Сварочные электроды с основным типом покрытия марки УОНИ13/55 — Герон
Дата последнего обновления: 11 февраля, 2017 Автор: Библиотечка Герон
В ручной дуговой сварке широко используются сварочные электроды с основным типом покрытия, матрицу которого составляют мрамор (основа карбонат кальция) и плавиковый шпат (основа фтористый кальций) взятые в определенной пропорции. Фтористо-кальциевые электроды главным образом используют в электродах для сварки наиболее ответственных конструкций, например в марках электродов УОНИ13/55; УОНИ13/45; LB-52U; ОК.53.70; ИТС-4; АНО-ТМ; АНО-Т…
Физические свойства основного покрытия электродов предопределяют наиболее полное удаление неметаллических включений из металла шва, а диссоциация карбонатов обеспечивает надежную газовую защиту сварочной ванны. Поэтому сварные соединения, выполненные такими электродами, должны быть пластичными, обладать высокой стойкостью против холодных трещин и хрупкого разрушения.
Для общего представления о качественном уровне электродов с основным покрытием, выпускаемых в настоящее время передовыми электродными заводами в России, была проведена их выборочная проверка на предмет содержание диффузионного водорода (Ндиф) в наплавке. При проверке электродов марки УОНИ13/55 и ее аналогов (выпущенных в РФ в 2014-2016гг) в наплавляемом металле выявили сильный разброс по содержанию диффузионного водорода от 7 до 16 см3 на 100 г наплавки. Для сравнения, в наплавках, выполняемых УОНИ13/55, серийно выпускаемыми в 80-х годах, содержание Ндиф колебалось от 3,5 до 6 см3 на 100 г. К лучшим, по этой характеристике, сейчас можно отнести электроды LB-52U (Kobe Steel), выпускаемые в Японии — 1,5-2,5 см 3 на 100г. Из полученных результатов видно, что общий уровень качества современных среднестатистических электродов с основным покрытием существенно снизился, относительно выпускаемых во времена СССР.
Более низкое содержание Ндиф – это важное преимущество, способствующее повышению стойкости металла шва против коррозии и хрупкого разрушения. Возрастающие требования к надежности судовых сварных конструкций, применение новых высокопрочных марок сталей, запрос на долговечность свариваемых конструкций, увеличивающиеся объемы сварочных работ в районах крайнего севера, повышают спрос на электроды с основным покрытием. Но только качественные электроды могут обеспечить надежность сварных конструкций, работающих в условиях статических и динамических знакопеременных нагрузок, когда металл сварных швов, будет обладать высокой ударной вязкостью при пониженных температурах, и отличаться длительной прочностью (быть не склонными к ускоренному старению).
Наряду с преимуществами, фтористо-кальциевые электроды обладают и существенными недостатками, чувствительностью к порообразованию при увлажнении покрытия, а также к наличию влаги или окалины на свариваемых кромках, низкими сварочно-технологическими свойствами (СТС), выражающимися в крупнокапельном переносе электродного металла, и в низкой стабильности горения дуги, особенно на переменном токе. Это обусловлено наличием, входящего в состав покрытия фтора, содержащегося в плавиковом шпате. Увеличение его содержания приводит к снижению устойчивости горения дуги, а сокращение уменьшает защиту дугового промежутка от водорода. К сожалению, в последние годы наметилась общая тенденция на сокращение содержания фтора в рецептурах покрытий электродов, производителям это дает некоторое улучшение СТС, но в ущерб качеству сварки. Следует отметить, что электроды нельзя оценивать, опираясь только на СТС, в первую очередь они должны соответствовать своему назначению и заявленным характеристикам.
Принимая во внимание недостатки, свойственные электродам с основным покрытием, ЗАО «Герон» доработало марку УОНИ13/55. В результате полученная хорошо сбалансированная шлаковая система позволила уменьшить размер капель при переносе металла и обеспечила более стабильное горение дуги. При этом благодаря высоким стабилизирующим свойствам покрытия удалось увеличить эластичность дуги, что дало возможность вести сварку в монтажных условиях от источников питания с напряжением холостого хода от 65 В как на постоянном, так и на переменном токе. Вследствие технологических преимуществ, отмеченных выше, сварщику легче манипулировать электродом и проще контролировать процесс сварки, а это способствует повышению качества шва.
Химический состав | Углерод | Кремний | Марганец | Сера | Фосфор |
Нормативный | не более 0,12 | 0,18-0,6 | 0,65-1,6 | не более 0,03 | не более 0,035 |
Типичный | 0,09 | 0,30 | 1,05 | 0,011 | 0,024 |
Механические свойства (требования) | Временное сопротивление разрыву, МПа | Предел текучести, МПа | Относительное удлинение, % | Ударная вязкость, Дж/см2 | ||||||
KCV 00C | KCV —200C | KCV —400C | KCV —500C | KCU +200C | KCU -300C | KCU -600C | ||||
ГОСТ9467 (минимальные) | 490 | 375 | 20 | — | — | — | 130 | 35 | — | |
Речной Регистр (минимальные) | 490-560 | 375 | 22 | 59 | — | — | — | — | — | — |
Типичные значения | 530 | 440 | 30 | — | 155 | 122 | 110 | — | — | 123 |
Норматив | 8,5-9,6 |
Типичные значения |
Электроды УОНИ13/55 производства ЗАО «Герон» подходят для выполнения качественных заполняющих и облицовочных слоев. При этом типичное содержание Ндиф в наплавленном металле составляет 5-6 см3 на100 г наплавки, что отвечает запросам самых требовательных заказчиков. Свойства и технические характеристики электродов в полном объеме соответствуют требованиям ГОСТ9467, предъявляемым к электродам типа Э-50А, а также РД 03-613-03 и нормативным документам, действующим для технических устройств опасных производственных объектов, поэтому электроды допущены к применению при изготовлении, реконструкции, монтаже и ремонте группы технических устройств: ПТО, КО, ГО, ОХНВП, ОТОГ, СК, НГДО, МО, ГДО. А также допущены для сварки ответственных судостроительных сталей нормальной прочности с классом Речного Регистра (относятся к 3 категории сварочных материалов). Назначение и основные технические характеристики электродов УОНИ13/55, производства ЗАО «Герон», сравнимы с заявленными показателям электродов ОК.53.70 ESAB.
Основное покрытие УОНИ 13/55 Э-50А
Покрытие электродов: основное, рутиловое, кислое, целлюлозное
Содержание:
- Назначение покрытия
- Размеры покрытия
- Виды покрытия
- Интересное видео
Электрод, предназначенный для соединения отдельных деталей, в большинстве случаев, представляет собой стержень из металла, который снаружи защищен специальным покрытием. Оно также известно под названием обмазка.
Покрытие электродов осуществляет функцию преграды между зоной сварки и воздухом, что исключает возникновение окислительного процесса. Обмазка применяется для электродов, предназначенных для соединения изделий из различных материалов, но имеет некоторые различия в зависимости от типов этих расходных элементов.
Назначение покрытия
Все виды электродов делятся на неметаллические, к которым относятся графитовые и угольные, и металлические. В свою очередь электроды, изготовленные из металла, разделяются на неплавящиеся и плавящиеся. Неплавящимся электродам покрытие не требуется, зато плавящиеся элементы нуждаются в защите. Эту функцию осуществляет специальная обмазка металлического внутреннего стержня, состоящая из нескольких компонентов.
Электроды с покрытием способствую образованию прочного, качественного шва без трещин и пор. Во время сварочного процесса образует оболочка из шлака, которая осуществляет защиту от негативного внешнего влияния. Она увеличивает время остывания соединения, благодаря чему из шва успевают выходить все посторонние включения, снижающие его качество.
Сварка покрытыми электродами обеспечивает стабильность горения дуги и простоту ее зажигания. Благодаря содержанию в обмазке ферросплавов из сварочной ванны происходит удаление кислорода — главного виновника образования пор в месте соединения.
Покрытие позволяет формировать облачко, состоящее из угарного и других газов. Оно осуществляет предохранение от окисления атмосферным воздухом. Насыщение расплава легирующими элементами улучшает качество соединения. Следствием удаления из расплава кислорода является процесс раскисления, что обеспечивается находящимися в обмазке таких веществ, как алюминий, титан, молибден, хром, марганец, графит. Эти компоненты более активно, чем кислород взаимодействуют с кислородом, связывая его.
Для придания соединению пластичности в обмазку добавляют бентонит и каолин. Для некоторых видов электродов в обмазку добавляют железный порошок, чтобы увеличить коэффициент наплавки.
Ручная дуговая сварка покрытыми электродами обеспечивает получение надежного и долговечного соединения металлических изделий.
Размеры покрытия
При осуществлении различных сварочных работ большую роль играет правильный выбор электродов. Чем большую толщину имеет свариваемое изделие, тем большим диаметром должен обладать электрод. В зависимости от этого выставляется величина тока на оборудовании.
Дуговая сварка покрытыми электродами требует грамотный выбор этих расходных элементов. При выборе электродов следует подвергать анализу величину размеров покрытия на нем. Каждое значение диаметра требует конкретную толщину покрытия. Обмазка наносится на определенной длине стержня.
Градация этого габарита, определенная в ГОСТе 9466-75, начинается с тонких, и заканчивается особо толстыми. Между ними находятся средние и толстые. Покрытия, имеющие статус тонких, обозначаются как «М», средние как «С». Толстые имеют обозначение «Д», а особо толстые носят обозначение «Г».
Эти буквы являются частью общего обозначения электродов с покрытием.
Для электродов, считающихся наиболее качественными, толщина обмазки находится в диапазоне от 0,5 до 2,5 миллиметров. У электродов с маленьким диаметром этот размер не превышает 0,3 миллиметра. Масса покрытия составляет примерно половину от значения общего веса расходного элемента.
Обмазкой, представляющей собой твердое пористое вещество, покрывают практически весь стержень, за исключением небольшого участка на его краю, размером приблизительно 20-30 миллиметров. Этот участок оставляют для того, чтобы поместить электрод в специальный держатель для его фиксации, что приводит к удобству работы с ним.
Виды покрытия
Виды покрытия электродов разделяются на некоторое количество групп, каждая из которых имеет свое обозначение. Типы покрытия электродов разделяются на:
- основное, обозначаемое как «Б», белого или бежевого цвета;
- кислое, обозначаемое «А», серого цвета;
- целлюлозное, имеющее обозначение «Ц», светло-серое с коричневатым оттенком;
- рутиловое, имеющее обозначение «Р», различных цветов, таких как серый, синий, зеленый, красноватый.
Также существуют покрытия смешанного типа, что отражается в их обозначении. Так, например, сочетание букв РЦ следует расшифровывать как рутилово-целлюлозное, а «РА» соответственно как рутилово-кислое. Буква «П» — обозначение других видов покрытий. Такая градация определяется наличием химических элементов, входящих в состав покрытия. Выбор покрытия следует осуществлять в зависимости от металлов, подвергаемых соединению.
Основное
Основное покрытие электродов содержит в основной массе карбонаты кальция и магния. Для того, чтобы произошло разбавление шлаковой корки в обмазку добавляют особый элемент в виде плавикового шпата. Это несколько ухудшает возможность работы при использовании переменного тока, поэтому электроды с основным покрытием рекомендуется использовать при работе с током постоянной величины.
Отличие этого вида покрытия состоит в том, что в образующейся газовой среде отсутствует водород, который может привести к образованию трещин холодного вида. Шов при использовании электродов с основным покрытием получается повышенной пластичности.
Большим преимуществом является возможность выполнения сварки при всех положениях, однако, следует учитывать, что шов вследствие значительной вязкости будет несколько выпуклым и не совсем эстетичным.
Кислое
Электроды с кислым покрытием обладают обмазкой, содержащей железную и марганцевую руды. Это способствует выделению на место сварки значительного количества кислорода. Результатом является повышение температуры и одновременно снижение поверхностного натяжения, что придает ему текучесть.
Увеличивается скорость сварочного процесса, но возникает опасность возникновения подрезов. Кислые электроды несут с собой некоторую опасность, поскольку в их покрытии содержатся оксиды марганца, обладающие токсичностью. Существуют марки электродов с кислым покрытием, однако более предпочтительными являются электроды с рутилово-кислым покрытием.
Целлюлозное
Соответственно названию основной элемент этого вида покрытия — целлюлоза. Также туда входят органические вещества в виде смол. Особенностью является то, что при сгорании в сварной дуге образуется значительное количество защитного газа. При этом шлака, наоборот, образуется мало.
Электроды с целлюлозным покрытием имеют некоторый недостаток, заключающийся в том, что при сварке появляются раскаленные брызги металла. Кроме того, металл шва имеет низкую пластичность. Это обусловлено наличием немалого количества водорода, выделяющегося при горении органических веществ.
Существующие марки электродов с целлюлозным покрытием характерны высокой скоростью осуществления сварочного процесса. К их достоинствам является возможность сварки во всех положениях, даже такому, при котором движение электрода происходит сверху вниз, что не под силу большинству электродов. Недостатками являются большое разбрызгивание горячего металла, образование подрезов на кромках, грубая поверхность получаемого шва.
Рутиловое
Такое покрытие содержит такой элемент, как природный концентрат рутил. Добавками являются полевой шпат, магнезит. Двуокись титана гарантирует легкое разжигание дуги. Брызг образуется немного.
Электроды обладают хорошими технологическими характеристиками. Вредность работы с ними менее, чем с другими электродами. Еще одно достоинство состоит в том, что зажигание дуги может происходить без непосредственного контакта электрода с поверхностью детали, поскольку пленка, образуемая в кратере, играет роль проводника. Особое значение это имеет, когда сваривание осуществляется короткими стежками.
Электродами можно осуществлять соединение даже загрунтованных поверхностей и шов при этом не будет уступать по прочности и надежности. Дуга обладает стабильностью, имеется возможность использования любого вида тока. Практически отсутствуют брызги раскаленного металла. Шов получается свободным от пор.
Интересное видео
Чем отличаются импортные и российские сварочные электроды
Технология соединения металлов с помощью сварки используется повсеместно. Современный рынок сварочных материалов может предложить не одно решение для выполнения одинаковых задач. Наряду с отечественными предприятиями свою продукцию в Россию поставляют зарубежные производители. Сопоставимы ли они по качеству?
Несмотря на то, что профессия сварщика считается вредной, кровь людей этой специальности обладает повышенной свертываемостью и содержит большее количество полезных микроэлементов. По этой причине таким посетителям всегда рады в донорских пунктах приема крови.
Швеция
Компания Elektriska Svetsnings-Aktiebolaget или сокращенно ESAB является известным производителем оборудования и расходных материалов для сварки. Сварочные электроды ESAB широко представлены на российском рынке. Они пользуются уважением и популярностью у специалистов. Продукция маркируется аббревиатурой ОК.
Одна из популярных марок электродов – ОК 53.70. Они работают на переменном или постоянном токе прямой полярности. Выпускаются с основным покрытием с низким содержанием водорода. Электроды применяются при сборке трубопроводов или других конструкций из низколегированных или малоуглеродистых сталей для односторонней сварки. Они обеспечивают стабильное горение дуги и надежную работу в любом пространственном положении. В результате их применения образуется плоский сварной шов с легко удаляемым шлаком и гарантируется качественная сварка корневого прохода с формированием обратного валика. Электроды прекрасно зарекомендовали себя в условиях крайнего Севера за счет высокой ударной вязкости при отрицательных температурах (100 Дж/см2 при -50 °С) и хороших механических свойств металла шва. Российский аналог ОК 53.70 – АНО-1М. Одно из его явных отрицательных качеств – образование большого количества шлака, препятствующего проведению сварочных работ. Также можно отметить неравномерную толщину покрытия.
Еще одна известная марка ESAB – ОК 46.00. Это универсальные электроды с рутиловым покрытием. У них очень легкий первичный и вторичный розжиг. Они обеспечивают отличное качество швов. Электроды очень удобны для наложения прихваток, заварки коротких швов или больших зазоров. Они не чувствительны к ржавчине и другим поверхностным загрязнениям. С ним легко смогут работать даже сварщики с низкой квалификацией. Применяются для сварки судовых, конструкционных и углеродистых сталей. Их российский аналог – АНО-4 с такими же недостатками, как и АНО-1М. Кроме этого для работы с АНО-4 характерно большое разбрызгивание металла, прерывающаяся дуга и затрудненное повторное зажигание.
Результат разбрызгивания металла
Германия
Еще одной страной, поставляющей в Россию сварочные электроды, является Германия. Известнейший производитель – Klockner. Одна из марок их продукции – Phoenix K 50. Они изначально разрабатывались для использования при сборке трубопроводов. Электроды обеспечивают отличное качество корневого шва при односторонней сварке. Для них характерен чистый химический состав и хороший показатель ударной вязкости (47 Дж/см2 при -30 °С). Они обеспечивают качественный капельный перенос металла. Phoenix K 50 применяются для сварки трубопроводов и котельного оборудования. Их российским аналогом являются АНО-1М и Э-138/50Н. Для последних отрицательным качеством является затрудненный поджиг.
Электроды Kessel 5520 Mo этого же производителя выпускаются с основным покрытием. Они применяются для работы с низколегированными или углеродистыми сталями, имеющими предел прочности до 640 МПа. Электроды используются при строительстве мостов и трубопроводов. Они обеспечивают отличное качество швов при любых погодных условиях. Их российские аналоги ВСФ-65М или ВСФ-65У обеспечить такого не могут. Главный их недостаток – склонность к образованию пор и повышенная разбрызгиваемость металла.
Качественные электроды обеспечивают бездефектные швы
Япония
Японская компания Kobe Steel, известная под торговой маркой Kobelco, маркирует свою продукцию аббревиатурой LB. Одна из известных марок электродов – LB-52U. Они имеют основное покрытие с низким содержанием водорода, что существенно улучшает все параметры сварного шва. Электроды разрабатывались для сварки соединений, изготовленных из разных сталей. Их применяют при сборке резервуаров, трубопроводов и морских сооружений. Изделия обеспечивают стабильную дугу при работе, проплавление по всей длине шва и высокую ударную вязкость металла шва (60 Дж/см2 при -40 °С). При их одностороннем использовании получается бездефектный корневой шов. Ближайший отечественный аналог этих электродов – СЭЛБ-52. Он создавался как заменитель LB-52U, но при более низкой цене обеспечить такое же бездефектное качество швов пока не может.
В целом электроды для сварочных работ российского производства выигрывают в цене, но уступают по качеству зарубежным аналогам. Большинство из них характеризуется нестабильными характеристиками, составом и толщиной покрытия, повышенной разбрызгиваемостью металла. Последний параметр подавляющим большинством отечественных предприятий регламентируется в пределах 2-10 %, в то время как у зарубежных изготовителей 0,5-2 %. Вероятными причинами более низкого качества российских электродов являются нарушения технологии производства и недостаточный контроль при их изготовлении. Этим и объясняется популярность импортных электродов.
Сварочные электроды, сварочная проволока — EWM AG
- Марки проволочных электродов
- Нелегированные и низколегированные стали
- Высоколегированные стали и никелевые сплавы
- Алюминий и алюминиевые сплавы
- Прочие материалы
Марки проволочных электродов
Проволочные электроды для сварки MIG/MAG нелегированных сталей и мелкозернистых конструкционных сталей нормированы в стандарте EN 440. По химическому составу стандарт различает 11 марок сварочных электродов. Однако он упоминает также такие марки сварочных электродов, которые используются лишь в других странах Европы. В Германии для нелегированных сталей в значительном объеме применяются лишь марки G2Si1, G3Si1 и G4Si1. Они имеют возрастающее в указанной последовательности содержание кремния и марганца, в частности, в среднем 0,65-0,9 % кремния и 1,10-1,75 % марганца. Для мелкозернистых сталей применяются также марки G4Mo, G3Ni1 и G3Ni2. Порошковые электроды для сварки этих сталей указаны в EN 758. По составу наполнителя различают электроды с рутиловым, основным покрытием и металлическим порошком. Наряду с порошковыми сварочными проволоками для сварки MIG/MAG в стандарте EN 758 нормированы также порошковые проволоки с самозащитой, которыми сваривают без подачи защитного газа. Они часто используются для наплавки. Проволочные электроды для сварки жаростойких сталей нормированы в стандарте EN 12070, порошковые электроды для тех же сталей – в стандарте EN 12071. Проволочные электроды очень разнообразны – от варианта, легированного молибденом, и проволок с содержанием хрома 1, 2,5, 5 и 9 % до проволочного электрода с содержанием хрома 12 %.
Из других легирующих элементов присутствуют молибден, ванадий и вольфрам. Порошковые электроды содержат до 5 % хрома. Проволочные электроды для сварки нержавеющих и жаростойких сталей нормированы в стандарте EN 12072; порошковые электроды для тех же сталей – в стандарте EN 12073. Стандарты различают присадки для мартенситных/ферритных хромистых сталей, аустенитных сталей, ферритных/аустенитных сталей и полностью аустенитных коррозионностойких сталей, а также специальные и жаропрочные марки.
Нелегированные и низколегированные стали
Нелегированные и низколегированные стали свариваются в атмосфере газовой смеси M1, M2, M3 или в чистой двуокиси углерода. Однако из-за малого образования брызг, прежде всего в верхнем диапазоне мощности, в Германии доминируют газовые смеси. Эти стали обычно хорошо поддаются сварке методом MAG. Исключение составляют высокоуглеродистые марки, например, E 360, содержащие ок. 0,45 % C. Из-за большого провара процесса наплавляемый металл при перемешивании принимает в себя достаточно много углерода, что создает риск горячих трещин. Это можно устранить мерами, снижающими провар, а вместе с ним и перемешивание. К ним можно отнести выбор более низкой силы тока, а также сварку на утекающем наплавляемом металле – Осторожно: опасность непровара. Поры образуются на нелегированных и низколегированных сталях в основном из-за азота. Он может появляться из-за перемешивания при сварке сталей с высоким содержанием азота, например, нитрированных сталей. Однако в большинстве случаев азот попадает в металл через неполноценный колокол защитного газа из воздуха. Надежную защиту можно обеспечить, если настроить правильный расход защитного газа и исключить завихрения его потока, например, из-за брызг в сопле защитного газа или нестабильности процесса. Двуокись углерода как защитного газа менее чувствительна к этому виду порообразования, чем газовые смеси. При использовании газовой смеси чувствительность снижается с повышением содержания CO2.
Высоколегированные стали и никелевые сплавы
Эта группа материалов также хорошо поддается сварке методом MIG/MAG. В качестве защитного газа для высоколегированных сталей применяются смеси аргон/кислород с содержанием кислорода 1-5 % (M1.1) или аргон с содержанием CO2 до 2,5 % (M1.2). Серьезным недостатком при сварке коррозионностойких сталей является оксидная пленка, остающаяся после сварки на шве и рядом с ним. Ее следует полностью удалить щеткой, травлением или струйной обработкой, прежде чем заготовка будет направлена на производство, т. к. она ухудшает коррозионную стойкость детали. Затраты на очистку для швов, сваренных методом MAG, выше, чем при сварке MMA, при которой слой шлака перекрывает кислороду при высоких температурах доступ к поверхности шва. Поэтому экономические преимущества частичной механизации сварки могут быть упущены из-за более высоких затрат на доработку. CO2-содержание газовые смеси в этом отношении лучше, чем O2-содержащие. Поэтому их применение расширяется. Однако доля двуокиси углерода в защитном газе не должна быть слишком высокой, т. к. газ, распадающийся в сварочной дуге ведет к обуглероживанию наплавляемого металла, а вместе с этим – к снижению коррозионной стойкости.
Поэтому допустимое содержание CO2 ограничено 5 %. При сварке коррозионностойких сталей следует избегать перегрева, т. к. из-за выделения карбида хрома он может привести к охрупчиванию и снижению коррозинной стойкости. Поэтому следует контролировать внесение тепла, время от времени давать рабочему материалу возможность промежуточного охлаждения, делая паузы для его остывания. При работе с материалами из группы полностью аустенитных сталей применяется также «холодная» сварка для избежания горячих трещин. Поскольку аустенитные стали не охрупчиваются в присутствии водорода, к аргону для увеличения производительности (повышение скорости сварки) можно добавлять несколько процентов водорода. Однако из-за опасности появления пор содержание h3 не должно превышать 7 %. При этом, дуплексные стали, обладающие двухфазной структурой из аустенита и феррита, имеют склонность к трещинообразованию, вызванному водородом. Никелевые сплавы как правило свариваются методом MIG в среде аргона. У чистого никеля и некоторых сплавов небольшие добавки водорода могут снижать напряжения поверхности и тем самым улучшать рисунок шва.
Алюминий и алюминиевые сплавы
Алюминиевые материалы соединяются сваркой MIG. В качестве защитного газа как правило применяется аргон. Из-за высокой теплопроводности алюминия добавки гелия здесь оказываются весьма эффективны. Как уже говорилось, гелий улучшает теплопроводность и теплоемкость атмосферы защитного газа. Это обеспечивает более глубокий и широкий провар. Там, где глубокий провар не требуется, например, при сварке тонких листов, при той же форме провара сварка будет идти быстрее. Толстые сечения алюминия из-за высокой теплопроводности материала необходимо подогревать. Это не гарантирует достаточного провара, но снижает склонность к порообразованию, т. к. наплавляемый материал имеет больше времени для дегазации во время застывания. При использовании защитных газов, содержащих гелий (традиционное содержание – 25 или 50 %), подогрев можно уменьшить, а при малой толщине стенки можно вообще отказаться от подогрева. Это частично компенсирует более высокую стоимость гелий-содержащих газов. Сложности в устранении тугоплавкой оксидной пленки на ванне отсутствуют при сварке MIG, т. к. положительный полюс находится на электроде (катодная очистка). Тем не менее, рекомендуется удалять оксидную пленку непосредственно перед сваркой шабровкой или очисткой щеткой, поскольку она гигроскопична и вносит водород в наплавляемый металл. Водород – это единственная причина порообразования при сварке материалов, содержащих алюминий. Алюминий в жидком состоянии обладает относительно высокой растворимостью для водорода, однако в твердом металле этот газ практически не растворим. Поэтому любой водород, попавший в наплавляемый металл во время сварки, должен покинуть его до застывания металла, чтобы исключить порообразование. Это не всегда возможно, особенно при обработке толстых сечений. Поэтому при обработке алюминиевых материалов в случае большой толщины стенки добиться швов, полностью чистых от пор, практически невозможно. Полезный эффект подогрева ранее уже упоминался. Сплавы AlMg и AlSi при содержании Si ок.
1 % или содержании Mg ок. 2 % имеют склонность к появлению горячих трещин при сварке. Эту область сплавообразования при выборе присадочных материалов следует избегать. В большинстве случаев проволочный электрод с более высоким легированием будет лучше, чем другой аналогичный.
Прочие материалы
Кроме уже названных материалов сваркой MIG обрабатываются также медь и ее сплавы. Чистую медь из-за ее высокой теплопроводности приходится подогревать до высокой температуры во избежание непроваров. Наплавляемый материал бронзовой проволоки, например, из алюминиевой или оловянной бронзы, обладает хорошими свойствами скольжения. Поэтому они применяются для нанесения твердых наплавок на поверхности скольжения. При таких наплавках на черные металлы надлежащими мерами следует добиваться тонкого провара, т. к. железо имеет низкую растворимость в меди. Оно включается в наплавляемый материал в форме горошин и снижает технические характеристики. Условия при MIG-пайке аналогичны. Этот метод применяется, например, для соединения оцинкованных листов в автомобилестроении. В качестве присадок используются проволочные электроды из кремниевой или оловянной бронзы. Низкая температура плавления этих сортов бронзы снижает испарение цинка. Образуется меньше пор, и защита, которую обеспечивает слой цинка, сохраняется вплоть до шва с обратной стороны листов. При этом провар по возможности не должен заходить в саму сталь. Соединение должно быть достигнуто, как и при высокотемпературной пайке, только за счет сил диффузии и адгезии. Это достигается благодаря точному выбору сварочных параметров и особому положению горелки, благодаря которому сварочная дуга горит только на жидкой сварочной ванне.
Проволочные электроды MIG/MAG в магазине
Загрузить справочник по сварочным расходным материалам
Типы и марки сварочных электродов
Ниже, по возможности, приводятся наиболее распространенные марки электродов для сварки, сгруппированные по типам.
Электроды для сварки углеродистых и низколегированных сталей
Получение металла шва, равнопрочного основному, обеспечивается выбором типа сварочного электрода, который регламентирует прочностные характеристики сварного соединения. Следует учитывать, что применение электродов с повышенными механическими свойствами наплавленного металла, например, по пределу прочности при растяжении, может привести к снижению работоспособности сварной конструкции.
Для сварки кипящих сталей (низкоуглеродистая сталь, выпускаемая из печи слабораскисленной) используют электроды с любым покрытием.
Для сварки полуспокойных сталей (сталь, полученная при раскислении жидкого металла менее полно, чем при выплавке спокойной стали, но большем, чем при выплавке кипящей стали) при больших толщинах следует применять электроды с покрытиями основного или рутилового видов.
Сварка конструкций из спокойной стали, работающих при низких температурах или при динамических нагрузках, должна выполняться электродами с основным покрытием.
Стабильность горения дуги влияет на качество швов и на возможность сварки переменным током. Наиболее стабильно дуга горит у электродов с целлюлозным, кислым и рутиловым покрытиями. Это позволяет использовать сварочные трансформаторы. Для электродов с основным покрытием требуются только источники постоянного тока.
В нижнем, вертикальном и потолочном положениях шов лучше формируется у электродов с целлюлозным покрытием, так как мелкокапельный перенос электродного металла и высокая вязкость шлака обеспечивают качественное ведение сварки. Хуже формируется шов у электродов с основным покрытием.
При сварке толстостенных конструкций многослойными швами отделяемость шлака является существенным показателем. Электроды с рутиловым, целлюлозным и кислым покрытиями обеспечивают лучшую отделяемость шлака по сравнению с основным покрытием.
Сварка электродами с основным покрытием требует тщательной очистки кромок от ржавчины, масла, грязи во избежание порообразования. Кроме того, электроды с основным покрытием склонны к порообразованию в начальный момент сварки и при сварке длинной дугой.
Тип Э42 Для сталей с пределом прочности при растяжении до 412 МПа (42 кгс/мм2) |
||||
Марка, область применения и технологические особенности |
Пок- рытие |
Род, полярность тока | Коэф. нап- лавки, г/А•ч |
Поло- жение швов |
Огонек |
Р |
~, =(+) |
6,5 |
|
Для изделий из стали толщиной 1-3 мм. Сварку можно выполнять способом «сверху-вниз». | ||||
АНО-6 |
АР |
~, =(+,-) |
9,0 |
|
Сварка короткой или средней дугой.![]() |
||||
АНО-6М |
АР |
~, =(+,-) |
8,5 |
|
Сварка короткой или средней дугой. Легко отделяется шлак. Минимальное разбрызгивание. Малая склонность к образованию пор и горячих трещин. Uхх≥50В. | ||||
АНО-17 |
АРЖ |
~, =(+,-) |
11,0 |
|
Высокопроизводительные. Для сварки металла большой толщины длинными швами. Малая чувствительность к порообразованию при сварке по окисленной поверхности.![]() |
||||
ВСЦ-4 |
Ц |
=(+) |
10,0 |
|
Сварка трубопроводов без колебаний электрода опиранием на кромки «сверху-вниз». Корень шва — на постоянном токе любой полярности, «горячий» проход — на обратной полярности. Оставлять огарок не менее 50 мм. | ||||
ВСЦ-4М |
Ц |
=(+,-) |
9,0 |
|
Сварка корневого шва и «горячего» прохода стыков трубопроводов. Позволяют вести сварку способом «сверху-вниз» опиранием электрода. Обеспечивают стойкость против образования пор. | ||||
ОЗС-23 |
Р |
~, =(+) |
8,5 |
|
Для сварки конструкций малой толщины по окисленной поверхности.![]() |
||||
ОМА-2 |
АЦ |
~, =(+) |
10,0 |
|
Для сварки ответственных металлоконструкций малой толщины (0,8- 3,0 мм). Сварка удлиненной дугой по окисленной поверхности. Электроды с малой проплавляющей способностью. Uхх≥60В. | ||||
Тип Э42А Стали с пределом прочности при растяжении до 412 МПа (42 кгс/мм2) с высокими требованиями к шву по пластичности и ударной вязкости. |
||||
УОНИ-13/45 |
Б |
=(+) |
10,0 |
|
Для сварки ответственных конструкций, работающих при пониженных температурах.![]() |
||||
УОНИ-13/45А |
Б |
=(+) |
10,0 |
|
Для сварки ответственных конструкций из сталей типа СХЛ-4, МС-1, Ст3сп и им подобных. Сварка короткой дугой по тщательно зачищенным кромкам. | ||||
УОНИИ-13/45 |
Б |
=(+) |
10,0 |
|
Для сварки ответственных конструкций, работающих при пониженных температурах. Сварка предельно короткой дугой по тщательно зачищенным кромкам. | ||||
УОНИИ-13/45А |
Б |
=(+) |
9,5 |
|
Для сварки ответственных конструкций, работающих при пониженных температурах.![]() |
||||
УОНИИ-13/45Р |
Б |
=(+) |
9,5 |
|
Для сварки судостроительных сталей. Сварка короткой дугой по зачищенным кромкам. Высокая стойкость металла шва к образованию горячих трещин. | ||||
Тип Э46 Для сталей с пределом прочности при растяжении до 451 МПа (46 кгс/мм2) |
||||
АНО-4 |
Р |
~, =(+, -) |
8,7 |
|
Для сварки простых и ответственных конструкций всех групп и степеней раскисления.![]() |
||||
АНО-13 |
РЦ |
~, =(+, -) |
8,5 |
|
Для вертикальных угловых, нахлесточных и стыковых швов способом «сверху — вниз». Сварка короткой или средней дугой. Можно по незачищенным кромкам. Металл шва стоек к образованию горячих трещин. Покрытие гигроскопично. Uхх≥50В. | ||||
АНО-21 |
Р |
~, =(+, -) |
8,5 |
|
Для простых и ответственных конструкций из углеродистых сталей всех групп и степеней раскисления.![]() |
||||
АНО-24 |
АР |
~, =(+, -) |
8,5 |
|
Для сварки в монтажных условиях. Сварка удлиненной дугой по незачищенным кромкам. Малая склонность к образованию подрезов. Uхх≥50В. | ||||
АНО-34 |
Р |
~, =(+, -) |
8,5 |
|
В нижнем положении электрод отклонять на 20-40° от вертикали в направлении сварки. Сварка возможна удлиненной дугой по окисленной поверхности. Uхх≥50В. | ||||
ЭЛЗ-С-1 |
Р |
~, =(+) |
9,5 |
|
Для сварки низкоуглеродистых, углеродистых и низколегированных сталей с пределом прочности при растяжении до 490 МПа.![]() |
||||
МР-3 |
РБ |
~, =(+) |
8,5 |
|
Для ответственных конструкции. Сварка короткой или средней дугой. Поверхности тщательно зачистить от окалины. Хорошо перекрываются зазоры. При сварке на повышенных токах возможны поры. Uхх≥60В. | ||||
МР-3М |
РБ |
~, =(+, -) |
8,5 |
|
Для сталей с содержанием углерода до 0,25%. Возможна сварка влажного, ржавого, плохо очищенного от окислов металла. Высокопроизводительны. Сварка средних и больших толщин ведется на повышенных режимах «углом назад». Uхх≥60В. | ||||
ОЗС-3 |
АРЖ |
~, =(+) |
15,0 |
|
Для сварки ответственных деталей.![]() |
||||
ОЗС-4 |
Р |
~, =(-) |
9,0 |
|
Для высокопроизводительной сварки ответственных деталей. Допускается сварка удлиненной дугой и по незачищенным поверхностям. Uхх≥60В. | ||||
ОЗС-4И |
АР |
~, =(+, -) |
8,5 |
|
Для ответственных конструкций. Допускают сварку влажного, ржавого, плохо очищенного от окислов металла. Высокая производительность. Сварка в нижнем положении при средних и больших толщинах «углом назад». Средняя длина дуги.![]() |
||||
ОЗС-6 |
РЖ |
~, =(+) |
11,0 |
|
Для высокопроизводительной сварки. Допускается сварка удлиненной дугой, возможна и по окисленной поверхности. Uхх≥50В. | ||||
ОЗС-12 |
Р |
~, =(-) |
8,5 |
|
Рекомендуется для тавровых соединений с получением мелкочешуйчатых вогнутых швов. Легко отделяется шлак. Сварка удлиненной дугой и по окисленной поверхности. Uхх≥50В. | ||||
Тип Э46А Для сталей с пределом прочности при растяжении 451 МПа (46 кгс/мм2) при повышенных требованиях к швам по пластичности и ударной вязкости.![]() |
||||
ТМУ-46 |
Б |
~, =(+) |
9,0 |
|
Для ответственных конструкций, в том числе трубопроводов. Сварка короткой дугой по зачищенным кромкам. Uхх≥65В. | ||||
УОНИ-13/55К |
Б |
=(+) |
10,0 |
|
Для ответственных конструкций, работающих при отрицательных температурах и знакопеременных нагрузках. Сварка короткой дугой по зачищенным кромкам. Металл шва обладает высокой стойкостью к образованию горячих трещин и характеризуется низким содержанием водорода. | ||||
АНО-8 |
Б |
=(+) |
10,0 |
|
Для сварки конструкций из углеродистых и низколегированных сталей, работающих при пониженных температурах.![]() |
||||
Тип Э50 Для сталей с пределом прочности при растяжении 490 МПа (50 кгс/мм2) | ||||
ВСЦ-4А |
Ц |
=(+) |
11,0 |
|
Высокопроизводительная сварка корневого шва и «горячего» прохода стыков трубопроводов и ответственных конструкций. Сварка корневого шва без колебаний, опиранием, на постоянном токе любой полярности. «Горячий» проход — после зачистки корневого шва. Оба слоя сваривать «сверху-вниз». Оставлять огарок не менее 50 мм. | ||||
55-У |
Б |
~, =(+, -) |
8,5 |
|
Сварка короткой дугой или опиранием по тщательно зачищенным кромкам.![]() |
||||
Тип Э50А Для сталей с пределом прочности при растяжении 490 МПа (50 кгс/мм2) при повышенных требованиях к швам по пластичности и ударной вязкости. | ||||
АНО-27 |
БЖ |
~, =(+) |
10,5 |
|
Для сварки ответственных конструкций при температуре до -40°С. Сварка короткой дугой по тщательно зачищенной поверхности. Обеспечивают пониженное содержание водорода в швах. | ||||
АНО-Т |
Б |
=(+) |
10,0 |
|
Для сварки ответственных конструкций и трубопроводов во всех климатических зонах.![]() |
||||
АНО-ТМ/Н |
Б |
~, =(+) |
10,5 |
|
Для поворотных стыков нефте- и газопроводов диаметром 59-1420 мм и других ответственных конструкций. Сварка короткой дугой по зачищенным кромкам. Эффективны для односторонней сварки. Uхх≥65В. | ||||
АНО-ТМ |
Б |
~, =(+) |
10,5 |
|
Для ответственных конструкций, в том числе трубопроводов из низкоуглеродистых и низколегированных сталей. Сварка короткой дугой по зачищенным кромкам.![]() |
||||
ИТС-4 |
Б |
=(+) |
10,0 |
|
Для судокорпусных сталей Ст3сп, 09Г2, 09Г2С, 10ХСНД, 10Г2С1Д-35, 10Г2С1Д-40 и т.д. Сварка короткой дугой по тщательно зачищенным кромкам. Обеспечивают высокую коррозионную стойкость. | ||||
ИТС-4С |
Б |
~, =(+) |
9,5 |
|
Для сварки ответственных конструкций в судостроении; стали СХЛ-4, 09Г2 и др. Сварка короткой дугой по зачищенным кромкам. Uхх≥65В. | ||||
ОЗС-18 |
Б |
=(+) |
9,5 |
|
Для сварки ответственных конструкций из сталей 10ХСНД, 10ХНДП и др.![]() |
||||
ОЗС-25 |
Б |
=(+) |
9,5 |
|
Для сварки ответственных конструкций. Сварка короткой дугой по тщательно зачищенным кромкам. Хорошая отделяемость шлака. Отсутствие подрезов и мелкочешуйчатость шва. | ||||
ОЗС/ВНИИСТ-26 |
Б |
=(+) |
9,4 |
|
Для трубопроводов нефти и газа, загрязненных сероводородом. Сварка короткой дугой по тщательно зачищенным кромкам. Высокая коррозионная стойкость в среде увлажненного до 25% сероводорода.![]() |
||||
ОЗС-28 |
РБ |
~, =(+) |
9,5 |
|
Для ответственных конструкций из сталей 09Г2, 10ХСНД и др. Сварка короткой дугой по тщательно зачищенным кромкам. Uхх≥60В. | ||||
ОЗС-33 |
Б |
~, =(+, -) |
9,5 |
|
Для особо ответственных конструкций. Обеспечивают металл шва с высокой стойкостью к образованию горячих трещин и низким содержанием водорода. Сварка короткой или предельно короткой дугой по зачищенным кромкам. | ||||
ТМУ-21У |
Б |
=(+) |
9,5 |
|
Для сталей типа 15ГС и др.![]() |
||||
ТМУ-50 |
Б |
~, =(+) |
9,0 |
|
Для ответственных конструкций и трубопроводов. Сварка короткой дугой по зачищенным кромкам. Uхх≥65В. | ||||
УОНИ-13/55 |
Б |
=(+) |
9,5 |
|
Для ответственных конструкций, работающих при отрицательных температурах и знакопеременных нагрузках.![]() |
||||
УОНИ-13/55С |
Б |
~, =(+) |
9,5 |
|
Для особо ответственных конструкций. Обеспечивают металл шва высокой стойкостью к образованию горячих трещин. Низкое содержание водорода. Сварка только короткой дугой по зачищенным кромкам. | ||||
УОНИ-13/55ТЖ |
БЖ |
~, =(+) |
9,5 |
|
Для особо ответственных конструкций, работающих при пониженных температурах. Металл шва хорошо противостоит образованию горячих трещин.![]() |
||||
УОНИИ-13/55Р |
Б |
~, =(+) |
9,5 |
|
Для судостроительных сталей с пределом прочности до 490-660 МПа. Сварка короткой дугой или опиранием по тщательно зачищенным кромкам. | ||||
ЦУ-5 |
Б |
=(+) |
9,5 |
|
Для трубных деталей и теплообменников котлоагрегатов, работающих при температурах до 400°С. Пониженная склонность к порообразованию. Сварка короткой дугой по тщательно зачищенным кромкам. | ||||
ЦУ-7 |
Б |
=(+) |
9,0 |
|
Для ответственных конструкций, работающих при температурах до 400°С.![]() |
||||
ЦУ-8 |
Б |
=(+) |
9,5 |
|
Для ответственных конструкций, работающих при температурах до 400°С при малой толщине металла и для сварки труб малых диаметров. Сварка короткой дугой по тщательно зачищенным кромкам. | ||||
Э-138/50Н |
Б |
=(+) |
9,0 |
|
Для тяжелонагруженных швов подводной части судов. Для сталей Ст3С, Ст4С, 09Г2, СХЛ-1, СХЛ-45, МС-1 и др. Сварка короткой дугой по тщательно зачищенным кромкам. Металл шва стоек против коррозии в морской воде.![]() |
||||
Тип Э55 Для сталей с пределом прочности при растяжении до 539 МПа (55 кгс/мм2) | ||||
ОЗС/ВНИИСТ-27 |
Б |
=(+) |
9,5 |
|
Для трубопроводов и конструкций из хладостойких низколегированных сталей, работающих при температурах до -60°С. Сварка короткой дугой по тщательно зачищенным кромкам. Корневые швы — на постоянном токе прямой полярности. | ||||
УОНИ-13/55У |
Б |
~, =(+) |
9,5 |
|
Для сварки арматуры и рельсов ванным способом, для ответственных конструкций ручной дуговой сваркой.![]() |
||||
Тип Э60 Для сталей с пределом прочности при растяжении до 588 МПа (60 кгс/мм2) | ||||
АНО-ТМ60 |
Б |
~, =(+) |
10,5 |
|
Для стыковых соединений труб и других ответственных конструкций. Сварка короткой дугой по зачищенным кромкам. Формирование корневого шва без подкладных элементов и подварки с плавным переходом к основному металлу. | ||||
ВСФ-65 |
Б |
=(+) |
9,5 |
|
Для ответственных конструкций, в том числе магистральных трубопроводов.![]() |
||||
ОЗС-24М |
Б |
=(+) |
9,5 |
|
Для конструкций и трубопроводов из сталей 06Г2НАБ, 12Г2АФЮ, 10ГНМАЮ и др., работающих при температурах до -70°С. Сварка короткой дугой по зачищенным кромкам. Металл шва характеризуется высокой хладостойкостью. | ||||
УОНИ-13/65 |
Б |
=(+) |
9,0 |
|
Для ответственных конструкций из углеродистых низколегированных хромистых, хромомолибденовых, хромокремнемарганцевых сталей, работающих при низких температурах. Сварка короткой дугой по тщательно зачищенным кромкам.![]() |
Тип Э70 Для сталей с пределом прочности при растяжении до 686 МПа (70 кгс/мм2) |
||||
Марка, область применения и технологические особенности |
Пок- рытие |
Род, полярность тока | Коэф. нап- лавки, г/А•ч |
Поло- жение швов |
АНО-ТМ70 |
Б |
~, =(+) |
10,5 |
|
Для сварки ответственных конструкций и трубопроводов без подкладных элементов и подварки.![]() |
||||
АНП-1 |
Б |
=(+) |
9,0 |
|
Для сварки ответственных конструкции из сталей 14ХГ2МР, 14ХМНДФР и др., деталей транспортных и дорожных машин, работающих при низких температурах. Сварка короткой дугой по тщательно зачищенным кромкам. | ||||
АНП-2 |
Б |
=(+) |
9,0 |
|
Для сварки ответственных конструкций. Сварка короткой дугой по тщательно зачищенным кромкам. | ||||
ВСФ-75 |
Б |
=(+) |
9,5 |
|
Для трубопроводов и ответственных конструкций при сварке заполняющих и облицовочных слоев.![]() |
||||
Тип Э85 Для сталей с пределом прочности при растяжении до 833 МПа (85 кгс/мм2) | ||||
НИАТ-3М |
Б |
=(+) |
10,0 |
|
Для сварки ответственных конструкций из термически упрочняемых сталей. Сварка короткой дугой по тщательно зачищенным кромкам. | ||||
УОНИ-13/85 |
Б |
=(+) |
8,5 |
|
Для ответственных конструкций из термически упрочняемых сталей до высокого предела прочности: 30ХГСА, 30ХГСНА и др.![]() |
||||
УОНИ-13/85У |
Б |
~, =(+) |
9,5 |
|
Для арматуры и рельсов ванным способом и ручной дуговой сварки конструкций из высокопрочных сталей, работающих при тяжелых нагрузках. Сварка короткой дугой по зачищенным кромкам. При ванном способе использовать остающиеся или удаляемые формы. | ||||
Тип Э100 Для сталей с пределом прочности при растяжении до 980 МПа (100 кгс/мм2) | ||||
АН-ХН7 |
Б |
=(+) |
9,6 |
|
Сборка без зазоров.![]() |
||||
ВИ-10-6 |
Б |
=(+) |
8,0 |
|
Сборка без зазоров. Сварка короткой или средней дугой по тщательно зачищенным кромкам петлеобразными движениями электрода. При быстром охлаждении возможны трещины в кратерах. | ||||
ОЗШ-1 |
Б |
=(+) |
9,0 |
|
Сварка короткой дугой непрерывно, не допуская охлаждения, по тщательно зачищенным кромкам. Предварительный подогрев до 400-450°С. Можно использовать для наплавки штампов. |
Тип Э125 Для сталей с пределом прочности при растяжении свыше 980 МПа (100 кгс/мм2) |
||||
Марка, область применения и технологические особенности |
Пок- рытие |
Род, полярность тока | Коэф.![]() лавки, г/А•ч |
Поло- жение швов |
НИИ-3М |
Б |
=(+) |
9,5 |
|
Для сталей 30ХГСНА, 30ХГСН2А и др., термически обрабатываемых на прочность до 1274 МПа (130 кгс/мм2). Сварка короткой дугой по зачищенным кромкам. | ||||
Тип Э150 Для сталей с пределом прочности при растяжении до 1470 МПа (150 кгс/мм2) | ||||
НИАТ-3 |
Б |
=(+) |
10,0 |
|
Для высокопрочных сталей типа 30ХГСНА с пределом прочности до 1470 МПа (150 кгс/мм2) |
Электроды для наплавки
Наплавочные электроды обеспечивают получение наплавленного металла разнообразного по химическому составу, структуре и свойствам. По ГОСТ 10051-75 «Электроды покрытые металлические для ручной дуговой наплавки поверхностных слоев с особыми свойствами» существует 44 типа таких электродов.
Все они имеют основное покрытие. Это обеспечивает лучшую сопротивляемость образованию трещин при наплавке деталей из стали с повышенным содержанием углерода и при высокой жёсткости конструкции.
В зависимости от условий работы конструкций с наплавленными покрытиями, электроды для наплавки могут быть условно разделены на 6 групп.
Первая группа Электроды для наплавки, обеспечивающие получение низкоуглеродистого низколегированного наплавленного металла с высокой стойкостью в условиях трения металла о металл и ударных нагрузок (по назначению к этой группе относятся некоторые марки электродов 3-ей группы). | ||||
Марка электрода /тип металла, область применения и технологические особенности |
Пок- рытие |
Род, полярность тока | Коэф.![]() лавки, г/А•ч |
Поло- жение швов |
ОЗН-300М /11Г3С |
Б |
~, =(+) |
10,5 |
|
Для деталей из углеродистых и низколегированных сталей, работающих в условиях трения и ударных нагрузок, например: валы, оси, автосцепки, крестовины и др. детали автомобильного и ж/д транспорта. | ||||
ОЗН-400М /15Г4С |
Б |
~, =(+) |
10,5 |
|
То же, с увеличенной твердостью наплавленного металла. | ||||
НР-70 /Э-30Г2ХМ |
Б |
=(+) |
9,0 |
|
Для деталей, работающих в условиях интенсивных ударных нагрузок и трения по металлу: рельсы, крестовины и другое.![]() |
||||
ЦНИИН-4 /Э-65Х25Г13Н3 |
Б |
=(+) |
10,5 |
|
Для заварки дефектов литья железнодорожных крестовин и других деталей из высокомарганцовистых сталей 110Г13Л. | ||||
Вторая группа Электроды, обеспечивающие получение среднеуглеродистого низколегированного наплавленного металла с высокой стойкостью в условиях трения металла о металл и ударных нагрузок при нормальной и повышенной температурах (до 600-650°С). | ||||
ЭН-60М /Э-70Х3СМТ |
Б |
=(+) |
8,5 |
|
Для штампов всех типов, работающих с нагревом контактных поверхностей до 400°С, и быстроизнашивающихся деталей в станочном оборудовании: шестерни, эксцентрики, направляющие и др.![]() |
||||
ЦН-14 |
Б |
=(+) |
12,0 |
|
Для оборудования горячей штамповки и резки, в том числе ножей, ножниц, штампов и др. | ||||
13КН/ЛИВТ /Э-80Х4С |
Б |
~, =(+) |
6,5 |
|
Для зубьев ковшей экскаваторов, черпаков, земснарядов, ножей дорожных машин, работающих при абразивном износе без значительных ударов и давлений. | ||||
ОЗШ-3 /Э-37Х9С2 |
Б |
=(+) |
9,5 |
|
Для обрезных и вырубных штампов холодной и горячей штамповки (до 650°С) и быстроизнашивающихся деталей машин и оборудования.![]() |
||||
ОЗИ-3 /Э-90Х4М4ВФ |
Б |
=(+) |
9,5 |
|
Для штампов холодного и горячего (до 650°С) деформирования металлов, а также для быстроизнашивающихся деталей горнометаллургического и станочного оборудования. | ||||
Третья группа Электроды, обеспечивающие получение углеродистого, легированного (или высоколегированного) наплавленного металла с высокой стойкостью в условиях абразивного изнашивания и ударных нагрузок. | ||||
ОЗН-6 /90Х4Г2С3Р |
Б |
=(+) |
11,0 |
|
Для быстроизнашивающихся деталей горно-добывающих, строительных машин и др.![]() |
||||
ОЗН-7 /75Х5Г4С3РФ |
Б |
=(+) |
12,0 |
|
Для быстроизнашивающихся деталей преимущественно из высокомарганцовистых сталей 110Г13Л, работающих при интенсивном износе и при значительных ударных нагрузках. | ||||
ВСН-6 /Э-110X14В13Ф2 |
П |
=(+) |
9,5 |
|
Для быстроизнашивающихся деталей из углеродистых и высокомарганцовистых сталей при значительных ударных нагрузках в условиях абразивного износа. | ||||
Т-590 /Э-320Х25С2ГР |
П |
~, =(+) |
9,0 |
|
Для деталей, работающих в условиях абразивного износа при умеренных ударных нагрузках.![]() |
||||
Четвертая группа Электроды, обеспечивающие получение углеродистого высоколегированного наплавленного металла с высокой стойкостью в условиях больших давлений и высоких температур (до 680-850°С). | ||||
ОЗШ-6 /10Х33Н11М3СГ |
Б |
=(+) |
13,0 |
|
Для бойков радиально-ковочных машин, штампов холодного и горячего (до 800-850°С) деформирования металлов, ножей горячей резки металла, быстроизнашивающихся деталей оборудования, работающих в тяжелых термо-деформационных условиях. | ||||
УОНИ-13/Н1-БК /Э-09Х31Н8АМ2 |
Б |
=(+) |
10,5 |
|
Для уплотнительных поверхностей арматуры, работающих в контакте со средами высокой агрессивности.![]() |
||||
ОЗИ-5 /Э-10К18В11М10Х3СФ |
П |
=(+) |
10,5 |
|
Для металлорежущего инструмента, штампов горячей (до 800-850°С) штамповки и деталей, работающих в особо тяжелых температурно-силовых условиях. | ||||
Пятая группа Электроды, обеспечивающие получение высоколегированного аустенитного наплавленного метала с высокой стойкостью в условиях коррозионно-эрозионного изнашивания и трения металла о металл при повышенных температурах (до 570-600°С). | ||||
ЦН-6Л /Э-08Х17Н8С6Г |
Б |
=(+) |
14,0 |
|
Для уплотнительных поверхностей деталей арматуры котлов, работающих при температуре до 570°С и давлении до 7800 МПа (780 кг/мм2).![]() |
||||
Шестая группа Электроды, обеспечивающие получение дисперсноупрочняемого высоколегированного наплавленного металла с высокой стойкостью в тяжелых температурно-деформационных условиях (до 950-1100°С). | ||||
ОЗШ-6 /10Х33Н11М3СГ |
Б |
=(+) |
8,5 |
|
Для кузнечно-штамповой оснастки холодного и горячего деформирования металлов, деталей металлургического и станочного оборудования, работающих в тяжелых условиях термической усталости (до 950°С) и больших давлений. | ||||
ОЗШ-8 /11Х31Н11ГСМ3ЮФ |
Б |
=(+) |
14,0 |
|
Для кузнечно-штамповой оснастки горячего деформирования металла, работающего в сверхтяжелых условиях термической усталости (до 1100°С) и больших давлений.![]() |
Электроды для сварки и наплавки чугуна
Такие электроды предназначены для устранения дефектов в чугунных отливках и для восстановления поврежденных и изношенных деталей. Их можно применять и для изготовления сварно-литых конструкций. Электроды для холодной сварки и наплавки чугуна без предварительного подогрева дают наплавленный металл в виде стали, сплавов на основе меди, никеля и железоникелевого сплава. Это марки ЦЧ-4, ОЗЧ-2, ОЗЧ-6 и др. Иногда целесообразно использовать электроды иного назначения. Так, при ремонте чугунных тюбингов в условиях большой загрязненности и высокой влажности лучше брать марку ОЗЛ-25Б. Первые слои на загрязненных чугунах можно выполнять марками ОЗЛ-27 и ОЗЛ-28. Успешно применяют и марку ОЗБ-2М, предназначенную для сварки бронз.
Марка электрода /основной металл шва, область применения и технологические особенности |
Пок- рытие |
Род, полярность тока | Коэф.![]() лавки, г/А•ч |
Поло- жение швов |
ЦЧ-4 /FeV |
Б |
=(+) |
10,0 |
|
Для сварки и заварки дефектов литья в деталях из серого, высокопрочного и ковкого чугуна. Сварка серого и высокопрочного чугунов. | ||||
ОЗЧ-2 /Cu |
АЖ |
=(+) |
13,5 |
|
Для сварки, наплавки и заварки дефектов литья в деталях из серого и ковкого чугунов. | ||||
ОЗЧ-6 /Cu |
Б |
=(+) |
15,5 |
|
Для сварки тонкостенных деталей из серого и ковкого чугунов.![]() |
||||
МНЧ-2 /NiCu |
П |
=(+) |
11,5 |
|
Для сварки, наплавки и заварки дефектов литья в деталях из серого и ковкого чугунов. | ||||
ОЗЧ-3 /Ni |
Б |
=(+) |
11,0 |
|
Для сварки и заварки дефектов литья в деталях из серого и высокопрочного чугунов, когда к соединениям предъявляются повышенные требования по чистоте обработки поверхности. | ||||
ОЗЧ-4 /Ni |
Б |
=(+) |
11,5 |
|
Для сварки и наплавки деталей из серого и высокопрочного чугунов.![]() |
Электроды для сварки цветных металлов
Предназначены для сварки алюминия, меди, никеля и их сплавов. Титан и его сплавы ручной дуговой сваркой покрытым электродом не сваривают из-за интенсивной окисляемости.
Электроды для сварки алюминия. Основная трудность при сварке алюминия и его сплавов — наличие окисной пленки. Температура её плавления 2060°С, тогда как температура плавления алюминия 660°С. Плотная тугоплавкая пленка может нарушить стабильность процесса сварки и таким образом повлиять на качество формирования шва, вызвав появление внутренних дефектов в наплавленном металле. Для удаления окисной пленки в состав покрытия электродов вводят хлористые и фтористые соли щелочных и щелочно-земельных металлов. Эти вещества и обеспечивают качественную сварку.
Марка электрода /основной металл шва, область применения и технологические особенности |
Пок- рытие |
Род, полярность тока | Коэф.![]() лавки, г/А•ч |
Поло- жение швов |
ОЗА-1 /Al |
Псол. |
=(+) |
6,5 |
|
Для деталей и конструкций из технически чистого алюминия А0, А1, А2, А3. Сварка с предварительным подогревом до 250-400°С по зачищенным кромкам. Шлак удалять горячей водой и щетками. | ||||
ОЗА-2 /Al |
Псол. |
=(+) |
6,5 |
|
Для заварки литьевого брака и наплавки деталей из алюминиево-кремнистых сплавов АЛ-4, АЛ-9, АЛ-11 и др. Сварка с предварительным подогревом до 250-400°С по зачищенным кромкам. Шлак удалять горячей водой и стальными щетками.![]() |
||||
ОЗАНА-1 /Al |
Псол. |
=(+) |
8,0 |
|
Для деталей и конструкций из технически чистого алюминия. Сварка изделий толщиной более 10 мм с предварительным подогревом до 250-400°С по зачищенным кромкам. | ||||
ОЗАНА-2 /Al |
Псол. |
=(+) |
8,0 |
|
Для заварки литьевого брака и наплавки деталей из алюминиево-кремнистых сплавов АЛ-4, АЛ-9, АЛ-11 и др. Сварка деталей толщиной до 10 мм без подогрева, при больших толщинах — с подогревом до 200°С по зачищенным кромкам. |
Электроды для сварки меди и ее сплавов. При сварке меди основная проблема — образование пор в металле шва из-за высокой ее активности при взаимодействии с газами, особенно с кислородом и водородом. Чтобы этого избежать, применяют только хорошо раскисленную медь и тщательно прокаленные электроды. Сварку выполняют по зачищенным до металлического блеска кромкам.
Сварка латуней сложна и опасна для здоровья из-за интенсивного выгорания цинка.
Сварка бронз доставляет трудности ввиду высокой хрупкости и недостаточной прочности в нагретом состоянии.
Марка электрода /основной металл шва, область применения и технологические особенности |
Пок- рытие |
Род, полярность тока | Коэф. нап- лавки, г/А•ч |
Поло- жение швов |
Комсомолец-100 /Cu |
Пспец. |
=(+) |
14,0 |
|
Для сварки и наплавки изделий из технически чистой меди М1, М2, М3. Возможна сварка меди со сталью. Сварка с предварительным местным подогревом до 300-700°С. | ||||
АНЦ/ОЗМ-2 /Cu |
Пспец. |
=(+) |
17,5 |
|
Для сварки и наплавки изделий из технически чистой меди с содержанием кислорода не более 0,01%. Сварка при толщине более 10 мм с предварительным подогревом до 150-350°С. | ||||
АНЦ/ОЗМ-3 /Cu |
Пспец. |
=(+) |
16,5 |
|
Для сварки и наплавки технически чистой меди (кислорода не более 0,01%).![]() |
||||
ОЗБ-2М /CuSn |
Б |
=(+) |
14,0 |
|
Для сварки и наплавки бронз, заварки дефектов бронзового и чугунного литья. Возможна сварка и наплавка латуней. | ||||
ОЗБ-3 /Cu |
Пспец. |
=(+) |
12,5 |
|
Для наплавки при изготовлении и восстановлении электродов машин контактной точечной сварки, в том числе для сварки стержневой арматуры. |
Электроды для сварки никеля и его сплавов. Сварка никеля и его сплавов затруднена из-за большой чувствительности к растворенным в сварочной ванне газам: азоту, кислороду и водороду, что вызывает образование горячих трещин и пор. Для предупреждения появления этих дефектов необходимо применять основной металл и сварочные электроды высокой чистоты и качественно их подготавливать.
Марка электрода, область применения и технологические особенности |
Пок- рытие |
Род, полярность тока | Коэф. нап- лавки, г/А•ч |
Поло- жение швов |
ОЗЛ-32 |
РБ |
=(+) |
12,0 |
|
Для изделий из никеля НП-2, НА-1, для наплавки на углеродистые и высоколегированные стали в аппаратуре, работающей в щелочных и хлоросодержащих средах содового производства, мыловарения, производства синтетических волокон и др.![]() |
||||
В-56У |
РБ |
=(+) |
11,5 |
|
Для сварки изделий из монель-металла и аппаратуры из двухслойных сталей (Ст3сп + монель-металл) со стороны коррозионностойкого слоя, а также для наплавки. Возможна сварка монель-металла с низкоуглеродистыми сталями. Сварка валиками шириной до 12 мм. |
Электроды для резки металла
Дуговая резка металла покрытыми электродами часто используется при монтаже и ремонте металлоконструкций. Она эффективна, так как не требует дополнительного оборудования и специальной квалификации рабочих. Электроды для резки отличаются от электродов для сварки высокой тепловой мощностью дуги, высокой теплостойкостью покрытия, интенсивной окисляемостью жидкого металла. Эти электроды целесообразно применять для удаления дефектных швов или их участков, удаления прихваток, заклепок, болтов, разделки трещин и т.п. Прокалка перед сваркой: 170°С; 1ч.
Марка электрода, область применения и технологические особенности |
Пок- рытие |
Род, полярность тока | Коэф. нап- лавки, г/А•ч |
Поло- жение швов |
ОЗР-1 |
Пспец. |
~, =(+, -) |
12,0 |
|
Резка, строжка, прошивка отверстий, удаление дефектных участков сварных соединений и отливок, разделка свариваемых кромок и корня шва, выполнение других подобных работ при изготовлении, монтаже и ремонте деталей и конструкций из сталей всех марок (в т.![]() |
||||
ОЗР-2 |
Пспец. |
~, =(+, -) |
12,0 |
|
Резка стержневой арматуры, строжка. Резка, прошивка отверстий, удаление дефектных участков сварных соединений и отливок, разделка свариваемых кромок и корня шва, выполнение других подобных работ при изготовлении, монтаже и ремонте деталей и конструкций из сталей всех марок (в т.ч. высоколегированных), чугуна, меди и алюминия и их сплавов. Обеспечивают получение чистого реза (без грата и натеков на поверхности реза).![]() |
Электроды для сварки легированных теплоустойчивых сталей
Электроды для сварки легированных теплоустойчивых сталей, должны в первую очередь обеспечить необходимую жаропрочность сварных соединений — способность противостоять механическим нагрузкам при высоких температурах.
Для конструкций, работающих при температурах до 475°С, используют молибденовые электроды типа Э-09М, а при температурах до 540°С — хромомолибденовые электроды типов Э-09МХ, Э-09Х1М, Э-09Х2М1 и Э-05Х2М.
Для конструкций, работающих при температурах до 600°С, применяют хромомолибденованадиевые электроды Э-09Х1МФ, Э-10Х1М1НБФ, Э-10Х3М1БФ.
Электроды Э-10Х5МФ с повышенным содержанием хрома предназначены для сварки конструкций из сталей с повышенным содержанием хрома (12Х5МА, 15Х5М, 15Х5МФА и др.), работающих в агрессивных средах при температурах до 450°С.
Для сварки теплоустойчивых сталей чаще используют электроды с основным покрытием, обеспечивающие прочность наплавленного металла при повышенных температурах, а также малую склонность к образованию горячих и холодных трещин.
Тип Э-09М Для молибденовых сталей | ||||
Марка, область применения и технологические особенности |
Пок- рытие |
Род, полярность тока | Коэф. нап- лавки, г/А•ч |
Поло- жение швов |
ЦЛ-6 |
А |
~, =(+, -) |
10,5 |
|
УОНИ-13/15М |
Б |
=(+) |
9,0 |
|
ЦУ-2М |
Б |
=(+) |
9,5 |
|
Для сталей 16М, 20М и др.![]() |
||||
Тип Э-09Х1М Для хромомолибденовых сталей с повышенным содержанием хрома. | ||||
УОНИ-13ХМ |
Б |
=(+) |
9,0 |
|
Для сталей 15ХМ, 20ХМ и др., в том числе для сварки трубопроводов и деталей энергетического оборудования, работающих при температурах до 520°С. Сварка предельно короткой дугой по зачищенным кромкам с предварительным и сопутствующим подогревом до 150-200°С. | ||||
ТМЛ-1 |
Б |
=(+) |
10,0 |
|
Для паропроводов, работающих при температурах до 500°С.![]() |
||||
ТМЛ-1У |
Б |
=(+) |
9,0 |
|
Для сталей 12МХ, 15МХ и др., для сварки трубопроводов и деталей энергетического оборудования, работающих при температурах до 540°С. Сварка короткой дугой по зачищенным кромкам. Возможна сварка в узкую разделку с углом скоса кромок до 15°. Дуга очень стабильна. Хорошо отделяется шлак. | ||||
Тип Э-05Х2М Для хромомолибденовых сталей с повышенным содержанием хрома. | ||||
Н-10 |
Б |
=(+) |
9,5 |
|
Для сварки легированных теплоустойчивых хромомолибденовых сталей, паропроводов из сталей 10Х2М, 12ХМ, 12Х2М1-Л и др.![]() |
||||
Тип Э-09Х2М1 Для хромомолибденовых сталей с повышенным содержанием хрома и молибдена | ||||
ЦЛ-55 |
Б |
=(+) |
9,0 |
|
Для сталей 10Х2М и др., в том числе для сварки трубопроводов, работающих при температурах до 550°С. Сварка короткой дугой по зачищенным кромкам с предварительным и сопутствующим подогревом до 150-300°С | ||||
Тип Э-09МХ Для хромомолибденовых сталей. | ||||
УОНИ-13/45МХ |
Б |
=(+) |
9,5 |
|
Для сталей 12МХ, 15ХМ и др.![]() |
||||
ОЗС-11 |
РБ |
~, =(+) |
8,5 |
|
Для сталей 12МХ, 15МХ, 12ХМФ, 15Х1М1Ф и др., для сварки паропроводов, работающих при температурах до 500°С. Сварка короткой дугой по зачищенным кромкам. Сварка сталей толщиной более 12 мм с предварительным и сопутствующим подогревом до 150-200°С. Рекомендуются для монтажных работ. | ||||
Тип Э-09Х1МФ Для хромомолибденованадиевых сталей | ||||
ТМЛ-3 |
Б |
=(+) |
9,5 |
|
Для сварки неповоротных стыков трубопроводов, работающих при температурах до 575°С.![]() |
||||
ТМЛ-3У |
Б |
=(+) |
9,5 |
|
Для сталей 12МХ, 15МХ,12Х2М1, 12Х1МФ, 15Х1М1Ф, 20ХМФ1, 15Х1М1Ф-Л и др., в т.ч. для трубопроводов, работающих при температурах до 565°С. Сварка короткой дугой по зачищенным кромкам с предварительным и сопутствующим подогревом до 350-400°С. Сварка в узкую разделку с углом скоса кромок до 15°. | ||||
ЦЛ-39 |
Б |
=(+) |
9,0 |
|
Для сталей 12Х1МФ, 12Х2МФСР, 12Х2МФБ и др.![]() |
||||
Тип Э-10Х1М1НФБ Для хромомолибденованадиевых сталей | ||||
ЦЛ-27А |
Б |
=(+) |
10,0 |
|
Для сталей 15Х1М1Ф, конструкций из литых, кованых и трубных деталей, работающих при температурах до 570°С. Сварка короткой дугой по зачищенным кромкам с предварительным и сопутствующим подогревом до 350-400°С. | ||||
ЦЛ-36 |
Б |
=(+) |
10,5 |
|
Для сталей 15Х1М1Ф, 15Х1М1Ф-Л и др.![]() |
||||
Тип Э-10Х3М1БФ Для хромомолибденованадиевониобиевых сталей | ||||
ЦЛ-26М |
Б |
=(+) |
10,0 |
|
Для сталей 12ХМФБ поверхностей нагрева котлов, работающих при температурах до 600°С, а также для тонкостенных труб пароперегревателей в монтажных условиях. Сварка короткой дугой по зачищенным кромкам с предварительным и сопутствующим подогревом до 300-350°С. | ||||
ЦЛ-40 |
Б |
~, =(+) |
9,0 |
|
Для сталей 12Х2МФБ, в т.![]() |
||||
Тип Э-10Х5МФ Для хромомолибденованадиевых и хромомолибденовыхсталей | ||||
ЦЛ-17 |
Б |
=(+) |
10,5 |
|
Для сталей 15Х5М (Х5М), 12Х5МА, 15Х5МФА в ответственных конструкциях, работающих в агрессивных средах при температурах до 450°С. Сварка короткой дугой по зачищенным кромкам с предварительным и сопутствующим подогревом до 350-450°С. |
Электроды для сварки высоколегированных сталей
Стали, содержащие 13% хрома, считаются высокохромистыми нержавеющими. Они обладают стойкостью против атмосферной коррозии и в слабоагрессивных средах. Это стали 08X13, 12X13, 20X13, которые различаются свариваемостью в зависимости от содержания углерода.
При выборе электродов для сварки таких сталей необходимо обеспечить следующие свойства металла шва: стойкость против атмосферной коррозии и в слабо агрессивных средах, жаростойкость до температуры 650°С и жаропрочность до температуры 550°С. Этим требованиям удовлетворяют электроды типа Э-12Х13 марок ЛМЗ-1, АНВ-1 и др., которые обеспечивают химический состав, структуру и свойства металла шва, близкие характеристикам основного металла.
Для сварки сталей с пониженным содержанием углерода и дополнительно легированных никелем рекомендуются электроды типа Э-06Х13Н марки ЦЛ-41.
С увеличением количества хрома возрастает коррозионная стойкость и жаростойкость высокохромистых сталей. Содержание 17-18% дает коррозионную стойкость в жидких средах средней агрессивности. Такие стали относятся к кислотостойким: 12X17, 08X17Т, 08Х18Т и др. Если количество хрома достигает 25-30%, то возрастает жаростойкость — стойкость против газовой коррозии при температурах до 1100°С. Это жаростойкие стали: 15Х25Т, 15X28 и др. Для серосодержащих сред пригодны стали и электроды, в которых не менее 25% хрома.
Выбор электродов для сварки высокохромистых сталей зависит от количества хрома в свариваемых сталях. Так, для сварки сталей с 17% хрома, к которым предъявляются требования по коррозионной стойкости в жидких окислительных средах или по жаростойкости при температурах до 800°С, рекомендуются электроды типа Э-10X17Т марок ВИ-12-6 и др.
Для сварки сталей с 25% хрома следует применять электроды типа Э-08Х24Н6ТАФМ, придающие металлу шва после отпуска высокие пластичность, ударную вязкость и стойкость против межкристаллитной коррозии.
Сварку высокохромистых сталей следует выполнять при умеренных режимах с уменьшенной погонной энергией. После каждого прохода рекомендуется охлаждать металл околошовной зоны до температуры ниже 100°С, что обеспечивает минимальный рост зерна.
Высокохромистые стали на основе 13% хрома с дополнительным легированием молибденом, ванадием, вольфрамом и ниобием относятся к жаропрочным. Они способны противостоять механическим нагрузкам при высоких температурах. При выборе электродов для этих сталей основное требование — обеспечить необходимый уровень жаропрочности металла шва. Это достигается за счет получения химического состава швов, близкого основному металлу. Такому условию наиболее полно удовлетворяют электроды типов Э-12Х11НМФ марки КТИ-9А, Э-12Х11НВМФ марки КТИ-10, Э-14Х11НВМФ марки ЦЛ-32.
Тип Э-12Х13 Для коррозионностойких сталей | ||||
Марка, область применения и технологические особенности |
Пок- рытие |
Род, полярность тока | Коэф.![]() лавки, г/А•ч |
Поло- жение швов |
УОНИ-13/НЖ 12X13 |
Б |
=(+) |
10,5 |
|
Для сварки сталей 08X13, 12X13, 20X13 и др., работающих при температурах до 600°С, а также наплавки уплотнительных поверхностей стальной арматуры. Сварка с предварительным нагревом до 200-250°С. В атмосфере пара и на воздухе обеспечивают жаропрочность до 540°С, жаростойкость до 650°С. | ||||
ЛМЗ-1 |
Б |
=(+) |
11,0 |
|
Для сталей 08X13, 1X13, 2X13 и др., работающих в пресной воде и слабоагрессивных средах при нормальной температуре.![]() |
||||
АНВ-1 |
Б |
=(+) |
11,0 |
|
Для сталей 08X13, 12X13 и др., работающих в пресной воде и слабоагрессивных средах при нормальной температуре. Пригодны для наплавки уплотнительных поверхностей арматуры. После сварки обязателен отпуск. В атмосфере пара и воздуха обеспечивают жаропрочность до 540°С и жаростойкость до 650°С. | ||||
Тип Э-10Х17Т Для коррозионностойких и жаростойких сталей | ||||
УОНИ-13/НЖ 10Х17Т |
Б |
=(+) |
11,0 |
|
Для сталей 12X17, 08Х17Т и др.![]() |
||||
ВИ-12-6 |
Б |
=(+) |
11,0 |
|
Для сталей 12X17, 08X17Т и др., работающих в окислительных средах при температурах до 800°С. Сварка короткой дугой по зачищенным кромкам. | ||||
Тип Э-06Х13Н Для коррозионностоиких сталей, легированных никелем | ||||
ЦЛ-41 |
РБ |
=(+) |
11,5 |
|
Для сталей 0Х12НД, 10Х12НД-Л, 06Х12Н3Д, 06Х14Н5ДМ и др.![]() |
||||
Тип Э-12Х11НМФ Для жаропрочных сталей | ||||
КТИ-9А |
Б |
=(+) |
9,5 |
|
Для сталей 15Х11МФ, 15Х11ВФ и др., работающих при температурах до 565°С. Сварка короткой дугой по зачищенным кромкам. | ||||
Тип Э-12Х11НВМФ Для жаропрочных сталей | ||||
КТИ-10 |
Б |
=(+) |
9,2 |
|
Для сталей 15Х11МФ, 15Х12ВНМФ и 15Х11МФБ-Л, работающих при температурах до 580°С.![]() |
||||
Тип Э-14Х11НВМФ Для жаропрочных сталей | ||||
ЦЛ-32 |
Б |
=(+) |
9,5 |
|
Для сварки паронагревателей котлов паропроводов из сталей 10Х11В2МФ и др., работающих при температурах до 610°С. Сварка короткой дугой по зачищенным кромкам. | ||||
Тип Э-10Х16Н4Б Для коррозионностойких и жаропрочных сталей. | ||||
УОНИ-13/ЭП-56 |
Б |
=(+) |
9,0 |
|
Для конструкций из сталей 09X16Н4Б и др.![]() |
Электроды для коррозионностойких кислотостойких сталей. Основное требование при выборе электродов для сварки кислотостойких сталей — это обеспечение коррозионной стойкости металла шва в жидких агрессивных средах при нормальных и повышенных температурах и давлениях. К наиболее агрессивным жидким средам относятся кислоты и их растворы, которые обладают как окислительными, так и неокислительными свойствами.
Для сварки конструкций из кислотостойких сталей, работающих в неокислительных жидких средах при температурах до 360°С и не подвергающихся термической обработке после сварки, рекомендуются электроды марок ЭА-400/10Т, ЭА-400/10У и др., марок ОЗЛ-8 и др., марки ЭА-606/10 и т.п. Термическая обработка сварных соединений, выполненных этими электродами, не допускается.
Для конструкций, работающих в неокислительных или малоокислительных жидких средах, для которых после сварки необходим отпуск, рекомендуются электроды марки ЭА-898/19 и др. , которые обеспечивают стойкость шва против межкристаллитной коррозии как в исходном состоянии, так и после отпуска.
Конструкции, которые эксплуатируются в окислительных жидких средах, например в азотной кислоте, рекомендуется сваривать электродами типа Э-08Х19Н10Г2Б марок ЦТ-15, ЗИО-3 и др.
Для низкоуглеродистых кислотостойких сталей, содержащих до 0,03% углерода, используются электроды типов Э-04Х20Н9 марок ОЗЛ-14А, ОЗЛ-36; Э-02Х20Н14Г2М2 марок ОЗЛ-20 и др.
Тип Э-08Х19Н10Г2Б | ||||
Марка, область применения и технологические особенности |
Пок- рытие |
Род, полярность тока | Коэф. нап- лавки, г/А•ч |
Поло- жение швов |
ЦТ-15 |
Б |
=(+) |
11,0 |
|
ЗИО-3 |
Б |
=(+) |
12,5 |
|
Для сталей с содержанием никеля до 16% — 08Х18Н10Т, 12Х18Н12Т, 08Х18Н12Б и др.![]() |
||||
Тип Э-07Х20Н9 | ||||
ОЗЛ-8 |
Б |
=(+) |
14,0 |
|
ОЗЛ-14 |
РБ |
~, =(+, -) |
11,0 |
|
УОНИ-13/НЖ 04Х19Н9 |
Б |
=(+) |
10,5 |
|
Для сталей 08Х18Н10, 12Х18Н9, 12Х18Н10Т и др., когда к металлу шва не предъявляются жесткие требования по стойкости против межкристаллитной коррозии. Сварка короткой дугой по зачищенным кромкам. | ||||
ЛЭЗ-8 |
Р |
~, =(+) |
12,5 |
|
Для сталей 08Х18Н10, 12Х18Н9, 12Х18Н10Т и др.![]() |
||||
ОЗЛ-8 |
П |
=(+) |
12,0 |
|
Для сталей 08Х18Н10, 12Х18Н9, 12Х18Н10Т и др., когда к металлу шва не предъявляются жесткие требования по стойкости против межкристаллитной коррозии. Сварка короткой дугой по зачищенным кромкам. | ||||
ЦТ-50 |
РБ |
~, =(+) |
11,0 |
|
Для сталей 08Х18Н10, 12Х18Н9, 12Х18Н10Т и др., когда к металлу шва предъявляются жесткие требования по стойкости против межкристаллитной коррозии.![]() |
||||
Тип Э-08Х19Н9Ф2Г2СМ | ||||
ЭА-606/10 |
Б |
=(+) |
11,0 |
|
Для сталей 09X17Н7Ю, 09X15Н8Ю и других, а также для сталей 14Х17Н2 и др. | ||||
Тип Э-07Х19Н11М3Г2Ф | ||||
ЭА-400/10У |
Б |
=(+) |
12,0 |
|
ЭА-400/10Т |
Б |
=(+) |
12,0 |
|
Для сталей 08Х18Н10Т, 12Х18Н10Т, 08Х17Н13М2Т и др.![]() |
||||
Тип Э-08Х19Н9Ф2С2 | ||||
ЭА-606/11 |
Б |
=(+) |
12,0 |
|
Для сталей 08Х18Н10Т, 12Х18Н9Т и др., работающих при температурах до 350°С и не подвергающихся после сварки термической обработке. Не рекомендуются для сварки сталей, не легированных титаном или ниобием.![]() |
||||
ГЛ-2 |
Б |
=(+) |
10,5 |
|
Для сталей 08Х18Н10Т, 12Х18Н9Т и др., работающих при температурах до 350 °С и не подвергающихся после сварки термической обработке. Не рекомендуются для сварки сталей, не легированных титаном или ниобием | ||||
Тип Э-08Х19Н10Г2МБ | ||||
ЭА-898/19 |
Б |
=(+) |
10,0 |
|
Для сталей 08Х18Н10Т, 08Х17Н13М2Т и др., работающих в окислительных и малоокислительных средах при температурах до 350°С и подвергаемых после сварки термической обработке.![]() |
||||
Тип Э-04Х20Н9 | ||||
ОЗЛ-36 |
РБ |
=(+) |
13,5 |
|
ОЗЛ-14А |
Р |
~, =(+) |
11,0 |
|
АНВ-32 |
Б |
=(+) |
10,5 |
|
УОНИ-13/НЖ-2 /04Х19Н9 |
Б |
=(+) |
10,5 |
|
Для сталей 08Х18Н10Т, 06Х18Н11, 08Х18Н12Т, 04Х18Н10 и др., когда к металлу шва предъявляются требования по стойкости против межкристаллитной коррозии как в исходном состоянии, так и после кратковременных выдержек в интервале критических температур.![]() |
||||
Тип Э-02Х20Н14Г2М2 Для коррозионностойких сталей с пониженным содержанием углерода | ||||
ОЗЛ-20 |
П |
=(+) |
13,5 |
|
Для сталей 03Х16Н15М3, 03Х17Н14М2 при жестких требованиях к швам по стойкости против межкристаллитной коррозии. |
Электроды для сварки коррозионностойких высокопрочных сталей. Выбор электродов для таких сталей весьма ограничен. Так, для сталей 12X21Н5Т, 08Х21Н6М2Т рекомендуются электроды, дающие металл шва по структуре не однотипный с основным металлом, а иной. В этом случае применяют электроды типов Э-08Х20Н9Г2Б марок ЦЛ-11, ОЗЛ-7 и др. Можно использовать электроды типа Э-09Х19Н10Г2М2Б марок ЭА-902/14, АНВ-36, ЭА-400/13 и др. Для высоколегированных сталей 12Х25Н5ТМФЛ и 10Х25Н6АТМФ предусмотрен один тип электродов — Э-08Х24Н6ТАФМ, к которому относятся электроды марки Н-48. Металл шва равнопрочен основному металлу толщиной до 200 мм. Электроды этого типа можно использовать и для сталей 12Х21Н5Т, 08Х21Н6М2Т. Для сталей 08Х22Н6Т и 08X21Н6М2Т разработаны электроды ОЗЛ-40 и ОЗЛ-41, которые повышают коррозионную стойкость швов при работе в щелочных средах.
Тип Э-08Х20Н9Г2Б | ||||
Марка, область применения и технологические особенности |
Пок- рытие |
Род, полярность тока | Коэф. нап- лавки, г/А•ч |
Поло- жение швов |
ЦЛ-11 |
Б |
=(+) |
10,5 |
|
Для сварки конструкций из коррозионностойких и жаропрочных сталей аустенитного класса типа 08Х18Н10Т, 08Х18Н12Т, 08Х18Н12Б и им подобных, работающих в агрессивных средах при температуре не более 400°С, когда к металлу шва предъявляются жесткие требования по стойкости против межкристаллитной коррозии.![]() |
||||
ОЗЛ-40 и ОЗЛ-41 |
БР |
=(+) |
13,5 |
|
Для сталей 08Х22Н6Т, 08X21Н6М2Т и др., работающих в агрессивных средах. | ||||
ЦТ-15К |
РБ |
=(+) |
11,0 |
|
Для сталей 10Х17Н13М2Т, 08Х18Н10 и др., работающих при температурах до 600°С. Пригодны для наплавки антикоррозионного слоя. | ||||
ОЗЛ-7 |
Б |
=(+) |
11,5 |
|
Для сталей 08X18Н10, 08Х18Н10Т, 08Х18Н12Б и др.![]() |
||||
Тип Э-09Х19Н10Г2М2Б | ||||
ЭА-902/14 |
Б |
=(+) |
11,0 |
|
ЭА-400/13 |
Б |
=(+) |
12,0 |
|
НЖ-13 |
Б |
=(+) |
13,0 |
|
АНВ-36 |
Н |
~, =(+) |
13,0 |
|
Для конструкций из сталей 10Х17Н13М3Т, 08Х17Н15М3Т, 10Х17Н13М2Т, Х18Н22В2Т2 и др.![]() |
||||
СЛ-28 |
Б |
=(+) |
11,0 |
|
Для конструкций из сталей 10Х17Н13М3Т, 08Х17Н15М3Т, 10Х17Н13М2Т, Х18Н22В2Т2 и др., работающих при температурах до 550°С, когда к швам предъявляют жесткие требования по стойкости против межкристаллитной коррозии, не подвергаемых термообработке после сварки. Сварка короткой дугой по зачищенным кромкам «ниточными»швами без поперечных колебаний. | ||||
Тип Э-08Х24Н6ТАФМ | ||||
Н-48 |
Б |
~, =(+, -) |
11,0 |
|
Для сталей 12Х25Н5ТМФЛ, 12Х21Н5Т, 08Х22Н6Т и др.![]() |
Электроды для сварки жаростойких (окалиностойких) сталей. Жаростойкими (окалиностойкими) считаются стали, способные противостоять химическому разрушению поверхности в воздухе или в другой газовой среде при температурах выше 850°С в ненагруженном или слабонагруженном состояниях. Они содержат до 20-25% хрома и работают при температурах до 1050°С и выше.
Жаростойкость наплавленного металла до 1000°С на сталях 20Х23Н13, 20Х23Н18 и др. достигается электродами типа Э-10Х25Н13Г2 марок СЛ-25, ОЗЛ-6, ЦЛ-25.
Для сварки жаростойких сталей, долго работающих при температурах выше 1000°С, следует применять электроды типа Э-12Х24Н14С2 марок ОЗЛ-5, ЦТ-17 и др., а также электроды типа Э-10Х17Н13С4 марки ОЗЛ-29, обеспечивающие жаростойкость до температуры 1100°С в окислительных и науглероживающих средах. Для конструкций, работающих в серосодержащих средах, применяют безникелевые высокохромистые жаростойкие стали 15Х25Т, 15X28 и др.
Тип Э-10Х25Н13Г2 | ||||
Марка, область применения и технологические особенности |
Пок- рытие |
Род, полярность тока | Коэф. нап- лавки, г/А•ч |
Поло- жение швов |
УОНИ-13/НЖ-2 /07Х25Н13 |
Б |
=(+) |
12,0 |
|
ЗИО-8 |
РБ |
=(+) |
13,0 |
|
ЦЛ-25 |
Б |
=(+) |
10,5 |
|
ОЗЛ-6 |
Б |
=(+) |
11,5 |
|
Для 10Х23Н18, 20Х23Н13, 20Х23Н18 и др.![]() |
||||
СЛ-25 |
Б |
=(+) |
10,0 |
|
То же, для жаростойких сталей. | ||||
Тип Э-12Х24Н14С2 | ||||
ОЗЛ-5 |
Б |
=(+) |
12,5 |
|
ЦТ-17 |
Б |
=(+) |
10,5 |
|
Для сталей 20Х25Н20С2, 20Х20Н14С2 и др.![]() |
||||
Тип Э-10Х17Н13С4 | ||||
ОЗЛ-29 |
Б |
=(+) |
15,5 |
|
ОЗЛ-3 |
Б |
=(+) |
12,0 |
|
Для сталей 20Х20Н14С2, 20Х25Н20С2, 45Х25Н20С2 и др., работающих при температурах до 1100°С в окислительных и науглероживающих средах, а также для стали 15Х18Н12С4ТЮ, работающей в агрессивных средах без высоких требований по стойкости к межкристаллитной коррозии. |
Электроды для сварки жаропрочных сталей. К жаропрочным относятся стали, которые работают в нагруженном состоянии при высоких температурах в течение определенного времени и обладают при этом достаточной стойкостью против образования окалин. Высокая жаропрочность хромоникелевых сталей достигается за счет увеличения содержания никеля и дополнительного легирования титаном, ниобием, молибденом, вольфрамом и др.
Следует учитывать, что жаропрочность сварных соединений может существенно отличаться от жаропрочности основного и наплавленного металлов. Поэтому выбор электрода по принципу равной или близкой жаропрочности шва и основного металла оправдывается только для кратковременных ресурсов работы сварных соединений. Для длительных ресурсов лучше брать электроды, дающие более пластичный металл шва. Этому принципу соответствуют электроды, легирующие металл шва молибденом, — типа Э-11Х15Н25М6АГ2 марок ЭА-395/9, ЦТ-10, НИАТ-5 и типа Э-08Х16Н8М2 марки ЦТ-26.
Для сварки жаропрочных сталей, содержащих до 16% никеля и работающих при температурах до 600-650°С, а также если сварные соединения после сварки подвергаются термообработке посредством отпуска, применяются электроды типов Э-09Х19Н11Г3М2Ф марок КТИ-5, ЦТ-7 и Э-08Х19Н10Г2Б (см. выше) марок ЦТ-15 и ЗИО-3.
При сварке корневых слоев многослойных стыковых швов жаропрочных сталей, когда перемешивание основного металла с наплавленным велико и не обеспечивает технологическую прочность швов, следует применять электроды типа Э-08Х20Н9Г2Б марки ЦТ-15-1.
Для сварки жаропрочных сталей, содержащих 35% никеля и легированных ниобием, которые работают при температурах до 700-750°С, применяют электроды типа Э-27Х15Н35В3Г2Б2Т марок КТИ-7 и КТИ-7А.
Для сварки жаропрочных сталей с 35% никеля, но без ниобия, однако легированных молибденом и марганцем, используют электроды типов Э-11Х15Н25М6АГ2 марок ЭА-395/9, НИАТ-5, ЦТ-10 и Э-09Х15Н25М6АГ2Ф марки ЭА-981/15. При этом надо учесть, что наплавленный такими электродами металл не стоек против межкристаллитной коррозии в состоянии после сварки и после термической обработки, Поэтому такие электроды непригодны, если конструкция работает еще и в жидкой агрессивной среде. Слои, контактирующие с агрессивной средой, следует выполнять электродами типа Э-07Х19Н11М3 (см. выше) марок ЭА-400/10У и ЭА-400/10Т.
Тип Э-11Х15Н25М6АГ2 | ||||
Марка, область применения и технологические особенности |
Пок- рытие |
Род, полярность тока | Коэф. нап- лавки, г/А•ч |
Поло- жение швов |
ЭА-395/9 и ЦТ-10 |
Б |
=(+) |
11,5 |
|
Для сталей и сплавов ХН35ВТ, Х15Н25АМ6 и др., содержащих до 35% никеля, но без ниобия, работающих при температурах до 700°С. Для разнородных соединений высоколегированных сталей с углеродистыми и низколегированными.![]() |
||||
НИАТ-5 |
Б |
=(+) |
12,5 |
|
Для сталей и сплавов ХН35ВТ, Х15Н25АМ6 и др., содержащих до 35% никеля, но без ниобия, работающих при температурах до 700°С. Для разнородных соединений высоколегированных сталей с углеродистыми и низкоуглеродистыми. Для конструкций, работающих при температурах до -196°С. Короткая дуга. Зачистить кромки. | ||||
Тип Э-08Х16Н8М2 | ||||
ЦТ-26 |
Б |
=(+) |
10,5 |
|
Для сталей 10Х14Н14В2М, 08Х16Н13М2Б и др.![]() |
||||
Тип Э-08Х20Н9Г2Б | ||||
ЦТ-15-1 |
Б |
=(+) |
11,0 |
|
Для сварки корневых слоев швов, выполняемых электродами ЦТ-15. | ||||
Тип Э-09Х19Н11Г3М2Ф | ||||
КТИ-5 |
Б |
=(+) |
12,0 |
|
Для сталей 08Х16Н13М2Б, 15Х14Н14М2ВФБТЛ (ЛА-3) и др., работающих при температурах до 600°С и подвергаемых после сварки термической обработке, а также для заварки дефектов литья из этих сталей.![]() |
||||
ЦТ-7 |
Б |
=(+) |
12,0 |
|
Для сталей 08Х16Н13М2Б, 15Х14Н14М2ВФБТЛ (ЛА-3) и др., работающих при температурах до 600°С и подвергаемых после сварки термической обработке, а также для заварки дефектов литья из этих сталей. Сварка короткой дугой по зачищенным кромкам короткими валиками без поперечных колебаний. | ||||
Тип Э-27Х15Н35В3Г2Б2Т | ||||
КТИ-7 |
Б |
=(+) |
11,0 |
|
Для сплавов на железоникелевой основе ХН35ВТ, ХН35ВТЮ и др.![]() |
||||
КТИ-7А |
Б |
=(+) |
10,0 |
|
Для сплавов на железоникелевой основе ХН35ВТ, ХН35ВТЮ и др., долго работающих при температурах до 750°С, а также для реакционных труб в печах конверсии металла из сталей 45Х20Н35С, 25Х20Н35 и др., работающих при температурах до 900°С. Сварка короткой дугой узкими валиками без поперечных колебаний. | ||||
Тип Э-09Х15Н25М6АГ2Ф | ||||
ЭА-981/15 |
Б |
=(+) |
11,5 |
|
Для сварки высоколегированных коррозионностойких хромоникелемолибденовых и хромоникелемолибденованадиевых сталей, а также высокопрочных сталей типа АК и высокомарганцовистых сталей типа 110Г13-Л.![]() |
Электроды для сварки разнородных сталей и сплавов
Разнородными сталями и сплавами считаются материалы, резко отличающиеся физико-механическими свойствами, химическим составом и свариваемостью. По признаку разнородности стали условно можно разделить на 4 группы: углеродистые и легированные, легированные повышенной и высокой прочности, теплоустойчивые, высоколегированные.
Сварка разнородных сталей и сплавов может существенно отличаться от сварки однородных материалов, так как возрастает вероятность появления трещин в металле шва, возникновения в зоне оплавления участков со структурной неоднородностью, чрезмерного роста остаточных напряжений из-за большой разницы в коэффициентах расширения свариваемых материалов.
Большинство электродов, используемых при сварке разнородных сталей и сплавов, относятся к электродам, предназначенным для сварки высоколегированных сталей и легированных сталей повышенной и высокой прочности, которые дают шов с однородной высокопластичной структурой металла.
Выбор электрода можно делать по таблице, составленной с учетом отечественного опыта сварки разнородных металлов.
Выбор электродов для сварки разнородных сталей и сплавов
Марка электрода, область применения и технологические особенности |
Пок- рытие |
Род, полярность тока | Коэф. нап- лавки, г/А•ч |
Поло- жение швов |
АНЖР-1 |
П |
=(+) |
15,0 |
|
АНЖР-2 |
Б |
=(+) |
14,5 |
|
Сварка теплоустойчивых сталей с высоколегированными жаропрочными сталями.![]() |
||||
ОЗЛ-27 |
РБ |
~, =(-) |
10,5 |
|
ОЗЛ-28 |
РБ |
~, =(+) |
9,5 |
|
Сварка углеродистых сталей с легированными, в том числе с трудносвариваемыми сталями. | ||||
ОЗЛ-6 |
Б |
=(+) |
12,0 |
|
ОЗЛ-6С |
Б |
=(+) |
11,0 |
|
Сварка углеродистых и низколегированных сталей с высоколегированными сталями.![]() |
||||
НИАТ-5 |
Б |
=(+) |
13,0 |
|
Сварка низколегированных и легированных сталей с высоколегированными сталями. | ||||
ЭА-395/9 |
Б |
=(+) |
11,5 |
|
Сварка низколегированных и легированных сталей с высоколегированными сталями. | ||||
ОЗЛ-25Б |
Б |
=(+) |
14,0 |
|
Сварка разнородных сталей: коррозионностойких, жаростойких, жаропрочных и сплавов на никелевой основе.![]() |
||||
ИМЕТ-10 |
РБ |
=(+) |
14,0 |
|
Сварка разнородных жаропрочных сталей и сплавов. | ||||
ЦТ-28 |
РБ |
=(+) |
10,5 |
|
Сварка углеродистых, низколегированных и хромистых сталей со сплавами на никелевой основе. | ||||
НИИ-48Г |
Б |
=(+) |
12,0 |
|
Сварка низколегированных, специальных и высокомарганцовистых сталей с высоколегированными сталями |
© 2018 Лаборатория сварки
Создание и продвижение сайтов компания «ИДЕЯ!»
Придерживайтесь основ — производительность сварки
Рекомендации по повторной сушке стержневых электродов с низким содержанием водорода.
Различные стержневые электроды с низким содержанием водорода используются в качестве присадочного металла для процесса дуговой сварки в среде защитного газа (SMAW). Электроды с низким содержанием водорода являются наиболее популярным типом стержневых электродов, используемых в Северной Америке. Независимо от того, опытный сварщик или новичок в профессии, полезно понимать, как работают электроды с низким содержанием водорода и почему они используются.
Стержневые электроды с низким содержанием водорода имеют плавные характеристики дуги, легкое удаление шлака, хорошую форму валика, более высокую скорость наплавки, и большинство из них можно использовать во всех положениях сварки. Они используются в различных отраслях промышленности, связанных со сваркой. Строительство мостов и зданий, морское бурение, сосуды под давлением, трубопроводы и производство электроэнергии — все это хорошие примеры.
Любые сварочные работы, связанные с чувствительными основными материалами, такими как высокопрочные стали, защемленные соединения или те, к которым применяются более строгие правила сварки, скорее всего, будут включать использование присадочного металла с низким содержанием водорода.
Электроды с низким содержанием водорода должны быть сухими для правильной работы. Поглощение влаги может ухудшить качество сварки несколькими способами. Чрезмерная влажность может вызвать пористость сварного шва, которая может быть видимой на поверхности сварного шва, или она может быть только подповерхностной, и для ее обнаружения требуется какой-либо тип неразрушающего или разрушающего контроля. Высокая влажность покрытия электрода также может привести к чрезмерной текучести шлака, шероховатой поверхности сварного шва и затрудненному удалению шлака. Наконец, чрезмерная влажность в электродах с низким содержанием водорода приводит к повышенному уровню диффузионного водорода, что, в свою очередь, может привести к водородному растрескиванию сварного шва и растрескиванию под валиком.
Водород естественным образом поглощается жидким металлом (т. е. расплавленной сварочной ванной) и естественным образом выходит из твердого металла (т. е. затвердевшего металла сварного шва). Сталь выше температуры плавления естественным образом поглощает водород. По мере того как сталь охлаждается ниже температуры плавления и снова затвердевает (замерзает), водород, который находится внутри металла сварного шва, стремится мигрировать или диффундировать наружу, и со временем это происходит. Однако, когда начальные уровни диффундирующего водорода внутри металла сварного шва повышены, существует большая вероятность водородного растрескивания, которое обычно происходит в зоне термического влияния (ЗТВ).
HAZ не является результатом только повышенного уровня диффузионного водорода. Кроме того, основной материал должен иметь более чувствительную микроструктуру, такую как высокоуглеродистые и высокопрочные низколегированные стали, которые более подвержены растрескиванию из-за более высокого содержания углерода и легирующих элементов. Кроме того, должны присутствовать более высокие внутренние напряжения в сварном шве, например, в случае более толстых стальных профилей или пластин, ограниченных рамками. Например, пластины на большом корабле ограничены и не могут двигаться, создавая напряжение.
Поиск источника
Откуда берется водород при сварке? Одним из источников являются загрязняющие вещества на основном материале. Краска, масло, грунтовка, прокатная окалина и ржавчина на поверхности стали — все это потенциальные источники углеводородов. Они могут производить водород в результате химических реакций, поскольку они расходуются в тепле сварочной дуги и, таким образом, вводят водород в металл сварного шва. Поэтому материал должен быть максимально чистым.
Вторым источником водорода является окружающая атмосфера – влажность воздуха. Сварка в очень влажных условиях потенциально может привести к попаданию большего количества водорода в металл сварного шва.
Третий источник водорода – конденсация влаги на покрытии электрода. Стержневые электроды имеют в сердцевине токопроводящий стальной стержень, который плавится и становится присадочным металлом. Этот сердечник покрыт флюсовым покрытием, которое также плавится, защищая дугу и образуя защитный шлаковый покров над сварным швом. Если влага конденсируется на этом внешнем флюсе, она связывается с пористым флюсом, вводя водород в металл сварного шва.
Следует отметить, что поддержание определенного уровня диффузионного водорода является проблемой только для электродов с флюсом, таких как стержневые электроды, флюсы для дуги под флюсом и порошковые проволоки (конденсация на внутреннем флюсе происходит из-за влаги через шов проволоки) .
Водород, однако, не является проблемой для стальных стержней для сварки TIG, проволоки для сварки MIG или проволоки для сварки под флюсом, поскольку они не имеют флюса. На присадочном металле все еще может оставаться влага из-за конденсата, но она не связывается со сталью или медным покрытием на стальном электроде. Он просто испаряется при нагревании в дуге. Таким образом, все стержни для сварки TIG, проволоки для сварки MIG и проволоки для сварки под флюсом считаются электродами с низким содержанием водорода, что некоторые могут не осознавать.
Стержневые электроды с низким содержанием водорода кондиционируются в процессе производства, чтобы свести к минимуму уровень водорода в их покрытиях, тем самым уменьшая возможность осаждения диффундирующего водорода в металле сварного шва. Стержневой электрод с низким содержанием водорода идентифицируется по обозначению типа покрытия в его классификационном номере. Он также может иметь необязательное обозначение максимального количества диффузионного водорода после его классификационного номера, как это определено Американским обществом сварщиков (AWS).
Обозначения «HX» указывают максимальное количество миллилитров диффузионного водорода на 100 граммов наплавленного металла. h5, H8 и h26 являются типичными обозначениями. Для стержневых электродов обозначение h26 или ниже считается низким содержанием водорода, но технология продвинулась до такой степени, что большинство стержневых электродов с низким содержанием водорода теперь имеют обозначение H8 или ниже.
Рекомендации по повторной сушке электродов с низким содержанием водорода.
Как обращаться
Несмотря на то, что стержневые электроды с низким содержанием водорода поставляются с завода с покрытием с низким содержанием водорода, они могут быстро поглощать дополнительный водород из-за конденсации, если их не хранить и не обращаться с ними должным образом. Вот почему они обычно поставляются в герметично закрытой или воздухонепроницаемой таре, где их можно хранить неограниченное время.
После открытия контейнера стандартные электроды с низким содержанием водорода должны находиться на открытом воздухе не более четырех часов. После этого электроды необходимо хранить в герметичном контейнере с регулируемой температурой и выдерживать при повышенной температуре в соответствии с рекомендациями производителя присадочного металла. Это предотвращает образование конденсата на покрытии.
Lincoln Electric рекомендует для своей продукции с низким содержанием водорода хранить открытые банки и незакрепленные электроды в герметичном контейнере при температуре от 250° до 300° F (от 120° до 150° C). Наиболее распространенные контейнеры для электродов с низким содержанием водорода называются стержневыми печами.
Некоторые стержневые электроды с низким содержанием водорода изготавливаются с влагостойкими покрытиями и обозначаются добавлением буквы «R» к их обозначению AWS с максимальным диффузионным водородом (например, E7018-h5R). В то время как время воздействия на открытом воздухе электродов с низким содержанием водорода ограничено примерно четырьмя часами, электроды с обозначением R потенциально могут подвергаться воздействию до девяти часов. И это важно, потому что их можно оставлять вне стержневой печи на всю рабочую смену. Тем не менее, некоторые требования кода могут указывать пределы воздействия, отличные от этих рекомендаций.
Электроды с низким содержанием водорода, которые не были запечатаны или хранились должным образом и превысили допустимые пределы воздействия на открытом воздухе, могут быть восстановлены (повторно высушены) перед использованием. Это делается путем повышения температуры в стержневой печи до определенного уровня и сушки электродов в течение одного часа при этой температуре. Их следует разложить в духовке, чтобы каждая могла достичь температуры сушки. Производитель присадочного металла предоставляет конкретные рекомендации по температуре восстановления (см. Таблицу 1).
Электроды с низким содержанием водорода не следует подвергать повторной сушке при температурах выше рекомендуемых или в течение нескольких часов при температурах ниже рекомендуемых. Кроме того, электроды с низким содержанием водорода, такие как целлюлозные и рутиловые, не следует хранить или повторно сушить при тех же температурах, что и электроды с низким содержанием водорода.
Электроды низколегированные низководородные не подлежат восстановлению более трех раз. Любой электрод с низким содержанием водорода, будь то углеродистая или низколегированная сталь, следует выбросить, если чрезмерная повторная сушка приводит к тому, что покрытие становится хрупким и отслаивается или отрывается во время сварки, или если наблюдается заметная разница в характеристиках дуги.
Пример типовых рабочих процедур.
Советы по технике
В дополнение к получению наплавленного металла с минимальным количеством диффундирующего водорода успех при использовании штучных электродов с низким содержанием водорода также зависит от использования правильной техники. Это включает в себя использование определенного типа электрода с низким содержанием водорода в его предполагаемом положении для сварки, сварку с соответствующим уровнем тока для данного типа и диаметра электрода и с использованием правильной скорости перемещения. Это также включает в себя использование правильного угла наклона электрода, длины дуги и так далее.
Рекомендуемые настройки тока по диаметру и полярности обычно можно найти в документации производителя присадочного металла. Сила тока измеряется в амперах или амперах. В качестве отправной точки сварщики должны выбрать настройку тока в середине диапазона.
Другое эмпирическое правило для настройки тока с электродами со средним покрытием, такими как E7018, заключается в умножении каждой тысячи дюймов диаметра электрода на один ампер. Например, 1/8 дюйма. электрод в десятичной форме до разряда тысяч составляет 0,125 дюйма. Таким образом, машина должна быть установлена около 0,125 х 1000 или 125 ампер. И наоборот, 5/32-дюймовый. электрод должен быть установлен примерно на 0,156 x 1000 или 156 ампер. Если ток слишком мал для данного диаметра, может быть трудно запустить и поддерживать дугу. Кроме того, сварной шов будет бугристым. Слишком большой ток может преждевременно разрушить покрытие и вызвать дефекты сварного шва (см. табл. 2).
При изготовлении стрингерных валиков стержневые электроды обычно имеют оптимальную скорость перемещения, которая обеспечивает наилучший контроль за лужей и форму валика. Размер полученного сварного шва увеличивается по мере увеличения диаметра электрода (см. Таблицу 3).
При использовании электродов с низким содержанием водорода сварщики всегда должны использовать угол перемещения, оставляя шлак за ванной, и поддерживать короткую длину дуги. Они всегда должны держать электрод близко к ванне, а не «длинную дугу», так как это может привести к нестабильности дуги и пористости сварного шва.
Обратите внимание, что при сварке в нерабочем положении целлюлозными стержневыми электродами (например, E6010) сварщики часто выхватывают электрод из ванны, а затем возвращают его обратно. Этот метод взбивания с длинной дугой позволяет слегка покрытой шлаком ванне замерзнуть перед наплавкой большего количества металла сварного шва. Однако этот метод взбивания не следует использовать с электродами с низким содержанием водорода.
Как правило, сварщики должны делать сварные швы или использовать прямую последовательность. Для более крупных сварных швов несколько небольших многопроходных стрингерных валиков обычно обеспечивают лучшие механические свойства, особенно ударную вязкость по сравнению с меньшим количеством проходов больших широких валиков. Однако в некоторых ситуациях сварщикам может потребоваться манипулировать сварочной ванной с использованием какой-либо техники плетения, стараясь не плести более 3/4 дюйма. широкий.
Согласно статье, написанной Джозефом Коласа, инструктором Школы сварки Lincoln Electric, и Джозефом Мурлином, менеджером по расходным материалам для сварки SMAW, первое, что должны сделать сварщики при начале сварки, — это удерживать очень короткую дугу. Более длинные дуги значительно увеличивают возможность получения пористости в начале дуги.
Также не следует устанавливать слишком высокий уровень контроля горячего старта (на сварочных аппаратах с этой функцией). Это может привести к увеличению длины дуги и преждевременному расплавлению покрытия электрода, создавая недостаточную защиту и, в конечном итоге, пористость сварного шва.
Распространенной проблемой перезапуска дуги при сварке вертикально вверх является «забивание» покрытия (т. е. когда одна сторона покрытия пригорает дальше, чем другая сторона, что может привести к проблемам с пористостью). Это происходит, когда сварщики используют слишком большой угол наклона вверх. Многие сварщики перезапускаются слишком высоко в сварном шве, а затем затягиваются до кратера. Они могут избежать этих сценариев при перезапуске штучного электрода, начиная примерно на 1/4–1/2 дюйма выше предыдущего сварного шва. Они должны направить электрод прямо в сустав, используя угол толкания не более 5° или 10°.
Повторный запуск частично израсходованного электрода с низким содержанием водорода после охлаждения наконечника может быть затруднен. На конце электрода естественным образом образуется шарик шлака. Этот твердый, хрупкий шлак действует как изолятор, что затрудняет установление дуги. Большинство сварщиков предпочитают помещать электрод в электрододержатель и стучать им по пластине, как молотком. Это может привести к отслаиванию покрытия электрода. Вместо этого им следует вынуть электрод из держателя и грубо потереть наконечник о поверхность сварочного стола, пока он не доберется до стального стержня. Это обеспечивает хорошее электрическое соединение для зажигания дуги без повреждения покрытия.
Многие сварщики предпочитают использовать стержневые электроды с низким содержанием водорода из-за их плавных характеристик дуги, легкого удаления шлака, хорошей формы валика и более высокой скорости наплавки. Их также выбирают, потому что они могут выполнять сварку во всех положениях. Однако лучшее понимание того, почему, где и как использовать электроды с низким содержанием водорода, а также как их хранить и обращаться с ними, также может сделать сварщиков еще умнее. Поскольку использование электродов с низким содержанием водорода продолжает расти, эти знания и набор навыков сделают любого сварщика еще более ценным для отрасли.
Типы электродов с низким содержанием водорода
Расшифровка классификационных номеров электродов.Общий номер классификации AWS с низким содержанием водорода — E7018-h5R. Конкретный классификационный номер для конкретного электрода рассказывает о нем историю. Расшифровка этих номеров показана в Таблице 4.
Первые две или три цифры в номере указывают минимальный предел прочности металла сварного шва на растяжение. Электрод с низким содержанием водорода из углеродистой стали (мягкой стали) имеет минимальный предел прочности на разрыв 70 тысяч фунтов на квадратный дюйм, в то время как большинство низколегированных электродов с низким содержанием водорода имеют минимальный предел прочности на разрыв от 80 до 120 тысяч фунтов на квадратный дюйм. За исключением нескольких целлюлозных электродов с пределом прочности 80 тыс.фунтов/кв.дюйм, все низколегированные электроды также являются электродами с низким содержанием водорода.
Предпоследняя цифра в номере указывает рекомендуемое положение сварки. «1» означает все положения (плоское, горизонтальное, вертикальное и над головой), «2» означает рабочее положение (только плоское и горизонтальное), а «4» означает только вертикальное вниз. Электроды, которые можно сваривать вне положения или против силы тяжести, имеют систему быстрого замерзания шлака, имеют меньший диаметр и обладают более низкой скоростью наплавки. Принимая во внимание, что электроды, которые можно использовать только в положении или под действием силы тяжести, имеют более медленную систему замерзания шлака, имеют больший диаметр и обладают более высокой скоростью наплавки.
Последняя цифра в номере указывает на тип покрытия электрода и рекомендуемую полярность сварки. Электроды, оканчивающиеся на «5» (на основе натрия), «6» (на основе калия) и «8» (на основе калия с добавлением порошка железа), являются электродами с низким содержанием водорода. Все они также считаются имеющими «базовое» покрытие — по сравнению с целлюлозным (органическим), рутиловым (диоксид титана) или покрытиями на основе оксида железа.
Из трех типов покрытие «8» на сегодняшний день является самым популярным. Электрод типа «28», устанавливаемый только в положении, имеет 50-процентное добавление железного порошка к покрытию для максимальной скорости осаждения и считается электродом с толстым покрытием. Добавление железного порошка увеличивает скорость наплавки этих электродов, поскольку железный порошок в покрытии плавится и становится частью металла сварного шва вместе с сердечником.
Всепозиционный электрод типа «18» имеет 30-процентное содержание железного порошка в покрытии и считается электродом со средним покрытием. Несмотря на то, что он по-прежнему имеет систему быстрого замерзания шлака, дополнительные 30 процентов железного порошка в покрытии обеспечивают максимальную скорость наплавки электрода при сварке в нерабочем положении. Кроме того, поскольку электрод «18» имеет тяжелую шлаковую систему, его не рекомендуется использовать для вертикальной подачи вниз, так как шлак может вытекать из ванны и задерживаться под ней. В вертикальном положении электрод «18» следует использовать только с вертикальным продвижением вверх.
В таблице 5 приведены примеры различных типов электродов с низким содержанием водорода с указанием их конкретного номера классификации AWS, описания и типичных областей применения.
Нидриг- и Миттельлегьерт | |
Interweld E 210 | Универсальный (для соединения и ремонта) всепозиционный электрод из мягкой стали. Хорошая работоспособность и легкое удаление шлака |
Interweld E 220 | Электрод с рутиловым покрытием с толстым покрытием, предназначенный для плоской сварки или присадочной сварки, когда требуется хороший внешний вид сварного шва |
Interweld E 250 | Универсальный (для соединения, ремонта и корневого прохода) основной электрод с двойным покрытием.![]() |
Interweld E 270 | Электрод с основным покрытием с низким содержанием водорода для мелкозернистых сталей. |
Interweld E 290 | Электрод с основным покрытием, обладающий высокой устойчивостью к растрескиванию и высокой прочностью, для мелкозернистых сталей |
Interweld E 291 | Электрод с основным покрытием с низким содержанием водорода и молибденом для сварки жаропрочных сталей, используемых при температурах до 500°C |
Interweld E 293 | Электрод с основным покрытием с низким содержанием водорода с Cr и Mo для сварки жаропрочных сталей (1% Cr – 0,5% Mo) |
Elektroden zum Ausfugen, Nuten und Schneiden | |
Interweld E 007 | Электрод для снятия фасок, канавок и строжки всех металлов без сжатого воздуха |
Interweld Кохлеэлектроден | Используется для резки, устранения дефектов сварки, просверливания отверстий и удаления сваренных деталей сжатым воздухом |
Электроден для rostfreie Stähle | |
Interweld E 308 | Электрод из аустенитной нержавеющей стали с низким содержанием углерода и рутиловым покрытием, с мягким плавлением и без брызг |
Interweld E 309 | Низкоуглеродистый рутил-основной электрод (аустенитный, нержавеющий) для сварки разнородных сталей |
Interweld E 310 | Электрод на рутиловой основе с жаростойким покрытием из аустенитной нержавеющей стали.![]() |
Interweld E 316 | Низкоуглеродистый электрод из аустенитной нержавеющей стали с рутиловым основным покрытием и покрытием из молибдена |
Interweld E 318 | Электрод с рутиловым покрытием, стабилизированный ниобием (колумбием), аустенитная нержавеющая сталь 18Cr 12Ni 3Mo |
Interweld E 347 | Электрод с рутиловым покрытием, нержавеющая сталь типа 18%Cr8% Ni, стабилизированный ниобием/колумбием |
Электроден для электрощита schweißbare Stähle | |
Interweld E 307 | Аустенитный электрод для наплавки и сварки трудносвариваемых сталей. Соединение разнородных сталей и марганцевых сталей |
Interweld E 309 Mo | Электрод для наплавки и сварки трудносвариваемых сталей.![]() |
Interweld E 312 | Электрод с рутиловым покрытием с высоким выходом (160 %) для наплавки и сварки трудносвариваемых сталей. |
Interweld E 360 | Соединение разнородных сталей, а также марганцевых сталей/наращивание режущих инструментов. Подходит для буферных слоев перед наплавкой |
Interweld E 363 | Универсальный электрод для ремонта и обслуживания. Высочайшая устойчивость к трещинам. |
Электроден для Gusseisenschweißen | |
Interweld E 815 | Электрод с графитовым основным покрытием для горячей сварки чугуна с шаровидным графитом с соответствующим по цвету и структуре налетом.![]() |
Interweld E 816 | Электрод со специальной железной основой для ремонтной сварки некачественного, шлакового или маслосодержащего старого чугуна |
Interweld E 820 | Электрод с графитовым основным покрытием и ферроникелевой проволокой для сварки и ремонта чугуна с шаровидным графитом. |
Interweld E 824 | Электрод с графито-основным покрытием. Наплавленный металл состоит из чистого никеля. Холодная сварка и ремонт серого чугуна |
Interweld E 836 | Рекомендуется для холодной сварки и ремонта серого чугуна, ремонта трещин. Соединение серых отливок с C-сталью. |
Interweld E 880 | «Биметаллическая» жильная проволока с высокой электропроводностью для холодной и горячей сварки (полугорячей сварки) чугуна.![]() |
Электроден на основе алюминия и меди | |
Interweld E 100 | Электрод для сварки медно-оловянных бронз (CuSn 68%) и в некоторых случаях латуни (CuZn) Также используется для сварки разнородных соединений |
Interweld E 101 | Электрод для сварки и наплавки алюминиевых бронз с содержанием алюминия до 10 % и для разнородных соединений |
Interweld E 103 | Электрод для сварки AlBz и наплавки углеродистых сталей, стального литья и чугуна. |
Interweld E 104 | Электрод из марганцовистой бронзы для сварки и наплавки на AlBz и для разнородных соединений между сталями и медными сплавами |
Interweld E 505 | Алюминиевый электрод с 5% Si для сварки и ремонта деталей из алюминия или алюминиевых сплавов |
Interweld E 512 | Алюминиевый электрод с 12% Si для сварки и ремонта деталей из алюминия или алюминиевых сплавов |
Никельбазиэлектроден | |
Interweld E 364 | Электрод для буферных слоев и сварки подобных сталей или соединения углеродистых/нержавеющих сталей и сталей с содержанием 5-9% Ni |
Interweld E 365 | Электрод с легированной основной проволокой для сварки сплавов NiCrMo между собой и с низколегированными сталями |
Interweld E 366 | Электрод с выходом 170% для сварки сплавов NiCrMo между собой и с низколегированными сталями |
Interweld E 367 | Электрод на никелевой основе с легированной основной проволокой для наплавки низколегированных сталей, сварки сплавов Fe и Ni |
Interweld E 368 | Электрод с наплавкой Ni-Cu, предназначенный для стыковой сварки и наплавки NiCu, CuNi |
Interweld E 369 | Электрод с наплавкой никеля, содержащий 1-2% Ti, предназначенный для стыковой сварки чистого никеля и наплавки NiCu |
Interweld E 394 | Электрод с проволокой из легированного сердечника для сварки сплавов на основе никеля (сплав С276) и других сплавов Ni Cr Mo |
Электроден для Hartauftragungen | |
Interweld E 395 | Покрытие с превосходными сварочными характеристиками.![]() |
Interweld E 395 Co | Депозит устойчив к коррозии, образованию накипи, окислению и термическим ударам |
Interweld E 601 | Самый твердый сплав на основе кобальта. Очень хорошая стойкость к износу металл-металл и к коррозии до 800°C. |
Interweld E 606 | Очень хорошая стойкость к износу металл-металл и коррозии до 800°C. Очень низкий коэффициент трения. |
Interweld E 612 | Очень хорошая стойкость к истиранию металлами и минералами в сочетании с коррозией при умеренных ударах |
Interweld E 621 | Очень хорошая стойкость к износу металл-металл при температуре до 1000°C, даже в присутствии сернистой атмосферы |
Interweld E 622 | Наплавленный металл устойчив к износу металла/металла при более высоких температурах и может подвергаться старению |
Interweld E 632 | Наплавка и наплавка деталей, подвергающихся ударам, сжатию и износу, используемых при рабочих температурах до 550°С.![]() |
Interweld E 633 | Используется для наплавки и наплавки деталей, подвергающихся ударам, сжатию и износу при температуре до 550°C. |
Interweld E 634 | Используется для наплавки и наплавки деталей, подвергающихся ударам, сжатию и износу при температуре до 550°C. |
Interweld E 635 | Используется для наплавки и наплавки деталей, подвергающихся ударам, сжатию и износу при температуре до 650°C. |
Interweld E 636 | Для наплавки всех видов режущих инструментов, таких как токарные и строгальные инструменты. Полученная резкость имеет исключительное качество |
Interweld E 642 | Для защиты деталей от сильных ударов и кавитации в сочетании с коррозией.![]() | .
Interweld E 643 | Детали, подверженные сильным ударам, для дефектных отливок и амортизирующих слоев перед наплавкой толстых покрытий |
Interweld E 658 | Наплавка деталей, подверженных ударному, компрессионному и абразивному износу |
Interweld E 660 | Устойчив к среднему истиранию, ударам и давлению. Закалка на воздухе. |
Interweld E 662 | Устойчив к истиранию тяжелыми минералами и умеренному удару |
Interweld E 663 | Используется для наплавки деталей, подверженных сильному истиранию, трению, нагреву и коррозии |
Interweld E 665 | Наплавка деталей, подверженных сильному истиранию, трению, нагреву и коррозии |
Interweld E 672 | Трубчатый электрод, наполненный порошком карбида хрома.![]() |
Interweld E 680 | Трубчатый электрод с графитовым покрытием для максимальной износостойкости отложений. Состоит примерно на 60 % из карбида вольфрама |
Электроды с покрытием из недрагоценных металлов для дуговой сварки | OEC
О
#постоянная ссылка на раздел Обзор Эта страница содержит последние торговые данные Электроды с покрытием из недрагоценных металлов для дуговой сварки. В 2020 году Электроды покрытые из недрагоценных металлов для дуговой сварки были 1797-м самым продаваемым продуктом в мире с общим объемом торговли 1,1 миллиарда долларов. В период с 2019 по 2020 год экспорт Электроды с покрытием из недрагоценных металлов для дуговой сварки сократился на -8,21%, с 1,2 млрд долларов до 1,1 млрд долларов. Торговля Электроды с покрытием из недрагоценных металлов для дуговой сварки составляют 0,0066% от общего объема мировой торговли.
Электроды с покрытием из недрагоценных металлов для дуговой сварки входят в состав продуктов для пайки металлов с покрытием.
Экспорт В 2020 году крупнейшими экспортерами Электродов с покрытием из недрагоценных металлов для дуговой сварки были Китай (306 млн долларов США), Чехия (58,8 млн долларов США), США (56,9 млн долларов США), Австрия (53,5 млн долларов США) и Беларусь. (46,3 млн долларов).
Импорт В 2020 году крупнейшими импортерами Электродов с покрытием из недрагоценных металлов для дуговой сварки были Россия (70,9 млн долларов), Чехия (51,2 млн долларов), Объединенные Арабские Эмираты (41,6 млн долларов), Китай (41,3 млн долларов) и Индонезия (32,1 млн долларов).
Тарифы В 2018 году средний тариф на Электроды с покрытием из недрагоценных металлов для дуговой сварки составил 10%, что делает его 2237-м самым низким тарифом с использованием классификации продуктов HS6.
Странами с самыми высокими импортными тарифами на Электроды с покрытием из недрагоценных металлов для дуговой сварки являются Багамы (41,8%), Иран (32%), Судан (35%) и Кения (34,2%). . Страны с самыми низкими тарифами — Маврикий (0%), Гонконг (0%), Шри-Ланка (0%), Сингапур (0%) и Швейцария (0%).
Рейтинг Электроды с покрытием из недрагоценных металлов для дуговой сварки занимает 3067-е место в индексе сложности продукта (PCI).
Описание Электроды являются расходным материалом в процессе дуговой сварки. Электроды бывают разных размеров и форм и состоят из сплава основного металла и покрытия. Покрытие обычно изготавливается из смеси меди и фосфора. Электрод является расходным материалом, так как после использования покрытие стирается и электрод необходимо заменить. Электроды обычно используются в процессе дуговой сварки. Дуговая сварка — это процесс, при котором ток проходит между плавящимся электродом и заготовкой. Ток нагревает электрод и заготовку до тех пор, пока заготовка не расплавится
Последние тенденции
#permalink в разделПоследние данные
#permalink к разделуПросмотр
Поток
Scale
. показаны последние тенденции в области электродов с покрытием из недрагоценных металлов для дуговой сварки. Страны показаны на основе наличия данных.
Для получения полной информации о структуре торговли посетите обозреватель тенденций или продукт в профиле страны.
* С использованием обменных курсов на январь 2020 г., если торговые данные представлены в местной валюте.
Explore Latest Trends
Historical Data
#permalink to sectionExporters and Importers
#permalink to sectionTrade By Country
Yearcaret-down2020201920182017201620152014201320122011201020092008200720062005200420032002200120001999199819971996
Electrodes, coated, of base metal, for дуговая сварка занимают 1797-е место в мире по объемам продаж.
В 2020 году ведущими экспортерами Электродов с покрытием из недрагоценных металлов для дуговой сварки были Китай (306 млн долларов), Чехия (58,8 млн долларов), США (56,9 млн долларов), Австрия (53,5 млн долларов), и Беларусь (46,3 млн долларов).
В 2020 году крупнейшими импортерами Электродов с покрытием из недрагоценных металлов для дуговой сварки были Россия (70,9 млн долларов), Чехия (51,2 млн долларов), Объединенные Арабские Эмираты (41,6 млн долларов), Китай (41,3 млн долларов). и Индонезия (32,1 млн долларов).
Explore Visualizations
Market Dynamics
#permalink to sectionTrade by country
Startingcaret-down20192018201720162015201420132012201120102009200820072006200520042003200220012000199919981997Endingcaret-down202020192018201720162015201420132012201120102009200820072006200520042003200220012000199919981997
Value
Between 2019 and 2020, the exports of Electrodes, coated, of base metal, for дуговая сварка 9Номер 0523 быстрее всего рос в Беларуси (7,86 млн долларов), Китайском Тайбэе (3,44 млн долларов), Турции (3,25 млн долларов), Украине (2,93 млн долларов) и Объединенных Арабских Эмиратах (2,53 млн долларов).
В период с 2019 по 2020 год самыми быстрорастущими импортерами Электродов с покрытием из недрагоценных металлов для дуговой сварки были Камбоджа (4,8 млн долларов США), Гана (4,57 млн долларов США), Танзания (4,49 млн долларов США), Судан (3,52 млн долларов США). ) и Кении (3,44 млн долларов).
Изучение визуализаций
Концентрация рынка
#постоянная ссылка на разделСовокупная доля рынка
Стоимость
На этой диаграмме показано изменение рыночной концентрации экспорта Электроды с покрытием из недрагоценных металлов для дуговой сварки.
В 2020 году концентрация рынка, измеренная с помощью энтропии Шеннона, составила 4,51. Это означает, что большая часть экспорта Электроды с покрытием из недрагоценных металлов для дуговой сварки приходится на 22 страны.
Просмотр визуализаций
Net Trade
#permalink в разделГодовой карет-вуд20201019201820172016201520142013201220112020200920082007200200520042003200220012000199919981997
0020012000199919981997
0020012000199919981997
0020012000199991998197
9 0002.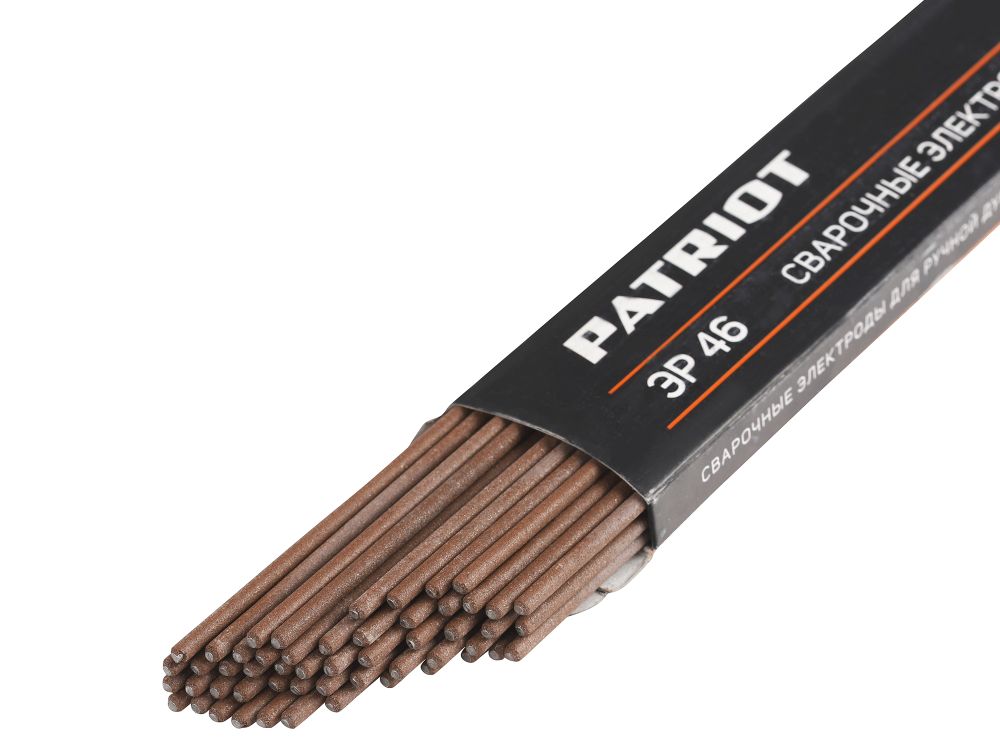
Электроды с покрытием из недрагоценных металлов для дуговой сварки были произведены в Китае (264 млн долларов), Австрии (50,4 млн долларов), Швеции (39,6 млн долларов), Турции (36 млн долларов) и Беларуси (35,3 млн долларов).
В 2020 году странами, которые имели наибольшую торговую стоимость в импорте, чем в экспорте Электроды с покрытием из недрагоценных металлов для дуговой сварки , были Россия (55,1 млн долларов США), Саудовская Аравия (27,9 млн долларов США), Объединенные Арабские Эмираты Эмирейтс (24 миллиона долларов), Казахстан (21,5 миллиона долларов) и Индонезия (20,4 миллиона долларов).
Сравнение стран
#permalink to sectionContinentscaret-downAllAfricaAntarcticaAsiaEuropeNorth AmericaOceaniaSouth America
Flow
Measure
Ranking
Эта визуализация показывает страны, которые имеют важное соотношение основных металлов для электродуговой сварки6, 9009, . Можно выбрать основные страны, экспортирующие или импортирующие Электроды с покрытием из недрагоценных металлов для дуговой сварки в мире или по континентам, а также выбрать интересующую меру.
Сложность продукта
#постоянная ссылка на разделГраница диверсификации
#постоянная ссылка на разделСпециализация
На диаграмме сложность-связь сравниваются риск и стратегическая ценность потенциальных экспортных возможностей продукта. Связанность предсказывает вероятность того, что страна увеличит свой экспорт продукта. Сложность связана с более высокими уровнями доходов, потенциалом экономического роста, меньшим неравенством доходов и меньшими выбросами.
Nicrotec
AVISO LEGAL
1. Общая информация.
Las Presentes Condiciones (en adelante, Condiciones de Uso) regulan el uso licensedo de la pgina con URL www. nicrotec.com,
que SOLDADURAS NICROTEC, S.A. (en adelante, el Prestador del Servicio), pone a disposicin de los usuarios de Internet (en adelante, los Usuarios).
Se pone a disposicin de los Usuarios los siguientes medios donde podrn dirigir sus peticiones, cuestiones y quejas:
Direccin Postal: calle Joiers, 5 Pligono Industrial Riera de Caldes, 08184 Palau Solit i Plegamans
Direccin de correo electrornico: [email protected]
Тел. для абонентов: 93 863 96 76
Datos registrales de SOLDADUR, SOLDEC. : inscrita en el el Registro Mercantil de Barcelona, en el tomo 31638, folio 25, hoja B-196701.
2. Интеллектуальная и промышленная собственность.
2.1 Los derechos de propiedad intelectual de la pgina www.nicrotec.com, su cdigo fuente, diseo, fotografas, textos, estructura de
navegacin, bases de datos y los distintos elementos en l contenidos, son titularidad del Prestador del Servicio a quien reporte el
ejercicio exclusivo de los derechos de explotacin de los mismos en cualquier forma y, en especial, los derechos de reproduccin, distribucin,
коммуникацин пблика и трансформацин.
2.2 El Prestador del Servicio es titular de los derechos de propiedad Industrial Referidos a sus productos y servicios, y especficamente de los relativos a la marca registrada Nicrotec, quedando prohibido su uso, salvo autorizacin expresa y firmada por parte del Prestador дель Сервисио.
2.3 Использование без авторизации на информацию, содержащуюся в Интернете, на ревенте, как комо-ла-ла-лесин-де-лос-дерехос-де-Интеллектуал o Industrial de el Prestador del Servicio dar lugar a las responsabilidades legalmente establecidas.
2.4 El usuario asume la responsabilidad del uso que effecte en la Web. El usuario se compromete a hacer un uso adecuado de los
contenidos y servicios que NICROTEC ofrece a travs del mismo. En este sentido, con carcter enunciativo pero no limitativo, el usuario se
compromete (i) a no utilizar las imgenes para un mal uso (ii) incurrir en actividades ilcitas, ilegales o contrarias a la buena fe y al orden
пблико; (iii) provocar daos en los sistemas fsicos y lgicos de NICROTEC, de sus proofedores o de terceras personas; (iv) introducir o difundir
en la redvirus informticos o cualesquiera otros sistemas fsicos o lgicos que sean visibles de provocar cualquier tipo de daos.
3. Aceptacin de las Condiciones de Uso.
Estas Condiciones de Uso regulan el acceso y utilizacin del site www.nicrotec.com que el Prestador del Servicio pone gratuitamente a disposicin де лос Usuarios. El acceso al mismo implica su aceptacin sin reservas.
4. Разрешения на использование.
Se autoriza la visualizacin, impressin y descarga parcial del contenido de la Web slo y exclusivamente si concurren las siguientes condiciones:
4.1. Que морской совместимый кон-лос-штрафы де-ла-Web.
4.2. Que se realice con el exclusivo nimo de obtener la informacin contenida para uso personal y privado. Se prohbe expressamente su utilizacin ограничивается коммерческими или пунктами su distribucin, comunicacin pblica, transformacin или descompilacin.
4.3. Que ninguno de los contenidos relacionados en la Web Шон modificados де Manera Alguna.
4.4. Queningn grfico, icono или imagen disponible en la Web sea utilizado, copyado или distribuido separadamente del texto or resto de imgenes que lo acompaan.
5. Modificaciones en la Web y las Condiciones de Uso.
El Prestador del Servicio se reserva la facultad de efectuar, en cualquier momento y sin necesidad de previo aviso, modificaciones y актуализирует de la informacin contenida en la Web, de la configuracin y Presentacin de sta y de las condiciones de acceso. Как mismo эль Prestador дель Servicio себе резерва эль derecho де актуализа лас представляет Condiciones де Uso грех previo aviso лос Usuarios, дие сын лос nicos responsables де су Consulta Como Paso previo a acceder а-ля Интернет.
6. Limitacin de responsabilidad.
6.1 El Prestador del Servicio не гарантирует несуществование прерываний или ошибок в доступе к сети или в отношении су contenido, ni que ste se encuentre actizado. El Prestador del Servicio llevar a cabo, siempre que no concurran causas que lo hagan imposible o de difcil ejecucin, y tan pronto tenga noticia de los errores, desconexiones o falta de actizacin en los contenidos, todas aquellas Labores tendentes a subsanar los errores, restablecer ла comunicacin у актуализировать лос contenidos.
6.2 Tanto el accesso a la Web como el uso inconsentido que pueda efectuarse de la informacin contenida en la misma, es de la exclusiva responsabilidad de quien lo realiza. El Prestador del Servicio не отвечает ninguna consecuencia, dao o perjuicio que pudieran derivarse de dicho acceso o uso. El Prestador del Servicio no se hace responsable de los errores de seguridad, que se puedan producir ni de los daos que puedan causarse al sistema informtico de los Usuarios (аппаратное и программное обеспечение), o a los ficheros o documentos almacenados en el mismo, como consecuencia de :
(i) la presencia de un virus en el ordenador de los Usuarios que sea utilizado para la conexin a los servicios y contenidos de la Web,
(ii) un mal funcionamiento del navegador o
(iii) del uso de versiones no actizadas del мимо.
6.3 El Prestador del Servicio no asume responsabilidad alguna derivada de los contenidos enlazados desde la Web, siempre que sean ajenos a la misma, ni garantiza la ausencia de virus u otros elementos en los mismos que puedan producir alteraciones en sistema inform аппаратное и программное обеспечение), en los documentos o los ficheros de los Usuarios, excluyendo cualquier responsabilidad por los daos de cualquier clase causados a los Usuarios por este motivo.
8. Законодательство применимо к компетентной юрисдикции.
Las Presentes Condiciones де Uso estn sometidas лас leyes espaolas у cualquier споров се dirimir ан лос juzgados де ла Сьюдад-де-Сабадель.
Poltica de privacidad
1. SOLDADURAS NICROTEC, S.A. (en adelante, NICROTEC), informa a los usuarios que respeta la legislacin vigente en materia de proteccin de datos personales, la privacidad de los usuarios y el secreto y seguridad de los datos personales, acceptando para ello las medidas tcnicas y organizativas necesarias para evitar la prdida, mal uso, alteracin, acceso no autorizado y robo de los datos personales facilitados, habida cuenta del estado de la tecnologa, la naturaleza de los datos y лос-риесгос лос-куе estn expuestos.
2. El accesso a los contenidos de esta web est exclusivamente dirigida a mayores de 18 aos 146 aos, por lo que cualquier persona que entregue sus datos personales, manifestate tener dicha edad, quedando prohibido el uso de www. nicrotec.com y ла entrega де datos personales персоны menores де esa edad.
3. NICROTEC tratar los datos de conformidad con los principios de calidad exigidos por la Ley Orgnica 15/1999, de 13 de diciembre de Proteccin de Datos (LOPD), de forma confidencial y con las medidas de seguridad exigidas por el Real Decreto 1720/2007, 21 декабря, por el que se aprueba el Reglamento de desarrollo de la Ley Orgnica 15/1999, de 13 de diciembre, de proteccin de datos de carcter personal.
4. Los datos de carcter personal que se faciliten en la Web, quedarn registradossern tratados en un fichero de NICROTEC debidamente declarado e inscrito en el Registro General de la Agencia Espaola de Proteccin de Datos, con la finalidad de llevar a cabo la prestacin de los servicios ofrecidos, as como para enviar por cualquier medio, incluido el correo electrornico, ofertas de productos y servicios personalizados, mejorar la relacin Comercial y gestionar las peticiones realizadas por nuestros Clientes.
5. El simple hecho de enviar un usuario sus datos de carcter personal a NICROTEC supondr el acceptimiento para su incorporacin al fichero y tratamiento.
NICROTEC facilitar лос-проверки, которые запрашивают una contrasea para acceder al sistema dedicado a ellos. La contrasea ser личное и непередаваемое. En todo caso deber mantener dicha contrasea bajo su control y en caso de que sospechara que un tercero no autorizado ha tenido acceso a la misma deber comunicarlo a NICROTEC.
6. NICROTEC se reserva el derecho de modificar las contraseas en cualquier momento.
5.7. El usuario pod revocar el acceptimiento prestado, sin que tenga efectos retroactivos, y ejercer los derechos de acceso, rectificacin, cancelacin y opposicin dirigindose mediante carta adjuntando su DNI u otro documento identificativo a NICROTEC C/ Joiers, 5 P.I. Риера-де-Кальдес CP 08184 Палау-Солит-и-Плегаманс.
6.8. El usuario garantiza que los datos personales facilitados a NICROTEC son veraces y se hace responsable de comunicar cualquier modificacin de los mismos para que, en todo momento responsean a su situacin fact.
7.9. Если вы хотите, чтобы вы написали свой отзыв о форме в NICROTEC, используйте данные своих пользователей, escrbanos a [email protected].
ELECTRODES FOR ALLOYED STEEL – Aweld
Aweld > ELECTRODES FOR ALLOYED STEEL
XII – ELECTRODES FOR ALLOYED STEEL
E6013 | C : 0,07 SI: 0,3 | Электрод средней толщины с покрытием из рутиловой целлюлозы для сварки в труднодоступных местах. Он подходит для универсального применения в металлоконструкциях, судостроении и автомобилестроении. YS=420 TS=510 IV=>47 E=>22 approvals : TÜV, DB,Ü |
E6013 E 38 0 RC 11 | C : 0,07 SI: 0,3 Mn : 0,50 | Электрод средней толщины с рутиловым целлюлозным покрытием для сварки в труднодоступных местах. YS=380 TS=500 IV=>47 E=>22 допуски: TÜV, DB,Ü |
C : 0,08 SI:0,4 | Электрод с рутиловым покрытием средней толщины для сварки в труднодоступных местах. Он подходит для универсального применения в металлоконструкциях, промышленном машиностроении, судостроении и автомобилестроении. YS=420 TS=510 IV=>47 E=>22 допуски: TÜV,GDL,DB,Ü | |
E6013 E 42 o RR 12 | C : 0,06 SI:0,4 | Электрод с рутиловым основным покрытием с быстротекучим наплавленным металлом, подходит для сварки строительных элементов из конструкционных сталей до L385N. ГС=420 ТС=490 IV=>47 E=>22 approvals : TÜV,GDL,DB,Ü |
E7018 E42 4 B 42 H 5 | C : 0,07 SI:0.5 | Универсальный электрод с основным покрытием для безопасной сварки высоконагруженных соединений. Стойкость к холодному растрескиванию, легкое удаление шлака. Очень хорошие сварочные характеристики, также можно использовать для сварки в труднодоступных местах. Быстро затвердевающий металл шва, позволяет выполнять сварку в высоком положении. YS = 420 TS = 530 IV => 47 E => 22 Утверждаемые: Tüv, GDL, DB, ü |
E7016 E42 3 B 32 H 10 |
| Электрод с двойным основным покрытием с превосходными сварочными характеристиками в сочетании с выдающимися механическими свойствами. Очень хорошо подходит для сварки переменным током (также с небольшими трансформаторами). Двойное покрытие обеспечивает оптимальные характеристики сварки даже при сварке в труднодоступных местах. Гладкая поверхность сварного шва, без сквозных насечек. ys = 420 TS = 530 IV => 47 E => 22 Утверждения: Tüv, GDL, DB, ü |
E7024 E 42 0 RR 73 | 9 C: 0,0 0002 C: 0,0 0002 C: 0,0 0002 C: 0,0 0002 C: 0,0 0002 C: 0,0000 C: 0,0000 C: 0,0000 C: 0,0000 C: 0,0000 C: 0,0000 3 E 42 0 RR 73 | Электрод с толстым рутиловым покрытием, коэффициент извлечения 180%. Подходит для универсального применения в металлоконструкциях, промышленном строительстве, судостроении и автомобилестроении. YS=420 TS=510 IV=>47 E=>22 approvals : TÜV,GDL,DB,Ü |
E7018-1 E 46 4 B32 H5 | C : 0,06 Si:0,5 Mn: 1,4 | Наплавленный наплавленный металл обладает выдающимися механическими свойствами, что делает эту продукцию пригодной для строительных работ с высокими механическими нагрузками. Это универсальный электрод, но обычно его используют для сварки рельсов с высоким содержанием углерода (до 0,6%). YS=460 TS=600 IV=>47 E=>22 approvals : TÜV,GDL,DB,Ü |
E11018-M E 69 4 Mn 2NiCrMo BT 42 H5 | C : 0,05 Si:0,3 Mn: 1,7 Ni:2 Cr: 0,4 Mo:0,4 | Электрод с основным покрытием для сварки высокопрочных низколегированных сталей, таких как S500-S690 (StE500-StE690V) или N-X-TRA55-70 . YS=730 TS=830 IV=>47 E=>18 допуски: TÜV,GDL,DB,Ü |
E8018-G E 46 5 ZB 09 32 800923 90: 6 Si:0,4 Mn: 1,0 Ni:0,4 Cr: 0,6 | Электрод с основным покрытием для атмосферостойких сталей. Наплавленный металл устойчив к погодным условиям и воздействию морской воды. YS=460 TS=580 IV=>47 E=>22 | |
C7018-A1 E Mo D 42 | C: 0,07 Si: 0,6 Mn: 0,9 Mo: 0,5 | Электрод, легированный молибденом, с основным покрытием для сварки трубопроводов, котлов и конструкционных сталей с зернистой структурой. Нестареющий сварочный металл, в том числе при низких температурах. Стойкий к растрескиванию и пригодный для эксплуатации при температурах до 550°C. |
C7013-G EMoR12 | C: 0,07 Si: 0,8 Mn с покрытием 0,9 Mo-80 9 Mo: 0,5 0,5 легированный электрод для сварки трубных и котельных сталей, а также линейно-зернистых конструкционных сталей. Металл вельда не стареет, а также прочен при низких температурах, устойчив к растрескиванию и пригоден для эксплуатации при температуре до 550°С. YS=490 TS=600 IV=>47 F=>22 Одобрения: TÜV | |
E8018-B2 E CrMo 1 B12H5 | C: 0,07 Si: 0,7 Mn:0,9 Cr: 099 0990 8 80035 Mo: Легированный CrMo электрод для сварки высокопрочных соединений низколегированных закаленных сталей до 880 Н/мм2. Подходит для сварки жаропрочных хромомолибденовых сталей при строительстве котлов и трубопроводов. Термостойкость до 500°C. Нестареющий сварочный наплав, устойчивый к щелочным растворам, поддающийся термообработке и цементации. ![]() | |
E9018-B3 E CrMo 2 B12 H5 | C: 0,05 Si: 0,6 Mn: 1,0 Cr:2,3 Mo:1,0 | С основным покрытием для высокопрочных сварных соединений CrMo легированные закаленные стали до 1100 Н/мм2. Подходит для сварки жаропрочных хромомолибденовых сталей при строительстве котлов и трубопроводов. Термостойкость до 500°C. Нестареющий сварочный наплав, устойчивый к щелочным растворам, поддающийся термообработке и цементации. Отжиг 30 мин. при 760°С YS=510 TS=650 IV=80 E=22 |
E 8015-86 E CrMo 5 B42 H5 | C: 0,06 Si: 0,5 Mn: 1,0 Cr: 5,1 Mo: 0,5 закаленные с последующим отпуском стали до 1275 Н/мм кв. Подходит для сварки термообрабатываемых, закаленных и впоследствии отпущенных сталей, а также для смазочных материалов. ![]() |