Рекомендуем приобрести: Установки для автоматической сварки продольных швов обечаек — в наличии на складе! Сварочные экраны и защитные шторки — в наличии на складе! Горячими трещинами называются хрупкие межкристаллитные разрушения сварного шва или околошовной зоны, возникающие в области температурного интервала хрупкости в результате воздействия термодеформационного сварочного цикла. Горячие трещины чаще всего возникают в сплавах, обладающих выраженным крупнокристаллическим строением, с повышенной локальной концентрацией легкоплавких фаз. Согласно общепринятым представлениям, они возникают в том случае, если интенсивность нарастания деформаций в металле сварного соединения в период остывания приводит к деформациям большим, чем его пластичность в данных температурных условиях. В МВТУ им. Н. Э. Баумана Н. Н. Прохоровым была разработана теория технологической прочности металлов при сварке, согласно которой сопротивляемость сварного соединения образованию горячих трещин определяется тремя основными факторами: пластичностью металла в температурном интервале хрупкости, значением этого интервала и характером нарастания деформации при охлаждении (темпом деформации сварного соединения). Графически эти представления наглядно могут быть проиллюстрированы графиками, представленными на рис. 12.43. Кривые пластичности П характеризуют изменение пластичности сварного соединения в т.и.х., а кривые е — интенсивность нарастания деформаций в свариом соединении в процессе остывания или темп деформации дe/дT. На рис. 12.43,а показано влияние величины минимальной пластичности в т.и.х. на сопротивляемость сварного соединения образованию горячих трещин. У сплава, пластичность которого характеризуется кривой 2, в момент, определяемый точкой А, значения пластичности и возникающей деформации равны — кривые касаются. Это критический случай. В сплаве, обладающем пластичностью в т.и.х., характеризуемой кривой 1, при том же темпе деформации е и температуре, соответствующей точке Б, произойдет исчерпание пластических свойств и образуется трещина. Таким образом, чем больше пластичность сплава в т.и.х., тем при равных прочих условиях меньше вероятность образования горячих трещин. Значение пластичности П и характер ее изменения в т. На рис. 12.43, б представлен случай, когда сплавы при одинаковой минимальной пластичности отличаются протяженностью температурного интервала хрупкости. При этом принято, что характер изменения пластичности в т.и.х. у всех трех рассматриваемых сплавов одинаков и пластичность остается практически неизменной на всем протяжении т.и.х. В этом случае чем больше протяженность температурного интервала хрупкости, тем больше вероятность возникновения трещины. Значение т.и.х., так же как и значение минимальной пластичности, зависит от многих факторов, поддающихся управлению,главные из которых — химический состав свариваемых материалов и применяемых присадочных проволок, покрытия электродов, флюсы, режим сварки, определяющий форму шва, схему кристаллизации, и процессы структурообразования в шве и околошовной зоне, размер зерна, характер и интенсивность протекания ликвационных и сегрегационных процессов и др. На рис. 12.43, в рассмотрено влияние темпа деформации de/dT при одинаковых значениях П и т.и.х. В сварном шве, при кристаллизации которого возникает темп деформации е, характеризуемый кривой 1, при температуре T1 появится трещина, так как в этот момент значение деформации превысит пластичность соединения в т.и.х. Для соединения, темп деформации которого обозначен кривой 2, точка касания при температуре Т Сплав, характеризуемый кривой 3, трещины не образует; более того, он имеет еще и некоторый запас пластичности ΔП. Таким образом, чем меньше темп деформации в т.и.х., тем меньше вероятность образования горячих трещин. Темп деформации, характеризуемый наклоном кривой е к оси температур и кривизной самой кривой, зависит от усадки сплава и деформаций, развивающихся в околошовной зоне. Следует иметь в виду, что деформация в сварном шве, обусловленная кристаллизационными и структурными процессами при остывании, распределяется по сечению весьма неравномерно: участки шва с более высокими температурами и вследствие этого менее прочные деформируются больше, чем участки, прилегающие к зоне сплавления и охлаждающиеся более интенсивно. Для равновесных условий кристаллизации акад. А. А. Бочвар связывает вероятность образования горячих трещин с эффективным интервалом кристаллизации Тэф, определяемым как интервал температур, заключенный между температурой образования кристаллического каркаса внутри расплава и температурой солидуса. На рис. 12.44 изображен участок бинарной диаграммы состояния. По вертикальной оси отложены температура Т, линейная усадка сплава г и критическая скорость vкр, определяющая уровень технологической прочности сплава. Штриховой линией нанесены температуры образования кристаллического каркаса. Заштрихованная область соответствует значениям эффективного интервала кристаллизации Тэф. Из приведенных кривых видно, что с увеличением Тэф возрастает линейная усадка ε, а уровень технологической прочности (vкр) падает. Далее: Виды горячих трещин |
Горячие и холодные трещины при сварке металлов и причины их образования
Горячие и холодные трещины при сварке металлов и причины их образования
Дефекты при сварке металлов плавлением образуются вследствие нарушения требований нормативных документов к сварочным материалам, подготовке, сборке и сварке соединяемых элементов, термической и механической обработке сварных соединений и конструкции в целом.
Согласно ГОСТ 30242-97 дефекты классифицируются на шесть групп: трещины, полости и поры, твердые включения, несплавления и непровары, нарушение формы шва, прочие дефекты (дефекты, не включенные в вышеперечисленные группы).
Трещина — это несплошность, вызванная местным разрывом шва, которая может возникнуть в результате охлаждения или действия нагрузок.
Микротрещина — это трещина,
имеющая микроскопические В зависимости от температуры, при которой
образуются трещины, их условно подразделяют
на горячие и холодные. Горячие трещины
в сталях возникают при температуре, превышающей
1000 °С, а холодные — при более низкой. Трещины
являются самым серьезным дефектом сварного
соединения, как правило не подлежащим
устранению.
Горячие трещины — это хрупкие межкристаллические разрушения металла шва и околошовной зоны, возникающие в твердожидком состоянии в процессе кристаллизации, а также при высоких температурах в твердом состоянии. Они извилисты, в изломе имеют темный цвет, сильно окислены, распространяются по границам зерен. По современным представлениям горячие трещины вызываются действием двух факторов: наличием жидких прослоек между зернами в процессе кристаллизации и деформациями укорачивания.
В интервале температур плавления
и полного затвердевания Неравномерность
линейной и объемной усадок шва и основного
металла при охлаждении приводит к возникновению
внутренних напряжений, являющихся причиной
появления микро- и макроскопических трещин
как вдоль, так и поперек шва.
Причинами образования
большое количество вредных примесей (особенно серы и фосфора) в металле свариваемых заготовок;
наличие в металле шва элементов, образующих химические соединения с низкой температурой затвердевания (хром, молибден, ванадий, вольфрам, титан), нарушающие связь между зернами;
жесткое закрепление свариваемых заготовок или повышенная жесткость сварного узла, затрудняющая перемещение заготовок при остывании.
Холодные трещины — это локальные
меж- или транскристаллические разрушения
сварных соединений, образующиеся в
металле при остывании до относительно
невысоких температур (как правило,
ниже 200 °С) или при вылеживании
готового изделия. Холодные трещины
в шве и переходной зоне расположены под
любым углом ко шву — в изломе светлые или
со слабыми цветами побежалости и возникают
преимущественно при дуговой сварке низколегированной
стали большой толщины. Чаще всего трещины
возникают в переходной зоне вследствие
неправильной техники сварки или неправильно
выбранного присадочного материала. Для
предупреждения образования холодных
трещин применяют:
прокаливание флюсов и электродов перед сваркой;
предварительный подогрев свариваемых заготовок до 250-450 °С;
ведение процесса сварки в режиме с оптимальными параметрами;
наложение швов в правильной последовательности;
медленное охлаждение изделия после сварки;
проведение непосредственно
Общими причинами появления трещин, как горячих, так и холодных, в швах сварных соединений являются:
слишком высокая жесткость соединений;
слишком малый размер сварного шва для данной толщины соединения;
несоблюдение или неправильный выбор технологии сварки;
дефекты в сварном шве;
t неправильная подготовка
неудовлетворительное качество или неправильный выбор типа электродов;
использование повышенных значений сварочного
тока, которое может привести к
появлению крупнозернистых
высокое содержание углерода или легирующих
элементов в основном металле, не
учтенное при выборе технологии сварки.
Для предупреждения
разрабатывать металлоконструкции и технологию сварки, которые позволяют исключить применение соединений с высокой жесткостью;
при сварке изделий достаточно большой толщины увеличивать размеры сварных швов;
не допускать при сварке
узких валиков, производить
выбирать последовательность выполнения сварных швов такой, чтобы максимально долго оставлять незаваренными концевые участки соединения, с тем чтобы они обладали максимально возможной подвижностью;
обеспечить сплошность и хорошее сплавление сварных швов;
в некоторых случаях обеспечить предварительный подогрев свариваемых частей;
сборку соединений производить с одинаковым и требуемым по технологии зазором, при необходимости для выравнивания зазора применять стягивающие сборочные приспособления;
не допускать при сварке завышенных по сварочному току режимов сварки;
по возможности сварной шов
делать многопроходным, так как однопроходные
швы могут быть более хрупкими,
а в многопроходных швах происходит
отжиг каждого предыдущего слоя
разделку заполнять сразу
Продольные, поперечные и др.виды трещин при сварке металлов
Продольная трещина — это трещина, ориентированная параллельно оси сварного шва. Продольные трещины могут возникать в металле сварного шва, на границе сплавления, в зоне термического влияния и в основном металле. Конфигурация трещин в основном определяется очертаниями линии сплавления основного металла и шва. Продольные трещины возникают как из-за наличия высокотемпературной хрупкости сплавов (горячие трещины), так и при замедленном разрушении металла (холодная трещина).
Продольные трещины в основном металле, смежном со сварным швом, возникающие из-за высокого напряжения, вызванного сжатием в сварном шве, называют скрытыми трещинами. Разрыв вызывается нарушением сцепления и связей вдоль рабочего направления основного металла. Трещины обычно проходят строго параллельно линии сплавления и внешне похожи на ступеньки.
Большие сварочные напряжения,
вызывающие скрытые трещины, в
большей или меньшей степени
присущи всем сварным Основные причины, вызывающие
недопустимые сварочные
Для снижения уровня
во время сварки допускать небольшие перемещения свариваемых частей;
по возможности использовать многопроходную сварку;
производить проковку каждого слоя наплавленного металла;
отжигать
готовое изделие при
применять
сварочную технологию, снижающую
вероятность образования
применять сварочную технологию, при которой все свариваемые части имеют неограниченную свободу перемещения;
при сварке
сталей, склонных к образованию горячих
и холодных трещин, производить наплавку
высокопластичного промежуточного слоя,
если это позволяет получаемая прочность
соединения.
При сварке тавровых соединений при толщине металла более 20 мм следует учитывать, что двухсторонний сварной шов вызывает меньшие напряжения, чем односторонний. Двухсторонний сварной шов без разделки кромок имеет меньшие напряжения в околошовной зоне, чем двухсторонний с разделкой кромок и полным проплавлением корня. Односторонний сварной шов с большой величиной катета следует заменять на двухсторонний с меньшим катетом. Изменение формы разделки углового соединения является наиболее эффективной мерой предупреждения образования скрытых трещин. Наплавка мягкой, высокопластичной прослойки на 15-25 мм шире сварного шва и толщиной 5-10 мм или наложение на одну из поверхностей разделки высокопластичных валиков за счет пластической деформации мягкой прослойки позволяет в значительной мере уменьшить напряжения в околошовной зоне.
Поперечная трещина — это трещина,
ориентированная поперек оси
сварного шва. Поперечные трещины
могут возникать в металле. Ориентация
связана с направлением продольных компонент
сварочных напряжений. Причина их возникновения
такая же, что и у продольных трещин.
Радиальные трещины — это трещины, радиально расходящиеся из одной точки. Трещины этого типа, расходящиеся в разные стороны, известны как звездоподобные трещины. Радиальные трещины могут располагаться в металле сварного шва, в зоне термического влияния и в основном металле. Конфигурация трещины определяется макроструктурой зон сварных соединений, а также характером внутренних напряжений. Причина их возникновения такая же, что и у продольных трещин.
Трещина в кратере — это трещина в углублении на поверхности шва в месте отрыва дуги. Трещины могут быть продольными, поперечными и звездообразными. Конфигурация трещины определяется микроструктурой зон сварных соединений, а также характером термических, фазовых и механических напряжений.
Раздельные трещины — это группа
не связанных друг с другом трещин. Они могут возникать в металле
сварного шва, в зоне термического влияния
и в основном металле. Конфигурация трещины
определяется микроструктурой зон сварных
соединений, а также характером термических,
фазовых, лик-вационных и механических
напряжений. Причина их возникновения
такая же, что и у продольных трещин.
Разветвленные трещины — это группа трещин, возникающих из одной трещины. Они могут располагаться в металле сварного шва, в зоне термического влияния и в основном металле. Конфигурация трещины определяется микроструктурой зон сварных соединений, а также характером термических, фазовых, ликвационных и механических напряжений. Причина их возникновения такая же, что и у продольных трещин.
Разновидности пор
Поры. Данный термин используется для
описания несплошностей глобулярной
формы, полых по своей структуре. Подобные
дефекты часто встречаются в металле сварных
швов. По сути своей и по механизму образования
очень напоминают включения, ибо являются
результатом протекающих в сварочной
ванне химических реакций. Поры отличаются
от включений тем, что внутри пор чаще
всего находится газ, а не твердое вещество,
как у включений.
Источником появления газов, которые содержатся в порах, являются газы, выделяющиеся из охлаждающегося металла из-за уменьшения растворимости при снижении температуры металла, и газы, образующиеся в результате химических реакций в металле сварного шва.
Пористость, за исключением случаев,
когда она появляется в очень
больших количествах, как правило,
не оказывает значительного
Появление в металле сварного шва пор вызвано:
плохим качеством или
неправильным выбором
малым временем существования сварочной ванны, газы не успевают выйти из расплавленного металла;
плохим качеством металла.
Слишком высокая температура При
использовании повышенных токов для сварки
покрытыми электродами может произойти
избыточное выгорание раскисляющих элементов
из покрытия электрода, что приводит к
недостатку раскислителей, сохранившихся
в металле шва, для взаимодействия с газами,
содержащимися в расплавленном металле.
Аналогичный эффект наблюдается при сварке
с применением слишком большой длины дуги.
Применение ряда мероприятий позволяет
значительно снизить, а в некоторых случаях
даже избежать образования пор и полостей
в сварных швах. При сварке:
необходимо подбирать тип
перемешивание жидкого металла
увеличивает время
в сварных швах, выполненных в виде серии узких валиков, наплавляемых без поперечных колебаний, обычно появляются цепочки пор; использование при сварке поперечных колебаний электрода часто устраняет пористость шва;
следует не допускать применения слишком больших значений сварочного тока;
следует производить прокалку электродов перед сваркой;
при подозрении на плохое качество металла
проверить его на наличие сегрегации
и включений.
Газовая полость — это полость произвольной формы, образованная газами, задержанными в расплавленном металле, которая не имеет углов. Газовая полость образуется в результате выделения газов при кристаллизации сварного соединения. Мелкодисперсные включения на поверхности границ раздела фаз служат центрами зарождения пузырьков газа.
Газовая пора — это газовая полость, обычно сферической формы, содержащая задержанный металлом газ. Поры образуются в результате перенасыщения жидкого металла газами, которые не успевают выйти на поверхность во время его быстрой кристаллизации.
Равномерно распределенная пористость — это группа газовых пор, распределенных равномерно в металле сварного шва (не путать с цепочкой пор). Сплошную пористость вызывает большое количество ржавчины и масла на кромках заготовок, а также влажный или крупный флюс.
Скопление пор — это группа газовых
полостей (три или более), расположенных
кучно с расстоянием между ними менее
трех максимальных размеров большей из
полостей. Вызывается локальным скоплением
ржавчины или масла на кромках заготовок.
Рекомендуем приобрести: Установки для автоматической сварки продольных швов обечаек — в наличии на складе! Сварочные экраны и защитные шторки — в наличии на складе! По температуре возникновения горячие трещины подразделяют на кристаллизационные, возникающие в области температур солидуса, и подсолидусные, температура образования которых ниже температуры окончания процесса затвердевания. По расположению в сварном соединении различают горячие трещины в шве, в зоне сплавления, в околошовной зоне, а также в зависимости от ориентировки их относительно направления сварки — продольные и поперечные. Во всех случаях вероятность образования трещин определяется соотношением пластических свойств соединений в т. Кристаллизационные трещины образуются, как правило, в сварном шве и реже в зоне полуоплавленных зерен. На рис. 12.45 представлены характерные места расположения горячих кристаллизационных трещин в сварном соединении. Подсолидусные трещины возникают в интервале температур второго минимума пластичности, расположенного ниже температуры солидуса. Сварной шов вследствие неравновесного процесса кристаллизации пересыщен дефектами кристаллической решетки, в том числе и вакансиями, которые при растяжении активно перемещаются к границам, расположенным перпендикулярно действующим усилиям. Преимущественные места зарождения подсолидусных трещин — ослабленные включениями и несовершенствами строения границы кристаллитов, где межзеренные проскальзывания наиболее выражены; чаще всего это участки, прилегающие к зоне сплавления, и поперечные границы зерен в центре шва. |
2 Горячие и холодные трещины в отливках, причины их возникновения
1.2. Горячие и холодные трещины в отливках, причины их возникновения. Причины коробления отливок. Технологические и конструктивные мероприятия, снижающие коробление. Горячие трещины в отливках возникают в процессе кристаллизации и усадки металла при переходе из жидкого состояния в твердое при температуре, близкой к температуре солидуса. Горячие трещины проходят по границам кристаллов и имеют окисленную поверхность. Склонность сплавов к образованию горячих трещин увеличивается при наличии неметаллических включений, газов (водорода, кислорода), серы и других примесей. Кроме того, образование горячих трещин вызывает резкие переходы тонкой части отливки к толстой, острые углы, выступающие части и т. д.
Для предупреждения возникновения горячих трещин в отливках необходимо создавать условия, способствующие формированию мелкозернистой структуры обеспечивать одновременное охлаждение тонких и толстых частей отливок; увеличивать податливость литейных форм, по возможности снижать температуру заливки сплава.
Холодные трещины возникают в области упругих деформаций, когда сплав полностью затвердел. Тонкие части отливки охлаждаются и сокращаются быстрее, чем толстые. В результате в отливке образуются напряжения, которые и вызывают появление трещин. Холодные трещины чаще всего образуются в тонкостенных отливках сложной конфигурации и тем. больше, чем выше упругие свойства сплава, чем значительнее его усадка при пониженных температурах и чем ниже его теплопроводность. Опасность образования холодных трещин в отливках усиливается наличием в сплаве вредных примесей (например, фосфора в сталях). Для предупреждения образования в отливках холодных трещин необходимо обеспечивать равномерное охлаждение отливок во всех сечениях путем использования холодильников; применять сплавы для отливок с высокой пластичностью; проводить отжиг отливок и т. п. Коробление—изменение формы и размеров отливки под влиянием напряжений, возникающих при охлаждении. Коробление увеличивается при усложнении конфигурации отливки и повышении скорости охлаждения, которая вызывает неравномерное охлаждение между отдельными частями отливки и различную усадку. Коробление отливки может быть также вызвано сопротивлением формы усадке отдельных частей отливки. Для предупреждения короблений в отливках необходимо увеличивать податливость формы; создавать рациональную конструкцию отливки и т. д.
Как предотвратить сварку горячих трещин?
Сварочная трещина является одним из наиболее распространенных серьезных дефектов при сварке заготовок. Сварочные трещины могут быть классифицированы различными способами в зависимости от их положения, размера, причины и механизма. В соответствии с состоянием образования трещин, его можно разделить на горячую трещину, холодную трещину, разогрев трещины и пластинчатую слезу.
Как следует из названия, трещины, возникающие при высокой температуре во время сварки, называются горячими трещинами (термические трещины / тепловые трещины), которые генерируются при высокой температуре вблизи линии твердой фазы и характеризуются распределением вдоль границы зерна. Но иногда он может образовываться вдоль полигональных границ при температурах ниже линии твердого тела. Горячие трещины обычно возникают в металле сварного шва, но они также могут образовываться в основном металле вблизи линии сварки.
Различные металлические материалы (низколегированная высокопрочная сталь, нержавеющая сталь, чугун, алюминиевый сплав и некоторые специальные металлы и т. Д.) Будут давать различную морфологию и температурный диапазон термической трещины во время сварки. Горячие трещины можно разделить на кристаллизационные трещины, разжижения трещины и многосторонние трещины в зависимости от их процесса образования. Сегодня мы разрабатываем конкретные причины, характеристики и профилактику и лечение горячих трещин.
Кристаллизация трещины
Эти трещины в основном образуются при сварке примесей, содержащих углеродистую сталь, низколегированную сталь (например, с высоким содержанием S, P, C, Si) и однофазную аустенитную сталь, сплавы на основе никеля и некоторые алюминиевые сплавы. Эта трещина произошла вблизи линии твердой фазы в процессе кристаллизации пайки. Из-за усадки затвердевшего металла и недостаточного количества остаточного жидкого металла, которые приводят к межкристаллитному растрескиванию, происходящему под напряжением.
Как предотвратить кристаллизацию трещин?
Металлургия: с одной стороны, правильно отрегулировать состав металла при сварке, сократить диапазон хрупких температурных зон, контролировать содержание серы, фосфора, углерода и других вредных примесей при сварке; С другой стороны, очистить первичное зерно металла сварного шва, то есть, соответствующим образом добавив Mo, V, Ti, Nb и другие элементы;
Технический процесс: предварительный нагрев перед сваркой, контроль энергии в линии и уменьшение связывания стыков.
Сжиженная трещина
Это тип микротрещины, которая растрескивается вдоль границы зерен аустенита и обычно происходит в зоне термического влияния вблизи зоны трещин или между слоями. Обычно это происходит из-за переплавления эвтектических компонентов на границе зерен аустенита в ближнем шве. зона или между сварными слоями при высокой температуре и растрескиванием аустенитных зерен под действием растягивающего напряжения.
Как предотвратить разжижение трещины в зоне трещины?
Эти меры по предотвращению образования трещин в основном соответствуют кристаллической трещине. Особенно с точки зрения металлургии, эффективно снизить содержание эвтектических элементов, таких как сера, фосфор, кремний и бор, насколько это возможно. С точки зрения технологии, энергия линии и вогнутость линии плавления могут быть уменьшены.
Полигональная трещина
Полигонизационная трещина образуется в процессе полигонизации, высокая температура приводит к очень низкой пластичности. Такого рода трещина не распространена, и мы не разрабатываем ее здесь сегодня. Профилактические меры по добавлению таких элементов, как Mo, W и Ti, к сварному шву могут улучшить энергию поляризации.
По сравнению со сталью общего назначения никельсодержащая нержавеющая сталь с большей вероятностью может создавать термические трещины, которые могут возникать в сварочных швах и зоне термического влияния. Чем выше содержание никеля, тем больше тенденция к образованию горячих трещин и тем больше неконтролируемый. Поэтому при сварке 304 заготовок необходимо уделять внимание предотвращению образования горячих трещин.
Сварка Горячие трещины — Энциклопедия по машиностроению XXL
Стойкость аустенитных швов к образованию трешин зависит от химического состава и структуры металла шва. Наиболее радикальный способ предупреждения трешин при сварке и повышения коррозийной стойкости швов — получение двухфазных аустенитно-ферритных швов путем подбора сварочных проволок, флюсов, электродных покрытий и режима сварки. Горячие трещины наиболее часто встречаются в кратерах, которые следует особенно тщательно заваривать. [c.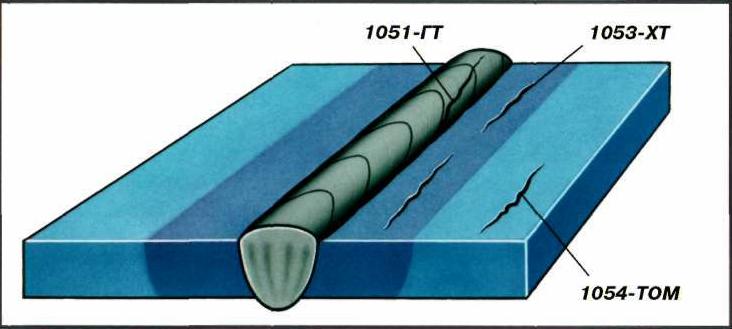
На рис. 40 схематически показана зависимость между содержанием углерода, серы и марганца и образованием горячих трещин в сварных угловых швах, выполняемых на конструкционной стали автоматом. Эти данные относятся к дуговой сварке под флюсом АН-348. При увеличении содержания серы и углерода, чтобы предотвратить образование горячих трещин, необходимо повысить содержание марганца, причем склонность к трещинам уменьшается при содержании одновременно не более 0,16% углерода и не более 0,03% серы. При электрошлаковой сварке горячие трещины в швах чаще всего образуются при значительной глубине металлической ванны, обусловленной применением повышенного сварочного тока (большой скорости подачи электрода), и располагаются между торцами кристаллитов в центре шва (рис. 41). Бывают случаи, когда горячие трещины в швах, выполненных электрошлаковым способом, образуются между соседними столбчатыми кристаллитами.

При электрошлаковой сварке горячие трещины чаще всего образуются при глубокой металлической ванне. Трещины при этом располагаются между торцами кристаллов в середине шва, не выходя на поверхность. [c.50]
Применяя присадочный металл соответствующего состава, можно регулировать и химический состав металла шва, достигая этим, например, повышения стойкости против образования при сварке горячих трещин. Более устойчивые результаты при ручной сварке могут быть обеспечены присадкой в виде закладок, что обеспечивает более стабильное соотношение долей между расплавленным основным, металлом (7) и металлом присадки (1— () в металле шва. Также устойчивые результаты достигаются и применением автоматической сварки с механизированной подачей в дугу присадочной проволоки с бухты. Такие автоматы, в основном разработанные НИАТ, например типа АТВ (для труб диамет- [c.106]
Таким образом, оказывается возможным подбирать такие составы сварочных материалов, которые при достаточно высоких эксплуатационных свойствах обладают и необходимой стойкостью против образования при сварке горячих трещин.
[c.322]
Хромоникелевые стали имеют низкую теплопроводность (коэффициент теплопроводности 16,7 Вт/(м-К) и высокий коэффициент линейного расширения (а= 17-10 град ), что вызывает повышенные деформации, горячие трещины и коробление изделий при газовой сварке. Горячие трещины не возникают, если в наплавленном металле содержится 2,5…8,5% ферритной фазы. Титан и ниобий способствуют получению двухфазной аустенит-но-ферритной структуры наплавленного металла. [c.405]
При дуговой сварке аустенитных сталей возможно образование в сварных швах горячих трещин. Они обусловлены широким интервалом кристаллизации вследствие повышенного содержания легирующих элементов и наличия вредных примесей (S). Образованию трещин способствует также крупнозернистая столбчатая макроструктура шва, при которой его кристаллизация завершается при наличии жидких прослоек большой протяженности. [c.233]
Увеличение силы сварочного тока при неизменной скорости сварки влечет за собой увеличение объема сварочной ванны.
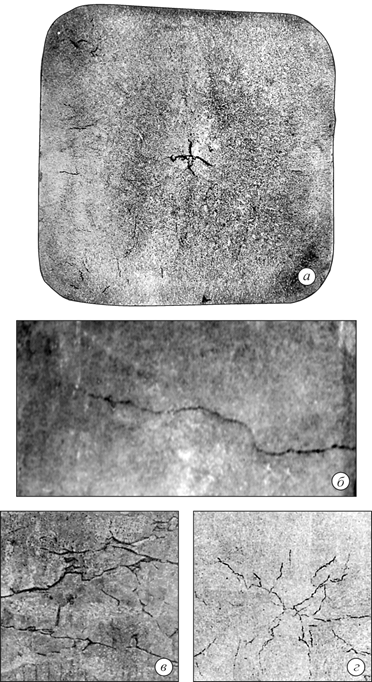
Площадь нагрева электронным лучом может быть по сравнению с газовым пламенем и дугой в 1000 раз меньше (см. табл. 1), при плотности энергии в 1000 раз большей. При использовании фотонного луча эта разница еще значительнее. Высокая плотность энергии в малом пятне нагрева определяет основные преимущества при сварке электронным лучом и лазером — выгодную форму проплавления (ножевая, кинжальная) и возможность получения прецизионных соединений. Вместе с тем при сварке глубоко внедренным лучом возникают дополнительные трудности большая опасность пор и горячих трещин, колебания глубины проплавления и подрезы. [c.15]
Для оценки свариваемости металлов по критерию сопротивляемости горячим трещинам применяют два основных вида испытаний — сварку технологических проб и машинные способы испытаний.
[c.42]
Основные меры по обеспечению качественного сварного соединения. До сварки при составлении технологии главное внимание должно быть уделено рациональному выбору материалов основного и присадочного металла, защитных средств. Основной металл с пониженным содержанием углерода и примесей (серы, фосфора) обладает более высокой стойкостью против холодных и горячих трещин. [c.124]
Природа образования горячих трещин при сварке [c.478]
Горячими трещинами называются хрупкие межкристаллитные разрушения сварного шва или околошовной зоны, возникаюш,ие в области температурного интервала хрупкости в результате воздействия термодеформационного сварочного цикла. Горячие трещины чаще всего возникают в сплавах, обладающих выраженным крупнокристаллическим строением, с повышенной локальной концентрацией легкоплавких фаз. Согласно общепринятым представлениям, они возникают в том случае, если интенсивность нарастания деформаций в металле сварного соединения в период остывания приводит к деформациям большим, чем его пластичность в данных температурных условиях. Способность сварного соединения воспринимать без разрушения деформации, вызванные термодеформационным циклом сварки, определяет уровень его технологической прочности.
[c.478]
В МВТУ им. Н. Э. Баумана Н. Н. Прохоровым была разработана теория технологической прочности металлов при сварке, согласно которой сопротивляемость сварного соединения образованию горячих трещин определяется тремя основными факторами пластичностью металла в температурном интервале хрупкости, значением этого интервала и характером нарастания деформации при охлаждении (темпом деформации сварного соединения). [c.478]
По расположению в сварном соединении различают горячие трещины в шве, в зоне сплавления, в околошовной зоне, а также в зависимости от ориентировки их относительно направления сварки — продольные и поперечные. Во всех случаях вероятность образования трещин определяется соотношением пластических свойств соединений в т.и.х. и темпом деформаций. Однако степень влияния отдельных технологических и металлургических факторов для каждого вида может быть существенно различной в связи с неодинаковыми условиями формирования химической и физической неоднородности в различных зонах сварного соединения. Особо следует выделить трещины повторного нагрева, образующиеся в ранее наложенных валиках при многослойной сварке в результате термодеформационного воздействия от сварки последующих слоев.
[c.481]
ОБРАЗОВАНИЮ ГОРЯЧИХ ТРЕЩИН ПРИ СВАРКЕ [c.482]
Очевидно, что этот запас пластичности и будет определять степень надежности сварного соединения образования горячих трещин при сварке. [c.483]
На практике нашли применение и несколько жестких проб, в которых в качестве критерия оценки принят изменяющийся от образца к образцу режим сварки. В основу этих проб положено известное обстоятельство, что увеличение скорости сварки приводит к снижению сопротивляемости шва образованию горячих трещин, так как уменьшается пластичность в т.и.х., ввиду более неблагоприятной схемы кристаллизации. [c.486]
Для повышения сопротивляемости сварных соединений образованию горячих трещин необходимо в процессе производства стремиться к такому сочетанию их свойств в т.

Влияние режима сварки на сопротивляемость образованию горячих трещин весьма важно вследствие следующих причин он представляет собой главный фактор, определяющий форму [c.488]
При плазменно-дуговой сварке сварочной проволокой СВ-07Х25Н12Г2Т (/ = 300 А, U = 25 В, = 10 м/ч) выделения карбидов по границам кристаллитов в металле шва более дисперсны, чем при ручной дуговой сварке. Горячие трещины отсутствуют. Механические свойства сварных соединений по отдельным показателям соответствуют следующим значениям = 683 МПа, б = 24,7 %, = 21,5, угол загиба 150° K U металла шва и ЗТВ соответственно 1,69 и 1,13 МДж/м,
[c. 284]
Марганец является ценным элементом, так как предупреждает появление при сварке горячих трещин. Марганец способствует раскислению наплавленного металла и удалению из него серы. Марганец в металл шва может вводиться через флюс или электродную проволоку. В соответствии с этим при сварке малоуглеродистой стали применяют флюсы высокомарганцовистые, содержащие более 30% МпО среднемарганцовистые, содержащие от 15 до 30% МпО, и низкомарганцовистые, содержащие менее 15% МпО, или безмарганцовистые. [c.175]
Механизированная сварка под флюсом. Конструктивные элементы подготовки кромок под автоматическую и полуавтоматическую сварку под флюсом выполняют такими же, как и при сварке углеродистых и низколегированных незакаливающихся конструкционных сталей, т. е. в соответствии с рекомендациями ГОСТ 8713—70. Однако в диапазоне толщин, для которого допускается сварка без разделки и со скосом кромок, последней следует отдать предпочтение. Наряду с затруднениями, связанными с образованием холодных трещин в околошовпой зоне и получением металла шва и других зон сварного соединения со свойствами, обеспечивающими высокую работоспособность сварных соединений, при механизированной сварке под флюсом швы имеют повышенную склонность к образованию горячих трещин. Это связано с тем, что при данном способе сварки доля основного металла в металле шва достаточно велика.
[c.252]
В связи с этим в шов с расплавленным основным металлом поступают легирующие элементы, содержащиеся в свариваемой стали, в том числе и углерод, концентрация которого в сталях этой группы достаточно высока. Влияние содержания углерода, серы и марганца в шве на склонность к образованию горячих трещин схематически представлепо на рис. 124. Линия I служит границей раздела составов с низким содержанием углерода ( ] m. при которых образуются или не образуются горячие трещины. При повышенном содержании углерода [С] , ш такой границей будет линия 5, в этом случае даже при низком содержании серы и большой концентрации марганца в шве могут возникнуть горячие трещины. При механизированной сварке под флюсом необходимы подготовка кромок, техника и режимы сварки, при которых доля основного металла в шве будет минимальной. [c.252]
Для предупреждения горячих трещин в шве необходимо выполнять сварку на режимах, обеспечивающих получение относительно неглубокой и широкой металлической ванны. При этом столбчатые криста.ллитьт по мере приближения их к оси изгибаются кверху, вследствие чего отсутствует резко выраженная встреча кристаллитов (рис. 126, б). Наоборот, при сварке на режимах, при которых образуется узкая и глубокая сварочная ванна, столбчатые кристаллиты, растущие от противоположных кромок, почти не изменяют своего направления, и при их встрече образуется резко выраженная плоскость слабииы (рис. 126, а). Для предупреждения трещин в околошовпой зоне при сварке жестко закрепленных элементов необходимо применять предварительный подогрев до температуры 150—200 °С.
[c.257]
Свариваемость рассматриваемых сталей и сплавов затрудняется мпогокомпонеитностью их легирования и разнообразием условий эксплуатации сварных конструкций (коррозионная стойкость, жаростойкость или жаропрочность). Общей сложностью сварки является предупреждение образования в шве и околошовной зоне кристаллизационных горячих трещин, имеющих межкристаллит-пый характер, наблюдаемых в виде мельчайших микронадрывов и трещин. Горячие трещины могут возникнуть и при термообработке или работе конструкции нри повышенных температурах. Образование горячих трещин наибо,лее характерно для крупнозернистой структуры металла шва, особенно выраженной в многослойных швах, когда кристаллы последующего слоя продолжают кристаллы предыдущего слоя.
[c.286]
Одна из основных трудностей при сварке рассматриваемых сталей и сплавов — предупреждение образования в швах и ojtoflo-шовной зоне горячих трещин. Предупреждение образования этих дефектов достигается [c.292]
Кристаллизация сварного шва начинается от границ оплавленного основного металла и протекает путем роста столбчатых кристаллитов к центру И1ва. При этом оси кристаллита, как правило, остаются перпендикулярными к поверхности движущейся сварочной ванны, в результате чего кристаллиты изгибаются и вытягиваются Б направленирг сварки (рис. 5.8). Вследствие дендритной ликвации примеси располагаются по границам кристаллитов, где они могут образовать легкоплавкие эвтектики и неметаллические включения. Это снижает механические свойства шва и в отдельных случаях люжет быть npii4HH0if образования горячих трещин.
[c.190]
Трудности при сварке алюминия и его сплавов обусловлены образованием тонкой прочной и тугоплавкой поверхностной пленки оксида AI2O3, плавящегося при температуре 2050 °С склонностью к образованию газовой пористости склонностью к образованию горячих трещин. [c.236]
При анализе свариваемости основное внимание обычрю уделяют оценке опасности образования холодных и горячих трещин при сварке. [c.150]
Низколегированные низкоуглеродистые стали хорошо свариваются они не образуют при сварке холодных и горячих трещин поэтому свойства сварного соединения и участков, прилегаюи1их к нему (зоны термического влияния), близки к свойствам основного металла. [c.257]
Наиболее широкое применение находят коррозионно-стойкие хромоникелевые стали (12Х18НЮТ, 10Х23Н18 и др. ). Главными трудностями при сварке этих сталей являются склонность к горячим трещинам при сварке и к межкристаллитной коррозии при эксплуатации.
[c.126]
Склонность к образованию горячих трещин в связи с большой литейной усадкой кристаллизующегося металла, грубой столбчатой структурой сварного шва и наличием примесей. Для борьбы с горячими трещинами ограничивают содержание примесей в свариваемом металле, для измельчения структуры добавляют в металл и сваг рочную проволоку модификаторы (2г, Т , В), регулируют режимы сварки. [c.134]
Удаление шлаками нежелательных примесей из металла при сварке. В любом металле или сплаве сера — вредная примесь, резко увеличиваюшая склонность металлов к образованию горячих трещин и снижающая технологическую прочность. Сера хорошо удаляется восстановительными и основными шлаками в соответствии с уравнением реакции [c.366]
Содержание в покрытии нескольких раскислителей позволяет получить хорошо восстановленный металл, содержащий мало серы и не склонный к образованию горячих трещин. При сварке высокопрочных, жаропрочных сталей применяют покрытия с пониженным содержанием СаСОз (15…20%), увеличивая aFa (60…80%). В этом случае удается избежать поглощения углерода сварочной ванной и обеспечить содержание углерода в металле шва на уровне (0,05…0,02%) С, как это требуется по техническим условиям. Недостаток этих электродов — малая устойчивость дугового разряда, требующая сварки на постоянном токе обратной полярности. Таким образом, технологические возможности электродов группы Б несколько ниже, чем электродов группы А. Повышенное содержание СаРг вызывает образование токсичных соединений и требует создания надежной вентиляции.
[c.395]
При разработке новых сварочных материалов, обладающих повышенной технологической прочностью, часто важно знать не только интегральную оценку их сопротивляемости образованию горячих трещин при сварке, но и отдельно каждую из характеристик, определяющую вероятность их появления. Главная из этих характеристик — значение температурного интервала хрупкости, минимальная пластичность в этом интервале и темп нарастания деформации а в = де1дТ.
[c.487]
При сварке аустенитными сварочными материалами поил лгается предрасположенность швов к образованию горячих грещин. Они могут возникать при неблагоприятном сочетании факторов, связанных с понижением деформационной способности металла шва вследствие наличия в струюуре легкоплавких эвтектик, дефектов кристаллического строения, выделения хрупких фаз, а также под действием внутренних и внешних напряжений. Методы повышения стойкости против горячих трещин обычно сводятся к уменьшению содержания элементов, способствующих их возникновению, снижению [c.81]
Обычная сварка стали 15Х5М аустенитными электродами с подогревом до 300-350°С приводит к образованию развитых (до 8-10 мм) твердых прослоек (рис. 2.8, 1-а). Макро- v микроструктура аустенитного шва грубая (дендритная столбчатая и транскристаллитная, склонная к образованик горячих трещин. У такого металла более низкий предел текучести Ст и низкие показатели пластических свойств по показателям относительного удлинения 5 и сужения ц/.
[c.100]
причины образования и методы борьбы
Виды холодных трещин при сварке
По месту образования холодные дефекты подразделяются на наружные и внутренние подвиды. По направленности относительно стыка видам холодных трещин даны следующие названия:
- откол ― продольные на участках рядом с соединением;
- отрыв ― направленные вдоль шва;
- частокол ― образующиеся поперек шва или в зоне термического воздействия перпендикулярно к соединению.
Разновидности холодных трещин при сварке
На сложных стыках холодные трещины могут образоваться:
- между швами при двухсторонней сварке;
- на границе между швом и металлом детали;
- на нижней стороне соединения под валиком.
Холодные трещины. Причины образования
При сварке с помощью машину контактной сварки могут появляться и холодные трещины. Они образуются в сварных соединениях при более низких температурах, а именно порядка 300-500 градусов. Главным их отличием от горячих трещин является то, что они появляются не только в межкристаллических прослойках, но и проходят по самим зернам металла. Причинами возникновения при контактной сварке трещин этого типа могут служить:
- наличие в материале свариваемых деталей повышенного содержания легирующих элементов или углерода;
- перегрев металла при сварке;
- содержание в сварном шве водорода;
- большие напряжения металла;
- всевозможные дефекты сварного шва.
Наличие в металле легирующих элементов или углерода делает его очень чувствительным к быстрому охлаждению (свойственно контактной сварке). Быстрое падение температуры после отключения трансформатора от электрической цепи аппарата контактной сварки ведет к образованию трещин в месте сварки или около нее.
Причины образования
Самая высокая вероятность появления холодных трещин после сварки у высокоуглеродистых и легированных марок стали, сплавов титана и алюминия. Холодный дефект образуется, если:
- Структура шва и заготовок чувствительна к действию водорода. Таким свойством обладают закаливающиеся марки стали даже когда холодные.
- В сварной зоне содержится достаточное количество водорода, который проникает из шва.
- Внутри соединения действует растягивающее напряжение.
Ученые установили, что основной причиной образования холодных трещин при сварке является негативное влияние водорода на структуру стали. Его источником может быть электродное покрытие, флюс, влага из воздуха. Водород в расплавленный металл может попасть из загрязнений на заготовках и присадочном материале или как составная часть защитного газа. Если кромки заготовок не очистить перед сваркой от ржавчины, она при нагреве начнет активно насыщать шов газом.
Как избежать появления холодных трещин
Методы борьбы всегда органично вытекают из условий образования. Для того чтобы воспрепятствовать образованию холодных трещин в сварных швах, необходимо: во-первых, устранить факторы, способствующие закалке металла при сварных работах; во-вторых, добиться максимального снижения содержания водорода в металле шва и околошовной зоне; в-третьих, обеспечить равномерное охлаждение шва.
Как показывает практика, учет перечисленных выше особенностей и соблюдение рекомендаций по проведению тех или иных сварочных работ, позволяют соединять широкий спектр металлов швами высочайшего качества.
Холодные трещины
Холодные трещины свое название получили в связи с тем, что их появление наблюдается при относительно низкой температуре. Например, при сварке сталей, способных закаливаться, холодные трещины образуются при температурах распада остаточного аустенита (120 °С и ниже) или при нормальной температуре спустя некоторое время после сварки (десятки минут, часы, иногда и через более длительное время). Характерный признак холодных трещин — блестящий излом без следов высокотемпературного окисления.
Для объяснения природы образования холодных трещин ранее использовали две гипотезы — закалочную и водородную. Согласно закалочной гипотезе образование холодных трещин объясняется мартенситным превращением, приводящим к возникновению высоких внутренних напряжений, вызванных изменением объема при фазовом превращении и одновременно снижением пластичности металла.
Согласно водородной гипотезе возникновение трещин объясняется выделением растворенного в металле водорода в микронесплошности, имеющиеся в металле, и созданием в них высокого давления молекулярным водородом из-за очень малой степени диссоциации молекулярного водорода при низких температурах. Повышенное давление водорода создает вокруг микронесплошностей поле высоких напряжений, что приводит к развитию деформаций и разрушению металла. При этом предполагается, что растворенный в металле водород облегчает разрушение, так как при наличии водорода снижается работа образования новой поверхности.
Использование современных представлений о механизме разрушения металлов позволило дать более глубокое объяснение механизма образования холодных трещин. Образование холодных трещин связано с действием растягивающих напряжений и протекает в две стадии: зарождение очага разрушения критического размера и последующее его развитие до макротрещины. Используются две модели механизма образования очага разрушения критического размера: вакансионная и дислокационная.
В соответствии с вакансионным механизмом в результате воздействия термического цикла сварки в металле околошовной зоны на стадии охлаждения возникает избыток вакансий, которые под действием напряжений мигрируют к границам зерен, конденсируются на них, образуя каверны и зародышевые микро-несплошности. Если значение действующих напряжений превышает критическое, при котором зародыш трещины приобретает способность к росту, то в этом случае происходит образование макротрещины и разрушение.
Если действующие напряжения ниже критических, то в этом случае развитие релаксационных процессов приводит к снижению напряжений и уменьшению вероятности образования макротрещины. В связи с этим повышение температуры также способствует снижению вероятности образования холодных трещин из-за более интенсивного развития релаксационных процессов.
Дислокационный механизм базируется на том известном факте, что хрупкому разрушению всегда предшествует определенная локальная пластическая деформация. В процессе локальной пластической деформации в местах блокировки полос скольжения препятствиями (например, границей зерна) образуются скопления дислокаций. Скопления дислокаций вызывают образование растягивающих напряжений. При определенных условиях растягивающие напряжения, возникающие вокруг скопления дислокаций, могут превзойти прочность атомных связей. В этом случае в результате разрыва автомных связей сформируется субмикротрещина, которая в зависимости от внешних условий способна или исчезнуть (в результате снятия или перераспределения напряжений, а также упорядочения структуры), или перерасти в микротрещину. При достижении критических размеров трещина может развиться в макротрещину.
Во всех случаях критические размеры микротрещины, способной развиться в макротрещину, зависят от действующих растягивающих напряжений и свободной поверхностной энергии образующейся трещины. Повышение растягивающих напряжений, а также снижение величины свободной поверхностной энергии образующейся трещины уменьшают размеры критического зародыша. Поскольку водород снижает величину свободной поверхностной энергии образующейся трещины, его повышенное содержание в металле увеличивает вероятность образования холодных трещин.
Из рассмотрения механизма образования холодных трещин (замедленного разрушения) следует, что неоднородная структура, формирующаяся в околошовной зоне, будет способствовать формированию неоднородного поля растягивающих напряжений и деформаций. В связи с этим будут создаваться условия для локального направленного перемещения вакансий и дислокаций и формирования каверн и скопления дислокаций. Следовательно, основные приемы предотвращения образования холодных трещин следующие:
- снижение внутренних напряжений (например, за счет использования высокого отпуска после сварки),
- получение более однородной структуры металла в околошовной зоне,
- снижение концентрации водорода.
Трещины при холодной сварке
Во время ремонтных процессов в сварочном шве могут появиться холодные трещины. Многие люди не знают, как с ними бороться и предотвратить их появление. Холодная трещина – это разрушение шва межкристаллического типа, она относится к категории локальных разрушений. В отличие от горячих трещин, появление которых можно заметить и предотвратить во время процесса сварки, холодные проявляются только после того как работы подойдут к концу и шов остынет. Их можно заметить на шве, сделать это достаточно легко, потому что излом будет блестеть. Холодная трещина появляется из-за температурного окисления шва во время сварки.
Разнообразные материалы имеют разную склонность к появлению данного дефекта. Чем больше углерода в составе металлической детали, тем более высок шанс появления холодной трещины. Она может появиться в любой момент, гарантии на то, что её не будет никто дать не сможет. Однако за многолетний опыт использования сварки было замечено, что трещины уже могут проявиться, когда температура остывающего металла пересекает отметку в двести градусов по Цельсию. Наиболее подверженными материалами к данному дефекту являются высоколегированные стали, но это не говорит о том, что трещина не может появиться на низколегированном металле. Просто на нем шанс возникновения данного дефекта значительно уменьшается. Отличительной особенностью данного дефекта является то, трещины чаще всего возникают в области около шва.
Классификация трещин при сварке
Самым часто встречающимся дефектом при сварке являются холодные изломы. Трещины другого типа, если судить по статистическим данным, появляются не так часто. Их можно встретить в изделиях, которые созданы из металла с аустенитной структурой. Трещины могут делиться по нескольким характеристикам. Одна из них – это её расположение.
Очень часто трещина появляется из мельчайшего, не видимого человеческому глазу дефекта, и уже из него в течение нескольких часов или дней дефект увеличивается в размерах. В швах, с количество слоёв отличным от одного, возникновение трещин более вероятно, так как мест где они могут появиться – больше. В этом случае дефекты можно разделить на следующие типы:
Почему образуются холодные трещины?
Существует множество причин, из-за которых холодные трещины могут появиться. Однако чаще всего это происходит по трём популярным факторам.
- Наличие микроскопической структуры в так называемой зоне термовлияния или непосредственно внутри шва. При сваривании сталей с высоким уровнем прочности, создаётся мартенситная структура, которая и обладает такой восприимчивостью.
- Диффузный водород проявляется в зоне термовлияния, он способен проникать как в сам шов, так и в область около него.
- Помимо вышеперечисленных факторов, обязательным является присутствие растягивающего напряжения в зоне термовлияния.
Все вышеописанные причины можно объединить в одну, ей является наличие водорода. Чаще всего в шве он появляется из флюса, которым обработаны электроды. Он может выделяться из загрязнений, из проволоки и защитных газов даже при газовой сварке. Также источником является наличие ржавчина на металле, однако чаще всего причиной его появления является флюс на электроде.
Механизм, по которому образуются холодные трещины
Сразу же после завершения сварки металлическая деталь оказывается под влиянием водорода. Именно оно может ухудшить качество финального результата. В шлаковых включениях и порах образуется диффузия водорода, в этих же местах химический элемент принимает молекулярную структуру, которая создаёт повышенное давление на шов, поэтому на соединении образуются блестящие изломы.
Особенностью данного процесса является то, что водород может принять молекулярную форму только в момент остывания изделия, когда значение его температуры пересекает отметку в двести градусов по Цельсию. Если температура выше данного значения, структура водорода остаётся в атомном состоянии. Во время постоянного воздействия водородом приводит к уменьшению уровня прочности материала. Высокая хрупкость делает все изменения в структуре необратимыми.
Что сделать, чтобы предотвратить появление холодной трещины?
Узнав причины возникновения трещин при сварке, можно сразу же провести определённые процессы, задача которых будет направлена на предотвращение появление трещин. Распространённым способом, к которому прибегают чаще всего, является периодическая смена приёмом в сварке. Также обязательной процедурой, которую необходимо выполнять непосредственно перед началом работ, является сушка электродом. Это позволяет понизить концентрацию водорода, следовательно, снижает шанс возникновения холодной трещины.
Если вы используете газовую сварку, то перед выполнением работы не стоит обрабатывать проволоку в соляной кислоте, так как она обладает повышенной концентрацией водорода. Многие опытные сварщики после окончания работ некоторое время подогревают шов, тем самым увеличивая время до того, как температура соединения опустится ниже 200 градусов, за это время из шва успевает выйти большее количество водорода. Данную манипуляцию желательно выполнять в течение двадцати-тридцати минут. В том случае если свариваемый материал имеет большую толщину, то в процессе работы лучше всего несколько раз прерываться и осуществлять прогрев шва, так как шанс появления холодной трещины при сварке толстого материала повышен.
Оценка склонности к образованию холодных трещин
Основными параметрами оценки склонности сталей к образованию холодных трещин являются эквивалент углерода (Сэкв) и параметр трещинообразования Pсм
Для определения значения эквивалента углерода в мировой практике используется несколько различных параметрических уравнений, наиболее полное из них
С экв= C + M n / 6 + C r / 5 + M o / 4 + V / 14 + N i / 15 + C u / 15 + N b / 4 + T i / 4 + P / 2 + 5 ∗ B {\displaystyle C+Mn/6+Cr/5+Mo/4+V/14+Ni/15+Cu/15+Nb/4+Ti/4+P/2+5*B}
- при Сэкв>0.45 — сталь склонна к образованию холодных трещин
- при Сэкв<0.25 — сталь не склонна к образованию холодных трещин
Однако для современных феррито-бейнитных и бейнитных сталей образования холодных трещин не происходит при значениях С экв>0.45
Параметр Рсм определеяется по параметрическому уравнению Ито-Бессио
Pсм= C + S i / 30 + M n / 20 + C r / 20 + C u / 20 + N i / 60 + M o / 15 + V / 15 + 5 ∗ B {\displaystyle C+Si/30+Mn/20+Cr/20+Cu/20+Ni/60+Mo/15+V/15+5*B}
Что такое горячее растрескивание (растрескивание при затвердевании)?
И растрескивание при затвердевании, и горячее растрескивание относятся к образованию усадочных трещин во время затвердевания металла шва, хотя горячее растрескивание также может относиться к ликвационному растрескиванию.
Трещины затвердевания могут появляться в нескольких местах и в разных направлениях, но чаще всего это продольные центральные трещины (совпадающие с пересечением зерен, растущих с противоположных сторон сварного шва) или трещины «расширяющиеся», опять же продольные, но под углом к сварному шву. направление по толщине ( рис.1 ). Если в пластине есть центральная сегрегированная полоса, растрескивание может распространяться от этого места на границе плавления ( Рис. 2 ). Трещины во всех местах могут быть заглубленными ( Рис.3 ) или поверхностным разрушением.
Растрескивание возникает, когда доступный запас жидкого сварочного металла недостаточен для заполнения промежутков между затвердевающим металлом сварного шва, которые открываются деформациями усадки. Таким образом, основными причинами появления трещин являются:
Чтобы контролировать растрескивание при затвердевании, необходимо управлять тремя основными факторами: составом металла сварного шва; образец затвердевания сварного шва; деформации затвердевающего металла шва.
Состав металла сварного шва влияет на образование трещин при затвердевании (поскольку состав определяет диапазон замерзания металла шва). Металлы сварных швов — это неизменно сплавы с диапазоном температур замерзания. Компоненты с низкой температурой плавления отклоняются затвердевающими дендритами, в результате чего образуется тонкая пленка жидкости, сохраняющаяся до низких температур и, следовательно, на некотором расстоянии от основной ванны жидкого металла. Эта пленка не выдерживает деформации сжатия, и если ее нельзя успешно подавать из сварочной ванны, то образуется трещина.
Было обнаружено несколько элементов, которые увеличивают риск растрескивания при затвердевании. [1] . Как правило, это те, которые образуют вторую фазу, так что небольшие добавки могут увеличить интервал замерзания сплава.
Форма сварного шва определяет характер затвердевания металла шва и, в свою очередь, в значительной степени зависит от параметров сварки. Выбор соответствующих параметров сварки и подгонки дает сварные швы, которые затвердевают в восходящем, а не внутреннем направлении — т. е.е. те, которые имеют широкую неглубокую сварочную ванну — снижают риск образования трещин при затвердевании; но если бассейн будет слишком широким, растрескивание при затвердевании все равно может произойти. Важно добиться хорошего контроля формы сварного шва; отношение ширины к глубине 0,5 обычно является лучшим для сопротивления растрескиванию при затвердевании. См. Раздел Как минимизировать риск образования трещин при затвердевании в сварных швах под флюсом (SAW)?
Скорость хода является критическим параметром сварки: высокая скорость движения приводит к получению длинной сварочной ванны с хвостом, который трудно подавать из передней части ванны.
Деформацию сварочной ванны часто трудно определить количественно, но на нее влияют ограничение стыка, толщина и прочность материала, а также используемая температура предварительного нагрева. Некоторые детали изготовления могут привести к тому, что более ранние части сварного шва могут вызвать дополнительную деформацию усадки в затвердевающих областях, например сварка вокруг выступа или небольшого сопла.
Все сварные швы подвержены растрескиванию при затвердевании. Подробные сведения о том, как избежать трещин при затвердевании в ферритных сталях, приведены в руководстве по передовой практике механизмов растрескивания при изготовлении.Информация о некоторых аспектах предотвращения образования трещин при затвердевании в различных свариваемых материалах приведена в серии «Рабочие знания»: Дефекты — трещины при затвердевании; Свариваемость материалов — нержавеющая сталь. Также см. Здесь информацию о склонности ферритных нержавеющих сталей к горячему растрескиванию.
Номер ссылки
- «Влияние серы и фосфора на растрескивание при затвердевании металла шва». Metal Construction и British Welding Journal, август 1970, 2, 8, 333-338.
См. Дополнительную информацию о материалах и коррозионном растрескивании или свяжитесь с нами.
Горячие трещины — обзор
XI.A Горячие трещины
Горячие трещины возникают из-за охрупчивания металла шва или частично расплавленной зоны (PMZ) во время охлаждения между температурами ликвидуса и солидуса или чуть ниже солидуса (рис. 26). Горячие трещины имеют межзеренный или междендритный характер. На горячее растрескивание большое влияние оказывает перераспределение растворенных веществ, которое происходит во время затвердевания.Этот процесс перераспределения делает три важных вещи, каждая из которых способствует горячему растрескиванию: он расширяет диапазон замерзания, вызывает сегрегацию растворенных веществ и вызывает неплоское затвердевание. Без этого перераспределения растворенных веществ крутой положительный градиент температуры в сварочной ванне делал бы горячие трещины маловероятными.
РИСУНОК 26. Схематическое изображение различных частей сварного шва. [После Сэвиджа, У. Ф., Ниппеса, Э. Ф. и Секереса, Э. С. (1976). Сварной шов. J . 55 , 260С.]
Форма сварочной ванны важна, поскольку она влияет на растрескивание по средней линии. Осевое растрескивание — это горячее растрескивание, которое развивается по средней линии сварного шва (т. Е. Вдоль оси, проходящей через вершину каплевидной сварочной ванны). В крайних случаях горячая трещина может пройти по длине сварного шва; в менее тяжелых случаях растрескивание может состоять из коротких трещин, идущих в направлении движения горелки и расположенных по средней линии сварного шва. Центральная линия с высоким содержанием растворенных веществ, образованная каплевидной сварочной ванной, делает эту область очень восприимчивой к горячему растрескиванию.
Эмпирические уравнения показывают, что склонность сталей к горячему растрескиванию увеличивается с увеличением содержания углерода, серы, фосфора, кремния и никеля, в то время как молибден, ванадий и кислород обычно замедляют растрескивание. Некоторые исследования показали, что хром, медь и марганец вредны, в то время как другие подтвердили обратное. В таблице IV приведен относительный коэффициент эффективности (RPF) для ряда растворенных веществ в железе. Такие элементы, как фосфор, мышьяк, углерод, бор и сера в железе, имеют большие значения RPF (> 40 ° C / вес.%) И, следовательно, должны делать железо и сплавы железа склонными к горячему растрескиванию. Однако следует помнить, что RPF — это только показатель общей тенденции к горячему растрескиванию. Фактическое растрескивание зависит от других факторов, таких как природа фазового равновесия между железом и растворенным веществом и взаимодействия между растворенными веществами в многослойных системах, таких как промышленные стали.
ТАБЛИЦА IV. Способность элементов к горячему растрескиванию в железобинарных системах
Элемент | Фактор относительной активности | Элемент | Фактор относительной активности |
---|---|---|---|
Be | 5.41 | Cu | 3,61 |
Si | 1,75 | Mn | 26,2 |
P | 121,1 | Co | 0,3 |
Ti | 13,8 | Ni | 2,93 |
As | 40,2 | Nb | 28,8 |
Sn | 16,8 | Ta | 13,0 |
Sb | 5,04 | B | 917.![]() |
Al | 1,52 | S | 925,0 |
C | 322,0 | Zn | 15,2 |
Нержавеющие стали обычно хорошо свариваются, но они также могут иметь микротрещины в сваривать металл при затвердевании. Присутствие некоторого количества дельта (δ) феррита в сварном шве необходимо для подавления образования микротрещин при затвердевании. Одна из причин, по которой δ-феррит оказывает такое положительное влияние, заключается в том, что он обладает высокой растворимостью для фосфора и серы и, следовательно, удаляет их из жидкости на ранних этапах процесса затвердевания.Оптимальный сварной шов из нержавеющей стали должен содержать 5–10% δ-феррита и примерно 20% хрома (% Cr + Mo + 1,5 ×% Si + 0,5 ×% Nb) и никелевый эквивалент (% Ni + 30 ×% C + 30%). ×% N + 0,5 ×% Mn) примерно 12. Увеличение содержания марганца и молибдена также уменьшит микротрещины. Марганец является хорошим средством предотвращения образования микротрещин, хотя он и является стабилизатором аустенита, поскольку он образует MnS. Молибден является таким же сильным стабилизатором феррита, как и хром, и его присутствие приводит к образованию большего количества δ-феррита в сварном шве.Параметры сварки также могут влиять на склонность к образованию горячих трещин. Минимальный сварочный ток и скорость перемещения уменьшат размер ванны и скорость затвердевания, соответственно, и тем самым уменьшат склонность к горячему растрескиванию.
Состав сварного шва в сплавах нержавеющей стали часто контролируется добавлением присадочного металла в сварочную ванну. Этот присадочный металл часто будет содержать сильные стабилизаторы δ-феррита, так что правильное количество этой фазы будет присутствовать в сварном шве. Примером присадочного металла является нержавеющая сталь 308.К сожалению, не весь материал в сварном шве можно регулировать присадочным металлом. Материал в зоне сварного шва без перемешивания вблизи границы шва имеет состав основного металла. Таким образом, такие сплавы, как нержавеющая сталь 310 (27Cr – 22Ni), которые первоначально затвердевают до аустенита, будут склонны к образованию горячих трещин в несмешанной зоне сварного шва. Состав нержавеющей стали 304 таков, что она начинает затвердевать в виде феррита и, следовательно, менее склонна к горячему растрескиванию, чем нержавеющая сталь 310.Чтобы избежать растрескивания в этой несмешанной зоне на границе между сварным швом и основным металлом, необходимо уделять особое внимание составу основного металла. Повышение уровней марганца и молибдена и уменьшение количества серы и фосфора в основном металле уменьшит тенденцию к образованию горячих трещин без перемешивания.
представляют собой еще один класс гранецентрированных кубических сплавов, подверженных горячему растрескиванию. В этих сплавах затвердевает до аустенита, поэтому они особенно чувствительны к присутствию серы и фосфора, которые отделяются до последней жидкости и понижают температуру плавления.Например, было обнаружено, что фосфор и сера способствуют горячему растрескиванию в Inconel-600. Марганец, кремний, титан и алюминий оказались полезными в предотвращении этого горячего растрескивания: марганец из-за его эффекта связывания серы, марганца и кремния, потому что они увеличивают межфазную энергию, и всех четырех элементов, потому что они раскисляют сварной шов. бассейн.
Суперсплавы, такие как A286 (сплав на основе Fe, но с высоким содержанием никеля) и Hastelloy-X (сплав на основе Ni), подвержены горячему растрескиванию.A286 особенно склонен к растрескиванию из-за образования фазы Лавеса Fe 2 Ti. Было обнаружено, что сульфиды с низкой температурой плавления способствуют растрескиванию сварных швов из сплава Hastelloy-X. Inconel-718 и Inconel-X750 не особенно склонны к горячему растрескиванию.
ПМЗ (рис. 26) часто является местом образования горячих трещин. Частичное плавление происходит из-за того, что температура в этой области сварного шва становится достаточно высокой для плавления материала с низкой температурой плавления, но недостаточно высокой для плавления всего объема.Материал с низкой температурой плавления может существовать из-за сильной сегрегации в основном металле или локальной сегрегации на границах зерен. Пленки с низкой температурой плавления на границах зерен и локальных лужах жидкости создают границы зерен жидкости, которые могут быть раздвинуты во время охлаждения. Этот тип горячего растрескивания PMZ был отмечен во многих различных типах сплавов, таких как низколегированные стали, суперсплавы на основе Ni и аустенитные нержавеющие стали.
Включения, такие как сульфиды, карбиды, фосфиды и бориды, могут быть источником скоплений жидкости, которые при смачивании границы зерен вызывают горячее растрескивание.Этот процесс плавления был назван конституционной ликвацией. Было показано, что этот процесс работает в мартенситностареющих сталях 18Ni, где осадки сульфидов ответственны за ликвацию. Ликвидация карбида (MC) и борида (M 3 B 2 ) также наблюдалась в Udimet 700 и Waspalloy; в сталях наблюдались сульфидные и боридные ликворы.
Конституционная ликвация очень чувствительна к скорости нагрева, скорости растворения осадка и скорости диффузии в твердом состоянии.Если скорость нагревания низкая по сравнению со скоростью растворения и диффузии осадка, ликвации не произойдет. Обычно это имеет место при растворении Fe 3 C в сталях для большинства сварочных процессов. Исключение составляет точечная контактная сварка, при которой скорость нагрева очень высока. Fe 3 C не обязательно должен растворяться для возникновения проблем. Он может растворяться выше эвтектоидной температуры и вызывать образование аустенита. Этот аустенит будет обогащен углеродом до уровня, превышающего эвтектоидный (точный уровень зависит от максимальной достигнутой температуры).Когда этот аустенит охлаждается, он превращается в высокоуглеродистый мартенсит, который является хрупким и поэтому нежелательным.
Сравнение горячего крекинга и холодного крекинга
Недавно мы помогли клиенту определить причину появления трещин на сварных швах. Было установлено, что трещины на их деталях возникли из-за быстрого охлаждения и неправильного размера сварных швов. Обсуждения, которые у нас были до и после определения причины, были весьма интересными. Мы обсудили с нашим клиентом типичные причины взлома.Вот краткое изложение наших встреч. Обратите внимание, что это не все причины появления трещин.
Вообще говоря, мы можем разделить трещины на две группы, которые связаны со временем появления трещин: горячие и холодные. По существу, горячее растрескивание происходит во время сварки или вскоре после нее, в то время как холодное растрескивание может возникать через несколько часов или даже дней после завершения сварки.
Горячий крекинг
Горячее растрескивание в основном происходит из-за большого количества элементов с низкими температурами плавления в основном материале.Слегка повышенного количества этих элементов обычно недостаточно, чтобы вызвать растрескивание, это скорее связано с другими проблемами, такими как неправильное соотношение ширины к глубине сварного шва. Некоторые элементы, используемые в производстве стали, такие как сера и фосфор, имеют низкие температуры плавления. Из-за этих низких температур плавления эти элементы смещаются к центру сварного шва по мере его затвердевания. Эти элементы могут застрять в середине сварного шва, когда лужа не остается в расплавленном состоянии достаточно долго. Когда это происходит, мы получаем трещину по средней линии, как показано на рисунке ниже.
Центральная трещина, вид сверху. Иногда эти трещины едва заметны невооруженным глазом, поэтому используются методы неразрушающего контроля, такие как жидкий пенетрант.
Поперечный разрез осевой трещины.
Расплавленная лужа затвердеет снаружи по направлению к середине сварного шва. Если сварной шов будет слишком глубоким по сравнению с его шириной, он будет захватывать элементы с низкой температурой плавления в середине сварного шва, независимо от того, находится ли количество в основном материале в пределах спецификации.Это называется растрескиванием, вызванным формой валика. На рисунке ниже показано, как затвердевает сварной шов.
Точно так же, как вода в стакане замерзает, сварочная лужа затвердевает от внешних краев к середине. Иногда попадающие элементы попадают в середину, вызывая трещины.
Для предотвращения горячего растрескивания мы хотим сделать следующее:
- Обеспечьте правильное соотношение ширины и глубины на сварных швах (идеально от 1: 1 до 1,4: 1).
Иногда для этого требуется совместный редизайн.
- Тщательно выбирайте основные материалы.
- Выберите правильный процесс. Такие процессы, как SAW, которые обеспечивают лучшее проникновение, иногда могут быть проблемой в зависимости от деталей соединения.
Холодное крекинг
Холодное растрескивание намного хуже горячего просто потому, что до появления трещины могут пройти часы или дни. Это означает, что сварная сборка может уже быть в эксплуатации. Холодное растрескивание характеризуется появлением трещины на основном материале, а не на сварном шве, как в случае горячего растрескивания.Иногда это называют растрескиванием в зоне термического влияния (HAZ) или растрескиванием под водородом.
Холодное растрескивание происходит при наличии трех условий: достаточно чувствительного материала, достаточного уровня водорода и высокого уровня остаточного напряжения. Обычно мы мало контролируем уровень остаточного напряжения, поэтому цель состоит в том, чтобы контролировать две другие переменные.
Высокие скорости охлаждения и материалы с высоким содержанием углерода создают условия, подверженные холодному растрескиванию.Чем выше скорость охлаждения, тем больше вероятность образования холодных трещин. Такие вещи, как большая толщина основного материала, низкое тепловложение и более низкие температуры основного металла, увеличивают скорость охлаждения. При высоких скоростях охлаждения в ЗТВ образуется твердый и хрупкий мартенсит. Он также имеет более низкую пластичность, чем сварной шов, поэтому остальной основной материал сжимается с разной скоростью по мере охлаждения сварного шва. Водород попадает в мартенсит, и при приложении напряжения возникает трещина.Со временем водород покидает ЗТВ и металл сварного шва; Вот почему Структурный кодекс D1.1 требует, чтобы проверка проводилась через 48 часов после сварки. Это гарантирует, что водород уйдет из сварной конструкции в сталях, чувствительных к растрескиванию, вызванному водородом, после проверки.
Чтобы предотвратить холодное растрескивание, мы хотим сделать следующее:
- Предварительно нагрейте основной материал, чтобы снизить скорость охлаждения — это также приведет к диффузии водорода и позволит сварному шву и основному материалу сжиматься с одинаковой скоростью при охлаждении.
- Выполните процедуры увеличения погонной энергии, если предварительный нагрев не предусмотрен
- Выберите присадочные материалы с низким содержанием водорода (обычно имеют обозначение h3, h5 или H8).
- Выполнять термообработку шва после сварки (отжиг водородом)
- Уменьшите скорость охлаждения, используя тепловые одеяла
Существуют и другие типы взлома, вызванные проблемами, не упомянутыми здесь. Были ли у вас проблемы с растрескиванием сварных швов?
Источник: Руководство изготовителей и монтажников по сварным стальным конструкциям
Горячая трещина
A Горячая трещина — это повреждение детали, вызванное сваркой.Трещина возникает во время затвердевания при температурах между температурами солидуса и ликвидуса, и поэтому является типичным дефектом сварного шва с солидусом.
Определение
Согласно техническому паспорту DVS 1004-1 [1], термин «горячая трещина» означает трещины, которые возникают из-за присутствия легкоплавких, хрупких веществ на границах зерен. Они вызваны высокими температурами во время или после завершения процесса сварки. В зависимости от характера разрушения при испытаниях на разрыв в горячем состоянии горячие трещины в специальной литературе также называются «хрупкими», т. Е. Разделениями материала без деформации в металле сварного шва и в зоне термического влияния основного материала.
Отличие от холодной трещины
Холодные трещины возникают в твердом состоянии после того, как температура солидуса упала ниже, например, из-за большой разницы в твердости, напряжения усадки при сварке или водородной хрупкости.
Механизм горячего растрескивания
Материалы с большим интервалом затвердевания между температурой ликвидуса и солидуса, высоким содержанием фосфора, серы и углерода так же склонны к горячему растрескиванию, как и материалы с низкой вязкостью при высоких температурах.В случае сплавов эвтектическая или неметаллическая фаза образуется перед затвердевающими дендритами или на них. Во время роста зерна эти примеси вытесняются растущим зерном и остаются в расплаве. Сегрегация остаточного расплава с неметаллическими веществами снижает температуру затвердевания оставшегося расплава и вызывает относительно длительный период жидкой фазы, остающейся между уже затвердевшими дендритами. Следовательно, риск горячего растрескивания увеличивается с увеличением загрязнения стали, поскольку температура солидуса увеличивается с увеличением степени загрязнения.Затем этот расплав может быть разорван напряжениями, возникающими во время сварки. Таким образом, образование горячих трещин (ранее известных как «горячие трещины») связано с присутствием жидких, полужидких, легкоплавких или даже хрупких фаз на границах зерен, которые могут возникать или уже присутствовать в результате процессы кристаллизации и превращения в интервале температур солидуса. Разрыв террасы). Даже после того, как свариваемый компонент остынет, могут оставаться горячие трещины, обычно в виде микротрещин, в результате усадочных напряжений или других внешних нагрузок.Высоколегированные аустенитные стали особенно подвержены риску образования горячих трещин.
Способность аустенитных дендритов растворять серу, фосфор и углерод значительно ниже, чем у ферритных сталей. [2]
Типы горячих трещин
В зависимости от причины их образования различают трещины затвердевания и расплавления. [3]
Трещины затвердевания
Трещины затвердевания лежат в металле сварного шва и возникают при кристаллизации материала из жидкой фазы.Внутри сварного шва сначала появляются микротрещины, которые могут распространяться на поверхность по мере продолжения затвердевания и становиться видимыми там в виде макротрещин. В этом случае поверхности трещин представляют собой не оголенный металл, а покрыты оксидами. Трещины затвердевания в основном перпендикулярны сильнейшей деформации усадки. Эти трещины обычно можно увидеть в увеличительное стекло, но часто также и невооруженным глазом (например, трещины в центре шва, трещины на концах кратера). Если они распространяются на поверхность, их можно обнаружить с помощью методов испытания поверхностных трещин.
Во избежание образования горячих трещин рекомендуется предварительно нагревать компонент и использовать небольшие неглубокие сварочные ванны. Небольшие сварочные ванны можно изготавливать, например, с помощью технологии многослойной сварки или путем выбора подходящей формы шва. Эти меры снижают усадочные напряжения и предотвращают выраженное дендритное затвердевание сварочной ванны.
Трещины плавления или переплавки
Трещины плавления, также называемые трещинами переплава, возникают в зоне термического влияния (ЗТВ), прилегающей к сварочной ванне.Тогда это может быть как основной материал, так и, в случае многослойной сварки, также зона термического влияния сварных валиков, расположенная ниже или рядом с ним. Они возникают преимущественно в точке перехода между жидким металлом сварного шва и ЗТВ и часто проникают в основной материал. Причиной появления трещин при переплаве является повторное разжижение выделений, расположенных на границах зерен. При этом растягивающие напряжения возникают в результате охлаждения металла шва из-за его уменьшения в объеме. Осадки были прямым результатом процесса сварки, но не привели к трещинам затвердевания, описанным выше.
Как и в случае трещин затвердевания, риск образования горячих трещин во время сварки можно снизить за счет уменьшения подводимого тепла, например, за счет линейных валиков и многослойной сварки.
Трещины из-за снижения деформируемости
Трещины из-за снижения деформируемости материала в результате сварки расположены в ЗТВ или непосредственно рядом с ней.Это межкристаллитные разделения, возникающие после охлаждения материала. Границы зерен не плавились.
Обнаружение горячих трещин
Обычно горячие трещины небольшие и редко превышают несколько миллиметров или даже сантиметров. Это, в частности, относится к трещинам и трещинам при переплаве в результате снижения пластичности или ударной вязкости (растрескивание при погружении в пластичность «DDC»), которые в основном возникают в виде микротрещин и часто не достигают поверхности. Поэтому микротрещины не всегда можно обнаружить с помощью методов неразрушающего контроля.
Причину трещины и ее отграничение от холодных трещин можно определить с помощью металлографического разреза. Направление затвердевания обычно четко видно на микрофотографии. Исследование с помощью сканирующего электронного микроскопа позволяет лучше отделить трещины затвердевания от холодных трещин и раковин. Поверхность излома трещины затвердевания в аустенитном металле сварного шва затем проходит вдоль по-разному ориентированных пакетов дендритов. Закругленные кончики дендритов ясно показывают, что расплав, лежащий на поверхности дендритов, свободно затвердел после разрыва. [4]
Индивидуальные свидетельства
- ↑ Проспект DVS 1004-1 «Технического комитета Немецкой ассоциации сварочных технологий»: Метод испытания на горячие трещины — основы.
- ↑ Образование горячих трещин
- ↑ IWT Ingenieurbüro für Werkstofftechnik: Явление трещин в сталях I и II (Памятка от 22 января 2005 г. в Интернет-архиве ), стр. 4: Подразделение типов трещин; Листы 5–7: Изображения горячих трещин с помощью сканирующего электронного микроскопа
- ↑ Volker Schmidt, Martin Möser, TH Magdeburg, страница 11, изображение 21 + изображение 22, изображения горячих трещин с помощью сканирующего электронного микроскопа (PDF; 981 kB).
Как предотвратить образование горячих трещин при сварке?
Сварочная трещина — один из наиболее частых серьезных дефектов сварных деталей. Сварочные трещины можно классифицировать по-разному в зависимости от их положения, размера, причины и механизма. По условию образования трещины ее можно разделить на горячую трещину, холодную трещину, трещину повторного нагрева и пластинчатый разрыв.
Как следует из названия, трещины, возникающие при высокой температуре во время сварки, называются горячими трещинами (термические трещины / тепловые трещины), которые возникают при высокой температуре вблизи линии твердой фазы и характеризуются распределением по границе зерен.Но иногда он может образовываться по полигональным границам при температурах ниже линии твердых тел. Горячие трещины обычно возникают в металле сварного шва, но они также могут образовываться в основном металле вблизи линии плавления шва.
Различные металлические материалы (низколегированная высокопрочная сталь, нержавеющая сталь, чугун, алюминиевый сплав и некоторые специальные металлы и т. Д.) Будут давать различную морфологию и температурный диапазон термических трещин во время сварки. Горячие трещины можно разделить на трещины кристаллизации, трещины разжижения и многосторонние трещины в соответствии с различными процессами их образования.Сегодня мы подробно рассмотрим конкретные причины, характеристики, профилактику и лечение горячих трещин.
Эти трещины в основном возникают при сварке примесей, содержащих углеродистую сталь, низколегированную сталь (например, с высоким содержанием S, P, C, Si) и однофазную аустенитную сталь, Сплавы на основе никеля и некоторые алюминиевые сплавы. Эта трещина возникла около линии твердой фазы во время процесса кристаллизации при пайке.Из-за усадки затвердевшего металла и недостаточного количества остаточного жидкого металла, которое приводит к межкристаллитному растрескиванию под действием напряжения.
Как предотвратить кристаллизационные трещины?
Металлургия: с одной стороны, правильно отрегулировать состав металла сварки, сократить диапазон хрупкой температурной зоны для контроля содержания серы, фосфора, углерода и других вредных примесей при сварке; С другой стороны, измельчить первичное зерно металла сварного шва, то есть соответствующим образом добавив Mo, V, Ti, Nb и другие элементы;
Технический процесс: предварительный нагрев перед сваркой, контроль энергии линии и уменьшение заедания стыков.
Трещина сжижения
Это тип микротрещины, которая растрескивается по границе зерен аустенита и обычно возникает в зоне термического влияния около зоны трещины или между слоями. Обычно она возникает в результате переплавления эвтектических компонентов на границе аустенита. зерна в околошовной зоне или между слоями сварного шва при высокой температуре и растрескивание зерен аустенита под действием растягивающего напряжения.
Как предотвратить образование трещин в зоне разжижения?
Эти меры по предотвращению трещин в основном соответствуют кристаллической трещине.В частности, в области металлургии эффективно максимально снизить содержание эвтектических элементов, таких как сера, фосфор, кремний и бор. С точки зрения технологии, можно уменьшить энергию линии и вогнутость линии плавления.
Полигональная трещина
Трещина полигонизации образуется в процессе полигонизации, высокая температура приводит к очень низкой пластичности. Этот вид трещин не является обычным явлением, и мы не будем здесь подробно останавливаться на этом. Профилактические меры, связанные с добавлением элементов, таких как Mo, W и Ti, в сварной шов, могут улучшить энергию поляризации.
По сравнению со сталью общего назначения никельсодержащая нержавеющая сталь более склонна к образованию термических трещин, которые могут возникать в сварных швах и зонах термического влияния. Чем выше содержание никеля, тем больше склонность к образованию горячих трещин и тем более неконтролируемым. Поэтому при сварке 304 заготовок необходимо обращать внимание на предотвращение образования горячих трещин.
Причины трещин литья и шесть видов общих дефектов и их предотвращение — китайский поставщик трубопроводных решений
В отливке бывают двух типов трещин: горячая трещина и холодная трещина.
Горячее растрескивание
Горячее растрескивание — это вид горячего растрескивания, который характеризуется искривленной формой трещины, неровной поверхностью излома, широкой поверхностью и более узкой внутренней стороной. Механизм следующий: расплавленная сталь начинает конденсироваться после того, как ее впрыснули в полость кристаллизатора. Когда кристаллический каркас сформирован и начинается линейная усадка, усадка блокируется, поскольку расплавленная сталь в это время не затвердевает до твердого состояния, и в отливке возникает напряжение или пластическая деформация.Когда они превышают предел прочности материала при такой высокой температуре, отливка треснет.
Морфология и характеристика горячих трещин
Горячая трещина — это разновидность трещины, которая возникает из-за заблокированной твердой усадки отливки, когда прочность и пластичность отливки очень низки в конце или вскоре после затвердевания. Горячие трещины — один из распространенных дефектов стальных отливок, отливок из ковкого чугуна и некоторых отливок из легких сплавов.Горячие трещины возникают и распространяются вдоль границы зерен, и их форма неровная, извилистая и неправильная. Поверхность трещины окрашена в оксидный цвет, без металлического блеска. Поверхность трещин стального литья почти черная, а у алюминиевого сплава — темно-серая. Внешнюю трещину можно увидеть невооруженным глазом и отличить от холодной трещины по форме и характеристикам излома.
Горячую трещину можно разделить на внешнюю и внутреннюю. Горячая трещина, которую можно увидеть на поверхности отливки, называется внешней трещиной.Наружные трещины часто возникают на углу отливки, резком изменении толщины сечения, медленном затвердевании и концентрации напряжений. Он отличается широкой поверхностью, узким внутренним пространством и рвущейся формой. Иногда трещина проходит через весь участок отливки. Другой характеристикой горячей трещины является то, что трещина распространяется по границе зерен. Внутренняя трещина обычно возникает на этапе окончательного затвердевания отливки. Форма трещины очень неправильная, а поперечное сечение часто сопровождается дендритами.Обычно внутренняя трещина не распространяется на поверхность отливки.
Причины образования горячих трещин
Существует множество теоретических и практических причин образования горячих трещин, но основной причиной является режим затвердевания, а также термическое напряжение и напряжение усадки во время затвердевания.
После заливки жидкого металла в форму потери тепла в основном происходят через стенку формы, поэтому затвердевание всегда начинается с поверхности отливки.Когда большое количество дендритов появляется на более поздней стадии затвердевания и формирует полный каркас, начинается сплошная усадка. Однако между дендритами есть слой жидкометаллической пленки (жидкой пленки). Если не препятствовать усадке отливки, дендритный каркас может свободно сокращаться без силы. Когда усадке дендритного каркаса препятствует песчаная форма или песчаная сердцевина, возникает растягивающее напряжение, если оно не может свободно сжиматься. Когда растягивающее напряжение превышает предел прочности материала, дендриты растрескиваются.Если скорость вытягивания каркаса дендрита очень мала и жидкого металла вокруг вытягивающей части достаточно, чтобы вовремя влить в трещину, отливка не вызовет горячих трещин. Напротив, если трещину не восполнить жидким металлом, в отливке появятся горячие трещины.
Видно, что сплав с широким диапазоном температур затвердевания и режимом затвердевания с мягкой или губчатой сеткой наиболее склонен к горячему растрескиванию. При сужении диапазона температур затвердевания склонность сплава к горячему растрескиванию уменьшается, и сплав с эвтектическим составом, затвердевающий при постоянной температуре, с наименьшей вероятностью образует горячее растрескивание.Горячее растрескивание происходит в период затвердевания отливок, но это не обязательно означает, что горячее растрескивание происходит во время затвердевания. В основном это зависит от термического напряжения и усадочного напряжения во время затвердевания. Термическое напряжение в твердом зернистом каркасе в области затвердевания отливки легко может вызвать горячее растрескивание или подкожное горячее растрескивание; Усадочное напряжение, вызванное внешними факторами, является основным условием образования горячих трещин. Когда литая оболочка находится в состоянии затвердевания, ее линейной усадке препятствуют внешние факторы, такие как песчаный стержень, формовочный песок, поверхностное трение между литейной поверхностью и песчаной формой, в оболочке возникает усадочное напряжение (растягивающее напряжение).
Тонкая оболочка, образованная горячей точкой, особенно острый угол в горячей точке, становится местом концентрации усадочного напряжения, и отливка, скорее всего, вызовет горячие трещины в этих местах.
- Причины появления горячих трещин отражаются на процессе и структуре отливки, в том числе неравномерная толщина стенки и небольшой внутренний угол;
- В нахлесточном соединении слишком много бифуркаций, которые препятствуют нормальной усадке отливки;
- Например, разливочный стояк расположен близко к ленточному конвейеру или прочность песка между разливочным стояком очень высока, что ограничивает свободную усадку отливки;
- Подступенок слишком маленький или слишком большой;
- Линейная усадка сплава слишком велика;
- Формирующие элементы со средней и низкой температурой плавления в сплаве превышают норматив, а содержание серы и фосфора в литой стали и чугуне высокое;
- Коробку открывать рано, охлаждение идет слишком быстро.
Как предотвратить образование горячих трещин
01. Улучшение структуры отливки
Толщина стенки должна быть одинаковой, а угол должен быть скругленным, чтобы уменьшить концентрацию напряжений. Спицы колесных отливок при необходимости можно гнуть.
02. Повышение качества плавления легированных материалов.
Для удаления оксидных включений и газов из жидкого металла используются процессы рафинирования и дегазации. Контролируйте содержание вредных примесей и применяйте разумный процесс плавления, чтобы предотвратить образование холодных трещин.
03. Принятие мер по правильному процессу литья
Это не только полезно для предотвращения горячих трещин, но также помогает предотвратить холодные трещины, одновременно заставляя отливку затвердеть. Положение и размер стояка должны быть установлены разумно, чтобы сделать скорость охлаждения каждой части отливки как можно более равномерной и уменьшить склонность к образованию холодных трещин.
Правильное определение времени пребывания отливок в песчаной форме Песчаная форма — это хороший контейнер для сохранения тепла, который может дополнительно гомогенизировать температуру более толстых и более тонких частей отливок, уменьшать разницу температур между ними, уменьшать термическое напряжение и уменьшать склонность холодных трещин. Увеличьте время пребывания отливки в форме, чтобы избежать больших внутренних напряжений и холодных трещин в отливке, вызванных преждевременной распаковкой.
Это эффективная мера для предотвращения холодного растрескивания отливок из-за усадочного напряжения за счет увеличения уступа песчаной формы и песчаного стержня, удаления прессованного железа как можно скорее после затвердевания и ослабления крепежного устройства песочницы. Песчаная форма и песчаная сердцевина больших отливок могут быть удалены заранее после заливки, чтобы уменьшить их сопротивление усадке отливкам и способствовать равномерному охлаждению всех частей отливок.В процессе осыпания песка, очистки и погрузочно-разгрузочных работ следует избегать столкновений и выдавливания, чтобы предотвратить образование холодных трещин.
04. Термическая обработка старением
Отливку с большим напряжением отливки следует своевременно обрабатывать термообработкой старением, чтобы избежать холодных трещин, вызванных чрезмерным остаточным напряжением. При необходимости следует провести термообработку старением после резки стояка или сварки.
Холодное растрескивание
Холодная трещина вызвана локальным напряжением отливки, превышающим предел прочности сплава, когда отливка охлаждается до упругого состояния после затвердевания.Холодная трещина всегда возникает в том месте, где при охлаждении концентрируется растягивающее напряжение. Холодная трещина отличается от горячей трещины. Холодная трещина обычно распространяется по всему сечению и имеет форму прямой или ломаной линии с одинаковой шириной. Поверхность излома холодной трещины имеет чистый металлический блеск или цвет со слабым окислением, а тенденция трещины гладкая, а не вдоль границы зерен. Это значительно отличается от горячего растрескивания. Холодные трещины можно увидеть невооруженным глазом, и их можно отличить от горячих трещин по их макроскопической морфологии и микроскопическим характеристикам трансгранулярного роста.
Когда литейное напряжение в отливке превышает предел прочности металла, отливка будет давать холодные трещины. Следовательно, все факторы, увеличивающие напряжение и снижающие прочность металла, могут вызвать холодные трещины в отливке.
Основные причины холодных трещин
01. Конструкция отливки
Неравномерная толщина стенок отливок вызывает напряжение отливки и иногда дефекты холодных трещин. Из-за препятствий жесткой конструкции отливка легко подвергается термическому напряжению, в результате чего отливка образует холодные трещины.Например, отливка ящика с однородной толщиной стенки «тонкая стенка и большой стержень» будет создавать временное напряжение усадки из-за засорения песчаного стержня. Когда он превышает предел прочности материала сплава, отливка вызывает холодное растрескивание.
02. Необоснованная конструкция подъемной системы
Для отливок с неравномерной толщиной стенки, если внутренний затвор установлен в части толщины стенки отливки, скорость охлаждения толстостенной части отливки будет ниже, что приведет к или усугубит разницу в скорости охлаждения каждой части отливки, увеличит термическое напряжение отливки и будет способствовать образованию холодных трещин в отливке. Неправильная установка заливки и стояка напрямую препятствует усадке отливок и вызывает образование холодных трещин в отливках. Поскольку ворота тоньше литого, они сначала затвердевают. Когда отливка сжимается внутрь и затрудняется воротами, возникает растягивающее напряжение, и на стене между двумя воротами легко могут образоваться холодные трещины. Во-вторых, высокотемпературная прочность или прочность в сухом состоянии формовочного песка или стержневого песка слишком высока, а высокотемпературный предел текучести является низким, что препятствует усадке отливки и создает большое напряжение при растяжении, что приводит к образованию холодных трещин в отливке.
03. Неопределенный химический состав материала сплава
Высокое содержание углерода и других легирующих элементов в стали делает отливку склонной к образованию холодных трещин. Из пластичных сплавов непросто образовать холодные трещины, из хрупких сплавов легко образоваться холодные трещины. Фосфор является вредным элементом в стали ω (P). Когда соотношение превышает 0,05%, хладноломкость стали увеличивается, и легко могут возникать холодные трещины. В сером чугуне наличие чрезмерных антиграфитирующих элементов также увеличивает усадку отливок, что приводит к образованию холодных трещин.
04. Контролируйте время распаковки
Если отливку открыть слишком рано и температура капель песка слишком высока, отливка потрескается при ударе и сжатии во время очистки от песка.
Общие дефекты шести видов отливок
01. Воздушное отверстие (пузырек, штуцер, воздушный карман)
Характеристики: воздушное отверстие — это отверстие круглой, овальной или неправильной формы на поверхности или внутри отливки. Иногда несколько отверстий для воздуха образуют воздушную массу, а кожа обычно имеет грушевидную форму.Форма штуцера неправильная, поверхность шероховатая. Воздушный карман представляет собой вогнутую часть поверхности отливки, и поверхность гладкая. Его можно обнаружить при осмотре внешнего вида открытого отверстия, а обнаружить его можно только путем механической обработки подкожных пор.
Причины следующие:
- 1. Температура предварительного нагрева формы слишком низкая, и жидкий металл слишком быстро остывает при прохождении через литниковую систему.
- 2.Плохая конструкция выхлопа пресс-формы, и газ не может отводиться плавно.
- 3. Плохое покрытие и плохой выхлоп, даже если он испаряет или разлагает газ.
- 4. На поверхности полости формы есть отверстия и ямки. После впрыска жидкого металла газ в отверстиях и ямках быстро расширяется и сжимает жидкий металл, образуя закупоривающие отверстия.
- 5. Поверхность полости формы заржавела и не очищена.
- 6.Сырье (песчаный стержень) не хранится должным образом и не нагревается перед использованием.
- 7. Плохой раскислитель, недостаточная дозировка или неправильная работа.
Методы профилактики:
- 1. Форма должна быть полностью нагрета, размер частиц покрытия (графита) не должен быть слишком мелким, а воздухопроницаемость должна быть хорошей.
- 2. Используйте метод наклонной заливки.
- 3. Сырье следует хранить в проветриваемом и сухом месте и предварительно нагревать во время использования.
- 4. Выберите раскислитель (магний) с лучшим раскисляющим эффектом.
- 5. Температура заливки не должна быть слишком высокой.
02. Усадка (пористость)
Характеристики: усадочная полость — это своего рода шероховатое отверстие на поверхности или внутри отливки. Небольшая усадочная полость представляет собой множество рассеянных мелких усадочных полостей, то есть усадочную пористость, а зерна в усадочной полости или усадочной пористости являются крупными. Это часто происходит возле желоба, корня стояка, толстых и больших частей, перехода толщины стенки и толстых и тонких частей с большой плоскостью.
Причины следующие:
- 1. Контроль рабочей температуры пресс-формы не соответствует требованиям направленного затвердевания.
- 2. Неправильный выбор покрытия и плохой контроль толщины покрытия на разных деталях.
- 3. Неправильная конструкция положения отливки в кристаллизаторе.
- 4. Конструкция заливки и стояка не сыграла роли полноценной подачи.
- 5. Температура заливки слишком низкая или слишком высокая.
Методы профилактики и борьбы:
- 1. Увеличьте температуру абразивных инструментов.
- 2. Отрегулируйте толщину слоя покрытия, равномерно распылите покрытие и не создавайте локальных скоплений покрытия, когда покрытие отваливается и перекрашивается.
- 3. Локальный нагрев формы или локальная изоляция изоляционным материалом.
- 4. Вставьте медный блок в горячую точку, чтобы охладить локальную часть.
- 5.спроектировать теплоотвод на матрице или ускорить скорость местного охлаждения с помощью воды, или распылить воду за пределы формы, распылить.
- 6. Съемный охлаждающий блок по очереди помещается в полость формы, чтобы избежать недостаточного охлаждения самого охлаждающего блока при непрерывном производстве.
- 7. Устройство давления расположено на стояке формы.
- 8. Необходимо точно спроектировать литниковую систему и выбрать подходящую температуру заливки.
03.Шлаковая лунка (шлаковые включения флюса или оксида металла)
Характеристики: шлаковая лунка — это открытая или темная лунка на отливке. Отверстие полностью или частично заполнено шлаком. Форма неправильная, мелкие пятна шлакового включения найти сложно. После удаления шлака появляется ровное отверстие, которое, как правило, располагается в нижней части места разливки, возле горловины или мертвого угла отливки. Включение оксидного шлака в основном распределяется по поверхности отливки вблизи отливки сеткой, иногда в виде тонкого листа. В процессе разрушения часто отрывается от промежуточного слоя, в котором оксид является одной из причин появления трещин. .
Причины следующие:
Шлаковое отверстие в основном вызвано процессом плавления сплава и процессом разливки (включая неправильную конструкцию системы разливки). Сама форма не вызовет образование шлакового отверстия, а металлическая форма является одним из эффективных способов избежать образования шлакового отверстия.
Методы профилактики и борьбы:
- 1. Система вентиляции настроена правильно или используется фильтр из литого волокна.
- 2. Применяется метод наклонной заливки.
- 3. Выберите флюс и строго контролируйте качество.
04. Трещина (горячая трещина, холодная трещина)
Характеристики: трещина имеет вид прямой или неправильной кривой, поверхность излома горячей трещины сильно окислена до темно-серого или черного цвета, без металлического блеска, а поверхность холодной трещины излом чистый и металлический блеск. Как правило, внешние трещины отливок можно увидеть непосредственно, а внутренние трещины можно увидеть только другими методами. Трещины часто связаны с усадочной пористостью, включениями шлака и другими дефектами, которые часто возникают на внутренней стороне острого угла отливки, на стыке толстых и тонких участков, а также в области горячей точки, где стояк соединяется с отливкой.
Причины следующие:
Отливка металлической формы легко вызывает дефекты трещин, потому что сама металлическая форма не уступает, скорость охлаждения высокая, легко вызвать увеличение внутреннего напряжения отливки, открытие формы слишком рано или слишком поздно, угол заливки слишком мал или слишком велик, слой покрытия слишком тонкий и т. д., которые легко могут вызвать трещины в самой полости формы.
Методы профилактики и борьбы:
- 1. Следует обратить внимание на конструкционные и технологические свойства отливок, чтобы детали с неравномерной толщиной стенки могли проходить равномерно, и следует выбрать соответствующий размер галтели.
- 2. Отрегулируйте толщину покрытия, чтобы каждая часть отливки достигла требуемой скорости охлаждения, насколько это возможно, чтобы избежать образования слишком большого внутреннего напряжения.
- 3. Обратите внимание на рабочую температуру металлической формы, отрегулируйте наклон формы, своевременное вытягивание стержня и растрескивание, а также выньте отливку для медленного охлаждения.
05. Холодная изоляция (плохое плавление)
Характеристики: холодный затвор — это своего рода сквозной шов или поверхностная трещина с круглым краем, который отделен оксидной пленкой посередине и не полностью интегрирован.Когда холодное закрытие серьезно, оно становится «под гипсом». Холодный затвор часто появляется на верхней стенке отливки, тонкой горизонтальной или вертикальной плоскости, толстом тонкостенном соединении или тонкой вспомогательной пластине.
Причины следующие
- 1. Вытяжная конструкция металлической формы неразумна.
- 2. Слишком низкая рабочая температура.
- 3. Низкое качество покрытия (искусственного, материального).
- 4. Неправильное положение бегуна.
- 5. Слишком низкая скорость заливки.
Методы профилактики и борьбы:
- 1. Правильно спроектируйте бегунок и выхлопную систему.
- 2. Для тонкостенных отливок большой площади покрытие не должно быть слишком тонким, и правильное утолщение слоя покрытия способствует формованию.
- 3. Правильно увеличьте рабочую температуру матрицы.
- 4. Применяется метод наклонной заливки.
- 5. Заливка металлической формой с механической вибрацией.
06.Песок (песчаная яма)
Характеристики: на поверхности или внутри отливки образуются относительно правильные отверстия, форма которых соответствует форме песчинок. Частицы песка, внедренные на поверхность отливки, можно увидеть, когда отливка только что выходит из формы, из которой можно извлечь частицы песка. Когда одновременно существует несколько отверстий для песка, поверхность отливки покрыта апельсиновой коркой.
Причины следующие.
Частицы песка, падающие с поверхности песчаного стержня, покрываются жидкой медью и образуют отверстия на поверхности отливки.
- 1. Поверхностная прочность песчаного сердечника плохая, обгорелая или не полностью затвердела.
- 2. Размер песчаного стержня не соответствует размеру внешней формы, и песчаный стержень раздавливается при закрытии формы.
- 3. Форма погружается в графитовую воду, загрязненную песком.
- 4. Песок, падающий в результате трения между ковшом и песчаным сердечником на желобе, с медной водой устремляется в полость кристаллизатора.
Методы профилактики и борьбы:
- 1.Ядро из песка должно производиться строго в соответствии с технологическим процессом и проверяться на качество.
- 2. Размер песчаного ядра соответствует размеру внешней формы.
- 3. Чернила необходимо вовремя очищать.
- 4. Избегайте трения между ковшом и песчаным стержнем.
- 5. Очистите песок в полости формы при установке песчаного стержня.
Источник: Network Arrangement — Китайский производитель трубопроводной арматуры — Yaang Pipe Industry (www.epowermetals.com)
(Yaang Pipe Industry — ведущий производитель и поставщик изделий из никелевых сплавов и нержавеющей стали, включая фланцы из супердуплексной нержавеющей стали, фланцы из нержавеющей стали, фитинги из нержавеющей стали, трубы из нержавеющей стали. Продукция Yaang широко используется в судостроении, атомной энергетике, судостроении. машиностроение, нефтяная, химическая, горнодобывающая промышленность, очистка сточных вод, резервуары для природного газа и высокого давления и другие отрасли).
Если вы хотите получить дополнительную информацию об этой статье или поделиться с нами своим мнением, свяжитесь с нами по адресу sales @ epowermetals.com
Как избежать растрескивания в алюминиевых сплавах
Большинство сплавов на основе алюминия можно успешно сваривать дуговой сваркой без проблем, связанных с растрескиванием, однако, использование наиболее подходящего присадочного сплава и проведение сварочных операций с надлежащим образом разработанной и испытанной процедурой сварки имеет большое значение для успеха . Чтобы оценить потенциальные проблемы, связанные с растрескиванием, необходимо понимать множество различных алюминиевых сплавов и их различные характеристики.Эти предварительные знания помогут избежать ситуаций взлома.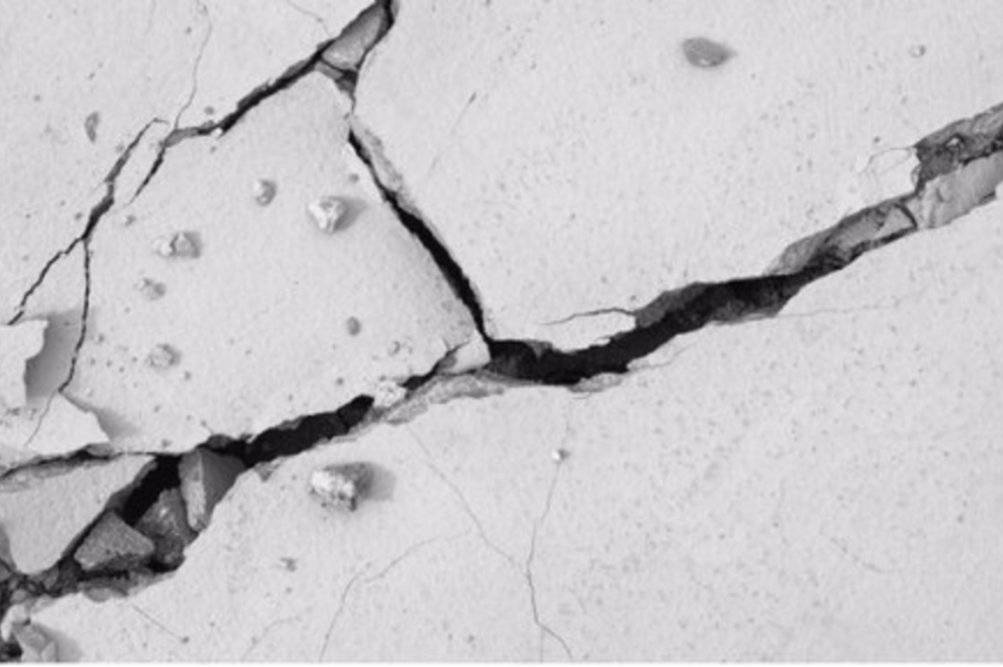
Механизм первичного растрескивания в сварных швах алюминия
Существует ряд механизмов растрескивания, связанных со сваркой металлических сплавов. Одним из самых известных является водородный крекинг, также называемый холодным крекингом. Водородное растрескивание часто является серьезной проблемой при сварке углеродистых сталей и высокопрочных низколегированных сталей. Однако при сварке алюминиевых сплавов водородное растрескивание возникнуть не может.
Горячее растрескивание является причиной почти всех трещин в сварных алюминиевых деталях. Горячее растрескивание — это механизм высокотемпературного растрескивания, который в основном зависит от того, как системы металлических сплавов затвердевают. Этот механизм растрескивания также известен как горячая непродолжительность, горячее растрескивание, растрескивание при затвердевании и ликвационное растрескивание.
Есть три области, которые могут существенно повлиять на вероятность возникновения горячих трещин в алюминиевой сварной конструкции. Они чувствительны к химическому составу основного сплава, выбору и использованию наиболее подходящего присадочного сплава и выбору наиболее подходящей конструкции соединения.
Кривые чувствительности к растрескиванию алюминия (рис. 1) — полезный инструмент для понимания причин растрескивания сварных швов алюминия и того, как выбор присадочного сплава и конструкции соединения может повлиять на чувствительность к трещинам. На диаграмме показано влияние четырех различных добавок сплава — кремния (Si), меди (Cu), магния (Mg) и силицида магния (Mg 2 Si) — на чувствительность алюминия к растрескиванию. Кривые чувствительности к трещинам (рис. 1) показывают, что при добавлении небольших количеств легирующих элементов чувствительность к трещинам становится более высокой, достигает максимума, а затем падает до относительно низких уровней.Изучив кривые чувствительности к трещинам, легко понять, что большинство сплавов на основе алюминия, считающихся несвариваемыми автогенно (без добавления присадочного сплава), имеют химический состав на пиках чувствительности к трещинам или около них. Кроме того, на рисунке показаны сплавы с низкими характеристиками растрескивания, химический состав которых находится далеко от пиков чувствительности к растрескиванию.
На основании этих фактов становится ясно, что трещиностойкость сплава на основе алюминия в первую очередь зависит от его химического состава.Используя те же принципы, можно сделать вывод, что чувствительность к растрескиванию алюминиевого сварного шва, который обычно состоит как из основного сплава, так и из присадочного сплава, также зависит от его химического состава.
Зная важность химии для чувствительности алюминиевого сварного шва к растрескиванию, применяются два основных принципа, которые могут снизить вероятность возникновения горячих трещин. Во-первых, при сварке основных сплавов с низкой чувствительностью к растрескиванию всегда используйте присадочный сплав с аналогичным химическим составом.Во-вторых, при сварке основных сплавов, которые имеют высокую чувствительность к образованию трещин, используйте присадочный сплав с химическим составом, отличным от химического состава основного сплава, чтобы создать химический состав металла сварного шва, который имеет низкую чувствительность к трещинам. При рассмотрении сварки наиболее часто используемых сплавов на алюминиевой основе серии 5xxx (Al-Mg) и серии 6xxx (Al-Mg-Si) эти принципы четко проиллюстрированы.
Сплавы серии 5xxx (Al-Mg)
Большинство базовых сплавов 5xxx, которые содержат около 5% Mg, обладают низкой чувствительностью к образованию трещин.Эти сплавы, часто свариваемые автогенно (без присадочного сплава), легко свариваются с присадочным сплавом, который имеет немного больше Mg, чем основной сплав. Это может обеспечить сварной шов с превосходной трещиностойкостью и температурой затвердевания немного ниже, чем у основного сплава. Эти сплавы не следует сваривать с присадочным сплавом серии 4ххх, поскольку в сварном шве может образоваться небольшое количество силицида магния, что приведет к образованию соединения с нежелательными механическими свойствами.
В эту группу входят базовые сплавы, такие как 5052, содержание Mg в которых очень близко к пику чувствительности к образованию трещин. В случае основного сплава 5052 с содержанием Mg около 2,5% определенно избегайте автогенной сварки. Сплавы на основе Mg с содержанием Mg менее 2,5%, такие как 5052, можно сваривать как с присадочными сплавами 4xxx, такими как 4043 или 4047, так и с присадочными сплавами 5xxx, такими как 5356. При сварке основных сплавов с содержанием Mg менее 2,5% необходимо: изменить химический состав затвердевающего сварного шва от высокого пикового уровня трещин основного сплава. Мы изменяем химический состав сварного шва, выбирая присадочный сплав с гораздо более высоким содержанием Mg, например 5356 (5.0% Mg) или с добавлением кремния в случае 4043.
Сплавы серии 6xxx (Al-Mg-Si)
Сплавы на основе алюминия / магния / кремния (серия 6xxx) очень чувствительны к образованию трещин, поскольку большинство этих сплавов содержат примерно 1,0% силицида магния (Mg 2 Si), что близко к пику кривой чувствительности к трещинам при затвердевании. Содержание Mg 2 Si в этих материалах является основной причиной отсутствия присадочных сплавов серии 6xxx. Использование присадочного сплава серии 6xxx или автогенная сварка неизбежно вызовут проблемы с растрескиванием (см. Рис. 2). Во время дуговой сварки склонность этих сплавов к растрескиванию доводится до приемлемого уровня путем разбавления основного материала избыточным магнием (за счет использования присадочных сплавов Al-Mg серии 5xxx) или избыточного кремния (за счет использования сплавов Al- Si-присадочные сплавы).
Особая осторожность необходима при сварке TIG (GTAW) тонких участков этого типа материала. Часто возможно произвести сварку, особенно на внешних угловых соединениях, без добавления присадочного материала, путем плавления обоих краев основного материала вместе.Однако в большинстве случаев дуговой сварки с этим основным материалом требуется добавление присадочного материала для создания однородных сварных швов без трещин. Одним из возможных исключений может быть противодействие механизму растрескивания путем поддержания сжимающего усилия на деталях во время операции сварки. Это требует специальных методов изготовления и рассмотрения. По этой причине метод используется редко.
Наиболее подходящий и успешный метод, используемый для предотвращения растрескивания основных материалов серии 6xxx, заключается в добавлении соответствующего присадочного сплава во время операции сварки.
Другими соображениями при сварке этой группы сплавов (6xxx) являются влияние конструкции соединения на разбавление основного сплава и присадочного сплава, а также профиль сварного шва, связанный с склонностью к растрескиванию. Сварные швы с квадратной канавкой в этом материале чрезвычайно уязвимы для растрескивания, потому что очень мало присадочного сплава смешивается с основным материалом во время сварки. Часто необходимо оценить использование подготовки сварного шва с V-образной канавкой, которая добавит больше присадочного сплава в смесь металла шва и снизит чувствительность к образованию трещин.Кроме того, вогнутые угловые швы с уменьшенной толщиной горловины и вогнутые корневые проходы в стыковых швах могут иметь тенденцию к растрескиванию (см. Рис. 3).
Дополнительные сведения
Кривые чувствительности к растрескиванию служат отличным ориентиром для определения вероятности образования горячих трещин, однако есть и другие вопросы, которые необходимо учитывать, чтобы понять растрескивание в алюминиевых сплавах. Одной из этих проблем является влияние легирующих элементов, отличных от основных легирующих элементов, учитываемых на кривых чувствительности к трещинам.Несомненно, некоторые сплавы на основе алюминия могут быть трудными для сварки и вызывать проблемы с растрескиванием, особенно без полного понимания их свойств и / или при неправильном обращении. Фактически, некоторые сплавы на основе алюминия непригодны для дуговой сварки, и по этой причине их обычно соединяют механически с помощью клепок или болтов. Эти алюминиевые сплавы трудно поддаются дуговой сварке без проблем во время и / или после сварки. Эти проблемы обычно связаны с растрескиванием, чаще всего с горячим растрескиванием, а иногда и с коррозионным растрескиванием под напряжением (SCC).
Алюминиевые сплавы, которые относятся к этой категории трудных для сварки, можно разделить на разные группы. Всегда помните о небольшом количестве алюминиевых сплавов, предназначенных для обработки, а не свариваемости. Такими сплавами являются 2011 и 6262, которые содержат 0,20-0,6 Bi, 0,20-0,6 Pb и 0,40-0,7 Bi, 0,40-0,7 Pb соответственно. Добавление элементов (висмута и свинца) к этим материалам обеспечивает отличное стружкообразование в этих сплавах, не подвергающихся механической обработке. Однако из-за низких температур затвердевания они могут серьезно снизить возможность получения качественных сварных швов в этих материалах.В дополнение к сплавам для свободной механической обработки, упомянутым выше, многие другие алюминиевые сплавы могут быть весьма восприимчивыми к горячему растрескиванию при дуговой сварке. Эти сплавы обычно подвергаются термообработке и чаще всего встречаются в группах материалов серии 2xxx (Al-Cu) и серии 7xxx (Al-Zn).
Чтобы понять, почему некоторые из этих сплавов непригодны для дуговой сварки, необходимо рассмотреть причины, по которым некоторые алюминиевые сплавы могут быть более восприимчивыми к горячему растрескиванию.
Горячее растрескивание или растрескивание при затвердевании возникает в алюминиевых сварных швах, когда присутствуют высокие уровни термического напряжения и усадка при затвердевании, когда сварной шов подвергается различной степени затвердевания.Сочетание механических, термических и металлургических факторов влияет на чувствительность любого алюминиевого сплава к образованию горячих трещин. Комбинируя различные легирующие элементы, были разработаны многие высокоэффективные термически обрабатываемые алюминиевые сплавы для улучшения механических свойств материалов. В некоторых случаях комбинация требуемых легирующих элементов дает материалы с высокой чувствительностью к образованию горячих трещин.
Когерентность Диапазон
Возможно, наиболее важным фактором, влияющим на чувствительность алюминиевых сварных швов к горячим трещинам, является температурный диапазон когерентности дендритов, а также тип и количество жидкости, доступной во время процесса замораживания. Когерентность возникает, когда дендриты начинают сцепляться друг с другом, так что расплавленный материал начинает образовывать мягкую стадию.
Диапазон когерентности — это температура между образованием когерентных взаимосвязанных дендритов и температурой солидуса. Чем шире диапазон когерентности, тем более вероятно возникновение горячего растрескивания из-за накапливающейся деформации затвердевания между взаимосвязанными дендритами.
Сплавы серии 2ххх (Al-Cu)
Чувствительность к образованию горячих трещин в сплавах Al-Cu увеличивается при добавлении примерно 3% Cu; однако затем он снижается до относительно низкого уровня — 4.5% Cu и выше. Сплав 2219 с 6,3% Cu показывает хорошее сопротивление горячему растрескиванию из-за его относительно узкого диапазона когерентности. Сплав 2024 содержит около 4,5% меди, что вызывает ощущение относительно низкой чувствительности к образованию трещин. Однако сплав 2024 также содержит небольшое количество магния (Mg). Небольшое количество Mg в этом сплаве снижает температуру солидуса, но не влияет на температуру когерентности; следовательно, увеличивается диапазон когерентности и возрастает склонность к образованию горячих трещин.Проблема при сварке 2024 заключается в том, что высокая температура операции сварки позволит сегрегацию легирующих компонентов на границах зерен, а присутствие Mg, как указано выше, снизит температуру солидуса. Поскольку эти легирующие компоненты имеют более низкие фазы плавления, напряжение затвердевания может вызвать растрескивание на границах зерен и / или создать условия внутри материала, способствующие коррозионному растрескиванию под напряжением позже. Высокое тепловложение во время сварки, повторяющиеся проходы сварного шва и большие размеры сварных швов — все это может увеличить проблему сегрегации границ зерен (сегрегация зависит от температуры и времени) и последующей тенденции к растрескиванию.
Сплавы серии 7xxx (Al-Zn)
Сплавы серии 7xxx, с учетом свариваемости, содержат две отдельные группы: типы Al-Zn-Mg и Al-Zn-Mg-Cu.
Al-Zn-Mg Сплавы , такие как 7005, лучше сопротивляются горячему растрескиванию и демонстрируют лучшие характеристики соединения, чем сплавы Al-Zn-Mg-Cu, такие как 7075. Содержание Mg в этой группе (Al-Zn-Mg) сплавы обычно повышают чувствительность к растрескиванию. Однако добавление Zr для уменьшения размера зерна эффективно снижает тенденцию к растрескиванию.Эта группа сплавов легко сваривается с присадочными сплавами с высоким содержанием магния, такими как 5356, что гарантирует, что сварной шов содержит достаточно магния для предотвращения растрескивания. Рекомендация присадочных сплавов на основе кремния, таких как 4043, для этих сплавов нежелательна, потому что избыток Si, вводимый присадочным сплавом, может привести к образованию чрезмерного количества хрупких частиц Mg 2 Si в сварном шве.
Al-Zn-Mg-Cu Сплавы , такие как 7075, содержат небольшое количество меди.Небольшие количества Cu вместе с Mg расширяют диапазон когерентности и, следовательно, увеличивают чувствительность к трещинам. Подобная ситуация может возникнуть с этими материалами, как и со сплавами типа 2024. Напряжение затвердевания может вызвать растрескивание на границах зерен и / или создать условия в материале, способствующие коррозионному растрескиванию под напряжением позже.
Будьте в курсе:
Проблема повышенной подверженности горячему растрескиванию из-за увеличения диапазона когерентности не ограничивается сваркой этих более восприимчивых основных сплавов, таких как 2024 и 7075.Чувствительность к образованию трещин может быть существенно увеличена при сварке несовместимых разнородных основных сплавов (которые обычно легко свариваются сами с собой) и / или путем выбора несовместимого присадочного сплава. Например, путем соединения идеально свариваемого основного сплава серии 2ххх с идеально свариваемым основным сплавом серии 5ххх или использования присадочного сплава серии 5ххх для сварки основного сплава серии 2ххх или присадочного сплава серии 2ххх на базовом сплаве серии 5ххх, мы можем создать такой же сценарий. Если мы смешиваем во время сварки высокое содержание Cu и высокое содержание Mg, мы можем расширить диапазон когерентности и, следовательно, повысить чувствительность к образованию трещин.
Резюме:
Избегайте горячего растрескивания алюминиевых сплавов, применяя один или несколько из следующих подходящих принципов:
- Избегайте чрезвычайно чувствительных к растрескиванию основных материалов, которые обычно считаются несвариваемыми.
- Используйте таблицу выбора подходящего присадочного сплава для выбора наиболее подходящего присадочного сплава для конкретного основного сплава, тем самым избегая критических диапазонов химического состава (диапазонов чувствительности к трещинам) в сварном шве.
- Выберите присадочный сплав с точкой затвердевания, близкой или ниже точки затвердевания основного материала.
- Выберите наиболее подходящую подготовку кромки и корневой зазор, чтобы допустить добавление достаточного количества присадочного материала, таким образом создавая химический состав металла сварного шва за пределами критического диапазона химического состава.
- Чтобы противодействовать растрескиванию, используйте хорошо зарекомендовавшие себя присадочные сплавы с добавлением измельчителей зерна, таких как титан или цирконий.
- Используйте максимально возможную скорость сварки. Чем быстрее проводится сварка, тем выше скорость охлаждения и тем меньше времени сварка находится в диапазоне температур горячего растрескивания.
- Старайтесь использовать последовательности и методы сварки и сборки, которые минимизируют ограничение, уменьшают остаточное напряжение и обеспечивают сварные швы приемлемого профиля.
- Приложите сжимающую силу к сварному соединению во время сварки, чтобы противодействовать механизму растрескивания.
Рис. 1. На этом рисунке показано влияние четырех различных добавок сплава на трещиностойкость алюминия
.Рис. 2 Вот два сварных шва GTAW (TIG), выполненных бок о бок на опорной плите 6061-T6.
1. Верхний сварной шов был наплавлен без присадочного сплава, а затем подвергнут испытаниям на проникновение жидкости. Метод испытаний выявил множество мелких линейных признаков (трещин) на поверхности сварного шва.
2. Нижний шов, выполненный также без присадочного сплава, использовал более высокий ток и меньшую скорость перемещения. Чрезмерное тепловложение во время сварки этого валика привело к возникновению гораздо большего напряжения в сварном шве, что привело к гораздо более очевидной ситуации растрескивания. Как легко видеть, без испытания проникающей жидкостью большая продольная трещина образовалась по центру сварного шва.
Вывод состоит в том, что можно ожидать горячего растрескивания той или иной формы, если основные сплавы серии 6ххх сваривать без добавления присадочного материала.
Рис. 3. На этом рисунке показаны два окончания углового шва в углу сварной конструкции. Трещины видны в обоих кратерах прекращения. Также видны трещины по центру обоих сварных швов. Причина этого горячего растрескивания — нежелательный профиль сварного шва из-за плохой техники сварки.