Алюминий, производство алюминия: технология, процесс и описание
Алюминий обладает массой свойств, которые делают его одним из самых используемых материалов в мире. Он широко распространен в природе, занимая среди металлов первое место. Казалось бы, и трудностей с его производством быть не должно. Но высокая химическая активность металла приводит к тому, что в чистом виде его не встретить, а производить – сложно, энергоемко и затратно.
Сырье для производства
Из какого сырья получают алюминий? Производство алюминия из всех минералов, его содержащих, дорого и нерентабельно. Добывают его из бокситов, которые содержат до 50% оксидов алюминия и залегают прямо на поверхности земли значительными массами.
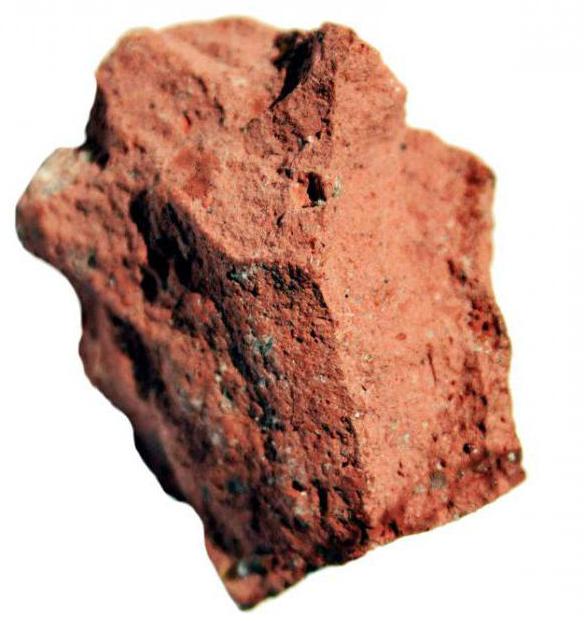
Эти алюминиевые руды имеют достаточно сложный химический состав. Они содержат глиноземы в количестве 30-70% от общей массы, кремнеземы, которых может быть до 20%,окись железа в пределах от 2 до 50%, титан (до 10%).
Глиноземы, а это окись алюминия и есть, состоят из гидроокисей, корунда и каолинита.
В последнее время окиси алюминия стали получать из нефелинов, которые содержат еще и окиси натрия, калия, кремния, и алунитов.
Для производства 1 т чистого алюминия нужно около двух тонн глинозема, который, в свою очередь, получают из примерно 4,5 т боксита.
Месторождения бокситов
Запасы бокситов в мире ограничены. На всем земном шаре всего семь районов с его богатыми залежами. Это Гвинея в Африке, Бразилия, Венесуэла и Суринам в Южной Америке, Ямайка в Карибском регионе, Австралия, Индия, Китай, Греция и Турция в Средиземноморье и Россия.
В странах, где есть богатые месторождения бокситов, может быть развито и производство алюминия. Россия добывает бокситы на Урале, в Алтайском и Красноярском краях, в одном из районов Ленинградской области, нефелин — на Кольском полуострове.
Самые богатые месторождения принадлежат именно российской объединенной компании UC RUSAL. За ней идут гиганты Rio Tinto (Англия-Австралия), объединившийся с канадской Alcan и CVRD. На четвертом месте находится компания Chalco из Китая, затем американо-австралийская корпорация Alcoa, которые являются и крупными производителями алюминия.
Зарождение производства
Датский физик Эрстед выделил первым алюминий в свободном виде в 1825 году. Химическая реакция проходила с хлоридом алюминия и амальгамой калия, вместо которой спустя два года немецкий химик Велер использовал металлический калий.
Калий – материал достаточно дорогой, поэтому в промышленном производстве алюминия француз Сент-Клер Девиль вместо калия в 1854 году использовал натрий, элемент значительно более дешевый, и стойкий двойной хлорид алюминия и натрия.
Русский ученый Н. Н. Бекетов смог вытеснить алюминий из расплавленного криолита магнием. В конце восьмидесятых годов того же века эту химическую реакцию использовали немцы на первом алюминиевом заводе. Во второй половине XVIII века было получено около химическими способами 20 т чистого металла. Это был очень дорогой алюминий.
Производство алюминия с помощью электролиза зародилось в 1886 году, когда одновременно были поданы практически одинаковые патентные заявки основоположниками этого способа американским ученым Холлом и французом Эру. Они предложили растворять глинозем в расплавленном криолите, а затем электролизом получать алюминий.
С этого и началась алюминиевая промышленность, ставшая за более чем вековую историю одной из самых крупных отраслей металлургии.
Основные этапы технологии производства
В общих чертах технология производства алюминия не изменилась с момента создания.
Процесс состоит из трех стадий. На первой из алюминиевых руд, будь это бокситы или нефелины, получают глинозем – окись алюминия Al2O3 .
Затем из окиси выделяют промышленный алюминий со степенью очистки 99,5 % , которой для некоторых целей бывает недостаточно.
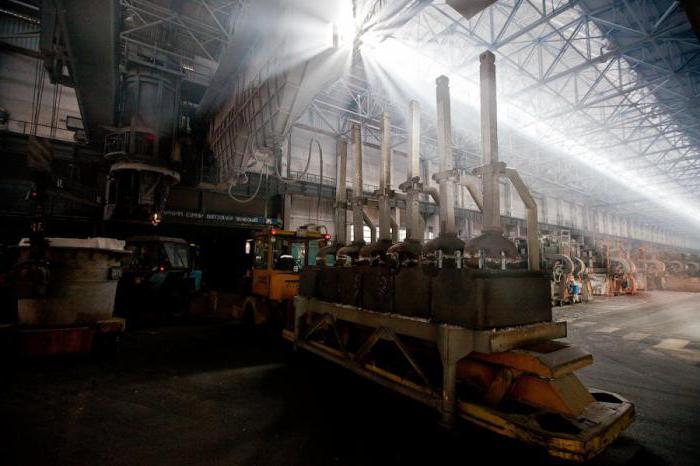
Поэтому на последней стадии рафинируют алюминий. Производство алюминия завершается его очисткой до 99,99 %.
Получение глинозема
Существует три способа получения окиси алюминия из руд:
— кислотный;
— электролитический;
— щелочной.
Последний способ — наиболее распространенный, разработанный еще в том же XVIII веке, но с тех пор неоднократно доработанный и существенно улучшенный, применяется для переработки бокситов высоких сортов. Так получают около 85 % глиноземов.
Сущность щелочного способа заключается в том, что алюминиевые растворы с большой скоростью разлагаются, когда в них вводится гидроокись алюминия. Оставшийся после реакции раствор выпаривается при высокой температуре около 170° С и опять используется для растворения глинозема;
Сначала боксит дробится и измельчается в мельницах с едкой щелочью и известью, затем в автоклавах при температурах до 250°С происходит его химическое разложение и образовывается алюминат натрия, который разбавляют щелочным раствором уже при более низкой температуре – всего 100° С. Алюминатный раствор промывается в специальных сгустителях, отделяется от шлама. Затем происходит его разложение. Через фильтры раствор перекачивают в емкости с мешалками для постоянного перемешивания состава, в который для затравки добавлена твердая гидроокись алюминия.
В гидроциклонах и вакуум-фильтрах выделяется гидроокись алюминия, часть которой возвращается в качестве затравочного материала, а часть идет на кальцинацию. Фильтрат, оставшийся после отделения гидроокиси, тоже возвращается в оборот для выщелачивания следующей партии бокситов.

Процесс кальцинации (обезвоживания) гидроокиси во вращающихся печах происходит при температурах до 1300° С.
Для получения двух тонн окиси алюминия расходуется 8,4 кВт*ч электроэнергии.
Прочное химическое соединение, температура плавления которого 2050° С, это еще не алюминий. Производство алюминия впереди.
Электролиз окиси алюминия
Основным оборудованием для электролиза является специальная ванна, футерованная углеродистыми блоками. К ней подводят электрический ток. В ванну погружаются угольные аноды, сгорающие при выделении из окиси чистого кислорода и образующие окись и двуокись улглерода. Ванны, или электрилизеры, как их называют специалисты, включаются в электрическую цепь последовательно, образуя серию. Сила тока при этом составляет 150 тысяч ампер.
Аноды могут быть двух типов: обожженные из больших угольных блоков, масса которых может быть больше тонны и самообжигающиеся, состоящие из угольных брикетов в алюминиевой оболочке, которые спекаются в процессе электролиза под действием высоких температур.
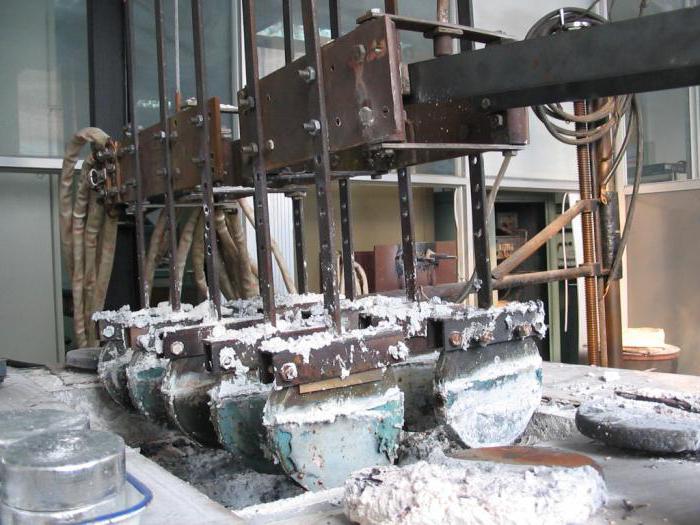
Рабочее напряжение на ванне обычно составляет около 5 вольт. Оно учитывает и напряжение, необходимое для разложения окиси, и неизбежные потери в разветвленной сети.
Из растворенной в расплаве на основе криолита окиси алюминия жидкий металл, который тяжелее солей электролита, оседает на угольном основании ванны. Его периодически откачивают.
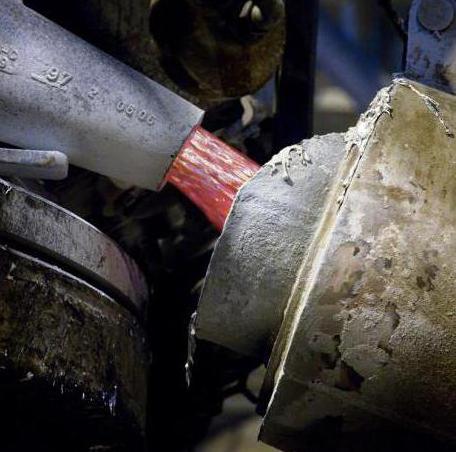
Процесс производства алюминия требует больших затрат электроэнергии. Чтобы получить одну тонну алюминия из глинозема, нужно израсходовать около 13,5 тысяч кВт*ч электроэнергии постоянного тока. Поэтому еще одним условием создания крупных производственных центров является работающая рядом мощная электростанция.
Рафинация алюминия
Наиболее известный метод – это трехслойный электролиз. Он также проходит в электролизных ваннах с угольными подинами, футерованных магнезитом. Анодом в процессе служит сам расплавленный металл, который подвергается очистке. Он располагается в нижнем слое на токопроводящей подине. Чистый алюминий, который из электролита растворяется в анодном слое, понимается вверх и служит катодом. Ток к нему подводится с помощью графитового электрода.
Электролит в промежуточном слое – это фториды алюминия или чистые или с добавлением натрия и хлорида бария. Нагревается он до температуры 800°С.
Расход электроэнергии при трехслойном рафинировании составляет 20 кВт*ч на один кг металла, то есть на одну тонну нужно 20 тысяч кВт*ч. Вот почему, как ни одно производство металлов, алюминий требует наличия не просто источника электроэнергии, а крупной электростанции в непосредственной близости.
В рафинированном алюминии в очень малых количествах содержатся железо, кремний, медь, цинк, титан и магний.
После рафинирования алюминий перерабатывается в товарную продукцию. Это и слитки, и проволока, и лист, и чушки.
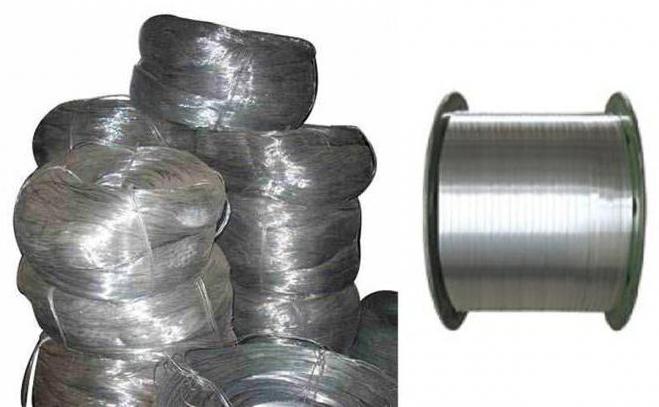
Продукты сегрегации, полученные в результате рафинирования, частично, в виде твердого осадка, используются для раскисления, а частично отходят в виде щелочного раствора.
Абсолютно чистый алюминий получают при последующей зонной плавке металла в инертном газе или вакууме. Примечательной его характеристикой является высокая электропроводность при криогенных температурах.
Переработка вторичного сырья
Четверть общей потребности в алюминии удовлетворяется вторичной переработкой сырья. Из продуктов вторичной переработке льется фасонное литье.
Предварительно отсортированное сырье переплавляется в пороговой печи. В ней остаются металлы, имеющие более высокую температуру плавления, чем алюминий, например, никель и железо. Из расплавленного алюминия продувкой хлором или азотом удаляются различные неметаллические включения.
Более легкоплавкие металлические примеси удаляются присадками магния, цинка или ртути и вакуумированием. Магний удаляется из расплава хлором.
Заданный литейный сплав получают, введя добавки, которые определяются составом расплавленного алюминия.
Центры производства алюминия
По объемам потребления алюминия КНР занимает первое место, оставляя далеко позади находящиеся на втором месте США и обладательницу третьего места Германию.
Китай – это и страна производства алюминия, с огромным отрывом лидирующая в этой области.
В десятку лучших, кроме КНР, входят Россия, Канада, ОАЭ, Индия, США, Австралия, Норвегия, Бразилия и Бахрейн.
В России монополистом в производстве глинозема и алюминия является объединенная компания RUSAL. Она производит до 4 млн т алюминия в год и экспортирует продукцию в семьдесят стран, а присутствует на пяти континентах в семнадцати странах.
Американской компании Alcoa в России принадлежат два металлургических завода.
Крупнейший производитель алюминия в Китае – компания Chalco. В отличие от зарубежных конкурентов, все ее активы сосредоточены в родной стране.
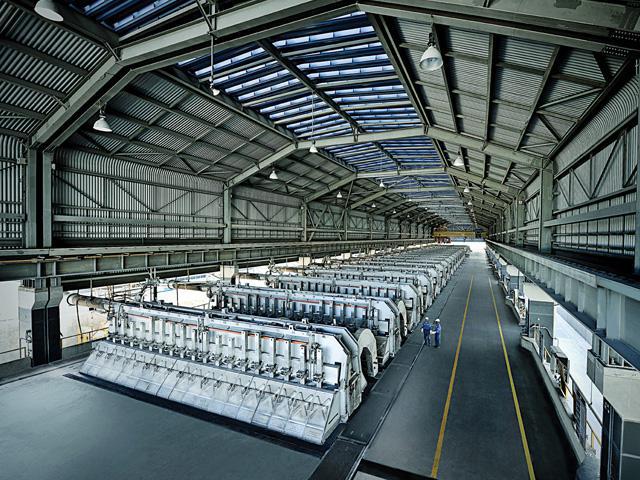
Подразделение Hydro Aluminium норвежской компании Norsk Hydro владеет алюминиевыми заводами в Норвегии, Германии, Словакии, Канаде, и Австралии.
Австралийская BHP Billiton владеет производством алюминия в Австралии, Южной Африке и Южной Америке.
В Бахрейне находится Alba (Aluminium Bahrain B. S. C.) – едва ли не самое крупное производство. Алюминий этого производителя занимает более 2 % общего объема «крылатого» металла, выпускаемого в мире.
Итак, подводя итоги, можно сказать, что главными производителями алюминия являются международные компании, владеющие запасами бокситов. А сам исключительно энергоемкий процесс состоит из получения глинозема из алюминиевых руд, производства фтористых солей, к которым относится криолит, углеродистой анодной массы и угольных анодных, катодных, футеровочных материалов, и собственно электролитического производства чистого металла, которое является главной составляющей металлургии алюминия.
Алюминиевая промышленность — Википедия
Материал из Википедии — свободной энциклопедии
Текущая версия страницы пока не проверялась опытными участниками и может значительно отличаться от версии, проверенной 21 июня 2019; проверки требуют 2 правки. Текущая версия страницы пока не проверялась опытными участниками и может значительно отличаться от версии, проверенной 21 июня 2019; проверки требуют 2 правки.Алюминиевая промышленность — отрасль цветной металлургии, объединяющая предприятия по выработке металлического алюминия[1]. По масштабам производства и потребления алюминий занимает первое место среди подотраслей цветной металлургии, а среди отраслей металлургии по объёму уступает лишь производству стали[2]. Важнейшими потребителями продукции алюминиевой промышленности являются: авиационная, электротехническая, автомобильная и ряд других отраслей машиностроительной и металлообрабатывающей промышленности, а также строительство, железнодорожный транспорт, химическая, пищевая промышленность.
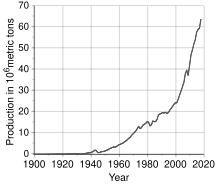
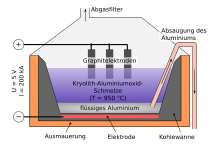
В 1854 году французским учёным Анри Этьеном Сент-Клер Девилем (Sainte-Claire Deville), был открыт способ промышленного производства алюминия, основанный на вытеснении алюминия металлическим натрием из двойного хлорида натрия и алюминия NaCl·AlCl3. За 36 лет его применения, с 1855 по 1890 гг., способом Сент-Клер Девиля было получено 200 т металлического алюминия[3].
В 1856 году на заводе братьев Тисье в Руане Девилль организовал первое промышленное предприятие по выпуску алюминия. При этом стоимость 1 кг алюминия сначала равнялась 300 франкам. Через несколько лет удалось снизить продажную цену до 200 франков за 1 кг, но все равно она оставалась исключительно высокой. Алюминий в это время употребляли почти как драгоценный металл для производства различных изделий. Изделия из этого металла даже пользовались популярностью благодаря своему белому цвету и приятному блеску. По мере совершенствования химических методов выделения алюминия цена на него с годами падала. Например, завод в Олбери (Англия) в середине 1880-х годов выпускал до 250 кг алюминия в день и продавал его по цене 30 шиллингов за кг, иными словами, цена его за 30 лет снизилась в 25 раз. Уже в середине XIX века некоторые химики указывали на то, что алюминий можно получать путём электролиза. В 1854 году Бунзен получил алюминий путём электролиза расплава хлористого алюминия. Для производства алюминия путём электролиза уже более 100 лет используется технология Эру-Холла — электролиз растворенного глинозема Al 2O3
Рост производства был особенно быстрым во время и после Второй мировой войны. Производство первичного алюминия (без учёта производства Советского Союза) составляло только 620 тыс. т в 1939 году. В 1943 году оно возросло до 1,9 млн т. В 1956 году во всем мире производилось 3,4 млн т первичного алюминия, в 1965 году мировое производство алюминия составило 5,4 млн т, в 1980 — 16,1 млн т, а в 1990 — 18 млн т. Производство алюминия в мире в 2007 году составило 37,41 млн тонн (по данным Международного института алюминия (International Aluminium Institute, IAI)[5] и продолжает развиваться очень большими темпами. Применяются Технология Содерберга и другие технологии.
Структура алюминиевой промышленности[править | править код]
Алюминиевая промышленность охватывает следующие основные производства,Основным природным сырьём для получения глинозёма с целью последующего получения из него алюминия, являются бокситы. Для производства одной тонны металлического алюминия требуется примерно 1930 кг глинозёма, 50 кг фтористых солей, 550 кг угольных электродов (анодной массы или обожжённых анодов) и до 18 000 квт-ч электроэнергии. Алюминиевая промышленность — одна из наиболее энергоёмких отраслей промышленности, поэтому важнейшим условием её развития является наличие мощных источников дешёвой электроэнергии.
Развитие и размещение алюминиевой промышленности в мире[править | править код]
Сырьевая база[править | править код]
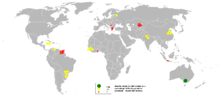
Боксит является основным минеральным сырьём для алюминиевой промышленности. Его запасы в мире распределены очень неравномерно и ограничены. В мире существует семь бокситоносных районов:
По данным Геологической службы США мировые ресурсы бокситов оцениваются в 55 — 75 млрд т, которые распределяются между отдельными регионами следующим образом: Африка — 32 %, Океания — 23 %, Южная Америка и страны Карибского бассейна — 21 %, Азия — 18 %, прочие регионы — 6 %. В целом мировые запасы природных ресурсов бокситов достаточны для удовлетворения мировых потребностей в алюминии в течение продолжительного времени
Понимая важность сырьевой базы, крупнейшие производители алюминия в мире поделили основные месторождения бокситов высокого качества с содержанием глинозёма не менее 50 %. Другим компаниям остается либо приобретать глинозём на открытом рынке и быть всецело зависимыми от рыночного колебания цен, либо объединять усилия с владельцами месторождений[2].
Основные производители алюминия в мире[править | править код]

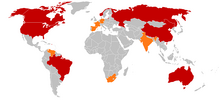

Список стран, крупнейших производителей алюминия[править | править код]
По данным Геологической службы США[7] крупнейшими производителями алюминия в мире явились следующие страны:
Список компаний — крупнейших производителей алюминия[править | править код]
Десятка крупнейших компаний-производителей алюминия выглядит следующим образом[8]:
Самым крупным предприятием по производству алюминия является Братский алюминиевый завод, который первым в мире стал производить более 1 миллиона тонн алюминия в год. Завод производит 30 % российского алюминия и 4 % мирового. Завод потребляет 75 % электроэнергии, вырабатываемой Братской ГЭС[9].
Производство алюминия: факторы размещения производства, процесс
Алюминий является одним из самых распространенных химических элементов на Земле, используется в машиностроении, энергетике и строительстве. Ежегодно добыча и потребление этого металла увеличивается на 7%. Производство алюминия является сложным техническим процессом и требует большого количества энергетических, транспортных, трудовых и сырьевых ресурсов.
Производство алюминия в России и мире
Объем производства алюминия в 2019 году составляет 72 млн тонн. Международный алюминиевый рынок находится в дефиците, составляющем 277 тыс. тонн.Крупнейшими странами-изготовителями данного металла являются Китай, Россия, США, Австралия, Бразилия и Индия. Страны Северной и Южной Америки активно сокращают добычу бокситов. Рост производства чистого алюминия обеспечивается государствами Ближнего Востока и Азии. В этих регионах содержится свыше 73% мировых запасов алюминиевых руд, залегающих на земной поверхности. В них отсутствует большое число металлических и газообразных веществ. Крупнейшими производителями алюминия в мире являются следующие транснациональные компании:
- UCRUSAL: российский концерн, производящий 13% всех алюминиевых сплавов в мире. Объем производства компании составляет 3,75 млн тонн в год. РУСАЛ обладает собственной инженерно-технической базой и экспортирует свою продукцию в страны Европы, Северной Америки и Юго-Восточной Азии.
- Chalco: китайская государственная корпорация, являющаяся вторым крупнейшим производителем алюминиевых материалов в мире. Объем производства составляет 3,4 млн тонн в год.
- RioTinto: австралийско-британская горно-металлургическая компания, производящая глинозем. Объем производства концерна составляет 3,1 млн тонн в год. RioTinto образует с канадской организацией Alcan совместное предприятие по добыче бокситов.
На рынке стран-лидеров по производству чистого алюминия наблюдается переизбыток мощностей. Это обусловлено циклическим характером спроса и большим количеством конкурентоспособных предприятий. Для снижения переизбытка мощностей многие предприятия стали экспортировать алюминиевые полуфабрикаты. С 2015 г. продажи этой продукции ежегодно растут на 20%.
В Российской Федерации присутствует 17 заводов по изготовлению глинозема и алюминиевых листов. Большая часть предприятий располагается на Урале в и в Сибири. Высокая эффективность российских алюминиевых заводов обуславливается следующими факторами размещения производства:
- Сырьевой: предприятия расположены рядом с основными месторождениями алюминия. Это позволяет снизить затраты на транспортировку сырья и снизить стоимость готовой продукции
- Энергетический: чистый алюминий изготавливается посредством электролиза, поэтому заводы расположены рядом с крупными гидроэлектростанциями, вырабатывающими большое количество электрической энергии.
- Потребительский фактор: продукция российский компаний, производящих алюминий, покупается странами Южной и Северной Америки, Азии, Ближнего Востока, Европы и Африки.
- Транспортный: заводы располагаются рядом с крупными транспортными узлами, позволяющими эффективно перевозить сырье и готовую продукцию на большие расстояния. Для транспортировки металла чаще всего используются железнодорожные поезда.
В настоящее время производство алюминия в России снижается и составляет 7,3 млн тонн в год. Это связано с разрушением межотраслевых и хозяйственных связей со странами бывшего СССР.
Технология производства
Технология производства алюминия включает в себя 3 основных этапа:
- Добыча боксита.
- Переработка алюминийсодержащих руд в глинозем.
- Выделение чистого металла из глинозема посредством электролиза и его очистка от лишних примесей.
Производство данного химического элемента осуществляется в электролизном цехе. Он состоит из нескольких корпусов протяженностью 1000 м. В нем располагаются электролизные ванны с большими проводами, подключенными к источнику питания. Ванны оборудованы электродами, находящимися под напряжением 6 В.
Большая часть процессов в электролизном цехе автоматизированы. Перед началом электролиза емкость ванн наполняется расплавленным криолитом. Это вещество предназначено для создания токопроводящей среды при высоких температурах. Дно ванны выступает в качестве катода. Анодом являются угольные блоки, погруженные в криолит.
В промышленности алюминий получают методом пирометаллургии, разработанного немецким химиком Карлом Иосифом Байером. Этот способ представляется собой восстановление металла с помощью углекислого газа или оксида углерода. Все работы на предприятии выполняются в соответствии со схемами производства алюминия, где подробно расписан процесс электролиза глинозема. Изначально в ванну загружается порция глинозема. Под воздействием электричества вещество разлагается. В результате связь между частицами алюминия и кислорода разрывается.
После электролиза на дне электролитических ванне остается чистый алюминий, находящийся в расплавленном состоянии. Кислород, вступая в реакцию углеродом, образуется углекислый газ. Полученный материал разливают по вакуумным ковшам и доставляют в литейный цех. Здесь металл подвергается термической обработке. С помощью переплавки из сплава удаляются лишние примеси. В результате вещество приобретает твердую форму и сортируется по блокам весом до 22 кг.
Алюминий сохраняет свои свойства при длительной эксплуатации. Поэтому часть алюминиевой продукции перерабатывается и повторно используется для создания чистых металлов, что оказывает положительное влияние на экологию. Объем затрат на охрану окружающей среды в этой сфере промышленности составляет 4%. Власти используют множество экономических мер в области ООС, предоставляя льготы предпринимателям, соблюдающим экологические нормы и государственные стандарты в процессе хозяйственной деятельности.
Производство глинозема
Глинозем представляет собой порошок белого цвета, образованный в результате взаимодействия алюминия с кислородом. Технологический процесс производства этого вещества был разработан Байером в конце XIXстолетия. С помощью этой технологии изготавливается 90% глинозема в мире.
При получении порошкообразного оксида алюминия методом Байера можно использовать высококачественные бокситы с низким содержанием примесей. В процессе изготовления глинозема кристаллическая гидроокись алюминия растворяется в каустической щелочи высокой концентрации. Химическая реакция осуществляется при высоких температурах. Посторонние вещества, входящие в состав боксита, при взаимодействии с раствором едкого натра выпадают в осадок. Примеси, отделенные от гидроокиси алюминия, называются красным шламом. В процессе переработки из них можно извлечь соединения кремния, железа, титана и иных химических элементов.
Крупные алюминиевые частицы с помощью фильтрации отделяются от гидроокиси алюминия. Полученное вещество промывают, высушивают и нагревают до температуры кипения воды. В результате образуется глинозем. У него отсутствует срок годности. Хранить глинозем необходимо в сухих местах. Транспортировка вещества осуществляется в железнодорожных вагонах.
Получение алюминия из глинозема
Производители активно совершенствуют технологию производства алюминия из глинозема, стараясь изготавливать металл с минимальными затратами электроэнергии и наименьшим воздействием на окружающую среду. В современных электролитических цехах используются инертные аноды, что позволяет отказаться от использования угля. Их можно использовать в течение нескольких десятилетий.
В результате использования инновационных технологий при электролизе глинозема в атмосферу не выделяется углекислый газ. В электролизных ваннах вырабатывается чистый кислород. Это позволяет снизить траты на вентиляционные механизмы, предназначенные для своевременного удаления углекислого газа из помещения. При электролизе используется не менее 2 Т глинозема, 0,1 Т криолита и небольшое количество фторидов.
Рафинирование алюминия
Образованный в результате электролиза металл содержит небольшое количество металлических и газообразных веществ:
- кремний;
- железо;
- цинк;
- углерод;
- водород;
- азот;
- озон;
- углекислый газ.
Примеси ухудшают свойства металла. Поэтому во время производства их удаляют при помощи рафинирования. Эта процедура осуществляется 2 методами:
- Хлорирование: осуществляется при температуре 750°С. Алюминий подвергается продувке хлористым раствором. Хлорирование производится в специальных ковшах в течение 12 мин.
- Электролитический способ: осуществляется с применением фтористых и хлористых солей. Металл подвергается термической обработке и анодному растворению. В результате из расплавленного вещества удаляются лишние примеси.
После процедуры рафинирования чистота металла составляет 99,5 – 99,9%. При этой процедуры также из рафинируемого вещества также удаляется 1% алюминия.
Сырье
В естественной среде алюминий встречается только в виде руд – бокситов. Эти вещества представлены виде гидроксидов, корунда и каолинита. В них содержится свыше 40 химических элементов. Содержание глинозема в бокситах составляет 45%. Одним из важнейших параметров алюминиевых руд является кремниевый модуль, характеризующий отношение содержаний оксидов алюминия и кремния. Он должен составляет не менее 2,6. В недрах Земли находится свыше 18 млрд тонн бокситов. При нынешних темпах производства из этого сырья можно производить алюминий до 2122 г.
Необходимое оборудование
Для добычи бокситов, преобразования руд в глинозем и извлечения чистого металла требуется следующее оборудование:
- Механизмы раздачи глинозема: предназначены для транспортировки порошкообразного оксида алюминия внутри цеха и дозированной подачи глинозема к электролизным машинам.
- Катодная ошиновка: представляет собой гибкие ленты катодных спусков, прикрепленных к стержням катодных шин, выполненных из стальных материалов.
- Газоочистительные установки: используются для очистки помещения от газов, образующихся во время производства фторида алюминия сухим способом.
- Монтажное оборудование: краны линейного и технического предназначения.
- Электролизер: прибор для разделения основных компонентов глинозема при помощи электрического тока во время электролиза.
В зависимости от технологических особенностей производства требуется большое количество барабанных вращающихся печей. Они используются при сухих методах производства. При организации предприятия важно обеспечить оборудование для электролиза глинозема электроэнергией.
Как производят алюминий. Хакасский алюминиевый завод
Все посты в Интернете про заводы РУСАЛа блогеры и журналисты пишут со слов кого-либо из руководства предприятия, больше-то им информацию взять не у кого.Этот фотоотчет — исключение. По моей просьбе, все фотографии здесь подписаны обычным работником, специалистом среднего звена Саяногорского алюминиевого завода (лексика, орфография и пунктуация сохранены).
1. Производство алюминия — тут никакого волшебства 🙂 Сырье (криолит и глинозем) привозят на завод поездами с фабрик по добыче и обогащению глинозема. Эта смесь по аэрожелобам подается в ванны, там происходит расплав солей алюминия под воздействием температуры получаемой при воздействии электрического тока. В расплаве происходит растворения веществ в результате которого металюминий выпадает в осадок.
2. Алюминий становиться тяжелее электролита и тупо оседает на дно ванны, откуда его с помощью «носка» выливают.
Выливщик — самая невеселая и неблагодарная профессия. Весь день за этими котлами по корпусу бродить приходиться, наматывая более 10 км за смену. Круглый год зимой, когда в корпусе столько же, сколько на улице и летом, когда температура поднимается до 70 градусов. Самый комфорт с точки зрения хорошего климата в рабочей зоне это весна и осень — и не дубак и не пекло. Летом в шутку корпуса называем филиалом ада.
3. Чистка лЁток — хоть какое-то разнообразие и большая проблема если они завалены сырьем после засыпки.
4. Криолит содержит фтор. Фтор очень активное вещество и практически сразу взаимодействует со всем что рядом, образуя соединения. Вы если не заметили, то все окна в помещении помутневшие и белого цвета. Фтор соединяясь с водяным паром в воздухе образует плавиковую кислоту — одна из немногих, которая растворяет стекло, хотя другие агрессивные вещества и сильные кислоты могут спокойно храниться в таких посудах. Поэтому стекла, если с них не смывать пыль, за год становятся соовсем непрозрачными.
5. Бедолага Ноель (по названию фирмы-производителя кранов — Nkm Noel) как завели при пуске так и не глушили по сей день, работает, как говориться, на пределе своих возможностей и ресурса. Ушел не один год на доводку, чтобы это супердорогая железяка хоть как-то адекватно работала.
6. Все по старинке, никакие не новейшие технологии. Только на одном кране, и то не всегда, работает программа по автоматической установки. Вручную двое бедолаг меняют анодные блоки, тока вот кран помогает куски корки вытаскивать — грейферит. Анодный массив засыпан укрывным материалом — сырьем, оно под температурой спекается и получается корка. Грейферит — это потому-что тот инструмент, с помощью которого кран черпает эту корку из электролита при замене блоков, называется грейфер.
7. Если не прогрейферить, то будут отклонения на аноде, всякая шляпа поприлипает и ванна будет нестабильно работать. За это, если не делать, то начальство «чпокает» работяг. Хотя, когда сила тока была 320 кА, то на куски было пофигу, все их растворяло. И такая операция по замене анодов происходила в два раза быстрее.
8. Да здравствует ручной труд. Так-то вонь от этой мульды для сырья неимоверная, вся таблица Менделеева. Вот, правда, рабочие официально работают на экологически чистом предприятии. По документации рабочие место у них абсолютно безвредное (вредности нет), они операторы (многим из них на врят ли доживут до 50 без проблем для здоровья), а все операции делаются автоматически с кнопки. Нажал кнопку и спина вспотела ))
9.
10.
11. Вот так под ним вообще-то народ пытается как можно меньше времени проводить, вдруг в очередной раз что-то отвалиться и упадет кило так 200.
12.
13.
14. Работяги называют эти аноды в шутку шлакоблоками. Замена красных на черные.
15. Литейный цех.
16. Одна ванна в сутки нарабатывает около 3 т алюминия, его транспортируют в литейное отделении, где бодяжат до нужного состава сплавы и выливают в слитки.
17.
18.
19. Всех гостей обычно сюда водят на показуху. Метал вот он перед глазами, ни каких там ванн с бешеным магнитном полем рядом… И наглядный пример готовой продукции!
20.
21.
22.
23.
24.
25. Погрузка продукта в вагоны, китайцы и американцы уже заждались.
26.
27.
28.
29.
30.
31. Мы её называем Аврора. Но не всегда из нее приятный белый дым, иногда что-то идет не так, и выбрасывается темно-коричневый, отвратительного запаха. Аврора — это трубы мокрой газоочистки цеха производства электродов — анодов. Коэффициент её очистки около 80% + еще износ оборудования дает о себе знать, бывают сбои и нормально нифига воздух не чистит и это все в атмосферу. Хотя, если честно, в компании жРУСАЛо много что изношено до неприличия. Ведь у нашего бизнеса девиз — выжми все при мин вложении.
32. В строительстве Саянского алюминиевого завода принимал участие молодой Шойгу.
33. Вот так когда-то начинались многие великие строки страны. На благо советского народа. В 90 годы уже российской истории при достаточной туманный обстоятельствах прихватизации предприятие перешло бизнесу, хотя предприятие РАСАЛ заявляет, что оно «самое наикрутейшее в мире и каждый работник должен гордиться этим, пусть даже заправщику на соседней заправки платят больше» — это взято из ответа директора на вопрос рабочих. Отношение к работнику напоминает иной раз шарагу.
Этот крупный бизнес в свое время помешал ввести в строй другие планируемые перспективные производства в городе, чтобы ограничить поток (уход) кадров и удержания их более высокими зарплатами.
А так по существу это хорошо, что у нас в стране есть свое производство. Пусть даже 80% выпускаемой продукции уходит за бугор. У нас есть к чему стремиться и что развивать. Как никак оно свое родное, хоть и зарегистрировано на Сейшелах :))
Взят у danlux в Хакасский алюминиевый завод
Если у вас есть производство или сервис, о котором вы хотите рассказать нашим читателям, пишите пишите мне — Аслан ([email protected]) и мы сделаем самый лучший репортаж, который увидят не только читатели сообщества, но и сайта Как это сделано
Подписывайтесь также на наши группы в фейсбуке, вконтакте, одноклассниках и в гугл+плюс, где будут выкладываться самое интересное из сообщества, плюс материалы, которых нет здесь и видео о том, как устроены вещи в нашем мире.
Жми на иконку и подписывайся!
Производство алюминия: victorborisov — LiveJournal
АО «Казахстанский электролизный завод» (КЭЗ), входящий в состав ENRC (Eurasian Natural Resources Corporation) — единственный завод в Казахстане по производству первичного алюминия. Завод находится в Павлодаре. Открыт в 2007 году. Включает в себя электролизный цех, литейный цех, цех по изготовлению анодов и другие вспомогательные отделения. На его базе образован металлургический кластер с полным циклом производства: добыча бокситов, получение глинозема, выработка «крылатого металла». В настоящий момент производственная мощность завода — 125 000 тонн в год. Алюминий выпускается в двадцатикилограммовых слитках марки А-85 (содержит 99,85 % алюминия).
А мы тем временем приступим к изучению технологии производства алюминия в фотографиях.
Общая информация
Алюминий — химический элемент третьей группы периодической системы элементов Д. И. Менделеева. По содержанию в земной коре алюминий занимает первое место среди металлов и третье среди других элементов (после кислорода и кремния). Земная кора на 8,8% состоит из алюминия (для сравнения, содержание в земной коре железа – 4,2%, меди – 0,003, золота – 0,000005%). В природе алюминий встречается только в виде различных и очень разнообразных по своему составу соединений. Основная их масса приходится на оксид алюминия — в обиходе он называется глиноземом , или просто глиной. Глина примерно на треть состоит из оксида алюминия и является потенциальным сырьем для его производства.
Алюминий обладает целым рядом свойств, которые выгодно отличают его от других металлов. Это — небольшая плотность алюминия, хорошая пластичность и достаточная механическая прочность, высокие тепло- и электропроводность. Алюминий нетоксичен, немагнитен и коррозионностоек к ряду химических веществ.
Важнейшие потребители алюминия и его сплавов — авиационная и автомобильная отрасли промышленности, железнодорожный и водный транспорт, машиностроение, электротехническая промышленность и приборостроение, промышленное и гражданское строительство, химическая промышленность, производство предметов народного потребления.
Производство алюминия
Сущность процесса производства алюминия заключается в получении безводного, свободного от примесей оксида алюминия (глинозёма) с последующим получением металлического алюминия путем электролиза растворенного глинозема в криолите.
Технологический процесс получения алюминия состоит из двух основных стадий:
• Получение глинозема (Al2O3) из алюминиевых руд;
• Электролиз и рафинирование алюминия из глинозема;
Глинозем получают из бокситов путем их обработки щелочью. Полученный алюминат натрия подвергают гидролизу. В результате в осадок выпадают кристаллы гидроксида алюминия. Гидроксид алюминия обезвоживают путем нагрева во вращающихся печах и получают обезвоженный глинозем.
Для производства криолита сначала из плавикового шпата получают фтористый водород, а затем плавиковую кислоту. В раствор плавиковой кислоты вводят гидроксид алюминия, в результате чего образуется фторалюминиевая кислота, которую нейтрализуют содой и получают криолит, выпадающий в осадок. Его отфильтровывают и просушивают в сушильных барабанах.
Таким образом получают глинозем, представляющий из себя серый порошок. Следующая задача выделить из него чистый алюминий с помощью электролиза. Вот теперь начинается самое интересное:
Цех по изготовлению анодов
2. Алюминиевая промышленность является крупным потребителем угольных электродов, которые служат для подвода тока к электролиту в электролизерах.
3. Здесь производят прессованные предварительно обожженные электроды.
4. Анод представляет собой призматический блок, на верхней плоскости которого имеется несколько ниппельных гнезд (углублений).
5. Анодные блоки изготавливают из малозольных и малосернистых коксов.
6. Для подвода тока к аноду служат стальные ниппеля, которые вставляют в ниппельные гнезда и заливают расплавленным чугуном или заделывают углеродистой пастой.
7. Для производства углеродистых изделий применяют твердые углеродистые материалы, составляющие основу электрода, и связующие углеродистые вещества, заполняющие промежутки между зернами твердых углеродистых материалов. При обжиге изделий связующие вещества коксуются и прочно связывают зерна твердых углеродистых материалов между собой.
8.
9.
Электролизный цех
10. Современный цех электролиза представляет собой территориально и административно обособленную хозрасчетную единицу с полным циклом производства — от приемных складов сырья до складов товарной продукции, основу которого составляет одна или несколько серии последовательно соединенных электролизных ванн.
11. Электролизер представляет собой ванну с расплавленным криолитом, двойным фторидом натрия и алюминия, в котором растворено 3–5% глинозема, – плавающим на подушке из расплавленного алюминия. Стальные шины, проходящие через подину из углеродистых плит, используются для подачи напряжения на катод, а подвешенные угольные бруски, погруженные в расплавленный криолит, служат анодами. Рабочая температура процесса близка к 950° С, что значительно выше температуры плавления алюминия. Температура в электролизной ванне регулируется изменением зазора между анодами и катодным металлоприемником, на который осаждается расплавленный алюминий.
12.
13.
14. Жидкий алюминий выделившийся на подине, служащей катодом, тяжелее расплава соли электролита, поэтому собирается на угольном основании, откуда его периодически откачивают. Сверху в электролит погружены угольные аноды, которые сгорают в атмосфере выделяющегося из окиси алюминия кислорода, с выделением окиси углерода СО и двуокиси углерода CO2.
15. Сила тока на электролизерах составляет 150 000 А. Рабочее напряжение на ванне 4-5 В. Рядом с электролизерами присутствует сильное электромагнитное поле.
16. Специальная машина транспорта анодных паллет. Применяются для транспортировки свежих анодов и анодных огарков между анодо-монтажным отделением (АМО) и корпусом электролиза.
17. Общие размеры цеха впечатляют. Позади такой же ряд электролизеров, а также рядом находится второй цех аналогичных размеров.
18. Характерным для производства глинозема, фтористых солей и углеродистых изделий является требование максимальной степени чистоты этих материалов.
19. В состав электролита промышленных алюминиевых электролизеров, помимо основных компонентов — криолита, фтористого алюминия и глинозема, входят небольшие количества (в сумме до 8-9%) некоторых других солей, которые улучшают некоторые физико-химические свойства электролита и тем самым повышают эффективность работы электролизеров.
20. По мере обеднения электролита глиноземом в него вводят очередную порцию глинозема.
Литейный цех
21. Литейное отделение расположено на территории электролизного цеха с таким расчетом, чтобы транспортные пути жидкого металла из корпусов электролиза в литейное отделение были минимальными. Основное оборудование этого отделения — отражательные печи (миксеры) с электрическим обогревом.
22. Обычно для повышения качества продукции устанавливают последовательно две спаренные отражательные печи, одна из которых (отстойник) предназначается для приема, отстаивания, усреднения температуры и состава металла, а другая (разливочная) — для литья из нее различных видов продукции. Система стационарных печей в отличие от поворотных позволяет осуществить непрерывный процесс литья.
23. Жидкий алюминий выдерживают в электропечи в течение 30—45 минут при температуре 690—730 °С для всплывания неметаллических включений и выделения газов из металла.
24. Примеси удаляют рафинированием, для чего продувают хлор через
расплав алюминия. Образующийся парообразный хлористый алюминий, проходя через расплавленный металл, обволакивает частички примесей, которые всплывают на поверхность металла, где их удаляют. Хлорирование алюминия способствует также удалению Na, Ca, Mg и газов, растворенных в алюминии. После рафинирования чистота первичного алюминия составляет 99,5—99,85%.
25. Разливка мелкоформатной чушки производится в изложницы на разливочной машине конвейерного типа, оборудованной устройством для механического клеймения чушек и системой воздушного или водяного охлаждения изложниц.
26. Разливку металла в изложницы ведут короткой ровной струей. После заполнения изложниц с поверхности металла удаляют оксидную пленку.
27. Устройство для механического клеймения чушек.
28. Отлитые чушки укладываются в штабеля с помощью чушкоукладчика, установленного в конце конвейерной машины.
29. После этого готовая продукция упаковывается в паллеты по 1000 кг и отправляется на склад.
30. Для производства одной тонны алюминия требуется около 14 000 киловатт-часов электроэнергии и окол двух тонн глинозема. В то же самое время, для производства одной тонну глинозера требуется переработать около 5 тонн бокситовой руды. В настоящее время стоимость алюминия на лондонской бирже металлов составляет 2600 долларов за тонну.
Видео с электролизного завода. Я совершил небольшую ошибку пытаясь одновременно снимать фото и видео, в результате на видео имеются паузы в момент экспонирования.
Книга для самостоятельного изучения: Металлургия алюминия
Репортажи с этого завода также смотрите в ближайшее время в журналах russos и gelio (здесь).
Ранее в серии «Индустриальный Казахстан»:
Производство металлургического кремния
Производство стеклопластиковых труб
Локомотивосборочный завод по производству тепловозов ТЭ33А «Evolution»
Карьер золотоизвлекательной фабрики АО «Васильковский ГОК»
Алматинский метрополитен. Часть 1/2
По вопросам организации фотосессий со мной можно связаться по электронной почте — [email protected]
Металлургия алюминия. Как получают алюминий высокой чистоты?
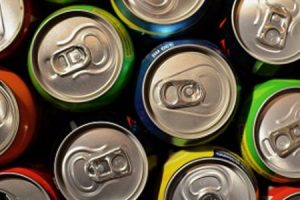
Этот металл хорошо известен уже более 2-х тысяч лет и характеризуется широким техническим применением. Для чего его можно использовать?
В промышленности алюминий в основном используется в сплавах с другими элементами, что улучшает его эксплуатационные свойства. В таком виде он представляет собой универсальный конструкционный материал с очень универсальным применением. Среди алюминиевых сплавов можно выделить, в частности, литейные сплавы и сплавы, используемые для пластической обработки. В их состав, кроме алюминия, входят такие элементы, как: медь, магний, кремний и марганец. Алюминиевые сплавы используют, в частности, в авиации, химической промышленности, автомобилестроении и даже в судостроении.
Алюминий широко используется в промышленности также и в чистом виде для изготовления разных предметов быта, таких как, например, зеркала, банки для напитков и продуктов питания, кухонные принадлежности или же всем известная алюминиевая фольга. Его используют также для изготовления химической аппаратуры, электрических проводов, а даже взрывчатых веществ. Чтобы выделить этот элемент из бокситовой руды, необходимо осуществить два следующих друг за другом этапа. Первый из них – это процесс Байера, который позволяет получить из минерала оксид алюминия. Затем это соединение подвергается электролизу, в результате чего образуется алюминий технической чистоты.
Из чего производят алюминий?
Чистый алюминий не встречается в природе из-за его способности к пассивации. Это явление заключается в окислении металла в присутствии воздуха, в результате чего на его поверхности образуется пассивный защитный слой. Алюминий покрывается слоем оксида алюминия (Al2O3) толщиной до нескольких нм. Затем, под воздействием влаги внешний слой подвергается частичному гидролизу, в результате чего дополнительно образуется гидроксид, т.е. Al(OH)
Алюминий входит в состав разных минеральных пород, встречающихся в природе в виде руд. Для производства чистого алюминия используется, прежде всего, глинистая бокситовая руда. Она образуется в основном в местах выветривания алюмосиликатных пород в жарком климате и содержит также соединения железа. Это порода с характерным красным или коричневым цветом, которая встречается в двух видах: силикатном и карбонатном.
Производство алюминия технической чистоты
Алюминий технической чистоты (более 99%) промышленно получают в результате двух последовательных процессов. В результате первого получают оксид алюминия (процесс Байера), а на следующем этапе проводят процесс электролитической редукции (электролиз методом Холла-Эру), благодаря которому получают чистый алюминий. Для снижения расходов, связанных с транспортировкой бокситовой руды, большинство перерабатывающих предприятий строят недалеко от шахт.
Процесс Байера
Первый этап после добычи руды заключается в ее мытье с помощью воды. Таким образом удаляют большую часть загрязнений, которые просто растворяются в воде. Затем, в обработанное водой сырье добавляют CaO, т.е. оксид кальция. После этого его измельчают с помощью специальных трубных мельниц до момента получения зерен с очень малым диаметром, т.е. меньше 300 мкм. Соответствующее измельчение сырья чрезвычайно важно, так как оно обеспечивает большую площадь поверхности зерен, что, в свою очередь, влияет на эффективность протекания процесса экстракции.
Следующий этап производства оксида алюминия заключается в растворении зерен при помощи водного раствора каустической соды. В Группе PCC гидроксид натрия производится методом мембранного электролиза. Полученный таким образом продукт характеризуется очень высоким качеством и чистотой, отвечая при этом требованиям последнего издания Европейской фармакопеи. Смесь, содержащая молотые зерна и гидроксид натрия, хранится в течение нескольких часов в специальных реакторах, называемых автоклавами. Во время протекающего процесса осаждения в реакторах поддерживаются высокое давление и повышенная температура. Таким образом, получают алюминат натрия, который затем очищают при помощи разных фильтров.
На следующем этапе очищенный раствор алюмината натрия подвергается разложению. В результате образуется натровый щелок (т.е. водный раствор каустической соды) и кристаллы гидроокиси алюминия высокой степени чистоты. Полученный в результате кристаллизации осадок отфильтровывают и промывают водой. А оставшийся натровый щелок нагревают и возвращают в процесс для повторного использования.
Последним этапом производства чистого оксида алюминия является кальцинация. Она заключается в нагревании гидроксида алюминия при температуре выше 1000oC, в результате чего происходит его разложение на Al2O3, который получают в виде чистого белого порошка. Так подготовленный оксид алюминия транспортируют в печи для получения металлического алюминия в процессе электролитической редукции.
Электролиз оксида алюминия
Следующим этапом получения чистого алюминия является проведение процесса электролиза методом Холла-Эру. В первую очередь, полученный в процессе Байера Al2O3 расплавляют с криолитом и таким образом приготовленный раствор подвергают процессу электролиза при температуре не выше 900oC. Полученный таким образом жидкий алюминий отделяют от электролита и удаляют из электролитических ванн с помощью т.н. вакуумных сифонов. Затем сырье попадает в литейное устройство, откуда на дальнейшем этапе его вкладывают в раскаленные печи, в которых происходит процесс переработки. Он заключается в очистке алюминия с целью достижения максимальной чистоты. В промышленных условиях алюминий может быть очищен двумя методами. Первый из них заключается в растопке алюминия и пропускании через него хлора, благодаря чему примеси связываются с хлором, образуя хлориды, которые затем удаляют из процесса. Второй метод заключается в электролитической редукции расплавленного с медью алюминия. Полученный таким образом конечный продукт характеризуется очень высокой чистотой.
Алюминий – материал будущего
Разработка метода получения чистого алюминия из боксита с помощью процесса Байера и электролиза Холла-Эру расширила область применения этого элемента. Кроме того, сочетание высокой прочности с легкостью позволило в некоторых случаях заменить алюминием более дорогую сталь. Устойчивость к воздействию атмосферных факторов дала возможность использовать алюминий в производстве оконных и дверных профилей. Еще одним преимуществом алюминия является возможность подвергать его многократной вторичной переработке, благодаря чему он считается относительно дружественным окружающей среде материалом.
Подводя итог, алюминий – это универсальный материал, широко используемый в пищевой, энергетической, химической, транспортной, строительной, автомобильной и авиационной промышленностях. Учитывая его многочисленные преимущества, безусловно, это не предел возможностей его применения и в ближайшем будущем он по-прежнему будет приобретать популярность.
Из чего делают алюминий сырье
Алюминий обладает массой свойств, которые делают его одним из самых используемых материалов в мире. Он широко распространен в природе, занимая среди металлов первое место. Казалось бы, и трудностей с его производством быть не должно. Но высокая химическая активность металла приводит к тому, что в чистом виде его не встретить, а производить – сложно, энергоемко и затратно.
Сырье для производства
Из какого сырья получают алюминий? Производство алюминия из всех минералов, его содержащих, дорого и нерентабельно. Добывают его из бокситов, которые содержат до 50% оксидов алюминия и залегают прямо на поверхности земли значительными массами.
Эти алюминиевые руды имеют достаточно сложный химический состав. Они содержат глиноземы в количестве 30-70% от общей массы, кремнеземы, которых может быть до 20%,окись железа в пределах от 2 до 50%, титан (до 10%).
Глиноземы, а это окись алюминия и есть, состоят из гидроокисей, корунда и каолинита.
В последнее время окиси алюминия стали получать из нефелинов, которые содержат еще и окиси натрия, калия, кремния, и алунитов.
Для производства 1 т чистого алюминия нужно около двух тонн глинозема, который, в свою очередь, получают из примерно 4,5 т боксита.
Месторождения бокситов
Запасы бокситов в мире ограничены. На всем земном шаре всего семь районов с его богатыми залежами. Это Гвинея в Африке, Бразилия, Венесуэла и Суринам в Южной Америке, Ямайка в Карибском регионе, Австралия, Индия, Китай, Греция и Турция в Средиземноморье и Россия.
В странах, где есть богатые месторождения бокситов, может быть развито и производство алюминия. Россия добывает бокситы на Урале, в Алтайском и Красноярском краях, в одном из районов Ленинградской области, нефелин — на Кольском полуострове.
Самые богатые месторождения принадлежат именно российской объединенной компании UC RUSAL. За ней идут гиганты Rio Tinto (Англия-Австралия), объединившийся с канадской Alcan и CVRD. На четвертом месте находится компания Chalco из Китая, затем американо-австралийская корпорация Alcoa, которые являются и крупными производителями алюминия.
Зарождение производства
Датский физик Эрстед выделил первым алюминий в свободном виде в 1825 году. Химическая реакция проходила с хлоридом алюминия и амальгамой калия, вместо которой спустя два года немецкий химик Велер использовал металлический калий.
Калий – материал достаточно дорогой, поэтому в промышленном производстве алюминия француз Сент-Клер Девиль вместо калия в 1854 году использовал натрий, элемент значительно более дешевый, и стойкий двойной хлорид алюминия и натрия.
Русский ученый Н. Н. Бекетов смог вытеснить алюминий из расплавленного криолита магнием. В конце восьмидесятых годов того же века эту химическую реакцию использовали немцы на первом алюминиевом заводе. Во второй половине XVIII века было получено около химическими способами 20 т чистого металла. Это был очень дорогой алюминий.
Производство алюминия с помощью электролиза зародилось в 1886 году, когда одновременно были поданы практически одинаковые патентные заявки основоположниками этого способа американским ученым Холлом и французом Эру. Они предложили растворять глинозем в расплавленном криолите, а затем электролизом получать алюминий.
С этого и началась алюминиевая промышленность, ставшая за более чем вековую историю одной из самых крупных отраслей металлургии.
Основные этапы технологии производства
В общих чертах технология производства алюминия не изменилась с момента создания.
Процесс состоит из трех стадий. На первой из алюминиевых руд, будь это бокситы или нефелины, получают глинозем – окись алюминия Al2O3 .
Затем из окиси выделяют промышленный алюминий со степенью очистки 99,5 % , которой для некоторых целей бывает недостаточно.
Поэтому на последней стадии рафинируют алюминий. Производство алюминия завершается его очисткой до 99,99 %.
Получение глинозема
Существует три способа получения окиси алюминия из руд:
Последний способ — наиболее распространенный, разработанный еще в том же XVIII веке, но с тех пор неоднократно доработанный и существенно улучшенный, применяется для переработки бокситов высоких сортов. Так получают около 85 % глиноземов.
Сущность щелочного способа заключается в том, что алюминиевые растворы с большой скоростью разлагаются, когда в них вводится гидроокись алюминия. Оставшийся после реакции раствор выпаривается при высокой температуре около 170° С и опять используется для растворения глинозема;
Сначала боксит дробится и измельчается в мельницах с едкой щелочью и известью, затем в автоклавах при температурах до 250°С происходит его химическое разложение и образовывается алюминат натрия, который разбавляют щелочным раствором уже при более низкой температуре – всего 100° С. Алюминатный раствор промывается в специальных сгустителях, отделяется от шлама. Затем происходит его разложение. Через фильтры раствор перекачивают в емкости с мешалками для постоянного перемешивания состава, в который для затравки добавлена твердая гидроокись алюминия.
В гидроциклонах и вакуум-фильтрах выделяется гидроокись алюминия, часть которой возвращается в качестве затравочного материала, а часть идет на кальцинацию. Фильтрат, оставшийся после отделения гидроокиси, тоже возвращается в оборот для выщелачивания следующей партии бокситов.
Процесс кальцинации (обезвоживания) гидроокиси во вращающихся печах происходит при температурах до 1300° С.
Для получения двух тонн окиси алюминия расходуется 8,4 кВт*ч электроэнергии.
Прочное химическое соединение, температура плавления которого 2050° С, это еще не алюминий. Производство алюминия впереди.
Электролиз окиси алюминия
Основным оборудованием для электролиза является специальная ванна, футерованная углеродистыми блоками. К ней подводят электрический ток. В ванну погружаются угольные аноды, сгорающие при выделении из окиси чистого кислорода и образующие окись и двуокись улглерода. Ванны, или электрилизеры, как их называют специалисты, включаются в электрическую цепь последовательно, образуя серию. Сила тока при этом составляет 150 тысяч ампер.
Аноды могут быть двух типов: обожженные из больших угольных блоков, масса которых может быть больше тонны и самообжигающиеся, состоящие из угольных брикетов в алюминиевой оболочке, которые спекаются в процессе электролиза под действием высоких температур.
Рабочее напряжение на ванне обычно составляет около 5 вольт. Оно учитывает и напряжение, необходимое для разложения окиси, и неизбежные потери в разветвленной сети.
Из растворенной в расплаве на основе криолита окиси алюминия жидкий металл, который тяжелее солей электролита, оседает на угольном основании ванны. Его периодически откачивают.
Процесс производства алюминия требует больших затрат электроэнергии. Чтобы получить одну тонну алюминия из глинозема, нужно израсходовать около 13,5 тысяч кВт*ч электроэнергии постоянного тока. Поэтому еще одним условием создания крупных производственных центров является работающая рядом мощная электростанция.
Рафинация алюминия
Наиболее известный метод – это трехслойный электролиз. Он также проходит в электролизных ваннах с угольными подинами, футерованных магнезитом. Анодом в процессе служит сам расплавленный металл, который подвергается очистке. Он располагается в нижнем слое на токопроводящей подине. Чистый алюминий, который из электролита растворяется в анодном слое, понимается вверх и служит катодом. Ток к нему подводится с помощью графитового электрода.
Электролит в промежуточном слое – это фториды алюминия или чистые или с добавлением натрия и хлорида бария. Нагревается он до температуры 800°С.
Расход электроэнергии при трехслойном рафинировании составляет 20 кВт*ч на один кг металла, то есть на одну тонну нужно 20 тысяч кВт*ч. Вот почему, как ни одно производство металлов, алюминий требует наличия не просто источника электроэнергии, а крупной электростанции в непосредственной близости.
В рафинированном алюминии в очень малых количествах содержатся железо, кремний, медь, цинк, титан и магний.
После рафинирования алюминий перерабатывается в товарную продукцию. Это и слитки, и проволока, и лист, и чушки.
Продукты сегрегации, полученные в результате рафинирования, частично, в виде твердого осадка, используются для раскисления, а частично отходят в виде щелочного раствора.
Абсолютно чистый алюминий получают при последующей зонной плавке металла в инертном газе или вакууме. Примечательной его характеристикой является высокая электропроводность при криогенных температурах.
Переработка вторичного сырья
Четверть общей потребности в алюминии удовлетворяется вторичной переработкой сырья. Из продуктов вторичной переработке льется фасонное литье.
Предварительно отсортированное сырье переплавляется в пороговой печи. В ней остаются металлы, имеющие более высокую температуру плавления, чем алюминий, например, никель и железо. Из расплавленного алюминия продувкой хлором или азотом удаляются различные неметаллические включения.
Более легкоплавкие металлические примеси удаляются присадками магния, цинка или ртути и вакуумированием. Магний удаляется из расплава хлором.
Заданный литейный сплав получают, введя добавки, которые определяются составом расплавленного алюминия.
Центры производства алюминия
По объемам потребления алюминия КНР занимает первое место, оставляя далеко позади находящиеся на втором месте США и обладательницу третьего места Германию.
Китай – это и страна производства алюминия, с огромным отрывом лидирующая в этой области.
В десятку лучших, кроме КНР, входят Россия, Канада, ОАЭ, Индия, США, Австралия, Норвегия, Бразилия и Бахрейн.
В России монополистом в производстве глинозема и алюминия является объединенная компания RUSAL. Она производит до 4 млн т алюминия в год и экспортирует продукцию в семьдесят стран, а присутствует на пяти континентах в семнадцати странах.
Американской компании Alcoa в России принадлежат два металлургических завода.
Крупнейший производитель алюминия в Китае – компания Chalco. В отличие от зарубежных конкурентов, все ее активы сосредоточены в родной стране.
Подразделение Hydro Aluminium норвежской компании Norsk Hydro владеет алюминиевыми заводами в Норвегии, Германии, Словакии, Канаде, и Австралии.
Австралийская BHP Billiton владеет производством алюминия в Австралии, Южной Африке и Южной Америке.
В Бахрейне находится Alba (Aluminium Bahrain B. S. C.) – едва ли не самое крупное производство. Алюминий этого производителя занимает более 2 % общего объема «крылатого» металла, выпускаемого в мире.
Итак, подводя итоги, можно сказать, что главными производителями алюминия являются международные компании, владеющие запасами бокситов. А сам исключительно энергоемкий процесс состоит из получения глинозема из алюминиевых руд, производства фтористых солей, к которым относится криолит, углеродистой анодной массы и угольных анодных, катодных, футеровочных материалов, и собственно электролитического производства чистого металла, которое является главной составляющей металлургии алюминия.
«В природе ничто не возникает мгновенно и ничто не появляется в свете в совершенно готовом виде».
Александр Герцен
русский публицист, писатель
Производство металла делится на три основных этапа: добыча бокситов – алюминийсодержащей руды, их переработка в глинозем – оксид алюминия, и, наконец, получение чистого металла с использованием процесса электролиза – распада оксида алюминия на составные части под воздействием электрического тока. Из 4-5 тонн бокситов получается 2 тонны глинозема, из которого производят 1 тонну алюминия.
В мире существуют несколько видов алюминиевых руд, но основным сырьем для производства этого металла являются именно бокситы. Это горная порода, состоящая, в основном, из оксида алюминия с примесью других минералов. Боксит считается качественным, если он содержит более 50% оксида алюминия.
Бокситы могут сильно отличаться друг от друга. По структуре они бывают твердые и плотные либо рыхлые и рассыпчатые. По цвету – как правило, кирпично-красные, рыжеватые или коричневые из-за примеси оксида железа. При небольшом содержании железа бокситы имеют белый или серый цвет. Но иногда встречаются руды желтого, темно-зеленого цвета и даже пестрые – с голубыми, красно-фиолетовыми или черными прожилками.
Около 90% мировых запасов бокситов сосредоточено в странах тропического и субтропического поясов – из них 73% приходится на пять стран: Гвинею, Бразилию, Ямайку, Австралию и Индию. В Гвинее бокситов больше всего – 5,3 миллиарда тонн (28,4%), при этом они высокого качества, содержат минимальное количество примесей и залегают практически на поверхности.
Следующим этапом является производственной цепочки является переработка бокситов в глинозем – это оксид алюминия Al2O3, который представляет собой белый рассыпчатый порошок. Основным способом получения глинозема в мире является метод Байера, открытый более ста лет назад, но актуальный до сих пор – около 90% глинозема в мире производятся именно так. Этот способ весьма экономичен, но использовать его можно только при переработке высококачественных бокситов со сравнительно низким содержанием примесей – в первую очередь кремнезема.
Метод Байера основан на следующем: кристаллическая гидроокись алюминия, входящая в состав боксита, хорошо растворяется при высокой температуре в растворе едкого натра (каустической щёлочи, NaOH) высокой концентрации, а при понижении температуры и концентрации раствора вновь кристаллизуется. Посторонние, входящие в состав боксита (так называемый балласт), не переходят при этом в растворимую форму или перекристаллизовываются и выпадают в осадок до того, как производится кристаллизация гидроокиси алюминия. Поэтому после растворения гидроокиси алюминия балласт легко может быть отделен – он называется красный шлам.
Это густая масса красно-бурого цвета, состоящая из соединений кремния, железа, титана и других элементов. Его складируют на тщательно изолированных территориях – шламохранилищах. Их обустраивают таким образом, чтобы содержащиеся в отходах щёлочи не проникали в грунтовые воды. Как только хранилище отрабатывает свой потенциал, территорию можно вернуть в первоначальный вид, покрыв её песком, золой или дёрном и посадив определённые виды деревьев и трав. На полное восстановление могут уйти годы, но в итоге местность возвращается в изначальное состояние.
Многие специалисты не считают красный шлам отходом, так как он может служить сырьем для переработки. Например, из него извлекают скандий для дальнейшего производства алюминиево-скандиевых сплавов. Скандий придает таким сплавом особую прочность, сферы использования – автомобиле- и ракетостроение, спортивная экипировка, производство электропроводов.
Также красный шлам может использоваться для производства чугуна, бетона, получения редкоземельных металлов.
У глинозема нет срока годности, но хранить его непросто, так как при малейшей он возможности активно впитывает влагу – поэтому производители предпочитают как можно быстрее отправлять его на алюминиевое производство. Сначала глинозем складывают в штабели весом до 30 тысяч тонн – получается своеобразный слоеный пирог высотой до 10-12 метров. Потом пирог «нарезают» и грузят для отправки в железнодорожные вагоны – в среднем, в один вагон от 60 до 75 тонн (зависит от вида самого вагона).
Существует еще один, гораздо менее распространенный способ получения глинозема – метод спекания. Его суть заключается в получения твердых материалов из порошкообразных при повышенной температуре. Бокситы спекают с содой и известняком – они связывают кремнезем в нерастворимые в воде силикаты, которые легко отделить от глинозема. Этот способ требует больших затрат, чем способ Байера, но в то же время дает возможность перерабатывать бокситы с высоким содержанием вредных примесей кремнезема.
Глинозем выступает непосредственным источником металла в процессе производства алюминия. Но для создания среды, в которой этот процесс будет происходить, необходим еще один компонент – криолит.
Это редкий минерал из группы природных фторидов состава Na3AlF6. Обычно он образует бесцветные, белые или дымчато-серые кристаллические скопления со стеклянным блеском, иногда – почти черные или красновато-коричневые. Криолит хрупкий и легко плавится.
Природных месторождений этого минерала крайне мало, поэтому в промышленности используется искусственный криолит. В современной металлургии его получают взаимодействием плавиковой кислоты с гидроксидом алюминия и содой.
Ток для производства алюминия
Для запуска двигателя автомобильный аккумулятор должен обеспечить электрический ток в 300-350 А в течение 30 секунд. То есть в 1000 раз меньше, чем нужно одному электролизеру для постоянной работы.
В каждой ванне происходит процесс электролиза алюминия. Емкость ванны заполняется расплавленным криолитом, который создает электролитическую (токопроводящую) среду при температуре 950°С. Роль катода выполняет дно ванны, а анода – погружаемые в криолит угольные блоки длиной около 1,5 метров и шириной 0,5 метра, со стороны они выглядят как впечатляющих размеров молот.
Каждые полчаса при помощи автоматической системы подачи глинозема в ванну загружается новая порция сырья. Под воздействием электрического тока связь между алюминием и кислородом разрывается – алюминий осаждается на дне ванны, образуя слой в 10-15 см, а кислород соединяется с углеродом, входящим в состав анодных блоков, и образует углекислый газ.
Примерно раз в 2-4 суток алюминий извлекают из ванны при помощи вакуумных ковшей. В застывшей на поверхности ванны корке электролита пробивают отверстие, в которое опускают трубу. Жидкий алюминий по ней засасывается в ковш, из которого предварительно откачан воздух. В среднем, из одной ванны откачивается около 1 тонны металла, а в один ковш вмещается около 4 тонн расплавленного алюминия. Далее этот ковш отправляется в литейное производство.
При производстве каждой тонны алюминия выделяется 280 000 м 3 газов. Поэтому каждый электролизер независимо от его конструкции оснащен системой газосбора, которая улавливает выделяющиеся при электролизе газы и направляет их в систему газоочистки. Современные «сухие» системы газоочистки для улавливания вредных фтористых соединений используют ни что иное, а глинозем. Поэтому перед тем как использоваться для производства алюминия, глинозем на самом деле сначала участвует в очистке газов, которые образовались в процессе производства металла ранее. Вот такой замкнутый цикл.
Для процесса электролиза алюминия требуется огромное количество электроэнергии, поэтому важно использовать возобновляемые и не загрязняющие окружающую среду источники этой энергии. Чаще всего для этого используются гидроэлектростанции – они обладают достаточной мощностью и не имеют выбросов в атмосферу. Например, в России 95% алюминиевого мощностей обеспечены гидрогенерацией. Однако есть в места в мире, где угольная генерация пока доминирует – в частности, в Китае на нее приходится 93% производства алюминия. В результате для производства 1 тонны алюминия с использованием гидрогенерации в атмосферу выделяется чуть более 4 тонн углекислого газа, а при использовании угольной генерации – в пять раз больше – 21,6 тонны.
А мы тем временем приступим к изучению технологии производства алюминия в фотографиях.
Общая информация
Алюминий — химический элемент третьей группы периодической системы элементов Д. И. Менделеева. По содержанию в земной коре алюминий занимает первое место среди металлов и третье среди других элементов (после кислорода и кремния). Земная кора на 8,8% состоит из алюминия (для сравнения, содержание в земной коре железа – 4,2%, меди – 0,003, золота – 0,000005%). В природе алюминий встречается только в виде различных и очень разнообразных по своему составу соединений. Основная их масса приходится на оксид алюминия — в обиходе он называется глиноземом , или просто глиной. Глина примерно на треть состоит из оксида алюминия и является потенциальным сырьем для его производства.
Алюминий обладает целым рядом свойств, которые выгодно отличают его от других металлов. Это — небольшая плотность алюминия, хорошая пластичность и достаточная механическая прочность, высокие тепло- и электропроводность. Алюминий нетоксичен, немагнитен и коррозионностоек к ряду химических веществ.
Важнейшие потребители алюминия и его сплавов — авиационная и автомобильная отрасли промышленности, железнодорожный и водный транспорт, машиностроение, электротехническая промышленность и приборостроение, промышленное и гражданское строительство, химическая промышленность, производство предметов народного потребления.
Производство алюминия
Сущность процесса производства алюминия заключается в получении безводного, свободного от примесей оксида алюминия (глинозёма) с последующим получением металлического алюминия путем электролиза растворенного глинозема в криолите.
Технологический процесс получения алюминия состоит из двух основных стадий:
• Получение глинозема (Al2O3) из алюминиевых руд;
• Электролиз и рафинирование алюминия из глинозема;
Глинозем получают из бокситов путем их обработки щелочью. Полученный алюминат натрия подвергают гидролизу. В результате в осадок выпадают кристаллы гидроксида алюминия. Гидроксид алюминия обезвоживают путем нагрева во вращающихся печах и получают обезвоженный глинозем.
Для производства криолита сначала из плавикового шпата получают фтористый водород, а затем плавиковую кислоту. В раствор плавиковой кислоты вводят гидроксид алюминия, в результате чего образуется фторалюминиевая кислота, которую нейтрализуют содой и получают криолит, выпадающий в осадок. Его отфильтровывают и просушивают в сушильных барабанах.
Таким образом получают глинозем, представляющий из себя серый порошок. Следующая задача выделить из него чистый алюминий с помощью электролиза. Вот теперь начинается самое интересное:
Цех по изготовлению анодов
2. Алюминиевая промышленность является крупным потребителем угольных электродов, которые служат для подвода тока к электролиту в электролизерах.
3. Здесь производят прессованные предварительно обожженные электроды.
4. Анод представляет собой призматический блок, на верхней плоскости которого имеется несколько ниппельных гнезд (углублений).
5. Анодные блоки изготавливают из малозольных и малосернистых коксов.
6. Для подвода тока к аноду служат стальные ниппеля, которые вставляют в ниппельные гнезда и заливают расплавленным чугуном или заделывают углеродистой пастой.
7. Для производства углеродистых изделий применяют твердые углеродистые материалы, составляющие основу электрода, и связующие углеродистые вещества, заполняющие промежутки между зернами твердых углеродистых материалов. При обжиге изделий связующие вещества коксуются и прочно связывают зерна твердых углеродистых материалов между собой.
10. Современный цех электролиза представляет собой территориально и административно обособленную хозрасчетную единицу с полным циклом производства — от приемных складов сырья до складов товарной продукции, основу которого составляет одна или несколько серии последовательно соединенных электролизных ванн.
11. Электролизер представляет собой ванну с расплавленным криолитом, двойным фторидом натрия и алюминия, в котором растворено 3–5% глинозема, – плавающим на подушке из расплавленного алюминия. Стальные шины, проходящие через подину из углеродистых плит, используются для подачи напряжения на катод, а подвешенные угольные бруски, погруженные в расплавленный криолит, служат анодами. Рабочая температура процесса близка к 950° С, что значительно выше температуры плавления алюминия. Температура в электролизной ванне регулируется изменением зазора между анодами и катодным металлоприемником, на который осаждается расплавленный алюминий.
14. Жидкий алюминий выделившийся на подине, служащей катодом, тяжелее расплава соли электролита, поэтому собирается на угольном основании, откуда его периодически откачивают. Сверху в электролит погружены угольные аноды, которые сгорают в атмосфере выделяющегося из окиси алюминия кислорода, с выделением окиси углерода СО и двуокиси углерода CO2.
15. Сила тока на электролизерах составляет 150 000 А. Рабочее напряжение на ванне 4-5 В. Рядом с электролизерами присутствует сильное электромагнитное поле.
16. Специальная машина транспорта анодных паллет. Применяются для транспортировки свежих анодов и анодных огарков между анодо-монтажным отделением (АМО) и корпусом электролиза.
17. Общие размеры цеха впечатляют. Позади такой же ряд электролизеров, а также рядом находится второй цех аналогичных размеров.
18. Характерным для производства глинозема, фтористых солей и углеродистых изделий является требование максимальной степени чистоты этих материалов.
19. В состав электролита промышленных алюминиевых электролизеров, помимо основных компонентов — криолита, фтористого алюминия и глинозема, входят небольшие количества (в сумме до 8-9%) некоторых других солей, которые улучшают некоторые физико-химические свойства электролита и тем самым повышают эффективность работы электролизеров.
20. По мере обеднения электролита глиноземом в него вводят очередную порцию глинозема.
21. Литейное отделение расположено на территории электролизного цеха с таким расчетом, чтобы транспортные пути жидкого металла из корпусов электролиза в литейное отделение были минимальными. Основное оборудование этого отделения — отражательные печи (миксеры) с электрическим обогревом.
22. Обычно для повышения качества продукции устанавливают последовательно две спаренные отражательные печи, одна из которых (отстойник) предназначается для приема, отстаивания, усреднения температуры и состава металла, а другая (разливочная) — для литья из нее различных видов продукции. Система стационарных печей в отличие от поворотных позволяет осуществить непрерывный процесс литья.
23. Жидкий алюминий выдерживают в электропечи в течение 30—45 минут при температуре 690—730 °С для всплывания неметаллических включений и выделения газов из металла.
24. Примеси удаляют рафинированием, для чего продувают хлор через
расплав алюминия. Образующийся парообразный хлористый алюминий, проходя через расплавленный металл, обволакивает частички примесей, которые всплывают на поверхность металла, где их удаляют. Хлорирование алюминия способствует также удалению Na, Ca, Mg и газов, растворенных в алюминии. После рафинирования чистота первичного алюминия составляет 99,5—99,85%.
25. Разливка мелкоформатной чушки производится в изложницы на разливочной машине конвейерного типа, оборудованной устройством для механического клеймения чушек и системой воздушного или водяного охлаждения изложниц.
26. Разливку металла в изложницы ведут короткой ровной струей. После заполнения изложниц с поверхности металла удаляют оксидную пленку.
27. Устройство для механического клеймения чушек.
28. Отлитые чушки укладываются в штабеля с помощью чушкоукладчика, установленного в конце конвейерной машины.
29. После этого готовая продукция упаковывается в паллеты по 1000 кг и отправляется на склад.
30. Для производства одной тонны алюминия требуется около 14 000 киловатт-часов электроэнергии и окол двух тонн глинозема. В то же самое время, для производства одной тонну глинозера требуется переработать около 5 тонн бокситовой руды. В настоящее время стоимость алюминия на лондонской бирже металлов составляет 2600 долларов за тонну.
Видео с электролизного завода. Я совершил небольшую ошибку пытаясь одновременно снимать фото и видео, в результате на видео имеются паузы в момент экспонирования.
Книга для самостоятельного изучения: Металлургия алюминия
Репортажи с этого завода также смотрите в ближайшее время в журналах russos и
gelio (здесь).