Водородный сварочный аппарат: преимущества работы
Водородное пламя используется как альтернатива ацетиленовому. С его помощью можно осуществлять процесс сваривания, резки, запаивания. Сварочный водородный аппарат обеспечивает эффективность и безопасность процесса. Использование водорода вместо ацетилена в процессе газовой сварки обеспечивает большую продуктивность. Сварочный шов получается качественным, а производительность остается на высоком уровне.
Суть процесса
Водородная сварка – разновидность газопламенной. Ее суть заключается в смешивании газов — водорода и кислорода. Работа позволяет получить пористый тонкий шов, однако в сварочной емкости остается большой шлаковый слой. Чтобы это избежать, в газовую смесь добавляют минимальное количество органики, а именно углеводородов. Эти вещества обладают способностью «гасить» кислород.
Сложным вопросом при организации водородной сварки считается выбор эффективного источника подачи газа.
Необходимо помнить, что этот газ пригоден для проведения сварки из малоуглеродистых сталей, железа, однако для сварки листов и труб из нержавеющей стали его применять нельзя.
Проблема возникает из-за взаимодействия водорода с никелем при высоких температурах. После охлаждения выделяется газ и образует повреждения на поверхности. Также такая сварка не применяется при обработке меди.
Варианты применения
Сварочный водородный аппарат подключают как к бытовой, так и к электрической сети с тремя фазами. Также его используют для ручной и автоматизированной работы.
Любой сварочный аппарат включается в эксплуатационный режим очень быстро – это зависит от температуры окружающей среды, а также величины расхода газа. Малые габариты прибора способны обеспечить его высокую мощность. Продукт горения водорода – пар, не имеющий токсических свойств. Поэтому как при работе, так и при хранении сварочный аппарат на основе этого газа абсолютно безопасен. Однако требования техники безопасности стоит соблюдать — нужно применять защитный костюм и очки при эксплуатации устройства.
Существуют следующие варианты применения оборудования:
- сваривание;
- выпаивание;
- порошковое напыление;
- кислородная резка;
- термическое упрочнение;
- наплавка.
Выбор режимов эксплуатации обеспечивает широкий спектр возможностей прибора — от сварки малой толщины до осуществления резки больших по толщине листов стали. Качественный сварочный аппарат – помощник стоматологов, ювелиров, также он часто применяется при ремонте холодильного оборудования, а также в пунктах технического обслуживания.
Помимо этого, оборудование используется при ремонте ступиц, двигателя, радиаторов, для проведения кузовных работ.
Безопасность устройства достигается благодаря системе автоматического отключения при достижении запредельного уровня давления и допустимой концентрации электролита. Это защищает от возможных взрывов и пожаров.
Плюсы водородной сварки
Преимущества данного типа сварочных работ таковы:
- эффективность;
- безопасность;
- экологичность;
- компактность;
- небольшая трудоемкость;
- широкий спектр материалов обработки: сталь, благородные и цветные металлы, стекло, чугун, керамика, стекло;
- для эксплуатации требуется только вода, бесперебойная работа не нуждается в других компонентах;
- водородная атмосфера создает защиту поверхности от окисления;
- нет необходимости перезарядки.
Новейшая разработка – сварочный аппарат, способный соединять трубы, толщина металлической поверхности которых составляет до 5 мм. Устройства применяются при заваривании участков с браком, а также для разрезания металлов толщиной до 30 мм. Такая сварка возможна при баллонной подаче кислорода. Так получают чистый срез. Металл подвергается закаливанию, но не происходит насыщения углеродом и нет побочного образования оксида азота. Такое оборудование эксплуатируется в метро, тоннельных помещениях и колодцах.
Таким образом, применение водородной сварки – отличное решение для широкого круга сфер деятельности. Главное достоинство метода заключается в его абсолютной безопасности при соблюдении всех условий эксплуатации.
Интересное по теме:
Водородный сварочный аппарат
Водородный сварочный аппарат ЭС-1000
Система водородной газосварки. Высокая температура пламени, отсутствие баллонов, резка металла до 10мм. Экономия на обслуживании до 100 раз по сравнению с ацетиленовой сваркой.
Водородный сварочный аппарат
Водородно – кислородное пламя имеет хорошую эффективность и является предпочтительной заменой ацетилено-кислородного пламени, для сварки, пайки и резки.
Водородно – кислородная сварка частично заменяет сварку и пайку в среде инертных газов (например, аргона), и в отличии от стандартных способов газосварки, является абсолютно безвредной, так как продуктом горения является водяной пар.
Водородно – кислородный сварочный аппарат можно использовать для широкого спектра обрабатываемых материалов: любой стали, цветные и благородные металлы, чугун, стекло, керамика, золото и т.д.
Для работы водородно – кислородного сварочного аппарата необходима только вода в маленьком количестве (примерно 0,2 литра в час).
Для обеспечения бесперебойной работы водородного сварочного поста, не нужно создавать запасы ацетилена и кислорода в баллонах.
Наш водородный сварочный аппарат позволяет выполнять широкий спектр работ – от сварки, микросварки и пайки пламенем размером с иголку до резки листовой стали толщиной до 10 мм и более. Обычно водородно – кислородная смесь превосходит ацетилено-кислородную по технологическим возможностям, а не просто является её более дешевым заменителем.
Водородный сварочный аппарат может работать непрерывно.
При применении водородно-кислородного пламени уменьшаются затраты на обслуживание рабочих мест, отсутствуют отходы производства, абсолютно безвредно – продуктом горения является водяной пар.
Преимущество этого аппарата перед аналогами
- 1. большая производительность при небольших габаритах
- 2. стабильное давление
- 3. специальная технология изготовления пластин обеспечивает большой ресурс работы
- 4. применение ШИМ (PWM) позволило уменьшить энергозатраты и снизить вес оборудования
- 5. интеллектуальное управление
- 6. Автоматическое и ручное управление
- 7.
удобство в использовании
- 8. долговечность и простота обслуживания
- 9. удобное управление мощностью
- 10. широкий спектр применения
- 11. высокое качество при небольшой стоимости
- 12. высокая эффективность и удобство, по сравнению с газобаллонным оборудованием
- 13. один аппарат можно использовать для работ на нескольких рабочих местах одновременно. Аппарат будет самостоятельно подстраиваться под действия персонала, автоматически удерживая нужное давление газа в системе.
Автоматика облегчает переход от использования баллонов к интеллектуальному, современному, экономичному оборудованию. У Вас в руках та же горелка, тот же принцип регулирования расхода газа, прибор сделает все остальное сам.
Сравнение затрат при эксплуатации сварочного оборудования
Стандартное газобалонное оборудование в Украине:
- Стоимость Ацетилен баллона 40 л. – 50$/шт.
- Заправка Ацетилен баллона 40 л. – 40$/шт.
- Стоимость Пропан-бутан баллона 50 л. – 35$/шт.
- Заправка Пропан-бутана 50 л. – 15$/шт.
- Стоимость Кислород баллон 40 л. – 50$/шт.
- Заправка Кислород баллон 40 л. – 6$/шт.
- Редуктор + манометр – 15$.
- Стоимость комплекта с баллоном Ацетилен – 161$.
- Стоимость комплекта с баллоном Пропан-бутан – 121$. (без шлангов, горелок и т.д)
Стоимость расходных материалов за 5 рабочих дней (30 рабочих часов).
- 1 баллон Ацетилена + 10 баллонов Кислорода = 100$.
- 1,3 баллон Пропан-бутан + 10 баллонов Кислорода = 80$.
- + доставка баллонов, стоимость которой часто превышает стоимость самого газа.
Стоимость водородно-кислородного газосварочного оборудования:
Ориентировочная стоимость – 1300$.
Стоимость расходных материалов за 5 рабочих дней (30 рабочих часов).
Мощность усредненная 2,5 кВт/час
2,5 х 30 = 75 кВт/час ( потребление ел. Энергии за 30 часов. )
75 х 0,05 = 3,75. (примерная стоимость ел. Энергии за 30 часов.)
Расход воды 15 л.
15 х 0,1 = 1,5$. (стоимость дистиллированой воды)
3,75 + 1,5 = 5,25$. (затраты на 30 рабочих часов)
Вывод:
Стоимость расходных материалов за 5 рабочих дней (30 рабочих часов).
- Ацетилена + Кислорода = 100$.
- Пропан-бутан + Кислорода = 80$.
- Вода + Эл. Энергия = 5, 25 $.
Сварочный аппарат водородный: зачем нужно подобное оборудование?
Водородное сварочное оборудование: особенности соединения материалов
Сварочный аппарат – устройство, без участия которого при строительстве, на производстве или в быту задача скрепления металлических деталей будет практически неосуществима. Водородный аппарат для производства сварочных работ – оборудование, достойное внимания, а поэтому постараемся рассмотреть все его полезные качества.
Описание и характеристики водородного аппарата
Водородный аппарат предназначен для резки, пайки и сварки металлов, при этом материалы могут быть цветными и черными.
Водородный аппарат послужит отличным помощником в ювелирном деле, в стоматологических целях, на станциях технического обслуживания. Такой сварочный аппарат пригодится в отраслях, где необходим высокотемпературный локальный нагрев.
Сварочный аппарат функционирует на водороде, вырабатываемом внутри устройства.
Заполучить водород выходит благодаря расщеплению молекул воды на атомы кислорода и водорода, при этом образуя газовую смесь с высокой потенциальной энергией, используемой для соединительных работ.
Для продуктивного функционирования данного оборудования понадобится полтора литра воды (дистиллированной), а также доступ к бытовой электрической сети (220В).
Технические характеристики:
- Питающая сеть – 220В,
- Потребляемая мощность – до 2 кВт,
- Производительность газа – до 480л/час,
- Расход дистиллированной воды – 150 мл.
/час.
Преимущества:
- Стабильное давление,
- Сварочный аппарат имеет значительную производительность при незначительных габаритах,
- Специализированная технология производства пластин обеспечивает существенный ресурс работы,
- Различные режимы функционирования,
- Удобство применения,
- Удобное управление мощностью,
- Долговечность, а также простота обслуживания,
- Широкий спектр использования,
- Высокое качество и стабильность наряду с незначительной стоимостью,
- Применение ШИМ дает возможность снизить энергетические затраты, снизить массу оборудования,
- Эффективность и удобство при сравнении с газосварочными баллонами,
- Возможность эксплуатации одного оборудования на нескольких рабочих местах одновременно,
- Универсальность.
Как сделать оборудования своими руками?
Водород, как известно, во время смешивания с воздухом способствует созданию взрывоопасной смеси – так называемого, гремучего газа. Температура горения водорода составляет 2800 градусов Цельсия.
Целесоо
бразно разобраться в собственноручном производстве такого полезного оборудования, как сварочный аппарат. Постараемся рассмотреть порядок работы и применяемые материалы с инструментами.
Инструменты и материалы:
- Листовая нержавеющая сталь,
- Болты с гайками,
- Оргстекло, либо стеклопластик,
- Резина или пластик,
- Герметик,
- Соединительные штуцера, а также патрубки.
Порядок работы:
- Начинать своими руками собирать качественный сварочный аппарат следует со сборки электролизера, а поэтому, сначала нарежьте пластины нержавеющей стали,
- Далее в пластинах стоит высверлить отверстия, предназначенные для циркуляции раствора, прохода газа между отсеками,
- Следующим образом понадобится нарезать изолирующие пластиковые промежутки, но лучше будет выполнить их из резины,
- Теперь нужно вырезать своими руками боковые основы из вышеупомянутого материала – оргстекла, после чего можно приступать к сворке оборудования.
Для того чтобы для болтов отверстия совпадали, желательно положить одно стекло на другое, после чего высверлить аккуратно по диагонали два отверстия. Далее надо зафиксировать их шурупами,
- Начинаем собирать сварочный аппарат. На оргстекло следует нанести герметик, уложить пластик на пластик, кладем нержавейку, после чего промазываем герметиком,
- Наиболее крайние пластины потребуется отвести таким образом, чтобы можно было зафиксировать контакты,
- Прежде чем как закрывать верхний отсек в стекле, надо выполнить пару отверстий своими руками вверху для выхода газа, а также для поддержки уровня раствора снизу,
- Нижний патрубок понадобится соединить с бутылкой, в которую будет заливаться раствор. Таким образом, раствор будет попадать в отсеки,
- Теперь можно приступать к производству водного затвора. Таким образом, в пробке выполняем два отверстия, при этом стоит знать, что в одну будет входить трубка электролизера и загружается в воду. Второе отверстие служит для трубки горелки,
- Роль горелки может исполнить обыкновенный шприц, то есть игла,
- Для питания можно использовать мощный источник постоянного тока, расчет напряжения – 2В на пластину нержавеющей стали.
То должен приравниваться не менее 7 А, при этом рабочий параметр подается на крайние пластины,
- В конце можно будет сделать самое главное – приготовить раствор, для чего добавим обычную пищевую соду. Концентрация воды должна рассчитываться по амперажу ток должен находиться в пределах 4-6А.
Изучив определенные шаги изготовления устройства, произвести сварочный аппарат, который будет эксплуатироваться при помощи водорода, и в будущем послужит отличную и долговечную службу.
Водородный сварочный аппарат: преимущества работы
- Суть процесса
- Варианты применения
- Плюсы водородной сварки
Водородное пламя используется как альтернатива ацетиленовому. С его помощью можно осуществлять процесс сваривания, резки, запаивания.
Сварочный водородный аппарат обеспечивает эффективность и безопасность процесса. Использование водорода вместо ацетилена в процессе газовой сварки обеспечивает большую продуктивность.
Сварочный шов получается качественным, а производительность остается на высоком уровне.
Водородная сварка – разновидность газопламенной. Ее суть заключается в смешивании газов — водорода и кислорода. Работа позволяет получить пористый тонкий шов, однако в сварочной емкости остается большой шлаковый слой. Чтобы это избежать, в газовую смесь добавляют минимальное количество органики, а именно углеводородов. Эти вещества обладают способностью «гасить» кислород.
Сложным вопросом при организации водородной сварки считается выбор эффективного источника подачи газа. Известно, что применять водородный баллон для этих целей опасно. Сжиженный водород при высокой концентрации вызывает удушье и головокружение.
Также проблемой является невидимость пламени в дневном свете. Днем применение такой сварки возможно только с использованием датчиков. Также проблема решается при помощи электролизеров – приборов, разлагающих воду на составляющие – кислород и водород.
Проблема возникает из-за взаимодействия водорода с никелем при высоких температурах. После охлаждения выделяется газ и образует повреждения на поверхности. Также такая сварка не применяется при обработке меди.
Сварочный водородный аппарат подключают как к бытовой, так и к электрической сети с тремя фазами. Также его используют для ручной и автоматизированной работы. При работе происходит подача по шлангу смеси газов в горелку. Температура регулируется в диапазоне 600-2600 градусов по Цельсию.
Любой сварочный аппарат включается в эксплуатационный режим очень быстро – это зависит от температуры окружающей среды, а также величины расхода газа. Малые габариты прибора способны обеспечить его высокую мощность.
Продукт горения водорода – пар, не имеющий токсических свойств. Поэтому как при работе, так и при хранении сварочный аппарат на основе этого газа абсолютно безопасен.
Однако требования техники безопасности стоит соблюдать — нужно применять защитный костюм и очки при эксплуатации устройства.
Существуют следующие варианты применения оборудования:
- сваривание,
- выпаивание,
- порошковое напыление,
- кислородная резка,
- термическое упрочнение,
- наплавка.
Выбор режимов эксплуатации обеспечивает широкий спектр возможностей прибора — от сварки малой толщины до осуществления резки больших по толщине листов стали. Качественный сварочный аппарат – помощник стоматологов, ювелиров, также он часто применяется при ремонте холодильного оборудования, а также в пунктах технического обслуживания.
Помимо этого, оборудование используется при ремонте ступиц, двигателя, радиаторов, для проведения кузовных работ.
Преимущества данного типа сварочных работ таковы:
- эффективность,
- безопасность,
- экологичность,
- компактность,
- небольшая трудоемкость,
- широкий спектр материалов обработки: сталь, благородные и цветные металлы, стекло, чугун, керамика, стекло,
- для эксплуатации требуется только вода, бесперебойная работа не нуждается в других компонентах,
- водородная атмосфера создает защиту поверхности от окисления,
- нет необходимости перезарядки.
Новейшая разработка – сварочный аппарат, способный соединять трубы, толщина металлической поверхности которых составляет до 5 мм. Устройства применяются при заваривании участков с браком, а также для разрезания металлов толщиной до 30 мм.
Такая сварка возможна при баллонной подаче кислорода. Так получают чистый срез. Металл подвергается закаливанию, но не происходит насыщения углеродом и нет побочного образования оксида азота.
Такое оборудование эксплуатируется в метро, тоннельных помещениях и колодцах.
Таким образом, применение водородной сварки – отличное решение для широкого круга сфер деятельности. Главное достоинство метода заключается в его абсолютной безопасности при соблюдении всех условий эксплуатации.
Водородная сварка своими руками
Газовая сварка позволяет аккуратно накладывать швы на тонкий металл. Смена сопла с разным диаметром выходного отверстия дает возможность производить работы как на трубах, так и на узких элементах. Но у пропан-ацетиленового пламени есть предел — существуют ограничения по использованию баллонов в замкнутом пространстве под землей в тоннелях.
Еще обычным пламенем не получится припаять сильно мелкие детали ювелирных украшений. Поэтому применяется водородная сварка. Метод аналогичен с ацетиленовым пламенем, и его легко освоить. Для реализации используется несложное оборудование. Возможна водородная сварка своими руками, что пригодится для ремонтных работ на дому или в небольших мастерских.
Суть и особенности
Газовая сварка происходит за счет горения газообразного вещества. Чаще всего применяют ацетилен в баллонах или из генератора, где карбид окисляется водой. Там, где требуется меньшая температура пламени на тонких изделиях, или в случае проведения работ по резке металла, используется газ пропан. Он подается по шлангам в трубку горелки и воспламеняется от поджига спичкой.
По второй шланге из соседнего баллона в смесительную камеру подается кислород. Он не горюч, но поддерживает пламя первого газообразного вещества. За счет высокого давления, можно разгонять температуру огня до 3000 градусов. Им можно выполнять сварку или резку. В качестве побочного действия в воздух выделяются продукты горения смеси.
По такому же принципу функционирует и водородная сварка, только вместо ацетилена по каналам горелки движется водород. Его опасно использовать в баллонах, ввиду легкой взрываемости большого объема газа. Утечка водорода и скопление в низине может привести к удушью и сильному головокружению. Поэтому его производят на месте сварки в специальной емкости. Для этого применяют углеводороды:
Проведение тока по этим жидкостям между двумя электродами дает достаточно водорода для сварки и резки, и безопасно в закрытых помещениях. Электролизный процесс позволяет уменьшить количество шлака в сварочной ванне, которого возникает очень много из-за чистого водорода в баллонах.
В результате шов получается плотным, без сильных пор. Для толстых металлов используются горелки с дополнительной подачей кислорода. В сварке мелких элементов достаточно только того, что получено в электролизере. Электрический разряд разделяет жидкость и содействует выработке как водорода, так и кислорода в виде пара.
Им, в зажженном состоянии, и осуществляются работы.
Применение метода
Сварка водородом широко применяется в сложных условиях. Это могут быть тоннели метро, шахты, глубокие монтажные колодцы и коллекторы.
Доставка баллонов в такие места либо невозможна, либо это чревато утечкой и взрывом. Сварочный метод с использованием электролиза позволяет безопасно проводить подобные работы.
Горящим веществом является пар, абсолютно безвредный для человека и окружающей среды.
Смена сопла на меньший диаметр, вплоть до иголки, делает возможным ювелирные работы, такие как:
- пайка шва золотых колец,
- ремонт цепочек,
- создание крепежных элементов для инкрустирования.
Этот вид пламени применяется в стоматологическом деле, для пайки металлических протезов. На производстве им обрабатывают стеклянные изделия. Больше всего водородная сварка подходит для углеродистой стали и дорогих металлов. Хорошо выполняется резка материалов как большой толщины на мощных моделях, так и тоненьких пластин игольчатыми соплами.
Преимущества водородной сварки
Сварка водородом завоевала широкое применение в определенных кругах благодаря следующим особенностям:
- аккуратные тонкие швы,
- возможность вести сварку и пайку на ювелирных украшениях,
- отсутствие вреда для органов дыхания человека,
- легкое небольшое оборудование, удобное для транспортировки,
- возможность вести работы в замкнутом пространстве, где запрещены другие технологии по сварке,
- пламя хорошо воздействует на все виды углеродистой стали и драгоценные металлы,
- для продолжительной работы не требуется частой перезарядки,
- возможность осуществлять резку материалов,
- подобный аппарат легко собрать своими руками.
Водородная сварка, несмотря на столько преимуществ, имеет и несколько минусов. Маленькие горелки и узкие сопла способны работать только на тонких деталях.
Чтобы вести сварку на толстых изделиях требуются мощные аппараты, с дополнительной подачей кислорода. При сваривании меди швы характеризуются многочисленными порами. Этот же дефект проявляется на легированных сталях.
Пламя от чистого водорода трудно разглядеть невооруженным глазом.
Создание водородной сварки своими руками
Чтобы производить мелкие сварочные работы водород-кислородным пламенем в домашних условиях потребуется смастерить небольшой аппарат по расщеплению жидкости и добыче этих газов. Свой электролизер можно сделать по разным схемам сложности. Самая простая состоит из двух емкостей и источника тока.
Основная емкость
Первая тара должна быть хорошо герметизирована. Она заполняется раствором едкого натра. Это гидроксид, который больше известен как щелочь. Соотношение с дистиллированной водой составляет 1/10. Именно этого будет достаточно для расщепления и получения газов, позволяющих полноценно вести сварку и пайку.
Емкость необходимо снабдить электродами, которые будут погружены в жидкость и, находясь под напряжением, запускать процесс добычи газа. Электродами могут быть пластины из нержавейки, шириной в 40 мм и толщиной 2-3 мм.
Потребуется сделать наборную конструкцию, которая позволит одновременно задействовать весь объем жидкости в таре. Для этого ряд пластин, просверливается по верхнему и нижнему краю и соединяется длинными шпильками на диэлектриках.
На сборном блоке делается три клеммы: два минуса по краям и один плюс по центру.
Верх каждой из трех клемм загибается под 90 градусов и болтом крепится к крышке емкости. С другой стороны на эти болты будут накидываться клеммы от источника тока.
В нижней части тары проделывается отверстие и монтируется штуцер, обжимаемый гайками и резиновыми прокладками с каждой части стенки. В него вставляется трубка для подпитки электролита.
В крышку емкости врезается второй штуцер на аналогичном креплении, по трубке которого будет отток пены и газа в обменную камеру. Когда основная емкость готова, происходит закрытие крышки, чтобы при вспенивании жидкость не брызгала.
Источник тока для водородной сварки
Источником тока может быть простой аккумулятор на 12 V. Но это не позволит регулировать силу пламени, ведь выработка водорода и кислорода будут производиться на одинаковом уровне.
Для сварки и резки на постоянной толщине металла этого хватит, а вот на тонких элементах потребуется регулировка. Поэтому лучше воспользоваться зарядным устройством для машинных аккумуляторов, настроив его на 3 V.
Это даст возможность варить тонкие пластины и ювелирные украшения.
Запитывать его можно от бытовой сети в 220V. Для работы с толстыми сталями потребуется трехфазная сеть и более мощное зарядное устройство. Но в небольшой мастерской можно обойтись и аккумуляторами меньших значений тока.
Обменная камера
Чтобы отбирать выработанный газ и подавать его в горелку, используется вторая емкость. В ней вырезается четыре отверстия:
- Верхняя горловина для заливки и дозаправки жидкости.
- Нижний штуцер для подачи электролита в основную емкость.
- Верхний штуцер для принятия пены, газа, и остатков электролита.
- Штуцер на крышке для подачи водорода и кислорода на горелку.
После сборки всех трубок и крышек, конструкцию необходимо загерметизировать, чтобы жидкость и пары газа не просачивались наружу. Это достигается путем хороших прокладок под штуцеры и клея «Момент», которым заливается крышка основной камеры. Используемые материалы должны быть устойчивы к щелочной среде.
Изготовление горелки
Чтобы осуществлять сварку и пайку водородом потребуется резиновый шланг по которому смесь паров будет поступать на рабочий элемент в руках сварщика. Последним может послужить обычная иголка от капельницы, имеющая более толстые стенки. Край шланги насаживается на пластиковый стержень основания иглы и затягивается хомутом. Второй хомут устанавливается на штуцер с обменной камерой.
Когда все коммуникации собраны, можно приступать к испытанию аппарата. На клеммы накидываются контакты от источника тока и подается напряжение.
Электролиз начинается очень быстро и уже через пару минут можно пытаться поджигать пламя на конце иглы. Чтобы регулировать силу горения уменьшают либо увеличивают напряжение на аппарате.
Водородное пламя отличается длинной структурой факела и необходимо приловчиться подносить его к изделию не обжигая окружающие детали.
Сварка водородом служит хорошей альтернативой пропану и кислороду, позволяя выполнять ювелирные работы с аккуратной пайкой. Резкой можно создавать разнообразные узоры на металле. А экологическая чистота делает этот метод безопасным в замкнутых помещениях без вентиляции.
Поделись с друзьями
Водородная сварка — экологическая чистота и легкость работы!
Безопасность водородной сварки, отличающей ее от других традиционных способов, обеспечивается тем, что продуктом горения, образованным в процессе, является пар.
Водородная сварка – это один из методов газопламенной обработки, при котором используются смесь кислорода с горючими газами.
Водородное пламя прекрасно заменяет ацетиленовое, когда необходимо выполнить резку, пайку и сварку разных материалов.
Особенности процесса
Использование водорода в качестве топливо заменяющего ацетилен приводит к покрытию сварочной ванны толстым слоем шлака. Шов, полученный таким способом, отличается низким качеством из-за повышенной пористости и тонкости.
Исключить подобные дефекты помогает применение органических соединений, связывающих кислород. Для этого используют подогретые до определенной температуры углеводороды: бензины, бензолы, толуолы, и другие.
Температура нагрева должна составлять от 30% до 80% от температуры кипения элементов.
Углеводы применяются в минимальном количестве, поэтому сварка водородом стоит почти столько же, сколько и другие способы газопламенного воздействия.
Основная сложность способа заключается в том, что часто не хватает эффективного источника водорода и кислорода. Использование баллонов с газом зачастую становится не целесообразным в связи с высоким риском возникновения обморожений и удуший при их эксплуатации.
Водородное пламя трудно заметить при дневном свете. Его возникновение обнаруживается только сверхчувствительными датчиками. Но все проблемы решаются применением специальных аппаратов, которые, воздействуя на воду электрической энергией, способствуют ее распаду на водород и кислород. Устройства – электролизеры, производят одномоментно два газа.
Приборы достаточно легки в применении, благодаря простоте и мобильности конструкции. Они являются отличной заменой крупногабаритному и тяжеловесному оборудованию, и могут использоваться при отсутствии прямых источников питания, что делает доступной водородную сварку своими руками в домашних условиях.
Оборудование для водородной сварки
Аппараты для сварки, проводимой таким способом, обладают различной мощность и работают от электрической сети. Они оснащены обычной горелкой, которая обеспечивается водородно-кислородной смесью посредством шланга.
Температура пламени варьируется от 600 до 2600ºС и устанавливается с помощью специальных устройств.
Водородно кислородная сварка может выполняться с помощью ручного и автоматического оборудования, которое не представляет никакой сложности при эксплуатации, благодаря низкой трудоемкости процесса и отсутствию нужды в постоянной перезарядке устройства.
Компактная аппаратура обладает большой мощностью и приводится в рабочее состояние за небольшой период времени, который зависит от температурных условий в месте проведения работ и количества газов, требуемых для сварочного процесса.
Атомно водородная сварка требует от сварщика только владения основными навыками и знаниями о газопламенной обработке, которые позволят без труда выполнить сварку элементов, и получить в месте соединения качественный и прочный шов.
Еще одним преимуществом водородной сварки является экологическая чистота процесса и его продуктивность. Например, ацетилен, используемый в качестве топливного газа, загрязняет окружающую среду соединениями, обладающими огромной токсичностью. А продуктом горения в процессе использования водородного оборудования является обычный пар.
Они предназначены как для сварочных работ, так и для ручной или автоматической кислородной резки, пайки, порошковой наплавки, термическом упрочнении и порошковом напылении. Компактное оборудование оснащено несколькими режимами работы, что позволяет выполнять с его помощью соединение материалов различной толщины и резку самых толстых металлических листов.
Применение
Ювелирное дело, стоматология, ремонт холодильного оборудования, сервисные центры, занимающиеся ремонтом и обслуживанием техники — не могут обойтись без применения сварочных аппаратов, с водородно-кислородным топливом. Устройства отлично подходят для использования их в помещениях, где запрещена эксплуатация взрывоопасных баллонов, наполненных кислородом или пропаном.
К преимуществам водородной сварки относятся также:
- низкая стоимость процесса,
- отсутствие отходов,
- отсутствие дорогих исходных материалов, для работы нужен небольшой объем воды,
- экологическая чистота производства,
- широкий спектр обрабатываемых материалов.
Атомно-водородная сварка, в основе которой лежит действие электродуги, прекрасно выполняет сваривание чугунных, легированных, низкоуглеродистых сталей. Но использование этого подвида сварки плавлением в промышленных целях ограничено высоким напряжением источников питания, которое представляет угрозу жизни человека.
Водородная сварка очень востребована при проведении сварочных работ в труднодоступных местах, например, колодцах, толях, железнодорожных цистернах, где нельзя использовать баллоны, наполненные пропаном и ацетиленом. Также существуют водородные сварочные приборы, с помощью которых можно соединять материалы в условиях низкой температуры.
Электролизная водородная HHO горелка | Катушки Тесла и все-все-все
Это восхитительный простотой своей идеи девайс, доступный к домашней сборке с минимумом использованных инструментов и навыков (разумеется, в продвинутом варианте всё усложняется за счёт примочек и заморочек). Суть очень проста: берём электроды, суём в электролит, подаём ток, собираем на выходе водород-кислород. 2): при большем токе будет иметь место перегрев электролита и закипание — то есть, пена, тысячи её, при меньшем — теряем в газовыделении. Падение на одной паре электродов для такого тока получается 2-3 вольта, в зависимости от концентрации электролита (я взял 10%, это соответствует примерно 2.2-2.3 вольта падения).
При таких обстоятельствах качать две огромных пластины сотнями ампер тока при двух вольтах представляется не очень разумным решением. Гораздо лучше соединить несколько ячеек последовательно: тогда мы сможем увеличить рабочее напряжение и площадь электродов во много раз при том же токе.
А теперь осталось только сообразить, что одна пластина электрода может быть с одной стороны катодом одной ячейки, а с другой — анодом другой.
Короче, просто набираем бигмак из чередующихся кольцеобразными прокладками пластин. Больше пластин — больше напряжение при том же токе, больше площадь одной каждой пластины — больший ток при том же напряжении. Увеличение числа пластин увеличивает суммарное падение на них напряжения. На схеме всё понятно видно.
Теперь о практических нюансах постройки. Первое и самое главное: материал электродных пластин. Поскольку работать им предстоит в агрессивной среде (сильная щёлочь, электролитические реакции, температура 50-80 градусов), выбор — из доступного — только один, нержавеющая сталь.
Но и тут не так просто, стали куча марок, и подходят далеко не все. Опытным (а также частично теоретическим и частично сравнительно-аналитическим — изучением описаний промышленных установок электролизной газосварки) путём была определена распространённая и подходящая сюда сталь: 12Х18Н10Т.
Не суть важно, это довольно модная и частая сталь и её не очень трудно отыскать в листах размерами типа 1000*2000 мм (способ раскройки листа на пластины оставляю на усмотрение желающих повторить девайс). Её аналог — AISI 321 — тоже должна теоретически подходить. Не знаю, не пробовал.
Безтитановая 08Х18Н10, например, ржавеет и окисляется, хотя, казалось бы, должна подходить вполне.
В каждой пластине необходимо проделать отверстия снизу и сверху на расстояниях чуть меньше диаметра прокладки друг от друга (но не менее 0.5-1 см от края прокладки) — для газообмена и для распределения электролита по ячейкам. Хватит где-то 5 мм сверла.
Не забыть припаять провода к внешним частям пластин перед сборкой.
Щёлочь. Подойдёт NaOH или KOH, желательно чистый, а не технический. Начинать с концентрации 10% по массе (в дистиллированной воде), дальше экспериментировать. Выше концентрация — выше ток, но больше пены.
Резиновые прокладки почти все из продающихся уже маслобензощелочестойкие. Я использовал о-ринги (кольца круглого сечения) где-то 130 мм диаметром. Их нужно на одну меньше чем пластин.
Стягивающие пластины. Требуется нечто очень слабо гнущееся и жёсткое.
Идеально и классика постройки — толстое, двухсантиметровое оргстекло. В нём же можно проделать выводы и резьбу под газ и доп. топливный бачок.
У меня не было оргстекла, я просто впаял медные трубки в последнюю нержавеющую пластину, а для стяжек использовал 27 мм фанеру.
Если все вышеназванные компоненты — сталь, прокладки, стяжки — есть, можно собрать их вместе, проверить небольшим поддувом давления — прокладки не должны выпячиваться и вообще не должно быть травления воздуха при давлении хотя бы 0.5-0.
6 атм, залить щёлочь — и переходить к внешнему обвесу.
Перво-наперво следует сделать водный затвор. Водород-кислородная смесь, HHO, невероятно злая штуковина.
Она с лёгкостью детонирует, да и сгорает весьма резво, не требуя притом никаких окислителей (кислород-то есть).
Если в процессе работы пламя почему-либо проскочит в шланги и дойдёт до электролизера — в лучшем случае по всему рабочему помещению будет размётана горячая щёлочь вперемешку с кусками прокладок. Но этого довольно легко избегнуть, поставив простую конструкцию, суть которой ясна из схемки.
Пламя не имеет шанса проскочить вниз по пузырькам сквозь слой воды или иной жидкости, и таким образом проскока горения в сам девайс не произойдёт. Конструкция чуть менее, чем полностью собирается из сантехники из магазина метизов.Далее следует озаботиться горелкой.
В качестве сопла лучшее, что удалось найти — толстые цельнометаллические иглы (типа «Рекорд» и подобные) от советских многоразовых шприцов. Но поскольку идея использовать ещё и сам шприц как часть горелки — не самая лучшая, я просто оторвал носик шприца и припаял его к насадке на полноценную пропан-кислородную горелку.
А далее следует важный момент.
Ввиду уже упомянутого выше злобства HHO в плане горения в целом и особенно его, горения, скорости, все возможные места в горелке следует плотно, утрамбовывая, забить спутанным мелким-мелким медным проводочком.Я использовал несколько метров МГТФа (там жила порядка 0.
07 и меньше), основательно перепутанного в медную кашицу, каковой забил почти весь «ствол» горелки и большую часть её носика. Это почти наверняка предотвратит проскок пламени в шланги даже при неправильном выключении (а совсем наверняка — при случайном таки проскоке — защитит уже гидрозатвор). Пренебрегать объёмом и количеством этой медной мотни очень не рекомендую.
И начинаться она должна от почти что самого сопла горелки.
Мелочи вроде шлангов, соединений, подводки манометра подробно расписывать не буду, они делаются из того что под рукой. Хорошо себя зарекомендовали виниловые и силиконовые медицинские трубки, их легко найти нужного, налезающего на стандартные сантехнические медные трубки диаметра.Питание.
В качестве питания всё просто, сколько_нужно вольт и 8-15 ампер. Я пока что использую ЛАТР и понижающий до 110 вольт трансформатор ОСМ-0,63 (600 ватт), после которых стоят диодный мост на 50 ампер (с запасом), фильтрующий электролит и амперметр для контроля тока. Потребляемое сейчас напряжение — 68 вольт, ток — 8-10А, соответственно мощность около 500-600 ватт.
Если расширить устройство до где-то 140 пластин, станет возможным прямое сетевое бестрансформаторное включение, что приведёт девайс в состояние неимоверной крутости и что и планируется сделать, как только достану резиновые прокладки — ещё 110 штук. Короче, если всё сделано, можно включать.
Расписывать возможные косяки, которые могут проявиться, очень лень, здесь всё же сайт не с набором инструкций «сделай сам для чайников». Вкратце так. Во-первых, может быть пена. Пена означает грязный электролит, грязь на пластинах или переток/перегрев. Если грязь, ждём минут 20-30 на небольшом токе, пока не исчезнет. Если переток/перегрев, снижаем ток или даём остыть.
Если грязный электролит — юзаем другую щёлочь и дистиллированую или хотя бы талую воду Далее, оно может плеваться щёлочью вместе с газом. Слишком большой уровень электролита, слить или дать поработать, пока не убавится. Давление не держится при закрытой горелке — где-то травит. Необходимо проверить.
Если девайс подтекает щёлочью между пластин — надо выяснить где именно, посмотреть, заменить прокладку или пластину. Течь ничего нигде не должно, ни газом, ни жидкостью. Слишком слабый поток газа, пламя проскакивает в горелку или сжигает иглу-сопло — уменьшить диаметр сопла или увеличить мощность газовыделения.
Кстати, при прогреве пластины могут прогибаться и замыкаться друг с другом — это надо отследить и положить между уголками что-нибудь.Проверять на горение рекомендую не в помещении (а то ещё ебанёт, простите мой французский, и будет всё в щёлочи). Я вытаскивал на улицу, когда убедился в безопасности — занёс назад внутрь.
Если всё сделано верно, на конце иглы загорится либо бледное жёлто-розоватое, либо довольно яркое жёлтое (последнее означает пробравшийся в пары натрий) пламя длиною несколько сантиметров, почти бесшумное, очень плохо задуваемое. Экспериментируя с подводимой мощностью, концентрацией электролита и диаметрами игл-сопел можно добиваться довольно интересных результатов.
Само по себе водород-кислородное пламя довольно жёсткое и не очень удобно для прогрева больших деталей, к тому же сильно окислительное. Если прогнать предварительно газ HHO через слой бензина, например, он обогатится его испарениями, которые, сгорая дадут дополнительную мощность пламени, и сделают его обогащённым. Обогащённое пламя имеет характерную кинжальную форму, большую мощность и размер, и характерный углеводородный сине-белый цвет. У меня обогатитель повторяет по конструкции гидрозатвор (только налит бензин вместо воды), и поэтому, поскольку они стоят вместе, можно плавно регулировать степень насыщенности пламени. С обогащённым пламенем виден истинный размер струи — около 30 сантиметров (в то время как с быстро сгорающим HHO видны от силы 5-7 см).
Сварочный аппарат на воде
Главная » Статьи » Сварочный аппарат на воде
Сжатые газы, используемые при сварке, как правило, весьма взрывоопасны. Сварочный аппарат, разработанный в рамках европейского проекта SafeFlame не нуждается в подобном топливе. Для его работы нужна лишь электроэнергия и вода.
Вода разлагается на кислород и водород в процессе электролиза, затем эти газы смешиваются и поджигаются на выходе из сопла горелки. Изменяя пропорции подаваемых к соплу газов, можно получать окислительное, восстановительное или нейтральное пламя, а температура сварки регулируется за счет изменения мощности, подаваемой на электролизер.
Такая технология позволяет не только снизить опасность взрывов и пожаров, отказавшись от хранения газов в баллонах, но и сократить расходы на покупку и транспортировку новых баллонов взамен опустошенных.
Информация о предполагаемой стоимости сварочных аппаратов SafeFlame пока отсутствует, но сообщается, что разработчики нашли способ снизить количество платины, используемой в электролизере, и тем самым сократить конечную стоимость устройства.
По сообщению Gizmag
Разработан уникальный сварочный аппарат, работающий на воде
Новый сварочный аппарат, а точнее новая технология сварки позволяет отказаться от хранения и использования взрывоопасных газов, например, ацетилена или пропана, сообщается в материалах «Популярной механики» со ссылкой на информацию портала «Gizmag».
Используемые при сварке сжатые газы, как правило, легковоспламеняющиеся и поэтому взрывоопасны. При ответе на вопрос, какой вы знаете не горючий и наиболее доступный материал, первое, что приходит в голову — это вода.
Именно от этого отталкивались разработчики европейского проекта «SafeFlame», создавая свой уникальный сварочный аппарат, работающий на подобном топливе.
Для генерации пламени не используется ничего, кроме воды и электричества.
В сварочном аппарате «SafeFlame» электрический ток генерирует электролиз обычной воды, разделяя ее на водород и кислород. Эти газы затем смешиваются и поджигаются при выходе из сопла горелки.
Путем тонкой настройки (изменения) пропорций поступающих к соплу газов, можно получать различные виды пламени: окислительное пламя, восстановительное или нейтральное, а для регулирования температуры сварки предусмотрено изменение мощности, подводимой к электролизеру.
Технология позволяет производить водород и кислород прямо на месте использования, никаких баллонов, заполненных горючими газами, не требуется. Это снижает опасность пожаров и взрывов, а также значительно уменьшает затраты на проведение сварочных работ: отпадает необходимость покупки газов, их транспортировки и обустройства безопасных мест для хранения.
Прототипы «SafeFlame» уже начали использоваться в Европе, коммерческое производство планируется начать в ближайшее время.
Информации о предполагаемой стоимости новых сварочных аппаратов пока нет, но говорится о том, что разработчикам удалось снизить количество используемой в электролизере платины, что тем самым сокращает и стоимость устройства в целом.
Новый сварочный аппарат, а точнее новая технология сварки позволяет отказаться от хранения и использования взрывоопасных газов, например, ацетилена или пропана, сообщается в материалах «Популярной механики» со ссылкой на информацию портала «Gizmag».
Используемые при сварке сжатые газы, как правило, легковоспламеняющиеся и поэтому взрывоопасны. При ответе на вопрос, какой вы знаете не горючий и наиболее доступный материал, первое, что приходит в голову — это вода.
Именно от этого отталкивались разработчики европейского проекта «SafeFlame», создавая свой уникальный сварочный аппарат, работающий на подобном топливе.
Для генерации пламени не используется ничего, кроме воды и электричества.
В сварочном аппарате «SafeFlame» электрический ток генерирует электролиз обычной воды, разделяя ее на водород и кислород. Эти газы затем смешиваются и поджигаются при выходе из сопла горелки.
Путем тонкой настройки (изменения) пропорций поступающих к соплу газов, можно получать различные виды пламени: окислительное пламя, восстановительное или нейтральное, а для регулирования температуры сварки предусмотрено изменение мощности, подводимой к электролизеру.
Технология позволяет производить водород и кислород прямо на месте использования, никаких баллонов, заполненных горючими газами, не требуется. Это снижает опасность пожаров и взрывов, а также значительно уменьшает затраты на проведение сварочных работ: отпадает необходимость покупки газов, их транспортировки и обустройства безопасных мест для хранения.
Прототипы «SafeFlame» уже начали использоваться в Европе, коммерческое производство планируется начать в ближайшее время.
Информации о предполагаемой стоимости новых сварочных аппаратов пока нет, но говорится о том, что разработчикам удалось снизить количество используемой в электролизере платины, что тем самым сокращает и стоимость устройства в целом.
Водородный сварочный аппарат
S400 ACS (Jeweller)
Генератор электролизного типа, для производства газовой смеси: водорода и кислорода, с системой обогащения углеродом.
Область применения: Сварка, пайка, обжиг, локальный высокотемпературный нагрев в ювелирных и стоматологических мастерских, а так же для обработки и плавки стекла и кварца, термической обработки пластмассы, акрила, других органических и синтетических полимеров.
Потребляемая мощность максимальная: 1300 Вт.
Производительность газа, номинальная: 450 л/час.
Разовый объем заправки углеводородной добавки: 200 мл.
Масса аппарата: 34 кг.
Генератор электролизного типа, для производства газовой смеси: водорода и кислорода, с системой обогащения углеродом.
Предназначен для сварки, пайки черных и цветных металлов, для нагрева, обжига или термической обработки металлов, пластмасс, дерева, полимеров, стекла или кварца.
Потребляемая мощность до: 3300 Вт.
Производительность газа до: 900 л/час.
Объем заправляемой воды: 3 литра.
Отличный выбор для домашнего использования,
для небольшого производства или частного бизнеса.
Генератор электролизного типа, для производства газовой смеси: водорода и кислорода, с жидкостной системой охлаждения.
Предназначен для очистки автомобильных двигателей от углеродистых отложений. Оснащен жидкостной системой охлаждения. Управление питанием осуществляется при помощи переносной сенсорной панели и брелока с радиусом действия до 50 метров.
Напряжение питания: 220 В, 50/60 Гц.
Потребляемая мощность до: 5000 Вт.
Максимальная производительность газа: 1500 л/час.
Время непрерывной работы 3-5 часов
Встроенный электрический счетчик потребленной энергии.
Встроенный контроллер управления системой охлаждения.
Отличный выбор, как для промышленного использования, так и для частного бизнеса. Приобретая наше оборудование Вы приобретаете готовый бизнес с высокой рентабельностью и коротким сроком окупаемости.
Генератор электролизного типа, для производства газовой смеси: водорода и кислорода, с воздушной системой охлаждения.
Предназначен для очистки автомобильных двигателей от углеродистых отложений. Также предназначен для сварки, пайки черных и цветных металлов, для нагрева, обжига или термической обработки металлов, пластмасс, дерева, полимеров, стекла или кварца.
Напряжение питания: 220 В, 50/60 Гц.
Потребляемая мощность до: 3800 Вт.
Номинальная производительность газа: 1000 л/час.
Время непрерывной работы 1-2 часа
Отличный выбор, как для домашнего использования,
так и для промышленного производства и частного бизнеса.
Генератор электролизного типа, для производства газовой смеси: водорода и кислорода, с жидкостной системой охлаждения
Предназначен для частного или коммерческого использования в области очистки автомобильных двигателей от углерод истых загрязнений (Hydrogen Carbon Cleaning)
Напряжение питания трехфазное: 380 В, 50 Гц.
Потребляемая мощность до: 6000 Вт.
Производительность газа: 2000 л/час.
Время непрерывной работы 5-6 часов.
Отличный выбор для промышленного производства и частного
бизнеса. Готовый бизнес с коротким сроком окупаемости.
цена: 5200 euro (2000 л/ч)
Генератор электролизного типа, для производства газовой смеси: водорода и кислорода, с жидкостной системой охлаждения
Предназначен для частного или коммерческого использования в области очистки автомобильных двигателей от углерод истых загрязнений (Hydrogen Carbon Cleaning)
Напряжение питания трехфазное: 380 В, 50 Гц.
Потребляемая мощность до: 9500 Вт.
Производительность газа: 3000 л/час.
Время непрерывной работы 5-6 часов.
Отличный выбор для промышленного производства и частного бизнеса.
Готовый бизнес с коротким сроком окупаемости.
цена: 7400 euro (3000 л/ч)
Водородная очистка ДВС, как это работает?
Коротко о физико-химическом процессе.
Вырабатываемый газ, через впускной коллектор автомобиля подается в камеру сгорания двигателя, на период, от 30 до 60 минут. В процессе окисления водорода в камере сгорания создается уникальное условие для эффективного окисления высоко концентрированного углерода. Сгорая, водород создает импульсивный толчок, энергия которого инициирует переход углерода из твердого агрегатного состояния в газообразное, то есть окисляясь, углерод становится газообразным веществом, обычным углекислым газом CO2, который покидает двигатель через выхлопную систему автомобильного двигателя. Большая часть закоксованного углерода, под воздействием энергии сгорания водорода разрушается, окисляется и выводится из ДВС в виде СО2, но огромное количество твердых частиц углерода в концентрированном состоянии оседает за пределами камеры сгорания и не подвергается прямому воздействию энергии сгорающего водорода. Но стоит помнить что сгорая, водород образует сверх-перегретый водяной пар, который оказывает на детали выхлопной системы автомобиля, газораспределительную систему, систему EGR и катализатор, кратковременное высокотемпературное и моющее воздействие, в следствии чего углеродистые отложения, растворяются и вымываются с поверхности деталей, вышеупомянутых систем двигателя. Окисленный углерод, в газообразном состоянии, вместе с твердыми частицами в процессе очистки, выводится из двигателя через выхлопную систему автомобиля. В результате очистки, увеличивается поршневая компрессия, снижается расход масла и топлива, уменьшаются показатели вредных выбросов. В целом, в значительной степени увеличивается эффективность работы двигателя автомобиля, увеличивается ресурс полезной работы и износостойкость внутренних подвижных деталей трения и качения.
Независимый Ювелирный Форум
Часовой пояс: UTC + 3 часа [ Летнее время ]
Правила форума
Подфорум для объявлений о покупке и продажи инструментов, оснастки и станков от частных лиц.
Разумеется речь об ювелирном оборудовании. Детские коляски будут удалены.
Каждое объявление должно включать в себя обязательно:
1. ФИО, контакты (телефон, email)
2. Место передачи или нахождения товара
3. ЦЕНУ
4. Новое-не новое
По возможности прикладывайте фото.
Водородные газогенераторы (пайка, сварка, плавка и нагрев)
- Изготовление под заказ водородного оборудования
для сварки, пайки, плавки и высокотемпературного нагрева
Водородный многофункциональный газогенератор “GreenWay” (Н2-2)
Цена: 3000$
Система позволяет:
– очистить ДВС автомобиля от всех углеродистых отложений
– использовать в качестве стационарного газосварочного оборудования для сварки черных
металлов и меди, для пайки цветных металлов, в том числе меди, латуни или алюминия.
При оснащении многофункциональным разветвителем, газогенератор можно применять в
качестве источника питания для нескольких рабочих постов в ювелирных или стоматологических
мастерских, в цехах по обработке стекла или кварца, в цехах по изготовлению КИП. При этом
один газогенератор может обеспечить питанием до пятнадцати рабочих постов в ювелирном
производстве, или до восьми рабочих постов в цехах обработки стекла или производстве КИП.
– использовать для отопления, водонагрева в быту.
– использовать в качестве источника топлива для бытовых газовых плит или каминов.
– использование газогенератора для локального и высокотемпературного нагрева
в кузовном цехе СТО, для осадки растянутого после аварии металла или в слесарном
цехе, для быстрого разогрева заржавевших деталей подвески или тормозной системы.
Как работает установка:
Установка представляет собой газогенератор. При помощи электрического тока, из воды в установке
генерируются газы, водород и кислород. Смесь полученных газов представляют собой высокоэффективное
горючее, топливо.
Технические параметры:
Водородный газогенератор “GreenWay-1”
Габаритные размеры – 90 х 40 х 44 см.
Потребляемая мощность – 4 кВт.
Напряжение питания – 220 В.
Расход воды – до 0,8 л/ч.
Вес устройства – 80 кг.
БЕЗОПАСНОСТЬ:
«… Несмотря на то, что многие люди имеют предубеждение по поводу безопасности водорода,
необходимо признать, что водород безопаснее, чем иные, обычно используемые газы, такие как пропан и ацетилен»
Keiichi Taniguchi, ведущий научный сотрудник, KOMATSU, Япония
Водородные газогенераторы в разы безопаснее любого газобаллонного оборудования или оборудования
работающего с применением бензина или керосина. В системе аппарата “Greenway” отсутствуют емкости
для хранения производимого газа, весь производимый газ сразу же подается в магистраль горелки, без
промежуточного хранения! Пустоты в которых газ собирается под рабочим давлением, защищены
системой водяного предотвращения проникновения пламени обратного хлопка. Но даже если произойдет
возгорание газа в пустотах, вы ни чего не увидите и не услышите кроме глухого хлопка, без
сопровождения открытым горением или разрушающего эффекта, так как все емкости внутри аппарата
изготовлены из очень прочной нержавеющей стали сваренной с применением дуговой сварки TIG в инертной
среде аргона.
Во время работы с водородным аппаратом “Greenway” достаточно использовать стандартные
знания по технике безопасности при проведении работ с применением открытого огня.
Сравнительная таблица свойств газов
Водородный газогенератор “GreenWay” оснащен следующей системой защиты:
– система автоматического отключения питания при образовании избыточного давления газа
– система контроля от воспламенения (водяной затвор, FBA)
– система принудительной системой охлаждения
Водород – горючий газ без цвета, вкуса и запаха. В обычных условиях в 14,5 раза легче воздуха. При нормальных условиях плотность водорода составляет 0,09 г/л. Среди газов является самым легким и обладает наибольшей теплопроводностью. Растворим во многих металлах (железе, никеле, платине и др.), мало растворим в воде. В жидком состоянии существует в температурном диапазоне от −252,8°C до −259,2 °C.
Водород наиболее распространен во Вселенной, составляя основную часть звезд и межзвездного газа. На Земле содержится в виде соединений (17% по числу атомов, 1% массовой доли в земной коре), лишь незначительное его количество присутствует в атмосфере в виде простого вещества (около 0,00005% по объему).
Водород получают химическими способами, самыми распространенными из которых являются:
- пропускание водяного пара над раскаленным коксом (t =
1000ºC):
H2O + C ↔ H2↑ + CO, взаимодействие водяного пара с метаном (t =
1100ºC):
12СН4 + 5Н2О(пар) + 5О2 → 29Н2↑ + 9СО + 3СО2,
2H2O → 2H2↑ + O2↑,
поскольку чистая вода почти не проводит электрический ток, в нее добавляют электролиты, например, KOH,
2NaCl + 2H2O → H2↑ + 2NaOH + Cl2.

Согласно ГОСТ Р 51673-2000 водород газообразный чистый (используемый в том числе для термической обработки металлопродукции) изготавливается трех сортов: высшего, первого и второго. Баллон с водородом окрашен в темно-зеленый цвет, с надписью «Водород» красного цвета (ПБ 10-115-96, ГОСТ 949-73).
Таблица. Характеристики марок газообразного чистого водорода
Водород поставляется в стандартных стальных баллонах вместимостью 40 и 50 л при давлении 14,7 МПа (ГОСТ 949), стальных бесшовных баллонах большого объема (до 1000 л) при давлении 39,2 МПа (ГОСТ 12247), по трубопроводам, а также в специальных крупногабаритных резервуарах для газа – газгольдерах, обычно под давлением не более 10 МПа.
Опасные факторы и меры безопасности при работе с водородом
- водород в смеси с кислородом и воздухом (гремучий газ) пожаро- и взрывоопасен, для водородно-воздушной смеси концентрационный предел распространения пламени составляет 4,12%–75% по объему, для смеси водорода с кислородом – 4,1%–96% по объему,
- температура самовоспламенения смеси водорода с воздухом – 510ºC, смеси водорода с кислородом – 450ºC,
- при дневном свете водородное пламя практически не видимо, поэтому для его обнаружения необходимо применять специальные датчики,
- сжиженный водород при попадании на кожу вызывает сильное обморожение, при испарении сжиженного водорода возможно образование взрыво- и пожароопасных смесей,
- при высоком давлении водород способен оказывать наркотическое действие,
- при высоких концентрациях водород вызывает кислородное голодание и удушье, при работе в его среде необходимо использовать изолирующие противогазы, а помещения оборудовать вентиляцией.
Применение водорода при сварке и резке
Водород получил ограниченное применение:
- при атомно-водородной сварке (как правило, сталей и алюминия толщиной до 5–10 мм),
- как горючий газ для газовой сварки (обычно сталей, алюминия толщиной до 5 мм) и резки,
- в качестве добавки к аргону, азоту при плазменной обработке.
В последние годы интерес к водороду для газопламенной обработки металлов возрастает благодаря появлению мобильных аппаратов, обеспечивающих получение водородно-кислородной смеси в результате гидролиза воды. При разложении воды электрическим током образуются кислород и водород в соотношении β = 1:2, однако такое пламя является окислительным и не обеспечивает качественного процесса сварки сталей. Чтобы пламя было нормальным (β = 0,25–0,4) газовая смесь в барботере электролизного-водного генератора обогащается парами углеводородных соединений – бензина, ацетона, спирта и др. При использовании бензина температура пламени составляет 2600°C. Исходным сырьем для получения водорода и кислорода служит 5–35%-ный раствор KOH в дистиллированной воде.
Водородно-кислородную сварку выполняют преимущественно левым способом. В качестве присадочного материала применяется сварочная проволока Св08ГС, Св08Г2С, Св10ГС, Св10ГСМ. Легирование кремнием и марганцем обеспечивает раскисление металла сварочной ванны, необходимое из-за избытка кислорода. Для водородно-кислородной сварки и резки выпускаются различные аппараты и установки – «Лига», «Энергия», «Москва» и др.
Фото. Аппараты «Лига-12» и «Лига-02» для водородно-кислородной сварки, пайки и резки методом электролиза воды
Данный вид газопламенной обработки металлов не требует баллонов с газами, экологичен, приводит к сокращению эксплуатационных расходов.
Применение водорода для сварки и резки металлов
При горении в кислороде некоторых газов, например водорода илн ацетилена (органическое вещество), достигается высокая температура.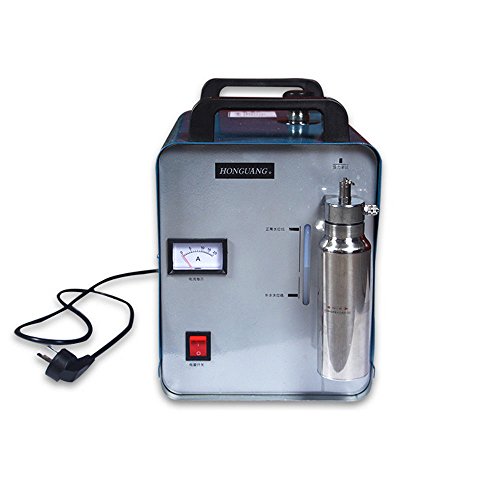
Кислород широко применяется для получения высоких температур, которые достигаются путем сжигания различных горючих газов (водорода, светильного газа и т. д.) в смеси не с воздухом, а с чистым кислородом. Особенно распространено применение кислорода в смеси с ацетиленом (температура пламени около 3000°С) для сварки и резки металлов. В медицине вдыхание чистого кислорода иногда назначается при некоторых отравлениях, заболеваниях легких и др. Очень большое практическое значение имеет использование кислорода (чаще — обогащенного им воздуха) для интенсификации ряда важнейших производственных процессов металлургической и химической промышленности. [c.48]
Водород находит широкое применение в металлургической и химической промышленности и смежных отраслях. Большие количества водорода расходуются в производстве аммиака, метанола и карбамида.

Практическое использование водорода началось с небольших количеств, потреблявшихся главным образом для воздухоплавания, освещения, гидрогенизации жиров и пайки свинца. В 20-х годах текущего столетия промышленное производство водорода резко возросло во всех странах мира, что было обусловлено разработкой и широким внедрением в практику процесса синтеза аммиака из водорода и азота. Этот процесс получил огромное развитие в связи с непрерывным увеличением производства и потребления минеральных удобрений. Большие количества водорода потребовались для производства метилового спирта, а с 50-х годов и для синтеза карбамида. В меньших количествах водород находит разнообразное применение во многих других отраслях народного хозяйства. Значительно увеличилось использование водорода для гидрогенизации жиров, гидрирования угля, тяжелых масел, при синтезе спиртов, жирных кислот, получении углеводородов, перекиси водорода, синильной и соляной кислот и других продуктов, а также для сварки, резки и обработки металлов, в производстве электрических ламп и аккумуляторов. [c.7]
Ацетилен — газ, он горит, давая ослепительный белый свет в свое время ацетиленовые лампы использовались в автомобильных и велосипедных фарах. Однако в настоящее время такие лампы находят применение только в бакенах и для освещения домов в отсутствие электричества. В смеси с кислородом газ дает кислородно-ацетиленовое пламя, температура которого достаточна для резки и сварки металлов (гл. 7). Вероятно, наиболее характерным химическим свойством ненасыщенных углеводородов является их тенденция превращаться в насыщенные соединения. Они энергично взаимодействуют с водородом, галогеноводородами и галогенами, образуя соответствующие насыщенные соединения. Такие реакции называются реакциями присоединения для иллюстрации ниже приводятся некоторые примеры [c.211]
Порядок проведения огневых работ. Пожарная опасность газовой сварки и резки металлов обусловливается применением горючего газа в смеси с чистым кислородом. Для газовой сварки и резки металлов в качестве горючего газа наиболее часто применяют ацетилен, а для огневой обработки свинца и чугуна — водород. Эти газы взрывоопасны. [c.34]
Как известно, синтезы с участием водорода обычно идут под давлением для сжатия газов применяют компрессоры на десятки и сотни атмосфер компрессия удорожает газы. Возможность получать газы из электролизера сразу под большим давлением вызывает значительный интерес. При разработке этого предложения встал также вопрос о целесообразности передачи сжатых газов на значительные расстояния (например, разводка газов для сварки и резки металлов на территории большого машиностроительного завода, передача энергии в виде сжатых газов, аккумуляция энергии и т. д.). Известны попытки применения электролиза воды под давлением на подводных лодках, на которых вместо батареи электрических аккумуляторов устанавливается водородно-кислородный двигатель, работающий при под- [c.42]
Кислород применяется для резки и сварки металлов (ацетиленово-кислородные и водородо-кислородные горелки) для плавления кварца и получения искусственных драгоценных камней и др. Кислород, или обогащенный кислородом воздух, находит большое применение в черной и цветной металлургии, в доменном процессе, в сталеплавильном производстве, в газогенераторах. Благодаря увеличению концентрации кислорода химические процессы протекают с большими скоростями, что приводит к интенсификации различных производств, потребляющих кислород. [c.560]
Применение. В химической промышленности водород служит сырьем для получения аммиака Nh4, хлороводорода H I, метанола СН3ОН и других органических веществ. В пищевой промышленности водород используют для выработки твердых жиров путем гидрогенизации растительных масел. В металлургии водород используется для восстановления некоторых цветных металлов из их оксидов. Как уже отмечалось выше, водород — очень легкий газ, поэтому им заполняют воздушные шары, зонды и другие летательные аппараты. Высокая экзотермич-ность реакции горения водорода в кислороде обусловливает использование водородной горелки для сварки и резки металлов (температура водородного пламени достигает 2600 °С). Жидкий водород является одним из наиболее эффективных видов ракетного топлива. [c.337]
После открытия кислорода (Шееле, Пристли, Лавуазье, 1775) последний долгое время получали только -Химическим способом. В дальнейшем нашедший себе применение метод электролиза позволил получать кислород разложением воды на ее составные части — кислород и водород. Однако наиболее экономичным оказался физический способ получения кислорода из атмосферного воздуха. Он открыл широкие возможности для внедрения кислорода в технику сначала при сварке и резке металлов, главнььм образом стали, а в дальнейшем при многих технологических процессах в промышленности (черная и цветная металлургия, химическая промышленность, газификация топлива и др. ). [c.64]
Применение обогащенного воздуха в качестве дутья в доменных печах позволяет значительно повысить их производительность. Широко внедряется в СССР обогащенный воздух в производстве стали. Благодаря применению кислорода увеличивается скорость горения топлива в рабочем пространстве мартеновской печи, повышается температура плавления, резко ускоряется процесс плавления шихты. При этом снижается расход горючего, так как уменьшаются потери тепла с дымовыми газами (уменьшается их количество), увеличивается выход стали. Расход кислорода на тонну стали на крупных печах в настоящее время значительно снижен. Для достижения наивысшей эффективности тепловой режим печи автоматизи руют и применяют термостойкие огнеупоры, например хромомагнезитовые Много кислорода требуется для газовой сварки и резки металлов (прежнее название — автогенная сварка и резка). Сварка, в том числе газовая в настоящее время почти полностью вытеснила клепку. Сварные конструк ции заменяют литые и кованые, даже при производстве таких аппаратов как колонны высокого давления для синтеза аммиака и спиртов (рис. 91) Газовая резка металлов заключается в окислении нагретого металла в струе кислорода (рис. 92). При газовой сварке и резке горючим служат ацетилен водород и другие вещества наиболее широко применяется ацетилен Чистота кислорода, применяемого для сварки, должна быть не ниже 99,0% Температура пламени горения ацетилена в кислороде достигает 3 100° [c.110]
Водород используют в химической промышленности для производства аммиака Nh4, метанола СНзОН и других спиртов, альдегидов, кетонов для гидрогенизации твердого и тяжелого жидкого топлива, жиров и различных органических соединений, для си)1теза хлороводорода НС1 для гидроочистки продуктов переработки нефти при сварке и резке ме-таллов горячим кислородно-водородным пламенем (температура до 2800 °С), а также при атомарно-водородной сварке (температура до 4000 °С). В металлургии водород применяют для восстановления металлов из их оксидов (получение молибдена, вольфрама и других металлов). Очень важное применение в атомной энергетике нашли изотопы водорода — дейтерий и тритий. [c.419]
Из других видов сварки следует отметить получившую распространение в последнее время дуговую сварку вольфрамовым электродом в защитном газе (аргоне) и применяемую в производстве изделий новой техники. Вольфрамовый электрод при нагревании энергично окисляется, поэтому сварку ведут в защитной среде, не содержащей кислорода. Возможно непрерывное вдувание в дугу инертного газа, в качестве которого используются аргон, гелий или водород, либо смеси этих газов. Наиболее часто используется аргон как наиболее дешевый. Дуга постоянного тока в аргоне при прямой полярности (минус на электроде) горит устойчиво и легко зал игается. Напряжение горения дуги составляет около 15 В, нагрев и расход электрода незначительны. Эта картина резко меняется при изменении полярности. При этом возникает катодное расаыление, приводящее к тому, что с поверхности основ юго металла в зоне сварки удаляются окислы и загрязнения. Очищающее действие дуги позволяет без применения флюсов сваривать спец-стали, алюминий, магний, различные легкие сплавы, тугоплавкие металлы, активные металлы с большим сродством к кислороду, а также металлы малых толщин. Для питания дуги используются обычные агрегаты постоянного тока и выпрямители для дуговой сварки. В некоторых случаях желательно применение дополнительных осцилляторов и специальных электродов с добавкой окиси тория или лантана (торированные или лантанированные электроды) с целью облегчения зажигания и повышения устойчивости дуги. [c.154]
В наплавленном металле водород может присутствовать в молекулярном, атомарном и ионизированном виде. Большая часть водорода в процессе кристаллизации успевает выделиться из сварочной ванны, однако в наплавленном металле остается значительное количество водорода (14. .. 22 мл/100 г металла при сварке электродами с целлюлозным покрытием [179]), который диффундирует к поверхности, задерживаясь внутренними порами и неметаллическими включениями, мик-ронесплошностями по границам зерен и т.п. В процессе сварки 1/3 часть водорода из металла шва через границу сплавления поступает к моменту снижения температуры до 500 °С в околошовную зону на расстояние 1,2. .. 1,6 мм, поэтому максимум концентрации водорода будет смещаться к границе сплавления. При переходе зоны термического влияния из аустенита, в котором водород хорошо растворяется, в феррит, атомарный водород выбрасывается и собирается в неметаллических включениях, порах или микроструктурных дефектах, присутствующих в металле шва и зоне термического влияния, где он превращается в молекулярный водород, вызывающий образование трещин [155]. Вблизи окклюдирующих водород несплошностей (непроваров, подрезов и т.д.) резко повышается содержание водорода, так, в соединении, сваренном электродами с целлюлозным покрытием, на расстоянии 300 мкм от глубокого подреза концентрация водорода в 1,5 раза больше, чем в бездефектном участке [179]. Для предотвращения возникновения водородных трещин стремятся обеспечить максимальную диффузию водорода из сварного соединения путем применения предварительного подогрева кромок до 150. .. 200 °С и поддержания этой температуры до завершения первого прохода [179]. [c.
87]
Сварка атомарным водородом — Atomic hydrogen welding
«AHW» перенаправляется сюда. Для использования в других целях, см AHW (значения) . Паяльная трубка с атомарным водородом, около 1930 года. Сварка атомарным водородом ( AHW ) — это процесс дуговой сварки, в котором используется дуга между двумя вольфрамовыми электродами в защитной атмосфере водорода . Этот процесс был изобретен Ирвингом Ленгмюром в ходе его исследований атомарного водорода . Электрическая дуга эффективно разбивает молекулы водорода, которые впоследствии рекомбинируют с огромным выделением тепла, достигая температуры от 3400 до 4000 ° C. Без дуги кислородно-водородная горелка может нагреваться только до 2800 ° C. Это третье по величине пламя после дицианоацетилена при 4987 ° C и цианогена при 4525 ° C. Ацетиленовой горелки только достигает 3300 ° C. Это устройство можно назвать атомным водород горелкой , зарождающейся горелкой водорода или Ленгмюра горелкой . Этот процесс также известен как дуговая атомная сварка .
Тепла, выделяемого этой горелкой, достаточно для сварки вольфрама (3422 ° C), самого тугоплавкого металла . Присутствие водорода также действует как защитный газ , предотвращая окисление и загрязнение углеродом , азотом или кислородом , которые могут серьезно повредить свойства многих металлов. Это устраняет необходимость в флюсе для этой цели.
Дуга поддерживается независимо от свариваемой детали или деталей. Газообразный водород обычно является двухатомным (H 2 ), но там, где температура около дуги превышает 6000 ° C (10800 ° F), водород распадается на атомарную форму, поглощая большое количество тепла от дуги. Когда водород попадает на относительно холодную поверхность (то есть на зону сварного шва), он рекомбинирует в свою двухатомную форму, высвобождая энергию, связанную с образованием этой связи. Энергию в AHW можно легко изменять, изменяя расстояние между струей дуги и поверхностью заготовки.
При сварке с атомарным водородом можно использовать или не использовать присадочный металл . В этом процессе дуга поддерживается полностью независимо от свариваемой работы или деталей. Изделие является частью электрической цепи только в той степени, в которой часть дуги входит в контакт с изделием, при этом между изделием и каждым электродом существует напряжение.
Этот процесс заменяется газовой дуговой сваркой , в основном из-за наличия недорогих инертных газов.
Видео документация
Смотрите также
Рекомендации
- Научная энциклопедия Norton, 1-е и 6-е издания, авторские права 1921–1950 и 1976 гг.
- Энциклопедия науки Ван Ностранда (стр. 1311)
- Справочник по сварке Том. 2 Библиотека Конгресса, номер 90-085465, авторское право 1991 г., Американское общество сварщиков
- Калпкчян, Сероп и Стивен Р. Шмид. Учебник производственной техники и технологии Пятое издание. Верхняя река Сэдл: Pearson Education, Inc.
, 2006 г.
- «Сварка атомарным водородом» . Специальные сварные швы . Архивировано из оригинала на 2014-10-19 . Проверено 26 января 2008 .
- «Атомно-водородная сварка» . Практическая и техническая энциклопедия Odhams . 1947. Архивировано из оригинала 11 января 2008 года . Проверено 26 января 2008 .
- «Паяльная лампа на атомарном водороде» . Латеральная наука . Архивировано из оригинала 11 января 2008 года . Проверено 26 января 2008 .
Влияние водорода при сварке | Сварка металлов и материалов
Водород, так же как кислород и азот, растворяется в расплавляемом при сварке металле. Ой попадает в металл из воздуха, содержащего пары воды, из влаги покрытия электродов; из ржавчины, находящейся на поверхности металла изделия и электродов. При высокой температуре влага превращается в пар и диссоциируется с поглощением тепла Q:
2Н2O → 2Н2 + O2 — Q;
2Н2O → 2OН + Н2 — Q.
Водород содержится также в электродных покрытиях, в таких, как крахмал, целлюлоза и др., а также в самом металле. В небольших количествах он растворим в металле даже при комнатной температуре, однако с повышением температуры его растворимость растет и при переходе металла из твердого состояния в жидкое увличивается с 0,0007 (8 см3 на 100 г металла) до 0,0025 % (28 см3 на 100 г).
Во время сварки при наличии значительного количества водорода во влаге или в покрытии электродов увеличивается разбрызгивание, так как с понижением температуры растворенный в ванне водород бурно выделяется из металла, вызывая его кипение и разбрызгивание. С началом кристаллизации ванны растворимость водорода резко падает, атомарный водород выделяется по реакции
2H←→H2 + Q,
образуя молекулярный водород, который нерастворим в стали и уходит в шлак или атмосферу. Однако скорость кристаллизации может препятствовать удалению всего водорода, и часть его остается в шве в виде наружных и внутренних пор. Процесс выделения водорода из металла происходит и при комнатной температуре в атмосферу и в микроскопические полости, имеющиеся внутри металла. В результате образуются внутренние поры, в которых накапливается водород, создавая большое давление, что часто приводит к образованию микротрещин и, следовательно, к ухудшению прочностных характеристик наплавленного металла, особенно пластичности и ударной вязкости. При изломе такого металла в нем обнаруживаются так называемые «рыбьи глаза» в виде светлых пятен небольшого диаметра с маленькой полостью (порой) в середине. Наличие «рыбьих глаз» в изломе металла всегда свидетельствует о насыщении его водородом. Для удаления водорода иногда прибегают к выдерживанию сварных конструкций при комнатной температуре. Выдержка при температуре 250-300 °С ускоряет процесс выделения водорода. Водород является вредной примесью в стали, и при сварке следует избегать попадания влаги в шов, тщательно очищать поверхность металла от ржавчины и влаги и применять электроды с хорошо прокаленным покрытием.
Некоторую отрицательную роль при сварке играет окись углерода СО. Она нерастворима в стали и, находясь в газовой среде, окружающей дугу, защищает расплавленный металл от воздуха. При образовании СО в самом металле по реакции
FeO + С → СО + Fe
она действует как раскислитель металла, удаляющий кислород и восстанавливающий Fe из FeO, что сопровождается кипением ванны при сварке. Если не хватает других раскислителей, то СО может оказаться причиной пористости шва и ухудшения качества стали.
При сварке незащищенной дугой расплавляемый металл свободно контактирует с окружающим воздухом и насыщается кислородом и азотом, вследствие чего металл шва обладает низким качеством. Предел его прочности равен 34-38 МПа (для низкоуглеродистой стали), относительное удлинение — 3-8% и ударная вязкость KCU=5-15 Дж/см2. Поэтому сварку незащищенной дугой не применяют, а для защиты расплавляемого металла от воздуха и для улучшения качества, а также технологических свойств процесса сварки электроды покрывают специальной обмазкой. Кроме того, применяют защитные газы: аргон, гелий и др.
Похожие материалы
ДИФФУЗИЯ ВОДОРОДА В СВАРНЫХ СОЕДИНЕНИЯХ КОНСТРУКЦИОННЫХ СТАЛЕЙ | Сергеев
1. Okuda N., Ogata Y., Nishikawa Y., Aoki T., Goto A., Abe T. Hydrogen-induced cracking susceptibility in high-strength weld metal. Welding Journal, 1987, vol. 66, pp. 141-146 s.
2. Yatake T., Yurioka N. Studies of delayed cracking in steel weldments (Report 3). Journal of the Japan Welding Society. 1981, vol. 50, no. 3, pp. 291-296.
3. Suzuki H., Yurioka N. Prevention against cold cracking in welding steels. Australian Welding Journal, 1982, vol. 27, pp. 9-27.
4. Karppi R. A. Stress Field Parameter for Weld Hydrogen Cracking. Technical Research Centre of Finland Publications. 1982, no. 9, 119 p.
5. Graville B.A. A survey review of weld metal hydrogen cracking. Welding in the World, 1986, vol. 24, no. 9/10, pp. 190-199.
6. An analysis of microstructure, strain and stress on the hydrogen accumulation in the weld heat-affected zone / Yurioka N., Ohshita S., Nakamura H., Asano K. IIW-Doc. IX-1161-80. Nippon Steel Corporation, The International Institute of Welding, Japan, 1980. 18 p.
7. Yurioka N. A review of numerical analyses on the hydrogen diffusion in welding of steel. IIW-Doc. IX-1553-89. Nippon Steel Corporation, The International Institute of Welding, Japan, July 1989. 15 p.
8. Yurioka N. Predictive methods for prevention and control of hydrogen assisted cold cracking. IIW-Doc. IX-1938-99. Nippon Steel Corporation, The International Institute of Welding, Japan, 1999. 16 p.
9. Yurioka N. Diffusion and accumulation of hydrogen in multiple-pass welds. Special Visitors Lectures. Nippon Steel Corporation, Chiba, Japan, 1999.
10. Porter D.A., Easterling K.E. Phase Transformations in Metals and Alloys. Chapman & Hall, London, U.K., 1992. 514 p.
11. Роль пиковых напряжений в образовании холодных трещин в сварных соединениях закаливающихся сталей / Ю.А. Стеренбоген, Д.В. Васильев, Э.Л. Демченко, Д.П. Новикова // Автомат. сварка. 2006. № 4. С. 11-20.
12. Махненко В.И. Ресурс безопасной эксплуатации сварных соединений и узлов современных конструкций. Киев: Наук. думка, 2006. 618 с.
13. Гавронойский А.А. Влияние диффузионного водорода на сопротивляемость замедленному разрушению сварных соединений высокоуглеродистой стали // Автомат. сварка. 2013. № 5. С. 15-21.
14. Yurioka N., Nakamura H. Investigation of the mass diffusion equation with activity as a variable. Journal of the Japan Welding Society, 1979, vol. 48, no. 9, pp. 726-730.
15. Sleptsov O.I., Mikhailov V.E., Smiyan O.D. Relationship between the delayed fracture process in-welds and kinetics of hidrogen reedistribution. Document MIS 1X-1557-89, 1989. 28 p.
16. Шаповалов В.И. Легирование водородом. Днепропетровск: Журфонд, 2013. 385 с.
17. Шоршоров М.Х. Металловедение сварки стали и сплавов титана. М.: Наука, 1965. 336 с.
18. Чернышева Т.А. Границы зерен в металле сварных соединений. М.: Наука, 1986. 125 с.
19. Сергеев Н. Н. Механические свойства и внутреннее трение высокопрочных сталей в коррозионных средах: автореф. дис.. д-ра. техн. наук: 01.04.07. Самара, 1996. 38 с.
20. Johnson E.W., Hill M.L. The diffusivity of hydrogen in alpha iron. Transactions of the Metallurgical Society of AIME, 1960, vol. 218, pp. 1104-1112.
21. Oriani R.A. The diffusion and trapping of hydrogen in steel. Acta Metall, 1970, vol. 18, pp. 147-157.
22. Процессы взаимной диффузии в сплавах: монография / И.Б. Боровский, К.П. Гуров, И.Д. Марчукова, Ю.Э. Угасте; под. ред. К.П. Гурова. М.:Наука, 1978. 359 с.
23. Взаимная диффузия в многофазных металлических системах / К.П. Гуров, Б.А. Карташкин, Ю.Э. Угасте; под ред. К.П. Гурова. М.: Наука, 1981. 350 с.
24. Технология металлов и сплавов: учебник / Н.Н. Сергеев, А.Е. Гвоздев, Н.Е. Стариков, В.И. Золотухин, А.Н. Сергеев, А.Д. Бреки, О.В. Кузовлева, Г.М. Журавлев, Д.А. Провоторов; под. ред. проф. Н.Н. Сергеева. Тула: Изд-во ТулГУ, 2017. 490 с.
25. Сопряженные поля в упругих, пластических, сыпучих средах и металлических труднодеформируемых системах: монография / Э.С. Макаров, В.Э. Ульченкова, А.Е. Гвоздев, Н.Н. Сергеев, А.Н. Сергеев; под ред. проф. А.Е. Гвоздева. Тула: Изд-во ТулГУ, 2016. 526 с.
26. Теория пластичности дилатирующих сред: монография / Э.С. Макаров, А.Е. Гвоздев, Г.М. Журавлев; под. ред. проф. А.Е. Гвоздева. 2-е изд. перераб. и доп. Тула: Изд-во ТулГУ, 2015. 337 с.
27. Роль процесса зародышеобразования в развитии некоторых фазовых переходов второго рода / А.Е. Гвоздев, Н.Н. Сергеев, И.В. Минаев, И.В. Тихонова, А.Г. Колмаков // Материаловедение. 2015. № 1. С. 15-21.
28. Влияние деформационной повреждаемости на формирование механических свойств малоуглеродистых сталей / Г.М. Журавлев, А.Е. Гвоздев, Н.Н. Сергеев, Д.А. Провоторов // Производство проката. 2015. № 12. С. 9-13.
29. Формирование механических свойств углеродистых сталей в процессах вытяжки с утонением / А. Е. Гвоздев, Г.М. Журавлев, А.Г. Колмаков // Технология металлов. 2015. № 11. С. 17-29.
30. Влияние разнозернистости аустенита на кинетику перлитного превращения в мало- и среднеуглеродистых низколегированных сталях / А.Е. Гвоздев, А.Г. Колмаков, Д.А. Провоторов, И.В. Минаев, Н.Н. Сергеев, И.В. Тихонова // Материаловедение. 2014. № 7. С. 23-26.
31. Особенности протекания процессов разупрочнения при горячей деформации алюминия, меди и их сплавов / А.Е. Гвоздев, А.Г. Колмаков, Д.Н. Боголюбова, Н.Н. Сергеев, И.В. Тихонова, Д.А. Провоторов // Материаловедение. 2014. № 6. С. 48-55.
32. Распределение температур и структура в зоне термического влияния для стальных листов после лазерной резки / А.Е. Гвоздев, Н.Н. Сергеев, И.В. Минаев, А.Г. Колмаков, И.В. Тихонова, А. Н. Сергеев, Д.А. Провоторов, Д.М. Хонелидзе, Д.В. Малий, И.В. Голышев // Материаловедение. 2016. № 9. С. 3-7.
33. Механизмы водородного растрескивания металлов и сплавов, связанные с усилением дислокационной активности / Н.Н. Сергеев, С.Н. Кутепов, А.Е. Гвоздев, Е.В. Агеев // Известия Юго-Западного государственного университета. 2017. Т. 21, № 2(71). С. 32-47.
34. Анализ теоретических представлений о механизмах водородного растрескивания металлов и сплавов / Н.Н. Сергеев, А.Н. Сергеев, С.Н. Кутепов, А.Е. Гвоздев, Е.В. Агеев // Известия Юго-Западного государственного университета. 2017. Т. 21, № 3(72). С. 6-33.
35. Перспективные стали для кожухов доменных агрегатов / Н.Н. Сергеев, А.Е. Гвоздев, А.Н. Сергеев, И.В. Тихонова, С.Н. Кутепов, О.В. Кузовлева, Е. В. Агеев // Известия Юго-Западного государственного университета. Серия: Техника и технологии. 2017. Т. 7, № 2(23). С. 6-15.
Взаимодействие с азотом и водородом при сварке плавлением
Основным источником азота при сварке является воздух. Молекулярный азот при высоких температурах диссоциирует на атомы
N2 = 2N – 170200 кал/моль.
Частично в присутствии кислорода при высоких температурах образуются и окислы азота, в частности NO.
Азот в некоторых металлах (медь, серебро, золото) практически нерастворим и может применяться при сварке таких металлов как защитный нейтральный (инертный) газ.
В железе и железных сплавах азот растворяется и при температурах ниже 600°С образует химические соединения – нитриды Fe2N, Fe4N. Зависимость растворимости азота в твердом и жидком железе от температуры показана на рис. 1.
Рис. 1. Зависимость растворимости азота и водорода в железе от температуры.
При переходе железа из жидкого состояния в твердое растворимость азота скачкообразно уменьшается; газ стремится из раствора в виде газовой фазы (нитриды при этих температурах не образуются), что может привести к образованию пор.
Источником водорода при сварке являются продукты горючих углеводородов (при газовой сварке) и углеводов из покрытий, а также продукты диссоциации паров воды.
Водород в газовой фазе может присутствовать в виде молекулярного, атомарного и ионизированного. Ионизация водорода происходит по реакции
Н2 = Н + Н+ + е— — 417480 кал/моль.
Различные металлы по-разному взаимодействуют с водородом. Одни из них (титан, тантал, ниобий, ванадий и др.) образуют с водородом химические соединения – гидриды (как правило, ухудшающие свойства металла). Многие гидридобразующие металлы сильно поглощают водород и в твердом состоянии. При более высоких температурах гидриды распадаются, вследствие чего водород может выделяться из металла (у титана при температурах более 700°С).
Другая группа металлов (железо, никель, кобальт, медь) гидридов не образует. Водород адсорбируется этими металлами; при плавлении растворимость водорода резко повышается. Растворимость водорода при постоянной температуре подчиняется зависимостям:
[Н] = К1рН; [Н] = К2√(рН2),
где К1, К2 – коэффициенты, зависящие от температуры; рН и рН2 – парциальные давления водорода (атомарного и молекулярного) в газовой фазе.
Общий характер изменения растворимости водорода в железе при различных температурах и рН2 = 1 кгс/см2 показан на рис. 1.
Для жидкого железа растворимость водорода [Н] (см3/100г) в зависимости от парциального давления рН2 (мм рт.ст.):
lg[H]ж = 0,5lg ph3 – 1745/Т + 0,888.
Часть водорода со временем удаляется из металла диффузией, а часть остается в металле в различных несплошностях. И диффузионно-подвижный остаточный водород в целом ухудшают свойства сварных соединений, в связи с чем его количество в металле следует ограничивать. Ограничение содержания водорода в металле в основном достигается уменьшением парциального давления свободного водорода в газовой фазе при сварке. Для этого:
1.Удаление и ограничение источников водорода при сварке;
2.Связывание газообразного водорода в стойкие при высоких температурах соединения;
3.Уменьшение растворимости водорода в жидком металле, в частности его окислением.
Методы удаления источников водорода сводятся к предварительной очистке кромок от водных окислов (например, ржавчины), их просушке от адсорбированной воды, очистке электродной проволоки от жиров, просушке и прокалке сварочных материалов (электродов, флюсов), предохранению флюсов от засорения ржавчиной и пр.
Связывание водорода в условиях сварки осуществляется либо во фтористый водород (HF), либо в гидроксил (ОН). Более распространенным является связывание во фтористый водород:
2CaF2 + 3SiO2 = 2CaSiO3 + SiF4
SiF4 + 3H = SiF + 3HF
SiF4 + 2H2O = SiO2 + 4HF.
Окисленность металла приводит к снижению содержания в нем водорода. Поэтому хорошо раскисленный металл является более чувствительным к водороду газовой фазы и требует применения более сильных мер защиты (введения фторидов, прокалки сварочных материалов и пр.).
Сварка на атомарном водороде — Baker’s Gas & Welding Supplies, Inc.
Сварка атомарным водородом, также известная как AHW, представляет собой метод дуговой сварки, в котором используется дуга, расположенная между двумя вольфрамовыми электродами, и водородный защитный газ. Этот способ сварки открыл Ирвинг Ленгмюр, изучая атомарный водород. Используемая электрическая дуга разрушает молекулы водорода, которые позже рекомбинируют и выделяют большое количество тепла, которое может достигать температуры от 3400 до 4000 градусов по Цельсию.Способность достигать таких высоких температур делает этот процесс сварки одним из третьих самых горячих источников пламени. По сравнению с ацетиленовой горелкой, которая способна достигать температуры только 3300 градусов по Цельсию, сварка с использованием атомарного водорода намного горячее, чем обычно работает средний сварщик.
Высокий уровень тепла, выделяемого при сварке с использованием атомарного водорода, достаточно высок, чтобы можно было плавить и сваривать вольфрам, который может быть самым твердым для сварки металлом. Водород, который используется в процессе сварки, действует как газовый экран и защищает свариваемый металл от загрязняющих веществ, таких как углерод, кислород и азот, которые могут вызывать дефекты во многих металлах.Это также избавляет сварщика от необходимости использовать флюс. Во время сварки атомарным водородом дуга поддерживается отдельно от свариваемых деталей. Газообразный водород обычно является двухатомным, но когда он достигает таких высоких температур, он распадается на атомарную форму и поглощает большое количество тепла, создаваемого дугой.
Когда водород контактирует с более холодной поверхностью, например, свариваемыми деталями, он рекомбинирует в свою двухатомную форму и быстро высвобождает накопленное тепло.Энергию, вырабатываемую при сварке атомарным водородом, можно довольно легко изменить, регулируя расстояние между струей дуги и свариваемыми деталями. Хотя сварка с использованием атомарного водорода является выгодным видом сварки, ее заменяют дуговой сваркой в среде защитного металла, прежде всего из-за недорогих инертных газов, которые используются в процессе.
Сварка атомарным водородом — полезный метод сварки, но из-за достижений в области инертных газов ее время может быть ограничено. Из-за высокого уровня тепла, выделяемого в этом процессе сварки, сварщикам необходимо еще больше осознавать опасности, которым они подвергаются.С высокими уровнями тепла необходимо обращаться с должным уважением и соблюдать все необходимые меры безопасности.
Сопутствующие товары
Газовые баллоны TurboTorch
Артикул: VIC-CYLINDER
Узнать больше
Шлем 3M Speedglas 9100 w Автозатемняющий фильтр 9100XX
Артикул: NAS711-06-0100-30SW
Узнать больше
Узел респиратора половинной стороны 3М с сажевым фильтром 6000 серии
Артикул: NAS142-6291
Узнать больше
Сообщение о сварке с использованием атомарного водорода впервые появилось на сайте Weld My World.
Что такое сварка атомарным водородом? — Мастер сварки
Все мы знаем о процессе дуговой сварки. Но слышали ли вы когда-нибудь о сварке атомарным водородом (AHW)? Что ж, этот процесс сварки является одним из видов дуговой сварки. Компания AHW известна своими превосходными сварочными технологиями. В этой статье мы сделаем краткий обзор, его плюсы, минусы, особенности и т. Д. Итак, давайте внимательно рассмотрим эту технику сварки.
ОпределениеЭто процесс дуговой сварки, при котором между двумя вольфрамовыми электродами в присутствии водорода используется электрическая дуга.Защитная атмосфера при сварке атомарным водородом состоит из водорода. Процесс сварки атомарным водородом сокращенно обозначается AHW.
История Мы знакомы с процессом дуговой сварки много лет. Но не всем было известно об использовании водорода в процессе дуговой сварки. Позже лауреат Нобелевской премии Ирвинг Ленгмюр изобрел AHW, когда изучал атомарный водород.
В сварке атомарным водородом решающую роль играют электрическая дуга и водород.Электрическая дуга очень эффективно разрушает молекулы водорода. Позже эти молекулы водорода рекомбинируют и выделяют огромное количество тепла. Во время выделения тепла достигаются температуры в диапазоне от 3400 º до 4000 º.
Что вы думаете о проведении этого процесса сварки в отсутствие водорода?
Из нескольких исследований было установлено, что без электрической дуги этот процесс становится совершенно неэффективным. Мы можем использовать кислородно-водородную горелку вместо электрической дуги, но в этом случае мы можем достичь температуры только до 2800 ºC.
Оборудование- 2 электрода вольфрама
- Электрододержатель или горелка
- Баллон водородного газа
- Присадочный стержень / из металла
- Контроллер с питанием 300 В. Источник питания переменного тока используется при сварке на атомарном водороде
Оборудование, используемое в AHW, включает сварочную горелку с двумя вольфрамовыми электродами. Эти два электрода наклонены друг к другу. Кроме того, они отрегулированы таким образом, чтобы поддерживать стабильную дугу.
Вокруг двух вольфрамовых электродов расположено угловое сопло, по которому проходит водород. Газовые баллоны используются для хранения необходимого газообразного водорода.
Почему используется источник переменного тока вместо постоянного?Этот вопрос может прийти вам в голову, когда вы думаете об источниках питания при сварке атомарным водородом. В этом процессе мы должны поддерживать равную подачу тепла на обоих концах электрода. Без равного питания на концах электрода мы не сможем выполнить этот процесс должным образом.Следовательно, чтобы получить необходимое равное количество тепла на обоих концах, мы должны использовать источник питания переменного тока вместо постоянного тока в процессе AHW.
Также читают:
Как работает сварка атомарным водородом? Возникновение дуги происходит, когда два вольфрамовых электрода находятся в контакте друг с другом. Кроме того, после контакта они разделены небольшим расстоянием 1,5 мм.
Ниже приведена диаграмма процесса AHW :
Когда электрическая дуга проходит через газообразный водород, он диссоциирует на атомарный водород.Эта диссоциация на атомарный водород происходит из-за поглощения большого количества тепла, производимого в процессе.
Здесь протекает эндотермическая реакция.
h3 = H + H -422 кДж
После этого происходит рекомбинация атомарного водорода. Эта рекомбинация происходит, когда атомарный водород касается холодной заготовки. Этот процесс выделяет большое количество тепла.
H + H = h3 = 422 кДж
Здесь при рекомбинации протекает экзотермическая реакция.
Процесс сварки атомарным водородом:Подаваемое тепло не должно быть слишком большим или слишком низким. Если процесс плавления длится долго, это признак недостаточного нагрева.
Необходимо поддерживать надлежащий дуговой зазор. Он не должен быть слишком большим или слишком маленьким. Если не поддерживать надлежащий дуговой зазор, выделяется очень мало тепла.
Чем меньше тепла, тем меньше будет бассейн. Поддерживать надлежащую пористость поверхности будет очень сложно, если будет меньше тепла.
Сильная жара приведет к образованию широкого бассейна. Избыточное количество тепла приводит к образованию больших отверстий в сварочном материале.
Четыре фактора, влияющие на успех процесса сварки атомарным водородом:- Скорость передвижения
- Размер дуги
- Настройка текущего
- Правильный контакт заготовки с дугой.
Для лучшего понимания просмотрите видео, представленное ниже:
Преимущества
- AHW производит очень меньше искажений.
Меньшее искажение происходит из-за очень интенсивного пламени. Это сильное пламя может быть сконцентрировано на определенном стыке.
- Сварка на атомарном водороде ускоряет процесс сварки. Ускорение процесса сварки всегда выгодно сварщикам, а также экономит время.
- В процессе AHW отдельный флюс не требуется. Газообразный водород действует как защитный газ и предотвращает окисление металлов, а также вольфрамового электрода.
- В некоторых процессах сварки заготовка является частью электрической цепи, и из-за таких ситуаций, как зажигание дуги и поддержание столба дуги, возникает.Но, поскольку деталь не является частью электрической цепи в AHW, таких проблем не возникает в течение всего процесса.
- Средняя температура пламени, образующегося в этом процессе, составляет около 4000º C. Это пламя считается 3-м по величине пламенем.
- Температура пламени дицианоацетилена составляет около 4987 ° C, а температура пламени цианогена составляет около 4525 ° C.
- При сварке с атомарным водородом срок службы электрода увеличивается за счет пропускания газообразного водорода через вольфрамовые электроды.Кроме того, когда газообразный водород проходит через электроды, электроды становятся холоднее.
- Недавно был разработан автоматический AHW. В этом процессе водород из баллонов высокого давления не используется. Вместо этого водород получают из безводного аммиака.
- Тепло, выделяемое в AHW, позволяет эффективно сваривать вольфрам.
- Для выполнения процесса сварки атомарным водородом требуется квалифицированная рабочая сила.Без квалифицированной рабочей силы этот процесс невозможно реализовать эффективно. Так что талантливый и опытный труд просто необходим.
- Стоимость этого процесса сварки немного выше, чем у других сварочных процессов. Итак, для выполнения AWH вам потребуется минимальный капитал.
- AHW ограничен только горизонтальными положениями.
Для других положений этот процесс сварки не подходит.
- Необходимо принять необходимые меры предосторожности, поскольку в этом процессе участвует водород. Водород — легковоспламеняющийся газ.
- Сварка атомарным водородом используется там, где требуется быстрая сварка. Этот процесс сварки в основном используется для нержавеющей стали и некоторых специальных сплавов.
- Может использоваться практически для всех черных и цветных металлов.
- Это идеальный процесс для сварки как тонких, так и толстых листов металлов диаметром от 2 до 10 мм.
В современном мире этот процесс иногда заменяют дуговой сваркой металла в газовой среде.Поскольку недорогие инертные газы присутствуют в большем количестве, вместо сварки атомарным водородом используется дуговая сварка металлическим газом.
Таким образом, в этой статье мы обсудили всю сварку атомарным водородом, ее историю, преимущества, применение, как она работает и все другие ее параметры. Спасибо, что прочитали эту статью, и дайте нам знать в комментариях свое мнение о ней.
Проблема водорода
Водород в наружной рабочей среде неизбежен. Почти все органические соединения содержат водород — от смазочных материалов и масел до веществ, встречающихся в природе в полевых условиях, и влаги в атмосфере.Растрескивание под воздействием водорода (HAC) или растрескивание в зоне термического влияния (HAZ) является одной из самых серьезных угроз целостности сварочных работ на линиях электропередачи (а также многих других сварочных работ). Подрядчики по сварке трубопроводов должны проявлять инициативу в снижении выбросов водорода в зоне сварки — и это начинается с понимания множества источников водорода и способов их устранения или минимизации.
В этой статье будет рассмотрена тема крекинга с помощью водорода и водородной хрупкости, а также представлены передовые методы управления водородной угрозой.В нем также будут указаны особые меры предосторожности для различных марок стали и присадочного металла. Как всегда, следует соблюдать предписанные процедуры сварки. Содержание этой статьи предназначено для ознакомления и не заменяет установленные процедуры и квалификацию процедур.
Проблема
Растрескивание с водородом, также называемое замедленным или холодным растрескиванием, может проявляться медленно и проявляться через несколько часов или дней после завершения сварки, что может привести к дорогостоящему ремонту и простоям.Ионы водорода чрезвычайно малы и очень подвижны, могут легко диффундировать за пределы зоны сварного шва и объединяться вдоль неоднородностей, присутствующих в микроструктуре. Ионы водорода могут рекомбинировать с образованием газообразного водорода, дополнительно нарушая микроструктуру. Эти скопления или карманы водорода в конечном итоге создают напряжения, которые могут привести к растрескиванию.
Для возникновения водородного крекинга должны присутствовать несколько факторов. К ним относятся микроструктура, подверженная образованию трещин, наличие остаточных напряжений и присутствие водорода. В общем, склонность к водородному растрескиванию увеличивается по мере увеличения прочности основного металла. Уменьшение количества диффундирующего водорода и принятие мер по уменьшению или устранению остаточных напряжений уменьшат вероятность образования трещин с участием водорода. Это может быть достигнуто за счет использования присадочных металлов с низким содержанием водорода, улучшения нагрева до и после сварки, поддержания температуры между проходами и, в некоторых случаях, изменения процесса сварки. Простое уделение большего внимания методам обращения с материалами и хранением для предотвращения поглощения влаги будет иметь большое значение для предотвращения растрескивания под действием водорода.
Проблема с присадочным металлом
Основным источником водорода в сварном шве является присадочный металл. Состав присадочного металла, а также окружающая среда и способ хранения присадочного металла могут влиять на уровень водорода в присадочном металле и образующемся металле сварного шва. Электроды для дуговой сварки металла с защитным покрытием из целлюлозы (SMAW, или стержневые) обеспечивают самые высокие уровни водорода в присадочных металлах, обычно используемых в трубопроводах электропередач, с уровнями, намного превышающими 16 мл на 100 г металла шва.Также доступны стержневые электроды с низким содержанием водорода с обозначениями h5 и H8, обеспечивающие менее 4 и 8 мл водорода на 100 г металла шва соответственно. К сожалению, стержневые электроды с низким содержанием водорода не обладают такими же характеристиками проплавления и эксплуатационными характеристиками, как целлюлозные электроды, и, как правило, неприемлемы для сварки корневого прохода трубы.
Переход на процесс нанесения металлической сердцевины для корневого прохода может снизить уровень водорода до 4 мл на 100 г металла шва или ниже, в то время как процесс самоэкранированной порошковой порошковой проволоки для заполняющих и закрывающих проходов позволяет использовать присадочный металл. что обычно составляет менее 8 мл на 100 г. Порошковые проволоки также содержат ряд поглотителей водорода, таких как фторидные соединения, которые в сочетании с водородом удаляют его из сварного шва. Эти проволоки особенно подходят для высокопрочных сталей, которые более склонны к образованию водородных трещин. Итог: используйте присадочный металл, который содержит самый низкий уровень диффундирующего водорода и при этом способен обеспечивать желаемые механические свойства.
Весь присадочный металл должен храниться в чистом, сухом месте в оригинальной упаковке до момента использования.Герметизация наплавочного металла помогает предотвратить попадание влаги в упаковку и разрушение наплавочного металла. Сведение к минимуму или исключение переноса присадочного металла из холодной в горячую среду также поможет минимизировать конденсацию, которая добавляет водород. Если присадочный металл перемещается из одного набора условий окружающей среды в другой, он должен быть защищен от окружающей среды и дать время для нормализации при температуре окружающей среды на рабочем месте.
Для применений с металлической или порошковой проволокой катушку с проволокой следует накрыть и / или снять и поместить в исходную коробку в конце рабочего дня.Полностью закрытые питатели типа чемодана также могут использоваться для полной изоляции провода от окружающей среды.
По возможности при работе с присадочными металлами следует использовать чистые сухие перчатки. Пот, масла и грязь на руках могут легко перейти на поверхность проволоки или электрода и внести дополнительный водород и загрязнения в сварной шов.
Целлюлозные стержневые электроды (т.е. электроды, относящиеся к классам EXX10 и EXX11, например E6010) представляют собой уникальный набор проблем, связанных с водородом.Электроды из целлюлозной палочки широко используются в трубопроводах, и никогда не следует хранить в электродной печи. Их следует хранить при комнатной температуре, в защищенном от окружающей среды месте. Влага, присутствующая в целлюлозных электродах, создает определенные характеристики дуги. Во время сварки целлюлоза разрушается в дуге и является источником углерода, водорода и кислорода в сварочной ванне. Производители понимают эту поломку и разрабатывают электроды для обеспечения определенного химического состава металла шва с учетом химических реакций, происходящих в расплавленной сварочной ванне.Высыхание покрытия электрода из целлюлозы приводит к изменению состава и может привести к растрескиванию металла сварного шва. Итог: хотя водород, как правило, нежелателен, целлюлозный стержневой электрод никогда не следует сушить для удаления влаги, образующейся в электроде. Если целлюлозный стержневой электрод, используемый в трубопроводах, становится влажным, его следует выбросить, и его нельзя восстанавливать путем сушки в стержневой печи. Точно так же, если электрод из целлюлозного стержня становится слишком сухим из-за непреднамеренного высыхания в электродной печи или из-за воздействия жаркой сухой погоды, его также следует выбросить.
Еще одно предостережение относительно электродов с целлюлозным стержнем: по возможности следует избегать сварки ими высокопрочных труб. Если приняты надлежащие меры предосторожности, эти электроды обычно приемлемы и обычно используются на трубопроводах X60 и более низкой прочности. Иногда они используются на трубопроводах класса X70, но не лучший выбор для высокопрочных сталей (некоторые операционные компании не разрешают их использование выше X65).
Хотя целлюлозные стержневые электроды не следует хранить в электродных печах, электроды с низким содержанием водорода (обозначения EXX18, EXX15 и EXX16, например E7018) всегда следует хранить в герметично закрытых контейнерах или в электродных печах.Обязательно следуйте рекомендациям производителя по хранению и ремонту стержневых электродов с низким содержанием водорода.
Важность нагрева (перед сваркой, после сварки и между проходами)
Водород оптимально диффундирует из сталей, используемых в строительстве трубопроводов, при температурах не ниже 250 градусов по Фаренгейту. Быстрый нагрев и охлаждение основного металла во время сварки создает напряжения в детали и может стимулировать создание твердых и прочных зернистых структур, подверженных водородному охрупчиванию. Быстрое охлаждение снижает вероятность диффузии водорода из сварного шва и ЗТВ и может привести к растрескиванию. Поддержание требуемой температуры предварительного нагрева и промежуточного прохода имеет решающее значение как для создания более мягкой, менее подверженной трещинам микроструктуры, так и для обеспечения диффузии водорода из металла шва и зоны термического влияния. В некоторых случаях может потребоваться выдержка после сварки (обычно от 24 до 48 часов при температуре 200–400 градусов по Фаренгейту), чтобы еще больше уменьшить количество водорода, который задерживается в сварном шве.Для некоторых типов стали может быть рекомендовано снятие напряжений с помощью послесварочной термообработки (PWHT).
При сварке многих трубопроводов используются старомодные газокислородные или пропановые горелки для нагрева сварного соединения. Это оборудование может представлять проблему, поскольку большинство топливных газов представляют собой углеводороды, а процесс зажигания горелки и приложения пламени к трубе фактически вводит водород в сварное соединение. Нагревание горелкой также не обеспечивает равномерного нагрева по всему стыку и ЗТВ, что приводит к появлению холодных участков, которые могут нагреваться и охлаждаться с неконтролируемой скоростью.Точно так же, если допускается падение температуры стыка ниже минимальной температуры между проходами, сварку необходимо прекратить и повторно нагреть стык, приложив к стыку горелку. Измерение температуры обычно выполняется вручную, и это остается на усмотрение сварщика или его помощника.
Индукционный нагрев рекомендуется для оптимальной диффузии водорода и равномерного нагрева по всей детали. Это также безопаснее, чем нагрев открытым пламенем (катушки индукционного нагрева фактически не нагреваются), и обеспечивает более быстрое время достижения температуры, чем другие методы нагрева.Тепло индуцируется в детали, помещая ее в переменное магнитное поле, создаваемое индукционными нагревательными кабелями с жидкостным или воздушным охлаждением. Индукционные кабели наматываются вокруг детали и создают в ней вихревые токи для генерации тепла. Автоматические записывающие устройства могут быть интегрированы в систему, которая создает постоянную запись, показывающую, что были выполнены надлежащие последовательности нагрева / охлаждения.
Ключевым фактором здесь является контроль. Оператор регулирует скорость нарастания, температуру между проходами и выдержку после сварки или снятие напряжений до точных параметров.Это контролирует охлаждение и гарантирует, что ЗТВ и сварной шов сохраняют желаемые механические свойства, и в то же время способствует удалению диффундирующего водорода. Этот контроль особенно важен при сварке электродами из целлюлозы, которые вводят более высокий уровень водорода в сварной шов, и при сварке более толстых высокопрочных сталей, которые обычно менее пластичны и с меньшей вероятностью деформируются, вызывая нарастание напряжений, в результате чего сталь еще более восприимчивы к водородному растрескиванию.
Сварочные мастерские
Хотя это и не основные инструменты для борьбы с водородом, есть некоторые изменения в технологии сварки, которые могут помочь уменьшить количество водорода, попадающего в сварной шов. В случае сплошной проволоки, металлической или порошковой проволоки сварка с большим расстоянием между контактным наконечником и заготовкой (в пределах рекомендуемого диапазона) может помочь удалить водород из зоны сварки. Более длинный электрический вылет приводит к большему предварительному нагреву проволоки и сжиганию большего количества водорода, прежде чем он пересечет дугу и перейдет в расплавленную сварочную ванну.Было показано, что разница в электрическом вылете в 1/8 дюйма может иметь существенное влияние на диффузионный водород. Однако использование слишком большого вылета может увеличить риск потери защитного газа и может привести к другим проблемам, включая уменьшение проникновения и плохую работоспособность. Как следствие, важно поддерживать электрический вылет и другие параметры сварки в пределах рекомендованных производителем диапазонов.
Другие распространенные источники водорода
Остаточные смазочно-охлаждающие жидкости от снятия фаски с труб, краски и некоторых покрытий, нанесенных на трубу, а также органических материалов, собранных в полевых условиях, таких как грязь, ржавчина или масло, вводят водород в сварной шов. Подготовка стыка имеет решающее значение: сварщики должны отшлифовать внутреннюю и внешнюю поверхности трубы на расстоянии одного дюйма от стыка, чтобы предотвратить попадание любого из этих загрязнений в сварочную ванну.
Остерегайтесь конденсата и влаги в сварном шве и вокруг него. Эта влажность может быть результатом колебаний температуры в течение дня, высокой влажности или других факторов окружающей среды. В частности, если температура окружающей среды упадет ниже точки росы (например, в течение ночи), влага будет конденсироваться на открытых поверхностях.Перед сваркой убедитесь, что соединение полностью высохло.
Сварочные процессы, для которых требуется защитный газ, могут создавать дополнительные проблемы из-за газового загрязнения или утечки шлангов и фитингов, которые всасывают воздух и тем самым вытягивают водород из атмосферы в газ. Все соединения и арматура защитного газа следует регулярно проверять. Защитные газы следует приобретать с указанием точки росы не выше -40 градусов по Фаренгейту.
Итог: приоритетной задачей должно быть сосредоточение внимания на методах сварки с низким содержанием водорода.Эти методы включают в себя упор на правильное обращение с трубой и присадочными металлами, выбор присадочных металлов с низким содержанием водорода и надлежащий предварительный, послесварочный и промежуточный нагрев. Металлы с низким содержанием водорода включают стержневые электроды с низким содержанием водорода, сплошные проволоки, электроды с металлическим сердечником, а также электроды с газовым и самозащитным сердечником. Внимательное отношение к этим факторам позволяет сварщикам свести к минимуму риск водородный крекинг в трубопроводах.
Дуговая сварка на атомарном водороде — Технические заметки
Сварка атомарным водородом — это процесс дуговой сварки, в котором используется газообразный водород для окружения и передачи тепла от дуги к основному металлу.Сварочная горелка на атомарном водороде содержит два металлических электрода из вольфрама, которые образуют электрическую дугу. Газообразный водород (h3) используется в качестве защитного газа, который при прохождении через дугу диссоциирует до своей элементарной формы (H +).
Разница между сваркой атомарным водородом и сваркой MMA или сваркой TIG заключается в том, что в последних случаях дуга образуется между электродом и основным металлом.
Вольфрамовые электроды не являются расходуемыми, и расстояние между ними можно изменять, чтобы контролировать тепло, выделяемое дугой. Трансформатор переменного тока обычно обеспечивает необходимый ток. Внешний присадочный металл может потребоваться, а может и не потребоваться, в зависимости от толщины основного металла.
Этот процесс был изобретен американским химиком и физиком Ирвином Ленгмюром в ходе его исследований атомарного водорода в начале 20 века.
Количество тепла, поглощаемого газообразным водородом (h3), равно энергии связи двух молекул водорода.
\ (H_2 \ rightleftharpoons H + H — 436 кДж / моль \)
Когда молекулы водорода ударяются о поверхность основного металла, происходит обратная реакция, и тепло, ранее поглощенное для разрыва связей, передается основному металлу. Соответствующая химическая реакция обеспечивает очень эффективную передачу тепла от дуги к основному металлу.
Помимо участия в теплопередаче, водород также служит защитным газом, который защищает сварочную ванну от атмосферного загрязнения.Например, любой кислород возле сварочной ванны соединяется с водородом с образованием воды, которая выходит в виде пара. Если кислород не удерживается вдали от сварочной ванны, образование оксида металла неизбежно.
Температуры, достигаемые с помощью этого процесса сварки, намного выше, чем при газовой кислородно-ацетиленовой сварке, с температурами до 4200 ° C. Поток водорода вокруг электрода также служит для охлаждения и предотвращения испарения вольфрама.
Процесс сварки атомно-водородной дугой очень универсален и может использоваться для сварки практически любого металла. Это особенно полезно при сварке легких металлов, черных сплавов и большинства цветных сплавов. Его также можно использовать для любого процесса, требующего прецизионной сварки, например для исправления ошибок обработки.
Сварка атомарным водородом — детали, работа, преимущества, недостатки и применение
Термохимическая сварка с использованием атомарного водорода (AHW) — это процесс сварки, при котором сварка выполняется с использованием дуги, возникающей между двумя вольфрамовыми электродами, и газообразным водородом, подаваемым из баллона с газообразным водородом.
Сварка называется атомарным водородом, потому что дуга разлагает водород на атомарную форму. Этот процесс также известен как атомно-дуговая сварка.
Этот процесс сварки был изобретен Ирвингом Ленгмюром, американским химиком и физиком в начале 20 века.
Присадочный стержень не является обязательным в этом процессе сварки, он может использоваться или не использоваться.
В этом процессе сварки высокая температура от 3400 до 4000 ° C достигается за счет использования электрической дуги и газообразного водорода.
Вольфрам и большая часть тугоплавких металлов можно сваривать, используя высокую температуру этого процесса сварки.
Газообразный водород в этом процессе сварки выполняет две функции, первая — обеспечивать эффект нагрева.
Кроме того, расплавленный металл, полученный во время сварки, окружен экраном, создаваемым газообразным водородом, и, таким образом, газообразный водород действует как защитный газ для расплавленного металла. Газообразный водород играет очень важную роль в этом процессе сварки.
Основное различие между процессом сварки атомарным водородом и сварочными процессами, такими как сварка MMA и сварка TIG, заключается в том, что в процессе сварки MMA и TIG дуга образуется между электродом и основным металлом, тогда как в AHW дуга образуется между двумя электродами.
Основные части вольфрамового электрода:
1) Вольфрамовый электрод:
В этом процессе сварки сварочная горелка оснащена двумя вольфрамовыми электродами, которые наклонены и регулируются для создания и поддержания стабильной дуги.
2) Держатель электрода:
Держатели электродов используются для удержания вольфрамовых электродов.
3) Сопла:
Вокруг вольфрамовых электродов имеются кольцевые сопла, через которые выходит водород, подаваемый из баллона с газообразным водородом.
4) Баллон с водородом:
Баллон, заполненный газообразным водородом, используется в этом процессе для подачи газообразного водорода в требуемое место в процессе сварки.
5) Источник питания переменного тока:
В этом процессе требуется источник питания переменного тока 300 В с контроллером. Этот источник питания будет использоваться для создания дуги между вольфрамовыми электродами.
AC предпочтительнее постоянного тока, потому что на обоих электродах требуется одинаковое количество тепла.
7) Трансформатор:
Трансформатор необходим для создания дуги и ее поддержания.Трансформатор должен иметь напряжение холостого хода 300 вольт.
8) Присадочный стержень:
Присадочный стержень не является обязательным. Его используют при необходимости, в противном случае этот процесс можно выполнить без присадочного стержня.
9) Клапан регулятора давления:
Клапан регулятора давления находится над баллоном с газообразным водородом. Он используется для измерения давления в баллоне и его отображения. Он также соединен с ручкой электрода, чтобы газообразный водород попадал в нужное место.
10) Пластины заготовки:
Сварочное соединение создается поверх этих пластин заготовки, и они соединяются вместе.
Грязь, оксиды и другие загрязнения удаляются с заготовки для получения сварного шва хорошего качества.
Рабочие:
Сначала, когда источник питания переменного тока включен и два электрода поднесены друг к другу, между этими двумя электродами возникает дуга, и эти электроды мгновенно разделяются на небольшое расстояние, равное почти 1. 5 мм. Электроды немного разделены, чтобы поддерживать стабильную дугу между электродами. Тепло, выделяемое дугой, можно контролировать, изменяя расстояние между электродами.
Кроме того, газообразный водород будет подаваться из баллона с газообразным водородом к электродам. Этот газообразный водород будет обеспечивать защиту от дуги, создаваемой электродами.
Водород будет подаваться из баллона и выходить из сопла, расположенного вокруг электродов. Этот газообразный водород будет действовать как защитный газ, а это значит, что он защитит сварное соединение от атмосферных газов и обеспечит хорошее качество сварного соединения.
Если атмосферный газ, например кислород, попадает в зону сварочного процесса, он соединяется с водородом с образованием воды и быстро испаряется из-за высокой температуры процесса сварки и предотвращает образование оксида металла. Водородная защита также защищает сварное соединение от загрязнения атмосферными газами, такими как углерод, азот или кислород.
Кроме того, когда дуга соприкасается со струей газообразного водорода, газообразный водород, который находится в двухатомной форме, деионизируется в отдельные ионы H +
H 2 = H + H — 422 кДж (эндотермическая реакция)
Когда эти деионизированные ионы H + подойдут к заготовке и ударяются о поверхность основного металла, они охлаждаются и объединяются с другими H + ионов.Но когда два иона H + объединяются, внезапно выделяется большое количество тепла, что обозначается следующей реакцией:
H + H = H 2 + 422 кДж (экзотермическая реакция)
Тепло, выделяющееся во время рекомбинации атомов водорода будут поглощены пластинами заготовки. Следовательно, металл будет плавиться, в результате чего между металлическими пластинами или деталями образуется плавкое соединение. Следовательно, между деталями образуется ванна расплава. В этом процессе может производиться тепло в диапазоне от 3500 o C до 4000 o C.
Заготовка в этом процессе сварки не полностью является частью электрической цепи. Заготовка становится частью электрической цепи только тогда, когда часть дуги входит в контакт с заготовкой, и, следовательно, между заготовкой и каждым электродом создается напряжение.
Преимущества сварки атомарным водородом:
1) Сварка в этом процессе выполняется быстрее.
2) Поскольку водород сам по себе действует как защитный газ, отдельный защитный газ не требуется.
3) Пламя очень мало искажается, так как получается интенсивное пламя, которое может концентрироваться на стыках.
4) Электроды остаются холодными, так как водород проходит мимо электродов в держателе, что также увеличивает срок службы электродов.
5) Оператор может легко контролировать поток газообразного водорода и дугу, и, следовательно, можно также контролировать выделяемое тепло. Таким образом, с помощью этого процесса сварки можно регулировать нагрев для сварки различных материалов.
6) Сплавы можно плавить без флюсов и без поверхностного окисления благодаря мощному восстановительному действию атомарного водорода.
Недостатки сварки на атомарном водороде:
1) Этот процесс более дорогостоящий по сравнению с другими сварочными процессами.
2) Для управления этим процессом сварки требуется опытный оператор.
3) С помощью этого процесса сварки нельзя наплавить большие количества металла.
4) Эта сварка может выполняться только на плоских участках.
5) Этот процесс сварки более опасен, так как водород является легковоспламеняющимся газом.
Применение сварки атомарным водородом:
1) В основном используется там, где требуется быстрая сварка, например, в случае нержавеющей стали и других специальных сплавов.
2) Может использоваться для сварки большинства черных и цветных металлов.
3) Также используется для сварки тонких листов металла и сплавов малого диаметра.
4) Этот процесс также используется при ремонте штампов и инструментов, наплавке твердых поверхностей и соединении деталей.
5) Может также использоваться для очень точной сварки, например для исправления ошибок обработки.
Смеси газообразного аргона и водорода
Смеси защитных газов Praxair HydroStar ® в основном используются для соединения аустенитных нержавеющих сталей с использованием процесса газовой вольфрамовой дуговой сварки (GTAW или TIG). Водород увеличивает подвод тепла к основным материалам, обеспечивая при этом восстановление атмосферу для повышения чистоты сварных швов. Могут быть получены значительные преимущества в скорости движения по сравнению с чистым аргоном.
Основные области применения
Добавки 2-5% обычно используются для ручной TIG-сварки оборудования для предприятий общественного питания, перил и аэрокосмических компонентов из нержавеющей стали. Добавки водорода 10-15% обычно используются при механизированной сварке труб из аустенитной нержавеющей стали.
Предупреждение: При смешивании аргона и водорода требуются особые меры безопасности. НЕ пытайтесь смешивать аргон и водород из отдельных баллонов.
Примечание: Кислород и диоксид углерода химически активны и не должны использоваться с GTAW.Их окислительный потенциал может вызвать сильную эрозию и деградацию вольфрамового электрода при температурах дуги.
Газовые смеси HydroStar H-2 и H-5
Эти смеси используются для ручной сварки. Смесь HydroStar H-5 предпочтительна для материалов толщиной более 1/16 дюйма. Эти смеси также подходят для использования с GTAW при сварке аустенитных нержавеющих сталей серии 300 и в качестве обратной продувочный газ для материалов из нержавеющей стали.
HydroStar H-10 Gas Blend
Эта смесь предпочтительна для механизированной высокоскоростной GTAW обработки аустенитной нержавеющей стали.
HydroStar H-15 Gas Blend
Эта смесь, содержащая 15% водорода, чаще всего используется для сварки стыковых соединений нержавеющей стали на скоростях, сравнимых с гелием, и на 50 процентов быстрее, чем аргон. Смесь HydroStar H-15 также используется для увеличения скорости сварки 300-й серии. нержавеющая сталь. Может использоваться с нержавеющей сталью любой толщины. Концентрации более 15% могут вызвать пористость металла шва при многопроходном применении.
HydroStar H-35 Gas Blend
Рекомендуется в качестве плазменного газа с плазменной дугой, при резке алюминия и нержавеющей стали, а также когда качество резки и внешний вид лицевых поверхностей имеют решающее значение.
Предотвращение водородного растрескивания при сварке сталей C-Mn
Углеродисто-марганцевые (C-Mn) стали являются преобладающими конструкционными сталями, которые используются в больших количествах в самых разных областях машиностроения. Стальные конструкции из C-Mn, как правило, можно успешно сваривать, если известен состав стали, принимаются соответствующие меры и выполняются квалифицированные процедуры.
C-Mn различается по простоте сварки или свариваемости. При соответствующем сочетании обстоятельств водородный крекинг, крекинг при затвердевании, крекинг с повторным нагревом — все возможные механизмы крекинга.Большинство современных композиций обеспечивают хорошее сопротивление этим типам проблем, но в случае водородного растрескивания, который, возможно, является наиболее важным фактором при применении конструкционной стали, процедура сварки очень важна.
Меры предосторожности, необходимые для предотвращения водородного крекинга:
- Не допускайте попадания влаги или водорода. Это можно сделать, обеспечив чистоту и сухость деталей, а также чтобы расходные детали были чистыми и сухими перед сваркой. Для ответственных применений обычно используются простые ручные металлические дуговые электроды с низким содержанием водорода.Низкие уровни диффундирующего водорода в металле сварного шва достигаются за счет использования электродов из запечатанных пакетов или их обжига перед использованием.
Сварка в среде с высокой влажностью также может повысить уровень водорода в металле шва, и могут потребоваться дополнительные меры, чтобы избежать растрескивания.
- Укажите химический состав свариваемой стали. Углеродный эквивалент (IIW CE) используется для характеристики влияния легирующих элементов на свариваемость и представляет вклад состава в подверженность стали водородному растрескиванию.При увеличении значения IIW CE (более высоколегированный) и толщины материала необходимо принять меры для смягчения неблагоприятных эффектов. Может потребоваться предварительный нагрев, и следует рассмотреть возможность использования сварочных материалов и процессов с низким содержанием водорода. Как правило, стали со значением IIW CE <0,4 не подвержены водородному растрескиванию, если используются процессы с низким содержанием водорода. Рекомендации по предотвращению водородного крекинга приведены в BS: EN 1011: 2001 Часть 2.
- Выберите подходящий электрод и сварочный процесс.
Одно из основных различий между процессами дуговой сварки — способ защиты расплавленной сварочной ванны во время сварки. Это достигается за счет использования либо флюса, образующего защитный расплавленный шлак, либо защитного газа. Для тонких сечений и материалов с низким уровнем IIW CE покрытые рутиловым флюсом электроды используются для общего производства при ручной дуговой сварке металлическим электродом (MMA) и дуговой сварке порошковой проволокой (FCAW), а плавленые флюсы используются при дуговой сварке под флюсом (SAW). Для сталей большего сечения и / или сталей с более высоким стандартом IIW CE необходимо учитывать более низкое потребление водорода.Для сварки MMA электроды запекаются, и электроды из основного флюса обеспечивают самые низкие водородные характеристики металла шва. Для SAW часто используются основные агломерированные флюсы. Сварка в среде инертного / активного газа (MIG / MAG) и вольфрамовым инертным газом (TIG) — это процессы с низким содержанием водорода, в которых используются защитные газы, а не флюсы.
Кольцевые сварные швы в материалах трубопроводов часто выполняются с использованием целлюлозных расходных материалов для MMA или автоматических установок TIG для увеличения скорости сварки, хотя в покрытиях из целлюлозного флюса содержание водорода может быть высоким, и необходимо соблюдать осторожность.
Меры предосторожности, необходимые для обеспечения удовлетворительных свойств сварного шва:
Требуемые механические свойства сварного соединения легко достигаются в стали C-Mn с использованием соответствующих сварочных материалов. Однако сложный характер структурных изменений, которые происходят во время термического цикла сварного шва, действительно означает, что требуется некоторая осторожность при оценке таких свойств, как ударная вязкость и твердость зоны термического влияния (HAZ).
- В некоторых случаях ухудшение характеристик в процессе эксплуатации может происходить из-за деформационного старения или коррозионного растрескивания под напряжением в стали C-Mn.
Этих проблем можно избежать, если принять правильные меры предосторожности, например: C-Mn-стали в кислой среде должны соответствовать указанным максимальным значениям твердости, чтобы исключить вероятность сульфидного коррозионного растрескивания под напряжением.
- Конструкционные стали более высокой прочности, используемые в условиях высоких напряжений, обычно должны соответствовать дополнительным требованиям к стандартным конструкционным классам, таким как минимальные требования к вязкости и максимальные требования к твердости, особенно в HAZ. Термическую обработку после сварки также необходимо учитывать во многих случаях, если твердость сварного шва является проблемой или если это требование правил производства.Закаленная и отпущенная сталь, используемая, например, в нефтяных и газовых скважинах для бурения, требует особой осторожности в отношении процедур сушки электродов, температуры предварительного нагрева, уровней подводимого тепла, термообработки после сварки и неразрушающего контроля после сварки.
Квалификация процедуры:
- Обычно требуется, чтобы процедура сварки была аттестована, а затем следовала ей, чтобы гарантировать, что сварка будет завершена удовлетворительно, и чтобы полученные свойства соединения соответствовали потребностям конкретного применения.Руководство по такой квалификации процедуры дано в BS EN ISO 15607: 2003 и BS EN ISO 15609-1: 2004.
Связанные статьи о сварке и свариваемости сталей C-Mn:
Список литературы
BS EN 1011-1: 2009 Сварка — Рекомендации по сварке металлических материалов.
Часть 1 — Общее руководство по дуговой сварке.
BS EN 1011-2: 2001 Сварка — Рекомендации по сварке металлических материалов
Часть 2 — Дуговая сварка ферритных сталей.
BS EN ISO 15607: 2003 Технические требования и аттестация процедур сварки металлических материалов.Общие правила (заменяет BS EN 288-1: 1992)
BS EN ISO 15609-1: 2004 Технические требования и аттестация процедур сварки металлических материалов.