Сварка выпускных коллекторов | Главный механик
Выпускной коллектор это важная и необходимая часть двигателя внутреннего сгорания автомобиля, которая в основном изготавливается из чугуна. При этом его местонахождение приводит к тому, что условия работы можно назвать скорее экстремальными. Это и огромный перепад температур, вследствие чего на внутренних стенках его труб появляется конденсат, и прохождение выхлопных газов, и резонирующие волны выхлопа – все это не лучшим образом влияет на его состояние и долговечность службы коллектора.
Конденсат приводит к коррозии, а это в свою очередь, к разрушению металла.
Выпускной коллекторКоллекторы могут быть как цельные, изготовленные из чугуна при помощи литья, так и трубчатые, сваренные из стальных труб и деталей.
Трубчатый выпускной коллекторТрубчатые ещё различают по виду соединения этих труб, а также по их длине и, как следует из этого, объем. Естественно, чем больше объем, тем лучше, и дороже коллектор. Например, на спортивные автомобили устанавливают коллекторы с длинными трубами одинаковой длины и сложными переплетениями.
Если вы услышали необычные звуки при работе на холостом ходу, не связные с работой двигателя или сам двигатель стал работать нестабильно или увеличилось потребления топлива, значит нужно проверить состояние коллектора.
Это может быть как разрушение крепёжной проушины или прокладки, которая устанавливается между блоком цилиндра и самим коллектором, так изменение геометрии соединительных фланцев под воздействием высоких температур. Может быть элементарный обрыв шпилек, а может и такая проблема, как появление трещины в корпусе. В зависимости от величины разрушения производится ремонт выпускного коллектора посредством сварки или, если дела совсем плохи, его замена.
Прокладка выпускного коллектора, которую меняют чаще всегоКоррозия и нагар могут стать причиной засора трубы, что требует своего решения.
Конечно, проще всего обратиться на станцию техобслуживания, но некоторый ремонт можно и произвести самому, причем не только супер опытному специалисту.
Для этого нужно подождать когда двигатель и сам коллектор остынут до той температуры, при которой можно с ними работать, после чего начинаем разбирать, начиная с кожуха двигателя, коллектора и прочее, что может помешать. Снимаем сам коллекторный узел путем откручивания крепежа. Меняем прокладку, если нужно, или другую деталь, и все устанавливаем назад в обратном порядке.
При обнаружении трещины в коллекторе её заваривают. Способ сварки зависит от материала, из которого он изготовлен. Если это чугун, он отличается от других сплавов с железом тем, что у него при плавке увеличивают содержание углерода, от 2 до 6 %, что отличает его от других черных металлов.
Сварной шов на чугунном коллектореСварка чугуна требует от сварщика определённой квалификации. Раннее считалось, что чугун из- за своей хрупкости вообще сварке не подлежит, сейчас, используя специальные электроды и отработав метод предварительного нагрева детали, сварной шов получается хорошего качества и с необходимыми свойствами.
Как упоминалось, деталь нагреваем непосредственно перед сваркой и стараемся поддержать температуру во время всего процесса сварки. Чугун имеет свойство быстро остывать.
Так как расплавленный чугун имеет повышенную текучесть, можно или высверливать отверстия по ходу трещины или применять графитовые прокладки под трещину. Также необходимо очистить хорошо место сварки.
Кроме того, при сварке происходит процесс выгорания углерода с образованием при этом СО, что приводит к порообразованию. А это также влияет на качество шва.
После того, как работа закончена, нужно обеспечить детали постепенное медленное остывание, что бы исключить появление новых трещин в районе сварного шва и появлению слоя «белого чугуна», который абсолютно никак не обрабатывается.
Сварка чугунного выпускного коллектора может быть произведена как горячим способом, так и холодным способом. Для каждого способа существуют свои типы электродов. Например, для горячей сварки используют марку ЦЧ-4, для холодной лучше ОЗЧ – 6, ОЗЧ – 2. Последние для коллектора более подходят, так как первые лучше применять для сварки изделий с тонкими стенками. Хорошо применять и электроды МНЧ – 2, которые применяют для ответственных изделий.
Для сварки с помощью этих электродов применяют ток обратной полярности.
При горячем способе всю деталь нагревают до температуры от 200 до 600 градусов, не более.
Очень хорошие результаты по качеству дает газовая сварка, которая защищает чугун от выгорания углерода и дает возможность нагреть деталь.
Холодная сварка для выпускного коллектора представляет собой технологию, при которой швы варятся короткими отрезками, в несколько слоев.
Технология заполнения швов при сварке чугунаОна применяется в случае, если нет возможности нагревать изделие, при этом используют электроды ОЗЧ -2, имеющие медную сердцевину, покрытую специальным слоем и МНЧ -2, с сердечником из меди, никеля, железа и марганца. Конечно. более доступен первый вариант. Дугу при сварочном процессе берут короткую. Отрезки швов выполняйте длиной от 3 до 5 см, делая небольшой перерыв, что бы шов остыл, но примерно до 50 градусов, затем его нужно слегка проковать. Этим мы предотвращаем образование трещин.
Выпускные коллекторы из нержавеющей стали также ремонтируются при помощи сварки, причем и здесь работа имеет свои особенности. Так как это сталь в сплаве с никелем или хромом и другими добавками, в процессе сварки в районе шва эти элементы могут выгорать, поэтому варить их нужно в среде защитных газов.
Кроме того, возможна деформация металла в разной степени при проведении сварочных работ.
Если процесс проводить по технологии, коллектор практически не нуждается в последующей обработке фланца. Обязательно нужно рассчитать силу тока, она должна быть невысокой, так как теплопроводность этой стали намного ниже, чем обыкновенной с низким содержанием углерода и добавок.
Процесс сварки нержавеющих труб с среде аргонаЕсли режим сварки не соблюдается, шов получается с меньшими антикоррозийными свойствами, чем основной металл. Это получается за счет того, что дуга нагревает металл до температуры выше 500 градусов, при этом происходит перераспределение молекул хрома и железа.
Наиболее распространёнными видами сварки нержавейки можно назвать:
- сварка электродами из вольфрама в среде аргона универсальным инвертором, например, DC/AC TIG;
- сварка, в основном ручная, при помощи электродов, покрытыми специальным составом;
- полуавтоматическая, с среде аргона, в качестве электрода применяется нержавеющая проволока;
- холодная, давлением, но для сварки коллекторов она не применяется.
Для сварки в домашних условиях, то есть в гараже, применяется сварка при помощи электродов со специальным покрытием (ММА).
Для этих работ подбираем электроды двух видов: с основанием из двуокисного титана и покрытые рутилом и покрытые карбонатом магния и кальция.
Первые применяются для сварки при переменном токе, вторые при постоянном. Толщину электрода лучше выбирать по ГОСТу 10052.
Если вы не сварщик профессионал, отличного качества сварного шва не гарантируется, хотя стремиться можно и нужно.
В основном сварочные работы лучше производить в специализированных мастерских, где есть разные виды оборудования. Хорошее оборудование, правильный режим и опытный мастер и ваш коллектор будет как новый.
Настоящие профессионалы не только отремонтируют выпускной коллектор, но могут модифицировать его или изготовить новый.
Изготовленный коллектор своими рукамиРемонт выпускного коллектора холодной сваркойХолодная сварка получила достаточно большое распространение среди домашних мастеров, которые умеют правильно применять этот метод.
Клей Холодная сварка для соединения металловЕсли следовать точно инструкциям, можно очень хорошо соединять металлические детали. Естественно, это не настоящий метод холодной сварки, который выполняется методом давления двух элементов до начала пластического деформирования соединяемых кромок деталей.
В нашем случае речь идёт о специальном клеящимся составе. При нанесении состава на место соединения металлов, получаем в итоге шов, который имеет свойства соединяемых металлов.
Применяют холодную сварку в таких случаях, если невозможно применить традиционные методы, например детали могут деформироваться в процессе сварки, форма деталей имеет сложную геометрию, соединяемые части состоят из разных металлов.
При этом соединение получается очень прочным и качественным, может выдерживать большие нагрузки, причем долгое время.
Но можно ли заклеить выпускной коллектор холодной сваркой – это очень интересный вопрос. Да, детали автомобиля, в том числе и трещины выхлопной трубы прекрасно соединяются при помощи этого состава, но нагрузки и большой перепад температур в коллекторе ставят под вопрос целесообразность его применение.
Хотя как временная мера, можно использовать. Есть отзывы, что при использовании такого клея машина прошла уже 800 км, другие советуют не рисковать, так как шов не работает ни на сдвиг и кручение.
Холодная сварка, как утверждает производитель, ремонтирует и коллекторыВозможно, дело в правильном использовании клея и в его качестве, то есть в производителе.
Внимание покупателей подшипников Уважаемые покупатели, отправляйте ваши вопросы и заявки по приобретению подшипников и комплектующих на почту или звоните сейчас: +7(499)403 39 91
Доставка подшипников по РФ и зарубежью.
Каталог подшипников на сайте themechanic.
|
Внимание покупателей подшипников
Уважаемые покупатели, отправляйте ваши вопросы и заявки по приобретению подшипников и комплектующих на почту или звоните сейчас:
+7 (495) 128 22 34
[email protected]
Доставка подшипников по РФ и зарубежью.
Каталог подшипников на сайте
themechanic.ru
Внимание покупателей подшипников
Уважаемые покупатели, отправляйте ваши вопросы и заявки по приобретению подшипников и комплектующих на почту или звоните сейчас:
+7 (495) 128 22 34
[email protected]
Доставка подшипников по РФ и зарубежью.
Каталог подшипников на сайте
themechanic.ru
Как заварить выпускной коллектор
Категории статей
- Все статьи
- Замена и ремонт катализаторов
- Замена и ремонт гофр
- Ремонт коллекторов
- Установка лямбдазонда
- Ремонт глушителей
- Тюнинг выхлопной системы
- Изготовление глушителей
- Ремонт автомобиля
26. 07.2022
Выпускной коллектор в автомобиле — важный элемент выхлопной системы, функция которого заключается в отводе отработанных газов из двигателя. К сожалению, деталь часто трескается в результате сильных вибраций, происходящих в процессе работы авто. В этом случае есть вариант заварить выпускной коллектор, эта услуга предоставляется профессионалами в автосервисах. Нежелательно заниматься этим самостоятельно, если только у вас нет опыта сварочных работ с чугуном.
Особенности компонента и причины поломки
Выпускные коллекторы находятся с обеих сторон ДВС, не прикасаясь один к другому, и как правило выполнены из разных материалов.
Как мы уже упоминали, коллектор может треснуть от вибрации, но есть и другие причины. Например, очень распространена ситуация с прогоранием детали, возникновением сплошных отверстий в ней. Отрицательно влияют и химикаты, используемые на дорогах зимой, и высокие температуры, и просто естественный износ, неизбежный со временем.
Если в салоне появился запах выхлопных газов, то это один из поводов проверить автомобиль на такой вид поломки.
Методы сварки коллектора выпускного
Можно использовать разные способы сварки — горячую (600-650 С), холодную (без нагрева), полугорячую (300-350 С) — и с применением разных вариантов оборудования. Расскажем о наиболее распространенных методах:
- Полуавтоматический сварочный аппарат. Наиболее простой способ, но требует определенных умений от сварщика — необходимо понимать, как подготовить запчасть и в какой последовательности осуществлять действия. От заблаговременной подготовки во многом зависит, насколько прочным по итогу будет шов. В качестве присадки используется специальная проволока.
- Газовая. Метод подразумевает медленное остывание и минимальное выгорание углерода. До начала работ допустимо нагревать изделие, тогда снижается риск появления трещин. В целом метод дает очень качественный шов.
- Инвертор. Из всех перечисленных здесь способов требует самой длительной подготовки. Сначала обрабатываемый участок зачищают до металлического блеска, потом тщательно обезжиривают при помощи ацетона либо Б-70.
Затем увеличивают глубину трещины, придавая ей форму конуса, и наконец слоями накладывают материал. В качестве опоры можно применять стальную шпильку.
- Аргоновая. Весьма дорогостоящий вариант из-за применения защитного газа аргона. Многие сварщики предпочитают использовать TIG сварку с вольфрамовым неплавящимся электродом.
Можно ли заварить выпускной коллектор холодной сваркой? Да, но здесь есть несколько нюансов. Нагрев отсутствует, а шов создается отдельными небольшими отрезками, после чего закрепляется сверху еще слоем. Это гарантирует, что металл не покоробится.
Монтаж и демонтаж коллектора
Большой объем времени (в среднем три часа) занимает процесс снятия детали и замены – установки обратно уже заваренной.
Потребуется такой набор инструментов, который следует подготовить до начала работ:
- Плоская и крестовая отвертки;
- Ключ-«трещотка», комплект насадок для него и удлинитель;
- Набор ключей — торцовые, накидные и рожковые;
- Домкрат — любого типа, какой вам удобен, от ручного до гидравлического;
- Наконец, емкость, куда будет сливаться антифриз.
Заодно следует поменять прокладки — между коллектором и приемной выпускной трубкой, а также между коллектором и головкой блока цилиндров.
Чтобы снять деталь для ремонта выпускного коллектора сваркой, а потом установить ее заново, потребуется выполнить следующую последовательность действий (лучше предоставить задачу профессионалам):
- Выключить аккумулятор. Слить охлаждающую жидкость в заранее подготовленный таз, используя гаечные ключи и желательно хозяйственные перчатки;
- Демонтировать воздушный фильтр. Снять ресивер инжектора, если актуально;
- Открутить болты, крепящие коллектор к ГБЦ. В двигателях с восемью клапанами система крепления устроена так, что необходимо сначала демонтировать впускной коллектор, и лишь после него выпускной;
- Очистить от изношенных остатков старой прокладки плоскости ГБЦ, установить новые прокладки;
- Одним из описанных выше способов заварить отверстия и повреждения коллектора.
Установить его на прежнее место, закрепить болтами, как и было;
- Соединить все необходимые трубы в выхлопной системе, проверить правильность установки запчастей и только после этого полноценно затянуть крепежи;
- Залить новую охлаждающую жидкость. Включить аккумулятор.
Эти действия в среднем занимают до 3 часов, но все зависит от профессионализма мастера и того, несколько часто он осуществлял процедуру. Сама же сварка чугунного выпускного коллектора обычно производится быстро, впрочем, это тоже зависит от мастерства и от количества повреждений.
Наш cервис ремонта глушителей в Санкт-Петербурге поможет отремонтировать или заменить любые компоненты выхлопной системы на авто и мототехнике. Цена вопроса зависит от сложности замены и прочих факторов.
Как заварить выпускной коллектор из чугуна
Содержание
- Сварка выпускных коллекторов своими руками
- Общая информация
- Ремонт выпускного коллектора
- Вместо заключения
- Сварка выпускного коллектора
- Выпускной коллектор: причины выхода из строя и обслуживание
- Сварка чугунного выпускного коллектора
- Сварка коллектора из нержавейки
- Холодная сварка при ремонте выпускного коллектора
- Заключение
- 3 пошаговых инструкции сварки выпускных коллекторов
- Что такое коллектор + причины его поломок
- Сварка выпускных коллекторов собственноручно: особенности и рекомендации
Сварка выпускных коллекторов своими руками
Выпускной коллектор — один из важнейших компонентов вашего автомобиля. Простейший коллектор состоит из нескольких труб, сваренных между собой в единую систему, по которой происходит вывод выхлопных газов. Выпускной коллектор есть в каждом автомобиле, независимо от его цены или года выпуска.
Поскольку это один из важнейших узлов, ему приходится выдерживать колоссальные нагрузки. В таких условиях коллектор не способен исправно работать и на нем образуются трещины, а иногда сквозные дыры. Особенно, если автомобиль старый и техническое обслуживание проводилось не часто. В таких ситуациях необходима сварка коллектора. С ее помощью можно отремонтировать агрегат и не приобретать новый. В этой статье мы расскажем все, что необходимо знать о сварке выпускных коллекторов.
Общая информация
Вне зависимости от автомобиля в нем может быть установлен трубчатый или цельный коллектор. Цельный агрегат отливается из чугуна и не имеет швов. Он наиболее прочный и долговечный. Трубчатый изготавливается путем сварки нескольких труб в единую систему. Такой вариант менее надежный, но более ремонтопригодный, поскольку зачастую лопаются именно швы и их можно без проблем наплавить заново.
Сами коллекторы изготавливаются из чугуна, жаростойкой стали или алюминия. Агрегат охлаждается с помощью воздуха, но порой этого недостаточно. В критических ситуациях коллектор сильно перегревается или переохлаждается, швы лопаются, образуются трещины или другие видимые дефекты.
Причиной возникновения трещин могут стать неисправности в двигателе, неправильная работа катализатора, неаккуратная езда по лужам и слякоти, неправильная мойка двигателя, агрессивная манера вождения и многое другое. Иногда частые поломки связаны с браком на производстве или желанием производителя сократить срок эксплуатации авто. Современные автоконцерны не ставят в приоритет качество своих автомобилей, часто изготавливая комплектующие из некачественного металла или допуская огрехи при сборке. Сварка коллектора необходима, если трещины достигли длины 5 сантиметров и больше, если фрагменты коллектора выгорели, сам коллектор раскололся на несколько составных частей, лопнули швы.
Ремонт выпускного коллектора
Многие автолюбители впадают в панику, увидев, что швы выпускного коллектора лопнули или он вовсе раскололся пополам. Если вашему агрегату не более 10 лет, то не спешите покупать новый взамен на неисправный коллектор. Его можно легко починить, если вы обладаете навыками сварки.
Сварка коллектора производится в проветриваемом (но без сквозняка) гараже, с использованием электродов. Также можно заварить трещину аргоном или наплавить чугун газопорошковой наплавкой. Если вы не обладаете достаточными навыками, то лучше не беритесь за эту работу. А всем опытным мастерам мы далее расскажем о нюансах ремонта.
Прежде всего, нужно засверлить края трещин или лопнувших швов. Разделайте кромки по всей глубине, только не используйте для этого стандартную болгарку. Теперь можно трещину заварить, используя метод аргонодуговой сварки, или наплавить газопорошковой наплавкой. Иногда встречаются коллекторы, которые настолько выгорели, что даже самый опытный сварщик не сможет их починить. Так что оцените свои силы и подумайте: может быть лучше потратиться на новый агрегат?
После сварки дайте коллектору остыть. При возможности лучше в работе использовать сварочный кондуктор. После того, как выполните сварку, обязательно отшлифуйте поверхность коллектора. Крайне важно восстановить все плоскости агрегата после ремонта, иначе швы гарантированно лопнут снова, а трещины разойдутся. Не стоит производить ремонт, если у коллектора нет прокладки. И обязательно контролируйте геометрию отверстий.
У опытного сварщика ремонт одного выпускного алюминиевого, чугунного или стального коллектора занимает в среднем 2-5 часов, в зависимости от характера поломки и условий работы. Это при условии сварки с аргоном или с электродами. Если применять метод газопорошковой наплавки, то ремонт может затянуться на несколько дней, поскольку коллектору необходимы минимум сутки на остывание.
Вместо заключения
Помните, что несоблюдение технологии сварки, нарушение техники безопасности и желание поскорее закончить ремонт выпускного коллектора могут привести к плачевным последствиям. Работу некоторых сварщиков порой невозможно переделать из-за огромного количества ошибок, и такой коллектор автоматически отправляется на свалку.
Сварка выпускного коллектора
Одной из составных частей ДВС является выпускной коллектор. В процессе эксплуатации он изнашивается. Такое характерно для автомобиля с любым пробегом. Причин для образования трещин немало: от заводского брака, некорректной сборки до динамического разрушения. При выходе детали из строя не спешите запчасть менять. Многие автосервисы специализируются на сварке выпускных коллекторов. Имея сварочный аппарат в гараже, можно реставрировать деталь своими руками. Сделать это можно несколькими методами. Коллектор производится из нержавеющих труб или чугуна. Сварке поддаются оба сплава, но любая технология со своими нюансами. Специалисты готовы поделиться опытом.
Выпускной коллектор: причины выхода из строя и обслуживание
В зависимости от марки машины и типа двигателя, на двигатель устанавливаются модели различных модификаций. Их можно разделить на две группы:
- цельнометаллические, они обычно делаются методом литья из чугуна;
- трубчатые, для их производства используются нержавеющие трубы различного диаметра.
К блоку ДВС коллекторы крепятся на фланцы. При каждом такте в камеру поступают под давлением отработанные газы. Их температура достигает 900 градусов. Понятно, что деталь, работая в таком режиме, способна сломаться.
Нарушение герметичности выпускного коллектора – самый сложный дефект. Возможные ситуации:
- прогорает одна из труб;
- от динамической нагрузки появляются трещины на коллекторе;
- полностью отламывается патрубок.
Все эти повреждения – проблема. Для многих автомобилей процедура замены детали затягивается на месяцы – «родные» запчасти иногда приходится заказывать.
На многих СТО их восстанавливают. Сварка коллекторов в зависимости от их модификации производится методами горячей, холодной или аргоновой сварки. Работы производят разным типом оборудования, с использованием электродов или присадочной проволоки. Реставрацией можно заняться во дворе дома или гараже. Как заварить выпускной коллектор самостоятельно? Рассмотрим подробно каждый из методов.
Сварка чугунного выпускного коллектора
Температурная обработка высокоуглеродистого сплава связана с определенными трудностями:
- углерод при термическом воздействии выгорает, металл становится рыхлым;
- у чугуна высокий коэффициент текучести;
- при быстром охлаждении, из-за внутреннего напряжения, литье начинает трескаться, становится белесым, это говорит об изменении структуры сплава.
Сварка выпускного коллектора из чугуна под силу стажистам. Новичкам лучше не браться за реставрацию детали автомобильного двигателя, или сначала нужно потренироваться на бросовых изделиях из чугуна. До недавнего времени за ремонт чугуна сварщики не брались. Шов получался с большим содержанием окалины, в зоне разогрева металл трещал. После появления специальных медесодержащих электродов, позволяющих снижать температуру в ванне расплава до +120°С, появилась возможность создавать прочные соединения.
Горячий и полугорячий способы принципиально не различаются. Трещина наплавляется медесодержащими присадками при предварительном прогреве детали. При горячем, деталь разогревают в печи до температуры +600°С, появляется малиновый отлив. Он заметен при затенении. После этого приступают к сварке. Чтобы деталь быстро не остывала, ее периодически прогревают паяльной лампой. При полугорячем способе деталь разогревают в пределах +300°С. Получается ровный шов. Очень важно поддерживать температуру во время охлаждения. Если глубина трещины большая, ее:
- предварительно разделают на всю глубину;
- края рассверливают с обеих сторон;
- кромки сглаживают под углом 30°.
Делают многослойное соединение. Каждый шов обязательно проковывается, длина проходки не более 3 см. Швы для надежности соединения делают перпендикулярно. При электродуговой сварке используют электроды марки ЦЧ-4.
Холодный способ не предусматривает предварительной подготовки. Трещина наплавляется в температурном режиме до 200°С. Для работы используют специальные электроды ОЗЧ-6, ОЗЧ-2.
Прочность на излом у холодного соединения ниже. Для ответственных соединений (когда патрубок выходного коллектора отломлен полностью) лучше брать электроды МНЧ-2. При газовой сварке полуавтоматом применяют медную присадочную проволоку.
Сварка коллектора из нержавейки
Трубчатые комплектующие обычно прогорают в местах изгибов. Сложности работы с нержавейкой:
- легированные сплавы в области рабочей зоны подвержены температурной деформации;
- никель, хром, другие компоненты при нагреве активно окисляются, это пагубно сказывается на качестве шва.
Для устранения дефектов применяется метод аргоновой сварки. Защитная атмосфера оберегает металл от окисления, из-за обдува меньше прогревается область, граничащая с рабочей зоной. Необходимо учитывать, что теплопроводность нержавейки ниже, чем у черных низкоуглеродистых сплавов. Нужна небольшая сила рабочего тока, она подбирается экспериментально. Важно соблюдать скорость образования шва. Металл варится большими проходами, чтобы не возникало межкристаллической коррозии в области соединения. Режим работы зависит от используемого оборудования.
- используя универсальный инвертор, для аргоновой сварки в режиме CD/АС TIG применяют тугоплавкие вольфрамовые электроды;
- для ручной электродуговой сварки нужны жаростойкие присадки марки ММА с рутиловым покрытием;
- для полуавтоматов выбирают проволоку по нержавейке, шов получается плотным, не требующим дополнительной обработки.
Холодная сварка при ремонте выпускного коллектора
Небольшие дефекты заделывают с использованием специальных клеевых составов, называемых «холодной сваркой». До нанесения смеси ремонтируемую зону необходимо обезжирить. Пользоваться клеями следует строго по инструкции. Тогда получается заплата, по физическим свойствам схожа с металлом. Такой метод удобен для устранения трещин и прогаров в труднодоступных местах. Клей – лишь временная мера устранения поломки. Под большой нагрузкой горячих отходящих из цилиндров газов латанная комплектующая долго не простоит. Клеевой состав не рассчитан на динамические нагрузки, зато отлично выносит статические. Перед приобретением клея важно изучить его характеристики.
Заключение
При сбоях в работе двигателя обязательно проверяют целостность выходного коллектора. Это – наиболее уязвимая деталь, эксплуатируемая в агрессивной среде под большим давлением. При обнаружении дефекта оцените, сможете ли произвести ремонт детали самостоятельно. Не имея опыта, за такую ответственную работу лучше не браться, доверить реставрацию специалисту.
3 пошаговых инструкции сварки выпускных коллекторов
Сварка выпускных коллекторов: классификация проблем выхлопной системы + алгоритм замены треснувшего коллекторы на новый + 3 способа сварки чугунного коллектора + 3 оптимальных вариации электродов для сварки + лучший вариант сварки выпускных коллекторов из нержавейки + анализ, можно ли сварить коллектор холодной сваркой.
Вопросы о коллекторах в сети довольно распространены, и касаются они автомобилей. Если мы говорим о транспорте, то здесь возможны 2 вариант коллекторов – впускной и выпускной.
Большим нагрузкам подвержен именно первый. Высокие температуры + остатки топлива буквально «прожигают» деталь, выводя ее из строя в транспортном средстве.
Как именно происходит сварка выпускных коллекторов + имеет ли смысл ее проводить вообще, мы рассмотрим в сегодняшней статье. Приступаем.
Что такое коллектор + причины его поломок
В системе автомобиля под коллектором подразумевают впускную или выпускную деталь, расположенную по обеим частям двигателя. Как правило, элементы не имеют точек соприкосновения, к тому же, в 90% случаев выполнены из различных сплавов металла.
Задачи коллектора определяются его типом:
- впускной. Задача детали – это подвод и помощь в смешивании смеси топлива до того, как она попадет в цилиндры двигательной системы;
- выпускной.
Выполняет отводящую функцию, где в качестве транспортного сырья выступают сгоревшие газы. Отходы поступают сначала в катализатор, а потом подаются на глушитель.
Структура обоих типов коллекторов также имеет большое сходство – это от 2 до 6 трубок, объединённые в одну, которые «одеваются» на цилиндры двигателя. Число трубок зависит от числа цилиндров, а в 2020 году могут встречаться как старые модели (та же «ОКА») с 2 цилиндрами, или продвинутые американские бензинопожирающие «монстры» с 6-ю цилиндрами. По классике – это 4 цилиндра.
Фото впускного коллектора представлено выше. Его подключение происходит к системе по подаче топлива + воздуха. В верхней части детали будет расположена или заслонка дросселя, или карбюратор.
Принцип работы выпускного коллектора:
- После поступления в двигатель топлива, клапаны закрываются.
- Происходит поджигание смеси свечей зажигания.
- Поршень смещается вниз благодаря получившейся взрывной силе.
- В работу вступают клапана на выпуске, которые отводят сгоревшие остатки топлива и газы в выпускной коллектор. К каждой трубе идет подвод коллектора, который в конце объединяет все ответвления в единое целое.
- Катализатор поджигает смесь из трубы.
- Горючие частички отправляются или в трубоотвод, или сразу в глушитель.
- Газы выходят во внешнюю среду.
Выходной коллектор + глушитель подавляют звуки от работы мотора, делая ход транспортного средства для окружающих, в звуковом плане, комфортным.
Важно: выпускной коллектор постоянно подвергается значительным температурным ударам – от 600 до 950 градусов по Цельсию. Логично предположить, что материал изготовления детали обязан иметь высокие показатели теплоустойчивости, а обеспечить это могут только тугоплавкие металлы.
Аналогичная ситуация и со сваркой. Если для залатывания коллектора будет использован низкокачественный материал, о долговечности проделанной работы не может быть и речи. В большинстве случаев отводящий коллектор дополняют специальным датчиком, который помогает отслеживать уровень кислорода в выхлопе. Он помогает корректировать состав топливной смеси, что подается в двигатель. Как итог – незримая взаимосвязь между составляющими системы.
Теперь поговорим о классификации проблем выхлопной системы.
Оговоренные проблемы возникают из-за влияния химических веществ, которые содержаться в смесях, распространяемых во время гололедицы. Вторая причина – износ детали. Система постоянно находится под влиянием высоких температур. Плавление и прогорание ее компонентов не диковинка.
Сварка выпускных коллекторов собственноручно: особенности и рекомендации
1) Как снять/установить выпускной коллектор в авто?
В зависимости от степени сложности проводимого ремонта, может возникнуть необходимость в покупке нового коллектора, ибо сварка обойдется по той же цене, а иногда даже дороже. Для большинства владельцев проще будет обратиться в СТО, но есть и категория автомобилистов, которые предпочитают производить мелкие ремонтные работы собственными руками.
Набор инструментов для замены старого коллектора на новый:
- емкость, в которую можно слить жидкость для охлаждения;
- ручной/гидравлический/пневматический или любой другой домкрат;
- комплект ключей рожкового, накидного и торцового типов;
- трещотка-ключ + набор насадок к нему + удлинитель;
- плоская отвертка и крестовинка.
Покупая новый коллектор, в комплекте сразу нужно менять 2 типа прокладок – в связке коллектор/ГБЦ и коллектор/приемная трубка системы выпуска. О том, какой именно брать коллектор, скажет маркировка старого + проконсультироваться у продавца – это святое.
Алгоритм замены выхлопного коллектора:
- Предварительно изучаем технику безопасности при ремонте двигательной системы транспортных средств.
- Выключаем аккумулятор.
- Сливаем жидкость для охлаждения. Для этого потребуются перчатки из резины, гаечные ключи, чистая вода и емкость для слива (зайдет обычный тазик).
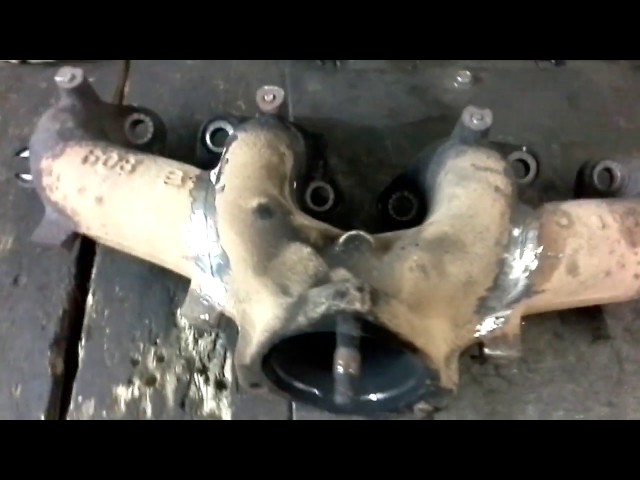

Всего 14 шагов. Весь процесс может занять от 1 до 3 часов. Конечно же, если у человека все в порядке с прямотой рук. Если не уверены в своих способностях, лучше обратиться в сервисный центр. Дороже, но качественней.
2) Как происходит сварка выпускных коллекторов из чугуна?
- Горячая технология. Когда заготовка разогревается до пиковой температуры от 600 до 660 градусов;
- Полугорячая технология. Процесс сварки протекает при температурных условиях 300-350 градусов по Цельсию;
- Холодная технология. Сварка производится в стандартных условиях, без какого-либо нагрева.
Последний вариант отличается методикой прокладки швов – короткие отрезки, на которые накладываются повторные слои. Такое подход позволяет избежать коробления материала выпускного коллектора.
Оценка статьи:
Загрузка…
Сохранить себе в:
Adblock
detector
Сварка выпускных коллекторов: ремонт запчасти
Содержание
- Выпускной коллектор – это
- Причины и признаки поломки деталей
- Ремонт выпускного коллектора
- Монтаж и демонтаж детали
- Сварка различных материалов в домашних условиях
- Из чугуна
- Из нержавейки
- Холодный метод
В процессе эксплуатации некоторые компоненты двигателя изнашиваются. Подобная ситуация характерна для автомобилей любого года выпуска. Однако при повреждении детали не стоит спешить покупать новую. Сварка выпускного коллектора помогает отложить процедуру замены на более благоприятное время.
Выпускной коллектор – это
Так называются детали, расположенные с обеих сторон двигателя. Элементы не соприкасаются друг с другом. В большинстве случаев для выпускных коллекторов используются разные материалы.
На этот элемент возложена отводящая функция. В роли сырья выступают выхлопные газы. Они подаются сначала в катализатор, затем в глушитель.
Причины и признаки поломки деталей
Самыми распространенными неисправностями бывают нарушение целостности патрубка или появление сквозного отверстия в коллекторе. Главный признак поломки – запах отработанных газов в салоне автомобиля. Неисправности возникают из-за негативного влияния химических веществ, которые содержатся в смесях, используемых во время гололедицы. Другой причиной является естественный износ детали под постоянным воздействием высоких температур. Прогорание компонентов выпускной системы не считается редкой поломкой.
Ремонт выпускного коллектора
Поскольку других проблем, кроме образования сквозных отверстий, не возникает, единственным способом устранения поломок считается сварка.
Если ремонт детали таким способом невозможен, ее заменяют новым элементом.
Монтаж и демонтаж детали
Для снятия и установки выпускного коллектора потребуются следующие инструменты:
- ручной или гидравлический домкрат;
- емкость для сбора охлаждающей жидкости;
- набор торцовых, накидных и рожковых ключей;
- ключ-трещотка;
- отвертки с плоской и крестовой насадками.
Демонтаж и установку детали выполняют так:
- Изучают технику безопасности при ремонте двигателей.
Сбрасывают клеммы аккумулятора.
- Сливают охлаждающую жидкость. Для этого потребуются гаечный ключ, тазик и резиновые перчатки.
- Демонтируют ресивер инжектора, снимают воздушный фильтр. С помощью ключа подходящего размера удаляют болты в местах прикрепления коллектора к блоку цилиндров.
- При ремонте 8-клапанного мотора демонтируют впускной коллектор. В таких системах крепежные элементы являются общими.
- Очищают головки цилиндров от остатков прогоревшей прокладки напильником или наждачной бумагой. В некоторых случаях требуется восстановление резьбы или монтаж новых шпилек, удерживающих коллектор.
- Устанавливают новые уплотнители. Монтируют коллектор. При ремонте автомобиля с 8-клапанным двигателем одновременно устанавливают впускную деталь.
- Завинчивают болты с гайками. Подключают коллектор к патрубкам отводящей системы.
- Проверяют правильность выполнения монтажных работ. Плотно затягивают гайки. Очищают радиатор, заполняют его новой охлаждающей жидкостью.
Подключают аккумуляторную батарею.
Сварка различных материалов в домашних условиях
Способ восстановления выбирают с учетом металла, из которого сделан коллектор.
Из чугуна
Для ремонта детали, сделанной из этого сплава, применяют следующие методы:
- Газовая сварка. Считается наиболее эффективным способом восстановления чугунных элементов. Позволяет получить шов высокой прочности.
- Полуавтоматическая сварка выпускного коллектора из чугуна. Для получения качественного шва требуется сложная подготовка элемента. В качестве присадочного материала используют специализированные виды проволоки.
- TIG-сварка. Процесс ведется в среде защитного газа, что предотвращает появление дефектов сварного соединения.
- Инверторный способ. В этом случае требуются тщательная зачистка поверхностей чугунного элемента, установка опорных шпилек.
Трещина наплавляется сразу после появления, не стоит ждать повреждения патрубка. Перед началом сварки детали прогревают. Во время работы учитывают свойства металла: он быстро остывает.
Из-за повышенной текучести материала вдоль шва просверливают отверстия или устанавливают графитовые прокладки.
Из нержавейки
Качественно заварить выпускной коллектор из этого материала можно только в среде защитного газа. При несоблюдении этого правила деталь деформируется из-за сильного нагрева. С учетом особенностей нержавеющей стали допускается применение только таких методов:
- Использование инвертора с подачей газа. В сочетании с таким сварочным аппаратом применяют неплавящиеся вольфрамовые электроды.
- Ручная сварка с покрытыми электродами. Требуется постоянное поддержание правильного режима работы агрегата.
- Полуавтоматическая сварка с электродом из нержавейки.
В бытовых условиях для получения качественных швов нужно использовать ММА-электроды, стержни с титановым или рутиловым покрытием.
» src=»https://www.youtube.com/embed/OF2mO3Iesms?feature=oembed&wmode=opaque» frameborder=»0″ allow=»accelerometer; autoplay; clipboard-write; encrypted-media; gyroscope; picture-in-picture» allowfullscreen=»»/>Холодный метод
Такой способ не имеет отношения к формированию классического сварного шва, однако для временного ремонта выпускной системы его использовать можно. Перед началом работы необходимо изучить технологию холодной сварки. Трещину устраняют так:
- Обрабатываемый участок зачищают и обезжиривают. Наносят клеящий состав согласно рекомендациям, содержащимся в инструкции.
- Дожидаются высыхания средства, устанавливают деталь на место. В результате работы получается заплатка, свойства которой сходны с характеристиками металла.
Под нагрузкой горячих выхлопных газов отремонтированная таким способ деталь служит недолго. Для сварки коллектора из нержавейки этот способ использовать можно, для ремонта чугунного элемента он не подойдет.
Ремонт выпускного коллектора своими руками
И так излазив просторы интернета, нашел в днепропетровске химию похожую на двухкомпонентный герметик или на эпоксидную смолу производства компании DoneDeal.
По утверждению завода изготовителя предназначен для ремонта чугунных и металлических коллекторов, ГБЦ и выхлопных систем. Не восприимчев к ударным нагрузкам и вибрациям, выдерживает температуру до 1400 градусов и после полного застывания его можно сверлить, нарезать резьбу и обрабатывать болгаркой)
Проверим на сколько это правда. Так как коллектор у меня уже был заварен какой то стремной сваркой то остается только 2 выхода: новый коллектор и стремная химия) -берем вариант №2, он дешевле, а к первому всегда можно вернутся)))
И так вот оно
По технологии зачистил место нанесения «Серой жижи» обезжирил, размешал ее до однородной массы и наляпал на трещину. По инструкции 5-6мм вокруг трещины, взял с запасом на все 10-12мм. Получилась коровья лепешка)))
Оставил эту лепешку сохнуть на ночь. Завтра посмотрим, что из этого получилось…))
Продолжение следует…
Первые полевые испытания показали что этот «Кизяк» держится молодцом.Пробовал ковырять его отверткой — не берет, довольно крепкая шняга, ну и выхлопными газами перестало вонять в салоне.
И так взялся я все таки за ремонт коллектора. Еще летом выяснилось что у меня в коллекторе трещина, рядом с первым лямбда датчиком. Как утверждал мой знакомый диагност это и являлось причиной увеличенного расхода и периодического подтраивания мотора. Хотя мозги ошибок не показали но показания с лябда датчиков говорили о том что они постоянно вносят корректировку в подачу топлива из за этой самой трещины. Вобщем проблем надо было решать.
Решения было два, точнее три, но третье отлетело сразу по причине невозможности его реализовать. Вариант первый это покупка нового коллектора, цена вопроса в районе 35000, как сами понимаете вариант не самый приемлемый. Вариант второй это заварить трещину, но тут возникла проблема, коллектор чугунный а варить чугунину я не умею и надо было искать сварщика. Ну и вариант третий это сварить альтернативный выпуск, этот вариант отлетел сразу потому как выпуск нужно варить с пламягасителем и делать его я тоже не умею, ни один спец по варке тазовских выхлопов за это дело тоже не брался. Третий вариант отлетел, осталось два и как вы понимаете остановился я на втором. Осталось дело за малым, найти хорошего мастера-чугуновара =))
И вот я нашел спеца. Через знакомых договорился пронести его на один завод где мне его и должны были заварить.
Перейдем к самому интересному. Процесс скажу я вам очень трудоемкий, ну по крайней мере мне так показалось. Вобщем приехал я на работу пораньше, загнал машину в бокс и принялся разбирать. Места в моторном отсеке не особо много и подлезть куда либо очень пролематично. Для удобства сначала снял вентилятор с радиатора чтобы освободить побольше места. Делается это очень просто:
1 отцепляем от каркаса все шланги охлаждения
2 в правой нижней части оцепляем разъем питания вентилятора
3 откручиваем два болта по бокам в верхней части
4 отцепляем в левой нижней части клипсу с проводом
5 вытаскиваем вентилятор вверх
Вентилятор снят и места стало чуточку больше =) Теперь откручиваем тепловой экран с коллектора, крепиться он на 3х болтах, два по краям и один посредине чуть ниже лямбда датчика. На одном из болтов крепиться щуп.
По уму перед снятием экрана надо открутить лямбду, но у меня она отворачиваться отказалась и это добавило гемороя. Вобщем из за того что лямбда не снялась я не мог вытащить экран, чтобы его вытащить мне пришлось открутить кронштейн для снятия движка. Потом методом дерганья во все стороны я снял экран и мягко говоря был в шоке.
В лажбинке возле датчика было 3 трещины сантиметра по 3-5 длинной, одна из них уходила чуть ниже датчика. Зрелище было не особо приятное. Обратная сторона тепловой защиты вся была в копоти.
Продолжаем разборку, коллектор крепиться на 11и шпильках к головке и 3х шпильках к приемной трубе снизу, так же есть еще два кронштейна снизу возле приемной трубы, дальше на фотках их будет видно.
Все гайки отвернулись на удивление легко, с небольшим усилием но легко, за 150 000 ничего особо не закисло и не прикипело. После того как все открутил сначала сдернул приемную трубу, а потом начал отковыривать коллектор от ГБЦ, чуть приложился монтировочкой и он оказался у меня в руках.
Первая часть данного процесса позади, я сложил все в сторонку, закрыл бокс с разобранной машиной и пошел работать работу, к слову процесс разборки занял около часа.
Одной из составных частей ДВС является выпускной коллектор. В процессе эксплуатации он изнашивается. Такое характерно для автомобиля с любым пробегом. Причин для образования трещин немало: от заводского брака, некорректной сборки до динамического разрушения. При выходе детали из строя не спешите запчасть менять. Многие автосервисы специализируются на сварке выпускных коллекторов. Имея сварочный аппарат в гараже, можно реставрировать деталь своими руками. Сделать это можно несколькими методами. Коллектор производится из нержавеющих труб или чугуна. Сварке поддаются оба сплава, но любая технология со своими нюансами. Специалисты готовы поделиться опытом.
Выпускной коллектор: причины выхода из строя и обслуживание
В зависимости от марки машины и типа двигателя, на двигатель устанавливаются модели различных модификаций. Их можно разделить на две группы:
- цельнометаллические, они обычно делаются методом литья из чугуна;
- трубчатые, для их производства используются нержавеющие трубы различного диаметра.
К блоку ДВС коллекторы крепятся на фланцы. При каждом такте в камеру поступают под давлением отработанные газы. Их температура достигает 900 градусов. Понятно, что деталь, работая в таком режиме, способна сломаться.
Нарушение герметичности выпускного коллектора – самый сложный дефект. Возможные ситуации:
- прогорает одна из труб;
- от динамической нагрузки появляются трещины на коллекторе;
- полностью отламывается патрубок.
Все эти повреждения – проблема. Для многих автомобилей процедура замены детали затягивается на месяцы – «родные» запчасти иногда приходится заказывать.
На многих СТО их восстанавливают. Сварка коллекторов в зависимости от их модификации производится методами горячей, холодной или аргоновой сварки. Работы производят разным типом оборудования, с использованием электродов или присадочной проволоки. Реставрацией можно заняться во дворе дома или гараже. Как заварить выпускной коллектор самостоятельно? Рассмотрим подробно каждый из методов.
Сварка чугунного выпускного коллектора
Температурная обработка высокоуглеродистого сплава связана с определенными трудностями:
- углерод при термическом воздействии выгорает, металл становится рыхлым;
- у чугуна высокий коэффициент текучести;
- при быстром охлаждении, из-за внутреннего напряжения, литье начинает трескаться, становится белесым, это говорит об изменении структуры сплава.
Сварка выпускного коллектора из чугуна под силу стажистам. Новичкам лучше не браться за реставрацию детали автомобильного двигателя, или сначала нужно потренироваться на бросовых изделиях из чугуна. До недавнего времени за ремонт чугуна сварщики не брались. Шов получался с большим содержанием окалины, в зоне разогрева металл трещал. После появления специальных медесодержащих электродов, позволяющих снижать температуру в ванне расплава до +120°С, появилась возможность создавать прочные соединения.
Горячий и полугорячий способы принципиально не различаются. Трещина наплавляется медесодержащими присадками при предварительном прогреве детали. При горячем, деталь разогревают в печи до температуры +600°С, появляется малиновый отлив. Он заметен при затенении. После этого приступают к сварке. Чтобы деталь быстро не остывала, ее периодически прогревают паяльной лампой. При полугорячем способе деталь разогревают в пределах +300°С. Получается ровный шов. Очень важно поддерживать температуру во время охлаждения. Если глубина трещины большая, ее:
- предварительно разделают на всю глубину;
- края рассверливают с обеих сторон;
- кромки сглаживают под углом 30°.
Делают многослойное соединение. Каждый шов обязательно проковывается, длина проходки не более 3 см. Швы для надежности соединения делают перпендикулярно. При электродуговой сварке используют электроды марки ЦЧ-4.
Холодный способ не предусматривает предварительной подготовки. Трещина наплавляется в температурном режиме до 200°С. Для работы используют специальные электроды ОЗЧ-6, ОЗЧ-2.
Прочность на излом у холодного соединения ниже. Для ответственных соединений (когда патрубок выходного коллектора отломлен полностью) лучше брать электроды МНЧ-2. При газовой сварке полуавтоматом применяют медную присадочную проволоку.
Сварка коллектора из нержавейки
Трубчатые комплектующие обычно прогорают в местах изгибов. Сложности работы с нержавейкой:
- легированные сплавы в области рабочей зоны подвержены температурной деформации;
- никель, хром, другие компоненты при нагреве активно окисляются, это пагубно сказывается на качестве шва.
Для устранения дефектов применяется метод аргоновой сварки. Защитная атмосфера оберегает металл от окисления, из-за обдува меньше прогревается область, граничащая с рабочей зоной. Необходимо учитывать, что теплопроводность нержавейки ниже, чем у черных низкоуглеродистых сплавов. Нужна небольшая сила рабочего тока, она подбирается экспериментально. Важно соблюдать скорость образования шва. Металл варится большими проходами, чтобы не возникало межкристаллической коррозии в области соединения. Режим работы зависит от используемого оборудования.
- используя универсальный инвертор, для аргоновой сварки в режиме CD/АС TIG применяют тугоплавкие вольфрамовые электроды;
- для ручной электродуговой сварки нужны жаростойкие присадки марки ММА с рутиловым покрытием;
- для полуавтоматов выбирают проволоку по нержавейке, шов получается плотным, не требующим дополнительной обработки.
Холодная сварка при ремонте выпускного коллектора
Небольшие дефекты заделывают с использованием специальных клеевых составов, называемых «холодной сваркой». До нанесения смеси ремонтируемую зону необходимо обезжирить. Пользоваться клеями следует строго по инструкции. Тогда получается заплата, по физическим свойствам схожа с металлом. Такой метод удобен для устранения трещин и прогаров в труднодоступных местах. Клей – лишь временная мера устранения поломки. Под большой нагрузкой горячих отходящих из цилиндров газов латанная комплектующая долго не простоит. Клеевой состав не рассчитан на динамические нагрузки, зато отлично выносит статические. Перед приобретением клея важно изучить его характеристики.
Заключение
При сбоях в работе двигателя обязательно проверяют целостность выходного коллектора. Это – наиболее уязвимая деталь, эксплуатируемая в агрессивной среде под большим давлением. При обнаружении дефекта оцените, сможете ли произвести ремонт детали самостоятельно. Не имея опыта, за такую ответственную работу лучше не браться, доверить реставрацию специалисту.
замена выпускного коллектора, ремонт и его взаимозаменяемость с другими элементами Фольксваген
Выпускной коллектор – важный элемент выпускного тракта любого автомобиля, который служит для объединения отработанных газов в одну трубу и транспортировки их в выхлопную трубу. Кроме того, эффективная работа этого навесного оборудования способствует эффективному продуванию и наполнению камер внутреннего сгорания ДВС.
Внимание! Работа детали происходит в условиях повышенного температурного режима, а значит сопряжена с высоким уровнем нагрузок.
Наши услуги для владельцев Поло Седан: замена выпускного коллектора
Наша автосервисная мастерская готова предложить все виды обслуживания выпускного тракта Поло Седан, в том числе замену и ремонт выпускного коллектора. Наши профессиональные мастера всегда готовы качественно и быстро устранить имеющиеся неисправности, с соблюдением сроков ремонта и за демократичную стоимость. Мы не предлагаем грамотно необоснованных технических мероприятий, и можем доказать необходимость проведения каждого из видов ремонта.
Для работы и диагностики наши специалисты используют только профессиональное оборудование и инструмент, которые рекомендованы производителем. Также в качестве расходных материалов мы используем только специализированные вещества и материалы, которые улучшают технологичность всех ремонтных работ. Опыт и квалификация сотрудников позволяет им определять даже скрытые повреждения в выпускном коллекторе, а также производить эффективный ремонт самых сложных поломок и неисправностей.
Мы строго контролируем технологические процессы, которым следуют автомастера, и проверяем их на соответствие рекомендациям производителя. Кроме того, мы всегда лояльно относимся к формированию цены и не предлагаем услуги по завышенной стоимости.
Важно! Своевременная замена выпускного коллектора Поло Седан – залог эффективной работы не только системы выхлопа, а и всего авто в целом.
В зависимости от состояния и степени повреждения выпускного коллектора Пол Седан наши специалисты могут предложить такие виды ремонта:
- Сварка трещин.
- Сварка отломанных фрагментов.
- Наплавка при истончении стенок.
- Полная замена детали.
Стоит доверять работу по ремонту коллектора только профессионалам, так как для этого требуется специализированное сварочное оборудование. И не каждый автовладелец имеет его в наличии, а также обладает необходимыми навыками его использования.
Когда и почему может потребоваться замена коллектора Поло Седан?
Самыми частыми причинами выхода из строя выпускного коллектора, являются:
- Выход из строя заслонки, что обусловлено высоким температурным режимом внутри системы, появлением конденсата, и низким качеством материала самого коллектора.
- Выход из строя клапана.
- Отслаивание трубки.
- Подсос коллектором воздуха.
- Попадание внутрь масла.
Для контроля работоспособности выпускного коллектора современные автомобили, в том числе и Фольксваген Поло Седан оснащается специальным датчиком. Он не только просигнализирует о неисправности коллектора, а и проверит состав воздушно-топливной смеси, что позволит оптимизировать ее состав.
Важными признаками, указывающими на то, что в работе системы выхлопа имеются проблемы с работой коллектора, являются:
- Увеличение уровня расхода горючего.
- Появление в салоне неприятного запаха.
- Работа двигателя сопровождается странными шумами.
- Электронные системы управления мотором стали давать сбои.
При обнаружении таких симптомов следует обращаться в автосервис для проведения качественной диагностики и определения последующей стратегии действий- замены или ремонта выпускного коллектора Поло Седан.
Ремонт выхлопного коллектора на Фольксваген Поло
Проведение работ по ремонту коллектора Фольксваген Поло Седан зависит от степени повреждения самого элемента. В любом случае необходимо использование сварочного оборудования, будь то ремонт и сварка дырок и трещин или полная замена элемента. Интересно то, что заводской выпускной коллектор Поло Седан взаимозаменяем на более бюджетный, но не менее эффективный выпускной коллектор ПАУК (Stinger 4-1). В связи с чем, автолюбители все чаще просят установить именно ПАУКа на место вышедшей из строя «родной» детали.
Специалисты нашего автосервиса предлагают быстро и качественно произвести замену коллектора в нашей мастерской, с учетом пожеланий автовладельца. Кроме того, в процессе ремонта автомастера оценят состояние каталитического нейтрализатора и проведут диагностику всего тракта выпуска.
Совет! Опытные мастера СТО, как и сами автомобилисты, рекомендуют не производить самостоятельный ремонт выхлопного коллектора на Фольксваген Поло, ведь он может привести к необратимым последствиям и полному выходу авто из строя.
Мы предлагаем выполнение ремонта с применением аргонно-дуговой сварки, которая способна на химическом уровне обеспечить качественное соединение металлических составляющих. Это гарантирует не только высокое качество, но и надежность швов.
После проведения всех видов работ, автомобиль в обязательном порядке подвергается повторной диагностике, для проверки качества выполненных работ.
Справедливое ценообразование на восстановительные работы выхлопной системы Поло Седан
Вас порадуют цены, которые предлагаются в нашем автосервисе. Их формирование происходит на основе таких важных принципов:
- Демократичность.
- Открытость.
- Справедливость.
- Лояльность.
- Персональный подход.
- Система скидок и бонусов для постоянных клиентов.
Каждый вид работ, проводимый при замене коллектора наши специалисты готовы технически грамотно обосновать, доказав необходимость его проведения. В каждом конкретном случае стоимость зависит от сложности работ и необходимости дополнительных видов обслуживания.
Гарантия качества на работы наших мастеров
Мы гарантируем качество, которое никогда не подведет в критической ситуации. На все виды работ наши специалисты обязательно дают гарантию, подтвержденную документально. Мы отвечаем за профессионализм каждого сотрудника и точно знаем, что они не подведут. На Поло Седан замена выпускного коллектора должна выполняться своевременно. Лучше всего для этого обращаться в автосервисную мастерскую. Так как если проблему запустить, то она может вылиться в более сложный и дорогостоящий ремонт в будущем.
Можно ли заварить треснувший выпускной коллектор? (Полезные советы)
Под редакцией Zak Dunn
Часы работыОбновлено
Направляющие для сварки
Выпускной коллектор может в конечном итоге треснуть из-за постоянных и высокотемпературных изменений.
Несмотря на то, что замена треснувшего выпускного коллектора также довольно дорогая, многие автовладельцы задумываются о сварке. Но можно ли заварить треснувший выпускной коллектор? Если да, то как?
Далее мы обсудили, можете ли вы заварить треснувший выпускной коллектор или нет . И мы включаем простой и быстрый метод ноу-хау для сварки треснувших выпускных коллекторов.
Содержание
Можно ли сваривать треснувший выпускной коллектор?
Да, можно. Но это более медленный процесс, и заварить треснувший выпускной коллектор можно любым сварочным аппаратом, подходящим для стали. Главное – правильно подготовиться, чтобы сварка прошла гладко.
Некоторые автовладельцы используют JB Weld ExtremeHeat для ремонта треснувших выпускных коллекторов.
Хотя это и более быстрое решение, оно не продлится долго. Поскольку можно заварить треснувший выпускной коллектор, и у вас есть простой процесс ноу-хау, рисковать будет неразумно.
Как заварить треснувший выпускной коллектор?
1. Извлеките треснутый выпускной коллектор из автомобиля.

Начните с снятия треснувшего выпускного коллектора с автомобиля. Сварка треснувшего выпускного коллектора и сохранение его на двигателе может сделать процесс чрезвычайно опасным.
Причина в том, что могут быть горючие химические вещества. В зависимости от года, модели и марки автомобиля процесс удаления может занять от 10 минут до часа или даже больше. Доступность и пространство также влияют на продолжительность процесса удаления.
2. Очистите коллектор
Очистите треснувший выпускной коллектор средством для удаления накипи, кальция или ржавчины. Тщательно очистите коллектор, чтобы в нем не осталось легковоспламеняющихся химикатов. Если на них есть какие-либо твердые вещества, используйте колесо или проволочную щетку, чтобы удалить их. После очистки коллектора высушите его должным образом.
3. Отшлифовать место с трещиной
Отшлифовать место, где нужно сварить. Таким образом, вы можете удалить ржавчину или мусор из области трещины и получить чистую поверхность для создания дуги.
Но не шлифуйте лишний материал. Вы стремитесь очистить место трещины на коллекторе и подготовить его к сварке. Если есть труднодоступные места для шлифовальной машины, примените проволочную щетку, чтобы максимально удалить загрязнения.
Также следует отшлифовать место, где вы будете присоединять зажим заземления. Эта практика обеспечит вам полную мощность во время сварки.
4. Заварить место трещины
В основном выпускные коллекторы сделаны из очень толстого металла. Таким образом, вам может потребоваться применить полную мощность вашего сварочного аппарата, особенно если он питается от сети 110 вольт.
Вы должны проникнуть достаточно глубоко, чтобы должным образом отремонтировать треснувшую область, а не латать поверхность. Начните с более медленной скорости при размещении сварного шва, чтобы получилась большая расплавленная лужа.
Если вы используете сварочный аппарат, вы можете добраться почти до всех областей коллектора. И наоборот, устройства с подачей проволоки не могут добраться до узких мест. Однако, если вы можете сварить оба конца трещины, они не уйдут дальше.
Другой вариант – порошковая проволока. Для этого устройства снимите насадку, чтобы сделать пистолет меньшего размера, чтобы вы могли добраться до крошечных участков.
5. Установите на место коллектор
После завершения сварки дайте ему остыть, прежде чем устанавливать коллектор на двигатель. Следуйте рекомендациям по крутящему моменту от производителя, чтобы прикрутить коллектор к автомобилю.
Тщательно проверьте прокладку на наличие повреждений. Если найдете, замените прокладку. После установки коллектора на выхлопную систему вы готовы к вождению автомобиля.
Подробнее: Как настроить давление газа для сварки MIG
Часто задаваемые вопросы
Можно ли сваривать MIG выпускной коллектор?
Профессиональные механики не рекомендуют сварку MIG по сравнению с любой формой сварки. Но если ваш выпускной коллектор сделан из автомобильного железа, вы можете сварить его сварочным аппаратом МИГ.
Сколько будет стоить ремонт выпускного коллектора?
Замена выпускного коллектора стоит в среднем от 996 до 1099 долларов. В частности, затраты на рабочую силу составляют от 248 до 314 долларов, а стоимость деталей — от 748 до 785 долларов. В эту стоимость не входят сборы и налоги.
Можно ли сварить чугунный выпускной коллектор?
Сварить чугунный выпускной коллектор можно, но проект за один раз не сделаешь. Для железного выпускного коллектора автомобиля вы должны приварить дюйм или меньше, а затем подождать минуту, чтобы дать ему остыть. Низкая скорость и более медленный процесс являются ключом к сварке чугуна.
Заключительные слова
Вы можете сварить треснувший выпускной коллектор с помощью обычного сварочного аппарата, подходящего для стали. Тем не менее, если вы нервничаете по поводу снятия и повторной установки треснувшего выпускного коллектора или использования сварочного аппарата, отнесите автомобиль в автомастерскую.
Зак Данн
Глава редактора @The Tool Reviews (это парень, ответственный за обеспечение того, чтобы каждый пост, который мы публикуем в блоге, был полезен для наших читателей.)
Похожие сообщения
Сварка выпускных коллекторов, нужен совет/помощь
14.08.2009 #1
Сварка выпускного коллектора, нужен совет/помощь
Привет, Мэтт здесь,
Я занимаюсь сваркой TIG уже пару лет и производил несколько довольно простых турбовыпускных коллекторов для 4 цилиндров.Я хочу попробовать вывести их на новый уровень и попробовать более сложные конструкции.
Моя главная проблема в том, что я в основном смущен тем, как вы на самом деле получаете горелку TIG в определенных местах, чтобы даже сделать сварку. Знаю, у сборщиков люди обычно сначала приваривают вот такие:Но как сварить в таком узком месте? У вас просто есть вольфрам, торчащий далеко от чашки, чтобы попасть туда?
Итак, после того, как вы сделаете коллектор, вы затем приварите 4 направляющих к верхней части этих 4 портов на коллекторах, и это в основном то, где возникает мой вопрос. Кажется, что есть неисчерпаемые места, которые нужно приварить, но я просто не понимаю, как туда засунуть горелку для сварки, вот несколько примеров:
Этот действительно узкий, большинство из них больше похожи на это:
Так что в основном смотрю, может ли кто-нибудь дать мне какие-либо указатели, даже такие, как размеры чашки, газовая линза? и вольфрамовые комбинации, которые я следует использовать, или как далеко я должен иметь вольфрам и т.
д. Любая помощь очень приветствуется, спасибо!
О P.S. Я делаю это из нержавеющей стали 304. Я использую присадочную проволоку ER308 для сварки нержавеющей стали с нержавеющей и ER309 для сварки нержавеющей стали с мягкой, правильно ли это?
Ответить с цитатой
14.08.2009 #2
Re: Сварка выпускного коллектора, нужен совет/помощь.
Вам нужно планировать заранее и приваривать то, что вы можете заранее, прежде чем приваривать остальные трубы или связывать их с коллекторами слияния.
Можно использовать газовую линзу с дополнительным вылетом в одних местах, микро налобные фонарики в других.
Ответить с цитатой
14.08.2009#3
Re: Сварка выпускного коллектора, нужен совет/помощь.
Предварительное планирование PPPPPP
предотвращает плохую работу.
Все трубные направляющие прибиты к фланцу коллектора и к коллектору и находятся в правильном положении. Затем они обрезаются у коллектора, у фланца или в стыке посередине прогона (это можно было бы оценить, когда все собрано). Затем все составные части свариваются, затем снова собираются и завершается окончательная сварка.
Ответить с цитатой
14.08.2009 #4
Re: Сварка выпускного коллектора, нужен совет/помощь.
Таким образом, несмотря на то, что все это скреплено вот так:
Затем они разорвут некоторые прихватки, а затем сварят их в разных местах, а не сделают все сварные швы как есть? Кстати, какие чашки и вольфрамы вы используете для подобных вещей?
Ответить с цитатой
14.
08.2009 #5
Re: Сварка выпускного коллектора, нужен совет/помощь.
когда я свариваю свои коллекторы, я просто использую стандартную горелку 17 с чашкой 8 на линзе для медицинского газа. 3/32 красный вольфрам кстати.
также при попытке сварки в труднодоступных местах может потребоваться вытягивание вольфрама из чашки примерно на дюйм или более для завершения работы. также мне пришлось согнуть вольфрам 45-90*, чтобы добраться в некоторых местах. и установили внешний шланг для продувки, чтобы получить надлежащее газовое покрытие.
Ответить с цитатой
14.
08.2009 #6
Re: Сварка выпускного коллектора, нужен совет/помощь.
А вот как согнуть вольфрам…
http://weldingweb.com/vbb/showthread.php…ghlight=copper
…зап!
Я не совсем сумасшедший..
Отсутствуют некоторые деталиПрофессиональный водитель на закрытом курсе….
Не пытайтесь.То, что я тупица, не означает, что и ты можешь быть таким же.
Так что НЕ пытайтесь ничего из того, что я делаю дома.Ответить с цитатой
14.
08.2009 #7
Re: Сварка выпускного коллектора, нужен совет/помощь.
Это здорово, я никогда не думал сделать что-то подобное, это похоже на хороший способ попасть в некоторые труднодоступные места, спасибо!
Ответить с цитатой
14.08.2009#8
Re: Сварка выпускного коллектора, нужен совет/помощь.
Первоначально Послано zapster
это хорошая передача знаний прямо здесь …Ответить с цитатой
19.08.2009 #9
Re: Сварка выпускного коллектора, нужен совет/помощь.
Первоначально Послано zapster
никогда не думал сделать это таким образом. Я только что использовал плоскогубцы и согнул его.снова хороший совет.
Ответить с цитатой
19.
08.2009 #10
Re: Сварка выпускного коллектора, нужен совет/помощь.
Первоначально Послано Mahonroy
Таким образом, даже несмотря на то, что все это скреплено вот так:
Затем они разорвут некоторые прихватки, а затем сварят их в разных местах, вместо того, чтобы делать все сварные швы как есть? Кстати, какие чашки и вольфрамы вы используете для подобных вещей?
Я сварил все, что мог, в состоянии, показанном на вашем рисунке, затем разобрал их, чтобы сварить последние недоступные части, а затем собрал их для окончательной сварки.Ответить с цитатой
23.08.2009 #11
Re: Сварка выпускного коллектора, нужен совет/помощь.
Убедитесь, что фланцы прикручены к чему-либо плоско. Я видел много коллекторов в мусоре, потому что кто-то деформировал фланец за точку невозврата.
Ответить с цитатой
24.
08.2009#12
Re: Сварка выпускного коллектора, нужен совет/помощь.
У меня был последний вопрос, я не знал, где его задать, поэтому решил просто бросить его сюда:
. В любом случае, я использую Autocad для изготовления фланцев головки, и я видел, что на многих фланцах края закруглены и выглядят намного лучше, например:Знаете ли вы, какой инструмент используется? для этого? Еще раз спасибо за помощь!
Ответить с цитатой
25.08.2009 №13
Re: Сварка выпускного коллектора, нужен совет/помощь.
Они обрабатываются на фрезерном станке с ЧПУ, кромки «скашиваются» фрезой под углом 45 градусов после того, как профиль был нарезан.
Ответить с цитатой
25.08.2009№14
Re: Сварка выпускного коллектора, нужен совет/помощь.
Первоначально Послано LenMann
Они обработаны на фрезерном станке с ЧПУ, края «скошены» 45-градусной фрезой после того, как профиль был вырезан.
Я также использовал массажер для удаления острых кромок на фланцах. это сокращает механическую обработку.Ответить с цитатой
09-17-2009 №15
Re: Сварка выпускного коллектора, нужен совет/помощь.
Хорошо, последний вопрос, лол.
Что вы, ребята, делаете с коллекторами, чтобы придать им красивый вид? Например, вы используете что-то вроде колеса заслонки на всех частях коллектора, прежде чем сваривать их все вместе (просто будьте осторожны, чтобы не поцарапать его?).Или вы бросаете весь коллектор в тумблер на время? Или какой-то другой метод? Я пытаюсь избежать бесчисленных часов шлифовки и полировки. Спасибо еще раз!
Ответить с цитатой
17.09.2009 №16
Re: Сварка выпускного коллектора, нужен совет/помощь.
перед подгонкой я использую подушечки Scotch Brite и обязательно использую максимально гладкий стол, чтобы не поцарапать.
.. надеюсь, это поможет
Ответить с цитатой
11.02.2010 # 17
Re: Сварка выпускного коллектора, нужен совет/помощь.
прежде чем приступить к работе с выпускным коллектором, убедитесь, что у вас есть сварочные перчатки, я бы порекомендовал совместить порты, а затем отполировать их с помощью небольшого колесика.
Ответить с цитатой
26.
10.2010 # 18
Re: Сварка выпускного коллектора, нужен совет/помощь.
Первоначально написал Mahonroy
Привет, Мэтт здесь,
Я занимаюсь сваркой TIG уже пару лет и производил несколько довольно простых турбовыпускных коллекторов для 4 цилиндров. Я хочу попробовать вывести их на новый уровень и попробовать более сложные конструкции.
Моя главная проблема в том, что я в основном смущен тем, как вы на самом деле получаете горелку TIG в определенных местах, чтобы даже сделать сварку.Знаю, у сборщиков люди обычно сначала приваривают вот такие:
Но как сварить там, в таком узком месте? У вас просто есть вольфрам, торчащий далеко от чашки, чтобы попасть туда?
Итак, после того, как вы сделаете коллектор, вы затем приварите 4 направляющих к верхней части этих 4 портов на коллекторах, и это в основном то, где возникает мой вопрос. Кажется, что есть неисчерпаемые места, которые нужно приварить, но я просто не понимаю, как туда засунуть горелку для сварки, вот несколько примеров:
Этот действительно узкий, большинство из них больше похожи на это:
Так что в основном смотрю, может ли кто-нибудь дать мне какие-либо указатели, даже такие, как размеры чашки, газовая линза? и вольфрамовые комбинации, которые я следует использовать, или как далеко я должен иметь вольфрам и т. д. Любая помощь очень приветствуется, спасибо!
О P.S. Я делаю это из нержавеющей стали 304. Я использую присадочную проволоку ER308 для сварки нержавеющей стали с нержавеющей и ER309 для сварки нержавеющей стали с мягкой, правильно ли это?
У вас получился неплохой дизайн.Сварка — непростая вещь, но видя, как вы свариваете, вы должны быть в порядке. Вы должны начать с плана.
Выпускной коллектор
Ответить с цитатой
Как использовать JB Weld ExtremeHeat » Блог ноу-хау NAPA
Опубликовано автором Jefferson Bryant1 Комментарий о том, как использовать JB Weld ExtremeHeat Know How
Купите JB Weld ExtremeHeat прямо сейчас! Одними из наиболее сложных для ремонта деталей являются те, которые должны выдерживать очень высокие температуры. Конечно, блок двигателя может нагреваться до 180-220 градусов, но это ничто по сравнению с экстремальным нагревом выхлопа, где температура может легко достигать 1200 градусов на стандартном немощном двигателе. Высокопроизводительные двигатели, такие как двигатели с наддувом или турбонаддувом, могут нагреваться еще больше, вплоть до того, что коллекторы или коллекторы раскаляются докрасна. Когда двигатель выключен, детали довольно быстро остывают, а затем снова нагреваются. Это циклическое нагревание наносит ущерб металлу, что в конечном итоге приводит к трещинам под напряжением.
Чугун очень трудно сварить, это можно сделать, но ремонт, как правило, довольно некрасивый и длится недолго. Надлежащий сварной шов чугуна требует изъятия детали из эксплуатации, предварительного нагрева детали до температуры, близкой к температуре сварки, сварки повреждений, а затем медленного доведения детали до комнатной температуры. Большинство ремонтных мастерских не имеют такой возможности, поэтому JB Weld ExtremeHeat так популярен для ремонта при высоких температурах.
Что может исправить JB Weld ExtremeHeat В отличие от стандартной эпоксидной смолы JB Weld, ExtremeHeat представляет собой продукт отверждения на воздухе, разработанный специально для применения при высоких температурах, выдерживающий до 2400 градусов по Фаренгейту непрерывного нагрева. Это означает, что ваш ремонт прослужит даже в условиях экстремальной жары. Однако все это идет с несколькими оговорками. JB Weld ExtremeHeat не является клеем, как эпоксидная смола JB Weld, то есть он не предназначен для соединения двух частей вместе; предназначен для ремонта трещин и отверстий в жаропрочных деталях.
Пример № 1. На вашем выпускном коллекторе образовалась трещина от напряжения возле болта. JB Weld ExtremeHeat — идеальное решение для ремонта.
Пример №2 – Выпускной коллектор раскололся на две части. JB Weld ExtremeHeat НЕ будет чинить две детали вместе, это ситуация замены или ремонта сваркой.
У этой ГБЦ сломано ушко для болтов выпускного коллектора. Это НЕ подлежит ремонту с помощью ExtremeHeat. Для этого вам понадобится JB Weld Original. Как пользоваться JB Weld ExtremeHeatИспользование JB Weld ExtremeHeat очень просто, всего четыре основных шага помогут вам вернуться к работе.
У нас в цеху оказался плохо сваренный участок выхлопной трубы. Протекает довольно плохо. Хотя мы могли бы сварить его, если у вас нет сварщика, ExtremeHeat может забрать его на машине.
Prep – Как и при любом ремонте, поверхность должна быть чистой, очень чистой. Любой мусор, грязь, масло, жир или другие загрязнения снижают эффективность ремонта. Используйте химический очиститель, чтобы удалить масло и жир, и наждачную бумагу, чтобы убрать мусор и сделать поверхность шероховатой, чтобы JB Weld ExtremeHeat хорошо держал деталь. Для этой работы достаточно наждачной бумаги с зернистостью 80.
Используя кусок Scotch-Brite™, мы придали трубке шероховатость, удалив всю ржавчину и грязь.Вот так должно выглядеть чисто.
Трещины и отверстия размером менее 1/8 дюйма должны быть раскрыты как минимум на 1/8 дюйма. Вместо того, чтобы поддевать трещину, используйте шлифовальную машину, напильник, сверло или наждачную бумагу, чтобы открыть трещину или отверстие.
Смесь – JB Weld ExtremeHeat представляет собой однокомпонентную замазку. Откройте контейнер и хорошо перемешайте до получения однородного цвета и консистенции.
Продукт оседает на полке, поэтому его нужно хорошенько перемешать.
После смешивания цвет должен быть однородным.
Нанесение – шпателем, деревянной палочкой или даже пальцем нанесите пасту на пораженный участок. Втирайте пасту в отверстие/трещину, пока она не будет полностью заполнена. Не беспокойтесь о том, что вы используете слишком много, вы всегда можете отшлифовать излишки после того, как он затвердеет. Отверстия представляют собой небольшую проблему, так как паста может просочиться и создать небольшой хвост на другой стороне, где вы не сможете его достать. Если это так, попробуйте работать в два этапа: сделайте меньший ремонт основания, дайте пасте застыть, а затем вернитесь и добавьте еще немного, чтобы завершить ремонт, поддерживая чистоту обратной стороны отверстия.
Мы зачерпнули немного ExtremeHeat на металлический шпатель. Вы можете положить то, что не используете, обратно в банку.На трубу нанесли замазку, протолкнув ее под зазор.
После нанесения мы оставляем его на несколько часов перед проверкой.

Отверждение — время отверждения JB Weld ExtremeHeat составляет 2-4 часа для установки, полное отверждение — через 24 часа. Очень важно дать пасте отвердиться в течение полных 24 часов, прежде чем возвращать деталь в эксплуатацию. Вы можете проверить завершение ремонта, надавив ногтем на ремонт. Если гвоздь уходит в ремонт, значит он не готов. По истечении времени подготовки вы можете ускорить процесс отверждения с помощью непламенного источника тепла, например, фена или тепловой пушки.
Если вы можете сделать отпечаток ногтем, он не установлен.После отверждения ремонт будет немного темнее, чем раньше, и твердым, как камень. При необходимости вы можете отшлифовать его и даже просверлить и нарезать резьбу JB Weld ExtremeHeat.
JB Weld ExtremeHeat идеально подходит для ремонта всех видов высокотемпературных деталей, включая выпускные коллекторы, глушители, каталитические нейтрализаторы, выхлопные трубы, блоки цилиндров, камины, коптильни/топки и многие другие детали, подверженные трещинам. Он хорошо работает со сталью, железом, медью, нержавеющей сталью и большинством других металлов, выдерживающих высокие температуры.
Ознакомьтесь со всеми химическими продуктами, доступными в NAPA Online, или доверьтесь одному из наших 17 000 пунктов обслуживания NAPA AutoCare для текущего обслуживания и ремонта. Для получения дополнительной информации о том, как использовать JB Weld ExtremeHeat, поговорите со знающим экспертом в вашем местном магазине АВТОЗАПЧАСТЕЙ NAPA.
Джефферсон Брайант, завсегдатай редукторов, проводит в магазине больше времени, чем где бы то ни было. Его карьера началась в автомобильной аудиоиндустрии в качестве менеджера магазина, а затем он проложил себе путь до должности дизайнера продукции в Rockford Fosgate. В 2003 году он начал писать технические статьи для журналов и с тех пор работает автомобильным журналистом. Его работы были представлены в Car Craft, Hot Rod, Rod & Custom, Truckin’, Mopar Muscle и многих других. Джефферсон также написал 4 книги и выпустил бесчисленное количество видеороликов. Джефферсон управляет Red Dirt Rodz, своей личной студией в гараже, где производятся все его журнальные статьи и технические видеоролики.
Как устранить утечку выхлопных газов с помощью сварки J-B — простые шаги
29 декабря 2021 г. 29 декабря 2021 г. / 6 минут чтения
J-B Weld не следует использовать на выпускных коллекторах или каталитических нейтрализаторах из-за высоких температур, которые могут достигаться в выхлопных системах. Когда непрерывный нагрев ниже 450°F, рекомендуется использовать наш эпоксидный клей-карандаш High Heat, но только в самых экстремальных случаях.
В случае утечки выхлопной трубы или глушителя JB Weld — отличный выбор. Утечку выхлопа можно устранить с помощью эпоксидной смолы и небольшого количества ткани. Протекающие выхлопы/глушители можно исправить с помощью эпоксидной смолы JB Weld, или, если отверстие достаточно маленькое, вы можете использовать JB Weld, чтобы полностью его закрыть.
Следующая статья предложит вам лучший способ действий, если у вас есть утечка выхлопных газов и вам нужно отремонтировать ее с помощью сварки J-B. Следующий пост также содержит ответы на другие часто задаваемые вопросы, что является отличным дополнением. Чтобы эффективно отремонтировать радиатор, вы должны обратить пристальное внимание на указания в этой статье и строго следовать им.
Содержание
- 1 Устранение утечки в выпускном коллекторе
- 1.1 Поиск утечки в выпускном коллекторе
- 1.1.1 #Необычные звуки
- 1.2 Принцип работы выпускного коллектора
- 1.3 Часто задаваемые вопросы:
- 1.1 Поиск утечки в выпускном коллекторе
- Поврежденные прокладки и уплотнения следует заменить. Чтобы снять коллектор, вам понадобится торцевой ключ и набор инструментов.
ii. Осмотрите фланец, которым выпускной коллектор крепится к двигателю. Если при снятии коллекторов не было прокладки, это вполне нормально.
III. Разберите и отремонтируйте сломанные коллекторы, если это возможно, или замените их более новой версией.
- Темно-серый оттенок достигается через 4-6 часов при комнатной температуре при использовании клея J-B Weld.
Через 15-24 часа достигается полное выздоровление. Этот продукт имеет предел прочности при растяжении 3960 фунтов на квадратный дюйм, который затвердевает до прочной связи через один-два часа после нанесения. При правильном закреплении он способен выдерживать температуры до 550°F.
- Поскольку большинство ремонтных предприятий не имеют необходимого оборудования, JB Weld Extreme Heat стала популярным решением для восстановления при высоких температурах. Например, Extreme Heat представляет собой раствор эпоксидной смолы воздушного отверждения, который может выдерживать температуры до 2400 ℉ в течение длительного периода времени, в отличие от обычной эпоксидной смолы JB Weld.
Поиск утечки в выпускном коллекторе
- Шаг 1
Чтобы правильно отремонтировать выхлопную систему, необходимо сначала определить источник проблемы. Поскольку выхлопная система сильно нагревается, может быть трудно заметить утечку выхлопных газов и определить источник неисправности.
Лучше не прикасаться к выхлопной системе, если вы ездили в машине в течение последних нескольких часов, потому что вы можете обжечь руки. Подождите, пока он станет комнатной температуры.
- Шаг 2
Начните с визуальной оценки. Выпускной коллектор можно найти, открыв капот и заглянув под него. Это место, где продукты сгорания двигателя автомобиля будут выбрасываться в атмосферу. Он определенно будет разрушен эрозией и будет состоять из нескольких труб или одной большой трубы. Из-за того, что их может скрыть теплозащитный экран, действуйте с осторожностью.
- Шаг 3
Следуйте по трубе обратно под автомобиль к задней части автомобиля. Произведите визуальный осмотр трубы на наличие трещин или мест, где она треснула или отделилась. На обратном пути внимательно осмотрите каждый из выпускных портов. Присутствие одного или нескольких каталитических нейтрализаторов, повторителей или даже глушителей может быть очевидным.
- Шаг 4
Для этого необходимо соединить большие металлические цилиндры или ящики вместе с выхлопной трубой. Трещины, изломы, складки следует проверять на каждом из них. Другие дефекты выхлопной трубы в некоторых случаях могут проявляться так же, как и признаки негерметичности выхлопной трубы. В результате крайне важно убедиться, что утечка происходит из коллектора, прежде чем приступать к какому-либо дополнительному ремонту.
#Необычные звукиВы также можете провести надлежащий осмотр, чтобы определить, существует ли утечка в выпускном коллекторе. Утечка через прокладку выхлопной системы обычно обнаруживается, когда вы поворачиваете ключ зажигания и замечаете все более громкий звук, исходящий от двигателя, когда он запускается.
Помните, что для вашего удобства между трубой выхлопной системы и двигателем расположена прокладка. Прокладка, как и труба, подвергается постоянному нагреву и охлаждению.
Осмотр прокладки на наличие дефекта необходим, если из трубы не идет трещина или течь. Когда вы нажимаете ногой на педаль газа, обратите внимание, не слышите ли вы что-нибудь необычное. Если вы обнаружите такие шумы, как утечка воздуха или слабый свист, у вас может быть проблема с кондиционером.
Большинство водителей с трудом различают различные звуки двигателя, шумы выхлопных газов и даже утечку вакуумной магистрали в своих автомобилях. Сконцентрируйтесь на точном времени, когда возникают шумы. Если вы сможете обнаружить проблему до того, как отправите свой автомобиль механику, самодиагностика может сэкономить вам много времени и нервов.
Принцип работы выпускного коллектора
Выпускной коллектор — это первый компонент, на который вы обращаете внимание, когда дело доходит до выхлопной системы вашего автомобиля. В этом случае он подключается к двигателю автомобиля и собирает загрязняющие вещества из автомобиля. Воздушная и топливная смеси из нескольких цилиндров двигателя автомобиля содержатся в выпускном коллекторе.
Топливно-воздушная смесь каждого цилиндра собирается во впускном коллекторе, независимо от количества цилиндров.
Из-за своей чрезвычайно высокой температуры выпускной коллектор не только собирает все отработавшие газы двигателя, но и полностью поглощает любые израсходованные или неполностью сгоревшие газы. Исходный кислородный датчик выхлопной системы также расположен в коллекторе и отвечает за контроль количества кислорода, проходящего через выхлопную систему.
Датчик кислорода анализирует уровень кислорода в атмосфере. Он сообщается с системой впрыска топлива, определяя, следует ли увеличивать или уменьшать количество кислорода в атмосфере и бензиновой смеси, используемой для обеспечения двигателя электричеством. Использование выхлопных коллекторов вместо стандартных выпускных коллекторов становится все более распространенным явлением в автомобилях. Ситуация особенно ужасна с высокопроизводительными автомобилями, когда увеличение мощности имеет приоритет над достижением максимальной производительности.
Поскольку коллекторы спроектированы так, чтобы иметь уменьшенные пределы расхода топлива, они могут быстро и эффективно удалять выхлопные газы из системы. Однако, в зависимости от того, как они спроектированы, они могут влиять на мощность при более низких скоростях и более высоких оборотах двигателя.
- Можно ли отремонтировать шов JB с помощью Extreme Heat?
Ответ; , если две детали нельзя отремонтировать с помощью JB Weld Extreme Heat, их необходимо заменить. На этой головке блока цилиндров оторвалась одна из гаек выпускного коллектора. Extreme Heat не может это исправить. Для этого требуется JB Weld Original.
Заключение
В заключение отметим, что хотя замена выхлопной системы коллектором возможна, обратное условие редко бывает верным, не вызывая значительного снижения производительности. Согласно техническим терминам, выпускной коллектор функционирует как воронка, собирающая все загрязняющие вещества, вырабатываемые двигателем.
После того, как загрязняющие вещества полностью сгорели в одном месте, загрязняющие вещества выбрасываются в остальную часть выхлопной трубы через коллектор.
Иногда, если трубы сломаны или заржавели, они могут привести к утечке выхлопных газов, что приведет к снижению производительности автомобиля. Из-за потери противодавления, вызванной утечкой выхлопных газов из-за поврежденной трубы, мощность, ускорение и эффективность автомобиля могут пострадать из-за проблемы. После того, как вы будете следовать приведенным рекомендациям и по-прежнему не исправите их должным образом, обратитесь за профессиональной помощью.
Автомобильная сварка: как работать с чугуном и другими материалами
Литые металлы отличаются от других металлов несколькими ключевыми моментами.
Во-первых, сплавы, используемые для литых деталей, отличаются от сплавов, используемых для изготовления кованых или механически обработанных деталей. Чугун или стальная отливка, например, содержат гораздо больше углерода, чем стальной прокат. Это создает определенные проблемы, когда вам нужно сваривать или адаптировать литые детали. Например, вы не можете легко нагреть и согнуть чугун — он просто треснет и развалится. Но вы можете сваривать литые детали с помощью соответствующего оборудования и методов.
Этот технический совет взят из полной книги АВТОМОБИЛЬНАЯ СВАРКА: ПРАКТИЧЕСКОЕ РУКОВОДСТВО. Подробное руководство по этой теме можно найти по этой ссылке:
УЗНАТЬ БОЛЬШЕ ОБ ЭТОЙ КНИГЕ ЗДЕСЬ
ПОДЕЛИТЬСЯ ЭТОЙ СТАТЬЕЙ: Поделитесь этой статьей на Facebook, на форумах или в любых клубах, которые вы принять участие. Вы можете скопировать и вставить эту ссылку, чтобы поделиться: https://musclecardiy.com/welding/automotive-welding-work-cast-iron-materials-part-8/
Поскольку литые детали более хрупкие, они могут растрескиваться и ломаться.
Поэтому большая часть этой главы посвящена ремонту сломанных литых деталей. В конце главы есть небольшой раздел по работе с другими металлами, такими как медь, свинец, бронза, олово и другие сплавы. Хотя эти металлы, как правило, нельзя сваривать, они обычно используются для пайки твердым припоем, пайки, изготовления кузовов, отделки и других автомобильных применений.
Литой металл можно эффективно сваривать, но для сварки чугуна вам потребуются немного другие навыки и некоторые специальные приспособления.
Фиксация сломанных литых деталей
Когда литые детали ломаются, они ломаются без повреждений. То есть, как разбитую керамическую кружку, вы можете собрать осколки вместе и получить форму, очень близкую к той, с которой вы начали. Это хорошая новость для ремонтных работ, ведь вам не придется возиться с кучей погнутых деталей. Тем не менее, вы можете иметь дело с невидимыми трещинами, поэтому, когда вы решите, что закончили, проверьте литые детали на наличие трещин в хорошем механическом цеху, прежде чем использовать их.
Выпускные коллекторы
Выпускные коллекторы являются одними из самых распространенных треснутых или сломанных литых деталей. Эти детали подвергаются регулярным циклам нагрева и вибрации при нормальной эксплуатации. Некоторые коллекторы сделаны из очень тонкого чугуна, а железо со временем изнашивается еще больше. Кроме того, есть фланцы, где коллектор крепится болтами к двигателю, и они особенно подвержены поломкам. Большинство выпускных коллекторов изготовлены из обычного чугуна и сравнительно легко свариваются.
Блоки двигателя
Блоки двигателя имеют преимущество перед выпускными коллекторами, поскольку обычно изготавливаются из более толстых отливок и из более качественных материалов. Тем не менее, применение, соответственно, более критично, поскольку в большинстве областей требуются точные машинные допуски. Заварка трещин в блоке цилиндров, вызванных замерзанием воды, под силу большинству любителей, но всегда перед тем, как использовать блок цилиндров, проверьте его на наличие трещин у профессионала.
Вы, возможно, устранили очевидную трещину во внешней оболочке, но если вы пропустили дефект в области опоры коленчатого вала или стенке цилиндра, вы могли бы потратить много денег впустую, когда этот двигатель выйдет из строя.
Компоненты подвески
Многие компоненты подвески, такие как шпиндели, тормозные фланцы и поворотные кулаки, также изготавливаются из чугуна или стали. В целом, в старинных автомобилях чаще используются литые детали. Если ваш проект включает в себя повышение производительности старинного автомобиля, внимательно осмотрите все детали рулевого управления и подвески. Они были разработаны для меньшей мощности двигателя и гораздо менее прочных шин, а дополнительные нагрузки, добавляемые хот-родом, могут привести к катастрофе. Хорошая новость заключается в том, что эти детали могут быть усилены, а в критических случаях доступны замены, изготовленные из современных высокопрочных материалов. Как всегда, если вы хотите использовать старые детали, проверьте их на наличие трещин у профессионалов, прежде чем они будут засчитаны.
Ремонт сломанной чугунной детали
В этом проекте мы будем заваривать трещину в чугунном выпускном коллекторе 50-летнего британского спортивного автомобиля. Коллектор изготовлен из толстого материала хорошего качества, поэтому он является хорошим кандидатом на ремонт. Для чугуна существует два основных типа электродов для сварки стержнями: 55% и 99% никеля. 99-процентный стержень оставляет более мягкий материал в сварном шве и подходит для механической обработки, если вам нужна плоская поверхность, когда вы закончите. 55-процентный стержень представляет собой более твердый сплав, и его немного легче сваривать.
Для этого ремонта мы выбрали сварочный электрод с 99-процентным никелевым покрытием и использовали этот электрод с насадкой для сварки электродом со сварочным аппаратом TIG. Мы установили TIG для работы на постоянном токе и отрицательной полярности и использовали мощность 75 ампер.
Для большинства чугунных деталей требуется предварительный нагрев перед сваркой.
Равномерно нагрейте всю деталь, чтобы свести к минимуму разницу температур сдвига при сварке. Вы можете предварительно нагреть деталь кислородно-ацетиленовой горелкой с наконечником в виде бутона розы. Просто подожгите деталь пламенем, пока она не станет горячей. Убедитесь, что вы не нагреваете какую-либо часть предмета до более чем тускло-красного свечения при просмотре в темной комнате.
Если вы соединяете две части, которые разошлись, верните их в исходное положение. Вы можете сделать на них несколько фасок, если они толстые и проникновение будет проблемой. Но особенно для автозапчастей вы хотите сохранить ключевые размеры.
1: Когда вы свариваете треснутую деталь, вы подвергаете ее сильному нагреву. Вы хотите быть уверены, что не приведете к дальнейшему распространению трещины, когда будете ее чинить! Итак, начните ремонт, просверлив два небольших отверстия на концах трещины. Это помогает снять внутренние напряжения, вызвавшие трещину, и позволяет выполнить ремонт, не вызывая дальнейшего повреждения.
Кроме того, отшлифуйте или отшлифуйте поверхность «кожи» вдали от зоны сварки. Эта оболочка имеет тенденцию поглощать примеси в процессе литья, и ее трудно сваривать.
Мы вырезали этот старый коллектор от британского спортивного автомобиля. Металл хороший и толстый, так что сварится очень хорошо.
Вы можете использовать свой аппарат для сварки TIG в качестве электродуховой сварки, что очень удобно, поскольку тогда у вас есть выбор работы на переменном или постоянном токе, а также вы можете выбрать полярность сварки в соответствии с используемыми материалами.
Помните, что на всех сварных швах необходимо удалить корку. Хорошая проволочная щетка никогда не повредит.
Готовый сварной шов можно отшлифовать или просто оставить приподнятым для большей поддержки детали.
2: Проверьте упаковку и документацию, прилагаемую к сварочным электродам, и начните с самой низкой номинальной мощности, подходящей для толщины сварного шва.
Начните с одного конца и медленно продвигайтесь вдоль трещины. Если вы не предварительно нагрели деталь, вы должны сваривать не более 1/2 дюйма за один раз, а затем останавливаться, чтобы нормализовать разницу температур в детали. Кроме того, останавливайте каждый дюйм или около того и удаляйте шлак и корку со сварного шва, прежде чем продолжить. Это также дает вам возможность убедиться, что трещина не расширяется и не распространяется.
3: Наконец, заварите отверстие на дальнем конце трещины, а затем, при необходимости, отшлифуйте или обработайте сварной шов. Если вы свариваете деталь, которая должна удерживать жидкости или газы, заглушите один конец и проверьте на наличие утечек. Небольшие дефекты сварного шва могут привести к образованию отверстий в материале и протечкам, когда деталь находится под давлением.
Сварка алюминия
Алюминий является наиболее распространенным цветным металлом, используемым в автомобилях.
Блоки двигателей, головки цилиндров, масляные поддоны, опоры подшипников, детали подвески и рулевого управления, панели кузова, конструктивные балки и другие детали могут быть изготовлены из литого или катаного алюминия.
Сварка алюминия является сложной задачей даже для опытных сварщиков. Наиболее распространенным методом, используемым для сварки алюминия, является TIG, но вы также можете использовать катушечную горелку и газ аргон, подключенный к вашему сварочному аппарату MIG. Если у вас есть кислородно-ацетиленовая горелка, вы также можете сваривать ею алюминий.
Работа со сварочным аппаратом MIG, оснащенным аргоном и шпульным пистолетом, ускоряет выполнение алюминиевых проектов. Вы должны использовать алюминиевую проволоку при проверке пистолета в магазине сварочных принадлежностей на предмет правильного материала. Если вы выбираете сварочный аппарат TIG для алюминия, аппарат должен быть настроен на работу на переменном токе. Сварка TIG постоянным током на алюминии приводит к проблемам с брызгами.
Вам также понадобятся алюминиевые стержни для сварки TIG.
Чистота даже важнее, чем обычно, при работе с алюминием, так как малейшие частицы смазки, пыли или частички черного металла вызывают точечную коррозию и шлак в сварном шве. Все алюминиевые детали, подлежащие сварке, должны быть тщательно очищены от масла или жира, а затем с ними следует обращаться осторожно.
По возможности используйте специальные алюминиевые пильные полотна и напильники. Это помогает предотвратить попадание мелких частиц железа или стали в алюминий. Даже мельчайшие частицы черных металлов в сварном шве загрязняют сварной шов, вызывая питтинг и пористость сварного шва.
Сварка алюминиевого масляного поддона
Для этого проекта мы адаптируем 2,5-литровый масляный поддон BMW для использования в 1,8-литровом двигателе, удалив примерно полдюйма из середины поддона. Помимо литого алюминиевого верхнего поддона, поддон картера из штампованной стали также нуждается в модификации.
И когда все будет готово, два поддона должны выровняться в отверстиях для болтов, а сопрягаемые поверхности должны быть достаточно гладкими, чтобы обеспечить герметичность. Это тонкая работа.
1: Тщательно очистите все детали в стиральной машине, затем прокалите алюминиевый верхний поддон в промышленной печи для удаления масла и жира. Когда они будут чистыми, отметьте место, чтобы сделать надрезы.
2: Отрежьте алюминиевый верхний поддон с помощью специального алюминиевого пильного диска, а штампованный стальной поддон — с помощью ленточной пилы по металлу. Затем используйте специальный алюминиевый напильник, чтобы сгладить и обрезать края алюминия, где вы собираетесь сваривать. Кроме того, снова протрите края, чтобы сохранить чистоту.
3: Закрепите алюминиевые детали на стальном столе. Это важно по двум причинам. Во-первых, вы хотите, чтобы детали оставались идеально выровненными, пока вы их скрепляете.
Вторая причина заключается в том, что алюминий имеет тенденцию коробиться при сварке, и вы хотите убедиться, что сопрягаемая поверхность остается как можно более плоской.
4: Включив сварочный аппарат на среднюю мощность, прикрепите две половинки на место в нескольких местах вдоль сопрягаемой поверхности. Затем постепенно заполняйте всю длину детали сварным швом. Важно дать каждому сегменту остыть, прежде чем переходить к следующему шагу, чтобы предотвратить деформацию.
5: Техника сварки алюминия заключается в перемещении дуги и создании горячей точки расплавленным алюминием, затем вдавливании небольшого количества сварочного стержня, чтобы заполнить зазор, затем сдвиньте его на пару миллиметров и повторите.
На алюминиевом верхнем поддоне и штампованном стальном поддоне отмечены места, откуда мы собираемся удалять материал.
Две части верхнего масляного поддона очищены, напилены и готовы к сварке.
Обратите внимание, что в этом случае глубина двух частей не одинакова. Нам нужно заполнить эти зазоры сваркой.
Установка детали на место в нескольких точках вдоль линии сварки помогает избежать деформации детали. Если сварить сплошным швом с одной стороны на другую, деталь деформируется.
Посмотрите, как техника нагрева, толчка и перемещения дает хороший равномерный результат. Обратите внимание на небольшое истирание и загрязнения с правой стороны — мы могли бы быть чище!
Расплавленный алюминий капнул внутрь, и его необходимо удалить, прежде чем можно будет наложить внутренний сварной шов. Обратите внимание на V-образные канавки по бокам.
Когда валик будет готов и нарастит на сопрягаемые поверхности прокладки, используйте специальный напильник, чтобы выровнять и сгладить поверхность.
Готовая сопрягаемая поверхность. Мы хотим использовать герметик для прокладок, но он будет работать хорошо.
Линейка показывает, что в результате нашей работы есть небольшая деформация. Другую кастрюлю делаем таким же образом, чтобы она лучше подходила.
Закрепите обе стороны стального поддона на месте болтами, затем приварите, чтобы убедиться, что отверстия под болты и контуры сопряженных поверхностей совпадут.
Соедините две половинки формы вместе в нескольких местах, прежде чем надевать валик. Это помогает избежать деформации.
Тепловое перемещение для наложения валика на штампованную сталь. Будьте осторожны с теплом при сварке — вы же не хотите сжечь деталь или проделать в ней дыру.
После сварки снаружи снова пройдитесь изнутри, чтобы закрыть все отверстия, которые могут протекать.
Готовый продукт. На это ушло около двух часов, и использовалась всего пара алюминиевых и пара стальных сварочных прутков.
6: При сварке наружной стороны спилите любые потеки, которые образовались внутри.
Затем повторите сварку вдоль внутренней стороны — эта часть должна удерживать масло без утечек. Обратите внимание на V-образный паз на каждом конце сопрягаемой поверхности прокладки. Соберите это с помощью сварочного стержня, затем отшлифуйте и разгладьте.
7: Когда закончите, возьмите линейку и поднесите ее к детали. Несмотря на все наши усилия, алюминий все же немного деформировался при охлаждении. Есть несколько способов исправить это. Если бы материала было достаточно, мы могли бы отнести деталь в механический цех и обработать ее плоско, но поскольку поддон присоединяется только одним способом, а верхний поддон лишь слегка деформирован, мы просто убедимся, что две половинки подходят друг к другу. Другой.
8: С помощью небольшой шлифовальной машины, проволочной щетки и напильников подготовьте края поддона из штампованной стали для сварки. Эту часть можно было выполнить с помощью сварочного аппарата MIG, но мы решили оставить TIG.
Конечно, вы должны переключиться на стальной сварочный пруток и на этот раз использовать более низкий уровень мощности постоянного тока, потому что эта часть работы связана со сталью. Чтобы получить хорошую посадку, надежно закрепите две части поддона на своих местах. Важно, чтобы отверстия под болты совпадали, а сопрягаемые поверхности прокладки были одинаковыми для герметизации маслом.
9: Как и прежде, соедините две детали вместе в нескольких местах, чтобы зафиксировать их на месте, не вызывая деформации. Штампованная листовая сталь может быть очень тонкой, поэтому уменьшите мощность сварки. Эти прихваточные швы также помогают обеспечить хорошее проплавление без риска прогорания тонкой стали сковороды.
10: Используйте тот же метод нагревания, чтобы наложить валик вдоль сварного шва листовой стали. Пройдитесь по кастрюле снаружи, прочно закрепив ее болтами. Затем снимите кастрюлю и повторите буртик внутри, чтобы заполнить возможные утечки.
11: Наконец, отшлифуйте сопрягаемую поверхность стального поддона и убедитесь, что все болты аккуратно крепятся к алюминиевому верхнему поддону. Штампованный листовой металл поддона немного прогибается, поэтому он должен хорошо удерживать масло, и все болты также совпадают. Это хорошо сделанная работа!
Работа с медью, свинцом, оловом, бронзой и другими сплавами и другие мягкие металлы. Но эти материалы заслуживают упоминания и могут быть полезны современному слесарю.
Медный лист используется для вырезания нестандартных прокладок и изготовления некоторых декоративных элементов. Чистая медь довольно мягкая и прощающая, поэтому вы можете формировать ее в холодном виде без особых проблем. Вы также можете использовать более толстые медные и латунные листы, чтобы сделать детали для украшения двигателя, такие как кронштейны для крепления катушки зажигания, указатели ВМТ для коленчатого вала и другие ненагруженные элементы.
Свинец можно увидеть в машине, когда слезает краска. Свинец имеет серебристый вид и демонстрирует больший эффект от взрыва носителя.
Такой кусок медного листа можно легко разрезать на специальную прокладку для антикварных изделий.
Свинец имеет давнюю историю в автомобилестроении. Он использовался в качестве основного наполнителя кузова до изобретения наполнителей кузова на основе пластика. Поскольку свинец плавится при температуре немногим более 600 градусов по Фаренгейту, вы можете расплавить его с помощью пропановой горелки и позволить ему заполнить вмятину или щель, а затем легко напилить или отшлифовать до гладкости. Делать кузовные работы со свинцом — это очень круто и старомодно, но, очевидно, примите все необходимые меры предосторожности, поскольку свинец ядовит для вашего мозга и со временем будет накапливаться в вашем теле.
В старых автомобилях, особенно в европейских, вы, скорее всего, найдете втулки и другие детали из бронзы.
Бронза — это сплав меди и олова, и хотя она тверже меди, большую часть времени найденные бронзовые детали будут безнадежно изношены. Замените их новыми втулками из нейлона, делрина или алюминия. Оригинальный автопроизводитель использовал бронзу, потому что она была недорогой, а теперь у нас есть лучшие материалы.
Пайка и пайка
Иногда вам нужно соединить разнородные металлы. Обычно это связано с крепежом — вы прикручиваете алюминиевую часть к стальной части или приклепываете алюминиевый лист к стальному кузову. Но иногда для взаимодействия требуется водонепроницаемое уплотнение или просто более прочное соединение.
Большинство людей использовали паяльник для электрических компонентов. Теория проста: вы плавите мягкий металлический наполнитель (обычно это сплав свинца, олова и других металлов) и используете его для приклеивания проволоки к фиксированной точке. Расплавленный припой течет и прилипает к обеим частям, а когда он замерзает, у него достаточно сцепления, чтобы удерживать деталь на месте до тех пор, пока никто не потянет ее слишком сильно.
Пайка и пайка являются аналогичными процессами в том, что они создают соединение без плавления одной из двух (или более) частей, удерживаемых на месте припоем. Паяльные стержни обычно изготавливают из бронзы, латуни или других сплавов мягких металлов.
Если посмотреть на металл под микроскопом, он не такой гладкий, как кажется невооруженным глазом. Он имеет шероховатую поверхность с пространством между металлическими кристаллами и волокнами. Расплавленные припои будут течь и впитываться в эти пространства, а когда припой замерзнет, он прилипнет к окружающему металлу.
Этот бачок радиатора изготовлен из меди, швы пропаяны, а фитинги AN также припаяны к бачку. Так прослужила не менее 20 лет без утечек.
Вы можете воспользоваться этим свойством и использовать пайку для соединения алюминия со сталью, например, сварным соединением. Соединение может быть таким же прочным, как сварной шов, но убедитесь, что пайка очищена, собрана и выполнена хорошо, чтобы получить эту прочность.
Изготовители гоночных автомобилей иногда припаивают детали подвески к гоночному автомобилю, так что в случае аварии эта часть ломается. Если подвеска оторвется при аварии, не повредив раму, ее легко починить! Это требует детального знания нагрузок на детали при нормальной эксплуатации и высокой степени уверенности в качестве пайки.
На многих старых автомобилях вы также можете увидеть свидетельства того, что пайка использовалась для устранения трещин в листовом металле и для заполнения небольших отверстий. Это было популярно среди любителей в течение многих лет, потому что пайка была проще и дешевле, чем ремонт сваркой.
Чаще всего пайка используется для сборки радиаторов, масляных радиаторов и других резервуаров, требующих герметичного уплотнения. Но этот процесс несколько утратил популярность с появлением широко распространенной и доступной сварки TIG для алюминия.
Для пайки соединения обе детали должны быть абсолютно чистыми. Также помогает проволочная щетка на сопрягаемых поверхностях.
Две части должны быть соединены как можно плотнее. Пайка не так хороша для заполнения зазоров, как сварка, потому что прочность пайки зависит от максимального сцепления с окружающим металлом.
Следствием того, чтобы обеспечить сцепление деталей, подлежащих пайке, является наличие достаточной сопрягаемой поверхности. Если вы попытаетесь припаять встык два тонких куска металла, вы не получите прочного соединения, потому что металла очень мало, чтобы выдержать припой всего один или два квадратных миллиметра. Поэтому всегда планируйте перекрытие деталей при пайке. Припой впитывается в соединение между двумя частями, что делает его прочным. Вы также можете припаять фитинги (например, алюминиевые и сантехнические) к латунным или алюминиевым резервуарам. Сопрягаемая поверхность невелика, но опять же, это ненапряженный сустав.
1: Возьмите два куска алюминия и тщательно очистите их. Немного обработайте их проволочной щеткой, чтобы придать им шероховатость. Убедитесь, что они хорошо подходят друг к другу — два куска плоской 1/8-дюймовой пластины хорошо подходят для пайки.
2: Положите кусочки алюминия на сварочный стол и насыпьте на них флюс для пайки алюминия. Перекрывайте их как минимум на дюйм. Убедитесь, что они плотно прилегают друг к другу без зазоров!
3: Начните пайку, нагрев окружающий металл до температуры плавления прутка, но не выше! Вы поймете, что это правильно, когда флюс растает и начнет течь. Сам алюминий в этот момент далек от плавления.
4: Окуните алюминиевый стержень для пайки в банку с флюсом и немного подайте в горячую зону. Он должен растаять и образовать лужу. Пусть лужа стечет в сустав и заполнит область. Затем продолжайте, как будто вы свариваете соединение газовой сваркой. Расплавленный стержень будет фактически всасываться в паяное соединение.
5: Переверните изделие и таким же образом припаяйте соединение внахлест с другой стороны. Затем дайте деталям нормально остыть и проверьте пайку.
Написано Расселом Найбергом и Джеффри Цуршмейде и опубликовано с разрешения CarTechBooks
Если вам понравилась эта статья, вам понравится вся книга.
Нажмите кнопку ниже, и мы вышлем вам эксклюзивное предложение на эту книгу.
Ремонт литья
ГОРЯЧАЯ трансформация!
Как этот сильно сломанный и грязный выпускной коллектор превратился в этот обновленный и изысканный кусок автомобильного чугуна? Продолжайте читать, чтобы узнать больше о нашем процессе.
Выпускной коллектор Chrysler 1955 года выпуска был доставлен к нам из Аризоны для ремонта. Он был сломан в трех местах, и из-за его возраста нам нужно было оценить наилучшую технику для сварки такой хрупкой детали.
При сварке чугуна на старинном выпускном коллекторе необходимо учитывать количество грязи и углеводородов, всосавшихся в отливки. Это может затруднить работу, потому что грязь выходит во время сварки. С чем-то таким старым невозможно удалить всю грязь, потому что она на самом деле находится внутри отливки. Крайне важно очистить чугун как можно лучше, прежде чем приступать к ремонту.Дробеструйная обработка — отличный способ тщательно очистить внешнюю поверхность отливки.
Первым шагом была прихватка деталей на месте (рис. 1-5)
Мы предварительно нагреваем отливку в нашей печи, и температура предварительного нагрева зависит от того, какой метод сварки вы будете использовать. Мы выбрали сварку пайкой, потому что температура предварительного нагрева не такая высокая, как при использовании чугунного стержня, и лучше всего подходит для такой старой детали.
Пайка после предварительного нагрева
После того, как все сварено, приступают к косметическому ремонту. Мы стремимся к тому, чтобы места сварки выглядели такими же красивыми, чистыми и свежими, как если бы они были новыми. Шлифуем сварные швы и наплавляем выпускной коллектор, так подгонка будет правильной.
Готовое изделие
Один из самых сложных и трудоемких ремонтов на сегодняшний день!В этой отливке была небольшая трещина, когда ее принесли «сварщику» для ремонта.
По сути, он взял сварочный аппарат и РАЗРУШИЛ отливку.Весь белый контур — это трещины, напряжение от сварки электродами фактически разорвало эту отливку. Они продолжали сварку и сварку, перекрывая бусины, и становилось все хуже и хуже.
1-й шаг – очистить его и подвергнуть дробеструйной обработке
2-й шаг – обработать отливку магнитным флюсом для обнаружения всех поверхностных и подповерхностных трещин для восстановления несущей конструкции отливки)
После этого место трещины было подготовлено, заземлено, а затем сварено пайкой.
После сварки пайкой сварной шов был подготовлен, а отливка повторно профлюсована. Была сделана третья процедура, называемая пиннингом.
После дробеструйной обработки и закрепления отливки следующим шагом было нанесение эпоксидного герметика (которое представляет собой зеленое покрытие).Затем нужно было расточить и изготовить втулку. Затем втулку необходимо было запрессовать.
Затем отливка была полностью собрана, и вся отливка была покрыта окончательным наружным герметиком.
Затем мы нанесли внутреннее покрытие для герметизации внутренней части
Затем на всю отливку было нанесено окончательное покрытие из высокотемпературного чугуна серого цвета и отвердено в печи.Успешно выполнен ремонт. Фотографии не отражают количество повреждений, которые эта отливка понесла из-за неправильной сварки электродом, которую почти никогда не следует делать на этих старых отливках. К счастью, нам удалось его отремонтировать, и заказчик смог снова запустить свой проект.
Интересный проект:
3 Необработанные отливки впускного коллектораОбработка сторон
Вид необработанной голой отливки и вид обработанных сторон
Специальная оснастка для обработки отверстия под магнето/распределителем под требуемым углом
Настоящая машина, принадлежащая Джеку А.
Посмотрите ниже, чтобы увидеть процесс ремонта этого драгоценного кусочка истории,
Как мы пришли от этого….. к тому…Боковые окантовки желтого цвета, полностью треснувшие
Очищен и подвергнут дробеструйной обработке, чтобы показать больше площади трещины
Подготовлено к ремонту
Ремонт деталей с помощью сварки пайкой
Штифты и сварка пайкой
Зона штифтов и замков
Нанесение окончательного пористого барьерного покрытия
Термическое отверждение три!
Готовое изделие«Тепловой стояк» для Buick 1930 года
Устаревший сломанный и не подлежащий ремонту радиатор для Buick 1930 года выпуска.
После объединения наших навыков, ноу-хау и деталей мы получили готовый продукт! Еще одна часть сохранена и очень счастливый клиент!
Отзыв клиента:
«Я просто хотел сообщить вам, что вы проделали отличную работу по ремонту «радиатора» для моего Бьюика 1930 года. Я буду рад порекомендовать вас своим друзьям, которым нужно сделать что-то подобное. Еще раз спасибо .» Томми СНесмотря на то, что это не ремонт литья, это экстраординарный ремонт, который могут выполнить только несколько мастерских в Соединенных Штатах.
Титановая выхлопная система стоимостью 3000 долларов США, которая больше не предназначена для гоночных мотоциклов Ducati. Что вы делаете, когда он дует в сторону?
TIG-сварка Титана требует специального процесса, специального стержня и большого количества технических знаний.
Готовый шов и еще одна сохраненная деталь!!
С годами «старое железо» становится все труднее и труднее достать, и иногда у вас есть этот идеальный номерной двигатель только для того, чтобы найти трещины.Ремонт отливок требует специальных знаний, а также оборудования, которое у нас есть. Будь то чугун или алюминий, латунь или бронза, мы можем это отремонтировать!
Трещины в долине подъемника и внешние трещины от замерзания обработаны магнитным флюсом, испытаны под давлением для определения протяженности трещин
Трещина от заморозки
Начало ремонта. Головная и основная крышки крепятся болтами и затягиваются на месте для создания и имитации напряжения блока во время процесса ремонта.
Линия трещины просверлена и снята фаска, сделан первоначальный ремонт штифта. Отверстия со скошенной кромкой завариваются, чтобы зафиксировать трещину вместе, затем между сварными швами используются специальные конические штифты, чтобы заделать трещину.
- Темно-серый оттенок достигается через 4-6 часов при комнатной температуре при использовании клея J-B Weld.