отличие инертных от активных, особенности аргона, ацетилена, кислорода и их смесей, какой из них выгоднее использовать? – Газовая сварка на Svarka.guru
Сварка претерпела множество модификаций и апгрейдов с момента своего появления.
Бесполезная, на первый взгляд, металлическая субстанция, которая реагировала с воздухом, показывала низкий КПД и производительность в сравнении с другими методами соединения и обработки поверхностей.
Переломный момент произошёл в тот момент, когда человек начал варить металл в защитной газовой среде, с целью повысить скорость работы и качество конечного изделия.
Содержание
- 1 Особенности
- 1.1 Разновидности
- 1.2 Активные и инертные
- 1.3 Горючие газовые смеси
- 2 Что использовать для резки?
- 3 Полезное видео
- 4 Заключение
Особенности
Большинство газов, которые применяются в ходе сварки активны, то есть не реагируют ни с металлом ни с воздухом, поэтому и называются «защитными». Они создают оболочку вокруг рабочих поверхностей, чтобы расплавленный металл попадал только в место назначения.
[stextbox id=’info’]Нередко используются и инертные газы, которые являются ингибиторами негативного влияния окружающей среды.[/stextbox]
Разновидности
- Смесь аргона с 1—5% кислорода. Применяется для сварки с плавящимися электродами. Подойдёт для и легированных сплавов и сталей с низким содержанием углерода. Добавление кислорода к аргону снизит критический ток, обеспечит защиту от появления пор, улучшит форму шва.
- Смесь аргона с 10—25% углекислого газа. Задействуют для варке плавящимися электродами. Включение углекислого газа при сварке углеродных сталей позволит избежать пор, немного повысит стабильность дуги и обеспечит надежную защиту для зоны сварки. При наличии сквозняка, улучшит форму шва при сварке тонких металлических листов.
- Смесь аргона с углекислым газом (до 20%) и 5% кислорода.
Применяется для сварки плавящимися электродами для углеродистых и легированных сталей. Добавление активных газов улучшит стабильность дуги, процесс формировки швов и предупредит пористость.
- Смесь углекислого газа с кислородом (до 20%). Используется при сварке плавящимися электродами углеродной стали.Такая комбинация имеет повышенную способность окисляться, что обеспечивает глубокую проплавку и красивую форму шва, а так же, предохраняет шов от появления пор.
Активные и инертные
Чтобы получить качественный металлический шов, применяются разные способы защиты. Например, газо-шлаковая или газовая защита, которая спасает от действия кислорода и азота в воздухе и обеспечивает расплавленное покрытие флюсом, что улучшает качество шва.
Газы делятся на две группы:
- химически инертные;
- химически активные.
Газы из 1 группы не взаимодействует с нагретым и расплавленным металлом и практически не растворяются в них. Для использования этих защитных газов дугувым методом, можно применять плавящиеся и неплавящиеся электроды. Защитные газы 2 группы обеспечивают защиту в зоне сварки, но они либо растворяются в жидком металле, либо вступают в реакцию с воздухом и нейтрализует его пагубное воздействие.
Рассмотрим конкретные газы, которые применяются в сварке. Наиболее распространённые из них это:
- Аргон. Химический элемент 8 группы в таблице Менделеева. Аргон добывают из воздушной атмосферы, так как этот источник никогда не кончится. Аргон не вступают в хим.реакцию и после использования опять возвращается в атмосферу. Он бывает трёх сортов:
- высшей,
- 1й категории
- 2й категории.
- Содержание аргона в них, соответственно равно 99,99%, 99,98%, 99,95% сотых процентов. Примеси, которые составляют остальное процент — это Кислород, Азот, Влага. Аргон гарантирует хорошую защиту сварочной ванны (это зависит от назначения и содержания азота), а именно от сорта.
Для газовой сварки могут использовать смесь аргона с другими газами, например кислородом или с углекислым газом. Хранить и транспортировать аргон нужно под давлением. Иногда допускается перевозка в жидком виде и последующая газификация.
- Ацетилен имеет углеродный состав с тройной углеродной связью. Он добывается способом кальцинирование карбида и гидрогена, благодаря этому он очень распространён в качестве горючего газа для сварки при повышенных температурах. Горение ацетилена приводит к тому, что выделяются твердые частицы углерода, которые светятся. Свет может быть как жёлтым так и белым. Это позволяет, в отличии от кислорода, применять ацетилен как наполнитель для газовых фонарей.
- Транспортировать и хранить его нужно в баллонах под давлением 1,6 мПа или в жидком. Он взрывоопасен, если вступит в связь с кислородом.
При высоком давлении. Посмотрим на конкретные характеристики этого газа. Первое, что бросается в глаза — это самая высокая температура горения среди всех сварочных газов.- высокая взрывоопасность
- большая загазованность помещения в процессе работы
- возможность появления дефектов (пережог, перегрев тонких металлических поверхностей).
- Кислород (при нормальных условиях) – газ, который не имеет цвета, вкуса и запаха, активно поддерживает процессы горения. Он незначительно тяжелее воздуха и плохо растворим в воде и спиртовой среде. При охлаждении становится прозрачной голубоватой жидкостью без запаха. Для сварки его используют часто, но качество шва, грубо говоря, черновое. Получить аккуратный стежок и хорошую детализацию — не так уж и просто, так как радиус разбрызгивания и рассеивания весьма большой. Главное преимущество- низкая цена и доступность.[stextbox id=’alert’] ВАЖНО! Учитывая обилие режимов сварки и автоматов для сваривания, практически любой газ может применяться эффективно.
Вся разница будет заключаться в расходах энергии и топлива.[/stextbox]
Горючие газовые смеси
Обычно, газы смешивают для того, чтобы обеспечить максимальную эффективность рабочего процесса, скрыть слабые стороны и усилить сильные. К тому же, не все газы одинаково хорошо подойдут для ручной, полу-автоматической и автоматической сварки.
В ходе разработки сварочного алгоритма также рассчитывают газовую смесь, которая подойдёт оптимальным образом. Активный основной газ смешиваю с инертным, в пропорции 90/10.
Самые популярные пары:
- аргон и углекислота;
- аргон и кислород;
- аргон и гелий;
- аргон и водород;
- аргон и активные газы.
Могут применяться и другие смеси, которая содержат в себе углекислоту, водород, углерод, гелий. В частности, они используются для обработки редких металлов и в тех случаях, когда нужно получить высокое качество сварочного шва, но пожертвовать временем, так как подготовка к сварочному процессу регулировка скорости подачи электрода, давления, требует времени. Также скорость сварки будет значительно ниже, чтобы в случае неисправности не испортить деталь.
Резка предполагает абсолютно другой принцип использования газа. Здесь нужно использовать те же газы, какие вступают в реакцию с кислородом с металлом, для того, чтобы как можно быстрее разрушать рабочую поверхность.
- Кислород. Самый дешёвый, но, в то же время, самый неэффективный газ.
- Ацетилен. Оптимальный выбор для всех типов сварки. Не подойдёт для слишком тонких поверхностей.
- Псевдо-ацетилен или его заменители. Не дешёвый вариант, особенно, если речь идёт о больших партиях. Обеспечивает премиальное качество и высокую скорость работы.
Полезное видео
Очень хорошую подробную лекцию по газам для сварки можно посмотреть в следующем видео:
Заключение
Не существует одного универсального газа для сварки, каждый из них обладает как плюсами. Так и минусами, к тому же, цена у всех разная. Для более точного подбора газа, нужно просчитать проект сварки, изучить спецификацию метала, из которого изготовлена деталь.
Только так достигается максимальная эффективность. Каждый производитель будет нахваливать свой газ и будет убеждать покупателя, что он эффективнее других, но это не более, чем маркетинговая уловка. Как гласит пословица: «7 раз отмерь и один раз отрежь», а в нашем случае «7 раз рассчитай, один раз свари»!
Газы, применяемые для сварки и резки металлов
ема: «Газы, применяемые для сварки и резки металлов.
ель: изучение газов, применяемых для сварки и резки
еталлов, что является неотъемлемой задачей моей
рофессии.
адачи: составить презентацию в которой максимально
росто и удобно перечислены газы, применяемые
ри сварке и резке металлов и их значение.
главление:
Газы, понятие——————————————————3
Резка металлов————————————————4-5
Сварка металлов————————————————-6
Газы, применяемые в сварке и резке металлов—7-9
1. Кислород———————————————————-10
2. Ацетилен——————————————————-11-12
3. Заменители ацетилена—————————————13
3. Газ (газообразное состояние) (от нидерл. gas, восходит к
др.-греч. χάος) — одно из трёх агрегатных состояний
вещества, характеризующееся очень слабыми связями
между составляющими его частицами (молекулами,
атомами или ионами), а также их большой подвижностью.
Частицы газа почти свободно и хаотически движутся в
промежутках между столкновениями, во время которых
происходит резкое изменение характера их движения.
Также термин «газ» можно определить как вещество,
температура которого равна или превышает критическую
точку, при такой температуре сжатие газа не приводит к
образованию жидкости. В этом и заключается отличие газа
от пара. При повышении давления насыщенный пар
частично превращается в жидкость, газ — нет.
Газообразное состояние вещества в условиях, когда
возможно существование устойчивой жидкой или твёрдой
фазы этого же вещества, обычно называется паром.
Подобно жидкостям, газы обладают текучестью и
сопротивляются деформации. В отличие от жидкостей,
газы не имеют фиксированного объёма[1] и не образуют
4. Что же такое сварка и резка металлов?
Резкой металлов называют отделение частей (заготовок) от
сортового, листового или литого металла. Различают
механическую (ножницами, пилами, резцами), ударную (рубка) и
термическую резку. Термической резкой называют обработку
металла (вырезку заготовок, строжку, создание отверстий)
посредством нагрева. Паз, образующийся между частями
металла в результате резки, называют резом. По форме и
характеру реза может быть разделительная и поверхностная
резка, по шероховатости поверхности реза — заготовительная и
чистовая. Термическая резка отличается от других видов
высокой производительностью при относительно малых
затратах энергии и возможностью получения заготовок любого,
сколь угодно сложного, контура при большой толщине металла.
Можно выделить три группы процессов термической резки:
окислением, плавлением и плавлением-окислением. При резке
окисление м металл в зоне резки нагревают до температуры его
воспламенения в кислороде, затем сжигают его в струе
кислорода, используя образующуюся теплоту для подогрева
следующих участков металла. Продукты сгорания выдувают из
реза струей кислорода и газов, образующихся при горении
5. К резке окислением относятся газопламенная
(кислородная) и кислородно-флюсовая резка. При
резке плавлением металл в месте резки нагревают
мощным концентрированным источником тепла выше
температуры его плавления и выдувают
расплавленный металл из реза с помощью силы
давления дуговой плазмы,, реакции паров металла,
электродинамических и других сил, возникающих при
действии источника тепла, либо специальной струей
газа. К способам этой группы относятся дуговая,
воздушно-дуговая, сжатой дугой (плазменная),
лазерная и термогазоструйная резка. При резке
плавлением-окислением применяют одновременно оба
процесса, на которых основаны две предыдущие
группы способов резки. К способам этой группы
относятся кислородно-дуговая, кислородноплазменная, кислородно-лазерная резка.
6. Теперь перейдем к процессу сварки металлов.
Сва́рка — процесс получения неразъёмных соединений
посредством установления межатомных связей между
свариваемыми частями при их местном или общем нагреве,
пластическом деформировании или совместном действии того
и другого[1].
Неразъёмное соединение, выполненное с помощью сварки,
называют сварным соединением[1]. Чаще всего с помощью
сварки соединяют детали из металлов. Однако сварку
применяют и для неметаллов — пластмасс, керамики или их
сочетания.
При сварке используются различные источники энергии:
электрическая дуга, электрический ток, газовое пламя, лазерное
излучение, электронный луч, трение, ультразвук. Развитие
технологий позволяет в настоящее время проводить сварку не
только в условиях промышленных предприятий, но в полевых
и монтажных условиях (в степи, в поле, в открытом море и т. п.),
под водой и даже в космосе. Процесс сварки сопряжён с
опасностью возгораний; поражений электрическим током;
отравлений вредными газами; поражением глаз и других частей
тела тепловым, ультрафиолетовым, инфракрасным излучением
7. Ну что же, мы подошли к кульминации нашего вопроса.
А именно, к самим газам, которые применяются для сварки
и резки металлов.
Газовая сварка, при которой происходит плавление кромок
свариваемых деталей в высокотемпературном пламени газовой
горелки (рис. 1) с дальнейшим формированием шва, имеет по
сравнению со сваркой электродуговой как преимущества, так и
недостатки. К первым относится тот факт, что при помощи
данного метода можно сваривать практически любые
материалы, более того, чугун, медь, латунь и свинец даже легче
поддаются газовой сварке, чем дуговой. При этом отсутствует
потребность в применении дорогого и сложного оборудования,
а также в подключении к источнику электропитания. В то же
время газовую сварку обычно применяют для обработки
относительно тонких изделий, так как с увеличением толщины
свариваемого металла в результате сравнительно медленного
его прогрева пламенем и невысокой концентрации тепла резко
падает ее производительность. Кроме того, стоимость газов,
применяемых для создания высокотемпературного пламени,
достаточно высока, поэтому эксплуатационные расходы в
процессе газовой сварки часто оказываются выше, нежели для
8. Температура пламени при газовой сварке должна быть не
меньше чем в два раза выше температуры плавления
свариваемого материала. Лучше всего удовлетворяет этому
условию ацетилен — при сжигании его в кислороде образуется
пламя с температурой порядка 3150 ˚С, что позволяет сваривать
практически любую сталь.
При этом в зависимости от соотношения ацетилен-кислород
горючая смесь может образовывать различные типы пламени,
по-разному влияющие на процесс сварки.
Нормальное пламя, образуется при подаче 1,1-1,3 объема
кислорода на один объем ацетилена. Этого недостаточно для
полного окисления горючего газа — как следствие в пламени
преобладает монооксид углерода(СО) и водород,
выделившийся при разложении ацетилена. Последний
защищает расплавленный металл шва от окисления.
Окончательное сгорание смеси до углекислого газа и воды
происходит за счет кислорода воздуха.
При подаче меньшего объема кислорода получается коптящее
науглероживающее пламя — недоокисленный углерод
9. Впрочем, избыток кислорода пользы также не приносит.
Образующееся при этом окислительное пламя, хотя и
характеризуется повышенной температурой, однако сообразно
со своим названием окисляет металл шва, снижая его
прочностные свойства. Оказывается, что при большом избытке
кислорода и должном давлении он вообще может полностью
окислить металл, выдувая из рабочей зоны продукты его
сгорания. На этом принципе основана технология газовой резки.
При ней ацетиленовое пламя исполняет скорее
вспомогательную роль, подогревая место разреза до
температуры, при которой металл начинает сгорать в струе
чистого кислорода, подающегося в зону резки параллельно с
горючей смесью. Основная теплота при этом выделяется
именно за счет окисления металла. Логическим продолжением
данного метода является копьевая резка, которая применяется
для разрезания низкоуглеродистой и легированной стали
большой толщины. Более того, копьевая резка позволяет
справиться и с железобетоном. Сущность метода заключается в
прожигании отверстий стальной трубкой(копьем), по которой
под большим давлением подается кислород, при этом
необходимую для процесса теплоту получают окислением
10. Теперь перейдем непосредственно к газам, которые
Участвуют при сварке и резке металлов, первый газ — кислород
Технический кислород различают по степени чистоты, так 1-ый
сорт содержит не менее 99,7% (объемных) кислорода, 2-й — не
менее 99,5%, 3-й — не менее 99,2%. Особенно большое значение
чистота кислорода имеет для кислородной резки.
С понижением содержания в нем газовых примесей
увеличивается скорость реза, и уменьшается расход самого
кислорода. Доставлять кислород к месту сварки можно как в
баллонах, так и в жидком состоянии.
В первом случае, полученный путем криогенной ректификации
из воздуха кислород закачивается в баллоны под давлением в
150-165 атм.
Второй метод, позволяющий уменьшить расходы на
содержание и транспортировку баллонов, заключается в
доставке жидкого кислорода прямо к месту сварки в
специальных сосудах с хорошей теплоизоляцией с
последующим его испарением. При этом из 1 дм3 жидкости
получают 860 дм3 газообразного кислорода (при нормальных
условиях).
11. Ацетилен
Ацетилен также можно либо получать в готовом виде на месте,
либо везти его издалека в баллонах. В первом случае
используются так называемые ацетиленовые генераторы, где
его получают реакцией карбида кальция с водой. Теоретически
одного килограмма чистого карбида достаточно для
образования 350 дм3 ацетилена, на практике же выход горючего
газа составляет не более 300 дм3/кг. Данный метод имеет
определенные недостатки, связанные с хлопотностью хранения
карбида кальция — он жадно поглощает воду из воздуха,
образуя взрывоопасные ацетилен-воздушные смеси.
Соответственно, загруженный в генератор кусок карбида
должен быть полностью превращен в ацетилен, а полученный
ацетилен — сожжен в горелке, во избежание проблем с
безопасностью труда. Отбор данного газа из баллона не создает
подобных трудностей.
В то же время, сама технология баллонного хранения и
перевозки ацетилена достаточно необычна, именно за счет его
чрезвычайной взрывоопасности. Которая понижается при
растворении ацетилена в ацетоне. В результате ацетиленовый
12. Ацетилен
При 10 атм. в стандартном 40-литровом баллоне помещается
порядка 5 кг ацетилена, что эквивалентно 4,5 м3 газа при
нормальных условиях. Отбор ацетилена из баллона
нежелательно производить со скоростью выше 1,5 м3/ч, так как
при более интенсивной откачке газа из емкости уносится и
часть ацетона.
Таким образом, при больших объемах потребляемого ацетилена
имеет смысл использовать ацетиленовые генераторы, для не
столь масштабных работ более подходящим решением
является отбор газа из баллонов.
Ацетилен для закачки в баллоны получают как из карбида
кальция, так и при пиролизе природного газа. Отметим, что
контакт с оксидом меди резко снижает температуру
воспламенения ацетилена, поэтому при изготовлении
оборудования для работы с этим газом стараются избегать
использования медьсодержащих деталей.
13. Заменители ацетилена
Дороговизна ацетилена зачастую вынуждает искать ему газызаменители, ведущее место среди которых занимает пропан,
или же пропан-бутановая смесь, обладающие высокой
теплотворной способностью. Впрочем, для
удовлетворительного сгорания пропана требуется примерно в
три раза больше кислорода, чем для ацетилена, что делает
выгодность его применения не столь однозначной. Самым же
большим недостатком пропана является более низкая, нежели у
ацетилена температура пламени, что существенно осложняет
его применение для сварки сталей. Поэтому пропан чаще
используют либо при сварке легко плавящихся цветных
металлов, либо для создания подогревающего пламени при
кислородной резке сталей.
Если все же пропановое пламя используют для сварки
углеродистых сталей, то приходится применять сварочную
проволоку, содержащую повышенную концентрацию кремния и
марганца, использующихся в качестве раскислителей, что
улучшает качество сварного соединения. Отметим, что большой
коэффициент объемного расширения пропана (и бутана)
накладывают ограничения на объем газа, который может быть
Газы применяемые при сварке и резке металлов
Главная » Статьи » Газы применяемые при сварке и резке металлов
Газы, применяемые для сварки и резки металлов
Газовая сварка, при которой происходит плавление кромок свариваемых деталей в высокотемпературном пламени газовой горелки (рис. 1) с дальнейшим формированием шва, имеет по сравнению со сваркой электродуговой как преимущества, так и недостатки. К первым относится тот факт, что при помощи данного метода можно сваривать практически любые материалы, более того, чугун, медь, латунь и свинец даже легче поддаются газовой сварке, чем дуговой. При этом отсутствует потребность в применении дорогого и сложного оборудования, а также в подключении к источнику электропитания. В то же время газовую сварку обычно применяют для обработки относительно тонких изделий, так как с увеличением толщины свариваемого металла в результате сравнительно медленного его прогрева пламенем и невысокой концентрации тепла резко падает ее производительность. Кроме того, стоимость газов, применяемых для создания высокотемпературного пламени, достаточно высока, поэтому эксплуатационные расходы в процессе газовой сварки часто оказываются выше, нежели для сварки электродуговой. Отметим, что при газовой сварке часто применяют присадочную проволоку, близкую по составу к свариваемому металлу, участвующую в образовании сварного соединения.
Рис. 1. Схема инжекторной горелки для газовой сварки: 1 — мундштук; 2 — сменный наконечник; 3 — смесительная камера; 4 — инжектор; 5 — кислородный вентиль; 6 — ацетиленовый вентиль
Температура пламени при газовой сварке должна быть не меньше чем в два раза выше температуры плавления свариваемого материала. Лучше всего удовлетворяет этому условию ацетилен — при сжигании его в кислороде образуется пламя с температурой порядка 3150 ˚С, что позволяет сваривать практически любую сталь.
При этом в зависимости от соотношения ацетилен-кислород горючая смесь может образовывать различные типы пламени, по-разному влияющие на процесс сварки.
Нормальное пламя, образуется при подаче 1,1-1,3 объема кислорода на один объем ацетилена. Этого недостаточно для полного окисления горючего газа — как следствие в пламени преобладает монооксид углерода(СО) и водород, выделившийся при разложении ацетилена. Последний защищает расплавленный металл шва от окисления. Окончательное сгорание смеси до углекислого газа и воды происходит за счет кислорода воздуха.
При подаче меньшего объема кислорода получается коптящее науглероживающее пламя — недоокисленный углерод переходит в расплавленный металл, ухудшая качество шва.
Впрочем, избыток кислорода пользы также не приносит. Образующееся при этом окислительное пламя, хотя и характеризуется повышенной температурой, однако сообразно со своим названием окисляет металл шва, снижая его прочностные свойства. Оказывается, что при большом избытке кислорода и должном давлении он вообще может полностью окислить металл, выдувая из рабочей зоны продукты его сгорания. На этом принципе основана технология газовой резки. При ней ацетиленовое пламя исполняет скорее вспомогательную роль, подогревая место разреза до температуры, при которой металл начинает сгорать в струе чистого кислорода, подающегося в зону резки параллельно с горючей смесью. Основная теплота при этом выделяется именно за счет окисления металла. Логическим продолжением данного метода является копьевая резка, которая применяется для разрезания низкоуглеродистой и легированной стали большой толщины. Более того, копьевая резка позволяет справиться и с железобетоном. Сущность метода заключается в прожигании отверстий стальной трубкой(копьем), по которой под большим давлением подается кислород, при этом необходимую для процесса теплоту получают окислением металла конца трубки(предварительно подогретого) и железа обрабатываемого изделия. Совершая копьем горизонтальные и вертикальные движения можно вырезать куски материала нужной формы.
Важнейшее значение для сварки и резки металлов имеет надлежащий выбор применяемых в этих процессах газов и способов их получения.
Кислород
Технический кислород различают по степени чистоты, так 1-ый сорт содержит не менее 99,7% (объемных) кислорода, 2-й — не менее 99,5%, 3-й — не менее 99,2%. Особенно большое значение чистота кислорода имеет для кислородной резки. С понижением содержания в нем газовых примесей увеличивается скорость реза, и уменьшается расход самого кислорода. Доставлять кислород к месту сварки можно как в баллонах, так и в жидком состоянии. В первом случае, полученный путем криогенной ректификации из воздуха кислород закачивается в баллоны под давлением в 150-165 атм. Второй метод, позволяющий уменьшить расходы на содержание и транспортировку баллонов, заключается в доставке жидкого кислорода прямо к месту сварки в специальных сосудах с хорошей теплоизоляцией с последующим его испарением. При этом из 1 дм3 жидкости получают 860 дм3 газообразного кислорода (при нормальных условиях).
Ацетилен
Ацетилен также можно либо получать в готовом виде на месте, либо везти его издалека в баллонах. В первом случае используются так называемые ацетиленовые генераторы, где его получают реакцией карбида кальция с водой. Теоретически одного килограмма чистого карбида достаточно для образования 350 дм3 ацетилена, на практике же выход горючего газа составляет не более 300 дм3/кг. Данный метод имеет определенные недостатки, связанные с хлопотностью хранения карбида кальция — он жадно поглощает воду из воздуха, образуя взрывоопасные ацетилен-воздушные смеси. Соответственно, загруженный в генератор кусок карбида должен быть полностью превращен в ацетилен, а полученный ацетилен — сожжен в горелке, во избежание проблем с безопасностью труда. Отбор данного газа из баллона не создает подобных трудностей. В то же время, сама технология баллонного хранения и перевозки ацетилена достаточно необычна, именно за счет его чрезвычайной взрывоопасности. Которая понижается при растворении ацетилена в ацетоне. В результате ацетиленовый баллон представляет собой наполненную пористой массой емкость. Пористая масса (например, активированный уголь) пропитана ацетоном, в ацетоне же растворяется ацетилен, закачиваемый в баллон под давлением 10-20 атм. При 10 атм. в стандартном 40-литровом баллоне помещается порядка 5 кг ацетилена, что эквивалентно 4,5 м3 газа при нормальных условиях. Отбор ацетилена из баллона нежелательно производить со скоростью выше 1,5 м3/ч, так как при более интенсивной откачке газа из емкости уносится и часть ацетона. Таким образом, при больших объемах потребляемого ацетилена имеет смысл использовать ацетиленовые генераторы, для не столь масштабных работ более подходящим решением является отбор газа из баллонов.
Ацетилен для закачки в баллоны получают как из карбида кальция, так и при пиролизе природного газа. Отметим, что контакт с оксидом меди резко снижает температуру воспламенения ацетилена, поэтому при изготовлении оборудования для работы с этим газом стараются избегать использования медьсодержащих деталей.
Заменители ацетилена
Дороговизна ацетилена зачастую вынуждает искать ему газы-заменители, ведущее место среди которых занимает пропан, или же пропан-бутановая смесь, обладающие высокой теплотворной способностью. Впрочем, для удовлетворительного сгорания пропана требуется примерно в три раза больше кислорода, чем для ацетилена, что делает выгодность его применения не столь однозначной. Самым же большим недостатком пропана является более низкая, нежели у ацетилена температура пламени, что существенно осложняет его применение для сварки сталей. Поэтому пропан чаще используют либо при сварке легко плавящихся цветных металлов, либо для создания подогревающего пламени при кислородной резке сталей.
Если все же пропановое пламя используют для сварки углеродистых сталей, то приходится применять сварочную проволоку, содержащую повышенную концентрацию кремния и марганца, использующихся в качестве раскислителей, что улучшает качество сварного соединения. Отметим, что большой коэффициент объемного расширения пропана (и бутана) накладывают ограничения на объем газа, который может быть безопасно закачан в баллон.
Аналогичные проблемы возникают и при использовании других заменителей ацетилена — водорода, коксового газа, бензина, керосина. Низкая температура пламени, поучаемая при сжигании данных веществ, затрудняет их применение при сварке сталей, однако позволяет использовать их в процессах резки, а также сварки и наплавки более легкоплавких металлов.
В общем, возможности выбора того или иного варианта состава горючей смеси, а также способов ее получения, для газовой сварки или резки достаточно широки, и всецело зависят от конкретной ситуации.
www.kriopass.com.ua
Какой газ применяется при сварке и резке металлов и сплавов?
Существует несколько видов сварки, отличающихся друг от друга методом получения сварочной ванны высокой температуры, предназначенной для резки или соединения различных металлов и сплавов: электрическая дуга, ультразвук, газовое пламя. Принцип действия заключается в том, что края конструкций подлежащих воссоединению, плавятся, и в месте их стыка образуется совершенно новая структурная единица – сварочный шов.
Сварочные газы
Показатель температуры зависит в первую очередь от того, какой газ используется при сварке. Например, в результате реакции воды с карбидом кальция, выделяется ацетилен, который взаимодействуя с кислородом, дает возможность получить температуру пламени более 3000 градусов. К сварочным газам относятся все разновидности пропанов, бутанов, МАФ (альтернатива ацетилену), бензолов, керосинов и прочих.
Присутствие кислорода, являющегося катализатором горения, обязательно в процессе применения любых сварочных газов. Подаваемый в горелку кислород, должен иметь высокое качество и чистоту. От этих показателей зависит максимальная температура, получаемая во время работы.
Элементы газовой смеси
Независимо от того, какой газ применяется при сварке, важно помнить, что получить высокую температуру горения и определенные свойства пламени, можно только при использовании в смеси технически чистого кислорода. От качества составляющей зависит полнота сгорания или испарения горючих элементов, а от количества – свойства, получаемые пламенем: восстановительные или окислительные.
Особые требования предъявляются к условиям хранения и подачи. Использование специальных отдельных баллонов необходимо в данном случае:
- технический кислород является мощным катализатором;
- многие газы, применяемые для сварки, очень токсичны.
Если применяется атмосферный кислород, то вряд ли удастся получить идеально ровные швы. При этом изменятся свойства металла, обретенные в процессе расплавления и соединения, что значительно снизит качество сделанного шва.
Считается не эффективным использование в сварочной газовой смеси обычного кислорода, содержащегося в атмосфере. Наличие примесей, существующих в воздухе, значительно уменьшает скорость сгорания элементов, что отражается на температуре пламени.
Сварочные газы
Независимо от того, какой газ используют при сварке, инертный или углекислый, следует помнить о соблюдении пропорций в смеси. Конкретный выбор зависит от металла. Например, в сварке стальных конструкций преобладает углекислый газ (около 18%), а при работе с нержавеющей сталью – аргон (почти 98%).
При сварке применяются инертные и активные газы. Инертные элементы, как правило, не ядовиты, не взаимодействуют с металлом и не растворяются в них.
- Аргон (Ar) – не имеет цвета и запаха, не горит, тяжелее воздуха в полтора раза. Различают два сорта. Высший сорт используется для сварки нагружаемых металлоконструкций из активных и редких металлов и сплавов. Первый сорт необходим для алюминиевых и стальных изделий.
- Гелий (He) – без цвета, запаха, легче воздуха. Различают два вида: высокой чистоты и технический элемент. Редкое использование гелия обусловлено его высокой стоимостью. Рекомендуется для чистых и активных металлов, алюминия и стали.
- Азот (N2) – не имеет цвета, запаха. Применяется для меди и медных сплавов. Бывает 4 сорта азота с разным содержанием вещества.
Газы активные служат защитой сварочной зоны от воздуха, вступают в химическое взаимодействие с металлами и растворяются в них.
- Кислород (О2) – не имеет цвета, запаха, вкуса.
Кислород не горит, но является мощным катализатором, поддерживающим горение. Применяется в смесях с инертными или активными компонентами.
- Углекислый газ (СО2) обладает запахом и ярко выраженными окислительными свойствами. Отлично растворяется в воде и весит в 1,5 раза тяжелее воздуха. Различают 3 сорта вещества, которые используют для соединения чугунных, низко и среднеуглеродистых металлов и сплавов, низколегированных конструкций и коррозийных сталей. Следует помнить, что двуокись углерода в сварке не применяется.
Улучшают процесс и качество шва с помощью сварочных смесей. Наиболее востребованы смеси:
- гелий и аргон;
- аргон и кислород;
- углекислый газ и аргон;
- кислород и углекислый газ;
- аргон, углекислый газ, кислород.
Выбирая, какой газ для сварки подойдет в конкретном случае, необходимо учитывать несколько факторов: характеристики соединяемого металла, тип оборудования, желаемую форму шва, условия выполнения работы, свойства химического состава.
Газовая сварка стоит дороже электрической, потому что цена ацетилена и кислорода значительно выше стоимости электрической энергии, требуемой при контактной или дуговой сварке.
stroitel5.ru
Газы, применяемые для сварки и резки металлов — online presentation










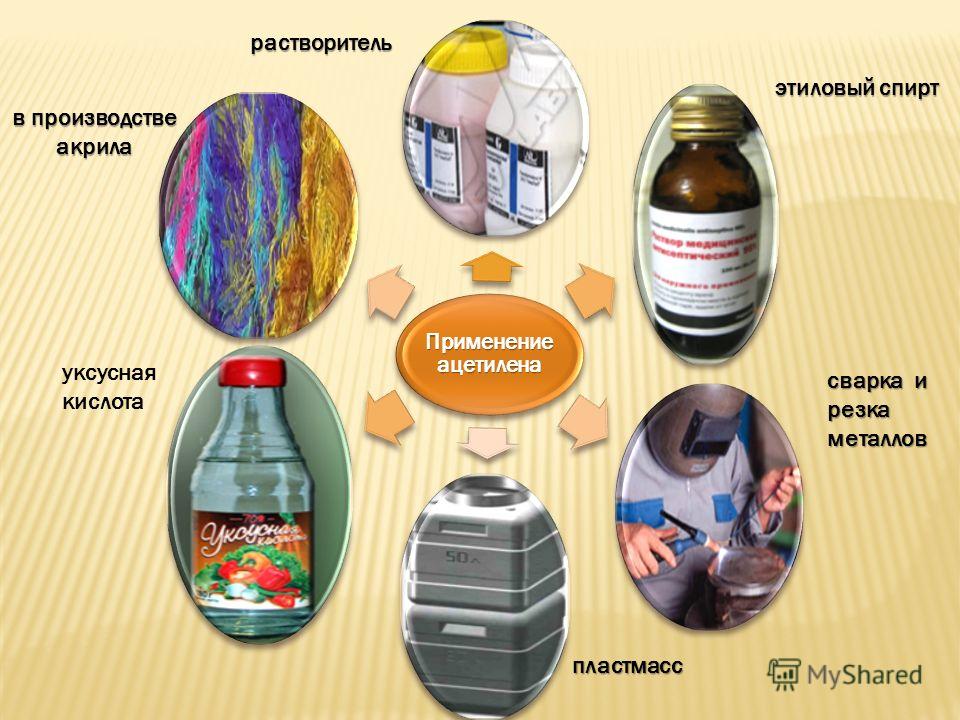
en.ppt-online.org
Газовая сварка и резка Газы, применяемые при сварке
Различают два вида газовой сварки: сварку плавлением и газопрессовую сварку.
В первом случае кромки свариваемых частей (основной металл) и присадочный металл расплавляют и образуют общую ванну, которая застывает швом.
Источником тепла для расплавления металла является сгорание горючего газа в струе кислорода.
Газы. В качестве горючих газов используют ацетилен, водород и другие газы. Чаще других применяют ацетилен, дающий наибольшую температуру пламени.
Кислород необходим для сжигания горючего газа. При промышленном использовании его получают из воздуха, который в жидком состоянии разлагают на кислород и азот.
Ацетилен (С2Н2) получают из карбида кальция (СаС2) в ацетиленовых генераторах. Из одного килограмма чистого карбида получают 250-300лацетилена.
Сварочное пламяслужит для расплавления металла, а также для восстановления, науглероживания или окисления ванны. В средней части пламени температура достигает 32000С. Получение пламени того или иного характера достигается изменением соотношения горючего газа и кислорода в смеси. Нормальное ацетиленовое пламя (С2Н2 : О2 = 1 :1) восстановительное. Оно применяется для сварки стали и цветных металлов.
Пламя с избытком ацетилена является науглероживающим. Оно применяется при сварке чугуна, так как за счет пламени пополняется углерод, выгорающий при сварке, и понижается температура плавления металла в шве.
Окислительное пламя применяется при сварке латуни для получения окисной пленки, уменьшающей испарение цинка.
Приемы газовой сварки и резки
При сварке горелку продвигают вдоль шва, причем соблюдают необходимый угол наклона горелки к свариваемой поверхности. Этот угол a(рис.80) колеблется от 200С (для сварки листов толщиной 1мм) до 800С (при толщине 15мм и выше).
Рис.80. Схема левой (а) и правой (б) газовой сварки: 1-шов;
2-разделка шва
Различают левую и правую сварку. При левой сварке горелку передвигают справа налево (рис.80,а) и пламя направляется на еще не сваренный участок шва. При правой сварке (рис.80,б) горелку передвигают слева направо и пламя направляется на сваренную часть шва. Конец проволоки погружен в расплавленный металл.
Правая сварка применяется для деталей толщиной — более 5 мм, левая — до 5мм. При правой сварке качество шва лучше вследствие более продолжительной защиты расплавленного и остывающего металла; однако на листах толщиной до 5ммлевая сварка оказывается производительнее, так как пламя подогревает впереди лежащие кромки.
Присадочный материалв виде прутков или проволоки продвигают в пламя горелки, он расплавляется и стекает в ванну, где смешивается с расплавленным основным металлом. Затвердевая металл образует сварной шов. Для сварки стали в качестве присадочного материала применяют стальную проволоку с содержанием до 0.18%С, а для легированных сплавов — проволоку, содержащую хром, марганец и другие легирующие элементы.
При сварке цветных металлов и сплавов применяют проволоку, близкую по своему химическому составу к основному металлу. Диаметр присадочной проволоки должен быть на 1-2 ммбольше половины толщины свариваемых листов.
Сварка чугунаприменяется для исправления дефектов литья. Она производится с подогревом свариваемых частей до 400-6000С. Подогрев нужен для предупреждения отбела и трещин вблизи сварочного шва, которые появляются вследствие больших местных напряжений, возникающих во время охлаждения. Для сварки чугуна с подогревом в качестве присадочного металла используют чугунные литые прутки диаметром 6-12ммс повышенным содержанием углерода (3-3. 6%) и кремния (3-4.8%), а при сварке без подогрева — латунную проволоку с содержанием 37-40%Zn.
Газовую сварку применяют для соединения тонкостенных стальных деталей, а также деталей из цветных металлов и сплавов. В этих случаях газовая сварка превосходит по качеству электродуговую. Газовую сварку используют также при наплавке твердых сплавов.
Газопрессовая сварка. Свариваемые части нагревают сварочным пламенем до пластического состояния и прикладывают усилие , сдавливающее эти части. Она применяется для соединения встык преимущественно труб больших диаметров (до 1000мм). Стыки нагревают кольцевой многопламенной горелкой. Кроме сварки труб, этим способом пользуются для сварки рельсов, бурильного оборудования и инструментов.
Контроль сварки. Качество сварных швов проверяют внешним осмотром, рентгеноанализом, магнитным дефектоскопом, а также по выборочным образцам с определением макро- и микроструктуры и механических свойств.
Газовая резкав струе кислорода применима лишь для тех металлов, у которых температура воспламенения ниже температуры плавления: железа, стали с содержанием углерода до 0. 7% и некоторых сортов легированной стали. Чугун, алюминий, а также медь и ее сплавы непосредственно струей кислорода не режутся, так как струя кислорода при плавлении быстро окисляет их, а при резке алюминия образуется тугоплавкая окись его. Для газовой резки этих металлов применяют порошковые флюсы, состоящие в основном из железа. Флюс сгорает в струе кислорода и повышает температуру в месте резки настолько, что образующиеся тугоплавкие окислы шлакуются с окислами железа и жидкий шлак выдувается струей.
Газовой резке поддаются детали большой толщины до 300 мм. Наряду с ацетиленом, резка которым производительнее, применяют водород или пары бензина.
studfiles.net
Ацетилен и другие горючие газы
Подробности
- Подробности
-
Опубликовано 27.
05.2012 13:27
- Просмотров: 14443
Ацетилен применяется в промышленности в качестве горючего для газовой сварки и резки металлов, а также в качестве сырья для различных химических производств.
Ацетилен является химическим соединением углерода и водорода. Технический ацетилен представляет собой бесцветный газ с резким характерным запахом. Длительное вдыхание его вызывает головокружение, тошноту и может привести к отравлению. Ацетилен легче воздуха, хорошо растворяется в различных жидкостях. Особенно хорошо он растворяется в ацетоне. Ацетилен при сгорании в смеси с чистым кислородом дает пламя температурой 3050— 3150° С. Он является взрывоопасным газом.
Ацетилен взрывается при следующих условиях:
1) при повышении температуры свыше 500° С и давления свыше 1,5 ат\
2) смесь ацетилена с кислородом при содержании в ней от 2,8 до 93% ацетилена взрывается при атмосферном давлении от искры, пламени, сильного местного нагрева и пр. ;
3) при тех же условиях ацетилено-воздушная смесь взрывается при содержании в ней от 2,8 до 80,7% ацетилена;
4) при длительном соприкосновении ацетилена с медью или серебром образуется взрывчатая ацетиленистая медь или ацетиленистое серебро, которые взрываются при ударе или повышении температуры.
Взрыв ацетилена сопровождается резким повышением давления и температуры и может вызвать тяжелые несчастные случаи и значительные разрушения.
При помещении ацетилена в узкие каналы способность его к взрыву при повышении давления значительно понижается. В промышленности ацетилен получают в результате разложения карбида кальция водой в специальных аппаратах — ацетиленовых генераторах. Получающийся таким образом технический ацетилен обычно содержит вредные примеси: сероводород, аммиак, фосфористый водород, кремнистый водород, которые придают ацетилену резкий запах и ухудшают качество сварки. Примеси удаляют из ацетилена путем промывки в воде и химической очистки специальными очистительными веществами. Кроме того, ацетилен может содержать пары воды и механические частицы (известковая и угольная пыль). Для удаления влаги ацетилен подвергается осушке. Очистка от пыли осуществляется матерчатым фильтром. Для сварки ацетилен можно отбирать из ацетиленопровода, идущего от ацетилено-генераторной станции, либо непосредственно от однопостового генератора. Ацетилен может поставляться также в баллонах под давлением 16ат, растворенный в ацетоне.
Кроме ацетилена, при сварке и резке металлов можно применять и другие горючие газы или пары горючих жидкостей: водород, нефтяной газ, пары бензина, керосина и др.
Водород представляет собой горючий газ без цвета и запаха. Водород — один из самых легких газов. Температура пламени при сгорании в кислороде 2300° С. Водород легко загорается и в определенной смеси с кислородом или воздухом дает взрывчатую смесь, которая носит название гремучего газа. Поэтому при производстве работ по сварке и резке водородом необходимо строго соблюдать правила техники безопасности во избежание взрыва. Получают водород путем разложения воды электрическим током. Хранят его и перевозят в стальных баллонах в газообразном виде под давлением 150ат.
Пропан бутановую смесь получают при добыче и переработке естественных нефтяных газов и нефти. Температура пламени при сгорании смеси в кислороде достигает 2100° С.
При небольшом давлении смеси пропана и бутана сжижаются. Хранение и транспортировка их производятся в стальных баллонах емкостью 33 и 45 кг под давлением до 16 ат, заполняемых жидкой смесью до половины объема, так как при нагревании баллона может значительно повыситься давление, что может привести к взрыву баллона. Смесь применяется для резки, пайки, закалки, сварки свинца, алюминия и стали небольшой толщины.
Нефтяной газ представляет собой смесь горючих газов, обладает неприятным запахом, бесцветен. Получается при переработке нефти и нефтепродуктов. Температура пламени при сгорании в кислороде 2300° С. Хранится и перевозится в газообразном состоянии в баллонах под давлением 150 ат. При этом давлении он частично сжижается. В установке для резки и сварки нефтяным газом требуется испаритель. Применяется для резки, пайки, закалки, сварки стали толщиной до 2—3 мм, сварки латуни, свинца, алюминия.
Коксовый газ — газообразная смесь горючих продуктов, получающихся на коксохимических заводах при выработке из углей кокса. Температура пламени при сгорании в кислороде — около 2000° С.
Доставляется к месту сварки по газопроводу или в баллонах под давлением 150ат. Коксовые газы загрязнены цианистыми соединениями, которые могут привести к отравлениям. Поэтому перед применением их тщательно очищают. Применяется для резки, пайки и сварки легкоплавких металлов.
Метан при нормальной температуре и давлении представляет собой бесцветный газ. Метан в больших количествах находится в естественных газах, где содержание его доходит до 95—98%, температура пламени при сгорании в кислороде 1850° С для дашавского и 2000° С для саратовского газа.
На места потребления природные газы, как правило, подаются по трубопроводам и сравнительно редко производится транспортировка в газообразном состоянии в баллонах под давлением 150ат. Применяется для сварки легкоплавких металлов, резки и пайки.
Городской газ (московский) является смесью коксового, нефтяного и природных газов. Получается при газификации твердого топлива. Температура пламени при сгорании в кислороде — около 2000° С.
На места потребления для резки и сварки легкоплавких металлов подается по газопроводам или в сжатом виде в баллонах под давлением 150ат.
Бензин представляет собой легко испаряющуюся прозрачную жидкость. Пары бензина при сгорании в кислороде дают температуру 2400° С. Бензин получается при переработке нефти. Хранится и перевозится в жидком виде в сосудах при атмосферном давлении. Для сварки и резки применяется специальная аппаратура. Бензин чаще применяется для резки, чем для сварки.
Керосин для газопламенной обработки используется, как и бензин, в виде паров. С этой целью применяются специальные горелки и резаки, снабженные испарителями. Керосинокислородное пламя имеет более низкую температуру (2700°С), чем бензинокислородное. Тем не менее керосин широко применяется при газовой резке.
Следует иметь в виду, что все рассмотренные газы, а также пары бензина являются взрывоопасными.
Читайте также
Добавить комментарий
Сварка, разновидности сварки
Сварка, разновидности сварки
Сварка является определённого рода искусством. Также
она является способом быстрого соединения двух кусков металла. Кроме этого,
она является чистой и эффективной технологией. И если вы всё делаете
самостоятельно, то газовая сварка является относительно недорогой. Для
автолюбителя лучшими методами сварки в домашних условиях являются газовая и
электрическая (дуговая) сварка. Если вы должны сделать выбор между двумя
этими методами, то мы рекомендуем газовую сварку. Она является более
универсальной. Конечно, если вы можете позволить себе дуговую сварку, то
пользуйтесь ей. Если вы решили серьёзно заняться кузовными работами и
планируете производить дорогостоящий ремонт, то электросварка вам потребуется
для приваривания таких деталей как опоры двигателя, детали рамы и элементы из
толстой стали, используемые для шасси и ходовой части. Хотя это можно сделать
и с помощью газовой сварки, она всё же лучше подходит для сварки кузовных
деталей из тонколистового металла.
Газовая сварка
С газовой сваркой обычно ассоциируются два типа
газов: кислород и ацетилен. Ацетилен является горючим веществом, “топливом”,
которое на самом деле сгорает. Кислород требуется для поддержания процесса
горения ацетилена в процессе сварки или резки металла. Оборудование для
газовой сварки включает в себя следующие детали: баллоны с кислородом и
ацетиленом. В верхней части каждого баллона имеется регулятор давления или
редуктор. К редуктору для кислорода подсоединяется шланг зелёного или чёрного
цвета; к редуктору для ацетилена подсоединяется шланг красного цвета.
Противоположные концы этих шлангов подсоединяются к горелке с наконечником
для сварки или резки. Теперь рассмотрим указанные детали подробнее.
Оборудование для газовой сварки
Баллоны
Кислородные баллоны больше ацетиленовых, так как при сварке и резке металла, особенно при резке, используется больше кислорода, чем ацетилена. В верхней части каждого баллона имеется клапан отсечки. К нижней части каждого клапана подсоединяется регулятор давления (редуктор). Редуктор (регулятор) давления требуется для уменьшения давления из баллона или регулировки давления на определённом уровне в процессе резки или сварки.
Внимание: никогда не используйте кислород
и ацетилен под высоким давлением.
Детали кислородного редуктора:
1 – входной штуцер редуктора
2 – винт регулировки давления
3 – манометр высокого давления
4 – манометр низкого давления
5 – выходной штуцер редуктора
6 – манометр низкого давления
7 – манометр высокого давления
8 – винт регулировки давления
9 – входное соединение
10 – выходное соединение.
Внимательно изучите эти детали “живьём” и
определите, как ими пользоваться для целей безопасности. Соединения на
ацетиленовом редукторе и на шлангах имеют левую резьбу; кислородные
соединения имеют правую резьбу. Гайки на соединениях для ацетилена также
имеют V-образную канавку вокруг центра плоского участка для идентификации. К
каждому редуктору подсоединены два манометра. Они являются точными приборами
и с ними нужно обращаться осторожно. Манометр с более высокими значениями
является манометром высокого давления ; он калибруется в килограмм-силах на
квадратный сантиметр (кгс/см2). Манометр с небольшими значениями является
манометром низкого давления и калибруется в тех же еденицах. Хотя давление в
баллоне снижается с уменьшением объёма газа, редуктор поддерживает линейное
давление в определённых пределах. Когда давление в баллоне снижается сильно,
линейное давление также спадает. Затем его нужно отрегулировать заново.
Винт регулировки давления
Регулировочные винты редуктора управляют линейным давлением в шлангах для кислорода и ацетилена и в горелке. При повороте по часовой стрелке редуктор увеличивает давление и, соответственно, потоки кислорода и ацетилена через шланги к горелке. Конечно, это предполагает, что клапан на баллоне открыт и газ поступает к редуктору.
Выходные соединения
Сварочные шланги подсоединяются к выходным штуцерам
редуктора. Мы рекомендуем использовать пламегаситель между редуктором и
шлангами для предотвращения возможности проникновения пламени обратно по
шлангу в баллон, что может привести к взрыву. Повторим, что на соединениях
для кислорода – правая резьба.
Никогда не смазывайте выходные соединения редуктора или любые детали сварочного оборудования! Эти соединения должны постоянно поддерживаться чистыми.
Шланги
Шланги подводят газы под низким давлением от редукторов к горелке. Они связываются вместе для удобства пользования.
Как указано выше, сварочные шланги кодируются
разными цветами: красным для ацетилена и зелёным или чёрным для кислорода.
Сварочные шланги изготовлены из чередующихся слоёв резины и оплёток. Центр
шланга сделан из резины, окружённой прорезиненной тканью, которая затем
покрывается провулканезированным резиновым защитным слоем. Большинство
сварочных шлангов являются огнеупорными. Они все же могут гореть, но
самостоятельно гаснут, если источник тепла удалён.
Правила обращения со шлангами
Если со шлангами правильно обращаться, то они будут долго и надёжно служить. Руководствуйтесь нижеперечисленными правилами обращения со шлангами:
Выдуйте защитный тальк из нового шланга перед его использованием для сварки или резки металла.
Держите сварочные шланги подальше от открытого пламени, падающих искр или капель металла.
Не ходите и ничего не кладите на шланги.
Заменяйте разрезанные, потрескавшиеся и перетёртые участки шлангов с помощью муфт правильного размера.
Никогда не путайте ацетиленовые и кислородные шланги.
Заменяйте сварочные шланги, если на них много
соединительных муфт или если они сильно растресканы или изношены.
Корпус сварочной горелки
Сварочная горелка представляет собой пару трубок с управляющими клапанами. Один клапан с трубкой управляют подачей ацетилена, другой – подачей кислорода. Корпус сварочной горелки не предназначен для смешивания газов. Это достигается с помощью сварочного или отрезного наконечника, который подсоединяется к корпусу горелки. Корпус служит в качестве ручки и для управления подачей газов к наконечнику.
Два уплотнительных кольца уплотняют сварочный наконечник на корпусе горелки. Маленькое уплотнительное кольцо уплотняет канал подачи ацетилена; большое кольцо — канал подачи кислорода.
Клапаны управления
В корпусе горелки есть два управляющих клапана у
выходных концов шлангов, один — для ацетилена, другой — для кислорода.
Кроме этого, специальные гайки могут потребовать небольшого подтягивания, но
никогда не смазывайте их. Убирайте грязь и пыль чистой тряпкой.
Цилиндр
Цилиндр (ручка) горелки является просто коллектором, который по отдельности подает кислород и ацетилен к сварочному наконечнику. Кислород подается через трубку в центре цилиндра; ацетилен подается через несколько отверстий, расположенных концентрично вокруг центральной трубы.
Наконечник
Сварочный или отрезной наконечник или головка накручивается на цилиндр горелки. Кислород из цилиндра направляется через центральный канал для кислорода в наконечнике; ацетилен поступает в отверстия вокруг канала для кислорода. Конусная поверхность внутри головки уплотнена кольцом для создания плотного соединения. Наружная резьба и внутренний конус могут быть восстановлены при повреждениях. Пыль и грязь убираются чистой тряпкой.
Запуск (зажигание) горелки
Предположим, что вам необходимо сварить листовой
металл толщиной 0,8 мм. Руководство, прилагаемое к вашему сварочному
аппарату, рекомендует использование наконечника № 0 при линейном
давлении кислорода и ацетилена 0,2 кгс/см2.
Начните с открывания клапанов баллонов, но с закрытыми клапанами горелки. Отрегулируйте давление редуктора до величины примерно 0,35 кгс/см2. Если вы решите заменить размер наконечника в процессе работы, то вы должны будете также отрегулировать линейные давления.
Теперь можно зажигать горелку. Всегда начинайте с
надевания защитных очков. Откройте клапан для ацетилена на горелке примерно
на ? оборота, клапан для кислорода — примерно на ? оборота. С помощью
специальной зажигалки зажгите горелку. Не пользуйтесь спичками, прикуривателем
ли другим источником открытого пламени. Направляйте горелку в сторону
от людей, животных и от баллонов с газами. Открывайте клапан для кислорода до
тех пор, пока не исчезнет черный дым или сажа. Теперь отрегулируйте редукторы
до рекомендуемого давления (в нашем случае 0,2 кгс/см2).
Когда изменяется линейное давление, подрегулируйте горелку так, чтобы пламя было нейтральным.
Каждый из четырёх типов сварочного пламени имеет специфическую цель. Нейтральное пламя используется чаще всего – оно предназначено для сварки.
Отрегулируйте клапаны горелки так, чтобы в пламени был яркий, светло-голубой конус. Когда “перистые” края пламени исчезают, виден острый внутренний конус и нет шипящего звука, то горелка отрегулирована правильно.
Отрегулируйте пламя, пока вы не будете уверены в том, что ваше пламя нейтральное. Если подаётся слишком много кислорода, то получится окисленное пламя. Этот тип пламени сопровождается громким шипящим звуком. Вместо расплавления металла окисленное пламя будет сжигать его.
Пламя, обогащённое ацетиленом, будет науглероженным
пламенем, которое определяется по длинному, оранжевому, грубо “оперенному”
концу. Науглероженное пламя вводит в металл избыточный углерод. Вместо этого
пламя должно быть светло-голубым с чётко определённым ярко-голубым внутренним
конусом. При получении хорошего нейтрального пламени можно начинать сварку.
Методы сварки
При кислородно-ацетиленовой сварке используются два способа: на себя и от себя.
Метод «на себя» используется для сварки стали толщиной менее 3 мм. Это метод, который используется для кузовных работ. Смысл использования состоит в прогреве металла перед сваркой, но не в перегреве расплавляемого металла, что приведет к образованию отверстия.
Сварка «на себя»
Производится, когда горелка направляется
под углом 450 к металлу и в направлении, в котором вы хотите создать шов;
сварочный электрод движется перед местом сварки вместе с расплавленным
пятном. Наконечник горелки движется, совершая круговые и полукруговые
движения, вдоль сварочного шва или соединения.
Электрод движется внутрь/ наружу в расплавленной точке. При этом тепло распределяется для формирования равномерного и прочного шва.
Сварка «от себя»
В основном производится так же, как и в методе «на себя», за исключением направления сварки (стрелка).
Горелка движется перед расплавленным пятном и перед электродом, образуя шов. Пламя идет за расплавленным пятном, поддерживая горячим его и базовый металл, т е. материал свариваемых частей. Это необходимо для качественного проникновения сварки при сварке толстой стали. Такое проникновение представляет собой полное совместное расплавление свариваемого металла и электрода или «заполняемого» металла при сварке. В противном случае качество шва будет плохим.
При газовой сварке располагайте горелку и электрод
под углом 45° к поверхности металла. Meжду электродом и горелкой будет угол
900. Двигайте горелку внутрь и наружу для контроля прогрева. “Смазывайте”
электрод в расплавленном пятне для заполнения шва.
Хорошее проникновение или пенетрация является одним из многих факторов, которые обеспечивают качество сварки. Сварка, которая имеет плохое проникновение может выглядеть хорошо, но она будет слабой. С другой стороны неаккуратная сварка с хорошей пенетрацией будет крепкой. Хорошая сварка начинается с хорошего соединения. Следовательно, будьте особенно внимательны при установке свариваемых деталей. В них не должно быть зазоров.
Для того, чтобы быть уверенным в том, что при сварке
не будет щелей, “прихватите” предварительно детали. “Прихватывание”
представляет собой несколько коротких сварных швов или точек. Такое
“прихватывание” не только удерживает детали вместе, но и предварительно
прогревает металл для получения равномерного и аккуратного окончательного
шва.
Как и любое другое дело, сварка требует большого опыта и практики. При работе старайтесь добиться того, чтобы ваши сварные швы были аккуратными. Чтобы достичь этого требуется практика, практика и ещё раз практика. Практика даст возможность вам делать швы различного типа – как внутренние, так и наружные. Когда вы будете считать, что ваша работа является как красивой, так и качественной, можете начинать сварные работы на кузове автомобиля.
Сварка с флюсом (пайка)
Теперь, когда вы уже думаете, что стали квалифицированным сварщиком, т.е. можете варить сверху вниз, изнутри наружу и сзади вперёд, то вы можете перейти к более лёгкому виду сварки. Это сварка с использованием флюса, которую можно также считать пайкой твёрдым припоем.
При такой сварке (пайке) используется электрод не
такой, который применяется при сварке с расплавлением – сделан из другого
металла. В этих случаях используется латунный или бронзовый электрод.
При такой сварке электрод заполняет стык, подобный V-образной канавке для образования шва, соединяющего две детали. Как и при “чистой” пайке, расплавленный электрод затекает в шов благодаря капиллярным эффектам. Тонкая плёнка материала электрода соединяет две детали из-за диффузии, что обеспечивает очень прочное соединение.
Флюс очищает свариваемый металл, позволяя материалу электрода затекать в шов и соединять детали. V-образная канавка заполняется материалом электрода.
Диффузия для пайки является тем же, чем является
проникновение (пенетрация) для сварки. Металлы электрода и свариваемого
металла диффундируют, т.е. проникают друг в друга в поверхностных слоях,
соединяя их друг с другом. Образуемый сплав, т.е. смесь металлов иногда
бывает даже прочнее, чем исходные металлы, особенно при использовании прочных
электродов.
Указанный метод может использоваться вместо обычной газовой сварки. К примеру, он используется для соединения друг с другом двух различных металлов, таких как сталь и медь или двух различных типов стали. Кроме этого, такая сварка производится при более низких температурах, чем сварка с плавлением металла, соответственно, при температурах порядка 4500C и 13000C, что обеспечивает меньшую деформацию. Это достаточно важно при проведении кузовных работ. Пониженные температуры являются преимуществом при работе с термочувствительными сталями.
Теперь, когда вы знаете о преимуществах пайки
твёрдым припоем, вам нужно знать о том, в каких областях нельзя использовать
сварку с флюсом (пайку). В частности, не используйте эту технологию для
соединения тех деталей, которые сильно нагружены, такие как детали подвески,
элементы рамы, несущие детали кузова и детали ходовой части. Для сварки этих
деталей используйте электросварку.
При подобной сварке критичной является одна вещь: соединяемые поверхности должны быть абсолютно чистыми и не иметь загрязнений. В противном случае припой (электрод) и свариваемые металлы не будут диффундировать. Тщательно очищайте детали механическим способом.
Легче всего очистить металл для пайки – использовать специальный состав – флюс или очищающее средство на основе бора. Однако, это может создать дополнительные проблемы. После использования флюса могут образоваться трудно удаляемые остатки. Для уменьшения вероятности их образования используйте комбинацию двух методов: механическая очистка соединения и нанесения флюса, не оставляющего следов.
Флюс может существовать в трёх основных формах:
порошок, паста или как покрытие на электродах (припое). При использовании
порошкового или пастообразного флюса вам нужно нагреть электрод на 5-7 см от конца, а затем окунуть его во флюс. При этом электрод покроется флюсом. По мере расходования
электрода эту процедуру нужно повторять на следующих 5-7 см. В продаже имеются электроды, уже покрытые флюсом, но они намного дороже.
Хорошо пропаянное соединение должно быть ровным и блестящим, с краями, входящими в основной металл. Поверхность с раковинами или с пузырями или с краями, которые заходят на основной металл, свидетельствует о некачественной работе. Обычной ошибкой при такой сварке является перегрев металла. Его следы проявляются как мелкий белый рыхлый порошок по обоим краям соединения.
Сварка внахлёст с использованием покрытого флюсом сварочного электрода (припоя). Подобная сварка, как и обычная пайка, работает благодаря капиллярным эффектам. Она действует подобно клею и не зависит от проникновения (пенетрации) в месте соединения.
Газовая сварка металлических сплавов
Да, вы сможете выполнить качественную газовую сварку
сплавов из цветных металлов или “белых” металлов. Это сплавы на
основе цинка, которые используются для крыльев или некоторых других кузовных
деталей. Для газовой сварки сплавов вам потребуется электрод (припой) без
флюса. Стоимость одного электрода – примерно 1 доллар.
Например повреждённый ободок фары можно отремонтировать с помощью сварки с использованием твёрдого припоя.
Температура плавления сплава составляет примерно 3900 C, как и для электрода. Ни электрод, ни сам свариваемый металл не разу переходят при нагревании
из твёрдого в жидкое состояние. Вместо этого оба материала имеют пастообразную
переходную фазу в близкой температурной области. Припой для автомобильных
кузовов реагирует подобным образом, по диапазонам температур для сварки
находится в этой пастообразной фазе, т.е. между точкой (температурой), в
которой металл начинает размягчаться и точкой жидкой фазы. Этот разброс
невелик и контроль температуры является определяющим параметром.
Очистка детали
Как практикуется для любого вида сварки, и в этом случае нужно механически зачистить детали из белого металла. Если деталь имеет трещину, то сделайте это напильником или отрезной машинкой V-образную канавку в нижней части трещины. Если деталь повреждена, то сделайте косую фаску на повреждённых краях. Убедитесь, что свариваемые края чистые до блеска. Даже электрод нужно зачистить.
Кроме этого, удалите механически весь хром с области, в которой будет производиться сварка, с помощью приспособления для зачистки. После сварки деталь придётся хромировать повторно.
Из-за пор в металле проверьте наличие влаги в
области трещины. Для сушки детали поместите её в духовку плиты примерно на
час. Начните с температур порядка 1000C и постепенно повышайте температуру примерно до 2000C. Не нагревайте деталь слишком быстро, иначе на поверхности
могут появиться трещины.
Крепление детали
Деталь нужно подпереть или надёжно закрепить в том месте, где будет производиться сварка. В противном случае при нагреве до температуры сварки рабочая область может провиснуть или сместиться. Чтобы этого не случилось, воспользуйтесь опорой. В качестве опоры можно воспользоваться любым материалом, который не плавится, не загорается и не разлагается при нагревании до температуры порядка 4000C.
Контроль температуры
Отрегулируйте горелку на минимально возможное пламя. Отрегулируйте пламя так, что примерно за 10 сек. На расстоянии примерно 5 см под его действием металл начал размягчаться. Более горячее пламя контролировать намного сложнее.
Вы должны нагревать электрод (припой) и основной
металл одновременно. Прижмите конец электрода непосредственно к той области,
где производится сварка. Направляйте пламя и на свариваемую область, и на
электрод. При прогреве прикладывайте электрод к поверхности основного металла
так, чтобы вы знали, когда электрод начнёт размягчаться и это будет
соответствовать правильной рабочей температуре.
На поверхности основного металла будут появляться маленькие блестки или небольшие провалы при приближении к нужной температуре сварки. Как только вы увидите их, вы должны быть готовы вставить размягчённый конец электрода (припоя) в ремонтируемую область, соединяя детали вместе. Держите горелку близко к рабочей области. Когда электрод и основной металл начнут плавиться, вы должны отвести горелку назад – оставьте пламя, чтобы оно было направлено непосредственно на место работы.
Если горелка находится слишком близко, то металл
будет перегреваться и всё закончится вспучиванием металла. Не направляйте
пламя от места работы, а затем не возвращайте его назад. Это станет причиной
того, что ремонтируемая область будет переходить из слишком горячего в слишком
холодное состояние. С помощью отведения пламени вертикально назад и оставив
его направленным на место сварки вы сможете контролировать нагрев более
точно. Когда оба металла перейдут в пастообразное состояние, добавляйте
электрод до тех пор, пока не образуется небольшой излишек заполнения шва.
Используйте низкое давление газов для сварки сплава. Избыточное давление может просто сдуть сварной шов.
Хотя место сварки выглядит и не очень красиво, проникновение составляет 100 %.
После окончания сварки деталей обработайте отремонтированное место механически так, чтобы оно не выступало за уровень окружающих деталей. Окончательная обработка производится с помощью мелкой наждачной шкурки.
Сварной шов зачищен. Шпаклёвка, грунтовка и окраска
восстановят вид ободка фары до уровня практически новой детали.
После этого деталь можно хромировать или покрасить и в конце концов она будет выглядеть не хуже новой.
Газовая сварка алюминия
Газовая сварка алюминия является более трудной, чем сварка стали или даже сплавов, так как требует более деликатного обращения. И в этом случае единственным путём улучшения уровня мастерства является практическая работа.
Выберите куски алюминия. Тщательно зачистите свариваемые области с помощью наждачной шкурки или проволочной щётки. Затем подберите специальный флюс для сварки алюминия.
Смешайте флюс с водой в соотношении 3 части флюса к одной части воды. Теперь нанесите раствор на свариваемую область. Лучше наносить его на обе стороны поверхности основного металла.
Когда флюс высохнет, вырежьте полоски из того же
металла, который будет свариваться, шириной 6мм и длинной 20-25 см. Он будет использоваться в качестве электрода (припоя). Конечно, можно купить электрод отдельно,
но вы должны быть уверены в том, что оба материала плавятся при одинаковой
температуре.
Теперь переходите к регулировке горелки. И в этом случае пользуйтесь нейтральным пламенем. Это очень важно, так как алюминий легко окисляется. Установите линейное давление низким – примерно от 0,15 кгс/см2 до 0,30 кгс/см2. Для более тонкого материала линейное давление должно быть ниже для предотвращения прожигания отверстий в основном материале.
Подобно сплавам, алюминий имеет узкий диапазон температур сварки. Этот диапазон температур немного шире, чем у сплавов, но небольшая практика легко покажет, что из этого диапазона довольно легко выйти.
Начните с предварительного “прихватывания”. Это
уменьшит деформации, которые приводят к появлению щелей, а прогревание металла
сделает окончательную сварку легче.
Соблюдая осторожность и при отсутствии зазоров, шов при сварке алюминия можно сделать без использования электрода (припоя).
Использование светофильтров при сварке алюминия
В отличие от расплавленной стали, которая имеет вишнёво-красный цвет, расплавленный алюминий в сочетании с флюсом дают интенсивное жёлтое свечение. Из-за этого сложно видеть сварной шов. Поэтому при сварке алюминия нужно использовать специальные светофильтры.
Мы настоятельно рекомендуем использовать светофильтры кобальтово-голубого цвета для защиты глаз и для лучшей видимости. Такие светофильтры продаются в магазинах сварочных пренадлежностей. Когда у вас есть нужные светофильтры, изготовленный самостоятельно сварочный электрод, горелка с установленным давлением газов 0,15-0,30 кгс/см2 и флюс на алюминии высох, можно начинать сварку.
Пользуйтесь таким же методом сварки, который был
описан для “белого” металла. Однако, перед началом сварки предварительно
прогрейте основной металл. Это хорошая практика для сварки любого металла, но
рекомендуется особенно для алюминия из-за его теплопроводности.
Нагрейте металл в том месте, где вы хотите начать сварку. Поддерживайте металл в пастообразном состоянии путём перемещения пламени рядом с участком металла. Одновременно нагревайте и свариваемый металл и электрод, но имейте в виду, что нагревание первым основного металла может привести к тому, что он будет вытекать ещё до того, как электрод перейдёт в расплавленное состояние.
Резка пламенем
Резка пламенем газовой горелки, вероятно, является самым быстрым способом резки металлов. Металл нагревается до расплавленного состояния газовой горелкой, а затем он выдувается, т.е. отрезается потоком кислорода.
Резка пламенем производится тем же самым
оборудованием, которое используется для газовой сварки, за исключением того,
что сварочный наконечник заменяется отрезным. Снимите сварочный наконечник с
газовой горелки и на его место закрутите наконечник для резки. Некоторые
газовые горелки для отрезания имеют встроенные корпуса. В этом случае шланги
отсоединяются от корпуса сварочной горелки и подсоединяются к отрезной
горелке.
Практическая резка пламенем
Прежде всего нужно нанести линию отрезания на металл. Это можно сделать с помощью мела. Когда линия разреза проведена, то переключите своё внимание на подготовку оборудования. После сборки отрезной горелки полностью откройте клапан кислорода на горелке, если отрезная насадка отделена от корпуса горелки. Затем откройте клапан управления кислородом для предварительного нагрева на горелке и отрегулируйте редуктор для кислорода на давление около 1,75 кгс/см2. После этого закройте клапан.
И в этот раз начинайте работу с надевания защитных
очков. Даже если пламя при резке не кажется таким ярким, как при сварке, всё
равно есть опасность повреждения глаз. На короткое время нажмите рычаг подачи
кислорода для очистки отверстия для кислорода. Слегка откройте клапан
управления подачей кислорода – примерно на 1/8 оборота. Затем откройте клапан
подачи ацетилена на ручке горелки примерно на ? оборота и подожгите ацетилен.
Увеличьте подачу ацетилена на ручке горелки, пока основание пламени не
отойдёт от конца наконечника примерно на 3 мм. Уменьшите подачу ацетилена для возврата пламени на наконечник. Теперь отрегулируйте нейтральное пламя.
Делайте это, медленно открывая клапан подачи
кислорода для предварительного нагрева, пока внутренний конус пламени не
станет острым. Это обеспечит желаемое нейтральное пламя. Прижмите рычаг
кислорода. Обратите внимание на то, что пламя предварительного нагрева слегка
изменится в сторону науглероженного пламени. Продолжайте нажимать рычаг и
открывайте клапан кислорода для предварительного нагрева до тех пор, пока
пламя для предварительного нагрева не станет нейтральным. Теперь вы готовы к
процессу резки.
Удобно возьмите отрезную горелку в одну руку для стабилизации отрезного наконечника. Оставьте другую руку свободной для работы с рычагом подачи кислорода.
Теперь сконцентрируйте пламя для предварительного нагрева в том месте, где должен начинаться разрез. Доведите разрезаемый металл до яркого вишнево-красного цвета.
Поверните наконечник в вертикальное положение.
Если разрез идёт по краю металла, то начинайте там. Когда появится красное пятно, слегка нажмите клапан (рычаг) подачи кислорода, и когда разрез начнётся, слегка поверните наконечник назад.
Теперь поверните наконечник в вертикальное положение, не перемещая его вперёд.
Поверните наконечник сильнее для небольшого наклона в направлении разреза.
Продвигайтесь вперёд с такой скоростью, чтобы обеспечить качественное резание.
При слишком медленном перемещении края разреза могут
сплавиться обратно. Слишком быстрое перемещение препятствует достаточному
прогреву и разреза не будет. При этом вы также получите сноп искр в лицо и на
колени. Держите рычаг подачи кислорода прижатым до конца линии разреза.
Не дергайте горелку резко, поддерживайте небольшой угол в направлении разреза.
Замедлите ход, позволяя линии разреза сделать острый край внизу.
Продолжайте движение вперёд, пока наконечник не окажется в пустом пространстве.
Повторите описанные операции несколько раз до получения удовлетворительного результата. Как и при сварке, ключом к качественной работе является практика. Первые разрезы будут выглядеть очень непривлекательно, но со временем вы сможете уверенно получать чистый и ровный разрез. Для удаления небольших следов оплавленного металла понадобится небольшая механическая обработка места разреза.
Дуговая сварка
Может показаться, что газовая (электрическая) сварка
никак не связаны друг с другом, но основная разница между ними состоит в
источниках нагрева для них. При электросварке для создания и поддержания
пятна расплавленного металла используется электрическая дуга, а не сгорающие
газы. В связи с этим, если вы освоили газовую сварку, то в течение короткого
времени сможете работать с электросваркой. Основное отличие состоит в
оборудовании.
Существует много типов электрических сварочных аппаратов, но мы рекомендуем использовать аппараты на сварочный ток 225-230 А. Вы можете приобрести аппарат на ток в 180 или даже 100 А, однако аппарат, рассчитанный на ток 225-230 А, будет лучше, тем более что разница в цене не очень большая.
Хотя сварочный аппарат и рассчитан на ток до 235 А,
но маловероятно, что при работе будет использоваться такой большой ток. Сталь
толщиной до 13 мм можно варить током 180 А, сталь толщиной 6 мм – током 130-145 А, а для сварки стали толщиной порядка 3 мм достаточно тока в 75 А. В связи с этим возникает вопрос: “Зачем нужен аппарат с током в 225-230 А ?” Ответ будет
таким же, как и при приобретении автомобиля с двигателем мощностью 300 л. с. – для дополнительного резерва. Даже если такая мощность никогда и не понадобится, то
сварочный аппарат не будет перегружаться.
Проконсультируйтесь относительно ваших требований к сварочному аппарату при его приобретении с учётом своих материальных возможностей. Продавец или консультант даст вам необходимые советы по приобретению. Помните, что вы покупаете аппарат для себя, а не для продавца.
Сварочный аппарат должен быть полностью готов к включению в бытовую электросеть напряжением 220 В, защищённую предохранителем на ток 50-60 А или автоматическим предохранителем. Не пользуйтесь розеткой для электрической кухонной плиты.
Мы рекомендуем приобретать аппарат отдельно, а не в
комплекте с маской, электрододержателем и с зажимами, а также с набором
электродов для сварки. Скорее всего, вам придётся выбросить прилагаемые к
аппарату дополнительные аксессуары и купить другие, специального назначения.
Но может случиться и так, что прилагаемые аксессуары могут подойти вам –
попробуйте. Имейте в виду, что в магазинах имеется широкий выбор аксессуаров
различного качества и назначения.
Провод питания вставляется в отверстие, соответствующее наименьшему значению необходимого сварочного тока для достаточного проникновения в шве. Слишком большой сварочный ток даёт слишком большой перегрев и прожжёт металл насквозь.
Электроды
Электрод поддерживает электрическую дугу. Он также подаёт металл электрода для сварочного соединения и флюс для защиты места сварки от загрязнения. Электроды для электросварки покрыты флюсом. Это расплавленное покрытие защищает свежую сварку, замедляя скорость охлаждения.
Для сварки различных типов стали имеются различные
электроды. Не покупайте больше электродов, чем вам нужно. Покрытие электрода
разрушается под действием влаги, поэтому нужно держать электроды в сухом
месте. При покупке электродов имеет смысл проконсультироваться со
специалистом.
Предварительные замечания
Практически всего в электросварке можно достичь практикой, в том числе подбор правильного электрода и установки правильного значения сварочного тока для конкретного металла, который вы собираетесь сваривать. Обратитесь к инструкциям, которые прилагаются к сварочному аппарату. На вопросы относительно скорости движения электрода, под каким углом его держать и т. д. можно дать надёжный ответ только в результате практической работы.
Перед тем как включить вилку сварочного аппарата в
сеть напряжением 220 В, отключите основной рубильник. Проверьте, что
заземление подсоединено к заземляющему проводу сварочного аппарата. Убедитесь
также, что плавкий или автоматический предохранитель способен выдержать то
50-60 А при работе сварочного аппарата. Если предохранитель не рассчитан на
такой ток, то он перегорит или отключится и аппарат не сможет работать
некоторое время. И наоборот, если предохранитель рассчитан на слишком большой
ток, то изоляция проводов может загореться.
В предположении, что указанные условия выполнены, включите сварочный аппарат в сеть и подсоедините заземляющий зажим к стальному рабочему столу или к свариваемой детали. Проверьте качество соединения.
Вообще говоря, большой и толстый кусок металла
требует электрода большего диаметра и большего значения сварочного тока для
большего тепловыделения. В инструкции к сварочному аппарату должны
приводиться данные по диаметрам электродов и значениям сварочного тока. Но
из-за того, что технические условия изменяются от аппарата к аппарату и для
различных фирм-изготовителей, нет определённых универсальных правил для
установки значений тока. Практика и эксперимент подскажут вам, правильно ли
вы устанавливаете значение тока.
При избыточном тепле в тонком или легкоплавком материале могут образовываться отверстия и шов будет плоским и пористым. Также шов будет проплавлять края металла. Такое проплавление имеет место, когда основной металл по бокам шва выплавляется и становится ниже по сравнению с “нормальной” поверхностью базового материала.
При недостаточном тепле шов выглядит так, что он просто наложен поверх места сварки – проникновение шва недостаточное. Шов будет нерегулярным и вам будет трудно поддерживать дугу. В заключение, если ток будет установлен слишком низким, то у вас возникнут сложности с дугой. Электрод будет стремиться “залипать” или же вам будет сложно поддерживать горение дуги.
При правильной установке величины тока дуга
загорается относительно легко, образуя ровный шов без рваных краёв. Вы
получите хорошее проникновение и без подплавления или прожигания отверстий.
Со временем вы по звукам при сварке сможете определить, правильно ли вы
варите. Звук при электросварке должен чем-то напоминать звук в процессе жарки
мяса на сковороде.
Скорость, с которой вы ведёте шов, также будет влиять на процесс проникновения. При слишком быстром движении проникновение будет плохим. Дуга должна двигаться медленно, используя волнообразное движение или движение, описанное далее для обеспечения хорошего проникновения и качества шва.
Внимание: Вы должны надевать маску перед зажиганием дуги. Защитная сварочная маска не только защитит ваши глаза от интенсивного свечения, но и защитит вас от радиации (излучения), летящих искр, капель расплавленного металла и дымов.
Защитная одежда
Перчатки защищают руки от ожогов. Плотная длинная куртка
защищает верхнюю часть тела. Сварка с оголёнными руками за пару часов
равносильна нахождению на открытом солнце в течении полудня. Для работы
необходимы длинные прочные брюки, лучше всего из материала типа брезента с
пропиткой. Для защиты от кусков расплавленного металла нужны плотно
закрывающиеся ботинки, внутрь которых не должны попадать искры и другие
посторонние предметы.
Зажигание дуги и создание шва
Теперь, когда вы знакомы с принципами работы дуговой сварки, обсудим, как нужно действовать на практике.
Начало сварки
Когда вы надели маску, защитную одежду и перчатки, возьмите электрододержатель в ту руку, которой вы обычно работаете.
Расположите конец электрода примерно в 2,5 см от того места, где вы хотите начать сварку. Откиньте вниз защитную маску. Качающим движением
поднесите электрод к металлу для зажигания дуги. Сразу же после этого
поднимите электрод на расстояние примерно в 3 мм от рабочей поверхности. Если этого не сделать, то электрод “залипнет”.
Если это всё же произошло, то качните электрододержатель из стороны в сторону, чтобы оторвать электрод. Если электрод не отрывается после нескольких качаний, то освободите его из держателя. Дайте электроду остыть перед повторной попыткой освобождения, так как он может быть раскалён докрасна. Ни в коем случае не беритесь за электрод голыми руками!
Зажигание дуги на практике с различными металлами и с разным сварочным током требует определённой практики. Повторяйте попытки до тех пор, пока не сможете успешно зажигать дугу и поддерживать её. Затем можно приступать к созданию шва.
После зажигания дуги подержите её примерно секунду
перед движением электрода, чтобы образовалось расплавленное пятно. Имейте в
виду, что сварочный электрод расходуется при работе – он расплавляется, как
только вы коснётесь им места сварки. Для поддержания дуги и создания шва вы
должны двигать электрод в направлении пятна расплавленного металла и
одновременно из стороны в сторону перекрёстными движениями. Концентрируйте
взгляд в той точке, где электрод касается металла, заполняйте её и
одновременно перемещайтесь.
Ровный шов
Легче всего создается ровный шов. Он делается одним непрерывным движением электрода без качающих и колебательных движений. Сварщик-правша двигает электрод слева направо, сварщик-левша – справа налево. В обоих случаях необходимо наклонять электрод под углом около 15 градусов. Средний шов от электрода диаметром 3 мм будет примерно 3 мм в высоту и примерно 6 мм в ширину. Попрактикуйтесь в изготовлении ровных швов, пока не сможете делать равномерные швы постоянной ширины и высоты с равномерно расположенными “волнами”.
Качающийся шов
Другим обычно используемым швом является “качающийся” шов. Этот тип швов используется для заполнения зазора между двумя кусками металла.
Качающийся шов выполняется путём перемещения
электрода в форме цифры 8 или буквы Z из стороны в сторону при одновременном
движении вдоль шва.
Моментальные колебания с каждой стороны обеспечивают одинаковое количество тепла по краям и в середине шва. Эти швы являются наиболее распространёнными, но какие есть ещё? Далее приведены ещё несколько распространённых швов:
Стыковой шов
Когда два куска металла соединяются краем к краю и свариваются, то это будет стыковой шов. Если металл толще 5 мм, то каждый край нужно скосить для обеспечения правильного проникновения. Углы скосов должны составлять примерно 45 градусов. Если материал толстый, для заполнения V-образной канавки, образованной от скошенных краёв может потребоваться сделать более одного прохода.
Внимание: Наши рассуждения относительно
процесса сварки являются сводными. На эту тему написаны сотни книг.
Специалистов по сварке готовят в различных учебных заведениях, во многих
странах существуют различные научно-исследовательские учреждения, занимающиеся
вопросами сварки. Ясно, что мы не сможем научить вас сварке. Мы можем только
вкратце описать суть процесса. Для настоящего обучения сварке вам нужна
большая практика, нужно читать книги и ещё раз практиковаться. Конечно, нет
нужды посвящать изучению тонкостей процесса сварки много времени, но вы
должны понимать, что сварка есть нечто большее, чем просто расплавление
электродов. Информация, приведённая в данной главе, поможет вам начать
изучение сварки и обеспечить основы знаний, необходимых для того, чтобы стать
хорошим сварщиком.
Ремонт панелей из высокопрочной стали
В конце 70-х – начале 80-х годов производители
автомобилей начали использовать новый тип материалов, которые были названы
высокопрочной сталью. Такая сталь благодаря своему повышенному соотношению
прочности и веса может быть прокатана до более тонкого состояния, чем
использованные ранее низкоуглеродистые мягкие стали, т. е. толщина составляет
примерно от 0,6 до 2,5 мм. Высокопрочная сталь может использоваться более
тонкой и сохраняет такую же абсолютную прочность, как и более толстая мягкая
сталь. Результатом были более лёгкие автомобили с такой же прочностью. Теперь
рассмотрим более подробно этот вид стали.
В соответствии с прогнозами мировых автопроизводителей мы можем предсказать более широкое использование высокопрочных сталей. В конце 70-х – начале 80-х годов фирмы “Форд” и “Крайслер” ограничивали использование этих материалов в структурах кузова, усилительных элементах, косынках, кронштейнах и опорах. Большинство наружных панелей из листового металла продолжали выпускаться из мягкой стали. Однако, некоторые японские производители, особенно “Тойота”, начали использовать высокопрочную сталь в кузовных деталях и для наружных панелей.
В чём состоит здесь проблема? Она в следующем: из-за
высокого содержания углерода высокопрочная сталь не может свариваться с
использованием обычных методов, особенно с использованием газовой сварки.
Некоторые стали могут нагреваться всего лишь до 370 – 380 градусов по
Цельсию. У других для предотвращения деформаций необходимо принимать
специальные меры. А мартенситная сталь вообще не может свариваться или
нагреваться. Кристаллическая структура зёрен стали окисляется и разрушается
под действием высокой температуры. Если она используется, то панель из такой
стали может стать причиной опасного повреждения.
Возможно, вы когда-нибудь видели старые кости, которые долго лежали. Эти кости, которые обычно очень плотные и твёрдые, со временем становятся пористыми и хрупкими. Наступите ногой на такую кость и она сразу же треснет. Это является результатом окисления, воздействия ультрафиолетовых лучей и других проблем. Этот пример иллюстрирует процессы, которые происходят в высокопрочной стали после воздействия температуры. Что же можно сделать для решения данной проблемы?
Снятие панелей
Для снятия панелей из высокопрочной стали или
отсоединения других панелей от панелей из этого материала высверлите места
точечной сварки или отрежьте сварные швы с помощью отрезной машинки. Не
производите резку с помощью газовой горелки. Для подсоединения панелей
прижмите новые панели на то место, где они должны быть и подсоедините деталь
с помощью сварки в атмосфере инертного газа с использованием сварочной
проволоки, если это возможно. В противном случае воспользуйтесь дуговой
сваркой.
Сварка высокопрочной стали
Первым решением является использование сварки металлов в атмосфере инертного газа. Сварка с инертным газом также известна как дуговая сварка металлов в атмосфере газа или аргоновая сварка.
Сварка в атмосфере инертного газа концентрирует
тепло в очень малой области. Путём использования ряда точечных стыков
(подобных обычной точечной сварке) вы сможете заменить деталь из
высокопрочной стали без нарушения её структурной целостности. Если сварка в
атмосфере газа не подходит, то можно использовать обычную дуговую сварку с
учётом приводимых далее указаний. Повторим, что газовая сварка не подходит
для сварки высокопрочной стали.
Сварка в атмосфере газа – предпочтительный метод
Сварка в атмосфере газа, называемая также сваркой с применением сварочной проволоки подобна дуговой сварке. Отличительной особенностью является использование “щита” из инертного газа, который защищает расплавленный металл от атмосферных загрязнений. Зажигается дуга и образуется пятно из расплавленного металла. Одновременно поток газа окутывает место сварки. В качестве газа обычно используется двуокись углерода. Часто используются такие инертные газы, как аргон или гелий. Газ не только защищает место сварки, но и помогает стабилизировать дугу.
Вместо использования покрытого флюсом электрода в
аргоновой сварке используется специальная проволока, которая автоматически
подаётся к сварочному шву с определённой скоростью. Хотя в этом методе сварки
используется проволока различных размеров, для сварки высокопрочной стали
используется проволока диаметра 0,7-0,9 мм.
Основными преимуществами аргоновой сварки является следующее:
Сварка происходит быстро.
Повреждение тонких листов металла минимизируется благодаря использованию небольшого тока; для сварки листа толщиной около 6 мм требуется напряжение менее 20 В.
Аргоновой сварке довольно легко научиться.
Зазоры легко заполняются с помощью нескольких швов, которые накладываются один поверх другого.
Сварка с перехлестом или вертикальная сварка производится относительно легко.
Металл различной толщины можно варить проволокой одинакового диаметра.
Металлы всех типов можно варить одним общим типом проволоки.
Таким образом, если вы имеете доступ к аргоновой сварке, то используйте ее для сварки высокопрочных сталей.
Дуговая сварка высокопрочной стали
Успешное использование дуговой сварки для
высокопрочной стали возможно при выполнении следующих правил: Пользуйтесь
только электродами диаметром 2,4 мм, которые специально предназначены для
сварки высокопрочной стали. При покупке электродов консультируйтесь в
магазине. Вместо непрерывных швов для соединения панелей воспользуйтесь
сваркой в нескольких местах. Это некое подобие точечной сварки. В тех местах,
где две панели перекрываются для соединения, сверлятся отверстия диаметром 6 мм через одну панель при перекрытии через каждые 2,5-5 см. Затем эти отверстия “заполняются”
материалом сварочного электрода при сварке. Это предотвращает нагрев от
выполнения непрерывного шва, что становится причиной ослабления соединения в
панели из высокопрочной стали.
(Данная статья взята из практического руководства «Ремонт, окраска кузовов автомобилей. Подготовка к покраске, сварка, рихтовка и многое другое». Под редакцией С. Афонина)
◄Вернуться в раздел статьи
Газы, применяемые для сварки и резки металлов | Пасс
Газовая сварка, при которой происходит плавление кромок свариваемых деталей в высокотемпературном пламени газовой горелки (рис. 1) с дальнейшим формированием шва, имеет по сравнению со сваркой электродуговой как преимущества, так и недостатки. К первым относится тот факт, что при помощи данного метода можно сваривать практически любые материалы, более того, чугун, медь, латунь и свинец даже легче поддаются газовой сварке, чем дуговой. При этом отсутствует потребность в применении дорогого и сложного оборудования, а также в подключении к источнику электропитания. В то же время газовую сварку обычно применяют для обработки относительно тонких изделий, так как с увеличением толщины свариваемого металла в результате сравнительно медленного его прогрева пламенем и невысокой концентрации тепла резко падает ее производительность. Кроме того, стоимость газов, применяемых для создания высокотемпературного пламени, достаточно высока, поэтому эксплуатационные расходы в процессе газовой сварки часто оказываются выше, нежели для сварки электродуговой. Отметим, что при газовой сварке часто применяют присадочную проволоку, близкую по составу к свариваемому металлу, участвующую в образовании сварного соединения.
Рис. 1. Схема инжекторной горелки для газовой сварки: 1 — мундштук; 2 — сменный наконечник; 3 — смесительная камера; 4 — инжектор; 5 — кислородный вентиль; 6 — ацетиленовый вентиль
Температура пламени при газовой сварке должна быть не меньше чем в два раза выше температуры плавления свариваемого материала. Лучше всего удовлетворяет этому условию ацетилен — при сжигании его в кислороде образуется пламя с температурой порядка 3150 ˚С, что позволяет сваривать практически любую сталь.
При этом в зависимости от соотношения ацетилен-кислород горючая смесь может образовывать различные типы пламени, по-разному влияющие на процесс сварки.
Нормальное пламя, образуется при подаче 1,1-1,3 объема кислорода на один объем ацетилена. Этого недостаточно для полного окисления горючего газа — как следствие в пламени преобладает монооксид углерода(СО) и водород, выделившийся при разложении ацетилена. Последний защищает расплавленный металл шва от окисления. Окончательное сгорание смеси до углекислого газа и воды происходит за счет кислорода воздуха.
При подаче меньшего объема кислорода получается коптящее науглероживающее пламя — недоокисленный углерод переходит в расплавленный металл, ухудшая качество шва.
Впрочем, избыток кислорода пользы также не приносит. Образующееся при этом окислительное пламя, хотя и характеризуется повышенной температурой, однако сообразно со своим названием окисляет металл шва, снижая его прочностные свойства. Оказывается, что при большом избытке кислорода и должном давлении он вообще может полностью окислить металл, выдувая из рабочей зоны продукты его сгорания. На этом принципе основана технология газовой резки. При ней ацетиленовое пламя исполняет скорее вспомогательную роль, подогревая место разреза до температуры, при которой металл начинает сгорать в струе чистого кислорода, подающегося в зону резки параллельно с горючей смесью. Основная теплота при этом выделяется именно за счет окисления металла. Логическим продолжением данного метода является копьевая резка, которая применяется для разрезания низкоуглеродистой и легированной стали большой толщины. Более того, копьевая резка позволяет справиться и с железобетоном. Сущность метода заключается в прожигании отверстий стальной трубкой(копьем), по которой под большим давлением подается кислород, при этом необходимую для процесса теплоту получают окислением металла конца трубки(предварительно подогретого) и железа обрабатываемого изделия. Совершая копьем горизонтальные и вертикальные движения можно вырезать куски материала нужной формы.
Важнейшее значение для сварки и резки металлов имеет надлежащий выбор применяемых в этих процессах газов и способов их получения.
Кислород
Технический кислород различают по степени чистоты, так 1-ый сорт содержит не менее 99,7% (объемных) кислорода, 2-й — не менее 99,5%, 3-й — не менее 99,2%. Особенно большое значение чистота кислорода имеет для кислородной резки. С понижением содержания в нем газовых примесей увеличивается скорость реза, и уменьшается расход самого кислорода. Доставлять кислород к месту сварки можно как в баллонах, так и в жидком состоянии. В первом случае, полученный путем криогенной ректификации из воздуха кислород закачивается в баллоны под давлением в 150-165 атм. Второй метод, позволяющий уменьшить расходы на содержание и транспортировку баллонов, заключается в доставке жидкого кислорода прямо к месту сварки в специальных сосудах с хорошей теплоизоляцией с последующим его испарением. При этом из 1 дм3 жидкости получают 860 дм3 газообразного кислорода (при нормальных условиях).
Ацетилен
Ацетилен также можно либо получать в готовом виде на месте, либо везти его издалека в баллонах. В первом случае используются так называемые ацетиленовые генераторы, где его получают реакцией карбида кальция с водой. Теоретически одного килограмма чистого карбида достаточно для образования 350 дм3 ацетилена, на практике же выход горючего газа составляет не более 300 дм3/кг. Данный метод имеет определенные недостатки, связанные с хлопотностью хранения карбида кальция — он жадно поглощает воду из воздуха, образуя взрывоопасные ацетилен-воздушные смеси. Соответственно, загруженный в генератор кусок карбида должен быть полностью превращен в ацетилен, а полученный ацетилен — сожжен в горелке, во избежание проблем с безопасностью труда. Отбор данного газа из баллона не создает подобных трудностей. В то же время, сама технология баллонного хранения и перевозки ацетилена достаточно необычна, именно за счет его чрезвычайной взрывоопасности. Которая понижается при растворении ацетилена в ацетоне. В результате ацетиленовый баллон представляет собой наполненную пористой массой емкость. Пористая масса (например, активированный уголь) пропитана ацетоном, в ацетоне же растворяется ацетилен, закачиваемый в баллон под давлением 10-20 атм. При 10 атм. в стандартном 40-литровом баллоне помещается порядка 5 кг ацетилена, что эквивалентно 4,5 м3 газа при нормальных условиях. Отбор ацетилена из баллона нежелательно производить со скоростью выше 1,5 м3/ч, так как при более интенсивной откачке газа из емкости уносится и часть ацетона.
Таким образом, при больших объемах потребляемого ацетилена имеет смысл использовать ацетиленовые генераторы, для не столь масштабных работ более подходящим решением является отбор газа из баллонов.
Ацетилен для закачки в баллоны получают как из карбида кальция, так и при пиролизе природного газа. Отметим, что контакт с оксидом меди резко снижает температуру воспламенения ацетилена, поэтому при изготовлении оборудования для работы с этим газом стараются избегать использования медьсодержащих деталей.
Заменители ацетилена
Дороговизна ацетилена зачастую вынуждает искать ему газы-заменители, ведущее место среди которых занимает пропан, или же пропан-бутановая смесь, обладающие высокой теплотворной способностью. Впрочем, для удовлетворительного сгорания пропана требуется примерно в три раза больше кислорода, чем для ацетилена, что делает выгодность его применения не столь однозначной. Самым же большим недостатком пропана является более низкая, нежели у ацетилена температура пламени, что существенно осложняет его применение для сварки сталей. Поэтому пропан чаще используют либо при сварке легко плавящихся цветных металлов, либо для создания подогревающего пламени при кислородной резке сталей.
Если все же пропановое пламя используют для сварки углеродистых сталей, то приходится применять сварочную проволоку, содержащую повышенную концентрацию кремния и марганца, использующихся в качестве раскислителей, что улучшает качество сварного соединения. Отметим, что большой коэффициент объемного расширения пропана (и бутана) накладывают ограничения на объем газа, который может быть безопасно закачан в баллон.
Аналогичные проблемы возникают и при использовании других заменителей ацетилена — водорода, коксового газа, бензина, керосина. Низкая температура пламени, поучаемая при сжигании данных веществ, затрудняет их применение при сварке сталей, однако позволяет использовать их в процессах резки, а также сварки и наплавки более легкоплавких металлов.
В общем, возможности выбора того или иного варианта состава горючей смеси, а также способов ее получения, для газовой сварки или резки достаточно широки, и всецело зависят от конкретной ситуации.
WebWISER — Главная
WISER — это система, предназначенная для оказания помощи аварийно-спасательным службам при инцидентах с опасными материалами. WISER предоставляет широкий спектр информации об опасных веществах, в том числе поддержка идентификации, физические характеристики, информация о здоровье человека и рекомендации по сдерживанию и подавлению. Для начала настройте свой профиль и выберите элемент ниже. Известные вещества Поиск вещества в базе данных известных веществ WISER. Помогите определить химическое вещество Определите неизвестное химическое вещество на основе его физических свойств, симптомов воздействия, окружающей среды и других критериев. Инструменты Ознакомьтесь с общими инструментами и справочными материалами. Последние новости
WebWISER лучше всего просматривать в следующих браузерах (указанная версия или выше): Internet Explorer 9, Firefox 26, Safari 7 или Google Chrome 30. WISER также доступен как отдельное приложение для ПК и различных мобильных платформ. включая устройства iOS и Android. Посетите домашнюю страницу WISER для бесплатных загрузок и получения дополнительной информации о WISER. | Другие ресурсы для чрезвычайных ситуаций с химическими веществами в NLM
Other Chemical Emergency Resources
|
Почему кислородно-ацетиленовое пламя используется при сварке и резке металлов?
Пламя имеет температуру около 2800 градусов по Цельсию. При этой температуре металл очень легко плавится . Поэтому он обычно используется для резки и плавки металла. Он также известен как кислородно-водородная горелка, потому что это газокислородная горелка, которая сжигает водород (действует как топливо) с кислородом (действует как окислитель).
Какое пламя используется для сварки и резки металлов?
Пламя кислородно-водородное используется для сварки и резки металлов.
Какое пламя используется для кислородно-ацетиленовой резки?
A Нейтральное кислородно-ацетиленовое пламя используется для сварки, пайки и пайки серебром большинства металлов и поэтому является наиболее распространенным типом пламени. Нейтральное пламя также используется для кислородно-ацетиленовой резки.
Для чего используется кислородно-водородное пламя?
Кислородно-водородная горелка (также известная как водородная горелка) представляет собой газокислородную горелку, которая сжигает водород (топливо) с кислородом (окислителем). Он используется для резки и сварки металлов , стекла и термопластов .
Как работает кислородно-ацетиленовый резак?
Газокислородные резаки используют медный наконечник с рядом отверстий, расположенных по кругу, для подачи смеси топливного газа и кислорода для создания пламени предварительного нагрева . Температура пламени предварительного нагрева будет варьироваться от 4440° до 6000°F в зависимости от используемого топливного газа и отрегулированного соотношения кислорода и топливного газа.
Можно ли сваривать кислородно-ацетиленовым электродом?
Ацетиленокислородная сварка, обычно называемая газовой сваркой, представляет собой процесс, основанный на сгорании кислорода и ацетилена . При смешивании в правильных пропорциях в ручной горелке или паяльной трубке образуется относительно горячее пламя с температурой около 3200 градусов.
Каковы преимущества окислительного пламени?
Естественное пламя имеет синхронизированную смесь топлива и кислорода, пламя науглероживания имеет больше топлива, а окислительное пламя имеет больше кислорода . В разных материалах использовалось разное пламя в зависимости от состояния сварки.
Что такое кислородно-ацетиленовое пламя и как его использовать?
Пояснение: Кислородно-ацетиленовое пламя представляет собой газовую горелку, которая сжигает смесь ацетилена и кислорода для получения высокотемпературного пламени, которое можно использовать для сварки, резки и другой обработки металлов .
Что такое пламя ацетилена?
Ацетилен (C 2 H 2 ) – легко воспламеняется и может вызывать удушье. Это один из горючих газов, используемых при кислородно-газовой сварке, составляющий любая процедура сварки, при которой горючий газ сочетается с кислородом для получения пламени . Теплота и температура, создаваемые ацетиленовым пламенем, зависят от количества кислорода, используемого для его сжигания.
Почему водород используется при резке и сварке?
Смесь кислорода и водорода используется для обработки заводских материалов. Потому что это пламя становится нейтральным и температура пламени повышается . Поскольку оба являются горючими газами и способствуют горению. Поэтому он также используется для резки и сварки.
Какой газ используется при газовой сварке?
Ацетилен является единственным горючим газом, подходящим для газовой сварки из-за его благоприятных характеристик пламени как при высокой температуре, так и при высокой скорости распространения. Другие горючие газы, такие как пропан, пропилен или природный газ, дают недостаточно тепла для сварки, но используются для резки, пайки и пайки.
Почему при газовой резке используется ацетилен?
Ацетилен выделяет почти 40% своего тепла во внутреннем конусе пламени . Поэтому ацетилен лучше для резки, чем пропан.
Почему кислородно-пламенные резаки предпочитают ацетилен пропану или природному газу?
Ацетилен выделяет почти 40% своего тепла во внутреннем конусе пламени . Поэтому ацетилен лучше для резки, чем пропан. Хотя с точки зрения температуры ацетилен горячее, чем пропан, факт заключается в том, что люди неправильно используют пропан для резки.
Для чего используется ацетилен при сварке?
Ацетилен используется для сварки и резки. Сварочный процесс, в котором используется ацетилен, известен как газокислородная резка или газовая резка. Этот метод используется для резки или сварки материалов, требующих температуры до 3500 °C (6330 °F) . Среди всех других газов ацетилен способен производить самое горячее пламя.
Где используется кислородно-ацетиленовая сварка?
Авиационная промышленность: кислородно-ацетиленовая сварка обычно используется для соединения различных деталей самолетов . Автомобильная промышленность: Используется для сварки деталей рамы и шасси. Соединение высокоуглеродистой стали: газовая сварка очень эффективна при плавлении высокоуглеродистой стали.
Что из следующего является преимуществом кислородно-газовой сварки?
Пламя кислородно-ацетиленового газа имеет температуру около 3200°C и, таким образом, может плавить все имеющиеся в продаже металлы .
В чем преимущество кислородно-ацетиленовой горелки по сравнению с воздушно-ацетиленовой горелкой?
В чем преимущество кислородно-ацетиленового пламени по сравнению с воздушным ацетиленовым? Нагревается быстрее , чем пламя ацетилена.
Почему газокислородная резка является наиболее предпочтительным методом резки в сварочной промышленности?
Газокислородная резка является одним из наиболее часто используемых процессов сварки, и на то есть веские причины. Первоначальная стоимость приобретения оборудования ниже, чем для других процессов, таких как плазменная резка . Оборудование может использоваться для широкого круга процессов, а не только для резки. Это быстро и легко настроить.
Какие металлы можно сваривать кислородно-ацетиленовой сваркой?
Металлы, которые можно сваривать кислородно-ацетиленовым пламенем, включают железо, сталь, чугун, медь, латунь, алюминий, бронзу, а также многие сплавы, которые можно сваривать . Кислородно-ацетиленовое пламя также используется для резки металла, цементации и отжига.
Каковы преимущества резки металла?
- Надежность.
- Требуется меньше человеческого труда.
- Высокая производительность.
- Идентичные продукты.
- Увеличьте прибыль и сократите усилия.
- Повышенная эффективность.
- Повышенная точность.
- Помочь вам опередить конкурентов.
Какова роль газообразного кислорода при газовой сварке?
Роль кислорода – Это окислитель, который химически соединяется с топливом для получения тепла для сварки . Это называется «окисление», но более конкретным и часто используемым термином в данном контексте является «сгорание». В случае водорода продуктом сгорания является просто вода.
Видео
youtube.com/embed/oOvZdVawbNM?enablejsapi=1&autoplay=0&cc_load_policy=0&cc_lang_pref=&iv_load_policy=1&loop=0&modestbranding=0&rel=1&fs=1&playsinline=0&autohide=2&theme=dark&color=red&controls=1&» title=»YouTube player» allow=»accelerometer; autoplay; clipboard-write; encrypted-media; gyroscope; picture-in-picture» allowfullscreen=»» data-no-lazy=»1″ data-skipgform_ajax_framebjll=»»>Другие статьи
Где производятся сварочные маски из стекла Speedglas?
Какой двигатель у сварочного аппарата Miller?
Как должны подходить сварочные перчатки?
Сколько стоит маска сварщика с автоматическим затемнением?
Где чаще всего используется сварка?
Уэс Роуз
Уэс Роуз — опытный сварщик с более чем 15-летним опытом. Он работал в различных областях сварки, в том числе в автомобилестроении, судостроении и строительстве. Он сертифицированный сварщик и выиграл несколько соревнований по сварке. Уэс увлечен обучением других сварке и любит делиться своими знаниями с другими.
oxy-fuel_welding_and_cutting
Oxy-fuel welding (commonly called oxyacetylene welding or oxy welding or in the U.S. gas welding ) and Oxy-fuel cutting are processes that use fuel gases and oxygen для сварки или резки металлов.
Между ними есть несколько различий. При кислородно-топливной сварке для сварки металлов используется сварочная горелка. При газокислородной резке черный металл нагревается с помощью резака до температуры воспламенения (около 9°С).80°С). Поток чистого кислорода направляется на горячий металл, который химически соединяется с железом, которое затем вытекает из разреза или пропила в виде шлака оксида железа [1] .
Горелки, которые не смешивают чистый кислород с топливом внутри горелки, а сжигают его с атмосферным воздухом, не являются кислородно-топливными горелками и могут быть идентифицированы по их единственному баку. (Для кислородно-топливной сварки/резки требуется два резервуара, топливный и кислородный.) Большинство металлов невозможно расплавить такими однобаковыми горелками, поэтому их можно использовать только для пайки и пайки, но не для сварки.
Примечание. Иногда резак по металлу в просторечии называют «газовым топором», «дымовым ключом», «горячим ключом», «синим ключом» или «горячим синим гаечным ключом» (в Великобритании). В просторечии многие ошибочно называют сварочную горелку паяльной лампой. В США слово паяльная лампа также используется для обозначения того, что в Великобритании называют паяльной лампой.
Дополнительные рекомендуемые знания
Содержимое
|
Использование
Газокислородные горелки используются или использовались для:
- Сварочный металл: см. ниже. Водородная сварка
- Резка металла: см.
ниже.
- Кроме того, кислородно-водородное пламя используется для:
- В стекольной промышленности под названием «огневая полировка».
- В ювелирном производстве под наименованием «водяная сварка» используется «водяная горелка». [1].
- Раньше для нагревания куска негашеной извести для получения яркого белого света, называемого центральным светом, в театрах или в оптических («волшебных») фонарях.
- Ранее на платиновых заводах, так как платина плавится только в кислородно-водородном пламени и в электрической печи.
Аппарат
Аппарат, используемый для газовой сварки, состоит в основном из источника кислорода и источника горючего газа (обычно баллоны), двух регуляторов давления и двух гибких шлангов (по одному на каждый баллон) и горелки. Этот тип горелки также можно использовать для пайки и пайки. Баллоны часто перевозятся на специальной колесной тележке.
Были примеры наборов для кислородно-водородной резки с небольшими (размером с акваланг) газовыми баллонами, которые носят на спине пользователя в привязи рюкзака, для спасательных работ и т. п.
Существуют также образцы резаков на жидком топливе под давлением, обычно использующих бензин. Они используются для их повышенной мобильности.
Регулятор
Регулятор используется для контроля давления в резервуарах путем снижения давления и регулирования расхода. Газокислородные регуляторы обычно имеют две ступени: первая ступень регулятора выпускает газ из баллона с постоянной скоростью, несмотря на то, что давление в баллоне становится меньше по мере использования газа в баллоне, как на первой ступени акваланга. — водолазный регулятор. Вторая ступень регулятора управляет снижением давления от промежуточного до низкого давления. Это постоянный поток. Узел клапана имеет два манометра, один из которых показывает давление в цилиндре, а другой — промежуточное давление.
Некоторые кислородно-газовые регуляторы имеют только одну ступень и один манометр. С ними поток газа уменьшается по мере падения давления в баллоне.
Газовые шланги
Используемые шланги специально разработаны для сварки и резки. Шланг обычно представляет собой конструкцию с двойным шлангом, что означает, что два шланга соединены вместе. Кислородный шланг черный (в Великобритании) или зеленый, а топливный шланг красный. Тип газа, который будет проходить по шлангу, важен, потому что соединения будут иметь разную резьбу для разных типов газа. Для топливных газов (красный) используется левая резьба и канавка, вырезанная в гайке, а для кислорода (зеленый) используется правая резьба. Это мера предосторожности для предотвращения неправильного подсоединения шлангов. [2]
В основном можно использовать два типа соединений. Первый использует юбилейный клип. Второй вариант – использование обжимного соединителя. Второй вариант, вероятно, более безопасен, так как этот тип соединения труднее ослабнуть. Шланги также должны быть скреплены клипсами на расстоянии примерно 1 метр друг от друга.
Обратный клапан
Между регулятором и шлангом, а в идеале между шлангом и горелкой как на кислородной, так и на топливной линиях, следует установить пламегаситель и/или обратный клапан, чтобы предотвратить попадание пламени или кислородно-топливной смеси обратно в какой-либо из цилиндров и повреждение оборудование или привести к взрыву баллона.
Пламегаситель (не путать с обратным клапаном) предотвращает обратное движение ударных волн вниз по шлангам и попадание в цилиндр (возможно его разрыв), так как внутри частей оборудования находится большое количество топливно-кислородных смесей ( особенно в смесителе и паяльной трубке/форсунке), которые могут взорваться при неправильном выключении оборудования; а ацетилен разлагается при избыточном давлении или температуре. Пламегаситель останется выключенным до тех пор, пока кто-нибудь не сбросит его, на случай, если волна давления создаст утечку после разрядника.
Обратный клапан
Обратный клапан пропускает газ только в одном направлении. Не путать с пламегасителем: обратные клапаны не предназначены для блокирования ударной волны. Волна давления может возникать, когда шар находится так далеко от впускного отверстия, что волна давления проходит мимо до того, как шар достигает положения выключения. Обратный клапан обычно представляет собой камеру, содержащую шарик, который прижимается к одному концу пружиной: поток газа в одну сторону выталкивает шарик в сторону, а отсутствие потока или потока в другую сторону позволяет пружине протолкнуть шарик во входное отверстие. блокируя его.
Факелы
Горелка — это часть, которую сварщик держит и которой манипулирует для сварки. Он имеет соединение и клапан для топливного газа и соединение и клапан для кислорода, ручку для захвата сварщиком, смесительную камеру (установленную под углом), где топливный газ и кислород смешиваются, с наконечником, где пламя формы.
Сварочная горелка
Головка сварочной горелки используется для сварки металлов. Его можно определить по наличию только двух труб, идущих к соплу, и отсутствию спускового крючка кислородного дутья.
Резак
Головка резака используется для резки металла. Он похож на сварочную горелку. Кислород соединяется с ацетиленом в факеле, что дает высокотемпературное пламя. Его можно определить по трем трубкам, которые идут к соплу под углом 90 градусов, и по триггеру подачи кислорода, который подает кислород для выброса материала во время резки.
Факел в виде бутона розы
Горелка в виде бутона розы используется для нагрева металлов для гибки, правки и т. д., когда необходимо нагреть большую площадь. Называется он так потому, что пламя на конце похоже на бутон розы. Сварочная горелка также может использоваться для нагрева небольших участков, таких как ржавые гайки и болты. В этом случае с горелкой не используется присадочная проволока.
Инжекторная горелка
В большинстве горелок два газа просто смешиваются: это горелка с равным давлением. Но в некоторых горелках (называемых инжекторными горелками) внутри головки горелки кислород выходит из небольшого сопла под давлением, поэтому он увлекает за собой топливный газ за счет эффекта Вентури.
Топливо
В кислородно-топливных процессах могут использоваться различные горючие газы, наиболее распространенным из которых является ацетилен. Другими газами, которые могут быть использованы, являются пропилен, сжиженный нефтяной газ (LPG), пропан, природный газ, водород и газ MAPP.
Примечание: не существует ни одного газа под названием «оксиацетилен».
Ацетилен
- См. также: Ацетилен
Ацетилен — это топливо, впервые использованное для кислородно-топливной сварки, и остается предпочтительным топливом для ремонтных работ, резки и сварки общего назначения. Газообразный ацетилен поставляется в специальных баллонах, предназначенных для растворения газа. Цилиндры заполнены различными пористыми материалами (например, капоковым волокном, диатомовой землей или, ранее, асбестом), а затем примерно наполовину заполнены ацетоном. Ацетилен растворяется в ацетоне. Этот метод необходим, потому что ацетилен под давлением выше 207 кПа (30 фунтов силы / дюйм²) (абсолютное давление) нестабилен и может взорваться. Давление в заполненном баке составляет около 1700 кПа (250 фунтов силы/кв. дюйм). Ацетилен при сжигании с кислородом дает температуру от 3200 ° C до 3500 ° C (от 5800 ° F до 6300 ° F), что является самой высокой температурой любого из обычно используемых газообразных топлив. Его главный недостаток – сравнительно высокая стоимость.
Поскольку ацетилен нестабилен при давлении, эквивалентном примерно 33 футам = 10 метрам под водой, при резке и сварке под водой вместо ацетилена должен использоваться водород.
Бензин
Было обнаружено, чтокислородно-бензиновые (= кислородно-бензиновые) горелки очень хорошо работают, особенно там, где газовое топливо в баллонах недоступно или его трудно транспортировать на рабочую площадку. Испытания показали, что кислородно-бензиновая горелка режет стальной лист толщиной до 0,5 дюйма, а также кислородно-ацетиленовую; и толщиной от 0,5 до 4 дюймов лучше: в 3 раза лучше при толщине 4 дюйма. [ нужна ссылка ]
Бензин подается из напорного бака, давление в котором можно накачать вручную или подать из газового баллона. [3]
Водород
- См. также: оксиводород
Водород имеет чистое пламя и подходит для использования на алюминии. Он может использоваться при более высоком давлении, чем ацетилен, и поэтому подходит для подводной сварки и резки. Это хороший тип пламени для нагрева большого количества материала. Температура пламени высокая, около 2000°С при атмосферном давлении. [4]
Для некоторых кислородно-водородных горелок кислород и водород получают путем электролиза воды в аппарате, который подсоединяется непосредственно к горелке. Типы такого фонаря:
- Кислород и водород выводятся из электролизера отдельно и подаются в два газовых соединения обычной кислородно-газовой горелки. Это происходит в водяном факеле, который иногда используется в небольших факелах, используемых при изготовлении украшений и электроники.
- Кислород и водород смешиваются из электролизера и направляются в специальную горелку, предназначенную для предотвращения обратного воспламенения. См. оксиводород.
Согласно Юлиусу Томсену, при сгорании кислорода и водорода выделяется 34 116 калорий тепла на каждый грамм сожженного водорода: это 286 кДж/моль. То, как протекает процесс, влияет на температуру пламени: она, очевидно, наиболее высока при горении чистой стехиометрической смеси [ цитирования ] (смеси водорода ровно с половиной его объема кислорода, количество, с которым он соединяется, превращаясь в вода, немецкий Knallgas). Он становится меньше, когда «оксиводород» смешивается с избытком кислорода или водорода [ citation need ] , или инертный газ, такой как азот, потому что там такое же количество тепла распространяется на большее количество вещества.
МАПП газ
Газ MAPP является зарегистрированным продуктом Dow Chemical Company. Это сжиженный нефтяной газ, смешанный с метилацетилен-пропадиеном. Он имеет характеристики хранения и транспортировки сжиженного нефтяного газа и имеет теплотворную способность немного меньше, чем ацетилен. Поскольку его можно отправлять в небольших контейнерах для продажи в розничных магазинах, он используется любителями, а также крупными промышленными компаниями и верфями, поскольку при хранении в баллонах он так же летуч, как вода, и поэтому гораздо менее опасен, чем ацетилен. Газ MAPP можно использовать при гораздо более высоких давлениях, чем ацетилен, иногда до 40 или 50 фунтов на квадратный дюйм в газовых резаках большого объема, которые могут резать сталь толщиной до 12 дюймов. Другие сварочные газы, которые развивают сопоставимые температуры, требуют специальных процедур для безопасной транспортировки и обращения. Утечку газа MAPP легко идентифицировать из-за его особенно ужасного запаха.
Пропан
Пропан не горит так же сильно, как ацетилен во внутреннем конусе, поэтому его нельзя использовать для сварки. Пропан, однако, имеет очень большое количество БТЕ на кубический фут во внешнем конусе, и поэтому с правильной горелкой (тип инжектора) может выполнять более быструю и чистую резку, чем ацетилен, и гораздо полезнее для нагрева и гибки, чем ацетилен. .
Пропан дешевле ацетилена и его легче транспортировать.
Как и пропиленовые, большинство пропановых наконечников состоят из двух частей. Пропан часто подвергается несправедливой критике, потому что для достижения наилучшей производительности действительно требуется замена горелки (с горелки равного давления на горелку с инжектором), а не просто замена наконечника. Большинство горелок имеют одинаковое давление и предназначены для таких газов, как ацетилен, который легче кислорода. Пропан намного тяжелее и намного лучше проходит через инжекторную горелку низкого давления с настройкой от нескольких унций до примерно двух фунтов на квадратный дюйм при резке.
Пропилен
Пропилениспользуется в производственной сварке и резке. Режет аналогично пропану. При использовании пропилена очистка наконечника горелки требуется редко. Резка инжекторной горелкой (см. #пропан) часто имеет существенное преимущество перед горелкой с равным давлением при использовании пропилена.
Роль кислорода
Кислород не является топливом: это то, что химически соединяется с топливом для производства тепла для сварки. Это называется «окисление», но более общий и часто используемый термин — «сгорание». В случае водорода продуктом сгорания является просто вода. Для других видов углеводородного топлива образуются вода и двуокись углерода. Тепло выделяется потому, что молекулы продуктов сгорания имеют более низкое энергетическое состояние, чем молекулы топлива и кислорода.
Слово «кислород» часто сокращается до «окси», как в термине «окси-ацетиленовая горелка».
Кислород обычно производится в другом месте путем перегонки сжиженного воздуха и доставляется к месту сварки в сосудах высокого давления (обычно называемых «цистернами» или «баллонами») под давлением около 21000 кПа (3000 фунтов силы/дюйм² = 200 атмосфер). Его также отправляют в жидком виде в сосудах типа Дьюара (например, в большом термосе) в места, где используется большое количество кислорода.
Также можно отделить кислород от воздуха, пропуская воздух под давлением через цеолитовое сито, которое избирательно поглощает азот и пропускает кислород (и аргон). Это дает чистоту кислорода около 93%. Это хорошо работает для пайки.
Виды пламени
Сварщик может отрегулировать кислородно-ацетиленовое пламя, чтобы оно было карбонизирующим (т. е. восстановительным), нейтральным или окислительным. Регулировка производится добавлением большего или меньшего количества кислорода в пламя ацетилена. Нейтральное пламя чаще всего используется при сварке или резке. Сварщик использует нейтральное пламя в качестве отправной точки для всех других регулировок пламени, потому что его очень легко определить. Это пламя достигается, когда сварщики, медленно открывая кислородный клапан на корпусе горелки, сначала видят только две зоны пламени. В этот момент ацетилен полностью сгорает в сварочном кислороде и окружающем воздухе [1] . Пламя химически нейтрально. Две части этого пламени — светло-голубой внутренний конус и внешний конус от темно-синего до бесцветного. Во внутреннем конусе смешиваются ацетилен и кислород. Кончик этого внутреннего конуса является самой горячей частью пламени. Она составляет приблизительно 6000 градусов по Фаренгейту и обеспечивает достаточно тепла, чтобы легко расплавить сталь [1] . Во внутреннем конусе ацетилен распадается и частично сгорает до водорода и монооксида углерода, которые во внешнем конусе соединяются с большим количеством кислорода из окружающего воздуха и сгорают.
Избыток ацетилена создает обугливающее пламя. Это пламя характеризуется тремя зонами пламени; горячий внутренний конус, раскаленное добела «ацетиленовое перо» и синий внешний конус. Это тип пламени, наблюдаемый при первом добавлении кислорода к горящему ацетилену. Перо регулируется и становится еще меньше, добавляя в пламя все большее количество кислорода. Сварочное перо измеряется как 2X или 3X, где X — длина внутреннего конуса пламени. Несгоревший углерод изолирует пламя и снижает температуру примерно до 5000 градусов по Фаренгейту. Восстановительное пламя обычно используется для операций наплавки или сварки труб с обратной стороны. Перо вызвано неполным сгоранием ацетилена, вызывающим избыток углерода в пламени. Часть этого углерода растворяется в расплавленном металле для его карбонизации. Науглероживающее пламя стремится удалить кислород из оксидов железа, которые могут присутствовать, и этот факт привел к тому, что пламя стало известно как «восстановительное пламя» 9.0582 [1] .
Окислительное пламя является третьей возможной регулировкой пламени. Это происходит, когда соотношение кислорода и ацетилена, необходимое для нейтрального пламени, было изменено, чтобы получить избыток кислорода. Этот тип пламени наблюдается, когда сварщики добавляют больше кислорода в нейтральное пламя. Это пламя горячее, чем два других пламени, потому что горючим газам не придется искать так далеко, чтобы найти необходимое количество кислорода, или нагревать столько же термически инертного углерода. [1] Его называют окислительным пламенем из-за его воздействия на металл. Эта регулировка пламени обычно не является предпочтительной. Окислительное пламя создает нежелательные оксиды, наносящие структурный и механический ущерб большинству металлов. В окислительном пламени внутренний конус приобретает пурпурный оттенок, сужается и сужается на конце, а звук пламени становится резким. Слабо окисляющее пламя используется при сварке пайкой и наплавке бронзы, тогда как более сильно окисляющее пламя используется при сварке плавлением некоторых видов латуни и бронзы [1]
Размер пламени можно регулировать в ограниченной степени клапанами на горелке и настройками регулятора, но в основном это зависит от размера отверстия в наконечнике. На самом деле, наконечник должен быть выбран в первую очередь в соответствии с выполняемой работой, а затем соответствующим образом настроены регуляторы.
Сварка
Пламя прикладывают к основному металлу и держат до тех пор, пока не образуется небольшая лужица расплавленного металла. Ванна перемещается по траектории, где требуется сварной шов. Обычно в ванну добавляется больше металла по мере ее перемещения посредством погружения металла из сварочного стержня или присадочного стержня в ванну расплавленного металла. Металлическая лужа будет перемещаться туда, где металл является самым горячим. Это достигается за счет манипулирования горелкой сварщиком.
Количество тепла, подаваемого на металл, зависит от размера сварочного наконечника, скорости перемещения и положения сварки. Размер пламени определяется размером сварочного наконечника. Правильный размер наконечника определяется толщиной металла и конструкцией соединения.
Давление сварочного газа с использованием кислородно-ацетиленового газа устанавливается в соответствии с рекомендациями производителя. Сварщик изменит скорость перемещения сварного шва, чтобы поддерживать одинаковую ширину валика. Однородность является качественным признаком, указывающим на хорошее качество изготовления. Обученных сварщиков учат поддерживать одинаковый размер валика в начале сварного шва и в конце. Если валик становится слишком широким, сварщик увеличивает скорость сварки. Если валик становится слишком узким или сварочная ванна теряется, сварщик снижает скорость перемещения. Сварка в вертикальном или потолочном положении обычно выполняется медленнее, чем сварка в плоском или горизонтальном положении.
Сварщик должен добавить присадочную проволоку в расплавленную ванну. Сварщик также должен держать присадочный металл в зоне горячего внешнего пламени, когда он не добавляется в ванну, чтобы защитить присадочный металл от окисления. Не позволяйте сварочному пламени сжечь присадочный металл. Металл не впитается в основной металл и будет выглядеть как серия холодных точек на основном металле. В холодном сварном шве прочность очень мала. Когда присадочный металл правильно добавлен в расплавленную ванну, полученный сварной шов будет прочнее исходного основного металла.
Резка
Для резки настройка немного отличается. Резак имеет головку, расположенную под углом 60 или 90 градусов, с отверстиями, расположенными вокруг центральной форсунки. Внешние форсунки предназначены для предварительного нагрева пламени кислорода и ацетилена. Центральная струя несет только кислород для резки. Использование нескольких факелов предварительного нагрева, а не одного факела, позволяет изменять направление реза по желанию без изменения положения сопла или угла, который факел образует с направлением реза, а также обеспечивает лучший баланс предварительного нагрева [1] . Производители разработали специальные наконечники для газов Mapp, пропана и полипропилена, чтобы оптимизировать пламя этих альтернативных топливных газов.
Пламя предназначено не для плавления металла, а для доведения его до температуры воспламенения.
Спусковой крючок резака подает дополнительный кислород под более высоким давлением по третьей трубке резака из центрального жиклера в заготовку, вызывая горение металла и выдувание образовавшегося расплавленного оксида на другую сторону. Идеальный пропил — это узкий зазор с острыми краями по обе стороны от заготовки; перегрев заготовки и, таким образом, ее проплавление вызывает закругление кромки.
Резка начинается путем нагрева кромки стали до температуры воспламенения (приблизительно ярко-вишнево-красного цвета) с использованием только форсунок предварительного нагрева, затем с помощью отдельного режущего кислородного клапана для выпуска кислорода из центральной форсунки [1] . Кислород химически соединяется с железом в металлическом материале, мгновенно окисляя железо в расплавленный оксид железа, производя разрез. Здесь стоит отметить несколько моментов:
- Скорость потока кислорода имеет решающее значение — слишком малая скорость приведет к медленному рваному разрезу; слишком много приведет к потере кислорода и созданию широкого вогнутого разреза.
Кислородные копья и другие горелки, изготовленные по индивидуальному заказу, не имеют отдельного регулятора давления кислорода для резки, поэтому давление кислорода для резки необходимо контролировать с помощью кислородного регулятора. Давление кислорода при резке должно соответствовать кислородному отверстию режущего наконечника. Обратитесь к данным производителя наконечника по оборудованию, чтобы узнать о надлежащем давлении кислорода при резке для конкретного режущего наконечника [1] .
- Окисление железа этим методом сильно экзотермическое. Однажды начав, сталь можно резать с удивительной скоростью, намного быстрее, чем если бы она была просто проплавлена. В этот момент форсунки предварительного нагрева служат исключительно для помощи. Повышение температуры будет заметно по яркому ослеплению выбрасываемого материала даже через надлежащие защитные очки. ( Термическое копье — это инструмент, который также использует быстрое окисление железа для разрезания практически любого материала.
)
- Поскольку расплавленный металл вытекает из заготовки, на противоположной стороне заготовки должно быть место для выхода струи. Когда это возможно, куски металла режут на решетке, которая позволяет расплавленному металлу свободно падать на землю. Одно и то же оборудование можно использовать для кислородно-ацетиленовых паяльных и сварочных горелок, заменив часть горелки перед клапанами горелки.
Для базовой кислородно-ацетиленовой установки скорость резки легкого стального профиля обычно почти в два раза выше, чем у шлифовальной машины с бензиновым двигателем. Преимущества при резке больших секций очевидны: газокислородная горелка легкая, маленькая и тихая, и для ее использования требуется очень мало усилий, в то время как шлифовальная машина для резки тяжелая и шумная, требует значительных усилий оператора и может сильно вибрировать, что приводит к поломке. скованность рук и возможные длительные повторяющиеся травмы от перенапряжения. Кислородно-ацетиленовые горелки могут легко резать железосодержащие материалы толщиной более 50 мм (2 дюйма). Кислородные фурмы используются в операциях по разборке и резке секций толщиной более 200 мм (8 дюймов). Отрезные шлифовальные машины бесполезны для таких применений.
Роботизированные газокислородные резаки иногда используют высокоскоростное расширяющееся сопло. При этом используется кислородная струя, которая слегка открывается по ходу ее прохождения. Это позволяет сжатому кислороду расширяться при выходе, образуя высокоскоростную струю, которая распространяется меньше, чем сопло с параллельным отверстием, что обеспечивает более чистый срез. Они не используются для резки вручную, так как требуют очень точного позиционирования над работой. Их способность изготавливать практически любую форму из больших стальных листов обеспечивает им надежное будущее в судостроении и во многих других отраслях промышленности.
Кислородно-пропановые горелки обычно используются для резки металлолома, чтобы сэкономить деньги, так как сжиженный нефтяной газ намного дешевле джоуля на джоуль, чем ацетилен, хотя пропан не дает очень аккуратного профиля резки ацетилена. Пропан также находит применение в производстве для резки очень больших профилей.
Безопасность
Оксиацетиленовая сварка/резка не сложна, но есть много тонких моментов, которые следует изучить, таких как
- Не следует использовать более 1/7 вместимости баллона в час.
- Ацетилен опасен при давлении выше 15 psi.
- Необходимо всегда носить надлежащую защиту.
Утечка топлива
Топливные газы тяжелее воздуха (такие как пропан, пропилен, MAPP и бутан) могут скапливаться в низинах, если им позволено выходить, поэтому следует соблюдать особую осторожность, чтобы не использовать эти газы в местах, где они могут скапливаться (например, над подвалы, раковины, ливневые стоки и др.).
Безопасность с цилиндрами
При использовании топливных и кислородных баллонов они должны быть надежно закреплены в вертикальном положении на стене, стойке или переносной тележке. Кислородный баллон особенно опасен по той причине, что кислород в наполненном состоянии находится под давлением 21 МПа (3000 фунтов силы/кв. стать чрезвычайно смертоносной летающей ракетой, приводимой в движение сжатым кислородом. По этой причине никогда не перемещайте кислородный баллон без завинченной крышки клапана.
В системе кислородно-ацетиленовой горелки будет три типа клапанов: клапан резервуара, регулирующий клапан и клапан горелки. Для каждого газа будет по одному. Газ в баллонах или баллонах находится под высоким давлением. Кислородные баллоны обычно наполняют примерно до 2200 фунтов на квадратный дюйм. Регулятор преобразует газ высокого давления в поток низкого давления, пригодный для сварки. Никогда не пытайтесь напрямую использовать газ под высоким давлением.
См. также
- Водяная горелка Уильям Август Тилден. Химические открытия и изобретения в двадцатом веке . Adamant Media Corporation, 80. ISBN 05434 .
- Современная сварка от Althouse, Turnquist и Bowditch. Компания Гудхарт-Уиллкокс, 1970 г.
- Энциклопедия сварки , Инженер по сварке, девятое изд. 1938 г.
- Не следует использовать более 1/7 емкости баллона в час . Это приводит к тому, что ацетон внутри ацетиленового баллона выходит из баллона и загрязняет шланг и, возможно, горелку.
- Ацетилен опасен при давлении выше 1 атм (15 фунтов на кв. дюйм). Он нестабилен и разлагается со взрывом.
- Надлежащая вентиляция при сварке поможет избежать сильного химического воздействия.
- Oxygen fitting
- Acetylene fitting
- Oxygen torch valve
- Acetylene torch valve
- Torch body
- Oxygen cutting lever
- Oxygen preheat valve
- Tip nut
- Slip-in tip
- Отверстие предварительного нагрева — нагревает металл до точки воспламенения (вишнево-красного цвета) приблизительно 1600 градусов по Фаренгейту
- Резкое отверстие — прибавляет окисленный металл
- Недостаточное давление ацетилена или кислорода
- Ослабленный режущий наконечник
- Грязный наконечник
- Перегрев режущего наконечника
- Плохое уплотнительное кольцо в корпусе горелки
- Пламя на мгновение возвращается обратно в наконечник
- Результат громкого щелчка или хлопка
- Пожар внутри факела
- Исчезновение пламени с последующим
- Закрыть
- Экскурсная единица
- Перезагрузку
- 1036
- Храните баллоны в хорошо проветриваемом месте, предпочтительно на открытом воздухе
- Место хранения должно находиться вдали от источников тепла, искр и пожароопасности
- Баллоны должны храниться в вертикальном положении и надежно закреплены
- Баллоны с кислородом следует хранить на расстоянии не менее 3 м от баллонов с топливным газом или отделять их 30-минутным огнестойким барьером
- Зона магазина должна быть обозначена как «Не курить».
- Баллоны очень тяжелые и должны быть всегда надежно закреплены
- Клапаны баллонов или кожухи клапанов никогда не должны ослабляться
- Проверить соответствие регулятора давлению в цилиндре
- При креплении регулятора к цилиндру стыки должны быть чистыми, герметик не должен использоваться
- Перед установкой регулятора необходимо выкрутить винт регулировки давления для предотвращения нерегулируемого поступления газа в систему при открытом клапане баллона
- При очистке резьбы цилиндра, подсоединении регулятора и продувке шлангов защищайте лицо и глаза, надев соответствующий головной щиток
- Используйте подходящий сварочный щиток с соответствующим фильтром для защиты глаз
- Носить негорючую одежду
- Убедитесь, что цилиндр не нагревается пламенем или блуждающими дугами от соседнего электрооборудования
- закрыть регулирующие клапаны нагнетательных трубок (сначала топливный газ)
- проверить герметичность форсунки
- проверить давление на регуляторах
- повторно зажгите горелку в соответствии с рекомендуемой процедурой
- закрыть кислородный клапан на горелке (во избежание внутреннего возгорания)
- закрыть ацетиленовый клапан на горелке
- закрыть клапаны баллонов или запорные клапаны точек подачи газа как для кислорода, так и для ацетилена
- закрыть выпускные отверстия регулируемых регуляторов давления, вывернув винты регулировки давления
- открыть оба клапана горелки, чтобы сбросить давление в оборудовании
- закрыть клапаны горелки
- проверить герметичность форсунок и давление на регуляторах
- повторно зажгите горелку в соответствии с рекомендуемой процедурой
- перекрыть подачу кислорода и топливного газа на вентилях баллонов или точках выхода газа (только если это может быть сделано безопасно)
- если нет риска получения травм, тушите пожар с помощью противопожарного оборудования первой помощи
- , если пожар невозможно потушить сразу, звоните в аварийно-спасательную службу .
- после того, как оборудование остынет, осмотрите оборудование и замените неисправные компоненты
- Регуляторы, установленные на баллонах, должны быть рассчитаны на используемый газ. Следует иметь в виду, что ацетиленовый регулятор нельзя использовать с водородом или угольным газом.
- Баллоны с кислородом и ацетиленом должны храниться раздельно и только в огнеупорных помещениях, лишенных горючих материалов. В случае пожара их можно легко снять.
- Необходимо соблюдать действующую или рекомендуемую цветовую кодировку для идентификации баллонов и принадлежностей. Например, кислород должен храниться в черных баллонах с синим шлангом, баллоны с ацетиленом темно-бордового цвета с красным шлангом (см. рис. 04), а другие горючие газы — в красных баллонах. Индийский стандарт IS 4379(1981): Идентификация содержимого промышленных газовых баллонов, рекомендации по цвету для различных баллонов, которым можно следовать.
- Руководство по предотвращению несчастных случаев: инженерия и технологии, 12-е издание, Чикаго, Национальный совет по безопасности, 2000 г.
- Американское общество сварщиков – Безопасность при сварке, резке и смежных процессах (ANSI Z49.1), Майами, AWS, 2012 г.
- Канадский центр охраны труда и техники безопасности – Газовая сварка и резка (Инфограмма безопасности – D01, D02, D03 и D04), Гамильтон, CCOHS.
- Канадский центр гигиены труда и техники безопасности – Воздействие сварочного дыма и газов на здоровье, Пол Сампара, Гамильтон, CCOHS, 1985.
- Энциклопедия охраны труда и техники безопасности — 2 тома. (Сварка и термическая резка, Линдон, Г.С.) Женева, Международное бюро труда, 1998 г.
- ЭСАБ – Меры предосторожности и безопасные методы дуговой сварки, резки и строжки (F-52-529), 2009 г.
- http://www.technologystudent.com/equip_flsh/acet1.html.
- https://en.wikipedia.org/wiki/Oxy-fuel_welding_and_cutting.
- Индия, Правила обращения с газовыми баллонами, 2005 г.
- Индия, Закон об охране окружающей среды, 1986 г. Аллахабад, Юридические публикации, 1992 г.
- Индия, Закон о фабриках, 1948 г. с поправкой 1987 г., Мумбаи, Агентство трудового права, 2011 г.
- Индия, Правила фабрик Махараштры, 1963 г. – Бомбей, Агентство трудового права, 1994 г.
- IS-1179:1967 – Технические требования к оборудованию для защиты глаз и лица во время сварки, Нью-Дели, Индийский институт стандартов, 1967 г.
- ИС-4379: 1981 — Идентификация содержимого промышленных газовых баллонов, рекомендации по цвету для различных баллонов, Нью-Дели, Индийский институт стандартов, 1981 г.
- IS-5983:1980 – Спецификация средств защиты глаз, Нью-Дели, Индийский институт стандартов, 1980 г.
- Клец, Тревор А. – Что пошло не так? 2-е изд., Хьюстан, Техас, Галф, 1986. .
- Мадан Мохан и Наир, Р.Р. – Средства индивидуальной защиты – нереспираторные (Публикация AICTE-CEP – 670), Бангалор, Всеиндийский совет по техническому образованию, 1997.
- Морган, W.K.C. и Ситон, А. – Профессиональные заболевания легких, 2-е изд.
, Торонто, В.Б. Сондерс, 1984.
- Наир, Р. Р. – Безопасное обращение со сжатыми газами, Обзор промышленной безопасности, март 2012 г.
- Наир, Р. Р. – Безопасная работа в замкнутых пространствах, Обзор промышленной безопасности, февраль 2013 г.
- Наир, Р. Р. и другие — Аудит безопасности, проведенный на различных заводах PAN India, Navi Mumbai, SHIB.
- Национальная ассоциация противопожарной защиты – Стандарт по предотвращению пожаров при сварке, резке и других огневых работах (NFPA-51B), Куинси, NFPA, 2014 г.
- Национальный институт гигиены труда – Безопасность и гигиена труда в области «Дуговая сварка и газовая резка» (издание: 78-138), Цинциннати, NIOSH, 1978.
- Справочник по безопасности и противопожарной защите, под редакцией Р. Виарагавана, 2-е издание, Мумбаи, безопасные технологии, 2009 г.
- Соединенное Королевство, Управление по охране труда и технике безопасности – электродуговая сварка (Серия безопасности на рабочем месте № 46), Лондон, HMSO.
Дальнейшее чтение
Резка — сварка — класс
Кислород — ацетиленовая резка/сварка (OAC) (OAW) Термины и определения
1. Воспоминание — Формарный факел (осторожность: это очень опасное состояние.) —Мгновенное вжигание пламени обратно в наконечник
3. Резка пламенем — Процесс, посредством которого железо или сталь нагревается до температуры, при которой он может быстро окислять с помощью высокой чистоты кислорода, протекающего под давлением через режущую факел
(примечание: при окисленном металле пламя предварительного нагревания поддерживает температуру, необходимую для сохранения процесс окисления, протекающий в узкой зоне по длине основного металла.)
4. Шлаковый ящик — Металлический контейнер со слоем воды или песка для сбора горячего шлака
5. Волочащая линия — Относится к ситуации, когда самая дальняя часть режущего потока отстает от потока — Участок, где металл был удален в виде оксида в процессе резки0567 (Примечание: кислород в сочетании с металлом, вызывающим оксиды.)
8. Окислительный -сопоставление кислорода с другим веществом
Пример: металл окисляется, когда металл разрезает
. сварка , кислородная сварка или газовая сварка в США) и газокислородная резка — это процессы, в которых для сварки и резки металлов используется топливный газ и кислород. Кислородно-ацетиленовая сварка была впервые разработана французскими инженерами в 1903. Чистый кислород вместо воздуха используется для повышения температуры пламени, чтобы обеспечить локальное плавление обрабатываемого материала.
ТЕМПЕСТЬ ТЕМПЕРГА ФЛАМЕ* F FUEL* F* C
Ацетилен 5589* 3087*
MAPP 5301* 2927*
Природный газ 4600* 2538*
Propane 4579* 2526*
Пропилен 5193* 2867*
Hydrogen 4820* 2660*
Оксид-топлив является одним из старейших сварных процессов, помимо сварки кузницы. Все еще используемый в промышленности, в последние десятилетия он менее широко использовался в промышленных приложениях, поскольку были приняты другие специально разработанные технологии. Он до сих пор широко используется для сварки труб и труб, а также ремонтных работ. Он также часто хорошо подходит и предпочтителен для изготовления некоторых видов произведений искусства на основе металла. Кроме того, газокислородная сварка имеет преимущество перед процессами электросварки и резки в ситуациях, когда доступ к электричеству (например, через удлинитель или портативный генератор) может вызвать трудности; он более автономен и, следовательно, часто более портативный.
В газокислородной сварке для сварки металлов используется сварочная горелка. Сварка металла происходит, когда две детали нагреваются до температуры, при которой образуется общая ванна расплавленного металла. Ванна расплава обычно снабжается дополнительным металлом, называемым наполнителем. Присадочный материал зависит от свариваемых металлов.
При газокислородной резке горелка используется для нагрева металла до температуры воспламенения. Затем поток кислорода направляется на металл, сжигая его до оксида металла, который вытекает из пропила в виде шлака.
Безопасность
Сварка/резка кислородно-ацетиленовым электродом не сложна, но есть много тонкостей безопасности, которые следует изучить, например:
Газокислородная сварка
станция | Защитные очки для газовой сварки/резки и защитная каска/сварочный колпачок |
Важность защиты глаз
Необходимо постоянно носить соответствующие средства защиты, такие как сварочные очки, в том числе для защиты глаз от яркого света и летящих искр. Необходимо использовать специальные защитные очки — как для защиты сварщика, так и для обеспечения четкого обзора сквозь желто-оранжевые блики, испускаемые раскаленным флюсом.
Утечка топлива
Топливные газы, плотность которых превышает плотность воздуха (пропан, пропилен, MAPP, бутан и т. д.), могут скапливаться в низких местах, если дать им возможность выйти. Во избежание опасности воспламенения следует соблюдать особую осторожность при использовании этих газов в таких местах, как подвалы, раковины, ливневые стоки и т. д. Кроме того, протекающие фитинги могут загореться во время использования и представлять опасность для персонала и имущества.
Безопасность с баллонами
При использовании топливных и кислородных баллонов они должны быть надежно закреплены в вертикальном положении на стене, стойке или переносной тележке. В системе кислородно-ацетиленовой горелки будет три типа клапанов: клапан резервуара, регулирующий клапан и клапан горелки. Для каждого газа будет комплект из этих трех клапанов. Кислородный баллон особенно опасен по той причине, что кислородные баллоны обычно заполнены примерно до 2200 фунтов на квадратный дюйм. Регулятор преобразует газ высокого давления в поток низкого давления, пригодный для сварки, и если бак упадет, а его клапан ударится обо что-нибудь и сломается, бак фактически превратится в чрезвычайно смертоносную летающую ракету, приводимую в движение сжатым кислородом, способную даже пробить кирпичную стену. По этой причине никогда не перемещайте кислородный баллон без завинченной крышки клапана.
Химическое воздействие
Менее очевидной опасностью сварки является воздействие вредных химических веществ. Воздействие некоторых металлов, оксидов металлов или угарного газа часто может привести к серьезным заболеваниям. Вредные химикаты могут быть получены из топлива, из заготовки или из защитного покрытия на заготовке. Увеличивая вентиляцию места сварки, сварщики сводят к минимуму воздействие вредных химических веществ из любого источника.
А. Cutting torch
B. Режущий наконечник
(Примечание. Выбор Правильный наконечник для работы определяется толщиной металла , размер кончиков и окисленные резки давления . рекомендации производителя.)
Причины плохого резания:
Причины обратной вспышки
)
Результат обратного выстрела
a. Пламя может погаснуть
b. Пламя может продолжать гореть обычным образом
Результаты воспоминаний
a. Визг или шипение внутри резака
b. Искры от горелки
c. Дым, поступающий из Torch
Шаги, которые следует выполнить в случае воспоминания
Ресурсы: задание:
|
|
ОСНОВНЫЕ ТЕРМИНЫ 0567 Агрочная режущая газовая плазменная дуга Ресурсы: Задания:
дуговая плазма джоулс плазменная дуга вытаскивает
чашка стека Керф. 0567 Electrode STACK SOLBACE Изолятор воды вода кожух
Электродная наконечник наконечника Накрытие Вода Таблица
Плотная зона.
Download File Plasma Cutting Tips
Intro to Plasma Cam |
CARBON ARC CUTTING (CAC)
Ключевые термины https://quizlet.com/join/ffxxpdtfq
0567 Синхронизированная графитовая синхронизированная форма волны воздушной углеродной дуги (CAC-A).0567 Экзотермические газы Монохроматические
Газовый лазерный кислород, копчатая резка
Ресурсы: назначения:
Загрузить файл
Оксицетилен Сварка, резка и нагревание
Руководства для обеспечения для здоровья и обеспечения для обеспечения для здоровья. безопасные методы сварки.
Нажмите здесь, чтобы посмотреть наши последние технические подкасты на YouTube .
Оксиацетиленовый процесс
Оксиацетиленовый процесс дает высокотемпературное пламя, превышающее 3000 градусов C, за счет сжигания чистого кислорода и ацетилена. Это единственная газовая смесь, достаточно горячая, чтобы расплавить сталь; другие газы (пропан, сжиженный нефтяной газ или водород) могут использоваться для цветных металлов с более низкой температурой плавления, для пайки твердым припоем и серебряным припоем, а также в качестве газа для предварительного нагрева/прошивки при резке.
Безопасное хранение
Газы обычно подаются под высоким давлением в стальных баллонах; в Великобритании цветовая кодировка баллонов находится в процессе согласования по всей Европе. Для ацетилена плечо баллона темно-бордовое, а для кислорода плечо белое, хотя черные кислородные баллоны еще какое-то время будут оставаться в обращении. Баллон также должен иметь этикетку с указанием типа газа. Для предотвращения перестановки фитингов между баллонами, содержащими горючие и негорючие газы, кислородные баллоны имеют правую, а ацетиленовые — левую резьбу. Все цилиндры открываются поворотом ключа или ручки против часовой стрелки и закрываются поворотом их по часовой стрелке.
Кислород вызовет более сильное пламя, а смесь кислорода и горючего газа может вызвать взрыв. Поэтому важно, чтобы кислородные баллоны были отделены от баллонов с топливным газом и хранились в месте, свободном от горючих материалов.
Безопасность и предотвращение несчастных случаев
Работа со сжатыми газами
Баллоны оснащены регуляторами для снижения давления газа в баллоне до рабочего давления горелки. Регулятор имеет два манометра: манометр высокого давления для газа в цилиндре и манометр низкого давления для газа, подаваемого на горелку. Расход газа регулируется винтом регулировки давления, который устанавливает давление газа на выходе. Кодекс практики BCGA CP7 рекомендует ежегодно проверять датчики и заменять их каждые 5 лет.
Необходимо учитывать следующие факторы: газовая система соответствует номинальному давлению и шланги подсоединены без утечек. Перед ввинчиванием регулятора необходимо очистить резьбу клапана. Клапан ацетиленового баллона можно слегка приоткрыть, чтобы продуть резьбу, но резьбу кислородного баллона лучше всего чистить чистым сжатым воздухом (резьбу водородного баллона всегда следует продувать сжатым воздухом).
Поскольку кислород может бурно реагировать с маслами и смазками, нельзя использовать смазочные масла или герметик для резьбы.
Безопасность и предотвращение несчастных случаев
Использование сжатых газов
Газы смешиваются в ручной горелке или паяльной трубке в правильных пропорциях. Шланги между регулятором и горелкой должны иметь цветовую маркировку; в Великобритании красный для ацетилена и синий для кислорода. Шланги должны быть как можно короче, и пользователи должны периодически проверять, не находятся ли они рядом с горячими или острыми предметами, которые могут повредить стенку шланга. Баллоны с ацетиленом всегда должны использоваться в вертикальном положении.
При подсоединении системы и, по крайней мере, в начале каждой смены шланги и горелку необходимо продуть для удаления горючих газовых смесей. Очень важно, чтобы поток кислорода не вступал в контакт с маслом, которое может самовозгораться. Продувку также нельзя проводить в закрытых помещениях.
Факел следует зажигать фрикционной зажигалкой или стационарным пилотным пламенем, чтобы не обжечь руки; нельзя использовать спички и нельзя повторно зажигать пламя от горячего металла, особенно при работе в замкнутом пространстве.
Цилиндры не должны нагреваться, например, при локальном нагреве стенок цилиндра пламенем горелки. Точно так же дуговая сварка слишком близко к цилиндру может привести к образованию дуги между цилиндром и заготовкой/электродом.
Несмотря на то, что излучается очень мало ультрафиолета, сварщик должен носить затемненные очки. Качество фильтра определяется интенсивностью пламени, которая зависит от толщины свариваемого металла; рекомендации для фильтров по расходу ацетилена приведены в таблице (BSEN 169:1992).
Марка фильтра, рекомендуемая по расходу ацетилена:
Рабочий | расход ацетилена в л/ч | |||
---|---|---|---|---|
до 70 | 70 — 200 | 200 — 800 | свыше 800 | |
Сварка и пайка тяжелых металлов, в т.ч. стали, меди и их сплавов | 4 | 5 | 6 | 7 |
Сварка с эмиссионными флюсами (особенно легких сплавов) | 4а | 5а | 6а | 7а |
Техника безопасности и предотвращение несчастных случаев
Обнаружение утечек
Соединения и шланги должны быть проверены на наличие утечек, прежде чем приступать к сварке. В то время как ацетилен можно определить по характерному запаху (обычно при содержании менее 2%), кислород не имеет запаха.
Обнаружение утечек лучше всего проводить с помощью слабого (обычно 0,5%) раствора моющего средства в воде или раствора для обнаружения утечек от одной из газоснабжающих компаний. Его наносят на швы с помощью кисти, и выходящий газ образует пузырьки. После устранения течи область следует очистить, чтобы удалить остатки раствора для обнаружения утечек. Утечки в шлангах могут быть устранены, но должны использоваться утвержденные сменные шланги и муфты в соответствии с BSEN 560:1995 и BSEN 1256:19.96.
Обратный огонь и воспоминание
Обратный огонь (одиночный треск или «хлопок») возникает, когда пламя воспламеняет газы внутри сопла и гаснет. Это может произойти, если резак находится слишком близко к заготовке.
Воспоминание (пронзительный шипящий звук), когда пламя горит внутри факела, более серьезное. Пламя может проходить обратно через смесительную камеру горелки в шланг. Наиболее вероятной причиной является неправильное давление газа, что приводит к слишком низкой скорости газа. В качестве альтернативы ситуация может быть создана за счет подачи газа с более высоким давлением (ацетилена) в поток газа с более низким давлением (кислород). Это может произойти, если кислородный баллон почти пуст, но другими возможными причинами могут быть протечки шлангов, ослабление соединений или неспособность должным образом продуть шланги.
Обратные клапаны, установленные на шлангах, обнаруживают и останавливают обратный поток газа, предотвращая образование горючей смеси кислорода и ацетилена в шланге. Пламегаситель представляет собой автоматический пламегаситель, предназначенный не только для гашения пламени, но и для предотвращения попадания пламени в регулятор.
Процедура обратного воспламенения или воспламенения
После непродолжительного обратного возгорания, при котором пламя погасло:
Если пламя продолжает гореть:
В случае обратного возгорания в шланге и оборудовании или пожара в шланге, соединениях регулятора или точках выхода газа:

После расследования обратного пламени и устранения неисправности фонарь можно снова зажечь. После вспышки, поскольку пламя распространилось на регулятор, важно не только осмотреть горелку, но и проверить шланги и компоненты и, при необходимости, заменить их. Пламегаситель также следует проверить в соответствии с инструкциями производителя, и в некоторых конструкциях может потребоваться его замена. Кодекс практики BCGA CP7 рекомендует заменять обратные клапаны и пламегасители каждые 5 лет.
Информация была подготовлена в сотрудничестве с Роджером Сайксом, руководителем отдела здравоохранения и безопасности, Ньюкасл-апон-Тайн.
Эта статья о вакансиях была первоначально опубликована в журнале Connect в мае 1997 г. Она была обновлена, поэтому веб-страница больше не отражает точно печатную версию.
Опасности при сварке и резке | ОБЗОР ПРОМЫШЛЕННОЙ ОХРАНЫ И БЕЗОПАСНОСТИ | Журнал «Пожарная промышленность» | Журнал безопасности Индия | Журнал безопасности Индия | Журнал безопасности жизнедеятельности
Воздействие сварочного дыма и газов следует максимально контролировать, соблюдая меры безопасности и надлежащие меры гигиены труда. Желательно носить соответствующие средства индивидуальной защиты. Подходящие средства пожаротушения также должны быть размещены рядом с местом, где выполняются операции по сварке и резке. – R. R. Nair
1.0 ВВЕДЕНИЕ
Сварка, резка и аналогичные операции выполняются в самых разных местах и в самых разных условиях. Эти операции проводятся на заводах, строительных площадках, карьерах, чанах, рудниках, резервуарах, судовых отсеках и буквально везде, где происходит соединение или резка металлов. Это основной промышленный процесс, в котором для соединения металлов используется тепло и/или давление. Среди различных способов сварки наибольшее распространение получила дуговая сварка. Несчастные случаи, происходящие в процессе сварки, очень типичны и связаны с многочисленными травмами. Горячий металлический шлак и брызги часто могут быть опасны для оператора и окружающей среды. Многие процессы сварки, резки и сходные с ними процессы производят дым и газы, которые могут быть вредны для здоровья рабочих. В замкнутых пространствах газы могут вытеснять воздух для дыхания и вызывать удушье. Избыточный шум представляет собой известную опасность для здоровья при сварке, резке и подобных операциях. Дуговая сварка испускает вредные лучи, такие как ультрафиолетовые лучи, инфракрасные лучи и пары, которые могут вызвать неприятные ощущения.
Эта статья посвящена некоторым опасностям, связанным с операциями сварки и резки, и мерам предосторожности, которые необходимо предпринять для их снижения. Прежде чем мы обсудим различные опасности, связанные с операциями сварки и резки, будет полезно кратко обсудить некоторые популярные методы, применяемые при операциях сварки и резки.
2.0 МЕТОДЫ СВАРКИ
Методы сварки можно разделить в основном на две группы, а именно: (i) кислородно-ацетиленовая сварка и (ii) дуговая сварка, которые кратко рассматриваются ниже.
2.1 Сварка в кислородно-ацетиленовой среде
Сварка в кислородно-ацетиленовой среде является очень распространенным сварочным процессом. Сочетание кислорода и ацетилена обеспечивает температуру пламени более 3100°C, что делает его идеальным для сварки и резки. Кислородно-ацетиленовая сварка также известна как кислородно-топливная сварка или кислородная сварка или газовая сварка и кислородная резка, при которой для сварки и резки металлов используются топливные газы и кислород. В последние десятилетия кислородно-ацетилен менее широко использовался в промышленных операциях, поскольку были приняты другие специально разработанные технологии. Однако он широко используется для сварки труб и труб, а также ремонтных работ. Он также часто хорошо подходит и предпочтителен для изготовления некоторых видов произведений искусства на основе металла. Следует иметь в виду, что кислородно-ацетиленовая сварка имеет преимущество перед электросваркой и процессами резки в ситуациях, когда доступ к электричеству может быть затруднен.
При кислородно-ацетиленовой сварке пламя, создаваемое комбинацией газов, плавит металлические поверхности соединяемых деталей, заставляя их течь вместе. Обычно добавляют присадочный металлический сплав, который иногда используется для предотвращения окисления и облегчения соединения металлов.
Аппарат, используемый при газовой сварке, состоит в основном из источника кислорода и источника топливного газа (обычно баллоны), двух регуляторов давления и двух гибких шлангов (по одному на каждый баллон) и горелки (см. рис. 01 и 02). . Обычно сварочный наконечник крепится на конце рукоятки горелки, и через него проходит горюче-газовая смесь, питающая пламя. Сварочные наконечники имеют только одно отверстие, в то время как режущие наконечники имеют центральное отверстие с несколькими меньшими отверстиями, расположенными вокруг него по кругу. Во время резки кислород поступает из центрального отверстия, а пламя предварительного нагрева исходит из отверстий вокруг центрального отверстия. В настоящее время доступны горелки различных конструкций, включающие множество предохранительных устройств (см. рис. 03).
Баллоны с кислородом
Газообразный кислород обычно сжимают в баллонах. Полный баллон обычно содержит кислород под давлением 139,2 кг/см2. Кислород бесцветен и не имеет запаха. Он поддерживает и способствует горению, но не воспламеняется. Для идентификации кислородные баллоны окрашены в черный цвет.
Ацетиленовые баллоны
Ацетилен – это горючий газ, обычно используемый для сварки и резки. Он образуется в результате химической реакции между водой и карбидом кальция. Это легковоспламеняющийся газ, взрывоопасный при смешивании с воздухом или кислородом в пропорции от 2% до 82%. Ацетилен легко определить по его характерному резкому запаху. Баллоны с ацетиленом окрашены в темно-бордовый цвет для идентификации. При смешивании ацетилена с кислородом из баллона в соотношении один к одному при воспламенении смеси газов на сопле дутьевой трубы получается пламя, имеющее температуру примерно 3140°С.
Баллоны с ацетиленом заправлены давлением 17,57 кг/м2. В основании баллона и на клапане баллона установлено предохранительное устройство с разрывной мембраной для защиты от чрезмерного повышения давления внутри баллона. Следует иметь в виду, что пользователь ни при каких обстоятельствах не должен вмешиваться в эти фитинги. Никогда не используйте медную трубу для соединения, потому что медь при контакте с ацетиленом может образовать опасно взрывоопасное соединение ацетиленида меди.
2.2 Дуговая сварка
В области дуговой сварки наблюдается огромный рост. Точечная сварка сопротивлением является одним из старейших процессов электросварки, используемых сегодня в промышленности. Сварка производится комбинацией тепла, давления и времени. При дуговой сварке дуга зажигается между электродом и деталями, подключенными к источнику переменного или постоянного тока. Температура составляет около 4000°С, когда заготовки сплавляются друг с другом. Обычно в соединение добавляют расплавленный металл либо путем расплавления самого электрода, либо путем расплавления отдельного присадочного стержня, не проводящего ток.
Обычная дуговая сварка выполняется вручную с помощью плавящегося электрода с покрытием или с покрытием, который удерживается вручную в электрододержателе. Тем не менее, многие полностью автоматические электронные процессы сварки также используются в промышленности. Дуговая сварка использует непрерывный электрический разряд (электрическую дугу) для создания высокой температуры от 3000°С до 30000°С. Электрическая дуга поддерживается в зазоре между электрическими проводниками, т.е. электродом и заготовкой. Дугу можно поддерживать и перемещать, чтобы расплавить часть заготовки и заполнить присадочным металлом по мере необходимости для формирования сварного шва.
Сварочные дымы и газы образуются в процессе сварки как побочные продукты в виде сварочного шлейфа. Тепловое и ультрафиолетовое излучение сварочной дуги также приводит к образованию потенциально вредных газов в окружающем воздухе. Сварщики и другие рабочие поблизости подвергаются воздействию всех этих веществ.
Подсчитано, что около 80% всей сварки приходится на три основных метода дуговой сварки, а именно: (i) Дуговая сварка металлическим электродом с защитой (ii) Сварка металла в среде инертного газа и (iii) Сварка вольфрамовым электродом в среде инертного газа. Эти методы используются для сварки четырех основных типов металлов, а именно:
(i) Мягкая сталь (ii) Нержавеющая сталь и высоколегированная сталь и (iii) Алюминий и оцинкованная сталь.
Дуговая сварка в среде защитного газа
Дуговая сварка в среде защитного металла (SMAW) является наиболее распространенным процессом дуговой сварки. Она также известна как ручная дуговая сварка металлом. В нем используется короткий расходуемый электрод, который плавится при поддержании дуги. Металл с характеристиками, аналогичными свариваемому металлу, расплавляется с электрода и проходит через дугу, становясь присадочным металлом сварного шва. Электрод подается в дугу по мере плавления, чтобы поддерживать постоянную длину дуги. Электрод покрыт сложной смесью химических соединений, которые выполняют важные функции в процессе сварки. Основная роль покрытия заключается в высвобождении защитного слоя инертного газа, такого как углекислый газ, для предотвращения попадания воздуха в зону дуги и предотвращения окисления и загрязнения во время сварки. Состав покрытий зависит от свариваемого металла.
Сварка металлов в среде инертного газа
Сварка металлов в среде инертного газа (MIG) использует расходуемую проволоку без покрытия, которая непрерывно подается по центру сварочной горелки. Кольцевая трубка вокруг проволоки транспортирует инертный газ, такой как аргон, гелий или углекислый газ, из внешнего источника в зону дуги, чтобы предотвратить окисление сварного шва. Дуговая сварка флюсовой проволокой (FCAW) представляет собой разновидность сварки MIG. В этом процессе используется полая расходуемая проволока, сердцевина которой содержит различные химические вещества, выделяющие защитные газы и укрепляющие сварной шов.
Сварка вольфрамовым электродом в среде инертного газа
Сварка вольфрамовым электродом в среде инертного газа (TIG) использует неплавящийся вольфрамовый электрод, который поддерживает дугу и обеспечивает достаточное количество тепла для соединения металлов. Если необходим присадочный металл, его добавляют в виде стержня, удерживаемого близко к дуге, чтобы он расплавился и осадился на сварном шве. Защитные газы, подаваемые извне, могут использоваться или не использоваться в TIG, в зависимости от свариваемого металла.
3.0 ОПАСНОСТИ ПРИ СВАРКЕ
Опасности, связанные с операциями сварки и резки, можно разделить на две группы, а именно: (i) опасности пожара и взрыва и (ii) опасности для здоровья, которые рассматриваются ниже:
3.1 Опасность пожара и взрыва
Сварка, резка и аналогичные процессы приводят к образованию расплавленного металла, искр, шлака и горячих рабочих поверхностей. Несоблюдение мер предосторожности может привести к пожару или взрыву. Во время работы летят искры и брызги. Разлетающиеся искры являются основной причиной пожаров и взрывов при сварке и резке. Искры и расплавленный металл могут преодолевать большие расстояния при падении. Следует иметь в виду, что искры могут распространяться на расстояние до 36 футов от рабочей зоны. Искры могут даже проходить сквозь щели, отверстия для труб и другие небольшие отверстия в полах, стенах или перегородках, а также крышах или застревать в них, что приводит к контакту с горючими материалами. К горючим материалам на рабочем месте или в зданиях относятся: дерево, бумага, тряпки, одежда, пластик, химические вещества, легковоспламеняющиеся жидкости, газы и пыль. Части рабочих мест или зданий, такие как полы, перегородки и крыши, также могут быть горючими. Типичные горючие материалы вне рабочих мест или зданий включают сухие листья, сухой газ и кусты.
3.1.1 Общие меры предосторожности
Хотя при обычной дуговой сварке используется ток низкого напряжения, сварочные токи являются высокими из-за использования оборудования, работающего от сетевого напряжения. Нельзя игнорировать риск поражения электрическим током, особенно в тесных помещениях или в страховочных положениях. Поэтому перед началом сварки всегда следует проверять заземление на оборудовании для дуговой сварки. Кабели и соединения должны быть прочными и иметь достаточную мощность. Всегда следует использовать надлежащий заземляющий зажим или клемму с болтовым креплением. Если два или более сварочных аппарата заземлены к одной и той же конструкции или используются другие переносные электроинструменты, заземление должно контролироваться компетентным лицом.
Рабочее место или место, используемое для сварки и резки, должно быть сухим, безопасным и свободным от опасных препятствий. Большое значение имеет благоустроенное, хорошо освещенное, должным образом проветриваемое и чистое рабочее место. Если работа выполняется в ограниченном пространстве или в опасных местах, в сварочном контуре может быть установлена дополнительная электрическая защита, обеспечивающая подачу на электрододержатель тока только крайне низкого напряжения, когда сварка не ведется.
Зажимы и соединения электрододержателей следует периодически очищать и подтягивать во избежание перегрева. Следует также предусмотреть безопасное крепление держателя электрода, когда он не используется, с помощью изолированного крючка или следует использовать полностью изолированный держатель. Для всех подводов от трансформатора к электрододержателю следует использовать пластиковые трубы и кабели с ПВХ-покрытием.
Следует избегать протаскивания кабеля и пластиковых труб подачи газа по нагревательным плитам или сварным швам. Тяжелые предметы, оставленные горячими после завершения сварки, всегда должны быть помечены как «горячие» в качестве предупреждения для других рабочих. Резиновые трубки и кабели с резиновым покрытием нельзя использовать вблизи источников высокочастотного разряда, так как образующийся озон вызывает гниение резины.
Грязь и металлическая пыль могут привести к выходу из строя блока высокочастотного разряда, который необходимо регулярно очищать, продувая сжатым воздухом.
В установках для газовой сварки высокого давления как кислород, так и горючие газы, такие как ацетилен, водород, пропан, подаваемые в горелку, получают из баллонов, в которых они хранятся под высоким давлением. Опасности и многочисленные меры предосторожности, необходимые при использовании баллонов со сжатым газом, подробно описаны в Индийских правилах обращения с газовыми баллонами 2005 года. Сварщикам и контролерам рекомендуется следовать этим положениям. Кроме того, при газовой сварке и связанных с ней операциях необходимо строго соблюдать следующие меры предосторожности:
3.1.2 Обратные вспышки и вспышки
Обратные вспышки и вспышки являются наиболее распространенными опасностями при сварке и резке. Обратный огонь возникает в самой горелке и достигает только наконечника горелки для сварки или резки и никогда не выходит за пределы горелки. Однако самым опасным видом является вспышка, и в этом случае пламя явно достигает источника подачи топливного газа через резак и шланги. Пламя возвращается обратно в смесительную камеру или даже за ее пределы и может распространяться по шлангам.
Здесь можно отметить, что если возникает обратная вспышка и если горелка не выключается немедленно, и если условия, вызвавшие встречную вспышку, не устраняются, возникает обратная вспышка. В случае воспоминаний действие пламени имеет взрывную силу. Воспламенение может произойти как в кислородном шланге, так и в ацетиленовом шланге.
При проведении кислородно-газовой резки и сварки операторы могут столкнуться с обратным или обратным воспламенением. Обратные клапаны и пламегасители являются одними из предохранительных устройств, используемых для защиты рабочих, участвующих в кислородно-топливной резке и смежных операциях. Обратный клапан — это устройство, предназначенное для предотвращения непреднамеренного обратного потока газов. Пламегаситель (пламегаситель) — это устройство, препятствующее распространению пламени вверх по потоку. Обратите внимание, что эти устройства уменьшают объем газов, доступных на наконечнике / сопле, что, в свою очередь, предотвращает потенциальные обратные вспышки и вспышки. Типичные обратные клапаны и пламегасители показаны на рис. 3.
3.1.3 Противопожарная безопасность
Поскольку вероятность возгорания во время газовой сварки очень высока, следует обратить внимание на окружающие стены, полы, близлежащие предметы или отходы. Все горючие материалы должны быть удалены или должным образом защищены листовым металлом. Следует иметь в виду, что брезент никогда не следует использовать для защиты горючих материалов. Следует избегать или защищать деревянные конструкции. Если сварочные работы проводятся на деревянном полу, его следует тщательно накрыть или смочить. Если легковоспламеняющиеся материалы хранятся в соседних помещениях или на полу ниже рабочей зоны, их следует убрать в безопасное место. Рабочее место и прилегающая территория должны быть свободны от всего, что может загореться от сварочных аппаратов, содержащих легковоспламеняющиеся вещества. Сплавы, богатые магнием или другими горючими металлами, следует держать вдали от сварочного пламени.
При наличии пожароопасности ответственное лицо должно держать место сварки под наблюдением не менее часа после окончания работ. Поскольку многие металлы, одежда и другие материалы становятся активно горючими в присутствии кислорода, кислород для газовой сварки никогда не должен выбрасываться в воздух в замкнутом пространстве. Операции газовой резки нельзя проводить в замкнутом пространстве без надлежащей вентиляции.
Подходящие средства пожаротушения всегда должны быть под рукой. В случае установки низкого давления, использующей ацетиленовый генератор, необходимо иметь в наличии пожарные ведра с сухим песком. Для предотвращения пожара можно использовать огнетушители сухого порошка или двуокиси углерода. Ни в коем случае нельзя использовать воду для предотвращения пожара.
3.1.4 Предотвращение взрыва
Вероятность взрыва во время газовой сварки высока. Взрывы могут произойти, когда газообразный ацетилен присутствует в воздухе в любой пропорции от 2% до 80%. Таким образом, при использовании баллонов с ацетиленом для газовой сварки необходимо обеспечить достаточную вентиляцию. Сварка и резка могут привести к взрыву в помещениях, содержащих легковоспламеняющиеся газы, пары, жидкости или пыль.
Все операции дуговой сварки должны быть экранированы, чтобы защитить других людей, работающих поблизости. Если работа выполняется на стационарных столах или в сварочных цехах, по возможности должны быть установлены постоянные экраны, в противном случае следует использовать временные экраны. Экраны должны быть непрозрачными, прочной конструкции и из огнеупорного материала.
Использование черных красок внутри сварочных камер стало общепринятой процедурой, но используемая краска должна давать матовую поверхность. Должно быть обеспечено достаточное окружающее освещение, чтобы предотвратить напряжение глаз, ведущее к головным болям. Сварочные кабины и переносные экраны следует регулярно проверять, чтобы убедиться, что они обеспечивают достаточную защиту работающих поблизости людей.
Меры предосторожности, которые необходимо соблюдать при дуговой резке, существенно не отличаются от тех, которые требуются при дуговой сварке. Однако, поскольку используемые токи, как правило, выше, обычно требуется более тяжелая защитная одежда. При использовании метода резки угольной дугой лучше использовать хороший шлем, а не ручной щиток. Следует надеть гетры из кожи или асбеста, чтобы защитить ноги от падения расплавленного металла.
3.2 Опасность для здоровья
Флюсы, содержащие фториды, часто используются при серебряной пайке и сварке алюминия, магния и сплавов. Фтористый водород, если его производить в достаточной концентрации, будет раздражать и наносить вред сварщикам. Некоторые серебряные припои могут содержать кадмий. Материалы, покрытые токсичными материалами, такими как свинец, кадмий, могут оказывать вредное воздействие при сварке любым способом. Коричневые пары кадмия чрезвычайно опасны, вызывая серьезные и смертельные повреждения легких при кратковременном воздействии. Лихорадка от паров металлов может возникнуть в результате воздействия паров цинка в результате операций на оцинкованных материалах, латуни или бронзе, а иногда и в результате использования бронзового наполнителя. Сварка цистерн и контейнеров любого типа, из которых не было тщательно удалено содержимое, может создать ряд опасностей вследствие улетучивания или разложения остатков.
3.2.1 Тепло и ожоги
Ожоги глаз и открытых частей тела могут возникнуть из-за разбрызгивания раскаленных металлических частиц. Интенсивное излучение пламени и раскаленного металла в сварочной ванне может вызвать дискомфорт у оператора и человека, находящегося вблизи места проведения операции, поэтому необходимы меры предосторожности. Чрезмерное воздействие ультрафиолетового излучения также может вызвать перегрев и ожог кожи и лица, затылка и других открытых частей тела, которые должны быть соответствующим образом защищены. Высокочастотная искра, используемая для индикации дуги, может вызвать небольшие глубокие ожоги, сконцентрированные в точке на коже. Ожоги из-за контакта с горячими материалами также могут быть устойчивыми, как правило, из-за отсутствия ухода или неиспользования надлежащей защитной одежды, очищенной от масла и жира. Рабочее место должно быть чистым и не загроможденным горючими материалами. Руки и предплечья должны быть защищены подходящими перчатками или рукавами. При потолочной сварке необходимы защитный плащ и колпак.
3.2.2 Травмы глаз
Существует два типа излучений, а именно:
(i) ионизирующее (например, рентгеновское) и (ii) неионизирующее (например, ультрафиолетовое, видимое или инфракрасное) ). Неионизирующие излучения связаны со сварочными работами.
При сварке и резке сильное излучение испускается нагретыми твердыми телами или газами. Сильные ультрафиолетовые лучи способны вызывать сильные воспаления, похожие на солнечные ожоги, в глазах и на открытых участках кожи. Чрезвычайно интенсивные видимые лучи могут вызвать напряжение глаз или даже временную слепоту. Инфракрасные лучи не поглощаются, но проникают в глаз. Предполагается, что они являются причиной катаракты, травм сетчатки, а также помутнения роговицы. Поскольку интенсивность этих излучений зависит от температуры источника сварки. Опасность от дуговой сварки больше, чем от газовой сварки или резки.
Свет, излучаемый электродной дугой, содержит высокую долю ультрафиолетового излучения. Большинство процессов дуговой сварки и резки; лазерная сварка и газовая сварка; резка и пайка; или пайка производят дозы радиации, требующие мер предосторожности. Некоторые процессы, такие как контактная сварка и сварка холодным давлением, обычно производят незначительное количество лучистой энергии.
Ультрафиолетовые и инфракрасные лучи
Ультрафиолетовые лучи следует опасаться не только потому, что они невидимы, но и потому, что у нас, людей, нет органов чувств, чтобы их обнаружить. При поглощении этих лучей хрусталик может флуоресцировать, т. е. светиться в темноте, что может нарушать зрение. Ультрафиолетовое излучение может воздействовать на глаза так же, как солнечный ожог. К этим лучам можно отнести обычное явление «дугового глаза».
Воздействие лучей в течение нескольких секунд может вызвать ощущение песка в глазах с болью, слезотечение и, возможно, головную боль, и эти симптомы могут развиться через четыре-восемь часов. Это известно как «дуговой глаз». Восстановление завершается через 24–48 часов, и не следует опасаться необратимых последствий. Все сварщики должны быть защищены от лучей, создаваемых сварочной дугой, с помощью соответствующего ручного щитка или защитных очков с цветными фильтрующими стеклами соответствующего класса (см. рис. 05).
Инфракрасные лучи обычно называют тепловыми лучами, потому что, когда они сталкиваются с каким-либо материалом, через который они не могут проникнуть, они поглощаются и превращаются в тепловые волны. Эти лучи производят ощущение тепла, когда они падают на кожу. Длительное воздействие на кожу приведет к солнечному ожогу. Медицинские власти считают, что более 90% этих излучений достигают сетчатки. Радужная оболочка может поглощать от 75% до 80% этого излучения. Следовательно, воздействие этих лучей на незащищенный глаз может быть серьезным – подобно солнечному ожогу глаз. Поэтому очень необходимо оберегать глаза от этого излучения.
3.2.3 Воздействие дыма и газов
Все операции по сварке и резке приводят к образованию определенного количества дыма и загрязнению атмосферы. Были случаи, когда сварщики, работающие внутри резервуаров, труб, туннелей или других ограниченных и плохо проветриваемых мест, теряли сознание. В некоторых из этих случаев причиной были признаны пары, тогда как истинной причиной была простая нехватка воздуха. По этой причине желательно предусмотреть средства для улавливания этих паров и улучшения вентиляции, особенно когда сварка происходит в таких замкнутых пространствах. Пары могут вызывать такие симптомы, как тошнота, головные боли, головокружение и лихорадка от паров металлов. Существует возможность более серьезных последствий для здоровья, когда речь идет о высокотоксичных материалах, таких как марганец, кадмий и т. д.
Количество и состав дыма и газов, выделяемых при сварке, резке и подобных процессах, зависят от состава присадочного металла и основного материала, процесса сварки, уровня тока, длины дуги и других факторов. При сварке некоторых металлов с покрытием или обработанных материалов могут образовываться опасные пары, поэтому требуется хорошая вентиляция или средства защиты органов дыхания. Особое внимание следует уделить также вентиляции при сварке цветных металлов и легированных сталей, а также защите от опасностей озона, угарного газа и фосгена, которые могут образовываться.
Сварочный дым
При всех сварочных процессах образуются дымы, но состав и концентрация дымов могут сильно различаться. Почти весь дым возникает из-за присадочного металла и покрытий, содержащихся в расходуемых электродах. Крупнейшим компонентом всех сварочных дымов является оксид железа. В зависимости от процесса сварки и свариваемого материала пары могут также содержать различные комбинации металлов, таких как алюминий; кадмий; хром; медь; фториды; привести; марганец; молибден; никель; банка; титан; ванадий; цинк и другие химические соединения. Медь, алюминий и другие металлы иногда сплавляют с бериллием, который является высокотоксичным металлом. Когда такой металл сваривается или режется, высокая концентрация токсичного бериллия может привести к одышке, хроническому кашлю, потере веса, усталости и общей слабости. Если свариваемый металл был окрашен или покрыт ингибиторами коррозии или ржавчины, эти покрытия могут разлагаться. Например, при сварке оцинкованной стали в дымовых газах образуется большое количество цинка или кадмия. Сварка окрашенных металлов может привести к высокому уровню паров свинца, если краска содержит свинец. Воздействие паров оксида цинка может привести к болезни, называемой «металлической лихорадкой», и в некоторых случаях может привести к летальному исходу. Наибольшую обеспокоенность по поводу потенциального воздействия сварки на здоровье вызывают кадмий, хром, оксид железа, никель и цинк.
Большинство сварочных дымов очень малы (менее одной тысячной миллиметра), поэтому их легко вдохнуть. При воздействии этих паров некоторые частицы дыма могут растворяться в легких и переноситься кровью или лимфатической системой в другие части тела, где они могут оказывать токсическое воздействие. Потенциальное воздействие сварочного дыма на здоровье зависит от общего количества вдыхаемого дыма и конкретных токсичных металлов или соединений, присутствующих в дыме. Дыхательная система человека имеет несколько способов удаления большей части осевших частиц за период от нескольких дней до многих месяцев. Исследователи обнаружили, что даже после продолжительной работы сварщиком в легких сварщиков редко можно обнаружить более нескольких граммов частиц сварочного дыма.
Сварочные газы
Газы, образующиеся при сварке незагрунтованных металлов, включают озон, оксиды азота, монооксид углерода и диоксид углерода. Озон и оксиды азота образуются под действием ультрафиолетового излучения сварочной дуги. Воздействие этих газов трудно контролировать, поскольку они образуются на расстоянии до нескольких метров от сварочной дуги. Сварка металла в среде инертного газа создает более высокий уровень ультрафиолетового излучения, чем дуговая сварка в среде защитного металла, что приводит к образованию большего количества озона и оксидов азота.
Углекислый газ и окись углерода, образующиеся при плавлении покрытий плавящихся электродов при высоких температурах сварочной дуги, могут представлять опасность для здоровья только в том случае, если сварка проводится в закрытых или закрытых помещениях с недостаточной вентиляцией. Точно так же, если дуговая сварка в среде защитного газа выполняется в закрытых помещениях с недостаточной вентиляцией, то защитные газы, такие как углекислый газ или аргон, могут вытеснять кислород из окружающего воздуха.
Типы выделяемых газов связаны с химическими веществами, содержащимися в покрытиях. Например, полиуретановые покрытия могут выделять большое количество формальдегида и толуолдиизоцианата, тогда как сварка металлов, покрытых эпоксидными смолами, может привести к воздействию цианистого водорода и угарного газа. Обезжиривающие растворители, такие как трихлорэтилен и перхлорэтилен, обычно используются для очистки металлов перед сваркой. Ультрафиолетовое излучение или тепло сварочной дуги разрушают эти соединения с образованием высокотоксичных газов, таких как фосген, фосфин, хлор или хлористый водород. Воздействие этих газов также может иметь место, если процесс обезжиривания проводится вблизи места сварки.
Было проведено несколько исследований, чтобы определить, может ли длительное воздействие сварочного дыма и газов вызывать заболевания легких, такие как бронхит, эмфизема и астма у сварщиков. Некоторые исследования показывают, что сварщики чаще страдают этими заболеваниями легких по сравнению с другими работниками или населением в целом. Однако другие исследования не обнаружили такого увеличения, если принять во внимание возраст, курение и воздействие других загрязняющих веществ, таких как асбест.
4.0 ЗАЩИТНОЕ ОБОРУДОВАНИЕ
Расплавленный металл имеет тенденцию лопаться и брызгать при воздействии тепла и реакции кислорода с перегретым металлом. При выбросе расплавленного металла или горячих частиц следует надевать кожаный фартук. При резке следует надевать кожаные гетры, чтобы предотвратить попадание горячих частиц в сапоги или обувь. Для защиты рук от тепловых брызг, шлака и т. д. достаточно перчаток типа рукавиц, за исключением ремонта крупных отливок, когда необходимо носить куртку из асбестовой ткани или фартук и нарукавную защиту из этого материала.
Защитные очки и/или лицевые щитки защищают глаза от искр и летящих частиц раскаленного металла. В очках или защитной маске используются специальные линзы для защиты глаз от повреждения светом. В зависимости от типа сварки или резки, типа материала и толщины материала используются различные линзы. Если защитная маска для глаз не используется, на поверхности глаза могут возникнуть болезненные ожоги, которые могут привести к необратимому повреждению. Линза, используемая для защиты глаз оператора, должна соответствовать определенным установленным стандартам. В связи с этим можно сослаться на IS-59.83: Спецификация средств защиты глаз и IS-1179: Спецификации оборудования для защиты глаз и лица во время сварки. Между прочим, Бюро индийских стандартов опубликовало серию индийских стандартов для сварки. Здесь следует отметить, что защитные крышки на стекле фильтра следует очищать по мере необходимости и заменять, если они поцарапаны или повреждены.
Сварка металлов, обработанных грунтовками, красками или другими защитными покрытиями, может быть потенциальным источником воздействия токсичных газов. При сварке металлов с покрытием или обработанных материалов следует надевать соответствующие средства защиты органов дыхания. Отсутствие защиты от ударов, ультрафиолетового, инфракрасного и синего света вызывало сильное напряжение глаз и повреждение глаз. Сегодня можно найти очень хорошую защиту для глаз, особенно для газовой сварки алюминия, которая полностью отсекает натриевый оранжевый блик и обеспечивает необходимую защиту от ультрафиолетового, инфракрасного, синего света и ударов. Поэтому необходимо постоянно носить соответствующую защиту, такую как сварочные очки.
Хотя соблюдение норм безопасности и использование средств индивидуальной защиты очень важны, при выполнении сварочных работ значительное количество рабочих не заботятся о соблюдении основных норм безопасности, возможно, из-за недостаточной осведомленности об опасностях, связанных с операции сварки и резки. Аудит безопасности, проведенный автором этой статьи на нескольких объектах, таких как фабрики, мастерские, строительные площадки и т. д., PAN India, показал, что многие сварщики выполняют операции по сварке и резке без соблюдения норм безопасности (см. рис. 06, 07, 08). & 09) и без необходимых средств защиты (см. рис. 10), что видно по фотографиям.
5.0 ЗАКЛЮЧЕНИЕ
Ацетиленокислородная сварка и дуговая сварка являются двумя основными методами, используемыми при сварке, резке и родственных процессах. Основными опасностями, связанными с этими операциями, являются пожары и взрывы, а также опасность для здоровья. Небезопасные методы труда и условия труда привели к ряду встречных и внезапных возгораний, в конечном итоге приведших к пожарам и взрывам. Подходящие средства пожаротушения должны быть размещены вблизи места проведения сварочных работ.
Рис. 06: Сильно поврежденный сварочный аппарат работает на заводе. Предоставлено: Shib Отсутствие защиты от ультрафиолетовых и инфракрасных лучей приводило к сильному напряжению и повреждению глаз сварщиков. Травма глаза, известная как «дуговые глаза», затрагивает тех, кто видит дугу без очков правильного типа.
Все операции по сварке и резке приводят к образованию определенного количества дыма и атмосферного загрязнения. В большинстве случаев эти пары безвредны, хотя иногда они могут вызывать раздражение. Однако были случаи, когда сварщики, работающие внутри резервуаров, труб, туннелей или других ограниченных и плохо проветриваемых мест, теряли сознание.
Рис. 07: Баллон со сжиженным нефтяным газом и около 20 баллонов с кислородом разбросаны по фабрике с нарушением норм безопасности. Предоставлено: ShibДым и газы, выделяемые при сварочных работах, в основном связаны с химическими веществами, содержащимися в покрытиях. Несмотря на огромное количество опубликованной литературы, вопрос о влиянии на здоровье многолетнего воздействия сварочного дыма и газов до сих пор остается без ответа. Определенной связи между сваркой и раком не установлено, хотя некоторые исследования указывают на повышенный риск рака легких среди сварщиков нержавеющей стали.
Рис. 08: Поврежденный электрический кабель, прикрепленный к сварочному аппарату.
Воздействие сварочного дыма и газов следует максимально контролировать, соблюдая правила гигиены труда, такие как замена продукта, модификация процесса и вентиляция. При сварке желательно обеспечить хорошую вентиляцию, особенно в ограниченном пространстве.
Рис. 09: Поврежденные шланги, прикрепленные к сварочной горелке. Предоставлено: ShibТакже желательно носить соответствующие средства индивидуальной защиты, такие как защитные очки, перчатки, фартуки, сапоги, гетры, сварочные маски, сварочные капюшоны, подходящие линзы для фильтрации ультрафиолетовых и инфракрасных лучей и т. д. во время сварки и резки. . Также наблюдалась неосведомленность операторов и контролеров в отношении безопасных операций сварки и резки.
Рис. 10: Сварщик использует осколки стекла вместо сварочного колпака. Предоставлено: Shib