание наибольшую протяженность зоны термического влияния 5 мм, тогда ширина зоны охлаждения будет изменяться в пределах 22-26 мм.
На протяженность зоны термического влияния, которая определяется температурой нагрева металла в данной области и длительность его пребывания при этом температуре, наибольшее влияние оказывает скорость охлаждения металла. Эксперименты показали, что для всех марок термоупрочняемых и нагартованных алюминиевых сплавов в диапазоне толщин листов 3-12 мм оптимальный величина скорости охлаждения водо-воздушной смесью должна быть не менее 0,5°С/с. Выбор скорости охлаждения менее 0,5°С/с не приводит к уменьшению протяженности зоны термического влияния и повышению прочности сварных соединений. Повышение скорости охлаждения более 35°С/с не приводит к заметному повышению свойств, но сопровождается увеличением расхода охлаждающей жидкости. Поэтому такое действие является не целесообразным. При охлаждении металла шва и зоны термического влияния регулирование скорости охлаждения осуществляют изменением расхода охлаждающей смеси или ее состава (соотношения воздуха в жидкости).
В качестве примера конкретного выполнения способа сварки трением с перемешиванием выполняли сварку с охлаждением шва и зоны термического влияния позади рабочего инструмента водо-воздушной смесью сплавов 1565чН и 1460Т1. Результаты испытаний сварных соединений листов сплавов 1565чН и 1460Т1, выполненных на оптимальных режимах для каждого из этих сплавов, в зависимости от скорости охлаждения металла шва и зоны термического влияния, представлены в таблице 2.
Представленные данные свидетельствуют, что применение охлаждения шва и зоны термического влияния при сварке трением с перемешиванием нагартованных и термически упрочненных алюминиевых сплавов позволяют решить задачу повышения прочностных свойств сварных соединений.
Таблица 2
Параметры режима СТП | Ширина зоны термического влияния (ЗТВ), мм | Механические свойства соединений | |||||
Частота вращения инструмента ω, об/мин | Скорость сварки Vсв, мм/мин | Подача инструмента на один оборот Vсв/ω, мм/об | Скорость охлаждения металла шва и ЗТВ, °С/с | Прел прочности сварного соединенияσВ, МПа | Предел прочности металла шва σВш, МПа | Угол изгиба α, град. | |
Термически неупрочняемый нагартованный алюминиевый сплав 1565чН | |||||||
720 | 180 | 0,25 | 0 | 5,3 | 390 | 415 | 160 |
720 | 180 | 0,25 | 0,2 | 5,0 | 395 | 418 | 160 |
720 | 180 | 0,25 | 0,5 | 2,3 | 438 | 472 | 180 |
720 | 180 | 0,25 | 10 | 1,8 | 445 | 477 | 180 |
720 | 180 | 0,25 | 35 | 1,2 | 447 | 486 | 180 |
720 | 180 | 0,25 | 80 | 1,2 | 447 | 488 | 180 |
Термически упрочняемый алюминиевый сплав 1460Т1 | |||||||
900 | 63 | 0,29 | 0 | 4,4 | 319 | 336 | 145 |
900 | 63 | 0,29 | 0,25 | 4,25 | 330 | 345 | 150 |
900 | 63 | 0,29 | 0,5 | 0,92 | 510 | 544 | 180 |
900 | 63 | 0,29 | 35 | 0,85 | 518 | 562 | 180 |
900 | 63 | 0,29 | 70 | 0,84 | 518 | 563 | 180 |
Полученные экспериментальные результаты подтверждают эффективность охлаждения металла шва и зоны термического влияния со скоростью не менее 0,5°С/сдля повышения прочностных и пластических свойств сварных соединений.
Реализация сварки трением с перемешиванием с принудительным охлаждением металла шва и зоны термического влияния возможно также при полном погружении свариваемых заготовок, рабочего инструмента и зажимного приспособления в ванну (емкость) с циркулирующей охлаждающей жидкостью (фиг. 5).
Свариваемые заготовки 1 прижимаются к подкладке 10 усилием Р от действия прижимов 11. В зоне свариваемого стыка в материал заготовок 1 внедрен наконечник 5, а заплечик 4 только касается поверхности заготовок и осуществляет их нагрев за счет сил трения при своем вращении. При этом заплечик 4 прижимается к поверхности заготовок усилием F.
Свариваемые заготовки 1, рабочий инструмент с заплечиком 4 и наконечником 5, подкладка 10 и прижимы 11 погружаются в ванну 12 с охлаждающей жидкостью 13 ниже ее уровня. Процесс сварки трением с перемешиванием осуществляется с охлаждением заготовок, рабочего инструмента и оснастки циркулирующей охлаждающей жидкостью 13.Необходимая скорость охлаждения при этом поддерживается за счет регулирования расхода на входе охлаждающей жидкости в ванну.
В табл. 3 представлены сравнительные результаты механических испытаний сварных соединений нагартованного сплава 1565чН и термически упрочняемого сплава 1460Т1, полученных по различным вариантам. В качестве охлаждающей жидкости в примере конкретного выполнения была использована вода.
Таблица 3
Вариант охлаждения металла шва | Параметры режима СТП | Механические свойства сварного соединения | ||||
Частота вращения инструмента ω, об/мин | Скорость сварки Vсв, мм/мин | Подача инструмента на один оборот Vсв/ω, мм/об | Скорость охлаждения металла шва и ЗТВ, °С/с | Прел прочности сварного соединенияσВ, МПа | Предел прочности металла шва σВш, МПа | Угол изгиба α, град. |
Термически неупрочняемый нагартованный алюминиевый сплав 1565чН | |||||||
Охлаждение жидкостно-воздушной смесью | 720 | 180 | 0,25 | 5 | 445 | 477 | 180 |
Охлаждение при сварке в ванне | 720 | 180 | 0,25 | 7 | 440 | 475 | 180 |
Термически упрочняемый алюминиевый сплав 1460Т1 | |||||||
Охлаждение жидкостно-воздушной смесью | 900 | 63 | 0,29 | 8 | 510 | 544 | 180 |
Охлаждение при сварке в ванне | 900 | 63 | 0,29 | 9 | 505 | 547 | 180 |
При использовании другой охлаждающей жидкости (имеющей отличные от воды теплофизические свойства) необходимо корректировать ее расход, чтобы поддерживать необходимую скорость охлаждения шва и зоны термического влияния соединения.
В случае применения при сварке трением с перемешиванием инструмента типа Боббин Тул шов 1 (фиг. 6) формируется при большей эффективности нагрева по сравнению со схемой, показанной на фиг. 1 примерно в 1,50-2 раза за счет выделения теплоты при трении по поверхности соединяемых заготовок заплечика 2 с хвостовиком 3 и стягивающей гайки 5, закрепленной на на резьбе на наконечнике 4. Поэтому для обеспечения необходимой скорости охлаждения шва и зоны термического влияния со скоростью не менее 0,5°С/с подачу охлаждающей струи жидкостно-воздушной смеси 6 осуществляют с обеих сторон соединения.
В качестве примера конкретного выполнения данного способа сварки трением с перемешиванием может служить эксперимент по сварке сплавов 1565чН и 1460Т1. Результаты механических испытаний полученных сварных соединений приведены в таблице 4.
Таблица 4
Вариант охлаждения металла шва | Параметры режима СТП | Механические свойства сварного соединения | |||||
Частота вращения инструмента ω, об/мин | Скорость сварки Vсв, мм/мин | Подача инструмента на один оборот Vсв/ω, мм/об | Скорость охлаждения металла шва и ЗТВ, °С/с | Прел прочности сварного соединенияσВ, МПа | Предел прочности металла шва σВш, МПа | Угол изгиба α, град. | |
Термически неупрочняемый нагартованный алюминиевый сплав 1565чН | |||||||
Охлаждение жидкостно-воздушной смесью с двух сторон | 720 | 180 | 0,25 | 7,2 | 445 | 477 | 180 |
Охлаждение жидкостно-воздушной смесью с одной стороны | 720 | 180 | 0,25 | 2,4 | 428 | 455 | 170 |
Без охлаждения | 720 | 180 | 0,25 | 2,5 | 390 | 415 | 145 |
Термически упрочняемый алюминиевый сплав 1460Т1 | |||||||
Охлаждение жидкостно-воздушной смесью с двух сторон | 900 | 63 | 0,29 | 4,9 | 510 | 544 | 180 |
Охлаждение жидкостно-воздушной смесью с одной стороны | 900 | 63 | 0,29 | 1,8 | 505 | 537 | 155 |
Без охлаждения | 900 | 63 | 0,29 | 0,26 | 325 | 355 | 130 |
Таким образом, полученные данные подтверждают эффективность применения принудительного охлаждения металла шва и зоны термического влияния при сварке трением с перемешиванием нагартованных и термически упрочняемых алюминиевых сплавов, а также достижении технического результата, заключающегося в повышении на 10-30% прочностных свойств сварных соединений при сохранении их высокой пластичности.
1. Способ сварки трением с перемешиванием соединений алюминиевых сплавов, преимущественно нагартованных и термически упрочняемых, включающий погружение вращающегося инструмента, состоящего из наконечника в виде тела вращения и заплечика, в стык свариваемых деталей до контакта заплечика с их поверхностью и выдержку, после чего осуществляют перемещение инструмента вдоль стыка, отличающийся тем, что скорость перемещения инструмента вдоль стыка поддерживают в пределах 0,08-0,48 мм/об, а непосредственно за инструментом осуществляют охлаждение шва и зоны термического влияния со скоростью не менее 0,5°С/с.
2. Способ сварки трением с перемешиванием соединений алюминиевых сплавов по п. 1, отличающийся тем, что охлаждение шва и зоны термического влияния осуществляют путем подачи струи охлаждающей жидкости или ее смеси с воздухом.
3. Способ сварки трением с перемешиванием соединений алюминиевых сплавов по п. 1, отличающийся тем, что сварку осуществляют при погружении свариваемых деталей и рабочего инструмента в ванну с циркулирующей охлаждающей жидкостью.
4. Способ сварки трением с перемешиванием соединений алюминиевых сплавов по п.1, отличающийся тем, что при сварке инструментом типа Боббин Тул охлаждение шва и зоны термического влияния осуществляют одновременно с лицевой и обратной стороны соединения.